DOI:
10.1039/D4SU00228H
(Paper)
RSC Sustain., 2024,
2, 1963-1968
Halogen-free bleaching of shellac using electrochemically generated peroxodicarbonate†
Received
11th May 2024
, Accepted 5th June 2024
First published on 6th June 2024
Abstract
Industrial bleaching of shellac with sodium hypochlorite causes bleaching damages, such as double bond chlorination. Peroxodicarbonate, generated from the anodic oxidation of carbonates, acts as peroxide source for a novel acetonitrile mediated bleaching protocol, applicable on shellac. Only 6 and 9 mmol gshellac−1 of peroxodicarbonate and acetonitrile, respectively, is required to bleach shellac at room temperature with a bleaching efficiency of 94% and an acid value of 109. Furthermore, this method was demonstrated on unprocessed seedlac where the ionic strength of the peroxodicarbonate buffer facilitates dewaxing. A decreased aldehyde and acetal quantity, as well as ester hydrolysis are the major bleaching damages, visualised by FT-IR and NMR spectroscopy.
Sustainability spotlight
With the expectation that renewable electricity will completely replace fossil-fuel based energy in the near future, water electrolysis will be the ideal CO2-neutral method for hydrogen production. Peroxodicarbonate, a strong oxidizer available from inexpensive carbonate salts can be generated along hydrogen gas. In this work, peroxodicarbonate is proven to be a sustainable replacement for sodium hypochlorite, which form persistent chlorinated organic compounds, for the bleaching of shellac. We also want to emphasize the revival of shellac, a renewable resource, with great potential for replacing fossil-fuel based polymers in multiple applications. This work addresses SDG 7 (affordable and clean energy), SDG 9 (industry, innovation and infrastructure) SDG 13 (climate action) and SDG 14 (life below water).
|
Introduction
Lac is a natural resin secreted by lac insects, mostly Kerria lacca, found in Asian countries.1 During their life cycle, the lac insects settle on the host plant and feed from its sap.2 The female insects secrete the protective resin, which is then harvested and processed to obtain shellac flakes.3
Shellac is a renewable resource without competing nutrition purposes and has been used in several industries for centuries due to its exceptional properties such as film-forming,4 adhesion,5 thermoplasticity,6 water-repellant7 and good solubility in ethanol and alkaline water.1 Shellac-based food coating protects it from drying out.8 Shellac can serve as a pharmaceutical coating with selective drug release in the small intestines due to the pH increase.9 Shellac is used in cosmetics,10 dentistry,11 as a wood finisher12 and food packaging.13 Moreover, 9,10,16-trihydroxyhexadecanoic acid (aleuritic acid) can be isolated from hydrolysed shellac14 and is used for the production of musk aroma frequently applied in perfume.15 In the past century, shellac has been replaced by fossil-fuel based polymers in many applications. However, due to an increasing demand of renewable feedstocks and biodegradable materials, there has been a revival of interest in shellac.16
As most natural resins, the structure of shellac is complex and varies in structural units connected with ester bonds and inter- and intramolecular hydrogen bonding between alkyl carboxylic acids and sesquiterpenic acids (Chart 1).17,18 The main component is aleuritic acid (approx. 35%),14 followed by various sesquiterpenic acids from the cedrene family (approx. 25%).19 The resin mainly varies in the oxidative state of the sesquiterpenic moiety and the length of the oligomers.20,21
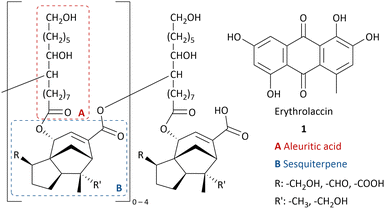 |
| Chart 1 General structure of shellac and 1. | |
As a result of the presence of lac dyes, known as laccaic acids, the unprocessed lac resin has a red to dark brown colour, which is influenced by the sap of the host tree and the lac insects.22,23 Most of the water-soluble dyes can be removed by washing with water. However, the presence of water-insoluble dyes, mainly erythrolaccin (1), hampers the complete decolourisation by washing.24 Further decolourisation is possible by filtration over activated carbon to obtain shellac in different yellow to orange grades, depending on the properties of the crude lac and the physical decolourisation procedure.4 For many applications, including food and pharmaceutical coatings, a completely colourless shellac coating is desired. Therefore, shellac can be chemically bleached. Half of all consumed shellac is bleached.3 Industrial bleaching processes use active chlorine species such as sodium hypochlorite (NaOCl).25–27 However, bleaching damages include oxidation of alcohol and aldehyde functionalities as well as double bond chlorination of the sesquiterpenes.28 Consequently, the obtained bleached shellac contains toxic organochlorine moieties, causing rapid aging and polymerization, limiting the shelf life of the bleached shellac.29 Furthermore, organochlorine species and excess hypochlorite in the waste-water stream can have harmful consequences on aquatic ecosystems.30 Dechlorination processes have been developed, mostly employing toxic and expensive metals such as palladium.29,31,32 Attempts have been made to minimize or even exclude the use of active chlorine species. By applying a mixture of hydrogen peroxide (2) and sodium hypochlorite, the amount of active chlorine could be diminished.33 Unfortunately, bleaching solely with hydrogen peroxide requires elevated temperature (90 °C), alkaline pH 9.0–11.0 and prolonged reaction times (7.2 h),34 which results in severe bleaching damage due to ester hydrolysis.28 It is worth mentioning that solid sources of hydrogen peroxide such as sodium perborate (3), sodium percarbonate (4) or urea hydrogen peroxide (5), suffered from similar issues.33 Furthermore, serious safety precautions are required for the handling and storage of high concentration hydrogen peroxide on industrial scale, both in liquid and solid equivalents.35,36
To lower the high temperature required for bleaching, activators have been developed. Current bleaching systems mainly use tetraacetylethylenediamine (6), decanoyloxybenzoic acid (7), sodium nonanoyloxybenzenesulfonate (8), sodium lauroyloxybenzenesulfonate (9) in combination with an oxygen bleach to form peroxy acids (Scheme 1). However, these are less mass-efficient due to their activation mechanism and are economically less feasible. Several nitriles, so called ‘nitrile quats’ (10), have been investigated as mass-efficient bleach activators, which release peroxyimidic acids on perhydrolysis.36,37 However, most used nitrile quats are not readily biodegradable and are too aggressive for domestic laundry detergents.
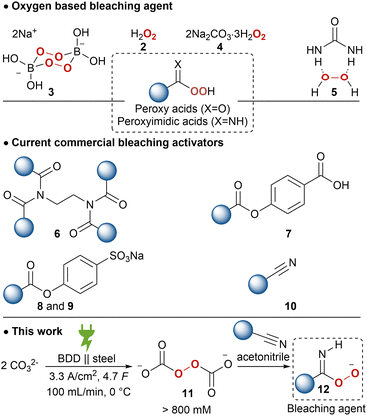 |
| Scheme 1 Classical oxygen bleaching agents and activators compared to electrochemically generated peroxodicarbonate (11). | |
In recent years, electrosynthesis has gained increasing attention due to its potential to render more sustainable and atom-economical processes, in particular when electricity from renewable energy is applied.38,39 However, translation into application is usually highly dependent on the downstream processing.40–42 The electrochemical water splitting for hydrogen production mostly uses oxygen evolution as anodic counter reaction. However, the formation of more valuable platform oxidizers as counter reaction might be an attractive solution. Waldvogel and co-workers have developed a scalable electrochemical and green synthesis of periodates as a platform oxidizer for active pharmaceutical ingredients (APIs) and for the valorization of renewable feedstocks.43–47
The potential of peroxodicarbonate 11, obtained by anodic oxidation of inexpensive, safe and environmentally benign alkali carbonate, has been recognized early on as a “green” oxidizer.48,49 However, the low concentration and limited thermal stability of 11 hampered the application of this potential platform oxidizer. Recently, a circular flow electrolysis setup was established for efficient generation of high concentration 11 (900 mm).50 The undivided flow cell with a boron-doped diamond (BDD) anode and stainless-steel cathode works at a high current density of 3.33 A cm−2. The synthetic features of this electrochemically generated ex-cell oxidant are already proven in a plethora of transformations, including; sulphoxidation,50,51N-oxidation,50,52,53 epoxidations,50 organo-boron oxidation,54 Dakin reaction,55 and also in selective lignin degradation.56 Further applications of 11 are drinking water treatment57 and bleaching of black tea as well as wood veneers, pulp and cardboard have been briefly explored and a higher bleaching activity and efficiency was reported compared to 2 or 4.58,59
Herein, we established an environmentally benign bleaching protocol applicable on shellac and wax-containing seedlac by in situ activation of 11 with acetonitrile as a mass efficient, inexpensive, and environmentally benign activator. Furthermore, the bleached product and waste-stream are completely halogen-free, offering high-quality dewaxed shellac in an economically feasible process.
Results and discussion
Bleaching optimisation
For the optimisation of the bleaching protocol, commercially refined dewaxed shellac was used. The bleaching performance is quantified on the reduced light absorbance at 430 nm. An acid–base titration is used for the quantification of free carboxylic acids and can be used to detect bleaching damages due to oxidation and ester hydrolysis. This acid value is expressed as mgKOH required to neutralize 1 g of shellac.
To obtain an economically feasible and technically viable process, an inexpensive liquid activator is desired. Therefore, acetonitrile was suggested as peroxodicarbonate activator, forming peroxyacetimidic acid 12in situ.37 Optimisation of this bleaching process started with the use of a constant amount of 11 (2 mmol g−1) and aimed to maximize the bleaching efficiency and minimize an increase in acid value. Noteworthy, dropwise addition of the strongly ionic peroxodicarbonate solution is needed to avoid shellac precipitation. First, the acetonitrile quantity was optimized (Fig. 1a). Sub-stoichiometric quantities of acetonitrile (0.3 eq. and 0.5 eq. relative to 11) lead to low bleaching efficiencies (34% and 48%, respectively). A small excess of 1.5 eq. induced an optimal bleaching efficiency of 62%. Further addition did not lead to significantly higher bleaching efficiency. The acid value did increase with increasing bleaching efficiency, presumably due to undesired oxidations of aldehyde and primary alcohol functionalities. At the optimal acetonitrile quantity, the acid value increased from 70 to 92. No bleaching was observed in the absence of acetonitrile while the acid value did increase to 77, presumably due to ester hydrolysis.
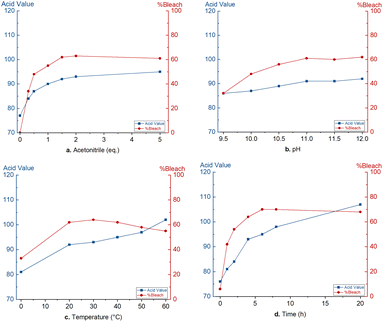 |
| Fig. 1 Optimisation of the peroxodicarbonate bleaching: a. acetonitrile quantity, (b) pH, (c) temperature, (d) time. | |
Peroxodicarbonate is stable in a pH range between 8 and 13.5. Electrochemically generated peroxodicarbonate 11 solution is strongly alkaline (pH 12.1). Therefore, the pH of the peroxodicarbonate solution was varied between 9.5 and 12. In Fig. 1b, it can be seen that prior neutralisation of 11 to pH 11 was possible without a significant loss of bleaching efficiency. However, also the acid value did not change significantly. Further neutralisation did lead to a decrease in bleaching efficiency associated with a decrease in acid value. Therefore, it is concluded that pH adjustment does not lead to a major advantage.
The influence of temperature was studied in the range of 0 °C to 60 °C (Fig. 1c). At 0 °C, bleaching decreased to 33%, while between 20 °C and 40 °C, shellac was bleached for 62–64%. However, increasing the temperature above 40 °C causes a decrease in bleaching efficiency, presumably due to the fast degradation of peroxodicarbonate and peroxyimidic acid (Fig. S4† shows stability test of 11 at different temperatures). Furthermore, elevated temperatures negatively affect the acid value due to ester hydrolysis.28 A bleaching temperature between 25 and 30 °C was chosen to be optimal.
Lastly, we investigated the change in bleaching efficiency and acid value over time (Fig. 1d). It should be noted that the time was started after complete addition of peroxodicarbonate (∼30 min) and the first sample was directly taken after. Over the first 3 hours, the bleaching efficiency increases strongly. Afterward, a slower increase is noticed significant increase is observed. This trend is also observed with the acid value. However, the acid value keeps raising slowly due to ester hydrolysis. To ensure complete bleaching with larger amounts of peroxodicarbonate, an optimal bleaching time of 8 hours was selected.
Comparison with other bleaching methods
To compare our protocol with existing literature methods, shellac was bleached with different amounts of oxidant and the bleaching efficiency and change in acid value were compared. Bleaching shellac with NaOCl is very efficient at room temperature and reaches 98% with 1.5 mmolox gshellac−1 (Fig. 2a).27 Also the acid value increase is limited to 83 (Fig. 2b). Our novel protocol reaches a bleaching efficiency of 94% with 6 mmolox gshellac−1 (Fig. 2a). The initial increase of the acid value from 70 to 90 is presumably due to ester hydrolysis in alkaline conditions (Fig. 2b). Next, the acid value increases gradually to 98 with 4 mmolox gshellac−1 bleaching shellac for 84%. Addition of more 11 leads to 94% bleaching of shellac, however, the acid value increases rapidly to 109. Lastly, shellac was bleached with 2 at 90 °C according to a literature procedure.34 A significantly larger amount of 2 is required (15 mmolox gshellac−1) to bleach shellac for 89% efficiency. Furthermore, the acid value increases drastically over the complete range up to reach 176, due to significant ester hydrolysis.
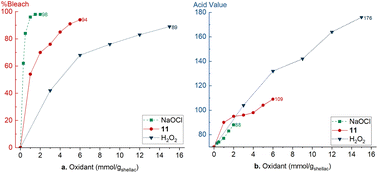 |
| Fig. 2 Comparison of different bleaching methods: NaOCl, H2O2 and this work with 11. (a) Bleaching efficiency, (b) acid value. | |
Bleaching and dewaxing of seedlac
Bleaching is usually performed on unprocessed seedlac. However, seedlac contains wax (approx. 2–5.5%) which is partly soluble in ethanol and not in water and can in that way be removed from shellac. Filtration becomes difficult due to wax ‘cloud’ precipitation. Addition of sodium hypochlorite to a wax-containing seedlac solution facilitated coagulation of wax and its separation.33 The ionic strength of the solution of 11 can therefore also be used in its advantage for dewaxing. Our bleaching method was applied on wax containing seedlac, which consists of more insoluble matter, such as twigs and insect bodies. However, these do not affect our bleaching method. More bleaching agent was required (10 mmolox gshellac−1 of 11), presumably due to a larger quantity of dye in seedlac. Upon dropwise addition of 11, wax starts to coagulate. To facilitate the filtration of the wax, the seedlac solution was stored at 4 °C for two hours without agitation followed by filtration prior to the shellac precipitation. From 10 g of seedlac, 7.4 g of 85% bleached shellac with an acid value of 112 were obtained.
Characterisation
The Fourier-transformed infrared spectra (FT-IR) of unbleached dewaxed shellac, peroxodicarbonate bleached shellac and sodium hypochlorite bleached shellac are compared (Fig. 3). There are no large changes in the IR spectra of all samples. However, there are small changes in the ratio of some absorbance bands. The broad band at 3390.70 cm−1 is attributed to O–H stretching of hydroxyls and carboxylic acids and is decreased for the NaOCl bleached shellac, while its band at 1710 cm−1, corresponding to the C
O stretch of carboxylic acids and esters increases. This might be due to ester formation caused by rapid aging in NaOCl bleached shellac. Bleaching with peroxodicarbonate did not lead to this change. Furthermore, the C–O stretching band at 1146 cm−1 for unbleached shellac has a shoulder at 1164 cm−1, which is growing slightly for peroxodicarbonate bleached shellac but becomes the major band in NaOCl bleached shellac. This hints that molecular changes in the shellac structure might be less then with NaOCl. Lastly, it was priorly stated that a peak at 1565 cm−1 in unbleached shellac is caused by C
C stretching vibration of the aromatic dyes, and the absence of the peak in the IR of H2O2-bleached shellac is a sign of dye removal.34 However, this peak is absent in all measured samples, including the unbleached shellac in this work. Therefore, we suggest that this peak is originating from asymmetric C
O stretching of deprotonated carboxylate, which agrees with IR spectra of shellac salt.4,60
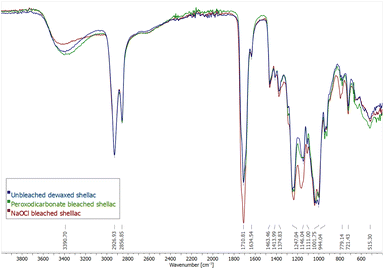 |
| Fig. 3 FT-IR spectra of unbleached shellac (blue), bleaching with 11 (green) and NaOCl bleached shellac (red). | |
A 1H, 13C and HSQC NMR were measured of unbleached shellac and bleached shellac with 11 and NaOCl (ESI†). In the 1H NMR, a moderate decrease of aldehyde resonance (9.7 ppm) and acetal functionality (1H: 4.45–4.30 ppm) for bleaching with 11 is noticeable. This is also visible in the 13C NMR. The decrease of these functionalities is less for NaOCl, leading to the conclusion that oxidation of aldehyde is more pronounced with 11 and acid catalysed acetal hydrolysis is minimal during precipitation.
Proposed mechanism
A tentative reaction mechanism is proposed (Scheme 2). For simplicity, 1 is used as example. The reaction sequence is initiated by mono-decarboxylation of 11.55 This nucleophilic peroxide species 13 attacks the nitrile with subsequent protonation to form 14, which further decarboxylates. 12 acts as an electrophilic peroxide reacting with 1. The phenolic peroxide in 15 is instable and will expel water to form ortho-quinone 16. ortho-Quinones are susceptible for nucleophilic attack of water and form quinoid intermediate 17, which will further degrade in various pathways with degradation fragments such as phthalic acid derivatives.61
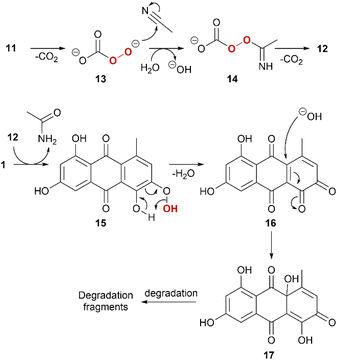 |
| Scheme 2 Proposed mechanism for the oxidative bleaching with 12. | |
Conclusions
A sustainable, halogen-free protocol at ambient temperature for the bleaching of shellac and seedlac was established. Combination of 11, as a platform oxidizer, and acetonitrile as an atom-economical inexpensive activator, results in a strong bleaching system for shellac. Peroxodicarbonate 11 provides the mildly alkaline conditions required for bleaching and facilitates dewaxing due to its strong ionic buffer system. Furthermore, 11 can be synthesised on demand via electrolysis of ecologically safe aqueous carbonate solutions, avoiding the storage of potentially dangerous peroxides. The optimized bleaching procedure requires 1.5 eq. acetonitrile relative to 11 and is performed at room temperature for 8 hours. The required amount of 11 highly depends on the shellac or seedlac grade used and the desired colour index after bleaching. Bleaching damages were examined via acid value, infrared and NMR (1H and 13C). FT-IR and NMR analysis suggest that molecular changes in shellac are limited in this new bleaching method. However, there has been considerable acetal breakage and aldehyde oxidation, as can be seen in the 1H NMR, in part leading to the increased acid value. Other bleaching damages mainly include ester hydrolysis. This ecological bleaching process is a step forward in the chlorine-free bleaching of shellac under ambient conditions with decreased bleaching damage, while still being economically feasible.
Author contributions
All authors have given approval to the final version of the manuscript.
Conflicts of interest
There are no conflicts to declare.
Acknowledgements
The authors are grateful for funding by the Deutsche Forschungsgemeinschaft (DFG, German Research Foundation) under FOR 2982/2-UNODE (WA 1276/23-2). The support and discussions by the late Manfred Penning are greatly appreciated.
References
- N. Thombare, S. Kumar, U. Kumari, P. Sakare, R. K. Yogi, N. Prasad and K. K. Sharma, Int. J. Biol. Macromol., 2022, 215, 203–223 CrossRef CAS PubMed
.
- T. H. Shah, M. Thomas and R. Bhandari, Int. J. Curr. Res., 2015, 7, 13652–13659 Search PubMed
.
-
J. Derry, Masters Thesis, University of Oslo, 2012 Search PubMed
.
- Y. Farag and C. S. Leopold, Eur. J. Pharm. Sci., 2011, 42, 400–405 CrossRef CAS PubMed
.
- M. Islam, N. Prasad and P. K. Ghosh, Res. Ind., 1974, 19, 167–169 Search PubMed
.
- R. Lausecker, V. Badilita, U. Gleißner and U. Wallrabe, Biomicrofluidics, 2016, 10, 044101 CrossRef CAS PubMed
.
- A. Cannon and J. Inst, J. Inst. Conserv., 2015, 38, 92–106 CrossRef
.
- Y. Yuan, N. He, Q. Xue, Q. Guo, L. Dong, M. H. Haruna, X. Zhang, B. Li and L. Li, Trends Food Sci. Technol., 2021, 109, 139–153 CrossRef CAS
.
- Y. Yuan, N. He, L. Dong, Q. Guo, X. Zhang, B. Li and L. Li, ACS Nano, 2021, 15, 18794–18821 CrossRef CAS PubMed
.
- M. Rademaker, J. D. Kirby and I. R. White, Contact Dermatitis, 1986, 15, 307–308 CrossRef CAS PubMed
.
- A. Azouka, R. Huggett and A. Harrison, J. Oral Rehabil., 1993, 20, 393–400 CrossRef CAS PubMed
.
- V. Landry, G. Boivin, D. Schorr, M. Mottoul, A. Mary, L. Abid, M. Carrère and B. Laratte, Curr. For. Rep., 2023, 9, 319–331 CrossRef
.
- A. Ahuja and V. K. Rastogi, Sustainability, 2023, 15, 3110 CrossRef CAS
.
- M. Ali, D. K. Hazra, Y. B. Kumar and R. Karmakar, Sep. Sci. Technol., 2022, 57, 2916–2922 CrossRef CAS
.
- F. Elterlein, N. Bugdahn and P. Kraft, Chem.–Eur. J., 2024, 30, e202400006 CrossRef CAS PubMed
.
- A. Gandini, Green Chem., 2011, 13, 1061–1083 RSC
.
- S. K. Sharma, S. K. Shukla and D. N. Vaid, Def. Sci. J., 2014, 33, 261–271 CrossRef
.
- D. Tamburini, J. Dyer and I. Bonaduce, Sci. Rep., 2017, 7, 14784 CrossRef PubMed
.
- G. B. V. Subramanian, J. Iqbal, K. N. Ganesh and N. Sriram, J. Chem. Soc., Perkin Trans. 1, 1976, 2045–2049 RSC
.
- S. Limmatvapirat, C. Limmatvapirat, M. Luangtana-anan, J. Nunthanid, T. Oguchi, Y. Tozuka, K. Yamamoto and S. Puttipipatkhachorn, Int. J. Pharm., 2004, 278, 41–49 CrossRef CAS PubMed
.
- K. Buch, M. Penning, E. Wächtersbach, M. Maskos and P. Langguth, Drug Dev. Ind. Pharm., 2009, 35, 694–703 CrossRef CAS PubMed
.
- R. Burwood, G. Read, K. Schofield and D. E. Wright, J. Chem. Soc. C, 1967, 842–851 RSC
.
- G. Shamim, K. S. Ranjan, M. D. Pandey and R. Ramani, Eur. J. Entomol., 2014, 111, 149–164 CrossRef CAS
.
- A. Tschirch and F. Lüdy jun, Helv. Chim. Acta, 1923, 6, 994–1008 CrossRef CAS
.
- B. B. Khanna, J. Appl. Chem., 1970, 20, 392–396 CrossRef CAS
.
- S. Saengsod, S. Limmatvapirat and M. Luangtana-Anan, Adv. Mater. Res., 2012, 506, 250–253 CAS
.
- S. Saengsod, S. Limmatvapirat and M. Luangtana-anan, J. Food Process Eng., 2019, 42, e13291 CrossRef
.
- K. Li, B. Tang, W. Zhang, Z. Shi, X. Tu, K. Li, J. Xu, J. Ma, L. Liu and H. Zhang, ACS Omega, 2020, 5, 22551–22559 CrossRef CAS PubMed
.
- Y. Liao, J. Zhou and F. Huang, Trop. J. Pharm. Res., 2015, 14, 1953–1960 CrossRef CAS
.
- K. R. Solomon, Pure Appl. Chem., 1996, 68, 1721–1730 CrossRef CAS
.
- Y. Liao, X. Chai and F. Xu, Adv. Mater. Res., 2011, 152–153, 372 CAS
.
- Y. Liao, F. Xu and D. Li, Adv. Mater. Res., 2009, 79–82, 1879 CAS
.
-
B. Baboo and D. N. Goswami, Processing, Chemistry and Applications of Lac, Indian Council of Agricultural Research New Delhi, New Delhi, 2010 Search PubMed
.
- K. Li, H. Zheng, H. Zhang, W.-w. Zhang, K. Li and J. Xu, RSC Adv., 2016, 6, 55618–55625 RSC
.
- D. J. Wu, X. M. Qian and P. Huang, Appl. Mech. Mater., 2011, 79, 215–220 CAS
.
- G. O. Bianchetti, C. L. Devlin and K. R. Seddon, RSC Adv., 2015, 5, 65365–65384 RSC
.
- G. B. Payne, P. H. Deming and P. H. Williams, J. Org. Chem., 1961, 26, 659–663 CrossRef CAS
.
- C. Schotten, T. P. Nicholls, R. A. Bourne, N. Kapur, B. N. Nguyen and C. E. Willans, Green Chem., 2020, 22, 3358–3375 RSC
.
- D. Pollok and S. R. Waldvogel, Chem. Sci., 2020, 11, 12386–12400 RSC
.
- S. Möhle, M. Zirbes, E. Rodrigo, T. Gieshoff, A. Wiebe and S. R. Waldvogel, Angew. Chem., Int. Ed., 2018, 57, 6018–6041 CrossRef PubMed
.
- A. Wiebe, T. Gieshoff, S. Möhle, E. Rodrigo, M. Zirbes and S. R. Waldvogel, Angew. Chem., Int. Ed., 2018, 57, 5594–5619 CrossRef CAS PubMed
.
- J. Seidler, J. Strugatchi, T. Gärtner and S. R. Waldvogel, MRS Energy Sustain., 2021, 7, 42 CrossRef
.
- S. Arndt, D. Weis, K. Donsbach and S. R. Waldvogel, Angew. Chem., Int. Ed., 2020, 59, 8036–8041 CrossRef CAS PubMed
.
- S. Arndt, R. Rücker, A. Stenglein and S. R. Waldvogel, Org. Process Res. Dev., 2022, 26, 2447–2455 CrossRef CAS
.
- S. Arndt, P. J. Kohlpaintner, K. Donsbach and S. R. Waldvogel, Org. Process Res. Dev., 2022, 26, 2564–2613 CrossRef CAS
.
- C. M. Kisukuri, R. J.-R. Bednarz, C. Kampf, S. Arndt and S. R. Waldvogel, ChemSusChem, 2022, 15, e202200874 CrossRef CAS PubMed
.
- J. Klein, K. Alt and S. R. Waldvogel, Adv. Sustainable Syst., 2022, 6, 2100391 CrossRef CAS
.
- E. J. Ruiz, R. Ortega-Borges, J. L. Jurado, T. W. Chapman and Y. Meas, Electrochem. Solid-State Lett., 2009, 12, E1 CrossRef CAS
.
- E. J. Constam and A. von Hansen, Z. Elektrochem., 1896, 3, 137–144 CrossRef
.
- A.-K. Seitz, P. J. Kohlpaintner, T. van Lingen, M. Dyga, F. Sprang, M. Zirbes, S. R. Waldvogel and L. J. Gooßen, Angew. Chem., Int. Ed., 2022, 61, e202117563 CrossRef CAS PubMed
.
- M. Klein, D. L. Troglauer and S. R. Waldvogel, JACS Au, 2023, 3, 575–583 CrossRef CAS PubMed
.
- A.-K. Seitz, T. van Lingen, M. Dyga, P. J. Kohlpaintner, S. R. Waldvogel and L. J. Gooßen, Synlett, 2022, 33, 1527–1531 CrossRef CAS
.
- P. J. Kohlpaintner, N. Schupp, N. Ehlenz, L. Marquart, L. J. Gooßen and S. R. Waldvogel, Org. Lett., 2024, 26, 1607–1611 CrossRef CAS PubMed
.
- P. J. Kohlpaintner, L. Marquart, L. J. Gooßen and S. R. Waldvogel, Eur. J. Org Chem., 2023, 26, e202300220 CrossRef CAS
.
- F. Sprang, N. Schupp, P. J. Kohlpaintner, L. J. Gooßen and S. R. Waldvogel, Green Chem., 2024, 26, 5862–5868 RSC
.
- M. Zirbes, T. Graßl, R. Neuber and S. R. Waldvogel, Angew. Chem., Int. Ed., 2023, 62, e202219217 CrossRef CAS PubMed
.
- T. Furuta, H. Tanaka, Y. Nishiki, L. Pupunat, W. Haenni and P. Rychen, Diamond Relat. Mater., 2004, 13, 2016–2019 CrossRef CAS
.
- C. P. Chardon, T. Matthée, R. Neuber, M. Fryda and C. Comninellis, ChemistrySelect, 2017, 2, 1037–1040 CrossRef CAS
.
- A. Ziogas, J. Belda, H.-J. Kost, J. Magomajew, R. A. Sperling and P. Wernig, Curr. Res. Green Sustainable Chem., 2022, 5, 100341 CrossRef CAS
.
- S. Limmatvapirat, C. Limmatvapirat, S. Puttipipatkhachorn, J. Nuntanid and M. Luangtana-anan, Eur. J. Pharm. Biopharm., 2007, 67, 690–698 CrossRef CAS PubMed
.
-
P. Hodge, in Quinonoid Compounds, ed. S. Patai, Wiley & Sons: London, 1974, ch. 11 Search PubMed
.
|
This journal is © The Royal Society of Chemistry 2024 |