DOI:
10.1039/D3MA00609C
(Review Article)
Mater. Adv., 2023,
4, 6152-6174
Recent advances in Ni-materials/carbon nanocomposites for supercapacitor electrodes
Received
28th August 2023
, Accepted 3rd November 2023
First published on 7th November 2023
Abstract
Recent advancements in Ni material-based supercapacitors have focused on their composites with carbon nanomaterials. These composites demonstrate improved electrical conductivity, enhanced surface area, and superior electrochemical performance by addressing critical issues related to cycling stability and low energy density. This review provides an overview of Ni material-based carbon nanocomposites including graphene (Ni/graphene), carbon nanotubes (Ni/CNTs), and activated carbon (Ni/AC) as potential electrodes for supercapacitors. The synergistic effects of Ni and carbon in nanocomposites on electrochemical properties such as capacitance, cycling stability, and specific capacitance are systematically outlined. The findings will serve as a valuable resource for understanding the structure–property–performance relationship of Ni-based composite materials for energy storage applications.
1. Introduction
The development of stationary and automotive systems requires effective and efficient energy storage devices. Supercapacitors were introduced as promising energy storage systems due to their high-power density and long cycle life. Recently, the development of supercapacitors has mostly focused on increasing their energy density by fabricating advanced electrode materials and electrolytes. Ni materials are highly regarded in the realm of supercapacitors due to their remarkable electrochemical properties including long cycle life, fast charge/discharge rates, and high specific capacity. Ni material supercapacitors find wide applications in energy storage systems, hybrid vehicles, portable electronics, and renewable energy systems. Fig. 1 shows the advantages of supercapacitors and the properties of carbon nanomaterials as an electrode of supercapacitors. Also, different types of Ni materials/carbon nanomaterials supercapacitors are shown in Fig. 1.
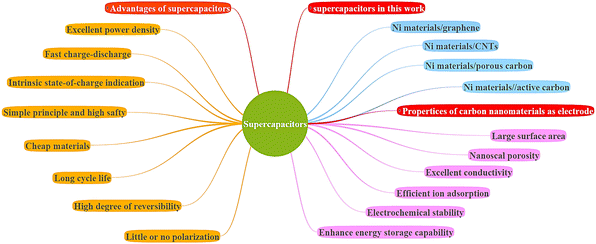 |
| Fig. 1 Advantages of supercapacitors and the properties of carbon nanomaterials as an electrode of supercapacitors. | |
The choice of materials for supercapacitor electrodes plays a critical role in determining the performance and characteristics. Some of the common types of materials used in supercapacitor electrodes are activated carbon, CNTs, graphene, metal oxides, conducting polymers, transition metal carbides, carbon aerogels, and hybrids and composites. Ni itself is a good conductor of electricity, which allows for rapid electron transport within the electrode material. Some Ni-based materials, such as nickel hydroxide, exhibit pseudocapacitance. This property leads to higher specific capacitance and overall energy storage capacity. Ni is a relatively abundant and cost-effective material compared to precious metals, is eco-friendly, easy to use in manufacturing processes, and has good stability and longevity. Ni-based materials can be combined with other substances to form composites or hybrid electrodes. This versatility enables researchers to develop supercapacitor electrodes. The composite of Ni materials with carbon nanomaterials in supercapacitors improves performance by enhancing conductivity, increasing surface area, improving stability, facilitating ion diffusion, and leveraging synergistic effects between the materials. These improvements contribute to higher energy storage capacity, faster charging/discharging rates, and improved overall device performance.1–5Fig. 2 shows the cumulative growth of published articles in recent years on Ni material supercapacitors. During the last decade, the growth of scientific research on using nickel materials to fabricate supercapacitor electrodes has increased significantly. The cumulative number of scientific studies has reached more than 3000 published articles, of which about 71% are from China, 10% from India, 9% from South Korea, 5% from the United States, and the share of other countries is 5%. Co-occurrence analysis is the way to investigate using keywords. In this analysis, the information related to the relationship between keywords in different reports, the amount of repetition of keywords, and the identification of different materials in the fabrication of supercapacitor electrodes that use nickel materials in their structure can be obtained. The VOSviewer image of Ni material-based supercapacitors from Scopus for 2022–2023 publications is shown in Fig. 3.
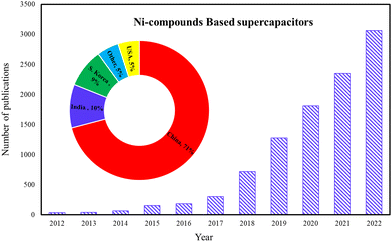 |
| Fig. 2 The cumulative growth in Ni material-based supercapacitor publications. | |
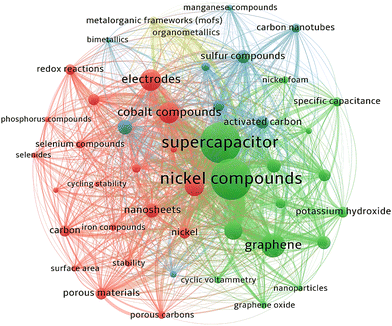 |
| Fig. 3 Co-occurrence keyword analysis of Ni material-based supercapacitors using VOSviewer. | |
As shown in Fig. 3, electrodes based on Ni materials and carbon nanomaterials are prominent keywords. Recently, nanocomposites of Ni materials with carbon nanomaterials as supercapacitor electrodes such as NiCo2S4/graphene,6 Ni(OH)2/graphene,7 NiCo2O4/graphene,8,9 Ni–Co/graphene,10–17 NiMoO4/graphene,18–20 Ni(OH)2/CNTs,21,22 Ni–Co/CNTs,23–25 NiCo2S4/CNTs,26–29 Ni–Co/porous carbon,30 NiCo2S4/porous carbon,31 NiCo2O4//AC,32 Ni–Co//AC,33–36 Ni(OH)2//AC,37 and other materials have been developed.
NiCo2S4 due to its high electrochemical stability offers advantages such as good cycling stability, and compatibility with flexible devices. Their primary components are widely available, making them cost-effective. NiCo2S4/carbon nanomaterial electrodes combine the advantages of NiCo2S4 and carbon nanomaterials to enhance energy storage. The synergy of both materials results in an improved power density and faster charge rates.38–43 NiCo2O4 belongs to the class of transition metal oxides and exhibits favorable electrochemical properties. Additionally, the properties of NiCo2O4 can be tuned by adjusting its synthesis parameters, allowing for optimization of its electrochemical performance to meet specific application requirements. The key distinction between NiCo2O4 and NiCo2S4-based supercapacitors lies in the redox reactions occurring at the electrode material. NiCo2O4 undergoes redox reactions involving oxygen atoms, while NiCo2S4 involves sulfur atoms. Recently, several kinds of research have been reported on supercapacitors based on NiCo2O4/carbon nanomaterials.44–48 Ni(OH)2-based supercapacitors are widely used due to efficient charge storage and are environmentally friendly. In supercapacitors based on Ni(OH)2/carbon nanomaterials, the performance characteristics are improved.49–54 The specific capacitance, power density, energy density, and cycle stability are important parameters in the classification of supercapacitors. Cycle stability refers to their ability to maintain a consistent performance over repeated charge and discharge cycles without significant degradation. It involves mitigating factors such as capacitance loss, resistance increase, leakage current, and mechanical stress. These degradation mechanisms can impact the specific capacitance, power delivery, and overall efficiency of the supercapacitor.55,56 Wu et al.57 reported a supercapacitor based on Ni3Se4@Co3Se4-1
:
3//rGO-Zn electrodes with a specific capacitance of 1120 F g−1. Ternary nanocomposites of nickel molybdate/reduced graphene oxide/polypyrrole (NiMoO4/rGO/PPy), as a supercapacitor electrode were investigated in ref. 58 This paper mentioned that with NiMoO4/rGO-450/PPy@NF//AC/graphite@NF electrodes, the energy and power densities of the supercapacitor were 43.65 W h kg−1 and 600 W kg−1, respectively. In another study, a supercapacitor based on FeNiS2 nanosheets decorated on rGO showed a specific capacitance of 1013 F g−1.59 Flexible supercapacitors play a significant role in soft, wearable, and portable electronics. Li et al.60 investigated a CoNiP2O7/CNT nanocomposite as a positive electrode for micro-supercapacitors. They obtained an areal capacitance of 20.9 mF cm−2 at 0.08 mA cm−2 and an energy density of 2.9 μW h cm−2. A supercapacitor based on the MWCNTs@Ni3S2/CuxS electrode presented a specific capacitance of 1388.7 F g−1 using the galvanostatic charge–discharge method and cycling stability of 100% after 10
000 cycles.61 Ni3P2O8 nanodot anchored MWCNT nanocomposites as a supercapacitor electrode were reported in ref. 62 This structure achieved a specific energy of 72.3 W h kg−1 with a power density of 6.4 kW kg−1. Recent research on Ni materials and porous carbon nanocomposites as electrodes has shown good progress.63–68 Nanomaterials and nanocomposites are receiving more attention in making energy storage devices, sensors, and different applications.69–75 In this review, the developments of Ni material/carbon nanomaterial-based supercapacitors for 2022–2023 publications (Scopus) are studied and compared. We have discussed the specific capacitance, power density, energy density, cycling stability, and rate capability of Ni-materials/carbon nanocomposites in supercapacitor applications. This article provides valuable insights into the introduction and development of recent Ni-based supercapacitors with high performance. It serves as a comprehensive resource for researchers and engineers working in the field of energy storage, facilitating further advancements in the design of efficient and sustainable energy storage systems.
2. Materials manufacturing for supercapacitors
2.1. Graphene-based supercapacitors
Various nanocomposites containing Ni and graphene have been frequently employed in supercapacitor and electrochemical applications and the novel results from the reported papers are tabulated in Table 1. From Table 1 the specific capacitance of Ni-materials/graphene-based supercapacitors is obtained, which is shown in Fig. 4. As can be seen from Fig. 4 the specific capacitance of Ni-materials/graphene-based supercapacitors reached 3268 F g−1. For better comparison, the energy density as a function of power density is also plotted in Fig. 4. From Fig. 4 the power density of most Ni-materials/graphene-based supercapacitors is less than 2 KW kg−1 and the energy density is less than 100 W h kg−1.
Table 1 The electrochemical results collected from various studies done on Ni/graphene nanocomposites
Electrode material |
Capacitance retention (CR%/Cycle) |
Specific capacitance (F g−1) |
Energy density (W h kg−1) |
Power density (W kg−1) |
Ref. |
NiMoO4/rGO |
91.1/1000 |
2056 |
60.2 |
750.2 |
76
|
NiMoO4/rGO–Ni/ZnFe2O4 |
89.6/7000 |
— |
58.6 |
799 |
77
|
NiFe2O4/rGO/polyaniline |
— |
1134.28 |
19.29 |
610 |
78
|
NiFe2O4/rGO |
94/5000 |
1320 C g−1 |
75 |
2343 |
79
|
Ni–Cu/rGO |
91.8/13 000 |
1075 C g−1 |
64 |
801 |
80
|
Ni molybdate/rGO |
— |
1805 |
43.65 |
600 |
81
|
NiCoSe4/rGO |
93/5000 |
120 mA h g−1 |
14 |
902 |
82
|
CoNi2S4/rGO/MoS2 |
— |
3268 |
41 |
700 |
83
|
Ni2ZnS4/rGO/ZIF-8 |
59.7/2000 |
1150 |
31.06 |
750.44 |
84
|
Ni cobaltite/rGO |
96/2500 |
2695 |
93.57 |
250 |
85
|
Ni–Mo/rGO |
83.4/— |
1220 |
60.5 |
1470 |
86
|
NiSe2/rGO |
99/8000 |
1845.5 |
12.66 |
3999.84 |
87
|
NiSe/rGO |
90/5000 |
781 C g−1 |
52.8 |
930 |
88
|
NiMoS4/rGO/polyaniline |
93/6000 |
194 mA h g−1 |
30.75 |
1500 |
89
|
NiSe/rGO/C |
75/5000 |
448.9 mA h g−1 |
60.5 |
13 340 |
90
|
NiSe2/rGO |
78.13/5000 |
224.75 mA h g−1 |
25.85 |
730 |
91
|
Ni3S2/rGO |
95.4/10 000 |
1960 mF cm−2 |
67.9 |
535.7 |
92
|
NiCoO2/rGO/MXene |
77.29/10 000 |
1614 |
45.15 |
394.52 |
93
|
Ni/rGO |
70/— |
52.64 mA h g−1 |
18.72 |
547.52 |
94
|
Ni/graphene |
— |
1900 |
37 |
5000 |
95
|
Ni phosphide/graphene |
85.2/10 000 |
1338.8 |
33.4 |
792.1 |
96
|
Ni/GO |
92.5/10 000 |
1115.6 |
52.5 |
18 000 |
97
|
Ni–Fe/graphene |
— |
1541 mA h g−1 |
190 |
9600 |
98
|
NiWO3/GO/PANI |
92.6/10 000 |
1380 |
47.8 |
— |
99
|
NiGa/graphene quantum dots |
87.5/5000 |
2160 |
78.8 |
1432.7 |
100
|
Ni–Co/rGO |
— |
1913.5 |
59.2 |
750 |
103
|
Ni–Co/Co3O4/graphene |
99.8/10 500 |
1866 |
66.7 |
800 |
104
|
Ni–Co phosphide/rGO |
90/10 000 |
2384 |
39.7 |
8820 |
105
|
Ni–Co selenide/rGO |
80.8/5000 |
2009 |
38 |
388 |
106
|
Ni–Co selenide/graphene |
84.6/5000 |
421.3 C g−1 |
40.4 |
533.3 |
107
|
Ni–Co sulfide/MnS/rGO |
83.6/10 000 |
1248 C g−1 |
42.0 |
793.8 |
108
|
Ni–Co/graphene |
89.6/10 000 |
1740 |
41.6 |
750 |
109
|
Ni–Co/graphene |
83.2/10 200 |
— |
40.6 |
400 |
110
|
Ni–Co/rGO |
87.3/10 000 |
2137.8 |
54.25 |
750 |
111
|
Ni–Co/N-GH/NF//GH/CNT |
— |
209 |
63.33 |
260 |
112
|
Ni–Co/rGO/MXene |
70.87/10 000 |
248.13 mA h g−1 |
29.46 |
700.34 |
113
|
Ni–Co/rGO |
85.1/10 000 |
582.1 mA h g−1 |
56.0 |
515.0 |
114
|
Ni–Co/graphene quantum dots |
86.2/8000 |
1628 |
46 |
7440 |
115
|
Ni–Co/MWCNTs–GO |
91.92/10 000 |
2532.80 |
77.61 |
850 |
116
|
Ni–Co/rGO |
75.5/5000 |
2020 mF cm−2 |
117.3 μW h cm−2 |
34 000 μW cm−2 |
117
|
NiCo2S4/rGO/g-C3N4 |
93.6/6000 |
1938 |
66 |
751 |
120
|
NiCo2S4/graphene |
— |
1325.9 |
30.72 |
1280 |
121
|
NiCo2S4/graphene/Ni–Mo |
80/10 000 |
1346 |
59.38 |
808.19 |
122
|
NiCo2S4/rGO/CoNi |
80.52/10 000 |
1846.66 |
28.88 |
— |
123
|
NiCo2S4/graphene |
74.5/5000 |
1145 |
33.8 |
799.8 |
124
|
NiCo2S4/rGO |
82/3000 |
1072 |
41.52 |
1067 |
125
|
NiCo2O4/NG/MnOOH |
88/2000 |
525.72 |
7.2 |
548.72 |
126
|
NiCo2O4/ZnCo2O4/rGO/CNTs |
84.0/6000 |
1128.6 |
50.8 |
800 |
127
|
NiCo2O4/Fe/rGO |
78.8/12 000 |
2772 |
93.5 |
455 |
128
|
NiCo2O4/GO |
— |
530 |
37.8 |
1350 |
129
|
NiCo2O4/graphene |
85/50 000 |
369.8 |
24.7 |
799.6 |
130
|
NiCo2O4/rGO |
134/30 000 |
871 |
29.3 |
790.8 |
131
|
NiCo2O4/graphene |
95.04/5000 |
1118 |
9.37 |
250 |
132
|
NiCo2O4/graphene/AC |
100/1000 |
854 |
2.2 mW h cm−2 |
45.1 mW cm−2 |
133
|
NiCo2O4/rGO |
92/5000 |
758 C g−1 |
61 |
— |
134
|
NiCo2O4/rGO/polymer |
61/10 000 |
3160 mF cm−2 |
0.64 mW h cm−2 |
2.7 mW cm−2 |
135
|
Ni(OH)2:polyaniline/rGO |
— |
381.67 |
76.33 |
3.3109 |
136
|
Ni(OH)2/rGO |
91.4/10 000 |
2776 |
39.24 |
1962 |
137
|
Ni(OH)2/silver/graphene/PPy |
108.37/5500 |
237.25 C g−1 |
43.26 |
750.00 |
138
|
Ni(OH)2/GO/AC |
80/1000 |
322 mF cm−2 |
0.134 mW h cm−2 |
33.6 mW cm−2 |
139
|
Ni(OH)2/Ni foam/graphene |
73.1/2000 |
2667.2 mF cm−2 |
143 μW h cm−2 |
1400 μW cm−2 |
140
|
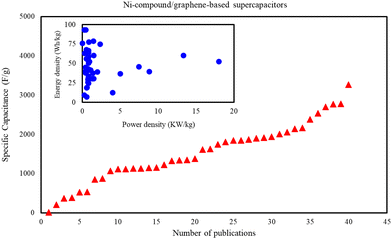 |
| Fig. 4 Specific capacitance, power, and energy densities of Ni-materials/graphene-based supercapacitors. | |
The specific capacitance of the NiMoO4/rGO composite reached 2056 F g−1 at a current density of 2 A g−1. Using NiMoO4/rGO as the (+) electrode in supercapacitors combined with AC as the (−) electrode led to the high-power density.76 ZnFe2O4/NiMoO4 nanosheet/rGO-NF as the cathode and MOF-derived hollow porous carbon as the anode was used in the supercapacitor leading to a high energy density of 58.6 W h kg−1 at a power density of 799 W kg−1 with prolonged cycling.77 Polyaniline/NiFe2O4/rGO hydrogel nanocomposites on carbon cloth showed high characteristics that led to the high properties in the corresponding supercapacitors attributed to its well-designed 3D microstructure and diffusion-controlled mechanism.78 Also, rGO/NiFe2O4 exhibited high electrochemical characteristics including a high specific capacity of 1320 C g−1 as well as high characteristics in the corresponding supercapacitor.79
Porous CuNi phosphide spheres/rGO as the cathode electrode have advantages such as fast electrolyte diffusion, better electron transfer, and better structural stability. Its supercapacitor with AC-anode represented a satisfactory energy density.80,81 The 450 °C annealed nanocomposite of NiMoO4/rGO-450/polypyrrole exhibited a specific capacitance of 1805 F g−1. NiCoSe4/N-rGO were fabricated using a solvothermal method and NiCoSe4/N-rGO-20 presents a specific capacity of 120 mA h g−1. The NiCoSe4/N-rGO-20 (anode)//N-rGO (cathode) supercapacitor demonstrated an ultra-high energy density of 14 W h kg−1 and good circulation stability.82 The spongy nanocomposite of CoNi2S4//MoS2/rGO has a specific capacitance of 3268 F g−1 at 1.0 A g−1. Its use in supercapacitors led to the optimal potential window and the high energy density of 41 W h kg−1.83 rGO/Ni2ZnS4 was used as a cathode material with a specific capacitance of 1150 F g−1. The capacitor composed of AC//rGO/Ni2ZnS4-1.5 h has an energy density of 31.06 W h kg−1.84 Spinel Ni cobaltite nanoflowers/rGO as an electrode material demonstrated a specific capacitance of 2695 F g−1 at 1 A g−1 and also exhibited a maximum energy density of 93.57 W h kg−1.85 The chalcogen-modified Ni–Mo selenide/rGO composites indicated that the Se-based electrode revealed the highest electrochemical properties. Also, a supercapacitor of this (+) electrode and thermally rGO electrode (−) presented a maximum energy density of 60.5 W h kg−1.86 NiSe2/rGO with various rGO weight ratios were fabricated and the NiSe2 (16%) rGO electrode outperformed the others due to its interconnected network topology and decreased effect of volume expansions. A supercapacitor with NiSe2-16% rGO (anode) and AC (cathode) exhibited a high retention of capacitance and energy density of 12.66 W h kg−1.87 Nanorod Ni-MOF-74 derived NiSe nanoparticles/rGO have been successfully prepared (NiSe/rGO) and showed an improved electrochemical performance so that the supercapacitor of NiSe/rGO (+)//(−) AC delivered energy density of 52.8 W h kg−1 and outstanding long-term cycling retention.88 The optimized rGO/polyaniline/NiMoS4 electrode exhibited a high specific capacitance of 194 mA h g−1 and the GO/PANI/NiMoS4//AC supercapacitor also showed a high energy density, good cycle stability, and capacity retention. Polyaniline can provide an additional Faradaic redox reaction.89 The selenized Ni/graphene oxide (Ni-MOF/GO) composites containing a hexa(4-carboxyl-phenoxy)-cyclotriphosphazene (NiSe/C/rGO) electrode displayed a high specific capacity of 448.9 mA h g−1 at 0.1 A g−1. The battery-type electrode NiSe/C/rGO with improved rate capacity and cycling stability enables an optimal SIHC with good properties.90 NiSe2 nanospheres/rGO showed an excellent specific capacity of 224.75 mA h g−1 at 1 A g−1, and good cycling performance. Also, the NiSe2/rGO//AC supercapacitor showed a high energy density and good capacity retention.91 The Ni3S2/rGO electrode with 20 mg GO precursor showed the optimal areal and mass-specific capacitances. Using Ni3S2-20 as both the anode and cathode led to the supercapacitor with a wide potential window and high electrochemical parameters.92 The (+) electrode of rGO/MXene/NiCoO2-5 wt% has a specific capacitance of 1614 F g−1 at 0.5 A g−1 which is maintained at 1257.5 F g−1 when increasing the current density to 10 A g−1. The supercapacitor of this electrode with rGO/MXene as the (−) electrode revealed an energy density of 45.15 W h kg−1.93 The positive electrode of thermally reduced graphene oxide (TrGO)/Ni-Foam (NF) showed a specific capacity of 52.64 mA h g−1 at 0.5 A g−1. The supercapacitor of TRGO/NF//PAC revealed a high specific energy and outstanding stability.94 The supercapacitor of pure graphene (−) with a Ni/graphene (+) electrode reached a specific energy of 37 W h kg−1 at 5 kW kg−1 and good reversibility.95 Moreover, carbon-coated nano-Ni2P (phosphides)/rGO (Ni2P/C/rGO) was constructed and the optimal Ni2P/C/rGO exhibited an excellent capacitance of 1338.8 F g−1. It was enabled for use in supercapacitors containing an N-doped porous carbon sheet (as the opposite electrode) representing an excellent energy density of 33.4 W h kg−1 at 792.1 W kg−1.96 The holey graphene oxide (HGO)/nano two-dimensional Ni (Ni(BDC)-HGO30) (30 = the added HGO amount) was applied by Wang et al.97 in a supercapacitor with AC (−) electrode and delivered a high outstanding property. Ni–Fe layered double hydroxide/graphene as the anode and superlong graphene nanoscrolls as the cathode were used as an anode, delivered a stable discharge capacity of 1541 mA h g−1, and were employed for synthesizing a supercapacitor with the energy density of 190 kW kg−1.98 N-doped GO/NiWO3/PANI nanocomposite showed an enhanced specific capacitance of 1380 F g−1, and thus was found to be useful in highly stable supercapacitors.99 The structure of LDH is prone to collapse during the redox reaction. A study assembled nitrogen-doped graphene quantum dots (N-GQD) on nickel gallium-layered double hydroxide (NiGa-LDH).100 That study described the electrochemically interesting electrode of NiGa-LDH/N-GQD/NF was employed in the structure of a supercapacitor device containing a carbon (−) electrode. The asymmetric supercapacitor with NiGa-LDH/N-GQD/NF electrode stated a specific capacitance of 2160 F g−1 at 1 A g−1 and capacitance retention of 87.5% after 5000 cycles. The fabrication schematic of NiGa-LDH/N-GQD/NF and carbon nanosheets derived from Co-MOF electrode and the electrical properties of the asymmetric supercapacitor with electron transport of NiGa-LDH/N-GQD/NF is shown in Fig. 5. The N-GQD nanosheets can enhance the electrical conductivity, material surface polarity, and surface area with more active sites. The N-GQD nanosheets also improved the ion flow efficiency, reduced the ion transport resistance, and enhanced the redox reaction.101,102
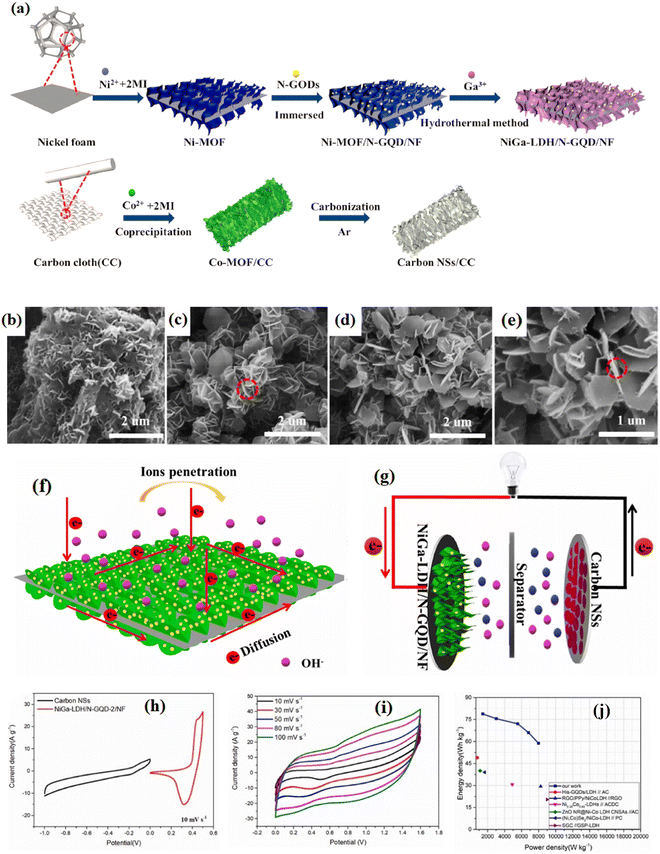 |
| Fig. 5 (a) The fabrication of NiGa-LDH/N-GQD/NF and carbon nanosheets derived from Co-MOF electrode. The SEM images of (b) Ni-MOF/NF, (c) NiGa-LDH/NF, and (d) and (e) NiGa-LDH/N-GQD/NF. (f) A schematic of the electron transport of NiGa-LDH/N-GQD/NF. (g) The assembly diagram of NiGa-LDH/N-GQD-2/NF//Carbon NSs. (h) The CV curves of NiGa-LDH/N-GQD-2/NF and carbon NSs at 10 mV s−1. (i) The CV graphs of an asymmetric supercapacitor at different scan rates. (j) A Ragone plot.100 | |
2.1.1. Nickel cobalt/selenide and graphene composites.
NiCo-based supercapacitors, also known as hybrid supercapacitors, combine the high energy density of batteries with the high-power density of traditional electrochemical capacitors. They are designed to provide both high energy and power capabilities for rapid energy storage and release. NiCo-based supercapacitors offer advantages such as high-power density, enabling them to deliver and absorb large amounts of energy quickly. They also have a long cycle life and good thermal stability, operating over a wide temperature range. However, their energy density is lower compared to lithium-ion batteries. NiCo-based supercapacitors are used in devices like portable electronics, electric vehicles, regenerative braking systems, and renewable energy integration, benefiting from their high-power density and rapid charge/discharge capabilities. NiCo-layered double hydroxides (NC-LDH)/rGO composites were prepared as high-performance electrodes for employment as the positive electrode in supercapacitors and AC as the negative electrode, which displayed a high electrochemical performance.103 3D hierarchical Ni–Co layered double hydroxides (LDH) wrapped around a porous Co3O4 nanocube derived from ZIF-67 were synthesized as an electrode (Ni–Co LDH/Co3O4 Nc). The supercapacitor constructed from this electrode and three-dimensional spongy graphene (3DSGr) showed a high energy density and superior recyclability.104 The NiCo phosphide nano horns are formed by the Kirkendall effect for preparing the NiCo phosphide/phosphorus-doped rGO as the anode with a specific capacity of 384 F g−1 at 1 A g−1.105 The synthesized process of NiCo phosphides wrapped with phosphorus-doped rGO the and electrical properties of the asymmetric supercapacitor were presented in Fig. 6. The supercapacitor prepared from this electrode and AC (cathode) yields an energy density of 39.7 W h kg−1 at a high power density of 8.82 kW kg−1. The (Ni0.85Se)3(Co0.85Se)/rGO composite was synthesized by microwave heating followed by a solvothermal method to present the microstructure with an excellent specific capacitance of 2009 F g−1 at a current density of 2 A g−1. The (Ni0.85Se)3(Co0.85Se)/rGO//AC supercapacitor exhibited a high energy density.106 Ni/Co selenide/GO (NiCoSe/G) was synthesized using a water bath and selenization process and the optimized electrode (NiCoSe/G-10) exhibited a high specific capacity and an excellent cycling performance as well as a high performance of NPC//NiCoSe/G-10 supercapacitor as tabulated in Table 1.107
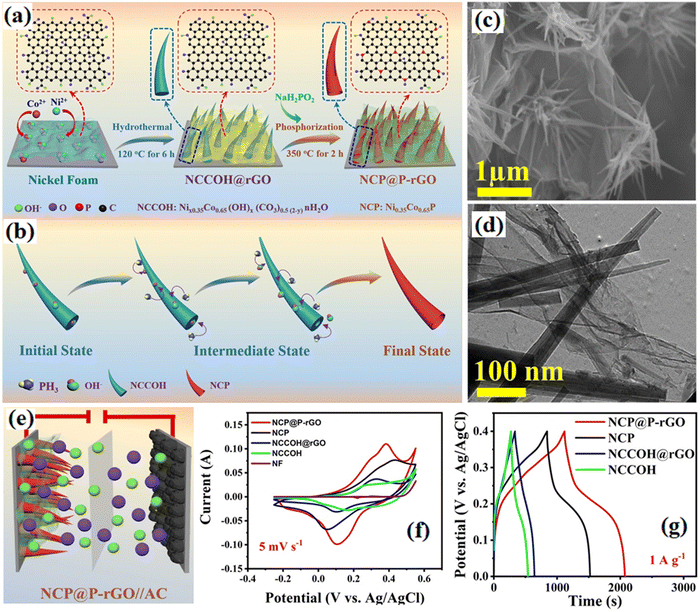 |
| Fig. 6 (a) Synthesis of NiCo phosphides wrapped with phosphorus-doped rGO and (b) ion-exchange reaction and morphology transition mechanism of NCP@P-rGO. (C) SEM image of NCCOH@rGO. (d) TEM image of NCCOH@rGO. (e) Schematic of the supercapacitor. (f) Comparison of CV curves at 5 mV s−1. (g) Comparison of GCD curves at 1 A g−1.105 | |
Ni–Co sulfide/crystalline MnS/rGO cathodes have long-term cyclic stability and a high specific capacity of 1248 C g−1 at 2 A g−1 while ultra-small Fe2O3 nanodots/rGO anode showed a specific capacity of 734.2 C g−1 at 2 A g−1. The corresponding supercapacitor showed a high specific energy of 42.0 W h kg−1.108 A supercapacitor based on 3D carbon microtubes and a vertical graphene nanosheet electrode (+) with AC electrode (−) revealed high power and energy densities.109 The Ni–Co LDH/graphene supercapacitor showed 87.1% capacity at a high rate, whereas only 50.5% was retained for Ni–Co LDH.110 The NiCoP/rGO-NF electrode (prepared using a hydrothermal method and low-temperature phosphating method) has a specific capacitance of 2137.8 F g−1 (at 1 A g−1 current density). The NiCoP/rGO-NF//AC supercapacitor exhibited novel electrochemical traits.111 The NiCo-LDH/N-doped graphene hydrogel (N-GH)/Nickel foam composites were prepared using a simple one-pot hydrothermal method. The NiCo-LDH/N-GH/NF//GH/CNT supercapacitor showed novel electrochemical behavior as reported in Table 1.112 rGO/MXene/Fe2O3 (−) and rGO/MXene/NiCo-P (+) have an interconnected nanostructure with specific surface areas at 17.1 and 131.9 m2 g−1. An asymmetric supercapacitor showed a maximum energy density of 29.46 W h kg−1 at a power density of 700.34 W kg−1.113 A Hausmannite/sulfur rGO (MO/rGO-S)/Co–Ni layered double hydroxide (MO/rGO-S-50/CN) composite and the device consisting of MO/rGO-S-50/CN (+) and AC (−) delivered excellent results for using in a high specific energy supercapacitor.114 NiCo-LDH hollow micro-tunnels strongly coupled with a higher-Fermi-level graphene quantum dots (GQDs) (GQDs/LDH-2) electrode yield an excellent capacitance of 1628 F g−1 at 1 A g−1 that when coupled with an rGO electrode (−) showed a 46 W h kg−1 energy density.115 MWCNT/GO nanoribbon/Graphitic carbon nitride NNi-colayered double hydroxide/Ni foam was prepared and exhibited high specific capacitance and exceptional performance. Its supercapacitor with AC delivers a high capacitance and long cycle life.116 The Ni–Co layered double hydroxide/rGO fibers (NCLDH/rGOFs) exhibited an outstanding area-specific capacitance of 2020 mF cm−2 at 5 mA cm−2 in a three-electrode system. Using NCLDH/rGOFs and FeOOH/rGOFs electrodes in the supercapacitor structure led to excellent properties.117 Nickel selenide (NiSe) is used as an electrode in hybrid supercapacitors, although it is limited by poor conductivity and sluggish ion kinetics. The electrochemical performance of NiSe is improved by the addition of rGO, which can be attributed to the raised interfacial interaction and enhanced access to the active sites. Khaladkar et al.118 fabricated an asymmetric supercapacitor with NiSe/rGO(+)//AC (−) electrodes and found an energy density of 49.6 W h kg−1 at 748.37 W kg−1 with a capacitance retention of 83.3% after 5000 cycles. They mentioned the possible chemical reaction processes to form NiSe as follows:118
| 3Se + 6OH− → 2Se2− + SeO32− + 3H2O | (1) |
The Se in an alkaline atmosphere becomes Se
2− and SeO
32− and Ni
2+ ions interacting with Se
2− create NiSe. The defects on the rGO matrix act as nucleation centers and help the growth of NiSe structures on rGO. In another study,
119 the NiSe nanoparticles on graphitic carbon nitride (g-C
3N
4) nanosheets were coated and the asymmetric supercapacitor with NiSe/g-C
3N
4//AC electrodes showed an energy density of 52.5 W h kg
−1 at 1488 W kg
−1 with a capacitance retention of 84.9% after 8000 cycles. This study reported the NiSe/g-C
3N
4 nanocomposite was created using the hydrothermal method and the obtained g-C
3N
4 was used during the procedure of NiSe fabrication and provided several active sites during the reaction. The reaction mechanism can be obtained from:
| Ni(CH3CO2)2·4H2O → Ni2+ + 2(CH3CO2)− + 4H2O | (3) |
| 2Ni2+ + 6N2H4 + 4OH− → 2[Ni(N2H4)3]2+ + 4OH− | (4) |
| 3Se + 6OH− → 2Se2− + SeO32− + 3H2O | (5) |
| [Ni(N2H4)3]2+ +Se2− → NiSe + 3N2H4 | (6) |
The surface charge distribution of g-C
3N
4 promotes the attachment of nanoparticles on its surface. In the reaction mechanism nickel acetate is dissociated into ions in the solution (
eqn (3)). The hydrazine hydrate helps in the reduction of Ni
2+ and dissolves Se powder in DI water (
eqn (4)). After dissolution the Se under highly basic pH conditions forms Se
2− ions (
eqn (5)). Then, the nickel complex and the Se
2− react together to form NiSe as a final product (
eqn (6)).
2.1.2. Ternary nickel cobalt sulfide/oxides and graphene composites.
Nickel and cobalt sulfides such as NiCo2S4 have emerged as exceptionally effective electrode materials for supercapacitors.120–125 Their selection stems from a combination of advantageous characteristics, including abundant availability of raw materials, remarkable electrochemical reactivity, superior electrical conductivity, weakened metal–sulfur bonds, and enhanced thermal stability. The growth of NiCo2S4 on the g-C3N4/rGO heterostructure as an electrode led to the high specific capacitance of 1938 F g−1 at a current density of 2 A g−1.120 NiCo2S4-β-cyclodextrin graphene composite has been used as an electrode with good characteristics due to the increase in the binding force between NiCo2S4 nanoparticles and substrates.121 The supercapacitor based on the NiCo2S4/Ni–Mo electrode exhibited a specific capacitance of 1346 F g−1.122
The composite of CoNi Hydroxide/NiCo2S4/rGO was synthesized by Guo et al.123 and showed attractive traits for the prepared supercapacitor of CoNi-LDH/NiCo2S4/rGO//AC. The cathode electrode of NiCo2S4/N, S co-doped graphene used in the supercapacitor device consisting of the graphene anode, demonstrated an outstanding energy density of 33.8 W h kg−1 and other characteristics.124 Abdel-Salam et al.125 employed the NiCo2S4/rGO nanocomposite with outstanding electrochemical behavior in the hybrid supercapacitor of NiCo2S4/rGO(+)//AC (−) with good electrochemical traits. Nickel cobaltite (NiCo2O4) has garnered attention as a promising energy storage material for electrochemical supercapacitors. It belongs to a new class of materials with favorable properties for energy storage applications. NiCo2O4 exhibits impressive electrochemical performance, including high specific capacitance, cycling stability, and rapid charge/discharge rates, enabling efficient energy storage and delivery. The abundance and cost-effectiveness of its constituents, nickel, and cobalt, make NiCo2O4 attractive for large-scale production. The combination of nickel and cobalt in NiCo2O4 synergistically enhances its electrochemical performance, leading to improved capacitance, conductivity, and stability, thereby advancing supercapacitor capabilities. NiCo2O4 holds promise for addressing energy storage challenges and plays a crucial role in advancing supercapacitor technology. The nanocomposite of graphene/NiCo2O4/MnOOH prepared by Yadav et al.,126 showed remarkable capacitive behavior for use in a novel coin cell supercapacitor device. NiCo2O4/ZnCo2O4/graphene/carbon nanotubes with significant electrochemical properties were combined with AC electrodes for preparing supercapacitors with good energy and power densities.127 That study presented a hybrid supercapacitor fabricated based on the NZ@GC and activated carbon electrodes, with an energy density of 50.8 W h kg−1 at a power density of 800 W kg−1. The fabrication process of NiCo2O4/ZnCo2O4@rGO/CNTs and the electrical properties of the hybrid supercapacitor are presented in Fig. 7.
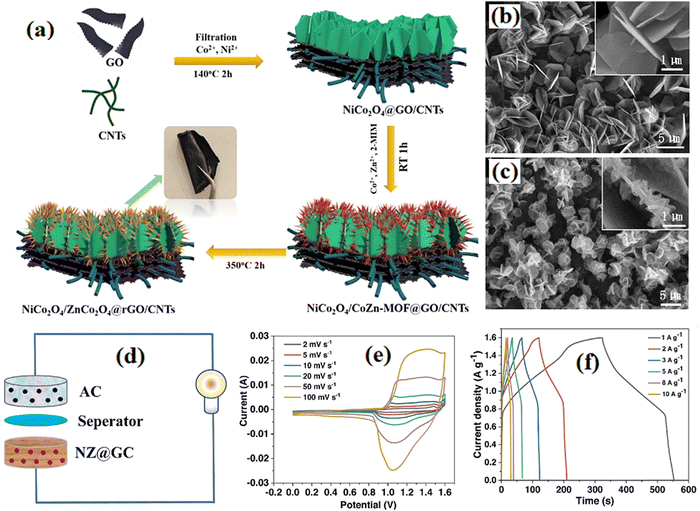 |
| Fig. 7 (a) Fabrication process of NiCo2O4/ZnCo2O4@rGO/CNTs. (b) SEM image of NiCo2O4@GO/CNTs. (c) SEM image of NiCo2O4/ZnCo2O4@rGO/CNTs film. (d) Assembly illustration of the NZ@GC//AC hybrid supercapacitor. (e) CV and (f) GCD curves of the supercapacitor.127 | |
An asymmetric supercapacitor based on the Fe-doped NiCo2O4/rGO hybrid (with highly electrochemically properties) delivered superb characteristics.128 This electrode was elaborated in hydrothermal and ultrasonic ways. An asymmetric supercapacitor device fabricated from GO/NiCo2O4/nano petals and in 1 M TEABF4 acetonitrile organic electrolyte.129 Nano-Ni cobaltate (NiCo2O4)/crumpled graphene microspheres (CGM) due to the porous spherical architecture and good dispersion displayed ideal electrochemical properties in the aqueous supercapacitor with a negative electrode of N-doped CGM (N-CGM).130 NiCo2O4/rGO composite with a hierarchical structure was fabricated using a facile one-step ultrasonic spray on Ni foam and directly used for supercapacitors in aqueous KOH electrolyte. Besides, the assembled NiCo2O4/rGO//AC supercapacitor displayed a maximum energy density of 29.3 W h kg−1 at 790.8 W kg−1.131 The obtained NiCo2O4/graphene electrode manifests a high specific capacitance as well as good steady electrochemical performances of the assembled supercapacitor under different tortuosity.132
The porous graphene/wood-derived carbon (GWC) aerogels were fabricated by chemical reduction of GO/wood hydrogels.133 An activated GWC anode was prepared by activating GWC using ZnCl2 while the cathode was synthesized by the growth of NiCo2O4 in the channels of GWC for use in a novel supercapacitor (with an areal capacitance of 7116 mF cm−2 at 1 mA cm−2). Nanoribbon-like NiCo2O4/rGO nanocomposites were prepared using an oxalate-assisted hydrothermal method with various rGO contents (10, 20, and 30 wt%).134 The NiCo2O4–30 wt% rGO//AC capacitor showed a high electrochemical characteristic. NiCo2O4/rGO nanosheets were assembled with the cement of KOH/polyacrylic acid, LiOTf/PAA, KOH/polyethylene oxide, and LiOTf/PEO into four structural supercapacitors.135 The (13%) NiCo2O4/rGO electrode presents the best areal capacitance. The corresponding supercapacitors showed superior electrochemical performances, e.g., areal capacitances of 330.4 mF cm−2.
2.1.3. Nickel hydroxide anchored graphene.
Nickel hydroxide (Ni(OH)2) is highly regarded as a cathode material for supercapacitors due to its superior electrochemical activity, well-understood reaction mechanism, and cost-effectiveness. Its excellent electrochemical activity facilitates efficient charge transfer, enabling effective energy storage and release. A clear understanding of its reaction mechanism aids in optimizing supercapacitor system design for enhanced performance. Additionally, its affordability compared to other electrode materials makes it economically viable for large-scale production and widespread adoption of supercapacitor technology. Ni(OH)2 has emerged as a promising choice for supercapacitor cathodes. The enhanced electrochemical results have been obtained in Ni(OH)2:polyaniline/rGO/acetic acid composites using 0.4 M CH3SO3H as the supporting electrolyte for 0.4 M H2SO4 as tabulated in ref. 136. The specific capacitance of the Ni(OH)2/rGO electrode was found to be remarkable and its combination with active carbon led to a supercapacitor with a high energy density.137 A supercapacitor based on the Ag/GN/polypyrrole–Ni(OH)2//AC electrodes showed a specific capacity of 237.25 C g−1 1 M potassium hydroxide (KOH) solution with the observable specific capacity used in the supercapattery containing AC as a (−) electrode displaying an eminent energy density of 43.26 W h kg−1.138 This particular configuration yielded an outstanding energy density of 43.26 W h kg−1, accompanied by a corresponding power density of 750 W kg−1, achieved at a current density of 1.0 A g−1. Moreover, that paper exhibited the cyclic stability of the supercapattery exceptional performance with a high cyclic stability of 108.37% even after enduring 5500 cycles. Fig. 8 shows the electrical properties of the Ag/GN/PPy–Ni(OH)2//AC supercapacitor. The nanocomposite of Ni(OH)2 nanoplates/highly-oxidized GO (HGO) was employed by Wu et al.139 in a Ni(OH)2/HGO//AC supercapacitor showing outstanding electrochemical properties. The electrode prepared by applying a constant potential to the Ni fiber in the alkaline solution containing GO was used in the supercapacitor of Ni(OH)2/Ni foam//AC/Ni foam and showed a high specific capacitance of 543.6 mF cm−2.140 Pseudocapacitive materials are significant to the development of energy storage devices despite usually suffering from poor conductivity. A study showed the specific capacitance of Ni(OH)2/GO electrode was 4.3 times higher than that of the pure Ni(OH)2.141 That study displayed the asymmetric supercapacitor with Ni(OH)2/HGO//AC electrodes exhibited an energy density of 0.134 mW h cm−2 and 33.6 mW cm−2. Also, the electrochemical performances of Ni(OH)2, Ni(OH)2/GO, and Ni(OH)2/HGO electrodes are evaluated with 6 M KOH as the electrolyte and observed a typical pseudocapacitive nature with the following reaction of:142 | Ni(OH)2 + OH− ↔ NiOOH + H2O + e− | (7) |
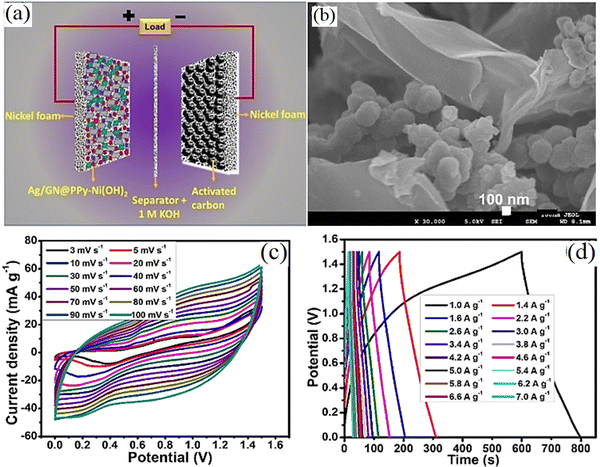 |
| Fig. 8 (a) Schematic of supercapattery structure. (b) SEM image. (c) C–V curves. (d) Discharge curves of the Ag/GN/PPy–Ni(OH)2//AC supercapattery.138 | |
Lai et al.143 prepared an asymmetric supercapacitor with rGO/Ni(OH)2 electrode, in which rGO has some oxygen-containing functional groups that supply more sites for Ni(OH)2. They achieved an energy density, power density, and specific capacitance of 1670.4 F g−1, 54.1 W h kg−1, and 1 kW kg−1 respectively, and also reported the good pseudocapacitance of Ni(OH)2 is due to its rapid reversible redox reaction on the surface (eqn (7)).
2.2. Carbon nanotube-based nickel composites
Yousefipour et al.144 prepared MWCNTs/NiMoO4 using blending and ball-milling and it delivered outstanding supercapacitive properties because of its fast kinetics, outstanding conductivity, good surface area, and many active sites. The CNT incorporation into NiMn sulfide (NiMnS) led to the NiMnS/CNTs composites and significantly improved the storage capacity. The supercapattery was designed using NiMnS75/CNTs25 as the anode and an AC cathode with an outstanding specific capacity.145 A flexible FSC was prepared based on carbon fiber/multi-layer alternating Ni–Al layered double hydroxide/mono-dispersed CNTs ([Ni–Al LDH-x/CNTs-y]/CF) as the (+) electrode, and tremella-derived AC/CF as the (−) electrode. This structure benefits from mechanical stress release, effective ion diffusion, rapid electron transfer, and high-quality loading resulting in the meaningful characteristics.146 The highly redox-active octamethyl-substituted Ni(II)phthalocyanine (NiMe2Pc)/CNTs-COOH dendritic nanocomposite provides rapid electron/electrolyte ion-transport pathways and represents excellent structural stability, resulting in highly-impressive cycling stability and capacity activity. The optimized weight ratio of NiMe2Pc
:
CNTs-COOH (6
:
10) showed the highest specific capacitance of 330.5 F g−1 at 0.25 A g−1. The SC device containing this electrode showed excellent performance with a maximum energy density of 22.8 W h kg−1 and outstanding cycling stability (111.6% retained after 35
000 cycles).147 Also, between the Ni phosphate (NiP)/MWCNTs (10, 30, and 50 wt%) samples, NiP50CNT50 revealed a better specific capacity of 845 C g−1 at 0.6 A g−1 and better supercapacitor performance with a specific capacity of 400 C g−1 at 0.4 A g−1.148 In another study, the MWCNTs/Ni–Mn–S were prepared and achieved excellent properties. The as-prepared MWCNTs/Ni–Mn–S (3
:
2) exhibit a specific capacitance of 1041 mA h g−1 at 1 A g−1 and good cycling stability. The MWCNT/Ni–Mn–S (3
:
2)//AC supercapacitor also showed outstanding cycling stability of 93.3%/20
000.149
2.2.1. Carbon nanotubes decorated with nickel cobalt.
A high-performance supercapacitor can be created by integrating Ni materials/CNTs. This combination enhances the energy storage capacity and facilitates rapid charge transfer. The supercapacitor exploits the reversible redox reactions of the Ni materials and the conductivity of CNTs to store and release charge efficiently. Through careful optimization of synthesis methods, electrode designs, and electrolyte selection, a powerful Ni-material/CNT-based supercapacitor can be developed. Su et al.150 prepared P-doped Ni–Co sulfides (P-NCS)/C/CNT composites by gas-solid phosphorization that revealed high specific capacity (932.0 C g−1 at 1 A g−1) and remarkable rate capability and also were used in flexible supercapacitors containing AC (as an opposite electrode), which exhibited high energy and power densities. Alternatively, the composites of NiCo-P (phosphate)/CNTs/lightweight carbonized wood were synthesized by chemical vapor deposition and electrodeposition showing a promising notable capacitance retention and rate areal capacitance. Also, its usage in supercapacitors composed of self-activated carbonized wood (SCW) electrodes as a cathode delivered outstanding traits.151 CNTs/Ni–Co sulfide composites exhibited the synergy between the components. It was used by Huang et al.152 as a positive electrode with a high specific capacity of 734 C g−1 in the supercapacitor of CNTs/Ni–Co–S-3//AC HSC with an energy density of 42.15 W h kg−1 and long-term stability. Another study reported an asymmetric fiber-shaped FSC made of carbon fiber, Ni–Co layered double hydroxide, and mono-dispersed CNTs (Ni–Co LDH-x/CNTs-y/CF) as the positive electrode and tremella-derived activated carbon/CF (TDC-z/CF) as the negative electrode. The prepend FSC achieved a high energy density of 26.20 W h kg−1 and a superior cycling stability of 112.5% over 5000 cycles.153 A supercapacitor based on the NiCo-phosphide/NiCo-layered double oxide-CNTs (NCP/LDO-CNTs) composite showed a specific capacity of 901.2 mA h g−1.154 The porous NiCo nanoparticles/N-doped CNTs/carbon cloth/NiCo hydroxide was prepared so that NiCo@NCNTs can act as a good conductor and structural scaffold to grow NiCo-LDH nanosheets. It displayed novel electrochemical traits as a (+) electrode. Also, its usage in a supercapacitor with a Co(OH)2/NiCo@NCNTs/CC negative electrode led to 52.8 W h kg−1 of energy density.155 Yuan et al.156 investigated a supercapacitor based on the Ni–Co–Se/C-CNTs electrode and achieved a specific capacitance of 1108.2 F g−1. They mentioned the power and energy densities of Ni–Co–Se/C-CNTs//AC supercapacitors were 38.2 W h kg−1 and 1602.1 W kg−1, respectively. Fig. 9 shows the electrical properties of the Ni–Co–Se/C-CNTs//AC supercapacitors.
 |
| Fig. 9 (a) Schematic of the supercapacitor structure. (b) SEM image. (c) C–V curves. (d) Discharge curves of the Ni–Co–Se/C-CNTs//AC supercapacitor.156 | |
2.2.2. Ternary nickel cobalt sulfide/oxides and carbon nanotube composites.
The electrochemical properties of supercapacitors on the basis of Ni materials and CNTs composite electrodes are reported in Table 2144–163 The nanocomposite CNTs/NiCo2S4 showed remarkable capacitive properties. In the structure of the asymmetric supercapacitor, it exhibited energy and power densities of 43.3 W h kg−1 and 800 W kg−1. The exceptional electrochemical capacity is attributed to the enhanced conductivity, refined grains, and structural features.157 NiCo sulfide (NiCo2S4) was prepared with the help of a shadow mask printing method on a flexible PET substrate using homemade ink comprised of PTFEm, CNTs, NiCo2S4, carbon nanotubes, and terpineol. The NiCo2S4 electrode revealed a high specific capacitance of 1401 F g−1 while the device delivered a value of 13.6 mF cm−2.158 A typical battery-type electrode of NiCo2S4/CNTs prepared by Yao et al.159 exhibited an ultrahigh specific capacitance of 1123 F g−1 at 0.5 A g−1, superior stability, and good energy storage ability. A supercapacitor constructed from this electrode (cathode) and treated carbon cloth (anode) showed a high energy density of 11.7 W h kg−1 with good cycling stability. The porous NiCo2S4 nanosheet/conductive carboxylated CNTs (CNTs-h-COOH) composite was synthesized and the deposition potential and time played important roles in influencing the morphology and electrochemical performance of the composite. This electrode and a supercapacitor contained commercial AC (as the anode) resulting in outstanding specific capacity and energy density.160 In the case of N-doped CNTs/NiCo layered double hydroxides(N-CNTs/NiCo-LDH), the samples of N-CNTs/Ni1Co2-LDH had the best electrochemical performance. Also, the N-CNTs/Ni1Co2-LDH(+)//AC(−) supercapacitor had a high energy density of 27.19 W h kg−1 at 750 W kg−1.161 The bimetal oxide (NiCoO2)/CNTs with a novel mesoporous grape-like structure were prepared that due to the synergistic effect, showed impressive properties. The supercapacitor (NiCoO2/CNTs//AC) exhibited an outstanding cycling property with 92% maintained after 5000 cycles.162 A kapok-derived proper-curved quasi-2D carbon tile (CT)/SWNTs/NiCo2O4 electrode was constructed via a scalable and controllable extrusion-based 3D printing strategy. A corresponding supercapacitor delivered a high specific capacitance (588 mF cm−2) and superior capacity even at large electrode thickness.163 Transition metal sulfides are promising electrodes due to the high conductivity and lower electronegativity of sulfur. Sammed et al.164 fabricated a composite of carbon nanocoils/nickel foam (CNCs/NF) substrate that was decorated with nickel cobalt sulfide (NiCoSx) nanosheets and CNTs. They elucidated that the specific capacitance of the CNTs/NiCoSx/CNCs/NF electrode was 3184 F g−1 with a capacitance retention of 97.2% after 3000 cycles. The redox reactions of NiCo2O4 and NiCo2S4 in the alkaline electrolyte can be obtained from:165 | NiCo2O4 + OH− + H2O → NiOOH + 2CoOOH + 2e− | (8) |
| CoOOH + 2OH− → NiSOH + 2CoSOH + 2e− | (9) |
| NiCo2S4 + 2OH− → NiSOH + 2CoSOH + 2e− | (10) |
| CoSOH + OH− → CoSO + H2O + e− | (11) |
Table 2 The electrochemical results collected from various studies done on Ni/CNT nanocomposites
Material |
Capacitance retention (CR%/Cycle) |
Specific capacitance (F g−1) |
Energy density (W h kg−1) |
Power density (W kg−1) |
Ref. |
NiMoO4/CNTs |
86.8/2000 |
727.2 |
40.9 |
918.5 |
144
|
NiMnS75/CNTs |
— |
1188 C g−1 |
9 |
1600.8 |
145
|
Ni/CNTs |
124.8/5000 |
1800 |
35.6 |
7531.90 |
146
|
NiMe2Pc/CNTs |
95.4/35 000 |
330.5 |
52.1 |
— |
147
|
Ni phosphate/CNTs |
— |
845 C g−1 |
94.4 |
340 |
148
|
Ni–Mn/CNTs |
83.3/10 000 |
1041 mA h g−1 |
25.33 |
829 |
149
|
Ni–Co sulfides/CNTs |
— |
932.0 C g−1 |
34.875 |
375 |
150
|
Ni–Co phosphate/CNTs |
92.4/10 000 |
11.2 F cm−2 |
12.1 |
39.5 |
151
|
Ni–Co–S-3/CNTs/AC |
88.46/10 000 |
734 C g−1 |
42.15 |
852 |
152
|
Ni–Co/CNTs |
112.5/5000 |
— |
26.20 |
7569.23 |
153
|
Ni–Co phosphide/CNTs |
117.4/4500 |
1888 |
21.3 |
748.5 |
154
|
Ni–Co/CNTs |
100/8000 |
1898 mF cm−2 |
52.8 |
— |
155
|
Ni–Co–Se/C-CNTs |
96.4/5000 |
1108.2 |
38.2 |
1602.1 |
156
|
NiCo2S4/CNTs |
83.5/5000 |
890 C g−1 |
43.3 |
800 |
157
|
NiCo2S4/PET/CNTs/PTFE |
90/3000 |
13.6 mF cm−2 |
2.1 μW h cm−2 |
0.189 mW cm−2 |
158
|
NiCo2S4/CNTs |
|
443 F cm−3 |
11.7 |
1320 |
159
|
NiCo2S4/CNT |
96.08/10 000 |
2498.12 |
76.47 |
201.01 |
160
|
NiCo2/CNTs |
76.4/2500 |
1311.8 |
27.19 |
750 |
161
|
NiCoO2/CNTs |
92/5000 |
1587 |
41.8 |
412 |
162
|
NiCo2O4/CNTs |
82/50 000 |
588 mF cm−2 |
138 μW h cm−2 |
— |
163
|
2.3. Dispersion of Ni materials in porous carbon
Table 3
166–181 demonstrates that supercapacitor electrodes based on a combination of Ni materials and porous carbon materials are widely used to enhance energy storage applications. Porous carbon, such as activated carbon or carbon nanotubes, provides a large surface area for electrochemical reactions and ion adsorption. Ni materials offer excellent electrical conductivity and redox properties. The performance of the supercapacitor is evaluated using tests like cyclic voltammetry and galvanostatic charge–discharge cycling. Panicker et al.166 synthesized porous carbon self-repairing g-C3N4 (pCCN)/NiCo2S4 for supercapacitor electrodes that showed a remarkably high specific capacitance. The constructed pCRNCS//AC exhibited a remarkable capacitance retention of 93.6% and 6000 cycles and an energy density of 66 W h kg−1. The porous and three-dimensional AC (BPC) was prepared by calcining and etching the Platanus fluff. The NiCo2S4/BPC electrode displayed a better characteristic than that of the pure NiCo2S4. The supercapacitor of NiCo2S4/BPC displayed a high energy density and superior cycling stability.167 N-doped lignite-based porous carbon (NPC)/CoNi2S4 (CoNi2S4/NPC) as the electrode material displayed excellent specific capacitance and good cycle performance. The supercapacitor of CoNi2S4/NPC (cathode)//AC (anode) demonstrated an energy density of 48.58 W h kg−1 and power density of 400 W kg−1, with a capacitance retention of 82.42% after 5000 cycles.168 Wang et al.169 synthesized the composites of NiCo2O4-4x nanowires (O vacancies-rich)/porous carbon (derived from discarded cigarette ash) named Ov-NCO/PC-Y resulting in a superior specific capacitance of 1002.2 F g−1. Moreover, the Ov-NCO/PC-0.1//AC-based supercapacitor delivered an elevated energy density. N-doped porous carbon nanofiber/NiCo2O4 nanoneedles (NiCo2O4/NPCNFs) electrode materials resulted in a competitive specific capacitance as well as good rate performance (78.0% at 10 A g−1). Also, the corresponding supercapacitors exhibited a high energy density.170
Table 3 The electrochemical results collected from various studies done on Ni/porous carbon nanocomposites
Electrode material |
Capacitance retention (CR%/cycle) |
Specific capacitance (F g−1) |
Energy density (W h kg−1) |
Power density (W kg−1) |
Ref. |
NiCo2S4/porous carbon/g-C3N4/rGO |
93.6/6000 |
211 |
66 |
751 |
166
|
NiCo2S4/porous carbon |
— |
175 |
38.5 |
738.1 |
167
|
CoNi2S4/porous carbon |
82.42/5000 |
1534.24 |
48.58 |
400 |
168
|
NiCo2O4/porous carbon |
— |
1002.2 |
32.7 |
160.2 |
169
|
NiCo2O4/porous carbon |
78/— |
1474.2 |
53 |
— |
170
|
NiCo2O4/porous carbon |
80/— |
1730 |
56.1 |
349 |
171
|
NiFe2O4/porous carbon |
90.2/10 000 |
2894 |
135.2 |
10 040 |
172
|
NiMoO4/porous carbon |
90.7/3000 |
1600 |
55.33 |
999.89 |
173
|
Ni–Co/porous carbon/GO |
92.6/3000 |
407.5 |
12.32 |
499.99 |
174
|
Ni–Co/porous carbon |
90.76/3000 |
1504 |
33.33 |
— |
175
|
Ni–Co/porous carbon |
60/— |
250 |
78 |
— |
176
|
Ni–Co/porous carbon |
87.87/10 000 |
415 |
35.6 |
500.1 |
177
|
Ni–sulfide/porous carbon |
95.7/10 000 |
360 |
19.65 |
450 |
178
|
Ni–cobalt/porous carbon |
75.9/4000 |
2390 |
52.47 |
375 |
179
|
Ni-MXene/porous carbon |
81.7/30 000 |
152.6 |
47.6 |
375 |
180
|
Ni(OH)2-MXene/porous carbon |
90/5000 |
— |
29.3 |
800 |
181
|
A supercapacitor based on the porous carbon-NiCo2O4 electrode was reported in ref. 171. This report determined the specific capacitance of the supercapacitor to be 1730 F g−1 with energy and power densities of 56.1 W h kg−1 and 349 W kg−1 respectively. Fig. 10 shows the electrical properties of the supercapacitor based on the porous carbon–NiCo2O4 electrode. Ni ferrite nanoparticle/carboxymethyl cellulose-derived porous carbon (NiFe2O4/CPC) was prepared so that the best-performing sample (NiFe2O4/CPC-800) exhibited a superior capacitance. A supercapacitor with (+) electrode of NiFe2O4/CPC-800 and AC (−) electrode delivered a high characteristic.172 Yan et al.173 produced the NiMoO4 (nanosheet-like)/Porous sub microfibers (HPCMFs) showing good electrochemical characteristics. A supercapacitor containing NiMoO4/HPCMFs electrodes showed a high flexibility and energy and power density.
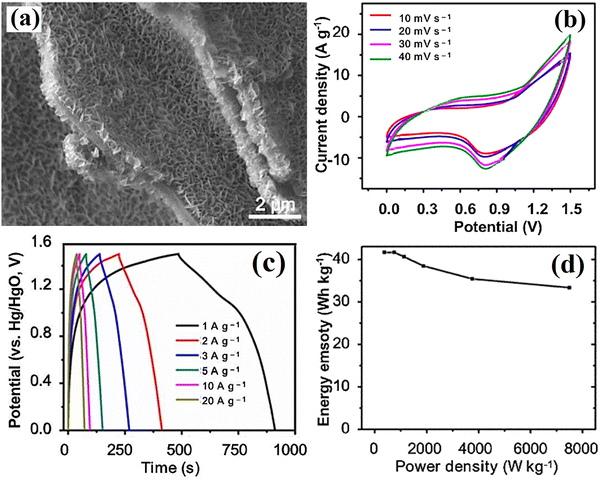 |
| Fig. 10 (a) SEM image, (b) C–V curves, (c) discharge curves, and (d) energy and power densities of the supercapacitor based on the porous carbon–NiCo2O4 electrode.171 | |
The mixture of lignin-removed poplar powder, graphene oxide, melamine, diammonium hydrogen phosphate, and nickel sulfate was carbonized and activated with KOH for preparing a porous carbon material with a pore volume of 0.93 cm3 g−1 and a surface area of 1214.1 m2 g−1. The prepared sample showed good performances such as outstanding power and energy densities for a supercapacitor.174 A highly graphitized N self-doped hierarchical porous carbon aerogel (HPCA) was prepared using biomass chitosan particles as the precursor and then composited with NiCo double hydroxide (NiCo-LDH) nanosheets. A NiCo-LDH/HPCA-30 composite was designated as an optimized sample with the highest electrochemical performance.175 The biomass lignin-derived and N-doped carbons (LPCs), i.e., the activated N-doped LPCs (N-LPCs) with the porous microstructure (BET surface area: 1990.49 m2 g−1) were synthesized and showed excellent electrochemical parameters. Also, as an anode, it was used in a supercapacitor combined with the cathode of NiCo double hydroxide (NiCo-LDH) and demonstrated an excellent specific capacitance.176 The green cellulose-based N/Ni co-doped porous carbon (PC) was prepared with a high specific surface area and total pore volume and outstanding specific capacitance and excellent cycling stability. Also, the form of supercapacitor led to an energy density of 35.6 W h kg−1.177
Ni sulfide composite with porous carbon (Ni3S2/HPCs) derived from coke solid waste was synthesized. The optimized Ni3S2/HPC-3 exhibited a high capacitance of 360 F g−1 and its existence in the supercapacitor structure led to a high cycle stability and energy density.178 In another study, hydrophilic NiCo/layered double hydroxides (LDHs)/biomass waste-derived porous carbon (BC) was prepared. Due to the ultrathin thickness of LDHs, large specific surface area, low charge transfer resistance, and high wettability with electrolyte, the Ni2Co1-LDHs/BC50 electrode revealed an ultra-high S.C. and the Ni2Co1-LDHs/BC50//YP-80F HSC delivered a maximum specific energy of 52.47 W h kg−1.179 Nanda et al.180 synthesized Ni MXene (cathode) and Euphorbia milii plant leaf-originated and N, S, P self-doped AC (EMAC-700) (anode). NiMX and EMAC-700 delivered high capacitances of 474.3 and 575.8 F g−1, respectively, attributed to the pseudo nature of NiMX, the presence of heteroatoms, and the large surface area of EMAC-700. The prepared supercapacitor also showed a 152.6 F g−1 capacitance as well as an ultrahigh energy density of 47.6 W h kg−1. Alternatively, 50MXene/50Ni(OH)2 was developed as the α-Ni(OH)2 petals are slid within the MXene structure for use as a cathode in combination with the biomass-derived porous carbon as the anode in the supercapacitor system. The good electrochemical performance was manifested (energy density of 29.3 W h kg−1, and capacitance retention of 90% after 5000 cycles) for this supercapacitor.181
2.4. Ni materials//active carbon-based asymmetric supercapacitors
Active carbon, with its high surface area and porosity, finds significant application as an electrode material in supercapacitors. Its porous structure allows for efficient ion adsorption, resulting in enhanced capacitance. Active carbon electrodes enable rapid charge and discharge, making them suitable for applications requiring high power output and quick response times. They contribute to the overall energy density of supercapacitors, albeit lower than batteries, by delivering a significant amount of energy in short bursts. Active carbon exhibits excellent stability and longevity, ensuring a long cycle life and reliable performance of the supercapacitor electrodes. These electrodes have been instrumental in the development of high-performance supercapacitors used in energy storage systems, portable electronics, hybrid vehicles, and renewable energy technologies. The various supercapacitors based on the Ni materials//active carbon electrodes have been employed in electrochemical applications, and the novel results of the reported papers are tabulated in Table 4.182–219 The utilization of active carbon in supercapacitors highlights its valuable role in improving energy storage capabilities and supporting advancements in various fields where efficient power delivery and rapid energy transfer are essential. Ni(OH)2/ZIF-67-derived CoS core/carbon cloth (Ni(OH)2/CoS/CC) was used in the supercapacitor of Ni(OH)2/CoS/CC (cathode)//AC (anode) that revealed a remarkable energy density as well as its excellent electro-catalytic activity towards methanol oxidation.182 La/Ni(OH)2 nanosheets were prepared and the La–Ni(OH)2(0.3) with 0.3 mmol of the La showed the best electrochemical traits. La–Ni(OH)2(0.3)//AC delivered an energy density of 47.5 W h kg−1 and excellent stability of 89.3% after 2000 cycles.183 Flower-like Zn-doped Ni(OH)2/CNTs were synthesized assisted by cetyltrimethylammonium bromide (CTAB) and NaBH4. This electrode showed prominent electrochemical properties and the supercapacitor of Zn doped Ni(OH)2@CNTs(+)//(−)AC exhibited high electrochemical performance.184 A 3D 2-nodal (3,8)-c tfz-d metal–organic framework (MOF 1) of {[Co1.5(TCPB)(1.3-bomb)0.5·(DMF)·(dioxane)1.5]}n has been synthesized and calcined at 700 °C under a N2 atmosphere to obtain Co/C composite (NC1). 2D flake Ni(OH)2 was coated on the surface of NC1 to prepare Ni(OH)2/NC1 (NC2). The specific capacitances of 866.8 F g−1 for the NC2-based electrode were more than three times as much as that of the NC1-based electrode (264.5 F g−1). The supercapacitor of AC (−)//(+) NC2@NF showed an energy density of 39.7 W h kg−1.185
Table 4 The electrochemical results collected from supercapacitors with Ni//active carbon electrodes
Electrode material |
Capacitance retention (CR%/cycle) |
Specific capacitance (F g−1) |
Energy density (W h kg−1) |
Power density (W kg−1) |
Ref. |
Ni(OH)2/CoS/CC//AC |
— |
561.6 mA h g−1 |
90.8 |
800 |
182
|
Ni(OH)2-La//AC |
89.3/2000 |
1510.7 |
47.5 |
375 |
183
|
Ni(OH)2/CNTs/Zn//AC |
— |
750.5 C g−1 |
51.3 |
409.6 |
184
|
Ni(OH)2/Co/C//AC |
97.3/1000 |
866.8 |
39.7 |
213.1 |
185
|
Ni3Se2–Li2//AC |
92/3000 |
236 mA h g−1 |
77 |
4000 |
186
|
Ni3S2/Co9S8//AC |
80.8/10 000 |
9.79 F cm−2 |
0.63 mW h cm−2 |
1.66 mW cm−2 |
187
|
Ni3S4/MnCo2O4//AC |
— |
904.7 C g−1 |
50.7 |
405.8 |
188
|
Ni3S2–Co3S4/Ni foam//AC |
92.8/2000 |
2825.5 mF cm−2 |
40.9 |
1566.4 |
189
|
Ni-MOF/polypyrrole//AC |
90.2/3000 |
1815.4 |
38.5 |
7001 |
190
|
Ni-MOF/C//AC |
100/5000 |
828 |
23.84 |
849.74 W g−1 |
191
|
Ni–Co-MOF//AC |
82.4/7000 |
832.6 C g−1 |
45.3 |
7160 |
192
|
NiCoS/NiMo//AC |
54/— |
1302.5 μAh cm−2 |
1096.6 μW h cm−2 |
2.8 mW cm−2 |
193
|
SnNiCoS//AC |
82.9/8000 |
18.6 F cm−2 |
937.2 μW h cm−2 |
4000 μW cm−2 |
197
|
NiMn/CuCo2O4//AC |
94.6/2500 |
2156.53 |
92.2 |
730 |
198
|
NiCo2O4@NiCo2O4//AC |
83.6/5000 |
1398.73 |
46.46 |
269.77 |
199
|
Ni–Mn–S/rGO//AC |
77.78/5000 |
2042.22 |
77.95 |
750 |
200
|
NixMn1−x(OH)2//AC |
94.4/3000 |
758.7 |
40.7 |
800 |
201
|
NixCoy(OH)2/Co(BO2)2//AC |
98/10 000 |
2257 |
56.5 |
800 |
202
|
Ni–Co//AC |
92.5/10 000 |
2458.1 |
62.7 |
714.3 |
203
|
Ni–Co//AC |
90.5/— |
3483 |
34.6 mW cm−2 |
— |
204
|
Ni–Co–P(6)//AC |
— |
1384 |
51.2 |
749.8 |
205
|
Ni–Co//AC |
91/5000 |
325.6 mA h g−1 |
50.5 |
750 |
206
|
Ni–Co/NF/MnCo2O4//AC |
78.7/5000 |
4555 |
21.3 |
160 |
207
|
Ni–Co/ZnO//AC |
86.78/2000 |
667.3 mF cm−2 |
0.044 mW h cm−2 |
1.17 mW cm−2 |
208
|
NiCoZnSx//AC |
80/10 000 |
1928 |
270 μW h cm−2 |
80.3 mW cm−2 |
208
|
NiCoP/CC//AC |
99.7/10 000 |
1149.2 C g−1 |
78.5 |
799.5 |
210
|
NiCoP//AC |
90.2/10 000 |
1088.9 C g−1 |
78.2 |
799.9 |
211
|
NiCoAl//AC |
87.5/10 000 |
23.85 F cm−2 |
3.29 mW h cm−2 |
18 mW cm−2 |
212
|
NiCoMn/C//AC |
92.05/5000 |
888.3 C g−1 |
46.5 |
792.5 |
213
|
NiCo2S4//AC |
81/10 000 |
857 C g−1 |
48.7 |
801 |
214
|
NiCo2S4/Co9S8//AC |
62.8/— |
1026 |
30 |
731.8 |
215
|
NiCo2S4//AC |
88.9/5000 |
559.3 C g−1 |
28.8 |
375.0 |
216
|
NiCo2O4//AC |
80.9/3000 |
2690 |
52.6 |
1100 |
217
|
NiCo2O4–In/CF//AC |
89.3/10 000 |
2375.1 |
60.2 |
985.5 |
218
|
NiCo2O4/MXene//AC |
— |
73.8 |
94.46 |
2882.0 |
219
|
The optimized pre-lithiated Ni3Se2 cathode (Li2–Ni3Se2) was prepared and presents a high specific capacitance of 236 mA h g−1as well as excellent cycling stability of 92% after 3000 cycles. It is far superior to other battery-type TMC cathodes reported in previous studies. The supercapacitor Li2–Ni3Se2//AC delivered a high energy density of 77 W h kg−1 and high capacitance retention.186 The hollow Ni3S2/Co9S8 (NiS/CoS) were prepared with a high active area and showed remarkable electrochemical properties. The supercapacitor of NiS/CoS(+)//AC(−) achieved a high energy density of 0.63 mW h cm−2.187 The MnCo2O4/Ni3S4 nanocomposite was prepared to solve the low MnCo2O4 electrical conductivity. The high performances of this electrode and its supercapacitor with active carbon were observed.188 Co3S4–Ni3S2 on Ni foam (NF) with the assistance of a chelating agent sodium 5-sulfosalicylic (SSS) (CS4–Ni3S2/F-SSS) revealed a specific capacitance of 2825.5 mF cm−2. Moreover, the supercapacitor of CS4–Ni3S2/F-SSS//AC/NF represents an energy density of 40.9 W h kg−1 with excellent durability.189
Ni-based metal–organic framework (Ni-MOF)/polypyrrole (PPy) had a specific capacitance of 1815.4 F g−1 and Ni-MOF/PPy(+)//(−)AC supercapacitors can provide capacitance retention of 90.2% after 3000 cycles, an energy density of 38.5 W h kg−1 and power density of 7001 W kg−1.190 Ni-metal–organic framework (MOF)/nanocarbon (NC) electrode materials were synthesized and delivered 828 F g−1. The supercapacitor of Ni-MOF/NC//AC showed a capacitance retention of 100% after 5000 cycles.191 A hydrangea-like NiCo-MOF (metal–organic framework) was well prepared revealing superior gravimetric capacity (832.6 C g−1 at 1 A g−1). The supercapacitor of NiCo-MOF (cathode)//AC (anode) delivered a desirable energy density (45.3 W h kg−1) and a favorable power density (7160.0 W kg−1).192 The NiCoS(sulfur)/NiMo-LDH electrode exhibited a very high capacitance of 1302.5 μAh cm−2. The supercapacitor of the NiCoS/NiMo-LDH//AC exhibited an energy density of 1096.6 μW h cm−2.193 Tao et al.194 encapsulated iron carbide nanoparticles into carbon nanofibers (Fe3C@CNF-650), and then nickel–cobalt sulfide nanoparticles were grown on electrospun carbon nanofibers (CNF@NiCoS-650). The conductivity of carbon nanofibers facilitates Faradaic charge transport. They reported the asymmetric supercapacitor with Fe3C@CNF-650 (−)//CNF@NiCoS-650 (+) electrodes achieved an energy density of 43.2 W h kg−1 at 800 W kg−1. The electrochemical processes involve fast reversible redox reactions of Ni2+/Ni3+, Co2+/Co3+, and Co3+/Co4+ reacting with OH− anions and can be obtained from:185–196
| NiS + OH− ↔ NiSOH + e− | (12) |
| CoS + OH− ↔ CoSOH + e− | (13) |
| CoSOH + OH− ↔ CoSO + H2O + e− | (14) |
SnNiCoS sulfide in the supercapacitors showed the best performance in that a specific capacitance of 18.6 F cm
−2 and an energy density of 937.2 μW h cm
−2 was achieved.
197 Zhao
et al.198 prepared the CuCo
2O
4@NiMn LDH//AC as supercapacitor electrodes and exhibited a specific capacity of 2156.53 F g
−1 with a rate capability retention of 94.6% after 2500 cycles. A supercapacitor based on the NiCo
2O
4@NiCo
2O
4//AC electrodes is reported in ref.
199. That paper reported that the energy density of the supercapacitor was 46.46 W h kg
−1 and the power density was 269.77 W kg
−1.
Fig. 11 shows the electrical properties of the supercapacitor based on the CuCo
2O
4@NiMn LDH//AC and NiCo
2O
4@NiCo
2O
4//AC electrodes.
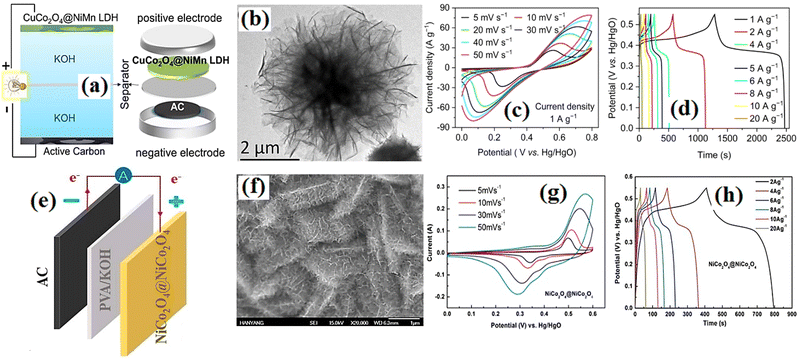 |
| Fig. 11 (a) Graphical structure. (b) TEM image. (c) C–V curves. (d) Discharge curves of CuCo2O4@NiMn LDH//AC supercapacitor.197 (e) Graphical structure. (f) SEM image. (g) C–V curves. (h) Discharge curves of the NiCo2O4@NiCo2O4//AC supercapacitor.199 | |
The optimized Ni–Mn–S/rGO composite revealed a superior specific capacitance of 2042.22 F g−1 and the supercapacitor prepared by using this electrode showed a high energy density of 77.95 W h kg−1 with good cycle stability.200 The optimal composition of Ni3/4Mn1/4(OH)2 hydroxide showed a capacitance of 758.7 F g−1. While the Ni3/4Mn1/4(OH)2//AC supercapacitors exhibited a high energy density of 40.7 W h kg−1 capacitance retention of 94.4% after 3000 cycles.201 2D Ni–Co hydroxide/BO2 ((NixCoy)(OH)2/Co(BO2)2) was prepared and the optimized electrode of (Ni0.5Co0.5)(OH)2/Co(BO2)2 delivered a remarkable specific capacitance of 2257 F g−1. The (Ni0.5Co0.5)(OH)2/Co(BO2)2//AC supercapacitors provided a high energy density and excellent cyclic stability.202
2.4.1. Nickel cobalt composite//active carbon-based asymmetric supercapacitors.
The optimal honeycomb NiCo-LDH (layered double hydroxide)/carbonized polydopamine (PDA-C/NiCo-LDH) exhibited a high capacitance along with superior rate performance and cyclic stability. PDA-C/NiCo-LDH(cathode)//AC(anode) exhibited a high energy density of 62.7 W h kg−1 and exceptional cyclic performance of 10
000 cycles with a capacitance retention of 92.5%.203 Gamma-phase Ni–Co oxyhydroxides were prepared and displayed a high electrical properties. Ni–Co oxyhydroxides//AC showed an ultrahigh energy density of 92.6 W h kg−1 and capacitance retention of 91% after 7000 cycles.204 NiCo-metal–organic frameworks (MOF) micro flowers possessed a high specific capacitance. Also, NiCo-P was prepared via a low-temperature phosphating method using the precursor of NiCo-MOF micro flowers. The NiCo-P(6) revealed the superior rate capability with the specific capacitances. NiCo-P(6)//AC supercapacitor exhibited a high energy density and outstanding cycling stability.205 NiCo double hydroxide (NiCo-DH)/MOF was prepared and showed an electrode ultrahigh specific capacitances capacitance of 325.6 mA h g−1. As a cathode for NiCo-Zn batteries, it exhibited high specific capacitances while the NiCo-DH//AC supercapacitor exhibited a remarkable performance.206 A core-sheath of MnCo2O4/NiCo-layered double hydroxide (NiCo-LDH)/Ni foam (MnCo2O4/NiCo-LDH/NF) has been prepared and used as a cathode in supercapacitors that led to the specific capacitances of 4555.0 F g−1. Also, the MnCo2O4/NiCo-LDH/NF//AC supercapacitor exhibited an outstanding energy density and can light up the green LED indicator for more than 30 min.207 The ZnO/NiCo-LDH/carbon cloth (CC) is synthesized so that ZnO/NiCo-LDH300s shows excellent electrochemical performance. The supercapacitor of ZnO/NiCo-LDH300s//AC exhibited an energy density of 0.044 mW h cm−2.208
In the production of NiCo-LDH (layered double hydroxide) nanosheets on an ultrathin NiCoZnSx (sulfide) microplate were prepared and exhibited a high specific capacitance of 1928 F g−1 and outstanding rate capability as well as a high energy density and good cycling stability of its supercapacitor with AC electrode.209 NiCoP (phosphide) composites with carbon cloth (NiCoP@CC) and Co-based ZIF-67 (Co-ZIF-67) were prepared and the NiCoP@CC electrode showed a remarkable specific capacity of 1149.2 C g−1 and good traits. The supercapacitor of the NiCoP@CC cathode and AC as the anode delivered a high specific energy.210 The hollow microcube of NiCoP (phosphide) was synthesized (NiCoP-HMC) as an electrode and exhibited a remarkable specific capacity of 1088.9 C g−1. Furthermore, an asymmetry supercapacitor was fabricated by using the NiCoP-HMCs of the (+) electrode and AC as the negative electrode with a high specific energy of 78.2 W h kg−1.211 Stable α-phase NiCoAl hydroxides were used in a NiCoAl-10 supercapacitor electrode with excellent specific capacitances of 19.27 F cm−2. A supercapacitor of NiCoAl-10//AC also exhibited a remarkable energy density and capacity retention.212 The hollow carbon-incorporated NiCoM layered double hydroxide nanocages (NiCoM-LDH/C, M = Mn, Cu, and Zn) are successfully synthesized and the optimized NiCoMn-LDH/C showed a meaningful capacity performance of 888.3 C g−1. Also, the HSC device of NiCoMn-LDH/C and AC revealed a remarkable energy density of 46.5 W h kg−1 and capacitance retention of 92.05% after 5000 cycles.213
2.4.2. Ternary nickel cobalt sulfide/oxides and active carbon-based asymmetric supercapacitors.
NiCo2S4 composites were prepared with citric acid as an inductive agent. Among the samples, NiCo2S4 mesoporous microspheres display the best electrochemical properties. Moreover, the NiCo2S4//AC supercapacitor yields an energy density of 48.7 W h kg−1.214 Tremella-like core-shellCo9S8/NiCo2S4/nickel foam (NF) was synthesized and the prepared Co9S8/NiCo2S4/NF electrode presents a high specific capacitance with a superior rate capability. Furthermore, the fabricated Co9S8/NiCo2S4/NF//AC supercapacitor displays a high energy density of 30 W h kg−1.215 The foam-structured NiCo2S4 (FSNCS) was synthesized by using the framework of the well-dispersed SiO2 nanospheres. It exhibited 559.3 C g−1 at a current density of 1 A g−1 which was 173.3 C g−1 higher than the performance of the free SiO2 NCS. The FSNCS//AC displays an energy density of 28.8 W h kg−1 with a good cyclic life of 88.9% after 5000 cycles.216 The ultrathin and porous NiCo2O4 nanosheet-based electrodes were synthesized and exhibited a high area capacity of 2690 F g−1. The corresponding supercapacitor if NiCo2O4(+)//(−)AC delivered a superior energy density of 52.6 W h kg−1 with a capacitance retention of 80.9% after 3000 cycles.217 The (In)-doped NiCo2O4 (In-NiCo2O4) nanoneedles with oxygen vacancies (Vo) on the carbon fiber (CF) (In-NiCo2O4/CF) were synthesized using a simple laser-assisted technique. This electrode exhibited a high specific capacitance of 2375.1 F g−1 as well as the good parameters of the In-NiCo2O4/CF//AC supercapacitor.218 Ti3C2Tx/NiCo2O4 (s-Ti3C2/NiCo2O4) were designed and used in the supercapacitors of s-Ti3C2/NiCo2O4 (+)//(−)AC with a widened voltage window of 1.6 V, which is almost twice wider than that of the common symmetric one. The device delivered high electrochemical performance.219
Graphene, CNTs, porous carbon, and nanomaterials are widely used in supercapacitor electrodes and industry.220–222 Graphene-based supercapacitors leverage the unique properties of graphene, a single layer of carbon atoms, for energy storage. They offer a high power density, rapid charging, and discharging, a large surface area for increased energy storage, long cycle life, and environmental friendliness. Carbon nanomaterials offer a high surface area, nanoscale porosity, and excellent conductivity, providing efficient ion adsorption and increased capacitance. Ni materials are widely used in supercapacitor electrodes. They offer high capacitance, excellent conductivity, and electrochemical stability. These materials can store a substantial amount of charge, provide a high power performance, and exhibit a long cycle life. Incorporating Ni materials enhances energy storage capabilities, driving the development of high-performance devices. In summary, supercapacitor electrodes based on nickel material composites with graphene, CNTs, and porous carbon show acceptable electrochemical behavior. The porous CuNi phosphide spheres/rGO as the cathode electrode has advantages such as fast electrolyte diffusion, better electron transfer, and better structural stability. The holey graphene oxide (HGO)/nano two-dimensional Ni (Ni(BDC)-HGO30) indicated an energy density of 52.5 W h kg−1 and an excellent power density of 18
000 W kg−1.97 NiCo-based supercapacitors offer advantages such as high-power density, enabling them to deliver and absorb large amounts of energy quickly. They also have a long cycle life and good thermal stability, operating over a wide temperature range. The NiCo phosphide nano horns are formed by the Kirkendall effect for preparing the NiCo phosphide/phosphorus-doped rGO as an anode achieving an energy density of 39.7 W h kg−1 and a distinguished power density of 8820 W kg−1.105 An asymmetric supercapacitor based on the Fe-doped NiCo2O4/rGO electrode displayed an outstanding energy density of 93.5 W h kg−1 and specific capacitance of 2772 F g−1.128 The Ni phosphate (NiP)/MWCNTs revealed a superior energy density of 94.4 W h kg−1 at 340 W kg−1.148 Ni ferrite nanoparticle/carboxymethyl cellulose-derived porous carbon (NiFe2O4/CPC) exhibited a major energy density of 135.2 W h kg−1 at 10
040 W kg−1.172 A supercapacitor with Ti3C2Tx MXene/NiCo2O4//AC electrodes delivered a high electrochemical performance with energy and power densities of 94.46 W h kg−1 and 2882 W kg−1, respectively.219 A comparison of power density as a function of energy density for supercapacitors based on the Ni-materials/graphene, Ni-materials/CNTs, Ni-materials/porous carbon, and Ni-materials//active carbon structures is shown in Fig. 12. As can be seen from Fig. 9, the Ni-materials/graphene-based supercapacitors have better power and energy densities of up to 10 kW kg−1 and 100 W h kg−1 respectively.
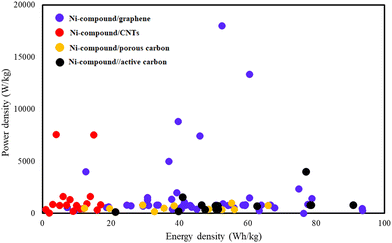 |
| Fig. 12 Comparison of power density as a function of energy density for supercapacitors based on the Ni-materials/graphene, Ni-materials/CNTs, Ni-materials/porous carbon, and Ni-materials//active carbon structures. | |
In this review the power and energy densities and specific capacitance of supercapacitors based on Ni cobalt/selenide and graphene composites, ternary nickel cobalt sulfide/oxides and graphene composites, Ni(OH)2 anchored graphene, CNTs-based nickel composites, CNTs decorated with nickel cobalt, ternary nickel cobalt sulfide/oxides and CNT composites, and dispersion of Ni materials in porous carbon have been investigated. It seems that the comparison between recent advances in Ni materials/carbon nanocomposites shows that most of the supercapacitors are limited to the sub-region of 100 W h kg−1 and 5000 W kg−1. The Ni compound/graphene-based supercapacitors achieve a higher power density than other nanocomposites of Ni materials and CNTs, porous carbon, and active carbon and they can overcome this limitation. Also, among the supercapacitors, Ni materials/graphene electrodes show a higher specific capacitance.
3. Conclusion
In conclusion, the appearance of supercapacitors based on Ni materials/graphene, Ni materials/CNTs, Ni materials/porous carbon, and Ni materials//active carbon has demonstrated significant advancements in energy storage. These innovative materials have enabled the development of supercapacitors with remarkable energy and power densities. These supercapacitors have achieved an impressive energy density of up to 10 kW kg−1, allowing for efficient and long-lasting energy storage. This high energy density makes them suitable for diverse applications such as renewable energy systems, electric vehicles, and portable electronics. Moreover, these supercapacitors exhibit a power density of up to 100 W h kg−1, enabling rapid energy release and meeting high power demands. This characteristic proves valuable in applications that require quick energy bursts, such as regenerative braking and power backup systems. This high specific capacitance ensures effective energy storage and swift charge–discharge cycles. The development of supercapacitors based on Ni-materials/graphene, Ni-materials/CNTs, Ni-materials/porous carbon, and Ni materials//active carbon has opened up new horizons for high-performance energy storage. With their impressive energy and power densities, along with their high specific capacitance, these supercapacitors hold great promise as a sustainable and efficient energy storage solution for the future.
Data Availability Statement
Data are contained within the article.
Conflicts of interest
The authors declare no conflicts of interest.
Acknowledgements
This research work was financially supported by East Tehran Branch, Islamic Azad University and the Iran National Science Foundation (INSF) and grant number (INSF: 97003234).
References
- N. R. Chodankar, H. D. Pham, A. K. Nanjundan, J. F. S. Fernando, K. Jayaramulu, D. Golberg, Y. Han and D. P. Dubal, Small, 2020, 16, e2002806 CrossRef PubMed.
- O. Maurya, S. Khaladkar, M. R. Horn, B. Sinha, R. Deshmukh, H. Wang, T. Kim, D. P. Dubal and A. Kalekar, Small, 2021, 17, 2300013 CrossRef PubMed.
- S. M. Mahadik, N. R. Chodankar, Y. Han, D. P. Dubal and S. Patil, ChemSusChem, 2021, 14, 5384–5398 CrossRef CAS PubMed.
- L. F. Aval, M. Ghoranneviss and G. B. Pour, Heliyon, 2018, 4, e00862 CrossRef PubMed.
- G. Behzadi pour, H. Nazarpour fard, L. Fekri aval and P. Esmaili, Ionics, 2019, 26, 549–563 CrossRef.
- Y. Tian, F. Yang, Z. Qiu, J. Jing, J. He and H. Xu, J. Energy Storage, 2023, 63, 107086 CrossRef.
- W. Wu, T. Liu, X. Zhang, C. Zhao, D. Yi, Y. Fang, J. Diwu, L. Wang and J. Zhu, J. Mater. Sci.: Mater. Electron., 2023, 34 DOI:10.1007/s10854-023-10202-6.
- M. Zhang, D. Jiang, F. Jin, Y. Sun, J. Wang, M. Jiang, J. Cao, B. Zhang and J. Liu, J. Colloid Interface Sci., 2023, 636, 204–215 CrossRef CAS PubMed.
- V. Shanmugavalli, R. D. Kumar, A. J. Kumar, R. Kavitha, C. Brundha, V. Sampath and M. Lee, J. Mater. Sci.: Mater. Electron., 2023, 34 DOI:10.1007/s10854-023-10248-6.
- R. Liu, J. Huang, Y. Diao, W. Zhao and H.-C. Chen, J. Colloid Interface Sci., 2023, 639, 263–273 CrossRef CAS PubMed.
- Z. Yuan, Y. Ma, P. Zhang, M. Zhai, C. Qin and X. Jiang, Energy Fuels, 2023, 37, 2420–2430 CrossRef CAS.
- S. Jo, N. Kitchamsetti, H. Cho and D. Kim, Polymers, 2023, 15, 454 CrossRef CAS PubMed.
- Y.-C. Hsiao, C.-H. Liao, C.-S. Hsu, S. Yougbaré, L.-Y. Lin and Y.-F. Wu, J. Energy Storage, 2023, 57, 106171 CrossRef.
- Y.-F. Wu, Y.-C. Hsiao, C.-H. Liao, C.-S. Hsu, S. Yougbaré and L.-Y. Lin, J. Colloid Interface Sci., 2022, 628, 540–552 CrossRef CAS PubMed.
- J. H. Kim, Y. Ko, S. Y. Lee, Y. S. Lee, S. K. Kim, Y. A. Kim and C. Yang, Int. J. Energy Res., 2022, 46, 23564–23577 CrossRef CAS.
- L. Wei, J. Li, R. Chen, Q. Wu and J. Li, J. Nanopart. Res., 2022, 24 DOI:10.1007/s11051-022-05606-0.
- S. Su, L. Sun, J. Qian, X. Shi and Y. Zhang, ACS Appl. Energy Mater., 2021, 5, 685–696 CrossRef.
- M. Jiang, Z. Hu, Y. Wang, C. Xiang, Y. Zou, F. Xu, Q. Yang, J. Zhang and L. Sun, J. Alloys Compd., 2022, 927, 166824 CrossRef CAS.
- J. Li, Y. Zou, L. Jin, F. Xu, L. Sun and C. Xiang, J. Energy Storage, 2022, 50, 104639 CrossRef.
- B. Huang, D. Yao, J. Yuan, Y. Tao, Y. Yin, G. He and H. Chen, J. Colloid Interface Sci., 2022, 606, 1652–1661 CrossRef CAS PubMed.
- Q. Xu, X. Liu, J. Zhang, Y. Xu, M. Zhou, J. Li, M. Du, K. Zhang, X. Qian, B. Xu, X. Wang, B. Wang and K. Zhang, J. Mater. Chem. A, 2023, 11, 5309–5319 RSC.
- C. Shi, J. Sun, Y. Pang, Y. Liu, B. Huang and B.-T. Liu, J. Colloid Interface Sci., 2022, 607, 462–469 CrossRef CAS PubMed.
- Y. J. Yang, S. Chen, C. Jiang, N. Wang, P. Yang, M. Liu and Y. Cheng, J. Alloys Compd., 2023, 930, 167466 CrossRef CAS.
- L. Xue’an, T. Liyi, Q. Jian, T. Dajiang, T. Zhangfa and Q. Huiying, CIESC J., 2022, 73, 3287–3297, DOI:10.11949/0438-1157.20220391.
- C. Hou, T. Li, Z. Zhang, C. Chang and L. An, Mater. Lett., 2022, 309, 131361 CrossRef CAS.
- J. Chen, Z. Du, K. Cheng, J. Bao, G. Wang, Y. Yao, J. Song, J. Yue, K. Xu, W. Xie, W. Qiang, Y. Liu and X. Wang, RSC Adv., 2022, 12, 34904–34909 RSC.
- S. Ramesh, K. Karuppasamy, D. Vikraman, H. M. Yadav, H.-S. Kim, A. Sivasamy and H. S. Kim, Ceram. Int., 2022, 48, 29102–29110 CrossRef CAS.
- J. Xiao, H. Tong, F. Jin, D. Gong, X. Chen, Y. Wu, Y. Zhou, L. Shen and X. Zhang, J. Power Sources, 2022, 518, 230763 CrossRef CAS.
- G. B. Pour, H. Ashourifar, L. F. Aval and S. Solaymani, Symmetry, 2023, 15, 1179 CrossRef CAS.
- M. B. Poudel, A. A. Kim, P. C. Lohani, D. J. Yoo and H. J. Kim, J. Energy Storage, 2023, 60, 106713 CrossRef.
- R. Wang, X. Li, Z. Nie, Y. Wang, Y. Zhao and H. Wang, Energy Fuels, 2022, 36, 13256–13265 CrossRef CAS.
- Y. Fang, H. Wang, X. Wang, J. Ren and R. Wang, Front. Chem. Sci. Eng., 2023, 17, 373–386 CrossRef CAS.
- Z. Qin, J. Liu, B. Sun, H. Zou, L. Chen, Y. Xu, Y. Cao and C. Chen, Electrochim. Acta, 2022, 435, 141370 CrossRef CAS.
- X. Dong, Z. Liu, H. Tan, P. Hu, Z. Zhang, Z. Huang and C. Shang, Mater. Today Chem., 2022, 26, 101234 CrossRef CAS.
- Y. Cao, N. Wu, F. Yang, M. Yang, T. Zhang, H. Guo and W. Yang, Colloids Surf., A, 2022, 646, 128954 CrossRef CAS.
- B. Geng, W. Hu, X. Wu, M. Du, G. Shan and Q. Zheng, J. Electrochem. Soc., 2022, 169, 082521 CrossRef CAS.
- M. Liang, X. Li, Y. Kang, N. Ur RehmanLashari, X. Zhang, Y. Zhao, H. Wang, Z. Miao and C. Fu, J. Power Sources, 2022, 535, 231486 CrossRef CAS.
- S. Ramesh, K. Karuppasamy, D. Vikraman, H. M. Yadav, H.-S. Kim, J.-H. Kim and H. S. Kim, J. Energy Storage, 2022, 55, 105728 CrossRef.
- M. Pathak and C. S. Rout, Adv. Compos. Hybrid Mater., 2022, 5, 1404–1422 CrossRef CAS.
- L. Cui, H. Xu, Y. An, M. Xu, Z. Lei and X. Jin, New J. Chem., 2022, 46, 12419–12426 RSC.
- D. N. Sangeetha, M. Selvakumar, P. Selvaraj and S. Senthilkumar, Mater. Lett., 2022, 313, 131765 CrossRef CAS.
- M. Pathak, S. R. Polaki and C. S. Rout, RSC Adv., 2022, 12, 10788–10799 RSC.
- M. Ding, Z. Wei, S. Huang, C. Li and Q. Lu, Current Nanoscience, 2022, 18, 399–407 CrossRef CAS.
- X. Wang, C. Deng, X. Hong, W. Dong and B. Liang, J. Energy Storage, 2022, 55, 105837 CrossRef.
- K. Venkatesh, C. Karuppiah, R. Palani, G. Periyasamy, S. K. Ramaraj and C.-C. Yang, Mater. Lett., 2022, 323, 132609 CrossRef CAS.
- H. Zhang, J. Han, J. Xu, Y. Ling and X. Ou, J. Mater. Sci., 2022, 57, 5566–5576 CrossRef CAS.
- Y. Tian, Z. Xue, Q. Zhao, J. Guo, K. Tao and L. Han, Dalton Trans., 2022, 51, 4406–4413 RSC.
- T. Kavinkumar, N. Naresh, G. Mathew and B. Neppolian, J. Alloys Compd., 2022, 891, 162052 CrossRef CAS.
- B. Deng, Y. Yang, Y. Liu, B. Yin and M. Yang, J. Colloid Interface Sci., 2022, 618, 399–410 CrossRef CAS PubMed.
- M. Aghazadeh and H. F. Rad, J. Mater. Sci.: Mater. Electron., 2022, 33, 11038–11054 CrossRef CAS.
- J. Fan, A. Chen, X. Xie and L. Gu, J. Energy Storage, 2022, 48, 103964 CrossRef.
- X. Liu and J. Xie, J. Mater. Sci.: Mater. Electron., 2022, 33, 4081–4092 CrossRef CAS.
- J. R. Junaqani, M. Kazazi, M. J. S. Shahraki and M. D. Chermahini, JOM, 2022, 74, 808–816 CrossRef CAS.
- X. Liu, S. Du, X. Zuo, X. Zhang and Y. Jiang, RSC Adv., 2022, 12, 1177–1183 RSC.
- G. B. Pour, L. F. Aval and M. Mirzaee, Nanotechnology, 2020, 14, 163–170 CAS.
- T. Chen and L. Dai, Mater. Today, 2013, 16, 272–280 CrossRef CAS.
- Y. Wu, X. Jia, H. Zhang, F. Zhou, Z. Fu, X. Jia, Z. Li, F. Liu, L. Wang and Z. Xiao, J. Energy Storage, 2023, 62, 106855 CrossRef.
- R. Ghanbari and S. R. Ghorbani, J. Energy Storage, 2023, 60, 106670 CrossRef.
- M. Miah, P. Hota, T. K. Mondal, R. Chen and S. K. Saha, J. Alloys Compd., 2023, 933, 167648 CrossRef CAS.
- M. Li, C. Jia, D. Zhang, Y. Luo, Y. Ma, G. Luo, L. Zhao, L. Wang, Z. Li, Q. Lin, P. Yang, N. Zhu, R. Boukherroub and Z. Jiang, J. Energy Storage, 2023, 64, 107144 CrossRef.
- Y. Abbasi, F. Jalali and S. Sheikhi, J. Alloys Compd., 2023, 938, 168450 CrossRef CAS.
- A. Agarwal, S. Majumder and B. R. Sankapal, J. Energy Storage, 2023, 58, 106396 CrossRef.
- E. Baasanjav, T. G. Senthamaraikannan, P. Bandyopadhyay, D.-H. Lim and S. M. Jeong, Chem. Eng. J., 2023, 466, 143064 CrossRef CAS.
- H. Lv, Z. Xiao, S. Zhai, X. Wang, J. Hao, Y. Tong and Q. An, Ind. Crops Prod., 2023, 194, 116320 CrossRef CAS.
- S. Demirel, M. S. Nas, A. Kocyigit, M. H. Calimli and M. H. Alma, J. Mater. Sci.: Mater. Electron., 2023, 34 DOI:10.1007/s10854-023-09894-7.
- X. Sun, Y. Liu, Z. Xu, X. Gao, X. Yin and X. Ma, Phys. Chem. Chem. Phys., 2022, 24, 29817–29826 RSC.
- R. Liu, X.-R. Shi, Y. Wen, X. Shao, C. Su, J. Hu and S. Xu, J. Energy Chem., 2022, 74, 149–158 CrossRef CAS.
- Y. Li, G. Huang, Q. Geng, Y. Liu, X. Li, Y. Yao, Y. Liu, B. Xing, Q. Liu, J. Jia and C. Zhang, J. Alloys Compd., 2022, 895, 162652 CrossRef CAS.
- L. F. Aval, M. Ghoranneviss and G. B. Pour, Mater. Renew. Sustainable Energy, 2018, 7 Search PubMed.
- Y. F. Avval, G. B. Pour and M. M. Aram, Int. Nano Lett., 2022, 12, 421–426 CrossRef CAS PubMed.
- C.-Y. Hsu, A. M. Rheima, Z. Sabri Abbas, M. U. Faryad, M. M. Kadhim, U. S. Altimari, A. H. Dawood, A. Dhari jawad al-bayati, Z. T. Abed, R. S. Radhi, A. S. Jaber, S. K. Hachim, F. K. Ali, Z. H. Mahmoud, G. Behzadi Pour and E. Kianfar, S. Afr. J. Chem. Eng., 2023, 46, 286–311 Search PubMed.
- S. Khatami, G. B. Pour, S. F. Aval and M. Amini, Plasma Chem. Plasma Process., 2023, 43, 1131–1147 CrossRef CAS.
- A. K. Alkhawaldeh, A. M. Rheima, M. M. Kadhim, Z. Sabri Abbas, A. Dhari Jawad al-Bayati, Z. Talib Abed, F. Mohamed Dashoor Al-Jaafari, A. Salam Jaber, S. K. Hachim, F. K. Ali, Z. H. Mahmoud, G. Behzadi Pour and E. Kianfar, Case Stud. Chem. Environ. Eng., 2023, 8, 100372 CrossRef CAS.
- S. Khatami, L. Fekri Aval and G. Behzadi Pour, NANO, 2018, 13, 1850062 CrossRef CAS.
- G. Behzadi Pour and L. Fekri Aval, Micro Nano Lett., 2018, 13, 149–153 CrossRef.
- T. Nandagopal, G. Balaji and S. Vadivel, J. Electroanal. Chem., 2023, 928, 116944 CrossRef CAS.
- J. Acharya, B. Pant, G. Prasad Ojha and M. Park, J. Colloid Interface Sci., 2022, 610, 863–878 CrossRef CAS PubMed.
- S. Sardana, K. Aggarwal, S. Malik, A. Saini, S. Dahiya, R. Punia, A. S. Maan, K. Singh and A. Ohlan, Electrochim. Acta, 2022, 434, 141324 CrossRef CAS.
- B. Carmel Jeeva Mary, J. J. Vijaya, B. Saravanakumar, M. Bououdina and L. J. Kennedy, Synth. Met., 2022, 291, 117201 CrossRef CAS.
- M. Amiri, A. Mohammadi Zardkhoshoui and S. S. Hosseiny Davarani, Nanoscale, 2023, 15, 2806–2819 RSC.
- M. Amiri, A. Mohammadi Zardkhoshoui and S. S. Hosseiny Davarani, Nanoscale, 2023, 15, 2806–2819 RSC.
- Q. Yang, Q. Feng, X. Xu, Y. Liu, X. Yang, F. Yang, J. Li, H. Zhan, Q. Wang and S. Wu, Nanotechnology, 2022, 33, 345401 CrossRef PubMed.
- M. Farshadnia, A. A. Ensafi, K. Zarean Mousaabadi and B. Rezaei, J. Alloys Compd., 2022, 906, 164278 CrossRef CAS.
- Y. Cui, C. Zhao, L. Zhao, H. Yu, J. Wang and Z. Zhang, Diamond Relat. Mater., 2022, 125, 108965 CrossRef CAS.
- M. Imranullah, T. Hussain, R. Ahmad, U. Shuaib, P. O. Agboola and I. shakir, Ceram. Int., 2022, 48, 12460–12466 CrossRef CAS.
- S. Ghosh, P. Samanta, W. Jang, C.-M. Yang, N. C. Murmu and T. Kuila, ACS Appl. Energy Mater., 2022, 5, 1528–1541 CrossRef CAS.
- B. A. Khan, R. Hussain, A. Shah, A. Mahmood, M. Z. U. Shah, J. Ismail, S. Ur Rahman, M. Sajjad, M. A. Assiri, M. Imran and M. S. Javed, Ceram. Int., 2022, 48, 5509–5517 CrossRef CAS.
- J. Wang, S. Li, Y. Zhu, S. Zhai, C. Liu, N. Fu, S. Hou, Y. Niu, J. Luo, S. Mu and Y. Huang, J. Electroanal. Chem., 2022, 919, 116548 CrossRef CAS.
- R. Xiong, X. Zhang, X. Xu, Z. Zhang, X. Tian and C. Wang, Diamond Relat. Mater., 2022, 127, 109183 CrossRef CAS.
- X. Shi, Q. Liu, W. Liang, B. Chen, L. Shao, J. Cai, Z. Sun, Y. Zhang, H. Huang and Y. Wu, Mater. Today Sustainability, 2022, 18, 100151 CrossRef.
- Z. Lu, H. Zhao, J. Luo and J. Wang, J. Phys. Chem. Solids, 2022, 163, 110593 CrossRef CAS.
- J. Miao, D. Wu, X. Gao, W. Wang, W. Wu, S. Tao, Y. Fang, Z. Han, B. Qian, X. Jiang and L. Zhang, J. Alloys Compd., 2022, 890, 161435 CrossRef CAS.
- C. Li, G. Jiang, T. Liu, Z. Zeng, P. Li, R. Wang and X. Zhang, J. Energy Storage, 2022, 49, 104176 CrossRef.
- V. M. Maphiri, D. T. Bakhoum, S. Sarr, N. F. Sylla, G. Rutavi and N. Manyala, J. Energy Storage, 2022, 52, 104967 CrossRef.
- A. Morenghi, S. Scaravonati, G. Magnani, M. Sidoli, L. Aversa, R. Verucchi, G. Bertoni, M. Riccò and D. Pontiroli, Electrochim. Acta, 2022, 424, 140626 CrossRef CAS.
- Y. Jia, D. Hu, X. Wang, H. Zhang and P. Du, J. Energy Storage, 2022, 50, 104713 CrossRef.
- H. Wang, P. Zhao, X. Zhang, S. Zhang, X. Lu, Z. Qiu, K. Ren, Z. Xu, R. Yao, T. Wei and Z. Fan, Nano Res., 2022, 15, 9047–9056 CrossRef CAS.
- K. K. Sarigamala, A. Struck, S. Shukla and S. Saxena, Electrochim. Acta, 2023, 450, 142266 CrossRef CAS.
- M. Hammad Aziz, F. Shaheen, R. Ahmad, A. Khan, S. Sharif, H. Muhammad Fahad and Q. Huang, Mater. Lett., 2023, 333, 133658 CrossRef CAS.
- C. Li, G. Zhang, X. Li, H. Wang, P. Huo and X. Wang, J. Phys. Chem. Solids, 2022, 163, 110591 CrossRef CAS.
- Q. Luo, Z. Zhong, Y. Zheng, D. Gao, Z. Xia and L. Wang, Talanta, 2021, 224, 121869 CrossRef CAS PubMed.
- A. B. Ganganboina and R.-A. Doong, Environ. Sci.: Nano, 2020, 7, 228–237 RSC.
- P. Rosaiah, N. G. Prakash, P. Divya, S. Sambasivam, M. Shkir, H. Algarni and T. J. Ko, J. Energy Storage, 2022, 56, 106133 CrossRef.
- A. G. El-Deen, M. K. Abdel-Sattar and N. K. Allam, Appl. Surf. Sci., 2022, 587, 152548 CrossRef CAS.
- U. Javed, G. Dhakal, A. M. Rabie, S. Iqbal, Y. R. Lee, J. Lee and J.-J. Shim, Mater. Today Nano, 2022, 18, 100195 CrossRef CAS.
- T. Zhou, S. Tang, H. Yu, L. Shen, Q. Huang, S. Yang, L. Yu and L. Zhang, New J. Chem., 2022, 46, 10328–10338 RSC.
- Y. Wang, F. Mo and X. Wu, J. Electroanal. Chem., 2022, 924, 116863 CrossRef CAS.
- Y. Zhou, L. Wei, C. Li, Y. Han, J. Xu, Z. Jia, J. Sun, H. Chen, Y. Song, X. Ouyang, X. Wang, J. Zhu and Y. Fu, J. Energy Storage, 2022, 45, 103765 CrossRef.
- X. Yin, L. Han, Y. Fu, J. Lu, Q. Song and H. Li, J. Energy Storage, 2022, 53, 105205 CrossRef.
- J. Zou, D. Xie, J. Xu, X. Song, X. Zeng, H. Wang and F. Zhao, Appl. Surf. Sci., 2022, 571, 151322 CrossRef CAS.
- X. Wang, Y. Xu, L. Shao, Y. Wei, X. Zhang, X. An, J. Liu, C. Zhou, Y. Chen and G. Wang, J. Energy Storage, 2023, 63, 107056 CrossRef.
- L. Chen, X. Zhao, G. Tian, Y. Wei and T. Liu, Mater. Lett., 2023, 334, 133698 CrossRef CAS.
- C. Li, G. Jiang, M. Demir, Y. Sun, R. Wang and T. Liu, J. Energy Storage, 2022, 56, 105986 CrossRef.
- G. Rutavi, D. J. Tarimo, V. M. Maphiri and N. Manyala, Int. J. Energy Res., 2022, 46, 11214–11227 CrossRef CAS.
- T. Zhao, C. Liu, T. Meng, W. Deng, L. Zheng, F. Yi, A. Gao and D. Shu, Small, 2022, 18, 2201286, DOI:10.1002/smll.202201286.
- H. Qiu, Q. Ma, X. Sun, X. Han, G. Jia, Y. Zhang and W. He, Appl. Surf. Sci., 2022, 578, 152019 CrossRef CAS.
- Y. Liu, X. Li, M. Gao, X. Hao, J. Li, Y. Liu, Y. Li and K. Cai, ACS Appl. Energy Mater., 2022, 5, 9605–9615 CrossRef CAS.
- S. Khaladkar, G. Gund, O. Maurya, B. Sinha, P. Salame, D. Dubal, R. Deshmukh and A. Kalekar, Adv. Energy Sustainability Res., 2023, 4 Search PubMed.
- S. R. Khaladkar, O. Maurya, G. Gund, B. Sinha, D. Dubal, R. R. Deshmukh and A. Kalekar, J. Energy Chem., 2023, 87, 304–313 CrossRef CAS.
- N. J. Panicker, J. C. Dutta and P. P. Sahu, Chem. Eng. J., 2023, 463, 142376 CrossRef CAS.
- X. Zang, L. Liang, X. Wang, C. Li, P. Li, Q. Shao and N. Cao, Energy Technol., 2022, 10, 2200490, DOI:10.1002/ente.202200490.
- C. Cheng, Y. Zou, F. Xu, C. Xiang, Q. Sui, J. Zhang, L. Sun and Z. Chen, J. Energy Storage, 2022, 52, 105049 CrossRef.
- Y. Guo, C. Hao, X. Wang, Y. Yang, X. Wang, J. Wu and Y. Shen, Ceram. Int., 2022, 48, 17644–17653 CrossRef CAS.
- D. He, F. Li, Y. Xiao, S. Chen, Z. Zhu, H. Chen, X. Hu, W. Peng, S. Xin and Y. Bai, Electrochim. Acta, 2022, 404, 139751 CrossRef CAS.
- A. I. Abdel-Salam, S. Y. Attia, F. I. El-Hosiny, M. A. Sadek, S. G. Mohamed and M. M. Rashad, Mater. Chem. Phys., 2022, 277, 125554 CrossRef CAS.
- S. Yadav, A. S. Ghrera and A. Devi, J. Energy Storage, 2022, 56, 105949 CrossRef.
- X. Chen, N. Xin, Y. Li, C. Sun, L. Li, Y. Ying, W. Shi and Y. Liu, J. Mater. Sci. Technol., 2022, 127, 236–244 CrossRef CAS.
- R. Nasser, X.-L. Wang, A. B. G. Trabelsi, F. H. Alkallas, H. Elhouichet and J.-M. Song, J. Energy Storage, 2022, 52, 104619 CrossRef.
- S. Pappu, S. Anandan, T. N. Rao, S. K. Martha and S. V. Bulusu, J. Energy Storage, 2022, 50, 104598 CrossRef.
- R. Yuan, W. Chen, J. Zhang, L. Zhang, H. Ren, T. Miao, Z. Wang, K. Zhan, M. Zhu and B. Zhao, Dalton Trans., 2022, 51, 4491–4501 RSC.
- Z. Shi, G. Sun, R. Yuan, W. Chen, Z. Wang, L. Zhang, K. Zhan, M. Zhu, J. Yang and B. Zhao, J. Mater. Sci. Technol., 2022, 99, 260–269 CrossRef CAS.
- Y. Jiang, X. Li, F. Liu, B. Wang, W. Zhou, S. Dong and X. Fan, Appl. Surf. Sci., 2022, 576, 151801 CrossRef CAS.
- M.-J. Zeng, X. Li, S.-M. Hao, J. Qu, W. Li, J. Wu, T. Zhao and Z.-Z. Yu, New J. Chem., 2022, 46, 533–541 RSC.
- J. Barqi, S. M. Masoudpanah, M. Hasheminiasari and X. Liu, J. Alloys Compd., 2023, 930, 167509 CrossRef CAS.
- C. Fang and D. Zhang, J. Electrochem. Soc., 2022, 169, 060528 CrossRef CAS.
- A. Viswanathan and A. N. Shetty, J. Energy Storage, 2023, 65, 107337 CrossRef.
- B. Guo, Y. Gao, Y. Li, X. Sun, S. Chen and M. Li, ACS Appl. Nano Mater., 2022, 5, 7471–7480 CrossRef CAS.
- R. Jafer, S. A. Alsufyani, J. Iqbal, M. O. Ansari, A. Numan, S. Bashir, P. M. Z. Hasan and S. Wageh, Polymers, 2023, 15, 1267 CrossRef CAS PubMed.
- X. Wu, F. Zeng, X. Song, X. Sha, H. Zhou, X. Zhang, Z. Liu, M. Yu and C. Jiang, Chem. Eng. J., 2023, 456, 140947 CrossRef CAS.
- A. Rahmanian and L. Naji, Colloids Surf., A, 2022, 640, 128450 CrossRef CAS.
- X. Wu, F. Zeng, X. Song, X. Sha, H. Zhou, X. Zhang, Z. Liu, M. Yu and C. Jiang, Chem. Eng. J., 2023, 456, 140947 CrossRef CAS.
- J. Li, H. Hao, J. Wang, W. Li and W. Shen, J. Alloys Compd., 2019, 782, 516–524 CrossRef CAS.
- J. Tian, Q. Shan, X. Yin and W. Wu, Adv. Powder Technol., 2019, 30, 3118–3126 CrossRef CAS.
- K. Yousefipour, R. Sarraf-Mamoory and A. Chaychi Maleki, J. Energy Storage, 2023, 59, 106438 CrossRef.
- M. W. Iqbal, M. H. Khan, A. M. Afzal, H. Hassan, H. A. Alzahrani and S. Aftab, J. Appl. Electrochem., 2022, 53, 949–962 CrossRef.
- D. Zhang, M. Zhao, H. Zhang, M. Terrones and Y. Wang, Carbon, 2023, 201, 1081–1089 CrossRef CAS.
- Y. Wang, M. Li, R. Ramachandran, H. Shan, Q. Chen, A. Luo, F. Wang and Z.-X. Xu, J. Energy Chem., 2023, 76, 214–225 CrossRef CAS.
- W. Shehzad, M. R. A. Karim, M. Z. Iqbal, N. Shahzad and A. Ali, J. Energy Storage, 2022, 54, 105231 CrossRef.
- Y. Hao, H. Guo, F. Yang, J. Zhang, N. Wu, M. Wang, C. Li and W. Yang, J. Alloys Compd., 2022, 911, 164726 CrossRef CAS.
- S. Su, L. Sun, F. Xie, J. Qian and Y. Zhang, Front. Chem. Sci. Eng., 2023, 17, 491–503 CrossRef CAS.
- Y. Chen, H. Hou, B. Liu, M. Li, L. Chen, C. Chen, S. Wang, Y. Li and D. Min, Chem. Eng. J., 2023, 454, 140453 CrossRef CAS.
- M. Huang, K. Zhao, D. He, J. He and Y. Wang, Energy Fuels, 2022, 36, 15234–15243 CrossRef CAS.
- M. Zhao, H. Zhang, S. Zhai, L. Sun, Z. Huang, M. Guo, Y. Liu, D. Zhang, M. Terrones and Y. Wang, J. Alloys Compd., 2022, 909, 164664 CrossRef CAS.
- J. Qian, L. Sun, X. Shi, L. Wu, S. Su, K. Wang and Y. Zhang, Chem. Eng. J., 2022, 429, 132482 CrossRef CAS.
- Z. Shi, X. Xu, P. Jing, B. Liu and J. Zhang, ACS Appl. Mater. Interfaces, 2023, 15, 7263–7273 CrossRef CAS PubMed.
- Y. Yuan, P. Cui, J. Liu, W. Ding, Y. Wang and L. Lv, Molecules, 2022, 27, 7507 CrossRef CAS PubMed.
- J. Chen, Z. Du, K. Cheng, J. Bao, G. Wang, Y. Yao, J. Song, J. Yue, K. Xu, W. Xie, W. Qiang, Y. Liu and X. Wang, RSC Adv., 2022, 12, 34904–34909 RSC.
- Z. Tian, D. Wang, C. Zhang, F. Meng, L. Cao and H. Lin, J. Mater. Sci., 2022, 57, 19381–19395 CrossRef CAS.
- M. Yao, X. Ji, X. Ou, P. Wu and S. Cheng, J. Power Sources, 2022, 543, 231829 CrossRef CAS.
- T. Feng, H. Jiao, H. Li, J. Wang, S. Zhang and M. Wu, Energy Fuels, 2022, 36, 2189–2201 CrossRef CAS.
- C. Hou, H. Wang, T. Li, Z. Zhang, C. Chang and L. An, Chem. Res. Chin. Univ., 2022, 43, 20220351, DOI:10.7503/cjcu20220351.
- B. Q. Wang, S. H. Gong, Q. S. Sun, F. Liu, X. C. Wang and J. P. Cheng, Electrochim. Acta, 2022, 402, 139575 CrossRef CAS.
- Z. Yang, X. Yang, T. Yang, Y. Cao, C. Zhang, Y. Zhang, P. Li, J. Yang, Y. Ma and Q. Li, Energy Storage Mater., 2023, 54, 51–59 CrossRef.
- S. Khan Abdul, K. Anuj, F. Amjad, T. Mohammad, A. Muhammad, U. Muhammad, A. Akmal, A. Saira, P. Lujun and Y. Ghulam, J. Energy Storage, 2022, 56, 106041 CrossRef.
- X. Wang, X. Han, M. Lim, N. Singh, C. L. Gan, M. Jan and P. S. Lee, J. Phys. Chem. C, 2012, 116, 12448–12454 CrossRef CAS.
- N. J. Panicker, J. C. Dutta and P. P. Sahu, Chem. Eng. J., 2023, 463, 142376 CrossRef CAS.
- J. Feng, X. Zhang, Q. Lu, E. Guo and M. Wei, Energy Fuels, 2022, 36, 5424–5432 CrossRef CAS.
- C. Han, X. Ding and J. Zhu, Ionics, 2023, 29, 1199–1207 CrossRef CAS.
- C. Wang, G. Sui, D. Guo, J. Li, X. Ma, Y. Zhuang and D.-F. Chai, J. Energy Storage, 2022, 50, 104280 CrossRef.
- J. Zhu, Q. Zhang, Y. Zhao, R. Zhang, L. Liu and J. Yu, Carbon, 2023, 202, 13–25 CrossRef CAS.
- J. Yang, H. Li, S. He, H. Du, K. Liu, C. Zhang and S. Jiang, Polymers, 2022, 14, 2521 CrossRef CAS PubMed.
- H. Lv, Z. Xiao, S. Zhai, J. Hao, Y. Tong, G. Wang and Q. An, J. Colloid Interface Sci., 2022, 622, 327–335 CrossRef CAS PubMed.
- T. Yan, M. Wang, K. Li, X. Ni, X. Du, M. Xi, H. Chen and A. Ju, J. Alloys Compd., 2022, 898, 162834 CrossRef CAS.
- Z. Yuan, Y. Ma, P. Zhang, M. Zhai, C. Qin and X. Jiang, Energy Fuels, 2023, 37, 2420–2430 CrossRef CAS.
- K. Zhao, X. Sun, Z. Wang, C. Huang, D. Li and J. Liu, J. Alloys Compd., 2022, 921, 166036 CrossRef CAS.
- D.-Y. Kim, C.-H. Ma, Y. Jang, S. Radhakrishnan, T. H. Ko and B.-S. Kim, Colloids Surf., A, 2022, 652, 129785 CrossRef CAS.
- Z.-W. Zhang, C.-Y. Lu, G.-H. Liu, Y.-J. Cao, Z. Wang, T. Yang, Y.-H. Kang, X.-Y. Wei and H.-C. Bai, J. Mater. Res. Technol., 2022, 19, 3034–3045 CrossRef CAS.
- Y. Hou, Q. Sun and H. Du, J. Alloys Compd., 2023, 937, 168399 CrossRef CAS.
- Y. Wang, Y. Liu, Z. Chen, M. Zhang, B. Liu, Z. Xu and K. Yan, Green, Chem. Eng., 2022, 3, 55–63 Search PubMed.
- O. P. Nanda, A. G. Prince, L. Durai and S. Badhulika, Energy Fuels, 2023, 37, 4701–4710 CrossRef CAS.
- R. S. Karmur, D. Gogoi, M. R. Das and N. N. Ghosh, Energy Fuels, 2022, 36, 8488–8499 CrossRef CAS.
- G. Wang, Z. Xu, Z. Li, Y. Ding, R. Ge, M. Xiang, G. Wang and Z. Yan, Electrochim. Acta, 2023, 443, 141980 CrossRef CAS.
- G. Wang, K. Qi, Z. Yan, L. Yue, Y. Ding, W. Li and Z. Xu, Appl. Surf. Sci., 2022, 592, 153293 CrossRef CAS.
- X. Ren, Z. Gan, M. Sun, Q. Fang, Y. Yan, Y. Sun, J. Huang, B. Cao, W. Shen, Z. Li and Y. Fu, Electrochim. Acta, 2022, 414, 140208 CrossRef CAS.
- T. Hu, L. Gao, W. Zhou and J. Zhang, J. Alloys Compd., 2022, 895, 162577 CrossRef CAS.
- Y. He, T. Liu, J. Song, Y. Wang, Y. Zhang, J. Feng, A. Meng, G. Li, L. Wang, J. Zhao and Z. Li, J. Energy Chem., 2023, 78, 37–46 CrossRef CAS.
- Y. Lin, X. Chen, P. Chang, Z. Liu, G. Ren and J. Tao, J. Alloys Compd., 2022, 900, 163503 CrossRef CAS.
- Q. Fang, M. Sun, X. Ren, Y. Sun, Y. Yan, Z. Gan, J. Huang, B. Cao, W. Shen, Z. Li and Y. Fu, J. Colloid Interface Sci., 2022, 611, 503–512 CrossRef CAS PubMed.
- Z. Li, J. Ren, C. Yang, Y. He, Y. Liang, J. Liu, G. I. N. Waterhouse, J. Li and D. Qian, J. Alloys Compd., 2021, 889, 161661 CrossRef.
- Z. Qin, Y. Xu, L. Liu, M. Liu, H. Zhou, L. Xiao, Y. Cao and C. Chen, RSC Adv., 2022, 12, 29177–29186 RSC.
- R. Liang, Y. Du, J. Lin, J. Chen and P. Xiao, Energy Fuels, 2022, 36, 7115–7120 CrossRef CAS.
- H. Li, X. Wang, L. Dai, F. Guo, H. Mi, C. Ji and L. Sun, Inorg. Chem., 2022, 61, 3866–3874 CrossRef CAS PubMed.
- D. P. Luo, Y. H. Chen, Y. B. Chen, Z. H. Wei, L. Zhang, X. Y. Ye, Q. T. Wang and L. A. Ma, Mater. Lett., 2023, 333, 133611 CrossRef CAS.
- B. Tao, W. Yang, M. Zhou, L. Qiu, S. Lu, X. Wang, Q. Zhao, Q. Xie and Y. Ruan, J. Colloid Interface Sci., 2022, 621, 139–148 CrossRef CAS PubMed.
- Y. Luan, H. Zhang, F. Yang, J. Yan, K. Zhu, K. Ye, G. Wang, K. Cheng and D. Cao, Appl. Surf. Sci., 2018, 447, 165–172 CrossRef CAS.
- J. Yang, C. Yu, X. Fan, S. Liang, S. Li, H. Huang, Z. Ling, C. Hao and J. Qiu, Energy Environ. Sci., 2016, 9, 1299–1307 RSC.
- T. Dai, B. Cai, X. Yang, Y. Jiang, L. Wang, J. Wang, X. Li and W. Lü, Nanotechnology, 2023, 34, 225401 CrossRef PubMed.
- W. Zhao, X. Xu, N. Wu, X. Zhao and J. Gong, Nanomaterials, 2023, 13, 730 CrossRef CAS PubMed.
- X. Chen, H. Li, J. Xu, F. Jaber, F. Musharavati, E. Zalnezhad, S. Bae, K. S. Hui, K. N. Hui and J. Liu, Nanomaterials, 2020, 10, 1292 CrossRef CAS PubMed.
- Y. Guo, C. Hao, Y. Yang, X. Wu, C. Ni, X. Wang and X. Wang, Ceram. Int., 2022, 48, 9558–9568 CrossRef CAS.
- S.-C. Hsu, H.-H. Chiang, T.-Y. Huang, S.-H. Chao, R. T. Wu, C.-Z. Lu, J.-H. Huang, C.-W. Chang-Jian, H. C. Weng and H.-C. Chen, Electrochim. Acta, 2022, 403, 139692 CrossRef CAS.
- C. Chen, M. Liu, Z. Liu, M. Xie, L. Wan, J. Chen, Y. Zhang, C. Du and D. Li, J. Colloid Interface Sci., 2022, 614, 66–74 CrossRef CAS PubMed.
- M. Fu, Z. Zhang, W. Chen, Y. Huang and H. Yu, J. Alloys Compd., 2023, 938, 168527 CrossRef CAS.
- X. Ren, M. Li, L. Qiu, X. Guo, F. Tian, G. Han, W. Yang and Y. Yu, J. Mater. Chem. A, 2023, 11, 5754–5765 RSC.
- Y. Cao, N. Wu, C. Li, Y. Chen, H. Zhang, H. Guo and W. Yang, Colloids Surf., A, 2023, 658, 130683 CrossRef CAS.
- W. Wang, Y. Fang, S. Wang, Z. Zhang, R. Zhao and W. Xue, J. Alloys Compd., 2022, 900, 163532 CrossRef CAS.
- Y. Wang, Z. Wang, X. Zheng, X. Teng, L. Xu, Y. Yuan, X. Liu, A. Fu, Y. Li and H. Li, J. Alloys Compd., 2022, 904, 164047 CrossRef CAS.
- Y. B. Chen, L. A. Ma, X. Zhang, L. K. Huang, H. X. Chen and Q. T. Wang, Mater. Technol., 2021, 37, 1146–1155 CrossRef.
- W. Hu, L. Chen, B. Geng, M. Du, G. Shan, Y. Song, Z. Wu and Q. Zheng, ACS Appl. Energy Mater., 2023, 6, 2781–2792 CrossRef CAS.
- X. Chen and J. Zhu, J. Energy Storage, 2022, 55, 105877 CrossRef.
- X. Chen and Y. Zhuang, Dalton Trans., 2022, 51, 16017–16026 RSC.
- Z. Xu, X. Li, S. Sun, X. Wang, Z. Zhang, H. Li and S. Yin, J. Power Sources, 2022, 546, 231982 CrossRef CAS.
- Z. Sheng, X. Lin, H. Gao, L. Huang, Y. Zhang, Y. Zhao, H. Wei, C. Wang, D. Xu and Y. Wang, Int. J. Hydrogen Energy, 2022, 47, 29195–29206 CrossRef CAS.
- H. Xu, P. Chen, Y. Zhu, Y. Bao, J. Ma, X. Zhao and Y. Chen, J. Electroanal. Chem., 2022, 921, 116688 CrossRef CAS.
- Y. Yang, D. Qian, H. Zhu, Q. Zhou, Z. Zhang, Z. Li and Z. Hu, J. Alloys Compd., 2022, 898, 162850 CrossRef CAS.
- J. Wang, J. Wang, G. Zhu, H. Xu, X. Zhang, Y. Zhao, J. Zhang, K. Jiang and A. Yu, J. Energy Storage, 2022, 46, 103907 CrossRef.
- F. Ren, Z. Tong, S. Tan, J. Yao, L. Pei, Y. Ji and A. Abulizi, J. Electrochem. Energy Convers. Storage, 2021, 19, 011004 CrossRef.
- X. Luo, Q. Zhou, M. Guo, X. Peng, D. Wu, Y. Ito and Y. Liu, Chem. Eng. J., 2022, 431, 134220 CrossRef CAS.
- L. Wang, J. Cao, Y.-H. Zhou and X. Liu, J. Electroanal. Chem., 2022, 923, 116787 CrossRef CAS.
- G. Behzadi Pour, E. Shajee Nia, E. Darabi, L. Fekri Aval, H. Nazarpour-Fard and E. Kianfar, Case Stud. Chem. Environ. Eng., 2023, 8, 100527 CrossRef CAS.
- L. F. Aval and S. M. Elahi, Electron. Mater. Lett., 2016, 13, 77–85 CrossRef.
- E. Akbarnejad, Z. Ghorannevis, E. Mohammadi and L. Fekriaval, J. Electroanal. Chem., 2019, 849, 113358 CrossRef CAS.
|
This journal is © The Royal Society of Chemistry 2023 |