DOI:
10.1039/C6LC01346E
(Paper)
Lab Chip, 2017,
17, 186-197
A novel micromixer based on the alternating current-flow field effect transistor†
Received
31st October 2016
, Accepted 1st December 2016
First published on 1st December 2016
Abstract
Induced-charge electroosmosis (ICEO) phenomena have been attracting considerable attention as a means for pumping and mixing in microfluidic systems with the advantage of simple structures and low-energy consumption. We propose the first effort to exploit a fixed-potential ICEO flow around a floating electrode for microfluidic mixing. In analogy with the field effect transistor (FET) in microelectronics, the floating electrode act as a “gate” electrode for generating asymmetric ICEO flow and thus the device is called an AC-flow FET (AC-FFET). We take advantage of a tandem electrode configuration containing two biased center metal strips arranged in sequence at the bottom of the channel to generate asymmetric vortexes. The current device is manufactured on low-cost glass substrates via an easy and reliable process. Mixing experiments were conducted in the proposed device and the comparison between simulation and experimental results was also carried out, which indicates that the micromixer permits an efficient mixing effect. The mixing performance can be further enhanced by the application of a suitable phase difference between the driving electrode and the gate electrode or a square wave signal. Finally, we performed a critical analysis of the proposed micromixer in comparison with different mixer designs using a comparative mixing index (CMI). The novel methods put forward here offer a simple solution to mixing issues in microfluidic systems.
Introduction
Microfluidic devices have drawn extensive attention in a variety of practical applications such as chemical synthesis,1 single cell analysis,2–4 medical diagnostics5 and tissue engineering.6 Their enormous advantages lie in large scale integration with rapid and simple fabrication processes,7 reduced analysis time,5 the possibility for in situ operation, and high sensitivity with small volumes of samples.8,9 One of the key characteristics for successful operation of microfluidic systems is the capability to accurately handle small amounts of fluids in microsystems.10 Compared to the mixing process mainly based on convection in macroscopic fluids, fluid flow in parallel without eddies and the occurrence of mixing only depend on the diffusion of molecules due to the low Reynolds number (Re),11 which denotes the ratio of inertial to viscous forces, in micro-systems.6 For the sake of accomplishing efficient mixing in microsystems, specific components or external energy input is required.12 Thus, the development of various types of micro-mixers has become a research hotspot in the field of micro-liquid handling.13 The mixing strategies can usually be classified into two categories: passive and active. Passive mixers primarily rely on the transverse diffusion and chaotic advection via their intricate geometries14–18 or strategic surface patches.19 The weakness of the passive mixers is the hydrodynamic dispersion of the sample deriving from spreading it out longitudinally, which may give rise to a loss of assay sensitivity.14,20 Active mixers always need external forces such as ultrasonic,21,22 magnetic23 and electrical24–28 actuation to induce mixing effects. Among them, electrokinetically driven mixing devices with the advantage of simplicity, no moving parts and ease of integration with microelectrodes are more attractive and under extensive investigations. Oddy et al.29 utilized electrokinetic instability to stir fluid streams at low frequencies (below 100 Hz) and high electric fields (more than 100 V mm−1), which may lead to electrolysis or bubble formation. A novel type of electrokinetic flow called induced-charge electroosmosis (ICEO) proposed by Bazant and Squires,30,31 in which a double-layer charge induced by the applied field is driven by the same field (Fig. 1), has attracted significant attention in the field of microfluidics due to its notable feature, the micro-flow generation near a polarizable conducting surface in an external electric field.32–34 Thus, ICEO flow is a promising way to achieve efficient mixing. Qian et al.35 and Zhao et al.36 demonstrated the ability of chaotic advection flow, arising from the spatially varying potential distribution, to stir and mix fluids via analytical and simulation methods. Mani et al.37 also discovered a chaotic ICEO flow phenomenon at high voltages which is capable of generating mixing. However, the experimental verification has not yet been conducted. Bazant et al.30,31 put forward a design for an ICEO mixer using an array of transverse conducting posts. Harnett et al.20 and many other scholars24,25,38–42 also proposed microfluidic mixers driven by ICEO vortex flow; nevertheless, an array of posts of various shapes and arrangements within the micro-channel or arbitrarily shaped obstacle embedded in the channel wall is required to induce the ICEO flow. However, in many cases, ease of fabrication and simplicity of design take preference. Based on the fixed-potential ICEO flow, we design a micromixer via an easy and reliable fabrication process. The fixed-potential ICEO was first proposed by Squires and Bazant,31 which requires charges to flow onto and off the conducting surface by actively controlling the potential of the gate electrode surface. The ICEO flow pattern in microchannels can be modified by applying an electric signal to the floating electrode and then changing the surface charge and the zeta potential on them. In analogy with the field effect transistor (FET) in microelectronics,43 the floating electrode acts as a “gate” electrode for generating asymmetric ICEO flow and thus the device is called an AC-flow FET (AC-FFET). FETs have been exploited by several scholars44–51 to generate net pumping due to the capability of FETs to flexibly control the fluid flow behavior. To our knowledge, few researchers have taken advantage of the AC-FFET to achieve efficient mixing. This context led us to shift our focus to fixed-potential ICEO mixing by exploiting the AC-FFET.
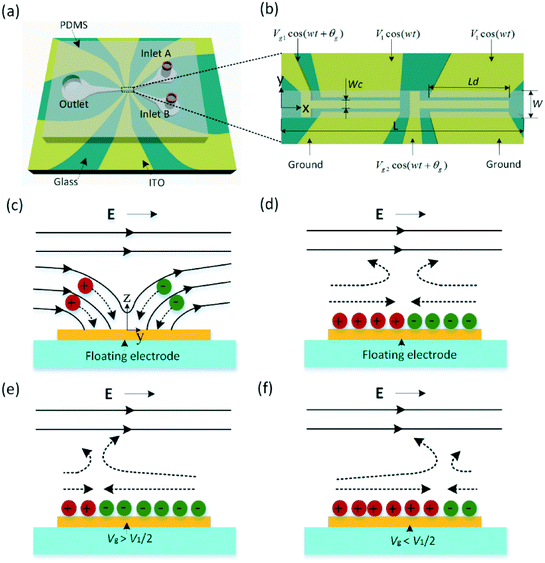 |
| Fig. 1 (a) 3D schematic diagram of the proposed micro-mixer, (b) the top view of the main channel. The length, width and height of the main channel are L, W and H, respectively. The illustration of the basic physics behind ICEO: as soon as the electric field is applied, the electric field lines perpendicularly intersect the electrode at first (c), driving ions from the solution onto the gate electrode. When the double layer is fully formed (d), the electric field is screened from the gate electrode and parallel to the electrode surface, resulting in a slip velocity and two counter-rotating rolls by driving the ions in the double layer. (e) When the gate electrode is energized with Vg (Vg > V1/2), a negatively charged double layer forms, which drives the fluid away from the grounded electrode, giving rise to asymmetric vortexes. (f) A positively charged double layer occurs when the gate electrode is energized with Vg (Vg < V1/2), driving the fluid towards the grounded electrode. | |
Herein, we present the first effort to design a novel micromixer on the basis of the AC-FFET, which makes use of a tandem electrode configuration containing two biased center metal strips arranged in sequence at the bottom of the channel (Fig. 1b). The incoming fluids are disturbed by the transverse AC-FFET vortex generated by applying an AC electric signal to the gate electrodes (Fig. 3a and b). The proposed micromixer is expected to have advantages such as low cost, easy implementation, simple operation, and robust and stable performance over other control methods. Therefore, the current micro-mixer provides a new approach for efficient electrokinetic mixing with broad applications in microfluidic systems.
Theoretical background
The governing equations for the coupled electric potential, flow, and concentration field can be found in the ESI.†
According to eqn (S6†), the flow stagnation line (FSL) can be achieved by making 〈νs〉 equal to zero. The FSL is located at the center of the floating electrode (x = 0) when the gate electrode is set as floating; whereas, the FSL can be changed (
) by altering the electric signal Vg
cos(wt). For instance, when the gate electrode is energized with Vg
cos(wt) (Vg > V1/2), positive charges will be accumulated at the top surface of the gate electrode, resulting in the formation of a negatively charged double layer in the liquid above the gate electrode. Consequently, an asymmetric ICEO flow occurs and the FSL is directed away from the ground electrode, as shown in Fig. 1e. On the other hand, when Vg < V1/2, a positively charged double layer forms and the FSL is directed toward the ground electrode (Fig. 1f). Eqn (S5) and (S6†) show that altering the electric potential applied to the gate electrode will change the zeta potential above the gate electrode, resulting in a shift of the flow stagnation line and generation of asymmetric flow across the channel. The direction of the asymmetry can also be reversed by changing the potential of the gate electrode. With the ability to actively fix the potential of the gate electrode, the asymmetric ICEO vortex can be used to generate effective mixing.
In terms of eqn (S4†), an ICEO flow driven by the electric field occurs as long as the double layer has time to form when the applied frequency is low enough (w < 1/τc).
is the “RC time” of an equivalent circuit of double-layer capacitors and bulk resistors of size L (here, L is the length scale and is equal to 0.19W in the present case). When the metal strip is subjected to an external electric field initially, the electric field lines intersect normal to the surface (Fig. 1c), driving negative ions in solution toward one half of the surface (x > 0) and positive ions to the other half, resulting in formation of a dipole-induced double layer. After a characteristic double layer charging time τc, the steady state can be achieved, in which the double layer totally insulates the surface and the field lines outside the double layer become tangential to the surface, leading to an ICEO flow (Fig. 1d).
When an electric signal is applied to the floating electrode, the potential of the floating electrode is coupled to the external circuit. The floating electrode acts like a driving electrode, thus fixed-potential ICEO is closely related to ACEO. Besides, it also shows the same fundamental physical mechanism of ICEO, because the primary ICEO flow can occur in polarizable surfaces.
Quantification of mixing
In order to quantify the mixing performance from the numerical results, concentration variation of fluid species in the micromixer is calculated. The performance of mixing is determined in a cross-sectional area of the micromixer that is perpendicular to the x-axis in terms of the mixing index (M):52–54 | 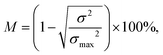 | (1) |
where
, in which Ci (from 0 to 1) is the value of the concentration at grid i (i = 0…n) and C∞ is the concentration value resulting from perfect mixing. σmax is the maximum standard deviation (no mixing at the inlet). The value of M ranges from 0 for no mixing or diffusion to 1 for perfect mixing.
Materials and methods
The micromixer proposed in this study consists of a Y-shaped microchannel with a tandem electrode configuration (Fig. 1a). Two center metal strips are placed in sequence from upstream to downstream of the main channel, denoted as gate electrodes, and the outer metal strips are the driving electrodes (Fig. 1b). The main channel has a length of L, a width of W and a height of H. The length and width of the center electrode are Lc and Wc, respectively. The gap size of the driving electrode pair is Gd and the distance between a driving electrode and a center electrode is G1. The gap between the center electrodes is Gc. Dimensional parameters are given in detail in Table 1.
Table 1 Geometrical parameters for the structure of the proposed micromixer
Parameters |
Value (μm) |
Implication |
L
|
2300 |
Length of the main channel |
W
|
180 |
Width of the main channel |
H
|
100 |
Height of the main channel |
L
c
|
1000 |
Length of the center electrode |
W
c
|
80 |
Width of the center electrode |
G
c
|
100 |
The gap between the center electrodes |
L
d
|
800 |
Length of the driving electrode |
G
1
|
30 |
The distance between a driving electrode and a center electrode |
G
d
|
140 |
The gap of the driving electrode pair |
Device fabrication
A schematic illustration of the fabrication process of the proposed micromixer is given in Fig. 2a. The major fabrication steps include: (1)–(4) PDMS channel fabrication, (5)–(7) ITO electrode patterning, and (8) plasma bonding. A photograph of the current device with electrical connections and tubing is shown in Fig. 2b. A microscopy image of the micromixer is shown in Fig. 2c.
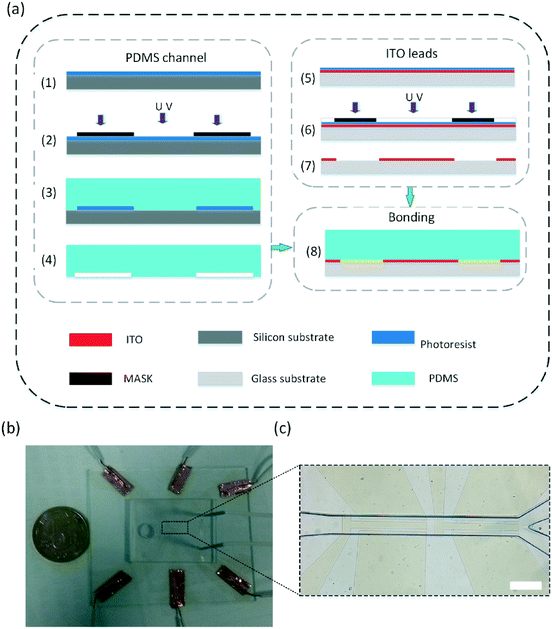 |
| Fig. 2 (a) Schematic illustration of the fabrication process of the micromixer including: (1)–(4) fabrication of the microchannel, (5)–(7) ITO electrode patterning, and (8) plasma bonding. (b) A photograph showing the assembled device with electrical connections and tubing. (c) A microscopy image of the dashed line area in (b) showing the main channel and the ITO electrodes. Scale bar, 200 μm. | |
The device fabrication began with creating the channel mold by conventional UV-lithography using a negative SU-8 2050 photoresist (MicroChem, Inc.). The microchannel was fabricated in poly(dimethylsiloxane) (PDMS, Sylgard 182, Dow Corning). A silicon wafer 3 inches in diameter and 2 mm in thickness was cleaned and then baked in an oven at 150 °C for 20 min before spin coating with the SU-8 photoresist. The photoresist was first spin coated on the silicon wafer at 1500 rpm for 30 s, generating a thickness of 100 μm. To evaporate the solvent, a pre-bake process was conducted with ramping from 60 °C to 95 °C for 70 min and then keeping at 95 °C for 1 h. After the SU-8 photoresist layers were exposed to UV light under a mask of desired geometry, a post-exposure bake process was carried out to accelerate the cross-linking of the exposed areas with ramping from 60 °C to 95 °C for 35 min and then keeping at 95 °C for 30 min. A SU-8 mold was attained after the UV-exposed wafer was developed in a SU-8 developer solution (MicroChem, Inc.) for 10 min and hard baked. A PDMS mixture of the base agent and curing agent with a mass ratio of 10
:
1 was poured onto the SU-8 mold and cured at 80 °C for 2 h. Finally, the channel was punched to generate inlets and outlets after the cured PDMS was peeled off the template.
For the sake of clear observation of fluid motion, transparent indium tin oxide (ITO) is selected as the electrode material. A glass substrate coated with an ITO film (Kaivo Optoelectronic Technology, China) was cleaned first and dried at 120 °C for 25 min. The positive photoresist AZ4620 was coated on an ITO substrate at 3100 rpm for 40 s. After a soft bake process was performed at 100 °C for 6 min, the photoresist was exposed to UV light. Then, the ITO substrate was developed in an AZ developer solution (NMD-W, 2.38%) for 4 min. The ITO electrodes and leads were obtained after etching using HCl solution. Lastly, the PDMS channel was bonded with the ITO substrate using oxygen plasma treatment (Fig. 2b).
Experimental setup
The dilution experiment has been widely conducted to quantify the mixing performance, in which an undyed fluid is mixed with a dyed fluid with a known concentration. We take advantage of a dilution technique to document the effect of fixed-potential ICEO flow and to quantitatively evaluate the performance of our micro-mixer. Fluorescein (Kermel Tianjin) is used as the fluorescent dye for the mixing process visualization. In the experiments, two laminar streams of aqueous solutions are utilized and only one is dyed (3 × 10−5 mol L−1). The concentration of each solution is adjusted by adding KCl, and the pH of each solution is adjusted to 9.2 with ammonia. Two solutions with identical conductivity (0.001 m S−1) are simultaneously injected into the main channel through two inlets using a syringe pump (PHD Ultra, Harvard Apparatus). Flow fields are observed using a fluorescence microscope (BX53, Olympus) with a CCD camera (RETIGA-2000R). The AC voltages are applied to the driving electrodes with a function generator (TGA12104, TTi).
Results and discussion
Numerical analysis
A commercial finite element simulation software package (COMSOL Multiphysics 5.0) was used to conduct the simulation analysis. The electrode surfaces were meshed extremely finely compared to the remaining part. To ensure that the numerical results are not dependent on the grid size, a grid-independence test is essential and the mixing performance was evaluated using the mixing index. The computational domain is covered fully by tetrahedral meshes. Six different tetrahedral grid systems with an element number ranging from 1.38 × 104 to 8.9 × 105 were analyzed. The simulation results show that the effect of gradual increment in the node number can be negligible when the node number exceeds 6.1 × 105 (Fig. 3c). Thus, a grid system with 6.1 × 105 nodes is selected as the optimum grid system in terms of its competency and efficiency for the current structure.
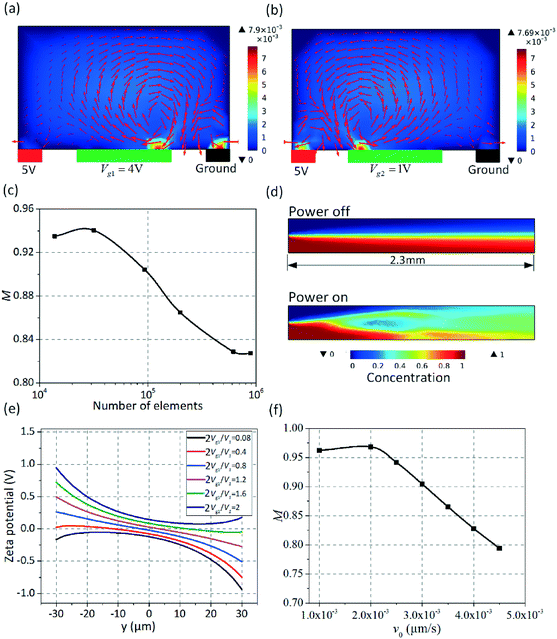 |
| Fig. 3 (a) Asymmetric vortexes above the left gate electrode in the upstream (x = 500 μm) under an AC field of V1 = 5 V, f = 500 Hz and Vg1 = 4 V. (b) Asymmetric vortexes above the right gate electrode in the upstream (x = 1500 μm) under an AC field of V1 = 5 V, f = 500 Hz and Vg2 = 1 V. (c) Grid-independence test. (d) 3D simulations of the concentration field at mid-depth of the main channel, top row: without an AC electric field, bottom row: at Vg1 = 4 V, Vg2 = 1 V, V1 = 5 V and f = 500 Hz. (e) Relationship between the zeta potential distribution along the gate electrode width direction and various applied voltages Vg1. (f) Dependence of mixing efficiency (M) on the inlet velocity. | |
The presence of a double layer on the surfaces of both the driving electrodes and gate electrodes is taken into account by imposing the boundary conditions in eqn (S2c) and (S8a†) on the driving electrodes. When the gate electrode is energized with an electric signal Vg
cos(wt), which will modify the zeta potential distribution above the gate electrode, leading to the occurrence of asymmetric vortexes across the channel. As shown in Fig. 3, asymmetric vortexes (Fig. 3a) were produced due to a negatively charged double layer forming in the fluid above the left gate electrode under an AC electric field of Vg1 = 4 V, driving the fluid away from the grounded electrode. In contrast, the double layer becomes positively charged when an electric potential of Vg2 = 1 V was applied to the right gate electrode, giving rise to similar asymmetric vortexes which drive the fluid towards the grounded electrode (Fig. 3b). Clearly, the asymmetric vortexes generated above the left gate electrode are mainly utilized to stir the fluid that flows near one side of the channel, whereas the fluid flowing near the other side of the channel will be mixed by the asymmetric vortexes produced above the right gate electrode. Fig. 3d displays the concentration field within the midplane of the main channel. In Fig. 3d, the upper (blue) layer is at tracer concentration around C-0 and the lower (red) layer is at tracer concentration around C-1. It is noted that, in the absence of electrical excitation (top row), the two fluids are mixed slightly by the diffusion across the contact interface of both liquids at a rate of ν0 = 3000 μm s−1. Electric signals were applied to the electrodes (Vg1 = 4 V, Vg2 = 1 V, V1 = 5 V and f = 500 Hz) producing asymmetric vortexes above the gate electrodes that enhance the mixing performance (bottom row). Fig. 3e shows the zeta potential distribution at the gate electrode surface in the upstream (x = 500 μm) at different applied voltages Vg1, confirming that the zeta potential distribution at the gate electrode surfaces can be adjusted by controlling the voltage applied to the gate electrode, which can be utilized to actively generate asymmetric vortexes, promoting the mixing performance. The mixing efficiency decreases monotonically with the inlet velocity under an AC field of V1 = 5 V, Vg1 = 4 V, Vg2 = 1 V and f = 500 Hz (Fig. 3f). The mixing efficiency would be less than 90%, once the inlet velocity surpassed 3000 μm s−1.
Then, the influence of the gate electrode voltages (Vg1 and Vg2) on the mixing performance was also analyzed in detail as shown in Fig. 4a. When a fixed value was given to Vg2, the mixing performance would be improved with increasing the applied voltage Vg1 (1 < 2Vg1/V1 < 2). Meanwhile, the mixing efficiency would be reduced as the applied voltage Vg2 (0 < 2Vg2/V1 < 1) increases when Vg1 was set as a fixed value. The dependence of mixing efficiency on the applied frequency at different medium conductivities of 0.001–0.1 S m−1 is shown in Fig. 4b. It is obvious that the applied frequency at which the maximum efficiency can be achieved increases with increasing medium conductivity in view of the characteristic frequency σλD/εL. What is more, the zeta potential ζ = Vg
cos(wt + θg) − ϕ(t) can be changed by adjusting the phase difference between the driving electrodes and the gate electrodes. Thus, the effect of the phase difference on mixing performance was likewise investigated as shown in Fig. 4c. It can be seen that the mixing efficiencies would reach 95%, 97% and 95%, respectively, when the phase differences between the driving electrodes and the gate electrodes are 60°, 180° and 300° at ν0 = 3000 μm s−1.
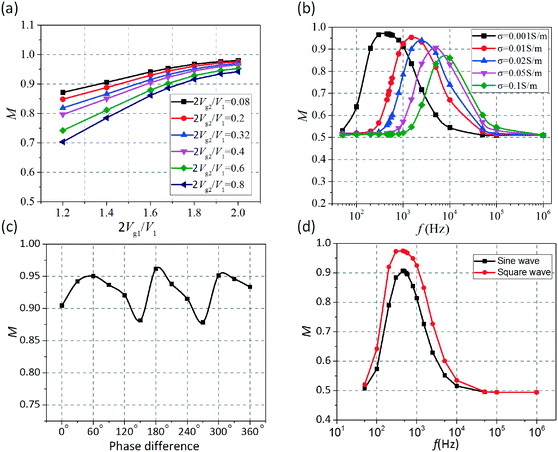 |
| Fig. 4 (a) A plot of mixing efficiency versus the voltages Vg1 applied to the left gate electrode at different voltages Vg2 when the inlet velocity ν0 is 3000 μm s−1 and V1 = 5 V. (b) A plot of the mixing efficiency versus the applied frequency for electrolytes with different conductivities at Vg2 = 1 V (2Vg2/V1 = 0.4), Vg1 = 4 V (2Vg1/V1 = 1.6) and ν0 = 2000 μm s−1. (c) Dependence of mixing efficiency on the phase difference between the driving electrodes and the gate electrodes at Vg1 = 4 V, Vg2 = 1 V, V1 = 5 V, f = 500 Hz and ν0 = 3000 μm s−1. (d) A plot of the mixing efficiency versus the applied frequency when square wave and sine wave signals are applied to the electrodes respectively at f = 500 Hz, Vg2 = 1 V (2Vg2/V1 = 0.4), Vg1 = 4 V (2Vg1/V1 = 1.6) and ν0 = 3000 μm s−1. | |
In a sinusoidal electric field, the oscillation between the two optimal values occurs in a progressive manner. For the sake of keeping the electric field intensity at its maximum value as long as possible, the square-wave electric field, which oscillates between a negative and a positive value in terms of a step function, was utilized to energize the electrodes. Herein, we also numerically investigate the influence of the wave shape on the mixing performance. When the driving electrodes are energized with the square wave signals instead of the sinusoidal signals, we carry out the simulation analyses by decomposing the square wave into the sum of simple sine waves in terms of a Fourier series. The voltage applied to the electrodes (V1 in a half period and −V1 in the other) can be written as a superposition of sinusoidal waves:
|  | (2) |
We assume that the first harmonic of the Fourier series predominates (4V1/π
sin(wt)) when approximating the original periodic function.
Fig. 4d shows the dependence of the mixing efficiency on the applied frequency when square wave and sine wave signals are applied to the electrodes respectively, indicating the superiority of the square electric field in mixing enhancement over the sinusoidal electric field.
Experimental verification
The comparison between the theoretical results and the experimental results is performed concerning the dependence of the mixing efficiency on the applied electric signal. To predict the trend of the mixing performance scientifically, every experiment was repeated three times independently and the mixing performance in each experiment was evaluated through 3 independent measurements. Fig. 5 shows typical fluorescence images of solute distributions in the device where fluorescent dye solution and water are injected into the two inlets simultaneously via a syringe pump, generating a continuous flow (2000 μm s−1). Images without power and with power are shown, where a function generator was used to generate an electric field at V1 = 5 V, Vg1 = 4 V, Vg2 = 1 V and f = 500 Hz. For the sake of better evaluating the mixing efficiency, the images were taken in white and black as shown in Fig. 5. The results of simulation and experiment both show that, in the absence of an electric field (Fig. 5a and c), the two fluids are slightly mixed as the dye remains on the upper side of the main channel, but the dye is distributed evenly at the outlet of the channel while the field is on (Fig. 5b and d). The corresponding intensity profiles across the channel are shown in Fig. 5e and f. It is noteworthy that the fluid motion and mixing process in the experiments demonstrate good agreement with the simulation results as shown in Fig. 5.
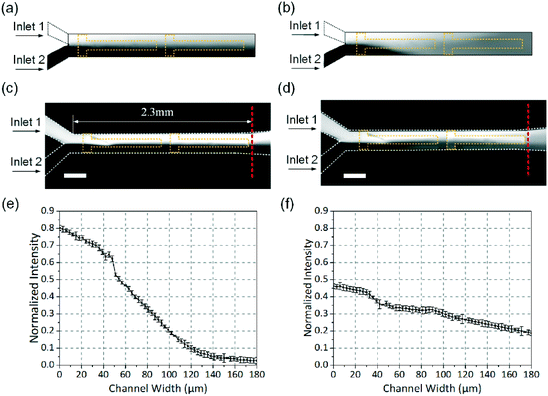 |
| Fig. 5 Comparison of calculated (a and b) and experimental (c and d) results for the solute distribution with (b and d) and without (a and c) an electric field. The location of the floating electrodes is indicated by the yellow lines. Fluorescence intensity profiles across the channel width obtained from the confocal micrographs before (e) and after (f) application of voltages. The red dashed line, located at a distance of 2.3 mm down the main channel, is the point where the fluorescence intensity profiles were evaluated. Error bars indicate the standard deviations. Scale bar, 200 μm. | |
In order to quantitatively estimate the mixing performance, the mixing efficiency (Me) was calculated according to the following equation:55
| 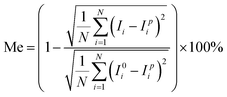 | (3) |
where
N,
Ii,
Ipi and
I0i are the total number of pixels, the intensity at pixel
i, the intensity of perfectly mixed solution at pixel
i and the intensity at pixel
i if no mixing or diffusion occurs, respectively. For unmixed fluids, Me is 0, and for the perfectly mixed fluids, Me is 1. A mixing efficiency of 0.9 or above usually indicates excellent mixing.
The effect of flow rate on mixing performance was investigated in detail. Fig. 6a shows the dependence of the mixing efficiency (Me) on different flow rates, ranging from 500 to 3500 μm s−1. The other conditions were V1 = 5 V, Vg1 = 4 V, Vg2 = 1 V and f = 500 Hz. It is observed that Me reaches 91% when the inlet velocity is less than 1700 μm s−1 and Me is merely 84% at the inlet velocity of 2000 μm s−1. The mixing images at different flow rates (1000 μm s−1, 2000 μm s−1 and 3000 μm s−1) are shown in Fig. 6b. It can be seen that the mixing efficiency decreases with increasing the inlet flow rate. Compared to the experiment results, the flow velocity is systematically overestimated by the current model which may be caused by various factors, such as Faradaic reactions, surface conduction within the double layer, surface contamination and so on.20,56
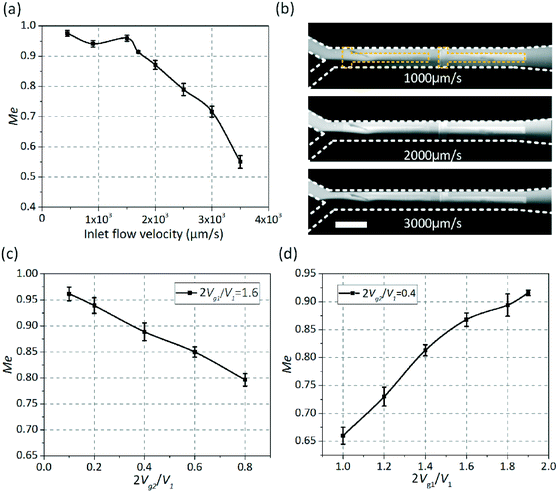 |
| Fig. 6 (a) Dependence of mixing efficiency (Me) on the inlet velocity. (b) Mixing images at different flow rates. Top row: ν0 = 1000 μm s−1. Middle row: ν0 = 2000 μm s−1. Bottom row: ν0 = 3000 μm s−1. The location of the floating electrodes is indicated by the yellow lines. Scale bar, 200 μm. (c) A plot of mixing efficiency versus the voltages Vg2 applied to the right gate electrode at ν0 = 2000 μm s−1, Vg1 = 4 V (2Vg1/V1 = 1.6) and V1 = 5 V. (d) A plot of mixing efficiency versus the voltages Vg1 applied to the left gate electrode at ν0 = 2000 μm s−1, Vg2 = 1 V (2Vg2/V1 = 0.4) and V1 = 5 V. Error bars indicate the standard deviations. | |
The zeta potential distribution above the gate electrode can be changed by applying an electric signal Vg
cos(wt) to the gate electrode which is then energized, leading to the occurrence of asymmetric vortexes across the channel. The effect of gate voltages was analyzed and the results are shown in Fig. 6c and d. The mixing efficiency increased as the voltage Vg2 applied to the right gate electrode decreased when the voltage Vg1 was 4 V (2Vg1/V1 = 1.6) (Fig. 6c). On the other hand, when a fixed voltage Vg2 = 1 V (2Vg2/V1 = 0.4) was applied to the left gate electrode, the mixing efficiency increased with increasing the voltage Vg1 (Fig. 6d). To avoid adverse factors such as Faradaic reactions and bubble generation, the following experiments were conducted at V1 = 5 V, Vg1 = 4 V and Vg2 = 1 V.
Furthermore, the effect of the phase difference between the driving electrode and the gate electrode on the mixing performance was investigated by simultaneously changing the electric signal phases applied to the gate electrodes with time (Fig. 7a). It is obvious that the mixing efficiencies will be improved remarkably and can reach 92%, 94% and 93%, respectively, when the phase differences between the driving electrodes and the gate electrodes are 60°, 180° and 300°, which proves the similarity between the experimental results and the simulation results. Fig. 7b shows the mixing images when the phase differences are 30° (top row) and 180° (bottom row). Hence, in terms of the overall flow structure and the basic trends, the agreement between the current model and experiment is good.
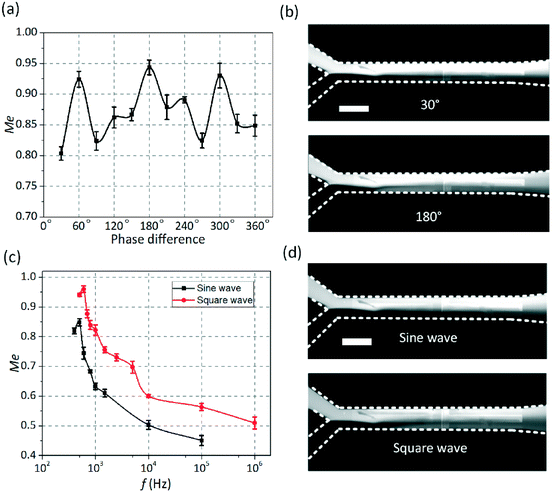 |
| Fig. 7 (a) Dependence of mixing efficiency on the phase difference between the driving electrodes and the gate electrodes at Vg1 = 4 V, Vg2 = 1 V, V1 = 5 V, f = 500 Hz and ν0 = 2000 μm s−1. (b) Mixing images at different phase differences, top row: 30° and bottom row: 180°. Scale bar, 200 μm. (c) A plot of the mixing efficiency versus the applied frequency when square wave and sine wave signals are applied to the electrodes respectively. Measurement at each data point was repeated three times. Error bar indicates the standard deviation. (d) Mixing images for the sinusoidal (top row) and square (bottom row) electric fields. Scale bar, 200 μm. | |
The influence of the wave shape on the mixing performance was also studied through experiments, as shown in Fig. 7c. The experiments were not carried out at frequencies below 100 Hz to minimize electrochemical reactions. Fig. 7d shows the mixing images when the electrodes are energized with a sinusoidal electric field (top row) and a square electric field (bottom row) at 600 Hz. It is noteworthy that the mixing performance improved when the square wave signal instead of the sine wave signal was applied to the electrodes. The comparison of the two curves (Fig. 7c) clearly indicates the superiority of the square electric field in comparison with the sinusoidal electric field. In addition, the effect of the frequency on mixing performance was investigated. In consistence with the simulation results, the maximum mixing efficiency would be achieved at f = 400–600 Hz when the sinusoidal field was used. It is also noted that the application of the square field allows us to keep good mixing performance up to relatively high frequencies.
Besides, to further enhance the mixing performance, we also investigate the effect of a DC bias voltage. When the left and right gate electrodes are energized with Vg1
cos(wt) + VDC1 and Vg2
cos(wt) + VDC2, respectively, four cases are analyzed (Table SI†) and the mixing images under different conditions are shown in Fig. S1.† The mixing efficiencies could reach up to 84% for case B (2Vg2/V1 = 0.4 and 2Vg1/V1 = 1.6) and 89% for case C ((2Vg2 + VDC2)/V1 = 0.4 and (2Vg1 + VDC1)/V1 = 1.6).
Compared to case B, the mixing performance for case D could be enhanced apparently when applying a DC bias voltage to the gate electrodes. When an AC voltage with a DC bias was applied to the gate electrodes, Faradaic reactions occurred, which is qualitatively different from the AC capacitive charging mechanism. The charge injection arising from the Faradaic reactions by the application of a small DC offset has been proven to be able to control the magnitude and direction of fluid flow.59 The ions generated by the Faradaic reactions possess the same polarity as the electrode, amplifying the external field instead of screening it. Due to the lack of screening, the velocity produced by the Faradaic charging is expected to have an exponential dependence on the applied voltage and increases monotonically.57,60 Therefore, the application of a small DC offset can be carried out to further improve the mixing performance. However, as the applied DC bias voltage increases, the electrode degradation and bubble formation from electrolysis will also occur.
Lastly, we carry out a critical analysis of our micromixer in comparison with different mixer designs using the methods proposed by Jain et al.61,62 Generally, the mixing index (Me) is obtained at the channel outlet by evaluating the deviation from the perfectly mixed state without considering the variation in flow rates or channel lengths among different designs. In fact, it is desirable to achieve great mixing performance by increasing the interfacial contact area and decreasing the diffusion length, instead of reducing the flow rate and increasing the residence time. The residence time, directly relevant to the time available for diffusion, should be taken into account when comparing different device designs. By accommodating the residence time in comparative analysis, the current index (CMI) can identify the non-diffusive mixing enhancement for various micromixers over the T-mixer.
| 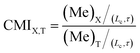 | (4) |
The above index can be utilized to compare any arbitrary designs (X) by benchmarking the mixing efficiency with respect to T-mixers for the same residence time and identify the true non-diffusive mixing enhancement for any given micromixer (X). The theoretical limits for CMI are between one and infinity. Therefore, when the micromixers with different designs (channel length) are compared under different experimental conditions (flow rates), the “true” non-diffusive mixing improvement can be obtained by normalizing the effect of residence time. So, to some extent, it would be reasonable and useful to compare various micromixer designs in terms of CMI. Based on the CMI, the mixing performance was assessed in comparison to those of the Tesla mixer,16 sigma mixer,58 and DC-biased ACEO57 (Table 2).
Table 2 Comparison of mixing performance of (a) the proposed micromixer, (b) micromixer with coplanar electrodes based on DC-biased ACEO flow,57 (c) sigma micromixer,58 and (d) micromixer with Tesla structures16
Micromixers |
L
|
(Me)T |
Me |
CMI |
V
|
(a) |
2.3 mm |
45% |
98% |
2.17 |
10 Vpp |
(b) |
0.6 mm |
31% |
92% |
2.96 |
20 Vpp, DC-bias = 2.5 V |
(c) |
17 mm |
46% |
80% |
1.7 |
|
(d) |
17 mm |
46% |
62% |
1.37 |
|
Table 2 shows that the mixing improvement of the proposed micromixer (a) reaches up to 217%, with a mixing efficiency close to 98% for electrolytes with 1 mS m−1. Although this mixing enhancement is lower than that of micromixer (b) of 296%, the AC voltage applied to the electrodes is much larger, which might give rise to water electrolytic reactions at the electrode surface. The non-diffusive mixing enhancements of passive micromixers with sigma (c) and Tesla (d) structures are only 170% and 137%, respectively. The channel length and flow rates are ignored when conducting comparisons because of the CMI and the normalized effect of residence time. More importantly, the current micromixer (a) based on the AC-FFET is much easier to fabricate in comparison with many other ICEO micromixers20,24,25,38–42 which always require an array of posts of various shapes and arrangements within the micro-channel. Therefore, the present design based on the AC-FFET can offer obvious advantages in improving the mixing performance over the other micromixers.
Conclusions
A microfluidic mixer is designed and fabricated herein to demonstrate the capacity of AC-FFET for mixing. The current device makes use of a tandem electrode configuration containing two biased center metal strips arranged in sequence at the bottom of the channel to directly manipulate the zeta potential and generate asymmetric vortexes in the gate electrode region through the control of the gate potential. The mixing performance of the micromixer was thoroughly investigated experimentally and numerically. The mixing efficiency can reach more than 95% within 2.3 mm mixing length under an AC field of 5 V and 500 Hz when the inlet flow velocity is 2000 μm s−1. Furthermore, the phase difference between the gate electrode and the driving electrode potentials and the wave shape are also taken into account. It was demonstrated that the mixing performance would be improved remarkably when the phase differences were 60°, 180° and 300° and the square wave signal was utilized. Lastly, based on the comparative mixing index (CMI), the mixing performance of our micromixer is compared with several micromixers appropriately. It can be seen that the current micro-mixer is expected to have advantages such as low cost, easy implementation, simple operation, and robust and stable performance over other control methods and provides a new approach for efficient electrokinetic mixing with broad applications in microfluidic systems.
Acknowledgements
This work is supported by the National Natural Science Foundation of China (No. 51305106, 11672095 and 11372093), the Fundamental Research Funds for the Central Universities (No. HIT. NSRIF. 2014058 and HIT. IBRSEM. 201319), the Self-Planned Task (No. 201510B and SKLRS201606C) of State Key Laboratory of Robotics and System (HIT) and the Programme of Introducing Talents of Discipline to Universities (No. B07018).
References
- K. S. Elvira, X. Casadevall i Solvas, R. C. Wootton and A. J. deMello, Nat. Chem., 2013, 5, 905–915 CrossRef CAS PubMed.
- P. Y. Chiou, A. T. Ohta and M. C. Wu, Nature, 2005, 436, 370–372 CrossRef CAS PubMed.
- K. Chung, Y. Kim, J. S. Kanodia, E. Gong, S. Y. Shvartsman and H. Lu, Nat. Methods, 2011, 8, 171–176 CrossRef CAS PubMed.
- A. M. Skelley, O. Kirak, H. Suh, R. Jaenisch and J. Voldman, Nat. Methods, 2009, 6, 147–152 CrossRef CAS PubMed.
- P. M. Valencia, O. C. Farokhzad, R. Karnik and R. Langer, Nat. Nanotechnol., 2012, 7, 623–629 CrossRef CAS PubMed.
- G. M. Whitesides, Nature, 2006, 442, 368–373 CrossRef CAS PubMed.
- T. Thorsen, S. J. Maerkl and S. R. Quake, Science, 2002, 298, 580–584 CrossRef CAS PubMed.
- S. Li, H. Cui, Q. Yuan, J. Wu, A. Wadhwa, S. Eda and H. Jiang, Biosens. Bioelectron., 2014, 51, 437–443 CrossRef CAS PubMed.
- T. A. Duncombe, A. M. Tentori and A. E. Herr, Nat. Rev. Mol. Cell Biol., 2015, 16, 554–567 CrossRef CAS PubMed.
- F. C. Leinweber, J. C. Eijkel, J. G. Bomer and A. van den Berg, Anal. Chem., 2006, 78, 1425–1434 CrossRef CAS PubMed.
- C. Liu, C. Xue, X. Chen, L. Shan, Y. Tian and G. Hu, Anal. Chem., 2015, 87, 6041–6048 CrossRef CAS PubMed.
- C.-C. Chang and R.-J. Yang, Microfluid. Nanofluid., 2007, 3, 501–525 CrossRef CAS.
- Y. Wang, Q. Lin and T. Mukherjee, Lab Chip, 2005, 5, 877–887 RSC.
- A. D. Stroock, S. K. Dertinger, A. Ajdari, I. Mezic, H. A. Stone and G. M. Whitesides, Science, 2002, 295, 647–651 CrossRef CAS PubMed.
- T. J. Johnson, D. Ross and L. E. Locascio, Anal. Chem., 2002, 74, 45–51 CrossRef CAS PubMed.
- C. C. Hong, J. W. Choi and C. H. Ahn, Lab Chip, 2004, 4, 109–113 RSC.
- F. Schonfeld, V. Hessel and C. Hofmann, Lab Chip, 2004, 4, 65–69 RSC.
- S. C. Jacobson, T. E. McKnight and J. M. Ramsey, Anal. Chem., 1999, 71, 4455–4459 CrossRef CAS.
- E. Biddiss, D. Erickson and D. Li, Anal. Chem., 2004, 76, 3208–3213 CrossRef CAS PubMed.
- C. K. Harnett, J. Templeton, K. A. Dunphy-Guzman, Y. M. Senousy and M. P. Kanouff, Lab Chip, 2008, 8, 565–572 RSC.
- Y. Gao, P. Tran, K. Petkovic-Duran, T. Swallow and Y. Zhu, Biomed. Microdevices, 2015, 17, 79 CrossRef PubMed.
- M. Bengtsson and T. Laurell, Anal. Bioanal. Chem., 2004, 378, 1716–1721 CrossRef CAS PubMed.
- K. S. Ryu, K. Shaikh, E. Goluch, Z. Fan and C. Liu, Lab Chip, 2004, 4, 608–613 RSC.
- M. Jain, A. Yeung and K. Nandakumar, J. Microelectromech. Syst., 2009, 18, 376–384 CrossRef CAS.
- Y. Daghighi and D. Li, Anal. Chim. Acta, 2013, 763, 28–37 CrossRef CAS PubMed.
- Y. Wu, Y. Ren and H. Jiang, Electrophoresis, 2016 DOI:10.1002/elps.201600106.
- G. Wang, F. Yang, W. Zhao and C. P. Chen, Lab Chip, 2016, 16, 1030–1038 RSC.
- Q. Zhang and M. Gong, J. Chromatogr. A, 2014, 1324, 231–237 CrossRef CAS PubMed.
- M. H. Oddy, J. G. Santiago and J. C. Mikkelsen, Anal. Chem., 2001, 73, 5822–5832 CrossRef CAS PubMed.
- M. Z. Bazant and T. M. Squires, Phys. Rev. Lett., 2004, 92, 066101 CrossRef PubMed.
- T. M. Squires and M. Z. Bazant, J. Fluid Mech., 2004, 509, 217–252 CrossRef.
- Y. Ren, W. Liu, Y. Jia, Y. Tao, J. Shao, Y. Ding and H. Jiang, Lab Chip, 2015, 15, 2181–2191 RSC.
- Y. Tao, Y. Ren, W. Liu, Y. Wu, Y. Jia, Q. Lang and H. Jiang, Electrophoresis, 2016, 37, 1326–1336 CrossRef CAS PubMed.
- Y. Ren, J. Liu, W. Liu, Q. Lang, Y. Tao, Q. Hu, L. Hou and H. Jiang, Lab Chip, 2016, 16, 2803–2812 RSC.
- S. Qian and H. H. Bau, Anal. Chem., 2002, 74, 3616–3625 CrossRef CAS PubMed.
- H. Zhao and H. H. Bau, Phys. Rev. E: Stat., Nonlinear, Soft Matter Phys., 2007, 75, 066217 CrossRef PubMed.
- S. M. Davidson, M. B. Andersen and A. Mani, Phys. Rev. Lett., 2014, 112, 128302 CrossRef PubMed.
- H. Sugioka, Phys. Rev. E: Stat., Nonlinear, Soft Matter Phys., 2010, 81, 036306 CrossRef PubMed.
- Z. Wu and D. Li, Microfluid. Nanofluid., 2007, 5, 65–76 CrossRef.
- Z. Wu and D. Li, Electrochim. Acta, 2008, 53, 5827–5835 CrossRef CAS.
- M. Jain, A. Yeung and K. Nandakumar, Biomicrofluidics, 2009, 3, 22413 CrossRef PubMed.
- H. Sugioka, J. Phys. Soc. Jpn., 2015, 84, 094603 CrossRef.
- R. B. M. Schasfoort, S. Schlautmann, L. Hendrikse and A. van den Berg, Science, 1999, 286, 942–945 CrossRef CAS PubMed.
- E. J. van der Wouden, D. C. Hermes, J. G. Gardeniers and A. van den Berg, Lab Chip, 2006, 6, 1300–1305 RSC.
- N. J. Sniadecki, C. S. Lee, P. Sivanesan and D. L. DeVoe, Anal. Chem., 2004, 76, 1942–1947 CrossRef CAS PubMed.
- R. Karnik, R. Fan, M. Yue, D. Li, P. Yang and A. Majumdar, Nano Lett., 2005, 5, 943–948 CrossRef CAS PubMed.
- E. J. V. D. Wouden, T. Heuser, D. C. Hermes, R. E. Oosterbroek, J. G. E. Gardeniers and A. V. D. Berg, Colloids Surf., A, 2005, 267, 110–116 CrossRef.
- A. Plecis, J. Tazid, A. Pallandre, P. Martinhon, C. Deslouis, Y. Chen and A. M. Haghiri-Gosnet, Lab Chip, 2010, 10, 1245–1253 RSC.
- L.-H. Yeh, S. Xue, S. W. Joo, S. Qian and J.-P. Hsu, J. Phys. Chem. C, 2012, 116, 4209–4216 CAS.
-
S. Muthu, F. Svec, C. H. Mastrangelo, J. M. Fréchet and Y. B. Gianchandan, 17th IEEE International Conference on Micro Electro Mechanical Systems, IEEE, Maastricht, 2004, pp. 850–853, ISBN: 0-7803-8265-X Search PubMed.
- W. Liu, J. Shao, Y. Ren, J. Liu, Y. Tao, H. Jiang and Y. Ding, Biomicrofluidics, 2016, 10, 034105 CrossRef PubMed.
- M. A. Ansari, K.-Y. Kim, K. Anwar and S. M. Kim, J. Micromech. Microeng., 2010, 20, 055007 CrossRef.
- Y.-T. Chen, W.-F. Fang, Y.-C. Liu and J.-T. Yang, Microfluid. Nanofluid., 2011, 11, 339–352 CrossRef CAS.
- Y. Lin, X. Yu, Z. Wang, S.-T. Tu and Z. Wang, Chem. Eng. J., 2011, 171, 291–300 CrossRef CAS.
- X. Feng, Y. Ren and H. Jiang, Biomicrofluidics, 2014, 8, 034106 CrossRef PubMed.
- J. A. Levitan, S. Devasenathipathy, V. Studer, Y. Ben, T. Thorsen, T. M. Squires and M. Z. Bazant, Colloids Surf., A, 2005, 267, 122–132 CrossRef CAS.
- W. Y. Ng, S. Goh, Y. C. Lam, C. Yang and I. Rodriguez, Lab Chip, 2009, 9, 802–809 RSC.
- E. Yakhshi Tafti, R. Kumar and H. J. Cho, Appl. Phys. Lett., 2008, 93, 143504 CrossRef.
- W. Y. Ng, Y. C. Lam and I. Rodriguez, Biomicrofluidics, 2009, 3, 22405 CrossRef PubMed.
- D. Lastochkin, R. Zhou, P. Wang, Y. Ben and H.-C. Chang, J. Appl. Phys., 2004, 96, 1730 CrossRef CAS.
- M. Jain and K. Nandakumar, Comput. Chem. Eng., 2013, 49, 18–24 CrossRef CAS.
- M. Jain and K. Nandakumar, Biomicrofluidics, 2010, 4, 31101 CrossRef PubMed.
Footnote |
† Electronic supplementary information (ESI) available. See DOI: 10.1039/c6lc01346e |
|
This journal is © The Royal Society of Chemistry 2017 |
Click here to see how this site uses Cookies. View our privacy policy here.