DOI:
10.1039/D1PY01283E
(Paper)
Polym. Chem., 2022,
13, 44-57
Controlling mechanical properties of 3D printed polymer composites through photoinduced reversible addition–fragmentation chain transfer (RAFT) polymerization†
Received
24th September 2021
, Accepted 13th October 2021
First published on 13th October 2021
Abstract
Reversible addition–fragmentation chain-transfer (RAFT) polymerization has been widely exploited to produce homogeneous and living polymer networks for advanced material design. In this work, we incorporate silica nanoparticles (SNPs) into a RAFT polymerization system to prepare a series of photocurable composite resins. These resins are applied to stereolithographic 3D printing to produce composite materials with enhanced mechanical properties. Relatively high loadings of SNPs (30 wt%) within the resins are achieved, allowing an increase in the 3D printed composite material tensile strength by 165% while simultaneously increasing the fracture toughness by 168%, compared with the pristine polymer materials. In addition, the inclusion of small amounts (1 wt%) of RAFT agent into the 3D printing resins also provide efficient control over thermomechanical, tensile, and fracture properties of the resulting materials. In particular, 3D printed SNP composite materials containing 30 wt% SNPs and 1 wt% RAFT show a 37% increase in elongation at break values and a 60% increase in tensile strength compared with free radical polymerization-based counterparts. The increased ductility of composite materials imparted via RAFT agent addition has not been reported and could provide a useful tool for optimizing the performance of composite materials prepared by 3D printing. Additionally, photoinduced reactivation of thiocarbonylthio groups provides access to spatially controlled post-printing functionalization of the surface of the composite materials. As such, RAFT-mediated 3D printing of composite resins is shown to be an effective strategy for developing composite materials with arbitrary combinations of well-defined mechanical properties and diverse chemical functionalities for material post-modification.
Introduction
Originating from the concept of layer-by-layer processes, 3D printing techniques have rapidly emerged as powerful approaches for the fabrication of advanced materials.1 Due to this infatuation with 3D printing technologies, a range of 3D printing processes have been developed, including photoinduced techniques (e.g. stereolithography (SLA) and digital light processing (DLP))2 and thermal-based fused deposition modeling (FDM), inject printing, and so on.3 Compared with thermal 3D printing processes, techniques using light as the stimulus provide easier access to geometrically complex structures in a time and resource efficient manner.4 Indeed, photoinduced 3D printing techniques intrinsically provide advantages over thermal-based processes, in terms of high resolution, rapid building speeds, spatiotemporal control, and biocompatible process temperatures.5 Additionally, the ease of producing bulk materials from resins significantly improves material design freedom and has enabled applications in the fields of medicine, energy, robotics, etc.6–8
Concurrently with the advancement of 3D printing techniques, the development of advanced photocurable resins has also garnered significant attention in recent years. Numerous chemistries have been leveraged to impart novel functionalities like post-printing reinforcement,9 self-healing,10 recyclability,9 stimuli responsiveness,11 and shape-memory effects.12 However, materials made using these chemistries may not satisfy mechanical requirements that are necessary for typical engineering applications and other high-performance applications.3 To overcome this issue, nanofillers have been proposed as promising additives for imparting functions and enhancing mechanical properties of photocurable resins.3,4 Indeed, an extensive range of nanofillers such as aluminum oxide nanoparticles,13 multi-walled carbon nanotubes (MWCNTs),14 graphene nanosheets,15 and silica nanoparticles (SNPs)16 have been introduced to endow photocured polymer systems with multiple functionalities including enhanced mechanical, electrical, and magnetic functionalities. In these systems, chemical surface modification (i.e. salinization) of nanoparticles has also enabled their higher loading into resins, and has improved the reinforcing efficiency of nanofillers in 3D printable composites.8 For example, Lee, Yang and coworkers demonstrated that a high content (20 wt%) of surface modified SNPs could be dispersed in a photocurable resin, resulting in significant increases in tensile strength and hardness of the 3D printed material, albeit with a reduction in the ductility of the 3D printed material.17
The above-mentioned photocurable resins and composites utilized free radical polymerization (FRP) for network formation, which is intrinsically associated with some limitations such as the production of heterogeneous polymer networks and the absence of livingness.18–20 Alternatively, reversible deactivation radical polymerization (RDRP) processes,21–25 such as atom transfer radical polymerization (ATRP),23,26–30 reversible addition–fragmentation chain transfer (RAFT) polymerization20,31–38 and other techniques,35,39–44 have been shown to impart favorable reactivation ability and homogeneity in polymer networks.20,29,45–49 Specifically, it was reported that the RAFT agent-mediated polymer network formation process features mild autoacceleration compared with FRP, which reduces intramolecular cyclization and microgel formation, resulting in the formation of more homogeneous polymer networks.50 In contrast to FRP polymer networks, networks formed via RDRP have displayed slightly lower Young's modulus but a noticeably increased strain at break.51 Beyond the distinctive mechanical properties, other properties, such as swelling ratio52 and self-healing properties,48 can be improved using RAFT polymerization as demonstrated by Matyjaszewski's group47 and others.20,53–55 Therefore, it follows that RDRP can be leveraged to develop 3D printable materials which are not achievable via FRP.
Limited by relatively slow polymerization rates, RDRP-based photocurable resins for 3D printing have seldom been reported, with some notable exceptions.56–61 For example, our group applied oxygen tolerant PET-RAFT polymerization under green light to produce 3D and 4D printed responsive polymer materials.62 Interestingly, other works by Liska's group using addition–fragmentation chain transfer (AFCT) agents,63 and by our group using multifunctional RAFT agents,64 have shown that reversible chain-transfer during network synthesis can impart increased toughness to 3D printed objects. More recently, our group also implemented a type I photoinitiated RAFT process in visible light mediated 3D printing.56 Compared with previous systems, this system provided a 7-fold increase in printing speeds with relatively low ratios of crosslinkers, enabling arbitrary design of materials with varying mechanical properties. Although there are novel features presented in the above-mentioned RDRP systems, the resulting pure polymer materials cannot provide exceptional mechanical properties, thus restricting their application under demanding conditions.3
In this work, for the first time, silane-modified SNPs have been incorporated into a type I photoinduced RAFT polymerization system to provide a series of photocurable nanocomposites for 3D printing. The influence of RAFT agent and modified SNPs on the polymerization was examined, and suitable resins were applied for the composite material fabrication using a commercial visible light 3D printer. 3D printed materials were analyzed via a suite of (thermo)mechanical testing procedures, which showed that objects 3D printed from composite resins containing RAFT agents and SNPs synergistically increased tensile strength of the 3D printed objects. Notably, these materials also showed increased fracture toughness, which was supported via scanning electron microscopy (SEM) images of fracture surfaces. Intricate lattice structures were also successfully manufactured, demonstrating the utility of the 3D printing process in creating geometrically complex materials. Finally, the reactivation of RAFT agents was exploited for spatially controlled surface modification of the 3D printed parts. The new photocurable PET-RAFT nanocomposites developed in this study promise a new paradigm for producing strong and tough composite materials with arbitrary designs that could advance various fields including aerospace, automotive, flexible electronics, recreational goods, and medical devices.
Results and discussion
Preparation and characterization of surface-modified silica nanoparticles
In this work, hydrophilic fumed silica nanoparticles (50 nm in diameter) were utilized as fillers for the composite photocurable resins. Fumed silica nanoparticles have been used in photocurable dental composites for many years, and have proven to be efficient fillers for mechanical reinforcement.65,66 Some typical issues associated with the use of these nanofillers include the lack of dispersion stability and presence of large aggregates due to the poor compatibility between the inorganic nanoparticles and the organic polymer matrix. One common strategy to reduce these issues is to modify the surface of silica nanoparticles (SNPs) via silane coupling agents, which allows the SNPs to improve their compatibility in organic solution and chemically bind to the polymeric matrix, thus increasing their dispersibility within the polymer matrix.67 In this work, 3-methacyloxypropyltrimethoxysilane (MPS) was grafted to the surface of the SNPs following the method reported by Karabela (Fig. 2A).66 The detailed experimental process is provided in the ESI (ESI,† Experimental).
Fourier-transform infrared (FTIR) spectroscopy was used to compare unmodified SNPs and MPS modified SNPs (MPS-SNPs). As shown in Fig. 2B, the characteristic peak at ∼1710 cm−1 corresponding to the carbonyl group was identified in the MPS-SNPs, indicating the successful attachment of MPS onto the surface of the SNPs.65,66 In addition, thermogravimetric analysis (TGA) was conducted to investigate the grafting density of MPS on the SNP surface. A one step weight loss of 2% between 270 and 600 °C was observed, as shown in Fig. 2C, which is attributed to the decomposition of chemically bound MPS, because mass losses related to physically adsorbed MPS occur before 150 °C.66 Subsequently, TEM was performed on both unaltered SNPs and MPS-SNPs to visualize the morphology and size of the particles before and after modification (Fig. 2D and E). The primary particles in both cases showed an average diameter of ca. 50 nm, however, they tended to form aggregates. Nonetheless, DLS results showed that MPS modification efficiently reduced the tendency of the particles to agglomerate. Specifically, the z-average diameter and polydispersity index were 249 nm and 0.109, respectively, for MPS-SNPs, compared with 365 nm and 0.192 for unmodified SNPs (ESI, Fig. S1†). As such, the MPS-SNPs were incorporated as fillers into photocurable resins for the remainder of this work.
Polymerization kinetics of different formulas
To develop a 3D printable resin, 2-hydroxyethyl acrylate (HEA) was selected as the linear chain building monomer, while poly(ethylene glycol) diacrylate (PEGDA, Mn = 250 g mol−1) was used as crosslinker. In all formulations, weight ratios of HEA
:
PEGDA were 100
:
50. To this mixture, 0.5 wt% of diphenyl(2,4,6-trimethylbenzoyl) phosphine oxide (TPO) relative to the overall weight of monomer and crosslinker was added. The initial ratio of HEA, PEGDA and TPO was selected based on our previous work56 and was found to provide a serviceable printing speed (20 s per layer). Varied amounts of the RAFT agent methyl 2-(n-butylthiocarbonothioylthio) propanoate (MBTP) and MPS-SNPs were added into the formulations to afford a series of 3D printable resins (Fig. 1A). Resins that contained no MPS-SNPs and no RAFT agent are herein referred to as free radical polymerization (FRP) resins (Fig. 1C), while those that contained MPS-SNPs but no additional RAFT agents are referred to as FRP-SNP resins (Fig. 1D). Correspondingly, systems that contain RAFT agent but no MPS-SNPs are referred to as RAFT resins (Fig. 1E), and the systems that contain both SNPs and RAFT agents are referred to as RAFT-SNP resins (Fig. 1F).
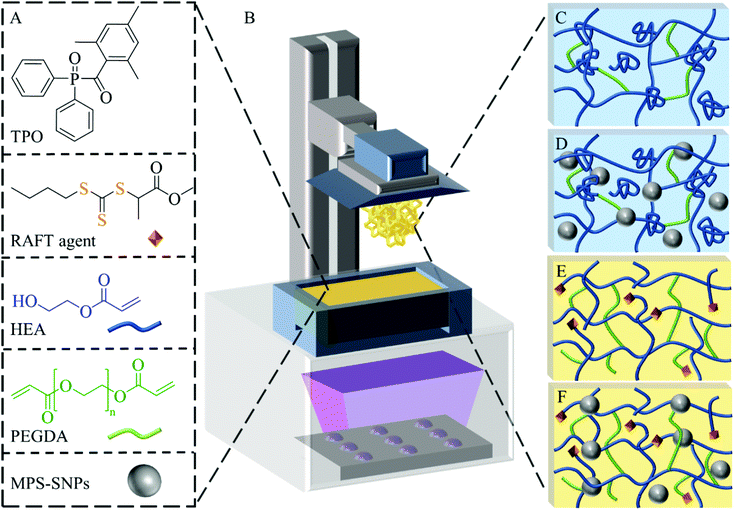 |
| Fig. 1 (A) Components used for the photocurable resins and composites developed in this work. (B) 3D printing by digital light projection (DLP) 3D printing. Representative network structures formed via 3D printing using (C) free-radical polymerization (FRP) resin; (D) FRP resin with MPS-SNPs; (E) RAFT resin; and (F) RAFT-SNP composite resin. | |
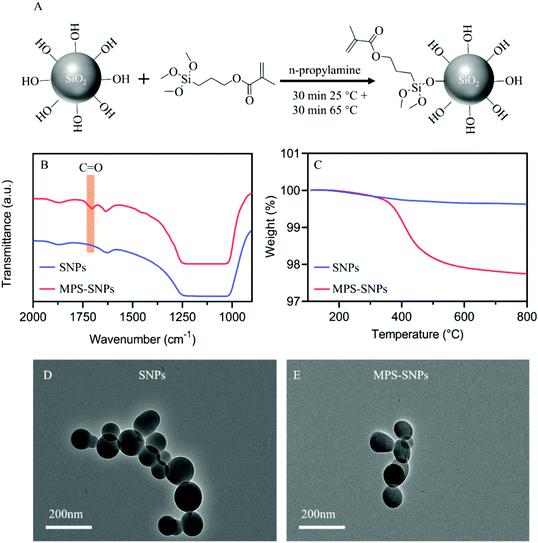 |
| Fig. 2 Surface modification of silica nanoparticles (SNPs) with 3-methacyloxypropyltrimethoxysilane (MPS). (A) Schematic reaction pathway and conditions for modification of SNPs with MPS. (B) FTIR spectra of unaltered SNPs and MPS modified SNPs, (C) temperature dependent weight loss of SNPs and MPS modified SNPs, (D) TEM image of unaltered SNPs. (E) TEM image of MPS modified SNPs. | |
The polymerization kinetics of these resins under violet light (λmax = 405 nm, 3.7 mW cm−2) was initially studied via attenuated total reflectance-Fourier-transform infrared (ATR-FTIR) spectroscopy. The monomer and crosslinker conversions were determined by monitoring the signals at ∼1620 cm−1 assigned to the C
C group. As presented in Fig. 3A, the induction period of polymerization for the neat resin was 5 s and 95% monomer conversion was reached in 10 s, indicating its great potential for photoinduced 3D printing. Comparatively, a longer induction period and a reduced polymerization rate was found for the resin containing RAFT agent, which is in accord with previously reported systems.62 For the RAFT resin with 2 wt% MBTP, the induction period was estimated to be around 20 s, and the monomer conversion reached 95% after 100 s (Fig. 3A). A similar reduction in polymerization rate has been observed in many studies applying photoinduced RAFT polymerization for network polymer formation,51,68 which has been attributed to the competitive light absorption by RAFT agent and a delayed onset of gelation.46 Indeed, UV-vis spectroscopy (ESI, Fig. S2†) showed that resins containing RAFT agents displayed higher absorption at 405 nm due to light absorption by the RAFT agent (MBTP). The competitive light absorption by RAFT agent resulted in a reduced rate of radical generation from TPO via photoinitiation and consequently reduced the polymerization rate of RAFT resins.
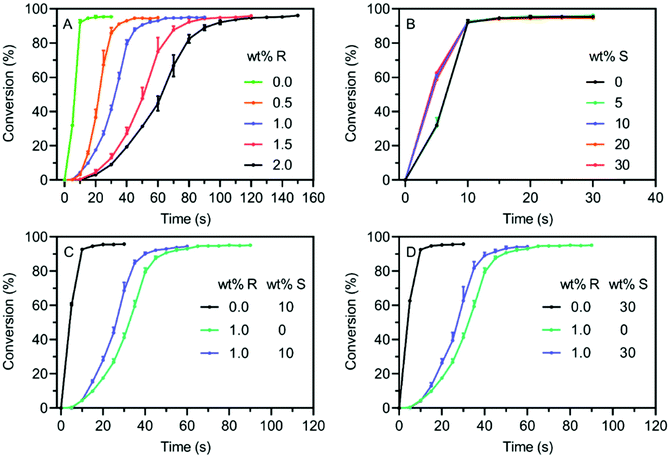 |
| Fig. 3 Effect of resin formulation on polymerization kinetics. (A) Effect of concentration of MBTP in RAFT resins. (B) Effect of concentration of MPS-SNPs in FRP-SNP resins. (C) Comparison of FRP-SNP resin (10 wt% MPS-SNPs), RAFT resin (1 wt% MBTP), and RAFT-SNP resin (1 wt% MBTP, 10 wt% MPS-SNPs). (D) Comparison of FRP-SNP resin (30 wt% MPS-SNPs), RAFT resin (1 wt% MBTP), and RAFT-SNP composite resin (1 wt% MBTP, 30 wt% MPS-SNPs). Fixed weight ratio of [HEA] : [PEGDA] : [TPO] = 100 : 50 : 0.75 were applied in all cases. Vinyl bond conversion was determined following the signals at 1620 cm−1 using ATR-FTIR under 3.7 mW cm−2 violet light (λmax = 405 nm). | |
To investigate the influence of MPS-SNPs, polymerization kinetics were also studied for FRP-SNP resins with varied amounts of MPS-SNPs.69 Interestingly, the incorporation of silica nanoparticles led to faster polymerization kinetics. Specifically, the vinyl group conversion reached 60% within 5 s for FRP-SNP resin with 10 wt% of MPS-SNPs, compared with less than 40% vinyl conversion for the FRP resin (Fig. 3B). Further addition of MPS-SNPs did not obviously increase the polymerization rate. The increased polymerization rate in the presence of SNPs was also reported by Su et al.69 The higher viscosity in SNPs contained resins reduced the frequency of diffusion-controlled termination events, which resulted in an increased propagating radical concentrations and faster polymerization rates.70 Subsequently, 1 wt% of MBTP was added to the FRP-SNPs resins to yield RAFT-SNPs resins. As shown in Fig. 3C, the presence of RAFT agent again resulted in a noticeable reduction of polymerization rate compared with the corresponding FRP-SNP resin (10 wt% MPS-SNPs), as indicated by the significantly slower kinetics, with an inhibition period of 10 s and a 60 s interval required to reach full monomer conversion. However, the higher viscosity of RAFT-SNPs resins resulted in slightly faster polymerization kinetics compared to the pure RAFT resins. The same trend was also observed when the RAFT-SNP resin was prepared with 30 wt% MPS-SNPs (Fig. 3D). It is important to note that addition of MPS-SNPs did not affect the optical properties of both FRP and RAFT systems, as indicated by the comparable UV-vis spectra with and without MPS-SNPs (ESI, Fig. S2†). Therefore, it was assumed that light penetration was not an issue regarding the printability of SNP composites.
Thermomechanical properties of 3D printed samples
Following analysis of the polymerization kinetics, the developed resins were applied in a stereolithographic 3D printing process to fabricate different 3D objects. For comparison, layer thickness for all the resin formulations was set to 50 μm. However, the cure time per layer (tc) was varied between different resin formulations to achieve similar vinyl group conversions for all the 3D printed objects. Experimental details of 3D printing conditions can be found in the ESI (ESI,† Experimental section). Although the conversion of the 3D printed objects was very high (typically α >95%), the objects were post-cured after 3D printing to consume any residual monomers within the 3D printed material.1,71 Indeed, the presence of unreacted vinyl groups is a common issue in stereolithography, which is due to the low diffusion of monomer and pendant vinyl groups in highly-crosslinked polymer networks at high monomer conversion.72 The presence of residual monomer often results in materials with poor mechanical properties, and can restrict potential applications due to the potential toxicity associated with the delayed leaching of monomer from the material.2,38 The monomer conversions of printed samples were determined from the disappearance of the characteristic peak of vinylic C–H stretching in FT-NIR spectrums. After post-curing, the 3D printed materials showed complete conversion (ESI, Fig. S6†), therefore, a 10 min post-cure treatment was conducted for all samples in this study to ensure the observed mechanical property differences were not caused by variation in vinyl group conversion.
To compare the thermomechanical properties of post-cured and non-post-cured samples, dynamic mechanical analysis (DMA) was conducted using rectangular samples (l × w × t = 40 × 8 × 3 mm). The glass transition temperature (Tg), measured as the peak of tan
δ curve, was ∼25 °C for both post-cured and non-post-cured samples (ESI, Fig. S3A†). As expected, post-curing of 3D printed samples resulted in a significant increase in storage modulus (G′) in the rubbery state (T >50 °C), from 14 MPa for the non-post-cured samples to 19 MPa for the post-cured samples. Additionally, no obvious change of storage modulus in the rubbery state and Tg was identified when varied tc was applied (ESI, Fig. S2B†). On this basis, variation of mechanical properties in the following study should be caused by formulation instead of different printing parameters.
Fig. S4† presents the storage modulus and tan
δ in the range of −50 °C to 60 °C for formulations with varying concentrations of RAFT agent. Notably, the rubbery state G′ (T >50 °C) of the materials printed with RAFT resin (1 wt% MBTP) were lower (13 MPa) compared to those printed with FRP resin (19 MPa), which was in agreement with previous publications.51,62 On the other hand, no obvious difference could be identified between Tg for FRP resin and RAFT resin. Additionally, 3D printed samples from FRP-SNPs resins were also analysed via DMA to determine their Tg and G′. The results showed that the variation of Tg was negligible, however, G′ at rubbery state increased from 19 MPa for 3D objects fabricated with the FRP resin to 31 MPa for objects 3D printed using FRP-SNP resins consisting of 10 wt% of MPS-SNPs (ESI, Fig. S5†).
Thermogravimetric analysis (TGA) was also conducted to evaluate the thermal stability of the 3D printed samples. Fig. S7A† shows that thermal degradation takes place at around 310 °C for samples prepared with or without MPS-SNPs. As expected, the incorporation of SNPs did not affect the temperature of decomposition. In addition, after full degradation of polymer matrix, it was found that the residual mass was very close to the designed loading of SNPs, indicating that a uniform incorporation of MPS-SNPs was achieved during the 3D printing process. The same trend was also identified in specimens printed from RAFT-SNP resins (ESI, Fig. S7B†).
Tensile properties of 3D printed samples
Inspired by the significant influence of RAFT agent on polymerization kinetics and DMA results, its effect on the tensile properties of 3D printed dumbbell-shaped specimens was also examined. Fig. 4A compares the stress–strain curves of specimens printed using RAFT resins with varied concentrations of RAFT agent. It was observed that the addition of RAFT agent extended the elongation at break and increased the tensile strength despite a marginal reduction in Young's modulus. For example, the addition of 1.5 wt% RAFT agent increased the elongation at break from 46% to 62% and simultaneously increased the tensile strength from 2.3 MPa to 2.9 MPa (Table 1).
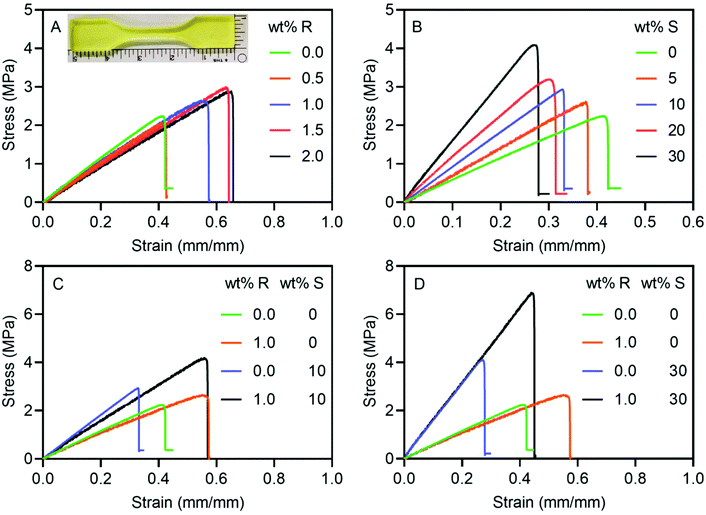 |
| Fig. 4 Tensile properties of dumbbell-shaped specimens. 3D printing performed using (A) variable concentrations of MBTP in RAFT resins, (B) variable concentrations of MPS-SNPs in FRP-SNP resins. (C) Comparison between tensile properties of specimens printed with FRP resin, RAFT resin (1 wt% MBTP), FRP-SNP resin (10 wt% MPS-SNPs), and RAFT-SNP resin (1 wt% MBTP and 10 wt% MPS-SNPs). (D) Comparison between tensile properties of specimens printed with FRP resin, RAFT resin (1 wt% MBTP), FRP-SNP resin (30 wt% MPS-SNPs), and RAFT-SNP resin (1 wt% MBTP and 30 wt% MPS-SNPs). A fixed weight ratio of [HEA] : [PEGDA] : [TPO] = 100 : 50 : 0.75 was applied in all cases. Samples were printed using 0.4 mW cm−2 violet light (λmax = 405 nm) with a layer thickness of 50 μm. | |
Table 1 Summary of the mechanical properties of specimens 3D printed in this work using various neat, SNP composite, RAFT, and RAFT-SNPs composite resins
|
Formula # |
wt% MBTP |
wt% SNPs |
Tensile strength (MPa) |
Young's modulus (MPa) |
Elongation at break (%) |
K
Ic (MPa m1/2) |
FRP resin |
1 |
0.0 |
0 |
2.3 |
6.1 |
46 |
0.35 |
|
RAFT resins |
2 |
0.5 |
0 |
2.0 |
5.6 |
42 |
0.35 |
3 |
1.0 |
0 |
2.6 |
6.1 |
54 |
0.29 |
4 |
1.5 |
0 |
2.9 |
5.8 |
62 |
0.23 |
5 |
2.0 |
0 |
2.9 |
4.8 |
64 |
0.22 |
|
FRP-SNP resins |
6 |
0.0 |
5 |
2.4 |
7.3 |
35 |
0.43 |
7 |
0.0 |
10 |
2.6 |
8.3 |
34 |
0.54 |
8 |
0.0 |
20 |
2.9 |
10.8 |
33 |
0.61 |
9 |
0.0 |
30 |
4.3 |
16.6 |
32 |
0.80 |
|
RAFT-SNP resins |
10 |
1.0 |
10 |
4.5 |
9.2 |
51 |
0.44 |
11 |
1.0 |
30 |
6.9 |
16.3 |
44 |
0.78 |
Subsequently, the effect of MPS-SNPs on the tensile properties of 3D printed samples was investigated. Notably, both Young's modulus and tensile strength increased significantly with the addition of MPS-SNPs (Fig. 4B). For example, Young's modulus (16.6 MPa) and tensile strength (4.3 MPa) for the samples printed with FRP-SNP resins containing 30 wt% of MPS-SNPs were about 2.5 and 1.8 times the values for those 3D printed using FRP resins (Table 1). This enhancement is usually attributed to the large surface area of SNPs as well as the strong interfacial interaction between the fillers and the polymeric matrix.65,73 Especially, silane coupling groups on the surface of SNPs can not only facilitate more homogeneous dispersion, but also enhance the polymer-filler interactions at the interfaces due to the vinyl groups from MPS on the SNP surface.65,74 Despite the increased strength of these composites, the elongation at break consecutively declined with the addition of MPS-SNPs and reduced from 46% for the FRP resin to 32% for the composite material 3D printed with 30 wt% MPS-SNPs (Fig. 4B). This result is in agreement with the studies of composite resins containing different nanoparticles by Lee,17 Wicker14 and Zhang et al.75 The loss of ductility can be a consequence of constrained chain movement by nanofillers within the polymer network.74
Fig. 4C compares the tensile properties of 3D printed dumbbell-shaped specimens using FRP, FRP-SNP, RAFT, and RAFT-SNP resins. Despite the lower Young's modulus, the specimens printed using the RAFT resin (1 wt% MBTP) featured the same tensile strength (2.6 MPa) as those from FRP-SNP resin (10 wt% MPS-SNPs, Table 1), due to the significantly increased ductility. Interestingly, RAFT-SNP composite materials showed a synergistic increase in tensile strength (4.5 MPa) compared with materials formed using only RAFT agent (2.6 MPa) or SNPs (2.6 MPa) alone (Table 1). Furthermore, the materials obtained using the RAFT-SNP resin containing 1 wt% of MBTP and 10 wt% MPS-SNPs showed a dramatically increased elongation at break (51%) compared to samples printed using FRP-SNP resin with 10 wt% MPS-SNPs (34%). Similar trends were observed for the RAFT-SNP resin with 1 wt% MBTP and 30 wt% MPS-SNPs (Fig. 4D), where the inclusion of RAFT increased the elongation at break (44%) and tensile strength (6.9 MPa) compared to the 30 wt% MPS-SNPs FRP-SNPs system (32% and 4.3 MPa). Critically, these results indicate that RAFT agent can efficiently strengthen and improve ductility of photocurable composite materials, independent of the loading of nanofillers.
Fracture toughness of 3D printed specimens
In practice, strong materials often fail under a much lower load than their tensile strength because of the formation and development of microcracks.76 Fracture toughness represents the ability of materials to resist the extension of crack propagation and prevent catastrophic failure that is hard to detect and predict. It is important to note, however, that unlike strength, the fracture toughness of 3D printed materials have been seldom investigated;69,77 a high resistance to crack propagation in a material is critical for real applications as the occurrence of defects cannot be avoided during the manufacture and service life of typical polymer materials.76,78 Therefore, the fracture toughness of the developed 3D printed materials were investigated at room temperature via single-edge notched bending (SENB) tests described in the ASTM D5045-14 standard. Fig. 5A presents a typical specimen 3D printed using RAFT resin (1 wt% MBTP), with the print direction normal to (coming out of) the page. The force required for pre-crack propagation was monitored using a setup shown in Fig. 5B.
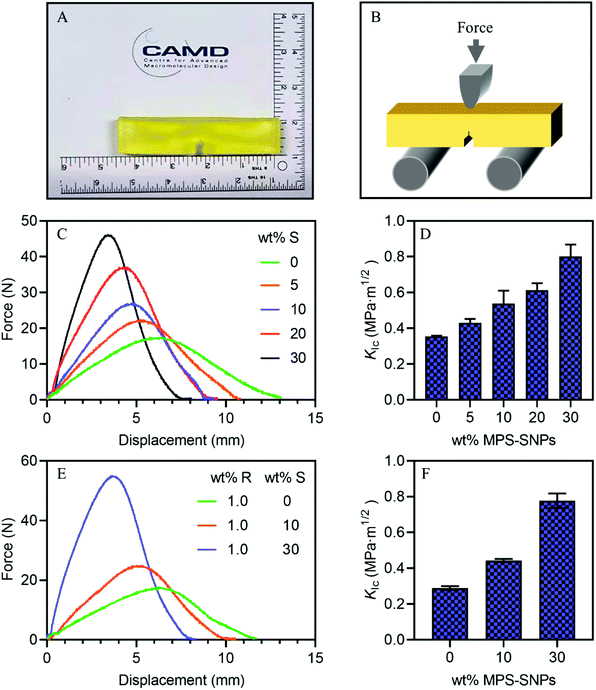 |
| Fig. 5 Investigation of fracture toughness of 3D printed SENB specimens. (A) Typical 3D printed specimen for SENB test using RAFT resin (1 wt% MBTP). Print direction is normal to the page. (B) The setup for SENB test. (C) Load-displacement curves of specimens 3D printed from FRP-SNP resins with variable concentration of MPS-SNPs. (D) KIC values of specimens 3D printed from FRP-SNP resins with variable concentration of MPS-SNPs. (E) Load-displacement curves of specimens 3D printed from RAFT-SNP resins with variable concentration of MPS-SNPs and 1 wt% MBTP. (F) KIC values of specimens 3D printed from RAFT-SNP resins with variable concentration of MPS-SNPs and 1 wt% MBTP. Fixed weight ratio of [HEA] : [PEGDA] : [TPO] = 100 : 50 : 0.75 was applied in all cases. Samples were printed under 0.4 mW cm−2 violet light (λmax = 405 nm) with layer thickness = 50 μm. | |
Fig. 5C compares the load-displacement curves of 3D printed SENB specimens from FRP-SNP resins containing increasing amounts of MPS-SNPs. In general, the load-displacement curves indicate ductile failure from the 3D printed SENB specimens.79 The inclusion of increasing concentrations of MPS-SNPs in the initial resins led to materials with a higher maximum failure load required to induce crack propagation and a reduced final displacement at break. Consequently, the stress-intensity factors (KIC) more than doubled from 0.35 MPa m1/2 for the FRP resin to 0.80 MPa m1/2 for the samples printed using FRP-SNP resin with 30 wt% of MPS-SNPs (Fig. 5D). The increased fracture toughness of the specimens from FRP-SNP resins was attributed to many factors including polymer/filler interfacial interactions, attraction among nanoparticles, as well as the movement of fillers and polymer chains.74
The fracture toughness of 3D printed objects prepared with RAFT resins was also examined by the SENB test. With increasing concentrations of RAFT agent in the RAFT resins, the resulting materials showed slightly reduced KIC values (Table 1). To examine the toughening effect of SNPs in the presence of RAFT agents, RAFT-SNPs resins consisting of 1 wt% MBTP and 0, 10, or 30 wt% of MPS-SNPs were applied to fabricate SENB specimens. It was found that the Fmax increased from 17 N for the material made with RAFT resin (0 wt% MPS-SNPs) to 25 and 55 N for materials made with RAFT-SNPs resins with 10 and 30 wt% MPS-SNPs, respectively (Fig. 5E). As a result, the KIC values for the SENB specimens increased from 0.29 MPa m1/2 for the RAFT resin to 0.44 and 0.78 MPa m1/2 for the 10 and 30 wt% RAFT-SNP resins, respectively. The increased KIC values represent a respective increase of 150% and 270% for the RAFT-SNP resins, verifying the effectiveness of MPS-SNPs for toughening the RAFT system (Fig. 5F). It was also found that the KIC values for RAFT-SNP composites were very similar to those from FRP-SNP resins, indicating the negligible effect of RAFT agent on the fracture toughness of the studied composite systems (Table 1).
To evaluate the filler dispersion in the polymer matrix and investigate the toughening mechanism, the fractography of the SENB specimens was observed using SEM. For specimens fabricated from FRP resin, the fracture surface was rather flat with no distinguished features (ESI, Fig. S8A†). Comparatively, the 3D printed samples from FRP-SNP resins containing 10 wt% MPS-SNPs displayed localized shear bands of polymer matrix caused by stress concentrations around the periphery of SNPs, and microvoids on the relatively rough fracture surface with randomly distributed SNPs (Fig. 6A). Together, these results are indicative of a more energy-dissipative fracture mode.80 Additionally, some nanovoids remained in the SNP concentrated region due to the particle-polymer debonding, which also contributed to prohibition of crack propagation.80 Indeed, MPS modified nanosized SNPs can yield stronger interfacial adhesion than unmodified SNPs, and therefore contribute to a higher energy debonding processes.81Fig. 6B shows the fracture surface of the composite materials prepared using the FRP-SNP resin with a weight loading of 30 wt% MPS-SNPs, on which the more abundant SNPs were homogeneously dispersed and significantly increased amount of nanovoids were observed. As such, it can be concluded that much more energy was required for SNP debonding and subsequent plastic void growth, resulting in a significant increase in fracture toughness. In the RAFT-SNP (1 wt% MBTP) system containing 10 or 30 wt% MPS-SNPs (Fig. 6C and D), similar fractography to the corresponding SNP composites was observed, indicating the negligible role of RAFT on improving the fracture toughness.
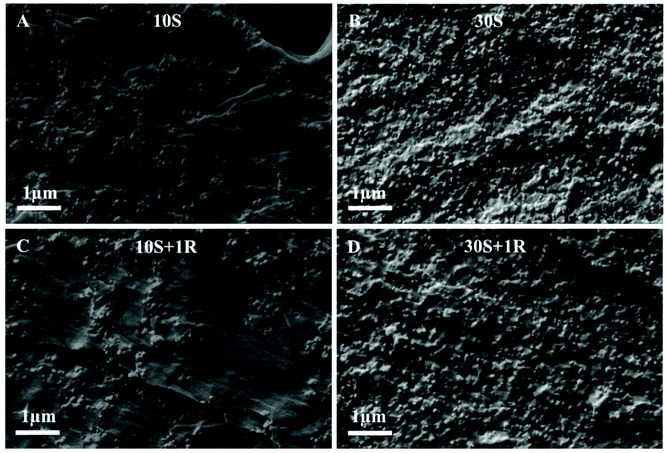 |
| Fig. 6 SEM images of the fracture surface of composite specimens 3D objects printed using (A) FRP-SNP resin containing 10 wt% MPS-SNPs, (B) FRP-SNP resin containing 30 wt% MPS-SNPs, (C) RAFT-SNP resin containing 10 wt% MPS-SNPs and 1 wt% MBTP, and (D) RAFT-SNP resin containing 30 wt% MPS-SNPs and 1 wt% MBTP. | |
3D printing complex objects and RAFT agent mediated surface modification
To design practically applicable photocurable resins, one of the most important criteria is high resolution during 3D printing process.82,83 The developed FRP-SNP resin (10 wt% MPS-SNPs), RAFT resin (1 wt% MBTP), and RAFT-SNP resin (1 wt% MBTP and 10 wt% MPS-SNPs) were thus applied to fabricate complex 3D structures to evaluate their resolution. Fig. 7A–C present the 3D printed lattice structures using FRP-SNP, RAFT and RAFT-SNP resins. Different curing times were applied according to the polymerization kinetics of these systems (ESI, Table S1†). To simplify the fabrication process, 4 bottom layers with extended curing time (120 s) were applied to ensure sufficient adhesion of printed objects toward the building platform without the addition of extra supports to the original 3D model. As a result, the bottom area of the lattice structure fabricated from the FRP-SNP resin (Fig. 7A) appeared to be overcured due to the fast polymerization rate of this system. On the other hand, this issue was not observed in the lattice structures fabricated using RAFT or RAFT-SNP resins. The effect of RAFT agent on preventing overcuring and improving resolution has been reported previously.38,56 Indeed, the RAFT agent can partially function as a dye to absorb the scattered light (ESI, Fig. S2†) and prevent undesired gelation outside of the irradiated areas.38,56,84
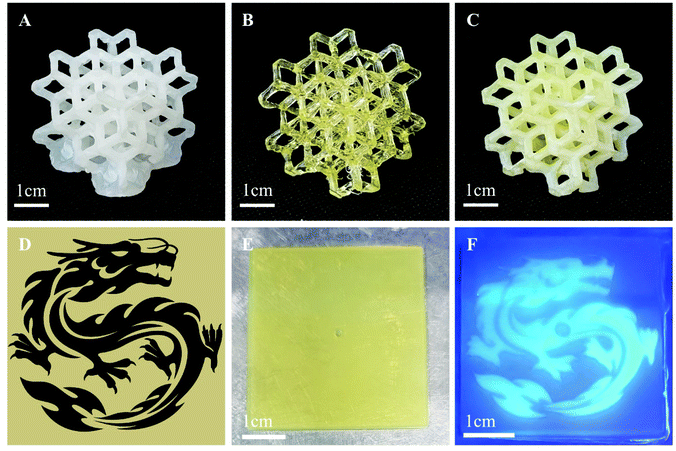 |
| Fig. 7 3D printing of complex structures and surface modification of printed parts. (A) Lattice structure 3D printed using FRP-SNP resin (10 wt% MPS-SNPs). (B) Lattice structure 3D printed using RAFT resin (1 wt% MBTP). (C) Lattice structure 3D printed using RAFT-SNP resin (1 wt% MBTP and 10 wt% MPS-SNPs). (D) Original dragon pattern applied for surface modification of 3D printed substrate. (E) Surface-modified substrate 3D printed using RAFT-SNP resin (1 wt% MBTP and 10 wt% MPS-SNPs) under white light. (F) Surface-modified substrate 3D printed using RAFT-SNP resin (1 wt% MBTP and 10 wt% MPS-SNPs) under UV light (λ = 312 nm). A fixed weight ratio of [HEA] : [PEGDA] : [TPO] = 100 : 50 : 0.75 was applied in all cases. Samples were printed under 0.4 mW cm−2 violet light (λmax = 405 nm) with layer thickness = 50 μm. | |
Accompanied by enhanced mechanical properties, the introduction of inorganic nanoparticles into photocurable resins inevitably changes the surface properties of 3D printed objects.85 RAFT polymerization has been widely applied in many studies to provide an efficient tool for the modification of surface properties relying on the dormant thiocarbonylthio species.86–89 In an attempt to independently control mechanical and surface properties, reactivation of dormant RAFT agent at the surface of the 3D objects from RAFT-SNPs materials (1 wt% MBTP and 10 wt% MPS-SNPs) was examined. Specifically, a 3D printed square prism with dimensions 40 × 40 × 1 mm (l, w, t) was modified with the fluorescent monomer 1-pyrene methyl methacrylate (PyMMA) utilizing the reported method by our group (Scheme S1†).56 Briefly, the square prism was 3D printed and kept on the build platform, washed with ethanol, and post-cured under 405 nm light to remove unreacted vinyl bonds prior to surface modification. Subsequently, the post-cured object was modified using a dilute reagent mixture containing 15 wt% total monomer in DMF, at a ratio [PyMMA]
:
[HEA]
:
[TPO] = 40
:
960
:
10. A single layer 3D printing program (tc = 180s) of the designed dragon pattern (Fig. 7D) was used to spatially confine the surface functionalization. The surface functionalized 3D printed objects were then washed with ethanol and dried before investigation. Fig. 7E displays the surface functionalized composite materials under white light, with no observable surface patterning. Under 312 nm irradiation, the modified composite material showed a detailed reproduction of the original design via the fluorescent PyMMA moieties in the grafted polymer, demonstrating the excellent spatial control of the applied surface functionalization technique for the developed composite material (Fig. 7F). In contrast, when FRP-SNP composite resins (with 10 wt% MPS-SNPs) were used for an analogous surface functionalization, details of the dragon were not well produced owing to the lack of polymerization control (ESI, Fig. S9†). In this case, some fluorescence was observed, presumably due to physical adsorption of the uncontrolled fluorescent polymers to the surface. Regardless, the inclusion of RAFT agents in the 3D printed material clearly plays a key role in providing high resolution spatial control over the surface functionalization process.
Conclusion
In this work, photocurable resins consisting of varied concentrations of RAFT agents and MPS-SNPs were developed and successfully 3D printed. The resulting 3D printed materials displayed tuneable mechanical properties and also provided reactive functional handles, i.e., thiocarbonylthio groups, for post-fabrication modification. The inclusion of MPS-SNPs into 3D printing resins simultaneously enhanced the tensile properties and fracture toughness of the resulting 3D printed specimens. An SEM study of fractography revealed homogeneously distributed SNPs in the resin matrix and the rough fracture surfaces with ductile shear bands, microvoids, nanosized particle-matrix debonding sites that all contributed to significant toughening in the FRP-SNP and RAFT-SNP materials. Interestingly, inclusion of RAFT agents in the 3D printing resins resulted in noticeable increase of elongation at break and tensile strength for materials 3D printed using RAFT and RAFT-SNP resins, indicating the advantages of constructing homogenous polymer networks with concurrently increased strength and ductility; this behaviour presents a significant benefit over previous SNP polymer composites that display increased strength at the cost of reduced ductility.
In addition, 3D printed composite materials fabricated using RAFT-SNP resins displayed improved resolution compared to materials fabricated using FRP-SNP resins. The presence of thiocarbonylthio end groups on the surfaces of these 3D printed RAFT-SNP composite materials also allowed a facile route to obtain spatially controlled, high resolution surface modification under violet light irradiation. Based on this preliminary work, the combined adoption of nanoparticles and RAFT polymerization for photoinduced 3D printing could extensively expand the ability to produce materials with multiple independently tuneable functionalities such as high strength, high toughness, higher ductility and other non-mechanical performance enhancements.
Conflicts of interest
There are no conflicts to declare.
Acknowledgements
This work was supported by the Australian Research Council and UNSW Australia via Discovery Research program (DP190100067 and DP210100094). We acknowledge the facilities and technical assistance provided by Dr Yin Yao and the Mark Wainwright Analytical Centre at UNSW Sydney.
References
- S. C. Ligon, R. Liska, J. Stampfl, M. Gurr and R. Mulhaupt, Polymers for 3D Printing and Customized Additive Manufacturing, Chem. Rev., 2017, 117(15), 10212–10290 CrossRef CAS PubMed.
- H. Quan, T. Zhang, H. Xu, S. Luo, J. Nie and X. Zhu, Photo-curing 3D printing technique and its challenges, Bioact. Mater., 2020, 5(1), 110–115 CrossRef.
- X. Wang, M. Jiang, Z. Zhou, J. Gou and D. Hui, 3D printing of polymer matrix composites: A review and prospective, Composites, Part B, 2017, 110, 442–458 CrossRef CAS.
- T. Ngo, A. Kashani, G. Imbalzano, K. Nguyen and D. Hui, Additive manufacturing (3D printing): A review of materials, methods, applications and challenges, Composites, Part B, 2018, 143, 172–196 CrossRef CAS.
- K. Jung, N. Corrigan, M. Ciftci, J. Xu, S. E. Seo, C. J. Hawker and C. Boyer, Designing with Light: Advanced 2D, 3D, and 4D Materials, Adv. Mater., 2020, 32, 1903850 CrossRef CAS.
- G. A. Appuhamillage, N. Chartrain, V. Meenakshisundaram, K. D. Feller, C. B. Williams and T. E. Long, 110th anniversary: Vat photopolymerization-based additive manufacturing: Current trends and future directions in materials design, Ind. Eng. Chem. Res., 2019, 58(33), 15109–15118 CrossRef CAS.
- T. J. Wallin, J. H. Pikul, S. Bodkhe, B. N. Peele, B. C. Mac Murray, D. Therriault, B. W. McEnerney, R. P. Dillon, E. P. Giannelis and R. F. Shepherd, Click chemistry stereolithography for soft robots that self-heal, J. Mater. Chem. B, 2017, 5(31), 6249–6255 RSC.
- H. Cui, R. Hensleigh, D. Yao, D. Maurya, P. Kumar, M. G. Kang, S. Priya and X. R. Zheng, Three-dimensional printing of piezoelectric materials with designed anisotropy and directional response, Nat. Mater., 2019, 18(3), 234–241 CrossRef CAS PubMed.
- Z. Biao, K. Kavin, S. Ahmad, L. D. Martin and G. Qi, Reprocessable thermosets for sustainable three-dimensional printing, Nat. Commun., 2018, 9(1), 1–7 CrossRef.
- X. Kuang, K. Chen, C. K. Dunn, J. Wu, V. C. Li and H. J. Qi, 3D printing of highly stretchable, shape-memory, and self-healing elastomer toward novel 4D printing, ACS Appl. Mater. Interfaces, 2018, 10(8), 7381–7388 CrossRef CAS PubMed.
- S. Dutta and D. Cohn, Temperature and pH responsive 3D printed scaffolds, J. Mater. Chem. B, 2017, 5(48), 9514–9521 RSC.
- Q. Ge, A. H. Sakhaei, H. Lee, C. K. Dunn, N. X. Fang and M. L. Dunn, Multimaterial 4D Printing with Tailorable Shape Memory Polymers, Sci. Rep., 2016, 6(1), 31110 CrossRef PubMed.
- T. Zheng, W. Wang, J. Sun, J. Liu and J. Bai, Development and evaluation of Al2O3–ZrO2 composite processed by digital light 3D printing, Ceram. Int., 2020, 46(7), 8682–8688 CrossRef CAS.
- J. H. Sandoval and R. B. Wicker, Functionalizing stereolithography resins: effects of dispersed multi–walled carbon nanotubes on physical properties, Rapid Prototyp. J., 2006, 12(5), 292–303 CrossRef.
- Y. Li, Z. Feng, L. Huang, K. Essa, E. Bilotti, H. Zhang, T. Peijs and L. Hao, Additive manufacturing high performance graphene-based composites: A review, Composites, Part A, 2019, 124, 105483 CrossRef CAS.
- Z. Weng, Y. Zhou, W. Lin, T. Senthil and L. Wu, Structure-property
relationship of nano enhanced stereolithography resin for desktop SLA 3D printer, Composites, Part A, 2016, 88, 234–242 CrossRef CAS.
- G. Jeong, C. H. Park, B.-Y. Kim, J. Kim, S.-D. Park, H. Yang and W. S. Lee, Photocurable Elastomer Composites with SiO2-Mediated Cross-Links for Mechanically Durable 3D Printing Materials, ACS Appl. Polym. Mater., 2020, 2(11), 5228–5237 CrossRef CAS.
- N. Corrigan and C. Boyer, In the Limelight: 2D and 3D Materials via Photo-Controlled Radical Polymerization, Trends Chem., 2020, 2(8), 689–706 CrossRef CAS.
- Y. Gu, J. Zhao and J. A. Johnson, Polymer Networks: From Plastics and Gels to Porous Frameworks, Angew. Chem., 2020, 59(13), 5022–5049 CrossRef CAS.
- G. Moad, RAFT (Reversible addition–fragmentation chain transfer) crosslinking (co) polymerization of multi–olefinic monomers to form polymer networks, Polym. Int., 2015, 64(1), 15–24 CrossRef CAS.
- K. Parkatzidis, H. S. Wang, N. P. Truong and A. Anastasaki, Recent Developments and Future Challenges in Controlled Radical Polymerization: A 2020 Update, Chem, 2020, 6(7), 1575–1588 CAS.
- N. Corrigan, K. Jung, G. Moad, C. J. Hawker, K. Matyjaszewski and C. Boyer, Reversible-deactivation radical polymerization (Controlled/living radical polymerization): From discovery to materials design and applications, Prog. Polym. Sci., 2020, 111, 101311 CrossRef CAS.
- K. Matyjaszewski and J. Spanswick, Controlled/living radical polymerization, Mater. Today, 2005, 8(3), 26–33 CrossRef CAS.
- G. Moad, E. Rizzardo and S. H. Thang, Toward Living Radical Polymerization, Acc. Chem. Res., 2008, 41(9), 1133–1142 CrossRef CAS PubMed.
- Y. Zhao, M. Ma, X. Lin and M. Chen, Photoorganocatalyzed Divergent Reversible–Deactivation Radical Polymerization towards Linear and Branched Fluoropolymers, Angew. Chem., 2020, 132(48), 21654–21658 CrossRef.
- A. Anastasaki, V. Nikolaou, G. Nurumbetov, P. Wilson, K. Kempe, J. F. Quinn, T. P. Davis, M. R. Whittaker and D. M. Haddleton, Cu(0)-Mediated Living Radical Polymerization: A Versatile Tool for Materials Synthesis, Chem. Rev., 2016, 116(3), 835–877 CrossRef CAS.
- V. Percec, T. Guliashvili, J. S. Ladislaw, A. Wistrand, A. Stjerndahl, M. J. Sienkowska, M. J. Monteiro and S. Sahoo, Ultrafast Synthesis of Ultrahigh Molar Mass Polymers by Metal-Catalyzed Living Radical Polymerization of Acrylates, Methacrylates, and Vinyl Chloride Mediated by SET at 25 °C, J. Am. Chem. Soc., 2006, 128(43), 14156–14165 CrossRef CAS PubMed.
- D. J. Siegwart, J. K. Oh and K. Matyjaszewski, ATRP in the design of functional materials for biomedical applications, Prog. Polym. Sci., 2012, 37(1), 18–37 CrossRef CAS PubMed.
- K. Matyjaszewski, Advanced Materials by Atom Transfer Radical Polymerization, Adv. Mater., 2018, 30(23), 1706441 CrossRef PubMed.
- M. Ouchi and M. Sawamoto, 50th Anniversary Perspective: Metal-Catalyzed Living Radical Polymerization: Discovery and Perspective, Macromolecules, 2017, 50(7), 2603–2614 CrossRef CAS.
- G. Moad, E. Rizzardo and S. H. Thang, Living Radical Polymerization by the RAFT Process, Aust. J. Chem., 2005, 58(6), 379–410 CrossRef CAS.
- G. Moad, J. Chiefari, Y. K. Chong, J. Krstina, R. T. A. Mayadunne, A. Postma, E. Rizzardo and S. H. Thang, Living free radical polymerization with reversible addition – fragmentation chain transfer (the life of RAFT), Polym. Int., 2000, 49(9), 993–1001 CrossRef CAS.
- M. R. Hill, R. N. Carmean and B. S. Sumerlin, Expanding the Scope of RAFT Polymerization: Recent Advances and New Horizons, Macromolecules, 2015, 48(16), 5459–5469 CrossRef CAS.
- S. Perrier, 50th Anniversary Perspective: RAFT Polymerization—A User Guide, Macromolecules, 2017, 50(19), 7433–7447 CrossRef CAS.
- Y. Qiang, W. Li and A.-C. Shi, Stabilizing Phases of Block Copolymers with Gigantic Spheres via Designed Chain Architectures, ACS Macro Lett., 2020, 9(5), 668–673 CrossRef CAS.
- K. Hakobyan, T. Gegenhuber, C. S. P. McErlean and M. Müllner, Visible-Light-Driven MADIX Polymerisation via a Reusable, Low-Cost, and Non-Toxic Bismuth Oxide Photocatalyst, Angew. Chem., Int. Ed., 2019, 58(6), 1828–1832 CrossRef CAS PubMed.
- Q. Quan, M. Ma, Z. Wang, Y. Gu and M. Chen, Visible–Light–Enabled Organocatalyzed Controlled Alternating Terpolymerization of Perfluorinated Vinyl Ethers, Angew. Chem., Int. Ed., 2021, 60, 20443–20451 CrossRef CAS.
- B. J. Green and C. A. Guymon, Modification of mechanical properties and resolution of printed stereolithographic objects through RAFT agent incorporation, Addit. Manuf., 2019, 27, 20–31 CAS.
- D. H. Solomon, Genesis of the CSIRO polymer group and the discovery and significance of nitroxide-mediated living radical polymerization, J. Polym. Sci., Part A: Polym. Chem., 2005, 43(23), 5748–5764 CrossRef CAS.
- C. J. Hawker, A. W. Bosman and E. Harth, New Polymer Synthesis by Nitroxide Mediated Living Radical Polymerizations, Chem. Rev., 2001, 101(12), 3661–3688 CrossRef CAS PubMed.
- J. Nicolas, Y. Guillaneuf, C. Lefay, D. Bertin, D. Gigmes and B. Charleux, Nitroxide-mediated polymerization, Prog. Polym. Sci., 2013, 38(1), 63–235 CrossRef CAS.
- S. Yamago, Precision Polymer Synthesis by Degenerative Transfer Controlled/Living Radical Polymerization Using Organotellurium, Organostibine, and Organobismuthine Chain-Transfer Agents, Chem. Rev., 2009, 109(11), 5051–5068 CrossRef CAS PubMed.
- A. Debuigne, R. Poli, C. Jérôme, R. Jérôme and C. Detrembleur, Overview of cobalt-mediated radical polymerization: Roots, state of the art and future prospects, Prog. Polym. Sci., 2009, 34(3), 211–239 CrossRef CAS.
- J. Sarkar, L. Xiao and A. Goto, Living Radical Polymerization with Alkali and Alkaline Earth Metal Iodides as Catalysts, Macromolecules, 2016, 49(14), 5033–5042 CrossRef CAS.
- A. R. Wang and S. Zhu, Branching and gelation in atom transfer radical polymerization of methyl methacrylate and ethylene glycol dimethacrylate, Polym. Eng. Sci., 2005, 45(5), 720–727 CrossRef CAS.
- H. Gao, P. Polanowski and K. Matyjaszewski, Gelation in living copolymerization of monomer and divinyl cross-linker: Comparison of ATRP experiments with Monte Carlo simulations, Macromolecules, 2009, 42(16), 5925–5932 CrossRef CAS.
- J. Cuthbert, A. C. Balazs, T. Kowalewski and K. Matyjaszewski, STEM Gels by Controlled Radical Polymerization, Trends Chem., 2020, 2(4), 341–353 CrossRef CAS.
- Y. Amamoto, J. Kamada, H. Otsuka, A. Takahara and K. Matyjaszewski, Repeatable photoinduced self–healing of covalently cross–linked polymers through reshuffling of trithiocarbonate units, Angew. Chem., Int. Ed., 2011, 50(7), 1660–1663 CrossRef CAS PubMed.
- P. Wen, Y. Zhao, Z. Wang, J. Lin, M. Chen and X. Lin, Solvent-Free Synthesis of the Polymer Electrolyte via Photo-Controlled Radical Polymerization: Toward Ultrafast In-Built Fabrication of Solid-State Batteries under Visible Light, ACS Appl. Mater. Interfaces, 2021, 13(7), 8426–8434 CrossRef CAS PubMed.
- Q. Yu, Y. Zhu, Y. Ding and S. Zhu, Reaction Behavior and Network Development in RAFT Radical Polymerization of Dimethacrylates, Macromol. Chem. Phys., 2008, 209(5), 551–556 CrossRef CAS.
- R. Henkel and P. Vana, The Influence of RAFT on the Microstructure and the Mechanical Properties of Photopolymerized Poly (butyl acrylate) Networks, Macromol. Chem. Phys., 2014, 215(2), 182–189 CrossRef CAS.
- R. Nicolay, J. Kamada, A. Van Wassen and K. Matyjaszewski, Responsive gels based on a dynamic covalent trithiocarbonate cross-linker, Macromolecules, 2010, 43(9), 4355–4361 CrossRef CAS.
- M. Chen, Y. Gu, A. Singh, M. Zhong, A. M. Jordan, S. Biswas, L. T. J. Korley, A. C. Balazs and J. A. Johnson, Living Additive Manufacturing: Transformation of Parent Gels into Diversely Functionalized Daughter Gels Made Possible by Visible Light Photoredox Catalysis, ACS Cent. Sci., 2017, 3(2), 124–134 CrossRef CAS PubMed.
- G. M. Scheutz, J. L. Rowell, S. T. Ellison, J. B. Garrison, T. E. Angelini and B. S. Sumerlin, Harnessing Strained Disulfides for Photocurable Adaptable Hydrogels, Macromolecules, 2020, 53(10), 4038–4046 CrossRef CAS.
- M. W. Lampley and E. Harth, Photocontrolled Growth of Cross-Linked Nanonetworks, ACS Macro Lett., 2018, 7(6), 745–750 CrossRef CAS.
- K. Lee, N. Corrigan and C. Boyer, Rapid High-Resolution 3D Printing and Surface Functionalization via Type I Photoinitiated RAFT Polymerization, Angew. Chem., 2021, 60(16), 8839–8850 CrossRef CAS PubMed.
- A. Bagheri, C. M. Fellows and C. Boyer, Reversible Deactivation Radical Polymerization: From Polymer Network Synthesis to 3D Printing, Adv. Sci., 2021, 8(5), 2003701 CrossRef CAS PubMed.
-
(a) L. Zhang, X. Shi, Z. Zhang, R. P. Kuchel, R. Namivandi-Zangeneh, N. Corrigan, K. Jung, K. Liang and C. Boyer, Porphyrinic Zirconium Metal–Organic Frameworks (MOFs) as Heterogeneous Photocatalysts for PET–RAFT Polymerization and Stereolithography, Angew. Chem., 2021, 133(10), 5549–5556 CrossRef;
(b) L. Zhang, G. Ng, N. Kapoor-Kaushik, X. Shi, N. Corrigan, R. Webster, K. Jung and C. Boyer, 2D Porphyrinic Metal–Organic Framework Nanosheets as Multidimensional Photocatalysts for Functional Materials, Angew. Chem., 2021, 60(42), 22664–22671 CrossRef CAS PubMed.
- A. Bagheri, C. W. A. Bainbridge, K. E. Engel, G. G. Qiao, J. Xu, C. Boyer and J. Jin, Oxygen Tolerant PET-RAFT Facilitated 3D Printing of Polymeric Materials under Visible LEDs, ACS Appl. Polym. Mater., 2020, 2(2), 782–790 CrossRef CAS.
- A. Bagheri, K. E. Engel, C. W. A. Bainbridge, J. Xu, C. Boyer and J. Jin, 3D printing of polymeric materials based on photo-RAFT polymerization, Polym. Chem., 2020, 11(3), 641–647 RSC.
-
A. Bagheri and J. Jin, in 3D Printing with Light. In Chapter 9 3D printing mediated by photoRAFT polymerization process, ed. X. Pu and Z. Jing, De Gruyter, 2021, pp. 295–316 Search PubMed.
- Z. Zhang, N. Corrigan, A. Bagheri, J. Jin and C. Boyer, A Versatile 3D and 4D Printing System through Photocontrolled RAFT Polymerization, Angew. Chem., 2019, 131(50), 18122–18131 CrossRef.
- C. Gorsche, K. Seidler, P. Knaack, P. Dorfinger, T. Koch, J. Stampfl, N. Moszner and R. Liska, Rapid formation of regulated methacrylate networks yielding tough materials for lithography-based 3D printing, Polym. Chem., 2016, 7(11), 2009–2014 RSC.
- X. Shi, J. Zhang, N. Corrigan and C. Boyer, PET-RAFT facilitated 3D printable resins with multifunctional RAFT agents, Mater. Chem. Front., 2021, 5(5), 2271–2282 RSC.
- M. Du and Y. Zheng, Modification of silica nanoparticles and their application in UDMA dental polymeric composites, Polym. Compos., 2007, 28(2), 198–207 CrossRef CAS.
- I. D. Sideridou and M. M. Karabela, Effect of the amount of 3-methacyloxypropyltrimethoxysilane coupling agent on physical properties of dental resin nanocomposites, Dent. Mater., 2009, 25(11), 1315–1324 CrossRef CAS PubMed.
- J. Ma, M.-S. Mo, X.-S. Du, P. Rosso, K. Friedrich and H.-C. Kuan, Effect of inorganic nanoparticles on mechanical property, fracture toughness and toughening mechanism of
two epoxy systems, Polymer, 2008, 49(16), 3510–3523 CrossRef CAS.
- D. Zhuo, Y. Ruan, X. Zhao and R. Ran, Kinetics of UV-initiated RAFT crosslinking polymerization of dimethacrylates, J. Appl. Polym. Sci., 2011, 121(2), 660–665 CrossRef CAS.
- Y. Y. C. Choong, S. Maleksaeedi, H. Eng, S. Yu, J. Wei and P.-C. Su, High speed 4D printing of shape memory polymers with nanosilica, Appl. Mater. Today, 2020, 18, 100515 CrossRef.
-
K. Matyjaszewski and T. P. Davis, Handbook of radical polymerization, John Wiley & Sons, 2003 Search PubMed.
- L. J. Tan, W. Zhu and K. Zhou, Recent progress on polymer materials for additive manufacturing, Adv. Funct. Mater., 2020, 30(43), 2003062 CrossRef CAS.
- C. Decker, Photoinitiated crosslinking polymerisation, Prog. Polym. Sci., 1996, 21(4), 593–650 CrossRef CAS.
- M. Gurr, D. Hofmann, M. Ehm, Y. Thomann, R. Kübler and R. Mülhaupt, Acrylic nanocomposite resins for use in stereolithography and structural light modulation based rapid prototyping and rapid manufacturing technologies, Adv. Funct. Mater., 2008, 18(16), 2390–2397 CrossRef CAS.
- J. Yang, J.-J. Zhao, C.-R. Han and J.-F. Duan, Keys to enhancing mechanical properties of silica nanoparticle composites hydrogels: the role of network structure and interfacial interactions, Compos. Sci. Technol., 2014, 95, 1–7 CrossRef CAS.
- Q. Mu, L. Wang, C. K. Dunn, X. Kuang, F. Duan, Z. Zhang, H. J. Qi and T. Wang, Digital light processing 3D printing of conductive complex structures, Addit. Manuf., 2017, 18, 74–83 CAS.
- M. E. Launey and R. O. Ritchie, On the fracture toughness of advanced materials, Adv. Mater., 2009, 21(20), 2103–2110 CrossRef CAS.
- E. Shukrun, I. Cooperstein and S. Magdassi, 3D-Printed Organic–Ceramic Complex Hybrid Structures with High Silica Content, Adv. Sci., 2018, 5(8), 1800061 CrossRef PubMed.
- R. O. Ritchie, The conflicts between strength and toughness, Nat. Mater., 2011, 10(11), 817–822 CrossRef CAS PubMed.
- A. Van der Wal, J. Mulder and R. Gaymans, Fracture of polypropylene: The effect of crystallinity, Polymer, 1998, 39(22), 5477–5481 CrossRef CAS.
- H. Zhang, L.-C. Tang, Z. Zhang, K. Friedrich and S. Sprenger, Fracture behaviours of in situ silica nanoparticle-filled epoxy at different temperatures, Polymer, 2008, 49(17), 3816–3825 CrossRef CAS.
- J. Lee and A. Yee, Inorganic particle toughening I: micro-mechanical deformations in the fracture of glass bead filled epoxies, Polymer, 2001, 42(2), 577–588 CrossRef CAS.
- J. Stampfl, S. Baudis, C. Heller, R. Liska, A. Neumeister, R. Kling, A. Ostendorf and M. Spitzbart, Photopolymers with tunable mechanical properties processed by laser-based high-resolution stereolithography, J. Micromech. Microeng., 2008, 18(12), 125014 CrossRef.
- D. Ahn, L. M. Stevens, K. Zhou and Z. A. Page, Rapid High-Resolution Visible Light 3D Printing, ACS Cent. Sci., 2020, 6(9), 1555–1563 CrossRef CAS PubMed.
- C. S. Pfeifer, N. D. Wilson, Z. R. Shelton and J. W. Stansbury, Delayed gelation through chain-transfer reactions: mechanism for stress reduction in methacrylate networks, Polymer, 2011, 52(15), 3295–3303 CrossRef CAS PubMed.
- M. Parvinzadeh, S. Moradian, A. Rashidi and M.-E. Yazdanshenas, Effect of the addition of modified nanoclays on the surface properties of the resultant polyethylene terephthalate/clay nanocomposites, Polym.-Plast. Technol. Eng., 2010, 49(9), 874–884 CrossRef CAS.
- T. Ameringer, F. Ercole, K. M. Tsang, B. R. Coad, X. Hou, A. Rodda, D. R. Nisbet, H. Thissen, R. A. Evans and L. Meagher, Surface grafting of electrospun fibers using ATRP and RAFT for the control of biointerfacial interactions, Biointerphases, 2013, 8(1), 16 CrossRef PubMed.
- F. Audouin and A. Heise, Surface-initiated RAFT polymerization of NIPAM from monolithic macroporous polyHIPE, Eur. Polym. J., 2013, 49(5), 1073–1079 CrossRef CAS.
- K. J. Barlow, X. Hao, T. C. Hughes, O. E. Hutt, A. Polyzos, K. A. Turner and G. Moad, Porous, functional, poly (styrene-co-divinylbenzene) monoliths by RAFT polymerization, Polym. Chem., 2014, 5(3), 722–732 RSC.
- Q. Ma, H. Zhang, J. Zhao and Y.-K. Gong, Fabrication of cell outer membrane mimetic polymer brush on polysulfone surface via RAFT technique, Appl. Surf. Sci., 2012, 258(24), 9711–9717 CrossRef CAS.
Footnote |
† Electronic supplementary information (ESI) available: Materials and method, Fig. S1–S9, Scheme S1 and Table S1. See DOI: 10.1039/d1py01283e |
|
This journal is © The Royal Society of Chemistry 2022 |
Click here to see how this site uses Cookies. View our privacy policy here.