DOI:
10.1039/D0RA01277G
(Paper)
RSC Adv., 2020,
10, 11039-11045
Understanding the mechanism of the competitive adsorption in 8-methylquinoline hydrogenation over a Ru catalyst†
Received
10th February 2020
, Accepted 6th March 2020
First published on 17th March 2020
Abstract
The competitive adsorption of 8-methylquinoline (8-MQL) and partially hydrogenated product, 4H-8-MQL, was studied by performing a combination of experiments and first-principles calculations over a selected Ru catalyst. A series of hydrogenation reactions were conducted with 8-MQL and 4H-8-MQL as initial reactants, respectively. 8-MQL exhibits stronger adsorption on catalyst surface active sites compared with 4H-8-MQL and the massive adsorption of 8-MQL hampers the further adsorption of 4H-8-MQL. The effects of temperature, pressure and solvent on the selectivity in 8-MQL hydrogenation were investigated as well. Full hydrogenation of 8-MQL to 10H-8-MQL was achieved within 120 min when the catalyst dosage increased from 5 wt% to 7 wt% under 160 °C and a hydrogen pressure of 7 MPa. The electronic charge of the N-heteroatom in 8-MQL and 4H-8-MQL was analyzed and the adsorption geometries of 8-MQL and 4H-8-MQL on the Ru(001) surface were optimized by DFT calculations to explain the competitive adsorption behaviors of 8-MQL and 4H-8-MQL.
Introduction
The direct hydrogenation of quinoline (QL) and its derivatives is considerably interesting for the industrial synthesis of a variety of petrochemicals, pharmaceuticals and fine chemicals.1–3 Both partially hydrogenated products and fully hydrogenated products are valuable chemicals as well as liquid organic hydrogen storage materials.4–8 Therefore, the role of reaction parameters in the selectivity of QLs hydrogenation is widely investigated for obtaining the required product.9–13 Two hydrogenated intermediates, 1,2,3,4-4H-QL and 5,6,7,8-4H-QL, were generated along with the completely hydrogenated product, 10H-QL. It is found that the selectivity to 4H-QL or 10H-QL is affected dramatically by the catalysts and solvents used in QL hydrogenation.14–16 Heterogeneous catalysts based on Rh,3,17 Pd,18,19 Ru20,21 and Pt22 were successfully used in selective hydrogenation of QLs to 4H-QLs. Yu et al. reported that 99.8% 4H-QL can be achieved over prepared Ru/OMNC (ordered mesoporous N-doped carbon) catalyst with EtOH as solvent under 40 °C and 1 MPa H2.21 Pt/CeO2 was found to be highly efficient and chemoselective hydrogenation of QL into 4H-QL at 60 °C, which was attributed to the metal-support interaction between Pt and basic CeO2.23 98% 4H-QL was achieved over cobalt-based catalyst under 120 °C and 2 MPa H2 with toluene as the solvent reported by Chen et al.24 Higher hydrogenation rates of 4H-QLs were observed in aqueous solvent compared to that in an aprotic and apolar solvent using supported Pd and Ru catalyst.10,18 Ionic liquid stabilized Ni and Pt nanoparticles were also selected as highly efficient catalysts in chemoselective hydrogenation of QLs.25–27 In addition, homogeneous catalysts based on Ir,28 Ru,29,30 Mo,31 Co32,33 were proposed to hydrogenate quinolines selectively as well.
The further hydrogenation, 4H-QL to 10H-QL, was proved to be more difficult, which requires longer reaction time and harsher conditions (T > 100 °C, P > 5 MPa).34,35 Only 0.6% 10H-QL was converted from 4H-QL after QL hydrogenation for 14 h over supported Ru at 150 °C and 5 MPa.36 This was explained mostly by the irreversible adsorption of QL and/or 4H-QL on the catalyst surface, also called catalyst poisoning, leading to the hydrogenation stops after 4H-QL production.37,38 Actually, some effective methods have been developed to realize selective hydrogenation by adjusting the adsorption behaviors of QL and 4H-QL. Addition of a Lewis base39 or introduction of aprotic solvent such as n-hexane40,41 to the reaction mixture was in favor of 10H-QL formation. Fan et al. reported an excellent catalyst for complete hydrogenation of QL, Rh/AlO(OH).40 They proposed that the hydrogen bond formed between hydroxyl group of Rh/AlO(OH) and the aromatic cycle of 4H-QL promotes 10H-QL production. However, the particular research on the competitive adsorption behaviors of QLs and 4H-QLs have been rarely reported.
In the present work, 8-methylquinoline (8-MQL) hydrogenation was investigated over commercial Ru/Al2O3 under designed conditions to elaborate the competitive adsorption between 8-MQL and 4H-8-MQL. A series of hydrogenation reactions were conducted with 8-MQL and 4H-8-MQL as initial reactants, respectively. It is found that the adsorption of 4H-8-MQL on Ru/Al2O3 is weaker than that of 8-MQL and 4H-8-MQL is not responsible for the catalyst poisoning. The role of reaction parameters including temperature, pressure and solvent in 8-MQL hydrogenation was studied in detail. In addition, the adsorption geometries of 8-MQL and 4H-8-MQL was optimized by DFT calculations and the corresponding adsorption energies were also compared.
Results and discussion
Hydrogenation of 8-MQL to form 4H-8-MQL
The standard hydrogenation conditions designed in the present work were: 0.2 g Ru/Al2O3 catalyst, 4 g 8-MQL, 40 ml dioxane with the hydrogen pressure of 7 MPa and reaction temperature range of 160–180 °C. As shown in Fig. 1, almost 100% of 8-MQL was converted to form 4H-8-MQL under designed conditions detected by GCMS. The structure of the produced 4H-8-MQL was determined to be 1,2,3,4-4H-8-MQL by 1H NMR, implying that 8-MQL hydrogenation firstly occurred in N-heterocycle as a result of the strong interaction between N atom and the catalyst active site. The NMR spectrum was presented in Fig. S1.† Increase temperature from 160 °C to 180 °C, the conversion rate of 8-MQL was accelerated obviously whereas only a trace of fully hydrogenated products (yield < 1%), 10H-8-MQL, was detected. Similarly, hydrogenation of QL to produce 10H-QL catalyzed by supported noble metal catalyst was also found to be very difficult, which was roughly attributed to the strong adsorption of QL and/or 4H-QL on the effective active sites.23,40
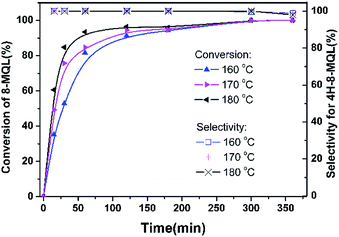 |
| Fig. 1 Hydrogenation of 8-MQL at different temperatures over Ru/Al2O3 with catalyst dosage proportion of 5 wt% and hydrogen pressure of 7 MPa. | |
Hydrogenation of 4H-8-MQL to form 10H-8-MQL
The 4H-8-MQL produced from 8-MQL hydrogenation was used as reactant after distillation. The standard conditions in this experiment were: 0.2 g Ru/Al2O3, 4 g 4H-8-MQL, 40 ml dioxane, 7 MPa hydrogen pressure and 160 °C reaction temperature. Fig. 2 demonstrates that the fully hydrogenated product, 10H-8-MQL was obtained as soon as the reaction started. Moreover, the same catalyst was reused 3 times for 4H-8-MQL hydrogenation. No significant decrease in hydrogenation rate was observed, indicating that Ru/Al2O3 is highly active to catalyze 4H-8-MQL to form 10H-8-MQL and that 4H-8-MQL is not responsible for poisoning the catalyst surface active sites.
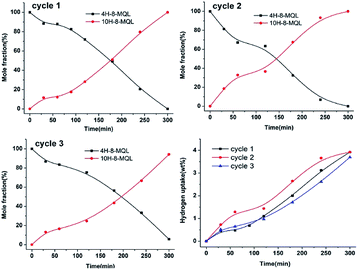 |
| Fig. 2 Hydrogenation of 4H-8-MQL at 160 °C and 7 MPa with the same Ru/Al2O3 catalyst for 3 cycles. | |
The reaction pathway for 8-MQL and 4H-8-MQL hydrogenation has been described in Scheme 1. Both of process (1) and (3) can be realized successfully. In contrast, the process (2) of 10H-8-MQL formation in hydrogenation of 8-MQL was rarely observed even when the reaction temperature was increased to 180 °C. By comparing process (1) and process (3), the conversion rate of 4H-8-MQL was slower than that of 8-MQL under the same reaction conditions. 85% of 8-MQL can be converted to 4H-8-MQLwithin 120 min at 160 °C and 7 MPa, while only 30% of 4H-8-MQL was consumed to produce 10H-8-MQL.
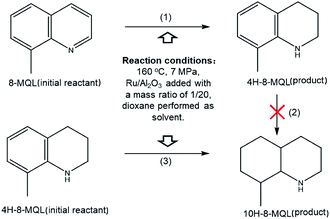 |
| Scheme 1 Hydrogenation pathway of 8-MQL and 4H-8-MQL at 160 °C and 7 MPa over Ru/Al2O3 catalyst with the dosage proportion of 5 wt%. | |
It is widely acknowledgement that adsorption on the catalyst active sites was an essential prerequisite for hydrogenation reaction to occur. Therefore, we speculated that 8-MQL were more easily adsorbed on the active sites such as metal surface and acid sites than that of 4H-8-MQL, leading to the desorption of 4H-8-MQL and thus 10H-8-MQL was rarely produced. The re-exposure of active sites was in favor of the continuous hydrogenation of 8-MQL. This hypothesis was proved by adding a new portion of 8-MQL after the previous 8-MQL was almost totally converted to 4H-8-MQL. The results showed that a further 50% conversion of the fresh 8-MQL to 4H-8-MQL can be obtained within 60 min. The weaker interaction of 4H-8-MQL with surface active sites compared with that of 8-MQL probably results in the difficulty in effective adsorption on active sites and low conversion rate for its further hydrogenation.
Hydrogenation of 8-MQL to form 10H-8-MQL
In the view of the previous studies, it is can be deduced that 4H-8-MQL could probably be further hydrogenated to form 10H-8-MQL if there were enough effective active sites in 8-MQL hydrogenation. Hence, another dose of fresh catalyst was introduced to the reaction mixture after complete 8-MQL was converted to 4H-8-MQL. The result has been presented in Fig. 3. 4H-8-MQL was consumed rapidly as soon as the reaction started. Finally, 10H-8-MQL with a yield of 100% was obtained. The results confirmed that the absence of 10H-8-MQL in 8-MQL hydrogenation is attributed to the catalyst poisoning caused by strong adsorption of 8-MQL occurred in the process of 8-MQL to 4H-8-MQL. However, it is believed that Ru/Al2O3 is essentially capable of hydrogenation of 8-MQL to form 10H-8-MQL. This assumption was confirmed by adding different dosage proportion of Ru/Al2O3 in the range of 4 wt% to 20 wt% for 8-MQL hydrogenation at 160 °C and 7 MPa. The hydrogen uptake curves vs. reaction time have been displayed in Fig. 4.
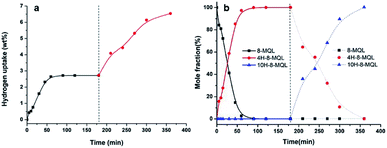 |
| Fig. 3 Hydrogenation of 8-MQL at 160 °C and 7 MPa over Ru/Al2O3 (4 g 8-MQL, 0.2 g Ru/Al2O3, 40 ml dioxane, 7 MPa H2, 160 °C). After 180 min of reaction time another 0.1 g of fresh Ru/Al2O3 was introduced. (a) The hydrogen uptake curves for the whole process of 8-MQL hydrogenation, (b) evolutions of 8-MQL and the hydrogenated products during the whole hydrogenation process. | |
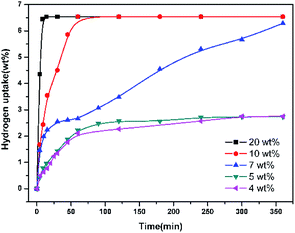 |
| Fig. 4 Influence of catalyst dosage proportions on the hydrogenation of 8-MQL. General reaction conditions: 4 g 8-MQL, 40 ml dioxane as solvents, 160 °C, 7 MPa H2. | |
Table 1 summarizes the conversion and selectivity during 8-MQL hydrogenation with catalysts introduced in different mass ratios. At the catalyst dosage proportion of 4 wt% and 5 wt%, the rapid consumed 8-MQL was totally converted to 4H-8-MQL in the first 120 min. Keeping the reactions for another 4 hours, still almost no 10H-8-MQL was observed. Differently, 4H-8-MQL was gradually converted to form 10H-8-MQL after 30 min when the dosage proportion of Ru/Al2O3 was increased from 5 wt% to 7 wt%. Further increase the dosage proportion to 20 wt%, 100% of 10H-8-MQL can be produced within 15 min. This can be attributed to the more effective active sites given by the catalyst with higher mass ratio, which makes more opportunities for successful adsorption of 4H-8-MQL on catalyst surface and benefits the further hydrogenation of 4H-8-MQL.
Table 1 Conversion and selectivity of 8-MQL hydrogenation with different catalyst dosage proportions at 160 °C and 7 MPa
Test |
Catalyst dosage proportion (wt%) |
Reaction time (h) |
Conversion (%) |
Selectivity (%) |
4H-8-MQL |
10H-8-MQL |
1 |
4 |
2 |
83.4 |
100 |
0 |
5 |
100 |
99.1 |
0.9 |
2 |
5 |
2 |
91.3 |
100 |
0 |
5 |
100 |
99.5 |
0.5 |
3 |
7 |
2 |
100 |
78.2 |
20.9 |
5 |
100 |
23.1 |
76.9 |
4 |
10 |
2 |
100 |
0 |
100 |
5 |
100 |
0 |
100 |
5 |
20 |
2 |
100 |
0 |
100 |
5 |
100 |
0 |
100 |
Fig. 5a and b display the hydrogen uptake curves vs. time of 8-MQL hydrogenation at different temperatures and pressures with the catalyst dosage proportion of 10 wt%, respectively. It is found that complete 10H-8-MQL can be produced within 60 min at 160 °C and 7 MPa. The apparent active energy of 8-MQL consumption was derived to be 75.2 kJ mol−1 based on the first order reaction kinetics model. The products concentration distribution curves of 8-MQL hydrogenation at different temperatures and pressures have been presented in Fig. S2 and S3,† respectively. The consumption of 8-MQL gives rise to a fast accumulation of 4H-8-MQL. Subsequently, the conversion from 4H-8-MQL to 10H-8-MQL starts. Particularly worth mentioning, the production rates of 10H-8-MQL accelerate sharply when the concentration of 4H-8-MQL reaches the maximum, indicating that the 8-MQL hydrogenation undergoes two steps: 8-MQL → 4H-8-MQL and 4H-8-MQL → 10H-8-MQL, and the second step is the rate-controlling step as stated previously.
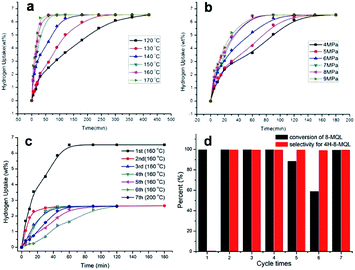 |
| Fig. 5 Time-dependent hydrogen uptake curves of 8-MQL hydrogenation (a) at different temperatures (conditions: 4 g 8-MQL, 0.4 g Ru/Al2O3, 40 ml dioxane, 7 MPa H2) and (b) at different H2 pressures (conditions: 4 g 8-MQL, 0.4 g Ru/Al2O3, 40 ml dioxane, 160 °C) and (c) with the reused Ru/Al2O3 catalyst (conditions: 4 g 8-MQL, 0.4 g Ru/Al2O3, 40 ml dioxane, 160 °C, 7 MPa H2); (d) conversion and selectivity of 8-MQL hydrogenation in 60 min for the 7 times cycles. | |
In order to make an investigation on the catalyst degradation, the same catalyst was reused for 7 times hydrogenation of 8-MQL at 160 °C and 7 MPa. The results have been displayed in Fig. 5c and d. Clearly, full hydrogenation of 8-MQL was observed only in the first hydrogenation catalyzed by the fresh Ru/Al2O3. However, as expected, almost 100% of 4H-8-MQL was obtained and very few 10H-8-MQL was observed in the remaining cycles. In addition, the conversion rates of 8-MQL gradually decreased with the increase of cycle times. This is probably because more effective active sites were covered by strong adsorption of 8-MQL. Besides, the carbon deposits may be also responsible for the decrease of hydrogenation rate after recycling of the catalyst.42 For the first cycle, the active sites of fresh Ru/Al2O3 are enough to catalyze 8-MQL to form 4H-8-MQL and 10H-8-MQL. For the remaining cycles, the new 8-MQL competes for effective active sites, some of which were probably gradually occupied by 8-MQL with the increase of cycle numbers, thus hydrogenation rates decreased and 4H-8-MQL was difficult to be further hydrogenated to form 10H-8-MQL. At the 7th cycle, the temperature was raised from 160 °C to 200 °C, which benefits the hydrogenation rate but still 10H-8-MQL was rarely obtained.
Competitive adsorption shows a huge impact on the reaction rates in 8-MQL hydrogenation. For quinoline substitutes, the adsorption of the reactant and its intermediate(s) was mainly through aromatic ring and nitrogen electron double. The solvents used in hydrogenation of quinoline derivatives play an important role in adsorption equilibrium.39,43 Fig. 6 shows the concentration distributions of intermediates and products in 8-MQL hydrogenation with different solvents. The reactions were conducted at 160 °C and 7 MPa with Ru/Al2O3 dosage proportion of 5 wt%. In the non-protic solvents, dioxane and toluene, almost complete conversion of 8-MQL was found to form 4H-8-MQL with only a trace of 10H-8-MQL produced after 240 min. However, the conversion from 4H-8-MQL to 10H-8-MQL was observed in 120 min with ethanol as solvent in our experiment. A reason might be due to the hydrogen bonds formed between hydroxyl and N-heterocycle of 8-MQL,15 which weakens the strong adsorption of 8-MQL on the active sites and benefits the adsorption of 4H-8-MQL. For the base solvent, N,N-isopropylethylamine, the steric hindrance produced by the amine and its electronic interaction with the catalyst active sites probably avoided the strong adsorption of 8-MQL,43 thus 100% 10H-8-MQL can be obtained in 240 min over Ru/Al2O3 in the presence of N,N-diisopropylethylamine (10 ml) and dioxane (30 ml) as solvent.
 |
| Fig. 6 The effects of solvents on hydrogenation of 8-MQL over Ru/Al2O3: (a) dioxane (40 ml), (b) toluene (40 ml), (c) ethanol (40 ml), (d) N,N-diisopropylethylamine (10 ml) + dioxane (30 ml). General reaction conditions: 4 g 8-MQL, 0.2 g Ru/Al2O3, 7 MPa H2, 160 °C. | |
Adsorption of 8-MQL and 4H-8-MQL on Ru(0 0 1) surface
The geometries of 8-MQL and 4H-8-MQL were optimized by DFT calculations using Material Studio Dmol.3 The electronic charges of N-heteroatom in 8-MQL and 4H-8-MQL were −0.158 and −0.124 calculated by Hirshfeld method as displayed in Fig. 7a. The adsorption geometries of 8-MQL and 4H-8MQL were also optimized as shown in Fig. 7b. Kinds of possible adsorption geometries of 8-MQL were investigated. It is found that the optimized adsorption geometry of 8-MQL kept the two rings aligned parallel to the surface at a Ru–N distance of 2.150 Å with the adsorption energy of 1.8 eV. Preferential hydrogenation of 8-MQL occurs in N-heterocycle in the view of large amount of 1,2,3,4-4H-8-MQL formed in hydrogenation. It is can be explained by the strong coordination interaction of N atom to Ru surface. Two types of geometries of 4H-8-MQL adsorbed on Ru(001) were optimized. Its aromatic ring aligned parallel to the surface was recorded as 4H-8-MQL-p and the aromatic ring was positioned inclined to the Ru surface recorded as 4H-8-MQL-i. The distance between N atom and the nearest Ru atom for 4H-8-MQL-p and 4H-8-MQL-i were 2.605 Å with the adsorption energy of 0.6 eV and 2.657 Å with the adsorption energy of 0.4 eV, respectively. Obviously, 4H-8-MQL-p exhibited a stronger adsorption to 4H-8-MQL-i. This suggests that the adsorption of 4H-8-MQL was mainly via configuration 4H-8-MQL-p, which can be attributed to the π-coordination of phenyl at Ru surface.44
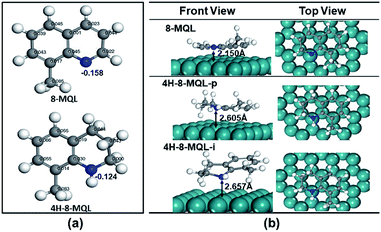 |
| Fig. 7 (a) The atomic charges distributions of 8-MQL and 4H-8-MQL; (b) the optimized adsorption geometries of 8-MQL and 4H-8-MQL over Ru(0 0 1) surface with showing the distance between the N atom and the nearest Ru surface atom. Green: Ru atoms, blue: N, gray: C, white: H. | |
Scheme 2 summarized the conversion and selectivity in hydrogenation of 4H-8-MQL and 8-MQL with reused catalysts. With more electronegativity of the N atom, basic 8-MQL is easier to adsorb on the metal surface by coordination and occupy the acid sites on the support with higher adsorption energy. 4H-8-MQL can be hydrogenated to form 10H-8-MQL with reused Ru/Al2O3 in 3 cycles, indicating that 4H-8-MQL was not responsible for poisoning the catalyst. For the process of 8-MQL hydrogenation, the occupied acid sites on the supported by 8-MQL prevent the 4H-8-MQL from adsorbing and being active. Consequently, 10H-8-MQL was rarely produced with limited catalyst active sites. Increase of the catalyst dosage proportion was benefit of the formation of 10H-8-MQL. However, the new added 8-MQL competes for effective active sites, some of which were probably gradually occupied by 8-MQL with the increase of cycle numbers, thus very little 10H-8-MQL was obtained in the remaining cycles. It is noted that the adsorption energies of the aromatic molecules are involved with the adsorption geometries, activated sites and adsorption sites. Nevertheless, the adsorption of QL substitutes benefits from the electronic charges of N atom, which leads to the strong interaction with the catalyst surface.
 |
| Scheme 2 Summary of catalyst cycles in hydrogenation of 4H-8-MQL and 8-MQL under designed conditions. | |
Experimental
Materials
8-MQL was provided from Alligator Reagent, which was further purified by vacuum distillation. Commercial 5 wt% Ru/Al2O3 catalyst was supplied by Shanxi Kaida Chemical Engineering Company Limited. Sinopharm Chemical Reagent Company Limited supplied 1,4-dioxane, ethanol and toluene. Energy Chemical Company provided N,N-diisopropylethylamine. All solvents and catalysts were used as received. Ultra-high purity of H2 and Ar were provided by Sichuan Ally High-Tech Company. All liquid samples taken from reactors during experiments were regularly detected by Gas Chromatography and Mass Spectrometry (Agilent 7890/5975C, GCMS) to determine the composition. The samples diluted by hexane were carried by ultra-high purity He at a flow rate of 1.5 ml min−1 into the chromatographic column (HP-5, 30 m × 320 μm × 0.25 μm). The injection temperature was 300 °C and split ratio was 1
:
100. The oven temperature started at 90 °C, then increased to 220 °C by 12 °C min−1 subsequently and kept 220 °C for 1 min. Nuclear magnetic resonance (Bruker 400, NMR) was applied to determine the structure of 4H-8-MQL produced in 8-MQL hydrogenation.
Hydrogenation of 8-MQL and 4H-8-MQL
Hydrogenation process was carried out at a 600 ml stainless steel batch reactor (Parr 4568). After the reactants were loaded, the reactor was sealed and flushed with hydrogen to remove air for 4 times. Then the reactor was heated to the designed temperature and pressurized to the designed pressure. The pressure kept unchanged over the entire experiment by adding hydrogen continuously. The reaction time was recorded as zero when the magnetic stirring was started with a speed of 600 rpm. The liquid samples were taken periodically and analyzed by GCMS.
DFT calculations
The geometry configurations of 8-MQL and 4H-8MQL were optimized by the software of Material Studio DMol.3 The double numerical plus polarization (DNP) was applied to analyze valence electron orbitals.45,46 Perdew–Wang-91 (PW91) was used to calculate nonlocal exchange and interrelation energies based on the generalized gradient approximation (GGA).47 The charges of N-heteroatom in 8-MQL and 4H-8-MQL were calculated by Hirshfeld method.48 The Ru(0 0 1) surface with a 5 × 5 supercell and three Ru layers with 20 Å vacuum region was built. The adsorption geometries of 8-MQL and 4H-8-MQL was optimized by stabilizing the last layer of Ru atoms in the supercell and relaxing the molecule on the top two layers of Ru(0 0 1). The adsorption energy was calculated by the Vienna Ab initio Simulation Package (VASP) according to the equation below:
Eadsorption = Esurface + Emolecule − Esurface–molecule |
The Esurface, Emolecule and Esurface–molecule were the energy of the surface, the energy of absorbed molecule and the adsorption energy of the system. A plane wave basis set with a cutoff energy of 400 eV was used to solve the Kohn–Sham equation and the electron–ion interactions were described by the projector augmented wave (PAW) method.49 The Brillouin zone was sampled within a 2 × 2 × 1 Monkhorst–Pack k-point mesh. Electron smearing was employed by using the Methfessel–Paxton technique with a width of 0.2 eV to minimize the errors in the Hellmann–Feynman forces. Structural optimizations were performed until the total energy of the system was converged to less than 10−3 eV.
Conclusions
4H-QLs are formed as the main products in hydrogenation of QLs under mild conditions in general. This was explained mostly by the irreversible adsorption of QL and/or 4H-QL on the catalyst surface. The particular research on the adsorption behaviors of QLs and 4H-QLs have been rarely reported. In our work, it is demonstrated that 4H-8-MQL is not responsible for the catalyst poisoning. The competitive adsorption behaviors of 8-MQL and 4H-8-MQL on Ru/Al2O3 was compared by a series of hydrogenation reactions and DFT calculations. The adsorption geometries and adsorption energies of 8-MQL and 4H-8-MQL were confirmed. It is found 8-MQL is easier to adsorb on the catalyst active sites by the interaction of N atom and Ru atoms compared with 4H-8-MQL. Hydrogenation of 8-MQL in mild conditions mainly generates 4H-8-MQL. It is probably because of the strong adsorption of 8-MQL, which occupies most of the active sites on the support and metal active sites. Fully hydrogenated product can be detected by increasing the catalyst dosage proportion of Ru/Al2O3. In addition, the production of 10H-8-MQL can be promoted by introducing a protic solvent or Lewis base. The selectivity to 4H-8-MQL or 10H-8-MQL is related with the competitive adsorption between 8-MQL and 4H-8-MQL. Increasing the metal dispersion and the amount of acid sites on the supported is probably another way to benefit the formation of 10H-8-MQL in 8-MQL hydrogenation.
Conflicts of interest
There are no conflicts to declare.
Acknowledgements
The authors gratefully acknowledge the financial support from the National Key Research and Development Program of China (No. 2018YFB1502903), the National Natural Science Foundation of China (No. 21603195 and No. 21875225), the Zhejiang Provincial Natural Science Foundation of China (No. LGG20B030001), the Fundamental Research Funds for Central Universities (CUGL170405 and CUG180604), Major Project of Technical Innovation of Hubei Province (No. 2019AAA163).
Notes and references
- F. Sotoodeh, B. J. M. Huber and K. J. Smith, Int. J. Hydrogen Energy, 2012, 37, 2715–2722 CrossRef CAS.
- A. M. Maj, I. Suisse, C. Hardouin and F. Agbossou-Niedercorn, Tetrahedron, 2013, 69, 9322–9328 CrossRef CAS.
- M. Campanati, M. Casagrande, I. Fagiolino, M. Lenarda, L. Storaro, M. Battagliarin and A. Vaccari, J. Mol. Catal. A: Chem., 2002, 184, 267–272 CrossRef CAS.
- T. Ben Issa, C. Ben Ali Hassine, H. Ghalla, H. Barhoumi and L. Benhamada, J. Mol. Struct., 2018, 1162, 71–80 CrossRef CAS.
- V. Sridharan, P. A. Suryavanshi and J. C. Menendez, Chem. Rev., 2011, 111, 7157–7259 CrossRef CAS PubMed.
- D. Ventura-Espinosa, A. Marza-Beltran and J. A. Mata, Chem.–Eur. J., 2016, 22, 17758–17766 CrossRef CAS PubMed.
- P. T. Aakko-Saksa, C. Cook, J. Kiviaho and T. Repo, J. Power Sources, 2018, 396, 803–823 CrossRef CAS.
- Y. Wu, Z. Chen, W. C. Cheong, C. Zhang, L. Zheng, W. Yan, R. Yu, C. Chen and Y. Li, Chem. Sci., 2019, 10, 5345–5352 RSC.
- C. H. Yang, X. Chen, H. Li, W. Wei, Z. Yang and J. Chang, Chem. Commun., 2018, 54, 8622–8625 RSC.
- D. M. Zhu, H. B. Jiang, L. Zhang, X. L. Zheng, H. Y. Fu, M. L. Yuan, H. Chen and R. X. Li, ChemCatChem, 2014, 6, 2954–2960 CrossRef CAS.
- X. Qiao, M. El-Shahat, B. Ullah, Z. Bao, H. Xing, L. Xiao, Q. Ren and Z. Zhang, Tetrahedron Lett., 2017, 58, 2050–2053 CrossRef CAS.
- M. G. Manas, L. S. Sharninghausen, E. Lin and R. H. Crabtree, J. Organomet. Chem., 2015, 792, 184–189 CrossRef CAS.
- P. Ryabchuk, A. Agapova, C. Kreyenschulte, H. Lund, H. Junge, K. Junge and M. Beller, Chem. Commun., 2019, 55, 4969–4972 RSC.
- F. Fache and O. Piva, Synlett, 2004, 1294–1296, DOI:10.1055/s-2004-825603.
- H. Mao, C. Chen, X. Liao and B. Shi, J. Mol. Catal. A: Chem., 2011, 341, 51–56 CrossRef CAS.
- C. Wan, Y. An, F. Chen, D. Cheng, F. Wu and G. Xu, Int. J. Hydrogen Energy, 2013, 38, 7065–7069 CrossRef CAS.
- M. Campanati, S. Franceschini, O. Piccolo and A. Vaccari, New ways for the full hydrogenation of quinoline in mild conditions, CRC Press-Taylor & Francis Group, Boca Raton, 2005 Search PubMed.
- M. M. Dell'Anna, V. F. Capodiferro, M. Mali, D. Manno, P. Cotugno, A. Monopoli and P. Mastrorilli, Appl. Catal., A, 2014, 481, 89–95 CrossRef.
- Y. Gong, P. Zhang, X. Xu, Y. Li, H. Li and Y. Wang, J. Catal., 2013, 297, 272–280 CrossRef CAS.
- B. Sun, D. Carnevale and G. Süss-Fink, J. Organomet. Chem., 2016, 821, 197–205 CrossRef CAS.
- X. Yu, R. Nie, H. Zhang, X. Lu, D. Zhou and Q. Xia, Microporous Mesoporous Mater., 2018, 256, 10–17 CrossRef CAS.
- H. Bernas, N. Kumar, A. Aho, R. Leino and D. Y. Murzin, Catal. Commun., 2014, 56, 41–44 CrossRef CAS.
- S. Zhang, Z. Xia, T. Ni, Z. Zhang, Y. Ma and Y. Qu, J. Catal., 2018, 359, 101–111 CrossRef CAS.
- F. Chen, A. E. Surkus, L. He, M. M. Pohl, J. Radnik, C. Topf, K. Junge and M. Beller, J. Am. Chem. Soc., 2015, 137, 11718–11724 CrossRef CAS PubMed.
- H. Y. Jiang, S. S. Zhang and B. Sun, Catal. Lett., 2018, 148, 1336–1344 CrossRef CAS.
- X. Yuan, N. Yan, C. Xiao, C. Li, Z. Fei, Z. Cai, Y. Kou and P. J. Dyson, Green Chem., 2010, 12, 228–233 RSC.
- Y. Hu, Y. Yu, Z. Hou, H. Yang, B. Feng, H. Li, Y. Qiao, X. Wang, L. Hua, Z. Pan and X. Zhao, Chem.–Asian J., 2010, 5, 1178–1184 CrossRef CAS PubMed.
- Á. Vivancos, M. Beller and M. Albrecht, ACS Catal., 2017, 8, 17–21 CrossRef.
- R. A. Sánchez-Delgado and E. González, Polyhedron, 1989, 8, 1431–1436 CrossRef.
- R. H. Fish, A. D. Thormodsen and G. A. Cremer, J. Am. Chem. Soc., 1982, 104, 5234–5237 CrossRef CAS.
- G. Zhu, K. Pang and G. Parkin, J. Am. Chem. Soc., 2008, 130, 1564–1565 CrossRef CAS PubMed.
- R. B. Xu, S. Chakraborty, H. M. Yuan and W. D. Jones, ACS Catal., 2015, 5, 6350–6354 CrossRef CAS.
- I. Sorribes, L. Liu, A. Doménech-Carbó and A. Corma, ACS Catal., 2018, 8, 4545–4557 CrossRef CAS.
- Z. Wei, Y. Chen, J. Wang, D. Su, M. Tang, S. Mao and Y. Wang, ACS Catal., 2016, 6, 5816–5822 CrossRef CAS.
- F. Martinez-Espinar, P. Blondeau, P. Nolis, B. Chaudret, C. Claver, S. Castillón and C. Godard, J. Catal., 2017, 354, 113–127 CrossRef CAS.
- Y. P. Sun, H. Y. Fu, D. l. Zhang, R.-X. Li, H. Chen and X.-J. Li, Catal. Commun., 2010, 12, 188–192 CrossRef CAS.
- L. M. Kustov, A. L. Tarasov and B. P. Tarasov, Int. J. Hydrogen Energy, 2013, 38, 5713–5716 CrossRef CAS.
- R. M. Zhang, G. Y. Fan, C. Li, Y. Y. Wang, R. X. Li, H. Chen and X. J. Li, Acta Phys.-Chim. Sin., 2008, 24, 965–970 CAS.
- M. C. M. Campanati, I. Fagiolino, M. Lenarda, L. Storaro, M. Battagliarin and A. Vaccari, J. Mol. Catal. A: Chem., 2002, 184, 6 CrossRef.
- G. Y. Fan and J. Wu, Catal. Commun., 2013, 31, 81–85 CrossRef CAS.
- F. A. K. Bing Sun, A. Vallat and G. Süss-Fink, Appl. Catal., A, 2013, 467, 5 Search PubMed.
- B. F. M. F. Williams, A. Jentys, C. Breitkopf, J. A. R. van Veen and J. A. Lercher, J. Phys. Chem. C, 2010, 114, 10 Search PubMed.
- A. V. M. Campanati and O. Piccolo, J. Mol. Catal. A: Chem., 2002, 179, 6 CrossRef.
- I. Favier, S. Massou, E. Teuma, K. Philippot, B. Chaudret and M. Gomez, Chem. Commun., 2008, 3296–3298, 10.1039/b804402c.
- F. W. Averill and D. E. Ellis, J. Chem. Phys., 1973, 59, 6412–6418 CrossRef CAS.
- A. D. Becke and R. M. Dickson, J. Chem. Phys., 1988, 89, 2993–2997 CrossRef CAS.
- A. D. Becke, Int. J. Quantum Chem., 1985, 27, 10 CrossRef.
- X. Y. Zhou, C. Y. Rong, T. Lu and S. B. Liu, Acta Phys.-Chim. Sin., 2014, 30, 2055–2062 CAS.
- G. Kresse and D. Joubert, Phys. Rev. B: Condens. Matter Mater. Phys., 1999, 59, 1758–1775 CrossRef CAS.
Footnote |
† Electronic supplementary information (ESI) available. See DOI: 10.1039/d0ra01277g |
|
This journal is © The Royal Society of Chemistry 2020 |
Click here to see how this site uses Cookies. View our privacy policy here.