DOI:
10.1039/C8QM00104A
(Research Article)
Mater. Chem. Front., 2018,
2, 1397-1402
High performance low dielectric polysiloxanes with high thermostability and low water uptake†
Received
13th March 2018
, Accepted 24th May 2018
First published on 24th May 2018
Abstract
Two novel low dielectric polysiloxanes with high thermostability and low water uptake were developed. These polymers were formed via a thermo-crosslinking reaction of two BCB-containing organosiloxanes. They exhibited dielectric constants (Dk) of less than 2.60 for frequencies ranging from 0.15 to 30.0 MHz, and good thermostability with a 5% weight loss temperature of up to 460 °C. In particular, the polymer derived from a monomer containing three BCB units displayed a Tg of 350 °C. These polymers exhibited water uptakes of less than 0.20% when they were immersed in boiling water for 72 h. These data reflect that these polysiloxanes are suitable as high performance low dielectric resins in the microelectronics industry.
Introduction
Polymers and oligomers containing benzocyclobutene (BCB) moieties have attracted much attention in the past few decades because they can yield cross-linked networks with high thermostability, and satisfactory mechanical and dielectric properties via a direct thermo-polymerization undergoing a ring-opening reaction of the four-membered-ring on the BCB units.1–15 These materials also exhibit desirable film-forming ability resulting in very low roughness and high hydrophobicity of the formed films. Hence, they have been well investigated and widely used in the microelectronics industry as encapsulation resins. Among various BCB-based polymers and macromolecules, those containing siloxane units have gathered increasing interest in recent years.16–22 The reason is that the combination of the good toughness of organic siloxanes and the high thermostability of BCB-containing resins can endow the polymers with excellent physical and chemical properties. Moreover, introducing BCB units to a siloxane succeeds in facilitating the preparation of organic siloxanes because BCB units can directly convert to a cross-linking network evolving no volatile components, requiring no solvents and catalysts.15,23 However, some organic siloxanes prepared from the conventional procedures usually involve –Si–OH or –CH2–CH2– groups in their main chains, which have negative effects on the thermal and dielectric properties of the materials.24–27 It is noted that the Piers–Rubinsztajn reaction can easily produce organosiloxanes excluding the above mentioned unfavourable groups.28 In particular, these organosiloxanes are generated by adding only a catalytic amount (about 0.5 mol% or even less) of B(C6F5)3. Inspired by this reaction, we design and synthesize two new siloxanes with BCB units, namely M1 and M2, whose chemical structures are exhibited in Scheme 1. These BCB-functionalized siloxanes are readily converted into cross-linked polysiloxanes at high temperature, and their cross-linked thermosets showed an average dielectric constant (Dk) below 2.60 for frequencies ranging from 0.15 to 30.0 MHz. These results are better than those of the reported BCB-functionalized siloxanes prepared from alcoholysis and hydrolysis.16,18 Moreover, these cross-linked polysiloxanes exhibited a high Tg over 200 °C and even as high as 350 °C (a TMA result). These data indicate that the Piers–Rubinsztajn reaction offers a satisfying chemical structure to the BCB-functionalized siloxanes. That is to say, the Piers–Rubinsztajn reaction is suitable for the production of the high performance organic siloxanes, and the formed resins have potential applications in the electronics and microelectronics industry as the encapsulation resins and the precursors of matrix resins. Here, we report the details.
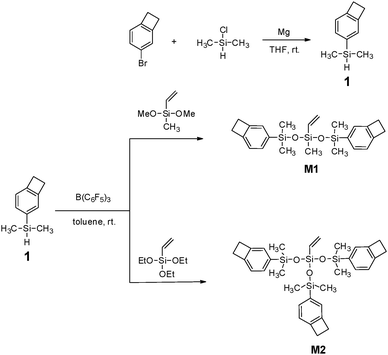 |
| Scheme 1 Procedures for the synthesis of the new monomers. | |
Experimental
Materials
4-Bromobenzocyclobutene was purchased from Chemtarget Technologies Co., China. Chlorodimethylsilane and triethoxyvinylsilane were purchased from J&K company and used as received. Dimethoxy(methyl)vinylsilane and tris(pentafluorophenyl)borane were purchased from Alfa company and used without purification. All solvents were purified by distillation before use.
Measurements
1H NMR and 13C NMR spectra were recorded on a JEOL 400YH instrument. Elemental analysis (EA) was examined by an Elemental vario EL III. High resolution mass spectra (HRMS) were recorded on a Water Micromass GCT Premier. Fourier transform infrared (FT-IR) spectroscopy was conducted on a Nicolet spectrometer with KBr pellets at room temperature. Thermogravimetric analysis (TGA) was obtained on a TG 209F1 apparatus with a heating rate of 10 °C min−1 in N2. Differential scanning calorimetric (DSC) analysis was collected on a TA Instrument DSC Q200 with a heating rate of 10 °C min−1 under a nitrogen flow. Thermo-mechanical analysis (TMA) was carried out on a TMA Q400 V7.1 Build 89, performed with a load of 0.05 N and a heating rate of 3 °C min−1. Dielectric properties were examined on a 4294A precision impendance analyzer (Agilent) with a range of frequencies from 40 Hz to 30 MHz. Atomic force microscope (AFM) images were captured by a Nanonavi E-sweep. Static contact angles were collected via a JC2000C of Shanghai Zhongchen Equipment Ltd, China. Water uptake was determined by weighing the changes in the cured sample before and after immersing in boiling water. The transparency of the sample was investigated using a Varian CARY 5000 at room temperature.
Synthesis
Synthesis of compound 1.
To a mixture of Mg turnings (5.13 g, 0.21 mol), chlorodimethylsilane (26.97 g, 0.28 mol) and THF (100 mL) was added dropwise a solution of 4-bromobenzocyclobutene (26.08 g, 0.14 mol) in THF (100 mL). After being stirred for 15 h at room temperature, the reaction mixture was filtered through Celite. The filtrate was washed with water and concentrated under reduced pressure to obtain a light-yellow liquid, which was purified by distillation under reduced pressure. Compound 1 was obtained in a yield of 88.5% as a colourless oil. 1H NMR (400 MHz, CDCl3, ppm) δ 7.39 (d, 1H), 7.24 (s, 1H), 7.07 (d, 1H), 4.41 (dt, 1H), 3.19 (s, 4H), 0.323 (m, 6H). 13C NMR (101 MHz, CDCl3, ppm) δ 147.29, 145.66, 135.43, 132.28, 127.70, 122.01, 29.83, −3.54. HRMS-EI (m/z): calcd for C10H14Si [M]+ 162.0865; found 162.0869. The detailed 1H NMR and 13C NMR spectra are depicted in ESI.†
Synthesis of monomers M1 and M2.
A solution of compound 1 (2.00 g, 12.32 mmol) in toluene (5 mL) was added dropwise to a mixture of B(C6F5)3 (6.31 mg, 12.32 μmol), diethoxy(methyl)vinylsilane (0.82 g, 6.16 mmol) and toluene (5 mL) at room temperature in N2. After addition, the reaction mixture was stirred at room temperature for an additional 15 h, filtered via Celite, and concentrated under vacuum. The residue was purified by column chromatography on silica gel using petroleum ether (60–90 °C) as the eluent. M1 was prepared in a yield of 63% as a colourless liquid. 1H NMR (400 MHz, CDCl3, ppm) δ 7.42 (d, 2H), 7.27 (s, 2H), 7.07 (d, 2H), 6.09–5.74 (m, 3H), 3.21 (s, 8H), 0.34 (m, 12H), 0.15 (s, 3H). 13C NMR (101 MHz, CDCl3, ppm) δ 147.37, 145.43, 137.85, 137.41, 132.92, 131.40, 126.87, 121.82, 29.90, 1.05, −0.31. Anal. calcd for C23H32O2Si3: C, 65.04, H, 7.59, found: C, 64.78, H, 7.33.
Analogously, M2 was prepared in a yield of 70%. 1H NMR (400 MHz, CDCl3, ppm) δ 7.37 (d, 3H), 7.22 (s, 3H), 7.01 (d, 3H), 5.87 (dd, 3H), 3.16 (s, 12H), 0.28 (d, 18H). 13C NMR (101 MHz, CDCl3, ppm) δ 147.29, 145.32, 137.56, 134.19, 133.40, 131.40, 126.88, 121.71, 29.84, 1.17, 0.87, 0.56. Anal. calcd. for C32H42O3Si4: C, 65.47, H, 7.21, found: C, 64.88, H, 6.83.
Preparation for fully cured siloxane sheets.
A flat-bottom glass tube with a diameter of 5 mm containing M1 of 0.7 g was heated to 160 °C and kept at that temperature for 1 h. Then the tube was heated to a higher temperature. After being treated at 180 °C for 1 h, 185 °C for 1 h, 200 °C for 2 h, 230 °C for 2 h, 250 °C for 3 h, 280 °C for 1 h, and 300 °C for 1 h, respectively, a fully cured M1 sheet was obtained. The cured M2 sheet was also prepared in a similar way.
Preparation for fully cured siloxane films.
A solution of M1 in mesitylene (350 mg mL−1) was stirred at 180 °C for 24 h. After being cooled to room temperature, the resulting pre-polymer was applied on the surface of a silicon wafer by a spin-coating route. The cured film was formed by treating the pre-polymer film at high temperature. The cured M2 sheet was also prepared in a similar way.
Measurement of water uptake.
A cured siloxane disc with a diameter of 10.0 mm and a thickness of about 5.0 mm was dried under vacuum until a constant weight was achieved. The disc was then immersed into boiling water and kept at the boiling temperature for an appropriate time. Water uptake was determined according to a formula of WA (%) = (M − M0)/M0. Here, WA refers to water absorption and M and M0 are the sample weight before and after immersing in boiling water, respectively.
Results and discussion
Synthesis and characterization
The procedure for the synthesis of the new BCB-siloxanes (M1 and M2) is depicted in Scheme 1. As shown in Scheme 1, the intermediate (compound 1) is prepared via a one-pot procedure. Usually, alkyl or aryl halides were able to react with Mg to form Grignard regents, whereas in our case chloroethylsilane did not react with Mg. This result implies that there is a big difference between a chloroalkylsilane and an alkyl or aryl halide. Such a difference provides a possibility for the synthesis of compound 1 in a one-pot route. In particular, the obtained compound 1 is easily purified by washing the resulting mixture with water to remove the inorganic salt while most siloxanes are sensitive to moisture, indicating that compound 1 is stable in water.
By using the Piers–Rubinsztajn reaction, M1 and M2 were obtained in a moderate yield in the presence of B(C6F5)3. All these monomers were low viscosity liquids and soluble in common solvents, suggesting that they possessed good processability.
The chemical structures of M1 and M2 were characterized by 1H NMR, 13C NMR and elemental analysis. Fig. 1 exhibits the 1H NMR spectra of M1 and M2. As shown in Fig. 1, the protons of the four-membered-ring of the BCB group (Ha) are observed at 3.16–3.21 ppm and the protons of the vinyl bond (Hf and Hg) appear at 5.7–6.1 ppm. The protons for the aromatic ring (Hb, Hc, Hd) are present at 7.00–7.40 ppm. In the 13C NMR spectrum of M2 (see Fig. S3 of ESI†), the carbons of the four-membered-ring (Ca) in BCB are observed at 29.84 ppm. The signals of aromatic carbons (Cb–Cg) and the carbons of the vinyl bond (Ci and Cj) appear at 120–150 ppm. Thus, all data are consistent with the proposed structures of the monomers.
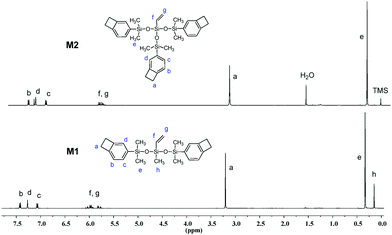 |
| Fig. 1
1H NMR (400 MHz, CDCl3) spectra of M1 and M2. | |
Curing behaviour
The four-membered-ring on a BCB unit easily undergoes a ring-opening reaction to produce a highly active o-quinodimethane intermediate at high temperature.14,15,29 This intermediate has a tendency to participate in a [4+2] (Diels–Alder) reaction with a vinyl group or run a [4+4] cycloaddition reaction with another intermediate.14,15,29
In our case, the curing behaviour of the BCB-siloxane monomers was investigated by DSC, and the results are demonstrated in Fig. 2. It is seen that the two monomers show a curing onset temperature below 190 °C and a maximum exothermic peak around 250 °C. Besides, M1 and M2 exhibit similar heat enthalpies of 749 J g−1 and 709 J g−1, respectively. At the second scan, no obvious exothermic peak is observed, indicating that these monomers have been completely cured.
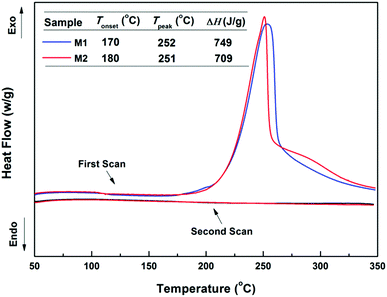 |
| Fig. 2 DSC traces of the new monomers at a heating rate of 10 °C min−1 in N2. | |
To well understand the polymerization of the new BCB-siloxanes, a schematic curing mechanism is described in Scheme 2. The curing degree was monitored by FT-IR spectroscopy. As shown in Fig. 3, the absorption at 1463 cm−1, ascribed to the BCB moieties, disappears after curing. The absorption peak at 958 cm−1 derived from vinyl groups also disappears after curing. These FT-IR data further imply that all the monomers have fully converted to the cross-linked networks.
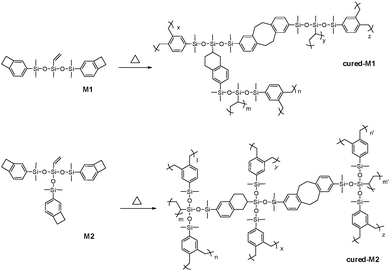 |
| Scheme 2 A schematic polymerization mechanism of the monomers. | |
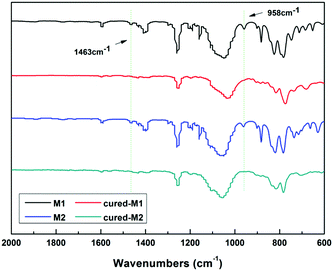 |
| Fig. 3 FT-IR spectra of the monomers before and after thermo-curing. | |
Dielectric properties
The BCB-functionalized siloxanes prepared from alcoholysis and hydrolysis usually display dielectric constants (Dk) of more than 2.7 because of the negative effect from the –Si–OH groups in the polymers.14,18 In our case, the BCB-siloxane monomers prepared via the Piers–Rubinsztajn reaction did not contain Si–OH groups, and thus the cured product would have a low dielectric constant. In fact, cross-linked M1 and M2 exhibit Dk of 2.62 and 2.52, respectively for frequencies ranging from 0.15 to 30.0 MHz, as shown in Fig. 4. Such low Dk values are better than those of BCB-functionalized siloxanes previously reported.5,20,21 Moreover, these low Dk values are also comparable to that of DVS-BCB (k ≈ 2.65),29 a commercial low k material from the Dow Chemical Company and widely used in the microelectronics industry. Our new siloxanes are also better than polyimides (2.9–3.5)30–32 and polyaryle ethers (2.7–2.8).31,33,34 Additionally, cured-M1 and cured-M2 also displayed low dissipation factors with tan
δ values of less than 3 × 10−3.
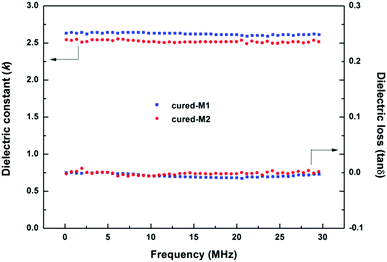 |
| Fig. 4 Dielectric constant (Dk) and dissipation factor (Df) of the cured monomers at different frequencies. | |
Thermostability
The thermostability of the cured monomers was characterized by TGA and TMA. As illustrated in Fig. 5, two cured monomers exhibit satisfying thermostability with a 5% weight loss temperature (T5d) of up to 460 °C. Among them, cured-M2 exhibits a higher T5d (482 °C), which is better than that of many BCB-based low-k materials.4,8,20 For example, DVS-BCB had a T5d of 467 °C.22
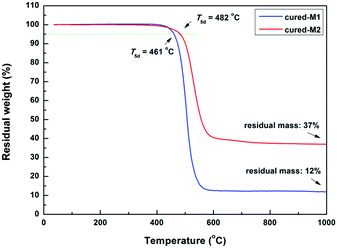 |
| Fig. 5 TGA curves of the cured monomers at a heating rate of 10 °C min−1 in N2. | |
Thermal mechanical analysis (TMA) was adopted to assess the glass-transition temperature (Tg) and coefficient of thermal expansion (CTE) of the cured monomers. As depicted in Fig. 6, cured-M1 shows a lower Tg of 208 °C, while cured-M2 displays a higher Tg of 350 °C. This Tg of cured-M2 is higher than that of DVS-BCB (343 °C TMA).22 For CTE, cured-M2 has a low CTE of 64.46 ppm °C−1, which is comparable to that of BCB-functionalized siloxanes previously reported.5,7,19 In addition, it can be seen that introducing more BCB moieties is conducive to improving the thermostability of the final resins. These results may be attributed to the fact that the cured monomers possess different crosslinking densities. Cured-M2 has a higher crosslinking density than cured-M1; thus, the later displays lower thermostability.
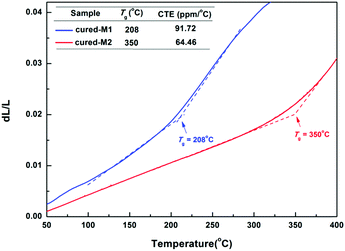 |
| Fig. 6 TMA curves of the cured monomers at a heating rate of 3 °C min−1 in N2. | |
Water uptake
Water uptake is an important parameter for evaluating the physical properties of materials. Low water absorption is helpful to maintain the high performance of the materials when they are utilized under humid conditions.35 In this work, the water absorption of the cured monomers was measured by immersing them in boiling water for a certain time. As summarized in Table 1, both cured monomers exhibit water uptake of less than 0.2% after being immersed in boiling water for 72 h. These low water uptakes are much lower than those of the commercial epoxy resins, such as DGEBA (2.81%), TGAP (4.8%) and TGDDM (3.97%).36
Table 1 Static contact angles of water on the surface of the cured polymer films and water absorption
Sample |
Cured-M1 |
Cured-M2 |
|
|
|
Static contact angle |
96° |
100° |
Water absorption |
0.19% |
0.15% |
In order to investigate the reason why the cured monomers possessed very low water absorption, the contact angle of water on the surface of the cured monomer films was measured. Table 1 lists the contact angle data. It is seen that the cured monomers exhibit contact angles of more than 95°, meaning that the cured monomers have high hydrophobicity. Thus, the low water uptake of the cured monomers is attributed to their high hydrophobicity.
Transparency and surface morphology
The transparency of the cured monomers was measured, and the results are depicted in Fig. 7. As exhibited in Fig. 7, two cured monomer sheets with a thickness of about 1.0 mm display a transmittance of more than 86% for wavelengths varying from 460 to 1100 nm. These data suggest that the cured monomers have good transmittance in the visible region, and they may have potential applications as optical materials with heat-resistance in industry.
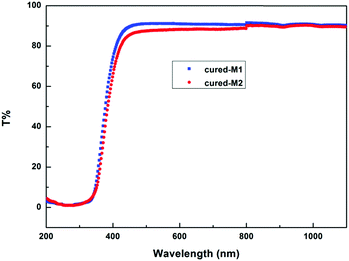 |
| Fig. 7 UV-vis-NIR spectrum of the cured BCB-siloxane sheets with an average thickness of 1.0 mm. | |
By means of atomic force microscopy (AFM), the film uniformity of the cured monomers was investigated. Fig. 8 exhibits images of cured M1 and M2. As seen from Fig. 8, the films of the two cured monomers are quite planar and uniform with a surface roughness (Ra) of less than 0.5 nm, a root-mean-square roughness (Rq) of not more than 0.6 nm and a maximum height difference (Rt) of below 8 nm over a 5 μm × 5 μm area. These data show that the cured monomers possess good surface morphology, which is desirable for application as a coating in the microelectronics industry.
 |
| Fig. 8 AFM images of the cured monomer films on the silicon wafers. Top: Cured-M1, bottom: cured-M2. | |
Conclusions
In summary, we have successfully synthesized two new BCB-functionalized siloxanes via the Piers–Rubinsztajn reaction. These new siloxanes were readily converted to highly cross-linked polymers via a thermal polymerization reaction. The formed resins exhibited good properties including high thermostability, low dielectric constants, good transparency, low water uptake and good film-forming ability. These data imply that these new siloxanes have a potential application as high performance resins in the microelectronics industry.
Conflicts of interest
There are no conflicts to declare.
Acknowledgements
Financial support from the Ministry of Science and Technology of China (2015CB931900), the Natural Science Foundation of China (NSFC, No. 21574146, 21774140 and 21774142), and the Science and Technology Commission of Shanghai Municipality (15ZR1449200 and 16JC1403800) is gratefully acknowledged. The authors are also grateful to the Strategic Priority Research Program of the Chinese Academy of Sciences (Grant XDB 20020000).
Notes and references
- Y. Huang, S. Zhang, H. Hu, X. Wei, H. Yu and J. Yang, J. Polym. Sci., Part A: Polym. Chem., 2017, 55, 1920 CrossRef.
- Y. Tao, F. He, K. Jin, J. Wang, Y. Wang, J. Zhou, J. Sun and Q. Fang, Polym. Chem., 2017, 8, 2010 RSC.
- S. Zhang, H. Hu, H. Yu, Y. Huang and J. Yang, Macromol. Res., 2017, 25, 381 CrossRef.
- F. He, K. Jin, Y. Wang, J. Wang, J. Zhou, J. Sun and Q. Fang, ACS Sustainable Chem. Eng., 2017, 5, 2578 CrossRef.
- Y. Cheng, W. Chen, Z. Li, T. Zhu, Z. Zhang and Y. Jin, RSC Adv., 2017, 7, 14406 RSC.
- J. Wang, I. Piskun and S. L. Craig, ACS Macro Lett., 2015, 4, 834 CrossRef.
- L. Kong, Y. Cheng, Y. Jin, Z. Ren, Y. Li and F. Xiao, J. Mater. Chem. C, 2015, 3, 3364 RSC.
- H. Hu, L. Liu, Z. Li, C. Zhao, Y. Huang, G. Chang and J. Yang, Polymer, 2015, 66, 58 CrossRef.
- J. Tong, S. Diao, K. Jin, C. Yuan, J. Wang, J. Sun and Q. Fang, Polymer, 2014, 55, 3628 CrossRef.
- S. Tian, J. Sun, K. Jin, J. Wang, F. He, S. Zheng and Q. Fang, ACS Appl. Mater. Interfaces, 2014, 6, 20437 Search PubMed.
- K. Cao, L. Yang, Y. Huang, G. Chang and J. Yang, Polymer, 2014, 55, 5680 CrossRef.
-
J. Yang, Y. Huang and K. Cao, in Polymerization, ed. A. D. S. Gomes, InTech, 2012 Search PubMed.
- Y. Cheng, J. Yang, Y. Jin, D. Deng and F. Xiao, Macromolecules, 2012, 45, 4085 CrossRef.
- M. F. Farona, Prog. Polym. Sci., 1996, 21, 505 CrossRef.
- R. A. Kirchhoff and K. J. Bruza, Prog. Polym. Sci., 1993, 18, 85 CrossRef.
- Y. Cheng, S. Tian, Y. Shi, W. Chen, Z. Li, T. Zhu and Z. Zhang, Eur. Polym. J., 2017, 95, 440 CrossRef.
- X. Huang, Q. Zhang, G. Deng, Z. Meng, X. Jia and K. Xi, RSC Adv., 2016, 6, 24690 RSC.
- J. Wang, Y. Luo, K. Jin, C. Yuan, J. Sun, F. He and Q. Fang, Polym. Chem., 2015, 6, 5984 RSC.
- J. Yang, Y. Cheng, Y. Jin and F. Xiao, Polym. Int., 2013, 62, 1684 CrossRef.
- X. Zuo, R. Yu, S. Shi, Z. Feng, Z. Li, S. Yang and L. Fan, J. Polym. Sci., Part A: Polym. Chem., 2009, 47, 6246 CrossRef.
- X. Zuo, J. Chen, X. Zhao, S. Yang and L. Fan, J. Polym. Sci., Part A: Polym. Chem., 2008, 46, 7868 CrossRef.
- J. Yang, Y. Cheng and F. Xiao, Eur. Polym. J., 2012, 48, 751 CrossRef.
- J. L. Segura and N. Martí, Chem. Rev., 1999, 99, 3199 CrossRef PubMed.
- W. Jiajia, S. Jing, Z. Junfeng, J. Kaikai and F. Qiang, ACS Appl. Mater. Interfaces, 2017, 9, 12782 Search PubMed.
- C. Yuan, J. Wang, K. Jin, S. Diao, J. Sun, J. Tong and Q. Fang, Macromolecules, 2014, 47, 6311 CrossRef.
- A. A. Bychkova, F. V. Soskov, A. I. Demchenko, P. A. Storozhenko and A. M. Muzafarov, Russ. Chem. Bull., 2011, 60, 2384 CrossRef.
-
M. Bogdan, M. Hieronim, P. Cezary and P. Piotr, in Advances in Silicon Science, ed. B. Marciniec, Springer, 2009, vol. 1 Search PubMed.
- S. Rubinsztajn and J. A. Cella, Macromolecules, 2005, 38, 1061 CrossRef.
- M. E. Mills, P. Townsend, D. Castillo, S. Martin and A. Achen, Microelectron. Eng., 1997, 33, 327 CrossRef.
- X. Chen, H. Huang, X. Shu, S. Liu and J. Zhao, RSC Adv., 2017, 7, 1956 RSC.
- W. Volksen, R. D. Miller and G. Dubois, Chem. Rev., 2010, 110, 56 CrossRef PubMed.
- Y.-T. Chern and J.-Y. Tsai, Macromolecules, 2008, 41, 9556 CrossRef.
- C. Wang, C. Xu, Q. Li, W. Chen and X. Zhao, Colloid Polym. Sci., 2014, 293, 313 Search PubMed.
- X. Zuo, X. Zhao, B. Liu, S. Yang and L. Fan, J. Appl. Polym. Sci., 2009, 112, 2781 CrossRef.
- Y. Li, I. Ciofi, L. Carbonell, N. Heylen, J. Van Aelst, M. R. Baklanov, G. Groeseneken, K. Maex and Z. Tőkei, J. Appl. Phys., 2008, 104, 034113 CrossRef.
- O. Becker, R. J. Varley and G. P. Simon, Eur. Polym. J., 2004, 40, 187 CrossRef.
Footnote |
† Electronic supplementary information (ESI) available. See DOI: 10.1039/c8qm00104a |
|
This journal is © the Partner Organisations 2018 |
Click here to see how this site uses Cookies. View our privacy policy here.