DOI:
10.1039/D3CY00242J
(Minireview)
Catal. Sci. Technol., 2023,
13, 2877-2898
Recent advances on g-C3N4-based Z-scheme photocatalysts for organic pollutant removal
Received
21st February 2023
, Accepted 24th March 2023
First published on 25th March 2023
Abstract
Graphitic carbon nitride (g-C3N4)-based Z-scheme photocatalysts have attracted growing interest in organic pollution removal because of their strong light absorption capacity, abundant active sites, and outstanding photocatalytic performance. This review provides a survey of the latest advances of g-C3N4-based Z-scheme photocatalysts for organic pollution removal, beginning with the fundamentals of g-C3N4-based Z-scheme photocatalysts. Subsequently, the characterization strategies and preparation approaches for g-C3N4-based Z-scheme photocatalysts are discussed. Various typical g-C3N4-based Z-scheme photocatalysts for organic pollutant degradation are described. Finally, this work provides some new insights into the major challenges, favorable circumstances, heuristic perspectives, and future development direction.
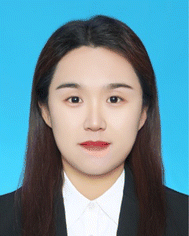 Chunxue Li | Chunxue Li obtained her B.Sc. (2016) and M.S. (2019) from Jilin Normal University. She then obtained her Ph.D. from Jiangsu University. Presently, she is a Lecturer at Fujian University of Technology. Her current research focuses on the synthesis and application of semiconductor nanomaterials for photocatalytic hydrogen evolution. She has received some awards, including the Graduate Student National Scholarship, Xue Liang Scholarship, and Excellent Graduation Thesis of Jilin Normal University. |
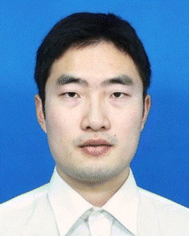 Hao Lu | Hao Lu received his Ph.D. degree in Physics from Soochow University in 2017. He is currently working at the School of Materials Science and Engineering, Suzhou University of Science and Technology, as an Associate Professor. His research interest involves the fabrication of high-performance optoelectronic devices by exploiting the morphology, surface and boundary of materials and energy bands. So far, he has published more than 60 high-profile SCI papers, such as Adv. Mater., Adv. Funct. Mater., Adv. Sci., Nano Energy, Sci. Bull., and Phys. Rev. Letters. |
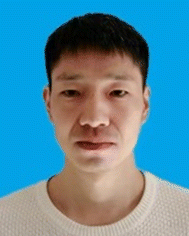 Guixiang Ding | Guixiang Ding received his B.S. degree from the College of Chemical Engineering at Liaoning Normal University in 2022. His current research focuses on the study of the photocatalytic CO2 reduction and on the development of photocatalytic materials. He has published one SCI as the first author and four SCI as the second author. |
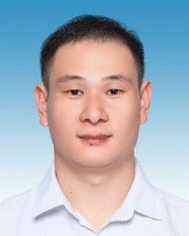 Qing Li | Qing Li obtained his B.Sc. (2012), M.S. (2015) and Ph.D. (2018) from Hubei University. Presently, he is an Associate Professor at Hubei University. His current research focuses on the synthesis and application of Ag-based catalytic materials. He has received some awards, including the Graduate Student National Scholarship, Excellent Innovation and Entrepreneurship Mentor, and others. |
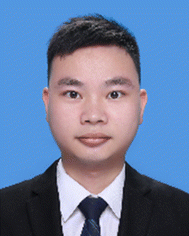 Guangfu Liao | Guangfu Liao received his Ph.D. degree in Material Physics & Chemistry from Sun Yat-sen University in 2020. Then, he joined the laboratory of Prof. Yi-Chun Lu at The Chinese University of Hong Kong, where he worked as a Research Associate. Subsequently, he became a Researcher at the China University of Geosciences. Now, he is a Professor at Fujian Agriculture and Forestry University. His research interests involve photo- and electrocatalysis, polymer synthesis and applications, polymer membranes, redox flow batteries, nanoporous and nanostructured materials, biomaterials, gas storage and energy conversion, and others. The broader impacts of his research include polymeric photocatalysts, polymer design and synthesis, nanostructure engineering, and biomaterials. So far, he has published more than 60 high profile SCI papers, such as Matter, Progress in Materials Science, Energy & Environmental Science, Applied Catalysis B: Environmental, Nano Energy, ACS Catalysis, Chemical Science, Small, Chemical Engineering Journal, Journal of Materials Chemistry A, Journal of Catalysis, and others. The awards he has received up to now include the National Endeavor Fellowship, Guanghua Scholarship, 2022 Journal of Materials Chemistry A Emerging Investigators, and others. He also serves as an Associate Editor for Frontiers in Energy Research, Guest Editor for Polymers, and Youth Editorial Board for Advanced Fiber Materials. |
1. Introduction
Water pollution has attracted growing interest because of the rapid industrial development and expanding population.1–6 The exploration and development of advanced technologies, such as adsorption,7–10 electrocatalysis,11,12 and photocatalysis13–19 (especially visible-light-responsive photocatalysis),20–24 are very promising for overcoming these issues. Among them, the most promising strategy is photocatalysis because of its unique advantage in simply using inexhaustible solar energy to organic pollution removal.19,25–31 Graphitic carbon nitride (g-C3N4)-based materials, as one of the most up-and-coming photocatalysts, have gained dramatically growing interests in organic pollution removal owing to their easy functionalization, suitable electronic and band structure, excellent physicochemical stability and photocatalytic property.32–47 Although great progress has been made, the photocatalytic performance of single g-C3N4 is still far from practical production demand owing to the fast electron–hole (e−–h+) recombination and poor light absorption capacity.48–51 Hence, it is crucial to explore new g-C3N4-based photocatalysts with strong light absorption capacity and high e−–h+ separation for organic pollutant removal.
To enhance the photocatalytic property of g-C3N4, various approaches have been proposed, e.g., doping,52,53 obtaining porous architectures,54,55 achieving highly crystalline structures,56 metal loading,57,58 heterojunction construction,59–61 exfoliation,62,63 defect engineering,64,65 and molecular and electronic structure engineering.66–69 Among these approaches, the integration of two semiconductors to fabricate type-II heterojunctions is a promising method for enhancing the photocatalytic performance since the band alignment between the two semiconductors will provide high separation efficiency of the photogenerated carrier.70,71 However, their photocatalytic activity is not significantly enhanced because of electrostatic repulsion.72 To overcome this disadvantage, an emerging g-C3N4-based Z-scheme system was proposed by the Yu group73 that created a more negative conduction band (CB) and more positive valence band (VB), and further achieved stronger photocatalytic ability.74,75 When compared to type-II heterojunctions, the charge migration of Z-scheme systems is more favorable. Owing to their strong light absorption capacity, abundant active sites, and outstanding photocatalytic performance,76 g-C3N4-based Z-scheme photocatalysts have achieved increasing attention for organic pollutant removal.
Although there have been many inspired reviews on g-C3N4-based photocatalysts for various applications,32,33,71,77–88 a comprehensive review about g-C3N4-based Z-scheme photocatalysts for organic pollutant removal is nonexistent despite the great interest in this research topic. In this review, the fundamentals of g-C3N4-based Z-scheme photocatalysts are firstly discussed. Subsequently, the characterization strategies and preparation methods for g-C3N4-based Z-scheme photocatalysts are illustrated. Next, some typical g-C3N4-based Z-scheme photocatalysts for organic pollutant removal are described. Finally, this work provides some advanced insights into the major challenges, favorable circumstances, heuristic perspectives, and future development direction.
2. What are g-C3N4-based Z-scheme photocatalysts?
Before introducing the g-C3N4-based Z-scheme photocatalysts, it is crucial to fully comprehend g-C3N4-based type-II heterojunctions, e.g., CeO2/g-C3N4,89 Co3O4/g-C3N4,90 Cu2O/g-C3N4,91 Fe2O3/g-C3N4,92 g-C3N4/g-C3N4,93 h-BN/flower-ring g-C3N4,94 which display outstanding photocatalytic property owing to their high separation efficiency of photogenerated charges through the band alignment.74,95 In these type-II heterojunctions, both CB and VB potentials of semiconductor 1 are lower than those of g-C3N4 (Fig. 1A). The e− in the CB of semiconductor 1 have a tendency to migrate to the CB of g-C3N4 owing to the band alignment. Similarly, the h+ in the VB of g-C3N4 easily migrate to the VB of semiconductor 1.96,97 Owing to the e− and h+ being concentrated on g-C3N4 and semiconductor 1, respectively, high separation efficiency of the photogenerated e− and h+ can be achieved through type-II heterojunctions.32,72,98,99 However, there are still some potential problems that need to be solved. The photocatalytic activity of the charges are not significantly enhanced.100,101 It is also very difficult for the e− in semiconductor 1 and h+ in g-C3N4 to migrate to the CB of g-C3N4 because of strong electrostatic repulsions, such as e−–e− or h+–h+ interactions, respectively.74 Thus, it is critical to fabricate a new type of photocatalytic system to relieve this disadvantage.
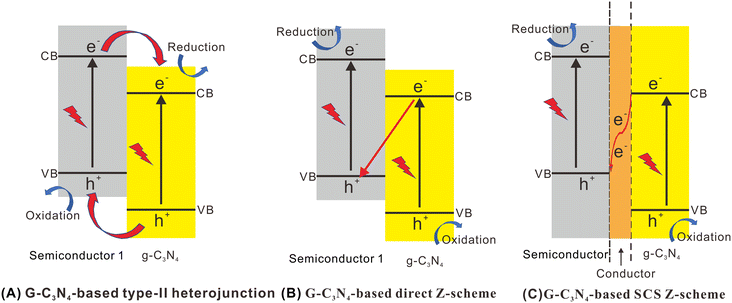 |
| Fig. 1 Comparative analysis of the charge transfer mechanism on g-C3N4-based type-II heterojunctions (A), g-C3N4-based Z-scheme (B) and (C) g-C3N4-based SCS Z-scheme systems. | |
Inspired by bionic photosynthesis, there is great potential in the development of the Z-scheme photocatalysts for enhancing photocatalytic performance.71,102 In 2013, the Yu group reported on the first use of a direct Z-scheme mechanism to explain the outstanding photocatalytic formaldehyde (HCHO) oxidation performance over TiO2/g-C3N4 hybrids.73 Especially, the direct Z-scheme systems exhibit a structure similar to that of type-II heterojunctions (Fig. 1A), but they possess an evidently dissimilar charge migration mechanism.103,104 The charge migration path of the direct Z-scheme photocatalysts resembles the letter “Z” (Fig. 1B), in which the e− in g-C3N4 with stronger oxidation ability will integrate with the h+ in semiconductor 1 with strong reduction ability.105 Therefore, the e− in semiconductor 1 with stronger reduction ability and h+ in g-C3N4 with stronger oxidation ability may be retained. As a result, the photocatalytic property of the direct Z-scheme systems can be evidently enhanced. Moreover, the charge migration path of the direct Z-scheme systems is more favorable than that of type-II heterojunctions. This is because the migration of the photogenerated e− from the CB of g-C3N4 to the VB of semiconductor 1 with adequate photogenerated h+ is very favorable owing to the effective electrostatic attraction.72 It is believed that g-C3N4-based Z-scheme systems exhibit faster charge transfer101 when compared with g-C3N4-based type-II heterojunctions.
Until now, there have been two main types of g-C3N4-based Z-scheme systems, including g-C3N4-based direct Z-scheme (Fig. 1B) without an electron mediator and g-C3N4-based semiconductor–conductor–semiconductor (SCS) Z-scheme system (Fig. 1C) with an electron mediator (conductor), e.g., conductive polymer, graphene, noble metal.106,107 The g-C3N4-based direct Z-scheme systems (e.g., TiO2/g-C3N4,73 ZnO/g-C3N4,108 WO3/g-C3N4,109 Ag3PO4/g-C3N4,110 BiVO4/g-C3N4,111 Bi2WO6/g-C3N4,112 BiOCl/g-C3N4,113 AgBr/g-C3N4 (ref. 114)) display outstanding photocatalytic performance by keeping a very negative CB and a very positive VB.115 As for g-C3N4-based SCS Z-scheme systems (e.g., WO3/Cu/gC3N4,116 Ag3PO4/Ag/g-C3N4,117 CdS/Au/g-C3N4 (ref. 106)), a conductor acting as a mediator is utilized to link two components for more favorable migration of photogenerated carriers.118 Moreover, the p–n Z-scheme systems (e.g., C3N4–Pd–Cu2O,119 LaFeO3/g-C3N4,120 g-C3N4/CaFe2O4,121 black phosphorus nanosheets/FeSe2/g-C3N4 (ref. 122)) favorably formed by combining p-type and n-type materials have received increasing attention. In the comprehensive consideration of the photocatalytic activity and fabrication cost, we must compare the advantages and disadvantages of the two g-C3N4-based Z-scheme systems, and develop a more appropriate photocatalytic system to achieve optimal photocatalytic property. The balance of charge utilization is also vital.123 The consumption of e− and h+ for redox reactions should be unified. Otherwise, the accumulation of charges may lead to the self-oxidation/reduction of the photocatalysts or the mediators.124
3. Characterization strategies for g-C3N4-based Z-scheme photocatalysts
As shown above, the Z-scheme systems exhibit similar structures with type-II heterojunctions. Therefore, it is important to prove that the charge migration mechanism occurs via multifarious characterization strategies, e.g., self-confirmation via photocatalytic reactions, products, and radical species, selective photodeposition of noble metal, X-ray photoelectron spectroscopy (XPS), surface photovoltage (SPV) techniques, density function theory (DFT) calculation, and others.
3.1. Self-confirmation via photocatalytic reactions, products, and radical species
It is generally known that not all photogenerated charges centered on the photocatalysts' surface are utilized for the photocatalytic reaction. Typically, there are only some photogenerated e− in a semiconductor with enough redox potential that can be utilized for photocatalytic reactions.76,125,126 Some commonly used standard redox potentials are shown in Fig. 2. Z-scheme systems can be confirmed via standard redox potentials and by investigating the photocatalytic reactions, products, and radical species.
 |
| Fig. 2 Standard redox potentials of some commonly used semiconductors. Reproduced with permission from ref. 35. | |
Considering the g-C3N4/WO3 photocatalysts as an example, a tight contact between g-C3N4 and WO3 can be found (Fig. 3A), and the individual g-C3N4 and WO3 components exhibit low photocatalytic performance (Fig. 3B and C). Interestingly, the g-C3N4/WO3 composites display enhanced photocatalytic performance. This phenomenon is mainly attributed to the fabrication of a direct Z-scheme system (Fig. 3D), which accelerated the separation of photogenerated e−–h+. The g-C3N4/WO3 composites also exhibited good stability (Fig. 3E).127 If it follows type II mechanism, the photogenerated e− will transfer from the CB of g-C3N4 to the CB of WO3. In this way, the g-C3N4/WO3 composites would display reduced redox capability, which conflicts with the experimental results. Therefore, it should obey the Z-scheme direct mechanism.
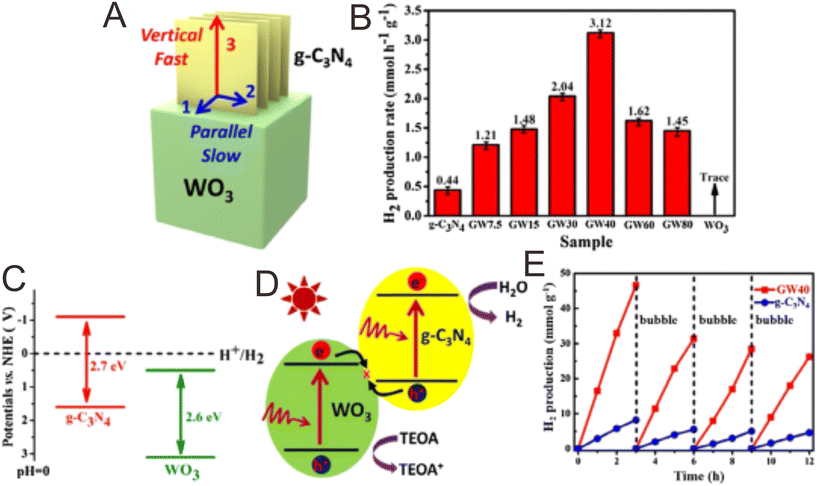 |
| Fig. 3 (A) The growth and extension of g-C3N4 parallel with and perpendicular to the flat surface of the WO3 nanocuboids. (B) Comparison of the photocatalytic H2 production properties. (C) Band structure of g-C3N4 and WO3. (D) The direct Z-scheme charge migration path in the g-C3N4/WO3 composites. (E) The photocatalytic stability tests of the g-C3N4 and g-C3N4/WO3 composites. Reproduced with permission from ref. 127. | |
We can also prove the Z-scheme mechanism through analyzing the photocatalytic products. Tao and co-workers128 proved the successful fabrication of the g-C3N4/CoTiO3 direct Z-scheme heterojunctions through analyzing the photocatalytic products. The single CoTiO3 displayed very low photocatalytic activity due to its low reduction ability, but the single g-C3N4 exhibited moderate photocatalytic performance owing to its adequate reduction ability. After the successful construction of a direct Z-scheme photocatalyst, the photogenerated carrier separation efficiency and the redox ability of g-C3N4/CoTiO3 were evidently improved. If the migration route of the photogenerated carriers follows the type-II mechanism, the photogenerated e− would be focused on CoTiO3 without adequate reduction potential, which would result in very low photocatalytic activity. Nevertheless, the experimental results unveiled that g-C3N4/CoTiO3 exhibited enhanced photocatalytic property, suggesting that the g-C3N4/CoTiO3 composites should follow the Z-scheme direct mechanism. This work demonstrated that the photocatalytic tests feasibly study the charge migration mechanism.
3.2. Selective photodeposition of noble metals
As for Z-scheme systems, the photogenerated charges can be efficiently separated. Photodeposition of several noble metals, e.g., Au, Ag, Cu, on electron-rich areas is a promising strategy to unlock the photocatalytic reaction sites.129 On the basis of the photodeposition sites of noble metals, the charge migration route and Z-scheme mechanism can be further proved. For example, Yu and co-workers130 proposed Fe2O3/g-C3N4 photocatalysts, which showed improved photocatalytic performance when compared with the pure Fe2O3 and g-C3N4 components. The TEM image (Fig. 4) showed that Pt nanoparticles were deposited on g-C3N4, but not on Fe2O3, suggesting that the photogenerated e− mainly focused on g-C3N4. If there were no close contacts between g-C3N4 and Fe2O3, Pt nanoparticles would randomly photodeposit on g-C3N4 and Fe2O3. If it followed the type II mechanism, the Pt nanoparticles would mainly concentrate on Fe2O3. Instead, the Pt nanoparticles mainly concentrated on g-C3N4. Therefore, the Fe2O3/g-C3N4 systems should follow the Z-scheme mechanism.
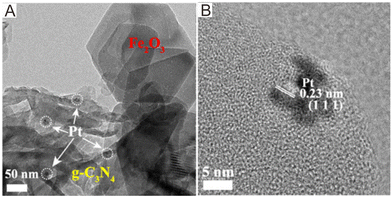 |
| Fig. 4 (A) TEM image and (B) HRTEM image of the Fe2O3/g-C3N4 composites after photodeposition of Pt nanoparticles. Reproduced with permission from ref. 130. | |
3.3. XPS characterization
XPS is a promising technique for analyzing the photocatalysts' surface chemistry,9,131–135 and it is also used for investigating the transformations in the electronic density on the photocatalysts' surface via probing the shift in the binding energies.98,136 A positive shift indicates a decrease of the electron density. Therefore, a shift in the binding energy can be used to study the migration path of photogenerated e−. For g-C3N4/MnO2,137 the Mn 2p spectrum of the MnO2 nanosheets (Fig. 5A) displayed two main peaks located at 641.9 and 654.0 eV, corresponding to Mn 2P3/2 and Mn 2P1/2, respectively, which shifted to 641.6 and 653.7 eV. However, the pure g-C3N4 sample only exhibited the adsorbed oxygen species and other oxygen impurities (Fig. 5B). In view of g-C3N4/MnO2, a combined O 1s spectrum was obtained (Fig. 5B) with the binding energy of the lattice oxygen shifted to 529.3 eV. The N 1s spectrum of g-C3N4 (Fig. 5C) can be divided into three main peaks at 398.2, 399.7, and 401.2 eV, which can be assigned to the sp2-hybridized nitrogen (C
N–C), bridging nitrogen ((C)3–N), and N–H bonding in the g-C3N4 framework, respectively. When compared with the MnO2 nanosheets, the N 1s binding energy of the C
N–C bond displayed a minor shift to higher value (Fig. 5D). These results suggested the formation of a Z-scheme system through the coating of MnO2 onto the g-C3N4 nanosheets with electrons flowing from g-C3N4 to MnO2 and achieving thermodynamic equilibrium. The XPS valence band spectra are also used for calculating band edge potentials, which can further explain the Z-scheme mechanism.138
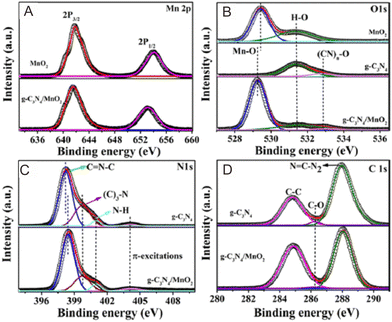 |
| Fig. 5 XPS spectra of (A) Mn 2p, (B) O 1s, (C) N 1s, and (D) C 1s for g-C3N4, MnO2, and g-C3N4/MnO2. Reproduced with permission from ref. 137. | |
3.4. SPV techniques
Recently, the SPV strategy has provided some new opportunities to study the charge transfer path of Z-scheme systems.139 Typically, Kelvin probe force microscopy (KPFM) can easily obtain the photocatalysts' surface potential distribution with high spatial resolution and potential sensitivity.140–143 Therefore, using KPFM-based SPV techniques to study the carrier transfer path of Z-scheme systems is an efficient technology. Guan and co-workers144 reported a g-C3N4-based Z-scheme system through encapsulation of g-C3N4 into hollow In2O3 tubules. To gain a deeper understanding of the charge migration route, KPFM was proposed (Fig. 6A–D). Under dark conditions, the difference in potential between the sample surface and substrate surface was 51.87 mV. Conversely, under visible light illumination, the surface potential of the whole area is greatly reduced, suggesting the concentration of photogenerated e− and h+. Meanwhile, the difference in potential between the sample surface and substrate surface were decreased to 50.57 mV. This change confirmed that the photogenerated e− migrated from the surface of g-C3N4 to the interior of In2O3, further illustrating the Z-scheme mechanism. Therefore, the SPV strategy is also very promising for the confirmation of the Z-scheme mechanism.
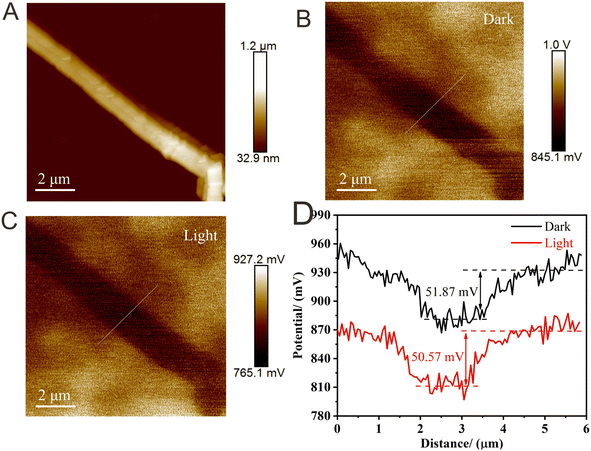 |
| Fig. 6 (A) Atomic force microscopy image of the samples. (B) KPFM potential image of the samples under dark conditions. (C) KPFM potential image of the samples under light illumination. (D) The corresponding surface curves correspond to the white light. Reproduced with permission from ref. 144. | |
3.5. DFT calculation
It is well known that DFT calculation is a promising technology to explore the charge migration mechanism.145,146 In detail, the first-principles simulation with a DFT calculation is commonly utilized for studying the charge transfer through analyzing the effective mass of its charge to estimate the recombination efficiency of the photogenerated carrier.108,127,147 The DFT calculation is conducted based on the crystal and electronic band structures (Fig. 7).127 The effective masses of the charges of WO3 and g-C3N4 can be calculated through the parabolic fitting of their CB minimum and VB maximum based on eqn (1) and (2), respectively, and the separation efficiency of the photogenerated h+ to the e− based on eqn (3): |  | (3) |
where ħ, d2E/dk2, k, m*, v, D,
, and
respectively signify the reduced Planck constant, the coefficient of the second-order term in a quadratic fit of E(k) curves for the band edge, the wave vector, the effective mass of a charge, the transfer efficiency of a charge, separation efficiency of the photogenerated h+ to the e−, and the effective mass of photogenerated h+ and e−.
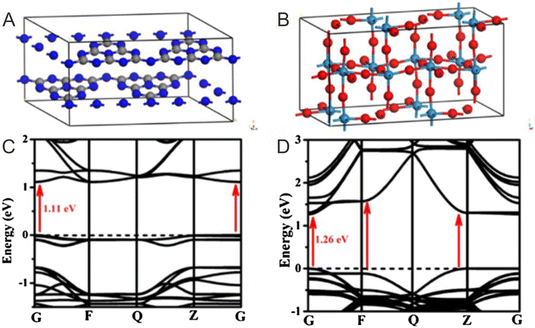 |
| Fig. 7 Crystal structures of (A) g-C3N4 and (B) monoclinic WO3. The calculated electronic band structures of (C) g-C3N4 and (D) WO3. Reproduced with permission from ref. 127. | |
The calculated effective masses of photogenerated e− and h+ and the relevant separation efficiency in G–Z and G–F directions are summarized in Table 1. The smaller D value for g-C3N4 (D = 1.36) indicates its faster recombination efficiency. In contrast to g-C3N4, the excited electrons of WO3 exhibit a higher transfer efficiency from bulk to interface, and then transfer into g-C3N4. In this way, the interfacial electron transfer path in g-C3N4/WO3 occurs from WO3 to g-C3N4, which follows the direct Z-scheme mechanism.127
Table 1 Calculated effective masses of the charges of g-C3N4 and WO3
Species |
Effective mass |
G–F direction |
G–Z direction |
F–Q direction |
Z–Q direction |
g-C3N4 |
|
0.72 |
71 |
— |
— |
|
0.53 |
1.8 |
— |
— |
D
|
1.36 |
39.44 |
— |
— |
WO3 |
|
0.53 |
— |
0.49 |
0.51 |
|
0.16 |
— |
0.17 |
0.14 |
D
|
3.31 |
— |
2.88 |
3.64 |
4. Preparation methods for g-C3N4-based Z-scheme photocatalysts
Until now, there have been a lot of approaches utilized for the preparation of g-C3N4-based Z-scheme photocatalysts, and selecting a suitable method is crucial. In the following sections, different preparation methods for g-C3N4-based Z-scheme photocatalysts are described. Their advantages and disadvantages are also discussed in Table 2.
Table 2 Comparison between different methods for the preparation of Z-scheme photocatalysts
Synthesis strategy |
Merits |
Demerits |
Deposition–precipitation strategy |
High-efficiency, simple, and low-cost |
Uncontrollable morphology and easy aggregation |
Hydrothermal and solvothermal strategy |
(i) Facile, eco-friendly, and highly efficient |
Complicated preparation process |
(ii) Produced photocatalysts with a relatively high crystallinity, narrow size distribution, and controllable morphology |
Solid-state synthesis |
High-efficiency, simple, and low-cost |
Uncontrollable morphology and easy aggregation |
Ion-exchange strategy |
The formation of closely contact interface, and the initial morphology can be well preserved |
Time- and cost-consuming and complicated preparation process |
Electrospinning strategy |
Very suitable for the preparation of 1D materials |
Time- and cost-consuming, complicated preparation process, and low efficiency |
Self-assembly strategy |
Narrow size distribution and uniform morphology |
Time- and cost-consuming, and complicated preparation process |
Photo-deposition strategy |
Facile, eco-friendly, and highly efficient |
Easy aggregation |
Mechanical agitation strategy |
Facile, eco-friendly, and highly efficient, and reduced aggregation |
Relatively poor interface contacts between the two semiconductors |
4.1. Deposition–precipitation strategy
Deposition–precipitation strategy is regarded as an effective method for fabricating g-C3N4-based Z-scheme photocatalysts.148 Narayanan and co-workers reported on a AgCl@g-C3N4 direct Z-scheme photocatalyst through a modified deposition-precipitation method.149 AgNO3 was firstly introduced into the g-C3N4 suspension, and then vigorously stirred to ensure full adsorption of Ag+ on the g-C3N4 surface. Subsequently, the Cl− ions and Ag+ ions were fully coated on the g-C3N4 surface, and then reacted to form the AgCl@g-C3N4 direct Z-scheme photocatalysts. The coating of AgCl on g-C3N4 was proved via XRD and FTIR spectra, which also confirmed the close interface between AgCl and g-C3N4 for greatly enhancing the photocatalytic performance.
4.2. Hydrothermal and solvothermal strategy
Hydrothermal and solvothermal approaches are usually conducted in a sealed autoclave under high temperature and pressure conditions, endowing the obtain semiconductors with high crystallinity, regulatable morphology, and homogeneous size distribution.13,150–155 Therefore, this strategy is commonly utilized for fabricating g-C3N4-based Z-scheme photocatalysts without further post-treatment. Liu and co-workers156 reported on Bi2WO6 quantum dots/g-C3N4 binary Z-scheme systems via a simple one-pot hydrothermal strategy. In this work, porous g-C3N4 ultrathin nanosheets provided a high specific surface area for decorating Bi2WO6 quantum dots, leading to a strong interaction between the Bi2WO6 quantum dots and g-C3N4 nanosheets.
4.3. Solid-state strategy
The solid-state strategy is commonly defined as the calcination of one precursor or multiple precursors in a gas atmosphere at an elevated temperature.157,158 The homogeneous dispersion of the precursors plays an important role in affecting the quality and uniformity of the prepared materials. Several methods, such as intensive ball milling159 and dissolving precursors in a solvent followed by drying,160 can evidently stop the agglomeration of the precursors and maintain uniformity. The calcination parameters, such as heating rate and calcination temperature and time, can regulate the crystallinity, microstructure morphology, surface performance, and phase structure, which further affect the photocatalytic performance. Wang and co-workers161 explored the effect of calcination temperature on the preparation of hierarchical TiO2/g-C3N4 Z-scheme photocatalysts. The insertion of g-C3N4 nanoparticles on the porous TiO2 framework was confirmed via SEM and XRD (Fig. 8A–G). The BET results indicated the effect of the calcination temperature on the porous structure (Fig. 8H and I). The specific surface area and pore volume gradually increased with increasing temperature to 550 °C, but a further increase in the temperature would lead to a reduction.
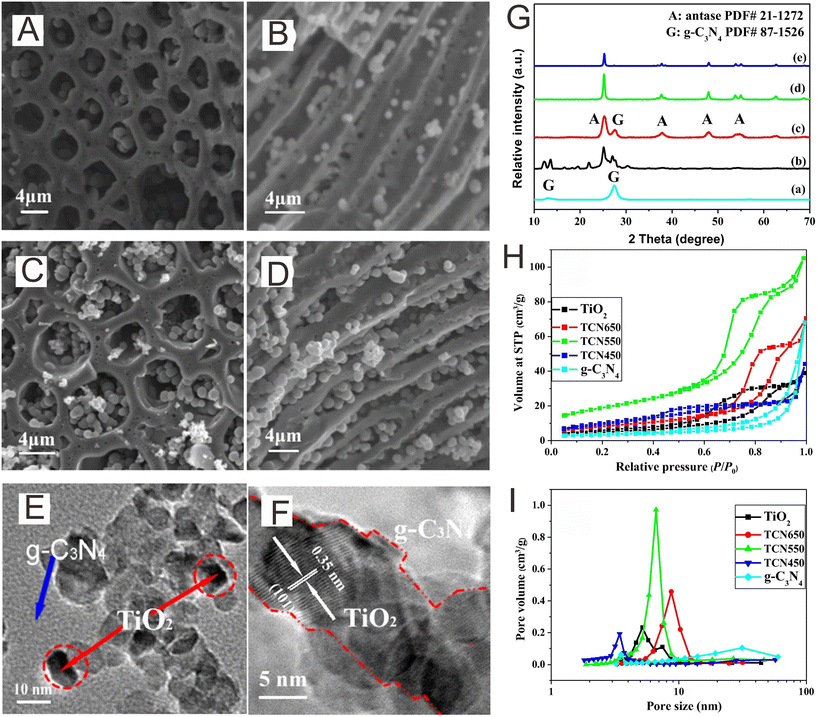 |
| Fig. 8 SEM images at different perspective views of (A and B) the pure hierarchical TiO2 framework and (C and D) the TiO2/g-C3N4 Z-scheme photocatalyst calcination at 550 °C (denoted as TCN550). TEM (E) and HRTEM (F) images of the TCN550. XRD (G), N2 adsorption isotherms (H), and pore size distribution (I) for the different samples. Reproduced with permission from ref. 161. | |
4.4. Ion exchange strategy
The ion exchange method mainly involves exchanging ions in an ionic crystal, but the framework still keeps close intact with each other.162–164 Additionally, the ion exchange can be quickly accomplished when the temperature is raised. Wang and co-workers165 prepared CdxZn1−xS/Au/g-C3N4 Z-scheme photocatalysts through the ion exchange approach, which displayed improved photocatalytic H2 production activity. Furthermore, when the ion exchange strategy is used, it is much easier to control the final product via adjusting the reaction conditions. Additionally, the Janus-like structures ensured them with improved visible light absorption and enlarged absorption range. Thus, the ion exchange method is an efficient approach for post-modification of Z-scheme systems.
4.5. Electrospinning strategy
It is well known that the electrospinning method is a versatile strategy to fabricate 1D materials, e.g., nanofibers, nanotubes, nanobelts.166,167 It can also be utilized for the preparation of 1D Z-scheme photocatalysts. A 1D nanostructure can boost the mobility of charge and enhance the absorption of visible light, and thus decrease the recombination of charge and enhance the photocatalytic performance.168,169 Li and co-workers170 prepared a TiO2/g-C3N4/RGO ternary Z-scheme heterojunction via an electrospinning coupled approach. The crystal structure, morphology, composition, specific surface area, photoelectrochemical properties, and photocatalytic performance can be adjusted via electrospinning condition.
4.6. Self-assembly strategy
The self-assembly approach involves the spontaneous organization of a disordered component into an ordered structure and the optimization of the free energy.8,171–174 Cheng and co-workers175 proposed a simple electrostatic self-assembly approach for preparing g-C3N4/ZnO Z-scheme photocatalysts. In this system, the electrostatic force between g-C3N and ZnO was very strong, which can concurrently enhance the charge separation and stability. When N-doped ZnO nanoplates were added to the exfoliated g-C3N4 suspension, the ZnO nanoplates' surface was spontaneously coated with g-C3N4 nanosheets to minimize the surface energy, resulting in the formation of a core–shell N-doped ZnO/g-C3N4 Z-scheme photocatalyst.176 Therefore, the self-assembly method endows the Z-scheme photocatalysts with a narrow size distribution, regulatable morphology, and strong interaction.
4.7. Photo-deposition strategy
The photo-deposition method is the phenomenon in which a semiconductor is decorated on the other's surface via light illumination.177–179 In this method, the CB potential of the semiconductor must be much lower than the reduction potential, and the VB potential must be higher than the oxidation potential.129 The photo-deposition method is very promising for preparing Z-scheme photocatalysts. A Bi2O3/g-C3N4 direct Z-scheme photocatalyst was fabricated through the simple photoreductive deposition of Bi3+ on the g-C3N4 surface under light illumination, followed by air oxidation of Bi3+ to Bi2O3 (Fig. 9A).180 The uniform dispersion of quantum-sized Bi2O3 on the g-C3N4 nanosheet surface could be observed from the XRD pattern, FESEM, TEM and HRTEM images (Fig. 9B–G). Wu and co-workers181 reported a novel BiVO4(040)–Ag@CdS Z-scheme photocatalyst in which Ag was selectively photo-deposited on the (040) facets of BiVO4, and the CdS nanorods were decorated on BiVO4(040)–Ag. Thus, the photo-deposition strategy is also a promising technology for decorating one semiconductor with the other semiconductor, which further improves the charge separation.
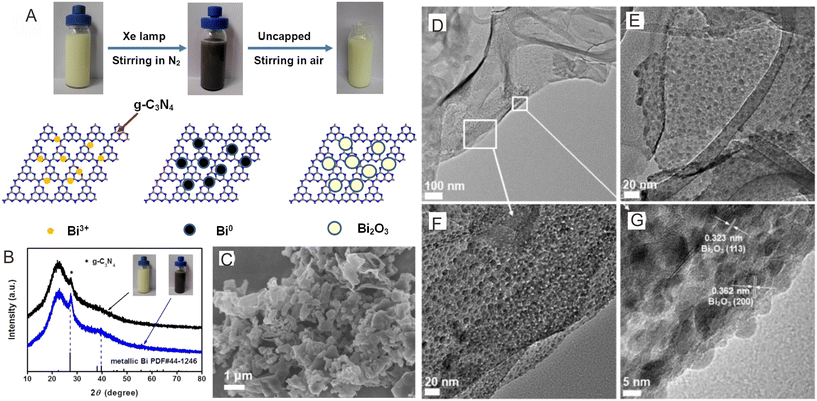 |
| Fig. 9 (A) Diagrammatic sketch of the preparation of Bi2O3/g-C3N4. (B) XRD patterns of the intermediate products. (C) FESEM image of Bi2O3/g-C3N4. TEM (D–F) and HRTEM (G) images of Bi2O3/g-C3N4. Reproduced with permission from ref. 180. | |
4.8. Mechanical agitation approach
The conventional mechanical agitation strategy involves the attachment of two pre-prepared semiconductors via physical methods, such as grinding,182 impregnation,183 planetary ball-milling,184 and reflux.185 However, the semiconductors assembled through these methods have no close interface, and they are easily separated from each other, resulting in a low charge transfer efficiency and moderate photocatalytic performance.186 Ohno and coworkers187 fabricated three kinds of g-C3N4/WO3 Z-scheme photocatalysts via grinding, impregnation assisted with sonication, and planetary ball-milling methods. Different from the agglomerated WO3 decorated on the g-C3N4 nanoplate prepared through the first two methods, WO3 prepared through planetary ball-milling strategy was uniformly dispersed on the g-C3N4 nanoparticles, which was beneficial for improving the specific surface area and photocatalytic performance.
Among the various fabrication strategies, deposition–precipitation, hydrothermal and solvothermal, solid-state synthesis, ion-exchange, electrospinning, self-assembly, and photo-deposition strategies are beneficial for achieving a strong interaction and intimate interface between the two semiconductors, which will lead to improved charge migration efficiency.76,188 The strong interaction (e.g., covalent bond, ionic bond, and coordination bond) and wear interaction (hydrogen bond and van der Waals force) can be formed between the two semiconductors, serving as charge transfer channels and enhancing the interface contact. Especially, the ion-exchange strategy is very promising for forming a close contact interface, and the initial morphology can be retained.189,190 The self-assembly method can ensure the two semiconductors with a narrow size distribution and uniform morphology.191 In contrast, the mechanical agitation method exhibits relatively poor interface contact between the two semiconductors, resulting in low photocatalytic performance.192 Nevertheless, this strategy is simple and cost effective, and shows great potential in practical production (Table 2).
5. Photocatalytic organic pollutant degradation
Many organic pollutants, such as methylene blue (MB), methyl orange (MO), 4-nitrophenol (4-NP), rhodamine B (RhB), basic fuchsin (BF), bisphenol A (BPA), brilliant blue (BB), 2,4-dichlorophenol (2,4-DCP), tetracycline (TC), sulfamethoxazole (SMX), indomethacin (IDM), and others have recently been excessively discharged to soil and water, which have negative influences on the environment and human health.193–201 g-C3N4-based Z-scheme photocatalysts have gained growing attention for organic pollutant removal because of their enhanced photocatalytic efficiency and stability (Fig. 10).77,101,202 Some important examples for photocatalytic organic pollutant degradation are shown below, and their property comparison is shown in Table 3.
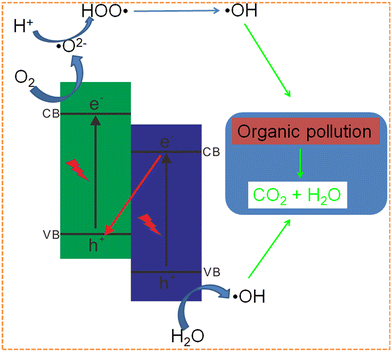 |
| Fig. 10 Diagrammatic explanation of organic pollutant degradation over g-C3N4-based Z-scheme photocatalysts. | |
Table 3 Comparison of the photocatalytic organic pollution degradation performance over g-C3N4-based Z-scheme photocatalysts
Photocatalysts |
Preparation strategy |
Mass (mg) |
Light source |
Target pollutant/initial concentration |
Degradation time (min) and rate (%) |
K
app
[10−2 min−1] |
Ref. |
K
app represents the reaction rate constant.
|
g-C3N4/TiO2 |
Calcination route |
300 |
15 W UV lamp, 365 nm |
HCHO/170 ppm |
60 (∼94) |
7.36 |
73
|
g-C3N4/TiO2 |
Electrochemical route |
— |
300 W xenon lamp, >420 nm |
RhB/5 mg L−1 |
300 (∼77) |
4.48 |
205
|
g-C3N4/rTiO2 |
Calcination route |
50 |
500 W xenon lamp, >420 nm |
RhB/5 mg L−1 |
240 (∼98) |
11.5 |
206
|
g-C3N4/TiO2/CuO |
Hydrothermal strategy |
50 |
500 W xenon lamp |
RhB/0.5 mg L−1 |
120 (∼97) |
0.95 |
208
|
g-C3N4/TiO2-HNB |
Microwave-assisted strategy |
— |
3 W LED lamp, 365 nm |
Brilliant red X-3B/1.0 × 10−4 mmol L−1 |
45 (∼99) |
5.1 |
209
|
WO3/g-C3N4 |
Ball milling and heat treatment methods |
10 |
500 W xenon lamp, >470 nm |
MB and BF/0.9 × 10−5 and 1.0 × 10−5 mol L−1 |
MB 120 (∼99) BF 120 (∼97) |
— |
213
|
WO3/g-C3N4 |
In situ liquid phase process |
50 |
300 W xenon lamp, >400 nm |
MB/50 mg L−1 |
90 (∼97) |
1.90 |
214
|
WO3/g-C3N4 |
One-step heating procedure |
30 |
500 W xenon lamp, >420 nm |
RhB/5 mg L−1 |
120 (∼90) |
— |
215
|
C-doped g-C3N4/WO3 |
Cellulose-assisted strategy |
100 |
500 W xenon lamp, >420 nm |
TC/10 mg L−1 |
60 (∼70) |
— |
217
|
WO3/g-C3N4/Bi2O3 |
One step co-calcination way |
100 |
300 W xenon lamp, >420 nm |
TC/10 mg L−1 |
60 (∼80) |
2.37 |
159
|
g-C3N4/MnO2 |
Wet-chemical method |
50 |
300 W xenon lamp |
RhB/10 mg L−1 |
180 (∼77) |
3.3 |
137
|
Bi2O3/g-C3N4 |
Ball milling and heat treatment methods |
5 |
500 W xenon lamp, 470 nm |
MB and RhB/1.1 × 10−5 and 1.0 × 10−5 mol L−1 |
MB 120 (∼76) RhB 120 (∼73) |
2.53 and 1.01 |
223
|
g-C3N4/Bi2O3/BiPO4 |
Calcination route |
15 |
— |
MO/10 mg L−1 |
160 (∼88) |
1.15 |
225
|
β-Bi2O3/g-C3N4 |
Hydrothermal calcination approach |
40 |
350 W xenon lamp, >420 nm |
RhB/1 × 10−5 mol/L |
80 (∼97) |
4.22 |
226
|
g-C3N4/Bi4O7 |
Calcination method |
80 |
500 W halogen lamp, 420–800 nm |
MB and RhB/— and — |
90 (∼80) |
1.73 |
227
|
g-C3N4/Bi2WO6 |
Mixing and heating method |
50 |
300 W xenon lamp, 350–780 nm |
2,4-DCP/20 mg L−1 |
120 (>99) |
1.13 |
228
|
g-C3N4/Bi2WO6 |
One-pot hydrothermal strategy |
50 |
Xenon lamp (XL-300, Yirda) |
RhB/10 mg L−1 |
30 (>99) |
8.17 |
156
|
g-C3N4/RGO/Bi2WO6 |
Hydrothermal method |
250 |
500 W xenon lamp, >420 nm |
TCP/20–100 mg L−1 |
120 (>99) |
3.15 |
229
|
Ag-decorated g-C3N4/Bi2WO6 |
Polymerization method |
40 |
300 W xenon lamp, 400 nm |
RhB/10 mg L−1 |
90 (>99) |
— |
230
|
Bi3O4Cl/g-C3N4 |
Solid-phase calcination method |
50 |
250 W xenon lamp, >420 nm |
RhB and TC/10 and 10 mg L−1 |
RhB 60 (>98) TC 60 (>76) |
— and 2.05 |
231
|
BiOBr/RGO/pg-C3N4 |
Solvothermal method |
50 |
300 W xenon lamp, 420 nm |
RhB and TC/10 and 10 mg L−1 |
RhB 7.5 (>99) TC 60 (>97) |
— and — |
232
|
Bi12GeO20/g-C3N4 |
Sol–gel method |
300 |
300 W Dy lamp, 400 nm |
RhB/5 mg L−1 |
50 (>99) |
2.55 |
233
|
g-C3N4/C@Bi2MoO6 |
Hydrothermal deposition method |
100 |
500 W xenon lamp, >420 nm |
β-Naphthol/15 mg L−1 |
150 (>62) |
0.63 |
234
|
Ag3PO4/g-C3N4 |
In situ precipitation method |
5 |
300 W xenon lamp, >400 nm |
SMX/1 mg L−1 |
10 (∼98) |
6.3 |
238
|
Ag3PO4/g-C3N4 |
In situ precipitation method |
30 |
300 W xenon lamp |
MO/10 mg L−1 |
5 (>99) |
— |
239
|
g-C3N4/Ag2WO |
In situ precipitation method |
30 |
300 W xenon lamp |
MO/10 mg L−1 |
150 (∼98) |
— |
240
|
Ag2CrO4/g-C3N4 |
Precipitation method |
20 |
300 W xenon lamp, >400 nm |
MO and RhB/10 and 10 mg L−1 |
MO 21 (∼90) RhB 40 (∼97) |
9.64 and 9.21 |
241
|
Ag@AgBr/g-C3N4 |
Deposition–precipitation method |
100 |
300 W xenon lamp |
MO and MB/10 and 10 mg L−1 |
MO 10 (∼97) RhB 10 (∼96) |
— and — |
117
|
Ag2CrO4/Ag/g-C3N4 |
In situ growth and photoreduction methods |
50 |
500 W xenon lamp, <420 nm |
2,4-DCP/10 mg L−1 |
120 (∼96) |
1.52 |
243
|
g-C3N4/Ag/MoS2 |
In situ growth and precipitation methods |
100 |
300 W xenon lamp, >420 nm |
RhB/20 mg L−1 |
60 (>99) |
— |
247
|
g-C3N4/ZnO |
Ultrasonically exfoliated method |
100 |
300 W xenon lamp, >420 nm |
4-CP/10−4 mol L−1 |
90 (>99) |
5.09 |
248
|
CdS/RGO/g-C3N4 |
Hydrothermal method |
20 |
350 W xenon lamp |
Atrazine/— |
300 (∼92) |
0.71 |
249
|
g-C3N4–RGO–TiO2 |
Liquid-precipitation strategy |
50 |
300 W xenon lamp, >420 nm |
RhB/30 mg L−1 |
180 (∼92) |
1.37 |
250
|
MoO3/g-C3N4 |
Calcination method |
30 |
350 W xenon lamp, >420 nm |
TC/20 mg L−1 |
90 (∼90) |
2.23 |
251
|
p-type Cu3P/n-type g-C3N4 |
Calcination method |
10 |
300 W xenon lamp, 400 nm |
RhB/— |
20 (>99) |
— |
252
|
NiTiO3/g-C3N4 |
Calcination method |
40 |
30 W visible LED |
RhB/10 mg L−1 |
— |
3.09 |
253
|
LaFeO3/g-C3N4 |
Calcination method |
30 |
300 W xenon lamp, >420 nm |
RhB/25 mg L−1 |
60 (∼98) |
6.22 |
120
|
V2O5/g-C3N4 |
In situ growth strategy |
50 |
250 W xenon lamp, 420 nm |
RhB and TC/10 and 10 mg L−1 |
120 (∼77) |
4.91 and — |
107
|
SnO2x/g-C3N4 |
Calcination method |
100 |
350 W xenon lamp, >420 nm |
RhB/10 mg L−1 |
40 (>99) |
1 |
254
|
InVO4/Bi2S3/g-C3N4 |
Wet-impregnation method |
200 |
300 W xenon lamp, >420 nm |
RhB19/15 mg L−1 |
100 (∼96) |
0.57 |
255
|
CDs/g-C3N4/SnO2 |
Thermal polymerization |
10 |
300 W xenon lamp, >420 nm |
IDM/10 mg L−1 |
40 (>99) |
2.33 |
256
|
g-C3N4/ZnFe2O4/UiO-66 |
Hydrothermal method |
— |
300 W xenon lamp, >420 nm |
RhB/— |
40 (>99) |
4.89 |
256
|
g-C3N4/BiVO4/CoFe2O4 |
High-temperature solid-state route |
50 |
300 W xenon lamp, >400 nm |
RhB/— |
25 (>99) |
2.84 |
257
|
g-C3N4/g-C3N4 |
Bottom-up approach |
10 |
50 W xenon lamp, >400 nm |
RhB/10 mg L−1 |
240 (>99) |
1.39 |
246
|
5.1. g-C3N4/TiO2 Z-scheme photocatalysts
TiO2 is valuable in the photocatalytic fields because of its unique advantages, e.g., excellent controllability, large surface area, amazing stability, and ease of recycling.203,204 Some investigations have focused on combining TiO2 with g-C3N4 to develop Z-scheme photocatalysts for achieving better photocatalytic property. The first example was reported by Yu and co-workers,73 who achieved markedly enhanced photocatalytic properties by g-C3N4/TiO2 Z-scheme photocatalysts. Dong and co-workers205 fabricated an all-solid-state (ASS) Z-scheme photocatalyst through decorating g-C3N4 nanosheets on TiO2 nanotube arrays (TNTAs). The as-prepared photocatalyst displayed improved photocatalytic property for RhB degradation, which was about 4 times greater than that exhibited by pure TiO2 TNTAs. Ho and co-workers206 prepared the g-C3N4 quantum dots (QDs)-modified rutile TiO2 (rTiO2) (g-C3N4 QDs-rTiO2) hybrid via calcination of the mixture of P25 TiO2 and melamine under 500 °C for 4 h, which displayed excellent photocatalytic properties for the RhB degradation. Facet engineering is crucial for improving the photocatalytic performance. The exposed {010} and {110} crystal facets of BiVO4 have been demonstrated to be the active reduction and oxidation sites, respectively.207 Raj and co-workers208 fabricated a g-C3N4/TiO2/CuO Z-scheme heterostructure via a simple hydrothermal strategy, which displayed improved photocatalytic performance of (90.3%) RhB dye degradation within 120 min. In addition, almost no loss in photocatalytic activity after 5 cycles was found. The Lv group209 studied the influence of the exposed {001} and {101} facets of TiO2 on the photocatalytic activity. They first fabricated TiO2 nanosheets (NSs) and TiO2 nanoboxes (NBs), and then combined them with g-C3N4 to prepare TiO2 NS/g-C3N4 and TiO2 NBs/g-C3N4, respectively (Fig. 11A and B). The {001} facets of TiO2 NSs came into contact with g-C3N4 (Fig. 11A and C), and the {101} facets of TiO2 NBs came into contact with g-C3N4 (Fig. 11B and D). Under visible light illumination, the photogenerated carriers on TiO2 were separately accumulated on the {101} and {001} facets.210 The photogenerated electrons were subsequently centered on the {101} facets of the TiO2 NBs, which could transfer to g-C3N4 for photocatalytic reactions, which is in line with the direct Z-scheme mechanism (Fig. 11F). Thus, the e−–h+ separation efficiency of TiO2 NBs/g-C3N4 is much higher than that of TiO2 NSs/g-C3N4, and the TiO2 NBs/g-C3N4 displayed the highest photocatalytic efficiency (Fig. 11E). This work offers us a new design concept, wherein the suitable interface engineering of the exposed facets of a pure semiconductor in a direct Z-scheme photocatalyst is able to effectively enhance the e−–h+ separation, which can further improve the photocatalytic property.
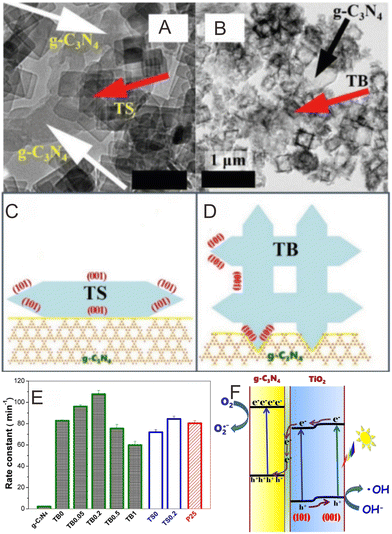 |
| Fig. 11 TEM images of (A) TiO2 NSs/g-C3N4 and (B) TiO2 NBs/g-C3N4. Diagrammatic sketch of the contact interface between TiO2 and g-C3N4 on (C) TiO2 NSs/g-C3N4 and (D) TiO2 NBs/g-C3N4. (E) Comparison of the photocatalytic activity of the synthesized photocatalysts for the photocatalytic degradation of brilliant red X3B. (F) Diagrammatic sketch for the photoinduced charge carrier migration mechanism in the TiO2/g-C3N4 hybrids. Reproduced with permission from ref. 209. | |
5.2. g-C3N4/WO3 Z-scheme photocatalysts
WO3 is gradually becoming recognized as one of the most promising photocatalysts, owing to its outstanding photocatalytic performance, chemical inertness, and optical stability.211,212 In comparison with TiO2, WO3 possesses a smaller band gap (2.7 eV) and more positive CB level. Thus, it is also favorable for combining with g-C3N4 to construct Z-scheme photocatalysts. The Chen group213 developed a WO3/g-C3N4 Z-scheme photocatalyst. The reaction rate constants for degrading MB and BF over WO3(5.0 wt%)/g-C3N4 were found to be 4.77 and 3.84 times greater than that of the bare g-C3N4, respectively. The Jia group214 developed a new bifunctional WO3/g-C3N4 Z-scheme photocatalyst by in situ liquid phase strategy. The photocatalytic degradation efficiency of the 30 wt%WO3/g-C3N4 was found to be 2.5 and 2.7 times higher than the individual g-C3N4 and WO3, respectively. Kang and co-workers215 fabricated WO3/g-C3N4 Z-scheme photocatalysts through a simple one-step simultaneous heating approach utilizing urea as the starting material, which exhibited markedly improved photocatalytic property for MB degradation. Chai and co-workers216 constructed a WO3/g-C3N4 Z-scheme photocatalyst through in situ acidic precipitation and subsequent calcination processes, which also showed improved photocatalytic property for RhB degradation. Zheng and co-workers217 reported a C-doped g-C3N4/WO3 Z-scheme photocatalyst through the hydrothermal strategy. Benefiting from high specific areas, C-substitution, and Z-scheme mechanism, the prepared Z-scheme photocatalysts displayed a narrow band-gap, and improved visible-light absorption and separation efficiency of charge. All of the abovementioned improved photocatalytic properties of the WO3/g-C3N4 composites were mainly because of the unusual merits of the Z-scheme photocatalytic systems.
5.3. g-C3N4/MnO2 Z-scheme photocatalysts
MnO2 is gradually becoming recognized as an efficient photocatalyst owing to its excellent photocatalytic performance, suitable bandgap value, and optical stability.218 Xu and co-workers137 prepared g-C3N4/MnO2 Z-scheme photocatalysts. There were many functional groups and exposed lone pair electrons from N atoms on the g-C3N4 surfaces, which provided abundant adsorption sites for Mn2+ ions (Fig. 12A). It should be noted that the thicknesses of the g-C3N4 nanosheets, MnO2 nanosheets, and the g-C3N4/MnO2 hybrid were approximately 3.4, 2.2, and 5.7 nm, respectively, which were roughly equal to the stacking distance of the g-C3N4 and MnO2 nanosheets (Fig. 12B–D). The electrostatic potentials of MnO2 (001) and g-C3N4 (001) were measured to be 6.8 and 4.5 eV, respectively, suggesting that the electrons on the g-C3N4 will spill onto MnO2via the interface (Fig. 12E–G).219,220 Thus, g-C3N4 was more positively charged. Photocatalytic experiments suggested that the prepared g-C3N4/MnO2 exhibited better photocatalytic property when compared with the bare g-C3N4 and MnO2 (Fig. 12H and I). Herein, electronic paramagnetic resonance (EPR) analysis can be used to survey the reactive species. The results indicated that the transfer of the photogenerated carrier in g-C3N4/MnO2 should obey the direct Z-scheme mechanism (Fig. 12J and K). Moreover, the positive slopes of the Mott–Schottky plots indicated that both g-C3N4 and MnO2 are typical n-type semiconductors (Fig. 12J and K). With regard to n-type semiconductors, the flat-band potential is nearly that same as that for CB,221,222 and the CB of g-C3N4 and MnO2 were measured to be −1.61 and 1.22 V, respectively (Fig. 12L and N). The VB positions were calculated by XPS spectroscopy (Fig. 12M), and the results showed that the VB of g-C3N4 and MnO2 were about 1.81 and 3.26 V, respectively. Therefore, a Z-scheme transfer mechanism can be used to illustrate the enhanced photocatalytic property over the g-C3N4/MnO2 hybrids. As for the individual g-C3N4 or MnO2, the photogenerated h+ in g-C3N4 cannot oxidize OH− to produce ˙OH radicals and the photogenerated e− in MnO2 cannot generate ˙O2− radicals, respectively, because of the thermodynamic equilibrium limit. After the Z-scheme heterojunction was formed, the photogenerated e− in the CB of MnO2 will migrate to the VB of g-C3N4 and then combine with the h+. The Z-scheme configuration can explain the enhanced photocatalytic property well (Fig. 13O).
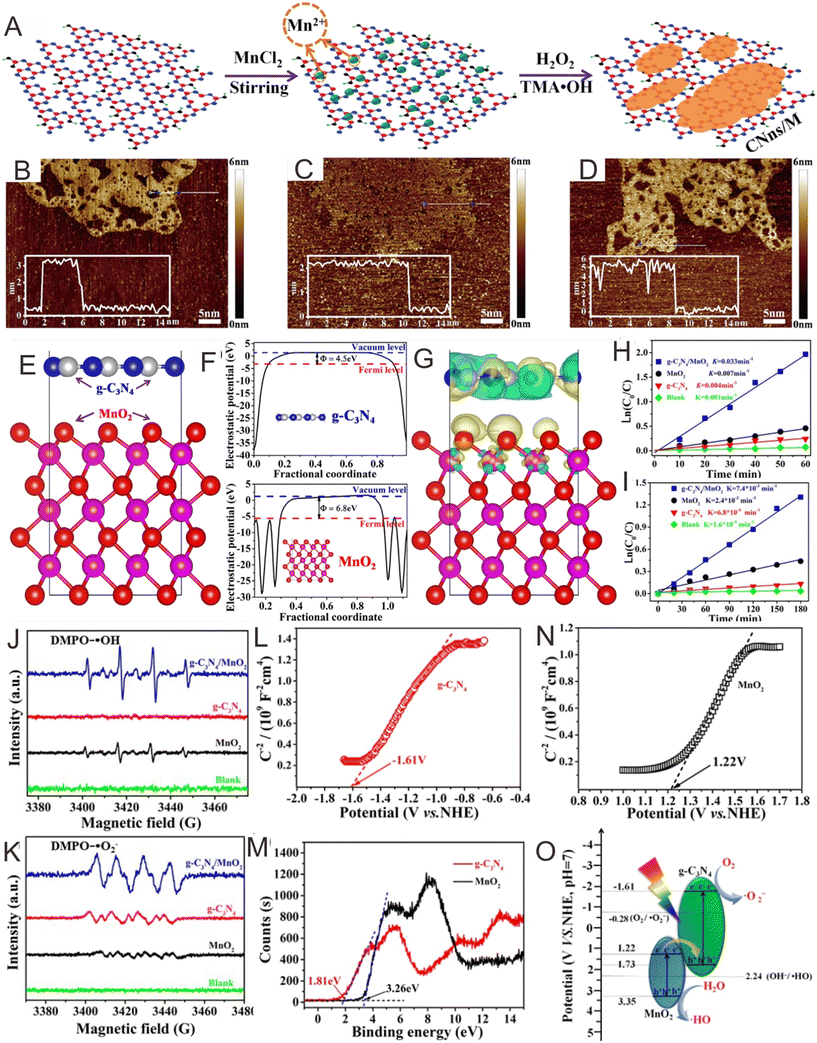 |
| Fig. 12 (A) Diagrammatic sketch of g-C3N4/MnO2 prepared through in situ growth of MnO2 on the g-C3N4 nanosheets. AFM images of the (B) g-C3N4 nanosheets, (C) MnO2 nanosheets, and (D) g-C3N4/MnO2. (E) Optimized structure model of g-C3N4/MnO2. (F) Calculated electrostatic potentials for g-C3N4 and the MnO2 nanosheets, respectively. (G) Charge density difference model of g-C3N4/MnO2. Photocatalytic degradation efficiency of (H) RhB and (I) phenol over g-C3N4, MnO2, and g-C3N4/MnO2 under light irradiation. (J) EPR spectra of DMPO–˙OH through irradiation for 120 s in an aqueous dispersion and (K) DMPO–˙O2− through irradiation for 120 s in a methanol dispersion in the existence of g-C3N4, MnO2, and g-C3N4/MnO2. Mott–Schottky plots for (L) g-C3N4 and (M) MnO2 nanosheets. (N) XPS valence band spectra of MnO2 and g-C3N4 nanosheets. (O) Photocatalytic mechanism of g-C3N4/MnO2. Reproduced with permission from ref. 137. | |
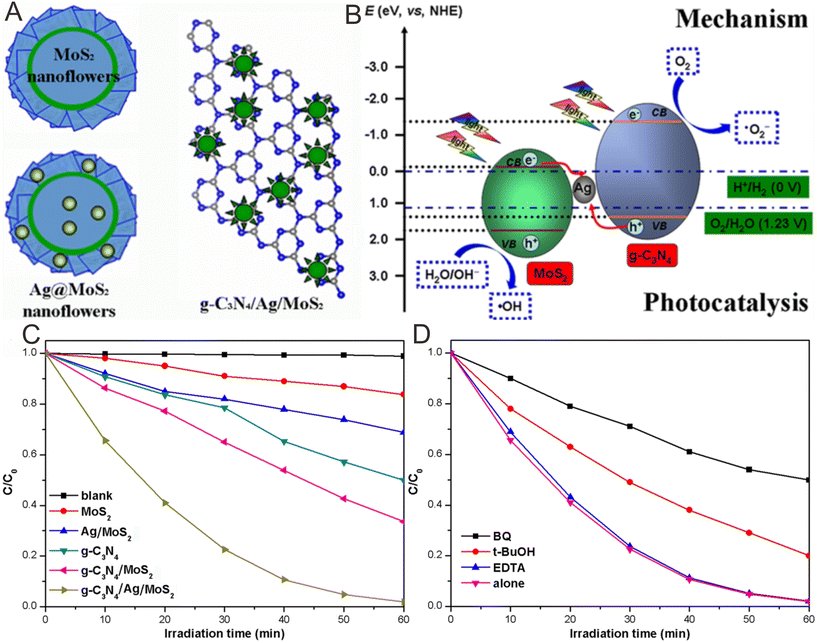 |
| Fig. 13 (A) The nanostructures of Ag/MoS2 and g-C3N4/Ag/MoS2. (B) Diagrammatic sketch for the separation and migration of the photogenerated charges over g-C3N4/Ag/MoS2. (C and D) Photocatalytic property of the fabricated MoS2, Ag/MoS2, g-C3N4, g-C3N4/MoS2, and g-C3N4/Ag/MoS2 photocatalysts for RhB solution. Reproduced with permission from ref. 247. | |
5.4. g-C3N4/bismuth oxide Z-scheme photocatalysts
Recently, multifarious bismuth-based semiconductors, e.g., Bi2O3,159,180,223–225 β-Bi2O3,226 Bi4O7,227 Bi2WO6,156,228–230 Bi3O4Cl,231 BiOBr,232 Bi12GeO2,233 Bi2MoO6,234 have been reported for combining with g-C3N4 to form Z-scheme photocatalysts because of their unique characteristics, such as outstanding electrical property, appropriate energy band positions, and highly efficient photocatalytic performance.235–237 For example, Chen and co-workers223 prepared a Z-scheme Bi2O3/g-C3N4 photocatalyst. The reaction rate constants of Bi2O3 (1.0 wt%)/g-C3N4 for MB and RhB degradation were approximately 3.4 and 5 times greater that of the bare g-C3N4 and Bi2O3, respectively. The Z-scheme mechanism was confirmed through various technologies (e.g., ESR, PL-TA and PL, etc.), which resulted in enhanced photocatalytic property. Du and co-workers227 fabricated a high-performance g-C3N4/Bi4O7 Z-scheme photocatalyst via a simple way. In contrast to the single photocatalysts, the as-prepared g-C3N4/Bi4O7 photocatalyst displayed enhanced degradation efficiency toward MB, phenol, RhB, and BPA. The improved photocatalytic performance should be attributed to the improved light utilization and the highly efficient Z-scheme charge migration. Zhao and co-workers228 reported a simple mixing and heating strategy to fabricate the g-C3N4/Bi2WO6 Z-scheme photocatalyst. The optimal dechlorination rate constant of 2,4-DCP over g-C3N4/Bi2WO6 was 1.13 h−1, exceeding those of the bare g-C3N4 and Bi2WO6 by 7.6 and 8.9 times, respectively. Yin and co-workers233 prepared a new ASS Bi12GeO20/g-C3N4 Z-scheme photocatalyst. The obtained Bi12GeO20/g-C3N4 photocatalyst displayed improved photocatalytic property for degrading microcystin-LR and RhB in contrast to the individual Bi12GeO20 and g-C3N4. The enhanced photocatalytic property is because of the enhanced light utilization efficiency and effective spatial separation of the photo-generated carriers. In short, bismuth-based semiconductors can couple well with g-C3N4 to fabricate Z-scheme photocatalysts for enhancing photocatalytic properties owing to their suitable CB and CB values.
5.5. g-C3N4/Ag-containing semiconductor Z-scheme photocatalysts
Ag-containing photocatalysts can greatly improve the photocatalytic property of g-C3N4 through the Z-scheme mechanism. Some examples of Ag-containing photocatalysts with improved properties include Ag3PO4/g-C3N4,238,239 Ag2WO4/g-C3N4,240 and Ag2CrO4/g-C3N4.241 In particular, utilizing noble metal Ag as the electron mediator for fabrication of Ag-containing semiconductors/g-C3N4 SCS Z-scheme photocatalysts can achieve more effective photocatalytic performance.242 The Guo group117 fabricated various Ag@AgBr/g-C3N4 Z-scheme photocatalysts via the photoreduction of AgBr/g-C3N4 hybrids. A dramatically improved photocatalytic property of Ag@AgBr/g-C3N4 was achieved, and is mainly attributed to the high light utilization and Z-scheme mechanism. Quan and co-workers243 prepared Ag2CrO4/Ag/g-C3N4 Z-scheme photocatalysts via simple in situ growth and photoreduction strategies. Because of the strong light utilization, effective separation of the photogenerated e− and h+, and the excellent redox ability, the obtained Ag2CrO4/Ag/g-C3N4 hybrids showed remarkably improved photocatalytic performance for 2,4-DCP degradation, exceeding that of the pure g-C3N4 by 5.2 times.
5.6. Metal-free g-C3N4-based Z-scheme photocatalysts
Fabricating metal-free g-C3N4-based Z-scheme photocatalysts is a very promising and environmentally friendly method for degrading organic pollutants.244,245 Huang and co-workers246 constructed a metal-free 2D g-C3N4/g-C3N4 Z-scheme photocatalyst via utilization of a bottom-up approach. Profiting from the 2D morphology with the large exposed active site and the Z-scheme mechanism with the efficient separation of the photoinduced carriers, the fabricated 2D g-C3N4/g-C3N4 Z-scheme photocatalysts showed better photocatalytic performance when compared to the conventional g-C3N4/g-C3N4 homojunction and bulk g-C3N4. This work provides some new design concepts for Z-scheme systems with specific 2D morphology for enhanced organic pollutant removal.
5.7. g-C3N4-based SCS Z-scheme photocatalysts
As mentioned above, the g-C3N4-based SCS Z-scheme photocatalysts seem to be more promising for organic pollutant degradation. Among them, conductors acting as intermediates are utilized to link two semiconductors for the more favorable migration of the photogenerated carriers.33 A typical example was presented by the Fang group.247 They prepared a Z-scheme g-C3N4/Ag/MoS2 ternary plasmonic Z-scheme photocatalyst with flowerlike nanostructures with a diameter of ∼0.4–0.6 μm (Fig. 13A). The prepared g-C3N4/Ag/MoS2 showed significantly enhanced photocatalytic performance, exceeding that of the Ag/MoS2 and g-C3N4/MoS2 systems by 9.43 and 3.56 times, respectively (Fig. 13C and D). The excellent photocatalytic property was mainly because of the synergetic effects of the Ag, g-C3N4, and MoS2 nanophase structures, which led to a Z-scheme-mechanism-induced rapid separation of the photogenerated e−–h+ pairs and further enhanced photocatalytic property (Fig. 13B).
5.8. Others
In addition to the above common g-C3N4-based Z-scheme photocatalysts, researchers have made many attempts to explore other candidates to fabricate g-C3N4-based Z-scheme systems, e.g., g-C3N4/ZnO,248 CdS/RGO/g-C3N4,249 g-C3N4–RGO–TiO2,250 MoO3/g-C3N4,251 Cu3P/g-C3N4,252 NiTiO3/g-C3N4,253 LaFeO3/g-C3N4,120 V2O5/g-C3N4,107 SnO2x/g-C3N4,254 InVO4/Bi2S3/g-C3N4,255 CDs/g-C3N4/SnO2,256 g-C3N4/ZnFe2O4/UiO-66,256 and g-C3N4/BiVO4/CoFe2O4.257 They have been extensively utilized as an efficient visible-light-guided photocatalyst with enhanced photocatalytic degradation activity. The recovery of the photocatalyst is also very important for efficient removal. Thus, the magnetic g-C3N4-based Z-scheme photocatalysts258,259 are also very useful in this field. The use of g-C3N4-based Z-scheme photocatalysts to degrade organic pollutions in actual water bodies is also very important.260 Of course, a more in-depth comprehension of the charge transfer route and photocatalytic mechanism is crucial for further clarification and amelioration. Some theoretical calculations and advanced characterization techniques, such as in situ FTIR, in situ XPS, and synchrotron radiation, are vital for further providing the specific charge transfer route and photocatalytic mechanism. Beyond question, g-C3N4-based Z-scheme systems will have enormous potential in photocatalytic organic pollutant degradation.
6. Conclusions and outlook
g-C3N4-based photocatalysts have attracted increasing interests because of their easy functionalization, suitable band structure, outstanding physicochemical stability and high photocatalytic property. However, the fast charge recombination and low light utilization greatly limit their practical organic pollution removal application. Luckily, g-C3N4-based Z-scheme photocatalysts can greatly boost the spatial separation of the photogenerated carrier and enhance their photocatalytic activity and light utilization. Thus, g-C3N4-based Z-scheme photocatalysts exhibit great potential for organic pollution removal. Although many achievements have been obtained, the research studies on g-C3N4-based Z-scheme photocatalysts are still at their initial stage, and further explorations are evidently needed. Some opportunities and challenges need to be further emphasized and explored, as shown below:
(1) A more in-depth comprehension of the charge transfer route and photocatalytic mechanism is crucial for further clarification and amelioration. Some theoretical calculations and characterization techniques, such as in situ FTIR, in situ XPS, and synchrotron radiation, are vital for further providing the specific charge transfer route and photocatalytic mechanism. Additionally, the step-scheme (S-scheme) mechanism261 is more reasonable and powerful for illustrating the evidently improved photocatalytic property.
(2) The physicochemical property of the g-C3N4-based Z-scheme photocatalysts should be further optimized. The main attempts should concentrate on the construction of advanced semiconductors with high light utilization efficiency, low charge-carrier-transfer resistance, and good physicochemical stability. In addition, dimension engineering (e.g., 0D quantum dots, 1D nanowires and nanorods, 2D nanosheets and 3D sphere and core–shell, etc.) should be considered more.
(3) The crystalline structure of g-C3N4-based Z-scheme photocatalysts is also vital for the enhanced charge migration efficiency. Normally, the transfer efficiency of photogenerated charges will be greatly decreased owing to the defects, mismatch of lattice parameters, and electronic configurations. Therefore, the optimization of the crystalline structure of the g-C3N4-based Z-scheme photocatalysts is a promising method for improving their photocatalytic performance.
(4) The photocatalytic performance of g-C3N4-based Z-scheme systems can be further improved via fabricating ternary or multicomponent systems. A practical method is to load suitable co-catalysts on the g-C3N4-based Z-scheme photocatalysts that will be very good for further enhancing its e−–h+ separation and light utilization.
(5) Considering the unique advantages of g-C3N4-based Z-scheme systems, widening their application scope (i.e., energy gas conversion, desulfurization, organic photosynthesis) is critical to building a sustainable society.
(6) In regard to g-C3N4-based Z-scheme systems for organic pollution removal, only considering the photocatalytic property is not enough. Other aspects, including cost, environment, and ecology, should also be focused on.
(7) In order to achieving a practical application of g-C3N4-based Z-scheme systems, some efficient enhancement approaches, e.g., morphology regulation, loading co-catalysts, interface engineering, doping and vacancy, and exposing more reactive facets, should be highly considered.
Looking to the future, there has been a lot of opportunities and challenges for g-C3N4-based Z-scheme photocatalysts for organic pollution removal. It is believed that this review can provide some new and advanced insights for guiding the rational design of g-C3N4-based Z-scheme systems for organic pollution removal. Certainly, the g-C3N4-based Z-scheme systems can achieve practical industrial applications in the near future.
Conflicts of interest
There are no conflicts of interest to declare.
Acknowledgements
This work was supported by the National Natural Science Foundation of China (Grant No. 52203110), the Knowledge Innovation Program of Wuhan-Shuguang Project (Grant No. 2022010801020216), the Scientific Research Foundation of Fujian University of Technology (Grant No. GY-Z220182), the China Postdoctoral Science Foundation (Grant No. 2021M693795), and the Excellent Youth Foundation of Jiangsu Science Committee (Grant No. BK20220118).
References
- Q. Wu, J. Wang, Z. Wang, Y. Xu, Z. Xing, X. Zhang, Y. Guan, G. Liao and X. Li, J. Mater. Chem. A, 2020, 8, 13685–13693 RSC.
- H. Zhu, S. Cai, G. Liao, Z. F. Gao, X. Min, Y. Huang, S. Jin and F. Xia, ACS Catal., 2021, 11, 14751–14771 CrossRef CAS.
- Y. Zhang, J. Cheng, Y. Xing, Z. Tan, G. Liao and S. Liu, Mater. Sci. Semicond. Process., 2023, 161, 107463 CrossRef CAS.
- Z. Li, J. Zhang, Y. Huang, J. Zhai, G. Liao, Z. Wang and C. Ning, Coord. Chem. Rev., 2022, 471, 214723 CrossRef CAS.
- R. Jia, C. He, Q. Li, S.-Y. Liu and G. Liao, Trends Biotechnol., 2022, 40, 1425–1438 CrossRef CAS PubMed.
- S. Liu, Y. Guo, S. Yi, S. Yan, C. Ouyang, F. Deng, C. Li, G. Liao and Q. Li, Sep. Purif. Technol., 2023, 307, 122727 CrossRef CAS.
- W. Xiao, X. Jiang, X. Liu, W. Zhou, Z. N. Garba, I. Lawan, L. Wang and Z. Yuan, J. Cleaner Prod., 2021, 284, 124773 CrossRef CAS.
- Z. Yan, T. Wu, G. Fang, M. Ran, K. Shen and G. Liao, RSC Adv., 2021, 11, 4713–4722 RSC.
- G. Liao, L. Zhong, C. S. Cheung, C. Du, J. Wu, W. Du, H. Zheng and H. Gao, Microporous Mesoporous Mater., 2020, 307, 110469 CrossRef CAS.
- D. Pathania, S. Sharma and P. Singh, Arabian J. Chem., 2017, 10, S1445–S1451 CrossRef CAS.
- Z. Wang, A. Berbille, Y. Feng, S. Li, L. Zhu, W. Tang and Z. L. Wang, Nat. Commun., 2022, 13, 130 CrossRef CAS PubMed.
- X. Ma, L. Xing, K. Liu and L. Liu, Catal. Sci. Technol., 2023, 13, 788–801 RSC.
- C. Li, H. Che, C. Liu, G. Che, P. A. Charpentier, W. Z. Xu, X. Wang and L. Liu, J. Taiwan Inst. Chem. Eng., 2019, 95, 669–681 CrossRef CAS.
- R. Acharya, B. Naik and K. Parida, Beilstein J. Nanotechnol., 2018, 9, 1448–1470 CrossRef CAS PubMed.
- F. Tian, X. Wu, S. Liu, Y. Gu, Z. Lin, H. Zhang, X. Yan and G. Liao, Sustainable Energy Fuels, 2023, 7, 786–796 RSC.
- J.-Z. Cheng, L.-L. Liu, G. Liao, Z.-Q. Shen, Z.-R. Tan, Y.-Q. Xing, X.-X. Li, K. Yang, L. Chen and S.-Y. Liu, J. Mater. Chem. A, 2020, 8, 5890–5899 RSC.
- C. Li, H. Che, P. Huo, Y. Yan, C. Liu and H. Dong, J. Colloid Interface Sci., 2021, 581, 764–773 CrossRef CAS PubMed.
- C. Li, X. Liu, Y. Yan, X. Song, Y. Yan, C. Liu, R. Xu and P. Huo, Chem. Eng. J., 2021, 410, 128316 CrossRef CAS.
- C. Li, Y. Zhao, X. Liu, P. Huo, Y. Yan, L. Wang, G. Liao and C. Liu, J. Colloid Interface Sci., 2021, 600, 794–803 CrossRef CAS PubMed.
- R. Acharya and P. Pani, Mater. Today: Proc., 2022, 67, 1276–1282 CAS.
-
R. Acharya, L. Acharya and K. Parida, in Perovskite Materials for Energy and Environmental Applications, 2022, pp. 167–216 Search PubMed.
- V. Hasija, A. Kumar, A. Sudhaik, P. Raizada, P. Singh, Q. Van Le, T. T. Le and V.-H. Nguyen, Environ. Chem. Lett., 2021, 19, 2941–2966 CrossRef CAS.
- A. Kumar, P. Raizada, A. Hosseini-Bandegharaei, V. K. Thakur, V.-H. Nguyen and P. Singh, J. Mater. Chem. A, 2021, 9, 111–153 RSC.
- C. Li, H. Che, Y. Yan, C. Liu and H. Dong, Chem. Eng. J., 2020, 398, 125523 CrossRef CAS.
- S. Li, S. Shan, S. Chen, H. Li, Z. Li, Y. Liang, J. Fei, L. Xie and J. Li, J. Environ. Chem. Eng., 2021, 9, 105967 CrossRef CAS.
- C. Li, X. Liu, P. Huo, Y. Yan, G. Liao, G. Ding and C. Liu, Small, 2021, 17, 2102539 CrossRef CAS PubMed.
- C. Li, G. Ding, X. Liu, P. Huo, Y. Yan, Y. Yan and G. Liao, Chem. Eng. J., 2022, 435, 134740 CrossRef CAS.
- C. Li, X. Liu, G. Ding, P. Huo, Y. Yan, Y. Yan and G. Liao, Inorg. Chem., 2022, 61, 4681–4689 CrossRef CAS PubMed.
- B. Yang, X. Li, Q. Zhang, X. Yang, J. Wan, G. Liao, J. Zhao, R. Wang, J. Liu, R. D. Rodriguez and X. Jia, Appl. Catal., B, 2022, 314, 121521 CrossRef CAS.
- B. Yang, Z. Wang, J. Zhao, X. Sun, R. Wang, G. Liao and X. Jia, Int. J. Hydrogen Energy, 2021, 46, 25436–25447 CrossRef CAS.
- Z.-R. Tan, Y.-Q. Xing, J.-Z. Cheng, G. Zhang, Z.-Q. Shen, Y.-J. Zhang, G. Liao, L. Chen and S.-Y. Liu, Chem. Sci., 2022, 13, 1725–1733 RSC.
- G. Liao, Y. Gong, L. Zhang, H. Gao, G.-J. Yang and B. Fang, Energy Environ. Sci., 2019, 12, 2080–2147 RSC.
- W.-J. Ong, L.-L. Tan, Y. H. Ng, S.-T. Yong and S.-P. Chai, Chem. Rev., 2016, 116, 7159–7329 CrossRef CAS PubMed.
- G. Liao, F. He, Q. Li, L. Zhong, R. Zhao, H. Che, H. Gao and B. Fang, Prog. Mater. Sci., 2020, 112, 100666 CrossRef CAS.
- G. Liao, C. Li, X. Li and B. Fang, Cell Rep. Phys. Sci., 2021, 2, 100355 CrossRef CAS.
- B. Yang, J. Han, Q. Zhang, G. Liao, W. Cheng, G. Ge, J. Liu, X. Yang, R. Wang and X. Jia, Carbon, 2023, 202, 348–357 CrossRef CAS.
- F. Su, Z. Wang, H. Cao, H. Xie, W. Tu, Y. Xiao, S. Shi, J. Chen, X. Jin and X. Y. Kong, Catal. Sci. Technol., 2023, 13, 1325–1334 RSC.
- V. Hasija, P. Raizada, A. Sudhaik, K. Sharma, A. Kumar, P. Singh, S. B. Jonnalagadda and V. K. Thakur, Appl. Mater. Today, 2019, 15, 494–524 CrossRef.
- T. Wu, Q. He, Z. Liu, B. Shao, Q. Liang, Y. Pan, J. Huang, Z. Peng, Y. Liu, C. Zhao, X. Yuan, L. Tang and S. Gong, J. Hazard. Mater., 2022, 424, 127177 CrossRef CAS PubMed.
- Y. Pan, X. Liu, W. Zhang, B. Shao, Z. Liu, Q. Liang, T. Wu, Q. He, J. Huang, Z. Peng, Y. Liu and C. Zhao, Chem. Eng. J., 2022, 427, 132032 CrossRef CAS.
- Q. Liang, X. Liu, B. Shao, L. Tang, Z. Liu, W. Zhang, S. Gong, Y. Liu, Q. He, T. Wu, Y. Pan and S. Tong, Chem. Eng. J., 2021, 426, 130831 CrossRef CAS.
- Q. Liang, B. Shao, S. Tong, Z. Liu, L. Tang, Y. Liu, M. Cheng, Q. He, T. Wu, Y. Pan, J. Huang and Z. Peng, Chem. Eng. J., 2021, 405, 126951 CrossRef CAS.
- Z. Zhou, Y. Zhang, Y. Shen, S. Liu and Y. Zhang, Chem. Soc. Rev., 2018, 47, 2298–2321 RSC.
- Y. Bai, Y. Zheng, Z. Wang, Q. Hong, S. Liu, Y. Shen and Y. Zhang, New J. Chem., 2021, 45, 11876–11892 RSC.
- H. Yang, Z. Wang, S. Liu, Y. Shen and Y. Zhang, Chin. Chem. Lett., 2020, 31, 3047–3054 CrossRef CAS.
- H. L. Tan, F. F. Abdi and Y. H. Ng, Chem. Soc. Rev., 2019, 48, 1255–1271 RSC.
- S. Wang, G. Liu and L. Wang, Chem. Rev., 2019, 119, 5192–5247 CrossRef CAS PubMed.
- B. He, M. Feng, X. Chen, D. Zhao and J. Sun, Appl. Surf. Sci., 2020, 527, 146737 CrossRef CAS.
- G. Liao, C. Li, S.-Y. Liu, B. Fang and H. Yang, Phys. Rep., 2022, 983, 1–41 CrossRef CAS.
- G. Liao, C. Li, S.-Y. Liu, B. Fang and H. Yang, Trends Chem., 2022, 4, 111–127 CrossRef CAS.
- C. Bie, B. Cheng, J. Fan, W. Ho and J. Yu, EnergyChem, 2021, 3, 100051 CrossRef CAS.
- J. Fu, B. Zhu, C. Jiang, B. Cheng, W. You and J. Yu, Small, 2017, 13, 1603938 CrossRef PubMed.
- Y. Jiang, Z. Sun, C. Tang, Y. Zhou, L. Zeng and L. Huang, Appl. Catal., B, 2019, 240, 30–38 CrossRef CAS.
- H. Che, C. Liu, G. Che, G. Liao, H. Dong, C. Li, N. Song and C. Li, Nano Energy, 2020, 67, 104273 CrossRef CAS.
- X. Chen, R. Shi, Q. Chen, Z. Zhang, W. Jiang, Y. Zhu and T. Zhang, Nano Energy, 2019, 59, 644–650 CrossRef CAS.
- K. Schwinghammer, M. B. Mesch, V. Duppel, C. Ziegler, J. Senker and B. V. Lotsch, J. Am. Chem. Soc., 2014, 136, 1730–1733 CrossRef CAS PubMed.
- O. Fontelles-Carceller, M. J. Muñoz-Batista, M. Fernández-García and A. Kubacka, ACS Appl. Mater. Interfaces, 2016, 8, 2617–2627 CrossRef CAS PubMed.
- J. Xue, S. Ma, Y. Zhou, Z. Zhang and M. He, ACS Appl. Mater. Interfaces, 2015, 7, 9630–9637 CrossRef CAS PubMed.
- X.-J. Wang, W.-Y. Yang, F.-T. Li, Y.-B. Xue, R.-H. Liu and Y.-J. Hao, Ind. Eng. Chem. Res., 2013, 52, 17140–17150 CrossRef CAS.
- K. Wang, J. Li and G. Zhang, ACS Appl. Mater. Interfaces, 2019, 11, 27686–27696 CrossRef CAS PubMed.
- J. Wang, Y. Chen, Y. Shen, S. Liu and Y. Zhang, Chem. Commun., 2017, 53, 2978–2981 RSC.
- L. Acharya, S. P. Pattnaik, A. Behera, R. Acharya and K. Parida, Inorg. Chem., 2021, 60, 5021–5033 CrossRef CAS PubMed.
- S. P. Pattnaik, A. Behera, S. Martha, R. Acharya and K. Parida, J. Mater. Sci., 2019, 54, 5726–5742 CrossRef CAS.
- L. Acharya, B. P. Mishra, S. P. Pattnaik, R. Acharya and K. Parida, New J. Chem., 2022, 46, 3493–3503 RSC.
- Z. Wang, M. Xiao, J. You, G. Liu and L. Wang, Acc. Mater. Res., 2022, 3, 1127–1136 CrossRef CAS.
- J. Ma, X. Peng, Z. Zhou, H. Yang, K. Wu, Z. Fang, D. Han, Y. Fang, S. Liu, Y. Shen and Y. Zhang, Angew. Chem., Int. Ed., 2022, 61, e202210856 CAS.
- P. Kumar, E. Vahidzadeh, U. K. Thakur, P. Kar, K. M. Alam, A. Goswami, N. Mahdi, K. Cui, G. M. Bernard, V. K. Michaelis and K. Shankar, J. Am. Chem. Soc., 2019, 141, 5415–5436 CrossRef CAS PubMed.
- H. Yang, Q. Zhou, Z. Fang, W. Li, Y. Zheng, J. Ma, Z. Wang, L. Zhao, S. Liu, Y. Shen and Y. Zhang, Chem, 2021, 7, 2708–2721 CAS.
- J. Mahmood, E. K. Lee, M. Jung, D. Shin, H.-J. Choi, J.-M. Seo, S.-M. Jung, D. Kim, F. Li, M. S. Lah, N. Park, H.-J. Shin, J. H. Oh and J.-B. Baek, Proc. Natl. Acad. Sci. U. S. A., 2016, 113, 7414–7419 CrossRef CAS PubMed.
- H. Wang, L. Zhang, Z. Chen, J. Hu, S. Li, Z. Wang, J. Liu and X. Wang, Chem. Soc. Rev., 2014, 43, 5234–5244 RSC.
- J. Fu, J. Yu, C. Jiang and B. Cheng, Adv. Energy Mater., 2018, 8, 1701503 CrossRef.
- J. Low, J. Yu, M. Jaroniec, S. Wageh and A. A. Al-Ghamdi, Adv. Mater., 2017, 29, 1601694 CrossRef PubMed.
- J. Yu, S. Wang, J. Low and W. Xiao, Phys. Chem. Chem. Phys., 2013, 15, 16883–16890 RSC.
- J. Low, C. Jiang, B. Cheng, S. Wageh, A. A. Al-Ghamdi and J. Yu, Small Methods, 2017, 1, 1700080 CrossRef.
- K. Qi, B. Cheng, J. Yu and W. Ho, Chin. J. Catal., 2017, 38, 1936–1955 CrossRef CAS.
- Q. Xu, L. Zhang, J. Yu, S. Wageh, A. A. Al-Ghamdi and M. Jaroniec, Mater. Today, 2018, 21, 1042–1063 CrossRef CAS.
- J. Wen, J. Xie, X. Chen and X. Li, Appl. Surf. Sci., 2017, 391, 72–123 CrossRef CAS.
- D. Masih, Y. Ma and S. Rohani, Appl. Catal., B, 2017, 206, 556–588 CrossRef CAS.
- Z. Zhao, Y. Sun and F. Dong, Nanoscale, 2015, 7, 15–37 RSC.
- M. Inagaki, T. Tsumura, T. Kinumoto and M. Toyoda, Carbon, 2019, 141, 580–607 CrossRef CAS.
- B. Zhu, L. Zhang, B. Cheng and J. Yu, Appl. Catal., B, 2018, 224, 983–999 CrossRef CAS.
- S. Zhang, P. Gu, R. Ma, C. Luo, T. Wen, G. Zhao, W. Cheng and X. Wang, Catal. Today, 2019, 335, 65–77 CrossRef CAS.
- M. Xiao, B. Luo, S. Wang and L. Wang, J. Energy Chem., 2018, 27, 1111–1123 CrossRef.
- C. Zhang, Y. Li, D. Shuai, Y. Shen, W. Xiong and L. Wang, Chemosphere, 2019, 214, 462–479 CrossRef CAS PubMed.
- A. Nikokavoura and C. Trapalis, Appl. Surf. Sci., 2018, 430, 18–52 CrossRef CAS.
- F. Bairamis, I. Rapti and I. Konstantinou, Curr. Opin. Green Sustainable Chem., 2022, 100749 Search PubMed.
- J. Jia, Q. Zhang, K. Li, Y. Zhang, E. Liu and X. Li, Int. J. Hydrogen Energy, 2023, 48, 196–231 CrossRef CAS.
- J. Fernández-Catalá, R. Greco, M. Navlani-García, W. Cao, Á. Berenguer-Murcia and D. Cazorla-Amorós, Catalysts, 2022, 12, 1137 CrossRef.
- M. Li, L. Zhang, M. Wu, Y. Du, X. Fan, M. Wang, L. Zhang, Q. Kong and J. Shi, Nano Energy, 2016, 19, 145–155 CrossRef CAS.
- P. Qiu, H. Chen and F. Jiang, RSC Adv., 2014, 4, 39969–39977 RSC.
- J. Chen, S. Shen, P. Guo, M. Wang, P. Wu, X. Wang and L. Guo, Appl. Catal., B, 2014, 152–153, 335–341 CrossRef CAS.
- X. Liu, A. Jin, Y. Jia, J. Jiang, N. Hu and X. Chen, RSC Adv., 2015, 5, 92033–92041 RSC.
- J. Zhang, M. Zhang, R.-Q. Sun and X. Wang, Angew. Chem., Int. Ed., 2012, 51, 10145–10149 CrossRef CAS PubMed.
- L. Sun, W. Wang, C. Zhang, M. Cheng, Y. Zhou, Y. Yang, H. Luo, D. Qin, C. Huang and Z. Ouyang, Chem. Eng. J., 2022, 446, 137027 CrossRef CAS.
- T. Su, Z. Qin, H. Ji and Z. Wu, Nanotechnology, 2019, 30, 502002 CrossRef CAS PubMed.
- K. Li, F.-Y. Su and W.-D. Zhang, Appl. Surf. Sci., 2016, 375, 110–117 CrossRef CAS.
- X. Li, J. Yu, J. Low, Y. Fang, J. Xiao and X. Chen, J. Mater. Chem. A, 2015, 3, 2485–2534 RSC.
- T. Su, Q. Shao, Z. Qin, Z. Guo and Z. Wu, ACS Catal., 2018, 8, 2253–2276 CrossRef CAS.
- S. J. A. Moniz, S. A. Shevlin, D. J. Martin, Z.-X. Guo and J. Tang, Energy Environ. Sci., 2015, 8, 731–759 RSC.
- K. Maeda, ACS Catal., 2013, 3, 1486–1503 CrossRef CAS.
- Z. Li, G. Weng, Q. Zou, G. Cong and Y.-C. Lu, Nano Energy, 2016, 30, 283–292 CrossRef CAS.
- D. Huang, S. Chen, G. Zeng, X. Gong, C. Zhou, M. Cheng, W. Xue, X. Yan and J. Li, Coord. Chem. Rev., 2019, 385, 44–80 CrossRef CAS.
- X. Cao, Z. Chen, R. Lin, W.-C. Cheong, S. Liu, J. Zhang, Q. Peng, C. Chen, T. Han, X. Tong, Y. Wang, R. Shen, W. Zhu, D. Wang and Y. Li, Nat. Catal., 2018, 1, 704–710 CrossRef CAS.
- Y.-C. Zhang, N. Afzal, L. Pan, X. Zhang and J.-J. Zou, Adv. Sci., 2019, 6, 1900053 CrossRef PubMed.
- R. He, D. Xu, B. Cheng, J. Yu and W. Ho, Nanoscale Horiz., 2018, 3, 464–504 RSC.
- D. Zheng, C. Pang and X. Wang, Chem. Commun., 2015, 51, 17467–17470 RSC.
- Y. Hong, Y. Jiang, C. Li, W. Fan, X. Yan, M. Yan and W. Shi, Appl. Catal., B, 2016, 180, 663–673 CrossRef CAS.
- W. Yu, D. Xu and T. Peng, J. Mater. Chem. A, 2015, 3, 19936–19947 RSC.
- K. Kailasam, A. Fischer, G. Zhang, J. Zhang, M. Schwarze, M. Schröder, X. Wang, R. Schomäcker and A. Thomas, ChemSusChem, 2015, 8, 1404–1410 CrossRef CAS PubMed.
- S. Meng, X. Ning, T. Zhang, S.-F. Chen and X. Fu, Phys. Chem. Chem. Phys., 2015, 17, 11577–11585 RSC.
- N. Tian, H. Huang, Y. He, Y. Guo, T. Zhang and Y. Zhang, Dalton Trans., 2015, 44, 4297–4307 RSC.
- M. Li, L. Zhang, X. Fan, Y. Zhou, M. Wu and J. Shi, J. Mater. Chem. A, 2015, 3, 5189–5196 RSC.
- Y. Bai, P.-Q. Wang, J.-Y. Liu and X.-J. Liu, RSC Adv., 2014, 4, 19456–19461 RSC.
- Y. Feng, J. Shen, Q. Cai, H. Yang and Q. Shen, New J. Chem., 2015, 39, 1132–1138 RSC.
- H. Cheng, J. Hou, O. Takeda, X.-M. Guo and H. Zhu, J. Mater. Chem. A, 2015, 3, 11006–11013 RSC.
- H. Li, H. Yu, X. Quan, S. Chen and Y. Zhang, ACS Appl. Mater. Interfaces, 2016, 8, 2111–2119 CrossRef CAS PubMed.
- Y. Yang, W. Guo, Y. Guo, Y. Zhao, X. Yuan and Y. Guo, J. Hazard. Mater., 2014, 271, 150–159 CrossRef CAS PubMed.
- F. Shi, L. Chen, M. Chen and D. Jiang, Chem. Commun., 2015, 51, 17144–17147 RSC.
- W. Yin, L. Bai, Y. Zhu, S. Zhong, L. Zhao, Z. Li and S. Bai, ACS Appl. Mater. Interfaces, 2016, 8, 23133–23142 CrossRef CAS PubMed.
- Y. Wu, H. Wang, W. Tu, Y. Liu, Y. Z. Tan, X. Yuan and J. W. Chew, J. Hazard. Mater., 2018, 347, 412–422 CrossRef CAS PubMed.
- S. Shenoy, C. Chuaicham, T. Okumura, K. Sekar and K. Sasaki, Chem. Eng. J., 2023, 453, 139758 CrossRef CAS.
- C. Liu, S. Sun, M. Yu, Y. Zhou, X. Zhang and J. Niu, Sep. Purif. Technol., 2023, 311, 123359 CrossRef CAS.
- L. Sruthi, B. Janani and S. Sudheer Khan, Sep. Purif. Technol., 2021, 279, 119709 CrossRef CAS.
- S. Zhu and D. Wang, Adv. Energy Mater., 2017, 7, 1700841 CrossRef.
- T. Di, Q. Xu, W. Ho, H. Tang, Q. Xiang and J. Yu, ChemCatChem, 2019, 11, 1394–1411 CrossRef CAS.
- J. K. Stolarczyk, S. Bhattacharyya, L. Polavarapu and J. Feldmann, ACS Catal., 2018, 8, 3602–3635 CrossRef CAS.
- W. Yu, J. Chen, T. Shang, L. Chen, L. Gu and T. Peng, Appl. Catal., B, 2017, 219, 693–704 CrossRef CAS.
- R. Ye, H. Fang, Y.-Z. Zheng, N. Li, Y. Wang and X. Tao, ACS Appl. Mater. Interfaces, 2016, 8, 13879–13889 CrossRef CAS PubMed.
- K. Wenderich and G. Mul, Chem. Rev., 2016, 116, 14587–14619 CrossRef CAS PubMed.
- Q. Xu, B. Zhu, C. Jiang, B. Cheng and J. Yu, Sol. RRL, 2018, 2, 1800006 CrossRef.
- G. Liao, L. Zhang, C. Li, S.-Y. Liu, B. Fang and H. Yang, Matter, 2022, 5, 3341–3374 CrossRef CAS.
- X. Li, T. Liu, Y. Zhang, J. Cai, M. He, M. Li, Z. Chen and L. Zhang, Adv. Fiber Mater., 2022, 4, 1620–1631 CrossRef CAS.
- H. Zhai, Z. Liu, L. Xu, T. Liu, Y. Fan, L. Jin, R. Dong, Y. Yi and Y. Li, Adv. Fiber Mater., 2022, 4, 1595–1608 CrossRef CAS.
- Z. Qin, M. Qiu, Q. Zhang, S. Yang, G. Liao, Z. Xiong and Z. Xu, J. Mater. Chem. B, 2021, 9, 8882–8896 RSC.
- Y. Zou, F. Sun, C. Liu, C. Yu, M. Zhang, Q. He, Y. Xiong, Z. Xu, S. Yang and G. Liao, Chem. Eng. J., 2019, 357, 237–247 CrossRef CAS.
- Y. Zhao, G. I. N. Waterhouse, G. Chen, X. Xiong, L.-Z. Wu, C.-H. Tung and T. Zhang, Chem. Soc. Rev., 2019, 48, 1972–2010 RSC.
- P. Xia, B. Zhu, B. Cheng, J. Yu and J. Xu, ACS Sustainable Chem. Eng., 2018, 6, 965–973 CrossRef CAS.
- R. Acharya, S. Pati and K. Parida, J. Mol. Liq., 2022, 357, 119105 CrossRef CAS.
- H. S. Moon, K.-C. Hsiao, M.-C. Wu, Y. Yun, Y.-J. Hsu and K. Yong, Adv. Mater., 2023, 35, 2200172 CrossRef CAS PubMed.
- H. Li, Y. Gao, Y. Zhou, F. Fan, Q. Han, Q. Xu, X. Wang, M. Xiao, C. Li and Z. Zou, Nano Lett., 2016, 16, 5547–5552 CrossRef CAS PubMed.
- Y. Jiang, H.-Y. Chen, J.-Y. Li, J.-F. Liao, H.-H. Zhang, X.-D. Wang and D.-B. Kuang, Adv. Funct. Mater., 2020, 30, 2004293 CrossRef CAS.
- X. Xia, M. Song, H. Wang, X. Zhang, N. Sui, Q. Zhang, V. L. Colvin and W. Y. William, Nanoscale, 2019, 11, 11071–11082 RSC.
- Y. Jiang, J.-F. Liao, H.-Y. Chen, H.-H. Zhang, J.-Y. Li, X.-D. Wang and D.-B. Kuang, Chem, 2020, 6, 766–780 CAS.
- R. Chen, H. Yin, L. Wang, Z. Zhang, J. Ding, J. Zhang, H. Wan and G. Guan, J. Colloid Interface Sci., 2023, 631, 122–132 CrossRef CAS PubMed.
- B. Nian, G. Liao, Y. Song, Y. Su, C. Cao and Y. Liu, J. Catal., 2020, 384, 159–168 CrossRef CAS.
- G. Liao, Z. Xiao, X. Chen, C. Du, L. Zhong, C. S. Cheung and H. Gao, Macromolecules, 2020, 53, 256–266 CrossRef CAS.
- W. Yu, J. Zhang and T. Peng, Appl. Catal., B, 2016, 181, 220–227 CrossRef CAS.
- X. Wang, J. Song, Y. Lu, W. Zhu and G. Hu, J. Mater. Sci.: Mater. Electron., 2021, 32, 2061–2074 CrossRef CAS.
- P. Murugesan, S. Narayanan, M. Manickam, P. K. Murugesan and R. Subbiah, Appl. Surf. Sci., 2018, 450, 516–526 CrossRef CAS.
- F. Wang, W. Li, S. Gu, H. Li, X. Wu, C. Ren and X. Liu, J. Photochem. Photobiol., A, 2017, 335, 140–148 CrossRef CAS.
- A. H. Mamaghani, F. Haghighat and C.-S. Lee, Appl. Catal., B, 2020, 269, 118735 CrossRef CAS.
- Q. Li, G. Liao, S. Zhang, L. Pang, H. Tong, W. Zhao and Z. Xu, Appl. Surf. Sci., 2018, 427, 437–450 CrossRef CAS.
- P. Xu and G. Liao, Materials, 2018, 11, 1616 CrossRef PubMed.
- Z. Mo, X. Pan, X. Pan, L. Ye, H. Hu, Q. Xu, X. Hu, Z. Xu, J. Xiong, G. Liao and S. Yang, J. Mater. Chem. B, 2022, 10, 8760–8770 RSC.
- L. Zhang, G. Oudeng, F. Wen and G. Liao, Biomater. Res., 2022, 26, 61 CrossRef CAS PubMed.
- W. Chen, T.-Y. Liu, T. Huang, X.-H. Liu, J.-W. Zhu, G.-R. Duan and X.-J. Yang, Appl. Surf. Sci., 2015, 355, 379–387 CrossRef CAS.
- S. T. Aruna and A. S. Mukasyan, Curr. Opin. Solid State Mater. Sci., 2008, 12, 44–50 CrossRef CAS.
- X. Xia, M. Song, H. Wang, X. Zhang, N. Sui, Q. Zhang, V. L. Colvin and W. W. Yu, Nanoscale, 2019, 11, 11071–11082 RSC.
- L. Jiang, X. Yuan, G. Zeng, J. Liang, X. Chen, H. Yu, H. Wang, Z. Wu, J. Zhang and T. Xiong, Appl. Catal., B, 2018, 227, 376–385 CrossRef CAS.
- S. Liu, J. Chen, D. Xu, X. Zhang and M. Shen, J. Mater. Res., 2018, 33, 1391–1400 CrossRef CAS.
- L. Lu, G. Wang, M. Zou, J. Wang and J. Li, Appl. Surf. Sci., 2018, 441, 1012–1023 CrossRef CAS.
- J. B. Rivest and P. K. Jain, Chem. Soc. Rev., 2013, 42, 89–96 RSC.
- R. K. Khamizov, V. A. Ivanov and A. A. Madani, React. Funct. Polym., 2010, 70, 521–530 CrossRef CAS.
- J. Wu, S. Nie, H. Liu, C. Gong, Q. Zhang, Z. Xu and G. Liao, J. Mater. Chem. A, 2022, 10, 19914–19924 RSC.
- H. Zhao, X. Ding, B. Zhang, Y. Li and C. Wang, Sci. Bull., 2017, 62, 602–609 CrossRef CAS PubMed.
- J. Liang, H. Zhao, L. Yue, G. Fan, T. Li, S. Lu, G. Chen, S. Gao, A. M. Asiri and X. Sun, J. Mater. Chem. A, 2020, 8, 16747–16789 RSC.
- C. Bavatharani, E. Muthusankar, S. M. Wabaidur, Z. A. Alothman, K. M. Alsheetan, M. M. Al-Anazy and D. Ragupathy, Synth. Met., 2021, 271, 116609 CrossRef CAS.
- R. C. Pawar, S. Kang, J. H. Park, J.-H. Kim, S. Ahn and C. S. Lee, Sci. Rep., 2016, 6, 31147 CrossRef CAS PubMed.
- M. Nehra, N. Dilbaghi, G. Marrazza, A. Kaushik, R. Abolhassani, Y. K. Mishra, K. H. Kim and S. Kumar, Nano Energy, 2020, 76, 104991 CrossRef CAS.
- L. Hu, J. Yan, C. Wang, B. Chai and J. Li, Chin. J. Catal., 2019, 40, 458–469 CrossRef CAS.
- H. Cölfen and S. Mann, Angew. Chem., Int. Ed., 2003, 42, 2350–2365 CrossRef PubMed.
- J. Peet, A. J. Heeger and G. C. Bazan, Acc. Chem. Res., 2009, 42, 1700–1708 CrossRef CAS PubMed.
- Z. Yan, G. Liao, X. Zou, M. Zhao, T. Wu, Y. Chen and G. Fang, J. Agric. Food Chem., 2020, 68, 8341–8349 CrossRef CAS PubMed.
- Z. Yan, B. Song, G. Fang, T. Wu, N. Chen, M. Zhao, X. Zou and G. Liao, ACS Sustainable Chem. Eng., 2021, 9, 10403–10423 CrossRef CAS.
- N. Nie, L. Zhang, J. Fu, B. Cheng and J. Yu, Appl. Surf. Sci., 2018, 441, 12–22 CrossRef CAS.
- S. Kumar, A. Baruah, S. Tonda, B. Kumar, V. Shanker and B. Sreedhar, Nanoscale, 2014, 6, 4830–4842 RSC.
- Y. Lin, S. Yang, Y. Liu, S. Zhang, H. Wang, H. Yu and F. Peng, Int. J. Hydrogen Energy, 2017, 42, 19942–19950 CrossRef CAS.
- Z. Gan, C. Huang, Y. Shen, Q. Zhou, D. Han, J. Ma, S. Liu and Y. Zhang, Chin. Chem. Lett., 2020, 31, 513–516 CrossRef CAS.
- C. Huang, Y. Wen, J. Ma, D. Dong, Y. Shen, S. Liu, H. Ma and Y. Zhang, Nat. Commun., 2021, 12, 320 CrossRef CAS PubMed.
- R. He, J. Zhou, H. Fu, S. Zhang and C. Jiang, Appl. Surf. Sci., 2018, 430, 273–282 CrossRef CAS.
- Y. Xue, Z. Wu, X. He, Q. Li, X. Yang and L. Li, J. Colloid Interface Sci., 2019, 548, 293–302 CrossRef CAS PubMed.
- D. Ni, H. Shen, H. Li, Y. Ma and T. Zhai, Appl. Surf. Sci., 2017, 409, 241–249 CrossRef CAS.
- D. Zhou, B. Yu, Q. Chen, H. Shi, Y. Zhang, D. Li, X. Yang, W. Zhao, C. Liu, G. Wei and Z. Chen, Mater. Res. Bull., 2020, 124, 110757 CrossRef CAS.
- A. Abdolhoseinzadeh and S. Sheibani, Adv. Powder Technol., 2020, 31, 40–50 CrossRef CAS.
- D. Majhi, K. Das, R. Bariki, S. Padhan, A. Mishra, R. Dhiman, P. Dash, B. Nayak and B. G. Mishra, J. Mater. Chem. A, 2020, 8, 21729–21743 RSC.
- M. S. Khan, F. Zhang, M. Osada, S. S. Mao and S. Shen, Sol. RRL, 2020, 4, 1900435 CrossRef CAS.
- T. Ohno, N. Murakami, T. Koyanagi and Y. Yang, J. CO2 Util., 2014, 6, 17–25 CrossRef CAS.
- U. Ghosh and A. Pal, J. Ind. Eng. Chem., 2019, 79, 383–408 CrossRef CAS.
- M. Pang, J. Hu and H. C. Zeng, J. Am. Chem. Soc., 2010, 132, 10771–10785 CrossRef CAS PubMed.
- T. Zhang, M. Long, K. Yan, M. Qin, X. Lu, X. Zeng, C. M. Cheng, K. S. Wong, P. Liu, W. Xie and J. Xu, Adv. Energy Mater., 2017, 7, 1700118 CrossRef.
- W. Deng, X. Zhang, H. Dong, J. Jie, X. Xu, J. Liu, L. He, L. Xu, W. Hu and X. Zhang, Mater. Today, 2019, 24, 17–25 CrossRef CAS.
- D. F. Fletcher and G. J. Brown, Int. J. Comput. Fluid Dyn., 2009, 23, 173–187 CrossRef.
- R. Das, C. D. Vecitis, A. Schulze, B. Cao, A. F. Ismail, X. Lu, J. Chen and S. Ramakrishna, Chem. Soc. Rev., 2017, 46, 6946–7020 RSC.
- G. Liao, J. Chen, W. Zeng, C. Yu, C. Yi and Z. Xu, J. Phys. Chem. C, 2016, 120, 25935–25944 CrossRef CAS.
- G. Liao, Q. Li, W. Zhao, Q. Pang, H. Gao and Z. Xu, Appl. Catal., A, 2018, 549, 102–111 CrossRef CAS.
- G. Liao, J. Fang, Q. Li, S. Li, Z. Xu and B. Fang, Nanoscale, 2019, 11, 7062–7096 RSC.
- G. Liao, W. Zhao, Q. Li, Q. Pang and Z. Xu, Chem. Lett., 2017, 46, 1631–1634 CrossRef CAS.
- G. Liao, Y. Gong, L. Zhong, J. Fang, L. Zhang, Z. Xu, H. Gao and B. Fang, Nano Res., 2019, 12, 2407–2436 CrossRef CAS.
- H. Zhu, C. Zhang, K. Xie, X. Li and G. Liao, Chem. Eng. J., 2023, 453, 139775 CrossRef CAS.
- L. Acharya, S. Nayak, S. P. Pattnaik, R. Acharya and K. Parida, J. Colloid Interface Sci., 2020, 566, 211–223 CrossRef CAS PubMed.
- X. Zhang, S. Tong, D. Huang, Z. Liu, B. Shao, Q. Liang, T. Wu, Y. Pan, J. Huang, Y. Liu, M. Cheng and M. Chen, Coord. Chem. Rev., 2021, 448, 214177 CrossRef CAS.
- M. Z. Rahman and C. B. Mullins, Acc. Chem. Res., 2019, 52, 248–257 CrossRef CAS PubMed.
- R. Qian, H. Zong, J. Schneider, G. Zhou, T. Zhao, Y. Li, J. Yang, D. W. Bahnemann and J. H. Pan, Catal. Today, 2019, 335, 78–90 CrossRef CAS.
- G. Liao, X. Tao and B. Fang, Matter, 2022, 5, 377–379 CrossRef CAS.
- D. Zhou, Z. Chen, Q. Yang, C. Shen, G. Tang, S. Zhao, J. Zhang, D. Chen, Q. Wei and X. Dong, ChemCatChem, 2016, 8, 3064–3073 CrossRef CAS.
- Y. Li, K. Lv, W. Ho, F. Dong, X. Wu and Y. Xia, Appl. Catal., B, 2017, 202, 611–619 CrossRef CAS.
- H. L. Tan, X. Wen, R. Amal and Y. H. Ng, J. Phys. Chem. Lett., 2016, 7, 1400–1405 CrossRef CAS PubMed.
- R. Rajendran, S. Vignesh, S. Suganthi, V. Raj, G. Kavitha, B. Palanivel, M. Shkir and H. Algarni, J. Phys. Chem. Solids, 2022, 161, 110391 CrossRef CAS.
- Z. A. Huang, Q. Sun, K. Lv, Z. Zhang, M. Li and B. Li, Appl. Catal., B, 2015, 164, 420–427 CrossRef CAS.
- C. P. Sajan, S. Wageh, A. A. Al-Ghamdi, J. Yu and S. Cao, Nano Res., 2016, 9, 3–27 CrossRef CAS.
- A. Srinivasan and M. Miyauchi, J. Phys. Chem. C, 2012, 116, 15421–15426 CrossRef CAS.
- Z.-F. Huang, J. Song, L. Pan, X. Zhang, L. Wang and J.-J. Zou, Adv. Mater., 2015, 27, 5309–5327 CrossRef CAS PubMed.
- S. Chen, Y. Hu, X. Jiang, S. Meng and X. Fu, Mater. Chem. Phys., 2015, 149–150, 512–521 CrossRef CAS.
- X. Liu, A. Jin, Y. Jia, T. Xia, C. Deng, M. Zhu, C. Chen and X. Chen, Appl. Surf. Sci., 2017, 405, 359–371 CrossRef CAS.
- L. Cui, X. Ding, Y. Wang, H. Shi, L. Huang, Y. Zuo and S. Kang, Appl. Surf. Sci., 2017, 391, 202–210 CrossRef CAS.
- B. Chai, C. Liu, J. Yan, Z. Ren and Z.-J. Wang, Appl. Surf. Sci., 2018, 448, 1–8 CrossRef CAS.
- C. Zhao, F. Ran, L. Dai, C. Li, C. Zheng and C. Si, Carbohydr. Polym., 2021, 255, 117343 CrossRef CAS PubMed.
- S.-L. Chiam, S.-Y. Pung and F.-Y. Yeoh, Environ. Sci. Pollut. Res., 2020, 27, 5759–5778 CrossRef CAS PubMed.
- J. Liu, B. Cheng and J. Yu, Phys. Chem. Chem. Phys., 2016, 18, 31175–31183 RSC.
- L. Sun, Y. Qi, C.-J. Jia, Z. Jin and W. Fan, Nanoscale, 2014, 6, 2649–2659 RSC.
- D. Xu, B. Cheng, S. Cao and J. Yu, Appl. Catal., B, 2015, 164, 380–388 CrossRef CAS.
- S. Sakthivel and H. Kisch, Angew. Chem., Int. Ed., 2003, 42, 4908–4911 CrossRef CAS PubMed.
- J. Zhang, Y. Hu, X. Jiang, S. Chen, S. Meng and X. Fu, J. Hazard. Mater., 2014, 280, 713–722 CrossRef CAS PubMed.
- Y. Yang, B. Tan and C. D. Wood, J. Mater. Chem. A, 2016, 4, 15072–15080 RSC.
- J. Li, H. Yuan and Z. Zhu, Appl. Surf. Sci., 2016, 385, 34–41 CrossRef CAS.
- L. Zhang, G. Wang, Z. Xiong, H. Tang and C. Jiang, Appl. Surf. Sci., 2018, 436, 162–171 CrossRef CAS.
- M. Sun, Y. Wang, Y. Shao, Y. He, Q. Zeng, H. Liang, T. Yan and B. Du, J. Colloid Interface Sci., 2017, 501, 123–132 CrossRef CAS PubMed.
- G. Long, J. Ding, L. Xie, R. Sun, M. Chen, Y. Zhou, X. Huang, G. Han, Y. Li and W. Zhao, Appl. Surf. Sci., 2018, 455, 1010–1018 CrossRef CAS.
- D. Ma, J. Wu, M. Gao, Y. Xin, T. Ma and Y. Sun, Chem. Eng. J., 2016, 290, 136–146 CrossRef CAS.
- B. Chong, L. Chen, W. Wang, D. Han, L. Wang, L. Feng, Q. Li and C. Li, Mater. Lett., 2017, 204, 149–153 CrossRef CAS.
- H. Che, G. Che, H. Dong, W. Hu, H. Hu, C. Liu and C. Li, Appl. Surf. Sci., 2018, 455, 705–716 CrossRef CAS.
- Y. Bao and K. Chen, Appl. Surf. Sci., 2018, 437, 51–61 CrossRef CAS.
- Z. Wan, G. Zhang, X. Wu and S. Yin, Appl. Catal., B, 2017, 207, 17–26 CrossRef CAS.
- T. Ma, J. Wu, Y. Mi, Q. Chen, D. Ma and C. Chai, Sep. Purif. Technol., 2017, 183, 54–65 CrossRef CAS.
- H. Huang, K. Xiao, Y. He, T. Zhang, F. Dong, X. Du and Y. Zhang, Appl. Catal., B, 2016, 199, 75–86 CrossRef CAS.
- H. Huang, X. Han, X. Li, S. Wang, P. K. Chu and Y. Zhang, ACS Appl. Mater. Interfaces, 2015, 7, 482–492 CrossRef CAS PubMed.
- H. Huang, R. Cao, S. Yu, K. Xu, W. Hao, Y. Wang, F. Dong, T. Zhang and Y. Zhang, Appl. Catal., B, 2017, 219, 526–537 CrossRef CAS.
- L. Zhou, W. Zhang, L. Chen and H. Deng, J. Colloid Interface Sci., 2017, 487, 410–417 CrossRef CAS PubMed.
- H. Katsumata, T. Sakai, T. Suzuki and S. Kaneco, Ind. Eng. Chem. Res., 2014, 53, 8018–8025 CrossRef CAS.
- B. Zhu, P. Xia, Y. Li, W. Ho and J. Yu, Appl. Surf. Sci., 2017, 391, 175–183 CrossRef CAS.
- Y. Deng, L. Tang, G. Zeng, J. Wang, Y. Zhou, J. Wang, J. Tang, Y. Liu, B. Peng and F. Chen, J. Mol. Catal. A: Chem., 2016, 421, 209–221 CrossRef CAS.
- X. Yang, Z. Chen, J. Xu, H. Tang, K. Chen and Y. Jiang, ACS Appl.
Mater. Interfaces, 2015, 7, 15285–15293 CrossRef CAS PubMed.
- Y. Gong, X. Quan, H. Yu and S. Chen, Appl. Catal., B, 2017, 219, 439–449 CrossRef CAS.
- S. Qin, Y. Lei, J. Guo, J.-F. Huang, C.-P. Hou and J.-M. Liu, ACS Appl. Mater. Interfaces, 2021, 13, 25960–25971 CrossRef CAS PubMed.
- G. Liao, C. Li and B. Fang, Matter, 2022, 5, 1635–1637 CrossRef CAS.
- Q. Qiao, W.-Q. Huang, Y.-Y. Li, B. Li, W. Hu, W. Peng, X. Fan and G.-F. Huang, J. Mater. Sci., 2018, 53, 15882–15894 CrossRef CAS.
- D. Lu, H. Wang, X. Zhao, K. K. Kondamareddy, J. Ding, C. Li and P. Fang, ACS Sustainable Chem. Eng., 2017, 5, 1436–1445 CrossRef CAS.
- J. Wang, Y. Xia, H. Zhao, G. Wang, L. Xiang, J. Xu and S. Komarneni, Appl. Catal., B, 2017, 206, 406–416 CrossRef CAS.
- W.-K. Jo and N. C. S. Selvam, Chem. Eng. J., 2017, 317, 913–924 CrossRef CAS.
- F. Wu, X. Li, W. Liu and S. Zhang, Appl. Surf. Sci., 2017, 405, 60–70 CrossRef CAS.
- Z. Xie, Y. Feng, F. Wang, D. Chen, Q. Zhang, Y. Zeng, W. Lv and G. Liu, Appl. Catal., B, 2018, 229, 96–104 CrossRef CAS.
- S. Hua, D. Qu, L. An, W. Jiang, Y. Wen, X. Wang and Z. Sun, Appl. Catal., B, 2019, 240, 253–261 CrossRef CAS.
- Z. Huang, X. Zeng, K. Li, S. Gao, Q. Wang and J. Lu, ACS Appl. Mater. Interfaces, 2017, 9, 41120–41125 CrossRef CAS PubMed.
- Y. He, L. Zhang, M. Fan, X. Wang, M. L. Walbridge, Q. Nong, Y. Wu and L. Zhao, Sol. Energy Mater. Sol. Cells, 2015, 137, 175–184 CrossRef CAS.
- Y. Li, S. Tan, Y. Meng, Y. Xia, L. Gao and W. Chen, J. Mater. Sci.: Mater. Electron., 2022, 33, 13887–13904 CrossRef CAS.
- D. Li, J. Huang, R. Li, P. Chen, D. Chen, M. Cai, H. Liu, Y. Feng, W. Lv and G. Liu, J. Hazard. Mater., 2021, 401, 123257 CrossRef CAS PubMed.
- F. Yu, F. Gong, Q. Yang and Y. Wang, Diamond Relat. Mater., 2022, 125, 109004 CrossRef CAS.
- A. Sudhaik, P. Raizada, A. A. P. Khan, A. Singh and P. Singh, Nanofabrication, 2022, 7, 280–313 CrossRef.
- G. Zhao, J. Ding, F. Zhou, X. Chen, L. Wei, Q. Gao, K. Wang and Q. Zhao, Chem. Eng. J., 2021, 405, 126704 CrossRef CAS.
- S. Das, T. Deka, P. Ningthoukhangjam, A. Chowdhury and R. G. Nair, Appl. Surf. Sci. Adv., 2022, 11, 100273 CrossRef.
- A. Kumar, P. Raizada, P. Singh, R. V. Saini, A. K. Saini and A. Hosseini-Bandegharaei, Chem. Eng. J., 2020, 391, 123496 CrossRef CAS.
|
This journal is © The Royal Society of Chemistry 2023 |
Click here to see how this site uses Cookies. View our privacy policy here.