DOI:
10.1039/D0AY01789B
(Paper)
Anal. Methods, 2021,
13, 56-63
A one-step electrochemically reduced graphene oxide based sensor for sensitive voltammetric determination of furfural in milk products
Received
20th September 2020
, Accepted 18th November 2020
First published on 19th November 2020
Abstract
Designing of fast, inexpensive and sensitive furfural determination methods for dairy milk is crucial in analytical and food chemistry. In this study, an electrochemical sensor was developed for the cathodic determination of furfural using a one-step electrochemically reduced graphene oxide (ErGO) modified glassy carbon electrode (GCE). The morphology and chemical constituents of the obtained ErGO/GCE were characterized by scanning electron microscopy (SEM), transmission electron microscopy (TEM), X-ray diffraction (XRD), and Raman and X-ray photoelectron spectroscopy (XPS). The results showed that the fast and green electrochemical reduction process effectively eliminated the oxygen-containing groups in GO and produced reduced graphene with a high surface area and improved electron transfer kinetics. In addition, the ErGO based sensor displayed excellent responses for furfural in a Na2HPO4–NaH2PO4 solution (pH = 9.18) with a wide linear range from 2 to 2015 μM and a low detection limit of 0.4 μM (S/N = 3). The reduction mechanism of furfural was also discussed. Furthermore, the feasibility of the sensor was confirmed by the determination of furfural in three milk samples which generated acceptable outputs.
1. Introduction
Furfural is a colorless and volatile oily liquid with a pungent aromatic odor. It is widely used in synthetic plastics, medicine, pesticides, and other fields.1 Furfural can also be found in a variety of dairy products and is generated by the degradation of saccharides as a result of thermal processing or long storage times.2 The appearance of furfural can lead to color, texture, and flavor changes in these dairy products.3,4 Furfural has negative impacts on the human central nervous system, liver, kidneys, heart, and other organs when its concentration exceeds a certain limit of body absorption.5,6 Therefore, it is of vital importance to develop a fast and sensitive method to determine the presence of furfural in different dairy products.
Several chromatography methods coupled with different detectors have been developed for the determination of furfural in dairy products, such as gas chromatography coupled with a tandem mass spectrometry (GC-MS/MS) detector,7 liquid chromatography with an MS detector,8 and high-performance liquid chromatography (HPLC) with diode array (DAD),9–12 fluorescence,13 and UV-Vis14–17 detectors. However, chromatography methods had several drawbacks such as high cost, use of toxic reagents, the requirement of sophisticated equipment and the need for specially trained people. Therefore, there is still an urgent need for simple, fast, portable and inexpensive methods for the assay of furfural in a variety of dairy samples.
The electrochemical method features high sensitivity, simplicity of operation, low cost, and short analysis times.18,19 Additionally, it is capable of being incorporated into robust, portable or miniaturized devices for targeted applications in the food analysis field.20 Although the electrochemical behavior of furfural has been investigated using glassy carbon,21 mercury pool,22 nickel and copper,23 carbon nanotube (CNT),24 and nanoTiO2–CNT complex film25 electrodes, a few attempts have been made to determine furfural quantitatively in real samples. Shamsipur and his coworkers found that a glassy carbon electrode (GCE)4 or PVC-calixarene membrane electrode26 could be used to determine traces of furaldehyde in oil and related wastewaters when using three different ionic liquids as electrolyte solutions. Gold,27 mercury film,28 static mercury drop29 and platinum electrodes30 have been reported for determination of furfural in transformer oil. Silva et al.3 developed an electroanalytical method for the determination of furfural in sugarcane bagasse using a nickel nanoparticle modified GCE. Among these reports, no facile electrochemical sensor was available for assay of furfural in dairy products.
The sensing material is vital to the performance of the sensor. Graphene, an allotrope of carbon with sp2-hybridization arranged as a honeycomb structure, is an ideal material for sensing applications because of its large surface area, excellent electron mobility and conductivity, and wide electrochemical window.31–33 The most common and scalable technique for the synthesis of graphene at a low cost involves the oxidation of graphite to graphene oxide (GO) followed by chemical, thermal or electrochemical reduction.34 Significantly, the electrochemical reduction of GO is relatively economical, fast, and eco friendly.35,36 It not only eliminates the excessive use of toxic and hazardous chemicals involved in chemical reduction of GO to reduced graphene oxide (rGO) which could contaminate the resulting product and even be harmful to human health and the environment,37 but also avoids the use of high temperatures to remove the oxygen functionalities in thermal reduction which suffers from high production cost and tedious control of experimental conditions.38 The electrochemical reduction uses a standard electrochemical cell in the presence of a nonhazardous aqueous buffer solution at room temperature via a one-step39 or two-step route.35 The one-step route allows the reduction of a GO colloidal suspension directly to insoluble rGO attached to the electrode surface, known as electrochemically reduced graphene oxide (ErGO). Moreover, the one-step route can more precisely control the film thickness and uniformity.40,41
In this work, a facile electrochemical furfural sensor was developed based on the one-step electrochemical reduction of GO on a GCE. After the preparation conditions were optimized, the morphology and chemical constituents of ErGO/GCE were characterized. The electrocatalytic performance of the prepared electrode was explored for furfural. The results showed that the modified electrode has good electrocatalytic activity for furfural reduction with a wide linear range and low limit of detection (LOD). Furthermore, a sensitive and reliable method for furfural detection in three different milk samples was established. Prospectively, the fast and economic strategy might be extended to other electroanalytical applications in dairy products.
2. Experimental
2.1. Materials and methods
Graphite powder (99.95%, 750–850 mesh), sodium phosphate, sodium nitrate, sulfuric acid, potassium ferricyanide, potassium chloride, and ethanol were purchased from Chemical Reagent Co. Ltd. (Tianjin, China). Potassium permanganate, hydrogen peroxide, and furfural were purchased from Aladdin Chemistry Co. Ltd (Shanghai, China). Three different milk samples were purchased from the local supermarket. All other reagents were of analytical grade and used as received without further purification. Ultrapure fresh water was obtained from a Millipore water purification system (MilliQ, specific resistivity > 18 MΩ cm, S.A., Molsheim, France) and used in all the runs. The solutions of furfural were prepared in a 0.1 M Na2HPO4–NaH2PO4 solution (pH 9.18) adjusted with 0.1 M NaOH.
The morphology of the modified electrode was obtained using scanning electron microscopy (SEM, Hitachi S-4800, Tokyo, Japan). Transmission electron microscopy (TEM) images were obtained on a Jeol JEM 2011. TEM samples were prepared by carefully removing the material from the GCE, followed by ultrasonication in isopropanol and coating of the TEM grids with a few microliters of the solution. Further compositional evidence was inferred by X-ray photoelectron spectroscopy (XPS), using a K-Alpha XPS spectrometer (Scientific ESCALAB 250) with Al Kα X-ray radiation (1486.6 eV) for excitation. X-ray diffraction (XRD) analysis was carried out on a German Bruker D8 ADVANCE with a graphite monochromatized Cu Kα radiation source (λ = 1.54056 Å). Raman spectra were acquired on a Renishaw RM1000 spectrometer with a He/Ne laser at a wavelength of 633 nm.
All electrochemical experiments were performed on a CHI 660C electrochemical workstation (Chenhua Instrument Co. Shanghai, China) with a three-electrode configuration. The ErGO/GCE, a saturated calomel electrode (SCE) and a platinum wire were used as the working electrode, the reference electrode and the auxiliary electrode, respectively. In furfural sensing, nitrogen-saturated solutions were obtained by passing high purity nitrogen gas for 10 min through the solution prior to voltammetric experiments and maintained using a flow of gas over the solution to eliminate oxygen from the solutions.
Electrochemical impedance spectroscopy (EIS) experiments were performed on an IM6e impedance measurement unit (Zahner, Germany). The solution was 0.1 M KCl containing 5 mM K3Fe(CN)6/K4Fe(CN)6 at open circuit potential with a frequency range from 0.01 Hz to 100 kHz and 50 mV amplitude.
2.2. Fabrication of the ErGO/GCE
GO was first synthesized from natural graphite powder by a modified Hummers method.42 The prepared GO suspension was then electrodeposited on a GCE according to Chen's method.39 Typically, 10 mg mL−1 GO dispersed in 0.067 M Na2HPO4 (pH 9.18) was electrochemically reduced on the surface of the GCE by running cyclic voltammetry (CV) in a potential window of −1.5 to 0.5 V with a varied number of scans. The obtained ErGO/GCE was washed with water and dried for further characterization.
2.3. Real sample analysis
Milk samples including charcoal yogurt, fresh milk and coconut milk were selected. Sample preparation was based on the Van Boekel and Rehman43 procedure. 15 g of the milk sample was mixed with 5 mL of 0.3 mol L−1 oxalic acid in a 25 mL sealed tube. Then, 3 mL of 40% (w/v) trichloroacetic acid (TCA) was added. After shaking for 10 min, the mixture was centrifuged at 6000 rpm for 15 min. The supernatant was collected in a 25 mL volumetric flask and another 10 mL of 4% (w/v) TCA was added into the solid residue. After shaking for 10 min, the new mixture was centrifuged at 6000 rpm for 15 min. The two supernatants were combined to give the final sample solution.
To perform the electrochemical measurements, the treated samples were first adjusted to pH = 9.18 with 0.1 M NaOH. 5 mL of the sample was then added into 5 mL of a 0.1 M Na2HPO4–NaH2PO4 solution (pH = 9.18). Each sample was measured in triplicate using the spike and recovery method with five furfural standard solutions after the pretreated sample was first analyzed. The electrochemical response of the ErGO/GCE was measured using the differential pulse voltammetry (DPV) technique in the potential range between −1.6 and −1.2 V. The reduction current obtained from the sensor responses was inserted into the calibration equation to determine the content of furfural.
3. Results and discussion
3.1. Characterization of the ErGO/GCE
GO used for preparing the ErGO was obtained by a modified Hummers method.42 As shown in Fig. 1A, graphite oxide was entirely exfoliated from graphite to smooth individual GO sheets which can form well-dispersed aqueous colloids (inset in Fig. 1A). The ErGO/GCE was obtained by direct electrochemical reduction of GO via CV in 0.067 M Na2HPO4. The typical cyclic voltammograms of GO reduced on the GCE have one anodic peak (I) and two cathodic peaks (II and III) (Fig. 1B). The redox pair (peaks I and II) exhibited by the ErGO/GCE in a 0.1 M phosphate solution (inset in Fig. 1B) is ascribed to the redox pair of some oxygen-containing groups on the graphene plane that are too stable to be reduced by CV.39,44 Peak III is generated from the irreversible electrochemical reduction of GO.39,45 The increased peak currents along with successive potential scans indicate the successful deposition of conducting graphene on the GCE. The formation of the ErGO film on the GCE can also be directly confirmed in the SEM and TEM images as shown in Fig. 1C and D, where typical wrinkled textures of ErGO are observed.
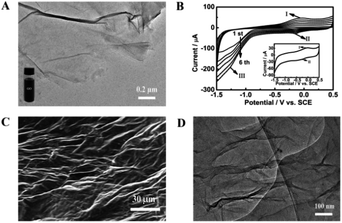 |
| Fig. 1 (A) TEM image of GO obtained by a Hummers method. Inset: the photo of GO colloids. (B) CV curves depicting electrochemical reduction of 10 mg mL−1 GO on a GCE at 10 mV s−1. Inset: CV curve of an ErGO/GCE in a 0.1 M Na2HPO4–NaH2PO4 solution (pH 9.18) at 10 mV s−1. (C) SEM image of the ErGO film (6 electrodeposition cycles) modified GCE. (D) TEM image of the ErGO removed from the GCE. | |
The successful preparation of ErGO was further verified using XRD, Raman, and XPS techniques together with pristine graphite and GO as the control. The XRD patterns of pristine graphite, GO and ErGO are presented in Fig. 2A. The main graphitic peak at 2θ = 26.5° (corresponding to an interlayer distance d = 0.336 nm) in graphite gradually disappears with the oxidation process while a new peak in GO appears at a lower angle (2θ ≈ 10.8°, d = 0.87 nm), indicating the complete oxidation of graphite.34,46 After electrochemical reduction, the diffraction peak at 2θ = 26.5° does not reappear as seen in the graphene produced with other methods,47,48 which suggests that all stacking of graphene layers in ErGO may be lost or some remaining stacking may be disordered.47,49,50
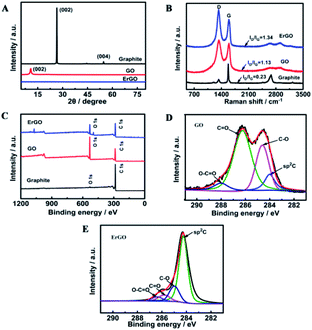 |
| Fig. 2 (A) XRD patterns, (B) Raman spectra and (C) XPS survey of graphite, GO, and ErGO. C1s high-resolution XPS spectra of (D) GO and (E) ErGO. | |
Raman spectroscopy is another useful and non-destructive technique used to reveal the structural information of carbon-based materials. The Raman spectrum (Fig. 2B) of pristine graphite shows a prominent and sharp G peak at 1581 cm−1 which is related to the in-plane motion of the carbon atoms. Pristine graphite also displays a less pronounced D band located at 1330 cm−1, which is associated with the presence of disorder and defects, either edge or topological (basal-plane) defects, in the graphene sheet.51 Structural defects induced by the oxidation of graphite significantly intensify the D band and blueshift the G band to 1590 cm−1 in the Raman spectrum of GO. On the other hand, the redshift of the G band in the Raman spectrum of ErGO to 1579 cm−1 is observed due to the reduction of GO. Such a shift back is consistent with previous reports of both chemical and thermal reductions of GO.52–54 The D/G intensity ratio in the Raman spectrum is often used to evaluate the size of the sp2 ring clusters in a network of sp2 and sp3 bonded carbons.55 As can be seen, the ID/IG value increases dramatically from the graphite powder (0.23) to GO (1.13), indicating a decreased average size of sp2 domains induced by the extensive oxidation. Noticeably, the ID/IG in ErGO is found to be slightly increased as well (from 1.13 to 1.34), which is consistent with that from most of the Raman spectra reported previously for ErGOs.56
Changes of carbon-based groups during the oxidation and reduction stages were further investigated by XPS. As shown in Fig. 2C, pristine graphite mainly has a C1s peak (285 eV), whereas GO and ErGO both have C1s and O1s (533 eV) peaks. The carbon to oxygen ratio (C/O) is a widely accepted criterion for evaluation of the reduction process.34,53 According to the XPS survey spectra, the C/O ratio increased from 0.6 in GO to 1.4 in ErGO, verifying a successful electrochemical reduction process. The high-resolution C1s XPS spectra of GO and ErGO display more detailed information on the functional groups involved in the reduction of GO. In GO, the C1s spectrum exhibits a saddle-like pattern, which is a signature of extreme oxidization in GO (Fig. 2D). The oxidation stage transforms the sp2 component in graphite into the sp3 hybridization in GO, while ErGO exhibits a much higher intensity of olefinic sp2 carbon, indicating a recovery of most of the sp2 bonds by electrochemical reduction (Fig. 2E). In addition to the increased sp2 graphitic component, deconvolution of the C1s peak in ErGO and GO reveals the considerable degrees of reduction: sharply decreased C–O and C
O functional groups and a slightly decreased carboxylic acid carbon (O–C
O).57
3.2. Electrochemical investigation of the furfural sensor
3.2.1. Optimization of ErGO/GCE preparation.
The electrochemical properties of the ErGO/GCE are sensitive to CV cycles during the reduction of GO to ErGO on the GCE. As shown in Fig. 3A, the current response of the ErGO/GCE for the redox probe [Fe(CN)6]3−/4− increases with the CV cycles from 0 to 15, indicating the successful surface modification of ErGO on the GCE. Additionally, the anodic-to-cathodic peak potential separation (ΔEp) initially becomes smaller and then larger than that for the bare GCE (Fig. 3B). The ΔEp and Ipa/Ipc ratio of [Fe(CN)6]3−/4− obtained on the ErGO/GCE with different electrodeposition cycles were compared and are listed in Table 1. As seen, the Ipa/Ipc ratio deviates more and more from a value of 1 when the electrodeposition cycles increase from 3 to 15. The narrowed ΔEp and the value of the Ipa/Ipc ratio close to 1 of [Fe(CN)6]3−/4− suggest the improved electron transfer kinetics and better reversibility on the ErGO/GCE, which is ascribed to the reactive edge defects on graphene.58,59 When the electrodeposition cycles are greater than 3, the increased ΔEp and Ipa/Ipc ratio of [Fe(CN)6]3−/4− can be ascribed to the hindered charge transfer which results from the increased thickness of the graphene film on the GCE.60,61 Finally, 6 cycles were used for subsequent electrode modification when both current sensitivity and electron transfer kinetics were taken into consideration at the same time.
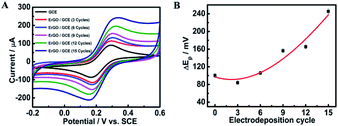 |
| Fig. 3 (A) CV curves of 5.0 mM [Fe(CN)6]3−/4− in 0.1 M KCl at the bare GCE and ErGO/GCE prepared under various electrodeposition cycles at 50 mV s−1. (B) The corresponding response curve of ΔEp on the CV cycle. | |
Table 1
I
pa/Ipc ratio and ΔEp values recorded by CV for [Fe(CN)6]3−/4− on the ErGO/GCE with different electrodeposition cycles
Electrodeposition cycle |
I
pa/Ipc ± SD (×10−4) |
ΔEp ± SD |
0 |
0.9951 ± 9.1 |
100 ± 4.51 |
3 |
0.9999 ± 4.7 |
84 ± 4.58 |
6 |
1.011 ± 11.4 |
106 ± 3.60 |
9 |
1.023 ± 10.1 |
156 ± 4.42 |
12 |
1.032 ± 11.5 |
165 ± 4.35 |
15 |
1.041 ± 15.9 |
222 ± 2.52 |
3.2.2. Electrochemical reduction of furfural at the ErGO/GCE.
In order to investigate the electrocatalytic behaviors of the resulting ErGO/GCE, cyclic voltammograms were first recorded (the GCE was prepared for comparison) in [Fe(CN)6]3−/4− solution. As shown in Fig. 4A, a higher current with a decreased ΔEp and a Ipa/Ipc ratio closer to 1 are observed, indicating a larger surface area and faster electron transfer of the ErGO/GCE. The Nyquist diagram (Fig. 4B) of the ErGO/GCE system shows a straight line while that of the GCE shows a depressed semicircle. As calculated from the equivalent circuit inset in Fig. 4B, the charge transfer resistance (Rct) values of the ErGO/GCE and GCE are 194 and 125 Ω, respectively. The lower Rct means that the ErGO film exhibits a lower electron transfer resistance and greater electron transfer rate.62
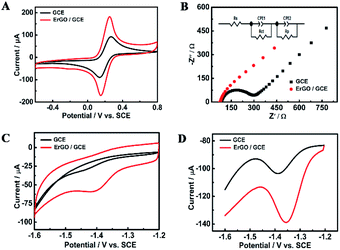 |
| Fig. 4 (A) CV curves and (B) EIS fitted curves of the bare GCE and ErGO/GCE in a 0.1 M KCl solution containing 5 mM [Fe(CN)6]3−/4−, respectively. The inset shows the respective equivalent circuit diagrams, where Rs, Rct, CPE and Rp represent solution resistance, charge transfer resistance, constant phase elements and polarization resistance, respectively. (C) CV and (D) DPV curves of different electrodes in a pH = 9.18 Na2HPO4–NaH2PO4 solution with 0.5 mM furfural. Scan rate: 50 mV s−1. | |
Fig. 4C compares the CV curves of a solution containing 0.5 mM furfural in a 0.1 M Na2HPO4–NaH2PO4 solution (pH 9.18) recorded at the bare GCE and ErGO/GCE. Furfural has an irreversible cathodic peak located at −1.41 V which is 40 mV positive than that at the GCE. The cathodic peak current obtained at the ErGO/GCE is 15 μA, which is 5 times larger than that at the bare GCE. Similar electrocatalytic activity for furfural (Fig. 4D) was also found in the DPV results, which occurs with an increased peak current and a smaller overpotential at the ErGO/GCE compared with that at the bare GCE, indicating the improved sensing ability of the ErGO/GCE.
3.2.3. The reduction mechanism of furfural at the ErGO/GCE.
The effect of the scan rate on the CV responses of furfural at the ErGO/GCE was investigated and the results are shown in Fig. 5. The reduction peak currents of furfural increase with the increasing scan rate, while the reduction peak potentials gradually shift to negative values (Fig. 5A). The plot of the cathodic peak current as a function of the square root of the scan rate in the range of 5–400 mV s−1 shows a linear relationship (Fig. 5B), which indicates that the electrode reaction of furfural is a diffusion-controlled process.
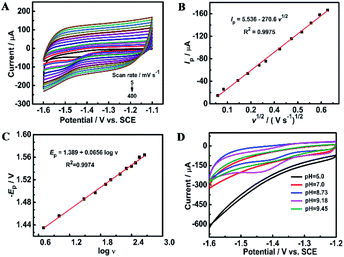 |
| Fig. 5 (A) CV curves of 0.5 mM furfural in 0.1 M pH = 9.18 NaH2PO4–Na2HPO4 at different scan rates: 5, 10, 30, 50, 80, 100, 150, 200, 250, 300, 350 and 400 mV s−1. (B) Plot of the cathodic peak current against the square root of the scan rate. (C) Plot of Ep against log ν. (D) CV responses of 1 mM furfural in different pH systems: pH = 5.0 HAc–NaAc, pH = 7.0 PBS, pH = 8.73 Na3C6H5O7, pH = 9.18 NaH2PO4–Na2HPO4, and pH = 9.45 NH3–NH4Cl. Scan rate: 10 mV s−1; electrodeposition cycles: 6. | |
For an overall irreversible electron transfer, the peak potential (Ep) depends on the scan rate (v) and can be expressed as the following Tafel equation:29,63
| Ep = (0.0591/αn)log ν + constant | (1) |
where
α is the transfer coefficient (
α = 0.5) and
n is the number of electrons participating in the redox reaction. According to the slope of the linear regression of
Ep to log
ν (
Fig. 5C),
n is determined roughly to be 2. Therefore, furfural reduction is related to a 2e
− irreversible process.
Fig. 5D shows the voltammetric responses of the prepared electrodes in different pH systems. It can be seen that no reduction peak of furfural appears in acidic and neutral media. The reduction of furfural favors a solution system of a pH = 9.18 Na2HPO4–NaH2PO4 solution which has the largest current response. The possible mechanism of furfural reduction with two electrons transferred in the alkaline electrolyte is outlined in Scheme 1. At the anode, hydroxide ions (OH−) are attracted and oxygen and electrons are produced.64–67 At the cathode, carbonyls first react with one H+/e− pair generating a radical intermediate (C˙–OH). Then, these radicals can be further converted by another H+/e− to yield the alcohol product.
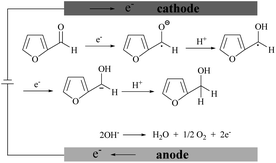 |
| Scheme 1 Furfural reduction mechanism in the alkaline electrolyte. | |
3.2.4. Detection of furfural.
Since DPV offers a preferable current sensitivity to CV, it was used for the determination of furfural. As shown in Fig. 6, the cathodic peak current response of furfural increases linearly with the increase in furfural concentration. The linear range for the determination of furfural is from 2 to 2015 μM with a detection limit of 0.4 μM (S/N = 3). The performance of the as-prepared sensor was also compared with those obtained by other detection methods, as summarized in Table 2. The comparable or improved furfural electrocatalytic performance of the ErGO/GCE is ascribed to the good catalytic performance of ErGO.
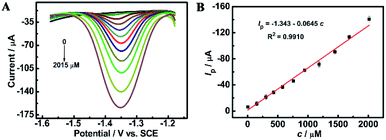 |
| Fig. 6 (A) DPV profiles at the ErGO/GCE in 0.1 M NaH2PO4–Na2HPO4 (pH = 9.18) containing different concentrations of furfural from 0–2015 μM. (B) The plot of the reduction peak current as a function of furfural concentration. | |
Table 2 Comparison of furfural detection performance with that of other sensors
Technique |
Electrode |
Linear range (μg mL−1) |
LOD (μg mL−1) |
Ref. |
PVC-calixarene membrane electrode.
Square wave voltammetry.
Static mercury drop electrode.
Pulsed amperometric detection.
Dual pulse staircase voltammetry.
|
DPV |
NiNPs/GCE |
0.48–28.8 |
0.24 |
3
|
DPV |
GCE |
6.10–117.9 |
1.81 |
4
|
SWV |
PMEa |
4.8–9600 |
2.0 |
26
|
CV |
Au cylinder electrode |
1.0–8.0 |
0.8 |
27
|
DPV |
Hg/GCE |
1.0–10.0 |
0.05 |
28
|
SWVb |
SMDEc |
— |
0.40 |
29
|
PADd/DPSVe |
Pt electrode |
2.0–10 |
0.56 |
30
|
DPV |
ErGO/GCE |
0.19–194 |
0.038 |
This work |
3.2.5. Repeatability, stability, reproducibility and selectivity of the ErGO/GCE.
The repeatability of the ErGO membrane was investigated with 100 successive measurements in a 1 mM furfural solution. As shown in Fig. 7A, the results show a relative standard deviation of 5.2% from the 1st to 100th cycle, indicating that the directly reduced ErGO electrode is not subjected to surface fouling by the reduction products. The satisfying repeatability of ErGO films results from the strong interaction between ErGO flakes.
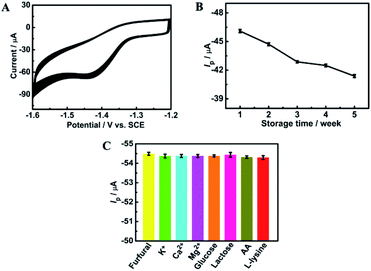 |
| Fig. 7 (A) CV profiles of 100 consecutive potential scans of 1 mM furfural in a pH 9.18 NaH2PO4–Na2HPO4 solution at the ErGO/GCE and (B) the current responses after storage in a refrigerator for 1, 2, 3, 4, and 5 weeks, respectively. Scan rate: 50 mV s−1. (C) Histogram for current responses of the ErGO/GCE sensor with 0.8 mM furfural containing 80 mM K+, Ca2+, and Mg2+ and 40 mM glucose, lactose, AA and L-lysine, respectively. | |
The long-term storage stability of the ErGO/GCE was also evaluated. As shown in Fig. 7B, after storing the prepared electrode in a refrigerator for 5 weeks, the corresponding reduction peak current can still retain 89.5% of the original, demonstrating the excellent storage stability of the ErGO/GCE.
Additionally, three parallel electrodes were prepared for the detection of furfural in a pH = 9.18 NaH2PO4–Na2HPO4 solution. The results show a relative standard deviation (RSD) of 2.0%. The small RSD value suggests that the reproducibility of the ErGO/GCE is satisfactory.
Interference studies were further carried out to evaluate the specificity of the ErGO/GCE sensor by recording the DPV current for 0.8 mM furfural with the existence of some common interferences in the milk sample such as 100-fold K+, Ca2+ and Mg2+ and 50-fold glucose, lactose, vitamin C (AA) and L-lysine. As seen in Fig. 7C, all the tested substances have no significant interferences in the determination of furfural with a less than 5% change in the peak current, indicating the excellent selectivity of the fabricated sensor.
3.3. Real sample analysis
The feasibility of the sensor was verified by its application in analyzing the three selected milk samples. Each sample was measured in triplicate using the spike and recovery method with five furfural standard solutions after the pretreated samples were first measured. As shown in Table 3, furfural was not detected in the three samples. After the manual addition of furfural at different concentrations, the recovery is in the range of 91.6–104.1% and RSD is 1.72–4.26%. These results indicate that the proposed electrochemical furfural sensor can be used for real sample analysis with excellent veracity and reliability.
Table 3 Determination of furfural in three different milk samples with the ErGO/GCE (n = 3)
Sample |
Added (μM) |
Found (μM) |
Recovery (%) |
RSD (%) |
Charcoal yogurt |
0 |
Not detected |
— |
— |
10 |
9.78 |
97.8 |
2.63 |
25 |
24.6 |
98.4 |
1.91 |
75 |
77.4 |
103.2 |
2.08 |
100 |
96.3 |
96.3 |
3.51 |
150 |
153.9 |
102.6 |
2.72 |
Fresh milk |
0 |
Not detected |
— |
— |
25 |
23.7 |
94.8 |
1.72 |
75 |
73.2 |
97.6 |
2.85 |
100 |
101.5 |
101.5 |
3.15 |
150 |
142.8 |
95.2 |
4.26 |
200 |
187.4 |
93.7 |
2.03 |
Coconut milk |
0 |
Not detected |
— |
— |
25 |
22.9 |
91.6 |
3.25 |
75 |
78.1 |
104.1 |
2.53 |
100 |
97.3 |
97.3 |
1.92 |
150 |
141.5 |
94.3 |
3.63 |
200 |
192.8 |
96.4 |
2.24 |
4. Conclusions
In summary, an electrochemical sensor for determination of furfural in dairy products was fabricated by direct electroreduction of GO in a PBS dispersion. The results showed that one-step cyclic voltammetry reduction effectively reduced the sp3 carbon in GO to the sp2 graphitic component, avoiding not only any reductants used in chemical reduction but also the cumbersome purification and drying procedures in thermal reduction. Moreover, the obtained wrinkled ErGO/GCE has a larger surface area and improved electron transfer capability. The resulting ErGO/GCE has excellent sensing sensitivity to furfural and is reliable for furfural detection in milk samples. The method reported here is simple and efficient and provides a reliable guideline towards rational fabrication of an electrochemical platform for furfural detection with high sensitivity and good stability.
Conflicts of interest
All authors declare that they have no conflict of interest.
Acknowledgements
The authors greatly appreciate the support of the National Key R&D Program of China (No. 2017YFC1600404), the Open Project Program of the State Key Laboratory of Dairy Biotechnology (No. SKLDB2019-003), and the Natural Science Foundation of Zhejiang Province (No. LY18B050004).
References
- R. Mariscal, P. Maireles-Torres, M. Ojeda, I. Sádaba and M. López Granados, Energy Environ. Sci., 2016, 9, 1144–1189 RSC.
-
Y. Liu, Rapid detection method of furfural and its application in brewing liquor, Master thesis, Hubei University of Technology, 2013.
- J. L. da Silva, M. A. Beluomini and N. Ramos Stradiotto, Anal. Methods, 2017, 9, 826–834 RSC.
- M. Shamsipur, A. A. Beigi, M. Teymouri, Y. Ghorbani, M. Irandoust and A. Mehdizadeh, Talanta, 2010, 81, 109–115 CrossRef CAS.
-
C. Centers for Disease, MMWR Morbidity and Mortality Weekly Report, 1990, vol. 39, pp. 367–368 Search PubMed.
- H. L. Li, X. F. Chen, J. L. Ren, H. Deng, F. Peng and R. C. Sun, Biotechnol. Biofuels, 2015, 8, 127 CrossRef.
- Y. Y. Cui, X. M. Shi, Y. Tang, Y. F. Xie and Z. X. Du, Food Chem., 2020, 313, 125930 CrossRef.
- V. Gökmen and H. Z. Senyuva, J. Agric. Food Chem., 2006, 54, 2845–2849 CrossRef.
- J. L. Chavez-Servin, A. I. Castellote and M. C. Lopez-Sabater, J. Chromatogr. A, 2005, 1076, 133–140 CrossRef CAS.
- B. Er Demirhan, B. Demirhan, C. Sonmez, H. Torul, U. Tamer and G. Yentur, J. Dairy Sci., 2015, 98, 818–822 CrossRef CAS.
- J. L. Chavez-Servin, K. de la Torre Carbot, T. Garcia-Gasca, A. I. Castellote and M. C. Lopez-Sabater, Food Chem., 2015, 166, 486–491 CrossRef CAS.
- Q. Q. Xing, Y. R. Ma, X. F. Fu, Q. Cao, Y. Zhang and C. P. You, J. Sci. Food Agric., 2020, 100, 5276–5282 CrossRef CAS.
- Y. Sun, Z. B. Guan, H. W. Cai, Y. Y. Huang, Y. W. Lin and X. S. Hu, Anal. Chim. Acta, 2017, 987, 47–55 CrossRef CAS.
- S. Albalá-Hurtado, M. T. Veciana-Nogués and M. Izquierdo-Pulido, J. Agric. Food Chem., 1997, 45, 2128–2133 CrossRef.
- M. Madani-Tonekaboni, M. Kamankesh and A. Mohammadi, J. Food Compos. Anal., 2015, 40, 1–7 CrossRef CAS.
- E. Ferrer, A. Alegria, R. Farré, P. Abellan and F. Romero, J. Chromatogr. A, 2002, 947, 85–95 CrossRef CAS.
- E. Ferrer, A. Alegria, G. Courtois and R. Farre, J. Chromatogr. A, 2000, 881, 599–606 CrossRef CAS.
- V. S. Bhat, S. Supriya and G. Hegde, J. Electrochem. Soc., 2020, 167, 037526 CrossRef CAS.
- A. Aziz, M. Asif, G. Ashraf, M. Azeem, I. Majeed, M. Ajmal, J. Wang and H. F. Liu, Microchim. Acta, 2019, 186, 671 CrossRef CAS.
- J. A. Ribeiro, P. M. V. Fernandes, C. M. Pereira and F. Silva, Talanta, 2016, 160, 653–679 CrossRef CAS.
- A. A. Saczk, L. L. Okumura, M. F. d. Oliveira, M. V. B. Zanoni and N. R. Stradiotto, Chromatographia, 2006, 63, 45–51 CrossRef CAS.
- L. Torben and L. Henning, Acta Chem. Scand., 1985, 39, 429–435 Search PubMed.
- P. Parpot, A. P. Bettencourt, G. Chamoulaud, K. B. Kokoh and E. M. Belgsir, Electrochim. Acta, 2004, 49, 397–403 CrossRef CAS.
- Y. P. Lin, Y. H. Fu, T. S. Chen and L. S. Wang, Journal of Shanghai Normal University, 2012, 41, 75–79 CrossRef.
- D. B. Chu, L. Y. Zhang, J. H. Zhang, X. M. Zhang and X. J. Yin, J. Phys. Chem., 2006, 22, 373–377 CAS.
- M. Shamsipur, A. A. M. Beigi, M. Teymouri, S. Rasoolipour and Z. Asfari, Anal. Chem., 2009, 81, 6789–6796 CrossRef CAS.
-
Y. H. Fu, Electrochemical detection of furfural in transformer oil, Master thesis, South China University of Technology, 2013.
-
R. L. Wang, Determination of Furfural in Insulating Oil and Preliminary Study on Growth of Pt Nanoparticles on Polyfurfural Membrane, South China University of Technology, 2016.
- M. Shamsipur, A. A. M. Beigi, M. Teymouri, S. A. Tash and V. Samimi, Electroanalysis, 2010, 22, 1314–1322 CrossRef CAS.
- T. Bosworth, S. Setford and R. Heywood, Anal. Chim. Acta, 2001, 450, 253–261 CrossRef CAS.
- T. Sattar, Top. Curr. Chem., 2019, 377, 10 CrossRef.
- A. Nag, A. Mitra and S. C. Mukhopadhyay, Sens. Actuators, A, 2018, 270, 177–194 CrossRef CAS.
- Y. Zhao, X.-g. Li, X. Zhou and Y.-n. Zhang, Sens. Actuators, B, 2016, 231, 324–340 CrossRef CAS.
- S. Y. Toh, K. S. Loh, S. K. Kamarudin and W. R. W. Daud, Chem. Eng. J., 2014, 251, 422–434 CrossRef CAS.
- H. L. Guo, X. F. Wang and Q. Y. Qian, ACS Nano, 2009, 3, 2653–2659 CrossRef CAS.
- M. Zhou, Y. Wang, Y. Zhai, J. Zhai, W. Ren, F. Wang and S. Dong, Chem.–Eur. J., 2009, 15, 6116–6120 CrossRef CAS.
- K. K. H. De Silva, H. H. Huang, R. K. Joshi and M. Yoshimura, Carbon, 2017, 119, 190–199 CrossRef CAS.
- T. Tomai, Y. Nakayasu, Y. Okamura, S. Ishiguro, N. Tamura, S. Katahira and I. Honma, Carbon, 2020, 158, 131–136 CrossRef CAS.
- L. Chen, Y. Tang, K. Wang, C. Liu and S. Luo, Electrochem. Commun., 2011, 13, 133–137 CrossRef CAS.
- G. Eda and M. Chhowalla, Adv. Mater., 2010, 22, 2392–2415 CrossRef CAS.
- G. Scott, H. Song, W. Minsheng, W. L. Kang and K. B. Richard, Nano Lett., 2007, 7, 3394–3398 CrossRef.
- J. Chen, B. W. Yao, C. Li and G. Q. Shi, Carbon, 2013, 64, 225–229 CrossRef CAS.
- M. A. J. S. Boekel and R. Zia Ur, Neth. Milk Dairy J., 1987, 41, 297–306 Search PubMed.
- S. Rastgar and S. Shahrokhian, Talanta, 2014, 119, 156–163 CrossRef CAS.
- C. Liu, K. Wang, S. Luo, Y. Tang and L. Chen, Small, 2011, 7, 1203–12306 CrossRef CAS.
- D. A. Dikin, S. Stankovich, E. J. Zimney, R. D. Piner, G. H. B. Dommett, G. Evmenenko, S. T. Nguyen and R. S. Ruoff, Nature, 2007, 448, 457–460 CrossRef CAS.
- M. J. McAllister, J. L. Li, D. H. Adamson, H. C. Schniepp, A. A. Abdala, J. Liu, M. Herrera-Alonso, D. L. Milius, R. Car, R. K. Prud’homme and I. A. Aksay, Chem. Mater., 2007, 19, 4396–4404 CrossRef CAS.
- G. X. Wang, J. Yang, J. Park, X. L. Gou, B. Wang, H. Liu and J. Yao, J. Phys. Chem. C, 2008, 112, 8192–8195 CrossRef CAS.
- M. Hilder, B. Winther-Jensen, D. Li, M. Forsyth and D. R. MacFarlane, Phys. Chem. Chem. Phys., 2011, 13, 9187–9193 RSC.
- Y. Shao, J. Wang, M. Engelhard, C. Wang and Y. Lin, J. Mater. Chem., 2010, 20, 743–748 RSC.
- V. Nagyte, D. J. Kelly, A. Felten, G. Picardi, Y. Shin, A. Alieva, R. E. Worsley, K. Parvez, S. Dehm, R. Krupke, S. J. Haigh, A. Oikonomou, A. J. Pollard and C. Casiraghi, Nano Lett., 2020, 20, 3411–3419 CrossRef CAS.
- X. Díez-Betriu, F. J. Mompeán, C. Munuera, J. Rubio-Zuazo, R. Menéndez, G. R. Castro and A. de Andrés, Carbon, 2014, 80, 40–49 CrossRef.
- L. G. Guex, B. Sacchi, K. F. Peuvot, R. L. Andersson, A. M. Pourrahimi, V. Strom, S. Farris and R. T. Olsson, Nanoscale, 2017, 9, 9562–9571 RSC.
- H.-J. Kil, K. Yun, M.-E. Yoo, S. Kim and J.-W. Park, RSC Adv., 2020, 10, 22102–22111 RSC.
- J. S. Bulmer, J. E. Mizen, T. S. Gspann, A. Kaniyoor, J. B. Ryley, P. J. Kiley, M. R. Sparkes, B. O'Neill and J. A. Elliott, Carbon, 2019, 153, 725–736 CrossRef CAS.
- S. Z. Xiang, ACS Nano, 2008, 2, 1033–1039 CrossRef.
- S. Yumitori, J. Mater. Sci., 2000, 35, 139–146 CrossRef CAS.
- K. Chu, J. Wang, Y.-p. Liu and Z.-r. Geng, Carbon, 2018, 140, 112–123 CrossRef CAS.
- S. Shanmugam, S. Nachimuthu and V. Subramaniam, J. Mater. Sci., 2020, 55, 5920–5937 CrossRef CAS.
- M. Velický, D. F. Bradley, A. J. Cooper, E. W. Hill, I. A. Kinloch, A. Mishchenko, K. S. Novoselov, H. V. Patten, P. S. Toth and A. T. Valota, ACS Nano, 2014, 8, 10089–10100 CrossRef.
- A. T. Valota, I. A. Kinloch, K. S. Novoselov, C. Casiraghi, A. Eckmann, E. W. Hill and R. A. W. Dryfe, ACS Nano, 2011, 5, 8809–8815 CrossRef CAS.
- S. Biswas and L. T. Drzal, Chem. Mater., 2010, 22, 5667–5671 CrossRef CAS.
-
A. J. Bard and L. R. Faulkner, Electrochemical Methods, John Wiley & Sons, 2nd edn, 2005, pp. 157–161 Search PubMed.
- C. J. Gagliardi, A. K. Vannucci, J. J. Concepcion, Z. Chen and T. J. Meyer, Energy Environ. Sci., 2012, 5, 7704–7717 RSC.
- X. H. Chadderdon, D. J. Chadderdon, J. E. Matthiesen, Y. Qiu, J. M. Carraher, J. P. Tessonnier and W. Li, J. Am. Chem. Soc., 2017, 139, 14120–14128 CrossRef CAS.
- Y. Cao and T. Noel, Org. Process Res. Dev., 2019, 23, 403–408 CrossRef CAS.
- S. Shiva Kumar and V. Himabindu, Mater. Sci. Energy Technol., 2019, 2, 442–454 Search PubMed.
|
This journal is © The Royal Society of Chemistry 2021 |