DOI:
10.1039/D4SU00411F
(Tutorial Review)
RSC Sustainability, 2024,
2, 2805-2832
Greener nanobiopolymers and nanoencapsulation: environmental implications and future prospects
Received
24th July 2024
, Accepted 22nd August 2024
First published on 23rd August 2024
Abstract
To minimize the consumption of nonrenewable resources and ensure environmental sustainability, there ought to be greater utilization of abundant and renewable greener nanobiopolymers, particularly those derived from various plants and microbes. This article discusses the various types, origins, and synthesis methods of biopolymers, including those that come from natural resources and microorganisms, with a focus on their properties in nanoformat; the most common and recently researched nanobiopolymers have been deliberated. In addition, discussion on various synthesis steps and structural characterization of green polymeric materials such as cellulose, chitin, and lignin is also incorporated. A comprehensive discussion of greener nanobiopolymers with illustrative examples has been presented for the last five years comprising their diverse types and topologies including the environmental improvements realized via the deployment of nanoencapsulation, especially the applications of polymer nanoencapsulated materials in wastewater and soil treatment. The emphasis on the use of greener nanobiopolymers for sustainable environmental remediation is specifically highlighted for the decontamination of soil, water, and air with the main objective being to offer an overview of their adaptability embracing nanotechnology. This effort could stimulate additional research in their deployment in practical environmental applications.
Sustainability spotlight
Environmental pollution remains a pressing global issue, posing significant risks to ecosystems and human health. Addressing this challenge is crucial for ensuring a sustainable future. Our review, “Modernizing Environmental Cleanup: Harnessing Greener Nanobiopolymers for a Sustainable Tomorrow,” explores innovative, eco-friendly nanobiopolymers as advanced solutions for remediation. These materials offer efficient, non-toxic alternatives to conventional methods, significantly reducing environmental impact. By leveraging cutting-edge technology, our work aligns with the United Nations Sustainable Development Goals (SDGs) 6 (Clean Water and Sanitation) and 9 (Industry, Innovation, and Infrastructure), promoting sustainable practices and fostering a healthier planet.
|
1. Introduction
Year after year, environmental pollution continues to increase and is now considered one of the most critical issues that society faces, causing irrevocable damage. Despite being a long-standing challenge, environmental pollution has become a significant problem as a result of ongoing urbanization and the incessant development of industry around the globe. The growing human population, vehicles, industrial smoke, and other essential components of modern life have increased our use of natural resources to the fullest, contributing to the degradation of the environment. Hazardous substances, such as toxic heavy metal ions, leftover pharmaceutical compounds or their metabolites, pathogens, various classes of sulfur compounds, or other chemicals dispersed in the air, soil, or water, pose a threat to both human health and the ecological system even at low concentrations. Thus, the search for a sustainable solution to address the degradation of the environment has become increasingly important with continuous search for cost-effectiveness and eco-friendly solutions.1 However, the challenge of eliminating toxins in an environmentally friendly and cost-effective manner using readily accessible technology remains a challenge.2,3 Many conventional techniques for environmental clean-up involve the consumption of chemicals and the generation of toxic by-products that are hazardous to the environment.4,5 Numerous techniques, namely adsorption, ion exchange, chemical precipitation, membrane-based filtration, photodegradation, solvent extraction, and reverse osmosis, are available for the treatment of pollutants. Nanotechnology, a powerful emerging technology of the 21st century, can help assist in the sustainable development of solutions for social communities. The unique properties of nanomaterials, such as their surface area, size, and reactivity, have enabled the development of novel, high-tech materials, such as nanosorbents, which are more efficient and faster in accomplishing wastewater remediation than traditional materials. In particular, due to their new physical and chemical characteristics—which differ significantly from those of the bulk phase—and their relatively small size (generally ranging from 1–100 nm in diameter), high surface-to-volume area, catalytic activity (in the form of adsorption), efficient interfacial reactions, and specific functions, nanomaterials are being developed into newly miniaturized, precise, and highly sensitive nanosensors.6 Biopolymers are polymers that are naturally synthesised by the cells of living organisms and often comprise monomeric units that are covalently bonded to form larger structures. The related polymer nanocomposites exhibit markedly improved properties compared to their individual counterparts.7,8 In the design of such polymer matrix nanocomposites, a variety of natural or synthetic polymers are employed due to their remarkable chemical structure, low weight, ease of processing, and recyclability; however, they lack mechanical and thermal stability.9 Polymers may be incorporated in nanocomposites as such, or as a monomer, which could be polymerized via an in situ mechanism. In order to improve their properties, large numbers of additives known as “nanofillers” are added to polymeric matrices. Recent developments in the generation of nanobiopolymers from living organisms have generated a great deal of interest in several scientific and technical fields.10 Unlike synthetic polymers, which are made from petroleum, these nano-based materials are renewable and environmentally friendly. Biopolymers, also referred to as organic plastics, are manufactured from renewable biomass namely corn starch, pea starch, and vegetable oil, among others. By placing more emphasis on the utilization of such biopolymers, it is possible to conserve fossil fuels which will in turn reduce CO2 emissions and thus help support sustainable development. All these materials are machinable due to their unique nano-dimensional effects such as ultra-high aspect ratios and length-to-diameter ratios. Nanobioremediation offers an excellent alternative for removing pollutants by utilizing nanobiopolymeric composites.11–13
The present article discusses the application of various bionanopolymeric materials, for the general remediation applicable to water, soil, and air pollutants. Assorted processes for the removal of heavy metals and dyes and other aspects, namely the need for air filter masks, comparison of current air filters and their traditional counterparts, and the clogging effect of biopolymers over various other soil treatment methods, are deliberated. All these factors govern the need for specific biopolymers in assorted environmental domains. A quantitative methodology for evaluating the environmental impact of nanobiopolymer isolation technologies is offered via life-cycle assessment encompassing crucial steps namely goal and scope definition, life-cycle inventory modelling, life-cycle impact assessment, and interpretation which are among the first three steps.14Fig. 1 presents the life cycle assessment process for nanobiopolymers.
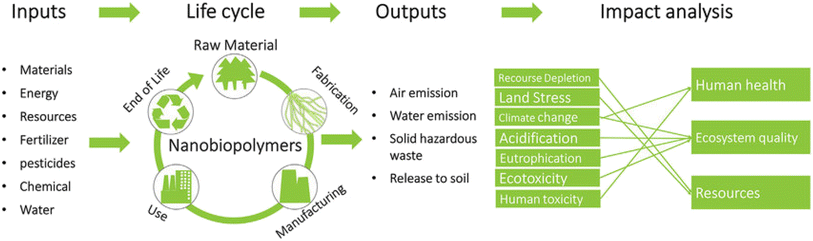 |
| Fig. 1 Life cycle assessment for nanobiopolymers. Copyright (2018) Wiley. Used with permission from Nanobiopolymers Fabrication and Their Life Cycle Assessments.14 | |
Fig. 2 reveals the extent of the growing field of biopolymers, nanobiopolymers, and finally, greener nanobiopolymers, in terms of their publications. The prominent increase in the number of articles every 4 years is an indication of the growing usefulness and popularity of green nanobiopolymers, owing to their various attributes such as adaptable design and modification based on the requirements of the current scientific and industrial demands. The biopolymers are ascertained to be biocompatible, biodegradable, and good adsorbents, rendering them useful in a variety of applications, including edible films, emulsions, packaging materials, medical implants, and environmental pollution remediation.
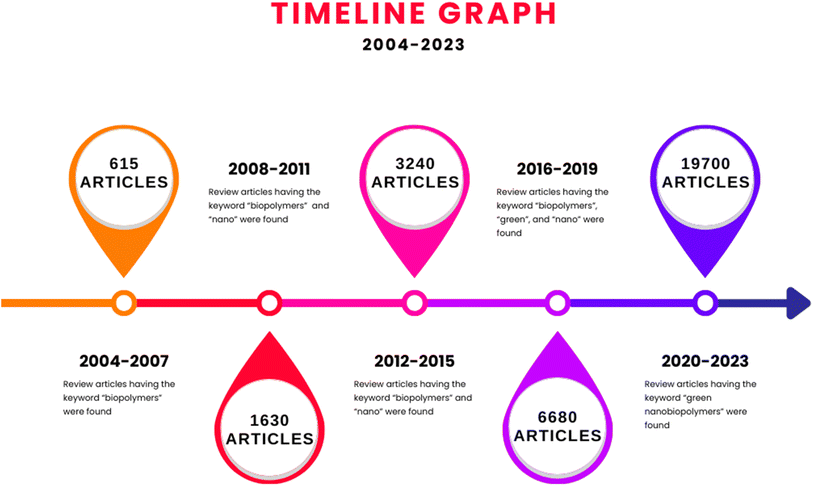 |
| Fig. 2 Depiction of the number of publications that include the keywords “biopolymers”, “nano”, and “green nanobiopolymers” which were uncovered, from the year 2004–2023, acquired from Google Scholar. | |
2. Biopolymers
The phrase “biopolymer” can be used to refer to the class of polymers that are made up of monomeric units that are covalently bonded to form oligomeric substances and are typically obtained from biological sources, such as plant, animal, or plant-based origins; “bio” means the material is created by living things.15 Materials originating from plant or animal sources, such as vegetable oil, sugar, fat, resin, protein, amino acids, and others, are examples of biopolymers.
The differentiation of biopolymers from synthetic polymers is through their sophisticated molecular assembly, which takes on a clear-cut, well-defined 3D shape and structure with their functionality in vivo. Renewable biopolymers offer an alternative to polymers derived from fossil fuels, as they are often created from starchy substances, sugars, natural fibers, or other organic, biodegradable elements and are amenable to decomposition upon exposure to microorganisms from compost, soil, or marine environments.16
2.1. Types of biopolymers
Biopolymers can be divided into several subgroups according to different contents, origins, and sizes (Fig. 3). They can be classified on the basis of their origin: (i) natural biopolymers, (ii) synthetic or man-made biopolymers, and (iii) based on repeating units.
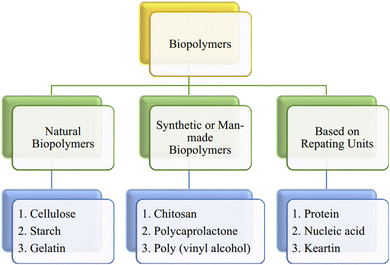 |
| Fig. 3 Different classes of biopolymers.17 Reproduced from Biopolymers and their Industrial Applications, with permission from Elsevier. | |
2.1.1. Natural biopolymers.
Natural biopolymers are polymers found in nature that regulate different aspects of an organism's life cycle. Among many of the favourable qualities are their non-toxicity, biodegradability, and biocompatibility as exemplified by discussion on cellulose, starch, and gelatine.
2.1.1.1. Cellulose.
The first thermoplastic polymer identified in plants is cellulose with chemical formula (C6H10O5)n, where n is the number of cellulose's repeating units.18 Cellulose is known by the IUPAC name (6,5)-2-(hydroxymethyl)-6-(3-S-4,5,6-trihydroxy-2-(hydroxymethyl)oxan-3-yl)oxyoxane-3,4,5-triol.19 It is a polysaccharide with a linear structure made up of 100–1000 (1–4) b-linked glucose repeating units.20 The glucose unit with (1–5) OH and CH2OH groups in the same plane is called D-glucose. Strong intra- and intermolecular hydrogen bonds exist between the oxygen atom and the hydroxyl group of the D-glucose unit. It is crystalline in nature, has a high molecular weight, and varies in Dp ranges between 8000 and 10
000 dpi. It serves as a structural element in plants' main cell walls.
2.1.1.2. Starch.
Starch is the main energy source with 60% to 75% of its weight made up of grain products consumed by humans.21 Its structure is similar to cellulose's, but its internal bonding is different.22 It finds use as a thickening agent, adhesive, and moisture retention material in numerous applications23 and is a homopolymer of D-glucopyranose units that are connected by α-(1/4) and α-(1/6) glycosidic bonds. A D-glucopyranose molecule is created when the C1 and C4 or C6 carbons of the glucopyranose ring combine.24 Because of the aldehyde group, starch molecules have one free reducing end. Amylose and amylopectin are the two forms of starch, with amylopectin being a larger molecule with a highly branched structure, while amylose is an essential carbohydrate with a linear assembly. Generally speaking, plant cells use a complicated biosynthesis pathway that is regulated by enzymes to produce starch. In green photosynthetic tissues, chloroplasts are the site of starch biosynthesis.
2.1.1.3. Gelatine.
Gelatine is a naturally occurring biopolymer obtained from the meat industry, which is derived from raw collagen. Collagen, hydrolysate, and denatured collagen are other terms for gelatine. It has eighteen different kinds of essential amino acids that are included in a normal diet. It is created through the hydrolysis of raw collagen found in many animal connective tissues, including skin and bones.24 Based on the method and composition, there are two types of gelatine. Raw collagen is hydrolyzed in the presence of acid to produce type-A gelatine 18% of it being nitrogen. Alkaline hydrolysis of collagen, which has 18% nitrogen atoms without the amide group (–CONH–), produces type-B gelatine. At both high and low temperatures, it is a temperature-sensitive biopolymer; at elevated temperatures, it melts and forms into a coil and shapes as a coil-to-helix at lower temperatures. Because of the reactive groups (such as –CONH–, –SH–, and –COOH–), it can be altered in the form of nanocomposites. It can form hydrogels, which are used in biomedical applications, and has a special crosslinking attribute. Gelatine is used to speed up the healing process following sports injuries and also for enhancing the quality of hair.
2.1.2. Synthetic or man-made biopolymers.
Synthetic nanobiopolymers are polymers that have been modified from natural nanopolymers or chemically synthesized from artificial monomers such that they can degrade naturally without generating hazardous residues in the living and natural surroundings.25 Synthetic nanobiopolymers have garnered a lot of interest in recent years due to their unique advantages over natural nanopolymers in terms of stability and flexibility for a wide range of applications.
2.1.2.1. Chitosan.
The largest structural polysaccharide based on nitrogen, chitosan is composed of repeating modified glucose subunits and is found in acetylated form as chitin among fish, insects, and many other vertebrates. Chitin's organisation resembles that of cellulose because monomer units have hydroxyl and amine substituents wherein a methyl amide group takes the place of the hydroxyl group.26 Living things and vertebrates may readily digest it because it is created by organisms.27 The fibrous chitin can be broken down into smaller constitutional glucose units by symbiotic bacteria and protozoa.
2.1.2.2. Polycaprolactone.
Polycaprolactone (PCL), with (1,7)-polyoxepan-2-one as the IUPAC name, is a biopolymer of synthetic polyester and is created by polymerising caprolactone through ring opening in the presence of a catalyst, such as stannous octate and finds utility in biological contexts.28 In order to reduce cost, boost biodegradability, and enhance impact strength, it is also added to starch. Some of the special qualities of PCL include its high toughness, biocompatibility, and cost-effectiveness. Compared to other biopolymers, PCL degrades considerably more slowly29 and its special characteristic makes it useful for drug delivery applications. Because of its hydrophobic nature, it has strong chemical resistance towards biological fluids. It combines seamlessly with other man-made polymers. In view of the easy cleavage of its ester bond, PCL readily breaks down and is often deployed as a biomaterial in tissue-engineering applications.
2.1.2.3. Polyvinyl alcohol.
Polyvinyl alcohol (PVA) is a thermoplastic biopolymer that is produced through the hydrolysis of its precursor, polyvinyl acetate, and can be degraded by biological microbes being very soluble in water.30 PVA is employed in the production of numerous polymer end products, including food packaging, liquors, and surgical threads. It is an extremely flexible, ductile, and robust polymer. The physical and chemical characteristics of PVA are based on grade, molecular weight, and the percentage of degree of hydrolysis. Its gas barrier qualities, flexibility, and tensile strength are all outstanding attributes.31 This biopolymer is highly prevalent and has the ability to form chemical bonds with many surfaces, including water. PVA is a biodegradable and nontoxic polymer and is often used in food packaging and in the biomedical fields as wound dressing, medication delivery, cardiac surgery, and contact lenses.
2.1.3. Polymers based on other repeating units.
2.1.3.1. Proteins.
Proteins are necessary building blocks for daily existence of humans32 and comprise fundamental components that make up bodily tissues. Peptide bonds allow the individual amino acids that make up proteins to be conjugated and are created via the combination of amino and carboxylic groups.33 A polypeptide bond holds the lengthy protein macromolecular chain together as proteins are essential for numerous biological functions including as catalysts for the movement or storage of other molecules (oxygen). They also offer the immune system mechanical support, with keratin being the primary example of a protein.
2.1.3.2. Keratin.
A protein polymer called keratin is found in horns, claws, and hooves and is a combination of floating proteins, enzymes, and many keratinized filaments.34 It is described as a specific filament-floating protein with superior physiochemical characteristics often derived from cells and tissues. Keratins are generally divided into two categories: (i) primary keratin: this keratin, which includes K8/K18, is generated from both stratified and epithelial cells. (ii) Secondary keratin: other byproducts are used to make these epithelial cells; K7 and K19 being the examples.35 Keratins are found in fibre connections and cellular binding and are frequently deployed in biological applications such as cell adhesion. In the cosmetics industry, they are utilized as skin care ingredients, fertilisers, and sites for cellular attachment.
2.1.3.3. Nucleic acids.
RNA is the earliest known biomolecule which stores and transfers the information contained in cells. All portions of polymeric chains, including genes, require DNA to store genetic information36 where every nucleic acid component is essential for transmitting the genetic information. Nucleotides are tiny monomeric components that make up this polymer.37 Three components make up each nucleotide monomer: a phosphate group, a nitroglycogenous base, and two types of pentasugars namely ribose and deoxyribose sugar that are present in the natural world.
2.2. Sources and synthesis of biopolymers
As mentioned earlier, bio-based polymers are substances that are composed of replenishable resources as exemplified by agricultural products such as corn, potatoes, and other plants rich in carbohydrates. Due to significant technical breakthroughs, the emphasis is now placed on resources other than those derived from food.38 Polymeric biopolymers are also created synthetically with a variety of applications through novel developments via plant engineering.39
These polymers are produced in bulk and then moulded for specific end uses. In addition, a variety of biopolymers, such as polyesters, polyamides, and polysaccharides, which are used to create everything from plastics to viscous solutions, depend on microbes for their production. Their physical characteristics rely on the molecular weight and contents of the polymer.
2.2.1. Biopolymers derived from natural plant resources: polysaccharides.
Polysaccharides are composed of complex carbohydrates that are widely present in nature or the environment and serve as structural components in both plants and animals. The three most common biopolymers derived from natural plant resources are starch, chitosan, and cellulose. Starch is a large polysaccharide and is the most prevalent and dominant polysaccharide in nature. Natural starch is frequently found as a granular substance that can be processed using customary methods for making plastics or used as a filler for polymers including as a drug delivery agent in tissue engineering applications, microcellular foams, and the food industry. Its main drawback is its hydrophilic nature, which limits its application in environments with high moisture content. Starch can be coupled with biodegradable polymers such as polyvinyl alcohol (PVA), polycaprolactone (PCL), chitosan, and others to generate fully biodegradable materials. Due to its biocompatibility, biodegradability, low toxicity, wide availability, and affordability, chitosan, the most exceptional biopolymer, is generated by deacetylation of naturally abundant chitin and is often deployed in drug delivery systems. Because of its reactive amino and hydroxyl functional groups, chitosan can be combined with other polymers to enhance their functional characteristics through inter- or intramolecular crosslinking in the polymer matrix.40,41
Cellulose, a vital biopolymer that is abundantly present in our environment in plant cell walls, is another important candidate. High sorption capacity, biocompatibility, biodegradability, relative thermostability, mechanical toughness, and adjustable visual appearance are only a few of its fascinating properties. Not surprisingly, numerous industries utilize cellulose in various ways as exemplified by the formation of bio-composites. Some leading examples of polysaccharides are presented in Table 1.
Table 1 Prominent examples of polysaccharides
Name |
Chemical formula |
Structure |
Chitosan |
C56H103N9O39 |
|
Starch |
(C6H10O5)n |
|
Cellulose |
(C6H12O5)n |
|
2.2.2. Biopolymers derived from natural animal resources: proteins.
For a variety of hierarchically complex biological material scales, proteins are crucial building blocks which are essentially polypeptide-based polymers created by condensation polymerization of amino acids; keratin, collagen, casein, and fibroin are significant animal proteins. Collagen is a protein that is abundantly found in the extracellular matrix of vertebrate animals and is employed widely in the food and pharmaceutical sectors. Collagen fibrils offer the main mechanical support and structural organization of connective tissues and they find predominant applications in areas such as wound healing, cosmetics, and tissue engineering.42
The main challenge and opportunities in biopolymer research and developmental endeavors are to find acceptable modification pathways to improve the properties of natural polymers as exemplified by the production of natural polymers based on proteins or wheat gluten.43,44 Due to its excellent thermoplastic qualities, superior processability, and amazing biodegradability, wheat gluten, a by-product of the starch industry with high protein content, could be regarded as an ideal candidate for many applications. Some leading examples of animal proteins are listed in Table 2.
Table 2 Examples of animal proteins
Name |
Chemical formula |
Structure |
Keratin |
(Gly-X–Y)n |
|
Collagen |
C4H6N2O3R2 |
|
Casein |
C81H125N22O39P |
|
Gelatin |
C6H12O6 |
|
Fibroin |
(Gly- Ser-Gly-Ala-Gly-Ala)n |
|
Whey protein |
The proteins consist of α-lactalbumin, β-lactoglobulin, serum albumin and immunoglobulins |
|
2.2.3. Biopolymers obtained from microorganisms: polyesters.
Microorganisms produce a wide variety of biopolymers, such as polysaccharides, polyesters, and polyamides, which vary from viscous solutions to plastics with their physical properties being defined by their molecular weight and composition. Genetically modified bacteria are especially suitable for high-value medical applications such as drug delivery and tissue engineering which is facilitated by the alteration of various biopolymers produced with the assistance of microorganisms.45
Microorganisms require a certain set of nutrients and a controlled environment to produce biopolymers which can be accomplished chemically via the polymerization of monomers; they can be created often through fermentation as well. A higher proportion of biopolymers of bacterial origin are biocompatible and have no harmful effects on biological systems as they are synthesized either as a part of their defense mechanism or for storage purposes.46,47
Algae are among the microorganisms that offer suitable feedstock for manufacturing plastic in view of their high productivity and adaptability to varied environmental conditions. It is now possible to employ algae to consume carbon and lessen the impact of greenhouse gas emissions from manufacturing facilities and power plants. In the era of bioplastics, algae-based plastics have become more popular relative to conventional techniques that employ corn and potatoes as plastic feedstocks. The leading examples of polyesters are presented in Table 3.
Table 3 Some examples of polyesters
Name |
Chemical formula |
Structure |
Poly(ethylene glycol) |
C2nH4n+2On+1 |
|
Polylactic acid (PLA) |
(C3H4O2)n |
|
Poly(e-caprolactone) (PCL) |
(C6H10O2)n |
|
2.3. Biopolymers-advantages and challenges
The most intriguing features of biodegradable polymers are their ability to survive a variety of environmental conditions and their disposability in the presence of bioactive molecules. Due to their expanding applications in environmental safety, packaging, biomedical implementation, and agricultural usage, biodegradable polymers play an extraordinary role. In view of its readily hydrolyzable ester linkages along with economical manufacture, poly(lactic acid) (PLA) is one of the most readily available and widely deployed polyesters. According to Rasal et al.'s48 research, the manufacture of PLA uses 25–55 percent less energy as compared to that of polymers derived from petroleum, although this figure may increase in the near future. Consequently, there is now more interest in producing lactic acid through fermentation using renewable resources rather than petrochemicals as the biotechnological pathway offers many advantages over chemical synthesis. Given that they are disposable and produced using sustainable resources, biodegradable polyesters can be considered a potential material to help with the problem associated with the disposal of solid waste. These polyesters' low immunogenicity and biological origin make them ideally suitable for usage in food packaging as well as other consumer goods.49
Despite the fact that biodegradable polymers have numerous uses, some of their properties, such as brittleness, low heat deflection temperature, low melt viscosity, poor thermal and mechanical resistance, and slow degradation rate, limit their deployment in industrial settings. The aforementioned drawbacks can be resolved, however, by improving the material's thermomechanical characteristics through various means such as copolymerization, mixing, and the use of fillers. Another notable downside of biodegradable polymers is the cost-effective manufacturing and recovery of biopolymers through the fermentation process as it is limited by the cell's ability to utilize inexpensive carbon sources, especially agricultural waste products. Since microorganisms grow slowly in agricultural waste or on inexpensive media, fewer polymer–plastic technologies and materials are created, which boosts the cost of downstream processing. It is crucial to isolate and screen potent and efficient microorganisms (especially fungal and bacterial strains) from the natural environment to employ relatively inexpensive feed stock. In order to reduce production costs and achieve the best productivity under optimum conditions, research has now focused on culture strategies to expand growth media using affordable carbon substrates.50
3. Greener nanobiopolymers
Organic compounds made from naturally replenishable resources include nanoforms of biopolymers as well. They are widely distributed in nature too and are accessible via biological monomer chain reactions. Because of their ease of production and them being economical, they are employed in ecologically sensitive applications. In natural systems, polysaccharides often comprise the most prevalent biopolymers and they are made up of sugar monomers which are further connected by glycosidic linkages. They perform a variety of crucial tasks in living things, encompassing supporting the structure, providing energy, and facilitating the transition of certain cells; cellulose, starch, chitin, and silk are nanobiopolymers that can be produced via metabolism.
3.1. Types and structural properties of greener nanobiopolymers
3.1.1. Nanocellulose.
Cellulose, the most prevalent polymer on earth, is made by plants, microorganisms, and cell-free systems, and chemically, it consists of repeating β-D-glucose monomers held together by β-(1,4)-glycosidic bonds. Natural cellulose usually has a fibrous form with interspersed crystalline and amorphous parts. Nanocellulose, also known as cellulose nanocrystals (CNCs), cellulose nanowhiskers (CNWs), and cellulose nanofibers (CNFs), is produced by fiber separation and occurs in a variety of morphologies. Microbial cellulose, also known as bacterial nanocellulose (BNC) and acellular cellulose, is the cleanest type of cellulose available compared to plant cellulose, which contains lignin and hemicellulose as additional components.51,52 Nanocellulose possesses characteristic structural, physicochemical, mechanical, and biological features such as a three-dimensional reticular network fibre structure, hydrophilicity, biodegradability, good mechanical strength, biocompatibility, high crystallinity, light transmission, high specific surface area, multi-functionality, and its ability to be molded into complex three-dimensional shapes.53 Nanocellulose is a sustainable material that can be produced using cell-free systems, various microbial strains, and via the degradation of plant and animal cellulose. Nanocellulose is widely deployed in a variety of fields as a tuneable material, both on its own and in composite form with other materials; usage includes tissue engineering, wound dressing, textiles and clothing, cosmetics, bioprinting, regenerative medicine, energy, optoelectronics, and environmental remediation, among others.54,55
The structural qualities of nanocellulose are better than those of microcrystalline cellulose (MCC), in terms of high mechanical strength and its ability for easy surface-modification using a variety of techniques. This is in view of a higher concentration of hydroxyl (OH) groups, rendering it more hydrophilic and amenable to various chemical and physical modifications. Nanocellulose has thus garnered a lot of attention as an ideal nanostructure for creating novel, high-value nanomaterials due to its excellent biocompatibility, high mechanical strength, renewability, and low cost.
3.1.2. Nanochitin.
Like cellulose, chitin is a natural polymer that occurs abundantly in nature. Many terrestrial arthropod creatures, including insects and spiders, have exoskeletons made of a polysaccharide called chitin, which is fuelled by the shells of crabs and shrimp that are consumed as seafood. The chitin molecule (C8H13O5N) is a long-chain polymer of N-acetylglucosamine, a glucose derivative, and has a long-chain structure generated by the repetition of two N-acetylglucosamine units joined by β-1,4 bonds.56 Like cellulose, chitin's structure is made up of nanofibers. The most prevalent types of these protein-embedded nanofibers, which range in size from 2 to 5 nm in diameter and 300 nm in length, are α-chitin and β-chitin.57 Chitin's application is constrained since it is a hydrophobic substance and is insoluble in most organic solvents. Chitin's deacetylated derivative, chitosan, currently satisfies some of the essential requirements namely dissolution in mildly acidic liquids such as acetic acid. Chitin and chitosan are often utilized in a variety of goods, including natural packaging materials, cosmetics, and food preservatives. Chitosan is a wonderful option for usage in biomedical sectors and has broader applications due to its lower degree of acetylation. There are other nanocomposite materials that can be combined with chitosan and chitin namely strengthening of chitosan with chitin whiskers. Such materials display better water absorption resistance and tensile strength as a result of the combination of their distinct characteristics. Chitosan may be incorporated into various systems and mixed with other natural polymers.58
In terms of structure, nanochitin is an assembly of highly oriented nanocrystals of semicrystalline chitin packed into highly oriented microfibrils or fibril bundles that are held together by van der Waals forces and hydrogen bonds (H-bonding). Nanometer lateral dimensions, tailorable crystallinity, fibrillar or rod-like structure, and other characteristics of nanochitin contribute to its appealing qualities. In the exoskeleton of arthropods, nanochitin is chemically contained by a sheath of proteins and formed into elongated fibrils that are encased in a mineral-protein matrix. Therefore, removing minerals and proteins is an essential process that must be completed before isolating nanochitin, and unlike natural nanopolysaccharides, this nitrogen-bearing biopolymer is an essential component of life.59
3.1.3. Nanostarch.
A well-known carbohydrate, starch bears resemblance to cellulose as well as chitin. D-Glucose units comprise the two macromolecules amylose and amylopectin that make up starch. One of the substantial naturally occurring polymers on earth, amylose is a chain with few branches that has an average mass of 370–350 Da,60 whereas amylopectin forms a branch at every 22–77 units of glucose and possesses (1–4) linkage.61 The biological and physical characteristics of starch are based on its crystal structure which is controlled by branches. Besides this, starch may also accommodate phosphate and lipids, which further depends on the botanical source from which it is derived, and these components might alter the starch's properties through the Maillard process.62 Starch nanoparticles at the nanoscale have diameters ranging from 50 and 200 nm across. The potential to inexpensively generate starch nanoparticles is closely correlated with the availability of starch in nature. Additionally, due to its biocompatibility as well as its ability to degrade without producing harmful or toxic waste, starch at the nanoscale has a large surface area and thus offers a wide range of applications. However, it is susceptible to a wide range of chemical processes because of the abundance of hydroxyl groups on its surface,63 a property that enables the utilization of starch nanoparticles in various composites. Starch nanocrystals have become a prominent research topic in recent years because of their intelligibility in degradation as well as their competence for regeneration.64
3.1.4. Nanosilk.
The natural glycoprotein polymer known as silk fibroin (SF) encompasses an H-chain as well as an L-chain and originates from spiders and silkworms. The morphologies of SF, like films, scaffolds, hydrogels, microspheres, and nanofibers, can be very diverse. Due to its excellent biocompatibility, lack of toxicity, ease of degradation, and anti-inflammatory properties, this protein-based nanomaterial is particularly well suited for use in biomedical research.65 Additionally, SF has the ability to inhibit the growth of bacteria and reduce metal ions in aqueous solutions. The scope of the material investigation is restricted because pure silk fibroins have the drawback of completely and quickly mixing in water, but this problem can be resolved by mixing nano-silk with other materials. For the usage of SF, sericin which is a glue-like protein found in silk fibroin, has been implicated in allergic reactions to silk. Hence its removal is considered crucial66 which is later refuted as the sericin protein has been shown to be a biocompatible substance;67 the allergic reaction is ascribed to the mixture of sericin and fibroin. Degumming is a thermochemical procedure that moves apart the protein fibroin and sericin from one another. High glycine content with strong binding in silk nanofibroins results in highly stable-sheet nanocrystals68 characterized by hydrogen bonds as the main molecular interactions in these crystalline layers. Despite their reputation as weak bonds, hydrogen bonds impart silk its stiffness and tensile strength. Amazing benefits such as self-assembly, as well as self-healing, are offered by weak hydrogen bonding in silk nanofibroins.
3.2. The versatility of greener nanocomposites
Greener nanocomposites are polymers that are basically combined with environment-friendly nanofillers, such as cellulose, starch, chitin, clay, or metal oxides.69 They differ from traditional nanocomposites in various manners, including price, weight, strength, biocompatibility, and environmental friendliness. They have been deployed in several energy devices such as solar cells, batteries, light-emitting diodes, etc. Energy storage, particularly in capacitors, is one of the principal uses for greener nanocomposites.70
Biopolymer nanocomposites have been a cutting-edge research area in nanotechnology with several fields being beneficiaries over the past ten years. In this context, challenges include (i) achieving a resemblance between polymer grids and nanofortifications, (ii) effective detachment pathways for dividing sustainable assets from nano-fortifications, and (iii) appropriate analysis.71 Cost and energy usage are also significant factors in the commercialization of such products comprising bio-nanocomposites. It is important to note that the most frequently employed method for modifying the properties of biopolymers is the addition of a nano-support to the polymer network (Fig. 4) although this strategy still needs improvement.72
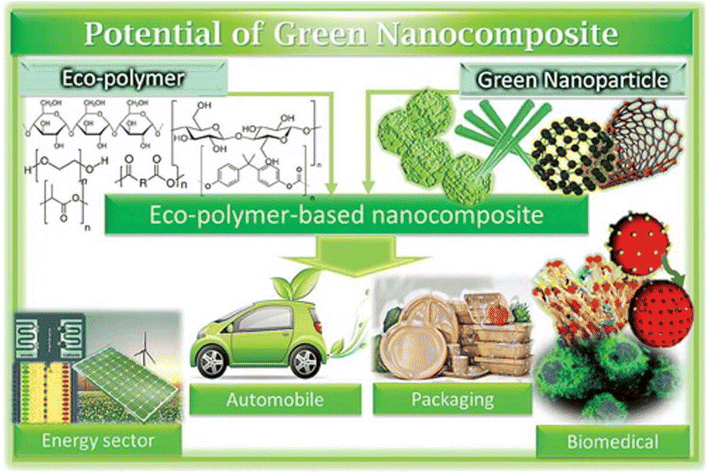 |
| Fig. 4 Applications of polymer-based nanocomposites11 Reprinted with permission from RSC Advances (2023). | |
Chitin appears in a high proportion as its fibres are employed to make fillers for polycaprolactone (PCL)-based nanocomposites realized via the use of a variety of manufacturing techniques, such as hot pressing and freeze-drying; ideal stiffness can be achieved with a 2.96 weight% of chitin.56 Further investigations with FTIR spectroscopy and X-beams demonstrated the presence of chitin in the PVA grid, which was followed by the confirmation of chitin hairs in the conventional flexible lattice. Numerous characteristics, including elasticity, weight reduction, and diffusion coefficient, further attested to their existence.73
Several entities such as starch's morphological properties and nanocrystals have been created for conventional elastic combinations. The rates of oxygen and water emission penetrability are also being studied though their effects have been marginal. Starch nanocrystals have enhanced water-retaining properties and decreased cost.74 Several studies have been published pertaining to polylactic acid (PLA) nanocomposites. The controllable and flexible strength of the KENAF fibrous content was observed to have increased by 50% when the effect of fibre content on the characteristics of KENAF fiber-based PLA composite was investigated.75 It has been predicted that the mechanical characteristics of PLA composites will be affected by the KENAF fibre content. Accordingly, the mechanical properties of the PLA network and 30% KENAF fibre-soluble composite were changed. At a 25-weight percent improvement, the polylactic acid (PLA) lattice showed improved mechanical characteristics.
The mechanical properties of a 25-weight% steam-exploded bamboo (SEB) strand infusion from PLA composites were dominant; SEB/PLA strands were twice as strong and solid as PLA strands.76
4. Nanoencapsulation
In recent years, there has been a great deal of interest in the deployment of micro- and nano-sized encapsulation methods which entail encapsulating the desired active material within a carrier matrix or semi-porous membrane. This allows for the transfer of the material between the matrix and a reaction medium, thus enabling the generation of particles with a regulated or trigger-release mechanism; generally, pH, and temperature- and pressure-sensitive agents are employed to control the release of the core material from the encapsulated particles.77 Various applications, ranging from water treatment and energy storage to agricultural practices, have been using encapsulated materials, particularly in the micro- and nano-size range; improved stability and reusable adsorbents for the removal of pollutants have been observed in water treatment. Subsequently, the applications for encapsulated materials have been extended in various energy storage systems, including phase change materials (PCMs). In the agricultural sector, encapsulated particulates enable the controlled and prolonged delivery of agricultural chemicals at the intended site, as well as the protection of core materials from adverse environmental conditions.78
Composite particles are created through encapsulation techniques and typically comprise a core material that has been covered in a valuable secondary material. Depending on the characteristics of the coating, encapsulation may offer properties such as discharge of core material in a controlled manner, protection from nonspecific interactions amongst chemicals, convenience of handling and transportation, and ease of separation from the matrix to composite particles.
4.1. Components of encapsulation
Typically, encapsulated particles consist of two parts: an inactive polymeric material (shell) and a core active component material that can be in different physical states. The coating material should be compatible with the core material and is often an inert polymer that can be applied to the core material in a desired thickness.79 Natural, synthetic, and sensitive polymers, created with biological moieties to change their chemical and physical characteristics responsive to internal and external factors, such as pH and temperature, are examples of common coating polymers.80
Encapsulated particles can be divided into two main categories based on the core material's dispersion, vesicular and matrix (Fig. 5).
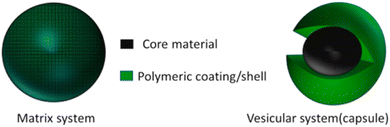 |
| Fig. 5 Visual representation of encapsulation components.77 | |
Matrix systems are characterized by the physical and uniform dispersion of the active component, or core. Vesicular systems, on the other hand, are portrayed by the encapsulation of the core within a cavity surrounded by a polymer membrane, also referred to as capsules. Both the terms “matrix” and “vesicular” can be denoted differently, depending on the composition, shape, coating material, and techniques of fabrication (Fig. 6).
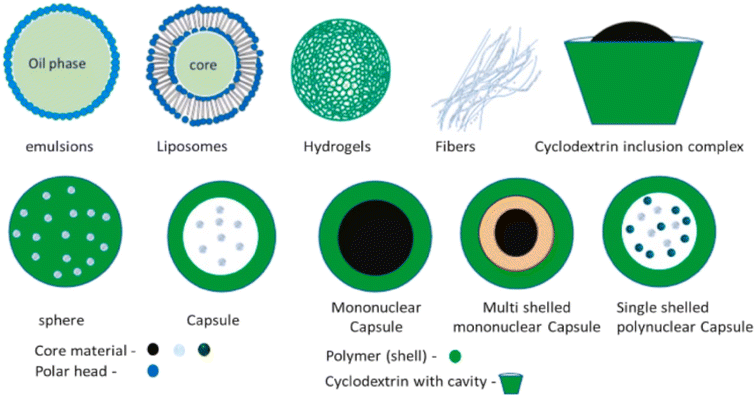 |
| Fig. 6 Visual representation of encapsulated particle types.77 Reprinted with permission from Elsevier (2023). | |
4.2. Environmental applications of polymer nano-encapsulated materials
Lately, there has been increasing interest in the deployment of micro- and nano-materials for encapsulation in various environmental contexts, particularly in the areas of water treatment, agriculture, and energy. The use of encapsulation techniques has the potential to significantly enhance a number of processes and features in environmental applications, such as the removal of various pollutants such as dyes and heavy metals from contaminated water; renewable energy, agricultural processes, and soil treatment for sustained release of herbicides, changes in release properties and soil sorption are some of the additional application avenues.
4.2.1. Wastewater treatment.
Encapsulated particles comprise an emerging field of study in wastewater treatment systems.81 These nanocomposites and materials enable the adsorption and decomposition of various pollutants in wastewater, thus contributing to the sustainability of water usage.82 For example, matrix-based hydrogels, nano-encapsulated membranes, and membranes encapsulated by metals have been deployed in the estimation of pharmaceuticals and heavy metals in wastewater through surface-enhanced Raman spectroscopy.83 Recycling of encapsulated materials is an additional benefit of their use in wastewater treatment. For instance, alginate-based magnetic beads containing Cyanex 272® have been demonstrated to remove Co2+ ions from aqueous solutions with successive 3 times reusability of the adsorbent without altering its initial properties.84 Additionally, a study demonstrated 67% Sr2+ removal from the seawater samples.85 In industrial and textile wastewater treatment, encapsulated bio-adsorbents, microorganisms encapsulated in polymeric matrices, have also been used to enhance their performance.86
4.2.2. Utilization in soil treatment and agriculture.
Encapsulation is a promising technology for agricultural and applications in soil treatment as this sustainable application may include the protection and growth of plants via the encapsulation of bio-active molecules, agrochemicals, and fertilizers, with the aim of delivering them to the intended sites.87 Additionally, encapsulated polymers, such as absorbent hydrogels and gels, are employed in a variety of forestry, agricultural, industrial, and horticultural applications, as well as in drought management and water conservation.88 These hydrogels offer a range of benefits, including improved soil quality, water conservation, improved soil fertilization activity, reduced runoff, and enhanced activity of soil microbes. Insect detection and disease detection in plants can also be achieved through encapsulated nanosensors.89 Encapsulation also offers eco-friendliness, sustainability, and the controlled release of fertilizers, plant nutrients, and herbicide.90 The catalytic and photocatalyst properties of encapsulated materials are commonly deployed for the adsorption and degradative adsorption of pesticides.
5. Environmental remediation using greener nanobiopolymers
Greener nanoforms of biopolymers are considered environmentally beneficial because of their biodegradability attributes and they being part of renewable feed stocks.91 The frequently deployed nanoparticles for environmental remediation comprise single enzyme nanoparticles (SENs), metallic oxides, and zero-valent metals.92 The abiding interest in metallic nanoparticles (NPs) of iron groups, for example, Co, Cu, Fe, and Ni, is due to their magnetic and chemical catalytic properties and hence, these classes of NPs and their composites with carbon, silica, polymers and noble metals have found significant appliances in environmental remediation endeavors.93 Also, various other polymeric substances, such as resin, cellulose, chitosan, alginate, carboxymethyl cellulose, etc. are combined with nanobiopolymers to enhance their mechanical and thermal properties; nanobiopolymers have been deployed for decontamination of water, soil, and air.94 This usage basically comprises two exclusive environmental domains namely remediation and monitoring.
5.1. Eliminating environmental pollutants with nanotechnology
Eliminating pollution has been the biggest environmental challenge95 as pollutants in air, water, and soil have detrimental short- and long-term effects. It is imperative to get rid of pollution at the sources of contamination. Nanotechnology has been explored to treat industrial and urban effluents to prevent water pollution, reduce soil pollutants, and decrease many air pollutants in towns and factories to a manageable level.96
5.2. Nanotechnology-based environmental pollution monitoring
This is conceivable because nanoparticles have fascinating chemical and physical features such as enormous surface area, composition, electrical properties, magnetic properties, mechanical capabilities, and optical qualities. Nanosensors detect contaminants by detecting pollutants' surface markers or by boosting the analytical signal.97 In comparison to conventional procedures, these unique characteristics of nanosensors are reliable for the sensitive detection of extremely low quantities of contaminants.98 Scientists have expressed a curiosity in developing nanomaterial-based biosensors for detecting environmental pollutants such as heavy metals, pesticides, and bacterial infections.99 For the creation of biosensors to sense and seek out environmental contaminants, many types of nanomaterials such as quantum dots and metallic and carbonaceous nanoparticles have been employed. According to a study, nano-porous materials such as metal/metal oxides offer a viable platform for the creation of sensors that can detect contaminants in polluted samples rapidly and efficiently.100 Nanoporous metal oxide-based gas sensors have been created to investigate environmental contaminants emitted by agricultural and medical sectors. Pollutants in water, food, and farmland have been identified using nano-based technologies such as biosensors.
5.3. Remediation of pollutants in water
Various studies have investigated the manipulation and formation of biopolymers by the diverse microbial species discovered during wastewater treatment100,101 and found it to be a slow process because of the inherent complexity of the systems involved. Removal of heavy metals or various other impurities is necessary102 which is accomplished using various polymers (nanocellulose, graphene oxide, etc.) and some basic oxides (Fe2O4, Al2O3, ZrO2,etc.).103,104 The removal of fluorides and chlorophenols involves some of the polymers deploying processes such as adsorption, precipitation, electrolysis, and membrane separation.105,106 In addition, inexpensive adsorbing materials have been explored such as spent bleaching earth, kaolinitic clay, agricultural by-products, and biogas residual slurry for use in the defluorination of water.107
5.3.1. Nanocellulose.
In general, nanocellulose-based materials are in high demand because of their versatility, large surface area, and renewable nature and can be broadly divided into two categories namely monocrystalline cellulose (MCC) and nanofibrillated cellulose (NFC).108 Due to the presence of the amorphous and crystalline nature of NFC, at low concentrations (below 1 weight%), their long fibrils entangle and produce highly viscous suspensions.109 One unit of nanocellulose polymer has the formula (C6H12O5)n and its structure is depicted in Fig. 7. All these properties contribute to the removal of F− and other such contaminations from water with appropriate modifications (Fig. 8).
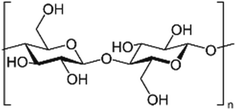 |
| Fig. 7 Structure of a unit of nanocellulose. | |
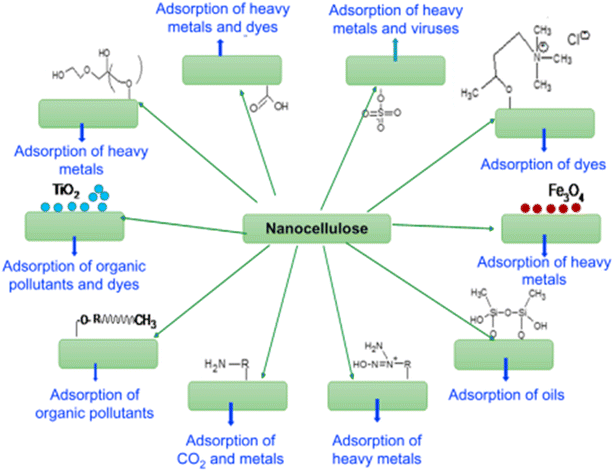 |
| Fig. 8 Possible strategies for surface modification of nanocellulose according to the pollutant class.110 Reprinted with permission from Woodhead Publishing Series (2017). | |
5.3.2. Nanochitin.
After cellulose, chitin is the biopolymer that is most widely available owing to its ideal properties such as its nontoxic, biodegradable, and renewable nature. Electrostatic action and filling are two important aspects of nanochitin. When chitin functions as an emulsifier and a saltiness-enhancing agent, electrostatic action is expressed. Because of their positive charge, nanofibers can absorb negatively charged particles such as oil droplets, which decreases the digestion of lipids, increases the release of sodium, and enhances the bioavailability of fat-soluble vitamins. A double layer of chloride is adsorbed on the surface of chitin nanofibers in response to static electricity, thus increasing the amount of free sodium and enhancing the salty flavour. Nanochitin can be added as a filler to certain composite membranes, such as those based on starch or gelatin, to enhance their antifungal, thermal, and physical characteristics. Additionally, chemical derivatization or post-functionalization can be used to chemically modify and functionalize a significant amount of hydroxyl and acetamide groups that are exposed on the surface of nanochitin. By filling in gaps and creating winding pathways between water molecules, nanochitin can enhance the gelatin film's ability to withstand water vapour. F–SiO2 can aid in the composite membrane's development of a superhydrophobic surface. Biomimetics enables the development of composite materials containing iron and silica to produce specific functionalities (both nutritional and physical).111
5.3.3. Graphene oxide (GO).
A mono-layer carbon sheet that is held together by a hexagonal honeycomb lattice is known as graphene. According to the Hummers' method, graphite can be oxidized with a strong oxidant and then exfoliated to produce graphene oxide (GO).112 Due to its thickness and various other unique properties, GO is used for the purification of water and can be further changed, creating hybrid nanocomposites deploying additional nanoparticles, suitable for multicomponent pollutant removal such as cationic, anionic, and amphiphilic pollutants;113 GO enhances the removal effectiveness and reusability of other materials. Besides graphite, GO can also be produced using some biological and natural resources such as coal, lignocellulose, and cellulose, among others. For wastewater treatment, both single-walled and multi-walled GO are used.114
5.3.4. Removal of heavy metals.
Heavy metal contamination of water supplies is a major issue that affects the environment as these metals enter aquatic ecosystems directly through industrial effluent discharge, leaching of heavy metal-contaminated soil, refineries, etc. The contaminating heavy metals comprise Cu2+, Cd2+, As5+, Pb2+, Hg2+, Cr6+, Mn2+, Zn2+, and Ni2+.115–117 All these pose a very serious threat to human health; for example Hg2+ causes severe damage to the nervous system, Cu2+ causes liver and kidney damage, etc. Thus, the removal of heavy metals from the polluted water is absolutely necessary.8,115,118
Table 4 lists a number of studies that have deployed polymer-based nanocomposites to remove heavy metals from water along with their adsorption capacities towards heavy metals. Additionally, pH significantly affects how much pollutant is taken up by composites120 as in the case of absorption of Cr6+ which decreased with an increase in pH because the –NH2 groups on the composite's surface are less protonated; at pH 2.0, the composite could absorb 171.5 mg g−1 of Cr6+ at its maximum rate. For the removal of Cr6+, polypyrrole has been used which is essentially an organically modified montmorillonite clay nanocomposite deployed as the absorbent121 wherein the amount of clay in the composite had a big impact on how well Cr6+ could bind in aqueous solutions.122
Table 4 Polymer composites as adsorbents for the removal of heavy metals119
Nanocomposites |
Names of heavy metals |
Maximum adsorption capacity (mg g−1) |
Chitosan–rectorite |
Cu2+, Cd2+, and Ni2+ |
13.32-Ni2+ |
(MWCNT/PU) multiwalled carbon nanotube–polyurethane |
Pb2+ |
270.27 |
Chitosan montmorillonite |
Cu2+ |
134.62 |
Chitosan-clay composite with epichlorohydrin cross-linking |
Cd2+ and Ni2+ |
72.31-Cd2+ |
32.36-Ni2+ |
Chitosan montmorillonite |
Co2+ |
150 |
Graphene oxide/chitosan |
Cu2+ and Cr6+ |
78.80-Cu2+ |
32.76-Cr6+ |
Chitosan–clay |
Cu2+ |
181.5 |
Magnetic cellulose with an amino functional group |
Cr6+ |
171.5 |
Exfoliated montmorillonite modified organically with polypyrrole |
Cr6+ |
209.0 |
Mercapto-functionalized Fe3O4 nanoparticles |
Hg2+ |
256.4 |
Nanohydroxyapatite–alginate |
Pb2+ |
270.3 |
Nano-hydroxyapatite–chitosan |
Cd2+ |
122.0 |
Chitin/chitosan-nano-hydroxyapatite |
Cu2+ |
6.2 |
Alginate/Mauritanian clay |
Cu2+ |
47.6 |
Mesoporous silica/polyacrylamide |
Hg2+ |
177.0 |
Poly(vinyl alcohol)clay/carboxymethyl chitosan |
Cd2+, Co2+, and Cu2+ |
2470-Cd2+ |
385-Co2+ |
794-Cu2+ |
TMSPEDA hybrid polymeric nanocomposite/PMDA |
Pb2+, Zn2+, and Cd2+ |
49.72-Pb2+ |
41.75-Zn2+ |
45.22-Cd2+ |
The Hg2+ ions have been removed from water using a composite of mesoporous silica and polyacrylamide (PAAM) where the physical adsorption of Hg2+ onto the composite proved a reversible process as the composite can be regenerated without losing its capacity to adsorb Hg2+.123 In the case of physical adsorption, the temperature affects the adsorption of the adsorbate negatively, and as the temperature increases, the uptake of heavy metals decreases; the highest amount of Hg2+ that the composite could have absorbed on an increase in temperature from 25–40 °C was reduced to 157.5 mg g−1.
5.3.5. Removal of dyes.
Since the dawn of human civilization, dyes have been employed as coloring agents and back then the majority of them came from natural sources. However, today thousands of synthetic dyes in the market have nearly completely replaced the natural ones.124
Synthetic dyes are typically categorized into various groups such as acid dyes, direct dyes, basic dyes, reactive dyes, disperse dyes, vat dyes, and sulphur dyes. Both acid and basic dyes are water-soluble; acid dyes have a carboxyl or sulfur-based group in their chemical structure, while basic dyes have amino groups, which impart them a (+)ve charge upon dissolution in water.125 Sulphur dyes and vat dyes are among the inexpensive dyes for coloring and are water-insoluble too. Reactive dyes are highly coloured organic substances that undergo hydrolysis as they are colored because their functional group is bonded to water. Water-soluble dyes include direct and dispersed dyes.126 The chemical structures of direct dyes typically have unmetallized azo structures, while the molecular structures of dispersed dyes normally contain anthraquinone or azobenzene with one or more functional groups attached to them.127 Some examples of polymer composites as dye-removal adsorbents are mentioned in Table 5.128
Table 5 Polymer composite adsorbents deployed in the removal of dyes119
Nanocomposite |
Dyes |
Maximum adsorption capacity (mg g−1) |
Montmorillonite–organocellulose acetate composites that resemble paper |
Acid scarlet G |
95.1 |
Montmorillonite/chitosan-g-(N-vinylpyrrolidone) |
Rhodamine 6G |
36.6 |
Basic yellow 28 571.4 montmorillonite amidated pectin |
Basic yellow 28 |
571.4 |
Anionic clay and alginate that resemble hydrotalcite |
Orange II |
2.8 (mmol g−1) |
Chitosan clay |
Methylene blue |
142 |
Acrylic copolymer–bentonite and chitosan |
Methyl violet; malachite green |
2280 for malachite green; 3057 for methyl violet |
Poly HEMA–chitosan–MWCNT |
Methyl orange |
416.6 |
Carbon tubes/spherical cellulose |
Hybrid methylene blue |
302.1 |
Graphene oxide/chitosan |
Methylene blue and methyl orange |
508.56 for methylene blue; 245.49 for methyl orange |
Even in low quantities, the majority of synthetic colors are visible in the water, and therefore, effluent containing synthetic colors must be treated before being released into the environment. The ideal approach for treating wastewater containing colors is the adsorption procedure and assorted polymeric nanocomposites have been utilized as adsorbents (Table 6) even for the large-scale wastewater treatment process.130
Table 6 Biopolymers with their characteristics and uses towards soil remediation
Serial no. |
Biopolymers |
Composition |
Structure |
Characteristics |
Behaviour towards soil remediation |
References |
1 |
Chitosan |
C56H103N9O39 |
|
- Soluble in acidic solvents |
- Coagulant effects |
129
|
- Biodegradable |
- Removal of heavy metals from water |
12
|
- Low mechanical strength |
|
|
- Low-temperature response rate |
|
|
2 |
Agar gum |
C14H24O9 |
|
- Ability to form reversible gels |
- Pore clogging |
12
|
- Thickening agent |
- Erosion reduction |
3 |
Xanthan gum |
C36H58O29P2 |
|
- High viscous rheology |
- Drilling mud thickener |
12
|
-Strengthening |
4 |
Dextran |
C18H32O16 |
|
- Flexible biopolymer |
- Drilling muds |
12
|
- Emulsifier |
- Erosion reduction |
5.4. Soil remediation
The strengthening of the soil, with increased cohesion and strength, and resistance to erosion, including reduced permeability, are all desirable traits for soft soil. Improving all these soil properties is an anticipated process, in terms of environmental concerns131 where ideal solutions are offered by using biopolymers132 The effects of applying different concentrations of biopolymers on the enhancement of soil strength have been experimentally investigated using direct shear tests and splitting tensile unconsolidated undrained triaxial; specimens treated with biopolymers demonstrated better resistance to environmental influences.132Fig. 8 presents a laboratory vegetation growth experiment which shows that both seed germination and overall growth in cultured soil are promoted by using biopolymers (Fig. 9(a)) and natural inorganic silty loam (Fig. 9(b)). Some examples of biopolymers with their behavior toward soil remediation are presented in Table 6.
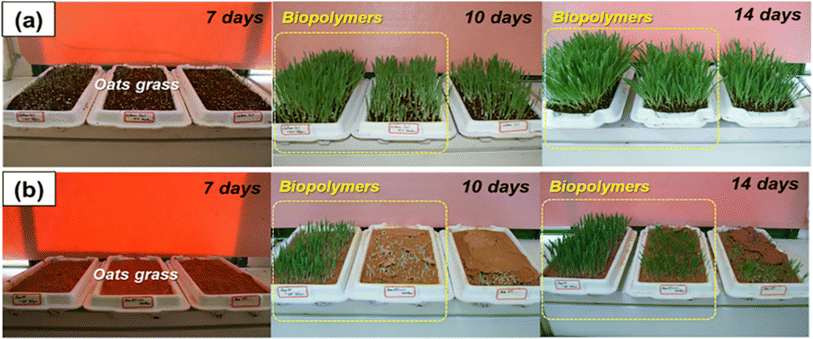 |
| Fig. 9 Vegetation promotion effect assessed in the laboratory. (a) Culture soil. (b) Inorganic silty loam.133 Reprinted with permission from Elsevier (2020). | |
5.4.1. Chitosan.
Chitosan is a deacylated form of chitin and NaOH treatment is usually employed to extract it. This biodegradable, biocompatible, renewable, and hydrophilic biopolymer has been deployed in a wide range of applications134 in various fields such as materials science, food and nutrition, medical science, immunology, microbiology, agriculture, and wastewater treatment products.135 Chitosan has been demonstrated to have the ability to decontaminate groundwater that contains contaminants such as Cu2+ and P− in geotechnical and geoenvironmental settings.136 By lowering the hydraulic conducting capacity of sandy soils, chitosan-coated sand particles can produce a suitable plugging effect in filters for the treatment of polluted groundwater.128,137
5.4.2. Agar gum.
Agar gum is a polysaccharide from the Rhodophyceae family and is made up of linked galactose molecules. After being dissolved in boiling water, agar gum, due to its thermoregulation quality, enables the formation of solid gels upon cooling to room temperature. Sand's strength is effectively increased by agar gum without endangering the environment wherein results showed that using 3% thermally treated agar gum increased the soil's unrestricted compressive strength by up to 10 MPa upon drying.136
5.4.3. Xanthan gum.
Xanthan gum is a polysaccharide made by the bacteria Xanthomonas campestris and it exhibits hydrocolloid rheology and is used as a viscosity thickener. Through pore filling and raising the liquid limit, it has been added for the reduction of the hydraulic conductivity of silty sand and for enhancing the soil's undrained shear strength. Another recent study examined the xanthan gum's potential to strengthen the soil and demonstrated that xanthan gum preferably forms firm clayey soil matrices through hydrogen bonding.138
5.4.4. Dextran.
Dextran is an adaptable biopolymer that can create coils in an aqueous medium that has a low level of permeability and a high density. This polymer is one of the first industrially utilized extracellular microbial polymers, commonly used as blood plasma extenders. The significant use of dextran has been in the industrial separation of plasma proteins, especially pro-insulin, albumin, and other factors of blood. Dextran increases the surface erosion and scouring resistance of saturated silty sands, according to recent experimental research but it has no effect on soil water retention, according to a study examining its impact on the desiccation and rehydration of sand and clays.
5.4.5. Clogging effect of biopolymers and hydro-dependency.
Dehydrated biopolymer gels or biopolymer-clay matrices tend to absorb and transmit water to hydrogels leading to volumetric expansion when soils contain a greater quantity of water. As the water content increases, the elastic properties of the biopolymers (e.g., tensile strength and stiffness) decrease exponentially, which results in a significant decrease in soil strength (roughly one-tenth of its strength in the dried state) when the soil is fully saturated.139 However, when the soil is rewetted with a biopolymer mixture (e.g., clay soil (200 kPa) versus sandy soil (50 kPa) in most cases), the uncompressed strength of the rewetted soil is much greater than the strength of untreated soils.136
In addition, the swelling of the hydrating biopolymer material fills the pores of the soil (especially in sand) thus causing it to become more clogged, resulting in a reduction of hydraulic conductivity by more than three to four orders of magnitude. As a result, biopolymers have potential applications in hydraulic engineering, e.g., slurry walls, seepage barriers, and grouting.140
5.4.6. Biopolymers in geotechnical engineering.
Biopolymers, in contrast to other ground improvement techniques, perform well in the midst of fine soils. Furthermore, they can be incorporated into the soil through a variety of practical methods, such as mixing, injecting, spraying, or grouting.141 Additionally, they can be employed in the construction industry, as well as in the construction of earth pavement and the prevention of erosion in farmland (Fig. 10). They tend to form a permanent gel matrix within the soil, which does not adversely affect the local environment. In combination with their water-retaining properties in the soil, it is assumed that biopolymers may be able to stimulate vegetation growth.142
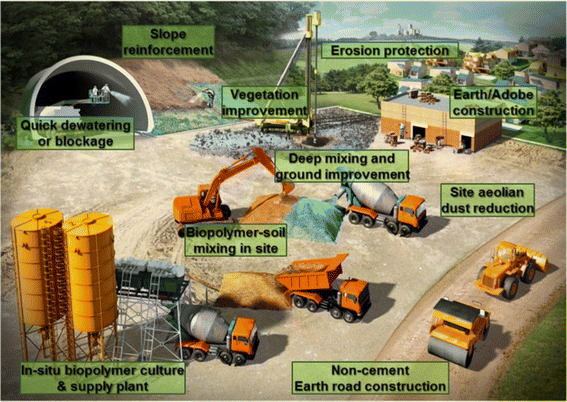 |
| Fig. 10 Schematic representation of applications of biopolymers in the field of geotechnical engineering.136 Reprinted with permission from Sustainability (2016). | |
Direct biopolymer implementation has several advantages over other bio-soil approaches, but the main one is that biopolymers can be generated ex situ and used in situ with a higher level of quality control, whereas Microbially Induced Calcium Carbonate Precipitation (MICP) requires time-consuming in situ cultivation. Biopolymers, being economically mass-produced, can react with soil particles quickly after mixing, making them useful for temporary or urgent support.
5.5. Air remediation
There are only a few methods and biopolymers available for the filtration of air143 applications because of the structural complexity of these polymers which makes the process challenging and difficult.144
This includes the deployment of some additional techniques for producing nanofibers, such as electrospinning, template synthesis, and thermally induced phase separation. The primary capturing mechanisms identifying the pollutant preservation on the filter media are particulate matter (PM) size and physical effects, delineating the function of particulate air filters in filtration.145
Inertial impaction, straining, gravitation, electrostatic attraction, diffusion, and fiber–pollutant interaction on the filter's surface are some of the filtration mechanisms that work for particles smaller than the pore size of the filter.146 It should be emphasized that for nanofibers, interception, and diffusion mechanisms are more effective than gravitation, straining, and inertial impaction. These mechanisms are often most common for capturing particles with a diameter of 0.5 μm.147 According to studies, interception and Brownian diffusion can cause particles with sizes between 50 and 500 nm to be removed by the nanofibrous media. Numerous studies have demonstrated that nanofibers with a higher packing density and a smaller fibre diameter enhance the interception effect.148 The strength of the diffusion mechanisms and interception is indicated using the Peclet number; a strong diffusion mechanism requires a lower Peclet number and a higher Knudsen number.149 It is also realized that biopolymer-based nanofilters primarily use the same size-based filtration and physical mechanisms. Additionally, these mechanisms support the biopolymer-based nanofilters' ability to achieve better particulate filtration efficiency, particularly for smaller, charged, or functionalized particles.150 Some examples of biopolymers with their behaviour toward air remediation are presented in Table 7.
Table 7 Biopolymers with their characteristics and behaviour towards air remediation
Serial no. |
Biopolymer |
Formula |
Structures |
Characteristics |
Environmental application |
References |
1 |
Chitosan |
C56H103N9O39 |
|
- Soluble in acidic solvents |
- Agricultural bio-pesticide |
6
|
- Biodegradable |
- Used for its antibacterial properties |
2 |
Cellulose |
(C6H12O5)n |
|
- Excellent mechanical properties |
- Acts as an aerogel and a hydrogel towards air filtration |
6
|
- Hydrophilic in nature |
5.5.1. Gaseous pollutants.
Gaseous pollutants can be captured through two primary capture mechanisms: physisorption (intermolecular attraction) and chemisorption (chemical action). Physisorption is the capture of gaseous pollutants through the surface pores of a fibre structure whereas more selective chemisorption entails the conversion of pollutants into simpler compounds through a chemical reaction, such as catalytic or non-catalyst reduction.151 The higher surface area of nanofibers increases the capacity for physisorption, and hence a fibrous filter ought to be designed with a very high surface area; functionalized electro-spun nano-membranes made from various polymers may be useful for this purpose. For the measurement of gaseous pollutants, various experimental configurations are available152 as illustrated in Fig. 11.
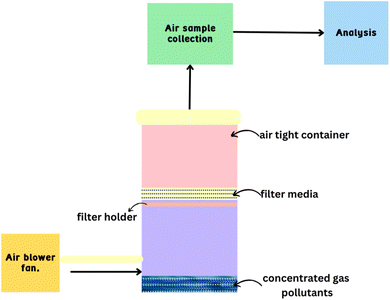 |
| Fig. 11 Schematics of the experimental setup for characterization of gas filters. | |
5.5.2. Antimicrobial air filters.
Bioaerosols are among the dangerous pollutants that endanger humans, wherein a high-performance air filter can be deployed to trap and destroy biohazards. However, the buildup of the collected bioaerosols in air filters poses a serious problem since, given enough moisture and nutrients, bacteria may proliferate and spread throughout the whole filter.153 Additionally, the particulate and chemical contaminants that are trapped in the filter may help promote the development of bacteria, which might significantly reduce the effectiveness of filtration and eventually cause the filter to degrade (bioporation).154 The possibility of the volatile compounds generated by the microbial metabolism being discharged from broken filters to the air again is another concern with such filters. The purpose of antimicrobial air filters is to remove or kill biological contaminants from the air.155
Both in research labs and in real-world applications, a wide range of synthetic polymers and biopolymers with or without the addition of additives may be utilized to create nanofiber membranes.152 The most popular and advanced polymers, as well as the fabrication methods, often deployed to create nanofibers for filtering applications are presented in Table 8
Table 8 Most popular and cutting-edge polymers deployed to create nanofibers for filtration applications and manufacturing processes
Polymer materials |
Method/application |
Commonly used plastics
|
(PP) polypropylene |
Filtration; electric whirling melts |
(PE) polyethylene |
Filtration; electric whirling melts |
(PVC) poly(vinyl chloride) |
Filtration; electrospinning |
(PS) polystyrene |
Matrix for composite materials and filtering; electrospinning |
![[thin space (1/6-em)]](https://www.rsc.org/images/entities/char_2009.gif) |
Advanced and special polymers
|
(PAN) polyacrylonitrile |
Filtration; electrospinning; a forerunner to the production of CNF |
(PEO) poly(ethylene oxide) |
Electrospinning. Filtration; model components |
(PVA) poly(vinyl alcohol) |
Electrospinning; conductive polymer-carriers; food packaging; filtering |
(PU) polyurethane |
Electrospinning; protective gear; filtering; composite material matrix |
(PA) polyamides |
Electrospinning; strengthening; filtering; model materials |
Traditional antimicrobial agents, namely metals such as Ag nanoparticles and metal oxides, which are expensive and can permanently harm both humans and the environment, have been used to treat or combine fibrous filters to achieve antimicrobial properties.156
5.5.2.1. Current air filters vs. traditional air filters.
Presently, three primary kinds of air filters are available commercially: antimicrobial air filters (Ag particles), chemical air filters (carbon C in its activated form), and particulate air filters (such as high-efficiency particulate air, HEPA) (Fig. 12). Air filters comprise porous materials such as fibrous non-woven mats with micro-sized fibres arranged in a random pattern. The fibres are created using chemically created polymers based on petroleum.157
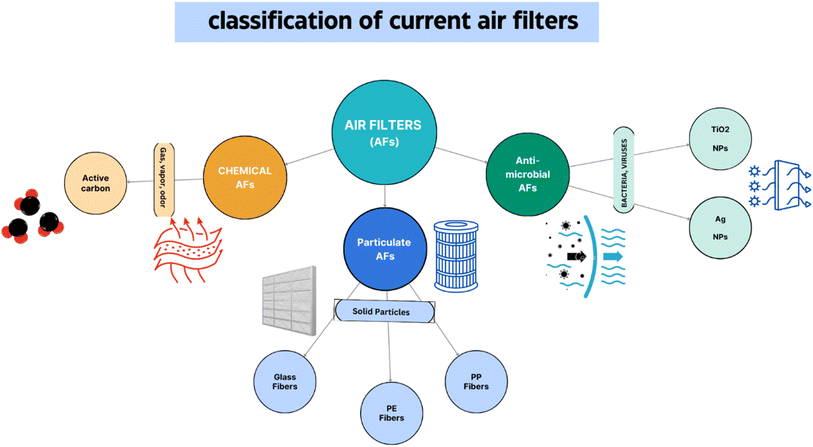 |
| Fig. 12 Classification and types of the air filters that are currently deployed. | |
Large concentrations of expensive nanoparticles, such as Ag or TiO2, that have antibacterial properties, are frequently found in antimicrobial air filters. However, it has been shown that both chemical filters and PM provide poor protection against risks. Therefore, in modern air filtration systems, a variety of filters may be used to achieve high-quality air, including regular particulate filters, HEPA filters, activated carbon filters, and antimicrobial filters, among others.158 As is to be expected in such systems, there is a significant pressure drop downstream from the filters, resulting in the additional cost of active air exchange filtration and an increase in energy consumption. There are a number of challenges associated with the current air filter materials that are being studied and are worth discussing.159 Firstly, in addition to cellulose-based filters, none of the conventional polymeric materials used, such as PP and PE, various additives, and glass fiber are environmentally friendly; they cannot be disposed of easily. Secondly, existing air filters may not be able to filter out a wide range of pollutants due to insufficient interactions with the filter materials.160 Thirdly, additional additives loaded into or on the filter mats, such as activated carbon and nanoparticles, may lessen the filter's effectiveness and increase the amount of active air exchange fuel used.161
The fabrication of air filtering materials is a complex and costly process, particularly for those that require the use of selected catalysts or nanoparticles. Furthermore, the filtration process in most common filters is decided by mechanisms based on size and physical properties, which are only effective for the capture of particulate matter.162 These mechanisms are not suitable for the elimination of toxic gas molecules or antimicrobial filtration.163 Consequently, the creation of bio-based multifunctional air filtering materials with high removal efficiencies ought to be affordable for various types of pollutants (such as particulate matter, toxic gases, and biological hazards) while also maintaining low airflow resistance, a challenging task for the development of advanced bio-based materials for air filtration systems.164
5.5.2.2. Air mask filter.
An appealing substitute for filter materials that may be able to solve the aforementioned issues is offered by biopolymers, being widely accessible, frequently inexpensive, and easily processed. They mostly include polysaccharides and proteins derived from both plant and animal sources, such as cotton cellulose, animal wool, silkworm silk, and soy and corn proteins (Fig. 13).150 Biopolymers possess chemical and physical characteristics that are crucial for the elimination and absorption of particular chemical pollutants or offer viricidal or bactericidal action that can be helpful in filter applications.
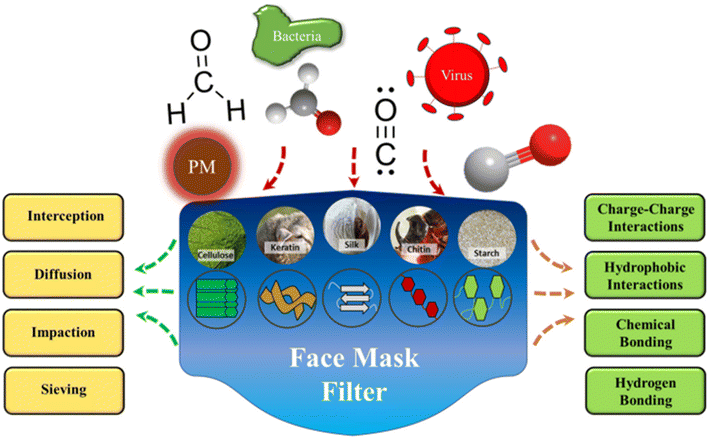 |
| Fig. 13 Materials for biopolymer-based filtration made from various protein and polysaccharide sources. Particulate matter (PM), viruses, bacteria, and smoke pollutants can all be filtered out due to their particular surface chemistries and varied molecular interactions.150 Reprinted with permission from ACS Publication (2021). | |
There are two main categories of air filtering methods. Through a process known as physical adsorption, harmful pollutants initially cling to the embedded particle or filter surface on the filter. The other is chemisorption, where the pollutant interacts with either the surface of the filter membrane or a particle that is embedded in it to produce an inert product.165 The accessibility of the active sites inside the filter is the limiting element in both situations. In other words, the leftover toxins may still pass through the porosity filter when there are no longer any active sites for them to bind. Fig. 14 deliberates the earlier air filters that used synthetic polymers to filter particles based on interception, impaction, electrostatic interaction, and diffusion.
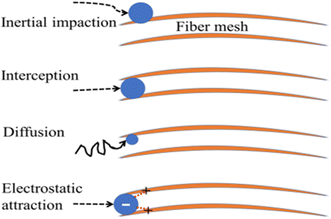 |
| Fig. 14 Impaction, diffusion, interception, and electrostatic interaction are frequently used filtration mechanisms for biopolymers (orange lines). The pollutant, represented as a blue sphere, moves along a black path, and interactions between the pollutant and the biopolymer are shown as red dotted lines.150 | |
The interactions also hold true for biopolymer-filters based on biopolymers. The type of the pollutant and its size are the major factors affecting the filtration interaction; (Fig. 15(a)), where large sized pollutants (>1000 nm) may be easily stopped, smaller pollutants are largely filtered through biological processes. Fig. 15(b) reflects the fractional collection effectiveness of various mechanical filters in relation to the contaminant's diameter.166
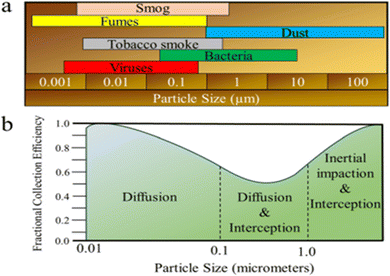 |
| Fig. 15 (a) Size proportions of common air pollutants and (b) fractional collection effectiveness for various mechanical filters in relation to the contaminant diameter.150 Reprinted with permission from ACS Publication (2021). | |
6. Conclusion and future prospects
The integration of greener nanobiopolymers into environmental cleanup represents a significant advancement towards achieving sustainability in addressing pollution. As the environmental challenges grow in scale and complexity, the deployment of these innovative materials has delivered promising results in remediating contaminated sites, removing pollutants from water, and mitigating the release of toxic substances into the ecosystem.167
In conclusion, greener nanobiopolymers offer a unique combination of biodegradability, renewability, and effectiveness in environmental cleanup processes. Their ability to be engineered at the nanoscale enhances their surface area, reactivity, and specificity toward targeted pollutants, making them superior to traditional remediation materials. Additionally, the use of biopolymers derived from natural resources aligns with the global push towards reducing carbon footprints and promoting circular economy practices.168
However, the journey toward widespread adoption of these materials is still in its early stages. Future research should focus on scaling up production processes, reducing costs, and improving the functionalization of these materials to target a broader range of pollutants. Moreover, the long-term environmental impact of deploying nanobiopolymers at a large scale remains a critical area of investigation. While these materials are designed to be eco-friendly, their interactions with different ecosystems, particularly in the case of nanoscale materials, need to be thoroughly assessed.
Future prospects in this field also include the development of hybrid materials that combine the properties of nanobiopolymers with other sustainable technologies, such as bio-based catalysts and green energy sources, to enhance their effectiveness and applicability. The integration of smart technologies, such as sensors and responsive materials, could also pave the way for more efficient and autonomous environmental remediation systems.
Furthermore, the detection and quantification of toxic matter in the environment can be significantly improved through the use of nanobiopolymers, offering more sensitive, selective, and rapid monitoring tools.169 This would not only facilitate the early detection of pollutants but also enable more precise interventions, thereby minimizing the environmental impact.170
The potential for greener nanobiopolymers to revolutionize environmental cleanup is immense, but it requires a concerted effort from the scientific community, industry stakeholders, and policymakers to fully realize their benefits.171 By fostering interdisciplinary collaborations and promoting sustainable innovation, the future of environmental remediation looks promising with greener nanobiopolymers at the forefront.172
Abbreviations
BNC | Bacterial nanocellulose |
CNCs | Cellulose nanocrystals |
CNFs | Cellulose nanofibers |
CNWs | Cellulose nanowhiskers |
FTIR | Fourier transform infrared |
GO | Graphene oxide |
MCC | Microcrystalline cellulose |
NFC | Nanofibrillated cellulose |
NPs | Nanoparticles |
OH | Hydroxyl |
PCL | Polycaprolactone |
PCM | Polychlorinated biphenyls |
PLA | Polylactic acid |
PVA | Polyvinyl alcohol |
SEB | Steam-exploded bamboo |
SENs | Single enzyme nanoparticles |
SF | Silk fibroin |
Data availability
No primary research results, software or code have been included and no new data were generated or analysed as part of this review.
Conflicts of interest
The authors declare no conflict of interest.
References
-
S. Gulati and K. S. Shikha, Chapter 22 – Functionalized carbon nanomaterials (FCNMs): Green and sustainable vision, in Funct. Carbon Nanomater Theranostic Appl., ed. Mallakpour S. and Hussain C. M., Elsevier, 2023, pp. 525–547, DOI:10.1016/B978-0-12-824366-4.00009-1.
- Z. Fallah, E. N. Zare, M. Ghomi, F. Ahmadijokani, M. Amini and M. Tajbakhsh,
et al., Toxicity and remediation of pharmaceuticals and pesticides using metal oxides and carbon nanomaterials, Chemosphere, 2021, 275, 130055, DOI:10.1016/j.chemosphere.2021.130055.
- B. Feizi Mohazzab, B. Jaleh, M. Nasrollahzadeh, S. Khazalpour, M. Sajjadi and R. S. Varma, Correction to “Upgraded Valorization of Biowaste: Laser-Assisted Synthesis of Pd/Calcium Lignosulfonate Nanocomposite for Hydrogen Storage and Environmental Remediation.”, ACS Omega, 2023, 8, 14855–14856, DOI:10.1021/acsomega.3c01351.
- Y. Monga, P. Kumar, R. K. Sharma, J. Filip, R. S. Varma and R. Zbořil,
et al., Sustainable Synthesis of Nanoscale Zerovalent Iron Particles for Environmental Remediation, ChemSusChem, 2020, 13, 3288–3305, DOI:10.1002/cssc.202000290.
- S. S. Lam, V.-H. Nguyen, M. T. Nguyen Dinh, D. Q. Khieu, D. D. La and H. T. Nguyen,
et al., Mainstream avenues for boosting graphitic carbon nitride efficiency: towards enhanced solar light-driven photocatalytic hydrogen production and environmental remediation, J. Mater. Chem. A, 2020, 8, 10571–10603, 10.1039/D0TA02582H.
- A. Mamun, T. Blachowicz and L. Sabantina, Electrospun Nanofiber Mats for Filtering Applications—Technology, Structure and Materials, Polymers, 2021, 13, 1368, DOI:10.3390/polym13091368.
- M. Hassanisaadi, R. Saberi Riseh, A. Rabiei, R. S. Varma and J. F. Kennedy, Nano/micro-cellulose-based materials as remarkable sorbents for the remediation of agricultural resources from chemical pollutants, Int. J. Biol. Macromol., 2023, 246, 125763, DOI:10.1016/j.ijbiomac.2023.125763.
- A. T. Hoang, S. Kumar, E. Lichtfouse, C. K. Cheng, R. S. Varma and N. Senthilkumar,
et al., Remediation of heavy metal polluted waters using activated carbon from lignocellulosic biomass: An update of recent trends, Chemosphere, 2022, 302, 134825, DOI:10.1016/j.chemosphere.2022.134825.
-
M. K. Murthy, P. Khandayataray, D. Samal, R. Pattanayak and C. S. Mohanty, Green Nanotechnology: A Roadmap to Long-Term Applications in Biomedicine, Agriculture, Food, Green Buildings, Coatings, and Textile Sectors, in Nanomater. Build. Blocks Mod. Technol. Synth. Prop. Appl., ed. Khan T., Jawaid M., Ahmad K. A. and Singh B., Springer Nature, Singapore, 2023, pp. 231–261, DOI:10.1007/978-981-99-4149-0_12.
- S. Iravani and R. S. Varma, Bacteria in Heavy Metal Remediation and Nanoparticle Biosynthesis, ACS Sustain. Chem. Eng., 2020, 8, 5395–5409, DOI:10.1021/acssuschemeng.0c00292.
- A. Thomas, G. Karmakar, A. Y. Shah, S. V. Lokhande, A. Y. Kulkarni and A. Tyagi,
et al., Molecular precursor-mediated facile synthesis of photo-responsive stibnite Sb2S3 nanorods and tetrahedrite Cu12Sb4S13 nanocrystals, Dalton Trans., 2022, 51, 12181–12191, 10.1039/D2DT01814D.
-
P. P. Singh, Ambika. 10 – Environmental remediation by nanoadsorbents-based polymer nanocomposite, in New Polym. Nanocomposites Environ. Remediat., ed. Hussain C. M. and Mishra A. K., Elsevier, 2018, pp. 223–241, DOI:10.1016/B978-0-12-811033-1.00010-X.
-
A. Denizli, N. Ali, M. Bilal, A. Khan and T. A. Nguyen, Nano-biosorbents for Decontamination of Water, Air, and Soil Pollution, 2022 Search PubMed.
- N. Yang, W. Zhang, C. Ye, X. Chen and S. Ling, Nanobiopolymers Fabrication and Their Life Cycle Assessments, Biotechnol. J., 2018, 14, 1700754, DOI:10.1002/biot.201700754.
- K. Van de Velde and P. Kiekens, Biopolymers: overview of several properties and consequences on their applications, Polym. Test., 2002, 21, 433–442, DOI:10.1016/S0142-9418(01)00107-6.
-
S. Mohan, O. S. Oluwafemi, N. Kalarikkal, S. Thomas and S. P. Songca, Biopolymers – Application in Nanoscience and Nanotechnology, in Recent Adv. Biopolym., ed. Perveen F. K., IntechOpen, Rijeka, 2016, DOI:10.5772/62225.
-
R. Singh, S. Gautam, B. Sharma, P. Jain and K. D. Chauhan, Biopolymers and Their Classifications, Elsevier Inc., 2021, DOI:10.1016/b978-0-12-819240-5.00002-x.
-
L. Avérous and E. Pollet, Environmental Silicate Nano-Biocomposite, 2012, vol. 50, DOI:10.1007/978-1-4471-4108-2.
- K. Khosravi-Darani and D. Z. Bucci, Application of poly(hydroxyalkanoate) in food packaging: Improvements by nanotechnology, Chem. Biochem. Eng. Q., 2015, 29, 275–285, DOI:10.15255/CABEQ.2014.2260.
- P. Lu, H. Xiao, W. Zhang and G. Gong, Reactive coating of soybean oil-based polymer on nanofibrillated cellulose film for water vapor barrier packaging, Carbohydr. Polym., 2014, 111, 524–529, DOI:10.1016/j.carbpol.2014.04.071.
- H. Wang, D. Wei, Z. Ziaee, H. Xiao, A. Zheng and Y. Zhao, Preparation and Properties of Nonleaching Antimicrobial Linear Low-Density Polyethylene Films, Ind. Eng. Chem. Res., 2015, 54, 1824–1831, DOI:10.1021/ie504393t.
- B. Kaur, A. Fazilah, R. Bhat and A. Karim, Progress in Starch modification in the last decade, Food Hydrocolloids, 2012, 26, 398–404, DOI:10.1016/j.foodhyd.2011.02.016.
- P. M. Visakh and S. Thomas, Preparation of Bionanomaterials and their Polymer Nanocomposites from Waste and Biomass, Waste Biomass Valorization, 2010, 1, 121–134, DOI:10.1007/s12649-010-9009-7.
- B. Hu, Q. Lu, X. Jiang, J. Liu, M. Cui and C. Dong,
et al., Formation mechanism of hydroxyacetone in glucose pyrolysis: A combined experimental and theoretical study, Proc. Combust. Inst., 2018, 37, 2741–2748, DOI:10.1016/j.proci.2018.05.146.
-
M. Rahman and M. R. Hasan, Synthetic Biopolymers, in Funct. Biopolym., ed. Jafar Mazumder M. A., Sheardown H. and Al-Ahmed A., Springer International Publishing, Cham, 2019, pp. 1–43, DOI:10.1007/978-3-319-95990-0_1.
- Y. Xu, F. Zhou, D. Zhou, J. Mo, H. Hu and L. Lin,
et al., Degradation Behaviors of Biodegradable Aliphatic Polyesters and Polycarbonates, J. Biobased Mater. Bioenergy, 2020, 14, 155–168 CrossRef CAS.
- C. K. S. Pillai, W. Paul and C. P. Sharma, Chitin and chitosan polymers: Chemistry, solubility and fiber formation, Prog. Polym. Sci., 2009, 34, 641–678, DOI:10.1016/j.progpolymsci.2009.04.001.
-
M. Das, B. Mandal and V. Katiyar, Sustainable Routes for Synthesis of Poly(ε-Caprolactone): Prospects in Chemical Industries, 2020, pp. 21–33, DOI:10.1007/978-981-15-1251-3_2.
- C. Mellinas, M. Ramos, A. Grau-Atienza, A. Jordà, N. Burgos and A. Jimenez,
et al., Biodegradable Poly(ε-Caprolactone) Active Films Loaded with MSU-X Mesoporous Silica for the Release of α-Tocopherol, Polymers, 2020, 12, 137, DOI:10.3390/polym12010137.
- T. Maharana, B. Mohanty and Y. Negi, Melt–solid polycondensation of lactic acid and its biodegradability, Prog. Polym. Sci., 2009, 34, 99–124, DOI:10.1016/j.progpolymsci.2008.10.001.
- G. Luckachan and C. Pillai, Chitosan/oligo L-lactide graft copolymers: Effect of hydrophobic side chains on the physico-chemical properties and biodegradability, Carbohydr. Polym., 2006, 64, 254–266, DOI:10.1016/j.carbpol.2005.11.035.
- G. Marianela and S. E. Vaillard, Evolution of Reactive mPEG Polymers for the Conjugation of Peptides and Proteins, Curr. Org. Chem., 2013, 17, 975–998, DOI:10.2174/1385272811317090010.
- M. Conda-Sheridan and M. Krishnaiah, Protecting Groups in Peptide Synthesis, Methods Mol. Biol., 2020, 2103, 111–128, DOI:10.1007/978-1-0716-0227-0_7.
- R. K. Donato and A. Mija, Keratin Associations with Synthetic, Biosynthetic and Natural Polymers: An Extensive Review, Polymers, 2020, 12, 32, DOI:10.3390/polym12010032.
- M. Rajabi, A. Ali, M. McConnell and J. Cabral, Keratinous materials: Structures and functions in biomedical applications, Mater. Sci. Eng., C, 2020, 110, 110612, DOI:10.1016/j.msec.2019.110612.
- L. Zhou, X. Jiao, S. Liu, M. Hao, S. Cheng and P. Zhang,
et al., Functional DNA-based hydrogel intelligent materials for biomedical applications, J. Mater. Chem. B, 2020, 8, 1991–2009, 10.1039/C9TB02716E.
- M. Rahman, K. S. Alharbi, N. K. Alruwaili, N. Anfinan, W. H. Almalki and I. Padhy,
et al., Nucleic acid-loaded lipid-polymer nanohybrids as novel nanotherapeutics in anticancer therapy, Expert Opin. Drug Delivery, 2020, 17, 805–816, DOI:10.1080/17425247.2020.1757645.
- A. Sarma and M. K. Das, Improving the sustainable performance of Biopolymers using nanotechnology, Polym. -Plast. Technol. Mat., 2021, 60, 1935–1965 CAS.
- G. P. Udayakumar, S. Muthusamy, B. Selvaganesh, N. Sivarajasekar, K. Rambabu and S. Sivamani,
et al., Ecofriendly biopolymers and composites: Preparation and their applications in water-treatment, Biotechnol. Adv., 2021, 52, 107815, DOI:10.1016/j.biotechadv.2021.107815.
- A. V. Samrot, T. C. Sean, T. Kudaiyappan, U. Bisyarah, A. Mirarmandi and E. Faradjeva,
et al., Production, characterization and application of nanocarriers made of polysaccharides, proteins, bio-polyesters and other biopolymers: A review, Int. J. Biol. Macromol., 2020, 165, 3088–3105, DOI:10.1016/j.ijbiomac.2020.10.104.
- A. Koyyada and P. Orsu, Natural gum polysaccharides as efficient tissue engineering and drug delivery biopolymers, J. Drug Delivery Sci. Technol., 2021, 63, 102431, DOI:10.1016/j.jddst.2021.102431.
- A. Lisitsyn, A. Semenova, V. Nasonova, E. Polishchuk, N. Revutskaya and I. Kozyrev,
et al., Approaches in Animal Proteins and Natural Polysaccharides Application for Food Packaging: Edible Film Production and Quality Estimation, Polymers, 2021, 13, 1592, DOI:10.3390/polym13101592.
-
V. Wankhade, Chapter 6 – Animal-derived biopolymers in food and biomedical technology, in Biopolym. Formul., ed. Pal K., Banerjee I., Sarkar P., Kim D., Deng W.-P., Dubey N. K., et al., Elsevier, 2020, pp. 139–152, DOI:10.1016/B978-0-12-816897-4.00006-0.
- P. Yadav, H. Yadav, V. G. Shah, G. Shah and G. Dhaka, Biomedical Biopolymers, their Origin and Evolution in Biomedical Sciences: A Systematic Review, J. Clin. Diagn. Res., 2015, 9, 21–25, DOI:10.7860/JCDR/2015/13907.6565.
- J. G. Tirrell and D. A. Tirrell, Synthesis of biopolymers: proteins, polyesters, polysaccharides and polynucleotides, Curr. Opin. Solid State Mater. Sci., 1996, 1, 407–411, DOI:10.1016/S1359-0286(96)80033-7.
- N. Koyama and Y. Doi, Continuous production of poly(3-hydroxybutyrate-co-3-hyhroxyvalerate) byAlcaligenes eutrophus, Biotechnol. Lett., 1995, 17, 281–284, DOI:10.1007/BF01190637.
- A. Sukan, I. Roy and T. Keshavarz, Dual production of biopolymers from bacteria, Carbohydr. Polym., 2015, 126, 47–51, DOI:10.1016/j.carbpol.2015.03.001.
- R. M. Rasal, A. V. Janorkar and D. E. Hirt, Poly(lactic acid) modifications, Prog. Polym. Sci., 2010, 35, 338–356, DOI:10.1016/j.progpolymsci.2009.12.003.
- K. Hamad, M. Kaseem, Y. G. Ko and F. Deri, Biodegradable polymer blends and composites: An overview, Polym. Sci., Ser. A, 2014, 56, 812–829, DOI:10.1134/S0965545X14060054.
- P. K. Annamalai, D. Depan, N. Tomer and R. Singh, Nanoscale particles for polymer degradation and stabilization-Trends and future perspectives, Prog. Polym. Sci., 2009, 34, 479–515, DOI:10.1016/j.progpolymsci.2009.01.002.
- F. Vilarinho, A. S. Silva, M. F. Vaz and J.
P. Farinha, Nanocellulose in green food packaging, Crit. Rev. Food Sci. Nutr., 2018, 58, 1526–1537, DOI:10.1080/10408398.2016.1270254.
- S. P. Bangar and W. S. Whiteside, Nano-cellulose reinforced starch bio composite films- A review on green composites, Int. J. Biol. Macromol., 2021, 185, 849–860, DOI:10.1016/j.ijbiomac.2021.07.017.
- S. H. Othman, Bio-nanocomposite Materials for Food Packaging Applications: Types of Biopolymer and Nano-sized Filler, Agric. Agric. Sci. Procedia, 2014, 2, 296–303, DOI:10.1016/j.aaspro.2014.11.042.
- K. Samborska, S. Boostani, M. Geranpour, H. Hosseini, C. Dima and S. Khoshnoudi-Nia,
et al., Green biopolymers from by-products as wall materials for spray drying microencapsulation of phytochemicals, Trends Food Sci. Technol., 2021, 108, 297–325, DOI:10.1016/j.tifs.2021.01.008.
- S. Moradi, K. Sadrjavadi, N. Farhadian, L. Hosseinzadeh and M. Shahlaei, Easy synthesis, characterization and cell cytotoxicity of green nano carbon dots using hydrothermal carbonization of Gum Tragacanth and chitosan bio-polymers for bioimaging, J. Mol. Liq., 2018, 259, 284–290, DOI:10.1016/j.molliq.2018.03.054.
- J. Liao, Y. Zhou, B. Hou, J. Zhang and H. Huang, Nano-chitin: Preparation strategies and food biopolymer film reinforcement and applications, Carbohydr. Polym., 2023, 305, 120553, DOI:10.1016/j.carbpol.2023.120553.
- X. Yang, J. Liu, Y. Pei, X. Zheng and K. Tang, Recent Progress in Preparation and Application of Nano-Chitin Materials, Energy Environ. Mater., 2020, 3, 492–515, DOI:10.1002/eem2.12079.
- L. Bai, L. Liu, M. Esquivel, B. L. Tardy, S. Huan and X. Niu,
et al., Nanochitin: Chemistry, Structure, Assembly, and Applications, Chem. Rev., 2022, 122, 11604–11674, DOI:10.1021/acs.chemrev.2c00125.
- T. M. Le, C. L. Tran, T. X. Nguyen, Y. H. P. Duong, P. K. Le and V. T. Tran, Green Preparation of Chitin and Nanochitin from Black Soldier Fly for Production of Biodegradable Packaging Material, J. Polym. Environ., 2023, 31, 3094–3105, DOI:10.1007/s10924-023-02793-2.
- T. Suortti, M. V. Gorenstein and P. Roger, Determination of the molecular mass of amylose, J. Chromatogr., 1998, 828, 515–521, DOI:10.1016/S0021-9673(98)00831-0.
-
S. Srinivasan, V. Ramachandran, R. Murali, V. Vinothkumar and D. Raajasubramanian and A. Kanagalakshimi, Biogenic Metal Nanoparticles and Their Antimicrobial Properties, 2020, pp. 126–162, DOI:10.1201/9780429342776-17.
- A. Kaanane and T. P. Labuza, The Maillard reaction in foods, Prog. Clin. Biol. Res., 1989, 304, 301–327 CAS.
- H. Angellier, S. Molina-Boisseau, M. N. Belgacem and A. Dufresne, Surface Chemical Modification of Waxy Maize Starch Nanocrystals, Langmuir, 2005, 21, 2425–2433, DOI:10.1021/la047530j.
- J.-L. Putaux, S. Molina-Boisseau, T. Momaur and A. Dufresne, Platelet nanocrystals resulting from the disruption of waxy maize starch granules by acid hydrolysis, Biomacromolecules, 2003, 4, 1198–1202, DOI:10.1021/bm0340422.
- X. Fei, M. Jia, X. Du, Y. Yang, R. Zhang and Z. Shao,
et al., Green Synthesis of Silk Fibroin-Silver Nanoparticle Composites with Effective Antibacterial and Biofilm-Disrupting Properties, Biomacromolecules, 2013, 14, 4483–4488, DOI:10.1021/bm4014149.
- Y. Duan, X. Chen and Z.-Z. Shao, The Silk Textile Embedded in Silk Fibroin Composite: Preparation and Properties, Chin. J. Polym. Sci., 2018, 36, 1043–1046, DOI:10.1007/s10118-018-2117-8.
- T. V. Chirila, S. Suzuki, L. J. Bray, N. L. Barnett and D. G. Harkin, Evaluation of silk sericin as a biomaterial: in vitro growth of human corneal limbal epithelial cells on Bombyx mori sericin membranes, Prog. Biomater., 2013, 2, 14, DOI:10.1186/2194-0517-2-14.
- S. Keten and M. J. Buehler, Nanostructure and molecular mechanics of spider dragline silk protein assemblies, J. R. Soc., Interface, 2010, 7, 1709–1721, DOI:10.1098/rsif.2010.0149.
- K. E. Rivadeneira-Velasco, C. A. Utreras-Silva, A. Díaz-Barrios, A. E. Sommer-Márquez, J. P. Tafur and R. M. Michell, Green Nanocomposites Based on Thermoplastic Starch: A Review, Polymers, 2021, 13, 3227, DOI:10.3390/polym13193227.
- V. S. K. Sonika, S. Samanta, A. K. Srivastava, S. Biswas and R. M. Alsharabi,
et al., Conducting Polymer Nanocomposite for Energy Storage and Energy Harvesting Systems, Adv. Mater. Sci. Eng., 2022, 2022, 2266899, DOI:10.1155/2022/2266899.
- N. Basavegowda and K.-H. Baek, Advances in Functional Biopolymer-Based Nanocomposites for Active Food Packaging Applications, Polymers, 2021, 13, 4198, DOI:10.3390/polym13234198.
- J. R. A. Pires, C. Rodrigues, I. Coelhoso, A. L. Fernando and V. G. L. Souza, Current Applications of Bionanocomposites in Food Processing and Packaging, Polymers, 2023, 15, 2336, DOI:10.3390/polym15102336.
- P. Chincholikar, K. R. Singh, A. Natarajan, R. G. Kerry, J. Singh and J. Malviya,
et al., Green nanobiopolymers for ecological applications: a step towards a sustainable environment, RSC Adv., 2023, 13, 12411–12429, 10.1039/d2ra07707h.
- J. W. Rhim, H. M. Park and C. S. Ha, Bio-nanocomposites for food packaging applications, Prog. Polym. Sci., 2013, 38, 1629–1652, DOI:10.1016/j.progpolymsci.2013.05.008.
- N. A. Abu Hassan, S. Ahmad, R. S. Chen and V. D. Natarajan, Synergistically enhanced mechanical, combustion and acoustic properties of biopolymer composite foams reinforcement by kenaf fibre, Composites, Part A, 2022, 155, 106826, DOI:10.1016/j.compositesa.2022.106826.
- R. Tokoro, V. Minh Duc, K. Okubo, T. Tanaka, T. Fujii and T. Fujiura, How to Improve Mechanical Properties of PolyLactic Acid with Bamboo Fibers, J. Mater. Sci., 2008, 43, 775–787, DOI:10.1007/s10853-007-1994-y.
- S. S. Ayyaril, A. Shanableh, S. Bhattacharjee, M. Rawas-Qalaji, R. Cagliani and A. G. Shabib,
et al., Recent progress in micro and nano-encapsulation techniques for environmental applications: A review, Results Eng., 2023, 18, 101094, DOI:10.1016/j.rineng.2023.101094.
- Y. Shang, M. K. Hasan, G. J. Ahammed, M. Li, H. Yin and J. Zhou, Applications of Nanotechnology in Plant Growth and Crop Protection: A Review, Molecules, 2019, 24, 2558, DOI:10.3390/molecules24142558.
- P. de Vos, M. M. Faas, M. Spasojevic and J. Sikkema, Encapsulation for preservation of functionality and targeted delivery of bioactive food components, Int. Dairy J., 2010, 20, 292–302, DOI:10.1016/j.idairyj.2009.11.008.
- P. N. Ezhilarasi, P. Karthik, N. Chhanwal and C. Anandharamakrishnan, Nanoencapsulation Techniques for Food Bioactive Components: A Review, Food Bioprocess Technol., 2013, 6, 628–647, DOI:10.1007/s11947-012-0944-0.
- Z. Wang, S. Ishii and P. J. Novak, Encapsulating microorganisms to enhance biological nitrogen removal in wastewater: recent advancements and future opportunities, Environ. Sci.: Water Res. Technol., 2021, 7, 1402–1416, 10.1039/D1EW00255D.
- S. Thakur, B. Sharma, A. Verma, J. Chaudhary, S. Tamulevicius and V. K. Thakur, Recent progress in sodium alginate based sustainable hydrogels for environmental applications, J. Cleaner Prod., 2018, 198, 143–159, DOI:10.1016/j.jclepro.2018.06.259.
- Y. Zhang, S. Xu, Y. Luo, S. Pan, H. Ding and G. Li, Synthesis of mesoporous carbon capsules encapsulated with magnetite nanoparticles and their application in wastewater treatment, J. Mater. Chem., 2011, 21, 3664–3671, 10.1039/C0JM03727C.
- A.-F. Ngomsik, A. Bee, J.-M. Siaugue, D. Talbot, V. Cabuil and G. Cote, Co(II) removal by magnetic alginate beads containing Cyanex 272®, J. Hazard. Mater., 2009, 166, 1043–1049, DOI:10.1016/j.jhazmat.2008.11.109.
- H.-J. Hong, H. Jeong, B.-G. Kim, J. Hong, I.-S. Park and T. Ryu,
et al., Highly stable and magnetically separable alginate/Fe3O4 composite for the removal of strontium (Sr) from seawater, Chemosphere, 2016, 165, 231–238, DOI:10.1016/j.chemosphere.2016.09.034.
- I.-S. Chang, C.-I. Kim and B.-U. Nam, The influence of poly-vinyl-alcohol (PVA) characteristics on the physical stability of encapsulated immobilization media for advanced wastewater treatment, Process Biochem., 2005, 40, 3050–3054, DOI:10.1016/j.procbio.2005.02.009.
- D. Jíménez-Arias, S. Morales-Sierra, P. Silva, H. Carrêlo, A. Gonçalves and J. F. T. Ganança,
et al., Encapsulation with Natural Polymers to Improve the Properties of Biostimulants in Agriculture, Plants, 2023, 12, 55, DOI:10.3390/plants12010055.
- H. S. Elshafie and I. Camele, Applications of Absorbent Polymers for Sustainable Plant Protection and Crop Yield, Sustainability, 2021, 13, 3253, DOI:10.3390/su13063253.
- H. El-Ramady, N. Abdalla, D. Sári, A. Ferroudj, A. Muthu and J. Prokisch,
et al., Nanofarming: Promising Solutions for the Future of the Global Agricultural Industry, Agronomy, 2023, 13, 1600, DOI:10.3390/agronomy13061600.
-
M. Sohail, A. Waris, M. Ayub, M. Usman, M. Zia-ur-Rehman, M. Sabir, et al., Environmental Application of Nanomaterials: A Promise to Sustainable Future, 2019, pp. 1–54, DOI:10.1016/bs.coac.2019.10.002.
- J. Baranwal, B. Barse, A. Fais, G. L. Delogu and A. Kumar, Biopolymer: A Sustainable Material for Food and Medical Applications, Polymers, 2022, 14, 983, DOI:10.3390/polym14050983.
- M. Khatami, H. Q. Alijani, M. S. Nejad and R. S. Varma, Core@shell nanoparticles: Greener synthesis using natural plant products, Appl. Sci., 2018, 8, 1–17, DOI:10.3390/app8030411.
- I. Khan, K. Saeed and I. Khan, Nanoparticles: Properties, applications and toxicities, Arabian J. Chem., 2019, 12, 908–931, DOI:10.1016/j.arabjc.2017.05.011.
- J. Joshi, S. V. Homburg and A. Ehrmann, Atomic Force Microscopy (AFM) on Biopolymers and Hydrogels for Biotechnological Applications—Possibilities and Limits, Polymers, 2022, 14, 1267, DOI:10.3390/polym14061267.
- A. Roy, A. Sharma, S. Yadav, L. T. Jule and R. Krishnaraj, Nanomaterials for Remediation of Environmental Pollutants, Bioinorg. Chem. Appl., 2021, 2021, 1764647, DOI:10.1155/2021/1764647.
- F. D. Guerra, M. F. Attia, D. C. Whitehead and F. Alexis, Nanotechnology for Environmental Remediation: Materials and Applications, Molecules, 2018, 23, 1760, DOI:10.3390/molecules23071760.
- N. Yadav, V. K. Garg, A. K. Chhillar and J. S. Rana, Detection and remediation of pollutants to maintain ecosustainability employing nanotechnology: A review, Chemosphere, 2021, 280, 130792, DOI:10.1016/j.chemosphere.2021.130792.
- H. Zhu, R. Jiang, L. Xiao, Y. Chang, Y. Guan and X. Li,
et al., Photocatalytic decolorization and degradation of Congo Red on innovative crosslinked chitosan/nano-CdS composite catalyst under visible light irradiation, J. Hazard. Mater., 2009, 169, 933–940, DOI:10.1016/j.jhazmat.2009.04.037.
- K. A. Lukyanenko, I. A. Denisov, V. V. Sorokin, A. S. Yakimov, E. N. Esimbekova and P. I. Belobrov, Handheld Enzymatic Luminescent Biosensor for Rapid Detection of Heavy Metals in Water Samples, Chemosensors, 2019, 7, 16, DOI:10.3390/chemosensors7010016.
- N. Goyal, A. Amar, S. Gulati and R. S. Varma, Cyclodextrin-Based Nanosponges as an Environmentally Sustainable Solution for Water Treatment: A Review, ACS Appl. Nano Mater., 2023, 6, 13766–13791, DOI:10.1021/acsanm.3c02026.
- S. Gulati, B. H. N. Lingam, A. Baul, S. Kumar, R. Wadhwa and M. Trivedi,
et al., Recent progress, synthesis, and application of chitosan-decorated magnetic nanocomposites in remediation of dye-laden wastewaters, New J. Chem., 2022, 46, 17114–17139, 10.1039/D2NJ03558H.
-
R. K. Sharma, S. Gulati and A. Puri, Green Chemistry Solutions to Water Pollution, Elsevier Inc., 2014, DOI:10.1016/B978-0-12-411645-0.00003-1.
- J. Yang, B. Hou, J. Wang, B. Tian, J. Bi and N. Wang,
et al., Nanomaterials for the Removal of Heavy Metals from Wastewater, Nanomaterials, 2019, 9, 424, DOI:10.3390/nano9030424.
- M. Nasrollahzadeh, M. Sajjadi, S. Iravani and R. S. Varma, Starch, cellulose, pectin, gum, alginate, chitin and chitosan derived (nano)materials for sustainable water treatment: A review, Carbohydr. Polym., 2021, 251, 116986, DOI:10.1016/j.carbpol.2020.116986.
- S. Manna, D. Gopakumar, D. Roy, P. Saha and S. Thomas, Nanobiomaterials for removal of fluoride and chlorophenols from water, New Polym. Nanocompos. Environ. Rem., 2018, 487–498, DOI:10.1016/B978-0-12-811033-1.00020-2.
- V. V. T. Padil, J. Y. Cheong, K. P. Akshay Kumar, P. Makvandi, E. N. Zare and R. Torres-Mendieta,
et al., Electrospun fibers based on carbohydrate gum polymers and their multifaceted applications, Carbohydr. Polym., 2020, 247, 116705, DOI:10.1016/j.carbpol.2020.116705.
- M. Mahramanlioglu, I. Kizilcikli and İ. Biçer, Adsorption of Fluoride from Aqueous Solution by Acid Treated Spent Bleaching Earth, J. Fluorine Chem., 2002, 115, 41–47, DOI:10.1016/S0022-1139(02)00003-9.
- R. K. Mishra, A. Sabu and S. K. Tiwari, Materials chemistry and the futurist eco-friendly applications of nanocellulose: Status and prospect, J. Saudi Chem. Soc., 2018, 22, 949–978, DOI:10.1016/j.jscs.2018.02.005.
- T. Abitbol, A. Rivkin, Y. Cao, Y. Nevo, E. Abraham and T. Ben-Shalom,
et al., Nanocellulose, a tiny fiber with huge applications, Curr. Opin. Biotechnol., 2016, 39, 76–88, DOI:10.1016/j.copbio.2016.01.002.
-
N. Mahfoudhi and S. Boufi, 12 – Nanocellulose: A challenging nanomaterial towards environment remediation, in Cellul. Nanofibre Compos., ed. Jawaid M., Boufi S. and Abdul Khalil H. P. S., Woodhead Publishing, 2017, pp. 277–304, DOI:10.1016/B978-0-08-100957-4.00012-7.
- L. Serventi, Q. He, J. Huang, A. Mani and A. J. Subhash, Advances in the preparations and applications of nanochitins, Food Hydrocolloids Health, 2021, 1, 100036, DOI:10.1016/j.fhfh.2021.100036.
- S. K. Tiwari, S. Sahoo, N. Wang and A. Huczko, Graphene research and their outputs: Status and prospect, J. Sci.: Adv. Mater. Devices, 2020, 5, 10–29, DOI:10.1016/j.jsamd.2020.01.006.
- A. Sahu, R. Dosi, C. Kwiatkowski, S. Schmal and J. C. Poler, Advanced Polymeric Nanocomposite Membranes for Water and Wastewater Treatment: A Comprehensive Review, Polymers, 2023, 15, 540, DOI:10.3390/polym15030540.
- T. Shahnaz, A. Jayakumar, D. Bedadeep and S. Narayanasamy, A review on tailored graphene material for industrial wastewater, J. Environ. Chem. Eng., 2021, 9, 105933, DOI:10.1016/j.jece.2021.105933.
-
A. Singh, A. Sharma, R. K. Verma, R. L. Chopade, P. P. Pandit, V. Nagar, et al., Heavy Metal Contamination of Water and Their Toxic Effect on Living Organisms, in Toxic. Environ. Pollut., ed. Dorta D. J. and de Oliveira D. P., IntechOpen, Rijeka, 2022, DOI:10.5772/intechopen.105075.
- S. Iravani and R. S. Varma, Genetically Engineered Organisms: Possibilities and Challenges of Heavy Metal Removal and Nanoparticle Synthesis, Clean Technol., 2022, 4, 502–511, DOI:10.3390/cleantechnol4020030.
- E. Kasiri, P. Arabkhani, H. Haddadi, A. Asfaram and R. S. Varma, A silanized magnetic amino-functionalized carbon nanotube-based multi-ion imprinted polymer for the selective aqueous decontamination of heavy metal ions, New J. Chem., 2022, 46, 21704–21716, 10.1039/D2NJ04105G.
- R. Taghavi, S. Rostamnia, M. Farajzadeh, H. Karimi-Maleh, J. Wang and D. Kim,
et al., Magnetite Metal–Organic Frameworks: Applications in Environmental Remediation of Heavy Metals, Organic Contaminants, and Other Pollutants, Inorg. Chem., 2022, 61, 15747–15783, DOI:10.1021/acs.inorgchem.2c01939.
- M. S. A. Darwish, M. H. Mostafa and L. M. Al-Harbi, Polymeric Nanocomposites for Environmental and Industrial Applications, Int. J. Mol. Sci., 2022, 23, 1023, DOI:10.3390/ijms23031023.
- U. Upadhyay, I. Sreedhar, S. A. Singh, C. M. Patel and K. L. Anitha, Recent advances in heavy metal removal by chitosan based adsorbents, Carbohydr. Polym., 2021, 251, 117000, DOI:10.1016/j.carbpol.2020.117000.
- X. Yuan, J. Li, L. Luo, Z. Zhong and X. Xie, Advances in Sorptive Removal of Hexavalent Chromium (Cr(VI)) in Aqueous Solutions Using Polymeric Materials, Polymers, 2023, 15, 388, DOI:10.3390/polym15020388.
- C.-H. Weng, Y. C. Sharma and S.-H. Chu, Adsorption of Cr(VI) From Aqueous Solutions by Spent Activated Clay, J. Hazard. Mater., 2008, 155, 65–75, DOI:10.1016/j.jhazmat.2007.11.029.
- A. Saad, I. Bakas, J.-Y. Piquemal, S. Nowak, M. Abderrabba and M. Chehimi, Mesoporous silica/polyacrylamide composite: Preparation by UV-graft photopolymerization, characterization and use as Hg(II) adsorbent, Appl. Surf. Sci., 2016, 367, 181–189, DOI:10.1016/j.apsusc.2016.01.134.
- L. D. Ardila-Leal, R. A. Poutou-Piñales, A. M. Pedroza-Rodríguez and B. E. Quevedo-Hidalgo, A Brief History of Colour, the Environmental Impact of Synthetic Dyes and Removal by Using Laccases, Molecules, 2021, 26, 3813, DOI:10.3390/molecules26133813.
-
A. Kumar, U. Dixit, K. Singh, S. P. Gupta and M. S. J. Beg, Structure and Properties of Dyes and Pigments, in Dye. Pigment., ed. Papadakis R., IntechOpen, Rijeka, 2021, DOI:10.5772/intechopen.97104.
- M. D. Teli, R. Paul, S. Landage and A. Aich, Ecofriendly processing of sulphur and vat dyes - An overview, Indian J. Fibre Text. Res., 2001, 26, 101–107 CAS.
- Y. Y. Lams, P. O. Nkeonye, K. A. Bello, M. K. Yakubu and A. O. Lawal, Synthesis of Disperse Dyes from Pyridone and Resorcinol Coupled to Diazotized 2-Amino-4-chloro-5-formylthiazole and Application to Polyester, Adv. Chem., 2014, 2014, 864286, DOI:10.1155/2014/864286.
- K. Ramakrishnan R, V. V. T. Padil, S. Wacławek, M. Černík and R. S. Varma, Eco-Friendly and Economic, Adsorptive Removal of Cationic and Anionic Dyes by Bio-Based Karaya Gum—Chitosan Sponge, Polymers, 2021, 13, 251, DOI:10.3390/polym13020251.
- I. Chang, A. K. Prasidhi, J. Im and G.-C. Cho, Soil strengthening using thermo-gelation biopolymers, Constr. Build. Mater., 2015, 77, 430–438, DOI:10.1016/j.conbuildmat.2014.12.116.
- R. Al-Tohamy, S. S. Ali, F. Li, K. M. Okasha, Y. A.-G. Mahmoud and T. Elsamahy,
et al., A critical review on the treatment of dye-containing wastewater: Ecotoxicological and health concerns of textile dyes and possible remediation approaches for environmental safety, Ecotoxicol. Environ. Saf., 2022, 231, 113160, DOI:10.1016/j.ecoenv.2021.113160.
- L. Wang, Y. Yao, J. Li, K. Liu and F. Wu, A State-of-the-Art Review of Organic Polymer Modifiers for Slope Eco-Engineering, Polymers, 2023, 15, 2878, DOI:10.3390/polym15132878.
- A. Soldo, M. Miletić and M. L. Auad, Biopolymers as a sustainable solution for the enhancement of soil mechanical properties, Sci. Rep., 2020, 10, 267, DOI:10.1038/s41598-019-57135-x.
- I. Chang, M. Lee, A. T. P. Tran, S. Lee, Y.-M. Kwon and J. Im,
et al., Review on biopolymer-based soil treatment (BPST) technology in geotechnical engineering practices, Transp. Geotech., 2020, 24, 100385, DOI:10.1016/j.trgeo.2020.100385.
- K. Piekarska, M. Sikora, M. Owczarek, J. Jóźwik-Pruska and M. Wiśniewska-Wrona, Chitin and Chitosan as Polymers of the Future—Obtaining, Modification, Life Cycle Assessment and Main Directions of Application, Polymers, 2023, 15, 793, DOI:10.3390/polym15040793.
- N. Karami, A. Mohammadpour, M. R. Samaei, A. M. Amani, M. Dehghani and R. S. Varma,
et al., Green synthesis of sustainable magnetic nanoparticles Fe3O4 and Fe3O4-chitosan derived from Prosopis farcta biomass extract and their performance in the sorption of lead(II), Int. J. Biol. Macromol., 2024, 254, 127663, DOI:10.1016/j.ijbiomac.2023.127663.
- I. Chang, J. Im and G.-C. Cho, Introduction of Microbial Biopolymers in Soil Treatment for Future Environmentally-Friendly and Sustainable Geotechnical Engineering, Sustainability, 2016, 8, 251, DOI:10.3390/su8030251.
- N. Hataf, P. Ghadir and N. Ranjbar, Investigation of soil stabilization using chitosan biopolymer, J. Cleaner Prod., 2018, 170, 1493–1500, DOI:10.1016/j.jclepro.2017.09.256.
- D. Petri, Xanthan gum: A versatile biopolymer for biomedical and technological applications, J. Appl. Polym. Sci., 2015, 132, 42035, DOI:10.1002/app.42035.
- A. Mendonça, P. V. Morais, A. C. Pires, A. P. Chung and P. V. Oliveira, A Review on the Importance of Microbial Biopolymers Such as Xanthan Gum to Improve Soil Properties, Appl. Sci., 2021, 11, 170, DOI:10.3390/app11010170.
- W. Gates, A. Bouazza and P. G. Ranjith, Hydraulic conductivity of biopolymer-treated silty sand, Geotechnique, 2009, 59, 71–72, DOI:10.1680/geot.2007.00137.
- H. Fatehi, D. E. L. Ong, J. Yu and I. Chang, Biopolymers as Green Binders for Soil Improvement in Geotechnical Applications: A Review, Geosciences, 2021, 11, 291, DOI:10.3390/geosciences11070291.
- A. I. Osman, S. Fawzy, M. Farghali, M. El-Azazy, A. M. Elgarahy and R. A. Fahim,
et al., Biochar for agronomy, animal farming, anaerobic digestion, composting, water treatment, soil remediation, construction, energy storage, and carbon sequestration: a review, Environ. Chem. Lett., 2022, 20, 2385–2485, DOI:10.1007/s10311-022-01424-x.
- S. Gulati, B. H. N. Lingam, S. Kumar, K. Goyal, A. Arora and R. S. Varma, Improving the air quality with Functionalized Carbon Nanotubes: Sensing and remediation applications in the real world, Chemosphere, 2022, 299, 134468, DOI:10.1016/j.chemosphere.2022.134468.
- A. K. Rana, E. Mostafavi, W. F. Alsanie, S. S. Siwal and V. K. Thakur, Cellulose-based materials for air purification: A review, Ind. Crops Prod., 2023, 194, 116331, DOI:10.1016/j.indcrop.2023.116331.
- Y. Zhou, Y. Liu, M. Zhang, Z. Feng, D.-G. Yu and K. Wang, Electrospun Nanofiber Membranes for Air Filtration: A Review, Nanomater, 2022, 12, 1077, DOI:10.3390/nano12071077.
- A. Tcharkhtchi, N. Abbasnezhad, M. Zarbini Seydani, N. Zirak, S. Farzaneh and M. Shirinbayan, An overview of filtration efficiency through the masks: Mechanisms of the aerosols penetration, Bioact. Mater., 2021, 6, 106–122, DOI:10.1016/j.bioactmat.2020.08.002.
- A. C. C. Bortolassi, S. Nagarajan, B. de Araújo Lima, V. G. Guerra, M. L. Aguiar and V. Huon,
et al., Efficient
nanoparticles removal and bactericidal action of electrospun nanofibers membranes for air filtration, Mater. Sci. Eng., C, 2019, 102, 718–729, DOI:10.1016/j.msec.2019.04.094.
- V. V. Kadam, L. Wang and R. Padhye, Electrospun nanofibre materials to filter air pollutants – A review, J. Ind. Text., 2018, 47, 2253–2280, DOI:10.1177/1528083716676812.
- G. Berry, I. Beckman and H. Cho, A comprehensive review of particle loading models of fibrous air filters, J. Aerosol Sci., 2023, 167, 106078, DOI:10.1016/j.jaerosci.2022.106078.
- C. R. Gough, K. Callaway, E. Spencer, K. Leisy, G. Jiang and S. Yang,
et al., Biopolymer-Based Filtration Materials, ACS Omega, 2021, 6, 11804–11812, DOI:10.1021/acsomega.1c00791.
- O. D. Agboola and N. U. Benson, Physisorption and Chemisorption Mechanisms Influencing Micro (Nano) Plastics-Organic Chemical Contaminants Interactions: A Review, Front. Environ. Sci., 2021, 9, 1–27, DOI:10.3389/fenvs.2021.678574.
- L. C. T. Kenry, Nanofiber technology: current status and emerging developments, Prog. Polym. Sci., 2017, 70, 1–17, DOI:10.1016/j.progpolymsci.2017.03.002.
- K.-H. Kim, E. Kabir and S. A. Jahan, Airborne bioaerosols and their impact on human health, J. Environ. Sci., 2018, 67, 23–35, DOI:10.1016/j.jes.2017.08.027.
- R. Maus, A. Goppelsröder and H. Umhauer, Survival of Bacterial and Mold Spores in Air Filter Media, Atmos. Environ., 2001, 35, 105–113, DOI:10.1016/S1352-2310(00)00280-6.
- S. B. Jeong, K. J. Heo and B. U. Lee, Antimicrobial Air Filters Using Natural Sea Salt Particles for Deactivating Airborne Bacterial Particles, Int. J. Environ. Res. Public Health, 2019, 17, 190, DOI:10.3390/ijerph17010190.
- L. Wang, C. Hu and L. Shao, The antimicrobial activity of nanoparticles: present situation and prospects for the future, Int. J. Nanomed., 2017, 12, 1227–1249, DOI:10.2147/IJN.S121956.
- A. Sabirova, S. Wang, G. Falca, P.-Y. Hong and S. P. Nunes, Flexible isoporous air filters for high-efficiency particle capture, Polymer, 2021, 213, 123278, DOI:10.1016/j.polymer.2020.123278.
- M. Kaloti and A. Kumar, Synthesis of Chitosan-Mediated Silver Coated γ-Fe2O3 (Ag-γ-Fe2O3@Cs) Superparamagnetic Binary Nanohybrids for Multifunctional Applications, J. Phys. Chem. C, 2016, 120, 17627–17644, DOI:10.1021/acs.jpcc.6b05851.
- G. Liu, M. Xiao, X. Zhang, C. Gal, X. Chen and L. Liu,
et al., A review of air filtration technologies for sustainable and healthy building ventilation, Sustain. Cities Soc., 2017, 32, 375–396, DOI:10.1016/j.scs.2017.04.011.
- M. al-Shaeli, R. A. Al-Juboori, S. Al Aani, B. P. Ladewig and N. Hilal, Natural and recycled materials for sustainable membrane modification: Recent trends and prospects, Sci. Total Environ., 2022, 838, 156014, DOI:10.1016/j.scitotenv.2022.156014.
- H. Souzandeh, Y. Wang, A. Netravali and W. Zhong, Towards Sustainable and Multifunctional Air-Filters: A Review on Biopolymer-Based Filtration Materials, Polym. Rev., 2019, 59, 1–36, DOI:10.1080/15583724.2019.1599391.
- S. Han, J. Kim and S. H. Ko, Advances in air filtration technologies: structure-based and interaction-based approaches, Mater. Today Adv., 2021, 9, 100134, DOI:10.1016/j.mtadv.2021.100134.
- A. Saravanan, P. Senthil Kumar, S. Jeevanantham, S. Karishma, B. Tajsabreen and P. R. Yaashikaa,
et al., Effective water/wastewater treatment methodologies for toxic pollutants removal: Processes and applications towards sustainable development, Chemosphere, 2021, 280, 130595, DOI:10.1016/j.chemosphere.2021.130595.
- X. Ji, J. Huang, L. Teng, S. Li, X. Li and W. Cai,
et al., Advances in particulate matter filtration: Materials, performance, and application, Green Energy Environ., 2023, 8, 673–697, DOI:10.1016/j.gee.2022.03.012.
- J. Cao, Y. Huang and Q. Zhang, Ambient Air Purification by Nanotechnologies: From Theory to Application, Catalysts, 2021, 11, 1276, DOI:10.3390/catal11111276.
- W. M. Saleh, M. I. Ahmad, E. B. Yahya and H. P. S. Abdul Khalil, Nanostructured Bioaerogels as a Potential Solution for Particulate Matter Pollution, Gels, 2023, 9, 575, DOI:10.3390/gels9070575.
-
Y. Musa and I. B. Bwatanglang, Chapter 6 – Current role and future developments of biopolymers in green and sustainable chemistry and catalysis, in Sustain. Nanocellulose Nanohydrogels from Nat. Sources, ed. Mohammad F., Al-Lohedan H. A. and Jawaid M., Elsevier, 2020, pp. 131–154, DOI:10.1016/B978-0-12-816789-2.00006-7.
-
K. Kumaş and A. Akyüz, An Overview on the Use of Nanotechnology in the Renewable Energy Field, 2020, pp. 143–148, DOI:10.31593/ijeat.764240.
- T. O. Machado, J. Grabow, C. Sayer, P. H. H. de Araújo, M. L. Ehrenhard and F. R. Wurm, Biopolymer-based nanocarriers for sustained release of agrochemicals: A review on materials and social science perspectives for a sustainable future of agri- and horticulture, Adv. Colloid Interface Sci., 2022, 303, 102645, DOI:10.1016/j.cis.2022.102645.
- A. H. Tayeb, E. Amini, S. Ghasemi and M. Tajvidi, Cellulose Nanomaterials—Binding Properties and Applications: A Review, Molecules, 2018, 23, 2684, DOI:10.3390/molecules23102684.
-
S. Palit and C. Hussain, Chapter 28 – Green sustainability and the application of polymer nanocomposites—a vast vision for the future, in Micro Nano Technol., ed. Hussain C. M., Elsevier, 2021, pp. 733–747, DOI:10.1016/B978-0-12-821497-8.00028-9.
-
S. Palit, C. M. Hussain and S. Mallakpour, Sustainable Future with Nanoproducts, Handb. Consum. Nanoproducts, Springer Nature Singapore, Singapore, 2022, pp. 1409–1431, DOI:10.1007/978-981-16-8698-6_80.
|
This journal is © The Royal Society of Chemistry 2024 |
Click here to see how this site uses Cookies. View our privacy policy here.