DOI:
10.1039/C9GC02992C
(Paper)
Green Chem., 2020,
22, 803-813
Hybridised sustainability metrics for use in life cycle assessment of bio-based products: resource efficiency and circularity†
Received
24th August 2019
, Accepted 27th November 2019
First published on 8th January 2020
Abstract
The development, implementation and social acceptance of resource efficient, circular, bio-based economies require critical understanding of the whole supply chain from feedstock to end-use. Trust, transparency and traceability will be paramount. Though life cycle assessment (LCA) is a universally chosen approach to fulfil this purpose, the nature of data required and the depth of analysis lead to complex interpretations of the findings. Herein, a new set of hybridised, first-line sustainability indicators, drawn from the principles of green chemistry and resource (material and energy) circularity, are reported. These flexible, potentially stand-alone metrics are demonstrated via application to an exemplary comparative LCA, incorporating the hybridised indicators including hazardous chemical use, waste generated, resource circularity and energy efficiency, from the “gate-to-gate” stages for the bio-based case studies and their petro-derived commercial counterparts. These metrics were observed to quantify critical new information relevant to our transition to a circular economy, bridging significant gaps in contemporary environmental impact assessment methodologies. Appropriate additional evaluations that examine the performance of metrics, when the embedded resource efficiency and circularity strategies are omitted, have also been undertaken and reported. The data drawn from employing these methods are crucial to inform and encourage operational optimisation, transparency in sustainability reporting and practices to a significant number of value-chain actors including manufacturers, policy makers and consumers.
Introduction
Bio-based products have been identified as a promising pathway for a transition from linear to a resilient bio-based circular economy and could potentially contribute to 14 (out of the 17) United Nations Sustainable Development Goals.1,2 The sustainability and performance potential of the bio-based sector are determined by a number of factors, including the spatial spread of the supply-chain, agricultural systems, impact on the ecosystem, technology readiness and local skill-level, which are captured via life cycle assessment (LCA) methodologies. LCA is a robust certified approach that offers an impact-led sustainability analysis measuring the environmental impacts/credits associated with the use and reuse of resources3,4 (similar to that presented in Fig. 1).
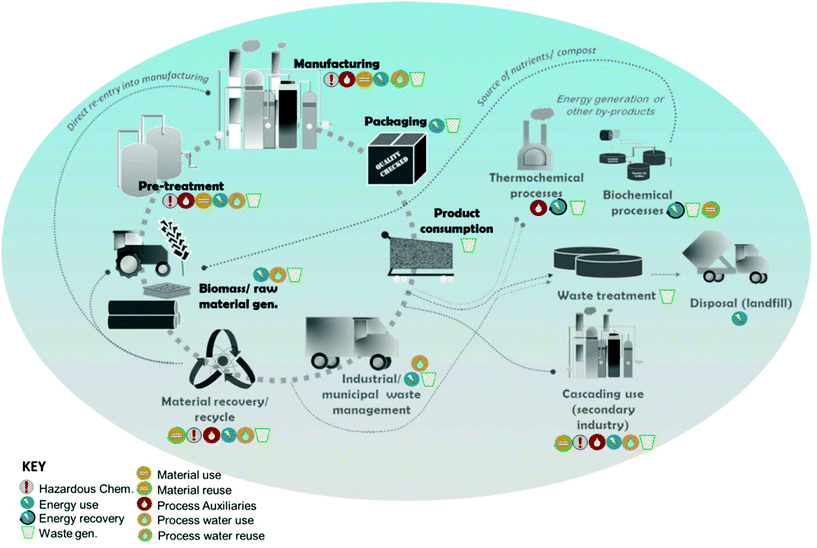 |
| Fig. 1 An overview of resource consumption, re-circulation and losses as waste within a typically circular bio-based value chain. | |
In reality, a number of present value-chain actors opt for an array of techniques comprising a mix of LCA and non-LCA metrics to report their responsible product (not restricted to bio-based) development and production operations, including
• BASF Eco-efficiency;5
• Dow's Chemical Index;6
• Green chemistry and other resource efficiency metrics;7–14
• Portfolio Sustainability Assessment (PSA) methodology;15
• Ellen MacArthur Foundation-Material Circularity.16
Review of these methodologies stresses the currently needed trajectory for sustainable development towards a resource-efficient circular economy, whilst highlighting significant gaps in the existing environmental assessment approaches. The European Commission Product Environmental Footprint (PEF) also recommends the use of a proposed set of impact categories for communication of a product's environmental performance within the industrial sector.17 Following these recommendations, a set of 7 LCA impact-categories were selected for this study (Table 1). Though LCA's single score quantification is valuable for the overall environmental comparison of products and processes, it provides limited visibility on process-level disaggregated impacts based on material-flow, wastage and utilisation efficiency. This is crucial for industrial sustainable production practitioners to help responsibly monitor resource and waste hotspots, optimise productivity, improve value-addition capabilities and communicate these practices, to the non-specialist stakeholders (upstream and downstream supply-chain actors).
Table 1 List of selected LCA methodologies as per the recommendations of the EU-PEF guidance on product sustainability evaluation
Environmental impact |
Impact category |
Unit |
Method |
Emissions to air |
Global warming potential BIO |
kg of CO2 eq. |
IPCC GWP100 complemented by GWP-BIO for biogenic carbon20 |
Particulate matter |
Disease incidence |
UNEP recommended model |
Acidification (terrestrial and freshwater) |
mol H+eq |
Accumulated exceedance model21 |
Emissions to water |
Freshwater Eutrophication |
kg P−eq |
EUTREND model – ReCIPe 2008 |
Human health |
Human toxicity, cancer |
CTUh |
USEtox model |
Abiotic resources |
Fossil resource depletion |
MJ |
Abiotic resource depletion-fossil fuels (CML 2002) |
Water use |
Water scarcity |
m3 water deprived |
Available Water Remaining (AWARE): user deprivation potential22 |
These critical parameters must also be quantified and featured alongside the main outcomes of LCA. Indicators are proposed to fulfil the criteria.
The proposed indicators must
• Act as first-line metrics prior to a comprehensive LCA;
• Facilitate result interpretation that helps non-expert value-chain actors implement appropriate operational optimisations;
• Facilitate cross-functional applications, without major modifications, across the different life cycle stages and to a wide range of products and processes;
• Adhere and contribute to the wider sustainable development and resource-efficiency targets;18,19
The overall aim of this study was to develop and investigate the performance of a unique environmental methodology that assesses the resource efficiency and circular characteristics of products and processes, across the “gate-to-gate” stages encompassing “product manufacturing to distribution of end-products to consumers”. For the purpose of its demonstration, a comparative LCA focussing on two bio-based products, bio-based packaging films and mulch films (from manufacturing processes which embed resource circularity strategies), was undertaken, weighing their environmental performance against that of their linearly produced petro-derived commercial equivalents. Refer to Fig. 2 for further clarity on the system boundary set for this study.
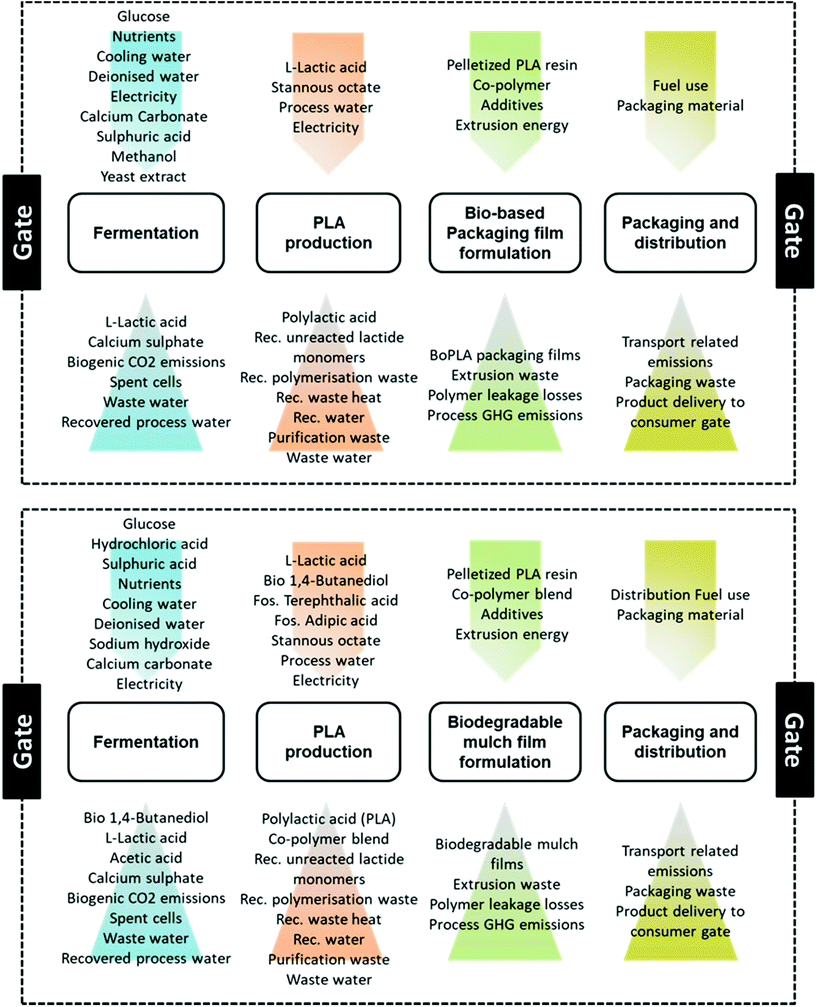 |
| Fig. 2 Process inventory and system boundary for manufacturing the BoPLA packaging film and the biodegradable mulch film. | |
Methodology
The selected impact assessment and resource efficiency indicators were applied to two case studies for a “gate-to-gate” environmental LCA. The first case study related to packaging films, where a comparative environmental performance was undertaken between BoPLA (Biaxially-oriented polylactic acid) films, weighed against BoPP (Biaxially-oriented polypropylene) films. A single BoPLA film (350 mm × 250 mm × 0.05 mm) was chosen as the functional unit for this study. Its baseline competitor, BoPP, has a similar functional unit of one film (450 mm × 250 × 0.05 mm).23–25 The second case study involves mulch films, where a similar comparative environmental assessment was undertaken between PLA-based mulch films and LLDPE (Linear-Low Density Polyethylene) mulch films. The functional unit chosen for the partially bio-based, biodegradable mulch film is the amount required to mulch 1 ha of agricultural land. The mulch film was synthesised from bio-based polylactic acid (PLA) (45%) and a co-polymer (55%) with UV-stabilisers and carbon black which is 0.015 mm thick (to enable biodegradation) with a density of 0.8 kg L−1. The baseline competitor, LLDPE mulch film, was synthesised from fossil-derived LLDPE, containing the same additives with an average thickness of 0.025 mm (to enable removal after use) and a density of 0.925 kg L−1.24
The starting material for the polymer resin (PLA), from which the two end-products are prepared, was assumed to be sourced from three different feedstocks which include glucose syrup derived from conventional corn, corn stover (a lignocellulose-rich agricultural residue) and sugar-beet pulp (a pectin-rich industrial by-product stream). Within the scope of this study, the starting material is glucose, which is then transformed into the building blocks of the polymer resin (i.e. lactic acid and 1,4-butanediol) needed for the end-products. In both case studies, PLA is used as the main or an allied compositional material. While the packaging films are made of 99% bio-based PLA,26 the mulch film is only 70% bio-based, drawn from blending 100% bio-based PLA and an only partially bio-based co-polymer (made of bio-based 1,4-butanediol and petro-derived adipic and terephthalic acids) and additives that confer thermal stability and colour to the final product.27–29
To produce PLA, glucose is fermented into lactic acid, followed by an array of downstream monomer separation and purification processes. The purified lactic acid is then polymerised in a process divided into three stages which include pre-polymer production, lactide production and PLA production via ring-opening polymerisation. The polymer is next blended with essential additives and co-polymers to produce the end-product.26,27 During the production, downstream processing and fabrication procedures, some consumables including deionised water, some inorganic acids and the trimmings from the extrusion process were assumed to be recovered and reused. (This is only applicable to processes of BoPP packaging films and PLA-based and LLDPE mulch films.) Unreacted components, such as the lactide monomers, during their polymerisation to PLA, are also recovered and recycled with an efficiency of 99.8%. The impact of absence of any resource efficiency and circularity (RE&C) strategy has also been examined through appropriate sensitivity analyses. The bio-based PLA and bio-1,4-butanediol production processes are described in greater detail in the supplementary section, providing further details on the embedded material valorisation steps to aid responsible resource use and waste reduction.
The process inventory was screened against the known databases (SINLIST and SUBSPORT) for hazardous chemicals. In addition to the conventional impact categories, crucial information such as wastes generated from the production, logistics and formulation processes has been taken into account and quantified. A more detailed description of the production and distribution processes and adopted assumptions relevant to the production and processing of materials to end-products is provided as the ESI.† The inventory for the production of PLA and the BoPLA packaging film can be found in Table 2 while the data for the production of PLA-mulch films and other assumptions can be found in Table 3.
Table 2 Inputs and outputs of PLA production and BoPLA packaging film production
Life cycle stages |
Inputs/outputs |
Material/energy |
Values |
Units |
Source: ref. 26, 30 and 31. |
Refinery |
Inputs |
Glucose |
1.284 |
kg kg−1 of PLA |
Stannous octoate (catalyst) |
0.0011 |
kg kg−1 of PLA |
Calcium carbonate |
0.843 |
kg kg−1 of PLA |
Water |
0.022 |
kg kg−1 of PLA |
Methanol |
0.0009 |
kg kg−1 of PLA |
Sulphuric acid |
1.35 |
kg kg−1 of PLA |
Cooling water |
299.3 |
kg kg−1 of PLA |
Electricity |
1.307 |
kW h kg−1 of PLA |
Outputs |
Polylactic acid (main-product) |
1 |
kg |
Unreacted lactide mixture (re-used) |
0.293 |
kg kg−1 of PLA |
Polymerisation residues (process waste) |
0.054 |
kg kg−1 of PLA |
|
Formulation |
Inputs |
PLA resin |
5.58 |
g functional per unit |
Co-polymer |
0.0155 |
g functional per unit |
Extrusion energy |
0.0245 |
kW h functional per unit |
Outputs |
BoPLA packaging film |
1 |
Piece (functional unit) |
Extrusion waste |
0.27 |
g functional per unit |
|
Transport |
|
Manufacturing to formulation site |
250 |
km |
|
Formulation to regional warehouse |
150 |
km |
|
Regional warehouse to retailer |
50 |
km |
|
Retailer to consumer |
5 |
km |
Table 3 Inputs and outputs for the formulation of PLA mulch film production
Inputs/outputs |
Inputs/outputs |
Material/energy |
Values |
Units |
Source: ref. 27, 28, 30 and 32–34. |
Formulation |
Inputs |
PLA resin |
0.55 |
kg kg−1 of mulch film |
Co-polymer blend |
0.43 |
kg kg−1 of mulch film |
Carbon black |
0.02 |
kg kg−1 of mulch film |
Extrusion energy |
0.0418 |
kW h kg−1 of mulch film |
Outputs |
PLA mulch film |
152 |
kg functional per unit |
Extrusion waste |
23.67 |
kg functional per unit |
|
Transport |
|
Manufacturing to formulation site |
250 |
km |
|
Formulation to regional warehouse |
150 |
km |
|
Regional warehouse to retailer |
50 |
km |
|
Retailer to consumer |
5 |
km |
Hybridised indicators
Hazardous chemical use.
Hazardous chemical use is an indicative parameter that “flags-up” the use of substances within a given product's inventory (including solvents, catalysts, additives or other chemicals) that could be used in the manufacturing process(es) and/or products, but may be classified as “hazardous” under the ECHA-REACH (European Chemical Agency-Registration, Evaluation, Authorisation and Restriction of Chemicals). While the REACH process is being carried out by the assessor, this analysis may be temporarily undertaken by screening the product's inventory against the known databases for hazardous chemicals, such as SIN LIST35 and SUBSPORT,36 which list substances of very high concern (SVHC). While these lists are not official and are largely based on incomplete data, they have been widely used by chemical companies. As part of the Innovative Medicines Initiative, the CHEM21 project developed a ‘flag’ system to indicate the presence of such undesirable substances. For example, a ‘solid black’ flag (■) indicates a need for a greener substitute,8,9 while a lighter flag (□) indicates the absence of such substances. This indicator may be applied to all life cycle stages involving synthesis, formulation and reprocessing that employ solvents, catalysts or other auxiliaries that may be known as or suspected of being substances of concern.
Feedstock intensity (FI) and circular-process feedstock intensity (CPFI).
Feedstock intensity (FI) quantifies raw material consumption and is the ratio of the total amount of the main raw materials used to the total amount of useful outputs (end-products and co-products). Measured as a kg of feedstock, FI (eqn (1)) can be calculated for either just the target product for a conservative estimate or for a functional unit of analysis when used in an LCA. For a linear process, FI may be used. | 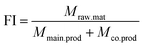 | (1) |
where Mraw.mat is the total mass of primary feedstock fed into the process (kg); Mmain.prod is the total mass of the target end-product synthesised in a process (kg); and Mco.prod is the total mass of any useful co-products synthesised in a process (kg).
Besides the application of this metric across the different stages of a product's life cycle (pre-treatment, manufacturing, refining and formulation), this quantitative indicator may also be utilised to measure material economy through product design for recovery via recycling of any primary production waste or material recovered from its end of life processes (EoL). For such circular processes, the circular-process feedstock intensity (CPFI) may be used (eqn (2)).
| 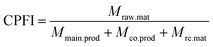 | (2) |
where
Mre.mat is the total mass of the material recovered /recycled from production waste or EoL (kg).
In terms of performance interpretation, this quantitative indicator is the best used in a comparative manner, for example, for comparison between bio-based products or between bio-based and fossil-derived products. The feedstock intensity of a product may ideally be 1 kg kg−1 of all the useful outputs.
Waste factor (WF) and circular-process waste factor (CPWF).
Waste factor (WF) measures the ratio of the total mass (kg) of solid, liquid or gaseous waste, generated as process wastes or lost from the system via leaks or spills, with respect to the total mass (kg) of the end-product and co-products (eqn (3)). | 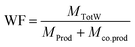 | (3) |
where MTotW is the total mass of waste generated from the production process (kg); MProd is the total mass of the end-product generated from the process (kg); and Mco.prod is the total mass of useful co-products generated (kg).
In the case of circular processes that demonstrate their capability to reduce process and production waste via valorisation strategies, the following expression for CPWF (eqn (4)) may be used.
| 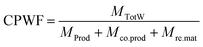 | (4) |
The quantification associated with waste-factor is variable depending on the goal and scope of the analysis. When used independently, a product waste-factor of “0” is considered ideal (if probably not realistic).
Product renewability (PR).
The renewable nature of the materials used in a product must be demonstrated to substantiate the bio-based claims of such products. Consumers and other relevant stakeholders see the use of bio-materials as a sign of renewability and an adherence to the principles of bioeconomy and therefore, due credit must be provided to such products. Though there are experimental standards (EN16640), a preliminary prediction would be a good starting point prior to substantiating the claims with an experimental test. Measured as a percent of the product, the product renewability (PR) (eqn (5)) should result in a figure from 0 to 100, with “0” representing non-renewability and “100” representing the ideal scenario of 100% renewability. | 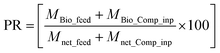 | (5) |
where MBio_feed is the net mass of bio-derived primary feedstock incorporated into the product (kg); MBio_Comp_inp is the net mass of bio-derived substances incorporated into the final formulation (compositional inputs) (kg); Mnet_feed is the net mass of all primary feedstocks incorporated into the product (kg); and Mnet_Comp_inp is the net mass of all the materials incorporated into the final formulation (compositional inputs) (for example, polymer additives) (kg).
Process material circularity (PMC).
Responsible material circularization strategies employed to recover and reuse some or all of the process auxiliaries consumed during the product synthesis (including solvents, catalysts, stabilising chemicals, columns and other items) must ideally be demonstrated. The process material circularity (PMC) is calculated as the summation of all the net mass of process auxiliaries used in the process deducting specific process auxiliaries that have been recovered and reused (eqn (6)). | 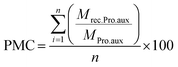 | (6) |
where MPro.aux is the net mass of specific process auxiliaries (deducting losses during use) used in the production process (kg); Mre.Pro.aux is the net mass of process auxiliaries that have been recovered and reused (kg); n is the total number of all the process auxiliaries; and i is the list of process auxiliaries used in the end-product synthesis at a given stage.
Measured as a %, similar to product renewability, “0%” represents an absolutely linear process and “100%” represents all the employed process auxiliaries being 100% recovered and reused.
Energy intensity (EI) and circular-process energy intensity (CPEI).
Energy intensity (EI) is defined as the ratio of the total amount of energy (fossil-derived, renewable energy, deducting any internally derived energy) to the total amount of products and co-products generated within the process (eqn (7)). All the energy invested is made accountable using this expression since, in accordance to the principles of green chemistry, a conversion process must be optimised to the lowest possible energy consumption for optimal product yield. The expression for a linear production process is presented below. | 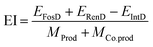 | (7) |
where EFosD is the fossil-derived energy used (kW h); ERenD is the renewable energy used (kW h); EIntD is the internally derived energy used (kW h); MProd is the total mass of the target product generated (kg); and MCo.prod is the total mass of the co-product generated (kg).
For a circular process demonstrating waste valorisation and material circularisation strategies, the circular process energy-intensity (CPEI) may be calculated according to eqn (8).
| 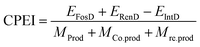 | (8) |
where
Mre.prod is the mass of the recovered and recycled product (kg).
NOTE: Though the methods have been presented as a stand-alone approach, in the upcoming sections quantifying the parameters for a total amount of process outputs, the empirical expressions have been modified to present the outcomes per functional unit of analysis for the purpose of consistency in result interpretation.
Results and discussion
Packaging films
The impact assessment and quantifications associated with the production of a functional unit of BoPLA packaging films set in the chosen scenario are presented in Table 4. The GWP100, measured as kgCO2eq for BoPLA was observed to deliver a GHG saving of roughly 40–70%, compared to the conventional BoPP packaging films. Biogenic CO2, released during the fermentation process, made up 35% of the total CO2 emissions to air released during the production process. The capability of the process to recover and reuse process auxiliaries such as inorganic acids and process water was effectively captured by process material circularity (PMC). The availability of this disaggregated material flow information helps the demonstration of resource recovery strategies implemented as part of the process design which in turn was observed to contribute nearly 20% of the overall GHG saving. Similarly, the water consumed downstream during the extraction and purification stages was reprocessed and reused, reducing the overall demand for process water. Disposal of fermentation waste onto landfills led to an increased eutrophication potential, which is conventionally overcome by redirecting this waste to an on-site anaerobic digester. However, this scenario was not considered in this analysis due to lack of supporting industrial data. In terms of hazardous chemicals present in the final product, a review of the material inventory for both BoPLA and BoPP packaging films against the hazardous substance databases (SIN LIST and SUBSPORT) resulted in the identification of no substances of very high concern and was thus highlighted with a “lighter” flag. This is particularly relevant within the industrial sector, where there are an evolving stringency, awareness and a requirement for responsible custodianship of products and/or components as required by the standards relevant to specific products (EN16751 in the case of bio-based products).
Table 4 “Gate-to-gate” environmental impacts and circularity characteristics of manufacturing a functional unit of packaging films
Impact indicators |
BoPLA (corn) |
BoPLA (corn stover) |
BoPLA (sugarbeet pulp) |
BoPP (petroleum derived) |
Units (per functional unit) |
Global warming potential (GWP100) |
4.46 × 10−3 |
2.4 × 10−3 |
2.7 × 10−3 |
8.1 × 10−3 |
kgCO2eq |
Respiratory inorganics |
1.67 × 10−9 |
6.05 × 10−10 |
9.84 × 10−10 |
5.58 × 10−9 |
Deaths |
Human toxicity, cancer |
2.10 × 10−7 |
1.55 × 10−7 |
1.60 × 10−7 |
3.52 × 10−7 |
CTUh |
Acidification, terrestrial and freshwater |
1.35 × 10−4 |
3.57 × 10−5 |
1.26 × 10−4 |
6.11 × 10−4 |
mol H+eq |
Freshwater eutrophication |
5.23 × 10−6 |
4.50 × 10−6 |
4.99 × 10−6 |
3.52 × 10−6 |
kg Peq |
Water scarcity |
6.2 × 10−4 |
6.11 × 10−4 |
5.51 × 10−4 |
1.54 × 10−2 |
m3 deprived |
Fossil resource depletion |
0.234 |
0.162 |
0.176 |
0.397 |
MJ |
Hybridised indicators |
BoPLA (bio-based) |
BoPP (petroleum derived) |
Units (per functional unit) |
Functional unit (1 packaging film that is 350 mm × 250 mm with a thickness of 0.05 mm). Mass of the BoPLA film: 5.58 g; mass of BoPP film = 4.67 g. □ = Non-hazardous chemical present; ■ = Hazardous chemical present (substitution required). |
Presence of hazardous chemicals |
□ |
□ |
— |
Feedstock intensity |
7.5 × 10−3 |
7.77 × 10−3 |
kg of feedstock |
Waste factor |
0.4 × 10−2 |
0.35 × 10−2 |
kg of waste |
Process material circularity |
85 |
No data |
% |
Renewability |
100 |
0 |
% |
Energy intensity |
7.2 × 10−3 |
5.14 × 10−3 |
kWh of energy required |
Transformation of the starting material to the end-product (packaging film) was more or less similar for both the BoPLA and BoPP packaging film synthesis, as demonstrated by feedstock intensity (FI/CPFI). We could further reduce feedstock demand for the bio-based case study by employing technical strategies to improve product purification stages. Post-fermentation waste and loss of some process auxiliaries, in addition to the inability of the process to recover and reuse the biopolymer trimmings (since the reuse of the scraps will negatively affect the optical clarity of the product26) from the extrusion phase, resulted in a relatively greater amount of waste factor (WF) (+14.3%) from the PLA production process. In the case of the BoPP packaging films, the extrusion waste can be recovered and reused.
From the perspective of recovering and reusing process auxiliaries, the process design employed for the bio-based case study showed 85% process material circularity (PMC) by recovering and reusing process water, catalysts and other inorganic acids from the downstream processes. The data source, for the process of producing polypropylene,37 sheds limited information on process material circularity, thus making a similar quantification for the baseline case-study a challenge. BoPLA films were also based on 100% bio-based PLA and 99.2% bio-based polymer additives. In terms of energy intensity (EI), BoPLA film synthesis was 40% more energy intense due to the added burden of energy-intense downstream processes. A visualisation of these impacts can be found in Fig. 3.
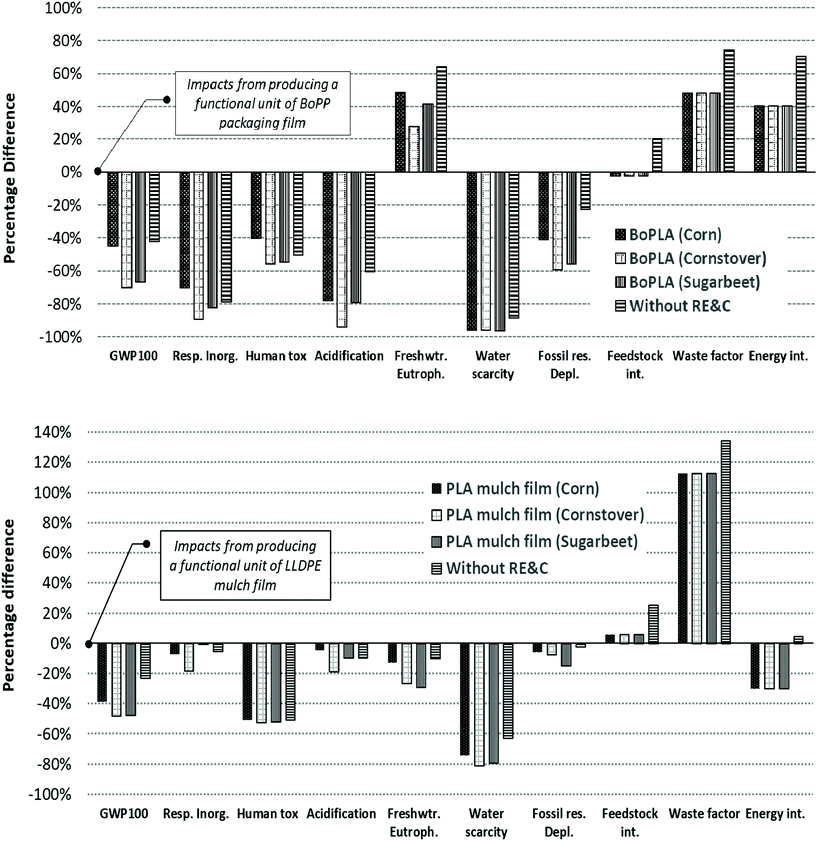 |
| Fig. 3 Difference in environmental impact and resource utilisation efficiency during the production of bio-based products, relative to that of their baseline fossil-derived case studies (including impacts of elimination of process-level resource efficiency and circularity strategies [Without RE&C]) [GWP100, Global Warming potential; Resp.Inorg, Respiratory Inorganics; Human tox, Human Toxicity; Freshwtr.Eutroph, Freshwater Eutrophication; Fossil res.Depl, Fossil Resource Depletion; Feedstock int., Feedstock Intensity; Energy int., Energy Intensity]. | |
Mulch film
A comparison of the overall outcomes from the impact assessment for the mulch film candidates is presented in Table 5. Based on the process specification modelled for the proposed functional unit of mulch films, the PLA based mulch film (sourced from the different bio-based feedstock) delivered GHG savings in the range of 35–50%, compared to the LLDPE mulch film. It is essential to note that the PLA-based film is only partially bio-based (70%) since the adipic acid and terephthalic acid components used in the preparation of the co-polymer are petro-chemically sourced. Adipic acid, in particular, was determined to be GHG intense, contributing nearly 40% of the overall process emissions, followed by the purified terephthalic acid that contributes nearly 20%. The GHG savings are, however, attributable mainly to two factors: (i) the biogenic carbon that is released during the fermentation of these sugars and (ii) the process's intrinsic capability to recover and reuse process auxiliaries, which reduced the overall material demand and the associated production-level impacts. This GHG deduction has been applied only to the bio-based components of the product, in compliance with the guidance provided in the EN16760 for the life cycle assessment of bio-based products.38
Table 5 “Gate-to-gate” environmental impacts and circularity characteristics of manufacturing a functional unit of biodegradable mulch
Impact indicators |
PLA-based mulch (corn) |
PLA-based mulch (corn stover) |
PLA-based mulch (sugarbeet pulp) |
LLDPE-mulch (petroleum derived) |
Units (per functional unit) |
Global warming potential (GWP100) |
352.42 |
292.47 |
304 |
574 |
kgCO2eq |
Respiratory inorganics |
2.87 × 10−5 |
2.52 × 10−5 |
3.08 × 10−5 |
3.09 × 10−5 |
Deaths |
Human toxicity, cancer |
8.20 × 10−6 |
7.90 × 10−6 |
8.01 × 10−6 |
1.67 × 10−5 |
CTUh |
Acidification, terrestrial and freshwater |
3.89 |
3.31 |
3.68 |
4.08 |
mol H+eq |
Freshwater eutrophication |
0.126 |
0.106 |
0.102 |
0.144 |
kg Peq |
Water scarcity |
4.86 |
3.51 |
3.84 |
18.72 |
m3 deprived |
Fossil resource depletion |
1.66 × 103 |
1.63 × 103 |
1.50 × 103 |
1.76 × 103 |
MJ equivalent |
Hybridised indicators |
PLA-based mulch (bio-derived) |
LLDPE-mulch (petroleum derived) |
Units (per functional unit) |
Functional unit (1 ha of mulched agricultural land). Mass of the PLA based mulch film: 152 kg functional per unit; mass of the LLDPE film = 185 kg functional per unit. □ = Non-hazardous chemical present; ■ = Hazardous chemical present (substitution required). |
Presence of hazardous chemicals |
□ |
□ |
— |
Feedstock intensity |
2.20 × 102 |
2.08 × 102 |
kg of feedstock required |
Waste factor |
0.155 |
8.12 |
kg of waste |
Process material circularity |
78 |
No data |
% |
Renewability |
70 |
0 |
% |
Energy intensity |
2.03 × 102 |
2.96 × 102 |
kWh of energy required |
Significant saving in other impact indicators including human toxicity, freshwater eutrophication and water scarcity was demonstrated by the production process associated with the PLA-based mulch film, resulting primarily from a limited release of volatile organic compounds, recovery and reuse of inorganic acids (used during downstream processes) and the treatment and reuse of process water from the fermentation phase of PLA synthesis. The feedstock intensity (FI) associated with the production of the bio-based candidate was observed to be 7–8% higher compared to the baseline case study. It is essential to reach a universal bio-processing industry-level consensus on where exactly the most optimal feedstock intensity lies for processing each of the bio-based feedstocks into a target product. For the time being, however, this metric informs the economic operator how efficient the employed process is in terms of resource utilisation capability, stimulating the need for techno-economically optimising the process. The waste factor (WF) associated with the production of the PLA-based mulch films, however, was determined to be relatively higher (+113%), despite the biopolymer recovery and re-use, compared to that generated from LLDPE mulch film production. The waste generated from the purification and evaporation of fermentation products, during lactic acid production, was determined to be some of the major waste hotspots. Process water, catalysts utilised in the polymerisation step and other inorganic acids consumed in the downstream processing phases were effectively reused over multiple cycles, leading to 78% process material circularity (PMC). Downstream processes are known to be generally energy intensive in fermentation processes. However, employing strategies to reuse waste heat from the downstream processes (evaporation heat-exchanger) resulted in an overall lower energy intensity (−30%), resulting from the production of bio-based candidates, compared to the conventional case study. The bio-based nature of the product must also be quantitatively communicated to the chain-actors downstream of the production process, particularly to the consumers and those within the end-of-life management. Transformation of fermentation waste (spent cells and the fermentation broth) into biogas via an on-site AD (anaerobic digester) facility is an established industrial process to further reduce the process's energy intensity.39 However, this has not been taken into consideration in this study due to the lack of appropriate data from the industrial source supporting this study. Refer to Fig. 3 for a visualisation of the impacts discussed above, relative to that of their baseline fossil-based counterpart.
Sensitivity study: elimination of resource efficiency and circularity strategies
Both the bio-based case studies were subjected to a sensitivity evaluation, where all the embedded resource efficiency and waste valorisation strategies were eliminated.
BoPLA packaging film.
For this sensitivity study, the energy demand of the recovery step and the recovered and re-used fraction of some inorganic acids were omitted. The inorganic acids were assumed to be disposed as a waste through the liquid waste stream. Recovery and reuse of unreacted components from the L-lactic acid production step was also omitted, reducing the overall productivity of the process. During the extrusion stage, an industrial average of +10% polymer wastage resulting from formulation of the resin to the associated end product BoPLA (in addition to the 4% resulting from spillage from transportation that was assumed in the benchmark) was taken into account for this study.40–42
The need for additional quantities of raw feedstock to make up for the loss of monomers and loss of/need for additional quantities of consumables within the process, in combination with the landfilling of solid waste, led to a significant increase in GWP100 (+18–25%). Energy demand related to the additional feedstock requirement also resulted in an increase in the release of acidifying and eutrophication emissions (+23% and +25% respectively). Any savings in energy consumption stemming from cancellation of the RE&C approaches were nullified by the additional demand for energy, glucose and other process materials (+30%). The loss of invested process water, due to the lack of its recovery, re-processing and re-use step in the original assessment, increased the water scarcity indicator (+8%). Elimination of any waste reduction approaches employed within the PLA packaging film production process is demonstrated by the +26% increase in waste factor.
PLA-based mulch film.
Similar to that elaborated in the case of packaging films, the step involving the recovery and reuse of the inorganic acids was omitted and the energy consumption for this sub-process was appropriately adjusted. Unreacted lactic acid monomers, which were originally recovered and recirculated, were also assumed to be lost as process waste. Quantitative evaluation of the model led to an outcome where the overall GHG emissions increased by 22%. Disposal of wastes and potentially recoverable resources onto a landfill contributed to a 20% increase in eutrophication potential of the process. Loss of process water, which originally would have been recovered and reused, led to an increase in impacts, resulting in an increase in process water consumption contributing to +21% water scarcity. Energy savings from abandoning resource circularity strategies, in combination with the additional energy demand from the need for processing virgin feedstock into process intermediates and end-products, resulted in +32% energy intensity and 23% increased virgin feedstock (processable sugars) requirement. Elimination of waste reduction strategies is also evident from the process's waste factor (WF) that has increased to 24% from its standard (baseline) production figures.
Conclusions
In the future, consumer acceptance of bio-based products within the confines of a circular economy will be driven by trust, transparency and traceability delivered through an evidence-based, fit-for-purpose, sustainability framework and its indicators. This study was dedicated to the development of new impact assessment indicators, set against a background of resource circularity, to evaluate the environmental performance of (bio-based) products, independently or in comparison with their commercial counterparts. Upon extensive literature review and careful assessment, a set of LCA indicators were identified. A set of guidance criteria was set to aid the development of some novel, hybridised indicators that could be flexibly applied to bridge gaps for both bio-based products and fossil-based products, by combining industrially used resource efficiency indicators with green chemistry metrics and principles. The LCA indicators were instrumental in highlighting the resource and energy hotspots and toxicity to the environment and human health and the quantification of impacts from minimisation of resource use while the hybridised indicators were instrumental in directly quantifying resource consumption and wastage, embedded resource circularity, renewable nature of the product and the process inventory, and use of any substances that are restricted/facing potential restriction. The proposed framework is dedicated to the value-chain actors operating within the circular/bio-economy hemisphere and operators who wish to transform into sustainable, green-manufacturers. To measure is to know. Setting operational key performance indicators (KPIs) based on resource consumption, recovery and re-utilisation metrics, as proposed in this paper, will provide positive short-term goals and impacts which could potentially be extended to a point where the manufacturing supply-chain is optimised for sustainable production and consumption. These metrics, in combination with the LCA impact indicators, could aid the sector's quest to attain sustainable consumption and production, in accordance to the UN-SDG 12. It is also acknowledged that during the preparation of a PEF-compliant process inventory, any internal strategies for improvised resource (material and energy) utilisation are seldom provided. This becomes an additional data need. Moreover, their application and performance in second-life products and other bio-based product groups needs to be undertaken. These limitations, however, could be overcome with further refinement of the approaches which is also a recommendation for future work.
Conflicts of interest
There are no conflicts to declare.
Acknowledgements
The contents of the paper are part of the findings of the project STAR-ProBio. STAR-ProBio has received funding from the European Union's Horizon 2020 program research and innovation programme under grant agreement No. 727740. Re-use of information contained in this document for commercial and/or non-commercial purposes is authorised and free of charge, on the conditions of acknowledgement by the re-user of the source of the document, not distorting the original meaning or message of the document and the non-liability of the STAR-ProBio consortium and/or partners for any consequence stemming from the re-use. The STAR-ProBio consortium does not accept responsibility for the consequences, errors or omissions herein enclosed. This document is subject to updates, revisions and extensions by the STAR-ProBio consortium. Questions and comments should be addressed to http://www.star-probio.eu/contact-us/. We would like to convey a special thanks to our partners from the University of Santiago Compostela, Spain, who contributed to the research undertaken in this paper.
References
-
Spatial Foresight, SWECO, ÖIR, Nordregio, Berman Group and Infyde, Bioeconomy development in EU regions. Mapping of EU Member States’/regions’ Research and Innovation plans & Strategies for Smart Specialisation (RIS3) on Bioeconomy for 2014–2020, DG Research & Innovation, European Commission, Brussels, 2017 Search PubMed.
- K. Lokesh, L. Ladu and L. Summerton, Sustainability, 2018, 10, 1695 CrossRef.
- CEN European Committee for Standardization, 2017.
- K. Lokesh, C. West, J. Kuylenstierna, J. Fan, V. Budarin, P. Priecel, J. A. Lopez-Sanchez and J. Clark, Green Chem., 2017, 19, 4380–4395 RSC.
-
P. Saling, A. Kicherer, B. Dittrich-krämer, R. Wittlinger, W. Zombik and I. Schmidt, Life Cycle Management Eco-efficiency Analysis by BASF: The Method 2002 Search PubMed.
- R. K. Helling, S. E. Hunter, E. Ocampo and H. Zhang, ACS Sustainable Chem. Eng., 2018, 6, 2250–2255 CrossRef CAS.
- R. A. Sheldon, Green Chem., 2017, 19, 18–43 RSC.
- C. R. McElroy, A. Constantinou, L. C. Jones, L. Summerton and J. H. Clark, Green Chem., 2015, 17, 3111–3121 RSC.
- D. Prat, A. Wells, J. Hayler, H. Sneddon, C. R. McElroy, S. Abou-Shehada and P. J. Dunn, Green Chem., 2015, 18, 288–296 RSC.
- G. J. Ruiz-Mercado, R. L. Smith and M. A. Gonzalez, Ind. Eng. Chem. Res., 2012, 51, 2309–2328 CrossRef CAS.
- J. Hildebrandt, A. Bezama and D. Thrän, Waste Manage. Res., 2017, 35, 367–378 CrossRef PubMed.
-
L. Pelkmans, B. Elbersen, U. Fritsche, L. Iriarte and C. Panoutsou, Guidelines and indicators for the evaluation of sustainable resource efficient biomass value chains: Deliverable 2.6 of the Biomass Policies* project, 2014 Search PubMed.
-
http://vlaanderen-circulair.be, Indicators for a Circular Economy - Vlaanderen Circulair, http://vlaanderen-circulair.be/en/summa-ce-centre/publications/indicators-for-a-circular-economy, (accessed September 13, 2018).
-
A. Behrens, I. Taranic, V. Rizos and B. Centre for European Policy Studies, Resource efficiency indicators for policy-making, Brussels, 2015 Search PubMed.
- World Business Council for Sustainable Development (WBCSD), 2018.
- Ellen MacArthur Foundation, Circularity Indicators, https://www.ellenmacarthurfoundation.org/resources/apply/circularity-indicators, (accessed December 17, 2018).
-
L. Zampori and R. Pant, Suggestions for updating the Product Environmental Footprint (PEF) method, European Commission Joint Research Centre, Brussels, 2019 Search PubMed.
- European Commission, 2014.
- European Commission, 2011.
- G. Guest, R. M. Bright, F. Cherubini and A. H. Strømman, Environ. Impact Assess. Rev., 2013, 43, 21–30 CrossRef.
- J. Seppälä, M. Posch, M. Johansson and J.-P. Hettelingh, Int. J. Life Cycle Assess., 2006, 11, 403–416 CrossRef.
- A.-M. Boulay, J. Bare, L. Benini, M. Berger, M. J. Lathuillière, A. Manzardo, M. Margni, M. Motoshita, M. Núñez, A. V. Pastor, B. Ridoutt, T. Oki, S. Worbe and S. Pfister, Int. J. Life Cycle Assess., 2018, 23, 368–378 CrossRef.
- R. Auras, B. Harte and S. Selke, Macromol. Biosci., 2004, 4, 835–864 CrossRef CAS PubMed.
- B. Choi, S. Yoo and S. Park, Sustainability, 2018, 10, 2369 CrossRef CAS.
-
C. Belley, Comparative Life Cycle Assessment report of Food Packaging products, InterUniversity Research Centre for the Life cycle of Products, Processes and Services, Quebec, Canada, 2011 Search PubMed.
- Taghleef Industries, 2018.
- BASF SE, 2018.
- BASF SE, 2013.
- OWS nv, 2017.
- E. T. H. Vink, K. R. Rábago, D. A. Glassner and P. R. Gruber, Polym. Degrad. Stab., 2003, 80, 403–419 CrossRef CAS.
- S. Madival, R. Auras, S. P. Singh and R. Narayan, J. Cleaner Prod., 2009, 17, 1183–1194 CrossRef CAS.
- A. Forte, A. Zucaro, R. Basosi and A. Fierro, Materials, 2016, 9, 563 CrossRef.
- D. L. Schrijvers, F. Leroux, V. Verney and M. K. Patel, Green Chem., 2014, 16, 4969–4984 RSC.
- K. H. Kang, U. G. Hong, Y. Bang, J. H. Choi, J. K. Kim, J. K. Lee, S. J. Han and I. K. Song, Appl. Catal., A, 2015, 490, 153–162 CrossRef CAS.
- The International Chemical Secretariat, SINLIST, https://chemsec.org/sin-list/, (accessed November 26, 2018).
-
E. Schmitz-Felten, I. Banduch, S. Pérez, D. Romano, A. Lennquist, J. Ligthart and L. Ankjær, SUBSPORT – Substitution Support Portal- Moving towards safer alternatives, https://www.subsport.eu/, (accessed November 26, 2018).
- Plastics Europe, 2016.
- CEN European Committee for Standardization, 2015.
-
D. Humbird, R. Davis, L. Tao, C. Kinchin, D. Hsu, A. Aden, P. Schoen, J. Lukas, B. Olthof, M. Worley, D. Sexton and D. Dudgeon, Process Design and Economics for Biochemical Conversion of Lignocellulosic Biomass to Ethanol: Dilute-Acid Pretreatment and Enzymatic Hydrolysis of Corn Stover, 2011 Search PubMed.
- Association of Plastics manufacturers Europe, Belgium, 2016.
- BioIntelligence Service S.A.S, 2012.
- V. Piemonte, J. Polym. Environ., 2011, 19, 988–994 CrossRef CAS.
Footnote |
† Electronic supplementary information (ESI) available. See DOI: 10.1039/c9gc02992c |
|
This journal is © The Royal Society of Chemistry 2020 |