DOI:
10.1039/D3PY01006F
(Paper)
Polym. Chem., 2024,
15, 106-117
From RAFT emulsion polymerization to RAFT dispersion polymerization: a facile approach to tuning dispersities and behaviors of self-assembled block copolymers†
Received
5th September 2023
, Accepted 27th November 2023
First published on 30th November 2023
Abstract
Heterogeneous reversible addition–fragmentation chain transfer (RAFT) polymerization coupled with polymerization-induced self-assembly (PISA) can be performed through either RAFT emulsion polymerization or RAFT dispersion polymerization, providing opportunities for the synthesis of block copolymers with low dispersities and polymer nanoparticles with various morphologies. In this study, we have demonstrated the successful transition from photoinitiated RAFT emulsion polymerization to photoinitiated RAFT dispersion polymerization by solely changing the solvent composition from water to water/ethanol. Kinetic studies indicated that slower polymerization was observed with higher ethanol content. Size exclusion chromatography (SEC) analysis demonstrated that narrower molecular weight distributions were achieved on increasing the ethanol content due to faster radical diffusion within the micellar core. The dispersity of block copolymers can be changed by varying the ethanol content used in photoinitiated heterogeneous RAFT polymerization. Moreover, the reaction temperature has also been explored as a parameter to control the diffusion of radicals within the micellar core and therefore dispersities of block copolymers. Finally, the morphological evolution of block copolymer nanoparticles during the transition from RAFT emulsion polymerization to RAFT dispersion polymerization was also investigated. The present study is anticipated to significantly expand the scope of heterogeneous RAFT polymerization by allowing access to a wide range of block copolymers with different dispersities and polymer nanoparticles with diverse morphologies.
Introduction
Reversible deactivation radical polymerizations (RDRPs), such as nitroxide-mediated polymerization (NMP),1 atom transfer radical polymerization (ATRP),2 and reversible addition–fragmentation chain transfer (RAFT) polymerization,3 have revolutionized research in polymer chemistry, allowing the synthesis of well-defined polymers with low dispersity, high end-group fidelity, and predetermined molecular weight.4–8 Furthermore, these RDRP techniques allow for the facile synthesis of complex polymers, such as block copolymers, star-shaped polymers, branched polymers, etc. Of all the RDRP techniques, RAFT polymerization is of particular interest due to its compatibility with a large array of solvents and monomer families, benign reaction conditions, and the absence of metal-containing catalysts.9 These features make RAFT polymerization an attractive method for the synthesis of advanced polymer materials with unique properties for various applications.4
When compared to homogeneous RAFT polymerization, heterogeneous RAFT polymerization presents several advantages, such as low viscosity, good heat transfer, high polymerization rate, and excellent polymerization controllability. Additionally, this technique can be used to create polymer nanoparticles with diverse structures like multilayered, core–shell, and hollow particles, which are useful for specific applications in coating, separation, biomedical analysis, and drug delivery areas.10–13 Initial attempts at heterogeneous RAFT polymerization involved the addition of a small-molecular RAFT agent into a conventional heterogeneous polymerization. However, the poor transportation of small-molecular RAFT agents within the heterogeneous polymerization system often resulted in poor control over the polymerization, polydisperse particle sizes, and colloidal instability.14–16 To overcome these issues, the use of solvophilic macromolecular RAFT (macro-RAFT) agents in heterogeneous polymerization became an attractive strategy.17 During the polymerization process, the macro-RAFT agent grows to generate a block copolymer. As the second block increases to a critical molecular weight, the block copolymer self-assembles into nanoparticles embedded with RAFT moieties. This process follows a so-called polymerization-induced self-assembly (PISA) mechanism. Over the past decade, RAFT–PISA has emerged as a powerful technique to prepare various block copolymer nanoparticles with high solids content (10–50%).18–34 Moreover, RAFT–PISA is also a useful synthetic tool for the synthesis of well-defined polymers with low dispersities.35–39 However, recent progress in controlling dispersities of polymers has shown that dispersity is also an important parameter that is used to tune properties of polymer materials.40–44 For example, Fors’ group42 reported that the domain spacing of self-assembled polystyrene-b-poly(methyl methacrylate) (PSt-b-PMMA) thin films could be controlled by varying dispersities and molecular weight distribution shapes. The same group43 also reported that strong, stiff, and tough thermoplastic elastomers could be prepared by controlling the dispersity and molecular weight distribution shape of the polystyrene-b-polyisoprene-b-polystyrene triblock copolymer. Furthermore, the dispersity of block copolymers also significantly influences their behaviors when self-assembled.40,45,46 These examples demonstrate that low dispersity is not always beneficial for the properties and applications of polymer materials. Therefore, exploring RAFT–PISA as a synthetic tool to control dispersities of block copolymers is highly desirable.
RAFT–PISA can be performed through either RAFT emulsion polymerization or RAFT dispersion polymerization.30,31 In RAFT emulsion polymerization, water-soluble initiators and hydrophobic monomers are required. Hydrophobic monomers exist as monomer droplets in the aqueous medium. Since coagulative homogeneous nucleation is more likely together with radical entry in pre-existing particles, polymerization is unlikely to occur inside monomer droplets. After micellar or homogeneous nucleation, hydrophobic monomers need to diffuse from monomer droplets to the formed block copolymer micelles (Scheme 1). It should be noted that the direct monomer droplet/particle collision is also accepted as a monomer transport mechanism to the loci of polymerization. This unique in-built monomer-feeding mechanism is particularly beneficial for the preparation of cross-linked polymer nanoparticles and multiblock copolymers.47–54 Very recently, Armes’ group55,56 and our group47,57 have reported that the aqueous solubility of monomers is critical for the formation of higher-order morphologies. Furthermore, if the reaction temperature is way above the glass transition temperature of the assembled hydrophobic part of the polymer, fusion between nanoparticles can also occur to generate higher-order morphologies.47 Block copolymer nanoparticles with various morphologies can also be easily prepared by RAFT dispersion polymerization.29,30,58 In RAFT dispersion polymerization, all ingredients (including the monomer, initiator, and macro-RAFT agent) are soluble in the reaction medium to form a transparent solution. As the polymerization proceeds, the formed block copolymer precipitates from the reaction medium and self-assembles into micelles (Scheme 1). After nucleation, the main polymerization locus should be inside the monomer-swollen micelles. Although great progress has been made in RAFT–PISA, direct comparisons between RAFT emulsion polymerization and RAFT dispersion polymerization have rarely been reported.59 Taking advantage of these two methods, we also expect that the combination of RAFT emulsion polymerization and RAFT dispersion polymerization would offer new opportunities for controlling the dispersities and behaviors of self-assembled block copolymers.
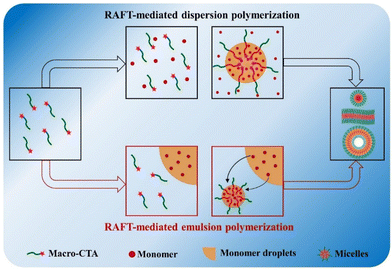 |
| Scheme 1 Schematic illustration for processes of RAFT dispersion polymerization and RAFT emulsion polymerization using a macro-RAFT agent. | |
In this study, we report the transition from RAFT emulsion polymerization to RAFT dispersion polymerization by solely changing the solvent composition from water to water/ethanol. It should be mentioned that these are batch reactions rather than semi-continuous reactions. We investigated the effect of polymerization process on the polymerization kinetics in detail and also explored the evolution of dispersities of block copolymers through the change of solvent composition. Taking advantage of the temperature-insensitive property of photoinitiation, heterogeneous RAFT polymerizations at different temperatures were performed to control the dispersities of block copolymers. Finally, the effects of the polymerization process and temperature on the morphologies of block copolymer nanoparticles were investigated.
Results and discussion
Synthesis and characterization of macro-RAFT agents
First, 4-cyano-4-(dodecylsulfanylthiocarbonyl) sulfanylpentanoic acid (CDPA) was reacted with methanol through esterification to obtain a non-carboxyl-functional RAFT agent, denoted as CDPA–Me (Fig. 1a). CDPA–Me was then used to mediate RAFT polymerization of poly(ethylene glycol) methyl ether methacrylate (PEGMA, 475 g mol−1) in 1,4-dioxane at 70 °C using azobisisobutyronitrile (AIBN) as the initiator (Scheme 2). The purified polymers were denoted as PPEGMAn–CDPA–Me, where n is the mean degree of polymerization (DP), as confirmed by 1H NMR spectroscopy. The polymers were then characterized by tetrahydrofuran (THF) size exclusion chromatography (SEC) with a reflective index (RI) detector. Fig. 1b shows THF SEC data of PPEGMAn–CDPA–Me (n = 7.6, 10.2), and low dispersities (Đ ≤ 1.13) were observed in both polymers. A small shoulder at high molecular weight was observed in each sample, which may be attributed to the presence of a small number of uncontrolled polymers that formed from radical–radical termination.
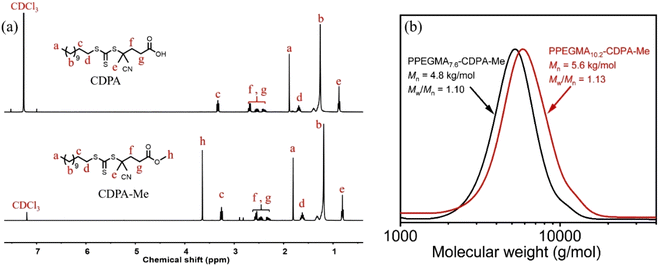 |
| Fig. 1 (a) 1H NMR spectra of CDPA and CDPA–Me. (b) THF SEC data of PPEGMAn–CDPA–Me (n = 7.6, 10.2) synthesized by RAFT solution polymerization of PEGMA (against polystyrene standards). | |
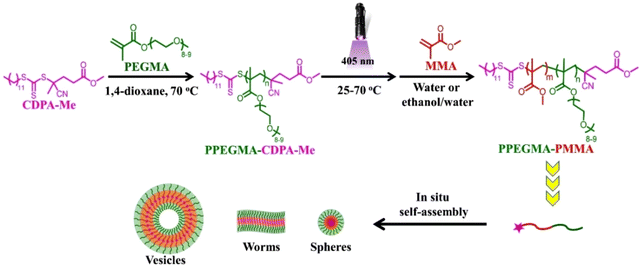 |
| Scheme 2 Schematic illustration for the synthesis of PPEGMAn–CDPA–Me macro-RAFT agents by RAFT solution polymerization of PEGMA in 1,4-dioxane mediated by CDPA–Me and the synthesis of PPEGMAn–PMMAm diblock copolymer by heterogeneous RAFT polymerization of MMA in water or ethanol/water mediated by PPEGMAn–CDPA–Me. | |
Evolution of molecular weight distributions of block copolymers in photoinitiated heterogeneous RAFT polymerization
PPEGMA10.2–CDPA–Me was then used for photoinitiated RAFT emulsion polymerization of methyl methacrylate (MMA, 10% w/w) at 25 °C using sodium phenyl-2,4,6-trimethylbenzoylphosphinate (SPTP) as the photoinitiator (λ = 405 nm, 0.45 mW cm−2) (Scheme 2). The target block copolymer composition was PPEGMA10.2–PMMA100. As shown in Fig. 2, a turbid solution was observed at the beginning of the polymerization due to the presence of MMA droplets in the aqueous medium. After 1 h of light irradiation (over 98% monomer conversion), a bluish solution was formed, indicating the formation of polymer nanoparticles. Ethanol is a good solvent for MMA and is miscible with water. To induce the transition from RAFT emulsion polymerization to RAFT dispersion polymerization, the reaction medium was then changed from pure water to a mixed solvent of ethanol and water. It should be noted that other reaction conditions were maintained. At ethanol/water ratios of 5/95–20/80 (w/w), a certain amount of MMA should be dissolved in the reaction medium (Table S1†), although turbid solutions were still observed at the beginning of polymerizations (Fig. 2). In these cases, a noticeable concentration of monomers dissolved in the reaction medium, while remaining monomers existed as monomer droplets; the heterogeneous polymerizations should undergo a mixed mechanism of RAFT emulsion polymerization and RAFT dispersion polymerization. The observed bluish solutions after light irradiation also indicate the formation of block copolymer nanoparticles. When the ethanol/water ratio was increased to 30/70 (w/w), MMA could be fully dissolved in the mixed solvent and an optically transparent solution was observed at the beginning of polymerization (Fig. 2). It should be mentioned that the presence of macro-RAFT agents should facilitate the dissolution of MMA in ethanol/water (Table S1†). After 1 h of light irradiation, over 95% monomer conversion was still achieved and transmission electron microscopy (TEM) characterization confirmed the formation of nanoparticles. In this case, MMA should have polymerized via RAFT dispersion polymerization.
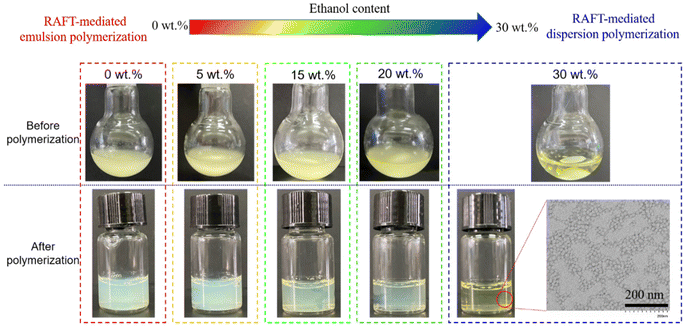 |
| Fig. 2 Digital images of reaction mixtures for heterogeneous RAFT polymerization of MMA (10% w/w, target DP of 100) mediated by PPEGMA10.2–CDPA–Me in a water/ethanol mixture with different ethanol contents. Note that a TEM image was provided at a 30 wt% ethanol content to demonstrate the formation of polymer nanoparticles. | |
The kinetics of polymerization targeting PPEGMA10.2–PMMA100 in water or ethanol/water mixtures was then monitored, as shown in Fig. 3a. It is evident that increasing the ethanol content could significantly slow down the MMA polymerization. Nevertheless, over 95% monomer conversion was still achieved in each case within 1 h of light irradiation at 25 °C. In previous works on heterogeneous RAFT polymerizations conducted under either emulsion polymerization or dispersion polymerization conditions, rate enhancements after an initial induction period have been observed.55,60 In this study, polymerizations conducted in water or ethanol/water mixtures also exhibit two-stage kinetics, as shown in the corresponding semilogarithmic plots (Fig. 3b). This can be attributed to the onset of nucleation of block copolymers according to time-resolved small-angle X-ray scattering (SAXS) investigations by Armes’ group,61,62 and the main polymerization locus is inside the monomer-swollen micelles. Regardless of the solvent composition, the slopes for the first polymerization stage were the same, which suggests that the change in solvent composition has no influence on the polymerization rate in the nucleation stage. Similarly, the slopes for the second polymerization stage were also the same. The difference in the polymerization behaviors should be mainly attributed to the different durations in the first phase of polymerization. The longer the first phase of polymerization, the more time is spent on the initial stage of polymerization. This means that less time is available for the subsequent stage of polymerization. Interpolations of two lines indicate that the initial polymerization period increased from ∼8 min in water to ∼11.9 min in ethanol/water (15/85, w/w) to ∼25 min in ethanol/water (30/70, w/w). Moreover, it was found that increasing the ethanol content led to an increase in the critical PMMA DP estimated from the kinetic plots. This can be explained by two possible reasons: (i) compared with water, ethanol is a relatively good solvent for both MMA and PMMA63 and (ii) MMA is also a good solvent for PMMA, and the dissolved MMA in ethanol/water also improves the solubility of PMMA in the reaction medium. These results suggest that the transition from RAFT emulsion polymerization to RAFT dispersion polymerization not only leads to different polymerization behaviors but also changes the PISA behavior of block copolymers.
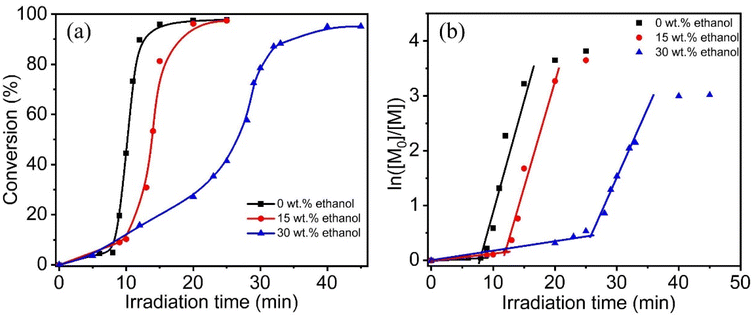 |
| Fig. 3 (a) Polymerization kinetics for heterogeneous RAFT polymerization of MMA (10% w/w, target DP of 100) at 25 °C mediated by PPEGMA10.2–CDPA–Me in a water/ethanol mixture with different ethanol contents. (b) Plots of ln([M]0/[M]) vs. irradiation time for heterogeneous RAFT polymerization of MMA (10% w/w, target DP of 100) mediated by PPEGMA10.2–CDPA–Me in a water/ethanol mixture with different ethanol contents. | |
Samples obtained during the kinetics experiments were also checked by THF SEC (Fig. 4 and Fig. S1†). In each case, the SEC curve shifted to higher molecular weight as the polymerization time (and the monomer conversion) increased, indicating the successful chain extension under heterogeneous RAFT polymerization conditions. It should be mentioned that high-molecular-weight shoulders were observed, as shown in Fig. 4a and c, which indicate the occurrence of a certain degree of uncontrolled RAFT polymerization in these cases and this will be discussed in the following section. Regardless of the solvent composition, a linear evolution of number-average molecular weight (Mn) with monomer conversion was observed (Fig. 4b, d and f), indicating that moderate RAFT control was maintained. Higher ethanol contents were found to achieve lower dispersities, with the final sample synthesized by RAFT emulsion polymerization (ethanol content of 0 wt%) achieving a dispersity of 1.67, while this value was decreased to 1.39 at an ethanol content of 15 wt% and to 1.33 at an ethanol content of 30 wt%. Fig. 5a shows THF SEC traces of PPEGMA10.2–PMMA100 block copolymers synthesized by photoinitiated heterogeneous RAFT polymerization at different ethanol contents (reaction temperature of 25 °C and irradiation time of 1 h). Narrower molecular weight distributions were observed on increasing the ethanol content (Fig. 5a), and it should be highlighted that the dispersity decreased linearly with the ethanol content used in the photoinitiated heterogeneous RAFT polymerization (Fig. 5b). Moreover, Mn values were close for all samples. These results suggest that the transition from RAFT emulsion polymerization to RAFT dispersion polymerization provides a facile strategy to change dispersities of block copolymers. To illustrate the versatility of this strategy, other monomers including benzyl methacrylate (BzMA), glycidyl methacrylate (GlyMA), tert-butyl acrylate (tBA), and isobronyl acrylate (IBOA) were also used in photoinitiated heterogeneous RAFT polymerizations. Due to the different solubility of monomers in ethanol/water, the amount of ethanol for photoinitiated RAFT dispersion polymerization was varied in each case. Initial experiments were conducted at room temperature. However, the heterogeneous RAFT polymerization of IBOA became unstable with precipitates being formed. This can be attributed to the weak mobility of PIBOA chains at room temperature, making it difficult to solvate the micellar cores effectively. After nucleation, the unreacted monomer tends to be excluded from the micelles and the heterogeneous polymerization should mainly occur in the reaction medium, leading to the occurrence of precipitation. Therefore, all polymerizations were performed at 45 °C to ensure the stability of heterogeneous RAFT polymerization. As shown in Fig. S2,† replacing a certain amount of water with ethanol in the heterogeneous RAFT polymerization could also decrease dispersities of block copolymers regardless of the monomer type.
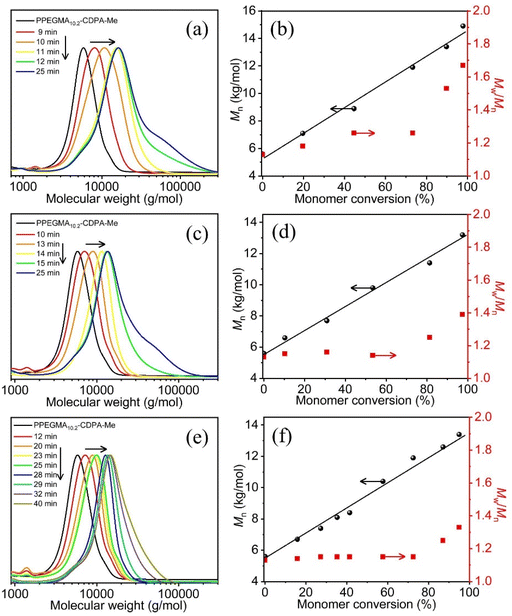 |
| Fig. 4 (a, c and e) THF SEC traces of PPEGMA10.2–CDPA–Me and samples obtained at different times during the kinetic study of heterogeneous RAFT polymerization of MMA (10% w/w, target DP of 100) mediated by PPEGMA10.2–CDPA–Me in a water/ethanol mixture with different ethanol contents: (a) 0 wt%, (c) 15 wt%, (e) 30 wt%. (b, d and f) Evolution of Mn and Mw/Mn with monomer conversion for heterogeneous RAFT polymerization of MMA (10% w/w, target DP of 100) mediated by PPEGMA10.2–CDPA–Me in a water/ethanol mixture with different ethanol contents: (b) 0 wt%, (d) 15 wt%, (f) 30 wt%. | |
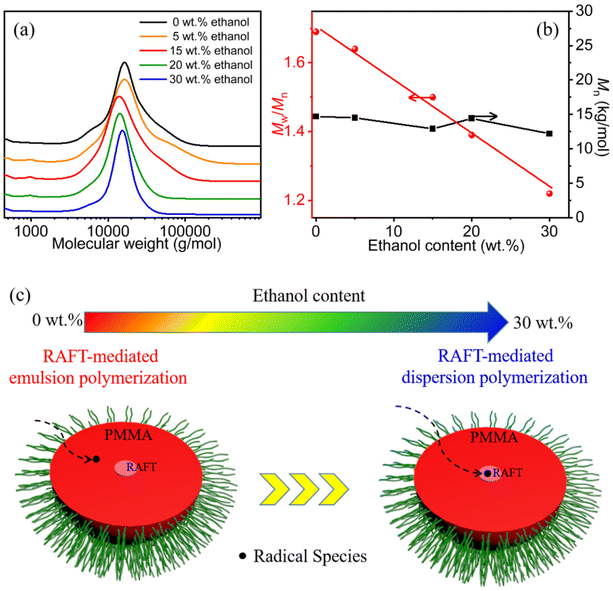 |
| Fig. 5 (a) THF SEC traces of PPEGMA10.2–PMMA100 block copolymers synthesized by photoinitiated heterogeneous RAFT polymerization of MMA (10% w/w) in ethanol/water at 25 °C with different ethanol contents. (b) Evolution of Mw/Mn and Mn with the ethanol content for PPEGMA10.2–PMMA100 block copolymers synthesized by photoinitiated heterogeneous RAFT polymerization of MMA (10% w/w) in ethanol/water at 25 °C. (c) Schematic illustration of faster radical diffusion with increasing ethanol content in heterogeneous RAFT polymerization. Note that increasing the ethanol content leads to the transition from RAFT emulsion polymerization to RAFT dispersion polymerization. | |
Based on the abovementioned results, it is evident that dispersities of block copolymers synthesized by heterogeneous RAFT polymerization can be varied by changing the solvent composition. Under RAFT emulsion polymerization conditions, due to the hydrophobic nature and the relatively high glass transition temperature (Tg) of PMMA (Tg = ∼125 °C),47 propagating radicals have difficulty diffusing to the RAFT end-groups embedded inside PMMA cores before bimolecular termination occurs (Fig. 5c). Therefore, a certain degree of uncontrolled radical polymerization occurs in RAFT emulsion polymerization, leading to a broad molecular weight distribution and higher dispersity. This effect should be more pronounced at higher DP of the core-forming block since radical penetration becomes progressively more difficult on increasing the particle size.64 As shown in Fig. 4, the dispersity was relatively low at low monomer conversions and increased significantly at high monomer conversions. When replacing a certain amount of water with ethanol, both ethanol and the dissolved MMA monomer act as plasticizers to the PMMA block, which can increase the extent of radical penetration (Fig. 5c). It should be pointed out that the number of living chains with RAFT moieties should be the same because radicals generated from the decomposition of initiators eventually terminate, and the RAFT moieties remain intact. On assuming bulk kinetics, the addition step of the RAFT process is also slowed down, thereby increasing the number of propagation steps (the effective kinetic chain length), and therefore causing loss of RAFT control.
As reported by Zetterlund et al.,64 the chain mobility of the core-forming block also has a significant effect on the radical penetration process during RAFT emulsion polymerization. Therefore, the level of control over molecular weight distributions is remarkably enhanced under conditions where the Tg of the core-forming block is low. However, in their system, it is difficult to control the chain mobility without changing the composition of the core-forming block. Taking advantage of the temperature-insensitive characteristic of photoinitiation,65,66 we expected that one could easily control the chain mobility by solely changing the reaction temperature. Photoinitiated RAFT emulsion polymerizations of MMA (10% w/w, target composition of PPEGMA10.2–PMMA100) at different temperatures (25–70 °C) were then performed. High monomer conversions (>95%) were achieved in all cases, as determined by 1H NMR spectroscopy. Fig. 6a shows SEC traces of diblock copolymers synthesized at different temperatures. It is clear that the molecular weight distribution becomes narrower with increasing reaction temperature. The dispersity decreases significantly with the reaction temperature and levels off at 60 °C or higher (Fig. 6b). For example, the dispersity at 30 °C was 1.69 and decreased to 1.49 at 35 °C and 1.27 at 60 °C. Moreover, it was found that the variation in reaction temperature had little influence on the molecular weight. Similar results were observed for heterogeneous RAFT polymerization in a mixed solvent with an ethanol/water ratio of 20/80 (w/w) (Fig. 6c). The dispersity was 1.49 at 25 °C and reached 1.11 at 70 °C (Fig. 6d). These results suggest that radical penetration toward RAFT moieties in the core region of polymer nanoparticles is more successful at a higher temperature, providing a facile strategy to change molecular weight distributions of block copolymers synthesized by heterogeneous RAFT polymerization.
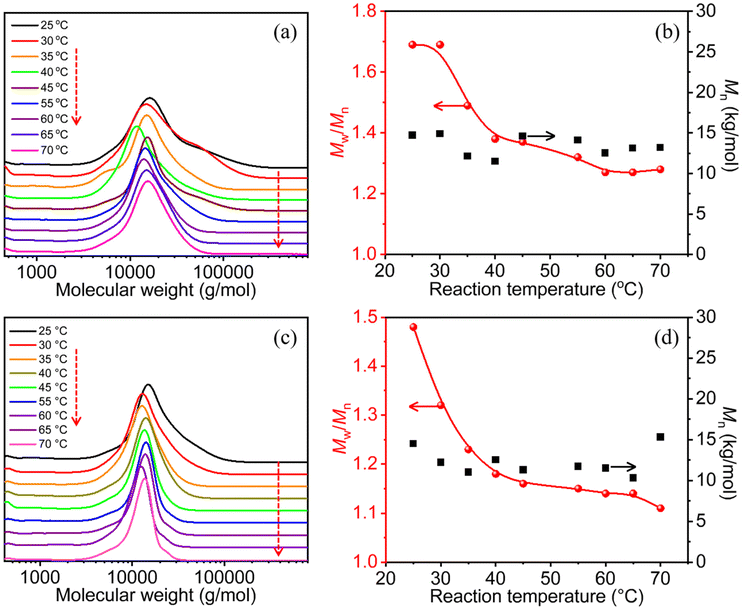 |
| Fig. 6 (a) THF SEC traces of PPEGMA10.2–PMMA100 block copolymers prepared by photoinitiated RAFT emulsion polymerization of MMA (10% w/w) at different temperatures. (b) Evolution of Mw/Mn and Mn with reaction temperature for PPEGMA10.2–PMMA100 block copolymers prepared by photoinitiated RAFT emulsion polymerization of MMA (10% w/w). (c) THF SEC traces of PPEGMA10.2–PMMA100 block copolymers prepared by photoinitiated heterogeneous RAFT polymerization of MMA (10% w/w) in ethanol/water (20/80, w/w) at different temperatures. (d) Evolution of Mw/Mn and Mn with reaction temperature for PPEGMA10.2–PMMA100 block copolymers prepared by photoinitiated heterogeneous RAFT polymerization of MMA (10% w/w) in ethanol/water (20/80, w/w). | |
Morphological evolution of block copolymer nanoparticles in photoinitiated heterogeneous RAFT polymerization
Heterogeneous RAFT polymerization is not only an efficient method for the synthesis of block copolymers but also enables the direct production of polymer nanoparticles with various morphologies.10,12,67Fig. 7 shows TEM images of PPEGMA10.2–PMMA100 nanoparticles prepared by heterogeneous RAFT polymerization of MMA (10% w/w) at different temperatures (30, 50, and 70 °C) in either water (Fig. 7a–c) or ethanol/water (20/80, w/w) (Fig. 7d–f). However, only spheres were formed regardless of the reaction temperature or the solvent composition. PPEGMA10.2–PMMA200 block copolymer nanoparticles were also prepared in either water or ethanol/water (20/80, w/w) at 50 °C. As shown in Fig. S3,† spheres mixed with vesicles were observed in water, while pure spheres were formed in ethanol/water (20/80, w/w). Nevertheless, these results suggest that the use of PPEGMA10.2–CDPA–Me favors the formation of kinetically trapped spheres. This can be attributed to the efficient stabilization of the PPEGMA10.2 corona toward nanoparticles, which restricts the morphological transition from lower-order morphologies to higher-order ones. To further induce the morphological transition, PPEGMA7.6–CDPA–Me, a shorter macro-RAFT agent, was then used to mediate heterogeneous RAFT polymerization of MMA at different temperatures (30, 50, and 70 °C) in water (Fig. 8). For PPEGMA7.6–PMMAm (m = 125, 150, 175), pure spheres were obtained at 30 °C, while mixed morphologies of spheres, worms, and vesicles were obtained at 50 °C. At 70 °C, a mixed morphology of vesicles and worms was formed for PPEGMA7.6–PMMA125, while tubular vesicles mixed with worms were formed for PPEGMA7.6–PMMA150 and large-compound vesicles mixed with worms were formed for PPEGMA7.6–PMMA175. These results suggest that increasing the reaction temperature could also promote the formation of higher-order morphologies. This can be explained by two possible reasons: (i) the PMMA block has higher chain mobility at a higher reaction temperature, facilitating the adjustment of chain conformations and therefore the morphological evolution, and (ii) the relatively poorer aqueous solubility of the PPEGMA stabilizer block at a higher reaction temperature could weaken its performance in steric stabilization, facilitating the fusion between nanoparticles.68 It should be noted that the difference in molecular weight distributions might also lead to the morphological difference of block copolymer nanoparticles, which clearly warrants further investigations.
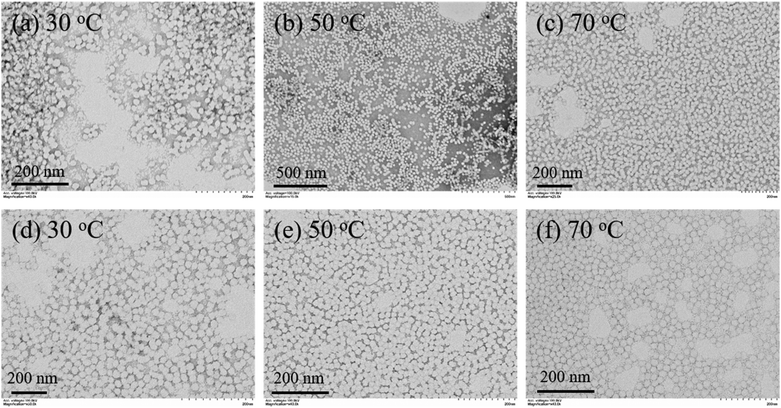 |
| Fig. 7 (a–c) TEM images of PPEGMA10.2–PMMA100 nanoparticles prepared by photoinitiated RAFT emulsion polymerization of MMA (10% w/w) at different temperatures: (a) 30 °C, (b) 50 °C, and (c) 70 °C. (d–f) TEM images of PPEGMA10.2–PMMA100 nanoparticles prepared by photoinitiated heterogeneous RAFT polymerization of MMA (10% w/w) in ethanol/water (20/80, w/w) at different temperatures: (d) 30 °C, (e) 50 °C, (f) 70 °C. | |
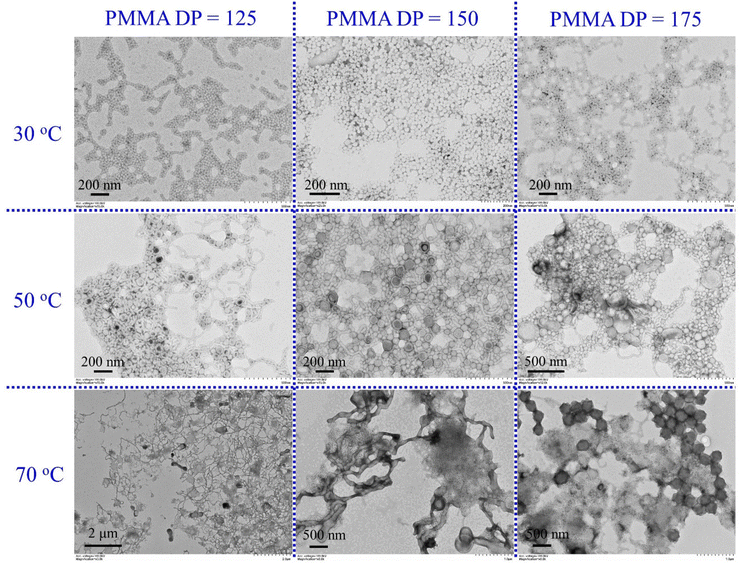 |
| Fig. 8 TEM images of PPEGMA7.6–PMMAm (m = 125, 150, 175) block copolymer nanoparticles prepared by photoinitiated RAFT emulsion polymerization of MMA (20% w/w) at different temperatures. | |
In order to investigate the morphological evolution during the transition from RAFT emulsion polymerization to RAFT dispersion polymerization, PPEGMA7.6–PMMA125 block copolymer nanoparticles were also prepared at different ethanol contents (Fig. 9). The reaction temperature was maintained at 70 °C in each case. In the absence of ethanol, worms mixed with a few vesicles were formed. As the ethanol content increased, the morphologies transformed into spheres even at 15 wt% ethanol content. A similar phenomenon was observed for PPEGMA7.6–PMMA150 and PPEGMA7.6–PMMA175 block copolymer nanoparticles prepared under the same conditions. For example, the morphology of PPEGMA7.6–PMMA150 block copolymer nanoparticles transformed from a mixed morphology of worms and tubular vesicles at 0 wt% ethanol content to pure worms at 15 wt% ethanol content. Further increasing the ethanol content in the polymerization system led to the formation of spheres. In this study, increasing the ethanol content leads to better solubility of the monomer in the reaction medium, resulting in lower local monomer concentration in monomer-swollen micelles. Moreover, the critical DP of the core-forming block is higher at higher ethanol contents, leading to a decrease in the amount of monomer for polymerization after micellization. Therefore, the transition from RAFT emulsion polymerization to RAFT dispersion polymerization should favor the formation of lower-order morphologies. It should be pointed out that the morphological evolution in RAFT dispersion polymerization could be further promoted by increasing the monomer concentration and the DP of the core-forming block,69,70 which is beyond the scope of this study.
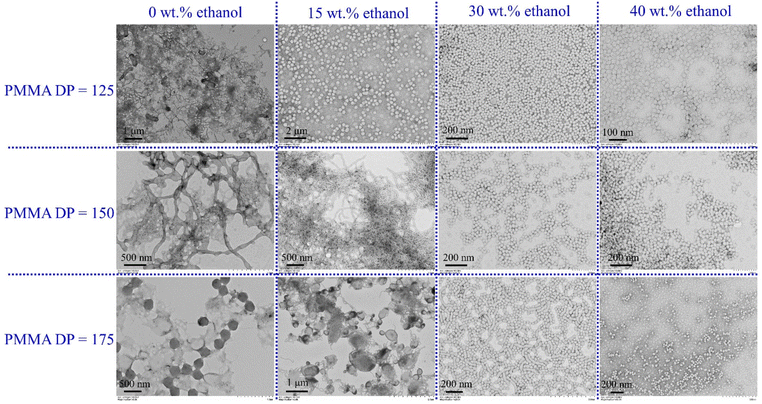 |
| Fig. 9 TEM images of PPEGMA7.6–PMMAm (m = 125, 150, 175) block copolymer nanoparticles prepared by heterogeneous RAFT polymerization of MMA (20% w/w) in ethanol/water at 70 °C with different ethanol contents. | |
Conclusion
In summary, we report the successful transition from photoinitiated RAFT emulsion polymerization to photoinitiated RAFT dispersion polymerization of MMA by replacing a certain amount of water with ethanol. Kinetics studies indicated that high monomer conversion (>95%) was achieved within 1 h of light irradiation in each case. A decrease in the rate of polymerization was observed on increasing the ethanol content in the polymerization system. SEC analysis indicated that moderate RAFT control was achieved in each case, as is evident by the linear evolution of Mn with monomer conversion. It was found that narrow molecular weight distributions were achieved on increasing the ethanol content and the dispersity could be controlled by varying the ethanol content, which can be attributed to the enhanced radical diffusion within the micellar core on increasing the ethanol content. Without changing the composition of block copolymers, radical diffusion within the micellar core can also be controlled by changing the reaction temperature. Narrower molecular weight distributions were also observed on increasing the reaction temperature, providing a facile strategy to tune dispersities of block copolymers. Finally, the effects of the reaction temperature and the ethanol content on morphologies of block copolymer nanoparticles were investigated. It was found that increasing the reaction temperature could promote the creation of higher-order morphologies. Moreover, the transition from RAFT emulsion polymerization to RAFT dispersion polymerization by increasing the ethanol content favored the formation of lower-order morphologies (e.g., spheres).
Conflicts of interest
There are no conflicts to declare.
Acknowledgements
The authors acknowledge support from the National Natural Science Foundation of China (Grant 52222301, 22171055, and 21971047) and the Guangdong Natural Science Foundation for Distinguished Young Scholars (Grant 2022B1515020078).
References
- J. Nicolas, Y. Guillaneuf, C. Lefay, D. Bertin, D. Gigmes and B. Charleux, Prog. Polym. Sci., 2013, 38, 63–235 CrossRef CAS
.
- J.-S. Wang and K. Matyjaszewski, J. Am. Chem. Soc., 1995, 117, 5614–5615 CrossRef CAS
.
- J. Chiefari, Y. K. (Bill) Chong, F. Ercole, J. Krstina, J. Jeffery, T. P. T. Le, R. T. A. Mayadunne, G. F. Meijs, C. L. Moad, G. Moad, E. Rizzardo and S. H. Thang, Macromolecules, 1998, 31, 5559–5562 CrossRef CAS
.
- N. Corrigan, K. Jung, G. Moad, C. J. Hawker, K. Matyjaszewski and C. Boyer, Prog. Polym. Sci., 2020, 111, 101311 CrossRef CAS
.
- M. R. Hill, R. N. Carmean and B. S. Sumerlin, Macromolecules, 2015, 48, 5459–5469 CrossRef CAS
.
- J. Phommalysack-Lovan, Y. Chu, C. Boyer and J. Xu, Chem. Commun., 2018, 54, 6591–6606 RSC
.
- S. Shanmugam, J. Xu and C. Boyer, Macromol. Rapid Commun., 2017, 38, 1700143 CrossRef PubMed
.
- R. Whitfield, K. Parkatzidis, N. P. Truong, T. Junkers and A. Anastasaki, Chem, 2020, 6, 1340–1352 CAS
.
- S. Perrier, Macromolecules, 2017, 50, 7433–7447 CrossRef CAS
.
- D. Liu, J. He, L. Zhang and J. Tan, ACS Macro Lett., 2019, 8, 1660–1669 CrossRef CAS PubMed
.
- P. B. Zetterlund, Y. Kagawa and M. Okubo, Chem. Rev., 2008, 108, 3747–3794 CrossRef CAS PubMed
.
- P. B. Zetterlund, S. C. Thickett, S. Perrier, E. Bourgeat-Lami and M. Lansalot, Chem. Rev., 2015, 115, 9745–9800 CrossRef CAS PubMed
.
- F. Jasinski, P. B. Zetterlund, A. M. Braun and A. Chemtob, Prog. Polym. Sci., 2018, 84, 47–88 CrossRef CAS
.
- J.-S. Song and M. A. Winnik, Macromolecules, 2006, 39, 8318–8325 CrossRef CAS
.
- P. J. Saikia, J. M. Lee, K. Lee and S. Choe, J. Polym. Sci., Part A: Polym. Chem., 2008, 46, 872–885 CrossRef CAS
.
- M. J. Monteiro, M. Hodgson and H. De Brouwer, J. Polym. Sci., Part A: Polym. Chem., 2000, 38, 3864–3874 CrossRef CAS
.
- C. J. Ferguson, R. J. Hughes, B. T. T. Pham, B. S. Hawkett, R. G. Gilbert, A. K. Serelis and C. H. Such, Macromolecules, 2002, 35, 9243–9245 CrossRef CAS
.
- D. Lin, L. Zhang and J. Tan, Acta Polym. Sin., 2023, 54, 761–777 CAS
.
- J. Cao, Y. Tan, Y. Chen, L. Zhang and J. Tan, Macromol. Rapid Commun., 2021, 42, 2100498 CrossRef CAS PubMed
.
- B. Niu, Y. Chen, L. Zhang and J. Tan, Polym. Chem., 2022, 13, 2554–2569 RSC
.
- S. Zhao, L. Zhang and J. Tan, Chin. J. Chem., 2023, 41, 1517–1525 CrossRef CAS
.
- J. He, Y. Chen, L. Zhang and J. Tan, Chin. Chem. Lett., 2023, 34, 107344 CrossRef CAS
.
- D. Lin, Y. Li, L. Zhang, Y. Chen and J. Tan, Macromolecules, 2023, 56, 440–447 CrossRef CAS
.
- W. Cai, S. Yang, L. Zhang, Y. Chen, L. Zhang and J. Tan, Macromolecules, 2022, 55, 5775–5787 CrossRef CAS
.
- S. Yang, L. Zhang, Y. Chen and J. Tan, Macromolecules, 2022, 55, 8472–8484 CrossRef CAS
.
- C. Liu, C.-Y. Hong and C.-Y. Pan, Polym. Chem., 2020, 11, 3673–3689 RSC
.
- W.-J. Zhang, C.-Y. Hong and C.-Y. Pan, Macromol. Rapid Commun., 2019, 40, 1800279 CrossRef PubMed
.
- X. Wang, L. Shen and Z. An, Prog. Polym. Sci., 2018, 83, 1–27 CrossRef CAS
.
- N. J. Warren and S. P. Armes, J. Am. Chem. Soc., 2014, 136, 10174–10185 CrossRef CAS PubMed
.
- S. L. Canning, G. N. Smith and S. P. Armes, Macromolecules, 2016, 49, 1985–2001 CrossRef CAS PubMed
.
- N. J. W. Penfold, J. Yeow, C. Boyer and S. P. Armes, ACS Macro Lett., 2019, 8, 1029–1054 CrossRef CAS PubMed
.
- P. Gurnani and S. Perrier, Prog. Polym. Sci., 2020, 102, 101209 CrossRef CAS
.
- S. Li, G. Han and W. Zhang, Polym. Chem., 2020, 11, 4681–4692 RSC
.
- Y. Liu, Y. Sun and W. Zhang, Chin. J. Chem., 2022, 40, 965–972 CrossRef CAS
.
- R. A. E. Richardson, T. R. Guimarães, M. Khan, G. Moad, P. B. Zetterlund and S. Perrier, Macromolecules, 2020, 53, 7672–7683 CrossRef CAS
.
- W. Hou, Z. Li, L. Xu, Y. Li, Y. Shi and Y. Chen, ACS Macro Lett., 2021, 10, 1260–1265 CrossRef CAS PubMed
.
- G. M. Scheutz, J. I. Bowman, S. Mondal, J. Y. Rho, J. B. Garrison, J. Korpanty, N. C. Gianneschi and B. S. Sumerlin, ACS Macro Lett., 2023, 12, 454–461 CrossRef CAS PubMed
.
- J. Wu, L. Zhang, Y. Chen and J. Tan, ACS Macro Lett., 2022, 11, 910–918 CrossRef CAS PubMed
.
- D. Liu, S. Yang, S. Peng, Y. Chen, L. Zhang and J. Tan, Macromol. Rapid Commun., 2022, 43, 2100921 CrossRef CAS PubMed
.
- K. E. B. Doncom, L. D. Blackman, D. B. Wright, M. I. Gibson and R. K. O'Reilly, Chem. Soc. Rev., 2017, 46, 4119–4134 RSC
.
- D. T. Gentekos, L. N. Dupuis and B. P. Fors, J. Am. Chem. Soc., 2016, 138, 1848–1851 CrossRef CAS PubMed
.
- D. T. Gentekos, J. Jia, E. S. Tirado, K. P. Barteau, D.-M. Smilgies, R. A. DiStasio Jr. and B. P. Fors, J. Am. Chem. Soc., 2018, 140, 4639–4648 CrossRef CAS PubMed
.
- S. I. Rosenbloom and B. P. Fors, Macromolecules, 2020, 53, 7479–7486 CrossRef CAS
.
- S. R. George, R. Champagne-Hartley, G. A. Deeter, J. D. Campbell, B. Reck, D. Urban and M. F. Cunningham, Macromolecules, 2017, 50, 315–323 CrossRef CAS
.
- S. R. George, R. Champagne-Hartley, G. A. Deeter, J. D. Campbell, B. Reck, D. Urban and M. F. Cunningham, Macromolecules, 2017, 50, 315–323 CrossRef CAS
.
- S. Han, J. Wu, Y. Zhang, J. Lai, Y. Chen, L. Zhang and J. Tan, Macromolecules, 2021, 54, 4669–4681 CrossRef CAS
.
- X. Dai, L. Yu, Y. Zhang, L. Zhang and J. Tan, Macromolecules, 2019, 52, 7468–7476 CrossRef CAS
.
- J. Cao, Y. Tan, X. Dai, Y. Chen, L. Zhang and J. Tan, Polymer, 2021, 230, 124095 CrossRef CAS
.
- S. W. Thompson, T. R. Guimarães and P. B. Zetterlund, Polym. Chem., 2022, 13, 5048–5057 RSC
.
- T. R. Guimarães, M. Khan, R. P. Kuchel, I. C. Morrow, H. Minami, G. Moad, S. Perrier and P. B. Zetterlund, Macromolecules, 2019, 52, 2965–2974 CrossRef
.
- G. K. K. Clothier, T. R. Guimarães, M. Khan, G. Moad, S. Perrier and P. B. Zetterlund, ACS Macro Lett., 2019, 8, 989–995 CrossRef CAS PubMed
.
- N. G. Engelis, A. Anastasaki, G. Nurumbetov, N. P. Truong, V. Nikolaou, A. Shegiwal, M. R. Whittaker, T. P. Davis and D. M. Haddleton, Nat. Chem., 2017, 9, 171–178 CrossRef CAS PubMed
.
- M. Khan, T. R. Guimarães, K. Choong, G. Moad, S. Perrier and P. B. Zetterlund, Macromolecules, 2021, 54, 736–746 CrossRef CAS
.
- J. Zhou, Q. Huang, L. Zhang and J. Tan, ACS Macro Lett., 2023, 1457–1465 CrossRef CAS PubMed
.
- E. E. Brotherton, F. L. Hatton, A. A. Cockram, M. J. Derry, A. Czajka, E. J. Cornel, P. D. Topham, O. O. Mykhaylyk and S. P. Armes, J. Am. Chem. Soc., 2019, 141, 13664–13675 CrossRef CAS PubMed
.
- F. L. Hatton, M. J. Derry and S. P. Armes, Polym. Chem., 2020, 11, 6343–6355 RSC
.
- J. Tan, X. Dai, Y. Zhang, L. Yu, H. Sun and L. Zhang, ACS Macro Lett., 2019, 8, 205–212 CrossRef CAS PubMed
.
- F. D'Agosto, J. Rieger and M. Lansalot, Angew. Chem., Int. Ed., 2020, 59, 8368–8392 CrossRef PubMed
.
- F. Zhong and C.-Y. Pan, Macromol. Rapid Commun., 2022, 43, 2100566 CrossRef CAS PubMed
.
- A. Blanazs, J. Madsen, G. Battaglia, A. J. Ryan and S. P. Armes, J. Am. Chem. Soc., 2011, 133, 16581–16587 CrossRef CAS PubMed
.
- A. Czajka and S. P. Armes, J. Am. Chem. Soc., 2021, 143, 1474–1484 CrossRef CAS PubMed
.
- A. Czajka and S. P. Armes, Chem. Sci., 2020, 11, 11443–11454 RSC
.
- J. Tan, X. Rao, X. Wu, H. Deng, J. Yang and Z. Zeng, Macromolecules, 2012, 45, 8790–8795 CrossRef CAS
.
- G. K. K. Clothier, T. R. Guimarães, G. Moad and P. B. Zetterlund, Macromolecules, 2021, 54, 3647–3658 CrossRef CAS
.
- J. Tan, D. Liu, Y. Bai, C. Huang, X. Li, J. He, Q. Xu, X. Zhang and L. Zhang, Polym. Chem., 2017, 8, 1315–1327 RSC
.
- X. Luo, S. Zhao, Y. Chen, L. Zhang and J. Tan, Macromolecules, 2021, 54, 2948–2959 CrossRef CAS
.
- K. Zhang, M. Xiao, L. Zhang, Y. Chen and J. Tan, ACS Macro Lett., 2022, 11, 716–722 CrossRef CAS PubMed
.
- Y. Zhang, J. He, X. Dai, L. Yu, J. Tan and L. Zhang, Polym. Chem., 2019, 10, 3902–3911 RSC
.
- E. R. Jones, M. Semsarilar, A. Blanazs and S. P. Armes, Macromolecules, 2012, 45, 5091–5098 CrossRef CAS
.
- S. J. Byard, M. Williams, B. E. McKenzie, A. Blanazs and S. P. Armes, Macromolecules, 2017, 50, 1482–1493 CrossRef CAS PubMed
.
Footnotes |
† Electronic supplementary information (ESI) available: Full experimental detail and additional results. See DOI: https://doi.org/10.1039/d3py01006f |
‡ These authors contributed equally to this work. |
|
This journal is © The Royal Society of Chemistry 2024 |