DOI:
10.1039/D2PY01560A
(Paper)
Polym. Chem., 2023,
14, 2617-2623
Economical synthesis of functional aromatic polythioamides from KOH-assisted multicomponent polymerizations of sulfur, aromatic diamines and dialdehydes†
Received
14th December 2022
, Accepted 24th April 2023
First published on 25th April 2023
Abstract
Polythioamides with fascinating properties such as unique metal ion coordination ability, excellent thermal stability, good solubility, and high refractive index have attracted much attention recently, but their synthesis remains challenging, especially for aromatic polythioamides. In this work, multicomponent polymerizations of elemental sulfur, aromatic diamines, and aromatic dialdehydes with wide and economical sources were developed with the assistance of KOH. The polymerizations featured commercially available monomers with low cost, general applicability to various diamine and dialdehyde monomers, feasibility of large-scale synthesis, high atom economy, and no release of harmful byproducts, producing a series of aromatic polythioamides with high molecular weights of up to 54
700 g mol−1 and high yields of up to 96%. These polythioamides generally exhibited excellent thermal stability, good solubility, high thin film-light refractivity of 1.87 at 633 nm, and could be used for gold extraction. The MCP has provided an economical and efficient method to access unique aromatic polythioamides on a large scale, accelerating the exploration of sulfur-containing polymers as high-performance functional polymer materials.
Introduction
Polythioamides with similar structures to classical polyamide materials whose oxygen atoms are replaced by sulfur atoms are a group of fascinating sulfur-containing polymer materials with unique metal ion coordination ability,1 excellent thermal stability,2 high refractive indices,3 and non-traditional luminescence properties.4 Moreover, it has been reported that when oxygen atoms in polymer materials are replaced by sulfur atoms, the crystallinity,5 thermal stability,6 solubility and processibility2 could be improved, demonstrating a great opportunity for developing new sulfur-containing polymer materials. Although polythioamides are attractive materials with potential practical value, their synthesis has remained challenging. The limited reports on the synthesis of polythioamides included the polymerizations of diamines with dithiocarboxylic acid-O,O-diethyl esters, dithioisophthalamide, or dithioesters,7–9 and the modification of polyamide with Lawesson's reagent with incomplete conversion.10 These synthetic approaches generally involve synthesized difunctional sulfur-containing monomers and expensive, toxic and smelly sulfur-containing reagents,11 causing great difficulty in the exploration of new polythioamide structures and materials.
Multicomponent polymerization (MCP) has been developed as a powerful method to concisely synthesize polymers from simple monomers, which have a series of advantages such as high efficiency, simple operation, mild conditions, high atom economy, and so on.12–14 Considering that elemental sulfur is an abundantly existing industrial byproduct whose profitable utilization is a global concern,15 a series of elemental sulfur-based multicomponent polymerizations were developed to directly convert elemental sulfur to sulfur-containing functional polymers such as polythioamides and polythioureas.2–4,16–20 For example, the MCP of sulfur, aliphatic diamines, and aromatic dialdehydes was first reported by Kanbara et al. to afford aliphatic polythioamides at 115 °C in DMAc;17,18 later, we reported a catalyst-free MCP of sulfur, aliphatic diamines, and aromatic diynes to produce seven aliphatic polythioamides with 100% atom economy at 100 °C in pyridine.4 A series of hyperbranched polythioamides with various topological structures, well-characterized chemical structures, and good solubility were also synthesized through these MCPs.19 Room temperature synthesis of polythioamides was also realized through this catalyst-free MCP with a pyridyl-activated diyne monomer.20 However, these catalyst-free sulfur-based MCPs were only applicable for aliphatic amine monomers, because the aromatic amines with weak alkalinity could not open the S8 ring to form reactive polysulfide anion species,2 which could hence only afford aliphatic polythioamides with non-conjugated flexible structures.
It is well-known that, compared with aliphatic polyamides, rigid aromatic polyamides possess superior thermal stability and mechanical properties, and are developed into high-performance engineering plastics,21 the development of aromatic polythioamides is hence desired to obtain advanced polymer materials. Recently, we have developed an MCP of sulfur, diamines, and benzyl diacids to synthesize aliphatic and aromatic polythioamides on a large scale through a decarboxylate process.2 It was found that through the assistance of K2CO3, less reactive aromatic diamine monomers could be included in this MCP to afford rigid aromatic polythioamides, with both sides of the thioamide moieties being directly linked to aromatic rings. However, commercially available benzyl diacids were limited, and it was crucial to develop new polymerizations with superior monomer choices in terms of cost, source, structural variations, and atom economy to realize economical and efficient synthesis of diverse aromatic polythioamides.
Considering that aromatic aldehydes have abundant natural sources, great structural diversity, low price, and are usually generated from biomass,22–24 in this work, we applied the inorganic base-assisted polymerization strategy to the MCP of sulfur, aromatic diamines and aromatic dialdehydes. In this reaction, elemental sulfur first underwent ring-opening reaction with the assistance of a base to form a polysulfide anion, which was then reacted with a Schiff base intermediate formed from an aldehyde and an amine, to furnish a thioamide product,18 and K2CO3 was reported to promote the aqueous phase reaction for the production of aromatic thioamides in water at 100 °C.25 Herein, an efficient KOH-assisted MCP of sulfur, aromatic diamines and aromatic dialdehydes was developed in organic solvent, affording various aromatic polythioamides with well-defined structures and high molecular weights (Mws) in high yields. Compared with previous synthetic approaches of aromatic polythioamides,2,7,9,26 more diversified polymer structures, lower cost, higher atom economy, scaled-up synthesis and no gas release were realized, demonstrating great potential in future large-scale preparation of these unique aromatic polythioamide materials.
Results and discussion
Base-assisted model reaction of sulfur, aromatic amine and aromatic aldehyde
To study the practicability of polymerization involving aromatic amines in organic solvents, a multicomponent small molecular reaction of sulfur 1, aromatic diamine 4,4′-methylenedianiline 2a, and 4-methylbenzaldehyde 3 was investigated in pyridine with the assistance of KOH. All the reagents were added in one portion and the reaction was conducted at 105 °C under nitrogen for 24 h. After purification, a yellow solid product 4 was obtained in 72% yield (Fig. 1A), proving that the inorganic base could facilitate the reaction of the aromatic amine in organic solvent. The high-resolution mass spectrum of compound 4 suggested its molecular weight of 467.1613 (calcd 467.1610) (Fig. S1†), together with the single-crystal structure of compound 4 (Fig. 1B and Table S1†), confirming its dithioamide structure. Two strong intermolecular S⋯H–N hydrogen bonds with a distance of 2.668 Å and 2.705 Å, respectively, were formed between each two neighboring molecules, forming ladder-shaped supramolecular polymers within the crystal (Fig. 1B), indicating potential intermolecular interaction mode in the corresponding polymer structures.
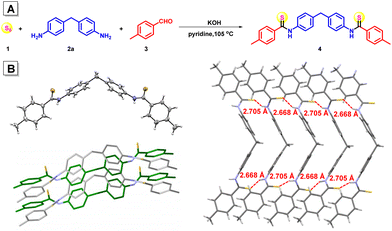 |
| Fig. 1 (A) The model reaction and (B) single crystal structure of the model compound 4. | |
KOH-assisted multicomponent polymerizations of sulfur, aromatic diamines and dialdehydes
The aromatic diamine monomer-participated MCP with sulfur and dialdehyde was then studied, selecting 4,4′-methylenedianiline 2a and m-phthalaldehyde 5a as monomers. The MCP of 1, 2a, and 5a was first carried out in different polar solvents at 105 °C under nitrogen for 12 h, while keeping the monomer loading ratio 1/8[S8]
:
[2a]
:
[5a] = 4.0
:
1.0
:
1.5 and monomer concentration [2a] = 0.4 M (Table S2†). Among all the tested polar solvents including pyridine, dimethylacetamide (DMAc), and dimethylformaldehyde (DMF), pyridine afforded the best polymerization result and polymer product with a Mw of 10
300 g mol−1 was obtained in 68% yield, suggesting that the alkalinity of pyridine may facilitate polymerization. Temperature was reported to be critical to the synthesis of polythioamides from sulfur-based MCPs.2,4 Similarly, in this polymerization, the polyimine intermediate formed from diamine and dialdehyde possessed poor solubility, which might cause its precipitation from the polymerization solution, hindering its further reaction with a polysulfide anion to produce thioamide moieties.17,18 Therefore, the polymerization temperature was fine-tuned from 90 to 115 °C, with a 5 °C interval to capture the sensitive influence of temperature on the MCP (Table S3†). Both the yield and Mw of the polymer product increased when the temperature was raised to 110 °C, and further heating to the boiling point of pyridine (115 °C) could cause a slight decrease in the yield and Mw. The monomer loading ratio was also crucial for the polymerization. An excess amount of dialdehyde was found to improve both yield and Mw, and when [2a]
:
[5a] = 1
:
2, a polymer with a Mw of 19
000 g mol−1 was obtained in 80% yield (Table S4,† entries 1–7). Considering the possible side reactions of aldehyde in the presence of KOH such as the Cannizaro reaction to consume aldehyde and result in stoichiometric imbalance of the amine and aldehyde, an excess amount of aldehyde in the MCP is beneficial for the polymerization. Moreover, when an excess amount of amine was adopted, only a low-molecular-weight product was afforded in low yield (Table S4,† entry 1). Similar to the reported sulfur-based MCPs,2,4,16 an excess amount of sulfur was also found to be beneficial for the polymerization, and the best result was obtained with the loading ratio of 1/8[S8]
:
[2a]
:
[5a] = 4.5
:
1.0
:
2.0, and a polymer with a Mw of 34
300 g mol−1 was furnished in 81% yield (Table S4,† entry 10).
In this polymerization, the inorganic base played a crucial role. Either weak bases such as Na2CO3, K2CO3, Cs2CO3, KF, and CsF, or a relatively dilute KOH (<0.4 M) aqueous solution could only afford an insoluble product, indicating that the reaction was probably stopped at the polyimine intermediate stage, which failed to convert to a polythioamide product. When [KOH] = 0.8 M and [2a] = 0.4 M, a satisfactory polymerization result was obtained; when [KOH] reached 1.2 M, only a low-molecular-weight product was generated (Table S4,† entry 13), due to the stoichiometric imbalance of the monomers caused by the aforementioned side reactions of the dialdehyde monomer and the potential degradation of these polythioamide structures at high temperature in the presence of a concentrated strong base. The monomer concentration was then optimized based on the loading ratio 1/8[S8]
:
[2a]
:
[5a]
:
[KOH] = 4.5
:
1.0
:
2.0
:
2.0. Increasing the monomer concentration was generally beneficial for the polymerization yield and Mw of the product, and the best result of a Mw of 41
700 g mol−1 and 87% yield was afforded when [2a] = 0.8 M (Table S5†). A further increase of the monomer concentration to 1.0 M caused gelation. Last but not least, the polymerization time was also optimized from 4 to 16 h. While elongation of the reaction time from 4 to 8 h could dramatically increase the yield and Mw to 94% and 54
700 g mol−1, respectively (Table S6†), further extension of the polymerization time to 16 h resulted in the reduction of both yield and Mw, suggesting a potential balance between polymerization and degradation of the polymer product at high temperature in the presence of a strong base with long reaction time.
Most importantly, with the three commercially available inexpensive monomers, the MCP of sulfur, 2a and 5a was conducted on a 50 mmol-scale under the above-mentioned optimal conditions, and 16.4 g of polymer product with a Mw of 19
600 g mol−1 was obtained in 91% yield, indicating the potential convenient and economical large-scale production of aromatic polythioamides (Table 1, entry 6).
Table 1 MCPs of sulfur 1, aromatic diamine 2a, and dialdehyde 5aa
The MCPs were carried out in the presence of KOH in pyridine with [KOH] : [2a] = 2 : 1 and a 0.5 mmol scale of 2a.
50 mmol of 2a was used.
|
|
Furthermore, the MCPs of sulfur, aromatic diamines and aromatic dialdehydes could be widely applicable to various aromatic amine and aldehyde monomers, which could afford diverse aromatic polythioamides. A series of commercially available, inexpensive aromatic diamines 2a–c and dialdehydes 5a–d were selected as the monomers (Table 2). In view of the different reactivity and solubility of each aromatic diamine and dialdehyde monomer, as well as their Schiff base intermediate, the polymerization conditions such as monomer concentrations, time, and loading ratio should be varied accordingly. The polymerizations generally proceeded well, affording polythioamides P2–P7 with satisfactory yields (up to 96%) and Mws (up to 25
300 g mol−1) (Fig. S2†). m-Phthalaldehyde 5a was found to produce polymers with higher Mws compared with those synthesized from p-phthalaldehyde 5b, probably owing to the improved solubility of the nonlinear-shaped polymer backbone with irregular intermolecular interactions. Besides, while the MCP of the relatively electron-rich aromatic dialdehyde 5c and electron-deficient aromatic dialdehyde 5d could proceed smoothly to afford polythioamides, the latter showed higher yield and Mw. It is worth mentioning that there were large numbers of commercially available, inexpensive aromatic dialdehydes, including those derived from biomass,22,23 to serve as monomers to tune the polymer backbone structures, which could greatly expand the aromatic polythioamide structure scope built from the previous MCPs of sulfur, aromatic diamines, and benzyl diacid monomers.2
Table 2 (A) MCPs of sulfur 1, aromatic diamines 2a–c and aromatic dialdehydes 5a–d. (B) The polymerization results of different monomers
A |
|
B |
Entry |
Monomers |
1/8[S8] : [2a–c] : [5a–d] |
[2a–c] (M) |
t (h) |
Yield (%) |
M
w a (g mol−1) |
M
w/Mn a |
Solubility |
The reactions were carried out at 110 °C under nitrogen in pyridine and the yield was calculated based on the diamine monomers, [KOH] : [2a] = 2 : 1. Mw and Mn were determined by GPC in DMF based on the polymethyl methacrylate standard samples. Mw and Mn were determined by GPC with partially soluble polymers. √: the product is completely soluble, Δ: the product is partially soluble. |
P2
|
1 + 2b + 5a |
4.5 : 1.0 : 2.0 |
0.8 |
8 |
92 |
25 300 |
2.20 |
√ |
P3
|
1 + 2c + 5a |
4.5 : 1.0 : 2.0 |
0.5 |
12 |
93 |
14 200 |
1.67 |
√ |
P4
|
1 + 2a + 5b |
4.5 : 1.0 : 1.8 |
0.5 |
12 |
96 |
11 800 |
1.54 |
Δ |
P5
|
1 + 2b + 5b |
4.5 : 1.0 : 1.8 |
0.4 |
12 |
88 |
9100 |
1.33 |
Δ |
P6
|
1 + 2a + 5c |
4.5 : 1.0 : 1.5 |
0.5 |
12 |
42 |
5900 |
1.20 |
√ |
P7
|
1 + 2a + 5d |
4.5 : 1.0 : 1.8 |
0.5 |
12 |
69 |
14 800 |
1.48 |
√ |
Structural characterization of the aromatic polythioamides
The well-defined structures of these aromatic polythioamides were confirmed by their 1H, 13C NMR, and FT-IR spectra. Take the 1H NMR spectrum of P1 for example, the characteristic –NH– proton resonance of the thioamide group appeared at δ 11.84, which was in good accordance with the corresponding resonance peak of the model compound 4 at δ 11.59. Meanwhile, the aromatic proton peaks from monomers 2a and 5a remained in the spectrum of P1, while the –NH2 peak of 2a at δ 4.80 and the –CHO peak of 5a at δ 10.12 both disappeared, proving that the amine and aldehyde groups in the monomers had converted to the thioamide group in the product (Fig. 2). Similar to P2–P7, the characteristic thioamide proton peaks emerged at δ 11.65–12.40 (Fig. S3†), and no obvious impurity peak was observed in this region, suggesting that the polymer products were well-defined polythioamide structures. In the 13C NMR spectrum of P1, the carbon resonance of –CHO from 5a at δ 192.69 was converted to the HN–C
S carbon peak of the thioamide group in P1 at δ 196.33 (Fig. S4†), and similar characteristics of HN–C
S carbon resonance were also observed at δ 189.13–196.51 in the 13C NMR spectra of P2–P7 (Fig. S5†). The FT-IR spectra of P1–P7 were also similar to that of model compound 4 (Fig. S6 and S7†).
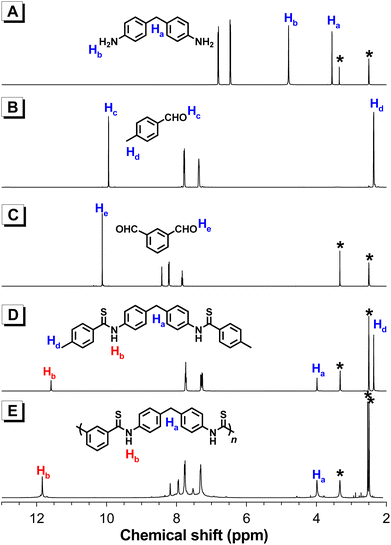 |
| Fig. 2
1H NMR spectra of (A) 2a, (B) 3, (C) 5a, (D) 4, and (E) P1 in DMSO-d6. The solvent peaks are marked with asterisks. | |
Furthermore, the existence of sulfur in these aromatic polythioamides was confirmed by X-ray photoelectron spectroscopy (XPS), and the binding energies of S 2p were observed at 162.20–163.81, which overlapped with those of model compound 4, but were not in the range of elemental sulfur, suggesting that the existing form of the sulfur atom in these polymers was indeed thioamide (Fig. S8†).
Solubility and thermal stability of the aromatic polythioamides
Aromatic polythioamides have similar structures to the high-performance aromatic polyamides, which are well-known for their high strength, good toughness, high thermal resistance and poor solubility.27 When the oxygen atoms in polyamides were replaced with sulfur atoms, the solubility of polythioamides was significantly improved. The aromatic polythioamides P1–P7 actually possessed satisfactory solubility in polar solvents such as DMSO and DMF, enabling structural and property study in solution and bringing more opportunities for materials processing and application.
Moreover, thermogravimetric analysis (TGA) suggested that these aromatic polythioamides possessed high thermal resistance with their decomposition temperatures at 5 wt% weight loss ranging from 295 to 363 °C, and high char yields of 50–67% at 800 °C, owing to their strong intermolecular and intramolecular interactions including hydrogen bonds among the abundant thioamide moieties and π–π stacking interactions among the large number of aromatic rings (Fig. 3). Their crystallinity was also studied by powder XRD, and diffraction peaks of P5 were observed (Fig. S9†), suggesting that the linear-shaped polymer backbone was beneficial for its regular alignment and packing.
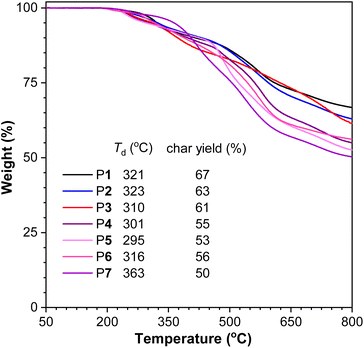 |
| Fig. 3 TGA curves of polythioamides P1–P7 with a heating rate of 10 °C min−1 under nitrogen. | |
Gold extraction by aromatic polythioamides
While it is of great economic and environmental significance to recycle precious metals from electronic waste,28–30 aromatic polythioamides with abundant sulfur coordination sites to metal ions, especially to Au3+,2 were then investigated for gold extraction from aqueous solutions. The metal coordination selectivity of the polythioamides among various metal ions was first studied. An identical amount of solid powder of P1 was directly added into the aqueous solutions of different metal ions including Au3+, Cu2+, Fe3+, Mn2+, Ni2+, Co2+, Pb2+, and Cd2+, respectively, with the metal ion concentration of 100 mg L−1. The polymer solid powder was removed by centrifugation after the aqueous suspension was stirred at room temperature for 1 h, and the remaining concentrations of the corresponding metal ions in the supernatants were measured by atomic absorption spectroscopy (AAS) to calculate the extraction efficiency. Of all the eight metal ions, a high extraction efficiency of 99.88% was realized only for Au3+ (Fig. S10†).
Different polythioamides P1–P7 were then utilized for gold extraction, using different amounts of solid powder (Fig. 4 and Table S7†). P7, prepared from 2,6-pyridinedicarboxaldehyde, showed the best performance among these polymers and its extraction capacity was 788 mg Au3+ g−1 calculated from the extraction efficiency obtained with 1 mg polymer to extract Au3+ from an aqueous solution with [Au3+]0 = 100 mg L−1, which showed higher efficiency and capacity with the best polythioamides in the literature.2 The pyridine moieties in P7 might also serve as a metal coordination ligand to extract Au3+, together with thioamide moieties, to improve the gold extraction performance.
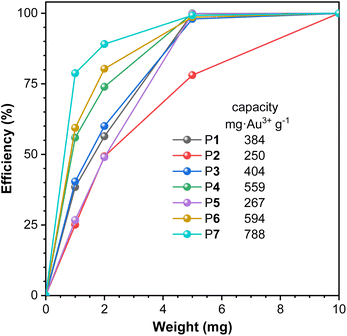 |
| Fig. 4 The extraction efficiency of Au3+ with different amounts of solid powder of aromatic polythioamides P1–P7. [Au3+]0 = 100 mg L−1. VAu3+ = 10 mL. | |
Light refractivity
One major advantage of aromatic polythioamides compared with aliphatic polythioamides is the high light refractivity, owing to the large amount of conjugation system of these sulfur-rich polymers. Polymer materials with high light refractivity above 1.80 are highly desired for optoelectronic devices,31–34 only limited examples of organic polymer materials possessing high thin film refractive indices have been reported. While introducing chalcogen atoms into the polymer structure or increasing the content of aromatic structure in the polymer is an effective approach to increase the refractive indices of polymers,35–41 the aromatic polythioamides synthesized in this work may be promising polymer materials with high refractive indices. P1 was investigated as an example, and the wavelength-dependent refractivity of the thin film of P1 was studied. The thin film of P1 possesses large n values of 2.0634–1.7287 in a wide wavelength range of 400–1700 nm, and a high n value of 1.8702 at 633 nm (Fig. 5), which is much higher than those of the reported polythioamides,4 and is among the highest values of chalcogen-containing organic polymer materials.3,41
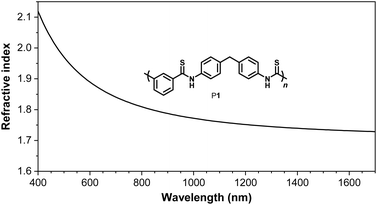 |
| Fig. 5 The wavelength dependence of the refractive index of the thin film of P1. | |
Conclusions
In this work, a KOH-assisted multicomponent polymerization of elemental sulfur, aromatic diamines, and aromatic dialdehydes was developed for the facile and economical synthesis of aromatic polythioamides. The polymerization featured commercially available monomers, simple operation, high atom economy, high efficiency, general monomer applicability, and potential scaled-up production, releasing H2O as the side product, and no gas was released. Compared with the reported aromatic polythioamide synthesis, this MCP could use aromatic dialdehydes as monomers, which possess great structural diversity, widespread and economical sources that could be prepared from biomass, making them an ideal monomer source for the preparation of various aromatic polythioamide structures. Moreover, the efficiency and specificity of this MCP were significantly improved, and the aromatic polythioamide products possessed clean structures without obvious side reactions observed from the structural characterization data. Besides well-defined structures, these polythioamides also possessed satisfactory molecular weight, excellent solubility, high thermal stability, and solid powder crystallinity. With the strong and selective coordination between the thiocarbonyl group and Au3+, the polythioamides could also serve as convenient and efficient gold extraction materials. Moreover, the high sulfur content and the aromatic structures of these aromatic polythioamides have endowed them with a high refractivity of 1.87 at 633 nm. The MCP of sulfur, aromatic diamines, and aromatic dialdehydes has hence provided an economical, efficient, and convenient method for the synthesis of unique aromatic polythioamides, bringing the opportunity of future scaled-up production of these new materials. It is anticipated that the advancement in polymer synthetic approaches can accelerate the development of high-performance advanced functional polymer materials and their potential applications.
Author contributions
Y. Hu, L. Zhang and R. Hu conceived the project and wrote the manuscript. Y. Hu and L. Zhang performed the experimental work. All authors contributed to the writing and editing of the manuscript.
Conflicts of interest
There are no conflicts to declare.
Acknowledgements
This work was partially supported by the Ministry of Science and Technology of China (2021YFA1501600), the National Natural Science Foundation of China (52173005 and 21822102), and the Guangdong Provincial Key Laboratory of Luminescence from Molecular Aggregates (2019B030301003).
References
- A. Yasin, Y. Chen, Y. Liu, L. Zhang, X. Zan and Y. Zhang, Polym. Chem., 2020, 11, 810–819 RSC.
- W. Cao, F. Dai, R. Hu and B. Z. Tang, J. Am. Chem. Soc., 2020, 142, 978–986 CrossRef CAS PubMed.
- Z. Sun, H. Huang, L. Li, L. Liu and Y. Chen, Macromolecules, 2017, 50, 8505–8511 CrossRef CAS.
- W. Li, X. Wu, Z. Zhao, A. Qin, R. Hu and B. Z. Tang, Macromolecules, 2015, 48, 7747–7754 CrossRef CAS.
- T.-J. Yue, W.-M. Ren, L. Chen, G.-G. Gu, Y. Liu and X.-B. Lu, Angew. Chem., Int. Ed., 2018, 57, 12670–12674 CrossRef CAS PubMed.
- K. Choi, W. Jang, W. Lee, J. S. Choi, M. Kang, J. Kim, K. Char, J. Lim and S. G. Im, Macromolecules, 2022, 55, 7222–7231 CrossRef CAS.
- K. Sanui, Y. Kishimoto and N. Ogata, Polym. J., 1971, 2, 789–798 CrossRef CAS.
- Y. Kishimoto and N. Ogata, Polym. J., 1973, 4, 637–643 CrossRef CAS.
- I. Delfanne and G. Levesque, Macromolecules, 1989, 22, 2589–2592 CrossRef CAS.
- M. Deletre and G. Levesque, Macromolecules, 1990, 23, 4876–4878 CrossRef CAS.
- K. Vellingiri, A. Deep and K.-H. Kim, ACS Appl. Mater. Interfaces, 2016, 8, 29835–29857 CrossRef CAS PubMed.
- H. Xue, Y. Zhao, H. Wu, Z. Wang, B. Yang, Y. Wei, Z. Wang and L. Tao, J. Am. Chem. Soc., 2016, 138, 8690–8693 CrossRef CAS PubMed.
- A. C. Boukis, A. Llevot and M. A. R. Meier, Macromol. Rapid Commun., 2016, 37, 643–649 CrossRef CAS PubMed.
- M. Li, X. Duan, Y. Jiang, X. Sun, X. Xu, J. He, Y. Zheng, W. Song and N. Zheng, CCS Chem., 2022, 4, 3402–3415 CrossRef CAS.
- T. Lee, P. T. Dirlam, J. T. Njardarson, R. S. Glass and J. Pyun, J. Am. Chem. Soc., 2022, 144, 5–22 CrossRef CAS PubMed.
- T. Tian, R. Hu and B. Z. Tang, J. Am. Chem. Soc., 2018, 140, 6156–6163 CrossRef CAS PubMed.
- Y. Kawai, T. Kanbara and K. Hasegawa, J. Polym. Sci., Part A: Polym. Chem., 1999, 37, 1737–1740 CrossRef CAS.
- T. Kanbara, Y. Kawai, K. Hasegawa, H. Morita and T. Yamamoto, J. Polym. Sci., Part A: Polym. Chem., 2001, 39, 3739–3750 CrossRef CAS.
- S. Liu, F. Li, W. Cao, R. Hu and B. Z. Tang, Chin. J. Chem., 2022, 40, 725–733 CrossRef CAS.
- L. Zhang, Y. Hu, R. Hu and B. Z. Tang, Chem. Commun., 2022, 58, 1994–1997 RSC.
- J. A. Reglero Ruiz, M. Trigo-López, F. C. García and J. M. García, Polymer, 2017, 9, 414 Search PubMed.
- S.-H. Park, C. Yang, N. Ayaril and G. Szekely, ACS Sustainable Chem. Eng., 2022, 10, 998–1007 CrossRef CAS.
- H. Qi, F. Liu, L. Zhang, L. Li, Y. Su, J. Yang, R. Hao, A. Wang and T. Zhang, Green Chem., 2020, 22, 6897–6901 RSC.
- K. Hong, Q. Sun, X. Zhang, L. Fan, T. Wu, J. Du and Y. Zhu, ACS Sustainable Chem. Eng., 2022, 10, 1036–1046 CrossRef CAS.
- H. Xu, H. Deng, Z. Li, H. Xiang and X. Zhou, Chem. – Eur. J., 2013, 2013, 7054–7057 CAS.
- K. Bayram, B. Kiskan and Y. Yagci, Polym. Chem., 2021, 12, 534–544 RSC.
- X. Lu, Y. Ye, W. Shang, S. Huang, H. Wang, T. Gan, G. Chen, L. Deng, Q. Wu and X. Zhou, J. Mater. Chem. A, 2022, 10, 21379–21389 RSC.
- K. He, Y. Jiang, T. Wang, Z. Liu, M. Wang, L. Pan and X. Chen, Aggregate, 2022, 3, e57 CAS.
- N. A. Dogan, Y. Hong, E. Ozdemir and C. T. Yavuz, ACS Sustainable Chem. Eng., 2019, 7, 123–128 CrossRef CAS.
- S. Yang, T. Li, Y. Cheng, W. Fan, L. Wang, Y. Liu, L. Bian, C.-H. Zhou, L.-Y. Zheng and Q.-E. Cao, ACS Sustainable Chem. Eng., 2022, 10, 9719–9731 CrossRef CAS.
- H. N. S. Krishnamoorthy, G. Adamo, J. Yin, V. Savinov, N. I. Zheludev and C. Soci, Nat. Commun., 2020, 11, 1692 CrossRef CAS PubMed.
- J.-H. Huh, J. Lee and S. Lee, Nano Lett., 2020, 20, 4768–4774 CrossRef CAS PubMed.
- Z. Chen, Y. Shi, M. Wei, Y. Luo, H. Ma, R. Tang, Y. Weng, H. Dai, C. Zhong, C. Sun, L. Wang, K. Si, W. Gong, H. Lin and L. Li, Adv. Opt. Mater., 2023, 2202824, DOI:10.1002/adom.202202824.
- D. H. Kim, W. Jang, K. Choi, J. S. Choi, J. Pyun, J. Lim, K. Char and S. G. Im, Sci. Adv., 2020, 6, eabb5320 CrossRef CAS PubMed.
- Y. Jeon, J. Choi, D. Seo, S. H. Jung and J. Lim, Polym. Chem., 2023, 14, 1117–1123 RSC.
- T. Badur, C. Dams and N. Hampp, Macromolecules, 2018, 51, 4220–4228 CrossRef CAS.
- S. Mavila, J. Sinha, Y. Hu, M. Podgorski, P. K. Shah and C. N. Bowman, ACS Appl. Mater. Interfaces, 2021, 13, 15647–15658 CrossRef CAS PubMed.
- M.-C. Fu, M. Ueda, S. Ando and T. Higashihara, ACS Omega, 2020, 5, 5134–5141 CrossRef CAS PubMed.
- E. K. Macdonald, J. C. Lacey, I. Ogura and M. P. Shaver, Eur. Polym. J., 2017, 87, 14–23 CrossRef CAS.
- Q. Li, S. Liu, M. Xu, X. Pan, N. Li, J. Zhu and X. Zhu, Eur. Polym. J., 2020, 122, 109358 CrossRef CAS.
- X. Wu, J. He, R. Hu and B. Z. Tang, J. Am. Chem. Soc., 2021, 143, 15723–15731 CrossRef CAS PubMed.
Footnotes |
† Electronic supplementary information (ESI) available: Materials and instruments, synthetic procedures and characterization data; single crystal data and MS spectrum of 4; effect of solvent, temperature, monomer loading ratio, base and monomer concentrations, polymerization time, and monomer structures on the MCP; GPC curves of P1–P7; 1H, 13C NMR and FT-IR spectra of P1–P7 and model compound; XPS spectra and XRD patterns of the polythioamides; selectivity test and effect of polymer dosages about gold extraction. CCDC 2225162. For ESI and crystallographic data in CIF or other electronic format, see DOI: https://doi.org/10.1039/d2py01560a |
‡ These authors have equally contributed to this work. |
|
This journal is © The Royal Society of Chemistry 2023 |
Click here to see how this site uses Cookies. View our privacy policy here.