DOI:
10.1039/D3GC02155F
(Paper)
Green Chem., 2024,
26, 2571-2576
Reductive amination of carboxylic acids under H2 using a heterogeneous Pt–Mo catalyst†
Received
16th June 2023
, Accepted 20th December 2023
First published on 22nd December 2023
Abstract
Reductive amination of carboxylic acids is a green and sustainable method for alkylamine synthesis because carboxylic acids are abundant and accessible carbon sources. Herein, we present an aluminum oxide-supported platinum–molybdenum (Pt–Mo/γ-Al2O3) catalyst that enables mild and selective reductive amination of carboxylic acids under H2. Pt–Mo/γ-Al2O3 exhibited high performance even under ambient H2 pressure. A broad range of carboxylic acids and amines were transformed into alkylamines with good functional group tolerance. Notably, the amination of biomass-derived fatty acids led to the successful formation of the corresponding fatty amines. The catalyst was reusable at least four times without any significant loss in activity. The development of highly active heterogeneous Pt–Mo catalysts with wide applicability and reusability will significantly contribute to sustainable alkylamine production.
Introduction
Alkylamines are an important class of chemicals that can be used as polymers, pharmaceuticals, dyes, agrochemicals, and surfactants.1 To date, there have been numerous reports on alkylamine syntheses based on stoichiometric or catalytic methods, including N-alkylation with organohalides, coupling of aryl halides with amines,2–4 and reductive amination of carbonyl compounds.5–7 Among these methods, the reductive amination of aldehydes or ketones to produce alkylamines is a reliable and widely accepted method in both research and industry. Meanwhile, carboxylic acids have been applied less frequently for reductive amination,8–11 despite their natural abundance and availability.12–14 In the previously reported reductive amination of carboxylic acids, stoichiometric amounts of NaBH415,16 or hydrosilanes17–21 were adopted as reductants (Scheme 1(I)). However, these methods produce large amounts of waste. In contrast, H2 is an ideal reductant because water is the sole co-product. Research efforts have been devoted to developing homogeneous Ru or Co catalysts for the reductive amination of carboxylic acids using H2 (Scheme 1(II)).22–27 Nevertheless, these catalyst systems have serious drawbacks, including difficulty in reusing the catalyst and the requirement of expensive phosphine ligands or additives. To address these problems, heterogeneous catalysts have been employed because of their easy recovery and reuse; however, the reported catalyst systems require high H2 pressures and temperatures (Scheme 1(III)).28–30 To attain green and sustainable reductive amination of carboxylic acids, the development of highly active heterogeneous catalysts is required.
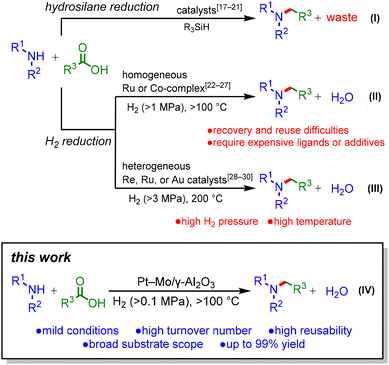 |
| Scheme 1 Catalytic reductive amination of carboxylic acids. | |
Herein, we report the mild reductive amination of carboxylic acids with H2 using a supported Pt–Mo catalyst (Scheme 1(IV)). This study represents the first catalyst for the reductive amination of carboxylic acids that operates under H2 at atmospheric pressure. Furthermore, the Pt–Mo catalyst exhibits a wide substrate scope, including biomass-derived carboxylic acids, and demonstrates high reusability.
Results and discussion
Catalyst performance
Pt–Mo and the other catalysts were prepared using the co-impregnation method (see Table S1† for details). The obtained catalysts were evaluated for the reductive amination of acetic acid (2a) with piperidine (1a) to N-ethylpiperidine (3a) under 2 MPa H2 at 100 °C for 12 h without any pre-reduction step (Table 1, see Table S2† for details). Notably, the aluminum oxide-supported platinum–molybdenum (Pt–Mo/γ-Al2O3) catalyst showed high activity, providing 3a in a 98% yield (entry 1). Catalysts using platinum-group metals (Rh, Pd, and Ru) and metal oxides (Re, W, and V) resulted in low yields of 3a (entries 2–7). The single-metal catalysts (Pt/γ-Al2O3 and Mo/γ-Al2O3) were ineffective in the reductive amination (entries 8 and 9). These results indicated that the co-presence of Pt and Mo is important for efficient reductive amination. The support effect of the Pt–Mo catalysts was also examined (Tables S3 and S4, Fig. S1 and S2† for details); consequently, the γ-Al2O3 and TiO2-supported catalysts showed high yield and selectivity for the reductive amination. The turnover number (TON) value of Pt–Mo/TiO2 surpassed that of Pt–Mo/γ-Al2O3. Then, the reusability of the Pt–Mo/γ-Al2O3 and Pt–Mo/TiO2 catalyst was investigated (Fig. 1 and Table S5†). After the reaction, Pt–Mo catalyst was recovered by centrifugation and reused for the next run. The Pt–Mo/γ-Al2O3 maintained its activity in the 2nd run, but the yield of 3a decreased to 85% in the 6th run. In sharp contrast to Pt–Mo/γ-Al2O3, the 3a yield using Pt–Mo/TiO2 significantly decreased in the 2nd run, clearly representing the superior reusability of Pt–Mo/γ-Al2O3 to Pt–Mo/TiO2. Therefore, Pt–Mo/γ-Al2O3 catalyst was selected as the most suitable catalyst in terms of activity and durability (see Tables S6, S7, and Fig. S3† for details).
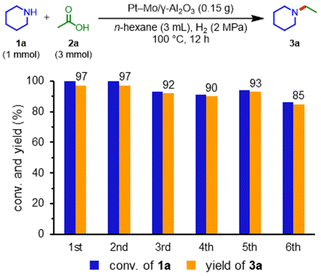 |
| Fig. 1 Reusability of the Pt–Mo/γ-Al2O3 catalyst for reductive amination. | |
Table 1 Reductive amination of acetic acid (2a) with piperidine (1a) to N-ethylpiperidine (3a) over various supported metal catalystsa
The high performance of the Pt–Mo/γ-Al2O3 catalyst was further demonstrated under H2 at atmospheric pressure (Scheme 2a); the Pt–Mo/γ-Al2O3 catalyst promoted the amination of 2a with 1a to afford 3a in a 71% yield, outperforming previously reported catalysts that require 1–6 MPa of H2.22–30 To the best of our knowledge, the Pt–Mo/γ-Al2O3 catalyst is the first example of a catalyst that can promote the reductive amination of carboxylic acid using H2 at atmospheric pressure. The Pt–Mo/γ-Al2O3 catalyst was also applicable to gram-scale amination (Scheme 2b); 1a (1 g) and 2a (2 g) were stirred at 160 °C for 48 h, and 3a was obtained in a 93% isolated yield with a high TON of 363 for the reductive amination of carboxylic acids (Table S8†). Overall, Pt–Mo/γ-Al2O3 showed high activity and good reusability in reductive amination.
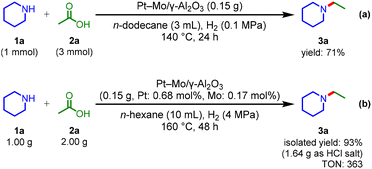 |
| Scheme 2 (a) Pt–Mo/γ-Al2O3 catalyzed reductive amination under H2 at atmospheric pressure. (b) Preparative-scale reductive amination. | |
Substrate scope
Using the Pt–Mo/γ-Al2O3 catalyst, the reductive amination of various carboxylic acids with 1a was investigated (see Scheme 3a and Table S9† for the products distribution). Notably, the Pt–Mo/γ-Al2O3 catalyst was applicable to naturally abundant carboxylic acids (2a–2g and 2k). Short-chain fatty acids obtained from the waste stream, such as 2a, propionic acid (2b), and butyric acid (2c),31 were successfully converted to 3a, N-propyl (3b), and N-butyl piperidine (3c) in 98%, 97%, and 85% yields, respectively. Triglyceride-derived medium- and long-chain fatty acids such as caproic acid (2d), lauric acid (2e), palmitic acid (2f), and stearic acid (2g) reacted well with 1a to generate the corresponding alkylamines in over 93% yield. Carboxylic acids bearing trifluoromethyl (2h), ether (2i and 2j), and heterocycles (2k) were aminated in good-to-moderate yields, but slight cleavage of the C–O bond occurred. The amination of acetic acid-d4 (2l) afforded N-ethyl piperidine with H–D scrambling. The Pt–Mo/γ-Al2O3 catalyst converted relatively bulky carboxylic acids (2m and 2n) to produce the corresponding amines at a high reaction temperature (160 °C). Furthermore, leptacline (3o), which has been reported to be a respiratory stimulant,32 was obtained from cyclohexanecarboxylic acid (2o). 3o was also directly produced from readily available benzoic acid (2p), along with the hydrogenation of the aromatic ring. The tertiary carboxylic acid (2q), with high steric hindrance around the acyl carbonyl carbon, was unfavorable for this catalytic system, and formic acid (2r) and sodium acetate (2s) were hardly aminated.
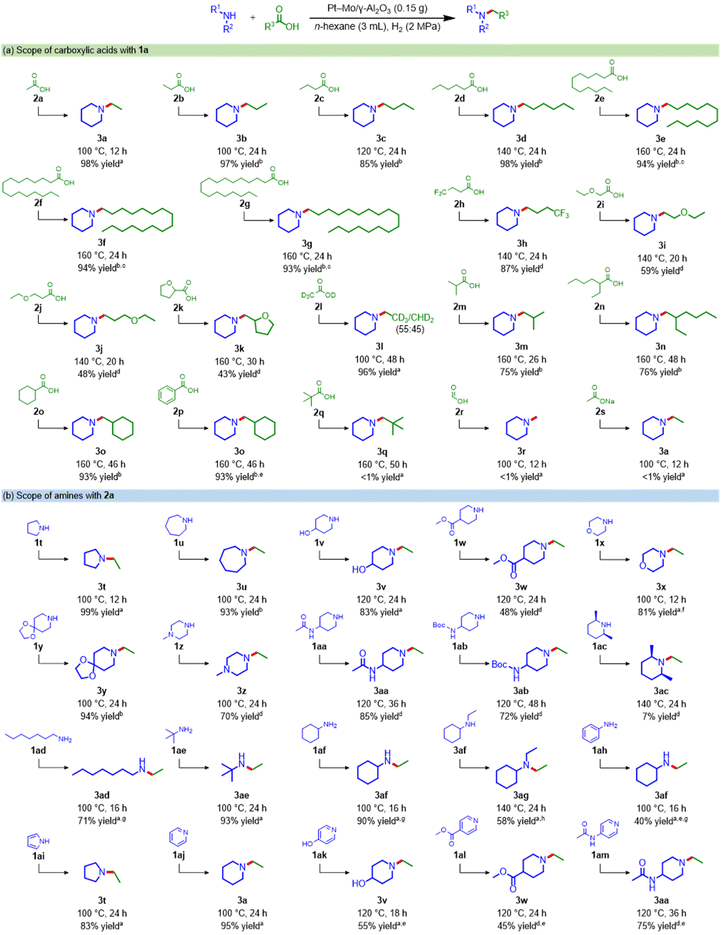 |
| Scheme 3 Reductive amination of various carboxylic acids with amines under H2. Reaction conditions: Pt–Mo/γ-Al2O3 (0.15 g, Pt: 8 mol% and Mo: 2 mol%), amine (1 mmol), carboxylic acid (3 mmol), n-hexane (3 mL), H2 (2 MPa). a GC-FID yield. b Isolated yield as a hydrochloride salt. c Carboxylic acid (1.5 mmol). d 1H NMR yield. e H2 (3 MPa). f H2 (4 MPa). g Carboxylic acid (4 mmol). h Carboxylic acid (5 mmol). | |
Next, we applied the Pt–Mo/γ-Al2O3 catalyst to the reductive amination of 2a using a wide range of amines (Scheme 3b and Table S10†). The Pt–Mo/γ-Al2O3 catalyst exhibited high activity toward various cyclic amines, aliphatic amines, and pyridine derivatives, producing the corresponding alkylamines in high yields. Secondary cyclic amines with different ring sizes (1a, 1t, and 1u) were smoothly alkylated to afford N-ethyl amines in excellent yields. Importantly, various functional groups, including hydroxyl (1v), ester (1w), ether (1x), acetal (1y), amino (1z), amide (1aa), and carbamate (1ab), were tolerated. However, the reaction using a bulky amine, cis-2,6-dimethylpiperidine (1ac), resulted in only 7% yield. The Pt–Mo/γ-Al2O3 catalyst was also applicable to amination with primary amines; heptyl (1ad), tert-butyl (1ae), and cyclohexyl amines (1af) were efficiently transformed into the corresponding secondary amines. 3af was further alkylated to produce N,N-diethyl cyclohexylamine (3ag) in 58% yield. Amination with aniline (1ah) gave 3af in a 40% yield. Heteroaromatics are also potential substrates for synthesizing alicyclic amines; pyrrole (1ai) and pyridine derivatives (1aj–1am) were hydrogenated and converted to their corresponding tertiary alicyclic amines. These results clearly demonstrate the broad applicability of this Pt–Mo/γ-Al2O3 catalyst for the synthesis of a variety of alkylamines from carboxylic acids and amines.
Characterization
To investigate the catalyst structure during the reaction, Pt–Mo/γ-Al2O3 was pre-reduced with H2 under the reaction conditions and characterized (see ESI† for details). Transmission electron microscopy (TEM) images of the reduced Pt–Mo/γ-Al2O3 revealed the presence of nanoparticles (NPs) with a mean diameter of 2.3 nm (Fig. 2a). A high-resolution TEM image of the NPs showed that the measured d-spacing value of the lattice fringe was approximately 0.20 nm, which corresponds to the (200) plane of face-centered cubic Pt NPs (Fig. 2b). High-angle annular dark-field scanning TEM (HAADF-STEM), coupled with energy-dispersive X-ray spectroscopy (EDX), confirmed the dispersion of Pt and Mo (Fig. 2c and d). The local structures of the Pt and Mo species in Pt–Mo/γ-Al2O3 were characterized by X-ray absorption fine structure (XAFS) analysis. The white lines in the Pt L3-edge X-ray absorption near-edge structure (XANES) spectra of fresh and reduced Pt–Mo/γ-Al2O3 were similar to those of PtO2 and Pt foil, respectively, indicating the in situ formation of metallic Pt species (Fig. 2e). In the Mo K-edge XANES spectra, the absorption edge energy of reduced Pt–Mo/γ-Al2O3 shifted toward a lower energy relative to that of fresh Pt–Mo/γ-Al2O3, indicating the partial reduction of Mo6+ (Fig. 2f and S4†). Overall, Pt(0) and partially reduced Mo-oxide species (MoOx) were generated on the γ-Al2O3 surface under reductive amination conditions.
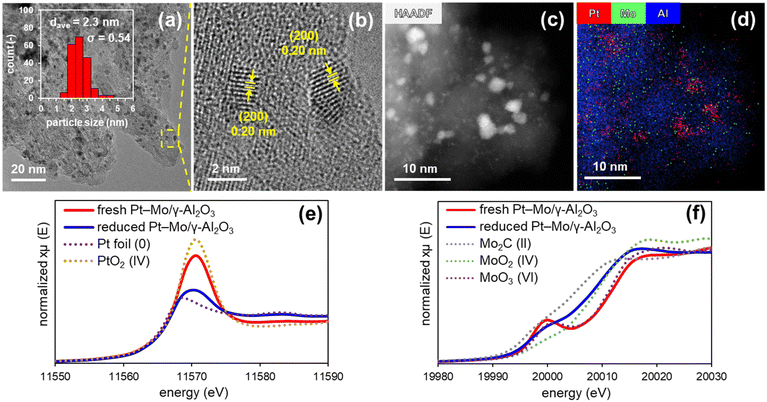 |
| Fig. 2 (a) TEM image and size distribution histogram (inset) of reduced Pt–Mo/γ-Al2O3. (b) High-resolution TEM image of reduced Pt–Mo/γ-Al2O3 showing one-dimensional lattice fringes of the (200) lattice planes in Pt NPs. (c) HAADF-STEM image of reduced Pt–Mo/γ-Al2O3. (d) Composite overlay of the elemental mapping of Pt, Mo, and Al in reduced Pt–Mo/γ-Al2O3. (e) Pt L3-edge XANES spectra of fresh Pt–Mo/γ-Al2O3, reduced Pt–Mo/γ-Al2O3, Pt foil, and PtO2. (f) Mo K-edge XANES spectra of fresh Pt–Mo/γ-Al2O3, reduced Pt–Mo/γ-Al2O3, Mo2C, MoO2, and MoO3. | |
Reaction pathway
In the reductive amination of carboxylic acids, three possible pathways can occur via amide, aldehyde, or alcohol intermediates (Scheme 4).22–29 As shown in Scheme 3b, amide and hydroxyl groups (3aa and 3v) are tolerated, suggesting that amides or alcohols are unlikely to be the major reaction intermediates. Indeed, the hydrogenation of N-propionylpiperidine (4b) in the presence of 2b or the amination of 1-propanol with 1a resulted in low yields of 3b (Scheme S1a and b†). In contrast, the reductive amination of propionaldehyde with 1a afforded 3b in a 70% yield, indicating that the aldehyde is the major intermediate (Scheme S1c and Fig. S5†). Based on the above results, a main reaction pathway is proposed (Scheme S2†). Pt NPs dissociate H2 to reduce MoO3 to MoOx,33,34 and carboxylic acid is adsorbed on MoOx35 and hydrogenated to give an aldehyde intermediate.36 The nucleophilic attack of the amine on the aldehyde, followed by hydrogenation of the generated hemiaminal, affords an alkylamine.37 Partially reduced MoOx serves as a Lewis acid site for carbonyl activation (see Fig. S6 and S7† for details).38–40 Therefore, cooperative catalysis between the Pt NPs and MoOx successfully promotes the reductive amination of carboxylic acids under H2.
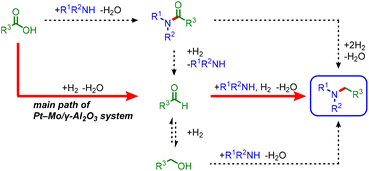 |
| Scheme 4 Possible reaction pathways for the Pt–Mo/γ-Al2O3-catalyzed reductive amination of carboxylic acids. | |
Conclusions
We developed a highly efficient Pt–Mo/γ-Al2O3 catalyst for the reductive amination of carboxylic acids under H2. This is the first catalytic system that achieves the reductive amination of carboxylic acids under ambient H2 pressure. The Pt–Mo/γ-Al2O3 catalyst was applicable to preparative-scale reactions with a high TON value (363). Furthermore, Pt–Mo/γ-Al2O3 was easily separated from the reaction mixture and the reaction could be repeated at least five times while maintaining high activity and selectivity. A wide range of substrates, including biomass-derived fatty acids, and high functional group tolerance were demonstrated, thus offering a simple and clean methodology for the reductive amination of carboxylic acids. We propose that the high catalytic performance of the Pt–Mo/γ-Al2O3 catalyst originates from cooperative catalysis between Pt NPs and MoOx, and this study makes a significant contribution to the development of future sustainable reaction processes.
Author contributions
K. S. and S. Y. designed the experiments, conducted the catalytic activity tests, and characterized the catalysts. K. H. and Y. K. performed the DFT calculations. T. Mit. discussed the experiments and results. T. Miz. directed and conceived the project. K. S. and S. Y. wrote the manuscript with input from all the authors. All the authors commented on the manuscript and approved the final version.
Conflicts of interest
There are no conflicts to declare.
Acknowledgements
This work was supported by a JSPS Research Fellowship for Young Scientists (23KJ1473), JSPS KAKENHI Grant Numbers 20H02523, 21K04776, and 22H02050, and JST PRESTO Grant Number JPMJPR21Q9. This study was partially supported by JST-CREST, Grant Number JPMJCR21L5. A portion of the experimental analysis was supported by the “Advanced Research Infrastructure for Materials and Nanotechnology in Japan (ARIM)” (JPMXP1222HK0062) of the Ministry of Education, Culture, Sports, Science and Technology (MEXT). We thank Dr Toshiaki Ina and Dr Tetsuo Honma (SPring-8) for the XAFS measurements (2021B1945, 2022B1699, 2022B0519, and 2022B0586). This work was the result of using the research equipment shared in the MEXT Project for promoting public utilization of advanced research infrastructure (Program for supporting the construction of core facilities) (Grant Numbers JPMXS0441200022 and JPMXS0441200023).
References
-
S. A. Lawrence, Amines: Synthesis, Properties and Application, Cambridge University Press, Cambridge, 2004 Search PubMed.
- S. V. Ley and A. W. Thomas, Angew. Chem., Int. Ed., 2003, 42, 5400–5449 CrossRef CAS PubMed.
- P. Ruiz-Castillo and S. L. Buchwald, Chem. Rev., 2016, 116, 12564–12649 CrossRef CAS PubMed.
- R. Dorel, C. P. Grugel and A. M. Haydl, Angew. Chem., Int. Ed., 2019, 58, 17118–17129 CrossRef CAS PubMed.
- T. Irrgang and R. Kempe, Chem. Rev., 2020, 120, 9583–9674 CrossRef CAS PubMed.
- K. Murugesan, T. Senthamarai, V. G. Chandrashekhar, K. Natte, P. C. J. Kamer, M. Beller and M. R. V. Jagadeesh, Chem. Soc. Rev., 2020, 49, 6273–6328 RSC.
- M. Sheng, S. Fujita, S. Yamaguchi, J. Yamasaki, K. Nakajima, S. Yamazoe, T. Mizugaki and T. Mitsudome, JACS Au, 2021, 1, 501–507 CrossRef CAS PubMed.
- A. Corma, S. Iborra and A. Velty, Chem. Rev., 2007, 107, 2411–2502 CrossRef CAS PubMed.
- P. Foley, A. Kermanshahi-pour, E. S. Beach and J. B. Zimmerman, Chem. Soc. Rev., 2012, 41, 1499–1518 RSC.
- J. R. Cabrero-Antonino, R. Adam and M. Beller, Angew. Chem., Int. Ed., 2019, 58, 12820–12838 CrossRef CAS PubMed.
- J. Li, C.-Y. Huang and C.-J. Li, Angew. Chem., Int. Ed., 2022, 61, e202112770 CrossRef CAS PubMed.
-
T. Werpy and G. Petersen, Top Value Added Chemicals from Biomass: Volume I – Results of Screening for Potential Candidates from Sugars and Synthesis Gas, 2004, DOI:10.2172/15008859.
- J. J. Bozell and G. R. Petersen, Green Chem., 2010, 12, 539–554 RSC.
- K. Tomishige, M. Yabushita, J. Cao and Y. Nakagawa, Green Chem., 2022, 24, 5652–5690 RSC.
- G. W. Gribble, P. D. Lord, J. Skotnicki, S. E. Dietz, J. T. Eaton and J. L. Johnson, J. Am. Chem. Soc., 1974, 96, 7812–7814 CrossRef CAS.
- P. Marchini, G. Liso and A. Reho, J. Org. Chem., 1975, 40, 3453–3456 CrossRef CAS.
- I. Sorribes, K. Junge and M. Beller, J. Am. Chem. Soc., 2014, 136, 14314–14319 CrossRef CAS PubMed.
- M.-C. Fu, R. Shang, W.-M. Cheng and Y. Fu, Angew. Chem., Int. Ed., 2015, 54, 9042–9046 CrossRef CAS PubMed.
- K. G. Andrews, R. Faizova and R. M. Denton, Nat. Commun., 2017, 8, 15913 CrossRef PubMed.
- E. L. Stoll, T. Tongue, K. G. Andrews, D. Valette, D. J. Hirst and R. M. Denton, Chem. Sci., 2020, 11, 9494–9500 RSC.
- L. Ouyang, R. Miao, Z. Yang and R. Luo, J. Catal., 2023, 418, 283–289 CrossRef CAS.
- A. A. N. Magro, G. R. Eastham and D. J. Cole-Hamilton, Chem. Commun., 2007, 3154–3156 RSC.
- I. Sorribes, J. R. Cabrero-Antonino, C. Vicent, K. Junge and M. Beller, J. Am. Chem. Soc., 2015, 137, 13580–13587 CrossRef CAS PubMed.
- Y. Shi, P. C. J. Kamer, D. J. Cole-Hamilton, M. Harvie, E. F. Baxter, K. J. C. Lim and P. Pogorzelec, Chem. Sci., 2017, 8, 6911–6917 RSC.
- Y. Shi, P. C. J. Kamer and D. J. Cole-Hamilton, Green Chem., 2017, 19, 5460–5466 RSC.
- W. Liu, B. Sahoo, A. Spannenberg, K. Junge and M. Beller, Angew. Chem., Int. Ed., 2018, 57, 11673–11677 CrossRef CAS PubMed.
- B. Emayavaramban, P. Chakraborty and B. Sundararaju, ChemSusChem, 2019, 12, 3089–3093 CrossRef CAS PubMed.
- T. Toyao, S. M. A. H. Siddiki, Y. Morita, T. Kamachi, A. S. Touchy, W. Onodera, K. Kon, S. Furukawa, H. Ariga, K. Asakura, K. Yoshizawa and K. Shimizu, Chem. – Eur. J., 2017, 23, 14848–14859 CrossRef CAS PubMed.
- R. Coeck and D. E. De Vos, Green Chem., 2020, 22, 5105–5114 RSC.
- R. Coeck, J. Meeprasert, G. Li, T. Altantzis, S. Bals, E. A. Pidko and D. E. De Vos, ACS Catal., 2021, 11, 7672–7684 CrossRef CAS.
- M. Atasoy, I. Owusu-Agyeman, E. Plaza and Z. Cetecioglu, Bioresour. Technol., 2018, 268, 773–786 CrossRef CAS PubMed.
- J. R. Boissier, C. Dumont and R. Ratouis, Arch. Int. Pharmacodyn. Ther., 1967, 167, 273–284 CAS.
- K. Murugappan, E. M. Anderson, D. Teschner, T. E. Jones, K. Skorupska and Y. Román-Leshkov, Nat. Catal., 2018, 1, 960–967 CrossRef CAS.
- K. Sakoda, S. Yamaguchi, T. Mitsudome and T. Mizugaki, JACS Au, 2022, 2, 665–672 CrossRef CAS PubMed.
- C. Kaku, S. Suganuma, K. Nakajima, E. Tsuji and N. Katada, ChemCatChem, 2022, 14, e202200399 CrossRef CAS.
- L. A. Gomez, R. Bababrik, M. R. Komarneni, J. Marlowe, T. Salavati-fard, A. D. D'Amico, B. Wang, P. Christopher and S. P. Crossley, ACS Catal., 2022, 12, 6313–6324 CrossRef CAS.
- Y. Nakamura, K. Kon, A. S. Touchy, K. Shimizu and W. Ueda, ChemCatChem, 2015, 7, 921–924 CrossRef CAS.
- A. S. Touchy, S. M. A. H. Siddiki, K. Kon and K. Shimizu, ACS Catal., 2014, 4, 3045–3050 CrossRef CAS.
- T. Mizugaki, Y. Nagatsu, K. Togo, Z. Maeno, T. Mitsudome, K. Jitsukawa and K. Kaneda, Green Chem., 2015, 17, 5136–5139 RSC.
- M. Shetty, E. M. Anderson, W. H. Green and Y. Román-Leshkov, J. Catal., 2019, 376, 248–257 CrossRef CAS.
|
This journal is © The Royal Society of Chemistry 2024 |