DOI:
10.1039/D3MA00188A
(Review Article)
Mater. Adv., 2023,
4, 3989-4010
MXene and their integrated composite-based acetone sensors for monitoring of diabetes
Received
21st April 2023
, Accepted 7th August 2023
First published on 25th August 2023
Abstract
For present-day technological advancements, the MXene family is a highly investigated material in the family of van der Waals heterostructures. MXenes possess exceptional physical, optical, electrical, and electronic properties. Herein, their vast electroactive surfaces, MXene-based sensors and their integration with other materials for enhanced sensing performance are discussed. The challenges and future directions of MXene-based VOCs sensors are also considered. This review emphasizes the potential of MXene in addressing environmental and health-related concerns, particularly in acetone sensing. Acetone, a volatile organic compound (VOC), is dangerous due to its explosiveness and toxicity, causing various health issues. Detecting acetone gas has medical and environmental applications, including diabetes diagnosis and environmental monitoring. This review aims to analyze recent advancements in chemiresistive sensors for acetone gas detection using MXene and MXene composite materials, discussing the synthesis methods, characterization, response and recovery time, and sensing mechanisms to achieve further improvements in sensor performance. The average amount of acetone detected in the breath of healthy people is less than 1 ppm (0.3–0.9 ppm), but it increases to 2.2 and 1.7 ppm in type 1 and type 2 diabetic patients, respectively. As a result, the ability to recognize acetone concentrations at levels sub-ppm, or even at ppb levels, is crucial for the early detection of diabetes. Nowadays, breath analysis has attracted much attention as a potentially powerful tool for studying medical diagnosis diseases due to its noninvasive nature and real-time monitoring ability. In VOCs, acetone is considered to be an important breath biomarker for diabetes.
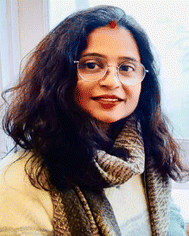
Monu Gupta
| Mrs. Monu Gupta has received her MSc Physics degree in 1998 from R.D.V.V. University, Jabalpur, M.P., India. Currently, she is pursuing PhD Degree from Nanomaterials and Sensors Research Laboratory under the supervision of Prof. B. C. Yadav from the Department of Physics, Babasaheb Bhimrao Ambedkar University, U.P., India. Her area of research interest includes the preparation and properties of MXenes integrated with metal/metal-oxide/metal sulfide, especially for the gas-sensing applications relevant to the disease biomarkers. |
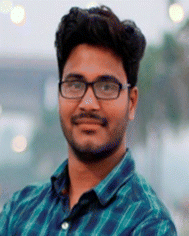
Arpit Verma
| Mr. Arpit Verma received his MSc degree in Applied Physics from Babasaheb Bhimrao Ambedkar University Lucknow, UP, India in 2018. Currently, he is pursuing a PhD degree from the Nanomaterials and Sensors Research Laboratory under the supervision of Prof. B. C. Yadav from the same university. His research interest includes the preparation and properties of metallopolymer-based functional nanomaterials for renewable energy applications, especially photovoltaics, photodetectors, sensors and energy-storing devices. |
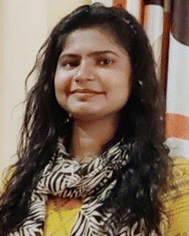
Priyanka Chaudhary
| Ms. Priyanka Chaudhary is pursuing a PhD degree from BBA (Central) University, Lucknow. She received her BSc and MSc, MPhil (Gold Medalist) degrees in 2012, 2014 and 2016, respectively, from University of Lucknow, Lucknow and BBA (Central) University, Lucknow, U.P., India. She was selected for a six-month internship in the Taiwan Experience Education Program (TEEP) 2020 sponsored by the Ministry of Education Taiwan. Her research interest includes investigations on nanometallopolymers, quantum dots and 2D materials, and their applications in humidity and gas sensing. |
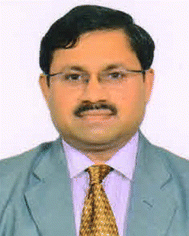
B. C. Yadav
| Prof. (Dr) B. C. Yadav was born in Hardatt Nagar Girant, Shravasti, Uttar Pradesh, India. Prof. Yadav received his PhD degree in 2001 from the Department of Physics, University of Lucknow, India. Currently, he is a Professor and the Head of the Department of Physics, School of Physical & Decision Sciences at Babasaheb Bhimrao Ambedkar University, Lucknow. Dr Yadav is also working as the Director of the University Sophisticated Instrumentation Center (USIC). He was the recipient of the prestigious Young Scientist Award (2005) instituted by the State Council of Science and Technology. Dr Yadav was also selected in 2011 for the Brain Pool International Fellowship of South Korea. He has published more than three hundred research/review papers in reputed international journals and authored two books. Dr Yadav has guided 24 PhD, 3 MPhil and 13 MTech students. Dr Yadav was nominated as a member of the National Academy of Sciences, India. His current research interests include the synthesis and characterization of metal oxide nanoparticles, metallopolymers, and Mxene with their applications as physical, chemical and biosensors. |
1. Introduction
MXene and its associated nanocomposites cover a wide range of uses, including energy storage, biomedicine, and photocatalysis, and are not solely concentrated on gas sensing.1 Because of their exceptional physical, optical, electrical, and electronic properties, as well as their vast electroactive surfaces, MXene is a rapidly increasing family of novel materials in the post-graphene period.2 The recently discovered carbides and nitrides have gained popularity and significant interest for gas sensing applications because of their outstanding chemistry and physical properties.3 MXene features enormous surface areas, high surface-to-volume ratio, and different electronic structures with atomically thin layers due to their chemical and physical structure, which cannot be obtained with normal bulk structures.4 The development of high-performance gas-sensing materials has drawn a lot of attention recently in comparison to conventional metal oxide-based gas sensors (MOS). A thorough review of the work on nanostructured gas sensors for VOC detection was previously presented by Mirzaei et al.5 They addressed other VOC gas sensors in their review paper, although acetone received less focus. A review paper on room-temperature chemiresistive gas sensors by Joshi et al.6 solely concentrated on room-temperature gas sensors, and covered other types of gases besides acetone. A solid and complete review on acetone gas sensors, which reviewed nearly all forms of gas sensors, was published by Alizadeh et al.7 However, the review did not address metal oxide gas sensors specifically, and did not include a study that Masikini et al.8 just released on the use of metal oxides to identify acetone in breath. Due to their numerous active sites, metallic conductivity, varied surface chemistry, and outstanding durability, MXene is preferred for gas sensing applications.9 Given the substantial amount of research performed on them, MXene-based sensors may be one of the likely future materials for gas sensing in this context. The focused characteristics of MXene, such as their high flexibility, facile solution processability, and ease of functionalization, make it possible to combine them with other nanomaterials to create composites, opening up a new field of study for enhanced sensing performances.10
Toxins abound in the environment, endangering both humans and the environment. Every year, around 3.8 million people are killed by a variety of fatal illnesses caused by air pollution.11 Additionally, according to the World Health Organization (WHO), these air pollutants harm the human nervous, immune, and respiratory systems, making people more vulnerable to risky diseases such as coronavirus disease (COVID-19), lung cancer, Chronic Obstructive Pulmonary Disease (COPD), ischemic heart disease, and stroke. Gas/vapor sensor devices are still used today to determine the concentrations of poisonous and non-toxic gases and to compute their amounts.12 As industry and daily activities increase, along with the burning of fossil fuels, harmful gases and volatile organic compounds (VOCs) are emitted into the environment.13 These VOCs and hazardous gases are poisonous to living things, including people and pets, when inhaled. Furthermore, the threats to our biosphere and other living beings are a concern. Among the several VOCs, acetone vapor is hazardous and possesses major human health problems.14 At 300–500 parts per million (ppm), the potential effects of acetone vaporing in adults are nausea and irritation to body parts.15 When a person has diabetes, either their body cannot produce enough insulin or they cannot use it efficiently. Typically, insulin works to metabolize blood glucose so that it may enter cells and produce energy. If the body is unable to obtain enough energy from glucose, it begins to burn fat as fuel.16 Ketones are byproducts that are produced when fat is broken down for energy. Actually, acetone is a kind of ketone that the body produces as it breaks down fat for energy. Diabetics' bodies may produce a high level of ketones, resulting in diabetic ketoacidosis (DKA). DKA is a critical diabetes complication that can be dangerous for diabetic people. The presence of acetone in the breath implies that the body is producing a sufficient number of ketones, the acetone levels in a diabetic's breath can be used to determine their risk of DKA. A high quantity of acetone in the breath indicates that the body is creating a large quantity of ketones. So, acetone levels in the breath should be checked on a regular basis, and maintained within a diabetic's safe zone by medical therapy.17 Diabetes mellitus is currently one of the top causes of death, with 0.451 billion diabetics globally in 2017 and a predicted increase to 0.693 billion by 2045. There are 200 different substances that have been identified in human breath, including the biomarker for diabetes known as acetone.18,19 VOC and acetone sensors are gaining prominence because of their potential applications in health monitoring and self-monitoring. Because acetone is a specific biomarker for diabetes, its presence in human breath has been identified as an important indicator of the disease.20 The average amount of acetone in the breath of healthy people is less than 1 ppm (0.3–0.9 ppm), but it increases to 2.2 and 1.7 ppm in type 1 and type 2 diabetic patients, respectively. As a result, recognizing acetone concentrations at less than 1 ppm, even at ppb levels, is crucial for detecting diabetes early.21,22 Thus, the early detection of acetone is crucial in a range of disciplines, including indoor air quality monitoring, medical diagnostics, and the industrial sector, to reduce health risks.23 As a result, it has become increasingly crucial in recent years to create high-performance gas monitoring sensors that can recognize minuscule amounts of acetone. Standardized techniques including high-performance liquid chromatography, proton transfer reaction mass spectrometry, and gas chromatography–mass spectrometry (GC-MS) can be used to determine the concentration of VOCs. These instruments cannot be used in portable healthcare applications since they are complex, challenging to use, and need time-consuming procedures to analyze the target gases.24
Due to their ease of fabrication, low cost, and high responsiveness, chemiresistive gas sensing materials have been used for a few years in the detection of several hazardous VOCs. Operation at high temperatures uses more energy, reduces the stability and longevity of the sensor, and puts the environment at risk of fire.25 The primary responsibility of every sensor is to provide information about a variable that is essential to the operation. Every measuring device needs at least one sensing element. Another element found in the majority of measurement technique is the transducer.26 The various types of gas sensors include chemiresistive, electrochemical, and infrared ones. With their superior accuracy, ease of use, and relative inexpensiveness, the chemiresistive sensors have received more attention than the other types.27 The chemiresistive gas sensor detects gas by adjusting the sensor's electrical resistance, which is dependent on the sensing materials and the target gas, via a chemical process that occurs when the target gases come into direct contact with the sensing element.28,29 This explains why chemical sensors have so many applications, especially in the medical field, where they are employed in portable healthcare monitoring systems.30
One of the most pressing issues in the realm of gas detection is the development of high-performance sensing materials at room temperature (RT).31 Traditional techniques for detecting various VOCs have good sensitivity and accuracy. However, these techniques require large, intricate, costly, and time-consuming equipment, and necessitate the use of professional gas monitoring tools. As a result, small, transportable, and fast dynamic acetone detection instruments are needed.32 When the target gases are present, electrical gas sensors can create an electrical signal. A useful gas sensor must have high sensitivity, selectivity, speed, stability, and affordability, as well as low cost and little power usage.33 Gas sensors should also have a high signal-to-noise ratio (S/N), which evaluates the relative strength of the gas signal over the noise intensity. It is possible to assess the electrical noise of gas sensors by keeping an eye on the average resistance fluctuation before injecting the target gas.34 A high electrical conductivity can typically create a low noise level. For calculating the limit of detection (LOD), at least three parameters among the five described above are required. N stands for the root mean square noise, and S is defined as average signal.35
In this review, we concentrated on the most recent developments in the study of bare MXene and its integrated nanocomposites for the detection of volatile organic compounds (VOCs). A road plan for commercializing MXene-based sensors is provided in this critical study, along with a thorough summary of current developments in sensor technology. Chemical, biological, and physical sensors are the three main classifications of the current sensors exhibited in Fig. 1.36 Depending on whether a sensor uses an electrical, electrochemical, structural, or optical detecting mechanism, the four main ways that sensors function in each category are then divided into a variety of subcategories.37 The most effective structural and electrical tactics for enhancing the performance of each category are provided. Finally, problems that prevent the commercialization of MXene-based sensors are examined, and many innovations for making MXene-based sensors readily available on a commercial scale are proposed. The production, properties, and uses of MXene in gas sensing devices are covered in this paper, along with information on their structural characteristics.
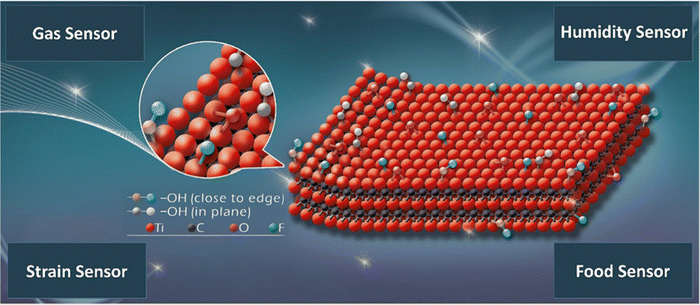 |
| Fig. 1 Schematic diagram of MXene. Reprinted with permission from ref. 38. Copyright 2022, American Chemical Society Omega. | |
2. Classification of 2D materials
Owing to their morphology, high surface-to-volume ratio, and structural properties, 2D materials are applicable for gas sensing39 because of their tunable chemistry, larger specific surface area, and fabrication techniques, 2D sensing nanomaterials have also been extensively studied in terms of the three S parameters (selectivity, sensitivity, and stability) and five essential R parameters (room temperature operation, repeatability, reproducibility, range of detection, response and recovery time).40 Single-layer 2D materials with minimal or no interlayers have highly fascinating electrical properties that distinguish them from monolayers.41Fig. 2 shows many kinds of 2D materials, such as graphene, including Xenes, Xanes, Fluro-Xenes, Transition Metal Dichalcogenides (TMDCs), Sheet Moulding Compounds (SMCs), MXenes, and other 2D materials. These 2D materials are moderately fascinating to researchers owing to their physical and chemical properties, which vary from those of 2D bulk materials.42,43 In these 2D materials, free charges do not move in one dimension, but move in the other spatial dimension. This feature of the 2D materials made it exceptional from other available bulk materials.44 Additionally, 2D materials have a wide variety of elemental compositions that improve their insulating, semiconducting, spanning metallic characteristics, and fine-tuning can improve their electrical properties, which are good for gas sensing.45 Ultra-thin 2D layered materials are famous for their unique chemical, physical, and electrical properties. This is why these materials are acceptable for energy storage, electronic application, and catalysis.46 For room temperature gas sensing, the use of 2D materials is promising owing to their morphology and electrical properties.45 These materials could be used in photocatalysts, field effect transistors, photovoltaics, composite materials, biosensors, photosensors and other applications.47 Due to their associated difficult synthesis processes, rough surface functionalization, and low selectivity, the 2D materials cannot be employed to produce sensing signals at the commercial level.
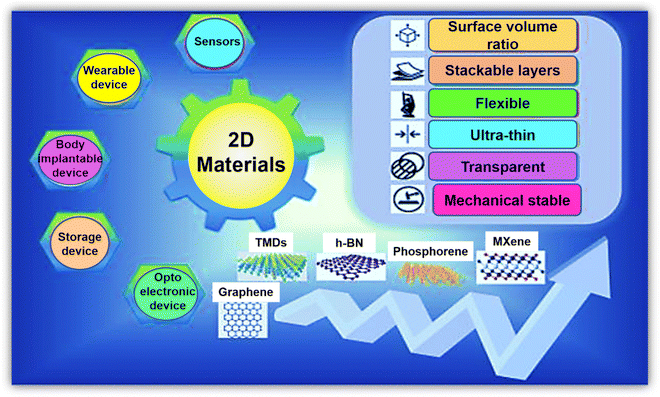 |
| Fig. 2 A schematic illustration of 2D nanomaterials with their properties and application. Reprinted with permission from ref. 48. Copyright 2022 iScience. | |
3. MXene: structures and properties
MXene has been accepted as a highly developed biosensing podium due to its excellent metallic conductivity, good biocompatibility, large surface volume ratio, and ease of functionalization.49 It has already achieved much attention in the research field of electronics, sensors, catalysis, and energy.50 MXene use in the biomedical sector has become a popular subject of research in the last two years, with studies on photothermal therapy for cancer, biosensors, neural electrodes, theragnostic, dialysis, and other applications.51 In the field of biosensors, Xu and his coauthor began recommending 2D materials to study neural activity in 2015.52 The MAX phase, as well as other layer nitrides and carbides, have been the focus of research for the last 10 years, and novel MXene precursors are now being developed since 2017.53 The modern 2D material MXene is increasingly gaining acceptance in the realm of gas sensors. MXene, a brand-new material from the 2D family, was created in 2011 at Drexel University.54 Shown in Fig. 3, as the forerunner of MXene, the MAX phase is frequently a sequence of triplex layered compounds, with M as the transition metal (Ti, Cr, Sc, V, Nb, Ta, Hf, Mo, and W), and A as an element such as Al or Ga, from group IIIA or IVA in the periodic table. This MAX phase is utilized as a precursor for the preparation of MXene.55 MXenes are two-dimensional metal carbide, nitride, or carbonitride materials with layered hexagonal lattice formations with P63/mmc symmetry and the formula Mn+1XnTx.56 Here, M is a transition metal (13 and 14 group element from the periodic table), X is a carbide, nitride, or carbonitride, and Tx is a terminated functional group, such as –O, –F, –OH.57 By using the appropriate acid solution, such as HF, to etch the interlayer A atoms, MXene can be produced from the metal-ceramic MAX phase (Mn+1AXn). In the MAX phase, M–A may be a covalent, ionic, or metallic bond and M–X may be a pure metallic bond.58 Hence, at high-temperature, the M–A bond breaks down into Mn+1Xn, which brings about recrystallization and arrangement of 2D layered Mn+1Xn, and the MXene sheet is maintained with van der Waals force and hydrogen bond.59 Recent studies have revealed a rapid increase in the variety of MXene compositions that have been synthesized.60 To date, over 30 MXene compounds have been published, and over a dozen have been surveyed by using computational methods.61 When two transition metals are mixed in the MXene structure, this is a characteristic property that is displayed.62 Transition metals can be arranged in an ordered structure in a single exfoliated 2D MXene, either by creating atomic sandwiches of transition metals in the plane (n = 1) arrangement structure like (Mo2/3Y1/3)2CTx or for planes (n > 2) like Mo2TiC2Tx. MXenes were synthesized in 2014 and published in 2015.63 The research on the MAX phase is exciting due to the numerous synthesized unique structured 2D carbide phases. The properties of the novel ordered double transition metal MAX phases have been studied, along with their magnetic properties. MXenes have an exclusive combination of properties. Along with the mechanical properties and electrical properties of the transition metal nitride/carbide, the functionalization surface of MXene makes it hydrophilic and prepared to attach with various species. This facilitates the creation of a durable colloidal solution in water with extra negative zeta potential and proper adsorption of electromagnetic waves. This is why there are a large number of MXene applications.64
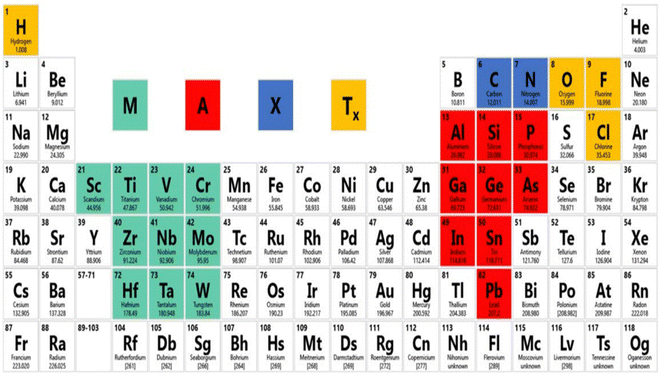 |
| Fig. 3 Chemical elements for the design of the MAX phase and MXene. Adopted with permission from ref. 69. Copyright 2017, American Chemical Society. | |
The appeal of MXene stems primarily from the fact that, in contrast to other 2D materials (like graphene, transition metal disulfide, and hexagonal boron nitride sheets) that require difficult synthesis procedures, folding or re-stacking sheets, and have limited hydrophilicity, MXene is advanced in all features.65 When a target gas comes into contact with 2D materials, the surface adsorption process can also affect the conductivity of the material.66 However, with MXene, this is not always the case because the interlayer puffiness can drastically alter the surface properties. As a result, mechanisms other than adsorption may be required for gas detection. MXenes have adaptable surface chemistry, graphene-like morphology, redox capability with high conductivity, terminated function development on the surface, and overall outstanding hydrophilicity, which make them an ideal candidate for various sensor devices.67 MXenes are now regarded as versatile gas-sensing materials, and it was noted that low concentrations of acetone can be detected at room temperature by utilizing an MXene-based sensing element.68 The largely undiscovered members of MXene, which have a unique mixture of properties, open the door to a diverse array of applications.
3.1 Structure of MXene
The structure of MXene is similar to that of the MAX phase. However, the M atoms are tightly packed in a group, while the X atoms are located in octahedral interstitial positions.70 In the hexagonal closed packed (HCP) configuration of the MXene structure, M atoms are arranged in M2X in the same manner as they are arranged in M3C2 and M4C2 in an ABABAB and ABCABC sequence, respectively.58 The MAX phase has a layered structure of carbides and nitrides with the formula Mn+1AXn, where M is a transition metal (groups 3–7 in the periodic table), A is an element such as Al or Ga, from group IIIA or IVA in the periodic table, and X is either carbon or nitrogen. MXene is created when the A layer is eliminated by any etching method.71 With the unstable M–A bond broken in the MAX phase, as shown in Fig. 4b, the elemental layers can be specifically eliminated, resulting in MXene with the formula Mn+1XnTx (n = 1, 2, 3) and Tx as a surface termination functionality. The most significant change in the MXene structure occurs when the –O, –F, and –OH functional groups replace the transition metal surfaces in the M–X layers as a result of the removal of the A layer from the MAX phase using fluoride acid, as illustrated in Fig. 4b and 4c (i and ii). Additionally, these functional groups, which are indicated by the symbol Tx in the MXene formula Mn+1XnTx, acquired some inherent flaws, such as atomic vacancies, during the preparation of the MXene flakes.72 A. N. Enyashin et al.73 used DFT (density functional theory) to determine the relationship between the properties and structure of MXene. In Ti3C2Tx, there are three different ways that –OH groups can be arranged. In configuration I, –OH groups are placed above the hollow space between the C atoms; in configuration II, –OH groups are positioned above the C atoms on both sides of layers; and in configuration III, they are mixed together. The structural stability of the term –OH configuration was assessed by contrasting their respective DFT energies. Configuration I is the most stable, whereas configuration II is the least stable because of the underlying C layers and strong attraction between Tx groups.73 As a result, it was discovered that configuration I contains the functional groups –OH and –F. Different terminal groups provide MXene with a wide range of characteristics.
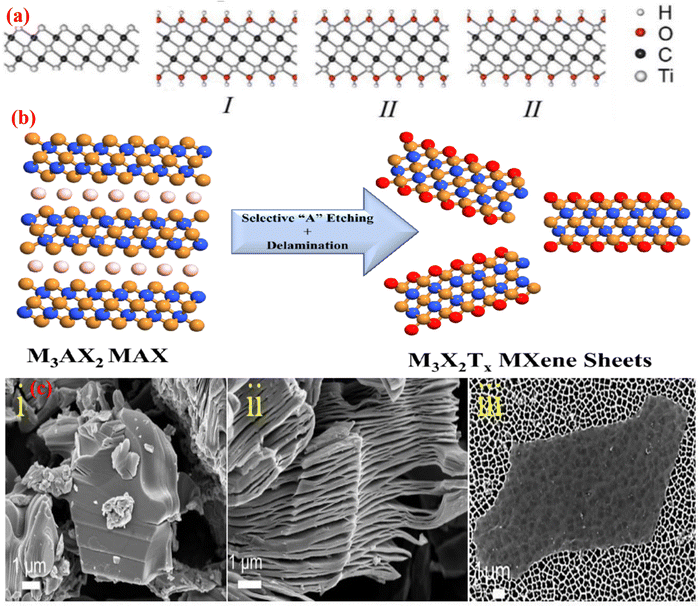 |
| Fig. 4 (a) Configuration of the OH groups: (i) Ti3C2(OH)2, (ii) Ti2C(OH)2, (iii) Ti3C2(OH)2. Adopted with permission from ref. 73. Copyright 2012, Computational and Theoretical Chemistry, Elsevier. (b) Schematic illustration of the MXene synthesis process from the MAX phase.74 (c) SEM images of the (i) MAX phase, (ii) Multilayer MXene, and (iii) MXene assembled flakes in a colloidal solution. Adopted with permission from ref. 62. Copyright 2017, American Chemical Society. | |
3.2. Properties of MXene
3.2.1 Tunable band gap.
The shape and surface termination of MXene, which have a significant impact on sensory functions, may be efficiently controlled by the synthesis process. Micro/nano morphology, for instance, may be used to modify electrical characteristics when mechanical force is applied. Furthermore, multi-layer morphology can aid the transport of enzymes for biosensors and allow for quick diffusion of certain compounds.75 A handful of the newly discovered semiconducting MXene structures have band gaps greater than 1 eV, making them potentially useful for the production, delivery, and storage of renewable energy.76 By examining the orbital decomposed electronic structures and density of states (DOS), we can provide information on the characteristics of semiconductors, such as Mott or charge-transfer insulators, as well as the primary excitation mechanism.77 The core layer exhibits the leading N-2p to Ti-3d excitation, and the band margins of the surface layer exhibit a strong dominance of the M-3d states.78 Layer-dependent and inter-atomic band edge-produced excitations in the two selected semiconducting MXene, which are accordingly charge–transfer semiconductors, permit careful research for novel optical properties.79 The d states of Hf are the major source of the Hf2CO2 conduction band. This suggests that the band gap may be tuned by substituting Ti for Hf since Ti has lower d levels. The quasiparticle band gap of the semiconductor alloy Hf2−2xTi2xCO2 can be continuously adjusted from 2.45 to 1.15 eV, which is in line with the estimated quasiparticle band gap of Ti2CO2 of around 1.15 eV.80 It is anticipated that adding Zr to the alloy system will lessen the lattice strain while essentially maintaining the same basic gap. MXene synthesis and modification are quite interesting, particularly in the context of sensors.
3.2.2 Physical properties.
The physical properties of MXene are strongly influenced by their surface terminations. The elastic stiffness of MXene with –F and –OH terminations is lower than that of O-terminated MXene, even though MXenes with an O-termination are anticipated to have exceptionally high stiffness.81 Here, the –O and –OH groups make MXene more stable because the –F group is replaced with the –OH group. When MXene is stored in water, –OH groups can also be replaced with –O groups by high-temperature treatment or metal adsorption method.82 Most importantly, when MXene comes into contact with Al, Mg, Ca, or other metals, it can stimulate the breakdown of the –O groups into true MXene. The highest Young's modulus of MXene for a solution-processed 2D system is 330 GPa. Theoretically, MXene with lighter M elements and fewer layers (n = 1) is projected to have greater elastic moduli.82 MXenes have a significant deal of potential for usage in composite materials due to their excellent elastic characteristics, as well as their strong electrical conductivity and hydrophilicity. Due to its suitability for intercalating a variety of organic molecules and metal cations, MXenes can be used in energy-storage applications. From Fig. 5b, we can observe the bending rigidity of the Tin+1Cn, MoS2, and graphene multilayer as a result of their thickness. Thick MXene nanoribbons have a greater bending rigidity value. This is because it depends on different parameters, like the shape, size and temperature of the sample.83
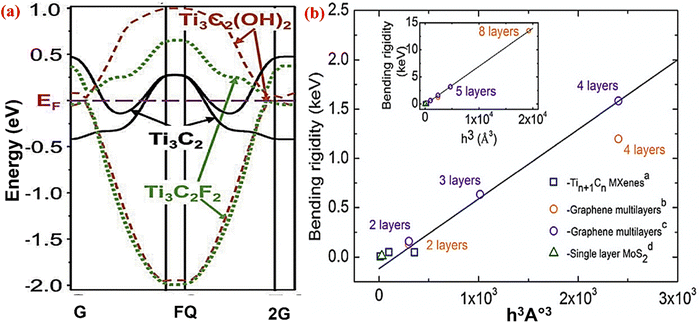 |
| Fig. 5 (a) Electronic structure of the Ti3C2 MXene with OH, F functional groups, and no termination adopted with permission from ref. 96. Copyright 2011 John Wiley and Sons. (b) The bending rigidity of the Tin+1Cn MXene, MoS2, and graphene multilayer in relation to their thickness. Reprinted with permission from ref. 83. Copyright 2018 Elsevier. | |
3.2.3 Chemical properties.
Many applications require the ability to produce exceptionally robust colloidal suspensions, particularly when fabricating thin films. The interlayer force is extremely strong in the bulk MAX phase, but it weakens after exfoliation in MXene. The formation of monolayers or few layers of MXene nanosheets is aided by the weak hydrogen bonding force between the –O/–F atoms on one surface and the –OH functional groups on the opposite surface, as well as the van der Waals force connecting the MXene layers.84 This means that the surface termination configurations are highly dependent on the etching and exfoliation process with ambient temperatures, such as when Ti3AlC2 is etched with a low concentration of HF solution, to obtain Ti3C2Tx and the amount of –O group will be greater than that of the –F group. In contrast, when Ti3AlC2 is etched with HCl–LiF solution for exfoliation, it contains the –O/–OH group with water molecules.85 Consequently, the intercalation of water molecules and cations improves the Ti3C2Tx dispersion behavior in various solvents. Furthermore, during the intercalation process and when cations and water molecules are introduced between the layers, they act as spacers.10 Studies were performed to determine the most successful method for separating the forcefully bonded structure of MXene when intercalated with molecules, such as DMSO, urea, and isopropyl amine.86 After exfoliation, a strong hydrophilic characteristic developed due to the creation of the surface termination on the Ti3C2Tx nanosheets. As a result, the Ti3C2Tx MXene shows the maximum dispersion stability in aqueous solution.87 Thus, Ti3C2Tx-based materials like composite materials still blend with polymers, free-standing paper by filtration, and thin film for deposition.88
3.2.4 Electrical properties.
MXene features a single-layer structure, metal-like electrical conductivity, and electron and Fermi level densities that are very close. The electrical conductivity of Ti3C2Tx MXene is higher in comparison to other MXenes reported in the literature.89 The electrical conductivity of MXene is affected by its shape, surface characteristics, and nanoflake size. Previous studies have reported that the least defective Ti3C2Tx nanosheet had an electric conductivity of 6.5 × 10−3 S cm−1 and the largest defect obtained by Ti3C2Tx etching with HF had an electrical conductivity of 1000 S cm−1.90 The MXene structure (Mn+1CnTx) contains n + 1 layers of M that are extremely close to one another, with C or N occupying the octahedral space between them to demonstrate the arrangement of [MX]nM.91 A metallic behavior is observed in the MXene family, such as Tin+1Xn. However, when the value of n grows, the metallic characteristics weaken due to the creation of an additional Ti–X bond. Titanium has greater metallic characteristics than titanium carbides in terms of X because N atoms have one more electron than C atoms.92 By distinction, functionalized MXene sheets are small band gap metals or semiconductors, calculated by the species and position of surface groups. By literature survey, different terminated MXenes such as Hf2CO2, Ti2CO2, Zr2CO2, and Sc2CF2 have band gaps of 1.8, 1.03 0.45, and 0.24 eV, respectively. Here, Sc2C(OH)2 has a small direct band gap because its electronic structure can be tuned.93 Strain can alter the interatomic distance and corresponding positions of atoms in materials. Therefore, when the tensile strain increases, the associated band gaps steadily become narrower. At the correct tensile strain, the indirect band gaps will become direct band gaps. So, under an external electric field in Sc2CO2 MXene, the indirect band gap changes into a direct band gap.94
DFT calculations also show that the band gap of MXene can be changed by changing the surface termination, as shown in Fig. 5a. MXene in Ti3C2 exhibits metallic behavior, whereas Ti3C2Tx has functional groups with –OH and –F and behaves as a semiconductor with band gaps of 0.05 eV and 0.1 eV, respectively. As a result of their band gaps, these materials can be used in applications ranging from field effect transistors to semiconductors. The band gap of MXene can be changed by changing the elemental composition of the M layers. Anasori et al.95 worked on the metallic nature of MXene like Ti3C2(OH)2. When the top two layers of Ti were replaced with Mo and produced Mo2TiC2(OH)2, the semiconducting properties were changed with a new bandgap at 0.05 eV. The density of state and atomic ordering calculation of Ti3C2(OH)2 and Mo2TiC2(OH)2 displayed this transition, which was verified by the negative and positive magneto-resistance values of both MXenes at 10 K.
4. Synthesis methods for MXene and Integrated MXene composite
4.1 Etching method of MXene (HF etching, intercalation, dispersion)
There are a variety of ways to make MXene from the MAX phase, including fluoride in an acidic solution, chemical vapor deposition, hydrothermal synthesis, alkali etching, and many others, which are given in Table 1. The two main methods for creating MXene are the bottom-up technique, which frequently begins with tiny atoms or molecules after crystallization and may be combined into a 2D layered MXene, and another one is the top-down method, which transforms bulk MAX phase transitions into single-layered MXene nanosheets.97 From 2011 to 2020, the most widely used technique for producing MXene was the hydrofluoric acid (HF) etching process. The hydrofluoric acid (HF) etching technique was first employed in the Ti3AlC2 MAX phase by Naguib et al. in 2011 to remove Al layers by simple displacement reaction, and create hydrogen gas (H2) using Ti3C2 MXene.98 Ti3C2 MXene is generated as a result of DI water and HF acid solution, with different functional groups like Ti3C2Tx (Tx as a functional group like –OH, –F, or –O). This was further processed, centrifuged and filtered because the supernatant contained the isolated solid form. In the next process, the layered structured MXene was found by washing with DI water and maintaining a pH of ∼6. The hydrofluoric acid etching method is mostly used to synthesize MXene materials.99 The MXene particles in Fig. 4c(ii) have an accordion-like shape that is clearly visible. The temperature, duration, and F ion density all have a big impact on how well the MXene layers develop during the etching process. However, harder acid etching may give larger surface defects and may reduce the quantity of MXene.100Fig. 6a displays the good layered shaped Ti3C2Tx MXene, which was produced by high concentration hydrofluoric acid. Chemical reactions used in the formation of MXene by HF etching are represented by eqn (1)–(3) | Mn+1AlXn + 3HF → AlF3 + Mn+1Xn + 1:5H2 | (1) |
| Mn+1X2 + 2H2O → Mn+1Xn(OH)2 + H2 | (2) |
| Mn+1X2 + 2HF → Mn+1X2F2 + H2 | (3) |
Table 1 Different etching processes of MXene are used by etchants
MXene |
Precursors |
Etchants |
Time (h) |
T (°C) |
Yield (%) |
Ref. |
CrTiC2Tx |
Cr2AlC2 |
5 M LiF + 6 M HCl |
42 |
55 |
80 |
63
|
Ti3C2Tx |
Ti3AlC2 |
50% HF |
2 |
RT |
100 |
96
|
Ta3C3Tx |
Ta3AlC2 |
50% HF |
72 |
RT |
90 |
98
|
Hf3C2Tx |
Hf3[Al(Si)]4C6 |
35% HF |
60 |
RT |
NA |
102
|
Ti3C2Tx |
Ti3AlC2 |
3 M LiF + 6 M HCl |
45 |
40 |
100 |
103
|
Nb2CTx |
Nb2AlC |
50% HF |
90 |
RT |
100 |
109
|
Zr3C2Tx |
Zr3AlC2 |
50% HF |
60 |
RT |
NA |
110
|
Mo2CTx |
Mo2Ga2C |
3 M LiF + 12 M HCl |
398 |
35 |
NA |
111
|
W4/3CTx |
(W2/3Sc1/3)2AlC |
4 g LiF + 12 M HCl |
48 |
35 |
NA |
112
|
Ti3C2Tx |
Ti3AlC2 |
1 M NH4HF2 |
12 |
80 |
NA |
113
|
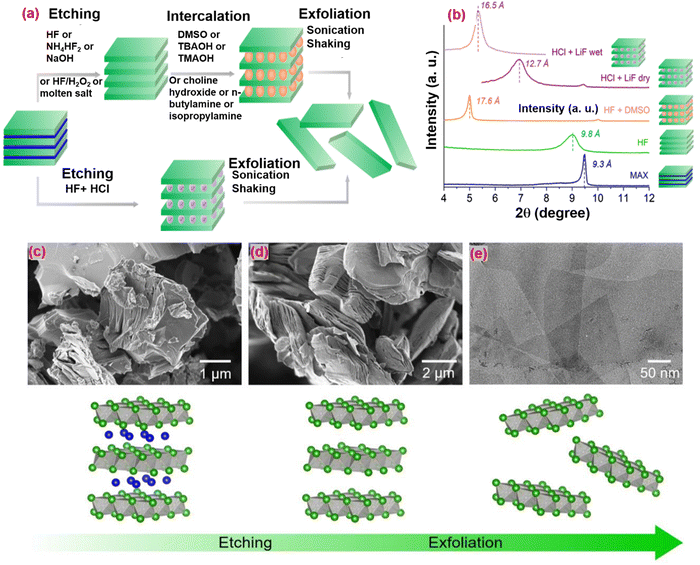 |
| Fig. 6 (a) Pathway to obtain 2D MXene single flakes by top-down synthesis: first, selective etching of atomic layer(s) from a 3D layered precursor is required, followed by exfoliation into single flakes. (b) XRD patterns for Ti3AlC2 (blue), dry Ti3C2Tz multilayers after etching with HF and washing (green) and after intercalation with DMSO (orange), dry (solid line purple) and wet (dotted line purple) Ti3C2Tz multilayers etched with HCl+LiF. (c) SEM micrograph of Ti3AlC2 particles. (d) SEM micrograph of Ti3C2Tz multilayers after etching of the Al layer. (e) TEM micrograph of overlapping Ti3C2Tz single layers. Schematics of the MAX-to-multilayers MXene transformation and their exfoliation are shown in the bottom row.71 Copyright 2019 Current Opinion in Solid State & Materials Science. | |
Lower concentrated HF does not produce a layered morphology, whereas etching with high concentrations of HF results in a suitable separated layered structure with low MXene crystallinity.72 The etching procedure depends on many variables, including the type of etchant, etching duration, temperature, and MAX phase quality, MXenes Ti3C2Tx,96 Nb2CTx,101 Hf3C2Tx,102etc. MXene is produced using this process, resulting in enormous amounts of very poisonous HF fumes that are hazardous to health.
To ensure safety and halt the disastrous results of concentrated HF, an alternative method must be used. The MAX phase was immersed for 45 hours at 40 °C in a solution of lithium fluoride (LiF) and hydrochloric acid (HCl) to etch the aluminum layers from the MAX phase. This process was introduced by Ghidiu et al.103 due to the mild nature of LiF + HCl. However, some defects appeared, so other combinations of fluoride salts can be used, such as NaF, CsF, CaF2, KF with HCl or H2SO4.
| LiF(aq) + HCl(aq) → HF(aq) + LiCl(aq) | (4) |
This method is less harmful, produces fewer defects, and requires less sonication time. Most importantly, HF etching failed for the nitride-based MXene.
104 Using this method, many MXenes, such as V
2CT
x,
105 Mo
2CT
x,
106 and W
4/3CT
x,
107 have been prepared. Only NH
4HF
2 should be used for the MAX phase of the Ti
3AlC
2 etchant, rather than a strong acid. In addition, as the MXene layers were being etched, NH
4+ (ammonium) ions were intercalated into them. This technique produced layers with a larger lattice parameter than HF etching in Ti
3C
2, which was the previous approach used. The etching process of Ti
3AlC
2 by NH
4HF
2 is explained through
eqn (5).
| Ti3AlC2 + 3NH4HF2 → (NH4)AlF6 + 3/2H2 + Ti3C2 | (5) |
To achieve high MXene quality, the etching procedure and suitable conditions must be gradually changed. For weak etchants, such as LiF/HCl, NH
4HF, and NH
4F, a long etching time or a high reaction temperature are required. The MXene structure verifies the outcome, requiring additional time and a higher temperature. A larger
n value requires a greater fluorine ion, as well as a high reaction time.
108
Multilayered MXene must then undergo a delaminating process to generate single-layered MXene.114 Reducing the contact between layers in MXene requires increasing the interlayer gap using intercalating materials.115 A suitable solvent is necessary for the delamination and intercalation processes to scatter the material and intercalate the products effectively. When the intercalated-like organic molecules dissolve in the solvent and are agitated for a few hours, they can fit between the 2D layers of multilayered MXene, resulting in a swollen shape as the interlayer distance rises. Furthermore, sonication in deionized water can convert the intercalated MXene multilayer into mono sheets.116 The sonication procedure is critical for the final nanosized sheets. Organic chemicals and ionic compounds are the two forms of intercalation. Organic chemicals are commonly employed as intercalants for HF-produced MXene because they mostly comprise polar organic molecules, such as isopropyl-amine, hydrazine, dimethyl sulfoxide (DMSO), urea, and tetrabutylammonium hydroxide (TBAOH).58 For delaminating, Ti3C2Tx and Nb2CTx have been used with DMSO and isopropyl-amine intercalants. Meanwhile, for the delamination of Mo2CTx, V2CTx, Ti4N3Tx, and Ti3CNTx, TBAOH was used as for intercalation.58
Due to a van der Waals force acting between the layers of MXene, MXene can be piled below its weight. It directs the increase of the ion transport pathway, and decreases the contact between electrolytic ions and active surface sites. This is why it is necessary to find a method that allows MXene to still be dispersed.117 Usually, two techniques are used together, not only in modifying MXene, but also in choosing various dispersants. Regarding dispersants, the most researched solvents have been organic. Maleski et al.118 dispersed the MXene in ethanol, acetone, water, methanol, and other solvents. The ease of dispersing the 2D substance with the solvent increases with surface tension. Except for ethanol, all other organic solvents have extremely high surface tension. For example, the solution-phase flocculation technique primarily used ammonium ions to resolve the MXene re-stacking issue. This technique was first used by Zhang et al.119 for the preparation of Ti3C2Tx MXene, although the direct preparation of MXene powder was possible using the solution-phase flocculation technique.
4.2 Synthesis of the integrated MXene composite
MXenes are regarded as ideal prospects for the synthesis of multifunctional composites due to their 2D morphology, multilayered structures, and remarkable flexibility, which has sparked a rise in the research of MXene-based composites. Many unique composites have been created by mixing MXenes with other materials, such as polymers, metal oxides, and carbon nanotubes.
4.2.1 Mxene–polymer composites.
MXenes with superior mechanical characteristics, metallic conductivity and hydrophilic surfaces can improve the mechanical and thermal properties of polymers when building composites with polymers. Single-layer MXenes have easily accessible surface hydrophilicity and polymer compatibility compared to multi-layered MXenes. As a result, MXenes are often delaminated before interacting with polymers. Ling et al.120 described the production of a single-layered Ti3C2Tx–polyvinyl alcohol (PVA) composite by combining a colloidal solution of Ti3C2Tx films with an aqueous solution of PVA. The PVA was spread between Ti3C2Tx films in the Ti3C2Tx–PVA composite, which is a layered structure. Naguib et al.121 used a two-step approach to create a Ti3C2Tx–polyacrylamide (PAM) composite. First, DMSO was inserted into the Ti3C2Tx interlayers to enhance the Ti3C2Tx layer separation and obtain complete delamination of the individual Ti3C2Tx layers. The produced Ti3C2Tx and PAM solutions were then evenly mixed and dried for 4–5 days at room temperature.
4.2.2 MXene-metal/metal oxide composites.
MXene-metal/metal oxide composites have excellent electrochemical stability and strong electrical conductivity. The synthesis of the Au/Ti3C2Tx nanocomposite was accomplished by chemical reduction. In this procedure, a reducing agent was introduced to decrease the metal-containing solution, and stirring was also used to help. The previous combination was then added with Ti3C2Tx MXene. After 30 minutes, the chemical was ultrasonically treated. After the reaction was finished, the solution was drained using cellulose filter paper with 0.1 μm pore size and rinsed three times with deionized water. After that, the filtered material was dried for two hours at 80 °C in a vacuum oven.122 Wang et al.123 offered a straightforward method for producing a Li4Ti5O12–Ti3C2Tx composite. The comparable synthetic process comprises two steps. To begin, by combining Ti3C2Tx, different hydrogen peroxides, and LiOH·H2O in deionized (DI) water, lithium ions can enter the interlamination of Ti3C2Tx and increase its interlayer spacing. The acquired products are then washed multiple times with DI water and dried at 40 °C for 24 hours before being calcined at 550 °C for 4 hours under N2 atmosphere to achieve the final products. Zhu et al.124 created TiO2–Ti3C2Tx nanocomposites in a hydrothermal environment. The TiO2–Ti3C2Tx nanocomposite is formed by heating the sample at 500 °C for 4 hours after tetra butyl titanate (TBOT) combines with Ti3C2Tx to create precipitates of TiO2 particles that attach to the surface of Ti3C2Tx.
4.2.3 MXene-carbon nanotube composite.
These composites were created through mechanical mixing, co-dispersion, self-assembly, electrophoretic deposition, in situ CNT growth on MXene by chemical vapor deposition, thermal processing, hydrothermal methods, and microwave-assisted synthesis.125 Three-dimensional (3D) nano-fillers of MXene (Ti3C2Tx)/CNTs have been synthesized with high stability and enhanced interfacial attachment between adjacent fiber yarns, as well as increased tensile and flexural strength, demonstrating excellent roughness on the surface and elasticity even after 18 weeks of immersion in alkali solutions.126
4.3 Characterizations of MXene and its integrated composite
4.3.1 X-ray diffraction analysis.
The best technique to ensure that there are no interacting MAX phases is by using X-ray diffraction (XRD) after imparting considerable texture to the powders. Because MAX phases are extremely anisotropic, when pressure is applied to the powders, the particles arrange along the (002) direction. This points out (00l) peaks in all MAX phases, making it simpler to identify conflicting MAX phases. It should be noted that texturing the materials in this manner makes complete phase quantification by Rietveld refinement. As a result, it is preferable to run the scan twice, once untextured and then again textured.127 In addition, the formation of the MXene composite increases the space between interlayers and specific surface area. Due to these remarkable properties, the adsorption and sensitivity performance are enhanced. MXene is identified by the XRD peak (110) at the 2θ value of 60° for the layered configuration form. In the etching process at the proper time, the peak (002) gets shifted at a lower angle. Fig. 6b and 7c exhibit the XRD pattern of the Mo2Ga2C MAX phase and Mo2CTx MXene after being HF etched. Hence, a strong peak (002) can be observed at a lower angle (<10°), and the XRD pattern also indicates the expanded interlayer spacing after etching with HF.
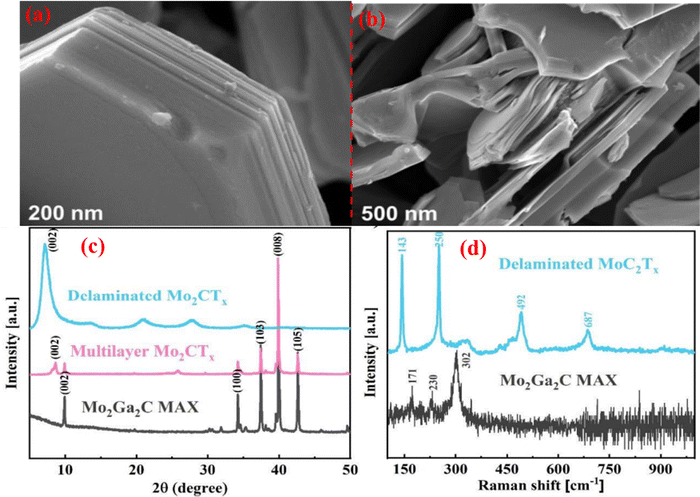 |
| Fig. 7 SEM images of the (a) Mo2Ga2C Max phase, (b) after HF etched Mo2CTx MXene, (c) XRD pattern of Mo2Ga2C during HF etching, (d) Mo2Ga2C MAX phase and delaminated Mo2CTx MXene Raman spectra. Reprinted with permission from ref. 130. Copyright 2020 American Chemical Society. | |
4.3.2 Raman spectroscopy.
Vibrational spectroscopies are powerful techniques for identifying molecular patterns, and have been widely utilized to detect the structure of 2D materials. Raman- or infrared-active vibrations are determined by the space group of the material. Fig. 7d shows that material uniformity should be addressed when interpreting a vibrational spectrum. The structure of MXene is characterized as a deformed P63/mmc space group. Surface groups are responsible for the distortion. This causes the vibrational bands to enlarge,128 because only one unit cell is included in simulations, the available estimations are based on the structure, which assumes homogeneous surface groups. In practice, the MXene synthesis method produces several surface groups that are randomly distributed around the flake. This causes a superposition and overlap of the surface group vibrations, and peak widening, making Raman spectral interpretation extremely difficult. Furthermore, the presence of water between the layers has an effect on the IR spectrum. However, good sample preparation may decrease this impact and allow infrared spectroscopy to reach its full potential, particularly for composite materials. In place of FT-IR, Raman spectroscopy was employed to demonstrate the presence of MXene in the composite materials.129
4.3.3 Scanning electron microscopy.
SEM enables identification of the structure, and typically provides immediate confirmation that MXene is being produced. However, not every single etched sample seems to be the same. Since the first MXenes were formed by immersion in extremely concentrated HF, the “accordion” form is thought to be indicative of a successful synthesis, as exhibited in Fig. 6c and d. Fig. 7a shows a pure layered stature of the Mo2Ga2C MAX phase and the multilayered structure of Mo2CTx MXene, which can be obtained after etching with HF. However, its accordion structure, which is now virtually synonymous with MXene, does not characterize all multilayer MXenes.62Fig. 7a and b show the difference between the MAX phase and the MXene morphology. Energy dispersive X-ray spectroscopy (EDS) is frequently used in conjunction with SEM as a supplementary method. While this method provides good qualitative information regarding the M element, it is critical to recognize that it is not accurate for analyzing the surface terminations or X ratios. Even when analyzing multiple-M MXenes, it is preferable to employ a qualitative comparison rather than an exact quantitative study. This is because most of the EDS detectors in use are not quantitative and calibrated as such. It is feasible to employ EDS as a quantitative approach.131
5. MXene-based acetone sensors: a mechanism
MXenes have high conductivity and typically exhibit metallic characteristics. The donor or acceptor gas molecules, as well as the p-type or n-type sensing materials, determine whether resistance increases or decreases in the semiconductor gas mechanism.132 In 2D materials, the space between the layers is a crucial for electrical transport. Large gaps between the 2D MXene provide a fundamental pathway for the movement of electrons. Junkaew and others133 have worked on the interlayer expansion that would change the conductivity of the materials and enhance the gas sensing performance. In 2D materials, the interlayer spacing is enhanced as a result of layer expansion, and electrons are unaffected. Additional active sites for gas adsorption may be added to MXene by the active terminations. In comparison to gas sensors based on other 2D materials, MXene-based gas sensors have extremely high signal-to-noise ratios and low limit of detection (LOD).134 Furthermore, despite the MXene gas sensor's ability to detect both electron acceptor gas and electron donor gas, the change in MXene resistance constantly rises. Chen et al.135 found that in the detection of acetone and ethanol, the resistance changes were typically positive. While the MXene carriers shrank and the MXene surface started to take up gas molecules. As the output increases, the MXene resistance increases. MXene can be characterized as having strong hydrophilicity and solution processability.136 The primary reason that MXene constantly shows a positive resistance is that the barrier on the surface of MXene makes it harder for the electrons to move around. This causes MXene to have more resistance, whereas other 2D materials do not experience it.
Following the etching procedure, MXene absorbed H2O and O molecules. This caused p-type MXene doping, which changed the metallic MXene behavior into that of a semiconductor. The MXene gas sensing mechanism is now understood similarly to semiconductor materials. The MXene sensor takes in oxygen when it is exposed to air. O2 molecules may be adsorbed on semiconductors by gaining an electron,137 and finally change them into chemically adsorbed oxygen molecules like O2−, O2−, and O−. After the surface produced the oxygen molecule O2, layers of hole accumulation formed, lowering electron resistance. O2 on the surface of sensor reacts with the target gas when the MXene sensor is submerged in it. Due to electron–hole recombination, which decreases the carriers of the MXene sensor and increases resistance, the electrons taken by the O2 molecule are free to return to the MXene surface.138 When metallic MXene and n-type semiconductors are mixed, the Fermi level remains constant, while electron transport occurs between the two materials and creates an electric field and Schottky barrier as a result. The MXene gas sensor's gas sensing mechanism is improved as a result of the interfacial generation of p-n junctions. As a result, the electron acceptor or donor property of the target gas molecule determines whether the sensor resistance negatively or positively changes. For instance, the p–n heterojunction of SnO–SnO2/Ti3C2Tx is shown in Fig. 8b and c. The energy level structure prior to contact and the acceptable band diagrams for SnO, SnO2, Ti3C2Tx MXene are shown. The band bending is caused by the differing Fermi levels after the combination (Fig. 8b), as the charge carrier changes until the Fermi energy is equal. Both p-type MXene and n-type semiconductor have a lower work function. The electron transfers from the n-type semiconductor and p-type MXene to the n-type semiconductor with oxygen adsorption/desorption occurring on the sensing material surface through exposure to sensing analyte. The oxygen is then removed by the target gas, and creates a depletion layer, as shown in Fig. 8c. Before exposure to air, the electron resistance of the n-type semiconductor/p-type MXene will increase.139 As seen in Fig. 8d, when acetone gas is introduced, it oxidizes the oxygen that has been adsorbed. Electrons are then released and returned to the n-type semiconductor/p-type MXene sensing materials. The hole reacts with the liberated electron, raising the Schottky barrier height, which is the cause of the increased resistance. The n-type semiconductor/p-type MXene has a higher resistance than n-type semiconductors as a result of the electron depletion layer's thickness, which decreases. The following eqn (6) and (7) explain how the adsorbed oxygen and acetone undergo an oxidation–reduction reaction.
| CH3COCH3 + 4O2− → 3CO2 + 3H2O + 4e− | (7) |
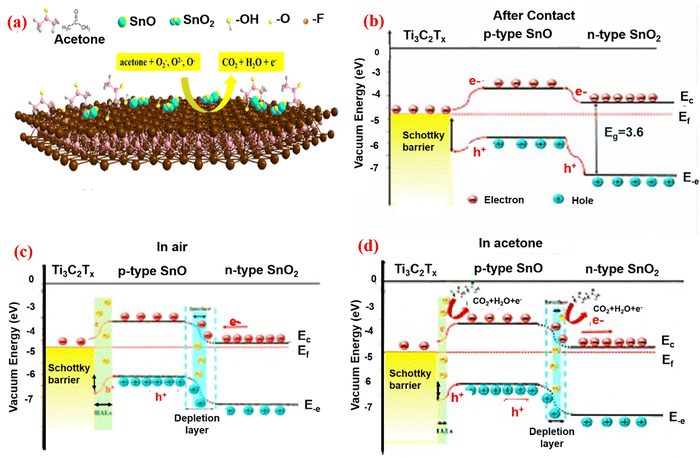 |
| Fig. 8 Schematic illustration of the band diagram of the p–n heterojunction and the combination of the SnO–SnO2/Ti3C2Tx sensor. Adopted with permission from ref. 139. Copyright 2020 Material Science Technology. | |
The n-type semiconductor/p-type MXene sensor will exhibit a hamburger-like morphology due to the wide surface area, which provides sufficient adsorption and reactivity for oxygen and the target gas. This is only one example of numerous contributions of MXene toward improving gas sensing performance. MXene has a significant amount of additional oxygen functional groups (–OH, –O) on its surface.139 MXene is now viewed as a versatile gas sensor, and the first finding of low-concentration acetone at room temperature was detected.
5.1 VOCs sensing by MXene
Gas sensing is a growing research direction because of its utilization in air quality management for monitoring air pollution, diagnosis, and breath analysis.140 Apart from reactive gases like NO2, H2S, and NH3, the identification of VOCs at ppm/ppb concentrations is essential for the early prediction of serious disorders like peptic ulcers. Normally, high noise and signal bandwidth are the two important factors for generating sensitive gas sensors.141,142 In this way, the sensing podium can accommodate numerous active sites and high conduction for interfacial interaction.143 There is a trade-off relationship in traditional materials like metal oxide, graphene, and black phosphorus, which can be categorized as materials that are considered but not optimal for sensing applications.144
Due to their special qualities and possible benefits over conventional sensing materials, MXenes are crucial for the detection of volatile organic compounds (VOCs). Because MXenes have a wide surface area, there are many active sites for gas adsorption.145 This quality makes MXene-based sensors more sensitive towards VOCs, and enables the detection of low quantities. MXenes can be tailored in terms of composition by using different transition metals and functional groups in the synthetic process.146 The selectivity and sensor performance of MXenes can be improved for certain VOCs because of its tunable characteristics. Good electrical conductivity, which is essential for creating capacitive or resistive gas sensors, is exhibited by MXenes.1 Changes in gas adsorption on MXene surfaces can result in changes in electrical characteristics, allowing for the conversion of quantifiable signals from the gas concentration. Even in the presence of VOCs and other reactive gases, MXenes remain chemically stable. MXene-based gas sensors reliably operate over an extended time because of their stability, which is beneficial for applications requiring continuous monitoring.132 Real-time VOC identification is made possible by the demonstrated quick response times of MXenes. The huge surface area is responsible for their quick response time since it enables quick gas adsorption and desorption processes. Thin films, nanosheets, composites, and three-dimensional structures are just a few of the sensor configurations that may include MXenes. This adaptability enables the creation of several sensing systems specifically suited for various VOC sensing applications. When compared to other 2D materials like graphene, MXenes are comparatively inexpensive.147 They are appealing for mass manufacture and extensive use as VOC sensors due to their cost-effectiveness. Owing to these attributes, MXenes are promising materials for VOC sensing, opening the way to the creation of sensitive, focused, and dependable gas sensors for use in applications, such as environmental monitoring, workplace safety, and indoor air quality. The performance and usability of MXene-based gas sensors are being further explored and improved via ongoing research, which will help with VOC sensing.134
MXene is a potential candidate in sensing materials due to its unique properties of having a hydrophilic surface, metallic conductivity, and 2D layered structure. As a result, MXene has been included in the field of gas-sensing biosensors, piezoresistive sensors, optical sensors, and gas-adsorptive sensors.163 In 2015, Xu and his collaborator started to recommend 2D materials in the biosensor field for exploring neural activities. They utilized a thin MXene micropattern to recognize highly sensitive FET biosensors for the label-free testing of small molecules in a proper biological environment and quick detection of action potential in initial neurons.164 This work developed a new space for biosensing applications to utilize MXene, showing that MXene can be a favorable candidate for expanding biosensors due to their outstanding electrical properties, large surface-to-volume ratio, and excellent biocompatibility. The MXene biosensor shows outstanding stability, repeatability, and reproducibility. Even though further extensive research has been performed on MXene-based sensors, these excellent properties do not meet all of the requirements of different applications.165 Hence, surface moderation and functionalization are compulsory to improve their performance. Meanwhile, a different potential problem is that physical adsorption interaction and noncovalent bonds are not durable in some biomedical applications. So, a possible interpretation could be to adopt the improved functional group on the surface of MXene-based materials to include some unique and controllable binding on the surface to enhance the surface properties.166
According to Table 2, the most recent research suggests that Ti2C MXene works well as a sensor for NH3 gas detection. Similar to whole cell application, lowering the applied biaxial strain makes it easy to release the NH3 that has been absorbed on single-layered Ti2CO2. However, once NH3 is omitted, Ti2CO2's electrical conductivity rises.167 The most popular option for NH3 sensors is the O-terminated MXene. When Ti3C2Tx MXene electrodes are used, the confined biological receptors on the surface of the nanosheet act as transducers, resulting in efficient sensing performance. This enables a direct electron transfer (DET) between the electrode surface and the redox enzyme to occur. Enzymes and proteins can be freely immobilized on the surface of MXene.168 As a result, they can be utilized to assist DET, lower detection thresholds, increase sensitivity and selectivity, and increase electrode kinetics. Ti3C2Tx MXene has been used to electrochemically identify several biomolecular components.169,170 Recently, a Ti3C2Tx/Nafion/AuNP nanohybrid created a glucose biosensor having a glassy carbon electrode coated with a material that can immobilize glucose oxidase (Gox).171 Due to the large specific surface area and unique organ-like structure of the hybrid Ti3C2/TiO2, the limitation of the substrate was confirmed. Additionally, a successful collision between redox proteins and substrate would occur when enzymes mounted on the surface of Ti3C2/TiO2 nanosheets were found. As a result, the sensing capabilities of biosensors were improved.172
Table 2 Summary of MXene-based VOC sensors
MXene |
Method |
Gas |
Concentration (ppm) |
Temp (°C) |
Response/recovery time (s) |
Ref. |
Mo2CTx |
HF |
Toluene |
140 |
RT |
— |
130
|
Ti3C2Tx |
3.2 g + 9 M HCl |
Ethanol |
120 |
RT |
39/139 s |
135
|
Ti3C2Tx/rGO/CuO |
|
Acetone |
100 |
RT |
6.5/7.5 s |
137
|
SnO–SnO2/Ti3C2Tx |
|
Acetone |
100 |
RT |
18/9 s |
139
|
Ti3C2Tx/SnO2 |
HF |
Ethanol |
10 |
230 °C |
14/26 s |
148
|
Co3O4/Ti3C2Tx |
— |
Ethanol |
50 |
|
50/45 s |
149
|
Ti3C2Tx/WSe2 |
|
Ethanol |
40 |
RT |
9.7/6.6 s |
147
|
Ti3C2Tx/PANI |
HF |
Ethanol |
200 |
RT |
0.4/0.5 s |
150
|
S-Ti3C2Tx |
LiF-HCl |
Toluene |
10 |
RT |
— |
151
|
Ti3C2Tx/CuO |
HF |
Toluene |
50 |
250 |
270/10 s |
152
|
rGO/N-Ti3C2Tx/TiO2 |
LiF-HCl |
Formaldehyde |
10 |
20 |
27.6/4.8 s |
153
|
Ti3C2Tx/CO3O4 |
LiF-HCl |
Formaldehyde |
10 |
25 |
83/5 s |
154
|
ZnSnO3/Ti3C2Tx |
|
Formaldehyde |
100 |
RT |
6.2/5.1 s |
155
|
W18O49/Ti3C2Tx |
|
Acetone |
170 ppb |
|
5.6/6 s |
156
|
V4C3Tx MXene |
HF |
Acetone |
1 |
25 |
— |
157
|
α-Fe2O3/Ti3C2Tx |
|
Acetone |
5 |
RT |
5/5 s |
158
|
α-/γ-Fe2O3/ex-Ti3C2Tx |
Solvothermal |
Acetone |
100 |
250 |
13/8 s |
159
|
1D/2DKWO/Ti3C2Tx |
HF |
Acetone |
|
RT |
— |
160
|
Nitrogen-doped Ti3C2Tx |
HF |
Acetone |
— |
150 |
36/9 s |
161
|
Accordion-like Ti3C2Tx |
HF |
Acetone |
250 ppb |
RT |
53/120 s |
162
|
To manage the health risk, acetone must first be identified by judgment in a variety of disciplines, including medical diagnosis, indoor air quality monitoring, and industrial area. Because of this, it is imperative to create high-quality monitoring sensors that are capable of detecting acetone at ppm or ppb levels. For diabetics, acetone is a crucial biomarker; thus, acetone sensors should be used to detect acetone concertation in human breath. Yongshan Xo et al. reported on a W18O49/α-Fe2O3 hollow structure for the detection of acetone. Its response/recovery time is 10/31 s and a detection limit of 86 ppb.173 S. Sun et al.156 reported on the W18O49/Ti3C2Tx composite fabrication for acetone sensing. MXene is a suitable candidate for use in gas sensing and biosensors due to the availability of functional groups on its surface. These functional groups can efficiently generate active sites for gas adsorption. Furthermore, Ti3C2Tx MXene-based gas sensors have a very low detection limit of 50–100 ppb for VOCs contaminants at room temperature. Because of its good chemical stability, easy synthesis technique, low cast, and structural variety, WOx≤3 (tungsten oxide) has received significant attention. WOx≤3 has a lot of oxygen vacancies, which function as extra-active sites for gas adsorption. W18O49/Ti3C2Tx nanocomposites were successfully created by using a simple solvothermal technique for acetone gas sensing to boost sensing performance at lower concentrations. To create the 1D/2D W18O49/Ti3C2Tx composite, 1D W18O49 nanorods were evenly distributed on 2D Ti3C2Tx nanosheets. The W18O49/Ti3C2Tx nanocomposite showed a strong response at low concentrations (11.6–20 ppm acetone), great selectivity, short response-recovery times, excellent stability, and a low threshold for detecting acetone (170 ppb) with a response-recovery time of 5.6/6 s, respectively.156 Most research has been done on Ti3C2Tx MXene-based sensors for VOCs gases. Nowadays, the most studied V-based MXene are V2CTx, V3C2Tx, and V4C3Tx, as reported by W. N. Zho et al.157 The V4C3Tx MXene was created by etching the Al layer from the V4C3Tx MAX phase in an aqueous HF solution at room temperature. Fig. 9a–d shows SEM pictures that illustrate the changes in structure caused by HF etching, and Fig. 9c–d demonstrates the removal of the Al element from V4AlC3. V4C3Tx MXene exhibits semiconducting behavior. V4C3Tx MXene exhibits the highest overall performance for acetone, including low temperature (25 °C), strong selectivity, good ideal operating sensitivity, and short response-recovery time with a LOD of 1 ppm. According to Fig. 9n–q, this makes the V4C3Tx sensor suitable as a practical acetone sensor. As a result, the V4C3Tx-based sensor has a high potential for providing a room-temperature solution for noninvasive diabetes monitoring.
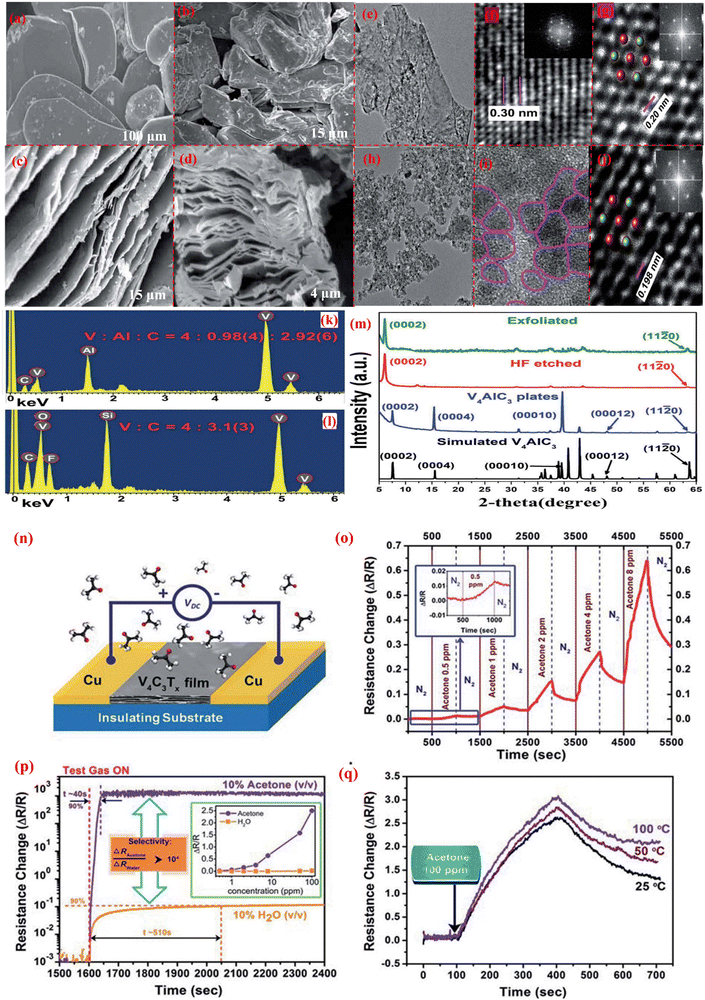 |
| Fig. 9 Characterization and investigation of the V4AlC3 MAX phase before and after etching with HF. (a) SEM image of the synthesized V4AlC3 plates. (b)–(d) Different magnification SEM images of V4AlC3 after HF (48% concertation) treatment. (e)–(j) TEM characterization of thin layer exfoliated V4AlC3 nanosheets: high-resolution TEM image, TEM with atomic resolution at Z contrast STEM, corresponding FET pattern and image of V4C3Tx at low magnification, high-resolution image, TEM image and STEM. (k and l) EDS measurement for the surface of V4AlC3 above SiO2/Si and V4C3Tx surface. (m) XRD characteristics of V4AlC3 before and after HF etching. (n) Fabricated V4C3Tx film sensor above an insulating substrate with a copper electrode for mechanical support. (o) Sensor response of the V4C3Tx film at various concentrations of acetone for acetone sensing. (p) Comparison of the sensing response of the V4C3Tx film between acetone and water vapor. (q) Gas-sensing response of the V4C3Tx film at various temperatures; reprinted ref. 157. Copyright RSC Advances. | |
Madeshwari et al.174 reported on a V2O5 nanowires-based acetone sensor. Its response/recovery time are 49/19 s for 50 ppm acetone at 30 °C. Sanjit Manohar Maji et al.175 reported on the urchin-like V2CTx/V2O5 hybrid sensors, which demonstrated fast response/recovery times of 115/180 s for very low acetone detection limit at 250 ppb, and superb reproducibility with long-term stability (21 days) at room temperature. Its increased response is S(%) = 11.9 around 15 ppm at ambient temperature.
W. Q. Li et al.176 reported on the SnO2 nanobelt as an acetone sensor. Its response/recovery times are 38/9 s for 5 ppm acetone at 260 °C. Zijing Wang et al.139 reported on a hydrothermal technique for the fabrication of SnO–SnO2/Ti3C2Tx composites. By distribution of SnO–SnO2 (p–n junction) nanoparticles on the surface of 2D Ti3C2Tx nanosheets, an effective acetone detection sensor was developed. The SnO–SnO2/Ti3C2Tx based sensor exhibited increased acetone sensing responses of 12.1 with response/recovery times of 18/9 s at ambient temperature and an exceptional repeatability. Because of the different work functions, a Schottky barrier was formed between the SnO and Ti3C2Tx nanosheets, functioning as a layer of hole accumulation between the two materials.
Shurong Wang et al.177 reported on porous α-Fe2O3 hollow microspheres for acetone sensors. It showed response/recovery times of 17/30 s for 100 ppm acetone at 250 °C. Miao Liu et al.158 showed that the α-Fe2O3/Ti3C2Tx nanocomposite, which was well produced by a simple hydrothermal technique, demonstrated remarkable performance for acetone at ambient temperature. As a result, 250 nm sized α-Fe2O3 nanotubes were appropriately dispersed over the surface of a Ti3C2Tx nanosheet. The α-Fe2O3/Ti3C2Tx nanocomposite has a high response of 16.6% for an acetone concentration of 5 ppm, with a response/recovery time of 5/5 s with good linearity and significant repeatability at ambient temperature. Dandan Huang et al.159 reported that at ambient temperature, MOFs created a porous α/γFe2O3/ex-Ti3C2Tx nanocomposite that performed well as an acetone sensor due to a variety of heterojunction contacts, porosity, and surface defects. Solvothermal and calcination methods were used to produce this material. Here, the surface of the Ti3C2Tx nanosheets is evenly covered by bi-phase α-/γ-Fe2O3 nanoparticles, which improves the acetone-sensing performance. The α-/γ-Fe2O3/ex-Ti3C2Tx sensor has a rapid recovery/recovery time of 13/8 s with great repeatability and exceptional selectivity at 255 °C for 100 ppm of acetone.
Obinna Ama et al.160 reported on 1D/2DKWO nanorod/Ti3C2Tx nanocomposites for acetone sensing with different compositional ratios for room temperature sensing. KWO/Ti3C2Tx showed the best response at a 2
:
1 ratio. Z. Wang et al.161 showed the porous nitrogen-doped Ti3C2Tx used as an acetone gas sensor due to its three-dimensional structure, which was synthesized by the sacrificial template method. When heteroatoms such as nitrogen atoms are introduced into Ti3C2Tx nanosheets, certain defects are produced throughout the nitrogen atoms, which can improve the hydrophilicity and adsorption characteristics of the Ti3C2Tx nanosheet. Therefore, porous nitrogen-doped Ti3C2Tx has a good response/recovery time of 36 s/9 s at 150 °C for acetone detection.
Kampara Roopa Kishore et al.178 reported on the CuO nanograin for acetone sensing at an operating temperature of 350 °C. Its response/recovery times are 11/13 s for 693 ppm acetone. M Liu et al.137 reported that when superfine CuO nanoparticles are decorated on 3D Ti3C2Tx MXene and rGO (reduce graphene oxide) nanosheets, 3D Ti3C2Tx/rGO/CuO is formed. Because of the large surface area of the interconnected spongy network, the even dispersion of CuO nanoparticles, and the excellent electrical conductivity of 3D MXene/rGO/CuO, the sensing performance of acetone at room temperature is high, with a response-recovery time of 6.5 s/7.5 s for 100 ppm acetone, as well as good reproducibility and selectivity. Sanjit at al.162 presented the accordion-like Ti3C2Tx MXene, which was created using a suitable HF etching method at 60 °C for acetone vapor detection as a chemiresistive gas sensor. SEM images of the accordion-like Ti3C2Tx are exhibited in Fig. 10a and b, and EDS measurements of various functional groups are given in Fig. 10c–g. Fig. 10h and i are the TEM images of Ti3C2Tx, which indicate the presence of few-layered MXene flakes. Fig. 10j shows an XRD graph with a shifting peak at a lower angle (002). With p-type sensing characteristics, the sensor successfully identified acetone vapors at ppb levels. The sensing graph is displayed in Fig. 10k–n, with a satisfactory reaction time of 53 s and an acetone detection limit of roughly 250 ppb. At 23 °C, the sensor has great repeatability, long-term stability, and strong acetone vapor selectivity. As a breath sensor, it offers a lot of potential for diabetic patients because the MXene surface functional groups are chemically reactive and can be functionalized.
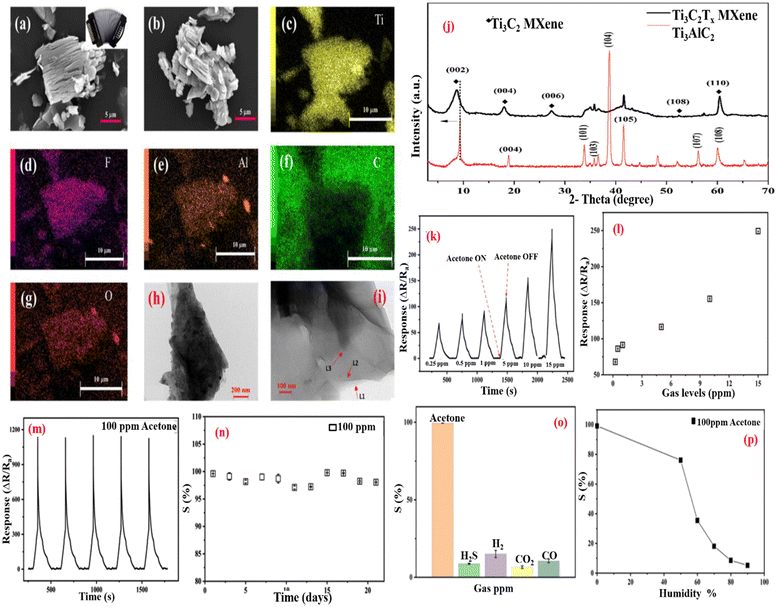 |
| Fig. 10 (a) and (b) SEM images of the exfoliated Ti3C2Tx MXene. (c)–(g) Related EDS elemental design of the Ti3C2Tx MXene exhibits Ti, Al, F, O, and C elements. (h)–(i) TEM images of the Ti3C2Tx MXene, representative of the few-layers MXene flakes. (j) XRD pattern of TI3AlC2 before and after HF treatment. (k) Sensing response of the Ti3CTx MXene sensor at various concentrations of acetone at RT. (l) Sensing response at a concentration of acetone gas levels (0.24–15 ppm). (m) and (n) Repeatability and stability test of the Ti3CTx MXene-based gas sensor for 100 ppm acetone at 23 °C. (o) Response nature of the Ti3CTx MXene gas sensor for 100 ppm of different gases. (p) Sensing response of the Ti3CTx MXene-based gas sensor as a function of RHs. Reprinted ref. 162. Copyright Applied Electronic Material ACS. | |
6. Other applications of MXene
MXenes have attracted much attention as a unique member of the 2D material family, and researchers are continuing to study its abundant composition, characteristics, and structure of 2D transition metal carbides, nitrides, and carbonitrides. The large surface area, surface functionalization, great hydrophilicity, high conductivity, outstanding optical characteristics, and biocompatibility are just a few unique characteristics of MXene, and they may be employed successfully in a variety of applications, as explained in Fig. 11. For instance, the outstanding optical and electrical properties of 2D MXenes may be exploited to create sensors.179 MXenes have been hugely studied as electrode materials for different types of rechargeable batteries (Li, K, and Na-ions), electromagnetic interface shields, photothermal conversion, water treatment, hydrogen storage, and supercapacitor, and other applications. MXenes have tremendous potential for usage as an electrode material for supercapacitor applications due to its high electrical conductivity and wide surface chemistry. It was found that Ti3C2Tx MXene was perhaps intercalated automatically using cations like NH4+, K+, Al+, Na+, and Mg2+ in related salt solutions.180 Sun et al. used 2D Ti3C2 MXene obtained after intercalation with DMSO, focusing on the production of anode materials for Li+ batteries. The electrochemical performance of the intercalated 2D Ti3C2 MXene is much higher than that of 2D Ti3C2 with groups –F terminated.181 In electrocatalysis and photocatalysis, MXene exhibits attractive chemical properties due to its superb electroconductivity, functionalization, and durability. Only limited catalytic reactions have been reported with MXene like CO oxidation,182 oxygen reduction reaction,183 dehydration of hydrogen storage materials,184 oxygen evolution reaction,90 and the hydrogen evolution reaction.185 In all of these reactions, MXene behaves as a catalyst, supporting substance, and co-catalyst. As for hydrogen storage material, the catalysts should have the following important properties: high cycle stability, and low dehydrogenation temperature. Zhou et al. reported on the synthesis of Ti3C2(OHxF1−x) and A0.9R0.1–TiO2/C materials, which exhibited anomalous catalytic activity for the dehydrogenation of NaAlH4. The materials demonstrated a capacity of 3.08 wt% in 240 minutes at 90 °C and 85 minutes at 100 °C, and were stable for 10 cycles.184 Fan and his group coated Ti3C2X2 with Ru nanoparticles with a 2.4 nm particle size, and this composite easily catalyzed the hydrolysis of NaBH4 at ambient temperature.186 According to a measured investigation, the optimal catalyst concentration is 6.99 wt% for a high hydrogen generation rate of 59.04 LH2 gRu−1 min−1.186 MXene has both metallic conductivity and hydrophilic surface characteristics, so it is good for electromagnetic interference shielding applications. Due to the 2D MXene structure, the high electrical conductivity and electronic coupling between layers are responsible for better EMI (Elctro-Magnetic Interference) shielding.88
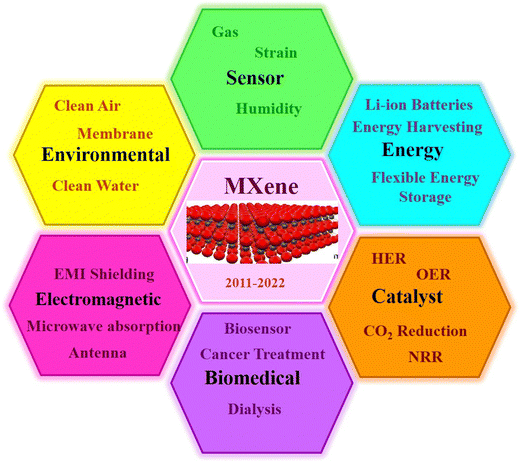 |
| Fig. 11 Schematic diagram illustrating the uses of MXene in different fields. | |
7. Conclusions
A history on the progress of 2D MXene materials, an explanation of how MXene is created from the MAX phase by selective etching with the proper etchant and a delaminating agent, and a comparison of the two states using morphology and XRD patterns show that MXene is the better candidate among all 2D materials. Along with their suitability for gas sensing, 2D MXene-based materials have several positive attributes, such as improved functional groups, a high surface-to-volume ratio, superior electrical, mechanical, chemical, and adjustable band gap capabilities, outstanding stability, and enhanced functional groups. A substantial amount of research on MXene nanocomposite-based VOC sensors has been conducted and is reported in this study. MXene-based materials have proven their particular advantage in biological sensing applications, with a focus on the most recent advancements in pure MXene and their nanocomposite-based acetone gas sensor. Finally, it has been explained how MXene nanocomposite detects ppb level acetone at ambient temperature, and how the related sensing performance summarizes the applicability of MXene in numerous sectors.
Conflicts of interest
The authors declare that they have no known competing financial interests or personal relationships that could have appeared to influence the work reported in this paper.
Acknowledgements
Monu Gupta acknowledges Babasaheb Bhimrao Ambedkar University, Lucknow, UP, India for providing a UGC non-NET fellowship. Mr Arpit Verma and the corresponding author Prof. B. C. Yadav acknowledge the Uttar Pradesh Council of Science and Technology, Lucknow for financial assistance in the form of Project Ref: CST/D-2290.
References
- R. Bhardwaj and A. Hazra, J. Mater. Chem. C, 2021, 9, 15735–15754 RSC.
- S. Yang, C. Jiang and S. Wei, Appl. Phys. Rev., 2017, 4, 21304 Search PubMed.
- H. Zhang and R. Lv, J. Mater., 2018, 4, 95–107 Search PubMed.
- C. Choi, Y. Lee, K. W. Cho, J. H. Koo and D.-H. Kim, Acc. Chem. Res., 2018, 52, 73–81 CrossRef PubMed.
- A. Mirzaei, S. G. Leonardi and G. Neri, Ceram. Int., 2016, 42, 15119–15141 CrossRef CAS.
- N. Joshi, T. Hayasaka, Y. Liu, H. Liu, O. N. Oliveira and L. Lin, Microchim. Acta, 2018, 185, 1–16 CrossRef CAS PubMed.
- S. Pirsa and N. Alizadeh, Sens. Actuators, B, 2010, 147, 461–466 CrossRef CAS.
- M. Masikini, M. Chowdhury and O. Nemraoui, J. Electrochem. Soc., 2020, 167, 37537 CrossRef CAS.
- X. Cai, Y. Luo, B. Liu and H.-M. Cheng, Chem. Soc. Rev., 2018, 47, 6224–6266 RSC.
- V. M. H. Ng, H. Huang, K. Zhou, P. S. Lee, W. Que, J. Z. Xu and L. B. Kong, J. Mater. Chem. A, 2017, 5, 3039–3068 RSC.
- W. E. O. Ghoma, H. Sevik and K. Isinkaralar, Air Qual. Atmos. Heal., 2022, 15, 415–424 CrossRef CAS.
- A. V. Tyurnina, I. Tzanakis, J. Morton, J. Mi, K. Porfyrakis, B. M. Maciejewska, N. Grobert and D. G. Eskin, Carbon, 2020, 168, 737–747 CrossRef CAS.
- L. Xuan, Y. Ma, Y. Xing, Q. Meng, J. Song, T. Chen, H. Wang, P. Wang, Y. Zhang and P. Gao, Environ. Pollut., 2021, 270, 116074 CrossRef CAS PubMed.
- S. H. Cho, J. M. Suh, T. H. Eom, T. Kim and H. W. Jang, Electron. Mater. Lett., 2021, 17, 1–17 CrossRef CAS.
- P. Srinivasan, A. J. Kulandaisamy, G. K. Mani, K. J. Babu, K. Tsuchiya and J. B. B. Rayappan, RSC Adv., 2019, 9, 30226–30239 RSC.
- S. Singh, U. Kumar, B. C. Yadav, K. Kumar, R. K. Tripathi and K. Singh, Results Phys., 2019, 15, 102772 CrossRef.
- A. S. Manolis, T. A. Manolis and A. A. Manolis, Int. J. Mol. Sci., 2023, 24, 3534 CrossRef CAS PubMed.
- N. H. Cho, J. E. Shaw, S. Karuranga, Y. Huang, J. D. da Rocha Fernandes, A. W. Ohlrogge and B. Malanda, Diabetes Res. Clin. Pract., 2018, 138, 271–281 CrossRef CAS PubMed.
- F. Chen, M. Yang, X. Wang, Y. Song, L. Guo, N. Xie, X. Kou, X. Xu, Y. Sun and G. Lu, Sens. Actuators, B, 2019, 290, 459–466 CrossRef CAS.
- K. Pathak, R. Saikia, H. Sarma, M. P. Pathak, R. J. Das, U. Gogoi, M. Z. Ahmad, A. Das and B. A. A. Wahab, J. Diabetes Metab. Disord., 2023, 1–15 Search PubMed.
- M. S. Sha, M. R. Maurya, S. Shafath, J.-J. Cabibihan, A. Al-Ali, R. A. Malik and K. K. Sadasivuni, ACS Omega, 2022, 7, 4257–4266 CrossRef CAS PubMed.
- H. R. Ansari, A. Mirzaei, H. Shokrollahi, R. Kumar, J.-Y. Kim, H. W. Kim, M. Kumar and S. S. Kim, J. Mater. Chem. C, 2023, 6528–6549 RSC.
- V. Longo, A. Forleo, A. Ferramosca, T. Notari, S. Pappalardo, P. Siciliano, S. Capone and L. Montano, Environ. Pollut., 2021, 286, 117410 CrossRef CAS PubMed.
- S. Halder, Z. Xie, M. H. Nantz and X.-A. Fu, J. Chromatogr. A, 2022, 1673, 463083 CrossRef CAS PubMed.
- A. Singh, S. Sikarwar, A. Verma and B. C. Yadav, Sens. Actuators, A, 2021, 332, 113127 CrossRef CAS.
- M. Catelani, L. Ciani and M. Venzi, Reliab. Eng. Syst. Saf., 2018, 180, 425–433 CrossRef.
-
K. Rana and R. K. Sonker, Smart Nanostructure Materials and Sensor Technology, Springer, 2022, pp. 179–199 Search PubMed.
- A. Verma, D. Yadav, A. Singh, M. Gupta, K. B. Thapa and B. C. Yadav, Sens. Actuators, B, 2022, 361, 131708 CrossRef CAS.
- B. K. S. Reddy and P. H. Borse, J. Electrochem. Soc., 2021, 168, 57521 CrossRef CAS.
- H. Teymourian, F. Tehrani, K. Mahato and J. Wang, Adv. Healthcare Mater., 2021, 10, 2002255 CrossRef CAS PubMed.
- J. Wang, H. Shen, Y. Xia and S. Komarneni, Ceram. Int., 2021, 47, 7353–7368 CrossRef CAS.
- T. Chen, T. Liu, T. Li, H. Zhao and Q. Chen, Clin. Chim. Acta, 2021, 515, 61–72 CrossRef CAS PubMed.
- D. J. Buckley, N. C. G. Black, E. G. Castanon, C. Melios, M. Hardman and O. Kazakova, 2D Mater., 2020, 7, 32002 CrossRef CAS.
- V. Amiri, H. Roshan, A. Mirzaei, G. Neri and A. I. Ayesh, Sensors, 2020, 20, 3096 CrossRef CAS PubMed.
- S. J. Ward, R. Layouni, S. Arshavsky-Graham, E. Segal and S. M. Weiss, ACS Sens., 2021, 6, 2967–2978 CrossRef CAS PubMed.
- T. Rasheed, Mater. Today Chem., 2022, 24, 100859 CrossRef CAS.
- D. H. Ho, Y. Y. Choi, S. B. Jo, J.-M. Myoung and J. H. Cho, Adv. Mater., 2021, 33, 2005846 CrossRef CAS PubMed.
- H. Riazi, G. Taghizadeh and M. Soroush, ACS omega, 2021, 6, 11103–11112 CrossRef CAS PubMed.
- X. Liu, T. Ma, N. Pinna and J. Zhang, Adv. Funct. Mater., 2017, 27, 1702168 CrossRef.
- J.-K. Qin, C. Wang, L. Zhen, L.-J. Li, C.-Y. Xu and Y. Chai, Prog. Mater. Sci., 2021, 122, 100856 CrossRef CAS.
- D. S. Schulman, A. J. Arnold and S. Das, Chem. Soc. Rev., 2018, 47, 3037–3058 RSC.
- C. Cui, F. Xue, W.-J. Hu and L.-J. Li, npj 2D Mater. Appl., 2018, 2, 1–14 CrossRef.
- X. Zhang, Y. Nie, Q. Zhang, Z. Liang, P. Wang and Q. Ma, Chem. Eng. J., 2021, 411, 128428 CrossRef CAS.
- Y. Li, Y.-L. Li, B. Sa and R. Ahuja, Catal. Sci. Technol., 2017, 7, 545–559 RSC.
- G. Neri, Chemosensors, 2017, 5, 21 CrossRef.
- M. Ko, L. Mendecki and K. A. Mirica, Chem. Commun., 2018, 54, 7873–7891 RSC.
- S.-T. Han, H. Peng, Q. Sun, S. Venkatesh, K.-S. Chung, S. C. Lau, Y. Zhou and V. A. L. Roy, Adv. Mater., 2017, 29, 1700375 CrossRef PubMed.
- S. Rana, V. Singh and B. Singh, iScience, 2022, 103748 CrossRef CAS PubMed.
- K. Khan, A. K. Tareen, M. Iqbal, L. Wang, C. Ma, Z. Shi, Z. Ye, W. Ahmad, R. U. R. Sagar and S. S. Shams,
et al.
, Prog. Solid State Chem., 2021, 63, 100326 CrossRef CAS.
- D. Cheng, P. Li, X. Zhu, M. Liu, Y. Zhang and Y. Liu, Chin. J. Chem., 2021, 39, 2181–2187 CrossRef CAS.
- J. Barman, A. Tirkey, S. Batra, A. A. Paul, K. Panda, R. Deka and P. J. Babu, Mater. Today Commun., 2022, 32, 104055 CrossRef CAS.
- B. Xu, C. Zhi and P. Shi, J. Phys. Mater., 2020, 3, 31001 CrossRef CAS.
- M. Dahlqvist, J. Lu, R. Meshkian, Q. Tao, L. Hultman and J. Rosen, Sci. Adv., 2017, 3, e1700642 CrossRef PubMed.
- S. K. Hwang, S.-M. Kang, M. Rethinasabapathy, C. Roh and Y. S. Huh, Chem. Eng. J., 2020, 397, 125428 CrossRef CAS.
- P. E. Lokhande, A. Pakdel, H. M. Pathan, D. Kumar, D.-V. N. Vo, A. Al-Gheethi, A. Sharma, S. Goel, P. P. Singh and B.-K. Lee, Chemosphere, 2022, 297, 134225 CrossRef CAS PubMed.
- Y. Wang, T. Guo, Z. Tian, K. Bibi, Y.-Z. Zhang and H. N. Alshareef, Adv. Mater., 2022, 34, 2108560 CrossRef CAS PubMed.
- R. Khan and S. Andreescu, Sensors, 2020, 20, 5434 CrossRef CAS PubMed.
- B. Anasori, M. R. Lukatskaya and Y. Gogotsi, Nat. Rev. Mater., 2017, 2, 1–17 CrossRef.
- C. Lamiel, I. Hussain, O. R. Ogunsakin and K. Zhang, J. Mater. Chem. A, 2022, 14247–14272 RSC.
- Q. Zhang, Y. Sun, M. Liu and Y. Liu, Nanoscale, 2020, 12, 1826–1832 RSC.
- S. De, S. Acharya, S. Sahoo and G. C. Nayak, Mater. Chem. Front., 2021, 5, 7134–7169 RSC.
- M. Alhabeb, K. Maleski, B. Anasori, P. Lelyukh, L. Clark, S. Sin and Y. Gogotsi, Chem. Mater., 2017, 29, 7633–7644 CrossRef CAS.
- B. Anasori, Y. Xie, M. Beidaghi, J. Lu, B. C. Hosler, L. Hultman, P. R. C. Kent, Y. Gogotsi and M. W. Barsoum, ACS Nano, 2015, 9, 9507–9516 CrossRef CAS PubMed.
- A. Petruhins, J. Lu, L. Hultman and J. Rosen, Mater. Res. Lett., 2019, 7, 446–452 CrossRef CAS.
- G. R. Bhimanapati, Z. Lin, V. Meunier, Y. Jung, J. Cha, S. Das, D. Xiao, Y. Son, M. S. Strano and V. R. Cooper,
et al.
, ACS Nano, 2015, 9, 11509–11539 CrossRef CAS PubMed.
- T. Tan, X. Jiang, C. Wang, B. Yao and H. Zhang, Adv. Sci., 2020, 7, 2000058 CrossRef CAS PubMed.
- R. A. Soomro, S. Jawaid, Q. Zhu, Z. Abbas and B. Xu, Chin. Chem. Lett., 2020, 31, 922–930 CrossRef CAS.
- Q. Li, Y. Li and W. Zeng, Chemosensors, 2021, 9, 225 CrossRef CAS.
- Y. Ibrahim, A. Mohamed, A. M. Abdelgawad, K. Eid, A. M. Abdullah and A. Elzatahry, Nanomaterials, 2020, 10, 1916 CrossRef CAS PubMed.
- M. Naguib, V. N. Mochalin, M. W. Barsoum and Y. Gogotsi, Adv. Mater., 2014, 26, 982 CrossRef.
- L. Verger, C. Xu, V. Natu, H.-M. Cheng, W. Ren and M. W. Barsoum, Curr. Opin. Solid State Mater. Sci., 2019, 23, 149–163 CrossRef CAS.
- E. Lee and D.-J. Kim, J. Electrochem. Soc., 2019, 167, 37515 CrossRef.
- A. N. Enyashin and A. L. Ivanovskii, Comput. Theor. Chem., 2012, 989, 27–32 CrossRef CAS.
- S. Mehdi Aghaei, A. Aasi and B. Panchapakesan, ACS Omega, 2021, 6, 2450–2461 CrossRef CAS PubMed.
- J. Zou, J. Wu, Y. Wang, F. Deng, J. Jiang, Y. Zhang, S. Liu, N. Li, H. Zhang and J. Yu,
et al.
, Chem. Soc. Rev., 2022, 51, 2972–2990 RSC.
- K. Hantanasirisakul and Y. Gogotsi, Adv. Mater., 2018, 30, 1804779 CrossRef PubMed.
- W. Sun, Y. Xie and P. R. C. Kent, Nanoscale, 2018, 10, 11962–11968 RSC.
- M. Magnuson and M. Mattesini, Thin Solid Films, 2017, 621, 108–130 CrossRef CAS.
- Y. Yin, L. Shi, S. Zhang, X. Duan, J. Zhang, H. Sun and S. Wang, Nano Mater. Sci., 2023, 1, 15–38 CrossRef.
- C. Ougherb, T. Ouahrani, M. Badawi and Á. Morales-García, Phys. Chem. Chem. Phys., 2022, 24, 7243–7252 RSC.
- A. Iqbal, J. Hong, T. Y. Ko and C. M. Koo, Nano Converge., 2021, 8, 1–22 CrossRef PubMed.
- Y. Zhang, L. Wang, N. Zhang and Z. Zhou, RSC Adv., 2018, 8, 19895–19905 RSC.
- V. N. Borysiuk, V. N. Mochalin and Y. Gogotsi, Comput. Mater. Sci., 2018, 143, 418–424 CrossRef CAS.
- Z. Lu, Y. Wei, J. Deng, L. Ding, Z.-K. Li and H. Wang, ACS Nano, 2019, 13, 10535–10544 CrossRef CAS PubMed.
- M. Benchakar, L. Loupias, C. Garnero, T. Bilyk, C. Morais, C. Canaff, N. Guignard, S. Morisset, H. Pazniak and S. Hurand,
et al.
, Appl. Surf. Sci., 2020, 530, 147209 CrossRef CAS.
- S. Munir, A. Rasheed, T. Rasheed, I. Ayman, S. Ajmal, A. Rehman, I. Shakir, P. O. Agboola and M. F. Warsi, ACS Omega, 2020, 5, 26845–26854 CrossRef CAS PubMed.
- D. Xiong, X. Li, Z. Bai and S. Lu, Small, 2018, 14, 1703419 CrossRef PubMed.
- F. Shahzad, M. Alhabeb, C. B. Hatter, B. Anasori, S. Man Hong, C. M. Koo and Y. Gogotsi, Science, 2016, 353, 1137–1140 CrossRef CAS PubMed.
- K. A. A. Usman, S. Qin, L. C. Henderson, J. Zhang, D. Hegh and J. M. Razal, Mater. Horiz., 2021, 8, 2886–2912 RSC.
- T. Y. Ma, J. L. Cao, M. Jaroniec and S. Z. Qiao, Angew. Chem., Int. Ed., 2016, 55, 1138–1142 CrossRef CAS PubMed.
- S. Qamar, K. Fatima, N. Ullah, Z. Akhter, A. Wasim and M. S. Sultan, Nanoscale, 2022, 14, 13018–13039 RSC.
- N. R. Hemanth and B. Kandasubramanian, Chem. Eng. J., 2020, 392, 123678 CrossRef CAS.
- Y.-Z. Zhang, Y. Wang, Q. Jiang, J. K. El-Demellawi, H. Kim and H. N. Alshareef, Adv. Mater., 2020, 32, 1908486 CrossRef CAS PubMed.
- Y. Lee, Y. Hwang, S. B. Cho and Y.-C. Chung, Phys. Chem. Chem. Phys., 2014, 16, 26273–26278 RSC.
- B. Anasori, C. Shi, E. J. Moon, Y. Xie, C. A. Voigt, P. R. C. Kent, S. J. May, S. J. L. Billinge, M. W. Barsoum and Y. Gogotsi, Nanoscale Horiz., 2016, 1, 227–234 RSC.
- M. Naguib, M. Kurtoglu, V. Presser, J. Lu, J. Niu, M. Heon, L. Hultman, Y. Gogotsi and M. W. Barsoum, Adv. Mater., 2011, 23, 4248–4253 CrossRef CAS PubMed.
-
B. Anasori and Y. Gogotsi, 2D Metal carbides and nitrides (MXenes), Springer, 2019, pp. 3–12 Search PubMed.
- M. Naguib, O. Mashtalir, J. Carle, V. Presser, J. Lu, L. Hultman, Y. Gogotsi and M. W. Barsoum, ACS Nano, 2012, 6, 1322–1331 CrossRef CAS PubMed.
- O. Salim, K. A. Mahmoud, K. K. Pant and R. K. Joshi, Mater. Today Chem., 2019, 14, 100191 CrossRef CAS.
- M. K. Aslam and M. Xu, Nanoscale, 2020, 12, 15993–16007 RSC.
- C. Zhang, M. Beidaghi, M. Naguib, M. R. Lukatskaya, M.-Q. Zhao, B. Dyatkin, K. M. Cook, S. J. Kim, B. Eng and X. Xiao,
et al.
, Chem. Mater., 2016, 28, 3937–3943 CrossRef CAS.
- J. Zhou, X. Zha, X. Zhou, F. Chen, G. Gao, S. Wang, C. Shen, T. Chen, C. Zhi and P. Eklund,
et al.
, ACS Nano, 2017, 11, 3841–3850 CrossRef CAS PubMed.
- M. Ghidiu, M. R. Lukatskaya, M.-Q. Zhao, Y. Gogotsi and M. W. Barsoum, Nature, 2014, 516, 78–81 CrossRef CAS PubMed.
- J. Zhu, E. Ha, G. Zhao, Y. Zhou, D. Huang, G. Yue, L. Hu, N. Sun, Y. Wang and L. Y. S. Lee,
et al.
, Coord. Chem. Rev., 2017, 352, 306–327 CrossRef CAS.
- M. Wu, Y. He, L. Wang, Q. Xia and A. Zhou, J. Adv. Ceram., 2020, 9, 749–758 CrossRef CAS.
- Y. Guo, S. Jin, L. Wang, P. He, Q. Hu, L.-Z. Fan and A. Zhou, Ceram. Int., 2020, 46, 19550–19556 CrossRef CAS.
- Y. Gong, X. Xing, Y. Wang, Z. Lv, Y. Zhou and S.-T. Han, Small Sci., 2021, 1, 2100006 CrossRef CAS.
- X. Zhan, C. Si, J. Zhou and Z. Sun, Nanoscale Horiz., 2020, 5, 235–258 RSC.
- M. Naguib, J. Halim, J. Lu, K. M. Cook, L. Hultman, Y. Gogotsi and M. W. Barsoum, J. Am. Chem. Soc., 2013, 135, 15966–15969 CrossRef CAS PubMed.
- J. Zhou, X. Zha, F. Y. Chen, Q. Ye, P. Eklund, S. Du and Q. Huang, Angew. Chem., Int. Ed., 2016, 55, 5008–5013 CrossRef CAS PubMed.
- J. Halim, S. Kota, M. R. Lukatskaya, M. Naguib, M.-Q. Zhao, E. J. Moon, J. Pitock, J. Nanda, S. J. May and Y. Gogotsi,
et al.
, Adv. Funct. Mater., 2016, 26, 3118–3127 CrossRef CAS.
- R. Meshkian, M. Dahlqvist, J. Lu, B. Wickman, J. Halim, J. Thörnberg, Q. Tao, S. Li, S. Intikhab and J. Snyder,
et al.
, Adv. Mater., 2018, 30, 1706409 CrossRef PubMed.
- J. Halim, M. R. Lukatskaya, K. M. Cook, J. Lu, C. R. Smith, L.-Å. Näslund, S. J. May, L. Hultman, Y. Gogotsi and P. Eklund,
et al.
, Chem. Mater., 2014, 26, 2374–2381 CrossRef CAS PubMed.
- C. Verma and K. K. Thakur, Eur. J. Mol. Clin. Med., 2020, 7, 4429–4450 Search PubMed.
- M. Naguib, R. R. Unocic, B. L. Armstrong and J. Nanda, Dalton Trans., 2015, 44, 9353–9358 RSC.
- O. Mashtalir, M. Naguib, V. N. Mochalin, Y. Dall’Agnese, M. Heon, M. W. Barsoum and Y. Gogotsi, Nat. Commun., 2013, 4, 1–7 Search PubMed.
- Y. Zhang, J. Cao, Z. Yuan, L. Zhao, L. Wang and W. Han, J. Colloid Interface Sci., 2021, 599, 109–118 CrossRef CAS PubMed.
- K. Maleski, V. N. Mochalin and Y. Gogotsi, Chem. Mater., 2017, 29, 1632–1640 CrossRef CAS.
- Q. Zhang, H. Lai, R. Fan, P. Ji, X. Fu and H. Li, ACS Nano, 2021, 15, 5249–5262 CrossRef CAS PubMed.
- Z. Ling, C. E. Ren, M.-Q. Zhao, J. Yang, J. M. Giammarco, J. Qiu, M. W. Barsoum and Y. Gogotsi, Proc. Natl. Acad. Sci. U. S. A., 2014, 111, 16676–16681 CrossRef CAS PubMed.
- M. Naguib, T. Saito, S. Lai, M. S. Rager, T. Aytug, M. P. Paranthaman, M.-Q. Zhao and Y. Gogotsi, RSC Adv., 2016, 6, 72069–72073 RSC.
- R. B. Rakhi, P. Nayak, C. Xia and H. N. Alshareef, Sci. Rep., 2016, 6, 1–10 CrossRef PubMed.
- J. Wang, S. Dong, H. Li, Z. Chen, S. Jiang, L. Wu and X. Zhang, J. Electroanal. Chem., 2018, 810, 27–33 CrossRef CAS.
- C. Zhang, Adv. Funct. Mater., 2016, 26, 4143–4151 CrossRef CAS.
- F. Mohajer, G. M. Ziarani, A. Badiei, S. Iravani and R. S. Varma, Nanomaterials, 2023, 13, 345 CrossRef CAS PubMed.
- Y. Qian, J. Zhong and J. Ou, Carbon N. Y., 2022, 190, 104–114 CrossRef CAS.
- N. C. Popa, J. Appl. Crystallogr., 1992, 25, 611–616 CrossRef.
- H.-W. Wang, M. Naguib, K. Page, D. J. Wesolowski and Y. Gogotsi, Chem. Mater., 2016, 28, 349–359 CrossRef CAS.
- A. S. Levitt, M. Alhabeb, C. B. Hatter, A. Sarycheva, G. Dion and Y. Gogotsi, J. Mater. Chem. A, 2019, 7, 269–277 RSC.
- W. Guo, S. G. Surya, V. Babar, F. Ming, S. Sharma, H. N. Alshareef, U. Schwingenschlogl and K. N. Salama, ACS Appl. Mater. Interfaces, 2020, 12, 57218–57227 CrossRef CAS PubMed.
- D. E. Newbury and N. W. M. Ritchie, Scanning, 2013, 35, 141–168 CrossRef CAS PubMed.
- W. Yuan, K. Yang, H. Peng, F. Li and F. Yin, J. Mater. Chem. A, 2018, 6, 18116–18124 RSC.
- A. Junkaew and R. Arroyave, Phys. Chem. Chem. Phys., 2018, 20, 6073–6082 RSC.
- D. Li, G. Liu, Q. Zhang, M. Qu, Y. Q. Fu, Q. Liu and J. Xie, Sens. Actuators, B, 2021, 331, 129414 CrossRef CAS.
- W. Y. Chen, S.-N. Lai, C.-C. Yen, X. Jiang, D. Peroulis and L. A. Stanciu, ACS Nano, 2020, 14, 11490–11501 CrossRef CAS PubMed.
- H.-J. Koh, S. J. Kim, K. Maleski, S.-Y. Cho, Y.-J. Kim, C. W. Ahn, Y. Gogotsi and H.-T. Jung, ACS Sens., 2019, 4, 1365–1372 CrossRef CAS PubMed.
- M. Liu, Z. Wang, P. Song, Z. Yang and Q. Wang, Sens. Actuators, B, 2021, 340, 129946 CrossRef CAS.
- T. He, W. Liu, T. Lv, M. Ma, Z. Liu, A. Vasiliev and X. Li, Sens. Actuators, B, 2021, 329, 129275 CrossRef CAS.
- Z. Wang, F. Wang, A. Hermawan, Y. Asakura, T. Hasegawa, H. Kumagai, H. Kato, M. Kakihana, J. Zhu and S. Yin, J. Mater. Sci. Technol., 2021, 73, 128–138 CrossRef CAS.
- M. Usman, Membranes, 2022, 12, 507 CrossRef CAS PubMed.
- M. Gupta, P. Chaudhary, A. Singh, A. Verma, D. Yadav and B. C. Yadav, Sens. Actuators, B, 2022, 368, 132102 CrossRef CAS.
- H. G. Shiraz, X. Crispin and M. Berggren, Int. J. Hydrogen Energy, 2021, 46, 24060–24077 CrossRef CAS.
- R. Malik, V. K. Tomer, Y. K. Mishra and L. Lin, Appl. Phys. Rev., 2020, 7, 021301 CAS.
- T. Srivastava and R. Jha, IEEE Photonics Technol. Lett., 2018, 30, 319–322 CAS.
- M. S. Bhargava Reddy, S. Kailasa, B. C. G. Marupalli, K. K. Sadasivuni and S. Aich, ACS Sens., 2022, 7, 2132–2163 CrossRef CAS PubMed.
- V. Chaudhary, N. Ashraf, M. Khalid, R. Walvekar, Y. Yang, A. Kaushik and Y. K. Mishra, Adv. Funct. Mater., 2022, 32, 2112913 CrossRef CAS.
- W. Y. Chen, X. Jiang, S.-N. Lai, D. Peroulis and L. Stanciu, Nat. Commun., 2020, 11, 1–10 CrossRef PubMed.
- C. Wang, R. Li, L. Feng and J. Xu, Chemosensors, 2022, 10, 109 CrossRef CAS.
- X. Bu, F. Ma, Q. Wu, H. Wu, Y. Yuan, L. Hu, C. Han, X. Wang, W. Liu and X. Li, Sens. Actuators, B, 2022, 369, 132232 CrossRef CAS.
- L. Zhao, K. Wang, W. Wei, L. Wang and W. Han, InfoMat, 2019, 1, 407–416 CrossRef CAS.
- S. N. Shuvo, A. M. Ulloa Gomez, A. Mishra, W. Y. Chen, A. M. Dongare and L. A. Stanciu, ACS Sens., 2020, 5, 2915–2924 CrossRef CAS PubMed.
- A. Hermawan, B. Zhang, A. Taufik, Y. Asakura, T. Hasegawa, J. Zhu, P. Shi and S. Yin, ACS Appl. Nano Mater., 2020, 3, 4755–4766 CrossRef CAS.
- Y. Wang, Y. Zhou and Y. Wang, Sens. Actuators, B, 2020, 323, 128695 CrossRef CAS.
- D. Zhang, Q. Mi, D. Wang and T. Li, Sens. Actuators, B, 2021, 339, 129923 CrossRef CAS.
- Z. Sima, P. Song, Y. Ding, Z. Lu and Q. Wang, Appl. Surf. Sci., 2022, 153861 CrossRef CAS.
- S. Sun, M. Wang, X. Chang, Y. Jiang, D. Zhang, D. Wang, Y. Zhang and Y. Lei, Sens. Actuators, B, 2020, 304, 127274 CrossRef CAS.
- W. N. Zhao, N. Yun, Z. H. Dai and Y. F. Li, RSC Adv., 2020, 10, 1261–1270 RSC.
- M. Liu, J. Ji, P. Song, M. Liu and Q. Wang, Sens. Actuators, B, 2021, 349, 130782 CrossRef CAS.
- D. Huang, H. Li, Y. Wang, X. Wang, L. Cai, W. Fan, Y. Chen, W. Wang, Y. Song and G. Han,
et al.
, Chem. Eng. J., 2022, 428, 131377 CrossRef CAS.
- O. Ama, M. Sadiq, M. Johnson, Q. Zhang and D. Wang, Chemosensors, 2020, 8, 102 CrossRef CAS.
- Z. Wang, F. Wang, A. Hermawan, J. Zhu and S. Yin, Funct. Mater. Lett., 2021, 14, 2151043 CrossRef CAS.
- S. M. Majhi, A. Ali, Y. E. Greish, H. F. El-Maghraby, N. N. Qamhieh, A. R. Hajamohideen and S. T. Mahmoud, ACS Appl. Electron. Mater., 2022, 4, 4094–4103 CrossRef CAS.
- K. Deshmukh, T. Kovávrik and S. K. K. Pasha, Coord. Chem. Rev., 2020, 424, 213514 CrossRef CAS.
- B. Xu, M. Zhu, W. Zhang, X. Zhen, Z. Pei, Q. Xue, C. Zhi and P. Shi, Adv. Mater., 2016, 28, 3333–3339 CrossRef CAS PubMed.
- Q. Wang, N. Han, Z. Shen, X. Li, Z. Chen, Y. Cao, W. Si, F. Wang, B.-J. Ni and V. K. Thakur, Nano Mater. Sci., 2023, 1, 35–52 Search PubMed.
- M. AhadiParsa, A. Dehghani, M. Ramezanzadeh and B. Ramezanzadeh, Adv. Colloid Interface Sci., 2022, 307, 102730 CrossRef CAS PubMed.
- X. Yu, Y. Li, J. Cheng, Z. Liu, Q. Li, W. Li, X. Yang and B. Xiao, ACS Appl. Mater. Interfaces, 2015, 7, 13707–13713 CrossRef CAS PubMed.
- S. Ramanavicius and A. Ramanavicius, Int. J. Mol. Sci., 2020, 21, 9224 CrossRef CAS PubMed.
- Y. Sun, P. Li, Y. Zhu, X. Zhu, Y. Zhang, M. Liu and Y. Liu, Biosens. Bioelectron., 2021, 194, 113600 CrossRef CAS PubMed.
- X. Zhu, Y. Zhang, M. Liu and Y. Liu, Biosens. Bioelectron., 2021, 171, 112730 CrossRef CAS PubMed.
-
Z. Xiao, S. Ruan, L. B. Kong, W. Que, K. Zhou, Y. Liu and T. Zhang, MXenes and MXenes-based Composites, Springer, 2020, pp. 303–404 Search PubMed.
- F. Wang, C. Yang, C. Duan, D. Xiao, Y. Tang and J. Zhu, J. Electrochem. Soc., 2014, 162, B16 CrossRef.
- Y. Xu, T. Ma, L. Zheng, Y. Zhao, X. Liu and J. Zhang, Sens. Actuators, B, 2019, 288, 432–441 CrossRef CAS.
- M. Ezhilan, J. B. B. Arockia Jayalatha and J. B. B. Rayappan, Mater. Res. Bull., 2021, 139, 111276 CrossRef CAS.
- S. M. Majhi, A. Ali, Y. E. Greish, H. F. El-Maghraby and S. T. Mahmoud, Sci. Rep., 2023, 13, 3114 CrossRef CAS PubMed.
- W. Q. Li, S. Y. Ma, J. Luo, Y. Z. Mao, L. Cheng, D. J. Gengzang, X. L. Xu and S. H. Yan, Mater. Lett., 2014, 132, 338–341 CrossRef CAS.
- S. Wang, L. Wang, T. Yang, X. Liu, J. Zhang, B. Zhu, S. Zhang, W. Huang and S. Wu, J. Solid State Chem., 2010, 183, 2869–2876 CrossRef CAS.
- K. Roopa Kishore, D. Balamurugan and B. G. Jeyaprakash, J. Mater. Sci.: Mater. Electron., 2021, 32, 1204–1220 CrossRef CAS.
- S. K. Bhardwaj, H. Singh, M. Khatri, K.-H. Kim and N. Bhardwaj, Biosens. Bioelectron., 2022, 202, 113995 CrossRef CAS PubMed.
- M. Hu, Z. Li, T. Hu, S. Zhu, C. Zhang and X. Wang, ACS Nano, 2016, 10, 11344–11350 CrossRef CAS PubMed.
- D. Sun, M. Wang, Z. Li, G. Fan, L.-Z. Fan and A. Zhou, Electrochem. Commun., 2014, 47, 80–83 CrossRef CAS.
- X. Zhang, J. Lei, D. Wu, X. Zhao, Y. Jing and Z. Zhou, J. Mater. Chem. A, 2016, 4, 4871–4876 RSC.
- X. Xie, S. Chen, W. Ding, Y. Nie and Z. Wei, Chem. Commun., 2013, 49, 10112–10114 RSC.
- G. Zou, B. Liu, J. Guo, Q. Zhang, C. Fernandez and Q. Peng, ACS Appl. Mater. Interfaces, 2017, 9, 7611–7618 CrossRef CAS PubMed.
- G. Gao, A. P. O’Mullane and A. Du, ACS Catal., 2017, 7, 494–500 CrossRef CAS.
- X. Li, G. Fan and C. Zeng, Int. J. Hydrogen Energy, 2014, 39, 14927–14934 CrossRef CAS.
|
This journal is © The Royal Society of Chemistry 2023 |