DOI:
10.1039/D3MA01058A
(Review Article)
Mater. Adv., 2024,
5, 2689-2718
Anti-corrosion properties of bio-inspired surfaces: a systematic review of recent research developments
Received
29th November 2023
, Accepted 6th February 2024
First published on 20th February 2024
Abstract
Strengthening measures for protecting metals against corrosion hold significant importance for environmental preservation, economic development, and the enhancement of people's well-being. It is crucial to research and implement effective protection technologies. Bio-inspired surfaces have emerged as a compelling avenue in corrosion protection research, owing to their unique design and functionality. This paper delves into the key findings and innovations in bio-inspired surfaces for anticorrosion through a systematic review organized into three distinct parts, each focusing on a specific category of bio-inspired coatings. In the first part, the paper examines self-healing coatings inspired by the regenerative properties of skin. Emphasis is placed on how the design and composition of these coatings draw inspiration from the remarkable self-repair ability of the skin. The second part delves into superhydrophobic coatings inspired by the lotus plant. The paper systematically presents the design curation, structural features, and research progress of superhydrophobic surfaces, with a focus on their role in self-cleaning, anti-pollution, and anti-corrosion. The third part explores slippery liquid-infused porous surfaces (SLIPSs) inspired by lubricating plants and animals, such as Nepenthes. This section provides a systematic overview of research advances in SLIPSs and their potential applications in corrosion protection. Through this systematic review, this paper offers a comprehensive perspective on various strategies employed in bio-inspired surfaces for corrosion protection. By summarizing and reviewing the latest developments in self-healing, superhydrophobic, and SLIPS surfaces, this paper provides valuable insights into current advancements in the field.
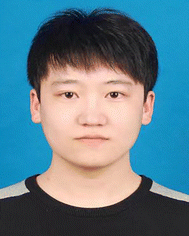
Qingyun Ma
| Dr Qingyun Ma is currently a PhD student in Prof. Feng Chen's group at Xi'an Jiaotong University. His research interests include bio-inspired design for corrosion, fouling and drag reduction. |
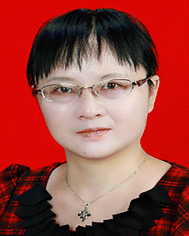
Qing Yang
| Prof. Qing Yang received her BS degree in Photoelectron Science and Technology in 1992 from Sichuan University. In 2009, she received her PhD from Xi'an Institute of Optics and Fine Mechanics, Chinese Academy of Science. She is currently an associate professor at Xi'an Jiaotong University. Her current research interests are femtosecond laser micro- and nanofabrication, laser biomimetic micro- and nanofabrication, ultrafast photonics and micro- and nanophotonics. |
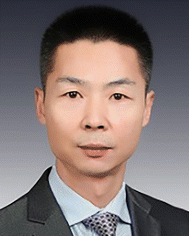
Feng Chen
| Prof. Feng Chen is a full professor of Electronic Engineering at Xi'an Jiaotong University, where he directs Ultrafast Photonic Laboratory (UPL), and has served as the director of Shaanxi key laboratory of Photonics Technology of Informtion (PTI) and the deputy director of the International Joint Research Center for Micro/Nano Manufacturing and Measurement Technologies. His current research interests are femtosecond laser microfabrication, bionic microfabrication and ultrafast photonics. Prof. Chen has published over 300 peer-reviewed papers in journals including Chem. Soc. Rev., Adv. Funct. Mater., Phys. Rev. Lett., etc. |
Introduction
Metals and alloys are extensively utilized in various industries such as engineering, transportation, construction, marine, and aerospace. However, these metallic materials are prone to corrosion when exposed to different environmental factors.1–5 Corrosion is a pervasive issue that leads to significant economic losses and causes severe environmental pollution.6–8 Consequently, the pursuit of effective methodologies to alleviate corrosion stands as a pivotal domain in scientific research, presenting an urgent imperative within the engineering discipline. To prevent the infiltration of corrosive agents into metals and the formation of microcells, measures can be instituted to decelerate and arrest this process, thereby realizing the objective of robust corrosion resistance efficiently. Polymer coating technology can provide protection and decoration for metals,9 while metal plating technology, such as thermal spraying,10 cold spraying,11 chemical plating,12 and electroplating,13 can form firmly adhered coatings on metal surfaces to enhance performance. Chemical conversion technology, including chromate conversion films,14 phosphate conversion films,15 and rare earth salt conversion films,16 can improve corrosion resistance through chemical reactions with metal surfaces. Anodic oxidation and micro-arc oxidation technology are also applicable to light metals like magnesium and aluminum,17,18 forming dense oxidation layers to increase surface hardness and abrasion resistance. The application of these technologies can result in enhanced durability, corrosion resistance, and aesthetic qualities for metal materials. Nevertheless, these coating technologies exhibit certain drawbacks, such as environmental considerations, heightened surface hydrophilicity, and constrained protective functionalities. In response to these challenges, researchers are actively engaged in the exploration and development of novel technologies aimed at augmenting the multifunctionality, intelligence, and overall performance of protective coatings for metals.
The intricate and dynamic ecological environment imposes rigorous selection and adaptation challenges on all natural organisms. In response, a diverse array of creatures have evolved optimal structures and functions tailored to their surroundings. For example, lotus leaves are renowned for their capacity to repel dirt and water, known as the lotus leaf effect. Butterflies, through the flapping of their wings, disperse water droplets radially, preventing them from wetting the butterfly's body. Geckos exhibit swift wall maneuverability due to their highly adhesive feet. Mosquitoes maintain exceptional visual acuity even in foggy and dark conditions. Fish scales demonstrate effective self-cleaning and drag-reduction properties under water. By scrutinizing and emulating the structures and characteristics of these organisms, researchers are actively exploring the realm of biomimetic intelligent materials that integrate both structure and function. This avenue of investigation stands at the forefront of scientific exploration. The rapid progress in bionics holds promise for addressing and preventing metal corrosion. Materials and coatings inspired by bionics principles offer innovative concepts and avenues to achieve diverse functions, intelligence, and high performance in metal protective surfaces.
Bio-inspired anticorrosion strategies are crafted by drawing inspiration from the shapes, functions, and other elements observed in nature to address intricate corrosion challenges. For instance, emulating biological tissues with self-healing properties facilitates the active repair of coatings following breakage. The replication of plant leaves possessing water-repellent properties leads to the development of inert coatings that minimize contact with the external environment. Furthermore, diverse organisms in nature have evolved various protective mechanisms to achieve effective anti-biofouling. Fig. 1 illustrates the escalating trend in publications focusing on bio-inspired anticorrosion strategies from 2014 to 2023. This trend signifies the growing interest among scholars over the past decade, highlighting the increasing attention directed toward these strategies.
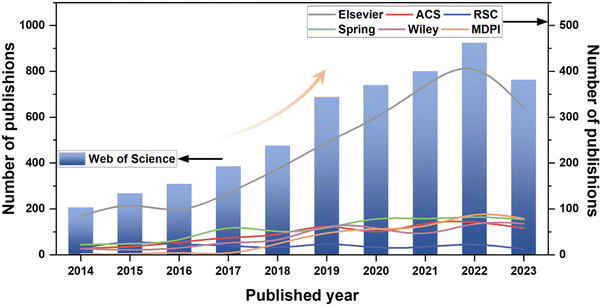 |
| Fig. 1 The number of publications that concern bioinspired anticorrosion studies, each year from 2014 to 2023 [search in Web of Science, search words: corrosion (Topic) or anticorrosion (Topic) and bioinspired (Title) or biomimetic (Title) and nature-inspired (Title)]. | |
Several review articles offer intriguing summaries and analyses of existing scientific research on bionic surfaces for anticorrosion.19–24 However, there is a relative scarcity of comprehensive overviews detailing the various types of bionic surface technologies. Particularly lacking are compilation and summarization of the corrosion prevention mechanisms, challenges, and response strategies associated with bionic surfaces developed in recent years. Biomimicry offers innovative solutions for preventing corrosion by emulating the structures and functions found in nature. Inspired by biological skin, researchers have created corrosion-resistant coatings with self-healing capabilities, reducing the incidence of corrosion. Morphological optimization, achieved through mimicking the structural forms of living organisms, facilitates the design of corrosion-resistant materials better suited to environmental conditions. For example, a coating with superhydrophobic properties has been developed by drawing inspiration from the surface texture of lotus leaves. This coating effectively prevents the adhesion of pollutants and corrosion of alloys. Despite the significant strides made in biomimetic strategies for corrosion prevention, challenges such as the feasibility and cost of practical applications persist. This review addresses this gap by presenting three nature-inspired anti-corrosion strategies, as shown in Fig. 2. These strategies encompass biomimetic self-healing coatings that emulate biological tissues, biomimetic superhydrophobic surfaces exemplified by lotus leaves, and biomimetic slippery lubricant-infused porous surfaces inspired by the exceptional liquid repellency of Nepenthes. This review further provides a summary of their relevant technologies, anti-corrosion mechanisms, and applications. Additionally, it organizes the challenges and research advances in anti-corrosion coatings witnessed in recent years.
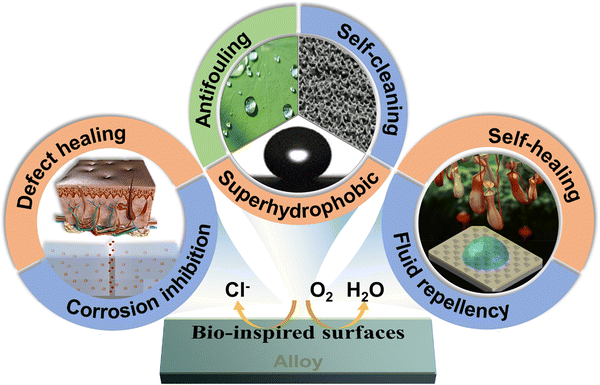 |
| Fig. 2 A graphical abstract of bio-inspired anti-corrosion surfaces, including biomimetic self-healing coatings, biomimetic superhydrophobic surfaces, and biomimetic slippery liquid-infused porous surfaces. | |
Biomimetic self-healing coatings
In the realm of nature, biological tissues exhibit remarkable adaptive capabilities to their external surroundings. These tissues effectively fulfill their biological functions even in challenging climates. Organisms, through a self-repair mechanism, possess the capacity to mend injuries inflicted upon them by the external environment. This reparative process aims to restore the original functionality of the wounded area, thereby ensuring the organism's optimal functioning and longevity. As an illustration, in the event of a skin injury, the blood emanating from the affected area carries coagulation factors,25 initiating an automatic hemostatic response to halt bleeding. Concurrently, the injury to the skin triggers cell division and proliferation in the vicinity of the wound. This cellular activity is aimed at repairing the damaged skin and reinstating its original protective function.26 It has become a hot research direction to imitate the self-healing ability of organisms and develop intelligent bionic materials that integrate sensing and driving and have good adaptive capacity to the external environment. Inspired by this, developing an anti-corrosion coating with a self-healing function to realize the active repair of a damaged layer is of great significance to extend the service life of the layer and reduce the maintenance cost. The definition of the self-healing function of the coating in the coating protection is different from that of the traditional self-healing function. In the classical understanding of the self-healing function, the self-healing function of a material requires the material to completely repair the damaged area and fully restore its original function. However, the most essential function of the anti-corrosion coating is to protect the base material from further damage by the surrounding corrosive media. Therefore, the protective coating has a self-healing function because its primary function is protection. Thus, only the recovery of the protective function of the coating can be realized at the damaged part of the coating without realizing all its functions, including the complete recovery of the original appearance of the coating.27 According to the different objects repaired by the coating, the self-healing coating can be divided into the defect healing type and the corrosion suppression type.
Defect healing type
Defect-healing coatings aim to restore the corrosion resistance of the coating by incorporating microcapsule-coated repair agents or utilizing the inherent physical and chemical attributes of the coating.
2.1.1. Multi-shelled microcapsules.
White et al.28 were the first to introduce microcapsule technology into material design and apply it to the development of smart materials with self-healing capabilities. This advancement has the potential to extend the service life of materials. Fig. 3 shows the design scheme and working principle of a smart self-healing material. A self-repair reagent monomer dicyclopentadiene (DCPD) was encapsulated in a urea–formaldehyde shell by situ polymerization, and the Grubbs catalyst, which can catalyze the polymerization of the DCPD monomer, was dispersed in the epoxy polymer matrix. When the epoxy polymer material ruptures, the microcapsule ruptures, releasing the DCPD monomer, which acts as a self-repairing reagent and undergoes a polymerization reaction catalyzed by the Grubbs catalyst in the matrix, thus repairing the rupture in the material. However, Grubbs catalysts are expensive, and the self-repairing reagents released upon rupture of the microcapsules depend on the catalyst dispersed in the polymer matrix material for the curing process. If the catalyst undergoes structural changes leading to the loss of its catalytic properties, for example, because of poor thermal stability, the self-repair reagent cannot be cured, leading to the loss of self-repair function. Therefore, the development of catalyst-free, self-healing core materials can expand the range of applications for self-healing materials and avoid the effects of catalyst failure. One-component self-healing systems without the aid of catalysts and curing agents, represented by dry oils,29–31 isocyanates,32–34 and active silicones,35–37 have been rapidly developed. The molecular structure of the repair agent of this system usually contains active functional groups that can polymerize under the action of O2, H2O, or light to realize the repair of coating defects and show good self-repair and corrosion resistance. For instance, Wang et al.38 synthesized isocyanate microcapsules with isophorone diisocyanate and hexamethylene diisocyanate (HDI) as functional additives. They were used as potential healing materials for the water-triggered process by utilizing the “water” in the corrosion process as a “trigger switch” for the repair process. When microcracks are generated, the isocyanate released from the rupture of the microcapsules undergoes a polymerization reaction at room temperature to bond the cracks, effectively preventing corrosion from occurring and prolonging the service life of the anticorrosion coating.
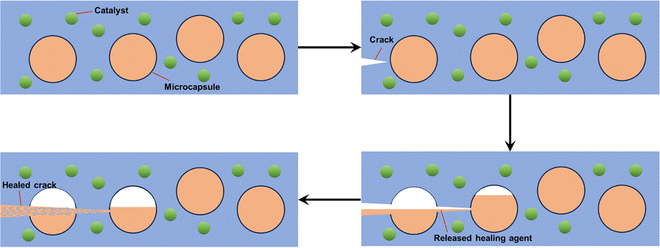 |
| Fig. 3 A microencapsulated healing agent is embedded in a structural composite matrix containing a catalyst capable of polymerizing the healing agent. | |
Furthermore, Wang et al.39 used a low-volatile HDI biuret as a healing material to prepare HDI biuret microcapsules by in situ polymerization instead of isocyanate, which is unfavorable to human health, and the study showed that it has an obvious self-healing effect under the trigger of water immersion, which strengthened the corrosion protection of the damaged area of the coating. Feng et al.40 prepared tung oil-loaded polyurethane (PU) microcapsules by interfacial polymerization and obtained tung oil-loaded PU/PANI double-shell microcapsules by in situ deposition of polyaniline (PANI) in a SiO2-stabilized Pickering emulsion system. The synergistic effect of the tung oil core and the polyaniline wall, through the formation of a self-healing film and a passivation layer, resulted in a coating with excellent self-healing and anti-corrosion properties.
Microcapsule preparation technology has reached a level of maturity and diversity, making it easily combinable with coating materials. Consequently, the design space for a microcapsule-embedded self-healing coating system is expansive, holding significant promise for widespread applications. While polymer self-repair materials based on microcapsules can accomplish the self-repair function of coatings, the loading capacity of microcapsules in the material is relatively limited. This constraint results in the material's ability to execute a one-time self-repair function at the point of rupture. Subsequent damage to the coating poses challenges as the self-repair reagents within the microcapsules become depleted, hindering the ability to sustain further repairs.
2.1.2. Microvascular networks.
It is necessary to supply a substantial amount of self-healing reagents continuously to address the challenge of multiple self-healing functions at the same break, ensuring a constant flow into the material break.41 Upon damage to the coating caused by external forces, the interwoven microvessel network becomes compromised. The self-repairing reagent is released from the damaged section of the microvessel network, initiating further curing and other reactions at the affected site. This autonomous repair process can be iteratively repeated numerous times. The construction of one-dimensional tubular structures in polymers is feasible through the utilization of hollow fibers, microtubes, or microchannels.42–45 With more sophisticated designs, a three-dimensional microvessel network embedded in the polymer becomes capable of transporting two-component self-healing reagents (Fig. 4). Hansen et al.46 demonstrated that dual-vessel-based self-healing composites are capable of achieving more than 30 repetitions of self-healing through their study. In addition, Hansen et al.47 suggested that the temperature and time of self-repair can be theoretically regulated by introducing a third independent microvessel network function, allowing the material to self-repair in harsh environments as well.
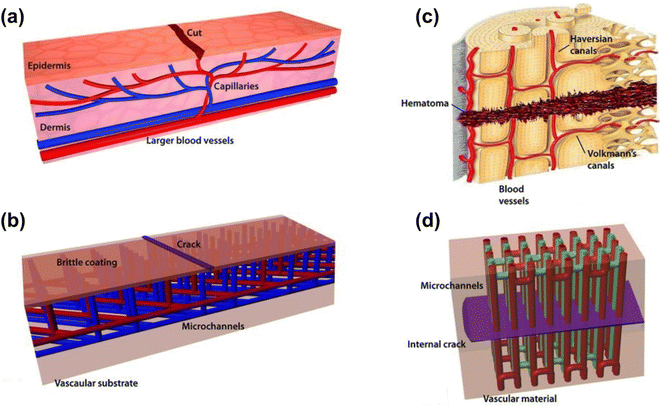 |
| Fig. 4 Schematic diagram of a microvascular structure (reproduced from ref. 41 with permission from [Wiley], copyright [2010]). | |
Despite the numerous advantages of self-repairing materials with microvascular network systems, several challenges must be addressed before practical applications. In the production and preparation process, efforts should be made to reduce the cost associated with microvessel network-based self-repair materials.48 Additionally, when designing such materials, special attention is required to ensure that the intelligent self-repair features do not compromise or adversely impact the properties and functions of the substrate material, which includes addressing concerns related to the circulation of self-repair reagents in microvessels and ensuring the feasibility of multiple self-repair processes.
Damage at the millimeter scale poses a challenge for a single self-healing material system to repair multiple scales of material damage simultaneously. Hence, the integration of multiple self-healing strategies can be employed in the design of self-healing materials. Gergely et al.49 designed a self-repairing material using both microcapsule and microvessel strategies, which is capable of autonomously repairing damage within the micrometer scale and millimeter scale at the same time. The microvessel network was used to deliver repair reagents with two-stage reaction characteristics to repair large-size damage due to punctures in the system. In contrast, microcapsules loaded with epoxy monomer-based self-repair reagents were used to repair damage such as microcracks generated. By adjusting the monomer self-repair reagent, the strength of the material after curing can be between 1.1 MPa and 1.4 GPa, thus ensuring that the strength of the material after the completion of self-repair at the damage is close to the strength of the material before damage. The experimental results show that the self-repair system with microcapsule-microvessel hybridization not only enables the self-repair efficiency of the matrix material to reach 100% but also enables the simultaneous repair of microcracks in the matrix material due to the microcapsule system, realizing the complete restoration of the morphology of the matrix material.
2.1.3. Core–shell nano- and micro-fibers.
Recent studies have identified core–shell structural epoxy coatings as an effective self-healing technique, providing a cost-effective alternative to microencapsulation.50 Nanofibers are popular due to their excellent mechanical and thermal properties combined with high porosity and large surface area to volume ratio. These characteristics contribute to the homogeneous dispersion of healing carriers in composites and ensure a benign interaction with the matrix and reinforcing fibers, preventing disruption to their surface morphology. Electrostatic spinning technology is commonly employed for fiber production. Sinha-Ray et al.51 pioneered the use of micro/nanofibers as a self-healing carrier, employing polyacrylonitrile (PAN) as the shell and encapsulating DCPD and isophorone diisocyanate via the electrostatic spinning technique. Wang et al.52 encapsulated self-healing epoxy resin and a curing agent in polyacrylonitrile by coaxial electrostatic spinning to form two-component core–shell nanofibers. The healing efficiency could reach 110.12% after self-healing for 1 h at 120 °C. Mao et al.53 synthesized PAN nanocore-shell fibers using the electrostatic spinning technique and incorporated them into a carbon fiber-reinforced polymer. The addition of core–shell nanofibers enabled the material to self-heal to 80% of its undamaged residual compressive strength when subjected to impacts with energies lower than 37.5 J.
Beyond the electrostatic spinning method, Lee et al.54 were the first to utilize commercial epoxy resins as healing agents embedded in nanofibers and microfibers formed through solution blow molding. Remarkably, this method has been successfully scaled up to an industrial level and is at least 30 times faster than the electrostatic spinning process.
2.1.4. Intrinsic self-healing materials.
Intrinsic-type materials can be designed through various mechanisms, including thermally reversible chemical reactions, ammonia bonding, ionomer rearrangements, diffusion and entanglement of molecular-level polymer chain segments, coordination chemistry, and host–guest interactions. Intrinsic materials possess a unique ability to self-heal at the molecular level, making them the closest to an ideal material compared to external additives like microcapsules or microvessels. In self-healing polymers relying on reversible Diels–Alder dynamic chemical reactions, thermally reversible covalent bonding facilitates the dynamic exchange of covalent bonds within the material when heated. This process effectively repairs microcracks that may occur in the material.55–57 The self-healing function is more readily achievable in thermoplastic polymers, primarily because they are linear polymers with polymer chain segments that exhibit greater mobility compared to thermoset polymers.58 Consequently, when thermoplastic polymers are subjected to heat, the polymer chain segments at the rupture interface can come into contact and entangle, effectively realizing the self-healing capability of the material. However, it is important to note that thermoplastic polymers generally exhibit lower mechanical strength. In contrast, thermosets possess a crosslinked network structure, resulting in higher mechanical strength.59 However, the presence of these crosslinked networks makes thermosets challenging to reuse multiple times. When compared to thermally reversible self-healing coatings, photoplastic self-healing coatings offer the advantage of remote and precise repair of damaged areas. This characteristic helps minimize the side effects of the self-healing process and reduce the risk of thermal damage to intact areas of the coating.60
Dopamine chemistry is a recently developed biomimetic chemical means in which the presence of the o-phenol hydroxyl group makes the dopamine-based materials have excellent bonding properties and self-repairing properties even under water,61 and the dopamine-based materials do not need any other stimulation to achieve rapid and efficient self-repairing properties of their materials.62–64 However, the small bond energy of dynamic non-covalent bonding leads to weak mechanical properties of self-healing materials prepared by dynamic bonding, which limits their further applications. Therefore, improving the mechanical properties of dynamic non-covalent bonded self-healing materials has become an important direction in the research of this class of self-healing materials. The mechanical properties of the self-healing materials were effectively enhanced by using inorganic materials for toughening, carbon materials, and the introduction of a dual network structure.65–67 Natural organisms exhibit remarkable self-healing abilities coupled with extraordinary mechanical strength, prompting researchers to delve into the structure and functions of these organisms. This exploration proves to be a highly rewarding endeavor. In the realm of biomimicry, the focus extends beyond mere imitation of a living organism's structure; it involves integrating structure and function to develop new materials that either replicate or surpass the structural attributes of the original organism. For instance, biological tissues like skin, with their layered structure, resilient bones, and the sturdy shells of mollusks, possess the capability to undergo complete self-repair following damage through a series of coordinated chemical and physical processes. Over hundreds of millions of years of natural evolution, these biological tissues have not only achieved structural excellence but have also optimized the repair process, maximizing resource and energy efficiency. Consequently, the development of materials that mirror the efficiency and environmental friendliness of biological tissues, coupled with high-strength self-repair capabilities, emerges as both a challenging task and an urgent priority in the domains of corrosion prevention and self-repair materials.
2.2. Corrosion inhibition type
In contrast to defect-healing self-healing coatings, corrosion-inhibiting self-healing coatings employ an alternative approach by impeding metal corrosion through the incorporation of an active substance into the coating.
2.2.1. Nanocontainers.
Direct doping of corrosion inhibitors into the coating poses challenges in achieving controlled release, potentially leading to the rapid depletion of the corrosion inhibitor over a short period. Moreover, there is a risk of the corrosion inhibitor reacting with certain components of the coating matrix, resulting in issues such as corrosion inhibitor failure or degradation of coating performance. In contrast, encapsulating the corrosion inhibitor in a nanocontainer before dispersing it into the coating provides an effective solution by isolating the corrosion inhibitor from the coating substrate. The presence of nanocontainers not only prevents direct contact between the corrosion inhibitor and the coating but also imparts a certain environmental responsiveness to the corrosion inhibitor, which allows controlled release and migration of the corrosion inhibitor to the corrosion site under external stimuli, such as a magnetic field, temperature, light, or pH. Subsequently, the released corrosion inhibitor can inhibit the electrochemical activity of the corrosion site through processes like adsorption, passivation, or chelating reactions with metal ions. This mechanism helps block the further expansion of corrosion.
Porous materials characterized by a high specific surface area serve as excellent candidates for nanocontainers loaded with corrosion inhibitors. Table 1 provides an overview of the research progress in nanocontainers based on corrosion inhibitors for the development of self-healing coatings.
Table 1 Summary of nanocontainers for self-heal coating
Group |
Type |
Corrosion inhibitor |
Applied coating |
Substrate |
Ref. |
Inorganic nanocontainers |
SiO2 |
2-Aminino-5-mercato-1,3,4-thiadizole, BTA |
Epoxy |
Copper, aluminum alloy |
68 and 69
|
TiO2 |
Molybdate |
Polypyrrole |
304 stainless steel |
70
|
ZrO2 |
IM |
Epoxy |
Carbon steel |
71
|
CeO2 |
BTA, dodecylamine, n-methylthiourea |
Silane-based coating, epoxy |
Copper, carbon steel |
72 and 73
|
Talc nanoparticles |
NaNO3 |
Epoxy |
Carbon steel |
74
|
HNTs |
IM |
Epoxy |
Carbon steel |
75
|
NaY zeolite |
BTA |
Epoxy |
Q235 low-carbon steel |
76
|
Graphene oxide (GO) |
BTA, 2-mercaptobenzothiazole |
Epoxy |
Q235 carbon steel |
77
|
MWCNT |
Polyaniline, Zn2+ |
Epoxy |
Mild steel |
78
|
Organic nanocontainers |
Cyclodextrin |
Dopamine |
Silane-based coating |
Steel |
79
|
Polydopamine |
Zn2+ |
Epoxy |
Mild steel |
80
|
Polyvinyl butyral |
Gallic acid and phenanthroline |
Epoxy |
Q235 steel |
81
|
Urea-formaldehyde |
Fluorinated alkyl silane |
Epoxy |
Q235 steel |
82
|
Organic–inorganic hybrids |
ZIF-8 |
Glutamate molecules, Zn2+ |
Epoxy |
ST12-grade low-carbon steel |
83
|
Inorganic nanocontainers predominantly consist of mesoporous nanoparticles like SiO2, TiO2, and CeO2, among others. The anti-corrosion mechanism typically involves loading the cavities of inorganic nanoparticles with both inorganic and organic corrosion inhibitors. The release of corrosion inhibitors is controlled in response to environmental stimuli, coupled with physical or chemical actions on the metal surface, thereby preventing corrosion. For instance, Habib et al.71 utilized ZrO2 nanoparticles as carriers loaded with a self-repairing agent polyethyleneimine (PEI) and a corrosion inhibitor imidazole (IM). Prolonged electrochemical tests in a 3.5 wt% NaCl solution demonstrated excellent corrosion resistance in the epoxy-based bilayer nanocomposite coatings after a 7-day immersion in the corrosive medium. Khan et al.75 incorporated a corrosion inhibitor IM into halloysite nanotubes (HNTs) and coated the surface with a polyelectrolyte multilayer film consisting of PEI and sulfonated polyether ether ketone, with insertion of dodecyl amine (DDA). Electrochemical impedance spectroscopy (EIS) tests revealed corrosion inhibition efficiencies of 92% and 99.8% for the modified and hybrid coatings, respectively.
HNTs are natural silica-aluminate nanomaterials with a versatile application scope in the field of anticorrosive coatings owing to their distinctive hollow tubular structure. However, the inherent corrosion inhibitor loading efficiency of pristine HNTs is relatively low. Many studies have employed sulfuric acid to etch HNTs, creating hybrid halloysite nanotubes as a smart carrier. This process increases pore volume and enhances loading efficiency. Nonetheless, the sulfuric acid treatment poses a risk of damaging or partially decomposing the hollow tubular structure of HNTs. In a recent study, Zhao et al.84 opted for a milder approach using acetic acid to etch HNTs, aiming to enhance the loading capacity of the corrosion inhibitor methyl benzotriazole (BTA). The loading of BTA increased from 1.57 wt% to 2.33 wt%. Notably, the authors applied polydopamine (PDA) to coat the HNTs, improving their dispersion in the epoxy resin and effectively reducing the release of BTA in the absence of corrosion.
Organic nanocontainers have been extensively utilized in the formulation and investigation of corrosion inhibitor coatings, primarily owing to their cost-effectiveness, straightforward synthesis, and high specific surface area. The corrosion prevention mechanism inherent in organic nanocontainers closely parallels that observed in inorganic nanocontainers. Drawing inspiration from mussel adhesive proteins, Shen et al.85 synthesized HNQ-EN via a Schiff base reaction involving 5-hydroxy-1,4-naphthalenedione (HNQ) and ethylenediamine (EN). The resultant HNQ-EN is subsequently combined with Ti3C2Tx, denoted as HE-Ti3C2Tx, functioning as a nanocontainer for cerium nitrate. This unique combination imparts self-healing properties to the epoxy coating. Experimental outcomes demonstrated a substantial enhancement in inhibition efficiency, increasing from the initial 7.8% to an impressive 91.1% after subjecting the samples to immersion in a 3.5 wt% NaCl solution for 36 hours.
2.2.2. Layer-by-layer coating technique.
The layer-by-layer (LBL) coating technique stands out as a versatile, cost-effective, relatively simple, and easily scalable method for the production of intelligent capsules with potential applicability in large-scale industrialized production. In a study reported by Chen et al.,86 the LBL method was employed to fabricate a novel pH-sensitive SnO2 nanocontainer. The process involved depositing a polypyridine layer onto SnO2 nanoparticles, synthesized through a hydrothermal method using in situ chemical polymerization. Subsequently, ultrasonic loading of the Na2MoO4 layer and stirring resulted in the acquisition of a PDA-modified nanocontainer. The incorporation of a polydopamine (PDA) outer layer exerted control over the on-demand release of the molybdate corrosion inhibitor, simultaneously modifying the cracked polymer network through the utilization of dopamine functional groups and iron oxide. This enhancement significantly bolstered the self-healing capability of the epoxy coating, showcasing commendable corrosion resistance. In a separate study, Fathabadi et al.87 synthesized intelligent multilayer pH-sensitive nanocapsules using the LBL strategy. The outer shell comprised multilayered polystyrenesulfonate (PSS)/PEI/PSS, while the inner shell consisted of PSS/cetyl trimethyl ammonium bromide (CTAB). ZrO2 was loaded with the corrosion inhibitor tolyltriazole, as illustrated in Fig. 5. The nanocapsules exhibited automatic release of the loaded corrosion inhibitor, providing surface protection under both strongly acidic and alkaline conditions.
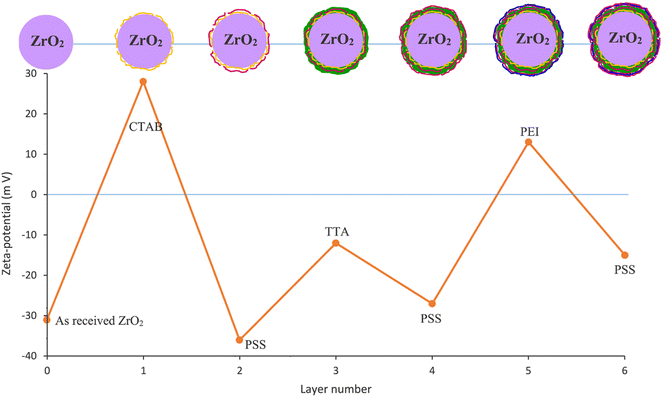 |
| Fig. 5 Zeta-potential measurement of ZrO2 nanoparticles and obtained compounds after each stage of the LBL process (reproduced from ref. 87 with permission from [Elsevier], copyright [2021]). | |
The integration of corrosion inhibitor loading techniques with emerging technologies, such as shape memory technology, has led to a rapid development of synergistic approaches to enhance various repair mechanisms. Li et al.88 explored the feasibility of depositing a SiO2/BTA/graphene quantum dot (GQD) coating on PDA (PSBG) as an effective LBL system for self-healing shape memory polymer (SMP) coatings on the AA2023 aluminum alloy. The remarkable passive and active corrosion protection capabilities of the PSBG can be delineated in three key aspects. The first key mechanism involves the PSBG composite nanofillers, which possess a robust photothermal conversion capability. This capability significantly facilitates the melting of Brazilian carnauba wax particles. This process serves a dual purpose: repairing coating defects and activating the occlusion effect within the SMP coating. The second mechanism operates at elevated temperatures, where the hydrogen bonding between the GQD cap and the polymeric shape (PS) container is disrupted. This disruption allows BTA to actively self-release, providing an additional layer of protection to the alloy. The final mechanism focuses on the enhanced corrosion resistance of the repaired PSBG-based coatings. This improvement is attributed to the presence of functional groups on the surface of GQDs, which contribute to the improved dispersion and compatibility of nanofillers within the SMP coatings.
3. Biomimetic superhydrophobic surfaces
Nature, over an extensive process of evolution, has bestowed various organisms with microscopically intricate structures, leading to the manifestation of captivating phenomena on a macroscopic scale. Notable examples include rose petals exhibiting dazzling color refraction in daylight when adorned with water droplets, a spectacle attributed to the structural intricacies of micron-sized bumps and nanometer-sized folds on the petal surface. Similarly, the enchanting sight of a butterfly fluttering in the rain is achieved through the combination of micron-sized scales and nanometer-sized grooves on the wing surface. In contrast, lotus leaves, growing in silt without staining, owe their hydrophobic nature to the micro- and nano-scale raised structures on their surfaces, as shown in Fig. 6. Inspired by these naturally occurring superhydrophobic phenomena, researchers have successfully enhanced corrosion resistance by introducing texture and reducing surface energy on metal or alloy substrates.89–92 Pioneering work reported by Liu et al.93 marked the first utilization of superhydrophobic surfaces (SHSs) for copper corrosion protection in seawater. They developed a superhydrophobic membrane covering the copper surface through an n-tetradecanoic acid etching process. EIS results unequivocally confirmed the outstanding corrosion resistance conferred by the membrane. The researchers highlighted that a synergistic effect of air-trapped valleys and capillary forces contributes significantly to the bolstered corrosion resistance. As research on SHSs for metal corrosion protection continues to expand, these coatings emerge as an effective strategy to combat metal corrosion in highly aggressive environments.
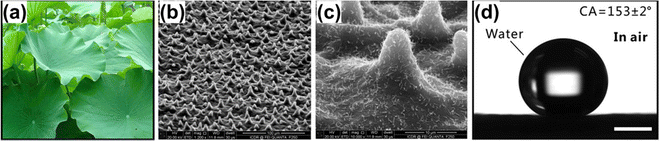 |
| Fig. 6 Superhydrophobicity of lotus leaves. (a) Photograph of lotus leaves, (b) and (c) surface microstructures on lotus leaves, (d) water droplets on lotus leaves in air (reproduced from ref. 94 with permission from [American Chemical Society], copyright [2017]). | |
3.1. Theoretical modeling of surface wettability
Wettability is one of the physicochemical properties of a solid surface and is expressed as the tendency of a liquid to diffuse to varying degrees on a solid surface. The contact angle of a liquid on a solid surface is the angle θ between the tangent of the gas–liquid interface at the gas–liquid–solid three-phase boundary and the solid–liquid interface on the liquid side (Fig. 7(a)). The sliding angle is defined as the critical angle formed between the solid surface and the horizontal plane when a liquid droplet precisely begins to roll on the solid surface. Both the contact angle and sliding angle are commonly employed parameters for characterizing the surface-wetting properties of materials. The wettability of a solid surface is intricately linked to interactions at the solid/liquid/gas interface. Notably, superhydrophobic surfaces stand out in the realm of wettability, typically showcasing a contact angle greater than 150° and a sliding angle less than 10°. These specific characteristics highlight the remarkable water-repellent nature of superhydrophobic surfaces, making them highly effective in resisting liquid contact and facilitating self-cleaning properties.
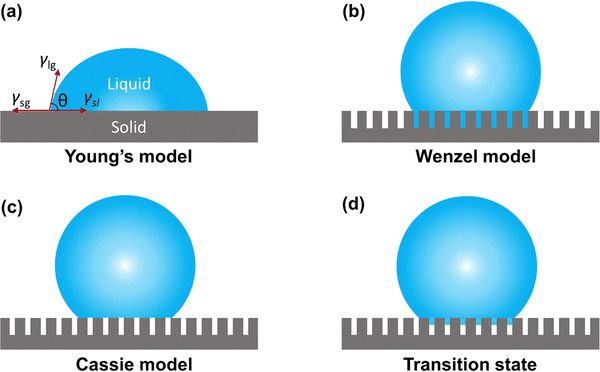 |
| Fig. 7 Typical wetting behavior of a droplet on a solid surface. (a) Young's model, (b) Wenzel model, (c) Cassie model, and (d) transition state. | |
To investigate the wettability characteristics of sample surfaces, researchers have developed and optimized wettability models for materials. In the case of an ideal solid substrate that is perfectly flat and chemically homogeneous, when a droplet is deposited on the solid surface, it initiates contact with the substrate, forming a three-phase contact line. The determination of the contact angle of the sample primarily relies on the surface energy and surface tension at the solid–gas, liquid–gas, and liquid–solid interfaces. This relationship is encapsulated in Young's equation:
| γls − γsg + γlg cos θ = 0 | (1) |
Here,
γls,
γsg, and
γlg represent the surface tension of the liquid–solid, solid–gas, and liquid–gas interfaces, respectively. This equation can also be alternatively expressed as:
|  | (2) |
Since the equation characterizes the contact angle of a droplet on a perfectly smooth ideal plane, the contact angle is also the intrinsic contact angle of the material. These equations encapsulate the fundamental relationship governing the contact angle of a droplet on an ideal solid substrate and are instrumental in the study of wettability characteristics on different surfaces.
Certainly, the condition for non-wettability of a solid surface often involves the presence of a rough structure. In such cases, the actual surface area of a rough substrate exceeds its apparent surface area. Wenzel introduced a new model to describe the contact angle on a rough surface, building upon Young's model. The relationship between the actual contact angle (θw) and the intrinsic contact angle (θs) of a droplet on a material surface is expressed as follows:
Here,
r represents the roughness factor. In this state, the droplets wet the surface and fill the rough surface voids (
Fig. 7(b)). In Wenzel's equation, when the solid surface
θs is less than 90°,
θw decreases with the increase of
r, which favors the wet contact between the droplet and the surface. When the solid surface
θs is greater than 90°,
θw increases with the increase of
r, and the hydrophobicity of the surface is enhanced. When
r of the hydrophobic surface is large, the penetration of the droplet will be hindered by the air trapped in the rough structure, and it is difficult to realize the wet contact between the droplet and the surface. Wenzel's equation is not suitable to explain this phenomenon.
The Cassie model presents a framework for elucidating the contact angle of droplets on the surface of an inhomogeneous material. In this model, water droplets adhere to a rough structure on a solid surface, comprising an air layer instead of directly wetting the surface, as illustrated in Fig. 7(c). By introducing the contact area fraction f1 between water droplets and the rough structure and the contact area fraction f2 between water droplets and air trapped in the rough structure (f1 + f2 = 1), the Cassie equation can be expressed as:
| cos θC = f1 cos θs + f2 cos θg | (4) |
Here,
θC is the apparent contact angle of the droplet in the Cassie state, and
θg is the contact angle of the droplet on the air surface. Given that the contact angle of the droplet with air is 180°,
eqn (4) can be formulated as follows:
| cos θC = rf1 cos θs + f1 − 1 | (5) |
When
f1 = 1, the Cassie equation is transformed into the Wenzel equation. When a fraction of the liquid infiltrates between rough structures, the contact state of the droplet lies between the Wenzel state and the Cassie state. This contact model is commonly referred to as the “transition state” or the “intermediate state,” as depicted in
Fig. 7(d). Therefore, it is essential to ensure the sustained stability of the surface state to maintain the Cassie state consistently.
3.2. Anti-corrosion mechanisms on superhydrophobic surfaces
Metal corrosion occurs under specific conditions, which include the presence of active corrosion sites serving as both the anode and cathode, electrical contact, a continuous electrolyte phase between the anode and cathode, and, finally, the existence of a cathodic reaction component capable of absorbing electrons produced through the ionization of the metal anode.95 SHSs exhibit micron-nanometer-scale roughness and possess low surface energy. The indentations on the non-uniform surface facilitate the easy entrapment of air. Consequently, corrosive substances, such as chloride ions, are effectively hindered by the air layer, preventing the degradation of the metal. With the growing research interest in superhydrophobic surfaces for metal corrosion prevention, scholars have discerned that the mechanism of SHS corrosion prevention extends beyond the mere isolation of the air layer. It also involves the synergistic impact of the hydrophobic agent layer, the textured structure, and the air layer.96–98
Regarding the hydrophobic agent layer, the hydrophobic molecules play a crucial role in preventing the adsorption of corrosive ions or molecular oxygen at the active corrosion sites (Fig. 8(a)). The hydrophobic agent forms an ordered chemisorption layer, acting as a barrier to charge transfer. Consequently, the hydrophobic molecular layer on the textured metal surface renders the metal less susceptible to corrosion. Furthermore, it influences the charging conditions at the interface where corrosion takes place. Metals/oxides typically carry a positive charge in neutral solutions, leading to the electrostatic attraction of aggressive anions. In contrast, hydrophobic materials exhibit a negative charge in a neutral solution, owing to their isoelectric point in the electrolyte at pH 2–4. The negative charge of the SHS results in an ion redistribution in the bilayer, diminishing the concentration of halide anions in the proximity of the solid surface (Fig. 8(b)).
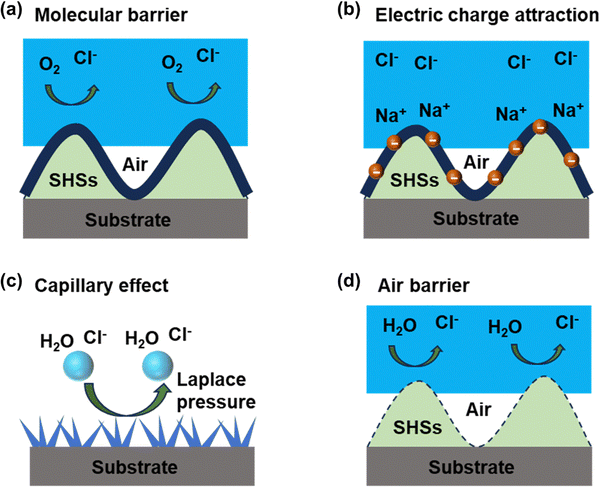 |
| Fig. 8 Schematic diagram of the anti-corrosion mechanism on SHSs. | |
In the context of the textured structure of SHSs, corrosion media are repelled from the surface grooves through capillary pressure within the microstructure, as depicted in Fig. 8(c). Certain preparation methods, such as laser ablation for constructing the textured structure, yield an oxide surface layer with favorable properties for blocking charge, chloride ions, and water molecule transfer, thereby further impeding corrosion reactions. SHSs also exhibit a water contact angle exceeding 150° and low wetting hysteresis. These characteristics ensure that an aqueous medium wets the coating material in a non-uniform wetting state, retaining air in the grooves of the textured surface. The liquid only contacts the material on the surface of the protruding peaks, resulting in a significantly smaller true wetting area between the liquid and the material compared to the apparent contact area (Fig. 8(d)).
3.3. Design strategies for superhydrophobic surfaces
Many organisms have developed a variety of micro/nanostructured surfaces that display biological properties to survive under natural stresses. For example, micro/nanostructures such as lotus leaves,98 shark skin,99 and butterfly wings100 endow each surface with excellent self-cleaning and degradable capabilities, allowing each organism to adapt to its surroundings. These natural strategies inspire the fabrication of artificial surfaces mimicking biological properties. The creation of biomimetic superhydrophobic surfaces typically involves two technological approaches: constructing micrometer and nano-rough structures on the surface of hydrophobic materials with low surface energy or modifying rough structures with low surface energy on the micrometer and nanometer scales. Various fabrication methods have been employed to create micro/nanostructured surfaces, and when preparing biomimetic anti-corrosion surfaces, considerations extend beyond performance and functionality to include cost and technical difficulty. Table 2 provides a summary of commonly used methods for preparing superhydrophobic surfaces, outlining their advantages and disadvantages.
Table 2 Methods commonly used to prepare SHSs and their advantages and disadvantages
Method |
Advantage |
Disadvantage |
Ref. |
Electrodeposition |
Simple operation and low process cost |
Poor bonding effect with the substrate |
101–104
|
Chemical etching |
Simple preparation process |
Higher cost and environmentally unfriendly |
105 and 106
|
Laser processing |
Simple operation, high precision, and high efficiency |
High cost |
107–110
|
Spray/spin coating |
Simple construction, high flexibility, and low cost |
Waste raw materials |
111–113
|
Sol–gel |
Low cost and simple preparation |
Poor durability |
114 and 115
|
3.3.1. Spray/spin coating.
The spray/spin coating method typically entails spraying a suspension of nanoparticles onto various substrates. This method is characterized by its simplicity, ease of implementation, and suitability for large-scale industrial production. Li et al.116 employed a hybrid approach to prepare EP + PDMS@SiO2 and uniformly sprayed it onto magnesium alloys. The results demonstrated a remarkable reduction in the corrosion current by two orders of magnitude compared to the initial state, showcasing superior corrosion resistance. Notably, the coating exhibited resistance to high-temperature fluids and demonstrated the ability to recover from storm leakage under low-temperature conditions.
Furthermore, it maintained superhydrophobic properties even after abrasion and tape stripping. In a similar vein, Shen et al.117 achieved superhydrophobic F-SiO2@PDMS coatings by initially spraying a PDMS layer on an aluminum alloy and subsequently applying a mixed solution of fluorinated silica and PDMS. The resulting non-wetting state, attributed to trapped air pockets, endowed the superhydrophobic F-SiO2@PDMS coatings with excellent corrosion resistance. The electrochemical impedance modulus exhibited a notable increase of up to three orders of magnitude compared to the pure aluminum alloy.
3.3.2. Electrodeposition.
Electrodeposition is a widely employed technique for depositing superhydrophobic surfaces onto metallic substrates. In this process, the application of an electrical potential between two electrodes initiates the dissolution of metal ions at the anode into the electrolyte, while those at the cathode undergo reduction, resulting in the formation of a metallic coating on the substrate. The manipulation of surface morphology is achievable by adjusting various parameters. Electrodeposition stands out as a promising method for crafting micrometers and nanostructures owing to its inherent advantages of low cost and simplicity.
Mousavi et al.118 prepared superhydrophobic surfaces on copper substrates using a distributed electrodeposition technique. The prepared surface has a water contact angle of more than 155° and exhibits excellent superhydrophobicity. The unique surface texture helps to trap large amounts of air and forms an air cushion underneath the water droplets, thus preventing the liquid from contacting the copper substrate. The superhydrophobic surface was shown to inhibit corrosion by two to four orders of magnitude compared to bare copper. Wang et al.119 achieved the preparation of superhydrophobic nickel films on copper foils using a one-step electrodeposition method, incorporating choline chloride as a crystal modifier. The static contact angle of the nickel film reached 162° under optimal parameters. Notably, this method obviated the need for organic surface modification to attain superhydrophobic properties. The resulting samples exhibited remarkable protection, with a corrosion inhibition efficiency of 99.6%. While the protective properties gradually diminished with immersion in a corrosive medium, even after 15 days, the film retained a high corrosion inhibition efficiency of 89.84%.
The presence of a superhydrophobic coating in the Cassie state can be considered a barrier, thus providing a perfect gas–liquid interface that inhibits the penetration of corrosive ions. However, surfaces prepared by electrodeposition have poor durability and stability due to poor adhesion strength and fragile micro/nanostructures. Combining electrodeposition with other techniques by adding nanofillers, such as nanoparticles or nanofibers,120–122 can enhance the mechanical strength and stability of superhydrophobic coatings.
3.3.3. Etching technique.
Etching techniques utilized for the preparation of SHSs commonly involve chemical etching and laser texturing. The underlying principle is to enhance surface roughness by selectively removing substrate materials through either physical or chemical reactions. Chemical etching is a commonly used method that utilizes a strong acidic or alkaline solution to form micro/nanostructures. Dou et al.123 successfully prepared superhydrophobic microneedle CuO surfaces on a copper surface using a simple chemical etching method and fluoride treatment. Based on the air-layer theory in the Cassie state, electrochemical tests showed that Icorr of the superhydrophobic samples was reduced by nearly three orders of magnitude compared with the untreated ones, providing excellent corrosion protection. However, chemical etching rates are difficult to control, and the etching reaction can be controlled and accelerated by adjusting the composition, concentration, or temperature of the etchant.
In recent years, laser processing has garnered significant attention from researchers due to its high efficiency, precision, and universality. Notably, femtosecond lasers, with ultrashort pulse times in the order of femtoseconds (10−15 s), possess a substantial peak power exceeding the damage threshold of most materials. This characteristic allows femtosecond lasers to process a wide range of materials, including metals, ceramics, polymers, and biomaterials, without significant limitations in material selection. Yong et al.124 have outlined advancements in manipulating the wettability of materials through femtosecond laser processing. By designing and machining various microstructures on substrates, they achieved superhydrophobic properties, underwater superhydrophobic properties, anisotropic wettability, and intelligent wettability. Additionally, materials like PDMS and PTFE could attain superhydrophobic properties solely through femtosecond laser processing. The creation of micro-nano grooves on material surfaces enabled anisotropic wetting and droplet sliding, showcasing potential applications in droplet manipulation, microfluidics, biology, and other fields. Femtosecond laser technology has gained popularity for biomimetic applications due to its ability to mimic biological surface structures easily. In terms of corrosion resistance, the femtosecond laser process is adept at producing stable superhydrophobic coatings that exhibit strong water repellency, utilizing the formation of interfacial bubbles in the Cassie state. Moreover, Rajan et al.125 delved into the laser-induced amorphization of metal surfaces, attributing it to the increase in crystal dislocation density caused by femtosecond laser-induced stress and compressive strain. This phenomenon plays a pivotal role in enhancing corrosion resistance by significantly reducing the free energy of amorphous materials, thereby increasing the chemical stability of metal alloys and reducing the reactivity of their elements.
3.3.4. Other methods.
In addition to the previously mentioned methods, various approaches for preparing superhydrophobic materials include chemical vapor deposition (CVD), template methods, and electrostatic methods. Vilaró et al.126 etched the copper surface by alternating plasma to produce a layered structure and then deposited 1H,1H,2H,2H-perfluorodecyl acrylate-ethylene glycol diacrylate [p(PFDA-co-EGDA)] on top of the metal by the CVD method. The modified surfaces exhibit superhydrophobicity (WCA > 160°) and low hysteresis (<1°). These superhydrophobic coatings demonstrated resistance to acid, alkali, and salt solutions. Compared to bare copper, the superhydrophobic coating significantly improved corrosion protection by three orders of magnitude.
Chang et al.127 replicated the surface structure of fresh leaves of Xanthosoma sagittifolium using PDMS. They then obtained a superhydrophobic epoxy/organophilic clay (SEC) coating on cold-rolled steel through a 3D-bioprinting technique. The SEC obtained by this biomimetic technique effectively prevented corrosion of the metal substrate by O2, H2O, and aggressive ions. Similarly, Chang et al.128 prepared a hydrophobic epoxy/graphene composite coating using a nanocomposite casting method and simulated the leaf structure (Xanthosoma sagittifolium leaves) using a PDMS polymer template. The resulting hydrophobic surface provided higher corrosion resistance than uncoated rolled steel. Crosslinked polybenzoxazine (PBZ)-based coatings prepared by Zachariah et al.129 using lotus leaf and xanthosoma sagittifolium leaves as templates had a hierarchical surface structure and high hydrophobicity. The coating showed 99.93% protection efficiency compared to the corrosion rate of the normal PBZ coating. The biomimetic concept of introducing a hierarchical surface structure and hydrophobicity on the surface of anticorrosive coatings has a significant effect on improving corrosion protection efficiency.
Vicente et al.130 deposited poly(acrylic acid) + β-cyclodextrin (PAA + β-CD) onto an aluminum alloy substrate using electrostatic spinning. They then obtained a PTFE layer by simple spin-coating, and finally, a layer of PTFE particles was electrosprayed to provide high roughness, resulting in a superhydrophobic coating with a hydrophobicity angle greater than 170°. The Cassie state created by this method greatly reduced the contact area between the coating and the liquid, acting as an effective barrier against the penetration of corrosive media into the underlying metallic substrate. As a result, the corrosion rate was reduced by four orders of magnitude. The technique with the preparation of superhydrophobic surfaces is presented in Fig. 9.
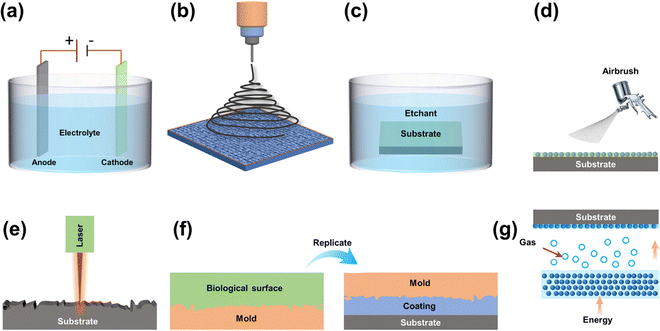 |
| Fig. 9 Schematic representation of a common manufacturing method for bio-inspired microtextured surfaces, including (a) electroplating, (b) electrospinning, (c) chemical etching, (d) spray coating, (e) laser processing, (f) template method, and (g) CVD. | |
3.4. Biomimetic superhydrophobic surface applications
3.4.1. Superhydrophobic self-cleaning anti-corrosion surfaces.
Self-cleaning surfaces inherently possess the capacity to eliminate dirt particles effortlessly. Specifically, superhydrophobic surfaces exhibit self-cleaning attributes by efficiently repelling water molecules, enabling water to smoothly roll over the surface and facilitate the removal of dirt. Conversely, the self-cleaning mechanism of hydrophilic surfaces operates through diffusion. In this process, water on the surface diffuses, effectively carrying away dirt particles from the solid surface. The widespread application and advancement of self-cleaning technology trace their origins to the innate superhydrophobic characteristics of lotus leaf surfaces.21
In a study reported by Li et al.131 superamphiphilic CuO films with exceptional self-cleaning and corrosion resistance were prepared on the surface of the steel, which was achieved through a combination of electrodeposition, solution immersion, and fluoride modification. The multilevel structure, comprising microfloral structures and secondary nanosheets, demonstrated the ability to repel both water and glycerol. The authors utilized fly ash with a particle size of tens of micrometers to dedust the superamphiphobic CuO film, with contaminants easily removed by 8 μL water droplets. Shu et al.132 employed nanosecond laser processing technology and the sol–gel method to design and fabricate mechanically robust micro- and nanostructures. They developed modified SiO2@PDMS superhydrophobic corrosion-resistant coatings on copper substrates. The authors utilized micron-sized fly ash particles as contaminants and relied on the ultra-low water adhesion (3.27 μN) on the surface to automatically remove dust within 200 s. Even after sandpaper abrasion, tape peeling, and cross-scratch tests, the coating maintained good superhydrophobicity. Jiang et al.133 prepared a ZnO@ZIF-8 superhydrophobic anti-corrosion coating on a magnesium alloy substrate, which involved micro-arc oxidation coating as a transition layer, followed by ZnO nanorods as a sacrificial template and Zn2+-induced growth of ZIF-8 on the surface through ligand solution etching. The corrosion resistance of the ZnO@ZIF-8 superhydrophobic coating significantly improved compared to that of untreated AZ91D. Chalk dust was used as a contaminant, and the study demonstrated that water droplets could easily carry away contaminants on the surface by tilting it at a certain angle.
3.4.2. Superhydrophobic anti-fouling anti-corrosion surfaces.
The marine environment serves as a highly corrosive electrolytic cell, where continual chemical and electrochemical reactions occur with the metal substrate. Furthermore, electrochemical corrosion results in the formation of material voids and gaps, creating favorable conditions for microbial adsorption and reproduction, thereby exacerbating biological corrosion. In scenarios such as sea-traveling cargo ships and submarines submerged in seawater, the adhesion of microorganisms leads to reduced navigation speed and increased fuel consumption. Undesirable adsorption and accumulation of microorganisms, algae, and organic matter in seawater contribute to the formation of biofouling—a gradual process encompassing four stages.134 In the initial stage, organic molecules and inorganic particles are adsorbed to the material surface, forming a base film within seconds or minutes through physical and electrostatic adsorption. Subsequently, algae in seawater attach to the base film within hours, constituting a reversible attachment. The third stage involves the growth and multiplication of bacteria over a few days, attracting other microorganisms and algae to form microfouling. In the fourth stage, organisms like barnacles and mussels attach to the microfouling biofilm within weeks, leading to the development of macrofouling. Microbial adhesion in complex environments accelerates material dissolution and metal oxidation, potentially resulting in holes and cracks formed by biofouling. Nature has developed various protective mechanisms against marine biofouling over evolutionary periods. One such mechanism involves the creation of an air cushion layer on the surface, mimicking the bionic superhydrophobic nature, which effectively blocks corrosive marine media such as Cl−. Importantly, superhydrophobic surfaces prevent the formation of a base film from the initial stage and exhibit superior repellent properties against biofouling adhesion.
Philip et al.135 reported the fabrication of superhydrophobic titanium surfaces using simultaneous anodic oxidation and adsorption with an ethanol solution of myristic acid and HCl. Exposure of these surfaces to microbial cultures for 48 hours resulted in a 50% reduction in bacterial adhesion compared to bare surfaces. Rasitha et al.136 developed robust SHSs by covalently bonding hydrolyzed glycidoxypropyltrimethoxysilane to a hydrophilic aluminum substrate as an intermediate layer, with hexamethyldisilazane-modified nano-silica as the top low surface energy material. The surface exhibited good self-cleaning ability, and the corrosion current density was significantly reduced compared to bare samples. Selim et al.137 synthesized silicone/GO-Fe3O4 nanocomposites inspired by composite mosquito eyes and dispersed into PDMS to obtain coatings with superhydrophobic properties showing high antifouling efficiency. The homogeneous dispersion of GO-Fe3O4 nanofillers had a good growth inhibition effect on microorganisms (Kocuria rhizophila, Pseudomonas aeruginosa, and Candida albicans) with good growth inhibition. Surface roughness and superhydrophobicity enhanced the antifouling adhesion and significantly reduced the number of adherent bacteria.
In a parallel approach, inspired by the multifaceted ability of kelp to inhibit marine pollution through a combination of physical micromorphology, chemical composition, and bioactive substances, Zhao et al.138 incorporated capsaicin into nanocapsules. These nanocapsules were stably deposited on modified PDMS surfaces, resulting in the development of novel PDMS antifouling coatings with multiple synergistic antifouling properties, utilizing the LBL assembly method. The microstructured surface of the biomimetic antifouling material played a crucial role in reducing the attachment points of fouling organisms, while the highly hydrated polymer film on the surface contributed to the reduction in algae adhesion. Moreover, the introduced nanocapsules demonstrated an additional enhancement of antifouling performance by leveraging bacteria as a stimulation switch, controlling the release rate of bioactives within the coatings.
3.5. Challenges and strategies for superhydrophobic anti-corrosive surfaces
As previously mentioned, biomimetic superhydrophobic surfaces have demonstrated significant self-cleaning, anti-pollution, and anti-corrosion effects, hinging on the maintenance of a stable liquid–air interface on the surface, earlier referred to as the Cassie state. However, several factors, including mechanical friction, chemical stability, and a gradual decline in air pressure within the confined cavity due to an elevation in liquid pressure, render the surface susceptible to transitioning from the Cassie state to the Wenzel state or even experiencing a complete loss of water resistance. The precarious stability of superhydrophobic surfaces poses a substantial challenge, acting as a hindrance to the advancement of their applications. Consequently, the construction of interface-strengthened superhydrophobic surfaces has emerged as a focal point of research in recent years.
3.5.1. Mechanical durability.
Superhydrophobic surfaces with high contact angles and low rolling angles can be obtained by introducing nano- or micrometer-scale morphologies. However, the stability of such structures is challenged as mechanical instability leads to a loss of robustness. Wang et al.139 used the concept of armored structures to improve mechanical stability and synthetic techniques for coatings on substrates to provide superior strength (Fig. 10). Using binders is considered to be an effective method to improve the robustness of SHSs. Typically, a binder is used to strengthen the interface between a substrate and a hydrophobic material, and hydrophobic particles are added to build up the rough structure. Specifically, there are several combinations of this technique, including mixing the adhesive and hydrophobic particles, using the adhesive as an intermediate layer and the hydrophobic particles as a surface layer, and mixing the adhesive and hydrophobic particles. Of these, the first two combinations are more common. For example, Chen et al.140 prepared hydrophilic nano-ZIF-8 with hydroxyl groups using MOF (ZIF-8) nanoparticles and organic resins as a substrate at room temperature and then hydrolytically condensed nano-ZIF-8 modified with low-surface-energy perfluoroalkyltriethoxysilanes (POTS) to produce SHSs.The coating was improved by introducing epoxy resin (EP) as an adhesive layer to improve its robustness and adhesion. The prepared ZIF-8/POTS/EP composite coatings exhibited good water repellency and mechanical and chemical stability and remained superhydrophobic after 300 days of aging in air or 60 days of immersion in 3.5 wt% NaCl aqueous solution. In addition, Zhang et al.141 successfully prepared purely hydrophobic PDMS surfaces and superhydrophobic candle soot (CS) deposited surfaces, as well as bilayer PDMS-CS coatings by scraping and CS incomplete combustion deposition. PDMS acted as a binder in the composite coatings, effectively connecting the outer layer of CS to the bottom aluminum substrate. The cohesive properties of PDMS, the nano-structures of the porous network, and the very low surface energy of the deposition due to incomplete combustion of candles together contribute to the formation of a corrosion-resistant and robust coating.
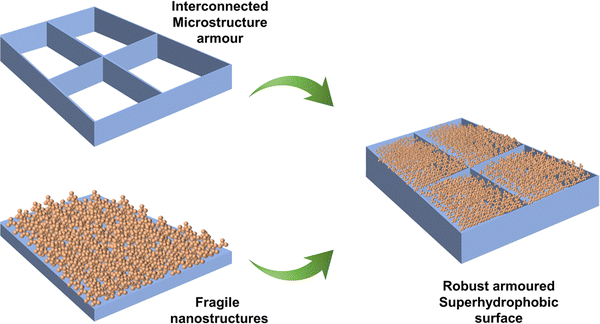 |
| Fig. 10 Design concept of the robust armoured superhydrophobic surface. | |
In addition to incorporating binders, the creation of durable SHSs can be achieved through the construction of ordered structures. These structures can generate micro/nanometer-scale deformations that exhibit cross-scale characteristics and are highly correlated with wear strength. Zhang et al.142 employed a one-step hydrothermal method to manufacture hierarchical micro/nanostructured superhydrophobic ZnO/Cu-ZnMOFs@SA composite coatings, exhibiting enhanced corrosion protection. This enhancement is attributed to both the hierarchical micro/nano-structures and the stearic acid (SA) modification, which collectively hinder aggressive ion transport. The hierarchical micro/nano-structure of ZnO/Cu-ZnMOFs@SA ensured that the surface retained its roughness even after rubbing, and delamination was visibly mitigated. Notably, the superhydrophobic properties could be easily restored by re-immersion in an ethanol solution containing SA.
3.5.2. Deep water pressure.
Apart from mechanical stability, one of the primary challenges encountered by SHSs during underwater use is the infiltration of water within air pockets due to the influence of high liquid pressures, leading to their instability. In underwater environments, such as submarine equipment exposed to seawater conditions, the coating surface experiences submergence under varying hydrostatic pressures at different depths. The disruption of air pockets on the superhydrophobic coating surface adversely affects the protective capability of the coating.143 Poetes et al.144 investigated the stability of underwater superhydrophobic surfaces and found that the air layer enclosed in the microstructure readily diffuses into the water, thus altering the surface wettability. Manoj et al.145 investigated the effect of water pressure on the wetting and corrosion behavior of superhydrophobic coatings. Under high hydrostatic pressure, the coating absorbs a large amount of water into the voids, which ultimately leads to the loss of superhydrophobicity and corrosion resistance. Typically, once a superhydrophobic surface is fabricated, it is not possible to adjust the solid–liquid contact area to the dynamic environment. Recently, smart surfaces with different air cushion ratios have been demonstrated, either using soft materials or multilayer structures in response to external stimuli.146–148 A better solution may be to develop superhydrophobic surfaces with adaptive morphology to the forces exerted by the liquid (i.e., liquid pressure) to regulate the solid–liquid stability in the face of dynamic environments. Tan et al.149 proposed a bilayer-structural liquid-pressure-guided superhydrophobic surface (LPGSS) consisting of a rigid micropillar array and a soft PDMS on top (Fig. 11). The results show that the LPGSS can maintain a stable Cassie state during droplet compression. The LPGSS can effectively adapt itself to the radius of the PDMS in response to changes in liquid pressure and protect the air cushion from damage. However, the mechanical durability of the soft surface still needs to be considered. Therefore, studying and improving the stability and durability of SHSs remains a key research direction to make it a reliable and long-lasting anti-corrosion technology.
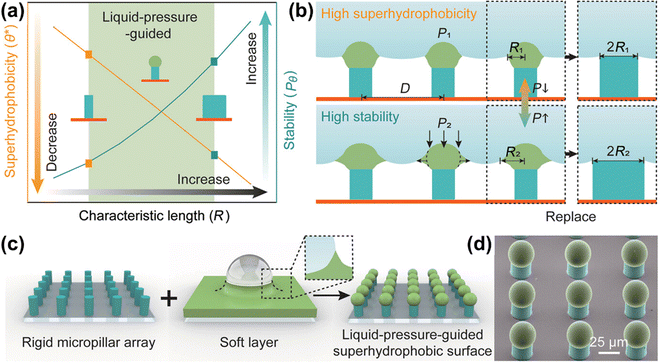 |
| Fig. 11 Design of a bilayer-structural liquid-pressure-guided superhydrophobic surface (reproduced from ref. 149 with permission from [Wiley], copyright [2022]). | |
3.5.3. Self-healing superhydrophobic surfaces.
Most SHSs are susceptible to scratches and abrasions during use, resulting in the degradation of their structures. Additionally, the low-surface-energy substances modified on these surfaces are susceptible to decomposition caused by factors such as light radiation, exposure to organic pollutants, and strong acids and bases. This decomposition leads to the loss of superhydrophobicity, significantly diminishing the service life of superhydrophobic surfaces and constraining their widespread adoption in practical applications. As discussed in Section 3.5.1, researchers have sought to enhance mechanical durability by incorporating adhesives into the fabrication of superhydrophobic surfaces. However, these surfaces are essentially “disposable” and cannot regain their original superhydrophobic properties after sustaining damage. To address this limitation, the integration of self-repairing features into superhydrophobic surfaces, making them self-healing, emerges as a promising strategy to extend their service life. Inspired by the natural regenerative abilities of damaged clover, where the rough structure and chemical composition can be regenerated, researchers have combined self-healing capabilities with superhydrophobicity to create self-healing superhydrophobic surfaces. These surfaces can be recycled, presenting an innovative approach for achieving the long-term durability of artificial superhydrophobic surfaces. Typically, the preparation of self-healing superhydrophobic surfaces involves inducing the migration of low surface energy substances or the reconstruction of rough structures.
Chemical or mechanical stimuli from within the coating or underlying low surface energy materials can drive the disrupted low surface energy materials to migrate to the surface in cases where the microstructures of SHSs remain intact or experience limited disruption. This migration helps in regaining the superhydrophobicity of the surface.150–152 Wang et al.153 conducted a simulation of the structure found on lotus leaves and employed a template method to fabricate a self-healing superhydrophobic PDMS/n-nonadecane wax composite surface. By replicating the nipple structure, the surface achieved the desired roughness, and the incorporation of n-nonadecane wax provided a low surface energy, imparting superhydrophobicity to the surface. Following an oxygen plasma treatment, the surface became rich in hydroxyl groups, undergoing a transition from superhydrophobic to superhydrophilic. Intriguingly, after 20 minutes of storage at room temperature, the surface was able to regain its superhydrophobicity. Fig. 12 illustrates the fundamental process of this self-healing behavior. The difference in interfacial free energy drives the transport of hydrophobic waxes from the PDMS matrix to the surface, reducing the surface energy and restoring rough fibers on the microscale structure. The high mobility of the PDMS molecular chains further facilitates the diffusion of n-nonadecane molecules within the PDMS network. The combined effect of these factors results in rapid transport kinetics of hydrophobic wax molecules from the physical structure to the outer surface, facilitating the repair of superhydrophobicity. Additionally, low surface energy substances can be stored in microcapsules in advance. In the event of chemical damage to the surface, the low surface energy substance is released from the container under external stimuli, migrating to the surface and thereby achieving the recovery of superhydrophobicity. Uzoma et al.154 utilized polymerization to synthesize microcapsules containing fluorosilane and urea-formaldehyde as core-shells. These microcapsules were incorporated into fluorocarbon resins and sprayed onto aluminum alloy substrates to develop self-healing superhydrophobic coatings. Following oxygen plasma treatment or alkali treatment, the coating initially lost its superhydrophobicity. However, after 8 days at room temperature, the coating managed to regain its initial superhydrophobicity due to the gradual release and migration of fluorosilane from the microcapsules to the coating surface. EIS results indicated that the released hydrophobic fluorosilane performed well in corrosion inhibition.
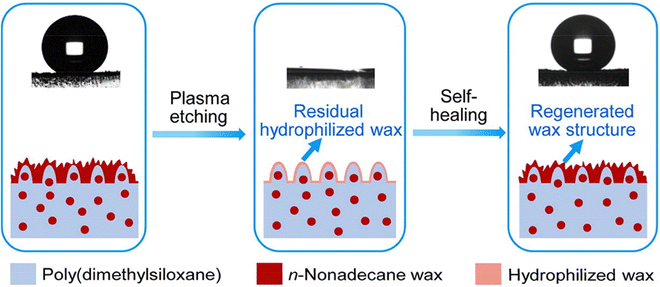 |
| Fig. 12 Schematic representation of the self-healing mechanism of SHSs (reproduced from ref. 153 with permission from [Elsevier], copyright [2020]). | |
The migration of low surface energy materials is typically suitable for repairing superhydrophobic surfaces under specific conditions such as plasma etching, chemical damage, and slight wear. However, in practical usage, superhydrophobic surfaces are more likely to face damage to their rough structures. In such cases, achieving the repair of superhydrophobic properties solely through the migration of low surface energy substances becomes challenging. Compared to the self-healing of low surface energy materials, the self-healing of surface-grade rough structures is more intricate, particularly when dealing with large-scale structural damage. To address this challenge, structural regeneration through rearranging components and polymers in the coating can effectively repair damage at the nano-scale or even micrometer scale.155–157 Wang et al.158 synthesized ACNTB-SiO2-KH570 particles by combining KH570-modified nano SiO2 with oriented carbon nanotube bundles (ACNTBs). These particles were used to prepare EP/ACNTB-SiO2-KH570 composite superhydrophobic surfaces together with EP. The particles provided the necessary hierarchical structure, ensuring the ideal mechanical stability of the surface. When the EP/ACNTB-SiO2-KH570 surface was damaged and removed with tape, the water contact angle decreased to 123°. Interestingly, after heating the damaged surface at 300 °C for 9 hours, the contact angle rebounded to 160°, and the water resistance remained stable after multiple cycles of structural damage and regeneration. The schematic self-healing mechanisms mediated by structural regeneration are illustrated in Fig. 13(a). During heating, the EP polymer partially breaks down, exposing layered nanoparticles. The heat energy weakens the interaction between ACNTB and SiO2. Gases generated from the EP polymer decomposition further accelerate the transport and assembly of SiO2 nanoparticles to reconstruct the rough structure on the damaged surface, facilitating the self-healing process triggered by structural regeneration.
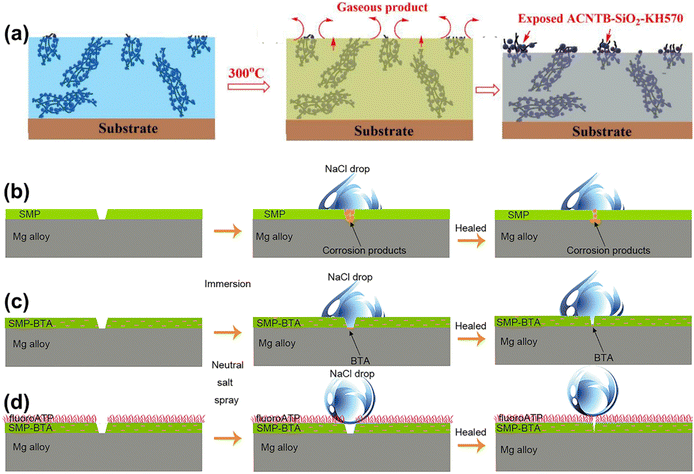 |
| Fig. 13 (a) Schematic of the self-healing mechanism of EP/ACNTB-SiO2-KH 570 of the damaged coating (reproduced from ref. 158 with permission from [Elsevier], copyright [2020]). Self-healing mechanism of the (b) SMP, (c) SMP-BTA, and (d) SMP-BTA/fluoroATP coatings (reproduced from ref. 161 with permission from [Elsevier], copyright [2021]). | |
Another approach to achieving the regeneration of shape relies on SMP. SMP is a stimulation-responsive material that can be restored from a temporarily deformed shape to its original form through external stimuli. Utilizing SMP for the preparation of superhydrophobic surfaces allows for the complete repair of deformed structures.159,160 Zhang et al.161 scraped SMP emulsion containing ceresine wax microparticles and BTA onto the surface of the magnesium alloy matrix and then sprayed fluorinated attapulgite (fluorine ATP) suspension to obtain SHSs (Fig. 13(d)). SMP is self-healing based on the shape memory effect, which can repair locally damaged areas. However, the formation of corrosion products prevents the closing of physical scratches, making it difficult for SMP coatings to recover their initial anti-corrosion properties. The introduction of BTA delays the occurrence of corrosion to a certain extent, so even if the SMP-BTA coating is not repaired in time, the coating can still partially recover its anti-corrosion properties. The top layer of fluorine ATP can effectively prevent corrosive electrolyte penetration into the coating by maintaining an air cushion at the solid–liquid interface. Therefore, the synergistic effect of SMP-BTA and the fluorine ATP layer results in the coating being almost completely self-healing, thus restoring the corrosion resistance.
The compensation of low surface energy materials and the reconstruction of rough structures enable the self-healing of superhydrophobic properties. However, many self-healing SHSs often require elevated temperature, light, or other external stimuli to expedite the repair process, making it challenging to achieve rapid repair at room temperature. Moreover, there has been relatively limited research on millimeter-scale or even centimeter-scale damage. Future development in this field is anticipated to focus on optimizing the design of coating structures and self-healing conditions. The aim is to develop superhydrophobic coatings that can efficiently and quickly self-repair large-size damage at room temperature. This optimization will be crucial for expanding the practical applications of self-healing superhydrophobic surfaces.
4. Biomimetic slippery liquid-infused porous surface
The bottle-shaped insect trap of Nepenthes features an inner wall with a porous microstructure and is filled with lubricating fluid. This unique attribute effectively prevents insects from escaping by leveraging the super-slip property of the inner wall. Fig. 14(a). Bohn et al.162 discovered that the inner wall's special microstructure securely traps the waxy mucus secreted by the inner wall, forming a continuous liquid surface within the cage. In 2011, Wong et al.163 pioneered the synthesis of slippery liquid-infused porous surfaces (SLIPSs), drawing inspiration from Nepenthes. SLIPSs utilize micro-textures to immobilize the lubricant on the substrate, serving as a repellent. By injecting the lubricant into the micro/nano-structures, a continuous and uniform dynamic liquid layer forms on the substrate's surface, effectively shielding the metal from corrosive media. The researchers conducted a comparison between the electrochemical impedance spectra and polarization curves of SLIPSs and SHSs. The results showed that the electrochemical impedance of SLIPSs is typically 2–3 orders of magnitude higher than that of SHSs, and the corrosion current density is 1–2 orders of magnitude lower than that of SHSs. Furthermore, the electrochemical impedance values of SHSs decreased more rapidly during long-term immersion in corrosive media, whereas SLIPSs demonstrated superior long-term corrosion resistance.164–168
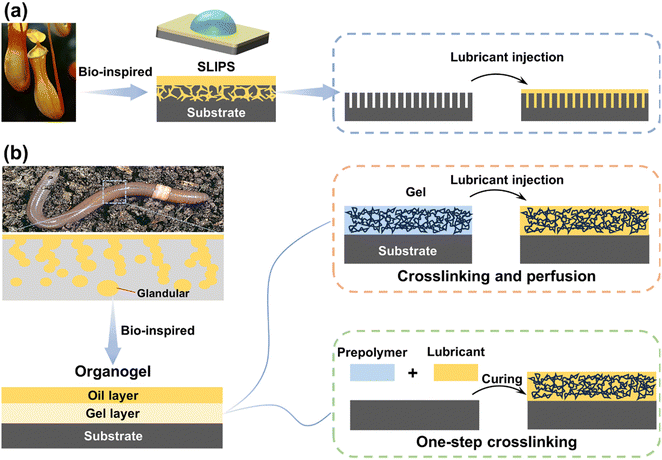 |
| Fig. 14 Schematic representation of the bio-inspired surfaces: (a) SLIPSs and (b) organogels and their preparation methods. | |
4.1. Challenges and strategies for SLIPSs
In contrast to the preparation of SHSs, where SLIPSs need to align matrix material properties with lubricant properties, chemical coatings can be applied to enhance material-lubricant affinity. Two common methods for inducing low-energy chemical coatings involve liquid phase deposition through a dip coating or spraying techniques in the first and the use of CVD to functionalize the surface in the second.
Wong et al.163 proposed three essential requirements for the thermodynamic stability of SLIPSs. First, the lubricant must quickly inhale, moisten, and stably attach to the substrate surface to prevent test fluid penetration and displacement of the lubricant. Second, the solid surface should be preferentially wet with the lubricant rather than the liquid to be repelled. Third, the lubricant and impact test fluid must be incompatible. Deterioration mainly stems from lubricant depletion and porous layer destruction, highlighting the importance of the matrix morphology and lubricant in designing SLIPSs with excellent sliding properties.
The size and nature of substrate holes are critical for strong lubricant anchoring. Suitable roughness enhances stable lubricant retention through capillary action and van der Waals forces. Small pore sizes and high porosity in substrates contribute to durability by generating high capillary pressure to retain the lubricant and allowing a larger contact area for effective self-cleaning. The creation of micro/nanostructures with roughness on SLIPSs substrates mirrors techniques used for SHSs, as described in Section 3.3.
The design and preparation of SLIPSs should center on selecting lubricants with properties suitable for the service environment. Table 3 outlines commonly used lubricants for anticorrosion SLIPSs. Additionally, extensive research has delved into the viscosity–durability relationship of SLIPSs.169–172 Findings reveal that higher viscosity lubricants facilitate droplet retention with superior durability, while low viscosity lubricants excel in sliding properties.
Table 3 Commonly used lubricants of SLIPSs for anti-corrosion
Type |
Substrate |
I
corr (A cm−2) |
E
corr (V) |
R
ct (Ω cm2) |
Ref. |
Silicone oil (DC-200) |
AZ31B Mg alloy |
1.918 × 10−6 |
−1.331 |
— |
164
|
Silicone oil (200 mPa s) |
1060 Al alloy |
1.85 × 10−10 |
3.17 |
— |
173
|
Silicone oil (20 mPa s) |
AZ31 Mg alloy |
1.17 × 10−9 |
— |
1.34 × 107 |
174
|
Silicone oil (10 mPa s) |
Al plates |
5.0 × 10−12 |
−0.35 |
1 × 107 |
175
|
Krytox 104 |
Al foil |
— |
−0.651 |
— |
176
|
Krytox GPL 103 |
AZ31 Mg alloy |
3.44 × 10−10 |
−0.210 |
55.9 × 106 |
177
|
Krytox 100 |
Mild steel |
3.687 × 10−8 |
−0.338 |
1.80 × 106 |
178
|
Plant oil |
Q235 steel |
— |
— |
1.42 × 1010 |
179
|
Ionic liquids |
Al alloy |
7.8 × 10−9 |
0.712 |
— |
180
|
Despite diligent research efforts made to enhance lubricant retention, depletion of lubricants remains an unavoidable occurrence across multiple application cycles. Drawing inspiration from the constant secretion of mucus by biological sebaceous glands to lubricate and moisturize the skin, solid materials with three-dimensional cross-linked networks that serve as reservoirs for lubricants are denoted as organogels, offering an alternative to SLIPSs. The synthesis of organogels can be achieved through two distinct approaches, as shown in Fig. 14(b). Firstly, by dissolving a well-cured polymer network, organogels are formed, where the lubricant interacts with the network structure, balancing the entropy and enthalpy of polymer chain mixing, thereby immobilizing the lubricant and giving rise to the organogel. Alternatively, the incorporation of the lubricant into the cured prepolymer results in the storage of the lubricant within the polymer network structure, leading to organogel formation.181–184 Organogels present several advantages, including tunability, dynamic self-healing capabilities, and facile synthesis. Nevertheless, the presence of the lubricant in the organogel diminishes its affinity with the metal substrate, predisposing the system to corrosion at the coating-metal interface. Consequently, enhancing the bond between the substrate and the organogel emerges as a crucial research direction.
4.2. Anticorrosion mechanism on SLIPSs
The lubricating liquid injected into the micro-nano structure of SLIPSs forms a continuous dynamic liquid film on the substrate surface. This film hinders direct contact between the substrate surface and the corrosive medium, preventing the transfer of electrons from the anode to the cathode and enhancing the corrosion resistance of the metal. Simultaneously, the low adhesion characteristics of the liquid film prevent direct contact between microorganisms and the matrix, effectively inhibiting microorganism adhesion and preventing microbial corrosion (Fig. 15(a)).185–188 In the organogel, the silicone oil layer on the surface acts as a barrier during the initial impregnation of the corrosion system, preventing the penetration of external water molecules into the coating. When the thin silicone oil layer is destroyed, water molecules reach the substrate surface through some unfilled voids, leading to local corrosion. However, the majority of the gel voids are still filled with silicone oil, inhibiting the diffusion of the corrosive medium (Fig. 15(b)).189
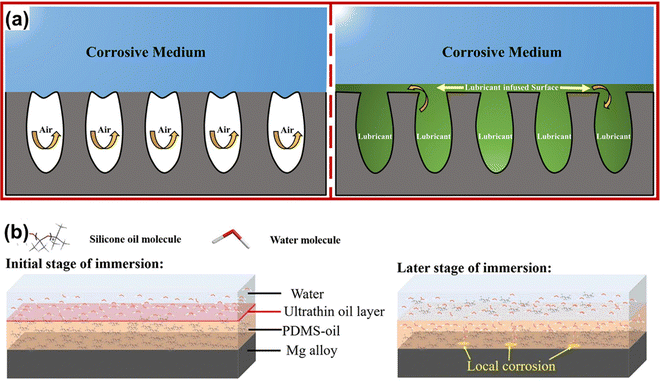 |
| Fig. 15 Corrosion prevention mechanism of (a) SHSs and SLIPSs (reproduced from ref. 188 with permission from [Wiley], copyright [2021]) and (b) organogel (reproduced from ref. 189 with permission from [Elsevier], copyright [2021]). | |
4.3. Application of SLIPSs in anticorrosion
4.3.1. Steel alloys.
Steel and its alloys stand as crucial engineering materials widely employed in daily life and various industrial fields.190 However, when exposed to aggressive ions, such as halogen ions, steel is susceptible to passivation film breakdown and pitting corrosion.191 Corrosion-induced structural failures and safety incidents are common, particularly for steel engineering structures operating in corrosive environments. The service life of these structures predominantly relies on the effectiveness of corrosion protection. Consequently, enhancing the stability of alloy steels in corrosive environments is a significant challenge. The investigation of SLIPSs holds great importance in enhancing the corrosion resistance of steel and broadening its application scope. Various methods are employed for preparing SLIPSs on steel, including electrodeposition, anodic oxidation, and spraying.
Xiang et al.192 utilized the electrodeposition method to create a coating with a porous metal film using a hydrogen bubble template. They injected a PDMS/paraffin mixture after FAS modification, forming a slippery surface composed of three solid layers (Fig. 16). This coating exhibits good corrosion resistance, with a corrosion current density of 6.402 × 10−9 A cm−2 and an impedance of 2.301 × 107 Ω cm−2, two orders of magnitude higher than those of the pure Ni coating. Additionally, Bae et al.193 employed anodization to generate a nano-porous oxide layer with microscopic roughness on the surface of stainless steel, providing storage conditions for lubrication. They coated the nano-porous oxide layer with a stearic acid solution without fluorine, transforming it into a hydrophobic surface. Finally, they impregnated the nano-porous oxide layer with edible oil to achieve corrosion resistance, environmental protection, and anti-condensation. Zhang et al.194 prepared a coral clustering structure SiO2 coating on carbon steel surfaces using a spraying method. The coating exhibited excellent silicone locking ability, as confirmed by the EIS results demonstrating outstanding corrosion resistance.
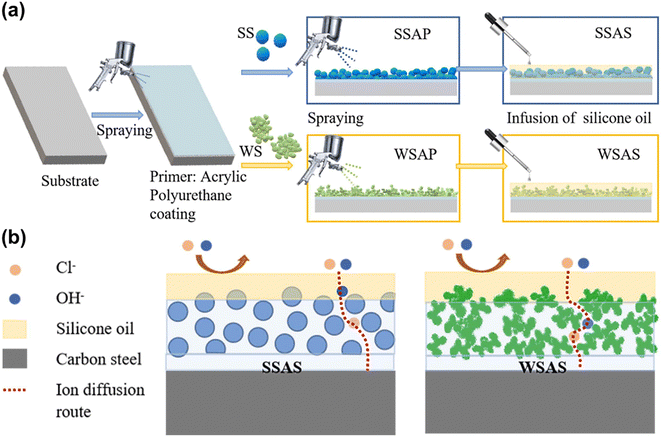 |
| Fig. 16 (a) The schematic image of the preparation process, and (b) schematic protection mechanism of coatings on carbon steel (reproduced from ref. 194 with permission from [Elsevier], copyright [2023]). | |
4.3.2. Titanium alloys.
Titanium alloys are recognized as the “marine metal” in the marine field due to their outstanding anti-corrosion properties and comprehensive mechanical characteristics.195 Despite their excellent corrosion resistance, titanium alloys may experience corrosion under specific conditions such as exposure to acid, alkali, salt solutions, and high temperatures. These environmental factors can induce chemical reactions in titanium alloys, leading to damage to their surface and internal structure.196 Additionally, titanium alloys, known for their good biocompatibility, are more susceptible to serious biological pollution in the marine environment compared to other structural materials, posing a significant threat to their long-term safety and function. Historically, paints containing toxic heavy metal ions were commonly used to repel or eliminate organisms attached to titanium alloy surfaces, a practice at odds with the growing global consensus on environmental protection.197 In the quest to enhance the corrosion resistance and biological adhesion resistance of titanium alloys, researchers are exploring new effective methods. Among these, slippery surface technology is considered to have significant application potential in the field of titanium alloy corrosion prevention.
Yue et al.198 employed micro-arc oxidation technology and chemical modification to in situ prepare SLIPSs on the surface of titanium alloys (Fig. 17(a)–(c)). SLIPSs comprise micro/nanopores produced by micro-arc oxidation, providing lubricant storage, and nano-skin spikes produced by the hydrothermal method that firmly retains the lubricant. Experimental results reveal that the coverage of chlorella and Phaeodactina trichotriangle on SLIPSs is 2 to 3 orders of magnitude lower than that on traditional titanium alloy surfaces, indicating that the new synovial material exhibits remarkable stability, durability, biological contamination resistance, and corrosion resistance. Wang et al.199 utilized anodic oxidation to grow in situ nanostructures with different diameters and depths, including nanopores and nanotubes, on the surface of titanium alloys (Fig. 17(d)–(g)). Fluorosilane is used to reduce the surface energy, ensuring easy immersion of the lubricant into the nano-structure. Owing to the super-slippery properties of the lubricant layer, this coating demonstrates significant stain resistance against E. coli and Navicula exigua. Simultaneously, SLIPSs improve the corrosion resistance of titanium alloys and play a synergistic role as the anode film, carburizing layer, and lubricant layer.
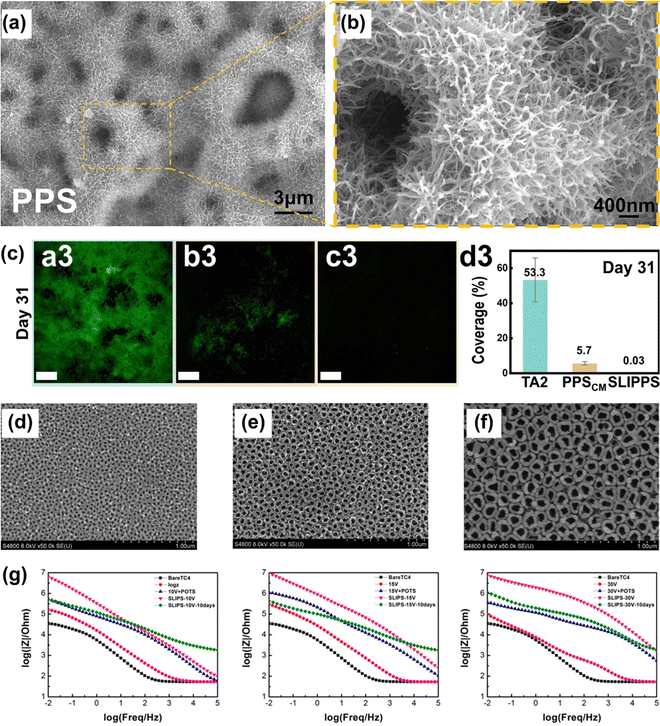 |
| Fig. 17 (a) and (b) SEM images of the surface morphologies of the PPS. (c) CLSM images of the Chlorella covering (reproduced from ref. 198 with permission from [Elsevier], copyright [2023]). (d)–(f) FE-SEM images of the TC4 anodic films formed at different voltages (10 V, 15 V, and 30 V). (g) Electrochemical impedance spectra of samples immersed in 3.5 wt% NaCl solution for 10 days (reproduced from ref. 199 with permission from [American Chemical Society], copyright [2019]). | |
4.3.3. Copper alloys.
Copper-based materials, renowned for their impressive mechanical properties and thermal conductivity, find widespread use across various industries. However, these materials encounter challenges in the form of environmental corrosion, especially when exposed to elements like seawater, acidity, and alkalinity.200,201 Shi et al.202 addressed this by oxidizing copper foil with copper chloride, sodium hydroxide, sulfuric acid, and other reagents to form nano-scale needle-like copper hydroxide on its surface. Subsequently, they modified it with an ethanol solution mixed with dodecyl mercaptan and injected a perfluorinated lubricant to achieve a super-smooth surface. The use of a Scanning Kelvin probe demonstrated an increase in electric potential from −850 mV to −500 mV, signifying a substantial improvement in corrosion resistance. Additionally, the impedance value of the super-slippery surface remained two orders of magnitude larger than that of copper foil even after prolonged seawater exposure, validating the long-term protective capability of the super-slippery surface. Wang et al.203 employed the immersion method to directly grow a graphdiyne layer on a copper substrate, as a protective layer in artificial seawater with a corrosion inhibition rate of ∼99.75%. To further enhance the coating's protective properties, the Graphdiyne layer was fluorinated, forming SLIPSs with a remarkable corrosion inhibition rate of 99.99%. Hussain et al.188 electrodeposited a layer of Ni–TiO2 micro-nano rough structure on the copper sheet's surface, modified it with fatty acids, and injected the Krytox lubricant to create a smooth, lubricant-injected surface. This surface exhibited excellent long-term corrosion resistance, with SLIPSs demonstrating a higher corrosion resistance (4.1 × 106 Ω cm−2) compared to the fatty acid-modified Ni–TiO2 surface (1.9 × 105 Ω cm−2). Ryu et al.204 initially prepared nano-rod-like Cu(OH)2via alkaline chemical etching to establish a microstructure and conditions for lubricant storage (Fig. 18). Introducing silica nanoparticles using the LBL method effectively prevented acidic substances from contacting the underlying nano-structures, addressing surface acid resistance issues. Compared with the unmodified copper tube's heat transfer performance, the SLIPSs on the copper substrate exhibited a higher heat transfer coefficient and was resistant to dust pollution due to its excellent self-cleaning performance.
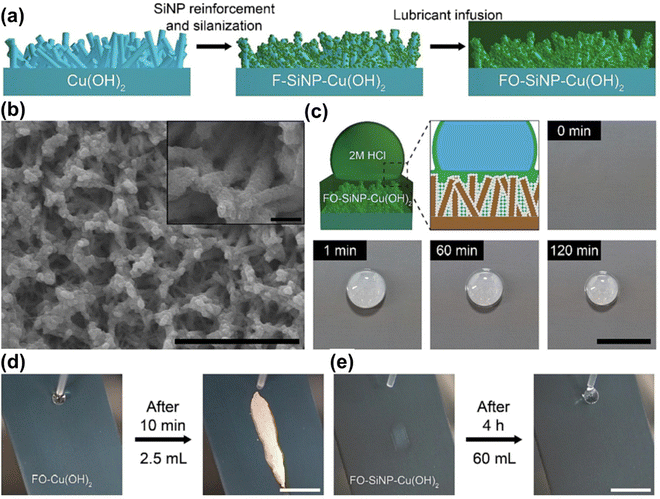 |
| Fig. 18 (a) Schematic illustrating the fabrication process of the SiNP-reinforced SLIPSs. (b) Low and high magnification electron micrographs of SiNP-reinforced SLIPSs. (c) Schematic and series of photographs showing the enhanced acid stability of SiNP-reinforced SLIPSs upon deposition of 2 M HCl droplet (100 μL). The scale bar represents 10 mm. (d) and (e) Acid resistance evaluation via continuous dispensing of 2 M HCl droplets on (d) SLIPSs and (e) SiNP-reinforced SLIPSs mounted at a tilting angle of 45° (reproduced from ref. 204 with permission from [Elsevier], copyright [2022]). | |
4.3.4. Aluminum alloys.
Aluminum alloys are widely utilized for their lightweight, high strength, good thermal and electrical conductivity, and corrosion resistance.205 With a density of approximately one-third that of steel, aluminum alloys offer crucial advantages in applications requiring weight reduction, making them ideal for fuel consumption reduction and achieving increased load capacity in aerospace and automotive industries. Aluminum alloys can form a stable oxide film in the air, exhibiting good corrosion resistance. Moreover, when damaged, the oxide film automatically repairs itself, extending the service life of the aluminum alloy.206,207 However, aluminum alloys are susceptible to corrosion in certain environments, such as acids, alkalis, and seawater, necessitating appropriate protective measures under these specific conditions. The anodizing process of aluminum alloys has a well-established preparation process and can be scaled up to meet commercial standards. The external porous layer ensures a stable lubricant-locking capability. Chen et al.180 introduced a layer of a polyionogel membrane, maintaining capillary force on the pore wall of the anodized aluminum layer. Stable bonding between the aluminum anodized porous surface and the polyionogel membrane was achieved through alkene polymerization with a coupling agent containing vinyl silane and an ionic liquid. Simultaneously, a strong intermolecular interaction formed between the unpolymerized ionic liquid and the polyionogel membrane. Through capillary action and intermolecular interactions, the unpolymerized ionic liquid is locked on the porous surface of the anodized aluminum, serving as the lubricating layer of the sliding sleeve, which effectively inhibits corrosion from the external environment. Sakuraba et al.208 initially prepared a nano-porous anodic alumina layer through an anodic oxidation method and then expanded the pore size by soaking it in a phosphoric acid solution (Fig. 19). After low surface energy treatment, the layer was infused with a lubricant containing organic additives that adsorbed on the porous surface, resulting in self-lubricating SLIPSs. Even in a corrosion system of acetic acid and sodium chloride mixed solution, the organic molecules added, if there are scratch defects on the surface, can be adsorbed again, maintaining high corrosion resistance and self-healing ability. Besides anodizing, SLIPSs can also be constructed using electrodeposition, chemical etching, and LDH methods to enhance the corrosion protection performance of aluminum due to its active characteristics.
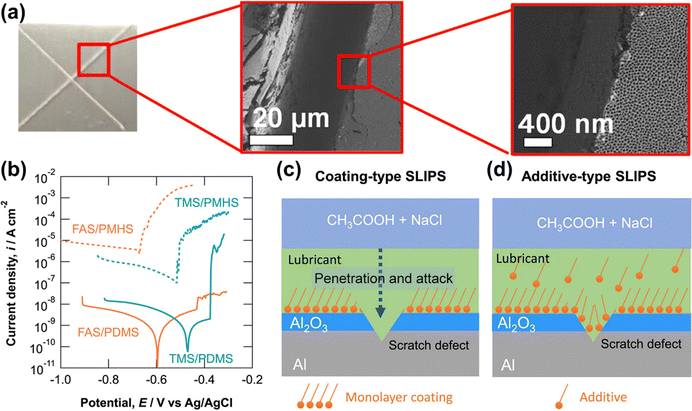 |
| Fig. 19 Potentiodynamic polarization curves of the additive-type SLIPSs measured after immersion in 2 g dm−3 acetic acid containing 10 g dm−3 NaCl (pH 3) for one week and subsequent introduction of the scratch defects, and schematic illustrations of coating-type and additive-type SLIPSs with a scratch defect (reproduced from ref. 208 with permission from [American Chemical Society], copyright [2021]). | |
4.3.5. Magnesium alloys.
Magnesium alloys are widely utilized in engineering applications due to their low elastic modulus, high specific strength, and vibration reduction capabilities.209 With advancements in low-cost production technology and efficient processing methods for magnesium alloys, coupled with the increasing demand for lightweight and energy-saving materials, magnesium alloys have garnered significant attention in industries such as aviation, aerospace, and 3C.210 Similar to aluminum alloys, magnesium alloys naturally form thin oxide films when exposed to air. However, the oxide films on the surface of magnesium alloys are not dense enough to effectively protect the magnesium alloy matrix.211 Consequently, magnesium alloys are susceptible to galvanic corrosion, environmental corrosion, and other forms of corrosion, limiting their widespread use. Enhancing the corrosion resistance of magnesium alloys has thus become a crucial challenge for their extensive application. One effective approach to improving corrosion resistance is the implementation of SLIPSs on the surface of magnesium and its alloys.
Yao et al.212 performed the in situ synthesis of MgAl-LDH nanovessels on the AZ31 magnesium alloy using the hydrothermal method. Sodium benzoate was intercalated into MgAl-LDH as an environmentally friendly corrosion inhibitor. The MgAl-LDH coating was then chemically modified to be superhydrophobic, and SiO2 nanoparticles, along with silicone oil, were mixed and injected into the superhydrophobic coating to form a composite SiO2-SLIPS eventually. The surface displayed good corrosion resistance (2.43 × 10−10 A cm−2) and wear resistance (0.041 mm3). Telmenbayar et al.177 created a layer of a PEO film on the surface of the magnesium alloy using the plasma electrolytic oxidation method. The Zn-MOF film was in situ grown on the surface of PEO (Fig. 20(a)–(e)). PEO-MOF-SLIPSs were obtained after modification and injection of a lubricant. After soaking for 7 days, the coating exhibited good corrosion resistance. Furthermore, the prepared coating demonstrated excellent robustness and stability, remaining hydrophobic even after undergoing 100 cm at a 100 g load and 80 cm at a 200 g load on 800 grid sandpaper. Joo et al.213 prepared a nano-porous hydroxide surface structure on the magnesium alloy substrate through plasma electrolytic oxidation and the hydrothermal method. They then constructed a super-slippery surface after modification and lubricating oil infiltration. The results demonstrated that in a 3.5 wt% NaCl solution, SLIPSs significantly enhanced the corrosion resistance of the magnesium alloy, with its corrosion current density being 5 orders of magnitude lower than that of the magnesium alloy matrix.
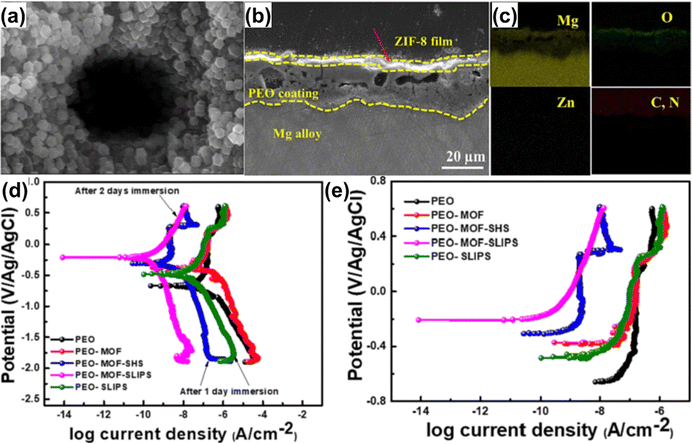 |
| Fig. 20 (a) and (f) Cross-sectional SEM images and elemental mapping analysis of the PEO-MOF sample. (g) and (h) Potentiodynamic polarization curves of different coatings in 3.5 wt% NaCl solution (reproduced from ref. 177 with permission from [Elsevier], copyright [2023]). | |
5. Summary and outlook
Significant progress has been achieved in the research and development of biomimetic self-healing coatings for corrosion prevention applications. However, opportunities for further development exist, especially in repairing large-scale or more complex damage defects. Strategies to improve the transport path of the coating matrix during corrosion or increase the active agent loading can be employed to develop self-healing solutions applicable to larger defects while maintaining overall barrier properties. Future research should focus on bionic self-healing coatings that are more sensitive to external and internal environmental stimuli, allowing quicker responses to maximize repair time and efficiency. Limited research exists on the corrosion resistance and anti-fatigue behavior of intrinsically self-healing materials, necessitating further exploration in this area. An unaddressed issue is the increase in the volume of self-healing coatings when the active agent is released, potentially creating a diffusion path for corrosive substances and leading to further coating failure and exploring methods to enable automatic coating shrinkage after the release of the active agent is an intriguing area of research.
Reviewing recent research on SHSs and SLIPSs reveals that despite various types applying to different metal substrates, many existing techniques face challenges like high costs, complex processes, limited generalization, and difficulties in scaling up production. The durability of these surfaces remains a significant hurdle, restricting practical applications. While some progress has been made in enhancing durability, it falls short of meeting engineering requirements. The development of both SHSs and SLIPSs has reached a bottleneck, primarily due to limited research being confined to laboratory-scale applications. Future research should prioritize environmentally friendly and cost-effective materials, rational preparation routes, and optimized methods for large-scale, low-cost, and easy preparation. Additionally, exploring new approaches to enhance mechanical stability and long-term durability, particularly for materials capable of self-repairing surface damage caused by friction and wear, will be a prominent area of future research.
Current research on the corrosion resistance or other functions of SHSs or SLIPSs has predominantly focused on replicating outermost surface functions found in organisms, such as hydrophobic effects and oily films. However, organism structures are complex, with a synergistic relationship between functions and structures. For example, fish has specialized epithelial cells secreting mucus for lubrication and defense against adhesive invasion. The outer surface of scaly fish skin, like carp, includes an ultrathin mineral layer on mineralized collagen fibrils, enhancing damage tolerance and serving as exceptional dermal armor.214 Adopting a multidimensional approach to designing bionic surface structures that integrate both structure and function can provide further inspiration for innovative surfaces.
Conflicts of interest
There are no conflicts to declare.
Acknowledgements
This work is supported by the National Science Foundation of China under the Grant no. 12127806, 62175195, and the International Joint Research Laboratory for Micro/Nano Manufacturing and Measurement Technologies.
References
- P. Rajala, D. Q. Cheng, S. A. Rice and F. M. Lauro, Microbiome, 2022, 10, 4 CrossRef CAS PubMed
.
- L. Yan, Y. Diao, Z. Lang and K. Gao, Sci. Technol. Adv. Mater., 2020, 21, 359–370 CrossRef CAS PubMed
.
- C. Cardell and I. Guerra, Sci. Adv., 2022, 8, eabn2541 CrossRef CAS PubMed
.
- D. Zhang, Y. Liu, R. Liu, X. Guan, S. Xing, X. Dou, Z. He and X. Zhang, Front. Chem., 2022, 10, 950768 CrossRef CAS PubMed
.
- H. Li, W. Song, X. Cui, Y. Li, B. Hou, L. Cheng and P. Zhang, Nanoscale Res. Lett., 2021, 16, 10 CrossRef CAS PubMed
.
- L. Zeng, Y. Chang, Y. Wu, J. Yang, J. F. Xu and X. Zhang, Sci. Adv., 2020, 6, eaba7524 CrossRef CAS PubMed
.
- S. Hong, Z. Wei, K. Wang, W. Gao, Y. Wu and J. Lin, Ultrason. Sonochem., 2021, 72, 105438 CrossRef CAS PubMed
.
- A. Vigneron, E. B. Alsop, B. Chambers, B. P. Lomans, I. M. Head and N. Tsesmetzis, Appl. Environ. Microbiol., 2016, 82, 2545–2554 CrossRef CAS PubMed
.
- C. Liu, B. Qian, P. Hou and Z. Song, ACS Appl. Mater. Interfaces, 2021, 13, 4429–4441 CrossRef CAS PubMed
.
- A. López-Ortega, O. Areitioaurtena, S. A. Alves, A. M. Goitandia, I. Elexpe, J. L. Arana and R. Bayón, Prog. Org. Coat., 2019, 137, 105376 CrossRef
.
- A. S. Jagadeeswar, S. Kumar, B. Venkataraman, P. S. Babu and A. Jyothirmayi, Surf. Coat. Technol., 2020, 399, 126138 CrossRef CAS
.
- G. Stremsdoerfer, H. Omidvar, P. Roux, Y. Meas and R. Ortega-Borges, J. Alloys Compd., 2008, 466, 391–397 CrossRef CAS
.
- M. Kultamaa, K. Mönkkönen, J. J. Saarinen and M. Suvanto, Coatings, 2021, 11, 949 CrossRef CAS
.
- H. Eivaz Mohammadloo, A. A. Sarabi, H. R. Asemani and P. Ahmadi, Prog. Org. Coat., 2018, 125, 432–442 CrossRef CAS
.
- K. Dong, Y. Song, D. Shan and E.-H. Han, Mater. Corros., 2018, 69, 481–491 CrossRef CAS
.
- D. Zhao, J. Sun, L. Zhang, Y. Tan and J. Li, J. Rare Earths, 2010, 28, 371–374 CrossRef
.
- S. Yu, L. Wang, C. Wu, T. Feng, Y. Cheng, Z. Bu and S. Zhu, J. Alloys Compd., 2020, 817, 153257 CrossRef CAS
.
- Y. Zhang, Y. Chen, X. Y. Duan, W. Q. Zheng and Y. W. Zhao, Mater. Res. Express, 2019, 6, 126416 CrossRef CAS
.
- M. Cui, B. Wang and Z. Wang, Adv. Eng. Mater., 2019, 21, 1801379 CrossRef
.
- P. P. Vijayan and D. Puglia, Emergent Mater., 2019, 2, 391–415 CrossRef
.
- J. S. George, P. Vijayan P, A. T. Hoang, N. Kalarikkal, P. Nguyen-Tri and S. Thomas, Prog. Org. Coat., 2022, 168, 106858 CrossRef CAS
.
- P. Nguyen-Tri, H. N. Tran, C. O. Plamondon, L. Tuduri, D.-V. N. Vo, S. Nanda, A. Mishra, H.-P. Chao and A. K. Bajpai, Prog. Org. Coat., 2019, 132, 235–256 CrossRef CAS
.
- Z. Wang, L. Scheres, H. Xia and H. Zuilhof, Adv. Funct. Mater., 2020, 30, 1908098 CrossRef CAS
.
- J. S. George, P. Vijayan P, J. K. Paduvilan, N. Salim, J. Sunarso, N. Kalarikkal, N. Hameed and S. Thomas, Prog. Org. Coat., 2022, 162, 106571 CrossRef CAS
.
- I. Martin-Martin, A. Paige, P. C. Valenzuela Leon, A. G. Gittis, O. Kern, B. Bonilla, A. C. Chagas, S. Ganesan, L. B. Smith, D. N. Garboczi and E. Calvo, Nat. Commun., 2020, 11, 2911 CrossRef CAS PubMed
.
- A. Stanley, E. D. Tichy, J. Kocan, D. W. Roberts, E. M. Shore and F. Mourkioti, NPJ Regener. Med., 2022, 7, 5 CrossRef CAS PubMed
.
- E. V. Skorb, D. Fix, D. V. Andreeva, H. Möhwald and D. G. Shchukin, Adv. Funct. Mater., 2009, 19, 2373–2379 CrossRef CAS
.
- S. R. White, N. R. Sottos, P. H. Geubelle, J. S. Moore, M. R. Kessler, S. R. Sriram, E. N. Brown and S. Viswanathan, Nature, 2001, 409, 794–797 CrossRef CAS PubMed
.
- Y.-K. Song, H.-W. Kim and C.-M. Chung, Polymers, 2022, 14, 2013 CrossRef CAS PubMed
.
- B. Oktay, J. H. Türkcan, O. K. Özdemir and N. Kayaman-Apohan, Macromol. Res., 2023, 31, 1077–1086 CrossRef CAS
.
- N. Z. Tomić, A. N. Mustapha, M. AlMheiri, N. AlShehhi and A. Antunes, Prog. Org. Coat., 2022, 172, 107070 CrossRef
.
- H. Wang, J. Xu, H. Wang, X. Cheng, S. Wang and Z. Du, Prog. Org. Coat., 2022, 167, 106837 CrossRef CAS
.
- H. Li, Y. Feng, Y. Cui, Y. Ma, Z. Zheng, B. Qian, H. Wang, A. Semenov and D. Shchukin, Prog. Org. Coat., 2020, 145, 105684 CrossRef CAS
.
- M. Attaei, L. M. Calado, M. G. Taryba, Y. Morozov, R. A. Shakoor, R. Kahraman, A. C. Marques and M. F. Montemor, Prog. Org. Coat., 2020, 139, 105445 CrossRef CAS
.
- J. Sun, J. Duan, X. Liu, X. Dong, Y. Zhang, C. Liu and B. Hou, Appl. Mater. Today, 2022, 28, 101551 CrossRef
.
- G. Chen, Z. Sun, Y. Wang, J. Zheng, S. Wen, J. Zhang, L. Wang, J. Hou, C. Lin and Z. Yue, Prog. Org. Coat., 2020, 140, 105483 CrossRef CAS
.
- J. Sun, C. Liu, J. Duan, J. Liu, X. Dong, Y. Zhang, N. Wang, J. Wang and B. Hou, J. Mater. Sci. Technol., 2022, 124, 1–13 CrossRef CAS
.
- W. Wang, L. Xu, X. Li, Y. Yang and E. An, Corros. Sci., 2014, 80, 528–535 CrossRef CAS
.
- W. Wang, W. Li, L. Song, W. Fan, C. Xiong, X. Gao, X. Zhang and X. Liu, J. Electrochem. Soc., 2017, 164, C635 CrossRef CAS
.
- Y. Feng, Y. Cui, M. Zhang, M. Li and H. Li, Macromol. Mater. Eng., 2021, 306, 2000581 CrossRef CAS
.
- A. R. Hamilton, N. R. Sottos and S. R. White, Adv. Mater., 2010, 22, 5159–5163 CrossRef CAS PubMed
.
- A. Adli, K. Shelesh-Nezhad, M. Khoshravan Azar and M. Mohammadi-Aghdam, Plast., Rubber Compos., 2020, 49, 79–90 CrossRef CAS
.
- S. J. Pety, J. E. Aw, A. C. Gendusa, P. R. Barnett, Q. A. Calvert, N. R. Sottos and S. R. White, Compos. Struct., 2018, 184, 428–436 CrossRef
.
- V. Vahedi, P. Pasbakhsh, C. S. Piao and C. E. Seng, J. Mater. Chem. A, 2015, 3, 16005–16012 RSC
.
- G. Postiglione, M. Alberini, S. Leigh, M. Levi and S. Turri, ACS Appl. Mater. Interfaces, 2017, 9, 14371–14378 CrossRef CAS PubMed
.
- C. J. Hansen, W. Wu, K. S. Toohey, N. R. Sottos, S. R. White and J. A. Lewis, Adv. Mater., 2009, 21, 4143–4147 CrossRef CAS
.
- C. J. Hansen, S. R. White, N. R. Sottos and J. A. Lewis, Adv. Funct. Mater., 2011, 21, 4320–4326 CrossRef CAS
.
- J. F. Patrick, M. J. Robb, N. R. Sottos, J. S. Moore and S. R. White, Nature, 2016, 540, 363–370 CrossRef CAS PubMed
.
- R. C. R. Gergely, W. A. Santa Cruz, B. P. Krull, E. L. Pruitt, J. Wang, N. R. Sottos and S. R. White, Adv. Funct. Mater., 2018, 28, 1704197 CrossRef
.
- H. Pulikkalparambil, S. Siengchin and J. Parameswaranpillai, Nano-Struct. Nano-Objects, 2018, 16, 381–395 CrossRef CAS
.
- S. Sinha-Ray, D. D. Pelot, Z. P. Zhou, A. Rahman, X. F. Wu and A. L. Yarin, J. Mater. Chem., 2012, 22, 9138–9146 RSC
.
- H. Wang, H. Cai, B. Chen and C. Mao, Polym. Compos., 2021, 42, 3281–3292 CrossRef CAS
.
- C. Mao, H. Cai, Y. Gan and M. Li, Polym. Compos., 2023, 44, 3435–3451 CrossRef CAS
.
- M. W. Lee, S. S. Yoon and A. L. Yarin, ACS Appl. Mater. Interfaces, 2016, 8, 4955–4962 CrossRef CAS PubMed
.
- Y. Zhang, J. Ye, D. Qu, H. Wang, C. Chai and L. Feng, Polym. Eng. Sci., 2021, 61, 2257–2266 CrossRef CAS
.
- M. Uzaki and M. Shibata, J. Polym. Res., 2022, 29, 453 CrossRef CAS
.
- M. Vauthier, L. Jierry, J. C. Oliveira, L. Hassouna, V. Roucoules and F. Bally-Le Gall, Adv. Funct. Mater., 2019, 29, 1806765 CrossRef
.
-
N. Patra, N. Mameda and M. Salerno, in Polymer-Based Nanoscale Materials for Surface Coatings, ed. S. Thomas and J. S. George, Elsevier, 2023, pp. 59–73 Search PubMed
.
-
P. Poornima Vijayan, J. S. George and R. V. Revathy, in Multifunctional Epoxy Resins: Self-Healing, Thermally and Electrically Conductive Resins, ed. N. Hameed, J. C. Capricho, N. Salim and S. Thomas, Springer Nature Singapore, Singapore, 2023, pp. 161–174 Search PubMed
.
- S.-L. Xiang, Q.-X. Hua, P.-J. Zhao, W.-L. Gong, C. Li and M.-Q. Zhu, Chem. Mater., 2019, 31, 5081–5088 CrossRef CAS
.
- M. A. North, C. A. Del Grosso and J. J. Wilker, ACS Appl. Mater. Interfaces, 2017, 9, 7866–7872 CrossRef CAS PubMed
.
- B. Qian, Z. Zheng, M. Michailids, N. Fleck, M. Bilton, Y. Song, G. Li and D. Shchukin, ACS Appl. Mater. Interfaces, 2019, 11, 10283–10291 CrossRef CAS PubMed
.
- H. Zhang, W. Sun, L. Wang, S. Ma, W. Xing, K. Liang and G. Liu, Chem. Eng. J., 2023, 473, 145164 CrossRef CAS
.
- W. Chen, J. Fan, Y. Jiang, S. Li, Y. Ying and H. Yang, Front. Mater., 2022, 9, 850362 CrossRef
.
- H. D. Zhang, A. Y. Chen, B. Gan, H. Jiang and L. J. Gu, J. Magnesium Alloys, 2022, 10, 1358–1367 CrossRef CAS
.
- J. Li, S. Li, C. Chen, H. Guo, B. Lei, P. Zhang, G. Meng and Z. Feng, Colloids Surf., A, 2023, 666, 131283 CrossRef CAS
.
- J. Huang, W. Zhang, H. Li, X. Yu, S. Ding and C. Wu, J. Mater. Sci., 2020, 55, 17255–17265 CrossRef CAS
.
- L. Song, Z. Gao, Q. Sun, G. Chu, H. Shi, N. Xu, Z. Li, N. Hao, X. Zhang, F. Ma and L. Wang, Prog. Org. Coat., 2023, 175, 107331 CrossRef CAS
.
- L. Ma, J. Wang, D. Zhang, Y. Huang, L. Huang, P. Wang, H. Qian, X. Li, H. A. Terryn and J. M. C. Mol, Chem. Eng. J., 2021, 404, 127118 CrossRef CAS
.
- Z. Chen, W. Yang, X. Yin, Y. Chen, Y. Liu and B. Xu, Prog. Org. Coat., 2020, 146, 105750 CrossRef CAS
.
- S. Habib, A. Hassanein, R. Kahraman, E. Mahdi Ahmed and R. A. Shakoor, Mater. Des., 2021, 207, 109839 CrossRef CAS
.
- H. H. Zhang, X. Zhang, H. Bian, L. Zhang, Y. Chen, Y. Yang and Z. Zhang, Colloids Surf., A, 2024, 682, 132844 CrossRef CAS
.
- S. Habib, E. Fayyad, M. Nawaz, A. Khan, R. A. Shakoor, R. Kahraman and A. Abdullah, Nanomaterials, 2020, 10, 791 CrossRef CAS PubMed
.
- S. Habib, E. Fayyed, R. A. Shakoor, R. Kahraman and A. Abdullah, Arabian J. Chem., 2021, 14, 102926 CrossRef CAS
.
- A. Khan, A. Hassanein, S. Habib, M. Nawaz, R. A. Shakoor and R. Kahraman, ACS Appl. Mater. Interfaces, 2020, 12, 37571–37584 CrossRef CAS PubMed
.
- D. Li, J. Zhuang, Z. Lin, D. Song, Q. Liu, J. Zhu, J. Yu, J. Liu, R. Chen and J. Wang, Prog. Org. Coat., 2023, 185, 107944 CrossRef CAS
.
- L. Cheng, C. Liu, H. Wu, H. Zhao and L. Wang, J. Colloid Interface Sci., 2022, 606, 1572–1585 CrossRef CAS PubMed
.
- P. Najmi, N. Keshmiri, M. Ramezanzadeh and B. Ramezanzadeh, Chem. Eng. J., 2021, 412, 128637 CrossRef CAS
.
- A. Dehghani, G. Bahlakeh, B. Ramezanzadeh and A. H. J. Mofidabadi, J. Environ. Chem. Eng., 2021, 9, 105457 CrossRef CAS
.
- M. Akbari, R. Naderi and B. Ramezanzadeh, Appl. Mater. Today, 2023, 33, 101880 CrossRef
.
- L. Cao, W. Wang, J. Cheng, T. Wang, Y. Zhang, L. Wang, W. Li and S. Chen, ACS Appl. Mater. Interfaces, 2023, 15, 48645–48659 CrossRef CAS PubMed
.
- C. Ma, J. Li, J. Wang, D. Bian and Y. Zhao, Polym. Eng. Sci., 2022, 62, 4173–4184 CrossRef CAS
.
- S. Mohammadkhah, M. Ramezanzadeh, H. Eivaz Mohammadloo, B. Ramezanzadeh and R. Ghamsarizade, J. Ind. Eng. Chem., 2023, 121, 358–377 CrossRef CAS
.
- C. Zhao, Y. Hu and W. Guo, Colloids Surf., A, 2023, 675, 132018 CrossRef CAS
.
- L. Shen, W. Xie, C. Ni, Y. Xie, L. Miao and W. Zhao, Mater. Today Nano, 2023, 24, 100395 CrossRef CAS
.
- Z. Chen, W. Yang, Y. Chen, X. Yin and Y. Liu, J. Colloid Interface Sci., 2020, 579, 741–753 CrossRef CAS PubMed
.
- H. E. Fathabadi, M. Ghorbani and H. M. Ghartavol, Nano-Struct. Nano-Objects, 2021, 26, 100760 CrossRef CAS
.
- X. Li, B. Gong, J. Zhang, Y. Di, Y. Ding, Z. Chen and W. Yang, Colloids Surf., A, 2023, 674, 131899 CrossRef CAS
.
- J. Yong, Q. Yang, X. Hou and F. Chen, Ultrafast Sci., 2022, 2, 9895418 Search PubMed
.
- D. Zhang, F. Chen, Q. Yang, J. Si and X. Hou, Soft Matter, 2011, 7, 8337–8342 RSC
.
- J. Yong, S. C. Singh, Z. Zhan, F. Chen and C. Guo, Langmuir, 2019, 35, 921–927 CrossRef CAS PubMed
.
- J. Yong, C. Zhang, X. Bai, J. Zhang, Q. Yang, X. Hou and F. Chen, Adv. Mater. Interfaces, 2020, 7, 1901931 CrossRef CAS
.
- T. Liu, Y. Yin, S. Chen, X. Chang and S. Cheng, Electrochim. Acta, 2007, 52, 3709–3713 CrossRef CAS
.
- J. Yong, F. Chen, Y. Fang, J. Huo, Q. Yang, J. Zhang, H. Bian and X. Hou, ACS Appl. Mater. Interfaces, 2017, 9, 39863–39871 CrossRef CAS PubMed
.
- L. B. Boinovich, A. M. Emelyanenko, A. D. Modestov, A. G. Domantovsky and K. A. Emelyanenko, Mendeleev Commun., 2017, 27, 254–256 CrossRef CAS
.
- X. Lai, J. Hu and J. Qu, Carbon, 2023, 212, 118155 CrossRef CAS
.
- D. Wei, J. Wang, S. Li, D. Wang and Y. Liu, Chem. Eng. J., 2023, 475, 146113 CrossRef CAS
.
- W. Gu, W. Li, Y. Zhang, Y. Xia, Q. Wang, W. Wang, P. Liu, X. Yu, H. He, C. Liang, Y. Ban, C. Mi, S. Yang, W. Liu, M. Cui, X. Deng, Z. Wang and Y. Zhang, Nat. Commun., 2023, 14, 5953 CrossRef CAS PubMed
.
- Q. Zhang, X. Bai, Y. Li, X. Zhang, D. Tian and L. Jiang, ACS Nano, 2022, 16, 16843–16852 CrossRef CAS PubMed
.
- X. Yan, B. Ji, L. Feng, X. Wang, D. Yang, K. F. Rabbi, Q. Peng, M. J. Hoque, P. Jin, E. Bello, S. Sett, M. Alleyne, D. M. Cropek and N. Miljkovic, ACS Nano, 2022, 16, 12910–12921 CrossRef CAS PubMed
.
- T. Zheng, Y. Hu, F. Pan, Y. Zhang and A. Tang, J. Magnesium Alloys, 2019, 7, 193–202 CrossRef CAS
.
- H. Wang, Y. Zhu, Z. Hu, X. Zhang, S. Wu, R. Wang and Y. Zhu, Chem. Eng. J., 2016, 303, 37–47 CrossRef CAS
.
- Y. Zou, Y. Wang, S. Xu, T. Jin, D. Wei, J. Ouyang, D. Jia and Y. Zhou, Chem. Eng. J., 2019, 362, 638–649 CrossRef CAS
.
- B. Zhang, Q. Zhu, Y. Li and B. Hou, Chem. Eng. J., 2018, 352, 625–633 CrossRef CAS
.
- Z. Bai and J. Zhu, Coatings, 2023, 13, 1151 CrossRef CAS
.
- Y. Wan, M. Chen, W. Liu, X. Shen, Y. Min and Q. Xu, Electrochim. Acta, 2018, 270, 310–318 CrossRef CAS
.
- W. Tong and D. Xiong, Mater. Today Phys., 2022, 23, 100651 CrossRef
.
- L. B. Boinovich, E. B. Modin, A. R. Sayfutdinova, K. A. Emelyanenko, A. L. Vasiliev and A. M. Emelyanenko, ACS Nano, 2017, 11, 10113–10123 CrossRef CAS PubMed
.
- V. A. Luchkina, M. S. Min'kin, A. Y. Luchkin and Y. I. Kuznetsov, J. Magnesium Alloys, 2023, 11, 3272–3286 CrossRef CAS
.
- W. Tong, L. Cui, R. Qiu, C. Yan, Y. Liu, N. Wang and D. Xiong, J. Mater. Sci. Technol., 2021, 89, 59–67 CrossRef CAS
.
- D. Li, L. Ma, B. Zhang and S. Chen, Chem. Eng. J., 2022, 450, 138429 CrossRef CAS
.
- A. Gong, Y. Zheng, Z. Yang, X. Guo, Y. Gao and X. Li, Mater. Today Commun., 2021, 26, 101828 CrossRef CAS
.
- B. Zhang, W. Xu, D. Xia, Y. Huang, X. Zhao and J. Zhang, Colloids Surf., A, 2020, 596, 124750 CrossRef CAS
.
- M. Hegde, J. Mohan, M. Q. Mushtaq Warraich, Y. Kavanagh, B. Duffy and E. F. Tobin, Wear, 2023, 524–525, 204766 CrossRef CAS
.
- A. V. Rao, S. S. Latthe, S. A. Mahadik and C. Kappenstein, Appl. Surf. Sci., 2011, 257, 5772–5776 CrossRef CAS
.
- D.-W. Li, H.-Y. Wang, Y. Liu, D.-S. Wei and Z.-X. Zhao, Chem. Eng. J., 2019, 367, 169–179 CrossRef CAS
.
- Y. Shen, K. Li, H. Chen, Z. Wu and Z. Wang, Chem. Eng. J., 2021, 413, 127455 CrossRef CAS
.
- S. M. A. Mousavi and R. Pitchumani, Corros. Sci., 2021, 186, 109420 CrossRef CAS
.
- S. Wang, C. Hou, M. Wu, X. Li, W. Wang, N. Mitsuzaki and Z. Chen, Colloids Surf., A, 2021, 614, 126185 CrossRef CAS
.
- M. Salehi, M. Mozammel and S. M. Emarati, Colloids Surf., A, 2019, 573, 196–204 CrossRef CAS
.
- H. Yin, H. Liu, X. Guo, Z. Cui, J. Tang, X. Lin and C. Hu, Vacuum, 2022, 195, 110699 CrossRef CAS
.
- Z. Kang, Y. He, J. Sang, H. Hirahara and D. Chen, Adv. Mater. Interfaces, 2021, 8, 2100651 CrossRef CAS
.
- H. Jie, Q. Xu, L. Wei and Y. Min, Corros. Sci., 2016, 102, 251–258 CrossRef CAS
.
- J. Yong, F. Chen, Q. Yang and X. Hou, Soft Matter, 2015, 11, 8897–8906 RSC
.
- R. A. Rajan, S. Rao Konda, C. Sajed Saraj, Y. Hang Lai, G. Verma, Z. Yu, W. Yu, D. Yan and J. Yang, Appl. Surf. Sci., 2022, 573, 151612 CrossRef CAS
.
- I. Vilaró, J. L. Yagüe and S. Borrós, ACS Appl. Mater. Interfaces, 2017, 9, 1057–1065 CrossRef PubMed
.
- C.-H. Chang, M.-H. Hsu, C.-J. Weng, W.-I. Hung, T.-L. Chuang, K.-C. Chang, C.-W. Peng, Y.-C. Yen and J.-M. Yeh, J. Mater. Chem. A, 2013, 1, 13869–13877 RSC
.
- K.-C. Chang, M.-H. Hsu, H.-I. Lu, M.-C. Lai, P.-J. Liu, C.-H. Hsu, W. F. Ji, T. L. Chuang, Y. Wei, J. M. Yeh and W.-R. Liu, Carbon, 2014, 66, 144–153 CrossRef CAS
.
- S. Zachariah, T.-W. Chuo and Y.-L. Liu, Polymer, 2018, 155, 168–176 CrossRef CAS
.
- A. Vicente, P. J. Rivero, U. Urdiroz, P. García, J. Mora, J. F. Palacio, F. J. Palomares and R. Rodríguez, Polymers, 2022, 14, 4356 CrossRef CAS PubMed
.
- H. Li, S. Yu and X. Han, Chem. Eng. J., 2016, 283, 1443–1454 CrossRef CAS
.
- Y. Shu, X. Lu, W. Lu, W. Su, Y. Wu, H. Wei, D. Xu, J. Liang and Y. Xie, Surf. Coat. Technol., 2023, 455, 129216 CrossRef CAS
.
- S. Jiang, W. Li, J. Liu, J. Jiang, Z. Zhang, W. Shang, N. Peng and Y. Wen, J. Magnesium Alloys, 2023, 11, 3287–3301 CrossRef CAS
.
- H. Jin, L. Tian, W. Bing, J. Zhao and L. Ren, Prog. Mater. Sci., 2022, 124, 100889 CrossRef CAS
.
- T. P. Manoj, T. P. Rasitha, S. C. Vanithakumari, B. Anandkumar, R. P. George and J. Philip, Appl. Surf. Sci., 2020, 512, 145636 CrossRef CAS
.
- T. P. Rasitha, S. C. Vanithakumari, D. Nanda Gopala Krishna, R. P. George, R. Srinivasan and J. Philip, Prog. Org. Coat., 2022, 162, 106560 CrossRef CAS
.
- M. S. Selim, N. A. Fatthallah, M. A. Shenashen, S. A. Higazy, H. R. Madian, M. M. Selim and S. A. El-Safty, Langmuir, 2023, 39, 2333–2346 CrossRef CAS PubMed
.
- L. Zhao, R. Chen, J. Liu, Q. Liu, J. Yu, J. Zhu, P. Liu and J. Wang, Prog. Org. Coat., 2023, 183, 107812 CrossRef CAS
.
- D. Wang, Q. Sun, M. J. Hokkanen, C. Zhang, F.-Y. Lin, Q. Liu, S.-P. Zhu, T. Zhou, Q. Chang, B. He, Q. Zhou, L. Chen, Z. Wang, R. H. A. Ras and X. Deng, Nature, 2020, 582, 55–59 CrossRef CAS PubMed
.
- H. Chen, F. Wang, H. Fan, R. Hong and W. Li, Chem. Eng. J., 2021, 408, 127343 CrossRef CAS
.
- B. Zhang, J. Duan, Y. Huang and B. Hou, J. Mater. Sci. Technol., 2021, 71, 1–11 CrossRef CAS
.
- J. Zhang, X. Pei, J. Huang, X. Ke, C. Xu, W. Zhao, L. Li, Y. Weng and J. Chen, ACS Appl. Mater. Interfaces, 2023, 15, 265–280 CrossRef CAS PubMed
.
- J. F. Ou, X. Z. Fang, W. J. Zhao, S. Lei, M. S. Xue, F. J. Wang, C. Q. Li, Y. L. Lu and W. Li, Langmuir, 2018, 34, 5807–5812 CrossRef CAS PubMed
.
- R. Poetes, K. Holtzmann, K. Franze and U. Steiner, Phys. Rev. Lett., 2010, 105, 166104 CrossRef PubMed
.
- A. Manoj, R. Ramachandran and P. L. Menezes, Int. J. Adv. Manuf. Technol., 2020, 110, 457–470 CrossRef
.
- S. F. Ahmadi, V. Umashankar, Z. Dean, B. Chang, S. Jung and J. B. Boreyko, ACS Appl. Mater. Interfaces, 2021, 13, 27567–27574 CrossRef CAS PubMed
.
- L. Zhang, X. Xue, H. Zhang, Z. Huang and Z. Zhang, Composites, Part A, 2021, 146, 106405 CrossRef CAS
.
- H. Teisala, F. Geyer, J. Haapanen, P. Juuti, J. M. Mäkelä, D. Vollmer and H.-J. Butt, Adv. Mater., 2018, 30, 1706529 CrossRef PubMed
.
- Y. Tan, J. Yang, Y. Li, X. Li, Q. Wu, Y. Fan, F. Yu, J. Cui, L. Chen, D. Wang and X. Deng, Adv. Mater., 2022, 34, 2202167 CrossRef CAS PubMed
.
- K. Zhang, F. Xu and Y. Gao, Appl. Mater. Today, 2021, 22, 100970 CrossRef
.
- Y. Liu, Y. Zheng, T. Li, D. Wang and F. Zhou, Nano Energy, 2019, 61, 454–461 CrossRef CAS
.
- X. Han, L. Ren, Y. Ma, X. Gong and H. Wang, Carbon, 2022, 197, 27–39 CrossRef CAS
.
- Y. Wang, Y. Liu, J. Li, L. Chen, S. Huang and X. Tian, Chem. Eng. J., 2020, 390, 124311 CrossRef
.
- P. C. Uzoma, F. Liu and E.-H. Han, J. Mater. Sci. Technol., 2020, 45, 70–83 CrossRef CAS
.
- X. Li, B. Li, Y. Li and J. Sun, Chem. Eng. J., 2021, 404, 126504 CrossRef CAS
.
- X. Ni, Y. Gao, X. Zhang, Y. Lei, G. Sun and B. You, Chem. Eng. J., 2021, 406, 126725 CrossRef CAS
.
- X. Liu, H. He, T. C. Zhang, L. Ouyang, Y.-X. Zhang and S. Yuan, Chem. Eng. J., 2021, 404, 127106 CrossRef CAS
.
- Z. Wang, L. Yuan, G. Liang and A. Gu, Chem. Eng. J., 2021, 408, 127263 CrossRef CAS
.
- X. Bai, Q. Yang, H. Li, J. Huo, J. Liang, X. Hou and F. Chen, Langmuir, 2022, 38, 4645–4656 CrossRef CAS PubMed
.
- J. Zhang, X. Zhao, J. Wei, B. Li and J. Zhang, Langmuir, 2021, 37, 13527–13536 CrossRef CAS PubMed
.
- J. Zhang, J. Wei, B. Li, X. Zhao and J. Zhang, J. Colloid Interface Sci., 2021, 594, 836–847 CrossRef CAS PubMed
.
- H. F. Bohn and W. Federle, Proc. Natl. Acad. Sci. U. S. A., 2004, 101, 14138–14143 CrossRef CAS PubMed
.
- T.-S. Wong, S. H. Kang, S. K. Y. Tang, E. J. Smythe, B. D. Hatton, A. Grinthal and J. Aizenberg, Nature, 2011, 477, 443–447 CrossRef CAS PubMed
.
- Y. Long, X. Yin, P. Mu, Q. Wang, J. Hu and J. Li, Chem. Eng. J., 2020, 401, 126137 CrossRef CAS
.
- Y. Yu, B. Li, Y. Wei, X. Ren, F. Bie, Y. Xu, R. Qiu, X. Li and Y. Ouyang, J. Ind. Eng. Chem., 2023, 118, 298–308 CrossRef CAS
.
- Y. Kan, F. Zheng, B. Li, R. Zhang, Y. Wei, Y. Yu, Y. Zhang, Y. Ouyang and R. Qiu, Colloids Surf., A, 2021, 630, 127585 CrossRef CAS
.
- J. Zhang, C. Gu and J. Tu, ACS Appl. Mater. Interfaces, 2017, 9, 11247–11257 CrossRef CAS PubMed
.
- P. Wang, T. Li and D. Zhang, Corros. Sci., 2017, 128, 110–119 CrossRef CAS
.
- J. Wang, Y. Wang, K. Zhang, X. Liu, S. Zhang, D. Wang and L. Xie, J. Colloid Interface Sci., 2024, 659, 289–298 CrossRef CAS PubMed
.
- M. Tonelli, S. Peppou-Chapman, F. Ridi and C. Neto, J. Phys. Chem. C, 2019, 123, 2987–2995 CrossRef CAS
.
- M. J. Hoque, S. Sett, X. Yan, D. Liu, K. F. Rabbi, H. Qiu, M. Qureshi, G. Barac, L. Bolton and N. Miljkovic, ACS Appl. Mater. Interfaces, 2022, 14, 4598–4611 CrossRef CAS PubMed
.
- A. Sasidharanpillai, Y. Lee and S. Lee, Colloids Surf., A, 2022, 646, 128923 CrossRef CAS
.
- T. Zhu, Y. Yuan, Q. Yu, H. Xiang, G. Liu, X. Dai and R. Liao, Mater. Chem. Phys., 2023, 306, 128073 CrossRef CAS
.
- W. Yao, Y. Chen, L. Wu, B. Jiang and F. Pan, J. Taiwan Inst. Chem. Eng., 2022, 131, 104176 CrossRef CAS
.
- J. Sun, C. Wang, J. Song, L. Huang, Y. Sun, Z. Liu, C. Zhao and Y. Li, J. Mater. Sci., 2018, 53, 16099–16109 CrossRef CAS
.
- H. Li, X. Fu and X. Chu, J. Mater. Sci., 2022, 57, 3746–3756 CrossRef CAS
.
- L. Telmenbayar, A. Gopal Ramu, D. Yang and D. Choi, Chem. Eng. J., 2023, 458, 141397 CrossRef CAS
.
- T. Xiang, M. Zhang, H. R. Sadig, Z. Li, M. Zhang, C. Dong, L. Yang, W. Chan and C. Li, Chem. Eng. J., 2018, 345, 147–155 CrossRef CAS
.
- Y. Jing, F. Meng, F. Wang and L. Liu, Appl. Surf. Sci., 2023, 639, 158214 CrossRef CAS
.
- Y. Chen and Z. Guo, J. Mater. Chem. A, 2020, 8, 24075–24085 RSC
.
- C. Urata, G. J. Dunderdale, M. W. England and A. Hozumi, J. Mater. Chem. A, 2015, 3, 12626–12630 RSC
.
- Y. Liu, W. Sun, K. Feng, Y. Wu, B. Yu, S. Liu and F. Zhou, Prog. Org. Coat., 2023, 174, 107311 CrossRef CAS
.
- J. Yu, R. Zhao, J. Wang, N. Wang, J. Xu, M. Jin and Y. Zhao, Tribol. Int., 2024, 192, 109220 CrossRef CAS
.
- H. Zhao, Q. Sun, X. Deng and J. Cui, Adv. Mater., 2018, 30, 1802141 CrossRef PubMed
.
- Y. Liang, C. Li, P. Wang and D. Zhang, Colloids Surf., A, 2021, 631, 127696 CrossRef CAS
.
- T. Zhu, Y. Yuan, Q. Yu, H. Xiang, X. Dai, G. Liu and R. Liao, J. Ind. Eng. Chem., 2023, 127, 454–466 CrossRef CAS
.
- X. Zhu, J. He, Y. Yao, J. Li, K. Li, X. Liu and M. Qu, Surf. Coat. Technol., 2022, 449, 128935 CrossRef CAS
.
- M. M. Hussain, A. Kunwar, M. K. Majeed, Y. Wang, A. Saleem and H. Ma, Adv. Eng. Mater., 2021, 23, 2100266 CrossRef CAS
.
- K. Xing, Z. Li, Z. Wang, S. Qian, J. Feng, C. Gu and J. Tu, Chem. Eng. J., 2021, 418, 129079 CrossRef CAS
.
- B. Gao, Q. Lai, Y. Cao, R. Hu, L. Xiao, Z. Pan, N. Liang, Y. Li, G. Sha, M. Liu, H. Zhou, X. Wu and Y. Zhu, Sci. Adv., 2020, 6, eaba8169 CrossRef CAS PubMed
.
- T. P. Hoar and W. R. Jacob, Nature, 1967, 216, 1299–1301 CrossRef CAS
.
- T. Xiang, H. Ren, Y. Zhang, Y. Qiang, Y. Yang, C. Li, P. Wang and S. Zhang, Mater. Des., 2022, 215, 110450 CrossRef CAS
.
- K. Bae, M. Kang, Y. Shin, E. Choi, Y.-M. Kim and J. Lee, Nanomaterials, 2023, 13, 807 CrossRef CAS PubMed
.
- K. Zhang, S. Xu, J. Tan, X. Li, L. Du, J. Ma and P. Qiu, Colloids Surf., A, 2023, 669, 131495 CrossRef CAS
.
- S. Yan, G.-L. Song, Z. Li, H. Wang, D. Zheng, F. Cao, M. Horynova, M. S. Dargusch and L. Zhou, J. Mater. Sci. Technol., 2018, 34, 421–435 CrossRef CAS
.
- W. Q. Zhu, S. Y. Shao, L. N. Xu, W. Q. Chen, X. Y. Yu, K. M. Tang, Z. H. Tang, F. M. Zhang and J. Qiu, J. Nanobiotechnol., 2019, 17, 55 CrossRef PubMed
.
- S. Kumar, F. Ye, B. Mazinani, S. Dobretsov and J. Dutta, Int. J. Mol. Sci., 2021, 22, 4513 CrossRef CAS PubMed
.
- D. Yue, X. Jiang, H. Yu and D. Sun, Chem. Eng. J., 2023, 463, 142389 CrossRef CAS
.
- Y. Wang, W. Zhao, W. Wu, C. Wang, X. Wu and Q. Xue, ACS Appl. Bio Mater., 2019, 2, 155–162 CrossRef CAS PubMed
.
- T. Yimyai, R. Thiramanas, T. Phakkeeree, S. Iamsaard and D. Crespy, Adv. Funct. Mater., 2021, 31, 2102568 CrossRef CAS
.
- G. Chilkoor, K. Jawaharraj, B. Vemuri, A. Kutana, M. Tripathi, D. Kota, T. Arif, T. Filleter, A. B. Dalton, B. I. Yakobson, M. Meyyappan, M. M. Rahman, P. M. Ajayan and V. Gadhamshetty, ACS Nano, 2020, 14, 14809–14819 CrossRef CAS PubMed
.
- Z. Shi, Y. Ouyang, R. Qiu, S. Hu, Y. Zhang, M. Chen and P. Wang, Prog. Org. Coat., 2019, 131, 49–59 CrossRef CAS
.
- J. Wang, H. Yan, Y. Zhao, D. Wu, H. Yang, X. Yin, R. Tan and T. Zhang, ACS Appl. Mater. Interfaces, 2023, 15, 12305–12314 CrossRef CAS PubMed
.
- M. Ryu, H. Choi, J. Yoon, Y.-N. Choi, S. Lee, H. Kim, M. Chae, J. W. Lee, J. Kang and H. Lee, Chem. Eng. J., 2023, 451, 138657 CrossRef CAS
.
- C. He, X. Zhao, Y. Lei, J. Nie, X. Lu, J. Song, L. Wang, H. Li, F. Liu, Y. Zhang and Q. Niu, Mol. Ther.--Nucleic Acids, 2021, 26, 1401–1417 CrossRef CAS PubMed
.
- Y. Liu, Z. Wang and W. Ke, Corros. Sci., 2014, 80, 169–176 CrossRef CAS
.
- R. I. Revilla, H. Terryn and I. De Graeve, Electrochem. Commun., 2018, 93, 162–165 CrossRef CAS
.
- K. Sakuraba, S. Kitano, D. Kowalski, Y. Aoki and H. Habazaki, ACS Appl. Mater. Interfaces, 2021, 13, 45089–45096 CrossRef CAS PubMed
.
- B. Y. Liu, Z. Zhang, F. Liu, N. Yang, B. Li, P. Chen, Y. Wang, J. H. Peng, J. Li, E. Ma and Z. W. Shan, Nat. Commun., 2022, 13, 1060 CrossRef CAS PubMed
.
- Y. Yan, X. Liu, H. Xiong, J. Zhou, H. Yu, C. Qin and Z. Wang, Nanomaterials, 2020, 10, 947 CrossRef CAS PubMed
.
- S. Leleu, B. Rives, J. Bour, N. Causse and N. Pébère, Electrochim. Acta, 2018, 290, 586–594 CrossRef CAS
.
- W. Yao, J. Qin, Y. Chen, L. Wu, B. Jiang and F. Pan, Mater. Des., 2023, 227, 111721 CrossRef CAS
.
- J. Joo, D. Kim, H.-S. Moon, K. Kim and J. Lee, Appl. Surf. Sci., 2020, 509, 145361 CrossRef CAS
.
- H. Quan, W. Yang, M. Lapeyriere, E. Schaible, R. O. Ritchie and M. A. Meyers, Matter, 2020, 3, 842–863 CrossRef
.
|
This journal is © The Royal Society of Chemistry 2024 |