DOI:
10.1039/D1NR06410J
(Minireview)
Nanoscale, 2021,
13, 20387-20395
Effect of light intensity on solar-driven interfacial steam generation
Received
29th September 2021
, Accepted 12th November 2021
First published on 16th November 2021
Abstract
Solar-driven interfacial steam generation (SISG) has attracted much attention in recent years as a solution to freshwater scarcity and the energy crisis. Currently, research interests are mainly focused on standard conditions under “1-sun” illumination, which we believe are insufficient on their own. Gaining insight and understanding about SISG under both weak and strong irradiation have important implications for real-world use that are rarely presented in relevant discussions. In this review, we aim to discuss SISG under weak (<1 sun) and strong solar irradiation (>1 sun), both of which are often undervalued but necessary for real application. By analyzing state-of-the-art techniques and recent research progress, we provide some possible strategies, in terms of both energy and water management, for improving the performance of SISG under different irradiation powers. Finally, we also give a summary and our perspectives on the directions that the future development of this exciting field might take.
 Yinghua Qiu | Yinghua Qiu received his bachelor's degree from Soochow University in 2020. He is currently pursuing a master's degree at the Institute of Functional Nano & Soft Materials (FUNSOM), Soochow University, under the supervision of Prof. Qiao Zhang. His research interests are focused on evaporators designs for solar-driven interfacial steam generation. |
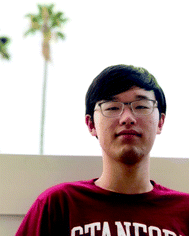 Michael Lee | Michael Lee worked with Prof. Jinxing Chen at Prof. Yadong Yin's lab at the University of California, Riverside and is now working towards a BS in chemistry at Stanford University. His current research interests include harnessing solar power for solar steam generation and electricity generation. |
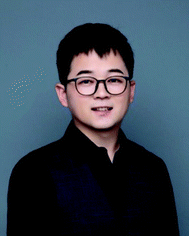 Jinxing Chen | Jinxing Chen received his B.S. in polymer materials and engineering from the University of Jinan in 2013, and Ph.D. in chemistry from the University of Science and Technology of China in 2018 under the supervision of Prof. Xuewu Ge. After working as a postdoctoral fellow at the University of California, Riverside, under the supervision of Prof. Yadong Yin, he joined the faculty at the Institute of Functional Nano & Soft Materials, Soochow University (2021). His research interests cover mainly nanomaterials for sustainability, including solar energy harvesting, plastic upcycling, and heterogeneous catalysis. |
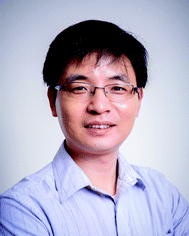 Qiao Zhang | Qiao Zhang is a Professor at the Institute of Functional Nano & Soft Materials (FUNSOM), Soochow University, China. He received his Ph.D. from the University of California Riverside (2012). After being a postdoctoral Fellow at the Department of Chemistry, University of California Berkeley (2012–2014), he joined Soochow University in 2014. His main research field is molecular level studies of surface and heterogeneous catalysis, controllable synthesis, and applications of metal halide perovskite nanocrystals. |
1. Introduction
As the population dramatically has increased over the past few decades, freshwater scarcity has become an increasingly more serious problem. Obtaining fresh, potable water from seawater through desalination has emerged as the primary strategy to address this. Due to complex equipment requirements and high energy consumption, traditional purification methods (e.g., reverse osmosis,1,2 electroosmosis,3,4 thermal desalination,5,6etc.) are difficult to widely implement, especially in economically underdeveloped areas. Solar-driven interfacial steam generation (SISG) has thus been suggested as a promising alternative technique. As a green, sustainable energy source, solar energy has been studied for multiple applications.7–11 SISG is a photothermal technique that aims to efficiently utilize solar energy to heat water. Unlike other heating desalination techniques that attempt to heat and evaporate the entirety of the bulk water,12,13 SISG focuses on heat localization at the water–air interface, minimizing heat loss and efficiently utilizing solar energy.
After being first reported by Chen et al. in 2014,10 improving evaporation performance has been the main focus of the field. Some suggestions have been made on different photothermal materials and structural designs for higher solar-thermal conversion and utilization efficiency, while more attention has been paid to practical application by focusing on useful properties such as salt-rejection and the design of complete evaporation-condensation systems. Most of these studies were carried out under “1-sun” illumination (1 kW m−2), which we believe is not enough of a strategy alone. Thus, studies of SISG under both weak (<1 kW m−2) and strong irradiation (>1 kW m−2) have important implications for real-world use.
For one, it is highly unrealistic to expect constant irradiation of exactly 1-sun during actual use. Many different factors, including the weather, climate, and geographical conditions, will cause real solar irradiation to fluctuate and often be weaker than 1-sun. As a result, evaporators that are not designed with this in mind will exhibit issues, in particular, lower evaporation efficiency due to relatively high heat loss10,14–16 and poor water generation rates caused by lower energy input, among others. Using only 1-sun irradiation to test new SISG designs does not accurately reflect the actual performance that a device would achieve if fully implemented.
Evaluating performance at over 1-sun irradiation is also important. Due to restrictive fabrication processes, materials availability, and usable space, evaporator sizes cannot be unlimited. According to the calculation equation of the evaporation rate (eqn (1)), assuming that the energy efficiency is constant, much higher solar irradiation power may be needed in some cases to increase performance for future large-scale clean water production within a limited evaporation area. When increasing the optical concentration, challenges may arise for conventional evaporators, in terms of complexity and cost of equipment, difficulties in achieving uniform and controlled concentration of solar irradiation, stability and durability under strong irradiation, rising energy loss (total amount but not percentage), insufficient water transport under a high evaporation rate, and so on. For any new SISG techniques that could see use alongside optical concentration, testing at high irradiations is essential to properly address these shortcomings.
Although studying SISG under different irradiations is crucial for further practical application development, testing at 1-sun is by far the most common in the current literature. This review first provides a primer discussion of solar steam generation, along with an overall summary of SISG and its development so far. We then present separate, in-depth investigations into SISG under high and low irradiation. Finally, we use what we established in the previous sections to provide some insights into the future direction of SISG evaporator design.
2. A primer on SISG
During the past few decades, several water desalination techniques such as osmosis and thermal desalination have been developed to combat severe water scarcity. Most of these desalination methods suffer from equipment complexity and high energy consumption. As a solution, inspired by the natural hydrological cycle, solar steam generation (SSG), which utilizes renewable solar power for direct water evaporation, has been suggested. SSG comprises several steps: solar irradiation absorption, solar thermal conversion, heat transfer for water evaporation, and vapor condensation. To date, classified by their heating methods, several modes of SSG have been proposed, which generally include bottom-heating, bulk-heating, and interfacial heating. As their names suggest, a different section of the water is being heated to produce steam in each method. In the bottom-heating method, the absorbers at the bottom of the bulk water naturally absorb sunlight and subsequently transfer heat to water and drive evaporation. This is the main mode of SSG used in classical solar stills13 and has been dismissed as being inefficient. The large distance between the heated region and the evaporation surface lowers energy efficiency and worsens performance. Bulk heating is intended to address these shortcomings by uniformly heating the entirety of the water. The most popular method to achieve this is through nanofluids,12 where nanoparticles dispersed throughout the water heat the system. Although this is more effective than bottom-heating, the energy conversion efficiency is still suboptimal. Additionally, the need for large amounts of materials, long-term durability, and stability under irradiation also posed great challenges to real applications. To this end, interfacial heating, or SISG, has been proposed, where the heat is localized at the water–air interface. Heating of the interface means that only the evaporation area is heated, with no need for extra bulk water heating. This leads to minimal heat loss and much higher energy efficiency. Furthermore, compared to other methods, the design of SISG evaporators, which will be explained next, resolves the materials cost and long-term use issues. This brand-new evaporation mode is well-balanced in terms of energy requirements, cost demands, and freshwater production needs, while also being environmentally sustainable. It presents a promising direction for the future of water production and is especially beneficial for solving the problem of safe water supply in undeveloped areas.
Due to these advantages, SISG has risen to the forefront of current research in freshwater production. In a conventional SISG system, the main components are an evaporator, a condenser, and feed water, analogous to traditional desalination methods. Most SISG evaporators have some mechanism to draw water into a separate, thermally insulated layer to be heated by the photothermal layer. The water transportation mechanisms usually differ between evaporator designs. In most cases with hydrophilic porous structures, the water transport is driven by hydrophilic adsorption and capillary forces, whereas diffusion mechanisms are more likely in nonporous structures. Other mechanisms, such as a passive siphon effect or an active injection method, have also been proven to be practical. Current efforts are focused on performance improvement of SISG, which is mainly focused on evaporator design. An evaporator with good performance typically follows several principles: broadband absorption that includes the full spectrum of sunlight; good photothermal conversion ability; low thermal conductivity to minimize heat loss; and a hydrophilic, porous structure to ensure sufficient water transport.
Since the first monolayer evaporator was reported, many different materials and structural designs have been suggested. For energy conversion, a wide range of photothermal materials, including carbon,10,11,17–22 plasmonic,16,23–30 and semi-conductor materials31–35 have been created with the purpose of converting as much sunlight to heat as possible while still respecting materials and environmental constraints. For further performance optimization through thermodynamic means, even more options have been proposed. The Zhu group, for example, suggested evaporators with a 2D confined water path to reduce heat loss to the bulk water.11 In order to break the theoretical limit of energy efficiency, Li et al. designed a 3D cylindrical evaporator that creates a temperature gradient between its sidewalls and the surroundings to harvest additional energy and further boost performance.14 Zhu and coworkers also achieved an ultrahigh performance with a 3D interconnected porous foam that ensures sufficient vapor diffusion with convective flow.36 Taking a different approach to exceed this limit, the Yu group proposed hydrogel-based evaporators with hydrophilic polymer frameworks that lower the water evaporation enthalpy within the hydrogel to allow for evaporation without the absorption of nearly as much solar energy.37,38 Other breakthrough attempts to maximize energy utilization were reported by Chiavazzo et al.39 and Hong et al.,40 who created passive multistage distillers and origami-based evaporators, respectively. Evaporators with properties designed for harsh conditions and long-term use have also been developed, such as salt-resistance,19,41,42 oil-resistance,43,44 antibacterial mechanisms,45,46 and more.
3. SISG under strong irradiation
As mentioned in the introduction, to maintain high efficiency for future, large-scale clean water production, a more concentrated source of irradiation may be necessary. The evaporation rate should theoretically scale to the energy input, meaning that stronger than 1-sun irradiation could both allow smaller evaporators to be useful and improve larger evaporators (eqn (1)). However, for many evaporators designed for 1-sun conditions, directly increasing the energy input usually results in decreasing efficiency. In our view, this can mainly be attributed to two aspects: thermal energy management and water transport. |  | (1) |
where ṁ represents the evaporation rate, Qin is the energy input, η denotes the energy utilization efficiency during the evaporation process, and HLV is the vaporization enthalpy of the water.
3.1. Thermal energy management
Because the evaporation rate is directly related to thermal energy, heat management is a dominant factor in the performance of SISG evaporators under different irradiation strengths. Designing SISG evaporators with this in mind will be an important step towards being able to take advantage of the benefits of high-intensity irradiation. Heat management in the context of future research on SISG under strong irradiation will be discussed in three parts: solar energy harvesting, the reduction of heat loss, and heat recovery.
3.1.1. Solar energy harvesting.
Solar-thermal energy conversion is a central part of the SISG process. For a functional evaporator, a photothermal material with a suitable light absorption range is necessary to provide thermal energy to the water. As shown in Fig. 1a, the solar irradiation wavelength mainly ranges from 200 to 2500 nm.47 To be able to absorb across the entirety of this range, materials with broadband absorption tend to be chosen to serve as the photothermal layer, which is often based on carbon or plasmonic-nanoparticles. In particular, under strong irradiation, these photothermal materials with high absorbances are much more important, as a low absorbance photothermal layer will fail to take full advantage of the increased solar irradiation.
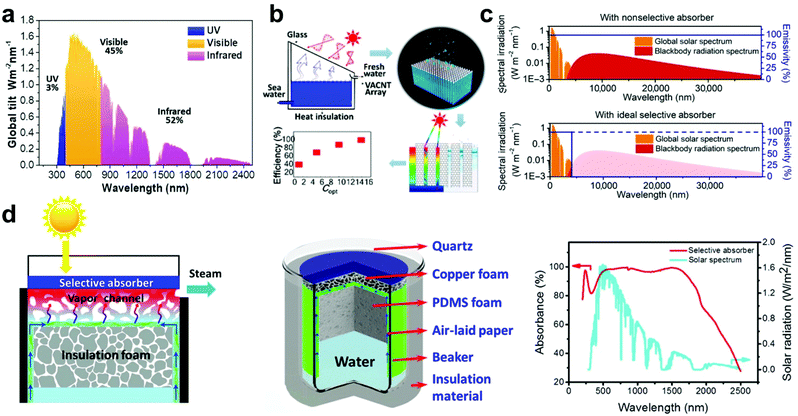 |
| Fig. 1 Solar energy absorption. (a) Solar spectral radiation (AM 1.5). This figure has been reproduced from ref. 47 with permission from The Royal Society of Chemistry, copyright 2019. (b) Evaporator with VACNT arrays as a photothermal layer. This figure has been reproduced from ref. 48 with permission from American Chemical Society, copyright 2017. (c) Emissivity of a nonselective absorber (upper) and an ideal selective absorber (below). This figure has been reproduced from ref. 51 with permission from American Association for the Advancement of Science, copyright 2019. (d) Schematic illustration of the evaporator with selective absorber and insulation layer, as well as the selective absorption spectrum. This figure has been reproduced from ref. 28 with permission from American Chemical Society, copyright 2019. | |
In 2017, Yin et al. applied vertically aligned carbon nanotube (VACNT) arrays as the photothermal layer in a SISG evaporator (Fig. 1b).48 VACNT arrays are known to be some of the blackest materials fabricated, as the forest-like structure formed by the imperfectly aligned nanotubes allows very little light to be reflected. ACNT arrays can reach an absorptivity of 0.98–0.99 throughout the entire solar spectrum with a wavelength range from 200 nm to 200 μm, which is extremely black, alongside a range that easily encompasses the solar spectrum.49 Testing the SISG evaporator with a VACNT array photothermal layer, the energy efficiency showed an increasing trend as the optical concentration increased, indicating that the heat loss to the surrounding environment decreases compared to the energy used for evaporation as the solar irradiation increases.50
However, research shows that, compared to non-selective absorbers, absorbers that can selectively absorb light in the solar spectrum range of 200–2500 nm seem to be more efficient due to lower radiative heat loss (Fig. 1c).51 For SISG under strong irradiation, higher energy input usually results in higher temperatures and more radiative heat loss. So, selective absorbers that only absorb sunlight and avoid thermal radiation are desirable. To this end, the Deng group designed spectrally selective absorbers and demonstrated their high performance under strong irradiation (Fig. 1d).28 Selective TiNOx absorbers in conjunction with copper and polymer foams showcased high efficiencies that increased with higher optical concentrations. Ensuring that a photothermal material has the absorbance necessary to scale effectively with stronger solar irradiation is an important step towards high-intensity SISG.
3.1.2. Heat loss reduction.
Heat loss reduction is another key point of heat management in SISG: while a higher absorbance means higher solar-thermal energy input, the heat loss directly relates to the energy utilization efficiency. A poorly designed SISG evaporator will lose more of its thermal energy to heat loss under stronger irradiation, lowering efficiency. There are three categories of heat loss: conduction, convection, and radiation. Since radiative loss has been discussed above, the following discussion will mainly focus on conductive and convective heat loss.
Conductive and convective heat loss mostly occurs between the evaporator and its surrounding environment, including both the atmosphere and bulk water beneath. This heat transfer is largely induced by the temperature difference between each surface. To negate these effects, many different strategies have been suggested.11,21,28,52–54 One efficient strategy is to isolate the evaporation surface from the bulk water to eliminate conductive heat loss (Fig. 2). Wu et al. reported an evaporator inspired by an oil lamp which can generate steam far above the water surface.54 In their design, the photothermal layer and the bulk water were separated by cotton strands. Due to the strong wicking effect and low thermal conductivity of cotton, the heat was localized in the top layer where evaporation occurred, effectively avoiding conductive heat loss to the bulk water and maintaining a high efficiency under strong irradiation.
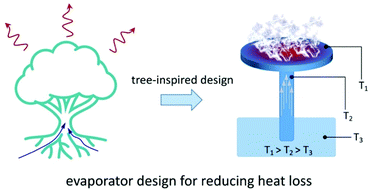 |
| Fig. 2 Reduction of heat loss. Design of the tree-inspired evaporator and its temperature field distribution under light illumination. | |
Liu et al. designed a mimetic transpiration system, consisting of carbonized wood embedded in expanded polyethylene (EPE) foam and air-laid paper, which imitates the water transport structures of trees.53 In this system, the EPE foam helps isolate the wood evaporator from the bulk water and neutralizes conductive heat loss, while the air-laid paper ensures the water supply. The work of the Deng group (Fig. 1d) mentioned before also applied this strategy: polydimethylsiloxane (PDMS) and EPE were used to avoid conductive heat loss to the bulk water and surroundings, respectively. Additionally, a transparent quartz cover was used to accomplish the more difficult task of limiting the convective heat loss. Ensuring that heat loss prevention methods hold up at higher optical concentrations is important for practical applications.
3.1.3. Heat recovery.
Another strategy to address the problem of heat loss is to recycle the heat used during SISG. While this is difficult to accomplish without the use of active pumps, Chiavazzo et al. suggested a passive SISG system that can recover the latent heat of condensation (Fig. 3).39 This system consists of multiple stages, with each stage consisting of an evaporation layer and a condensation layer, along with a photothermal absorber on the top stage. After the water in each layer evaporates, it will collect on the condenser below the air gap beneath the evaporator. As this clean water is collected, the heat from the condensation process is collected by the aluminium sheet of the next stage down so that it can effectively reutilize the heat of condensation to power multiple cycles of evaporation, potentially exceeding the theoretical limit for simple SISG. Although the author did not test this design under strong irradiation, we believe that, based on promising results, this could also be utilized to address the heat loss problem during the SISG process under strong irradiation. It is also worth mentioning that the heat loss can be reutilized for other applications (e.g., electricity production) in a similar manner,15 but here we just focus on improving the performance of SISG under strong irradiation.
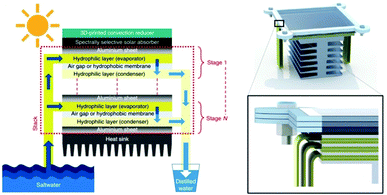 |
| Fig. 3 Heat recovery. Schematic illustration of a passive multistage steam generator. This figure has been reproduced from ref. 39 with permission from Springer Nature, copyright 2018. | |
3.2. Water transport
For SISG under strong irradiation, another limiting factor is the water supply. For many evaporator designs, although they exhibit good absorption of the solar spectrum, they still show worse performance under strong irradiation, which may be attributed to insufficient water supply. For these evaporators, the water transport is sufficient for evaporation under 1-sun irradiation but increasing the power input results in too high of an evaporation rate. The water supply then seems to not be able to match the increased evaporation rate, and the steam generation performance and efficiency decrease as a result. According to previous research and Fick's law (eqn (2)), the strategy to solve this problem seems to be clear—evaporators with a hydrophilic, interconnected structure will provide a strong driving force and large transport area to ensure a sufficient water supply. An example of an evaporator that does this well is one developed by the Hu group, who have designed several wood-based evaporators.32,55 A typical example is a plasmonic wood-based evaporator, which was produced by the deposition of plasmonic nanoparticles on wood.56 Plasmonic wood possesses multiple natural, hydrophilic microchannels through which water can be quickly drawn using capillary action (Fig. 4a). This both ensures sufficient, continuous water supply, and the plasmonic nanoparticles within the channels provide a waveguide effect for efficient light absorption, which results in high efficiency that increases under stronger irradiation. | 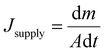 | (2) |
where Jsupply represents the water diffusion flux and dm/Adt denotes the amount of water that pass through an area within a certain time.
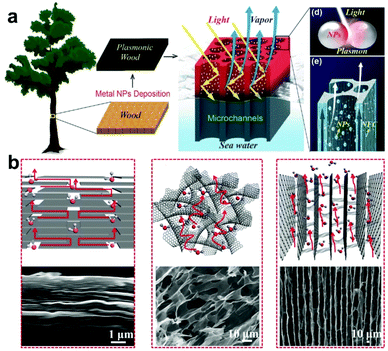 |
| Fig. 4 Water transport. (a) Schematic illustration of a plasmonic-wood-based evaporator. This figure has been reproduced from ref. 56 with permission from WILEY-VCH Verlag GmbH & Co. KGaA, Weinheim, copyright 2017. (b) Mechanism of the water transport channels of VA-GSM (right) and other rGO materials. This figure has been reproduced from ref. 18 with permission from American Chemical Society, copyright 2017. | |
Aside from biomass-derived materials, researchers have also explored artificial synthesis strategies. As shown in Fig. 4b, the Qu group applied a vertically aligned graphene sheet membrane (VA-GSM) as an evaporator for SISG.18 Compared to other reduced graphene oxide (rGO) materials, the well-aligned hydrophilic graphene sheets can provide sufficient water supply by forming several open channels for water transport while simultaneously improving light absorption, resulting in an ultra-high efficiency under strong irradiation. It should be noted that most evaporators that fail to provide sufficient water supply under strong irradiation follow the same principles for transporting water. This makes it even more imperative that testing is done at higher optical concentrations, as it is difficult to evaluate a design's water supply capabilities under strong irradiation without actual data.
4. SISG under weak irradiation
In terms of real applications, for many places around the world, the sunlight power density is usually weaker than “1-sun” (1 kW m−2) conditions.20,57,58 Due to the equipment requirements of SISG under strong irradiation, the approaches discussed in the previous section may be not fit for some areas. Thus, studying SISG under weak irradiation that can meet daily water requirements is also necessary. For weak irradiation, the main limiting factor is the energy input, which restricts the evaporation rate. Based on eqn (1), this could be solved through several approaches. One is to directly draw additional energy from the surrounding environment, while another is to decrease the energy required to evaporate the water. Moreover, improving energy utilization efficiency, in general, is also necessary for practical use under weak irradiation.
4.1. Harvesting energy from surroundings
As has been discussed, in a conventional 2D evaporator, solar power is absorbed by a photothermal layer and converted into thermal energy for further steam generation, which is based on heat transfer to the water. However, even at an efficiency of 100%, the limited energy input for SISG under weak irradiation is still far behind the requirements of daily water usage. Thus, extra energy input is necessary for real applications, and the environment surrounding the evaporator is a convenient source.
Heat transfer mainly depends on a temperature difference. As a result, if the temperature of the evaporator is lower than its surrounding environment, then it can draw additional energy from the surroundings and break the theoretical limit of the evaporation rate. To this end, the Zhu group designed a cylindrical evaporator, where the top surface absorbs solar energy. Because water evaporates on the side surfaces even though they are not absorbing solar irradiation, the side surfaces will have a lower temperature than the surroundings. This temperature gradient allows the evaporator to draw energy from its surroundings by heat transfer through the sides, as depicted in Fig. 5.14 As the irradiation is decreased, the enhancement factor shows an increasing trend, which can be attributed to the lower surface temperature, and results in greater environmental energy input under weaker irradiation. Song et al. suggested a 2D system based on carbon-coated paper on polystyrene foam (CP-foam), where the top surface is lower in temperature than the environment under weak irradiation. Because the CP-foam is colder than both the bulk water and the surroundings, energy can be drawn from both of these sources, reversing the heat loss that would normally occur.59 Like Zhu's work, this CP-foam shows increasing efficiency as the power density is decreased, because solar irradiation that is too strong will raise the temperature of the absorber, lessening the energy harvested from the environment.
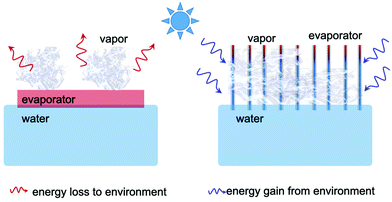 |
| Fig. 5 Harvesting energy from surroundings. Schematic work principles of 2D and 3D cylindrical evaporators. The color map of the evaporator indicates the temperature field distribution, and the red and blue areas represent high and low temperatures, respectively. | |
4.2. Decreasing the energy requirements
Since solar energy is limited, the energy available has an upper limit without harvesting extra environmental energy. However, another strategy for improving evaporation performance is to lower the energy required for evaporation. According to eqn (1), the energy required for evaporation is directly related to the vaporization enthalpy (HLV), indicating that decreasing the vaporization enthalpy is a valid method to increase the evaporation performance. As shown in Fig. 6, the Yu group reported a highly hydratable light-absorbing hydrogel (h-LAH) for use as an evaporator, within which the evaporation process needs less than 50% of the energy that would typically be needed in bulk water.60
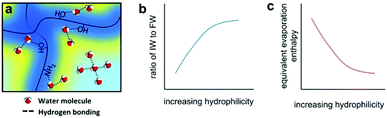 |
| Fig. 6 Enhancing evaporation by decreasing the vaporization enthalpy of water. Schematic illustration of the (a) water state, (b) intermediate water ratio, and (c) equivalent evaporation enthalpy of water in a hydrogel. This figure has been reproduced from ref. 37 with permission from American Association for the Advancement of Science, copyright 2019. | |
Based on molecular interactions, there are three different states of water inside the hydrogel: bound water (deep-blue area), free water (light-blue area) and intermediate water (yellow area). The bound water strongly interacts with the polymer molecules, while each free water molecule forms four hydrogen bonds with neighbouring water molecules. Between them, intermediate water molecules have a weaker molecular interaction with nearby water molecules and polymer chains, leading to a lower vaporization enthalpy. Tuning the polymer composition to increase the amount of intermediate water optimizes this drop in vaporization enthalpy. The steam generation performance is greatly improved because of this, and the lower energy supplied by weaker solar irradiation would no longer be an issue for the SISG process. Besides hydrogels, other materials can also achieve this goal. Lu and co-workers suggested a 1D-O-doped MoS2−x nanosheet assembly (1D-OMoSNSA) evaporator with hydrophobic nanoconfined water molecule channels (NCWMCs).61 According to molecular dynamics simulations, the NCWMCs can promote the evaporation of water molecules as clusters states and thus reduce the vaporization enthalpy. This allows for the 1D-OMoSNSA evaporator to maintain reasonable evaporation rates at low irradiation. Lowering the vaporization enthalpy is an effective strategy for functionalizing SISG evaporators without optical concentration.
4.3. Improvement of energy efficiency
Aside from the strategies discussed above, the energy utilization efficiency is still a primary factor for SISG due to the limited energy input under weak evaporation. Besides the heat isolation strategies mentioned above in the strong irradiation section, unique structural designs for energy capture are also feasible solutions. Based on their flexibility, Liu et al. applied origami-inspired techniques to the evaporator structure design (Fig. 7).46 By folding nanosheets together, a 3D structure that can reflect light is created. With this structure, the multiple-reflected light beam is effectively absorbed, and the heat loss to radiation can be well-recovered. Additionally, this origami structure can absorb sunlight with different incident angles without any obvious changes in evaporation performance.
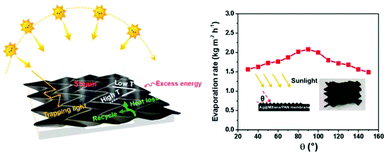 |
| Fig. 7 Improvement of energy efficiency. Schematic illustration of an origami-structured evaporator and evaporation rate under incident light with different incident angles. This figure has been reproduced from ref. 46 with permission from Elsevier, copyright 2021. | |
From another perspective, according to work by the Miao group, matching the input energy (IE, removing heat loss) to the required energy (RE) is also an important factor that influences the performance.62 On the one hand, if the IE is larger than the RE, this means that there will be insufficient water and thermal energy will be wasted. On the other hand, if the IE is less than the RE, the free water will consume some of the thermal energy, and thus the energy efficiency will decrease. Based on this, Miao et al. achieved increased performance by tuning the water transport rate. Improving energy efficiency in this manner is important for low-light SISG.
5. Conclusions
As a source of green, sustainable energy, solar power is regarded as an important potential energy source, and many different solar energy-based applications have been explored. Among them, SISG has drawn much attention as a novel but effective technique compared to traditional freshwater production techniques. Therefore, a great amount of effort has been directed towards improvement of the performance of SISG. However, insufficient attention has been paid to the effect of power on SISG, which is closely related to future applications. Although optical concentrators are important for future practical applications, many SISG evaporators suffer from poor energy management and insufficient water supply under strong solar irradiation. The resolution of these issues is necessary for the successful use of SISG evaporators alongside optical concentrators. SISG under low irradiation of under 1-sun is also important to consider, as consistent 1-sun irradiation is unrealistic and the equipment and materials for optical concentrators will not always be practical. The main barrier that prevents SISG evaporators from functioning well under low irradiation is simply poor performance. Evaluation at low irradiation is thus important to assess designs, but this is too often neglected. This review presents some of the research that has been carried out to date to investigate the low-energy constraints on SISG under weak irradiation.
Besides these, there are still several challenges that stand in the way of SISG evaporator integration. There is still much work to be done in fundamental SISG research. For example, the structural design of absorbers with ultrahigh absorption adapted to increased solar irradiation, photothermal materials with complementary absorption to achieve a desired selective spectrum range, and improved water supply and thermal insulation should still be pursued. Meanwhile, research on SISG for real applications is also important, including whole evaporation-condensation-collection system designs and designs that focus on stability and durability against harsh environmental conditions such as salt, oil, bacteria through either resistive properties or self-healing. It is worth noting that the condensation aspect of SISG is still largely unexplored, despite its importance. More strategies and solutions should be developed further, as it is crucial to the water harvesting process during SISG. Additionally, since concentrated steam is always generated with SISG, tandem designs that engage with other uses for steam, such as electricity generation, can also be achieved.63 Finally, large-scale steam generation still seems to be out of reach, either due to insufficient performance or the lack of scalable fabrication methods. Ingenious structural designs that achieve high performances while allowing for easy scaling should be prioritized. It should also be mentioned that research based on 1-sun irradiation is still necessary for basic research as a standard for comparation between different system designs. We hope that the summary of the work reported the field thus far will shine some light on future research, as well as emphasize the importance of considering the real-world conditions of SISG.
Author contributions
J. C. and Q. Z. conceived the manuscript. Y. Q., M. L., and J. C. wrote the manuscript. Y. Q. and M. L. contributed equally to the manuscript.
Conflicts of interest
There are no conflicts to declare.
Acknowledgements
J. C. acknowledges support from the National Natural Science Foundation of China (51901147). J. C. is grateful for the support of the Suzhou Key Laboratory of Functional Nano & Soft Materials, Collaborative Innovation Center of Suzhou Nano Science & Technology, the 111 Project. The authors thank Prof. Yadong Yin at UC Riverside and Zirui Zhou at the University of Chicago for their meaningful help in preparing the manuscript.
References
- L. Wang, M. S. H. Boutilier, P. R. Kidambi, D. Jang, N. G. Hadjiconstantinou and R. Karnik, Nat. Nanotechnol., 2017, 12, 509–522 CrossRef CAS PubMed.
- D. Cohen-Tanugi and J. C. Grossman, Desalination, 2015, 366, 59–70 CrossRef CAS.
- K. G. Zhou, K. S. Vasu, C. T. Cherian, M. Neek-Amal, J. C. Zhang, H. Ghorbanfekr-Kalashami, K. Huang, O. P. Marshall, V. G. Kravets, J. Abraham, Y. Su, A. N. Grigorenko, A. Pratt, A. K. Geim, F. M. Peeters, K. S. Novoselov and R. R. Nair, Nature, 2018, 559, 236–240 CrossRef CAS PubMed.
- Y. Mei and C. Y. Tang, Desalination, 2018, 425, 156–174 CrossRef CAS.
- S. Miller, H. Shemer and R. Semiat, Desalination, 2015, 366, 2–8 CrossRef CAS.
- D. von Eiff, P. W. Wong, Y. Gao, S. Jeong and A. K. An, Desalination, 2021, 503, 114925 CrossRef CAS.
- Y. Chen, Y. Lei, Y. Li, Y. Yu, J. Cai, M. H. Chiu, R. Rao, Y. Gu, C. Wang, W. Choi, H. Hu, C. Wang, Y. Li, J. Song, J. Zhang, B. Qi, M. Lin, Z. Zhang, A. E. Islam, B. Maruyama, S. Dayeh, L. J. Li, K. Yang, Y. H. Lo and S. Xu, Nature, 2020, 577, 209–215 CrossRef CAS PubMed.
- B.-w. Park, H. W. Kwon, Y. Lee, D. Y. Lee, M. G. Kim, G. Kim, K.-j. Kim, Y. K. Kim, J. Im, T. J. Shin and S. I. Seok, Nat. Energy, 2021, 6, 419–428 CrossRef CAS.
- A. Kumar, P. Choudhary, A. Kumar, P. H. C. Camargo and V. Krishnan, Small, 2021, 2101638 CrossRef PubMed.
- H. Ghasemi, G. Ni, A. M. Marconnet, J. Loomis, S. Yerci, N. Miljkovic and G. Chen, Nat. Commun., 2014, 5, 4449 CrossRef CAS PubMed.
- X. Li, W. Xu, M. Tang, L. Zhou, B. Zhu, S. Zhu and J. Zhu, Proc. Natl. Acad. Sci. U. S. A., 2016, 113, 13953–13958 CrossRef CAS PubMed.
- O. Neumann, A. S. Urban, J. Day, S. Lal, P. Nordlander and N. J. Halas, ACS Nano, 2013, 7, 42–49 CrossRef CAS PubMed.
- A. E. Kabeel and S. A. El-Agouz, Desalination, 2011, 276, 1–12 CrossRef CAS.
- X. Li, J. Li, J. Lu, N. Xu, C. Chen, X. Min, B. Zhu, H. Li, L. Zhou, S. Zhu, T. Zhang and J. Zhu, Joule, 2018, 2, 1331–1338 CrossRef CAS.
- X. Li, X. Min, J. Li, N. Xu, P. Zhu, B. Zhu, S. Zhu and J. Zhu, Joule, 2018, 2, 2477–2484 CrossRef.
- L. Zhou, Y. Tan, J. Wang, W. Xu, Y. Yuan, W. Cai, S. Zhu and J. Zhu, Nat. Photonics, 2016, 10, 393–398 CrossRef CAS.
- F. Jiang, H. Liu, Y. Li, Y. Kuang, X. Xu, C. Chen, H. Huang, C. Jia, X. Zhao, E. Hitz, Y. Zhou, R. Yang, L. Cui and L. Hu, ACS Appl. Mater. Interfaces, 2018, 10, 1104–1112 CrossRef CAS PubMed.
- P. Zhang, J. Li, L. Lv, Y. Zhao and L. Qu, ACS Nano, 2017, 11, 5087–5093 CrossRef CAS PubMed.
- X. Wu, Y. Wang, P. Wu, J. Zhao, Y. Lu, X. Yang and H. Xu, Adv. Funct. Mater., 2021, 31, 2102618 CrossRef CAS.
- C. Wang, J. Wang, Z. Li, K. Xu, T. Lei and W. Wang, J. Mater. Chem. A, 2020, 8, 9528–9535 RSC.
- H. Liang, Q. Liao, N. Chen, Y. Liang, G. Lv, P. Zhang, B. Lu and L. Qu, Angew. Chem., Int. Ed., 2019, 58, 19041–19046 CrossRef CAS PubMed.
- Z. Huang, Y. Wan, J. Liang, Y. Xiao, X. Li, X. Cui, S. Tian, Q. Zhao, S. Li and C. S. Lee, ACS Appl. Mater. Interfaces, 2021, 13, 31624–31634 CrossRef CAS PubMed.
- Z. Wang, Y. Liu, P. Tao, Q. Shen, N. Yi, F. Zhang, Q. Liu, C. Song, D. Zhang, W. Shang and T. Deng, Small, 2014, 10, 3234–3239 CrossRef CAS PubMed.
- K. Bae, G. Kang, S. K. Cho, W. Park, K. Kim and W. J. Padilla, Nat. Commun., 2015, 6, 10103 CrossRef CAS PubMed.
- Y. Liu, S. Yu, R. Feng, A. Bernard, Y. Liu, Y. Zhang, H. Duan, W. Shang, P. Tao, C. Song and T. Deng, Adv. Mater., 2015, 27, 2768–2774 CrossRef CAS PubMed.
- L. Zhou, Y. L. Tan, D. X. Ji, B. Zhu, P. Zhang, J. Xu, Q. Q. Gan, Z. F. Yu and J. Zhu, Sci. Adv., 2016, 2, e1501227 CrossRef PubMed.
- J. Chen, J. Feng, Z. Li, P. Xu, X. Wang, W. Yin, M. Wang, X. Ge and Y. Yin, Nano Lett., 2019, 19, 400–407 CrossRef CAS PubMed.
- C. Chang, P. Tao, B. Fu, J. Xu, C. Song, J. Wu, W. Shang and T. Deng, ACS Omega, 2019, 4, 3546–3555 CrossRef CAS PubMed.
- W. Guo, Y. L. Liu, Y. H. Sun, Y. W. Wang, W. Qin, B. Zhao, Z. Q. Liang and L. Jiang, Adv. Funct. Mater., 2021, 31, 2100768 CrossRef CAS.
- Y. Wang, J. Zhang, W. Liang, H. Yang, T. Guan, B. Zhao, Y. Sun, L. Chi and L. Jiang, CCS Chem., 2021, 2127–2142, DOI:10.31635/ccschem.021.202000732.
- J. Wang, Y. Li, L. Deng, N. Wei, Y. Weng, S. Dong, D. Qi, J. Qiu, X. Chen and T. Wu, Adv. Mater., 2017, 29, 1603730 CrossRef PubMed.
- H. Liu, C. Chen, H. Wen, R. Guo, N. A. Williams, B. Wang, F. Chen and L. Hu, J. Mater. Chem. A, 2018, 6, 18839–18846 RSC.
- X. Wu, M. E. Robson, J. L. Phelps, J. S. Tan, B. Shao, G. Owens and H. Xu, Nano Energy, 2019, 56, 708–715 CrossRef CAS.
- L. Zhu, L. Sun, H. Zhang, D. Yu, H. Aslan, J. Zhao, Z. Li, M. Yu, F. Besenbacher and Y. Sun, Nano Energy, 2019, 57, 842–850 CrossRef CAS.
- Q. Lu, Y. Yang, J. Feng and X. Wang, Sol. RRL, 2019, 3, 1800277 CrossRef.
- J. Li, X. Wang, Z. Lin, N. Xu, X. Li, J. Liang, W. Zhao, R. Lin, B. Zhu, G. Liu, L. Zhou, S. Zhu and J. Zhu, Joule, 2020, 4, 928–937 CrossRef CAS.
- X. Y. Zhou, F. Zhao, Y. H. Guo, B. Rosenberger and G. H. Yu, Sci. Adv., 2019, 5, eaaw5484 CrossRef CAS PubMed.
- X. Zhou, Y. Guo, F. Zhao, W. Shi and G. Yu, Adv. Mater., 2020, 32, e2007012 CrossRef PubMed.
- E. Chiavazzo, M. Morciano, F. Viglino, M. Fasano and P. Asinari, Nat. Sustainability, 2018, 1, 763–772 CrossRef.
- S. Hong, Y. Shi, R. Li, C. Zhang, Y. Jin and P. Wang, ACS Appl. Mater. Interfaces, 2018, 10, 28517–28524 CrossRef CAS PubMed.
- J. Chen, J. L. Yin, B. Li, Z. Ye, D. Liu, D. Ding, F. Qian, N. V. Myung, Q. Zhang and Y. Yin, ACS Nano, 2020, 14, 17419–17427 CrossRef CAS PubMed.
- H. Liu, R. Jin, S. Duan, Y. Ju, Z. Wang, K. Yang, B. Wang, B. Wang, Y. Yao and F. Chen, Small, 2021, 17, e2100969 CrossRef PubMed.
- Y. Zou, J. Zhao, J. Zhu, X. Guo, P. Chen, G. Duan, X. Liu and Y. Li, ACS Appl. Mater. Interfaces, 2021, 13, 7617–7624 CrossRef CAS PubMed.
- S. L. Wu, L. N. Quan, Y. T. Huang, Y. T. Li, H. C. Yang and S. B. Darling, ACS Appl. Mater. Interfaces, 2021, 13, 39513–39522 CrossRef CAS PubMed.
- Y. Guo, C. M. Dundas, X. Zhou, K. P. Johnston and G. Yu, Adv. Mater., 2021, 33, e2102994 CrossRef PubMed.
- H. Liu, Y. Liu, L. Wang, X. Qin and J. Yu, Carbon, 2021, 177, 199–206 CrossRef CAS.
- M. Gao, L. Zhu, C. K. Peh and G. W. Ho, Energy Environ. Sci., 2019, 12, 841–864 RSC.
- Z. Yin, H. Wang, M. Jian, Y. Li, K. Xia, M. Zhang, C. Wang, Q. Wang, M. Ma, Q. S. Zheng and Y. Zhang, ACS Appl. Mater. Interfaces, 2017, 9, 28596–28603 CrossRef CAS PubMed.
- K. Mizuno, J. Ishii, H. Kishida, Y. Hayamizu, S. Yasuda, D. N. Futaba, M. Yumura and K. Hata, Proc. Natl. Acad. Sci. U. S. A., 2009, 106, 6044–6047 CrossRef CAS PubMed.
- X. Luo, J. Shi, C. Zhao, Z. Luo, X. Gu and H. Bao, Appl. Energy, 2021, 302, 117581 CrossRef.
- Z. X. Wang, T. Horseman, A. P. Straub, N. Y. Yip, D. Y. Li, M. Elimelech and S. H. Lin, Sci. Adv., 2019, 5, eaax0763 CrossRef CAS PubMed.
- T. A. Cooper, S. H. Zandavi, G. W. Ni, Y. Tsurimaki, Y. Huang, S. V. Boriskina and G. Chen, Nat. Commun., 2018, 9, 5086 CrossRef CAS PubMed.
- P.-F. Liu, L. Miao, Z. Deng, J. Zhou, H. Su, L. Sun, S. Tanemura, W. Cao, F. Jiang and L.-D. Zhao, Mater. Today Energy, 2018, 8, 166–173 CrossRef.
- X. Wu, L. Wu, J. Tan, G. Y. Chen, G. Owens and H. Xu, J. Mater. Chem. A, 2018, 6, 12267–12274 RSC.
- C. Chen, Y. Li, J. Song, Z. Yang, Y. Kuang, E. Hitz, C. Jia, A. Gong, F. Jiang, J. Y. Zhu, B. Yang, J. Xie and L. Hu, Adv. Mater., 2017, 29, 1701756 CrossRef PubMed.
- M. Zhu, Y. Li, F. Chen, X. Zhu, J. Dai, Y. Li, Z. Yang, X. Yan, J. Song, Y. Wang, E. Hitz, W. Luo, M. Lu, B. Yang and L. Hu, Adv. Energy Mater., 2018, 8, 1701028 CrossRef.
- F. Zhao, X. Zhou, Y. Shi, X. Qian, M. Alexander, X. Zhao, S. Mendez, R. Yang, L. Qu and G. Yu, Nat. Nanotechnol., 2018, 13, 489–495 CrossRef CAS PubMed.
- W. Tu, Z. Wang, Q. Wu, H. Huang, Y. Liu, M. Shao, B. Yao and Z. Kang, J. Mater. Chem. A, 2020, 8, 10260–10268 RSC.
- H. Song, Y. Liu, Z. Liu, M. H. Singer, C. Li, A. R. Cheney, D. Ji, L. Zhou, N. Zhang, X. Zeng, Z. Bei, Z. Yu, S. Jiang and Q. Gan, Adv. Sci., 2018, 5, 1800222 CrossRef PubMed.
- X. Y. Zhou, F. Zhao, Y. H. Guo, B. Rosenberger and G. H. Yu, Sci. Adv., 2019, 5, eaaw5484 CrossRef CAS PubMed.
- Q. Lu, W. Shi, H. Yang and X. Wang, Adv. Mater., 2020, 32, e2001544 CrossRef PubMed.
- X. Mu, Y. Gu, P. Wang, J. Shi, A. Wei, Y. Tian, J. Zhou, Y. Chen, J. Zhang, Z. Sun, J. Liu, B. Peng and L. Miao, Sol. RRL, 2020, 4, 2000341 CrossRef.
- N. Xu, P. Zhu, Y. Sheng, L. Zhou, X. Li, H. Tan, S. Zhu and J. Zhu, Joule, 2020, 4, 347–358 CrossRef.
Footnote |
† These authors contributed equally. |
|
This journal is © The Royal Society of Chemistry 2021 |
Click here to see how this site uses Cookies. View our privacy policy here.