DOI:
10.1039/C3RA47954D
(Paper)
RSC Adv., 2014,
4, 17787-17796
Biodiesel production, characterization, engine performance, and emission characteristics of Malaysian Alexandrian laurel oil
Received
24th December 2013
, Accepted 19th March 2014
First published on 24th March 2014
Abstract
Biodiesel is a green fuel produced from renewable resources. It is a clean-burning alternative fuel, which has drawn the attention of energy researchers for the last two decades. This paper presents an experimental investigation on Alexandrian laurel oil as a potential feedstock for biodiesel development. Biodiesel was produced using a two-step esterification–transesterification process. Analysis of the physicochemical properties of diesel–biodiesel blends precedes the performance and emission study using 10% and 20% blends (ALB10 and ALB20). A 55 kW, 2.5 L, four-cylinder indirect injection diesel engine was used to carry out tests under conditions of constant load and varying speed. Brake power decreased 0.36–0.76%, and brake-specific fuel consumption (BSFC) increased 2.42–3.20% for these blends. In general, the exhaust emission profile was much better compared to diesel except for NOx emission, which increased by 2.12–8.32% compared to diesel. Thus, from overall performance and emission characteristics, both the blends are prospective fuels for diesel engines.
1. Introduction
Energy consumption is increasing throughout the world due to progress in lifestyle and substantial population growth. The transportation sector is one of the top consumers of energy. Previously, the increasing need for energy in this sector was catered to with fossil fuels like coal, gasoline, or diesel. However, burning of fossil fuels in transport vehicles results in serious ecological changes, which include increase in global surface temperature (global warming), changes in rainfall patterns, and changes in the frequency of extreme weather events. Hence, the increasing scarcity of conventional fossil fuels and negative effects on climate have driven scientists worldwide to look for new alternatives.1 During the last few decades, researchers have discovered many renewable sources of energy. Biodiesel is one of the renewable sources of energy that can partially replace diesel, which is the main fuel for vehicles worldwide.2 Nowadays, diesel engines are used in power generators, construction vehicles and industrial activities rather than automobiles. Increasing prices of fossil fuels, their limited reserves and environmental concerns have boosted research on biodiesel fuels.
Biodiesel, which refers to the fatty acid alkyl esters (FAAEs), is derived from lipid substances originating from products such as vegetable oil, animal fats, waste greases, or recycled cooking oils.3,4 To produce biodiesel, vegetable oils from edible sources were treated as one of the potential feedstocks; however, due to criticism on the use of edible oil for fuel production, other sources, such as non-edible oils of plant origin or waste fats with high free fatty acid (FFA) content, are now being used for biodiesel production; moreover, researchers are identifying newer feedstocks for biodiesel production.5,6 Advantages of biodiesel over petroleum diesel include production from renewable feedstocks, superior lubricity and biodegradability, lower toxicity, higher flash point and cetane number (CN), ability to blend with petro-diesel in any proportion, adaptability in an engine without major modification, positive energy balance and reduced emissions of carbon monoxide (CO), total hydrocarbon (THC), particulate matter (PM) and polyaromatic hydrocarbons (PAH).7,8 Disadvantages include limited feedstock availability, inferior oxidative and storage stability, lower volumetric energy content, inferior cold flow properties, higher specific fuel consumption, and higher nitrogen oxide exhaust emissions.9,10
Alexandrian laurel (Calophyllum inophyllum) is a member of the Clusiaceae or Guttiferae (mangosteen) family, and it is commonly known as Penaga Laut in Malaysia.11 It is also known by names, such as Kamani, Honne, Polanga, Tamanu, and Pinnai, in other parts of the world. It is a medium-to-large sized ornamental evergreen tree that averages 8–20 m in height with a broad spreading crown of irregular branches.12 It grows along coastal areas and adjacent lowland forests, although it occasionally occurs inland at higher elevations. The fruit is a round, green drupe reaching 2–4 cm in diameter, and it has a single large seed. The kernels have very high oil content (75%). The oil is non-edible in nature and obtained by cold expression, which results in dark green oil with an aromatic odor and an insipid taste, which is used mainly for medicinal purposes. The annual yield of a mature tree is about 100 kg of seeds, which produce approximately 18 kg of oil.13 Alexandrian laurel is native to East Africa; South, Southeast and East Asia; Australia; and the South Pacific; however, it has now been widely planted throughout the tropics. Due to growing interest in non-edible oils with high free fatty acid content for biodiesel production, AL oil has drawn the attention of researchers in the last decade.
Thus far, very few studies are available on AL biodiesel, and among these, most of the articles deal with biodiesel production and its process optimization. Sahoo et al.14 developed biodiesel from polanga oil (acid value 44 mg KOH g−1) using a three-stage transesterification process to form this oil. The first stage removes the organic materials and other impurities in which the extracted oil reacts with 35% (v/v) methanol and 5% (v/v) toluene. Second stage transesterification reduces the acid value below 2 mg KOH g−1 in order to make the oil suitable for experiencing base-catalyzed transesterification. An optimized quantity of methanol with a molar ratio of 6
:
1 and 0.65% (v/v) of anhydrous sulphuric acid (98.4%) was used in this stage with a reaction time of 4 h. The product of the second stage was reacted with methanol (molar ratio of 9
:
1) and 1.5% potassium hydroxide (KOH) (w/w oil) with a reaction duration of 4 h that yielded maximum amount of esters from this stage. To study its suitability in diesel engines, Sahoo et al.14 employed different percentages of blends with diesel in a single-cylinder diesel engine and found that pure biodiesel is the best fuel for diesel engine operation as it provided lower BSFC, higher BTE, and lower HC and NOx emission compared to diesel operation. Later, Sahoo and Das15 experimentally optimized the reaction parameters of CI biodiesel production by measuring the acid values of the product. The optimized reaction parameters of the first stage are 35% (v/v) methanol, 0.5% (v/v) toluene, and 0.5% (v/v) ortho-phosphoric acid with a 66 °C reaction temperature and 2 h time period. For the second stage, the parameters are 12% (v/v) methanol, 0.65% (v/v) sulfuric acid (H2SO4) with a 55 °C reaction temperature and 4 h time period. For the third stage, the parameters are 7.5% (v/v) methanol and 9% (w/w) KOH with a 66 °C reaction temperature and 4 h time period.
For producing biodiesel, Venkanna and Venkataramana Reddy16 employed one-step acid-catalyzed esterification, one-step alkali-catalyzed transesterification and post-treatment washing. The post-treatment stage employed here was washing with methyl esters. However, the acid value of their oil was very low (only 4.76 mg KOH g−1) compared to that in other studies. To obtain the maximum conversion efficiency, they performed each process at different reaction parameters with 100 g of moisture-free CI oil (acid value 44). The optimum conversion was attained for the first stage with a 4
:
1 molar ratio of methanol and 0.5 mL anhydrous H2SO4 with a reaction time of 120 minutes at 60 °C. Optimal parameters for transesterification were an 8
:
1 molar ratio of methanol to 1.25% KOH (w/w) with a reaction time of 120 minutes at 60 °C. In their study, SathyaSelvabala et al.17 employed one-step esterification using phosphoric acid-modified β-zeolite as catalyst and one-step transesterification process using 1% KOH as catalyst for biodiesel production. They optimized the reaction parameters of the esterification step using central composite design and response surface methodology. The global solution for the optimization was the oil–methanol ratio of 0.33 (wt%) and a catalyst amount of 1% and temperature of 60 °C. They performed the experiments using these values and found that the acid value dropped from 44 mg KOH g−1 to 1.9 mg KOH g−1 with 93% conversion efficiency. Venkanna and Reddy18 studied the effect of different blends of honne oil with diesel on a single-cylinder diesel engine. They concluded that up to a 20% blend with diesel could be used in diesel engines without any adverse effect. Belagur and Chitimi19 presented different fuel properties of 10–90% blends of AL oil, which are related to combustion in diesel engines. They concluded that up to a 50% blend with diesel meets the fuel specification limits set by ASTM D6751-08 and can be used as a substitute for neat diesel for short-term application. Rahman et al.20 studied the effect of AL biodiesel blends on high idling conditions of a four-cylinder diesel engine. They found the lowest CO and HC emissions for the 20% blend with diesel in this range of operation. In another study, Venkanna and Venkataramana Reddy21 studied the effect of injector opening pressure of a single-cylinder diesel engine on engine performance and found that at 100% load, the increase in BSFC was 16.18% and the decrease in BTE was 4.11%. However, with an increase in pressure, at 100% load, emission is reduced. For CO, it was 65–80% and for smoke opacity (SO) it was 45–60%; in contrast, the opposite trend was observed in case of NOx. With increasing load and pressure, NOx emission was generally slightly higher in the case of biodiesel. Belagur and Chitimini22 studied the effect of variation of static injection timing (SIT) of a single-cylinder diesel engine on engine performance and emission and found that at 28 crank angle bTDC (original 23 crank angle bTDC) and 100% load condition, BSFC decreases and BTE increases. However, BSFC was still about 16% higher and BTE was 4% lower compared to original diesel operation. Therefore, according to the literature, most of the studies on engine performance and emission were carried out in single-cylinder diesel engines, necessitating an investigation of AL biodiesel (ALBD) and its blends on a turbocharged heavy-duty diesel engine.
The present study is an endeavor to produce biodiesel from AL oil of Malaysian origin using a one-stage esterification and one-stage transesterification processes as well as characterization of produced biodiesel and its blends with diesel. ASTM D7467 allows blending of biodiesel with diesel from 6% to 20% (B6–B20). B20 represents a good balance of cost, emissions, materials compatibility, and cold weather performance.23 Thus, applicability of ALBD blends, e.g. ALB10 and ALB20, in an unmodified IDI diesel engine is experimentally investigated, and then compared with diesel in this study.
2. Materials and method
2.1 Material
In this study, crude AL oil was purchased from local markets. Other chemicals such as methanol, potassium hydroxide (KOH) and anhydrous sodium sulfate (Na2SO4) were obtained from Friendemann Schmidt Chemicals, USA. All purchased chemicals such as methanol, sulfuric acid (H2SO4) were of analytical grade, and catalysts and antioxidants were of 99.5% purity.
2.2 Biodiesel production
Crude AL oil had a high free fatty acid content of 20%, i.e. acid value of 40 mg KOH g−1. Canakci and Van Gerpen24 mentioned that if the oil contains more than 1% FFA, which corresponds to an acid value of 2 mg KOH g−1, then it cannot undergo alkaline-catalyzed transesterification reaction; moreover, if the FFA level exceeds this amount, the formation of soap will inhibit the separation of the ester from the glycerin and reduce the ester conversion rate. However, Ramadhas et al.25 showed that, if the acid value of oil is less than 4, then it can undergo transesterification. In this study, as free fatty acid content was very high, biodiesel conversion using one-step alkaline transesterification was not possible and pretreatment was required. Among the available pretreatment methods, including steam distillation or extraction of alcohol and esterification by acid catalysts, esterification of FFA with methanol in the presence of acidic catalysts is the most commonly used method because of its simplicity and utilization of acid catalysts to convert FFAs into biodiesel.26 Thus, for producing biodiesel, an acid-catalyzed pretreatment process was carried out first.
2.2.1 Pre-treatment process (acid-catalyzed esterification). In this process, crude AL oil was placed with a 12
:
1 molar ratio of methanol and 1.5% v/v (of oil) H2SO4 in a “FAVORIT jacket reactor.” The temperature was maintained at 60 °C using a circulating water bath for 3 h, and the mixture was stirred at 1000 rpm using an “IKA Eurostar motor stirrer.” Afterwards, a separation time of 1 h was given to this mixture for the separation of the esterified product and catalyst layer. After separation, the lower layer was taken out to remove excess methanol and water using an “IKA RV10 Control” rotary evaporator. The yield of this step was about 98%.
2.2.2 Alkali-catalyzed transesterification process. Product of pretreatment was heated to 60 °C and placed for transesterification with a 6
:
1 molar ratio of methanol and 1% w/w (of oil) KOH in the same setup. The temperature was maintained for 2 h, and the mixture was stirred at 1200 rpm. Afterwards, a separation time of 12 h was given to this mixture for the separation of glycerin from methyl ester. Then, the lower layer containing impurities and glycerin was discarded.
2.2.3 Post-treatment process. The methyl ester was washed with distilled water to remove the impurities and glycerin. For this process, 50% (v/v) distilled water at 60 °C was added to the esters and the mixture was stirred gently. This process was repeated several times until the methyl ester became neutral. The opaque lower layer containing water and impurities was taken out. Then, methyl ester was distilled under vacuum distillation at 65 °C for 30 minutes using an “IKA RV10 Control” rotary evaporator to remove water and methanol. Finally, methyl ester was dried using anhydrous Na2SO4 for 3 h and filtered using a qualitative filter paper. Table 1 provides the list of equipment and their accuracies for crude oil and biodiesel characterization. The characteristics of crude oil and ALBD are given in Table 2. Saponification number (SN), iodine value (IV) and cetane number (CN) of the produced biodiesel were calculated using the eqn (1)–(3), respectively:27 |
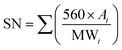 | (1) |
|
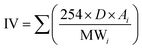 | (2) |
|
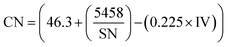 | (3) |
where Ai is the percentage of each component, D is the number of double bonds and MWi is the mass of each component. The molecular mass of each component is given in Table 4. The effects of blending of ALBD with diesel (B10 to B90) on different fuel properties such as kinematic viscosity, density, flash point and calorific value were examined and are presented in Fig. 1(a–d).
Table 1 List of equipment used in the characterization of fuelsa
Property |
Equipment |
Manufacturer |
Standard method |
ASTM D6751 limit |
Accuracy |
n.s. ≡ not specified in ASTM standard; min: minimum. |
Kinematic viscosity at 40 °C |
SVM 3000 – automatic |
Anton Paar, UK |
D 7042 |
1.9–6.0 |
±0.35% |
Dynamic viscosity at 40 °C |
SVM 3000 – automatic |
Anton Paar, UK |
D 7042 |
n.s. |
±0.35% |
Density at 40 °C |
SVM 3000 – automatic |
Anton Paar, UK |
D 7042 |
n.s. |
±0.1 kg m−3 |
Viscosity index |
SVM 3000 – automatic |
Anton Paar, UK |
|
n.s. |
|
Lower heating value |
C2000 basic calorimeter-automatic |
IKA, UK |
D 240 |
n.s. |
±0.1% |
Flash point |
Pensky-martens flash point – automatic NPM 440 |
Normalab, France |
D 93 |
130 (min) |
±0.1 °C |
Oxidation stability |
873 Rancimat – automatic |
Metrohm, Switzerland |
EN 14112 |
3 h (min) |
±0.01 h |
Cloud point |
Cloud and pour point tester – automatic NTE 450 |
Normalab, France |
D 2500 |
Report |
±0.1 °C |
Pour point |
Cloud and pour point tester – automatic NTE 450 |
Normalab, France |
D 97 |
|
±0.1 °C |
CFPP |
Cold filter plugging point – automatic NTL 450 |
Normalab, France |
D 6371 |
n.s. |
|
Acid value |
G-20 Rondolino automated titration system |
Mettler Toledo, Switzerland |
D 664 |
0.5 max |
±0.001 mg KOH g−1 |
Table 2 Physicochemical properties of crude oil, produced biodiesel and tested fuelsa
Property |
Units |
Crude AL oil |
ALBD |
PBDb |
JBDc |
ALB10 |
ALB20 |
ASTM D7467d |
Diesel |
n.s. ≡ not specified; PBD: Palm biodiesel; JBD: Jatropha biodiesel; min: minimum. Data obtained from ref. 28. Data obtained from ref. 28. Data obtained from ref. 23. |
Kinematic viscosity at 40 °C |
mm2 s−1 |
53.136 |
4.7128 |
4.6889 |
4.9476 |
3.1969 |
3.3538 |
1.9–4.1 |
3.0738 |
Dynamic viscosity at 40 °C |
m Pa s |
48.973 |
4.1470 |
4.0284 |
4.2758 |
2.7098 |
2.8695 |
n.s. |
2.5501 |
Density at 40 °C |
kg m−3 |
921.6 |
868.6 |
859.1 |
864.2 |
833.4 |
837.1 |
n.s |
829.6 |
Viscosity index |
|
159.2 |
174.7 |
203.6 |
194.6 |
132.7 |
133 |
n.s. |
152.6 |
Lower heating value |
MJ kg−1 |
38.511 |
39.389 |
40.009 |
39.738 |
44.656 |
44.111 |
n.s |
45.238 |
Flash point |
°C |
218.5 |
141.5 |
214.5 |
186.5 |
71.5 |
77.5 |
52 (min) |
69.5 |
Oxidation stability at 110 °C |
h |
3.28 |
6.01 |
23.56 |
4.84 |
25.65 |
18.73 |
6 (min) |
59.10 |
Cloud point |
°C |
8 |
10 |
12 |
10 |
8 |
8 |
Report |
8 |
Pour point |
°C |
8 |
8 |
15 |
10 |
4 |
4 |
n.s. |
7 |
Cold filter Plugging point |
°C |
27 |
8 |
12 |
10 |
8 |
8 |
n.s. |
8 |
Acid value |
mg KOH g−1 |
40 |
0.3 |
— |
— |
0.14 |
0.17 |
0.3 (max) |
|
Saponification number (SN) |
|
|
191.6 |
|
|
|
|
n.s. |
— |
Iodine value (IV) |
g I2/100 g |
|
82.1 |
|
|
|
|
|
— |
Cetane number (CN) |
|
|
56.3 |
|
|
|
|
40 (min) |
48 |
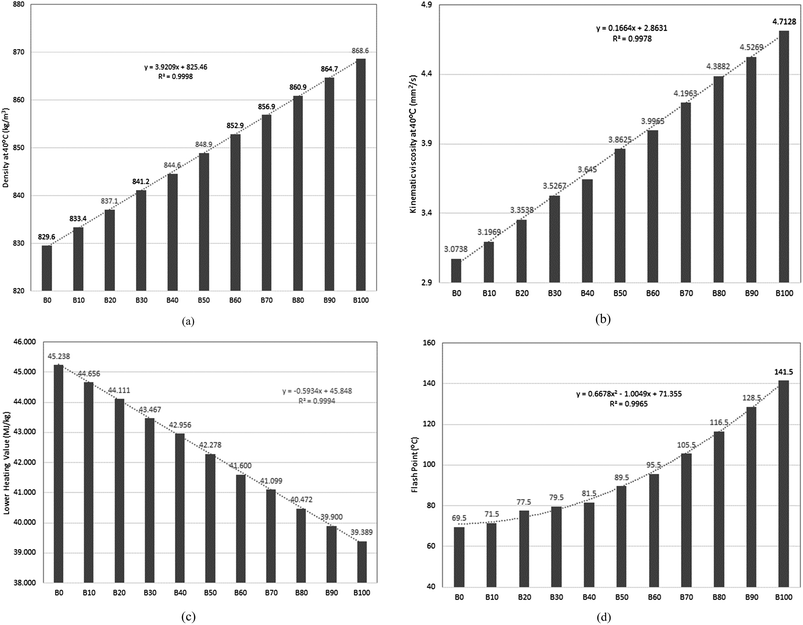 |
| Fig. 1 (a–d) Effect of biodiesel blending with diesel on physicochemical properties. | |
2.3 Fatty acid composition
The biodiesel sample was injected into a gas chromatograph (Agilent 7890 Series, USA) equipped with a flame ionization detector. Table 3 shows the GC operating conditions for fatty acid composition. Total ester content and methyl linolenate content was measured as per EN14103 standard. Monoglyceride content, diglyceride content, triglyceride content, free and total glycerin was measured as per EN 14105 standard. Table 4 shows the composition of produced biodiesel. It is found that ALBD contains 29.3% saturated methyl esters, 40.5% monounsaturated methyl esters and 25.8% polyunsaturated methyl ester.
Table 3 GC conditions for determination of fatty acid composition
Column |
0.32 mm × 30 m, 0.25 μm |
Injection volume |
1 μL |
Carrier gas |
Helium, 83 kPa |
Injector |
Split/splitless 1177, full EFC control |
Temperature |
250 °C |
Split flow |
100 mL min−1 |
Column 2 flow |
Helium at 1 mL min−1 constant flow |
Oven |
210 °C isothermal |
Column temperature |
60 °C for 2 min |
10 °C min−1 to 200 °C |
5 °C min−1 to 240 °C |
Hold 240 °C for 7 min |
Detector |
250 °C, FID, full EFC control |
Table 4 Fatty acid composition of ALBD
Fatty acid ester |
Structure |
Molecular mass |
Formula |
ALBD (% m m−1) |
Methyl palmitate |
16 : 0 |
270.45 |
CH3(CH2)14CO2CH3 |
13.9 |
Methyl palmitoleate |
16 : 1 |
268.43 |
CH3(CH2)5CH CH(CH2)7COOCH3 |
0.2 |
Methyl stearate |
18 : 0 |
298.50 |
CH3(CH2)16CO2CH3 |
15.1 |
Methyl oleate |
18 : 1 |
296.49 |
CH3(CH2)7CH CH(CH2)7CO2CH3 |
40.3 |
Methyl linoleate |
18 : 2 |
294.47 |
CH3(CH2)3(CH2CH CH)2(CH2)7CO2CH3 |
25.6 |
Methyl linolenate |
18 : 3 |
292.46 |
CH3(CH2CH CH)3(CH2)7COOCH3 |
0.2 |
Methyl arachidate |
20 : 0 |
326.56 |
CH3(CH2)18COOCH3 |
0.3 |
Total ester content |
|
|
|
95.6 |
Monoglyceride content |
|
|
|
0.32 |
Diglyceride content |
|
|
|
0.08 |
Triglyceride content |
|
|
|
0.12 |
Total glycerin |
|
|
|
0.109 |
Free glycerin |
|
|
|
0.003 |
2.4 Engine test
The experimental investigation was carried out in the Heat Engine Laboratory of the Mechanical Engineering Department, University of Malaya, on a turbocharged IDI four-cylinder diesel engine. The details of the engine are described in Table 5. The test engine was directly coupled to the Froude Hofman AG250 eddy current dynamometer. Fuel flow was measured using a Kobold ZOD positive-displacement type flow meter. Engine oil, cooling water, exhaust gas, and inlet air temperatures were measured using a K-type thermocouple. A REO-dCA Data Acquisition System collected the data. The engine fuel system was modified by adding separate tanks with two-way valves, which allowed for rapid switching of fuels. The exhaust gas composition CO, HC, and NOx emissions were measured by a gas analyzer (AVL DiCom4000). In this equipment, the CO and HC measuring instrument uses non-dispersive infrared (NDIR) detectors and the NOx analyzer uses an electrochemical method. Smoke opacity was measured by a continuous flow smoke meter (AVL DiSmoke 4000) working on the Hartridge principle.
Table 5 Detailed engine specifications
Description |
Specification |
No. and arrangement of cylinders |
4 in-line, longitudinal |
Rated power |
55 kW at 4200 rpm |
Combustion chamber |
Swirl chamber |
Total displacement |
2477 cc |
Cylinder bore × stroke |
91.1 × 95 mm |
Valve mechanism |
SOHC |
Compression ratio |
21 : 1 |
Valve timing |
IVO: 20°BTDC IVC: 49°ABDC |
EVO: 55°BBDC EVC: 22°ATDC |
Lubrication system |
Pressure feed, full flow filtration |
Fuel system |
Distributor type injection pump |
Air flow |
Turbocharged |
Fuel injection pressure |
157 bar |
Lift of plunger |
7°ATDC |
To carry out tests using biodiesel blends, the engine was run with diesel until a steady operating condition was achieved, and then the fuel was changed to biodiesel blend. After consumption of sufficient blend fuel, data acquisition was initiated to ensure the removal of residual diesel in the fuel line. After each test, the engine was again run with diesel to drain all of the blend fuel out of the fuel line, and this procedure was followed for all blends. The test fuels were diesel and 10% and 20% biodiesel in diesel (ALB10 and ALB20). The fuels were blended using a homogenizer device at a speed of 3000 rpm for 10 minutes. Table 2 shows some important characteristics of the tested fuels. The engine was operated between 1000 and 4500 rpm with a step of 500 rpm at 100% load condition. The performance and emission measurements were taken in triplicate. The results of each test were highly repeatable within that test series.
2.5 Accuracies and uncertainties
Uncertainties in the experiments can arise from instrument selection, experimental conditions, equipment calibration, ambient environment, observation, reading and test preparation; thus, uncertainty analysis is needed to establish the accuracy of the experiments. Uncertainty of measured quantities like torque, CO, HC, NOx and smoke were calculated using the uncertainties of various instruments used in the experiment. The relative uncertainty of calculated BSFC was determined using the linearized approximation method of uncertainty.29 Table 6 shows the accuracies and uncertainties of the measured and calculated parameters.
Table 6 The accuracies and uncertainties of the quantities
Measured qty |
Measuring range |
Accuracy |
Uncertainty |
Torque |
0–1200 Nm |
±3 Nm |
|
Fuel flow measurement |
0.5–36 l h−1 |
±0.089 l h−1 |
|
Speed |
0–6000 rpm |
±1 rpm |
|
Smoke opacity |
0–100% |
0.1% |
±0.5% |
CO |
0–10 vol% |
0.01 vol% |
±0.01 vol% |
HC |
0–20 000 ppm vol |
1 ppm vol |
±1 ppm |
NOx |
0–5000 ppm vol |
1 ppm vol |
±5 ppm |
|
Calculated results |
Power |
|
|
±0.1 kW |
BSFC |
|
|
±0.35 g kW−1 h−1 |
3. Results and discussion
3.1 Physicochemical properties of oil, biodiesel and its blends
The characteristic property of crude AL oil is its high free fatty acid content of 20%, i.e. acid value of 40 mg KOH g−1, which necessitates a pretreatment step before the transesterification step for biodiesel production. The crude oil has a very high kinematic viscosity (53.136 mm2 s−1) compared to other feedstocks such as palm oil (41.932 mm2 s−1), soybean oil (31.739 mm2 s−1), or canola oil (35.706 mm2 s−1).30 The kinematic viscosity of produced ALBD is 4.7128 mm2 s−1, which is 53.32% higher compared to diesel (3.0738 mm2 s−1). The mass energy content or lower heating value (LHV) of ALBD (39.389 MJ kg−1) is much less compared to diesel (45.238 MJ kg−1) due to its high oxygen content. The flash point is inversely related to fuel volatility. As ALBD contains mostly heavy constituents like methyl oleate and methyl linoleate (Table 4), its flash point is higher and meets the ASTM D6751 specification of 130 °C. The cetane number (CN) is a measure of a fuel's autoignition quality characteristic. Since ALBD has mostly unsaturated fatty acid esters (68.4%), it has a CN of 56.3, which meets the ASTM D6751 specification of CN ≥ 47. The oxidation stability improved after conversion of crude oil to biodiesel and met the ASTM D6751 specification. However, since its unsaturated ester content is high, it can quickly degrade and lose its oxidative stability.
Addition of biodiesel in diesel forms a non-separable liquid phase, which signifies biodiesel is dissolved in diesel at any proportion. As shown in Fig. 1(a) and (b), with an increasing percentage of biodiesel, density and kinematic viscosity increase linearly with coefficients of determination (R2) of 0.9998 and 0.9978, respectively. LHV decreases linearly with an R2 of 0.9994, and flash point increases in a second-degree polynomial nature with an R2 of 0.9965. From the graph, it is observed that ALB10 and ALB20 possess physicochemical properties similar to diesel fuel. Densities and kinematic viscosities of ALB10 are 833.4 and 3.1969 mm2 s−1, and those of B20 (837.1 kg m−3 and 3.3538 mm2 s−1) are 4% and 9.1% higher than those of diesel, respectively. The LHVs of ALB10 and ALB20 are 44.656 and 44.111 MJ kg−1, respectively, which are slightly less compared to the LHV of diesel (Fig. 1(c)). An increasing percentage of biodiesel results in an increasing percentage of oxygen in the fuel that reduces the number of carbon and hydrogen atoms present in the fuel. The flash points of the ALB10 and ALB20 blends are 71.5 °C and 77.5 °C, respectively (Fig. 1(d)). Thus, they meet the ASTM D7467 limit of 40 °C, which means they can be stored safely.
3.2 Engine performance characteristics
3.2.1 Brake power. The brake power outputs from the engine with different tested fuels are shown in Fig. 2. The maximum brake powers recorded at 4000 rpm for diesel, ALB10 and ALB20 were 48.5 kW, 48.3 kW and 48.2 kW, respectively. Thus, ALB10 and ALB20 showed 0.41% and 0.62% lower maximum power compared to diesel, respectively. This reduction can be attributed to its lower LHV and higher viscosity compared to diesel fuel.31 Higher kinematic viscosity results in higher resistance in the fuel line for pump line nozzle system as in the tested engine, which results in a greater delay in the start of injection,32 which also leads to poorer fuel atomization.33 Together with higher volumetric fuel consumption, these effects result in lower power output. Mofijur et al. reported about 4.67% and 8.86% average reductions in power with 10% and 20% Jatropha biodiesel blends, respectively.34 Furthermore, the average brake power reductions for ALB10 and ALB20 compared to diesel were 0.36% and 0.76%, respectively.
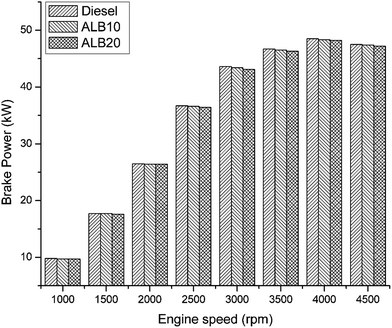 |
| Fig. 2 Variation of brake power for the test fuels with engine speed. | |
3.2.2 Brake-specific fuel consumption. Fig. 3 shows the variation of BSFC with engine speed for the test fuels. It is obvious from the figure that the BSFC of the engine was lowest at 2500 rpm, and then increased with increase in speed. The average values of BSFC for diesel, ALB10 and ALB20 were 300.49, 307.76 and 310.11 g kW−1 h−1, respectively; thus, ALB10 and ALB20 produced about 2.42% and 3.20% higher BSFC, respectively. Higher fuel consumption can be attributed to the volumetric effect of the constant fuel injection rate together with the higher viscosity and lower calorific value of biodiesel and its blends.35 The lower heating value is compensated through higher volumetric consumption of fuel to obtain the same power, higher viscosity (which reduces the back flow across the piston clearance of the injection pump) and higher lubricity of fuel (which also leads to friction loss reduction).36 With the increase in biodiesel content in the fuel, BSFC generally increases because a greater volume of fuel is consumed due to the higher density of the fuel.
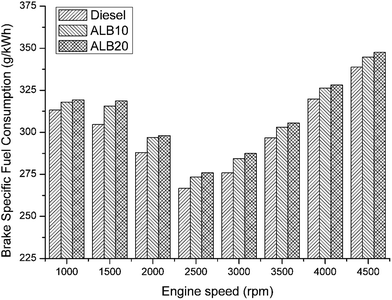 |
| Fig. 3 Variation of brake-specific fuel consumption (BSFC) for the test fuels with engine speed. | |
3.2.3 Brake thermal efficiency. The brake thermal efficiency is defined as the actual brake work per cycle divided by the amount of fuel chemical energy. The chemical energy input is the product of the injected fuel mass flow rate and the heating value. The comparison of brake thermal efficiency (BTE) with engine speed for different fuels is shown in Fig. 4. Thermal efficiency varies inversely with the product of BSFC and calorific value of the fuel. BTE is calculated using the following equation:
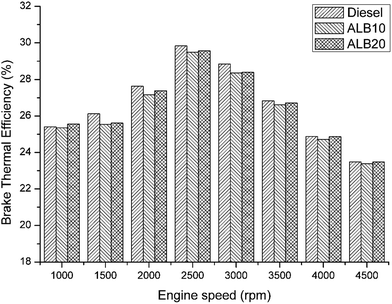 |
| Fig. 4 Variation of brake thermal efficiency (BTE) for the test fuels with engine speed. | |
The maximum BTEs calculated at 2500 rpm for diesel, ALB10 and ALB20 were 29.83%, 29.49% and 29.57%, respectively; thus, ALB10 and ALB20 showed 1.14% and 0.87% lower maximum BTEs compared to diesel, respectively. Lower efficiency can be attributed to higher BSFC with lower power output. This may be related to the atomization of the blends during injection and/or with the stability of the mixtures of fuels during storage, pumping and injection.37 The maximum BTE was observed at 2500 rpm.
3.3 Engine emission analysis
3.3.1 Nitrogen oxide emission. Fig. 5 illustrates the NOx emission from the test diesel engine for different test fuels. The thermal (Zeldovich), prompt (Fenimore), N2O pathway, fuel-bound nitrogen and NNH mechanism are the most common mechanisms for NOx formation in diesel combustion. NOx is the most deleterious pollutant and should be controlled at the combustion stage. It is well documented that factors, such as higher combustion temperature and longer combustion duration inside the combustion chamber or ample local oxygen concentration, are responsible for NOx formation.38 ALBD consists of higher molecular weight species, which burn in late combustion phases owing to poor atomization in the premixed region. Late phase combustion resulting in higher temperature together with oxygen content in the fuel results in the formation of greater amounts of NOx.39 The average NOx emissions for diesel, ALB10 and ALB20 were 10.778 g kW−1 h−1, 11.007 g kW−1 h−1 and 11.675 g kW−1 h−1, respectively. Thus, ALB10 and ALB20 resulted in 2.12% and 8.32% higher average NOx emission compared to diesel. This higher NOx emission compared to diesel can be validated from the literature.40,41
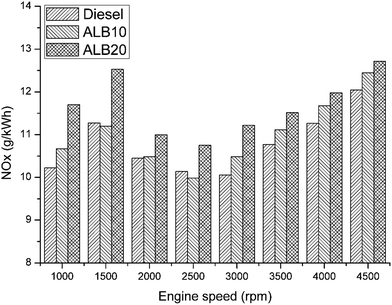 |
| Fig. 5 Variation of NOx emission for different test fuels with speed. | |
3.3.2 Carbon monoxide emission. CO is formed during combustion whenever charge is burned with an insufficient air supply and low flame temperature. The variation of CO emission as a function of engine speed with diesel, ALB10 and ALB20 is shown in Fig. 6. The average CO emissions for diesel, ALB10 and ALB20 over the entire speed range were 17.888 g kW−1 h−1, 15.184 g kW−1 h−1 and 13.086 g kW−1 h−1, respectively. Thus, average CO emission was reduced by 15.12% and 26.84% for ALB10 and ALB20, respectively. With increasing biodiesel percentage in the blend, the CO emission level decreases as the amount of oxygen content of biodiesel helps to achieve more complete combustion.42 Moreover, biodiesel possesses a slightly lower carbon/hydrogen (C/H) ratio than diesel fuel, which also assists in decreasing CO emissions.43
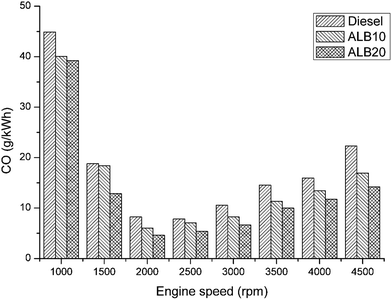 |
| Fig. 6 Variation of CO emission of different test fuels with speed. | |
3.3.3 Hydrocarbon emission. Two major causes for HC emission in diesel engine are as follows: (1) fuel mixed to leaner than the lean combustion limit during the delay period, and (2) undermixing of fuel that leaves the fuel injector nozzle late in the combustion process at low velocity. Fig. 7 shows the variation of HC emission at various speeds. The average HC emissions for diesel, ALB10 and ALB20 over the entire speed range were 0.270 g kW−1 h−1, 0.245 g kW−1 h−1 and 0.224 g kW−1 h−1, respectively. Thus, the average HC emission was reduced by 9.26% and 17.04% for ALB10 and ALB20, respectively. The oxygen content of biodiesel might have provided some advantageous conditions (such as post flame oxidation and higher flame speed) during air–fuel interactions, particularly in the fuel-rich regions, which enhanced the oxidation of unburned HC, thus reducing HC significantly.44
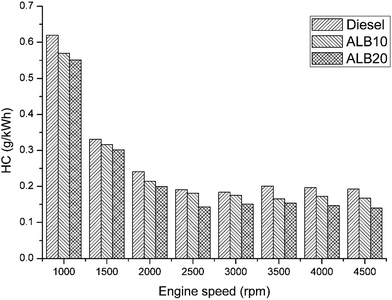 |
| Fig. 7 Variation of HC emission for different test fuels with speed. | |
3.3.4 Smoke opacity. Smoke opacity is indicative of dry soot emissions, which is one of the main components of particulate matter.45 Fig. 8 shows the exhaust smoke opacity of tested fuels. The average smoke opacities for diesel, ALB10 and ALB20 were 27.25%, 25.13% and 23.63%, respectively. Thus, an average reduction in smoke for ALB10 and ALB20 were 7.78% and 13.28% compared to diesel, respectively. The smoke opacity in all blends are well below the level of diesel. The lower smoke opacity can be explained by the reduction of probability of rich zone formation (high local fuel–air ratio) in the presence of fuel-borne oxygen and oxidation of soot nuclei during fuel combustion.46 This also explains ALB20 having a lower smoke opacity compared to ALB10.
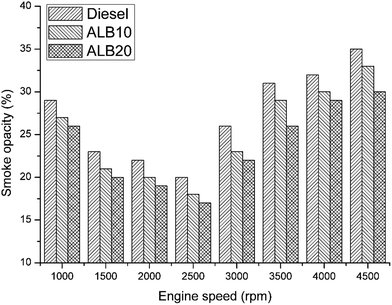 |
| Fig. 8 Variation in smoke opacity of different test fuels with speed. | |
4. Conclusions
Non-edible, high acid value Alexandrian laurel oil is a potential source for biodiesel production. In this study, biodiesel was obtained through one-step, acid-catalyzed esterification and a one-step, alkali-catalyzed transesterification step. Based on experimental observation, the following conclusions can be made:
• With an increase in the biodiesel content of the blend, density and kinematic viscosity increase linearly, calorific value decreases linearly and flash point increases in a second-degree polynomial nature.
• The average brake power reductions for ALB10 and ALB20 compared to diesel were 0.36% and 0.76%, respectively, due to their lower LHV and higher viscosity.
• ALB10 and ALB20 produced about 2.42% and 3.20% higher BSFC due to the volumetric effect of constant fuel injection rate together with higher viscosity and lower calorific value.
• Both ALB10 and ALB20 result in higher NOx emission (2.12–8.32%) because combustion mainly occurs in late combustion stage. Higher viscosity results in poor atomization, which hinders the fuel atomization and mixing in premixed combustion stage.
• CO and HC emission were reduced by 15.12–26.84% and 9.26–17.04% compared to those of diesel operation.
• Average smoke opacity reduction of smoke for ALB10 and ALB20 were 7.78% and 13.28% lower compared to diesel, respectively, due to the oxidation of soot nuclei by fuel borne oxygen.
Acknowledgements
The authors would like to thank University of Malaya for financial support through a High Impact Research grant titled: “Exhaust nanoparticles characterization from biodiesel fuelled internal combustion engine” with grant number RP016-2012E.
References
- B. M. Masum, H. H. Masjuki, M. A. Kalam, I. M. Rizwanul Fattah, S. M. Palash and M. J. Abedin, Renewable Sustainable Energy Rev., 2013, 24, 209–222 CrossRef CAS PubMed.
- M. H. Jayed, H. H. Masjuki, M. A. Kalam, T. M. I. Mahlia, M. Husnawan and A. M. Liaquat, Renewable Sustainable Energy Rev., 2011, 15, 220–235 CrossRef PubMed.
- A. Demirbas, Int. J. Green Energy, 2007, 4, 15–26 CrossRef CAS.
- I. M. Rizwanul Fattah, H. H. Masjuki, M. A. Kalam, M. Mofijur and M. J. Abedin, Energy Convers. Manage., 2014, 79, 265–272 CrossRef CAS PubMed.
- B. S. Chauhan, N. Kumar, H. M. Cho and H. C. Lim, Energy, 2013, 56, 1–7 CrossRef CAS PubMed.
- D.-V. Manh, Y.-H. Chen, C.-C. Chang, C.-Y. Chang, H.-D. Hanh, N.-H. Chau, T.-V. Tuyen, P.-Q. Long and C.-V. Minh, Energy, 2012, 48, 519–524 CrossRef CAS PubMed.
- I. M. Rizwanul Fattah, H. H. Masjuki, A. M. Liaquat, R. Ramli, M. A. Kalam and V. N. Riazuddin, Renewable Sustainable Energy Rev., 2013, 18, 552–567 CrossRef PubMed.
- L. A. H. Nogueira, Energy, 2011, 36, 3659–3666 CrossRef PubMed.
- M. Özcanlı, A. Keskin and K. Aydın, Int. J. Green Energy, 2011, 8, 518–528 CrossRef.
- M. S. Graboski and R. L. McCormick, Prog. Energy Combust. Sci., 1998, 24, 125–164 CrossRef CAS.
- H. C. Ong, T. M. I. Mahlia, H. H. Masjuki and R. S. Norhasyima, Renewable Sustainable Energy Rev., 2011, 15, 3501–3515 CrossRef CAS PubMed.
- J. Friday and D. Okano, Species Profiles for Pacific Island Agroforestry, 2006, vol. 2, pp. 1–17 Search PubMed.
- A. C. Dweck and T. Meadows, Int. J. Cosmet. Sci., 2002, 24, 1–8 CrossRef PubMed.
- P. K. Sahoo, L. M. Das, M. K. G. Babu and S. N. Naik, Fuel, 2007, 86, 448–454 CrossRef CAS PubMed.
- P. K. Sahoo and L. M. Das, Fuel, 2009, 88, 1588–1594 CrossRef CAS PubMed.
- B. K. Venkanna and C. Venkataramana Reddy, Bioresour. Technol., 2009, 100, 5122–5125 CrossRef CAS PubMed.
- V. SathyaSelvabala, D. K. Selvaraj, J. Kalimuthu, P. M. Periyaraman and S. Subramanian, Bioresour. Technol., 2011, 102, 1066–1072 CrossRef CAS PubMed.
- B. K. Venkanna and C. V. Reddy, Int. J. Green Energy, 2012 DOI:10.1080/15435075.2011.653850.
- V. K. Belagur and V. R. Chitimi, Fuel, 2013, 109, 356–361 CrossRef CAS PubMed.
- S. M. A. Rahman, H. H. Masjuki, M. A. Kalam, M. J. Abedin, A. Sanjid and H. Sajjad, Energy Convers. Manage., 2013, 76, 362–367 CrossRef CAS PubMed.
- B. Venkanna and C. Venkataramana Reddy, Environ. Prog. Sustainable Energy, 2013, 32, 148–155 CrossRef CAS.
- V. K. Belagur and V. R. Chitimini, Int. J. Ambient Energy, 2012, 33, 65–74 CrossRef CAS.
- National Renewable Energy Laboratory, Biodiesel Handling and Use Guide, Fourth Edition, NREL/TP-540-43672, 2009.
- M. Canakci and J. Van Gerpen, Trans. ASAE, 2001, 44, 1429–1436 CAS.
- A. S. Ramadhas, S. Jayaraj and C. Muraleedharan, Fuel, 2005, 84, 335–340 CrossRef CAS PubMed.
- M. Y. Koh and T. I. Mohd Ghazi, Renewable Sustainable Energy Rev., 2011, 15, 2240–2251 CrossRef CAS PubMed.
- P. K. Devan and N. V. Mahalakshmi, Fuel Process. Technol., 2009, 90, 513–519 CrossRef CAS PubMed.
- A. E. Atabani, T. M. I. Mahlia, H. H. Masjuki, I. A. Badruddin, H. W. Yussof, W. T. Chong and K. T. Lee, Energy, 2013, 58, 296–304 CrossRef CAS PubMed.
- M. Mofijur, H. H. Masjuki, M. A. Kalam, A. E. Atabani, I. M. R. Fattah and H. M. Mobarak, Industrial Crops and Products, 2014, 53, 78–84 CrossRef CAS PubMed.
- A. E. Atabani, T. M. I. Mahlia, I. Anjum Badruddin, H. H. Masjuki, W. T. Chong and K. T. Lee, Renewable Sustainable Energy Rev., 2013, 21, 749–755 CrossRef CAS PubMed.
- H. Aydin and H. Bayindir, Renewable Energy, 2010, 35, 588–592 CrossRef CAS PubMed.
- S. K. Hoekman, A. Broch, C. Robbins, E. Ceniceros and M. Natarajan, Renewable Sustainable Energy Rev., 2012, 16, 143–169 CrossRef CAS PubMed.
- C. Haşimoğlu, M. Ciniviz, İ. Özsert, Y. İçingür, A. Parlak and M. Sahir Salman, Renewable Energy, 2008, 33, 1709–1715 CrossRef PubMed.
- M. Mofijur, H. H. Masjuki, M. A. Kalam and A. E. Atabani, Energy, 2013, 55, 879–887 CrossRef CAS PubMed.
- F. Boudy and P. Seers, Energy Convers. Manage., 2009, 50, 2905–2912 CrossRef CAS PubMed.
- H. Hazar and H. Aydin, Appl. Energy, 2010, 87, 786–790 CrossRef CAS PubMed.
- S. Murillo, J. L. Míguez, J. Porteiro, E. Granada and J. C. Morán, Fuel, 2007, 86, 1765–1771 CrossRef CAS PubMed.
- S. M. Palash, M. A. Kalam, H. H. Masjuki, B. M. Masum, I. M. Rizwanul Fattah and M. Mofijur, Renewable Sustainable Energy Rev., 2013, 23, 473–490 CrossRef CAS PubMed.
- H. Sharon, K. Karuppasamy, D. R. Soban Kumar and A. Sundaresan, Renewable Energy, 2012, 47, 160–166 CrossRef CAS PubMed.
- E. Buyukkaya, S. Benli, S. Karaaslan and M. Guru, Energy Convers. Manage., 2013, 69, 41–48 CrossRef CAS PubMed.
- H. Serin and N. Y. Akar, Int. J. Green Energy, 2013, 11, 292–301 CrossRef.
- P. V. Bhale, N. V. Deshpande and S. B. Thombre, Renewable Energy, 2009, 34, 794–800 CrossRef CAS PubMed.
- M. Karabektas, Renewable Energy, 2009, 34, 989–993 CrossRef CAS PubMed.
- A. N. Ozsezen and M. Canakci, Energy Convers. Manage., 2011, 52, 108–116 CrossRef CAS PubMed.
- C. Sayin, Fuel, 2010, 89, 3410–3415 CrossRef CAS PubMed.
- L. M. Pickett and D. L. Siebers, Combust. Flame, 2004, 138, 114–135 CrossRef CAS PubMed.
|
This journal is © The Royal Society of Chemistry 2014 |