DOI:
10.1039/D4TA02241F
(Perspective)
J. Mater. Chem. A, 2024,
12, 13672-13681
Advancing low-dimensional flexible energy devices for wearable technology
Received
3rd April 2024
, Accepted 26th April 2024
First published on 27th April 2024
Abstract
Flexible batteries and supercapacitors have witnessed remarkable progress in recent years, making them integral to the field of wearable technology. These energy devices offer the unique ability to seamlessly conform to the wearer's movements, ensuring uninterrupted power supply for an array of smart devices. To meet the pressing demand for high-efficiency wearable batteries, it is crucial to explore various forms of flexibility and their impact on practical applications. This perspective critically examines the recent advancements in one-dimensional and two-dimensional flexible energy devices, emphasizing their pivotal roles in enabling wearable technology to reach their full potential. Lastly, the challenges and opportunities associated with these devices are discussed in detail, underscoring the paramount importance of low-dimensional flexible energy solutions in the ever-evolving landscape of wearable devices.
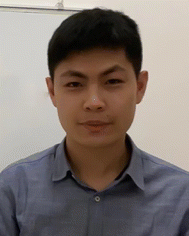 Tao Huang | Tao Huang is a doctoral student at the University of Technology Sydney. His doctoral research focuses on realizing flexible batteries from material to manufacturing process. He is not only proficient in making various batteries, but also good at applying batteries to various smart devices. |
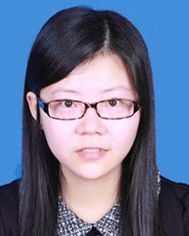 Hong Gao | Hong Gao is presently serving as an Associate Professor at Shanghai University. She completed her PhD in Material Science at the University of Wollongong, Australia, in 2018. Following her doctoral studies, she assumed the role of faculty postdoctoral fellow at Shanghai University before transitioning to the University of Technology Sydney as a Research Associate. Her research pursuits center on the synthesis and applications of advanced functional materials tailored for energy storage and conversion applications. |
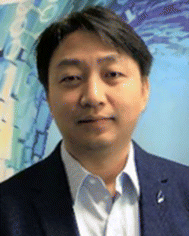 Hao Liu | Hao Liu is a Full Professor and ARC Future Fellow at University of Technology Sydney (UTS). He obtained his PhD degree from the University of Wollongong in 2011. He worked as a research associate at the University of Queensland and moved to the University of Technology Sydney as a Chancellor's postdoctoral research fellow. He is interested in the synthesis of nanostructured materials and their applications in the fields of lithium-ion batteries, sodium-ion batteries, lithium–sulfur batteries, lithium–oxygen batteries, supercapacitors, and electrocatalysts. |
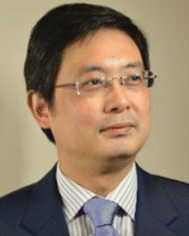 Guoxiu Wang | Guoxiu Wang is the director of the Centre for Clean Energy Technology and a distinguished professor at University of Technology Sydney (UTS), Australia. His research interests include lithium-ion batteries, lithium–air batteries, sodium-ion batteries, lithium–sulfur batteries, supercapacitors, hydrogen storage materials, fuel-cells, 2D materials such as graphene and MXene, and electrocatalysis for hydrogen production. Professor Wang has published more than 650 refereed journal papers with an h-index of 144. His publications have attracted over 67000 citations. He has been recognized as a highly cited researcher in both Materials Science and Chemistry by Clarivate Analytics. |
1 Introduction
Energy storage devices are indispensable components, and their design must cater to specific physical and chemical properties1–8 to meet diverse applications scenarios.9–14 Traditional power plants, like emerging wind power and solar power stations, demand energy storage devices with large capacity and cost-effectiveness,15–22 while volume and weight are less critical.23–25 In contrast, portable electronic devices, such as smartphones and smartwatches, require high energy densities and compact volume, often at the expense of cost considerations.26–29 Electric vehicles occupy an intermediate position, considering a delicate balance between endurance mileage, limited physical dimensions, and the necessity for extra-large capacity, high-energy Density, and cost-effectiveness.30–36 The emergence of wearable technology has introduced a novel requirement for battery devices – flexibility.33,37–39 These devices need to be capable of bending, twisting and stretching to accommodate the dynamic nature of wearable applications.40–46 This necessitates the development of low-dimensional structured flexible batteries and supercapacitors, tailored to varying timelines, battery dimensions, and device types (Fig. 1). Different wearable scenarios require different types of flexibility. For instance, when integrating flexible battery into soft robots, such as worm robots, stretchable batteries/supercapacitors are vital to accommodate the robots' deformations.47–49 In the case of a watch band (Fig. 2c), a great degree of bendability to conform to the wrist's shape while optimizing capacity and standby time.46,50–53 In addition, flexible energy devices can be designed into one-dimensional (1-D) rubber band44,54,55 or two-dimensional (2-D) films (Fig. 2a),56–59 both capable of stretching, bending and twisting (Fig. 2a and b).
 |
| Fig. 1 Timeline of the development of typical flexible batteries/supercapacitors. Panels reproduced with permission from Copyright (Wiley), (Elsevier), (Springer Nature), (Royal Society of Chemistry). | |
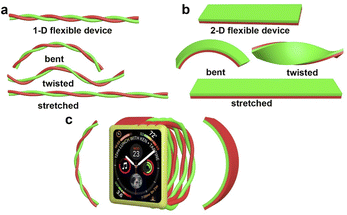 |
| Fig. 2 Schematic diagram of supercapacitor and battery with different dimensions and flexibility. (a) A one-dimensional flexible energy storage device and corresponding three flexible states. (b) A two-dimensional flexible energy storage device and corresponding three flexible states. (c) A hypothetical one-dimensional or two-dimensional flexible energy device for smart watches. | |
These energy devices feature similar components to traditional energy storage systems. They consist of two electrodes, cathode and anode,60–62 sometimes with multiple cathodes and anodes connected in series or parallel inside the battery.63 They serve as the source of energy storage.64 In addition, a diaphragm or separator is crucial for separating electrodes and preventing internal short circuit.65 The electrolyte within cell allows electrical current to flow between anode and cathode.66 All the above substances are encapsulated in a case to insulate them from the outside environment. Flexible energy devices incorporate the same components, albeit in flexible state. To be specific, the flexible energy device is realized from bendable electrode,67–71 elastic electrolyte/diaphragm,72–76 as well as pliable packaging material.77,78 Like the traditional energy storage systems, this type of flexible batteries/supercapacitors also can be applied to super capacitors, lithium-ion batteries, sodium-ion batteries, zinc-ion batteries,79–85etc.
2 1-D flexible energy devices
A 1-D flexible energy storage string has emerged as a transformative technology. They can be wound around devices or seamlessly woven into clothing, providing a means to store and deliver electrical energy for various electronic applications. This innovation empowers individuals to power electronic devices while wearing smart clothes, ushering in a new era of wearable technology.86 Like their traditional batteries' counterparts, 1-D flexible energy devices consist of electrodes, electrolyte, separator and packaging materials, among which electrode research is the main research object. Notably, Peng's group has made a lot of contributions to the research of 1-D flexible batteries/supercapacitors.7,44,45,87–92 They explored the fabrication of various 1-D flexible devices, including symmetric supercapacitors, asymmetric supercapacitors and lithium-ion batteries. These devices are further woven into wearable flexible batteries/supercapacitors.7,8 The remarkable progress made by Peng's research group has resulted in practical fiber batteries, several meters or even tens of meters in length. These extended fibers can be woven into fabrics, and they continue to function reliably after undergoing washing and enduring substantial pressing, and more importantly, these fiber batteries did not show any safety issues such as smoke, fire or explosion after these treatments.7,8
Generally, the one-dimensional electrode comes in two primary forms. One is coaxial mode87, in which an electrode is used as the axis, then gel electrolyte wraps on it, followed by a layer of coaxial tubular electrode further wraps on the outer layer as the opposite electrode. The outermost layer is the packaging material to form a coaxial one-dimensional flexible energy device. In the other mode, the two electrodes are wound together,88 in which the axes spiral each other. In this case, multiple electrodes can be wound to form a flexible 1-D hybrid energy device. Alternatively, one electrode remains stationary while the other electrode winds around it as the counter electrode.89,90 In this case, the axis of the non-rotating electrode is a straight line, while the counter electrode of axis forms a helix. The schematic representations of these three electrode combinations are depicted in Fig. 3a. All of these different combinations perform excellent flexibility, enabling them to be stretched, bent or twisted (Fig. 3b). These advancements in 1-D flexible energy devices are shaping the future of wearable technology and energy storage.
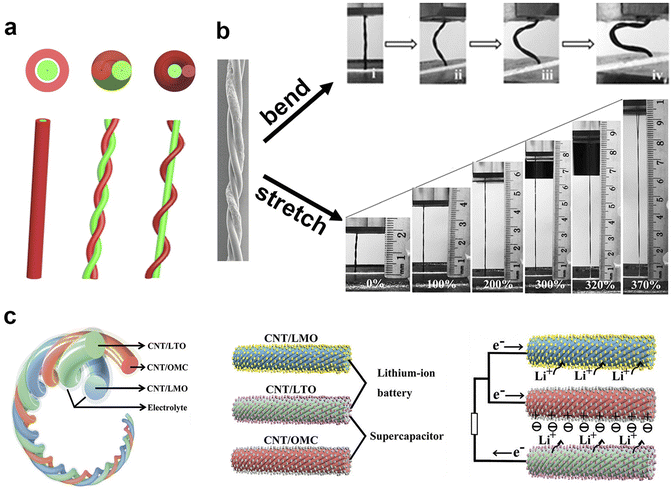 |
| Fig. 3 Various types of one-dimensional electrodes. (a) Schematic diagram of three different types of one-dimensional electrodes assembled into a one-dimensional device. (b) Bending and stretching photos of one-dimensional flexible batteries/supercapacitors, in which the distortion of flexible devices can be attributed to bending. (c) A hybrid flexible energy storage device composed of three different types of electrodes, two of which can be composed of a supercapacitor and two of which can be composed of a lithium-ion battery, in which high power density and high energy density can be achieved through different internal and external connections. Panels reproduced with permission from (b) Chen et al.91 (Wiley) and (c) Zhang et al.93 (Wiley). | |
2.1 Stretchable property of one-dimensional flexible batteries/supercapacitors
1-D energy devices are naturally inclined to bending and distortion, while achieving stretchability poses a significant challenge. In the case of 1-D electrode, resilience is an essential character. Dai's group91 reported a stretchable 1-D flexible capacitor. The flexible capacitor consists of two identical electrodes, forming a symmetric supercapacitor, and the electrolyte/diaphragm is composed of polyvinyl alcohol and phosphoric acid hydrogel, which also act as packaging materials. Two carbon nanotube (CNT) electrodes are twisted together to form a 1-D supercapacitor. The excellent tensile property of the capacitor guarantees a stable electrochemical performance (a capacity of 30.7 F g−1) even after experiencing a 200% stretch. This kind of flexible energy device can be woven into two-dimensional flexible fabrics, which can be made into clothing, effectively serving as an energy-storing textile. However, when creating clothing from these materials, it's imperative to consider the biocompatibility between the fabric and the wearer's skin. A high level of biocompatibility is essential to protect the wearer's skin or body from potential inflammation and provide a comfortable wearing experience. At present, biocompatibility research mainly focuses on natural materials and non-biotoxicity, aiming to ensure the safety and comfort of users in wearable energy storage clothing.
2.2 Bendable and twistable properties of one-dimensional flexible batteries/supercapacitors
Bending aligns with a natural characteristic of 1-D flexible devices, where the ability to bend makes warp formation feasible. An impressive example in this realm was presented by Peng's group.93 They reported a bendable 1-D hybrid lithium-ion battery, in which three different 1-D electrodes (lithium titanate, lithium manganate, and carbon) were twisted together (Fig. 3c). The hybrid fiber battery achieved a high energy density of 50 mW h cm−3 or 90 W h kg−1 and a power density of 1 W cm−3 or 5970 W kg−1. Accordingly, they also prepared a 1-D hybrid lithium-ion supercapacitor device, featuring lithium manganate and carbon electrodes. In comparison to 2-D electrodes, the 1-D multi-electrodes can be easily combined together. While the three 2-D electrodes need a lamination design, implying only two electrodes can close to each other. The flexible energy storage device offers an array of possibilities, as it can be bent and twisted into various configurations, making it highly adaptable to different application scenarios. The ease of integration and manipulation further emphasizes the potential of one-dimensional flexible energy devices for a wide range of practical applications. At present, the Peng group has successfully prepared 1D fiber batteries on a large scale using industrial equipment, and successfully woven this 1D fiber battery into cloth, achieving a huge upgrade from laboratory samples to industrial products.7,8 They creatively used metal wires as current collectors, effectively reducing the internal resistance of fiber batteries at ultra-long lengths, making it possible to industrially prepare and apply such batteries.
3 2-D flexible batteries/supercapacitors
2-D flat batteries represent one of the most prevalent forms of energy storage devices in use today.94 Generally, a 2-D flat energy storage device inherits a certain angle of bendability and torsion under a certain thickness, although stretching remains unattainable.95–98 In reality, due to requirement of a certain volume energy density, the devise is endowed with a limited length and width, resulting in a prescribed thickness. In order to meet the specific flexible energy storage systems, innovation is essential, whether through novel materials or advanced manufacturing processes. 2-D flexible devices necessitate compatible 2-D flexible electrodes, electrolyte/diaphragm, and packaging materials. Moreover, a 2-D electrode must exhibit stretchability, torsional flexibility, and bending capabilities. The pursuit of such innovative 2-D flexible energy devices has the potential to usher in a new era of versatile and adaptable energy storage solutions, pushing the boundaries of what is achievable in practical applications.
3.1 Stretchable properties of 2-D flexible batteries/supercapacitors
Innovative manufacturing processes have paved the way for the development of highly elastic electrode substrate materials, enabling the realization of stretchable property in two-dimensional flexible batteries and supercapacitors. Yang's team99 designed a stretchable accordion-like battery as show in Fig. 4a. The intelligent design separates the energy storage part from the stretchable part, achieving both high energy density and stretchability simultaneously.
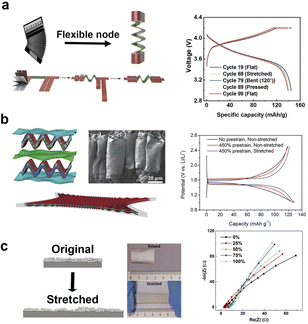 |
| Fig. 4 Different stretchability of flexible batteries and their electrical properties. (a) Diagram of the structure of flexible accordion-like battery and corresponding charge and discharge curves of the battery in different states.99 (b) Schematic diagram, overall picture and scanning electron microscope image of arch electrode structure, and corresponding charge and discharge curves of the battery in different states.92 (c) Schematic drawings and century photos of high elastic substrates with silver layers under normal and stretched conditions and their AC impedance curves.41 Panels reproduced with permission from (a) (Elsevier), (b) and (c) (Wiley). | |
The as-prepared stretchable lithium-ion battery employed lithium cobalt oxide as the electrochemically active material and aluminum foil as the current collector in the cathode, graphite and copper foil collector in the anode. The cathode and anode were wound together with the diaphragm to form a coil. At the joint of the coil, a conductive material is made into an accordion shape, allowing the entire battery to stretch.
The electrodes can also be molded into a certain shape to facilitate stretchability. For instance, Peng and his team92 created arch-shaped electrodes (Fig. 4b). These electrodes comprise lithium manganate with carbon nanotubes and a highly elastic substrate as cathode, and lithium titanate with carbon nanotubes and the same elastic substrate as anode. The as-prepared cell can be stretched up to 400% without any electrochemical performance loss. Under the 400% stretch state, the battery could deliver a capacity of about 100 mA h g−1. Another innovative approach involves the combination of elastic substrate and current collector. Niederberger's group41 laid a layer of conductive silver nanosheets on a highly elastic substrate (Fig. 4c). During stretching and retracting process, the silver nanosheets could connect to each other all the time, guaranteeing a stable electrical conductivity, thus a stretchable current collector. A high elastic and stretchable electrode can be formed by laying the active materials on the stretchable current collector. The silver nanosheets attached elastic substrate can be stretched to 100% with a low sheet resistance of about 2.7 Ω □−1.
In addition to these methods, active materials combined with graphene or carbon nanotubes offer a route to self-flexible electrodes. Such electrodes without current collector can be bent or twisted like paper. Ahn's group comprehensively explored the application of graphene-based active materials in flexible batteries, covering various types of graphene,100 including CVD-graphene, graphene flake, GO, rGO and graphene-based hybrid materials. In terms of carbon nanotube-based composite, Wei's group101 reported a stretchable composite electrode of carbon nanotube and lithium manganate (LMO) and applied in lithium-ion batteries. The as-prepared cell could achieve 100% stretchability and maintain electrochemical properties simultaneously.
3.2 Foldable properties of 2-D flexible batteries/supercapacitors
The foldable properties of two-dimensional flexible batteries and supercapacitors are harnessed through the use of polymer materials known for their flexibility. For instance, the polymer materials can be applied as the substrate to support the active material, and in some cases, they can also act as both flexible substrate and electrochemical active material. Schubert's group102 has systematically introduced and summarized the application of various polymer materials in flexible batteries. For example, polypyrroles (PPY), polythiophene (PT), poly(ethylenedioxythiophene) (PEDOT), and other alkoxy-sub-stituted polythiophene have been applied in various flexible batteries/supercapacitors due to their exceptional REDOX activities. While, these polymer materials have relatively low specific capacity (<100 mA h g−1), they eliminate the need for binders as electrodes, resulting in a slight overall specific capacity increase. The elimination of an additional flexible substrate further enhances the overall specific capacity of flexible electrodes. As a flexible and cost-effective substrate, carbon cloth with is commonly used for flexible electrode substrates. Wu's group103 adopted carbon cloth and thermoplastic polyurethane (TPU) as conductive and flexible substrate to load the 3,4,9,10-perylenetetracarboxylic diimide (PDI) active material (Fig. 5a). This innovative approach resulted in the creation of a foldable electrode with a specific capacity of about 120 mA h g−1. Such foldable electrodes have been successfully applied in flexible lithium-ion battery, showcasing their ability to power LED light perfectly when bent at 180°. These developments highlight the promising potential of foldable two-dimensional flexible batteries and supercapacitors for a wide range of applications.
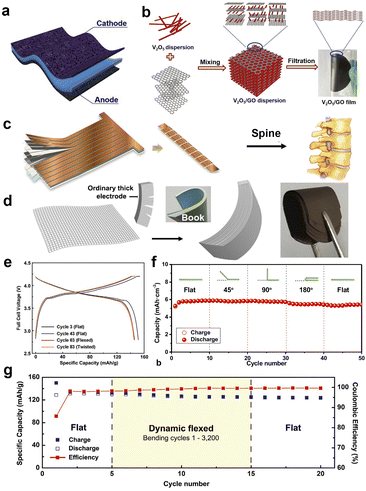 |
| Fig. 5 Diagram and electrochemical performance of different flexible batteries/supercapacitors that can be bent or twisted. (a) Schematic diagram of an electrode with carbon cloth loaded active materials.103 (b) Synthesis process of graphene oxide loaded vanadium pentoxide flexible electrode.104 (c) A fabrication process of spine-like flexible electrode.106 (d) Schematic diagram of book-like flexible electrode preparation and (f) cycling performances.105 (e and g) Charge–discharge curves and cycling performances of a spine-like battery in different flexible states.106 Panels reproduced with permission from (a) (Elsevier), (b), (c), (e) and (g) (Wiley) (d) and (f) (Royal Society of Chemistry). | |
As mentioned earlier, the graphene demonstrates its versatility by forming composites with various materials, especially 2-D REDOX active materials, to create flexible electrodes. In 2017, Feng's group104 made an exciting advancement by combining graphene with vanadium pentoxide (V2O5) nanobelt to prepare flexible electrodes for symmetric supercapacitors (Fig. 5b). The electrode was not limited to supercapacitors and could also function as a cathode in lithium-ion batteries. Both graphene and V2O5 exhibit 2-D sheet-like characteristics, and V2O5 readily attached on the surface of graphene layers, forming a 2-D flat and self-supporting electrode.
In addition to using flexible materials, innovative preparation methods can also make electrodes bendable and flexible. For example, in 2022, Wang's group simulated the bendable properties of books and produced book-like bendable flexible electrodes, which were successfully used in flexible lithium-ion batteries and sodium-ion batteries. Capacities of 5.88 mA h cm−2 and 5.24 mA h cm−2 were obtained in lithium-ion batteries and sodium-ion batteries. And the battery is used in smart insoles, flexible LED arrays and Android smart watches.105
3.3 Twistable property of 2-D flexible batteries/supercapacitors
In general, while stretchable energy devices can typically be twisted, it's important to note that not all twistable energy devices are necessarily stretchable. Highly elastic materials, such as polymers, are frequently used in flexible batteries and their electrodes. However, these materials have lower power and energy density compared to traditional metal foil substrates. Innovation in the electrodes manufacturing process is an effective way solve the above issue. In terms of torsional electrodes, Yang's group106 introduced a spine-like cell design with multiple sections and small intervals between them (Fig. 5c). When applied in lithium-ion batteries, the conventional lithium cobaltate (LCO) as cathode with aluminum foil as current collector and graphite as anode with copper foil as current collector. The as-prepared battery could maintain excellent capacity even when subjected to bending and twisting (Fig. 5d). Notably, innovations in electrode and cell manufacturing processes hold great potential for practical implementation in flexible battery production by battery manufacturers.
4 Flexible electrolyte & diaphragm
Except electrodes, suitable electrolyte and diaphragm are critical components in the development of flexible batteries/supercapacitors. Gel electrolytes are commonly used in flexible energy devices, serving as both electrolyte and diaphragm.107 Zhi's group108 prepared a super stretchable gel electrolyte using sodium polyacrylate and cellulose. The gel electrolyte can be stretched as large as 800% in a 2-D cell and 500% in a 1-D fiber cell. Kyu's group109 explored a polymer electrolyte with poly(ethylene oxide) (PEO), succinonitrile (SCN) (solid plasticizer) gels, and bis(trifluoromethane)sulfonimide (LiTFSI) as conductive salt (Fig. 6a and b). This polymer electrolyte with excellent ionic conductivity and certain stretchability was subsequently applied in the flexible lithium-ion battery by Peng's group (Fig. 6c).92 Niederberger's group dispersed LiTFSI in polyacrylamide hydrogel and applied as both diaphragm and electrolyte.41 Specifically, acrylamide monomer and ammonium persulfate were dissolved in water initially, and then obtained the polyacrylamide hydrogel via a polymerization process. After that a high concentration of LiTFSI aqueous solution was added and comprehensively stirred to prepare the flexible gel electrolyte. The as-prepared gel electrolyte inherits wide working voltage window, high elasticity and high ionic conductivity, as shown in Fig. 6d and e.
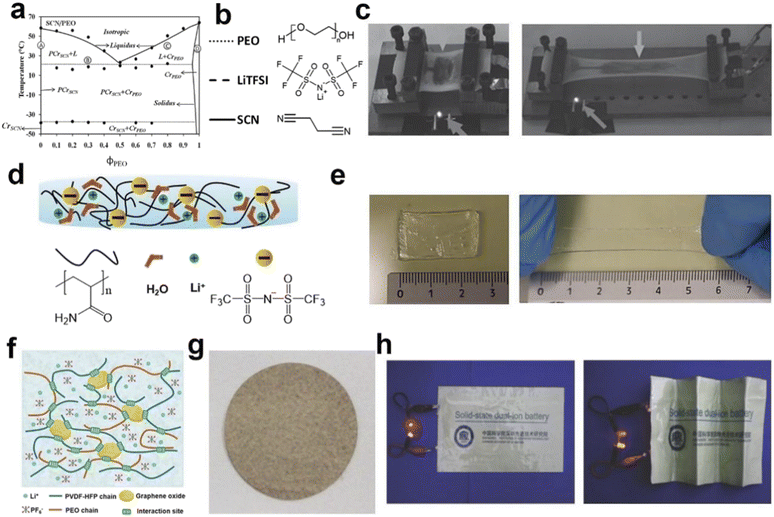 |
| Fig. 6 Schematic diagram of various flexible electrolytes. (a) Binary phase diagram of the PEO/SCN mixture, and (b) chemical structures of the LiTFSI electrolyte.109 (c) The gel electrolyte was applied to the stretchable lithium ion battery, and the battery photos before and after the stretching.92 (d) Schematic illustration of the design concept of PAM-WiS gel electrolyte, and (e) photos of the unstretched and stretched electrolyte.41 (f) Schematic of the 3D porous polymer network, and (g) optical photographs of the dual-ion gel electrolyte, and (h) the electrolyte is applied to a bendable dual-ion battery, and the battery photos before and after bending.110 Panels reproduced with permission from (a) and (b) (ACS Publications), (c)–(h) (Wiley). | |
The resulting flexible dual-ion cell could be folded freely. Additionally, cells utilizing the gel electrolyte, often referred to as solid-state batteries, are safer than their liquid electrolyte counterparts due to the gel's high operating voltage and temperature. In addition to conventional energy devices, gel electrolytes find utility in flexible dual-ion batteries. These environment ally friendly and cost-effective devices have high voltage and show promise in the realm of flexible energy devices. In 2018, a dual-ion gel electrolyte (Fig. 6f–h) was prepared by copolymerizing poly(vinylidene fluoride-hexafluoro propylene)(PVDF) with poly(ethylene oxide)(PEO) and then incorporating graphene oxide(GO).110–113 The electrolyte featured an abundance of 3D channels, facilitating the rapid movement of conductive ions. The resulting flexible dual-ion cell could be folded arbitrarily. Moreover, cells made with the gel electrolyte, also known as solid state batteries, are safer than their liquid electrolyte counterparts due to the relatively high operating voltage and high operating temperature of the gel electrolyte.
5 Flexible packaging materials
A flexible packaging is essential for isolating the interior components of a battery or capacitor from the surrounding environment. In certain prototype energy storage devices, gel electrolyte can even play the role of packaging material. For instance, some 1-D flexible energy devices lack traditional packaging and consist only electrodes and gel electrolyte.87 Some traditional materials, such as aluminum plastic film, are often used as packaging materials for the lithium-ion battery. The aluminum plastic film is composed of two layers of polymers and an aluminum foil in between, which can be bent and twisted. Through the above-mentioned new techniques, such as accordion-like and spine-like production processes, the aluminum-plastic film can also inherit the stretchable property. Other flexible polymers, such as polystyrene, polydimethylsiloxane (PDMS), and silicone rubber, are suitable choices for packaging. In flexible energy devices, packaging materials not only serve the purpose of environmental isolation but must also possess flexibility. Therefore, many packaging materials with the above-mentioned characteristics have potential to be applied in soft energy devices.
6 Conclusions and outlooks
In this perspective, we systematically overview the 1-D and 2-D forms flexible energy devices, taking into account various types of flexibility, including bending, twisting and stretching. We also delve into the essential components of these devices, including flexible electrodes, electrolyte/diaphragm and packaging materials. A comparative analysis of typical flexible batteries/supercapacitors are summarized in Table 1, highlighting their electrode characteristics, electrolytes, diaphragms, packaging materials, flexibility types, and bending performance.
Table 1 A summary of electrode, electrolyte/diaphragm, packaging materials, flexible type and bending performance of typical flexible batteries/supercapacitors
|
Type of device |
Flexible type |
Performance |
Electrode materials |
Electrolyte/diaphragm materials |
Packaging materials |
Ref. |
1D |
Supercapacitor |
Stretched, bent |
Maximum 370% |
CNT |
PVA/H3PO4/water hydrogel |
None |
91
|
Hybrid of lithium-ion battery and supercapacitor |
Bent |
>180° |
CNT, carbon, Li4Ti5O12, LiMn2O4 |
LiTFSI/SCN/PEO gel electrolyte |
None |
93
|
2D |
Li-ion battery |
Stretchable, bent |
Maximum 22% stretching, 180° bent |
LCO, graphite, metal foil |
LiPF6 in ethylene carbonate/diethyl carbonate, celgard separators |
Aluminized pouch bags |
99
|
Li-ion battery |
Stretchable |
Maximum 400% |
LTO, LMO, CNT, elastic substrate |
LiTFSI/SCN/PEO gel electrolyte |
PDMS film |
92
|
Li-ion battery |
Stretchable |
Maximum 300% |
LiMn2O4, V2O5, silver coated elastic substrate |
Polyacrylamide/water-in-salt hydrogel electrolyte |
PDMS film, epoxy glue |
41
|
Li-ion battery |
Bent |
180° |
PDI, TPU, carbon cloth |
LiPF6 in ethylene carbonate/diethyl carbonate, celgard separators |
Aluminized pouch bags |
103
|
Supercapacitor |
Bent |
180° |
Graphene, V2O5 |
LiPF6 in ethylene carbonate/diethyl carbonate, celgard separators |
Aluminized pouch bags |
104
|
Li-ion battery & Na-ion battery |
Bent |
180° |
CNT, PTCDI |
Commercial electrolyte |
Aluminized pouch bags |
105
|
Li-ion battery |
Bent, twisted |
About 180° bent, about 60° twist |
LiCoO2, graphite, metal foil |
LiPF6 in ethylene carbonate/diethyl carbonate, celgard separators |
Aluminized pouch bags |
106
|
Generally, the flexible electrodes with elastic substrates or special flexible nodes behave a lower energy density compared with non-flexible counterparts. Traditional metal foil can only be bent or distorted to a certain extent; thus, a high-elastic substrate is critical to obtain a flexible electrode that can be bent, twisted and stretched.
Compared to traditional liquid electrolytes and polymer membranes (e.g., PE, PP), the gel electrolyte is more widely used in flexible batteries/supercapacitors due to its natural flexible and ionic conductive properties. After dissolving salts, the gel electrolyte has the ionic conductivity as an electrolyte, and separates electrodes as a diaphragm. The packaging material is required to separate the inside of the device from the outside environment. In flexible energy devices, it must be endowed with flexibility as well.
Despite some significant progress made in flexible energy storage devices, there are still many challenges need to be overcame. Thus, the current challenges and prospective research focus in this field are summarized as follows:
The issue of reduced electrochemical performance after deformation is a critical concern. Adding conductive carbon materials into substrates or using conductive polymers are effective way to alleviate the performance loss of the distorted electrode. While the low density of polymers and carbon materials would reduce the power and energy density. Novel electrode fabrication processes, such as adding flexible nodes to the electrodes, could realize an improved volumetric power and energy densities compared to soft substrates. However, the conventional materials and current collectors tend to be unstretchable more or less, making it crucial to simultaneously enhance the power density, energy density and flexibility in electrodes for future research.
Similar to the elastic substrate, the gel electrolyte also behaves a low density. At present, the gel electrolyte displays the thickness of few hundred microns to a millimeter, which greatly affects the device volume energy density and power density. However, reducing the thickness of gel electrolyte may risk internal short circuit, especially in stretched state. Therefore, the development of ultra-thin and flexible solid-state electrolytes emerges as a promising avenue for future research.
Moreover, attention to flexible packaging material is also essential. Because the flexible packages are typically composed of polymers, research efforts in producing ultra-thin polymer materials hold promise in this field.
Conflicts of interest
There are no conflicts to declare.
Acknowledgements
HL thanks the financial support from Australian Research Council (FT180100705). HG acknowledges the support from the Science and Technology Commission of Shanghai Municipality (22010500400) and “Shanghai Pujiang Program” (23PJ1402800), “Joint International Laboratory on Environmental and Energy Frontier Materials” and “Innovation Research Team of High-Level Local Universities in Shanghai” at Shanghai University.
References
- Y. Zhang, J. Riexinger, X. Yang, E. Mikhailova, Y. Jin, L. Zhou and H. Bayley, Nature, 2023, 620, 1001–1006 CrossRef CAS PubMed.
- T. P. Nguyen, A. D. Easley, N. Kang, S. Khan, S.-M. Lim, Y. H. Rezenom, S. Wang, D. K. Tran, J. Fan and R. A. Letteri, Nature, 2021, 593, 61–66 CrossRef CAS PubMed.
- Y.-H. Chu, Science, 2021, 374, 33–34 CrossRef CAS PubMed.
- P. R. Kidambi, P. Chaturvedi and N. K. Moehring, Science, 2021, 374, eabd7687 CrossRef CAS PubMed.
- C. A. Aubin, S. Choudhury, R. Jerch, L. A. Archer, J. H. Pikul and R. F. Shepherd, Nature, 2019, 571, 51–57 CrossRef CAS PubMed.
- K. Kleiner, Nature, 2006, 441, 1046–1047 CrossRef PubMed.
- M. Liao, C. Wang, Y. Hong, Y. Zhang, X. Cheng, H. Sun, X. Huang, L. Ye, J. Wu, X. Shi, X. Kang, X. Zhou, J. Wang, P. Li, X. Sun, P. Chen, B. Wang, Y. Wang, Y. Xia, Y. Cheng and H. Peng, Nat. Nanotechnol., 2022, 17, 372–377 CrossRef CAS PubMed.
- J. He, C. Lu, H. Jiang, F. Han, X. Shi, J. Wu, L. Wang, T. Chen, J. Wang and Y. Zhang, Nature, 2021, 597, 57–63 CrossRef CAS PubMed.
- P. P. Lopes and V. R. Stamenkovic, Science, 2020, 369, 923–924 CrossRef CAS PubMed.
- C. Zhao, Q. Wang, Z. Yao, J. Wang, B. Sánchez-Lengeling, F. Ding, X. Qi, Y. Lu, X. Bai and B. Li, Science, 2020, 370, 708–711 CrossRef CAS PubMed.
- C. S. Ioakimidis, A. Murillo-Marrodán, A. Bagheri, D. Thomas and K. N. Genikomsakis, Sustainability, 2019, 11, 2527 CrossRef.
-
L. Held, H. Krämer, M. Zimmerlin, M. R. Suriyah, T. Leibfried, L. Ratajczak, S. Lossau and M. Konermann, 53rd International Universities Power Engineering Conference (UPEC), IEEE, 2018, pp. 1–6 Search PubMed.
- Y. Jiang, L. Kang and Y. Liu, Energy, 2020, 206, 118093 CrossRef.
- H. Sun, Y. Zhang, J. Zhang, X. Sun and H. Peng, Nat. Rev. Mater., 2017, 2, 17023 CrossRef CAS.
- W. Sun, F. Wang, B. Zhang, M. Zhang, V. Küpers, X. Ji, C. Theile, P. Bieker, K. Xu and C. Wang, Science, 2021, 371, 46–51 CrossRef CAS PubMed.
- Z. Peng, S. A. Freunberger, Y. Chen and P. G. Bruce, Science, 2012, 337, 563–566 CrossRef CAS PubMed.
- T. Janoschka, N. Martin, U. Martin, C. Friebe, S. Morgenstern, H. Hiller, M. D. Hager and U. S. Schubert, Nature, 2015, 527, 78–81 CrossRef CAS PubMed.
- X. Chi, M. Li, J. Di, P. Bai, L. Song, X. Wang, F. Li, S. Liang, J. Xu and J. Yu, Nature, 2021, 592, 551–557 CrossRef CAS PubMed.
- H. Gao, J. Li, F. Zhang, C. Li, J. Xiao, X. Nie, G. Zhang, Y. Xiao, D. Zhang, X. Guo, Y. Wang, Y.-M. Kang, G. Wang and H. Liu, Adv. Energy Mater., 2024, 14, 2304529 CrossRef.
- J. Chen, G. Zhang, J. Xiao, J. Li, Y. Xiao, D. Zhang, H. Gao, X. Guo, G. Wang and H. Liu, Adv. Funct. Mater., 2024, 34, 2307959 CrossRef CAS.
- X.-M. Lu, Y. Cao, Y. Sun, H. Wang, W. Sun, Y. Xu, Y. Wu, C. Yang and Y. Wang, Angew. Chem., Int. Ed., 2024, 63, e202320259 CrossRef CAS PubMed.
- H. Liu, X. Liu, W. Li, X. Guo, Y. Wang, G. Wang and D. Zhao, Adv. Energy Mater., 2017, 7, 1700283 CrossRef.
- Z. Li, R. Sun, Z. Qin, X. Liu, C. Wang, S. Lu, Y. Zhang and H. Fan, Mater. Chem. Front., 2021, 5, 7540–7547 RSC.
- X. Guo, H. Gao, S. Wang, G. Yang, X. Zhang, J. Zhang, H. Liu and G. Wang, Nano Lett., 2022, 22, 1225–1232 CrossRef CAS PubMed.
-
O. S. Burheim, Engineering Energy Storage, Academic press, 2017 Search PubMed.
- M. Wang, W. Yao, P. Zou, S. Hu, H. Zhu, K. Liu and C. Yang, J. Power Sources, 2021, 490, 229527 CrossRef CAS.
- C. Xia, C. Kwok and L. Nazar, Science, 2018, 361, 777–781 CrossRef CAS PubMed.
- X. Xiao, X. Xiao, Y. Zhou, X. Zhao, G. Chen, Z. Liu, Z. Wang, C. Lu, M. Hu and A. Nashalian, Sci. Adv., 2021, 7, eabl3742 CrossRef CAS PubMed.
- B. Kang and G. Ceder, Nature, 2009, 458, 190–193 CrossRef CAS PubMed.
- S. Ovshinsky, M. Fetcenko and J. Ross, Science, 1993, 260, 176–181 CrossRef CAS PubMed.
- J. F. Parker, C. N. Chervin, I. R. Pala, M. Machler, M. F. Burz, J. W. Long and D. R. Rolison, Science, 2017, 356, 415–418 CrossRef CAS PubMed.
- X. Zhou, Q. Liu, C. Jiang, B. Ji, X. Ji, Y. Tang and H. M. Cheng, Angew. Chem., Int. Ed., 2020, 59, 3802–3832 CrossRef CAS PubMed.
- Y. Lan, W. Yao, X. He, T. Song and Y. Tang, Angew. Chem., Int. Ed., 2020, 59, 9255–9262 CrossRef CAS PubMed.
- S. J. Gerssen-Gondelach and A. P. Faaij, J. Power Sources, 2012, 212, 111–129 CrossRef CAS.
- B. Nykvist and M. Nilsson, Nat. Clim. Change, 2015, 5, 329–332 CrossRef.
- S. Eaves and J. Eaves, J. Power Sources, 2004, 130, 208–212 CrossRef CAS.
- L. Manjakkal, L. Yin, A. Nathan, J. Wang and R. Dahiya, Adv. Mater., 2021, 2100899 CrossRef CAS PubMed.
- Z. Wu, Y. Wang, X. Liu, C. Lv, Y. Li, D. Wei and Z. Liu, Adv. Mater., 2019, 31, 1800716 CrossRef PubMed.
- C. Wang, T. He, J. Cheng, Q. Guan and B. Wang, Adv. Funct. Mater., 2020, 30, 2004430 CrossRef CAS.
- D. G. Mackanic, M. Kao and Z. Bao, Adv. Energy Mater., 2020, 10, 2001424 CrossRef CAS.
- X. Chen, H. Huang, L. Pan, T. Liu and M. Niederberger, Adv. Mater., 2019, 31, 1904648 CrossRef CAS PubMed.
- Y. Ma, Y. Zhang, S. Cai, Z. Han, X. Liu, F. Wang, Y. Cao, Z. Wang, H. Li and Y. Chen, Adv. Mater., 2020, 32, 1902062 CrossRef CAS PubMed.
- D. Wang, H. Li, Z. Liu, Z. Tang, G. Liang, F. Mo, Q. Yang, L. Ma and C. Zhi, Small, 2018, 14, 1803978 CrossRef PubMed.
- L. Wang, Y. Zhang, J. Pan and H. Peng, J. Mater. Chem. A, 2016, 4, 13419–13424 RSC.
- Y. Zhang, Y. Zhao, J. Ren, W. Weng and H. Peng, Adv. Mater., 2016, 28, 4524–4531 CrossRef CAS PubMed.
- A. Chen, X. Guo, S. Yang, G. Liang, Q. Li, Z. Chen, Z. Huang, Q. Yang, C. Han and C. Zhi, Energy Environ. Sci., 2021, 14, 3599–3608 RSC.
- N. Lu and D.-H. Kim, Soft Robot., 2014, 1, 53–62 CrossRef.
- Y. Li, H. Yang, T. Zhang, S. Li, S. Li, S. He, T. Chen, J. Y. Lee, Y. Zhao and P. Y. Chen, Adv. Energy Mater., 2021, 11, 2101862 CrossRef CAS.
- Y. Lee, W. Song and J.-Y. Sun, Mater. Today Phys., 2020, 15, 100258 CrossRef.
- J. Chen, K. Zou, P. Ding, J. Deng, C. Zha, Y. Hu, X. Zhao, J. Wu, J. Fan and Y. Li, Adv. Mater., 2019, 31, 1805484 CrossRef PubMed.
- J. Chang, Q. Huang, Y. Gao and Z. Zheng, Adv. Mater., 2021, 33, 2004419 CrossRef CAS PubMed.
- J. Q. Zhu, Y. L. Ban, Y. Zhang, Z. Yan, R. M. Xu and C. C. Mi, IET Power Electron., 2020, 13, 3428–3434 CrossRef.
-
R. Xiao, G. Laput and C. Harrison, Proceedings of the SIGCHI Conference on Human Factors in Computing Systems, 2014, pp. 193–196 Search PubMed.
- C. Song, Y. Li, H. Li, T. He, Q. Guan, J. Yang, X. Li, J. Cheng and B. Wang, Nano Energy, 2019, 60, 285–293 CrossRef CAS.
- P. Man, B. He, Q. Zhang, Z. Zhou, C. Li, Q. Li, L. Wei and Y. Yao, J. Mater. Chem. A, 2019, 7, 27217–27224 RSC.
- X. Guo, S. Zheng, G. Zhang, X. Xiao, X. Li, Y. Xu, H. Xue and H. Pang, Energy Storage Mater., 2017, 9, 150–169 CrossRef.
- P. Xiong, L. Peng, D. Chen, Y. Zhao, X. Wang and G. Yu, Nano Energy, 2015, 12, 816–823 CrossRef CAS.
- J.-Z. Wang, S.-L. Chou, J. Chen, S.-Y. Chew, G.-X. Wang, K. Konstantinov, J. Wu, S.-X. Dou and H. K. Liu, Electrochem. Commun., 2008, 10, 1781–1784 CrossRef CAS.
- L. Jabbour, C. Gerbaldi, D. Chaussy, E. Zeno, S. Bodoardo and D. Beneventi, J. Mater. Chem., 2010, 20, 7344–7347 RSC.
- W. Cao and J. Zheng, J. Electrochem. Soc., 2013, 160, A1572 CrossRef CAS.
- M. Asadi, B. Sayahpour, P. Abbasi, A. T. Ngo, K. Karis, J. R. Jokisaari, C. Liu, B. Narayanan, M. Gerard and P. Yasaei, Nature, 2018, 555, 502–506 CrossRef CAS PubMed.
- P. Srimuk, F. Kaasik, B. Krüner, A. Tolosa, S. Fleischmann, N. Jäckel, M. C. Tekeli, M. Aslan, M. E. Suss and V. Presser, J. Mater. Chem. A, 2016, 4, 18265–18271 RSC.
-
R. Boddula, R. Pothu and A. M. Asiri, Rechargeable Batteries: History, Progress, and Applications, John Wiley & Sons, 2020 Search PubMed.
- H. Liu, T. Xu, K. Liu, M. Zhang, W. Liu, H. Li, H. Du and C. Si, Ind. Crops Prod., 2021, 165, 113425 CrossRef CAS.
-
C. s. Yang, D. h. Han and M. Zhang, Rechargeable Batteries: History, Progress, and Applications, 2020, pp. 1–16 Search PubMed.
- J. Y. Kim and S. H. Kim, Solid State Ionics, 1999, 124, 91–99 CrossRef CAS.
- D.-W. Wang, F. Li, J. Zhao, W. Ren, Z.-G. Chen, J. Tan, Z.-S. Wu, I. Gentle, G. Q. Lu and H.-M. Cheng, ACS Nano, 2009, 3, 1745–1752 CrossRef CAS PubMed.
- Y. Huang, H. Li, Z. Wang, M. Zhu, Z. Pei, Q. Xue, Y. Huang and C. Zhi, Nano Energy, 2016, 22, 422–438 CrossRef CAS.
- R. K. L. Tan, S. P. Reeves, N. Hashemi, D. G. Thomas, E. Kavak, R. Montazami and N. N. Hashemi, J. Mater. Chem. A, 2017, 5, 17777–17803 RSC.
- X. Wu and S. Yao, Nano Energy, 2017, 42, 143–150 CrossRef CAS.
- J. He, N. Wang, Z. Cui, H. Du, L. Fu, C. Huang, Z. Yang, X. Shen, Y. Yi and Z. Tu, Nat. Commun., 2017, 8, 1–11 CrossRef PubMed.
- W. G. Moon, G.-P. Kim, M. Lee, H. D. Song and J. Yi, ACS Appl. Mater. Interfaces, 2015, 7, 3503–3511 CrossRef CAS PubMed.
- X. Lei, X. Liu, W. Ma, Z. Cao, Y. Wang and Y. Ding, Angew. Chem., Int. Ed., 2018, 57, 16131–16135 CrossRef CAS PubMed.
- Y. J. Kang, Y. Yoo and W. Kim, ACS Appl. Mater. Interfaces, 2016, 8, 13909–13917 CrossRef CAS PubMed.
- N. W. Li, Y. Shi, Y. X. Yin, X. X. Zeng, J. Y. Li, C. J. Li, L. J. Wan, R. Wen and Y. G. Guo, Angew. Chem., Int. Ed., 2018, 57, 1505–1509 CrossRef CAS PubMed.
- J.-K. Kim, Y. J. Lim, H. Kim, G.-B. Cho and Y. Kim, Energy Environ. Sci., 2015, 8, 3589–3596 RSC.
- A. N. Jansen, K. Amine, A. E. Newman, D. R. Vissers and G. L. Henriksen, JOM, 2002, 54, 29–32 CrossRef CAS.
- J. P. Thomas and M. A. Qidwai, JOM, 2005, 57, 18 CrossRef CAS.
- N. S. Shaikh, V. Lokhande, S. Praserthdam, C. D. Lokhande, F. Ezema, D. Salunkhe, J. S. Shaikh and P. Kanjanaboos, Energy Fuels, 2021, 35, 14241–14264 CrossRef CAS.
- J.-M. Ma and Y.-T. Li, Rare Met., 2021, 40, 246–248 CrossRef CAS.
- K. Yu, X. Pan, G. Zhang, X. Liao, X. Zhou, M. Yan, L. Xu and L. Mai, Adv. Energy Mater., 2018, 8, 1802369 CrossRef.
- L. Dong, X. Ma, Y. Li, L. Zhao, W. Liu, J. Cheng, C. Xu, B. Li, Q.-H. Yang and F. Kang, Energy Storage Mater., 2018, 13, 96–102 CrossRef.
- Z. Liu, H. Sun, L. Qin, X. Cao, J. Zhou, A. Pan, G. Fang and S. Liang, ChemNanoMat, 2020, 6, 1553–1566 CrossRef CAS.
- M. Ates, A. Chebil, O. Yoruk, C. Dridi and M. Turkyilmaz, Ionics, 2021, 1–26 Search PubMed.
- S. J. Uke, S. P. Mardikar, A. Kumar, Y. Kumar, M. Gupta and Y. Kumar, R. Soc. Open Sci., 2021, 8, 210567 CrossRef CAS PubMed.
- Y.-H. Lee, J.-S. Kim, J. Noh, I. Lee, H. J. Kim, S. Choi, J. Seo, S. Jeon, T.-S. Kim and J.-Y. Lee, Nano Lett., 2013, 13, 5753–5761 CrossRef CAS PubMed.
- X. Yu, J. Pan, J. Zhang, H. Sun, S. He, L. Qiu, H. Lou, X. Sun and H. Peng, J. Mater. Chem. A, 2017, 5, 6032–6037 RSC.
- J. Ren, W. Bai, G. Guan, Y. Zhang and H. Peng, Adv. Mater., 2013, 25, 5965–5970 CrossRef CAS PubMed.
- Z. Yang, H. Sun, T. Chen, L. Qiu, Y. Luo and H. Peng, Angew. Chem., 2013, 125, 7693–7696 CrossRef.
- J. Deng, L. Qiu, X. Lu, Z. Yang, G. Guan, Z. Zhang and H. Peng, J. Mater. Chem. A, 2015, 3, 21070–21076 RSC.
- T. Chen, R. Hao, H. Peng and L. Dai, Angew. Chem., Int. Ed., 2015, 54, 618–622 CrossRef CAS PubMed.
- W. Weng, Q. Sun, Y. Zhang, S. He, Q. Wu, J. Deng, X. Fang, G. Guan, J. Ren and H. Peng, Adv. Mater., 2015, 27, 1363–1369 CrossRef CAS PubMed.
- Y. Zhang, Y. Zhao, X. Cheng, W. Weng, J. Ren, X. Fang, Y. Jiang, P. Chen, Z. Zhang, Y. Wang and H. Peng, Angew. Chem., Int. Ed., 2015, 54, 11177–11182 CrossRef CAS PubMed.
- S. Arora, W. Shen and A. Kapoor, Renewable Sustainable Energy Rev., 2016, 60, 1319–1331 CrossRef.
- M. Koo, K.-I. Park, S. H. Lee, M. Suh, D. Y. Jeon, J. W. Choi, K. Kang and K. J. Lee, Nano Lett., 2012, 12, 4810–4816 CrossRef CAS PubMed.
- J.-Z. Wang, S.-L. Chou, H. Liu, G. X. Wang, C. Zhong, S. Y. Chew and H. K. Liu, Mater. Lett., 2009, 63, 2352–2354 CrossRef CAS.
- Y. J. Nam, S.-J. Cho, D. Y. Oh, J.-M. Lim, S. Y. Kim, J. H. Song, Y.-G. Lee, S.-Y. Lee and Y. S. Jung, Nano Lett., 2015, 15, 3317–3323 CrossRef CAS PubMed.
- B. Liu, X. Wang, B. Liu, Q. Wang, D. Tan, W. Song, X. Hou, D. Chen and G. Shen, Nano Res., 2013, 6, 525–534 CrossRef CAS.
- C. Shi, T. Wang, X. Liao, B. Qie, P. Yang, M. Chen, X. Wang, A. Srinivasan, Q. Cheng, Q. Ye, A. Li, X. Chen and Y. Yang, Energy Storage Mater., 2019, 17, 136–142 CrossRef.
- S. D. Kim, A. Sarkar and J. H. Ahn, Small, 2021, 17, 2006262 CrossRef CAS PubMed.
- T. Gu, Z. Cao and B. Wei, Adv. Energy Mater., 2017, 7, 1700369 CrossRef.
- M. D. Hager, B. Esser, X. Feng, W. Schuhmann, P. Theato and U. S. Schubert, Adv. Mater., 2020, 32, 2000587 CrossRef CAS PubMed.
- L. Ma, D. Lu, P. Yang, X. Xi, R. Liu and D. Wu, Electrochim. Acta, 2019, 319, 201–209 CrossRef CAS.
- H. Liu, Y. Tang, C. Wang, Z. Xu, C. Yang, T. Huang, F. Zhang, D. Wu and X. Feng, Adv. Funct. Mater., 2017, 27, 1606269 CrossRef.
- T. Huang, H. Gao, J. Chen, H. Liu, D. Wu and G. Wang, Chem. Commun., 2022, 58, 10158–10161 RSC.
- G. Qian, B. Zhu, X. Liao, H. Zhai, A. Srinivasan, N. J. Fritz, Q. Cheng, M. Ning, B. Qie, Y. Li, S. Yuan, J. Zhu, X. Chen and Y. Yang, Adv. Mater., 2018, 30, 1704947 CrossRef PubMed.
- Y. Li, J. Fu, C. Zhong, T. Wu, Z. Chen, W. Hu, K. Amine and J. Lu, Adv. Energy Mater., 2019, 9, 1802605 CrossRef.
- L. Ma, S. Chen, D. Wang, Q. Yang, F. Mo, G. Liang, N. Li, H. Zhang, J. A. Zapien and C. Zhi, Adv. Energy Mater., 2019, 9, 1803046 CrossRef.
- M. Echeverri, N. Kim and T. Kyu, Macromolecules, 2012, 45, 6068–6077 CrossRef CAS.
- G. Chen, F. Zhang, Z. Zhou, J. Li and Y. Tang, Adv. Energy Mater., 2018, 8, 1801219 CrossRef.
- Z. Cao, G. Liang, D. Ho, C. Zhi and H. Hu, Adv. Funct. Mater., 2023, 33, 2303060 CrossRef CAS.
- Y. Wu, N. He, G. Liang, C. Zhang, C. Liang, D. Ho, M. Wu and H. Hu, Adv. Funct. Mater., 2024, 34, 2301734 CrossRef CAS.
- J. Zhang, K. Wang, P. Lu, J. Gao, Z. Cao, F. Mo, D. Ho, B. Li and H. Hu, Adv. Funct. Mater., 2024, 34, 2310775 CrossRef CAS.
|
This journal is © The Royal Society of Chemistry 2024 |
Click here to see how this site uses Cookies. View our privacy policy here.