Biosurfactants' production with substrates from the sugar industry – environmental, cost, market, and social aspects†
Received
21st April 2023
, Accepted 24th August 2023
First published on 6th September 2023
Abstract
Transforming today's products and production processes towards a more sustainable bio-economy requires the consideration of environmental, cost and market related, as well as social aspects. In this study lab and pilot plant data were extended to industrial scale process chain designs for biosurfactant production. Considering different substrates from the sugar industry (molasses and sugar beet pulp) and different products (rhamnolipids (RL) and mannosylerythritol lipids (MEL)), advantageous process paths and possible specific hotspots were identified. To enable sustainability-oriented process development of microbial biosurfactants, assessment approaches such as Life Cycle Assessment (LCA), product cost analysis (CA) and market analysis were applied. Social aspects were addressed in a more general way. Regarding environmental impacts, the most contributing impact categories (e.g., resource use), process modules (e.g., solvent production) and stages (e.g., extraction stage) were determined. Results for environmental impacts show significant advantages for MEL production, while the choice of the substrate plays a minor role. CA has shown significantly lower costs for MEL production, which can reach the levels of comparable products on the market. The examined market framework and calculated production costs allowed estimations on the competitive position within the market of surfactants. The social aspects have also shown advantages for MEL production and, in the product-dependent variety of results, the importance of taking them into account. In summary, MEL production in an exemplary industrial scale scenario has shown essential advantages, which can be traced back mainly to the higher production yields. However, further design improvements were identified for RL and MEL production.
Sustainability spotlight
The quantification of different sustainability aspects during process development is an important tool to identify improvement options. Thus, biosurfactants can meet their expectations to be part of a future bio-economy and substitute fossil based products. For a classification in the overall context, a multidimensional assessment approach allows addressing several SDGs (e.g., SDG 12 by “resource depletion”, SDG 13 by “climate change”, SDG 14 by “ecotoxicity freshwater”, and SDG 5 by “gender wage gap”).
|
Introduction
To achieve a more sustainable chemical production, process improvement options should be addressed already during the development phase. Aligned with a sustainability-oriented development path, the project Bio2 was carried out to design production processes for novel so-called biosurfactants. In this study, the term biosurfactant is used in line with DIN EN 17035 for totally bio-based surfactants.1 The focus was on the biosurfactants rhamnolipid (hereinafter RL) and mannosylerythritol lipids (hereinafter MEL).2,3 These biosurfactants are naturally produced by the bacterium Pseudomonas putida (RL) and the fungus Ustilago maydis (MEL).4,5 Taking into account two different substrates (molasses (MOL) and sugar beet pulp (SBP) from the sugar industry), there are four process routes included in this study (two products and two substrates). By political initiatives such as the “European Green Deal” and civic engagements by NGOs or climate activism,6–8 the idea of sustainability was once again brought more into the spotlight of public discussions and necessities in recent years. Especially in the context of product development like the one described in this study, sustainability assessment provides instruments to consider the three dimensions of environmental, economic and social aspects according to the triple-bottom-line approach.9–11
The global surfactant manufacturing, with a production mass of ca. 17 m Mg and a revenue of ca. 36 bn€ per a,12–14 represents a constantly growing market with expected growth rates in a one-digit percentage range (5%revenue per a and 3%mass per a) for the next few years,15,16 neglecting the effects of the corona pandemic. With regard to the basic types of surfactants and the associated production principles and raw materials, the market can be divided into “petrochemical/non-bio-based” surfactants (44%mass_Global and 48%mass_Europe), “oleochemical/partly or mainly bio-based” surfactants (52%mass_Global and 49%mass_Europe), and “biosurfactants/totally bio-based” (4%mass_Global and 3%mass_Europe).17,18 The term bio-based surfactants describes surfactants based on biogenic raw material shares between 5% and 95%, while biosurfactants show biogenic raw material shares >95%.1 The surfactants RL and MEL are microbial biosurfactants, which are “extracellular compounds produced by microbes such as bacteria, fungi and actinomycetes” according to Thavasi (2011).19 Direct statements not only from global players of industry but also from NGOs20,21 confirm the need for a more sustainable production. As one major challenge, the pricing of surfactants can be named.22 While conventional synthetic surfactants come up with prices in the one digit range between 1 and 4 $ per kg,23–25 estimations for the pricing of biosurfactants may differ from this by a factor of 1.5, 10, or more.23,25–27 In general, different factors, such as substrates used and associated yields, purity, functional characteristics, and the processing and related manufacturing cost affect the total production costs and resulting supply prices.23,26 This logic of property-depending costs and prices is also applicable to conventional surfactants. Publications on the topic of cost analysis (CA) for RL and MEL are not available for an industrial scale scenario. Moreover, CA for other biosurfactants is also rarely found or not up-to-date, e.g. the study of Adlercreutz et al. on a 200 Mg per a alkanolamide production.28
The assessment of sustainability is inseparably associated with the environmental impact of products and their production. Since biosurfactant production processes are still under development or on the pilot scale, only a limited number of Life Cycle Assessment (LCA) studies are available on this subject. Different studies on specific bio-based surfactants and biosurfactants such as alkanolamides,28 sophorolipids,29,30 alkyl polyglucosides (APG),31 rhamnolipids,30 and different anionic and cationic detergents32 have been performed. Furthermore, different datasets for APG or detergents such as anionic fatty alcohol sulfates (FAS), anionic linear alkylbenzene sulfonate (LAS) or non-ionic alcohol ethoxylates (AE) can be found.33–35 Differences compared to the present study can be seen in the modelled system (cradle-to-gate and cradle-to-cradle), the time-related reference and the scale. On an industrial scale, LCAs for biosurfactants are missing. Related to non-bio-based or mainly and partly bio-based surfactants, the LCA database ERASM provides different datasets with industrial data of the European surfactants industry as a “black box”.36
In addition to the environmental and cost perspectives, the social impacts should not be neglected. These social impacts describe positive and negative effects along the life cycle for defined stakeholder groups resulting from the assessed product or service.37 Especially regarding negative impacts, which arise in complex upstream processes, social aspects should also be considered if the modeling is carried out for a “socially related safe ground” such as Europe. Previous studies on the social aspects of RL and MEL production as well as other biosurfactants are not available according to our knowledge. In this publication, social issues are addressed in more general terms, since the results are generally similar to LCA results due to their linear dependence on LCA input data and thus a qualitative description seems to be sufficient at first. However, to offer a broader understanding of the quantitative character of the “social dimension”, a detailed description and selected results can be found in the ESI (ESI chapter social Life Cycle Assessment (S-LCA)).†
With the present study, results for the newly developed production processes for RL and MEL regarding all dimensions of sustainability are determined. With a view of the current state of studies, it can be concluded that the present work is the first covering all aspects in general. In contrast to many previous assessment studies, the present study was carried out with current lab and pilot scale data, scaled up to an industrial scale scenario. The approach widens previous results of environmental impacts for a prospective industrial scale and adds CA and other economic aspects.38 Additionally, exemplary results of social impacts complete the sustainability assessment. The results allow an estimation of needs and options for process improvements as well as of needed further research.
Materials and methods
The present LCA study was carried out in line with ISO 14040/14044,39,40 wherein the implementation was realized by means of LCA software GaBi version 10.5.41 The economic aspects are basically aligned with an established CA method shown in Peters et al.,42 using cost data in real terms, complemented by research on today's (bio-) surfactant market, which allows a classification of results. The implementation was carried out by standard spreadsheet applications. Regarding the social dimension, an S-LCA was performed according to the S-LCA guidelines by the United Nations Environment Programme.43 The software tool used for S-LCA was openLCA 1.9.44 The application of the above mentioned methods and tools is enabled by a defined study framework, defined data sources and a reasonable selection of impact categories and indicators.
Study framework
Analogous to the dimensions of sustainability the goal of the study is the assessment of dimension-specific performances of the considered process chains. The production processes examined differ by the products generated and substrates used, which results in four process chains RL_MOL, RL_SBP, MEL_MOL, and MEL_SBP (product_substrate). For modelling process chains on a prospective industrial scale, an annual production of 15 Mg of the mentioned products was assumed, based on available substrate quantities generated in Germany. The assessed process chains represent cradle-to-gate systems, as the products are usually used for further processing in other industries. They involve all processing stages from the biomass production (allocated supply from sugar production) up to the supply of the products (RL or MEL). The perspective of assessment primarily relates to the viewpoint of process developers and surfactant producers. Consequently, the use and end-of-life (EoL) phase of the products are not considered here. As demonstrated in earlier LCA studies,38 the EoL phase of the production facilities is negligible, since the main impacts are generated during operation. The general geographic reference is, depending on data availability, Germany or Europe with conditions of 2020.
Regarding the environmental impacts the goal was the identification of energy-, material-, or impact-intensive processes. In addition to previously published results,38 the exploration of environmental impacts with high relevance on a global level and their sensitivity related to changes in the recycling rates of auxiliary materials (solvents) was quantified.
The goal of the CA was the identification of more cost-efficient process designs and products. Besides investment costs and derived product costs, the inclusion of current market conditions enabled an estimation of the position within the market. The underlying system boundaries and the yearly production of 15 Mg of product correspond to LCA conditions. In contrast to LCA, however, the costs of the production facilities' EoL phase (dismantling and recycling of production facilities) after a defined total operating time were taken into account. This different procedure is based on the assumption that the influence on production costs may not be negligible. Moreover, the modeling provides additional information for process developers and producers that may be relevant in the development phase (e.g., plant design).
To enable the achievement of these goals and a comparison of different products (RL and MEL), the functions of the examined systems must be consistent. The function is expressed by the functional unit (FU), which was set to the mass of the product, which is necessary to fulfill the same specific cleaning performance (SCP) like 1 kg of MEL. The ratio of product masses could be derived from the differences of critical micelle concentration (CMC), which describes the maximum decrease in surface tension.45,46 The CMC specifies the appropriate concentration for meaningful use (surfactant specific mass per volume (g L−1)), as the surface tension is not further reduced when CMC is reached. The CMC data used to determine mass ratios were assessed by Schonhoff et al.38 As a result, 1 kg MEL/SCP corresponds to 3.6 kg RL/SCP, which means that 3.6 times more mass of RL is needed to fulfill the same SCP as 1 kg MEL does. The FU is identical for LCA and CA. To facilitate rough comparisons with given market prices, the CA results are not given per SCP of 1 kg MEL, but per kg product to facilitate rough comparisons with given market prices, even though the same FU definition is used.
The goal of the social assessment was the identification of social risk hotspots within the process and the functional unit is the same like for LCA and CA, but the consideration was reduced to two production cases (RL_MOL and MEL_MOL). System boundaries and yearly production are the same as for LCA.
Data sources and supply
Basic data for the developed process chains (foreground processes) were generated within the project Bio2 by different partners involved and their specific studies.47–51 These data allowed the design and quantification of key components and their input and output flows (see the section “Assessed process chains”), primarily for LCA. Further background process data for the LCA (e.g., production of solvents or electricity) were taken from ecoinvent (version 3.7) and the GaBi professional databases.35,52 Additional data were taken from or based on the literature and statistics (e.g., for general fermenter design and potential substrates available).53,54 Noteworthy is the use of an existing LCA-study on the European sugar market, which included necessary data for modeling substrate supply.55 After an update of the economic data, the flows and their economic values were used for an economic allocation (see ESI Table S1†), in order to count exclusively the burdens of the respective substrate.
Regarding the CA data, the costs of process modules were determined by the use of databases,56 individual research,57–59 own calculations based on Knoll et al.,53 and in some cases assumptions. Additional data for waste disposal, wastewater treatment, energy supply, auxiliary materials and other flows of operation were taken from activity or flow specific sources, statistics, the literature, and other sources.60–63 Furthermore, data required for subsequent calculations (e.g., direct cost and indirect cost) are sourced from the literature or given by methods (CA) and used tools (e.g., tool for cost determination for deconstruction).64
The input data for the study of social impacts are based on the above described LCA and CA data. Furthermore, a generic database (PSILCA = Product Social Impact Life Cycle Assessment) for social data was used as shown in the ESI.†
65,66
A more in-depth description of the input/output data, the underlying process chains and framework conditions can be found in the sections “Assessed process chains” and “Applied data” below. The base for the transformation of the input and output data into impact-related results is the definition of suitable impact categories and indicators.
Impact categories and indicators
To represent issues of concern in terms of LCA, impact category indicators are used.40 For Life Cycle Impact Assessment (LCIA), the framework and recommendations of the European Environmental Footprint method EF 3.0 were used.67 The present study is narrowed to the normalized results (see explanation below) of the six most contributing (70–75% of total impact) impact categories, which were identified from the total number of 16 categories in a previous study.38 These analyzed impact categories are EF 3.0 acidification (unit: mole of H+ eq.), EF 3.0 climate change – total (unit: kg CO2 eq.), EF 3.0 ecotoxicity, freshwater – total (unit: CTUe), EF 3.0 eutrophication, freshwater (unit: kg P eq.), EF 3.0 resource use, fossils (unit: MJ), and EF 3.0 resource use, mineral and metals (unit: kg Sb eq.). The presented normalized total environmental impact is expressed by so-called person equivalents (PE, global level, in line with European standards).68 The normalization is realized by the applied EF 3.0 normalization method, which collates category-specific impact results with region specific reference scores and thus enables a comparison and aggregation of different impact categories. Weighting was considered by assuming weighting factors to be 1, implying that each environmental impact category is equally important.
In the case of CA, the only relevant impact category is cost. Focused indicators of the present study are investment cost, direct production cost, and plant overhead cost, which serve as the basis for an estimation of production cost. These costs are analyzed by the use of a standardized calculation method as it is presented in Peters et al.42 The structure, relevant cost items and the relative quantitative base of the method are presented in ESI Table S2.† Additionally, the production facilities' EoL costs were included as an indicator by considering decommissioning, utilization of used plant components, core removal of buildings, dismantling/demolition of buildings, unsealing of plant sites, and restoration of plant sites. Subsequently, the production cost per kilogram of the product (RL or MEL) is the main outcome. By comparing the four process chains, advantages can be identified. A rough comparison of the costs with the market conditions (prices) allows a first assessment of the market position.
The selection of social impact categories (fair salary, trade unionism, gender wage gap, and non-fatal accidents) strongly depends on the analysis of sustainability reports of chemical companies.69–72 These impact categories represent the most commonly used indicators in these reports. Information on categories and indicators of the social aspects, their selection and further methodological information can be found in the ESI† and in Springer et al.73
Limitations
Coming from the previous explanations and definitions, different limitations can be identified. The results of the presented study are limited by the transferability of data from the laboratory to the pilot scale. Data validation by intermediate steps such as a demonstration plant could, while keeping improvement options, help to minimize these limitations. Regarding the CA result of production costs, data for established market products are lacking for a proper discussion with the results from this study. The property of CMC for each product should be increased in its robustness by further data acquisition or own laboratory investigations (see Table 1). Furthermore, the results do not offer an integrated result (aggregation of all results to one single value) per considered process, so that an overall evaluation is up to the recipient and his or her interests. Due to the exceptional character of the current situation, war-related developments in the energy and resource markets are not considered.
Table 1 Main input and output of the process chains for RL and MEL production with substrate molasses (MOL) and sugar beet pulp (SBP) including quantitative data for process characteristics, input flows, intermediate products, and the output for LCA
Basic parameter |
Unit |
RL_MOL |
RL_SBP |
MEL_MOL |
MEL_SBP |
Source |
Average value generated from ten different data sources for each type of surfactant.
SCP = specific cleaning performance.
|
Product |
— |
RL |
RL |
MEL |
MEL |
— |
Substrate |
— |
MOL |
SBP |
MOL |
SBP |
— |
Content useable sugar |
kgglucose kgsubstrate−1 |
0.47 |
0.67 |
0.47 |
0.67 |
Data from project |
Yield coefficient |
kgproduct kgglucose−1 |
0.1 |
0.1 |
0.235 |
0.235 |
Data from project |
Conversion rate |
% |
10 |
10 |
21 |
21 |
Data from project |
Critical micelle concentration (CMC)a |
Nm m−1 |
96 |
96 |
27 |
27 |
Average value from literature sources |
Surfactant mass to fulfill a SCPb of 1 kg MEL |
kg per SCP |
3.6 |
3.6 |
1 |
1 |
Generated from the CMC ratio |
![[thin space (1/6-em)]](https://www.rsc.org/images/entities/char_2009.gif) |
Inputs
|
Substrate demand |
kgsubstrate kgproduct−1 |
241.0 |
171.0 |
43.5 |
30.9 |
Calculated |
Substrate per 5000 L fermentation |
kgsubstrate/fermentation |
3396 |
1762 |
3205 |
1686 |
Calculated |
Water per 5000 L fermentation |
kgwater/fermentation |
2447 |
2937 |
2309 |
2810 |
Calculated |
Mineral medium per 5000 L fermentation |
kgmineralmedium/fermentation |
65 |
65 |
287 |
234 |
Data from project |
Inoculum per 5000 L fermentation |
kginoculum/fermentation |
29 |
29 |
28 |
28 |
Data from project |
Precipitation agent (acetone) |
kg |
3555 |
3357 |
0 |
0 |
Data from project |
Extraction agent I (ethyl acetate) |
kg |
802 |
757 |
1350 |
1275 |
Data from project |
Acidification agent (sulphuric acid) |
kg |
0.535 |
0.505 |
0 |
0 |
Data from project |
Extraction agent II (n-hexane) |
kg |
0 |
0 |
360 |
335 |
Data from project |
Summed energy demand (gross calorific) |
MJ kgproduct−1 |
9563 |
11 340 |
1173 |
1429 |
GaBi database |
Summed energy demand (net calorific) |
MJ kgproduct−1 |
8952 |
10 625 |
1108 |
1352 |
GaBi database |
![[thin space (1/6-em)]](https://www.rsc.org/images/entities/char_2009.gif) |
Intermediate products
|
Fermentation broth |
kg |
5937 |
4792 |
5829 |
4758 |
Calculated based on data from project |
Theoretical contained RL |
kgbiosurfactant |
16.0 |
11.7 |
74.3 |
55.4 |
Calculated based on data from project |
Product losses |
kg |
1.9 |
1.4 |
4.8 |
3.6 |
Calculated based on data from project |
![[thin space (1/6-em)]](https://www.rsc.org/images/entities/char_2009.gif) |
Output
|
Product |
kg |
14.0 |
10.3 |
69.6 |
51.9 |
Calculated based on data from project |
Assessed process chains
As mentioned above, four different process chains were developed on a defined industrial scale, which differ with regard to microbiology and technology. Besides the different specific microorganisms and substrate-determined yields of fermentation processes, the specific energy and material flows describe the variations. The common feature of all process chains is the fermentation operation volume of 5000 L, which is the basis of design for a single process chain (exemplary shown in ESI Fig. S1† for the RL process chain based on SBP use (RL_SBP); see also “Applied data for CA”). A simplified flow diagram combining all four process chains is given in Fig. 1.
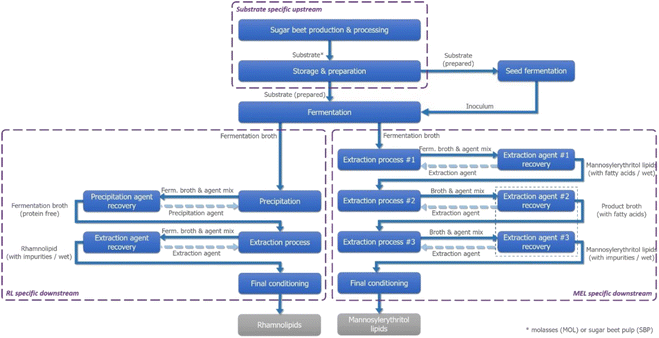 |
| Fig. 1 Simplified aggregated flow diagram of Bio2-processes for the production of rhamnolipids (RL) and mannosylerythritol lipids (MEL); process stages represent different pooled process modules; recycling flows lead back to modules of use by the dotted line. | |
The process modules are taken into account both in their operation (e.g., electricity) and in their manufacturing (e.g., storage tank production). The supply of auxiliary materials (e.g., water or extraction agent) includes the related background processes. The modelled default recycling includes the regular rejection of purge flows and the addition of “fresh” solvent/agent to prevent strong declines in quality. The consideration of recycling is realized by heating (distillation) and cooling (condensation) units and applies for all RL and MEL process chains. Further general presupposed conditions of all process chains assessed are a five-day operation time per volume change for the fermentation, as well as product losses and purge flows (agent recycling), whose extent is based on project data.
Process chains of RL
The nine basic process stages for RL production are illustrated in Fig. 1, wherein each stage stands for a variety of underlying process modules and associated upstream supply chains. The “sugar beet production & processing”-stage contains all steps from the cultivation up to the product (sugar) and its by-products. Since both substrates (MOL and SBP) are by-products and only responsible for specific shares of environmental burdens, the output is allocated by their economic values (see the section “Data sources and supply”). Spoerri et al. provided the data for this process stage.55 An overview of the used and modified data (mass shares and updated economic values) is given in ESI Table S1.† The second stage “storage and preparation” depends on the substrate used and includes its preparation (e.g., shredding of SBP), storage, and infrastructure. For the mentioned fermentation operation volume, the “seed fermentation”-stage is considered as a three-step tank layout (5 L, 50 L, and 500 L) and infrastructure (e.g., pumps). Included elements of the “fermentation stage” are the tank and its production, the bubble-free aeration modules (described in Bongartz et al.,51,74 0.1 Lgas Lferm.broth−1 min−1), and the supply of water, air, steam for sterilization, and electricity. Furthermore, a centrifuge (separation of solid (10% v/v) and liquid content), related pumps, etc. are included. Substrates are mixed in a volume ratio (substrate to water) Ψ = 1
:
1 for MOL and Ψ = 1
:
1.5 for SBP. In the present setting, the separated solid share is treated as bio-waste, and later it is intended to be recycled back to the process. In the “precipitation stage”, the liquid fermentation broth is mixed (Ψ = 1
:
1 (v/v)) with a precipitation agent (acetone) and a centrifugation unit separates precipitated proteins (bio-waste, no use). The following “precipitation agent recovery”-stage includes the precipitation agent storage and further modules (buffer tank, heating unit, cooling unit, and pumps) necessary for the recycling of the agent (80% recycled). A protein-free broth is forwarded to the “extraction stage”, which contains a storage and the supply of extraction and acidification agents, a mixer-settler unit, and further infrastructure. The extraction agent (ethyl acetate) is dosed in a volume ratio of Ψ = 1
:
5 (agent
:
broth), while the acidification agent is dosed in a range of 0.1% (v/v). The aqueous phase is treated as wastewater in the present setting. The product containing phase is pumped to the “extraction agent recovery”-stage with a storage for the agent and the further technical equipment (heating unit, cooling unit, and pumps) for the agent recycling (80% recycled). In the final “conditioning stage”, the separation of further fluids, a drying unit (natural gas operation), the final product storage and conveyors are considered. The product is stored in a powdery state. Based on lab and technical scale studies, the product can be described with a purity of >98% containing RL and HAA (=3-(3-hydroxyalkanoyloxy)alkanoate; share HAA max. 10–20%).75
Process chains of MEL
As can be seen in Fig. 1, the process chain of MEL production is divided into eleven process stages and is similar to the RL production. Like in RL production, the “storage and preparation stage” is substrate-driven. The principles of the “seed fermentation stage” are also the same. After the “fermentation stage” (incl. aeration 0.1 Lgas Lferm.broth−1 min−1, centrifugation included (15% solid contents)) the separated liquid fermentation broth is forwarded to mixer settler I of the “extraction process #1 stage”, where extraction agent I (ethyl acetate, Ψ = 1
:
3) is added to extract the product from the fermentation broth. While the aqueous phase is treated as wastewater (perspectively returned to the process), the light phase (solvent, product, and fatty acids) is recycled in the “extraction agent #1 recovery stage” (default setting: 80% recycled; 20% new). The remaining product and fatty acid mixture is forwarded to the “extraction process #2 stage”, where it is re-dissolved to water (ca. 50% (v/v) of before added solvent). Afterwards extraction agent II (n-hexane) and an acidification agent (0.1% (v/v)) are added into the mixer-settler unit II (Ψ = 1
:
3) and approximately 50% of the contained fatty acids are removed with the solvent. The remaining 50% of fatty acids are removed in the following “extraction process #3 stage” by the mixer settler unit III. The recycling of solvents is realized by the “extraction agent #2 recovery stage” (heating & cooling unit, tank, and infrastructure) in both stages, while the fatty acids are separated. The water-product mixture remaining in both stages contains the product, which is purified by a heating/drying unit, so that afterwards the product MEL is conveyed to a product storage in a powdery state.
Applied data
The following section quantifies and provides an overview of used data related to the applied approaches.
Applied data for LCA.
The main input and output data for LCA as well as further essential parameters of the four process chains are given in Table 1. Main distinctions can be noted regarding the choice of the substrate, targeted product, and related microorganism. Differences are amounts of useable sugars (Δ ≈ 40%), needed amounts of extraction agents (Δ ≈ 5–10%), and different product losses (Δ ≈ 35%). Crucial differences are varying specific yields and conversion rates (Δ > 200%) as well as needed mineral media (Δ ≈ 440%), wherein the latter difference is remarkably in favor of RL process chains. In contrast, aeration rates, the total fermentation operation volume (5000 L), or the recycling rates of different agents are the same for all process chains. Flows like separated biomass, fermentation broth residues, or purge flows are considered as waste in the present process chains.
Applied data for CA.
An overview of the main input and output data for CA is given in Table 2 below. The CA was set up on the technical structure described previously. The starting point of calculations was the technical equipment of a single process chain. A single process chain includes all technical components from substrate supply to product storage (process chain example shown in ESI Fig. S1† for RL_SBP). With an underlying scenario for the production of 15 Mgproduct per a, the number of specific equipment components varies in proportion to their temporal multiple use, which depends on the production volume and capacities. This means for example, an annual product output of 5000 kgproduct per fermentation unit leads to the consideration of three fermentation units (3 × 5000 kg = 15 Mg) in the defined scenario. Other components, such as the centrifugation unit, may be adequate to process the total throughput in the defined scenario and do not need to be considered more than one time. An exemplary visualization of a 15 Mg per a-scenario plant setup is given in ESI Fig. S2.† The number of considered equipment components, the number of each required, costs per process stage and in total are given in ESI Table S3† for the process chain MEL_MOL exemplarily. Significant differences in the numerical data can be found in the needed and built up area for the plant (Δ ≈ 230–490%), the substrate quantity used (Δ > 500%), and the different quantities used for agents (differences up to factor 10). The required plant size and area furthermore result in different labor and production facilities' EoL costs. Additionally, the basic cost positions of investment, fixed (e.g., labor cost) and variable costs (e.g., raw material) reflect these characteristics. Underlying sources and calculation data of different cost positions can be found in ESI Tables S2 and S5.† The quantified calculation structure to determine “total capital investment” (TCI) and “total production cost” (TPC; including production facilities' EoL cost) is shown in ESI Fig. S3.†
Table 2 Main input and output data of process chains for RL and MEL production with substrate molasses (MOL) and sugar beet pulp (SBP) for CA (data sources: see ESI Table S5)
Basic parameter |
Unit |
RL_MOL |
RL_SBP |
MEL_MOL |
MEL_SBP |
Source/description |
Product |
— |
RL |
RL |
MEL |
MEL |
— |
Substrate |
— |
MOL |
SBP |
MOL |
SBP |
— |
Yearly production |
kg per a |
15 000 |
15 000 |
15 000 |
15 000 |
Substrate availability based assumption |
Depreciation period |
a |
10 |
10 |
10 |
10 |
Assumption |
Needed area for plant (property size) |
m2 |
15 464 |
23 273 |
4750 |
6600 |
Derived from simplified construction plans for specific production sites (see the example in the ESI) |
Built-up area |
m2 |
6965 |
10 483 |
2155 |
2952 |
![[thin space (1/6-em)]](https://www.rsc.org/images/entities/char_2009.gif) |
Investment cost
|
Initial investment cost |
m € |
50.13 |
85.88 |
13.83 |
20.55 |
Calculation result (see the ESI; including equipment cost, installation, etc.) |
![[thin space (1/6-em)]](https://www.rsc.org/images/entities/char_2009.gif) |
End of life cost
|
Decommissioning cost |
€ |
325 558 |
489 964 |
100 000 |
138 947 |
Assumption in the area-depending relation |
Plant utilization cost |
€ |
−10 696 |
−21 799 |
−9939 |
−12 928 |
Net cost (deinstallation cost minus revenue from scrap) |
Core removal, dismantling/demolition, restoration cost |
€ |
916 644 |
1 383 468 |
283 888 |
390 358 |
Calculated by using the tender documents & LfU tool “cost determination for deconstruction and demolition work – REFINA” |
Total cost of EoL |
€ |
3 534 977 |
5 315 027 |
1 073 402 |
1 482 234 |
Calculated considering a lump sum cost addition of 30% and inflation |
![[thin space (1/6-em)]](https://www.rsc.org/images/entities/char_2009.gif) |
Fixed cost
|
Fixed costs |
m € per a |
14.21 |
23.45 |
4.34 |
6.10 |
Calculation result (see the ESI; including labor cost, maintenance, etc.) |
![[thin space (1/6-em)]](https://www.rsc.org/images/entities/char_2009.gif) |
Variable cost
|
Variable costs |
m € per a |
2.59 |
2.69 |
0.54 |
0.56 |
Calculation result (see the ESI; including raw material cost, laboratory cost, etc.) |
![[thin space (1/6-em)]](https://www.rsc.org/images/entities/char_2009.gif) |
Feedstock & material cost
|
Substrate molasses |
€ per a |
720 000 |
0 |
130 500 |
0 |
Assumption based on nine net supplier prices [200 € per Mg] |
Substrate sugar beet pulp |
€ per a |
0 |
513 000 |
0 |
92 700 |
Assumption based on six net supplier prices [200 € per Mg] |
Water |
€ per a |
20 870 |
30 780 |
3783 |
5562 |
Assumption based on ten net supplier prices [2 € per m3] |
Inoculum |
€ per a |
10 435 |
6926 |
1891 |
1251 |
Assumption of net supplier price [20 € per L] |
Precipitation agent (acetone) |
€ per a |
989 217 |
1 177 169 |
0 |
0 |
Assumption based on six net supplier prices [1200 € per Mg] |
Acidification agent (sulphuric acid) |
€ per a |
501 |
1368 |
91 |
99 |
Assumption based on six net supplier prices [400 € per Mg] |
Extraction agent I (ethyl acetate) |
€ per a |
281 739 |
277 020 |
51 065 |
50 058 |
Assumption based on eight net supplier prices [3 € per L] |
Extraction agent II (n-hexane) |
€ per a |
0 |
0 |
140 429 |
137 660 |
Assumption of net supplier prices [5 € per L] |
Energy |
€ per kW per h |
0.18 |
0.18 |
0.18 |
0.18 |
Industrial electricity prices Germany, https://www.statista.com |
Steam |
€ per kW per h |
0.024 |
0.024 |
0.024 |
0.024 |
Baerns et al. (2013) Technische Chemie |
Compressed air |
€ per N m3 |
0.017 |
0.017 |
0.017 |
0.017 |
Arithmetic mean of six literature values |
Total production cost |
m € per a |
16.80 |
26.14 |
4.88 |
6.66 |
Calculation result |
Results and discussion
For each dimension, the environmental, economic and social impacts related to the process chains are discussed separately.
Life cycle assessment
The following sections provide results from the perspectives of most contributing impact categories and process stages and a sensitivity analysis related to the recycling rates of auxiliary materials and their influence on the total environmental impact.
Impact per category, process module, and flow.
As shown in Fig. 2C, the normalized overall environmental impact of RL production is 1.740 PE using substrate MOL and 1.960 PE using substrate SBP per SCP (i.e. 3.6 kg of RL, which equals a SCP of 1 kg MEL). The difference of these impacts is Δ = 12%. The production of MEL causes environmental impacts of 0.073 PE for MOL and 0.085 PE for SBP per SCP (Δ = 15%), respectively. All environmental impact values per impact category can be found in Schonhoff et al.38 Thus, for both products, i.e., RL and MEL, at least 10% less impacts occur in process chains using molasses. MEL production has far lower environmental burdens than RL production due to its significantly higher efficiency in the SCP. This can be attributed, inter alia, to the higher specific product yields of Ustilago maydis and the associated difference in mass throughputs required per unit.
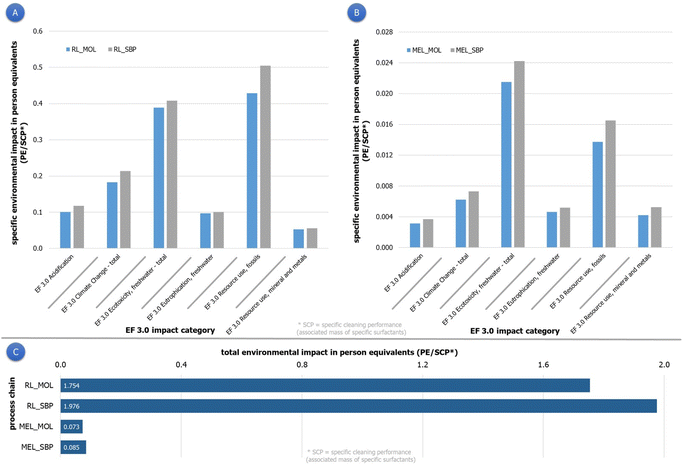 |
| Fig. 2 Normalized environmental impacts of the six selected impact categories in person equivalents (PE) per SCP for RL (A) and MEL (B); (C) total environmental impacts of four process chains (two different products and substrates) per SCP. | |
Fig. 2A and B show detailed results for six selected impact categories, which represent the most influencing impact categories (ca. 70–75% of total normalized impact), identified in an earlier paper.38 Large impact shares can be traced back to the impact categories of “ecotoxicity freshwater − total” (21–30%), “resource use, fossils” (19–26%), “climate change − total” (9–11%), “eutrophication, freshwater” (5–6%), “acidification” (4–6%), and “resource use, minerals and metals” (3–6%) (see ESI Table S4†). Once an assessment is narrowed to the category of climate change, other significant impacts do not become visible.
Previous results have shown that the environmental impact per process chain of the RL production is mainly associated with the process stages of precipitation agent recovery (RL_MOL: 38%PEtotal; RL_SBP: 43%PEtotal; includes agent production) and fermentation (RL_MOL: 25%PEtotal; RL_SBP: 29%PEtotal).38 The process chains for MEL production are dominated by extraction process #1 (MEL_MOL: 36%PEtotal; MEL_SBP: 39%PEtotal) and fermentation (MEL_MOL: 31%PEtotal; MEL_SBP: 36%PEtotal). Because of the limited informative value of arbitrarily set process stages, the following Fig. 3 gets more into detail. The illustration provides an overview of the most contributing process modules and underlying flows (lowest representation level) for each of the impact categories considered. For evaluation, the two main responsible process modules (e.g., acetone production) in each process stage (e.g., precipitation agent recovery) were identified. The subsequent counting of the appearance as the main responsible process module and a following summation of these appearances led to the numbers in Fig. 3. Specific process modules, responsible flows, and shares of these per impact category can be found in ESI Table S4.†
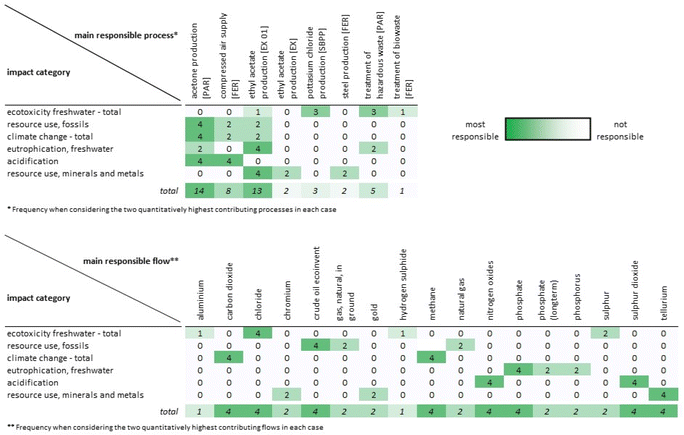 |
| Fig. 3 Frequency of two highest contributing process modules (top) and flows (bottom) per impact category for all considered process chains (RL_MOL, RL_SBP, MEL_MOL, and MEL_SBP). | |
A closer look into the underlying impact-responsible process modules shows that the primarily causing process modules differ by the impact category. In the case of “ecotoxicity freshwater − total”, waste utilization (purge flow and biowaste) and the potassium chloride production (fertilizer in sugar beet production) generate the largest relative contributions. The most impacting process modules in further impact categories are the acetone production (resource use, fossils; climate change − total; acidification) for precipitation in RL process chains, the ethyl acetate production (eutrophication, freshwater, resource use, minerals and metals) for the extraction in MEL process chains, and compressed air supply (acidification). The relative shares of the process modules in the total effects per impact category range between 3.8% and 39% (see ESI Table S4†). For example, the treatment of hazardous waste from MEL_SBP production represents 3.8% of the total “ecotoxicity freshwater − total”-category. In the same process chain the contribution of ethyl acetate production with a share of 36.4% in the “eutrophication freshwater”-category can be described as very dominant.
Regarding the underlying flows of the largest relative impact shares of process modules, the results in Fig. 3 and ESI Table S4† are very heterogeneous. Depending on the impact category, specific flows reveal smaller influences of 5% and considerable influences of up to 90% on the specific environmental impact category result. As in the case of the dominant process modules, it can be stated that the dominance of single flows can thus vary greatly and must be evaluated in relation to the remaining other influences.
A closer look at the detailed results indicates a strong correlation between the origin of category-specific impacts (process module) and the most impacting process stages identified in previous lab scale studies (precipitation (RL), extraction (MEL), fermentation (RL and MEL), sugar beet production and processing (RL and MEL)) (see Tiso et al.50). At the level of process modules, the most relevant modules were identified and improvement was assessed. The same applies for the identified flows, which are linked to the process modules. Exemplary production modules are the agents' production (ethyl acetate and acetone) and the linked waste utilization. A lowering of impacts would be possible by the decrease of newly added agents (acetone and ethyl acetate) or rather the increase of recycling rates. As an additional option, the type of aeration operation (e.g., full time aeration vs. demand-oriented aeration) should be characterized by a purposeful design in the further planning. It should also be considered that the use of non-fossil produced solvents and a renewable energy based or more energy efficient compressed air supply could be used.76
Variation of recycling rates.
To illustrate the influence of recycling rates of the solvents used, an exemplary variation of the rates was done for the MEL_MOL process chain (total impact result for a default recycling rate of 80%: ∑PE = 0.073 PE). Fig. 4 shows the effect of recycling rate decrease and increase, starting from a standard recycling rate of 80% in the present setting (MEL_MOL_RR 80). The variation of rates for ethyl acetate and n-hexane ranges from 25% (MEL_MOL_RR 25) to 75% (MEL_MOL_RR 75) in the decreasing trend and up to 90% (MEL_MOL_RR 90), 95% (MEL_MOL_RR 95) and 99% (MEL_MOL_RR 99) in the increasing trend. With a view to the lowest considered recycling rate of 25% (total impact: ∑PERR25 = 0.36), the results indicate that the doubling of the recycling rate to 50% leads to an impact decrease of 58% (total impact: ∑PERR50 = 0.15), while an increase of the recycling rate up to 99% leads to an impact decrease of 81% (total impact: ∑PERR99 = 0.05) in the examined process chain.
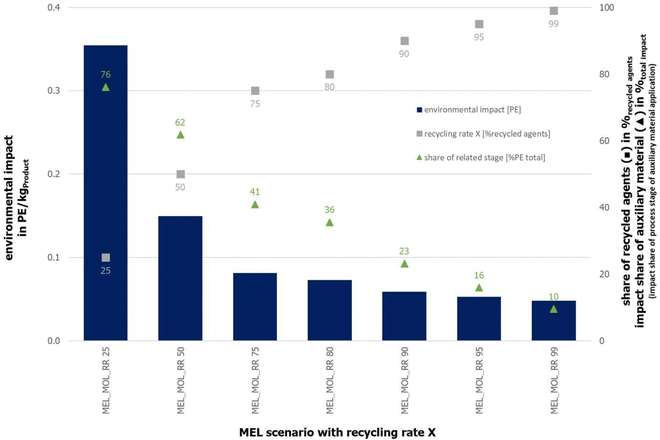 |
| Fig. 4 Environmental impact of the MEL_MOL process chain in dependence of the applied recycling rate of auxiliary materials (■; extraction agents acetone and n-hexane); illustration impact share of the process stage of auxiliary material application (e.g., extraction stage) (▲) (MEL_MOL_RR 80 = present setting = 80% recycling rate; MEL_MOL_RR 25 = 25% recycling, MEL_MOL_RR 50 = 50% recycling, MEL_MOL_RR 75 = 75%, MEL_MOL_RR 90 = 90% recycling, MEL_MOL_RR 95 = 95% recycling, and MEL_MOL_RR 99 = 99% recycling). | |
These results show the non-linear dependency of the recycling rate and illustrate the improvement potential. Combined with the findings of the previous section that the production of the recyclable flows has a large relative influence on the overall impact, the establishment of high recycling rates offers one of the highest improvement potentials within the process chain. To get a full impression of the effects caused by the recycling rate change, also the other process chains should be examined for validation. Moreover, the use of alternative agents could be taken into account and checked in an LCA comparison. The planned implementation of further recycling options (e.g., biomass or fermentation broth) should be examined in relation to their feasibility, effect (waste utilization vs. process-internal recycling), and improvement potential in relation to the environmental impacts. With regard to the quality protection of solvents and the product, the maximum possible recycling rates should be determined in practical trials, in order to avoid unwanted effects.
Economic aspects
The economic classification of the produced surfactants is based on the current market framework (possible sales markets, alternative product price range, etc.) and the results from the conducted CA for the establishment of an industrial setting for the production of 15 Mg of product.
Market framework.
Today's market for surfactants is dominated by petrochemical and oleochemical surfactants (market share >95%). To get an idea of the market relations, Fig. 5 shows the approximate current share of microbial biosurfactants, which is very low. Due to the fact that the underlying data are linked to different years and sources,17,77–79 the results are to be understood as orientation values. On the basis of a market volume of 35 bn€ per a (revenues, see the section “Introduction”), the financial contribution of biosurfactants (4%) is 1.4 bn€ per a, which is consistent with data from other sources (e.g.,80 1.6 bn$ per a). The financial market contribution of microbial surfactants was estimated to be approximately 15 m€ per a in 2020,79 which equals a share of less than 1% of the biosurfactants market revenues. In relation to the surfactant market in total (35 bn€ per a), this means that the share of microbial surfactants is less than 0.1%. Assuming a Compound Annual Growth Rate (CAGR) of 5% like in most surfactant-specific market reports, this shows that a significantly larger market share of microbial biosurfactants lies in the distant future. If these revenue-related shares are applied to the produced amounts of surfactants (17 m Mg), the yearly produced mass of microbial biosurfactants can be quantified as 5700 Mg per a. Since the transfer of shares from financial to mass aspects is not entirely appropriate, it can be assumed that the real production quantities of microbial surfactants are higher. Taking into account current developments regarding production plants of market actors such as Stepan chemicals (capacity 20
000 Mg per a) or Evonik (capacity “tens of thousands” Mg per a),81 the microbial biosurfactant production quantities can be estimated to be a low 6-digit amount per year.
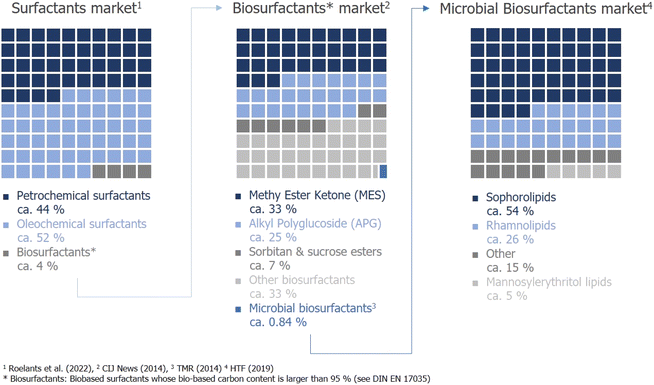 |
| Fig. 5 Illustration of the market shares of different groups and types of biosurfactants; own calculation based on listed sources. | |
The focus on biosurfactants' production and consumption can be seen in Europe,78 wherein their “demand is driven by extensive usage in cosmetics”.80 The fields of application in the total market of surfactants are dominated by the usage as detergents in Western Europe and globally. In Europe, the detergents segment makes up about half of total use (54%), followed by the sectors of cosmetics and pharmacy (15%) and textiles and fibers (10%). With market shares of 1 to 5%, all further application fields such as the chemical industry, mining, flotation, and oil production sectors as well as the food industry and others play a rather minor role (detailed data from TEGEWA).82
To get an idea of the pricing of surfactants, different parameters like the area of application and the related needed properties (e.g., purity, number of congeners, etc.), and the production scale, as well as feedstock prices and their volatilities can be named (for instance Van Bogaert et al.).83 As oil production applications only need minimum purities and, by contrast the pharmaceutical, cosmetic or food applications demand purities >90%,84,85 the costs for the production (biosurfactants: fermentation and downstream processing) differ significantly by efforts. While low purity solutions (3%) can be purchased for <10 $ per kg, highly purified solution (>98%) can be purchased for >500 $ per g, for example.86,87 A similar price structure was found for the prices of sophorolipids in dependence of the purity (see ESI Table S6†). The supply price of synthetic surfactants in the literature is often stated as 2 € per kg without any further description of parameters, whereas exemplary universal biosurfactant prices are up to ten times higher.88–90 Our own market research has shown a significantly larger variety of prices, whereby the exemplary data for RL (38 sources) can be described by a range which differs by a factor of up to 2000. The related data vary from 3% to 98% of purity, RL-types (mono-, di-, number of congeners, etc.), physical state (liquid and solid), purchase quantities, and providers. ESI Fig. S4† offers an overview of the collected pricing data, which are based on given supply prices from € per μg or € per mg to € per kg. As a comparison, the graphic shows the calculated costs (prices at the cost covering level) of the studies' surfactants.
The market framework shows that today's revenue-related shares of microbial biosurfactants are very low. An increase of market shares may be related to an increase of interest and visibility of these alternative production options. This suggests the need to improve attractiveness through cost-effective solutions. Such solutions could be addressed by keeping in mind possible “economies of scale” effects, which occur if a specific production volume is exceeded. Assuming that the substitution of petrochemical surfactants due to resource protection is intended, the establishment of the corresponding political framework conditions (e.g., subsidies or fiscal advantages for non-fossil substitutes), and considering further criteria, would be necessary.
Related to the potential market segments, the mass-related most promising fields of application are evident (detergents, cosmetics and pharmacy, textiles and fibers). Looking at generated products RL and MEL in the current setting (see the section “Assessed process chains”), it gets clear that these products' properties are more appropriate for pharmaceutical, cosmetic, or food applications (higher value use), for example. Beyond the product-related properties, attention should be paid to the legal and procedural criteria of the processor. For some sectors (e.g., food industries and cosmetic industries), the question arises if the use of microbial produced products is permitted and which conditions must be fulfilled for their use (e.g., certificates). To achieve market participation in application areas with lower requirements, a reduction of the efforts in downstream processing should be considered.
Cost analysis and market implications.
As shown in Fig. 6A, the equipment costs (purchased equipment) for a single process chain (design exemplary shown in ESI Fig. S1;† see also the section “Applied data for CA”) are very similar in all four process chains (2.0–2.2 m €). The clear differences for the total equipment costs (for 15 Mg production scenario) vary with significantly higher costs for RL production (12–21 m €) than for MEL production (3–5 m €). The differences can be traced back to chain-specific lower product yields for RL (see Table 1), which require a larger number of equipment units. After determining equipment costs for the four different process chains, the total capital investment appears to be very different in terms of the cost magnitude also, though the relative cost structure is similar. The same relative differences apply for the production facilities' EoL-costs and the yearly production costs. Additional cost elements of the TCI can be found in ESI Table S2.† RL process chains show significantly higher total capital investments (50–86 m €) and yearly production costs (17–26 m €) than the MEL process chains (investment: 14–21 m €; yearly production costs: 5–7 m €). Analogous to this, the previously mentioned fixed and variable costs (see Table 2) reflect these differences. Exemplary details of these costs can be found in ESI Table S2.† The production facilities' EoL costs for RL production (3.5–5.3 m €) vary from those of MEL production (1.1–1.5 m €) by a factor of 2–5, resulting from the yield-induced higher technical and space requirements. When the view is narrowed to one product, it becomes apparent that the use of molasses as a substrate leads to lower financial expenditures (35–55%). By taking into account the SCP like in LCA, the differences described would increase by a factor of 3.6 (see the definition in the section “Functional unit”), since the yearly produced surfactant mass would differ.
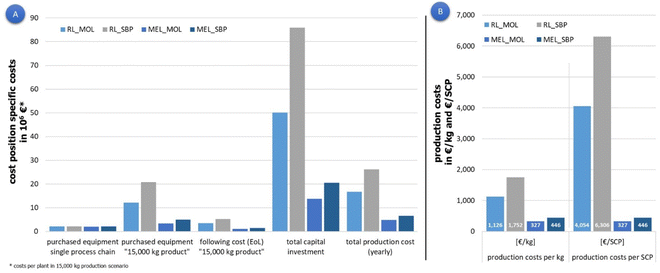 |
| Fig. 6 Results in a 15 Mg production scenario for (A) different purchased equipment data, capital investment, yearly production cost and End-of-Life (EoL) cost for the production plant per process chain and (B) production costs per process chain expressed per kg and per SCP. | |
The specific production costs were derived from total production cost data and the yearly product quantity, which results in cost covering supply prices as shown in Fig. 6B. While the calculated production costs for the process chains RL_MOL (1126 € per kg) and RL_SBP (1752 € per kg) are in a 4-digit range, for MEL_MOL (327 € per kg) and MEL_SBP (446 € per kg) these are clearly lower (left four columns in Fig. 6B). This difference is strengthened when the results are adjusted to the functional unit of € per SCP (right four columns in Fig. 6B). While the production costs for MEL production remain the same, the production costs for RL increase to 4054 € per kg for RL_MOL and 6306 € per kg for RL_SBP.
In the present 15 Mg per a production scenario with a fixed product quantity, the costs of the considered biosurfactants appear very different. Depending on the purchased equipment costs for 15 Mg yearly production and differing production costs per year the costs for RL and MEL production result in a difference in the order of a power of ten. Without precise specifications of target markets and application purposes, it is difficult to classify the results. Looking at the ESI Fig. S4† (prices for RL in the market) it can be seen that the calculated costs (prices at the cost covering level; correspond to the data in Fig. 6B) combined with the given purity are in a typical range for RL. Due to the limited availability of prices for MEL, prices for RL can be taken for preliminary pricing classification. Since costs for MEL are significantly lower, they can be classified as marketable. At the same time, it has to be noted that higher purities and qualities require a high-value use (e.g., use in pharmaceutical industries), which limits the market segments for the product. Assuming a selling intention on the mass market (e.g., detergents), the determined production costs and resulting supply prices are too high. A simplified downstream process (e.g., no or limited extraction) could lower the costs for MEL and RL and consequently the possible supply prices. On the other hand, it has to be discussed if it is realistic to produce these higher value biosurfactants in large amounts (15 Mg scenario).
Social Life Cycle Assessment
The results for the social impacts, described in more detail in the ESI† section, point in the same qualitative direction as the results of LCA and CA. They confirm that also with regard to social aspects a production of MEL is preferable, due to impacts that approximately are 15 times higher for RL in all categories. So, the supply chain of RL production bears a considerably higher social impact compared to the MEL production. It is to be expected that further categories would result in similar ratios between RL and MEL production. Current results for the considered categories reveal large contributions from the supply of chemicals, metals and plastics. However, in general a broader approach by taking into account further indicators can draw a clearer picture of social aspects. For further studies it would be useful to include alternative substrates as well as different geographical references (e.g., manufacturing of chemical products in alternative countries) to find the lowest impact level for the production of RL and MEL.
In summary, it is obvious that specific supply chains (e.g., manufacturing of chemical products such as solvents) are mainly responsible for social impacts. The identified impact sources may be influenceable by an adjusted process design and improvements in the field of resource consumption. As an indirect option of reducing the amount of needed chemicals and the coupled social impact, the increase of yields is applicable also in this case, for example.
Conclusions
The present study discusses the aspects of environmental, CA and selected social impacts of different process chains for biosurfactant production (RL and MEL) with different substrates (molasses and sugar beet pulp). The results have shown that the use of molasses as a substrate for fermentation and the production of MEL provides the lowest potential environmental burden (LCA) and production cost (CA). As a more influential choice than the substrate, the product was identified. Thus, RL can be categorized as less environmentally friendly and more expensive than MEL, assuming the same application for the product. By the LCA, acetone production, ethyl acetate production, waste utilization, and compressed air supply as well as the underlying specific flows (e.g., carbon dioxide or crude oil, etc.) were identified as the main contributors. The dominance of specific flows and process modules (e.g., phosphate in the ethyl acetate production of MEL extraction) was identified with the largest improvement potentials. As an example, the influence of the recycling rate for the MEL_MOL process showed impressive potential for improvement.
The observed market conditions combined with the determined supply costs showed that it is possible to reach market position levels. The high purity products from the considered process chains are related to costs in a low three- or four-digit range per kg of product, which offer the general option of competitiveness for higher value applications (e.g., pharmaceuticals or cosmetics). In mass-market applications such as detergents, where lower product qualities are needed, the present setting is not applicable. Although the calculations are based on a preliminary CA, the development's direction appears to be heading in the right direction.
Concerning the selected social impacts, results are qualitatively equivalent to LCA and CA outcomes with regard to a product and substrate choice. Furthermore, the relevance of the social aspects' consideration was illustrated by strongly differing impacts depending on the product choice. Hence, from the results presented in this paper, it can only be recommended to choose MEL over RL production.
In summary, MEL production appears more sustainable in environmental, economic, and social regards than RL production. The results of the LCA, CA, and S-LCA allow us to make this very clear conclusion, as the impact difference between RL and MEL production is impressive.
A verification and implementation of the identified improvement potentials in the design of process chains could lead to a further reduction of environmental impacts and thus justify the substitution of petroleum-based products. On the other hand, further cost reduction through the implementation is to be assumed. Further work should verify this and, if necessary, weigh up improvement alternatives against each other. It should also include the option of political measures to force the production of such substitutes. To complement, the S-LCA should be extended to the actual production and a check of alternative supply chain scenarios (e.g., change of production routes and related geographical references). In addition to the investigations that may be necessary for the future, however, this study has shown that the detailed investigation of all dimensions of sustainability offers the option of implementing a sustainability oriented approach of development. Furthermore, it was shown by results and analysis that the choice of production processes/flows outside the own development and the microorganisms used can have a major influence on the dimension-specific impacts. These findings should be kept in mind and taken into account from the outset for the development of different production processes in the sector of microbial biosurfactants. Recent developments regarding increasing global production capacities, mentioned in the market framework section, justify a further development of the presented process chains presented in this study. This is also needed due to the wide variety of products apart from today's major application of biosurfactants in the field of detergents, for example. A combination of higher value use specialization and assessment-indicated improvements offers the possibility of more sustainable biosurfactants.
Author contributions
The concept of the present study was established by A. S. and P. Z., and data curation was realized by A. S. with data resources provided by acknowledged project partners. Investigations were made by A. S. and G. S. in coordination with acknowledged project partners and supervisors. Applied project-specific methods were (further) developed by A. S. and G. S. The presented study was supervised by P. Z. The responsibility for the writing of the original draft and contained visualization was with A. S. and G. S., while C. W., W. K., and P. Z. performed the reviewing and editing. All authors have approved the final version of the manuscript.
Conflicts of interest
There are no conflicts to declare.
Acknowledgements
The presented results were generated within the Project Bio2, which is part of the NRW-Strategieprojekt BioSC and thus funded by the Ministry of Culture and Science of the German State of North Rhine-Westphalia. The used process engineering data were provided and generated by Maximilian Schelden (RWTH Aachen University, AVT – Chemical Process Engineering), Patrick Bongartz (RWTH Aachen University, AVT – Chemical Process Engineering), and Andreas Biselli (RWTH Aachen University, AVT – Fluid Process Engineering). Essential data that enabled the process development was offered and generated by Silke Jankowski/Marius Terfrüchte (Heinrich-Heine-University Düsseldorf – Institute for Microbiology – Department of biology), Isabell Bator (RWTH Aachen University – Institute of Applied Microbiology (iAMB)) and Sonja Kubicki (Heinrich-Heine-University Düsseldorf – Institute of Molecular Enzyme Technology (IMET)) related to the aspects of microorganism and microbiology. The research activities of the project “Bio2 – Integration of next generation biosurfactant production into biorefinery processes.” were financially supported by the Ministry of Culture and Research of the German federal state of North Rhine Westphalia within the framework of the NRW-Strategieprojekt BioSC (No. 313/323-400-002 13).
Notes and references
- DIN, DIN EN 17035 - Surface Active Agents - Bio-based surfactants - Requirements and test methods; German version CEN/TS 17035:2021, 2021, DIN EN 17035.
-
T. Tiso, S. Thies, M. Müller, L. Tsvetanova, L. Carraresi, S. Bröring, K.-E. Jaeger and L. M. Blank, in Consequences of Microbial Interactions with Hydrocarbons, Oils, and Lipids: Production of Fuels and Chemicals, ed. S. Y. Lee, Springer International Publishing, Cham, 2017, DOI:10.1007/978-3-319-31421-1_388-1, pp. 1–37.
- T. Morita, T. Fukuoka, T. Imura and D. Kitamoto, Appl. Microbiol. Biotechnol., 2013, 97, 4691–4700 CrossRef CAS PubMed.
- A. Loeschcke and S. Thies, Appl. Microbiol. Biotechnol., 2015, 99, 6197–6214 CrossRef CAS PubMed.
- M. Terfrüchte, S. Wewetzer, P. Sarkari, D. Stollewerk, M. Franz-Wachtel, B. Macek, T. Schlepütz, M. Feldbrügge, J. Büchs and K. Schipper, J. Biotechnol., 2018, 284, 37–51 CrossRef PubMed.
-
EC-COM640, Communication from the Commission - the European Green Deal - COM(2019) 640 Final, Report COM(2019) 640 Final, European Commission, 2019 Search PubMed.
-
EuropeanCommission-COM550, Communication from the Commission to the European Parliament, the Council, the European Economic and Social Committee and the Committee of the Regions - 'Fit for 55': Delivering the EU's 2030 Climate Target on the Way to Climate Neutrality, European Commission, Brusseles, 2021 Search PubMed.
-
J. Allan, The New Climate Activism, University of Toronto Press, Toronto, 2022 Search PubMed.
-
UNEP/SETAC, Towards a Life Cycle Sustainability Assessment - Making Informed Choices on Products, United Nations Environment Programme (UNEP) and Society for Environmental Toxicology and Chemistry (SETAC), Nairobi, 2011 Search PubMed.
-
J. Guinée, in Taking Stock of Industrial Ecology, ed. R. Clift and A. Druckman, Springer International Publishing, Cham, 2016, pp. 45–68, DOI:10.1007/978-3-319-20571-7_3.
- W. Klöpffer, Int. J. Life Cycle Assess., 2003, 8, 157–159 CrossRef.
- IHS-Markit, Assessing the sustainability and performance of green surfactants, https://ihsmarkit.com/research-analysis/assessing-sustainability-and-performance-of-green-surfactants.html, accessed 01.03.2023.
-
D. Saurabh, D. Rutuja and P. Eswara, Surfactants Market Outlook - 2027, 2020 Search PubMed.
- ResearchAndMarkets, Surfactants Market - Growth, Trends, COVID-19 Impact, and Forecasts (2022–2027), https://www.researchandmarkets.com/reports/4771655/surfactants-market-growth-trends-covid-19, accessed 04.03.2023.
- ResearchAndMarkets, Global Surfactants Market (Non-ionic, Anionic & Cationic): Insights, Trends and Forecast (2019-2023), https://www.researchandmarkets.com/reports/4845555/global-surfactants-market-non-ionic-anionic-and, accessed 03.12.2021.
- ResearchAndMarkets, Surfactants Market - Growth, Trends, and Forecast (2020-2025), https://www.researchandmarkets.com/reports/4771655/surfactants-market-growth-trends-and-forecast#relb1-4845555, accessed 10.11.2021.
-
S. Roelants and W. Soetaert, in Biosurfactants for the Biobased Economy, ed. R. Hausmann and M. Henkel, Springer Nature Switzerland AG, Cham (CH), 2022, vol. 181, pp. 1–15 Search PubMed.
- J. G. Tropsch, INFORM, 2017, 28, 20–22 Search PubMed.
- R. Thavasi, J. Biorem. Biodegrad., 2011, 2, 104e Search PubMed.
-
CHEManager, Solving Challenges at Interfaces - Surfactants are used in a Variety of Applications from Detergents to Crop Protection to Oil & Gas, CHEManager | Fine & Specialty Chemicals, 2019, vol. 13, 01, pp. 10–12 Search PubMed.
-
Frost&Sullivan/WWF, The Impact of the Consumption of Palm Oil in Poland on the Global Natural Environment and Analysis of the Possibility of Replacing it by Other Vegetable Oils, 2019 Search PubMed.
-
R. Marchant and I. M. Banat, in Biosurfactants for the Biobased Economy, ed. R. Hausmann and M. Henkel, Springer Nature Switzerland AG, Cham (CH), 2022, vol. 181, pp. 181–193 Search PubMed.
-
K. Andersen, Saponin-What Is it? what Can it Do in the Industry?, Agro Business Park A/S, 2015 Search PubMed.
- U. Kanbur, G. Zang, A. L. Paterson, P. Chatterjee, R. A. Hackler, M. Delferro, I. I. Slowing, F. A. Perras, P. Sun and A. D. Sadow, Chem, 2021, 7, 1347–1362 CAS.
- C. B. B. Farias, F. C. G. Almeida, I. A. Silva, T. C. Souza, H. M. Meira, R. d. C. F. Soares da Silva, J. M. Luna, V. A. Santos, A. Converti, I. M. Banat and L. A. Sarubbo, Electron. J. Biotechnol., 2021, 51, 28–39 CrossRef CAS.
-
N. Kosaric and F. V. Sukan, BIOSURFACTANTS: Production and Utilization—Processes, Technologies, and Economics, Taylor & Francis, 2015 Search PubMed.
- S. Lang and D. Wullbrandt, Appl. Microbiol. Biotechnol., 1999, 51, 22–32 CrossRef CAS PubMed.
- D. Adlercreutz, P. Tufvesson, A. Karlsson and R. Hatti-Kaul, Ind. Biotechnol., 2010, 6, 204–211 CrossRef CAS.
- N. Baccile, F. Babonneau, I. M. Banat, K. Ciesielska, A.-S. Cuvier, B. Devreese, B. Everaert, H. Lydon, R. Marchant, C. A. Mitchell, S. Roelants, L. Six, E. Theeuwes, G. Tsatsos, G. E. Tsotsou, B. Vanlerberghe, I. N. A. Van Bogaert and W. Soetaert, ACS Sustain. Chem. Eng., 2017, 5, 1186–1198 CrossRef CAS.
- A. Kopsahelis, C. Kourmentza, C. Zafiri and M. Kornaros, J. Chem. Technol. Biotechnol., 2018, 93, 2833–2841 CrossRef CAS.
- J. Guilbot, S. Kerverdo, A. Milius, R. Escola and F. Pomrehn, Green Chem., 2013, 15, 3337–3354 RSC.
-
S. Rebello, A. N. Anoopkumar, R. Sindhu, P. Binod, A. Pandey and E. M. Aneesh, in Refining Biomass Residues for Sustainable Energy and Bioproducts, ed. R. P. Kumar, E. Gnansounou, J. K. Raman and G. Baskar, Academic Press, 2020, pp. 511–521, DOI:10.1016/B978-0-12-818996-2.00023-5.
-
CPM, SPINE LCI Dataset: Production of Alkyl Polyglucosides (APG) from Coconut Oil, Chalmers University of Technology, Göteborg, 1995 Search PubMed.
-
R. Zah and R. Hischier, Life Cycle Inventories of Detergents. Final Report Ecoinvent Data v2.0, No. 12, Swiss Centre for Life Cycle Inventories, 2007 Search PubMed.
-
Ecoinvent-DB, The Ecoinvent Database, Ecoinvent Association, Zurich, 2021 Search PubMed.
-
CESIO/ERASM, Life Cycle Ecofootprinting (SLE), European Committee of Organic Surfactants and Their Intermediates (CESIO), Brussels, 2017 Search PubMed.
- LCI, Social Life Cycle Assessment (S-LCA), https://www.lifecycleinitiative.org/starting-life-cycle-thinking/life-cycle-approaches/social-lca/, accessed 01.03.2023, 2023.
- A. Schonhoff, N. Ihling, A. Schreiber and P. Zapp, ACS Sustain. Chem. Eng., 2022, 10, 9345–9358 CrossRef CAS.
- I. O. f. S. (ISO), ISO 14040:2006 - Environmental management - Life cycle assessment - Principles and framework, 2006, ISO 14040:2006.
- I. O. f. S. (ISO), ISO 14044:2006 - Environmental management - Life cycle assessment - Requirements and guidelines, 2006, ISO 14044:2006.
-
GaBi-S, GaBi Software Suite - #1 LCA Software, Sphera Solutions GmbH, Leinfelden-Echterdingen, 2021 Search PubMed.
-
M. S. Peters, K. D. Timmerhaus and R. E. West, Plant Design and Economics for Chemical Engineers, McGraw-Hill Education, 2003 Search PubMed.
-
UNEP, Guidelines for Social Life Cycle Assessment of Products and Organizations 2020, United NationsEnvironment Programme (UNEP)/Life Cycle Initiative/Social LC Alliance, Nairobi (KEN), 2020 Search PubMed.
-
GreenDelta, OpenLCA – the Life Cycle and Sustainability Modeling Suite, Green Delta GmbH, Berlin, 2019 Search PubMed.
- L. R. Rodrigues, J. Colloid Interface Sci., 2015, 449, 304–316 CrossRef CAS PubMed.
-
D. N. Ghista, Biomedical Science, Engineering and Technology, IntechOpen, 2012 Search PubMed.
- A. Biselli, A.-L. Willenbrink, M. Leipnitz and A. Jupke, Sep. Purif. Technol., 2020, 117031 CrossRef CAS.
- I. Bator, A. Wittgens, F. Rosenau, T. Tiso and L. M. Blank, Front. Bioeng. Biotechnol., 2020, 7, 1–18 Search PubMed.
-
S. Kubicki, I. Bator, S. Jankowski, T. Marius, K. Schipper, M. Feldbrügge, T. Tiso, L. Blank, K.-E. Jaeger and S. Thies, in Biosurfactants 2019 - Book of Abstracts, University of Hohenheim - Bioprocess Engineering, Hohenheim (DE), 2019 Search PubMed.
- T. Tiso, N. Ihling, S. Kubicki, A. Biselli, A. Schonhoff, I. Bator, S. Thies, T. Karmainski, S. Kruth, A.-L. Willenbrink, A. Loeschke, P. Zapp, A. Jupke, J. Büchs, K.-E. Jaeger and L. M. Blank, Front. Bioeng. Biotechnol., 2020, 8, 1–24 CrossRef PubMed.
- P. Bongartz, R. Keller, M. Schelden, G. Wandrey, J. Büchs and M. Wessling, Chem. Ing. Tech., 2018, 90, 1250 CrossRef CAS.
-
GaBi-DB, GaBi Professional Databases, Sphera Solutions GmbH, Leinfelden-Echterdingen, 2021 Search PubMed.
-
A. J. Knoll, Dissertation/PhD Thesis, RWTH Aachen, 2008.
-
WVZ, Futtermittel aus Zuckerrüben, 2020, http://www.zuckerverbaende.de/zuckermarkt/zahlen-und-fakten/zuckermarkt-deutschland/futtermittel-aus-zuckerrueben.html Search PubMed.
- A. Spoerri and T. Kaegi, Sugar Ind., 2015, 140, 492–499 Search PubMed.
- Matches, Matches' Process Equipment Cost Estimates, http://www.matche.com/equipcost/Default.html, accessed 01.05.2021.
- Alibaba, Alibaba B2B marketplace, https://www.alibaba.com/, accessed 01.06.2020, 2020.
- Eurolux, Eurolux production and distribution, http://eurolux-ag.com/en/, accessed 01.06.2020, 2020.
- MixerDirect, MixerDirect, https://www.mixerdirect.com/, accessed 01.06.2020, 2020.
- IHK-D, Gewerbemietpreisspiegel 2019 (engl.: business rent index), https://www.dortmund.ihk24.de/produktmarken/interessenvertretung/raumordnung-und-planung/gewerbeflaechen/gewerbemietpreisspiegel-314154, accessed 01.02.2021.
- TT-SRL, Schrottpreise (engl. scrap price), https://www.schrottpreis.org/, accessed 20.04.2020, 2020.
-
BDEW, BDEW Strompreisanalyse Januar 2020, Haushalte und Industrie, BDEW Bundesverband der Energie und Wasserwirtschaft e.V., Berlin, 2020 Search PubMed.
-
M. Baerns, A. Behr, A. Brehm, J. Gmehling, H. Hofmann and U. Onken, Technische Chemie, Wiley VCH, Weinheim, 2013 Search PubMed.
-
REFINA, EDV-werkzeug Zum Gebäuderückbau (Engl. EDP Tool for the Deconstruction of Buildings), Deutsches Institut für Urbanistik gGmbH; Hochschule Biberach, 2009 Search PubMed.
-
F. Eisfeldt and A. Ciroth, PSILCA – A Product Social Impact Life Cycle Assessment Database, GreenDelta GmbH, Berlin, 2017 Search PubMed.
-
PSILCA-DB, PSILCA - Understanding Social Impacts, Green Delta GmbH, Berlin, 2021 Search PubMed.
-
EU-JRC, EF Reference Package 3.0, European Commission, Brussels, 2019 Search PubMed.
-
European Commission, Commission Recommendation on the Use of the Environmental Footprint Methods to Measure and Communicate the Life Cycle Environmental Performance of Products and Organisations, European Commission, Brussels, 2021 Search PubMed.
-
BASF, BASF-Bericht 2019 - Ökonomische, ökologische und gesellschaftliche Leistung, BASF SE, Ludwigshafen, 2020 Search PubMed.
-
Henkel, Nachhaltigkeitsbericht, 2019, Henkel AG & Co. KG a A, Düsseldorf, 2020 Search PubMed.
-
Evonik, Nachhaltigkeitsbericht, 2019, Leading Beyond Chemistry, Evonik Industries AG, Essen, 2020 Search PubMed.
-
Bayer, Nachhaltigkeitsbericht, 2019, Bayer AG, Leverkusen, 2020 Search PubMed.
- S. K. Springer, C. Wulf and P. Zapp, Int. J. Hydrogen Energy, 2023 DOI:10.1016/j.ijhydene.2023.04.034.
- P. Bongartz, I. Bator, L. Blank and M. Wessling, Chem. Ing. Tech., 2020, 92, 1204 CrossRef CAS.
- A. Biselli, A.-L. Willenbrink, M. Leipnitz and A. Jupke, Sep. Purif. Technol., 2020, 250, 117031 CrossRef CAS.
- E. Budsberg, R. Morales-Vera, J. T. Crawford, R. Bura and R. Gustafson, Biotechnol. Biofuels Bioprod., 2020, 13, 154 CrossRef CAS PubMed.
-
CIJ, Global Market for Biosurfactants: Report, Clean India Journal, Mumbai (IND), 2014 Search PubMed.
-
HTF, Global Microbial Biosurfactants Market Insights, Forecast to 2025, 2019 Search PubMed.
-
TMR, Microbial Biosurfactants Market - Global Industry Analysis, Size, Share, Growth, Trends and Forecast, 2014-2020, Transparency Market Research, Albany, NY (US), 2014 Search PubMed.
-
K. Ahuja, S. Singh and GMI, Biosurfactants Market Size by Product, by Application, Industry Outlook Report, Regional Analysis, Application Potential, Price Trends, Competitive Market Share & Forecast, 2019 – 2025, Report GMI484, Global Market Insights, Selbyville, DE (US), 2019 Search PubMed.
-
C. Bettenhausen, Evonik Invests in Rhamnolipid Biosurfactants - New Capacity Is Slovakia Bolsters Partnership with Unilever, American Chemical Society, Washington DC, 2022, vol. 2022 Search PubMed.
-
TEGEWA, Die fleißigen Verbindungen Eine kurze Einführung in die Welt der Tenside, Verband der Hersteller von Textil-, Papier-, Leder- und Pelzhilfs- und -farbmitteln, Tensiden, Komplexbildnern, Antimikrobiellen Mitteln, Polymeren Flockungsmitteln, Kosmetischen Rohstoffen und Pharmazeutischen Hilfsstoffen oder verwandten Produkten, Frankfurt am Main (DE), 2014 Search PubMed.
-
I. Van Bogaert, K. Ciesielska, B. Devreese and W. Soetaert, in Biosurfactants: Production and Utilization-Processes, Technologies, and Economics, ed. N. Kosaric and F. V. Sukan, Taylor & Francis, 2014 Search PubMed.
- M. Irfan-Maqsood and M. Seddiq-Shams, Ind. Biotechnol., 2014, 10, 285–291 CrossRef CAS.
-
X. Yin, Formulations Combining Ramoplanin and Rhamnolipids for Combating Bacterial Infection, AGAE Technologies LLC, Corvallis, 2014 Search PubMed.
- Alibaba-Offer, Rhamnolipid,CAS: 4348-76-9, https://www.alibaba.com/product-detail/Rhamnolipid-CAS-4348-76-9_748580719.html?spm=a2700.7724857.normalList.57.25a07ae5LtNyee, accessed 01.06.2020, 2020.
- Glycosurf, Rhamnolipids, http://glycosurf.com/rhamnolipids/rhamnolipids/, accessed 01.06.2020, 2020.
- H. Chong and Q. Li, Microb. Cell Factories, 2017, 16, 137 CrossRef PubMed.
-
K. Andersen, Saponin - from Waste to Value, Aarhus, 2015 Search PubMed.
- BIOPRO, Rudolf Hausmann - Grüne Tenside aus Bakterien, https://www.biooekonomie-bw.de/fachbeitrag/aktuell/rudolf-hausmann-gruene-tenside-aus-bakterien, accessed 01.03.2023.
|
This journal is © The Royal Society of Chemistry 2023 |
Click here to see how this site uses Cookies. View our privacy policy here.