Inexpensive colloidal SnSb nanoalloys as efficient anode materials for lithium- and sodium-ion batteries†
Received
23rd December 2015
, Accepted 20th March 2016
First published on 21st March 2016
Abstract
The quest for higher energy densities of lithium-ion batteries (LIBs) and emerging sodium-ion analogues (SIBs) has motivated an intense research effort toward novel electrode materials. We report a simple and inexpensive colloidal synthesis of SnSb nanocrystals (NCs) and demonstrate their utility as lithium- and sodium-ion anode materials. In particular, SnSb NC Li-ion anodes deliver capacities of ∼890 mA h g−1 for 100 cycles at a current density of 200 mA g−1 and show excellent rate capability, reaching 90% and 80% of the theoretical capacity at current densities of 1000 and 5000 mA g−1, respectively. Similarly, SnSb NCs show also outstanding Na-ion storage properties with only ∼5% capacity loss over 100 cycles at a rate of 5000 mA g−1. Full-cells can be constructed with SnSb anodes and state-of-the-art cathodes, achieving anodic capacities of 600 and 400 mA h g−1 with an average discharge voltage of 3.0 and 2.7 V for lithium- and sodium-ions, respectively.
Introduction
Lithium-ion batteries (LIBs) with higher energy and power densities are actively sought to increase the competitiveness and widespread deployment of electric cars and stationary energy storage units, and for enabling new portable electronic devices.1,2 Great hopes have been extended to conceptually similar sodium-ion batteries (SIBs)3–5 due to the much greater natural abundance of Na and the possibility of replacing copper anode current collectors with aluminum foils. The eventual success of SIBs will require this technology to have the same energy density as LIBs.
The energy density of a battery is primarily determined by the charge storage capacity of the electrode materials and the overall voltage of the battery. In this regard, SIBs face a critical challenge: a lack of efficient anode materials. For instance, graphite, the commercialized anode material for LIBs, shows only negligible Na-ion capacity,6,7 causing a recent surge of research on Na-ion anode materials.8–25 Certain metals and metalloids that alloy with Na and Li are especially promising, such as Sb and Sn which both show 2–3 times higher gravimetric and volumetric energy densities than that of graphite (e.g., 992 mA h g−1 or ∼7300 mA h cm−3 for the reversible formation of Li4.4Sn). However, alloying leads to a much more intense reconstruction of the host material, as compared to intercalation. Such anode materials undergo massive volume changes of 120–300% upon lithiation (even greater for Na-ions), causing fast capacity fading due the formation of cracks, loss of electrical contact and eventual disintegration of the electrode. Nanostructuring of the electrode material has been demonstrated to efficiently mitigate the effects of mechanical stress on many systems.26–37 In this work, we focus on SnSb as a promising anode material and present a facile and inexpensive solution-based synthesis of nanocrystals (NCs) of this compound with a mean size of 10–30 nm, and demonstrate their efficient performance for Na-ion and Li-ion storage.
The choice of the SnSb system stems from several synergistic effects between Sn and Sb. First, both components of this alloy contribute to its high theoretical capacity of 824 mA h g−1:38
| SnSb + xLi+ + xe− → LixSnSb (x = 0–1.6) | (1) |
| Li1.6SnSb + 1.4Li+ + 1.4e− → Li3Sb + Sn | (2) |
| Sn + 4.4Li+ + 4.4e− → Li4.4Sn | (3) |
Similarly, the theoretical maximum capacity for Na-ion storage in SnSb is 752 mA h g−1 based on the formation of Na3Sb and Na3.75Sn; however, the exact mechanism of this reaction is not fully understood, except that it does not occur in analogy to Li and is not a mere combination of the separate processes taking place for Sb and Sn.39
Secondly, alloying/dealloying reactions of Sn and Sb occur at different potentials, which smoothens the mechanical stress somewhat. Finally, Sn and Sb are at least as inexpensive as common cathode materials comprising transition metals (e.g. Co and V). Notable examples of SnSb-based anode materials for both Li- and Na-ion storage are monodisperse SnSb NCs,40 SnSb–C nanofibers,32 CNT–Sn–Sb nanorods,41 and SnSb–C composites.18,42–44
A specific goal of this study was to develop a new synthesis route to SnSb NCs that is orders of magnitude cheaper than that in our previous study.40 That previous synthesis route involved the use of expensive, air-sensitive organic and coordination compounds (alkylamides as precursors, alkylamines as solvents, long-chain surfactants and reducing agents), as well as multiple steps of washing and removal of surface capping ligands, with a very low overall atomic economy.40 Here, we present a surfactant-free synthesis that is at least 1000 times cheaper, by utilizing metal chlorides as precursors and NaBH4 as a reducing agent, and which does not require any post-synthetic purification other than rinsing in water. We demonstrate that these SnSb NCs exhibit electrochemical performance which is the same as or better than that of the “expensive” NCs from the previous study.40 We also present results from full-cell experiments. Under anode-limiting operation, SnSb NCs retain Li-ion capacities of 600 mA h g−1 at an average voltage of 3.0 V when paired with a LiCoO2 cathode, and a Na-ion capacity of 400 mA h g−1 at an average voltage of 2.7 V when paired with a Na1.5VPO4.8F0.7 cathode.
Experimental
Synthesis of SnSb NCs
A solution of NaBH4 (32 mmol, 98%, ABCR) in anhydrous 1-methyl-2-pyrrolidone (NMP, 17 mL, 99.5%, Fisher BioReagents) was heated to 60 °C under nitrogen. Upon reaching 60 °C, a solution of SnCl2 (1 mmol, ≥99%, Alfa Aesar) dissolved in anhydrous NMP (1.5 mL) was injected, followed immediately by the injection of SbCl3 (1 mmol, 99%, ABCR) and cooling down to room temperature using a water-ice bath. The resulting black precipitate was separated from the solution by centrifugation and washed three times with water (30 mL) to remove side products such as NaCl or borates. After drying under vacuum at room temperature a fine black powder was obtained with a yield of ∼0.2 g (83%).
Synthesis of bulk SnSb
Micrometer-sized SnSb particles were synthesized by heating a mixture of Sn (1 mmol, 99.8%, Sigma-Aldrich) and Sb powder (1 mmol, 99.5%, Alfa Aesar) above their respective melting points to 700 °C under inert atmosphere. After 5 min at 700 °C the material was cooled naturally to room temperature and the resulting product was ground using a mortar and pestle.
Assembly and testing of half- and full-cells
The following battery components were used: carbon black (CB, Super C65, TIMCAL), carboxymethylcellulose (CMC, Grade: 2200, Daicel Fine Chem. Ltd.), NaClO4 (98%, Alfa Aesar, additionally dried), propylene carbonate (PC, BASF, battery grade), fluoroethylene carbonate (FEC, Solvay, battery grade), 1 M LiPF6 in a mixture of ethyl carbonate and dimethyl carbonate (EC
:
DMC, 1
:
1, Merck, battery grade), glass microfiber separator (GF/D, Whatman), and Cu foil (9 μm thick, MTI Corporation). SnSb-containing electrodes were prepared by mixing SnSb (NCs or bulk), CB and CMC (64%
:
21%
:
15%) with water using a Fritsch Pulverisette 7 classic planetary mill (500 rpm, 1 hour). The resulting slurries were coated onto Cu foil and dried at 80 °C for 12 h under vacuum. The final loading was ∼0.5 mg cm−2. Electrochemical measurements were conducted in airtight coin-type cells assembled in an Ar-filled glovebox (O2 < 0.1 ppm, H2O < 0.1 ppm). Elemental lithium and sodium were employed as both the reference and counter electrode in half-cells. LiCoO2 (MTI Corporation) coated onto Al foil was used as the Li-ion cathode for full-cells (the loading of active material was ∼20 mg cm−2). For Na-ion full-cell experiments, Na1.5VPO4.8F0.7 was prepared according to Park et al.45 as the cathode. Prior to electrode preparation, Na1.5VPO4.8F0.7 was carbon-coated by ball-milling with CB (20 wt%) and annealing at 450 °C for 12 h.46 Before the assembly of Na-ion full-cells, SnSb electrodes were charged/discharged for 5 cycles vs. elemental Na in the potential range of 0.005–2.0 V at a current of 200 mA g−1. As the electrolyte, 1 M LiPF6 in EC
:
DMC with 3% FEC was used for LIBs and 1 M NaClO4 in PC with 10% FEC was used for SIBs in this work. One layer of glass microfiber served as the separator in all cases. Galvanostatic cycling experiments were carried out at room temperature on an MPG2 multi-channel workstation (BioLogic). For Li-ion full-cell experiments, the batteries were cycled in the potential range of 2.0–3.9 V at a current of 400 mA g−1. Na-ion full-cell experiments were conducted within a limited charge and discharge capacity window of 400 mA h g−1, in the potential range of 1.5–4.3 V at a current density of 200 mA g−1. All capacities reported in this work correspond to the content of SnSb.
Materials characterization
Transmission electron microscopy (TEM) images were obtained using a Philips CM30 microscope operating at 300 kV using carbon-coated Cu grids as substrates (Ted-Pella). Powder X-ray diffraction (XRD) was performed on a STOE STADI P diffractometer (Cu-Kα1 irradiation). Scanning electron microscopy (SEM) and energy-dispersive X-ray spectroscopy (EDX) measurements were carried out using a NanoSEM 230 microscope.
Results and discussion
In the novel synthesis route to SnSb NCs (Fig. 1) developed herein, a solution of NaBH4 in 1-methyl-2-pyrrolidone (NMP) was heated under nitrogen to 60 °C, followed by the consecutive injections of SnCl2 and then SbCl3 dissolved in the same solvent. As in our previously reported “expensive” organometallic synthesis of SnSb NCs,40 Sb is introduced last to prevent the formation of Sb NCs. As seen in TEM images (Fig. 1b) the resulting SnSb NCs have a size distribution between 10 and 30 nm. XRD measurements confirm that the sole crystalline product is a cubic SnSb compound (space group Fm
m (225), a = 6.13 Å, COD entry 9008724), without any traces of Sn, Sb or their respective oxides (Fig. 1c). Notably, even for storage of eight months under ambient conditions no formation of crystalline oxides can be detected (Fig. S1†). Efficient removal of the main side product NaCl and potentially unreacted NaBH4, SnCl2 or SbCl3 is further evidenced by the absence of signals corresponding to sodium and chlorine in the energy dispersive X-ray (EDX) spectra of the purified SnSb NCs (Fig. S2†). Together, the use of inexpensive reagents, absence of surfactants, recycling of the solvent (NMP), high reaction yield and the non-essentiality of purification of the final product with organic solvents all lead to the low overall cost of this synthesis of ≤0.3 USD per gram of SnSb (which is essentially only the cost of the starting salts and reducing agent; see also Table S1†). In stark contrast to hydrothermal/solvothermal procedures,47,48 the synthesis presented herein is carried out at low temperatures, under ambient pressure and with short, sub-minute reaction times, ideal for up-scaling.
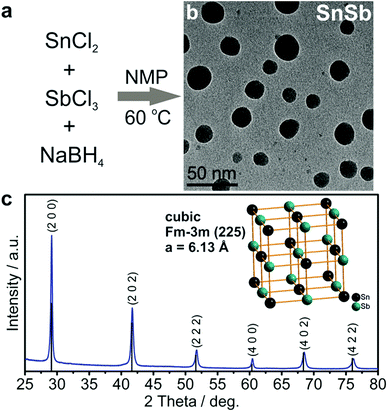 |
| Fig. 1 Synthesis and characterization of SnSb NCs. (a) Reaction scheme. (b) Transmission electron microscopy (TEM) image. (c) X-ray diffraction (XRD) pattern of SnSb NCs, indexed as cubic SnSb (COD entry 9008724). | |
Lithium- and sodium-ion half-cell tests
Half-cell experiments serve to shed initial light on the capacity, energy density and rate capability of the anodes investigated in this work (Fig. 2). Working electrodes were prepared by mixing the SnSb NCs with carbon black (CB) and carboxymethylcellulose (CMC) as a binder in water and coating the resulting slurry onto Cu foil (for Li- and Na-ion cells, respectively). In this regard, it should be noted that SnSb NCs retain their cubic structure after electrode preparation without the formation of crystalline oxides (Fig. S1†). Standard liquid electrolyte formulations were used: LiPF6 in EC:DMC for Li-ion and NaClO4 in PC for Na-ion cells. In both cases, FEC was added to the electrolyte because of its known beneficial effect on cycling stability due to the stabilization of the solid-electrolyte interface (SEI).49–52
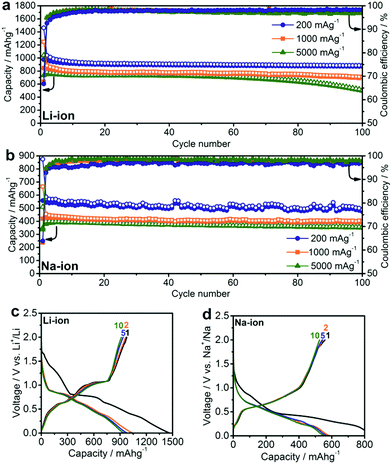 |
| Fig. 2 Electrochemical performance of SnSb NCs. Capacity retention of SnSb NCs in (a) Li-ion and (b) Na-ion half-cells at currents of 200, 1000 and 5000 mA g−1. Galvanostatic charge and discharge curves of SnSb NCs in (c) Li-ion and (d) Na-ion half-cells at a current of 200 mA g−1. All measurements were performed in the potential range of 0.005–2.0 V. | |
As is apparent in Fig. 2a, SnSb NCs deliver initial capacities close to the theoretical maximum at all tested current densities, with values of 980, 850 and 730 mA h g−1 at 200, 1000, and 5000 mA g−1, respectively, and retain 90%, 80% and 70% of these initial capacities after 100 cycles. The observation of capacities that are higher than the theoretical capacity (by up to 10%) may arise from a contribution by amorphous carbon of ∼100–200 mA h g−1 of carbon and also, possibly, due to reversible interfacial lithium storage mechanisms as previously reported for conversion-type materials53,54 or even reversible Li-ion storage by a polymeric gel-like layer formed by the electrolyte.55 A significant irreversible capacity is observed in the first few cycles, resulting in an initial coulombic efficiency of just 63–70% for both Li-ion and Na-ion cells. This irreversible capacity can be attributed to the formation of an SEI layer over the large surface area of the nanostructured electrode. During subsequent cycles, the coulombic efficiency rises to ∼97–98%, indicating that side reactions such as SEI reformation or electrolyte decomposition continue to occur, causing the remaining 2–3% deficit.
Despite only a minor difference in theoretical capacity between Na3Sb and Na3.75Sn, significantly lower capacities were observed for SnSb NC Na-ion anodes, as in previous reports.40,56 In particular, at currents of 200, 1000 and 5000 mA g−1, initial capacities of only 560, 420 and 380 mA h g−1 were obtained, respectively. However, contrary to Li-ion half-cells, a much higher fraction of the initial capacity was retained (∼90–95%) after 100 cycles at these current densities. This result is clearly an improvement over previous reports of Na-ion storage in SnSb (for a detailed comparison with existing literature reports, see Tables S2 and S3†).18,38,40–44,52,56–60 The small size of SnSb NCs enhances the kinetics of the charge/discharge reactions due to fast ionic and electronic transport, and also leads to improved cycling stability by more effectively accommodating the impact of volume changes during cycling.26,31 The importance of downsizing of the active material is further evidenced by comparison with electrochemical experiments using micrometer-sized SnSb particles, prepared by melting elemental Sn and Sb powders (Fig. S3†). Such bulk SnSb particles show much poorer capacity retention for both Li- and Na-ion half-cells (Fig. S4†), despite similar reaction mechanisms as indicated by the similarities of the charge/discharge curves (Fig. S5†). Notably, compared to monodisperse 20 nm particles,40 the herein presented SnSb NCs, show the same or even better electrochemical performance, indicating that narrow size distributions are not crucial for obtaining good electrochemical performance. Moreover, the absence of any surfactants during the reaction most likely leads to higher capacity levels compared to monodisperse 20 nm SnSb NCs, since the remaining insulating ligands on the surface can decrease the storage capacity. Apart from their high storage capacities, SnSb NCs show relatively low delithiation and desodiation potentials (Fig. 2c and d), making them highly attractive materials for full-cell applications. It should also be noted that for Li-ion storage the galvanostatic charge/discharge curves are essentially comprised of a combination of the features of the pure phase compounds (the delithiation of Sn occurring between 0.8 and 0.4 V and Sb at ∼1.1 V) whereas the alloying reaction of SnSb NCs with Na is clearly different.19 The same conclusion can be made from cyclic voltammetry measurements, which are fully consistent with previous reports on SnSb (Fig. 3).38,52
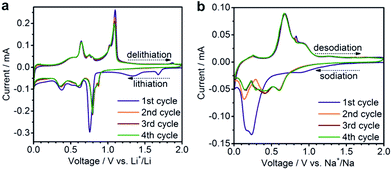 |
| Fig. 3 Cyclic voltammograms of SnSb NCs tested in (a) Li-ion or (b) Na-ion half-cells using a scan rate of 0.1 mV s−1 in the potential range of 0.005–2.0 V. | |
The reaction mechanism of SnSb with Na is not fully clarified due to difficulties to analyze the amorphous intermediates and products,61 whereas the reaction mechanism of Sb has been elucidated to proceed via the following steps (where c – crystalline, a – amorphous):62
| 1st sodiation: c-Sb → a-Na3−xSb + c-Na3−xSb → c-Na3−xSb | (4) |
| 1st desodiation: c-Na3−xSb → a-Na1.7Sb → a-Na1.0Sb → a-Na1.0Sb + c-Sb | (5) |
| 2nd sodiation: a-Na1.0Sb + c-Sb → a-Na1.7Sb + c-Sb → a-Na1.7Sb + a-Na3−xSb → a-Na3−xSb → c-Na3−xSb | (6) |
Transition through amorphous phases, helping in mitigating volumetric changes, has been hypothesized as one of the reasons for the relatively high cycling stability of Sb-based electrodes.62 In the case of Sn, the sodiation mechanism was proposed to take place according to the following sequence:63
| c-Sn → c-NaSn3 → a-NaSn → c-Na2.25Sn → c-Na3.75Sn | (7) |
However, it should be noted that this sequence was obtained at low current rates (C/50) with an additional potentiostatic step at 5 mV vs. Na+/Na. Under more practical cycling conditions, at higher rates, full sodiation of Sn to Na3.75Sn might in fact not occur,64 as supported by significantly lower capacities for Sn-based electrodes.65–67 Notably, in the case of SnSb electrodes Na3Sb could be crystallized at elevated temperatures, whereas Sn environments remain incompletely sodiated, as reported by Baggetto et al.61 Thus, the generally lower capacity of SnSb-based anodes for Na-ion storage compared to Li-ion storage40,56 – which is also observed for the herein presented SnSb NCs – might be attributed to not fully sodiated Sn-phases.
Lithium- and sodium-ion full-cell tests
To evaluate the practical utility of SnSb nanomaterials as anodes, Li- and Na-ion full-cells were assembled using standard cathode materials (Fig. 4). Anode-limited operation of a full-cell allows the assessment of the behavior of the anode under more practically relevant conditions. As in half-cell experiments, all specific currents and capacities correspond to the mass of the SnSb active material in the anode.
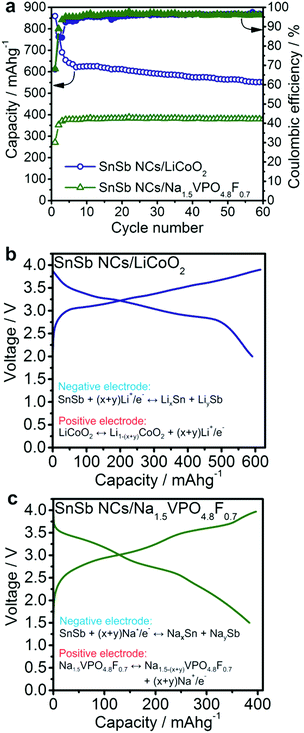 |
| Fig. 4 Electrochemical performance of SnSb NCs in lithium-ion and sodium ion full-cells using LiCoO2 and Na1.5VPO4.8F0.7 as the cathode materials, respectively. (a) Capacity retention of SnSb NCs at a current of 400 mA g−1 in Li-ion and at 200 mA g−1 in Na-ion full cells. Li-ion cells were cycled in the potential range of 2.0–3.9 V. Na-ion cells were cycled with a limitation of the charge and discharge capacity to 400 mA h g−1. Galvanostatic charge/discharge curves of the (b) Li-ion and (c) Na-ion full-cells, during the 30th cycle (see also Fig. S8†). The displayed specific capacities and currents correspond to the mass of SnSb NCs. | |
Li-ion full-cells were assembled using commercial LiCoO2 cathodes and then cycled in the potential range of 2.0–3.9 V with a current density of 400 mA g−1 (related to the anode). For at least 60 cycles, SnSb NCs deliver an average Li-ion storage capacity of 600 mA h g−1 (Fig. 4a) with an average discharge voltage of 3.0 V.
Na-ion full-cells were assembled using Na1.5VPO4.8F0.7 as the cathode, synthesized according to Park et al.45 and characterized by powder XRD (Fig. S6†). This cathode material exhibits high cycling stability and a high sodiation potential (∼3.8 V vs. Na+/Na, Fig. S7†).45 Prior to full-cell experiments, SnSb anodes were cycled vs. elemental Na at a current of 200 mA g−1 in the potential range of 0.005–2.0 V for 5 cycles in order to form a stable SEI layer and therefore minimize the charge loss during subsequent cycles. Both charge and discharge capacities were limited to 400 mA h g−1 within the potential range of 4.3–1.5 V and the cells were cycled at a current of 200 mA g−1. As can be seen in Fig. 4, the SnSb/Na1.5VPO4.8F0.7 Na-ion full-cell delivers a stable capacity of ∼400 mA h g−1 for at least 60 cycles, with an average discharge voltage of 2.7 V (Fig. S8†).
Based on the anodic capacities obtained for Li- and Na-ion full-cells and the theoretical capacities of the cathode materials (140 mA h g−1 for LiCoO2 and 129.7 mA h g−1 for Na1.5VPO4.8F0.7)45 the theoretical cell capacities can be estimated, using Ccell = CanodeCcathode/(Canode + Ccathode). This cell capacity multiplied by the average discharge voltage yields the theoretical energy density of the cell. In this way, the energy density of the SnSb/Na1.5VPO4.8F0.7 full-cell battery developed in this work compares favorably to other recently reported Na-ion full-cells.68–71 Similarly, the SnSb/LiCoO2 Li-ion full-cell exhibits an energy density of 340 W h kg−1, comparable to the graphite/LiCoO2 system. One possible advantage of SnSb over graphite lies in its three-fold higher density compared to graphite (6.9 g cm−3vs. 2.2 g cm−3, respectively). This potentially enables higher volumetric energy densities by up to 30%: 1796 W h L−1 for the SnSb/LiCoO2 full-cell compared to 1339 W h L−1 for graphite/LiCoO2, assuming a density of 5 g cm−3 for LiCoO2.72
Conclusions
In summary, we report an inexpensive and scalable synthesis of SnSb nanocrystals of 10–30 nm in size using metal chlorides as precursors and sodium borohydride as a reducing agent. The important advantages of this method over previous solution syntheses are its nearly quantitative reaction yield and its avoidance of the use of surfactants. The resulting NCs can thus be isolated simply by centrifugation or filtering, and purified by rinsing with water. Lithium-ion storage in such SnSb NCs is characterized by capacities close to the theoretical maximum, with an average value of 760 mA h g−1 for 100 cycles at a high current density of 1000 mA g−1. For sodium-ion storage, lower capacities are obtained, but with higher relative capacity retention upon cycling. The first results from Li-ion and Na-ion full-cell experiments, using LiCoO2 and Na1.5VPO4.8F0.7 as the cathodes, indicate stable cycling performance of SnSb NCs with specific Li- and Na-ion anodic capacities (average discharge voltage in parentheses) of 600 mA h g−1 (3.0 V) and 400 mA h g−1 (2.7 V), respectively.
Acknowledgements
This work was financially supported by the Swiss Federal Commission for Technology and Innovation (CTI, Project Nr. 14698.2 PFIW-IW), CTI Swiss Competence Centers for Energy Research (SCCER, “Heat and Electricity Storage”), ETH Zürich (Grant Nr. ETH-56 12-2), Competence Center for Energy and Mobility (CCEM, project SLIB) and by Belenos Clean Power Holding. Electron microscopy was performed at the Empa Electron Microscopy Center. We thank Dr Nicholas Stadie for reading the manuscript.
Notes and references
- R. Van Noorden, Nature, 2014, 507, 26–28 CrossRef CAS PubMed.
- D. Larcher and J. M. Tarascon, Nat. Chem., 2015, 7, 19–29 CrossRef CAS PubMed.
- V. Palomares, P. Serras, I. Villaluenga, K. B. Hueso, J. Carretero-Gonzalez and T. Rojo, Energy Environ. Sci., 2012, 5, 5884–5901 CAS.
- M. D. Slater, D. Kim, E. Lee and C. S. Johnson, Adv. Funct. Mater., 2013, 23, 947–958 CrossRef CAS.
- H. Pan, Y.-S. Hu and L. Chen, Energy Environ. Sci., 2013, 6, 2338–2360 CAS.
- P. Ge, Solid State Ionics, 1988, 28–30, 1172–1175 CrossRef.
- S. Komaba, Y. Matsuura, T. Ishikawa, N. Yabuuchi, W. Murata and S. Kuze, Electrochem. Commun., 2012, 21, 65–68 CrossRef CAS.
- Y. Wen, K. He, Y. Zhu, F. Han, Y. Xu, I. Matsuda, Y. Ishii, J. Cumings and C. Wang, Nat. Commun., 2014, 5, 4033 CAS.
- L. M. Wu, D. Buchholz, D. Bresser, L. G. Chagas and S. Passerini, J. Power Sources, 2014, 251, 379–385 CrossRef CAS.
- D. Y. Yu, P. V. Prikhodchenko, C. W. Mason, S. K. Batabyal, J. Gun, S. Sladkevich, A. G. Medvedev and O. Lev, Nat. Commun., 2013, 4, 2922 Search PubMed.
- Y. Wang, X. Yu, S. Xu, J. Bai, R. Xiao, Y. S. Hu, H. Li, X. Q. Yang, L. Chen and X. Huang, Nat. Commun., 2013, 4, 2365 Search PubMed.
- Y. Sun, L. Zhao, H. Pan, X. Lu, L. Gu, Y. S. Hu, H. Li, M. Armand, Y. Ikuhara, L. Chen and X. Huang, Nat. Commun., 2013, 4, 1870 CrossRef PubMed.
- Y. M. Lin, P. R. Abel, A. Gupta, J. B. Goodenough, A. Heller and C. B. Mullins, ACS Appl. Mater. Interfaces, 2013, 5, 8273–8277 CAS.
- J. Qian, X. Wu, Y. Cao, X. Ai and H. Yang, Angew. Chem., Int. Ed., 2013, 52, 4633–4636 CrossRef CAS PubMed.
- Y. Kim, Y. Park, A. Choi, N.-S. Choi, J. Kim, J. Lee, J. H. Ryu, S. M. Oh and K. T. Lee, Adv. Mater., 2013, 25, 3045–3049 CrossRef CAS PubMed.
- N. Yabuuchi, Y. Matsuura, T. Ishikawa, S. Kuze, J.-Y. Son, Y.-T. Cui, H. Oji and S. Komaba, ChemElectroChem, 2014, 1, 580–589 CrossRef.
- W.-J. Li, S.-L. Chou, J.-Z. Wang, H.-K. Liu and S.-X. Dou, Nano Lett., 2013, 13, 5480–5484 CrossRef CAS PubMed.
- L. Xiao, Y. Cao, J. Xiao, W. Wang, L. Kovarik, Z. Nie and J. Liu, Chem. Commun., 2012, 48, 3321–3323 RSC.
- A. Darwiche, M. T. Sougrati, B. Fraisse, L. Stievano and L. Monconduit, Electrochem. Commun., 2013, 32, 18–21 CrossRef CAS.
- Y. Zhu, X. Han, Y. Xu, Y. Liu, S. Zheng, K. Xu, L. Hu and C. Wang, ACS Nano, 2013, 7, 6378–6386 CrossRef CAS PubMed.
- X. Zhou, Z. Dai, J. Bao and Y.-G. Guo, J. Mater. Chem. A, 2013, 1, 13727–13731 CAS.
- D. H. Nam, K. S. Hong, S. J. Lim and H. S. Kwon, J. Power Sources, 2014, 247, 423–427 CrossRef CAS.
- L. Wu, X. Hu, J. Qian, F. Pei, F. Wu, R. Mao, X. Ai, H. Yang and Y. Cao, Energy Environ. Sci., 2014, 7, 323–328 CAS.
- B. Farbod, K. Cui, W. P. Kalisvaart, M. Kupsta, B. Zahiri, A. Kohandehghan, E. M. Lotfabad, Z. Li, E. J. Luber and D. Mitlin, ACS Nano, 2014, 8, 4415–4429 CrossRef CAS PubMed.
- C. Nithya and S. Gopukumar, J. Mater. Chem. A, 2014, 2, 10516–10525 CAS.
- P. G. Bruce, B. Scrosati and J.-M. Tarascon, Angew. Chem., Int. Ed., 2008, 47, 2930–2946 CrossRef CAS PubMed.
- M. R. Palacin, Chem. Soc. Rev., 2009, 38, 2565–2575 RSC.
- A. Magasinski, P. Dixon, B. Hertzberg, A. Kvit, J. Ayala and G. Yushin, Nat. Mater., 2010, 9, 353–358 CrossRef CAS PubMed.
- C. K. Chan, R. N. Patel, M. J. O'Connell, B. A. Korgel and Y. Cui, ACS Nano, 2010, 4, 1443–1450 CrossRef CAS PubMed.
- K. Kravchyk, L. Protesescu, M. I. Bodnarchuk, F. Krumeich, M. Yarema, M. Walter, C. Guntlin and M. V. Kovalenko, J. Am. Chem. Soc., 2013, 135, 4199–4202 CrossRef CAS PubMed.
- M. F. Oszajca, M. I. Bodnarchuk and M. V. Kovalenko, Chem. Mater., 2014, 26, 5422–5432 CrossRef CAS.
- N. Liu, Z. Lu, J. Zhao, M. T. McDowell, H.-W. Lee, W. Zhao and Y. Cui, Nat. Nanotechnol., 2014, 9, 187–192 CrossRef CAS PubMed.
- A. Jahel, C. M. Ghimbeu, L. Monconduit and C. Vix-Guterl, Adv. Energy Mater., 2014, 4, 1400025 Search PubMed.
- J. Liu, Y. Wen, P. A. van Aken, J. Maier and Y. Yu, Nano Lett., 2014, 14, 6387–6392 CrossRef CAS PubMed.
- H. Chen, C. Wang, W. Dong, W. Lu, Z. Du and L. Chen, Nano Lett., 2015, 15, 798–802 CrossRef CAS PubMed.
- M. Walter, R. Erni and M. V. Kovalenko, Sci. Rep., 2015, 5, 8418 CrossRef CAS PubMed.
- Y. Zhu, Y. Wen, X. Fan, T. Gao, F. Han, C. Luo, S.-C. Liou and C. Wang, ACS Nano, 2015, 9, 3254–3264 CrossRef CAS PubMed.
- S. Fan, T. Sun, X. Rui, Q. Yan and H. H. Hng, J. Power Sources, 2012, 201, 288–293 CrossRef CAS.
- A. Darwiche, M. T. Sougrati, B. Fraisse, L. Stievano and L. Monconduit, Electrochem. Commun., 2013, 32, 18–21 CrossRef CAS.
- M. He, M. Walter, K. V. Kravchyk, R. Erni, R. Widmer and M. V. Kovalenko, Nanoscale, 2015, 7, 455–459 RSC.
- Y. Wang and J. Y. Lee, Angew. Chem., Int. Ed., 2006, 45, 7039–7042 CrossRef CAS PubMed.
- L. Fan, J. Zhang, Y. Zhu, X. Zhu, J. Liang, L. Wang and Y. Qian, RSC Adv., 2014, 4, 62301–62307 RSC.
- D. Sun, B. An, B. Zhang, Q. Ru, X. Hou and S. Hu, J. Solid State Electrochem., 2014, 18, 2573–2579 CrossRef CAS.
- J. Li, Q. Ru, S. Hu, D. Sun, B. Zhang and X. Hou, Electrochim. Acta, 2013, 113, 505–513 CrossRef CAS.
- Y.-U. Park, D.-H. Seo, H.-S. Kwon, B. Kim, J. Kim, H. Kim, I. Kim, H.-I. Yoo and K. Kang, J. Am. Chem. Soc., 2013, 135, 13870–13878 CrossRef CAS PubMed.
- Y.-U. Park, D.-H. Seo, B. Kim, K.-P. Hong, H. Kim, S. Lee, R. A. Shakoor, K. Miyasaka, J.-M. Tarascon and K. Kang, Sci. Rep., 2012, 2, 704 Search PubMed.
- J. Xie, W. Song, Y. Zheng, S. Liu, T. Zhu, G. Cao and X. Zhao, Int. J. Smart Nano Mater., 2011, 2, 261–271 CAS.
- L. Li, K. Seng, D. Li, Y. Xia, H. Liu and Z. Guo, Nano Res., 2014, 7, 1466–1476 CrossRef CAS.
- V. Etacheri, O. Haik, Y. Goffer, G. A. Roberts, I. C. Stefan, R. Fasching and D. Aurbach, Langmuir, 2011, 28, 965–976 CrossRef PubMed.
- S. Komaba, T. Ishikawa, N. Yabuuchi, W. Murata, A. Ito and Y. Ohsawa, ACS Appl. Mater. Interfaces, 2011, 3, 4165–4168 CAS.
- A. M. Chockla, K. C. Klavetter, C. B. Mullins and B. A. Korgel, Chem. Mater., 2012, 24, 3738–3745 CrossRef CAS.
- L. Ji, M. Gu, Y. Shao, X. Li, M. H. Engelhard, B. W. Arey, W. Wang, Z. Nie, J. Xiao, C. Wang, J.-G. Zhang and J. Liu, Adv. Mater., 2014, 26, 2901–2908 CrossRef CAS PubMed.
- Y. F. Zhukovskii, P. Balaya, E. A. Kotomin and J. Maier, Phys. Rev. Lett., 2006, 96, 058302 CrossRef PubMed.
- Y.-Y. Hu, Z. Liu, K.-W. Nam, O. J. Borkiewicz, J. Cheng, X. Hua, M. T. Dunstan, X. Yu, K. M. Wiaderek, L.-S. Du, K. W. Chapman, P. J. Chupas, X.-Q. Yang and C. P. Grey, Nat. Mater., 2013, 12, 1130–1136 CrossRef CAS PubMed.
- S. Laruelle, S. Grugeon, P. Poizot, M. Dollé, L. Dupont and J.-M. Tarascon, J. Electrochem. Soc., 2002, 149, A627–A634 CrossRef CAS.
- J.-C. Kim and D.-W. Kim, Electrochem. Commun., 2014, 46, 124–127 CrossRef CAS.
- M.-S. Park, S. A. Needham, G.-X. Wang, Y.-M. Kang, J.-S. Park, S.-X. Dou and H.-K. Liu, Chem. Mater., 2007, 19, 2406–2410 CrossRef CAS.
- S. Chen, P. Chen, M. Wu, D. Pan and Y. Wang, Electrochem. Commun., 2010, 12, 1302–1306 CrossRef CAS.
- R. Yang, J. Huang, W. Zhao, W. Lai, X. Zhang, J. Zheng and X. Li, J. Power Sources, 2010, 195, 6811–6816 CrossRef CAS.
- X. Niu, H. Zhou, Z. Li, X. Shan and X. Xia, J. Alloys Compd., 2015, 620, 308–314 CrossRef CAS.
- L. Baggetto, H.-Y. Hah, J.-C. Jumas, C. E. Johnson, J. A. Johnson, J. K. Keum, C. A. Bridges and G. M. Veith, J. Power Sources, 2014, 267, 329–336 CrossRef CAS.
- P. K. Allan, J. M. Griffin, A. Darwiche, O. J. Borkiewicz, K. M. Wiaderek, K. W. Chapman, A. J. Morris, P. J. Chupas, L. Monconduit and C. P. Grey, J. Am. Chem. Soc., 2016, 138, 2352–2365 CrossRef CAS PubMed.
- L. D. Ellis, T. D. Hatchard and M. N. Obrovac, J. Electrochem. Soc., 2012, 159, A1801–A1805 CrossRef CAS.
- Z. Li, J. Ding and D. Mitlin, Acc. Chem. Res., 2015, 48, 1657–1665 CrossRef CAS PubMed.
- M. K. Datta, R. Epur, P. Saha, K. Kadakia, S. K. Park and P. N. Kumta, J. Power Sources, 2013, 225, 316–322 CrossRef CAS.
- Y. Xu, Y. Zhu, Y. Liu and C. Wang, Adv. Energy Mater., 2013, 3, 128–133 CrossRef CAS.
- H. Zhu, Z. Jia, Y. Chen, N. Weadock, J. Wan, O. Vaaland, X. Han, T. Li and L. Hu, Nano Lett., 2013, 13, 3093–3100 CrossRef CAS PubMed.
- P. R. Kumar, Y. H. Jung, K. K. Bharathi, C. H. Lim and D. K. Kim, Electrochim. Acta, 2014, 146, 503–510 CrossRef CAS.
- S.-M. Oh, S.-T. Myung, C. S. Yoon, J. Lu, J. Hassoun, B. Scrosati, K. Amine and Y.-K. Sun, Nano Lett., 2014, 14, 1620–1626 CrossRef CAS PubMed.
- S. Guo, H. Yu, P. Liu, Y. Ren, T. Zhang, M. Chen, M. Ishida and H. Zhou, Energy Environ. Sci., 2015, 8, 1237–1244 CAS.
- J. Ming, H. Ming, W. Yang, W.-J. Kwak, J.-B. Park, J. Zheng and Y.-K. Sun, RSC Adv., 2015, 5, 8793–8800 RSC.
- Y.-C. Lu, B. M. Gallant, D. G. Kwabi, J. R. Harding, R. R. Mitchell, M. S. Whittingham and Y. Shao-Horn, Energy Environ. Sci., 2013, 6, 750–768 CAS.
Footnote |
† Electronic supplementary information (ESI) available. See DOI: 10.1039/c5ta10568d |
|
This journal is © The Royal Society of Chemistry 2016 |
Click here to see how this site uses Cookies. View our privacy policy here.