Comparison of mechanochemical methods in the synthesis of binaphthol–benzoquinone based cocrystals†
Received
28th September 2023
, Accepted 8th April 2024
First published on 8th April 2024
Abstract
Mechanochemical methods either under neat or liquid assisted conditions have proven to be successful in making cocrystals. In this paper we compare the outcome of cocrystallization using two different mechanochemical methods, ball milling (BM) and resonant acoustic mixing (RAM), with solution crystallization. Racemic binaphthol and benzoquinone based binary and ternary cocrystals were investigated by BM and RAM. Both mechanochemical methods were successful in making the binary and ternary cocrystals that have been observed in solid state and solution. It is shown that the type of mechanochemical force imparted to the sample is very different between BM and RAM and this in turn leads to different cocrystallization outcomes. Thus, different mechanochemical methods should not be treated as the same and care must be taken when choosing a mechanochemical method for a particular application.
Introduction
Cocrystals are systems where two or more components which are solids at ambient temperature assemble into a crystalline state. Cocrystals have found uses as energetic and pharmaceutical materials. Especially in the field of pharmaceutics, a significant effort has been made to find new cocrystal forms of active pharmaceutical ingredients (API). Pharmaceutical cocrystals have been shown to improve several properties of an API such as solubility,1 physical/chemical stability,2,3 mechanical properties4 and bioavailability.5,6 Pharmaceutical cocrystals are typically prepared by solution crystallization. However, work in the last two decades has shown that solventless or solvent-assisted mechanochemical methods are powerful tools in the screening and scale-up of cocrystals. The main mechanochemical methods used to date to make cocrystals are ball milling (BM),7,8 twin screw extrusion (TSE)9–13 and resonant acoustic mixing (RAM).14–16 While there are many reports that describe the use of these mechanochemical methods to make cocrystals, only a few reports do a systematic comparison of the methods.
Coloristic cocrystals formed by grinding racemic BN and BQ were first reported by Kuroda et al. In their elegant work, they have shown that manual grinding of white powder of racemic BN with yellow powder of BQ produced striking red cocrystals of racemic binaphthol–benzoquinone (rBN–BQ) due to electron transfer. The authors showed manual grinding produced cocrystal I while solution crystallization produced cocrystal II.17 These results show that mechanochemical methods of preparation led to a different form of the cocrystal when compared to solution crystallization. Thus, this system is an ideal example system to investigate the effect of different mechanochemical methods on cocrystal formation in rBN–BQ systems.
In this study we used a BM and a RAM as the primary mechanochemical devices as they operate on different principles. BMs are available in many different configurations. For this study we have used shaker or mixer balls mill (cf. Fig. S1A, ESI†). In this setup the sample is loaded into stainless steel vessels along with stainless steel grinding balls. Two grinding vessels are horizontally clamped and are subjected to horizontal oscillating motion at defined frequencies and time periods. The movement of the chamber supplies the energy to the grinding balls which in turn is transferred to the sample during ball collisions. The final outcome of milling is dependent on the vessel configuration, the size, material and number of milling balls, the frequency, and the time period of milling. In the RAM setup, the sample is loaded into plastic containers and is clamped vertically on a spring-loaded platform (cf. Fig. S1B, ESI†). The machine operates at resonance and in theory can transfer all the mechanical energy in the springs to the sample in the vial in a contactless fashion. The mixing in the sample is facilitated by a low frequency and high intensity acoustic field. The final outcome of RAM is determined by the mixing intensity as measured by acceleration and the time period of mixing. Thus, RAM imparts mechanical energy to the sample in a fundamentally different way when compared to the BM. While RAM is an inherently contactless mixing technique, milling media can be used in conjunction with RAM to augment the mixing and mechanical energy provided by RAM.16,18 Since RAM is known to be more amenable to scale up than BM, such augmentation could prove very useful in expanding the applicability of RAM. Typically ZrO2 beads are used as milling media in the RAM.
In this paper, we report the comparison of BM and RAM in the synthesis of two component rBN–BQ and three component cocrystals of rBN–BQ with anthracene (AN) and naphthalene (NP).
Experimental
Materials
Racemic binaphthol (rBN), benzoquinone (BQ), anthracene (AN) and naphthalene (NP) were purchased from Fischer Scientific (Hampton, NH) and were used as received. rBN, BQ, AN, and NP samples were reported to >95% pure by the manufacturer. The structures of the molecules investigated are shown in Fig. 1. All solvents used in the work were purchased from Fischer Scientific (Hampton, NH) at purity level >99% and were used as received.
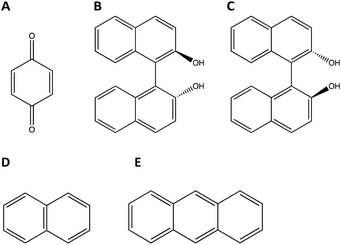 |
| Fig. 1 Chemical structures of molecules investigated in this study. (A) Benzoquinone (BQ), (B) R-Bi-naphthol (BN), (C) S-Bi-naphthol (BN), (D) naphthalene (NP), and (E) anthracene (AN). | |
Methods
X-ray powder diffraction (XRPD).
XRPD patterns of powder samples were collected using a PANalytical Empyrean X-ray diffractometer (Malvern Panalytical Ltd, Malvern, UK) equipped with Cu Kα source with a tube voltage of 45 kV and current of 40 mA. Samples were packed on a zero-background holder and scanned from 3.0° to 40.0° 2θ using a step size of 0.0263°. The incident beam path was equipped with a 0.02° Soller slit, a fixed 1° anti scatter slit, a fixed incident beam mask of 10 mm, and a programmable divergence slit in automatic mode. A beam knife for linear detectors was used. The diffracted beam was equipped with a 0.02° Soller slit, a programmable anti-scatter slit in automatic mode, and a nickel K-β filter. A PIXcel 1D detector was used in the scanning line detector (1D) mode. Data was collected in reflection mode at ambient conditions and analyzed using commercial software (HighScore Plus, version 5.0, Malvern Panalytical B.B., Almelo, Netherlands).
Differential scanning calorimetry (DSC).
DSC experiments were conducted using a Discovery DSC 2500 (TA instruments, New Castle, DE) equipped with a refrigerated cooling accessory. A sample size of approximately 5 mg was packed in non-hermetically crimped pans (Tzero™ aluminium) and heated from 0 °C to 200 °C and 250 °C for the 1
:
1 systems and 3
:
1 systems respectively, at 10 °C min−1 under dry nitrogen purge.
Ball milling (BM).
A Retsch ball mill model #MM301 (Irvine, CA) was used to mill rBN with either BQ, or with BQ/AN, and BQ/NP. The type of mill used in this study is often also referred to as a mixer mill. The samples to be milled at appropriate mole ratios were placed in a 25-mL chamber with two 12 mm stainless steel balls and milling was conducted at room temperature. The vibration frequency of the mill was varied between 10–30 Hz for all experiments. The samples were milled for varying lengths of time between 0 and 60 min. At predetermined times, the solid sample was removed from the mill for further characterization to understand the kinetics of the mechanochemical reaction. Details of milling parameters used for each sample is provided in the figure captions and in the discussion of results.
Resonant acoustic mixing (RAM).
All RAM experiments were performed on the LabRAM II (Resodyn Inc., Butte, Montana). The appropriate mole ratio of rBN/BQ, rBN/BQ/AN, or rBN/BQ/NP were weighed into a 20-mL scintillation vial. Details of the total amount of solid used in the experiments are provided in the figure captions. Neat RAM experiments were performed without solvent. For liquid assisted RAM (LA-RAM), the appropriate amount of the liquid additive was added to the contents of the scintillation vial. The amount of liquid added was calculated based on previously established η parameter, which is the ratio of the amount of liquid added in μL to the amount of solid in mg. A η value of 0.5 was used. In cases where milling media was used in RAM experiments, 2 mm ZrO2 beads at 3× the total mass of solids were used. The scintillation vial was secured to the RAM platform using a sample holder clamp. The RAM platform resonates at a frequency of 60 Hz. Two parameters, forcing energy (acceleration) and time, were varied for each experimental condition. The details of the RAM parameters used are provided in the figure captions and in the discussion of data.
Results and discussion
rBN–BQ cocrystal I
Kuroda and co-workers have shown that dry grinding of rBN with BQ produces the rBN–BQ cocrystal I. Cocrystal I crystallizes in a monoclinic space group C2/c and has a 1
:
1.5 mole ratio of rBN
:
BQ or 1
:
1
:
3 mole ratio of R-BN
:
S-BN
:
BQ.17 It should be noted that rBN crystallizes as homochiral columns of R-BN and S-BN while in cocrystal I, the BQ molecule is sandwiched between R- and S-BN molecules. The molecular packing diagram calculated from the published crystal structure17 is shown in ESI† (cf. Fig. S2). The cocrystal formation occurred when the constituents were co-ground manually in a mortar and pestle or in a planetary ball mill.19 The reaction could be followed visually as the color of the mixture changes from pale yellow to pink to dark red as a function of grinding time in a mortar and pestle. The reaction could also be followed quantitatively by using XRPD.19 Kuroda and co-workers also demonstrated that a threshold level of mechanical energy is necessary to induce the formation of cocrystal I. Below this threshold mechanical energy, no reaction occurred even when milled for extensive periods in the planetary mill.
We conducted this reaction in a Retsch ball mill using a 25 mL stainless steel milling jar and two stainless steel grinding balls at 20–25 Hz frequency. At the 1
:
1 ratio (cf. Fig. 2) the formation of the cocrystal occurs by 10 minutes, which was the shortest milling time investigated.
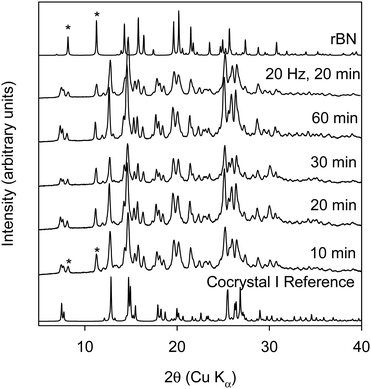 |
| Fig. 2 XRPD data of rBN/BQ ball milled at a 1 : 1 mole ratio shown in comparison to the reference powder data calculated from the published crystal structure of cocrystal I and the experimental powder data of rBN. Ball milling was done for different times at 25 Hz except for the one sample indicated in the figure. 480–490 mg of total solids were used for the experiments. The peaks marked with “*” at 8° and 11.1° 2θ are associated with unreacted rBN. | |
The data shows that under all conditions investigated, some unreacted rBN was found as evidenced by peaks (marked with “*”) at 8° and 11.1° 2θ. Single crystal data shows that the mole ratio of rBN
:
BQ is 1
:
1.5 in cocrystal I.17 Thus, at the 1
:
1 ratio which was used in this experiment, it is expected to see unreacted rBN with the formation of cocrystal I. The data shows that ball milling in a mixer mill is able to provide enough mechanical energy even at the shortest milling time under the described experimental conditions to facilitate the formation of cocrystal I. This observation is markedly different than what was reported by Kuroda et al. In their work, they showed that milling rBN and BQ for a period of 48 hours at 150 rpm did not lead to the formation of the cocrystal.20 However, increasing the RPM to 160 facilitated the partial formation of the cocrystal by 40 minutes. Thus, changing the type of mill used can change the kinetics of cocrystallization. Fig. 3 shows the XRPD data of rBN/BQ samples ball milled at a 1
:
1.5 ratio as a function of milling time at 25 Hz frequency. In this case, as the milling time is increased, the amount of unreacted rBN decreases, and finally at 60 minutes of milling time, nearly pure cocrystal I is formed. This result is in line with expectations (and consistent with previous literature) as a 1
:
1.5 mole ratio was used for these BM experiments. The DSC thermogram of cocrystal I shows an endothermic melting transition with an onset temperature of 108.6 °C with an associated heat of fusion of 68.2 J g−1 (cf. Fig. S3, thermogram E, ESI†).
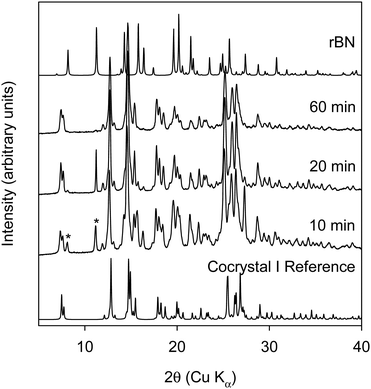 |
| Fig. 3 XRPD data of rBN/BQ ball milled at a 1 : 1.5 mole ratio shown in comparison to the reference powder data calculated from the published crystal structure of cocrystal I and the experimental powder data of rBN. Ball milling was done for different times at 25 Hz. 570 mg of total solids were used for the experiment. The peaks marked with “*” at 8° and 11.1° 2θ are associated with unreacted rBN. | |
Similar experiments were conducted by RAM to understand if a different mechanochemical technique can also produce cocrystal I. When RAM was performed at 75g for 90 minutes at both 1
:
1 and 1
:
1.5 ratios of rBN
:
BQ, cocrystal formation was not observed. XRPD data simply showed a mixture of the starting components (cf. Fig. S4, ESI†). Neat RAM experiment was then performed at 1
:
2.5 mole ratio at 90g and the mixing time was extended for 540 minutes. Even under these conditions, cocrystal formation was not observed. It is interesting to note that XRPD did not show any conversion to the cocrystal even though the color of the samples after RAM changed progressively from pink to dark red as a function of milling time in the RAM (cf. Fig. S5, ESI†). This observation is in contrast to what was reported by Kurda and co-workers. They showed that color change in rBN/BQ samples when ground with a mortar and pestle correlated with form change to the cocrystal I.19
As neat RAM did not lead to the formation of the cocrystal, neat RAM with beads was investigated. It was hypothesized that adding beads to the vial would provide more mechanical energy and thereby lead to the formation of the cocrystal in the RAM. 2-mm ZrO2 beads were added to the vial before starting RAM experiments. The amount of ZrO2 beads used was around three times the total powder samples mass. Fig. 4 shows the XRPD data of rBN/BQ sample at a 1
:
2 mole ratio subjected to RAM with ZrO2 beads.
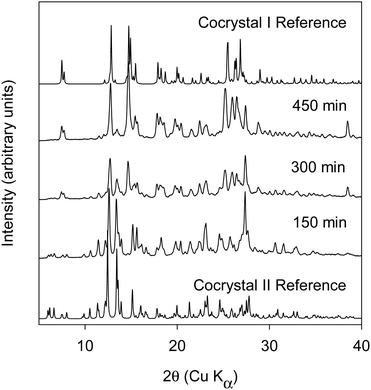 |
| Fig. 4 XRPD data of rBN/BQ at a 1 : 2 mole ratio subjected to RAM shown in comparison to the reference powder data calculated from the published crystal structures of cocrystals I and II. 440 mg of total solids and 1320 mg of zirconia beads were used for the experiment. RAM was done at 75g for all samples. | |
Surprisingly, when beads are used in RAM, cocrystal II is formed after 150 minutes at 75g. It should be noted that in all previous reports cocrystal I was predominantly formed under neat conditions (i.e. without the use of solvents). There is one report where after 48 hours of comilling of rBN/BQ, a small peak pertaining to cocrystal II was observed in the XRDP data.20 However, to our knowledge, formation of pure cocrystal II has not been observed from neat grinding conditions. Here we show that when mechanical energy is imparted in a different way with RAM, the form that is observed in solution can be realized under solventless RAM conditions. As different milling media was used in the RAM and ball milling experiments, we conducted a control experiment where the milling media was changed from steel balls to ZrO2 balls in the ball mill. Care was taken to keep the ratio of sample to ball weight approximately equal when steel balls were replaced with ZrO2 balls. rBN
:
BQ at a 1
:
1.5 ratio was milled at 25 Hz for 10 and 60 min using ZrO2 balls. The results are the same as what we obtained when steel balls for ball milling, i.e. only the formation of cocrystal I was observed after ball milling (cf. Fig. S6, ESI†). This observation lends further credence to the fact that the difference in form outcome observed in the RAM and ball mill is due to the type of mechanical energy imparted to the system by different milling methods.
Upon further acoustic mixing with beads, the gradual conversion of cocrystal II to cocrystal I was observed. Thus, increasing the total amount of mechanical energy eventually leads to the formation of cocrystal I. Given these results with the RAM, we wanted to see if this could be replicated in the ball mill. Ball milling of a 1
:
2 mole ratio sample was conducted at 10, 20, and 30 Hz for 10 minutes (cf. Fig. S7, ESI†). No conversion to cocrystal was observed at 10 Hz while conversion to cocrystal I was observed at 20 and 30 Hz frequency. At least within the scope of the experiments conducted here, it appears that ball milling will either result in no conversion or only conversion to cocrystal I. These observations clearly point to how type and nature of mechanical energy imparted by different techniques can influence the outcome of cocrystal formation.
rBN–BQ cocrystal II
It has been reported that cocrystal II is produced from solution crystallization using ether/hexane solvent system.17 Single crystal data shows that cocrystal II crystallizes in a triclinic space group P1 with a mole ratio of 1
:
1 (rBN
:
BQ).17 In contrast to cocrystal I, the BQ molecule is sandwiched between a pair of homochiral BN molecules. The molecular packing diagram calculated from the published crystal structure17 is shown in ESI† (cf. Fig. S8). Liquid assisted BM and RAM were investigated using heptane as the liquid additive. Heptane was used at an η of 0.5. For both 1
:
1 and 1.5 mole ratios, full conversion to the cocrystal II was observed in both BM and RAM (Data shown in Fig. 5). The DSC thermogram of cocrystal II shows an endothermic melting transition with an onset temperature of 99.7 °C and heat of fusion = 58.9 J g−1 (cf. Fig. S3, thermogram C, ESI†).
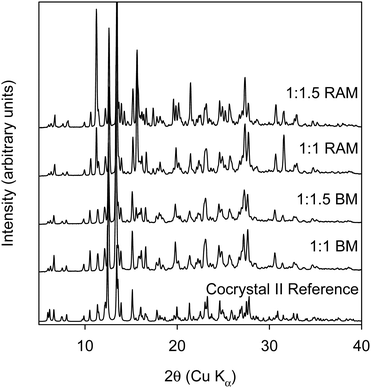 |
| Fig. 5 XRPD data of rBN/BQ subjected to RAM shown in comparison to the reference powder data calculated from the published crystal structure of cocrystal II. BM was performed at 25 Hz for 10 minutes. RAM was performed at 75g for 90 minutes. Heptane was used as a liquid additive at an η of 0.5 for all experiments. 490–540 mg of total solids was used for all experiments. | |
Thus, we are able to demonstrate the formation of cocrystal II with mechanochemical methods with the use of liquid additive. While it is an important demonstration, this is in line with expectations as cocrystal II was originally obtained from solution crystallization. RAM with small set liquid additives of different polarity were also examined to understand if the nature of the liquid additive would affect the form outcome. The liquid additives were used at an η of 0.5. This data is shown in Fig. S9 in the Section (ESI†). The data shows that cocrystal II is formed when acetonitrile, methanol, and ethyl acetate were used as liquid additives. However, when DMSO and THF were used as liquid additives, a different form was produced. Further investigations on the forms produced from DMSO and THF are beyond the scope of this report.
Three component cocrystals with AN and NP
Kuroda and co-workers have shown that grinding of rBN/BQ with either AN or NP leads to the formation of a three component cocrystal. The same form of rBN/BQ/NP cocrystal is obtained from grinding and solution crystallization while different forms are obtained from grinding and solution for the rBN/BQ/AN cocrystal. Structure solution revealed that rBN/BQ/NP cocrystal crystallizes in the P1 space group with a mole ratio of 2
:
1
:
2. We performed both BM and RAM at this mole ratio and obtained dark blue solids whose XRPD pattern matches well with that calculated from the single crystal structure. The data is shown in Fig. 6. The DSC thermogram of ternary rBN/BQ/NP shows an endothermic melting transition with an onset temperature of 78.6 °C and heat of fusion = 31.5 J g−1 (cf. Fig. S10, thermogram D, ESI†).
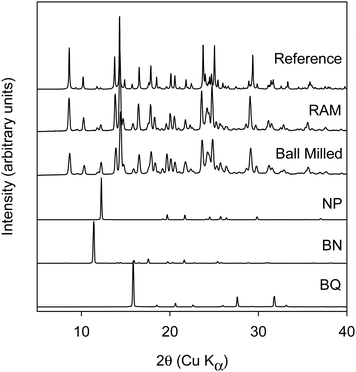 |
| Fig. 6 XRPD data of rBN/BQ/NP at a 2 : 1 : 2 mole ratio subjected to BM and RAM shown in comparison to the reference powder data calculated from the published single crystal structure of rBN/BQ/NP and experimental powder data of NP, rBN, and BQ. BM was performed at 30 Hz for 30 minutes. RAM was performed at 90g for 90 minutes. 470 mg of total solids were used for the BM experiments while 490 mg of total solids were used for the RAM experiments. | |
In order to see if we could make the ternary cocrystal of rBN/BQ/AN, we performed both BM and RAM at 2
:
2
:
1 mole ratio. The 2
:
2
:
1 mole ratio was chosen based on the reported crystal structure of the rBN/BQ/AN cocrystal made from grinding. Instead of single crystal structure determination, this structure was solved directly from powder XRPD pattern.21 It should be noted that the solution grown crystal is blue in color while the crystals obtained from solid state grinding are red in color. Moreover, the mole ratio of the solution grown crystal is 2
:
1
:
2. The data from the BM and RAM experiments is shown in Fig. 7. XRPD of the sample ball milled at 30 Hz for 30 minutes showed a pattern that was distinctly different from the three starting components. However, the XRPD of the neat RAM sample (75 G for 90 minutes) showed a pattern that was simply a superposition of the three starting components. Thus, like what was seen earlier for the cocrystal I rBN/BQ cocrystal, neat RAM is unable to make the rBN/BQ/AN cocrystal. Based on learnings from the previous system, RAM of rBN/BQ/AN system was tried after adding 2 mm ZrO2 beads to the starting mixture. In this case the XRPD of the RAM sample matched that of BM sample showing that the three component cocrystal had been made. The DSC thermogram of ternary rBN/BQ/AN shows an endothermic melting transition with an onset temperature of 120 °C (cf. Fig. S11, thermogram D, ESI†).
 |
| Fig. 7 XRPD data of rBN/BQ/AN subjected to BM and RAM shown in comparison to the experimental powder data of AN, rBN, and BQ. BM was performed at 30 Hz for 30 minutes. RAM was performed at 75g for 90 minutes. 340 mg of total solids were used for the BM experiments while 540 mg of total solids were used for the RAM experiments. | |
A full summary of the method used and cocrystallization outcome is shown in Table 1.
Table 1 Cocrystallization methods and the corresponding form outcomes
Method |
Cocrystallization outcome |
Based on data from literature.17,19
|
Neat grinding |
rBN/BQ cocrystal I 1 : 1.5 |
Neat RAM + beads |
Solutiona |
rBN/BQ cocrystal II 1 : 1 |
LA grinding |
LA RAM |
Neat RAM + beads |
Solutiona |
rBN/BQ/NP cocrystal 2 : 1 : 2 |
Neat grinding |
Neat RAM |
Neat grinding |
rBN/BQ/AN cocrystal 2 : 2 : 1 |
Neat RAM + beads |
Conclusions
In this paper we examined the effect of different mechanochemical techniques on the physical form of the cocrystal. rBN/BQ based binary and ternary cocrystals were selected as model systems to study this effect. Neat BM was found to produce cocrystal I of the rBN/BQ cocrystal while liquid assisted BM was found to produce cocrystal II of the rBN/BQ cocrystal. Similarly, liquid assisted RAM was found to produce cocrystal II of the rBN/BQ cocrystal. However, neat RAM was unable to produce the cocrystal I showing that the mechanical energy imparted by RAM was insufficient to produce cocrystal I. When ZrO2 beads were added to the starting mixture, RAM was found to produce pure cocrystal II after a mixing time of 150 minutes. This is the first demonstration of producing pure cocrystal II by a mechanochemical method without the use of solvents. Further mixing in RAM gradually converted the cocrystal II to cocrystal I.
Neat BM was also able to produce the ternary cocrystals of rBN/BQ/NP and rBN/BQ/AN in line with previous literature. While neat RAM was able to produce the rBN/BQ/NP cocrystal, it could not produce the rBN/BQ/AN cocrystal. Based on the results from the binary cocrystal, when beads were added to the components, neat RAM was able to produce the rBN/BQ/AN.
This work shows that the choice of mechanochemical technique can change the form outcome for cocrystals. In addition, by adding milling media to an inherently media free method like RAM can change the mechanical forces a sample experiences in the RAM, thereby leading to unexpected form outcomes. This work also shows that different mechanochemical methods should not be treated as the same and care must be taken when choosing a mechanochemical method for a particular application.
Author contributions
Siddarth Nagapudi was involved with investigation, data curation formal analysis and writing of parts of the manuscript. Karthik Nagapudi was involved with conceptualization, formal analysis, supervision and writing and revising of the manuscript.
Conflicts of interest
There are no conflicts to declare.
Acknowledgements
We would like to acknowledge Professor Tomislav Friscic for suggesting we work on the rBN/BQ cocrystal systems.
Notes and references
- S. L. Childs, L. J. Chyall, J. T. Dunlap, V. N. Smolenskaya, B. C. Stahly and G. P. Stahly, J. Am. Chem. Soc., 2004, 126, 13335–13342 CrossRef CAS PubMed.
- Y. Gao, H. Zu and J. Zhang, J. Pharm. Pharmacol., 2011, 63, 483–490 CrossRef CAS PubMed.
- A. V. Trask, W. D. S. Motherwell and W. Jones, Int. J. Pharm., 2006, 320, 114–123 CrossRef CAS PubMed.
- C. C. Sun and H. Hou, Cryst. Growth Des., 2008, 8, 1575–1579 CrossRef CAS.
- A. Bak, A. Gore, E. Yanez, M. Stanton, S. Tufekcic, R. Syed, A. Akrami, M. Rose, S. Surapaneni, T. Bostick, A. King, S. Neervannan, D. Ostovic and A. Koparkar, J. Pharm. Sci., 2008, 97, 3942–3956 CrossRef CAS PubMed.
- D. P. McNamara, S. L. Childs, J. Giordano, A. Iarriccio, J. Cassidy, M. S. Shet, R. Mannion, E. O'Donnell and A. Park, Pharm. Res., 2006, 23, 1888–1897 CrossRef CAS PubMed.
- T. Friščić, A. V. Trask, W. Jones and W. D. S. Motherwell, Angew. Chem., Int. Ed., 2006, 45, 7546–7550 CrossRef PubMed.
- T. Friščić, C. Mottillo and H. M. Titi, Angew. Chem., Int. Ed., 2020, 59, 1018–1029 CrossRef PubMed.
- D. Daurio, C. Medina, R. Saw, K. Nagapudi and F. Alvarez-Núñez, Pharmaceutics, 2011, 3, 582–600 CrossRef CAS PubMed.
- D. Daurio, K. Nagapudi, L. Li, P. Quan and F.-A. Nunez, Faraday Discuss., 2014, 170, 235–249 RSC.
- R. S. Dhumal, A. L. Kelly, P. York, P. D. Coates and A. Paradkar, Pharm. Res., 2010, 27, 2725–2733 CrossRef CAS PubMed.
- C. Medina, D. Daurio, K. Nagapudi and F. Alvarez-Nunez, J. Pharm. Sci., 2010, 99, 1693–1696 CrossRef CAS PubMed.
- T. Stolar, S. Lukin, M. Tireli, I. Sović, B. Karadeniz, I. Kereković, G. Matijašić, M. Gretić, Z. Katančić, I. Dejanović, M. D. Michiel, I. Halasz and K. Užarević, ACS Sustainable Chem., Eng., 2019, 7, 7102–7110 CrossRef CAS.
- D. J. Am Ende, S. R. Anderson and J. S. Salan, Org. Process Res. Dev., 2014, 18, 331–341 CrossRef CAS.
- M. Bui, P. Chakravarty and K. Nagapudi, Faraday Discuss., 2023, 241, 357–366 RSC.
- K. Nagapudi, E. Y. Umanzor and C. Masui, Int. J. Pharm., 2017, 521, 337–345 CrossRef CAS PubMed.
- R. Kuroda, Y. Imai and N. Tajima, Chem. Commun., 2002, 2848–2849, 10.1039/B207417F.
- D. H. Leung, D. J. Lamberto, L. Liu, E. Kwong, T. Nelson, T. Rhodes and A. Bak, Int. J. Pharm., 2014, 473, 10–19 CrossRef CAS PubMed.
- R. Kuroda, T. Sato and Y. Imai, CrystEngComm, 2008, 10, 1881–1890 RSC.
- R. Kuroda, K. Higashiguchi, S. Hasebe and Y. Imai, CrystEngComm, 2004, 6, 464–468 RSC.
- E. Y. Cheung, S. J. Kitchin, K. D. M. Harris, Y. Imai, N. Tajima and R. Kuroda, J. Am. Chem. Soc., 2003, 125, 14658–14659 CrossRef CAS PubMed.
|
This journal is © the Owner Societies 2024 |
Click here to see how this site uses Cookies. View our privacy policy here.