DOI:
10.1039/D3SE01564E
(Review Article)
Sustainable Energy Fuels, 2024,
8, 1105-1152
Current advances and future outlook of heterogeneous catalytic transesterification towards biodiesel production from waste cooking oil†
Received
2nd December 2023
, Accepted 30th January 2024
First published on 14th February 2024
Abstract
The judicious utilization of waste cooking oil (WCO) could be a viable option to curtail the production cost of biodiesel and mitigate the environmental issues related to waste disposal in landfills. The use of heterogeneous catalysts in biodiesel synthesis has been advocated as the most promising approach in recent years owing to their non-corrosive and easily separable nature and long catalytic life for recycling. However, WCO-derived biodiesel production by catalytic heterogeneous transesterification in large-scale industries is a barrier yet. Currently the majority of review articles emphasize on the progress of reactor configuration, and preparation of new catalyst based on the modifications of the catalyst's morphology. Concurrently, the synthesis of cost-competitive catalysts is also crucial for their commercial implementation. It is observed from a meticulous literature review that most of the catalysts used in biodiesel production are confined to the lab scale. For example, the synthesis of nanocatalysts is now an emerging area in biodiesel production, but practically it has not been feasible to use on a large scale. Therefore, biodiesel process development including cost effective heterogeneous catalysts is the need of the hour for its commercialization. In this paper, an integrated reactor design has been proposed for the heterogeneous catalytic transesterification process for biodiesel production towards commercial productivity and economic viability. Life cycle assessment of WCO-derived biodiesel production methods is also discussed. The efficiency and limitations of heterogeneous catalysts are summarized and compared in detail to assess their suitability in pragmatic applications with critical, theoretical, and scientific views. The present-day challenges and future outlooks are envisioned too.
1. Introduction
The world's population is growing at an accelerating rate, which means that there will be a greater and greater need for energy. Continuous expansion of the world's population led to a rise in fossil fuel demand and increased their costs globally.1 Worldwide production of refined oil products witnessed a sharp increase of 26.42% from 1990 to 2017 led by the Middle East and the USA.2 Being the most populated country in the world, India heavily relies on fossil fuels for its everyday energy demands. Diesel and gasoline represent 46% and 24% of India's total transportation fuel, respectively, which is expected to grow to 226 billion liters in 2026 from 134 billion liters in 2015.3 The Indian government has set a goal of decreasing its reliance on imports of natural gas and oil to half by 2030 to significantly strengthen the country's renewable energy dependency.4 The drive of research towards affordable renewable energy production would limit the dependency on non-renewable fossil fuels and mitigate the environmental issues related to fossil fuel combustion. A rise in the consumption of renewable energy is anticipated in 2040 and 2050 (Fig. S1 ESI File†).5 Biofuel has appeared as a very promising alternative to conventional fuel owing to its multifaceted solution due to its biodegradable and nontoxic nature.6 Biodiesel is a renewable fuel produced from natural oil sources, mainly edible oils, WCO, and animal fats. Biodiesel has a better combustion quality as compared to conventional fuel due to its higher cetane number and 10–11% oxygen by weight with an insignificant amount of sulphur, making it a clean alternative.7 Biodiesel also resolves the issue of environmental harm, as it is made of renewable materials and thus emits much fewer greenhouse gases than conventional diesel. These properties of biodiesel can effectively reduce the emission contribution in the exhaust gas.11 The zero aromatic hydrocarbon content and nearly negligible emissions of benzopyrenes and related chemicals are the two biggest advantages of biodiesel over diesel fuels from a pollution perspective.3 Not only does this solve the environmental problem posed by fossil fuels but this also reduces the economic pressure on countries due to their dependence on oil imports. Among the numerous techniques for producing biodiesel, including pyrolysis, microemulsion, and direct mixing, biodiesel is prepared through transesterification. Biodiesel is chemically termed a monoalkyl ester of vegetable oils or animal fats or a fatty acid methyl ester (FAME).356 Feedstock used for biodiesel is composed of 85–98 wt% triglycerides. It is produced when a triglyceride reacts with an alcohol in the presence of a catalyst.8 More than 95% of the world's biodiesel production is derived from consumable vegetable oils, making them the most common source of feedstock.9
Biodiesel is subdivided into four generations based on different feedstock as reported by the European Academies' Science Advisory Council (EASAC).10 Fig. S2† shows the different generations of feedstock in biodiesel production. Edible vegetable oils utilized for the production of first-generation biodiesel are soybean oil, palm oil, rapeseed oil, corn oil, mustard oil, coconut oil, olive oil, rice oil, etc.11 However, this generation of feedstock raises concerns about food security, increase in costs of these edible products, and the debate of food vs. energy.11 Several studies have discussed the use of second-generation oil including waste cooking oil, mahua oil, linseed oil, castor oil, and neem oil for the production of biodiesel.347 However, this again raises the concern of land security. The land used for the production of these crops could be used for the production of edible crops.12 Microalgae are now emerging as viable feedstock, owing to their high oil percentage and fast biomass production.6 This also solves the main disadvantage of biodiesel being costlier than conventional diesel, which is inexpensive, and can be replaced by algal oils.13 The fourth generation of biodiesel utilizes an artificial biological process, which are called ‘photo biological solar fuels’ or ‘electro-fuels’, prepared by the transformation of solar energy.348 In this case, the initial investment is extremely high and research in this area still has to be developed. During the transesterification reaction, catalysts from the homogeneous, heterogeneous, and enzymatic categories are all utilized. Homogeneous catalysts show very good activity in transesterifying fats to biodiesel, leading to good yields and high reaction rates.39 The difficulty in separating catalysts once the process is complete, leading to the loss of the catalyst, is a pivotal downside of producing biodiesel with homogeneous catalysts.14 Heterogeneous catalysts have subdued the problem of homogeneous catalysts. They allow easy separation of the produced ester and provide good reusability viz. MgO/clinoptilole, sulfonated synthetic coal, NaOH/chitosan–Fe3O4, K+ trapped clay nanotubes, bimetallic tungsten–zirconia (W–Zr), La3+/ZnO–TiO2 photocatalyst, FeCl3-modified resin, eggshell derived CaO, and alkalized SBC ash. Moreover, heterogeneous catalysts are comparatively less corrosive, omitting the water redemption step.336 The approximate utilization efficiency of WCO generation in densely populated nations like China, the United States of America, India, and Japan was stated to be 5.6 million tonnes, 1.2 million tonnes, 1.1 million tonnes, and 0.57 million tonnes, respectively.15 Based on a study, WCO is believed to be an alternative to replace edible oil in biodiesel production.16 The distribution of various oils utilized for the production of biodiesel is depicted in Fig. 1(a).10 The generation of WCO from various sources is depicted in Fig. 1(b).10
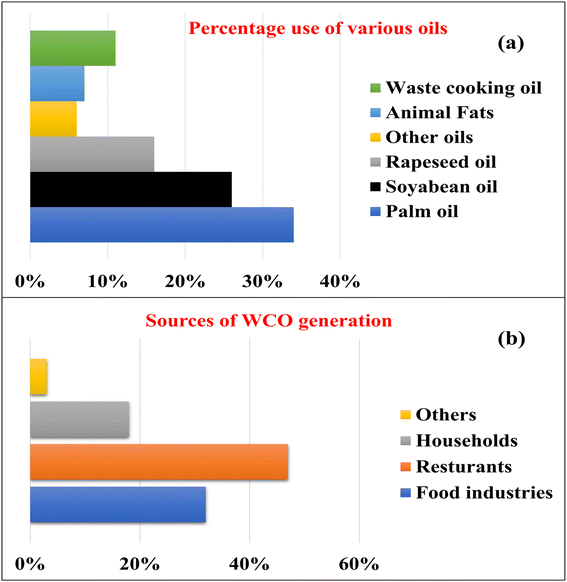 |
| Fig. 1 (a) Sources of WCO generation and (b) percentage share of different oils in biodiesel production.10 | |
This review has emphasized the utilization of various heterogeneous catalysts in biodiesel synthesis from WCO and assessed their efficiency and reusability. The life cycle assessment of WCO-derived biodiesel production methods will provide a comprehensive understanding of the cost-effectiveness and environmental friendliness of these processes to produce a cleaner and affordable alternative fuel. While there are numerous publications on the impact of catalysts on biodiesel production in the contemporary period, few researchers have thoroughly examined and studied them. As per the author's knowledge, this review study has considered multiple categories of heterogeneous catalysts reported for the last ten years on biodiesel production from only waste cooking oil. In addition to these, the emission parameters of WCO-derived biodiesel have been elucidated with critical vision, which were not available in the majority of the research assignments. The physicochemical parameters of WCO obtained from different sources were summarized and compared to get a better understanding of how these properties affect product efficacy. Moreover, an in-depth review and assessment of biodiesel properties were presented to identify the path of commercial scalability and cost-effective sustainability needed.
1.1 Emission perspective of biodiesel
The emissions from fossil fuel combustion are estimated to be 1122 gigatonnes of carbon dioxide (CO2) by 2050. This would raise the global average atmospheric temperature by about 1 °C. Burning of fossil fuels for various energy needs emits toxic carbon monoxide (CO), sulfur dioxide (SO2), and nitrogen oxides (NOx) together with CO2 in the atmosphere, creating serious damage to the environment.13 India is also affected by this threat of climate change and air pollution. The major emissions found in the most polluted region of the country i.e., Indo-Gangetic Plain, are contributed by fossil fuel exhaust.17,18 The threat posed by fossil fuel emissions in the form of global warming is thus very real and can be seen accelerating with the given trends of fossil fuel consumption.350,355 Biodiesel is utilized in conventional engines in the blended form, usually 5% biodiesel with 95% petroleum diesel. It has the same energy content as conventional diesel, but it produces fewer emissions when burned. The exhaust emissions of the engine are reduced by using this blend and the resulting lower level of PM is beneficial to human health. Biodiesel also produces less CO than petroleum diesel, so it does not contribute to air pollution as much. It is reported that, CO emissions decreased as the engine load climbed to half load when B10 (10% biodiesel and 90% petroleum diesel) and B20 blends (20% biodiesel and 80% petroleum diesel) were evaluated on a four-stroke single cylinder diesel engine. When compared to pure diesel fuel, CO emissions significantly decreased using biodiesel and its blend over the entire engine load range. This is because biodiesel has a greater oxygen percentage than diesel fuel, which causes complete burning.19 However, all biodiesel mixes had greater NOx emissions than diesel oil, due to higher cylinder combustion temperature, higher adiabatic flame temperature, and greater availability of oxygen. At half engine load, HC emissions for all tested fuels were decreased, but at increasing engine load, they had risen, because there was comparatively less oxygen available when more fuel was injected at higher loads. Smoke emissions are reduced as well, with biodiesel blends as contrasted to pure diesel. Correspondingly, when tested by Gad et al. with special attention to palm oil biodiesel, it was discovered that NOx emissions increased owing to a rise in the content of fuel consumed and a rise in the cylinder temperature, while CO and CO2 emissions decreased owing to the oxygen present in the molecular structure of biodiesel blend fuels.20 The high cetane number causes a decrease in HC emissions in biodiesel. Moreover, high oxygen content improves combustion, which lowers HC emissions. However, only reporting the emission parameters without discussing the consumption parameters in the same circumstances does not display the full picture. The amount of biodiesel mixed with diesel fuel affects how much fuel is consumed in oil blends, as biodiesel has lower calorific values than diesel fuel. The amount of fuel required by a diesel engine to produce the same amount of power increases when biodiesel and its mixes with diesel fuel are used. There is a decrease in thermal efficiency as well, due to higher viscosity, lower heating value, elevated density, and poor volatility of biodiesel. Biodiesel from WCO has also been tested for emission qualities, by Gad et al. They found that NOx emissions were reduced by about 12% when WCO-derived biodiesel was blended with diesel and used in a four-cylinder indirect ignition engine, compared to the use of diesel blended with WCO.21 A similar reduction was reported for the emissions of HC and CO by Kukana & Jakhar.22 The emission parameters of the CI engine are summarized in Table 1 during the use of WCO-derived biodiesel.
Table 1 Emission parameters of the CI engine operating on WCO biodiesel
Specification of the engine |
Biodiesel |
Emission parameter |
Reference |
CO% |
HC% |
Smoke% |
CO2% |
NOx% |
cyl: cylinder. CR: compression ratio. |
1 cyla 4-stroke, horsepower of 5.02 kW at 1500 rpm, CRb of 18 : 1 |
BD10 |
−31.46 |
−25.2 |
−3.61 |
|
+34.5 |
24 |
BD20 |
−27.3 |
−10.84 |
−6.82 |
+41.39 |
BD100 |
−44.05 |
−36.22 |
−18.63 |
+48.4 |
3 cyl, power 9.9 kW, 1500 rpm, CR 1 : 22 |
|
−15 |
|
|
+3 |
−4 |
25 |
Kirloskar & TV1, 1 cyl, 5.2 kW at 1500 rpm, CR 17.5 : 1 |
B20 |
−20 |
−15.4 |
−17.39 |
+3.12 |
+12.66 |
26 |
Kirloskar, 1 cyl, power 3.5 kW at 1500 rpm |
B20 |
−ve |
−ve |
|
+ve |
+9 |
27 |
B100 |
−16 |
−20 |
Yanmar L70N6, 4.4 kW @ 3600 rpm |
B100 |
−ve |
−ve |
|
−ve |
−ve |
28 |
Kirloskar AV-1, 1 cyl, 3.7 kW at 1500 rpm, CR 16 : 1 |
OOME-T100 |
−12.5 |
−18.7 |
−24 |
|
+10.4 |
29 |
1 cyl, 3.7 kW at 1500 rpm, CR 16 : 1 |
B10 |
−ve |
−ve |
— |
— |
+ve |
30 |
B20 |
B30 |
1 cyl, 7.8 kW at 2400 rpm, CR 17.7 : 1 |
B10 |
−52.2 |
−72.6 |
— |
— |
−1.8 |
31 |
B20 |
−8.2 |
Euro IV, in-line 4 cyl, turbocharged, 75 kW at 3600 rpm, CR 18.5 : 1 |
B20 |
−ve |
−ve |
— |
— |
+ve |
32 |
B50 |
B100 |
Kirloskar TV2 engine |
B20 |
−36 |
−14 |
— |
— |
−10 |
33 |
1.2 Waste cooking oil and its prospects
Waste cooking oil, commonly abbreviated as WCO, or referred to as used cooking oil (UCO) or spent cooking oil (SCO) is obtained by collecting oil that is used for cooking purposes, usually frying. If WCO is disposed in municipal solid waste landfills, it will also pollute the soil.23 The typical techniques for disposing of WCO also pose a concern to human health.35 To be more exact, WCO seeps into the soil and then it reaches groundwater supplies and drinking water.24 Moreover, the dangerous substances that are generated in WCO are ingested by marine species and passed back to people via the food chain as shown in Fig. 2(a).25 One of the most reliable and efficient methods for reducing environmental issues linked to trash disposal and addressing issues with conventional energy consumption, particularly carbon emissions, is waste-to-energy as shown in Fig. 2(b).25 Using WCO as feedstock not only mitigates the food and land security concerns of first and second-generation biodiesel but also provides a novel solution for recycling WCO, which is otherwise dumped as waste.26 At present the Indian government is taking necessary steps for producing biodiesel from WCO through a suitable collection mechanism to ensure a continuous supply of waste oil for the same. The Food Safety and Standards Authority of India (FSSAI) has set the limit at 25% for polar compounds in waste oil.40 It is disclosed that a single junk food center produces around 10 to 20 l of WCO daily.27 Recently, the FSSAI and the Biodiesel Association of India have jointly implemented a digital directory where all the data related to the acquisition and conversion of WCO to biodiesel are available.28 To enhance the biodiesel market, the Indian government has fixed the price of UCO per liter for 3 years (Aug 2019–Sep 2022). To ensure the implementation of policy under RUCO in all the states nodal officers have been appointed by the government.29 As per the report of the Biodiesel Association of India (BDAI), biodiesel production is 3.5 lac tons per annum only, although India has a total installed capacity of 12 lakh tons per annum. So, biodiesel can reserve roughly S$1.47 billion in foreign currency of India as a substitute for conventional diesel.30
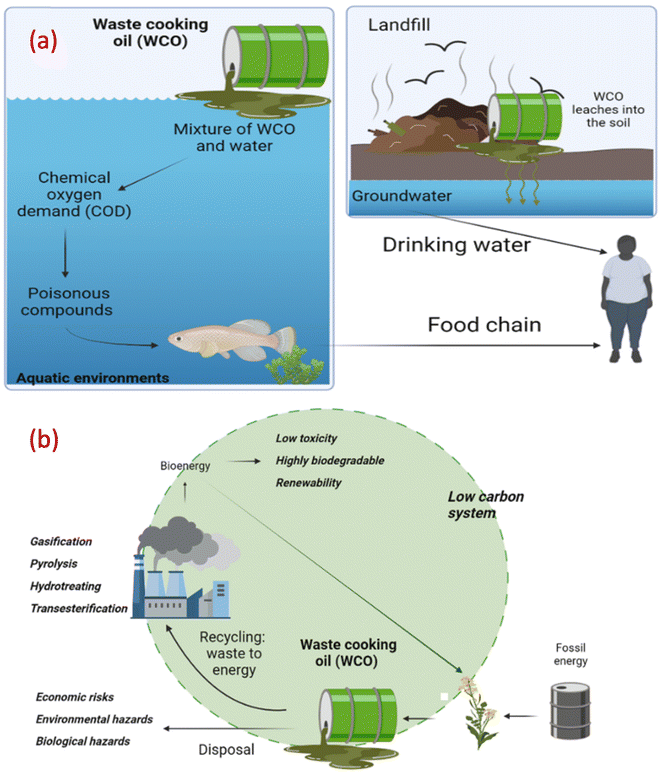 |
| Fig. 2 (a) Disposal chain and hazardous impacts of oil spill on human health, and (b) risks and opportunities of waste cooking oil (WCO) conversion into bioenergy vs. WCO disposal. Reprinted with permission from ref. 36 Copyright (2021) Elsevier. | |
Nevertheless, WCO goes through continuous heating and frying at high temperatures for which some chemical properties change in the used oil.21,34 In frying oil, the chemical reactions of hydrolysis, oxidation, and polymerization frequently occur and result in the production of volatile or non-volatile chemicals as shown in Fig. S3(a).†31 Deep-fat frying reduces the amount of unsaturated fatty acids in the oil and increases the amount of free fatty acids,42 polar materials, and polymeric compounds, as well as changes in foaming, color, viscosity, density, and specific heat.21,43 The acid value and FFA content of WCO are found to be substantially higher than those of edible oils and also happen to be the critical factors for deciding the catalyst and method to produce biodiesel from any oil. The majority of WCO contains FFA in the range of 2–15%.32 The hydrolysis, oxidation, and polymerization of the oil during frying are influenced by frying temperature and time, frying oil, antioxidants, and the type of fryer. The different chemical reactions are outlined as follows.
1.2.1 Hydrolysis. While food items are crisped in hot oil, vapor generates steam, which, combined with oxygen along with water, starts the chemical process in the hot oil. The ester bond of triglycerides is attacked by water, which possesses weak nucleophilic action, resulting in de-esterification and the production of FFA and di- and monoacylglycerols, which is why FFA content increases with the number of times a batch of oil is reused.44,45 The hydrolysis reaction of WCO is depicted in Fig. S3(b).† It is also reported that when oil is heated, more unsaturated fatty acids quickly decrease in proportion to less unsaturated or saturated fatty acids. Free fatty acids are more flammable and lower the smoke point of the oil.41 Polar mono- and diglycerides cause foaming. Using oil with long-chain fatty acids reduces hydrolysis since small-chain fatty acids are more soluble in water and enhance hydrolysis.
1.2.2 Oxidation. It occurs in stages, primary, secondary, and tertiary. The primary or initial oxidation of triglyceride molecules in frying oil results in hydroperoxides bound to a double bond of an unsaturated fatty acid, an unstable lipid species that cleaves to create non-volatile and volatile secondary oxidation products such as alcohols, carbonyls, and acids as shown in Fig. S3(c).† As a result of some of these secondary products' polymerizing (tertiary oxidation), the oil becomes viscous, becomes brown on the surface, and darkens.46 In oils that are high in free unsaturated fatty acids, like soybean oil, polymerization is prevalent.
1.2.3 Thermal polymerisation. High-molecular-weight cyclic fatty acid (FA) monomers, as well as dimers and oligomers, are produced in a non-radical mechanism by frying at high temperatures as shown in Fig. S3(d).† It is similar to tertiary oxidation, but unrelated and occurs at higher temperatures when oxygen is limited due to evaporated water from the food covering the oil in a ‘steam blanket’.47
1.3 Pre-treatment of WCO
The production of biodiesel from WCO faces one big challenge. During cooking, moisture gets adsorbed on the oil surface from various food items.10 This moisture leads to hydrolysis of the triglycerides in the oil and forms FFA. This increases the viscosity of WCO as well as the acidity.38 The increase in FFA and water content misbalances the biodiesel yield by forming soap along with the final product.48–50 The process of estimating AV and FFA comprises titrating a given amount of sample diluted in 10 milliliters of 2-propanol against a KOH solution of a given strength. Phenolphthalein was utilized as the end point indicator. Three separate estimates were made, and the mean figure was taken into account. FFA content and AV are computed using eqn (1) and (2).51 Hence, WCO, before it can be used to produce biodiesel, has to go through pre-treatment to reduce FFA by less than 2% for the base catalyzed process. Pre-treatment initially includes removing impurities and solids left over due to the cooking processes via filtration. Pre-treatment processes must also reduce the high FFA content of WCO, most commonly done by esterification. Moisture content is usually removed by preheating the oil above 100 °C or using adsorption or vacuum distillation (0.05 bar).52,53 It requires a two-step (when FFA > 2%) esterification process with an acid catalyst followed by transesterification with a basic catalyst.54 These challenges need to overcome by selecting a suitable catalyst with WCO. The fatty acid compositions and acid values of various WCO influence the biodiesel efficiency. The prescribed standard of biodiesel fuel such as viscosity, oxidation stability, acid value, and flash point gets influenced by the presence of FFA.55,56 |
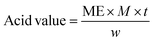 | (1) |
|
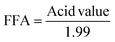 | (2) |
where ME – molecular weight of KOH, M – molarity, t – titrant value, and w – weight of oil (g).
Esterification as pre-treatment was studied and reported by Chai et al. who optimized the reaction parameters for used cooking oil with FFA 5.0 wt%. They discovered that the ideal reaction temperature was between 55 and 65 °C, the methanol to FFA molar ratio was 40
:
1, and 10 wt% sulfuric acid as a catalyst.57 Thoai et al. also carried out pre-treatment of WCO having FFA and moisture contents of 3.94 wt% and 0.54 wt% by esterification with sulphuric acid as a conventional acid catalyst. First, moisture was removed from the WCO by preheating it for 2 hours at 110 °C. They used response surface methodology (RSM) to optimize the process parameters and achieved 90% conversion to reduce the FFA to 0.40 wt% with a methanol to FFA molar ratio of 40
:
11 with a catalyst weight of 10.64 wt% at a temperature of 60 °C for 5 hours.58 Other ways of removing the acidity of the feedstock are neutralization and chemical refining by reaction with alkaline solutions with KOH or NaOH, which produces soaps and water. Once generated, the alkaline fatty acid salts are insoluble in the oil and must be extracted using decantation or centrifugation after being washed with water spray.59 After neutralization, vacuum distillation is used to remove the residual water from the WCO.60 Vacuum and stripping distillation is also used as a standalone physical process to reduce acidity, as the acidic components are more volatile.61 Other than esterification, biological treatment is also used as a chemical process to remove acidity in WCO. The free fatty acids are acted upon by microorganisms to break them down under specific conditions.59
2. Methods for biodiesel production
2.1 Dilution
In this method, produced biodiesel is simply blended with diesel without any chemical reaction. Raw materials like WCO or other oils like sunflower oil, rubber seed oil, rapeseed oil, etc. are blended with diesel fuel, ethanol, or solvent.62 While this lowers the density and viscosity of the raw materials, it does not reduce the high FFA or moisture content of WCO.10,63 Blending is not suitable in the long term, as the viscosity of the blend was more than the prescribed ASTM standards. B20 blends have also been used, with 20% vegetable oils and 80% diesel fuel.64 It was found that the calorific value of the mixed fuel is lower than that of gasoline, so the fuel consumption rate increases and the engine output decreases, even though there was no notable distinction in the thermal efficacy of the engine.63 The viscosity is reduced with an increased percentage of diesel fuel in the blend, but the high FFA and moisture lead to wear and tear of engines and reduce the performance of the produced biodiesel.10
2.2 Thermal cracking or pyrolysis
Pyrolysis is a thermochemical process, where feedstock is heated at medium temperature in the absence of air or oxygen or anaerobically under inert conditions, to produce oil (here, biodiesel), char, and gas.65 This may be performed with or without the help of a catalyst. The yield of oil produced from pyrolysis depends primarily on the process temperature, whereas the composition and quality of the oil depend on the lignin–cellulose content and type of feedstock used.66 A wide range of process conditions like temperature, rate of heating, solid residence time, the particle size of biomass, etc., are considered, depending on which, pyrolysis can be categorized as traditional (or slow), fast, and flash pyrolysis. Slow pyrolysis has a very high residence time, which requires a massive amount of energy due to the low heat transfer. Fast pyrolysis is found to give the best biodiesel yield above 80%.67 Flash pyrolysis produces up to 75% oil yield, but the product has many disadvantages such as poor thermal stability and high corrosiveness, and results in the production of pyrolytic water.68 This process' adequacy is enhanced by its lower processing cost, excellent resemblance to fuel qualities and standards, and feedstock flexibility. The fuel obtained through pyrolysis is identical to conventional diesel fuel in terms of qualities and characteristics. Wang et al. reports biodiesel produced from waste clay oil via catalytic pyrolysis with a carrier gas rate of 0.1 N L min−1, pyrolysis temperature of 550 °C and calcium oxide (CaO) as a catalyst with a catalyst ratio of 1/5 with a yield of 83%.69 The choice of the catalyst improves the efficiency of the production process in the pyrolysis temperature range. Also, it was outlined that waste cooking oil pyrolyzed with 1% NaOH catalyst concentration gave a 70% biofuel yield in a temperature range of 235–310 °C.70 However, this method needs sophisticated machinery, produces compounds with short chains, has limited volatility, and provides non-oxygenated value. Due to the outdated nature of this biodiesel production method, modern methods such as ultrasonic reactors, microwave technologies, and the supercritical process are currently used.71
2.3 Micro-emulsification
An immiscible mixture of oil and alcohol can be produced by using a surfactant and co-surfactant as a binder through micro-emulsification without any chemical reaction.72 They are isotropic, transparent, and thermodynamically stable mixtures of oil in water (O/W) or water in oil (W/O) along with surface-active agents (surfactants/co-surfactants).73,74 Alcohols like methanol, ethanol, and 1-butanol form a colloidal equilibrium dispersion with vegetable oils with optically isotropic fluid microstructures of dimensions normally in the span of 1–150 nm.75,76 This lowers the high viscosity of the oils, which allows them to be directly utilized in diesel engines. Micro-emulsified biofuels can be made from WCO, as reported by Bora et al. using ethanol as a dispersed phase and butane-2-ol as a co-surfactant. The fuel was found to have comparable fuel properties to biodiesel and superior cold flow properties.77 Micro-emulsification does not require heat energy, as compared to pyrolysis, which makes the process energy intensive. According to research by Chang et al., biodiesel with improved brake efficiency and significantly lower emissions of PM, NOx, and polycyclic aromatic hydrocarbons (PAHs) was produced. They used an emulsion of 20 vol% acetone–butanol–ethanol solution with 0.5 vol% water in diesel.78 WCO, ethanol, water, and Span 80 as a surfactant were used to create an emulsified fuel by using 70% WCO, 15%water, 10% ethanol, and 5% Span 80 as an ideal composition. The performance of the emulsified fuels was improved, and smoke, NOX, HC, and CO emissions were greatly decreased. Tan et al. reported the use of WCO as feedstock to produce biodiesel as a surfactant to produce a microemulsion with optimum volume ratios of diesel-80%, bioethanol-15%, and biodiesel-5%.79 The microemulsion was found to emit lower CO levels than conventional diesel at lower engine speeds. Similar trends were reported for NOx emissions, and it was found that no significant emissions of NO2 took place. However, micro-emulsified diesel fuels might give rise to problems such as incomplete combustion, carbon deposit, and nozzle failure. Also, this method needs sophisticated machines and extreme temperatures.80
2.4 Transesterification
Transesterification, or alcoholysis, is now the most preferred and simple procedure for preparing biodiesel from diverse feedstock and other oils.81 It is a chemical reaction between vegetable oils or fat with suitable short-chain alcohols to give biodiesel and glycerol as shown in Fig. 3(a). Large branched triglycerides in vegetable oils are converted to smaller straight-chain molecules of methyl esters via transesterification.61 It essentially exchanges the alkoxy group of an ester compound with another alcohol, mostly similar to hydrolysis as shown in Fig. 3(b), except that alcohol is used instead of water.82 The saponification reaction is shown in Fig. 3(c). The entire transesterification reaction occurs in three steps with intermediate products of diglycerides and monoglycerides, finally resulting in three moles of methyl esters and one mole of glycerol as shown in Fig. S4.†83 Alcohols are the acyl acceptors in the transesterification process. Methanol and ethanol are commonly used. These alcohols are economical and easily available as opposed to costlier short-chain alcohols like propanol, butanol, isopropanol, tert-butanol, octanol, etc.84 Methanol is preferred because of its shortest chain and polar nature, quick reaction with triglycerides, high solubility in NaOH, easier availability as compared to ethanol, and the fact that it does not form an azeotrope with water making it easy to separate from the product phase.85 Ethanol is of interest because it is cheaper than methanol, and biodiesel produced using ethanol is entirely bio-based and carbon-dioxide neutral, as opposed to petroleum-derived alcohols like methanol, propanol, and isopropanol. Hence, it is environmentally friendly and less toxic and can be considered an alternative to methanol which is toxic fossil-derived.86 Several studies have reported using blends of methanol and ethanol since they remove the difficulty of product separation after transesterification. Blends of methanol and ethanol show good complementary outcomes as an ester exchange agent. Also, oil (especially waste cooking oil, being non-polar) dissolves better in ethanol, a non-polar solvent, rather than methanol, leading to fewer mass transfer limitations when a methanol–ethanol blend is used.87 Stoichiometrically, one mole of triglyceride reacts with three moles of alcohol, to give three moles of fatty acid methyl esters or FAMEs and one mole of glycerol. However, transesterification is a reversible reaction, so adding alcohol in excess accelerates the forward reaction, shifting the equilibrium to the right, leading to faster formation of the products.88
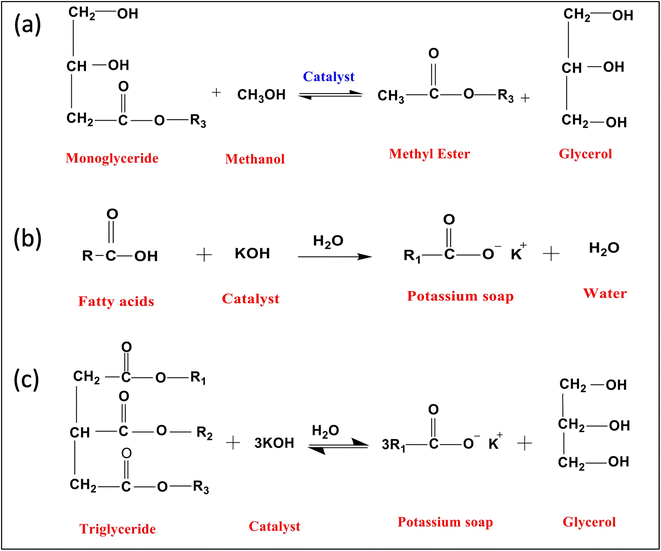 |
| Fig. 3 (a) Overall transesterification reaction mechanism, (b) hydrolysis reaction mechanism, and (c) saponification reaction mechanism. Reprinted with permission from ref. 70. Copyright (2022) Elsevier. | |
2.5 Ultrasonication
Ultrasonication is a widely accepted intensification technique for catalyzed transesterification of biodiesel, which improves mass transfer by augmenting the interfacial surface area between immiscible reactants and reducing the reaction time and production cost. It is less energy-intensive than conventional reactors.89 Ultrasonic cavitation, or the periodic development, growth, and collapse of small bubbles in the ultrasound-irradiated liquid, is caused by the propagation of ultrasound waves through a liquid as shown in Fig. 4(a).90 As a result, high local temperature and pressure spots, called “hotspots”, high-speed micro-jets, micro-streaming, and shockwaves emerge locally, increasing mass and heat transfers in the reaction mixture.91 The physical properties of ultrasonication help in mixing solutions effectively, breaking up unmixable liquid layers and promoting mass transfer at liquid–solid interfaces. Radial motion cavitation bubbles also create microturbulence, which is utilized to emulsify immiscible liquid reactants. Emulsion stability and viscosity are found to increase with sonication time.92 During the brief cavitation bubble collapse phases, free radicals are produced as one of the chemical effects. Low-frequency ultrasound (LFU, between 28 and 40 kHz) is an effective and time-saving method of agitation that is also financially feasible since it uses just a little amount of catalyst and one-third and half of the energy used by mechanical stirring.93 Ultrasonication can be done in one of two ways – continuous mode or pulse mode. Chand et al. have reported a comparison between the two methods, the efficiency of each method, and yield obtained by a conventional method. They found that biodiesel with a yield of 96 wt% was produced using pulse mode ultrasonic treatment in less than 90 seconds as opposed to 30–45 minutes in the conventional method with comparable yields (83–86%). The highest biodiesel output in the continuous sonication mode was 86 wt% and was attained in 15 s.94 Fallah Kelarijani et al. worked with nanomagnetic catalysts (Li/Fe3O4 or Li/ZnO–Fe3O4) and obtained a yield of 99.8% by employing ultrasonic waves at 37 kHz frequency. They compared it to mechanical stirring and found that the optimum yield only required 0.8% catalyst loading, at an ambient temperature of 35 °C for 35 minutes with ultrasonication.95 Ultrasonication has also been used in conjunction with enzymatic transesterification, as reported by Bhangu et al. They showed that the reaction time could be reduced considerably by using ultrasonic irradiation, from 22–24 h to 1.5 h.96
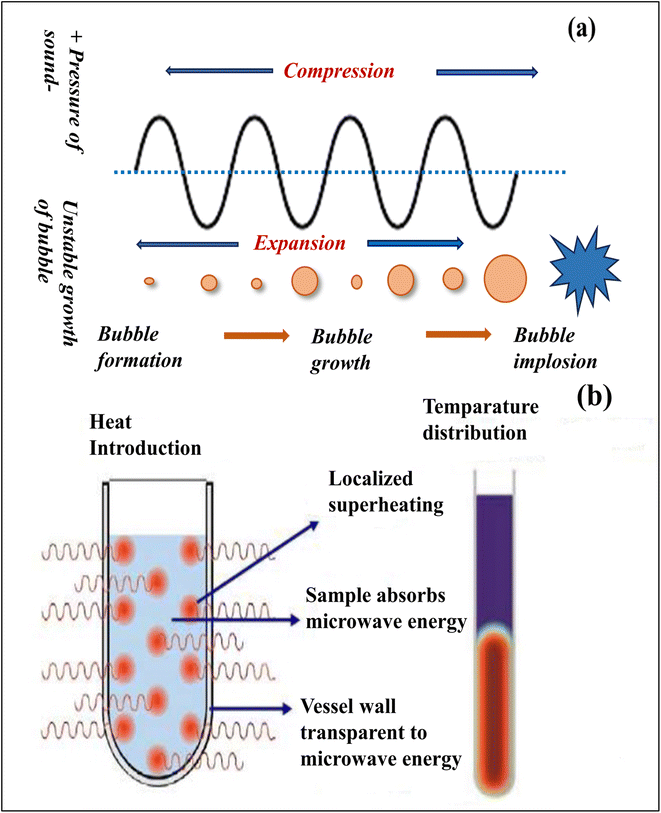 |
| Fig. 4 Mechanism of ultrasonication, (b) heating mechanism of conventional and microwave heating processes. Reprinted with permission from ref. 90. Copyright (2020) Elsevier. | |
2.6 Microwave-assisted transesterification
Another extensively used process intensification method is microwave-assisted transesterification.353 Compared to the ultrasonic process, microwave irradiation requires even shorter reaction times and lower solvent volumes, and is even more energy efficient.97 Microwaves are electromagnetic radiations that have the power to heat polar molecules already existing in the reactants, causing them to align with the microwaves' electromagnetic field and producing heat through friction as shown in Fig. 4(b).98 Dielectric loss results in microwave dielectric heating, which is a bulk effect. Thus, dielectric heating by irradiation with microwave energy at 2.45 GHz is made feasible by multiple species in the reaction mixture having a persistent dipole, for instance, methanol in the transesterification reaction.99 Microwave heating immediately transmits energy to reactants from the inside to the outside, unlike conventional heating methods, transferring heat energy via radiation rather than conduction or convection, and producing potent microwave hot spots. As a result, it increases the reaction rate process and overcomes the activation energy needed for transesterification for biodiesel production.100 A few benefits of microwave processing include quick heating and cooling, time efficiency, energy efficiency, precision, controlled processing, selective heating, uniform heating, and shorter processing times, which allegedly improve the attributes and characteristics of the final product. Rahul Soosai et al. reported on the use of microwave irradiation for producing biodiesel from in-edible Ceiba pentandra seed oil. The FFA of the oil was as high as 6.87%, so the oil was subjected to microwave-assisted esterification, which reduced the FFA to 0.83%. This esterified oil was transesterified with CaO as the catalyst, to give a yield of 97.4% in just 114 s reaction time at 270 W. The reaction time showed how considerably microwave irradiation reduces the reaction time.101 WCO has also been utilized as feedstock for microwave-assisted studies, as reported by Sharma et al., who used waste cotton seed oil, with KOH and CaO catalysts as conventional catalysts, respectively. With homogeneous catalysts, the reaction was completed in 9.6 minutes, with a yield of 96.55 ± 0.23% at 0.65 wt% catalyst loading with a 7
:
1 molar ratio for alcohol
:
oil. When the heterogeneous catalyst CaO was used, the yield obtained was 90.41 ± 0.02%, in 9.7 minutes with 1.33 wt% catalyst weight with an alcohol
:
oil molar ratio of 9.6
:
1.102
2.7 Supercritical method
Transesterification is a mechanism for the reaction between triglycerides and methanol in supercritical circumstances. As discussed earlier, transesterification employs the use of alcohol, usually methanol, ethanol, or a blend of the two. The utilization of high pressure and temperature settings over the utilized alcohol's critical point is implied by the term supercritical technology, e.g., 8.01 MPa and 512.6 K for methanol.103 Dramatic changes in methanol's mass density occur when the critical temperature and pressure are crossed, changing its solubility and mass-transfer properties. Triglycerides and methanol combine into a single phase in supercritical methanol as a result of methanol's increased density and decreased dielectric constant. Due to hydrogen bonding, the polarity of methanol decreases as density rises. To generate a homogeneous phase, it is, therefore, preferable to dissolve the non-polar triglyceride in methanol under supercritical conditions.104 Supercritical conditions also make scaling and continuous operation possible.105 At elevated pressures and temperatures, methanol attacks the carbonyl group present in triglycerides, releasing free monomers and creating an intermediary by the transfer of a methoxide molecule. The intermediate is then rearranged to produce diglycerides and biodiesel, two more stable molecules. Diglycerides similarly interact with a second methanol molecule to produce monoglycerides and biodiesel. Biodiesel and glycerol are produced when monoglyceride and methanol combine. Ghoreishi & Moein reported the application of waste vegetable oils as feedstock for the supercritical method in a batch reactor. They reported the requirement of a high methanol/oil molar ratio of 33.8
:
1, a temperature of 271.1 °C, a pressure of 23.1 MPa, and a reaction time of 20.4 minutes, to give a yield of 95.27%.106 There are some restrictions on the manufacture of supercritical biodiesel, such as the requirement for high oil-to-alcohol molar ratios, high pressure, and high temperature. Co-solvent and catalyst use has been suggested as a solution to these issues. DMC, methanol, and methyl acetate are just a few of the numerous reactants and reaction environments that have been investigated.107
3. The relevance of catalysis to biodiesel production
3.1 Homogeneous catalyst
In a reaction involving a homogeneous catalyst, the catalyst is present in the same phase as the medium, often a liquid.349 Homogeneous catalysts are subdivided into homogeneous acid and homogeneous base catalysts.108 They are most popularly used due to their high conversion efficiency. Alkaline metal hydroxides like NaOH and KOH as well as alkoxides like CH3ONa, CH3OK, and NaOC2H5 are the common catalysts in this group.109 The carbonyl group of the ester is protonated to form a carbocation and a tetrahedral intermediary during acid-catalyzed transesterification, which allows the elimination of glycerol to form a new ester. A nucleophilic attack on the alcohol revives the catalyst for recycling as shown in Fig. 5(a).110 In the presence of excess alcohol, the forward reaction exhibits pseudo-first-order kinetics, and the reverse reaction follows second-order kinetics.82 However, these catalysts work best with pure virgin oils that are low in acidity (1 mg KOH per g oil) and FFA concentration (0.5%). Pre-treatment procedures such as filtering and heating and esterification help in improving the yield of biodiesel produced from feedstock with high FFA and moisture.111 However, according to studies by Sheet et al. it is recommended to not heat the feedstock beyond the boiling point of alcohol, and the use of an alkali catalyst is suggested without preheating.112 KOH was also used by Hamze et al. to achieve 99.38% yield at 1.4 wt% catalyst loading, a methanol
:
oil molar ratio of 7.5
:
1, and 65 °C temperature.113 Similarly, Oza et al. also used KOH as a catalyst with an ultrasound technique having 250 W power and a fixed frequency of 20 kHz. With just 0.5 wt% catalyst weight and a 6
:
1 methanol
:
oil ratio, and a temperature of 50 °C for a reaction time of just 10 minutes, they also achieved a high yield of 98%.114 Sree et al. outlined the use of NaOH as a homogeneous catalyst on WCO feedstock with 1.5 g l−1 catalyst weight, a 6
:
1 methanol
:
oil molar ratio, and 65 °C temperature for 90 minutes, and achieved 90% biodiesel yield.115 When used with high-FFA feedstock, such as non-edible oils and waste oils, it is difficult to extract and purify the product due to excess soap formation. Acid catalysts are not affected by the high FFA content of the feedstock and can catalyze two-step esterification and transesterification reactions at the same time. The most commonly used homogeneous acid catalysts are sulphuric acid (H2SO4), sulfonic acid (H2SO3), and hydrochloric acid (HCl). Sulphuric acid is preferred due to its capability to catalyze the reaction under moderate conditions.111 AI Hatrooshi et al. used a H2SO4 acid catalyst to achieve a conversion of about 99% with 5.9 wt% catalyst loading, a 10.3
:
1 molar ratio of methanol
:
waste shark liver oil, and 60 °C for a reaction time of 720 minutes.116 Chakraborty et al. also used H2SO4 as a catalyst with waste goat tallow as feedstock at 59.93 wt% catalyst loading, 31.88
:
1 methanol
:
WCO and 69.97 °C for 2.5 hours to achieve 96.7% conversion. Process intensification was used in the form of infrared radiation for simultaneous esterification/transesterification.117 When producing biodiesel, utilizing an acid catalyst is preferable to a base catalyst since it allows for better performance at lower temperatures and pressure. Irrespective of these high yields, focus is shifting from homogeneous catalysts as they cannot be separated from the product stream, and thus cannot be reused. Separation issues following reactions and wastewater treatment, saponification creating a stable emulsion, the inability to reuse catalysts, and the sensitivity of basic catalysts to the presence of FFA and water are the main challenges faced by homogeneous catalysts.
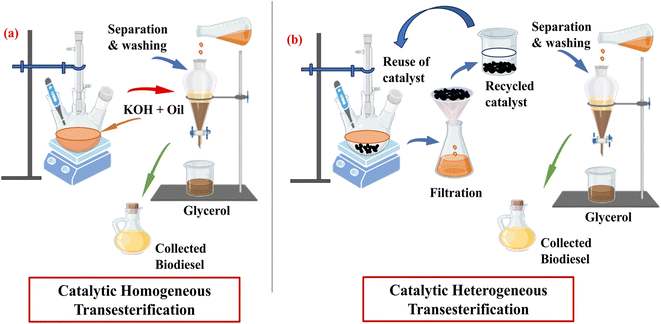 |
| Fig. 5 Mechanism of (a) homogeneous catalytic transesterification and (b) heterogeneous catalytic transesterification. | |
3.2 Heterogeneous catalysts
A heterogeneous catalyst maintains a different phase than the component of the reactant. They are also known as solid catalysts because they work by having the reactant components adhere to their surfaces.118,119 Heterogeneous catalysts primarily persist in the solid phase of biodiesel production (transesterification process), whereas alcohol and feedstock are in the liquid phase.352 During heterogeneous catalysis, a few of the reactants spread throughout the catalyst surface and are adsorbed onto the active phases by the creation of chemical affinity.120 After the reaction, the products spread and desorb from the catalyst's surface, leaving the active site free for a new molecule to adsorb on it and thus regenerating the catalyst.121 Heterogeneous catalysts have attracted a lot of scientific and industrial recognition in recent years for producing biodiesel from WCO because of their affordability, non-corrosive and recyclable nature as shown in Fig. 5(b), and environmental friendliness. Heterogeneous catalysts can be either acidic, basic or sometimes bifunctional, meaning they show both acidic and basic characteristics.122 For the production of biodiesel from oils with a high FFA concentration, solid acid catalysts concurrently favor esterification and transesterification; however, solid base catalysts have higher efficiency. Different catalyst supports, such as ceria, iron, silica, or alumina, can be made attached to the surface or to the internal pores to promote the grafting and trapping of the active molecules.123 Heterogeneous acid catalysts require a long reaction duration and exceptionally high temperature. Altered bifunctional catalysts can carry out both transesterification and esterification reactions concurrently under mild conditions.124 The surface of the catalyst, which is primarily dependent on a linked structure of large pores, surface acid sites, and hydrophobicity, affects heterogeneous acid-catalyzed reactions. Heterogeneous solid acid catalysts are being studied in biodiesel research because they have two different types of strengths: the Lewis type, which can acquire a negatron combination from amalgamated sulfonated oxides, and the Brønsted type, which can donate a proton to minerals that contain sulphonic acid.125 The main advantages of heterogeneous catalysts include cost effectiveness, being non-corrosive and recyclable, having fewer disposal issues, being easy to separate products from one another, having a higher selectivity, having a longer catalyst life, and acid catalysts being insensitive to the presence of water and FFA, providing simple and efficient recovery.126,127 The attributes and properties of dissimilar heterogeneous catalysts and the process variables for producing biodiesel from WCO are delineated in Table 2.
Table 2 Summary of heterogeneous catalysts used in biodiesel production from WCO with operating parameters and biodiesel yield
Feedstock |
Catalyst description |
M : O |
Temp °C |
Time (h) |
Yield (Y)/conversion (C) % |
Catalyst recycles |
Reference |
Source |
Surface area in m2 g−1 |
Average or total pore volume in cm3 g−1 |
wt% |
E : O – ethanol to oil ratio. |
Waste cooking oil |
Ni/zeolite |
81.925 ± 0.248 |
0.123 ± 0.007 |
3 |
12 : 1 |
60 |
4 |
89.4 (Y) |
3/73.3% |
128 |
Waste cooking oil |
CaO from clinoptilolite/industrial phosphoric waste |
20.1 |
0.0998 (T) |
8.08 |
15.65 : 1 |
54.72 |
119 min |
84.76 (purity) |
— |
129 |
Waste cooking oil |
CuO/ZnO (1 : 2) |
2.6939 |
0.00924 |
5 |
9 : 1 (E : O) |
65 |
2 |
93.5 (Y) |
6/81.4% |
130 |
Waste cooking oil |
Waste chicken eggshell derived CaO |
— |
— |
6.04 |
8.33 |
55 |
39.84 min |
98.62 (Y) |
— |
131 |
Waste cooking oil |
Empty fruit bunch-based activated carbon |
342.56 |
0.27 |
5 |
12 : 1 |
70 |
2 |
97.1 (Y) |
5/61.7% |
132 |
Waste vegetable oil |
KOH/corncob-derived activated carbon |
877 |
0.873 |
1 |
18 : 1 |
45 |
1 |
97.8 (Y) |
2/∼35% |
133 |
Waste cooking oil |
Z/GP |
106 |
0.058 |
3.25 |
12 : 1 |
40 |
1.5 |
98.1 (Y) |
5/>92% |
134 |
Waste cooking oil |
NiO@D (diatomite) |
400.5 |
0.117 |
3.97 |
11.6 : 1 |
63.7 |
117.4 min |
93.2 (Y) |
— |
135 |
Waste palm oil |
MgO/clinoptilole |
324.5 |
0.047 ml g−1 |
4 |
20 : 1 |
70 |
150 min |
97.6 (Y) |
5/>85% |
136 |
Waste sunflower oil |
(Sodium and potassium silicate-based catalysts) |
0.71 |
0.00421 |
3.5 |
9 : 1 |
70 |
2 |
93.7 (Y) |
— |
137 |
93.89 (C) |
Waste sunflower oil |
Sulfonated synthetic coal |
26.4 |
— |
3 g |
20 : 1 |
120 |
30 min |
99.5 (Y) |
5/89.6% |
138 |
Waste soybean oil |
Laboratory grade CaO |
3.8974 |
1.28 × 10−2 |
6.8 |
15.9 : 1 |
64.8 |
3 |
98.81 (Y) |
5/63.7% |
139 |
Waste sunflower oil |
Na–SiO2@TiO2 |
107.26 |
0.133 |
2.5 |
25 : 1 |
65 |
2 |
97 (Y) |
— |
133 |
Waste cooking oil |
CaO (MM-CaO) |
— |
— |
1.5 g |
3 : 1 |
50 |
3 |
86.8 (Y) |
— |
140 |
Waste cooking oil |
MoO3/SrFe2O4 |
— |
— |
10 |
40 : 1 |
164 |
4 |
95.4 (C) |
5 > 84% |
141 |
Waste cooking oil |
Lignin char |
30.31 |
0.03 |
15 |
18 : 1 |
60 |
15 min |
89.19 (Y) |
— |
142 |
Waste cooking oil |
Ba/MT |
370 |
0.409 ml g−1 |
3 |
11 : 1 |
60 |
3 |
97 (Y) |
— |
143 |
Waste cooking oil |
Acid catalyst derived from Amazon açaí berry seeds |
249.7 |
0.121 |
8.25 |
10 : 38 |
61 |
209 min |
89 (C) |
— |
144 |
Waste cottonseed oil |
α-Fe2O3/AlOOH |
323.3 |
— |
3 |
6 : 1 |
60 |
3 |
94.6 (Y) |
4/91.3% |
145 |
Waste frying oil |
Na+/zeolite |
3.731 |
0.02812 |
1 |
8 : 1 |
— |
30 min |
96.5 (Y) |
— |
146 |
Waste palm cooking oil |
[BSMBIM][CF3SO3] |
— |
— |
4 |
12 : 1 |
120 |
3 |
94.52 (Y) |
— |
147 |
Waste cooking oil |
[Bmim]OH with imidazolium cation IL/Mg–Al–La |
— |
— |
3 |
12 : 1 |
65 |
6 |
98.7 (Y) |
— |
148 |
Used cooking oil |
Modified calcium oxide (doped with zinc acetate dihydrate) |
— |
— |
5 |
12 : 1 |
60 |
3.5 |
97.3 (Y) |
— |
149 |
Waste soybean and sunflower oil |
Bi-functional alginate-based composite catalyst CaCl2 |
151 |
— |
3 |
21 : 1 |
65 |
1 min |
97 (C) |
— |
150 |
Waste cooking oil |
CaO nanocatalyst |
— |
— |
2.4 |
11.8 : 1 |
63.7 |
70 min |
94.74 (Y) |
5/58.92% |
151 |
Waste cooking oil |
Lipase enzyme immobilized magnetic nanocomposite |
— |
— |
1 g |
4 : 1 |
40 |
30 |
96 (Y) |
10/15% |
152 |
Waste cooking oil |
NaOH/chitosan–Fe3O4 |
3.731 |
3.14 |
0.5 |
6 : 1 |
25 |
4.5 |
92 (Y) |
5/79% |
153 |
Used cooking oil |
Sulfonated resin |
836 |
0.52 |
5 |
12 : 1 |
60 |
2 |
97 (C) |
5/80% |
154 |
Waste cooking oil |
Clay/CaO solid base catalyst |
— |
— |
9.6 |
1.94 (O : M) |
54.97 |
74.32 min |
97.16 (C) |
— |
155 |
Waste cooking oil |
([HMim][HSO4]) |
— |
— |
0.35 ml |
60 ml |
155 |
45 min |
97.6 (Y) |
— |
156 |
Waste cooking oil |
1-Allyl-1H-imidazole, 1,3-propyl sulfonic acid lactone |
— |
— |
5 |
25 : 1 |
60 |
20 |
87.58 (Y) |
— |
157 |
Used sunflower oil |
Hazelnut shell ash (base catalyst) |
4.9 |
— |
5 |
12 : 1 |
60 ± 0.1 |
10 min |
98 (Y) |
3/>96% |
158 |
Waste vegetable oil |
Iron-doped solid catalyst from cow horn |
711.92 |
0.63 |
3 |
13.3 |
58 |
60.4 min |
99.34 (Y) |
— |
159 |
Waste cooking oil |
La0.2Ce0.8O1.9–ZrO2 |
100.2 |
— |
5 |
15 : 1 |
120 |
3 |
91 (Y) |
— |
160 |
Waste cooking oil and honne seed oil blend |
Ba (OH)2 |
— |
— |
1.75 |
6 : 1 |
|
4 min |
100 (Y) |
— |
161 |
Waste edible oil |
MnFe2O4/graphene oxide |
51.22 |
0.147 |
3 |
18 : 1 |
65 |
4 |
96.47 (Y) |
|
162 |
Quaternary blend of Carica papaya – Citrus sinensis – Hibiscus sabdariffa – waste used oil |
CaO-based catalyst |
— |
— |
3 g |
6 : 1 (E : O) |
70 |
1 |
99.95 (Y) |
— |
163 |
Waste date seed oil |
Magnetic–Fe3O4 nanoparticles |
13.4 |
0.08 |
1.5 |
15 : 1 |
55 |
47 min |
91.4 (Y) |
— |
164 |
Waste chicken fat |
Nano-eggshell catalyst |
8.32 |
0.116 |
7.5 |
12 : 1 |
62 |
2 |
96.7 (Y) |
— |
165 |
Waste palm cooking oil |
(BMIMHSO4) |
— |
— |
5 |
15 : 1 |
160 |
60 min |
95.65 (Y) |
— |
166 |
Waste cooking oil |
Acai berry |
249.7 |
0.121 |
8.25 |
10 : 38 (w/v) |
61 |
209 min |
89 (C) |
— |
144 |
Waste cooking oil |
Modified wheat bran ash and CaO |
— |
— |
11.66 |
1.46 : 1 |
54.6 |
114.21 |
93.6 (purity) |
— |
155 |
Waste cooking oil |
ZnCuO/N-doped graphene |
228.8 |
— |
10 |
15 : 1 |
180 |
8 |
97.1 (Y) |
— |
167 |
Waste sunflower oil |
(MgAl-LDH) |
8.6 |
— |
4 |
15 : 1 |
120 |
4 |
94.6 (Y) |
— |
168 |
Waste cooking oil |
Mg/clino |
252.4 |
0.028 ml g−1 |
4 |
16 : 1 |
70 |
150 min |
98.7 (Y) |
5/94.5% |
169 |
Waste cooking oil |
KOH/clinoptilolite |
— |
— |
8.1 |
2.25 : 1 |
65 |
13.4 min |
97.4 (purity) |
— |
170 |
Waste oil |
Ionic liquid immobilization on PDVB |
— |
— |
50 mg |
2.91 g |
70 |
10 h |
99 (Y) |
— |
171 |
Waste oil |
HSO3(Pmim) HSO4 |
— |
— |
2 g |
12 : 1 |
120 |
8 h |
96 (Y) |
— |
172 |
Waste oil |
[MorMeA][Br] |
— |
— |
1 |
9 : 1 |
70 |
7 min |
89.1 (Y) |
— |
173 |
Waste cooking oil |
Nickel doped onto calcined chicken eggshell |
— |
— |
1 |
16 : 1 |
65 |
2 |
100 (Y) |
— |
174 |
Spent frying oil |
12-Tungstophosphoric acid loaded bentonite clay |
69.58 |
0.019 |
0.7 g |
10 : 1 |
85 |
4.5 |
96 (Y) |
6/82% |
175 |
Waste palm oil |
Chicken manure |
28.44 ± 0.11 |
0.14 ± 0.014 |
3 |
6 : 1 |
80 |
20 min |
98 (C) |
4/94% |
176 |
Waste sunflower oil |
K2O/fumed silica catalysts |
1 |
— |
10 |
12 : 1 |
60 |
4 |
99.9 (Y) |
3/99.9% |
177 |
Waste cooking oil |
Sulfonated carbon catalyst |
6.53 |
0.39 |
5 |
22 : 1 |
100 |
3 |
92.3 (Y) |
5/65.4% |
178 |
Waste cooking oil |
Palm kernel shell derived activated carbon |
3368.6 |
— |
4 |
12 : 1 |
70 |
2 |
95.36 ± 1.4% (Y) |
5/82.5 ± 2.5% |
132 |
Waste sunflower oil |
K+ trapped clay nanotubes |
112 |
0.55 |
6 |
15 : 1 |
90 |
4 |
98 (Y) |
6/>85% |
179 |
Waste vegetable oil |
[Bmim][FeCl4] |
— |
— |
5 |
10 : 1 |
55 |
8 |
97 (Y) |
— |
180 |
Waste oil |
α-Fe2O3/AlOOH(γ-Al2O3) |
323.3 |
0.322 ml g−1 |
3 |
6 : 1 |
60 |
3 |
94.3 (Y) |
— |
145 |
Waste cooking oil |
Yeast residue-based acid catalyst |
198 |
0.1 |
4 |
10 : 1 |
60 |
6 |
96.2 (Y) |
4/93.5% |
181 |
Waste cooking oil |
CaO catalyst from waste eggshells |
— |
— |
1.5 mg l−1 |
8 : 1 |
65 |
1.5 |
90 (Y) |
— |
115 |
Waste vegetable palm oil |
Bimetallic tungsten–zirconia (W–Zr) |
9.7 |
0.16 |
2 |
15 : 1 |
80 |
1 |
94 (Y) |
5/79.3% |
182 |
Waste frying oil |
Alumina supported coconut chaff |
78.25 |
0.182 |
1.5 |
12 : 1 |
65 |
2.5 |
91.05 (Y) |
5/75.57% |
183 |
Waste cooking oil |
Lithium metasilicate (Li2SiO3) |
3.5 |
— |
0.25 |
10 : 1 |
60 |
2 |
86.4 (Y) |
— |
184 |
Waste cooking oil |
Zinc aluminate |
— |
— |
5 |
18 : 1 |
100 |
3 |
94.88 (Y) |
— |
185 |
Waste cooking oil |
Core–shell SO4/Mg–Al–Fe3O4 |
123 |
— |
4 |
9 : 1 |
95 |
300 min |
98.5 (Y) |
— |
186 |
Used cooking oil |
Waste borosilicate glass Na2SiO3 |
— |
— |
5 |
12 : 1 |
65 |
90 min |
100 (FAME content) |
5/96.2% |
187 |
Waste cooking oil |
K+ trapped kaolinite |
18.2 |
— |
15 |
14 : 1 |
70 |
180 min |
94.76 (Y) |
5/83.33% |
188 |
Waste cooking oil |
SO4/Fe–Al–TiO2 |
49–78 |
— |
3 |
10 : 1 |
90 |
2.5 |
95.6 (Y) |
— |
189 |
Waste cooking oil |
Potassium impregnated zinc oxide |
3.01 |
— |
2.5 |
18 : 1 |
65 |
50 min |
98 (C) |
5/75.38% |
190 |
Waste cooking oil |
Mesoporous calcium titanate |
31.4 |
0.11 |
0.2 |
3 : 1 |
65 |
1 |
80 (Y) |
— |
191 |
Waste cooking oil |
CM-SO3H |
86 |
0.09 |
10 |
10 : 1 |
110 |
2 |
96.5 (Y) |
3/75.5% |
192 |
Waste palm oil |
CaO catalyst |
10.8 |
— |
7.5 |
15 : 1 |
65 |
3 |
90 (Y) |
4/58.1% |
193 |
Waste palm oil |
Cesium-modified silica catalyst |
5.92 |
0.03 |
3 |
20 : 1 |
65 |
3 |
90 (Y) |
4/65.3% |
194 |
Waste cooking oil |
Fe2O3–MnO–SO42−/ZrO2 |
72 |
— |
3 |
20 : 1 |
180 |
4 |
96.5 ± 0.02 (Y) |
— |
195 |
Waste cooking oil |
Alumina-supported Cs–Zr |
134.9 |
0.20 |
3 |
20 : 1 |
65 |
3 |
90 (Y) |
4/70.05% |
196 |
Waste palm oil |
Mn3.5xZr0.5yAlxO3 |
196 |
0.2 |
2.5 |
14 : 1 |
150 |
5 |
>93 (Y) |
— |
197 |
Waste cooking oil |
Waste marine Na–silica sponge |
5.08 |
0.08 |
3 |
9 : 1 |
55 |
30 min |
98.4 ± 0.4 (Y) |
7/86.3% |
198 |
Waste palm oil |
Clay based catalyst |
34.61 |
0.21 |
3.5 |
15 : 1 |
150 |
5 |
96 (Y) |
3/72% |
199 |
Waste frying oil |
Calcined snail shell |
24 |
0.0588 |
2 |
6.03 : 1 |
60 |
8 |
99.58 (C) |
— |
200 |
87.28 (Y) |
Waste frying oil |
Tetramethylguanidine |
— |
— |
3 |
12 : 1 |
— |
1.5 |
93.8 (Y) |
— |
201 |
Waste sunflower oil |
Sulfated montmorillonite clay |
— |
— |
6 |
12 : 1 |
55 |
120 min |
80.8 (C) |
3/52% |
202 |
Waste cooking oil |
Kettle limescale |
29.3 |
— |
8.87 |
1.7 : 3 |
61.7 |
15 min |
93.41 (purity) |
5/<2% |
203 |
Waste cooking oil |
Ficus carica leaves activated by KOH |
— |
— |
1 |
6 : 1 |
— |
2 |
92.73 (C) |
— |
204 |
Waste cooking oil |
Mn–Zr/CaO from waste eggshell |
12.6 |
0.23 |
3 |
15 : 1 |
80 |
3 |
92.1 (Y) |
5/79% |
205 |
Waste frying oil |
Anthill–eggshell–Ni–Co mixed oxides |
411.1 |
0.151 (T) |
3 |
12 : 1 |
70 |
2 |
90.23 (Y) |
4/77.05% |
206 |
Used vegetable cooking oil |
NH4OH precipitated solid Mg1−xZn1+xO2 catalyst |
9.67 |
30.46 (T) |
2.55 |
9 : 1 |
188 |
4 h 15 min |
80 (C) |
— |
207 |
Waste cooking oil |
KBr impregnated CaO |
— |
— |
3 |
12 : 1 |
65 |
1.83 |
82.48 (Y) |
— |
208 |
Waste frying oil |
Zinc-modified pumice |
22.81 |
0.0228 |
3 |
12 : 1 |
60 |
1 |
91.05 ± 0.04 (Y) |
— |
209 |
Waste frying oil |
Alumina supported eggshell |
78.2 |
0.341 (T) |
4 |
12 : 1 |
65 |
120 min |
77.56 (Y) |
4/18.92% |
210 |
Waste cooking oil |
Barium-modified montmorillonite |
13.114 |
0.056 (T) |
3.5 |
12 : 1 |
150 |
5 |
83.38 (Y) |
3/21.50% |
211 |
Waste cooking oil |
Egg shells |
1.8 |
— |
5.8 |
6 : 1 |
25 |
11 |
97 (Y) |
5/∼97% |
212 |
Waste edible oil |
CaO@MgO |
— |
— |
4.571 |
16.7 : 1 |
69.37 |
7.08 |
98.37 (Y) |
— |
213 |
Waste cooking oil |
Waste oyster shell derived CaO |
0.8142 |
— |
6 |
9 : 1 |
65 |
180 min |
87.3 (Y) |
— |
214 |
Waste cooking oil |
Waste chicken bone derived CaO |
3.38 |
0.0127 |
3 |
3 : 1 |
80 ± 5 |
3 |
96.31 ± 0.72 (Y) |
— |
215 |
Waste palm oil |
Quail eggshell derived CaO |
68 |
1.65 |
2 g |
— |
65 |
3 |
98 (Y) |
— |
216 |
Waste cooking oil |
CaO nanocatalyst |
— |
— |
1 |
8 : 1 |
50 |
90 min |
96 (C) |
— |
217 |
Waste cooking oil |
La3+/ZnO–TiO2 photocatalyst |
62.65 |
0.1131 |
4 |
12 : 1 (E : O) |
35 |
3 |
96.14 (C) |
5/>87% |
218 |
Waste animal tallow |
(NaOH) |
— |
— |
2.5 |
6.5 : 1 |
60 |
1.5 |
62 (Y) |
— |
219 |
Waste cooking oil |
Sodium silicate catalyst |
0.386 |
6.24 × 10−3 |
2.5 |
6 : 1 |
64 |
4 |
57.92 (Y) |
— |
220 |
Waste oil from date pits |
Biomass-derived waste date pits |
232.2 |
0.17 |
4.5 |
12 : 1 |
70 |
2 |
98.2 (Y) |
— |
221 |
Waste sunflower oil |
Zeolite tuft |
3.731 |
0.02812 |
6.4 |
11.5 : 1 |
50 |
2 |
96.7 (Y) |
3/1.21% |
222 |
Waste cooking oil |
Ni/Fe carbonate-fluorapatite |
— |
— |
10 |
8 : 1 |
70 |
2 |
97.5 (Y) |
3/54% |
223 |
Waste cooking oil |
Eggshell supported pyrolysis residue (char) |
23.48 |
0.1 |
10 |
12 : 1 |
65 |
3 |
>95 (C) |
— |
224 |
Waste soybean oil and animal fat |
FeCl3-modified resin |
— |
— |
8 |
10 : 1 |
90 |
2 |
92 (Y) |
9/73% |
225 |
Waste cooking oil |
SO42−/SnO2–SiO2 |
— |
— |
6 |
15 : 1 (mixed); E : M 9 : 6 |
150 |
1 |
81.4 (Y) |
— |
226 |
Waste cooking oil |
Mesoporous calcium titanate catalyst |
31.4 |
0.11 |
0.2 |
3 : 1 |
65 |
1 |
80 (Y) |
5/75% |
191 |
Waste cooking oil |
Silica impregnated calcium oxide |
12.29 |
0.0429 (T) |
3 |
15 : 1 |
60 |
2 |
95.75 (C) |
8/52.5% |
227 |
Waste cooking oil |
Fe/zeolite catalysts |
24.626 |
0.042 |
3 |
12 : 1 |
65 |
4 |
89.23 (Y) |
— |
228 |
Waste cooking oil |
Synthesized CaO |
— |
— |
5 |
10 : 1 |
75 |
1 |
96.6 ± 0.05 (Y) |
— |
229 |
Waste cooking oil |
Eggshell-CaDG |
48.35 |
— |
1.5 |
10 : 1 |
60 |
50 min |
96.07 (Y) |
— |
230 |
Waste cooking oil |
Calcium diglyceroxide |
— |
— |
1 |
9 : 1 |
60 |
1 |
93.15 (Y) |
3/50.5% |
231 |
Waste cooking oil |
Copper and calcium-based metal–organic framework |
118 Cu-MOF; 101 Ca-MOF |
0.035 |
1.0 g/100 ml |
20 : 1 |
60 |
60 min |
85 (Y) |
3/75.1% |
232 |
Used cooking oil |
CaO from river snail shell ash |
— |
— |
3 |
9 : 1 |
65 |
1 |
92.5 (Y) |
— |
233 |
Waste cottonseed oil |
α-Fe2O3/AlOOH |
323 |
0.322 |
3 |
6 : 1 |
60 |
3 |
94.6 (Y) |
4/91.3% |
234 |
Waste cooking oil |
SO42−/TiO2/La3+ |
229 |
— |
5 |
10 : 1 |
110 |
1 |
92.3 (C) |
5/90.2% |
235 |
Waste frying oil |
Eggshell derived CaO |
8.6401 |
— |
5 |
12 : 1 |
65 |
1 |
94.52 (C) |
6/>90% |
236 |
Waste cooking oil |
Calcined scallop shell |
7.33 |
— |
5 |
6 : 1 |
65 |
2 |
86 (Y) |
4/66% |
237 |
Waste sunflower oil |
Eggshell |
12.5 |
0.0033 |
3 |
30 : 1 |
65 |
3 |
96.11 (C) |
3/82.31% |
238 |
Chicken fat |
AC/CuFe2O4@CaO |
— |
— |
3 |
12 : 1 |
65 |
4 |
95.6 (Y) |
— |
239 |
Waste cooking oil |
Calcium oxide/cellulose/polyvinyl alcohol |
— |
— |
0.5 |
6 : 1 |
65 |
4 |
98.40 (Y) |
7/67.67% |
240 |
Waste Phoenix dactylifera L. kernel |
(Mn–MgO–ZrO2) |
45.78 |
0.12 |
3 |
15 : 1 |
90 |
4 |
96.4 (Y) |
— |
241 |
Waste soybean oil |
Alkalized SBC ash |
0.02 |
5.51 × 10−3 |
8 |
11 : 1 |
65 |
3 |
99.1 (Y) |
8/>95% |
242 |
Waste fish oil |
Sulfonated activated carbon |
884.26 |
0.479 |
11.4 |
14.85 : 1 |
328 K |
1 |
88 (C) |
— |
243 |
Waste sunflower oil |
CaO/Al2O3 |
13.001 |
0.08 |
2.5 |
12 : 1 |
60 |
5 |
98.23 (Y) |
5/76.379% |
244 |
Waste cooking oil |
Ripe and unripe plantain peels |
1.10 ± 0.0050 |
0.002366 |
0.5 |
6 : 1 |
45 |
45 min |
97.96 (Y) |
5/84.64% |
161 |
Beef tallow animal fat |
Calcium oxide catalyst |
586.272 |
0.2936 |
7.1 |
9 : 1 |
60 |
96 min |
72 (C) |
4/<50% |
245 |
Waste cooking oil |
Fused crab shell and plantain peels |
260.35 |
0.65 |
5 |
13.03 : 1 |
60 |
149.94 min |
93 (Y) |
6/>80% |
246 |
Used cooking oil |
(RHC/K2O-20%/Ni-5%) |
— |
— |
4 |
12 : 1 |
65 |
2 |
98.2 (Y) |
5/70% |
247 |
Waste sunflower oil |
TiO2–ZnO nanocatalyst |
— |
— |
267 mg l−1 |
6 : 1 |
66 |
— |
96.4 (Y) |
— |
248 |
Waste cooking oil |
K/Fe2O3/γ-Al2O3 |
65 |
0.2 |
4.6 |
9.73 : 1 |
— |
7.84 |
99 (Y) |
2/77% |
249 |
Waste cooking oil |
Carbon catalyst |
238 |
0.29 |
— |
10 : 1 |
65 |
1.5 |
93.07 (Y) |
— |
250 |
Waste cooking oil |
CRL-MgO–Al2O3 |
— |
— |
10 |
3 : 1 |
40 |
24 |
69.10 (C) |
— |
251 |
Edible waste oil |
Biochar/CaO/K2CO3 |
3.74 |
0.013 |
4 |
18 : 1 |
65 |
200 min |
98.83 (Y) |
5/90% |
252 |
Waste frying oil |
Carbon microsphere-based solid acid |
8 |
0.011 |
0.6 g |
16 : 1 |
140 |
4 |
92.2 (Y) |
5/65.9% |
253 |
Waste cooking oil |
Ba doped CaO |
4.86 |
— |
1 |
6 : 1 |
65 |
3 |
>98 (C) |
— |
254 |
Mixtures of refined palm oil and WCO |
Biomass fly ash catalyst |
9.028 |
0.01055 |
10 |
9 : 1 |
60 |
3 |
94.6 (Y) |
— |
255 |
Waste sunflower oil |
Amberlyst 15 |
— |
— |
3 |
12 : 1 |
65 |
9 |
78 ± 3.39 (Y) |
— |
256 |
Waste cooking oil |
Fe3O4@Al2O3 |
— |
— |
5 |
32.1 : 1 |
99.8 |
2.95 |
99.1 (C) |
4/67% |
257 |
Waste frying oil |
Magnetic solid acid catalyst |
92 |
|
50 mg |
15 : 1 |
70 |
5 |
98.9 (Y) |
6/98% |
258 |
Waste chicken fat |
MWCNT-SO3H |
— |
— |
25 |
30 : 1 |
90 |
3 |
93.7 (Y) |
— |
259 |
Waste palm oil |
Sulfonated carbon catalyst derived from coconut meal |
1.33 |
0.31 (A) |
5 |
12 : 1 |
65–70 |
10 |
92.7 (Y) |
4/>80% |
260 |
Waste frying oil |
MGO@MMO |
— |
— |
— |
8 : 1 |
60 |
1.5 |
94 (Y) |
4/86% |
261 |
Waste cooking oil |
GO@ZrO2–SrO |
68 |
0.08 |
0.2 g |
4 : 1 |
120 |
1.5 |
91 (Y) |
5/54% |
262 |
Waste vegetable oil |
Carbon-based solid acid catalyst |
7.48 |
— |
0.2 |
16.8 : 1 |
220 |
4.5 |
94.8 (C) |
— |
263 |
Waste cooking oil |
TiO2/RGO |
— |
— |
1.5 |
12 : 1 |
65 |
3 |
98 (C) |
3/78.86% |
264 |
Waste cooking oil |
TiO2–MgO |
36.3 |
0.16 |
10 |
50 : 1 |
160 |
6 |
92.3 (Y) |
4/81.2% |
265 |
Waste cooking oil |
LaPO4 supported nickel foam |
— |
— |
2.5 |
5 : 1 |
90 |
2 |
91 (Y) |
9/41% |
266 |
Waste cooking oil |
DMB catalyst |
68.13 |
— |
3 |
11 : 1 |
60 |
6 |
96.25 (Y) |
5/84.79% |
267 |
Waste corn oil |
MgO doped magnetic graphene |
— |
— |
8 |
13 : 1 |
65 |
7 |
93.55 (Y) |
— |
268 |
Waste cooking oil |
CaO–ZrO2 |
7.3 |
0.05 |
10 |
30 : 1 |
65 |
2 |
92.1 (Y) |
10/>80% |
269 |
Waste cooking oil |
Bagasse derived catalyst |
— |
— |
15 |
30 : 1 |
90 |
12 |
93.8 (Y) |
— |
270 |
Waste cooking oil |
Sulfonated rice husk char RHC–SO3H |
4 |
— |
5 |
20 : 1 |
110 |
3 |
98.17 (C) |
5/95.75% |
271 |
Waste cottonseed oil |
Solid acid CS0.073O0.541 |
— |
— |
5 |
20 : 1 |
80 |
12 |
∼90 (Y) |
— |
272 |
Waste cooking oil |
ZrO2–SrO2 mixed oxide nanocatalyst |
— |
— |
5 |
10 : 1 |
120 |
3 |
92 (Y) |
4/76% |
273 |
Waste cooking oil |
Activated carbon |
— |
— |
1 |
6 : 1 |
60 ± 1 |
2 |
93.95 (Y) |
— |
274 |
Waste cooking oil |
Solid mixed oxide catalyst from waste biomass |
78.681 |
0.349 |
2 |
9 : 1 |
60 |
3 |
95.23 (C) |
6/85.4% |
275 |
Waste cooking oil |
Sugarcane bagasse derived biochar |
— |
— |
10 |
1 : 2 |
65 |
2 |
98.94 (C) |
— |
276 |
Waste cooking oil |
Solid waste coral fragment |
— |
0.172 ± 0.012 |
100 |
15 : 1 |
65 |
2 |
>98 (Y) |
3/95% |
277 |
Waste palm oil |
Calcium-based Mo–Zr/CS catalyst |
6.5 |
— |
3 |
15 : 1 |
80 |
3 |
90.1 (Y)a |
3/>70% |
278 |
Waste cooking oil |
Musa balbisiana Colla peels |
14.036 |
0.074 |
2 |
6 : 1 |
60 |
3 |
100 (C) |
— |
279 |
Waste cooking oil |
Waste grooved razor shell |
— |
— |
5 |
15 : 1 |
65 |
3 |
93.5 (Y) |
6/93.6% |
280 |
Waste cooking oil |
MgO/MgSO4 |
82 |
0.047 |
8.9 |
9.4 : 1 |
|
46 min |
98.8 (Y) |
— |
281 |
Waste cooking oil |
MPANI@CO3O4 |
— |
— |
— |
10 : 1 |
90 |
4 |
>90 (Y) |
— |
282 |
Waste frying oil |
CO-doped Fe2O3–CaO |
— |
— |
3 |
16 : 1 |
70 |
150 min |
91.5 (Y) |
— |
283 |
Waste cooking oil |
CaO (10%)–Fe2O3 (10%)/AC |
— |
— |
3 |
18 : 1 |
65 |
3 |
98.3 (Y) |
6/>80% |
284 |
3.2.1 Zeolites. Zeolites are crystalline aluminosilicate materials with a large surface area and great thermal solidity that are found in nature. The pore shape, surface characteristics, and the inner electric field from the crystal vary across different zeolites. Zeolites also can increase the number of mobile phases in the core pores and enhance surface assimilation because of the strong electric field produced by the catalyst's efficient catalysis and high selectivity.125 They have molecular-scale pores, which results in very good shape selectivity and make it possible to synthesize transition metal nanoparticles that are catalytically active. The selection of the reaction species in the zeolite pores affects the yield and speed of reactions catalyzed by zeolites. Fig. 6 schematically illustrates three different transition metal–zeolite composites.285 Zeolites do, however, have several restrictions on the transesterification reaction, including their small pore size and diffusion.286 The catalytic efficiency of a Ni/zeolite catalyst was outlined for producing biodiesel from WCO through transesterification.128 According to BET analysis, the generated Ni/zeolite has a more surface area of 80.661 m2 g−1 and pore volume of 0.123 cm3 g−1 than the zeolite catalyst. This was due to calcination that forced agglomerates to break into smaller-sized agglomerates and effectively reduced the pore radius. The optimized parameters such as a methanol to WCO ratio of 12
:
1, 4 h reaction time, a reaction temperature of 60 °C, and 3 wt% catalyst loading obtained the maximum biodiesel efficiency of 89.4%. Compared with other studies, it was reported that the waste-based catalyst gave a relatively higher yield per 100 g of the catalyst and used a minimum amount of alcohol. The catalyst also showed good reusability for three consecutive cycles, and the process overall has good sustainability, being entirely waste-derived and reusable. Aghel et al. reported a zeolite-like material, clinoptilolite, obtained from calcium-rich industrial phosphoric waste as a catalyst with WCO and methanol for producing biodiesel.287 The preparation of the catalyst is simple, the clinoptilolite being ordinarily purified and then stirred with a weighed amount of calcium oxide and kept at 800 °C for 2 h. The result showed a highest biodiesel purity of 84.76%. Reusability studies indicated a loss of catalytic activity by 20% at the end of the last cycle, due to deactivation of active sites by absorption and by-products of unreacted oil.
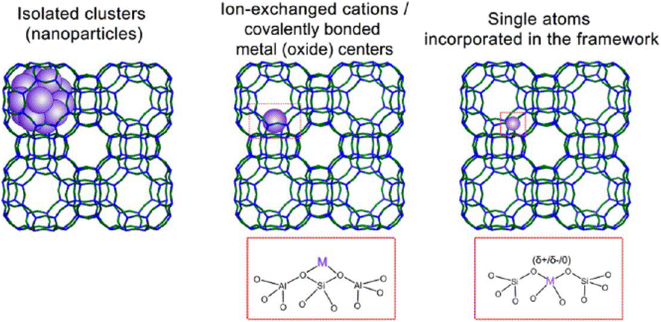 |
| Fig. 6 Possible zeolite–metal composite configurations. Reprinted with permission from ref. 285. Copyright (2018) ACS. | |
A zeolite/geopolymer (Z/GP) composite basic catalyst was synthesized from kaolinite and diatomite for producing biodiesel from spent cooking oil. The Z/GP catalyst showed a surface area of 106 m2 g−1, 4.2 nm pore size (diameter), and a basicity of 6.73 mmol OH per g. XRD analysis confirmed an alteration in the structural and crystalline properties of the raw materials used to produce Z/GP. This catalyst showed 98.1% biodiesel yield from WCO through the transesterification reaction with maximized conditions of a 12
:
1 methanol to oil ratio, catalyst weight of 3.25 wt%, and 90 min reaction time at a relatively low reaction temperature of 40 °C. The optimization study indicated that the yield could be increased to 99% with a reaction temperature of 54.9 °C for 81.9 minutes with the same molar ratio for methanol and oil with 3.48 wt% catalyst loading. The experimental yield obtained is high in comparison with other studies and the catalyst showed very good reusability for five runs.134 Fereidooni et al. explored a Na+/zeolite–chitosan biocomposite in the electrolytic transesterification of waste frying oil to biodiesel utilizing methanol solvent. TEM images in Fig. 7(a) show that holes with various sizes are highly porous in raw zeolite and Fig. 7(b) demonstrates that there are multiple cages and pores on the surface of the catalyst. The maximum 96.5% biodiesel yield was obtained with a relatively low molar ratio of methanol
:
oil of 8
:
1, 1 wt% catalyst concentration at ambient temperature, and a reaction time of 30 minutes with an electric voltage of 40 V and stirring at 400 rpm. This study made use of co-solvents to combat the low solubility of oil in alcohol by using acetone in the reaction phase. Reusability studies were reported for five runs with the yield decreasing from 96.5% to 92.9% in the final run, showing excellent reusability. The decrease in catalytic efficiency was attributed to the percolation of Na catalytic phases and by-product absorption on these active sites, leading to their deactivation.146
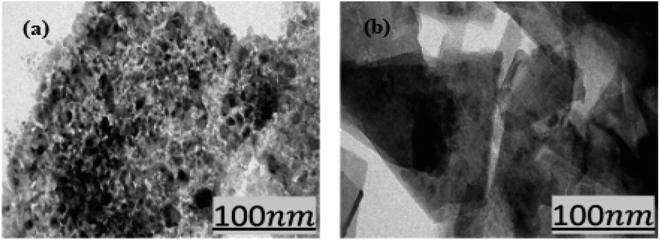 |
| Fig. 7 TEM of the zeolite (a) and composite (b). Reprinted with permission from ref. 146. Copyright (2021) Elsevier. | |
3.2.2 Alkaline earth metal oxides. Alkaline earth metal oxides are one of the most frequently utilized groups in heterogeneous catalysis for transesterification. The group mainly includes basic oxides like MgO, CaO, SrO, and BaO. All of these oxides are quite active because of the high percentage of surface basic sites,288 but to maximize their reusability and activity, it is recommended to mix them with other active metals.289 Their activity is determined by the quantity and basic strength or the alkalinity of these sites,290 and hence their activity usually follows the trend MgO < CaO < SrO < BaO.291 The appearance of a surface metal ion that works like a Lewis acid and an oxygen ion that works like Brønsted basic results in the formation of a basic site.127 BaO gives the best activity but can get diluted in methanol and produce harmful barium compounds,292 whereas SrO does not generate toxic components. However, SrO is smoothly leached in the reaction mixture and is easily deactivated by CO2 and ambient moisture and hence would require very delicately monitored reaction conditions.293 Support materials usually applied are ZrO2,195 La2O3,294 Al2O3, and silica.295 CaO specifically is reported to be active for the transesterification of vegetable oil in refluxing methanol by catalyzing the reaction through a nucleophilic reaction and speeding up the reaction due to its enhanced basic characteristics.296 It is non-toxic and non-corrosive, can be prepared easily, has low solubility in biodiesel and hence can be separated easily and requires mild reaction conditions. Similarly, the basic characteristics of MgO also catalyze the reaction, but its basic sites are activated at higher calcination temperatures. CaO is a very commonly used catalyst as it can be easily obtained from waste eggshells, thus being bioderived. These catalysts' basic sites can be readily affected by the appearance of FFA and water adsorption, which results in a reduction in activity and reduced overall efficiency.297 In 2021, Erchamo et al. prepared a CaO nanocatalyst by calcination of eggshell powder at 900 °C, followed by hydration-dehydration treatment to enhance its catalytic activity for biodiesel production with WCO through transesterification. XRD, SEM, and EDX studies were used to examine the catalyst's various physical characteristics. After hydration–dehydration, the catalyst underwent morphological modifications, changing from a rod-like pattern to a honeycomb structure, with a decrease in the particle size and an increase in the surface area. The highest efficiency of 94% was reported under the maximized set of preconditions (time: 120 min, temperature 60 °C, methanol
:
oil molar ratio of 12
:
1, and catalyst weight: 2.5 wt%). The produced biodiesel met the ASTM parameters concerning fuel properties. The study is of importance from a profitable point of view, being entirely waste-derived.298Bargole et al. prepared a CaO catalyst from marble waste powder. The marble waste was cleaned and calcined at 850 °C for 2 h. After that, it was subjected to acid nitric acid (HNO3) treatment to eliminate insoluble silica contaminants from the pre-calcined marble waste, and then filtered and dried. This was again additionally calcined at 850 °C for 2 h, to give calcium and magnesium oxides. The study revealed the application of ultrasonication for producing biodiesel from WCO through transesterification. The maximum biodiesel efficacy of 95.45% was attained from WCO under optimized process preconditions. RSM optimization showed that the effect of temperature was the greatest compared to the other reaction parameters. The acid-treated pre-calcined marble waste powder gave the best yields, as it had no SiO2 and MgO impurities and mainly consisted of CaO, which generates methoxy ions on the adsorption of methanol on the surface of the catalyst and stays in the aqueous phase with methanol due to its hydrophilicity. The conversion of biodiesel was 63.79% after the 5th cycle of recycling. This deactivation may occur owing to the adsorption of fatty acids on the catalytic sites, effectively blocking them.139 Attari et al. investigated waste chicken eggshells as CaO catalysts with WCO for the transesterification reaction equipped with an ultrasonic horn-type reactor and achieved 98.62% biodiesel yield. The waste eggshells were washed, dried, and finely crushed, and then calcined at 900 °C for 4 h, which converted the carbonate present in the shells to calcium oxide. The FESEM images showed that the raw chicken eggshell powder exerted irregular-sized particles as shown in Fig. S5(a),† and the calcined eggshell generates rod-like components in the form of lumps as shown in Fig. S5(b).† RSM with CCD was utilized to get the reaction parameters, and they found that the best yield was achieved at a catalyst weight of 6.04 w/w% with a methanol-to-oil ratio of 8.33
:
1 at an ultrasonic potential of 299.66 W for a reaction time of 39.84 minutes. Process intensification with ultrasonic energy helped maximize the yield in a shorter period as compared to similar studies with the catalyst in conventional reactors.131 In further work, Sahani et al. explored the catalytic efficiency of an altered strontium oxide catalyst for the transesterification of WCO. They used a Sr–Ti mixed oxide, synthesized by the sol–gel polymer precursor method using different Sr/Ti atomic ratios, and then calcined at 880 °C for 8 h to optimize the catalytic performance. The Sr–Ti mixed metal oxide at a 4
:
1 ratio resulted in the highest biodiesel conversion under optimized parameters, compared to the other catalysts. The pore diameter or pore size was deliberated to be 8.7125 nm, which indicated the mesoporous structure of the catalyst. Its high activity can be explained by its high surface area of 43.6 m2 g−1 and basicity of 15.0 < H_ < 18.4, measured through the Hammett titration process. The highest biodiesel conversion was 97.9 ± 0.5%, optimized by RSM using CCD. Moreover, a persistent catalytic efficacy directing to an 83% methyl ester conversion with an eight recycle was observed.299
3.2.3 Cation exchange resins. Cation exchange resins fall within the category of ion exchange materials, which contain Brønsted and Lewis acids in their metallic H+ and M+ forms. Ion–exchange materials can be broadly defined as insoluble matrices with labile ions that may exchange with ions in their surrounding media without significantly altering the structure of the material.300 They are essentially Brønsted acids that gradually gain Lewis acidic character as a result of an increased interchange with metallic cations. Inorganic substances like clays and zeolites are fundamentally Lewis's acids, and the presence of metallic cations and the petrology formation influence them.301 These acidic heterogeneous catalysts are widely used due to their reusability, non-corrosivity, eco-friendly nature, and their easy removal from the reaction medium, usually by elementary filtration or decantation due to their solid nature.302,303 These catalysts can prevent the interference of moisture in the transesterification process and the biodiesel process can be carried out efficiently.304 Using these catalysts in a packed tower removes the necessity of washing biodiesel for purification, thus cutting down the cost of production and reducing water wastage.305 Ma et al. investigated the effect of a modified macroporous styrene type cation-exchange resin, i.e., FeCl3 altered resin as a catalyst to transesterify WCO obtained from soybean oil and animal fat. They obtained a yield of 92% under the optimum conditions of a 10
:
1 molar ratio of methanol
:
oil, catalyst content of 8%, and a reaction temperature of 90 °C for a reaction time of 120 minutes. The conventional homogeneous catalyst H2SO4, with the same feedstock, took a long reaction time. The convenient catalyst segregation from the reaction made reusability studies feasible and economical. The conversion was maintained at 73% after the 9th recycle run.225 Shibasaki-Kitakawa et al. outlined biodiesel production from waste rice bran acid oil with over 95% FFA by weight using a porous type of cation-exchange resin with low crosslinking density, i.e., Diaion PK208LH. The cation-exchange resin was used for the esterification of FFA, after which they used an anion-exchange resin for transesterification. They achieved a complete conversion of FFA at a methanol to oil ratio of 2
:
1 for alcohol
:
fatty acid. They achieved greater yields with feedstock that contained more FFA than triglycerides, as triglycerides led to the occurrence of a side reaction with the anion exchange resin. Thus, this catalyst opened the path for using low-quality inedible and waste oils. The biodiesel produced met the required specifications, other than that for oxidative stability.306
3.2.4 Mixed metal oxides. These catalysts are prepared by mixing metals and their oxides, which enhances their properties as compared to their catalytic activity as individual species act in synergy. Mixing these oxides leads to enhancement in properties because of a better surface area. It also helps in the separation of the catalyst inducing magnetic separation and provides good catalytic activity. Mixing different metals gives better activity for feedstock with high moisture and FFA content. The stability, surface area, and basicity of catalysts are significantly impacted by the appearance of various active particles in the binary system.307 Dias et al. reported methanolysis of soybean oil over magnesia-supported SrO heterogeneous catalysts. The catalytic activity decays after three reuses as the residual Sr remains trapped in the MgO pores and is thus inaccessible to the reactants as shown in Fig. 8.308 Metals and their oxides can be mixed to provide bifunctional catalysts that can perform the acid-catalyzed esterification of FFA and base-catalyzed transesterification of triglycerides in a single step, reducing the reaction time and cost on a commercial scale.309 The majority of current research focuses on enhancing stability or regeneration methods such as solvent washing or recalcination. Lee et al. have reported the catalytic activity of various mixed metal oxides, like CaO–MgO, CaO–ZnO, CaO–La2O3, and MgO–ZnO, with Jatropha oil, and found that their activity as compared to their oxides enhanced in the order CaO–ZnO > CaO ∼ CaO–MgO ∼ CaO–La2O3 > MgO–ZnO > MgO > ZnO > La2O3. Additionally, they also found that CaO–ZnO displayed good separability and reusability.310 TiO2–MgO mixed oxides synthesized by a sol–gel method were analyzed by Wen et al. for biodiesel production from waste cooking oil. They prepared a set of catalysts with different atomic ratios and different calcination temperatures to optimize the catalytic activity. The results reported a 92.3% biodiesel yield for MT-1-923, with an Mg/Ti molar ratio of 1 and calcined at 923 K. They concluded that improving the molar ratio of Mg to 1 increased the yield drastically from 52.2% to 79.1%. The surface area of a catalyst affects its catalytic performance significantly. The surface area of the catalyst was determined to be 36.3 m2 g−1, and the pore diameter was determined to be 16.1 nm. For the reusability work, the catalyst was separated, cleaned with methanol, and dried for reuse and found to reduce to 81.2% after 4 recycles.311 Yusuff et al. reported the synthesis of anthill–eggshell–Ni–Co mixed oxide nanomaterials via co-precipitation transesterification of waste frying oil. The catalyst was prepared by co-precipitation. The catalyst was then calcined at 1000 °C for 4 h. The numerous properties of the nanocatalyst were examined by XRD, FTIR, XRF, BET, and SEM. The BET analysis showed that the surface area of the catalyst enhanced greatly, from 55.95 m2 g−1 to 411.10 m2 g−1 due to calcination, and a similar trend was followed for the pore volume and diameter. The reaction was optimized at 3 wt% catalyst weight, a molar ratio of 12
:
1, and 70 °C for 2 h to obtain 90.23% yield. Again, the catalyst was found to have good activity and stability for four reuse cycles. It had slight deactivation of basic sites after each cycle, which contributed to the decrease in activity, resulting in a 77.05% yield after the last cycle.206
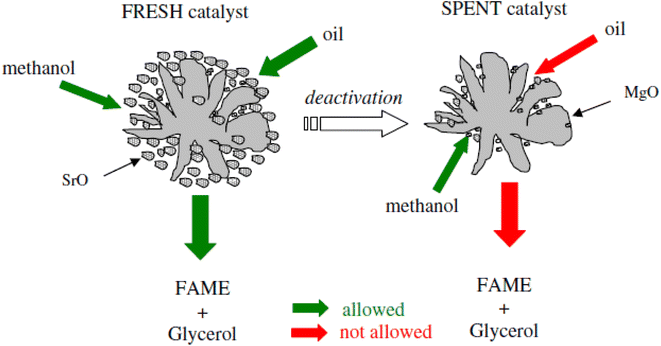 |
| Fig. 8 Scheme for the catalyst deactivation process. Reprinted with permission from ref. 308. Copyright (2012) Elsevier. | |
Apart from binary mixed systems, ternary systems with further modifications have also been investigated by Rezania et al. To create a heterogeneous nanocatalyst, MGO@MMO was prepared by a co-precipitation process with basic cations of cerium, zirconium, and strontium oxides as shown in Fig. 9, for the conversion of waste frying oil. The molar ratio of the mixed oxides was kept constant at 1
:
1
:
1, but the ratio of graphene oxide to mixed metal oxides was varied to optimize the catalytic performance. The delineation of the catalyst proved that the spherical metal oxide nanoparticles were dispersed onto the planar graphene oxide sheets and reduced the nano-particle agglomeration. It is evident that the MGO@MMO catalyst had bifunctional properties (MGO and MMO) that concurrently can attack the triglycerides. MMO acts as a Brønsted base and high proton acceptor and graphene oxide acts as a Brønsted acid and high proton donor. They achieved a high yield of 94% with WFO by utilizing a methanol
:
oil ratio of 8
:
1 at a temperature of 60 °C for 90 minutes. This catalyst in particular displayed good reusability due to its magnetic nature. They reported eight cycles of reuse but noted a substantial decrease in activity after the fourth cycle, up to which the yield was 86%. Then this activity decreased as a result of active site blockage, leaching, and coverage by glycerol and fatty acids.312
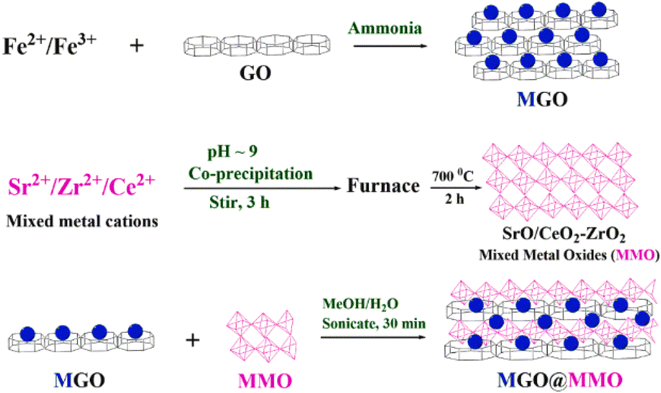 |
| Fig. 9 Schematic synthesis of the magnetic MGO@MMO nanocatalyst. Reprinted with permission from ref. 312. Copyright (2020) Elsevier. | |
3.2.5 Heteropoly acids. Oxygenated compounds, such as heteropolyacid and their related salts, are mostly used in the transesterification reaction. Keggin-type and Wells–Dawson-type are two usual formations of HPAs.313 The structure of Keggin-type HPAs is nearly rounded, while Wells–Dawson type has an egg-shaped formation.314 Heteropolyacids (HPAs) such as H4PNbW11O40, H3PW12O40, H4SiW12O40, and H4SiM12O40 were reported for better catalytic efficiency. HPAs were added to extremely porous materials with a large surface area to improve catalytic efficacy. Heteropolyacids are insensitive to FFA content, generally give higher yields at relatively lower catalyst loading, and can catalyze esterification and transesterification simultaneously, thus eliminating the need for an esterification pre-treatment step. They have easy separation as they do not require the product stream to be washed to get biodiesel and can be reused repeatedly due to their high stability against leaching. The elimination of water washing lowers the biodiesel production price, which makes the procedure environmentally friendly.315 Their flexible structure and strong acidity make them attractive choices for transesterification catalysis. Their high activity can be attributed to strong Brønsted acidity and proton mobility. For conventional catalysts, the formation of water around the catalysts leads to the blocking of active sites for the catalyst and the reaction is not able to proceed at those sites. This barrier formation by water does not hinder the activity of HPA catalysts, making them superior to solid acid catalysts. They show quick, reversible multi-electron redox reactions under very moderate circumstances, as they are effective oxidants. By altering the chemical composition, their acid–base and redox characteristics may be changed in a wide range of ways. HPAs however have a low surface area, so to make their acid sites more accessible, they are often modified with support materials.316 Support materials used include mesoporous silica317 and mesoporous SBA-15 (ref. 318), among others.Talebian-Kiakalaieh et al. used a heteropoly acid catalyst H3PW12O40.6H2O (PW12) for producing biodiesel from WCO. They used RSM and artificial neural networks (ANNs) to optimize the reaction parameters. The catalyst showed 88.6% conversion after a time of 14 h at 65 °C along with a 70
:
1 M ratio of methanol
:
oil, and a catalyst loading of 10 wt%. The catalyst could easily be separated by filtration and be reused, thus eliminating the need for washing the product, and no wastewater was generated. To conduct reusability studies, the separated catalyst was soaked in hexane overnight to aid in the desorption of the non-polar compounds from its surface. The catalyst reached 70% conversion in the fifth cycle of reuse but does not show a very significant drop in activity till the fourth cycle.319 Zou et al. investigated an altered form of HPA catalysts for the transesterification reaction of WCO. Their addition of a complex Cs2.5H0.5PW12O40 with bridged bis-cyclodextrin perfectly transesterified the oil with a yield of 94.2%. The optimum conditions were a catalyst loading of 3 wt%, a 9
:
1 molar ratio of methanol
:
oil, a stirring speed of 300 rpm, and a temperature of 65 °C for 180 minutes. The inclusion complex was calcined at 200 °C for 3 h. The BET result showed that the specific surface area was 153.4 m2 g−1. The catalyst calcined at 1000 °C showed a surface area of 111 m2 g−1. The produced biodiesel was found to meet the ASTM D6751 standards.320 Cao et al. reported the transesterification of WFO having a high acid number and high moisture quantity with the hexahydrate form of H3PW12O40.6H2O (PW12) to produce biodiesel. H3PW12O40.3H2O was calcined at 393 K overnight in the air to give H3PW12O40.6H2O, which gave the best activity for transesterification. It gave a yield of 87% at 65 °C, and a methanol
:
oil ratio of 70
:
1 in a reaction time of 14 h. The catalyst was easily separable and was treated with methanol before reuse. The catalyst was used five times with considerable stability and a very low leaching of 4.6%.321
3.2.6 Waste sources. Vinu & Binitha investigated a solid catalyst areca nut husk ash with lithium compound by chemical modification. The lithium-loaded ash catalyst exhibited excellent catalytic activity and stability from used cooking oil with 99.92% biodiesel conversion. The catalyst had a high basicity of 0.8797 mmol−1 for the transesterification process with the following process conditions: catalyst loading of 1 wt%, methanol and oil ratio: 15
:
1, temperature: 65 °C, and time: 120 min. This catalyst was used 3 times with a 99% FAME yield.322 Khan et al. showed a biodiesel conversion of 91.7% with waste biomass through the transesterification reaction of waste cooking oil with a duration of 4 hours. The waste biomass (quail beaks) was calcined at 900 °C for 4 h and the waste cooking oil was pre-treated before transesterification. XRD analysis showed that the crystallinity of hydroxyapatite (Hap) formation was improved by thermal calcination with a crystallite size of 37.33 nm. More than five times, without a significant yield loss, the catalyst's activity was seen to be quite stable. Yet, it seems that the output decreased in the sixth run.323 Zik et al. reported a catalyst source isolated from chicken bone (calcined at 900 °C for 4 h) with coconut residue by modification. The biodiesel yield of 98.40% was obtained in a transesterification reaction in a packed bed reactor. The catalyst was reusable 4 times with maintaining a biodiesel yield >90%. Examination of the kinetics of the reaction reported that the reaction accompanied a pseudo-first-order reaction with k-values ranging from 0.0092 min−1 to 0.0151 cm−1.324 Researchers have explored CaCO3 as an effective source of heterogeneous catalysts to produce biodiesel. CaO can be extracted from numerous waste sources such as chicken bone, snail shells, chicken eggshells, waste ostrich shells, seashells, crab shells, etc. Mostly these shells are composed of 95% calcium carbonate, and the remaining is MgCO3, organic matter, phosphate, and small traces of metals. Fig. 10 illustrates the schematic of CaO catalyst preparation from different waste shells.325
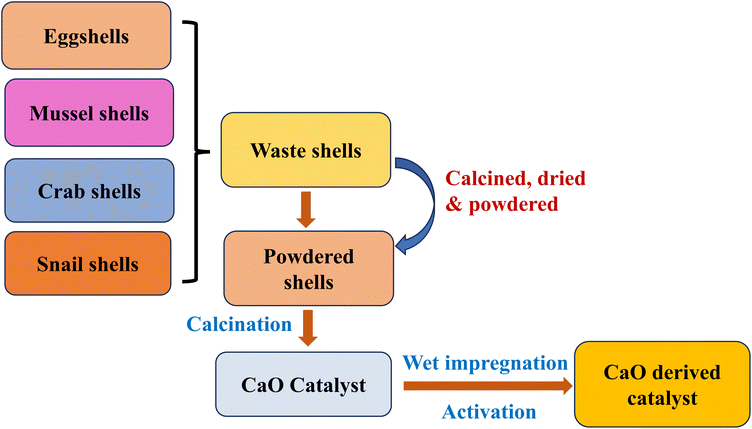 |
| Fig. 10 General method of preparation of a CaO derived catalyst from waste shells. Reprinted with permission from ref. 325. Copyright (2022) Elsevier. | |
Bharti et al. investigated the source of CaO as a solid catalyst from chicken eggshells to prepare biodiesel by the transesterification reaction of waste cooking oil using solar irradiation-based thermal energy and achieved 90.13% biodiesel conversion. The study delineated that the calcined shells generally contain calcium oxide (calcined at 900 °C for a reaction time of 3 h). The waste cooking oil was subjected to esterification due to its high acid value.326 Kamaronzaman et al. reported a strong base catalyst derived from eggshells with modification by doping nickel. The catalyst was prepared by calcined at 1000 °C for 4 h. The biodiesel yield reached 100% from waste cooking oil with a time of 2 h.327 Putra et al. presented a CaO/SiO2 catalyst isolated from cheap and abundant wastes of eggshells and peat clay. The waste shells were calcined at 700 °C for 4 h to get the desired catalyst. A biodiesel yield of 91% was achieved from waste cooking oil in a transesterification reaction in 60 min reaction time.328 Birla et al. showed the better efficacy of calcined snail shells as catalysts at 900 °C in the transesterification of waste frying oil (acid value of 1.948 mgKOH g−1). In a long 7 h reaction, a yield of 87.28% was reported. It was mentioned that the surface area of the catalyst was 3.5 m2 g−1 determined by BET when the calcination temperature was above 800 °C and the total pore volume was 0.09 cm3 g−1, and the mean pore diameter was 21.4 nm, and all of the factors enhanced the sturdy basic phases to the catalyst with super catalytic efficiency. The loss of catalytic activity after the fourth reuse was mainly from the leaching of CaO with 80% biodiesel yield.200
3.2.7 Ionic liquids. The application of Ionic Liquids (ILs) as a catalyst for biodiesel production has enhanced latterly owing to the impediment correlation with other catalysts. Ionic liquids (ILs) are salts having low liquefied points, which can be around or below ambient temperature. Ionic liquids are formed by combining cations and anions, which can be either organic or inorganic. ILs are an environmentally attractive alternative owing to their distinctive characteristics corresponding to insignificant or low vapor pressure, comparable chemical and thermal strengths, and the capability to disperse a broad range of organic and inorganic components. ILs would reduce the affiliated prices and relinquish requisites and hazards related to volatile organic compounds (VOCs). Divergence in cations and anions can produce millions of ILs. Ionic liquids' physical characteristics, such as boiling point, viscosity, and density, are controlled by the cations, but their chemical characteristics and reactivity are managed by the anion. Liu et al. developed a functionalized catalyst [HSO3pmim] HSO4 and reported a yield of 96% under the optimum conditions of a methanol to oil ratio of 12
:
1 and 15 g of waste oil at 120 °C for 8 h with a catalyst weight of 2 g. The catalyst was reusable 5 times.172 Yassin et al. showed a high biodiesel efficiency of 97% with a [BMIM][FeCl4] catalyst from waste vegetable oil in a reaction time of 8 h. The high biodiesel yield was acquired due to the chloride modification with the basic ionic liquid. The ionic liquid could be reusable 8 times.180 Ullah et al. proposed [BMIMHSO4] as an effective acid catalyst in the esterification reaction from waste palm cooking oil (acid value of 4.03 mgKOH g−1) and reported a yield of 95.65% in 1 h reaction time. The high biodiesel yield was obtained owing to the longer side chain of the catalyst with methanol.166 Caldas et al. investigated a ([HMim][HSO4]) catalyst to produce biodiesel from waste cooking oil and the yield was reported to be 97.6% under high temperatures along with supercritical ethanol in the reaction.156 Sun et al. synthesized [Bmim]OH modified with imidazolium cation IL/Mg–Al–La as a catalyst from waste cooking oil (acid value of 4.9 mgKOH g−1). The basicity of the catalyst improved with the addition of an immobilization cation. The 98.7% biodiesel yield was acquired in a reaction time of 6 h at 65 °C. The catalyst was reusable 6 times while maintaining the yield at 85.4%.148 Table 2 summarizes the efficiency of biodiesel produced from WCO using a variety of heterogeneous catalysts. The most frequently used WCO with heterogeneous catalysts include palm, sunflower, soybean, cottonseed, date seed, chicken fat, canola, fish oil, beef tallow animal fat, etc. WCO has shown high biodiesel efficiency with the used variety of catalysts. Sunflower and palm oil have contributed to the major source of WCO as it is globally used as edible oil for food consumption. As shown in Table 2, waste chicken bone derived CaO catalysts with WCO reported a biodiesel yield of 96.31 ± 0.72%. This biodiesel yield was achieved with a molar ratio of 3
:
1, which was reported as the minimum molar ratio used among all types of catalysts used with WCO.215 Hazelnut shell ash as a base catalyst used with used sunflower oil showed the maximum biodiesel efficiency of 98% in 10 min, which resulted an maximum efficiency within this shortest reaction time.158 Cong et al. showed an alkalized SBC ash catalyst with waste soybean seed oil with 99.1% efficiency. The results reported that efficiency was more than 85% after 8 cycles with the SBC ash catalyst. This catalyst reported the highest recyclability among the various catalysts reviewed so far.242 Another catalyst, (RS-SO3H) used with WCO, depicted better reusability for seven cycles with >91.1% yield.329 According to Table 2, a biodiesel efficiency of 99.9% was obtained with waste sunflower oil using K2O/fumed silica catalysts, which was the maximum reported efficiency reported so far.177 The lowest biodiesel efficiency recorded for a CaO-based catalyst was 72% from beef tallow, which is considered as the lowest efficiency.245 All three catalysts, namely, CuO/ZnO, zinc-modified anthill, K+ trapped clay nanotubes, fused crab shell and plantain peels (Table 2), showed recyclability till the sixth cycle with >70%. Different catalysts viz. waste chicken eggshell derived CaO,131 Z/GP,134 BaSnO3,330 and (TiO2/PrSO3H)331 catalysts reported a similar efficiency of 98% produced from WCO.
4. Parametric study
Several variables, including temperature, reaction duration, type of alcohol and quantity, FFA and moisture quantity of oil, and type of catalyst and quantity, impact the transesterification reaction. Several strategies have been devised to enhance the overall conversion and reaction rate; nonetheless, there is a big difference between the industrial practices of today and the optimum parametric process conditions. The factors affecting the trans/esterification reaction are shown in Fig. S6.†
4.1 Influence of reaction temperature
The influence of reaction temperature is very pronounced on the transesterification reaction. The biodiesel efficiency enhances with the enhancement in temperature as it would reduce the viscosity of the oil. The temperature and reaction rate are directly related; greater temperatures increase the reaction rate, but only to a certain extent, as high reaction temperature will require maximum power and will affect the operating cost.332 Biodiesel efficacy decreased when the temperature inflated past the highest result as it would enhance the soap formation of TGs. The ideal reaction temperature is observed to be close to the boiling point of the alcohol used.333 The diffusion defiance of the catalyst and feedstock including the alcohol combination has to be overcome by increasing the number of reactant–reactant contacts that are possible via supplying thermal energy or increasing the frequency of collisions between the reactants and the catalyst, or by increasing the temperature.37 Hence, an optimum range of temperature is observed to be followed, irrespective of the feedstock properties and the kind of catalyst used, usually between 50 °C and 70 °C. Guo et al. in their study reported that the yield gradually increased as the temperature varied from 35 °C to 65 °C, with the maximum yield reached at 93.5%. Above 65 °C, while the temperature was increased to 75 °C, the yield decreased as shown in Fig. S7(b).†130 The endothermic nature of transesterification makes it possible to accelerate the conversion by increasing the temperature, as reported by Aghel et al. and it was seen to drop slightly above 65 °C. They achieved 84.76% FAME conversion at 54.72 °C.129
4.2 Influence of calcination temperature
A major part of the catalyst synthesis depends on the calcination temperature for both acidic and basic heterogeneous catalysts. The primary catalytic properties, including the surface area, crystalline form, the volume of pores, basic and acidic site densities, and molecular composition, are significantly influenced by the calcination temperature. By removing the loosely attached carbon dioxide and water atoms from the catalyst surface, a maximum calcination temperature improves the active phases of catalysts. However, an increase in calcination temperature unnecessarily results in a lower FAME yield, signifying low catalytic activity. This could take place in the pores by gaseous dispersion during the thermal treatment, which ultimately results in a restriction of pores or partial removal of the joined molecules of moisture from the catalyst surface, which harms the catalyst's effectiveness and produces new species. According to Yusuff et al. calcining a barium-loaded zeolite catalyst enhanced the biodiesel output from waste frying oil. While the calcination temperature was raised from 600 °C to 700 °C, the yield was shown to improve from 76.55% to 88.21%, but when it was raised to 800 °C, the yield declined considerably, dropping below 60%, presumably because the catalyst structure disintegrated.334 Afsharizadeh et al. found that calcining a rare-earth metal oxides (REOx)–zirconia (ZrO2) nanocatalyst at temperatures ranging from 500 °C to 800 °C for 5 h led to a great difference in their activities. The conversion in the transesterification reaction was seen to increase from 71% to 89% when the calcination temperature was increased from 500 °C to 700 °C. Once the temperature was raised above 700 °C to 800 °C, there was no further increase in the reaction yield as shown in Fig. S7(a),† and hence 700 °C was the maximum calcination temperature for the synthesis of the catalyst.160
4.3 Influence of catalyst loading
Catalyst loading significantly affects biodiesel yield. The activation energy of the reaction is decreased by the catalyst, which speeds up the reaction process. By the percentage weight of oil, the dose of the catalyst is typically adjusted between different ranges, and the resultant efficiency is evaluated. Improving the catalyst amount beyond a certain optimum point leads to excess formation of soap and greater costs in product purification. In contrast, decreasing the catalyst amount indiscriminately leads to incomplete reactions and a lower yield of biodiesel.337 The amount of catalyst loading needed also depends on the surface area of the catalysts. Nanocatalysts with a very high surface area to volume ratio require a moderately low amount of catalyst loading owing to the presence of more active sites with lower amounts of catalyst as compared to greater-sized catalysts.10 The biodiesel yield reached 80% in a study by Erchamo et al. on increasing the eggshell-derived CaO nano-catalyst weight from 1 wt% to 2.5 wt%, but it was shown to decline when the catalyst loading was further increased to 4 wt%. By increasing the catalyst amount, the active surface area catalyzing the reaction was increased and it was ensured that there was enough catalyst present to fully convert the oils to methyl ester. On increasing the concentration to 4 wt%, the yield was reduced because the product became stickier and inhibited mass transfer in the reaction phase.298 Roy et al. also studied increase in the yield of biodiesel by increasing the concentration of de-oiled microalgal biomass from 1 wt% to 3 wt% which gave a maximum yield of 86.03% for WCO, but further increasing the concentration up to 6 wt% resulted in a lower yield of around 70% as presented in Fig. S7(c).†267
4.4 Influence of reaction time
Reaction time has a great impact on the yield of the final product. Given that it greatly affects the size, type, and refinery to be utilized for production, reaction time is a critical issue in optimizing the commercial production of biodiesel. Given that transesterification is a reversible reaction, enough reaction time is required for the reaction to obtain equilibrium. However, if the reaction time is increased beyond equilibrium, the backward reaction takes place and reduces the yield of biodiesel. The reaction time is moderately improved from low to high and the efficiency is measured. Process intensification techniques and usage of highly active heterogeneous catalysts may lead to the completion of the reaction in durations as short as 1 minute,338 whereas other catalysts might require as long as 12 h reaction time, as observed while using bagasse-derived catalysts.270 Odetoye et al. announced that the yield varied with the reaction time, with the maximum yield of 90.2% at an optimum reaction time of 3.42 h, which was seen to increase from 48.4% at 0.59 h and 46.9% at 1 h respectively.339 Al-Sakkari et al. showed an enhancement in conversion with an enhancement in the reaction time but also showed that increasing the time when sonication at high power is used may affect the conversion adversely. The optimum conversion was found to be 97%.150 Deeba et al. revealed the impact of reaction time on the biodiesel efficiency, which was seen to increase from 56% to 94.8% when the time was increased from 2 h to 8 h as shown in Fig. S7(d).† When the reaction time was enhanced beyond 8 h, the yield reduced significantly. The maximum time was obtained to be 6 h.181 Similarly, on varying the reaction time from 40 min to 80 min, Cholapandian et al. found that a maximum conversion was acquired at the reaction time of 60 min, which was 94%.151
4.5 Influence of the alcohol to oil molar ratio
The catalytic efficacy of a particular catalyst is greatly influenced by the methanol-to-oil ratio. Transesterification is a reversible reaction, so higher concentrations of the reactant drive the forward reaction and lead to the greater formation of the products. The alcohol to oil should be 3
:
1 as dictated by the transesterification chemical reaction stoichiometry. A large weight of methanol is required to ensure that the reaction occurs in a forward direction. A commonly used ratio is 6
:
1, which ensures that 100% excess alcohol is used. This ratio is often driven up to 30
:
1 as reported by Molaei Dehkordi & Ghasemi using Ca and Zr mixed oxides,340 or even 70
:
1 for heteropoly acid catalysts.341 The kind of catalyst and feedstock used does affect the amount of alcohol required. It is observed that homogeneous base catalysts require much less alcohol generally, than homogeneous acid catalysts which catalyze higher FFA feedstock. However, a too high molar ratio can lower the efficiency of biodiesel by generating a large quantity of glycerol. Nonetheless, the insufficiency of the molar ratio also affects the production of the endmost product by modifying the catalyst, resulting in the generation of waste. Rezania et al. reported transesterification of waste frying oil with magnetic graphene oxide (GO) combined with a ternary mixed metal oxide (MMO), where the methanol
:
oil molar ratio was varied from 1
:
1, 3
:
1, 5
:
1, 8
:
1, and 10
:
1, and it was seen that the efficiency of the process improved till reaching equilibrium at ratios 8
:
1 and 10
:
1, giving a yield of 94%.312 Naeem et al. observed that increasing the oil
:
alcohol molar ratio from 1
:
15 to 1
:
25 led to an improvement in the yield from 85% to 98%. However, once it was increased beyond 1
:
25 to 1
:
35, the yield dropped. This decrease was attributed to the reconversion of the product to triglyceride.342 Abukhadra et al. reported that increasing the methanol ratio to 10
:
1, 15
:
1, and 20
:
1 led to an improvement in yield initially from 81.6% to 95.2% and then a decrease to 88.12%, clearly indicating that the optimum ratio was 15
:
1 as shown in Fig. S7(e).†335
4.6 Effect of stirring speed
The yield of biodiesel is significantly impacted by stirring speed. The production of methyl ester can be improved by making sure that the oil and catalyst are properly in contact and mixed. By increasing the amount of catalyst and solvent collision, agitation quickens the reaction. While the mixing speed was changed from 200 to 800 rpm, Ullah et al. found a biodiesel output from used cooking oil. According to reports, 700 rpm stirring speed led to a maximum biodiesel production of 78.10%, and an increase to 800 rpm saw a modest improvement to 76.20%. Therefore, 700 rpm was chosen as the ideal mixing speed.166 Fereidooni et al. checked the influence of stirring speed in the range of 100 rpm to 700 rpm. The yield increased from 88.5% to 96.5% till 400 rpm, and beyond 500 rpm, super cavitation led to the breakage of cavities with reduced intensities, decreasing the yield thereby.146 Basyouny et al. reported the effect of stirring speed by varying the speed from 250 rpm to 1250 rpm. The yield was reported to enhance from 83.5% to 97.6% when the speed was raised from 250 rpm to 1250 rpm as shown in Fig. S7(f).†343 Fadhil et al. varied the stirring speed from 300 rpm to 900 rpm and reported that phase change occurred at multiple stirring speeds. At 300 rpm, very little phase change was noticed, and the yield was the lowest at 85.44% w/v. On increasing the stirring speed, the phase change formation increased and so did the yield, attaining a maximum of 95.20% at 600 rpm. At stirring speeds higher than this, the yield dropped due to the hydrolysis of the product, forming soap.344
5. Physicochemical properties of WCO and biodiesel
Generally most of the waste oils come from different types of edible sources after repeated use. Due to the frying process, the physicochemical characteristics of WCO are distinct from those of its parent vegetable oils. The hydrolysis and oxidation reactions (discussed earlier) that occur throughout the frying procedure are what cause the change in physicochemical qualities (Table S1†). In comparison to raw oil, these reactions enhance the FFA and moisture percentage in WCO, which ultimately results in soap formation during the manufacture of biodiesel.345 As oligomeric substances develop during frying, the volatile content of the oil drops, and its molar mass rises. Oleic acid (45.15%) and linoleic acid (39.74%) make up the bulk of WCO as shown in Fig. 11. The physicochemical properties of biodiesel alter as a result of variations in the FFA profile. The performance of biodiesel in CI engines is affected by changes in its physicochemical qualities. Engine components may corrode if WCO biodiesel has a high-water content. Engine wear is also a result of high FFA content in WCO. These elements drive pre-treating WCO before the trans-esterification reaction.346
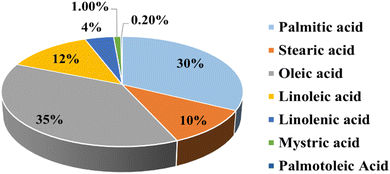 |
| Fig. 11 Percentage share of different free fatty acids present in waste cooking oil. | |
The discrete characteristics of WCO-derived biodiesel are briefly described in (Table 3) to check if the properties of the fuel altered depending on the type of WCO utilized as feedstock. The lower calorific value for WCO biodiesel ranges between 34 MJ kg−1 and 42 MJ kg−1. A maximum value of 50.245 MJ kg−1 is outlined for biodiesel produced from sunflower oil.185 According to the results obtained by Basyouny et al., it was seen that the source of waste cooking oil made a difference in the qualities of the biodiesel obtained even with the same catalyst and similar reaction parameters. It was seen that biodiesel acquired from waste corn oil gave biodiesel with a lower density, viscosity, flash point, cloud point, moisture content, and higher pour point and cetane number than biodiesel produced under relatively similar conditions from waste palm oil.343 The crucial fuel temperature ranges for CI engines are the pour point, flash point, and cloud point. This temperature range should be low to run the engine in cold weather. The WCO biodiesel should have a high flash point from the perspective of fuel storage. The fluctuation in WCO-derived biodiesel blend ratios in diesel fuel affects all these temperatures. The highest cloud and pour points are given at 23 and 13.1 °C, respectively,206,351 whereas the minimum flash points value reported is 49 °C.357 The lower values of cloud and pour point show promising flow properties, and it can be summarized that waste corn oil showed better properties than waste palm oil in transesterification. The fuel's ignition quality is determined by its cetane number (CN). A low CN fuel shortens the ignition delay time. The range of CN between 47–62 is the most adopted. The high cetane number makes it suitable for direct use in an engine. WCO biodiesel has a CN that ranges from 47.7 to 59.8. This variance occurs since biodiesel is made from waste oil originating from numerous vegetable oils including corn, canola, soybean, sunflower, rapeseed, cottonseed, animal, chicken fat, etc. Highly viscous fuels have excessive pump resistance, filter damage, poor combustion, enhanced exhaust smoke and emissions, and poor fuel atomization. Abukhadra et al. reported that the type of catalyst also influences the properties of the biodiesel produced from the same waste oil by transesterification. They used commercial waste cooking oil and alkali-modified clinoptilolite as a catalyst. Four types of catalysts were prepared and studied, namely K/clino, Na/clino, Ca/clino, and Mg/clino, respectively. It was outlined that the viscosity of the biodiesel samples produced by the four catalysts was all under the permissible limits by ASTM standards, but the waste oil catalyzed by Mg/clino gave the lowest viscosity. Similarly, the lowest moisture content, cloud point, and pour point were also recorded in the biodiesel sample produced by the Mg/clino catalyst. It gave the highest flash point of the four samples, indicating the safety related to transportation and storage. The highest density was reported in the biodiesel catalyzed by the Ca/clino catalyst. This means that, for the same engine, biodiesel with a higher density will move from the injection pump to the injector in a shorter amount of time. As a result, the higher density makes up for the reduced calorific or heating value. The lowest acid value was recorded for the sample catalyzed by K/clino, indicating the highest oxidative stability.169 Most of the WCO biodiesel reported density within ASTM standards with a few exceptions. As a result, it cannot be said with certainty that any single feedstock of WCO produced better biodiesel than the others. However, it can be concluded that there are a few designated properties of the feedstock oil that may indicate its feasibility to be used for the production of biodiesel. The acid number (AN) of WCO is reported to be high due to repeated frying. For instance, in a study outlined by Naeem et al. a mixture of waste sunflower and soybean oils with an acid value as high as 25 mg KOH per g oil was used. The feedstock was catalyzed by KOH/corncob-derived activated carbon through transesterification, the biodiesel formed was tested, and it was found that it had a remarkably high viscosity, 6 mm2 g−1 at 40 °C, which just barely falls within the ASTM standards. In contrast, waste oil feedstock with acid values <2.5 mgKOH g−1 produced biodiesel with a viscosity of 5 mm2 g−1 at 40 °C.133
Table 3 Characteristics of biodiesel generated from different sources of WCO in the presence of catalysts
Feedstock |
Viscosity (mm2 s−1) |
Density (g cm−3) |
Acid value (mgKOH g−1) |
Flash point (°C) |
Calorific value (MJ kg−1) |
Moisture content (wt%) |
Cloud point (°C) |
Pour point (pp) |
Cetane number |
Kinematic viscosity (mm2 s−1) |
Reference |
Waste cooking oil |
— |
0.880 |
0.1 |
160.5 |
— |
0.01 |
11 |
−3 |
51 |
3.3 |
358 |
Waste cooking oil |
6 |
0.880 |
0.8 |
140 |
41.30 |
— |
−1 |
−3 |
56.67 |
— |
359 |
Waste cooking oil |
3.43 |
0.873 |
0.27 |
122.8 |
45.2 |
0.041 |
3.4 |
5.2 |
53.3 |
— |
134 |
Waste cooking oil |
3.84 |
0.87 |
0.47 |
126.4 |
40.5 |
0.037 |
6.2 |
7.3 |
53.4 |
— |
135 |
Waste corn |
3.12 |
0.84 |
— |
146.7 |
— |
0.037 |
6.4 |
6.5 |
54.8 |
— |
343 |
Waste palm oil |
3.62 |
0.88 |
— |
170.3 |
— |
0.042 |
7.12 |
5.8 |
50.9 |
— |
Waste sunflower oil |
3.8 |
0.86 |
0.23 |
134.7 |
— |
0.036 |
5.7 |
4.8 |
62.4 |
— |
138 |
Waste cooking oil |
— |
0.83 |
0.39 |
133 |
— |
0.02 |
−1.57 |
— |
49.34 |
3.92 |
360 |
Waste cooking oil |
— |
0.89 |
0.5 |
140 |
41.34 |
|
2 |
6 |
49 |
4.3 |
330 |
Waste sunflower oil |
3.64 |
0.881 |
— |
161.2 |
49.65 |
0.038 |
3 |
0 |
60.4 |
— |
168 |
Waste cooking oil |
— |
0.8184 |
— |
117 |
50.245 |
— |
−12 |
0 |
— |
5.15 |
185 |
Waste cooking oil |
3.87 |
0.861 |
— |
128 |
— |
0.031 |
6.4 |
5.23 |
53.34 |
— |
188 |
Waste sunflower oil |
4.13 |
0.874 |
— |
143.6 |
— |
0.028 |
9.4 |
7.2 |
58.6 |
— |
179 |
Waste cooking oil |
— |
0.890 |
<0.1 |
144 |
42.61 |
— |
9 |
−5 |
— |
5.51 |
144 |
Waste frying oil |
— |
0.865 |
0.48 |
169 |
35.305 |
— |
1 |
−4 |
— |
5.4 |
361 |
Waste cooking oil |
4.5 |
0.864 |
0.36 |
156 |
— |
0.02 |
— |
— |
64.8 |
— |
130 |
Waste cooking oil |
— |
0.865 |
— |
170 |
9452 cal g−1 |
— |
−1 |
−5 |
— |
3.5 |
151 |
Quaternary blend of waste used oil |
— |
0.872 |
0.36 |
130 |
— |
0.001 |
−2 |
−12 |
64.38 |
1.82 |
362 |
Waste cooking oil |
5.83 |
0.876 |
0.6 |
171 |
37.2 |
— |
10.5 |
1 |
51.4 |
— |
214 |
Waste cooking oil |
4.45 |
0.861 |
0.38 |
154 |
40.6 |
0.002 |
— |
— |
61.5 |
— |
218 |
Waste animal tallow |
— |
0.9 |
0.9 |
190 |
8900 kcal kg−1 |
— |
−12 |
−8 |
35 |
22 |
219 |
Waste oil from date pits |
3.98 |
0.892 |
0.26 |
145 |
44.19 |
— |
3.6 |
−2.1 |
59.31 |
— |
221 |
Waste sunflower oil |
— |
— |
0.75–1.09 |
150 |
39.45 |
0.034 |
— |
— |
— |
5.63 |
222 |
Waste cooking oil |
4.3 |
0.886 |
0.32 |
153 |
25.7 |
0.012 |
10.24 |
7.2 |
57.4 |
— |
223 |
Waste cooking oil |
3.12 |
0.876 |
— |
133 |
38.431 |
0.022 |
3 |
3 |
51.4 |
— |
363 |
Waste cottonseed oil |
— |
0.8739 |
— |
142 |
— |
— |
— |
−9 |
52.9 |
4.95 |
234 |
Waste Phoenix dactylifera L. kernel |
4.24 |
0.881 |
0.32 |
141 |
43.24 |
— |
3.9 |
−1.4 |
60.31 |
— |
241 |
Mixture of waste cooking oil, Jatropha curcas oil, and palm oil |
— |
0.8779 |
0.05 |
185.6 |
39.98 |
— |
11.2 |
5.4 |
59.93 |
4.586 |
364 |
Beef tallow animal fat |
— |
0.928 |
0.836 |
154 |
— |
— |
11 |
5 |
56 |
5.4 |
245 |
Waste cooking oil |
— |
0.876 |
0.21 |
185 |
39.17 |
0.02 |
— |
— |
55 |
5.15 |
159 |
Waste cooking oil |
— |
0.889 |
0.41 |
152 |
43.24 |
— |
2.6 |
−2.1 |
64.23 |
6.63 |
250 |
Waste cooking oil |
5.83 |
0.874 |
0.6 |
— |
37.2 |
— |
10.5 |
1 |
51.48 |
— |
365 |
Waste cottonseed oil |
— |
0.880 |
0.3 |
— |
36.3 |
— |
−15 |
−8 |
— |
3.76 |
114 |
Composite of Pongamia pinnata, animal fat and waste cooking oil |
— |
0.851 |
0.13 |
211 |
42.50 |
— |
6 |
4 |
— |
5.25 |
354 |
Waste sunflower oil |
4.95 |
0.887 |
— |
163 |
— |
0.041 |
−3 |
−8 |
56 |
— |
366 |
Waste edible oil |
— |
0.872 |
0.25 |
— |
— |
— |
1 |
−5 |
57.64 |
4.1 |
213 |
Waste soybean and sunflower oil |
3.8 |
0.880 |
0.1 |
120 |
— |
100 mg kg−1 |
−5 |
−2 |
54 |
— |
367 |
Waste cooking oil |
5.5 |
0.91 |
— |
180 |
— |
— |
−3 |
−6 |
— |
— |
274 |
Waste cooking oil |
— |
0.87 |
0.06 |
150 |
40.3 |
— |
−6 |
−10 |
57 |
3.1 |
275 |
Waste cooking oil |
— |
0.867 |
— |
158 |
— |
— |
4 |
— |
— |
4.85 |
276 |
Waste cooking oil |
— |
0.874 |
0.25 |
238 |
— |
0.025 |
— |
— |
— |
4.33 |
277 |
Waste cooking oil |
— |
0.89 |
0.08 |
145 |
40.2 |
— |
−4 |
−9 |
55 |
3.12 |
368 |
Waste cooking oil |
4.4 |
0.908 |
0.44 |
139 |
— |
456 ppm |
— |
— |
52.2 |
— |
280 |
Castor seed oil and waste fish oil blend |
— |
0.8989 ± 0.0001 |
0.06 ± 0.002 |
84 ± 1.0 |
40.88 |
— |
5.0 ± 0.50 |
−2.0 ± 0.50 |
56.97 |
3.61 ± 0.03 |
344 |
6. Life cycle analysis of WCO-derived biodiesel production
For determining how produced biodiesel will affect the environment, life cycle analysis (LCA) is essential. Resource extraction is the primary step in the LCA technique, which concludes with the production of the final product and wastewater discharge. Throughout its entire life cycle, LCA assesses and evaluates system energy intake and results in the environmental sphere. The different stages that make up the life cycle evaluation procedure are shown in Fig. 12. Goal and scope analysis is done in the beginning, and inventory and impact analyses are done in the second and third stages. The final stage involves explaining the results. An LCA analysis of the production of biodiesel using single feedstock i.e., WCO and various catalysts has been carried out. Diverse objectives have been pursued, according to an analysis of the many LCA studies done to evaluate the impact of WCO-derived biodiesel on the environment. Throughout the life cycle of WCO biodiesel, this research has mostly concentrated on quantifying environmental loads and identifying the major environmental hotspots. These goals include quantifying and differentiating the environmental influence of biodiesel produced from WCO as well as other used feedstock, the harmful effects of WCO biodiesel including multiple additives, combustion related to biodiesel, and the consumption of resources associated with these activities.369–371 In consonance with the study's objectives, an LCA investigation can often be conducted in one of two ways: attributional LCA or consequential LCA. An attributional LCA, in short, calculates and provides information about the environmental effects of creating a product over the course of its life cycle. In contrast, data from consequential LCA show how environmental impacts alter because of a decision.
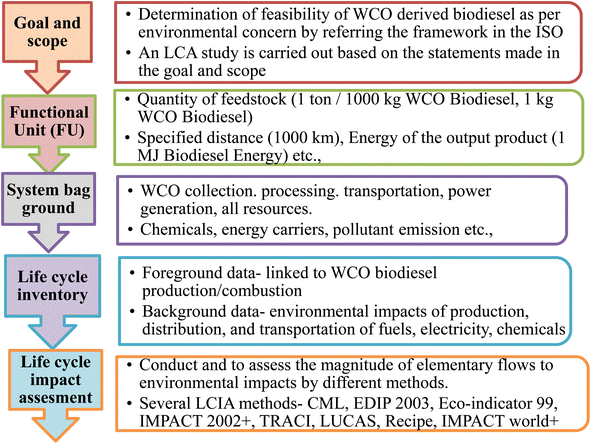 |
| Fig. 12 Schematic of different stages of life cycle assessment in WCO biodiesel production. | |
6.1 Functional unit and system background
An LCA study's functional unit (FU) is selected by its objectives and parameters, and it serves as a standard against which the inputs and results of the process under investigation are adjusted and represented. Different researchers have considered various masses of WCO feedstock such as 1000 kg,372,373 and 1 kg of WCO biodiesel369,370 as FU. This explanation of FU deliberates the mass/volume of WCO as the major attribute. Depending on the objectives and parameters stated, several FUs, including quantity, transportation distances, and energy-related FUs, could be taken into consideration for the assessment of WCO biodiesel on the environment.
The system background determines the infinitesimal components, or unit operations, that are evaluated for input and output checklist data and that are incorporated in the LCI analysis. To determine all significant inputs and outputs of UCO to the biodiesel production chain, Elin Verd SA was contacted for this task. Since they are inside the system boundary, these inputs and outputs are considered in the analysis. System boundaries in the manufacturing of WCO biodiesel are typically restricted to electricity generation, collection, processing, and transportation of WCO to production centers.374 Hence, different kinds of resources viz. chemicals, substances, energy conveyors, transportation of various materials, emissions of pollutants into the atmosphere including land and water bodies concerning each stage, and release of depleted gases concerning biodiesel ignition are incorporated in the analysis, i.e., they are inside the system boundary as shown in Fig. 13.372
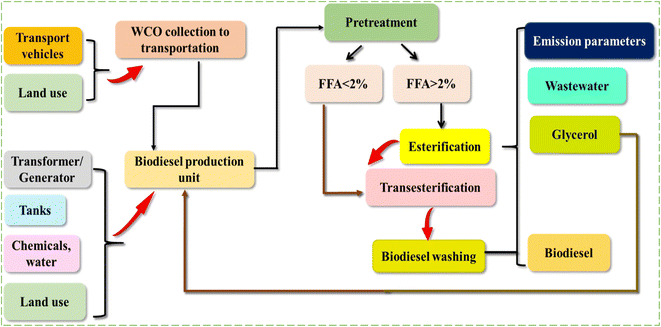 |
| Fig. 13 The system boundary of a second-generation biodiesel production system. Reprinted with permission from ref. 375. Copyright (2020) Elsevier. *FFA – free fatty acid. | |
6.2 Life cycle inventory and life cycle impact analysis
The utmost challenging, expensive, and lengthy LCA study phase is life cycle inventory (LCI). The input and results relating to the specified process are quantified and accumulated in this step. The ISO defines LCI as including the quantities of necessary energy and substance as input variables and the quantities of products, derivative products, discharge into the environment, and the quantities of wastes produced as outcomes throughout the processes taken into consideration. The background data include information on the environmental effects of the manufacture, dispensation, and transportation of biofuels, power, chemicals, and other additional materials that promptly interrelate with the foreground system of WCO derived biodiesel.376 Nonetheless, the production of biodiesel/combustion is precisely associated with foreground data. For existing and in-progress technologies utilized in WCO biodiesel production, the insufficient amount of the variable, especially that correlated to the treatment of solid waste and wastewater, innovative catalysts synthesis, etc., is also thought to be quite troublesome. This problem causes uncertainty and could reduce the reliability of the findings for making decisions, especially in relative studies. The foreground data are either simulated based on multiple sources or taken from case studies (lab or industrial size). One of the most significant methods for addressing the uncertainty problem is Monte Carlo analysis. This method has also been used to enhance the LCA of WCO biodiesel production decision-making. For instance, the different types of variation in WCO production of biodiesel are caused by the absence of accurate data indicating parameters viz. fuel consumption, power, synthesis of novel catalysts, alcohol, and the separation of catalysts through a filter.377
Biodiesel and glycerol are produced through the transesterification of WCO and alcohol aided by a catalyst. Glycerol is a useful by-product with over 2000 uses, including in meals, pharmaceuticals, cosmetics, and personal care products. Many studies have designated the environmental impact related to biodiesel and the co-product in terms of energy content369 or exergy content378 by the EU Directive. Cherubini et al. stated that the considerable cause of variability in LCA results is the allocation method used. For instance, the mass, energy, and exertion content of biodiesel and glycerol are not equal, yielding various outcomes. Moreover, the inability to compare the results of different studies is severely hindered by the absence of constancy in issuance.379 As a result, sensitivity analysis should be done in future research on biodiesel production while taking various allocation techniques into account.
According to the ISO standard, life cycle impact assessment (LCIA) is the third stage of an LCA analysis which comes before the interpretation of results step. To achieve a difficulty-oriented perspective, impacts are divided into 18 environmental categories (impact categories) at the midway level. Environmental impacts are translated into issues of problems such as human health, biosphere, and maneuver availability, via the endpoint or damage-oriented approach. Several LCIA techniques, including EDIP 2003, IMPACT 2002+, Eco-indicator 99, IMPACT world+, LUCAS, LIME, CML, TRACI, Recipe, etc., have been evolved and polished.376 Subsequently, it should be remembered that various techniques cover various numbers of chemicals. For instance, ReCiPe covers 3000 chemicals while IMPACT 2002+ only covers 1500. As a result, adopting various techniques in the LCIA of biodiesel production from WCO could result in differing degrees of environmental impact, restricting comparability. Additionally, different midpoint and endpoint categories as well as varied emission factors are used to run distinct procedures, producing various results.
6.3 Future scope and outlook
Population growth around the world, increasing urbanization, industrialization, and economic evolution drive the utilization of fossil fuels to fulfill rising energy demands. The pragmatic approach of replacing conventional fuel with biodiesel would decrease the amount of carbon emissions through fuel combustion. Despite multiple advantages and substantial developments in biodiesel production, the biodiesel industry is persistent with various obstacles. Inadequate biofuel policies, particularly in developing nations, insufficient investment in traditional and edible feedstock, inadequate energy generation, and ineffectual operating processes impeded its widespread commercial utilization. The hindrance concerning the availability of feedstock could be eliminated by utilizing new cost-effective feedstock, WCO. Around 500
000 tons of WCO are discarded into the environment each year in an improper manner worldwide, creating environmental concerns. The implementation of WCO in biodiesel production would be a sustainable cost-effective environmentally friendly practice. WCO-derived biodiesel production is feasible currently on a small scale due to logistical difficulties such as a lack of collection centres, improper infrastructure, inadequate supply chain, and the low recovery rate of the product. Studies on policies to boost biodiesel production at a pilot and commercial level using WCO are essential. Flexible techniques, simpler sample preparation methods, and accurate mass analyzers are required for the proper characterization of WCO due to the variety of available oil matrices and their heterogenicity and complicated structure of degraded components. Changes in the physical and chemical properties of the feedstock affect the selection of the catalyst, the transesterification reaction, biodiesel yield, quality of the product, and catalyst reusability. A pre-treatment of WCO before the transesterification to produce biodiesel would improve the final product yields. Tabatabei et al. have shown a conventional inert membrane reactor which was used to synthesize biodiesel by transesterifying oils. This arrangement typically consists of a feedstock/catalyst mixing chamber (for homogeneous catalysts) or a packed or fluidized bed of catalysts (for heterogeneous catalysts). It has been outlined that a high molar ratio enhanced the product efficiency.380 Li et al. produced biodiesel through transesterification of soybean oil using a packed-bed reactor. Here the boundary layer of the reactor was decreased across the heterogeneous catalyst, which ensures decrease in the resistance of mass transfer and improves the efficiency.381
• Here, an integrated reactor design has been proposed for the catalytic transesterification process for biodiesel production. As shown in Fig. 14, the setup consists of two separate tanks, the first of which is filled with alcohol and feedstock, and in the second reactor the catalyst is added.
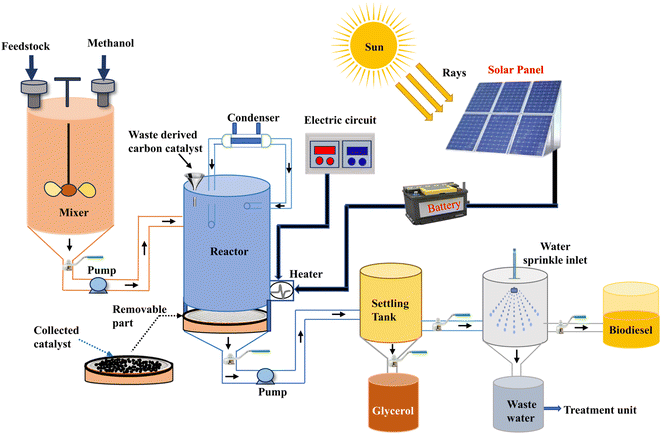 |
| Fig. 14 Proposed reactor design for biodiesel production employing heterogeneous catalytic transesterification. | |
• The reactor is supported with a reflux condenser to keep the alcohol inside the reactor to avoid the overconsumption of alcohol throughout the conversion. The produced glycerol remains in the settling tank and can later be separated from the remaining oil by ultracentrifugation.
• The suggested design is unique in that it produces biodiesel using waste-derived heterogeneous catalysts, and the reactor is constructed in such a way that the same catalyst can be recycled through the movable component and reused for the following batch of cycles.
• The total expense of the catalyst will be computed after taking into account the many sequential steps involved. It is one of the most important factors to consider in order to make the total process cost-effective for commercial deployment in large-scale applications.
7. Conclusion
Population growth around the world, increasing urbanization, industrialization, and economic evolution drive up the utilization of fossil fuels to keep up with rising energy demand. Identifying an acceptable and sustainable replacement for fossil fuels will become necessary due to ongoing emissions from fossil fuel combustion. Because of the environmental consequences of petroleum-based diesel, biodiesel has grown in popularity as a substitute fuel for diesel engines. Numerous investigations have revealed that the qualities of biodiesel are identical to those of conventional diesel fuel, making it an appropriate alternative energy source. Different feedstock and extraction techniques were initially examined to comprehend the initial stage of biodiesel manufacturing. The main barriers to this biofuel's market entry are its high cost and scarcity of feedstock such as fats and oils. WCO as second-generation and inedible feedstock is superior in contrast with other reported first and second-generation feedstock owing to its simple availability, economic viability, and less polluting nature. The gathering of various categories of leftover cooking oils reduces the price of biodiesel while minimizing the negative environmental impact of waste oil disposal. However, throughout the frying, the oil goes through various processes that result in the emergence of unwanted substances viz. polymers and FFA. This presents various difficulties in the transesterification of spent waste oil, necessitating an auxiliary pre-treatment stage to eliminate these contaminants. Despite the higher expenses of treatment, studies have demonstrated a decrease of up to 45% in direct manufacturing costs. This paper highlights an extensive assessment of the production of biodiesel from WCO and its application to internal combustion engines. In this paper, the FFA content, preliminary-treatment procedure, catalytic and non-catalytic biodiesel manufacturing methods, and their benefits and drawbacks are covered. A thorough overview of the diverse catalysts used in the production of biodiesel, including an analysis of the emissions from biodiesel synthesis was provided in this paper. The processes, which takes place inside a reactor, as well as process variables including reaction duration, temperature, feedstock, and catalyst concentration, were also covered in this review. Additionally, the aspects of process scalability for the synthesis of biodiesel from diverse WCOs are examined. A heterogeneous catalyst has suppressed most of the limitations of a homogeneous catalyst, and still, the high cost of the catalyst and its complicated synthetic route make it difficult to commercialize. Waste-acquired biomass is made up of industrial and biological waste and is composed of various components viz. calcium, magnesium, and potassium that can accelerate the catalytic biodiesel production. Waste-acquired catalysts are currently being studied as a promising replacement for conventional chemical catalysts because of their affordable price, permeability, large surface area, environmental friendliness, and special characteristics. It is important to use a few cutting-edge techniques that lead to successful biodiesel production for commercial and effective biodiesel manufacturing. Due to biodiesel's higher viscosity than diesel fuel, engines need more fuel specifically for the brakes, and their thermal efficiency is reduced. There has been a noticeable decrease in different emission parameters viz. CO and PM. Nevertheless, the emissions of NOx and CO2 have enhanced because of high oxygen compounds found in biodiesel. A previous study has demonstrated that using emulsion techniques can be used to reduce NOx and PM emissions.
Comprehensively, it can be said that WCO-derived biodiesel offers compression ignition engines a cheaper and cleaner alternative fuel source. So far, several reactors for biodiesel production have been used with various feedstock materials for biodiesel production. However, large-scale development of biodiesel synthesis employing heterogeneous catalytic methods supported by solar energy has not been reported so far. As a result, the recommended incorporated reactor design is an initiative to evaluate the technological viability of productive output from the proposed technique, and commercial scale-up of the process to meet the energy mandate through the introduction of environmentally benign green fuel, which is a current challenge. During the last decade, numerous research articles have been published on producing biodiesel through transesterification with heterogeneous catalysts, and further research is still mandatory to synthesise heterogeneous catalysts from waste biomass to improve catalytic activity by surface modifications. Along with waste feedstock, the application of waste material as a heterogeneous catalyst enhances biodiesel production on a large scale in the future. Moreover, life cycle assessment analysis aids in foreseeing and minimizing the economic and environmental effects of producing biodiesel.
Conflicts of interest
The authors declare that they have no known competing financial interests or personal relationships that could have appeared to influence the work reported in this paper.
Acknowledgements
The authors acknowledge the financial support from the Ministry of Science and Technology, Government of India vide project file: EEQ/2021/000167.
References
- B. Karmakar, A. Hossain, B. Jha, R. Sagar and G. Halder, Factorial optimization of biodiesel synthesis from castor-karanja oil blend with methanol-isopropanol mixture through acid/base doped Delonix regia heterogeneous catalysis, Fuel, 2021, 285, 119197, DOI:10.1016/j.fuel.2020.119197.
- T. Ahmad and D. Zhang, A critical review of comparative global historical energy consumption and future demand: The story told so far, Energy Rep., 2020, 6, 1973–1991, DOI:10.1016/j.egyr.2020.07.020.
- P. Maheshwari, M. B. Haider, M. Yusuf, J. J. Klemeš, A. Bokhari, M. Beg, A. Al-Othman, R. Kumar and A. K. Jaiswal, A review on latest trends in cleaner biodiesel production: Role of feedstock, production methods, and catalysts, J. Cleaner Prod., 2022, 355, 131588, DOI:10.1016/j.jclepro.2022.131588.
- A. Dewangan, A. K. Yadav and A. Mallick, Current scenario of biodiesel development in India: prospects and challenges, Energy Sources, Part A, 2018, 40, 2494–2501, DOI:10.1080/15567036.2018.1502849.
- O. Awogbemi, D. V. Von Kallon and V. S. Aigbodion, Trends in the development and utilization of agricultural wastes as heterogeneous catalyst for biodiesel production, J. Energy Inst., 2021, 98, 244–258, DOI:10.1016/j.joei.2021.06.017.
- I. B. Banković-Ilić, O. S. Stamenković and V. B. Veljković, Biodiesel production from non-edible plant oils, Renewable Sustainable Energy Rev., 2012, 16, 3621–3647, DOI:10.1016/j.rser.2012.03.002.
- M. K. Bharti, S. Chalia, P. Thakur, S. N. Sridhara, A. Thakur and P. B. Sharma, Nanoferrites heterogeneous catalysts for biodiesel production from soybean and canola oil: a review, Environ. Chem. Lett., 2021, 19, 3727–3746, DOI:10.1007/s10311-021-01247-2.
- M. U. H. Suzihaque, H. Alwi, U. Kalthum Ibrahim, S. Abdullah and N. Haron, Biodiesel production from waste cooking oil: A brief review, Mater. Today: Proc., 2022, 63, S490–S495, DOI:10.1016/j.matpr.2022.04.527.
- M. Abdul Hakim Shaah, M. S. Hossain, F. A. Salem Allafi, A. Alsaedi, N. Ismail, M. O. Ab Kadir and M. I. Ahmad, A review on non-edible oil as a potential feedstock for biodiesel: physicochemical properties and production technologies, RSC Adv., 2021, 11, 25018–25037, 10.1039/d1ra04311k.
- D. Singh, D. Sharma, S. L. Soni, C. S. Inda, S. Sharma, P. K. Sharma and A. Jhalani, A comprehensive review of biodiesel production from waste cooking oil and its use as fuel in compression ignition engines: 3rd generation cleaner feedstock, J. Cleaner Prod., 2021, 307, 127299, DOI:10.1016/j.jclepro.2021.127299.
- H. Wang, H. Zhou, Q. Yan, X. Wu and H. Zhang, Superparamagnetic nanospheres with efficient bifunctional acidic sites enable sustainable production of biodiesel from budget non-edible oils, Energy Convers. Manage., 2023, 297, 117758, DOI:10.1016/j.enconman.2023.117758.
- D. Singh, D. Sharma, S. L. Soni, S. Sharma, P. Kumar Sharma and A. Jhalani, A review on feedstocks, production processes, and yield for different generations of biodiesel, Fuel, 2020, 262, 116553, DOI:10.1016/j.fuel.2019.116553.
- A. S. Elgharbawy, W. A. Sadik, O. M. Sadek and M. A. Kasaby, A review on biodiesel feedstocks and production technologies, J. Chil. Chem. Soc., 2021, 65, 5098–5109, DOI:10.4067/S0717-97072021000105098.
- S. Islam, B. Basumatary, S. L. Rokhum, P. K. Mochahari and S. Basumatary, Advancement in utilization of nanomaterials as efficient and recyclable solid catalyst for biodiesel synthesis, Cleaner Chem. Eng., 2022, 3, 100043, DOI:10.1016/j.clce.2022.100043.
- B. R. Naidu and K. Venkateswarlu, Dried water extract of pomegranate peel ash (DWEPA) as novel and biorenewable heterogeneous catalyst for biodiesel production and biopotent quinoxalines synthesis, Bioresour. Technol. Rep., 2022, 18, 101107, DOI:10.1016/j.biteb.2022.101107.
- M. Lopes, S. M. Miranda and I. Belo, Microbial valorization of waste cooking oils for valuable compounds production–a review, Crit. Rev. Environ. Sci. Technol., 2020, 50, 2583–2616, DOI:10.1080/10643389.2019.1704602.
- S. H. Dhawane, B. Karmakar, S. Ghosh and G. Halder, Parametric optimisation of biodiesel synthesis from waste cooking oil via Taguchi approach, J. Environ. Chem. Eng., 2018, 6, 3971–3980, DOI:10.1016/j.jece.2018.05.053.
- M. Dutta and A. Chatterjee, Assessment of the relative influences of long-range transport, fossil fuel and biomass burning from aerosol pollution under restricted anthropogenic emissions: A national scenario in India, Atmos. Environ., 2021, 255, 118423, DOI:10.1016/j.atmosenv.2021.118423.
- M. M. Gogoi, S. S. Babu, K. K. Moorthy, P. K. Bhuyan, B. Pathak, T. Subba, L. Chutia, S. S. Kundu, C. Bharali, A. Borgohain, A. Guha, B. Kumar De, B. Singh and M. Chin, Radiative effects of absorbing aerosols over northeastern India: Observations and model simulations, J. Geophys. Res., 2017, 122, 1132–1157, DOI:10.1002/2016JD025592.
- K. A. Abed, M. S. Gad, A. K. El Morsi, M. M. Sayed and S. A. Elyazeed, Effect of biodiesel fuels on diesel engine emissions, Egypt. J. Pet., 2019, 28, 183–188, DOI:10.1016/j.ejpe.2019.03.001.
- M. S. Gad, R. El-Araby, K. A. Abed, N. N. El-Ibiari, A. K. El Morsi and G. I. El-Diwani, Performance and emissions characteristics of C.I. engine fueled with palm oil/palm oil methyl ester blended with diesel fuel, Egypt. J. Pet., 2018, 27, 215–219, DOI:10.1016/j.ejpe.2017.05.009.
- R. Kukana and O. P. Jakhar, Performance, combustion and emission characteristics of a diesel engine using composite biodiesel from waste cooking oil – Hibiscus Cannabinus oil, J. Cleaner Prod., 2022, 372, 133503, DOI:10.1016/j.jclepro.2022.133503.
- A. Dubey, R. S. Prasad, J. K. Singh and A. Nayyar, Combined effects of biodiesel − ULSD blends and EGR on performance and emissions of diesel engine using Response surface methodology (RSM), Energy Nexus, 2022, 7, 100136, DOI:10.1016/j.nexus.2022.100136.
- S. K. Nayak, A. T. Hoang, B. Nayak and P. C. Mishra, Influence of fish oil and waste cooking oil as post mixed binary biodiesel blends on performance improvement and emission reduction in diesel engine, Fuel, 2021, 289, 119948, DOI:10.1016/j.fuel.2020.119948.
- A. K. Hossain and P. A. Davies, Combustion and emission characteristics of a typical biodiesel engine operated on waste cooking oil derived biodiesel, SAE [Tech. Pap.], 2012, 9, 1624, DOI:10.4271/2012-01-1624.
- M. Dhanarasu, and P. Maadeswaran, Performance, Combustion and Emission Evaluation of Direct Injection Diesel Engine Fueled with ZnO Dispersed Waste Cooking Oil Biodiesel, 2021, pp. 1–32 Search PubMed.
- M. D. Harlapur, S. Bevinahalli and M. B. Sasi, Comparision of Performance and Emission Test Using Biodiesel from Simarouba and Waste Cooking Oil in CI Engine, Int. J. Sci. Res., 2016, 5, 1860–1863, DOI:10.21275/v5i6.nov164627.
- N. H. Said, F. N. Ani and M. F. M. Said, Emission and performance characteristics of waste cooking oil biodiesel blends in a single direct injection diesel engine, Int. J. Technol., 2018, 9, 238–245, DOI:10.14716/ijtech.v9i2.1204.
- A. M. Kumar, M. Kannan and G. Nataraj, A study on performance, emission and combustion characteristics of diesel engine powered by nano-emulsion of waste orange peel oil biodiesel, Renewable Energy, 2020, 146, 1781–1795, DOI:10.1016/j.renene.2019.06.168.
- M. A. Khote and P. A. Deshmukh, Reduction of NOx emission & Performance characteristics of Waste Cooking Oil from diesel engine using Exhaust gas Recirculation, Int. J. Curr. Eng. Technol., 2011, 5, 156–160, DOI:10.14741/ijcet/22774106/spl.5.6.2016.30.
- Y. H. Teoh, H. H. Masjuki, M. A. Kalam, M. A. Amalina and H. G. How, Impact of waste cooking oil biodiesel on performance, exhaust emission and combustion characteristics in a light-duty diesel engine, SAE [Tech. Pap.], 2013, 11, 2679, DOI:10.4271/2013-01-2679.
- H. An, W. M. Yang, A. Maghbouli, J. Li, S. K. Chou and K. J. Chua, Performance, combustion and emission characteristics of biodiesel derived from waste cooking oils, Appl. Energy, 2013, 112, 493–499, DOI:10.1016/j.apenergy.2012.12.044.
- A. Lobo, D. K. Ramesha, T. D. Kumar and L. Bharath, Experimental investigation of performance, emission and combustion characteristics of compression ignition engine using waste cooking oil derived biodiesel with ethanol, AIP Conf. Proc., 2021, 2316, 030023, DOI:10.1063/5.0036525.
- M. E. Ortner, W. Müller, I. Schneider and A. Bockreis, Environmental assessment of three different utilization paths of waste cooking oil from households, Resour., Conserv. Recycl., 2016, 106, 59–67, DOI:10.1016/j.resconrec.2015.11.007.
- N. Ghosh, D. Rhithuparna, S. L. Rokhum and G. Halder, Ethical issues pertaining to sustainable biodiesel synthesis over trans/esterification process, Sustainable Chem. Pharm., 2023, 33, 101123, DOI:10.1016/j.scp.2023.101123.
- H. Hosseinzadeh-Bandbafha, C. Li, X. Chen, W. Peng, M. Aghbashlo, S. S. Lam and M. Tabatabaei, Managing the hazardous waste cooking oil by conversion into bioenergy through the application of waste-derived green catalysts: A review, J. Hazard. Mater., 2022, 424, 127636, DOI:10.1016/j.jhazmat.2021.127636.
- T. A. Degfie, T. T. Mamo and Y. S. Mekonnen, Optimized Biodiesel Production from Waste Cooking Oil (WCO) using Calcium Oxide (CaO) Nano-catalyst, Sci. Rep., 2019, 9, 1–8, DOI:10.1038/s41598-019-55403-4.
- A. Avinash, P. Sasikumar and A. Murugesan, Understanding the interaction among the barriers of biodiesel production from waste cooking oil in India-an interpretive structural modeling approach, Renewable Energy, 2018, 127, 678–684, DOI:10.1016/j.renene.2018.04.079.
- A. Gaur, S. Mishra, S. Chowdhury, P. Baredar and P. Verma, A review on factor affecting biodiesel production from waste cooking oil: An Indian perspective, Mater. Today: Proc., 2020, 46, 5594–5600, DOI:10.1016/j.matpr.2020.09.432.
- FSSAI and RUCO-Repurpose Used Cooking Oil, Nucl. Phys., 2017, 13, 104–116 Search PubMed.
- S. Sharma, V. Saxena, A. Baranwal, P. Chandra and L. M. Pandey, Engineered nanoporous materials mediated heterogeneous catalysts and their implications in biodiesel production, Mater. Sci. Energy Technol., 2018, 1, 11–21, DOI:10.1016/j.mset.2018.05.002.
- B. X. Kumar Ganesan and K. Sukalingam, Impact of consumption and cooking manners of vegetable oils on cardiovascular diseases-A critical review, Trends Food Sci. Technol., 2017, 17, S0924–2244, DOI:10.1016/j.tifs.2017.11.003.
- S. Sirisomboonchai, M. Abuduwayiti, G. Guan, C. Samart, S. Abliz, X. Hao, K. Kusakabe and A. Abudula, Biodiesel production from waste cooking oil using calcined scallop shell as catalyst, Energy Convers. Manage., 2015, 95, 242–247, DOI:10.1016/j.enconman.2015.02.044.
- E. Choe and D. B. Min, Chemistry of deep-fat frying oils, J. Food Sci., 2007, 72, 1750–3841, DOI:10.1111/j.1750-3841.2007.00352.x.
- J. Chung, J. Lee and E. Choe, Oxidative Stability of Soybean and Sesame Oil Mixture during Frying of Flour Dough, J. Food Sci., 2004, 69, 574–578, DOI:10.1111/j.1365-2621.2004.tb13652.x.
- G. Goswami, R. Bora and M. S. Rathore, Oxidation of Cooking Oils Due to Repeated Frying and Human Health, Int. J. Sci. Technol. Manag., 2016, 4, 495–501 Search PubMed.
- D. Dana and I. S. Saguy, Frying of Nutritious Foods: Obstacles and Feasibility, Food Sci. Technol. Res., 2001, 7, 265–279, DOI:10.3136/fstr.7.265.
- I. M. Atadashi, M. K. Aroua, A. R. Abdul Aziz and N. M. N. Sulaiman, The effects of water on biodiesel production and refining technologies: A review, Renewable Sustainable Energy Rev., 2012, 16, 3456–3470, DOI:10.1016/j.rser.2012.03.004.
- I. M. Lokman, U. Rashid, R. Yunus and Y. H. Taufiq-Yap, Carbohydrate-derived solid acid catalysts for biodiesel production from low-cost feedstocks: A review, Catal. Rev.: Sci. Eng., 2014, 56, 187–219, DOI:10.1080/01614940.2014.891842.
- T. T. V. Tran, S. Kaiprommarat, S. Kongparakul, P. Reubroycharoen, G. Guan, M. H. Nguyen and C. Samart, Green biodiesel production from waste cooking oil using an environmentally benign acid catalyst, Waste Manage., 2016, 52, 367–374, DOI:10.1016/j.wasman.2016.03.053.
- N. Ghosh, D. Rhithuparna, R. Khatoon, S. Lalthazuala and G. Halder, Sulphonic-acid functionalized novel Limonia acidissima carbonaceous catalyst for biodiesel synthesis from Millettia pinnata oil : Optimization , kinetics , thermodynamics and cost analysis, J. Cleaner Prod., 2023, 394, 136362, DOI:10.1016/j.jclepro.2023.136362.
- Z. Yaakob, M. Mohammad, M. Alherbawi, Z. Alam and K. Sopian, Overview of the production of biodiesel from Waste cooking oil, Renewable Sustainable Energy Rev., 2013, 18, 184–193, DOI:10.1016/j.rser.2012.10.016.
- I. D. Casallas, E. Carvajal, E. Mahecha, C. Castrillón, H. Gómez, C. López and D. Malagón-Romero, Pre-treatment of waste cooking oils for biodiesel production, Chem. Eng. Trans., 2018, 65, 385–390, DOI:10.3303/CET1865065.
- S. Liu, T. McDonald and Y. Wang, Producing biodiesel from high free fatty acids waste cooking oil assisted by radio frequency heating, Fuel, 2010, 89, 2735–2740, DOI:10.1016/j.fuel.2010.03.011.
- F. Motasemi and F. N. Ani, A review on microwave-assisted production of biodiesel, Renewable Sustainable Energy Rev., 2012, 16, 4719–4733, DOI:10.1016/j.rser.2012.03.069.
- K. Nakajima and M. Hara, Amorphous carbon with SO3H groups as a solid brønsted acid catalyst, ACS Catal., 2012, 2, 1296–1304, DOI:10.1021/cs300103k.
- M. Chai, Q. Tu, M. Lu and Y. J. Yang, Esterification pretreatment of free fatty acid in biodiesel production, from laboratory to industry, Fuel Process. Technol., 2014, 125, 106–113, DOI:10.1016/j.fuproc.2014.03.025.
- D. N. Thoai, P. T. Le Hang and D. T. Lan, Pre-treatment of waste cooking oil with high free fatty acids content for biodiesel production: An optimization study via response surface methodology, Vietnam J. Chem., 2019, 57, 568–573, DOI:10.1002/vjch.201900072.
- J. Cárdenas, A. Orjuela, D. L. Sánchez, P. C. Narváez, B. Katryniok and J. Clark, Pre-treatment of used cooking oils for the production of green chemicals: A review, J. Cleaner Prod., 2021, 289, 125129, DOI:10.1016/j.jclepro.2020.125129.
- C. Vaisali, S. Charanyaa, P. D. Belur and I. Regupathi, Refining of edible oils: A critical appraisal of current and potential technologies, Int. J. Food Sci. Technol., 2015, 50, 13–23, DOI:10.1111/ijfs.12657.
- G. L. Maddikeri, A. B. Pandit and P. R. Gogate, Intensification approaches for biodiesel synthesis from waste cooking oil: A review, Ind. Eng. Chem. Res., 2012, 51, 14610–14628, DOI:10.1021/ie301675j.
- M. K. Delvi, M. E. M. Soudagar, H. Khan, Z. A. Shariff and I. Mokashi, Biodiesel production utilizing diverse sources, classification of oils and their esters, performance and emission characteristics: A research, Int. J. Recent Technol. Eng., 2019, 8, 976–983, DOI:10.35940/ijrte.B1183.0782S319.
- G. Vignesh, and D. Barik, Toxic Waste from Biodiesel Production Industries and its Utilization, Elsevier Ltd, 2018, DOI:10.1016/B978-0-08-102528-4.00006-7.
- S. P. Singh and D. Singh, Biodiesel production through the use of different sources and characterization of oils and their esters as the substitute of diesel: A review, Renewable Sustainable Energy Rev., 2010, 14, 200–216, DOI:10.1016/j.rser.2009.07.017.
- Y. Y. Gan, H. C. Ong, P. L. Show, T. C. Ling, W. H. Chen, K. L. Yu and R. Abdullah, Torrefaction of microalgal biochar as potential coal fuel and application as bio-adsorbent, Energy Convers. Manage., 2018, 165, 152–162, DOI:10.1016/j.enconman.2018.03.046.
- B. H. H. Goh, C. T. Chong, Y. Ge, H. C. Ong, J. H. Ng, B. Tian, V. Ashokkumar, S. Lim, T. Seljak and V. Józsa, Progress in utilisation of waste cooking oil for sustainable biodiesel and biojet fuel production, Energy Convers. Manage., 2020, 223, 113296, DOI:10.1016/j.enconman.2020.113296.
- C. Gutiérrez-Antonio, F. I. Gómez-Castro, J. A. de Lira-Flores and S. Hernández, A review on the production processes of renewable jet fuel, Renewable Sustainable Energy Rev., 2017, 79, 709–729, DOI:10.1016/j.rser.2017.05.108.
- T. Cornelissen, J. Yperman, G. Reggers, S. Schreurs and R. Carleer, Flash co-pyrolysis of biomass with polylactic acid. Part 1: Influence on bio-oil yield and heating value, Fuel, 2008, 87, 1031–1041, DOI:10.1016/j.fuel.2007.07.019.
- S. Wang, C. Yuan, S. Esakkimuthu, L. Xu, B. Cao, A. El-Fatah Abomohra, L. Qian, L. Liu and Y. Hu, Catalytic pyrolysis of waste clay oil to produce high quality biofuel, J. Anal. Appl. Pyrolysis, 2019, 141, 104633, DOI:10.1016/j.jaap.2019.104633.
- M. A. Mohamed, Biofuel Production from Used Cooking Oil Using Pyrolysis Process, Int. J. Res. Appl. Sci. Eng. Technol., 2017, V, 2971–2976, DOI:10.22214/ijraset.2017.11410.
- P. Maheshwari, M. B. Haider, M. Yusuf, J. J. Klemeš, A. Bokhari, M. Beg, A. Al-Othman, R. Kumar and A. K. Jaiswal, A review on latest trends in cleaner biodiesel production: Role of feedstock, production methods, and catalysts, J. Cleaner Prod., 2022, 355, 131588, DOI:10.1016/j.jclepro.2022.131588.
- P. Ekkpowpan, N. Arpornpong, A. Charoensaeng, and S. Khaodhiar, Life Cycle Assessment of Biofuel from Microemulsion and Transesterification Processes, 2014, pp. 610–614. DOI:10.15242/iie.e0314051.
- H. Kumar, A. K. Sarma and P. Kumar, A comprehensive review on preparation, characterization, and combustion characteristics of microemulsion based hybrid biofuels, Renewable Sustainable Energy Rev., 2020, 117, 109498, DOI:10.1016/j.rser.2019.109498.
- Y. Zhang, Y. Zhong, S. Lu, Z. Zhang and D. Tan, A Comprehensive Review of the Properties, Performance, Combustion, and Emissions of the Diesel Engine Fueled with Different Generations of Biodiesel, Processes, 2022, 10(6), 1178, DOI:10.3390/pr10061178.
- F. Ma and M. A. Hanna, Biodiesel production: a review1Journal Series #12109, Agricultural Research Division, Institute of Agriculture and Natural Resources, University of Nebraska, Lincoln.1, Bioresour. Technol., 1999, 70, 1–15, DOI:10.1016/s0960-8524(99)00025-5.
- E. Supriyanto, J. Sentanuhady, A. Dwiputra, A. Permana and M. A. Muflikhun, The recent progress of natural sources and manufacturing process of biodiesel: A review, Sustainability, 2021, 13(10), 5599, DOI:10.3390/su13105599.
- P. Bora, J. Boro, L. J. Konwar and D. Deka, Formulation of microemulsion based hybrid biofuel from waste cooking oil – A comparative study with biodiesel, J. Energy Inst., 2016, 89, 560–568, DOI:10.1016/j.joei.2015.07.001.
- Y. C. Chang, W. J. Lee, S. L. Lin and L. C. Wang, Green energy: Water-containing acetone-butanol-ethanol diesel blends fueled in diesel engines, Appl. Energy, 2013, 109, 182–191, DOI:10.1016/j.apenergy.2013.03.086.
- Y. H. Tan, M. O. Abdullah, C. Nolasco-Hipolito, N. S. A. Zauzi and G. W. Abdullah, Engine performance and emissions characteristics of a diesel engine fueled with diesel-biodiesel-bioethanol emulsions, Energy Convers. Manage., 2017, 132, 54–64, DOI:10.1016/j.enconman.2016.11.013.
- P. Bora, J. Boro, L. J. Konwar and D. Deka, Formulation of microemulsion based hybrid biofuel from waste cooking oil – A comparative study with biodiesel, J. Energy Inst., 2016, 89, 560–568, DOI:10.1016/j.joei.2015.07.001.
- L. Chen, L. He, B. Zheng, G. Wei, H. Li, H. Zhang and S. Yang, Bifunctional acid-activated montmorillonite catalyzed biodiesel production from non-food oil: Characterization, optimization, kinetic and thermodynamic studies, Fuel Process. Technol., 2023, 250, 107903, DOI:10.1016/j.fuproc.2023.107903.
- M. Koberg, and A. Gedanken, Using Microwave Radiation and SrO as a Catalyst for the Complete Conversion of Oils, Cooked Oils, and Microalgae to Biodiesel, Elsevier B.V., 2013, DOI:10.1016/B978-0-444-53878-9.00010-2.
- N. Ghosh and G. Halder, Current progress and perspective of heterogeneous nanocatalytic transesterification towards biodiesel production from edible and inedible feedstock: A review, Energy Convers. Manage., 2022, 270, 116292, DOI:10.1016/j.enconman.2022.116292.
- N. N. A. N. Yusuf, S. K. Kamarudin and Z. Yaakub, Overview on the current trends in biodiesel production, Energy Convers. Manage., 2011, 52, 2741–2751, DOI:10.1016/j.enconman.2010.12.004.
- J. Van Gerpen, Biodiesel processing and production, Fuel Process. Technol., 2005, 86, 1097–1107, DOI:10.1016/j.fuproc.2004.11.005.
- I. A. Musa, The effects of alcohol to oil molar ratios and the type of alcohol on biodiesel production using transesterification process, Egypt. J. Pet., 2016, 25, 21–31, DOI:10.1016/j.ejpe.2015.06.007.
- Y. Ma, Q. Wang, L. Zheng, Z. Gao, Q. Wang and Y. Ma, Mixed methanol/ethanol on transesterification of waste cooking oil using Mg/Al hydrotalcite catalyst, Energy, 2016, 107, 523–531, DOI:10.1016/j.energy.2016.04.066.
- B. Karmakar and G. Halder, Progress and future of biodiesel synthesis: Advancements in oil extraction and conversion technologies, Energy Convers. Manage., 2019, 182, 307–339, DOI:10.1016/j.enconman.2018.12.066.
- V. B. Veljković, J. M. Avramović and O. S. Stamenković, Biodiesel production by ultrasound-assisted transesterification: State of the art and the perspectives, Renewable Sustainable Energy Rev., 2012, 16, 1193–1209, DOI:10.1016/j.rser.2011.11.022.
- M. Athar and S. Zaidi, A review of the feedstocks, catalysts, and intensification techniques for sustainable biodiesel production, J. Environ. Chem. Eng., 2020, 8, 104523, DOI:10.1016/j.jece.2020.104523.
- W. W. S. Ho, H. K. Ng and S. Gan, Advances in ultrasound-assisted transesterification for biodiesel production, Appl. Therm. Eng., 2016, 100, 553–563, DOI:10.1016/j.applthermaleng.2016.02.058.
- Y. Kojima, H. Imazu and K. Nishida, Physical and chemical characteristics of ultrasonically-prepared water-in-diesel fuel: Effects of ultrasonic horn position and water content, Ultrason. Sonochem., 2014, 21, 722–728, DOI:10.1016/j.ultsonch.2013.09.019.
- J. Ji, J. Wang, Y. Li, Y. Yu and Z. Xu, Preparation of biodiesel with the help of ultrasonic and hydrodynamic cavitation, Ultrasonics, 2006, 44, e411–e414, DOI:10.1016/j.ultras.2006.05.020.
- P. Chand, V. R. Chintareddy, J. G. Verkade and D. Grewell, Enhancing biodiesel production from soybean oil using ultrasonics, Energy Fuels, 2010, 24, 2010–2015, DOI:10.1021/ef9011752.
- A. Fallah Kelarijani, N. Gholipour Zanjani and A. Kamran Pirzaman, Ultrasonic Assisted Transesterification of Rapeseed Oil to Biodiesel Using Nano Magnetic Catalysts, Waste Biomass Valorization, 2020, 11, 2613–2621, DOI:10.1007/s12649-019-00593-1.
- S. K. Bhangu, S. Gupta and M. Ashokkumar, Ultrasonic enhancement of lipase-catalysed transesterification for biodiesel synthesis, Ultrason. Sonochem., 2017, 34, 305–309, DOI:10.1016/j.ultsonch.2016.06.005.
- P. Cintas, S. Mantegna, E. C. Gaudino and G. Cravotto, A new pilot flow reactor for high-intensity ultrasound irradiation. Application to the synthesis of biodiesel, Ultrason. Sonochem., 2010, 17, 985–989, DOI:10.1016/j.ultsonch.2009.12.003.
- M. Athar, S. Imdad, S. Zaidi, M. Yusuf, H. Kamyab, J. Jaromír Klemeš and S. Chelliapan, Biodiesel production by single-step acid-catalysed transesterification of Jatropha oil under microwave heating with modelling and optimisation using response surface methodology, Fuel, 2022, 322, 124205, DOI:10.1016/j.fuel.2022.124205.
- S. Caddick and R. Fitzmaurice, Microwave enhanced synthesis, Tetrahedron, 2009, 65, 3325–3355, DOI:10.1016/j.tet.2009.01.105.
- S. N. Nayak, C. P. Bhasin and M. G. Nayak, A review on microwave-assisted transesterification processes using various catalytic and non-catalytic systems, Renewable Energy, 2019, 143, 1366–1387, DOI:10.1016/j.renene.2019.05.056.
- M. Rahul Soosai, I. M. G. Moorthy, P. Varalakshmi and C. J. Yonas, Integrated global optimization and process modelling for biodiesel production from non-edible silk-cotton seed oil by microwave-assisted transesterification with heterogeneous calcium oxide catalyst, J. Cleaner Prod., 2022, 367, 132946, DOI:10.1016/j.jclepro.2022.132946.
- A. Sharma, P. Kodgire and S. S. Kachhwaha, Biodiesel production from waste cotton-seed cooking oil using microwave-assisted transesterification: Optimization and kinetic modeling, Renewable Sustainable Energy Rev., 2019, 116, 109394, DOI:10.1016/j.rser.2019.109394.
- O. Farobie and Y. Matsumura, State of the art of biodiesel production under supercritical conditions, Prog. Energy Combust. Sci., 2017, 63, 173–203, DOI:10.1016/j.pecs.2017.08.001.
- S. Saka and D. Kusdiana, Biodiesel fuel from rapeseed oil as prepared in supercritical methanol, Fuel, 2001, 80, 225–231, DOI:10.1016/S0016-2361(00)00083-1.
- P. Andreo-Martínez, V. M. Ortiz-Martínez, M. J. Salar-García, J. M. Veiga-del-Baño, A. Chica and J. Quesada-Medina, Waste animal fats as feedstock for biodiesel production using non-catalytic supercritical alcohol transesterification: A perspective by the PRISMA methodology, Energy Sustainable Dev., 2022, 69, 150–163, DOI:10.1016/j.esd.2022.06.004.
- S. M. Ghoreishi and P. Moein, Biodiesel synthesis from waste vegetable oil via transesterification reaction in supercritical methanol, J. Supercrit. Fluids, 2013, 76, 24–31, DOI:10.1016/j.supflu.2013.01.011.
- N. Akkarawatkhoosith, A. Kaewchada and A. Jaree, Enhancement of continuous supercritical biodiesel production: Influence of co-solvent types, Energy Procedia, 2019, 156, 48–52, DOI:10.1016/j.egypro.2018.11.085.
- O. D. Okechukwu, E. Joseph, U. C. Nonso and N.-O. Kenechi, Improving heterogeneous catalysis for biodiesel production process, Cleaner Chem. Eng., 2022, 3, 100038, DOI:10.1016/j.clce.2022.100038.
- Z. Abelniece, L. Laipniece and V. Kampars, Biodiesel production by interesterification of rapeseed oil with methyl formate in presence of potassium alkoxides, Biomass Convers. Biorefin., 2022, 12, 2881–2889, DOI:10.1007/s13399-020-00874-z.
- U. Patel, A. Vaghela and N. M. Patel, Biodiesel Production by Trasesterification method review paper, Int. J. Res. Inf. Technol., 2013, 1, 17–30 Search PubMed.
- V. Mandari and S. K. Devarai, Biodiesel Production Using Homogeneous, Heterogeneous, and Enzyme Catalysts via Transesterification and Esterification Reactions: a Critical Review, BioEnergy Res., 2021, 15, 935–961, DOI:10.1007/s12155-021-10333-w.
- E. A. E. Sheet, Effect of preheating waste cooking oil on biodiesel production and properties, Energy Sources, Part A, 2018, 40, 207–213, DOI:10.1080/15567036.2017.1410594.
- H. Hamze, M. Akia and F. Yazdani, Optimization of biodiesel production from the waste cooking oil using response surface methodology, Process Saf. Environ. Prot., 2015, 94, 1–10, DOI:10.1016/j.psep.2014.12.005.
- S. Oza, N. Prajapati, P. Kodgire and S. S. Kachhwaha, An ultrasound-assisted process for the optimization of biodiesel production from waste cottonseed cooking oil using response surface methodology, Water-Energy Nexus, 2021, 4, 187–198, DOI:10.1016/j.wen.2021.11.001.
- J. V. Sree, B. A. Chowdary, K. S. Kumar, M. P. Anbazhagan and S. Subramanian, Optimization of the biodiesel production from waste cooking oil using homogeneous catalyst and heterogeneous catalysts, Mater. Today: Proc., 2019, 46, 4900–4908, DOI:10.1016/j.matpr.2020.10.332.
- A. S. Al Hatrooshi, V. C. Eze and A. P. Harvey, Production of biodiesel from waste shark liver oil for biofuel applications, Renewable Energy, 2020, 145, 99–105, DOI:10.1016/j.renene.2019.06.002.
- R. Chakraborty and H. Sahu, Intensification of biodiesel production from waste goat tallow using infrared radiation: Process evaluation through response surface methodology and artificial neural network, Appl. Energy, 2014, 114, 827–836, DOI:10.1016/j.apenergy.2013.04.025.
- V. Mandari and S. K. Devarai, Biodiesel Production Using Homogeneous, Heterogeneous, and Enzyme Catalysts via Transesterification and Esterification Reactions: a Critical Review, BioEnergy Res., 2021, 15, 935–961, DOI:10.1007/s12155-021-10333-w.
- A. L. De Lima, C. M. Ronconi and C. J. A. Mota, Heterogeneous basic catalysts for biodiesel production, Catal. Sci. Technol., 2016, 6, 2877–2891, 10.1039/c5cy01989c.
- L. He, L. Chen, B. Zheng, H. Zhou, H. Wang, H. Li, H. Zhang, C. C. Xu and S. Yang, Deep eutectic solvents for catalytic biodiesel production from liquid biomass and upgrading of solid biomass into 5-hydroxymethylfurfural, Green Chem., 2023, 25, 7410–7440, 10.1039/d3gc02816j.
- G. Sahu, N. K. Gupta, A. Kotha, S. Saha, S. Datta, P. Chavan, N. Kumari and P. Dutta, A Review on Biodiesel Production through Heterogeneous Catalysis Route, ChemBioEng Rev., 2018, 5, 231–252, DOI:10.1002/cben.201700014.
- B. Maleki, S. S. Ashraf Talesh and M. Mansouri, Comparison of catalysts types performance in the generation of sustainable biodiesel via transesterification of various oil sources: a review study, Mater. Today Sustainability, 2022, 18, 100157, DOI:10.1016/j.mtsust.2022.100157.
- B. Thangaraj, P. R. Solomon, B. Muniyandi, S. Ranganathan and L. Lin, Catalysis in biodiesel production – A review, Clean Energy, 2019, 3, 2–23, DOI:10.1093/ce/zky020.
- N. Mansir, S. H. Teo, U. Rashid, M. I. Saiman, Y. P. Tan, G. A. Alsultan and Y. H. Taufiq-Yap, Modified waste egg shell derived bifunctional catalyst for biodiesel production from high FFA waste cooking oil A review, Renewable Sustainable Energy Rev., 2018, 82, 3645–3655, DOI:10.1016/j.rser.2017.10.098.
- J. Gupta, M. Agarwal and A. K. Dalai, An overview on the recent advancements of sustainable heterogeneous catalysts and prominent continuous reactor for biodiesel production, J. Ind. Eng. Chem., 2020, 88, 58–77, DOI:10.1016/j.jiec.2020.05.012.
- A. A. Refaat and A. A. Refaat, Archive of SID Different techniques for the production of biodiesel from waste vegetable oil, Int. J. Environ. Sci. Technol., 2010, 7, 183–213 CrossRef CAS.
- A. K. Endalew, Y. Kiros and R. Zanzi, Inorganic heterogeneous catalysts for biodiesel production from vegetable oils, Biomass Bioenergy, 2011, 35, 3787–3809, DOI:10.1016/j.biombioe.2011.06.011.
- H. Satriadi, I. Y. Pratiwi, M. Khuriyah, H. Widayat and J. Prameswari, Geothermal solid waste derived Ni/Zeolite catalyst for waste cooking oil processing, Chemosphere, 2022, 286, 131618, DOI:10.1016/j.chemosphere.2021.131618.
- B. Aghel, A. Gouran and F. Nasirmanesh, Transesterification of waste cooking oil using clinoptilolite/industrial phosphoric waste as green and environmental catalysts, Energy, 2022, 244, 123138, DOI:10.1016/j.energy.2022.123138.
- M. Guo, W. Jiang, J. Ding and J. Lu, Highly active and recyclable CuO/ZnO as photocatalyst for transesterification of waste cooking oil to biodiesel and the kinetics, Fuel, 2022, 315, 123254, DOI:10.1016/j.fuel.2022.123254.
- A. Attari, A. Abbaszadeh-Mayvan and A. Taghizadeh-Alisaraie, Process optimization of ultrasonic-assisted biodiesel production from waste cooking oil using waste chicken eggshell-derived CaO as a green
heterogeneous catalyst, Biomass Bioenergy, 2022, 158, 106357, DOI:10.1016/j.biombioe.2022.106357.
- R. F. Abdullah, U. Rashid, M. L. Ibrahim, B. Hazmi, F. A. Alharthi and I. A. Nehdi, Bifunctional nano-catalyst produced from palm kernel shell via hydrothermal-assisted carbonization for biodiesel production from waste cooking oil, Renewable Sustainable Energy Rev., 2021, 137, 110638, DOI:10.1016/j.rser.2020.110638.
- A. Naeem, I. Wali Khan, M. Farooq, T. Mahmood, I. Ud Din, Z. Ali Ghazi and T. Saeed, Kinetic and optimization study of sustainable biodiesel production from waste cooking oil using novel heterogeneous solid base catalyst, Bioresour. Technol., 2021, 328, 124831, DOI:10.1016/j.biortech.2021.124831.
- M. R. Abukhadra, S. I. Othman, A. A. Allam and H. Elfayoumi, Insight into the catalytic properties zeolitized kaolinite/diatomite geopolymer as an environmental catalyst for the sustainable conversion of spent cooking oil into biodiesel; optimization and kinetics, Sustainable Chem. Pharm., 2021, 22, 100473, DOI:10.1016/j.scp.2021.100473.
- M. N. B. Jumah, S. M. Ibrahim, A. A. AL-Huqail, N. S. Bin-Murdhi, A. A. Allam, G. M. Abu-Taweel, N. Altoom, K. M. Al-Anazi and M. R. Abukhadra, Enhancing the catalytic performance of NiO during the transesterification of waste cooking oil using a diatomite carrier and an integrated Ni0Metal: Response surface studies, ACS Omega, 2021, 6, 12318–12330, DOI:10.1021/acsomega.1c01301.
- M. G. Basyouny, M. R. Abukhadra, K. Alkhaledi, A. M. El-Sherbeeny, M. A. El-Meligy, A. T. A. Soliman and M. Luqman, Insight into the catalytic transformation of the waste products of some edible oils (corn oil and palm oil) into biodiesel using MgO/clinoptilolite green nanocomposite, Mol. Catal., 2021, 500, 111340, DOI:10.1016/j.mcat.2020.111340.
- J. H. C. Wancura, A. L. Fantinel, G. A. Ugalde, F. F. Donato, J. Vladimir de Oliveira, M. V. Tres and S. L. Jahn, Semi-continuous production of biodiesel on pilot scale via enzymatic hydroesterification of waste material: Process and economics considerations, J. Cleaner Prod., 2021, 285, 124838, DOI:10.1016/j.jclepro.2020.124838.
- S. M. Ibrahim, A. M. El-Sherbeeny, J. J. Shim, A. A. AlHammadi and M. R. Abukhadra, SO3H-functionalization of sub-bituminous coal as a highly active acidic catalyst during the transesterification of spent sunflower oil; characterization, application, and mechanism, Energy Rep., 2021, 7, 8699–8710, DOI:10.1016/j.egyr.2021.11.139.
- S. S. Bargole, P. K. Singh, S. George and V. K. Saharan, Valorisation of low fatty acid content waste cooking oil into biodiesel through transesterification using a basic heterogeneous calcium-based catalyst, Biomass Bioenergy, 2021, 146, 105984, DOI:10.1016/j.biombioe.2021.105984.
- F. Nadeem, I. A. Bhatti, A. Ashar, M. Yousaf, M. Iqbal, M. Mohsin, J. Nisar, N. Tamam and N. Alwadai, Eco-benign biodiesel production from waste cooking oil using eggshell derived MM-CaO catalyst and condition optimization using RSM approach, Arabian J. Chem., 2021, 14, 103263, DOI:10.1016/j.arabjc.2021.103263.
- M. Arrais Gonçalves, E. Karine Lourenço Mares, J. Roberto Zamian, G. Narciso da Rocha Filho and L. Rafael Vieira da Conceição, Statistical optimization of biodiesel production from waste cooking oil using magnetic acid heterogeneous catalyst MoO3/SrFe2O4, Fuel, 2021, 304, 121463, DOI:10.1016/j.fuel.2021.121463.
- M. H. Nazir, M. Ayoub, I. Zahid, R. Bin Shamsuddin, S. Yusup, M. Ameen, Zulqarnain and M. U. Qadeer, Development of lignin based heterogeneous solid acid catalyst derived from sugarcane bagasse for microwave assisted-transesterification of waste cooking oil, Biomass Bioenergy, 2021, 146, 105978, DOI:10.1016/j.biombioe.2021.105978.
- P. Sharma and A. G. Bhavani, Green, cost effective barium loaded montmorillonite catalyst for biodiesel synthesis from waste cooking oil, Mater. Today: Proc., 2021, 45, 4544–4549, DOI:10.1016/j.matpr.2020.12.1202.
- D. Gualberto Zavarize, H. Braun and J. Diniz de Oliveira, Methanolysis of low-FFA waste cooking oil with novel carbon-based heterogeneous acid catalyst derived from Amazon açaí berry seeds, Renewable Energy, 2021, 171, 621–634, DOI:10.1016/j.renene.2021.02.112.
- M. M. Mohamed, W. A. Bayoumy, H. El-Faramawy, W. El-Dogdog and A. A. Mohamed, A novel α-Fe2O3/AlOOH(γ-Al2O3) nanocatalyst for efficient biodiesel production from waste oil: Kinetic and thermal studies, Renewable Energy, 2020, 160, 450–464, DOI:10.1016/j.renene.2020.07.006.
- L. Fereidooni, A. Abbaspourrad and M. Enayati, Electrolytic transesterification of waste frying oil using Na+/zeolite–chitosan biocomposite for biodiesel production, Waste Manage., 2021, 127, 48–62, DOI:10.1016/j.wasman.2021.04.020.
- Z. Ullah, M. A. Bustam, Z. Man, A. S. Khan, N. Muhammad and A. Sarwono, Preparation and kinetics study of biodiesel production from waste cooking oil using new functionalized ionic liquids as catalysts, Renewable Energy, 2017, 114, 755–765, DOI:10.1016/j.renene.2017.07.085.
- J. Sun, J. Yang, S. Li and X. Xu, Basic ionic liquid immobilized oxides as heterogeneous catalyst for biodiesel synthesis from waste cooking oil, Catal. Commun., 2016, 83, 35–38, DOI:10.1016/j.catcom.2016.05.002.
- R. Sipayung and Budiyono, Optimization of biodiesel production from used cooking oil using modified calcium oxide as catalyst and N-Hexane as solvent, Mater. Today: Proc., 2022, 63, S32–S39, DOI:10.1016/j.matpr.2021.12.562.
- E. G. Al-Sakkari, N. K. Attia, M. M. Habashy, O. M. Abdeldayem, S. R. Mostafa, S. T. El-Sheltawy, M. F. Abadir, M. K. Mostafa, E. R. Rene and S. S. E. H. Elnashaie, A bi-functional alginate-based composite for catalyzing one-pot methyl esters synthesis from waste cooking oil having high acidity, Fuel, 2021, 306, 121637, DOI:10.1016/j.fuel.2021.121637.
- K. Cholapandian, B. Gurunathan and N. Rajendran, Investigation of CaO nanocatalyst synthesized from Acalypha indica leaves and its application in biodiesel production using waste cooking oil, Fuel, 2022, 312, 122958, DOI:10.1016/j.fuel.2021.122958.
- E. Parandi, M. Safaripour, M. H. Abdellattif, M. Saidi, A. Bozorgian, H. Rashidi Nodeh and S. Rezania, Biodiesel production from waste cooking oil using a novel biocatalyst of lipase enzyme immobilized magnetic nanocomposite, Fuel, 2022, 313, 123057, DOI:10.1016/j.fuel.2021.123057.
- M. Helmi and A. Hemmati, Synthesis of magnetically solid base catalyst of NaOH/Chitosan-Fe3O4 for biodiesel production from waste cooking oil: Optimization, kinetics and thermodynamic studies, Energy Convers. Manage., 2021, 248, 114807, DOI:10.1016/j.enconman.2021.114807.
- N. A. Roslan, S. Zainal Abidin, N. Abdullah, O. U. Osazuwa, R. Abdul Rasid and N. M. Yunus, Esterification reaction of free fatty acid in used cooking oil using sulfonated hypercrosslinked exchange resin as catalyst, Chem. Eng. Res. Des., 2022, 180, 414–424, DOI:10.1016/j.cherd.2021.10.020.
- A. Gouran, B. Aghel and F. Nasirmanesh, Biodiesel production from waste cooking oil using wheat bran ash as a sustainable biomass, Fuel, 2021, 295, 120542, DOI:10.1016/j.fuel.2021.120542.
- B. S. Caldas, C. S. Nunes, P. R. Souza, F. A. Rosa, J. V. Visentainer, O. d. O. S. Júnior and E. C. Muniz, Supercritical ethanolysis for biodiesel production from edible oil waste using ionic liquid [HMim][HSO4] as catalyst, Appl. Catal., B, 2016, 181, 289–297, DOI:10.1016/j.apcatb.2015.07.047.
- Y. Cao, H. Zhou and J. Li, Preparation of a supported acidic ionic liquid on silica-gel and its application to the synthesis of biodiesel from waste cooking oil, Renewable Sustainable Energy Rev., 2016, 58, 871–875, DOI:10.1016/j.rser.2015.12.237.
- M. R. Miladinović, J. B. Krstić, M. V. Zdujić, L. M. Veselinović, D. N. Veljović, I. B. Banković-Ilić, O. S. Stamenković and V. B. Veljković, Transesterification of used cooking sunflower oil catalyzed by hazelnut shell ash, Renewable Energy, 2022, 183, 103–113, DOI:10.1016/j.renene.2021.10.071.
- A. N. Amenaghawon, N. I. Evbarunegbe and K. Obahiagbon, Optimum biodiesel production from waste vegetable oil using functionalized cow horn catalyst: A comparative evaluation of some expert systems, Cleaner Eng. Technol., 2021, 4, 100184, DOI:10.1016/j.clet.2021.100184.
- M. Afsharizadeh and M. Mohsennia, Novel rare-earth metal oxides-zirconia nanocatalysts for biodiesel production from corn oil and waste cooking oil, Fuel, 2021, 304, 121350, DOI:10.1016/j.fuel.2021.121350.
- O. A. Falowo, B. Oladipo, A. E. Taiwo, A. T. Olaiya, O. O. Oyekola and E. Betiku, Green heterogeneous base catalyst from ripe and unripe plantain peels mixture for the transesterification of waste cooking oil, Chem. Eng. J. Adv., 2022, 10, 100293, DOI:10.1016/j.ceja.2022.100293.
- L. Bai, A. Tajikfar, S. Tamjidi, R. Foroutan and H. Esmaeili, Synthesis of MnFe2O4@graphene oxide catalyst for biodiesel production from waste edible oil, Renewable Energy, 2021, 170, 426–437, DOI:10.1016/j.renene.2021.01.139.
- T. F. Adepoju, U. P. Eyibuo, R. E. Emberru and T. A. Balogun, Optimization conversion of beef tallow blend with waste used vegetable oil for fatty acid ethyl ester (FAEE) synthesis in the presence of bio-base derived from Theobroma cacao pod husks, Case Stud. Chem. Environ. Eng., 2022, 6, 100218, DOI:10.1016/j.cscee.2022.100218.
- K. S. Al-Mawali, A. I. Osman, A. H. Al-Muhtaseb, N. Mehta, F. Jamil, F. Mjalli, G. R. Vakili-Nezhaad and D. W. Rooney, Life cycle assessment of biodiesel production utilising waste date seed oil and a novel magnetic catalyst: A circular bioeconomy approach, Renewable Energy, 2021, 170, 832–846, DOI:10.1016/j.renene.2021.02.027.
- M. Kirubakaran and V. Arul Mozhi Selvan, Experimental investigation on the effects of micro eggshell and nano-eggshell catalysts on biodiesel optimization from waste chicken fat, Bioresour. Technol. Rep., 2021, 14, 100658, DOI:10.1016/j.biteb.2021.100658.
- Z. Ullah, M. A. Bustam and Z. Man, Biodiesel production from waste cooking oil by acidic ionic liquid as a catalyst, Renewable Energy, 2015, 77, 521–526, DOI:10.1016/j.renene.2014.12.040.
- M. Kuniyil, J. V. Shanmukha Kumar, S. F. Adil, M. E. Assal, M. R. Shaik, M. Khan, A. Al-Warthan and M. R. H. Siddiqui, Production of biodiesel from waste cooking oil using ZnCuO/N-doped graphene nanocomposite as an efficient heterogeneous catalyst, Arabian J. Chem., 2021, 14, 102982, DOI:10.1016/j.arabjc.2020.102982.
- M. R. Sayed, M. R. Abukhadra, S. Abdelkader Ahmed, M. Shaban, U. Javed, M. A. Betiha, J. J. Shim and A. M. Rabie, Synthesis of advanced MgAl-LDH based geopolymer as a potential catalyst in the conversion of waste sunflower oil into biodiesel: Response surface studies, Fuel, 2020, 282, 118865, DOI:10.1016/j.fuel.2020.118865.
- M. R. AbuKhadra, M. G. Basyouny, A. M. El-Sherbeeny, M. A. El-Meligy and A. E. E. Abd Elgawad, Transesterification of commercial waste cooking oil into biodiesel over innovative alkali trapped zeolite nanocomposite as green and environmental catalysts, Sustainable Chem. Pharm., 2020, 17, 100289, DOI:10.1016/j.scp.2020.100289.
- M. Mohadesi, B. Aghel, M. Maleki and A. Ansari, The use of KOH/Clinoptilolite catalyst in pilot of microreactor for biodiesel production from waste cooking oil, Fuel, 2020, 263, 116659, DOI:10.1016/j.fuel.2019.116659.
- X. Liang, Synthesis of biodiesel from waste oil under mild conditions using novel acidic ionic liquid immobilization on poly divinylbenzene, Energy, 2013, 63, 103–108, DOI:10.1016/j.energy.2013.10.043.
- S. Liu, Z. Wang, S. Yu and C. Xie, Transesterification of waste oil to biodiesel using brønsted acid ionic liquid as catalyst, Bull. Chem. Soc. Ethiop., 2013, 27, 289–294, DOI:10.4314/bcse.v27i2.14.
- Y. C. Lin, P. M. Yang, S. C. Chen and J. F. Lin, Improving biodiesel yields from waste cooking oil using ionic liquids as catalysts with a microwave heating system, Fuel Process. Technol., 2013, 115, 57–62, DOI:10.1016/j.fuproc.2013.04.004.
- M. F. F. Kamaronzaman, H. Kahar, N. Hassan, M. F. Hanafi and N. Sapawe, Biodiesel production from waste cooking oil using nickel doped onto eggshell catalyst, Mater. Today: Proc., 2020, 31, 342–346, DOI:10.1016/j.matpr.2020.06.159.
- I. W. Khan, A. Naeem, M. Farooq, T. Mahmood, B. Ahmad, M. Hamayun, Z. Ahmad and T. Saeed, Catalytic conversion of spent frying oil into biodiesel over raw and 12-tungsto-phosphoric acid modified clay, Renewable Energy, 2020, 155, 181–188, DOI:10.1016/j.renene.2020.03.123.
- F. Li, M. J. Hülsey, N. Yan, Y. Dai and C. H. Wang, Co-transesterification of waste cooking oil, algal oil and dimethyl carbonate over sustainable nanoparticle catalysts, Chem. Eng. J., 2021, 405, 127036, DOI:10.1016/j.cej.2020.127036.
- N. Ishak, J. Estephane, E. Dahdah, L. M. Chalouhi, S. Nassreddine, B. El Khoury and S. Aouad, Outstanding activity of a biodiesel coated K2O/fumed silica catalyst in the transesterification reaction, J. Environ. Chem. Eng., 2021, 9, 104665, DOI:10.1016/j.jece.2020.104665.
- S. Kumar, M. R. Shamsuddin, M. S. A. Farabi, M. I. Saiman, Z. Zainal and Y. H. Taufiq-Yap, Production of methyl esters from waste cooking oil and chicken fat oil via simultaneous esterification and transesterification using acid catalyst, Energy Convers. Manage., 2020, 226, 113366, DOI:10.1016/j.enconman.2020.113366.
- M. R. Abukhadra, M. Mostafa, A. M. El-Sherbeeny, A. T. Ahmed Soliman and A. E. E. Abd Elgawad, Effective transformation of waste sunflower oil into biodiesel over novel K+ trapped clay nanotubes (K+/KNTs) as a heterogeneous catalyst; response surface studies, Microporous Mesoporous Mater., 2020, 306, 110465, DOI:10.1016/j.micromeso.2020.110465.
- F. A. Yassin, F. Y. El Kady, H. S. Ahmed, L. K. Mohamed, S. A. Shaban and A. K. Elfadaly, Highly effective ionic liquids for biodiesel production from waste vegetable oils, Egypt. J. Pet., 2015, 24, 103–111, DOI:10.1016/j.ejpe.2015.02.011.
- F. Deeba, B. Kumar, N. Arora, S. Singh, A. Kumar, S. S. Han and Y. S. Negi, Novel bio-based solid acid catalyst derived from waste yeast residue for biodiesel production, Renewable Energy, 2020, 159, 127–139, DOI:10.1016/j.renene.2020.05.029.
- N. Mansir, S. H. Teo, N. A. Mijan and Y. H. Taufiq-Yap, Efficient reaction for biodiesel manufacturing using bi-functional oxide catalyst, Catal. Commun., 2021, 149, 106201, DOI:10.1016/j.catcom.2020.106201.
- A. S. Yusuff and J. O. Owolabi, Synthesis and characterization of alumina supported coconut chaff catalyst for biodiesel production from waste frying oil, S. Afr. J. Chem. Eng., 2019, 30, 42–49, DOI:10.1016/j.sajce.2019.09.001.
- Y. C. Chen, D. Y. Lin and B. H. Chen, Metasilicate-based catalyst prepared from natural diatomaceous earth for biodiesel production, Renewable Energy, 2019, 138, 1042–1050, DOI:10.1016/j.renene.2019.02.054.
- M. Shaban, R. Hosny, A. M. Rabie, J. J. Shim, S. A. Ahmed, M. A. Betiha and N. A. Negm, Zinc aluminate nanoparticles: Preparation, characterization and application as efficient and economic catalyst in transformation of waste cooking oil into biodiesel, J. Mol. Liq., 2020, 302, 112377, DOI:10.1016/j.molliq.2019.112377.
- J. Gardy, E. Nourafkan, A. Osatiashtiani, A. F. Lee, K. Wilson, A. Hassanpour and X. Lai, A core-shell SO4/Mg-Al-Fe3O4 catalyst for biodiesel production, Appl. Catal., B, 2019, 259, 118093, DOI:10.1016/j.apcatb.2019.118093.
- V. Vadery, S. K. Cherikkallinmel, R. M. Ramakrishnan, S. Sugunan and B. N. Narayanan, Green production of biodiesel over waste borosilicate glass derived catalyst and the process up-gradation in pilot scale, Renewable Energy, 2019, 141, 1042–1053, DOI:10.1016/j.renene.2019.04.053.
- M. R. Abukhadra and M. A. Sayed, K+ trapped kaolinite (Kaol/K+) as low cost and eco-friendly basic heterogeneous catalyst in the transesterification of commercial waste cooking oil into biodiesel, Energy Convers. Manage., 2018, 177, 468–476, DOI:10.1016/j.enconman.2018.09.083.
- J. Gardy, A. Osatiashtiani, O. Céspedes, A. Hassanpour, X. Lai, A. F. Lee, K. Wilson and M. Rehan, A magnetically separable SO4/Fe-Al-TiO2 solid acid catalyst for biodiesel production from waste cooking oil, Appl. Catal., B, 2018, 234, 268–278, DOI:10.1016/j.apcatb.2018.04.046.
- M. Yadav, V. Singh and Y. C. Sharma, Methyl transesterification of waste cooking oil using a laboratory synthesized reusable heterogeneous base catalyst: Process optimization and homogeneity study of catalyst, Energy Convers. Manage., 2017, 148, 1438–1452, DOI:10.1016/j.enconman.2017.06.024.
- N. Y. Yahya, N. Ngadi, M. Jusoh and N. A. A. Halim, Characterization and parametric study of mesoporous calcium titanate catalyst for transesterification of waste cooking oil into biodiesel, Energy Convers. Manage., 2016, 129, 275–283, DOI:10.1016/j.enconman.2016.10.037.
- T. T. V. Tran, S. Kaiprommarat, S. Kongparakul, P. Reubroycharoen, G. Guan, M. H. Nguyen and C. Samart, Green biodiesel production from waste cooking oil using an environmentally benign acid catalyst, Waste Manage., 2016, 52, 367–374, DOI:10.1016/j.wasman.2016.03.053.
- T. Maneerung, S. Kawi, Y. Dai and C. H. Wang, Sustainable biodiesel production via transesterification of waste cooking oil by using CaO catalysts prepared from chicken manure, Energy Convers. Manage., 2016, 123, 487–497, DOI:10.1016/j.enconman.2016.06.071.
- H. Amani, M. Asif and B. H. Hameed, Transesterification of waste cooking palm oil and palm oil to fatty acid methyl ester using cesium-modified silica catalyst, J. Taiwan Inst. Chem. Eng., 2016, 58, 226–234, DOI:10.1016/j.jtice.2015.07.009.
- F. H. Alhassan, U. Rashid and Y. H. Taufiq-Yap, Synthesis of waste cooking oil-based biodiesel via effectual recyclable bi-functional Fe2O3MnOSO42-/ZrO2 nanoparticle solid catalyst, Fuel, 2015, 142, 38–45, DOI:10.1016/j.fuel.2014.10.038.
- H. Amani, Z. Ahmad and B. H. Hameed, Highly active alumina-supported Cs-Zr mixed oxide catalysts for low-temperature transesterification of waste cooking oil, Appl. Catal., A, 2014, 487, 16–25, DOI:10.1016/j.apcata.2014.08.038.
- H. Amani, Z. Ahmad, M. Asif and B. H. Hameed, Transesterification of waste cooking palm oil by MnZr with supported alumina as a potential heterogeneous catalyst, J. Ind. Eng. Chem., 2014, 20, 4437–4442, DOI:10.1016/j.jiec.2014.02.012.
- N. Hindryawati and G. P. Maniam, Novel utilization of waste marine sponge (Demospongiae) as a catalyst in ultrasound-assisted transesterification of waste cooking oil, Ultrason. Sonochem., 2015, 22, 454–462, DOI:10.1016/j.ultsonch.2014.04.011.
- M. A. Olutoye and B. H. Hameed, A highly active clay-based catalyst for the synthesis of fatty acid methyl ester from waste cooking palm oil, Appl. Catal., A, 2013, 450, 57–62, DOI:10.1016/j.apcata.2012.09.049.
- A. Birla, B. Singh, S. N. Upadhyay and Y. C. Sharma, Kinetics studies of synthesis of biodiesel from waste frying oil using a heterogeneous catalyst derived from snail shell, Bioresour. Technol., 2012, 106, 95–100, DOI:10.1016/j.biortech.2011.11.065.
- G. Karavalakis, G. Anastopoulos and S. Stournas, Tetramethylguanidine as an efficient catalyst for transesterification of waste frying oils, Appl. Energy, 2011, 88, 3645–3650, DOI:10.1016/j.apenergy.2011.03.050.
- B. Devaraj Naik and M. Udayakumar, Optimization studies on esterification of waste cooking oil using sulfated montmorillonite clay acidic catalyst, Mater. Today: Proc., 2019, 46, 9855–9861, DOI:10.1016/j.matpr.2020.11.419.
- B. Aghel, M. Mohadesi, A. Ansari and M. Maleki, Pilot-scale production of biodiesel from waste cooking oil using kettle limescale as a heterogeneous catalyst, Renewable Energy, 2019, 142, 207–214, DOI:10.1016/j.renene.2019.04.100.
- D. A. Kamel, H. A. Farag, N. K. Amin, A. A. Zatout and Y. O. Fouad, Utilization of Ficus carica leaves as a heterogeneous catalyst for production of biodiesel from waste cooking oil, Environ. Sci. Pollut. Res., 2019, 26, 32804–32814, DOI:10.1007/s11356-019-06424-z.
- N. Mansir, S. H. Teo, I. Rabiu and Y. H. Taufiq-Yap, Effective biodiesel synthesis from waste cooking oil and biomass residue solid green catalyst, Chem. Eng. J., 2018, 347, 137–144, DOI:10.1016/j.cej.2018.04.034.
- A. S. Yusuff, O. D. Adeniyi, S. O. Azeez, M. A. Olutoye and U. G. Akpan, Synthesis and characterization of anthill-eggshell-Ni-Co mixed oxides composite catalyst for biodiesel production from waste frying oil, Biofuels, Bioprod. Biorefin., 2019, 13, 37–47, DOI:10.1002/bbb.1914.
- M. A. Olutoye and B. H. Hameed, Synthesis of fatty acid methyl ester from used vegetable cooking oil by solid reusable Mg1-x Zn1+xO2 catalyst, Bioresour. Technol., 2011, 102, 3819–3826, DOI:10.1016/j.biortech.2010.11.100.
- S. E. Mahesh, A. Ramanathan, K. M. M. S. Begum and A. Narayanan, Biodiesel production from waste cooking oil using KBr impregnated CaO as catalyst, Energy Convers. Manage., 2015, 91, 442–450, DOI:10.1016/j.enconman.2014.12.031.
- A. S. Yusuff and K. A. Bello, Synthesis of fatty acid methyl ester via transesterification of waste frying oil by a zinc-modified pumice catalyst: Taguchi approach to parametric optimization, React. Kinet., Mech. Catal., 2019, 128, 739–761, DOI:10.1007/s11144-019-01680-z.
- A. S. Yusuff and L. T. Popoola, Optimization of biodiesel production from waste frying oil over alumina supported chicken eggshell catalyst using experimental design tool, Acta Polytech., 2019, 59, 88–97, DOI:10.14311/AP.2019.59.0088.
- M. A. Olutoye, S. W. Wong, L. H. Chin, H. Amani, M. Asif and B. H. Hameed, Synthesis of fatty acid methyl esters via the transesterification of waste cooking oil by methanol with a barium-modified montmorillonite K10 catalyst, Renewable Energy, 2016, 86, 392–398, DOI:10.1016/j.renene.2015.08.016.
- A. Piker, B. Tabah, N. Perkas and A. Gedanken, A green and low-cost room temperature biodiesel production method from waste oil using egg shells as catalyst, Fuel, 2016, 182, 34–41, DOI:10.1016/j.fuel.2016.05.078.
- R. Foroutan, R. Mohammadi, H. Esmaeili, F. Mirzaee Bektashi and S. Tamjidi, Transesterification of waste edible oils to biodiesel using calcium oxide@magnesium oxide nanocatalyst, Waste Manage., 2020, 105, 373–383, DOI:10.1016/j.wasman.2020.02.032.
- Y. C. Lin, K. T. T. Amesho, C. E. Chen, P. C. Cheng and F. C. Chou, A cleaner process for green biodiesel synthesis from waste cooking oil using recycled waste oyster shells as a sustainable base heterogeneous catalyst under the microwave heating system, Sustainable Chem. Pharm., 2020, 17, 100310, DOI:10.1016/j.scp.2020.100310.
- P. Suwannasom, P. Tansupo and C. Ruangviriyachai, A bone-based catalyst for biodiesel production from waste cooking oil, Energy Sources, Part A, 2016, 38, 3167–3173, DOI:10.1080/15567036.2015.1137998.
- R. Mohadi, A. Sueb, K. Anggraini and A. Lesbani, Calcium Oxide Catalyst Based on Quail Eggshell for Biodiesel Synthesis from Waste Palm Oil, J. Pure Appl. Chem. Res., 2018, 7, 129–138, DOI:10.21776/ub.jpacr.2018.007.02.390.
- T. A. Degfie, T. T. Mamo and Y. S. Mekonnen, Optimized Biodiesel Production from Waste Cooking Oil (WCO) using Calcium Oxide (CaO) Nano-catalyst, Sci. Rep., 2019, 9, 1–8, DOI:10.1038/s41598-019-55403-4.
- M. Guo, W. Jiang, C. Chen, S. Qu, J. Lu, W. Yi and J. Ding, Process optimization of biodiesel production from waste cooking oil by esterification of free fatty acids using La3+/ZnO-TiO2 photocatalyst, Energy Convers. Manage., 2021, 229, 113745, DOI:10.1016/j.enconman.2020.113745.
- P. Hariprasath, V. Vijayakumar, S. T. Selvamani, M. Vigneshwar and K. Palanikumar, Some studies on waste animal tallow biodiesel produced by modified transesterification method using heterogeneous catalyst, Mater. Today: Proc., 2019, 16, 1271–1278, DOI:10.1016/j.matpr.2019.05.224.
- M. O. Daramola, D. Nkazi and K. Mtshali, Synthesis and evaluation of catalytic activity of calcined sodium silicate for transesterification of waste cooking oil to biodiesel, Int. J. Renewable Energy Res., 2015, 5, 517–523, DOI:10.20508/ijrer.v5i2.2164.g6606.
- A. H. Al-Muhtaseb, F. Jamil, L. Al-Haj, M. T. Zar Myint, E. Mahmoud, M. N. M. Ahmad, A. O. Hasan and S. Rafiq, Biodiesel production over a catalyst prepared from biomass-derived waste date pits, Biotechnol. Rep., 2018, 20, e00284, DOI:10.1016/j.btre.2018.e00284.
- N. Al-Jammal, Z. Al-Hamamre and M. Alnaief, Manufacturing of zeolite based catalyst from zeolite tuft for biodiesel production from waste sunflower oil, Renewable Energy, 2016, 93, 449–459, DOI:10.1016/j.renene.2016.03.018.
- M. R. Abukhadra, F. M. Dardir, M. Shaban, E. A. Ahmed and M. F. Soliman, Spongy Ni/Fe carbonate-fluorapatite catalyst for efficient conversion of cooking oil waste into biodiesel, Environ. Chem. Lett., 2018, 16, 665–670, DOI:10.1007/s10311-017-0695-2.
- A. R. K. Gollakota, V. Volli and C. M. Shu, Transesterification of waste cooking oil using pyrolysis residue supported eggshell catalyst, Sci. Total Environ., 2019, 661, 316–325, DOI:10.1016/j.scitotenv.2019.01.165.
- Y. Ma, Q. Wang, X. Sun, C. Wu and Z. Gao, Kinetics studies of biodiesel production from waste cooking oil using FeCl3-modified resin as heterogeneous catalyst, Renewable Energy, 2017, 107, 522–530, DOI:10.1016/j.renene.2017.02.007.
- M. K. Lam and K. T. Lee, Mixed methanol-ethanol technology to produce greener biodiesel from waste cooking oil: A breakthrough for SO42-/SnO 2-SiO2 catalyst, Fuel Process. Technol., 2011, 92, 1639–1645, DOI:10.1016/j.fuproc.2011.04.012.
- N. S. Lani, N. Ngadi, N. Y. Yahya and R. A. Rahman, Synthesis, characterization and performance of silica impregnated calcium oxide as heterogeneous catalyst in biodiesel production, J. Cleaner Prod., 2017, 146, 116–124, DOI:10.1016/j.jclepro.2016.06.058.
- N. L. Muna, A. A. Mu'alimah, D. B. Pridiana, A. K. Widodo, S. R. Adiyar and E. H. Elinda, The production of biodiesel from waste cooking oil (Simultaneous esterification and transesterification using fe/zeolite catalysts from waste geothermal), Mater. Sci. Forum, 2020, 990, 161–167, DOI:10.4028/www.scientific.net/MSF.990.161.
- T. S. Singh and T. N. Verma, Taguchi design approach for extraction of methyl ester from waste cooking oil using synthesized CaO as heterogeneous catalyst: Response surface methodology optimization, Energy Convers. Manage., 2019, 182, 383–397, DOI:10.1016/j.enconman.2018.12.077.
- A. R. Gupta and V. K. Rathod, Waste cooking oil and waste chicken eggshells derived solid base catalyst for the biodiesel production: Optimization and kinetics, Waste Manage., 2018, 79, 169–178, DOI:10.1016/j.wasman.2018.07.022.
- A. R. Gupta, S. V. Yadav and V. K. Rathod, Enhancement in biodiesel production using waste cooking oil and calcium diglyceroxide as a heterogeneous catalyst in presence of ultrasound, Fuel, 2015, 158, 800–806, DOI:10.1016/j.fuel.2015.05.064.
- U. Jamil, A. Husain Khoja, R. Liaquat, S. Raza Naqvi, W. Nor Nadyaini Wan Omar and N. Aishah Saidina Amin, Copper and calcium-based metal organic framework (MOF) catalyst for biodiesel production from waste cooking oil: A process optimization study, Energy Convers. Manage., 2020, 215, 112934, DOI:10.1016/j.enconman.2020.112934.
- S. Kaewdaeng, P. Sintuya and R. Nirunsin, Biodiesel production using calcium oxide from river snail shell ash as catalyst, Energy Procedia, 2017, 138, 937–942, DOI:10.1016/j.egypro.2017.10.057.
- M. Mokhatr Mohamed and H. El-Faramawy, An innovative nanocatalyst α-Fe2O3/AlOOH processed from gibbsite rubbish ore for efficient biodiesel production via utilizing cottonseed waste oil, Fuel, 2021, 297, 120741, DOI:10.1016/j.fuel.2021.120741.
- K. Wang, J. Jiang, Z. Si and X. Liang, Biodiesel production from waste cooking oil catalyzed by solid acid SO 42-/TiO2/La3+, J. Renewable Sustainable Energy, 2013, 5, 4820563, DOI:10.1063/1.4820563.
- S. Niju, M. M. M. S. Begum and N. Anantharaman, Modification of egg shell and its application in biodiesel production, J. Saudi Chem. Soc., 2014, 18, 702–706, DOI:10.1016/j.jscs.2014.02.010.
- S. Sirisomboonchai, M. Abuduwayiti, G. Guan, C. Samart, S. Abliz, X. Hao, K. Kusakabe and A. Abudula, Biodiesel production from waste cooking oil using calcined scallop shell as catalyst, Energy Convers. Manage., 2015, 95, 242–247, DOI:10.1016/j.enconman.2015.02.044.
- I. M. Rashid, M. A. Atiya and B. H. Hameed, Production of Biodiesel from Waste Cooking Oil using Cao-Egg Shell Waste Derived Heterogeneous Catalyst, Int. J. Sci. Res., 2017, 6, 94–103, DOI:10.21275/art20177723.
- K. Seffati, H. Esmaeili, B. Honarvar and N. Esfandiari, AC/CuFe2O4@CaO as a novel nanocatalyst to produce biodiesel from chicken fat, Renewable Energy, 2020, 147, 25–34, DOI:10.1016/j.renene.2019.08.105.
- N. A. F. A. Zik, S. Sulaiman and P. Jamal, Biodiesel production from waste cooking oil using calcium oxide/nanocrystal cellulose/polyvinyl alcohol catalyst in a packed bed reactor, Renewable Energy, 2020, 155, 267–277, DOI:10.1016/j.renene.2020.03.144.
- A. H. Al-Muhtaseb, F. Jamil, M. T. Z. Myint, M. Baawain, M. Al-Abri, T. N. B. Dung, G. Kumar and M. N. M. Ahmad, Cleaner fuel production from waste Phoenix dactylifera L. kernel oil in the presence of a bimetallic catalyst: Optimization and kinetics study, Energy Convers. Manage., 2017, 146, 195–204, DOI:10.1016/j.enconman.2017.05.035.
- W. J. Cong, Y. T. Wang, H. Li, Z. Fang, J. Sun, H. T. Liu, J. T. Liu, S. Tang and L. Xu, Direct production of biodiesel from waste oils with a strong solid base from alkalized industrial clay ash, Appl. Energy, 2020, 264, 114735, DOI:10.1016/j.apenergy.2020.114735.
- Z. Hajamini, M. A. Sobati, S. Shahhosseini and B. Ghobadian, Waste fish oil (WFO) esterification catalyzed by sulfonated activated carbon under ultrasound irradiation, Appl. Therm. Eng., 2016, 94, 141–150, DOI:10.1016/j.applthermaleng.2015.10.101.
- I. Simbi, U. O. Aigbe, O. Oyekola and O. A. Osibote, Optimization of biodiesel produced from waste sunflower cooking oil over bi-functional catalyst, Results Eng., 2022, 13, 100374, DOI:10.1016/j.rineng.2022.100374.
- B. Esther Olubunmi, A. Fatai Alade, S. Ogbeide Ebhodaghe and O. Tokunbo Oladapo, Optimization and kinetic study of biodiesel production from beef tallow using calcium oxide as a heterogeneous and recyclable catalyst, Energy Convers. Manage.: X, 2022, 14, 100221, DOI:10.1016/j.ecmx.2022.100221.
- A. N. Amenaghawon, K. Obahiagbon, V. Isesele and F. Usman, Optimized biodiesel production from waste cooking oil using a functionalized bio-based heterogeneous catalyst, Cleaner Eng. Technol., 2022, 8, 100501, DOI:10.1016/j.clet.2022.100501.
- B. Hazmi, U. Rashid, M. L. Ibrahim, I. A. Nehdi, M. Azam and S. I. Al-Resayes, Synthesis and characterization of bifunctional magnetic nano-catalyst from rice husk for production of biodiesel, Environ. Technol. Innovation, 2021, 21, 101296, DOI:10.1016/j.eti.2020.101296.
- M. A. Zahed, M. Revayati, N. Shahcheraghi, F. Maghsoudi and Y. Tabari, Modeling and optimization of biodiesel synthesis using TiO2–ZnO nanocatalyst and characteristics of biodiesel made from waste sunflower oil, Curr. Res. Green Sustainable Chem., 2021, 4, 100223, DOI:10.1016/j.crgsc.2021.100223.
- F. Yazdani, M. Akia, F. Khanbolouk, H. Hamze and H. Arandiyan, Novel heterogeneous base nanocatalysts supported on a spray dried gamma alumina applying optimized production of biodiesel from waste cooking oil, Biofuels, 2021, 12, 1275–1281, DOI:10.1080/17597269.2019.1613749.
- A. Inayat, F. Jamil, M. Raza, S. Khurram, C. Ghenai and A. H. Al-Muhatseb, Upgradation of waste cooking
oil to biodiesel in the presence of green catalyst derived from date seeds, Biofuels, 2021, 12, 1245–1250, DOI:10.1080/17597269.2019.1608036.
- N. N. Ramlee, R. Md Illias, S. Toemen, N. H. Abdul Manas and N. I. Wan Azelee, Esterification of a waste cooking oil using metal-hybrid catalysts for chemoenzymatic reactions, Mater. Today: Proc., 2020, 47, 1280–1286, DOI:10.1016/j.matpr.2021.02.795.
- R. Foroutan, R. Mohammadi, J. Razeghi and B. Ramavandi, Biodiesel production from edible oils using algal biochar/CaO/K2CO3 as a heterogeneous and recyclable catalyst, Renewable Energy, 2021, 168, 1207–1216, DOI:10.1016/j.renene.2020.12.094.
- S. Wang, Y. Xue, X. Zhao and H. Yuan, Preparation of a carbon microsphere–based solid acid application to waste frying oil transesterification, Diamond Relat. Mater., 2021, 116, 108420, DOI:10.1016/j.diamond.2021.108420.
- J. Boro, L. J. Konwar, A. J. Thakur and D. Deka, Ba doped CaO derived from waste shells of T striatula (TS-CaO) as heterogeneous catalyst for biodiesel production, Fuel, 2014, 129, 182–187, DOI:10.1016/j.fuel.2014.03.067.
- E. M. Vargas, M. C. Neves, L. A. C. Tarelho and M. I. Nunes, Solid catalysts obtained from wastes for FAME production using mixtures of refined palm oil and waste cooking oils, Renewable Energy, 2019, 136, 873–883, DOI:10.1016/j.renene.2019.01.048.
- N. Boz, N. Degirmenbasi and D. M. Kalyon, Esterification and transesterification of waste cooking oil over Amberlyst 15 and modified Amberlyst 15 catalysts, Appl. Catal., B, 2015, 165, 723–730, DOI:10.1016/j.apcatb.2014.10.079.
- A. Bayat, M. Baghdadi and G. N. Bidhendi, Tailored magnetic nano-alumina as an efficient catalyst for transesterification of waste cooking oil: Optimization of biodiesel production using response surface methodology, Energy Convers. Manage., 2018, 177, 395–405, DOI:10.1016/j.enconman.2018.09.086.
- J. Li and X. Liang, Magnetic solid acid catalyst for biodiesel synthesis from waste oil, Energy Convers. Manage., 2017, 141, 126–132, DOI:10.1016/j.enconman.2016.06.072.
- A. S. Rad, M. H. Nia, F. Ardestani and H. Nayebzadeh, Esterification of Waste Chicken Fat: Sulfonated MWCNT Toward Biodiesel Production, Waste Biomass Valorization, 2018, 9, 591–599, DOI:10.1007/s12649-016-9732-9.
- I. Thushari and S. Babel, Sustainable utilization of waste palm oil and sulfonated carbon catalyst derived from coconut meal residue for biodiesel production, Bioresour. Technol., 2018, 248, 199–203, DOI:10.1016/j.biortech.2017.06.106.
- S. Rezania, M. A. Kamboh, S. S. Arian, N. A. Al-Dhabi, M. V. Arasu, G. A. Esmail and K. Kumar Yadav, Conversion of waste frying oil into biodiesel using recoverable nanocatalyst based on magnetic graphene oxide supported ternary mixed metal oxide nanoparticles, Bioresour. Technol., 2021, 323, 124561, DOI:10.1016/j.biortech.2020.124561.
- B. H. Jume, M. A. Gabris, H. Rashidi Nodeh, S. Rezania and J. Cho, Biodiesel production from waste cooking oil using a novel heterogeneous catalyst based on graphene oxide doped metal oxide nanoparticles, Renewable Energy, 2020, 162, 2182–2189, DOI:10.1016/j.renene.2020.10.046.
- Q. Shu, J. Gao, Z. Nawaz, Y. Liao, D. Wang and J. Wang, Synthesis of biodiesel from waste vegetable oil with large amounts of free fatty acids using a carbon-based solid acid catalyst, Appl. Energy, 2010, 87, 2589–2596, DOI:10.1016/j.apenergy.2010.03.024.
- M. J. Borah, A. Devi, R. A. Saikia and D. Deka, Biodiesel production from waste cooking oil catalyzed by in-situ decorated TiO2 on reduced graphene oxide nanocomposite, Energy, 2018, 158, 881–889, DOI:10.1016/j.energy.2018.06.079.
- Z. Wen, X. Yu, S. T. Tu, J. Yan and E. Dahlquist, Biodiesel production from waste cooking oil catalyzed by TiO2-MgO mixed oxides, Bioresour. Technol., 2010, 101, 9570–9576, DOI:10.1016/j.biortech.2010.07.066.
- S. Rezania, Z. S. Korrani, M. A. Gabris, J. Cho, K. K. Yadav, M. M. S. Cabral-Pinto, J. Alam, M. Ahamed and H. R. Nodeh, Lanthanum phosphate foam as novel heterogeneous nanocatalyst for biodiesel production from waste cooking oil, Renewable Energy, 2021, 176, 228–236, DOI:10.1016/j.renene.2021.05.060.
- M. Roy and K. Mohanty, Valorization of de-oiled microalgal biomass as a carbon-based heterogeneous catalyst for a sustainable biodiesel production, Bioresour. Technol., 2021, 337, 125424, DOI:10.1016/j.biortech.2021.125424.
- T. Tamoradi, A. R. Kiasat, H. Veisi, V. Nobakht, Z. Besharati and B. Karmakar, MgO doped magnetic graphene derivative as a competent heterogeneous catalyst producing biofuels via transesterification: Process optimization through Response Surface Methodology (RSM), J. Environ. Chem. Eng., 2021, 9, 106009, DOI:10.1016/j.jece.2021.106009.
- A. Molaei Dehkordi and M. Ghasemi, Transesterification of waste cooking oil to biodiesel using Ca and Zr mixed oxides as heterogeneous base catalysts, Fuel Process. Technol., 2012, 97, 45–51, DOI:10.1016/j.fuproc.2012.01.010.
- W. Y. Lou, Q. Guo, W. J. Chen, M. H. Zong, H. Wu and T. J. Smith, A highly active bagasse-derived solid acid catalyst with properties suitable for production of biodiesel, ChemSusChem, 2012, 5, 1533–1541, DOI:10.1002/cssc.201100811.
- M. Li, Y. Zheng, Y. Chen and X. Zhu, Biodiesel production from waste cooking oil using a heterogeneous catalyst from pyrolyzed rice husk, Bioresour. Technol., 2014, 154, 345–348, DOI:10.1016/j.biortech.2013.12.070.
- G. Chen and B. Fang, Preparation of solid acid catalyst from glucose-starch mixture for biodiesel production, Bioresour. Technol., 2011, 102, 2635–2640, DOI:10.1016/j.biortech.2010.10.099.
- M. Afsharizadeh and M. Mohsennia, Catalytic synthesis of biodiesel from waste cooking oil and corn oil over zirconia-based metal oxide nanocatalysts, React. Kinet., Mech. Catal., 2019, 128, 443–459, DOI:10.1007/s11144-019-01622-9.
- D. A. Kamel, H. A. Farag, N. K. Amin and Y. O. Fouad, Biodiesel synthesis from non-edible oils by transesterification using the activated carbon as heterogeneous catalyst, Int. J. Environ. Sci. Technol., 2017, 14, 785–794, DOI:10.1007/s13762-016-1184-z.
- M. Gohain, K. Laskar, A. K. Paul, N. Daimary, M. Maharana, I. K. Goswami, A. Hazarika, U. Bora and D. Deka, Carica papaya stem: A source of versatile heterogeneous catalyst for biodiesel production and C–C bond formation, Renewable Energy, 2020, 147, 541–555, DOI:10.1016/j.renene.2019.09.016.
- S. Niju, R. Rabia, K. Sumithra Devi, M. Naveen Kumar and M. Balajii, Modified Malleus malleus Shells for Biodiesel Production from Waste Cooking Oil: An Optimization Study Using Box–Behnken Design, Waste Biomass Valorization, 2020, 11, 793–806, DOI:10.1007/s12649-018-0520-6.
- W. Roschat, M. Kacha, B. Yoosuk, T. Sudyoadsuk and V. Promarak, Biodiesel production based on heterogeneous process catalyzed by solid waste coral fragment, Fuel, 2012, 98, 194–202, DOI:10.1016/j.fuel.2012.04.009.
- N. Mansir, S. H. Teo, U. Rashid and Y. H. Taufiq-Yap, Efficient waste Gallus domesticus shell derived calcium-based catalyst for biodiesel production, Fuel, 2018, 211, 67–75, DOI:10.1016/j.fuel.2017.09.014.
- M. Gohain, A. Devi and D. Deka, Musa balbisiana Colla peel as highly effective renewable heterogeneous base catalyst for biodiesel production, Ind. Crops Prod., 2017, 109, 8–18, DOI:10.1016/j.indcrop.2017.08.006.
- A. Aitlaalim, F. Ouanji, A. Benzaouak, M. El Mahi, E. M. Lotfi, M. Kacimi and L. F. Liotta, Utilization of waste grooved razor shell (Grs) as a catalyst in biodiesel production from refined and waste cooking oils, Catalysts, 2020, 10, 1–17, DOI:10.3390/catal10060703.
- A. P. Bora, L. D. N. V. V. Konda, S. Pasupuleti and K. S. Durbha, Synthesis of MgO/MgSO4 nanocatalyst by thiourea–nitrate solution combustion for biodiesel production from waste cooking oil, Renewable Energy, 2022, 190, 474–486, DOI:10.1016/j.renene.2022.03.127.
- A. Bahadoran, S. Ramakrishna, B. Oryani, L. Ahmed Al-Keridis, H. Rashidi Nodeh and S. Rezania, Biodiesel production from waste cooking oil using heterogeneous nanocatalyst-based magnetic polyaniline decorated with cobalt oxide, Fuel, 2022, 319, 123858, DOI:10.1016/j.fuel.2022.123858.
- S. Xia, J. Li, G. Chen, J. Tao, W. Li and G. Zhu, Magnetic reusable acid-base bifunctional Co doped Fe2O3–CaO nanocatalysts for biodiesel production from soybean oil and waste frying oil, Renewable Energy, 2022, 189, 421–434, DOI:10.1016/j.renene.2022.02.122.
- N. A. Ibrahim, U. Rashid, B. Hazmi, B. R. Moser, F. A. Alharthi, S. L. Rokhum and C. Ngamcharussrivichai, Biodiesel production from waste cooking oil using magnetic bifunctional calcium and iron oxide nanocatalysts derived from empty fruit bunch, Fuel, 2022, 317, 123525, DOI:10.1016/j.fuel.2022.123525.
- N. Kosinov, C. Liu, E. J. M. Hensen and E. A. Pidko, Engineering of Transition Metal Catalysts Confined in Zeolites, Chem. Mater., 2018, 30, 3177–3198, DOI:10.1021/acs.chemmater.8b01311.
- R. Qin, P. Liu, G. Fu and N. Zheng, Strategies for Stabilizing Atomically Dispersed Metal Catalysts, Small Methods, 2018, 2, 1–21, DOI:10.1002/smtd.201700286.
- B. Aghel, A. Gouran and F. Nasirmanesh, Transesterification of waste cooking oil using clinoptilolite/industrial phosphoric waste as green and environmental catalysts, Energy, 2022, 244, 123138, DOI:10.1016/j.energy.2022.123138.
- J. A. Tavizón-Pozos, G. Chavez-Esquivel, V. A. Suárez-Toriello, C. E. Santolalla-Vargas, O. A. Luévano-Rivas, O. U. Valdés-Martínez, A. Talavera-López and J. A. Rodriguez, State of art of alkaline earth metal oxides catalysts used in the transesterification of oils for biodiesel production, Energies, 2021, 14, 1–24, DOI:10.3390/en14041031.
- F. Jamil, P. S. Murphin Kumar, L. Al-Haj, M. Tay Zar Myint and A. H. Al-Muhtaseb, Heterogeneous carbon-based catalyst modified by alkaline earth metal oxides for biodiesel production: Parametric and kinetic study, Energy Convers. Manage.: X, 2021, 10, 100047, DOI:10.1016/j.ecmx.2020.100047.
- C. L. Chen, C. C. Huang, D. T. Tran and J. S. Chang, Biodiesel synthesis via heterogeneous catalysis using modified strontium oxides as the catalysts, Bioresour. Technol., 2012, 113, 8–13, DOI:10.1016/j.biortech.2011.12.142.
- S. Yan, H. Lu and B. Liang, Supported CaO catalysts used in the transesterification of rapeseed oil for the purpose of biodiesel production, Energy Fuels, 2008, 22, 646–651, DOI:10.1021/ef070105o.
- S. Gryglewicz, Simulateur EIRL Notice et exemple commenté, 2011, vol. 70, pp. 1–16 Search PubMed.
- H. Li, S. Niu, C. Lu and J. Li, Calcium oxide functionalized with strontium as heterogeneous transesterification catalyst for biodiesel production, Fuel, 2016, 176, 63–71, DOI:10.1016/j.fuel.2016.02.067.
- Y. H. Taufiq-Yap, S. H. Teo, U. Rashid, A. Islam, M. Z. Hussien and K. T. Lee, Transesterification of Jatropha curcas crude oil to biodiesel on calcium lanthanum mixed oxide catalyst: Effect of stoichiometric composition, Energy Convers. Manage., 2014, 88, 1290–1296, DOI:10.1016/j.enconman.2013.12.075.
- M. Mohadesi, Z. Hojabri and G. Moradi, Biodiesel production using alkali earth metal oxides catalysts synthesized by sol-gel method, Biofuel Res. J., 2014, 1, 30–33, DOI:10.18331/BRJ2015.1.1.7.
- A. Islam, Y. H. Taufiq-Yap, C. M. Chu, E. S. Chan and P. Ravindra, Studies on design of heterogeneous catalysts for biodiesel production, Process Saf. Environ. Prot., 2013, 91, 131–144, DOI:10.1016/j.psep.2012.01.002.
- L. J. Konwar, J. Boro and D. Deka, Review on latest developments in biodiesel production using carbon-based catalysts, Renewable Sustainable Energy Rev., 2014, 29, 546–564, DOI:10.1016/j.rser.2013.09.003.
- Y. S. Erchamo, T. T. Mamo, G. A. Workneh and Y. S. Mekonnen, Improved biodiesel production from waste cooking oil with mixed methanol–ethanol using enhanced eggshell-derived CaO nano-catalyst, Sci. Rep., 2021, 11, 1–12, DOI:10.1038/s41598-021-86062-z.
- S. Sahani, T. Roy and Y. C. Sharma, Smart waste management of waste cooking oil for large scale high quality biodiesel production using Sr-Ti mixed metal oxide as solid catalyst: Optimization and E-metrics studies, Waste Manage., 2020, 108, 189–201, DOI:10.1016/j.wasman.2020.04.036.
- A. Chakrabarti and M. M. Sharma, Cationic ion exchange resins as catalyst, React. Polym., 1993, 20, 1–45, DOI:10.1016/0923-1137(93)90064-M.
- G. Gelbard, Organic synthesis by catalysis with ion-exchange resins, Ind. Eng. Chem. Res., 2005, 44, 8468–8498, DOI:10.1021/ie0580405.
- P. Of, M. J. Astle, J. A. Zaslowsky, and P. G. Lafyatis, Catalysis with Cation-Exchange Resins, 1954 Search PubMed.
- G. D. Yadav and M. B. Thathagar, Esterification of maleic acid with ethanol over cation-exchange resin catalysts, React. Funct. Polym., 2002, 52, 99–110, DOI:10.1016/S1381-5148(02)00086-X.
- R. Hartono, B. Mulia, M. Sahlan, T. S. Utami, A. Wijanarko and H. Hermansyah, The modification of ion exchange heterogeneous catalysts for biodiesel synthesis, AIP Conf. Proc., 2017, 1826, 020020, DOI:10.1063/1.4979236.
- L. Yun and W. Ling, Bio-diesel preparation from waste oil using cation exchange resin as heterogeneous catalyst, Chem. Technol. Fuels Oils, 2009, 45, 417–424, DOI:10.1007/s10553-010-0167-x.
- N. Shibasaki-Kitakawa, K. Hiromori, T. Ihara, K. Nakashima and T. Yonemoto, Production of high quality biodiesel from waste acid oil obtained during edible oil refining using ion-exchange resin catalysts, Fuel, 2015, 139, 11–17, DOI:10.1016/j.fuel.2014.08.024.
- F. Chang, Q. Zhou, H. Pan, X. F. Liu, H. Zhang, W. Xue and S. Yang, Solid Mixed-Metal-Oxide Catalysts for Biodiesel Production: A Review, Energy Technol., 2014, 2, 865–873, DOI:10.1002/ente.201402089.
- A. P. S. Dias, J. Bernardo, P. Felizardo and M. J. N. Correia, Biodiesel production by soybean oil methanolysis over SrO/MgO catalysts: The relevance of the catalyst granulometry, Fuel Process. Technol., 2012, 102, 146–155, DOI:10.1016/j.fuproc.2012.04.039.
- V. Enguilo Gonzaga, R. Romero, R. M. Gómez-Espinosa, A. Romero, S. L. Martínez and R. Natividad, Biodiesel Production from Waste Cooking Oil Catalyzed by a Bifunctional Catalyst, ACS Omega, 2021, 6, 24092–24105, DOI:10.1021/acsomega.1c03586.
- H. V. Lee, J. C. Juan, T. Y. Yun Hin and H. C. Ong, Environment-friendly heterogeneous alkaline-Based mixed metal oxide catalysts for biodiesel production, Energies, 2016, 9(8), 611, DOI:10.3390/en9080611.
- Z. Wen, X. Yu, S. T. Tu, J. Yan and E. Dahlquist, Biodiesel production from waste cooking oil catalyzed by TiO2-MgO mixed oxides, Bioresour. Technol., 2010, 101, 9570–9576, DOI:10.1016/j.biortech.2010.07.066.
- S. Rezania, M. A. Kamboh, S. S. Arian, N. A. Al-Dhabi, M. V. Arasu, G. A. Esmail and K. Kumar Yadav, Conversion of waste frying oil into biodiesel using recoverable nanocatalyst based on magnetic graphene oxide supported ternary mixed metal oxide nanoparticles, Bioresour. Technol., 2021, 323, 124561, DOI:10.1016/j.biortech.2020.124561.
- E. I. García-López, G. Marcì, I. Krivtsov, J. Casado Espina, L. F. Liotta and A. Serrano, Local Structure of Supported Keggin and Wells-Dawson Heteropolyacids and Its Influence on the Catalytic Activity, J. Phys. Chem. C, 2019, 123, 19513–19527, DOI:10.1021/acs.jpcc.9b03659.
- F. Esmi, V. B. Borugadda and A. K. Dalai, Heteropoly acids as supported solid acid catalysts for sustainable biodiesel production using vegetable oils: A review, Catal. Today, 2022, 404, 19–34, DOI:10.1016/j.cattod.2022.01.019.
- Y. C. Sharma, B. Singh and S. N. Upadhyay, Advancements in development and characterization of biodiesel: A review, Fuel, 2008, 87, 2355–2373, DOI:10.1016/j.fuel.2008.01.014.
- M. A. Hanif, S. Nisar and U. Rashid, Supported solid and heteropoly acid catalysts for production of biodiesel, Catal. Rev.: Sci. Eng., 2017, 59, 165–188, DOI:10.1080/01614940.2017.1321452.
- A. I. Tropecêlo, M. H. Casimiro, I. M. Fonseca, A. M. Ramos, J. Vital and J. E. Castanheiro, Esterification of free fatty acids to biodiesel over heteropolyacids immobilized on mesoporous silica, Appl. Catal., A, 2010, 390, 183–189, DOI:10.1016/j.apcata.2010.10.007.
- N. Narkhede, V. Brahmkhatri and A. Patel, Efficient synthesis of biodiesel from waste cooking oil using solid acid catalyst comprising 12-tungstosilicic acid and SBA-15, Fuel, 2014, 135, 253–261, DOI:10.1016/j.fuel.2014.06.062.
- A. Talebian-Kiakalaieh, N. A. S. Amin, A. Zarei and I. Noshadi, Transesterification of waste cooking oil by heteropoly acid (HPA) catalyst: Optimization and kinetic model, Appl. Energy, 2013, 102, 283–292, DOI:10.1016/j.apenergy.2012.07.018.
- C. Zou, P. Zhao, L. Shi, S. Huang and P. Luo, Biodiesel fuel production from waste cooking oil by the inclusion complex of heteropoly acid with bridged bis-cyclodextrin, Bioresour. Technol., 2013, 146, 785–788, DOI:10.1016/j.biortech.2013.07.149.
- F. Cao, Y. Chen, F. Zhai, J. Li, J. Wang, X. Wang, S. Wang and W. Zhu, Biodiesel production from high acid value waste frying oil catalyzed by superacid heteropolyacid, Biotechnol. Bioeng., 2008, 101, 93–100, DOI:10.1002/bit.21879.
- V. Vinu and N. N. Binitha, Lithium silicate based catalysts prepared using arecanut husk ash for biodiesel production from used cooking oil, Mater. Today: Proc., 2019, 25, 241–245, DOI:10.1016/j.matpr.2020.01.210.
- H. M. Khan, T. Iqbal, C. H. Ali, S. Yasin and F. Jamil, Waste quail beaks as renewable source for synthesizing novel catalysts for biodiesel production, Renewable Energy, 2020, 154, 1035–1043, DOI:10.1016/j.renene.2020.03.079.
- N. A. F. A. Zik, S. Sulaiman and P. Jamal, Biodiesel production from waste cooking oil using calcium oxide/nanocrystal cellulose/polyvinyl alcohol catalyst in a packed bed reactor, Renewable Energy, 2020, 155, 267–277, DOI:10.1016/j.renene.2020.03.144.
- S. Parida, M. Singh and S. Pradhan, Biomass wastes: A potential catalyst source for biodiesel production, Bioresour. Technol. Rep., 2022, 18, 101081, DOI:10.1016/j.biteb.2022.101081.
- R. Bharti, A. Guldhe, D. Kumar and B. Singh, Solar irradiation assisted synthesis of biodiesel from waste cooking oil using calcium oxide derived from chicken eggshell, Fuel, 2020, 273, 117778, DOI:10.1016/j.fuel.2020.117778.
- M. F. F. Kamaronzaman, H. Kahar, N. Hassan, M. F. Hanafi and N. Sapawe, Biodiesel production from waste cooking oil using nickel doped onto eggshell catalyst, Mater. Today: Proc., 2020, 31, 342–346, DOI:10.1016/j.matpr.2020.06.159.
- M. D. Putra, C. Irawan, Udiantoro, Y. Ristianingsih and I. F. Nata, A cleaner process for biodiesel production from waste cooking oil using waste materials as a heterogeneous catalyst and its kinetic study, J. Cleaner Prod., 2018, 195, 1249–1258, DOI:10.1016/j.jclepro.2018.06.010.
- R. M. Mohamed, G. A. Kadry, H. A. Abdel-Samad and M. E. Awad, High operative heterogeneous catalyst in biodiesel production from waste cooking
oil, Egypt. J. Pet., 2020, 29, 59–65, DOI:10.1016/j.ejpe.2019.11.002.
- T. Roy, S. Sahani, D. Madhu and Y. Chandra Sharma, A clean approach of biodiesel production from waste cooking oil by using single phase BaSnO3 as solid base catalyst: Mechanism, kinetics & E-study, J. Cleaner Prod., 2020, 265, 121440, DOI:10.1016/j.jclepro.2020.121440.
- J. Gardy, A. Hassanpour, X. Lai, M. H. Ahmed and M. Rehan, Biodiesel production from used cooking oil using a novel surface functionalised TiO2 nano-catalyst, Appl. Catal., B, 2017, 207, 297–310, DOI:10.1016/j.apcatb.2017.01.080.
- I. Raheem, M. N. Bin Mohiddin, Y. H. Tan, J. Kansedo, N. M. Mubarak, M. O. Abdullah and M. L. Ibrahim, A review on influence of reactor technologies and kinetic studies for biodiesel application, J. Ind. Eng. Chem., 2020, 91, 54–68, DOI:10.1016/j.jiec.2020.08.024.
- Z. Yaakob, M. Mohammad, M. Alherbawi, Z. Alam and K. Sopian, Overview of the production of biodiesel from Waste cooking oil, Renewable Sustainable Energy Rev., 2013, 18, 184–193, DOI:10.1016/j.rser.2012.10.016.
- A. S. Yusuff, A. K. Bhonsle, D. P. Bangwal and N. Atray, Development of a barium-modified zeolite catalyst for biodiesel production from waste frying oil: Process optimization by design of experiment, Renewable Energy, 2021, 177, 1253–1264, DOI:10.1016/j.renene.2021.06.039.
- M. R. Abukhadra, M. G. Basyouny, A. M. El-Sherbeeny, M. A. El-Meligy and A. E. E. Abd Elgawad, Transesterification of commercial waste cooking oil into biodiesel over innovative alkali trapped zeolite nanocomposite as green and environmental catalysts, Sustainable Chem. Pharm., 2020, 17, 100289, DOI:10.1016/j.scp.2020.100289.
- M. G. Basyouny, M. R. Abukhadra, K. Alkhaledi, A. M. El-Sherbeeny, M. A. El-Meligy, A. T. A. Soliman and M. Luqman, Insight into the catalytic transformation of the waste products of some edible oils (corn oil and palm oil) into biodiesel using MgO/clinoptilolite green nanocomposite, Mol. Catal., 2021, 500, 111340, DOI:10.1016/j.mcat.2020.111340.
- M. Agarwal, G. Chauhan, S. P. Chaurasia and K. Singh, Study of catalytic behavior of KOH as homogeneous and heterogeneous catalyst for biodiesel production, J. Taiwan Inst. Chem. Eng., 2012, 43, 89–94, DOI:10.1016/j.jtice.2011.06.003.
- O. A. Falowo, O. E. Apanisile, A. O. Aladelusi, A. E. Adeleke, M. A. Oke, A. Enamhanye, L. M. Latinwo and E. Betiku, Influence of nature of catalyst on biodiesel synthesis via irradiation-aided transesterification of waste cooking oil-honne seed oil blend: Modeling and optimization by Taguchi design method, Energy Convers. Manage.: X, 2021, 12, 100119, DOI:10.1016/j.ecmx.2021.100119.
- T. E. Odetoye, J. O. Agu and E. O. Ajala, Biodiesel production from poultry wastes: Waste chicken fat and eggshell, J. Environ. Chem. Eng., 2021, 9, 105654, DOI:10.1016/j.jece.2021.105654.
- A. Molaei Dehkordi and M. Ghasemi, Transesterification of waste cooking oil to biodiesel using Ca and Zr mixed oxides as heterogeneous base catalysts, Fuel Process. Technol., 2012, 97, 45–51, DOI:10.1016/j.fuproc.2012.01.010.
- I. Noshadi, N. A. S. Amin and R. S. Parnas, Continuous production of biodiesel from waste cooking oil in a reactive distillation column catalyzed by solid heteropolyacid: Optimization using response surface methodology (RSM), Fuel, 2012, 94, 156–164, DOI:10.1016/j.fuel.2011.10.018.
- A. Naeem, I. Wali Khan, M. Farooq, T. Mahmood, I. Ud Din, Z. Ali Ghazi and T. Saeed, Kinetic and optimization study of sustainable biodiesel production from waste cooking oil using novel heterogeneous solid base catalyst, Bioresour. Technol., 2021, 328, 124831, DOI:10.1016/j.biortech.2021.124831.
- M. G. Basyouny, M. R. Abukhadra, K. Alkhaledi, A. M. El-Sherbeeny, M. A. El-Meligy, A. T. A. Soliman and M. Luqman, Insight into the catalytic transformation of the waste products of some edible oils (corn oil and palm oil) into biodiesel using MgO/clinoptilolite green nanocomposite, Mol. Catal., 2021, 500, 111340, DOI:10.1016/j.mcat.2020.111340.
- A. B. Fadhil, E. T. B. Al-Tikrity and M. A. Albadree, Biodiesel production from mixed non-edible oils, castor seed oil and waste fish oil, Fuel, 2017, 210, 721–728, DOI:10.1016/j.fuel.2017.09.009.
- S. H. Dhawane, T. Kumar and G. Halder, Biodiesel synthesis from Hevea brasiliensis oil employing carbon supported heterogeneous catalyst: Optimization by Taguchi method, Renewable Energy, 2016, 89, 506–514, DOI:10.1016/j.renene.2015.12.027.
- B. Karmakar and G. Halder, Accelerated conversion of waste cooking oil into biodiesel by injecting 2-propanol and methanol under superheated conditions: A novel approach, Energy Convers. Manage., 2021, 247, 114733, DOI:10.1016/j.enconman.2021.114733.
- A. Al-Saadi, B. Mathan and Y. He, Biodiesel production via simultaneous transesterification and esterification reactions over SrO–ZnO/Al2O3 as a bifunctional catalyst using high acidic waste cooking oil, Chem. Eng. Res. Des., 2020, 162, 238–248, DOI:10.1016/j.cherd.2020.08.018.
- F. Li, M. J. Hülsey, N. Yan, Y. Dai and C. H. Wang, Co-transesterification of waste cooking oil, algal oil and dimethyl carbonate over sustainable nanoparticle catalysts, Chem. Eng. J., 2021, 405, 127036, DOI:10.1016/j.cej.2020.127036.
- F. H. Alhassan, U. Rashid and Y. H. Taufiq-Yap, Synthesis of waste cooking oil-based biodiesel via effectual recyclable bi-functional Fe2O3MnOSO42-/ZrO2 nanoparticle solid catalyst, Fuel, 2015, 142, 38–45, DOI:10.1016/j.fuel.2014.10.038.
- J. V. Sree, B. A. Chowdary, K. S. Kumar, M. P. Anbazhagan and S. Subramanian, Optimization of the biodiesel production from waste cooking oil using homogeneous catalyst and heterogeneous catalysts, Mater. Today: Proc., 2019, 46, 4900–4908, DOI:10.1016/j.matpr.2020.10.332.
- T. Maneerung, S. Kawi, Y. Dai and C. H. Wang, Sustainable biodiesel production via transesterification of waste cooking oil by using CaO catalysts prepared from chicken manure, Energy Convers. Manage., 2016, 123, 487–497, DOI:10.1016/j.enconman.2016.06.071.
- E. Soria-Figueroa, V. Y. Mena-Cervantes, M. García-Solares, R. Hernández-Altamirano and J. Vazquez-Arenas, Statistical optimization of biodiesel production from waste cooking oil using CaO as catalyst in a Robinson-Mahoney type reactor, Fuel, 2020, 282, 118853, DOI:10.1016/j.fuel.2020.118853.
- J. Milano, H. C. Ong, H. H. Masjuki, A. S. Silitonga, W. H. Chen, F. Kusumo, S. Dharma and A. H. Sebayang, Optimization of biodiesel production by microwave irradiation-assisted transesterification for waste cooking oil-Calophyllum inophyllum oil via response surface methodology, Energy Convers. Manage., 2018, 158, 400–415, DOI:10.1016/j.enconman.2017.12.027.
- P. Harisha, B. N. Anil Kumar, S. R. Tilak and C. Ganesh, Production and optimization of biodiesel from composite Pongamia oil, animal fat oil and waste cooking oil using RSM, Mater. Today: Proc., 2021, 47, 4901–4905, DOI:10.1016/j.matpr.2021.06.322.
- N. S. Topare, K. D. Patil and S. V. Khedkar, Synthesis of Biodiesel from Waste Cooking Oil and Emission Characteristics of Its blends, IOP Conf. Ser.: Mater. Sci. Eng., 2020, 983, 012015, DOI:10.1088/1757-899X/983/1/012015.
- I. Thushari, S. Babel and C. Samart, Biodiesel production in an autoclave reactor using waste palm oil and coconut coir husk derived catalyst, Renewable Energy, 2019, 134, 125–134, DOI:10.1016/j.renene.2018.11.030.
- N. S. Topare and K. D. Patil, Biodiesel from waste cooking soybean oil under ultrasonication as an alternative fuel for diesel engine, Mater. Today: Proc., 2020, 43, 510–513, DOI:10.1016/j.matpr.2020.12.025.
- R. F. Abdullah, U. Rashid, M. L. Ibrahim, B. Hazmi, F. A. Alharthi and I. A. Nehdi, Bifunctional nano-catalyst produced from palm kernel shell via hydrothermal-assisted carbonization for biodiesel production from waste cooking oil, Renewable Sustainable Energy Rev., 2021, 137, 110638, DOI:10.1016/j.rser.2020.110638.
- M. M. Naeem, E. G. Al-Sakkari, D. C. Boffito, M. A. Gadalla and F. H. Ashour, One-pot conversion of highly acidic waste cooking oil into biodiesel over a novel bio-based bi-functional catalyst, Fuel, 2021, 283, 118914, DOI:10.1016/j.fuel.2020.118914.
- M. H. Nazir, M. Ayoub, I. Zahid, R. B. Shamsuddin, Zulqarnain, M. Ameen, F. Sher and S. Farrukh, Waste sugarcane bagasse-derived nanocatalyst for microwave-assisted transesterification: Thermal, kinetic and optimization study, Biofuels, Bioprod. Biorefin., 2022, 16, 122–141, DOI:10.1002/bbb.2264.
- A. Birla, B. Singh, S. N. Upadhyay and Y. C. Sharma, Kinetics studies of synthesis of biodiesel from waste frying oil using a heterogeneous catalyst derived from snail shell, Bioresour. Technol., 2012, 106, 95–100, DOI:10.1016/j.biortech.2011.11.065.
- T. F. Adepoju, M. A. Ibeh, E. N. Udoetuk and E. O. Babatunde, Quaternary blend of Carica papaya – Citrus sinesis – Hibiscus sabdariffa – Waste used oil for biodiesel synthesis using CaO-based catalyst derived from binary mix of Lattorina littorea and Mactra coralline shell, Renewable Energy, 2021, 171, 22–33, DOI:10.1016/j.renene.2021.02.020.
- A. M. Rabie, M. Shaban, M. R. Abukhadra, R. Hosny, S. A. Ahmed and N. A. Negm, Diatomite supported by CaO/MgO nanocomposite as heterogeneous catalyst for biodiesel production from waste cooking oil, J. Mol. Liq., 2019, 279, 224–231, DOI:10.1016/j.molliq.2019.01.096.
- M. N. A. M. Yusoff, N. W. M. Zulkifli, N. L. Sukiman, M. A. Kalam, H. H. Masjuki, A. Z. Syahir, M. S. N. Awang, M. A. Mujtaba, J. Milano and A. H. Shamsuddin, Microwave irradiation-assisted transesterification of ternary oil mixture of waste cooking oil – Jatropha curcas – Palm oil: Optimization and characterization, Alexandria Eng. J., 2022, 61, 9569–9582, DOI:10.1016/j.aej.2022.03.040.
- S. S. Sahar, J. Iqbal, I. Ullah, H. N. Bhatti, S. Nouren, H. ur-Rehman, J. Nisar and M. Iqbal, Biodiesel production from waste cooking oil: An efficient technique to convert waste into biodiesel, Sustainable Cities Soc., 2018, 41, 220–226, DOI:10.1016/j.scs.2018.05.037.
- N. S. Topare, K. D. Patil and S. V. Khedkar, Effects of operating parameters on biodiesel production from waste cooking oil under ultrasonic irradiation, Mater. Today: Proc., 2021, 46, 10638–10641, DOI:10.1016/j.matpr.2021.01.379.
- H. Hamze, M. Akia and F. Yazdani, Optimization of biodiesel production from the waste cooking oil using response surface methodology, Process Saf. Environ. Prot., 2015, 94, 1–10, DOI:10.1016/j.psep.2014.12.005.
- M. Gohain, A. Devi and D. Deka, Musa balbisiana Colla peel as highly effective renewable heterogeneous base catalyst for biodiesel production, Ind. Crops Prod., 2017, 109, 8–18, DOI:10.1016/j.indcrop.2017.08.006.
- C. Caldeira, P. Quinteiro, E. Castanheira, A. M. Boulay, A. C. Dias, L. Arroja and F. Freire, Water footprint profile of crop-based vegetable oils and waste cooking oil: Comparing two water scarcity footprint methods, J. Cleaner Prod., 2018, 195, 1190–1202, DOI:10.1016/j.jclepro.2018.05.221.
- M. Tabatabaei, M. Aghbashlo, B. Najafi, H. Hosseinzadeh-Bandbafha, S. Faizollahzadeh Ardabili, E. Akbarian, E. Khalife, P. Mohammadi, H. Rastegari and H. S. Ghaziaskar, Environmental impact assessment of the mechanical shaft work produced in a diesel engine running on diesel/biodiesel blends containing glycerol-derived triacetin, J. Cleaner Prod., 2019, 223, 466–486, DOI:10.1016/j.jclepro.2019.03.106.
- C. B. H. Chua, H. M. Lee and J. S. C. Low, Life cycle emissions and energy study of biodiesel derived from waste cooking oil and diesel in Singapore, Int. J. Life Cycle Assess., 2010, 15, 417–423, DOI:10.1007/s11367-010-0166-5.
- Z. Sajid, F. Khan and Y. Zhang, Process simulation and life cycle analysis of biodiesel production, Renewable Energy, 2016, 85, 945–952, DOI:10.1016/j.renene.2015.07.046.
- Z. L. Chung, Y. H. Tan, Y. S. Chan, J. Kansedo, N. M. Mubarak, M. Ghasemi and M. O. Abdullah, Life cycle assessment of waste cooking oil for biodiesel production using waste chicken eggshell derived CaO as catalyst via transesterification, Biocatal. Agric. Biotechnol., 2019, 21, 101317, DOI:10.1016/j.bcab.2019.101317.
- D. S. Khang, R. R. Tan, O. M. Uy, M. A. B. Promentilla, P. D. Tuan, N. Abe and L. F. Razon, Design of experiments for global sensitivity analysis in life cycle assessment: The case of biodiesel in Vietnam, Resour., Conserv. Recycl., 2017, 119, 12–23, DOI:10.1016/j.resconrec.2016.08.016.
- S. Foteinis, E. Chatzisymeon, A. Litinas and T. Tsoutsos, Used-cooking-oil biodiesel: Life cycle assessment and comparison with first- and third-generation biofuel, Renewable Energy, 2020, 153, 588–600, DOI:10.1016/j.renene.2020.02.022.
- H. Hosseinzadeh-Bandbafha, A. S. Nizami, S. A. Kalogirou, V. K. Gupta, Y. K. Park, A. Fallahi, A. Sulaiman, M. Ranjbari, H. Rahnama, M. Aghbashlo, W. Peng and M. Tabatabaei, Environmental life cycle assessment of biodiesel production from waste cooking oil: A systematic review, Renewable Sustainable Energy Rev., 2022, 161, 112411, DOI:10.1016/j.rser.2022.112411.
- C. Caldeira, J. Queirós, A. Noshadravan and F. Freire, Incorporating uncertainty in the life cycle assessment of biodiesel from waste cooking oil addressing different collection systems, Resour., Conserv. Recycl., 2016, 112, 83–92, DOI:10.1016/j.resconrec.2016.05.005.
- H. Hosseinzadeh-Bandbafha, M. Tabatabaei, M. Aghbashlo, M. Khanali, E. Khalife, T. Roodbar Shojaei and P. Mohammadi, Data supporting consolidating emission indices of a diesel engine powered by carbon nanoparticle-doped diesel/biodiesel emulsion fuels using life cycle assessment framework, Data Brief, 2020, 30, 105428, DOI:10.1016/j.dib.2020.105428.
- F. Cherubini, N. D. Bird, A. Cowie, G. Jungmeier, B. Schlamadinger and S. Woess-Gallasch, Energy- and greenhouse gas-based LCA of biofuel and bioenergy systems: Key issues, ranges and recommendations, Resour., Conserv. Recycl., 2009, 53, 434–447, DOI:10.1016/j.resconrec.2009.03.013.
- M. Tabatabaei, M. Aghbashlo, M. Dehhaghi, H. K. S. Panahi, A. Mollahosseini, M. Hosseini and M. M. Soufiyan, Reactor technologies for biodiesel production and processing: A review, Prog. Energy Combust. Sci., 2019, 74, 239–303, DOI:10.1016/j.pecs.2019.06.001.
- Z. H. Li, P. H. Lin, J. C. S. Wu, Y. T. Huang, K. S. Lin and K. C. W. Wu, A stirring packed-bed reactor to enhance the esterification-transesterification in biodiesel production by lowering mass-transfer resistance, Chem. Eng. J., 2013, 234, 9–15, DOI:10.1016/j.cej.2013.08.053.
|
This journal is © The Royal Society of Chemistry 2024 |