DOI:
10.1039/C7PY01873H
(Paper)
Polym. Chem., 2018,
9, 178-183
Main-chain benzoxazine precursor block copolymers
Received
7th November 2017
, Accepted 27th November 2017
First published on 28th November 2017
Abstract
A novel strategy for the preparation of block copolymers of polymeric benzoxazine precursors with polyetheramines by one-pot two-step or stepwise pathways is described. The method pertains to the use of simple chemicals such as 4-hydroxyaniline, formaldehyde and polyetheramines (Jeffamines). The structures and molecular weights of the polymers were characterized by FTIR, 1H NMR, and GPC. Successful block copolymer formation was evidenced by the clear shift of the molecular weight of the block copolymer to the higher molecular weight region. Thermal properties of the polymers were also investigated by using DSC and TGA. Block copolymers were shown to undergo thermally activated curing by the ring-opening polymerization of the benzoxazine block. The thermal stability of the cured product drastically increased compared to the precursor polyetheramine.
Introduction
Polybenzoxazines (PBZs) as contenders to classical phenolic resins have numerous superior properties, such as good mechanical strength, limited or no water absorption, dimensional and thermal stability, and chemical and flame resistivity.1–3 Moreover, their monomers, namely 1,3-benzoxazines (BZ), also have excellent storage life stability at room temperature. When BZ prepreg formulas were analyzed over one year, they demonstrated a slight change in differential scanning calorimetry (DSC) thermograms. Therefore, many resin producers established benzoxazine-bearing formulations and these resins have found numerous applications as high-performance materials in electronic circuit boards, composites, blends and alloys.4–7 Polybenzoxazines are synthesized by thermal ring-opening polymerization (ROP) of benzoxazine monomers. Typically, the polymerization takes place between 170 and 250 °C without using any catalyst or curative depending on the structure and purity of the monomer (Scheme 1).8–10 Purer monomers have higher curing temperatures than monomers containing phenolic residues, where these residues act as the catalyst in the polymerization.11–16 Another appealing aspect of the polybenzoxazines is their great molecular design flexibility, unlike traditional phenolic resins. Simply, most of the benzoxazine monomers can be synthesized by using a derivative of phenol, a primary amine and formaldehyde (Scheme 1).17 Hence, various polybenzoxazines can be designed with tailored properties for desired applications.18–22 For example, highly stiff polybenzoxazines can be obtained by using allyl,23,24 propargyl,25 coumarine,26,27 or di- and tri-oxazine functional benzoxazines that allow extra crosslinking.28,29 For some specific applications, room temperature viscosity of the monomers can be decreased by selecting alcohol functional or long-chain alkyl amines in the synthesis to give essentially fluid benzoxazines, which are important for moulding and similar uses.30,31
 |
| Scheme 1 Synthesis and polymerization of a benzoxazine monomer. | |
Apart from monomer synthesis, polymeric benzoxazine precursors have been synthesized using various methods. For example, polycondensation of diamines and diphenols yields polybenzoxazine precursors with relatively high molecular weights and good film properties.32,33 Other polymer types, such as polyesters,34 polysiloxanes,35,36 polysulfones,37 and polyethers,38 have also been synthesized from benzoxazines, successfully. Moreover, smart systems based on benzoxazines,39–42 such as self-healing,43–46 shape memory,47 and electro-responsive systems,48–50 can even be designed by selecting suitable phenols and amines. Consequently, benzoxazine chemistry has high design capacity to obtain task-specific benzoxazine monomers or polybenzoxazine precursors. Especially, polybenzoxazine precursors have huge potential in terms of applications since they have good film properties and can bear many features of general polymers. Thus, a wide range of main-, side- and end-chain polybenzoxazine precursors have been readily synthesized and used for different purposes.34,51–57 Obviously, each structural variation and the method used would reflect the characteristics of the polymer formed and modify the properties of the resulting polybenzoxazines. For example, flexible and tough materials could be produced from polybenzoxazine precursors by selecting siloxanes or ethers as the repeat units in the polymer.54 The length of the siloxane or etheric chain in the polymeric benzoxazine precursors affects both the toughness and thermal properties. Although several polybenzoxazine precursors have been reported, block copolymers of benzoxazines have scarcely been investigated and this subject has potential to combine the properties of two different polymer chains.38,58 In this study, we have shown that block copolymers of polybenzoxazine precursors can be synthesized using either one-pot two-step or sequential synthetic pathways by selecting suitable aminophenols.
Experimental
Materials
Paraformaldehyde (Aldrich, 95.0–100.5%), p-aminophenol (4-hydroxyaniline) (Merck, ≥99%), Jeffamine D-2000, Jeffamine D-4000, toluene (Merck, ≥99%), ethanol (EtOH, Carlo Erba, ≥99.9%), and methanol (MeOH, Aldrich, 99.8%) were used as received.
Characterization
All 1H NMR spectra were recorded on an Agilent NMR System VNMRS 500 spectrometer at room temperature in CDCl3 or DMSO-d6 with Si(CH3)4 as the internal standard. FTIR spectra were recorded on a PerkinElmer FTIR Spectrum One spectrometer. Differential scanning calorimetry (DSC) was performed on PerkinElmer Diamond DSC from 30 °C to 320 °C with a heating rate of 10 °C min−1 under nitrogen flow. A typical DSC sample was 2–5 mg in a 30 μL aluminum pan. Thermal gravimetric analysis (TGA) was performed on a PerkinElmer Diamond TA/TGA with a heating rate of 10 °C min−1 under nitrogen flow. Gel permeation chromatography (GPC) measurements were performed on a Viscotek GPC max auto sampler system consisting of a pump, a light-scattering detector (λ = 670 nm, Model 270 dual detector, Viscotek Corp.) consisting of two scattering angles: 7° and 90°, and a Viscotek differential refractive index (RI) detector with three ViscoGEL GPC columns (G2000H HR, G3000H HR, and G4000H HR, 7.8 mm internal diameter, 300 mm length) in series. The effective molecular weight ranges were 456–42
800, 1050–107
000, and 10
200–2
890
000, respectively. THF was used as an eluent at a flow rate of 1.0 mL min−1 at 30 °C. Both detectors were calibrated with PS standards with a narrow-molecular-weight distribution. Data were analyzed using ViscotekOmniSEC Omni-01 software.
Synthesis of main-chain benzoxazine precursor (MPBz)
Paraformaldehyde (0.87 g, 0.029 mol) and 4-aminophenol (1.5 g, 0.014 mol) were dissolved in a mixture of 40 mL of toluene and 20 mL of ethanol in a 150 mL flask equipped with a reflux condenser and a magnet for stirring. The solution was refluxed for 24 h at ca. 110 °C. After reflux, the flask was cooled to r.t. and the contents were filtered using an ordinary filter paper to remove solid particles. The clear solution was concentrated under vacuum, and then precipitated in 250 mL of methanol containing 2–3 mL of salty water. The polymer was filtered, washed with water and methanol, then dried in a vacuum chamber at ambient temperature for 48 h to obtain a brown powdery solid (yield ≈ 68%).
Synthesis of poly(benzoxazine-co-etheramine) (MPBz-co-PEA)
Paraformaldehyde (0.87 g, 0.029 mol) and 4-aminophenol (1.5 g, 0.014 mol) were dissolved in a mixture of 40 mL of toluene and 20 mL of ethanol in a 150 mL flask equipped with a reflux condenser and a magnet for stirring. The solution was refluxed for 24 h at ca. 110 °C. The whole mixture was cooled to r.t. Then, Jeffamine D-2000 (1.8 g) (or Jeffamine D-4000, 3.6 g) and extra paraformaldehyde (0.1 g, 0.014 mol) were admixed. The solution was again refluxed for 3 hours at ca. 110 °C. After reflux, the reaction mixture was filtered through an ordinary filter paper, concentrated, and finally precipitated in 250 mL of deionized water. The polymer was filtered under vacuum, washed with copious amounts of water, and dried in a vacuum chamber at ambient temperature for 48 h to obtain a brownish solid with a quantitative yield.
Results and discussion
Initially, AB type main-chain polybenzoxazine (MPBz) prepolymer was synthesized using a slightly modified procedure reported by Takeichi et al.59 In this synthesis p-aminophenol and formaldehyde were reacted in a molar ratio of 1
:
2 (Scheme 2). Ishida and Low reported non-polar solvent mixtures for the synthesis of benzoxazine monomer with high yields and purity.60 Moreover, the toluene
:
ethanol (2
:
1, v/v) binary system was found to reduce gelation and increase the molecular weight of main-chain polybenzoxazine prepolymers.61 Therefore, we applied a nonpolar solvent method by using the toluene
:
ethanol system. The purpose of MPBz synthesis is to produce a scaffold for further reactions and p-aminophenol was selected deliberately since the prepolymer is expected to possess a free phenol and amino group as end-chains. In this way, the polybenzoxazine prepolymer can be modified at the end-chains and further reactions over the phenolic group with polyetheramines and formaldehyde would yield ultimate block copolymers (Scheme 2). For this purpose, MPBz was reacted with two different commercially available polyetheramines (PEA), namely Jeffamine D-2000 and D-4000, with molecular weights of approximately 2000 and 4000 Da, respectively. In addition to the sequential approach, block copolymer formation was also performed in a one-pot two-step manner, which would essentially yield identical copolymers and eliminate the additional separation step for MPBz. The block copolymers were abbreviated as MPBz-co-PEA2000 and MPBz-co-PEA4000 according to molecular weights of the used PEAs.
 |
| Scheme 2 Sequential or one-pot two-step synthesis of MPBz-co-PEA2000 or 4000. | |
Block copolymer formations were monitored by using gel-permeation chromatography (GPC). The number average molecular weight of MPBz was measured as 1364 Da, which is in accordance with the literature.59 After the copolymerization with Jeffamine D-2000 and D-4000 the molecular weights increased to 3150 and 6160 Da, respectively in complete accordance with that of the precursor polymers, indicating that one MPBz and one PEA were connected from end-chains (Table 1). Although PEA has two amino groups at its two ends, the MPBz-PEA-MPBz polymer was not detected in the GPC chromatogram. The observed narrow molecular weight distribution also supports the hypothesis of one MPBz being connected with one PEA and no additional chain extension was noted. Moreover, unreacted end-chain amino group of MPBz-PEA2000 was also detectable with IR, which can be considered as further evidence (Fig. 1).
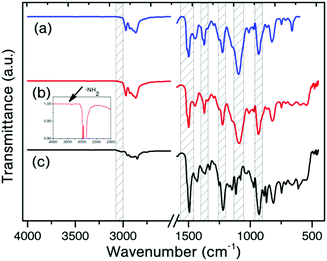 |
| Fig. 1 FT-IR spectra of MPBz-co-PEA4000 (a), MPBz-co-PEA2000 (b), and MPBz (c). | |
Table 1 Molecular weight characteristics of MPBz and its copolymers
Polymer |
M
n a |
M
w a |
M
w/Mn a |
Determined by GPC according to polystyrene standards.
|
MPBz |
1364 |
1466 |
1.08 |
MPBz-co-PEA2000 |
3150 |
3346 |
1.06 |
MPBz-co-PEA4000 |
6160 |
6641 |
1.08 |
The structure of the MPBz and MPBz-co-PEA polymers was confirmed by FTIR and 1H NMR spectroscopies. Fig. 1 shows the FTIR spectra of the copolymers and the main-chain precursor. The characteristic IR bands of benzoxazines were detected for MPBz at 1230 cm−1 (asymmetric stretching of C–O–C) and at 1375 cm−1 (CH2 wagging). Additionally, typical absorptions attributed to the tri-substituted benzene ring at 1498 cm−1 and out of plane bending of C–H at 927 cm−1 were observed, evidencing the presence of the oxazine ring in the backbone of the polymers.62 Moreover, an aromatic C–H stretching vibration band is visible at 3026 cm−1. Similarly, identical IR bands can be observed for both MPBz-co-PEA polymers, disclosing the oxazine ring preservation after copolymerization reactions. Apart from oxazine IR bands, etheric C–O stretching vibration of PEA block is visible as a strong band at 1084 cm−1 providing further evidence for the copolymer formation.
The 1H NMR spectrum of MPBz, shown in Fig. 2a, displayed the typical NMR peaks attributed to methylene protons of oxazine ring (O–CH2–N at 5.19 ppm and Ar–CH2–N at 4.42 ppm). The aromatic protons produced signals between 6.58 and 6.88 ppm. The 1H NMR spectrum of MPBz-co-PEA2000 is shown in Fig. 2b. Similar proton signals related to the benzoxazine ring appear at 5.17 ppm for O–CH2–N and at 4.41 for Ar–CH2–N, clearly indicating that the oxazine ring is preserved under copolymerization conditions. Moreover, aromatic protons slightly shifted between 6.61 and 6.87 ppm. Proton signals related to the PEA block appear at 3.40–3.46 ppm for O–CH2–CH2, at 3.34 ppm for O–CH2–CH2–, and at 1.01 ppm for branching –CH3 groups. A methylene group attached to an oxazine amino group is also visible at 2.97 ppm, showing the linkage between PEA and MPBz in accordance with the literature.45 It should be noted that synthesis of main-chain polybenzoxazine prepolymers is a kind of polycondensation reaction and as a consequence of the nature of the polymerization, the ring-closed ratio was found to be 85–95%.32,33,52,59,61,63 Therefore, peak areas for oxazine protons do not fit well in the NMR spectra. The ring-closed ratio was found to be ca. 86% for MPBz and reasonably high to be used as a benzoxazine precursor.
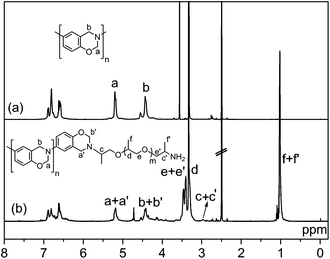 |
| Fig. 2 NMR spectra of MPBz (a) and MPBz-co-PEA2000 (b). | |
The ROP temperatures of benzoxazines generally lay between 170–260 °C depending on the structure. Fig. 3 shows the overlaid DSC profiles of MPBz and its copolymers. The curing of MPBz has an onset at 195 °C, end-set at 296 °C and the curing maximum at 257 °C, indicating that the ring-opening process occurs in a broad temperature range, ca. 100 °C. Moreover, the DSC thermogram of MPBz shows an endotherm between 123 and 147 °C, which may be related to evaporation of small molecule residues. These values were affected after connecting PEA to MPBz; the onset temperatures decreased in the range of 3–5 °C (Table 2) and the temperature interval of the whole ring-opening process dropped from 100 to 80 °C. However, the end-set and curing maximum temperatures reduced ca. 24 and 16 °C, respectively. The decrease in curing temperature can be explained as the effect of amino groups at the chain end of the block copolymer, since amines are known to catalyse ROP of benzoxazines.9,64 Moreover, the amount of exotherm gradually reduced with increasing PEA chain length due to its contribution as an extra mass.
 |
| Fig. 3 DSC thermograms of MPBZ (a), MPBZ-co-PEA2000 (b), and MPBZ-co-PEA4000 (c). | |
Table 2 DSCa characteristics of MPBz and its copolymers under N2 environment
Polymer |
Curing on-set (°C) |
Curing end-set (°C) |
Curing maximum (°C) |
Curing exotherm (J g−1) |
DSC analyses were performed under N2 stream (20 mL min−1.) with a 10 °C min−1 heating rate.
|
MPBz |
195 |
296 |
257 |
−137.5 |
MPBz-co-PEA2000 |
192 |
272 |
241 |
− 45.7 |
MPBz-co-PEA4000 |
190 |
275 |
242 |
−30.4 |
Apart from DSC behaviours of MPBz-co-PEA polymers, there are physical differences between cured MPBz and MPBz-co-PEAs. The cured MPBz has a macroporous structure and shows elastic behaviour. The MPBz network can be squeezed easily by hand and turns back to its original shape. Conversely, the MPBz-co-PEA2000 network is stiffer than cured MPBz in non-porous form (Fig. 4). The gas, presumably formed as by-products during ROP of MPBz block and captured by PEA block, is more slowly released which prevents pore formation.
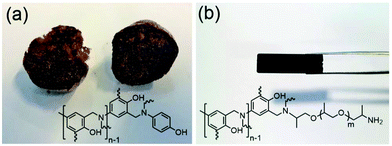 |
| Fig. 4 Images of cured MPBz (a), and MPBz-co-PEA2000 (b). | |
Thermal stabilities of the MPBz and its copolymers were investigated by thermo-gravimetric analysis (TGA) under N2 flow (200 mL min−1). The TGA curves of cured MPBz, MPBz-co-PEA2000, MPBz-co-PEA2000 and PEAs (D-2000 and D-4000) are shown in Fig. 5 and the results are tabulated in Table 3. Moreover, derivatives of TGA curves are displayed in Fig. 6. As expected, all the cured MPBz and its copolymers polymers exhibited better char yields, T5% and T10%, than PEAs. Accordingly, all the PEAs almost completely vaporized after 425 °C and only 0.02% remained at 800 °C. With the all polymers studied, the cured MPBz displayed the highest char of 67% due to the quantity of benzoxazines per mass of sample. Initial degradations of the cured MPBz-co-PEA2000 and MPBz-co-PEA4000 have identical temperatures at T5%, and relatively close values at T10% probably owing to the thermal stability of the ether linkages. Non-functional PEAs also showed comparable initial degradation temperatures and the ether cleavage reaches a maximum at ≈377 °C supporting the thermal stability of the ether linkages. Interestingly, there are two Tmax values for the cured MPBz and the derivative TGA is a broad curve. Although this polymer has a high char yield, the first Tmax value is between T5% and T10% temperatures and a rapid degradation is observed at the initial stages. Conversely, only one Tmax is recorded at 400 °C when the same structure connects to the PEA chain. Obviously, benzoxazine units significantly improve the char yield of bare PEA in accordance with previous reports. Another important point is the dependence of char yields on the molecular weight of the PEA block. As seen in the overlaid TGA curves, incorporation of each 2000 Da PEA unit results in an approximately 20% decrease of the char yield. However, the initial and maximum degradation temperatures are not affected by the PEA chain length.
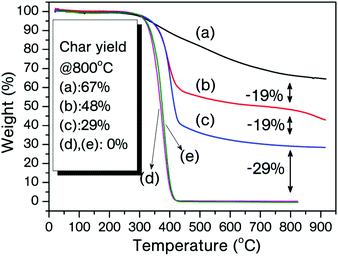 |
| Fig. 5 TGA traces of cured MPBz (a), MPBz-co-PEA2000 (b), MPBz-co-PEA4000 (c), pristine PEA (D-2000) (d), and PEA (D-4000) (e). | |
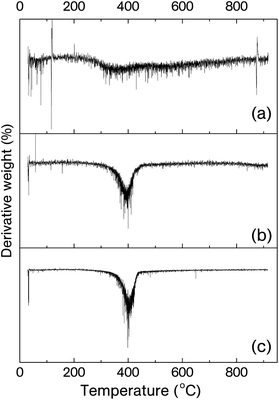 |
| Fig. 6 Derivative of TGA traces of cured MPBz (a), MPBz-co-PEA2000 (b) and MPBz-co-PEA4000 (c). | |
Table 3 Thermal characteristics of cured MPBz and its cured copolymers determined by TGA
Polymer |
T
5% (°C) |
T
10% (°C) |
T
max (°C) |
Y
c (%) |
Curing was performed in TGA at 240 °C for 15 min under N2 stream (200 mL min−1).
T
5%: The temperature for which the weight loss is 5%. T10%: The temperature for which the weight loss is 10%. Tmax: The temperature for maximum weight loss extracted from Fig. 6. Yc: Char yields at 800 °C under nitrogen atmosphere. |
Cureda MPBz |
339 |
389 |
358, 533 |
67 |
Cureda MPBz-co-PEA2000 |
339 |
363 |
393 |
48 |
Cureda MPBz-co-PEA4000 |
339 |
363 |
401 |
29 |
PEA (D-2000) |
319 |
332 |
376 |
≈0 |
PEA (D-4000) |
319 |
334 |
377 |
≈0 |
Conclusions
In conclusion, we have demonstrated that block copolymers of polybenzoxazines with polyetheramines can be synthesized from main-chain polybenzoxazines either in one-pot two-step or stepwise pathways. The synthetic methodology described here is relatively easy, which can be achieved by using simple and commercially available chemicals such as 4-hydroxyaniline, formaldehyde and polyetheramines (Jeffamines) by a straightforward process. In this context, the design flexibility of benzoxazine chemistry can provide a vast number of different possible block copolymers giving the opportunity to further extend the described approach for the fabrication of thermally stable materials. As demonstrated, copolymerization of MPBz with Jeffamines has a drastic impact on the physical behaviours compared to pristine MPBz. Apparently, the porous structure of MPBz can be easily converted to a smooth film. Furthermore, thermal stability of Jeffamines significantly increased in the copolymer form as one can expect from the contribution of benzoxazines. Consequently, the most appealing part of this strategy is its simplicity and the low cost of the chemicals that can be converted into advanced materials using the conditions outlined here in one-pot.
Conflicts of interest
There are no conflicts to declare.
Acknowledgements
The authors would like to thank Istanbul Technical University Research Fund (Project No. TYL-2017-40560).
Notes and references
- N. N. Ghosh, B. Kiskan and Y. Yagci, Prog. Polym. Sci., 2007, 32, 1344–1391 CrossRef CAS.
- C. P. R. Nair, Prog. Polym. Sci., 2004, 29, 401–498 CrossRef CAS.
-
H. Ishida and T. Agag, Handbook of Benzoxazine Resins, Elsevier, 2011 Search PubMed.
-
X. Kommann, K. Kaltenegger, J. Rocks and R. Weder, Eur. Pat, EP1901312A1, 2008 Search PubMed.
-
S. H. Shi, L. Wang and T. A. Chen, US Pat, US7179684B2, 2007 Search PubMed.
-
C. J. S. Rimdusit and S. Tiptipakorn, Alloys and Composites of Polybenzoxazines: Properties and Applications, Springer, New York, 2013 Search PubMed.
-
Advanced Materials, Benzoxazine Thermoset Resins: High-Performance Materials for Extreme Environments, Huntsman corporation guide, 2015 Search PubMed.
- C. Wang, C. Zhao, J. Sun, S. Huang, X. Liu and T. Endo, J. Polym. Sci., Part A: Polym. Chem., 2013, 51, 2016–2023 CrossRef CAS.
- J. Wang, Y. Z. Xu, Y. F. Fu and X. D. Liu, Sci. Rep., 2016, 6, 38584 CrossRef PubMed.
- X. Ning and H. Ishida, J. Polym. Sci., Part A: Polym. Chem., 1994, 32, 1121–1129 CrossRef CAS.
- A. Kocaarslan, B. Kiskan and Y. Yagci, Polymer, 2017, 122, 340–346 CrossRef CAS.
- L. Han, M. L. Salum, K. Zhang, P. Froimowicz and H. Ishida, J. Polym. Sci., Part A: Polym. Chem., 2017, 55, 3434–3445 CrossRef CAS.
- Y. X. Wang and H. Ishida, Polymer, 1999, 40, 4563–4570 CrossRef CAS.
- P. Chutayothin and H. Ishida, Macromolecules, 2010, 43, 4562–4572 CrossRef CAS.
- M. W. Wang, R. J. Jeng and C. H. Lin, Macromolecules, 2015, 48, 530–535 CrossRef CAS.
- H. Oie, A. Mori, A. Sudo and T. Endo, J. Polym. Sci., Part A: Polym. Chem., 2013, 51, 3867–3872 CrossRef CAS.
- G. Lligadas, A. Tuzun, J. C. Ronda, M. Galia and V. Cadiz, Polym. Chem., 2014, 5, 6636–6644 RSC.
- M. Imran, B. Kiskan and Y. Yagci, Tetrahedron Lett., 2013, 54, 4966–4969 CrossRef CAS.
- C. Zuniga, G. Lligadas, J. Carlos Ronda, M. Galia and V. Cadiz, Polymer, 2012, 53, 3089–3095 CrossRef CAS.
- C. Zuniga, M. S. Larrechi, G. Lligadas, J. C. Ronda, M. Galia and V. Cadiz, J. Polym. Sci., Part A: Polym. Chem., 2011, 49, 1219–1227 CrossRef CAS.
- Y.-C. Yen, C.-C. Cheng, Y.-L. Chu and F.-C. Chang, Polym. Chem., 2011, 2, 1648–1653 RSC.
- A. Van, K. Chiou and H. Ishida, Polymer, 2014, 55, 1443–1451 CrossRef CAS.
- T. Agag and T. Takeichi, Macromolecules, 2003, 36, 6010–6017 CrossRef CAS.
- H. Oie, A. Sudo and T. Endo, J. Polym. Sci., Part A: Polym. Chem., 2010, 48, 5357–5363 CrossRef CAS.
- T. Agag and T. Takeichi, Macromolecules, 2001, 34, 7257–7263 CrossRef CAS.
- B. Kiskan and Y. Yagci, J. Polym. Sci., Part A: Polym. Chem., 2007, 45, 1670–1676 CrossRef CAS.
- P. Froimowicz, C. Rodriguez Arza, S. Ohashi and H. Ishida, J. Polym. Sci., Part A: Polym. Chem., 2016, 54, 1428–1435 CrossRef CAS.
- C. W. Chang, C. H. Lin, H. T. Lin, H. J. Huang, K. Y. Hwang and A. P. Tu, Eur. Polym. J., 2009, 45, 680–689 CrossRef CAS.
- L. Puchot, P. Verge, T. Fouquet, C. Vancaeyzeele, F. Vidal and Y. Habibi, Green Chem., 2016, 18, 3346–3353 RSC.
- B. Kiskan, B. Koz and Y. Yagci, J. Polym. Sci., Part A: Polym. Chem., 2009, 47, 6955–6961 CrossRef CAS.
- T. Agag, S. Geiger, S. M. Alhassan, S. Qutubuddin and H. Ishida, Macromolecules, 2010, 43, 7122–7127 CrossRef CAS.
- A. Chernykh, J. P. Liu and H. Ishida, Polymer, 2006, 47, 7664–7669 CrossRef CAS.
- T. Takeichi, T. Kano and T. Agag, Polymer, 2005, 46, 12172–12180 CrossRef CAS.
- B. Kiskan, Y. Yagci and H. Ishida, J. Polym. Sci., Part A: Polym. Chem., 2008, 46, 414–420 CrossRef CAS.
- B. Aydogan, D. Sureka, B. Kiskan and Y. Yagci, J. Polym. Sci., Part A: Polym. Chem., 2010, 48, 5156–5162 CrossRef CAS.
- Y.-C. Wu and S.-W. Kuo, Polymer, 2010, 51, 3948–3955 CrossRef CAS.
- C. Altinkok, B. Kiskan and Y. Yagci, J. Polym. Sci., Part A: Polym. Chem., 2011, 49, 2445–2450 CrossRef CAS.
- C. Sawaryn, K. Landfester and A. Taden, Macromolecules, 2011, 44, 5650–5658 CrossRef CAS.
- B. Kiskan, React. Funct. Polym., 2017 DOI:10.1016/j.reactfunctpolym.2017.06.009 , in press.
- S. Akay, B. Kayan, D. Kalderis, M. Arslan, Y. Yagci and B. Kiskan, J. Appl. Polym. Sci., 2017, 134, 45306–45317 CrossRef.
- M. Arslan, B. Kiskan and Y. Yagci, Macromolecules, 2016, 49, 767–773 CrossRef CAS.
- S.-W. Kuo, Y.-C. Wu, C.-F. Wang and K.-U. Jeong, J. Phys. Chem. C, 2009, 113, 20666–20673 CAS.
- M. Arslan, B. Kiskan and Y. Yagci, Sci. Rep., 2017, 7, 5207 CrossRef PubMed.
- M. Arslan, B. Kiskan and Y. Yagci, Macromolecules, 2015, 48, 1329–1334 CrossRef CAS.
- B. Kiskan and Y. Yagci, J. Polym. Sci., Part A: Polym. Chem., 2014, 52, 2911–2918 CrossRef CAS.
- O. S. Taskin, B. Kiskan and Y. Yagci, Macromolecules, 2013, 46, 8773–8778 CrossRef CAS.
- R. Sarawut, L. Montha, H. Kasinee, K. Pornnapa and D. Isala, Smart Mater. Struct., 2013, 22, 075033 CrossRef.
- C. Aydogan, B. Kiskan, S. O. Hacioglu, L. Toppare and Y. Yagci, RSC Adv., 2014, 4, 27545–27551 RSC.
- L.-C. Lin, H.-J. Yen, Y.-R. Kung, C.-M. Leu, T.-M. Lee and G.-S. Liou, J. Mater. Chem. C, 2014, 2, 7796–7803 RSC.
- H.-K. Shih, Y.-L. Chu, F.-C. Chang, C.-Y. Zhu and S.-W. Kuo, Polym. Chem., 2015, 6, 6227–6237 RSC.
- M. Arslan, B. Kiskan and Y. Yagci, Macromolecules, 2016, 49, 5026–5032 CrossRef CAS.
- K. D. Demir, B. Kiskan, B. Aydogan and Y. Yagci, React. Funct. Polym., 2013, 73, 346–359 CrossRef CAS.
- B. Hanbeyoglu, B. Kiskan and Y. Yagci, Macromolecules, 2013, 46, 8434–8440 CrossRef CAS.
- B. Kiskan, B. Aydogan and Y. Yagci, J. Polym. Sci., Part A: Polym. Chem., 2009, 47, 804–811 CrossRef CAS.
- B. Koz, B. Kiskan and Y. Yagci, Int. J. Mol. Sci., 2008, 9, 383–393 CrossRef CAS PubMed.
- B. Kiskan, Y. Yagci, E. Sahmethogilu and L. Toppare, J. Polym. Sci., Part A: Polym. Chem., 2007, 45, 999–1006 CrossRef CAS.
- M. Kukut, B. Kiskan and Y. Yagci, Des. Monomers Polym., 2009, 12, 167–176 CrossRef CAS.
- E. A. Brown and D. A. Rider, Macromolecules, 2017, 50, 6468–6481 CrossRef CAS.
- T. Agag and T. Takeichi, J. Polym. Sci., Part A: Polym. Chem., 2007, 45, 1878–1888 CrossRef CAS.
- H. Ishida and H. Y. Low, J. Appl. Polym. Sci., 1998, 69, 2559–2567 CrossRef CAS.
- C. H. Lin, S. L. Chang, T. Y. Shen, Y. S. Shih, H. T. Lin and C. F. Wang, Polym. Chem., 2012, 3, 935–945 RSC.
- L. Han, D. Iguchi, P. Gil, T. R. Heyl, V. M. Sedwick, C. R. Arza, S. Ohashi, D. J. Lacks and H. Ishida, J. Phys. Chem., 2017, 121, 6269–6282 CrossRef CAS PubMed.
- T. Takeichi, T. Kano, T. Agag, T. Kawauchi and N. Furukawa, J. Polym. Sci., Part A: Polym. Chem., 2010, 48, 5945–5952 CrossRef CAS.
- J. Sun, W. Wei, Y. Xu, J. Qu, X. Liu and T. Endo, RSC Adv., 2015, 5, 19048–19057 RSC.
|
This journal is © The Royal Society of Chemistry 2018 |
Click here to see how this site uses Cookies. View our privacy policy here.