DOI:
10.1039/D3YA00631J
(Review Article)
Energy Adv., 2024,
3, 1869-1893
Challenges and opportunities using Ni-rich layered oxide cathodes in Li-ion rechargeable batteries: the case of nickel cobalt manganese oxides
Received
27th December 2023
, Accepted 19th June 2024
First published on 10th July 2024
Abstract
This review provides an overview of recent advances in the utilization of Ni-rich nickel–cobalt–manganese (NCM) oxides as cathode materials for Li-ion rechargeable batteries (LIBs). In the past decade, Ni-rich NCM cathodes have been extensively investigated because of their rational capacity and easy accessibility of constituent elements. However, huge capacity fading and irreversible structural disorder, associated with oxygen release, are the major limitations which hinder the desired electrochemical performance of these cathodes. The LIB performance can be improved through several strategies such as doping, coating, composite formation, microstructure manipulation and replacing the Mn ions. Attempts are also made to amend the crystal orientation and achieve additive-induced surface engineering of NCM cathodes. However, the practical application of high-performance LIBs demand an effective modification of the intrinsic properties of NCMs. Substandard thermal stability is another safety aspect to be resolved in the Ni-rich NCMs. However, efforts in this context are not enough. Apart from designing NCM cathodes, there are major issues such as cost-effectiveness, supply and demand for constituent elements, and the reuse of spent batteries, which hinder the realisation of LIBs with high electrochemical performance. Keeping in mind the current research interests, this review article presents concise and in-depth strategies to design NCM cathodes for future energy demands of mankind by considering the cost and Co abundance-related issues.
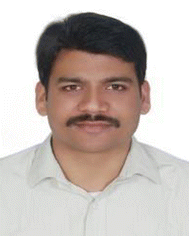
Jitendra Pal Singh
| Jitendra Pal Singh is currently working at Manav Rachna University as a Ramanujan Fellow. He received PhD from Govind Ballabh Pant University of Agriculture and Technology, Pantnagar, Uttarakhand, in 2010. He worked as Research Associate at Inter-University Accelerator Centre, New Delhi, during the period 2010–2011 and as a post-doc researcher at Taiwan SPIN Research Centre, National Chung Cheng University, Taiwan, for a brief period during 2011–2012. He was Assistant Professor at Krishna Engineering College, Ghaziabad, India, from 2012 to 2014. In 2014, he joined the Korea Institute of Science and Technology, Korea. He moved to Pohang Accelerator Laboratory, Pohang, South Korea, and worked there from December 2018 to May 2022. His research interests include irradiation studies in nanoferrites, thin films, magnetic multilayers, biomaterials and cathode materials. He has expertise in X-ray absorption spectroscopy and hard X-ray imaging. Dr Singh is a member of the Magnetics Society of India, Indian Physics Association, and Ion Beam Society of India. |
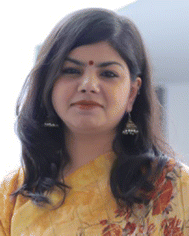
Harsha Devnani
| Harsha Devnani earned her PhD in Chemistry from Dayalbagh Educational Institute, Agra (India), in 2017. She has worked as a research associate at IOCL, R&D Centre, Faridabad (2018), and at IIT Delhi (2018–2019). She is currently Assistant Professor at the Department of Sciences, Manav Rachna University, Faridabad (India). She is also associated with the University Instrumentation Centre at ManavRachna University. She has worked as Assistant Professor at Lingaya's University, Faridabad (2019–2020). Her research interests include electrochemistry and materials chemistry with applications in sensors, energy storage and catalysis. |
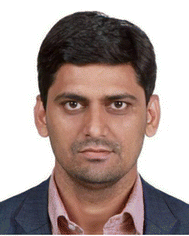
Aditya Sharma
| Aditya Sharma is currently working as an Associate Professor in Physics, UPES, Dehradun. He has been a Post Doctoral Research Fellow in the Spectro-Nano-Scopy group at Pohang Accelerator (synchrotron) Laboratory (PAL), South Korea and also functioned as a Visiting Research Scientist in the X-ray division of Korea Institute of Science and Technology (KIST) South Korea. Dr Sharma's current research endeavors revolve around energy harvesting and conversion through developing up-conversion persistent luminescent nanomaterials, photo/electro catalysts, battery/super-capacitor materials and solar-cell devices. |
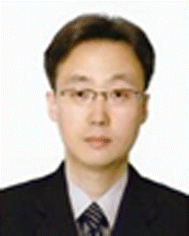
Weon Cheol Lim
| Weon Cheol Lim received PhD in advanced materials engineering from Korea University in 2023. As a senior research scientist at the Korea Institute of Science and Technology, he is studying material modification via ion implantation using a wide variety of ion beams, and he uses ion irradiation to test the reliability of materials and devices used in high-radiation environments such as space and nuclear fusion and fission reactor materials. He currently runs 0.4/2.0/6.0 MV accelerators at KIST. |
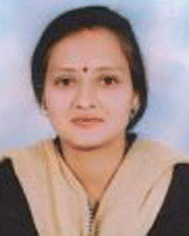
Archana Dhyani
| Archana Dhyani has received her PhD in physics from G.B. Pant University of Agriculture and Technology, Pantnagar, India in 2009. She is Assistant Professor at the Shri Guru Ram Rai University, Dehradun, India. She has also been associated with the University of Petroleum and Energy Studies (UPES), Dehradun, India, 2012–23, as Assistant Professor. She has authored several publications, including articles in reputed journals, edited books, chapters in standard books, etc. She has also been an external expert member for the National Science Center, Poland, and life-time member of the Indian Physics Association (IPA). Her current research interest is to study the spectral and transport properties of quantum dot–based nano-junctions for their various applications. |
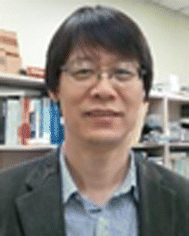
Keun Hwa Chae
| Keun Hwa Chae received his BSc degree in Physics in 1986 and MSc degree in Physics in 1988 from Yonsei University, Seoul, Korea. In 1994, he received his PhD in Physics from Yonsei University, Seoul, Korea. He was a postdoctoral fellow from 1995 to 1997 at Rutgers-The State University of New Jersey, USA. His research fields are ion beam modification of materials and characterization of materials using synchrotron radiation. He has been working as a principal research scientist in the Korea Institute of Science and Technology, Korea, since 2000. |
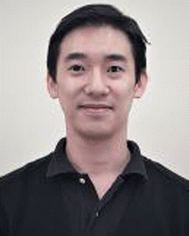
Sangsul Lee
| Sangsul Lee is Senior Scientist at the Pohang Accelerator Laboratory (PAL) and Affiliate Professor in the Department of Semiconductor Engineering at POSTECH. He has actively pursued research in soft X-ray, EUV and hard X-ray analysis methods for approximately 20 years. Since 2020, he has been leading a compact EUV synchrotron and metrology project at PAL, with a focus on establishing soft X-ray-dedicated material and component testing infrastructure, as well as developing evaluation techniques. |
Introduction
Rechargeable batteries have emerged as an alternative to fulfill the future energy demands of society.1–3 In the past 15 years, the use of rechargeable batteries for mobile and other portable electronic devices has been well established.4,5 Their role in the utilization of electrical vehicles (EVs)6–9 together with other high-energy applications such as grid-scale storage systems10,11 needs to be proven. Despite their higher cost and unsafe nature compared to internal combustion engines (ICEs),11 rechargeable batteries are getting optimized in terms of energy capacity, safety and cost-effectiveness before their practical applications.12,13 Hence, extensive research efforts have been made to develop rechargeable batteries with higher energy density, reversibility14,15 and cycling efficiency16,17 to compete with the existing ICEs.
Numerous rechargeable batteries are designed for fulfilling the required parameters of high electrochemical performance.18 Some of these batteries, which have drawn significant attention, are Pb-acid,19 aqueous rechargeable,20 Mg-ion,21 Ca-ion,22 K-ion23 and Al-ion batteries.24 Various parameters such as specific energy, energy density, charging/discharging efficiency and life of several batteries are collated in Table 1.25–28 The comparative analysis presented in Table 2 conveys the superiority of Li-ion batteries (LIBs) over other rechargeable batteries. Thus, LIBs show potential to compete with ICEs in terms of performance.29,30 Work done to date has depicted an advancement in battery parameters for better functionality by engineering cathode31–35 and anode36–39 properties. Thus, LIBs are classified into different categories with regard to the nature of their components such as cathodes, anodes and electrolytes.40,41Table 3 summarizes the various types of LIBs based on these components.42–59 Among these, LIBs based on NCM, commonly termed as NCM batteries, have received considerable attention in recent years because of their high lithium diffusion coefficient.60,61 Thus, NCM batteries, especially those with excess Ni contents (Ni-rich),62–64 received great attention for scientific research to make their commercialization successful. This is reflected in the recent reviews on various aspects of NCM cathodes such as commercialization,65 electrochemical performance,66–68 cost-effectiveness,69 and recovery70 independently. Though these reviews provide authenticated and independent analyses of these aspects, there is lack of a comprehensive review combining all aspects at one place. Thus, this review is an attempt to fill this gap, by combining most of the challenges associated with NCM cathodes in a concrete and concise manner by providing an understanding of the layered structure and Li-migration in NCM materials.
Table 1 Characteristic parameters of various rechargeable batteries. Values of different parameters are adopted from the description available at https://circuitdigest.com/article/different-types-of-batteries
Battery |
Characteristic parameters |
Specific energy (W h kg−1) |
Energy density (W h L−1) |
Specific power (W kg−1) |
Charge/discharge efficiency (%) |
Self-discharge rate (% month) |
Life (cycles) |
Ni–Cd25 |
40–60 |
50–150 |
150 |
70–90 |
10 |
2000 |
Ni–MH26 |
60–120 |
140–300 |
250–1000 |
66–92 |
1.3–2.9 |
180–2000 |
Li-ion27 |
265 |
693 |
340 |
80–90 |
— |
1200 |
Zn-ion28 |
250 |
450 |
— |
80 |
— |
1000 |
Table 2 General components of electric batteries. Permission obtained from C Iclodean et al., IOP Conf. Ser.: Mater. Sci. Eng.252 (2017) 012058
Name |
Value for battery type |
Unit |
Li-ion |
Na–NiCl2 |
Ni–MH |
Li–S |
Maximum charge |
75 |
84 |
85 |
80 |
A h |
Nominal voltage |
323 |
289 |
288 |
305 |
V |
Stored energy |
24.2 |
24.2 |
24.2 |
24.2 |
kW h |
Maximum/minimum voltage |
339/308 |
275/304 |
274/302 |
290/320 |
V |
Initial charge |
100 |
100 |
100 |
100 |
% |
Number of cells per cell-row |
12 |
12 |
20 |
26 |
— |
Number of cell-row |
17 |
30 |
20 |
1 |
— |
Internal resistance charge/discharge |
1/1 |
1/1 |
1/1 |
1/1 |
Ω |
Operating temperature |
33 |
270 |
36 |
30 |
°C |
Specific heat transition |
0.4 |
6 |
0.4 |
0.08 |
W K−1 |
Specific heat capacity |
795 |
950 |
677 |
1650 |
J kg−1 K−1 |
Mass of battery |
318 |
457 |
534 |
173 |
kg |
Battery price |
300 |
500 |
400 |
250 |
£ |
Table 3 Various types of Li rechargeable batteries and their abbreviations based on cathodes, anodes and the nature of electrolytes
Type |
Abbreviation |
Basis |
Lithium ion cobalt oxide battery42 |
LCO |
LiCoO2 |
Lithium ion manganese oxide battery43,44 |
LMO |
LiMnO2 |
Lithium ion nickel oxide battery45 |
LNO |
LiNiO2 |
Lithium iron phosphate battery46,47 |
LFP |
LiFePO4 |
Lithium nickel manganese battery48 |
LNMO |
LiNi0.5Mn1.5O4 |
Lithium nickel cobalt aluminium oxide49 |
NCA |
LiNiCoAlO2 |
Lithium nickel cobalt manganese oxide50 |
NCM |
LiNiCoMnO2 |
Lithium–titanate battery51 |
LTO |
Li4Ti5O12 |
Lithium–sulphur battery52 |
Li–S |
Li as anode and Li2S as cathode |
Lithium–air battery53 |
Li–air |
|
Lithium-ion polymer battery54,55 |
LIP |
Polymer as electrolyte |
Thin film lithium-ion battery/microbattery56–58 |
|
Based on the nature of electrolyte and thickness of electrodes |
Lithium ceramic battery/solid state battery59 |
|
Based on nature of electrolyte |
Layered oxide cathodes
The advanced pedagogical developments of layered oxide cathode materials have opened up new avenues to offer high cumulative capacity of batteries designed for high-energy applications. These layered oxides are successfully used in various batteries such as LIBs,71,72 Na-ion batteries,73–76 K-ion batteries77,78 and Ca-ion batteries.79,80 Thus, numerous layered oxide cathodes are investigated for LIBs to optimize their performance.81–86 The chemical formula of layered oxides is LiMO2, where M is a transition metal (TM). Most common metals are iron, manganese, cobalt, nickel, titanium and vanadium. Layered LiMnO2 and Li2MnO3, as LIB cathodes, are known for significant values of theoretical capacities.86,87 Other oxides with similar values of cumulative capacity are LiCoO2, LiNiO2 and LiVO2.88 Among these oxides, layered LiNiO2 has a theoretical capacity of 275 mA h g−1
89,90 but it is not preferred because of low electrochemical stability. Another major issue related to this cathode is the presence of local John Teller distrotions91,92 and is responsible for phase transition.93
These drawbacks are proposed to be minimized by doping the cathodes94,95 with similar elements and developing other layered oxides such as LiNi1−xMxO2 (M–Co, Fe, Mn, Ti, Mg and Al), LiNi1−x−yMgxMy′O2 (M′ = Ti and Al) and LiNi1−x−yCoxAlyO2 (NCA).96 The growth of layered oxides such as NCA and NCM is the result of such efforts. Table 4 depicts the characteristics of selected layered oxides along with their cumulative capacities.97–112 Thus, it is clear from Table 4 that layered structures, in which, M has a combination of two or more TMs, exhibit improved electrochemical performance, thereby deeming the NCM cathodes to be effective for a typical LIB.
Table 4 Characteristics of selected layered oxide cathode materials
Cathode material |
Cumulative capacity (mA h g−1) |
Capacity retention (%)/cycle/charging rate |
Discharge voltage (V) |
LiNiO297 |
183.4 |
91.9/20 cycle |
3.8 |
LiNi0.92Co0.08O298 |
212.8 |
75.4/100 cycle/0.1C |
2.75–4.3 |
LiNi1−xFexO299 |
|
|
|
LiNi0.5Mn0.5O2100 |
186.3 |
87.5 (100 cycle/20 mA g−1) |
2.5–4.7 |
LiNi0.975Ti0.025O2101 |
171 |
95.9/30 cycle/0.2C |
4.3 |
LiNi1−xMgxO2102 |
— |
— |
— |
LiNi0.995Al0.005O2103 |
164 |
0.65 mA h per g per cycle |
|
LiNi0.8Co1.9Ti0.05Mg0.05O2104 |
120 |
93/40 cycle/0.4C |
2.5–4.4 |
LiNi0.90Al0.05Mg0.05O2105 |
180 |
— |
— |
LiNi0.9Co0.06Ti0.04O2106 |
214 |
98.7/50 cycle/0.1C |
4.3 |
LiNi0.84Co0.14Al0.02O2107 |
190 |
96.8/30 cycle/0.1C |
4.3 |
LiNi0.7Co0.2Mn0.1O2108 |
148 |
95.2/14 cycle/0.2C |
|
LiMnO2109 |
270 |
|
|
Li2MnO3110 |
400 |
|
|
Li2Mn0.9Al0.1O3111 |
99.4 |
97.1/40 cycles/0.1C |
2.0–4.8 |
LiNi0.90Co0.07Mg0.03O2112 |
228.3 |
84.3/300 cycle/0.1C |
4.2 |
Nickel cobalt manganese oxide (NCM)
The widespread use of NCM cathode materials in the current scenario is evident from Table 4 as well as the work reported by research groups working in this direction.113–116 The electrochemical performance of the NCM cathode can be optimized by altering the chemical compositions117 as observed from compositions such as LiNi1/3Co1/3Mn1/3O2 (NCM333),118 Li1.2Mn0.54Ni0.13Co0.13O2,119 LiNi0.4Co0.4Mn0.2O2 (NCM442),120 LiNi0.5Co0.3Mn0.2O2 (NCM532),121 LiNi0.6Co0.2Mn0.2O2 (NCM622),122,123 and LiNi0.8Co0.1Mn0.1O2 (NCM811).124,125 As a result, several investigations are continuing on NCM cathodes, particularly those with excess Ni ions and surpassing Ni content to 0.8.126,127 In effect, NCM cathodes with excess Ni contents in the range of 0.8 to 0.99 are being designed by researchers in order to increase the cumulative capacity.128–130 Some cathodes in this range of Ni content are LiNi0.88Mn0.06Co0.06O2,131 LiNi0.91Co0.06Mn0.03O2,132 Li1+x(Ni0.88Mn0.06Co0.06)1−xO2 (NMC88),133 LiNi0.83Co0.11Mn0.06O2,134 LiNi0.895Co0.085Mn0.02O2135 and LiNi0.96Co0.03Mn0.01O2.136 Interestingly, among different compositions, the NCM811 cathode material is seen to offer an amazing value of cumulative capacity (200 mA h g−1) and is therefore deemed the most effective Ni-rich composition of the NCM cathode.137,138
For the understanding of the layered structure of NCM oxides, the unit cell of NCM111 cathode material (hexagonal α-NaFeO2 layered structure the with R
m space group) is shown in Fig. 1a.139 In this structure, oxygen atoms form a cubic close-packed (ccp) lattice with rhombohedral distortion along the c-direction, resulting in layers formed by edge-sharing octahedra. The octahedral sites of the somewhat thinner layer (Wyckoff position 3a) are occupied mainly by TM layers, whereas those of the somewhat thicker layer (Wyckoff position 3b) are occupied mainly by lithium (Li layer), yielding [Li]3b[TM]3a[O2]. Especially, in the presence of manganese, the material becomes Li rich, which leads to fractional occupancy of 3a sites by the Li ions. Hence, NCM is frequently denoted as Li1+z(Ni1−x−yCoxMny)1−zO2. By contrast, LNO tends towards Li deficiency, meaning that nickel occupies some of the 3b sites. In case of layered oxides, this type of structure is often referred to as H1-type structure.140–143 The structure is stable for various compositions of NCM oxides.144 The atomic models of crystal structure for NCM811 in different planes are depicted in Fig. 1b and c. With the change in composition, the unit cell parameters of the NCM structure vary (Table 5).145 The TM and Li layer distances for various compositions are shown in Fig. 1d.
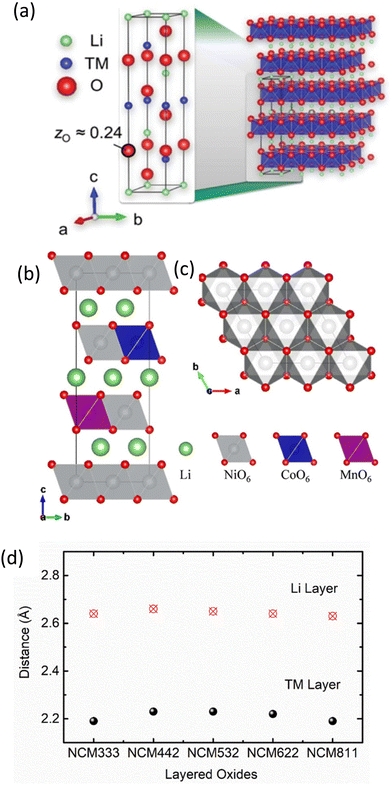 |
| Fig. 1 Structure of layered oxides: (a) layered crystal structure of NCM. Reprinted with permission from L. de Biasi, A. O. Kondrakov, H. Geßwein, T. Brezesinski, P. Hartmann and J. Janek, J. Phys. Chem. C, 2017, 121, 26163.139 Atomic models of Ni-rich LiNi0.8Co0.1Mn0.1O2 (NCM811) layered oxides (R m) projected onto the (b) bc and (c) ab planes. Reprinted with permission from J.-M. Lim, T. Hwang, D. Kim, M.-S. Park, K. Cho and M. Cho, Sci. Rep., 2021, 7, 39669.144 (d) Distance of the TM and Li layer with various compositions of cathodes. Values are adopted from H. Sun and K. Zhao, J. Phys. Chem. C, 2017, 121, 6002.145 | |
Table 5 Average bond length (Å) of TM–TM and TM–O pairs
Composition |
Ni–Mn |
Mn–Co |
Ni–Co |
Mn–O |
Ni–O |
Co–O |
Reprinted with permission from H. Sun and K. Zhao, J. Phys. Chem. C 2017, 121, 6002.145 |
NCM333 |
2.93 |
2.89 |
2.92 |
1.95 |
2.06 |
1.99 |
NCM442 |
2.93 |
2.91 |
2.92 |
1.95 |
2.07 |
1.99 |
NCM532 |
2.91 |
2.91 |
2.92 |
1.94 |
2.05 |
1.98 |
NCM622 |
2.91 |
2.88 |
2.91 |
1.94 |
2.02 |
1.97 |
NCM811 |
2.91 |
2.85 |
2.88 |
1.94 |
2.00 |
1.94 |
Fig. 2 shows a schematic of the Li intercalation process in the NCM cathode.146 Delithiated NCM materials experience crystalline structure change at elevated temperatures. Although the detailed phase transition process differs in various reports, most studies agree that the delithiated NCM cathodes experience a three-stage transition with the increase in temperature: from layered structure (R
m) to spinel phase (Fd
m), and then to rock salt phase (MO-type).147,148 The spinel phase can split into two sequential stages: spinel phase I (LiMn2O4-type) and II (M3O4-type).149 Only a few research studies reported metallic phases (nickel or cobalt) as the final products, which might be generated under extremely high pressures or temperatures (above 900 °C).150,151 The three-stage phase transition reactions release heat and oxygen. The oxygen reacts with electrolytes and lithiated anodes152–155 and is chiefly responsible for the thermal runway (TR) in Ni-rich oxide cathodes.156,157 The thermal stability of NCM cathodes is intricately linked to the composition of Ni, Mn, and Co. Notably, the presence of Mn4+ plays a pivotal role in enhancing the thermal stability as it remains electrochemically inert, providing stabilization to the oxide matrix even in a deep delithiated state.158,159 Conversely, higher concentrations of Ni in delithiated NCM lead to a lower onset temperature for phase transitions towards spinel and rock salt phases, accompanied by an increased release of oxygen.127 This liberated oxygen contributes to solvent combustion and heat generation. Consequently, formulations with elevated Ni contents and reduced levels of Mn and Co generally exhibit higher self-heating rate values, coupled with lower temperatures for exothermic reactions to initiate. The phase stability in Ni-rich cathode materials also shows the manifestation of structure with temperature.127,146
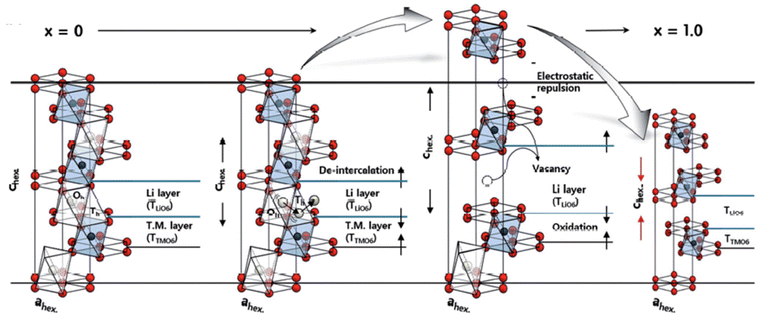 |
| Fig. 2 De-intercalation process in the NCM cathode: structural description of the NCM622 cathode material during the first de-intercalation process (x = 0 to x = 1.0). Reprinted with permission from W. Lee, S. Muhammad, T. Kim, H. Kim, E. Lee, M. Jeong, S. Son, J.-H. Ryou and W.-S. Yoon, Adv. Energy Mater., 2018, 8, 1701788.146 | |
Challenges with NCM cathodes
NCM cathodes represent a pivotal component in the advancement of LIB technology, owing to their commendable energy density and cycling stability, as discussed in the previous section. However, this section delves into the multifaceted challenges that confront the design and application of NCM cathodes. Notably, the cation disorder within the crystal lattice poses a significant hurdle, as it disrupts the ordered arrangement of nickel, manganese, and cobalt ions, leading to compromised electrochemical properties. Additionally, the delicate balance in material composition, particularly in mitigating the reliance on cobalt, necessitates intricate optimization strategies. Furthermore, the intricacies of surface coatings and modifications, as well as the understanding of voltage fade mechanisms, demand meticulous investigations. Thermal stability and safety concerns, which become paramount in applications exposed to elevated temperatures, represent another substantial research avenue. Following are some recent literature highlights of these challenges and overcoming of these may pave the way for enhanced NCM cathodes that drive the evolution of high-performance lithium-ion batteries.
Cation disorder
The phenomenon of cation disorder within the crystal lattice presents a significant challenge to NCM optimization. This disorder leads to variations in the electronic structure and local environments around the transition metal sites, affecting the key electrochemical parameters. In layered NCM oxide cathodes, there is existence of Ni2+ ions at the Li+ site and vice versa,160 which is termed cation disorder/mixing (Fig. 3a). This factor affects Li mobility in these materials,161–163 which consequently influences the capacity of LIBs.164Fig. 3b shows that intermixing decreases with the increase of Mn ions.161 Studies have shown that the disorderly distribution of cations in NCM cathodes can result in reduced capacity, voltage fade, and deteriorated cycling stability,165 which ultimately affects the electrochemical performance of batteries. Hence, efforts are made to control cation ordering through tailored synthesis techniques and doping strategies166,167 for the improvement of NCM cathode performance.
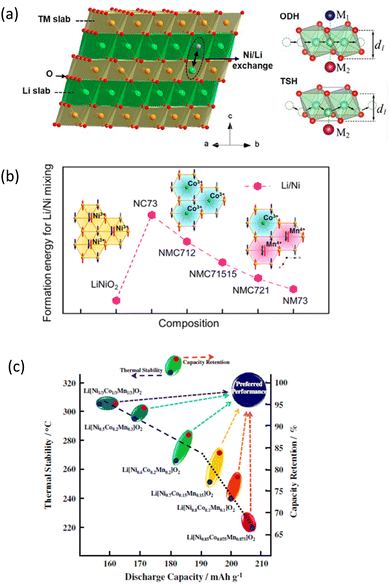 |
| Fig. 3 Issues related to NCM cathodes: (a) α-NaFeO2-type structure of layered NMC materials with one pair of Ni/Li exchange (left panel) and illustration of the ODH (oxygen dumbbell hopping) and TSH (tetrahedral site hopping) types of Li-ion diffusion pathways (right panel). Permission obtained from J. Zheng, Y. Ye, T. Liu, Y. Xiao, C. Wang, F. Wang and F. Pan, Acc. Chem. Res., 2019, 52, 2201.160 (b) Variation of Ni/Li exchange in various compositions of NCM oxides Permission obtained from D. Wang, C. Xin, M. Zhang, J. Bai, J. Zheng, R. Kou and J. Y. P. Ko et al., Chem. Mater., 2019, 31, 2731.161 (c) Thermal stability, capacity retention and discharge capacity of various Ni-rich cathode materials. Permission obtained from H.-J. Noh, S. Youn, C. S. Yoon and Y.-K. Sun, J. Power Sources, 2013, 233, 121.168 | |
Cumulative capacity and retention
These materials have the potential to be utilized for EV applications due to their high theoretical capacity of 230 mA h g−1.11,169,170 The composition of NCM cathodes plays a crucial role in determining both the cumulative capacity and capacity retention of a battery. On the contrary, higher nickel contents can reduce the thermal stability of the cathode material, potentially affecting capacity retention over extended cycling (Fig. 3c).168 An optimal Mn content ensures a balance between capacity and structural stability. It also plays a crucial role in stabilizing the crystal structure of the cathode material. This can enhance the cathode's ability to retain capacity over repeated cycles. Cobalt contributes to the overall capacity of the cathode. However, it is often limited due to cost and ethical considerations. Reduced cobalt content may not significantly affect the initial capacity but can influence capacity retention. Further, the disordered distribution of Ni, Mn, and Co ions within the crystal lattice can hinder the efficient movement of lithium ions, leading to reduced cumulative capacity.171 Optimizing the NCM cathode composition involves a delicate balance between maximizing specific capacity, ensuring structural stability, and managing factors such as thermal stability and cost. Researchers work to strike this balance to achieve the optimal performance of NCM batteries.
Thermal stability
Thermal stability is necessary for the development of a risk-free battery. Thus, investigating the thermal stability of cathodes is equally important.172–174 Unfortunately, thermal stability decreases with the increase in Ni content (Fig. 5b). The onset temperature of TR for the battery with the NCM811 cathode is 20 °C lower than that with the NCM622 cathode; however, this value is 13 °C lower for single-crystal NCM811.175 Atomic substitutions to NCM can help suppress the TR behavior.176 Ca doping to NCM811 increases the onset temperature by almost 30 °C.177 The addition of a negative-thermal-expansion (NTE) material of Al2(WO3)4 leads to improvement in the thermal stability.178 The formation of the rock-salt layer on the surface of NCM811 is reported to enhance the thermal stability of an NCM cathode with high Ni contents.179 The change in the total heat generation with degradation suggests a strong correlation between the heat generation and crystal structure changes during cycling, as indicated by differential scanning calorimetry (DSC) measurements and XAS measurements. Studies focusing on the thermal stability of layered NCM materials envisaged the correlation between the thermal stability and its electrochemical performance.180,181
Cost, efficiency, abundance and demand
The optimal use of NCM cathodes in LIBs is not only limited to the optimization of electrochemical performance but the factors affecting their cost also play an important role. Thus, the projected cost of the designed NCM battery,182 abundance, supply and demand of elements such as Ni, Co, Mn have always been a concern and are being reviewed by the scientific community.169 Despite the numerous efforts, vehicles based on LIBs are costlier than ICEs (Fig. 4a).183 Strategies are planned to reduce their cost comparable to the value of ICE-based vehicles in the next 5–6 years. Fig. 4b depicts the cost of various NCM batteries by describing the cost of various components.184 If the example of LMO is considered, the production cost for a solid-state process is $7 per kg and requires 6 kW h kg−1 of energy. The cost of automotive batteries based on LMO cathode may be reduced by cutting LMO price and plat production volume.185 Thus, the reduction in cathode price is an effective choice for reducing the cost of LIBs; however, the case of NCM is different. In this case, the use of Co ions is not considered favourable at the industrial level, as Co has issues related to the abundance and cost (Fig. 5a).169 It is expected that the demand of lithium, cobalt, and nickel will be increased by the factors of 18–20, 17–19, and 28–31, respectively, from 2025 to 2050. In addition to that, a factor of 15–20 of existing cost will be hiked for other auxiliary materials used in LIBs (Fig. 5b).186 This requires drastic expansion of lithium, cobalt, and nickel supply chains and likely additional resource discovery.187,188
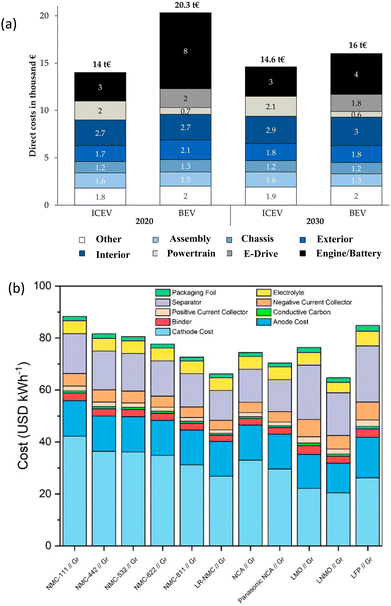 |
| Fig. 4 Cost of li-rechargeable batteries: (a) Comparison of costs in the next 10 years for internal combustion engine battery electrical vehicles (ICEVs) and. Reprinted with permission from A. König, L. Nicoletti, D. Schröder, S. Wolff, A. Waclaw and M. Lienkamp, World Electr. Veh. J., 2021, 12, 21183 (b) cost of Li rechargeable batteries for various NCM compositions, Reprinted with permission from M. Wentker, M. Greenwood and J. Leker, A Bottom-Up Approach to Lithium-Ion Battery Cost Modelling with a Focus on Cathode Active Materials, Energies, 2019, 12, 504. open access.184 | |
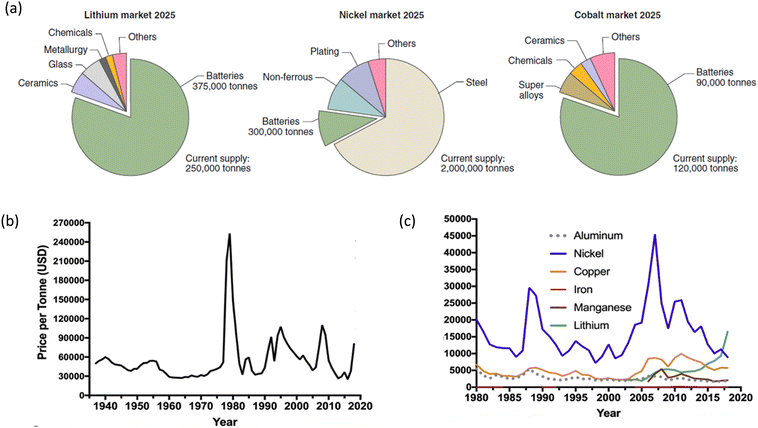 |
| Fig. 5 Market statistics of the NCM cathode: (a) market of various elements by 2025. Reprinted with permission from W. Li, E. M. Erickson and A. Manthiram, Nat. Energy, 2020, 5, 26.169 (b) Prices per tonne (USD) for Co and (c) other elements related to NCM cathodes. Reprinted with permission from S. W. D. Gourley, Tyler and Z. Chen, iScience, 2020, 23, 101505.186 | |
Thus, structural degradation,189 capacity retention,190 lower thermal stability191 and production cost192 are the major challenges towards the development of efficient NCM cathodes. Apart from these challenges specific to the cathode, effects such as release of CO2/O2193,194 and metal ion dissolution195,196 are major concerns when the cathode comes into contact with the electrolyte. Thus, the scientific community is working towards overcoming these issues for making global use of LIBs by investigating cathodes,197,198 cathode/electrolyte interfaces199,200 and gas evolution phenomena.201–203 Therefore, this review is focused on exploring the nature of NCM cathodes, and efforts related to this cathode are discussed in the following sections.
Strategies to improve the electrochemical performance
Several strategies including microstructural modifications,199 doping,204–206 co-doping207–209 or coating210,211 are applied to improve the electrochemical performance212,213 of parent cathode materials. Studies focusing on air stability,214 correlating the surface structure with the internal strain, and capacity deterioration215–217 along with correlation among the structural changes with Li diffusion218 also provide the opportunities to resolve the electrochemical performance–related issues. Thus, the present section describes the strategies utilized for the improvement of the electrochemical performance of cathodes.
Coating
Coating is an effective strategy to improve the electrochemical performance of the LIBs based on NCM cathodes.219–221Fig. 6a shows the schematic of surface coating processes. As the surface coating of cathode materials may enhance the life and rate capability of LIBs,222–224 various materials are investigated for the NCM811 cathode as coating materials.225,226 Carbon seems to be very common to use as a coating material as the presence of carbon on the surface of the cathode is effective to enhance the cycle life by altering the following behaviors.
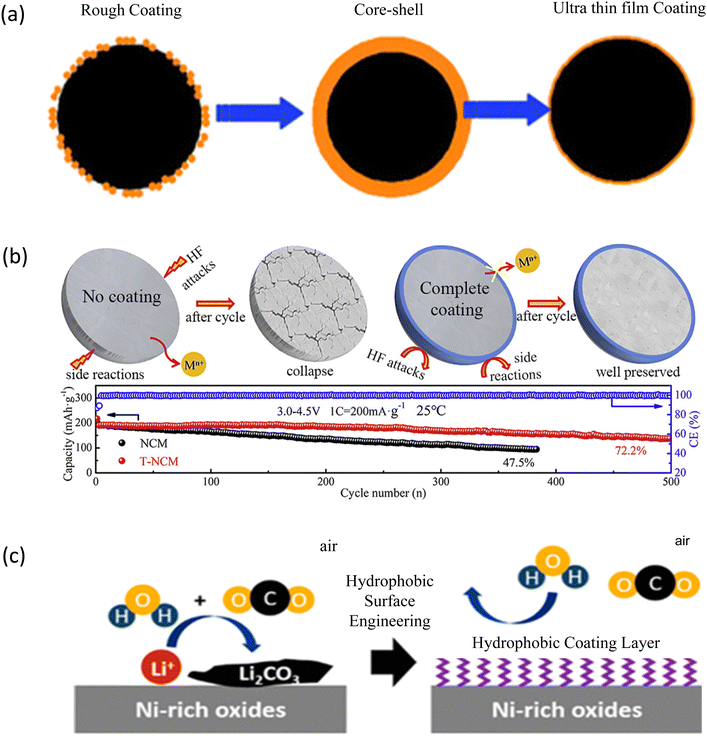 |
| Fig. 6 Coating of the NCM cathodes: (a) surface coating approaches to cathode materials. Reprinted with permission from Z. Chen, Y. Qin, K. Amine and Y.-K. Sun, J. Mater. Chem., 2010, 20, 7606.219 (b) Representation of TiO2 coating on the NCM cathode along with the electrochemical behavior of pure and doped counterparts. Reprinted with permission from Q. Fan, S. Yang, S. Guan. J. Chen, S. Feng, J. Liu, L. Liu, J. Li and Z. Shi, J. Power Sources, 2020, 477, 228745.227 (c) Hydrophobic Coating Layer for NCM cathode Materials Reprinted with permission from SungWookDooSungWook Doo, More by S. Wook Doo, S. Lee, H. Kim, J. H. Choi and K. Tae Lee, ACS Appl. Energy Mater., 2019, 2, 6246.228 | |
1. increase in electrode conductivity,
2. improvement in the surface chemistry of the active material and
3. protection of the electrode from direct contact with the electrolyte.
Super-P carbon black (SPB 0.5 wt%)-coated NCM811 delivers excellent cyclability (87.8% after 80 cycles) and rate capability (86.5% at 2C) compared to those of pristine NCM811.229 The discharge capacity of the 4 nm coating of carbon on NMC811 showed only a 1.26% decrease after 100 cycles at a rate of 0.2C, while pristine NMC811 lost 6.85% of its initial reversible capacity.230 N-doped carbon-coated NCM maintained good cycling performance (210.2 mA h g−1 at 0.1C after 40 cycles and 188.5 mA h g−1 at 1C after 100 cycles) and rate ability (131.7 mA h g−1 at 5C rate). In comparison, the uncoated (NCM) electrode retained only 56.60% of its capacity (102.5 mA h g−1 at 1C after 100 cycles).231
Oxides such as Al2O3, ZrO2, Li2O–2B2O3 (LBO), and Li2MnO3 are also used as coating materials232–234 apart from utilizing carbon-derived materials such as graphene oxides and polymers. The schematic of the TiO2 coating procedure is shown in Fig. 6b, which exhibits a significant improvement in the electrochemical performance of LIBs.227 In Table 6, the capacity retention values of bare and oxide cathodes are collated.234–252 These observations clearly reflect the improvement in the electrochemical performance of NCM cathodes.
Table 6 Capacity retention (%) of bare and coated cathode materials
Coated materials |
Cathode |
Bare cathode |
Coated cathodes |
Cycles |
Specification |
Metal oxides |
3%Li2MnO3234 |
NCM811 |
74 |
93 |
100 |
0.1C |
63 |
81 |
100 |
1C |
TiO2227 |
NCM811 |
|
72.2 |
500 |
4.5 V |
|
63.4 |
1000 |
1000 cycles-4.3 V |
Li3PO4235 |
NCM811 |
|
88.4 |
100 |
1C |
|
84.6 |
100 |
1C _exposed to air for 7 days |
Li3PO4236 |
NCM811 |
86 |
92.6 |
100 |
1C |
4.53 wt% Li FePO4237 |
NCM811 |
78 |
97 |
100 |
2.7–4.5 V |
|
|
63 |
86 |
400 |
|
2% Li2MoO4238 |
NCM811 |
85.5 |
93.99 |
100 |
1C |
LiNbO3239 |
NCM523 |
73 |
92 |
100 |
1C |
2 wt% |
LiNi0.83 |
|
|
|
|
Li1.3Al0.3Ti1.7(PO4)3240 |
Co0.06Mn0.06Al0.05O2 |
80.9 |
90.9 |
300 |
5C |
MoO3241 |
NCM811 |
|
84.5 |
100 |
0.1C |
|
|
|
79.8 |
|
5C |
|
Graphene oxides and nitrides |
r-GO242 |
NCM811 |
|
92.8 |
100 |
1C |
g-C3N4243 |
NCM811 |
130 mA h g−1 |
140 |
225 |
0.178 mA cm−2 |
Gr244 |
LiNi0.8Co0.15Al0.05O2 |
|
|
|
|
|
Polymers245,246 |
Oxy-thiophosphate247 |
NCM811 |
128 mA h g−1 |
|
|
|
Polypyrrole248 |
NCM811 |
|
90.7 |
100 |
|
Poly(thiophene)249 |
NCM811 |
84.2 |
91.3 |
|
|
Polypropylene250 |
NCS* |
94.7 |
96.2 |
|
3.0–4.3 V |
Polyvinylpyrrolidone (PVP), and polyaniline (PANI)251 |
NCM811 |
|
88.7 |
100 |
|
PMMA252 |
NCM811 |
181.1 mA h g−1 |
|
|
1C |
Furthermore, the coating of NMC811 with hydrophobic materials is effective in protecting the cathode surface from environmental moisture or humidity.253Fig. 6c shows hydrophobic coating with di hexadecyl phosphate (DHP) on the NCM particle surface. It consists of two layers: (i) an outer-layer hydrophobic alkyl surface, which alleviates the absorption of H2O/CO2 on the particle surface in the humid environment and (ii) an inner-layer phosphate-based coating with O
POLi covalent bonds. This layer improves the Li+ transportation coefficient during the charge–discharge process. As a result, profiting from these two synergistic effects, the DHP-coated NCM cathodes have shown excellent rate performance and cycling stability, particularly, after 14 days of exposure to air. The DHP-coated NCM cathodes delivered an initial capacity of 168.7 mA h g−1 at 2C rate, but only 134.7 mA h g−1 for the pristine NCM.228 Hydrophobic polydimethylsiloxane-grafted NCM811 suppresses the formation of residual Li+ even in humid air. This leads to the negligible surface degradation of NCM811 and the modified cathode shows excellent electrochemical performance even after storage in humid air for 2 weeks.
Dual coating
Dual coating is considered an effective approach for the improvement of the electrode/electrolyte interface.254,255 It not only improves the discharge capacity but also increases the cyclic performance.256 It involves applying two separate layers of protective materials onto the surface of the cathode particles. The first coating layer is typically designed to act as a barrier between the cathode material and the electrolyte. It helps prevent unwanted side reactions that can occur at the electrode–electrolyte interface. It is especially important for high–nickel content NCM cathodes, which are much prone to such reactions. The second coating layer is often chosen to enhance the structural stability of the cathode material. It helps maintain the integrity of the crystal lattice during charge and discharge cycles, reducing structural degradation and extending the lifespan of the cathode.257 The initial specific discharge capacity of NCA, Y2O3-decorated NCA, and graphene/Y2O3/NCA was found to be >190 mA h g−1 at 0.5C, but the capacity retention of the graphene/Y2O3/NCA composite was about 48% higher than that of the bare material during 100 cycles. NCA, Y2O3/NCA, and graphene/Y2O3/NCA materials deliver specific discharge capacities of 109, 136 and 164 mA h g−1, respectively at 2C.258 The capacity retention of the polypyrrole LiAlO2-coated NCM (PPy-LA) is 92.8% after 100 loops and a capacity of 128 mA h g−1 is obtained at 2 A h g−1.259 Dimethyl sulfone (DMS) and dimethyl sulfoxide (DMSO)-modified NCM811 cathodes are reported to exhibit improved specific capacity retention (DMS-NCM811: 99.4%; DMSO-NCM811: 88.6%; and NCM811: 78.4%).260 The capacity retention of Li3PO4 and PPy for layered Ni-rich cathodes is 95.1% at 0.1C after 50 cycles, whereas the bare sample exhibits only 86% retention. The coated cathode delivers a cumulative capacity of 159.7 mA h g−1 at 10C compared to 125.7 mA h g−1 for the bare cathode (Fig. 7a).261 Heating polyacrylonitrile with NCM811 can simultaneously construct a cyclized polyacrylonitrile outer layer and a rock-salt bridge-like inner layer, forming a compact dual-coating of NCM811.262 The modified cathode leads to a high reversible capacity of 183 mA h g−1 and a high capacity retention of 83% after 300 cycles at 1C rate (Fig. 7b).
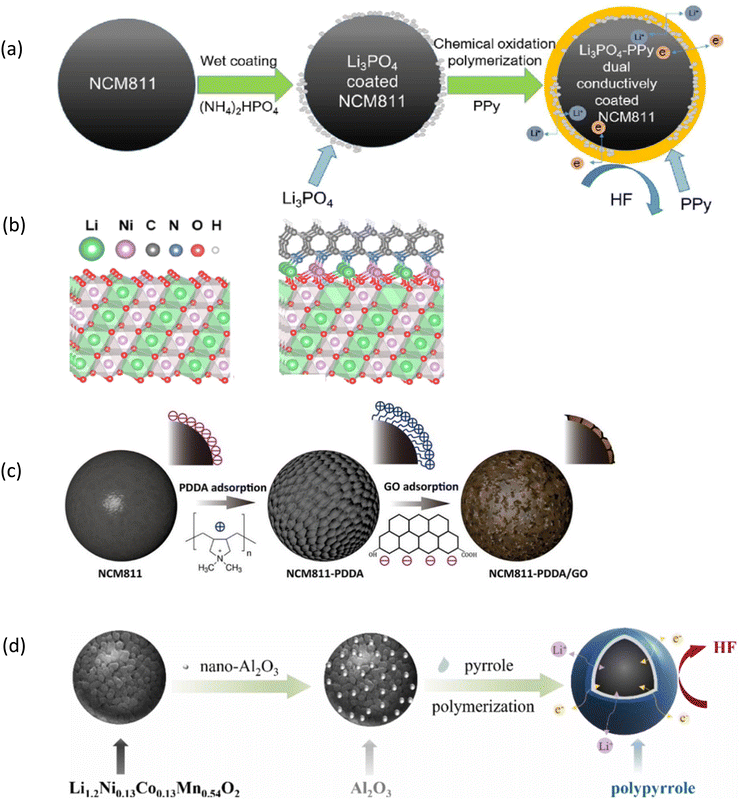 |
| Fig. 7 Dual-coating process: (a) schematic representation of Li3PO4–PPy Dual coating on the NCM811 cathode. Reprinted with permission from S. Chen, T. He, Y. Su, Y. Lu, L. Bao, L. Chen, Q. Zhang, J. Wang, R. Chen and F. Wu, ACS Appl. Mater. Interfaces, 2017, 9, 29732–29743.261 (b) Reprinted with permission from J. Wang, Q. Yuan, Z. Ren, C. Sun, J. Zhang, R. Wang, M. Qian, Q. Shi, R. Shao, D. Mu, Y. Su, J. Xie, F. Wu and G. Tan, Nano Lett. 2022, 22, 5221.262 (c) Coating of PDDA/Go on NCM811. Reprinted with permission from J. Yu, J. Zhang, Y. Zhang, Z. Wang, Z. Chen, A. Gao, J. Zhang, Y. Wang and R. Zhao, Appl. Surf. Sci., 2022, 577, 151716.263 (d) Nano-Al2O3 and pyrrole coating on the Li-rich NCM cathode. Reprinted with permission from Y. Beia, Y. Zhang, Y. Li, Y. Song, L. Liu, J. Ma, and J. Liu, J. Alloys Compds, 2022, 928, 167140.264 | |
Dual coating of polydimethyldiallyl ammonium chloride/graphene oxide (PDDA/GO) on a single-crystalline NCM811 cathode leads to 77% capacity retention after 500 cycles at a current density of 50 mA g−1, against 28% for pristine NCM811 (Fig. 7c).263 The nano-Al2O3 and PPy double-layer coating forms a firm protective shell on the surface of the Li1.2Ni0.13Co0.13Mn0.54O2 cathode to alleviate external side reactions (Fig. 7d). This type of double-layer coating was helpful to achieve a discharge capacity retention rate of 90.74% after 100 cycles at 1C rate.264 Wu et al. have investigated the impact of LiAlO2/Al2O3 dual coating on the NCM811 cathode. The optimal electrochemical performance is reported to be an appropriate ratio of ion-conducting LiAlO2 and chemical-inert Al2O3 phases.265
Doping and co-doping
Introducing certain dopants can help stabilize the crystal structure of NCM cathodes.266–268 This improves the structural integrity during charge and discharge cycles, reducing degradation. Doping may also enhance the material's ability to withstand high temperatures, reducing the risk of thermal runaway events.269–271 Dopants can be strategically chosen to influence the distribution of nickel (Ni), manganese (Mn), and cobalt (Co) ions within the crystal lattice. This helps reduce the cation disorder, which can have a negative impact on the electrochemical performance.272–274 Strategic doping can help stabilize the redox chemistry of NCM cathodes, reducing the phenomenon of voltage fade, where the voltage of the cell decreases over repeated cycles. The doping of NCM811 with cations such as Mg2+, Al3+, Si4+, Ti4+, Zr4+, and Ta5+ following “top–down” approach concludes that Ta5+ cations are very promising dopants for Ni-rich NCM cathodes.275 LIB prototypes, consisting of tungsten-stabilized Ni-rich cathode materials (x > 0.9), exhibit specific capacities greater than 220 mA h g−1. This study enables the superiority of doping for enhancing the energy density of LIB without compromising the durability.276 This is also reflected in the improvement in in the capacity retention of NCM cathodes by various ions such as B,277,278 V,279 Mg,280 F,281 ZrB2,282 Nb,283 Ti,284 Dy,285 Al,286 Nb5+,287 Nb (dual site),288 Mg,289 Ga,290 and Mo.291 Capacity retention of doped and their pristine counterparts is shown in Fig. 8a. The doping of ions into NCM cathodes, especially rare earth (RE) ions, suppresses the Ni/Li cation mixing effect.292 The functional trace doping of dual-elements has been an effective strategy to address issues such as internal strain accumulation, structural/mechanical degradation, and surface parasitic reaction.293,294 Titanium and boron co-doped into NMC811 improve the rate performance (183.1 mA h g−1 at 1C and 155.5 mA h g−1 at 10C) and cycling stability (capacity retention of 94.7% after 100 cycles at 1C). This co-doping also reduces charge transfer impedance and suppresses phase change of NCM811.295 For La3+ and Al3+ co-doped NCM811, initial discharge specific capacities of 218.6 mA h g−1 (0.05C) and 178.6 mA h g−1 (1C) are observed to reduce to 134.6 mA h g−1 with 75.4% capacity retention after 100 cycles at 1C (Fig. 8b).296 In the voltage range of 2.8–4.3 V, the discharge capacity of dual-doped NCM811 with Mg2+ and Al3+ (NCM-MA) is 138.8 mA h g−1 after 200 cycles at 1C, which is 31 mA h g−1 higher than that of the pristine NCM (Fig. 8c). NCM-MA also delivers a high discharge capacity of 150.33 mA h g−1 at 5C, due to the improvement of Li+ diffusion kinetics.297
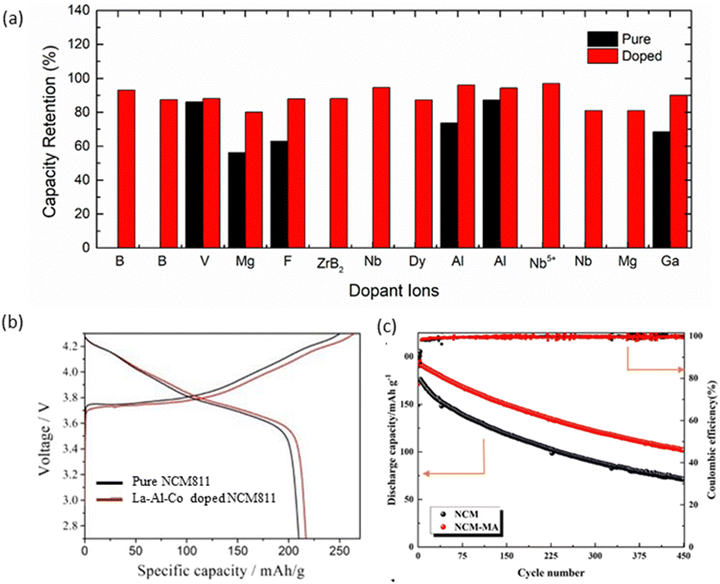 |
| Fig. 8 Doping effect on electrochemical performance: (a) capacity retention in NCM811 cathodes by doping with various ions. Doping improves the retention in these cathodes. The values are taken from previously published work.277–291 (b) Behaviour of La–Al Co doped NCM811 and pure NCM811. Reprinted with permission from Mi. Zhang, C. Wang, J. Zhang, G. Li and L. Gu, ACS Omega, 2021, 6, 16465296 (c) discharge capacity of Mg and Al co-doped NCM811. Reprinted with permission from L. Xiao, X. Tang, Z. Ban et al., An Mg–Al dual doping strategy to enhance the structural stability and long cycle life of LiNi0.8Co0.1Mn0.1O2 cathode material, Ionics, 2022, 28, 3101.297 | |
Doping, co-doping followed by coating or dual modifications of NCM cathodes
Doping followed by coating is used by several researchers to improve the electrochemical performance of LIBs.189,298 Doping can be used in conjunction with surface coatings to further mitigate unwanted side reactions between the cathode material and the electrolyte. For the NCM950505 cathode, doped with Zr and simultaneously coated with an Li2ZrO3 layer, the capacity-retentions are reported as 86.08%, 92.12%, and 96.85% at the 50th cycle for pristine NCM, S-NCM (synthesized by the solid method), and L-NCM (synthesized by the liquid/solvent method), respectively. In the 300th cycle, in the voltage range of 2.8–4.35 V, the capacity-retentions for S-NCM and L-NCM are 77.72% and 81.95%, respectively.299 The 1% Zr-NCM831205 cathode maintains a discharge capacity of 173.9 mA h g−1 at 1C after 200 cycles in the 2.5–4.3 V voltage range at 25 °C, corresponding to a capacity retention of 94.6%; however, the unmodified NCM exhibits a capacity retention of 68.6%. The synergistic effect of bulk Zr doping and surface Li6Zr2O7 coating is shown to further improve the cycling stability of this cathode.300 The La2Li0.5Al0.5O4-coated and La-and-Al-doped NCM811 exhibits an excellent capacity retention of 97.2% at 1C in the voltage range of 3.0–4.4 V after 100 cycles, which is 18.5% higher than that of the pristine form. With regard to the rate performance, it shows a retention of 95.1% in capacity at 5C after 80 cycles from 3.0 V to 4.4 V, 6.4% higher than that of the pristine form.301 ZrO2-coated/Zr-doped NCM811 exhibits enhanced cycling stability and lower impedance.302 The co-doping of cobalt and titanium in NCM811 cathodes is reported to improve the reversible capacity together with the rate capability by obviously alleviating the lattice structure degradation and microscopic inter-granular cracks. Titanium doping effectively reduces the cation mixing and also stabilizes the crystal structure, while the spinel phase formed at the surface by a cobalt oxide coating is more stable than the layered phase at high voltages, which can alleviate the generation of micro-cracks. After 0.5% Co oxide coating and 1% Ti doping (Ti1Co0.5-NCM), a superior rate capability of 121.75 mA h g−1 at 20C between 2.7 and 4.5 V and a predominant capacity retention of 74.2% are observed compared with the pristine NCM811 with a capacity retention of 59.5% after 400 cycles between 2.7 and 4.7 V.303 Ti-doped and La4NiLiO8-coated NCM811 cathodes show improved electrochemical performance due to the synergetic effect of the conductive La4NiLiO8 coating layer and the strong Ti–O bond.304 Trace Zr-doping and the conductive Li3BO3 layer are simultaneously adopted to modify the NCM cathode.305 The results have indicated that the Zr4+ dopants, diffused to the surface during annealing, are responsible for the improved electrochemical performance compared to the unmodified cathode without additional coatings (Fig. 9a).306 A maximum discharge capacity of 129.8 mA h g−1 at 5C high rate and enhanced cycling performance with a capacity retention of 90.1% after 300 cycles are reported for PPy-coated LiNi0.835Co0.05Mn0.10B0.015O2. The pristine cathode demonstrates a fast decaying capacity and delivers a capacity retention of only 81.9%.307Fig. 9b shows that the sample containing 0.5% Sm has the highest initial discharge specific capacity (1C, 184.2 mA h g−1), capacity retention rate (2.7–4.3 V, 100th cycle, 94.2%), and rate performance (5C, 152.2 mA h g−1).308 WO3-coated and Mg2+-doped NCM811 cathodes are synthesized by the co-precipitation and wet coating methods and the electrochemical performance is compared. In Fig. 9c, the WO3-coated and Mg2+-doped NCM811 cathode exhibits a capacity retention of 73.5% at 1C after 100 cycles, which is considerably higher than that of the raw materials (53.6%).309 The bulk Zr4+-doped and surface Al2O3-coated cathode delivered a high discharge capacity of 120 mA h g−1 after 200 cycles at 0.5C.310
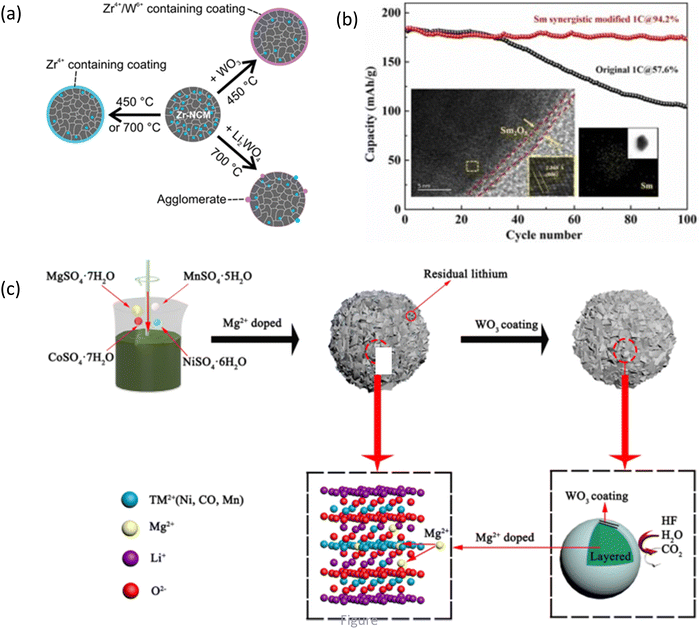 |
| Fig. 9 Dual modification strategy: (a) Zr4+/W6+-coated Zr-doped NCM cathode. Reprinted with permission from F. Reissig, M. A. Lange, L. Haneke, T. Placke, W. G. Zeier, M. Winter, R. Schmuch and A. Gomez-Martin, ChemSusChem, 2022, 15, e202102220306 (b) electrochemical performance of the Sm-coated and Sm-doped NCM811 cathode. Reprinted with permission from M. Zhang, M. Lv, D. Zhang, Y. Yan, Y. Wang, J. Li, Z. Li, Enhanced electrochemical properties of NCM811 cathode material due to synergistic modification with Sm as doping and coating agent, J. Alloys Compd., 2022, 909, 164712308 (c) schematic process of the designing of the WO3-coated and Mg2+-doped NCM811 cathode. Reprinted with permission from Z. Xiao, C. Zhou, L. Song, Z. Cao and P. Jiang, Dual-modification of WO3-coating and Mg-doping on LiNi0.8Co0.1Mn0.1O2 cathodes for enhanced electrochemical performance at high voltage, Ionics, 2021, 27, 1909.309 | |
Composites, morphology/microstructure manipulation and some specialized structures
In the context of NCM batteries, composites can be tailored to optimize the conductivity, stability, and capacity. For example, incorporating conductive additives or coatings within the cathode composite can enhance the electron transport, ultimately improving the overall battery performance. Furthermore, morphology and microstructure manipulation involve controlling the size, shape, and arrangement of particles within the cathode material. This manipulation enables the optimization of key electrochemical properties. For instance, designing cathode materials with well-defined particle sizes and surface areas can enhance ion diffusion kinetics, leading to improved charge/discharge rates and overall efficiency. Additionally, tailoring the microstructure can help mitigate issues such as particle cracking or phase transformation during cycling, ultimately prolonging the battery's lifespan.311 Allahyari et al. designed an NCM811/LFP/Al composite cathode and reported that the addition of 20 wt% of LiFePO4 to the cathode materials reduces the internal resistance of the electrode and the charge transfer resistance. This is due to the strong P–O bond of PO4 in LiFePO4 involved in the side reactions between the active electrode and the electrolyte. Al is added to control the ionic conductivity.312 Carbon nanotube (CNT) and graphene (GN)-based hybrid materials of NCM333 (NCM333/CNT/graphene) form a three-dimensional (3D) spider web-like network structure. This material exhibits a high discharge capacity of 134 mA h g−1 at 3.0C.313
The NCM811 compound, after the addition of ethylene glycol (EG) and surfactant PVP, delivers the highest discharge capacity of 220.18 mA h g−1 for the initial cycle, and the capacity retention rate of the spherical-like cathode material is 82.36% at 20 mA g−1 after 100 cycles.314 The hybrid structure of the Li[Ni0.9Co0.045Mn0.045Al0.01] cathode compositionally partitioned into inner Li[Ni0.92Co0.04Mn0.03Al0.01]O2 and outer Li[Ni0.845Co0.067Mn0.078Al0.01]O2 develops radially aligned, size-refined primary particles with a high aspect ratio. This type of microstructure is helpful to improve its cycling stability, which retains 84.7% of its initial capacity after 1500 cycles.315
The optimization of cathode active materials in terms of size and morphology is a prerequisite for achieving good rate capability in Ni-rich NCMs.316,317 The electrode material obtained from microwave-assisted co-precipitation followed by a hydrothermal modification (NCM-WH) method possesses a pure α-NaFeO2 phase and a regular spheroidal morphology with a proper size over 10 μm, which exhibits more excellent discharge capacity of 150 mA h g−1 after 200 cycles and a better capacity retention of 88.3% than those obtained by the microwave-assisted co-precipitation method (NCM-W) or the normal co-precipitation method (NCM-N) alone. The improved electrochemical properties are confirmed by their ordered phase structure, regular spheroidal morphology and high tap density, which result in lower Li/Ni cation mixing, faster solid-state ion diffusion, higher electrochemical reversibility and better structure stability during the long-term cycles.318
Water washing and surface modification (gases and molecular species)
Washing is a commonly used, easy and cost-effective method to remove the surface impurities of cathode materials for LIBs,130,319 therefore, it is used to improve the cycling performance and structural stability. In the case of NCM811 cathodes, the untreated sample usually transforms into the spinel phase, whereas the washed sample remains as a layered hexagonal phase. Fig. 10a shows the electrochemical performance of the treated cathode.320 The crystal and electronic structures are the same in the bulk aspect after the water-washing process for the NCM88 cathode, but there are differences in the surface environment. The amount of Li2CO3 decreases while the NiO-like rock-salt phase increases on the surface of the water-washed cathode, and it deteriorates the rate performance by elevating the surface resistances.321 Heat treatment after washing LiNi0.88Co0.11Al0.01O2 with a stable activation process has a lower increment in the cation disorder and a better local structural retentivity after 300 cycles and, consequently, shows a superior cycle life.322 A dry cobalt hydroxide coating on high-Ni cathodes, as shown in Fig. 10b, has not only reduced residual lithium contents but also leads to the formation of a Co-rich concentration gradient layer on the surface that suppresses Li leaching when in contact with water (Fig. 10b).323 The SO2-treated LiNi0.85Co0.10Mn0.05O2 (NCM85105) material is also found to be significantly thermally stable, demonstrating lower heat evolution upon thermal reactions with standard EC-EMC/LiPF6 solutions by 12–20%, compared to the untreated material (Fig. 10c).324
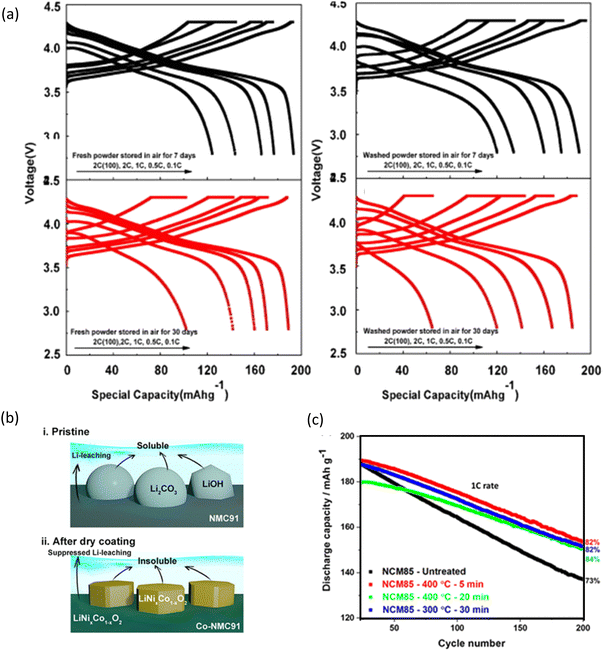 |
| Fig. 10 Washing impact on the electrochemical performance: (a) first charge–discharge curves under different current densities and cycling performance of fresh and washed powders after storage in air for 7 and 30 days. Reprinted with permission from X. Xiong, Z. Wang, P. Yue, H. Guo, F. Wu, J. Wang and X. Li, J. Power Sources, 2013, 222, 318.320 (b) Approach towards the exaggeration of the LiOH content in residual lithium. Reprinted with permission from Y. Kim, H. Park, J. H. Warner and A. Manthiram, ACS Energy Lett., 2021, 6(3), 941–948.276 (c) Electrochemical performance of NMC85 under different SO2 treatments. Reprinted with permission Required from F. A. Susai, H. Sclar, S. Maiti, L. Burstein, O. Perkal, J. Grinblat, M. Talianker, S. Ruthstein, C. Erk, P. Hartmann, B. Markovsky and D. Aurbach, ACS Appl. Energy Mater., 2020, 3, 3609.324 | |
Crystalline orientation
For industrial applications, single-crystal cathodes (SCCs) have numerous benefits over other forms including good crystallinity, high mechanical strength,325 high reaction uniformity, small specific surface area, strong structural stability, and high thermal stability.326,327 The rate performance of the single-crystal NCM333 is 10–15% more than that of polycrystalline NCM333, whereas the capacity retention of single-crystal NCM333 is enhanced by ∼12% after 300 cycles at 0.5C.328 The single-crystal NMC622 exhibits a pronounced improvement in rate performance, especially at high rates (∼28.6% better at 5C and ∼129% better at 10C) and has a comparable cycle performance to polycrystalline NMC622.328 Studies carried out on single crystals of NMC811, LiNi0.80Mn0.15Co0.05O2 (NMC80155), and NCM85105 show that while a higher Ni content leads to overall increased reactivity, the presence of Mn provides a stabilizing effect on thermal, structural, and chemical properties.329 Considering the important observations on single crystals, researchers are putting efforts to understand the involved responsible phenomena330,331 and working towards the use of surface engineering modification methods to further improve the electrochemical performance.332–334
Replacement of Mn ions
It is evidenced from the previous experimental research that a complete replacement of Mn ions with B216 and W,217 in Ni-rich cathode compositions, has also improved the electrochemical performance. When Mn is replaced with Ta (Li[Ni0.90Co0.09Ta0.01]O2), a newly designed cathode (NCT) exhibits 90% capacity retention after 2000 cycles at full depth of discharge (DOD) and a cathode energy density >850
W h
kg−1.335 LiNi0.90Co0.07Mg0.03O2 microspheres exhibit a high value of capacity (228.3 mA h g−1 at 0.1C) and almost 84.3% capacity retention after 300 cycles.111
Strategies for cost optimization and recovery
Co-free Ni-rich oxides: an approach towards cost-effectiveness
Considering the low abundance and high cost of Co,189,336 efforts are made to design Co-free layered oxides by understanding the role of Co ions.337,338 However, one has to compromise with cumulative capacity and other factors while designing such cathodes.339,340 Various research groups around the globe are working effortlessly towards designing Co-free Ni-rich layered oxide cathodes by replacing Co ions with suitable ions.341,342 This is clear from few studies on the development of LiNi0.9Mn0.05Zn0.05O2 (NMZ955) cathodes,343,344 introduction of Mo Ni-rich oxides345 and Co-free LiNi0.9Mn0.1O2 with lattice Ge-doping and interface Li4GeO4-coating (NMGe).346 Tan et al., designed a Co-free Ni-rich LiNi0.96Mn0.04O2 cathode material (NM) by doping with Al and Zr.347 The synthesized material exhibits better thermal and structural stability than that of the NM material. Lv et al. reported that the replacement of Co with Al and In/Sn prolongs the cycle life of the Ni-rich Co-free cathode (InSn–LiNi0.85Mn0.09Al0.06O2, InSn–NMA85) at a high voltage ≥4.5 V as well as a high temperature (≥45 °C).348 The search for Co-free cathodes is not limited to the Ni-rich materials but they are also adopted to optimize Li-rich NCM cathodes.349,350
Recovery, recycling and reuse of cathodes after cycling
With the rapid development of the EV industry, there is a significant increase in the number of spent power batteries. The recycling of such batteries is profitable and necessary not only to eliminate environment pollution but also to reduce the resource use.351,352 Thus, many efforts are made by the scientific community in this direction. In this context, a novel green process involving natural L-tartaric acid leaching is reported for the sustainable recovery of Mn, Li, Co, and Ni from spent LIBs. For the first stage, the activation energies (Eas) for the leaching of Mn, Li, Co, and Ni were 66.00, 54.03, 58.18, and 73.28 kJ mol−1, respectively. For the second stage, the Eas values for the leaching of Mn, Li, Co, and Ni were 55.68, 53.86, 58.94, and 47.78 kJ mol−1, respectively.353 After single-stage leaching, the spent NCM recovery using NH3–(NH4)2CO3–Na2SO3 leaching has exhibited 79.1% of lithium, 86.4% of cobalt, and 85.3% of nickel. For multistage leaching, almost all metals (98.4% of the lithium, 99.4% of the cobalt, 97.3% of the nickel) could be leached and a high-purity (>99%) MnCO3 product was simultaneously obtained.354 A dual-function electro-oxidation strategy is helpful for highly selective recovery of Li+ from spent NCM batteries. Under the optimal conditions, the selective recovery rate of Li+ exceeded 99%. After electro-oxidation, the electrolyte can be directly heated and concentrated to obtain Li2CO3.355
Perspectives
Fig. 11 summarises the various strategies that are helpful to optimize the NCM cathode materials. Though these strategies are helpful to design cathodes, complexities affecting the battery performance must be overcome to scale up the manufacture of lithium-ion batteries. The pre-preparation process, extreme environments, defective quality, and the risk of lithium volatilization are obstacles. The development of economic and safe LIBs is the need of the hour. Solid-state electrolytes offer a solid interface that mitigates safety risks associated with nickel-rich cathodes. This could lead to the development of safer, more dependable lithium-ion batteries that have an enhanced energy density. Cobalt-free NCM versions are the subject of research to reduce supply chain difficulties and environmental hazards. The development of nickel-rich, cobalt-free NCM batteries marked a significant advancement in lithium-ion battery technology. Although cobalt increases battery efficiency, its scarcity and the geopolitical issues associated with its extraction provide challenges for the environment, ethics, and supply chain. NCM batteries without cobalt provide a sustainable alternative that alleviates these concerns while maintaining the performance and energy density. In order to overcome these obstacles, creative mitigation techniques and a thorough understanding of the underlying degradation mechanisms are needed. To ensure compatibility and optimal battery performance, cobalt-free NCM cathodes must be integrated carefully with other battery components, such as electrolytes and anodes. To improve the performance and safety of cobalt-free NCM batteries, research is done to optimize the electrolyte composition, electrode/electrolyte contact, and cell design. To sum up, nickel-rich, cobalt-free NCM batteries show great potential for the development of lithium-ion battery technology. To overcome lingering obstacles and realize the full potential of these high-performance and sustainable energy storage systems, extensive research and innovation in this area are necessary.
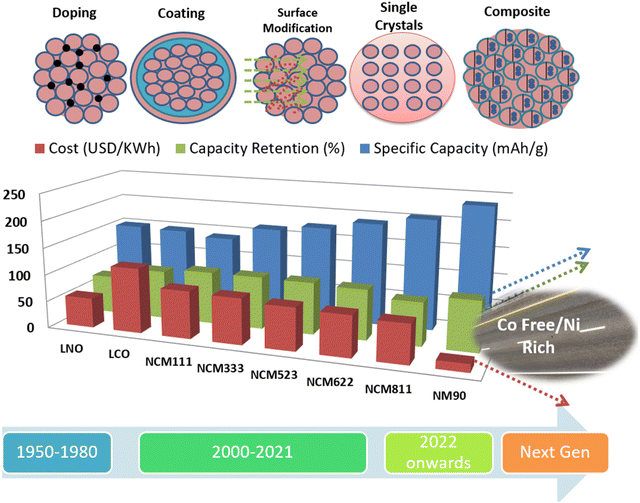 |
| Fig. 11 Strategies for the optimization of NCM cathode materials. | |
Conclusions
This review presents an overview of the opportunities and problems associated with the use of Ni-rich NCM cathodes. Because of the layered structure of these cathodes, intercalation processes result in delithiation and lithiation. High cumulative capacity of the NCM cathode can be achieved by increasing the Ni content, but capacity retention and thermal stability are reduced as a result. This article critically elaborates the effects of doping, coating, morphology, and crystalline orientation on the electrochemical performance of LIBs based on the NCM cathode. These tactics assist in optimizing the Li/Ni disorder and thermal stability in addition to controlling capacity retention. The design of Co-free, Ni-rich NCM cathodes is in progress in order to address the manufacturing cost and demand of LIBs. Furthermore, these batteries may be more successful if different elements are recovered from spent batteries. In the same way, the creation of a thin-film, Co-free, Ni-rich NCM cathode may continue down the path of environmentally friendly technology and a pollution-free atmosphere at a low cost of transportation.
Author's contribution
JPS & SL – conceptualization & funding; JPS – manuscript preparation; HD, AD, AS & WCL – data acquisition & manuscript view; KHC & SL – supervision; manuscript view.
Data availability
Data will be made available on request.
Conflicts of interest
The authors declare no competing financial interests.
Acknowledgements
JPS is thankful to Science and Engineering Research Board, New Delhi for providing financial support via research grant RJF2021/000115. This work was supported by the National Research Foundation of Korea (NRF) grant funded by the Korea government (MSIT) (NRF-2020M3H4A3081917).
References
- M. Fichtner, K. Edström, E. Ayerbe, M. Berecibar, A. Bhowmik, I. E. Castelli, S. Clark, R. Dominko, M. Alejandro, A. Franco, A. Grimaud, B. Horstmann, A. Latz, H. Lorrmann, M. Meeus, R. Narayan, F. Pammer, J. Ruhland, H. Stein, T. Vegge and M. Weil, Adv. Energy Mater., 2022, 12, 2102904 CrossRef CAS.
- J. Xiao, F. Shi, T. Glossmann, C. Burnett and Z. Liu, Nat. Energy, 2023, 8, 329 CrossRef.
- C. P. Grey and D. S. Hall, Nat. Commun., 2020, 11, 6279 CrossRef CAS PubMed.
- Y. Liang, C.-Z. Zhao, H. Yuan, Y. Chen, W. Zhang, J.-Q. Huang, D. Yu, Y. Liu, M.-M. Titirici, Y.-L. Chueh, H. Yu and Q. Zhang, InfoMat, 2019, 1, 6 CrossRef CAS.
- A. G. Olabi, Q. Abbas, P. A. Shinde and M. A. Abdelkareem, Energy, 2023, 266, 126408 CrossRef CAS.
- Y. Ding, Z. P. Cano, A. Yu, J. Lu and Z. Chen, Electrochem. Energy Rev., 2019, 2, 1 CrossRef CAS.
- G. Zubi, R. Dufo-López, M. Carvalho and G. Pasaoglu, Renewable Sustainable Energy Rev., 2018, 89, 292 CrossRef.
- W. Lee, S. Muhammad, C. Sergey, H. Lee, J. Yoon, Y.-M. Kang and W.-S. Yoon, Angew. Chem., Int. Ed., 2020, 59, 2578 CrossRef CAS PubMed.
- Y. K. Sun, ACS Energy Lett., 2019, 4, 1042 CrossRef CAS.
- T. Chen, Y. Jin, H. Lv, A. Yang, M. Liu, B. Chen, Y. Xie and Q. Chen, Trans. Tianjin Univ., 2020, 26, 208 CrossRef.
- R. Kakodkar, G. He, C. D. Demirhan, M. Arbabzadeh, S. G. Baratsas, S. Avraamidou, D. Mallapragada, I. Miller, R. C. Allen, E. Gençer and E. N. Pistikopoulos, Renewable Sustainable Energy Rev., 2022, 160, 112277 CrossRef CAS.
- J. Furch, V. Konečný and Z. Krobot, Sci. Rep., 2022, 12, 10661 CrossRef CAS.
- J. Wang, H. Li, N. Xu and J. Qiao, Ionics, 2018, 24, 3877 CrossRef CAS.
- Y. E. Durmus, H. Zhang, F. Baakes, G. Desmaizieres, H. Hayun, L. Yang, M. Kolek, V. Küpers, J. Janek, D. Mandler, S. Passerini and Y. E. Eli, Adv. Energy Mater., 2020, 10, 2000089 CrossRef CAS.
- L. Ma, M. A. Schroeder, O. Borodin, T. P. Pollard, M. S. Ding, C. Wang and K. Xu, Nat. Energy, 2020, 5, 743 CrossRef CAS.
- R. Boraha, F. R. Hughson, J. Johnstona and T. Nanna, Mater. Today Adv., 2020, 6, 100046 CrossRef.
- C. H. Lee, Z. Y. Wu, S. H. Hsu and J. A. Jiang, IEEE Trans. Energy Conv., 2000, 35, 1475 Search PubMed.
- A. E. Kharbachi, O. Zavorotynsk, M. Latroche, F. Cuevas, V. Yartys and M. Fichtner, J. Alloys Compd., 2020, 817, 153261 CrossRef.
- G. F. May, A. Davidson and B. Monahov, J. Energy Storage, 2018, 15, 145 CrossRef.
- J. Liu, C. Xu, Z. Chena, S. Ni and Z. X. Shen, Green Energy Environ., 2018, 3, 20 CrossRef.
- Z. Ma, D. R. MacFarlane and M. Kar, Batteries Supercaps, 2019, 2, 115 CrossRef.
- R. J. Gummow, G. Vamvounis, M. B. Kannan and Y. He, Adv. Mater., 2018, 30, 1801702 CrossRef.
- T. Hosaka, K. Kubota, S. Hameed and S. Komaba, Chem. Rev., 2020, 120, 6358 CrossRef CAS.
- K. Zhang, K. Zhang, K. O. Kirlikovali, J. M. Suh, J.-W. Choi, H. W. Jang, R. S. Varma, O. K. Farha and M. Shokouhimehr, ACS Appl. Energy Mater., 2020, 3, 6019 CrossRef CAS.
- M. A. Zelinsky, J. M. Koch and K.-H. Young, Batteries, 2018, 4, 1 CrossRef.
-
S. Arya and S. Verma, in Rechargeable Batteries, ed. R.Boddula, Inamuddin, R. Pothu and A. M. Asiri, 2020, p. 131 Search PubMed.
- J. Xie and Y.-C. Lu, Nat. Commun., 2020, 11, 2499 CrossRef CAS PubMed.
- J. Ming, J. Guo, C. Xia, W. Wang and H. N. Alshareef, Mater. Sci. Eng., R, 2019, 135, 58 CrossRef.
- A. Manthiram, Nat. Commun., 2020, 11, 1550 CrossRef CAS PubMed.
- C. Iclodean, B. Varga, N. Burnete, D. Cimerdean and B. Jurchiş, IOP Conf. Ser.: Mater. Sci. Eng., 2017, 252, 012058 Search PubMed.
- L. Ghadbeigi, J. K. Harada, B. R. Lettiere and T. D. Sparks, Energy Environ. Sci., 2015, 8, 1640 RSC.
- N. Li, M. Sun, W. H. Kan, Z. Zhuo, S. Hwang, S. E. Renfrew, M. Avdeev, A. Huq, B. D. McCloskey, D. Su, W. Yang and W. Tong, Nat. Commun., 2021, 12, 2348 CrossRef CAS PubMed.
- L.-X. Yuan, Z.-H. Wang, W.-X. Zhang, X.-L. Hu, J.-T. Chen, Y.-H. Huang and J. B. Goodenough, Energy Environ. Sci., 2011, 4, 269 RSC.
- B. Wang, F.-L. Zhang, X.-A. Zhou, P. Wang, J. Wang, H. Ding, H. Dong, W.-B. Liang, N.-S. Zhang and S.-Y. Li, J. Mater. Chem. A, 2021, 9, 13540 RSC.
- B. Chua, Y.-J. Guo, J.-L. Shi, Y. X. Yin, T. Huang, H. Su, A. Yu, Y.-G. Guo, Y. Lie, F. Wu and G. Yushin, Energy Environ. Sci., 2017, 10, 435 RSC.
- H. Chang, Y.-R. Wu, X. Han and T.-F. Yi, Energy Mater., 2021, 1, 100003 CrossRef CAS.
-
C. Kim and M. Endo, Anode Performance of the Li-Ion Secondary Battery, in Design and Control of Structure of Advanced Carbon Materials for Enhanced Performance, ed. B. Rand, S. P. Appleyard and M. F. Yardim, NATO Science Series, Springer, Dordrecht, 2001, vol. 374 DOI:10.1007/978-94-010-1013-9_15.
- K.-H. Nam, S. Jeong, B.-C. Yu, J.-H. Choi, K.-J. Jeon and C. M. Park, ACS Nano, 2022, 16, 13704 CrossRef CAS PubMed.
- D. Li, F. Chu, Z. He, Y. Cheng and F. Wu, Mater. Today, 2022, 58, 80 CrossRef CAS.
- T. Khan, A. K. Garg, A. Gupta, A. K. Madan and P. K. Jain, J. Energy Storage, 2023, 57, 106204 CrossRef.
- K. Xu, Nat. Energy, 2021, 6, 763 CrossRef CAS.
- C. Sun, X. Liao, F. Xia, Y. Zhao, L. Zhang, S. Mu, S. Shi, Y. Li, H. Peng, G. V. Tendeloo, K. Zhao and J. Wu, ACS Nano, 2020, 14, 6181 CrossRef CAS PubMed.
- P. G. Bruce, A. R. Armstrong and H. Huang, J. Power Sources, 1997, 68, 19 CrossRef CAS.
- J. Xiu, J. Wang, Y. Ni, Y. Zhang, J. Luo, F. Cheng and J. Chen, Small Methods, 2019, 3, 1900350 CrossRef.
- C. S. Yoon and U.-H. Kim, ACS Energy Lett., 2018, 3, 1634 CrossRef CAS.
- W. Zhang, J. Power Sources, 2011, 196, 2962 CrossRef CAS.
- W. C. Chien, J. S. Jhang, S. H. Wu, Z. H. Wu and C. C. Yang, J. Alloys Compd., 2020, 847, 156447 CrossRef CAS.
- G. Liang, V. K. Peterson, K. W. See, Z. Guo and W. K. Pang, J. Mater. Chem. A, 2000, 8, 15373 RSC.
- S. Vadivel, N. Phattharasupakun, J. Wutthiprom, S. Duangdangchote and M. Sawangphruk, ACS Appl. Mater. Interfaces, 2019, 11, 30719 CrossRef CAS.
- S.-J. Kwon, S.-E. Lee, J.-H. Lim, J. Choi and J. Kim, Electronics, 2018, 7, 406 CrossRef CAS.
- T. Nemeth, P. Schroer, M. Kuipers and D. U. Sauer, J. Energy Storage, 2020, 31, 101656 CrossRef.
- X.-Q. Zhang, C. Liu, Y. Gao, J.-M. Zhang and Y.-Q. Wang, NANO, 2020, 15, 2030002 CrossRef CAS.
- N. Imanishi and O. Yamamoto, Mater. Today Adv., 2019, 4, 100031 CrossRef.
- L. Long, S. Wang, M. Xiao and Y. Meng, J. Mater. Chem. A, 2016, 4, 10038 RSC.
- J. M. Amanor-Boadu and A. Guiseppi-Elie, Appl. Sci., 2020, 10, 895 CrossRef CAS.
- J. B. Bates, N. J. Dudney, B. Neudecker, A. Ueda and C. D. Evans, Solid State Ionics, 2000, 135, 33 CrossRef CAS.
- J. P. Singh, Prabha Mater. Sci. Lett., 2022, 2, 26 Search PubMed.
- Y. Lu, Z. Wang, M. Li, Z. Li, X. Hu, Q. Xu, Y. Wang, H. Liu and Y. Wang, Adv. Funct. Mater., 2023, 2310966 Search PubMed.
- C. Sun, J. Liu, Y. Gong, D. P. Wilkinson and J. Zhang, Nano Energy, 2017, 33, 363 CrossRef CAS.
- A. Van der Ven, J. Bhattacharya and A. A. Belak, Acc. Chem. Res., 2013, 46, 1216 CrossRef CAS PubMed.
- T. Schied, A. Nickol, C. Heubner, M. Schneider, A. Michaelis, M. Bobeth and G. Cuniberti, ChemPhysChem, 2021, 22, 885–893 CrossRef CAS PubMed.
- M. Ahangari, B. Szalai, J. Lujan, M. Zhou and H. Luo, Materials, 2024, 17, 801 CrossRef CAS.
- A. Butt, G. Ali, K. T. Kubra, R. Sharif, A. Salman, M. Bashir and S. Jamil, Energy Technol., 2022, 10, 2100775 CrossRef CAS.
- J. Yang, X. Liang, H.-H. Ryu, C. S. Yoon and Y.-K. Sun, Energy Storage Mater., 2023, 63, 102969 CrossRef.
- J. Kim, H. Lee, H. Cha, M. Yoon, M. Park and J. Cho, Adv. Energy Mater., 2018, 8, 1702028 CrossRef.
- S. S. Zhang, Energy Storage Mater., 2020, 24, 247 CrossRef.
- A. Manthiram, B. Song and W. Li, Energy Storage Mater., 2017, 6, 125 CrossRef.
- A. Rajkamal, A. Sharma, B. K. Pullagura, R. Thapa and H. Kim, Chem. Eng. J., 2024, 481, 148223 CrossRef CAS.
- A. Sakti, J. J. Michalek, E. R. H. Fuchs and J. F. Whitacre, J. Power Sources, 2015, 273, 966 CrossRef CAS.
- N. Zhang, Z. Xu, W. Deng and X. Wang, Recycling and Upcycling Spent LIB Cathodes: A Comprehensive Review, Electrochem. Energy Rev., 2022, 33, 5 Search PubMed.
- A. Chakraborty, M. Dixit, D. Aurbach and D. T. Major, npj Comput. Mater., 2018, 4, 60 CrossRef.
- D. Luo, H. Zhu, Y. Xia, Z. Yin, Y. Qin, T. Li, Q. Zhang, L. Gu, Y. Peng, J. Zhang, K. M. Wiaderek, Y. Huang, T. Yang, Y. Tang, S. Lan, Y. Ren, W. Lu, C. M. Wolverton and Q. Liu, Nat. Energy, 2023, 8, 1078 CrossRef CAS.
- Z.-X. Huang, X.-L. Zhang, X.-X. Zhao, Y.-L. Heng, T. Wang, H. Geng and X.-L. Wu, Sci. China: Mater., 2023, 66, 79 CrossRef CAS.
- Z.-Y. Gu, X.-T. Wang, Y.-L. Heng, K.-Y. Zhang, H.-J. Liang, J.-L. Yang, E. H. Ang, P.-F. Wang, Y. You, F. Du and X.-L. Wu, Sci. Bull., 2023, 68, 2302 CrossRef CAS.
- Z.-X. Huang, X.-L. Zhang, X.-X. Zhao, H.-Y. Lü, X.-Y. Zhang, Y.-L. Heng, H. Geng and X.-L. Wu, J. Mater. Sci. Technol., 2023, 160, 9 CrossRef CAS.
- T.-T. Wei, X. Liu, S.-J. Yang, P.-F. Wang and T.-F. Yi, J. Energy Chem., 2023, 80, 603 CrossRef CAS.
- X. Niu, J. Qu, Y. Hong, L. Deng, R. Wang, M. Feng, J. Wang, L. Zeng, Q. Zhang, L. Guo and Y. Zhu, J. Mater. Chem. A, 2021, 9, 13125 RSC.
- P. K. Jha, S. N. Totade, P. Barpanda and G. S. Gautam, Inorg. Chem., 2023, 62, 14971 CrossRef CAS PubMed.
- Z.-L. Xu, J. Park, J. Wang, H. Moon, G. Yoon, J. Lim, Y.-J. Ko, S.-P. Cho, S.-Y. Lee and K. Kang, Nat. Commun., 2021, 12, 3369 CrossRef CAS PubMed.
- H. Song and C. Wang, Adv. Energy Sustainable Res., 2022, 3, 2100192 CrossRef CAS.
- A. Chakraborty, S. Kunnikuruvan, S. Kumar, B. Markovsky, D. Aurbach, M. Dixit and D. T. Major, Chem. Mater., 2020, 32, 915 CrossRef CAS.
- X. Zheng, Z. Cai, J. Sun, J. He, W. Rao, J. Wang, Y. Zhang, Q. Gao, B. Han, K. Xia, R. Sun and C. Zhou, J. Energy Storage, 2023, 58, 106405 CrossRef.
- M. Wang and A. Navostsky, J. Solid State Chem., 2005, 178, 1230 CrossRef CAS.
- S. Laubach, S. Laubach, P. C. Schmidt, D. Ensling, S. Schmid, W. Jaegermann, A. Thiben, K. Nikolowski and H. Ehrenberg, Phys. Chem. Chem. Phys., 2009, 11, 3278 RSC.
- M. Tabuchi and R. Kataoka, J. Electrochem. Soc., 2019, 166, A2209 CrossRef CAS.
- K. Hoang, Phys. Rev. Appl., 2015, 3, 024013 CrossRef CAS.
- P. He, H. Yu, D. Li and H. Zhou, J. Mater. Chem., 2012, 22, 3680 RSC.
- M. M. Thackeray, J. Electrochem. Soc., 1995, 142, 2558 CrossRef CAS.
- L. D. Dyer, B. S. Borie and G. P. Smith, J. Am. Chem. Soc., 1954, 76, 1499 CrossRef CAS.
- M. Bianchini, M. Roca-Ayats, P. Hartmann, T. Brezesinski and J. Janek, Angew. Chem., 2019, 58, 10434 CrossRef CAS PubMed.
- I. Nakai, K. Takahashi, Y. Shiraishi, T. Nakagome and F. Nishikawa, J. Solid State Chem., 1998, 140, 145 CrossRef CAS.
- S. Sicolo, M. Mock, M. Bianchini and K. Albe, Chem. Mater., 2020, 32, 10096 CrossRef CAS.
- A. R. Genreith-Schriever, A. Alexiu, G. S. Phillips, C. S. Coates, L. A. V. Nagle-Cocco, J. D. Bocarsly, F. N. Sayed, S. E. Dutton and C. P. Grey, Chem. Mater., 2024, 36, 2289 CrossRef CAS PubMed.
- R. Prasad, R. Benedek, A. J. Kropf, C. S. Johnson, A. D. Robertson, P. G. Bruce and M. M. Thackeray, Phys. Rev. B: Condens. Matter Mater. Phys., 2003, 68, 012101 CrossRef.
- Z. Xiao, F. Xia, L. Xu, X. Wang, J. Meng, H. Wang, X. Zhang, L. Geng, J. Wu and L. Mai, Adv. Funct. Mater., 2022, 32, 2108244 CrossRef CAS.
- A. Manthiram, J. C. Knight, S.-T. Myung, S.-M. Oh and Y.-K. Sun, Adv. Energy Mater., 2016, 6, 1501010 CrossRef.
- Y. Sun, P. Wan, J. Pan, C. Xu and X. Liu, Solid State Ionics, 2016, 177, 1173 CrossRef.
- L. Tang, G. Li, P. Xiao, X. Chen and W. Yang, RSC Adv., 2019, 9, 9079 RSC.
- K. Zhu, T. Wu, Y. Zhu, X. Li, M. Li, R. Lu, J. Wang, X. Zhu and W. Yang, ACS Energy Lett., 2017, 2, 1654 CrossRef CAS.
- H. Li, Q. Xu, X.-X. Shi, D.-W. Song and L.-Q. Zhang, Rare Met., 2015, 34, 580 CrossRef CAS.
- H.-W. Ha, K. Hee and J. K. Kim, J. Power Sources, 2016, 161, 606 CrossRef.
- N. Murali, K. V. Babu, K. E. Babu and V. Veeraiah, Chem. Sci. Trans., 2015, 4, 1031 CAS.
- S. N. Kwon, M. Y. Song and H. R. Park, Ceram. Int., 2014, 40, 14141 CrossRef CAS.
- B. V. R. Chowdari, G. V. Subba Rao and S. Y. Chow, Solid State Ionics, 2001, 140, 55 CrossRef CAS.
- J. Kim, B. H. Kim, Y. H. Baik, P. K. Chang, H. S. Park and K. Amine, J. Power Sources, 2006, 158, 641 CrossRef CAS.
- H. S. Ko, J. H. Kim, J. Wang and J. D. Lee, J. Power Sources, 2017, 372, 107 CrossRef CAS.
- W. Chen, Y. Li, D. Yang, X. Feng, X. Guan and L. Mi, Electrochim. Acta, 2016, 190, 932 CrossRef CAS.
- Z. Liua, A. Yua and J. Y. Lee, J. Power Sources, 1999, 81–82, 416 CrossRef.
- A. R. Armstrong and P. G. Bruce, Nature, 1996, 381, 499 CrossRef CAS.
- Y. Zuo, B. Li, N. Jiang, W. Chu, H. Zhang, R. Zou and D. Xia, Adv. Mater., 2018, 30, 1707255 CrossRef PubMed.
- Y. Xiang and X. Wu, Ionics, 2018, 24, 83 CrossRef CAS.
- H. Li, P. Zhou, F. Liu, H. Li, F. Cheng and J. Chen, Chem. Sci., 2019, 10, 1374 RSC.
- S. Chen, X. Zhang, M. Xia, K. Wei, L. Zhang, X. Zhang, Y. Cui and J. Shu, J. Electroanal. Chem., 2021, 895, 115412 CrossRef CAS.
-
Y. Chen and Y. Liu, 2019. Development of Lithium Nickel Cobalt Manganese Oxide as Cathode Material for Commercial Lithium-Ion Batteries, in Nanostructured Materials for Next-Generation Energy Storage and Conversion, ed. Q. Zhen, S. Bashir, J. Liu, Springer, Berlin, Heidelberg DOI:10.1007/978-3-662-58675-4_8.
- M. M. Thackeray and K. Amine, Nat. Energy, 2021, 6, 933 CrossRef CAS.
- C. S. Yoon, M. Ho Choi, B.-B. Lim, E.-J. Lee and Y.-K. Sun, J. Electrochem. Soc., 2015, 162, A2483 CrossRef CAS.
- M. A. Kebede, Curr. Opin. Electrochem., 2023, 39, 101261 CrossRef CAS.
- D. Kwak, W.-G. Lim, K. Shin, I. W. Cheong, J. Lee and J. Joo, Korean J. Chem. Eng., 2020, 37, 1258 CrossRef CAS.
- F.-F. Wang, Y.-R. Ji, Y.-H. Chen, P.-F. Wang, Q.-Z. Lai, F. Qiu, Y.-R. Zhu and T.-F. Yi, J. Colloid Interface Sci., 2023, 652, 577 CrossRef CAS PubMed.
- F. Lin, I. M. Markus, D. Nordlund, T.-C. Weng, M. D. Asta, H. L. Xin and M. M. Doeff, Nat. Commun., 2014, 5, 3529 CrossRef PubMed.
- W. Sha, Y. Guo, D. Cheng, Q. Han, P. Lou, M. Guan, S. Tang, X. Zhang, S. Lu, S. Cheng and Y.-C. Cao, npj Comput. Mater., 2022, 8, 223 CrossRef CAS.
- Y. Xia, J. Zheng, C. Wang and M. Gu, Nano Energy, 2018, 49, 434 CrossRef CAS.
- J. Lin, Z. Chen, M. Li, J. Luo, B. Wu, S. C. Cao and W. J. Li, Mater. Today Commun., 2023, 36, 106701 CrossRef CAS.
- L. de Biasi, B. Schwarz, T. Brezesinski, P. Hartmann, J. Janek and H. Ehrenberg, Adv. Mater., 2019, 31, 1900985 CrossRef PubMed.
- H. Gupta and R. K. Singh, ChemElectroChem, 2020, 7, 3597 CrossRef CAS.
- U.-H. Kim, D.-W. Jun, K.-J. Park, Q. Zhang, P. Kaghazchi, D. Aurbach, D. T. Major, G. Goobes, M. Dixit, N. Leifer, C. M. Wang, P. Yan, D. Ahn, K.-H. Kim, C. S. Yoon and Y.-K. Sun, Environ. Sci., 2018, 11, 1271 CAS.
- S. M. Bak, E. Hu, Y. Zhou, X. Yu, S. D. Senanayake, S. J. Cho, K. B. Kim, K. Y. Chung, X. Q. Yang and K. W. Nam, ACS Appl. Mater. Interfaces, 2014, 6, 22594 CrossRef CAS PubMed.
- H.-H. Ryu, K.-J. Park, C. S. Yoon and Y.-K. Sun, Chem. Mater., 2018, 30, 1155 CrossRef CAS.
- U.-H. Kim, L.-Y. Kuo, P. Kaghazchi, C. S. Yoon and Y.-K. Sun, ACS Energy Lett., 2019, 4, 576 CrossRef CAS.
- D. Pritzl, T. Teufl, A. T. S. Freiberg, B. Strehle, J. Sicklinger, H. Sommer, P. Hartmann and H. A. Gasteiger, J. Electrochem. Soc., 2019, 166, A4056 CrossRef CAS.
- D. Ren, Y. Yang, L. Shen, R. Zeng and H. D. Abruña, J. Power Sources, 2020, 447, 227344 CrossRef CAS.
- S.-H. Lee, S. Lee, B.-S. Jin and H.-S. Kim, Sci. Rep., 2019, 9, 8901 CrossRef PubMed.
- Z. Yu, X. Qu, T. Wan, A. Dou, Y. Zhou, X. Peng, M. Su, Y. Liu and D. Chu, ACS Appl. Mater. Interfaces, 2020, 12, 40393 CrossRef CAS PubMed.
- X. Liu, G.-L. Xu, L. Yin, I. Hwang, Y. Li, L. Lu, W. Xu, X. Zhang, Y. Chen, Y. Ren, C.-J. Sun, Z. Chen, M. Ouyang and K. Amine, J. Am. Chem. Soc., 2020, 142, 19745 CrossRef CAS PubMed.
- S. H. Song, M. Cho, I. Park, J.-G. Yoo, K.-T. Ko, J. Hong, J. Kim, S.-K. Jung, M. Avdeev, S. Ji, S. Lee, J. Bang and H. Kim, Adv. Energy Mater., 2020, 10, 2000521 CrossRef CAS.
- Y.-T. Tsai, C.-Y. Wu and J.-G. Duh, Electrochim. Acta, 2021, 381, 138244 CrossRef CAS.
- G. Yang, X. Qin, B. Wang, F. Cai and J. Gao, J. Mater. Res., 2020, 35, 51 CrossRef CAS.
- J. P. Singh, J. Y. Park, K. H. Chae, D. Ahn and S. Lee, Nanomaterials, 2020, 10, 759 CrossRef CAS PubMed.
- L. de Biasi, A. O. Kondrakov, H. Geßwein, T. Brezesinski, P. Hartmann and J. Janek, J. Phys. Chem. C, 2017, 121, 26163 CrossRef CAS.
- L. de Biasi, B. Schwarz, T. Brezesinski, P. Hartmann, J. Janek and H. Ehrenberg, Adv. Mater., 2019, 31, 190035 CrossRef PubMed.
- W. Li, J. N. Reimers and J. R. Dahn, Solid State Ionics, 1993, 67, 123 CrossRef CAS.
- P. Rozier and J. M. Tarascon, J. Electrochem. Soc., 2015, 162, A2490 CrossRef CAS.
- C. Delmas, C. Fouassier and P. Hagenmuller, Phys. B+C, 1980, 99, 81 CrossRef CAS.
- J.-M. Lim, T. Hwang, D. Kim, M.-S. Park, K. Cho and M. Cho, Sci. Rep., 2021, 7, 39669 CrossRef PubMed.
- H. Sun and K. Zhao, J. Phys. Chem. C, 2017, 121, 6002 CrossRef CAS.
- W. Lee, S. Muhammad, T. Kim, H. Kim, E. Lee, M. Jeong, S. Son, J.-H. Ryou and W.-S. Yoon, Adv. Energy Mater., 2018, 8, 1701788 CrossRef.
- M. Gu, I. Belharouak, J. Zheng, H. Wu, J. Xiao, A. Genc, K. Amine, S. Thevuthasan, D. R. Baer, J.-G. Zhang, N. D. Browning, J. Liu and C. Wang, ACS Nano, 2013, 7, 760 CrossRef CAS PubMed.
- S. Choi and A. Manthiram, J. Electrochem. Soc., 2002, 149, A1157 CrossRef CAS.
- Y. Liu, H.-X. Zhuo, Y.-P. Yin, S.-G. Lu, Z.-Y. Wang and W.-D. Zhuang, ACS Appl. Mater. Interfaces, 2020, 12, 27226 CrossRef CAS PubMed.
- E.-Y. Hu, X.-L. Wang, X.-Q. Yu and X.-Q. Yang, Acc. Chem. Res., 2018, 51, 290 CrossRef CAS PubMed.
- C. Tian, F. Lin and M. M. Doeff, Acc. Chem. Res., 2018, 51, 89 CrossRef CAS PubMed.
- B. L. D. Rinkel, D. S. Hall, I. Temprano and C. P. Grey, J. Am. Chem. Soc., 2020, 142, 15058 CrossRef CAS PubMed.
- X. Liu, D.-S. Ren, H.-J. Hsu, X.-N. Feng, G.-L. Xu, M.-H. Zhuang, H. Gao, L.-G. Lu, X.-B. Han, Z.-G. Chu, J.-Q. Li, X.-M. He, K. Amine and M.-G. Ouyang, Joule, 2018, 2, 2047 CrossRef CAS.
- K. Nakayama, R. Ishikawa, S. Kobayashi, N. Shibata and Y. Ikuhara, Nat. Commun., 2020, 11, 4452 CrossRef CAS PubMed.
- S.-C. Li, Y.-Y. Liu, Y.-G. Zhang, W. He, H.-F. Zheng, W.-B. Guo, H.-L. Wu, G.-Y. Gao, B.-S. Sa, L.-S. Wang, Q.-S. Xie, J. Lin, J. Shi and D.-L. Peng, Chem. Eng. J., 2023, 462, 142194 CrossRef CAS.
- C. Xu, P. J. Reeves, Q. Jacquet and C. P. Grey, Adv. Energy Mater., 2012, 11, 20212003404 Search PubMed.
- L. Ma, M. Nie, J. Xia and J. R. Dahn, J. Power Sources, 2016, 327, 145 CrossRef CAS.
-
H. Kim, S.-M. Oh, B. Scrosati and Y.-K. Sun, in Advances in Battery Technologies for Electric Vehicles, ed. B. Scrosati, J. Garche and W. Tillmetz, Woodhead Publ., 2015, pp. 191–233 Search PubMed.
- K.-S. Lee, S.-T. Myung, K. Amine, H. Yashiro and Y.-K. Sun, J. Electrochem. Soc., 2007, 154, A971 CrossRef CAS.
- J. Zheng, Y. Ye, T. Liu, Y. Xiao, C. Wang, F. Wang and F. Pan, Acc. Chem. Res., 2019, 52, 2201 CrossRef CAS PubMed.
- D. Wang, C. Xin, M. Zhang, J. Bai, J. Zheng, R. Kou, J. Y. P. Ko, A. Huq, G. Zhong, C.-J. Sun, Y. Yang, Z. Chen, Y. Xiao, K. Amine, F. Pan and F. Wang, Chem. Mater., 2019, 31, 2731 CrossRef CAS.
- K. Märker, P. J. Reeves, C. Xu, K. J. Griffith and C. P. Grey, Chem. Mater., 2019, 31, 2545 CrossRef.
- K. Kang and G. Ceder, Phys. Rev. B: Condens. Matter Mater. Phys., 2006, 74, 94105 CrossRef.
- J. Cui, X. Ding, D. Luo, H. Xie, Z. Zhang, B. Zhang, F. Tan, C. Liu and Z. Lin, Energy Fuels, 2021, 35, 1842 CrossRef CAS.
- E. D. Orlova, A. A. Savina, S. A. Abakumov, A. V. Morozov and A. M. Abakumov., Symmetry, 2021, 13, 1628 CrossRef CAS.
- J. Li, G. Liang, W. Zheng, S. Zhang, K. Davey, W. K. Pang and Z. Guo, Nano Mater. Sci., 2023, 5, 404 CrossRef CAS.
- Y. Lei, J. Ai, S. Yang, H. Jiang, C. Lai and Q. Xu, J. Alloys Compd., 2019, 797, 421 CrossRef CAS.
- H.-J. Noh, S. Youn, C. S. Yoon and Y.-K. Sun, J. Power Sources, 2013, 233, 121 CrossRef CAS.
- W. Li, E. M. Erickson and A. Manthiram, Nat. Energy, 2020, 5, 26 CrossRef CAS.
- R. Shah, B. Gashi, S. G. Poggini, M. C. Lagrille and A. Rosenkranz, Adv. Mech. Eng., 2021, 13, 1 Search PubMed.
- R. N. Ramesha, D. Bosubabu, M. G. Karthick Babu and K. Ramesha, ACS Appl. Energy Mater., 2020, 3, 10872 CrossRef CAS.
- S. K. Martha, O. Haik, E. Zinigrad, I. Exnar, T. Drezen, J. H. Miners and D. Aurbach, J. Electrochem. Soc., 2011, 158, A1115 CrossRef CAS.
- Y. Xia, T. Fujieda, K. Tatsumi, P. P. Prosini and T. Sakai, J. Power Sources, 2001, 92, 234 CrossRef CAS.
- Y. Huang, Y.-C. Lin, D. M. Jenkins, N. A. Chernova, Y. Chung, B. Radhakrishnan, I.-H. Chull, J. Fang, Q. Wang, F. Omenya, S. P. Ong and M. S. Whittingham, ACS Appl. Mater. Interfaces, 2016, 8, 7013 CrossRef CAS PubMed.
- Y. Sun, D. Ren, G. Liu, D. Mu, L. Wang, B. Wu, J.-H. Liu, N.-N. Wu and X. He, J. Energy Res., 2021, 45, 20867 CAS.
- Y. Yoshimoto, T. Toma, K. Hongo, K. Nakano and R. Maezono, ACS Appl. Mater. Interfaces, 2022, 14, 23355 CrossRef CAS PubMed.
- Y. Lin, C. M. Abram, X. Shi, I. G. McKendry, Z. Wang, H. Zhong, H. Zhao, X. Yang, B. E. Koel, C. Yan and Y. Ju, ACS Appl. Energy Mater., 2022, 5, 10751 CrossRef CAS.
- F. Lou, Q. Xie, X. Luo, Y. Xie, M. Wang, H. Hao, Z. Wang, L. Yang, G. Wang, J. Chen and G. Wang, Ind. Eng. Chem. Res., 2022, 61, 4588 CrossRef CAS.
- S. Komagata, Y. Itou and H. Kondo, ACS Appl. Mater. Interfaces, 2022, 14, 8931 CrossRef CAS PubMed.
- L. Jiang, Q. Wang and J. Sun, J. Hazard. Mater., 2018, 351, 260 CrossRef CAS PubMed.
- Y. Wang, D. Ren, X.-N. Feng, L. Wang and M. Ouyang, J. Power Sources, 2021, 514, 230582 CrossRef CAS.
- R. Schmuch, R. Wagner, G. Hörpel, T. Placke and M. Winter, Nat. Energy, 2018, 3, 267–278 CrossRef CAS.
- A. König, L. Nicoletti, D. Schröder, S. Wolff, A. Waclaw and M. Lienkamp, World Electr. Veh. J., 2021, 12, 21 CrossRef.
- M. Wentker, M. Greenwood and J. Leker, Energies, 2019, 12, 504 CAS.
-
N. Susarla and A. Shabbir, OSTI.GOV: Technical Report: Estimating the cost and energy demand of producing lithium manganese oxide for Li-ion batteries DOI:10.2172/1607686.
- S. W. D. Gourley, T. Or and Z. Chen, iScience, 2020, 23, 101505186 CrossRef PubMed.
- C. Xu, Q. Dai, L. Gaines, M. Hu, A. Tukker and B. Steubing, Commun. Mater., 2020, 1, 99 CrossRef.
- A. Zeng, W. Chen, K. D. Rasmussen, X. Zhu, M. Lundhaug, D. B. Müller, J. Tan, J. K. Keiding, L. Liu, T. Dai, A. Wang and G. Liu, Nat. Commun., 2022, 13, 1341 CrossRef CAS PubMed.
- L. Britala, M. Marinaro and G. Kucinskis, J. Energy Storage, 2023, 73, 108875 CrossRef.
- C. M. Julien and A. Mauger, Energies, 2020, 13, 6363 CrossRef CAS.
- Z. He, M. Zhang, K. Zhou, Y. Cheng, M. Luo, Y. Su, J. Hao, Y. Sun, Y. Li and Y. Yang, ACS Appl. Energy Mater., 2023, 6, 3422 CrossRef CAS.
- S. Ahmed, P. A. Nelson, K. G. Gallagher, N. Susarla and D. W. Dees, J. Power Sources, 2017, 342, 733 CrossRef CAS.
- J. Zhang, Q. Guo, S. Liu, C. Zhou, Z. Huang and D. Han, J. Energy Storage, 2024, 80, 110201 CrossRef.
- T. Hatsukade, A. Schiele, P. Hartmann, T. Brezesinski and J. Janek, ACS Appl. Mater. Interfaces, 2018, 10, 38892 CrossRef CAS PubMed.
- H. Y. Asl and A. Manthiram, Science, 2020, 369, 140 CrossRef CAS PubMed.
- X. Zhang, Z. Cui, E. Jo and A. Manthiram, Energy Storage Mater., 2023, 56, 562 CrossRef.
- A. K. Paidi, A. T. Lee, V. K. Paidi, H. Ahn, J. Lim, K.-S. Lee, S. Lee and D. Ahn, J. Mater. Chem. A, 2023, 11, 12002 RSC.
- L. Fang, D. Han, S. Kang, U.-S. Heo, K.-W. Nam and Y.-M. Kang, Energy Environ. Sci., 2023, 16, 3053 RSC.
- F. Wu, J. Dong, L. Chen, L. Bao, N. Li, D. Cao, Y. Lu, R. Xue, N. Liu, L. Wei, Z. Wang, S. Chen and Y. Su, Energy Storage Mater., 2001, 41, 495 CrossRef.
- Y. Zou, Q. Zheng, Y. Tang, Y. Yan, S. Zhou, H.-G. Liao, Y. Qiao, J. Bao and S.-G. Sun, Chem. Eng. J., 2024, 488, 151153 CrossRef CAS.
- B. Rowden and N. Garcia-Araez, Energy Rep., 2020, 6, 10 CrossRef.
- J. Zahnow, T. Bernges, A. Wagner, N. Bohn, J. R. Binder, W. G. Zeier, M. T. Elm and J. Janek, ACS Appl. Energy Mater., 2021, 4, 1335 CrossRef CAS.
- Y. Zheng, N. Xu, S. Chen, Y. Liao, G. Zhong, Z. Zhang and Y. Yang, ACS Appl. Energy Mater., 2020, 8, 2837 CrossRef.
- S. S. Zhang, J. Energy Chem., 2020, 41, 135 CrossRef.
- X. Fan, B. Zhang, X. Ou, J. Zhang, W. Zhao, H. Jia, L. Zou, P. Li and Y. Yang, Nano Energy, 2020, 70, 104450 CrossRef CAS.
- R. Li, Y. Ming, W. Xiang, C. Xu, G. Feng, Y. Li, Y. Chen, Z. Wu, B. Zhong and X. Guo, RSC Adv., 2019, 9, 36849 RSC.
- D. Eum, B. Kim, S. J. Kim, H. Park, J. Wu, S. P. Cho, G. Yoon, M. H. Lee, S. K. Jung, W. Yang, W. M. Seong, K. Ku, O. Tamwattana, S. K. Park, I. Hwang and K. Kang, Nat. Mater., 2020, 19, 419 CrossRef CAS PubMed.
- N. Yabuuchi, Nat. Mater., 2020, 19, 372 CrossRef CAS PubMed.
- W. Yao, Y. Liu, D. Li, Q. Zhang, S. Zhong, H. Cheng and Z. Yan, J. Phys. Chem. C, 2020, 124, 2346 CrossRef CAS.
- R.-K. Yang, Z.-G. Wu, Y.-C. Li, R. Li, L. Qiu, D. Wang, L. Yang and X.-D. Guo, Ionics, 2020, 26, 3223 CrossRef CAS.
- L. Zou, Y. He, Z. Liu, H. Jia, J. Zhu, J. Zheng, G. Wang, X. Li, J. Xiao, J. Liu, J. G. Zhang, G. Chen and C. Wang, Nat. Commun., 2020, 11, 3204 CrossRef CAS PubMed.
- Q. An, X. Sun, J. Guo, S. Cai and C. Zheng, J. Electrochem. Soc., 2020, 167, 140528 CrossRef CAS.
- H. Q. Pham, E. H. Hwang, Y. G. Kwon and S. W. Song, Chem. Commun., 2019, 55, 1256 RSC.
- F. Zhang, S. Lou, S. Li, Z. Yu, Q. Liu, A. Dai, C. Cao, M. F. Toney, M. Ge, X. Xiao, W.-K. Lee, Y. Yao, J. Deng, T. Liu, Y. Tang, G. Yin, J. Lu, D. Su and J. Wang, Nat. Commun., 2020, 11, 3050 CrossRef CAS PubMed.
- C. Hong, Q. Leng, J. Zhu, S. Zheng, H. He, Y. Li, R. Liu, J. Wan and Y. Yang, J. Mater. Chem. A, 2020, 8, 8540 RSC.
- F. Friedrich, B. Strehle, A. T. S. Freiberg, K. Kleiner, S. J. Day, C. Erk, M. Piana and H. A. Gasteiger, J. Electrochem. Soc., 2019, 166, A3760 CrossRef CAS.
- H.-H. Ryu, N.-Y. Park, D. R. Yoon, U.-H. Kim, C. S. Yoon and Y.-K. Sun, Adv. Energy Mater., 2020, 10, 2000495 CrossRef CAS.
- H.-H. Ryu, K.-J. Park, D. R. Yoon, A. Aishova, C. S. Yoon and Y.-K. Sun, Adv. Energy Mater., 2019, 9, 1902698 CrossRef CAS.
- Z. Chen, Y. Qin, K. Amine and Y.-K. Sun, J. Mater. Chem., 2010, 20, 7606 RSC.
- J. Wang, J. Yang, Y. Tang, R. Li, G. Liang, T.-K. Sham and X. Sun, J. Mater. Chem. A, 2013, 1, 1579 RSC.
- Y. Su, G. Chen, L. Chen, Q. Li, Y. Lu, L. Bao, N. Li, S. Chen and F. Wu, Chin. J. Chem., 2020, 38, 1817 CrossRef CAS.
- P. Guan, L. Zhou, Z. Yu, Y. Sun, Y. Liu, F. Wu, Y. Jiang and D. Chu, J. Energy Chem., 2020, 43, 220 CrossRef.
- D. Zuo, X. Tan, M. Zhang, J. Li, D. Zhang, Y. Yan and Z. Li, Ceram. Int., 2020, 46, 21888 CrossRef.
- H. Li and H. Zhou, Chem. Commun., 2012, 48, 1201 RSC.
- Q. Hou, G. Cao, P. Wang, D. Zhao, X. Cui, S. Li and C. Li, J. Alloys Compd., 2018, 747, 796 CrossRef CAS.
- Z. Chen, Q. Zhang and Q. Liang, Nanomaterials, 2022, 12, 1936 CrossRef CAS PubMed.
- Q. Fan, S. Yang, S. Guan, J. Chen, S. Feng, J. Liu, L. Liu, J. Li and Z. Shi, J. Power Sources, 2020, 477, 228745 CrossRef CAS.
- S. Wook, S. Lee, H. Kim, J. H. Choi and K. T. Lee, ACS Appl. Energy Mater., 2019, 2, 6246 CrossRef.
- S.-J. Sim, S.-H. Lee, B.-S. Jin and H.-S. Kim, Sci. Rep., 2020, 10, 11114 CrossRef CAS PubMed.
- G. Chen, B. Peng, R. Han, N. Chen, Z. Wang and Q. Wang, Ceram. Int., 2020, 46, 20985 CrossRef CAS.
- Y. Qiu, X. Wei, N. Liu, Y. Song, L. Bi, X. Long, Z. Chen, S. Wang and J. Liao, Electrochim. Acta, 2022, 428, 140973 CrossRef CAS.
- H. Zhang, J. Xu and J. Zhang, Front. Mater., 2019, 6, 309 CrossRef.
- R. S. Negi and M. T. Elm, Sci. Data, 2022, 9, 127 CrossRef CAS PubMed.
- X. Huang, W. Zhu, J. Yao, L. Bu, X. Li, K. Tian, H. Lu, C. Quan, S. Xu, K. Xu, Z. Jiang, X. Zhang, L. Gao and J. Zhao, J. Mater. Chem. A, 2020, 8, 17429 RSC.
- P. Zou, Z. Lin, M. Fan, F. Wang, Y. Liu and X. Xiong, Appl. Surf. Sci., 2020, 504, 144506 CrossRef CAS.
- J. Zhu, Y. Li, L. L. Xue, Y. Chen, T. Lei, S. Deng and G. Cao, J. Alloys Compd., 2020, 773, 112 CrossRef.
- G. Zha, Y. Luo, N. Hu, C. Ouyang and H. Hou, ACS Appl. Mater. Interfaces, 2020, 12, 36046 CrossRef CAS PubMed.
- L. M. Babulala, C.-C. Yang, S.-H. Wu, W.-C. Chi, R. Jose and S. J. Lu, Chem. Eng. J., 2021, 413, 127150 CrossRef.
- H. Yu, S. Wang, Y. Hu, G. He, L. Quo, B. P. Parkin and H. Iang, Green Energy Environ., 2022, 7, 266 CrossRef CAS.
- F. Chen, X. Zhu, W. Dai, C. Yao, J. Qian, Z. Chen and C. Liu, J. Alloys Compd., 2022, 923, 166277 CrossRef CAS.
- S.-B. Park, C.-Y. Kang, D.-Y. Hwang, Y.-W. Y, H.-J. Park, J.-H. Park, H.-S. Kim and S.-H. Lee, Curr. Appl. Phys., 2022, 44, 1 CrossRef.
- R. Ning, K. Yuan, K. Zhang, C. Shen and K. Xie, Appl. Surf. Sci., 2021, 542, 148663 CrossRef CAS.
- S. She, Y. Zhou, Z. Hong, Y. Huang and Y. Wu, ACS Omega, 2022, 7, 24851 CrossRef CAS PubMed.
- C. W. Park, J.-H. Lee, J. K. Seo, W. Y. Jo, D. Whang, S. M. Hwang and Y.-J. Kim, Nat. Commun., 2021, 12, 2145 CrossRef CAS PubMed.
- G.-L. Xu, Q. Liu, K. K. S. Lau, Y. Liu, X. Liu, H. Gao, X. Zhou, M. Zhuang, Y. Ren, J. Li, M. Shao, M. Ouyang, F. Pan, Z. Chen, K. Amine and G. Chen, Nat. Energy, 2019, 4, 484 CrossRef CAS.
- Y. Cao, X. Qi, K. Hu, Y. Wang, Z. Gan, Y. Li, G. Hu, Z. G. Peng and K. Du, ACS Appl. Mater. Interfaces, 2018, 10, 18270 CrossRef CAS PubMed.
- J. Liang, Y. Zhu, X. Li, J. Luo, S. Deng, Y. Zhao, Y. Sun, D. Wu, Y. Hu, W. Li, T.-K. Sham, R. Li, M. Gu and X. Sun, Nat. Commun., 2023, 14, 146 CrossRef CAS PubMed.
- H. Nie, C. Shang, P. Hu and Y. Li, Mater. Lett., 2023, 335, 133768 CrossRef CAS.
- B. J. Chae, J. H. Park, H. J. Song, S. H. Jang, K. Jung, Y. D. Park and T. Yim, Electrochim. Acta, 2018, 290, 465 CrossRef CAS.
- G.-W. Yoo and J.-T. Son, J. Electrochem. Sci. Technol., 2016, 7, 179 CrossRef CAS.
- Q. Gan, Y. Zhu, Z. Huang, F. Zhang, S. Gu, J. Xie, K. Zhang, L. Lu and Z. Lu, ACS Appl. Mater. Interfaces, 2019, 11, 12594 CrossRef CAS PubMed.
- Y. Han, S. Heng, Y. Wang, Q. Qu and H. Zheng, ACS Energy Lett., 2020, 5, 2421 CrossRef CAS.
- L. Zeng, K. Shi, B. Qiu, H. Liang, J. Li, W. Zhao, S. Li, W. Zhang, Z. Liu and Q. Liu, Chem. Eng. J., 2022, 437, 135276 CrossRef CAS.
- P. Dai, X. Kong, H. Yang, S. Kuang, J. Zeng and J. Zhao, ACS Appl. Mater. Interfaces, 2022, 14, 39927 CrossRef CAS PubMed.
- B. Chu, R. Xu, G. Li, J. Chen, Z. Xu, T. Huang, B. Wang and A. Yu, J. Power Sources, 2023, 577, 233260 CrossRef CAS.
- R. Zhao, J. Liang, J. Huang, R. Zeng, J. Zhang, H. Chen and G. Shi, J. Alloys Compd., 2017, 724, 1109–1116 CrossRef CAS.
- W. Yan, S. Yang, Y. Huang, Y. Yang and G. Yuan, J. Alloys Compd., 2020, 819, 153048 CrossRef CAS.
- M. Mohsen, L. Rahim, E. Hossein and M. Manesha, J. Electroanal. Chem., 2020, 862, 113971 CrossRef.
- Y. Ma, M. Xu, J. Zhang, R. Liu, Y. Wang, H. Xiao, Y. Huang and G. Yuan, J. Alloys Compd., 2020, 848, 156387 CrossRef CAS.
- B.-J. Chae, H. Ji Song, J. Mun and T. Yim, J. Electrochem. Sci. Technol., 2020, 11, 361–367 CAS.
- S. Chen, T. He, Y. Su, Y. Lu, L. Bao, L. Chen, Q. Zhang, J. Wang, R. Chen and F. Wu, ACS Appl. Mater. Interfaces, 2017, 9, 29732 CrossRef CAS PubMed.
- J. Wang, Q. Yuan, Z. Ren, C. Sun, J. Zhang, R. Wang, M. Qian, Q. Shi, R. Shao, D. Mu, Y. Su, J. Xie, F. Wu and G. Tan, Nano Lett., 2022, 22, 5221 CrossRef CAS PubMed.
- J. Yua, J. Zhang, Y. Zhang, Z. Wang, Z. Chen, A. Gao, J. Zhang, Y. Wang and R. Zhao, Appl. Surf. Sci., 2022, 577, 151716 CrossRef.
- Y. Beia, Y. Zhang, Y. Li, Y. Song, L. Liu, J. Ma and J. Liu, J. Alloys Compd., 2022, 928, 167140 CrossRef.
- F. Wu, Q. Shi, L. Chen, J. Dong, J. Zhao, H. Wang, F. Gao, J. Liu, H. Zhang, N. Li, Y. Lu and Y. Su, Chem. Eng. J., 2023, 470, 144045 CrossRef CAS.
- G.-T. Park, H. H. Sun, T.-C. Noh, F. Maglia, S.-J. Kim, P. Lamp and Y.-K. Sun, Adv. Energy Mater., 2022, 12, 2202719 CrossRef CAS.
- L.-Y. Kuo, C. Roitzheim, H. Valencia, J. Mayer, S. Möller, S.-T. Myung, M. Finsterbusch, O. Guillon, D. Fattakhova-Rohlfing and P. Kaghazch, Small, 2024, 20, 2307678 CrossRef CAS PubMed.
- Y.-J. Guo, C.-H. Zhang, S. Xin, J.-L. Shi, W.-P. Wang, M. Fan, Y.-X. Chang, W.-H. He, E. Wang, Y.-G. Zou, X. Yang, F. Meng, Y.-Y. Zhang, Z.-Q. Lei, Y.-X. Yin and Y.-G. Guo, Angew. Chem., 2022, 61, e202116865 CrossRef CAS PubMed.
- J.-h Ge, M.-y Xie, Q.-f Zhao, S.-q Zhang and H. Sun, Int. J. Electrochem. Sci., 2023, 18, 100292 CrossRef.
- Y. Kim, W. M. Seong and A. Manthiram, Energy Storage Mater., 2021, 34, 250–259 CrossRef.
- R. Dang, Y. Qu, Z. Ma, L. Yu, L. Duan and W. Lü, J. Phys. Chem. C, 2022, 126, 151 CrossRef CAS.
- N.-Y. Park, G. Cho, S.-B. Kim and Y.-K. Sun, Adv. Energy Mater., 2023, 13, 2204291 CrossRef CAS.
- G. Ko, S. Jeong, S. Park, J. Lee, S. Kim, Y. Shin, W. Kim and K. Jung Kwo, Energy Storage Mater., 2023, 60, 102840 CrossRef.
- N. Yung Park, S.-B. Kim, M.-C. Kim, S.-M. Han, D.-H. Kim, M.-S. Kim and Y.-K. Sun, Adv. Energy Mater., 2023, 13, 2301530 CrossRef.
- T. Weigel, Fl Schipper, E. M. Erickson, F. A. Susai, B. Markovsky and D. Aurbach, ACS Energy Lett., 2019, 4, 508 CrossRef CAS.
- U.-H. Kim, D.-W. Jun, K.-J. Park, Q. Zhang, P. Kaghazchi, D. Aurbach, D. T. Major, G. Goobes, M. Dixit, N. Leifer, C. M. Wang, P. Yan, D. Ahn, K.-H. Kim, C. S. Yoon and Y.-K. Sun, Energy Environ. Sci., 2018, 11, 1271 RSC.
- C. Roitzheim, L.-Y. Kuo, Y. J. Sohn, M. Finsterbusch, S. Möller, D. Sebold, H. Valencia, M. Meledina, J. Mayer, U. Breuer, P. Kaghazchi, O. Guillon and D. Fattakhova-Rohlfing, ACS Appl. Energy Mater., 2022, 5, 524 CrossRef CAS.
- S.-H. Lee, B.-S. Jin and H.-S. Kim, Sci. Rep., 2019, 9, 17541 CrossRef PubMed.
- S.-J. Sim, S.-H. Lee, B.-S. Jin and H.-S. Kim, Sci. Rep., 2019, 9, 8952 CrossRef PubMed.
- Q. Xie, W. Li and A. Manthiram, Chem. Mater., 2019, 31, 938 CrossRef CAS.
- H. Kim, S.-B. Kim, D.-H. Park and K.-W. Park, Energies, 2020, 13, 4808 CrossRef CAS.
- Z. Feng, R. Rajagopalan, S. Zhang, D. Sun, Y. Tang, Y. Ren and H. Wang, Adv. Sci., 2021, 8, 2001809 CrossRef CAS PubMed.
- J. Li, M. Zhang, D. Zhang, Y. Yan and Z. Li, Chem. Eng. J., 2020, 402, 126195 CrossRef CAS.
- J. H. Kim, H. Kim, W.-J. Kim, Y.-C. Kim, J. Y. Jung, D. Y. Rhee, J. H. Song, W. Cho and M.-S. Park, ACS Appl. Energy Mater., 2020, 3, 12204 CrossRef CAS.
- C. Yan, X. Yang, H. Zhao, H. Zhong, G. Ma, Y. Qi, B. E. Koel and Y. Ju, Proc. Combust. Inst., 2021, 38, 6623 CrossRef CAS.
- S. J. Do, P. S. Kumar, S. H. Kang, K. Prasanna, Y. Nam, J. Chang and W. Lee, Ceram. Int., 2019, 45, 6972 CrossRef CAS.
- F. Tian, Y. Zhang, Z. Liu, R. S. Monteiro, R. M. Ribas, P. Gao, Y. Zhu, H. Yu, L. Ben and X. Huang, Solid State Ionics, 2021, 359, 115520 CrossRef CAS.
- M. Chu, M. Chu, Z. Y. Huang, T. Zhang, R. Wang, T. Shao, C. Wang, W. Zhu, L. He, J. Chen, W. Zhao and Y. Xiao, ACS Appl. Mater. Interfaces, 2021, 13, 19950 CrossRef CAS PubMed.
- X. Liu, S. Wang, L. Wang, K. Wang, X. Wu, P. Zhou, Z. Miao, J. Zhou, Y. Zhao and S. Zhuo, J. Power Sources, 2019, 438, 227017 CrossRef CAS.
- S. Jamil, L. Yue, C. Li, M. Fasehullah, M. AizazUd Din, W. Yang, S. Bao and M. Xu, Chem. Eng. J., 2022, 441, 135821 CrossRef CAS.
- T. Sattar, S.-H. Lee, B.-S. Jin and H.-S. Kim, Sci. Rep., 2020, 10, 8562 CrossRef CAS PubMed.
- M. Zybert, H. Rondula, K. Dabrowska, A. Ostrowski, K. Sobczak, D. Moszynski, B. Hamankiewicz, Z. Rogulski, W. Rarog-Pilecka and W. Wieczorek, Energy Rep., 2022, 8, 3995 CrossRef.
- X. Ou, T. Liu, W. Zhong, X. Fan, X. Guo, X. Huang, L. Cao, J. Hu, B. Zhang, Y. S. Chu, G. Hu, Z. Lin, M. Dahbi, J. Alami, K. Amine, C. Yang and J. Lu, Nat. Commun., 2022, 13, 2319 CrossRef CAS PubMed.
- F. Wu, N. Liu, L. Chen, N. Li, Y. Lu, D. Cao, M. Xu, Z. Wang and Y. Su, ACS Appl. Mater. Interfaces, 2021, 13, 24925 CrossRef CAS PubMed.
- F. Zhu, Y. Shi, G. Hu, Z. Peng, Y. Cao, Q. Sun, Z. Xue, Y. Zhang and K. Du, Ceram. Int., 2021, 47, 3070 CrossRef CAS.
- J. H. Lee, J. Kang, S.-W. Kim, W. Halim, M. W. Frey and Y. L. Joo, ACS Omega, 2021, 6, 16465 CrossRef PubMed.
- L. Xiao, X. Tang, Z. Ban, Z. Tang, H. Liu, C. Liu and Y. Lou, Ionics, 2022, 28, 3101 CrossRef CAS.
- J. Li, W. Zhong, Q. Deng, Q. Zhang and C. Yang, Int. J. Extrem. Manuf., 2022, 4, 042004 CrossRef CAS.
- K. Park, D. J. Ham, S. Y. Park, J. Jang, D.-H. Yeon, S. Moon and S. J. Ahn, RSC Adv., 2020, 10, 26756 RSC.
- Q. Li, Z. Li, S. Wu, Z. Wang, X. Liu, W. Li, N. Li, J. Wang and W. Zhuang, ACS Appl. Energy Mater., 2020, 3, 11741 CrossRef CAS.
- J. Yang, Y. Chen, Y. Li, S. Deng, S. Chang, G. Cao, D. Zhang, S. Wang and W. Li, Mater. Chem. Phys., 2020, 249, 123135 CrossRef CAS.
- F. Schipper, H. Bouzaglo, M. Dixit, E. M. Erickson, T. Weigel, M. Talianker, J. Grinblat, L. Burstein, M. Schmidt, J. Lampert, C. Erk, B. Markovsky, D. T. Major and D. Aurbach, Adv. Eng. Mater., 2018, 8, 1701682 Search PubMed.
- X. Zhang, Y. Qiu, F. Cheng, P. Wei, Y. Li, Y. Liu, S. Sun, Y. Xu, Q. Li, C. Fang, J. Han and Y. Huang, ACS Appl. Mater. Interfaces, 2021, 13, 17707 CrossRef CAS PubMed.
- H. P. Yang, H.-H. Wu, M. Y. Ge, L. J. Li, Y. F. Yuan, Q. Yao, J. Chen, L. F. Xia, J. M. Zheng, Z. Y. Chen, J. F. Duan, K. Kisslinger, X. C. Zeng, W.-K. Lee, Q. B. Zhang and J. Lu, Adv. Funct. Mater., 2019, 29, 1808825 CrossRef.
- J. Shen, B. Zhang, X. He, B. Xiao, Z. Xiao, X. Li and X. Ou, J. Colloid Interface Sci., 2023, 629, 388 CrossRef CAS PubMed.
- F. Reissig, M. A. Lange, L. Haneke, T. Placke, W. G. Zeier, M. Winter, R. Schmuch and A. Gomez-Martin, ChemSusChem, 2022, 15, e202102220 CrossRef CAS PubMed.
- M. Zhu, M. Zhang, H. Gu, X. Zhu, W. Dai, C. Yao and F. Chen, J. Electrochem. Soc., 2011, 168, 030527 CrossRef.
- M. Zhang, M. Lv, D. Zhang, Y. Yan, Y. Wang, J. Li and Z. Li, J. Alloys Compd., 2022, 909, 164712 CrossRef CAS.
- Z. Xiao, C. Zhou, L. Song, Z. Cao and P. Jiang, Ionics, 2021, 27, 1909 CrossRef CAS.
- Y. Hou, Y. Ren, T. Shi, J. Li, H. Li, L. Zhang, Y. Liu, Y. Wan, S. Zhang, Y. Liu, Y. Wan, S. Zhang and D. Zhu, J. Alloys Compd., 2023, 939, 168778 CrossRef CAS.
- P. Minnmann, F. Strauss, A. Bielefeld, R. Ruess, P. Adelhelm, S. Burkhardt, S. L. Dreyer, E. Trevisanello, H. Ehrenberg, T. Brezesinski, F. H. Richter and J. Janek, Adv. Energy Mater., 2022, 12, 2201425 CrossRef CAS.
- E. Allahyari, M. Ghorbanzadeh, R. Riahifar and S. M. M. Hadavi, Mater. Res. Express, 2018, 5, 055503 CrossRef.
- X. Li, X. Zhao, M.-S. Wang, K.-J. Zhang, Y. Huang, M.-Z. Qu, Z.-L. Yu, D.-S. Geng, W.-G. Zhao and J.-M. Zheng, RSC Adv., 2017, 7, 24359 RSC.
- H. Gu, J. Wang, Z. Wang, J. Tong, N. Qi, G. Han and M. Zhang, Appl. Surf. Sci., 2021, 539, 148034 CrossRef CAS.
- H.-H. Ryu, N.-Y. Park, T.-C. Noh, G.-C. Kang, F. Maglia, S.-J. Kim, C. S. Yoon and Y.-K. Sun, ACS Energy Lett., 2021, 6, 216 CrossRef CAS.
- Y. Liu, W. Yao, C. Lei, Q. Zhang, S. Zhong and Z. Yan, J. Electrochem. Soc., 2019, 166, A1300 CrossRef CAS.
- W. E. Gent, G. M. Busse and K. Z. House, Nat. Energy, 2022, 7, 1132 CrossRef CAS.
- N. Voronina, Y.-K. Sun and S.-T. Myung, ACS Energy Lett., 2020, 5, 1814 CrossRef CAS.
- L. Azhari, X. Zhou, B. Sousa, Z. Yang, G. Gao and Y. Wang, ACS Appl. Mater. Interfaces, 2020, 12, 57963 CrossRef CAS PubMed.
- X. Xiong, Z. Wang, P. Yue, H. Guo, F. Wu, J. Wang and X. Li, J. Power Sources, 2013, 222, 318 CrossRef CAS.
- W. Lee, S. Lee, E. Lee, M. Choi, R. Thangavel, Y. Lee and W.-S. Yoon, Energy Storage Mater., 2022, 44, 441 CrossRef.
- W. Lee, D. Lee, Y. Kim, W. Choi and W.-S. Yoon, J. Mater. Chem. A, 2020, 8, 10206 RSC.
- Y. Kim, H. Park, J. H. Warner and A. Manthiram, ACS Energy Lett., 2021, 6, 941 CrossRef CAS.
- F. A. Susai, H. Sclar, S. Maiti, L. Burstein, O. Perkal, J. Grinblat, M. Talianker, S. Ruthstein, C. Erk, P. Hartmann, B. Markovsky and D. Aurbach, ACS Appl. Energy Mater., 2020, 3, 3609 CrossRef CAS.
- Y. Wang, E. Wang, X. Zhang and H. Yu, Energy Fuels, 2021, 35, 1918 CrossRef CAS.
- Y. Han, Y. Lei, J. Ni, Y. Zhang, Z. Geng, P. Ming, C. Zhang, X. Tian, J.-L. Shi, Y. Guo and Q. Xiao, Small, 2022, 18, 2107048 CrossRef CAS PubMed.
- L. Ni, S. Zhang, A. Di, W. Deng, G. Zou, H. Hou and X. Ji, Adv. Energy Mater., 2022, 12, 2201510 CrossRef CAS.
- X. Ma, P. Vanaphuti, J. Fu, J. Hou, Y. Liu, R. Zhang, S. Bong, Z. Yao, Z. Yang and Y. Wang, NanoEnergy, 2021, 89, 106194 Search PubMed.
- Ref NCM801501.
- M. Kim, J. Zhu, L. Li, C. Wang and G. Chen, ACS Appl. Energy Mater., 2020, 3, 12238 CrossRef CAS.
- E. Trevisanello, R. Ruess, G. Conforto, F. H. Richter and J. Janek, Adv. Energy Mater., 2021, 11, 2003400 CrossRef CAS.
- G. Sun, S. Zhuang, S. Jiang, Y. Ren, Y. Sun, X. Pan, Y. Wen, X. Li and F. Tu, J. Alloys Compd., 2024, 976, 173097 CrossRef CAS.
- H. Bai, K. Yuan, C. Zhang, W. Zhang, X. Tang, S. Jiang, T. Jin, Y. Ma, L. Kou, C. Shen and K. Xie, Energy Storage Mater., 2023, 61, 102879 CrossRef.
- Y. Liu, T. Zeng, G. Li, T. Wan, M. Li, X. Zhang, M. Li, M. Su, A. Dou, W. Zeng, Y. Zhou, R. Guo and D. Chu, Energy Storage Mater., 2022, 52, 534 CrossRef.
- U.-H. Kim, G.-T. Park, B.-K. Son, G. W. Nam, J. Liu, L.-Y. Kuo, P. Kaghazchi, C. S. Yoon and Y.-K. Sun, Nat. Energy, 2020, 5, 860 CrossRef CAS.
- H. Ge, Z. Shen, Y. Wang, Z. Sun, X. Cao, C. Wang, X. Fan, J. Bai, R. Li, T. Yang and G. Wu, SusMat, 2024, 4, 48 CrossRef CAS.
- T. Liu, L. Yu, J. Liu, J. Lu, X. Bi, A. Dai, M. Li, M. Li, Z. Hu, L. Ma, D. Luo, J. Zheng, T. Wu, Y. Ren, J. Wen, F. Pan and K. Amine, Nat. Energy, 2021, 6, 277 CrossRef CAS.
- R. Wang, L. Wang, Y. Fan, W. Yang, C. Zhan and G. Liu, J. Ind. Eng. Chem., 2022, 110, 120 CrossRef CAS.
- S. Mallick, A. Patel, X.-G. Sun, M. P. Paranthaman, M. Mou, J. H. Mugumya, M. Jiang, M. L. Rasche, H. Lopez and R. B. Gupta, J. Mater. Chem. A, 2023, 11, 3789 RSC.
- B. Chu, Y.-J. Guo, J.-L. Shi, Y.-X. Yin, T. Huang, H. Su, A. Yu, Y.-G. Guo and Y. Li, J. Power Sources, 2022, 544, 231873 CrossRef CAS.
- Y. Cheng, X. Zhang, Q. Leng, X. Yang, T. Jiao, Z. Gong, M.-S. Wang and Y. Yang, Chem. Eng. J., 2023, 474, 145869 CrossRef CAS.
- H. Yan, Y. Ha, T. Ye, X. Gao, X. Yue and Z. Li, Chem. Eng. J., 2023, 465, 142926 CrossRef CAS.
- S. Jeong, S. Park, J. Park, M. Beak, J. Lee, E. E. Kwon and K. Kwon, Int. J. Energy Res., 2022, 46, 19177 CrossRef CAS.
- Z. Cui, Q. Xie and A. Manthiram, ACS Appl. Mater. Interfaces, 2021, 13, 15324 CrossRef CAS PubMed.
- J. Shen, B. Zhang, C. Hao, X. Li, Z. Xiao, X. He and X. Ou, Nat. Energy, 2022, 7, 914 CrossRef.
- Z. Yang, Z. Wang, Y. Zhu, H. Jiang and C. Li, Battery Energy, 2022, 2, 20220048 CrossRef.
- X. Tan, W. Peng, M. Wang, G. Luo, Z. Wang, G. Yan, H. Guo, Q. Li and J. Wang, Prog. Nat. Sci.: Mater. Int., 2023, 33, 108 CrossRef CAS.
- Y. Lv, S. Huang, S. Lu, T. Jia, Y. Liu, W. Ding, X. Yu, F. Kang, J. Zhang and Y. Cao, Chem. Eng. J., 2023, 455, 140652 CrossRef CAS.
- Z.-C. Lv, F.-F. Wang, J.-C. Wang, P.-F. Wang and T.-F. Y. Yi, J. Colloid Interface Sci., 2023, 649, 175 CrossRef CAS PubMed.
- T.-F. Yi, Y.-M. Li, S.-Y. Yang, Y.-R. Zhu and Y. Xie, ACS Appl. Mater. Interfaces, 2016, 8, 32349 CrossRef CAS PubMed.
- X. Zheng, Z. Zhu, X. Lin, Y. Zhang, Y. He, H. Cao and Z. Sun, Engineering, 2018, 4, 361–370 CrossRef CAS.
- G. Tian, G. Yuan, A. Aleksandrov, T. Zhang, Z. Li, A. M. Fathollahi-Fard and M. Ivanov, Sustain. Energy Technol. Assessments, 2022, 53, 102447 CrossRef.
- L.-P. He, S.-Y. Sun, Y.-Y. Mu, X.-F. Song and J.-G. Yu, ACS Sustainable Chem. Eng., 2017, 5, 714 CrossRef CAS.
- C. Wang, S. Wang, F. Yan, Z. Zhang, X. Shen and Z. Zhang, Waste Manage., 2020, 114, 253 CrossRef CAS PubMed.
- S. Dang, W. Hou, Y. Min, J. Wu, Q. Xu and P. Shi, Chem. Eng. J., 2022, 435, 135169 CrossRef CAS.
|
This journal is © The Royal Society of Chemistry 2024 |
Click here to see how this site uses Cookies. View our privacy policy here.