DOI:
10.1039/D4CC02088J
(Feature Article)
Chem. Commun., 2024,
60, 8497-8515
Recent advances in continuous flow synthesis of metal–organic frameworks and their composites
Received
30th April 2024
, Accepted 26th June 2024
First published on 27th June 2024
Abstract
Metal–organic frameworks (MOFs) and their composites have garnered significant attention in recent years due to their exceptional properties and diverse applications across various fields. The conventional batch synthesis methods for MOFs and their composites often suffer from challenges such as long reaction times, poor reproducibility, and limited scalability. Continuous flow synthesis has emerged as a promising alternative for overcoming these limitations. In this short review, we discuss the recent advancements, challenges, and future perspectives of continuous flow synthesis in the context of MOFs and their composites. The review delves into a brief overview of the fundamental principles of flow synthesis, highlighting its advantages over batch methods. Key benefits, including precise control over reaction parameters, improved scalability and efficiency, rapid optimization capabilities, enhanced reaction kinetics and mass transfer, and increased safety and environmental sustainability, are addressed. Additionally, the versatility and flexibility of flow synthesis techniques are discussed. The article then explores various flow synthesis methods applicable to MOF and MOF composite production. The techniques covered include continuous flow solvothermal synthesis, mechanochemical synthesis, microwave and ultrasound-assisted flow synthesis, microfluidic droplet synthesis, and aerosol synthesis. Notably, the combination of flow chemistry and aerosol synthesis with real-time characterization is also addressed. Furthermore, the impact of flow synthesis on the properties and performance of MOFs is explored. Finally, the review discusses current challenges and future perspectives in the field of continuous flow MOF synthesis, paving the way for further development and broader application of this promising technique.
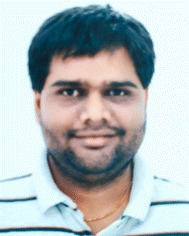
Duraisamy Senthil Raja
| Duraisamy Senthil Raja was born in the Tamil-speaking part of India, Erode, in 1985. After completing his MSc in Chemistry (2007) at Bharathiar University, he worked in the pharmaceutical industry for a year. Then, he moved back to Bharathiar University and did PhD in Bioinorganic Chemistry (2008–2012). He worked as postdoc with Prof. Chia-Her Lin, CYCU, Taiwan (2012–2017) on development of MOFs for functional applications. Later, he worked as postdoc with Prof. Shih-Yuan Lu, NTHU, Taiwan (2017–2023) on MOF-based/-derived materials for energy applications. From August 2023 on, he joined Prof. De-Hao Tsai's group as postdoc, working on MOF-based/-derived materials for catalytic applications. |
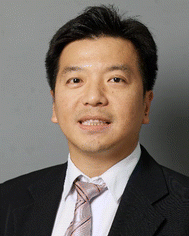
De-Hao Tsai
| De-Hao Tsai is a professor at the Department of Chemical Engineering, NTHU. He received his PhD degree from the University of Maryland (USA) and has worked at the National Institutes of Standards and Technology (USA) for many years. His research combines academic study and industrial applications, focusing on a combination of colloid & interface science, aerosol technology and chemical engineering to develop advanced nanomaterial dispersions used for specialized chemicals and energy & environmental applications. |
1. Introduction
Metal–organic frameworks (MOFs) have attracted significant interest in recent decades due to their exceptional properties and wide-ranging applications in the fields of gas storage, separation, catalysis, magnetism, sensing, energy storage and conversion, photoluminescence, drug delivery, environmental remediation and more.1–14 MOFs are composed of metal ions or clusters coordinated with organic ligands, forming highly porous crystalline structures.1–3,15 However, the inherent limitations of MOFs, such as poor mechanical stability, limited processability, and low conductivity, have spurred the development of MOF-based composites.16–18 MOF-based composites involve incorporating MOFs into matrices or combining them with other materials to create hybrid structures with synergistic properties.16–20 These composites leverage the unique features of both MOFs and the host materials, resulting in enhanced mechanical strength, improved stability, enhanced conductivity, or additional functionalities compared to pure MOFs.16–20 For instance, pristine MOFs have hardly been applied as direct catalysts for electrolytic water splitting applications due to their low conducting nature, lower stability under alkaline conditions and less mass permeability characteristics; however, the direct growth of MOFs on nickel foam (NF) to form MOF/NF composite materials showed outstanding electrocatalytic performances because of the positive synergistic effect between the conductive NF substrate and the MOFs.21–24 Predictably, the advantages and wide-ranging applications of MOFs and their composites have prompted their industrial-scale production.25,26 Pragmatically, MOFs can be bolstered through the efficient provision of top-quality products to facilitate their seamless formation and processing, as well as to yield MOFs with unparalleled properties. Nonetheless, to attain these objectives, three synthetic hurdles must be surmounted. Firstly, industrial-scale production necessitates the efficient synthesis of substantial quantities of high-quality MOFs.27 Unfortunately, such large-scale synthesis is time-consuming and tends to yield impurities like unreacted ligands, undesired complexes, or other MOFs, owing to the inherent variability of the reaction mixture. Moreover, the usage of large quantities of chemicals presents fire and explosion risks, rendering the scaling-up process challenging.26,28,29 Secondly, a technology incorporating continuous, adaptable processing is required to imbue the materials with the desired properties. While MOFs can be molded into various shapes to optimize their performance, bulk synthesis does not permit continuous product generation, thereby imposing certain constraints and underscoring the need for novel methods.28,30 Thirdly, MOFs exhibit a propensity to form polymorphs, leading to the production of unwanted MOFs as impurities. The MOF structure is known to be influenced by various factors such as reaction temperature and duration, yet it remains challenging to anticipate the conditions necessary for the selective and deliberate formation of any specific target structure.31–33 Therefore, ideally, one should possess the ability to deliberately choose the reaction pathway.
Conventional batch synthesis methods such as hydrothermal/solvothermal synthesis,34 sonochemical synthesis,35 mechanochemical synthesis,36 microwave-assisted synthesis37 and electrochemical synthesis38 have widely been used for the fabrication of MOFs due to their simplicity, versatility, and established protocols.39,40 While conventional batch synthesis methods have been traditionally employed for MOF production, they often encounter challenges such as lengthy reaction times, poor reproducibility, and difficulties in scale-up.32,39,40 Flow synthesis, also known as continuous flow synthesis or flow chemistry, involves the continuous addition of reagents into a reaction system, typically within a flow reactor or microfluidic device.32,39,41–43 Unlike batch synthesis, where reactions occur in a single vessel, flow synthesis allows for precise control over reaction parameters such as temperature, pressure, residence time, and flow rates.39,41,43 This enables improved mixing, heat transfer, and mass transfer, leading to enhanced reaction kinetics, product yields, and purity.32,39,41,43 Hence, here in, the review delves into the recent advances in continuous flow synthesis of MOFs and their composites (Fig. 1), highlighting key techniques, challenges and future prospects.
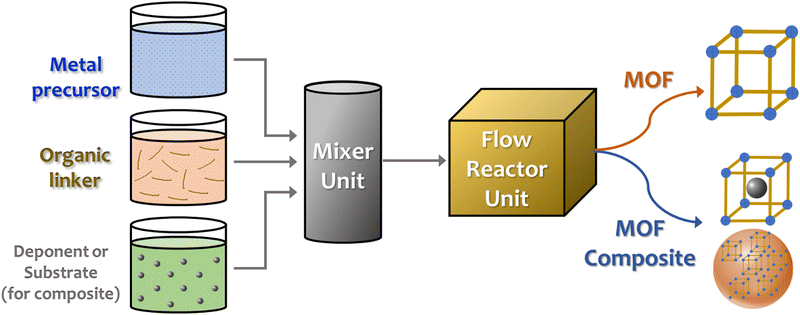 |
| Fig. 1 General schematic illustration of the continuous flow synthesis of MOFs and their composites. | |
2. Principles of flow synthesis
Flow chemistry, also known as continuous flow synthesis or microreactor technology, involves performing chemical reactions in a continuous stream of reagents flowing through a reactor system.44–47 Unlike batch reactors, where reagents are mixed in a single vessel and allowed to react over time, flow reactors enable precise control over reaction parameters such as temperature, pressure, residence time, and stoichiometry.45–48 The following are the main principles applied in flow synthesis.
2.1. Continuous flow reactors
Flow synthesis typically employs continuous flow reactors, where reagents are continuously pumped through a reaction chamber. This allows for precise control over reaction parameters such as temperature, pressure, and residence time, leading to improved reproducibility and scalability compared to batch synthesis.32
2.2. Precursor mixing and reaction
In flow synthesis, precise control over precursor mixing is crucial to ensure uniform nucleation and crystal growth. Various mixing strategies, such as passive mixing, active mixing, and segmented flow, can be employed to achieve homogeneous reaction conditions and enhance product quality.32,49
2.3. Temperature and pressure control
Flow reactors enable precise control over temperature and pressure gradients, which are essential for controlling nucleation, crystal growth, and phase transformations during material synthesis. Rapid heating and cooling rates can be achieved, allowing for material synthesis with specific crystalline structures and properties.32,50
2.4. Solvent selection and management
The choice of solvent plays a critical role in material synthesis, influencing crystal size, morphology, and purity. Flow synthesis allows for efficient solvent management, including solvent recycling and on-the-fly solvent exchange, leading to reduced waste generation and improved sustainability.51
2.5. Scalability and automation
Flow synthesis can be easily scaled up by parallelization of flow reactors or by increasing reactor dimensions. Furthermore, automation of flow synthesis processes allows for high-throughput screening of reaction conditions and rapid optimization of synthesis protocols.25,26,32
Recent publications offer valuable guidance for optimizing and troubleshooting flow synthesis, particularly for handling solids. The review by Hayes and Mallia52 addresses the challenges associated with solid particles in flow chemistry, proposing strategies for successful flow synthesis of materials involving solids. Ley and Baumann et al.53 discuss the potential of flow chemistry for discovering new reactions and enabling novel molecular assemblies. Their focus lies on photochemical, electrochemical, and temperature-sensitive processes where flow methods and machine learning can significantly impact reaction outcomes. In 2020, Williams and Kappe54 have summarized the advancements in sustainable flow photochemical processing over the past three years, highlighting developments in light source technology, reactor design, and process optimization. Noël et al.55 have reported a comprehensive review of recent technological advances in flow chemistry, including reactor design, scale-up, and the integration of photo- and electro-chemistry. Another review by Noël et al.48 demonstrates how microreactor technology can be used to explore new avenues in organic synthesis, achieving unique reactivity and selectivity. Baumann and Smyth et al.56 have discussed the challenges associated with scaling up flow processes from lab-scale to industrial quantities, focusing on inherently difficult reaction classes and handling solids in continuous flow setups. Hone and Kappe57 offer the guidance for scientists performing and reporting flow chemistry protocols. Their review emphasizes the importance of reporting critical experimental details to ensure reproducible, scalable, and safe protocols. These references offer practical advice and case studies for troubleshooting common challenges encountered in flow synthesis, along with effective approaches to achieve successful flow processes.
3. Advantages of flow synthesis over conventional batch synthesis
Flow synthesis, as a modern approach to synthesizing MOFs and MOF-based composite materials, offers several distinct advantages over conventional batch synthesis methods. The following are the main points of advantages.
3.1. Precise control of reaction parameters
Flow synthesis enables precise control over reaction parameters such as temperature, pressure, and residence time.58 In conventional batch synthesis, achieving uniform reaction conditions throughout the reaction vessel can be challenging, leading to variations in product quality and yield.58 Flow reactors allow for continuous and uniform mixing of reactants, ensuring consistent reaction conditions and reproducible results in the MOF synthesis.58,59 For example, in the flow synthesis of MIL-88B type MOFs, researchers have demonstrated control over particle size (ranging from 90 to 900 nm) by adjusting the residence time (from 20 to 600 s) within the flow reactor.60 In another case, during the flow synthesis of MOF-74(Ni), higher crystallinity was achieved by increasing the reaction temperature from 70 to 150 °C. In this case, the flow reactor precisely maintained the optimal temperature of 150 °C, leading to a high-quality product.61 In a different case, a series of Cu-BDC MOFs were synthesized via microdroplet flow synthesis with precisely controlled operating pressure, highlighting the influence of this parameter.62 Further, the precise control over reaction parameters enables the creation of well-defined MOF composite structures with desired functionalities.32,63 Nanoparticles or guest molecules can be introduced into the flow system along with the MOF precursors, enabling precise control over their encapsulation within the MOF pores during crystallization. For example, in the continuous synthesis of insulin- and gold nanoparticle-encapsulated ZIF-8, setting the residence time to just 1 second resulted in a high-yield (42 ± 3%) MOF composite.63
3.2. Scalability and efficiency
One of the most significant advantages of flow synthesis is its scalability and efficiency. In large scale batch synthesis, larger reactors pose challenges in achieving homogeneous mixing throughout the reaction volume, potentially leading to inconsistencies in MOF properties. Further, precise temperature and concentration control becomes increasingly challenging with larger batches. Variations in mixing, temperature profiles, and precursor concentrations across batches can lead to inconsistencies in MOF characteristics like crystal size, porosity, and surface area.64 Hence, it is hard to achieve good scalability and efficiency in large scale batch synthesis of MOFs. In flow synthesis, the production rates can be readily adjusted by simply manipulating the flow rates of precursor solutions, and thereby the amount of MOF produced per unit time can be easily scaled up.65 As a representative case, Polyzoidis and coworkers developed a method for the continuous, upscaled synthesis of UiO-66 and its derivatives using a simple milli-structured flow reactor.66 This method produces high-quality MOFs within 8 minutes, with exceptional reproducibility. The space-time yield (STY), a measure of production efficiency, reaches up to 7162 kg m−3 d−1. The reaction conditions were optimized in a smaller reactor and then successfully applied to a larger reactor capable of producing up to 200 grams of UiO-66 per day using only 40 mL of reaction volume.66 This demonstrates the remarkable scalability of flow synthesis. Moreover, connecting multiple flow reactors in series allows for further production rate amplification without compromising control.67 By overcoming the scalability and efficiency limitations of batch methods, continuous flow synthesis paves the way for the consistent, high-quality, and large-scale production of MOFs and their composites.68 This scalability is particularly advantageous for industrial applications where high throughput and production efficiency are paramount.
3.3. Rapid optimization and high-throughput screening
The quest for efficient MOFs and their composites with optimized properties often involves rapid exploration of a vast chemical space. Here, the continuous flow synthesis shines as a powerful tool for accelerating the optimization process and enabling high-throughput screening compared to traditional batch methods.69 Batch synthesis can be slow due to preparation of multiple reaction vessels, individual reaction runs, product isolation and analysis for each batch. Further, batch methods are inherently limited in the number of reactions that can be performed simultaneously, hindering efficient high-throughput screening. On the other hand, the continuous flow synthesis offers a transformative approach for rapid optimization and high-throughput screening of MOFs.70 In flow synthesis, multiple reaction conditions can be tested sequentially within the same flow setup, significantly accelerating the exploration of different parameter combinations.70 Also, multiple flow channels can be incorporated within a single setup, allowing for simultaneous testing of various reaction conditions. This significantly increases the throughput compared to batch methods. Automation of flow systems allows for the systematic variation of reaction parameters, such as reagent concentrations, flow rates, and temperature, leading to accelerated process optimization and discovery of novel MOF materials. This capability is invaluable for exploring the vast chemical space of MOFs and tailoring their properties for specific applications. For instance, Sels, Lammertyn et al. demonstrated the high-throughput potential of flow synthesis by using a microfluidic device to simultaneously synthesize a staggering number (up to 6400) of single HKUST-1 crystals.71 This device utilized femtoliter-scale droplets controlled by patterned hydrophilic–hydrophobic micropatches. Additionally, Maspoch et al. employed microfluidic pen lithography to mix femtoliter-scale droplets on a substrate, enabling the high-throughput screening of novel peptide MOFs.72 These studies showcase how isolated droplets within flow systems can serve as independent reaction and crystallization vessels.
3.4. Improved reaction kinetics and mass transfer
The synthesis of MOFs and their composites relies heavily on efficient reaction kinetics and mass transfer. While batch synthesis has served as the traditional method, continuous flow synthesis offers significant advantages in reaction kinetics and mass transfer, ultimately leading to superior MOF production.51 In batch synthesis, the batch reactors often rely on stirring or diffusion for mixing, which can be slow and inefficient. This leads to inhomogeneity within the reaction mixture, which can lead to variations in nucleation and crystal growth rates, resulting in inconsistent MOF properties.32,67 Further, the slow mixing delays the interaction between precursors, hindering control over the initial stages of MOF formation. Diffusion limitations can occur within the batch reactor, especially for larger reaction volumes. This can lead to slower crystal growth and non-uniform crystal size distribution.69 The continuous flow synthesis addresses these limitations and promotes faster, more efficient MOF production. Flow systems utilize microfluidic channels with precisely designed geometries which enables the precursor solutions to flow in layers within the microchannels, minimizing mixing time and promoting homogeneous distribution. In addition, the static mixers or T-junctions within the flow system further enhance mixing, ensuring rapid interaction between precursors at the outset of the reaction.32,50 More importantly, the microfluidic channels have smaller dimensions compared to batch reactors. This translates to shorter diffusion distances for precursors, enabling them to reach growing MOF crystals more readily.73 Continuous flow ensures a constant supply of fresh precursors to the reaction zone, facilitating faster crystal growth and promoting uniform crystal size distribution.74 By promoting efficient reaction kinetics and mass transfer, continuous flow synthesis paves the way for faster, more controlled, and higher-quality MOFs and their composites compared to batch methods.73,75 This is exemplified by the synthesis of UiO-67 in a microfluidic reactor, which produces the material in 30 minutes – a fraction of the traditional batch heating time of 24 hours.76 The flow-synthesized UiO-67 is also smaller with a narrower particle size distribution compared to its batch counterpart. Recently, a team of researchers employed a continuous flow reactor to study the crystallization kinetics of MOF-808 using time-resolved techniques.74 They found that at constant residence time, temperature, and composition, higher flow velocities increased the advective transport of precursors to nucleation sites, resulting in faster crystal growth rates and larger crystals. The increase of flow rate from 0.334 to 1.067 mL min−1 increased the size of the MOF-808 crystal from ∼105 ± 22 to ∼180 ± 19 nm. These examples showcase the advantages of flow systems in enhancing reaction kinetics for MOF synthesis.
3.5. Enhanced safety and environmental sustainability
Conventional batch synthesis methods for MOF production can raise safety concerns and environmental impact. The continuous flow synthesis emerges as a superior approach, promoting enhanced safety and environmental sustainability for MOF production. Batch synthesis often involves large quantities of air-sensitive or moisture-sensitive precursors. This can pose safety risks for researchers and production personnel if appropriate handling procedures are not strictly followed.77 The use of large reaction vessels makes it difficult to completely contain potential spills or leaks of hazardous materials. Batch processes typically consume significant volumes of solvents, some of which may be flammable or toxic.78 Improper solvent disposal can pose environmental hazards.77 Continuous flow synthesis offers significant advantages for safe and eco-friendly MOF production. Flow systems utilize smaller reaction volumes compared to batch methods.51 This translates to a reduction in the amount of hazardous precursors needed per reaction, minimizing potential risks associated with handling and storage. The confined nature of flow reactors allows for better containment of hazardous materials. This minimizes the risk of exposure for personnel working with the system. Flow systems can be readily integrated with safety features like automated shut-off valves and fume hood integration. These features further minimize the risk of accidents or exposure to hazardous materials. Flow processes are inherently solvent-efficient. Smaller reaction volumes and the potential for solvent recycling strategies within the flow system contribute to a significant reduction in solvent consumption compared to batch methods.79 Flow synthesis often leads to faster MOF formation compared to batch methods.80 In this regard, Gimeno-Fabra et al. showcased the power of continuous flow reactors by synthesizing high-quality HKUST-1 in just 1 second at high temperatures (300 °C) and pressures (250 bar).81 This represents a tremendous leap compared to the hours needed in conventional methods, while still maintaining a high surface area – a crucial property for MOF performance. Then, Kim et al. reported continuous production of high-yield, high-quality HKUST-1 crystals within 5 minutes using flow synthesis.82 Importantly, their method employed milder operating conditions (100 bar) compared to Gimeno-Fabra et al.'s approach. Rubio-Martinez et al. took flow synthesis a step further.59 They demonstrated the ability to continuously produce not only HKUST-1 but also UiO-66 and NOTT-400. Additionally, they successfully scaled up the reaction volume for HKUST-1 from 10 mL to a much larger 108 mL, all while maintaining its high surface area – even surpassing the results of Kim et al. Furthermore, their system operated at pressures closer to atmospheric conditions, reducing the inherent risks associated with high-pressure setups. This translates to lower energy consumption per unit of MOF produced. Flow synthesis can be integrated with continuous downstream processing steps like solvent removal and activation.83 This eliminates the need for multiple batch processes, further reducing energy consumption and solvent waste. By minimizing safety hazards, reducing environmental impact through lower solvent usage, and promoting efficient resource utilization, flow synthesis paves the way for a safer and more sustainable approach to MOF development.
3.6. Versatility and flexibility
Flow synthesis provides greater versatility and flexibility in MOF synthesis compared to batch methods. Flow reactors can accommodate a wide range of reaction conditions and configurations, allowing for the synthesis of various MOF structures, including those with challenging synthesis requirements such as high temperatures or pressures.59,68,84 For example, Zhao et al. demonstrated the versatility of flow synthesis by using an air–liquid segmented microfluidic flow reactor to synthesize a series of MOFs (Cu-BDC, HKUST-1, UiO-66, Co-MOF-74, MOF-801, and MOF-808) in just ten minutes.85 These flow-synthesized MOFs exhibited comparable crystallinity and quality to conventionally prepared samples. Importantly, the same microfluidic flow reactor can be used to synthesize different MOFs by simply changing the precursor solutions and reaction conditions. Notably, the synthesized MOFs displayed a smaller crystal particle size compared to their batch-synthesized counterparts. Additionally, the flow-synthesized MOFs showed significantly higher STY values (108.1, 41.6, 51.5, 1890.0, 97.0, and 133 kg m3 d−1 for HKUST-1, Co-MOF-74, Cu-BDC, MOF-801, UiO-66, and MOF-808 respectively) compared to batch methods (28.4, 11.3, 4.6, 81.9, 5.5, and 4.3 kg m3 d−1 for HKUST-1, Co-MOF-74, Cu-BDC, MOF-801, UiO-66, and MOF-808 respectively) for all tested MOFs.85 Furthermore, flow synthesis can be easily integrated with other process steps, such as post-synthetic modifications or encapsulation of MOFs into composite materials, enabling the rapid development of advanced functional materials.86–88 As an example for rapid functionalization of MOFs, researchers demonstrated a flow-based microfluidic route as a powerful platform for MOF synthesis and their functionalized analogs.89 Confining reactants within nanodroplets significantly enhanced heat and mass transfer, leading to rapid reaction rates. They successfully obtained functionalized UiO-66-NH2 MOF composites (acetyl and fluorescein isothiocyanate functionalized MOFs) in just 1 hour, compared to the 6–20 days required by batch processes. This approach combines four typical post-synthetic modification steps into a single, streamlined process, potentially paving the way for industrial-scale synthesis of MOFs with tailored functionalities.89
4. Various types of flow synthesis techniques for MOFs and their composites
Continuous flow synthesis techniques offer numerous advantages for the preparation of MOFs and their composites, including precise control over reaction conditions, enhanced scalability, and continuous production. Here, an overview of several types of flow synthesis techniques employed for MOFs and their composites is presented.
4.1. Continuous flow solvothermal synthesis
Solvothermal synthesis involve the reaction of metal precursors and organic ligands in solvent medium at elevated temperatures and pressures. Continuous flow solvothermal synthesis extends this approach to continuous processing in flow reactors, offering advantages such as improved heat and mass transfer, enhanced reproducibility, and scalability.90 In this method, the reaction mixture is continuously pumped through a heated reactor, where the solvothermal condition promotes the formation of MOFs or MOF composites.90,91 By adjusting parameters such as temperature, pressure, solvent composition, and residence time, one can control the size, morphology, and other important properties of the synthesized MOFs.88,90 Continuous flow solvothermal synthesis has been employed for the preparation of a wide range of MOFs and their composites with diverse structures and functionalities.88,90,92,93 This approach enables the rapid screening of reaction conditions and the continuous production of MOFs with tailored properties for specific applications. For example, Román-Leshkov et al. developed a continuous flow solvothermal process for producing Ni2Cl2(BTDD)-MOF, offering significant advantages over traditional batch methods.94 This flow approach achieves higher yields, faster crystallization times, and reduced solvent consumption. The flow reactor used a syringe pump and a positive displacement pump to inject the MOF precursor mixture and silicone oil (carrier) separately (Fig. 2). The reaction zone, made of polytetrafluoroethylene (PTFE) tubing housed within a heated furnace, ensured efficient heat transfer and near-isothermal operation. A back-pressure regulator (BPR) was used to maintain the reactor operating pressure at a value higher than the bubble-point pressure of the reaction mixture. (Here, we feel that the use of a BPR is necessary. Since the flow reaction in this case is operated under high temperature and pressure conditions, a BPR is required to maintain the reactor operating pressure at a value higher than the bubble-point pressure of the reaction mixture.) The precursor mixture formed segmented “slugs” within the flowing silicone oil stream upon injection. These slugs experienced a rapid temperature increase upon entering the heated zone. The flow reactor design allows for precise control over reaction conditions (residence time, temperature) for optimal MOF crystallinity. Residence times could be adjusted from minutes to days, and temperatures could reach 250 °C at a pressure of 25 atm. They investigated the influence of three key parameters: residence time, temperature, and solvent ratio. And, they found that optimal crystallinity was achieved at 140 °C for residence times between 30 and 60 minutes. Higher temperatures led to linker degradation, while lower temperatures hindered crystallization. Solvent composition optimization was conducted at 140 °C with a 60-minute residence time. Starting from the batch recipe (1
:
1
:
0.64 volumetric ratio of DMF, CH3OH, and HCl), the HCl content was reduced by 10%, 40%, and 60%, and CH3OH by 25% and 50%. The highest crystallinity in the flow reactor was achieved with a volumetric ratio of DMF/CH3OH/HCl = 1
:
0.5
:
0.38, representing a 50% reduction in CH3OH and a 40% reduction in HCl compared to the optimized batch composition. The present flow synthesis resulted in slightly higher yields (80%) compared to batch synthesis (75%). However, the most significant advantage was the dramatic increase in productivity. Flow synthesis achieved a productivity 190 times higher (12.24 kg m−3 day−1) than that achieved by batch synthesis (0.0643 kg m−3 day−1).94
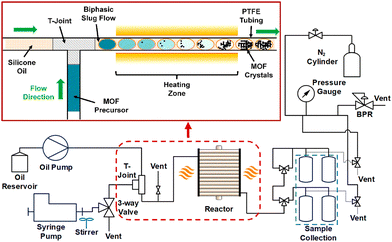 |
| Fig. 2 Schematic representation of the continuous flow solvothermal synthesis of MOFs. The inset picture with red boundaries illustrates the phenomenological model of crystallization using a biphasic slug flow generated from two immiscible fluids in a T-junction. Reprinted with permission from ref. 94. Copyright 2021, American Chemical Society. | |
The same research group (Román-Leshkov et al.) reported a continuous flow approach to synthesizing MOF-808 under mild solvothermal conditions, achieving highly crystalline products within minutes.90 They explored the effects of various synthesis parameters, including residence time, linker concentration, and the volumetric ratio of modulator to solvent, on the crystallization process. Fig. 3 illustrates both the conventional batch synthesis method and the continuous flow process developed in their study. In their continuous flow synthesis, reactions were conducted at a minimum pressure of 4 atm and a temperature of 150 °C to prevent gas bubble formation. The setup included a positive displacement pump and a syringe pump to inject the continuous phase (silicone oil) and the dispersed phase (precursor mixture) into a PTFE based T-joint, generating a biphasic slug flow. The heated reaction zone, or the crystallizer unit, used approximately 8 meters of tubing, and the system was pressurized with pure N2 gas. Further, a BPR was placed at the outlet of the flow reactor to maintain a constant pressure within the reactor. (As we discussed in the previous case, we feel that the use of a BPR is also necessary here. Since the flow reaction in this case is also operated under high temperature and pressure conditions, a BPR is required to maintain a constant pressure within the reactor. Further, it is also possible that by using high-performance pumps and carefully designed flow channels, precise control over the flow rates of all incoming streams can achieve the desired pressure within the reactor without a BPR. But the choice between using a BPR or an alternative approach depends on several factors, including the specific requirements of the MOF synthesis, complexity considerations, and the risk of clogging.) MOF-808 was synthesized under flow conditions at 150 °C with residence times ranging from 1 to 120 minutes to compare the crystallinity development with the batch reaction conditions (130 °C and 48 hours) using the same precursor composition. Crystallinity started developing as early as 2 minutes in the flow process. MOF-808 particles produced from flow synthesis were smaller (average size 140 nm) compared to those from batch synthesis (360 nm). The researchers investigated the influence of various parameters on MOF-808 formation in flow synthesis, including residence time, solvent ratios, and linker concentration. They found that residence times of 15–120 minutes resulted in crystalline MOF-808 at a formic acid (FA) to DMF ratio of 1 or 2; higher FA content (FA
:
DMF = 3 or 4) hindered crystallization due to competition with the linker for metal binding sites. A 5-minute residence time achieved the highest productivity (95
155 kg m−3 d−1), two orders of magnitude higher than that achieved with batch synthesis. Flow synthesis achieved an ∼80% yield compared to ∼75% for batch synthesis. The maximum productivity in batch synthesis was 335.5 kg m−3 d−1, while flow synthesis at a 5-minute residence time achieved 95
155 kg m−3 d−1. Longer residence times (>15 min) reduced productivity without significant surface area improvements. A 15-minute residence time in flow synthesis achieved the highest surface area (∼2000 m2 g−1), with lower productivity (31
730 kg m−3 d−1). A 5-minute residence time decreased the surface area (∼1600 m2 g−1) but increased the productivity to 95
155 kg m−3 d−1. Optimized flow synthesis reduced DMF usage by ∼84% and formic acid by ∼67%, demonstrating the direct benefits of flow synthesis for process intensification. Finally, they estimated the minimum cost of manufacturing MOF-808 in a laboratory-scale flow synthesis (∼$3 per gram), which was significantly lower than current MOF synthesis costs. This methodology offers a new approach for assessing and optimizing continuous manufacturing routes in a lab-scale environment, paving the way for more efficient MOF synthesis on an industrial scale.90
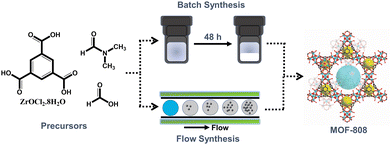 |
| Fig. 3 Synthesis scheme for MOF-808 using batch and flow reactors. Adopted with permission from ref. 90. Copyright 2021, Royal Society of Chemistry. | |
In another instance, a continuous solvothermal flow processing technique was effectively applied for the preparation of MOF composites with MgFe2O4@UiO-66-NH2 as a model material (Fig. 4).88 For the synthesis, MgFe2O4 nanoparticles were dispersed in a ZrCl4 solution in DMF, maintaining a molar ratio of MgFe2O4 to ZrCl4 of 0.6. The ligand (2-aminoterephthalic acid) and the modulator (benzoic acid) were also dissolved in DMF. The metal salt and magnetic nanoparticle suspension was then combined with the ligand and modulator solution. This mixture was injected into a loading coil and pumped into the reactor coil, using DMF as the carrier solvent. The reaction was carried out at 130 °C and 10 bar pressure in a 30 mL coil reactor, with a flow rate of 2 mL min−1 and a residence time of 15 min. A BPR installed at the end of the line controlled the reactor's backpressure. (Given the high-temperature (130 °C) and high-pressure (10 bar) conditions of this flow reaction, the BPR is essential for maintaining the reactor operating pressure above the bubble point of the reaction mixture. This prevents gas evolution and potential bubble formation that could disrupt flow or clog microchannels.) For scalability studies, the reactor size was increased to 52 mL and then to 1028 mL, using the same reagent mixture and maintaining the same residence times as in the 30 mL reactor. In the continuous flow reaction in the 52 mL reactor, the production rate and STY increased to 0.27 g h−1 and 215.3 kg m−3 day−1, respectively. Further scaling to the largest reactor (1028 mL) resulted in a production rate and STY of 12.8 g h−1 and 300.3 kg m−3 day−1, respectively. The synthesized MOF composite exhibited similar material properties to those obtained from a batch solvothermal synthesis method. Moreover, the study showcased the scalability of flow chemistry for MOF composite synthesis, transitioning from milligram-scale to gram-scale flow reactors with increased production rates. Additionally, it was demonstrated that these MOF composites synthesized via continuous flow could undergo magnetically induced regeneration and release of adsorbed CO2 gas molecules. The adsorbed gas was swiftly released, demonstrating comparable performance to that of the small-scale batch-synthesized analogs.88
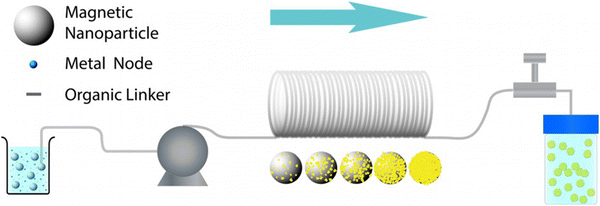 |
| Fig. 4 Schematic illustration of the continuous flow solvothermal synthesis of MOF composites. Pre-dispersed magnetic nanoparticles in a solution of metal salt and ligand are pumped into a temperature- and pressure-controlled reactor to form the MOF composite. Reprinted with permission from ref. 88. Copyright 2019, John Wiley and Sons. | |
Overall, the continuous flow solvothermal synthesis offers opportunities for process intensification and automation, leading to increased efficiency and throughput in the synthesis of MOFs and their composites.
4.2. Continuous flow mechanochemical synthesis
Mechanochemical synthesis has emerged as a promising alternative approach for the production of MOFs and their composites.95,96 This method utilizes mechanical energy, such as grinding or milling, to induce solid-state reactions between metal precursors and organic linkers, leading to the formation of MOFs.97 Mechanochemical synthesis can also be used to fabricate MOF composites, where MOFs are integrated with other functional materials. Nanoparticles or guest molecules can be physically mixed with the MOF precursors and co-ground. This can lead to their encapsulation within the MOF structure during mechanochemical synthesis.98 On the other hand, continuous flow mechanochemical synthesis combines milling with fluid flow in flow reactors, enabling the continuous production of MOFs with enhanced crystallinity, purity, and yield.99 In this method, solid reactants are continuously fed into a milling chamber, where mechanical forces generated by milling promote the formation of MOF crystals. The addition of fluid flow helps to disperse reactants, enhance mixing, and remove heat generated during the reaction. Continuous flow mechanochemical synthesis offers several advantages, including rapid reaction kinetics, reduced reaction times, and improved scalability compared to batch mechanochemical methods. For the first time, a recent study has shown that employing the continuous flow mechanochemical technique using air pressure can effectively synthesize MOFs.100 This reported method offers solvent-free synthesis and potentially higher production rates compared to traditional batch methods. MOF precursor powders are fed into an impact chamber using a dedicated feeder. Compressed air generates a supersonic airflow that accelerates these particles to speeds exceeding 300 m s−1 within an acceleration tube. Inside the chamber, violent collisions occur between the particles, triggering both particle breakdown and the chemical reactions needed to form MOFs. (It is to be noted that this study eliminates the need for a BPR because the mechanochemical synthesis process does not require supercritical fluids (high temperature and pressure) for MOF formation. Instead, this approach utilizes MOF precursor powders directly.) This study successfully synthesized Cd2(BTC)3 and HKUST-1 MOFs using this method. The continuous flow reaction yielded a significant amount of product (251.5 g Cd2(BTC)3 and 195.7 g HKUST-1) within just 10 minutes at a feed rate of 60 kg h−1. Following purification, the final yields were 82.5% for Cd2(BTC)3 (154.9 g) and 80.0% for HKUST-1 (121.0 g). Notably, the STY reached a remarkable 1.44 × 106 kg m−3 day−1, which is an order of magnitude higher than the 1.44 × 105 kg m−3 day−1 typically achieved with batch methods. Interestingly, the MOFs produced using this method exhibited slightly better surface areas and pore sizes compared to those synthesized using conventional batch methods.100 Notably, achieving a high STY was straightforward, with even greater rates possible with larger-scale equipment. This chemical synthesis approach, utilizing continuous flow mechanochemistry, offers numerous advantages over conventional methods, including enhanced efficiency, reduced cost, and scalability.101 On comparing other flow synthetic techniques, the continuous flow mechanochemical synthesis often operates at ambient temperatures, reducing energy consumption and mostly eliminates solvent waste and associated environmental concerns.102 Further, the grinding parameters can be tuned to influence crystal size and morphology, and potentially even induce the formation of amorphous phases.102 Overall, it paves the way for a new approach to MOF and their composite synthesis, addressing the limitations posed by the lack of continuous, large-scale, and environmentally friendly synthetic techniques.
4.3. Microwave-assisted and ultrasound-assisted flow synthesis
Microwave-assisted flow synthesis involves performing MOF synthesis reactions in a flow reactor under microwave irradiation. Microwave heating offers rapid and uniform heating, leading to shorter reaction times and enhanced yields compared to conventional heating methods.103 Recent advancements in microwave-assisted flow synthesis have focused on optimizing reaction conditions, exploring new MOF structures, and scaling up production for industrial applications.61,104–106
Ranocchiari et al. have pioneered the use of microwave-assisted continuous flow synthesis for MOFs, marking a significant advancement in the field. They thoroughly showcased the versatility and remarkable efficiency of this method by successfully synthesizing three distinct benchmark MOFs: UiO-66, MIL-53(Al), and HKUST-1.106 As illustrated in Fig. 5, three pumps discretely draw from the metal and ligand stock solutions, as well as fresh solvent, and are linked to a mixing unit with an in-line pressure gauge positioned downstream and BPRs (these BPRs likely play a critical role in maintaining pressure within the microfluidic channels before the various solutions are mixed) positioned upstream of the mixing unit. Another BPR unit (this BPR likely functions to control the backpressure within the reactor and prevent unwanted gas behaviour) is also connected before the gas outlet. The tubular reactor is placed within the heating cavity of a microwave synthesizer, and following the oven, the tube is directed into a pressurized collecting unit. Both the pumps and the microwave oven are remotely controlled via a laptop computer. First, UiO-66 MOF was prepared in DMF at one bar pressure using stoichiometric amounts of metal and ligand. A 94% conversion of reagents into the final product was achieved after seven minutes of irradiation at 280 W, with a STY of 7163 kg m−3 day−1. The synthesis was scaled up using a 53 mL reactor, processing 500 mL of synthetic mixture in 73 minutes. The larger reactor required lower power (200 W) and higher pressure (3 bar), achieving a 94% yield. The total amount of MOF obtained was 17.5 g, with a STY of 7204 kg m−3 day−1 and a production rate of 14.4 g h−1. Next, the synthesis of the MIL-53(Al) MOF was carried out in DMF at 3 bar pressure, achieving 90% conversion after four minutes of irradiation at 240 W, with a STY of 4795 kg m−3 day−1. Scaling up with a 53 mL reactor, they processed 400 mL of solution in 34 minutes. The scaled-up procedure required lower power (200 W) and higher pressure (6 bar), yielding 4.0 g of MOF with a 65% yield. The calculated STY was 3618 kg m−3 day−1 with a production rate of 7.1 g h−1. Finally, the HKUST-1 MOF was synthesized in DMF at 4 bar pressure by one minute of irradiation at 360 W, with a calculated STY of 66
650 kg m−3 day−1. The synthesis was scaled up using a 29.6 mL reactor, processing 500 mL of reaction mixture in 17 min at 6 bar pressure, producing 22.5 g of MOF. The corresponding STY was 64
800 kg m−3 day−1 with a production rate of 79.4 g h−1. Overall, by achieving high mass conversion and unprecedented STYs, they demonstrated the effectiveness of continuous flow microwave technology in rapidly producing multi-gram quantities of high-quality MOFs within minutes. These achievements transcend mere proof of concept, underscoring the potential of this technology for applications necessitating large-scale MOF synthesis.106
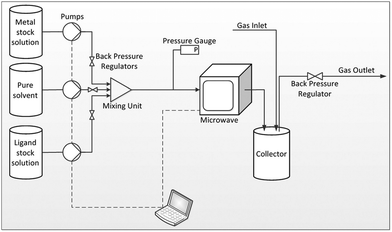 |
| Fig. 5 Schematic illustration of microwave-assisted continuous flow synthesis of MOFs. Reprinted with permission from ref. 106. Copyright 2016, John Wiley and Sons. | |
Like microwave-assisted flow synthesis, the ultrasound-assisted flow synthesis utilizes ultrasonic waves to enhance mixing and promote MOF formation in a continuous flow reactor. Ultrasonic irradiation generates cavitation bubbles in the reaction mixture, leading to localized heating, increased mass transfer, and enhanced reaction kinetics.107 Ultrasound-assisted synthesis offers advantages such as reduced reaction times, improved yield and purity of MOF and composite products, and the ability to synthesize MOFs under mild conditions.108 Recently, a polyethylene glycol (PEG)-MIL-101(Cr) MOF composite was synthesized through a two-step continuous ultrasound-assisted flow synthesis approach.108 Initially, NH2-MIL-101(Cr) was synthesized using ultrasound assistance (flow 1 in Fig. 6). Metal ions and ligand solutions were pumped into a reactor coil within an ultrasound reactor. The reaction occurred under controlled conditions: 40 kHz ultrasound, 600 W power, 160 °C temperature, 80 psi pressure, and a flow rate of 1.25 mL min−1 for each solution. Then, the product flow entered a BPR, which matched the pressure of flow 1 to that of flow 2. Following MOF formation, the PEG solution (0.06 mol L−1, pH 9.0) was introduced in flow 2, as depicted in Fig. 6. The flow rate of each flow was maintained at 2.5 mL min−1. These solutions were combined in a T-type mixer before entering another tubular reactor. The reactor temperature was maintained at 25 °C, and the resulting MOF composite product was collected and filtered. (This continuous flow synthesis setup utilizes a BPR downstream of the first reactor (flow 1) to achieve pressure equilibration with the second stream (flow 2) containing the PEG solution, prior to their confluence in the T-mixer. By maintaining a higher pressure in flow 1 compared to flow 2, the BPR safeguards against the backflow of the PEG solution into the MOF synthesis reactor. The BPR can also influence the flow rate of the MOF synthesis solution (flow 1) by regulating the pressure. It is possible that the BPR itself can be susceptible to clogging from precipitates in the reaction mixture. Employing high-precision pumps in tandem with precisely designed flow channels can potentially achieve the desired flow rates for both streams, eliminating the need for a BPR for pressure equilibration.) Additionally, they investigated the effects of synthesis conditions such as flow rate (1.0, 2.5, and 5 mL min−1), temperature (140, 160, and 180 °C), and applied ultrasound on the STY, yield, and crystallinity of the MOF, NH2-MIL-101(Cr). They found that the optimal conditions for a balance between production rate and product quality were a temperature of 160 °C, a pressure of 80 psi, a reactor volume of 7 mL and a flow rate of 2.5 mL min−1 (residence time: 2.8 min). A yield of 88% and a calculated STY of 5785 kg m−3 day−1 were observed under these conditions. Under these conditions, the process achieved a high yield of 88% for NH2-MIL-101(Cr) formation with a significant STY of 5785 kg m−3 day−1 for the final PEGylated MOF composite. While increasing the flow rate could further boost STY (up to 21
054 kg m−3 day−1), it compromised product quality. This highlights the importance of optimizing reaction parameters for both efficiency and quality. The crystallinity of the MOF composite produced via the ultrasound-assisted continuous flow method was consistent with that of batch production.108
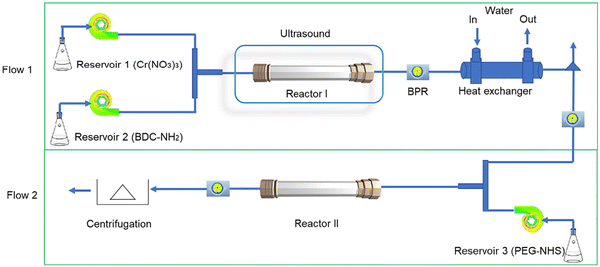 |
| Fig. 6 Schematic illustrations of two step ultrasound-assisted continuous-flow synthesis of the PEG-MIL-101(Cr) MOF composite. Reprinted with permission from ref. 108. Copyright 2021, Elsevier. | |
4.4. Continuous microfluidic droplet synthesis
Continuous microfluidic droplet synthesis has recently emerged as a powerful technique for the preparation of MOFs and their composites with precise control over composition, morphology, and other important material properties.82,109–111 Continuous microfluidic droplet synthesis involves the controlled generation, manipulation, and reaction of discrete droplets of reactants within microscale channels; the process typically utilizes microfluidic devices composed of interconnected channels and chambers, where precise control over flow rates, mixing, and reaction conditions can be achieved.112–114 By manipulating the flow rates of different reactant streams, droplets of controlled size and composition can be generated and transported through the microfluidic device, where they undergo reactions to form MOFs or their composites.82,109,110,115 Further, the microfluidic platforms offer precise control over reaction parameters, such as droplet size, composition, and residence time, enabling the synthesis of MOFs and their composites with uniform properties.111,115 The continuous operation allows for the rapid generation and processing of droplets, leading to high throughput production of MOFs and their composites.110 Microfluidic systems can be easily scaled up to meet production demands, making them suitable for both laboratory-scale research and industrial-scale manufacturing. The microscale volumes of reactants used in microfluidic droplet synthesis result in reduced reagent consumption and waste generation, making the process more environmentally friendly.109 By tuning the microfluidic parameters, such as flow rates and channel geometry, the morphology of the synthesized MOFs and their composites can be precisely controlled, leading to tailored properties for specific applications.
For instance, a team of researchers recently introduced a novel approach to synthesizing MOFs using a water-based droplet microfluidic system. In this system, they utilized ZIF-8 and MIL-100 as examples for ultrafast and continuous synthesis.109 As shown in Fig. 7, metal precursors and organic ligands were injected via syringe pumps, mixed in an 8 cm PFA tube, and then allowed to form droplets in a T-shaped configuration with a flow stabilizer ensuring continuous flow. For ZIF-8 synthesis, Zn salt and ligand solutions were pumped at equal flow rates (50 or 100 μL min−1) with a continuous phase flow rate of 330 μL min−1 and a 24 s reaction time. When the synthesis was carried out at various temperatures (40, 60, 80 °C), it was observed that room temperature synthesis produced truncated rhombic dodecahedral crystals, while higher temperatures yielded thermodynamically stable rhombic dodecahedra. This method achieved a STY of 10
1312 kg m−3 d−1, significantly outperforming hydrothermal batch synthesis. For MIL-100(Fe) synthesis, precursors were pumped at 100 μL min−1 with a continuous phase flow rate of 330 μL min−1. Reaction times were 24 and 160 s, depending on tube length, achieving a STY of 62
850 kg m−3 d−1. Higher temperatures (50 °C and above) improved crystallization, with the microfluidic method providing greater crystallinity and reduced reaction time compared to hydrothermal synthesis. (Interestingly, the reported reaction setup eliminates the need for a BPR unit. As discussed previously, the absence of high temperatures and pressures in the system negates the requirement for a BPR to maintain supercritical fluids. Additionally, the use of syringe pumps and the specified flow rates (e.g., 50 or 100 μL min−1) suggest that the researchers prioritized precise control over the flow rates of the precursor and ligand solutions. This approach, coupled with the microfluidic design, likely achieved the desired pressure within the system without a BPR.) Notably, they devised a two-phase method to generate droplets and prevent channel blockages, establishing a stable droplet flow pattern. By carefully controlling the flow rates of both phases, they boosted productivity and established a confined microreactor with minimal droplet formation. Their findings revealed a substantial enhancement in the crystallinity of ZIF-8 and MIL-100 with increasing synthesis temperatures. In summary, the described microfluidic system enabled rapid and scalable continuous production of MOFs under mild operating conditions.109
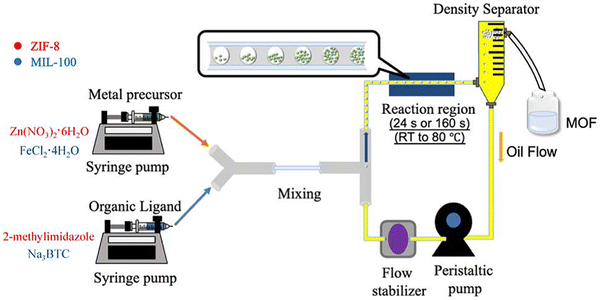 |
| Fig. 7 Setup of the microfluidic system. Reprinted with permission from ref. 109. Copyright 2023, Royal Society of Chemistry. | |
In another case, the enzyme–MOF composites were synthesized through a specialized mixing technique within a microfluidic flow system (Fig. 8), resulting in products exhibiting significantly enhanced enzyme activity.116 Employing a three-way mixing approach within the microfluidic laminar flow setup enabled precise control over diffusive mixing conditions, allowing the introduction of one component into the system after a defined time interval. For the synthesis, zinc nitrate (9.3 mg mL−1), 2-methylimidazole (2-MeIM, 102.5 mg mL−1), and enzyme (1 mg mL−1) water solutions were introduced into the inlets of a microfluidic chip at a flow rate of 0.5 μL min−1 using a syringe pump at room temperature. (Notably, the reported reaction setup eliminates the need for a BPR unit, as we have seen in the previous example. This is because the system operates at mild temperatures and pressures, eliminating the need for a BPR to maintain supercritical fluids. Furthermore, the use of syringe pumps and the controlled flow rates (e.g., 0.5 μL min−1) suggest a focus on precise control over the precursor and ligand solutions. This strategy, combined with the microfluidic design, likely generates the desired pressure within the system without requiring a BPR.) Three trials were conducted using a double-Y shaped microfluidic chip. In trial 1, enzyme molecules were added from the side channel after the organic ligands and metal ions were mixed. In trials 2 and 3, enzyme molecules were first mixed with metal ions and organic ligands, respectively, followed by adding the other component from the side channel. The study demonstrated a significant improvement in the activity of enzyme–MOF composites through microfluidic flow synthesis. Enzyme–MOF composites from trial 1 exhibited the highest activity (∼700% compared to the native enzyme), indicating a correlation between enzyme–MOF activity and the microfluidic mixing sequence of reactants. They suggested that the superior performance in trial 1 was due to more enzyme molecules being embedded near the outer surface of the particles, allowing better access for substrate molecules. Further, the researchers observed that the continuously varying concentrations of MOF precursors in the gradient mixing process of microfluidic flow synthesis led to structural defects in the enzyme–MOF composites, consequently improving substrate accessibility and enzyme activity. This defect-driven synthesis introduces a novel strategy for enhancing the performance of enzyme–MOF composites. In contrast to conventional methods for creating mesopores, which often involve complex templating processes potentially compromising enzyme activity during template removal, the proposed method spontaneously generates mesopores in a single step without the need for any templates. Leveraging the unique gradient mixing characteristics of microfluidic laminar flow synthesis, this strategy enables controllable, continuous, and rapid synthesis of enzyme–MOF composites with enhanced activity, thus presenting a promising new avenue for inducing defects in enzyme–MOF composites.116
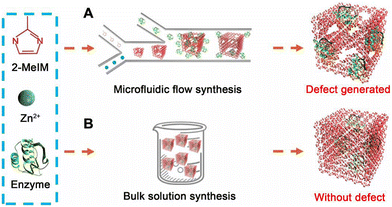 |
| Fig. 8 Schematics of microfluidic laminar flow synthesis and bulk solution synthesis of enzyme–MOF composites. (A) Synthesis of enzyme–MOF composites in a microfluidic laminar flow. Zinc nitrate, 2-MeIM, and enzymes were introduced into the three inlets; enzyme–MOF composites were formed in the microchannel via diffusion-based gradient mixing. (B) Synthesis of enzyme–MOF composites in bulk solution. The reactants were added into the beaker and mixed through stirring. Reprinted with permission from ref. 116. Copyright 2020, American Association for the Advancement of Science. | |
In brief, the continuous microfluidic droplet synthesis offers a versatile and efficient approach for the preparation of MOFs and their composites with tailored properties and enhanced functionalities. Despite existing challenges, ongoing research efforts are expected to further advance this promising technology and unlock new opportunities for the design and synthesis of advanced porous materials for various applications.
4.5. Aerosol synthesis
Spray-drying, also known as aerosol synthesis, has emerged as a versatile and scalable technique for the preparation of a variety of materials including MOFs and their derived composites.68,75,117–122 Spray-drying involves the atomization of a liquid precursor solution containing metal ions and organic ligands into fine droplets, which are then rapidly dried in a hot gas stream to form solid particles. The solid particles are conveyed to a collector, typically positioned at the base of a gas-stream cyclone formed by an aspirator situated downstream of the outlet filter. This configuration prevents particles from infiltrating the exhaust gas. Significantly, the entire process can be operated continuously within a closed loop, offering technical and environmental advantages. Atomization of the feed can be viewed as the pivotal stage of spray-drying. As the precursor solution is pumped into the inner channel, it encounters the gas stream flowing through the second channel, generating a shear field that atomizes the solution into droplets. Generally, prior to atomization, the precursor feed is introduced into the nozzle via uncomplicated peristaltic-pump tubing. This direct injection method is simple and convenient for precursor solutions that do not undergo undesired reactions before spray-drying.117 In the continuous flow-assisted approach, where a continuous-flow reactor is linked to the inlet of the spray dryer, the precursor solution is pumped and guided into a continuous coil flow reactor enclosed in a thermostatic oil tank, where it is heated to a specified temperature. Subsequently, the preheated solution is automatically injected into the spray dryer at the same feed rate, as the outlet of the continuous coil flow reactor is directly connected to the nozzle of the spray dryer.117 In MOF synthesis using the aerosol method, the rapid evaporation of the solvent promotes the nucleation and growth of MOF crystals within the droplets, leading to the formation of MOF particles with controlled size, morphology, and composition.84,119 The spray-drying process can be easily scaled up and offers advantages such as rapid production, uniform particle size distribution, and the ability to incorporate functional additives or dopants. Spray-drying is a highly scalable technique that can be easily adapted for industrial-scale production of MOFs and their composites, making it suitable for large-scale manufacturing applications.68,84,118 By adjusting the spray-drying parameters, such as feed composition, atomization conditions, and drying temperature, precise control over the particle size, morphology, and porosity of the synthesized MOFs and their composites can be achieved.119 Spray-drying allows for the incorporation of functional additives, such as nanoparticles, polymers, or biomolecules, into MOF particles, enabling the design of multifunctional composite materials with tailored properties and functionalities.68,118 The high surface area and porous structure of spray-dried MOF particles promote enhanced mass transport and reactivity, making them promising candidates for various applications. Recent studies have demonstrated the synthesis of MOF particles with tailored morphologies, including spheres, rods, fibers, and hollow structures, by controlling the spray-drying parameters and precursor composition.84,117,119
As a proof of concept, Maspoch and coworkers developed a continuous-flow spray-drying method for synthesizing and shaping spherical MOFs, specifically UiO-66-NH2 and Zr-fumarate.123 By adjusting the acetic acid concentration in water, they produced UiO-66-NH2 and Zr-fumarate beads. Fig. 9 shows a schematic of the aqueous continuous-flow spray-drying setup. An equimolar mixture of ZrOCl2 and 2-aminoterephthalic acid in water and acetic acid was injected into a coil-flow reactor in a silicone bath. The reaction was carried out at a specific temperature (Tc, °C) and liquid-feed rate (Qlf, mL min−1). The resulting yellow slurry was spray-dried at a set inlet temperature (Tin, °C) and drying-gas flow rate (Qdg, mL min−1) using a spray dryer. By optimizing reagent concentrations, they aimed to increase yield, identifying a maximum usable concentration of 0.2 M for ZrOCl2 and linker, with acetic acid concentration at 56% (v/v). This produced compact spherical UiO-66-NH2 beads (2–12 μm) with a high yield (72%) and a large surface area (1036 m2 g−1). They further explored the effect of acetic acid concentration (10% to 70%) on bead formation, finding that concentrations between 30% and 60% yielded better crystallinity. The process was extended to Zr-fumarate beads, with optimal crystallinity at 30% acetic acid. They demonstrated the scalability of this method by producing UiO-66-NH2 beads on a multigram scale (40 g) under optimized conditions, achieving a yield of 85% with a surface area of 1270 m2 g−1, similar to milligram-scale synthesis results. In summary, they reported a continuous-flow spray-drying method for the aqueous production of UiO-66-NH2 and Zr-fumarate, with an optimal acetic acid concentration of 30% (v/v). This method avoids post-synthetic shaping, preserving MOF porosity, and demonstrates the potential for industrial-scale green synthesis of shaped MOF microbeads using spray-drying.123 (Interestingly, the setup avoids the usage of a BPR unit. This spray-drying setup involves converting a liquid feedstock into dry particles using a hot gas stream. The key parameters for this process are the inlet temperature (150 °C) of the drying gas and the drying gas flow rate (336 mL min−1). These parameters are precisely controlled to achieve efficient atomization and drying of the particles. A BPR is not essential for this process. Further, Fig. 9 shows separate lines for the liquid feed and drying gas. The liquid feed flows through the coil-flow reactor and then enters the spray dryer. The drying gas stream likely pressurizes the spray dryer to facilitate atomization, but this pressure is independent of the pressure in the coil-flow. This independent control of flow rates eliminates the need for a BPR to regulate pressure across the entire system.)
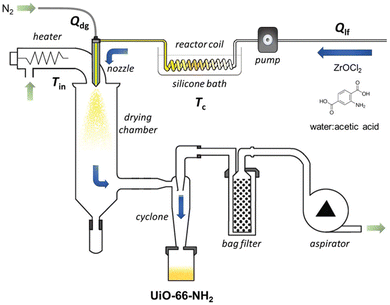 |
| Fig. 9 Schematic illustration of the set-up for the aqueous continuous-flow spray-drying synthesis of UiO-66-NH2. Reprinted with permission from ref. 123. Copyright 2018, Royal Society of Chemistry. | |
To give another example, we have recently developed a continuous aerosol technique for the synthesis of HKUST-1.87 Experiments were conducted using a spray dryer and a particle collector operating at an environmental pressure of 310 mmHg. As shown in Fig. 10(a), airflow (30 m3 h−1) at 170 °C was introduced into the instrument from the top for the spray drying process. Organic linker solutions (solution 1) and Cu precursor-stabilized ceria colloids (solution 2) were fed to a three-fluid nozzle through separate fluid channels operated by individual peristaltic pumps (step 1). The three-fluid nozzle simultaneously mixed and atomized the precursor solutions (step 2), producing micron-sized droplets (∼10 μm). In the drying chamber (step 3), the solvent in the droplets instantly evaporated at 170 °C, allowing Cu precursors and organic linkers to self-assemble into the Cu–MOF structure in the aerosol phase (step 4). The Cu–MOF@CeO2 nanoparticle clusters were then collected in the particle collector. The operating parameters were an inlet temperature of 170 °C, a solution feed rate of 2.5 mL min−1, and an atomizing gas flow rate of 6.9 L min−1. The continuous aerosol route was demonstrated for the gas-phase synthesis of MOF composite Cu–MOF@CeO2, which has further been used to fabricate the MOF-derived Cu@CeO2 nanocomposite material (Fig. 10(b)) for the catalysis of reverse water–gas shift (RWGS) reaction.87 Similarly, we have also used the continuous spray-drying approach to fabricate the MOF based composites Cu–MOF–Zn/Al2O3124 and Ni/ZIF-8@Al2O3.86
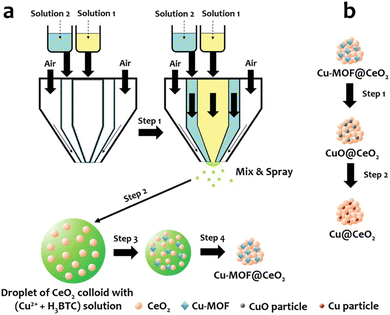 |
| Fig. 10 Cartoon depictions of (a) aerosol-based synthesis of the Cu–MOF@CeO2 composite, and (b) subsequent formation of the Cu–MOF-derived hybrid nanostructure (Cu@CeO2). Reprinted with permission from ref. 87. Copyright 2022, American Chemical Society. | |
4.6. Combined flow chemistry and aerosol synthesis with real-time characterization
The integration of flow chemistry with aerosol-based methods offers a novel and exciting approach for the synthesis of MOFs and their composites.83,125 This combination leverages the strengths of both techniques, potentially leading to the development of new MOFs with unique properties and improved production efficiency. Further, the real-time characterization of the MOFs synthesized via flow synthesis methods is crucial for gaining insights into the reaction process, optimizing reaction conditions, and ensuring consistent MOF quality. In this regard, we have demonstrated for the first time by using gas-phase electrophoresis the real-time quantitative characterization of MOF colloids synthesized via the droplet flow synthetic method.125 In detail, as illustrated in Fig. 11(a), the aqueous solution containing the metal precursor (solution 1) and the solution of organic linkers (solution 2) were introduced through separate channels into a mixing section. Following mixing, uniform water-in-oil droplets were generated within the droplet flow reaction system. To separate the oil phase from the reaction phase, an oil–water separator was attached to the outlet of the droplet reaction system. The reaction phase, possessing a lower density, was gathered at the top of the separator, while the oil, with a higher density, was extracted from the separator for subsequent reuse. An electrospray-differential mobility analysis (ES-DMA) was implemented to interface with the developed microdroplet synthetic system, facilitating real-time, high-resolution quantitative analysis of the continuously produced MOF colloids (Fig. 11(b)).125 It is to be noted that our previous research has shown that the standalone ES-DMA can effectively analyse colloidal materials produced through batch synthesis; this technique allows for the quantitative characterization of several key properties, including physical size, colloidal stability and size growth, by monitoring changes in the mobility size distribution of the colloidal materials.126–128
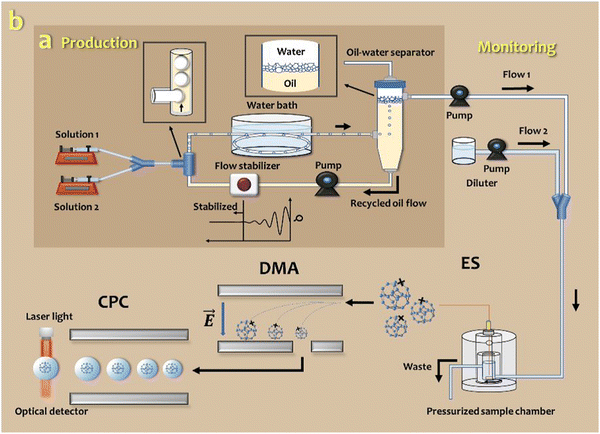 |
| Fig. 11 (a) Flow-mode microdroplet synthesis of MOF colloids followed by (b) real-time quantitative characterization of mobility size distribution by using a hyphenated electrospray differential mobility analysis system. Reprinted with permission from ref. 125. Copyright 2023, American Chemical Society. | |
Very recently, we devised an innovative and efficient method that integrates microfluidic and aerosol-based synthesis techniques with coupled ES-DMA.83 This approach enables the simultaneous synthesis and analysis of MOF-derived hybrid nanostructured products in an effective and continuous manner (Fig. 12). We explored the influence of precursor concentration and carrier selection on various properties of the resulting products, such as mobility size distribution, crystallization degree, surface area, and metal dispersion. Additionally, we investigated the relationship between the material properties of the synthesized MOF-derived materials and their catalytic performance in the RWGS reaction, including conversion ratio/rate, selectivity, and operational stability. Our findings demonstrated that the continuous microfluidic droplet system effectively synthesizes MOF colloids, followed by the continuous production of MOF-derived hybrid materials using the tandem aerosol spray-drying-reaction system.83 This work contributes to streamlining the production process and advancing the conceptualization of relevant MOF-derived hybrid nanostructured materials in continuous synthesis settings.
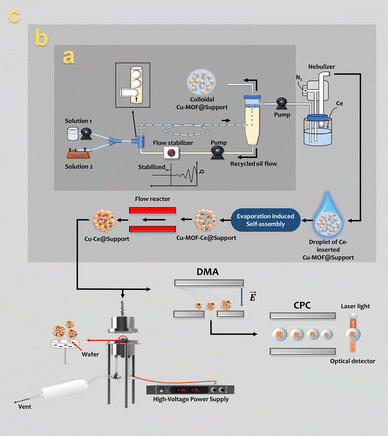 |
| Fig. 12 Schematic diagram of the continuous microfluidic droplet–aerosol combined material synthesis and characterization technology. (a) MOF@Support colloidal particle synthetic unit (via microfluidic droplet process); (b) MOF-derived material (Cu@Support) synthetic unit; and (c) real-time differential mobility analysis unit and electrostatic deposition for ex situ material characterization. Reprinted with permission from ref. 83. Copyright 2023, John Wiley and Sons. | |
5. Impact of flow synthesis on MOF properties and performance
The use of flow synthesis techniques has a significant impact on the properties and performance of the synthesized MOFs. Key factors influencing the properties of flow-synthesized MOFs include the following.
5.1. Crystallinity and phase purity
Continuous flow synthesis offers significant advantages for the production of MOFs with improved crystallinity and phase purity compared to traditional batch synthesis methods.59,90,100,129 Flow systems utilize microfluidic channels with precisely designed geometries that promote efficient and rapid mixing of precursor solutions. This minimizes precursor concentration gradients within the reaction zone, leading to more uniform nucleation and growth of MOF crystals.51,129 This uniformity translates to higher crystallinity with well-defined crystal structures. The short diffusion distances within microfluidic channels ensure efficient delivery of precursors to growing MOF crystals. This reduces the risk of precursor depletion in certain areas, which can lead to defects and imperfections within the crystal structure.129,130 Consequently, flow synthesis promotes the formation of MOFs with higher crystallinity. Flow systems allow for precise control over the residence time (reaction time) of precursors within the reactor. This enables optimization of reaction conditions to favour the formation of the desired MOF phase.129,130 By minimizing exposure to undesired side reactions or competing phases, flow synthesis promotes the production of MOFs with higher phase purity. The efficient mixing and mass transfer within the flow system minimize the formation of unwanted by-products due to incomplete or uncontrolled reactions which contributes to the production of purer MOF phases.129,130 Further, optimizing flow rate, temperature, and pressure within the flow system can significantly impact both crystallinity and phase purity. Careful optimization is crucial for achieving the desired MOF characteristics.74,108,131 Moreover, the choice of precursors and their compatibility with flow synthesis conditions can influence the final MOF properties. Selecting suitable precursors is essential for achieving high crystallinity and phase purity.
5.2. Particle size and morphology
Continuous flow synthesis offers a high degree of control over the particle size and morphology of MOFs compared to traditional batch methods.51,59,129,132 This controllability allows for the fine-tuning of MOF properties for targeted applications. Flow rate dictates the residence time of precursors within the microfluidic channels. Slower flow rates allow for longer contact time between precursors, promoting crystal growth and leading to larger MOF particles. Conversely, faster flow rates result in shorter contact times, favouring the formation of smaller MOF particles.129,132 Next, the reaction temperature plays a crucial role. Higher temperatures can accelerate nucleation and crystal growth, often leading to larger MOF particles. However, excessively high temperatures might promote uncontrolled aggregation, resulting in uneven particle size.59,132 The concentration of precursors in the reaction mixture can also influence the particle size. Lower precursor concentration often leads to the formation of smaller MOF particles due to limited availability of building blocks for crystal growth. Conversely, higher concentrations can promote the formation of larger crystals.59,74,132 Introducing specific additives like modulators or directing agents within the flow system can influence the growth kinetics and morphology of MOF crystals. These additives can promote the formation of specific crystal shapes or control the aspect ratio of the particles.51,129
5.3. Chemical composition and surface chemistry
Continuous flow synthesis offers significant advantages for controlling the chemical composition and surface chemistry of MOFs over traditional batch synthetic methods.50,51,90 Flow systems enable precise metering and mixing of precursor solutions within the microfluidic channels. This meticulous control over precursor ratios minimizes deviations from the desired stoichiometry, leading to MOFs with a more accurate and consistent chemical composition.50,51 Batch synthesis can suffer from inhomogeneity, potentially resulting in variations in MOF composition across different reaction batches. Efficient mixing within the flow system reduces the formation of unwanted side products or competing phases during the reaction. This contributes to the formation of MOFs with a purer chemical composition, reflecting the intended design.50 Flow synthesis allows for the introduction of dopants or functional groups directly into the reaction mixture within the flow system. This enables precise control over the incorporation of these modifying agents, leading to MOFs with well-defined chemical compositions for tailored functionalities.50,90 Flow synthesis offers precise control over reaction parameters like temperature and residence time. This allows for controlled nucleation and growth processes, influencing the density and distribution of functional groups on the MOF surface. By controlling the chemical composition and surface chemistry through flow synthesis, researchers can design MOFs with specific functionalities for targeted applications.50,51
6. Challenges and future perspectives
The continuous flow synthesis of MOFs and their composites presents both opportunities and challenges in the realm of materials science and engineering. The following are some of the key challenges faced in this area and offer insights into potential future perspectives:
1. Reaction kinetics and optimization: one of the primary challenges in flow synthesis of MOFs is optimizing reaction conditions to achieve high yields and desired properties. This involves understanding the kinetics of MOF formation under continuous flow conditions and developing efficient strategies for reaction control and optimization.
2. Scalability and continuous production: while flow synthesis offers advantages in terms of scalability and continuous production compared to batch synthesis methods, scaling up flow reactors for industrial-scale production of MOFs and their composites remains a significant challenge. Future research may focus on developing scalable flow reactor designs and process optimization strategies to enable large-scale production of MOFs.
3. Control over MOF properties: achieving precise control over the properties of MOFs synthesized under flow conditions, such as particle size, morphology, crystallinity, and pore structure, remains a key challenge. Future research efforts may explore novel reactor designs, reaction conditions, and post-synthesis treatments to fine-tune the properties of flow-synthesized MOFs for specific applications.
4. Reactor fouling and blockage: precipitate formation, a common occurrence during MOF synthesis, can obstruct the microchannels within the reactor. Blockages hinder the flow of reactants and products, ultimately reducing the overall production rate of MOFs. Frequent cleaning or redesign of reactor components becomes necessary to maintain functionality, resulting in higher maintenance costs. However, developing microfluidic reactors with improved flow characteristics and self-cleaning mechanisms can minimize blockage risks. Implementing real-time monitoring systems to detect the onset of blockage and trigger automated cleaning protocols can prevent complete flow disruption. Research into alternative MOF precursors that are less prone to generating problematic precipitates during the synthesis process can significantly reduce the risk of blockage.
5. Working with overheated solvents: continuous flow synthesis often necessitates using solvents at elevated temperatures to accelerate reactions. Overheated solvents can degrade or decompose, impacting MOF formation and potentially damaging the reactor itself. This necessitates defining a “novel process window” for each MOF system, balancing reaction efficiency with solvent stability. Selecting high-boiling point solvents with good thermal stability for the desired reaction temperature is crucial. Exploring alternative solvent systems or using additives that enhance solvent stability at high temperatures are potential solutions. Implementing efficient heat exchange mechanisms within the microfluidic chip can ensure precise temperature control and prevent solvent overheating. Utilizing microreactors with materials that can withstand higher temperatures can also be explored.
6. Integration of functional components: incorporating functional components into MOFs to impart specific properties or functionalities, such as catalytic activity, luminescence, or sensing capabilities, presents challenges in flow synthesis. Future perspectives may involve developing innovative strategies for the controlled incorporation of functional moieties into MOF frameworks under continuous flow conditions.
7. Characterization and quality control: reliable characterization techniques are essential for assessing the quality and properties of flow-synthesized MOFs and their composites. However, traditional characterization methods may need adaptation or development of new techniques suitable for analyzing materials produced under flow conditions. Future research may focus on advancing in situ and online characterization techniques tailored for flow synthesis of MOFs.
8. Green and sustainable synthesis: as with any chemical synthesis process, ensuring sustainability and minimizing environmental impact are critical considerations in flow synthesis of MOFs. Future perspectives may involve the development of greener and more sustainable synthesis routes, including the use of renewable starting materials, eco-friendly solvents, and energy-efficient reaction conditions.
9. Flow synthesis without back-pressure regulators (BPRs): BPRs are commonly used in continuous flow systems to maintain constant pressure throughout the reaction channel. However, their use adds complexity to the setup. Eliminating BPRs can simplify the flow system design and potentially reduce maintenance costs. Precise control over flow rates of all incoming streams using high-performance pumps is essential to maintain the desired pressure within the microfluidic chip without the need for a BPR. Microreactors with specifically designed channel geometries or integrated pressure control elements can be explored to achieve the desired pressure profile within the flow system.
10. Hybrid processes: integration of continuous flow with established batch processes can leverage the strengths of both approaches. This can optimize production throughput and offer greater flexibility in MOF design and synthesis. Additionally, designing systems capable of performing multiple sequential steps in a continuous manner can significantly reduce the need for intermediate handling and purification procedures.
11. Application-oriented research: while significant progress has been made in the synthesis of MOFs and their composites under flow conditions, there is still a need for application-oriented research to explore the practical utility of flow-synthesized materials in various fields, including catalysis, gas storage and separation, drug delivery, sensing, and environmental remediation. Future perspectives may involve interdisciplinary collaborations to bridge the gap between material synthesis and application-driven research.
Overall, though the continuous flow synthesis of MOFs and their composites holds great promise for advancing the field of porous materials, several challenges need to be addressed to realize its full potential. Future research efforts may focus on overcoming these challenges through innovation in reactor design, process optimization, characterization techniques, and sustainable synthesis strategies, ultimately paving the way for the development of next-generation functional materials with tailored properties and enhanced performance.
Author contributions
Duraisamy Senthil Raja: conceptualization, methodology, data curation, writing – original draft, writing – review & editing, visualization. De-Hao Tsai: conceptualization, writing – review & editing, supervision, project administration, funding acquisition.
Data availability statement
The manuscript is a review article. No primary research results, software or code have been included and no new data were generated or analysed as part of this review.
Conflicts of interest
There are no conflicts to declare.
Acknowledgements
The authors thank the National Science and Technology Council (NSTC) of Taiwan, ROC for financial support under the contract of NSTC 112-2221-E-007-014-MY3.
Notes and references
- H.-C. Zhou, J. R. Long and O. M. Yaghi, Chem. Rev., 2012, 112, 673–674 CrossRef CAS PubMed.
- H. Furukawa, K. E. Cordova, M. O’Keeffe and O. M. Yaghi, Science, 2013, 341, 1230444 CrossRef PubMed.
- X. Zhang, Z. Chen, X. Liu, S. L. Hanna, X. Wang, R. Taheri-Ledari, A. Maleki, P. Li and O. K. Farha, Chem. Soc. Rev., 2020, 49, 7406–7427 RSC.
- Y. Li, Y. Wang, W. Fan and D. Sun, Dalton Trans., 2022, 51, 4608–4618 RSC.
- W. Li, P. Xu, Z. Wang, Y. He, H. Qin, Y. Zeng, Y. Li, Z. Zhang and J. Gao, Mater. Chem. Front., 2023, 7, 5140–5170 RSC.
- L. Jiao, Y. Wang, H.-L. Jiang and Q. Xu, Adv. Mater., 2018, 30, 1703663 CrossRef PubMed.
- G. Mínguez Espallargas and E. Coronado, Chem. Soc. Rev., 2018, 47, 533–557 RSC.
- J. F. Olorunyomi, S. T. Geh, R. A. Caruso and C. M. Doherty, Mater. Horiz., 2021, 8, 2387–2419 RSC.
- Z. A. Sandhu, M. A. Raza, N. S. Awwad, H. A. Ibrahium, U. Farwa, S. Ashraf, A. Dildar, E. Fatima, S. Ashraf and F. Ali, Mater. Adv., 2024, 5, 30–50 RSC.
- J. Dong, D. Zhao, Y. Lu and W.-Y. Sun, J. Mater. Chem. A, 2019, 7, 22744–22767 RSC.
- Z. Sun, T. Li, T. Mei, Y. Liu, K. Wu, W. Le and Y. Hu, J. Mater. Chem. B, 2023, 11, 3273–3294 RSC.
-
A. Yohannes, Y. Su and S. Yao, Metal–Organic Frameworks for Environmental Remediation, American Chemical Society, 2021, vol. 1395, ch. 1, pp. 1–23 Search PubMed.
- D. Zhao, X. Wang, L. Yue, Y. He and B. Chen, Chem. Commun., 2022, 58, 11059–11078 RSC.
- T. M. Reichenau, F. Steinke, M. T. Wharmby, C. Näther, T. A. Engesser and N. Stock, Angew. Chem., Int. Ed., 2023, 62, e202303561 CrossRef CAS PubMed.
- O. M. Yaghi, M. O'Keeffe, N. W. Ockwig, H. K. Chae, M. Eddaoudi and J. Kim, Nature, 2003, 423, 705–714 CrossRef CAS PubMed.
- Q.-L. Zhu and Q. Xu, Chem. Soc. Rev., 2014, 43, 5468–5512 RSC.
- Q. Zhang, H. Yang, T. Zhou, X. Chen, W. Li and H. Pang, Adv. Sci., 2022, 9, 2204141 CrossRef CAS PubMed.
- Y. Xue, S. Zheng, H. Xue and H. Pang, J. Mater. Chem. A, 2019, 7, 7301–7327 RSC.
- Y. Ren and Y. Xu, Chem. Commun., 2023, 59, 6475–6494 RSC.
- Y. Zhu, T. Han, X. Lin, H. Zhang, C. Hu and J. Liu, Chem. Commun., 2023, 59, 2640–2643 RSC.
- D. Senthil Raja, X.-F. Chuah and S.-Y. Lu, Adv. Energy Mater., 2018, 8, 1801065 CrossRef.
- D. Senthil Raja, H.-W. Lin and S.-Y. Lu, Nano Energy, 2019, 57, 1–13 CrossRef CAS.
- H.-W. Lin, D. Senthil Raja, X.-F. Chuah, C.-T. Hsieh, Y.-A. Chen and S.-Y. Lu, Appl. Catal., B, 2019, 258, 118023 CrossRef CAS.
- D. Senthil Raja, C.-L. Huang, Y.-A. Chen, Y. Choi and S.-Y. Lu, Appl. Catal., B, 2020, 279, 119375 CrossRef CAS.
- X. Liu, A. Wang, C. Wang, J. Li, Z. Zhang, A. M. Al-Enizi, A. Nafady, F. Shui, Z. You, B. Li, Y. Wen and S. Ma, Nat. Commun., 2023, 14, 7022 CrossRef CAS PubMed.
- D. Chakraborty, A. Yurdusen, G. Mouchaham, F. Nouar and C. Serre, Adv. Funct. Mater., 2023, 2309089 CrossRef.
- M. Rubio-Martinez, C. Avci-Camur, A. W. Thornton, I. Imaz, D. Maspoch and M. R. Hill, Chem. Soc. Rev., 2017, 46, 3453–3480 RSC.
- D. Ma, X. Huang, Y. Zhang, L. Wang and B. Wang, Nano Res., 2023, 16, 7906–7925 CrossRef CAS.
- Q. He, F. Zhan, H. Wang, W. Xu, H. Wang and L. Chen, Mater. Today Sustain., 2022, 17, 100104 CrossRef.
- P. Li, F.-F. Cheng, W.-W. Xiong and Q. Zhang, Inorg. Chem. Front., 2018, 5, 2693–2708 RSC.
- J. Łuczak, M. Kroczewska, M. Baluk, J. Sowik, P. Mazierski and A. Zaleska-Medynska, Adv. Colloid Interface Sci., 2023, 314, 102864 CrossRef PubMed.
- Y. Tanaka, S. Yamada and D. Tanaka, ChemPlusChem, 2021, 86, 650–661 CrossRef CAS PubMed.
- J. Li, J.-Y. Huang, Y.-X. Meng, L. Li, L.-L. Zhang and H.-L. Jiang, Chem. Commun., 2023, 59, 2541–2559 RSC.
- Y. Sun and H.-C. Zhou, Sci. Technol. Adv. Mater., 2015, 16, 054202 CrossRef PubMed.
- W.-J. Son, J. Kim, J. Kim and W.-S. Ahn, Chem. Commun., 2008, 6336–6338, 10.1039/B814740J.
- F. Afshariazar and A. Morsali, J. Mater. Chem. A, 2022, 10, 15332–15369 RSC.
- I. Thomas-Hillman, A. Laybourn, C. Dodds and S. W. Kingman, J. Mater. Chem. A, 2018, 6, 11564–11581 RSC.
- H. Ren and T. Wei, ChemElectroChem, 2022, 9, e202200196 CrossRef CAS.
- Y. Li, G. Wen, J. Li, Q. Li, H. Zhang, B. Tao and J. Zhang, Chem. Commun., 2022, 58, 11488–11506 RSC.
- K. Pobłocki, J. Drzeżdżon, B. Gawdzik and D. Jacewicz, Green Chem., 2022, 24, 9402–9427 RSC.
- A. I. Alfano, M. Brindisi and H. Lange, Green Chem., 2021, 23, 2233–2292 RSC.
- B. K. Kaang, L. Ha, J.-U. Joo and D.-P. Kim, Nanoscale, 2022, 14, 10835–10843 RSC.
- J. Yu, J. Liu, C. Li, J. Huang, Y. Zhu and H. You, Chem. Commun., 2024, 60, 3217–3225 RSC.
- M. Guidi, P. H. Seeberger and K. Gilmore, Chem. Soc. Rev., 2020, 49, 8910–8932 RSC.
- J. Britton and C. L. Raston, Chem. Soc. Rev., 2017, 46, 1250–1271 RSC.
- J. Sui, J. Yan, D. Liu, K. Wang and G. Luo, Small, 2020, 16, 1902828 CrossRef CAS PubMed.
- A. Laybourn, K. Robertson and A. G. Slater, J. Am. Chem. Soc., 2023, 145, 4355–4365 CrossRef CAS PubMed.
- L. Capaldo, Z. Wen and T. Noël, Chem. Sci., 2023, 14, 4230–4247 RSC.
- W. D. Wong, M. F. Majnis, C. W. Lai, S. Sagadevan and N. Muhd Julkapli, Chem. Eng. Process., 2024, 198, 109729 CrossRef CAS.
- P. A. Bayliss, I. A. Ibarra, E. Pérez, S. Yang, C. C. Tang, M. Poliakoff and M. Schröder, Green Chem., 2014, 16, 3796–3802 RSC.
- M. P. Batten, M. Rubio-Martinez, T. Hadley, K.-C. Carey, K.-S. Lim, A. Polyzos and M. R. Hill, Curr. Opin. Chem. Eng., 2015, 8, 55–59 CrossRef.
- H. L. D. Hayes and C. J. Mallia, Org. Process Res. Dev., 2024, 28, 1327–1354 CrossRef CAS.
- A. I. Alfano, J. García-Lacuna, O. M. Griffiths, S. V. Ley and M. Baumann, Chem. Sci., 2024, 15, 4618–4630 RSC.
- J. D. Williams and C. O. Kappe, Curr. Opin. Green Sustainable Chem., 2020, 25, 100351 CrossRef.
- L. Buglioni, F. Raymenants, A. Slattery, S. D. A. Zondag and T. Noël, Chem. Rev., 2022, 122, 2752–2906 CrossRef CAS PubMed.
- M. Baumann, T. S. Moody, M. Smyth and S. Wharry, Eur. J. Org. Chem., 2020, 7398–7406 CrossRef CAS.
- C. A. Hone and C. O. Kappe, Chem.: Methods, 2021, 1, 454–467 CAS.
- A. Sivo, R. d S. Galaverna, G. R. Gomes, J. C. Pastre and G. Vilé, React. Chem. Eng., 2021, 6, 756–786 RSC.
- M. Rubio-Martinez, M. P. Batten, A. Polyzos, K.-C. Carey, J. I. Mardel, K.-S. Lim and M. R. Hill, Sci. Rep., 2014, 4, 5443 CrossRef CAS PubMed.
- L. Paseta, B. Seoane, D. Julve, V. Sebastián, C. Téllez and J. Coronas, ACS Appl. Mater. Interfaces, 2013, 5, 9405–9410 CrossRef CAS PubMed.
- G. H. Albuquerque, R. C. Fitzmorris, M. Ahmadi, N. Wannenmacher, P. K. Thallapally, B. P. McGrail and G. S. Herman, CrystEngComm, 2015, 17, 5502–5510 RSC.
- J. Chen, Z. Zhu, G. Monge and W.-N. Wang, Chem. Eng. J., 2022, 447, 137544 CrossRef CAS.
- N. Rohra, G. Gaikwad, P. Dandekar and R. Jain, ACS Appl. Mater. Interfaces, 2022, 14, 8251–8265 CrossRef CAS PubMed.
- N. Stock and S. Biswas, Chem. Rev., 2012, 112, 933–969 CrossRef CAS PubMed.
- X. Yu, J. Andreo, M. Walden, J. F. del Campo, L. Basabe-Desmonts, F. Benito-Lopez, T. P. Burg and S. Wuttke, Small Methods, 2024, 8, 2300603 CrossRef CAS PubMed.
- A. Polyzoidis, S. Reichle, M. Schwarzer, C. G. Piscopo, S. Löbbecke and D. Boskovic, React. Chem. Eng., 2021, 6, 679–684 RSC.
- Z. Liu, J. Zhu, C. Peng, T. Wakihara and T. Okubo, React. Chem. Eng., 2019, 4, 1699–1720 RSC.
- J. Sun, H. T. Kwon and H.-K. Jeong, Polyhedron, 2018, 153, 226–233 CrossRef CAS.
- V. Sebastian, S. A. Khan and A. A. Kulkarni, J. Flow Chem., 2017, 7, 96–105 CrossRef CAS.
- T. Lee, J.-O. Kim, C. Park, H. Kim, M. Kim, H. Park, I. Kim, J. Ko, K. Pak, S. Q. Choi, I.-D. Kim and S. Park, Adv. Mater., 2022, 34, 2107696 CrossRef CAS PubMed.
- D. Witters, N. Vergauwe, R. Ameloot, S. Vermeir, D. De Vos, R. Puers, B. Sels and J. Lammertyn, Adv. Mater., 2012, 24, 1316–1320 CrossRef CAS PubMed.
- C. Carbonell, K. C. Stylianou, J. Hernando, E. Evangelio, S. A. Barnett, S. Nettikadan, I. Imaz and D. Maspoch, Nat. Commun., 2013, 4, 2173 CrossRef PubMed.
- S. Chen, X. Zhou, G. Li and F. Yang, Chem. Eng. J., 2024, 480, 148208 CrossRef CAS.
- S. D. Bagi, A. S. Myerson and Y. Román-Leshkov, Cryst. Growth Des., 2021, 21, 6529–6536 CrossRef CAS.
- A. Carné-Sánchez, I. Imaz, M. Cano-Sarabia and D. Maspoch, Nat. Chem., 2013, 5, 203–211 CrossRef PubMed.
- T. Bailey, M. Pinto, N. Hondow and K.-J. Wu, MethodsX, 2021, 8, 101246 CrossRef CAS PubMed.
- H. U. Escobar-Hernandez, R. Shen, M. I. Papadaki, J. A. Powell, H.-C. Zhou and Q. Wang, ACS Chem. Health Saf., 2021, 28, 358–368 CrossRef CAS.
- T. Johnson, M. Fejzic, D. Tee and S. Bennett, Org. Process Res. Dev., 2021, 25, 754–759 CrossRef CAS.
- N. Al Amery, H. R. Abid, S. Al-Saadi, S. Wang and S. Liu, Mater. Today Chem., 2020, 17, 100343 CrossRef CAS.
- X. He, Z. Gan, S. Fisenko, D. Wang, H. M. El-Kaderi and W.-N. Wang, ACS Appl. Mater. Interfaces, 2017, 9, 9688–9698 CrossRef CAS PubMed.
- M. Gimeno-Fabra, A. S. Munn, L. A. Stevens, T. C. Drage, D. M. Grant, R. J. Kashtiban, J. Sloan, E. Lester and R. I. Walton, Chem. Commun., 2012, 48, 10642–10644 RSC.
- M. Faustini, J. Kim, G.-Y. Jeong, J. Y. Kim, H. R. Moon, W.-S. Ahn and D.-P. Kim, J. Am. Chem. Soc., 2013, 135, 14619–14626 CrossRef CAS PubMed.
- Y.-H. Sung, D. Senthil Raja, J.-H. Huang and D.-H. Tsai, Small Methods, 2023, 8, 2301435 CrossRef PubMed.
- A. Garcia Marquez, P. Horcajada, D. Grosso, G. Ferey, C. Serre, C. Sanchez and C. Boissiere, Chem. Commun., 2013, 49, 3848–3850 RSC.
- Q. Fu, W. Niu, L. Yan, W. Xie, H. Jiang, S. Zhang, L. Yang, Y. Wang, Y. Xing and X. Zhao, Mater. Lett., 2023, 343, 134344 CrossRef CAS.
- C.-B. Du, J.-Y. Tu, Z. X. Law and D.-H. Tsai, Int. J. Hydrogen Energy, 2024, 57, 1152–1163 CrossRef CAS.
- Y.-A. Hsueh, Y. C. Chuah, C.-H. Lin and D.-H. Tsai, ACS Appl. Nano Mater., 2022, 5, 8883–8893 CrossRef CAS.
- B. He, M. M. Sadiq, M. P. Batten, K. Suzuki, M. Rubio-Martinez, J. Gardiner and M. R. Hill, Chem. – Eur. J., 2019, 25, 13184–13188 CrossRef CAS PubMed.
- S. R. Jambovane, S. K. Nune, R. T. Kelly, B. P. McGrail, Z. Wang, M. I. Nandasiri, S. Katipamula, C. Trader and H. T. Schaef, Sci. Rep., 2016, 6, 36657 CrossRef CAS PubMed.
- S. Bagi, S. Yuan, S. Rojas-Buzo, Y. Shao-Horn and Y. Román-Leshkov, Green Chem., 2021, 23, 9982–9991 RSC.
- C. McKinstry, R. J. Cathcart, E. J. Cussen, A. J. Fletcher, S. V. Patwardhan and J. Sefcik, Chem. Eng. J., 2016, 285, 718–725 CrossRef CAS.
- Y. Denis, C. Elissalde, M. R. Suchomel, M. Gayot, F. Weill, C. Labrugère, L. Etienne, M. Vaudesca, N. Cam, U. C. Chung, H. Reveron, J. Chevalier, T. H. de Beauvoir, C. Estournès, C. Aymonier, G. Goglio and G. Philippot, Adv. Mater. Technol., 2024, 9, 2301474 CrossRef CAS.
- T. Stassin, S. Waitschat, N. Heidenreich, H. Reinsch, F. Pluschkell, D. Kravchenko, J. Marreiros, I. Stassen, J. van Dinter, R. Verbeke, M. Dickmann, W. Egger, I. Vankelecom, D. De Vos, R. Ameloot and N. Stock, Chem. – Eur. J., 2020, 26, 10841–10848 CrossRef CAS PubMed.
- S. Bagi, A. M. Wright, J. Oppenheim, M. Dincă and Y. Román-Leshkov, ACS Sustainable Chem. Eng., 2021, 9, 3996–4003 CrossRef CAS.
- M. Y. B. Zulkifli, Y. Yao, R. Chen, M. Chai, K. Su, X. Li, Y. Zhou, R. Lin, Z. Zhu, K. Liang, V. Chen and J. Hou, Chem. Commun., 2022, 58, 12297–12300 RSC.
- Y. Wang, Y. Lu, Z. Li, X.-W. Sun, W.-Y. Zhang, S. Zhang, J. Wang, T.-Y. Dang, Z. Zhang and S.-X. Liu, Chem. Commun., 2021, 57, 8933–8936 RSC.
- M. Klimakow, P. Klobes, A. F. Thünemann, K. Rademann and F. Emmerling, Chem. Mater., 2010, 22, 5216–5221 CrossRef CAS.
- W. Wang, M. Chai, M. Y. Bin Zulkifli, K. Xu, Y. Chen, L. Wang, V. Chen and J. Hou, Mol. Syst. Des. Eng., 2023, 8, 560–579 RSC.
- D. Crawford, J. Casaban, R. Haydon, N. Giri, T. McNally and S. L. James, Chem. Sci., 2015, 6, 1645–1649 RSC.
- Z. Guo, Q. Zhang, Z. Cheng, Q. Liu, J. Zuo, B. Jin and R. Peng, ACS Sustainable Chem. Eng., 2020, 8, 4037–4043 CrossRef CAS.
- R. S. Atapalkar and A. A. Kulkarni, React. Chem. Eng., 2024, 9, 10–25 RSC.
- R. R. A. Bolt, J. A. Leitch, A. C. Jones, W. I. Nicholson and D. L. Browne, Chem. Soc. Rev., 2022, 51, 4243–4260 RSC.
- R. Morschhäuser, M. Krull, C. Kayser, C. Boberski, R. Bierbaum, P. A. Püschner, T. N. Glasnov and C. O. Kappe, Green Process Synth., 2012, 1, 281–290 Search PubMed.
- C. McKinstry, E. J. Cussen, A. J. Fletcher, S. V. Patwardhan and J. Sefcik, Chem. Eng. J., 2017, 326, 570–577 CrossRef CAS.
- A. Laybourn, A. M. López-Fernández, I. Thomas-Hillman, J. Katrib, W. Lewis, C. Dodds, A. P. Harvey and S. W. Kingman, Chem. Eng. J., 2019, 356, 170–177 CrossRef CAS.
- M. Taddei, D. A. Steitz, J. A. van Bokhoven and M. Ranocchiari, Chem. – Eur. J., 2016, 22, 3245–3249 CrossRef CAS PubMed.
- D. Fernandez Rivas, P. Cintas and H. J. G. E. Gardeniers, Chem. Commun., 2012, 48, 10935–10947 RSC.
- J. Cao, X. Peng, H. Li, L. Ren, T. Xu, K. Sun, Y. Zhang and D. Li, Mater. Sci. Eng., C, 2021, 129, 112369 CrossRef CAS PubMed.
- H.-Y. Wu, C.-L. Wu, W. Liao, B. M. Matsagar, K.-Y. Chang, J.-H. Huang and K. C. W. Wu, J. Mater. Chem. A, 2023, 11, 9427–9435 RSC.
- G.-Y. Jeong, R. Ricco, K. Liang, J. Ludwig, J.-O. Kim, P. Falcaro and D.-P. Kim, Chem. Mater., 2015, 27, 7903–7909 CrossRef CAS.
- G. Hu, L. Yang, Y. Li and L. Wang, J. Mater. Chem. B, 2018, 6, 7936–7942 RSC.
- F. Long, Y. Guo, Z. Zhang, J. Wang, Y. Ren, Y. Cheng and G. Xu, Global Chall., 2023, 7, 2300063 CrossRef PubMed.
- K. Tsachouridis, Y. Zhou and A. D. Anastasiou, Chem. Eng. Sci., 2024, 293, 119956 CrossRef CAS.
- P. D. Patil, S. Salokhe, A. Karvekar, P. Suryavanshi, A. N. Phirke, M. S. Tiwari and S. S. Nadar, Int. J. Biol. Macromol., 2023, 253, 127358 CrossRef CAS PubMed.
- Y. Wang, L. Li, H. Liang, Y. Xing, L. Yan, P. Dai, X. Gu, G. Zhao and X. Zhao, ACS Nano, 2019, 13, 2901–2912 CrossRef CAS PubMed.
- C. Hu, Y. Bai, M. Hou, Y. Wang, L. Wang, X. Cao, C.-W. Chan, H. Sun, W. Li, J. Ge and K. Ren, Sci. Adv., 2020, 6, eaax5785 CrossRef CAS PubMed.
- J. Troyano, C. Çamur, L. Garzón-Tovar, A. Carné-Sánchez, I. Imaz and D. Maspoch, Acc. Chem. Res., 2020, 53, 1206–1217 CrossRef CAS PubMed.
- A. Carné-Sánchez, K. C. Stylianou, C. Carbonell, M. Naderi, I. Imaz and D. Maspoch, Adv. Mater., 2015, 27, 869–873 CrossRef PubMed.
- L. Garzón-Tovar, M. Cano-Sarabia, A. Carné-Sánchez, C. Carbonell, I. Imaz and D. Maspoch, React. Chem. Eng., 2016, 1, 533–539 RSC.
- T. T. Nguyen, T. Hirano, R. N. Chamida, E. L. Septiani, N. T. Nguyen and T. Ogi, Powder Technol., 2024, 440, 119782 CrossRef CAS.
- S. Wintzheimer, L. Luthardt, K. L. A. Cao, I. Imaz, D. Maspoch, T. Ogi, A. Bück, D. P. Debecker, M. Faustini and K. Mandel, Adv. Mater., 2023, 35, 2306648 CrossRef CAS PubMed.
- T. T. Nguyen, Y. Toyoda, N. S. N. Saipul Bahri, A. M. Rahmatika, K. L. A. Cao, T. Hirano, K. Takahashi, Y. Goi, Y. Morita, M. Watanabe and T. Ogi, J. Colloid Interface Sci., 2023, 630, 134–143 CrossRef CAS PubMed.
- C. Avci-Camur, J. Troyano, J. Pérez-Carvajal, A. Legrand, D. Farrusseng, I. Imaz and D. Maspoch, Green Chem., 2018, 20, 873–878 RSC.
- R.-Y. Huang, T. Truc Nguyen Hoang, Y.-A. Hsueh and D.-H. Tsai, Fuel, 2023, 349, 128647 CrossRef CAS.
- Y.-H. Sung, C.-L. Wu, J.-H. Huang and D.-H. Tsai, Anal. Chem., 2023, 95, 4513–4520 CrossRef CAS PubMed.
- J.-T. Tai, Y.-C. Lai, J.-H. Yang, H.-C. Ho, H.-F. Wang, R.-M. Ho and D.-H. Tsai, Anal. Chem., 2015, 87, 3884–3889 CrossRef CAS PubMed.
- Y.-C. Lai, C.-W. Kung, C.-H. Su, K.-C. Ho, Y.-C. Liao and D.-H. Tsai, Langmuir, 2016, 32, 6123–6129 CrossRef CAS PubMed.
- W.-C. Chang, S.-C. Cheng, W.-H. Chiang, J.-L. Liao, R.-M. Ho, T.-C. Hsiao and D.-H. Tsai, Anal. Chem., 2017, 89, 12217–12222 CrossRef CAS PubMed.
- B. He, L. K. Macreadie, J. Gardiner, S. G. Telfer and M. R. Hill, ACS Appl. Mater. Interfaces, 2021, 13, 54284–54293 CrossRef CAS PubMed.
- C. Echaide-Górriz, C. Clément, F. Cacho-Bailo, C. Téllez and J. Coronas, J. Mater. Chem. A, 2018, 6, 5485–5506 RSC.
- I. G. Koryakina, S. V. Bachinin, E. N. Gerasimova, M. V. Timofeeva, S. A. Shipilovskikh, A. S. Bukatin, A. Sakhatskii, A. S. Timin, V. A. Milichko and M. V. Zyuzin, Chem. Eng. J., 2023, 452, 139450 CrossRef CAS.
- A. Zuliani, M. Carmen Castillejos and N. Khiar, Green Chem., 2023, 25, 10596–10610 RSC.
|
This journal is © The Royal Society of Chemistry 2024 |