DOI:
10.1039/D3QM00627A
(Research Article)
Mater. Chem. Front., 2023,
7, 4952-4960
FeNi3 nanoparticles for electrocatalytic synthesis of urea from carbon dioxide and nitrate†
Received
1st June 2023
, Accepted 13th August 2023
First published on 16th August 2023
Abstract
Due to the environmental pollution and high energy consumption associated with the conventional industrial Bosch–Meiser method, electrocatalytic urea synthesis emerges as a promising and sustainable alternative route. In this work, we constructed and utilized nitrogen-doped porous carbon loaded with bimetallic FeNi3 alloy nanoparticles as an efficient electrocatalyst for synthesizing urea from carbon dioxide (CO2) and nitrate (NO3−). The created FeNi3 alloy within FeNi/NC served as the active site for the C–N coupling reaction, generating a higher urea yield of 496.5 μg h−1 mgcat.−1 with a correlating faradaic efficiency (FE) of 16.58% at −0.9 V versus the reversible hydrogen electrode (vs. RHE), when in comparison to monometallic Fe/NC and Ni/NC catalysts. Moreover, we also monitored the urea generation process via in situ Raman spectroscopy technology, which enabled the identification of two critical reaction species, namely O–C–O and N–C–N, inferring that C–N coupling acted as the key reaction step.
1. Introduction
Urea, an indispensable nitrogen source in agricultural fertilizers, plays a pivotal role in promoting robust crop growth.1–4 However, the conventional industrial technique employed for urea production necessitates the harsh reaction between ammonia (NH3) and CO2 with extreme conditions of elevated temperatures (150–200 °C) and pressures (100–200 atm).5–7 Regrettably, this approach not only engenders substantial energy consumption but also exacerbates environmental concerns by contributing to the release of CO2 emissions.8–10 To surmount these formidable challenges and foster the principles of sustainable development, it is imperative to explore alternative methodologies enabling the synthesis of urea under milder conditions.10–12 One particularly promising avenue lies in harnessing the potential of electrocatalytic C–N coupling to urea, which effectively utilizes CO2 and NO3− as reactants and operates under ambient conditions. However, the main issues present with NO3− pollutants, i.e., low concentration, complicated composition, heavy metals and chemical oxygen demand, will lead to decline in electrocatalytic performance.13 For other nitrogen sources, the intrinsic chemical inertness and low solubility of N2 significantly restrict urea yield and faradaic efficiency (FE);14 NO2− is unstable and susceptible to nitrate formation in aqueous solution.15 Thus, NO3− is more appealing from an application standpoint as a nitrogen source for the electrocatalytic production of urea with CO2. This indicates that the innovative approach of electrocatalytic synthesis of urea, which holds tremendous prospects for attaining efficient conversion to urea while significantly alleviating the demands for energy resources, still has a number of challenges that need to be addressed.16–19
As widely acknowledged, the composition and structure of catalysts are of utmost significance in the realm of electrocatalytic urea synthesis.20–22 Such as, the metal alloying strategy promotes electronic interactions among the various components, which facilitates the creation of more different active sites for the electrocatalytic reaction to cooperatively activate the reactants/intermediates and reduce the occurrence of side reactions.23–25 Thus, alloy catalysts have been widely applied in electrochemical application.26–28 As an exemplification of this concept, Wang et al. reported an AuPd nanoalloy, with Pd and Au as the active sites for carbon dioxide reduction reactions (CO2RR) and nitrate reduction reactions (NO3RR), respectively, to synergistically catalyze the formation of urea by C–N coupling reaction.26 Given the great potential of alloy electrocatalysts in the relevant electrocatalytic reaction of urea generation, and through extensive literature it can be found that bimetallic FeNi catalysts are expected to be the superior candidates for urea synthesis, i.e. nickel-based catalysts exhibit excellent performance in CO2RR, whereas iron-based catalysts display remarkable efficacy in NO3RR. For CO2RR, Chen et al. developed a nickel phthalocyanine (NiPPc) electrocatalyst, achieving up to 99.8% selectivity of CO.29 Similarly, Lu et al. introduced a pyridine nitrogen-coated nickel nanoparticle with core–shell structure, showing up to 90% FE in reducing CO2 to CO.30 For NO3RR, Zhang et al. used ultra-thin graphene nanosheets as protective armor, ensuring long-term catalytic performance by preventing oxidation and leakage of iron nanoparticles.31 Cu-doped hematite particles also achieved nearly 100% FE in converting NO3− to NH3.32 While cobalt-doping can precise tuning of the d-band center of Fe@Fe2O3, thus achieving NH3 selectivity up to 99%.33
Taking into consideration the individual advantages of Fe-based and Ni-based catalysts showcased in the aforementioned respective reactions, this study designed a FeNi3 alloy catalyst (FeNi/NC) capable of simultaneously adsorbing and activating CO2 molecules and NO3− ions, leading to efficient urea synthesis through the construction of C–N coupling active sites. The synergistic effect between Fe and Ni components yields remarkable improvements in the electrochemical synthesis of urea, with an impressive urea yield of 496.5 μg h−1 mgcat.−1 and a corresponding FE of 16.58%. This work emphasizes a feasible methodology for sustainable urea synthesis through metal alloying and C–N coupling.
2. Experimental section
2.1 Chemicals
Polyvinylidene chloride (PVDC), sodium ethylate (C2H5ONa, 96%) were bought from MACKLIN; lignin (Alkaline), Melamine (99%), and Nickel chloride hexahydrate (NiCl2·6H2O) were received from Aladdin Biochemical Technology; Iron chloride (FeCl3), nitrate of potash (KNO3, ≥99.99% metals basis), potassium hydroxide (KOH) were acquired through Sinopharm Chemical Reagent Co., Ltd; Carbon papers (HCP020N) were provided from Hesen company (Shanghai, China) and rinsed with acetone, ethanol, and distilled water before being used. Urease was purchased from Sigma, its activity and batch number are 20KU and Lot#SLCJ5647, respectively. Milli-Q ultrapure water (>18 Ω) was used in all experiments. All chemicals were used without further purification.
2.2 Synthesis of FeNi/NC
Firstly, 1 g PVDC, 1 g lignin, 1 g KOH, 0.5 g melamine, 2.04 g C2H5ONa, 0.3 g FeCl3, 0.15 g NiCl2·6H2O were meticulously mixed in an agate mortar and thoroughly ground. The resulting viscous liquid was then solidified by freezing it with liquid nitrogen and subsequently transferred to a freeze dryer where it underwent an 8 hour drying process. Following that, the carbonation procedure was initiated. The prepared precursors were carefully transferred to a quartz boat and placed in a tube furnace under a N2 atmosphere. The temperature was gradually increased at a rate of 5 °C per minute until reaching 950 °C, and the samples were maintained at this temperature for 2 h. Subsequently, the excess fractions of Fe and Ni were eliminated by subjecting the black powder to a reaction with 1 M H2SO4 at 90 °C for a duration of 12 h. The resulting powder was washed with deionized water until reaching neutrality and subsequently dried under vacuum conditions. Lastly, the obtained powder was once again subjected to carbonization at 950 °C under a N2 atmosphere for 2 h, resulting in the final formation of the FeNi/NC catalyst. In the aforementioned synthesis process, a combination of C2H5ONa and KOH can be employed to eliminate the Cl element from PVDC. Melamine is served as the nitrogen source.34 It is worth noting that lignin, which contains abundant hydroxyl and carboxyl groups, plays a vital role in effectively adsorbing metal ions and facilitating the dispersion of metal elements on the nitrogen-doped carbon carrier during the carbonization.35,36
2.3 Synthesis of Fe/NC
The synthesis procedure for Fe/NC followed a similar process to that of FeNi/NC, with the only difference being the use of 0.389 g of FeCl3 instead of the combination of 0.3 g of FeCl3 and 0.15 g of NiCl2·6H2O.
2.4 Synthesis of Ni/NC
The synthesis procedure for Ni/NC is the same as that for FeNi/NC, except that 0.3 g of FeCl3 and 0.15 g of NiCl2·6H2O are replaced by 0.570 g of NiCl2·6H2O.
2.5 Materials characterization
The morphology of catalysts was investigated by field emission Scanning electron microscopy (SEM, ZEISS VLTRA-55) and transmission electron microscopy (TEM, FEI Tecnai G2 F20). The Raman spectra were acquired on a Renishaw in via Raman microscope with the 532 nm laser. X-ray diffraction (XRD) measurements were performed on a D8 ADVANCE X-ray diffractometer (Bruker). The X-ray photoelectron spectroscopy (XPS) analyses were performed with an ESCALAB 250 Xi X-ray photoelectron spectrometer. The gaseous products for electrocatalytic reaction were quantified on a GC9790 plus (FULI instruments). The 1H NMR spectra were measured on an Ascend 800 MHz NMR spectrometer (Bruker) equipped with an ultralow temperature probe.
2.6 Electrochemical characterization
All electrochemical characterizations were conducted using a CHI 760E workstation integrated with a three-electrode configuration within a two-compartment cell, which was divided by a Nafion 117 membrane. The catalyst loading on the carbon paper (Hesen, HCP-020) was served as the working electrode, and the carbon rod and the Ag/AgCl (saturated KCl solution) were applied as the counter and reference electrodes, respectively. For the preparation of catalyst ink, 2 mg of catalyst was dispersed in the mixed solution of deionized water (500 μL), isopropanol (450 μL) and 5 wt% Nafion (50 μL). After ultrasonic treatment for 1 h, the homogenous ink was formed and 50 μL of the catalyst ink was drop-casted onto the carbon paper with a geometric surface of 1 × 1.5 cm2, thus the catalyst loading is 0.1 mg cm−2.
For the electrocatalytic synthesis of urea, the electrolyte was initially purged with CO2 (purity: 99.999%, flow rate: 100 sccm) for 0.5 h for degassing and CO2 saturation. The flow rate was then adjusted to 30 sccm and the continuous feeding of CO2 was kept during the electrochemical test of 1 h. Then, the cathode electrolyte was extracted for further analyzation. The all applied potentials in this work have been converted to the RHE scale:
E(vs. RHE) = E(vs. Ag/AgCl) + 0.0591 × pH + 0.197 |
The pH was 3.9 or 6.8 in the presence or absence of CO
2 saturation, respectively.
In situ Raman test.
A three-electrode flow cell with a quartz window (C031-3, Gaoss Union, Tianjin) was applied to collect in Raman spectra data (Renishaw: laser, λ = 532 nm; power, 5 mW). A gold plate loaded with powder catalyst, Ag/AgCl (Saturated KCl) and graphite rod were used as working, reference and counter electrode, respectively. The cathode and anode chambers were separated by the membrane (Nafion 117), and a CO2-saturated 0.1 M KNO3 electrolyte was continuously passed into the cathode chamber. The Raman signals at different applied potentials or electrolysis time were recorded using a 10 s acquisition time.
2.7 Determination of urea and NH3
The generated NH3 was quantified using the indophenol blue method. Three aqueous colorants were employed: (a) 1 M NaOH (5 wt% sodium citrate, 5 wt% salicylic acid); (b) 0.05 M NaClO; (c) 1 wt% sodium nitroferricyanide. Subsequently, the solution was added sequentially with the following volumes: 2 mL electrolyte, 2 mL (a) 1 mL (b) and 0.2 mL (c). The resulting mixture was then incubated under dark environment for 2 h, followed by the absorbance measurement, and obtain the amount of NH3 according to the calibration curve between NH3 concentration and the absorbance at 662 nm.10 The concentration of urea was determined utilizing the urease decomposition.34,35 The 1.8 mL electrolyte comprising urea underwent hydrolysis employing 0.2 mL urease (5 mg mL−1) for a duration of 1 h at 37 °C. The quantification of NH3 concentration before and after the hydrolysis experiment was accomplished utilizing the previously established calibration curve of NH3. The quantification of urea quantity was based on the stoichiometric conversion, whereby 1 urea molecule yields 1 CO2 and 2 NH3.
Calculations of urea yield and the faradaic efficiency.
The mole concentration of yielded urea (murea) can be calculated as followed:
m1 and m2 are the NH3 concentrations before and after the urease decomposition experiment, respectively.
The urea yield rate of urea was calculated from the following equation:
R (urea) represents the urea yield (mg h
−1 mg
cat.−1);
c for urea mass concentration (mg mL
−1);
v for electrolyte volume (mL);
t presents the reaction time (h);
m for catalyst mass (mg).
The FE of urea can be acquired through the following equation:
where
F for the Faraday constant (96485.3 C mol
−1),
Q for electric quantity,
c for generated urea concentration,
v for electrolyte volume,
n is the number of electron transfer, which is 16 for electro-coupling of CO
2 and NO
3−.
Calculations of the NH3 faradaic efficiency.
The FE of NH3 was calculated through the following equation:
where F denotes the Faraday constant (96
485.3 C mol−1), Q for electric quantity, c for generated NH3 concentration, v for electrolyte volume, and n represents the number of electron transfer, which is 8.
2.8 Determination of CO and H2
The thermal conductivity detector (TCD) on the gas chromatograph is used to identify H2, while its the flame ionization detector (FID) is used to detect CO and other hydrocarbons.
Calculations of the CO and H2 faradaic efficiency.
The FE of gas product is calculated as following equation:
where n represents the number of transferred electrons (n = 2), v (mL min−1) represents the gas flow rate of CO2, and the S1 represents the product peak area, the C2 represents the standard gas product concentration, the S2 represents the standard gas product peak area. The i is the total current measured during gas collection. P = 101
325 Pa, F = 96
485 C mol−1, R = 8.314 J mol−1 K−1, and T = 298.15 K.
2.9 Determination of NO2−
4 g of aminobenzenesulfonamide, 0.2 g of N-(1-teayl) ethylenediamine dihydrochloride, 10 mL of phosphoric acid (ρ = 1.685 g mL−1), and 50 mL of deionized water were mixed well as a coloring agent. Take 0.2 mL of electrolyte, dilute it to 5 mL, then add 0.1 mL of colouring agent and mix thoroughly. After the reaction at room temperature for 20 min, the absorption spectrum was measured by UV-Vis spectrophotometer, and recorded the absorption intensity at 540 nm. The NO2− standard concentration-absorbance curves were obtained using a series of standard solutions of different concentrations of KNO2.37
Calculations of NO2− faradaic efficiency.
The FE of NO2− is calculated as the following equation:
where F stands for the Faraday constant (96
485.3 C mol−1), Q for electric quantity, c for produced NO2−, v is electrolyte volume, n for the number of electron transfer, which is 2.
3. Results and discussion
The fabrication process of FeNi/NC was illustrated in Fig. 1a. After the metal source, carbon source, and nitrogen source were thoroughly mixed, this mixture was sequentially subjected to the procedures of freeze-drying, carbonization, acid washing, and pyrolysis to obtain the FeNi/NC sample. And the detailed procedures could be acquired in the Experimental section. The morphology of the FeNi/NC, Fe/NC and Ni/NC catalysts were characterized by SEM in Fig. 1b and Fig. S1 (ESI†), which revealed a porous structure with thinner carbon nanosheets randomly anchored or wrapped with metallic nanoparticles (from ∼20 nm to 200 nm in diameter). And high-angle annular dark-field scanning TEM (HAADF-STEM) also clearly showed uniform dispersion of the brighter metal nanoparticles in the porous carbon matrix (Fig. 1c). Meanwhile, in Fig. 1e–i, elemental mapping showed that C, N, and O elements are well distributed overall, while Fe and Ni elements are more concentrated on the alloy nanoparticles. Moreover, the interplanar spacing of 0.355 nm and 0.335 nm, corresponding to the (100) plane of FeNi3, and (111) plane of graphite carbon, respectively, can be seen by high-resolution TEM (HRTEM) in Fig. 1d and Fig. S2 (ESI†). Therefore, it can be inferred that FeNi/NC forms a nitrogen-doped porous carbon structure with a large specific surface area of randomly distributed FeNi3 alloy nanoparticles, which facilitates the exposure of active sites and promotes electron transfer and mass transfer.38
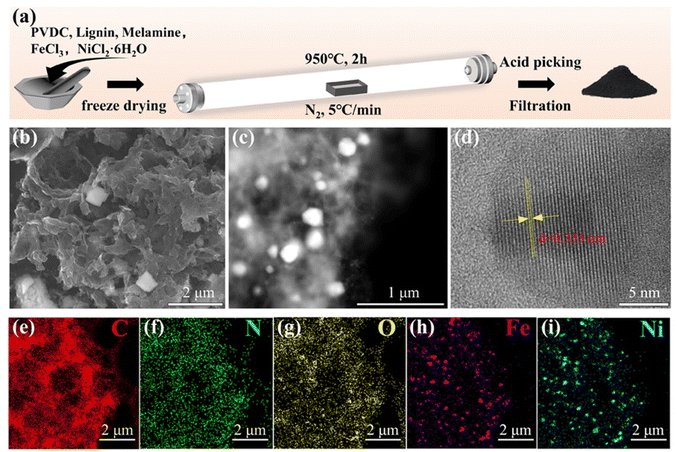 |
| Fig. 1 (a) Schematic illustration of the synthesis procedure. (b) SEM, (c) HAADF-STEM, (d) HRTEM, and (e–i) elemental mapping images of FeNi/NC. | |
XRD analysis was employed to investigate the composition properties of the theses materials. As shown in Fig. 2a, the diffraction peaks of FeNi3 (PDF#88-1715), Fe3O4 (PDF#75-0449), and graphitic carbon (PDF#75-2078) were observed in the XRD spectra of FeNi/NC, indicating the successful generation of a FeNi3 alloy. However, for Fe/NC and Ni/NC (Fig. S3 and S4, ESI†), only the respective Fe (PDF#87-0721), Fe3O4 (PDF#75-0033) and Ni (PDF#87-0712) metals were found. Fig. 2b showed the Raman spectra of these samples to characterize their degree of graphitization, which exists two typical D (∼1350 cm−1) and G (∼1580 cm−1) bands associated with lattice carbon defects and sp2 hybridized carbon, respectively. Among them, Fe/NC (1.01), Ni/NC (1.02), and FeNi/NC (1.06) exhibited similar intensity ratio of ID/IG, indicating that there is no significant difference in the degree of graphitization of these samples.39Fig. 2c presented the Fe 2p XPS spectrum, where four peaks at 733.5, 728.3, 725.7, and 723.9 eV correspond to Fe3+ (satellite), Fe2+ (satellite), Fe3+, and Fe2+ in the Fe 2p1/2 region, respectively. And in the Fe 2P3/2 region, similar peaks at 718.8, 714.7, 712.8, and 710.2 eV were found and attributed to Fe3+ (satellite), Fe2+ (satellite), Fe3+, and Fe2+, respectively. While the remaining peaks at 720.5 of Fe 2p1/2 and 707.7 eV of Fe 2p3/2 are assigned to Fe(0).37 In the deconvolution analysis of Ni 2p XPS spectra (Fig. 2d), there are two groups of peaks of Ni2+ (876.6/859.2 eV) and Ni (872.2/854.4 eV) accompanied by two shake-up satellite peaks (879.9/862.3 eV) in the Ni 2p1/2 and Ni 2p3/2.40
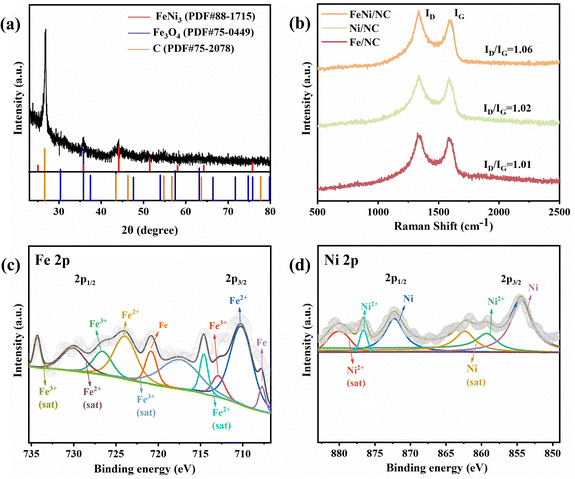 |
| Fig. 2 (a) XRD pattern of FeNi/NC. (b) Raman spectra of FeNi/NC, Fe/NC, and Ni/NC. (c) Fe 2p and (d) Ni 2p XPS spectra of FeNi/NC. | |
The electrochemical performance of FeNi/NC, Fe/NC, and Ni/NC have been investigated by using a 0.1 M KNO3 solution as the electrolyte, CO2 as feeding gas were continuously bubbled into the H-shaped cell (Fig. S5, ESI†). Linear sweep voltammetry (LSV) curves for FeNi/NC, Fe/NC, and Ni/NC in Ar or CO2 saturated electrolytes are shown in the Fig. 3a and Fig. S6 (ESI†). Their current densities from −0.2 to −1.4 V (vs. RHE) are significantly higher in CO2-saturated electrolyte than in Ar-saturated electrolyte, and the current densities of FeNi/NC were higher than those of Fe/NC and Ni/NC, indicating FeNi/NC possess better electrocatalytic activity towards the synthesis of urea from CO2 and NO3−. Meantime, the above three materials’ electrochemical impedance spectroscopy (EIS) data (Fig. S7, ESI†) were also shown to analyze their kinetics properties. Both of them presented similar charger transfer resistance of ∼20 Ω, while the slope of FeNi/NC in low frequency region was more vertical compared to the other two, which implies that it has the lowest Warburg impedance, fast ion diffusion and short diffusion distance.41 And in the double-layer (Cdl) measurement (Fig. S8, ESI†), it can be observed that the Cdl value of FeNi/NC is about 1.3 times that of Fe/NC and 1.6 times that of Ni/NC, which implies that the former has a larger electrochemically active surface area (ECSA).42
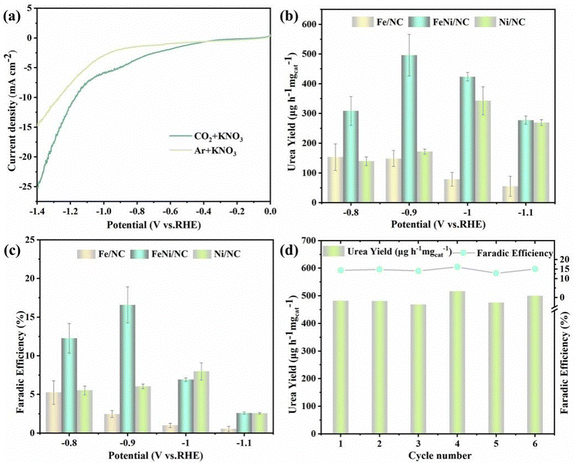 |
| Fig. 3 (a) LSV curves of FeNi/NC measured in Ar and CO2 saturated 0.1 M KNO3 electrolytes. (b) The urea yield and (c) urea FE for FeNi/NC, Fe/NC, and Ni/NC on the different applied potentials. (d) The cyclic stability test of FeNi/NC for urea synthesis. | |
To further quantitatively assess urea electrosynthesis activity, chronopotentiometry procedure with different applied potential from −0.8 to −1.1 V vs. RHE was carried out in CO2 saturated 0.1 M KNO3. The obtained liquid by-products, such NH3 and NO2−, were estimated through chromogenic method, the corresponding calibration curves of them are shown in Fig. S9 and S10 (ESI†). While the generated urea was analyzed by the urease method according to the principle that 1 mol urea can be decomposed into 2 mol NH3 (Fig. S11, ESI†).43 Meanwhile, 1H NMR was also employed to identify the produced urea and NH3 after 1 h electrolysis at −0.9 V vs. RHE (Fig. S12 and S13, ESI†). Moreover, the gaseous products, such as H2 and CO, were monitored by gas chromatography. As shown in Fig. 3b and c, the urea yield rate and corresponding FE on different potentials could be calculated through UV-vis spectra and corresponding calibration curve. It can be observed that as the applied potential increases, the urea yield rate and FE also increase, reaching a maximum yield of 496.5 μg h−1 mgcat.−1 and FE of 16.58% at −0.9 V (vs. RHE). FeNi/NC exhibited comparable or better urea production activity than previously reported catalysts (Table S1, ESI†). Furthermore, comparison of the variability of the crystalline compositions of the three catalysts mentioned above, it could be seen that FeNi/NC, Fe/NC, and Ni/NC each corresponded to FeNi3/Fe3O4, Fe/Fe3O4, and Ni. Among them, the electrocatalytic activity, both in terms of urea yield and FE, was the highest in FeNi/NC, and it differed significantly from the other samples as follows the presence of FeNi3 alloy nanoparticles, which implied that FeNi3 part played an indispensable role as an active part in the urea synthesis process.
However, these two values including yield and FE gradually decrease when the potential exceeds −0.9 V vs. RHE, mainly due to possible competitive hydrogen evolution reaction (HER), CO2RR, and NO3RR. To verify this speculation, all possible products during the electrocatalytic urea synthesis process were identified, including H2, CO, NH3, NO2−, and urea (Fig. S14, ESI†). It was found that the FE of the by-products increased significantly at higher negative potentials, leading to a poorer selectivity of urea. Subsequently, electrocatalytic stability tests of FeNi/NC, including cyclic experiments and chronoamperometry electrolysis, were carried out in CO2-saturated 0.1 M KNO3. The cyclic test was carried out for 6 cycles at −0.90 V vs. RHE with each cycle lasting 1 h of electrocatalysis and almost no decay in urea yield and FE (Fig. 3d), and the current density profile did not decay significantly after 30 h of continuity (Fig. S15, ESI†), showing the good reproducibility and durability of FeNi/NC materials. Also, after 30 h stability test, the XRD pattern and SEM image of the as-obtained FeNi/NC were demonstrated Fig. S16 and S17 (ESI†), respectively. It could be observed that the crystal structure and thinner carbon nanosheets morphology of FeNi/NC were well preserved, demonstrating its better robustness. In order to exclude the possible influence of environmental and chemical interferences on the experimental results, a series of control experiments were performed to further verify that the urea generated came from the simultaneous reduction of CO2 and NO3− and not from pollutants: (i) open-circuit potential of FeNi/NC in CO2-saturated 0.1 M KNO3 for 1 h; (ii) chronoamperometry of FeNi/NC at −0.9 V (vs. RHE) in Ar-saturated 0.1 M KNO3 for 1 h; (iii) chronoamperometry of FeNi/NC at −0.9 V (vs. RHE) in CO2-saturated 0.1 M KHCO3 for 1 h. In all three cases mentioned above, the absorbance of the two electrolytes (open circuit and blank electrolyte; with and without urease) was measured by UV-vis spectra, and no significant difference was found between them, which indicated that no urea was detected (Fig. S18 and S19, ESI†), suggesting that the urea generated via FeNi/NC catalysis was indeed from the coupling reaction of CO2 and NO3−.
Moreover, electrochemical in situ Raman spectroscopy was employed to detect the evolution of bond structures of intermediate species generated during the electrocatalytic process of FeNi/NC (Fig. 4a and Fig. S20, ESI†). In a CO2-saturated 0.1 M KNO3 solution of Fig. 4b, compared to the noticeable characteristic peak of O–C–O antisymmetrical stretching at 1050 cm−1 originating from CO32− in the open circuit potential,44,45 peak intensity of other potential gradually decreases with higher applied potential from −0.8 V to −1.1 V (vs. RHE), indicating that growth in the consumption rate of CO32−, which implies that for the urea synthesis provides sufficient key intermediates of *COOH and *CO.43,46 Meanwhile, in situ Raman spectra also appeared a weak peak at 1000 cm−1 with prolonged electroreduction time (Fig. 4c and d),47–49 which could be attributed to the N–C–N symmetric stretching model of the urea molecule and confirmed by the high concentration of the urea solution (Fig. S21, ESI†), indicating that a C–N coupling reaction between CO2 and NO3− was indeed occurred.50–56
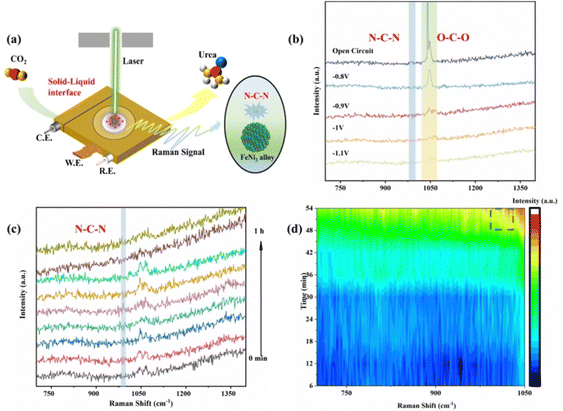 |
| Fig. 4 (a) In situ Raman schematic diagram, (b) in situ Raman spectra at different potentials, (c) in situ Raman plots at different reaction time at −0.9 V vs. RHE, and (d) corresponding contour plots. | |
4. Conclusions
In summary, numerous FeNi3 nanoparticles loaded on nitrogen-doped porous carbon were constructed through a simple carbonization strategy. Conductive carbon substrates with porous structures not only promote electrocatalytic kinetics, but also enhance full exposure of active sites. The obtained catalyst achieve the highest urea yield rate of 496.5 μg h−1 mgcat.−1 and FE of 16.58% in CO2-saturated 0.1 M KNO3 at −0.9 V vs. RHE. The in situ Raman spectroscopy and control experiments confirmed that the generated urea was originated from the C–N coupling reaction of CO2 and NO3−.
Conflicts of interest
There are no conflicts to declare.
Acknowledgements
This work was financially supported by the National Natural Science Foundation of China (22075211 and 51971157), Shenzhen Science and Technology Program (JCYJ20210324115412035, JCYJ20210324123202008, JCYJ20210324122803009 and ZDSYS20210813095534001), Guangdong Basic and Applied Basic Research Foundation (2021A1515110880), and Tianjin Science Fund for Distinguished Young Scholars (19JCJQJC61800).
References
- Y. Feng, H. Yang, Y. Zhang, X. Huang, L. Li, T. Cheng and Q. Shao, Te-Doped Pd Nanocrystal for Electrochemical Urea Production by Efficiently Coupling Carbon Dioxide Reduction with Nitrite Reduction, Nano Lett., 2020, 20, 8282–8289 CrossRef CAS PubMed.
- J. Li, G. Zhan, J. Yang, F. Quan, C. Mao, Y. Liu, B. Wang, F. Lei, L. Li, A. W. M. Chan, L. Xu, Y. Shi, Y. Du, W. Hao, P. K. Wong, J. Wang, S. X. Dou, L. Zhang and J. C. Yu, Efficient Ammonia Electrosynthesis from Nitrate on Strained Ruthenium Nanoclusters, J. Am. Chem. Soc., 2020, 142, 7036–7046 CrossRef CAS PubMed.
- Y. Huang, R. Yang, C. Wang, N. Meng, Y. Shi, Y. Yu and B. Zhang, Direct Electrosynthesis of Urea from Carbon Dioxide and Nitric Oxide, ACS Energy Lett., 2021, 7, 284–291 CrossRef.
- L. Han, P. Ou, W. Liu, X. Wang, H.-T. Wang, R. Zhang, C.-W. Pao, X. Liu, W.-F. Pong, J. Song, Z. Zhuang, M. V. Mirkin, J. Luo and H. L. Xin, Design of Ru–Ni diatomic sites for efficient alkaline hydrogen oxidation, Sci. Adv., 2022, 8, eabm3779 CrossRef CAS.
- G.-F. Chen, Y. Yuan, H. Jiang, S.-Y. Ren, L.-X. Ding, L. Ma, T. Wu, J. Lu and H. Wang, Electrochemical reduction of nitrate to ammonia via direct eight-electron transfer using a copper–molecular solid catalyst, Nat. Energy, 2020, 5, 605–613 CrossRef CAS.
- Y. Wang, Y. Yu, R. Jia, C. Zhang and B. Zhang, Electrochemical synthesis of nitric acid from air and ammonia through waste utilization, Natl. Sci. Rev., 2019, 6, 730–738 CrossRef CAS.
- S. Liu, M. Jin, J. Sun, Y. Qin, S. Gao, Y. Chen, S. Zhang, J. Luo and X. Liu, Coordination environment engineering to boost electrocatalytic CO2 reduction performance by introducing boron into single-Fe-atomic catalyst, Chem. Eng. J., 2022, 437, 135294 CrossRef CAS.
- M. Yuan, J. Chen, Y. Bai, Z. Liu, J. Zhang, T. Zhao, Q. Wang, S. Li, H. He and G. Zhang, Unveiling Electrochemical Urea Synthesis by Co-Activation of CO2 and N2 with Mott-Schottky Heterostructure Catalysts, Angew. Chem., Int. Ed. Engl., 2021, 60, 10910–10918 CrossRef CAS PubMed.
- C. Lv, C. Lee, L. Zhong, H. Liu, J. Liu, L. Yang, C. Yan, W. Yu, H. H. Hng, Z. Qi, L. Song, S. Li, K. P. Loh, Q. Yan and G. Yu, A Defect Engineered Electrocatalyst that Promotes High-Efficiency Urea Synthesis under Ambient Conditions, ACS Nano, 2022, 16, 8213–8222 CrossRef CAS PubMed.
- S. Liu, L. Wang, H. Yang, S. Gao, Y. Liu, S. Zhang, Y. Chen, X. Liu and J. Luo, Nitrogen-Doped Carbon Polyhedrons Confined Fe–P Nanocrystals as High-Efficiency Bifunctional Catalysts for Aqueous Zn–CO2 Batteries, Small, 2022, 18, 2104965 CrossRef CAS PubMed.
- J. Lim, C. A. Fernández, S. W. Lee and M. C. Hatzell, Ammonia and Nitric Acid Demands for Fertilizer Use in 2050, ACS Energy Lett., 2021, 6, 3676–3685 CrossRef CAS.
- Ö. Yildirim, K. Nölker, K. Büker and R. Kleinschmidt, Chemical Conversion of Steel Mill Gases to Urea: An Analysis of Plant Capacity, Chem. Ing. Tech., 2018, 90, 1529–1535 CrossRef.
- P. H. van Langevelde, I. Katsounaros and M. T. M. Koper, Electrocatalytic Nitrate Reduction for Sustainable Ammonia Production, Joule, 2021, 5, 290–294 CrossRef.
- N. Meng, X. Ma, C. Wang, Y. Wang, R. Yang, J. Shao, Y. Huang, Y. Xu, B. Zhang and Y. Yu, Oxide-Derived Core-Shell Cu@Zn Nanowires for Urea Electrosynthesis from Carbon Dioxide and Nitrate in Water, ACS Nano, 2022, 16, 9095–9104 CrossRef CAS PubMed.
- N. Meng, Y. Huang, Y. Liu, Y. Yu and B. Zhang, Electrosynthesis of urea from nitrite and CO2 over oxygen vacancy-rich ZnO porous nanosheets, Cell Rep. Phys. Sci., 2021, 2, 100697 CrossRef CAS.
- Y. Wang, X. Zheng and D. Wang, Design concept for electrocatalysts, Nano Res., 2021, 15, 1730–1752 CrossRef.
- Y. Liu, X. Tu, X. Wei, D. Wang, X. Zhang, W. Chen, C. Chen and S. Wang, C-Bound or O-Bound Surface: Which One Boosts Electrocatalytic Urea Synthesis?, Angew. Chem., Int. Ed. Engl., 2023, 62, e202300387 CrossRef CAS.
- W. Song, L. Yue, X. Fan, Y. Luo, B. Ying, S. Sun, D. Zheng, Q. Liu, M. S. Hamdy and X. Sun, Recent progress and strategies on the design of catalysts for electrochemical ammonia synthesis from nitrate reduction, Inorg. Chem. Front., 2023, 10, 3489–3514 RSC.
- L. Li, I. M. U. Hasan, Farwa, R. He, L. Peng, N. Xu, N. K. Niazi, J.-N. Zhang and J. Qiao, Copper as a single metal atom based photo-, electro-, and photoelectrochemical catalyst decorated on carbon nitride surface for efficient CO2 reduction: a review, Nano Res. Energy, 2022, 1, e9120015 Search PubMed.
- M. Yang, S. Liu, J. Sun, M. Jin, R. Fu, S. Zhang, H. Li, Z. Sun, J. Luo and X. Liu, Highly dispersed Bi clusters for efficient rechargeable Zn−CO2 batteries, Appl. Catal., B, 2022, 307, 121145 CrossRef CAS.
- J. Liang, Z. Li, L. Zhang, X. He, Y. Luo, D. Zheng, Y. Wang, T. Li, H. Yan, B. Ying, S. Sun, Q. Liu, M. S. Hamdy, B. Tang and X. Sun, Advances in ammonia electrosynthesis from ambient nitrate/nitrite reduction, Chem, 2023, 9, 1768–1827 CAS.
- Q. Liu, L. Xie, J. Liang, Y. Ren, Y. Wang, L. Zhang, L. Yue, T. Li, Y. Luo, N. Li, B. Tang, Y. Liu, S. Gao, A. A. Alshehri, I. Shakir, P. O. Agboola, Q. Kong, Q. Wang, D. Ma and X. Sun, Ambient Ammonia Synthesis via Electrochemical Reduction of Nitrate Enabled by NiCo2O4 Nanowire Array, Small, 2022, 18, 2106961 CrossRef CAS.
- Y. Nakaya and S. Furukawa, Catalysis of Alloys: Classification, Principles, and Design for a Variety of Materials and Reactions, Chem. Rev., 2023, 123, 5859–5947 CrossRef CAS PubMed.
- X. Xu, L. Hu, Z. Li, L. Xie, S. Sun, L. Zhang, J. Li, Y. Luo, X. Yan, M. S. Hamdy, Q. Kong, X. Sun and Q. Liu, Oxygen vacancies in Co3O4 nanoarrays promote nitrate electroreduction for ammonia synthesis, Sustainable Energy Fuels, 2022, 6, 4130–4136 RSC.
- W. Zhang, M. Jiang, S. Yang, Y. Hu, B. Mu, Z. Tie and Z. Jin, In situ grown CuOx nanowire forest on copper foam: A 3D hierarchical and freestanding electrocatalyst with enhanced carbonaceous product selectivity in CO2 reduction, Nano Res. Energy, 2022, 1, e9120033 CrossRef.
- H. Wang, Y. Jiang, S. Li, F. Gou, X. Liu, Y. Jiang, W. Luo, W. Shen, R. He and M. Li, Realizing efficient C–N coupling via electrochemical co-reduction of CO2 and NO3− on AuPd nanoalloy to form urea: Key C–N coupling intermediates, Appl. Catal., B, 2022, 318, 121819 CrossRef CAS.
- C. Chen, X. Zhu, X. Wen, Y. Zhou, L. Zhou, H. Li, L. Tao, Q. Li, S. Du, T. Liu, D. Yan, C. Xie, Y. Zou, Y. Wang, R. Chen, J. Huo, Y. Li, J. Cheng, H. Su, X. Zhao, W. Cheng, Q. Liu, H. Lin, J. Luo, J. Chen, M. Dong, K. Cheng, C. Li and S. Wang, Coupling N2 and CO2 in H2O to synthesize urea under ambient conditions, Nat. Chem., 2020, 12, 717–724 CrossRef CAS PubMed.
- Z. Li, J. Liang, Q. Liu, L. Xie, L. Zhang, Y. Ren, L. Yue, N. Li, B. Tang, A. A. Alshehri, M. S. Hamdy, Y. Luo, Q. Kong and X. Sun, High-efficiency ammonia electrosynthesis via selective reduction of nitrate on ZnCo2O4 nanosheet array, Mater. Today Phys., 2022, 23, 100619 CrossRef CAS.
- K. Chen, M. Cao, G. Ni, S. Chen, H. Liao, L. Zhu, H. Li, J. Fu, J. Hu, E. Cortés and M. Liu, Nickel polyphthalocyanine with electronic localization at the nickel site for enhanced CO2 reduction reaction, Appl. Catal., B, 2022, 306, 121093 CrossRef CAS.
- Q. Lu, C. Chen, Q. Di, W. Liu, X. Sun, Y. Tuo, Y. Zhou, Y. Pan, X. Feng, L. Li, D. Chen and J. Zhang, Dual Role of Pyridinic-N Doping in Carbon-Coated Ni Nanoparticles for Highly Efficient Electrochemical CO2 Reduction to CO over a Wide Potential Range, ACS Catal., 2022, 12, 1364–1374 CrossRef CAS.
- H. Zhang, C. Wang, H. Luo, J. Chen, M. Kuang and J. Yang, Iron Nanoparticles Protected by Chainmail-structured Graphene for Durable Electrocatalytic Nitrate Reduction to Nitrogen, Angew. Chem., Int. Ed. Engl., 2023, 62, e202217071 CAS.
- J. Wang, Y. Wang, C. Cai, Y. Liu, D. Wu, M. Wang, M. Li, X. Wei, M. Shao and M. Gu, Cu-Doped Iron Oxide for the Efficient Electrocatalytic Nitrate Reduction Reaction, Nano Lett., 2023, 23, 1897–1903 CrossRef CAS PubMed.
- S. Zhang, M. Li, J. Li, Q. Song and X. Liu, High-ammonia selective metal-organic framework-derived Co-doped Fe/Fe2O3 catalysts for electrochemical nitrate reduction, Proc. Natl. Acad. Sci. U. S. A., 2022, 119, e2115504119 CrossRef CAS PubMed.
- G. Zhang, L. Wang, Y. Hao, X. Jin, Y. Xu, Y. Kuang, L. Dai and X. Sun, Unconventional Carbon: Alkaline Dehalogenation of Polymers Yields N-Doped Carbon Electrode for High-Performance Capacitive Energy Storage, Adv. Funct. Mater., 2016, 26, 3340–3348 CrossRef CAS.
- Y. Ge and Z. Li, Application of Lignin and Its Derivatives in Adsorption of Heavy Metal Ions in Water: A Review, ACS Sustainable Chem. Eng., 2018, 6, 7181–7192 CrossRef CAS.
- N. Supanchaiyamat, K. Jetsrisuparb, J. T. N. Knijnenburg, D. C. W. Tsang and A. J. Hunt, Lignin materials for adsorption: Current trend, perspectives and opportunities, Bioresour. Technol., 2019, 272, 570–581 CrossRef CAS.
- J. Geng, S. Ji, M. Jin, C. Zhang, M. Xu, G. Wang, C. Liang and H. Zhang, Ambient Electrosynthesis of Urea with Nitrate and Carbon Dioxide over Iron-Based Dual-Sites, Angew. Chem., Int. Ed. Engl., 2023, 62, e202210958 CrossRef CAS.
- W. Ma, X. He, W. Wang, S. Xie, Q. Zhang and Y. Wang, Electrocatalytic reduction of CO2 and CO to multi-carbon compounds over Cu-based catalysts, Chem. Soc. Rev., 2021, 50, 12897–12914 RSC.
- J. Ding, Q. Sun, L. Zhong, X. Wang, L. Chai, Q. Li, T.-T. Li, Y. Hu, J. Qian and S. Huang, Thermal conversion of hollow nickel-organic framework into bimetallic FeNi3 alloy embedded in carbon materials as efficient oer electrocatalyst, Electrochim. Acta, 2020, 354, 136716 CrossRef CAS.
- Y. Wang, G. Qian, Q. Xu, H. Zhang, F. Shen, L. Luo and S. Yin, Industrially promising IrNi–FeNi3 hybrid nanosheets for overall water splitting catalysis at large current density, Appl. Catal., B, 2021, 286, 119881 CrossRef CAS.
- X. Wang, W. Zhang, Q. Yu, X. Liu, Q. Liang, X. Meng, X. Wang and L. Wang, Fe-doped CoNiP@N-doped carbon nanosheet arrays for hydrazine oxidation assisting energy-saving seawater splitting, Chem. Eng. J., 2022, 446, 136987 CrossRef CAS.
- D. Qi, F. Lv, T. Wei, M. Jin, G. Meng, S. Zhang, Q. Liu, W. Liu, D. Ma, M. S. Hamdy, J. Luo and X. Liu, High-efficiency electrocatalytic NO reduction to NH3 by nanoporous VN, Nano Res. Energy, 2022, 1, e9120022 CrossRef.
- X. Zhang, X. Zhu, S. Bo, C. Chen, M. Qiu, X. Wei, N. He, C. Xie, W. Chen, J. Zheng, P. Chen, S. P. Jiang, Y. Li, Q. Liu and S. Wang, Identifying and tailoring C–N coupling site for efficient urea synthesis over diatomic Fe–Ni catalyst, Nat. Commun., 2022, 13, 5337 CrossRef CAS.
- P. Li, J. Bi, J. Liu, Y. Wang, X. Kang, X. Sun, J. Zhang, Z. Liu, Q. Zhu and B. Han, p–d Orbital Hybridization Induced by p-Block Metal-Doped Cu Promotes the Formation of C2+ Products in Ampere-Level CO2 Electroreduction, J. Am. Chem. Soc., 2023, 145, 4675–4682 CrossRef CAS PubMed.
- W. Shan, R. Liu, H. Zhao, Z. He, Y. Lai, S. Li, G. He and J. Liu, In Situ Surface-Enhanced Raman Spectroscopic Evidence on the Origin of Selectivity in CO2 Electrocatalytic Reduction, ACS Nano, 2020, 14, 11363–11372 CrossRef CAS PubMed.
- V. Fawcett and D. A. Long, Raman spectroscopic studies of urea/n-paraffin clathrates, J. Raman Spectrosc., 1975, 3, 263–275 CrossRef CAS.
- P. Shen, X. Li, Y. Luo, N. Zhang, X. Zhao and K. Chu, Ultra-efficient N2 electroreduction achieved over a rhodium single-atom catalyst (Rh1/MnO2) in water-in-salt electrolyte, Appl. Catal., B, 2022, 316, 121651 CrossRef CAS.
- J. Liang, Q. Liu, A. A. Alshehri and X. Sun, Recent advances in nanostructured heterogeneous catalysts for N-cycle electrocatalysis, Nano Res. Energy, 2022, 1, e9120010 CrossRef.
- Z. Wang, D. Richards and N. Singh, Recent discoveries in the reaction mechanism of heterogeneous electrocatalytic nitrate reduction, Catal. Sci. Technol., 2021, 11, 705–725 RSC.
- J. Shao, N. Meng, Y. Wang, B. Zhang, K. Yang, C. Liu, Y. Yu and B. Zhang, Scalable Electrosynthesis of Formamide through C−N Coupling at the Industrially Relevant Current Density of 120 mA
cm−2, Angew. Chem., Int. Ed., 2022, 61, e202213009 CAS.
- Y. Huang, Y. Wang, Y. Wu, Y. Yu and B. Zhang, Electrocatalytic construction of the C–N bond from the derivates of CO2 and N2, Sci. China: Chem., 2022, 65, 204–206 CrossRef CAS.
- Q. Zhang, K. Lian, Q. Liu, G. Qi, S. Zhang, J. Luo and X. Li, High entropy alloy nanoparticles as efficient catalysts for alkaline overall seawater splitting and Zn–air batteries, J. Colloid Interface Sci., 2023, 646, 844–854 CrossRef CAS PubMed.
- S. Zhang, Q. Liu, X. Tang, Z. Zhou, T. Fan, Y. You, Q. Zhang, S. Zhang, J. Luo and X. Li, Electrocatalytic reduction of NO to NH3 in ionic liquids by P-doped TiO2 nanotubes, Front. Chem. Sci. Eng., 2023, 17, 726–734 CrossRef CAS.
- M. Tang, Q. Tong, Y. Li, R. Jiang, L. Shi, F. Shen, Y. Wei, Z. Liu, S. Liu, J. Zhang and G. Jiang, Effective and selective electrocatalytic nitrate reduction to ammonia on urchin-like and defect-enriched titanium oxide microparticles, Chin. Chem. Lett., 2023, 108410 CrossRef.
- W. Zhang, X. Qin, T. Wei, Q. Liu, J. Luo and X. Liu, Single atomic cerium sites anchored on nitrogen-doped hollow carbon spheres for highly selective electroreduction of nitric oxide to ammonia, J. Colloid Interface Sci., 2023, 638, 650–657 CrossRef CAS.
- T. Feng, F. Li, X. Hu and Y. Wang, Selective electroreduction of nitrate to ammonia via NbWO6 perovskite nanosheets with oxygen vacancy, Chinese, Chem. Lett., 2023, 34, 107862 CAS.
|
This journal is © the Partner Organisations 2023 |
Click here to see how this site uses Cookies. View our privacy policy here.