DOI:
10.1039/D3TA03482H
(Perspective)
J. Mater. Chem. A, 2023,
11, 22718-22736
Sustainable stretchable batteries for next-generation wearables
Received
13th June 2023
, Accepted 18th September 2023
First published on 20th September 2023
Abstract
Next-generation wearables will interface intimately with the human body either on-skin, implanted or woven into clothing. This requires electrical components that match the mechanical properties of biological tissues – stretchability (up to 60% strain) and softness (Young's modulus of ∼1 kPa to 1 MPa). As wearables become increasingly complex, the energy and mechanical requirements will increase, and an integrated power supply unit such as a soft and stretchable battery is needed to achieve autonomy and wireless operation. However, two key challenges remain for current stretchable battery technology: the mechanical performance (softness and stretchability) and its relation to the size and charge storage capacity (challenge I), and the sustainability and biocompatibility of the battery materials and its components (challenge II). Integrating all these factors into the battery design often leads to a trade-off between the various properties. This perspective will evaluate current strategies for achieving sustainable stretchable batteries and provide a discussion on possible avenues for future research.
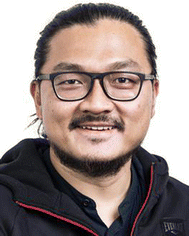 Aiman Rahmanudin | Aiman Rahmanudin obtained an MChem degree in Chemistry with Business and Management from the University of Manchester (UoM) in 2013. He then pursued his PhD in Chemistry at the École Polytechnique Fédérale de Lausanne under the supervision of Professor Kevin Sivula, and upon graduating in 2018, he went back to UoM as a postdoctoral research associate. In 2020, he joined the Laboratory of Organic Electronics at Linköping University after being awarded a Marie Skłodowska-Curie Actions Seal of Excellence research fellowship by the Swedish Governmental Agency for Innovation Systems (VINNOVA). His research is directed towards developing functional materials for soft, stretchable, and biodegradable electronics and energy devices. |
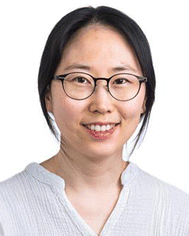 Nara Kim | Nara Kim received a BSc degree in Physics from Korea University in 2009 and a PhD degree in Materials Science and Engineering from the Gwangju Institute of Science and Technology in 2016 (PhD Supervisor: Prof. Kwanghee Lee). She joined the Laboratory of Organic Electronics at Linköping University as a postdoctoral researcher in 2017 and became an Assistant Professor in 2021 after receiving the Swedish Research Council (VR) Starting Grant. Her research interests include the structure–property relationship of conducting polymer composites and their applications in tissue-like energy harvesting/storage devices and bioelectronic devices. |
1 Introduction
Commercial wearable electronics are rigid or flexible smart devices worn either on the body or as clothing to provide functionalities like fitness data tracking and health monitoring, and for communication and entertainment. These devices improve the convenience and quality of human life by providing data connectivity between the user and their environment, especially in the era of digitalisation and big data. On the other hand, next-generation wearables will interface more intimately with the human body either on-skin, implanted or woven into clothing (Fig. 1a).1,2 They will advance healthcare technologies for applications in neuroscience, medical diagnostics and therapy, sensors for environmental and food monitoring and facilitate futuristic consumer electronics such as electronic (e-)skin, e-textile systems, and soft robotics.3–8 However, wearable devices have a variety of form factors and contain multiple electrical components (sensors, integrated circuits, transistors, capacitors, antennas, displays, conductive tracks, etc.) to perform intricate functions, which makes integration a challenge. Recently, significant advances have been made to enable the electronic components in wearables to match the mechanical attributes of biological tissues – stretchability (up to 60% strain) and softness (Young's modulus of ∼1 kPa to 1 MPa).9–11 This can facilitate stable contact between the device and the tissue during dynamic deformation while minimising inflammatory foreign body response and discomfort to the user.12 As wearables become increasingly complex and incorporate wireless communication, so would the demand for energy consumption, and to achieve autonomy, a reliable and continuous power supply unit such as a soft and stretchable battery is needed (Fig. 1a).13
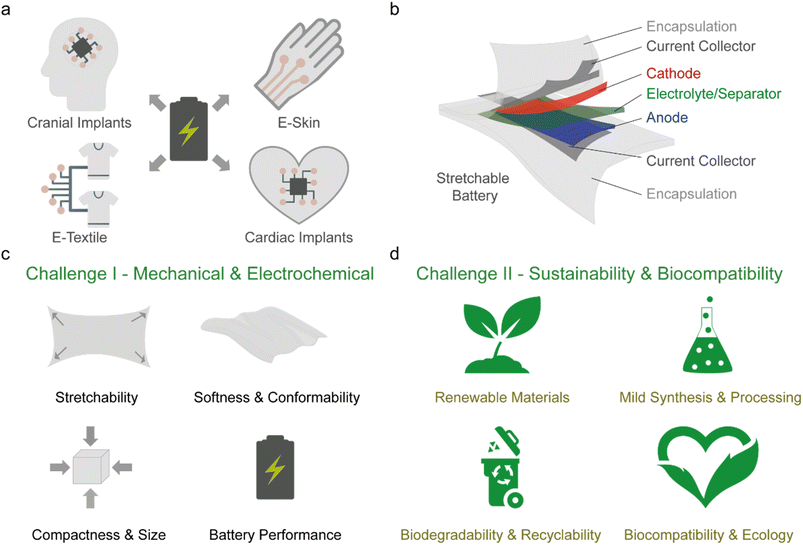 |
| Fig. 1 An overview of the key points discussed in the perspective. Illustrations of (a) the role of the battery in powering the next generation of wearables, (b) a stretchable battery and its respective components and (c and d) the key factors of the challenges discussed. | |
A variety of strategies have been proposed to achieve batteries (and their respective components, Fig. 1b) with stretchability over 50% strain.14–17 However, challenges remain with respect to the form factor, softness, biocompatibility, and sustainability. It is desirable to maximize the active material content of the battery to improve the attainable battery capacity, but this often results in stiffening of the electrodes thereby decreasing softness and stretchability.18 Furthermore, most reports do not consider size as a factor and it has been observed in commercial wearables that as the level of functionality increases, batteries occupy a larger volume within the device.19 This is more pertinent for next-generation wearables as miniaturisation is crucial for integration with the user,20 especially for implantable devices where volumetric space is a limitation.21–23
Another major issue lies in the dependence on unsustainable and non-biocompatible Li-ion battery (LIB) materials and chemistries. Despite their high energy density and long life cycle, active materials based on transition metals rely on finite resources that are mostly non-biodegradable,24,25 and the use of flammable and toxic organic solvent-based electrolytes poses safety risks for on-skin or implanted applications.26–28 This places stricter requirements on the barrier properties of the encapsulation that necessitates thicker layers to ensure hermeticity.29 The utilisation of non-biodegradable petroleum-based elastomers (silicone, styrene block copolymers, etc.) as binders, encapsulation, and separator materials,30,31 along with expensive and finite conductive metal nano-fillers (Au, Ag, etc.) in the current collectors32 contributes to the depletion of finite resources and complicates the disposability or recyclability of the battery after use, which adds to the growing problem of e-waste.33
Ultimately, to realise sustainable and autonomous next generation wearables, the development of soft, stretchable, compact, and biocompatible batteries that uses abundant or renewably sourced materials and are biodegradable or recyclable is crucial. However, integrating all mentioned factors in the battery design often leads to a trade-off between the various properties. Thus far, numerous comprehensive reviews have covered in detail the various strategies of achieving soft and stretchable batteries.14–18 There are also several focused reviews ranging from structural engineering to enable stretchability,34,35 battery systems such as aqueous,26,27,36 metal–air,37 nanowire,38 and microbattery,39 and application centred topics for skin-interfaced and implantable wearables.21,22,29 Here, we will not delve into details of the various strategies as they have been previously covered in review articles. Instead, we will provide our perspective on the challenges facing the current stretchable battery technology, which are the mechanical and electrochemical performance (challenge I) and its sustainability and biocompatibility (challenge II), as illustrated in Fig. 1c and d, respectively, and provide a guideline for future development.
2 Challenge I – mechanical and electrochemical properties
In this section, we will first describe the role of each battery component and the required design parameters (Section 2.1). It will be followed by a discussion on the balance between the dimensions, mechanical properties, and charge storage capacity of the battery (Section 2.2). Next, we made a critical assessment of the conventional metrics used to report the mechanical and electrochemical performances of stretchable batteries (Section 2.3). Based on this, we recommended several metrics that should be reported to reflect the overall battery performance. The discussion will then briefly compare the commonly used strategies to enable stretchability in batteries in Section 2.4 with an in-depth focus on the intrinsic method and its variants (fluid, elastomer, and gel-based) in Section 2.5. Lastly, in Section 2.6, the importance of the encapsulation will be deliberated.
2.1 Stretchable battery components and design parameters
The fundamental mechanism of storing and converting chemical energy to electrical energy is identical for conventional (rigid and flexible) and stretchable batteries, while the material selection and design parameters for the battery components differ. Significant efforts have been made to improve the performance of conventional batteries, with the primary focus placed on the active electrodes, electrolytes and separator components.40–44 To design a stretchable battery, a holistic approach, which considers all components (Fig. 1b), is required as each layer plays a distinct yet interconnected function that simultaneously demonstrates good electrochemical performance while accommodating mechanical stress during operation.
In its simplest form, a battery is an electrochemical cell consisting of two active electrodes (cathode and anode) separated by an electrolyte that facilitates the transport of the dissolved ions.45 The process of storing chemical energy involves electronic and ionic transport (and storage) in the active electrodes. Ions are transported and inserted into the bulk of the electrode, where redox reactions occur via a faradaic electron transfer process within the active material at a given electrochemical potential. The energy is thus stored in the bulk volume of the electrode and its capacity depends on the mass loading of the active material. A physical separator is also typically used to act as an electrical insulation barrier between the active electrodes while permitting ion-conduction within the electrolyte medium. The current collector interfaces with the active electrode and high electrical conductivity are essential to facilitate electrical transport within the electrodes to allow for efficient charging and discharging of the battery. Lastly, the encapsulation is necessary for holding the internal components in place, especially during mechanical deformation, and to protect the cell from internal leakage and gas/liquid permeation to and from the external environment.
The key differentiating material between conventional and stretchable batteries is that the latter typically utilises elastomers to induce stretchability and softness into the various components of the cell. Elastomers are commonly employed as a binder in the active electrode and current collector, as well as in the physical separator and encapsulation components. An essential design parameter is the Young's modulus of the full cell, which must be soft enough to ensure conformability with the surface of the biological tissue. Mechanical adhesion between each component is also crucial to ensure that delamination is avoided when the battery is place under strain.46
2.2 Balance between dimensions, mechanical properties, and energy storage capacity
The physical and mechanical properties of a wearable device such as its weight and size, and softness and stretchability are essential in ensuring that the user feels comfortable under prolonged contact and under dynamic movement. An effective approach to impart these properties is the utilisation of ultrathin form factors, as demonstrated by optoelectronic devices and thin-film transistors,47,48 which follows the relation:
(1) As the thickness (d) decreases, the bending stiffness (k) of an object exponentially decreases based on the equation, k = E × I = E(wd3/12), where E is the Young's modulus, I is the moment of inertia, and w is the width of the object.49
(2) As the thickness decreases, the bending radius (R) of an object that is subjected to a bending strain (ε) decreases linearly according to the equation, R = d/2ε (Fig. 2a).50
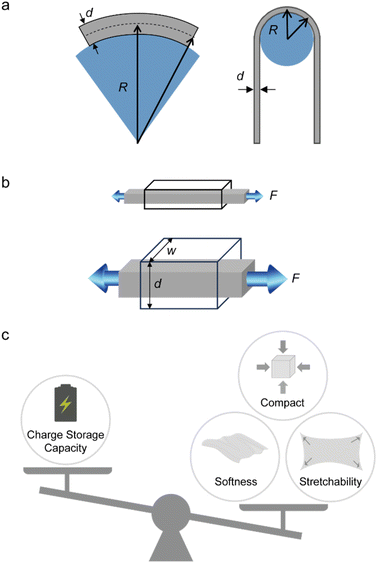 |
| Fig. 2 Illustrations of a rectangular shaped beam that is (a) bent and (b) stretched, where d is the thickness, R is the bending radius, and F is the force needed to deform the object. (c) The trade-off between the charge storage capacity and the mechanical properties of the battery. | |
Therefore, a material can be rigid in the axial direction, but if made thinner it can easily bend. However, such an approach cannot be applied to batteries due to the following relation:
(3) Increasing the mass loading of active material often leads to thicker and stiffer electrodes.
Indeed, the charge storage capacity increases with higher mass loading that leads to a larger volume of the electrode.40,42 Typically, batteries are made thick or with a large area to have enough energy to power the target device. For a relatively thick and large material system to conform on the dynamic and uneven surfaces of the human body, its Young's modulus (softness) and stretchability must closely match the mechanical properties of the surface that it is interfacing based on relation (1) and the following:
(4) As the thickness and the width increase, the force (F) that is needed to deform an object having a certain Young's modulus (E) linearly increases according to the equation, F = σ × A = E × ε × A = E × ε × (d × w), where σ, ε, and A, are the stress, tensile strain, and cross-sectional area of the object (Fig. 2b).
Essentially, there is a trade-off between the volume and the capacity of the electrodes, and the attainable softness and stretchability (Fig. 2c). This is likely due to a large volume percentage of inactive elastomer binder (with respect to the active material loading) that is needed to retain stretchability and softness, which often comes at the cost of reduced energy density.51–53 The difference in the mechanical properties of conventional battery materials, elastomers, and representative biological tissues is shown in Fig. 3. As such, new battery designs or the use of inherently softer materials could balance the dimensions, mechanical properties, and performance of the battery electrode.
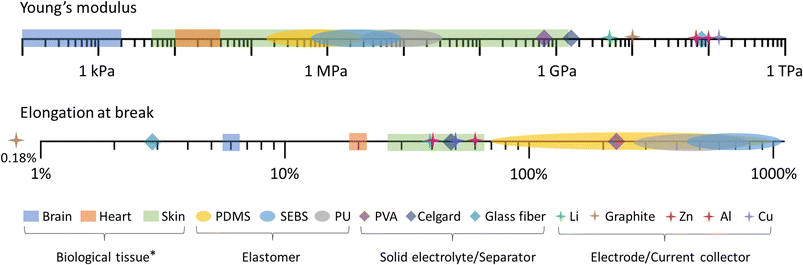 |
| Fig. 3 Young's modulus (top) and elongation at break (bottom) of conventional battery materials and elastomers in comparison with representative biological tissues (*maximum tensile strain in biomechanical environment).9,54–59 | |
2.3 Assessment of mechanical and battery performance metrics
2.3.1 Stretchability.
In Table 1, a summary of representative battery systems using the various strategies to enable stretchability is presented. The reported mechanical properties of stretchable batteries have mainly been focused on the capacity retention of the cell under uniaxial tensile strain. The stretchability reported in Table 1 varies from 20% to 300%, except for the 1300% compressibility of origami batteries.60–65 Reports on stretchable wearable devices typically emphasise on their high stretchability beyond 100% strain.9 However, the range of strain that most body parts experience is less than 20%, except for the joints (e.g., ankle, wrist, finger, knee, and elbow) and face with a maximum strain around 40% to 60%. As such, batteries that can withstand repeated biaxial stretching at 30% strain or more would satisfy the stretchability requirement for most wearable applications (Fig. 4). Elasticity is the ability of the material to return to its original shape after deformation. It is an essential mechanical property that needs to be characterised. In the case of devices that are applied onto growing tissues, viscoplasticity may be desirable and this has been achieved for neural electrodes consisting of stretchable conductors and substrates.66 Such properties can be investigated via cyclic stress–strain measurements, creep and stress relaxation tests, and dynamic mechanical analysis.67,68
Table 1 The representative examples of the various strategies used to enable stretchable batteries. Images reproduced with permission from ref. (see the bottom of table)
Yes at the tips of the cuts; no if soft and stretchable hinges are applied.
Yes for elastic materials such as elastomers and highly crosslinked gels; no for viscous materials such as fluids and poorly crosslinked gels.
|
Schematic
|
|
|
|
|
|
|
|
![[thin space (1/6-em)]](https://www.rsc.org/images/entities/char_2009.gif) |
Strategy
|
Rigid islands with stretchable interconnectors |
Wavy structure |
Origami/folding |
Twisted fibre shape |
Kirigami/cutting |
Porous microstructure |
Intrinsically stretchable materials |
![[thin space (1/6-em)]](https://www.rsc.org/images/entities/char_2009.gif) |
Form factors
|
Dimensionality |
2D |
3D |
3D |
1D |
2D |
2D/3D |
2D or freely adjustable |
Out-of-plane deformation |
Yes |
Yes |
Yes |
— |
Yes or noa |
No |
No |
Stretchable direction |
Biaxial |
Uniaxial |
Predefined direction |
Fibre axis |
Uniaxial or biaxial |
Omnidirectional |
Omnidirectional |
![[thin space (1/6-em)]](https://www.rsc.org/images/entities/char_2009.gif) |
Mechanical properties
|
Stretchability |
300% |
50% |
1300% compressibility |
Bending |
20% |
50% |
30% |
Young's modulus |
67 kPa (estimated value) |
— |
— |
— |
0.75 MPa for alginate separators |
— |
80 kPa |
Elasticity |
Yes |
Yes |
No |
— |
Yes |
Yes |
Yes or nob |
![[thin space (1/6-em)]](https://www.rsc.org/images/entities/char_2009.gif) |
Fabrication
|
Processes |
Spin-casting X2, electron beam evaporation photolithography and etching X3, PDMS curing X2, slurry casting X2, Wet transfer X2, lamination, electrolyte injection, sealing |
Electrospinning PU/PVDF separator, slurry casting X2, calendaring, electrolyte injection, sealing, moulding, PDMS curing |
CNT coating on paper, slurry casting X2, electrolyte soaking, packaging, folding |
Chemical vapor deposition of CNT, active material coating, dry spinning, gel coating, twisting |
Substrate synthesis and curing, laser patterning, slurry casting, gel formation, lamination |
PDMS infiltration into sugar cubes, PDMS curing and sugar washing, GO dip-coating, HI vapor reduction, slurry casting X2, gel formation, lamination, PDMS curing |
Gel formation X2, dehydration, lamination |
![[thin space (1/6-em)]](https://www.rsc.org/images/entities/char_2009.gif) |
Device performance
|
Battery chemistry |
Li ion |
Li ion |
Li ion |
Li ion |
Mg ion |
Na ion |
Li ion |
Cathode |
LCO |
LiCoO2 (LCO) |
LCO |
LiMn2O4 (LMO) |
MoO3 |
VOPO4 |
LMO |
Anode |
Li4Ti5O12 (LTO) |
Graphite |
LTO |
LTO |
Mg foil |
Hard carbon |
LiTi2(PO4)3 (LTP) |
Electrolyte |
EC/DMC/LiClO4–PEO gel |
EC/DEC/LiPF6 liquid |
EC:DMC:DEC/LiPF6 liquid |
SCN/LiTFSI-PEO gel |
CaCl2 alginate gel |
PC/FEC/NaClO4–P(VDF–HFP) gel |
PAM/LiCl hydrogel |
Current collector |
Al/Cu |
Al foil/Cu foil |
CNT-coated paper |
CNT |
Mo foil/Mg foils |
— |
— |
Capacity |
1.1 mA h cm−2 |
2.2 mA h cm−2 |
0.2 mA h cm−2 |
120.5 mA h g−1 |
|
103 mA h g−1 (∼0.6 mA h cm−2) |
82 mA h g−1 (∼0.2 mA h cm−2) |
Energy density |
|
110 W h L−1 |
|
98.6 W h kg−1 |
1.72 mW h cm−2 |
|
|
![[thin space (1/6-em)]](https://www.rsc.org/images/entities/char_2009.gif) |
Ref.
|
64
|
62
|
60
|
79
|
65
|
63
|
61
|
Copyright |
2013 Springer Nature Ltd |
2017 Wiley-VCH GmbH |
2014 Springer Nature Ltd |
2015 Wiley-VCH GmbH |
2022 The authors |
2017 Wiley-VCH GmbH |
2021 Wiley-VCH GmbH |
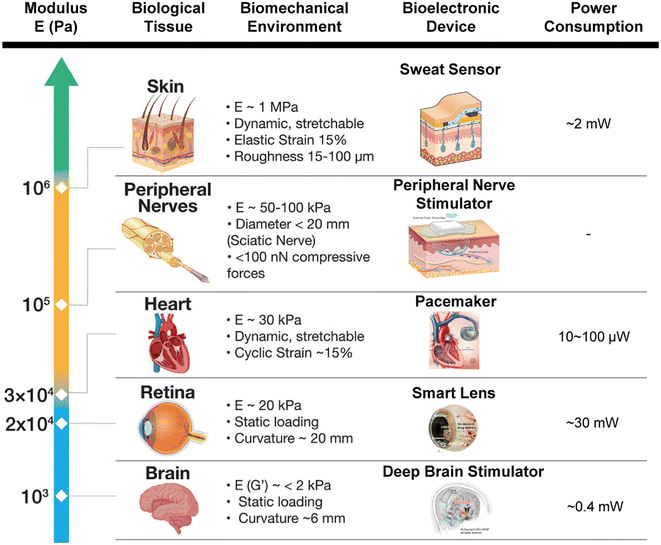 |
| Fig. 4 A table illustrating the relationship between the modulus of the biological tissues and its biomechanical environment with the corresponding bioelectronic devices and their power consumption. This figure was modified from the original figure. Reproduced with permission.3 © 2022 Wiley-VCH GmbH. Images of bioelectronic devices reproduced with permission: sweat sensor,71 peripheral nerve stimulator (courtesy of Bioventus), pacemaker (courtesy of MAYO Foundation), smart lens,72 and deep brain stimulator.73 © 2014 IEEE.71 © 2020 The Authors, some rights reserved; exclusive licensee AAAS.72 © 2021 The Authors, under exclusive licence to Springer Nature America, Inc.73 | |
2.3.2 Softness.
The softness of the battery has often been overlooked and arguably, it is more relevant for the conformability and comfortability of the battery for device integration than high stretchability. It is well known that the mechanical mismatch between the soft tissues (Young's moduli of 1–100 kPa) and rigid devices (1–100 GPa) for implants causes inflammatory foreign body response and discomfort.69 In the case of stretchable batteries, the Young's modulus of a full cell is not commonly reported.61,65,70 It was only recently that an all-hydrogel stretchable battery reported its Young's modulus of the full cell with a tissue-like softness of 80 kPa.61 The battery had adhesive catechol groups in the encapsulation layer that enabled stable attachment and conformability onto a porcine heart, where the battery powered an ultrasoft sensor that detected the change in strain induced by the heartbeat. The report also demonstrated the capacity retention of the battery beyond the standard uniaxial tensile stretching, to include bending at 180°, twisting at 90°, and lap-shearing mechanical tests. These conditions are more realistic compared to only the uniaxial tensile stretching data that are typically reported for stretchable batteries. Furthermore, reporting the overall Young's modulus of the full battery cell along with its dimensions would provide information on the force needed for deformation. These mechanical characterisation methods are essential for assessing meaningful functional information when designing stretchable batteries and for device integration considering the different mechanical properties of various parts of the body and internal organs (Fig. 4).
2.3.3 Electrochemical performance.
Besides the mechanical properties of stretchable batteries, a direct comparison of their electrochemical performance has been difficult since different normalisation metrics (areal, volumetric, and gravimetric) are used to report the battery capacity, and their energy and power densities. There have been efforts towards standardising the reporting of battery data, which are applicable for stretchable batteries.74–76 As shown in Table 1, areal capacities are typically used to report the performance of stretchable batteries (values in parentheses were estimated from the gravimetric capacities and mass loadings). As size and compactness are essential factors for stretchable batteries, normalising the battery performance (capacity, energy, and power densities) by its volume will be useful when comparing different systems and for device scaling and integration. Moreover, reporting of the gravimetric capacity could also be used to elucidate the efficiency of the active material in storing energy in the electrode when compared to its theoretical capacity. This can then be used to optimise the properties of the electrode (access to the active material, film morphology, electrical conductivity, tortuosity for ion diffusion, etc.) to improve the battery performance. Finally, the amount of charge stored (capacity) and the useable energy of a device (energy) should be reported as the latter is often omitted in battery data reporting.
2.4 Strategies to enable stretchable batteries
There are two broad categories, the structural engineering of rigid or flexible materials to impart stretchability, and the use of materials with stretchability that is intrinsic to the bulk of the system (Table 1). The most straightforward structural engineering method is connecting rigid islands of individual battery cells by stretchable serpentine interconnects.64,77 However, the unit size of individual cells is typically on the mm-scale and the majority of the occupied space within the battery is taken up by the inactive interconnects. Another method is fabricating wavy and origami structures. This involves the buckling or folding of the battery and its components to accommodate the release of strain along the folding direction to gain stretchability. The battery has a 3D structure on the mm-scale and deforms in the out-of-plane direction, which might limit the conformability and scaling of the cell dimensions.60,62 Fibre-shaped batteries have unique 1D structures, which consist of forming layered twisted fibres of each component to create a single battery cell and has shown promise for e-textile applications.78,79 The most promising structural engineering method is kirigami patterning via laser ablation.80 It enables both uniaxial and biaxial stretchability on otherwise intrinsically rigid materials and their conformability can be enhanced if they adapt soft and stretchable conductive hinges at the tips of the kirigami cuts.65,81 As for form factors, batteries that possess 2D structures, omnidirectional stretchability and deformation are well suited for conformability onto diverse surfaces.65,81 In this regard, batteries using porous micro-structured electrodes and intrinsically stretchable materials are favourable.61,63 Hybrid approaches using both structural and intrinsic methods have been applied for stretchable batteries with porous microstructure electrodes or kirigami electrodes where the other components such as the gel electrolyte/separator and elastomer substrate/encapsulant are intrinsically stretchable.63,65
2.5 Intrinsically stretchable batteries
Intrinsically stretchable battery designs are attractive due to their versatile form factor, omnidirectional stretchability, and tuneable softness. Such design strategies have the potential for commercialisation as the components can be manufactured using similar slurry casting and lamination processes used by conventional batteries.15,82 There are three variations of the intrinsic method as illustrated in Fig. 5.
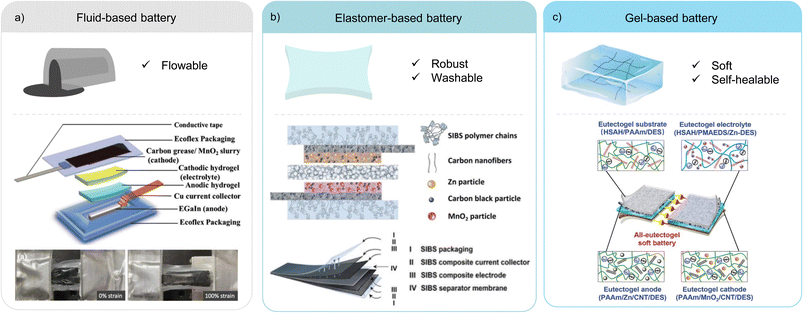 |
| Fig. 5 Representative examples of the three variations of the intrinsic strategy. (a) Fluid-based battery and a schematic showing the battery components (top) and a photograph of the cell before and after stretching to 100% strain (bottom). Reproduced with permission.83 © 2019 Wiley-VCH GmbH. (b) Elastomer-based battery and a schematic of the battery components (top), highlighting the use of a single SIBS elastomer in all components (bottom). Reproduced with permission.93 © 2021 The Authors. Advanced Energy Materials published by Wiley-VCH GmbH. (c) Gel-based battery and a schematic showing the eutectogel used in the encapsulation substrate, the electrolyte, and the anode and cathode. Reproduced with permission.100,102 © 2022 Wiley-VCH GmbH.100 © 2019 The Authors.102 | |
2.5.1 Fluid-based.
Firstly, a fluid is a substance that has no fixed shape and yields easily to external pressure. Fluid-based stretchable batteries exploit this property in the form of composites based on pastes or liquid metal alloys such as eutectic Gallium Indium (EGaIn) as either the active electrode, current collector, or both. Interestingly, the first stretchable battery reported in 2010 was fluid-based. It employed carbon grease as its current collector and a composite paste consisting of carbon black and electrolyte solution mixed with the corresponding Zn or MnO2 particles as the anode and cathode, respectively. As employed in many other stretchable batteries, gel electrolytes and elastomer packaging were used for the battery. Liquid metal-based stretchable batteries are particularly interesting as they have high electrical conductivity and redox activity of the Ga species (Fig. 5a).83–86 EGaIn can be directly employed as either the anode or the current collector in the form of a composite with Ag flakes and an elastomer, styrene-isoprene-styrene (SIS). In the latter case, a composite of melted Ga, carbon black, and SIS formed the anode.84 Owing to the fluid nature of the materials, printing techniques such as screen and 3D printing can be easily employed to fabricate the battery. The main concern is the risk of leakage, which places stricter requirements on the elastomer packaging.
2.5.2 Elastomer-based.
Another variation of the intrinsic method is the dispersion of filler materials within an elastomer matrix to form a stretchable conductive composite. The current collector is typically based on a composite of nano- and micro-structured conductive fillers such as carbon black, carbon nanotubes (CNTs), Ag flakes and nanowires (NWs), and Au nanosheets and nanoparticles with either silicone or styrene copolymer elastomers.70,87–91 In some cases, more than one conductive filler with different aspect ratios is introduced into the elastomeric matrix to improve the electromechanical properties of the current collector during deformation. Similarly, active electrode composites are formed in the same manner but with the addition of redox-active particles along with a carbon based conductive filler.70,87–89 Elastomers are also used as the separator to hold the liquid electrolyte and to electrically insulate the active electrodes, either as nanofiber mats or porous membranes.89,92
A key example of this variation is the use of poly(styrene-isobutylene-styrene) (SIBS) as a single elastomer in all components of a Zn–MnO2 battery (Fig. 5b).93 Composites of the current collectors and active electrodes were prepared by dispersing the conductive fillers and active material particles into a SIBS matrix and the inks were doctor bladed onto a SIBS encapsulation substrate. The porous SIBS separators were fabricated via solvent evaporation-induced phase separation. Due to the thermoplastic nature of SIBS, the components were assembled into a full cell by hot pressing, which created a strong adhesion between the different layers. The low gas and water permeability of the SIBS encapsulation allowed this battery to withstand 39 washing cycles and retain 78% of electrolyte after 523 days. The approach delivered good mechanical robustness, a high reversible specific capacity of 160 mA h g−1 and a capacity retention of 75% after 500 charge and discharge cycles. Interestingly, the volume fraction of the binder used in the active electrode composite was relatively low and the mechanical characterisation for the active electrode was not reported. It suggests that the key material design is to obtain good overall mechanical and electrochemical performance at the cell level, the adhesion and electrical connection between the intrinsically stretchable current collector and the active electrode composites, and a robust separator to electrically insulate the electrodes while permitting ion conduction.
The elastomer method was also applied into designing stretchable microbatteries.39 This unique battery concept is essential in addressing the size constraints for wearable applications, as mentioned earlier in Section 1. To enable this, recent reports utilised aqueous Zn-ion battery chemistries with an intrinsically stretchable current collector composite consisting of CNTs as the conductive filler with an elastomer binder, while the active-electrodes are either electrodeposited94 or slurry cast over the current collector.95 Both methods exploited electrode designs that enable stretchability and compactness at the battery cell level. The latter work by Bai et al.95 used an interdigitated electrode design that harnesses heterogeneous stiffness to create spatially non-uniform strain distributions to selectively reduce the actual strains on individual electrodes, achieving stretchability up to 200% strain, while retaining electrochemical performance (510 μA h cm−2). The former work by Li et al.94 used a concentric circle electrode structure that induced a high electrical field intensity and energy distribution to enhance the electrochemical performance (0.25 mW h cm−2) and enabled stretchability up to 40% strain.
Another interesting elastomer method to maximise the amount of active material is the use of AgNWs.96 They possess bifunctionality by acting as the current collector and the redox-active material for a Ag–Zn battery system. AgNWs can undergo reversible cathodic reaction into Ag oxides while Zn was electrodeposited on the AgNWs as the anode. Intrinsically stretchable composite electrodes were fabricated by embedding AgNWs into the polydimethylsiloxane (PDMS) elastomer matrix, which also acts as the encapsulation layer. The high-aspect ratio of the 1D AgNWs provided an interconnected percolation network and intrinsic stretchability into the composite. The full cell observed an increase in capacity from 0.19 mA h cm−2 at 0% strain to 0.27 mA h cm−2 at 80% strain. The full cell could withstand up to 1000 cycles without obvious capacity degradation at both relaxed and stretched states. However, the PDMS elastomer had limited insulating capability to prevent leakage of the electrolyte under prolonged periods.
Alternatively, organic active materials have shown potential as they are generally softer than their metal-based counterparts. An intrinsically soft and ultrathin stretchable organic-based battery with moderately large output currents (≈40 A g−1 and 400 μA cm−2) has been reported.97 The organic electrodes were based on hybridising CNT nanosheets with hydrophilic redox-active polymers, poly(TEMPO substituted acrylamide) and poly(anthraquinone-substituted ethyleneimine), as the cathode and anode polymers, respectively. The active electrodes were ultrathin (≈100 nm) and had 700% stretchability. In a full cell configuration, a 250 nm thick poly(styrene-butadiene-styrene) encapsulation layer and a 50 μm thick, soft polyethylene glycol electrolyte hydrogel based on a NaCl solution were used. The overall cell had a calculated flexural rigidity of 10−2 nN m, which allowed it to conform easily onto human skin. More importantly, despite the thinness of the active electrode, the battery achieved good current outputs. The utilisation of soft organic-based active materials could potentially lead to the design of thicker active electrodes (to gain higher capacity), while retaining softness.
2.5.3 Gel-based.
Gels are physically or chemically crosslinked polymer networks that can hold large amounts of fluids (water or organic solvents) through intermolecular interactions (e.g. ionic and/or hydrogen bonding) between the components.98 Due to the large amount of fluids within the polymer network, the young's modulus is closer to that of biological tissues and its ionic conductivity is generally higher. Intrinsically stretchable batteries using ion-conducting gels as both the electrolyte matrix and binder for the active electrode have recently gained much attention. Mackanic et al. developed a supramolecular composite containing an ion-conducting soft block copolymer segment, poly(propylene glycol)-pol(ethylene glycol)-poly(propylene glycol), and a strong quadruple hydrogen-bonding motif, 2-ureido-4-pyrimidone, which had high ionic conductivity (1.2 × 10−4 S cm−1) and mechanical toughness (29.3 MJ m−3) when mixed with an ionic liquid, lithium bis(trifluoromethanesulfonyl)imide, a SiO2 ceramic additive and diethylene glycol dimethyl ether as a plasticizer.99 The supramolecular ion conductor was also used as a binder in the active electrode and the LIB full cell could retain 92% of its capacity at 70% strain. In another example, Hong et al. developed a series of ion/organogels based on polyvinylidene difluoride (PVDF).91 When soaked in an ionic liquid carbonate electrolyte, PVDF formed a mass-spring elastomeric network consisting of rigid domains with high crystallinity and swollen amorphous domains with high ion mobility that functioned as the electrolyte component. PVDF was also functionalised with hydroxyl groups to increase the adhesion with the active materials when used as an elastomer binder. In combination with a stretchable current collector and a polyisobutylene (PIB) elastomer encapsulant, an intrinsically stretchable LIB printed on a stretchable fabric was demonstrated.
As described in Section 2.3.2, an all-hydrogel battery was demonstrated.61 In the paper, both LIB and Zn-ion battery (ZIB) chemistries were used. Despite exhibiting excellent softness and conformability, the aqueous system is limited by its narrow electrochemical window and poor temperature tolerance. An interesting approach to solve this issue is the replacement of water with a deep eutectic solvent (DES) to fabricate an all-eutectogel stretchable battery (Fig. 5c).100 DESs have similar characteristics to ionic liquids such as good thermal and chemical stability, a wide electrochemical potential window and low vapor pressure, but are potentially cost-effective and environmentally friendly compared to ionic liquids.101 The all-eutectogel battery used the same DES and a similar polymer network across all the components, which formed a strong dynamic hydrogen bonded network that enabled self-healing of the full cell. The all-gel-based strategy is an effective way to obtain tissue-like softness for stretchable batteries.
2.6 Encapsulation
The barrier properties of the battery encapsulation are an important factor to ensure hermetic seals from moisture and oxygen and minimising internal leakage of the electrolyte. However, stretchable and low-permeability materials do not exist, but in general, the commonly used stretchable elastomers based on butyl rubbers such as SIBS and styrene-ethylene-butadiene-styrene (SEBS) have lower permeability than PDMS and polyurethane (PU) based elastomers.103 Liquid metal alloys such as EGaIn have shown excellent barrier properties when coated as a thin layer over a polydimethylsiloxane (PDMS) elastomer encapsulation for a stretchable electronic device104 and on PU for a stretchable battery.105 Aside from protecting the battery components, the encapsulation plays a key role in determining its degradability or recyclability. It is the first layer that must disintegrate before the internal components can be broken down or be recycled. The challenge is identifying and designing suitable materials that are stable during battery operation and degrade at the end-of-life. This will be discussed further in Section 3.3.
3 Challenge II – sustainability and biocompatibility
Sustainability in conventional battery technologies has been evaluated extensively.106–108 It emphasizes the importance of considering the environmental, ethical, and social aspects associated with the life cycle of the battery in terms of mining of finite raw materials, their manufacturing processes, the battery chemistry used and the disposability or recyclability of the battery components at the end-of-life. A recent perspective by Maria-Magdelana Titirici pointed out that despite the tremendous progress in battery research, its focus has been on attaining high performance while often disregarding the sustainability aspects of the battery life cycle.109 A similar case can be made for stretchable batteries. As discussed in challenge I, a variety of strategies have been developed to enable and improve the mechanical and electrochemical performance of stretchable batteries. However, the prevalence of the use of unsustainable, non-degradable, and non-biocompatible battery materials and chemistries remains.
E-waste generated by current electronic devices accounts for approximately 50 million tons of solid waste and its plastic packaging adds another 150 million tons, with the majority ending up in landfills and incinerators that leach out toxic chemicals or microplastics, which are harmful to the environment.110 The ecological impact is even higher for the battery unit, as it is considered the most hazardous component in an electronic device. While recycling can mitigate the e-waste crisis, the huge variety of battery (and electronic device) configurations complicates the process.24 Furthermore, as the number of wearable devices is projected to reach one trillion by 2035,111 the use of finite resources and problems with e-waste will intensify if no sustainable solution is developed. Additionally, stringent biosafety requirements on the types of battery materials and chemistries are needed for stretchable batteries as they are expected to play a key role in powering wearables that interact closely with the human body.29,112 It is imperative that future stretchable battery design concepts not only focus on high performance but also encompass the sustainability and biocompatibility aspects of the battery system.
3.1 Stretchable transient and biodegradable batteries
A potential solution to the e-waste and biocompatibility issue is the emerging concept of transient and biodegradable batteries.113,114 They have limited life spans and undergo natural degradation processes into bioresorbable products that are safe for the human body and the environment. These batteries are highly suited for applications where long-term battery life is not essential, such as temporary medical implants and disposable sensors. Particularly, in vivo biodegradation of implants avoids the necessity for a secondary surgery to recover the device at the end-of-use, minimising the associated costs and risks of discomfort and harm to the patient. Similarly, the disposal of transient sensors (including the battery) used for environmental monitoring or on-skin application can potentially be compostable and thrown-away safely without harming the environment.8 However, despite being soft, most reported transient batteries have limited mechanical flexibility and stretchability.
In a prototypical transient battery, the active materials and current collectors are primarily based on abundant and degradable metallic electrodes such as Zn, Mg, Fe, W, Mo and Mn, and their oxide counterparts are typically MoO3 and MnO2 (Fig. 6a). These metals have irreversible ductility and are not stretchable, and so far only a couple of examples have integrated stretchability into biodegradable batteries.65,115 In both examples, laser ablation was used to structurally engineer kirigami patterns of the degradable metal component (Mg and Mo) to impart stretchability, while for one of the examples the oxide component (MoO3) was a paste-based composite using an edible plant derived polysaccharide xanthan gum as a binder. Natural polymers such as protein-based gelatin and another polysaccharide alginate were used as a stretchable hydrogel electrolyte separator, which contain biocompatible salts relevant to their battery chemistries. Only one of the examples used a biomass-derived biodegradable synthetic polyester-based elastomer, poly(glycerol-sebacate) (PGS) as the encapsulation,65 while a kirigami patterned cellulose paper was used in another report.115 In both cases, the disintegration of the battery was initiated by physiological fluids at a controlled rate and the degraded products can either be absorbed or excreted by the body's metabolic system. The abovementioned examples highlight a promising material selection and processing method that could pave the way to address the sustainability and biocompatibility challenges in stretchable batteries. In the following sections, we will discuss these points in detail.
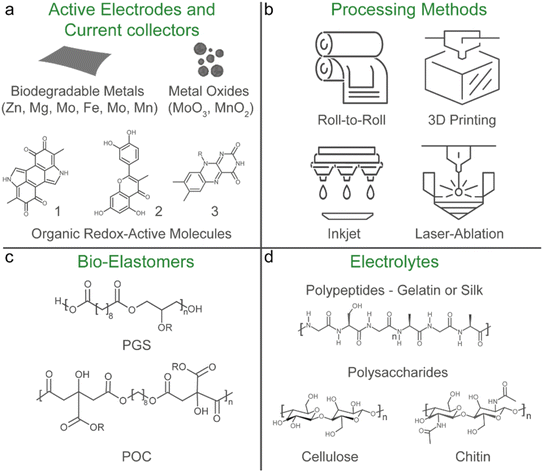 |
| Fig. 6 Illustrations of (a) representative examples of the active electrodes and/or current collectors used in transient and biodegradable batteries – biodegradable metals and metal oxides (top) and organic redox-active materials, Eumelanin (1), Quercetin (2) and Riboflavin (3) (bottom), (b) processing methods suitable for printing of the stretchable battery materials and components, and the chemical structures of (c) the biodegradable elastomers PGS and POC (Section 3.3), and (d) the natural biopolymers used as the hydrogel matrix for the electrolytes (Section 3.5). | |
3.2 Processing methods
Solution-based methods such as spray, gravure and flexographic printing are known for their scalable and large-area roll-to-roll processing and are widely used for commercial rigid or flexible batteries.41,82 They are applicable for stretchable batteries that have low resolution patterns, but for diversification of form factors other processing methods should be employed (Fig. 6b). Additive manufacturing such as 3D printing, inkjet, direct ink writing, and laser-ablation transfer printing are seen as a sustainable energy and material efficient production process that can construct complex multilayer structures with high resolution.116 This method is suited for manufacturing of battery arrays with different form factors or directly integrating the battery into the device.17 They are also applicable for high resolution patterning of stretchable electronic materials and devices.117 The main advantage of such methods is the avoidance of using tedious conventional clean-room lithography fabrication, which requires wet processing steps (such as washing, etching, developing, etc.) which are not environmentally friendly and have a limited scope of compatible substrates. This is particularly important for biodegradable materials as they are generally sensitive to humidity, heat and prone to oxidation, and thus compatible fabrication processes that can be conducted under ambient conditions are favourable.118–120
Laser-ablation techniques are particularly adapted to process a variety of transient organic and inorganic materials as they minimise the risk of degradation of the material through oxidation during fabrication80 and were used to pattern kirigami structures for the stretchable and biodegradable battery materials mentioned in Section 3.1. Recently, this method was also used to engineer intricate 3D micropillar active electrodes on metallic serpentine structures to assemble a stretchable microbattery with a high areal capacities of 2.5 mA h cm−2.121 However, LIB materials and chemistries and a petroleum-based PDMS encapsulation were used, but the potential of this technique to engineer 3D microbattery designs that enable more compact battery structures with higher capacities is preferable for device integration.39,122 Moreover, incorporating lasering techniques into the battery material production line for large-scale roll-to-roll manufacturing are potentially feasible.123
Solution-based methods such as inkjet, direct ink writing, and 3D printing open the possibility of printing of functional inks, gels and pastes that could enable the processing of a wider scope of stretchable battery designs (Section 2.4).37 Promisingly, a fully 3D printed biodegradable flexible supercapacitor has been reported.124 As for stretchable batteries, nano-cellulose was used as a binder to 3D print a Li-ion battery cell with serpentine structures to enable deformable electrodes and the separator.125 The full cell was able to withstand stretching at 50% strain over 50 cycles. Although unsustainable, the printing of fluid-based liquid126 and Li-ion126,127 electrode composites demonstrates the potential of this method as a feasible manufacturing process.84 The main challenge for solution-based methods is the preparation and optimisation of inks for battery components that consist of biodegradable materials and green solvents, an area which has not been widely explored.119,128 Nonetheless, the low energy consumption and ambient conditions required for printing of biodegradable materials could lead to a more environmentally friendly manufacturing process.
3.3 Elastomers (encapsulation and binder)
The elastomer plays a key role in embedding stretchability and softness into the materials and components of the battery, either as a binder in the form of a composite with the relevant filler (conductive and/or redox-active particles) as the current collector and active electrode, as a porous separator membrane or as the encapsulation layer. Moreover, as discussed in Section 2.6, the ability of the encapsulation to breakdown determines the biodegradability of the cell and the recyclability of the internal components. Petroleum-based thermoset elastomers such as PDMS form permanent covalent crosslinked networks that make them insoluble and difficult to disintegrate. On the other hand, thermoplastic elastomers based on styrene block copolymers dissolve easily in certain solvents and were recently shown to facilitate the recycling of the internal components (metal conductive fillers, microchips, etc.) of a soft electronic device when used as the binder and encapsulation materials.129 If appropriate recovery processes are in place, the utilisation of such elastomers can be considered sustainable as it emphasises on a closed-loop circular economy that promotes recycling of not just the elastomer but also the costly internal components likely sourced from finite raw materials.130
For transient batteries, biomass derived synthetic polyesters such as polylactide, poly(lactic-co-glycolic acid), and poly-caprolactone are commonly used as the encapsulation and the separator components.113,114 However, these polymers lack the tensile properties needed for stretchable applications.131 Synthetic biodegradable elastomers (bio-elastomers) typically have higher elongation, better elasticity and a lower Young's modulus, and if the monomers are derived from renewable biomass sources and can degrade into bioresorbable products, it addresses the sustainability and biocompatibility aspects of challenge II.132–134
The most promising bio-elastomers are polyester based poly(1,8-octanediol-co-citrate) (POC) and PGS and their derivatives, which are commonly used for soft tissue engineering (Fig. 6c).135 So far only a handful of examples have used these bio-elastomers for stretchable applications, primarily as the encapsulation substrate for batteries (as discussed in Section 3.1),65 supercapacitors,136 biosensors137 and soft printed circuit boards.138,139 PGS was also used as a dielectric component for a cardiovascular pressure sensor.140 A PGS derivative with photo-cross linkable groups has also been used as a binder with Ag nanowires for a flexible edible battery141 and was used in a 3D printable bioink with Zn metal.142
In conventional battery electrodes, sustainable binder alternatives such as water-processable polysaccharides (cellulose, alginate, chitosan, etc.) and protein-based (gelatin and caseinate) materials have been proposed to replace non-biodegradable and petrochemical-derived fluorinated and styrene rubber polymers.143–145 However, to embed stretchability and softness, a higher volume fraction of the elastomer is typically needed to maintain the mechanical properties of the composite.146 Here, the challenge remains of balancing high active material loading without affecting the mechanical properties of the active electrode. Regardless, synthetic bio-elastomers are potential candidates as the binder material along with natural biopolymers (silk, gelatin and alginate), which have been used to make stretchable electronic conducting composites.147,148 Similarly to conventional elastomers, the barrier properties are also another limitation. Sustainable alternatives to liquid metal-based barriers such as plant-derived hydrophobic coatings that have been used for cellulosic fibres in textiles could be integrated with bio-elastomers.99 It is recommended that future work should focus on evaluating the use of bio-elastomers as stretchable battery materials either as a binder, separator, and encapsulation.
3.4 Active materials and current collectors
As briefly highlighted in Section 3.1, biodegradable metals and metal oxides are commonly employed as the active materials for transient batteries. An advantage is that the metals also function as the current collector due to their relatively high conductivity, which can minimise the number of materials used within a battery cell. They also corrode naturally inside the body at controlled rates without harming human health.149 Similarly, the metal oxides (MoO3 and MnO2) undergo dissolution into their ionic compounds and are biocompatible at certain dosage limits, while the release of the ions can be controlled by the rate of degradation of the bio-elastomer encapsulation.141,150 The most promising sustainable stretchable battery system is Zn–MnO2 since the active components are abundant and biodegradable and it can operate in aqueous electrolytes.27,151,152 Various strategies to enable stretchability have been implemented for this system as highlighted in challenge I (Section 2.5), but non-biodegradable elastomers and materials were utilised for various components of the battery.153–158 A potential way forward would be to incorporate and evaluate the mechanical and electrochemical compatibility of the synthetic and natural bio-elastomers into the components of such battery systems.
These degradable metals are highly abundant, but they are still a finite resource, and the environmental concerns of mining are still problematic.159–161 Furthermore, high temperature synthesis processes for metal oxide-based cathodes are energy intensive and not environmentally friendly.152 Batteries based on organic active materials are poised as a cost-effective and sustainable alternative to their inorganic counterpart, due to their low temperature synthesis and processing, and especially if the precursors are based on renewable biomass feedstock.162–166 A couple of reports have shown the use of organic active materials for stretchable batteries either fully organic167 or as a cathode material paired with a biodegradable metal.168 However, the battery was not fully biodegradable, and the organic active materials were petrochemical based including its passive components. Additionally, organic active electrodes are well-suited for biocompatible alkali (Na+ and K+) and multivalent (Mg2+ and Zn2+) electrolyte systems and can be paired with the relevant biodegradable metal169,170 or be made fully organic.171
Biodegradable batteries using organic active materials have been reported but are not stretchable. Some key examples include the use of a biologically derived Eumelanin molecule (a melanin pigment), which is a quinone based redox-active species, as an anode material along with a MnO2 cathode and a biocompatible aqueous Na-ion electrolyte.172 Similarly, a recent report showed an edible battery made from entirely food ingredients and additives.173 The fully organic battery was based on riboflavin (cathode), which is Vitamin B, and quercetin (anode), which is a naturally occurring flavonoid molecule found in fruits and vegetables. These biologically derived materials have in vitro and in vivo biocompatibility and are biodegradable.174 Edible batteries are particularly interesting for applications such as disposable food monitoring sensors or to power biosensors that monitor gastrointestinal diseases. For these examples, stretchability was not demonstrated but the concept and materials can be applied to stretchable batteries especially since organic materials are generally softer than metal-based materials which could enable truly soft and stretchable components and material composites.
Another worthy mention is the development of stretchable aqueous metal–air batteries for wearables.37 These battery systems do not require water and/or oxygen free environments during assembly and have lenient encapsulation requirements and high operational safety due to the utilisation of oxygen from ambient air, and the required mass and volume of the electrode can be scaled down without sacrificing charge storage capacity. A handful of examples have demonstrated stretchable Zn–Air battery concepts using structural engineering methods of fibre and wavy shaped components with excellent stretchability (>500% strain) and high-power densities of 210.5 mW cm−2,175 and kirigami-patterning of the battery.176
3.5 Electrolytes
Aqueous electrolytes are well suited for stretchable batteries since they are non-flammable, which enhances battery safety, and are environmentally friendly, making them appropriate for greener manufacturing processes and minimising complications upon the disposal of the cell at the end-of-use.27,177 Natural biopolymers (gelatin, silk, cellulose, lignin, and chitosan) have been increasingly implemented for various types of battery chemistries as the hydrogel matrix.178,179 These hydrogels are biodegradable, intrinsically soft, and can easily be made stretchable.180 They can also provide better interfacial contact with the electrode material, which lowers the internal resistance of the cell,181 mitigate issues with dendrite formation of the biodegradable metal anodes,182–186 and dissolution of the cathode materials.187 However, the main drawback of aqueous electrolytes is their narrow electrochemical stability window of 1.23 V. Highly concentrated “water-in-salt” electrolytes can effectively expand this window by reducing the amount of “free” water that can undergo electrolysis.188 However, not much focus has been given to developing biodegradable natural polymer-based water-in-salt electrolyte systems.189 As mentioned in Section 2.5.3, DESs are a potential non-aqueous alternative to extend the electrochemical stability window, while retaining flame retardant and anti-freezing properties.101 It has been suggested that certain DESs are generally biocompatible and show favourable biodegradability.190 However, recent reports have put into question the true sustainability of DESs in terms of their production methods and their environmental and human impact.191–193 Thus it presents an opportunity to develop new sustainable electrolyte systems for stretchable batteries.
In general, the leakage of the battery electrolyte should be avoided at all costs due to the use of toxic electrolytes, or in the cases where it is biocompatible, to prevent the degradation of battery operation. This results in thick encapsulations, which will increase the volume of the battery and the eventual wearable device. To eliminate this issue, designing battery electrodes that can operate with physiological fluids (sweat, blood, serum, gastric fluids, etc.) as the electrolyte would remove the need for stringent encapsulation layers, and if the electrolyte were to leak out it will not be harmful to the human body or the environment. This has been referred to as an “opening-up system”.21 However, operating the battery on purely bodily fluids would limit the capacity due to the low electrolyte concentrations within the body. Nevertheless, a stretchable battery that can operate with bodily fluids using components and materials that are biocompatible and biodegradable would be ideal, but further developments are needed.
4 Conclusion
In conclusion, stretchable battery technology still faces several challenges that need to be addressed to progress the development of next-generation wearables (Fig. 7). We recommend that the evaluation of the mechanical performance should include realistic conditions (biaxial tensile stretch, twisting, bending, and lap-shearing) and the reporting of the cell young's modulus. Based on the biomechanical environment of various parts of the body (Fig. 3 and 4), softness is arguably more important to ensure conformability and easy integration into the wearable device, and batteries that can withstand cyclic stretching at 30% strain or more would satisfy the stretchability requirement for most wearable applications. The two categories, structural engineering and the intrinsic method, offer potential solutions to engineer stretchability into the various battery components and should be implemented according to the requirements of the wearable device application. Combining the common transient battery chemistries (e.g., Zn and Mg ions), softer organic-based redox materials, biocompatible electrolytes, and bio-elastomers such as PGS and POC derivatives could potentially integrate all the key factors (Fig. 1c and d). However, they require further investigation in terms of electrochemical stability and performance. Future research should also focus on developing sustainable processing methods (printing and additive manufacturing) that would suit biodegradable materials, especially the preparation and optimisation of inks for stretchable batteries. It is recommended that to study the impact of the battery on the environment and human health, the biodegradation and biocompatible experiments should follow the standard procedures.194–196 More importantly, performing a life cycle assessment for stretchable batteries including their materials selection, manufacturing processes, and disposal or recyclability at the end-of life would aid in establishing design rules and policies for the commercialisation of the technology.197
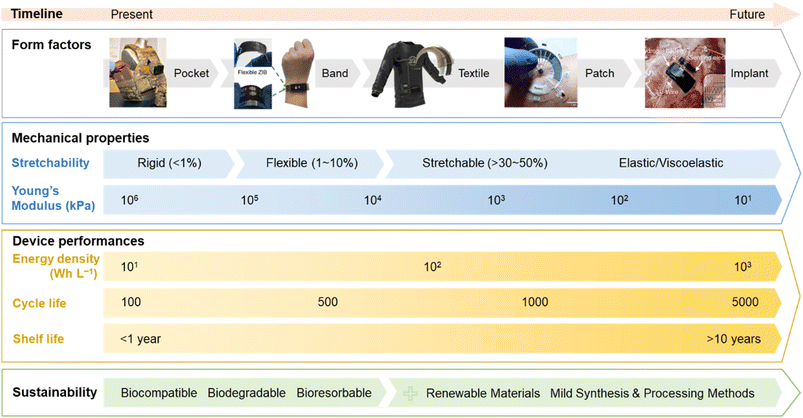 |
| Fig. 7 Illustration of the technology road map for sustainable stretchable batteries for next generation wearables. Images of wearable devices reproduced with permission: conformal batteries in a pocket vest (courtesy of Military & Aerospace Electronics) and a wristband,198 a textile battery (courtesy of Hackster), an epidermal battery,199 and an implantable battery.61 © 2021 American Chemical Society.198 © 2022 Springer Nature Ltd.199 © 2022 Wiley-VCH GmbH.61 | |
Conflicts of interest
There are no conflicts to declare.
Acknowledgements
AR acknowledges the financial support from the Marie Skłodowska-Curie Actions Seal of Excellence Fellowship program from the Swedish Governmental Agency for Innovation Systems, VINNOVA (grant 2021-01668). AR and KT were financially supported by the Knut and Alice Wallenberg Foundation, Linköping University, and industry through the Wallenberg Wood Science Centre. ZK acknowledges the Åforsk foundation for the project “anode free Zn-ion battery (21-130)”. NK acknowledges the Swedish Research Council (Starting Grant No. 2020-05218). NR and KT acknowledge the Swedish Government Strategic Research Area in Materials Science on Advanced Functional Materials at Linköping University (Faculty Grant SFO-Mat-LiU No. 2009-00971). This work was partially supported by the Wallenberg Initiative Materials Science for Sustainability (WISE) funded by the Knut and Alice Wallenberg Foundation.
Notes and references
- M. J. Cima, Nat. Biotechnol., 2014, 32, 642–643 CrossRef CAS PubMed.
- E. Gibney, Nature, 2015, 528, 26–28 CrossRef CAS PubMed.
- G. Balakrishnan, J. Song, C. Mou and C. J. Bettinger, Adv. Mater., 2022, 34, 2106787 CrossRef CAS PubMed.
- J. Y. Oh and Z. Bao, Adv. Sci., 2019, 6, 1900186 CrossRef PubMed.
- T. R. Ray, J. Choi, A. J. Bandodkar, S. Krishnan, P. Gutruf, L. Tian, R. Ghaffari and J. A. Rogers, Chem. Rev., 2019, 119, 5461–5533 CrossRef CAS PubMed.
- H.-R. Lim, H. S. Kim, R. Qazi, Y.-T. Kwon, J.-W. Jeong and W.-H. Yeo, Adv. Mater., 2019, 1901924 Search PubMed.
- J. C. Yang, J. Mun, S. Y. Kwon, S. Park, Z. Bao and S. Park, Adv. Mater., 2019, 31, 1904765 CrossRef CAS PubMed.
- C. Dincer, R. Bruch, E. Costa-Rama, M. T. Fernández-Abedul, A. Merkoçi, A. Manz, G. A. Urban and F. Güder, Adv. Mater., 2019, 1806739 CrossRef PubMed.
- S. Liu, Y. Rao, H. Jang, P. Tan and N. Lu, Matter, 2022, 5, 1104–1136 CrossRef CAS.
- J. M. R. Tan, Y. Farraj, A. Kamyshny and S. Magdassi, ACS Appl. Electron. Mater., 2023, 5, 1376–1393 CrossRef CAS.
- D. W. Kim, M. Kong and U. Jeong, Adv. Sci., 2021, 8, 2004170 CrossRef PubMed.
- O. Veiseh, J. C. Doloff, M. Ma, A. J. Vegas, H. H. Tam, A. R. Bader, J. Li, E. Langan, J. Wyckoff, W. S. Loo, S. Jhunjhunwala, A. Chiu, S. Siebert, K. Tang, J. Hollister-Lock, S. Aresta-Dasilva, M. Bochenek, J. Mendoza-Elias, Y. Wang, M. Qi, D. M. Lavin, M. Chen, N. Dholakia, R. Thakrar, I. Lacík, G. C. Weir, J. Oberholzer, D. L. Greiner, R. Langer and D. G. Anderson, Nat. Mater., 2015, 14, 643–651 CrossRef CAS PubMed.
- Y. Luo, M. R. Abidian, J.-H. Ahn, D. Akinwande, A. M. Andrews, M. Antonietti, Z. Bao, M. Berggren, C. A. Berkey, C. J. Bettinger, J. Chen, P. Chen, W. Cheng, X. Cheng, S.-J. Choi, A. Chortos, C. Dagdeviren, R. H. Dauskardt, C.-A. Di, M. D. Dickey, X. Duan, A. Facchetti, Z. Fan, Y. Fang, J. Feng, X. Feng, H. Gao, W. Gao, X. Gong, C. F. Guo, X. Guo, M. C. Hartel, Z. He, J. S. Ho, Y. Hu, Q. Huang, Y. Huang, F. Huo, M. M. Hussain, A. Javey, U. Jeong, C. Jiang, X. Jiang, J. Kang, D. Karnaushenko, A. Khademhosseini, D.-H. Kim, I.-D. Kim, D. Kireev, L. Kong, C. Lee, N.-E. Lee, P. S. Lee, T.-W. Lee, F. Li, J. Li, C. Liang, C. T. Lim, Y. Lin, D. J. Lipomi, J. Liu, K. Liu, N. Liu, R. Liu, Y. Liu, Y. Liu, Z. Liu, Z. Liu, X. J. Loh, N. Lu, Z. Lv, S. Magdassi, G. G. Malliaras, N. Matsuhisa, A. Nathan, S. Niu, J. Pan, C. Pang, Q. Pei, H. Peng, D. Qi, H. Ren, J. A. Rogers, A. Rowe, O. G. Schmidt, T. Sekitani, D.-G. Seo, G. Shen, X. Sheng, Q. Shi, T. Someya, Y. Song, E. Stavrinidou, M. Su, X. Sun, K. Takei, X.-M. Tao, B. C. K. Tee, A. V.-Y. Thean, T. Q. Trung, C. Wan, H. Wang, J. Wang, M. Wang, S. Wang, T. Wang, Z. L. Wang, P. S. Weiss, H. Wen, S. Xu, T. Xu, H. Yan, X. Yan, H. Yang, L. Yang, S. Yang, L. Yin, C. Yu, G. Yu, J. Yu, S.-H. Yu, X. Yu, E. Zamburg, H. Zhang, X. Zhang, X. Zhang, X. Zhang, Y. Zhang, Y. Zhang, S. Zhao, X. Zhao, Y. Zheng, Y.-Q. Zheng, Z. Zheng, T. Zhou, B. Zhu, M. Zhu, R. Zhu, Y. Zhu, Y. Zhu, G. Zou and X. Chen, ACS Nano, 2023, 17(6), 5211–5295 CrossRef CAS PubMed.
- Q. Yang, A. Chen, C. Li, G. Zou, H. Li and C. Zhi, Matter, 2021, 4, 3146–3160 CrossRef CAS.
- D. G. Mackanic, T.-H. Chang, Z. Huang, Y. Cui and Z. Bao, Chem. Soc. Rev., 2020, 49, 4466–4495 RSC.
- W. J. Song, S. Yoo, G. Song, S. Lee, M. Kong, J. Rim, U. Jeong and S. Park, Batteries Supercaps, 2019, 2, 181–199 CrossRef.
- K.-H. Choi, D. B. Ahn and S.-Y. Lee, ACS Energy Lett., 2018, 3, 220–236 CrossRef CAS.
- D. G. Mackanic, M. Kao and Z. Bao, Adv. Energy Mater., 2020, 10, 2001424 CrossRef CAS.
- C. L. Cobb and C. C. Ho, Electrochem. Soc. Interface, 2016, 25, 75 CrossRef CAS.
- H. C. Ates, P. Q. Nguyen, L. Gonzalez-Macia, E. Morales-Narváez, F. Güder, J. J. Collins and C. Dincer, Nat. Rev. Mater., 2022, 7, 887–907 CrossRef PubMed.
- M. Yu, Y. Peng, X. Wang and F. Ran, Adv. Funct. Mater., 2023, 33, 2301877 CrossRef CAS.
- B. Yan, Y. Zhao and H. Peng, Small Methods, 2023, 2300501 CrossRef PubMed.
- H. Sheng, X. Zhang, J. Liang, M. Shao, E. Xie, C. Yu and W. Lan, Adv. Funct. Mater., 2021, 10, 2100199 CAS.
- J. Neumann, M. Petranikova, M. Meeus, J. D. Gamarra, R. Younesi, M. Winter and S. Nowak, Adv. Energy Mater., 2022, 12, 2102917 CrossRef CAS.
- J. F. Peters, M. Baumann, B. Zimmermann, J. Braun and M. Weil, Renewable Sustainable Energy Rev., 2017, 67, 491–506 CrossRef CAS.
- J. Li, P. Ruan, X. Chen, S. Lei, B. Lu, Z. Chen and J. Zhou, ACS Energy Lett., 2023, 8, 2904–2918 CrossRef CAS.
- W.-J. Song, S. Lee, G. Song and S. Park, ACS Energy Lett., 2019, 4, 177–186 CrossRef CAS.
- K. Liu, Y. Liu, D. Lin, A. Pei and Y. Cui, Sci. Adv., 2018, 4, eaas9820 CrossRef PubMed.
- J. Li, J. Zhao and J. A. Rogers, Acc. Chem. Res., 2019, 52, 53–62 CrossRef CAS PubMed.
- D. Qi, K. Zhang, G. Tian, B. Jiang and Y. Huang, Adv. Mater., 2021, 33, 2003155 CrossRef CAS PubMed.
- I. You, M. Kong and U. Jeong, Acc. Chem. Res., 2019, 52, 63–72 CrossRef CAS PubMed.
- N. Matsuhisa, X. Chen, Z. Bao and T. Someya, Chem. Soc. Rev., 2019, 48, 2946–2966 RSC.
- A. K. Awasthi, J. Li, L. Koh and O. A. Ogunseitan, Nat. Electron., 2019, 2, 86–89 CrossRef.
- Y. Sun and W. G. Chong, Mater. Horiz., 2023, 10, 2373–2397 RSC.
- X. Xia, J. Yang, Y. Liu, J. Zhang, J. Shang, B. Liu, S. Li and W. Li, Adv. Sci., 2023, 10, 2204875 CrossRef CAS PubMed.
- X. Wang, T. He, J. Cheng, Y. Wu and B. Wang, Small Methods, 2023, 2300591 CrossRef PubMed.
- H. Li, J. Chen and J. Fang, Adv. Mater. Technol., 2023, 8, 2201762 CrossRef CAS.
- J. Jung, H. Cho, R. Yuksel, D. Kim, H. Lee, J. Kwon, P. Lee, J. Yeo, S. Hong, H. E. Unalan, S. Han and S. H. Ko, Nanoscale, 2019, 11, 20356–20378 RSC.
- M. Nasreldin, S. Mulatier, R. Delattre, M. Ramuz and T. Djenizian, Adv. Mater. Technol., 2020, 5, 2000412 CrossRef.
- Y. Kuang, C. Chen, D. Kirsch and L. Hu, Adv. Energy Mater., 2019, 9, 1901457 CrossRef.
- J. Li, J. Fleetwood, W. B. Hawley and W. Kays, Chem. Rev., 2022, 122, 903–956 CrossRef CAS PubMed.
- H. Sun, J. Zhu, D. Baumann, L. Peng, Y. Xu, I. Shakir, Y. Huang and X. Duan, Nat. Rev. Mater., 2019, 4, 45–60 CrossRef.
- P. Zhu, P. R. Slater and E. Kendrick, Mater. Des., 2022, 223, 111208 CrossRef CAS.
- A. Kraytsberg and Y. Ein-Eli, Adv. Energy Mater., 2016, 6, 1600655 CrossRef.
-
F. Nobili and R. Marassi, Fundamental Princicples of Battery Electrochemistry, in Encyclopedia of Electrochemistry, ed. A. J. Bard, 2020 Search PubMed.
- L. A. Wehner, N. Mittal, T. Liu and M. Niederberger, ACS Cent. Sci., 2021, 7, 231–244 CrossRef CAS PubMed.
- T. Yokota, P. Zalar, M. Kaltenbrunner, H. Jinno, N. Matsuhisa, H. Kitanosako, Y. Tachibana, W. Yukita, M. Koizumi and T. Someya, Sci. Adv., 2016, 2, e1501856 CrossRef PubMed.
- M. Kaltenbrunner, T. Sekitani, J. Reeder, T. Yokota, K. Kuribara, T. Tokuhara, M. Drack, R. Schwödiauer, I. Graz, S. Bauer-Gogonea, S. Bauer and T. Someya, Nature, 2013, 499, 458–463 CrossRef CAS PubMed.
- T. B. Abbott, Mater. Sci. Forum, 2009, 618–619, 3–6 Search PubMed.
- Z. Suo, E. Y. Ma, H. Gleskova and S. Wagner, Appl. Phys. Lett., 1999, 74, 1177–1179 CrossRef CAS.
- N. Matsuhisa, M. Kaltenbrunner, T. Yokota, H. Jinno, K. Kuribara, T. Sekitani and T. Someya, Nat. Commun., 2015, 6, 7461 CrossRef CAS PubMed.
- S. Kim, S. Choi, E. Oh, J. Byun, H. Kim, B. Lee, S. Lee and Y. Hong, Sci. Rep., 2016, 6, 34632 CrossRef PubMed.
-
J. Liu and L. Zhang, in Progress in Rubber Nanocomposites, ed. S. Thomas and H. J. Maria, Woodhead Publishing, 2017, pp. 523–555 Search PubMed.
- J. Shim, H. J. Kim, B. G. Kim, Y. S. Kim, D.-G. Kim and J.-C. Lee, Energy Environ. Sci., 2017, 10, 1911–1916 RSC.
-
A. J. Gallagher, A. N. Annaidh, K. Bruyère, M. Otténio, H. Xie and M. D. Gilchrist, IRCOBI Conf., 2012, vol. 40, p. 494 Search PubMed.
- N. Jain, V. K. Singh and S. Chauhan, J. Mech. Behav. Mater., 2017, 26, 213–222 CAS.
-
AZO materials, https://www.azom.com, accessed September 2023 Search PubMed.
-
Hydrogenated Styrenic Thermoplastic Elastomer (SEBS), https://www.akelastomer.com/en/products, accessed September 2023 Search PubMed.
-
Physical Properties of Polyurethane, https://americanurethane.com/urethane-polyurethane-properties, accessed September 2023 Search PubMed.
- Z. Song, T. Ma, R. Tang, Q. Cheng, X. Wang, D. Krishnaraju, R. Panat, C. K. Chan, H. Yu and H. Jiang, Nat. Commun., 2014, 5, 3140 CrossRef PubMed.
- T. Ye, J. Wang, Y. Jiao, L. Li, E. He, L. Wang, Y. Li, Y. Yun, D. Li, J. Lu, H. Chen, Q. Li, F. Li, R. Gao, H. Peng and Y. Zhang, Adv. Mater., 2022, 34, 2105120 CrossRef CAS PubMed.
- W. Liu, J. Chen, Z. Chen, K. Liu, G. Zhou, Y. Sun, M.-S. Song, Z. Bao and Y. Cui, Adv. Energy Mater., 2017, 7, 1701076 CrossRef.
- H. Li, Y. Ding, H. Ha, Y. Shi, L. Peng, X. Zhang, C. J. Ellison and G. Yu, Adv. Mater., 2017, 29, 1700898 CrossRef PubMed.
- S. Xu, Y. Zhang, J. Cho, J. Lee, X. Huang, L. Jia, J. A. Fan, Y. Su, J. Su, H. Zhang, H. Cheng, B. Lu, C. Yu, C. Chuang, T.-i. Kim, T. Song, K. Shigeta, S. Kang, C. Dagdeviren, I. Petrov, P. V. Braun, Y. Huang, U. Paik and J. A. Rogers, Nat. Commun., 2013, 4, 1543 CrossRef PubMed.
- M. Karami-Mosammam, D. Danninger, D. Schiller and M. Kaltenbrunner, Adv. Mater., 2022, 34, 2204457 CrossRef CAS PubMed.
- Y. Liu, J. Li, S. Song, J. Kang, Y. Tsao, S. Chen, V. Mottini, K. McConnell, W. Xu, Y.-Q. Zheng, J. B. H. Tok, P. M. George and Z. Bao, Nat. Biotechnol., 2020, 38, 1031–1036 CrossRef CAS PubMed.
- D. S. Jones, Int. J. Pharm., 1999, 179, 167–178 CrossRef CAS PubMed.
- J.-Y. Sun, X. Zhao, W. R. K. Illeperuma, O. Chaudhuri, K. H. Oh, D. J. Mooney, J. J. Vlassak and Z. Suo, Nature, 2012, 489, 133–136 CrossRef CAS PubMed.
- S. P. Lacour, G. Courtine and J. Guck, Nat. Rev. Mater., 2016, 1, 16063 CrossRef CAS.
- M. Gu, W.-J. Song, J. Hong, S. Y. Kim, T. J. Shin, N. A. Kotov, S. Park and B.-S. Kim, Sci. Adv., 2019, 5, eaaw1879 CrossRef CAS PubMed.
- J. Heikenfeld, IEEE Spectrum, 2014, 51, 46–63 Search PubMed.
- D. H. Keum, S.-K. Kim, J. Koo, G.-H. Lee, C. Jeon, J. W. Mok, B. H. Mun, K. J. Lee, E. Kamrani, C.-K. Joo, S. Shin, J.-Y. Sim, D. Myung, S. H. Yun, Z. Bao and S. K. Hahn, Sci. Adv., 2020, 6, eaba3252 CrossRef CAS PubMed.
- K. W. Scangos, A. N. Khambhati, P. M. Daly, G. S. Makhoul, L. P. Sugrue, H. Zamanian, T. X. Liu, V. R. Rao, K. K. Sellers, H. E. Dawes, P. A. Starr, A. D. Krystal and E. F. Chang, Nat. Med., 2021, 27, 1696–1700 CrossRef CAS PubMed.
- T. S. Mathis, N. Kurra, X. Wang, D. Pinto, P. Simon and Y. Gogotsi, Adv. Energy Mater., 2019, 9, 1902007 CrossRef CAS.
- A. Noori, M. F. El-Kady, M. S. Rahmanifar, R. B. Kaner and M. F. Mousavi, Chem. Soc. Rev., 2019, 48, 1272–1341 RSC.
-
Battery Data Reporting Checklist, https://onlinelibrary.wiley.com/pb-assets/assets/vch/msp/author_guidelines/data_reporting_checklist/Battery_Data_Reporting_Checklist-1643963769483.pdf, accessed September 2023 Search PubMed.
- S. Choi, S. I. Han, D. Jung, H. J. Hwang, C. Lim, S. Bae, O. K. Park, C. M. Tschabrunn, M. Lee, S. Y. Bae, J. W. Yu, J. H. Ryu, S.-W. Lee, K. Park, P. M. Kang, W. B. Lee, R. Nezafat, T. Hyeon and D.-H. Kim, Nat. Nanotechnol., 2018, 13, 1048–1056 CrossRef CAS PubMed.
- F. Mo, G. Liang, Z. Huang, H. Li, D. Wang and C. Zhi, Adv. Mater., 2020, 32, 1902151 CrossRef CAS PubMed.
- Y. Zhang, Y. Zhao, X. Cheng, W. Weng, J. Ren, X. Fang, Y. Jiang, P. Chen, Z. Zhang, Y. Wang and H. Peng, Angew. Chem., Int. Ed., 2015, 54, 11177–11182 CrossRef CAS PubMed.
- Q. Yang, Z. Hu, M.-H. Seo, Y. Xu, Y. Yan, Y.-H. Hsu, J. Berkovich, K. Lee, T.-L. Liu, S. McDonald, H. Nie, H. Oh, M. Wu, J.-T. Kim, S. A. Miller, Y. Jia, S. Butun, W. Bai, H. Guo, J. Choi, A. Banks, W. Z. Ray, Y. Kozorovitskiy, M. L. Becker, M. A. Pet, M. R. MacEwan, J.-K. Chang, H. Wang, Y. Huang and J. A. Rogers, Nat. Commun., 2022, 13, 6518 CrossRef CAS PubMed.
- S. Jiang, J. Liu, W. Xiong, Z. Yang, L. Yin, K. Li and Y. Huang, Adv. Mater., 2022, 34, 2204091 CrossRef CAS PubMed.
- A. Kraytsberg and Y. Ein-Eli, Adv. Energy Mater., 2016, 6, 1600655 CrossRef.
- D. Liu, L. Su, J. Liao, B. Reeja-Jayan and C. Majidi, Adv. Energy Mater., 2019, 9, 1902798 CrossRef CAS.
- G. Costa, P. A. Lopes, A. L. Sanati, A. F. Silva, M. C. Freitas, A. T. de Almeida and M. Tavakoli, Adv. Funct. Mater., 2022, 32, 2113232 CrossRef CAS.
- G. Liu, J. Y. Kim, M. Wang, J.-Y. Woo, L. Wang, D. Zou and J. K. Lee, Adv. Energy Mater., 2018, 8, 1703652 CrossRef.
- S. Park, G. Thangavel, K. Parida, S. Li and P. S. Lee, Adv. Mater., 2019, 31, 1805536 CrossRef PubMed.
- W.-J. Song, J. Park, D. H. Kim, S. Bae, M.-J. Kwak, M. Shin, S. Kim, S. Choi, J.-H. Jang, T. J. Shin, S. Y. Kim, K. Seo and S. Park, Adv. Energy Mater., 2018, 8, 1702478 CrossRef.
- X. Chen, H. Huang, L. Pan, T. Liu and M. Niederberger, Adv. Mater., 2019, 31, 1904648 CrossRef CAS PubMed.
- W.-J. Song, M. Kong, S. Cho, S. Lee, J. Kwon, H. B. Son, J. H. Song, D.-G. Lee, G. Song, S.-Y. Lee, S. Jung, S. Park and U. Jeong, Adv. Funct. Mater., 2020, 30, 2003608 CrossRef CAS.
- A. Zhou, R. Sim, Y. Luo and X. Gao, J. Mater. Chem. A, 2017, 5, 21550–21559 RSC.
- S. Y. Hong, S. M. Jee, Y. Ko, J. Cho, K. H. Lee, B. Yeom, H. Kim and J. G. Son, ACS Nano, 2022, 16, 2271–2281 CrossRef CAS PubMed.
- M. Shin, W.-J. Song, H. B. Son, S. Yoo, S. Kim, G. Song, N.-S. Choi and S. Park, Adv. Energy Mater., 2018, 8, 1801025 CrossRef.
- T. N. Nguyen, B. Iranpour, E. Cheng and J. D. W. Madden, Adv. Energy Mater., 2022, 12, 2103148 CrossRef CAS.
- R. Li, L. Li, R. Jia, K. Jiang, G. Shen and D. Chen, Small Methods, 2020, 4, 2000363 CrossRef CAS.
- C. Bai, K. Ji, H. Wang, J. Zhang, G. Hu and D. Kong, ACS Mater. Lett., 2022, 4, 2401–2408 CrossRef CAS.
- C. Yan, X. Wang, M. Cui, J. Wang, W. Kang, C. Y. Foo and P. S. Lee, Adv. Energy Mater., 2014, 4, 1301396 CrossRef.
- K. Hatakeyama-Sato, H. Wakamatsu, K. Yamagishi, T. Fujie, S. Takeoka, K. Oyaizu and H. Nishide, Small, 2019, 15, 1805296 CrossRef PubMed.
- H. Yuk, J. Wu and X. Zhao, Nat. Rev. Mater., 2022, 7, 935–952 CrossRef CAS.
- D. G. Mackanic, X. Yan, Q. Zhang, N. Matsuhisa, Z. Yu, Y. Jiang, T. Manika, J. Lopez, H. Yan, K. Liu, X. Chen, Y. Cui and Z. Bao, Nat. Commun., 2019, 10, 5384 CrossRef PubMed.
- C. Gu, M. Wang, K. Zhang, J. Li, Y.-L. Lu, Y. Cui, Y. Zhang and C.-S. Liu, Adv. Mater., 2023, 35, 2208392 CrossRef CAS PubMed.
- J. Wu, Q. Liang, X. Yu, Q.-F. Lü, L. Ma, X. Qin, G. Chen and B. Li, Adv. Funct. Mater., 2021, 31, 2011102 CrossRef CAS.
- Q. Shi, H. Liu, D. Tang, Y. Li, X. Li and F. Xu, NPG Asia Mater., 2019, 11, 64 CrossRef CAS.
- P. Le Floch, S. Meixuanzi, J. Tang, J. Liu and Z. Suo, ACS Appl. Mater. Interfaces, 2018, 10, 27333–27343 CrossRef CAS PubMed.
- Q. Shen, M. Jiang, R. Wang, K. Song, M. H. Vong, W. Jung, F. Krisnadi, R. Kan, F. Zheng, B. Fu, P. Tao, C. Song, G. Weng, B. Peng, J. Wang, W. Shang, M. D. Dickey and T. Deng, Science, 2023, 379, 488–493 CrossRef CAS PubMed.
- N. Ochirkhuyag, Y. Nishitai, S. Mizuguchi, Y. Isano, S. Ni, K. Murakami, M. Shimamura, H. Iida, K. Ueno and H. Ota, ACS Appl. Mater. Interfaces, 2022, 14, 48123–48132 CrossRef CAS PubMed.
- M. Li, J. Lu, Z. Chen and K. Amine, Adv. Mater., 2018, 30, 1800561 CrossRef PubMed.
- J. Piątek, S. Afyon, T. M. Budnyak, S. Budnyk, M. H. Sipponen and A. Slabon, Adv. Energy Mater., 2021, 11, 2003456 CrossRef.
- S. Dühnen, J. Betz, M. Kolek, R. Schmuch, M. Winter and T. Placke, Small Methods, 2020, 4, 2000039 CrossRef.
- M. M. Titirici, Adv. Energy Mater., 2021, 11, 2003700 CrossRef CAS.
-
V. Forti, C. P. Balde, R. Kuehr and G. Bel, The Global E-Waste Monitor 2020: Quantities, Flows and the Circular Economy Potential, United Nations University/United Nations Institute for Training and Research, International Telecommunication Union, and International Solid Waste Association, Bonn, Geneva and Rotterdam, 2020 Search PubMed.
-
P. Sparks, White Paper: The Route to a Trillion Devices, ARM, 2017 Search PubMed.
- S. Gong and W. Cheng, Adv. Energy Mater., 2017, 7, 1700648 CrossRef.
- N. Mittal, A. Ojanguren, M. Niederberger and E. Lizundia, Adv. Sci., 2021, 8, 2004814 CrossRef CAS PubMed.
- K. Rajaram, S. M. Yang and S.-W. Hwang, Adv. Energy Sustainability Res., 2022, 3, 2100223 CrossRef CAS.
- Z. Wang, X. Li, Z. Yang, H. Guo, Y. J. Tan, G. J. Susanto, W. Cheng, W. Yang and B. C. K. Tee, EcoMat, 2021, 3, e12073 CrossRef CAS.
- E. Sanchez-Rexach, T. G. Johnston, C. Jehanno, H. Sardon and A. Nelson, Chem. Mater., 2020, 32, 7105–7119 CrossRef CAS.
- D. F. Fernandes, C. Majidi and M. Tavakoli, J. Mater. Chem. C, 2019, 7, 14035–14068 RSC.
- Y. Liu, Y. Zheng, X. H. Chen, J. A. Yang, H. Pan, D. Chen, L. Wang, J. Zhang, D. Zhu, S. Wu, K. W. K. Yeung, R. C. Zeng, Y. Han and S. Guan, Adv. Funct. Mater., 2019, 29, 1805402 CrossRef.
- J. Li, J. Liu, W. Huo, J. Yu, X. Liu, M. J. Haslinger, M. Muehlberger, P. Kulha and X. Huang, Mater. Today Nano, 2022, 18, 100201 CrossRef.
- Y. Qin, P. Wen, H. Guo, D. Xia, Y. Zheng, L. Jauer, R. Poprawe, M. Voshage and J. H. Schleifenbaum, Acta Biomater., 2019, 98, 3–22 CrossRef CAS PubMed.
- M. Nasreldin, R. Delattre, C. Calmes, M. Ramuz, V. A. Sugiawati, S. Maria, J.-L. d. B. d. l. Tocnaye and T. Djenizian, Energy Storage Mater., 2020, 33, 108–115 CrossRef.
- Z. Lyu, G. J. H. Lim, J. J. Koh, Y. Li, Y. Ma, J. Ding, J. Wang, Z. Hu, J. Wang, W. Chen and Y. Chen, Joule, 2021, 5, 89–114 CrossRef CAS.
- W. Pfleging, Int. J. Extreme Manuf., 2020, 3, 012002 CrossRef.
- X. Aeby, A. Poulin, G. Siqueira, M. K. Hausmann and G. Nyström, Adv. Mater., 2021, 33, 2101328 CrossRef CAS PubMed.
- J. Qian, Q. Chen, M. Hong, W. Xie, S. Jing, Y. Bao, G. Chen, Z. Pang, L. Hu and T. Li, Mater. Today, 2022, 54, 18–26 CrossRef CAS.
- S. Praveen, T. Kim, S. P. Jung and C. W. Lee, Small, 2023, 19, 2205817 CrossRef CAS PubMed.
- Y. Bao, Y. Liu, Y. Kuang, D. Fang and T. Li, Energy Storage Mater., 2020, 33, 55–61 CrossRef.
- R. R. Jose, M. J. Rodriguez, T. A. Dixon, F. Omenetto and D. L. Kaplan, ACS Biomater. Sci. Eng., 2016, 2, 1662–1678 CrossRef CAS PubMed.
- M. Tavakoli, P. Alhais Lopes, A. Hajalilou, A. F. Silva, M. Reis Carneiro, J. Carvalheiro, J. Marques Pereira and A. T. De Almeida, Adv. Mater., 2022, 34, 2203266 CrossRef CAS PubMed.
- D. E. Fagnani, J. L. Tami, G. Copley, M. N. Clemons, Y. D. Y. L. Getzler and A. J. McNeil, ACS Macro Lett., 2021, 10, 41–53 CrossRef CAS PubMed.
- Z. Zhai, X. Du, Y. Long and H. Zheng, Front. Electron., 2022, 3, 985681 CrossRef.
- Q. Liu, L. Jiang, R. Shi and L. Zhang, Prog. Polym. Sci., 2012, 37, 715–765 CrossRef CAS.
- M. J. L. Tschan, E. Brulé, P. Haquette and C. M. Thomas, Polym. Chem., 2012, 3, 836–851 RSC.
- D. Gao, J. Lv and P. S. Lee, Adv. Mater., 2022, 34, 2105020 CrossRef CAS PubMed.
- H. Ye, K. Zhang, D. Kai, Z. Li and X. J. Loh, Chem. Soc. Rev., 2018, 47, 4545–4580 RSC.
- H. Lee, G. Lee, J. Yun, K. Keum, S. Y. Hong, C. Song, J. W. Kim, J. H. Lee, S. Y. Oh, D. S. Kim, M. S. Kim and J. S. Ha, Chem. Eng. J., 2019, 366, 62–71 CrossRef CAS.
- S.-W. Hwang, C. H. Lee, H. Cheng, J.-W. Jeong, S.-K. Kang, J.-H. Kim, J. Shin, J. Yang, Z. Liu, G. A. Ameer, Y. Huang and J. A. Rogers, Nano Lett., 2015, 15, 2801–2808 CrossRef CAS PubMed.
- M. Held, A. Pichler, J. Chabeda, N. Lam, P. Hindenberg, C. Romero-Nieto and G. Hernandez-Sosa, Adv. Sustainable Syst., 2022, 6, 2100035 CrossRef CAS.
- B. L. Turner, J. Twiddy, M. D. Wilkins, S. Ramesh, K. M. Kilgour, E. Domingos, O. Nasrallah, S. Menegatti and M. A. Daniele, npj Flexible Electron., 2023, 7, 25 CrossRef CAS.
- C. M. Boutry, A. Nguyen, Q. O. Lawal, A. Chortos, S. Rondeau-Gagné and Z. Bao, Adv. Mater., 2015, 27, 6954–6961 CrossRef CAS PubMed.
- Y. J. Kim, S.-E. Chun, J. Whitacre and C. J. Bettinger, J. Mater. Chem. B, 2013, 1, 3781–3788 RSC.
- A. A. Kazemzadeh Farizhandi, S. Z. Khalajabadi, V. Krishnadoss and I. Noshadi, J. Mech. Behav. Biomed. Mater., 2020, 110, 103960 CrossRef CAS PubMed.
- D. Bresser, D. Buchholz, A. Moretti, A. Varzi and S. Passerini, Energy Environ. Sci., 2018, 11, 3096–3127 RSC.
- S. Scott, J. Terreblanche, D. L. Thompson, C. Lei, J. M. Hartley, A. P. Abbott and K. S. Ryder, J. Phys. Chem. C, 2022, 126, 8489–8498 CrossRef CAS.
- Y. Wu, H. Li, T. Liu and M. Xu, Adv. Mater., 2023, 2305063 CrossRef PubMed.
- S. Choi, S. I. Han, D. Kim, T. Hyeon and D.-H. Kim, Chem. Soc. Rev., 2019, 48, 1566–1595 RSC.
- C. Wang, T. Yokota and T. Someya, Chem. Rev., 2021, 121, 2109–2146 CrossRef CAS PubMed.
- C. Wang, K. Xia, Y. Zhang and D. L. Kaplan, Acc. Chem. Res., 2019, 52, 2916–2927 CrossRef CAS PubMed.
- H. Li, Y. Zheng and L. Qin, Prog. Nat. Sci.: Mater. Int., 2014, 24, 414–422 CrossRef CAS.
- X. Huang, D. Wang, Z. Yuan, W. Xie, Y. Wu, R. Li, Y. Zhao, D. Luo, L. Cen, B. Chen, H. Wu, H. Xu, X. Sheng, M. Zhang, L. Zhao and L. Yin, Small, 2018, 14, 1800994 CrossRef PubMed.
- H. Dong, J. Li, J. Guo, F. Lai, F. Zhao, Y. Jiao, D. J. L. Brett, T. Liu, G. He and I. P. Parkin, Adv. Mater., 2021, 33, 2007548 CrossRef CAS PubMed.
- W. Zhao, S. J. B. Rubio, Y. Dang and S. L. Suib, ACS ES&T Engg, 2022, 2, 20–42 Search PubMed.
- K. Ji, S. Li, Y. Lin, J. Zhang, M. Wang, C. Bai and D. Kong, ACS Mater. Lett., 2023, 5, 955–961 CrossRef CAS.
- T. N. Nguyen, B. Iranpour, E. Cheng and J. D. W. Madden, Adv. Energy Mater., 2022, 12, 2103148 CrossRef CAS.
- C. Bai, K. Ji, S. Feng, J. Zhang and D. Kong, Energy Storage Mater., 2022, 47, 386–393 CrossRef.
- D. Danninger, F. Hartmann, W. Paschinger, R. Pruckner, R. Schwödiauer, S. Demchyshyn, A. Bismarck, S. Bauer and M. Kaltenbrunner, Adv. Energy Mater., 2020, 10, 2000467 CrossRef CAS.
- A. M. Gaikwad, A. M. Zamarayeva, J. Rousseau, H. Chu, I. Derin and D. A. Steingart, Adv. Mater., 2012, 24, 5071–5076 CrossRef CAS PubMed.
- M. Kaltenbrunner, G. Kettlgruber, C. Siket, R. Schwödiauer and S. Bauer, Adv. Mater., 2010, 22, 2065–2067 CrossRef CAS PubMed.
- É. Lèbre, M. Stringer, K. Svobodova, J. R. Owen, D. Kemp, C. Côte, A. Arratia-Solar and R. K. Valenta, Nat. Commun., 2020, 11, 4823 CrossRef PubMed.
- F. P. Carvalho, Food Energy Secur., 2017, 6, 61–77 CrossRef.
- M. Iturrondobeitia, O. Akizu-Gardoki, O. Amondarain, R. Minguez and E. Lizundia, Adv. Sustainable Syst., 2022, 6, 2100308 CrossRef CAS.
- J. Kim, Y. Kim, J. Yoo, G. Kwon, Y. Ko and K. Kang, Nat. Rev. Mater., 2023, 8, 54–70 CrossRef.
- S. Zhang, N. Ericsson, P.-A. Hansson, M. Sjödin and Å. Nordberg, J. Cleaner Prod., 2022, 337, 130454 CrossRef CAS.
- L. Liu, N. Solin and O. Inganäs, Adv. Energy Mater., 2021, 11, 2003713 CrossRef CAS.
- C. Liedel, ChemSusChem, 2020, 13, 2110–2141 CrossRef CAS PubMed.
- H. Wang, Y. Yang and L. Guo, Adv. Energy Mater., 2017, 7, 1700663 CrossRef.
- K. Hatakeyama-Sato, H. Wakamatsu, K. Yamagishi, T. Fujie, S. Takeoka, K. Oyaizu and H. Nishide, Small, 2019, 15, 1805296 CrossRef PubMed.
- C. Wang, W. Zheng, Z. Yue, C. O. Too and G. G. Wallace, Adv. Mater., 2011, 23, 3580–3584 CrossRef CAS PubMed.
- P. Poizot, J. Gaubicher, S. Renault, L. Dubois, Y. Liang and Y. Yao, Chem. Rev., 2020, 120(14), 6490–6557 CrossRef CAS PubMed.
- Z. Li, J. Tan, Y. Wang, C. Gao, Y. Wang, M. Ye and J. Shen, Energy Environ. Sci., 2023, 16, 2398–2431 RSC.
- C. Friebe, A. Lex-Balducci and U. S. Schubert, ChemSusChem, 2019, 12, 4093–4115 CrossRef CAS PubMed.
- Y. J. Kim, W. Wu, S.-E. Chun, J. F. Whitacre and C. J. Bettinger, Proc. Natl. Acad. Sci. U. S. A., 2013, 110, 20912–20917 CrossRef CAS PubMed.
- I. K. Ilic, V. Galli, L. Lamanna, P. Cataldi, L. Pasquale, V. F. Annese, A. Athanassiou and M. Caironi, Adv. Mater., 2023, 35, 2211400 CrossRef CAS PubMed.
- B. Lee, Y. Ko, G. Kwon, S. Lee, K. Ku, J. Kim and K. Kang, Joule, 2018, 2, 61–75 CrossRef CAS.
- L. Ma, S. Chen, D. Wang, Q. Yang, F. Mo, G. Liang, N. Li, H. Zhang, J. A. Zapien and C. Zhi, Adv. Energy Mater., 2019, 9, 1803046 CrossRef.
- S. Qu, B. Liu, J. Wu, Z. Zhao, J. Liu, J. Ding, X. Han, Y. Deng, C. Zhong and W. Hu, ACS Appl. Mater. Interfaces, 2020, 12, 54833–54841 CrossRef CAS PubMed.
- Y. Liang and Y. Yao, Nat. Rev. Mater., 2022, 8, 109–122 CrossRef.
- E. Lizundia and D. Kundu, Adv. Funct. Mater., 2021, 31, 2005646 CrossRef CAS.
- A. Raghavan and S. Ghosh, ChemistrySelect, 2021, 6, 13647–13663 CrossRef CAS.
- S. Chen, Z. Wu, C. Chu, Y. Ni, R. E. Neisiany and Z. You, Adv. Sci., 2022, 9, 2105146 CrossRef CAS PubMed.
- N. Boaretto, L. Meabe, M. Martinez-Ibañez, M. Armand and H. Zhang, J. Electrochem. Soc., 2020, 167, 070524 CrossRef CAS.
- H. Li, C. Han, Y. Huang, Y. Huang, M. Zhu, Z. Pei, Q. Xue, Z. Wang, Z. Liu, Z. Tang, Y. Wang, F. Kang, B. Li and C. Zhi, Energy Environ. Sci., 2018, 11, 941–951 RSC.
- Y. Huang, J. Liu, J. Zhang, S. Jin, Y. Jiang, S. Zhang, Z. Li, C. Zhi, G. Du and H. Zhou, RSC Adv., 2019, 9, 16313–16319 RSC.
- K. Wang, J.-B. Le, S.-J. Zhang, W.-F. Ren, J.-M. Yuan, T.-T. Su, B.-Y. Chi, C.-Y. Shao and R.-C. Sun, J. Mater. Chem. A, 2022, 10, 4845–4857 RSC.
- Y. Lu, T. Zhu, N. Xu and K. Huang, ACS Appl. Energy Mater., 2019, 2, 6904–6910 CrossRef CAS.
- P. Yang, J. Li, S. W. Lee and H. J. Fan, Adv. Sci., 2022, 9, 2103894 CrossRef CAS PubMed.
- J. Xu, X. Hu, M. A. Alam, G. Muhammad, Y. Lv, M. Wang, C. Zhu and W. Xiong, RSC Adv., 2021, 11, 35280–35286 RSC.
- T. Liang, R. Hou, Q. Dou, H. Zhang and X. Yan, Adv. Funct. Mater., 2021, 31, 2006749 CrossRef CAS.
- L. Sun, Y. Yao, L. Dai, M. Jiao, B. Ding, Q. Yu, J. Tang and B. Liu, Energy Storage Mater., 2022, 47, 187–194 CrossRef.
- B.-Y. Zhao, P. Xu, F.-X. Yang, H. Wu, M.-H. Zong and W.-Y. Lou, ACS Sustain. Chem. Eng., 2015, 3, 2746–2755 CrossRef CAS.
- A. Sharma, R. Sharma, R. C. Thakur and L. Singh, J. Energy Chem., 2023, 82, 592–626 CrossRef CAS.
- J. Afonso, A. Mezzetta, I. M. Marrucho and L. Guazzelli, Green Chem., 2023, 25, 59–105 RSC.
- Q. Zaib, M. J. Eckelman, Y. Yang and D. Kyung, Green Chem., 2022, 24, 7924–7930 RSC.
- T. P. Haider, C. Völker, J. Kramm, K. Landfester and F. R. Wurm, Angew. Chem., Int. Ed., 2019, 58, 50–62 CrossRef CAS PubMed.
- L. Filiciotto and G. Rothenberg, ChemSusChem, 2021, 14, 56–72 CrossRef CAS PubMed.
- J. Tropp and J. Rivnay, J. Mater. Chem. C, 2021, 9, 13543–13556 RSC.
- J. F. Peters, Nat. Sustain., 2023, 6, 614–616 CrossRef.
- J. Zhao, Z. Xu, Z. Zhou, S. Xi, Y. Xia, Q. Zhang, L. Huang, L. Mei, Y. Jiang, J. Gao, Z. Zeng and C. Tan, ACS Nano, 2021, 15, 10597–10608 CrossRef CAS PubMed.
- L. Yin, M. Cao, K. N. Kim, M. Lin, J.-M. Moon, J. R. Sempionatto, J. Yu, R. Liu, C. Wicker, A. Trifonov, F. Zhang, H. Hu, J. R. Moreto, J. Go, S. Xu and J. Wang, Nat. Electron., 2022, 5, 694–705 CrossRef.
|
This journal is © The Royal Society of Chemistry 2023 |