DOI:
10.1039/C4RA14328K
(Paper)
RSC Adv., 2015,
5, 19807-19817
Application of electrodialysis to remove copper and cyanide from simulated and real gold mine effluents
Received
11th November 2014
, Accepted 27th January 2015
First published on 27th January 2015
Abstract
In this study, a laboratory-scale electrodialysis (ED) system with an effective area of 88 cm2 was used to remove copper and cyanide in simulated and real gold mine effluents. The membrane fouling was characterized by FTIR, SEM-EDX, membrane resistance measurements and static contact angle. The effects of applied voltage, initial concentration, and flux rate on the removal rate of copper and cyanide were investigated. The highest copper (99.41%) and cyanide (99.83%) removal rates were achieved under the following conditions: applied voltage of 25 V, initial concentration of C2 (concentration of copper and cyanide were 47 mg L−1 and 242 mg L−1), and a flux rate of 4.17 mL s−1. In addition, the lowest concentration of copper (0.44 mg L−1), cyanide (0.48 mg L−1) and zinc (0.34 mg L−1) in the treated effluent were all below regulatory limits (copper, cyanide <0.5 mg L−1, zinc <2.0 mg L−1). The results showed the presence of CuCN, [Cu(CN)3]2−, Cu(OH)2, and Zn(OH)2 in the precipitate, and the fouling of anion-exchange membranes (AEMs) could be decreased significantly via pH adjustment. This research provides a new insight into the removal of copper and cyanide from gold mine effluent.
1 Introduction
Due to the dwindling resources of simple cyanide extractable gold deposits, a large proportion of the gold production is currently recovered from complex gold ores, many of which contain soluble copper minerals.1 The cyanidation based extraction of gold from its host minerals has remained fundamentally unchanged since its inception over 100 years ago.2 However, using cyanidation generates a large amount of effluent, which contains copper and cyanide.3 The discharge of these effluents into the environment is strictly controlled. Many countries and environmental protection agencies have imposed limiting standards for the discharge of gold mine effluent.4 In view of these considerations, the recovery/removal of copper and cyanide is necessary.
In order to achieve the regulated concentration of cyanide and copper in the discharged effluent (<0.5 mg L−1),5 several treatment systems have been developed. The majority of current approaches are based on cyanide destruction by chemical oxidation and/or recovery by acidification.4,6 The chemical oxidation is very efficient in detoxifying free cyanide bearing wastes; however, it is less-effective in the case of cyanide based metal complexes (such as copper) due to slow reaction kinetics.6,7 Moreover, the toxic intermediates (cyanogen chlorides) produced during the oxidation process could produce additional environmental pollution.8 On the other hand, the acidification treatment approach has been adopted in gold processing facilities, whereas the high consumption and cost of reagents have significantly limited their application.9 Other recent emerging treatment methods, including the Inco SO2-air process, hydrogen peroxide oxidation, active carbon adsorption, biological degradation, ozone oxidation, electrochemical oxidation and ion-exchange resins, have been explored.1,10–14 The comparison of all those methods and a discussion of their advantages and disadvantages have been listed in ref. 4.
The Inco SO2-air process involves the use of SO2 (or other sulfite source), which reacts together with oxygen and copper cyanide complexes, resulting in the oxidation of cyanide to cyanate. At the end of the reaction, copper is precipitated out as copper hydroxide. In order to meet stringent environmental regulations, the operational cost increases significantly.1,4,15 As for hydrogen peroxide oxidation, excess reagent is decomposed to water and oxygen, which results in high cost of reagent.9 Activated carbon adsorption has an affinity for many metal cyanide compounds, including the soluble cyanide species of copper, zinc, nickel and iron. However, their low adsorption capability has severely hampered their wide application in practice, which is used only for low concentrations of cyanide.8,11 Biological degradation is environmentally friendly and relatively inexpensive, but the technology is not well established and it tends to be very site specific with specific evaluation.12 Ozone oxidation is efficient for cyanide removal, and some regeneration of cyanide is possible. However the reagent and equipment are costly.10 In the electrochemical oxidation process, all cyanide baths can be treated regardless of the concentration but it requires post treatment by a number of oxidation methods.13 The use of ion-exchange resins is an efficient method but a pretreatment is required, and it is difficult to find suitable resin, which limits their application.14
As mentioned above, some of these methods are hindered due to either high consumption of reagents or technical obstacles, few require special equipment or further treatment, and others are not well established yet. Thus, there is an urgent need for the development of an alternative treatment process, which is capable of achieving high removal efficiency with low reagent consumption without secondary pollution.16,17 Electrodialysis (ED) could not only lower the concentrations of the targeted pollutant, but also concentrate the useful ingredients in wastewater for further reuse.18 It has proven to be an efficient technology for industrial applications, which includes brackish water desalination, boiler feed and process water purification, demineralization of food products, table salt production and waste treatment.19,20 The investment cost and operating cost (energy consumption) of ED are becoming more acceptable in these applications, and the cost of this method can be further reduced because of space saving, chemical saving and the recovery of useful ingredients.21–23
More recently, the ED technology has attracted increasing attention in effluent treatment in galvanic industries because of its inherent advantages including lower reagent consumption, convenient operation, environmental-friendly, compactness and the utilization of durable equipment.18,24,25 However, there are only a few works on the application of ED to remove toxic substances and reuse ionized species in gold mine effluent.26,27 The satisfactory removal of cyanide and metals is necessary to be achieved in order to meet the discharge limits. On the other hand, ion-exchange membrane fouling is one of the major problems that affects the ED process, which can reduce the flux, increase membrane resistance and energy consumption, and even destroy the membranes.18 There are some studies about ion-exchange membranes fouling in the treatment of other effluents such as cadmium electroplating wastewater, seawater and polymer-flooding produced wastewater.24,28–30 To the best of our knowledge, the ion-exchange membrane fouling has rarely been investigated in the treatment of gold mine effluent.
In this research, the feasibility of using ED technology to treat both real and simulated gold mine effluents was investigated to remove cyanide and copper, and the operational parameters were optimized to improve the removal efficiency. In addition, the membrane fouling was studied to understand the fouling behavior during the gold mine effluent treatment process.
2 Experimental
2.1 Solutions
The gold mine effluent was provided by the Zhaoyuan gold smelter plant, (Shandong, China) and the main compositions of the effluent are shown in Table 1. The simulated solutions were made up from CuCN (A R Grade, Aladdin) and NaCN (A R Grade, Aladdin) by referring to the mole ratio of cyanide and copper in the effluent. The concentrations of cyanide and copper in simulated solutions are presented in Table 2. Sodium hydroxide solution was added to adjust the pH of the simulated solution to 9.5. In this work, with the copper/or zinc and cyanide mole relationship used in the solutions, copper and cyanide were predominately present in the [Cu(CN)4]3−, [Cu(CN)3]2−and CN− forms2,31–34 and zinc and cyanide were mainly present in the form of [Zn(CN)4]3−.35
Table 1 The main composition of the gold mine effluent
Parameter |
Concentration (mg L−1) |
Sodium |
275 |
Copper |
47 |
Zinc |
31.2 |
Potassium |
6.3 |
Iron |
0.59 |
Aluminum |
0.06 |
Gold |
0.02 |
Cyanide |
242 |
Chloride |
159 |
Table 2 The concentrations of total copper and cyanide in simulated solutions
Concentration |
Cyanide (mg L−1) |
Copper (mg L−1) |
C1 |
121 |
23.5 |
C2 |
242 |
47 |
C3 |
363 |
70.5 |
C4 |
484 |
94 |
2.2 Apparatus
The experimental set-up consisted of three separated circuits, and each one included a centrifugal pump (CXB-30 Wenzhou Erle Pump Co., Ltd.), a rotameter (0–25 L h−1) and a 5 L tank (Fig. 1a). The direct current was supplied by a CV/CC regulated power supply (WYL1702, Hangzhou Siling Electrical Instrument Ltd.). The ED stack was composed of two electrodes made of a titanium plate coated with ruthenium, five anion exchange membranes (AEM) and six cation exchange membranes (CEM). Ionic species transportation in the ED stack is shown in Fig. 1b.
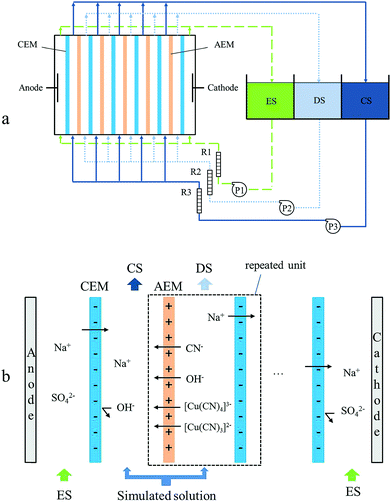 |
| Fig. 1 Flow diagram of the experimental setup (a) and ionic species transport in the ED stack with the simulated solution (b) (AEM, anion exchange membrane; CEM, cation exchange membrane; DS, diluted solution; CS, concentrated solution; ES, electrode solution; P1—pump for ES, P2—pump for DS, P3—pump for CS; R1—rotameter for ES, R2—rotameter for DS, R3—rotameter for CS). | |
Ion-exchange membranes can be considered as ion-exchange resins in film form. There are two different types of ion-exchange membranes: (1) CEMs, which contain negatively charged groups (typically –SO3−, –COO−, –PO32−, –PO3H− and C6H4O−) fixed to the polymer matrix, and (2) AEMs, which contain positively charged groups (typically –NH3+, –NRH2+, –NR2H+ and –NR3+) fixed to a polymer matrix. In a CEM, the fixed anions are in electrical equilibrium with mobile cations in the interstices of the polymer. The mobile cations in solution are referred to as counter-ions. The mobile anions are called co-ions and are more or less completely excluded from the membrane matrix because of their electrical charge which is identical to that of the fixed ions. Due to the exclusion of the co-ions, a CEM is preferentially permeable to cations. AEMs carry positive charges fixed on the polymer matrix. They therefore exclude cations and are preferentially permeable to anions.19,36
The homogeneous anion exchange membranes and the cation exchange membranes were purchased from the Qianqiu Environmental Protection & Water Treatment Corporation (China) and their main characteristics are listed in Table 3. The effective areas of both the membrane and electrode were 88 cm2. The whole experimental set-up was fixed by brackets in stainless steel, which was purchased from Shandong Tianwei Membrane Technology Co., Ltd (Shandong, China).28
Table 3 The main characteristics of the ion-exchange membranes
Membrane |
Thickness (mm) |
Exchange capacity (meq g−1) |
Area resistance (Ω cm2) |
Selectivity (%) |
Heat stability (≤°C) |
AEM |
0.16–0.23 |
1.8–2.0 |
5–9 |
90–95 |
40 |
CEM |
0.16–0.23 |
1.8–2.2 |
2–5 |
95–99 |
40 |
2.3 Experimental procedure
Laboratory-scale tests were mainly performed to investigate the technological parameters of the ED process. 5% sodium sulfate solution was added to the electrode compartment, and the diluted compartment and concentrated compartment were fed with effluents. Each tank contained 2 L solution and all the solutions had an alkaline pH in order to avoid HCN formation. The experiments were performed at room temperature in potentiostatic mode.
The effects of applied voltage, initial concentration and flux rate on the removal rate, current efficiency and energy consumption were investigated with the simulated solution. After the treatment of the simulated solution, the real gold mine effluent was treated by ED with the optimized operational parameters. The total time of each experimental run was 100 or 140 min. During each run, current was recorded and the concentrations of copper and cyanide were measured in the diluted sample.
The measurement of pH was made with a pH-meter (DELTA 320, Mettle–Toledo international incorporated company) using a combined glass electrode. The contents of copper and zinc in the solution were determined through an AA320N atomic absorption spectrophotometer (Shanghai Precision & Scientific Instrument Co., Ltd.). The content of cyanide (total cyanide) was analyzed by distillation and the content of free cyanide (CN−) was analyzed by titration with silver nitrate.7 It is worth mentioning that three replicates of each experiment were performed and then the average value was reported in order to minimize the experimental errors. The ion removal rate, current efficiency and energy consumption were calculated accordingly.
2.4 Data analysis
The ion removal rate (η) is calculated from eqn (1): |
 | (1) |
where η is the ion removal rate (%), and C0 and Ct are the concentration of cyanide (or copper) in the dilute compartment at time 0 and t (s) (mol L−1), respectively.
The current efficiency (ce%) is given by eqn (2):
|
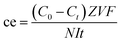 | (2) |
where
Ct and
C0 are the concentration of free cyanide (CN
−) in the diluted compartment at time
t (s) and 0 (mol L
−1), respectively.
Z is the ion's absolute valence (
Z = 1), and
V is the circulated volume of the solution in the salt cycle (L).
I is the current (A),
F is the Faraday constant (96
![[thin space (1/6-em)]](https://www.rsc.org/images/entities/char_2009.gif)
485 A s mol
−1),
N is the number of stack triplets (
N = 5), and
t is the operation time (s). Because the volume change in each compartment is negligible during the entire operation,
V was fixed at 2 L.
The energy consumption (E, kW h m−3) (not including the energy consumption used in driving solution circulation in the different compartments) can be defined by eqn (3):
|
 | (3) |
where
U is the potential (V),
I is the current (A),
V is the circulated volume in the salt cycle (0.002 m
3), and
t is the operation time (h).
2.5 Membrane fouling analysis
According to the previously reported methods,35 fouling of anion-exchange membrane could be characterized by measuring the membrane resistance and static contact angle, using scanning electron microscopy and surface elemental analysis. To measure the electrical resistance of ion-exchange membranes, a six compartment cell with a four-electrode arrangement was used. The measurement set-up was made from plexiglass and consisted of six separate compartments with a solution volume of 2 dm3.37 The measurement of the static contact angle was performed by the sessile drop method (DSA100, Germany KRUSS) at 298.15 K with a relative humidity of 30% ± 2%. The SEM (scanning electron microscopy) images and elemental analyses were performed with a scanning electron microscope (S-4800, Hitachi High-Technologies Corporation, Japan) and an X-ray energy dispersive spectrometer (EDX) (EMAX 7593H, Horiba, Japan), respectively. FTIR (Tensor 27, BRUKER OPTIK GmbH) was employed and the spectra were recorded in the range of 400–4000 cm−1.
3 Results and discussion
3.1 Current density of the ED process in potentiostatic operation mode
Fig. 2 shows the influence of applied voltage on the current density over time. For certain solutions, the current density across the membrane stack was proportional to voltage. This is because the ratio of the irreversible (the voltage drop or energy used to overcome the electrical resistance) to reversible contribution to the electric potential became larger with increasing current density.28 During the initial 70 min of ED operation, the current density decreased rapidly over time, which was closely related to the conductivity of the stack with constant voltage (including the conductivity of the membranes and the DS, CS and ES). The decrease of DS concentration resulted in lower conductivity and higher electrical resistance of the stack, and thus the stack current density was decreased rapidly according to Ohm's law.38 Then, the current density kept relatively unchanged in the remaining period of ED operation (70–100 min) because the equilibrium of ion migration determined the constant value for the total conductivity of DS and CS.
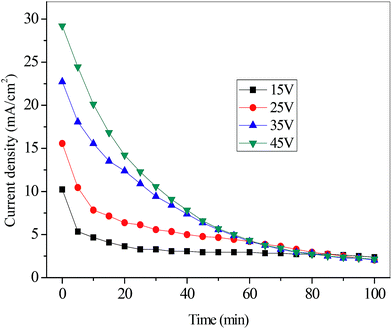 |
| Fig. 2 The current density across the stack at various voltages (initial concentration of C2, flux rate of 4.17 mL s−1). | |
3.2 The effects of the ED operation conditions in the circulation experiment
3.2.1 Effect of applied voltage. Applied voltage is one of the most important parameters for the removal efficiency in potentiostatic mode.36 Fig. 3 depicts the removal rates of cyanide and copper as a function of operation time under different applied voltages. As expected, the removal rate was improved with the increase of voltage due to the higher driving force (direct current, DC) accompanied with higher voltage. Under a higher voltage, ions were faster transferred from the diluted compartment to the concentrated compartment through the ion-exchange membrane. When the applied voltage was 45 V, the removal of cyanide and copper were 99.83% and 99.41%, respectively. After 100 min, both of the concentrations of copper (0.28 mg L−1) and cyanide (0.41 mg L−1) in DS were below 0.5 mg L−1, which met grade one of “the national integrated wastewater discharge standards” GB8978-1996.5
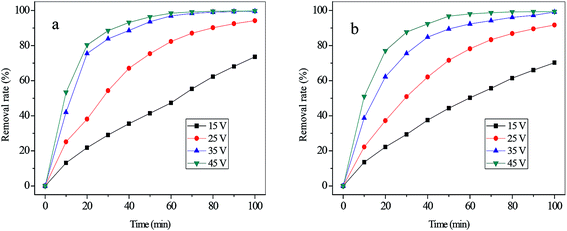 |
| Fig. 3 The removal rates of cyanide (a) and copper (b) with various applied voltages (initial concentration of C2, flux rate of 4.17 mL s−1). | |
Fig. 4 shows that the current efficiency of CN− increased sharply from 14.31% at 15 V to 21.37% at 25 V and then relatively plateaued after 35 V at a level of around 22%. According to the eqn (2), this phenomenon could be attributed to the variation of the removal rate and current with time. In terms of the energy consumption, it increased linearly from 3.72 kW h m−3 to 28.47 kW h m−3 with the voltage increasing from 15 V to 45 V. This trend is mainly attributed to the fact that a greater part of the total electrical energy was consumed to overcome the electrical resistance as the voltage increased.23 As a result, in the view of removal rate, energy consumption and current efficiency, 25 V was adopted as the optimal applied voltage for ED process in the simulated gold mine effluent treatment.
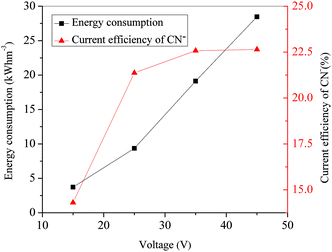 |
| Fig. 4 Variation of the energy consumption and current efficiency of CN− with various applied voltages (initial concentration of C2, flux rate of 4.17 mL s−1). | |
3.2.2 Effect of initial concentration. The effect of the initial concentration of effluents is of great importance in order to assess the optimum domain of applicability of the ED process investigated.39 In order to study the influence of the initial concentrations of cyanide and copper, four effluents with different concentrations were used in this experiment and their detailed compositions are presented in Table 2. Fig. 5 shows that the removal rates of cyanide and copper increased with more operation time, and a higher ion removal rate could be achieved with a lower initial concentration. Fig. 6 shows that the higher concentrated solution led to higher energy consumption of the ED process, which could be attributed to the fact that the higher concentrated solution led to higher electrical conductivity of solution and lower electrical resistance. According to Ohm's Law,38 the operating current would be higher at a constant voltage, which would result in higher energy consumption in accordance with eqn (3). In terms of the current efficiency, increasing the initial concentration increases the current efficiency of CN− up to a maximum value of 21.37% at an initial concentration of C2 (concentration of copper and cyanide were 47 mg L−1 and 242 mg L−1) and then decreases it to about 19.86% for the more concentrated effluent. This variation of current efficiency with initial concentration could be also explained by the decrease in the electrical resistance of the solutions when increasing the concentration.39 Hence, the data in Fig. 6 suggests that the enhancement in the migration rate was greater than the increase in current intensity in the concentration range C1 to C2, and therefore, current efficiency increased in accordance with eqn (2), whereas the situation was reversed for the concentrations higher than C2 investigated here and thus resulted in a lowering of the current efficiency values.
 |
| Fig. 5 The removal rate of cyanide (a) and copper (b) with various initial concentrations (applied voltage of 25 V, flux rate of 4.17 mL s−1). | |
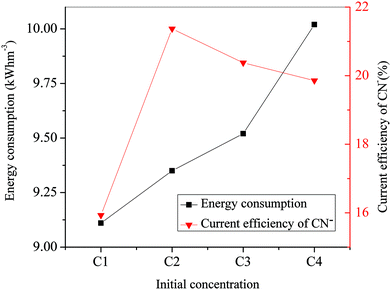 |
| Fig. 6 Variation of the energy consumption and current efficiency of CN− with various initial concentrations (applied voltage of 25 V, flux rate of 4.17 mL s−1). | |
3.2.3 Effect of flux rate. Fig. 7 shows that the removal rate of cyanide increased from 66.12% to 94.21% after 100 minutes of operation. With the initial increase of the operational flux, the removal rate of copper increased as well with the highest removal rate obtained at 4.17 mL s−1. This could be ascribed to the fact that the increase of flow rate could shorten the cycle time and increase the cycle number. The turbulence in compartments could be strengthened so that the migration rate of [Cu(CN)4]3−, [Cu(CN)3]2−and CN− could also be increased. As a result, the removal rate of cyanide and copper was increased with the initial rise of the flux rate. Further increasing the flux rate to higher than 4.17 mL s−1 did not significantly improve the removal rate of cyanide and even led to a reduced removal rate for copper. This phenomenon could be attributed to the fact that over-high flow rate could limit the retention time of solution in DC, and some ions in solution were taken out of ED stack without penetrating through the membrane. Therefore, the removal rate of copper or cyanide was not increasing sustainably as the flow rate increased. Moreover, the increase of flow rate could raise the hydraulic pressure between membranes. It might also damage membranes and shorten the membrane life.39 At the same time, the energy consumption of ED process could also be increased due to the energy requirement of the higher flux. As a result, in the view of the ions removal rate, the best flux rate was 4.17 mL s−1 (average flow velocity at the membrane water interphase 1.32 cm s−1) for the ED system.
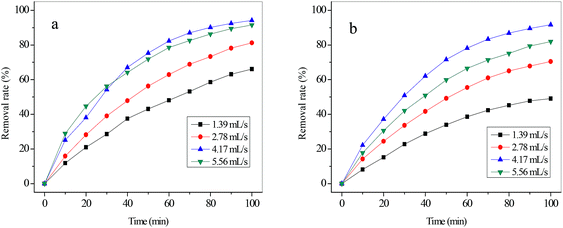 |
| Fig. 7 The removal rate of cyanide (a) and copper (b) with various flux rates (applied voltage of 25 V, initial concentration of C2). | |
As shown in Fig. 8, the energy consumption increased slowly with the flux rate increasing from 1.39 mL s−1 to 4.17 mL s−1, whereas it increased sharply with the flux rate increasing from 4.17 mL s−1 to 5.56 mL s−1. This variation of energy consumption was closely related to the conductivity of the solutions in compartments with a constant voltage. It could be explained by the increase of current intensity as the flux rate was increased according to eqn (3). The increased electrical energy was consumed as the current intensity increased. The current efficiency of CN− with various flux rates was also calculated, which is also presented in Fig. 8. It increased nearly linearly from 12.99% at 1.39 mL s−1 to 21.37% at 4.17 mL s−1 but decreased from 21.37% at 4.17 mL s−1 to 19.61% at 5.56 mL s−1. As mentioned above, the ion migration rate was closely related to the flux rate. The variation of current efficiency can be ascribed to the fact that the migration rate of CN− increased with the initial rise of the flux rate but decreased with the continuing increase of the flow rate. On the other hand, according to eqn (1) and (2), the increase of removal rate (η) of CN− could lead to an increase of the current efficiency of CN− with constant values of C0, Z, N, V, F and t. Therefore, the variation trend of current efficiency of CN− with various flux rates was similar to that of the removal rate. For our simulated solution, the optimized operational parameters were a voltage of 25 V, initial concentration of C2 (concentration of copper and cyanide were 47 mg L−1 and 242 mg L−1), and flux rate of 4.17 mL s−1 with the removal rate of 94.21% (cyanide) and 91.72% (copper).
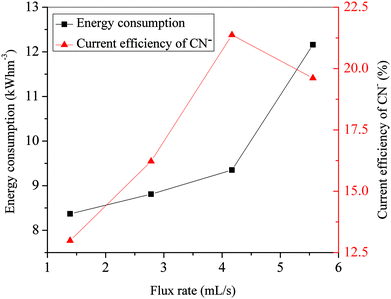 |
| Fig. 8 Variation of the energy consumption and current efficiency of CN− with various flux rates (applied voltage of 25 V, initial concentration of C2). | |
3.3 The removal of cyanide and copper from gold mine effluent
After the optimization of the ED parameters with the simulated solution, the real gold mine effluent was also treated by applying the optimized parameters (voltage of 25 V and flux rate of 4.17 mL s−1). In addition to copper, zinc is also a toxic heavy metal that was present in the gold mine effluent, and thus the content of zinc in the samples was determined and the removal rate was calculated. The results are represented in Table 4. On the other hand, in order to lower the concentrations of copper and cyanide, a voltage of 45 V was applied in the ED process, and the results are represented in Table 5. Due to the higher current flowing through the ED stack, the energy consumption values obtained from the experiments performed with the gold mine effluent were higher than that of simulated solution. This could be explained by the presence of salts, particularly sodium cyanide, which was used excessively in the process of gold extraction.18
Table 4 Performance of ED in real gold mine effluent (25 V)
Time (min) |
Current (A) |
Removal rate of cyanide (%) |
Removal rate of copper (%) |
Removal rate of zinc (%) |
Current efficiency of CN− (%) |
Energy consumption (kW h m−3) |
0 |
1.73 |
0 |
0 |
0 |
0 |
0 |
20 |
1.04 |
32.14 |
22.00 |
19.45 |
6.50 |
5.77 |
40 |
0.74 |
53.94 |
38.54 |
36.37 |
7.67 |
9.48 |
60 |
0.52 |
71.49 |
55.82 |
57.28 |
9.64 |
12.10 |
80 |
0.41 |
82.35 |
68.18 |
67.33 |
10.56 |
14.04 |
100 |
0.34 |
88.44 |
80.34 |
78.51 |
10.94 |
15.60 |
120 |
0.27 |
91.02 |
85.67 |
86.18 |
11.82 |
16.88 |
140 |
0.21 |
93.22 |
91.00 |
91.50 |
13.34 |
17.88 |
Table 5 Performance of ED in real gold mine effluent (45 V)
Time (min) |
Current (A) |
Removal rate of cyanide (%) |
Removal rate of copper (%) |
Removal rate of zinc (%) |
Current efficiency of CN− (%) |
Energy consumption (kW h m−3) |
0 |
2.76 |
0 |
0 |
0 |
0 |
0 |
20 |
1.37 |
55.12 |
42.55 |
43.80 |
8.46 |
15.49 |
40 |
0.83 |
73.96 |
65.91 |
68.26 |
9.37 |
23.74 |
60 |
0.55 |
87.05 |
79.53 |
79.50 |
11.10 |
28.91 |
80 |
0.36 |
94.16 |
89.63 |
92.11 |
13.75 |
32.33 |
100 |
0.24 |
96.73 |
95.04 |
94.07 |
16.95 |
34.58 |
120 |
0.21 |
98.94 |
97.51 |
96.95 |
16.52 |
36.26 |
140 |
0.20 |
99.80 |
99.07 |
98.90 |
14.99 |
37.80 |
It could also be seen from the Tables 4 and 5 that the removal rate of copper was close to that of zinc, whereas the removal rate of cyanide was higher than that of copper or zinc. The reason is that [Cu(CN)4]3−, [Cu(CN)3]2− or [Zn(CN)4]3− are more voluminous than CN−, and it is more difficult to transport larger ions through the anion exchange membrane.24 When the real gold mine effluent was tested, the current efficiency of CN− decreased, and longer times were required for the same removal rates. In terms of cyanide, with the simulated solution, a removal of 93.0% was achieved after 80 min with an energy consumption of 9.35 kW h m−3, whereas with the gold mine effluent, the removal of 93.0% was achieved after 140 min with an energy consumption of 17.88 kW h m−3. The reason is associated with the competition between the considerably more anions, which are present in real gold mine effluent ([Cu(CN)4]3−, [Cu(CN)3]2−, [Zn(CN)4]3−, CN−, and Cl−)25 Still, the concentrations of copper (0.44 mg L−1), cyanide (0.48 mg L−1) and zinc (0.34 mg L−1) in treated effluent were all below the regulatory limits (copper, cyanide <0.5 mg L−1, zinc <2.0 mg L−1).5 The highest removal rates were 99.80%, 99.07% and 98.90%. Another point that should be noted is that the removal rates of cyanide and copper in this work were higher than that in other similar research (cyanide 93.3%, copper 93.9%).8,27 Thus, the results could verify the feasibility of the removal copper and cyanide in gold mine effluent using the ED technique. The removal rate of cyanide and metals had been improved after optimizing the conditions.
3.4 Ion-exchange membranes fouling analysis
It is well known in ED that the precipitation on ion-exchange membranes can be a consequence of operating above the limiting current density.24 In this case water could be dissociated into H+ and OH− ions, which might cause changes in the pH of the boundary layer formed at the membrane/solution interface, leading to a local change in the characteristics of the ionic species presented in the solution. Insoluble compounds can be formed and then precipitated on the ion-exchange membrane.25 In order to understand the membrane fouling behavior during the gold mine effluent ED treatment process, experiments were carried out with following parameters: for test 1, a voltage of 25 V and flux rate of 4.17 mL s−1 were used, and the sodium hydroxide was added to adjust the pH of DS to alkaline range of 9–10 during ED process. For test 2, the voltage of 25 V and the flux rate of 4.17 mL s−1 were used, and without pH adjustment, pH of DS in the late process changed from 9.89 to 7.02, and even 3.57.
3.4.1 Analysis by FTIR. The FTIR spectrum of the original and used membranes is presented in Fig. 9. Compared with the FTIR spectrum of the original membrane (spectrum a-1), the absorption bands at 2174 cm−1 (spectrum a-2) and 2175 cm−1 (spectrum a-3) could be attributed to the presence of CuCN, and the absorption bands at 2099 cm−1 (spectrum a-2) and 2098 cm−1 (spectrum a-3) could be attributed to the presence of [Cu(CN)3]2−.2,40,41 The two peaks in spectrum a-3 are considerably stronger. Moreover, the absorption bands at 3571 cm−1 and 686 cm−1 arise from the stretching and bending vibrations of bulk OH groups of Cu(OH)2, strongly suggesting the presence of Cu(OH)2 on the surface of AEM a-3.42,43 Metal–oxygen characteristic bands are typically observed in an interval from 600 cm−1 to 400 cm−1. A band at 445 cm−1 and a shoulder at around 500 cm−1 can be due to Zn–O and Zn–OH lattice vibrations.44–47 In addition, the absorption band at 1617 cm−1 (HOH bending) and the broad bands around 3400 cm−1 (O–H stretching) are assigned to both the OH group of the precipitates and water molecules absorbed from the air.41,43,48
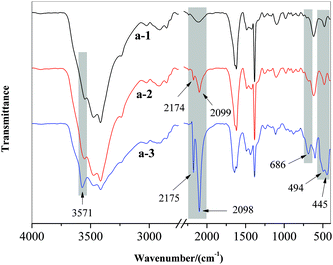 |
| Fig. 9 The FTIR spectra of the original AEM (a-1), the used AEM (a-2) in test 1, and the used AEM (a-3) in test 2. | |
3.4.2 Analysis by SEM-EDX. In order to further understand the fouling compositions and surface morphologies of the membranes, samples including original membranes, and used membranes in two tests were analyzed by SEM-EDX. The SEM images are shown in Fig. 10. It could be clearly seen that the surface morphologies of AEMs and CEMs were distinctly different. Compared to AEMs, the surfaces of CEMs were smooth and no evident fouling was found (Fig. 10(b)). However, the surfaces of the AEMs were rough with crevices, and membrane fouling was more likely to happen, as shown in Fig. 10(a). In terms of AEMs, the precipitation was observed clearly on the surface of a-3 (test 2), which was considerably more than that on the surface of a-2 (test 2).
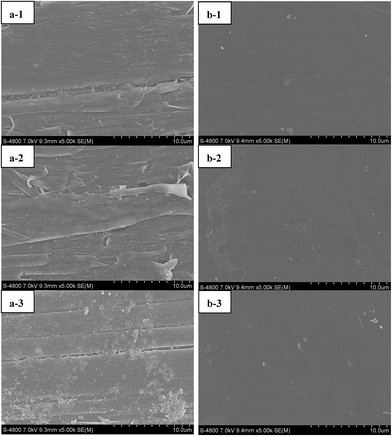 |
| Fig. 10 SEM images (original magnification, 5000×) of the original AEM (a-1), the used AEM (a-2) in test 1, the used AEM (a-3) in test 2; the original CEM (b-1), the used CEM (b-2) in test 1 and the used CEM (b-3) in test 2. | |
The results of elemental analysis are presented in Table 6. It was observed that the surface of the original AEM a-1 consisted of two elements: carbon (C) and oxygen (O). Compared with a-1, the used AEM a-2 has a decrease in C content but there exists 2.3% of Cu and 3.01% of N in its surface indicating that precipitation occurred. This phenomenon is in agreement with the presence of CuCN and [Cu(CN)3]2−, which has been proven via FTIR spectroscopy. On the other hand, the used AEM a-2 has even more decrease in C content and a large amount of Cu. The contents of O and N also increased on the surface of a-3. This can be ascribed to the increase of CuCN and [Cu(CN)3]2− and the presence of Cu(OH)2, which has been mentioned in the results of molecular analysis (FTIR). In addition to the increase of O, N and Cu, the increase of Zn and the presence of Fe, Na, and Cl also resulted in the decrease of C percent.
Table 6 The elemental analysis (expressed as atomic percentage %) of AEMs
Membrane |
Atomic percentage (%) |
C |
O |
N |
Cu |
Zn |
Fe |
Na |
Cl |
a-1 |
90.32 |
9.68 |
|
|
|
|
|
|
a-2 |
83.88 |
9.98 |
3.01 |
2.34 |
0.79 |
|
|
|
a-3 |
49.63 |
15.59 |
13.82 |
15.47 |
3.46 |
1.38 |
0.36 |
0.29 |
According to ref. 13, 31 and 49, the copper cyanide complex might be destructed and subsequently formed on the electrode and membrane surface of CuOOH (eqn (4-1)), which could change into Cu(OH)2 and/or CuO species (eqn (4-2)).
|
[Cu(CN)n]1−n + 2H2O ⇔ CuOOH + 3H+ + nCN− + 2e−
| (4-1) |
|
CuOOH + e− ⇆ Cu(OH)2 + CuO
| (4-2) |
Combined with the results of molecular analysis (FTIR), the species presented on the membrane (a-3) surface was Cu(OH)2. In addition to copper and cyanide, zinc and cyanide were mainly present in the forms of [Zn(CN)4]3− in the gold mine effluent as mentioned above. There is equilibrium between compounds with cyanide and hydroxyl, as it can be seen in the reaction below (eqn (5)):50
|
[Zn(CN)4]2− + 4OH− ⇔ [Zn(OH)4]2− + 4CN−
| (5) |
This demonstrates that Zn could present in the forms of zinc cyanide or zinc hydroxide on the surface of membrane. Combined with the existence of Zn–O and Zn–OH characteristic bands in the FTIR spectrum, it is evident that Zn(OH)2 exists in the precipitate (a-3).
3.4.3 Analysis by membrane resistance and static contact angle. The membrane resistance and static contact angle were also measured before and after the experiments, and the results are shown in Table 7. Compared to Original membranes (a-1 and b-1), no significant increase of membrane resistance was observed from the used CEMs (b-2 and b-3) and AEM a-2, whereas the membrane resistance of a-3 increased evidently. This phenomenon suggested that there was more fouling on the surface of a-3.28,29 On the other hand, in comparison to a-1, the significant decrease of the static contact angle is only observed for a-3 and the static contact angle of a-2 decreased slightly. This result is in agreement with the membrane resistance and demonstrates that the ion-exchange membrane fouling of AEM can be decreased significantly via pH adjustment, which has been proven in the results of FTIR and SEM-EDX.
Table 7 Membrane resistance and contact angle of the membranes in the experiment
Project |
Original |
Test 1 |
Test 2 |
AEM (a-1) |
CEM (b-1) |
AEM (a-2) |
CEM (b-2) |
AEM (a-3) |
CEM (b-3) |
Membrane resistance (Ω cm−2) |
5.78 |
3.67 |
5.82 |
3.73 |
6.12 |
3.77 |
Static contact angle (°) |
64.05–66.56 |
60.90–62.28 |
61.21–63.17 |
58.12–60.87 |
33.04–41.35 |
56.91–64.13 |
4 Feasibility analysis
ED has proven to be an efficient technology for many industrial applications. In this research, the removal rates of cyanide (99.80%) and copper (99.07%) has been improved and were higher than that in other similar studies.8,27 The concentration of copper (0.44 mg L−1) and cyanide (0.48 mg L−1) in the treated effluent were below the regulatory discharge limits (<0.5 mg L−1). In addition, the ion-exchange membrane fouling can be controlled to a minimum with pH adjustment. Generally, the capital and operating costs of an ED plant depend strongly on the quality of the feed and product water, the total membrane area, the plant capacity, the site characteristics, the membrane cost, and other plant components and their useful life under operating conditions; therefore, it is difficult to analyze and compare the costs of electrodialysis and other methods.51,52 However, many industrial applications and studies have proven the economic feasibility of ED in many cases.19–21 The ion-exchange membranes, electrodes and spacers are easy to acquire and their cost is becoming more inexpensive along with the development of related technologies.19,22,23 Therefore, ED is worth to be studied and be used for the treatment of gold mine effluent. At least it can be used as a complementary method in some cases.
This method has advantages such as it consumes minimal chemicals and there are no sludge problems. However, the experiment was carried out without considering the further treatment of CS. In addition to the application mentioned above for the treatment of gold mine effluent, the operating cost of this method could be further reduced by reusing the useful ingredients in CS. Thus, it is indispensable for further study to recover the cyanide and metals in concentrated gold mine effluent.
5 Conclusions
In the present work, ED was proposed for the treatment of simulated and real gold mine effluents. The effects of applied voltage, initial concentration, and flux rate on ED performance were investigated. The results showed that increasing the flow rate and initial concentration increased the current efficiency to a maximum value and further increasing decreased the efficiency. The increase of the removal rate and current efficiency were fast initially and then slowed when the applied voltage was increased from 15 to 45 V. It was found out that the removal rates of cyanide and copper had been improved after optimizing the conditions. Then, the lowest concentration of copper and cyanide in the treated effluent were below the regulatory discharge limits. Therefore, the results could verify the feasibility of the removal copper and cyanide in gold mine effluent using the ED technique. In addition, ion-exchange membrane fouling was studied and the results showed the presence of CuCN, [Cu(CN)3]2−, Cu(OH)2, and Zn(OH)2 in the precipitate, and the ion-exchange membrane fouling of AEM could be decreased significantly via a pH adjustment. This research provides a new insight into the removal of copper and cyanide from gold mine effluent.
Acknowledgements
This research was supported by the National Science & Technology Pillar Program during the 12th Five-year Plan Period (no. 2015BAE06B03) and the Public Science and Technology Research Funds Projects of Ocean (no. 201405035).
References
- X. Dai, A. Simons and P. Breuer, A review of copper cyanide recovery technologies for the cyanidation of copper containing gold ores, Miner. Eng., 2012, 25, 1–13 CrossRef CAS PubMed.
- G. C. Lukey, J. S. J. van Deventer, S. T. Huntington, R. L. Chowdhury and D. C. Shallcross, Raman study on the speciation of copper cyanide complexes in highly saline solutions, Hydrometallurgy, 1999, 53, 233–244 CrossRef CAS.
- D. Donato, O. Nichols, H. Possingham, M. Moore, P. Ricci and B. Noller, A critical review of the effects of gold cyanide-bearing tailings solutions on wildlife, Environ. Int., 2007, 33, 974–984 CrossRef CAS PubMed.
- R. R. Dash, A. Gaur and C. Balomajumder, Cyanide in industrial wastewaters and its removal: A review on biotreatment, J. Hazard. Mater., 2009, 163, 1–11 CrossRef CAS PubMed.
- National Environmental Protection Agency, National integrated wastewater discharge standard GB 8978-1996, China Environmental Science Press, Beijing, 1996, In Chinese Search PubMed.
- O. Alonso-González, F. Nava-Alonso and A. Uribe-Salas, Copper removal from cyanide solutions by acidification, Miner. Eng., 2009, 22, 324–329 CrossRef PubMed.
- Y. B. Patil and K. M. Paknikar, Development of a process for biodetoxification of metal cyanides from wastewater, Process Biochem., 2000, 35, 1139–1151 CrossRef CAS.
- F. Xie and D. Dreisinger, Recovery of copper cyanide from waste cyanide solution by LIX 7950, Miner. Eng., 2009, 22, 190–195 CrossRef CAS PubMed.
- D. Pak and W. Chang, Oxidation of aqueous cyanide solution using hydrogen peroxide in the presence of heterogeneous catalyst, Environ. Technol., 1997, 18, 557–561 CrossRef CAS.
- F. Barriga-Ordonez, F. Nava-Alonso and A. Uribe-Salas, Cyanide oxidation by ozone in a steady-state flow bubble column, Miner. Eng., 2006, 19, 117–122 CrossRef CAS PubMed.
- W. Zhang, W. Liu, Y. Lv, B. Li and W. Ying, Enhanced carbon adsorption treatment for removing cyanide from coking plant effluent, J. Hazard. Mater., 2010, 184, 135–140 CrossRef CAS PubMed.
- F. Gurbuz, F. Ciftci and A. Akcil, Biodegradation of cyanide containing effluents by Scenedesmus obliquus, J. Hazard. Mater., 2009, 162, 74–79 CrossRef CAS PubMed.
- S. C. Cheng, M. Gattrell, T. Guena and B. MacDougall, The electrochemical oxidation of alkaline copper cyanide solutions, Electrochim. Acta, 2002, 47, 3245–3256 CrossRef CAS.
- D. Bachiller, M. Torre, M. Rendueles and M. Diaz, Cyanide recovery by ion exchange from gold ore waste effluents containing copper, Miner. Eng., 2004, 17, 767–774 CrossRef CAS PubMed.
- N. Kuyucak and A. Akcil, Cyanide and removal options from effluents in gold mining and metallurgical processes, Miner. Eng., 2013, 50–51, 13–29 CrossRef CAS PubMed.
- J. Hou, G. Dong, B. Luu, R. G. Sengpiel, Y. Ye, M. Wessling and V. Chen, Hybrid membrane with TiO2 based bio-catalytic nanoparticle suspension system for the degradation of bisphenol-A, Bioresour. Technol., 2014, 169, 475–483 CrossRef CAS PubMed.
- J. Hou, G. Dong, Y. Ye and V. Chen, Enzymatic degradation of bisphenol-A with immobilized laccase on TiO2 sol–gel coated PVDF membrane, J. Membr. Sci., 2014, 469, 19–30 CrossRef CAS PubMed.
- A. Güvenc and B. Karabacakoglu, Use of electrodialysis to remove silver ions from model solutions and wastewater, Desalination, 2005, 172, 7–17 CrossRef PubMed.
- H. Strathmann, Electrodialysis, a mature technology with a multitude of new applications, Desalination, 2010, 264, 268–288 CrossRef CAS PubMed.
- D. C. Buzzi, L. S. Viegas, M. A. S. Rodrigues, A. M. Bernardes and J. A. S. Tenório, Water recovery from acid mine drainage by electrodialysis, Miner. Eng., 2013, 40, 82–89 CrossRef CAS PubMed.
- R. K. McGovern, A. M. Weiner, L. Sun, C. G. Chambers, S. M. Zubair and J. H. Lienhard V, On the cost of electrodialysis for the desalination of high salinity feeds, Appl. Energy, 2014, 136, 649–661 CrossRef PubMed.
- A. H. Galama, M. Saakes, H. Bruning, H. H. M. Rijnaarts and J. W. Post, Seawater predesalination with electrodialysis, Desalination, 2014, 342, 61–69 CrossRef CAS PubMed.
- Y. Wei, Y. Wang, X. Zhang and T. Xu, Comparative study on the treatment of simulated brominated butyl rubber effluent by using bipolar membrane electrodialysis (BMED) and conventional electrodialysis (ED), Sep. Purif. Technol., 2013, 110, 164–169 CrossRef CAS PubMed.
- L. Marder, G. O. Sulzbach, A. M. Bernardes and J. Z. Ferreira, Removal of Cadmium and Cyanide from Aqueous Solutions through Electrodialysis, J. Braz. Chem. Soc., 2003, 14, 610–615 CrossRef CAS PubMed.
- L. Marder, A. M. Bernardes and J. Z. Ferreira, Cadmium electroplating wastewater treatment using a laboratory-scale electrodialysis system, Sep. Purif. Technol., 2004, 37, 247–255 CrossRef CAS PubMed.
- C. A. Young and T. S. Jordan, Cyanide remediation: current and past technologies, in Proceedings of the 10th Annual Conference on Hazardous Waste Res, 1995, pp. 104–129 Search PubMed.
- X. J. Luo and K. Luo, Application of liquit membrane technology in treating cyanide leach solution of gold ore, Miner. Eng., 2004, 2, 58–62 Search PubMed . (In Chinese).
- Y. Yang, X. Gao, A. Fan, L. Fu and C. Gao, An innovative beneficial reuse of seawater concentrate using bipolar membrane electrodialysis, J. Membr. Sci., 2014, 449, 119–126 CrossRef CAS PubMed.
- V. Lindstrand, G. Sundström and A. S. Jönsson, Fouling of electrodialysis membranes by organic substances, Desalination, 2000, 128, 91–102 CrossRef CAS.
- X. Zuo, L. Wang, J. He, Z. Li and S. Yu, SEM-EDX studies of SiO2/PVDF membranes fouling in electrodialysis of polymer-flooding produced wastewater: Diatomite, APAM and crude oil, Desalination, 2014, 347, 43–51 CrossRef CAS PubMed.
- J. Lu, D. B. Dreisinger and W. C. Cooper, Thermodynamics of the aqueous copper–cyanide system, Hydrometallurgy, 2002, 66, 23–36 CrossRef CAS.
- G. C. Lukey, J. S. J. van Deventer, R. L. Chowdhury and D. C. Shallcross, The effect of salinity on the capacity and selectivity of ion exchange resins for gold cyanide, Miner. Eng., 1999, 12, 769–785 CrossRef CAS.
- O. Alonso-González, F. Nava-Alonso, A. Uribe-Salas and D. Dreisinger, Use of quaternary ammonium salts to remove copper–cyanide complexes, Miner. Eng., 2010, 23, 765–770 CrossRef PubMed.
- A. J. B. Dutra, G. P. Rocha and F. R. Pombo, Copper recovery and cyanide oxidation by electrowinning from a spent copper-cyanide electroplating electrolyte, J. Hazard. Mater., 2008, 152, 648–655 CrossRef CAS PubMed.
- J. M. Chiaplello and J. Y. Gal, Recovery by electrodialysis of cyanide electroplating rinse waters, J. Membr. Sci., 1992, 68, 283 CrossRef.
- F. Karas, J. Hnat, M. Paidar, J. Schauer and K. Bouzek, Determination of the ion-exchange capacity of anion-selective membranes, Int. J. Hydrogen Energy, 2014, 39, 5054–5062 CrossRef CAS PubMed.
- P. Długołęcki, K. Nymeijer, S. Metz and M. Wessling, Current status of ion exchange membranes for power generation from salinity gradients, J. Membr. Sci., 2008, 319, 214–222 CrossRef PubMed.
- M. Sadrzadeh and T. Mohammadi, Treatment of sea water using electrodialysis: Current efficiency evaluation, Desalination, 2009, 249, 279–285 CrossRef CAS PubMed.
- C. V. Gherasim, J. Křivčík and P. Mikulášek, Investigation of batch electrodialysis process for removal of lead ions from aqueous solutions, Chem. Eng. J., 2014, 256, 324–334 CrossRef CAS PubMed.
- R. A. Penneman and L. H. Jones, Infrared absorption studies of aqueous complex ions: II Cyanide complexes of Cu(I) in aqueous solution, J. Chem. Phys., 1956, 24, 293–296 CrossRef CAS PubMed.
- W. Zheng, Y. Wang, L. Yang, X. Li, L. Zhou and Y. Li, Novel adsorbent of polymeric complex derived from chaleting resin with Cu(II) and its removal properties for cyanide in aqueous solution, Colloids Surf., A, 2014, 455, 136–146 CrossRef CAS PubMed.
- B. J. W. Eerd, A. G. Young, N. I. A. Salim, T. Kemmitt and N. M. Strickland, Ligand-functionalised copper(II) hydroxide for quantum dot photoluminescence quenching, J. Colloid Interface Sci., 2010, 346, 288–295 CrossRef PubMed.
- H. Niu, Q. Yang and K. Tang, A new route to copper nitrate hydroxide microcrystals, Mater. Sci. Eng., B, 2006, 135, 172–175 CrossRef CAS PubMed.
- D. Japic, M. Bitenc, M. Marinšek and Z. C. Orel, The impact of nano-milling on porous ZnO prepared from layered zinc hydroxide nitrate and zinc hydroxide carbonate, Mater. Res. Bull., 2014, 60, 738–745 CrossRef CAS PubMed.
- M. Y. Ghotbi, N. Bagheri and S. K. Sadrnezhaad, Nanocrystalline copper doped zinc oxide produced from copper doped zinc hydroxide nitrate as a layered precursor, Adv. Powder Technol., 2012, 23, 279–283 CrossRef CAS PubMed.
- M. Z. B. Hussein, M. Y. Ghotbi, A. H. Yahaya and M. Z. Abd Rahman, The effect of polymers onto the size of zinc layered hydroxide salt and its calcined product, Solid State Sci., 2009, 11, 368–374 CrossRef PubMed.
- M. Z. B. Hussein, M. Y. Ghotbi, A. H. Yahaya and M. Z. Abd Rahman, The effect of polymers onto the size of zinc layered hydroxide salt and its calcined product, Mater. Chem. Phys., 2009, 113, 491–496 CrossRef PubMed.
- H. S. Jung, J. K. Lee, J. Y. Kim and K. S. Hong, Crystallization behaviors of nanosized MgO particles from magnesium alkoxides, J. Colloid Interface Sci., 2003, 259, 127–132 CrossRef CAS.
- I. G. Casella and M. Gatta, Anodic electrodeposition of copper oxide/hydroxide films by alkaline solutions containing cuprous cyanide ions, J. Electroanal. Chem., 2000, 494, 12–20 CrossRef CAS.
- M. A. S. Rodrigues, C. Korzenovski, E. Gondran, A. M. Bernardes and J. Z. Ferreira, Evaluation of changes on ion-selective membranes in contact with zinc-cyanide complexes, J. Membr. Sci., 2006, 279, 140–147 CrossRef CAS PubMed.
- S. Lahnid, M. Tahaikt, K. Elaroui, I. Idrissi, M. Hafsi, I. Laaziz, Z. Amor, F. Tiyal and A. Elmidaoui, Economic evaluation of fluoride removal by electrodialysis, Desalination, 2008, 230, 213–219 CrossRef CAS PubMed.
- M. Turek, Cost effective electrodialytic seawater desalination, Desalination, 2002, 153, 371–376 CrossRef.
|
This journal is © The Royal Society of Chemistry 2015 |