DOI:
10.1039/D4RA05102E
(Review Article)
RSC Adv., 2024,
14, 30566-30581
Recent advances in noble metal-based catalysts for CO oxidation
Received
15th July 2024
, Accepted 20th September 2024
First published on 24th September 2024
Abstract
Carbon monoxide, one of the major pollutants in the air, is mainly produced due to the incomplete combustion of fossil fuels such as coal and oil. Among all the techniques developed for removing CO, catalytic oxidation has been considered one of the most effective approaches, and the commonly used catalysts include metal oxides and noble metals. Noble metal attracted extensive attention due to its good catalytic performance at low temperatures and high resistance to poisoning. The review summarizes the recent advances of noble metals including Pt, Pd, Au, Ru, Rh, and Ir in CO oxidation. The effect of support, metal doping, the particle size of noble metals, and the hydroxyl groups on CO oxidation is discussed. Besides, the metal-support interaction on the stability and activity is also involved in this review. Finally, the challenges and opportunities of supported noble metal catalysts in practical CO oxidation are proposed.
1 Introduction
Industrial exhaust and automobile exhaust have become the primary sources of atmospheric pollution, and CO is one of the most abundant components in exhaust gas.1–6 CO is mainly produced from the incomplete combustion of fuel in oxygen-deficient conditions. It was reported that 90% of the CO emission in urban areas is from motor vehicles. CO is also derived to numerous environmental and health issues. For example, when the CO concentration in the environment reaches 0.1% above, humans may be poisoned and die within minutes. Therefore, it is essential to find an effective method to purify CO. Among all the techniques, catalytic oxidation is one of the simple, inexpensive, and effective methods to remove CO. Besides, CO oxidation was considered an important probe reaction to investigate the structure and metal-support interaction of the supported catalysts. In the past few decades, transition metal oxides and noble metal catalysts have been developed for the catalytic purification of CO. Among them, noble metal catalysts received much attention due to their excellent low-temperature CO oxidation activity.7–11 For example, it was reported that the supported Au nanoparticles could oxidize CO even at −70 °C, though the bulk Au is generally inert.12 Pt and Pd have been extensively applied as the main components of three-way catalysts to purify CO in diesel vehicle exhaust. Apart from the purification of CO emitted from the industrial exhaust and automobile exhaust, the selective removal of trace amount of CO in H2-rich conditions is vital for H2 fuel cell, as the H2 produced from methane streaming and water gas shift reaction usually contains a low concentration of CO, which deactivated the Pt electrode in the proton-exchange membrane fuel cells. In this scenario, the key was to fully remove CO without H2 oxidation. Various catalyst including both noble and non-noble catalysts have been developed for preferential CO oxidation. It was recently reported that single-atom catalysts showed decent preferential CO activity, which might be due to the relatively weak H2 activation ability. On the other hand, the stability of the single-atom catalysts remains challenging. The coordination unsaturated single-atom noble metal species tend to aggregate into nanoparticles under reductive conditions. A knowledge gas on how to develop a catalyst with high stability, activity and selectivity for CO preferential CO still existed. The noble metal species were generally supported on metal oxides in those catalysts. Apart from the intrinsic properties of noble metal, the characteristics of the metal oxides also significantly affected the CO catalytic oxidation performance.
This paper reviewed the recent progress of supported noble metal catalysts (including Pt, Pd, Au, Ru, Rh, and Ir.) in CO catalytic oxidation. Although some reviews have summarized the progress of supported catalysts in CO oxidation, a comprehensive review of the recent advances (particularly past three years) of noble metal-based catalysts in CO oxidation is still limited Table 1. This review critically reviewed the characteristics of different supported noble metal catalysts and the key factors affecting CO catalytic oxidation are discussed, including catalyst carrier, dopant, metal particle size, hydroxyl group, etc. This review aims to provide an overview of the practical application of noble metal catalysts in CO catalytic purification Fig. 1.
Table 1 The CO oxidation performance of parts of noble metal-based catalysts reported in the literature
Catalysts |
Reaction conditions |
CO conversion (%) |
Temperature (°C) |
Ref. |
Temperature (°C) |
WHSV (mL g−1 h−1) |
CO (ppm) |
O2 (%) |
Gaseous hourly space velocity (h−1). |
0.5%Ptn/ND@G |
30–200 |
12 000 |
10 000 |
1 |
100 |
120 |
13 |
Pt/TiO2 |
60–160 |
47 900 |
8000 |
16 |
100 |
100 |
14 |
4.5%Pt/CeO2 |
50–500 |
60 000 |
1000 |
10 |
50 |
85 |
15 |
CoOx/Pt/CeO2 |
−50–85 |
75 000 |
10 000 |
20 |
100 |
20 |
16 |
Pt-CD/Al2O3 |
−80–80 |
18 000 |
10 000 |
1 |
100 |
−20 |
7 |
1%Pt-2%Bi/SiO2 |
20–160 |
134 000 |
10 000 |
20 |
100 |
100 |
17 |
1%Pt/SiO2 |
20–160 |
134 000 |
10 000 |
20 |
100 |
150 |
17 |
0.1%Pt/Sb–SnO2 |
100–450 |
120 000 |
10 000 |
1 |
100 |
240 |
18 |
0.1%Pt/SnO2 |
100–450 |
120 000 |
10 000 |
1 |
100 |
270 |
18 |
0.1%Pt/SiO2 |
100–450 |
120 000 |
10 000 |
1 |
100 |
270 |
18 |
Pt/CeO2 |
50–250 |
80 000 |
6000 |
0.6 |
100 |
180 |
19 |
Pt/Nb2O5 |
50–250 |
80 000 |
6000 |
0.6 |
14.9 |
180 |
19 |
Pd/CeO2(111) |
50–300 |
60 000 |
20 000 |
2 |
100 |
150 |
20 |
Pd/CeO2(100) |
50–300 |
60 000 |
20 000 |
2 |
100 |
200 |
20 |
Pd/CeO2–SnO2-800 |
−10–450 |
240 000a |
2000 |
1 |
50 |
45 |
21 |
Pd/CeO2-800 |
−10–450 |
240 000a |
2000 |
1 |
50 |
60 |
21 |
Pd/Ce0.3Zr0.7O2 |
100–300 |
600 000 |
10 000 |
0.5 |
50 |
134 |
10 |
Pd/Ce0.7Zr0.3O2 |
100–300 |
600 000 |
10 000 |
0.5 |
50 |
163 |
10 |
Pd1@HEFO |
50–300 |
40 000 |
10 000 |
20 |
100 |
170 |
22 |
Pd@CeO2 |
50–300 |
40 000 |
10 000 |
20 |
100 |
253 |
22 |
Pd/α-Fe2O3 |
−50–250 |
15 000 |
10 000 |
20 |
100 |
120 |
23 |
Pd/γ-Fe2O3 |
−50–250 |
15 000 |
10 000 |
20 |
100 |
80 |
23 |
Pd/MnOx–CeO2 |
50–450 |
40 000a |
20 000 |
5 |
100 |
50 |
24 |
Co0.24Pd0.76 |
25–200 |
60 000 |
10 000 |
4 |
100 |
110 |
25 |
Au3Pd7/TiO2 |
50–250 |
48 000a |
1000 |
10 |
50 |
139 |
26 |
PdFe/CeO2-HT |
25–160 |
120 000 |
10 000 |
1 |
100 |
125 |
27 |
Pd-SBA-15 |
40–180 |
30 000 |
40 000 |
20 |
100 |
115 |
28 |
Au–Rh/NT |
0–300 |
150 000 |
10 000 |
1 |
100 |
68 |
29 |
Au/NT |
0–300 |
150 000 |
10 000 |
1 |
100 |
179 |
29 |
CeOx@Au/SiO2 |
50–450 |
16 000 |
20 000 |
16 |
100 |
180 |
30 |
Au/SiO2 |
50–450 |
16 000 |
20 000 |
16 |
100 |
340 |
30 |
Au/La(6.6)/HAP |
40–120 |
60 000 |
10 000 |
1 |
100 |
60 |
31 |
Au/HAP |
40–120 |
60 000 |
10 000 |
1 |
80 |
60 |
31 |
Au/CuO |
0–250 |
15 000 |
10 000 |
21 |
100 |
55 |
32 |
Au/Cu2O |
0–250 |
15 000 |
10 000 |
21 |
100 |
200 |
32 |
Ru–ZrO2 |
80–200 |
12 000a |
10 000 |
0.5 |
95 |
100 |
11 |
Ru–TiO2 |
80–200 |
12 000a |
10 000 |
0.5 |
90 |
100 |
11 |
5Ru/CeO2(110) |
25–425 |
36 000 |
10 000 |
20 |
10 |
71 |
33 |
5Ru/CeO2(111) |
25–425 |
36 000 |
10 000 |
20 |
10 |
99 |
33 |
5Ru/CeO2 (100) |
25–425 |
36 000 |
10 000 |
20 |
10 |
96 |
33 |
Cu0.2Ru0.8/γ-Al2O3 |
80–160 |
20 000 |
10 000 |
1 |
50 |
109 |
34 |
Ru/γ-Al2O3 |
80–160 |
20 000 |
10 000 |
1 |
50 |
155 |
34 |
Rh/Ce-MCM-41 |
100–350 |
75 000 |
10 000 |
1 |
100 |
167 |
35 |
Rh/MCM-41 |
100–350 |
75 000 |
10 000 |
1 |
78 |
270 |
35 |
Rh1/ZnO-nw |
150–400 |
40 000 |
10 000 |
1 |
100 |
210 |
8 |
3%Ir/BFA |
0–220 |
20 000 |
10 000 |
1 |
100 |
20 |
9 |
2Fe/Ir/SiO2-350 |
20–220 |
18 000 |
10 000 |
1 |
100 |
80 |
36 |
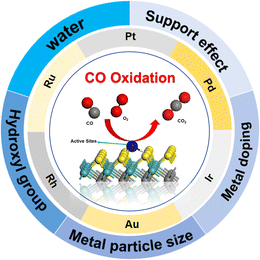 |
| Fig. 1 The overview of the noble-based catalysts in CO oxidation. | |
The conventional methods to prepare noble-metal based catalysts including coprecipitation, impregnation, hydrothermal and et al. For example, it was reported that atomically dispersed Pt1/FeOx was fabricated by co-precipitation via finely controlling the Pt loading, pH value and temperature for CO oxidation.37 Similarly, Au single-atom and nanoparticle species, isolated Ir species dispersed on FeOx were also fabricated via the coprecipitation for CO oxidation,38 in which CO and O2 molecules reacted in the interface of sites through a Langmuir–Hinshelwood mechanism. Apart from coprecipitation, other approaches were also applied. Via optimizing the solution pH during the synthesis procedure, atomically dispersed Pt species was anchored on TiO2 and displayed higher CO oxidation performance than the nanoparticle counterparts.39 Zhang and co-workers anchored isolated Pt atoms within the pore structure of Al2O3 via a Pluronic P-123 assisted sol–gel approach for CO oxidation.40 Other unconventional methods such photochemical reduction, flame spray pyrolysis, and electrochemical deposition were also reported for CO oxidation.41–43 The methods to prepare noble-metal based catalysts for CO oxidation is not the focus of the manuscript. The following section will be discussed based on the type of noble metals.
2 Pt-based catalyst
Pt-based catalysts were extensively studied in CO oxidation and have been considered as one of the most active noble metals for CO catalytic oxidation.44–50 The following section will summarize the recent progress of Pt-based catalysts in CO oxidation. Particular effort was given to the structure–performance relationship investigation, including the effect of Pt particle size, metal doping, the role of the hydroxyl group, and the support effect.51–61
2.1 Effect of metal particle size
The particle size of Pt significantly affected the activity of CO catalytic oxidation. It is still controversial which one was more active in CO oxidation among Pt single-atom, nanoclusters, and nanoparticles. Beniya et al. investigated the relationship between CO oxidation activity and the size of Pt species and successfully established the relationship of CO oxidation activity as a function of Pt sizes on TiO2.62 The ratio of metal to cationic Pt atoms is linearly correlated to the CO oxidation activity. Jia et al. loaded Pt single atoms (Pt1), clusters (Ptn), and nanoparticles (Ptp) onto nanodiamond/graphene (ND@G) composite carriers and explored the structure of the active sites of the catalysts for the oxidation of CO.63 Due to the weak CO adsorption, strong O2 dissociative adsorption of Pt clusters, and the near 100% Pt dispersion, the fully exposed Pt cluster (0.5 wt%) loaded on ND@G possessed optimal low-temperature CO oxidation activity (Fig. 2a). Dessal et al. investigated the structural stability of Pt/γ-Al2O3 single-atom catalysts for CO oxidation and their catalytic properties.64 It was indicated that isolated Pt ions gradually aggregated to form partially oxidized Pt clusters during the reaction. Since clusters had better activity than isolated atoms, the formation of Pt clusters during the reaction process or after hydrogen treatment increased the CO oxidation activity of Pt species. Cai et al. showed that the Pt species on Pt/TiO2 catalyst had higher dispersion and smaller Pt particle size after calcination pretreatment of TiO2 at 700 °C.14 The reduced adsorption capacity of the catalyst for CO and CO2 allowed the complete conversion of CO at 100 °C, which was 40 °C lower than that of the samples without calcination pretreatment. The concentration of noble metal on the catalyst surface also significantly affected the CO oxidation activity. By increasing Pt loading, Maurer et al. increased the surface noble metal concentration (SNMC) of the Pt/CeO2 catalyst by four times, thereby reducing the distance between Pt species. The high surface noble metal concentration promoted the formation of active Pt clusters at low temperatures. It increased the reaction rate of CO oxidation, which further proved that the surface noble metal concentration was the key to affecting the low-temperature activity of the Pt/CeO2 catalyst (Fig. 2b).15 Chen and co-workers demonstrated that CO-rich conditions induced the reconstruction of Pt species from Pt1(CO) to Pt8(CO)9 complex using first-principles investigation.45 Besides, a linear scaling relationship was established between CO2 formation rate and O adsorption energy among single atoms, clusters, and nanocatalysts (Fig. 2c).
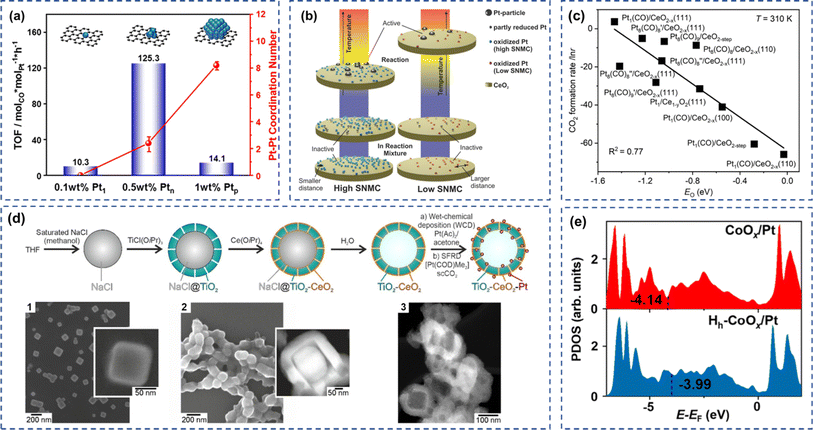 |
| Fig. 2 (a) Relationship between the Pt–Pt shell coordination numbers and their TOF over Pt single, nanocluster, and nanoparticle. Reproduced with permission from ref. 63 Copyright 2022, American Chemical Society. (b) The scheme of cluster formation model under reaction conditions and the dependence of CO oxidation activity on the surface noble metal concentration (SNMC). Reproduced with permission from ref. 15 Copyright 2022, American Chemical Society. (c) Copyright 2024, American Chemical Society. (d)The synthesis of TiO2–CeOx–Pt hollow catalyst by a liquid-phase strategy Reproduced with permission from ref. 44 Copyright 2024, Wiley-VCH GmbH. (e) The projected density of states of Co species in CoOx/Pt(111) and HhCoOx/Pt(111).60 Copyright 2024, American Chemical Society. | |
2.2 Elemental doping
Elemental doping is a conventional method to improve the CO catalytic activity of Pt-based catalysts.65 Wang et al. doped BaO as an additive into Pt/La–Al2O3 catalyst to effectively stabilized the PtOx catalytic sites on the La–Al2O3 surface.66 The catalyst still had almost 100% atomic dispersion after hydrothermal aging at 650 °C, indicating the good stability and sintering resistance of the catalyst. Lee et al. investigated the effect of MnOx doping on the CO oxidation activity of Pt/Al2O3 catalysts by atomic layer deposition (ALD).67 Compared with the unmodified Pt/Al2O3 catalyst, the addition of MnOx improved the durability of the catalysts and inhibited the agglomeration of Pt particles after thermal aging at 1073 K. The modified catalysts generated highly active Pt–MnOx interfacial sites to increase the CO oxidation rate. Song et al. introduced transition metal oxides (MOx, M = Fe, Co, and Ni) into Pt/CeO2 catalysts and investigated the role of transition metal oxides in CO oxidation.16 The variable chemical valence states of Fe and Co-promoted the electron transfer from Pt to MOx, enhancing the carrier's redox properties and the ability to activate oxygen molecules. The stability of the catalysts mainly depended on the ability of the carriers to provide oxygen. CoOx–Pt/CeO2 and NiOx–Pt/CeO2 were highly stable under high humidity conditions due to their ability to reversibly restore the reactive oxygen species consumed by the reaction. CoOx was the optimal choice for improving the CO oxidation performance of Pt/CeO2 catalysts because it could simultaneously enhance the activity and stability of Pt/CeO2. Nan et al. modified the Pt-based catalyst by adding BiOx.17 The strong interaction between BiOx and Pt resulted in PtxBiyOz clusters with excellent sintering resistance in the CO oxidation reaction. The addition of BiOx resulted in the formation of a unique Pt–[O]x–Bi cluster structure on the surface of the catalysts, which allowed the efficient activation and dissociation of oxygen molecules at low temperatures. At the same time, this structure prevented poisoning of Pt species due to CO supersaturation adsorption and efficiently activated CO molecules, thereby reducing the activation energy of CO oxidation. Liebertseder designed a TiO2–CeOx–Pt hollow catalyst by a liquid-phase strategy using NaCl as a template (Fig. 2d).44 The prepared catalyst showed stable performance in the low-temperature CO oxidation.
2.3 Effects of hydroxyl groups
Hydroxyl species played a crucial role in improving the catalytic oxidation of CO over Pt-based catalysts. Chen et al. synthesized the Pt/Al2O3 catalyst by a refined colloidal deposition method with 100% CO conversion at low temperatures.10 Structural characterization combined with theoretical calculations demonstrated that CO adsorbed on the kink sites of Pt(OH)x could react with OH on the platform sites to form CO2, whereas O2 molecules were activated on the terrace sites of Pt(OH)x to regenerate OH groups. The kink and terrace sites of Pt species synergy suppressed the competitive adsorption between CO and O2, thus decreasing the reaction energy barrier for CO oxidation. Similarly, they also tested the activity of the Pt/Al2O3 in CO catalytic oxidation under hydrogen-rich conditions.68 The Pt/Al2O3 catalyst possessed the active sites with both Pt(OH)x and metallic Pt, weakening the competitive adsorption between CO and H2 and facilitating O2 activation. The catalyst exhibited 100% CO conversion and 100% CO2 selectivity in the temperature range of −30 to 120 °C. Chai et al. reported that water molecules on Pt(111) affected the low-temperature oxidation of CO under near-ambient conditions.1 The results showed that H2O was activated on Pt(111) to generate the key intermediates (the reversibly adsorbed OH groups and the irreversibly adsorbed COOH groups), which significantly increased the CO oxidation in the temperature range of 290–320 K. Liu et al. investigated the surface chemistry of ZnO/Pt(111) catalysts for CO oxidation.69 The reaction rate of ZnO/Pt(111) was 30% higher than that of Pt(111) in the range from room temperature to 410 K. Meanwhile, the carboxyl groups formed at low temperature, and the OH species located at the Pt/ZnO acted as the intermediates and co-catalysts respectively to promote the CO oxidation due to the synergistic interaction between ZnO and Pt. Apart from experimental investigation, theoretical calculations were also applied to study the effect of OH groups on CO oxidation.60 Fig. 2e showed that the d-band center of Co is shifted from −4.14 to −3.99 eV in the presence of the OH group, indicating the activity enhancement of Co species by OH modification.
2.4 Support effect
The catalytic activity of Pt-based catalysts in CO oxidation is also related to the support. Bae et al. compared the catalytic performance of Pt/Sb–SnO2, Pt/SnO2, and Pt/SiO2 catalysts with the same Pt loading in CO oxidation.18 It was discovered that Pt/Sb–SnO2 showed the best catalytic activity and high durability. Further studies demonstrated that Pt/Sb–SnO2 had the most abundant surface oxygen and was hard to form surface carbonates during the reaction process, thus promoting the CO oxidation reaction. Cai et al. prepared Pt/CoOx by dispersing Pt on CoOx nanoclusters via the selective atomic layer deposition method. The highly dispersed Pt maximized the interface and enhanced the CO-PROX activity of Pt/CoOx, resulting in almost 100% CO conversion and CO2 selectivity at room temperature of Pt/CoOx.70 Compared with conventional Pt/Co3O4, Pt/CoOx exhibited weaker adsorption of CO and lower O2 activation energy barriers, which indicated that different preparation methods could significantly affect the state of the active sites on the support, thus in turn affecting the catalytic performance. Wang et al. compared the CO oxidation performance of Pt/CeO2 and Pt/Nb2O5 catalysts.19 The Pt/CeO2 catalysts showed higher activity than the Pt/Nb2O5 catalysts for CO oxidation due to the easier activation of oxygen on CeO2, which has abundant oxygen vacancies.
3 Pd-based catalysts
Apart from Pt, Pd-based catalysts were also extensively studied in CO oxidation.71–74 The influence of the support, bimetallic doping, and Pd particle size will be summarized in the following section.
3.1 Support effect
The support also markedly affected the catalytic performance of Pd-based catalysts. Spezzati et al. demonstrated that the different catalytic activity in CO oxidation of Pd/CeO2(111) and Pd/CeO2(100) was mainly attributed to the difference in free energy barriers.20 Slavinskaya et al. prepared Pd/CeO2, Pd/SnO2, and Pd/CeO2–SnO2 catalysts and compared their catalytic activity in CO oxidation.21 The results indicated that Pd/CeO2–SnO2 had more active lattice oxygen and more thermally stable PdOx(s)/Pd–O–Ce(s) clusters, which resulted in relatively better low-temperature CO oxidation activity and excellent thermal stability. Li et al. investigated the effect of Pd-support interactions on CO oxidation performance for Pd/CeO2 and Pd/CeO2–ZrO2 catalysts.10 As shown in Fig. 3a, the interactions between Pd and the support were attributed to the surface reactive oxygen species of the support. Pd existed in an ionic state on Pd/CeO2 but in a metallic state on Pd/Ce0.3Zr0.7O2. Although the dispersion of Pd was higher in the Pd/CeO2, the weaker adsorption of CO by Pd in the ionic state resulted in lower TOFs. In addition, further studies demonstrated that the pretreatment conditions could dramatically change the Pd-support interactions. The hydrothermal-aged Pd/CeO2 showed weak Pd–CeO2 interactions and poor catalytic performance, while the hydrothermal-aged Pd/Ce0.7Zr0.3O2 exhibited higher Pd dispersion and excellent activity. Xu et al. synthesized a sinter-resistant Pd single-atom catalyst Pd1@HEFO by a combination of mechanical milling and high-temperature calcination method.22 The results of characterizations indicated that the Pd atoms were doped into the crystal lattice of HEFO through the formation of stable Pd–O–M (M = Ce/Zr/La) bonds. Compared with conventional Pd@CeO2 catalysts, Pd1@HEFO showed higher reducibility of lattice oxygen and had more stable Pd–O–M species, resulting in superior CO oxidation activity and better thermal stability. Wang et al. prepared Pd/Fe2O3 catalysts with different Fe2O3 crystal types by deposition precipitation method and found that Pd/γ-Fe2O3 showed better catalytic performance than Pd/α-Fe2O3 in CO oxidation.23 Further characterization showed that the strong interaction between Pd and γ-Fe2O3 increased the concentration of Fe2+, promoted the redox cycle between Fe3+ and Fe2+, and facilitated the activation of oxygen molecules, thus exhibiting higher catalytic activity for CO oxidation. In contrast, when Pd was loaded on α-Fe2O3, the carbonate and bicarbonate species were easily formed on the catalyst surface, which inhibited the oxygen activation process, resulting in lower catalytic activity. Wang et al. investigated the low-temperature CO oxidation activity of Pd-doped MnOx–CeO2 (MC) solid solution catalysts.24 In the process of calcination, highly dispersed PdO that exhibited catalytic activity toward CO oxidation was formed on CeO2 and MC supports. However, Pd2+ on CeO2 would be reduced to Pd0 during CO oxidation, whereas MC can promote the transfer of lattice oxygen and thus stabilize Pd2+. In addition, CO/O2 transient pulse experiments confirmed that MC showed higher reducibility than CeO2 and could facilitate CO oxidation at 50 °C.
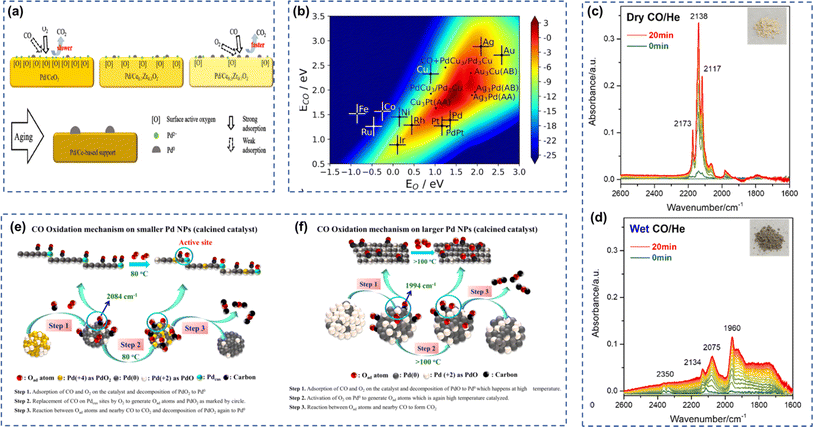 |
| Fig. 3 (a) The scheme of CO oxidation on Pd/CeO2, Pd/Ce0.7Zr0.3O2 and Pd/Ce0.3Zr0.7O2 catalysts. Reproduced with permission from ref. 10 Copyright 2020, American Chemical Society. (b) CO oxidation rate contour plot as a function of the binding energy of O and CO. Reproduced with permission from ref. 75 Copyright 2024, Wiley-VCH GmbH. DRIFTS spectra while flowing (c) CO/He and (d) CO + H2O/He on Pd/FER. Reproduced with permission from ref. 71 Copyright 2023, American Chemical Society. The proposed scheme of CO oxidation on (e) small and (f) large Pd nanoparticles. Reproduced with permission from ref. 28 Copyright 2020, Elsevier. | |
3.2 Bimetallic catalysts
Pd-based bimetallic catalysts are also widely used in CO oxidation reactions.76 Wu et al. investigated the surface evolution of CoPd alloy nanoparticles under CO oxidation reaction and revealed the correlation between its catalytic activity and surface composition.25 The synergistic effect between Pd and CoOx promoted the CO oxidation activity of the bimetallic catalysts, as Co was biased to the nanoparticle surface in the form of CoOx during the CO oxidation reaction, and CO at high temperatures led to the migration of Pd to the surface. Further studies showed that this synergy could be further optimized by adjusting the ratio of Co/Pd, and the results showed that Co0.24Pd0.76 had the best CO conversion at low temperatures. Tofighi and coworkers synthesized bimetallic AuxPdy nanoparticles with different Au
:
Pd ratios and loaded them on TiO2.26 The strong electronic interactions existed between Au and Pd due to interatomic charge transfer and electronic modification in the d-bands of Au and Pd. In this bimetallic catalyst, Pd atoms adsorb and activate O2 molecules, while CO is adsorbed at both Au and Pd sites, and the synergistic interaction between Pd and Au atoms results in the highest catalytic activity in CO oxidation over the Au3Pd7/TiO2 catalyst. Choi et al. studied the influence of hydrothermal treatment on the activity of Pd-based bimetallic (Pd–Fe, Pd–Ni, and Pd–Co) catalysts deposited on CeO2.27 The hydrothermal treatment promoted the dispersion of Pd atoms and enhanced the interactions between Pd atoms and transition metals, which in turn improved the CO oxidation activity, resulting in the PdFe/CeO2-HT catalysts showing the highest catalytic activity. Grabow and co-workers examined the activity of PdCu alloy in CO oxidation.75 As shown in Fig. 3b, the CO oxidation activity was correlated to the binding energy of O and CO. It was predicted that PdCu3 alloys display comparable CO oxidation activity as that of PdPt. The PdCu3 was able to achieve full oxidation of CO below 150 °C even in the presence of H2O.
3.3 Effect of particle size
Soni and coworkers loaded small-sized (about 1 nm) Pd nanoparticles on SBA-15 by a modified deposition precipitation method.28 The readily decomposable high-valent PdOx species were present on the ligand-unsaturated Pd sites (Pdcus) over smaller Pd nanoparticles. The weaker adsorption of CO on the small-sized Pd nanoparticles promoted the low-temperature CO oxidation activity. The CO oxidation mechanism on two different sizes of Pd nanoparticles was illustrated in Fig. 3e and f. Mehar and coworkers investigated the CO oxidation capacity of catalysts prepared by depositing Pd on ordered monolayer AgOx/Ag (111) surfaces to probe the transfer of oxygen from AgOx to Pd and how the size of the Pd clusters affects the oxygen transfer process.77 The results showed that the high oxygenophilicity of Pd induced the transfer of oxygen atoms from AgOx to Pd. The smaller the Pd cluster size, the more efficient the oxygen transfer and the higher the CO oxidation activity. The asymmetric edge sites of the Pd clusters had higher oxygen concentrations, which in turn led to a higher CO oxidation rate near the interface of Pd and AgOx. Liu and co-workers reported that the transformation of Pd nanoclusters to nanoparticles occurred in the gas containing CO and H2O.53 As displayed in Fig. 3c, CO adsorbed on positively charged Pd species were observed when only CO was injected to the in situ cell in DRIFTS. On the other hand, when both CO and H2O were injected, CO adsorbed on metallic Pd were identified indicating the transformation of highly dispersed Pd to nanoparticles (Fig. 3d).
4 Au-based catalysts
Bulk Au with filled d-orbital electrons showed lower activity for O2 activation and therefore displayed lower oxidation activity.78,79 However, when the Au particle downsized to the nanoscale, it showed excellent CO oxidation performance.80–85 Current studies on Au-based catalysts focused on the effect of metal dopants, supported carriers, and water molecules on CO oxidation performance.
4.1 Effect of dopant
Doping components have been justified as an effective strategy to boost the CO oxidation performance of Au-based catalysts. Calzada et al. prepared bimetallic AuRu/TiO2 catalysts by urea deposition precipitation and investigated their synergistic effect in CO oxidation.86 The activity evaluation results indicated that the bimetallic catalysts displayed higher activity than Au/TiO2. The Au–Rh/TiO2 catalysts prepared by Camposeco et al. exhibited superior performance to monometallic catalysts. The results indicated that in the bimetallic system new CO adsorption sites were constructed, thereby improving the performance of the catalyst.29 Wang et al. modified silica-loaded Au nanoparticle catalysts with CeOx nanoparticles.30 The CeOx nanomodification significantly boosted the concentration of Auδ+ on the surface of Au nanoparticles, leading to better activity and stability of CeOx@ Au/SiO2 catalysts than Au/SiO2. Manzorro et al. prepared CeO2-modified Au/Y2O3–ZrO2 catalysts and elaborated that an atomic layer thickness of CeO2 was generated on the surface of Y2O3–ZrO2 microcrystals. This strengthened the interactions between CeO2 and the loaded metal, and improved the CO oxidation activity and stability of the catalysts at high temperatures.87 Boukha et al. investigated the CO oxidation performance of La-modified Au/HAP catalysts under hydrogen-enriched conditions.31 The results showed that Au species existed in the form of Auσ+ and Au+ after La doping. The addition of La boosted the chemisorption of CO and weakened the interaction of the catalyst with H2 and H2O, while the reducibility and oxygen mobility of the catalyst were also enhanced. The catalyst with the highest content of La (Au/La(6.6)/HAP) exhibited a CO conversion of 100% and the widest active temperature range.
4.2 Effects of carriers
The properties of the carrier have been proven to influence the CO oxidation performance of the Au-based catalysts. Mochizuki et al. synthesized Au1/NiO catalysts and investigated the relationship between the surface state of NiO and the stability of Au monoatoms.88 The experimental results indicated that Au monoatoms were more prone to be anchored on the surface of NiO with Ni vacancies than on the original NiO. Au atoms were positively charged on the NiO surface and their charge state depended on the carrier crystal structure. In addition, Au1/NiO displayed high catalytic stability for CO oxidation reactions. Campbell et al. explored the relationship between the CO oxidation activity of Au/TiO2 catalysts and the nature of the titanium dioxide carriers.89 The amorphous TiO2 carriers exhibited better activity than crystalline TiO2 due to the presence of more active sites. Qi et al. deposited Au nanoparticles on Cu2O nanoparticles with different morphologies and investigated the CO oxidation performance of the prepared catalysts under hydrogen-rich and oxygen-rich conditions.32 The Au atoms were mainly adsorbed on the surface of Cu2O, which did not change its initial morphology and the crystal structure. The results also revealed that Au nanoparticles smaller than 10 nm were deposited on the CuO surface with a strong interaction, which boosted the activity of the Au/CuO catalyst. Furthermore, Lin et al. prepared Au-deposited Ta2O5 catalysts with different crystalline structures (hexagonal, rhombohedral, and pyrochlore).90 The results demonstrated that the Au-loaded hexagonal Ta2O5 (TT-Ta2O5) synthesized by the hydrothermal method possessed the highest CO oxidation activity. Further research revealed that the differences in the catalytic activity of CO oxidation were mainly attributed to the differences in oxygen activation and adsorption capacity of CO when Au was loaded on carriers with different crystal structures. Liu and co-workers reported the geometric edge effect on the interface of Au/CeO2 in CO oxidation.81 Au nanoparticles were dispersed on CeO2 with various morphologies including cube, octahedron, and nanorod, among which nanorod CeO2 showed the highest CO oxidation activity due to the unsaturated coordination environment, thus lowering the oxygen formation energy and promoting the CO adsorption (Fig. 4a–f). Similarly, Au nanoparticles were also anchored on ZnO nanorod or nanopyramid for CO oxidation.79 Au loaded on ZnO nanorod showed a lower activation energy, thus displaying a higher CO oxidation activity (Fig. 4g and h).
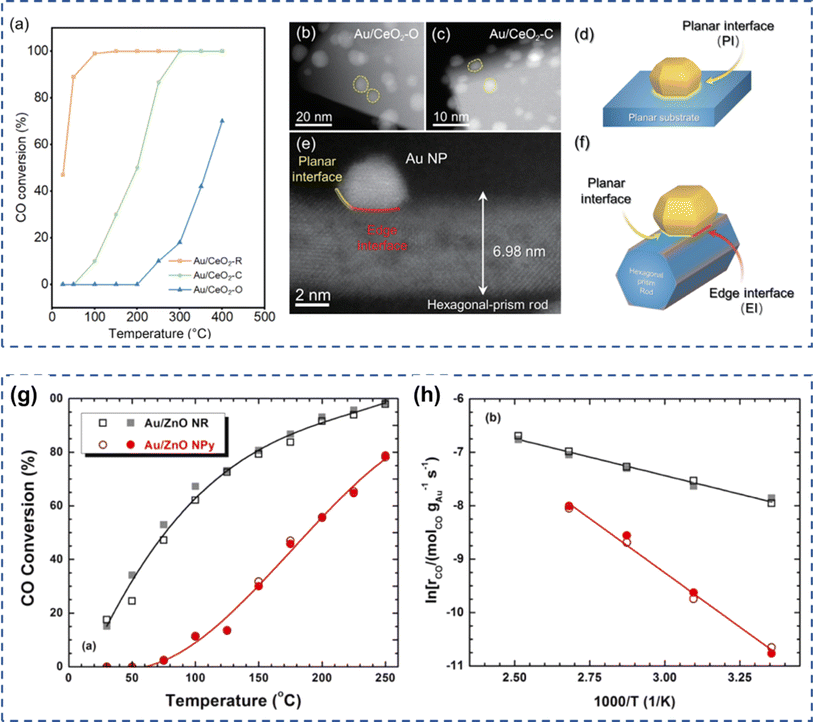 |
| Fig. 4 (a) The CO oxidation performance over Au nanoparticles dispersed on various CeO2. The TEM images of Au dispersed on (b) octahedron, (c) cube, and (e) nanorod. The scheme of (d) planar and (f) edge interface. Reproduced with permission from ref. 81 Copyright 2024, Springer. (g) The activity of CO oxidation and apparent activation (h) energy barrier for Au dispersed on ZnO nanorod and nanopyramid. Reproduced with permission from ref. 79 Copyright 2023, Elsevier. | |
4.3 The effect of water
H2O has a significant effect on the catalytic oxidation activity of CO oxidation. To clarify the role of H2O on CO oxidation performance on Au/TiO2 catalyst at low temperatures, Fujitani et al. first deposited Au nanoparticles on the surface of single-crystal TiO2(110), adsorbed H2O to saturation, and then conducted a temperature-programed desorption analysis.91 Two desorption peaks were observed in the H2O-TPD spectrum: the peak at 370 K was attributed to molecular desorption of H2O, while the peak at 510 K was attributed to recombinative desorption of H2O. H2O dissociated into H and OH at the interface of Au and TiO2, and H2O dissociation and CO oxidation were carried out at the same active sites. The authors claimed that the dissociation of H2O triggered the oxidation of CO. Tran-Thuy et al. also investigated the effect of adsorbed H2O molecules on the CO oxidation over Au/BN catalysts that were calcined at different temperatures.92 The results showed that an increase in calcination temperature promoted the dispersion of Au particles on BN carriers. Besides, the high calcination temperature also improved the adsorption of water molecules on the surface, increased the defect density on the BN carriers, and enhanced the CO oxidation activity at room temperature and higher relative humidity conditions. The CO oxidation activity over the Au/BN catalysts increased with increasing relative humidity, and the TOF of the reaction at high humidity was correlated with physically adsorbed H2O in a volcano-shape relationship with the adsorption intensity and the density of H2O adsorbed on the surface. The increase in TOF under high humidity conditions could be attributed to the formation of CO(H2O)n and H2Oad species, in which CO(H2O)n was generated by COad on Au0 and H2Oad on BN, indicating the importance of the Au–BN interface sites. Zhao et al. also studied the promotion effect of H2O on the oxidation activity of CO.93 Compared to Au nanoparticles loaded on CeO2 (Au/CeO2-NP), water significantly affected the catalytic performance of Au single-atom catalysts (Au1/CeO2). In the Au1/CeO2 single-atom catalysts, the positively charged Au atoms as electron acceptors provided a more effective active site for the reaction of CO and OH groups due to their higher oxidation state change. On the other hand, the near zero-valent Au interfacial atoms in the supported Au nanoparticle catalysts were not conducive to this oxidation reaction, thus significantly hindering the CO + OH reaction pathway.
5 Ru-based catalysts
Though Ru was less applied in CO oxidation compared to Au, Pt, and Pd-based catalysts, the effect of supports and metal doping on the catalytic performance of Ru-based catalysts was also reported in the literature.
5.1 Effects of supports
The nature of the carrier significantly affected the catalytic CO oxidation performance of Ru-based catalysts. Mohamed et al. investigated the CO oxidation over Ru/TiO2 and Ru/ZrO2 catalysts, and the results showed that the Ru–ZrO2 catalysts were more active.11 Zhang and co-workers prepared CeO2 nanorod and nanocube via a hydrothermal method and examined the effect of CeO2 morphology on Ru nanoparticles for CO oxidation (Fig. 5a).94 Similarly, Li et al. designed and synthesized Ru catalysts loaded on CeO2 nano-rods (NR), nano-cubes (NC), and nano-octahedra (NO) to investigate the effect between the shape and exposed crystalline surfaces ((100), (110), and (111)) of the nano-CeO2 carriers on their low-temperature CO oxidation activity.33 As shown in Fig. 5b–e, the (111) face of CeO2 nanorods had a higher number of defects, while the nano-cubes and octahedra were surrounded by relatively flat (111) and (100) faces, respectively. The strong metal-support interaction between CeO2 nanorods and RuOx species rendered RuOx to exhibit high stability in CO oxidation reactions. Run+ species were dominated in the 5Ru/CeO2 NR-r catalyst, and those species could diffuse into the surface lattice and form a Ru–O–Ce structure on the surface of CeO2 nanorods, promoting the formation of oxygen vacancies. Therefore, CeO2 nanorods-loaded Ru catalysts exhibited the strongest Ru–CeO2 interactions, as well as strong reducibility and the highest low-temperature CO oxidation activity. Qin et al.94 loaded Ru onto CeO2 nano-rods (NR) and CeO2 nano-cubes (NC) to investigate the effect of Ru–CeO2 interaction on CO oxidation activity. The results showed that the interaction of Ru with CeO2-NC was stronger than that with CeO2-NR, which promoted the activation of lattice oxygen on CeO2-NC while weakening the redox ability of RuOx. The moderate interaction of Ru with CeO2-NR resulted in a high redox capacity of RuOx but a weak lattice oxygen activation ability of CeO2-NR. Thus, the Ru/CeO2-NR catalyst exhibited higher catalytic activity than Ru/CeO2-NC in low-temperature CO oxidation reactions.
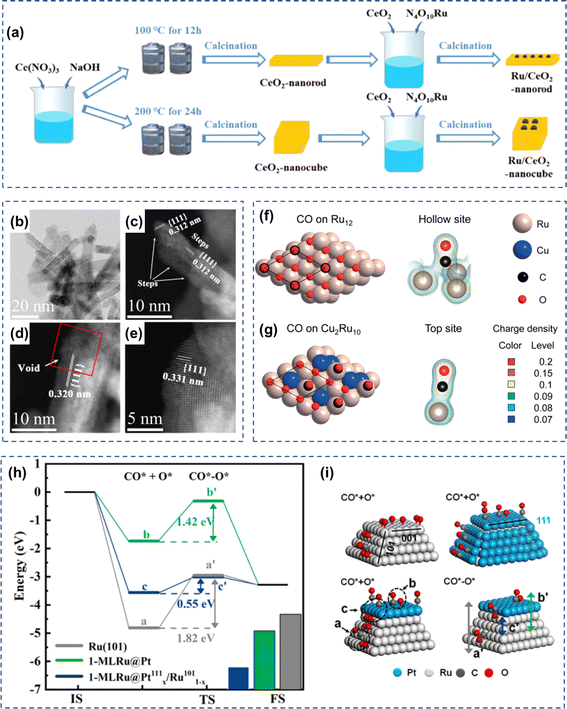 |
| Fig. 5 (a) The illustration for the preparation of Ru/CeO2. Reproduced with permission from ref. 94 Copyright 2022, American Chemical Society. (b) Low-magnification TEM image and (c and d) HAADF-STEM images of Ru/CeO2NR catalyst after reduction treatment; (e) the enlarged image of the red square shown in (d). Reproduced with permission from ref. 33 Copyright 2019, American Chemical Society. CO adsorption models on (f) Ru12(111) and (g) Cu2Ru10 surface. Reproduced with permission from ref. 34 Copyright 2019, Wiley. (h) The reaction energy barrier and (i) CO adsorption model on Ru(101), 1-MLRu@Pt, and 1-ML Ru@Pt(111)x/Ru(101)1−x catalyst. Reproduced with permission from ref. 95 Copyright 2021, Elsevier. | |
5.2 Elemental doping
Elemental doping also significantly affected the CO oxidation performance of Ru-based catalysts. Du et al. selectively deposited Pt on the (001) facet of Ru while exposing adjacent Ru surfaces by selective atomic layer deposition.95 As shown in Fig. 5h and i, for the bifunctional faceted Pt/Ru catalysts, the deposition of a single layer of Pt atoms on Ru (001) effectively reduces the competitive adsorption of CO and lowers the reaction barriers; and the neighboring exposed Ru surfaces have higher dissociation activity of O2, which in turn improves the catalytic performance of the catalysts in the reaction. Huang et al. synthesized CuxRu1−x solid solution alloyed nanoparticles, and the CO oxidation activity of CuxRu1−x nanoparticles (x = 0.05–0.7) were all enhanced compared to Ru nanoparticles, and the highest CO oxidation activity was observed for Cu0.2Ru0.8 nanoparticles (Fig. 5f–g).34 The Ru atoms in the CuxRu1−x nanoparticles mainly acted as the active sites, and the Cu atom alloying attenuates the adsorption energy of CO on Ru atoms, thus enhancing the CO oxidation activity of CuxRu1−x nanoparticles.
6 Rh-based catalysts
The catalyst carrier affects the effectiveness of CO oxidation on Rh-based catalysts. Rafaj et al. investigated the oxygen exchange properties between Rh nanoparticles and the carriers CeO2(111) or CeO2(110) in CO oxidation.96 In a low-pressure reaction cycle at 300–770 K, the CO2 produced by Rh/CeO2(111) and Rh/CeO2(110) contained 53% and 70% oxygen atoms originating from the carriers, respectively, and the oxygen mobility of CeO2(110) was higher than that of CeO2(111). The CO desorption energy of Rh/CeO2(111) was 2.39(7) × 10−19 J and that of Rh/CeO2(110) was 2.28(7) × 10−19 J. The catalytic performance of Rh/CeO2(110) was better due to the weaker CO–Rh bonding and higher oxygen exchange activity of the catalyst. González Vargas et al. synthesized 1 wt% Rh/Ce-MCM-41 catalyst using mesoporous Ce-MCM-41 material as a carrier.35 In this catalyst, the small particle size of Rh and its high dispersion on the carrier surface, as well as the presence of silica hydroxyl groups on the catalyst surface would produce a synergistic effect, which enabled the Rh/Ce-MCM-41 catalyst to realize the complete conversion of CO at temperatures close to 440 K, whereas the reference samples Rh/CeO2 and Rh/MCM-41 were inactive at this temperature. The mechanistic study of the low-temperature CO oxidation reaction of Rh/Ce-MCM-41 showed that CO adsorbed on Rh3+ clusters to form intermediate species, and Ce4+ doped in the mesoporous MCM-41 silica structure, along with an abundance of O–OH reactive oxygen species on the surface. Lin et al. deposited CaTiO3 with a thickness of 1 nm on MgAl2O4 by atomic layer deposition, SrTiO3 and BaTiO3 films with a thickness of 1 nm on MgAl2O4, and investigated their CO catalytic oxidation performance as catalyst carriers loaded with Rh.97 The interaction strengths of Rh with the three chalcogenide films followed the order of Rh/CaTiO3/MgAl2O4 > Rh/SrTiO3/MgAl2O4 > Rh/BaTiO3/MgAl2O4. When Rh was loaded on MgAl2O4 or BaTiO3 films, Rh species formed larger particles after redox cycling at 1073 K, but small particles were formed on SrTiO3 films and remained better atomically dispersed on CaTiO3 films. Rh/SrTiO3/MgAl2O4 showed strong oxidizing activity for CO after reduction at 1073 K, while Rh/CaTiO3/MgAl2O4 showed low oxidizing activity for CO. Rh monoatomic catalysts also showed high reactivity for CO oxidation. Han et al. prepared Rh, Au and Pt monoatomic catalysts with ZnO nanowires (ZnO-nw) as carriers and studied their CO oxidation performance.8 As shown in Fig. 6a–c, the reaction proceeds following the Mars-van Krevelen mechanism and the dissociation of oxygen molecules at the surface oxygen vacancies is the rate-controlling step of the reaction. Among the three noble metals studied, the Rh1/ZnO-nw catalysts have the lowest energy barriers, and thus they have the highest CO oxidation activity, and the Rh1/ZnO-nw catalysts have better resistance to high-temperature sintering. Hulsey et al. explored the active center of Rh-HPA catalysts in CO oxidation and demonstrated that atomically dispersed Rh-catalyzed CO oxidation follows an unconventional M–vK mechanism and that heteropolyacid carriers are directly involved in the reaction Fig. 6e–f.98 Rh cycles between Rh3+ and Rh+ and the reoxidation of the carrier is a rate-controlling step.
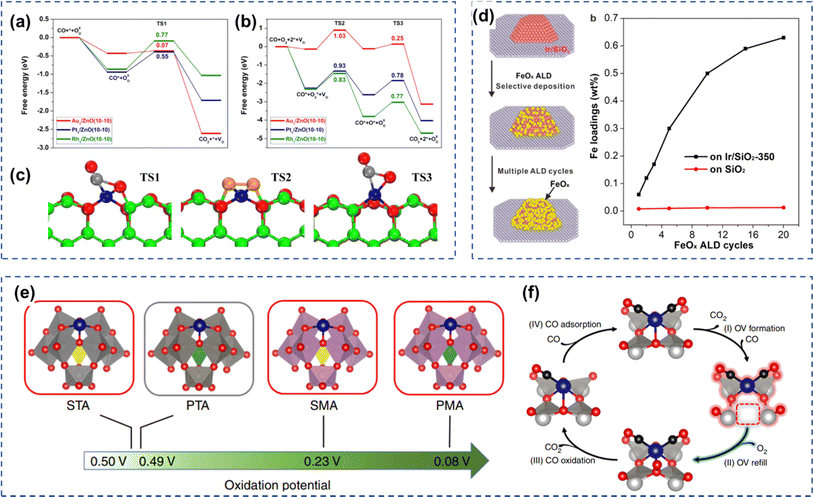 |
| Fig. 6 (a and b) The free energy of CO oxidation via the M–vK mechanism over Rh1/ZnO, Pt1/ZnO, and Au1/ZnO SACs catalysts, respectively; (c) the optimized state of the elementary step in CO oxidation, where the green, blue, red, orange, and gray balls represent Zn Rh/Pt/Au, O, O from O2, and C atoms, respectively. Reproduced with permission from ref. 8 Copyright 2019, Elsevier. (d) The effect of FeOx ALD cycling on the activity of Ir in CO oxidation. Reproduced with permission from ref. 36 Copyright 2019, American Chemical Society. (e) The oxidation potential of single-atom Rh dispersed on four heteropoly acids. (f) The proposed reaction mechanism of CO oxidation over single-atom Rh anchored on heteropoly acid. Reproduced with permission from ref. 98 Copyright 2019, Nature Publishing Group. | |
7 Ir-based catalysts
Hong et al. used Fe-substituted hexaaluminate as a support to disperse Ir nanoparticles (Ir/BaFeAl11O19) for CO oxidation.9 The interaction between Ir species on the crystalline surface of hexaaluminate and the Fe species in the matrix of support resulted in Fe oxidation state of +2, and the moderate adsorption of CO on the Ir sites, thus the catalyst showed good catalytic performance in the CO-PROX reaction with high conversion, good stability, and strong resistance to CO2 and H2O poisoning. Wang et al. adopted atomic layer deposition strategies to selectively deposit FeOx onto SiO2 and then further loaded Ir nanoparticles with different particle sizes (Fig. 6d).36 The activity of FeOx-coated Ir/SiO2 samples was significantly higher compared to the uncoated Ir/SiO2 samples and showed a volcano-shaped pattern as the number of FeOx deposition cycles increased. Among them, the 1.5 nm Ir/SiO2 sample showed the best catalytic performance by achieving the complete conversion of CO in a wide temperature range of 60–180 °C after two FeOx cycles.
8 Conclusion and outlook
With the development of modern industry, the negative effect of CO on the environment is becoming more and more serious. CO catalytic oxidation is an effective approach to reducing CO. Noble metal catalysts have been widely used for CO catalytic oxidation due to their better catalytic performance. Most of the current studies focused on the influences of elemental doping, the particle size of precious metals, carrier type, oxygen vacancies, and surface hydroxyl groups on CO catalytic oxidation. Despite the tremendous progress has been made in the design and fabrication of noble metal-based catalysts for CO oxidation, the practical application of those catalysts still faces some problems and challenges that can not be ignored. In this section, the challenges and opportunities in the development of efficient catalysts for CO oxidation will be offered.
(1) The stability and poisoning resistance of noble metal-based catalysts still need to be improved. The composition of the exhaust gases is complex, containing a certain percentage of water vapor and SO2, etc. It was widely accepted that the SO2 poisoned and deactivated the noble metal-based catalysts to form sulfate or sulfite. The development of precious metal catalysts with high SO2 poisoning resistance is urgent. One of the possible strategies is to coat the noble-metal catalysts with a thin layer of acidic metal oxides, which suppressed the adsorption of SO2, thus protecting the noble-metal sites from poisoning. Considering that the size of CO is smaller than SO2, the other possible approach was to the confine the noble-metal atoms within the small size pore of the zeolites, in which the pore only allowed the adsorption of CO on metal sites, and protected the noble metals from interacting with SO2. Other strategies to enhance the SO2 resistance are still highly desirable. Besides, the methods to regenerate the poisoned catalysts are also needed.
(2) The design and selection of catalytic materials are the key to efficiently remove CO. Though noble metal-based catalysts were demonstrated effective, the high price limits the large application of noble metals. The cost of precious metals accounts for more than 90% of the catalyst production. How to reduce the loading of precious metals without compromising the catalytic performance is the focus of the research. Thanks to the emergence of single-atom catalysts, which were characterized by the 100% exposure of the metal atoms, the effective removal of CO molecules with acceptable cost is becoming possible. On the other hand, non-noble metal catalysts with comparable catalytic performance as noble metal catalysts are more desirable. The transition metal nitride and carbide behave like noble metals in electrochemical reactions, such as the oxygen reduction reactions, and the hydrogen evolution reactions. The application of transition metal nitride and carbide in CO might be able to further decrease the cost of the catalysts. It should be noted that the metal nitride/carbide could be oxidized to metal oxides under oxygen-rich conditions. The formed metal nitride@oxide structure might possess unique electronic and geometric properties that enable effective CO oxidation.
(3) The active sites of CO oxidation over noble metal-based catalysts were still ambiguous. Some research reported that atomically dispersed metal species were responsible for the CO oxidation, while it was also claimed that the nanoclusters were the sites where the reaction occurred. The current techniques to identify the single-atom sites heavily rely on HAADF-STEM, XAFS, and DRIFTS. Though those techniques can provide the general structure information of the sample, it is still challenging to precisely reveal the electronic and coordination environment with spatial resolution under working conditions. Besides, a wide range of metal particle sizes were present in the heterogeneous catalysts. It is challenging to distinguish the real active sites.
(4) Apart from studying the structure of the catalysts, it is also critical to investigate the reaction mechanism as well as the structure–performance relationship under working conditions. The understanding of the reaction mechanism and the structure–performance relationship are the cornerstone for the development of efficient CO oxidation catalysts. Although enormous progress has been made in the mechanism study, most of the studies were carried out under ideal conditions. How the molecules such as H2O and SO2 that are generally present in the exhaust affected the reaction mechanism still needs to be further investigated. Besides, theoretical calculation combined with experimental measurement is another area to explore.
(5) Artificial intelligence should be applied in the design of CO oxidation catalysts. Artificial intelligence is playing a more and more important role in catalysis. The rapid development of both the hardware and software makes it possible to acquire a huge amount of catalysis data, including reaction rate, kinetic behavior, and the operando spectroscopy. All the information can help to predict the CO oxidation activity of a particular catalyst. On the other hand, the machine learning-based technique enables the discovery of the key descriptors, such as work function, d-band center and Fermi energy, governing the CO oxidation reaction rate. Based on the descriptor, we can design a catalyst with excellent CO oxidation activity. We also expected that the research along this line will promote the identification of the best catalysts in CO oxidation.
Data availability
No primary research results, software or code have been included and no new data were generated or analysed as part of this review.
Conflicts of interest
The authors declare that they have no known competing financial interests or personal relationships that could have appeared to influence the work reported in this paper.
Acknowledgements
This work is supported by the Open Project Program of the State Key Laboratory of Clean and Efficient Coal-Fired Power Generation and Pollution Control (D2022FK093). The authors also would like to acknowledge the Natural Science Foundation of Jiangsu Province (BK20220847) for the financial support.
References
- P. Chai, Z. Wu, L. Wu, H. Wang, C. Fu and W. Huang, An Operando Study of H2O-Enhanced Low-Temperature CO Oxidation on Pt(111) under Near Ambient Pressure Conditions, ACS Catal., 2022, 13292–13299 CrossRef CAS
. - C. A. Whitcomb, A. Shrestha, C. Paolucci and R. J. Davis, Low temperature CO oxidation over Rh supported on N-doped carbon, Catal. Sci. Technol., 2024, 2479–2488 RSC
. - X. Mao, Y. Zhang, Y. Xu, Y. Zhou, K. Zhuang, K. Shen and S. Ding, The lattice oxygen determines the methanol selectivity in CO2 hydrogenation over ZnZrOx catalysts, Catal. Sci. Technol., 2024, 14(2), 419–430 RSC
. - L. Xiang, S. Wang and L. Kuai, Superior single-atom Pt/TiO2 mesoporous microspheres via microdrops-confined pyrolysis/deposition for low-temperature CO oxidation, Microporous Mesoporous Mater., 2024, 363, 112809 CrossRef CAS
. - Z. Cui, X. Wang, R. Li, L. Kuai and C. Fang, Spatially confined (Au core)/CeO2–(Au nanoclusters) hierarchical nanostructures as highly active and stable catalysts for CO oxidation, J. Alloys Compd., 2023, 938, 168655 CrossRef CAS
. - C. Fang, X. Jiang, J. Hu, J. Song, N. Sun, D. Zhang and L. Kuai, Ru Nanoworms Loaded TiO(2) for Their Catalytic Performances toward CO Oxidation, ACS Appl. Mater. Interfaces, 2021, 13(4), 5079–5087 CrossRef CAS PubMed
. - Y. Chen, Y. Feng, L. Li, J. Liu, X. Pan, W. Liu, F. Wei, Y. Cui, B. Qiao, X. Sun, X. Li, J. Lin, S. Lin, X. Wang and T. Zhang, Identification of Active Sites on High-Performance Pt/Al2O3 Catalyst for Cryogenic CO Oxidation, ACS Catal., 2020, 10(15), 8815–8824 CrossRef CAS
. - B. Han, R. Lang, H. Tang, J. Xu, X.-K. Gu, B. Qiao and J. Liu, Superior activity of Rh1/ZnO single-atom catalyst for CO oxidation, Chin. J. Catal., 2019, 40(12), 1847–1853 CrossRef
. - B. Hong, J.-X. Liang, X. Sun, M. Tian, F. Huang, Y. Zheng, J. Lin, L. Li, Y. Zhou and X. Wang, Widening Temperature Window for CO Preferential Oxidation in H2 by Ir Nanoparticles Interaction with Framework Fe of Hexaaluminate, ACS Catal., 2021, 11(9), 5709–5717 CrossRef CAS
. - H. Li, M. Shen, J. Wang, H. Wang and J. Wang, Effect of Support on CO Oxidation Performance over the Pd/CeO2 and Pd/CeO2–ZrO2 Catalyst, Ind. Eng. Chem. Res., 2020, 59(4), 1477–1486 CrossRef CAS
. - Z. Mohamed, V. D. B. C. Dasireddy, S. Singh and H. B. Friedrich, TiO2 and ZrO2 supported Ru catalysts for CO mitigation following the water-gas shift reaction, Int. J. Hydrogen Energy, 2018, 43(49), 22291–22302 CrossRef CAS
. - C. Feng, X. Liu, T. Zhu and M. Tian, Catalytic oxidation of CO on noble metal-based catalysts, Environ. Sci. Pollut. Res. Int., 2021, 28(20), 24847–24871 CrossRef CAS
. - Z. Jia, M. Peng, X. Cai, Y. Chen, X. Chen, F. Huang, L. Zhao, J. Diao, N. Wang, D. Xiao, X. Wen, Z. Jiang, H. Liu and D. Ma, Fully Exposed Platinum Clusters on a Nanodiamond/Graphene Hybrid for Efficient Low-Temperature CO Oxidation, ACS Catal., 2022, 9602–9610 CrossRef CAS
. - J. Cai, Z. Yu, X. Fan and J. Li, Effect of TiO(2) Calcination Pretreatment on the Performance of Pt/TiO(2) Catalyst for CO Oxidation, Molecules, 2022, 27(12), 3875 CrossRef CAS PubMed
. - F. Maurer, A. Beck, J. Jelic, W. Wang, S. Mangold, M. Stehle, D. Wang, P. Dolcet, A. M. Gaenzler, C. Kuebel, F. Studt, M. Casapu and J.-D. Grunwaldt, Surface Noble Metal Concentration on Ceria as a Key Descriptor for Efficient Catalytic CO Oxidation, ACS Catal., 2022, 12(4), 2473–2486 CrossRef CAS
. - S. Song, Y. Wu, S. Ge, L. Wang, Y. Wang, Y. Guo, W. Zhan and Y. Guo, A Facile Way To Improve Pt Atom Efficiency for CO Oxidation at Low Temperature: Modification by Transition Metal Oxides, ACS Catal., 2019, 9(7), 6177–6187 CrossRef CAS
. - B. Nan, Q. Fu, J. Yu, M. Shu, L.-L. Zhou, J. Li, W.-W. Wang, C.-J. Jia, C. Ma, J.-X. Chen, L. Li and R. Si, Unique structure of active platinum-bismuth site for oxidation of carbon monoxide, Nat. Commun., 2021, 12(1), 3342 CrossRef CAS
. - J. Bae, J. Kim, H. Jeong and H. Lee, CO oxidation on SnO2 surfaces enhanced by metal doping, Catal. Sci. Technol., 2018, 8(3), 782–789 RSC
. - W. Wang, D. Li, H. Yu, C. Liu, C. Tang, J. Chen, J. Lu and M. Luo, Insights into Different Reaction Behaviors of Propane and CO Oxidation over Pt/CeO2 and Pt/Nb2O5: The Crucial Roles of Support Properties, J. Phys. Chem. C, 2021, 125(35), 19301–19310 CrossRef CAS
. - G. Spezzati, A. D. Benavidez, A. T. DeLaRiva, Y. Su, J. P. Hofmann, S. Asahina, E. J. Olivier, J. H. Neethling, J. T. Miller, A. K. Datye and E. J. M. Hensen, CO oxidation by Pd supported on CeO2(100) and CeO2(111) facets, Appl. Catal., B, 2019, 243, 36–46 CrossRef CAS
. - E. M. Slavinskaya, A. V. Zadesenets, O. A. Stonkus, A. I. Stadnichenko, A. V. Shchukarev, Y. V. Shubin, S. V. Korenev and A. I. Boronin, Thermal activation of Pd/CeO2–SnO2 catalysts for low-temperature CO oxidation, Appl. Catal., B, 2020, 277, 119275 CrossRef CAS
. - H. Xu, Z. Zhang, J. Liu, C. L. Do-Thanh, H. Chen, S. Xu, Q. Lin, Y. Jiao, J. Wang, Y. Wang, Y. Chen and S. Dai, Entropy-stabilized single-atom Pd catalysts via high-entropy fluorite oxide supports, Nat. Commun., 2020, 11(1), 3908 CrossRef CAS PubMed
. - L. Wang, C. Pu, L. Xu, Y. Cai, Y. Guo, Y. Guo and G. Lu, Effect of supports over Pd/Fe2O3 on CO oxidation at low temperature, Fuel Process. Technol., 2017, 160, 152–157 CrossRef CAS
. - C. Wang, C. Wen, J. Lauterbach and E. Sasmaz, Superior oxygen transfer ability of Pd/MnOx–CeO2 for enhanced low temperature CO oxidation activity, Appl. Catal., B, 2017, 206, 1–8 CrossRef CAS
. - C. H. Wu, C. Liu, D. Su, H. L. Xin, H.-T. Fang, B. Eren, S. Zhang, C. B. Murray and M. B. Salmeron, Bimetallic synergy in cobalt–palladium nanocatalysts for CO oxidation, Nat. Catal., 2018, 2(1), 78–85 CrossRef
. - G. Tofighi, X. Yu, H. Lichtenberg, D. E. Doronkin, W. Wang, C. Wöll, Y. Wang and J.-D. Grunwaldt, Chemical Nature of Microfluidically Synthesized AuPd Nanoalloys Supported on TiO2, ACS Catal., 2019, 9(6), 5462–5473 CrossRef CAS
. - M. S. Choi, H. Jeong and H. Lee, Re-dispersion of Pd-based bimetallic catalysts by hydrothermal treatment for CO oxidation, RSC Adv., 2021, 11(5), 3104–3109 RSC
. - Y. Soni, S. Pradhan, M. K. Bamnia, A. K. Yadav, S. N. Jha, D. Bhattacharyya, T. S. Khan, M. A. Haider and C. P. Vinod, Spectroscopic Evidences for the Size Dependent Generation of Pd Species Responsible for the Low Temperature CO Oxidation Activity on Pd-SBA-15 Nanocatalyst, Appl. Catal., B, 2020, 272, 118934 CrossRef CAS
. - R. Camposeco, M. Hinojosa-Reyes, S. Castillo, N. Nava and R. Zanella, Synthesis and characterization of highly dispersed bimetallic Au-Rh nanoparticles supported on titanate nanotubes for CO oxidation reaction at low temperature, Environ. Sci. Pollut. Res. Int., 2021, 28(9), 10734–10748 CrossRef CAS PubMed
. - L. Wang, L. Wang, J. Zhang, H. Wang and F.-S. Xiao, Enhancement of the activity and durability in CO oxidation over silica-supported Au nanoparticle catalyst via CeO modification, Chin. J. Catal., 2018, 39(10), 1608–1614 CrossRef CAS
. - Z. Boukha, J. R. González-Velasco and M. A. Gutiérrez-Ortiz, Viability of Au/La2O3/HAP catalysts for the CO preferential oxidation reaction under reformate gas conditions, Appl. Catal., B, 2022, 312, 121384 CrossRef CAS
. - C. Qi, Y. Zheng, H. Lin, H. Su, X. Sun and L. Sun, CO oxidation over gold catalysts supported on CuO/Cu2O both in O2-rich and H2-rich streams: Necessity of copper oxide, Appl. Catal., B, 2019, 253, 160–169 CrossRef CAS
. - J. Li, Z. Liu, D. A. Cullen, W. Hu, J. Huang, L. Yao, Z. Peng, P. Liao and R. Wang, Distribution and Valence State of Ru Species on CeO2 Supports: Support Shape Effect and Its Influence on CO Oxidation, ACS Catal., 2019, 9(12), 11088–11103 CrossRef CAS
. - B. Huang, H. Kobayashi, T. Yamamoto, T. Toriyama, S. Matsumura, Y. Nishida, K. Sato, K. Nagaoka, M. Haneda, W. Xie, Y. Nanba, M. Koyama, F. Wang, S. Kawaguchi, Y. Kubota and H. Kitagawa, A CO Adsorption Site Change Induced by Copper Substitution in a Ruthenium Catalyst for Enhanced CO Oxidation Activity, Angew Chem. Int. Ed. Engl., 2019, 58(8), 2230–2235 CrossRef CAS PubMed
. - O. A. González Vargas, J. A. de Los Reyes Heredia, V. A. Suarez-Toriello, S. M. Anderson, L. F. Chen and J. A. Wang, Enhanced catalytic performance of Ce-MCM-41-supported Rh for CO oxidation, Res. Chem. Intermed., 2021, 47(7), 2857–2880 CrossRef
. - C. Wang, Q. Yao, L. Cao, J. Li, S. Chen and J. Lu, Precise Tailoring of Ir-FeOx Interfaces for Improved Catalytic Performance in Preferential Oxidation of Carbon Monoxide in Hydrogen, J. Phys. Chem. C, 2019, 123(48), 29262–29270 CrossRef CAS
. - B. Qiao, A. Wang, X. Yang, L. F. Allard, Z. Jiang, Y. Cui, J. Liu, J. Li and T. Zhang, Single-atom catalysis of CO oxidation using Pt1/FeOx, Nat. Chem., 2011, 3(8), 634–641 CrossRef CAS PubMed
. - B. Qiao, J.-X. Liang, A. Wang, C.-Q. Xu, J. Li, T. Zhang and J. Liu, Ultrastable single-atom gold catalysts with strong covalent metal-support interaction (CMSI), Nano Res., 2015, 8(9), 2913–2924 CrossRef CAS
. - L. Jiao and J. R. Regalbuto, The synthesis of highly dispersed noble and base metals on silica via strong electrostatic adsorption: I. Amorphous silica, J. Catal., 2008, 260(2), 329–341 CrossRef CAS
. - Z. Zhang, Y. Zhu, H. Asakura, B. Zhang, J. Zhang, M. Zhou, Y. Han, T. Tanaka, A. Wang, T. Zhang and N. Yan, Thermally stable single atom Pt/m-Al2O3 for selective hydrogenation and CO oxidation, Nat. Commun., 2017, 8, 16100 CrossRef CAS PubMed
. - Z. Zhang, C. Feng, C. Liu, M. Zuo, L. Qin, X. Yan, Y. Xing, H. Li, R. Si, S. Zhou and J. Zeng, Electrochemical deposition as a universal route for fabricating single-atom catalysts, Nat. Commun., 2020, 11(1), 1215 CrossRef CAS
. - P. Liu, Y. Zhao, R. Qin, S. Mo, G. Chen, L. Gu, D. M. Chevrier, P. Zhang, Q. Guo, D. Zang, B. Wu, G. Fu and N. Zheng, Photochemical route for synthesizing atomically dispersed palladium catalysts, Science, 2016, 352(6287), 797–801 CrossRef CAS
. - S. Ding, H.-A. Chen, O. Mekasuwandumrong, M. J. Hülsey, X. Fu, Q. He, J. Panpranot, C.-M. Yang and N. Yan, High-temperature flame spray pyrolysis induced stabilization of Pt single-atom catalysts, Appl. Catal., B, 2021, 281, 119471 CrossRef CAS
. - M. Liebertseder, C. B. Maliakkal, M. Crone, G. Nails, M. Casapu, J.-D. Grunwaldt, M. Tuerk, C. Kuebel and C. Feldmann, TiO2–CeOx–Pt Hollow Nanosphere Catalyst for Low-Temperature CO Oxidation, Chemcatchem, 2024, 16(2), e202301358 CrossRef CAS
. - C. Chen, J.-L. Chen, L. Feng, J. Hu, X. Chai, J.-X. Liu and W.-X. Li, Reactant-Induced Dynamic Stabilization of Highly Dispersed Pt Catalysts on Ceria Dictating the Reactivity of CO Oxidation, ACS Catal., 2024, 14(5), 3504–3513 CrossRef CAS
. - Z. Zhang, J. Tian, Y. Lu, S. Yang, D. Jiang, W. Huang, Y. Li, J. Hong, A. S. Hoffman, S. R. Bare, M. H. Engelhard, A. K. Datye and Y. Wang, Memory-dictated dynamics of single-atom Pt on CeO2 for CO oxidation, Nat. Commun., 2023, 14(1), 2664 CrossRef CAS PubMed
. - L. Xu, Y. Pan, H. Li, R. Xu and Z. Sun, Highly active and water-resistant Lanthanum-doped platinum-cobalt oxide catalysts for CO oxidation, Appl. Catal., B, 2023, 331, 122678 CrossRef CAS
. - H. J. Wallander, D. Gajdek, S. Albertin, G. Harlow, N. Braud, L. Buss, J.-O. Krisponeit, J. I. Flege, J. Falta, E. Lundgren and L. R. Merte, Dynamic Behavior of Tin at Platinum Surfaces during Catalytic CO Oxidation, ACS Catal., 2023, 13(24), 16158–16167 CrossRef CAS
. - I. V. Zagaynov, E. Y. Liberman and A. V. Naumkin, Influence of Pt/Pd state on ceria-based support in CO oxidation, J. Rare Earths, 2023, 41(12), 1963–1968 CrossRef CAS
. - T. Ueda, T. Matsuo, T. Hyodo and Y. Shimizu, Effects of heat treatments of Pt-loaded Al2O3 on catalytic activities of CO oxidation and combustion-type CO sensors, J. Mater. Sci., 2023, 9459–9472 CrossRef CAS
. - E. M. Slavinskaya, A. I. Stadnichenko, J. E. Q. Dominguez, O. A. Stonkus, M. Vorokhta, B. Smid, P. Castro-Latorre, A. Bruix, K. M. Neyman and A. I. Boronin, States of Pt/CeO2 catalysts for CO oxidation below room temperature, J. Catal., 2023, 421, 285–299 CrossRef CAS
. - K. Shen, R. J. Gorte and J. M. Vohs, H2O Promotion of CO Oxidation On Oxidized Pt/CeFeOx, Catal. Lett., 2023, 2414–2421 Search PubMed
. - X. Liu, Y. Zou, X. Li, T. Xu, W. Cen, B. Li and T. Zhu, Ultralow Doping of Mn Species into Pt Catalyst Enhances the CO Oxidation Performance in the Presence of H2O and SO2, ACS Catal., 2023, 13(22), 14580–14597 CrossRef CAS
. - Y. Li, H. Wang, H. Song, N. Rui, M. Kottwitz, S. D. Senanayake, R. G. Nuzzo, Z. Wu, D.-e. Jiang and A. I. Frenkel, Active sites of atomically dispersed Pt supported on Gd-doped ceria with improved low temperature performance for CO oxidation, Chem. Sci., 2023, 14(44), 12582–12588 RSC
. - D. Kim, D. Park, H. C. Song, B. Jeong, J. Lee, Y. Jung and J. Y. Park, Metal Encapsulation-Driven Strong Metal-Support Interaction on Pt/Co3O4 during CO Oxidation, ACS Catal., 2023, 13(8), 5326–5335 CrossRef CAS
. - S. Hu, M. Huang, J. Li, J. He, K. Xu, X. Rao, D. Cai and G. Zhan, Tailoring the electronic states of Pt by atomic layer deposition of Al2O3 for enhanced CO oxidation performance: Experimental and theoretical investigations, Appl. Catal., B, 2023, 333, 122804 CrossRef CAS
. - S. Hong, D. Kim, K.-J. Kim and J. Y. Park, Facet-Controlled Cu2O Support Enhances Catalytic Activity of Pt Nanoparticles for CO Oxidation, J. Phys. Chem. Lett., 2023, 14(23), 5241–5248 CrossRef CAS
. - J. Dong, Y. Zhang, D. Li, A. Adogwa, S. Huang, M. Yang, J. Yang and Q. Jin, Reaction-driven evolutions of Pt states over Pt–CeO2 catalysts during CO oxidation, Appl. Catal., B, 2023, 330, 122662 CrossRef CAS
. - S. Dhakar, A. Sharma, N. K. Katiyar, A. Parui, R. Das, A. K. Singh, C. S. Tiwary, S. Sharma and K. Biswas, Utilization of structural high entropy alloy for CO oxidation to CO2, Mater. Today Energy, 2023, 37, 101386 CrossRef CAS
. - D. Wang, R. Li, X. Sun, L. Lin, K. Li, R. Zhang, R. Mu and Q. Fu, Hydroxide Structure-Dependent OH Promotion Mechanism over a Hydroxylated CoOx/Pt(111) Catalyst toward CO Oxidation, ACS Catal., 2024, 14(7), 5147–5155 CrossRef CAS
. - X. Wang, S. Zeng, G. Qi, Q. Wang, J. Xu and F. Deng, CO oxidation over embedded Pt nanoparticles on Al2O3 with Al coordination flexibility, Chem. Commun., 2023, 59(50), 7783–7786 RSC
. - A. Beniya, S. Higashi, N. Ohba, R. Jinnouchi, H. Hirata and Y. Watanabe, CO oxidation activity of non-reducible oxide-supported mass-selected few-atom Pt single-clusters, Nat. Commun., 2020, 11(1), 1888 CrossRef CAS PubMed
. - Z. Jia, M. Peng, X. Cai, Y. Chen, X. Chen, F. Huang, L. Zhao, J. Diao, N. Wang, D. Xiao, X. Wen, Z. Jiang, H. Liu and D. Ma, Fully Exposed Platinum Clusters on a Nanodiamond/Graphene Hybrid for Efficient Low-Temperature CO Oxidation, ACS Catal., 2022, 12(15), 9602–9610 CrossRef CAS
. - C. Dessal, T. Len, F. Morfin, J.-L. Rousset, M. Aouine, P. Afanasiev and L. Piccolo, Dynamics of Single Pt Atoms on Alumina during CO Oxidation Monitored by Operando X-ray and Infrared Spectroscopies, ACS Catal., 2019, 9(6), 5752–5759 CrossRef CAS
. - J. Chen, S. Xiong, H. Liu, J. Shi, J. Mi, H. Liu, Z. Gong, L. Oliviero, F. Mauge and J. Li, Reverse oxygen spillover triggered by CO adsorption on Sn-doped Pt/TiO2 for low-temperature CO oxidation, Nat. Commun., 2023, 14(1), 3477 CrossRef CAS
. - H. Wang, J. Dong, L. F. Allard, S. Lee, S. Oh, J. Wang, W. Li, M. Shen and M. Yang, Single-site Pt/La–Al2O3 stabilized by barium as an active and stable catalyst in purifying CO and C3H6 emissions, Appl. Catal., B, 2019, 244, 327–339 CrossRef CAS
. - S. Lee, C. Lin, S. Kim, X. Mao, T. Kim, S.-J. Kim, R. J. Gorte and W. Jung, Manganese Oxide Overlayers Promote CO Oxidation on Pt, ACS Catal., 2021, 11(22), 13935–13946 CrossRef CAS
. - Y. Chen, J. Lin, L. Li, X. Pan, X. Wang and T. Zhang, Local structure of Pt species dictates remarkable performance on Pt/Al2O3 for preferential oxidation of CO in H-2, Appl. Catal., B, 2021, 282, 119588 CrossRef CAS
. - H. Liu, A. Zakhtser, A. Naitabdi, F. Rochet, F. Bournel, C. Salzemann, C. Petit, J.-J. Gallet and W. Jie, Operando Near-Ambient Pressure X-ray Photoelectron Spectroscopy Study of the CO Oxidation Reaction on the Oxide/Metal Model Catalyst ZnO/Pt(111), ACS Catal., 2019, 9(11), 10212–10225 CrossRef CAS
. - J. Cai, Z. Liu, K. Cao, Y. Lang, S. Chu, B. Shan and R. Chen, Highly dispersed Pt studded on CoOx nanoclusters for CO preferential oxidation in H2, J. Mater. Chem. A, 2020, 8(20), 10180–10187 RSC
. - I. Song, I. Z. Koleva, H. A. Aleksandrov, L. Chen, J. Heo, D. Li, Y. Wang, J. Szanyi and K. Khivantsev, Ultrasmall Pd Clusters in FER Zeolite Alleviate CO Poisoning for Effective Low-Temperature Carbon Monoxide Oxidation, J. Am. Chem. Soc., 2023, 145(50), 27493–27499 CrossRef CAS PubMed
. - H. Liu, S. Wu, C. Sun, Z. Huang, H. Xu and W. Shen, Fabricating Uniform TiO2-CeO2 Solid Solution Supported Pd Catalysts by an In Situ Capture Strategy for Low-Temperature CO Oxidation, ACS Appl. Mater. Interfaces, 2023, 15(8), 10795–10802 CrossRef CAS PubMed
. - A. S. Khder, H. M. Altass, R. S. Jassas, M. M. Al-Rooqi, M. A. Khder, M. Morad, A. Gebreil, Z. Moussa and S. A. Ahmed, Room-Temperature CO Oxidation over Au-Pd Monometallic and Bimetallic Nanoparticle-Supported MgO, ACS Appl. Nano Mater., 2023, 6(6), 4243–4252 CrossRef CAS
. - J. Chen, Y. Su, Q. Meng, H. Qian, L. Shi, J. A. Darr, Z. Wu and X. Weng, Palladium Encapsulated by an Oxygen-Saturated TiO2 Overlayer for Low-Temperature SO2-Tolerant Catalysis during CO Oxidation, Angew. Chem., Int. Ed., 2023, 62(49), e202310191 CrossRef CAS
. - Y. Song, S. Svadlenak, T. Bathena, M. J. Hazlett, W. S. Epling, K. A. Goulas and L. C. Grabow, PdCu Alloy Catalyst for Inhibition-free, Low-temperature CO Oxidation, Chemcatchem, 2024, 16(1), e202301024 CrossRef CAS
. - S. Shigenobu, H. Hojo and H. Einaga, Catalytic Oxidation of CO to CO2 over CeO2-Supported Pd–Cu Catalysts under Dilute O2 Conditions, Ind. Eng. Chem. Res., 2022, 15856–15865 CAS
. - V. Mehar, A. Almithn, T. Egle, M.-H. Yu, C. R. O'Connor, M. Karatok, R. J. Madix, D. Hibbitts and J. F. Weaver, Oxophilicity Drives Oxygen Transfer at a Palladium–Silver Interface for Increased CO Oxidation Activity, ACS Catal., 2020, 10(23), 13878–13889 CrossRef CAS
. - H. Dong, M. Jung, Y. Zhang, S. Wang and S. Ding, Supported noble metal-based catalysts for thermal CO2 hydrogenation to CO, Mol. Catal., 2024, 560, 114133 CrossRef CAS
. - M. Lotfi, A. A. Gomaa, J. Wei, X. Zhang, K. Qadir, A. Goldbach and W. Shen, Surface-dependent CO oxidation over Au/ZnO nanopyramids and nanorods, Appl. Catal., A, 2023, 666, 119436 CrossRef CAS
. - R. E. Tankard, F. Romeggio, S. K. Akazawa, A. Krabbe, O. F. Sloth, N. M. Secher, S. Colding-Fagerholt, S. Helveg, R. Palmer, C. D. Damsgaard, J. Kibsgaard and I. Chorkendorff, Stable mass-selected AuTiOx nanoparticles for CO oxidation, Phys. Chem. Chem. Phys., 2024, 26(12), 9253–9263 RSC
. - H. Liu, Z. Cao, S. Yang, Q. Ren, Z. Dong, W. Liu, Z.-A. Li, X. Chen and L. Luo, Geometric edge effect on the interface of Au/CeO2 nanocatalysts for CO oxidation, Nano Res., 2024, 4986–4993 CrossRef CAS
. - Q. Huang, D. Ren, J. Ding, C. Tang, H. Wang, W. Huang, X. Wen and Z. Zhang, Tailoring Au–CuO interfaces for enhanced activity in CO oxidation, Appl. Surf. Sci., 2024, 651, 159231 CrossRef CAS
. - A. Holm, B. Davies, S. B. Bibi, F. Moncada, J. Halldin-Stenlid, L. Paskevicius, V. Claman, A. Slabon, C.-W. Tai, E. C. dos-Santos and S. Koroidov, A Water-Promoted Mars-van Krevelen Reaction Dominates Low-Temperature CO Oxidation over Au–Fe2O3 but Not over Au–TiO2, ACS Catal., 2024, 14(5), 3191–3197 CrossRef CAS PubMed
. - X. Wang, J. Zhao, H. Eliasson, R. Erni, A. Ziarati, S. McKeown Walker and T. Burgi, Very Low Temperature CO Oxidation over Atomically Precise Au25 Nanoclusters on MnO2, J. Am. Chem. Soc., 2023, 145(50), 27273–27281 CrossRef CAS PubMed
. - Y. Adachi, J. Brndiar, M. Konopka, R. Turansky, Q. Zhu, H. F. Wen, Y. Sugawara, L. Kantorovich, I. Stich and Y. J. Li, Tip-activated single-atom catalysis: CO oxidation on Au adatom on oxidized rutile TiO2 surface, Sci. Adv., 2023, 9(39), eadi4799 CrossRef CAS
. - L. A. Calzada, C. Louis, C. Wan Han, V. Ortalan and R. Zanella, Au-Ru/TiO2 prepared by deposition-precipitation with urea: Relevant synthesis parameters to obtain bimetallic particles, Appl. Catal., B, 2020, 264, 118503 CrossRef
. - R. Manzorro, W. E. Celín, J. A. Pérez-Omil, J. J. Calvino and S. Trasobares, Improving the Activity and Stability of YSZ-Supported Gold Powder Catalyst by Means of Ultrathin, Coherent, Ceria Overlayers. Atomic Scale Structural Insights, ACS Catal., 2019, 9(6), 5157–5170 CrossRef CAS
. - C. Mochizuki, Y. Inomata, S. Yasumura, M. Lin, A. Taketoshi, T. Honma, N. Sakaguchi, M. Haruta, K.-i. Shimizu, T. Ishida and T. Murayama, Defective NiO as a Stabilizer for Au Single-Atom Catalysts, ACS Catal., 2022, 6149–6158 CrossRef CAS
. - C. T. Campbell, N. Lopez and S. Vajda, Catalytic properties of model supported nanoparticles, J. Chem. Phys., 2020, 152(14), 140401 CrossRef CAS PubMed
. - M. Lin, C. Mochizuki, B. An, Y. Inomata, T. Ishida, M. Haruta and T. Murayama, Elucidation of Active Sites of Gold Nanoparticles on Acidic Ta2O5 Supports for CO Oxidation, ACS Catal., 2020, 10(16), 9328–9335 CrossRef CAS
. - T. Fujitani, I. Nakamura and A. Takahashi, H2O Dissociation at the Perimeter Interface between Gold Nanoparticles and TiO2 Is Crucial for Oxidation of CO, ACS Catal., 2020, 10(4), 2517–2521 CrossRef CAS
. - T.-M. Tran-Thuy, T.-L. Yu and S. D. Lin, How H2O may influence ambient CO oxidation over Au/BN, Appl. Catal., B, 2022, 314, 121492 Search PubMed
. - S. Zhao, F. Chen, S. Duan, B. Shao, T. Li, H. Tang, Q. Lin, J. Zhang, L. Li, J. Huang, N. Bion, W. Liu, H. Sun, A. Q. Wang, M. Haruta, B. Qiao, J. Li, J. Liu and T. Zhang, Remarkable active-site dependent H(2)O promoting effect in CO oxidation, Nat. Commun., 2019, 10(1), 3824 CrossRef
. - X. Qin, M. Chen, X. Chen, J. Zhang, X. Wang, J. Fang and C. Zhang, Effects of the Metal–Support Interaction in Ru/CeO2 Nanostructures on Active Oxygen Species for HCHO/CO Oxidation, ACS Appl. Nano Mater., 2022, 5(10), 15574–15582 CrossRef CAS
. - X. Du, Y. Lang, K. Cao, J. Yang, J. Cai, B. Shan and R. Chen, Bifunctionally faceted Pt/Ru nanoparticles for preferential oxidation of CO in H2, J. Catal., 2021, 396, 148–156 CrossRef CAS
. - Z. Rafaj, J. Krutel and V. Nehasil, Oxygen Exchange between Catalyst and Active Support during CO Oxidation on Rh/CeO2(111) and Rh/CeO2(110): Isotope Labeled 18O Study, J. Phys. Chem. C, 2021, 125(29), 15959–15966 CrossRef CAS
. - C. Lin, A. C. Foucher, Y. Ji, E. A. Stach and R. J. Gorte, Investigation of Rh–titanate (ATiO3) interactions on high-surface-area perovskite thin films prepared by atomic layer deposition, J. Mater. Chem. A, 2020, 8(33), 16973–16984 RSC
. - M. J. Hulsey, B. Zhang, Z. Ma, H. Asakura, D. A. Do, W. Chen, T. Tanaka, P. Zhang, Z. Wu and N. Yan, In situ spectroscopy-guided engineering of rhodium single-atom catalysts for CO oxidation, Nat. Commun., 2019, 10(1), 1330 CrossRef PubMed
.
|
This journal is © The Royal Society of Chemistry 2024 |
Click here to see how this site uses Cookies. View our privacy policy here.