DOI:
10.1039/D4IM00048J
(Review Article)
Ind. Chem. Mater., 2024,
2, 393-423
Progress on fiber engineering for fabric innovation in ecological hydrophobic design and multifunctional applications
Received
5th May 2024
, Accepted 2nd July 2024
First published on 11th July 2024
Abstract
The application of fluorinated coatings on textiles has garnered substantial research interest over the past years, owing to their ability to endow fabrics with exceptional hydrophobic characteristics, thereby mitigating issues associated with high moisture absorption and susceptibility to contamination. Nevertheless, the deployment of fluorinated substances has been proscribed due to concerns regarding their ecological impact and potential human toxicity. Consequently, there has been a burgeoning demand for hydrophobic textile alternatives derived from non-fluorinated, natural materials that are both sustainable and environmentally benign. This paper presents a thorough overview of the advancements in the development and functionalization of eco-friendly, hydrophobic textiles. Initially, the natural materials and their derivatives utilized in the creation of superhydrophobic textiles are delineated, including cellulose, lignin and chitosan, among others. Subsequently, methodologies for crafting efficient, stable, and resilient hydrophobic textiles are elucidated, encompassing conventional techniques as well as novel, inventive concepts. Furthermore, the current state of research and the obstacles faced in the evolution of multifunctional textiles based on superhydrophobic fabrics are examined. In conclusion, this discussion presents incisive insights into the impending direction of advancements in functional textiles.
Keywords: Eco-friendly; Superhydrophobic; Bioinspired; Multifunctional textiles; Natural materials.
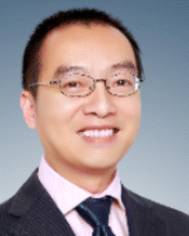 Wei Li | Wei Li is an associate professor at the College of Materials Science and Engineering at Fujian University of Technology. He received his PhD degree from the College of Materials Science and Engineering at Fuzhou University. His current research topics are microstructure and properties of materials (multifunctional fabric surface, optical properties of nanomaterials), advanced structural materials and preparation of novel materials. |
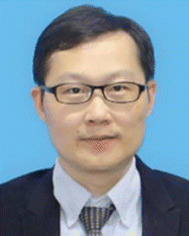 Yuekun Lai | Yuekun Lai is a Fujian province “Minjiang Scholar” Chair Professor at the College of Chemical Engineering at Fuzhou University, and served as Editor of Chemical Engineering Journal. He received his PhD degree from the Department of Chemistry, Xiamen University. He is selected as the 2018–2023 Highly Cited Researchers (Clarivate Analytics) and the recipient of the 2016 Journal of Materials Chemistry A (JMCA, RSC) Emerging Investigators and 2019 Advanced Materials Interfaces (AMI, Wiley) Hall of Fame award. His current research topics are bioinspired intelligent materials with special wettability, multifunctional fabrics, conductive hydrogels and functional nanostructures for energy and environmental applications. |
1 Introduction
In recent years, there has been an increasing concern over personal health, which has spurred the development of an increasing number of sensors designed to monitor human physiological and chemical parameters. The conventional mechanical and electronic sensors are often cumbersome and uncomfortable for prolonged wear, prompting researchers to engineer intelligent devices for the human body using innovative materials such as hydrogels,1–5 aerogels,6–10 and flexible textiles.11–15 In addition, electronic skins16–20 and human implantable devices21–25 are also proposed with prototypes developed. Typically, these devices are expected to be harmless to both living organisms and the environment. However, the current research primarily concentrates on achieving the desired functionalities, and significant challenges remain in realizing devices that are both environmentally benign and biocompatible.
Natural materials have garnered significant interest due to their exceptional biocompatibility. Plant-derived extracts, including fibers, natural leather, animal fur, and shells, along with their derivatives, have been extensively incorporated into the fabrication of functional textiles.26–28 These materials are endowed with a wealth of functional groups and intricate molecular structures, enabling them to form bonds with the plethora of hydroxyl, carboxyl, and other moieties present in textiles. Consequently, a diverse array of techniques for the creation of functional textiles has emerged, encompassing impregnation, spraying,29,30 sol–gel processes,31 and in situ polymerization methods.32 Additionally, the advanced maturity of processes for crafting hydrophobic textiles, coupled with the tangible utility of these functionalities, has predisposed researchers towards the development of multifunctional textiles on hydrophobic substrates. In this vein, numerous eco-friendly, hydrophobic, and multifunctional textiles have been innovatively designed, such as high-performance sensors, alarm systems, and energy-harvesting devices constructed from conductive materials like carbon nanotubes (CNT),33 MXene,34,35 graphene,36,37 among others,38–40 integrated with textile fibers, plant fibers, and other natural materials. The field of green and multifunctional hydrophobic textile design has thus witnessed rapid and progressive advancements.
This manuscript presents an exhaustive examination of eco-friendly techniques for the production of hydrophobic textiles and their functional augmentation. It commences with an elucidation of the wetting state model and the biological orchestration of droplets. The treatise then delves into the exploration of verdant materials utilized in the creation of superhydrophobic fabrics, encompassing natural substances and derivatives obtained from soybeans, plant fibers, seaweed, and crustacean shells, as well as the methodologies employed to engineer highly efficacious and stable hydrophobic textiles. This includes the application of biomimetic principles and sophisticated structural design for bolstering the stability of hydrophobic coatings, coupled with energy-efficient and low energy consumption manufacturing techniques. The third segment elucidates on the versatile textiles spawned from hydrophobic materials, featuring applications such as personal buoyancy aids, proactive perspiration management apparel, and fabrics conducive to monitoring human motor activities. Finally, this paper introduces the obstacles encountered by green hydrophobic textiles and prognosticates the prospective trajectory of their development (Fig. 1).
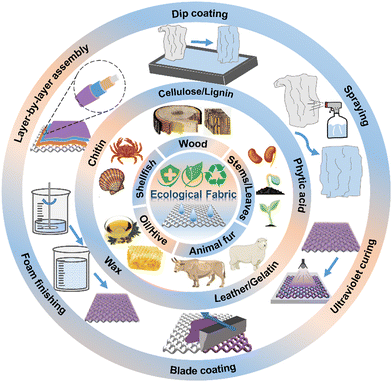 |
| Fig. 1 Natural materials and preparation method for ecological hydrophobic fabrics. | |
2 The exploration process of surface wetting mechanism
In the natural world, the phenomenon of bio-manipulation of droplets is ubiquitous. A notable instance of this is the superhydrophobic property exhibited by lotus leaves, which facilitates the unrestricted movement of droplets across their surfaces.41,42 This behavior is not unique to lotus leaves but is also observed in other species, such as the feathers of swans and the legs of water striders.43 Researchers have deciphered the enigma of surface wetness and developed techniques for fabricating superhydrophobic surfaces. These surfaces are implemented in various applications requiring water repellency or self-cleaning properties, including the exterior walls of buildings, glass panels, and textile fabrics. The wettability of a surface is commonly measured by the static water contact angle (WCA) and the contact angle hysteresis (CAH).
As illustrated in Fig. 2f, the Young's model proposes that a surface is considered hydrophilic if the WCA is less than 90°, implying a tendency for the droplet to spread out on the surface, thus forming a significant solid–liquid contact area. On the contrary, when the WCA surpasses 90°, the surface is deemed hydrophobic, indicating a reduction in the attractive forces between the droplet and the surface. The WCA can be calculated using the Young's equation, as shown in eqn (1):
| γSV = γSL + γLV cos θ | (1) |
where
γSV,
γSL, and
γLV represent the interfacial tensions of solid–vapor, solid–liquid, and liquid–vapor, respectively,
θ denotes the water contact angle at the interface. It can be deduced from Young's equation that a diminution in the surface energy of a solid leads to an elevation of the static WCA (
θ). Young's state is predicated on an ideally smooth and chemically homogeneous solid surface. However, in practice, surfaces invariably exhibit some degree of roughness, which exerts a significant influence on the water contact angle at the interface. As shown in
Fig. 2f Wenzel state, when a surface is roughened, a liquid droplet may entirely imbue the rough cavities. To measure the relationship between surface tension and water contact angle with greater precision, Wenzel introduced the roughness factor “
r” and proposed the Wenzel equation based on Young's equation:
where
r represents the ratio of the actual area to the geometrical surface area,
θ*/
θ denotes the external/internal CA. According to the Wenzel equation, when the surface is sufficiently rough, with
r ≫ 1, the Wenzel formula ceases to be applicable. In real scenarios, if the surface is adequately rough, air pockets exist between the droplet and the solid. To further elucidate the wetting relationship between the droplet and the surface, Cassie and Baxter proposed the existence of a composite contact on rough surfaces (
Fig. 2f), where contact occurs not only between the solid and the liquid but also between the solid and air. This is described by the Cassie–Baxter equation:
where
fi denotes the percentage of the total contact area occupied by the contact interface between substance and the droplet, with ∑
fi = 1. Within the context of a generally rough surface, trapped air is present under nano-pits, allowing for the presumption of two distinct contact scenarios during droplet interfacing: namely, the percentage of the total area in contact between the solid and the liquid (
f1), or between the air and the liquid (
f2). Because of the WCA = 180°, the Cassie–Baxter equation can thus be reformulated as:
| cos θ* = f1(cos θ + 1) − 1 | (4) |
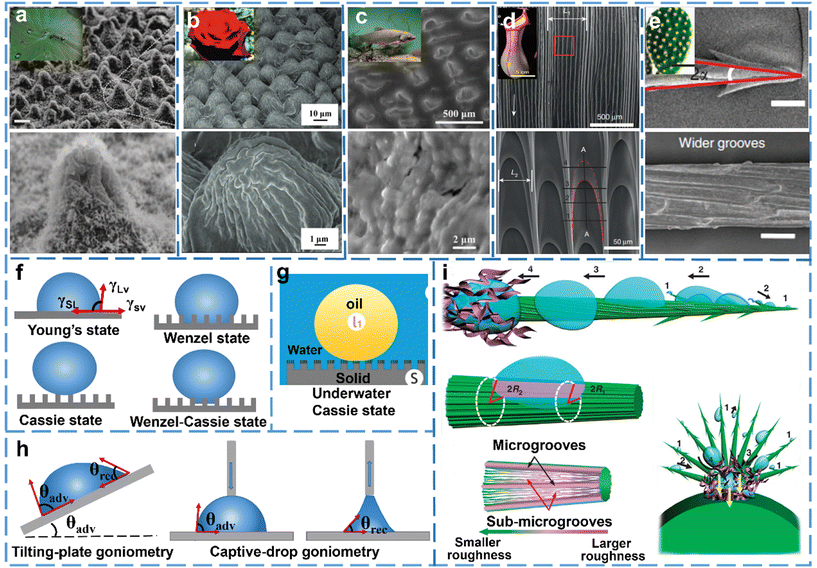 |
| Fig. 2 Surface microstructure of cacti (a) Lotus leaf,42 Copyright 2008 Wiley-VCH; (b) rose petal,44 Copyright 2008 American Chemical Society; (c) fish scale,45 Copyright 2009 Wiley-VCH; (d) peristome surface,46 Copyright 2016 Springer Nature; (e) cactus,47 Copyright 2012 Springer Nature; (f) droplet surface contact model; (g) underwater Cassie state,45 Copyright 2009 Wiley-VCH; (h) the means for characterization of the contact angle hysteresis,48 Copyright 2022 Wiley-VCH; (i) droplet transport model on cactus thorns,47 Copyright 2012 Springer Nature. | |
The Wenzel and Cassie models represent ideal states of solid–liquid contact. However, the interaction between solid and liquid surfaces may be an intermediate state, not fully conforming to either model, as the droplet does not completely fill the nano-pits indentations of the surface. Grounded in these models and their respective equations, we are justified in believing that the WCA of droplet correlates with the surface energy and the roughness. The Fig. 2a shows the micro-structure of a lotus leaf, revealing the rough, protrusive architecture coupled with hydrophobic wax materials adhered to it. This is pivotal in endowing the lotus leaf surface with its exceptional water-repellency and lends credence to the validity of our inference from a tangential perspective.
Typically, two distinct superhydrophobic states are found on rough surfaces. We previously discussed the non-wettability contact mode exemplified by the Cassie state, wherein water droplets facilely roll off the surface. Another mode is the Wenzel state of wetted contact, in which the droplets are secured in place on the surface. As shown in Fig. 2b, demonstrating the “petal effect” with the surface of a rose as an example, the droplets assume a spherical form yet maintain a high adhesion to the petals.44 Hence, the crucial notion of contact angle hysteresis is introduced. The advancing angle (θadv) is higher than the receding angle (θrec), when droplets roll off on an inclined surface, as depicted in Fig. 2h, and their difference is defined as the contact angle hysteresis (CAH). A lower CAH suggests that droplets can roll off the surface with ease. Fig. 2h illustrates the inclined plane method and the addition/subtraction of liquid method for measuring the CAH.48,49 On the petal, one can observe numerous closely-packed micro-papillae, each topped with an abundance of intricate folds, which is pivotal for ensuring the superhydrophobicity of the petal. The waxy covering on the surface of lotus leaves prevents droplets from being trapped in nano-pits, yet the micro-dimensions on the petal surface are larger than those of the lotus, causing droplets to settle into the larger pits and form a Cassie wetting state.
Similarly, when a school of fish swims through water contaminated with oil, they can maintain their cleanliness. The surface of fish scales exhibits superoleophobic properties in water, yet in air, it shows superhydrophilicity and superoleophilicity. As shown in Fig. 2c, regularly arranged micro-papillae are observed on the fish scales, and further magnification reveals rough structures on these micro-papillae. In water, the surface of the fish scales forms a Cassie state with oil droplets, as shown in Fig. 2g. This state is similar to the superhydrophobicity of a solid surface in an atmospheric environment. At this time, water fills the nanoscale pits between the fish scales and the oil droplets, preventing the oil droplets from penetrating.45,50 From the “lotus effect” and the “petal effect” to the special oil-repellent behavior of fish scales, the secrets of surface hydrophobicity have been unveiled. To ensure the isolation between the two substances, a third substance needs to be introduced to isolate and maintain this stable state. Just like the “Leidenfrost Phenomenon”, the steam insulates the droplet from the hot pot, and the droplet exhibits superhydrophobic behavior.51
Further, the manipulation of droplet behavior is crucial for engineering applications. As shown in Fig. 2d, presenting the inner surface structure of the pitcher plant, with regularly arranged micro-channels on the rocky walls of the pitcher plant's water sac, allowing unidirectional droplet transport without energy gradients.46 The inner wall of the pitcher plant consists of multiple first-order micro-grooves, each made up of about 10 second-order micro-grooves, which are arch-shaped and regularly distributed. It is this unique structure that enables continuous upward transport of the liquid, while downward movement is impeded. In deserts, cacti convey droplets to the root's absorptive trichomes by utilizing their spines. As shown in Fig. 2e, the microscopic structure of a cactus spine is conical with neatly arranged retroverted barbs.47 These droplets are driven in a directed motion by the Laplace pressure gradient produced by the conical structure, together with the surface energy gradient due to the surface roughness. As illustrated in Fig. 2i, the spine of the cactus has a grooved cone shape, with the Laplace pressure difference generated at different radii of the cone being:
|  | (5) |
where
R1 and
R2 represent the radius of spikes at different positions,
R0 is the radius of the water droplet,
γ stands for the surface tension of water,
α is the half-vertex angle of the spine, and d
z is the incremental radius of the spike. It is evident that the Laplace pressure in the area of smaller spike radius is greater than that in the area of larger spike radius, creating a pressure difference that drives the movement of the droplet. In addition, the surface near the tip of the needle is rougher than the tail end surface. According to the Wenzel equation (
formula (2)), the rougher tip has better hydrophobicity and higher surface free energy. Therefore, this free energy driving force can be written as follows:
|  | (6) |
In the formula, θA and θR represent the advancing and receding WCA at the midpoint of the spine, respectively, and dl is the integral variable in the direction of length from the area near the tip to the area near the base along the midpoint of the spine. In addition, the parallel grooves produce anisotropic contact angle hysteresis, and such grooves make it easier for droplets to be transported horizontally along the spine, which is similar to the directional transport guided by the grooves of the pitcher plant. Similarly, directional movement of droplets can also be observed on spider silk,52 and microscopic observation of the spider silk can also reveal similar conical structures and changes in surface roughness.
From the superhydrophobic phenomena observed on the surfaces of lotus leaves and on petals, to the special movement of droplets exhibited by the spines of cacti and the inner walls of pitcher plants, we have discovered the secrets of droplet behavior in nature. In the textile industry, especially in the development of multifunctional fabrics, hydrophobic behavior is a hot topic of research.
In the past time, the construction of superhydrophobic fabrics often involves the use of fluorine-containing materials. Fluoropolymers have unique physicochemical properties such as excellent hydrophobicity and lipophobicity, good chemical stability and bio-inertness.53 The van der Waals forces between fluoropolymers and other materials are small, so they have a low surface energy when treating the surface of the fabric, which the manufacture of superhydrophobic fabrics becomes easier. However, the fluorine materials significantly impact the ecosystem and pose threats to human health, also limits its use. Of course, it is not necessary to use fluorine materials to improve the hydrophobicity of fabric, where natural materials are also widely developed for superhydrophobic fabrics.
3 The natural material used in hydrophobic fabrics
Although many natural materials are hydrophilic,54,55 their excellent biocompatibility and environmental friendliness, have become the subject of heightened interest, in recent years, the researchers have turned their focus to natural materials. In fact, the natural materials can be used in the fabricate of superhydrophobic fabrics.56,57 We provide the application cases of different natural materials and their derivatives on hydrophobic fabrics, including the use of natural hydrophobic materials to prepare green hydrophobic fabrics, and there are bold attempts to prepare hydrophobic fabrics using nature hydrophilic materials. Finally introduce other natural materials that provide additional properties on hydrophobic fabrics.
3.1 Natural wax
Wax is one of the hydrophobic substances in nature. Waxy materials come from plants, animals and mineral oils, mainly composed of long chain fatty aliphatic compounds.58,59 Hydrophobic fabric can be prepared directly from natural wax. Such as, superhydrophobic coatings were prepared from castor oil spherulites,60 carnauba wax,61 paraffin wax etc.62 In this process, wax is directly applied to the fabric. Either made into wax particles or mixed with other nanoparticles and used in the preparation of hydrophobic fabrics.
Other components extracted from wax are used in the preparation of hydrophobic fabrics. Such as, fatty acid (stearic acid,63 lauric acid,64 oleic chloride,65et al.66,67) are almost always present in the wax of all plants. Waxy materials also contain alkanes, triterpenoids, alcohols,68,69 which are effective in reducing the surface free energy of fabrics, and are widely used in hydrophobic treatment, but they are not completely non-toxic and harmless.
3.2 Phytic acid
Phytic acid (PA) is an organic phosphorus compound predominantly found in plant seeds.70,71 It has strong acidity and metal chelating capacity and is widely utilized.72,73 Zhang et al.74 employed phytic acid to etch cotton fabrics to create rough surfaces, and combined with the thermosetting resin to prepared superhydrophobic textiles. Phytic acid exhibits a strong negative charge that binds firmly to most cationic charged compounds even at room temperature. It can also form coordination complexes with metal ions. Wang et al.75 used phytic acid chelated with iron ions to produce PA–Fe particles for the preparation of hydrophobic fabrics. In addition, the excellent flame retardant and conductive properties of phytic acid are also commonly used in the preparation of green fabrics.76–78
3.3 Cellulose
Cellulose is one of the most abundant and widely distributed polysaccharides in nature, and it constitutes the primary component of plant cell walls.79,80 Cellulose has excellent mechanical properties and low cost, which makes cellulose based fabrics are widely used. Cellulose is a hydrophilic material,81 but it is easily hydrophobic modified to prepare green hydrophobic fabrics. For example, direct hydrophobic modification of cellulose fabrics.82,83
Moreover, nanocellulose and cellulose derivatives are also widely used in hydrophobic fabrics modification.84,85 The modified hydrophobic nanocellulose particles can not only improve the fabric surface, but also have low surface energy. Such as, Sun et al.86 mixing the cellulose powder with oleoyl chloride to make hydrophobic cellulose powder, Zeng et al.87 used cellulose nanocrystals to construct the rough surface of fabric, and combined with cured epoxidized soybean oil to produce superhydrophobic cotton textiles.
3.4 Lignin
Lignin, as a kind of recyclable biological resource with multifunctional properties, is widely used in biomedicine, material chemistry and other fields.88,89 Unlike cellulose, lignin possesses a complex chemical structure and is highly resistant to acid, alkali and thermally stable.90,91 Similar to cellulose, lignin can also be hydrophobic modified,92 prepared nanoparticle,93 its derivatives extracted,94 and used in the preparation of hydrophobic fabrics. In addition, lignin has a polyphenol structure, which allows itself to coordinate with metal ions to form hydrophobic particles. Zhang et al.95 utilized lignin and its metal ion chelation properties to fabricate fabrics with high hydrophobicity for oil–water separation.
3.5 Chitosan
Chitosan is a natural polysaccharide found in the exoskeletons of animals, bacterial cell walls, and membranes of algae.96 Its excellent biodegradability and cell affinity have led to its widespread application in bio-functional materials.97,98 Although natural chitosan is hydrophilic, but it can be used in the preparation of hydrophobic fabrics after modification technology. The common method is to improve the surface roughness of hydrophobic fabric by chitosan nanoparticles.99 Moreover, chitosan hydrophobic films were also prepared by hydrophobic modification.100 There are also some reports that demonstrate the potential of chitosan in the preparation of hydrophobic fabrics. Raeisi et al.101 preparation a superhydrophobic cotton fabric using chitosan and nano TiO2, and found that the cotton fabric with added chitosan solution changed from superhydrophilic (WCA = 0°) to hydrophilic (WCA = 62°). Furthermore, the unpredictable surface hydrophobicity created by hydrophilic chitosan and tannic acid,102 this novel method can replace the traditional fluorine-free or fluorine hydrophobic materials. In this process, chitosan not only improves the surface roughness but also reduces the surface free energy of the fabric.
Moreover, the unique properties of chitosan, including the antimicrobial and flame-retardant qualities, are extensively utilized in the fabrication of functional textiles.103,104
3.6 Other natural materials
Other natural materials are also employed in the preparation of multifunctional textiles. For instance, in methods such as producing waterproof leather from animal hides.105 Silkworms are fed with silver nanoparticles to enable the secretion of silver silk.106 Hydrogel composite textile materials synthesized using substances like sodium alginate are applied in the creation of wearable multipurpose textiles.107 Biodegradable oil–water separation textiles are also produced using natural grasses as the raw materials.108 Furthermore, materials such as taurine, epoxidized soybean oil, edodes polysaccharides, and sodium lignosulfonate are utilized in the fabrication of flame-retardant textiles (Fig. 3).109–111
 |
| Fig. 3 Natural material structural formula. | |
4 The design strategies for hydrophobic fabric
To imbue hydrophilic fabrics with the capacity to resist droplets, enhancing their surface characteristics through material modification is essential, yet the methods of preparation play a pivotal role as well. In this section, we first discuss several ways of designing hydrophobic fabrics through some common preparation methods. Secondly, we introduce some energy saving and fast preparation strategies. Finally, we introduce some inspiring and innovative strategies.
4.1 Recreate the “lotus leaf” surface structure
Most hydrophobic interfaces are designed to mimic the lotus leaf effect, so common manufacture methods of hydrophobic fabrics are based on low energy surface and nano-rough structures.112
Depending on the hydrophilic and lipophilic properties of natural fabrics, hydrophobic materials can enter the fabric with the solution. Then, the fabric is heat-treated and solvent restored. The fiber is covered with hydrophobic material, and the surface free energy is reduced quickly, so that the fabric can obtain hydrophobic properties. Moreover, the surface of natural fabrics usually has great number of hydroxyl groups, which allows hydrophobic materials to interact with it to form stable chemical bonds. The dipping is one of the most widely used preparation method of hydrophobic fabric in industry.113,114 Similarly, spraying, spin coating, and padding also use solvents to transfer hydrophobic materials.
The low surface energy hydrophobic agent is very effective for hydrophobic modification of fabrics, meanwhile, it also important to improving the nano roughness of fabric surface.115 There are three main ways to improve the roughness of fabric:
First, the surface roughness of fabric can be improved by adding nanoparticles. For example, the Fig. 4a proposed a superhydrophobic fabric preparation method based on dopamine polymerization promoted by the Fenton reaction.116 The design promotes dopamine polymerization through the Fenton reaction, and the nanoparticles are firmly wrapped on the fabric, thus forming a surface of nano-rough structure. Moreover, Then the long-term stability between the nanoparticles and fabric was achieved by van der Waals forces.
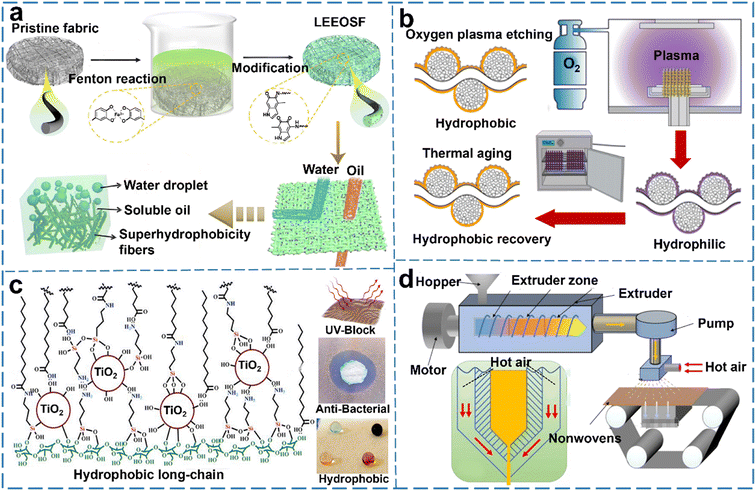 |
| Fig. 4 Preparation of superhydrophobic fabric by (a) Fenton reaction,116 Copyright 2023 Elsevier; (b) oxygen plasma etching and thermal aging,117 Copyright 2020 Elsevier; (c) hydrophobic branches on fabric long chains,118 Copyright 2023 Elsevier; (d) melt-blow method,119 Copyright 2022 MDPI. | |
Secondly, the surface of the fabric can be roughened directly. The Fig. 4b shows a superhydrophobic fabric through a combination of plasma etching and thermal aging.117 The surface of nano-rough structure is effectively formed by plasma etching, and the modification of low surface materials, the formation of hydrophobic fabric. Besides physical etching, the surface roughness of the fabric can be improved by chemical etching (acid-etching)74 and biological etching (enzyme-etching).120
Thirdly, long-chains are grafted onto the fabric to create a rough surface. As shown in Fig. 4c, long chemical chains are grafted on the superhydrophobic fabric, which are formed by myristate acid and nano-titanium dioxide.118
In addition to the means commonly used for fabric preparation mentioned earlier, nonwovens construct fabrics directly from hydrophobic fibers, such as melt-blowing and electrospinning.121 As shown in Fig. 4d, the polylactic acid (PLA) and propylene-based elastomer (PBE) polymer are dissolved at high temperature and squeezed into a small spine-jet hole. At the same time, the PLA/PBE polymer are pulled by high pressure and high speed compressed gas, and solidified in the air to form microfibers. This blended nanofiber fabric is hydrophobic.119 Similar to melt-blowing, electrospinning is a process of atomizing polymer fluid to form nanofibers under the action of high voltage electric field.122 The fluorine-free fabric by green electrospinning technology has a highly hydrophobic porous structure, the hydrophobic film has ultra-highly water resistance and air permeability.123
4.2 Eco-friendly and efficient treatment methods
Efficient and rapid preparation methods are vital for enhancing production economic benefit of fabrics.124,125 Furthermore, traditional preparation methods typically suffer from high water usage and subsequent effluent liquor generation, leading to secondary pollution within the preparation process.126 To tackle these issues, Lai et al.127,128 have introduced a foam finishing technique for hydrophobic textile treatment. Notably, this method of preparing hydrophobic textiles can reduce the use of aqueous solutions without significantly affecting the breathability and weight of the fabric. As depicted in Fig. 5a, the process involves using surfactants turn an aqueous solution into the foams, replacing water with air as a solvent, thereby decreasing the solution usage. The Fig. 5b demonstrates the impacts of different finishing methods on the liquid pickup, weight gain and breathability of fabrics. The foam finishing method has a lower liquid pickup and weight gain, which means the fabric is quicker drying and energy-efficient. Furthermore, the textile treated with this method are lighter and thinner. Foam finishing method offers advantages, it presented a new idea for the preparation of green hydrophobic textiles.
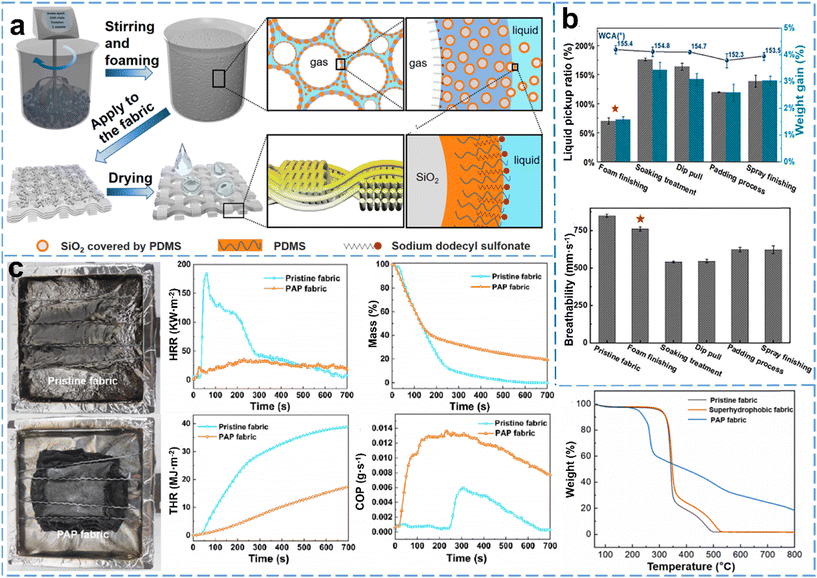 |
| Fig. 5 (a) Preparation process of foam finishing; (b) liquid carrying rate and air permeability of fabric treated by different means,127 Copyright 2021 Elsevier; (c) fabric cone calorimetry and thermogravimetric test,128 Copyright 2023 Elsevier. | |
The foam finishing method constructs a thin and intact film on the textile surface, using a little amount of material, yielding effective protection for the fabric. As illustrated in Fig. 5c, the treated textiles underwent cone calorimetry and thermogravimetric analyses, revealing that the modified fabrics exhibit a stable flame-retardant process. In contrast to traditional methods such as dipping and spraying, which thoroughly impregnate the fabric from the outside, the foam finishing approach predominantly deposits materials on the surface of the textile with limited penetration into the fibers.
The sudden change of interface energy will cause huge influence in surface wettability. As shown in Fig. 6, a water-based coating that can be rapidly switched between hydrophobic and hydrophilic.129 Taking inspiration from seashells, the team designed an eco-friendly, biodegradable, and naturally derived hydrophobic flame-retardant coating. It is noteworthy that after being processed with a hydrophobic coating, wall surfaces exhibited persistent superhydrophobic and flame resistance, yet upon respraying with a hydrophilic salt solution, the surfaces could be rapidly transformed from hydrophobic to hydrophilic. This design inspiration lays the groundwork for rapidly transforming textiles from hydrophobic to hydrophilic, further enhancing the convenience of practical applications of fabrics.
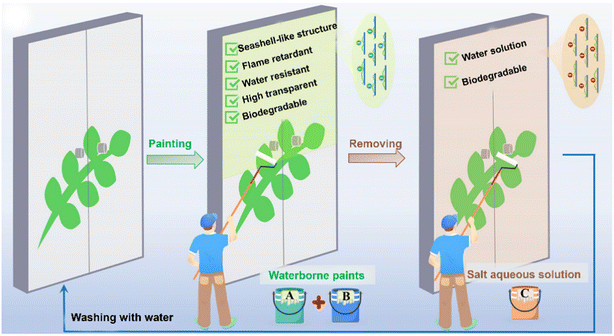 |
| Fig. 6 Switchable waterborne coatings,129 Copyright 2023 American Chemical Society. | |
4.3 Tough hydrophobic coating
The durability of fabric functionality is a critical factor that must be considered for the routine utilization of hydrophobic textiles. As described above, a more stable hydrophobic fabric can be obtained by physical and chemical means, and the mechanical properties of the fiber can also be improved.130,131 Besides, the hydrophobic stability of fabric can also be improved by reasonable surface structure design. Here are some innovative design strategies.
Deformable water-resistant surface structure. As shown in Fig. 7a, the superhydrophobic surface is composed of an array of rigid micropillars topped with a soft polydimethylsiloxane (PDMS) matrix.132 Under hydraulic pressure, the soft PDMS tips at the top of the structure undergo reversible deformation, in which compression of the PDMS spheres reduces the inter-pillar gaps under applied pressure. This alteration allows the superhydrophobic surface to maintain a stable Cassie state during compression and impact by water droplets, preventing droplet infiltration. This special structure balance between breathability and hydrophobic of the fabric under various complex wetting conditions.
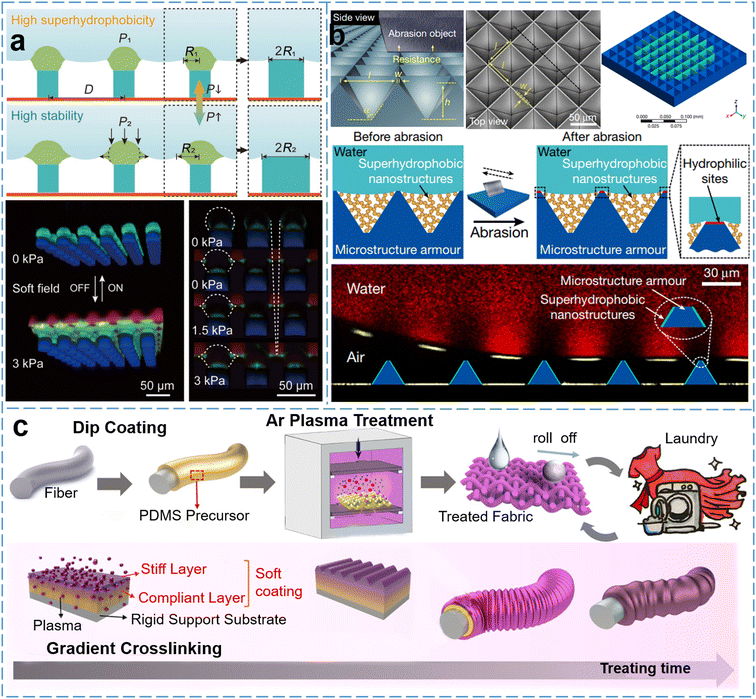 |
| Fig. 7 (a) Design of the LPGSS and its switching effect diagram,132 Copyright 2022 Wiley-VCH; (b) design of the microstructure armour,133 Copyright 2020 Springer Nature; (c) SH fabric is prepared by argon plasma treatment and a wrinkled surface is formed on the fiber,134 Copyright 2021 American Chemical Society. | |
The rigid structure combined with brittle materials. In general, the hydrophobic modified materials are easily damaged. It is a good strategy to improve the wear resistance of hydrophobic fabrics that using strong structure to protect hydrophobic materials. As depicted in Fig. 7b, a robust armored hydrophobic surface by wrapping waterproof materials in a high-strength array framework.133 When the coated surface is mechanically scratched, the high-strength framework protects the hydrophobic materials from being detached. The mechanical strength of the pyramid structured coating increases with the area of the frame. Although this case does not apply to the preparation of hydrophobic fabrics, it also provides us with a good idea. Similar thinking, the tough fibers can be used to protect hydrophobic materials, it is similarly adding nanomaterials to a body armor.135
Soft surfaces resist rigid damage. Xu et al.134 emulated the soft, wrinkled skin of earthworms and designed a super durable fabric with adaptive deformation, as illustrated in Fig. 7c. The reversible wrinkled surface and the interfacial viscoelastic layer can accommodate mechanical wear and shear forces encountered during washing and friction processes. The mimicking biological behaviors and surface structures has offered significant ideas for the design of hydrophobic surfaces.136–139
In addition to the previously mentioned passive defense mechanism of coatings under external aggression, and the durability of coatings can be enhanced through active self-healing strategies. The self-healing coating of fabric can be divided into internal healing repair and external stimulation repair.140–143 The intrinsic repair system refers to the ability of the coating to carry out the repair process independently of external conditions after damage, and thus inspires the design of microcapsules.144,145 The external repair coating can be repaired under the action of temperature, pH, humidity, ultraviolet light and other factors.146,147 For instance, ultra-thin autonomic healing vitrimer coatings,148 with the dynamic bonding of the coating material, endows it with self-healing and damage-resistant properties. The Fig. 8 shows the recovery process of the damaged vitreous after reheating.
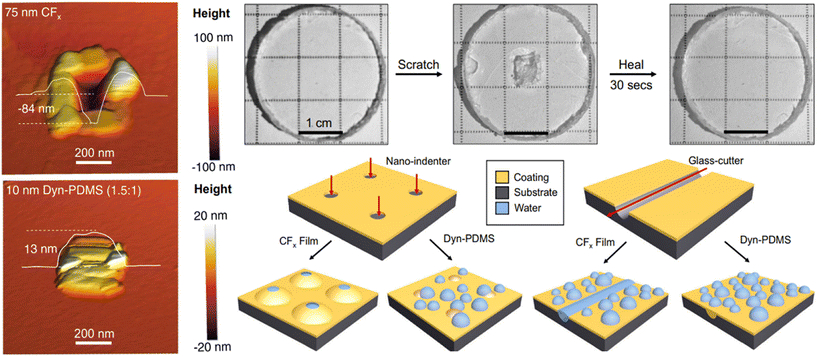 |
| Fig. 8 Self-healing of dynamic crosslinks films,148 Copyright 2021 Springer Nature. | |
5 The functional application of hydrophobic fabrics
Superhydrophobic fabrics are extensive application in engineering, with their simplest use being in the creation of waterproof fabric such as storm jackets and tents. The precise manipulation of droplet behavior can be achieved through the construction of specially wettability fabrics.149 Additionally, conductive modification hydrophobic fabrics, the conductive polymers can also control the wettability of the fabric and ensure the stability of the conductive stability.150,151 The versatility of hydrophobic fabrics is substantial, allowing for integration with numerous functionalities, thereby unlocking greater potential value.152,153
5.1 Functional fabric based on hydrophobic properties
5.1.1 Oil–water separation fabric.
The hydrophobic and oleophilic nature of hydrophobic fabrics imparts them with the capability for oil–water separation. The surface energy of oil is lower, allowing it to permeate through the hydrophobic fabric under the gravity and capillary forces, whereas the water unable to infiltrate the superhydrophobic fabric because of its higher surface energy.154–157 For example, Bai et al.158 synthesized a novel cashew phenol-KH550 benzoxazine (CKBO) by reacting it with 3-aminopropyltriethoxysilane (KH-550) and grafted it onto cotton fabrics. In practical tests, even under harsh conditions, the CKBO-modified cotton fabrics exhibited high separation efficiency for a variety of immiscible oil–water mixtures. Devices designed for this separation based on the fabric substrate are advantageous due to their mechanical robustness and low cost.
5.1.2 High buoyancy fabric.
Drawing upon the lotus effect, the rough surface of the lotus leaves traps air when it is in contact with the liquid, thereby preventing the penetration of the droplet and manifesting water repellence in the macroscopic world. The silver mirror phenomenon can be observed when droplets contact the superhydrophobic surface, which is the result of air isolation between liquid and surfaces. Therefore, when the superhydrophobic fabric is immersed in the liquid, a large amount of gas is confined to the surface rough texture, so that the surface has a buoyancy force beyond its own.159,160 Zhang et al.161 prepared superhydrophobic fabrics using a simple spray process. In the buoyancy tests, the coated filter paper was able to support a weight 39 times of its own. Inspired by this characteristic of hydrophobic fabrics, there are potential applications in drowning prevention or aquatic rescue equipment.162,163
5.1.3 Janus membrane and sweat monitoring.
The ease in handling of textile fabrics is a critical aspect in the design process of wearable materials. However, waterproofing and breathability have always represented two diametrically opposed extremes. High-density fabrics can mitigate the penetration of droplets into fibers, yet simultaneously, the breathability of the fabric tends to decrease accordingly.164,165 Consequently, the pursuit of fabric that embodies both efficient hydrophobicity and breathability remains a focal point of research.
Fabrics embedded with membranes that exhibit asymmetrical physical and chemical properties, manifested as variations in surface hydrophilicity or charge delineation, are referred to as Janus membranes. Due to their unique asymmetric surface topography, Janus membranes impart specialized fluid transport capabilities,166 which have drawn considerable interest in the realm of waterproof textile design.167,168Fig. 9a elucidates the diffusion process of water across the surface of Janus fabric.127 As water encounters the hydrophobic side, it continues to disperse towards the hydrophilic test direction due to the collective forces of gravity (Fg), capillary force (Fc), and surface tension (Fs), yielding a resultant force is greater than 0 ((F = Fg + Fc + Fs) > 0). Conversely, upon contacting the hydrophobic interface, droplets experience radial expansion driven by surface tension and capillary. In scenarios where the aggregate force is overcome by the capillary force, the resultant force is less than 0 ((F = Fg + Fc − Fs) < 0), penetration of the droplets through the fabric is inhibited.
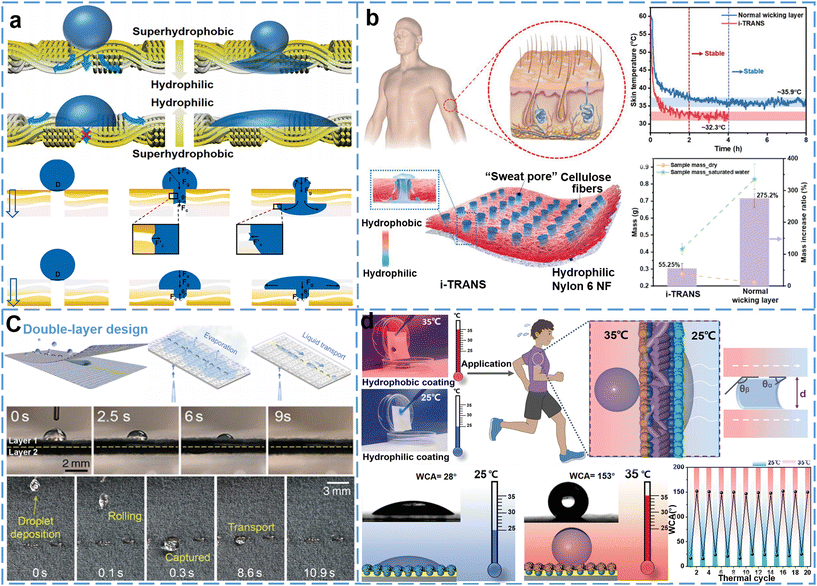 |
| Fig. 9 (a) Janus fabric one-way water transport mechanism,127 Copyright 2021 Elsevier; (b) concept illustration of integrated 3D hydrophilicity/hydrophobicity design for artificial sweating skin (i-TRANS),169 Copyright 2022 Wiley-VCH; (c) schematic of the fabrication of the double-layer fabric assembly,170 Copyright 2023 The Royal Society of Chemistry; (d) temperature triggered directional water transport fabric,171 Copyright 2023 Wiley-VCH. | |
For example, Soltani et al.170 have engineered a textile with a Janus membrane structure that facilitates rapid sweat expulsion to ensure human comfort. As depicted in Fig. 9c, the team created a wetting channel on the inner layer of the fabric by wearing two superhydrophobic textiles together. In this configuration, liquid is channeled through a slit into an internal passage, allowing droplets to be transported within the fabric while keeping its exterior dry. This design ensures effective droplet transfer even in highly humid environments. The droplet behavior can also be controlled by external stimulus.172 The Fig. 9d shows a thermally responsive dynamic Janus fabric.171 When thermosensitive Janus particles adhere to a textile, the surface becomes hydrophobic at temperatures above 32 °C and hydrophilic below this threshold. Therefore, when this composite fabric is worn, the side in contact with skin becomes hydrophobic due to body heat, whereas the opposite side remains hydrophilic, thereby creating a Janus membrane on two sides of the skin enabling directed sweat transfer. Moreover, there is also a biomimetic skin designed based on Janus membrane characteristics (Fig. 9b), which can effectively facilitate rapid evaporation of human sweat and regulate body temperature.169,173–175 It has been demonstrated that the judicious design of fabric structures, combined with the manipulation of physicochemical properties, can engender a differential pressure in droplets, thereby facilitating their autonomous movement.
5.1.4 Fog harvesting devices.
By manipulating the gradient of wettability and implementing specialized structural designs, researchers have also developed fog-harvesting and water-collection textiles.176–178 Fog harvesting devices, which collect atmospheric water vapor and convert it into liquid fresh water, hold practical significance for addressing freshwater needs in arid regions and for the desalination of seawater. Inspired by the prism-like structures of desert beetle's elytra,179 Yu et al.180 fabricated a biomimetic, ultralight, superhydrophilic–superhydrophobic (SHL–SHB) foldable fabric (Fig. 10a). Employing advanced textile manufacturing techniques, yarns with opposing wettability were interlaced, resulting in a vein-like, wedge-shaped structure. SHL yarns are distributed on both sides of the wedge to rapidly capture droplets, while SHB yarns facilitate droplet transport. This wedge-shaped structure, also discernible within the cacti. The curvature gradient along the wedge-shaped track, induces a Laplace pressure difference across the droplet, coupled with fibers of varying wettability, facilitates the directed movement of droplets through capillary action. Special structural is an effective means to drive the droplet, on the other hand, reasonable utilization of the external energy can also achieve on-demand functionality.181,182Fig. 10b depicted a device with high thermal conductivity interfaces and dual asymmetry structures.183 The thermal gradient formed on the fabric surface and accelerates the condensation of vapor, while the synergistic action of the wedge-shaped structure and asymmetric wettability gradient provides a potent driving force for the directed transfer of droplets. Experimental results revealed that the maximum water collection rate (WCR) of the fabric-based fog harvester reached 1538.4 mg h cm−2. Beyond the mentioned fog-harvesting devices, researchers have also developed devices for extracting clean water from wastewater and high-performance devices for seawater evaporation and fog harvesting to collect fresh water (Fig. 10c).184 Tan et al.185 shows the water collection process using the wedge-shaped structure, promising for application on sailboats to acquire freshwater at sea (Fig. 10d). Fog-harvesting apparatuses based on green fabrics offer favorable biocompatibility and can be widely utilized in natural settings without generating pollution. Additionally, leveraging the unique absorptive properties of the fabric fibers facilitates the control of droplets with greater ease.
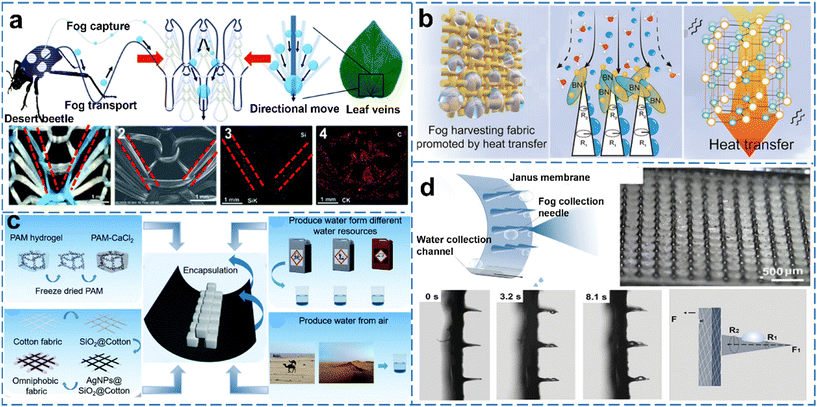 |
| Fig. 10 (a) Double bionic mist collection knitted fabric design,180 Copyright 2022 The Royal Society of Chemistry; (b) fog collecting process of thermodynamically induced interfacial condensation trap,183 Copyright 2023 Wiley-VCH; (c) application of mixed water vapor adsorbent design,184 Copyright 2021 The Royal Society of Chemistry; (d) observation of the fog collection process and analysis of the droplet transportation mechanism,185 Copyright 2022 Wiley-VCH. | |
5.2 Functional fabric based on hydrophobic and conductive materials
Owing to the effective isolation between hydrophobic fabrics and aqueous solutions, the introduction of electrical conductivity to hydrophobic textiles can yield more favorable outcomes and concurrently facilitate the realization of unique functionalities within the fabric.
5.2.1 Nanogenerator.
Nanogenerators have emerged as a research focal point in recent years. The nanogenerator is a nano-scale device, which converts mechanical energy into electrical energy. Nanogenerators mainly include piezoelectric nanogenerators, triboelectric nanogenerators, and thermoelectric nanogenerators, among others.186 Researchers have utilized the energy generated from human motion to fabricate textile-based nanogenerators, such as the inner and outer rings of fibers made of different materials can carry different charges,187 so a potential difference can be created on a single fiber (Fig. 11a left). Charge transfer occurs in external work such as fiber friction or compression, and current is generated under the difference of potential. Moreover, by placing the fibers in series and the fabric layer-by-layer, and the current is increased for use (Fig. 11a right). Furthermore, the repulsive effect of hydrophobic fabrics towards aqueous solutions can maintain the stability of the current produced by nanogenerators and protect the device, marking the development of hydrophobic fabric-based nanogenerators as bearing significant practical application value. Yang et al.188 proposed a novel bio-friendly triboelectric nanogenerator (SF-TENG) based on superhydrophobic conductive antibacterial cellulose. The team employed a unique bioremediation approach to prepare core–shell structures, thereby achieving a superhydrophobic layer on woven fibers. Another example, superhydrophobic cores composite fabric with conductive properties.189 Integrated nanogenerators boasted advantages such as simple structures and low wear characteristics. Due to the waterproof nature of the fabric surface, the textiles maintained high output performance even under high humidity conditions.190
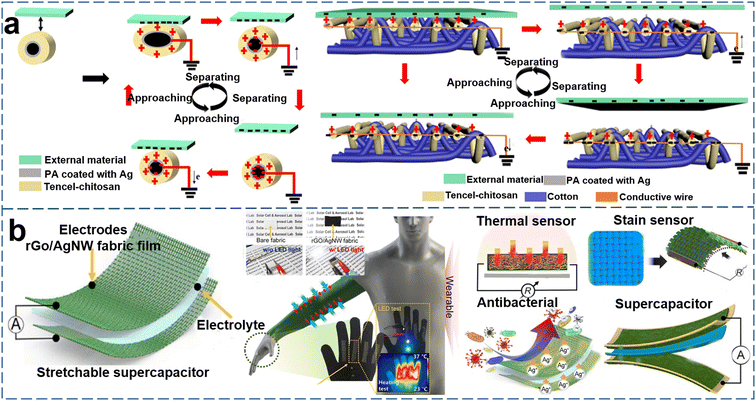 |
| Fig. 11 (a) Structure and working principle of friction nanogenerator,187 Copyright 2021 American Chemical Society; (b) wearable supercapacitors and human motion sensors,191 Copyright 2021 American Chemical Society. | |
Hydrophobic fabrics that integrate nanogenerators and body monitoring have also been extensively studied. Such as, combination of high moisture permeability fiber and nanogenerator,192 or body motion sensing combined with nano generation.193 For example, Hou et al.194 have developed a triboelectric structural material with superhydrophobic and sensing capabilities, which can ensure stable motion monitoring in a high humidity environment. In addition, the nanogenerator has wireless signal transmission function, and the motion information of the personnel is transmitted within a distance of ≈3 meters. Such cases provide some inspiration for the development of interconnection fabric and intelligent fabrics.
5.2.2 Supercapacitors.
Supercapacitors represent a promising energy storage device. They are equipped with advantages such as fast charging rates, stable electrical performances, and high cycle lives, which could meet the application requirements for future wearable devices.195 Kim et al.191 designed a multifunctional fabric that encompasses sensing, heating, and supercapacitor capabilities, along with antibacterial properties (Fig. 11b). Such multifunctional integrated portable electronic textiles hold excellent application prospects in medical monitoring, intelligent active wear, energy storage, and other fields. Additional related examples are also documented.196–198
5.2.3 Human motion sensor.
Unlike traditional mechanical devices, fabric sensing devices are thinner and more precise, are thus are promising to replace human sensing devices currently available on the market. A variety of human motion sensing devices,199 leveraging the advantages of the superhydrophobic coating, the sensor can operate under harsh conditions such as moisture, acid, alkali, and salt environments. The fabric is capable of detecting human motion (throat, neck, elbow, wrist, knee, fingers, etc.). Sensors for a variety of fields and applications. As shown in Fig. 12a, a fabric-based multifunctional strain sensor with excellent electromechanical performances that can be mounted on joints for activity monitoring, medical rehabilitation assessment, gesture recognition, and other functions.200 Motion monitoring based on waterproof fabrics can offer certain safety guarantees to individuals working in special environments, like outdoor research teams, divers, and athletes. Body sensors are used in human health monitoring, it has great application potential in the medical field. Wang et al.201 intercalated a high-sensitivity porous polyethylene terephthalate (PET) sensor between layers of superhydrophobic fabric to design a sensor with high sensitivity and outstanding breathability for sweat analysis. This fabric can be used to assess human life and health conditions such as thermoregulation and skin barrier functions (Fig. 12c). Reports on droplet-based control systems that enable precise measurements are uncommon, underscoring the suitability of conductive fabrics for integration with various functional textiles. Furthermore, the motion sensor applied in life safety field, Lai et al.202 developed a silver-rim sensor on superhydrophobic conductive knit polyester fabrics that make use of the characteristics of waterproof textiles. Utilizing the fabric's excellent hydrophobicity (Fig. 12b), conductivity, and mechanical properties, it is feasible to achieve underwater human motion monitoring and drowning alarms, laying a practical foundation for the commercialization of wearable functional fabrics for the human body.203,204
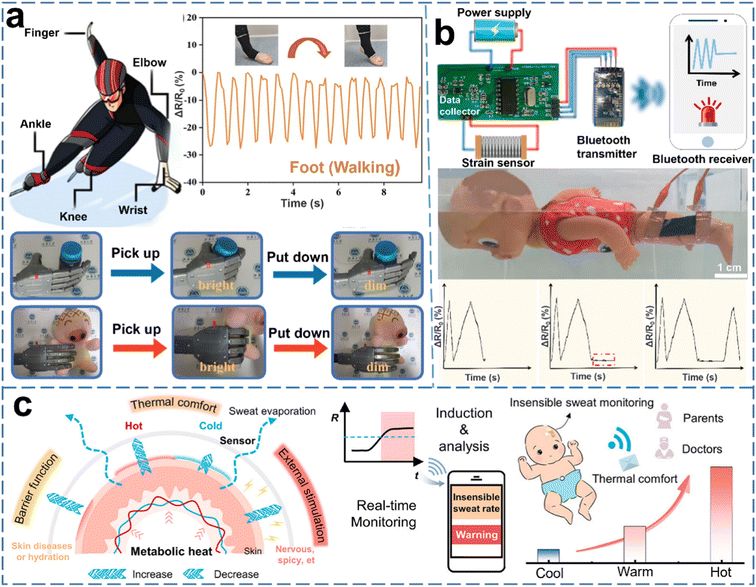 |
| Fig. 12 (a) Multifunctional fabric sensor,200 Copyright 2022 Springer Nature; (b) drowning alarm device based on fabric,202 Copyright 2022 American Chemical Society; (c) application of conductive fabric in medical treatment,201 Copyright 2023 American Chemical Society. | |
5.2.4 Electromagnetic shielding fabric.
With the continuous development of modern electronic communication technologies, there is a widespread need for effective electromagnetic wave shielding materials. These materials serve to protect electronic devices from electromagnetic radiation, safeguarding human health and safety, and they are also of great interest in the defense applications (Fig. 13b).205,206 Owing to the excellent flexibility of wearable fabrics and the electromagnetic absorption and shielding properties of fabric conductive materials, the electromagnetic shielding function of conductive fabrics has garnered attention. Conductive materials are treated on cotton fabrics to form conductive coatings, and the textiles offering outstanding electromagnetic shielding, hydrophobicity, and thermal conductivity.207,208
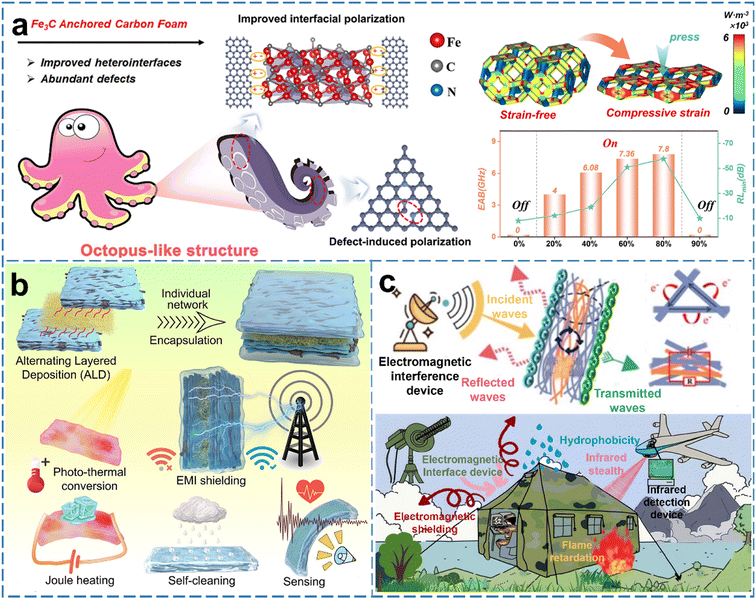 |
| Fig. 13 (a) Bionic octopus structure inspired stress-driven reconfigurable microwave absorption and electromagnetic switching process,209 Copyright 2023 Elsevier; (b) electromagnetic shielding fabric application scenario,205 Copyright 2022 American Chemical Society; (c) electromagnetic shielding fabrics are used in military neighborhoods,210 Copyright 2023 Elsevier. | |
In the defense domain, textiles with infrared stealth and electromagnetic shielding are widely utilized. Imitated the structure of octopus tentacles,209 achieving adjustable “on–off–on” electromagnetic absorption performance by altering the pore size of the foam skeleton through compressive strain (Fig. 13a). A hybrid strategy by fabricating highly anti-oxidative two-dimensional metal carbides/nitrides (MXene)@gallotannic acid (GA) through Fe3+ interactions and covalently grafting the coating onto cotton fabric.211 Leveraging the antioxidative nature and strong binding properties of GA materials, the fabric maintains good stability, washing resistance, and can withstand various extreme conditions, while achieving excellent conductivity and efficient electromagnetic shielding for infrared camouflage. As shown in Fig. 13c, a multi-function tent featuring electromagnetic shielding and infrared stealth capabilities along with hydrophobic and flame-retardant properties, suitable for tents in harsh conditions.210
Additionally, electromagnetic waves often interfere with the monitoring accuracy of the instrument. Han et al.212 developed a flexible piezoelectric sensor system based on high-performance electromagnetic shielding signal interference, which can accurately collect and analyze unique physiological sound patterns related to clinical applications, aiding in the diagnosis of heart disease. Liu et al.213 developed a highly stretchable, high-permeability liquid metal electronic textile that not only precisely monitors health vitals including respiration, energy generation, surface electromyography (sEMG), and electroencephalogram (EEG) signals, but also maintains commercial electromagnetic shielding requirements under 300% strain (Fig. 14). The preceding introduction outlines a distinct category of fabrics that are enhanced with the capability to shield against electromagnetic interference. This enhancement primarily relies on the creation of interconnected networks facilitated by the high conductivity of surface materials, which in turn serves as a foundation for developing innovative applications within the realm of textile design. However, research aimed at enhancing electromagnetic shielding performance through special designs on ultra-thin fabric coatings remains scarce, despite being a challenging endeavor.
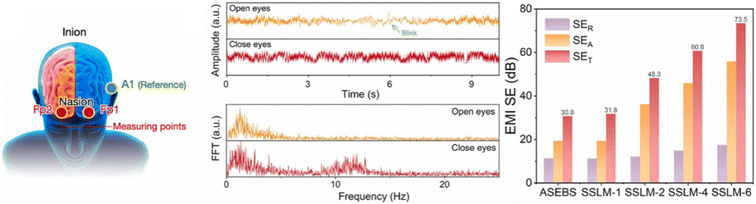 |
| Fig. 14 High precision human physiological signal monitoring wearable chip based on electromagnetic shielding structure,213 Copyright 2023 Elsevier. | |
Existing conductive fabrics are primarily functionally independent, capable of realizing only singular or partial functionalities. However, for the realization of highly intelligent fabrics, it is imperative that these textiles integrate multiple functions,214–217 such as being powered by nanogenerators, energy storage in supercapacitors, functionality execution within designated zones, and interconnecting communication with external devices. In the future, such intelligent fabrics might supersede our current smart devices, like smartphones and computers.
5.3 Based on hydrophobic fabrics with photocatalytic applications
5.3.1 Self-cleaning, anti-bacterial and ultraviolet shielding fabric.
Leveraging the low droplet adhesion and self-cleaning properties of hydrophobic fabrics, researchers have enhanced these materials by incorporating photocatalytic substances. For instance, by in situ deposition of photocatalytic materials on fabric substrates and then hydrophobic finishing, superhydrophobic and photodegradable fabrics have been prepared, endowing the fabric with self-cleaning and antibacterial surface characteristics.218 This combination gives the fabric excellent UV resistance, mechanical wear and photocatalytic self-cleaning capabilities.
Photocatalytic materials undergo redox reactions upon exposure to light, in conjunction with the fabric's superhydrophobic behavior, effectively degrading stains adhered to the fabric. Moreover, these materials can also reflect or absorb light waves, harnessing solar energy. Agrawal et al.219 reported a dual-stage silanization technique for creating superhydrophobic, antibacterial, and UV-protective fabrics. This straightforward fabrication strategy holds significant potential for commercial application in textile materials. There are other reports, a multifunctional fabric prepared with significant hydrophobicity and photothermal effects for oil removal and water evaporation purification.220 Converting waste textiles into multifunctional photothermal protective materials through carbonization.221
5.3.2 Active heating, deicing and anti-icing.
Ice is prevalent in nature and poses detrimental impacts on societal industrial production and daily human life. In general, de-icing strategies can be categorized into passive de-icing based on superhydrophobic surfaces and active de-icing utilizing photothermal and electrothermal materials (Fig. 15a).222 Zhao et al.223 introduced a highly efficient fluorine-free superhydrophobic photothermal fabric. Owing to its proficient photothermal conversion property, this fabric could heat the coating to 100 °C at room temperature in 120 s under simulated solar irradiation, demonstrating excellent anti-icing and de-icing performance.
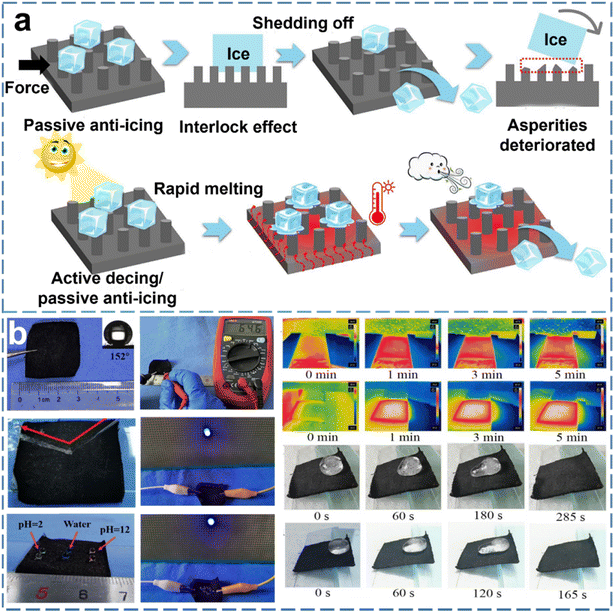 |
| Fig. 15 (a) Schematic overview of deicing/anti-icing surfaces,222 Copyright 2023 Elsevier; (b) conductive fabric active deicing process,224 Copyright 2022 Elsevier. | |
The deicing ability of the superhydrophobic fabric can also be improved by active heating.224Fig. 15b shows the electrical conductivity of the fabric and the rate of heating and deicing effect of the fabric under sunlight. Fabrics designed with anti-icing and de-icing functionalities based on these principles can be applied to materials such as storm jackets and outdoor travel tents under extreme ice and snow conditions.
5.3.3 Seawater desalination, solar energy harvesting.
Photothermal nanomaterials exhibit exceptional characteristics such as high photothermal conversion efficiency and broad absorption bandwidth, which can be harnessed for rapid de-icing and seawater desalination. Furthermore, they offer the potential to transform the abundant solar energy into forms of energy required by humans. Xiao et al.225 developed a superhydrophobic fabric composite material for interface-efficient evaporation, as illustrated in Fig. 16a. The fabric comprises a solar energy absorption layer, an insulation layer, and a top-down water transport channel. Utilizing highly hydrophilic PF as a water-absorbing material for efficient moisture wicking and polystyrene foam as an insulating layer, the solar energy absorption layer is constituted of a matrix fabric made from superhydrophobic PDMS and MXene materials. The surface roughness and photothermal properties of the fabric's hydrophobic layer enhance the light absorption efficiency. Moreover, the liquid pumped from below cannot reach the hydrophobic layer, thereby reducing thermal losses from interfacial evaporation, whereas high-concentration brine returns to the water body driven by a concentration gradient. The insulation layer keeps the upper layer's light and heat separated from the water below, preventing heat transfer to the water body. During the process of evaporation, it is often desirable to attain sufficiently elevated temperatures to expedite the vaporization of liquids. In addition to facilitating rapid temperature increases at the evaporative surface, Xiao et al. has also managed to minimize the thermal conduction of heat from the evaporative layer to the body of water.
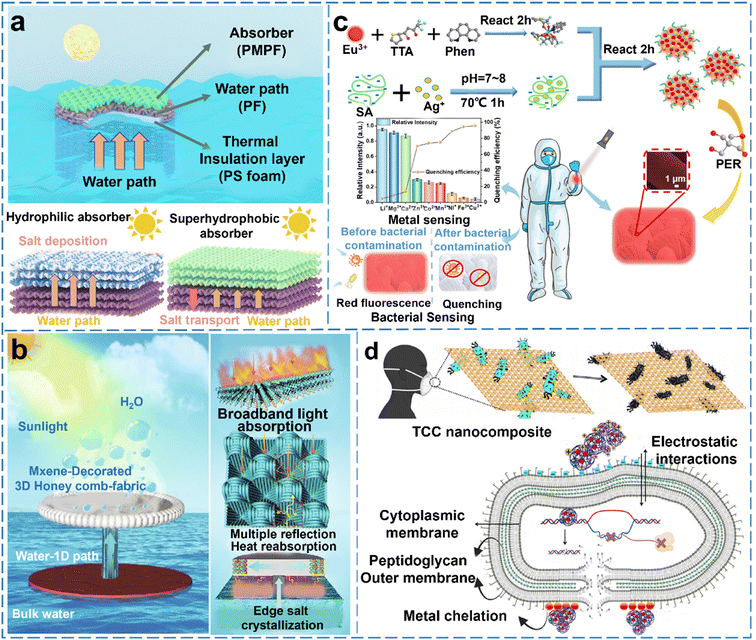 |
| Fig. 16 (a) Schematic diagram of salt deposition and salt tolerance in a brine evaporator,225 Copyright 2021 Elsevier. (b) Three-dimensional honeycomb fabric solar evaporation seawater desalination schematic diagram,226 Copyright 2022 Springer Nature; (c) experimental mechanism and performance of smart wearable fluorescent sensing fabric,227 Copyright 2022 American Chemical Society; (d) schematic diagram of antibacterial mechanism of nanocomposites,228 Copyright 2023 American Chemical Society. | |
The following example, employs a clever design that achieves efficient water transport through the construction of a moisture gradient within the fabric, thereby securing highly effective evaporation. Wu et al.229 constructed a novel cotton fabric evaporator with a superhydrophobic–hydrophobic–hydrophilic–superhydrophilic wetting gradient (CEF-WG). The wetting gradient design of CEF-WG efficiently prevents excessive brine from entering the evaporator and effectively reduces thermal losses. Portable solar water purification and processing provide an expandable evaporator for solar-thermal applications.
Other researchers have developed a range of solar liquid evaporation devices through special fabric weaving and structural design,226,230–233 presenting possibilities for the commercialization of accelerated wastewater treatment, seawater desalination, and drinking water collection (Fig. 16b). Moreover, wearable energy storage fabrics have been designed based on high energy storage capacity.234,235
5.3.4 Luminous quantum dots and fluorescent fabrics.
Additionally, there are special fabric materials made utilizing photonic quantum entities. For instance, the surface of the fiber is coated with luminescent nanomaterials, and leveraging the function of photoluminescent nanomaterials, the fabric emits different colors of light under varying frequencies of light radiation (green under ultraviolet irradiation, gray and white under sunlight irradiation, etc.).236
Moreover, wearable sensing fabrics have been designed based on the integration of fluorescent nanomaterials with antibacterial agents,227,228 achieving fluorescence tagging and colony suppression of bacteria (Fig. 16c) and toxic metal ions. Fig. 16d depicts the degradation process of bacterial colonies by antibacterial fluorescent nanomaterials. Such materials hold significant potential for applications in environmental monitoring and healthcare settings.
5.4 Other types of functional hydrophobic fabrics
5.4.1 Hydrophobic flame-retardant fabric.
Under natural conditions, fabrics are susceptible to combustion, posing a fire safety hazard. Therefore, the fabrication of durable flame-retardant fabrics is of significant importance for fire protection.237,238 Chattopadhyay et al.239 employed a two-step spray-coating approach to create multifunctional fabrics. The first layer was spray-coated with chitosan and phytic acid to form a flame-retardant coating, while the second layer was coated with PDMS–ZnO to establish a hydrophobic coating. Following modification, the cotton fabric's limiting oxygen index (LOI) increased from 18% to 30%, and its peak heat release rate (PHRR) and total heat release rate (THR) were reduced to 75% and 33%, respectively. The contact angle of the fabric with water was 148°. The combination of green natural materials tannic acid (TA), phytic acid (PA) and polydimethylsiloxane (PDMS) was used to construct an environmentally friendly and efficient hydrophobic flame-retardant coating on cotton fabric using a layer-by-layer self-assembly method (LBL).240,241
There are also instances for fire alarm and personal protection applications, such as the design a superhydrophobic, flame-retardant, multifunctional conductive fiber fabric suitable for all-weather wear and high-temperature alarm.242 He et al.243 designed a self-powered fire alarm ultra-lightweight electronic textile based on conductive aerogels (Fig. 17a). Despite the advanced stage of development attained by hydrophobic and flame-retardant fabrics, their presence in the market is surprisingly minimal, a circumstance that might be attributed to their lack of practicality. In the future, researchers might delve into the behaviors of creatures in the natural world, drawing inspiration from biomimicry to craft fabrics with superior functionalities.244 (Fig. 17b, inspired by the structure of camel humps, designed fabrics with personal thermal protection and thermal comfort management). Moreover, steering the development of functional textiles towards real-world applications could foster a paradigm conducive to the creation of more exemplary hydrophobic and flame-retardant materials.
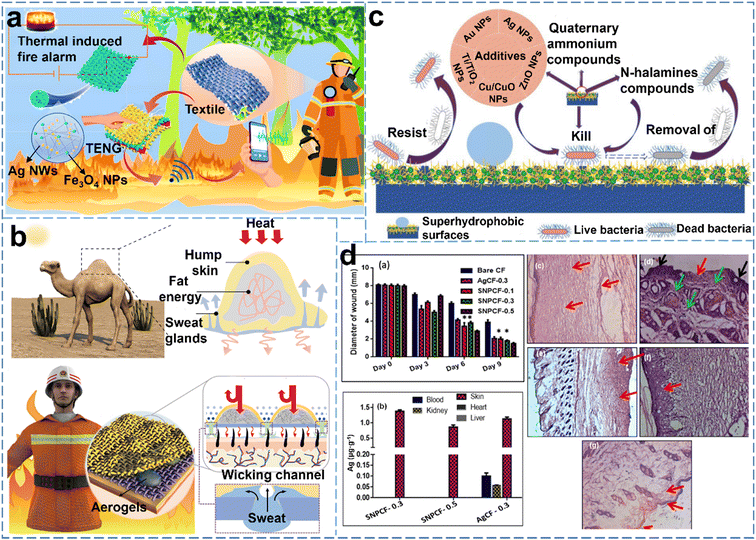 |
| Fig. 17 (a) Self-powered fireproof electronic textiles, with temperature monitoring and signal alarm, positioning,243 Copyright 2022 American Chemical Society; (b) hump-inspired layered flame retardant, heat management fabric,244 Copyright 2023 Wiley-VCH; (c) biomimetic superhydrophobic surfaces to inhibit microbial contamination,245 Copyright 2023 Springer Nature; (d) hydrophobic cotton to promote wound healing,246 Copyright 2021 American Chemical Society. | |
5.4.2 Hydrophobic antibacterial fabric.
Similarly, the self-cleaning properties of hydrophobic fabrics can effectively reduce the residual stains on the fabric surface and can also effectively inhibit the proliferation of bacteria and viruses on the fabric surface (Fig. 17c), making fabrics that combine hydrophobic and antibacterial functions a research focus.245 For instance, the fabric is coated with antibacterial materials and encapsulated with hydrophobic materials to achieve hydrophobic, antibacterial and other properties of the fabric.247 Suryaprabha et al.248 explored the blood repellency of cotton fabrics and their potential value in the medical field using a coating of chitosan–polyacrylonitrile–polyurethane. Additionally, photocatalytic materials have been introduced to decompose bacterial colonies through redox reactions under light irradiation.249–251
Beyond daily protection, the application of hydrophobic antibacterial fabrics in the healthcare sector is also expanding.252 For example, electronic textiles for human health monitoring and antibacterial properties,253 and antibacterial cotton fabrics incorporating silver nitrate nanoparticles can effectively accelerate wound healing and sterilization.246Fig. 17d represents the graphical depiction of wound closure caused by different treatments from day 0 to day 9. Histopathological analysis indicated that the epidermis of the mice treated with cotton fabric impregnated with silver nitroprusside nanoparticles (SNPCFs) was completely healed, with no signs of inflammation or fibrosis. The study suggests that SNPCFs can serve as a new type of agent for wound healing. Textiles hold an irreplaceable position in the realm of healthcare. Medical protective garments and masks crafted from ultra-hydrophobic fabrics can significantly reduce the adherence of bacteria and viruses, thereby diminishing the risk of occupational exposure. Furthermore, functional fabrics used in the production of band-aids and bandages offer assistance in patient recovery, providing a semblance of health assurance. Thus, the design of functional textiles for medical applications is of paramount importance. Table 1 summarizes the preparation process and application of hydrophobic fabrics.
Table 1 Preparation and properties of hydrophobic fabrics
Substrate |
Modified materials |
Fabrication strategy |
Wetting property |
Function & application |
Ref. |
WSA: water shedding angle; SA: sliding angle; UOCA: underwater oil contact angles; UWCA: underoil water contact angles; RHP: robust hydrostatic pressure.
|
Polyester cloth |
Hydrogenated castor oil |
Dipping |
WCA = 156.6°; aWSA = 4.8° |
Multi-substrate superhydrophobic coating |
60
|
Cotton fabric |
Stearic acid; Cu, rGo |
Dipping and in situ growth |
WCA = 153° |
Underwater, multifunctional superhydrophobic sensor |
63
|
Cotton fabric |
Lauric acid; γ-Fe2O3 |
Dipping |
WCA = 156° |
Oil/water separation; flame retardancy |
64
|
Polyester fabrics |
Cellulose oleoyl ester nanoparticles |
Coating |
WCA = 160.9°; aSA = 7 ± 1.6°; CAH = 2.5 ± 0.8° |
Triboelectric generator; multi-fabric hydrophobic coating |
65
|
Cotton fabric |
Phytic acid; stearic acid; epoxidized soybean oil |
Phytic acid etching and coating |
WCA = 156.3° |
Green superhydrophobic cotton fabrics |
74
|
Cellulose nonwoven |
Mono-isocyanate compounds |
Chemical branches |
WCA = 130–135° |
Green and breathable hydrophobic fabric |
82
|
Cotton fabric |
Lignocellulose |
Dipping |
WCA = 125.8°; aUOCA = 143.6°; aUCA = 151.7° |
Oil/water separation and seawater desalination |
83
|
Cotton fabric |
Oleoyl chloride; cellulose powder |
Spray coating |
WCA > 150° |
Ultraviolet resistant; oil/water separation |
86
|
Cotton fabric |
Lignin; Cu, Fe particles |
In situ deposition |
WCA = 149.9° |
Oil/water separation |
95
|
Cotton |
Chitosan; tannic acid polymer; PDMS |
Dipping |
WCA = 153.3° |
Ultraviolet resistant; photothermal; self-healing; oil/water separation |
102
|
Polyurethane fabric |
Dopamine; Fe nano-particles |
Fenton reaction; in situ polymerization |
WCA = 161.8° |
Structural robustness; oil/water separation |
116
|
Polypropylene fabric |
N.A. |
Plasma etching and thermal aging |
WCA = 180°; SA = 9.8° |
Efficient and simple preparation |
117
|
Silk fabrics |
Methyltrichlorosilane; papain, alkaline protease |
Enzyme-etching; CVD |
WCA = 156.7°; SA = 8.5° |
Oil/water separation |
120
|
Nonwoven |
Waterborne PU; long-chain alkyl polymer |
Electrospinning; in situ doping |
WCA = 137.1°; aRHP = 35.9 kPa |
Robust liquid water resistance and water vapor transmission capabilities |
121
|
Nonwoven |
Polylactic acid; propylene-based elastomer |
Melt-blown process |
WCA = 134° |
Oil/water separation |
119
|
Cotton fabric |
SiO2 nanoparticles; PDMS |
Foam finishing method |
WCA = 155.6 ± 1.7° |
Energy conservation, efficient and controllable fabric handling |
127
|
Polyester fabric |
Pentaerythritol oleate; 3-mercaptopropyltriethoxysilane |
Thiol-ene click reaction; spraying |
WCA = 171.2 ± 0.3° |
Durable hydrophobic coating for multiple substrates; self-healing |
146
|
Nonwoven |
TPU; MXene |
Electrospinning; dipping |
WCA = 145.3° |
Pressure–temperature sensing; rechargeable zinc–air battery |
163
|
Cotton |
Amino-silica PVDB/PANPAM |
Dipping |
WCA = 153° |
Temperature-triggered dynamic Janus fabrics for directional water transport |
171
|
Cellulose fiber |
SiO2 nanoparticles; gluconacetobacter xylinum |
Bio-fabricated |
WCA = 163.5 ± 4° |
Fabric-based triboelectric nanogenerators |
188
|
Knitted fabric |
Ni; ZnO |
Electroplated |
WCA = 125° |
Antibacterial; supercapacitor; pressure/temperature sensors |
196
|
Polyester fabrics |
PDMS; rGO |
Dipping |
WCA = 156° |
Underwater behavior monitoring and drowning alarm |
202
|
Cotton |
Polyphosphate; aluminium wire |
Dipping |
WCA = 130.2° |
Electromagnetic shielding, infrared stealth and flame retardance |
210
|
Cotton |
MXene; PPy; PDMS |
Dipping |
WCA = 152° |
Joule heating effects and light-to-heat conversion capabilities |
224
|
6 Conclusion and outlook
The realization of green sustainability and functionalization of hydrophobic fabrics still requires extensive research and consideration of industrial production. Current fabric design and manufacturing have been moving towards a green and sustainable approach. However, this ‘greenness’ is not all-encompassing, as the manufacturing process is not entirely green or might require a higher cost to make the fabrics healthier.254 Future designs should evolve towards a trend of being green throughout the entire process, cost-effective, and commercialization. With the rapid development of information technology, the Internet of Things, and artificial intelligence, the functionality of various smart textiles is becoming increasingly rich,255 while also gradually being applied in fields such as energy harvesting and resource recovery. Researchers should also focus on the sustainable development of functional fabrics and collaboration across multiple domains (Fig. 18).
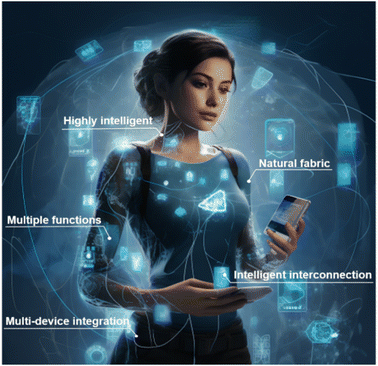 |
| Fig. 18 The future development direction of fabrics. | |
6.1 Material selection
As fabrics are intended for everyday use, they should meet basic standards of comfort, non-toxicity to the human body, and durability. In addition, the materials of the fabric should be cost-effective, environmentally friendly, and either naturally degradable or suitable for repeated use. In recent years, natural materials have garnered extensive attention in the preparation of multifunctional textiles due to their excellent biocompatibility and wide availability. Silk, cellulose, phytic acid, and chitosan, among others, have been utilized as foundational materials for multifunctional fabrics to replace other chemical substances. Moreover, the application of cross-linking agents or encapsulating materials to coat textiles can address the issues of wear and oxidation in superhydrophobic fabrics, thereby enhancing the durability of the fabric.
6.2 Process optimization
Today, the textile industry has evolved rapidly and established sophisticated assembly line manufacturing processes. However, high-efficiency production lines and flexible personalized design have traditionally been at odds with each other. In addition, the high efficiency and versatility of production lines are prerequisites for reducing the costs associated with fabric manufacturing and realizing personalized designs of functional fabrics. Therefore, bridging the gap between current industrial production lines and laboratory research conditions to facilitate the translation of functional fabrics from laboratory settings to production applications remains a topic that requires concerted efforts.
6.3 Functional development
Although numerous types of textile products have been invented in the research domain, their functions are mostly basic and discrete. Specifically, various performance textiles exist such as flame retardant, electromagnetic shielding, antibacterial, self-cleaning, etc. Likewise, there are textiles designed for applications like nano-generators, biosensors, supercapacitors, and so on. The integration of functionalities within textiles is of great importance. For instance, to achieve stable operation of textiles under all-weather conditions and across multiple environments with self-powering capabilities, textiles should fundamentally meet self-powering, energy storage, and functionality requirements. These objectives can be achieved by designing highly conductive circuits on the fabric and implementing zone segmentation, followed by an encapsulation process to ensure the durability of the integrated functional textiles.
6.4 Interdisciplinary integration
Research in special fabrics should also foster interdisciplinary collaborations, merging with communication technologies, artificial intelligence, and machine learning. First, to realize the Internet of Things and create intelligent fabrics capable of cognition, such as smart textiles that monitor human health information and intelligent home systems. Second, their application should span across various fields and settings, including healthcare (prevention, diagnosis, emergency response), exemplified by implanted human monitoring devices and artificial skin; defense applications (camouflage, interference), and space operations (radiation protection, lightweight, temperature control garments). Third, they should contribute to sustainable development through resource and energy harvesting. A widespread collaboration among engineers, scientists, and entrepreneurs is anticipated to facilitate the commercialization of intelligent textiles.
Data availability
All data generated or analyzed during this study are available from the corresponding authors upon request.
Conflicts of interest
The authors declare no conflict of interest.
Acknowledgements
This work was partly supported by the National Key Research and Development Program of China (2022YFB3804905 and 2022YFB3804900), the National Natural Science Foundation of China (22075046, 22375047, 22378068 and 22378071), Natural Science Foundation of Fujian Province (2022J01568).
References
- R. Zhong, S. Talebian, B. Mendes, G. Wallace, R. Langer, J. Conde and J. Shi, Hydrogels for RNA delivery, Nat. Mater., 2023, 22, 818–831 CrossRef CAS PubMed.
- L. Hu, P. Chee, S. Sugiarto, Y. Yu, C. Shi, R. Yan, Z. Yao, X. Shi, J. Zhi, D. Kai, H. Yu and W. Huang, Hydrogel-based flexible electronics, Adv. Mater., 2023, 35, 2205326 CrossRef CAS.
- Y. Xu, J. Hua, J. Hub, Y. Cheng, X. Chena, Z. Gu and Y. Li, Bioinspired polydopamine hydrogels: Strategies and applications, Prog. Polym. Sci., 2023, 146, 101740 CrossRef CAS.
- T. Zhu, Y. Ni, G. Biesold, Y. Cheng, M. Ge, H. Li, J. Huang, Z. Lin and Y. Lai, Recent advances in conductive hydrogels: Classifications, properties, and applications, Chem. Soc. Rev., 2023, 52, 473–509 RSC.
- K. Mendez, W. Whyte, B. Freedman, Y. Fan, C. Varela, M. Singh, J. Cintron-Cruz, S. Rothenbücher, J. Li, D. Mooney and E. Roche, Mechanoresponsive drug release from a flexible, tissue-Adherent, hybrid hydrogel actuator, Adv. Mater., 2023, 2303301 CrossRef.
- J. Guo, S. Fu, Y. Deng, X. Xu, S. Laima, D. Liu, P. Zhang, J. Zhou, H. Zhao, H. Yu, S. Dang, J. Zhang, Y. Zhao, H. Li and X. Duan, Hypocrystalline ceramic aerogels for thermal insulation at extreme conditions, Nature, 2022, 606, 909–916 CrossRef CAS PubMed.
- T. Xu, Q. Song, K. Liu, H. Liu, J. Pan, W. Liu, L. Dai, M. Zhang, Y. Wang, C. Si, H. Du and K. Zhang, Nanocellulose-assisted construction of multifunctional MXene-based aerogels with engineering biomimetic texture for pressure sensor and compressible electrode, Nano-Micro Lett., 2023, 15, 98 CrossRef CAS.
- J. Sun, T. Wu, H. Wu, W. Li, L. Li, S. Liu, J. Wang, W. Malfait and S. Zhao, Aerogel-based solar-powered water production from atmosphere and ocean: A review, Mater. Sci. Eng., R, 2023, 154, 100735 CrossRef.
- E. Abraham, V. Cherpak, B. Senyuk, J. Hove, T. Lee, Q. Liu and I. Smalyukh, Highly transparent silanized cellulose aerogels for boosting energy efficiency of glazing in buildings, Nat. Energy, 2023, 8, 381–396 CrossRef CAS.
- F. Wu, P. Hu, F. Hu, Z. Tian, J. Tang, P. Zhang, L. Pan, M. Barsoum, L. Cai and Z. Sun, Multifunctional MXene/C aerogels for enhanced microwave absorption and thermal insulation, Nano-Micro Lett., 2023, 15, 194 CrossRef CAS.
- W. Yan, G. Noel, G. Loke, E. Meiklejohn, T. Khudiyev, J. Marion, G. Rui, J. Lin, J. Cherston, A. Sahasrabudhe, J. Wilbert, I. Wicaksono, R. Hoyt, A. Missakian, L. Zhu, C. Ma, J. Joannopoulos and Y. Fink, Single fiber enables acoustic fabrics via nanometer scale vibrations, Nature, 2022, 603, 616–623 CrossRef CAS PubMed.
- F. Sun, H. Jiang, H. Wang, Y. Zhong, Y. Xu, Y. Xing, M. Yu, L. Feng, Z. Tang, J. Liu, H. Sun, H. Wang, G. Wang and M. Zhu, Soft fiber electronics based on semiconducting polymer, Chem. Rev., 2023, 123, 4693–4763 CrossRef CAS.
- M. Chen, J. Liu, P. Li, H. Gharavi, Y. Hao, J. Ouyang, J. Hu, L. Hu, C. Hou, I. Humar, L. Wei, G. Yang and G. Tao, Fabric computing: Concepts, opportunities, and challenges, Innovation, 2022, 3, 100340 Search PubMed.
- T. Lv, R. Cheng, C. Wei, E. Su, T. Jiang, F. Sheng, X. Peng, K. Dong and Z. Wang, All-fabric direct-current triboelectric nanogenerators based on the Tribovoltaic effect as power textiles, Adv. Energy Mater., 2023, 13, 2301178 CrossRef CAS.
- J. Dong, Y. Peng, Y. Zhang, Y. Chai, J. Long, Y. Zhang, Y. Zhao, Y. Huang and T. Liu, Superelastic radiative cooling metafabric for comfortable epidermal electrophysiological monitoring, Nano-Micro Lett., 2023, 15, 181 CrossRef.
- W. Wang, Y. Jiang, D. Zhong, Z. Zhang, S. Choudhury, J. Lai, H. Gong, S. Niu, X. Yan, Y. Zheng, C. Shih, R. Ning, Q. Lin, D. Li, Y. Kim, J. Kim, Y. Wang, C. Zhao, C. Xu, X. Ji, Y. Nishio, H. Lyu, J. Tok and Z. Bao, Neuromorphic sensorimotor loop embodied by monolithically integrated, low-Voltage, soft e-Skin, Science, 2023, 380, 735–742 CrossRef CAS.
- L. Massari, G. Fransvea, J. D'Abbraccio, M. Filosa, G. Terruso, A. Aliperta, G. D'Alesio, M. Zaltieri, E. Schena, E. Palermo, E. Sinibaldi and C. Oddo, Functional mimicry of Ruffini receptors with fibre Bragg gratings and deep neural networks enables a bio-inspired large-area tactile-sensitive skin, Nat. Mach. Intell., 2022, 4, 425–435 CrossRef.
- B. Xue, H. Sheng, Y. Li, L. Li, W. Di, Z. Xu, L. Ma, X. Wang, H. Jiang, M. Qin, Z. Yan, Q. Jiang, J. Liu, W. Wang and Y. Cao, Stretchable and self-healable hydrogel artificial skin, Natl. Sci. Rev., 2022, 9, 147 CrossRef PubMed.
- W. Cao, Z. Wang, X. Liu, Z. Zhou, Y. Zhang, S. He, D. Cui and F. Chen, Bioinspired MXene-based user-interactive electronic skin for digital and visual dual-channel sensing, Nano-Micro Lett., 2022, 14, 119 CrossRef CAS.
- Y. Kim, J. Suh, J. Shin, Y. Liu, H. Yeon, K. Qiao, H. Kum, C. Kim, H. Lee, C. Choi, H. Kim, D. Lee, J. Lee, J. Kang, B. Park, S. Kang, J. Kim, S. Kim, J. Perozek, K. Wang, Y. Park, K. Kishen, L. Kong, T. Palacios, J. Park, M. Park, H. Kim, Y. Lee, K. Lee, S. Bae, W. Kong, J. Han and J. Kim, Chip-Less wireless electronic skins by remote epitaxial freestanding compound semiconductors, Science, 2022, 377, 859–864 CrossRef CAS PubMed.
- Y. Choi, H. Jeong, R. Yin, R. Avila, A. Pfenniger, J. Yoo, J. Lee, A. Tzavelis, Y. Lee, S. Chen, H. Knight, S. Kim, H. Ahn, G. Wickerson, A. Guardado, E. Dempsey, B. Russo, M. Napolitano, T. Holleran, L. Razzak, A. Miniovich, G. Lee, B. Geist, B. Kim, S. Han, J. Brennan, K. Aras, S. Kwak, J. Kim, E. Waters, X. Yang, A. Burrell, K. Chun, C. Liu, C. Wu, A. Rwei, A. Spann, A. Banks, D. Johnson, Z. Zhang, C. Haney, S. Jin, A. Sahakian, Y. Huang, G. Trachiotis, B. Knight, R. Arora, I. Efimov and J. Rogers, A transient, closed-loop network of wireless, body-integrated devices for autonomous electrotherapy, Science, 2022, 376, 1006–1012 CrossRef CAS PubMed.
- J. Ausra, M. Madrid, R. Yin, J. Hanna, S. Arnott, J. Brennan, R. Peralta, D. Clausen, J. Bakall, I. Efimov and P. Gutruf, Wireless, fully implantable cardiac stimulation and recording with on-device computation for closed-loop pacing and defibrillation, Sci. Adv., 2022, 8, 7469 CrossRef.
- S. Flesher, J. Downey, J. Weiss, C. Hughes, A. Herrera, E. Kabara, M. Boninger, J. Collinger and R. Gaunt, A brain-computer interface that evokes tactile sensations improves robotic arm control, Science, 2021, 372, 831–836 CrossRef CAS.
- M. Hjort, A. Mousa, D. Bliman, M. Shameem, K. Hellman, A. Yadav, P. Ekström and F. Ek, Roger Olsson, In situ assembly of bioresorbable organic bioelectronics in the brain, Nat. Commun., 2023, 14, 4453 CrossRef CAS.
- C. Guimarães, A. Marques and R. Reis, Pushing the natural frontier: Progress on the integration of biomaterial cues toward combinatorial biofabrication and tissue engineering, Adv. Mater., 2022, 34, 2105645 CrossRef PubMed.
- C. Li, J. Wu, H. Shi, Z. Xia, J. Sahoo, J. Yeo and D. Kaplan, Fiber-based biopolymer processing as a route toward sustainability, Adv. Mater., 2022, 34, 2105196 CrossRef CAS PubMed.
- E. Jang, P. Banerjee, J. Huang and D. Madan, High performance scalable and cost-effective thermoelectric devices fabricated using energy efficient methods and naturally occuring materials, Appl. Energy, 2021, 294, 117006 CrossRef CAS.
- Y. Xie, H. Lu, J. Huang and H. Xie, Natural materials for sustainable organic solar cells: Status and challenge, Adv. Funct. Mater., 2023, 33, 2213910 CrossRef CAS.
- S. Zhang, S. Chen, H. Li, X. Lai and X. Zeng, Superhydrophobic, flame-retardant and magnetic polyurethane sponge for oil-water separation, J. Environ. Chem. Eng., 2022, 10, 107580 CrossRef CAS.
- R. Xu, M. She, J. Liu, S. Zhao, H. Liu, L. Qu and M. Tian, Breathable kirigami-shaped ionotronic e-textile with touch/strain sensing for friendly epidermal electronics, Adv. Fiber Mater., 2022, 4, 1525–1534 CrossRef.
- D. Lin, X. Zeng, H. Li, X. Lai and T. Wu, One-pot fabrication of superhydrophobic and flame-retardant coatings on cotton fabrics via sol-gel reaction, J. Colloid Interface Sci., 2019, 533, 198–206 CrossRef CAS PubMed.
- A. Gorgani, O. Avinc and R. Alborz, Sustainable antibacterial cotton fabrics with in situ formed silver nanoparticles by bio-inkjet printing, J. Cleaner Prod., 2023, 386, 135796 CrossRef.
- A. Franklin, M. Hersam and H. Wong, Carbon nanotube transistors: Making electronics from molecules, Science, 2022, 378, 726–732 CrossRef CAS PubMed.
- A. VahidMohammadi, J. Rosen and Y. Gogotsi, The world of two-dimensional carbides and nitrides (MXenes), Science, 2021, 372, 1165 CrossRef.
- Y. Wang, T. Guo, Z. Tian, L. Shi, S. Barman and H. Alshareef, MXenes for soft robotics, Matter, 2023, 6, 2807–2833 CrossRef.
- P. Tang, Z. Deng, Y. Zhang, L. Liu, Z. Wang, Z. Yu and H. Zhang, Tough, Strong, and conductive graphene fibers by optimizing surface chemistry of graphene oxide precursor, Adv. Funct. Mater., 2022, 32, 2112156 CrossRef CAS.
- G. Pace, M. Serri, A. Castillo, A. Ansaldo, S. Lauciello, M. Prato, L. Pasquale, J. Luxa, V. Mazanek, Z. Sofer and F. Bonaccorso, Nitrogen-doped graphene based triboelectric nanogenerators, Nano Energy, 2021, 87, 106173 CrossRef CAS.
- K. Wang, R. Hazra, Q. Ma, L. Jiang, Z. Liu, Y. Zhang, S. Wang and G. Han, Multifunctional silk fibroin/PVA bio-nanocomposite films containing TEMPO-oxidized bacterial cellulose nanofibers and silver nanoparticles, Cellulose, 2022, 29, 1647–1666 CrossRef CAS.
- Z. Ma, Q. Huang, Q. Xu, Q. Zhuang, X. Zhao, Y. Yang, H. Qiu, Z. Yang, C. Wang, Y. Chai and Z. Zheng, Permeable superelastic liquid-metal fibre mat enables biocompatible and monolithic stretchable electronics, Nat. Mater., 2021, 20, 859–868 CrossRef CAS.
- Y. Zheng, Z. Man, Y. Zhang, G. Wu, W. Lu and W. Chen, High-performance stretchable supercapacitors based on centrifugal electrospinning-directed hetero-structured graphene-polyaniline hierarchical fabric, Adv. Fiber Mater., 2023, 5, 1759–1772 CrossRef CAS.
- W. Barthlott and C. Neinhuis, Purity of the sacred lotus, or escape from contamination in biological surfaces, Planta, 1997, 202, 1–8 CrossRef CAS.
- V. Zorba, E. Stratakis, M. Barberoglou, E. Spanakis, P. Tzanetakis, S. Anastasiadis and C. Fotakis, Biomimetic artificial surfaces quantitatively reproduce the water repellency of a lotus leaf, Adv. Mater., 2008, 20, 4049–4054 CrossRef CAS.
- X. Gao and L. Jiang, Water-repellent legs of water striders, Nature, 2004, 432, 36–36 CrossRef CAS.
- L. Feng, Y. Zhang, J. Xi, Y. Zhu, N. Wang, F. Xia and L. Jiang, Petal effect: A superhydrophobic state with high adhesive force, Langmuir, 2008, 24, 4114–4119 CrossRef CAS.
- M. Liu, S. Wang, Z. Wei, Y. Song and L. Jiang, Bioinspired design of a superoleophobic and low adhesive water/solid interface, Adv. Mater., 2009, 21, 665–669 CrossRef CAS.
- H. Chen, P. Zhang, L. Zhang, H. Liu, Y. Jiang, D. Zhang, Z. Han and L. Jiang, Continuous directional water transport on the peristome surface of nepenthes alata, Nature, 2016, 532, 85–89 CrossRef CAS PubMed.
- J. Ju, H. Bai, Y. Zheng, T. Zhao, R. Fang and L. Jiang, A multi-structural and multi-functional integrated fog collection system in cactus, Nat. Commun., 2012, 3, 1247 CrossRef PubMed.
- X. Leng, L. Sun, Y. Long and Y. Lu, Bioinspired superwetting materials for water manipulation, Droplet, 2022, 1, 139–169 CrossRef.
- S. Li, J. Huang, Z. Chen, G. Chen and Y. Lai, A review on special wettability textiles: Theoretical models, fabrication technologies and multifunctional applications, J. Mater. Chem. A, 2017, 5, 31–55 RSC.
- J. Yong, F. Chen, Q. Yang, J. Huo and X. Hou, Superoleophobic surfaces, Chem. Soc. Rev., 2017, 46, 4168–4217 RSC.
- M. Jiang, Y. Wang, F. Liu, H. Du, Y. Li, H. Zhang, S. To, S. Wang, C. Pan, J. Yu, D. Quéré and Z. Wang, Inhibiting the Leidenfrost effect above 1,000 °C for sustained thermal cooling, Nature, 2022, 601, 568–572 CrossRef CAS PubMed.
- Y. Zheng, H. Bai, Z. Huang, X. Tian, F. Nie, Y. Zhao, J. Zhai and L. Jiang, Directional water collection on wetted spider silk, Nature, 2010, 463, 640–643 CrossRef CAS PubMed.
- J. Lv and Y. Cheng, Fluoropolymers in biomedical applications: State-of-the-art and future perspectives, Chem. Soc. Rev., 2021, 50, 5435–5467 RSC.
- M. Karahan, Experimental investigation of the effect of fabric construction on dynamic water absorbtion in terry fabrics, Fibres Text. East. Eur., 2007, 15, 74–80 Search PubMed.
- U. Baig, M. Faizan and A. Waheed, A review on super-wettable porous membranes and materials based on bio-polymeric chitosan for oil-water separation, Adv. Colloid Interface Sci., 2022, 303, 102635 CrossRef CAS PubMed.
- Y. Wang, W. Zhao, L. Han and K. Tam, Superhydrophobic surfaces from sustainable colloidal systems, Curr. Opin. Colloid Interface Sci., 2022, 57, 101534 CrossRef CAS.
- B. He, X. Hou, Y. Liu, J. Hu, L. Song, Z. Tong, X. Zhan, Y. Ren, Q. Liu and Q. Zhang, Design of fluorine-free waterborne fabric coating with robust hydrophobicity, water-resistant and breathability, Sep. Purif. Technol., 2023, 311, 123308 CrossRef CAS.
- V. Saji, Wax-based artificial superhydrophobic surfaces and coatings, Colloids Surf., A, 2020, 602, 125132 CrossRef CAS.
- F. Dent, G. Tyagi, F. Esat, J. Cabral and S. Khodaparast, Tuneable topography and hydrophobicity mode in biomimetic plant-based wax coatings, Adv. Funct. Mater., 2024, 34, 2307977 CrossRef CAS.
- H. Bai, L. Zhang and D. Gu, Micrometer-sized spherulites as building blocks for lotus leaf-like superhydrophobic coatings, Appl. Surf. Sci., 2018, 459, 54–62 CrossRef CAS.
- N. Zhang, C. Gao, L. Meng and X. Tang, Preparation and characterization of carnauba wax-based particle with hierarchical structure and its use as hydrophobic coating for chitosan films, Carbohydr. Polym., 2023, 319, 121224 CrossRef CAS PubMed.
- A. Atta, N. Mohamed, M. Rostom, H. Al-Lohedan and M. Abdullah, New hydrophobic silica nanoparticles capped with petroleum paraffin wax embedded in epoxy networks as multifunctional steel epoxy coatings, Prog. Org. Coat., 2019, 128, 99–111 CrossRef CAS.
- Y. Ni, J. Huang, S. Li, X. Wang, L. Liu, M. Wang, Z. Chen, X. Li and Y. Lai, Underwater, multifunctional superhydrophobic sensor for human motion detection, ACS Appl. Mater. Interfaces, 2021, 13, 4740–4749 CrossRef CAS PubMed.
- B. Wang, C. Zhang, B. Huang, H. Wang and X. Miao, A facile dip-coating approach to prepare robust superhydrophobic fabric modified by γ-Fe2O3/epoxy resin/lauric acid for oil/water separation, lossless water transportation, and flame retardancy, Surf. Interfaces, 2024, 45, 103896 CrossRef CAS.
- J. Xiong, M. Lin, J. Wang, S. Gaw, K. Parida and P. Lee, Wearable all-fabric-based triboelectric generator for water energy harvesting, Adv. Energy Mater., 2017, 7, 1701243 CrossRef.
- N. Patil and A. Netravali, Bioinspired process using anisotropic silica particles and fatty acid for superhydrophobic cotton fabrics, Cellulose, 2020, 27, 545–559 CrossRef CAS.
- E. Prudnikov, I. Polishchuk, A. Sand, H. Hamad, N. Massad-Ivanir, E. Segal and B. Pokroy, Self-assembled fatty acid crystalline coatings display superhydrophobic antimicrobial properties, Mater. Today Bio, 2023, 18, 100516 CrossRef CAS PubMed.
- W. Wu, B. Jiang, R. Liu, Y. Han, X. Fang, H. Mu, M. Farag, J. Simal-Gandara, M. Prieto, H. Chen, J. Xiao and H. Gao, Structures and functions of cuticular wax in postharvest fruit and its regulation: A comprehensive review with future perspectives, Engineering, 2023, 23, 118–129 CrossRef CAS.
- X. Zhao, T. Hu and J. Zhang, Superhydrophobic coatings with high repellency to daily consumed liquid foods based on food grade waxes, J. Colloid Interface Sci., 2018, 515, 255–263 CrossRef CAS PubMed.
- N. Sharma, S. Angural, M. Rana, N. Puri, K. Kondepudi and N. Gupta, Phytase producing lactic acid bacteria: Cell factories for enhancing micronutrient bioavailability of phytate rich foods, Trends Food Sci. Technol., 2020, 96, 1–12 CrossRef CAS.
- R. Wang and S. Guo, Phytic acid and its interactions: Contributions to protein functionality, food processing, and safety, Compr. Rev. Food Sci. Food Saf., 2021, 20, 2081–2105 CrossRef CAS PubMed.
- S. Xiong, S. Xu, A. Phommachanh, M. Yi and Y. Wang, Versatile surface modification of TFC membrane by layer-by-layer assembly of phytic acid-metal complexes for comprehensively enhanced FO performance, Environ. Sci. Technol., 2019, 53, 3331–3341 CrossRef CAS PubMed.
- C. Zhang, G. Chu, Z. Ruan, N. Tang, C. Song, Q. Li, W. Zhou, J. Jin, H. Haick, Y. Chen and D. Cui, Biomimetic self-assembling metal-organic architectures with non-iridescent structural coloration for synergetic antibacterial and osteogenic activity of implants, ACS Nano, 2022, 16, 16584–16597 CrossRef CAS PubMed.
- Q. Xu, X. Wang and Y. Zhang, Green and sustainable fabrication of a durable superhydrophobic cotton fabric with self-cleaning properties, Int. J. Biol. Macromol., 2023, 242, 124731 CrossRef CAS PubMed.
- K. Wang, T. Zhang, X. Xiao, X. Fang, X. Liu, Y. Dong, Y. Li and J. Li, Nature-inspired phytic acid-based hybrid complexes for fabricating green and transparent superhydrophobic and anti-mildew coating on bamboo surface, Colloids Surf., A, 2022, 651, 129769 CrossRef CAS.
- S. Chen, H. Li, X. Lai, S. Zhang and X. Zeng, Superhydrophobic and phosphorus- nitrogen flame-retardant cotton fabric, Prog. Org. Coat., 2021, 159, 106446 CrossRef CAS.
- Z. Zhang, Z. Zhou, J. Huang and Y. Wang, A flame retardant poly vinyl alcohol/graphene oxide/phytic acid composite for a quick response and ultra-long fire alarm check for updates, J. Mater. Chem. A, 2024, 12, 6050–6066 RSC.
- Z. Yu, Z. Zhu, Y. Zhang, X. Li, X. Liu, Y. Qin, Z. Zheng, L. Zhang and H. He, Biodegradable and flame-retardant cellulose-Based wearable triboelectric nanogenerator for mechanical energy harvesting in firefighting clothing, Carbohydr. Polym., 2024, 334, 122040 CrossRef CAS PubMed.
- X. Yang, S. Biswas, J. Han, S. Tanpichai, M. Li, C. Chen, S. Zhu, A. Das and H. Yano, Surface and interface engineering for nanocellulosic advanced materials, Adv. Mater., 2021, 33, 2002264 CrossRef CAS PubMed.
- L. Ross, S. Shah, B. Hankamer and N. Amiralian, Microalgal nanocellulose-opportunities for a circular bioeconomy, Trends Plant Sci., 2021, 26, 924–939 CrossRef PubMed.
- W. Zhang, X. Chen, J. Zhao, X. Wang, X. Li, T. Liu, B. Luo, Y. Qin, S. Zhang, M. Chi, S. Wang and S. Nie, Cellulose template-based triboelectric nanogenerators for self-powered sensing at high humidity, Nano Energy, 2023, 108, 108196 CrossRef CAS.
- M. Liu, C. Ma, D. Zhou, S. Chen, L. Zou, H. Wang and J. Wu, Hydrophobic, breathable cellulose nonwoven fabrics for disposable hygiene applications, Carbohydr. Polym., 2022, 288, 119367 CrossRef CAS PubMed.
- J. Li, J. Gao, J. Fang, T. Ling, M. Xia, X. Cao, Z. Han and Y. Chen, Environmental-friendly regenerated lignocellulose functionalized cotton fabric to prepare multi-functional degradable membrane for efficient oil-water separation and solar seawater desalination, Sci. Rep., 2023, 13, 5251 CrossRef CAS PubMed.
- A. Isogai, Emerging Nanocellulose technologies: Recent developments, Adv. Mater., 2021, 33, 2000630 CrossRef CAS PubMed.
- M. Zhang, H. Du, K. Liu, S. Nie, T. Xu, X. Zhang and C. Si, Fabrication and applications of cellulose-based nanogenerators, Adv. Compos. Hybrid Mater., 2021, 4, 865–884 CrossRef CAS.
- S. Sun, P. Xu, Q. Xiao, X. Qiang and X. Shi, One-step solvent-free fabrication of superhydrophobic cellulose powder with reversible wettability, Prog. Org. Coat., 2022, 173, 107170 CrossRef CAS.
- Q. Cheng, C. Guan, M. Wang, Y. Li and J. Zeng, Cellulose nanocrystal coated cotton fabric with superhydrophobicity for efficient oil/water separation, Carbohydr. Polym., 2018, 199, 390–396 CrossRef CAS PubMed.
- Y. Yang, Y. Guan, C. Li, T. Xu, L. Dai, J. Xu and C. Si, Application and carbon footprint evaluation of lignin-based composite materials, Adv. Compos. Hybrid Mater., 2024, 7, 61 CrossRef.
- L. Tardy, E. Lizundia, C. Guizani, M. Hakkarainen and M. Sipponen, Prospects for the integration of lignin materials into the circular economy, Mater. Today, 2023, 65, 122–132 CrossRef.
- J. Sternberg, O. Sequerth and S. Pilla, Green chemistry design in polymers derived from lignin: Review and perspective, Prog. Polym. Sci., 2021, 113, 101344 CrossRef CAS.
- P. Figueiredo, K. Lintinen, J. Hirvonen, M. Kostiainen and H. Santos, Properties and chemical modifications of lignin: Towards lignin-based nanomaterials for biomedical applications, Prog. Mater. Sci., 2018, 93, 233–269 CrossRef CAS.
- D. Wei, S. Liang, S. Lv, J. Zuo, S. Zhang and L. Liu, Preparation and properties of modified lignin/triphenol epoxy composite coatings for superhydrophobicity and corrosion protection, ACS Appl. Polym. Mater., 2024, 6, 5485–5495 CrossRef CAS.
- Y. Chen, Y. Jiang, D. Tian, J. Hu, J. He, G. Yang, L. Luo, Y. Xiao, S. Deng, O. Deng, W. Zhou and F. Shen, Fabrication of spherical lignin nanoparticles using acid-catalyzed condensed lignins, Int. J. Biol. Macromol., 2020, 164, 3038–3047 CrossRef CAS PubMed.
- N. Alwadani, N. Ghavidel and P. Fatehi, Surface and interface characteristics of hydrophobic lignin derivatives in solvents and films, Colloids Surf., A, 2021, 609, 125656 CrossRef CAS.
- X. Liu, X. Chen, H. Bian, S. Ni, Z. Li, N. Liu, M. Qin and F. Zhang, Highly hydrophobic cotton fabric by in-situ co-deposition of lignin/metal particles for oil/water separation, Ind. Crops Prod., 2023, 204, 117393 CrossRef CAS.
- J. Wang and S. Zhuang, Chitosan-based materials: Preparation, modification and application, J. Cleaner Prod., 2022, 355, 131825 CrossRef CAS.
- S. Lee, L. Hao, J. Park, D. Oh and D. Hwang, Nanochitin and nanochitosan: Chitin nanostructure engineering with multiscale properties for biomedical and environmental applications, Adv. Mater., 2023, 35, 2203325 CrossRef CAS PubMed.
- Z. Ma, Z. Zhang, F. Zhao and Y. Wang, A multifunctional coating for cotton fabrics integrating superior performance of flame-retardant and self-cleaning, Adv. Compos. Hybrid Mater., 2022, 5, 2817–2833 CrossRef CAS.
- S. Wang, J. Sha, W. Wang, C. Qin, W. Li and C. Qin, Superhydrophobic surfaces generated by one-pot spray-coating of chitosan-based nanoparticles, Carbohydr. Polym., 2018, 195, 39–44 CrossRef CAS PubMed.
- W. Song, V. Gaware, Ö. Rúnarsson, M. Másson and J. Mano, Functionalized superhydrophobic biomimetic chitosan-based films, Carbohydr. Polym., 2010, 81, 140–144 CrossRef CAS.
- M. Raeisi, Y. Kazerouni, A. Mohammadi, M. Hashemi, I. Hejazi, J. Seyfi and H. Khonakdar, Seyed Mohammad Davachi, Superhydrophobic cotton fabrics coated by chitosan and titanium dioxide nanoparticles with enhanced antibacterial and UV-protecting properties, Int. J. Biol. Macromol., 2021, 171, 158–165 CrossRef CAS PubMed.
- G. Zheng, Y. Cui, Z. Jiang, M. Zhou, Y. Yu, P. Wang and Q. Wang, Superhydrophobic, photothermal, and UV-resistant coatings obtained by polydimethylsiloxane treating self-healing hydrophobic chitosan-tannic acid surface for oil/water separation, Chem. Eng. J., 2023, 473, 145258 CrossRef CAS.
- S. Li, R. Tang and C. Yu, Flame retardant treatment of jute fabric with chitosan and sodium alginate, Polym. Degrad. Stab., 2022, 196, 109826 CrossRef CAS.
- P. Li, C. Liu, Y. Xu, Z. Jiang, Y. Liu and P. Zhu, Novel and eco-friendly flame-retardant cotton fabrics with lignosulfonate and chitosan through LBL: Flame retardancy, smoke suppression and flame-retardant mechanism, Polym. Degrad. Stab., 2020, 181, 109302 CrossRef CAS.
- Q. Guo, J. Guo, H. Chen, P. Zhou, C. Li, K. Yang, N. Hua, J. Wang and M. Weng, Multi-functional graphene/leather for versatile wearable electronics, J. Mater. Chem. A, 2023, 11, 11773–11785 RSC.
- H. Lu, M. Jian, Z. Yin, K. Xia, S. Shi, M. Zhang, H. Wang, X. Liang, W. Ma, X. Zhang and Y. Zhang, Silkworm silk fibers with multiple reinforced properties obtained through feeding Ag nanowires, Adv. Fiber Mater., 2022, 4, 547–555 CrossRef CAS.
- Y. Chen, H. Dai, Y. Yan, Z. Piao, H. Lu, Z. Hu, W. Wei, G. Zhang, W. Zhang and R. Guo, Polyacrylamide-poly(vinyl alcohol)-sodium alginate-reduced graphene oxide/nylon fabrics with multistimuli responses, ACS Appl. Polym. Mater., 2023, 5, 7766–7773 CrossRef CAS.
- Z. Xia, J. Li, H. Lu, J. Zhang, Q. Mi, J. Wu, X. Zheng and J. Zhang, Natural grass to all-biomass biodegradable tape and superior oil-water separation fabric, Resour., Conserv. Recycl., 2022, 182, 106320 CrossRef CAS.
- Y. Zhang, W. Tan, C. Zuo, L. Jiang, X. Chen, Y. Liu, Y. Ren and X. Liu, A cleaner and sustainable preparation of green flame retardant and antibacterial lyocell fabric, Cellulose, 2023, 30, 6081–6097 CrossRef CAS.
- F. Chen, P. Qi, J. Liu, G. Xia, B. Fei, J. Sun, J. Xin and S. Zhang, Rationally designed lentinan outer layer to improve the comprehensive performance of flame-retardant cotton fabrics, Chem. Eng. J., 2023, 476, 146427 CrossRef CAS.
- K. Safi, K. Kant, I. Bramhecha, P. Mathur and J. Sheikh, Multifunctional modification of cotton using layer-by-layer finishing with chitosan, sodium lignin sulphonate and boric acid, Int. J. Biol. Macromol., 2020, 158, 903–910 CrossRef CAS PubMed.
- X. Tian, T. Verho and R. Ras, Moving superhydrophobic surfaces toward real-world applications, Science, 2016, 352, 142–143 CrossRef CAS PubMed.
- L. Xu, Y. Liu, X. Yuan, J. Wan, L. Wang, H. Pan and Y. Shen, One-pot preparation of robust, ultraviolet-proof superhydrophobic cotton fabrics for self-cleaning, Cellulose, 2020, 27, 9005–9026 CrossRef CAS.
- J. Li, Y. Meng, J. Liu, F. Yu, X. Wang, T. Wang, K. Gao and Z. Zhang, Antibacterial waterborne polyacrylate coated fabric with underwater superoleophobicity and underoil superhydrophobicity for continuous oil/water separation, Prog. Org. Coat., 2022, 173, 107149 CrossRef CAS.
- M. Ghasemlou, F. Daver, E. Ivanova and B. Adhikari, Bio-inspired sustainable and durable superhydrophobic materials: From nature to market, J. Mater. Chem. A, 2019, 7, 16643–16670 RSC.
- X. Long, J. Xu, C. Li, J. Liu, Y. Qing and C. Long, Long-lived superhydrophobic fabric-based films via Fenton reaction for efficient oil/water separation, Sep. Purif. Technol., 2023, 324, 124523 CrossRef CAS.
- S. Kim, J. Oh and C. Park, Development of energy-efficient superhydrophobic polypropylene fabric by oxygen plasma etching and thermal aging, Polymer, 2020, 12, 2756 CAS.
- N. Ahmad, S. Rasheed, K. Ahmed, S. Musharraf, M. Najam-ul-Haq and D. Hussain, Facile two-step functionalization of multifunctional superhydrophobic cotton fabric for UV-blocking, self cleaning, antibacterial, and oil-water separation, Sep. Purif. Technol., 2023, 306, 122626 CrossRef CAS.
- H. Li, H. Zhang, J. Hu, G. Wang, J. Cui, Y. Zhang and Q. Zhen, Facile preparation of hydrophobic PLA/PBE micro-nanofiber fabrics via the melt-blown process for high-efficacy oil/water separation, Polymer, 2022, 14, 1667 CAS.
- Y. Cheng, T. Zhu, S. Li, J. Huang, J. Mao, H. Yang, S. Gao, Z. Chen and Y. Lai, A novel strategy for fabricating robust superhydrophobic fabrics by environmentally-friendly enzyme etching, Chem. Eng. J., 2019, 355, 290–298 CrossRef CAS.
- A. Ruhela, G. Kasinathan, S. Rath, M. Sasikala and C. Sharma, Waterborne electrospinning of fluorine-free stretchable nanofiber membranes with waterproof and breathable capabilities for protective textiles, Mater. Sci. Eng., C, 2021, 118, 111409 CrossRef CAS PubMed.
- D. Ji, Y. Lin, X. Guo, B. Ramasubramanian, R. Wang, N. Radacsi, R. Jose, X. Qin and S. Ramakrishna, Electrospinning of nanofibres, Nat. Rev. Methods Primers, 2024, 4, 1 CrossRef CAS.
- W. Zhou, X. Gong, Y. Li, Y. Si, S. Zhang, J. Yu and B. Ding, Waterborne electrospinning of fluorine-free stretchable nanofiber membranes with waterproof and breathable capabilities for protective textiles, J. Colloid Interface Sci., 2021, 602, 105–114 CrossRef CAS PubMed.
- H. Zhang, J. Gan, Y. Wu and Z. Wu, Biomimetic high water adhesion superhydrophobic surface via UV nanoimprint lithography, Appl. Surf. Sci., 2023, 633, 157610 CrossRef CAS.
- H. Ou, Z. Dai, Y. Gao and B. Zhou, Breathable fabrics with robust superhydrophobicity via in situ formation of hierarchical surface morphologies, ACS Appl. Mater. Interfaces, 2023, 15, 39989–40000 CrossRef CAS PubMed.
- R. Tohamy, S. Ali, F. Li, K. Okasha, Y. Mahmoud, T. Elsamahy, H. Jiao, Y. Fu and J. Sun, A critical review on the treatment of dye-containing wastewater: Ecotoxicological and health concerns of textile dyes and possible remediation approaches for environmental safety, Ecotoxicol. Environ. Saf., 2022, 231, 113160 CrossRef PubMed.
- X. Xie, S. Li, X. Wang, J. Huang, Z. Chen, W. Cai and Y. Lai, An effective and low-consumption foam finishing strategy for robust functional fabrics with on-demand special wettability, Chem. Eng. J., 2021, 426, 131245 CrossRef CAS.
- W. Li, L. Yang, X. Xie, K. Ng, F. Xu, C. Zheng, Z. Zhang, S. Li, J. Huang, W. Cai and Y. Lai, Environmentally-friendly foam-coating synthetic strategy for fabrics with robust superhydrophobicity, self-cleaning capability and flame retardance properties, Chem. Eng. J., 2023, 470, 144376 CrossRef CAS.
- Y. Wang, Y. Cheng, C. Yin, J. Zhang, X. Zhang and J. Zhang, Seashell-inspired switchable waterborne coatings with complete biodegradability, intrinsic flame-retardance, and high transparency, ACS Nano, 2023, 17, 12433–12444 CrossRef CAS PubMed.
- M. Ameer, K. Shaker, M. Ashraf, M. Karahan, Y. Nawab, S. Ahmad and M. Nasir, Interdependence of moisture, mechanical properties, and hydrophobic treatment of jute fibre-reinforced composite materials, J. Text. Inst., 2017, 108, 1768–1776 CrossRef CAS.
- A. Jabbar, J. Militky, J. Wiener and M. Karahan, Static and dynamic mechanical properties of novel treated jute/green epoxy composites, Text. Res. J., 2015, 86, 960–974 CrossRef.
- Y. Tan, J. Yang, Y. Li, X. Li, Q. Wu, Y. Fan, F. Yu, J. Cui, L. Chen, D. Wang and X. Deng, Liquid-pressure-guided superhydrophobic surfaces with adaptive adhesion and stability, Adv. Mater., 2022, 34, 2202167 CrossRef CAS PubMed.
- D. Wang, Q. Sun, M. Hokkanen, C. Zhang, F. Lin, Q. Liu, S. Zhu, T. Zhou, Q. Chang, B. He, Q. Zhou, L. Chen, Z. Wang, R. Ras and X. Deng, Design of robust superhydrophobic surfaces, Nature, 2020, 582, 55–59 CrossRef CAS PubMed.
- L. Xu, L. Yang, S. Yang, Z. Xu, G. Lin, J. Shi, R. Zhang, J. Yu, D. Ge and Y. Guo, Earthworm-inspired ultradurable superhydrophobic fabrics from adaptive wrinkled skin, ACS Appl. Mater. Interfaces, 2021, 13, 6758–6766 CrossRef CAS PubMed.
- M. Selim, S. El-Safty, M. Shenashen and A. Elmarakbi, Advances in polymer/inorganic nanocomposite fabrics for lightweight and high-strength armor and ballistic-proof materials, Chem. Eng. J., 2024, 493, 152422 CrossRef CAS.
- M. Wu, Z. Shao, N. Zhao, R. Zhang, G. Yuan, L. Tian, Z. Zhang, W. Gao and H. Bai, Biomimetic, knittable aerogel fiber for thermal insulation textile, Science, 2023, 382, 1379–1383 CrossRef CAS PubMed.
- Q. Liu, F. Chen, T. Dong, W. Yu, C. Chen, G. Jiang, Z. Dong and P. Ma, Large-scale fabrication of snake-skin-inspired protective composite textiles, Adv. Fiber Mater., 2024 DOI:10.1007/s42765-024-00396-7.
- B. Su, Y. Tian and L. Jiang, Bioinspired interfaces with superwettability: From materials to chemistry, J. Am. Chem. Soc., 2016, 138, 1727–1748 CrossRef CAS PubMed.
- S. Zhao and J. Ahn, Rational design of high-performance wearable tactile sensors utilizing bioinspired structures/functions, natural biopolymers, and biomimetic strategies, Mater. Sci. Eng., R, 2022, 148, 100672 CrossRef.
- W. Zhang, D. Wang, Z. Sun, J. Song and X. Deng, Robust superhydrophobicity: Mechanisms and strategies, Chem. Soc. Rev., 2021, 50, 4031–4061 RSC.
- Z. Zhang, M. Rong and M. Zhang, Self-healable functional polymers and polymer-based composites, Prog. Polym. Sci., 2023, 144, 101724 CrossRef CAS.
- S. Ramesh, S. Khan, Y. Park, E. Ford, S. Menegatti and J. Genzer, Self-healing and repair of fabrics: A comprehensive review of the application toolkit, Mater. Today, 2022, 54, 90–109 CrossRef CAS.
- J. Youngblood and N. Sottos, Bioinspired materials for self-cleaning and self-healing, MRS Bull., 2008, 33, 732–741 CrossRef CAS.
- K. Chen, J. Zhou, X. Che, R. Zhao and Q. Gao, One-step synthesis of core shell cellulose-silica/n-octadecane microcapsules and their application in waterborne self-healing multiple protective fabric coatings, J. Colloid Interface Sci., 2020, 566, 401–410 CrossRef CAS PubMed.
- J. Liu, N. Zheng, Z. Li, Z. Liu, G. Wang, L. Gui and J. Lin, Fast self-healing and antifouling polyurethane/fluorinated polysiloxane-microcapsules-silica composite material, Adv. Compos. Hybrid Mater., 2022, 5, 1899–1909 CrossRef CAS.
- H. Li, S. Tang, W. Chen, X. Yang, S. Dong, T. Xing, Y. Zhao and G. Chen, A fully waterborne coating system based on thiolene click reaction for robust and self-Healing superhydrophobic surfaces, Chem. Eng. J., 2022, 447, 137499 CrossRef CAS.
- J. Tao, Y. Liu, M. Li, Z. Li, Y. Zhang, X. Song, Q. Yang, F. Guan and J. Guo, Robust superhydrophobic composite fabric with self-healing and chemical durability, Small, 2024, 20, 2304894 CrossRef PubMed.
- J. Ma, L. Porath, Md. Haque, S. Sett, K. Rabbi, S. Nam, N. Miljkovic and C. Evans, Ultra-thin self-healing vitrimer coatings for durable hydrophobicity, Nat. Commun., 2021, 12, 5210 CrossRef CAS PubMed.
- M. Zhang, L. Chu, J. Chen, F. Qi, X. Li, X. Chen and D. Yu, Asymmetric wettability fibrous membranes: Preparation and biologic applications, Composites, Part B, 2024, 269, 111095 CrossRef CAS.
- T. Darmanin and F. Guittard, Wettability of conducting polymers: From superhydrophilicity to superoleophobicity, Prog. Polym. Sci., 2014, 39, 656–682 CrossRef CAS.
- G. Zhang, Z. Chen, C. Ahn and Z. Suo, Conducting polymer coatings prepared by mixed emulsions are highly conductive and stable in water, Adv. Mater., 2024, 36, 2306960 CrossRef CAS PubMed.
- W. Yang, S. Lin, W. Gong, R. Lin, C. Jiang, X. Yang, Y. Hu, J. Wang, X. Xiao, K. Li, Y. Li, Q. Zhang, J. Ho, Y. Liu, C. Hou and H. Wang, Single body-coupled fiber enables chipless textile electronics, Science, 2024, 384, 74–81 CrossRef CAS PubMed.
- J. Zhang, K. Peng, Z. Xu, Y. Xiong, J. Liu, C. Cai and X. Huang, A comprehensive review on the behavior and evolution of oil droplets during oil/water separation by membranes, Adv. Colloid Interface Sci., 2023, 319, 102971 CrossRef CAS PubMed.
- M. Wang, J. Huang, S. Li, Y. Ni, X. Dong, X. Wang, Z. Chen, X. Li, W. Cai and Y. Lai, A sandwich-like structured superhydrophobic fabric for versatile and highly efficient emulsion separation, Sep. Purif. Technol., 2021, 275, 119253 CrossRef CAS.
- Y. Su, T. Fan, W. Cui, Y. Li, S. Ramakrishna and Y. Long, Advanced electrospun nanofibrous materials for efficient oil/water separation, Adv. Fiber Mater., 2022, 4, 938–958 CrossRef CAS.
- Y. Yang, Z. Guo and W. Liu, Special superwetting materials from bioinspired to intelligent surface for on-demand oil/water separation: A comprehensive review, Small, 2022, 18, 2204624 CrossRef CAS PubMed.
- H. Bai, P. Li, X. Wang, Z. Li, T. Zhao, Y. Tian, M. Cheng, Y. Hong, X. Zhu and M. Cao, Bioinspired superhydrophobic cellular origami exhibiting improved and multifunctional floatability, Adv. Funct. Mater., 2024, 34, 2400574 CrossRef CAS.
- W. Bai, H. Lin, K. Chen, J. Xu, J. Chen, X. Zhang, R. Zeng, J. Lin and Y. Xu, Eco-Friendly stable cardanol-based benzoxazine modified superhydrophobic cotton fabrics for oil-water separation, Sep. Purif. Technol., 2020, 253, 117545 CrossRef CAS.
- D. Gandyra, S. Walheim, S. Gorb, P. Ditsche, W. Barthlott and T. Schimmel, Air retention under water by the floating Fern Salvinia: The crucial role of a trapped air layer as a pneumatic spring, Small, 2020, 16, 2003425 CrossRef CAS PubMed.
- Y. Zhao, C. Yu, H. Lan, M. Cao and L. Jiang, Improved interfacial floatability of superhydrophobic/superhydrophilic janus sheet inspired by lotus leaf, Adv. Funct. Mater., 2017, 27, 1701466 CrossRef.
- J. Zhang, L. Zhang and X. Gong, Large-scale spraying fabrication of robust fluorine-free superhydrophobic coatings based on dual-sized silica particles for effective antipollution and strong buoyancy, Langmuir, 2021, 37, 6042–6051 CrossRef CAS PubMed.
- Y. Wang, Y. Jiang, H. Wu and Y. Yang, Floating robotic insects to obtain electric energy from water surface for realizing some self-powered functions, Nano Energy, 2019, 63, 103810 CrossRef CAS.
- P. Wang, G. Liu, G. Sun, C. Meng, G. Shen and Y. Li, An integrated bifunctional pressure-temperature sensing system fabricated on a breathable nanofiber and powered by rechargeable zinc-air battery for long-term comfortable health care monitoring, Adv. Fiber Mater., 2024 DOI:10.1007/s42765-024-00398-5.
- A. Reza and T. Bagha, Waterproof breathable layers-A review, Adv. Colloid Interface Sci., 2019, 268, 114–135 CrossRef PubMed.
- X. Gong, Y. Ji, X. Liu, J. Yu, S. Zhang and B. Ding, Biomimetic and durably superhydrophobic nanofibrous membranes for high-performance waterproof and breathable textiles, Adv. Funct. Mater., 2024, 34, 2316030 CrossRef CAS.
- X. Zhang, Y. Zhu and S. Granick, Hydrophobicity at a Janus interface, Science, 2002, 295, 663–666 CrossRef CAS PubMed.
- L. Meng, W. Shi, Y. Li, X. Li, X. Tong and Z. Wang, Janus membranes at the water-energy nexus: A critical review, Adv. Colloid Interface Sci., 2023, 318, 102937 CrossRef CAS PubMed.
- L. Yan, X. Yang, Y. Zhang, Y. Wu, Z. Cheng, S. Darling and L. Shao, Porous Janus materials with unique asymmetries and functionality, Mater. Today, 2021, 51, 1369–7021 CrossRef.
- Y. Peng, J. Zhou, Y. Yang, J. Lai, Y. Ye and Y. Cui, An integrated 3D hydrophilicity/hydrophobicity design for artificial sweating skin (i-TRANS) mimicking human body perspiration, Adv. Mater., 2022, 34, 2204168 CrossRef CAS PubMed.
- M. Soltani, S. Lahiri, S. Shabanian and K. Golovin, Surface-engineered double-layered fabrics for continuous, passive fluid transport, Mater. Horiz., 2023, 10, 4293–4302 RSC.
- T. Yang, S. Wang, H. Yang, H. Gui, Y. Du and F. Liang, Temperature-triggered dynamic Janus fabrics for smart directional water transport, Adv. Funct. Mater., 2023, 33, 2214183 CrossRef CAS.
- C. Yang, Q. Zeng, J. Huang and Z. Guo, Droplet manipulation on superhydrophobic surfaces based on external stimulation: A review, Adv. Colloid Interface Sci., 2022, 306, 102724 CrossRef CAS PubMed.
- J. Hou, Y. Yang, D. Yu, Z. Chen, K. Wang, Y. Liu and G. Williams, Multifunctional fabrics finished using electro sprayed hybrid Janus particles containing nanocatalysts, Chem. Eng. J., 2021, 411, 128474 CrossRef CAS.
- X. Yu, Y. Li, X. Yin, X. Wang, Y. Han, Y. Si, J. Yu and B. Ding, Corncoblike, superhydrophobic, and phase-changeable nanofibers for intelligent thermoregulating and water-repellent fabrics, ACS Appl. Mater. Interfaces, 2019, 11, 39324–39333 CrossRef CAS PubMed.
- Z. Chen and Y. Wang, Ionic skin: From imitating natural skin to beyond, Ind. Chem. Mater., 2023, 1, 224–239 RSC.
- Z. Yu, T. Zhu, J. Zhang, M. Ge, S. Fu and Y. Lai, Fog harvesting devices inspired from single to multiple creatures: Current progress and future perspective, Adv. Funct. Mater., 2022, 32, 2200359 CrossRef CAS.
- H. Yue, Q. Zeng, J. Huang, Z. Guo and W. Liu, Fog collection behavior of bionic surface and large fog collector: A review, Adv. Colloid Interface Sci., 2022, 300, 102583 CrossRef CAS PubMed.
- X. Tang, Y. Tian, X. Tian, W. Li, X. Han, T. Kong and L. Wang, Design of multi-scale textured surfaces for unconventional liquid harnessing, Mater. Today, 2021, 43, 62–83 CrossRef CAS.
- W. Hamilton and M. Seely, Fog basking by the Namib Desert beetle, Onymacris unguicularis, Nature, 1976, 262, 284–285 CrossRef.
- Z. Yu, S. Li, M. Liu, R. Zhu, M. Yu, X. Dong, Y. Suna and S. Fu, A dual-biomimetic knitted fabric with a manipulable structure and wettability for highly efficient fog harvesting, J. Mater. Chem. A, 2022, 10, 304–312 RSC.
- B. Kennedy and J. Boreyko, Bio-inspired fog harvesting meshes: A review, Adv. Funct. Mater., 2023, 33, 2306162 CrossRef.
- A. Rao, A. Fix, Y. Yang and D. Warsinger, Thermodynamic limits of atmospheric water harvesting, Energy Environ. Sci., 2022, 15, 4025–4037 RSC.
- Y. Ji, W. Yang, X. Li, K. Hou, P. Du, H. Zhao, Z. Fan, B. Xu and Z. Cai, Thermodynamically induced interfacial condensation for efficient fog harvesting, Small, 2023, 19, 2304037 CrossRef CAS PubMed.
- R. Li, M. Wu, Y. Shi, S. Aleid, W. Wang, C. Zhang and P. Wang, Hybrid water vapor sorbent design with pollution shielding properties: Extracting clean water from polluted bulk water sources, J. Mater. Chem. A, 2021, 9, 14731–14740 RSC.
- W. Zhou, C. Zhou, C. Deng, L. Chen, X. Zeng, Y. Zhang, L. Tan, B. Hu, S. Guo, L. Dong and S. Tan, High-performance freshwater harvesting system by coupling solar desalination and fog collection with hierarchical porous microneedle arrays, Adv. Funct. Mater., 2022, 32, 2113264 CrossRef CAS.
- M. Shah, B. Pirzada, G. Price, A. Shibiru and A. Qurashi, Applications of nanotechnology in smart textile industry: A critical review, J. Adv. Res., 2022, 38, 55–75 CrossRef CAS PubMed.
- X. Tian and T. Hua, Antibacterial, scalable manufacturing, skin-attachable, and ecofriendly fabric triboelectric nanogenerators for self-powered sensing, ACS Sustainable Chem. Eng., 2021, 9, 13356–13366 CrossRef CAS.
- K. Chen, Y. Li, G. Yang, S. Hu, Z. Shi and G. Yang, Fabric-based TENG woven with bio-fabricated superhydrophobic bacterial cellulose fiber for energy harvesting and motion detection, Adv. Funct. Mater., 2023, 33, 2304809 CrossRef CAS.
- J. He, Y. Xue, H. Liu, J. Li, Q. Liu, Y. Zhao, L. Mu, C. Sun and M. Qu, Humidity-resistant, conductive fabric-based triboelectric nanogenerator for efficient energy harvesting and human-machine interaction sensing, ACS Appl. Mater. Interfaces, 2023, 15, 43963–43975 CrossRef CAS PubMed.
- C. Gao, T. Liu, B. Luo, C. Cai, W. Zhang, J. Zhao, J. Yuan, P. Fatehi, C. Qin and S. Nie, Cellulosic triboelectric materials for stable energy harvesting from hot and humid conditions, Nano Energy, 2023, 111, 108426 CrossRef CAS.
- T. Kim, C. Park, E. Samuel, S. An, A. Aldalbahi, F. Alotaibi, A. Yarin and S. Yoon, Supersonically sprayed washable, wearable, stretchable, hydrophobic, and antibacterial rGO/AgNW fabric for multifunctional sensors and supercapacitors, ACS Appl. Mater. Interfaces, 2021, 13, 10013–10025 CrossRef CAS PubMed.
- Y. Cheng, J. Wang, X. Lu and C. Wang, An all-nanofibrous Janus textile with directional perspiration for triboelectric nanogenerator and self-powered e-skin sensor, Nano Energy, 2023, 117, 108852 CrossRef CAS.
- S. Hu, J. Han, Z. Shi, K. Chen, N. Xu, Y. Wang, R. Zheng, Y. Tao, Q. Sun, Z. Wang and G. Yang, Biodegradable, Super-strong, and conductive cellulose macrofibers for fabric-based triboelectric nanogenerator, Nano-Micro Lett., 2022, 14, 2150–5551 Search PubMed.
- Z. Hou, T. Liu, M. Li, Y. Xu, X. Wu, S. Luo, C. Cai, Y. Mou, Y. Qiu, S. Nie and D. Lu, Superhydrophobic triboelectric structural materials enabled by hierarchical spatial assembly, Adv. Funct. Mater., 2024, 34, 2400750 CrossRef.
- C. Gopi, R. Vinodh, S. Sambasivam, I. Obaidat and H. Kim, Recent progress of advanced energy storage materials for flexible and wearable supercapacitor: From design and development to applications, J. Energy Storage, 2020, 27, 101035 CrossRef.
- T. Kim, C. Park, E. Samuel, Y. Kim, S. An and S. Yoon, Wearable sensors and supercapacitors using electroplated-Ni/ZnO antibacterial fabric, J. Mater. Sci. Technol., 2022, 100, 254–264 CrossRef CAS.
- Y. Yang, Q. Huang, L. Niu, D. Wang, C. Yan, Y. She and Z. Zheng, Waterproof, ultrahigh areal-capacitance, wearable supercapacitor fabrics, Adv. Mater., 2017, 29, 1606679 CrossRef PubMed.
- T. Xia, X. Zhang, J. Zhao, Q. Li, C. Ao, R. Hu, Z. Zheng, W. Zhang, C. Lu and Y. Deng, Flexible and conductive carbonized cotton fabrics coupled with a nanostructured Ni(OH)2 coating for high performance aqueous symmetric supercapacitors, ACS Sustainable Chem. Eng., 2019, 7, 5231–5239 CrossRef CAS.
- J. Peng, B. Wang, H. Cheng, R. Yang, Y. Yin, S. Xu and C. Wang, Highly sensitive and superhydrophobic fabric sensor based on AgNPs/polypyrrole composite conductive networks for body movement monitoring, Compos. Sci. Technol., 2022, 227, 109561 CrossRef CAS.
- D. Lu, S. Liao, Y. Chu, Y. Cai, Q. Wei, K. Chen and Q. Wang, Highly durable and fast response fabric strain sensor for movement monitoring under extreme conditions, Adv. Fiber Mater., 2023, 5, 223–234 CrossRef CAS.
- Y. Liu, X. Li, H. Yang, P. Zhang, P. Wang, Y. Sun, F. Yang, W. Liu, Y. Li, Y. Tian, S. Qian, S. Chen, H. Cheng and X. Wang, Skin-interfaced superhydrophobic insensible sweat sensors for evaluating body thermoregulation and skin barrier functions, ACS Nano, 2023, 17, 5588–5599 CrossRef CAS PubMed.
- T. Zhu, Y. Ni, K. Zhao, J. Huang, Y. Cheng, M. Ge, C. Park and Y. Lai, A breathable knitted fabric-based smart system with enhanced superhydrophobicity for drowning alarming, ACS Nano, 2022, 16, 18018–18026 CrossRef CAS PubMed.
- Y. Ni, X. Zang, J. Chen, T. Zhu, Y. Yang, J. Huang, W. Cai and Y. Lai, Flexible MXene-based hydrogel enables wearable human–Computer interaction for intelligent underwater communication and sensing rescue, Adv. Funct. Mater., 2023, 33, 2301127 CrossRef CAS.
- T. Zhu, L. Liu, J. Huang, S. Li, Y. Lei, W. Cai, Y. Lai and H. Li, Multifunctional hydrophobic fabric-based strain sensor for human motion detection and personal thermal management, J. Mater. Sci. Technol., 2023, 138, 108–116 CrossRef.
- Y. Shi, Z. Xiang, L. Cai, F. Pan, Y. Dong, X. Zhu, J. Cheng, H. Jiang and W. Lu, Multi-interface assembled N-doped MXene/HCFG/AgNW films for wearable electromagnetic shielding devices with multimodal energy conversion and healthcare monitoring performances, ACS Nano, 2022, 16, 7816–7833 CrossRef CAS PubMed.
- C. Wen, B. Zhao, Y. Liu, C. Xu, Y. Wu, Y. Cheng, J. Liu, Y. Liu, Y. Yang, H. Pan, J. Zhang, L. Wu and R. Che, Flexible MXene-based composite films for multi-spectra defense in radar, infrared and visible light bands, Adv. Funct. Mater., 2023, 33, 2214223 CrossRef CAS.
- Q. Wang, S. Zhu, H. He, J. Du, W. Li, Z. Kang and D. Chen, Conductive and superhydrophobic Ag/PDMS films with high stability for passive de-icing and electromagnetic shielding, Prog. Org. Coat., 2022, 169, 106919 CrossRef CAS.
- X. Li, Z. Zhang, L. Chen, J. Zhang, W. Chen, R. Feng and X. Wang, Multifunctional MnFe2O4/TiO2/Ti3C2Tx composites based on in-situ grown TiO2 for efficient microwave absorption, high hydrophobicity, and heat dissipation properties, J. Colloid Interface Sci., 2023, 654, 96–106 CrossRef PubMed.
- G. Fang, T. He, X. Hu, X. Yang, S. Zheng, G. Xu and C. Liu, Bionic octopus structure inspired stress-driven reconfigurable microwave absorption and multifunctional compatibility in infrared stealth and de-icing, Chem. Eng. J., 2023, 467, 143266 CrossRef CAS.
- Y. Zhang, G. Shen, S. Lam, S. Ansar, S. Jung, S. Ge, L. Hou, Z. Fan, F. Wang and W. Fan, A waste textiles-based multilayer composite fabric with superior electromagnetic shielding, infrared stealth and flame retardance for military applications, Chem. Eng. J., 2023, 471, 144679 CrossRef CAS.
- B. Yan, X. Bao, Y. Gao, M. Zhou, Y. Yu, B. Xu, L. Cui, Q. Wang and P. Wang, Antioxidative MXene@GA-decorated textile assisted by metal ion for efficient electromagnetic interference shielding, dual-driven heating, and infrared thermal camouflage, Adv. Fiber Mater., 2023, 5, 2080–2098 CrossRef CAS.
- L. Han, W. Liang, Q. Xie, J. Zhao, Y. Dong, X. Wang and L. Lin, Health monitoring via heart, breath, and Korotkoff sounds by wearable Piezoelectret patches, Adv. Sci., 2023, 20, 2301180 CrossRef PubMed.
- J. Dong, X. Tang, Y. Peng, C. Fan, L. Li, C. Zhang, F. Lai, G. He, P. Ma, Z. Wang, Q. Wei, X. Yan, H. Qian, Y. Huang and T. Liu, Highly permeable and ultrastretchable E-textiles with EGaIn-superlyophilicity for on-skin health monitoring, joule heating, and electromagnetic shielding, Nano Energy, 2023, 108, 108194 CrossRef CAS.
- B. Wang, Z. Yin, W. Cheng, Y. Zhang and Y. Hu, Flame-retardant aramid fabric with durable, self-cleaning, hydrophobic, and tunable electromagnetic interference shielding properties, Composites, Part A, 2023, 166, 107392 CrossRef CAS.
- L. Liu, Z. Ma, M. Zhu, L. Liu, J. Dai, Y. Shi, J. Gao, T. Dinh, T. Nguyen, L. Tang and P. Song, Superhydrophobic self-extinguishing cotton fabrics for electromagnetic interference shielding and human motion detection, J. Mater. Sci. Technol., 2023, 132, 59–68 CrossRef CAS.
- Y. Cheng, W. Zhu, X. Lu and C. Wang, Lightweight and flexible MXene/carboxymethyl cellulose aerogel for electromagnetic shielding, energy harvest and self-powered sensing, Nano Energy, 2022, 98, 107229 CrossRef CAS.
- X. Li, X. Sheng, Y. Fang, X. Hu, S. Gong, M. Sheng, X. Lu and J. Qu, Wearable Janus-type film with integrated all-season active/passive thermal management, thermal camouflage, and ultra-high electromagnetic shielding efficiency tunable by Origami process, Adv. Funct. Mater., 2023, 33, 2212776 CrossRef CAS.
- Y. Xie, P. Tu, Y. Xiao, X. Li, M. Ren, Z. Cai and B. Xu, Designing non-fluorinated superhydrophobic fabrics with durable stability and photocatalytic functionality, ACS Appl. Mater. Interfaces, 2023, 15, 40011–40021 CrossRef CAS PubMed.
- N. Agrawal, J. Tan, P. Low, E. Fong, Y. Lai and Z. Chen, Green synthesis of robust superhydrophobic antibacterial and UV-blocking cotton fabrics by a dual-stage silanization approach, Adv. Mater. Interfaces, 2019, 29, 1900032 CrossRef.
- S. Sun, Z. Chen and Q. Xiao, Multifunctional cotton fabric with favorable hydrophobicity, electrical conductivity and photothermal effect for contaminants removal and oil detection, Appl. Surf. Sci., 2023, 612, 155731 CrossRef CAS.
- Y. Li, H. Li, J. Wu, X. Jia, Z. Zhang, J. Yang, X. Miao, L. Feng and H. Song, Facile recycling of waste fabrics for preparing multifunctional photothermal protective materials, ACS Sustainable Chem. Eng., 2023, 11, 10566–10577 CrossRef CAS.
- Y. Wu, L. Dong, X. Shu, Y. Yang, P. Feng and Q. Ran, Recent advancements in photothermal anti-icing/deicing materials, Chem. Eng. J., 2023, 469, 143924 CrossRef CAS.
- Z. Zhao, Q. Zhang, X. Song, J. Chen, Y. Ding, H. Wu and S. Guo, Versatile melanin-like coatings with hierarchical structure toward personal thermal management, anti-icing/deicing, and UV protection, ACS Appl. Mater. Interfaces, 2023, 15, 3522–3533 CrossRef CAS PubMed.
- H. He and Z. Guo, Fabric-based superhydrophobic MXene@ polypyrrole heater with superior dual-driving energy conversion, J. Colloid Interface Sci., 2023, 629, 508–521 CrossRef CAS PubMed.
- W. Xiao, J. Yan, S. Gao, X. Huang, J. Luo, L. Wang, S. Zhang, Z. Wu, X. Lai and J. Gao, Superhydrophobic MXene based fabric composite for high efficiency solar desalination, Desalination, 2022, 524, 115475 CrossRef CAS.
- Z. Lei, X. Sun, S. Zhu, K. Dong, X. Liu, L. Wang, X. Zhang, L. Qu and X. Zhang, Nature inspired MXene-decorated 3D honeycomb-fabric architectures toward efficient water desalination and salt harvesting, Nano-Micro Lett., 2022, 14, 2311–6706 Search PubMed.
- C. Li, Q. Tang, H. Wei, J. Liu, Q. Wang, Y. Wang, Z. Du, J. Wang, R. Xu, Y. Bi, C. Snow, L. Belfiore and J. Tang, Smart wearable fluorescence sensing of bacterial pathogens and toxic contaminants by Eu3+-induced sodium alginate/Ag nanoparticle aggregates, ACS Appl. Nano Mater., 2022, 5, 8393–8403 CrossRef CAS.
- P. Das, M. Sherazee, P. Marvi, S. Ahmed, A. Gedanken, S. Srinivasan and A. Rajabzadeh, Waste-derived sustainable fluorescent nanocarbon-coated breathable functional fabric for antioxidant and antimicrobial applications, ACS Appl. Mater. Interfaces, 2023, 15, 29425–29439 CrossRef CAS PubMed.
- Y. Wu, C. Xue, X. Guo, M. Huang, H. Wang, C. Ma, X. Wang and Z. Shao, Highly efficient solar-driven water evaporation through a cotton fabric evaporator with wettability gradient, Chem. Eng. J., 2023, 471, 144313 CrossRef CAS.
- Z. Lei, S. Zhu, X. Sun, S. Yu, X. Liu, K. Liang, X. Zhang, L. Qu, L. Wang and X. Zhang, A multiscale porous 3D-fabric evaporator with vertically aligned yarns enables ultra-efficient and continuous water desalination, Adv. Funct. Mater., 2022, 32, 2205790 CrossRef CAS.
- J. Su, P. Zhang, R. Yang, B. Wang, H. Zhao, W. Wang and C. Wang, MXene-based flexible and washable photothermal fabrics for efficiently continuous solar-driven evaporation and desalination of seawater, Renewable Energy, 2022, 195, 407–415 CrossRef CAS.
- D. Xu, C. Ge, Z. Chen, Y. Liu, H. Du, H. Gong, C. Gao, Z. Shen, W. Xu and K. Liu, Composite braided fabric coupled with photothermal and electrothermal processes for stable and continuous all-day desalination, ACS Appl. Mater. Interfaces, 2022, 14, 52087–52095 CrossRef CAS PubMed.
- P. Zhou, Y. Wang and X. Zhang, Bi2Se3 nanosheets-based photothermal composites with hydrophobic surface for synergistic anti−/de-icing, Compos. Sci. Technol., 2023, 233, 109916 CrossRef CAS.
- X. Xu, Y. Xing, Y. Yin, W. Fang, B. Wu, P. Bei, J. Feng, H. Yu, G. Wang and W. Li, Flexible wearable fabrics for solar thermal energy storage and release in on-demand environments, Chem. Eng. J., 2023, 466, 143175 CrossRef CAS.
- L. Fei, Z. Zhang, Y. Tan, T. Ye, D. Dong, Y. Yin, T. Li and C. Wang, Efficient and robust molecular solar thermal fabric for personal thermal management, Adv. Mater., 2023, 35, 2209768 CrossRef CAS PubMed.
- A. Nafady, A. Alothman and S. Shaikh, Fabrication of photoluminescent electrically conductive and flame-retardant cellulose fabric incorporating polyaniline/strontium aluminate nanocomposite for a plethora of useful applications, Int. J. Biol. Macromol., 2023, 244, 125384 CrossRef CAS PubMed.
- P. Qi, F. Chen, Y. Li, H. Li, X. Gu, J. Sun and S. Zhang, A review of durable flame-retardant fabrics by finishing: fabrication strategies and challenges, Adv. Fiber Mater., 2023, 5, 731–763 CrossRef CAS.
- Q. Ge, J. Chu, W. Cao, F. Yi, Z. Ran, Z. Jin, B. Mao, Z. Li and K. Novoselov, Graphene-based textiles for thermal management and flame retardancy, Adv. Funct. Mater., 2022, 32, 2205934 CrossRef CAS.
- A. Vishwakarma, M. Singh, B. Weclawski, V. Reddy, B. Kandola, G. Manik, A. Dasari and S. Chattopadhyay, Construction of hydrophobic fire retardant coating on cotton fabric using a layer-by-layer spray coating method, Int. J. Biol. Macromol., 2022, 223, 1653–1666 CrossRef CAS PubMed.
- M. Yang, Y. Yang, J. Shi and W. Rao, Fabrication of eco-friendly flame-retardant and hydrophobic coating for cotton fabric, Cellulose, 2023, 30, 3267–3280 CrossRef CAS.
- F. Liang, Y. Xu, S. Chen, Y. Zhu, Y. Huang, B. Fei and W. Guo, Fabrication of highly efficient flame-retardant and fluorine-free superhydrophobic cotton fabric by constructing multielement-containing POSS@ZIF-67@PDMS micro-nano hierarchical coatings, ACS Appl. Mater. Interfaces, 2022, 14, 56027–56045 CrossRef CAS PubMed.
- J. Wang, J. He, L. Ma, Y. Zhang, L. Shen, S. Xiong, K. Li and M. Qu, Multifunctional conductive cellulose fabric with flexibility, superamphiphobicity and flame-retardancy for all-weather wearable smart electronic textiles and high-temperature warning device, Chem. Eng. J., 2020, 390, 124508 CrossRef.
- H. He, J. Liu, Y. Wang, Y. Zhao, Y. Qin, Z. Zhu, Z. Yu and J. Wang, An ultralight self-powered fire alarm e-textile based on conductive aerogel fiber with repeatable temperature monitoring performance used in firefighting clothing, ACS Nano, 2022, 16, 2953–2967 CrossRef CAS PubMed.
- D. Xu, Z. Chen, Y. Liu, C. Ge, C. Gao, L. Jiao, W. Guo, Q. Zhang, J. Fang and W. Xu, Hump-inspired hierarchical fabric for personal thermal protection and thermal comfort management, Adv. Funct. Mater., 2023, 33, 2212626 CrossRef CAS.
- H. Zhou, Q. Li, Z. Zhang, X. Wang and H. Niu, Recent advances in superhydrophobic and antibacterial cellulose-based fibers and fabrics: Bio-inspiration, strategies, and applications, Adv. Fiber Mater., 2023, 5, 1555–1591 CrossRef CAS PubMed.
- B. Rao, R. Kumar, S. Haque, J. Kumar, T. Rao, R. Kothapalli and C. Patra, Ag2[Fe(CN)5NO]-fabricated hydrophobic cotton as a potential wound healing dressing: An in vivo approach, ACS Appl. Mater. Interfaces, 2021, 13, 10689–10704 CrossRef CAS PubMed.
- Y. Fang, L. Chen, J. Liu and L. Wu, Multi-functionalization of cotton fabrics with excellent flame retardant, antibacterial and superhydrophobic properties, Int. J. Biol. Macromol., 2024, 254, 127889 CrossRef CAS PubMed.
- T. Suryaprabha, H. Ha, B. Hwang and M. Sethuraman, Self-cleaning, superhydrophobic, and antibacterial cotton fabrics with chitosan-based composite coatings, Int. J. Biol. Macromol., 2023, 250, 126217 CrossRef CAS PubMed.
- M. Chen, P. Ayaz, Y. Xiao, Y. Li, P. Wang, W. Huang, S. Zhao, F. Fu, X. Liu and S. Xiang, Hydrophobic, fireproof, UV-blocking and antibacterial cotton fabric activated by bio-based PA/ODA/TiO2, Cellulose, 2023, 30, 4713–4733 CrossRef CAS.
- T. Wright, M. Vlok, T. Shapira, A. Olmstead, F. Jean and M. Wolf, Photodynamic and contact killing polymeric fabric coating for bacteria and SARS-CoV-2, ACS Appl. Mater. Interfaces, 2022, 14, 49–56 CrossRef CAS PubMed.
- E. Pakdel, J. Sharp, S. Kashi, W. Bai, M. Gashti and X. Wang, Antibacterial superhydrophobic cotton fabric with photothermal, self-cleaning, and ultraviolet protection functionalities, ACS Appl. Mater. Interfaces, 2023, 15, 34031–34043 CrossRef CAS PubMed.
- Y. Chen, J. Ao, J. Zhang, J. Gao, L. Hao, R. Jiang, Z. Zhang, Z. Liu, J. Zhao and L. Ren, Bioinspired superhydrophobic surfaces, inhibiting or promoting microbial contamination, Mater. Today, 2023, 67, 1369–7021 CrossRef.
- Y. Peng, J. Dong, J. Sun, Y. Mao, Y. Zhang, J. Long, L. Li, C. Zhang, Y. Zhao, H. Lu, H. Qian, X. Yan, J. Zhao, F. Wang, Y. Huang and T. Liu, Multimodal health monitoring via a hierarchical and ultrastretchable all-in-one electronic textile, Nano Energy, 2023, 110, 108374 CrossRef CAS.
- Z. Hui, L. Zhang, G. Ren, G. Sun, H. Yu and W. Huang, Green flexible electronics: natural materials, fabrication, and applications, Adv. Mater., 2023, 35, 2211202 CrossRef CAS PubMed.
- T. Tat, G. Chen, X. Zhao, Y. Zhou, J. Xu and J. Chen, Smart textiles for healthcare and sustainability, ACS Nano, 2022, 16, 13301–13313 CrossRef CAS PubMed.
|
This journal is © Institute of Process Engineering of CAS 2024 |
Click here to see how this site uses Cookies. View our privacy policy here.