DOI:
10.1039/C2PY20611K
(Paper)
Polym. Chem., 2013,
4, 724-730
Synthesis of a diamine cross-linker containing Diels–Alder adducts to produce self-healing thermosetting epoxy polymer from a widely used epoxy monomer†
Received
6th August 2012
, Accepted 29th September 2012
First published on 1st October 2012
Abstract
A diamine cross-linker with thermal reversible Diels–Alder (DA) adducts of furan and maleimide groups has been designed and synthesised, which can be used to crosslink commercial epoxy monomers to achieve self-healing, cross-linked epoxy polymers. This new strategy to make self-healing epoxy polymer was successfully proved by incorporating the cross-linker with a widely used epoxy monomer, the diglycidyl ether of bisphenol A. The self-healing property of the new epoxy polymer was shown by complete elimination of cracks after the process of retro-DA and DA reactions which occurred in the cross-linker component of the network.
Introduction
In the past decades, self-healing polymers have become an exciting research field in the study of thermosetting polymers.1 Irreversible damage, such as microcracks which can significant reduce the load-carrying capacity properties of the materials and shorten their lifetime, can be healed.2–4 For thermosetting materials (as compared to thermoplastic materials), self-healing is both challenging and important due to the fact that thermosets do not readily flow under the post-processing application of heat, as do thermoplastics.
To date, there are two main strategies to cause self-healing in thermosetting/cross-linked polymers: autonomous mending and external stimuli mending.4 Autonomous mending is based on the incorporation of micro-containers or capsules which contain healing agents (monomers and/or catalysts) and are distributed throughout the cross-linked polymeric matrix. When damage occurs and a crack grows, it breaks the micro-containers, releasing the healing agents into the crack, the catalyst causing polymerization, and subsequent solidification and crack healing.5,6 The other strategy achieves mending based on the use of external stimuli which are related to the chemical properties of the polymer, and rely on the appropriate application of external stimuli. At the point of polymer design, special functional groups are introduced into the polymer molecules, which can react to heal the cracks by external stimuli. This kind of healing tends to be reversible and repeatable. The stimuli include heat and light,7 but various functional groups can be designed to allow a wide range of stimuli to be used.1,3,4,8 Wudl and co-workers successfully used Diels–Alder (DA) reaction/retro Diels–Alder (rDA) reaction strategy to produce self-healing polymers.2,9 The highly cross-linked polymer synthesised from multifunctional furan and maleimide could heal the cracks after a heating and cooling process.
Epoxy resins have many applications in a range of fields, including fibre-reinforced plastic materials, potting materials for electronics, coatings, civil engineering applications and as general purpose adhesives,10,11 many of which would be benefit if they could be made repairable. Following Wudl's approach, Liu and Hseih used epoxy compounds as precursors to simply synthesised trifunctional furan and maleimide.12 The thermally remendable cross-linked polymer prepared from those monomers can be seen as a new kind of epoxy polymer and it can be healed vis rDA and DA reactions. Tian et al. made a novel epoxy resin with a furan group in the structure.13 After reacting with difunctional maleimide and being cured with anhydride, it formed a new cross-linked epoxy which can heal the cracks through chain reconnection resulting from rDA and DA reactions. In a subsequent paper, they changed the structure of epoxy resin and finally get a new self-healing epoxy with a higher self-healing efficiency.14
Previous works have only focused on modifying the epoxy monomer to contain the DA group.13,14 Clearly this would be expensive to widely implement, and it would be desirable to be able to use common, commercially available epoxy monomers. In our research, a new strategy was researched, where the thermally reversible DA unit can be incorporated into the diamine cross-linker as the healable element. This has the advantage that it can be used for a range of different commercial epoxy monomers, including in the aerospace industry, which make often use a blend of epoxy systems, usually with different functionality. A new diamine cross-linker (4) with adducts of furan and maleimide groups was synthesised and used to cure epoxy monomers to yield new self-healing epoxy polymer. The diglycidyl ether of bisphenol A (DGEBA) was chosen as the epoxy monomer, as it is the most commonly used epoxy resin across a range of applications.
Experiment
Materials
1,8-Diaminooctane was obtained from Fluka. Maleic anhydride, furfurylamine and di-tert-butyl dicarbonate were supplied by Aldrich. DGEBA (DER331) was obtained from ATL composites. The Mn is 370 and the epoxide equivalent weight (EEW) is 185 g per eq. All other reactants and reagents were purchased from Merck. All the chemicals were used as received.
Characterization
1H NMR spectra were carried out on Bruker DRX 400 and chemical shifts were calibrated by CDCl3 (δ = 7.26), D2O (δ = 4.79) or DMSO-d6 (δ = 2.5).1513C NMR spectra were recorded on Bruker DRX 400 and chemical shifts were calibrated by the signal of CDCl3 (δ = 77.16) or DMSO-d6 (δ = 39.52).15 Mass spectrums (ESI) were recorded on Micro mass Platform. Fourier transform infrared (FTIR) spectra were record with a Bruker EQUINOX 55 FTIR fitted with an MCT detector. ATR sampler is a Specac ‘Golden Gate’ single bounce diamond ATR. The operation condition was 50 scans at a resolution of 4 cm−1. Near infrared spectra were obtained using a Bruker EQUINOX 55 FTIR spectrometer with 32 scans at resolution of 8 cm−1 in the region 9000–4000 cm−1. Differential scanning calorimetry (DSC) experiments were performed using a Perkin-Elmer DSC-7 using nitrogen purge and aluminium pans. The thermal stability was tested by thermogravimetric analysis (TGA) with EXSTAR TG/DTA6300 at heating rate of 10 °C min−1 under argon atmosphere. The images of the cracked sample and healed sample were recorded using a Nikon 80i microscope and a Nikon DS-Fi1 CCD camera.
Synthesis of tert-butyl (furan-2-ylmethyl)carbamate (1)
Furfurylamine (11.68 g, 0.12 mol) in CH2Cl2 (100 mL) was added under stirring to di-tert-butyl dicarbonate (28.88 g, 0.132 mol) in CH2Cl2 (100 mL) at 0 °C. The solution was stirred at room temperature for 1 day. After the reaction, CH2Cl2 was evaporated and EtOAc was added to the solution. The solution was washed with saturated Na2CO3 solution (2 × 30 mL) and dried over anhydrous Na2SO4. The solution was concentrated to yield compound 1 (26.23 g, 99%) as yellow crystal. 1H NMR (400 MHz, CDCl3) δ 7.34 (d, J = 1.9 Hz, 1H), 6.30 (dd, J = 3.2, 1.9 Hz, 1H), 6.20 (d, J = 2.9 Hz, 1H), 4.83 (s, 1H), 4.29 (d, J = 5.4 Hz, 2H), 1.45 (s, 9H). 13C NMR (100 MHz, CDCl3) δ 155.72, 152.21, 142.18, 110.48, 107.05, 37.90, 28.52. ESI-MS (m/z): [M + Na]+ calc. for C10H15NO3Na 220.1, found 220.1. FTIR ν (cm−1) 3338, 2978, 2932, 2362, 1698, 1507, 1392, 1367, 1273, 1250, 1166, 736.
1,8-Diaminooctane (4 g, 27.7 mmol) in CH2Cl2 (60 mL) was added under stirring to maleic anhydride (6 g, 61.2 mmol) in CH2Cl2 (60 mL) at 0 °C and stirred for an overnight at room temperature. After the reaction, CH2Cl2 was evaporated and residue was dissolved in acetone (120 mL) and acetic anhydride (11.45 g, 112.2 mmol), nick(II) acetate (0.14 g, 0.56 mmol) and triethylamine (1.58 mL, 11.4 mmol) were added to the solution under stirring. The mixture was heated at 65 °C for 2 days. The mixture was cooled to room temperature and acetone was evaporated and the residue was poured into ice water (400 mL) and stirred for 30 minutes. The mixture was filtered and washed with water (2 × 50 mL). After drying, the crude product was purified by flash chromatography (hexane–EtOAc = 3
:
1) to give the compound 2 (4.36 g, 52%) as white powder.161H NMR (400 MHz, CDCl3) δ 6.67 (s, 4H), 3.49 (t, J = 7.2, 4H), 1.67–1.46 (m, 4H), 1.38–1.14 (m, 8H). 13C NMR (100 MHz, CDCl3) δ 171.00, 134.18, 134.18, 38.00, 29.06, 28.60, 26.74. ESI-MS (m/z): [M + Na]+ calc. for C16H20N2O4Na 327.1, found 327.1. FTIR ν (cm−1) 3109, 3090, 2941, 2912, 2363, 2339, 1700, 1423, 1374, 1131, 841, 702.
Synthesis of di-tert-butyl ((2,2′-(octane-1,8-diyl)bis(1,3-dioxo-2,3,3a,4,7,7a-hexahydro-1H-4,7-epoxyisoindole-4,2-diyl))bis(methylene))dicarbamate (3)
Compound 1 (14.13 g, 71.71 mmol) and 2 (4.36 g, 14,34 mmol) were added in EtOAc (130 mL). The solution was heated at 78 °C for an overnight. The solution was cooled and concentrated after the reaction and the residue was purified by flash chromatography (hexane–EtOAc = 2
:
1) to give the compound 3 (6.63 g, 81%) as white solid. The compound 3 is a mixture of exo and endo (ratio of exo/endo = 7.5
:
1 as determined by 1H NMR) isomers. Exo isomer: 1H NMR (400 MHz, CDCl3) δ 6.53 (d, J = 5.6 Hz, 2H), 6.49 (d, J = 5.6 Hz, 2H), 5.27 (bs, 2H), 5.19 (d, J = 1.6 Hz, 2H), 3.79 (dd, J = 14.8, 6.7 Hz, 2H), 3.67 (dd, J = 14.7, 6.4 Hz, 2H), 3.45 (t, J = 7.3 Hz, 4H), 2.94 (d, J = 6.5 Hz, 2H), 2.85 (d, J = 6.4 Hz, 2H), 1.57–1.48 (m, 4H), 1.45 (s, 18H), 1.31–1.10 (m, 8H). 13C NMR (100 MHz, CDCl3) δ 176.08, 175.39, 156.17, 138.85, 137.08, 101.88, 91.07, 80.89, 79.78, 50.30, 48.25, 40.03, 39.07, 28.95, 28.52, 27.60, 26.56. ESI-MS (m/z): [M + Na]+ calc. for C36H50N4O10Na 721.3, found 721.1. FTIR ν (cm−1) 3366, 2978, 2933, 2857, 1766, 1693, 1526, 1435, 1399, 1291, 1247, 1164, 975, 862, 737.
Synthesis of 2,2′-(octane-1,8-diyl)bis(4-(aminomethyl)-3a,4,7,7a-tetrahydro-1H-4,7-epoxyisoindole-1,3(2H)-dione) (4)
Concentrated HCl solution (50 mL) was added under stirring to the solution of compound 3 (6.63 g, 9.5 mmol) in acetone (50 mL) at 0 °C. The mixture was stirred at room temperature for 2 hours. After the reaction, acetone was evaporated and the residue was washed with CHCl3 (3 × 30 mL) to remove the unreacted starting material. Water (100 mL) was added to the residue and 0.5 mol L−1 NaOH solution was used to adjust the pH to 9. CHCl3 (3 × 100 mL) was used to extract and combined to concentrate to get the compound 4 (4.63 g, 98%) as liquid. Exo and endo ratio of compound 4 was determined by 1H NMR as exo/endo = 6.7
:
1. Exo isomer: 1H NMR (400 MHz, CDCl3) δ 6.54 (d, J = 5.7 Hz, 2H), 6.50 (dd, J = 5.7, 1.6 Hz, 2H), 5.20 (d, J = 1.7 Hz, 2H), 3.43 (t, J = 8.0 Hz, 4H), 3.34–3.11 (m, 4H), 2.94 (d, J = 6.4 Hz, 2H), 2.83 (d, J = 6.4 Hz, 2H), 1.55–1.39 (m, 4H), 1.24 (s, 8H). 13C NMR (100 MHz, CDCl3) δ 176.27, 175.36, 138.57, 137.08, 92.45, 91.97, 82.99, 80.80, 50.46, 48.06, 41.46, 39.74, 28.94, 27.59, 26.55. ESI-MS (m/z): [M + H]+ calc. for C26H35N4O6 499.3, found 499.1. FTIR ν (cm−1) 3373, 2932, 2857, 1768, 1692, 1439, 1402, 1153, 731.
Preparation of the cross-linked epoxy polymer
Diamine cross-linker (4) (1.21 g, 2.43 mmol) and DGEBA (1.8 g, 4.86 mmol) were mixed directly and degased under vacuum (0.5 mm Hg) for 3 hours. After that, the mixture was heated at 60 °C for 10 hours to get the cross-linked epoxy polymer. FTIR ν (cm−1) 3431, 2927, 2858, 1766, 1691, 1604, 1506, 1400, 1238, 1180, 1032, 827.
Result and discussion
Synthesis and characterization of the diamine cross-linker (4)
The diamine cross-linker (4) with DA adducts was synthesized.
Scheme 1 shows the synthesis process. The 1,8-diaminooctane reacted with maleic anhydride under the catalysis of acetic anhydride, nick(II) acetate and triethylamine in refluxed acetone to obtain compound 2.16 Furfurylamine was protected by Boc group to get compound 1. Compound 1 and 2 reacted in EtOAc to obtain compound 3 as a mixture of exo and endo isomers under reflux. After two Boc groups were deprotected and HCl salt was neutralized using NaOH solution, the final product compound 4 was successfully obtained. It was a very viscous liquid with brown colour and it is a mixture of exo and endo isomers as same as compound 3. From the 1H NMR spectrum of compound 4, the ratio of exo/endo is 6.7
:
1 and exo isomer is the main product.17–20 However, the pure exo or endo isomer is not necessary for the self-healing epoxy polymer synthesis because both of the isomers undergo DA and rDA reactions and thus serve the self-healing purpose. This is the first time this kind of diamine cross-linker (4) was synthesised and reported.
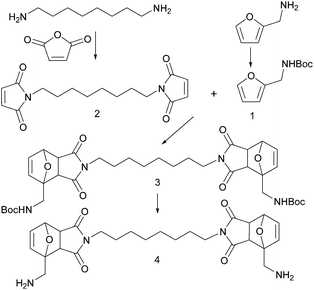 |
| Scheme 1 Synthesis of diamine cross-linker (4) with two adducts. | |
DA and rDA reactions in the diamine cross-linker
In this research, two pairs of furan and maleimide groups as healable units were put into the diamine cross-linker (4) in order to make the final epoxy polymer have the self-healing property. DA and rDA reactions are the chemical foundation of self-healing properties, so it was necessary to confirm whether the diamine cross-linker has the cycling reaction ability of DA and rDA reactions. Since the final epoxy polymer is a cross-linked polymer and cannot be dissolved in any solvents, it was necessary to determine whether the DA and rDA reactions occurred in the diamine cross-linker itself at this stage because of its better solubility in organic solvents. According to the literature,13,14 DA and rDA reaction temperatures of the current system were set at 75 °C and 120 °C. 1H-NMR was used to test the cycle of DA and rDA reactions. Pure diamine cross-linker (4) can not be exposed to these tests, because the C
C double bond in maleimide group readily reacts with the amine group when temperature is above 70 °C, due to Michael Addition.21 Upon the rDA reaction occurring, the amine group attacks the C
C double bond, which would stop the subsequent DA reaction. Thus, the Boc-protected diamine cross-linker (3) was used to do this test (Scheme 2).
 |
| Scheme 2 DA and rDA reactions in compound 3. | |
In order to investigate the DA and rDA reactions of the cross-linker itself, a series of experiments with compound 3 were carried out. Compound 3 was added to a NMR tube in DMSO-d6, which was selected as the solvent because of its high boiling point, 189 °C. The 1H-NMR was first run at room temperature, and the sample was then heated at 120 °C for 30 minutes and quenched quickly to room temperature before 1H-NMR test was run again. After that, the sample was treated at 75 °C for 20 hours and cooled to room temperature and retested. The resultant spectra are shown in Fig. 1. Peaks of 1, 2 and 3 stood for the DA adduct, and peaks of 1′, 2′ and 3′ ascribed to furan group in rDA product. Before heating, only peaks of 1, 2 and 3 were observed (Fig. 1a). After heating at 120 °C for 30 minutes, peaks of 1, 2 and 3 disappeared and peaks of 1′, 2′ and 3′ appeared (Fig. 1b). This showed the appearance of the furan groups and showed that the rDA reaction had occurred. The sample was then treated at 75 °C for 20 hours, following which peaks of 1, 2 and 3 appeared once again (Fig. 1c), proving that adducts of furan and maleimide groups reformed and the DA reaction occurred. The test thus verified the cycling of DA and rDA reactions in the system. As the experiment was in a NMR tube, the solution was not able to be stirred and the concentration of the solution was also not very high, so it took some 20 hours to get a better NMR spectrum (Fig. 1c) to show DA reaction happened. It would be quicker inside the epoxy polymer.
 |
| Fig. 1
1H NMR spectra of cycle of DA and rDA reaction. (a) Before heating; (b) heated at 120 °C for 30 minutes and quenched quickly to room temperature; (c) heated at 120 °C for 30 minutes, then treated at 75 °C for 20 hours and cooled to room temperature. | |
Preparation and characterization of the cross-linked epoxy polymer
The cross-linked self-healing epoxy polymer was synthesised by step growth polymerisation of epoxide and amine groups. DGEBA was chosen as the epoxy monomer because it is a common, widely used epoxy monomer.
The compound 4 was mixed with DGEBA at room temperature and degassed using a vacuum oven. The molar ratio of NH groups and epoxide groups was 1
:
1. After that, it was heated at 60 °C for 10 hours to get the final, self-healing epoxy thermosetting polymer (Scheme 3), which was found to be insoluble. Since one amine group can react with two epoxide groups, the diamine cross-linker is thus able to react with four epoxide groups to yield a cross-linked epoxy polymer.
 |
| Scheme 3 The curing reaction between the synthesised diamine cross-linker (4) and DGEBA. | |
Near infrared (NIR) spectroscopy can be used to monitor the reaction of the epoxy polymer formed, where peaks observed in Fig. 2 could be assigned on previous reports.22–24 Since samples used had slightly different thicknesses, internal peak standards were used to compare different spectra. The peaks at 4624 and 4678 cm−1 were from the phenyl group band, which did not change during the curing process and thus were a suitable internal standard. The spectrum of the uncured mixture of DGEBA and the diamine cross-linker (Fig. 2a) showed a strong peak at 4532 cm−1 from the epoxide group and two peaks at 4952 and 6532 cm−1 for the amine groups. After curing at 60 °C for 10 hours, the peak at 4532 cm−1 became very weak and the two peaks at 4952 and 6532 cm−1 nearly disappeared (Fig. 2b), whilst simultaneously a peak at 6981 cm−1 for the hydroxyl group appeared. These changes clearly showed that the curing reaction between epoxide and amine groups occurred, and hydroxyl group was produced as a result. Peak-fitting software (Igor Pro 6.2) was used to calculate the curing percentage by comparing the height of the epoxide group peak at 4532 cm−1 to that of original uncured mixture, normalised by the internal standard, and the resultant cure was 79.8%.
 |
| Fig. 2 Near infrared spectra of (a) an unreacted mixture of DGEBA and the diamine cross-linker, and (b) a mixture of DGEBA and diamine cross-linker cured at 60 °C for 10 hours. | |
In order to better understand the curing process, differential scanning calorimetry (DSC) was carried out on the reactive mixture. The DSC scan of the mixture of DGEBA and diamine cross-linker (4) was shown in Fig. 3. The DSC curve had two apparent exothermic peaks at 105 and 186 °C representing the curing reaction and an endothermic peak at 155 °C due to the rDA reaction. In order to better understand the 2nd peak at 186 °C, curing agent Ethacure 100 diamine was used to mix with DGEBA and the mixture was tested without curing. The DSC result was shown in Fig. S1 in the ESI.† The curing temperature range of the mixture of DGEBA and Ethacure 100 amine was from 100 °C to 250 °C. Because the diamine cross-liker (4) is less rigid than the Ethacure 100 diamine, the curing temperature range of the mixture of DGEBA and diamine cross-linker should be lower and the range from 50 °C to 200 °C is reasonable. It is clear that the curing reaction started from about 50 °C. When the temperature was above 105 °C, an endothermic peak appeared due to the rDA process occurring before the curing reaction finished, further heating shows a continued exotherm due to ongoing cure.
 |
| Fig. 3 DSC result of a mixture of unreacted DGEBA and diamine cross-linker (4). Heating rate is 2 °C min−1. | |
DSC was also used to obtain the Tg of the epoxy polymer, which was cured at 60 °C for 10 hours (Fig. 4). From the result, Tg was about 61 °C, which is lower than the temperature of rDA reaction (117 °C). The rDA peak in the uncured system appears at 155 °C (Fig. 3), but this is likely because it is the rDA peak combined with the curing reaction exothermic peak. Additional post curing was observed when the temperature was above 200 °C.
 |
| Fig. 4 DSC result of the cured epoxy polymer reacted at 60 °C for 10 hours. Heating rate is 5 °C min−1. | |
The cured cross-linked epoxy polymer sample was scanned by TGA (Fig. 5) showed that, the new self-healing epoxy polymer had 6% weight loss under 300 °C. When the temperature of the sample was above 140 °C, rDA reaction occurred and crosslink became partially cleaved, and the polymer effectively became a liner polymer. Since the curing percentage of the sample was 79.8%, some proportion of the 20% unreacted epoxy monomers were likely thermally released ca. 6%, mostly likely due to epoxy monomer (as opposed to pendent unreacted groups), whilst some of the remaining material continued to cure. The weight reduced to 60% at about 370 °C due to the loss of its more volatile side organic group.25 Cross-linked epoxy polymer cured with Ethacure 100 diamine, an aromatic amine without DA adducts, was also tested by TGA (Fig. S2 in the ESI†) for comparison and the degree of cure of that sample was 82.4% (preparation of the sample given in the ESI†). The weight loss was 2% under 300 °C, because the cross-like part cannot broke and the uncured epoxy monomer cannot be released. Compared with result of the sample without DA adducts, the stability of sample with DA adducts was a little lower from 200 °C to 300 °C. However it shows that the cross-linker is stable throughout the temperature range of the healing process (shown shortly).
 |
| Fig. 5 TGA result of the cured cross-linked epoxy polymer. | |
DA and rDA reactions in the cross-linked epoxy polymer
When the cross-linked epoxy polymer was prepared, it was not able to be dissolved in any solvents. FTIR was found to be the best option to observe the DA and rDA reactions in the system. 140 °C was chosen as the temperature for breaking adducts and the results were good. Whilst cooling the sample down should allow the reformation of sufficient adducts, it was found that annealing at temperature of 75 °C was useful to cause fuller regeneration of the adducts. The peak at 694 cm−1 is the peak of C–H bond attached the C
C in the maleimide ring (Scheme 2).26 The height change of that peak was used to know the difference in the (forward) DA and (backward) rDA reactions. The maleimide carbonyl peak at 1691 cm−1 was used as internal standard to allow quantification.26 The results are shown in Fig. 6. After the cross-linked epoxy polymer sample was heated at 140 °C for 30 minutes and quenched quickly to room temperature. The peak at 694 cm−1 then became bigger (Fig. 6b) compared to the original sample (Fig. 6a) due to the increasing amount of maleimide groups in the system after heating, and rDA reaction occurred to break adducts. The sample was then treated at 75 °C for 5 hours and cooled to room temperature. The peak at 694 cm−1 was reduced in height (Fig. 6c), becoming similar to that of the original sample (Fig. 6a). This shows that the amount of maleimide groups decreased to a similar level as that of original sample, with the DA reaction reforming the adducts. The results showed that the heating/cooling cycle of DA and rDA reactions in the reacted epoxy polymer system worked well with the above healing condition. This cycle was repeated for 3 times, and similar results were obtained each time.
 |
| Fig. 6 FTIR spectra of (a) the cured epoxy polymer; (b) heated at 140 °C for 30 minutes and quenched quickly to room temperature; (c) after that, treated at 75 °C for 5 hours and cooled to room temperature. | |
Self-healing property of the cross-linked epoxy polymer
The self-healing property of the cross-linked epoxy polymer can clearly be seen in Fig. 7. A razor blade was used to make a flaw on the sample surface (Fig. 7a), the crack being some 40 micrometres in width. The above condition for testing the DA and rDA reactions in the cured epoxy polymer was used. The sample was heated at 140 °C for 3 minutes and was partially healed. The crack width became smaller and was about 15 micrometres (Fig. 7b). After heated at 140 °C for 30 minutes, it can be clearly seen that scratches completely healed (disappeared) using an optical microscope (Fig. 7c). The fully healed sample was then heated at 75 °C for 5 hours to make it crosslink again. The round bubble inside the sample and the right edge of the sample helped to show that it was at the same position. According to the results of FTIR above (Fig. 6), DA and rDA reactions occurred in the epoxy polymer at these treatment temperatures, which helped to heal the cracks. Cross-linked epoxy polymer sample cured with Ethacure 100 diamine, which did not contain DA adduct, was used for comparison and the degree of cure of that sample was 82.4% (preparation of the sample given in the ESI†). The sample was subjected to the same conditions used to heal the polymers with the DA adducts (Fig. S3 in the ESI†). Although the crack became slightly less pronounced as a result of the enthalpy change during the heating process, it did not heal in the same way as the one with DA adducts did. The result showed that the epoxy polymer with the newly synthesised diamine cross-linker provided the expected self-healing behaviour. The same location on the polymer was used to be scratched and rehealed 3 times, indicating there was no “fatigue” or diminution of healing potential.
 |
| Fig. 7 Photos of (a) scratches made on the surface of the cross-linked epoxy polymer sample, (b) partially healed sample after heated at 140 °C for 3 minutes and (c) fully healed sample after heated at 140 °C for 30 minutes. | |
Conclusions
A new strategy of making a self-healing epoxy polymer by incorporating a diamine cross-linker synthesised with thermal reversible DA adducts of furan and maleimide groups is reported. A widely used epoxy monomer, DGEBA, was cured using the synthesised diamine cross-linker (4). The DA and rDA reactions in the cross-linked system of epoxy polymer thus formed were shown using FTIR. It was found that scratches on the epoxy polymer disappeared after treatment at 140 °C for 30 minutes. With the crack disappearing in a visible sense after the 140 °C heating, whilst the post-heat at 75 °C was suitable for getting maximal re-joining of the two adducts. The self-healing process was repeated a number of times and no diminution of healing potential was apparent. Further work is being undertaken to examine the temperature-dependence and kinetics of the healing process, including the minimum time required to cause the scratches to be healed.
Notes and references
- S. D. Bergman and F. Wudl, J. Mater. Chem., 2008, 18, 41–62 RSC.
- X. Chen, M. A. Dam, K. Ono, A. Mal, H. Shen, S. R. Nutt, K. Sheran and F. Wudl, Science, 2002, 295, 1698 CrossRef CAS.
- Y. C. Yuan, T. Yin, M. Z. Rong and M. Q. Zhang, eXPRESS Polym. Lett., 2008, 2, 238–250 Search PubMed.
-
S. Bergman and F. Wudl, in Self Healing Materials, 2007, pp. 45–68 Search PubMed.
- S. R. White, N. R. Sottos, P. H. Geubelle, J. S. Moore, M. R. Kessler, S. R. Sriram, E. N. Brown and S. Viswanathan, Nature, 2001, 409, 794–797 CrossRef CAS.
- M. R. Kessler, N. R. Sottos and S. R. White, Composites, Part A, 2003, 34, 743–753 CrossRef.
- M. Coursan, J. P. Desvergne and A. Deffieux, Macromol. Chem. Phys., 1996, 197, 1599–1608 CrossRef CAS.
- J. S. Park, K. Takahashi, Z. H. Guo, Y. Wang, E. Bolanos, C. Hamann-Schaffner, E. Murphy, F. Wudl and H. T. Hahn, J. Compos. Mater., 2008, 42, 2869–2881 CrossRef CAS.
- X. X. Chen, F. Wudl, A. K. Mal, H. B. Shen and S. R. Nutt, Macromolecules, 2003, 36, 1802–1807 CrossRef CAS.
-
Handbook of Epoxy Resins, ed. H. Lee and K. Neville, McGraw-Hill, New York, 1972 Search PubMed.
-
Handbook of Thermoset Plastics, ed. S. H. Goodman, Noyes Publications, Berkshire, 1998 Search PubMed.
- Y. L. Liu and C. Y. Hsieh, J. Polym. Sci., Part A: Polym. Chem., 2006, 44, 905–913 CrossRef CAS.
- Q. Tian, Y. C. Yuan, M. Z. Rong and M. Q. Zhang, J. Mater. Chem., 2009, 19, 1289–1296 RSC.
- Q. A. Tian, M. Z. Rong, M. Q. Zhang and Y. C. Yuan, Polym. Int., 2010, 59, 1339–1345 CrossRef CAS.
- H. E. Gottlieb, V. Kotlyar and A. Nudelman, J. Org. Chem., 1997, 62, 7512–7515 CrossRef CAS.
- G. Kossmehl, H. I. Nagel and A. Pahl, Angew. Makromol. Chem., 1995, 227, 139–157 Search PubMed.
- C. A. G. Haasnoot, F. Deleeuw and C. Altona, Tetrahedron, 1980, 36, 2783–2792 CrossRef CAS.
- F. Benito-Lopez, A. J. Mettelalj, R. J. M. Egberink, A. H. Velders, R. M. Tiggelaar, H. Gardeniers, D. N. Reinhoudt and W. Verboom, Chim. Oggi, 2010, 28, 56–59 Search PubMed.
- J. H. Cooley and R. V. Williams, J. Chem. Educ., 1997, 74, 582–585 CrossRef CAS.
- L. Rulíšek, P. Šebek, Z. Havlas, R. Hrabal, P. Čapek and A. Svatoš, J. Org. Chem., 2005, 70, 6295–6302 CrossRef CAS.
- A. M. Scutaru, M. Wenzel and R. Gust, Eur. J. Med. Chem., 2011, 46, 1604–1615 Search PubMed.
- B. G. Min, Z. H. Stachurski, J. H. Hodgkin and G. R. Heath, Polymer, 1993, 34, 3620–3627 CrossRef CAS.
- G. Lachenal, A. Pierre and N. Poisson, Micron, 1996, 27, 329–334 Search PubMed.
- N. Poisson, G. Lachenal and H. Sautereau, Vib. Spectrosc., 1996, 12, 237–247 Search PubMed.
- M. El Gouri, A. El Bachiri, S. E. Hegazi, M. Rafik and A. El Harfi, Polym. Degrad. Stab., 2009, 94, 2101–2106 CrossRef.
- S. Magana, A. Zerroukhi, C. Jegat and N. Mignard, React. Funct. Polym., 2010, 70, 442–448 CrossRef CAS.
Footnote |
† Electronic supplementary information (ESI) available. See DOI: 10.1039/c2py20611k |
|
This journal is © The Royal Society of Chemistry 2013 |
Click here to see how this site uses Cookies. View our privacy policy here.