DOI:
10.1039/D4GC01882F
(Critical Review)
Green Chem., 2024,
26, 9503-9528
Sustainability of flow chemistry and microreaction technology
Received
16th April 2024
, Accepted 10th July 2024
First published on 17th July 2024
Abstract
This critical review provides an overview of the sustainability outcomes associated with flow chemistry, as a new concept in process chemistry, and its related technology and engineering field, microreaction technology. This study is broad in scope and covers cost and life cycle assessment methodologies applied to flow chemistry. The present review differs from past studies by providing a mechanistic viewpoint, i.e., starting by listing key levers (e.g. mass transfer), and then unravelling their impact on costs and life cycle, using reported flow chemistry studies as examples to underline the sustainability capability. This way, this review transitions from informing on how flow chemistry and microreactors can improve fundamental principles in chemical engineering and chemistry to their translation to improved sustainability. Gaps and opportunities in the reporting of microreactor/flow chemistry are identified. To put the reported achievements into perspective, a life cycle assessment (LCA) study is conducted that reports on the effects of the key levers, as identified in this study, for a flow chemistry reaction at the pilot scale, conducted at an industrial site (technology readiness level 4). This way, this study provides a quantitative forecast of what principally can be achieved when maximising the key levers, in terms of the individual LCA impact categories and their total average outcome.
1. Introduction
Microreactors are microfabricated or otherwise structured devices with at least one (characteristic) dimension below 1 mm. The smallest structures typically used are a few tens of microns, though there are exceptions with even smaller dimensions. Microreaction technology utilizes microreactors for chemical reaction engineering. Flow chemistry is a related approach driven by chemical motivation (e.g., new synthesis protocols) that typically uses readily available commercial devices with internal sub-mm dimensions instead of microreactors. These devices may include commercial microcapillaries and fluidic connectors, commonly used in high-pressure liquid chromatography, but increasingly complex commercial full-system equipment, which is automated, and accessible at a price that researchers can afford.
Sustainability investigations of microreactors and flow chemistry are crucial for their justification of use, to demonstrate societal impact both via cost and environmental improvements. The first cost study1 of microreaction processing and the first environmental study2 using life cycle assessment were published in 2005 and 2006, respectively. Since then, sustainability assessments have increased and become common to monitor the societal and industrial impacts of the technology.3–6 This paper critically reviews the sustainability achievements of flow chemistry and identifies what is still missing in terms of sustainability demonstration and methodology.
Sustainability, as surveyed here, includes primarily cost and environmental assessments. A holistic sustainability assessment of a process encompasses green chemistry metrics, circularity assessment, and life cycle assessment (LCA).7 Cost assessments are typically given as techno-economic analysis (TEA), life cycle costing (LCC), or cash-flow analysis. Environmental assessments are typically performed using life cycle assessment (LCA). Recently, circular economy (CE) metrics and environmental, social, and governance (ESG) have complemented the sustainability tool portfolio.
While green chemistry metrics strongly emphasize design and process development (factory gate-to-gate), providing efficiency performance indicators and valuable insights into the environmental and resource efficiency of a chemical process, circularity assessment focuses on the promotion of resource efficiency through recycling raw materials and waste reduction (cradle-to-cradle).7 In between, LCA evaluates the environmental impacts of products and processes throughout their entire life cycle, from raw material extraction to end-of-life disposal (cradle-to-grave). LCA looks back in time (‘ecological backpack’) and green chemistry metrics reflect the current and near-future status, whereas CE metrics and ESG look deep into the future, predicting how the sustainability of a current laboratory tool might develop when used on an industrial scale and with new companies launched.
Flow chemistry is one of the emerging technologies, and sustainability is a major argument for its use. Sustainability should be put into perspective to even larger technological momenta that are currently changing the planet. A GoogleScholar search was conducted, restricting the search results to finding the keyword in the title only. Otherwise, the search can be done through the whole paper text; yet this deemed to be too unspecific, because the keyword may be used in the introduction or outlook sections without directly relating to the paper's content. The methodology chosen (“title only”) means that the actual manuscript numbers are somewhat larger. However, this method ensures sufficient data accuracy to identify trends, as mentioned earlier. All reports in the literature are considered, meaning no restriction has been made to the publication year.
Hydrogen (H2) and carbon dioxide (CO2) are likely the most extensively investigated emerging technologies. Table 1 shows 829
000 ‘Hydrogen’ and 152
000 ‘H2’ entries, respectively. Yet, these include titles that comprise a second term after ‘Hydrogen’ such as ‘Hydrogen peroxide’, for which 98
600 entries were found. As this is assumed to be the major portion of ‘non-Hydrogen’ entries, the number of ‘Hydrogen’ papers is set here as 700
000. For ‘Carbon Dioxide’ and ‘CO2’, 251
000 and 785
000 entries were found, respectively. Concerning the dual mentioning of ‘Hydrogen + LCA’ and ‘Carbon Dioxide + LCA’, 375 and 218 entries, respectively, were determined.
Table 1 Comparing the total number of papers on three emerging technologies, including ‘hydrogen’, ‘carbon dioxide’, and ‘flow’ as well as their related LCA studies
Entry |
‘Hydrogen’ combined |
‘Carbon dioxide’ combined |
‘Flow’ combined |
‘Hydrogen’ + LCA |
‘Carbon dioxide’ + LCA |
‘Flow’ + LCA |
Number of papers |
852 000 |
1 036 000 |
18 523 |
375 |
218 |
60 |
LCA share of entry papers [%] |
|
|
|
0.044 |
0.021 |
0.324 |
For ‘Flow Chemistry’, ‘Microreactor’, and ‘Continuous Flow’ 753, 2970, and 14
800 entries were found, respectively; altogether there were 18
523 entries on “flow” in the understanding of this review.
The search for LCA entries for emerging technologies was done considering, for example, ‘Carbon dioxide LCA’, ‘Carbon Dioxide Life Cycle Assessment’, ‘CO2 LCA’, and ‘CO2 Life Cycle Assessment’; the same as for hydrogen as the entry. The combined search for LCA and the three terms for “flow” in GoogleScholar does not reveal numbers that seem to be close to the real numbers, according to the authors’ expertise. This study cites about 60 “LCA-flow” papers; as there are more, a total number of 70 is assumed.
It is evident that LCA studies are rare, both for the major emerging technologies and “flow” as a medium-sized emerging technology; noting that ‘Flow + LCA’ has a share that is an order of magnitude higher than those for ‘Hydrogen + LCA’ and “Carbon Dioxide + LCA”. It is assumed, however, that for ‘Hydrogen’ and “Carbon Dioxide” many more sustainability studies have been published that do not carry the acronym LCA or the words “life cycle assessment” in their title.
To sum up, there is a need for more sustainability (LCA) studies, and this manuscript aims to encourage them. Sustainability achievements correlate to commercial and societal-impact success. This review aims to assess the current achievements of the technology in terms of its readiness level and impact release, and to explore potential improvements through the adoption of modern sustainability methodologies. This review uses a classification of fundamental process benefits of microreactor and flow chemistry, as commonly and unanimously quoted in all reviews of the technology. This structural element forms a narrative, through which it is discussed how each of these benefits translates into sustainability. In this way, the intrinsic sustainability potential is mirrored by its transition to practical sustainability achievements, also showing what gaps are left. This review gives a critical state-of-the art description of what has been practically achieved for each of the commonly agreed intrinsic potential goals of microreaction technology and flow chemistry.
2. Microreactor and flow chemistry opportunities and their relevance to sustainability
In lieu of the above, this review categorises flow chemistry/microreactors in terms of sustainability according to their intrinsic capabilities, which are extensively cited in reviews.7–12 These are briefly defined in the following, accompanied by a listing of sustainability assessment classes addressed (e.g., costs or LCA), and a description of demonstrated examples. This break down provides details and elaboration for the practitioner, Fig. 1.
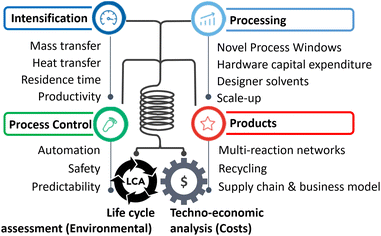 |
| Fig. 1 Connection between flow chemistry capabilities and sustainability metrics. | |
2.1. Hardware capital expenditure
The microreactor literature is full of reports on low-cost microfabrication approaches, in terms of ‘fast prototyping’ or ‘mass manufacturing’; sometimes adding quantitative cost estimations and studies on the qualitative assignment of ‘low-cost’. This way, microreactors and flow chemistry equipment have become commercial and industrial. The sustainability outcome is cost reduction, for which the present review provides several examples in the following.
2.2. Mass transfer
Microreactors mix much faster than conventional mixers, down to the millisecond range. Mass transfer, within one phase or between two phases, is similarly intensified. Sustainability outcomes are less waste, lower energy consumption, higher yield; relevant for costs and LCA (circularity). Example: A microreactor was developed for HCl-catalysed fructose dehydration to produce HMF in a short reaction time and at high temperature.13 The mixing time was determined as 0.03 to 4.8 s by particle image velocimetry monitoring. Coiled microchannels generate Dean vortices for advanced convection mixing. The HMF yield was 50%, which is among the best result reported in the literature.
2.3. Heat transfer
Microreactors can transfer heat even under thermal runaway or explosive scenarios and change from strong (adiabatic) heat release to a controllable isothermal operation.
Sustainability outcomes are less waste, lower energy, higher yield; relevant for costs and LCA (circularity).
Example: Microdevice design is essential for good heat transfer and a common design is a plate arrangement in a stack, with alternating plates comprising reactor and heat microchannels. Using such an alternating stacked commercial microreactor, the serpentine shape of the microchannels forces convection, which supports heat transfer (and mass transfer); especially at the very high Reynolds numbers studied from 400 to 2000.14 Silver thermal paste proved to be effective at intensifying conductive heat transfer between the plates; by up to 70% and the heat transfer coefficient reached up to 2200 W m−2 K−1. Temperature control was demonstrated for a highly exothermic reaction, dimethyl-oxalate and ethylmagnesium chloride forming methyl 2-oxobutanoate, which avoided forming local hot spots.
Full control of heat transfer (no thermal overshooting, no hot spots) is often related to concurrent full control of mass transfer. The Taylor flow mode of microreactors, regular gas–liquid slugs, enables, through both these avenues, the investigation of the subtle interplay of elemental reactions during the oxidation of isobutane to tertiary butyl hydroperoxide (TBHP) at relatively high temperature.15 TBHP as the peroxide is a thermally sensitive material and easily decomposed. TBHP has a dual function: initiating the reaction and as a kind of autocatalyst. Another common initiator, di-t-butyl peroxide (DTBP) decomposes at the high temperature employed, and thus, decreases the TBHP yield. Differentiation of these sophisticated effects is only possible with the superior heat transfer control provided by a microreactor.
2.4. Residence time
Microreactors can, dramatically, reduce reaction times; from days and hours to minutes and less.16 The possibility of reactions occurring on the shortest possible (intrinsic) timescale has been coined flash chemistry.17 The fastest reactions are completed in milliseconds.
Sustainability outcomes are less waste and higher yield; relevant for costs and LCA (circularity).
Example: Organolithium reactions are capable of occurring within a few milliseconds only, which is a timescale that conventional mixing can hardly cope with. Inefficient mixing in such short intervals promotes side reactions with functional groups in the organic reactant, e.g., with ketone groups, forcing them to be protected under the reaction conditions (which generates waste). Microreactors can mix faster, and an organolithium reaction, based on iodine–lithium exchange of aryl iodides with mesityllithium, leads straight to the aryllithium product, a precursor to the polyphenolic bioactive product pauciflorol F.18 As the main reaction dominates and side reactions are absent, protection-free chemistry can be used.
Mixing-assisted microreactor operation for polyether polyols enabled a significant reduction in reaction time compared to batch technology.19 95% conversion was achieved in less than 1 min at an unusually high reaction temperature.
2.5. Productivity
Faster reaction times, operation in former explosive regimes, and/or higher yields enable flow chemistry to boost productivity. The challenge is then to maintain high productivity when scaling-out. Productivity principally can be increased by reducing the reaction time or increasing the conversion (or both).
Sustainability outcomes are less waste and higher yield; relevant for costs and LCA (circularity).
Examples: Biodiesel is mass produced well at the industrial level, and a good benchmark for microreactors as emerging technology. Enzyme-catalysed transesterification for biodiesel production advances sustainability compared to current conventional methods relying on strong acids or bases, but is slower, which hinders the achievement of high productivity. Using a recyclable nanomagnetic immobilised enzyme, Candida rugosa lipase, the productivity was increased in a statistical analysis (using response surface methodology-Box–Behnken design).20 The highest immobilisation efficiency of 93% was determined for an optimised set of process conditions, and the immobilised enzyme was stable under relevant process conditions. The microreactor transesterification increased the productivity of transforming sesame cake oil into biodiesel to a maximum conversion of 97%. The biodiesel produced fulfils industrial standards (ASTM D6751).
2.6. Safety
Microreactors can achieve safe operation in process regimes that may otherwise lead to thermal runaway or explosions under conventional conditions, Fig. 2. Micro-flow operation can shift the explosion envelope out of typical operating conditions. Hazardous reactions are often road blocks to hinder scale-up in conventional reactors, and microreactors have proved to be safe for handling reactions using unstable intermediates or hazardous reagents and highly exothermic reactions for kilogram scale synthesis.21 This enables the transition of more laboratory chemical innovations to the pilot and production scale.
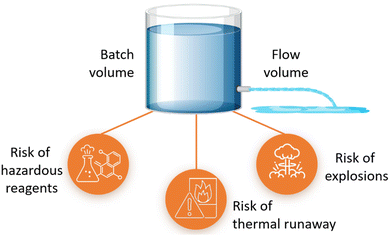 |
| Fig. 2 Main batch safety risks mitigated by the use of reduced volumes in flow chemistry. | |
The sustainability outcome is higher predictability towards commercial business; relevant for ESG.
Example: Thermal polymerisation of styrene is known to release huge thermal loads in a short time, which can be problematic for industrial usage. Computation fluid dynamics was used to delineate the thermal release in a batch reactor and microreactor.22 Polymerisation in the microreactor could be kept at 150 °C, whereas the batch reactor showed a large temperature rise to 371 °C. In 6 mm wide microchannels, the maximum temperature difference was 25 °C. Viscosity, as expected, has a significant effect, whereas other process conditions minimally affect heat transfer. The avoidance of any catastrophic system failure, i.e., adiabatic (=maximal) temperature release in one moment, through complete loss of (jacket) cooling was taken into a system design.
Reactions with three classes of heat production potential (HPP) were computed in microreactors, considering, as a design case study, microchannels <500 μm;23 it was found that the smaller the microchannel, the better the heat transfer. The heat transfer in category 1 reactions (HPP > 100 kW L−1) could not be managed in a microchannel (of common dimensions), while category 2 reactions (HPP > 10 kW L−1) could be kept under control when microchannels were properly dimensioned. Category 3 reactions (HPP < 10 kW L−1) with milder heat transfer can be handled even in millimeter-sized channels.
2.7. Multi-reaction networks/product complexity
Microreactors can integrate several reactions in a confined space and short time, minimizing waste. They enable the continuous synthesis of complex products; often without the need for separation or reaction interruption.17
Sustainability outcomes are lower energy, higher yield, and better products; relevant for costs, LCA, and circularity.
Examples: The electrophilic amination of organolithium intermediates with aminating reagents under mild reaction conditions in micro-flow leads to facile C–N bond formation; without the need for a catalyst or separation.24 Within 5 min, a 3-step integrated one-flow synthesis was conducted, including the intermediate synthesis of an aryllithium, an aminating reagent, and its reaction to the product. Via a 4-step integrated one-flow synthesis, the Swern–Moffatt oxidation of cyclohexanol was accomplished; at residence times as short as 10 ms and favourable temperatures ranging from −20 to 20 °C, significantly higher than for conventional batch synthesis (−50 °C),25Fig. 3.
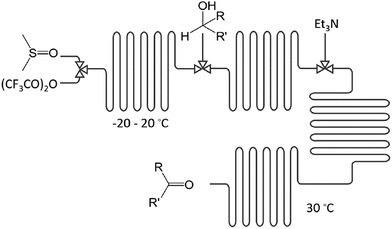 |
| Fig. 3 Flow chemistry applied to sequential multi-step Swern–Moffatt-type oxidation. | |
2.8. Novel process windows
Microreactors require dedicated processes (protocols), and the best are often far from conventional practice. These unusual (novel) process windows, which are unsuitable for conventional equipment, enable microreactors and flow chemistry to outperform their counterparts. The exploration of novel process windows (NPWs) can boost the performance of microreactors and flow chemistry, as illustrated in Fig. 4.
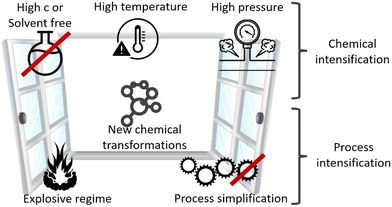 |
| Fig. 4 A schematic representation of intensification features via NPWs. | |
Sustainability outcomes are less waste, lower energy, higher yield, and better products; relevant for costs, LCA, and circularity.
Example: Peroxide synthesis is challenging for conventional processing due to its explosive nature. Yet using very fast kinetics makes any reaction highly productive. So how can this be exploited in a safe way? The two-stage synthesis of tert-butyl peroxy pivalate was performed in two flow regimes, namely, segmented flow and dispersed flow.26 The challenge of exploiting the very fast kinetics is to cope with the significant heat release of the reaction (126 kJ mol−1). The dispersed flow regime provides a large interfacial area for safe peroxide production, even at increased process temperatures (stating an NPW), strongly enhancing productivity; noting that peroxide synthesis is normally conducted at room temperature or under cooling. The comparison with an industrial patent demonstrates a microreactor space–time yield that is orders of magnitude higher.
2.9. Recycling
In the age of circularity, recycling has become essential in all processing, including that of flow chemistry. Flow separation, which is a part of recycling, still lacks being integrated into flow chemistry reactions despite two decades of investigations.
Sustainability outcomes include reduced waste and energy consumption; relevant for costs, LCA, and most notably circularity and ESG.
Examples: Enzyme reuse was achieved in a continuous-flow de-esterification using a water/ionic liquid biphasic system via recycling.27 Batch processing resulted in foaming because of shear forces from heavy stirring, which meant that the separation needed for recycling took unacceptably long. Micro-flow processing with its ‘soft convection stirring’ did not induce foaming, which led to fast and complete phase separation. Three recycling stages were demonstrated, each showing a gradual decline in enzyme activity, yet this was tolerable for proof of principle.
Recycling of the process components HCl, water, and n-butanal was demonstrated in the polycondensation reaction of polyvinyl alcohol and n-butanal in a membrane dispersion microreactor.28 This produced polyvinyl butyral, a chemical used in laminated vehicle glass. These ingredients were chosen for their ability to bring the polycondensations to the needed ultrahigh conversion. 99% n-butanal conversion was achieved, with recycling effectively reducing HCl usage by 86%.
2.10. Designer solvents
Designer solvents enable the design of solvent capability beyond what normal solvents can deliver; therefore, they are also termed ‘master solvents’.29 Microreactors generally involve small volumes, which suit the use of costly designer solvents, and require solvent performance at the highest standards. The co-use of microreactors and master solvents has yielded significant achievements at the laboratory scale,30Fig. 5.
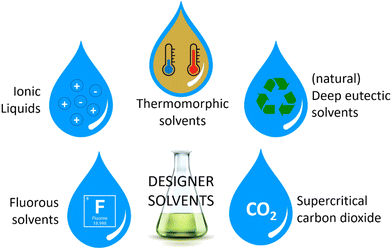 |
| Fig. 5 Classification of designer solvents used in flow chemistry. | |
Sustainability outcomes are less waste and lower energy costs; relevant for costs, LCA, and most notably circularity.
Example: A biphasic designer solvent system for enzymatic biotransformation was developed to demonstrate automatic purification and enzyme reuse via recycling.27 Three ionic liquids (ILs) were tested for the lipase-catalyzed hydrolysis of 4-nitrophenyl acetate; all with the 1-butyl-3-methyl-imidazolium cation and differing in their anions, namely, tetrafluoroborate, bis(trifluoromethylsulfonyl)-imide, and hexafluorophosphate. In the same reaction time and using water/IL biphasic systems, the flow reactor gave higher yields (90% at best) at the same degree of purification (97%). An additional benefit using the IL was much-improved recyclability of the enzymes; see below.
2.11. Automation/modularisation
Small, compact reactors like microreactors favour modularisation as a kind of ‘Lego of process modules’, Fig. 6. The opportunity to reach near-ideal process conditions requires computational intelligence to replace human operationalization; which is the essence of ‘process automation’ of flow chemistry.31 Automated flow chemistry has enabled on-demand drug production in a reconfigurable, modular system capable of performing a telescoped synthesis in one flow.32 It supports either many different reactions or the synthesis of many molecules through a common building block.33 The advantages of using flow include scalability, safety, speed, and reproducibility. Automated flow synthesis has integrated automatic design, API synthesis, and biological assay screening platforms.34
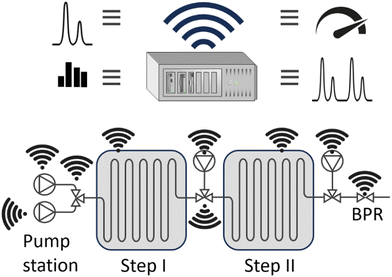 |
| Fig. 6 Example of process automation, including pumping stations, reactors, process conditions (i.e. temperature and pressure) and on-line analysers. | |
Sustainability outcomes encompass the categories listed above; relevant for ESG, contributing to achieving industrial standards.
Examples: Machine learning, via Gaussian process regression, was used to guide electrochemical microreactor processing to optimize the additive-free cyanosilylation reaction of benzaldehyde to cyanohydrins.35 A parametric reaction study identified reaction conditions that generated a high yield. This avoided extensive experimental parameter screening commonly applied, thereby reducing the number of experiments. The computations maximised productivity without the need for human expertise, through optimising the interplay between electrical (current) and chemical engineering (flow rate) settings. Sensors are crucial for flow process automation, as they perform essential metering and process control functions. A non-invasive sensor with a fast reaction time was developed to monitor changes in phase(s) and concentration in single- and multi-phase micro-flow.36 Also, advanced online detection methods are needed. Total internal reflection transient absorption microscopy (TIRTAM) was applied for the detection of excited-state dynamics in flow.37 Lastly, advanced process monitoring is needed to detect and diagnose blocked microreactors. For the parallel operation of Suzuki–Miyaura coupling in five microreactors, a split-and-recombine-type flow distributor (SRFD) was used for blockage detection.24 The channel resistances and sensor locations in the SRFD were adjusted via a pressure drop compartment model.
2.12. Scale-up/predictability
Microreactors are replicable reactor systems that ideally are just ‘numbered-up’ similar to nature's cells. While microreactor scaling-out reality is partly different from the ideal, it is nonetheless true that microreactor scale-up is faster and more facile than a conventional batch reactor setup. This viewpoint is shared by several industrial researchers, who brought microreactors to the production scale.
Sustainability outcomes are faster time to market, reduced costs, and increased cash-flow; relevant for TEA, and most notably ESG.
Example: Scale-up of sub-second micro-flow synthesis was performed by numbering up of 3D-printed and laminated metal microreactors.38 The initial one-flow-reactor synthesis was extended to a monolithic module with 4 numbered-up 3D-printed metal microreactors (4N-PMR). As the next and final scale-up step, 16 microreactors (16N-PMR) delivered 20 g of three drug scaffold products within 10 min of operation. This was achieved by stacking four 4N-PMR modules. A kilogram-scale synthesis of 2-ethylhexyl nitrate in a microreactor was developed via a statistical method, specifically a Box–Behnken experimental design, varying systematically process parameters.39 The experimental design was studied for four factors and at three levels. Determining key impact factors (sulphuric acid, temperature) and optimising liquid–liquid contact by using computational fluid dynamics led to a scaled-up microreactor design, capable of producing 16 kg h−2 ethylhexyl nitrate.
2.13. Supply chain and business model
As compact, modular units with easy installation/demounting and fast start-up/shutdown capabilities, microreactors lead to new business models, including decentralised small-scale production, and strengthen multi-product business models such as campaign production.
Sustainability outcomes are new product services, a reduction in environmental effects from transportation, personalisation of products, and improved product delivery reliability (resilience); relevant for LCA, and most notably ESG.
Examples: New types of chemical production plants (so called “future factories”) can provide new business windows. Containerised, mobile plants are promising for reducing the time-to-market (“50% idea”), leading to a higher cash-flow.40 This is, i.a., due to their modular construction and to embed smart-scale processing technologies such as microreactors. CAPEX and OPEX analyses have been conducted for microreactor-equipped container plants (Evonik Company's Evotrainer production platform). Three microreactor applications were evaluated across chemical market sectors: bulk chemistry, fine chemistry, and pharmacy. Containerized chemical plants demonstrate faster payback and higher earnings compared to conventional technology, particularly for high-value chemical products such as those in the pharmaceutical industry. Microreactor equipment uplifts the economics.
3. Costs of flow chemistry/microreactors
Cost studies of flow chemistry or microreactors often focus on either capital expenditure (CAPEX) or operational expenditure (OPEX); rarely putting an equal emphasis on both. As evident from the above, the main benefits of using microreaction technology are to improve OPEX costs, e.g., through higher yields, faster development time, reducing waste, etc. The quantification of cost improvements for chemical processes after the implementation of microreactors or flow chemistry is essential to demonstrate the technology's effectiveness. The following section shows first CAPEX cost studies and thereafter OPEX cost studies in the field.
3.1. Microreactor CAPEX costs
Innumerable microfluidic studies have aimed, for more than three decades, to invent new fabrication methods for microreactors, part of these comprise cost studies, as cost reduction is a major motivation for the studies. However, many of these innovations have not passed into today's flow chemistry and microreactor business, but rather have been implemented in lab-chip technology. This review retains, as previously stated, its holistic narrative, and presents in the following microfluidic CAPEX cost studies around microfabrication innovations. The hypothesis among all studies reported here is that fast prototyping is key to reducing the fabrication costs of microreactors, because chemical reactors are small-quantity campaign products, as opposed to the imperative of mass manufacturing, which is demanded for most microfabrication (and microelectronic) products.
3.1.1. Low-cost manufacturing.
A fast-prototyping study uses the combination of wire machining and fast laser microfabrication for low-cost polymeric microreactor machining, with polydimethylsiloxane (PDMS) and polymethylmethacrylate (PMMA) as construction materials,41Fig. 7. The microreactor was designed for the synthesis of SnS nanoparticles as catalysts for the photocatalysed degradation of an organic dye, with an achievement of 75% decomposition instantly.
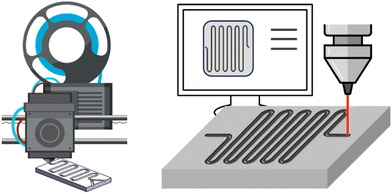 |
| Fig. 7 Flow chemistry enables fast and precise prototyping when combined with other technologies. Left: 3D printing; right: laser milling. | |
Another fast-prototyping study aimed to minimize all cost contributions. This included cheap construction materials (microscope glass slides from low-cost soda-lime glass) as well as a cost-effective micromachining process (deep etching, a simplified masking method).42 This allowed microchannels to be produced with depths of >100 μm with a very low surface roughness, below 10 nm. These microreactor devices were used for oligopeptide immobilisation.
A third study aimed to reduce costs via low-cost micromanufacturing through laser cutting of polymethyl methacrylate (PMMA)43 and proposed reusing the micromixers to prevent PMMA microdevices from becoming plastic waste. Three micromixers with different channel configurations, serpentine, triangular, and a 3D arrangement, were prototyped to conduct (nano)precipitation at optimal nucleation and growth, at the quality needed for drug delivery and bioremediation. Magnetite nanomaterials were generated with a narrow particle size distribution, homogeneous morphology, and crystalline structure.
3.1.2. Advanced machining.
Metal additive manufacturing and powder metallurgy processes can advance bonding processes in microreactor fabrication towards reduced material input. Many microstructured layers are bonded to metal shim stocks.44 Metal injection molding has a better cost profile than the binder-jetting additive technology, due to lower tooling costs and faster manufacturing. The microreactor, fabricated using those machining techniques, was designed for dimethyl ether production.
3.1.3. Materials.
Polydimethylsiloxane (PDMS) is a prime material for fast prototyping. A cost study was performed for a PDMS microreactor manufactured using an advanced print-and-peel (PAP) method.45 The manufacturing cost is reported to be fifty times lower than that of a commercial benchmark. The microreactor was used to form silver nanoparticles from silver nitrate and the fast reductant sodium borohydride. An average nanoparticle diameter of 24 nm was obtained, which was smaller than those produced by batch technology, ranging from 30 to 60 nm, and commercial samples.
3.1.4. Catalysts.
Catalyst implementation: Catalysts are crucial for microreactor function and sustainability, necessitating low-cost catalyst implementation techniques. Catalyst immobilisation was performed by loading a TiO2 suspension into polymer microtubes as the support for the photocatalyst,46 followed by a quick thermal treatment at 285 °C. The costs are determined by the number of catalytic coatings, the concentration of the catalyst precursor suspension, and the reactor's inner diameter. The reaction rates of photocatalytic phenol degradation in the microtube were an order of magnitude larger than those in a laboratory-scale batch reactor with a catalyst slurry.
Catalyst coating techniques and the prime materials used in fast prototyping do not always blend with each other, i.e., the coating might not be feasible and block a possible cost reduction. Conventional catalyst coating methods are unable to load catalysts firmly and uniformly on PDMS (polydimethylsiloxane). A casting-transfer method has been developed for loading catalysts on the PDMS substrate.47 This optofluidic microreactor was used for photocatalytic water splitting. The hydrogen production rate was higher than in a conventionally fabricated microreactor and the durability was superior.
Catalyst durability: The durability of catalysts is central, as catalyst replacement causes material costs and a pausing of continuous operation lowering the cash-flow. High durability (and recyclability) was achieved for TiO2 nanoparticle-coated ZnO nanorod arrays grown in the capillaries of a photocatalytic microreactor,48Fig. 8. To further reduce costs, simple catalyst incorporation was developed by pumping a TiO2 sol into capillaries containing preformed ZnO nanorod arrays. The capillary microreactors demonstrated high photocatalytic activity in response to the dye methylene blue.
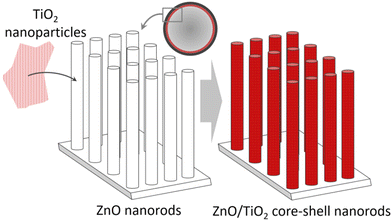 |
| Fig. 8 TiO2 nanoparticle-coated ZnO nanorod arrays grown in the capillaries of a photocatalytic microreactor. | |
Catalysts in gas–liquid–solid microreactors often exhibit poor durability. High durability was observed for Pd nanocatalyst49 coatings achieved via electroless deposition on a polydopamine-functionalized surface, followed by hydrogen reduction. Almost complete reduction of all palladium ions and uniform dispersion of the palladium nanoparticles were achieved. This catalyst proved to have higher durability at a high nitrobenzene (gas–liquid–solid) conversion compared to traditional electroless catalyst deposition. Yet, it was also noted that microreactor operation could compromise catalyst durability; this is a function of reactant concentration and can be minimised accordingly.
Catalyst regeneration: A nanosized Au/TiO2 catalyst was regenerated in situ and demonstrated reproducible conversion and yield in more than 50 test runs. Monometallic gold (Au) and palladium (Pd), as well as bimetallic Au–Pd nanoparticles, were supported on titania (TiO2) by sol immobilization.50 The catalytic activity of the coated microreactor was tested for the gas-phase partial oxidation of (bio-based) 1-butanol to n-butyraldehyde.
Regeneration (and durability) of a catalyst was also demonstrated for an Ag/ZnO catalyst coated on an aluminium microreactor by spray pyrolysis.51 The photocatalytic degradation of methylene blue under UV-A irradiation was investigated.
3.2. Flow chemistry OPEX costs
The economic benefits of implementing flow chemistry on a commercial scale are assessed in section 3.2 with a focus on savings in OPEX costs. As Fig. 9 suggests, sections 3.2.1–3.2.15 are structured by viewpoints based on reaction and catalyst engineering, process design, process automation, process economics, and similar. Fig. 9 does not include all these assets for reasons of clarity and simplicity.
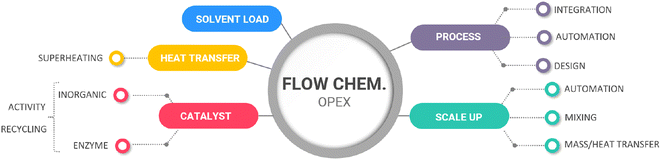 |
| Fig. 9 Flow chemistry OPEX costs sorted by relevant engineering and process viewpoints. | |
3.2.1. Superheated processing for soybean epoxidation.
The utilisation of unusually high reaction temperatures was tested to massively accelerate the kinetics of hydrogen peroxide-mediated soybean oxidation (to green plasticisers, epoxidized soybean oil, ESBO), a novel process window.52 This is only achievable in microreactors that are able to provide the high mass transfer demanded under these conditions; especially between the two immiscible phases used. For a pilot plant, the production costs were computed to be governed by variable costs (91%), with material costs having the highest share. Maximising yield is therefore key to NPW-guided process design. The cost study also confirmed savings in personnel costs due to decreased operation and supervision times when using microreactor operation, which offers shorter reaction times compared to the batch process.
3.2.2. Superheated processing for rufinamide drug synthesis.
A real-case study of industrial scale-up aimed to build on the environmental advantages of a promising reported lab-scale flow chemistry53 for the manufacturing of the pharmaceutical drug rufinamide.54 A mini-pilot plant was operated at an industrial site, and aimed to carry out the reported superheated processing (a novel process window) of the three-step flow chemistry cascade.55 Annual costs of five raw materials used in the three steps were computed and given as a function of the total yield of the mini-pilot flow chemistry plant, ranging from 47 to 83%. A cumulative cash-flow (CCF) analysis was conducted for depreciation over ten years, with CAPEX costs ranging from 0.5 to 2.0 million US$. The CCF increases with time, breaks through (positive cash outcome) after about 2 to 4 years depreciation, and is better for larger yields; approximately doubling the CCF when increasing the yield from 65 to 83% with hardly any CCF at 47%. The costs of the mini-pilot plant were only 25% higher than the former lab-scale plant, assuming 83% yield, despite the compromises needed during scale-up. In this case, CAPEX costs increased disproportionally when scaling-up the microreactor plant. The future achievement of the 83% total-yield performance by the mini-pilot plant requires improving the yield of the last step, while the yields of the first two steps are close to 90%.
3.2.3. Solvent loading and reaction time reduction (for flow-made catalysts).
The metal–organic framework (MOF) catalyst MOF-808 was manufactured using flow chemistry reactors. Relevant process parameters were the residence time, linker concentration, volumetric ratios of modulator, and solvent.56 The consumption of the solvents dimethylformamide (DMF) and formic acid was reduced by 84% and 67%, respectively. Highly crystalline MOF-808 nanoparticles were synthesized with 5 min residence time, in contrast to 48 h residence time in batch reactors. The costs of the laboratory-scale flow synthesis of MOF-808 was determined to be around $3 per g, lower than the current batch method.
3.2.4. Heat transfer.
A cost assessment was conducted via a thermodynamic analysis of the supercritical CO2 recompression Brayton cycle for a heat pipe-cooled microreactor, including heat exchanger and turbomachinery design sub-codes.57 A maximum cycle efficiency of 52% was determined. An LCOE score of 82 USD per MW h was calculated. When considering the transmission and distribution (T&D) electricity loss, the microreactor presented an economic opportunity compared to a nuclear power plant. The microreactor operation would be superior, for example, after 0.6 years in Hungary (high electricity costs), and after 23 years in South Korea (high electricity costs).
3.2.5. Catalyst costs.
A holistic cost study assessed the costs of combined microwave–microreactor processing for 14 process scenarios of the copper-catalyzed Ullmann cross-coupling to produce 4-phenoxypyridine, a pharmaceutical intermediate used in the production of commercial drugs like vancomycin or vancocin.58 Dominance of material costs (reactants, catalysts, pretreatment agents) in the OPEX costs was determined, which outweighed CAPEX costs by far. It was determined that microwave heating and the use of advanced catalysts was more economical than conventionally heated batch and continuous processes. The combination of microwave heating and microreactor processing is synergistic, resulting in even lower operational costs,59Fig. 10. Different provision of microwave heating (‘monomode’, ‘multimode’) impacted energy costs for heating and were compared with conventionally heated systems. Overall, the contribution of energy costs was low. In contrast, the catalyst costs, in particular the method of catalyst implementation, had a strong impact on the profitability. A conventional (bead) catalyst supply was more cost-effective than the use of advanced catalysts, including coated and nanocatalysts. A micro-packed-bed reactor was 20% more cost-effective than coating the catalyst on the walls of the microchannels.
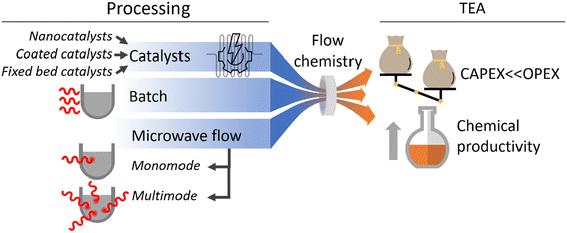 |
| Fig. 10 Effect of microwave flow and advanced catalyst processing on techno-economic assessment (TEA). | |
3.2.6. Enzyme activity and recycling.
A biodiesel production study determined that enzyme costs outperformed all other costs and were key to the implementation of biocatalytic flow chemistry when benchmarking costs against those of a real biodiesel production plant.60 Enzyme catalysts are generally expensive and necessitate recycling and reuse, while ensuring that the enzyme has great reaction activity. Concerning the latter, currently, at best, gram-scale product quantities can be produced, to fulfill production targets of the pharmaceutical industry.61 For biodiesel production, much greater productivity and consequently much larger enzyme loads are required. Immobilization of the enzyme is essential for both; yet this adds a mass transfer hurdle from liquid-phase reactants to the solid-phase enzyme, Fig. 11.
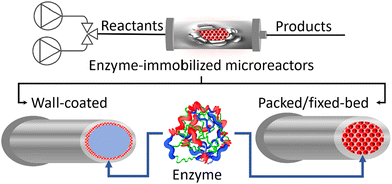 |
| Fig. 11 Strategies for enzyme immobilization in flow chemistry. | |
Costs were assessed for enzymatic biodiesel production from sunflower oil in small packed-bed reactors with internal micro-flow. A production scenario at 10
000 t a−1 capacity with 32 parallel reactors was cost evaluated and demonstrated the necessity to consider the costs of the ESI for the enzymes, typically a polymeric resin.60 This enzyme supports adds even higher costs than the enzyme itself does. Currently available support polymers are made for laboratory investigations so the outcome of the biodiesel study is to propose some cheaper polymer material options.
3.2.7. Enzyme loading and fixture.
A cost study determined how to achieve large enzyme loadings for economic viability in microreactor processing.61 Threonine aldolase can make complex, high-value pharmaceutical products with up to two chiral centres. It was immobilized to decrease costs by allowing reuse of the costly catalyst. The study demonstrated that achieving a high number of enzymes attached per unit support area was crucial, while retaining high activity after immobilization and in several process runs. The support is imperative here as it provides the total surface area available for immobilization. As the supports used for immobilization are costly themselves, compactness of the integration of diverse enzyme supports into a flow chemistry microreactor was investigated in terms of the integrated volume of immobilized enzymes; either by coating or packing. The same study also assessed the impact of high enzyme loadings for the example of glucose oxidase immobilization for gluconic acid synthesis for the food market, with its higher production quantities at lower price.
3.2.8. Enzyme-assisted waste-to-value conversion.
The decisive role of enzyme-immobilization costs on earnings and cash flow was demonstrated for lipase-catalyzed biodiesel production from waste cooking oil.62 This study showed a solution to this (currently) unavoidable high cost microreactor scenario, which was a reduction in material costs by using cheap waste materials, i.e., oil cake, Fig. 12. Earnings and cashflow for the new biodiesel flow chemistry process were computed. Still, it was determined that current commercial polymeric substrates were insufficient for enzyme immobilization, but that future microreactor production would demand the development of cheaper substrates, made for purpose.
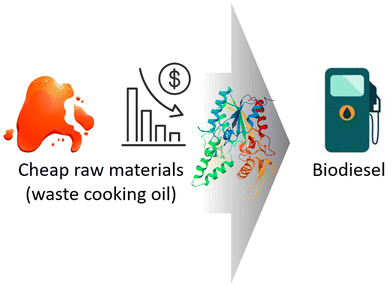 |
| Fig. 12 Lipase-catalyzed biodiesel production from waste cooking oil. | |
3.2.9. Catalyst recycling (in fine chemistry).
Cost computations demonstrated that reuse of the catalyst coatings on microstructured steel plates was preferable to the disposal of the used coatings and plates.63 The cost study targeted industrial-scale applications at a fine-chemistry level that necessitated plates of a much larger size and number than usual for reported laboratory-scale microreactor catalytic plates. Removal of the coatings was undertaken for recycling purposes, and several common removal methods were investigated. Harsh treatment with a strong acid changes the structural properties of the coatings and the steel supporting plates and accordingly their functionality, whereas mild conditions do not do the job. Coating renewal rates of 90% were achieved, requiring only a few fresh plates, which did not impact the overall sustainability of the recycling process.
3.2.10. Scale-up of process intensification.
A cost analysis of an industrial small-scale microreactor process to produce 4-cyanophenylboronic acid, run by the Azurchem Company, demonstrated that OPEX costs outweighed CAPEX costs by far; with 96% share.1 This cost analysis was the first published at the time, for a real industrial process with real cost data. The microreactor was cost effective by achieving a great yield via improved mixing (mass transfer) for expensive raw materials and/or high-value products, namely, 4-cyanophenylboronic acid. As a second driver, the reduction of operator costs (labour) was identified via the shorter flow processes. The study gained significance by generalising experimental findings via computed projection of case scenarios to a larger microreactor process capacity (scale-up). Numbering-up 10 times or 10 times the process intensification (meaning a faster process) were considered, and at scaled-up productivity, the microreactor OPEX benefits were even stronger.
3.2.11. Process design to scale.
A cost study was made to score process intensification enabled via microreactors and adsorption beds to produce hydroxy methyl furfural (HMF), made from renewable biomass. The impact of process design, “flowsheeting capability”, was investigated with the objective of maximising mass and heat transfer at different scales.64 The study demonstrated that scaling up microreactor modules reduced the sales price by 10% and emissions by 5% compared to conventional reactors. The recovery of HMF by adsorption beds as an alternative to vacuum distillation reduces the price between 10 and 50% and the CO2 emissions by up to 40%.
3.2.12. Process automation.
There are, to the best of our knowledge, no cost assessments on the impact of flow process automation. This is probably because automation by itself does not improve sustainability, but it does it indirectly via opening multiple optimization routes, e.g., helping to find a better yield. Evidently, automation saves personnel costs,65 and this has been quoted in the literature,66 but not quantified.
3.2.13. Process sheeting of modular units.
Decentralized production in modularized small-scale plants with microreactors was computed to produce liquid fuels from bioresources (the EU project BIOGO).67 The integrated process comprised coupled reforming of biogas and bio-oil, methanol synthesis, and conversion to gasoline. Process computing determined carbon efficiency of 56% and energy efficiency of 42%. The production cost of gasoline is €0.5 per L (in 1994), demonstrating compatibility with fossil fuel production and cost competitiveness compared to the Fischer–Tropsch route. Another advantage of using modular microreactors is the time to market, as the assessment of the construction time and operating costs of 35 decentralized modular plants revealed compared to one centralized large-scale plant.
3.2.14. Holistic process design with advanced downstream purification.
A cost and performance analysis of a pharmaceutical process was performed, by comparing an existing batch plant and a hypothetical continuous, modular plant.68 The data is reliable because it comes from an industrial batch plant operated by Sanofi, Fig. 13. The productivity of Sanofi's drug of 100 kg per year at a price of a few thousand euros per kg fits well with the capabilities of continuous-flow manufacturing. The assessment outcome can be considered generic for a multitude of drugs with similar characteristics. The genericness is also supported by a high-level scenario analysis applicable to the majority of drug manufacturing. Five scenarios were compared to the reference case at Sanofi, which were coined intensified reaction, continuous-flow, alternative catalysts, solvent switch, purification switch, product recovery, and intensified drying. This holistic economic analysis covered process parameters, including operation time, waste, and resource usage. Intensified continuous-flow processing at the millimetre scale, followed by continuous purification, emerged as the optimal solution among the five options, also pointing to opportunities for further optimisation. Costs are predicted to be decreased by 35%, the process time by 27%, and the labour efforts by 47%.
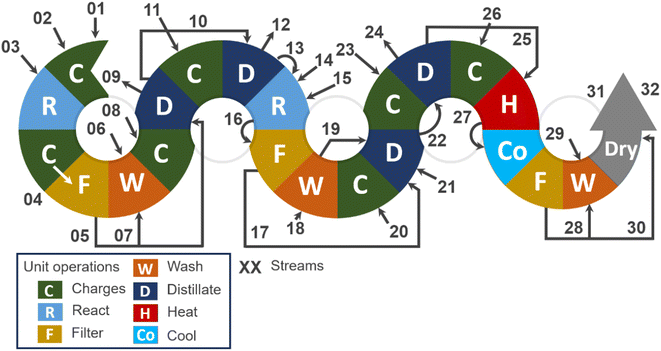 |
| Fig. 13 Scheme of a multi-step process and interactions as proposed by Sanofi. | |
3.2.15. Energy economics-by-design.
A study of microreactors for nuclear power confirms that the calculated levelized cost of electricity (LCOE) is much above market acceptance.69 It is concluded that using emerging technology intrinsically means accepting penalties from a low technological readiness level (TRL). The study instead proposed a ‘way-out’ to guide economic assessment through ‘design choices’, which provided guidance via bottom-up estimates. The so-called economics-by-design approach sets economic assessment at the center of the design process, meaning essentially to apply the principles that guide high TRL to low TRL. This methodology of a “microreactor-specific code of accounts at a range of cost equations” has been validated by existing frameworks, including design-to-cost and value engineering, Fig. 14. Market entry points are decisive for parametric design and rigorously push technical specifications until the performance meets the financial set point. The main outcome is to open the door to new markets (in the case studied, it means to approach niche markets “beyond the grid” towards remote communities), new attributes (beyond costs alone), and speed up the design cycle for earlier market entry (in the case studied, sequential unit deployments). The rapid evolution of design changes in microreactors, meaning they are factory-fabricated and rapidly deployable, is beneficial for these objectives. While TRL motivation promotes the economy of scale, microreactors stand for an alternative economic model based on offsetting gains standardization, simplification, passive safety, lower inventories (in the case studied, this refers to radionuclides), factory fabrication, fast installation, and low financing costs. The economics-by-design approach operates with learning rate (LR) assumptions, specific targets, to lower the largest cost contributors. In the case studied, this referred to changes in the neutron spectrum, the power output, and building structures.
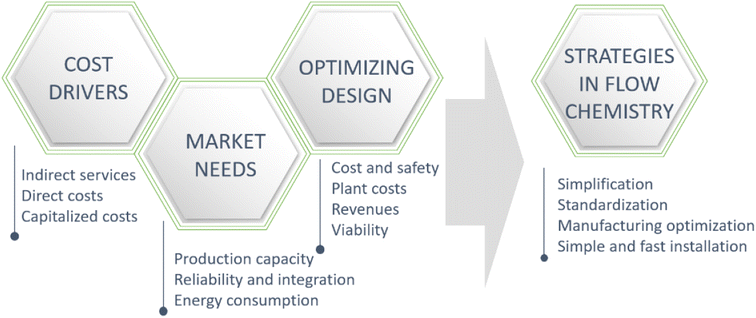 |
| Fig. 14 Benefits of the economics-by-design approach applied to flow chemistry. | |
4. Life cycle assessment, LCA
4.1. Micromachining
4.1.1. Advanced machining.
From the perspective of life cycle assessment, metal injection moulding is a better manufacturing choice than the binder-jetting additive technology.44 It has a low cumulative energy demand, global warming potential, and other favourable LCA impacts, through the use of mold plates and appropriate solvent management.
4.1.2. Microfabrication technology and design.
The so-called modular server–client–server methodology was used for combining process optimization with LCA, aiming at early-stage decision-making for microreactor design.70 LCA and process design modelling were connected via an interactive translator with the aim of achieving symbiotic time and cost saving automation. This approach predicted different design and manufacturing options for microstructured reactors made for gas-to-liquid-fuel conversion. The LCA impact of two microstructuring techniques for metal foils was compared, while considering several microreactor designs. Classification was made into improvable and non-improvable technical parameters for each fabrication step.
4.2. Materials
4.2.1. Reactants.
LCA rated the suitability of various CO2 precursors, including aqueous potassium hydrogen carbonate, hydrogen carbonate-based ionic liquids, DIMCARB, or sc-CO2 for the microreactor-enabled Kolbe–Schmitt synthesis.71 Yield is key for achieving a good LCA-sustainability profile. Using the ionic liquids [EMIM][HCO3] and [BMIM][HCO3] as combined solvent-reaction media led to the highest yields observed for all flow chemistry investigations of the Kolbe–Schmitt synthesis,72Fig. 15. The IL-flow chemistry has a high cumulative energy demand (CED) due to ecological backpack of the IL compounds. Recycling is imperative to improve the life cycle profile.
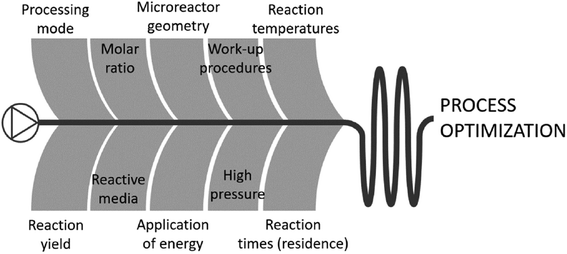 |
| Fig. 15 Process parameters used for the Kolbe–Schmitt synthesis intensification. | |
4.2.2. Catalysts and solvents.
Seven batch approaches and two flow chemistry approaches were compared by LCA for the synthesis of the drug intermediates 2-aryl benzoxazoles.73 Traditional chemistry is based on strong acids or toxic reagents with a related waste problem. The flow chemistry approaches demonstrated environmental benefits because these were able to use two recycling advantages. The first is related to the regeneration of an innovative molecular sieve catalyst and reduction of key metal (manganese) leaching. The second is the use of the green cyclopentyl methyl ether (CPME) solvent, due to its high recyclability and massively improved manganese recyclability (down to 0.002% loss). CPME is also a solvent with a significantly lower safety hazard compared to conventional ethers, containing fewer explosive peroxides. As a net effect of both innovations, carbon emissions are reduced by 85% in comparison with the batch approach, which chemically mirrors the flow chemistry process; the latter outperforming the other six batch processes studied. The flow chemistry process has a lower energy consumption and solvent loading, the share of which is up to 88% of the environmental impact.
Multi-step flow chemistry processes use much solvent through the aggregated process connection via telescoping. Solvent recycling, guided by LCA, was used to reduce the solvent loading for a three-step flow chemistry process.74
The impact of catalyst and solvent was also determined by LCA for the Buchwald–Hartwig amination of an API with a Pd-NHC based catalyst in both a lab-scale and a pilot-scale flow chemistry plant; NHC: N-heterocyclic carbene.75 Catalyst stability was investigated under solvent recycling conditions. Due to a higher space–time yield, the flow chemistry was an environmental improvement for almost all LCA impact categories compared to the batch synthesis; as well as being more economical. The LCA, which was the first done for complex molecularly defined catalysts, determined that catalyst synthesis could improve the profile of the entire flow chemistry process if the catalyst lifetime were short.
4.3. Mass transfer
4.3.1. Single-phase mass transfer (for wastewater).
LCA considered the environmental impact of water sources contaminated by dyes from the textile industry via remediation using catalytically active nanocomposites made in flow. These nanocomposites provide an alternative for the treatment of wastewater from the textile industry due to their high activity, low consumption, and short reaction times. Six different designs of micromixers were modelled and evaluated for the treatment of wastewater, Fig. 16.76 Velocity profiles, pressure drops, and flows were analyzed and compared under the same mixing conditions. The study shows a high contribution of the construction material, poly(methyl methacrylate) (PMMA) to the environmental profile, exhibiting 44% energy consumption, and 1% impact on human toxicity. The study shows that well-designed microdevices can reduce environmental impacts using flow chemistry. Micromixers with different microchannel designs, to force mass transfer by convection, had LCA impacts of 87%, 69%, 77%, 66%, and 58% for the LCA category of photochemical ozone formation.
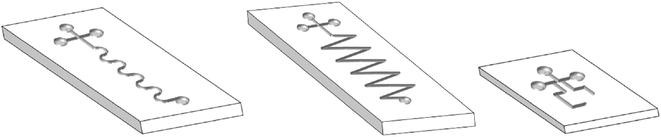 |
| Fig. 16 Micromixer designs used for wastewater treatment. | |
4.3.2. Single-phase mass transfer (for fuels).
An attributional life cycle assessment (LCA) was performed to determine the sustainability footprint of a new process design, enabled by microreactor technology, to utilize existing resources in a different way.77 NetMIX-microreactor technology converts natural gas from offshore resources via a gas-to-liquid (GtL) process combining steam methane reforming and the Fischer–Tropsch process (FT-SMR). The sustainability of the NetMIX-assisted process was compared with conventional crude oil production, with 1 MJ LHV as a functional unit. An additional assessment determined the impact to generate liquid fuel of 1 barrel volume. The latter allows one to judge the partial substitution of the existing crude-oil based technology, termed ‘add-on technology’. The synthetic fuel generated by the FT-SMR pathway has a net-negative score for the global warming potential, GWP. The emissions score is higher than the emissions caused by the NetMIX-microreactor process. Other life cycle impact categories increase because of the process complexity of the FT-SMR, which causes higher energy consumption and releases emissions. The GWP of the microreactor and conventionally made fuels are −0.34 kg CO2 eq. per MJ and 0.012 kg CO2 eq. per MJ, respectively, which is due to different yields. The GWP score impact per daily barrel of crude fuel is reduced from 70.3 to 64.6 kg CO2 eq. per barrel when adding the microreactor-assisted FT-SMR process, while reducing 34% of the flared gas.
4.3.3. Multiphase mass transfer (phase-transfer chemistry).
LCA has been applied to the green process design of a two-phase reaction, Fig. 17, the esterification of phenol and benzoyl chloride to give phenyl benzoate, including the synthesis of the phase transfer catalyst used, 1-butyl 3-methyl imidazolium chloride, [BMIM]Cl.78 [BMIM]Cl is advantageous for product recovery. The underlying engineering mechanism is the high surface-to-volume ratio of multi-phase microreactors, which causes high interfacial mass transfer rates. The human toxicity potential, HTP, is reduced by more than 60% when replacing the interdigital mixer with a herringbone-structured mixer. A similar trend is observed in global warming potential, GWP. Yet, this improvement comes at a price, which is the need to synthesize [BMIM]Cl. Conducting this by a batch and continuous process, the HTP scores 3.5% and 1.7 to 2.8%, respectively. The GWP of this process is 4 to 4.5% for the batch and 4 to 6.7% for the continuous process.
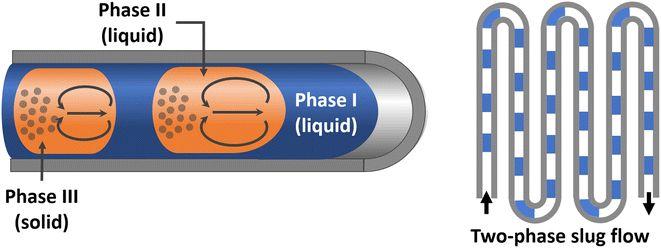 |
| Fig. 17 Continuous multiphase flow strategy. | |
4.3.4. Multiphase mass transfer (photochemistry).
Photochemistry is considered as mass transfer, as light penetration is much higher in small microvolumes compared to large vessels.79 An LCA study of vitamin D3 synthesis under UV-photoflow chemistry was based on a cradle-to-gate approach,80Fig. 18. Besides the reaction, extraction and purification by crystallization were considered.81 The flow chemistry process had a lower environmental impact than batch processing. It was found that the major LCA impact was made by solvents. Consequently, incorporating recycling loops for the two solvents used in extraction and precipitation improved the LCA profile.82
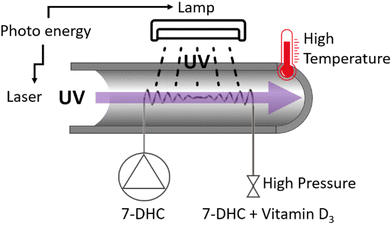 |
| Fig. 18 Scheme of continuous flow photo-high-p,T intensification reactor.83 | |
4.4. Heat transfer
4.4.1. Electromagnetic heat transfer.
In continuation of the LCA study reported in section 4.2.1, the environmental effect of the heating mode for the Kolbe–Schmitt synthesis of 2,4-dihydroxybenzoic acid was determined. Microwave irradiation was tested as an alternative to conventional oil-bath heating under superheated conditions, leading to higher yields but with the drawback of higher energy consumption.72 The recommendation is that microwave heating should only be applied when reaction yields are much higher.
4.4.2. Electrical heat transfer.
Electrical heating is another alternative and was tested in a tailor-made microdevice, which was amenable for the pilot scale through internal numbering-up.84 A productivity of 225 kg h−1 at 4 s residence time and 32% yield was determined. The space–time yield for electrical heat was 38
250 kg (m3 h)−1, while microwave heating achieved space–time yields up to 32
550 kg (m3 h)−1. The conclusion is that convective heating methods such as an oil bath or electrical heating are ecologically better than microwave irradiation.71
4.5. Master solvents
4.5.1. Ionic liquids.
LCA was performed for the environmental score of master solvents, as alternatives to normal solvents used in organic chemistry, as well as the possibility of solvent-free processing.85 The master solvent choice included the ionic liquid 1-hexyl-3-methylimidazolium tetrafluoroborate, [C6MIM][BF4], and a mixture of citric acid/N,N′-dimethyl urea as a deep eutectic solvent. These solvent alternatives were compared to commonly used solvents including methanol, cyclohexane, acetone and methanol/water. The test reaction chosen was the Diels–Alder cycloaddition of cyclopentadiene and methyl acrylate. The ecological and economic optimisation (ECO) method was used for scoring; this uses LCA together with an optimisation procedure. The life cycle inventory is large and holistic, including the production of reactants, solvents and auxiliary agents, synthesis and workup, as well as recycling and disposal. This way, the environmental effects of the solvents were computed, comparing the new master solvents to traditional solvents. At 25 °C, 98% conversion of methyl acrylate was computed with a 5.5 exo/endo ratio. For a solvent-free route at 25 °C, 98% conversion of methyl acrylate is achieved with a 2.9 exo/endo ratio. The LCA study showed a higher cumulative energy demand, CED, due to the use of the solvents (acetone, cyclohexane) and additives (DMU). A higher EF is determined in the workup, since additional solvents are used. The ionic liquid [C6MIM][BF4] is a threat to aquatic organisms, classified as water hazard class 3. The additives citric acid and DMU are not hazards here, classified as WGK-1.
4.6. Residence time/productivity
4.6.1. Faster reaction kinetics with novel process windows.
A real-case study of the industrial scale-up of a reported three-step, lab-scale flow chemistry cascade can build on environmental advantages, as demonstrated for a mini-pilot flow chemistry plant for manufacturing the anti-epilepsy drug rufinamide, operated at an industrial site,54Fig. 19. On the lab-scale and as one of three steps of the cascade, changing from batch to flow chemistry significantly reduced the reaction time from 28 to 0.17 h (about 10 min) for the 1,3-dipolar Huisgen cycloaddition.55 A novel process window speeds up reaction kinetics via an unusually high temperature of 210 °C instead of 135 °C possible under batch conditions. The laboratory yield of rufinamide, made by a three-step process, was practically the same for batch and flow chemistry, being 79% and 80%, respectively. The mini-pilot had only a slightly higher environmental impact than the laboratory plant, showing that the ‘environmental carry on’ was successful. The small difference is due to using somewhat higher temperatures and higher reactant excess for the mini-pilot plant to compensate for the slight increase in internal dimensions of the mini-pilot plant's reaction channels and to guarantee the same productivity as that for the laboratory-scale standard. The environmental benefits of the mini-pilot plant are much higher than those for the batch synthesis. The main winning point of the microreactor process is the higher yield, i.e., reduction in waste, in two out of three reaction steps. Yet, the last step of the rufinamide process, the Huisgen cycloaddition is slow, even under flow chemistry conditions, which negatively impacts the environmental profile and requires improvement to release the full potential of the multi-reaction network.
 |
| Fig. 19 Scheme of the 3-step synthesis of rufinamide precursor performed using flow chemistry. | |
4.7. Safety
To the best of our knowledge, there are no LCAs on the impact of flow chemistry safety. Safety, in general, is not a true part of LCA, which is primarily concerned with emissions (from chemical processes). Accordingly, a study proposed a new metric, the life cycle inherent toxicity, to adapt LCA with inherent hazard data of all the chemical flows to the final product.86 Toxicity is determined for the entire cradle-to-gate of a chemical, rather than just considering the starting materials as in conventional toxicity. Life cycle inherent toxicity is different from the latter and can provide genuine information. The usage of this potential for flow chemistry is yet to be achieved.
4.8. Multi-reaction networks/product complexity
4.8.1. Product quality, novel process windows.
An LCA study was conducted to assess the potential of microreactor chemistry to conduct multi-step syntheses in an end-to-end process design. Drugs are foremost examples of products made by multi-step synthesis.74 It was imperative was to ensure uninterrupted flow from the first step to the final product, also known as telescoping in flow. The LCA was made for the flow chemistry synthesis of the antiepileptic drug rufinamide starting from benzyl alcohol. Rufinamide is one of the best-selling 5-membered ring heterocyclic pharmaceuticals. Foreground process work explored harsh operating conditions (i.e., novel process windows) to obtain the activation needed for the low reactivity reagent. This enables the use of more environmentally friendly chlorides instead of the commonly used (more reactive) bromides in the first of three steps. Three such multi-step microreactor networks were rated by green metrics and LCA.74
4.9. Novel process windows
4.9.1. Superheated processing, precursors, and heat transfer.
An LCA study provided decision support toward a green process design for the Kolbe–Schmitt synthesis of 2,4-dihydroxybenzoic acid from resorcinol.71 The impact of various kinds of process intensification was investigated based on chemistry innovations, including different CO2 precursors such as aqueous potassium hydrogen carbonate, hydrogen carbonate-based ionic liquids, dimethyl carbonate, and supercritical CO2. The LCA study allowed a ranking of those impacts and informed the selection of the best chemistry. This chemical scenario analysis was complemented by a process-thermal study, including microwave irradiation for faster heating than that conventionally achievable and superheated process conditions (‘novel process windows’) at unusually high reaction temperatures. It is demonstrated that convective heating, such as on an oil bath or electrical heating, were environmentally more beneficial than heating by microwave irradiation. The environmental performance of microreactors, under those best heating conditions, was superior compared to conventional batch reactors. The holistic process study included the LCA determination of workup procedures.
4.9.2. Superheated processing.
An LCA study was conducted, based on process modelling and experiments, for an existing production process of plasticizers made of epoxidized soybean oil (ESBO).52 Superheated processing in novel process windows (NPWs) was used to improve the environmental profile. ESBO is produced at a yield of 75% in 300 min, while batch operation is on a 100 g scale at 60 to 80 °C. The flow chemistry ESBO process has a 12% improvement in the cumulative energy demand, CED. An environmental drawback, as for the batch process, is the use of hydrogen peroxide, which increases the human toxicity potential, HTP, above average. Knowing these LCA hot spots and the capability of NPW and green chemistry, a reduction of GWP and HTP by 11–12% was computed.
4.10. Recycling
4.10.1. Enzyme recycling.
Life cycle assessment (LCA) was done for a modified flow chemistry process (Bogdan) towards the drug ibuprofen, using enzymes in the last of three reaction steps, and was compared to the non-enzymatic three-step flow chemistry (Bogdan, name of the lead researcher) and the industrial BHC process (BHC company),87Fig. 20. The BHC process has received awards for its greenness improvements compared to previous commercial processes. A reduction of environmental impact was demonstrated for almost all LCA impact categories of the analysis, with the magnitude depending strongly on recycling in the production system. When 50% of the enzyme is recycled, the new enzyme-flow chemistry process has a lower environmental impact in impact categories like acidification, ecotoxicity of freshwater, human toxicity, particulate matter, and resource depletion. At a recycling efficiency near 100%, virtually all impact categories are improved. Then, the improvement compared to the BHC process can range from about 30 to 95%, and to 31 to 38% relative to the Bogdan process; the latter demonstrating how important recycling of a value component in one out of three flow chemistry steps is.
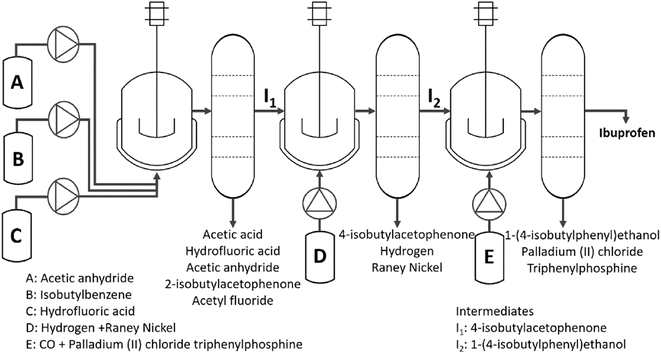 |
| Fig. 20 BHC's 3-step ibuprofen production process. | |
4.10.2. Construction material recycling.
An LCA was made for (nano)precipitation at optimal nucleation and growth, at the quality needed for drug delivery and bioremediation using three micromixers with different channel configurations, namely, serpentine, triangular, and a 3D arrangement.43 The environmental assessment aimed to demonstrate that recycling of the construction polymeric material had an impact; also from a flow chemistry process viewpoint. Assuming reuse of the micromixers in the first cycle, it was determined that energy and water consumption were reduced by 84% and 4%, respectively. In TB and SB mixers, an energy consumption of 0.2 kW h is observed, whereas in 3DB mixers it is 0.3 kW h. For reused micromixers, energy and water consumption declines by 95% and 50% for the second cycle, respectively.
4.11. Process simplification
4.11.1. Chlorine-free process.
An LCA study was made for a new chlorine-free process for producing tetrafluoroethylene (TFE) and hexafluoropropylene (HFP) in a microreactor, starting from partially fluorinated alkanes obtained from electrochemical fluorination.88 Tetrafluoroethylene (TFE) is a common monomer for the synthesis of fluoropolymers at the industrial scale, and is produced via multistep pyrolysis of chlorodifluoromethane, resulting in high energy demands and large amounts of acid waste, mainly HCl and HF. In the microreactor, high conversion rates of CHF3, which is used as a surrogate of electrochemical fluorination (ECF) streams, and high yields of fluoromonomers could be achieved. The conversion is 25% at 875 °C with 0.4 s residence time, at a maximum yield of 23% TFE at 875 °C in 0.4 s and 17% TFE and 35% HFE at 875 °C in 2.5 s. CHF3 pyrolysis needs 40% less energy than the industrial process. It has a 50% reduction in ozone depletion and climate change. The 100-year GWP of CHF3 is 11
700 kg CO2-eq. per kg. Incineration of the waste acid CHF3 requires 40% higher energy, whereas pyrolysis of CHF3 by the industrial method requires 40% less energy, and 50% reduction in climate change and ozone depletion.
4.12. Process design (end-to-end)
4.12.1. End-to-end modular process design.
For the process development of an active pharmaceutical ingredient (API) and motivated by the introduction of microreactor technology, a study involved holistic rethinking, redesigning, and optimization of an entire multi-step process, including downstream purification.89 An early process development stage of an API, produced in low-volume with high-value at Sanofi Company, was investigated, in the hope that it would leave more levers than a late-stage optimization. The LCA study computed through 6 batch and 6 flow chemistry scenarios that the most decisive impact factors were materials (reactants), solvent, and catalyst. Several future process scenarios were taken for hot-spot analysis, including increased yield, reduced solvent load/solvent recycling, and catalyst immobilisation to favour its recycling. As a bespoke approach, the impact of purification through multiparametric variations was computed when changing from batch to continuous production. The fixation of catalysts turned out to be a winning ecological point, but also indicated limits when changing protocols, as the reactant concentration needed to be changed. Using the Pareto approach, a cost ranking of the 12 process design options was achieved. The product cost is decreased by 35%, and the labour cost is decreased by 47%, the latter due to a reduction in reaction time by 27% compared to the industrial state of the art.68
4.13. Process automation/control/modularisation
There are, to the best of our knowledge, no LCAs (or cost assessments) on the impact of flow process automation. This is probably because automation by itself does not improve sustainability, but it does so indirectly by opening multiple optimization routes, e.g., helping to find a better yield. Evidently, automation saves personnel costs and increases safety, and this has been quoted in the literature,66 but not quantified.
4.14. Scale-up/predictability
4.14.1. Process development towards commercialization.
An LCA study aimed to elevate the role of environmental assessments within the early phase of process development of drugs (active pharmaceutical ingredient, APIs). It was imperative to shorten the development time to enable faster market launch for new drugs. The hypothesis is that it is beneficial to rethink, redesign, and optimize process strategies as early as possible, while implementing these at a later stage reduces their potential, as the processes are already established. An environmental study conducted life-cycle-based process optimization and intensification of a pharmaceutical production process targeting a high-value API.90 The LCA study was holistic by considering diverse enabling functions in a broad scenario, including the changeover from batch to flow-chemistry processing, using new catalysts, and following various process options.
Influential factors on the Sanofi API production process are the supply of KIM, solvent, and catalyst. These strategies bring ecological improvements along with enhanced yield, a reduction in solvent demand/solvent recycling, and fixation/change of the catalyst. Shifting from a batch to a continuous process has improved overall sustainability and efficiency of the process due to changing the catalyst. A cost saving potential of 33% has also been achieved by transitioning from API manufacturing process AP to CP 5a. Better heat management, a higher reaction rate, lower environmental impacts, and reduced human health risks are also expected.
In CP 5a, an 84% recovery rate is observed along with a reduction in AP, GWP, and HTP between 66 and 64%. A reduction in TETP by 71%, NLTP 65%, POFP 91%, MDP 85%, ODP 26%, TAP 99%, FEP 82%, and FDP 67% has been observed.
4.14.2. Scale-up predictability.
With the same generic ambition of predicting the performance of a whole class of reactions in one example, a multi-criteria decision supported by life cycle management, was developed to score the sustainability of process design and its scale-up.91 Three industrial cases are investigated, including an intensified reaction of renewable feedstock by epoxidation and transesterification, and the recovery of a catalyst from large-scale plate coating (relative to the scale of the microreactor used). Directions for the processes investigated themselves were determined to facilitate transfer to the pilot scale and beyond; this is also informative for opportunities for the whole class of reactions, as the innovations are generic scenarios, Fig. 21. Epoxidation is achieved by using minimum oxidative media and favourable use of supercritical processing with waste oil and methanol. Flow chemistry epoxidation reduces the global warming potential, GWP, by 12% and the human toxicity potential, HTP, by 11%. Continuing with flow chemistry innovations, it is computed to achieve a 70% reduction in GWP.
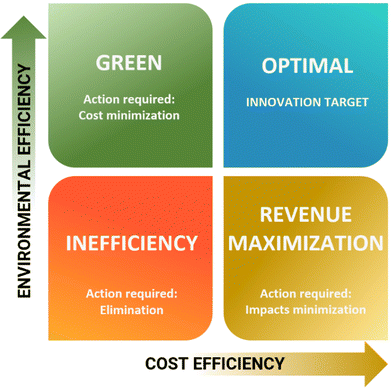 |
| Fig. 21 Correlation between cost and environmental efficiency for alternative scenarios. | |
4.15. Achievement summary of sections 4.1–4.14
This review analyses all references used in sections 4.1–4.14 to determine if the LCA studies do report benefits compared to conventional (batch) technology or just report on the emerging microreactor/flow chemistry LCA outcome, Fig. 22. Only 38% of these LCA papers report impact improvements against the benchmark, most of these are related to energy savings (51%), while 44% report improvement due to recycling (waste reduction).
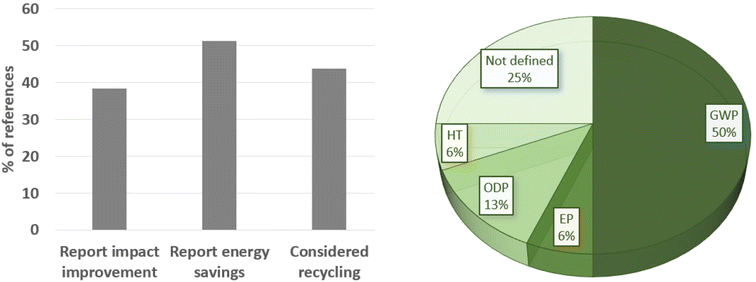 |
| Fig. 22 Statistics about the references in this review, showing the types of parameters considered (left) and the main categories that benefited from each published work (right). | |
Among all LCA impact categories, in about the half of cases, climate change (GWP) is determined as the most influential category, while the ozone toxicity potential (ODP) is 13%, and the eutrophication and human toxicity potentials are 6% each. In 25% of the studies considered here, the most influential category is not specifically defined. There is clearly a lack of reporting in the literature.
5. Potential of sustainability for future flow chemistry
5.1. Micromachining
A vision is given for the sustainability potential (costs and LCA) of flow chemistry, when being used (‘future’). Following the classifications of key levers, Table 2 lists the key processing issues listed in sections 2.1–2.13, their reasoning, and key levers for costs and LCA for microreactors/flow chemistry.
Table 2 Impact of key processing issues of microreactors/flow chemistry on key levers for costs and LCA
Section |
Key processing issue |
Reasoning |
Costs key lever |
LCA key lever |
2.1. |
Hardware capital expenditure |
Facilitated transition batch-to-flow and use of best equipment |
Costs |
Indirect, complex |
2.2. |
Mass transfer |
Much faster mixing |
Costs |
Waste, energy, yield |
2.3. |
Heat transfer |
Much faster heat transfer; even under thermal runaway or explosive scenarios |
Costs |
Waste, energy, yield |
2.4. |
Reaction time |
Dramatic reduced reaction times |
Costs |
Yield, waste, productivity |
2.5. |
Productivity |
Boosted productivity (elimination of transfer limitations, and intensified processing) |
Costs |
Productivity |
2.6. |
Safety |
Safe operation in former explosive or thermal runaway regimes |
Costs |
Productivity |
2.7. |
Multi-reaction networks/product complexity |
Connect, in a tight space and within a short time, several reactions to a complex product |
Indirect, complex |
Yield, energy, new products |
2.8. |
Novel process windows |
Boost reactivity and other performance |
Costs |
Yield, energy, productivity |
2.9. |
Recycling |
Increased circularity by reusing non-converted material |
Costs |
Waste, energy |
2.10. |
Designer solvents |
Extraordinary dissolution ability and performance beyond dissolution |
Costs |
Waste, energy |
2.11. |
Automation/-modularisation |
Highly controlled and standardised processing |
Indirect, complex |
Indirect, complex |
2.12. |
Scale-up/-predictability |
Equalling-up and facilitated reaction modelling |
Cost, time-to-market, cash-flow |
Indirect, complex |
2.13. |
Supply chain/-business model |
Compact, transportable, easy installation/demounting and fast start-up/shutdown |
New product services |
Indirect, complex |
11 of 13 key processing issues can lead to cost benefits. From the beginning of investigations, the microreactor/flow chemistry technology was supported by industry for that reason, and this motivation is also instrumental to process intensification, which also fuels microreactors/flow chemistry. As a second source of motivation, the concept of green chemistry has drawn attention to key sustainability levers for microreactors/flow chemistry, meaning research that can impact the LCA. 9 of 13 key processing issues can comprise benefits for LCA. The missing 7 assignments for costs and LCA, do not (necessarily) mean that there is no impact, but that the possible impact is indirect and complex, meaning it is difficult to trace. One main reason these 7 key processing issues are disconnected from direct impact on cost and LCA key levers is that microreactors/flow chemistry have their roots in microfluidics. Here, key levers are producing and handling large amounts of data (‘process automation’) at low costs; this is instrumental in the aim of using microfluidics to intensify analytics. This explains the three respective section entries 2.1, 2.11, and 2.12.
As listed in Table 2, LCA-relevant key levers of microreactors/flow chemistry are yield, waste, productivity, and energy efficiency. While a higher yield will automatically reduce waste, their dual listing is still required, as recycling can also reduce waste (at constant yield) and regain the reactant. Productivity is also LCA-relevant, as at a higher productivity yield the energy efficiency might be lower than at the pilot and laboratory scales; noting that the latter might also be higher, e.g., for reasons of energy integration. Energy efficiency in this context refers only to the capability of the microreactors/flow chemistry to transfer heat or cooling to the reaction medium (assuming the same energy source as for the batch reaction; typically, at this time still fossil energy).
LCA- and cost-relevant levers each take roughly one third of the reported key levers in Table 2. The last third (including process automation) has an indirect, complex impact on LCA and costs that is difficult to track.
This study demonstrates the impact of four LCA key levers on the final LCA outcome. The latter is determined in terms of the individual outcomes, the LCA impact categories, the total outcome, and the averaged normalised LCA result. A flow chemistry reaction that the authors of this study have previously conducted research on provides detailed reporting, including an LCA, and operates at an industrial site (TRL 4). Very few examples of that scale and openness in information are reported in the literature. The reaction was guided by a 6-membered industrial consortium.
This Huisgen dipolar cycloaddition has heat duties (heating to 175 °C), known scaled-up productivity, and a yield (55%) that still leaves room for improvement. To illustrate what is achievable by advanced setting of the key levers, we extend here the previous LCA study by a parametric extrapolation using the four key levers beyond the achievements of the former pilot study, Table 3, meaning, e.g., the yield is increased from 60% to 100% (and also lower for reasons of systematics) and the productivity is considered from 100 to 200%.
Table 3 Relative potential effects of the environmental impacts on the LCA when processing key processing issues of microreactors/flow chemistry. (Impact categories: AP acidification, GWP climate change, FET ecotoxicity: freshwater, CEDf energy resources: non-renewable, EPw eutrophication: freshwater, EPt eutrophication: terrestrial, HTc human toxicity: carcinogenic, HTnc human toxicity: non-carcinogenic, CEDm material resources: metals/minerals, Ph photochemical ozone formation: human health, WU water use)
|
|
Impact categories |
|
AP |
GWP |
FET |
CEDf |
EPw |
EPt |
HTc |
HTnc |
CEDm |
Ph |
WU |
Average |
Most affected category |
Yield, % |
60 |
1.06 |
1.01 |
1.04 |
1.07 |
1.05 |
1.03 |
1.03 |
1.05 |
1.02 |
1.06 |
1.05 |
1.04 |
AP |
70 |
0.99 |
1.00 |
0.98 |
0.99 |
0.98 |
0.99 |
0.99 |
0.98 |
0.99 |
1.00 |
0.98 |
0.99 |
80 |
0.93 |
0.98 |
0.95 |
0.94 |
0.93 |
0.96 |
0.96 |
0.93 |
0.97 |
0.95 |
0.93 |
0.95 |
90 |
0.88 |
0.97 |
0.92 |
0.89 |
0.89 |
0.94 |
0.93 |
0.88 |
0.96 |
0.91 |
0.89 |
0.92 |
100 |
0.85 |
0.96 |
0.89 |
0.86 |
0.86 |
0.92 |
0.91 |
0.85 |
0.95 |
0.88 |
0.85 |
0.89 |
Productivity, % |
125 |
1.08 |
0.96 |
1.03 |
1.07 |
1.06 |
1.01 |
1.01 |
1.07 |
0.98 |
1.05 |
1.07 |
1.03 |
GWP |
150 |
1.17 |
0.93 |
1.07 |
1.15 |
1.14 |
1.02 |
1.02 |
1.15 |
0.96 |
1.10 |
1.14 |
1.08 |
175 |
1.26 |
0.91 |
1.11 |
1.23 |
1.21 |
1.04 |
1.04 |
1.23 |
0.95 |
1.16 |
1.22 |
1.12 |
200 |
1.36 |
0.89 |
1.16 |
1.32 |
1.29 |
1.07 |
1.07 |
1.31 |
0.95 |
1.22 |
1.30 |
1.18 |
Waste, % |
20 |
0.98 |
0.97 |
0.99 |
0.97 |
0.99 |
0.96 |
0.98 |
0.99 |
0.91 |
0.97 |
0.98 |
0.97 |
CEDf |
40 |
0.95 |
0.94 |
0.97 |
0.93 |
0.98 |
0.92 |
0.96 |
0.98 |
0.82 |
0.93 |
0.96 |
0.94 |
60 |
0.93 |
0.90 |
0.96 |
0.90 |
0.98 |
0.89 |
0.95 |
0.96 |
0.73 |
0.90 |
0.93 |
0.91 |
80 |
0.91 |
0.87 |
0.94 |
0.86 |
0.97 |
0.85 |
0.93 |
0.95 |
0.64 |
0.86 |
0.91 |
0.88 |
100 |
0.88 |
0.84 |
0.93 |
0.83 |
0.96 |
0.81 |
0.91 |
0.94 |
0.56 |
0.83 |
0.89 |
0.85 |
Energy efficiency, % |
20 |
1.48 |
0.26 |
1.40 |
1.22 |
0.48 |
1.74 |
1.47 |
1.60 |
1.71 |
1.33 |
1.86 |
1.32 |
GWP |
40 |
1.12 |
0.82 |
1.10 |
1.05 |
0.87 |
1.18 |
1.12 |
1.15 |
1.18 |
1.08 |
1.22 |
1.08 |
80 |
0.94 |
1.09 |
0.95 |
0.97 |
1.07 |
0.91 |
0.94 |
0.92 |
0.91 |
0.96 |
0.89 |
0.96 |
100 |
0.90 |
1.15 |
0.92 |
0.96 |
1.10 |
0.85 |
0.91 |
0.88 |
0.86 |
0.93 |
0.83 |
0.94 |
This is to justify this study, compare the latter reported present studies, and to guide future investigations, by having information about the gap. The assessment is performed per kilogram of final rufinamide intermediate produced, using the Ecoinvent database and environmental footprint (EF 3.0) quantification methodology. Each impact quantification is normalised by the former LCA to obtain a non-dimensional value, from which a global sustainability coefficient is averaged. Whilst values above one (invariant) denote a relative increase in environmental impacts, values below one exhibit global environmental benefits.
For the rufinamide base case, 55% yield, 0% recycling, 100 g h−1 productivity (‘50%’), and 60% energy efficiency were taken according to the process data of our pilot plant at an industrial site.55 Yield was varied from 60 to 100%, productivity from 100 to 200% assuming 5% energy efficiency improvement per 25% scale increase, waste from 0 to 100% recycling, and energy efficiency from 20 to 100%, Table 3.
The LCA results, gained in this way of consecutive LCA (CLCA), demonstrated that the acidification potential (AP) exhibited the highest reduction for yield variations, while human toxicity (HTnc) and water usage (WU), and human toxicity (HTnc) and energy usage (CEDf), were only affected to a minor degree, Table 3. The cumulative energy demand (CEDf) is majorly reduced for waste variation, while the climate change (GWP) is based on the energy efficiency variation and productivity.
Fig. 23 plots the relative (%-wise) variations of the average environmental impact for the four key levers. Yield and waste variation give 11 and 15% reduction in the average environmental impacts, respectively. Productivity variation gives 18% difference. Lower energy efficiency at a smaller scale was assumed, while yield mildly decreased on a higher scale. The productivity impact would be minor, and even absent when considering ideal numbering-up (‘equalling-up’), which this study did not do because ‘scaling-out’ is the reality in industrial laboratories, as reported by the Lonza pharmaceutical company. The energy efficiency variation above the base case set value gives 6% decrease in the average environmental impacts, while a strong loss of 32% is determined for lower energy efficiencies than the base. Noting that the heat duty is moderate for the reaction chosen, some microreactor-conducted reactions are known to have a larger heat duty; yet this also holds for the levers of yield, waste, and productivity.
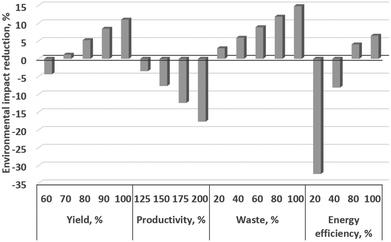 |
| Fig. 23 Normalised global reduction of the environmental impacts of alternative scenarios when compared with the LCA of the rufinamide process. Positive values denote a reduction of environmental impacts, while negative denote an increase. | |
Among all scenarios, energy efficiency exhibits the highest span (39%) between best and worst scenarios, but only when considering 20% as low energy efficiency. Productivity variation has 18% span, yet this is based on our assumptions (see above) and these will vary from equipment to equipment. Then waste variation would have the largest impact with 15% span, followed by yield with 12% span. The lesson learned is that optimising one of the four parameters has an impact, but it is clearly advised to optimise more than one for a substantial impact.
6. Perspective: flow chemistry/microreactors need more societal engagement
The perspective for future flow chemistry is to integrate most modern societal and industrial trends, and foremost the green energy transition.92 This puts photoflow chemistry into focus, to finally use sunlight as a renewable energy source.93 Yet the system integration of flow chemistry with electrochemistry,94 plasma chemistry,95 and microwave activation96 also provides pathways to profit from the renewable energy transition.
While photoflow chemistry studies have advanced considerably and the other named hybrid-technology studies were taken up, one cannot claim that a ‘flow chemistry transition’ has taken place; this means today's flow chemistry activities are still largely like those when the field emerged in the years 2004–2006. The flow chemistry community may follow up on using the momentum of the green energy transition by being more involved in respective projects.
The same is advised for using microreaction technology directly for the green energy transition, which means to design and test reactors for making hydrogen or other energy carriers from renewable resources.97 This has been investigated since the start of the field in 1998–2001,98 and while some academic progress and also industrial translation has been achieved, the real breakthrough is still to occur.
Extraction is a field that is much underexplored in industrial translation. While there is a vast demonstration of the benefits of microfluidics for most relevant extraction applications, such as to gain and recycle critical minerals,99 this has never been transferred to the industrial scale. This remains an unused opportunity, as the technology readiness level is advanced, i.e., industrial microreactor equipment is on the market and used by industry.100 The main reason for this gap is that microreactors/flow chemistry, while well accepted by the pharmaceutical industry, are only occasionally applied to other branches of the chemical industry and rarely to industries outside chemistry. The advice here is that the flow chemistry community needs to proactively engage more with the mining, biomass, and other large-scale industries that provide notable opportunities for (continuous-flow) extraction.
This assessment could list more global societal movements that provide opportunities for flow chemistry and microreactors. A pronounced one is ‘process automation’, following the trend of industrial digitalization (‘Industry 4.0’) and the deployment of artificial intelligence and quantum computing.101 More megatrends are listed in the compilation of the sustainable development goals (SDG's) of the United Nations,102 yet this perspective reached end-point and asks for conclusion.
To sum up, this review shows that the contribution of environmental engineers and scientists, social scientists, business school researchers, and economists to the field is small. It was always small but seems to have declined even more over the last decade. Prosperous mega-technologies like hydrogen splitting from water receive considerable pull from those scientists outside the traditional fields of chemical engineering and chemistry. Flow chemists may increase their awareness of those communications and societal engagement, moving across boundaries outside their traditional pharmaceutical market.
7. Conclusions
This review critically studied microreactor- or flow chemistry-based sustainability assessments, which over about 15 years, have contributed knowledge, but still left gaps to be filled in future research. Overall, the number of sustainability-based papers specifically addressing this topic is low compared to the total number of microreactor and flow chemistry papers. This gap is shared with major emerging technologies around hydrogen and carbon dioxide, topics of highest societal eminence. Yet, the sheer mass of papers and investigations means there is better coverage of sustainability.
The sustainability assessments in this study are classified by key levers, which are fundamental characteristics of microreactors/flow chemistry. These include microreactor machining, microdevice design, operating conditions, microprocess design, total process design, and so forth. This aims to link the sustainability assessment outcomes with the information provided in many reviews in the field, mirroring the knowledge of users, to narrow the above-mentioned gap and knowing that the fundamental characteristics motivate new researchers to enter the field.
Several microreactor studies are still driven by cost arguments and these studies often straddle the boundary between microreactor engineering and microfluidics. These heavily use inventions in microfluidic fabrication technologies, which has been a decent research topic over the last three decades. Low-cost manufacturing techniques, including rapid prototyping, and the use of cheap construction materials are an ongoing topic in these cost assessments. The gap noted is that these studies most often do not quantify the cost effect in a suitable engineering way (e.g., as a techno-economic assessment, TEA), so the cost issue is often only objective and not the goal (a goal splits into several objectives), and it does not reach the companies that produce and sell microreactor/flow chemistry equipment. The consideration of machining costs must also include the recyclability of key materials within a microreactor, foremost catalysts. Conversely, this requires considering the durability of those key materials (catalysts) during microreactor operation. It is a lack of communication between scientific communities, crossing discipline borders, that hampers the use of these valuable studies.
The microreactor/flow chemistry community, on its own, does not conduct sufficient cost or TEA studies. These are actually very rare. Sustainability assessment is better developed with life cycle assessment (LCA) studies. Some (ten) studies have determined a clear view of how microreactors/flow chemistry can improve the life cycle. Yet the assessment lacks details and bandwidth. It lacks reporting based on industrial data. Information in the literature is still proficient enough to guide future developments of emerging technology. It has contributed to industrial success, and it will continue.
Many LCA studies investigate the impact of different microreactor and process designs, targeting improved OPEX costs. Some LCA studies address how microreactors and flow chemistry facilitate entirely new ways to process. A multitude of environmental assessments studies have elucidated the process side of microreactor and flow chemistry.
The lesson learnt is that communication between those practising the technology and sustainability researchers should be improved. Yet, this gap exists for virtually all technology and science fields and thus is not a specific lack of awareness in this field. This common drawback is due to having sustainability studies with diverse and often non-holistic motivations; the latter is what this study is asking for. This has to do with the different research communities involved, including at least three of these – microreaction technology, flow chemistry, and microfluidics. The microfluidic community is focused on CAPEX cost studies, being confined to the device level, while the flow chemistry community is interested in improving OPEX costs.
Another drawback of reported sustainability studies is that these typically consider lab-scale devices, while it would be necessary to judge industrial operation at the production scale. This is obviously also due to the lack of disclosure of microreactor studies at scale; mostly for reasons of protecting industrial intellectual property. A final shortcoming identified in this study is that some key levers, including safe processing and process automation, are not assisted by sustainability assessments. Admittedly, assessing this is more complex than evaluating other enabling factors.
8. Outlook
The LCA and sustainability approach guidance should be more widely used for the development of a flow chemistry process; this is only found in rare cases, as demonstrated for a three-step flow chemistry reaction network, in which the reactants were selected and the whole synthesis pathway was designed based on green chemistry metrics and LCA criteria.74
The rareness is because most flow chemists work on the lab scale, and a prediction of costs at the industrial scale is beyond their expertise and research interests and is the domain of chemical engineers. Only very rarely do chemists and chemical engineers unite to publish a cost (or other sustainability) study.55
This leaves a large gap in opportunity. Flow chemistry and microreactor researchers and practitioners can profit much from LCA and other sustainability assessments, when realising that it is an integral methodology for process design, even at the early stages of innovation, and can be used as a decision support tool for R&D projects in industry and in the academic setting.103 In addition to the relevant sustainability literature in the field, a consideration of recent achievements is valuable; for example, learning can be taken from the recent approach of integrating a screening LCA into the development of a chemical (recycling) process.104
A uniform methodological approach for life cycle assessment and techno-economic assessment (costs) would aid increased transparency, comprehensiveness, and comparability, as demonstrated for recycling.105 Ongoing, new sustainability assessments are designed with the aim of being more accurate, holistic, and so on. A modified green chemistry metrics approach has been proposed via the 12 green chemistry principles and their metric combination.106 The idea is to avoid the resource intensive data collection common to LCA, but rather use readily available data from the globally harmonized system of classification and labeling of chemicals (GHS).
A holistic exploitation of all circular process opportunities, as forecasted by the 10R sustainability framework (e.g., R standing for recycle, repair, rethink, and refuse), is still lacking. As an exception, scarcely reported in flow chemistry, a catalyst was regenerated, which was a new approach to the more frequently used normal solvent and catalyst recycling strategies.73
To support the sustainability holism, microreactors/flow chemistry are on the verge of being applied (circularity economy metrics, CEM; environmental, social and governance, ESG).7 It is revealed that major microreactor benefits – safety, automation, and scale-up – have large potential for the emerging CEM and ESG.
Data availability
Data for this article are available at the repository of the University of Lleida at https://repositori.udl.cat/.
Conflicts of interest
There are no conflicts to declare.
References
- U. Krtschil, V. Hessel, D. Kralisch, G. Kreisel, M. Küpper and R. Schenk, Cost Analysis of a Commercial Manufacturing Process of a Fine Chemical Compound Using Micro Process Engineering, Chimia, 2006, 60, 611 CrossRef CAS.
- D. Kralisch and G. Kreisel, Assessment of the ecological potential of microreaction technology, Chem. Eng. Sci., 2007, 62(4), 1094–1100 CrossRef CAS.
-
A. Grunwald, Technology assessment: Concepts and methods, in Philosophy of technology and engineering sciences, Elsevier, 2009, pp. 1103–1146 Search PubMed.
- F. Siekmann, H. Schlör and S. Venghaus, Linking sustainability and the Fourth Industrial Revolution: a monitoring framework accounting for technological development, Energy Sustain. Soc., 2023, 13(1), 26 CrossRef.
-
M. Bennett, P. James and L. Klinkers, Sustainable measures: Evaluation and reporting of environmental and social performance, Routledge, 2017 Search PubMed.
- R. K. Singh, H. R. Murty, S. K. Gupta and A. K. Dikshit, An overview of sustainability assessment methodologies, Ecol. Indic., 2012, 15(1), 281–299 CrossRef.
- V. Hessel, M. Escribà-Gelonch, J. Bricout, N. N. Tran, A. Anastasopoulou, F. Ferlin, F. Valentini, D. Lanari and L. Vaccaro, Quantitative sustainability assessment of flow chemistry–from simple metrics to holistic assessment, ACS Sustain, Chem. Eng., 2021, 9(29), 9508–9540 CAS.
- T. Illg, P. Löb and V. Hessel, Flow chemistry using milli-and microstructured reactors—From conventional to novel process windows, BMCL, 2010, 18(11), 3707–3719 CAS.
- T. Y. Chen, Y. W. Hsiao, M. Baker-Fales, F. Cameli, P. Dimitrakellis and D. G. Vlachos, Microflow chemistry and its electrification for sustainable chemical manufacturing, Chem. Sci., 2022, 13(36), 10644–10685 RSC.
- A. Sivo, R. de Souza Galaverna, G. Rodrigues Gomes, J. Cezar Pastre and G. Vilé, From circular synthesis to material manufacturing: advances, challenges, and future steps for using flow chemistry in novel application area, React. Chem. Eng., 2021, 6(5), 756–786 RSC.
- J. Yue, Green process intensification using microreactor technology for the synthesis of biobased chemicals and fuels, Chem. Eng. Process., 2022, 177, 109002 CrossRef CAS.
- J. Yue, Multiphase flow processing in microreactors combined with heterogeneous catalysis for efficient and sustainable chemical synthesis, Catal. Today, 2018, 308, 3–19 CrossRef CAS.
- P. Desir, B. Saha and D. G. Vlachos, Ultrafast flow chemistry for the acid-catalyzed conversion of fructose, Energy Environ. Sci., 2019, 12(8), 2463–2475 RSC.
- E. Mielke, P. Plouffe, N. Koushik, M. Eyholzer, M. Gottsponer, N. Kockmann, A. Macchi and D. M. Roberge, Local and overall heat transfer of exothermic reactions in microreactor systems, React. Chem. Eng., 2017, 2(5), 763–775 RSC.
- T. Willms, H. Kryk and U. Hampel, Microreactor studies for efficient organic oxidation processes, Catal. Today, 2020, 346, 3–9 CrossRef CAS.
- M. Escribà, V. Hessel, S. Rothstock, J. Eras, R. Canela and P. Löbb, Applying a continuous capillary-based process to the synthesis of 3-chloro-2-hydroxypropyl pivaloate, Green Chem., 2011, 13, 1799–1805 RSC.
- J. I. Yoshida, Flash chemistry: flow microreactor synthesis based on high–resolution reaction time control, Chem. Rec., 2010, 10(5), 332–341 CrossRef CAS PubMed.
- H. Kim, A. Nagaki and J.-I. Yoshida, A flow-microreactor approach to protecting-group-free synthesis using organolithium compounds, Nat. Commun., 2011, 2(1), 264 CrossRef PubMed.
- J. Shu, L. Yu, R. Dinga and L. Zhang, Efficient synthesis of polyether polyols in simple microreactors, React. Chem.
Eng., 2021, 6(4), 685–693 RSC.
- E. Parandi, M. Mousavi, H. Kiani, H. R. Nodeh, J. Cho and S. Rezania, Optimization of microreactor-intensified transesterification reaction of sesame cake oil (sesame waste) for biodiesel production using magnetically immobilized lipase nano-biocatalyst, Energy Convers. Manage., 2023, 295, 117616 CrossRef CAS.
- X. Zhang, S. Stefanick and F. J. Villani, Application of microreactor technology in process development, Org. Process Res. Dev., 2004, 8(3), 455–460 CrossRef CAS.
- J. Wang, L. Ni, J. Cui, J. Jiang, K. J. Zhou and J. Wang, Thermal hazard analysis of styrene polymerization in microreactor of varying diameter, Processes, 2020, 8(12), 1650 CrossRef CAS.
- T. Westermann and L. Mleczko, Heat Management in Microreactors for Fast Exothermic Organic Syntheses – First Design Principles, Org. Process Res. Dev., 2016, 20(2), 487–494 CrossRef CAS.
- H. Kim, Y. Yonekura and J. I. Yoshida, A Catalyst–Free Amination of Functional Organolithium Reagents by Flow Chemistry, Angew. Chem., Int. Ed., 2018, 57(15), 4063–4066 CrossRef CAS PubMed.
- T. Kawaguchi, H. Miyata, K. Ataka, K. Mae and J.-I. Yoshida, Room–temperature Swern oxidations by using a microscale flow system, Angew. Chem., 2005, 117(16), 2465–2468 CrossRef.
- T. Illg, V. Hessel, P. Löb and J. C. Schouten, Novel Process Window for the safe and continuous synthesis of tert.-butyl peroxy pivalate in a micro-reactor, Chem. Eng. J., 2011, 167(2–3), 504–509 CrossRef CAS.
- Q. Deng, N. N. Tran, M. R. Asrami, L. Schober, H. Gröger and V. Hessel, Ionic liquid/water continuous-flow system with compartmentalized spaces for automatic product purification of biotransformation with enzyme recycling, Ind. Eng. Chem. Res., 2020, 59(48), 21001–21011 CrossRef CAS.
- X. Lin, S. Yan, B. Zhou, K. Wang, J. Zhanga and G. Luo, Highly efficient synthesis of polyvinyl butyral (PVB) using a membrane dispersion microreactor system and recycling reaction technology, Green Chem., 2017, 19(9), 2155–2163 RSC.
- V. Hessel, N. N. Tran, M. R. Asrami, Q. D. Tran, N. V. D. Long, M. Escribà-Gelonch, J. Osorio Tejada, S. Linke and K. Sundmacher, Sustainability of green solvents–review and perspective, Green Chem., 2022, 24(2), 410–437 RSC.
- M. R. Asrami, N. N. Tran, K. D. Prasad Nigam and V. Hessel, Solvent extraction of metals: role of ionic liquids and microfluidics, Sep. Purif. Technol., 2021, 262, 118289 CrossRef CAS.
- M. Escribà-Gelonch, E. Shahbazali, M. Honing and V. Hessel, Quality-In(Process)Line (QuIProLi) process intensification for a micro-flow UV-photo synthesis enabled by online UHPLC analysis, Tetrahedron, 2018, 74(25), 3143–3151 CrossRef.
- A. Adamo, R. L. Beingessner, M. Behnam, J. Chen, T. F. Jamison, K. F. Jensen, J.-C. M. Monbaliu, A. S. Myerson, E. M. Revalor, D. R. Snead, T. Stelzer, N. Weeranoppanant, S. Y. Wong and P. Zhang, On-demand continuous-flow production of pharmaceuticals in a compact, reconfigurable system, Science, 2016, 352(6281), 61–67 CrossRef CAS PubMed.
-
Á. Díaz-Ortiz and A. de la Hoz, Green Aspects of Flow Chemistry for Drug Discovery, in Flow Chemistry in Drug Discovery, Springer, 2021, pp. 23–70 Search PubMed.
- D. M. Parry, Closing the loop: developing an integrated design, make, and test platform for discovery, ACS Med. Chem. Lett., 2019, 10(6), 848–856 CrossRef CAS PubMed.
- E. Sato, M. Fujii, H. Tanaka, K. Mitsudo, M. Kondo, S. Takizawa, H. Sasai, T. Washio, K. Ishikawa and S. Suga, Application of an electrochemical microflow reactor for cyanosilylation: machine learning-assisted exploration of suitable reaction conditions for semi-large-scale synthesis, J. Org. Chem., 2021, 86(22), 16035–16044 CrossRef CAS PubMed.
- S. Höving, J. Bobers and N. Kockmann, Open-source multi-purpose sensor for measurements in continuous capillary flow, J. Flow Chem., 2022, 1–12 Search PubMed.
- B. A. Colon, M. R. Hassan, A. Saleheen, C. A. Baker and T. R. Calhoun, Total internal reflection transient absorption microscopy: an online detection method for microfluidics, J. Phys. Chem. A, 2020, 124(20), 4160–4170 CrossRef CAS PubMed.
- J.-H. Kang, G.-N. Ahn, H. Lee, S.-J. Yim, S. Lahore, H.-J. Lee, H. Kim, J. T. Kim and D.-P. Kim, Scalable Subsecond Synthesis of Drug Scaffolds via Aryllithium Intermediates by Numbered-up 3D-Printed Metal Microreactors, ACS Cent. Sci., 2021, 8(1), 43–50 CrossRef PubMed.
- S. Guo, L.-W. Zhan, G.-K. Zhu, X.-G. Wu and B.-D. Li, Scale-Up and Development of Synthesis 2-Ethylhexyl Nitrate in Microreactor Using the Box–Behnken Design, Org. Process Res. Dev., 2021, 26(1), 174–182 CrossRef.
- I. Vural-Gursel, V. Hessel, Q. Wang, T. Noel and J. Lang, Window of opportunity–potential of increase in profitability using modular compact plants and micro-reactor based flow processing, Green Process. Synth., 2012, 1(4), 315–336 Search PubMed.
- V. Katoch, M. Singh, A. Katoch and B. Prakash, Cost-effective microreactors for the synthesis of SnS nanoparticles and inline photocatalytic degradation of azo dyes, Mater. Lett., 2023, 333, 133677 CrossRef CAS.
- R. Mazurczyk, G. El Khoury, V. Dugas, B. Hannes, E. Laurenceau, M. Cabrera, S. Krawczyk, E. Souteyrand, J. P. Cloarec and Y. Chevolot, Low-cost, fast prototyping method of fabrication of the microreactor devices in soda-lime glass, Sens. Actuators, B, 2008, 128(2), 552–559 CrossRef CAS.
- S. L. Florez, A. L. Campaña, M. J. Noguera, V. Quezada, O. P. Fuentes, J. C. Cruz and J. F. Osma, CFD Analysis and Life Cycle Assessment of Continuous Synthesis of Magnetite Nanoparticles Using 2D and 3D Micromixers, Micromachines, 2022, 13(6), 970 CrossRef PubMed.
- K. Raoufi, S. Manoharan, T. Etheridge, B. K. Paul and K. R. Haapala, Cost and environmental impact assessment of stainless steel microreactor plates using binder jetting and metal injection molding processes, Procedia Manuf., 2020, 48, 311–319 CrossRef.
- R. M. N. Lintag, F. G. D. Leyson, M. S. B. Matibag and K. J. R. Yap, Low-cost fabrication of a polydimethylsiloxane (PDMS) microreactor using an improved Print-and-Peel (PAP) method and its performance testing in silver nanoparticle synthesis, Mater. Today: Proc., 2020, 22, 185–192 CAS.
- B. Ramos, S. Ookawara, Y. Matsushita and S. Yoshikawa, Low-cost polymeric photocatalytic microreactors: Catalyst deposition and performance for phenol degradation, J. Environ. Chem. Eng., 2014, 2(3), 1487–1494 CrossRef CAS.
- R. Chen, L. Li, X. Zhu, H. Wang, Q. Liao and M.-X. Zhang, Highly-durable optofluidic microreactor for photocatalytic water splitting, Energy, 2015, 83, 797–804 CrossRef CAS.
- Z. He, Y. Li, Q. Zhang and H. Wang, Capillary microchannel-based microreactors with highly durable ZnO/TiO2 nanorod arrays for rapid, high efficiency and continuous-flow photocatalysis, Appl. Catal., B, 2010, 93(3–4), 376–382 CrossRef CAS.
- X. Zhu, H. Feng, R. Chen, Q. Liao, D. Ye, B. Zhang, J. Liu, M. Liu and G. Chen, Experimental study on the durability of the polydopamine functionalized gas–liquid–solid microreactor for nitrobenzene hydrogenation, RSC Adv., 2018, 8(11), 5661–5669 RSC.
- Y. Khan, M. Marin, T. Viinikainen, J. Lehtonen, R. L. Puurunen and R. Karinen, Structured microreactor with gold and palladium on titania: Active, regenerable and durable catalyst coatings for the gas-phase partial oxidation of 1-butanol, Appl. Catal., A, 2018, 562, 173–183 CrossRef CAS.
- B. Akman and O. Aras, Usability, durability and regeneration of Ag/ZnO coated microreactor for photocatalytic degradation of methylene blue, J. Mol. Struct., 2022, 1251, 132003 CrossRef CAS.
- D. Kralisch, I. Streckmann, D. Ott, U. Krtschil, E. Santacesaria, M. Di Serio, V. Russo, L. De Carlo, W. Linhart, E. Christian, B. Cortese, M. H. de Croon and V. Hessel, Transfer of the epoxidation of soybean oil from batch to flow chemistry guided by cost and environmental issues, ChemSusChem, 2012, 5(2), 300–311 CrossRef CAS PubMed.
- S. Borukhova, T. Noel, B. Metten, E. de Vos and V. Hessel, Solvent–and Catalyst–Free Huisgen Cycloaddition to Rufinamide in Flow with a Greener, Less Expensive Dipolarophile, ChemSusChem, 2013, 6(12), 2220–2225 CrossRef CAS PubMed.
- F. Grimaldi, G. A. de Leon Izeppi, D. Kirschneck, P. Lettieri, M. Escribà-Gelonch and V. Hessel, Life cycle assessment and cost evaluation of emerging technologies at early stages: The case of continuous flow synthesis of Rufinamide, Adv. Manuf. Process., 2020, 2(2), e10043 CrossRef CAS.
- M. Escribà-Gelonch, G. A. de Leon Izeppi, D. Kirschneck and V. Hessel, Multistep Solvent-Free 3 m2 Footprint Pilot Miniplant for the Synthesis of Annual Half-Ton Rufinamide Precursor, ACS Sustainable Chem. Eng., 2019, 7(20), 17237–17251 CrossRef PubMed.
- S. Bagi, S. Yuan, S. Rojas-Buzo, Y. Shao-Horn and Y. Román-Leshkov, A continuous flow chemistry approach for the ultrafast and low-cost synthesis of MOF-808, Green Chem., 2021, 23(24), 9982–9991 RSC.
-
S. W. Lee, H. Jo, Y. Lee and N. Kim, Thermodynamic Analysis and Economic Evaluation of Supercritical CO2 Recompression Brayton Cycle for Heat Pipe Cooled Microreactor, available at SSRN 4196775.
- F. Benaskar, A. Ben-Abdelmoumen, N. G. Patil, E. V. Rebrov, J. Meuldijk, L. A. Hulshof, V. Hessel, U. Krtschil and J. C. Schouten, Cost analysis for a continuously operated fine chemicals production plant at 10 kg/day using a combination of microprocessing and microwave heating, J. Flow Chem., 2011, 1(2), 74 CrossRef.
- M. Escribà, J. Eras, M. Duran, S. Simon, C. Butchosa, G. Villorbina, M. Balcells and R. Canela, From glycerol to chlorohydrin esters using a solvent-free system. Microwave irradiation versus conventional heating, Tetrahedron, 2009, 65(50), 10370–10376 CrossRef.
- S. Budžaki, G. Miljić, S. Sundaram, M. Tišma and V. Hessel, Cost analysis of enzymatic biodiesel production in small-scaled packed-bed reactors, Appl. Energy, 2018, 210, 268–278 CrossRef.
- H. Fu, I. Dencic, J. Tibhe, C. A. Sanchez Pedraza, Q. Wang, T. Noel, J. Meuldijk, M. de Croon, V. Hessel, N. Weizenmann, T. Oeser, T. Kinkeade, D. Hyatt, S. Van Roy, W. Dejonghe and L. Diels, Threonine aldolase immobilization on different supports for engineering of productive, cost-efficient enzymatic microreactors, Chem. Eng. J., 2012, 207, 564–576 CrossRef.
- S. Budžaki, S. Sundaram, M. Tišma and V. Hessel, Cost analysis of oil cake-to-biodiesel production in packed-bed micro-flow reactors with immobilized lipases, J. Biosci. Bioeng., 2019, 128(1), 98–102 CrossRef PubMed.
- S. Kressirer, L. N. Protasova, M. H. J. M. de Croon, V. Hessel and D. Kralisch, Removal and renewal of catalytic coatings from lab-and pilot-scale microreactors, accompanied by life cycle assessment and cost analysis, Green Chem., 2012, 14(11), 3034–3046 RSC.
- B. Hernández, D. G. Vlachos and M. G. Ierapetritou, Coupling Process Intensification and Systems Flowsheeting for Economic and Environmental Analysis of 5-Hydroxymethyl Furfural Modular Microreactor Plants, ACS Sustainable Chem. Eng., 2022, 10(45), 14955–14971 CrossRef.
- M. Escribà-Gelonch, N. N. Tran and V. Hessel, Automated High-Pressure Atline Analysis of Photo-High-p,T Vitamin D3 Microfluidic Synthesis, Front. Chem. Eng., 2021, 3, 724036 CrossRef.
- C. Mateos, M. J. Nieves-Remacha and J. A. Rincón, Automated platforms for reaction self-optimization in flow, React. Chem. Eng., 2019, 4(9), 1536–1544 RSC.
- I. Vural-Gürsel, Q. Wang, T. Noël, G. Kolb, V. Hessel and A. C. van Veen, Heat-integrated novel process of liquid fuel production from bioresources–process simulation and costing study, Chem. Eng. Trans., 2014, 39, 931–936 Search PubMed.
- I. Denčić, D. Ott, D. Kralisch, T. Noël, J. Meuldijk, M. de Croon, V. Hessel, Y. Laribi and P. Perrichon, Eco-efficiency analysis for intensified production of an active pharmaceutical ingredient: a case study, Org. Process Res. Dev., 2014, 18(11), 1326–1338 CrossRef.
-
A. Abou-Jaoude, Y. Arafat, A. W. Foss and B. W. Dixon, An Economics-by-Design Approach Applied to a Heat Pipe Microreactor Concept, Idaho National Lab. (INL), Idaho Falls, ID, United States, 2021 Search PubMed.
- E. Zschieschang, P. Pfeifer and L. Schebek, Environmentally optimized microreactor design through Life Cycle Assessment, Green Process. Synth., 2012, 1(4), 375–384 CAS.
- S. Kressirer, D. Kralisch, A. Stark, U. Krtschil and V. Hessel, Agile green process design for the intensified Kolbe–Schmitt synthesis by accompanying (simplified) life cycle assessment, Environ. Sci. Technol., 2013, 47(10), 5362–5371 CrossRef CAS PubMed.
- S. Huebschmann, D. Kralisch, V. Hessel, U. Krtschil and C. Kompter, Environmentally benign microreaction process design by accompanying (simplified) life cycle assessment, Chem. Eng. Technol., 2009, 32(11), 1757–1765 CrossRef CAS.
- J. Osorio-Tejada, F. Ferlin, L. Vaccaro and V. Hessel, Life cycle assessment of multistep benzoxazole synthesis: from batch to waste-minimised continuous flow systems, Green Chem., 2022, 24(1), 325–337 RSC.
- D. Ott, S. Borukhova and V. Hessel, Life cycle assessment of multi-step rufinamide synthesis–from isolated reactions in batch to continuous microreactor networks, Green Chem., 2016, 18(4), 1096–1116 RSC.
- P. Yaseneva, P. Hodgson, J. Zakrzewski, S. Falß, R. E. Meadows and A. A. Lapkin, Continuous flow Buchwald–Hartwig amination of a pharmaceutical intermediate, React. Chem. Eng., 2016, 1(2), 229–238 RSC.
-
O. P. Fuentes, M. J. Noguera, P. A. Peñaranda, S. L. Flores, J. C. Cruz and J. F. Osma, Micromixers for Wastewater Treatment and Their Life Cycle Assessment (LCA), in Advances in Microfluidics and Nanofluids, 2021, pp. 1–15 Search PubMed.
- G. P. Rangel, R. M. Martinho, L. B. Dias, F. S. Coelho and B. Neto, Life cycle flaring emissions mitigation potential of a novel Fischer-Tropsch gas-to-liquid microreactor technology for synthetic crude oil production, Sci. Total Environ., 2022, 822, 153647 CrossRef CAS PubMed.
- S. Huebschmann, D. Kralisch, H. Loewe, D. Breuch, J. H. Petersen, T. Dietrich and R. Scholzd, Decision support towards agile eco-design of microreaction processes by accompanying (simplified) life cycle assessment, Green Chem., 2011, 13(7), 1694–1707 RSC.
- M. Escribà-Gelonch, T. Noël and V. Hessel, Microflow High-p,T Intensification of Vitamin D3 Synthesis Using an Ultraviolet Lamp, Org. Process Res. Dev., 2018, 22(2), 147–155 CrossRef PubMed.
- O. M. Morales-Gonzalez, M. Escribà-Gelonch and V. Hessel, Life cycle assessment of vitamin D3 synthesis: from batch to photo-high-p,T, Int. J. Life Cycle Assess., 2019, 24, 2111–2127 CrossRef CAS.
- M. Escribà-Gelonch, V. Hessel, M. C. Maier, T. Noël, M. F. Neira d'Angelo and H. Gruber-Woelfler, Continuous-Flow In-Line Solvent-Swap Crystallization of Vitamin D3, Org. Process Res. Dev., 2018, 22(2), 178–189 CrossRef PubMed.
- M. Escribà-Gelonch, J. Bricout and V. Hessel, Circular Economy Metrics for the Photo-High-p,T Continuous Multistep Synthesis of Vitamin D3, ACS Sustainable Chem. Eng., 2021, 9(4), 1867–1879 CrossRef.
- M. Escribà-Gelonch, A. Halpin, T. Noël and V. Hessel, Laser-Mediated Photo-High-p,T Intensification of Vitamin D3 Synthesis in Continuous Flow, ChemPhotoChem, 2018, 2, 922 CrossRef.
- U. Krtschil, V. Hessel, P. Löb, D. Reinhard, S. Hübschmann and D. Kralisch, Tailor-made microdevices for maximizing process intensification and productivity through advanced heating, Chem. Eng. J., 2011, 167(2–3), 510–518 CrossRef CAS.
- D. Reinhardt, F. Ilgen, D. Kralisch, B. König and G. Kreisel, Evaluating the greenness of alternative reaction media, Green Chem., 2008, 10(11), 1170–1181 RSC.
- M. J. Eckelman, Life cycle inherent toxicity: a novel LCA-based algorithm for evaluating chemical synthesis pathways, Green Chem., 2016, 18(11), 3257–3264 RSC.
- F. Grimaldi, N. N. Tran, M. M. Sarafraz, P. Lettieri, O. M. Morales-Gonzalez and V. Hessel, Life cycle assessment of an enzymatic ibuprofen production process with automatic recycling and purification, ACS Sustainable Chem. Eng., 2021, 9(39), 13135–13150 CrossRef CAS.
- K. Mierdel, A. Jess, T. Gerdes, A. Schmidt and K. Hintzer, Energy and Resource Efficient Production of Fluoroalkenes in High Temperature Microreactors, ChemEngineering, 2019, 3(4), 77 CrossRef CAS.
- R. Cao, Across the board: Rui Cao on electrocatalytic CO2 reduction, ChemSusChem, 2022, 15(21), e202201788 CrossRef CAS PubMed.
- D. Ott, D. Kralisch, I. Denčić, V. Hessel, Y. Laribi, P. D. Perrichon, C. Berguerand, L. Kiwi-Minsker and P. Loeb, Life cycle analysis within pharmaceutical process optimization and intensification: case study of active pharmaceutical ingredient production, ChemSusChem, 2014, 7(12), 3521–3533 CrossRef CAS PubMed.
- D. Kralisch, D. Ott, S. Kressirer, C. Staffel, I. Sell, U. Krtschil and P. Loeb, Bridging sustainability and intensified flow processing within process design for sustainable future factories, Green Process. Synth., 2013, 2(5), 465–478 CAS.
- S. A. Qadir, H. Al-Motairi, F. Tahir and L. Al-Fagih, Incentives and strategies for financing the renewable energy transition: A review, Energy Rep., 2021, 7, 3590–3606 CrossRef.
- D. Cambié, F. Zhao, V. Hessel, M. G. Debije and T. Noël, A Leaf-Inspired Luminescent Solar Concentrator for Energy-Efficient Continuous-Flow Photochemistry, Angew. Chem., Int. Ed., 2017, 56(4), 1050–1054 CrossRef PubMed.
-
B. Winterson and T. Wirth, Electrochemistry in Flow for Drug Discovery, in Flow Chemistry in Drug Discovery. Topics in Medicinal Chemistry, ed. J. Alcazar, A. de la Hoz and A. Díaz-Ortiz, Springer, 2021, vol. 38 Search PubMed.
- P. Lamichhane, N. Pourali, L. Scott, N. N. Tran, L. Lin, M. Escribà-Gelonch, E. V. Rebrov and V. Hessel, Critical review: ‘Green’ ethylene production through emerging technologies, with a focus on plasma catalysis, Renewable Sustainable Energy Rev., 2024, 189B, 114044 CrossRef.
- T. Mooney, M. Ilamanova and B. Török, Microwave-Assisted Flow Chemistry for Green Synthesis and Other Applications, Curr. Microwave Chem., 2022, 9(2), 65–69 CrossRef CAS.
- P. Panagiotopoulou, C. Papadopoulou, H. Matralis and X. Verykios, Production of renewable hydrogen by reformation of biofuels, Wiley Interdiscip. Rev.: Energy Environ., 2014, 3, 231–253 CrossRef CAS PubMed.
-
H. Löwe, W. Ehrfeld and V. Hessel, Microreactors: New Technology for Modern Chemistry, Wiley-VCH Verlag, Weinheim, 2000 Search PubMed.
- Q. Wang, E. Nakouzi, E. A. Ryan and C. V. Subban, Flow-Assisted Selective Mineral Extraction from Seawater, Environ. Technol. Lett., 2022, 9(7), 645–649 CAS.
-
I. Dencic and V. Hessel, Industrial Microreactor Process Development up to Production, in Microreactors in Organic Chemistry and Catalysis, ed. T. Wirth, 2013 Search PubMed.
- M. Escribà-Gelonch, S. Liang, P. van Schalkwyk, I. Fisk, N. van Duc Long and V. Hessel, Digital Twins in Agriculture: Orchestration and Applications, J. Agric. Food Chem., 2024, 72(19), 10737–10752 CrossRef PubMed.
-
https://sdgs.un.org/
(accessed June 2024).
-
A. A. Lapkin and P. Yaseneva, Life cycle assessment of flow chemistry processes, in Sustainable Flow Chemistry: Methods and Applications, 2017, pp. 249–276 Search PubMed.
- M. Johanning, M. Widenmeyer, G. Escobar Cano, V. Zeller, S. Klemenz, G. Chen, A. Feldhoff and A. Weidenkaff, Recycling process development with integrated life cycle assessment–a case study on oxygen transport membrane material, Green Chem., 2023, 25(12), 4735–4749 RSC.
-
F. Keller, R. Voss and R. P. Lee, Overcoming Challenges of Life Cycle Assessment (LCA) & Techno-Economic Assessment (TEA) for Chemical Recycling, Institute of Energy Process Engineering & Chemical Engineering, Freiberg, Germany, 2022 Search PubMed.
- A. DeVierno Kreuder, T. House-Knight, J. Whitford, E. Ponnusamy, P. Miller, N. Jesse, R. Rodenborn, S. Sayag, M. Gebel, I. Aped, I. Sharfstein, E. Manaster, I. Ergaz, A. Harris and L. Nelowet Grice, A method for assessing greener alternatives between chemical products following the 12 principles of green chemistry, ACS Sustainable Chem. Eng., 2017, 5(4), 2927–2935 CrossRef CAS.
|
This journal is © The Royal Society of Chemistry 2024 |