DOI:
10.1039/D3YA00638G
(Review Article)
Energy Adv., 2024,
3, 676-688
Possibilities and challenges of cathode materials for Zn-ion batteries
Received
31st December 2023
, Accepted 29th February 2024
First published on 29th February 2024
Abstract
The demand for energy storage solutions has been steadily rising with the increasing prevalence of renewable energy sources and the widespread use of portable electronic devices. In this context, zinc-ion batteries (ZIBs) have emerged as a promising alternative to lithium-ion batteries due to their high energy density, cost-effectiveness, and safety advantages. However, the practical application of ZIBs faces limitations due to the lack of suitable cathode materials. This comprehensive review explores the possibilities and challenges associated with various cathode materials suitable for ZIB applications. It also highlights key issues, discusses strategies to overcome these challenges, and provides insights into ongoing prospects in the research of cathode materials. In conclusion, the review offers a perspective on recycling, sustainability, and the efforts of various organizations in the development and promotion of ZIB research for energy storage systems.
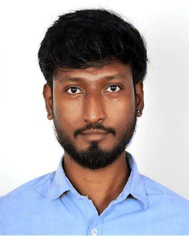
R. Ajay Rakkesh
| R. Ajay Rakkesh obtained his PhD in Nanoscience and Nanotechnology from the National Centre for Nanosciences and Nanotechnology, University of Madras, Chennai. Presently, he serves as an Assistant Professor in the Department of Physics and Nanotechnology at SRM Institute of Science and Technology, Kattankulathur, Chennai. His research focuses on Graphene-based Nanoarchitectronics for Energy Conversion and Storage. |
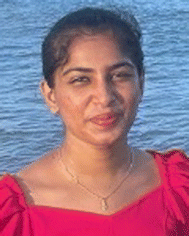
S. Shalini
| S. Shalini is a PhD student in the Department of Physics and Nanotechnology at SRM Institute of Science and Technology (SRMIST), Kattankulathur, Chennai. She earned his master's in Physics at SRMIST. Her research focused on developing Metal Oxides based nanostructures for advanced energy storage and conversion applications. |
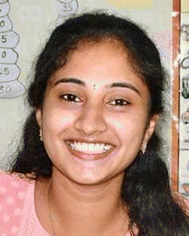
S. Tharani
| S. Tharani is pursuing her PhD in the Department of Physics and Nanotechnology at SRM Institute of Science and Technology, located in Kattankulathur, Chennai. Before this, she earned her master's degree in Physics from the Madras Christian College, Chennai. Her research is focused on Zn-ion Batteries. |
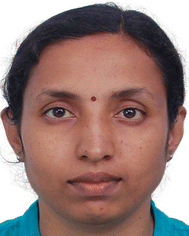
D. Durgalakshmi
| D. Durgalakshmi has obtained her PhD in Nanoscience and Nanotechnology from the National Centre for Nanoscience and Nanotechnology, University of Madras, Chennai. She is an Assistant Professor in the Department of Medical Physics at Anna University, Chennai. Her research interests focus on biomass-derived graphene and its applications in biosensors, bone and dental regenerations. |
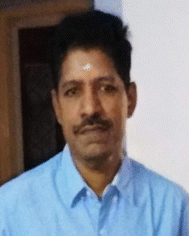
S. Balakumar
| S. Balakumar is a professor and the director of the National Centre for Nanoscience and Nanotechnology at the University of Madras, Chennai, India. He obtained his PhD from Anna University and gained post-doctoral experience at the Chinese University of Hong Kong and the National University of Singapore. His primary research focuses on multifunctional nano-materials, exploring their applications in the energy, environmental, and healthcare sectors. |
Introduction
Batteries have become an indispensable cornerstone of modern society, permeating nearly every facet of our daily lives. These energy storage devices quietly power the electronic devices we rely on, from the ubiquitous smartphones that keep us connected to the electric vehicles (EVs) revolutionising our transportation and the grid energy storage systems securing our energy future. For decades, lithium-ion batteries have reigned supreme as the reigning workhorse of energy storage technology, powering everything from our pocket-sized gadgets to our electric dreams. Nevertheless, as our reliance on batteries grows, so do the concerns surrounding their sustainability, safety, and long-term availability.1
The relentless demand for lithium, a finite resource, raises questions about the long-term viability of lithium-ion batteries as the go-to energy storage solution. Moreover, recurring safety incidents, including thermal runaway events and overheating, have underscored the need for safer alternatives. These factors have catalysed a fervent exploration of alternative battery chemistries that can promise a sustainable, safer, and more affordable energy storage landscape.2
Zinc-ion batteries (ZIBs) have emerged as a compelling candidate in recent years among the contenders striving to unseat lithium-ion batteries. The allure of ZIBs lies in their abundance and relatively low cost, qualities that resonate with the imperatives of scalability and affordability, especially in large-scale energy storage applications. Further adding to their appeal, ZIBs exhibit an improved safety profile compared to their lithium-ion counterparts, offering a pathway to mitigate some of the safety concerns that have plagued the battery industry.3
Within the intricate architecture of a battery, the cathode material plays a role of paramount significance. The linchpin dictates the entire energy storage system's overall performance, energy density, and efficiency. The cathode is where the magic happens; electrons shuttle back and forth during charging and discharging, and the electrochemical reactions that store and release energy occur. Consequently, understanding, optimising, and innovating upon cathode materials are pivotal in the quest for next-generation energy storage solutions.4a,b
This comprehensive review embarks on an exploratory journey into the intricate world of cathode materials for ZIBs. By delving into these materials' possibilities and elucidating their multifaceted challenges, we seek to illuminate the evolving landscape of energy storage technology. In the pages that follow, we will uncover the diverse array of cathode materials vying for a role in the ZIB revolution, examine the intricacies of their electrochemical behaviour, and scrutinise the strategies and innovations aimed at surmounting the hurdles that stand between ZIBs and their full realisation as a game-changing energy storage solution.5
Cathode materials for Zn-ion batteries
Transition metal oxides
Transition metal oxides (TMOs) have emerged as significant candidates for cathode materials in zinc-ion batteries (ZIBs). Their attractiveness lies in their high theoretical capacities and commendable electrochemical performance, making them compelling options for energy storage applications. In this section, we explore the characteristics of particular TMOs, including manganese dioxide (MnO2), vanadium oxide (V6O13), and nickel oxide (NiO), accentuating their potential and addressing the challenges they encounter. Additionally, we have also cited recent research articles to substantiate our analysis.6,7a–c
Manganese dioxide (MnO2)
Manganese dioxide (MnO2) has garnered significant attention in ZIBs due to its abundant availability and high theoretical capacity as a cathode material. MnO2 exhibits a theoretical capacity of 308 mA h g−1, making it an attractive choice for energy storage applications. Furthermore, its eco-friendliness adds to its appeal. However, the practical application of MnO2 faces hurdles, notably in poor cyclability and limited rate capability. During cycling, MnO2 experiences substantial volume changes, leading to mechanical stress and gradual degradation of the electrode material. Researchers are actively working to address these challenges and enhance the performance of MnO2-based cathodes.
In 2018, Yuan et al. conducted a comparison between a control sample featuring conventional MnO2 electrodes and ZIBs with MnO2/rGO electrodes as depicted in Fig. 1a. In contrast, Fig. 1b and c illustrate the crumpled surface morphology, d-spacing, elemental distribution, and composition of the Zn–MnO2/rGO-based AZIB. The cyclic voltammogram (CV) in Fig. 1d reveals two distinct reversible redox peaks for the standard MnO2 cathode within the potential window of 1.0–1.9 V vs. Zn2+/Zn @ 0.2 mV s−1. MnO2/rGO electrodes also exhibit similar redox peaks but with enhanced peak current densities, indicating an improved specific capacity compared to MnO2 electrodes. Fig. 1e illustrates the charging and discharging curves of MnO2 and MnO2/rGO electrodes @ 0.3 A g−1, clearly showcasing the improved capacity of MnO2/rGO (≈332.2 mA h g−1) compared to MnO2 (≈259.1 mA h g−1) at the given current density. Fig. 1f demonstrates the extraordinary capacity retention and coulombic efficiency of the MnO2/rGO electrode even after 500 cycles @ 6 A g−1.8
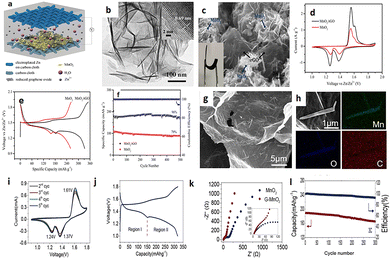 |
| Fig. 1 Morphology and electrochemical performance of MnO2/rGO. (a) Graphical representation of Zn–MnO2/rGO battery. (b) TEM image of MnO2/rGO. (c) SEM image and photographs of MnO2/rGO and EDX elemental mapping. (d) CV of MnO2/rGO. (e) Charging and discharging of the samples at 0.3 A g−1 current density. (f) The MnO2/rGO electrodes' coulombic efficiency and the MnO2/rGO and standard MnO2 electrode's cycling stability were measured at 6.0 A g−1. (g) G–MnO2 hybrid aerogel SEM images. (h) The matching aerogel Mn, O and C element mapping pictures. (i) CV curve for G–MnO2 at 0.2 mV s−1. (j) Charge–discharge curve for G–MnO2. (k) EIS curve for sample G–MnO2 and α-MnO2. (l) 300 cycle performance at 3C. | |
Chunyan et al. synthesized a G–MnO2 hybrid aerogel, as depicted in Fig. 1g, featuring a 3D porous network with interconnected graphene sheets, likely enhancing ion diffusion and electron transport. Elemental mapping in Fig. 1h demonstrates the electrode's homogeneous distribution of C, Mn, and O. Two cathodic and one anodic peak in the CV curves, along with overlapping CV curves in Fig. 1i, validate the stability of the G–MnO2 electrode. Galvanostatic charge and discharge profiles of G–MnO2 and α-MnO2 electrodes @ 0.2C are shown in Fig. 1j, displaying two voltage plateaus aligning with the respective CV curves. The G–MnO2 electrode demonstrates an excellent capacity of 321 mA h g−1 compared to α-MnO2 (248 mA h g−1) and rGO (26 mA h g−1), indicating superior Zn2+ ion storage capacity attributed to the conducting nature of rGO in the cathode material. EIS analysis in Fig. 1k reveals the low charge transfer resistance of the G–MnO2 cathode compared to pristine α-MnO2, validating enhanced conductivity.7 Furthermore, Fig. 1l demonstrates the extraordinary stability and capacity retention of the G–MnO2 electrode, remaining around 90% after 300 cycles @ 3C compared to pristine α-MnO2.9
Vanadium oxide (V6O13)
Vanadium oxide has captured the attention of researchers in the realm of ZIBs. With a specific capacity of approximately 294 mA h g−1, it stands as a strong contender for cathode materials. The layered crystal structure of V6O13, with its V5+ ions, facilitates the intercalation and de-intercalation of zinc ions, crucial for achieving efficient electrochemical performance. However, similar to MnO2, V6O13 encounters challenges such as limited cyclability and rate capability. The substantial volume changes experienced by V6O13 during charge–discharge cycles may lead to particle cracking and electrode degradation.10a–d
In the cyclic voltammetry (CV) profiling of the V5+-rich V6O13 cathode material, various scan rates were employed, revealing four distinct redox peaks. These peaks consist of two oxidation and two reduction peaks, as depicted in Fig. 2a. Fig. 2b illustrates the log(i) vs. log(v) fitted graph with a b value for the four redox peaks, indicating that the capacitive effect primarily contributes to the capacity. Fig. 2c demonstrates that the contribution of the diffusion process varies around 28%, while the capacitive process dominates at the mentioned scan rates.
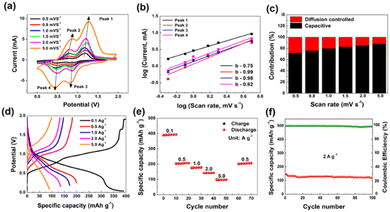 |
| Fig. 2 (a) CV curve at different scan rates. (b) Four primary redox CV peaks in a fitted plot. (c) Diffusion control and capacitive ratios at various scan rates. (d) GCD curves at different current densities. (e) Rate performance and (f) cyclic stability and coulombic efficiency @ 2 A g−1 for the V6O13 cathode respectively.8 | |
Fig. 2d displays the galvanostatic charge–discharge (GCD) curves at different current densities, highlighting the excellent specific capacity of the V5+-rich V6O13 electrode at 394.1 mA h g−1 @ 0.1 A g−1. Fig. 2e shows the cyclic performance for various current densities, while Fig. 2f exhibits the capacity retention and coulombic efficiency of the layered V6O13 nanostructure at 2 A g−1, around 94% and 96%, respectively.11
Nickel oxide (NiO)
Due to its favourable electrochemical properties, nickel oxide (NiO) is being investigated as a cathode material for ZIBs. NiO boasts a theoretical capacity of 718 mA h g−1, surpassing many other TMOs. Additionally, nickel is a relatively low-cost and abundant material. However, NiO faces challenges such as cyclability issues and limited rate capability, which arise from the same volume expansion problem observed in other TMOs like MnO2 and V6O13. Recent research on NiO-based cathodes has demonstrated the use of nanostructured NiO as an effective strategy to enhance the performance of NiO cathodes in ZIBs. Nanostructured NiO materials exhibit improved electrochemical stability and rate capability, addressing some of the challenges associated with this promising cathode material.
Liangyu et al. constructed a ZIB with zinc as the anode and NiOOH as the cathode, as depicted in Fig. 3a. A nanoporous zinc anode was utilized, achieving an excellent specific capacity of 759.32 mA h g−1 at 5 mA cm−2, utilizing a high zinc mass of approximately 92.6%. This showcased an enhanced power density of 264 mW cm−2 @ 196.4 mA cm−2 in a polarization test, as shown in Fig. 3b.
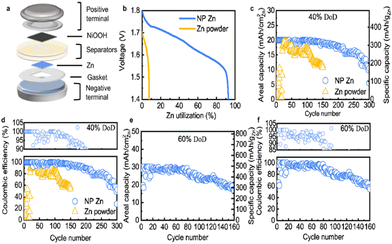 |
| Fig. 3 (a) Schematic of Zn II NiOOH coin cell. (b) Various anodes for zinc are used in primary Zn II NiOOH alkaline anodes. (c) Cycle number vs. discharging capacities of NP Zn and Zn powder sample. (d) Coulombic efficiency of NP Zn and Zn powder at 40% DoD. (e) At 60% depth of DoD, discharging capacities of the NP Zn anodes. (f) Coulombic efficiency of the sample at 60% DoD. | |
Observing Fig. 3c and d, it is evident that after 100 cycles, the capacity gradually decreases at a rate of 0.15% per cycle, reducing coulombic efficiency. When the depth of discharge (DoD) was increased to 60%, the nanoporous zinc anode maintained 80% of its specific capacity even after 120 cycles as shown in Fig. 3e. In summary, TMOs like MnO2, V6O13, and NiO show significant promise as cathode materials for ZIBs due to their high theoretical capacities. However, practical implementation faces challenges related to cyclability and rate capability. Recent research has made significant strides in mitigating these challenges through nanoscale engineering and advanced synthesis methods, bringing us closer to realizing efficient zinc-ion batteries for diverse energy storage applications.12
Polyanionic compounds
Polyanionic compounds, specifically iron phosphates (FePO4) and vanadium phosphates (VP), have emerged as notable candidates among cathode materials for zinc-ion batteries (ZIBs) due to their inherent advantages in terms of stability and structural flexibility. Recent research and articles have underscored the growing interest in these materials for energy storage applications.13
Iron phosphates (FePO4)
Iron phosphates have garnered significant attention as cathode materials for ZIBs, primarily owing to their exceptional stability and robust structural flexibility. These materials have been extensively explored in recent studies, with numerous investigations underscoring their potential. The latest advancements in FePO4 cathodes are presented in this study, showcasing innovative synthesis methods and advanced characterization techniques that have markedly enhanced the electrochemical performance and cycle life of FePO4-based cathodes. The authors accentuate the intrinsic safety of FePO4 materials, positioning them as a compelling choice for large-scale energy storage applications. While FePO4 exhibits noteworthy advantages, it is imperative to address its low electrical conductivity, which can limit its rate capability. Researchers have delved into various strategies to mitigate this constraint, including using conductive additives and composite materials to augment the electrical conductivity of FePO4 cathodes. This work encapsulates the latest advancements in this realm and underscores the potential for optimizing FePO4-based cathodes to enhance ZIB performance.14
In this study, Vinod et al. present an alcohol-assisted ambient temperature method for manufacturing amorphous metal phosphate cathodes, with a specific focus on porous iron(III) phosphate cathodes. Transmission electron microscopy (TEM) images as shown in Fig. 4a reveal amorphous FePO4 without fringes. Conversely, Fig. 4b and c display distinct fringes with varying widths corresponding to different diffraction planes, confirming the transformation of the FePO4 electrode from amorphous to crystalline phase during electrochemical Na/Li-insertion. The cyclic voltammetry (CV) curves of the cathode in an aqueous medium, depicted in Fig. 4d and e, along with a galvanostatic charge–discharge (GCD) curve, show an initial specific capacity of 96 mA h g−1. However, under non-aqueous electrolyte conditions and with magnesium ion insertion, amorphous FePO4 exhibits an impressive specific capacity of 131 mA h g−1 at 5 mA g−1, as illustrated in Fig. 4f. Additionally, the research group investigates the feasibility of aluminium ion (Al3+) insertion in the amorphous FePO4 cathode, exploring its potential application in aluminium-ion batteries.15
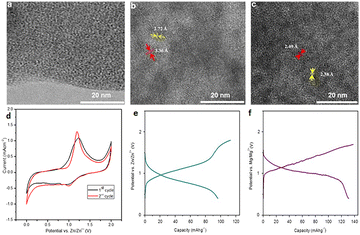 |
| Fig. 4 (a) STEM image of amorphous (FePO4). (b) Chemically sodiated. (c) Lattices fringe widths of lithiated (FePO4). (d) CV of amorphous (FePO4) versus zinc. (e) Electrochemical study of zinc insertion of amorphous (FePO4). (f) Electrochemical study of magnesium cell insertion of amorphous (FePO4). | |
Vanadium phosphates (VP)
Vanadium phosphates, precisely VP compounds, have also garnered significant attention in ZIBs due to their stability and structural flexibility. Recent research and articles have elucidated their potential as promising cathode materials. A recent report on VP materials' excellent cycle life and safety characteristics makes them attractive for ZIB applications. They also highlight the need for further research to improve VP cathodes' electrical conductivity.16
A recent study highlighting the exceptional cycle life and safety features of vanadium phosphate (VP) materials has positioned them as attractive candidates for ZIB applications. The report also underscores the imperative for further investigation to enhance the electrical conductivity of VP cathodes. Linfeng et al. synthesised layered VOP42H2O (VOP 7.4 Å) using a phenylamine (PA) intercalation technique through a straightforward solvothermal method. This method yielded three distinct PA–VOP samples with varying interlayer distances (14.8, 15.6, and 16.5 Å), as depicted in the XRD pattern in Fig. 5a. The relationship between solvothermal reaction time, interlayer spacing, and the saturation range is illustrated in Fig. 5b. Moreover, Fig. 5c confirms that the interlayer spacing of 16.5 Å surpasses that of other reported layered cathode materials for AZIBs.
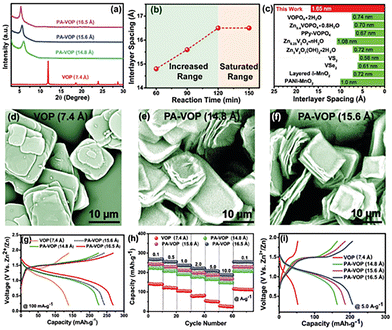 |
| Fig. 5 (a) XRD pattern for different temperatures and solvents of various samples of PA–VOP. (b) Solvothermal time and interlayer spacing. (c) Different interlayer spacing of aqueous ZIBs. (d)–(f) SEM images of different samples at various phases. (g) GCD curve of various samples. (h) The current density of samples with different interlayer spacing. (i) GCD curve of various samples with different interlayer spacing at a current density of 5 A g−1. | |
Fig. 5d–f showcases the remarkable thickness and plate-like morphology of the three PA–VOP cathodes resulting from phenylamine insertion. The researchers observed that alterations in interlayer spacing significantly impact the specific capacity exhibited by the cathode. Fig. 5g displays the discharge capacities of pristine VOP (7.4 Å) and the three PA–VOP samples, revealing enhanced specific capacity in Fig. 5h. Fig. 5i highlights the maximum discharge capacity for the PA–VOP cathode material with a 16.5 Å phase. Addressing the low electrical conductivity of VP cathodes remains a key challenge. Correspondingly, a recent work explores innovative approaches to bolster VP cathode conductivity. The work delves into advanced synthesis techniques and the development of VP-based composite materials as potential solutions. The authors stress these strategies' significance in unlocking VP's full potential as a cathode material for ZIBs.17
Furthermore, recent articles and research on polyanionic compounds, particularly iron phosphates (FePO4) and vanadium phosphates (VP), underscore their stability and structural flexibility as crucial for cathode materials in ZIBs. While these materials exhibit excellent cycle life and safety characteristics, the challenge of low electrical conductivity necessitates continuous research into conductive additives, composite materials, and innovative synthesis techniques to fully harness their capabilities in zinc-ion battery technology.
Organic cathode materials
Organic cathode materials encompass various organic compounds, including polymers, quinones, and tannins. These materials can potentially revolutionise the field of energy storage due to their unique properties and eco-friendly nature.18a,b Here, we explore some key categories of organic cathode materials and their recent advancements:
1. Organic polymers.
Organic polymers, including polyaniline, polypyrrole, and polythiophene, have garnered attention due to their notable redox activity and customizable properties. Recent research efforts have been directed towards developing organic polymers that exhibit improved electrochemical stability and high charge/discharge rates. In a study by Onur et al., a modified Diels–Alder reaction synthesised a redox-active porous organic polymer (rPOP) functionalized with quinones. This polymer serves as the cathode for aqueous ZIBs. Fig. 6a illustrates the cyclic voltammetry (CV) cycles of the rPOP polymer cathode within a potential window range of 0.1–1.6 V, with scan rates varying from 0.1 to 2.0 mV s−1, revealing one oxidation and three reduction peaks.
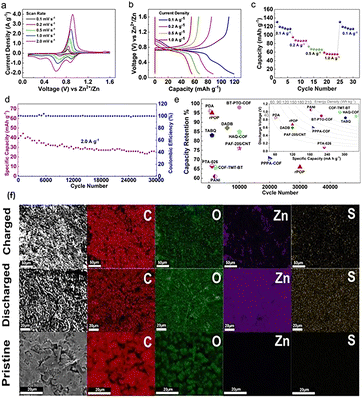 |
| Fig. 6 (a) CV curves at different scan rates. (b) GCD at different current densities. (c) Rate performance of samples with various current densities. (d) Cyclic stability of the sample. (e) Electrochemical performance of the sample compared with different organic cathode materials. (f) EDX elemental mapping of the sample and SEM images. | |
Fig. 6b illustrates the galvanostatic charge/discharge profiles of the rPOP cathode. The cathode demonstrates outstanding specific capacities of 120, 89, 69, and 58 mA h g−1 at various current densities ranging from 0.1 to 1.0 A g−1, as depicted in the figure. The rate performance of this cathode is further detailed in Fig. 6c. Remarkably, Fig. 6d showcases the exceptional cyclic stability of the rPOP cathode material at 2.0 A g−1, maintaining an impressive capacity retention of approximately 66% even after 30
000 cycles. Despite the rPOP's specific capacity being slightly lower than other polymeric cathodes, as illustrated in Fig. 6e, it stands out due to its remarkable conductivity, solubility, and prolonged cycle stability. These qualities surpass other cathode materials based on quinone-containing small organic compounds. Fig. 6f presents ex situ scanning electron microscope (SEM) images of discharged and charged cathodes, revealing a sheet-like formation characteristic of Zn4SO4(OH)6·5H2O. The energy-dispersive X-ray (EDX) mapping also demonstrates the uniform distribution of sulphur and zinc post-charging and discharging.19
2. Quinones.
Quinone-based organic cathode materials have emerged as promising candidates for ZIB applications, due to their abundance and cost-effectiveness. Recent research has introduced a novel quinone-based cathode material with outstanding electrochemical performance and impressive energy density. This study underscores the growing significance of quinones in advancing efficient ZIB technology. In the work conducted by Lulu et al., the synthesis of 8,21-dihydronaphtho-[2,3-a], an organic chemical employed in this research, involved a solvent-free condensation procedure to produce naphtha [2′,3′:7,8] quinoxalino [2,3-i] phenazine 5,11,16,22-tetraone (DADB) with multiple active centres (C
N and C
O).19 The scanning electron microscopy (SEM) image in Fig. 7a confirms the layered stacking morphology of the DADB sample, which proves beneficial for the rapid transportation of electrons and ions.
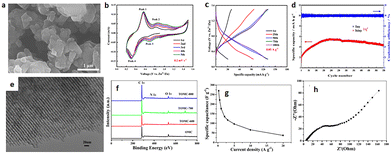 |
| Fig. 7 (a) SEM image of DADB. (b) CV curve of DADB under 0.2 mV s−1. (c) GCD of DADB under 0.05 A g−1. (d) Cyclic stability of DADB under 1 A g−1. (e) HRTEM images of TOMC-700. (f) XPS survey of the sample. (g) Specific capacitance at a series of current densities. (h) EIS spectrum of the ZHSC cathode respectively. | |
Cyclic voltammetry (CV) curves for DADB/Zn gel batteries, depicted in Fig. 7b, reveal two oxidation and two reduction peaks. Additionally, Fig. 7c demonstrates that the DADB electrode maintains an exceptional capacity of 134 mA h g−1 @ 0.05 A g−1 even after 55 cycles, remaining stable for 100 cycles. Moreover, Fig. 7d illustrates the DADB electrodes' remarkable cycling stability and capacity retention, with a retention rate of around 43 mA h g−1 (78.2%) even after 5500 cycles.20
3. Tannins.
Tannins, natural polyphenolic compounds in plants, have emerged as sustainable candidates for organic cathode materials. The utilisation of tannin-derived materials as cathodes showcases their eco-friendliness and potential for large-scale ZIB applications. Haichao et al. adopted an EISA (evaporation-induced self-assembly) technique using TEOS as the precursor to creating an ordered mesoporous carbon (OMC).21 The high-resolution transmission electron microscopy (HRTEM) image of the TOMC-700 microstructure is shown in Fig. 7e, and Fig. 7f displays the survey spectra of the cathode.22Fig. 7g presents the specific capacity of Zn/PAM-ZnSO4(gel)/TOMC-700 ZHSC at different current densities, while the electrochemical impedance spectroscopy (EIS) spectrum of the same ZHSC cathode is depicted in Fig. 7h.21
Typically, Zinc ion batteries exhibit six distinct energy storage mechanisms, encompassing (1) Zn2+ insertion/extraction, (2) conversion reactions, (3) H+/Zn2+ insertion/extraction, (4) dissolution/deposition, (5) ion coordination, and (6) multiple-ion insertion/extraction. Table 1 below provides a summary of appropriate cathode materials and the corresponding reaction mechanisms observed in Zinc-based batteries as shown in Fig. 8 (Table 2).
Table 1 Reaction mechanism summary for various cathodes of AZIB's
Cathode |
Cathode reaction |
Mechanism |
MnO2/rGO |
2MnO2 + Zn2+ + 2e− ↔ ZnMn2O4 |
Zn2+ insertion/extraction |
G–MnO2 |
2MnO2 + Zn2+ + 2e− ↔ ZnMn2O4 |
Zn2+ insertion/extraction |
MnO2 |
MnO2 + H+ + e− ↔ MnOOH |
Conversion |
K0.97Mn8O160.56H2O |
4Zn(s) + ZnMn3O7·3H2O(s) + MnO2(s) + SO4(aq)2− + 12H(aq)+ ↔ Zn4SO4(OH)6·5H2O(s) + Zn(aq)2+ + 4Mn(aq)2+ + H2O(1) |
Dissolution/deposition |
V6O13 |
V6O13 + (a + m)Zn 2+ + 2(a + m)e− ↔ ZnaV6O13 + ZnmV3O7 |
Conversion |
V3O7@C |
V3O7·H2O → Zn3(VO4)2(H2O)2.93 |
Conversion |
H–VHN |
V3O7 + V2O3 + aZn2+ + 2ae− + nH2O ⇌ ZnaV3O7·nH2O + ZnaV2O3 |
H+/Zn2+ insertion/extraction |
Zn0.25V2O5·nH2O |
Zn0.25V2O5·nH2O + 1.1Zn2+ + 2.2e− ↔ Zn1.35V2O5·nH2O |
Zn2+ insertion/extraction |
Ni3S2 doped with Zn and Co |
Zn, Co − Ni3S2 + 2OH− ↔ Zn, Co − Ni3S2O+ H2O + 2e − |
Multi-ion insertion/extraction |
NiOOH |
2β-NiOOH(s) + 2H2O(l) + 2e− → 2β-Ni(OH)2(s) + 2OH−(aq) |
Conversion |
VOPO4 |
VOy+PO4 + xZn2+ + (2x + y)e− ↔ ZnxVOPO4 |
Zn2+ insertion/extraction |
Na3V2(PO4)3 |
Na3V2(PO4)3 → (3−x)Na+ + (3−x)e− + NaxV2(PO4)3 (first charge) |
Multi-ion insertion/extraction |
NaxV2(PO4)3 + zZn2+ + yNa+ + (2z + y)e− ↔ ZnzNa(x+y)V2(PO4)3 (following cycles) |
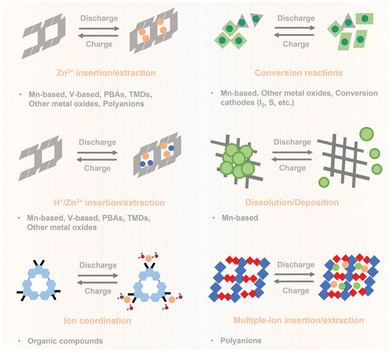 |
| Fig. 8 Pictorial representation of energy storage mechanism for various cathode materials of AZIB's. | |
Table 2 Advantages and disadvantages of various cathodes of AZIB's
Materials |
Advantages |
Disadvantages |
Mn-based |
High energy density, relatively higher operating voltage, low cost, abundant raw materials |
Complicated energy storage mechanism, poor cycle performance, unstable structure |
V-based |
High energy densities, high-rate performance, unique crystal structure, strong composite properties |
Low operating voltage, high-cost, toxicity, structural change |
Ni-based |
Acceptable energy densities, highly reliable, excellent safety record |
Low charge and discharge cycle, poor recycling |
FePO4-based |
Higher operating voltage, cost effective elements, low toxicity, good cyclic stability |
Poor electronic conductivity, kinetic limitations, limited capacity, |
VP-based |
Reversable intercalation, high voltage, cyclic stability, good thermal and chemical stability |
Low electronic conductivity, volume changes, |
Organic polymer-based |
Light weight, Flexibility, high energy densities |
Limited stability, poor conductivity, |
Quinones-based |
High theoretical capacity, eco-friendly, reversible redox chemistry |
Solubility issue, low conductivity, low charging cycle |
Tannins-based |
Renewable source, biodegradability, flexibility in structure, high energy densities |
Poor electronic conductivity, limit in redox reaction, scalability should be limited |
Challenges in cathode materials for Zn-ion batteries
1. Cycling stability
Cycling stability is one of the paramount challenges in developing cathode materials for ZIBs. The ability of a battery to maintain its capacity and performance over a significant number of charge–discharge cycles is critical for its practical applications in various fields, including energy storage, electric vehicles, and portable electronics. This extensive review delves into the complexities of cycling stability in ZIB cathode materials, exploring recent research findings and innovative strategies to address this challenge, as shown in Fig. 10.22a,b
(i). Understanding cycling stability.
Cycling stability, often measured as the number of charge–discharge cycles a battery can undergo while retaining a specific capacity, is crucial for the commercial viability and user acceptance of energy storage technologies. In the case of ZIBs, achieving long-term cycling stability is particularly challenging due to several factors. Some factors that affect the ways to improve the stability are discussed in detail in the upcoming pages.23
(ii). Structural changes during cycling.
One of the primary causes of capacity fade in ZIB cathode materials is the structural changes that occur during repeated cycling. When ZIB cathode materials undergo charge and discharge processes, they experience volume expansion and contraction. These structural changes can lead to particle cracking, pulverisation, and electrode–electrolyte interface instability, all contributing to a decline in cycling stability.24
(iii). Chemical reactions and side reactions.
In addition to structural changes, ZIB cathode materials may undergo chemical reactions with the electrolyte during cycling. These side reactions can result in forming SEI layers or other undesirable compounds on the surface of the cathode materials. SEI layers can impede ion transport and further deteriorate cycling stability.25 The different challenges associated with various cathode materials of AZIBs are summarized as schematically shown in Fig. 9.
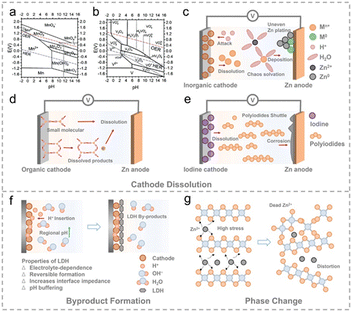 |
| Fig. 9 Pourbaix diagram for various (a) Mn and (b) V-based oxides. Pictorial diagram of different challenges associated with (c) inorganic, (d) organic and (e) iodine, cathodes. Schematic for (f) byproduct formation and (g) phase change. | |
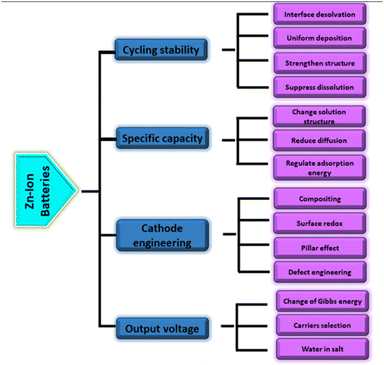 |
| Fig. 10 Challenges in cathode materials for Zn-ion batteries. | |
(iv). Strategies to improve cycling stability.
Researchers have been exploring various strategies and techniques to address the challenge of cycling stability in ZIB cathode materials. Recent studies have shed light on promising approaches to mitigate capacity fade and enhance the longevity of ZIBs.
(a). Nanoscale engineering.
Nanoscale engineering involves tailoring the size and morphology of cathode materials at the nanoscale regime. Recent research has demonstrated that nanostructured cathode materials exhibit improved cycling stability compared to their bulk counterparts. For instance, zinc oxide (ZnO) nanoparticles with controlled morphology have enhanced stability due to reduced mechanical stress during cycling.26
(b). Surface coatings.
Protective coatings on cathode materials can act as a barrier, shielding the material from direct contact with the electrolyte. Recent studies have explored coating techniques using graphene, carbon nanotubes, and metal oxides as coatings to mitigate undesirable side reactions. These coatings enhance cycling stability and improve overall electrochemical performance.27
(c). Novel synthesis methods.
Advancements in synthesis techniques have paved the way for the creation of cathode materials with enhanced structural stability. Recent innovations in hydrothermal, solvothermal, and chemical vapour deposition methods have yielded cathode materials with tailored properties. For example, researchers have reported the synthesis of layered transition metal oxides with improved cycling stability through precise control of synthesis parameters.28
(d). Advanced characterisation techniques.
Recent developments in characterisation techniques, such as in situ and operando analysis, have provided more profound insights into the mechanisms of capacity fade in ZIB cathode materials. By understanding the underlying processes, researchers can design more effective strategies to address cycling stability challenges.29
The challenge of achieving long-term cycling stability in cathode materials for Zn-ion batteries is a complex issue requiring multidisciplinary research. Recent studies and innovative approaches, including nanoscale engineering, surface coatings, novel synthesis methods, and advanced characterisation techniques, have shown promise in mitigating capacity fade and improving the overall performance of ZIBs. As researchers continue to explore these strategies and collaborate across various domains, the prospects for developing ZIBs with excellent cycling stability are becoming increasingly optimistic.
2. Low conductivity
The low electrical conductivity of cathode materials is a significant challenge in developing ZIBs. This limitation can adversely affect the rate capability, overall efficiency, and performance stability of ZIBs. In this section, we will delve into the issue of low conductivity in cathode materials for ZIBs, explore the strategies employed to mitigate this challenge and highlight recent research findings in the field.30
(i). Low conductivity: a critical challenge.
Low electrical conductivity is a common characteristic of many cathode materials for ZIBs. The intrinsic conductivity of these materials is often insufficient to support rapid electron transfer during charge and discharge cycles. This limitation results in sluggish kinetics and low-rate capability, hampering the practical application of ZIBs in high-power-demanding devices, such as electric vehicles and grid storage systems.31
(ii). Strategies to address low conductivity.
(a). Conductive additives.
One established strategy to enhance the electrical conductivity of cathode materials is the incorporation of conductive additives. Conductive materials like carbon black, graphene, and conductive polymers are frequently introduced into the cathode formulation. These additives create a conductive network within the electrode, facilitating electron transport and mitigating the low conductivity of the active cathode material.32
(b). Composite cathodes.
Composite cathode materials are another approach to overcome the low conductivity challenge. These composites combine the active cathode material with a conductive matrix, often carbon-based materials. Composite cathodes offer improved electron transport pathways by embedding the active material within a conductive framework, enhancing rate capability and overall electrochemical performance.33
(c). Novel materials with intrinsic conductivity.
Recent research efforts have focused on developing cathode materials with inherently high electrical conductivity. Scientists have explored a range of materials, including conductive polymers, metal oxides, and organic materials, with improved intrinsic conductivity. These materials can eliminate the need for external additives or composites, simplifying the manufacturing process and reducing costs.34
(iii). Recent research findings to mitigate low conductivity.
Recent articles and studies have significantly addressed the low conductivity challenge in ZIB cathode materials. Here are some noteworthy findings:
(a).
In Situ synthesis of conductive metal–organic frameworks (MOFs).
A study by Liu et al. demonstrated the in situ synthesis of conductive MOFs as cathode materials for ZIBs. These MOFs exhibited high intrinsic conductivity, improving rate capability and cycling stability. Zhang et al. explored the incorporation of carbon nanotubes (CNTs) into cathode materials. The study showed that CNT-enhanced cathodes significantly enhanced electrical conductivity and rate performance.35
(b). Metal–organic framework-derived cathodes.
A recent work by Wang et al. reported synthesising cathode materials derived from metal–organic frameworks (MOF-Ds). These MOF-D cathodes demonstrated high capacity and improved conductivity, addressing critical challenges in ZIBs. Moreover, the low electrical conductivity of cathode materials represents a critical challenge in developing zinc-ion batteries. While this limitation can hinder the rate capability and overall performance of ZIBs, ongoing research is making significant strides in addressing this issue. Strategies such as using conductive additives, composite cathodes, and developing novel materials with intrinsic conductivity are at the forefront of this effort. Recent articles and studies, as highlighted above, showcase promising advancements in the field, offering hope for the future of high-performance ZIBs in various applications. Continued research and innovation in cathode materials will play a pivotal role in unlocking the full potential of ZIB technology.36
3. Safety concerns
Safety is a critical aspect of battery technology, and it has gained increasing attention in recent years. As the demand for energy storage solutions continues to grow, ensuring the safety of batteries becomes even more crucial. The ZIBs have emerged as an attractive alternative to lithium-ion batteries due to their potential for improved safety, high energy density, and cost-effectiveness. However, ZIBs are not immune to safety concerns like any energy storage system. This section will delve into the safety challenges associated with cathode materials for ZIBs, highlighting recent research and developments.37
(i). Improved safety of Zn-ion batteries.
ZIBs have garnered attention for their enhanced safety compared to traditional lithium-ion batteries. This improvement is primarily attributed to the choice of zinc as the anode material. Zinc is less reactive and prone to dendrite formation than lithium, reducing the risk of short circuits and thermal runaway. Additionally, ZIBs do not suffer from the formation of lithium metal deposits on the anode, a process known to be a safety concern in lithium-ion batteries.38
(ii). Challenges in cathode material safety.
While ZIBs offer a higher level of safety, it is essential to recognise that safety concerns are not eliminated. The cathode materials used in ZIBs must still be carefully engineered to mitigate potential safety hazards. Some of the key challenges include:
(a). Thermal runaway.
Although zinc is less reactive than lithium, thermal runaway events can still occur if the cathode materials are not adequately designed. Elevated temperatures, internal shorts, and overcharging can lead to thermal instability. This can result in releasing toxic gases, fires, or even explosions.39
(b). Structural stability.
Cathode materials often undergo structural changes during cycling, compromising stability. This structural instability can lead to capacity fade, reduced cycle life, and safety concerns. Preventing these structural changes is a primary focus of research into safer cathode materials.40
(c). Compatibility.
Compatibility between the cathode and other components of the battery, including the electrolyte, separator, and anode, is critical for safety. Incompatibilities can lead to chemical reactions that generate heat or gas, posing safety risks.41
(iii). Ongoing research into safer cathode materials.
Addressing safety concerns in ZIBs requires continuous research and innovation. Recent articles highlight several strategies being pursued:
(a). Novel cathode materials.
Researchers are exploring new cathode materials with enhanced stability and reduced reactivity. For example, a recent study investigated a novel cathode material that demonstrated improved thermal stability and reduced capacity degradation over cycling.42
(b). Advanced coatings.
Coating cathode materials with protective layers can enhance stability and prevent unwanted reactions. Recent study investigated the development of advanced coatings that effectively mitigate safety concerns in ZIBs.43
(c). Electrolyte optimisation.
The choice of electrolyte plays a crucial role in battery safety. Recent research focused on developing electrolytes that are less prone to thermal decomposition, reducing the risk of thermal runaway.
(d). Advanced diagnostics.
Researchers are developing advanced diagnostic techniques to monitor the internal temperature, pressure, and chemical state of ZIBs in real-time. These diagnostics can help identify safety issues before they escalate.44
Safety concerns in cathode materials for zinc-ion batteries are a significant challenge, albeit one that is actively being addressed through ongoing research and innovation. While ZIBs offer improved safety compared to lithium-ion batteries, it is essential to continue developing safer cathode materials, advanced coatings, optimised electrolytes, and enhanced diagnostic tools to ensure the continued growth and adoption of this promising energy storage technology. Recent articles demonstrate the dedication of the scientific community to advancing the safety of ZIBs and expanding their applications in various industries.
4. Cost-effectiveness
As the demand for energy storage technologies continues to rise, the focus has shifted towards alternatives to lithium-ion batteries. ZIBs have garnered attention due to their potential to combine high energy density, safety, and affordability. However, for ZIBs to truly compete with lithium-ion batteries, it is essential to overcome the cost-effectiveness challenge. This article explores the multifaceted nature of this challenge, emphasising the importance of low-cost materials, optimised manufacturing processes, and recycling strategies. Furthermore, it highlights the critical role of government incentives and research initiatives in reducing costs to make ZIBs a viable and sustainable energy storage option.45
(i). Low-cost materials selection.
One of the fundamental aspects of achieving cost-effectiveness in ZIBs is carefully selecting low-cost cathode materials. Recent research has underscored the significance of materials cost in the overall cost structure of batteries. Materials such as TMOs, polyanionic compounds, and certain organic materials exhibit promising electrochemical performance and are abundant and cost-effective. These materials can significantly reduce the cost of ZIBs compared to cathode materials in lithium-ion batteries.46
(ii). Optimising manufacturing processes.
Optimising the manufacturing processes for ZIB cathode materials is another critical aspect of achieving cost-effectiveness. Recent studies have highlighted the need for improved scalability and efficiency in producing cathode materials. This includes advancements in synthesis techniques, such as scalable solvothermal methods and continuous-flow processes, to reduce manufacturing costs. The scaling up of production can lead to economies of scale, further driving down the cost per kilowatt-hour (kW h) of ZIBs.47
(iii). Recycling strategies.
In addition to selecting cost-effective materials and optimising manufacturing processes, implementing effective recycling strategies is pivotal for the cost-effectiveness of ZIBs. Recent work has shown that recycling cathode materials from spent batteries can significantly reduce the environmental impact and overall cost of battery production. By recovering and reusing valuable materials, ZIB manufacturers can lower the raw material costs and minimise waste disposal expenses.
(iv). Government incentives and research initiatives.
Government incentives and research initiatives are crucial drivers in pursuing cost-effective ZIBs. Governments worldwide have recognised the importance of advancing battery technologies to support renewable energy integration and reduce greenhouse gas emissions. Recent legislative actions (Energy Policy Act, 2022) have allocated funds to research and develop next-generation batteries, including ZIBs.
Research programs, such as the national battery initiative (NBI), have been established to promote collaborative efforts between academia, industry, and government agencies (NBI Annual Report, 2021). These initiatives offer grants, subsidies, and tax incentives to battery research, development, and production companies. Such support can accelerate the commercialisation of ZIBs and help offset the initial cost disadvantages compared to established lithium-ion technology.
In conclusion, addressing the cost-effectiveness challenge in cathode materials for Zn-ion batteries is essential for their widespread adoption and competitiveness with lithium-ion batteries. By selecting low-cost materials, optimising manufacturing processes, and implementing efficient recycling strategies, ZIBs can become a cost-competitive energy storage solution. Moreover, government incentives and research initiatives are pivotal in reducing costs and advancing ZIB technology. Collaborative efforts across the battery industry, academia, and government agencies are crucial in realising the full potential of ZIBs as a sustainable and affordable energy storage option for the future.48
5. Future prospects
Prospects in cathode materials for ZIBs are critical for advancing this emerging energy storage technology. As researchers and industry experts continue to explore and innovate, several vital areas show promise for the development and improvement of cathode materials for ZIBs. The challenges and prospects of AZIBs are pictorially represented in Fig. 11.
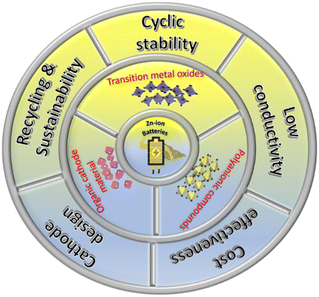 |
| Fig. 11 Challenges and prospects associated with AZIBs. | |
(i). Advanced synthesis techniques.
(a). Nanomaterials and nanostructuring.
Nanomaterials and nanostructuring techniques can significantly enhance the electrochemical performance of cathode materials. By reducing particle size and increasing surface area, these methods improve ion diffusion and increase active sites for charge transfer. Techniques such as solvothermal, hydrothermal, and chemical vapour deposition are being explored to synthesise cathode materials with controlled nanostructures.49
(b).
In situ characterization.
Real-time, in situ characterisation techniques enable researchers to monitor cathode materials' structural and chemical changes during charge–discharge cycles. This more profound understanding of the electrochemical processes can lead to the development of more stable and efficient materials.50
(ii). Material design and engineering.
(a). Tailored properties.
The rational design of cathode materials at the atomic and molecular levels allows for customising their properties. This tailoring can improve energy density, cycling stability, and rate capability. Computational modelling and high-throughput screening methods aid in identifying promising materials with desired characteristics.51
(b). Composite materials.
Composite cathode materials, combining multiple components with complementary properties, offer a way to overcome the limitations of individual materials. For example, combining a high-capacity but low-conductivity material with a highly conductive material can improve overall performance.52a,b
(iii). Integration into various applications.
(a). Electric vehicles (EVs).
To make ZIBs a viable option, cathode materials must be optimised for high energy density, long cycle life, and rapid charging capabilities. Research in this area focuses on developing materials that meet these criteria while maintaining safety and cost-effectiveness.53
(b). Grid energy storage.
Cathode materials for grid energy storage systems should prioritise long cycle life and high-power capability. Customised materials that can handle frequent charge–discharge cycles without significant capacity loss are essential for stabilising the grid and integrating renewable energy sources.54
(c). Portable electronics.
Cathode materials for portable electronic devices must be lightweight, compact, and safe. These applications often demand high energy density and fast charge–discharge rates, driving research toward materials that meet these requirements.55
6. Recycling and sustainability
(i). Sustainable materials.
Developing cathode materials using sustainable and environmentally friendly components is gaining importance. Researchers are exploring bio-based materials, organic compounds, and abundant elements as alternatives to reduce the environmental impact.56
(ii). Recycling technologies.
Recycling cathode materials from spent batteries is crucial for resource conservation and environmental sustainability. Developing efficient and cost-effective recycling processes is an ongoing research and innovation area.57,58
7. Collaborative efforts
(i). Public-private partnerships.
Collaborations between academia, industry, and government agencies are essential for accelerating the development and commercialisation of ZIBs. Public-private partnerships can provide funding, infrastructure, and expertise to drive research forward.
(ii). Global research initiatives.
International research initiatives and collaborations can facilitate knowledge sharing, standardising materials, and testing protocols. These efforts help create a unified approach to advancing ZIB technology.59,60
8. Safety innovations
(i). Advanced battery management systems (BMS).
The development of sophisticated BMS that monitor and control the battery's state in real-time can enhance the safety of ZIBs. These systems can help prevent overcharging, over-discharging, and thermal runaway events.61
(ii). Non-flammable electrolytes.
Research into non-flammable electrolytes can further improve the safety of ZIBs. The risk of fire or explosion is significantly reduced by eliminating flammable components.62
Furthermore, the prospects for cathode materials in ZIBs are promising, with ongoing research aimed at addressing key challenges and unlocking the full potential of this technology. Advanced synthesis techniques, material design, integration into diverse applications, sustainability efforts, and collaborative initiatives will be crucial in advancing ZIBs as a clean, safe, and sustainable energy storage solution. As these innovations evolve, ZIBs may become increasingly competitive with other energy storage technologies, offering a greener and more efficient way to store and utilise electrical energy.63,64
Conclusions
Cathode materials for Zn-ion batteries hold immense promise for addressing the growing demand for energy storage solutions. While challenges such as cycling stability, low conductivity, safety concerns, and cost-effectiveness persist, ongoing research and innovation in materials science and engineering offer hope for overcoming these hurdles. The future of ZIBs depends on the collective efforts of scientists, engineers, and policymakers to unlock their full potential as a clean, safe, and sustainable energy storage technology.
Author contributions
R. Ajay Rakkesh: conceptualization, investigation, methodology, writing – original draft, supervision, S. Shalini and S. Tharani: review & editing, conceptualization, D. Durgalakshmi: conceptualization, investigation, S. Balakumar: conceptualization, validation, review.
Data availability
All required data can be found within the main manuscript file.
Code availability
Not applicable.
Conflicts of interest
The authors declare that they have no conflict of interest.
Acknowledgements
The authors acknowledge the Department of Science and Technology – SERB research project file No. EEQ/2023/000314 for providing funds to conduct this work.
References
- B. Tang, L. Shan, S. Liang and J. Zhou, Energy Environ. Sci., 2019, 12, 3288–3304 RSC.
- R. Schmuch, R. Wagner, G. Horpel, T. Placke and M. Winter, Nat. Energy, 2018, 3, 267–278 CrossRef CAS.
- T. Famprikis, P. Canepa, J. A. Dawson, M. S. Islam and C. Masquelier, Nat. Mater., 2019, 18, 1278–1291 CrossRef CAS PubMed.
-
(a) G. Z. Li, B. Huang, Z. F. Pan, X. Y. Su, Z. P. Shao and L. An, Energy Environ. Sci., 2019, 12, 2030–2053 RSC;
(b) T.-F. Yi, L. Qiu, J.-P. Qu, H. Liu, J.-H. Zhang and Y.-R. Zhu, Coord. Chem. Rev., 2021, 446, 214124 CrossRef CAS.
- T.-H. Wu, Y. Zhang, Z. D. Althouse and N. Liu, Mater. Today Nano, 2019, 6, 100032 CrossRef.
- H. F. Li, L. T. Ma, C. P. Han, Z. F. Wang, Z. X. Liu, Z. J. Tang and C. Y. Zhi, Nano Energy, 2019, 62, 550–587 CrossRef CAS.
-
(a) W. Shi, W. S. V. Lee and J. Xue, ChemSusChem, 2021, 14, 1634–1658 CrossRef CAS PubMed;
(b) N. Zhang, J. Wang, Y. Guo, P.-F. Wang, Y.-R. Zhu and T.-F. Yi, Coord. Chem. Rev., 2023, 479, 215009 CrossRef CAS;
(c) N. Zhang, Y.-R. Ji, J.-C. Wang, P.-F. Wang, Y.-R. Zhu and T.-F. Yi, J. Energy Chem., 2023, 82, 423–463 CrossRef CAS;
(d) N. Zhang, J. Wang, X. Liu, P.-F. Wang, Y.-G. Liu, Y. Xie and T.-F. Yi, Compos. B: Eng., 2023, 260, 110770 CrossRef CAS.
- Y. Huang, J. Liu, Q. Huang, Z. Zheng, P. Hiralal, F. Zheng, D. Ozgit, S. Su, S. Chen, P.-H. Tan, S. Zhang and H. Zhou, npj Flex Electron., 2018, 2, 21 CrossRef.
- C. Wang, M. Wang, Z. He, L. Liu and Y. Huang, ACS Appl. Energy Mater., 2020, 3, 1742–1748 CrossRef CAS.
-
(a) G. Yang, Q. Li, K. Ma, C. Hong and C. Wang, J. Mater. Chem. A, 2020, 8, 8084–8095 RSC;
(b) L. Shan, J. Zhou, W. Zhang, C. Xia, S. Guo, X. Ma, G. Fang, X. Wu and S. Liang, Energy Technol., 2019, 7, 1900022 CrossRef;
(c) Y. Liu and X. Wu, J. Energy Chem., 2023, 87, 334–341 CrossRef CAS;
(d) C. Liu, G. Zhang, T. Ma, Y. Su, J. Dai, X. Su, X. Yue, C. Cong and W. Zhou, Next Energy, 2024, 2, 100089 CrossRef.
- T. Selvam, D. Dhinasekaran, B. Subramanian and A. R. Rajendran, ACS Appl. Mater. Interfaces, 2023, 15, 30350–30359 CrossRef CAS PubMed.
- L. Li, Y. C. A. Tsang, D. Xiao, G. Zhu, C. Zhi and Q. Chen, Nat. Commun., 2022, 13, 2870 CrossRef CAS PubMed.
- H. Dong, X. Hu, R. Liu, M. Ouyang, H. He, T. Wang, X. Gao, Y. Dai, W. Zhang, Y. Liu, Y. Zhou, D. J. L. Brett, I. P. Parkin, P. R. Shearing and G. He, Angew. Chem., Int. Ed., 2023, 62, e202311268 CrossRef CAS PubMed.
- L. He, H. Li, X. Ge, S. Li, X. Wang, S. Wang, L. Zhang and Z. Zhang, Adv. Mater. Interfaces, 2022, 9, 2200515 CrossRef CAS.
- V. Mathew, S. Kim, J. Kang, J. Gim, J. Song, J. P. Baboo, W. Park, D. Ahn, J. Han, L. Gu, Y. Wang, Y. S. Hu, Y.-K. Sun and J. Kim, NPG Asia Mater., 2014, 6, e138 CrossRef CAS.
- S. H. Hwang, S. D. Seo and D.-W. Kim, J. Mater. Chem. A, 2022, 10, 10638–10650 RSC.
- L. Hu, Z. Wu, C. Lu, F. Ye, Q. Liu and Z. Sun, Energy Environ. Sci., 2021, 14, 4095–4106 RSC.
-
(a) J. Cui, Z. Guo, J. Yi, X. Liu, K. Wu, P. Liang, Q. Li, Y. Liu, Y. Wang, Y. Xia and J. Zhang, ChemSusChem, 2020, 8, 2160–2185 CrossRef PubMed;
(b) G. Ma, Z. Ju, X. Xu, Y. Xu, Y. Sun, Y. Wang, G. Zhang, M. Cai, L. Pan and G. Yu, Chem. Sci., 2023, 14, 12589–12597 RSC.
- O. Buyukcakir, R. Yuksel, F. Begar, M. Erdogmus, M. Arsakay, S. H. Lee, S. O. Kim and R. S. Ruoff, ACS Appl. Energy Mater., 2023, 6, 7672–7680 CrossRef CAS.
- L. Huang, J. Li, J. Wang, H. Lv, Y. Liu, B. Peng, L. Chen, W. Guo, G. Wang and T. Gu, ACS Appl. Energy Mater., 2022, 5, 15780–15787 CrossRef CAS.
- H. Yu, X. Chen, J. Zhou and H. Wang, Ind. Eng. Chem. Res., 2023, 62, 62–71 CrossRef CAS.
-
(a) Q. Li, T. Wei, K. Ma, G. Yang and C. Wang, ACS Appl. Mater. Interfaces, 2019, 11, 20888–20894 CrossRef PubMed;
(b) G. Li, L. Sun, S. Zhang, C. Zhang, H. Jin, K. Davey, G. Liang, S. Liu, J. Mao and Z. Guo, Adv. Funct. Mater., 2024, 34, 2301291 CrossRef CAS.
- Z. Zeng, Y. Zeng, L. Sun, H. Mi, L. Deng, P. Zhang, X. Ren and Y. Li, Nanoscale, 2021, 13, 12223–12232 RSC.
- M. Du, Z. Miao, H. Li, Y. Sang, H. Liu and S. Wang, J. Mater. Chem. A, 2021, 9, 19245–19281 RSC.
- Y. Tan, F. An, Y. Liu, S. Li, P. He, N. Zhang, P. Li and X. Qu, J. Power Sources, 2021, 492, 229655 CrossRef CAS.
- M. I. Khan, X. Jia, Z. Wang and G. Cao, ACS Appl. Mater. Interfaces, 2023, 15, 25980–25989 CrossRef CAS PubMed.
- N. Mohamed and N. K. Allam, RSC Adv., 2020, 10, 21662 RSC.
- B. Li, J. Xue, X. Lv, R. Zhang, K. Ma, X. Wu, L. Dai, L. Wang and Z. He, Surf. Coat. Technol., 2021, 421, 127367 CrossRef CAS.
- F. E. Kouihen, Z. Kharbouch and A. Faik, J. Electrochem. Soc., 2023, 170, 100520 CrossRef.
- J. Lu, T. Wu and K. Amine, Nat. Energy, 2017, 2, 17011 CrossRef CAS.
- H. Ahn, D. Kim, M. Lee and K. W. Nam, Commun. Mater., 2023, 4, 37 CrossRef.
- X. Jiao, A. V. Kirianova, X. Xu, O. O. Kapitanova, V. A. Krivchenko, F. S. Napolskiy, V. S. Volkov, M. O. Gallyamov and Y. Liu, ACS Appl. Energy Mater., 2023, 6, 2855–2862 CrossRef CAS.
- S. Y. Kim, H. Cha, R. Kostecki and G. Chen, ACS Energy Lett., 2023, 8, 521–528 CrossRef CAS.
- H. Luo, J. Deng, Q. Gou, O. Odunmbaku, K. Sun, J. Xiao, M. Li and Y. Zheng, Chin. Chem. Lett., 2023, 34, 107885 CrossRef CAS.
- K. W. Nam, S. S. Park, R. Reis, V. P. Dravid, H. Kim, C. A. Mirkin and J. F. Stoddart, Nat. Commun., 2019, 10, 4948 CrossRef PubMed.
- X. Li, Q. Liu, X. Ma, P. Liu, D. Wang, X. Yu and Y. Liu, J. Mater. Chem. A, 2023, 11, 19566–19577 RSC.
- B. Tang, L. Shan, S. Liang and J. Zhou, Energy Environ. Sci., 2019, 12, 3288–3304 RSC.
- T. Mageto, S. D. Bhoyate, K. Mensah-Darkwa, A. Kumar and R. K. Gupta, J. Energy Storage, 2023, 70, 108081 CrossRef.
- S. Rana, R. Kumar and R. S. Bharj, Chem. Eng., 2023, 463, 142336 CrossRef CAS.
- S. Shahid and M. Agelin-Chaab, Energy Convers. Manage.: X, 2022, 16, 100310 CAS.
- W. Kaoian, A. A. Mohamad, W.-R. Liu, R. Pornprasertsuk, S. Siwamogsatham and S. Kheawhom, Batteries Supercaps., 2022, 5, e202100361 CrossRef CAS.
- S. Chen, H. Wang, M. Zhu, F. You, W. Lin, D. Chan, W. Lin, P. Li, Y. Tang and Y. Zhang, Nanoscale Horiz., 2023, 8, 29–54 RSC.
- H. Cui, L. Ma, Z. Huang, Z. Chen and C. Zhi, SmartMat, 2022, 3, 565–581 CrossRef CAS.
- Y. Xing, K. Feng, C. Kong, G. Wang, Y. Pei, Q. Huang and Y. Liu, Coatings, 2023, 13, 1457 CrossRef CAS.
- A. Ejigu, L. W. Le Fevre, A. Elgendy, B. F. Spencer, C. Bawn and R. A. W. Dryfe, ACS
Appl. Mater. Interfaces, 2022, 14, 25232–25245 CrossRef CAS PubMed.
- T. R. Tanim, E. J. Dufek, L. K. Walker, C. D. Ho, C. E. Hendricks and J. P. Christophersen, eTransportation, 2020, 3, 100045 CrossRef.
- L. Mauler, F. Duffner, W. G. Zeier and J. Leker, Energy Environ. Sci., 2021, 14, 4712–4739 RSC.
- N. Zhang, X. Chen, M. Yu, Z. Niu, F. Cheng and J. Chen, Chem. Soc. Rev., 2020, 49, 4203–4219 RSC.
- H. Karaki, M. Thomitzek, T. Obermann, C. Herrmann and D. Schröder, Energy Technol., 2023, 11, 2201032 CrossRef CAS.
- Z. J. Baum, R. E. Bird, X. Yu and J. Ma, ACS Energy Lett., 2022, 7, 712–719 CrossRef CAS.
- Y. Buravleva, D. Tang and B. J. Bethel, Sustainability, 2021, 13, 8309 CrossRef CAS.
-
(a) Y. Li, Z. Wang, Y. Cai, M. E. Pam, Y. Yang, D. Zhang, Y. Wang and S. Huang, Energy Environ. Sci., 2022, 5, 823–851 CAS;
(b) Y. Guo, Y. Zhang and H. Lu, Battery Energy, 2022, 1, 20210014 CrossRef CAS.
- R. Jain, A. S. Lakhnot, K. Bhimani, S. Sharma, V. Mahajani, R. A. Panchal, M. Kamble, F. Han, C. Wang and N. Koratkar, Nat. Rev. Mater., 2022, 7, 736–746 CrossRef CAS.
- S. M. Bak, Z. Shadike, R. Lin, X. Yu and X.-Q. Yang, NPG Asia Mater., 2018, 10, 563–580 CrossRef.
- S. Haghi, A. Summer, P. Bauerschmidt and R. Daub, Energy Technol., 2022, 10, 2200657 CrossRef.
- X. Jia, C. Liu, Z. G. Neale, J. Yang and G. Cao, Chem. Rev., 2020, 120, 7795–7866 CrossRef CAS PubMed.
- G. Zhao, X. Wang and M. Negnevitsky, iScience, 2022, 25, 103744 CrossRef CAS PubMed.
- C. J. Jafta, Curr. Opin. Electrochem., 2022, 36, 101130 CrossRef CAS.
- C. Xu, Y. Song, M. Han and H. Zhang, Microsyst. Nanoeng., 2021, 7, 25 CrossRef PubMed.
- X. Yu and A. Manthiram, Adv. Energy Sustainability Res., 2021, 2, 2000102 CrossRef CAS.
- M. Iturrondobeitia, O. Akizu-Gardoki, O. Amondarain, R. Minguez and E. Lizundia, Adv. Sustainable Syst., 2022, 6, 2100308 CrossRef CAS.
- N. G. Panwar, S. Singh, A. Garg, A. K. Gupta and L. Gao, Energy Technol., 2021, 9, 2000984 CrossRef.
- G. Ma, L. Miao, W. Yuan, K. Qiu, M. Liu, X. Nie, Y. Dong, N. Zhang and F. Cheng, Chem. Sci., 2022, 13, 11320–11329 RSC.
- D. Han, C. Cui, K. Zhang, Z. Wang, J. Gao, Y. Guo, Z. Zhang, S. Wu, L. Yin, Z. Weng, F. Kang and Q.-H. Yang, Nat. Sustainability, 2022, 5, 205–213 CrossRef.
|
This journal is © The Royal Society of Chemistry 2024 |