DOI:
10.1039/D2GC04145F
(Critical Review)
Green Chem., 2023,
25, 4878-4911
Sustainable valorisation of renewables through dialkyl carbonates and isopropenyl esters
Received
4th November 2022
, Accepted 12th April 2023
First published on 14th April 2023
Abstract
This review showcases a thorough analysis of reactions and applications of the most widespread linear and alkylene organic carbonates (DACs), dimethyl-, diethyl-, ethylene-, and propylene-carbonates (DMC, DEC, EC, and PC, respectively), and a representative enol ester isopropenyl acetate (iPAc), for the chemical functionalisation and upgrading of renewable compounds, including both bio-based platform molecules and biopolymers. The work, which follows a previous survey published by us in 2018 and limited to DMC only, is organised into five sections where the literature screening encompasses the past 4 years in the case of DMC and a wider timespan of 5–6 years for other homologues/analogues carbonates and iPAc. After a general introductory section on benign-by-design processes for the conversion of biomass derivatives, a description of synthetic methods of DACs follows. Most of the review content is then focused on reactions in which DACs and iPAc act as alkylating, carboxylating, and acylating agents, respectively, and processes where the same compounds are used as solvents. Topics are grouped starting from the valorisation of small renewable molecules such as glycerol, cyclic carbonates, carbonyl derivatives of furfural and HMF, then proceeding with bio-monomers, and ending up with the synthesis and functionalisation of biopolymers. The investigated examples have been detailed by providing conditions and scope, the proposed reaction mechanisms when available, and a rationale behind the choice of reaction/process parameters (T, p, catalyst(s), etc.). Criticism and comments have been put forward on the pros and cons of the described methods and their perspectives, as well as on those studies which still require follow-ups and more in-depth analyses.
Introduction
Environmental sustainability and the green transition are central goals of modern societies and economies wherein the use of renewable feedstocks represents a fundamental tool and, at the same time, one of the greatest challenges to cope with. An exemplificative assessment of this scenario comes from the analysis of the European Green Deal (EGD, Fig. 1). EGD is a long-term financial commitment of the European Commission, developed with the aim of supporting Europe in becoming the first carbon-neutral continent by 2050.1 Over the next decade, EGD will provide finance of €1 trillion divided into two main financing streams: direct EU funds, and co-financing by Member States as well as private/public partnerships.2 Such an ambitious plan combines policy instruments and revisions of regulations with the design and adoption of a new industrial policy strategy towards a green and circular economy. Research and innovation are the main drivers towards a green transition, not only as instruments to meet policy objectives, but also to help tackle societal challenges. Green chemistry and green chemical engineering actively contribute to this field by establishing novel bio-based value chains integrating biomass processing with circularity principles for the production of renewable molecules, materials and energy (Fig. 2). Although it is expected that biomass valorisation into molecules and materials will require the use of fossil-derived chemicals to some extent, at least in the next 30–40 years, only safe and non-toxic petrochemical derivatives are currently integrated into benign-by-design processes and technologies for the conversion of food waste and lignocellulosic residues into a variety of high added-value products such as pharmaceuticals, bioactive compounds, and bio(nano)-materials.3,4 For example, Pereira and co-workers developed an effective strategy to achieve C5–C6 sugar polyols as low-calorie sweeteners and emulsifiers that combines the chemical hydrolytic breakdown of the holocellulose fraction (cellulose and hemicellulose in biowaste feedstocks) with hydrogenation or transfer hydrogenation reactions, both catalysed by metals (Ru, Ni).5 Likewise, the Borregaard process allows for the production of vanillin, a well-known flavouring agent in the food, fragrance, and pharmaceutical industries and a relevant renewable-based building block for active pharmaceutical ingredients (APIs) from an aqueous alkaline solution upon O2-mediated oxidation of lignosulfonates which, in turn, are obtained by sulfite pulping of wood waste. The overall transformation accounts for 15% (ca. 3000 T y−1) of the vanillin market, while the residual major segment (85%) comes from petrochemistry.6 Finally, another relevant biorefining scheme involves sugar beet pulp (SBP) which is the main solid by-product of the European sugar production industry (ca. 10.4 Mt y−1 in 2016).7 SBP is still mainly used as animal feed, but alternative “zero waste discharge” approaches are in the pipeline based on multistep sequences in which the solvent extraction of the phenolic-rich fraction and pectin of SBP is followed by the chemical/enzymatic recovery of carbohydrates for the production of chemicals and polymers.9 Albeit far from being exhaustive, this preliminary analysis highlights the role of green technologies towards primary transformation of renewable feedstocks in platform chemicals, effectively combining sustainability with environmental protection and safety. This concept was also explored within our long-standing interest in the design of eco-friendly protocols using clean reagents and solvents. Particularly, some of our contributions in 2018–2019 surveyed the role of carbon dioxide (CO2) and one of its most interesting commercial derivatives, dimethyl carbonate (DMC), in the chemical upgrading of bio-based compounds and polymers through a variety of reactions including catalytic, photocatalytic and thermal transformations of insertion, CH-bond activation, methylation, methoxycarbonylation (transcarbonation and carbamation), and polymerization.10–12 This lively sector is constantly fuelled by new findings describing benefits and innovations not only in terms of efficiency and safety, but more generally, of process intensification, low-to-zero waste/emissions and carbon footprint minimisation. The lack of toxicity and the versatile reactivity of DMC make it an ideal green reagent to convey both CO2 and/or methyl function in chemical processes. However, there are some bottlenecks associated with the sustainability of these strategies, mainly related to the synthesis of DMC which still requires fossil/toxic reagents such as ethylene oxide or propylene oxide, both downstream products of ethylene and propylene, and may be affected by the fluctuating price of H2 (further details will be discussed later on this section).13,14
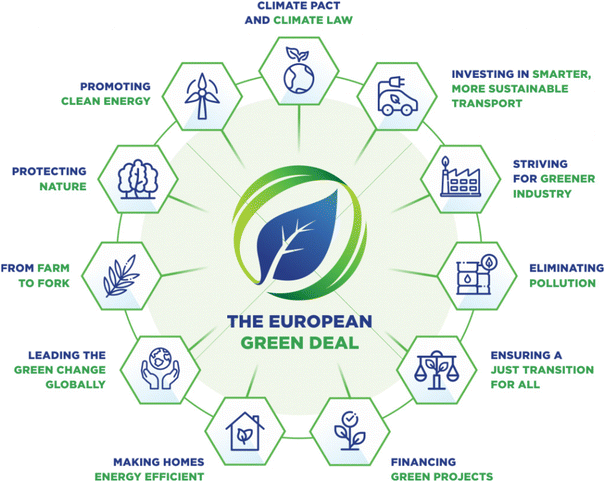 |
| Fig. 1 The overarching aim of the European Green Deal.8 | |
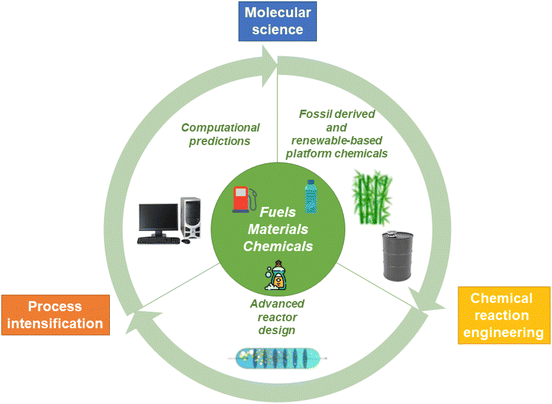 |
| Fig. 2 Green chemistry and green engineering in the upgrading of biomass derivatives. | |
The present review aims at providing a critical and updated overview of the most promising chemical valorisation and upgrading strategies applied to renewable-based compounds, exploiting the reactivity of dialkylcarbonates (DACs) and isopropenyl esters (iPEs). Each class of compounds will be introduced identifying the main current synthetic methodologies and highlighting the most relevant commercial derivatives. Recent advances in the synthesis of glycerol carbonate (GC), which can be selectively obtained reacting glycerol, a well-known bio-based raw material, with DMC will be used to introduce the main reactivity pathways occurring in chemical upgrading of renewable compounds with DACs. An up-to-date overview of the main applications of commercially relevant linear and alkylene carbonates (e.g. diethyl carbonate, DEC; ethylene carbonate, EC; and propylene carbonate, PC) in alkylation and/or carboxyalkylation reaction with renewable-based co-reactants will then follow. More recently, DACs have found increasing applications as solvents in thermo- and photochemical processes, as well as in selected biological and analytical applications.
Finally, recent applications of DACs in polymer and biopolymer synthesis and processing will be critically evaluated. iPEs represent another promising class of environmentally benign chemicals suitable for the valorization of both biopolymers and bio-based derivatives. Non-toxic isopropenyl acetate (iPAc), in particular, was recently employed for the sustainable acylation of cellulose pulps, rayon, xylan, pullulan, dextrin, sugar cane bagasse and Kraft lignin. iPAc reactivity was also exploited for the development of acid-catalyzed esterification-acetalization tandem sequences with renewable-based 1,2-diols and/or glycerol.
Synthesis of dialkyl carbonates (DACs)
Dimethyl carbonate (DMC)
The protocols available for the preparation of DMC have been reviewed extensively and are generally classified as conventional and CO2-based processes.15,16 It is beyond the scope of this paper to offer a thorough analysis of this subject. However, some sustainability considerations related to DAC synthesis must be taken into account. Early conventional processes, developed before 1980 and based on the stoichiometric phosgenation of methanol have been gradually abandoned worldwide because of the extreme toxicity and dangers associated with the use of phosgene. Two relevant alternative processes were developed in the mid-80s: the oxidative carbonylation of methanol and the carbonylation of methyl nitrite, which were flagship productions of Enichem and UBE industries, respectively. Both these transformations are much safer compared with phosgene-mediated reactions, and have been conceived under a pioneering green chemistry vision using effective catalysts and producing minimal, if any, waste to be disposed of. At the current rate of consumption of DMC of about 90 Kt y−1, oxidative carbonylation of methanol is still appreciated as one of the most widespread methods for the production DMC.17–19 Notwithstanding this, the risks of explosion due to the presence of oxygen and NO/O2 mixture, the toxicity of NOx and the difficult catalyst/product separation have pushed research forward to the use of CO2 as a starting feedstock. Nevertheless, at present the most attractive reactions for the preparation of DMC are based on transcarbonation of alkylene carbonates (EC and PC) with methanol, and direct or indirect urea methanolysis (Scheme 1).
 |
| Scheme 1 Synthesis of DMC. Top: CO2 insertion into epoxides (a) followed by transcarbonation of alkylene carbonate (b) (red box); bottom: direct and indirect urea methanolysis (c) and (d), respectively (blue box). Cat. 1: bifunctional catalyst, cat. 2: amphoteric catalyst; cat. 3 and 4: amphoteric heterogeneous catalyst. | |
The first sequence (route a and b, Scheme 1) has been successfully integrated in the phosgene-free production of polycarbonate by the Asahi-Kasei Japanese group.20 Particularly, the transcarbonation of EC with methanol (red box: b; R = H) was carried out by a new reactive distillation process which achieved both DMC and ethylene glycol (EG) in yields higher than 99.8%, in the presence of catalyst comprising an anion exchange resin or an alkali metal hydroxide.21 This process has been claimed as one of the major breakthroughs in polymer synthesis, and the best process in the world in terms of productivity for DMC and EG, which reached 3.340 t h−1 and 2.301 t h−1, respectively. Moreover, thanks also to the recovery of waste CO2 in the preparation of EC (Scheme 1, red box: a, R = H), the Life Cycle Assessment (LCA) of the polymer production confirmed that in 2016, CO2 emissions were reduced by 1.93 Mt compared with those of a conventional phosgene-based PC process. All these innovations and benefits were recognized by the American Chemical Society, which awarded Asahi Kasei Chemicals the prestigious Heroes of Chemistry Award in 2014.22 As mentioned above, however, concerns related to the sustainability/safety of this protocol have emerged because of the use of alkylene oxides that not only are toxic compounds, but are also obtained from crude oil, with production costs directly affected by ethylene and propylene prices. These aspects have been a major driver to explore alternative strategies. Among them, recent analyses have highlighted how processes based on the methanolysis of urea (Scheme 1, blue box: c) are gaining momentum and competitiveness because of the cheapness, non-toxicity, and commercial availability of the involved reagents, and the moderate reaction conditions. The transformation can be carried out either directly (Scheme 1, c) or indirectly through an initial step of nucleophilic addition of a 1,2-diol (ethylene or propylene glycol) to urea, which affords an alkylene carbonate (EC or PC, Scheme 1, d), following the same transcarbonation reaction described for the Asahi Kasei process. A 1.000 t pilot plant based on the indirect route via PC has been operated by the Chinese Academy of Science since 2014 using metal oxides (ZnO and ZnO-Cr2O3) as catalysts.13 This strategy takes advantage of sustainable methods of achieving reactants: indeed, gasification and anaerobic digestion of biomass such as switchgrass, and technologies based on renewable (RE) powered H2O electrolysis have been recently proposed and are under investigation to generate renewable ammonia and H2 for the synthesis of urea and methanol from CO2 (Scheme 2).23,24
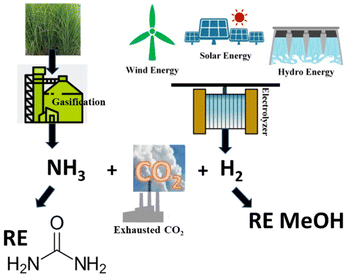 |
| Scheme 2 Sustainable production of MeOH (right) and urea (left) for the synthesis of DMC. | |
Techno-economic analyses on simulated processes have demonstrated that even compared with a mature technology such as the oxidative carbonylation of methanol, urea methanolysis exhibits a higher energy efficiency of 48.5% and a lower cost of manufacturing of 2.19 € per lDE (DE: diesel equivalent).13
A concluding note on this section is dedicated to the direct reaction of methanol and CO2 (Scheme 3). Thermodynamic constraints have severely limited any large-scale application of the process; water is obviously a desirable side-product, but it also represents one of the major drawbacks since it shifts the equilibrium backwards and deactivates the catalyst, resulting in lower yields of DMC.16 The reaction, however, is considered the epitome of the sustainable synthesis of DMC and it is therefore receiving great attention.25,26 Among the plethora of heterogeneous catalysts based on metal oxides (ZrO2, CeO2, SiO2, Al2O3, TiO2, ZnO, MoO3, Bi2O3, MgO, Y2O3, HfO2, La2O3, Ga2O3, GeO2, In2O3, Sb2O3),27 alcoholates and their mixtures, used in combination with powerful organic and inorganic dehydrating agents (dicyclohexylcarbodiimide, CaC2, trimethyl phosphate, orthoesters, ketals and nitriles),28,29 ceria (CeO2) in the presence of 2-cyanopyridine (2-CP) is probably the best system so far reported, with which DMC was achieved with selectivity and yields of >99% and >95%, respectively.30 Interestingly, the direct reaction of CO2 with an alcohol has entered a demonstration phase in industry on the basis of this equilibrium shift concept.31
 |
| Scheme 3 The synthesis of DMC via the direct reaction of CO2 and methanol. | |
Diethyl carbonate (DEC) and alkylene carbonates (EC, PC)
The synthesis of diethyl carbonate (DEC) is carried out through protocols analogous to those described for DMC, including the urea alcoholysis, the transcarbonation reaction, the direct reaction of ethanol and CO2, and ethanol oxidative carbonylation (EOC).32,33 Suffice it to add here that most approaches in the current literature are aimed at catalyst optimization: for example, innovative chloride-free Cu-based systems synthesized by in situ carbothermal reduction have been proposed for the EOC process,34 while the reaction of CO2 and ethanol has been described using CeO2, ZrO2, and mixed CexZr1−xO2 metal oxides as catalysts in combination with ketals (2,2-diethoxypropane), tetraethylorthosilicate, and microporous membranes for the removal of water.35–37 Other catalysts displaying tunable acid–base properties such as mixed oxides in the form of Mg2ZrxAl1−x and Zn-based imidazolate-frameworks (ZIF) have been, instead, proposed for synthesizing DEC (in yields up to 38%) via the ethanolysis of urea.38,39 For a comprehensive view of the main existing catalytic methodologies for the direct synthesis of DMC from CO2via direct alcohol carbonylation or through an indirect route via urea alcoholysis, the reader is referred to recent reviews by Paul et al. and Sharma and co-workers, respectively.40–42 The preparation of alkylene carbonates is consistent with the above-described protocol of cycloaddition of CO2 to epoxides (Scheme 1, a), particularly PO and EO which are the most used reactants for industrial applications in the synthesis of propylene carbonate and ethylene carbonate. This subject has been extensively reviewed in the recent literature, and mainly relies on non-reductive CO2 valorisation approaches in the presence of bifunctional single-component catalytic systems or binary mixtures where the two catalytic species act simultaneously as Lewis acids and bases.43–46 The coordination of such catalysts at both the O- and C-atoms of the epoxide ring promotes ring opening and further CO2 insertion (Scheme 4). Typically, the Lewis acid site is provided by one or more metal centres or metal-free hydrogen bond donor species, while the Lewis base is a halide anion ([X]− = Cl, Br, I). Robust air- and moisture-stable complexes have been developed based on inexpensive and low-toxic metals (e.g. Al and Fe), but active research trends in the field of homogeneous catalysts are towards systems comprising renewable hydrogen bond donors in combination with organic halides such as, for example, ascorbic acid and tetrabutylammonium iodide (TBAI) or amino acids-derived ionic liquids (ILs, e.g. 1-butyl-3-methylimidazolium glycinate, [C4C1im][GLY]).47,48 The most active heterogeneous catalysts reported include metal organic frameworks (MOFs), porous organic polymers (POPs) functionalized by the inclusion of metal complexes (Mg- or Al-porphyrins),49,50 -onium salt-based ILs covalently bound to silica,51 carboxyl-bearing ILs immobilized on mesoporous terephthalate-based materials (MIL101),52 and nanotubes and nanowires with supported imidazolium salts.53 Original strategies have been proposed for carrying out the cycloaddition of CO2 to epoxides also under continuous flow (CF) conditions in the presence of both supported ionic liquids and binary mixtures of salts/complexes of alkali and alkaline earth metals and cation coordinating agents as glycols, crown ethers and polyethers.54 Most of the quoted catalytic systems allow selectivity and yields to alkylene carbonates above 99% at T and p in the range of 70–150 °C and 1–50 bar, respectively. An alternative green approach for the reaction involves the simultaneous use of oxidants and CO2 for the direct one-pot two-step conversion of olefins into the corresponding cyclic organic carbonates (Scheme 5).55,56 This method not only avoids the purification/isolation of toxic intermediate epoxides, but it represents a process intensification archetype towards a more efficient use of chemicals. This topic has been recently reviewed by our group, surveying a variety of examples including auto tandem, assisted tandem, and orthogonal tandem processes that have been described using green oxidants, mostly H2O2, and catalysts based on several different metals (Nb, Ru, Mo, Mn, Ti, Zn–W, Cu–Mo, Co, Au) with and without the use of organic halides as co-catalysts.57
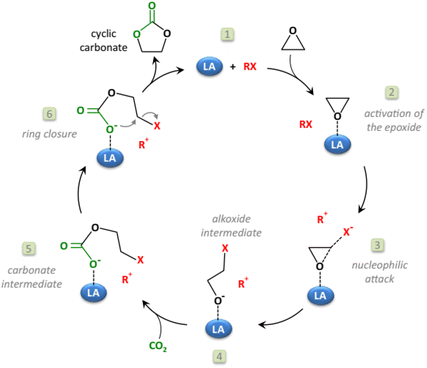 |
| Scheme 4 The mechanism of coordination of a bifunctional (acid/base) catalyst to an epoxide in the synthesis of alkylene carbonates. Reprinted with permission from “Cyclic carbonates synthesised from CO2: applications, challenges and recent research trends” P. P. Pescarmona, Curr. Opin. Green Sustainable Chem., 2021, 29, 100457 (ref. 43), https://www.sciencedirect.com/science/article/pii/S2452223621000134. | |
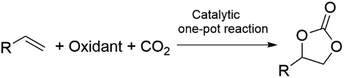 |
| Scheme 5 One-pot two-step conversion of olefins to alkylene carbonates. | |
Novel methodologies for DACs synthesis
Hintermair, Sankar and O'Neill developed and tested experimentally a novel thermodynamic model for calculating equilibrium yields of DMC and DEC in a wide range of experimental conditions, employing the corresponding alcohol and CO2 as reagents and CeO2 as heterogeneous catalyst. They observed that performing DAC synthesis in CF conditions (scCO2 at 200 bar, T = 140 °C, productivities of 235 mmol (L h)−1 for DMC and 241 mmol (L h)−1 for DEC) allowed for continuous removal of both water and DAC product, preventing progressive surface M–O–M hydrolysis on the heterogeneous catalyst and paving the road towards low-temperature direct carboxylation of alcohols.58 Aricò and co-workers developed a scalable procedure for the synthesis of non-commercial symmetrical and unsymmetrical DACs incorporating alkyl, alkoxyalkyl, aminoalkyl, and thioalkyl moieties, depicted in Scheme 6. DAC synthesis occurred via TBD-promoted transcarbonylation (10% mol); interestingly, the reported procedure allowed for large-scale production of DACs (up to 100 mL) and DAC products were purified by distillation.59
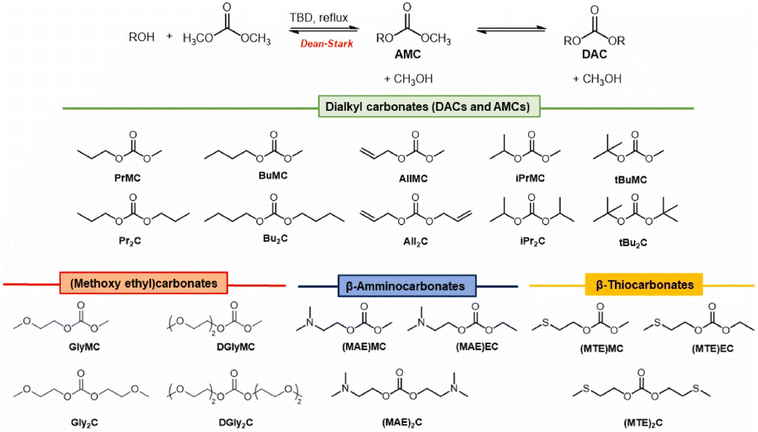 |
| Scheme 6 Synthesis of DACs via TBD-promoted transcarbonylation. Reproduced with permission from ref. 59. Copyright 2022 Elsevier Ltd. | |
Upgrading of renewables with dialkyl and alkylene carbonates
DACs offer several advantages as solvents since they are a class of non-toxic, (bio)degradable solvents, stable under ambient conditions and available in large amounts at relatively low prices. Besides, DACs’ polarity and boiling points can be easily tuned by varying the length and nature of the alkyl groups.60 DACs are considered aprotic polar solvents like DMSO or DMF, although, differently from DMSO and DMF, DACs generally show only limited miscibility with water. The main established solvent applications of DACs include electrochemical applications, in particular, as non-aqueous electrolytes, as well as extractive procedures. In recent years, DACs have emerged as possible alternatives to replace VOCs or as co-solvents in cleaning processes and in cosmetics.61,62 DACs have also found numerous applications in synthetic organic chemistry, as sustainable alkylating and/or carboxymethylating agents. This dual reactivity is ascribed to their ambident electrophile features. Analysing the model case of DMC, this molecule contains two distinct electrophilic sites: the sp2 carbonyl carbon and the sp3 carbons of the methyl groups, which are hard and soft electrophilic centres, respectively. Their reactivity can be fine-tuned towards BAc2- or BAl2-nucleophilic substitutions by selecting the reaction T, the catalysts and the nature of the nucleophilic co-reactant, to give, respectively, methoxycarbonylation or methylation reactions, as depicted in Scheme 7. Low reaction T (T ∼ 90 °C) and the presence of hard nucleophiles (e.g. ROH, RO–) as co-reactants favour the carboxymethylation reaction, occurring via a BAc2 mechanism (Scheme 7, right). This is an equilibrium reaction which is right-shifted by using overstoichiometric quantities of DMC or by continuously removing the by-product alcohol from the reaction mixture via azeotrope distillation. Conversely, at a high T (T > 120 °C) and with soft nucleophiles as co-reactants (e.g. RSH, ArOH, R3P) the methylation reaction is favoured according to a BAl2 mechanism (Scheme 7, left). This is an irreversible process: upon formation of the methylated product, methyl carbonic acid is released. Due to its instability above T = −36 °C, the acid readily decomposes forming CO2 and MeOH.63 Currently, DMC and DEC are the most commercially relevant DACs, while EC and PC are the main commercially available COCs. As summarized in Table 1, these compounds combine desirable properties in terms of mild toxicologic properties, environmental pollution, and biodegradability with practically relevant features, such as UV transparency, high flash points, chemical stability, and easy separation and recycling, as well as potential synthetic routes from renewable resources.
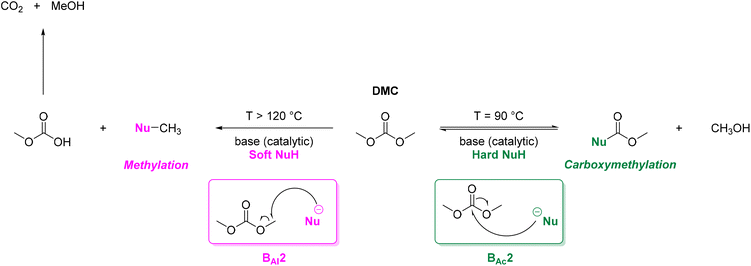 |
| Scheme 7 DMC reactivity. | |
Table 1 Physicochemical properties of commercially relevant dialkyl and alkylidene carbonates
Abbreviation |
DMC |
DEC |
EC |
PC |
Ref. |
Structure |
|
|
|
|
— |
Formula |
C3H6O3 |
C5H10O3 |
C3H4O3 |
C4H6O3 |
43, 64 and 65 |
Molecular mass [g mol−1] |
90.08 |
118.13 |
88.06 |
102.09 |
43 and 65 |
T
m [°C] |
4.6 |
−43 |
36 |
−49 |
43, 64, 65 and 66 |
T
eb [°C] |
90.3 |
126 |
248 |
242 |
43, 64, 65 and 66 |
Flash point [°C] |
21.7 |
46 |
143 |
135 |
43, 64 and 65 |
d [g mL−1] |
1.069 |
0.975 |
1.321 |
1.205 |
43, 64, 66 and 67 |
Viscosity, η [mPa s] |
0.59 (25 °C) |
0.75 (25 °C) |
1.93 (40 °C) |
2.53 (25 °C) |
43, 65 and 68 |
Dielectric constant, ε |
3.20 (25 °C) |
2.83 (25 °C) |
89.78 (40 °C) |
66.14 (20 °C) |
43, 65 and 68 |
Dipole moment, μ [D] |
0.93 |
1.07 |
4.9 |
4.9 |
43 and 65 |
Refractive index, nD |
1.3699 (25 °C) |
1.3845 (20 °C) |
1.4148 (20 °C) |
1.4189 (20 °C) |
43, 65, 67 and 69 |
ΔHf [kJ mol−1] |
−613.78 (25 °C, liquid) |
−637.9 |
−581.6 (25 °C, solid) |
−613.2 (25 °C, liquid) |
43, 64 and 70 |
C
p [J (mol K)−1] |
165.48 (25 °C, liquid) |
152.1 (n.d.) |
133.9 (50 °C, liquid) |
218.6 (25 °C, liquid) |
43, 71 and 72 |
Solubility |
Solubility in H2O: 1.39 g L−1. Miscible with alcohols, ethers, esters, ketones |
Soluble in diethyl ether, ethanol, and chloroform. Miscible with ketones, esters, aromatic hydrocarbons, some aliphatic solvents |
Miscible in H2O, ethanol, ethyl acetate, acetic acid, ethyl ether, chloroform, benzene |
Very soluble in H2O (240 g L−1) |
43 and 64 |
Hazards |
Highly flammable liquid and vapor |
Flammable liquid and vapor |
Harmful if swallowed, causes serious eye irritation, may cause damage to organs (kidney) through prolonged or repeated exposure if swallowed |
Causes serious eye irritation |
43 and 64 |
An archetype for sustainable reactions: synthesis of glycerol carbonate (GC)
The synthesis of glycerol carbonate (GC) via catalytic transcarbonation (carbonate interchange reaction) of organic carbonates, mostly DMC, with glycerol derived from the biodiesel manufacture, is among the most investigated applications for the valorisation of biobased feedstocks.
This subject has been extensively surveyed by several papers over the past ten years,10,73,74 and it continues to be the object of recent review articles,75–77 which testify two major aspects: (i) compared with other strategies of glycerol upgrading (e.g. reduction, oxidation, dehydration, pyrolysis, reforming, etc.) that often require harsh reaction conditions, the production of GC is a benign-by-design route. The reaction occurs in the proximity of ambient T and at atmospheric pressure, with safe non-toxic reagents; (ii) GC is an excellent substrate and intermediate for a variety of uses spanning the synthesis of polymers (polyurethane, polycarbonates, polyesters, and polyamides) and glycerol-derived surfactants to other applications as a high-boiling protic polar solvent, an electrolyte for batteries, a blowing agent, etc. This broad spectrum of interests is clearly highlighted also by multinational manufacturers such as Huntsman and Ube Industries Limited, which include GC in their portfolio of key products for sustainability and USDA-certified bio-based derivatives.78Table 2 summarizes some of the best results and reaction conditions reported in the past four years’ (2018–2021) literature on the synthesis of glycerol carbonate from DMC. As mentioned above, quantitative reactions are achieved under mild conditions: at T in the range of 65–90 °C (below or at the refluxing point of DMC), excellent selectivity (≥97%) and yields (≥90%) of GC are reported more often in times no longer than two hours. The poor mutual miscibility of glycerol and DMC and the reversible nature of the process impose the use of excess carbonate, usually from 2 to 5 molar equiv. with respect to the stoichiometric ratio. It should be noted that higher amounts of DMC may compromise the selectivity, mostly due to the formation of glycerol dicarbonate as a by-product.
Table 2 Synthesis of glycerol carbonate (GC) from dimethyl carbonate (DMC).79–94
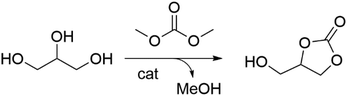
|
Entry |
Catalyst |
Glyc : DMCa (mol : mol) |
T, t (°C, h) |
Conversion/selectivitya (%) |
Yield (%) |
Ref. |
Glyc : DMC is the glycerol (Glyc) to DMC molar ratio, while conversion and selectivity refer to Glyc and glycerol carbonate (GC), respectively. All reactions were carried out at atmospheric pressure.
1,4-Diazabicyclo[2.2.2]octane modified poly(divinylbenzene-co-vinylbenzyl chloride).
Soybean oil was used as the starting feedstock: DMC acted as a transcarbonation agent of both the natural oil and the coproduct glycerol. The vegetable oil and DMC were mixed in 1 : 10 v/v ratio, in methyl tert-butyl ether (MTBE).
Yield was not determined; however, a productivity of 16 × 10−2 g of GC h−1 U−1 of the biocatalyst was reported under continuous flow conditions.
Total basicity (TB) of the solid catalysts was determined. Entry 5: TB up to 8.8 mmol g−1 mostly due to alkaline mineral salts including potassium carbonate and potassium silicate; entry 7: TB up to 1.36 mmol g−1 due to to Li+ and O2− ions as a surface oxide; entry 8: TB up to 26.3 mmol g−1 due to both the aluminate salt (NaAlO2) and the inorganic support; entry 11: TB up to 16.6 mmol g−1 due to Na2CO3 present in the original absorbent material.
Supports: Al2O3, MgO, TiO2, SiO2.
Crude glycerol (70% purity) was the starting feedstock: authors observed a discrepancy between the yield of GC and the conversion of glycerol which was attributed to impurities such as methanol and fatty acid esters present in the crude glycerol.
SAP: superabsorbent polymer in disposable baby diapers waste.
[HPTPA]OH: hydroxypropyltripentylammonium hydroxide.
nr: conversion not reported.
|
1 |
DABCO on poly(DVB-co-VBCl)b |
1 : 3 |
85/1 |
9–82/97–100 |
9–80 |
79
|
2 |
Na2CO3 |
1 : 3 |
75/2 |
98 |
>99% |
80
|
3 |
Lipases on epoxy resins |
|
60/5 |
100/99 |
n.d.d |
81
|
4 |
mesoporous CaO-ZrO2 |
1 : 3 |
90/8 |
97/93 |
90 |
82
|
5 |
Calcined corncob residuee |
1 : 3 |
80/1.5 |
98 |
94 |
83
|
6 |
Mg/ZnO |
1 : 4 |
80/2 |
98 |
97 |
84
|
7 |
Li/CFA (coal fly ash)f |
1 : 4 |
90/2 |
96 |
92 |
85
|
8 |
Supported NaAlO2e,f |
1 : 3 |
90/1 |
96/100 |
96 |
86
|
9 |
CaO |
1 : 2.5 |
65/3 |
|
97 |
87
|
10 |
MgO nanoparticles |
1 : 5 |
90/1.7 |
82/93 |
n.d. |
88
|
11 |
Carbonized SAP e,h |
1 : 4 |
75/1 |
97 |
94 |
89
|
12 |
[HPTPA]OH i |
1 : 3 |
80/1.5 |
96 |
88 |
90
|
13 |
Spray-dried NaAlO2 |
1 : 4 |
30/2 |
nr/100j |
85 |
91
|
14 |
[C2C1im][OAc] |
1 : 2 (DEC) |
120/2 |
98/93 |
91 |
92
|
15 |
Ce/NiO |
1 : 3 (DEC) |
80/6 |
97/99 |
98 |
93
|
16 |
CaO |
1 : 1 (PC) |
80/5 |
80/98 |
78 |
94
|
Alternatively, polar solvents such as, for example, methyl tert-butyl ether (MTBE), have been proposed to ensure single-phase reactions in the design of enzymatic processes (entry 3, Table 2).81 The catalyst, however, plays the most crucial role. Both the studies reported in Table 2 and the above-mentioned review articles agree that a correlation exists between the basicity of the catalytic systems and their performance: the higher the density of strong basic sites, the faster the transcarbonation reaction.10,73–77 This behaviour has been confirmed even in the case of catalysts obtained by calcination/carbonization of waste solids (corncobs and superabsorbent polymers) whose basicity is due to alkaline mineral salts, e.g. K2CO3 and Na2CO3, present in the starting materials (entries 5 and 11, Table 2).83,89 In particular, Wang et al. pointed out that a change in the total basicity from 0.6 to 16.6 mmol g−1 in the catalytic samples derived from corncobs (entry 5, Table 2) corresponded to a dramatic increase of the glycerol conversion from 2 to >95%, respectively.83 The mechanism proposed for the DMC-mediated transcarbonation is consistent with the basicity/performance correlation. The most accepted hypotheses describe the role of the base catalyst for the nucleophilic activation of glycerol and the generation of glyceroxide anion species which, through two subsequent NAcS (nucleophilic acyl substitution) reactions, produce a glyceryl methyl carbonate as an intermediate and the final cyclic product, glycerol carbonate, along with methanol.10,77 Interestingly, a recent study of the reaction catalyzed by CaO under microwave (MW) irradiation has demonstrated that for very fast reactions occurring in 3 min, no intermediates were observed and the overall process followed an irreversible second-order kinetic model from 45 to 65 °C, with an activation energy up to 12 times lower than that of a conventional heating system.95 Another promising approach for the synthesis of effective base heterogeneous catalysts has been described through a spray-drying technique by which, with organic templates such as polyvinylpyrrolidone and glycerol as a template, NaAlO2 was achieved as a spherical highly porous material (entry 13, Table 2 and Fig. 3).91 Among other DACs, DEC and PC have been recently reported for the preparation of GC over both homogeneous and heterogeneous catalysts. In the case of DEC, two representative examples described the use of 1-ethyl-3-methylimidazolium acetate ([C3C1im][AcO]) as a basic ionic liquid and a Ce-NiO mixed oxide to catalyze the conversion of glycerol into GC with yields in the range of 83–94% at T = 65–120 °C.92,93 The reaction over Ce-NiO was consistent with a three-order kinetic equation of glycerol (second order) and DEC (first order). In the case of PC, one of the best results was obtained by a calcium-doped hydrotalcite (Ca-HT) catalyst that allowed a 84% conversion and almost complete GC selectivity (T = 160 °C, t = 5 h). The authors hypothesized that the HT lamellar sheet-like structure provided easy accessibility of reactant glycerol and PC onto the catalyst, while interlayer carbonate anions were responsible for the deprotonation (nucleophilic activation) of glycerol. For the sake of completeness, two other approaches for the synthesis of GC should be mentioned here, based on the oxidative carbonylation of glycerol (OCG) and the direct reaction of glycerol with carbon dioxide [Scheme 8(a) and (b)]. In a recent example, the OCG process was carried out using a rod-like CeO2-supported Pd catalyst (Pd/CeO2-r) and NaI as a co-catalyst [Scheme 8(a)].96 Under optimized conditions, at 140 °C and 50 bar total pressure [p(O2) = 17 bar; p(CO) = 33 bar], the GC selectivity was 98% at 93% conversion. The redox cycle responsible for the catalytic activity was based on two subsequent oxidations, 2I− → I2 + 2e− and Pd(0) → Pd2+, mediated by O2 and I2, respectively. Thereafter, in the presence of CO, Pd2+ promotes the conversion of glycerol to GC and it is concurrently restored/reduced to Pd(0). The oxygen vacancy on the CeO2-r surface helps the reaction by adsorbing the reactant oxygen. The activation of non-toxic CO2 for its direct insertion into glycerol represents the most attractive design for the sustainable preparation of GC. However, alike the reaction discussed in the above-described Scheme 3, the thermodynamic limitations of the reaction (b) in Scheme 8 impose the use of stoichiometric amounts of dehydrating agents to shift the process to the product side. One of the best results reported so far was recently achieved using a combination of a strong Lewis acid catalyst as Zn(OTf)2, 1,10-phenanthroline (phen) as a ligand, and CaC2: at T = 180 °C, GC was obtained in a 92% yield (isolated 88%) by reacting glycerol under a CO2 pressure of 50 bar in the presence of N-methylpyrrolidone (NMP) solvent.97 The authors emphasized the role of CaC2 not only for its powerful dehydration capability, but also for its sustainable nature, being derived from a not endangered metal (Ca).
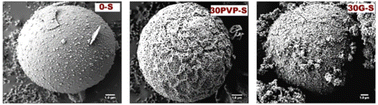 |
| Fig. 3 SEM images of NaAlO2 catalysts prepared through a spray-drying (S) method without an organic template (left) or with the addition of polyvinylpyrrolidone (PVP, centre) or glycerol (G, right) as a template. Reproduced from “Production of Glycerol Carbonate from Glycerol over Templated-Sodium-Aluminate Catalysts Prepared Using a Spray-Drying Method” P. Rittiron, C. Niamnuy, W. Donphai, M. Chareonpanich and A. Seubsai, ACS Omega, 2019, 4, 9001–9009 (ref. 91), https://pubs.acs.org/doi/10.1021/acsomega.9b00805. | |
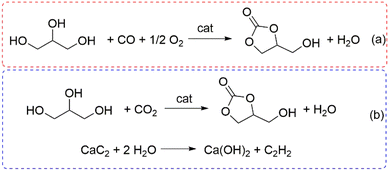 |
| Scheme 8 Synthesis of GC via: (a) catalytic oxidative carbonylation of glycerol (top, red box); (b) direct catalytic insertion of CO2 into glycerol in the presence of CaC2 as a dehydrating agent (bottom, blue box). | |
Valorization of renewable-based molecules and platform chemicals with DACs as reagents and solvents
DACs as reagents
Lui et al. employed Me2S as an inexpensive bio-derived catalyst/co-reagent for the cost-effective methylation of phenols, benzoic acids, and arylacetonitriles in DMC, employing non-carcinogenic alkylating agents and avoiding waste salts production. The proposed mechanism is depicted in Scheme 9 for the methylation of phenols. The overall sequence encompasses an initial alkylation of Me2S by DMC that generates an ionic intermediate, [Me3S][OCO2Me]. This species combines a strong methylating agent ([Me3S]+) with a strong Brønsted base ([OCO2Me]−), which allows the activation of the nucleophile (ArOH → ArO−) and its further methylation to the desired ether product (ArOMe). Differently substituted phenols, benzoic acids and arylacetonitrile substrates were selectively methylated applying this protocol (22 examples, yields up to >99%).98 Li et al. reported the first example of a phosgene-free, two-step sustainable methodology for the synthesis of carboxylic anhydrides (NCAs) from γ-benzyl-L-glutamate (BLG) and DMC, upon initial formation of the N-methoxycarbonyl-γ-benzyl-L-glutamate intermediate (NOM-BLG, 84% yield) followed by intramolecular cyclization to give NCA-BLG in 67% yield.99
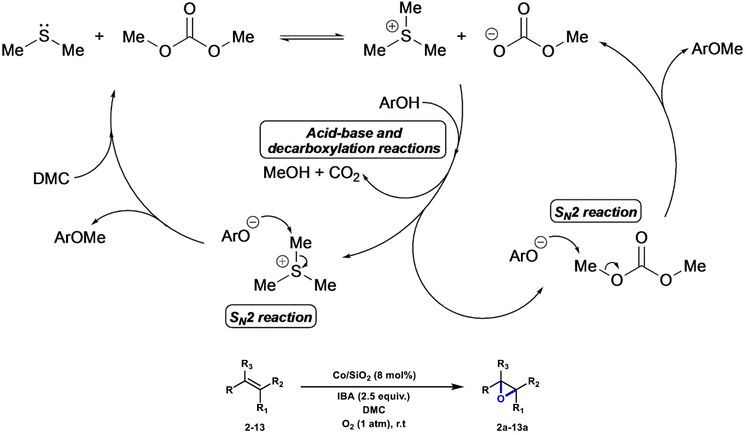 |
| Scheme 9 Proposed mechanistic pathway for phenol methylation with DMC/Me2S. Reproduced with permission from ref. 98. Copyright 2022 Wiley-VCH. | |
In the last 5 years, DMC was the main DAC employed in chemical valorisation of bio-derived platform chemicals, developing novel effective and sustainable methylation protocols accessing both aromatic platform chemicals and/or valuable renewable-based monomers (e.g. NCAs).
DACs as solvents
Gusevskaya, Robles-Azocar and co-workers recently developed a widely applicable alkene aerobic oxidation protocol, in the presence of supported M-catalysts (e.g. Co/SiO2) using DMC as solvent. Intriguingly, several different terpene-derived epoxides were synthesized employing this methodology with high chemo- and regioselectivity, as depicted in Scheme 10.100 Sneddon, Jordan and co-workers performed a high-throughput solvent-reagent conditions screening, to optimise a sustainable protocol for Steglich-type esterification reactions starting from equimolar amounts of carboxylic acid and alcohol, in the presence of Mukaiyama's reagent as coupling agent, 2,6-litidine as base and DMC as solvent (20 examples, up to 99% yield).101 Ok, Tsang and co-workers employed aqueous solutions of green solvents, PC and γ-valerolactone (GVL), for the microwave-assisted conversion of bread waste to 5-hydroxymethylfurfural (HMF) in the presence of SnCl4 as catalyst. HMF was synthesized in yield of up to ∼20% at T = 120 °C in t = 7.5 and 20 min employing PC/H2O and GVL/H2O 1
:
1 V/V, respectively. Moreover, these solvent mixtures played a key role in maintaining effective Lewis acid sites (Sn4+), to a greater extent compared with acetone/H2O and water only, preventing hydrolysis and the formation of catalytically inactive colloidal SnO2 particles.102 A DMC-based continuous process for HMF production was developed by Hatti-Kaul et al., employing a biphasic water/DMC system. Acid-catalysed fructose dehydration in a continuous mode was performed in the presence of 0.23 M HCl: the maximum HMF yield was achieved starting from 30% (w/v) fructose in water, performing the reaction in a tube reaction with H2O/DMC 1
:
3 V/V mixture at 1 min residence time and T = 200 °C, observing 96.5% fructose conversion and 87.2% HMF yield with a selectivity of 85.5% and 95.8% in the aqueous and organic phases, respectively. With this setup HMF could be synthesized in high selectivity (up to 74% yield) also from pure fructose and commercial fructose syrup. Moreover, this continuous process in a biphasic system required simple downstream processing, as depicted in Fig. 4. Interestingly, HMF's improved stability in the above-mentioned experimental conditions is ascribed to an increased DMC solubility in water at high temperatures.103 More recently, Das and co-workers developed an efficient and economic one-pot process for the conversion of untreated lignocellulosic biomass (e.g. corn cob, sugarcane bagasse, rice straw and corn straw) into HMF and furfural. DMC was employed as both solvent and carbonating agent, due to its partial decomposition promoted by AlCl3 and HCl as acid catalysts. Upon optimization, the maximum yield of 5-HMF and furfural from various biomass feedstocks was recorded as 35–60% and 61–98%, respectively, upon heating the mixture in a pressurized hydrothermal steel container at T = 180 °C for t = 6 h.104
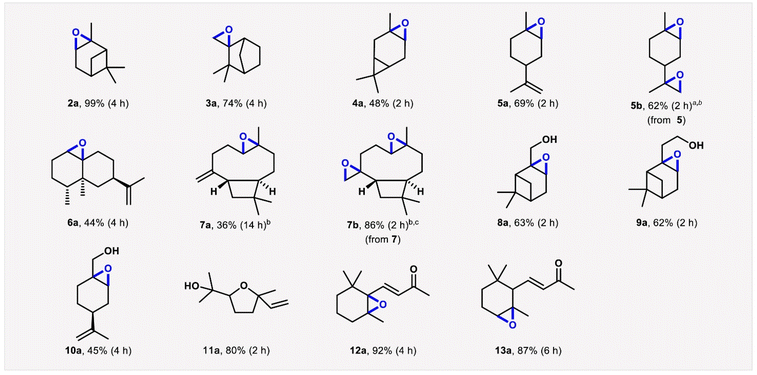 |
| Scheme 10 Cobalt catalysed epoxidation of bio-renewable alkenes (GC yields and reaction times). Substrate (0.5 mmol), isobutyraldehyde (IBA, 1.25 mmol), catalyst (8 mol%, 47 mg), dimethylcarbonate (5 mL), O2 (1 atm), room temperature. Conversions were nearly complete in all reactions except those performed to obtain products 3a (78%), 6a (79%) and 7a (55%). b40 °C. c5 equiv. of IBA. Reproduced with permission from ref. 100, Copyright 2022 Elsevier Ltd. | |
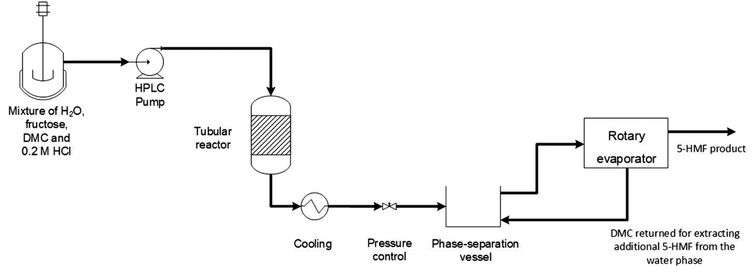 |
| Fig. 4 Biphasic continuous process for 5-HMF production from fructose: biphasic system of water/DMC with HCl as catalyst and fructose were pre-mixed and pumped into a tube reactor under pressure at T = 180–200 °C. Also, the strategy for 5-HMF recovery and purification from both organic and aqueous phase is shown. Reproduced with permission from ref. 103. Copyright 2020 Royal Society of Chemistry. | |
Aricò and co-workers reviewed the main applications of DACs as green reagents and solvents for the synthesis of several 5- and 6-membered heterocycles (e.g. tetrahydrofuran, furans, pyrrolidines, indolines, isoindolines, 1,4-dioxanes, piperidines, cyclic carbamates).61
Thanks to some key chemico-physical properties, such as their high boiling points, chemical inertness, and tuneable solvation behaviour, DACs have found increasing applications as solvents in the chemical valorisation of renewables-based starting materials. In particular, DMC and PC have promising application as solvents for the chemical valorisation of biomass, e.g. from monosaccharides to 5-HMF, thanks to the combination of their good solvent properties, extensive miscibility with most organic solvents, and inertness towards the desired 5-HMF product as well as towards heterogeneous metal-based catalysts: notably, using a solvent mixture containing a DAC preserved the presence of metal nanoparticles on the catalyst surface inhibiting the metal nucleation deactivation pathway.
Biological application of DACs as solvents
Cabri, Ferrazzano and co-workers formulated different green binary mixtures for solid-phase peptide synthesis as a safe and sustainable alternative to standard hazardous solvents such as DMF. Three different solvent mixtures, e.g. cyrene/DEC 30
:
70, sulfolane/DEC 30
:
70 and anisole/DMC 70
:
30 V/V, showed good swelling properties for PS and PEG resins and dissolved a large group of amino acids, in particular when adding DIC/Oxyma Pure as coupling reagents. In particular, the anisole/DMC 70
:
30 V/V mixture was further employed as solvent for the synthesis of the model peptide Aib-enkephalin (pentapeptide), Aib-ACP (decapeptide) and Octreotide, a pharmaceutically relevant peptide. All syntheses were performed on ChemMatrix-RinkAmide, observing HPLC purities comparable with reported DMF-based procedures.105 An up-to-date review on sustainable reaction media employed for amide bond formation, including DMC, DEC and PC, was recently compiled by Di Gioia and co-workers.106
Although solid-state polypeptides synthesis is a well-established chemical process commonly employed for the development of amino acid-based bioactive molecules, limited examples of environmentally benign processes have been reported so far. DACs represent a class of promising, sustainable, alternative solvents to commonly employed DMF in terms of chemical compatibility, solvation properties and spectroscopic properties; the latter is particularly relevant to combine in- and offline HPLC and HPLC-MS peptide quantitative determination approaches.
Dialkylcarbonates in photochemical processes as reagents and solvents
Zheng, Wang and co-workers reported the first example of light-assisted O-methylation of phenol with DMC over a layered double oxide heterogeneous catalyst. Light irradiation improved dramatically the reaction outcome: at T = 160 °C and t = 6 h, Mg3Al LDO (1.5% w/w, characterized by a Mg/Al ratio = 3
:
1) displayed the best catalytic activity for the O-methylation of phenol (2 equiv.) with DMC (1 equiv.), forming anisole in 82% yield and 96% selectivity. Although the irradiation wavelength(s) were not specified, the improved catalytic performance was ascribed to a synergistic effect of facile reactant coordination/deprotonation on the activated LDO and easy deprotonation of phenol in the light-promoted excited state.107 Yu, Jiang et al. optimized the light-promoted alkylation of 2H-indazoles upon decarboxylative C(sp3)–C(sp2) coupling between 2-aryl-2H-indazoles and alkyl N-hydroxyphthalimide esters using DMC as solvent and 1,2,3,5-tetrakis(carbazol-9-yl)-4,6-dicyanobenzene (4CzIPN) as photocatalyst. Various primary, secondary and tertiary alkylated 2-aryl-2H-indazoles were synthesized in moderate to good yields (31 examples, up to 91% yield). Moreover, the protocol was successfully applied to the late-stage modification of drug molecules, including renewable-based ones, and for the synthesis of unnatural amino acids, as depicted in Scheme 11.108 More recently, the same authors developed a catalyst-free blue light-induced acylation protocol employing 4-acyl-1,4-dihydropyridines (acyl-DHPs) as acylating agents in DMC as solvent at rt. Several different aroylated heterocycles were prepared applying this methodology, in particular derived from active pharmaceutical ingredients and natural products, i.e., thioflavones, benzimidazo[2,1-a]isoquinolin-6(5H)-ones, indolo[2,1-a]isoquinolin-6(5H)ones, quaternary 3,3-dialkyl 2-oxindoles, quinoxalin-2(1H)-ones, and benzo[e][1,2,3]oxathiazine 2,2-dioxides (55 examples, up to 95% yield). Interestingly, thioflavone 3a, obtained upon light-induced acylation of 1-(2-(methylthio)phenyl)-3-phenylprop-2-yn-1-one (1a) and 4-benzoyl-DHPs (2a), could be synthesized on a gram scale and under solar irradiation, as depicted in Scheme 12.109 Barham and co-workers optimized a photocatalytic protocol in CF conditions, suitable for the photocyclopropanation of various heterocycles, including potentially bioderived furans, with diazoesters using DMC as solvent. CF conditions drastically reduced the hazards associated with the use of diazo compounds, as N2 evolution upon reaction was safely contained by back pressure in a microfluidic module and by a small volume of reaction mixture exposed to the reaction conditions at any given time. The protocol was applied to a large scope of heterocyclic cores and diazoesters: employing DMC as solvent allowed for an easy scaling to gram-per-hour productivities, as depicted in Scheme 13.110
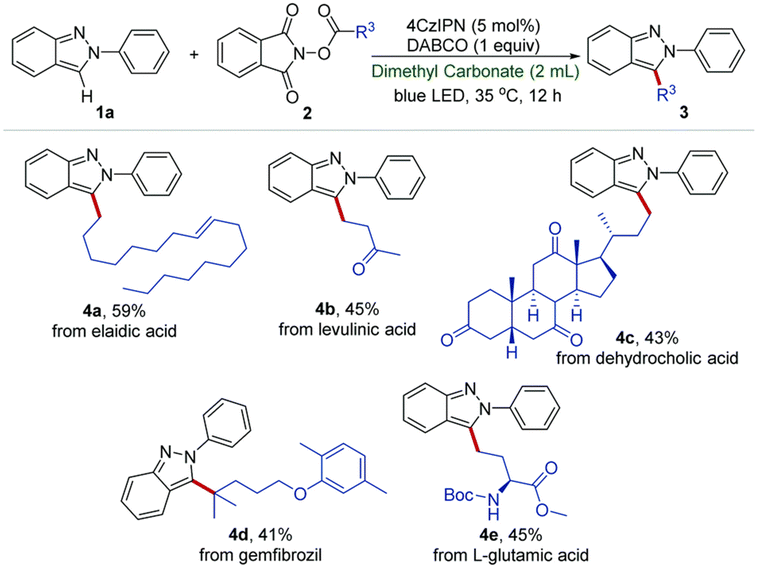 |
| Scheme 11 Late-stage modification of natural resources and drug molecules. Reaction conditions: 1a (0.2 mmol), 2 (2 equiv.), 4CzIPN (5 mol%), DABCO (1 equiv.), DMC (2 mL), T = 35 °C, blue LED, t = 12 h under N2 atmosphere. Reproduced with permission from ref. 108. Copyright 2021 Chinese Chemical Society (CCS), Shanghai Institute of Organic Chemistry (SIOC), and the Royal Society of Chemistry. | |
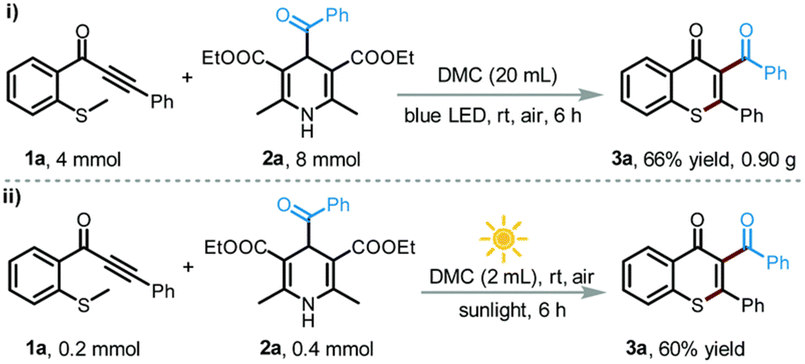 |
| Scheme 12 Visible-light-promoted synthesis of 3a in DMC: (i) gram-scale synthesis and (ii) solar light-induced protocol. Reproduced with permission from ref. 109. Copyright 2022 Royal Society of Chemistry. | |
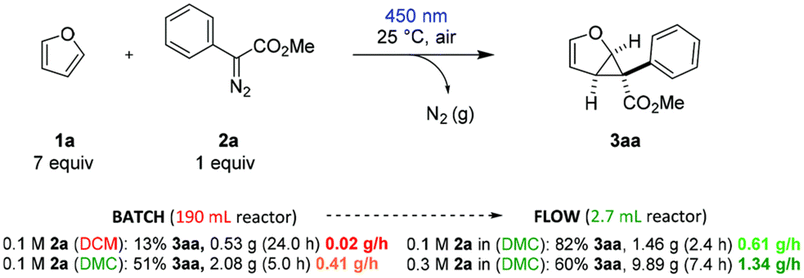 |
| Scheme 13 Comparison of large-scale batch reaction in DCM and DMC, respectively, with the long-term continuous flow reaction under optimal and more productive conditions, respectively. Reproduced with permission from ref. 110. Copyright 2021 Royal Society of Chemistry. | |
As previously detailed in Table 1, DACs are (bio)degradable renewable-based polar aprotic solvents, characterised by UV-Vis transparency, therefore not interfering with photochemical process. DACs are characterized by additional appealing features including large liquid-state windows, high boiling point and moderate viscosity. However, there are still some open challenges associated with the widespread use of DACs in photochemical processes, due to the limited number of commercially available dialkyl and alkylidene carbonates, their production costs, and the lack of solvent recyclability studies. Moreover, DACs are characterized by a limited stability in the presence of acidic catalysts, especially at high T (>150 °C).
Separation and purification applications of DACs
DACs are characterized by an ever-increasing number of separation and purification applications, including their emerging role as eco-friendly solvents for the selective extraction of biological metabolites, the fabrication of membranes with improved separation performances, and multiphasic extractions from aqueous matrixes.
Zhang et al. evaluated DMC as a solvent for the replacement of tert-butanol in the extraction of natural biomolecules. A three-phase system with DMC as an organic phase and sodium citrate as a salt phase was used for the partitioning of exopolysaccharide from the fermentation broth of Phellinus baumii, a functional fungi. The extract was characterized by higher carbohydrate and uronic acid contents compared with conventional solvents comprising tert-butanol/ammonium sulphate. Moreover, it displayed improved free-radical scavenging activity in in vitro antioxidant assays.111 Da Silva and co-workers employed DMC/EtOH solvent mixtures for the pressurized liquid extraction of oil and active compounds from crambe seeds. The optimal extraction mass yield was obtained employing DMC/EtOH 1
:
1 w/w mixtures at T = 150 °C and p = 50 bar with an extraction performance superior to the traditionally employed Soxhlet methodology; moreover, the extract was rich in valuable phytosterols and γ-tocopherol.112 Fu and co-workers reported an ultrasonic microwave-assisted extraction method with DMC as solvent for the extraction of Manchurian walnut kernel oil (MWKO). The extract was rich in unsaturated fatty acids (>90% of the total fatty acid content); in in vitro assays it displayed promising antioxidant properties and reduced liver lipid accumulation compared with conventionally obtained MWKO extracts.113 Ottolina and co-workers performed an ultrasound-assisted extraction of two added-value lignans, justicidin B and 6-methoxypodophyllotoxin, from Linum tissues in the presence of DMC as solvent, observing an improved performance in terms of purity and recovery rates and when compared with conventionally employed maceration.114 Fabbri et al. developed a novel methodology for the quantitative evaluation of volatile fatty acids (VFAs) produced by anaerobic digestion plants for biogas production, based on the direct analysis of DMC extracts of the digestates by GC-MS. This analytical methodology allowed for micro-scale studies of complex aqueous matrices; furthermore, MS detection enabled the identification of cyclic and aromatic VFAs.115 Abdel Azim and co-workers developed a novel poly(hydroxy)butyrates (PHB) extraction methodology, employing eco-friendly DMC and ethanol as eco-friendly alternatives as solvent and polishing agent to commonly employed VOCs, e.g. chloroform and hexane, observing comparable extraction yields.116
DMC and DACs are suitable bio-sourced solvents for membrane manufacture.117 For example, Pescarmona and co-workers evaluated the use of DACs as sustainable solvent alternatives in membrane fabrication, obtained from synthetic and artificial polymers. In all cases, membranes suitable for nanofiltration applications were prepared employing DACs (e.g. DMC, DEC, PC, GC, 1,2-butylene carbonate, 1,2-hexylene carbonate and styrene carbonate)-based solvent mixtures, upon casting from highly concentrated polymer solutions.118 Wang, Zhou and co-workers modified polyamide reverse osmosis membranes with tannic acid employing DMC as solvent. The resulting membranes were characterized by an improved performance ascribed to the combined effects of an increased number of superficial big leaves, obtained by using DMC, and a thinner and more compact active layer, caused by the presence of tannic acid.119 Prabakar et al. optimized an alternative leather tanning process employing PC as the carrier medium, gaining valuable insights into chrome tanning in non-aqueous solvents. For example, SAXS analysis on the collagen structure of chrome-tanned leather using propylene carbonate showed an increased Cr uptake and a more uniform penetration of Cr through the leather cross-section; this latter observation was further confirmed by DSC analysis.120
The increasing number of applications of DACs as solvent for the extraction of biologically active metabolites is ascribed to the combined effects of improved quality of the extracts (as proved by the higher antiproliferative activities), tuneable extraction conditions, effective combination with different pre-treatment technologies like sonication, and the development of one-pot extraction/concentration/quantitative determination protocols. The use of DACs in membrane applications is still in its infancy; however, it is expected to rapidly gain importance and expand the range of applications as the reported preliminary casting studies with DACs allow for tuneable membrane design combined with improved performances.
Dialkylcarbonates in polymer synthesis and biopolymers modification
Applications of dialkylcarbonates in monomer synthesis
D-Sorbitol (SOR) has gained increasing attention as a versatile bio-based platform chemical, characterised by a growing yearly production (8.0 × 105 t y−1) and demand increasing by 2–3% annually. The most relevant application of SOR is the synthesis of isosorbide (ISB), which can be obtained selectively upon double dehydration of SOR.121 One of the most attractive uses of both SOR and ISB is as monomers in polymer synthesis, for the preparation of bio-based polyesters, polycarbonates and non-isocyanate poly(hydroxy urethanes)s, NIPUs.122 DMC is useful for the preparation of sugar-derived cyclic carbonate monomers employed in NIPU synthesis.123 For example, DMC was employed to obtain SOR-based cyclic organic carbonates (COCs) in batch and semi-continuous conditions, as depicted in Scheme 14.124 The reaction occurred under mild operating conditions (T = 75 °C) in the presence of 1,3,5-triazabicyclo[4.4.0]dec-5-ene (TBD) as catalyst. ISB (1,4
:
3,6-dianyhdro-D-glucitol or 1,4
:
3,6-dianyhdro-D-sorbitol) is a rigid bicyclic diol consisting of two nearly planar 3,4-tetrahydrofuran rings forming a “V-shape” and overall angle of 120°. ISB is a commercially relevant bio-based diol, characterised by a production of 104 t y−1 and applications in polymer science, and the pharmaceutical, nutraceutical, food and cosmetics industries. The rigid, tridimensional structure of ISB imparts a different reactivity to the two –OH functional groups: in particular, thanks to an intramolecular hydrogen bond, the endo-hydroxy group is more acidic/nucleophilic compared with the exo-one. This has been exploited for the preparation of pharmaceutically active derivatives, solvents, additives (plasticizers and surfactants) and monomers.121,125 Ochoa-Gómez and co-workers reported a protocol for the selective preparation of isosorbide bis(methyl carbonate) (IBMC) by transesterification of ISB and DMC in a semi-continuous mode, at the reflux T (T = 90 °C) and in the presence of basic catalysts (e.g. K2CO3 and Cs2CO3: 0.02–0.4 mol%). The process required the continuous distillation of the co-product methanol to ensure quantitative IBMC formation. Oligomeric by-product formation was minimized when working at a high DMC/ISB ratio (30
:
1 mol/mol) with 0.2 mol% of Cs2CO3, obtaining IBMC in 97% purity.126 More recently, the same group employed dual basic-nucleophilic catalysts, including guanidine (TBD), amidine (DBN) and three cycloaliphatic secondary amines (N-methylpyrrolidine, quinuclidine and DABCO) as transesterification catalysts in 5% mol catalyst load.
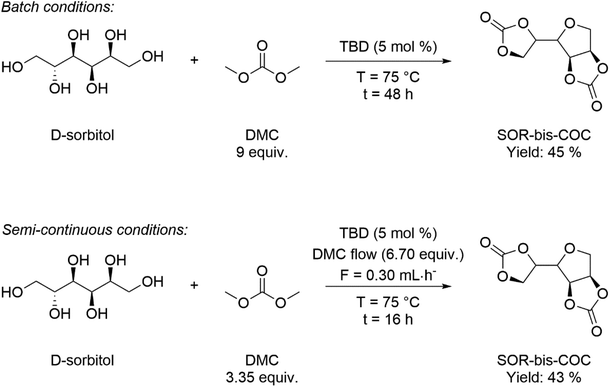 |
| Scheme 14 Optimised synthesis of SOR-bis-CC in batch (top) and semi-continuous experimental conditions (bottom). | |
The best results were observed in the presence of TBD; an ISB conversion of 93.2% was observed in t = 50 min, with formation of IBMC in 87.3% yield.127 Furanic compounds, such as furfural (FUR) and HMF, are promising platform chemicals which can be conveniently achieved from hemicellulose (FUR) and cellulose (HMF) in residual biomass. Some furanic derivatives are readily transformed in COC-functionalised monomers for NIPU synthesis.128 For example, Monbaliu and co-workers performed scalable DMC-based carbonylation reactions under sustainable, continuous flow (CF) conditions starting from DMC and FUR- and/or HMF-derived 1,2-diols without additional additives, as depicted in Scheme 15, bottom. CF carbonylation occurred in the presence of an organocatalyst, tetrabutylammonium bromide (TBAB). Interestingly, this CF carbonylation protocol could be applied to different sugar-derived polyols, including glycerol ether and erithrytol derivatives (20 examples, 45–95% yield). The CF setup could be scaled up employing reactors with internal volumes up to 60 mL. The COC products were quantitatively recovered by extraction with solvents.129 Aricò and co-workers prepared a library of alkyl carbonate derivatives suitable for polycarbonates and NIPU synthesis (Scheme 16). Reactions started from 2,5-bis(hydroxymethyl)furan (BHMF) and excess dialkylcarbonate(s), including DMC, DEC, diallyl carbonate (DAlC), bis(2-methoxyethyl) carbonate (DMOEC), bis(2-(2-methoxyethoxy)ethyl) carbonate (DMEOEC) and dibenzyl carbonate (DBnC) in alkoxycarbonylation conditions (2 equiv. K2CO3, T = 90–140 °C, t = 6–24 h, 15–87% yield).130 Pyo, Cheng and co-workers synthesised quantitatively di(trimethylpropane)cyclic carbonate (DiTMPCC, 98% isolated yield; Fig. 5) from di(trimethylol)propane and excess DMC under thermal conditions (T = 200 °C). The corresponding DiTMPCC-derived polycarbonate was obtained upon chain transfer polymerisation in the presence of organic bases.
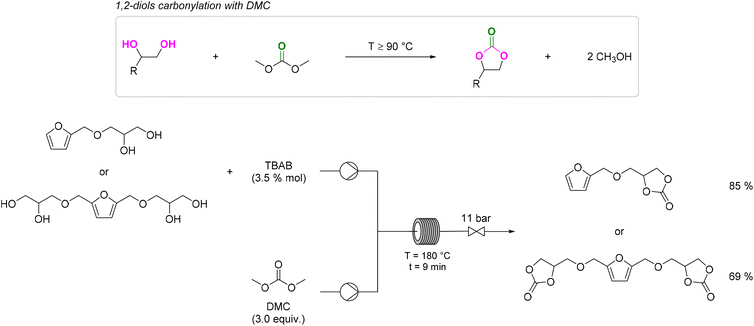 |
| Scheme 15 1,2-diols carbonylation with DMC (top) and CF carbonylation of FUR and HMF derived 1,2-diols with DMC (bottom). 3.5 mol% of TBAB and 3 equiv. of DMC were added per 1,2-diol functional group. TBAB = tetrabutylammonium bromide. Reproduced with permission from ref. 128. Copyright 2021 Elsevier Ltd. | |
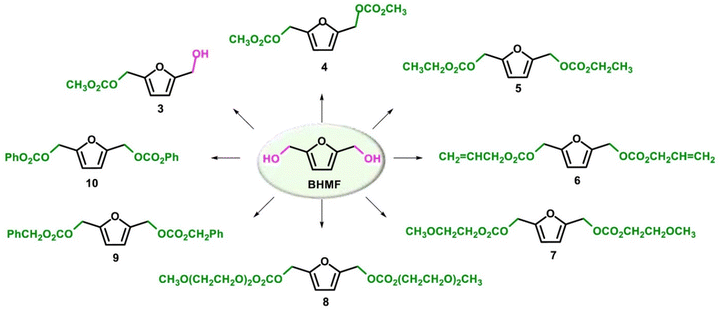 |
| Scheme 16 Reactivity of BHMF with dialkyl carbonates. Reproduced with permission from ref. 130. Copyright 2021 Elsevier Ltd. | |
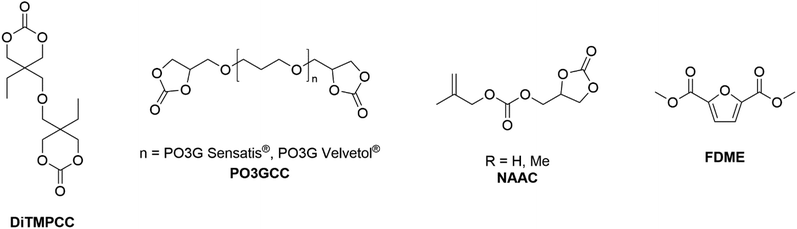 |
| Fig. 5 Organic carbonate-based monomers. | |
For example, a 99% DiTMPCC conversion was achieved in the presence of 0.03% mol DBU and 10 equiv. of 1,3-propanediol at T = 150 °C for t = 30 min. The resulting homopolymers were thermally stable up to T = 200 °C and characterised by high optical transparency and hardness and low swelling property in organic solvents. Interestingly, C3H10T1/2 cells seeded directly on the PC films surface displayed high cell viabilities and cyto-compatibilities.131DiTMPCC was also employed as co-monomer for the synthesis of NIPUs, following a two-step synthesis: an initial thermal ring-opening reaction of DiTMPCC in the presence of bio-based diamine co-monomers (e.g. putrescine, spermidine, spermine and cadaverine) was followed by a UV polymerization of the resulting diallyl diurethane prepolymer with thiol cross-linkers by thiol–ene click chemistry. The mechanical properties of the resulting co-polymers were evaluated by frequency-related dynamic and tension-related elastic-deformation tests, and swelling analysis was performed. NIPUs displayed good cytocompatibilities and adhesion properties towards stained murine myoblast cultures, leading to potential applications as anti-biofouling materials. Interestingly, 3D multi-material biocompatible structures with micro-features were printed via light-based 3D printing.132 Datta and co-workers prepared and characterised a series of five-membered bis(cyclic carbonate)s (PO3GCC, Fig. 5) derived from commercially available bio-based polyether polyols (PO3G) with different molecular weights (250, 650 and 1000 g mol−1):133 the authors described a sustainable two-step synthetic procedure consisting of an initial alkylation with epichlorohydrin followed by TBAB-catalysed CO2 insertion. The resulting bis(cyclic)carbonate monomers were used in the preparation of NIPU thermosets in combination with a bio-based diamine hardener, Priamine 1071, derived from dimerized fatty acids. The thermal, chemical and mechanical properties of the NIPUs were compatible with further vibration damping (sound absorption) applications.134 Meier and co-workers synthesised different renewable-based non-activated allylic carbonate monomers (NAACs, Fig. 5) via a solventless TBD-catalysed one-pot transesterification reaction between glycerol and diallylcarbonate (R = H) or dimethylallylcarbonate (R = Me), respectively.135,136 These monomers were further employed for the preparation of renewable co-polymers. Co-polymers with vinyl acetate were obtained upon Co-mediated radical polymerisation (CMRP) (Mw up to 14.0 × 103 g mol−1, PDI up to 1.17). These materials were purified by supercritical carbon dioxide (scCO2) extractions, which allowed recovery of up to 58% of unused carbonate-based monomer.135 More recently, partially renewable polyethylenes (PE) were prepared by Detrembleur, Meier et al. upon organometallic-mediated radical polymerization with allyl(2-oxo-1,3-dioxolan-4-yl)methyl carbonate (Mw up to 14.6 × 103 g mol−1, PDI up to 1.19). The carbonate co-monomer content of PE was easily tuned by changing the working pressure. Moreover, the cyclic carbonate functional groups were selectively hydrolysed under mild conditions to form PE-bearing vicinal diols, with hydrolysis degree up to 71%.137 Very recently, Aricò and co-workers optimized a DMC-based methodology for the scalable preparation of 2,5-furandicarboxylic acid dimethyl ester (FDME, Fig. 5) starting from galactaric acid, the main product of galactose oxidation. FDME was obtained in up to 70% isolated yield, upon reacting galactaric acid and excess DMC in the presence of Amberlyst-36 (50 wt%) as catalyst for t = 2 h at T = 200 °C.138
DACs have found application as environmentally benign reagents for the selective functionalisation of renewable-based derivatives with –OH functional groups, as in the notable case of SOR/ISB platform chemicals. In particular, when using DMC, DACs’ reactivity was easily tuned to selectively form the corresponding COC or carboxymethylated derivative: while COC derivatives are useful for non-NIPU polyurethane synthesis, carboxymethylated derivatives are mainly employed in PE synthesis by polycondensation. To improve and expand both the array of DACs-derived bio-based monomers and the corresponding polymeric products, two main strategies are foreseen for future development: (a) synthesis of large COCs derivatives, including ≥6-membered rings and (b) expansion of the heterocyclic derivatives pool, targeting thiocarbonates and/or oxazolidinone derivatives. In the former case, COCs’ synthesis via carbonation with DMC represents a reliable, low-cost, environmentally benign and versatile synthetic methodology for the selective preparation of COCs with >5 membered rings, which are not easily accessible via CO2 insertion into oxetane synthetic methodologies. In the latter case, bio-based S- and N-containing platform chemicals and molecules could be easily functionalised exploiting the well-established DACs chemistry, avoiding the preparation of complex and (often) toxic and chemically unstable heterocyclic derivatives.
Applications of dialkylcarbonates in polymer synthesis
Poly(isosorbide)carbonate, PIC, is a fully renewable-based polycarbonate characterised by useful physico-chemical properties to ensure a wide processability window, between the glass transition temperature, Tg = 167 °C, and 5% decomposition temperature (T5% > 250 °C), and optical transparency. The polymer can be synthesised in a single-step procedure from ISB, a glucose-derived monomer, and DMC, as depicted in Scheme 17. Zhang et al. developed a novel methodology for the preparation of high molecular weight poly(isosorbide carbonate), PIC, obtained via melt polymerization of isosorbide (ISB) and dimethyl carbonate (DMC) (entry 1, Table 3). Starting from a DMC/ISB 7
:
1 mol/mol feed and employing sodium tert-butoxide (0.8 mol%) as the basic catalyst, PIC was obtained with a Mw = 55.1 × 103 g mol−1 (PDI = 1.9), which is the highest value reported for one-step polycondensations, at T = 205 °C and in t = 2.5 h with a ISB conversion >99.0%. The high polycondensation temperature was required to ensure an efficient removal of the MeOH by-product released upon condensation and to decrease PIC viscosity. The resulting PIC samples displayed random polymerisation features by 1H NMR characterisation with no regioselectivity in the polycondensation step. End-group analysis was performed by MALDI-TOF on PIC oligomers and showed prevailing formation of monocarboxymethylated end groups.139 Different metal-free, organocatalytic systems were employed for the synthesis of PIC via polycondensation of DMC and ISB. Xu and co-workers reported a metal-free one-pot transesterification/polycondensation PIC synthesis employing TBD as the basic organocatalyst (entry 2, Table 3). A dual activation mechanism was proposed for the TBD-catalysed one-pot process.140 ILs have emerged as active and tuneable catalysts for both the transesterification and polycondensation step. For example, Luo, Xu and co-workers tested a library of amino acid ionic liquids (AAILs) as catalysts, and found that the most active catalyst was tetramethylammonium arginate, [N1111][Arg] (entry 3, Table 3): this IL displayed high catalytic activity and >99% selectivity towards ISB transesterification with DMC and, thanks to its dual activation mechanism, catalysed the preparation of high Mw PIC with improved thermal properties (Td5% > 310 °C, Tdmax > 378 °C, Tg = 143–157 °C), suitable for food packaging applications.141 A synergic effect of both the cationic and anionic moiety of the IL catalyst was also observed by Zhang et al. when employing imidazolium-based ILs such as 1-ethyl-3-methylimidazolium bromide, [C1C2im][Br] or 1-butyl-3-methylimidazolium 4-iodophenolate, [C1C4im][4-I-OPh] as transesterification/polycondensation catalyst for the synthesis of PIC from ISB and DMC (entries 4 and 5, Table 3): both ILs performed a dual activation mechanism involving both the anionic and cationic moieties, obtaining high Mw PIC (up to 52.1 × 103 g mol−1) with promising thermal properties (Td5% up to 345 °C and Tg up to 160 °C).142,143 IL catalysis was further improved by employing bis(tetraethylammonium) hydroquinone, [N2222]2[HQ], the most active IL catalyst for PIC one-step synthesis, observing quantitative PIC formation with a Mw of 53.6 × 103 g mol−1 and a 98% ISB conversion (entry 6, Table 3).144 Recently, Luo, Xu and co-workers evaluated the activity of several different acylamido-based tetrabutylphosphonium ILs, characterised by low anion–cation interaction as ISB/DMC transesterification/polycondensation catalysts: tetrabutylphosphonium phthalimide, [P4444][Pthth] (entry 7, Table 3) was the most active PIL in terms of activity (ISB conversion up to 99.6%) and DMC carboxymethylation selectivity (99.0%).145 Remarkable improvements in terms of PIC Mw and Tg were observed when employing diphenyl carbonate (DPC) instead of DMC in the presence of trace amounts (1.5–4.5 × 10−2 mol%) of an imidazolium-based gemini IL catalyst, bis-(3-methyl-1-imidazolium)ethylene dibromide, [C2(C1im)2][Br]2 (entry 8, Table 3) obtaining PIC samples with Mw as high as 97.8 × 103 g mol−1.146 Deep eutectic solvents (DESs) were also effective catalysts for the synthesis of high Mw PIC from ISB and DPC. pH played a crucial role with this latter class of catalysts: near neutral [C1C2OHim]Cl·2EG (pH = 6.63) was the most active DES catalyst, leading to formation of high Mw PIC (Mw = 102.0 × 103 g mol−1) in t = 25 min (entry 9, Table 3). The polycondensation stage was perturbed by the presence of basic or acidic DESs: the former class of DESs caused extensive depolymerization of the macromolecular chains, limiting the molecular weight of the PIC product, while fast PIC yellowing was observed with both acidic and basic DESs, which was ascribed to ISB hydrolysis.147 Xu and co-workers developed a DMC-based polycondensation strategy for the preparation of flexible isosorbide-based co(polycarbonates), BDM-PIC, with tuneable thermal property, upon one-pot direct melt polycondensation of ISB, DMC and various diol co-monomers (Scheme 18). In an initial study, TBD was employed as the active organocatalyst, observing for the first time a dual activation of the secondary hydroxyl group of ISB as well as of the primary hydroxyl group present on the diol co-monomers (Scheme 18, top). The best result was obtained with 1,4-benzenedimethanol (BDM) as co-monomer and a ISB/diol ratio of 80
:
20 mol/mol: under optimized conditions (TBD 0.1% wt., DMC/ISB/diol 5
:
0.8
:
0.2 mol/mol; transesterification: p = 0.1 MPa, T = 120–180 °C, t = 8 h; polycondensation: p = 0.1–5 × 10−6 MPa, T = 180–240 °C, t = 4 h) the resulting PBMIC co-polymer displayed a Mw of 47.2 × 103 g mol−1 and a PDI of 1.73.140 Sodium tert-butoxide was the most efficient catalyst when used in combination with DPC and different commercial diols (Scheme 18, centre). For example, PBMIC was obtained with Mw up to 80.3 × 103 g mol−1 and PDI = 1.72 (other conditions for transesterification: NaOtBu 0.8% mol, DMC/ISB 7
:
1 mol/mol, p = 0.1 MPa, T = 160–180 °C, t = 3 h; and for polycondensation: NaOtBu 0.8% mol, ISB/BDM 4
:
6 mol/mol p = 5 × 10−6 MPa, T = 220 °C, t = 0.5 h). The Tg values of BDM-PIC varied between 69 and 164 °C just by increasing the BDM content of the copolymer. Moreover, the presence of BDM improved the overall polymer flexibility.148 Xu, Zhang and co-workers prepared a series of isosorbide-based co(polycarbonates) including bis-phenol A-derived monomers (Scheme 18, bottom). Copolymerisation occurred via melt polycondensation in the presence of an IL catalyst, 1,4-(1,4-diazabicyclo[2.2.2]octane)butyl dibromide, [(C4)2DABCO][Br]2 (transesterification: [(C4)2DABCO][Br]2 0.005% mol, DPC/ISB 7
:
1 mol/mol, p = 0.1 MPa, T = 160–180 °C, t = 2.25 h; polycondensation: [(C4)2DABCO][Br]2 0.005% mol, ISB/bis(phenol) comonomer 7
:
3 mol/mol, p < 1.3 × 10−4 MPa, T = 280 °C, t = 0.5 h). The co-polymers so achieved were suitable for the preparation of bio-based optical lenses: compared with PIC, they displayed higher refractive indices (1.511–1.573) and improved physico-chemical properties including thermal stability, flexibility, hydrophobicity, processing-friendly Tgs and pencil hardness.149 Allais, Fadlallah et al. reported on the copolymerisation between ISB, DMC and bis-γ-lactone, a monomer derived from levoglusenone, observing almost exclusive fast homopolymerisation of the bis-γ-lactone co-monomer.150
 |
| Scheme 17 PIC synthesis via polycondensation of ISB and DMC. | |
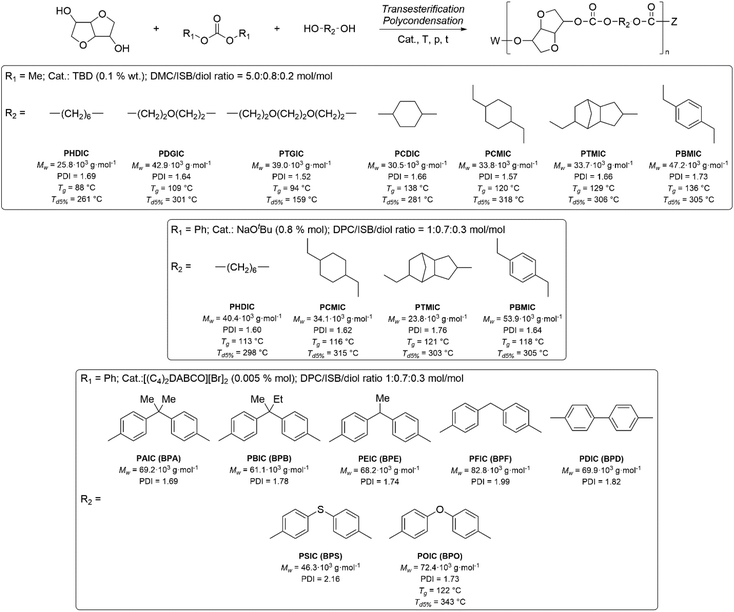 |
| Scheme 18 Diol co-monomers employed for the preparation of isosorbide-based co(polycarbonates). | |
Table 3 PIC synthesis via polycondensation between dialkylcarbonates and ISB
DACs/diols polycondensation represents a promising strategy for the preparation of commercially relevant renewable-based polyesters. It is likely that this technology will reach high TRLs in the next 10–15 years; therefore, the commercial relevance of this process must be combined with a detailed assessment of its economic and environmental viability, as well as with an evaluation of the toxicity, ecocompatibility and end-of-life fate of the resulting polyesters.
Biopolymer modification with DACs and COCs
Lignin is a promising and abundant bio-based feedstock for the preparation of platform chemicals and monomers for polymer synthesis which has not been yet fully exploited, in particular towards wood-derived NIPUs.151,152 Only recently, Lehnen and co-workers developed a novel two-step synthetic approach for the preparation of COC-functionalised lignin, comprising an initial oxyalkylation step, requiring GC as the bio-based alkylating agent. The etherification occurred in the presence of a basic catalyst, 1,8-diazabicyclo[5.4.0]undec-7-ene (DBU). The resulting functionalised lignin was then quantitatively carbonated upon transesterification with DMC (conversion up to 96%) in mild conditions (T = 75 °C, t = 6 h) with K2CO3 (20–40% mol) as catalyst (entry 1, Table 4).153 This environmentally benign synthetic protocol was also extended to the oxyalkylation of non-depolymerised and non-fractioned industrial Kraft lignin: the corresponding COC-functionalised lignin was obtained in a quantitative yield (up to 98%) following a similar two-step synthetic protocol comprising a 1,5,7-triazabicyclo 4.4.0 dec-5-ene (TBD)-catalysed oxyalkylation reaction, followed by a K2CO3-catalysed transesterification step in the presence of DMC. COC-functionalised Kraft lignin was employed as co-monomer, in combination with Priamine 1074, for the preparation of 100% bio-based shape memory NIPU foams (entry 2, Table 4).154 Partially bio-based NIPUs were also prepared combining 1,6-hexamethylenediamine and COC-functionalised beech lignosulfonate (entry 3, Table 4).155 The first example of uniform lignin hydroxyethylation was reported by Renneckar et al., employing EC as both solvent and reagent for the functionalization of lignin aromatic hydroxyl groups and carboxylic acids. In the optimized reaction conditions for softwood Kraft lignin (20 equiv. of EC, T = 120 °C, t = 20 h), 95% conversion of phenolics into primary hydroxyalkyl ethers (90% for hardwood Kraft lignin) was observed with a total hydroxyl content of 5.02 mmol g−1 (4.56 mmol g−1 for hardwood Kraft lignin). The lignin hydroxyethyl ethers were further functionalized via sustainable, solventless esterification reactions. Interestingly, the hydroxyethyl lignin derivatives showed an increased thermally stability compared with the unmodified analogues, as well as a slight decrease in Tg relative to pristine lignin.156 Xiong et al. synthesised a lignin-based heterogeneous deep eutectic solvent (DES) catalyst, lignin-ChCl-PABA, composed of lignin, choline chloride (ChCl) as salt and p-aminobenzoic acid (PABA) as H-bond donor, as depicted in Scheme 19. This catalyst was active for the preparation of COC via CO2 insertion in terminal epoxides (cat. 100 mg, TBAB = 10% mol, T = 110 °C, p(CO2) = 1.0 MPa, t = 3 h, 10 examples, 91–99% yield), and it was recycled and reused up to 5 times with minimal loss of activity.157 Similarly, Crespy and co-workers developed novel heterogeneous catalysts containing H-bond donors as microparticles obtained from bio-derived melanin combined with Kraft lignin nanoparticles.
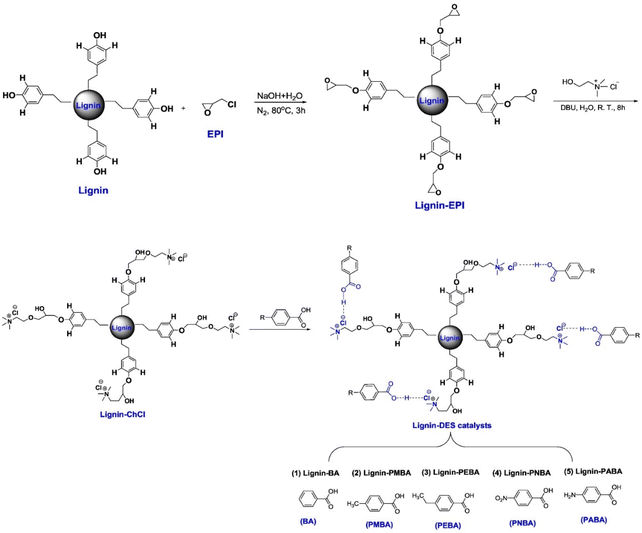 |
| Scheme 19 Synthetic route of DESs-modified lignin heterogeneous catalysts through hydrogen bonds interaction. Reproduced with permission from ref. 157. Copyright 2020 Elsevier Ltd. | |
Table 4 Lignin-derived COCs
Entry |
Lignin structure |
Glycidation conditions |
Transesterification conditions |
Product structure and yield |
Ref. |
Determined by gravimetry measurements.
Determined by quantitative 31P NMR.
|
1 |
|
GC (10 equiv.) |
DMC (5 equiv.) |
|
153
|
DBU (1 equiv.) |
K2CO3 (0.4 equiv.) |
T = 170 °C |
DMSO |
t = 3 h |
T = 150 °C |
N2 |
t = 6 h |
Conversion = n.d. |
Conversion = 96%a |
2 |
|
GC (10 equiv.) |
DMC (5 equiv.) |
|
154
|
TBD (0.05 equiv.) |
K2CO3 (0.4 equiv.) |
T = 150 °C |
DMSO |
t = 1.5 h |
T = 75 °C |
N2 |
t = 4 h |
Conversion = n.d. |
Conversion = n.d. |
3 |
|
GC (15 equiv.) |
DMC (260 mmol) |
|
155
|
TBD (0.13 equiv.) |
DBU (0.01 equiv.) |
T = 170 °C |
T = 75 °C |
t = 18 h |
t = 12 h |
N2 |
Conversion = n.d. |
Conversion = n.d. |
|
The resulting materials displayed catalytic activity in combination with TBAI for CO2 insertion in terminal epoxides under mild conditions (cat. 100 mg, TBAI = 10% mol, T = 60 °C, p(CO2) = 0.1 MPa, t = 24 h, 6 examples, 97–99% yield).158 Socha and co-workers prepared a series of novel benzyl alkylammonium ILs combining starting materials derived from grass, softwood, and hardwood lignin with methyl carbonate ion exchange chemistry, following a three-step synthetic procedure, depicted in Scheme 20. Such ILs, obtained in >90% yield, were able to dissolve microcrystalline cellulose up to 10 wt% and converted up to 71% of the glucans and xylans contained in raw switchgrass to fermentable sugars (e.g. glucose and xylose).159 Heiskanen and Sirviö developed a methodology for the functionalization of polysaccharides with DMC in the presence of DBU as the basic catalyst. Starch carbamation occurred upon DBU (20% mol)-catalysed reaction with DMC and n-octylamine (OA) via an in situ formation of the carbamation intermediate methyl octyl carbamate: at T = 70 °C and t = 24 h, starch was functionalised with a degree of substitution (DS) of 15. The same reaction in the absence of OA yielded both cyclic and linear carbonate ester-functionalised derivatives.160 Selva, Perosa and co-workers employed DMC for the functionalization of chitosan, optimizing the single-step synthesis of N,N,N-trimethylchitosan (TMC) upon methylation of chitosan with DMC in [C4C1im][Cl]. Under the optimized conditions (T = 90 °C, t = 12 h), TMC was obtained in 9% yield and characterized by 1H NMR.161
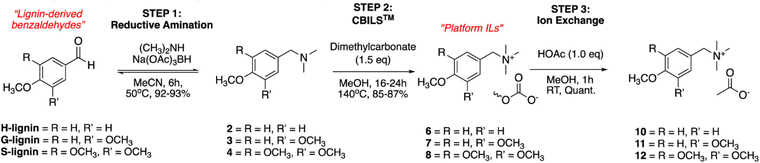 |
| Scheme 20 Three-step synthesis of lignin derived ILs from methylated lignin-derived benzaldehydes. Reproduced with permission from V. Diez, A. DeWeese, R. S. Kalb, D. N. Blauch and A. M. Socha, Ind. Eng. Chem. Res., 2019, 58, 16009–16017 (ref. 159). Copyright 2020 American Chemical Society. | |
The tuneable reactivity of DACs can be exploited for the chemical modification of biopolymers, developing novel, fully renewable-based functional molecules and materials. Alkylation and/or carboxyalkylation typically improve the overall biopolymer solubility in organic solvents: in the future, this should be combined with novel insights into the reactivity of asymmetric DACs and COCs in organic synthesis.
Biopolymer depolymerisation
Bolm and co-workers employed DMC as solvent for the base-promoted depolymerisation of lignin, employing alkali earth metal catalysts to produce methylated phenol derivatives as the final products. Lignin depolymerisation was performed on different lignin samples (including 1 Kraft and 3 organosolv lignin samples) in the presence of catalytic quantities (5 mol%) of LiOtBu or Cs2CO3 as base catalysts, at T = 180 °C for t = 8–12 h. In all cases, high yields (52–67% w/w) of low-molecular weight oils were obtained. Oils were quantified and characterised by HSQC 2D NMR, 31P NMR, GPC and GC-MS measurements. The oil fractions obtained from the Cs2CO3-catalysed depolymerisation contained a range of methoxy-capped aromatic monomers, as depicted in Fig. 6. The scope of the reaction system was further expanded to commercially available lignocellulosic biomass such as milled beechwood chips and to cheaper and widely employed base catalysts, such as KOH.162 Barta and co-workers reported a lignin fractionation protocol relying on a mild lignin-first acidolysis process (T = 140 °C, t = 40 min) using DMC as solvent and EG as co-solvent and stabilization agent, to produce aromatic monophenols from softwood lignocellulose (pine, spruce, cedar, and Douglas fir) with depolymerisation efficiencies ranging from 77 to 98%. Under the optimized conditions pinewood delignification occurred in 77% yield (1.5 g of softwood lignocellulose, 30 mL of DMC, T = 140 °C, t = 40 min, 400 wt% EG and 2 wt% H2SO4 based on pinewood), producing up to 9 wt% of the aromatic monophenol products, while the cellulosic fraction remained unaffected.163 Tsang and co-workers optimized a protocol for depolymerisation of cellulosic paper towel waste employing aqueous solution of DACs (e.g. PC/H2O, EC/H2O, DMC/H2O 1
:
1 V/V). Using PC/H2O and EC/H2O 1
:
1 V/V mixtures, depolymerisation of paper towel waste occurred under mild conditions (T = 130 °C, t = 20 min) with an improved total sugar yield (up to ∼25 mol% of glucose) compared with H2O only (up to ∼11 mol% of glucose). The improved activity and selectivity were attributed to higher availability of reactive protons in the catalytic system, facilitating efficient acid hydrolysis of recalcitrant cellulosic fibres combined with their stability in tandem hydrolysis/dehydration process.164
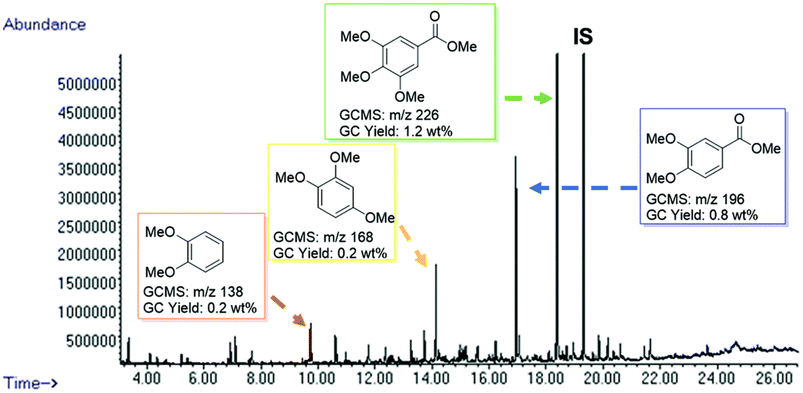 |
| Fig. 6 GC-FID trace of the product mixture obtained from the depolymerisation of milled beechwood chips (100 mg) using Cs2CO3 (10% w/w) in DMC (V = 5 mL) at T = 180 °C for t = 8 h. Identification of the major peaks is based on the GC-MS data. Quantification is based on the standardization of individual products, using n-octadecane as an internal standard. Reproduced with permission from ref. 162. Copyright 2018 Royal Society of Chemistry. | |
Miscellaneous
Salerno et al. employed DMC as solvent for the preparation of polycaprolactone (PCL) mould to optimize the tunable three-dimensional architecture of scCO2 PCL scaffolds for tissue engineering applications.165
Isopropenyl acetate for the conversion of renewables
Synthesis of isopropenyl acetate (iPAc)
Isopropenyl acetate (iPAc) belongs to the general family of enol esters and is characterized by the presence of a methyl-substituted vinyl group directly bound to an acetate functionality. The non-toxicity, the commercial availability and cheapness of iPAc are contributing to its increasing popularity in the design of protocols of irreversible transesterification and carbamation of alcohols, phenols, and amines. Indeed, iPAc is currently produced on an industrial scale via the thermal cracking of acetic acid (Scheme 21).
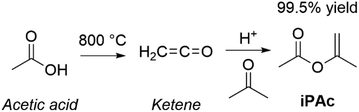 |
| Scheme 21 Industrial synthesis of iPAc. | |
The process generates ketene that, in turn, reacts with acetone in the presence of acid catalysts.166,167 Manufacturers of iPAc are some of the top players among world chemical companies, including Eastman, Dow, Wacker Chemie, and Hebei Ascend Chemical Co, and the overall synthesis is likely to attract more and more attention in the future through sustainable approaches based on acetic acid obtained by the catalytic reforming of biomass waste streams and acetone prepared by the ABE fermentation of sugars.168 However, the high toxicity and poisoning effects of ketene pose restrictions and safety precautions.169,170
Acylation of biopolymers
Conventional esterification and transesterification processes are among the major transformations in organic synthesis and are extensively used also for large-scale sequences of biomass valorization. To mention just one example, the catalytic conversion of natural triglycerides into biodiesel belongs to this family. These reactions, however, are reversible, which means that over-stoichiometric quantities of reactants (alcohol or ester) and active catalytic systems are required to ensure quantitative product formation. iPAc offers a privileged transesterification pathway because of the formation of an enol, prop-1-en-2-ol, as a reaction co-product that quickly converts into the corresponding ketone (acetone). This feature makes the overall transformation irreversible.171Scheme 22 depicts an iPAc-mediated acetylation of an alcohol. Acetone continuously released during the reaction can be either used as a solvent/co-solvent or it is easily distilled off and recycled during work-up. iPAc-based transesterifications have been successfully applied to a variety of substituted alcohols and polyfunctional substrates such as polyols and amino alcohols.172 Particularly, in the chemical upgrading of renewable feedstocks, iPAc has been described as a versatile acylating reagent of biopolymers such as cellulose and lignin, and sugars. Table 5 summarizes the conditions and the results reported in some representative works published in the last five years. A remarkable contribution in this sector has been given by the investigations of Takahashi, Wada, and Kakuchi, who were among the first introducing the combined use of ILs, in particular 1-ethyl-3-methylimidazolium acetate, [C2C1im][OAc], as both organocatalyst and co-solvent in the presence of iPAc as the acylating agent (entries 1–6, Table 5).173–178 Due to the high viscosity and cost associated with the use of [C2C1im][OAc], the latter was recovered according to the strategy shown in Fig. 7 for the preparation of cellulose acetate.174
 |
| Scheme 22 A model transesterification reaction of iPAc with an alcohol. The process is made irreversible due to the tautomerization of the enol leaving group. | |
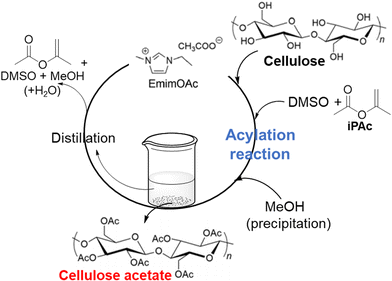 |
| Fig. 7 Recycle of the [C2C1im][AcO]/DMSO mixed solvent system used for the organocatalytic transesterification cellulose with iPAc. | |
Table 5 Recent examples of biomass acylation with iPAc
Entry |
Starting biomass |
Solvent, co-solvent |
Catalyst |
Product |
Ref. |
[C2C1im][OAc]: 1-ethyl-3-methylimidazolium acetate.
[DBNH][OAc]: 1,5-diazabicyclo[4.3.0]non-5-enium acetate.
|
1 |
Cellulose |
[C2C1im][OAc] |
[C2C1im][OAc]a |
Acylated cellulose |
173
|
2 |
Pulps |
DMSO |
[C2C1im][OAc] |
Acylated polysaccharides |
174
|
Rayon |
[C2C1im][OAc] |
Xylan |
|
Pullulan |
|
Dextrin |
|
3 |
Pretreated sugar cane bagasse |
DMSO |
[C2C1im][OAc] |
Cellulose triacetate |
175
|
[C2C1im][OAc] |
4 |
Sugarcane bagasse |
DMSO |
[C2C1im][OAc] |
Thermoplastics |
176
|
[C2C1im][OAc] |
5 |
Kraft lignin |
DMSO |
[C2C1im][OAc] |
Acylated lignin at aliphatic OH groups |
177
|
[C2C1im][OAc] |
6 |
Kraft lignin |
DMSO |
[C2C1im][OAc] |
Electrospun carbon fibers |
178
|
[C2C1im][OAc] |
7 |
Wood chips |
[DBNH][OAc]b |
[DBNH][OAc] |
Acetylated autohydrolysed wood |
179
|
8 |
Vacuum dried pulp |
[DBNH][OAc]b |
[DBNH][OAc] |
Cellulose triacetate (ioncell-F fibers) |
180
|
9 |
Microcrystalline cellulose, cotton linters, rice straw |
AcOH |
MeSO3H |
Cellulose triacetate |
181
|
iPAc |
10 |
Glucose, maltose, and maltotriose |
NH4AcO |
Acyltransferases |
Acylated sugars |
182
|
The transesterification of cellulose was conducted at T = 80 °C for t = 30 min in a [C2C1im][OAc]/DMSO mixed solvent system providing cellulose acetate which was isolated by precipitation from methanol. Thereafter, distillation of the methanol layer allowed separation of [C2C1im][OAc] with a 99.2 wt% recovery ratio. The protocol proved scalable up to 2.5 g of different polysaccharide sources including Avicel® (microcrystalline) cellulose, various pulps, xylan, dextrin, and pullulan. The efficiency of iPAc as an acylating agent was very high in all cases, with a degree of substitution (DS) of ca. 2.9 for the achieved cellulose acetates (entries 1 and 2, Table 5).173,174 The same procedure ([C2C1im][OAc]/DMSO/iPAc: EDI) was successful for the synthesis of cellulose triacetate and thermoplastics starting from a lignocellulosic feedstock.
For example, bagasse with a mild-acid pretreatment and untreated bagasse, were compared as iPAc mediated acylation substrates (cfr. entries 3 and 4, Table 5, respectively).175,176 The precipitation step from methanol allowed fractionation of an (insoluble) polysaccharide acetate and (soluble) lignin acetate; both were high-value-added materials for bio-based polymers (Fig. 8).175 Interestingly, lignocellulosic thermoplastics composed of cellulose, hemicellulose, and lignin-mixed ester derivatives were achieved by fine tuning of the acylation conditions. Combining 25 mol% He (hexanoyl) and 74 mol% Ac groups in the esterified bagasse (Bag-AcHe) provided a material with excellent melt flowability (Tflow = 182 °C) and good mechanical properties (tensile strength: 35 ± 4 MPa and Young's modulus: 1.6 ± 0.1 GPa) (entry 4, Table 5). The EDI protocol was claimed as a facile, sustainable method for the selective modification of aliphatic hydroxy (R–OH) groups in Kraft lignin (entry 5, Table 5).177 Based on the different basicity and nucleophilicity of aromatic OH functions compared with their aliphatic counterparts, the authors were able to design a one-pot two-step reaction: (i) by using a calibrated amount of iPAc (ca. 3 equiv. with respect to [ROH]), a fast Ar–OH acetylation and a relatively slow R–OH acetylation were first performed at T = 80 °C for t = 1 h; (ii) thereafter, at the same temperature, a selective deacetylation of the (less stable) Ar–OAc groups occurred by adding water (2 equiv. with respect to [Ar–OH]) as a proton donor. The overall transformation resulted in the selective R–OH functionalization (>99%) while almost all Ar–OH groups were preserved (93%). The final material was isolated in an 85% yield. In a similar approach, electrospun carbon fibers were fabricated starting from a 1
:
1 mixture of polyacrylonitrile (PAN) and iPAc-acetylated lignin (entry 6, Table 5).178 The degree of substitution (DS) of lignin was finely tuned to make the material less hydrophilic and improve “phase compatibilization” with PAN, but at the same time to preserve enough structural hydroxyl groups (s-OH) essential for free radical reactions during the steps of themostabilization and carbonization in the preparation of fibers. A variety of samples were prepared by modifying the s-OH amount (total including carboxylic, phenolic, and aliphatic OH functions) from less than 1 up 7 mmol g−1. Interestingly, an interfiber fusion was noticed after a certain DS was reached (Fig. 9, B and C, middle and right).178 Overall, carbon fibres showed better mechanical performance when partially acetylated Kraft lignin was used, with an almost 3-fold improvement in tensile strength (about 2-fold increase in elastic modulus) compared with the unmodified lignin-based fibrous materials. Other than [C2C1im][OAc], 1,5-diazabicyclo[4.3.0]non-5-enium acetate ([DBNH][OAc]) obtained by the direct reaction of DBN (1,5-diazabicyclo[4.3.0]non-5-ene) with AcOH proved a successful ionic liquid for the dissolution of wood samples. An initial study reported an autohydrolytic processing of birch and spruce wood chips in hot water (T = 180–220 °C, t = 20–50 min) followed by their subsequent acetylation mediated by iPAc in [DBNH][OAc] as a solvent (T = 80–130 °C) (entry 7, Table 5).179 It was demonstrated that the resulting materials were dramatically more soluble in chloroform compared with the untreated specimens. This could pave the way to chemical modification strategies of wood chips as a low-cost feedstock. In another investigation (entry 8, Table 5), cellulose was dissolved in [DBNH][OAc] and in situ esterified with iPAc (0.05–0.75 equiv. per anhydroglucose unit of cellulose, T = 70 °C, t = 1 h) to provide a low DS of 0.05–0.75.180 This reaction environment proved excellent for dry-jet wet-fibre spinning, by which modified cellulose filaments (Ioncell-F Fibers) were fabricated.183 These were characterized by a high tensile strength value (525–750 MPa conditioned and 315–615 MPa wet) and elastic moduli between 10–26 GPa and were claimed as innovative materials for producing high-value products such as textiles, biocomposites, filters, and membranes. An interesting standpoint on the sustainability of protocols based on IL for chemical modification of cellulose under homogeneous conditions was offered by Meier and co-workers, who proposed an analysis of the subject based on the evaluation of E-factors together with basic toxicity information.184 Considering the specific case of the acetylation of cellulose in [DBNH][AcO] solvent, the authors compared the reaction carried out with four different acetylating agents, vinyl acetate, vinyl propionate, acetic anhydride, and iPAc, and estimated the corresponding E-factors of 3.7, 3.7, 3.6, and 2.9, respectively, with the IL recovery.185 It was concluded that the reduction of the carbon footprint in the synthesis of new bio-based polymers could not be based only on the renewability of starting feedstock, but also on the design of efficient procedures for its chemical functionalization. An ILs-free approach for the conversion of either microcrystalline cellulose (MCC) and non-forage crop residues such as cotton linters, and rice straw, into cellulose triacetate (CTA) was instead described by using iPAc as the acetyl donor in the presence of methanesulfonic acid as a cheap and green acid catalyst, and AcOH as a co-solvent (entry 9, Table 5).181 For example, at T = 40 °C, CTA was achieved in >70% yield from rice straw, meaning that ca. 90% of the cellulose content of the starting material was acetylated. iPAc was described also for the bio-catalyzed acylation of sugars (glucose, maltose, and maltotriose) to sugar esters (entry 10, Table 5).182 Compared with other methods for sugar acylation involving lipases or proteases in organic solvents or ionic liquids, which are often toxic and expensive media, the iPAc-mediated protocol was successful in a monophasic aqueous environment thanks to the introduction of a novel class of enzyme catalysts based on promiscuous acyltransferase MsAcT from Mycobacterium smegmatis. It was demonstrated that a selective 6-O-acetylation of sugars took place with the formation of glucose acetate, maltose acetate, and maltotriose acetate in 34.1 ± 5.9%, 77.5 ± 9.4%, and 53.7 ± 1.0% amounts, respectively, after a very short times ranging from 15 min to 2 h.
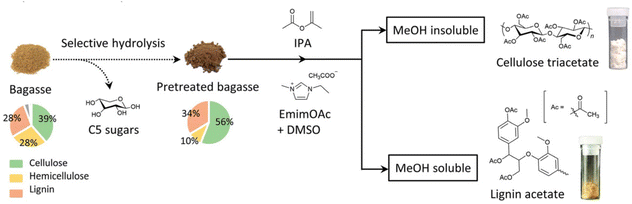 |
| Fig. 8 The organocatalytic transesterification of bagasse and the subsequent fractionation into cellulose triacetate and lignin acetate. Reprinted from “A mechanistic insight into the organocatalytic properties of imidazolium-based ionic liquids and a positive co-solvent effect on cellulose modification reactions in an ionic liquid” S. Suzuki, Y. Shibata, D. Hirose, T. Endo, K. Ninomiya, R. Kakuchi and K. Takahashi, RSC Adv., 2017, 8, 21768–21776 (ref. 175), https://pubs.rsc.org/en/content/articlelanding/2018/ra/c8ra03859g. | |
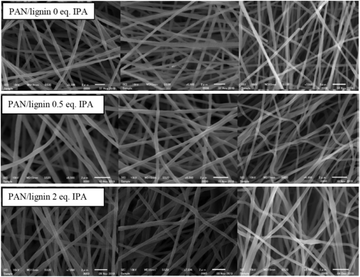 |
| Fig. 9 SEM images of electrospun fibers (left), after thermostabilization (middle; T = 250 °C for t = 1 h at 0.5 °C min−1), and carbonization (right; T = 1000 °C at 5 °C min−1) steps using acetylated lignin with different amounts of iPAc and s-OH. Adapted with permission from ref. 178. Copyright 2021 Elsevier Ltd. | |
A two-step procedure was developed to produce thermosets comprising Kraft lignin (KL) and the cross-linker adipic acid (AdA) by activating the reaction with iPAc. At reflux temperature, the H2SO4-catalysed reaction of AdA with excess iPAc yielded a cross-linking mixture (CLM) by which lignin was partially esterified to achieve thermoset materials suitable for coatings, with tensile strength in the range of 15–0.33 MPa.186 Mechanistic studies, carried out by solid-state 13C MAS NMR and FT-IR, confirmed that both the aliphatic and aromatic hydroxyl groups of lignin were reactive towards the desired transesterification process.
Upgrading of bio-based molecules via iPAc-mediated tandem reactions
The release of acetone as a by-product in iPAc-mediated reactions is a key aspect to make transesterification/amidation processes irreversible and therefore to increase their synthetic potential (Scheme 22). Acetone can be distilled off after the reaction and recycled, or it can be used in situ as a reagent to promote subsequent reactions in a tandem sequence. The latter (tandem) approach is not new: the first examples of coupled acetylation and acetalization of diols, sugars and sugar glycosides with enol acetates date back to the early 2000s.187,188 Only very recently, however, has this topic been revisited by some of us to design novel eco-friendly procedures for the upgrading of bio-based molecules. An acid-catalysed tandem sequence of esterification-acetalization of renewable 1,2-diols, such as propylene glycol (PG) and ethylene glycol (EG), with iPEs was developed (Scheme 23, top).172 An overall 100% carbon efficient (CE) protocol was achieved, affording water as the sole byproduct and a ≥99% tandem yield of acetals and esters. The tandem sequence was successfully transferred to CF mode, where the catalyst (Amberlyst-15) could be used virtually indefinitely without loss of performance, and the solvent (acetic acid) was quantitatively recovered and reused. Similarly, a pool of innocuous reactants (iPAc, AcOH and acetone) allowed the conversion of glycerol through selective acetylation and acetalization processes.189 Tuning of conditions, mostly by changing the reactant molar ratio and optimizing the reaction time, was successful to steer the observed reactions towards the synthesis of either a 1
:
1 mixture of acetal acetates (97% of which was solketal acetate) and triacetin, or acetal acetates. At 30 °C, the conversion of glycerol was quantitative, and yields were up to 91% (Scheme 23, centre). By combining batch and CF protocols, the tandem approach was also exploited to convert two aminodiol regioisomers derived from glycerol, i.e., 3-amino-1,2-propanediol (3-APD) and 2-amino-1,3-propanediol (2-APD), into the corresponding acetalized amides (49–99% yield; Scheme 23, bottom).190 A tandem sequence comprising acetylation and aldol condensation was also successfully implemented for the upgrading of another relevant bio-based chemical, HMF: the OH group of HMF was first subjected to an iPAc-mediated acetylation affording an ester derivative that was used in situ for an aldol condensation with acetone released from the former acetylation reaction. The final tandem product was achieved in an overall 88% isolated yield.191
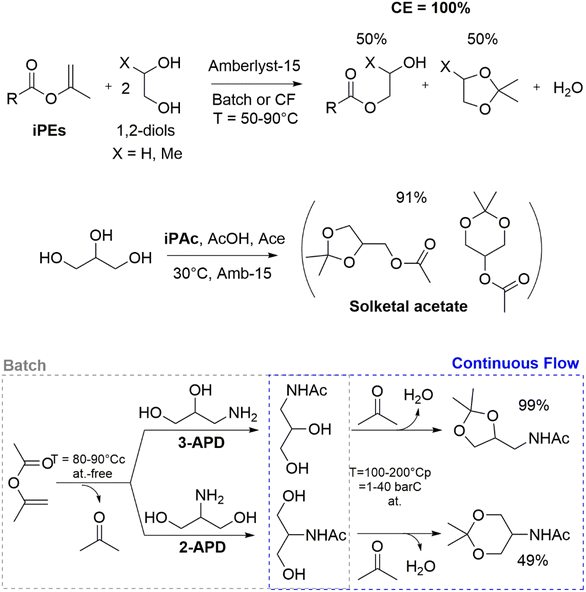 |
| Scheme 23 Top: 100% CE tandem acetylation-acetalization of 1,2-diols. Centre: tandem synthesis of solketal acetate with iPAc. Bottom: concatenated tandem procedures of amidation-acetalization. | |
iPAc reactivity represents a low-cost, eco-compatible strategy for the preparation of diol-based monomers and co-monomers for renewable-based co-polymers and composites. Interestingly, iPAc-based protocols have been applied to structurally and chemically different biopolymers, in particular lignins. iPAc-based acetylations are suitable for mono- and polysaccharide functionalisation, as the Brønsted acid additive is only required in catalytic quantities. Moreover, iPAc can be employed in combination with neoteric solvents, such as ILs and DESs, which are known to solubilise biomass effectively. iPAc-mediated amidations represent another promising approach for biomass valorisation, as they do not require pre-activation of the acyl moieties, overcoming a widely used, non-sustainable approach in organic synthesis. Moreover, a significant contribution to expanding the chemical valorisation opportunities for nitrogen-rich biomass, such as microalgae, is expected and for the preparation of N-containing platform chemicals from biomass, effectively combining tandem protocols with reductive amination reactivity.
Conclusions
A substantial part of this critical review (first four sections) deals with the synthesis, properties and reactivity of light homologues of dialkyl and alkylidene carbonates, particularly dimethyl-, diethyl-, ethylene-, and propylene carbonates (DACs). Modern methods for the preparation of DACs are based on the catalytic activation of CO2 as a renewable C1 building block, for the reaction of insertion into epoxides and the alcoholysis of urea from renewable ammonia. These pathways are not only intrinsically green, but they impart characteristics of low/non-toxicity to DACs that make them outstanding candidates for the design of strategies aimed at the valorisation of biomass derivatives, both biopolymers and bio-based molecules. Accordingly, DACs find an increasing number of applications as dual electrophilic reagents for the alkylation and the carboxyalkylation of families of nucleophiles derived from biomass. A well-known example is the catalytic transcarbonation between DACs and glycerol, one of the most promising platform chemicals, to produce glycerol carbonate, which is a key product of the sustainability portfolio of major multinational manufacturers. Notwithstanding this transcarbonation process has operated on a commercial scale for a long time, the subject is still a vivid area of research, especially focused on the design of new catalysts and reaction conditions. A variety of other examples taken from the literature of the past 4–5 years testifies that DAC-mediated alkylation and carboxyalkylation reactions have been successfully addressed for the preparation of bio-monomers based on sugars, furfural and HMF, and bio-derived polycarbonate, in particular poly(isosorbide)carbonate (PIC) and isosorbide-based co-poly carbonates. The resulting materials display physico-chemical properties suitable for the development of engineered bio-based materials, particularly suitable for optical applications.
Moreover, the presence of carbonate functional groups in both polycarbonates and block co-polymers containing polycarbonate subunits is suitable for stimuli-responsive, biocompatible applications and can be exploited for the development of chemical end-of-life valorization strategies on these degradable renewable-based materials.
Another emerging area in the field of sustainable valorization of renewables includes the use of DACs as solvents not only for the synthesis of fine chemicals and electrochemical processes, but also for membrane fabrication, photochemical processes, separation and purification of untreated feedstocks, and energy storage applications. This versatility is ascribed to some key physico-chemical properties of organic carbonates, such as their polar aprotic nature, low dipole moment, moderate viscosity, and immiscibility with water.
The last (fifth) section of this review has been dedicated to isopropenyl acetate (iPAc). The use of iPAc is becoming increasingly attractive for multiple reasons, such as its non-toxicity, the potential for its synthesis via fermentative/sustainable pathways starting from acetic acid and acetone, and its reactivity to promote irreversible acetylation processes. In particular, iPAc allows unique acylation conditions, suitable for the functionalization of biopolymers (lignin, cellulose, dextrin, sugar cane bagasse), platform chemicals (1,n-diols, glycerol, aminoglycerols) and acid or base-sensitive substrates, and is compatible with the development of sustainable tandem and/or sequential muti-step reaction protocols, even in a continuous-flow mode.
A concluding note is on the degree of technological maturity of the work presented here, meaning how far the current scenario is from the implementation of DACs- or iPAc-mediated reactions on a commercial scale. If we adopt the concept of sustainable development according to the Venn representation (environmental, social, and economic approaches), the synthetic selectivity and the clean, safe, and non-toxic character of both DACs and iPAc make the chemistry of these compounds/solvents suited to the upgrading of biomass derivatives, with a processing which is both socially and environmentally acceptable. An open issue, however, is with the economics of these transformations. Not only are the intrinsic costs of DACs higher, but also the activation barriers of transesterifications and alkylations promoted by these compounds are usually greater compared with those of conventional (and highly toxic) carboxylating and alkylating agents such as phosgene, CO/alcohols, alkyl halides, and dialkylsulphates. Our opinion is that a virtuous circle can be triggered by integrating the use of DACs for large-scale applications within modern biorefinery plants where available technologies for the recovery of waste/excess heat and recycling of reactants/solvents can make the difference to the overall energy/costs balance. This strategy would clearly imply a more extensive use of such compounds (DACs), with a positive impact on their price and competitiveness on the market in the future.
Author contributions
GF, AP and MS conceived the presented idea and performed the initial formal analysis. GF and MS wrote the original draft. Manuscript revision and editing was performed jointly by GF, AP and MS.
Conflicts of interest
There are no conflicts to declare.
References
-
https://www.euromemo.eu/show/10813271.html
(last access, December 22nd, 2021).
-
https://ec.europa.eu/commission/presscorner/detail/en/qanda_20_24
.
- C. Espro, E. Paone, F. Mauriello, R. Gotti, E. Uliassi, M. L. Bolognesi, D. Rodrıguez-Padron and R. Luque, Chem. Soc. Rev., 2021, 50, 11191–11207 RSC.
- T. Maschmeyer, R. Luque and M. Selva, Chem. Soc. Rev., 2020, 49, 4527–4563 RSC.
- L. S. Ribeiro, J. J. Delgado, J. J. M. Órfão and M. F. R. Pereira, Appl. Catal., B, 2017, 217, 265–274 CrossRef CAS.
- L. A. Zevallos Torres, A. Lorenci Woiciechowski, V. O. de Andrade Tanobe, S. G. Karp, L. C. Guimaraes Lorenci, C. Faulds and C. R. Soccol, J. Cleaner Prod., 2020, 263, 121499 CrossRef CAS.
- S. M. Ioannidou, C. Pateraki, D. Ladakis, H. Papapostolou, M. Tsakona, A. Vlysidis, I. K. Kookos and A. Koutinas, Bioresour. Technol., 2020, 307, 123093 CrossRef CAS PubMed.
-
https://euinasean.eu/eu-green-deal/
.
- M. Alexandri, R. Schneider, H. Papapostolou, D. Ladakis, A. Koutinas and J. Venus, ACS Sustainable Chem. Eng., 2019, 7, 6569–6579 CrossRef CAS.
- G. Fiorani, A. Perosa and M. Selva, Green Chem., 2018, 20, 288–322 RSC.
- M. Selva, A. Perosa, D. Rodríguez-Padrón and R. Luque, ACS Sustainable Chem. Eng., 2019, 7, 6471–6479 CrossRef CAS.
-
M. Selva, A. Perosa, G. Fiorani and L. Cattelan, in Green Synthetic Processes and Procedures, ed. R. Ballini, Royal Society of Chemistry, Cambridge, 2019, ch. 14, pp. 319–342 Search PubMed.
- H. Huang, R. C. Samsun, R. Peters and D. Stolten, Green Chem., 2021, 23, 1734–1747 RSC.
- A. Sánchez, L. M. Gil and M. Martín, J. CO2 Util., 2019, 33, 521–531 CrossRef.
- P. Kongpanna, V. Pvarajarn, R. Gani and S. Assabumrungrat, Chem. Eng. Res. Des., 2015, 93, 496–510 CrossRef CAS.
- P. Kumar, V. C. Srivastava, U. L. Štangar, B. Mušič, I. M. Mani and Y. Meng, Catal. Rev., 2021, 63, 363–421 CrossRef CAS.
- S. H. Pyo, J. H. Park, T. S. Chang and R. Hatti-Kaul, Curr. Opin. Green Sustainable Chem., 2017, 5, 61–66 CrossRef.
- Y. Peia, Y. Quana, X. Wanga, J. Zhaoa, R. Shia, Z. Li and J. Ren, Appl. Catal., B, 2022, 300, 120718 CrossRef.
- J.-M. Woo, J. Y. Seo, H. Kim, D.-H. Lee, Y. C. Park, C.-K. Yi, Y. S. Park and J.-H. Moon, Ultrason. Sonochem., 2018, 44, 146–151 CrossRef CAS PubMed.
- S. Fukuoka, M. Tojo, H. Hachiya, M. Aminaka and K. Kasegawa, Polym. J., 2007, 39, 91–114 CrossRef CAS.
- S. Fukuoka, I. Fukawa, T. Adachi, H. Fujita, N. Sugiyama and T. Sawa, Org. Process Res. Dev., 2019, 23, 145–169 CrossRef CAS.
-
https://www.asahi-kasei.co.jp/asahi/en/news/2014/e140813.html
.
- A. Sanchez, M. Martín and P. Vega, ACS Sustainable Chem. Eng., 2019, 7, 9995–10007 CrossRef CAS.
- C. Hank, S. Gelpke, A. Schnabl, R. J. White, J. Full, N. Wiebe, T. Smolinka, A. Schaadt, H.-M. Henning and C. Hebling, Sustainable Energy Fuels, 2018, 2, 1244–1261 RSC.
- S. Kumar, M. B. Gawande, I. Medřík, M. Petr, O. Tomanec, V. Kupka, R. S. Varma and R. Zbořil, Green Chem., 2020, 22, 5619–5627 RSC.
- Z. Fu, Y. Zhong, Y. Yu, L. Long, M. Xiao, D. Han, S. Wang and Y. Meng, ACS Omega, 2018, 3, 198–207 CrossRef CAS PubMed.
- D. Stoian, F. Medina and A. Urakawa, ACS Catal., 2018, 8, 3181–3193 CrossRef CAS.
- Z. Zhang, S. Liu, L. Zhang, S. Yin, G. Yang and B. Han, Chem. Commun., 2018, 54, 4410–4412 RSC.
- A. A. Marciniak, O. C. Alves, L. G. Appel and C. J. A. Mota, J. Catal., 2019, 371, 88–95 CrossRef CAS.
- H. Ohno, M. Ikhlayel, M. Tamura, K. Nakao, K. Suzuki, K. Morita, Y. Kato, K. Tomishige and Y. Fukushima, Green Chem., 2021, 23, 457–469 RSC.
- M. Poor Kalhor, H. Chermette and D. Ballivet-Tkatchenko, Ind. Eng. Chem. Res., 2020, 59, 6867–6873 CrossRef CAS.
- K. Shukla and V. C. Srivastava, RSC Adv., 2016, 6, 32624–32645 RSC.
- K. Shukla and V. C. Srivastava, Can. J. Chem. Eng., 2018, 96, 414–420 CrossRef CAS.
- H. Wang, Y. Xiang, M. Guo, J. Su, G. Wang, W. Cui and Z. Deng, Energy Fuels, 2020, 34, 8697–8706 CrossRef CAS.
- T. Chang, M. Tamura, Y. Nakagawa, N. Fukaya, J.-C. Choi, T. Mishima, S. Matsumoto, S. Hamura and K. Tomishige, Green Chem., 2020, 22, 7321–7327 RSC.
- W. S. Putro, A. Ikeda, S. Shigeyasu, S. Hamura, S. Matusmoto, W. Y. Lee, J.-C. Choi and N. Fukaya, ChemSusChem, 2021, 14, 842–846 CrossRef CAS PubMed.
- J. Wang, Z. Hao and S. Wohlrab, Green Chem., 2017, 19, 3595–3600 RSC.
- T. Yan, W. Bing, M. Xu, Y. Li, Y. Yang, G. Cui, L. Yang and M. Wei, RSC Adv., 2018, 8, 4695–4702 RSC.
- A. Dibenedetto, A. Angelini, M. Aresta, S. Fasciano, M. E. Cucciolito, F. Ruffo, B. M. Aresta, D. Curulla-Ferré and E. De Giglio, Appl. Catal., A, 2015, 493, 1–7 CrossRef CAS.
- D. Shi, S. Heyte, M. Capron and S. Paul, Green Chem., 2022, 24, 1067–1089 RSC.
- K. Kohli, B. K. Sharma and C. B. Panchal, Energies, 2022, 15, 5133 CrossRef CAS.
- A. Brege, R. Grignard, R. Méreau, C. Detrembleur, C. Jerome and T. Tassaing, Catalysts, 2022, 12, 124 CrossRef CAS.
- P. P. Pescarmona, Curr. Opin. Green Sustainable Chem., 2021, 29, 100457 CrossRef CAS.
- Q.-W. Song, Z.-H. Zhou and L.-N. He, Green Chem., 2017, 19, 3707–3728 RSC.
- L. Guo, K. J. Lamb and M. North, Green Chem., 2021, 23, 77–118 RSC.
- V. Aomchad, À. Cristòfol, F. Della Monica, B. Limburg, V. D'Elia and A. W. Kleij, Green Chem., 2021, 23, 1077–1113 RSC.
- S. Arayachukiat, C. Kongtes, A. Barthel, S. V. C. Vummaleti, A. Poater, S. Wannakao, L. Cavallo and V. D'Elia, ACS Sustainable Chem. Eng., 2017, 5, 6392–6397 CrossRef CAS.
- E. Hernandez, R. Santiago, C. Moya, S. Vela, P. Navarro and J. Palomar, J. CO2 Util., 2021, 52, 101656 CrossRef CAS.
- V. Abdelsayed, T. H. Gardner, A. H. Kababji and Y. Fan, Appl. Catal., A, 2019, 586, 117225 CrossRef.
- Y. Chen, R. Luo, Q. Xu, J. Jiang, X. Zhou and H. Ji, ChemSusChem, 2017, 10, 2534–2541 CrossRef CAS PubMed.
- A. Sainz Martinez, C. Hauzenberger, A. R. Sahoo, Z. Csendes, H. Hoffmann and K. Bica, ACS Sustainable Chem. Eng., 2018, 6, 13131–13139 CrossRef CAS.
- T. Wang, X. Song, Q. Luo, X. Yang, S. Chong, J. Zhang and M. Ji, Microporous Mesoporous Mater., 2018, 267, 84–92 CrossRef CAS.
- W. F. Monteiro, M. O. Vieira, A. S. Aquino, M. O. de Souza, J. de Lima, S. Einloft and R. Ligabue, Appl. Catal., A, 2017, 544, 46–54 CrossRef CAS.
- D. Rigo, R. Calmanti, A. Perosa, M. Selva and G. Fiorani, ChemCatChem, 2021, 13, 2005–2016 CrossRef CAS.
- N. Eghbali and C.-J. Li, Green Chem., 2007, 9, 213–215 RSC.
- J.-L. Wang, J.-Q. Wang, L.-N. He, X.-Y. Dou and F. Wu, Green Chem., 2008, 10, 1218–1223 RSC.
- R. Calmanti, M. Selva and A. Perosa, Green Chem., 2021, 23, 1921–1941 RSC.
- M. F. O'Neill, M. Sankar and U. Hintermair, ACS Sustainable Chem. Eng., 2022, 10, 5243–5257 CrossRef PubMed.
- G. Trapasso, C. Salaris, M. Reich, E. Logunova, C. Salata, K. Kümmerer, A. Figoli and F. Aricò, Sustainable Chem. Pharm., 2022, 26, 100639 CrossRef CAS.
- B. Schäffner, F. Schäffner, S. P. Verevkin and A. Börner, Chem. Rev., 2010, 110, 4554–4581 CrossRef PubMed.
- P. Tundo, M. Musolino and F. Aricò, Front. Chem., 2019, 7, 300 CrossRef PubMed.
- A. Jordan, C. G. J. Hall, L. R. Thorp and H. F. Sneddon, Chem. Rev., 2022, 122, 6749–6794 CrossRef CAS PubMed.
- P. Tundo, M. Musolino and F. Aricò, Green Chem., 2018, 20, 28–85 RSC.
- S. Huang, B. Yan, S. Wang and X. Ma, Chem. Soc. Rev., 2015, 44, 3079–3116 RSC.
-
CRC Handbook of Chemistry and Physics, ed. W. M. Haynes, CRC Press, Boca Raton, 91st edn, 2010 Search PubMed.
- K. Shukla and V. C. Srivastava, RSC Adv., 2016, 6, 32624–32645 RSC.
- A. Rodríguez, J. Canosa, A. Domínguez and J. Tojo, J. Chem. Eng. Data, 2003, 48, 146–151 CrossRef.
- R. Naejus, D. Lemordant and R. Coudert, J. Chem. Thermodyn., 1997, 29, 1503–1515 CrossRef CAS.
- M. Moosavi, A. Motahari, A. Vahid, V. Akbar, A. A. Rostami and A. Omrani, J. Chem. Eng. Data, 2016, 61, 1981–1991 CrossRef CAS.
- Q. Cai, B. Lu, L. Guo and Y. Shan, Catal. Commun., 2009, 10, 605–609 CrossRef CAS.
- M. A. Rivas, S. M. Pereira and T. P. Iglesias, J. Chem. Thermodyn., 2002, 34, 1897–1907 CrossRef CAS.
- V. Pokorný, V. Štejfa, M. Fulem, C. Červinka and K. Růžička, J. Chem. Eng. Data, 2017, 62, 3206–3215 CrossRef.
- J. R. Ochoa-Gomez, O. Gomez-Jimenez-Aberasturi, C. Ramirez-Lopez and M. Belsue, Org. Process Res. Dev., 2012, 16, 389–399 CrossRef CAS.
- M. O. Sonnati, S. Amigoni, E. P. Taffin de Givenchy, T. Darmanin, O. Choulet and F. Guittard, Green Chem., 2013, 15, 283–306 RSC.
- S. Sahani, S. N. Upadhyay and Y. C. Sharma, Ind. Eng. Chem. Res., 2021, 60, 67–88 CrossRef CAS.
- D. Procopio and M. L. Di Gioia, Catalysts, 2022, 12, 50 CrossRef CAS.
- Y. Ji, Catalysts, 2019, 9, 58 CrossRef.
-
(a)
https://www.ulprospector.com/en/na/Coatings/Detail/848/34431/JEFFSOL-GLYCERINE-CARBONATE; ;
(b)
https://ube.es/products/fine-chemicals/glycerine-carbonate/
.
- Y. Wan, Y. Lei, G. Lan, D. Liu, G. Li and R. Bai, Appl. Catal., A, 2018, 562, 267–275 CrossRef CAS.
- P. de Caro, M. Bandres, M. Urrutigoïty, C. Cecutti and S. Thiebaud-Roux, Front. Chem., 2019, 7, 308 CrossRef CAS PubMed.
- M. A. do Nascimento, L. E. Gotardo, R. A. C. Leao, A. M. de Castro, R. O. M. A. de Souza and I. Itabaiana Jr., ACS Omega, 2019, 4, 860–869 CrossRef CAS.
- X. Zhang, S. Wei, X. Zhao, Z. Chen, H. Wu, P. Rong, Y. Sun, Y. Li, H. Yu and D. Wang, Appl. Catal., A, 2020, 590, 117313 CrossRef CAS.
- S. Wang, J. Wang, P. U. Okoye, S. Chen, X. Li, L. Duan, H. Zhou, S. Li, T. Tang, L. Zhang and A. Zhang, BioResources, 2020, 15, 142–158 CAS.
- G. Pradhan and Y. C. Sharma, Fuel, 2021, 284, 118966 CrossRef CAS.
- S. Arora, V. Gosu, V. Subbaramaiah and B. H. Hameed, J. Environ. Chem. Eng., 2021, 9, 105999 CrossRef CAS.
- J. Keogh, G. Deshmukh and H. Manyar, Fuel, 2022, 310, 122484 CrossRef CAS.
- W. K. Teng, R. Yusoff, M. K. Aroua and G. C. Ngoh, Sustainable Energy Fuels, 2021, 5, 274–282 RSC.
- M. Manikandan and P. Sangeetha, ChemistrySelect, 2019, 4, 6672–6678 CrossRef CAS.
- S. Wang, J. Wang, P. Sun, L. Xu, P. U. Okoye, S. Li, L. Zhang, A. Guo, J. Zhang and A. Zhang, J. Cleaner Prod., 2019, 211, 330–341 CrossRef CAS.
- E. Elhaj, H. Wang and Y. Gu, Mol. Catal., 2019, 468, 19–28 CrossRef CAS.
- P. Rittiron, C. Niamnuy, W. Donphai, M. Chareonpanich and A. Seubsai, ACS Omega, 2019, 4, 9001–9009 CrossRef CAS PubMed.
- Z. I. Ishak, N. A. Sairi, Y. Alias, M. K. T. Aroua and R. Yusoff, Chem. Eng. J., 2016, 297, 128–138 CrossRef CAS.
- J. Zhang, Y. Wu, X. Song, S. Xu, S. Li, Y. Zhu, L. Gao, J. Zhang and G. Xiao, Chemurg. Pap., 2018, 72, 2909–2919 CrossRef CAS.
- S. Kondawar and C. Rode, Energy Fuels, 2017, 31, 4361–4371 CrossRef CAS.
- W. K. Teng, R. Yusoff, M. K. Aroua and G. C. Ngoh, Sustainable Energy Fuels, 2021, 5, 274–282 RSC.
- Z. Wang, S. Guo, Z. Wang, F. Li, W. Xue and Y. Wang, RSC Adv., 2021, 11, 17072–17079 RSC.
- Q. Zhang, H.-Y. Yuan, X.-T. Lin, N. Fukaya, T. Fujitani, K. Sato and J.-C. Choi, Green Chem., 2020, 22, 4231–4239 RSC.
- Y. W. Lui, B. Chan and M. Y. Lui, ChemSusChem, 2022, 15, e202102538 CrossRef CAS PubMed.
- Z. Zhang, K. Su and Z. Li, Org. Lett., 2019, 21, 749–752 CrossRef CAS PubMed.
- L. D. Almeida, F. G. Delolo, A. P. S. Costa, E. V. Gusevskaya and P. A. Robles-Azocar, Mol. Catal., 2022, 527, 112400 CrossRef CAS.
- A. Jordan, K. D. Whymark, J. Sydenham and H. F. Sneddon, Green Chem., 2021, 23, 6405–6413 RSC.
- I. K. M. Yu, D. C. W. Tsang, A. C. K. Yip, A. J. Hunt, J. Sherwood, J. Shang, H. Song, Y. S. Ok and C. S. Poon, Green Chem., 2018, 20, 2064–2074 RSC.
- M. Sayed, N. Warlin, C. Hulteberg, I. Munslow, S. Lundmark, O. Pajalic, P. Tunå, B. Zhang, S.-H. Pyo and R. Hatti-Kaul, Green Chem., 2020, 22, 5402–5413 RSC.
- R. Bains, A. Kumar, A. S. Chauhan and P. Das, Renewable Energy, 2022, 197, 237–243 CrossRef CAS.
- L. Ferrazzano, D. Corbisiero, G. Martelli, A. Tolomelli, A. Viola, A. Ricci and W. Cabri, ACS Sustainable Chem. Eng., 2019, 7, 12867–12877 CrossRef CAS.
- D. Procopio, C. Siciliano, S. Trombino, D. E. Dumitrescu, F. Suciu and M. L. Di Gioia, Org. Biomol. Chem., 2022, 20, 1137–1149 RSC.
- X. Wang, R. Wang, X. Gu, J. Jia and Z. Zheng, Catal. Sci. Technol., 2019, 9, 1774–1778 RSC.
- C. Ma, Z. Feng, J. Li, D. Zhang, W. Li, Y. Jiang and B. Yu, Org. Chem. Front., 2021, 8, 3286–3291 RSC.
- F.-L. Zeng, K.-C. Xie, Y.-T. Liu, H. Wang, P.-C. Yin, L.-B. Qu, X.-L. Chen and B. Yu, Green Chem., 2022, 24, 1732–1737 RSC.
- V. Klöpfer, R. Eckl, J. Floß, P. M. C. Roth, O. Reiser and J. P. Barham, Green Chem., 2021, 23, 6366–6372 RSC.
- Y.-Y. Wang, H. Ma, J.-K. Yana, K.-D. Wang, Y. Yang, W.-H. Wang and H.-N. Zhang, Int. J. Biol. Macromol., 2019, 131, 941–948 CrossRef CAS PubMed.
- N. Postaue, C. E. Borba and C. da Silva, Fuel, 2022, 324, 124827 CrossRef CAS.
- C. Liu, H.-Y. Ni, Y.-H. Chang, Z.-L. Wang, N. Wan, L. Cao, Z.-G. Liu and Y.-J. Fu, J. Food Process. Preserv., 2022, e16603 CAS.
- M. Alfieri, I. Mascheretti, R. A. Dougué Kentsop, M. Mattana, M. Laura and G. Ottolina, Molecules, 2022, 27, 2732 CrossRef CAS PubMed.
- M. Ghidotti, D. Fabbri, C. Torri and S. Piccinini, Anal. Chim. Acta, 2018, 1034, 92–101 CrossRef CAS PubMed.
- B. Mongili, A. Abdel Azim, S. Fraterrigo Garofalo, E. Batuecas, A. Re, S. Bocchini and D. Fino, Biotechnol. Biofuels, 2021, 14, 13 CrossRef CAS PubMed.
- D. Kim and S. P. Nunes, Curr. Opin. Green Sustainable Chem., 2021, 28, 100427 CrossRef CAS.
- M. A. Rasool, P. P. Pescarmona and I. F. J. Vankelecom, ACS Sustainable Chem. Eng., 2019, 7, 13774–13785 CrossRef CAS.
- M. Shi, W. Yan, Y. Zhou, Z. Wang, L. Liu, S. Zhao, Y. Ji, J. Wang, C. Gao, P. Zhang and X. Cao, J. Membr. Sci., 2020, 595, 117474 CrossRef.
- Y. Zhang, J. K. Buchanan, G. Holmes, B. W. Mansel and S. Prabakar, J. Leather Sci. Eng., 2019, 1, 8 CrossRef.
- F. Aricò, Curr. Opin. Green Sustainable Chem., 2020, 21, 82–88 CrossRef.
- M. Ghasemlou, F. Daver, E. P. Ivanova and B. Adhikari, Eur. Polym. J., 2019, 118, 668–684 CrossRef CAS.
- M. A. C. Mhd. Haniffa, K. Munawar, Y. C. Ching, H. A. Illias and C. H. Chuah, Chem. – Asian J., 2021, 16, 1281–1297 CrossRef CAS PubMed.
- P. Furtwengler and L. Avérous, Sci. Rep., 2018, 8, 9134 CrossRef PubMed.
- F. Delbecq, M. Reza Khodadadi, D. Rodriguez Padron, R. Varma and C. Len, Mol. Catal., 2020, 482, 110648 CrossRef CAS.
- R. Ochoa-Gómez, S. Gil-Río, B. Maestro-Madurga, O. Gómez-Jimènez-Aberasturi and F. Río-Pérez, Arabian J. Chem., 2019, 12, 4764–4774 CrossRef.
- J. R. Ochoa-Gómez, L. Lorenzo-Ibarreta, C. Diñeiro-García and O. Gómez-Jiménez-Aberasturi, RSC Adv., 2020, 10, 18728–18739 RSC.
- N. Bragato and G. Fiorani, Curr. Opin. Green Sustainable Chem., 2021, 30, 100479 CrossRef CAS.
- R. Gérardy, J. Estager, P. Luis, D. P. Debecker and J.-C. M. Monbaliu, Catal. Sci. Technol., 2019, 9, 6841–6851 RSC.
- A. G. Sathicq, M. Annatelli, I. Abdullah, G. Romanelli and F. Aricò, Sustainable Chem. Pharm., 2021, 19, 100352 CrossRef CAS.
- P. Wang, J. H. Park, M. Sayed, T.-S. Chang, A. Moran, S. Chen and S.-H. Pyo, Polym. Chem., 2018, 9, 3798–3807 RSC.
- J. J. Warner, P. Wang, W. M. Mellor, H. H. Hwang, J. H. Park, S.-H. Pyo and S. Chen, Polym. Chem., 2019, 10, 4665–4674 RSC.
- K. Błażek, J. Datta and A. Cichoracka, Polym. Int., 2019, 68, 1968–1979 CrossRef.
- K. Błażek, H. Beneš, Z. Walterová, S. Abbrent, A. Eceiza, T. Calvo-Correas and J. Datta, Polym. Chem., 2021, 12, 1643–1652 RSC.
- P. B. V. Scholten, C. Detrembleur and M. A. R. Meier, ACS Sustainable Chem. Eng., 2019, 7, 2751–2762 CrossRef CAS.
- P. B. V. Scholten, D. Moatsou, C. Detrembleur and M. A. R. Meier, Macromol. Rapid Commun., 2020, 41, 2000266 CrossRef CAS PubMed.
- P. B. V. Scholten, G. Cartigny, B. Grignard, A. Debuigne, H. Cramail, M. A. R. Meier and C. Detrembleur, ACS Macro Lett., 2021, 10, 313–320 CrossRef CAS PubMed.
- G. Trapasso, M. Annatelli, D. Dalla Torre and F. Aricò, Green Chem., 2022, 24, 2766–2771 RSC.
- Z. Yang, L. Liu, H. An, C. Li, Z. Zhang, W. Fang, F. Xu and S. Zhang, ACS Sustainable Chem. Eng., 2020, 8, 9968–9979 CrossRef CAS.
- W. Fang, Z. Zhang, Z. Yang, Y. Zhang, F. Xu, C. Li, H. An, T. Song, Y. Luo and S. Zhang, Green Chem., 2020, 22, 4550–4560 RSC.
- W. Fang, Y. Zhang, Z. Yang, Z. Zhang, F. Xu, W. Wang, H. He, Y. Diao, Y. Zhang and Y. Luo, Appl. Catal., A, 2021, 617, 188111 CrossRef.
- W. Qian, X. Ma, L. Liu, L. Deng, Q. Su, R. Bai, Z. Zhang, H. Gou, L. Dong, W. Cheng and F. Xu, Green Chem., 2020, 22, 5357–5368 RSC.
- W. Qian, L. Liu, Z. Zhang, Q. Su, W. Zhao, W. Cheng, L. Dong, Z. Yang, R. Bai, F. Xu, Y. Zhang and S. Zhang, Green Chem., 2020, 22, 2488–2497 RSC.
- Z. Yang, X. Li, F. Xu, W. Wang, Y. Shi, Z. Zhang, W. Fang, L. Liu and S. Zhang, Green Chem., 2021, 23, 447–459 RSC.
- W. Fang, F. Xu, Y. Zhang, H. Wang, Z. Zhang, Z. Yang, W. Wang, H. He and Y. Luo, Catal. Sci. Technol., 2022, 12, 1756–1765 RSC.
- W. Wang, Y. Zhang, Z. Yang, Z. Zhang, W. Fang, D. Niu, H. He and F. Xu, Green Chem., 2021, 23, 973–982 RSC.
- W. Wang, Z. Yang, Y. Zhang, H. He, W. Fang, Z. Zhang and F. Xu, Green Chem., 2021, 23, 4134–4143 RSC.
- Z. Yang, Z. Zhang, M. Fu, W. Wang, Y. Shi, C. Li, W. Fang and F. Xu, J. Macromol. Sci., Part A: Pure Appl.Chem., 2021, 58, 398–407 CrossRef CAS.
- J. Chu, H. Wang, Y. Zhang, Z. Li, Z. Zhang, H. He, Q. Zhang and F. Xu, React. Funct. Polym., 2022, 170, 105145 CrossRef CAS.
- S. Fadlallah, A. L. Flourat, L. M. M. Mouterde, M. Annatelli, A. A. M. Peru, A. Gallos, F. Aricò and F. Allais, Macromol. Rapid Commun., 2021, 42, 2100284 CrossRef CAS PubMed.
- C. Carré, Y. Ecochard, S. Caillol and L. Avérous, ChemSusChem, 2019, 12, 3410–3430 CrossRef PubMed.
- J. Sternberg, O. Sequerth and S. Pilla, Prog. Polym. Sci., 2021, 113, 101344 CrossRef CAS.
- I. Kühnel, B. Saake and R. Lehnen, Macromol. Chem. Phys., 2018, 219, 1700613 CrossRef.
- J. Sternberg and S. Pilla, Green Chem., 2020, 22, 6922–6935 RSC.
- V. Mimini, H. Amer, H. Hettegger, M. Bacher, I. Gebauer, R. Bischof, K. Fackler, A. Potthast and T. Rosenau, Holzforschung, 2020, 74, 203–211 CAS.
- L.-Y. Liu, M. Cho, N. Sathitsuksanoh, S. Chowdhury and S. Renneckar, ACS Sustainable Chem. Eng., 2018, 6, 12251–12260 CrossRef CAS.
- X. Xiong, H. Zhang, S. L. Lai, J. Gao and L. Gao, React. Funct. Polym., 2020, 149, 104502 CrossRef.
- W. Jaroonwatana, T. Theerathanagorn, M. Theerasilp, S. Del Gobbo, D. Yiamsawas, V. D'Elia and D. Crespy, Sustainable Energy Fuels, 2021, 5, 5431–5444 RSC.
- V. Diez, A. DeWeese, R. S. Kalb, D. N. Blauch and A. M. Socha, Ind. Eng. Chem. Res., 2019, 58, 16009–16017 CrossRef CAS.
- J. A. Sirviö and J. P. Heiskanen, ACS Omega, 2019, 4, 15702–15710 CrossRef PubMed.
- E. B. Hemming, A. F. Masters, A. Perosa, M. Selva and T. Maschmeyer, Molecules, 2019, 24, 3986 CrossRef CAS PubMed.
- S. Dabral, J. Engel, J. Mottweiler, S. S. M. Spoehrle, C. W. Lahive and C. Bolm, Green Chem., 2018, 20, 170–182 RSC.
- A. De Santi, M. V. Galkin, C. W. Lahive, P. J. Deuss and K. Barta, ChemSusChem, 2020, 13, 4468–4477 CrossRef CAS PubMed.
- S. Dutta, I. K. M. Yu, D. C. W. Tsang, J. Fan, J. H. Clark, Z. Jiang, Z. Su, C. Hu and C. S. Poon, ACS Sustainable Chem. Eng., 2020, 8, 13100–13110 CrossRef CAS.
- A. Salerno, A. B. Leonardi, P. Pedrama, E. Di Maio, M. A. Fanovich and P. A. Nettia, Mater. Sci. Eng., C, 2020, 109, 110518 CrossRef CAS PubMed.
-
R. Miller, C. Abaecherli, A. Sais and B. Jackson, in Ullmann's Encyclopedia of Industrial Chemistry, ed. B. Elvers, Wiley, New York, 2001, vol. 20, pp. 171–185 Search PubMed.
-
Z. Yan, CN Pat., 105777540, 2016 Search PubMed.
- M. Sauer, FEMS Microbiol. Lett., 2016, 363, 134 CrossRef PubMed.
-
S. C. Moldoveanu, in Pyrolysis of Organic Molecules: Applications to Health and Environmental Issues, Elsevier, Amsterdam, 2018, ch. 10, pp. 391–418 Search PubMed.
- T. T. Tidwell, Angew. Chem., Int. Ed., 2005, 44, 5778–5785 CrossRef CAS PubMed.
- R. Calmanti, M. Galvan, E. Amadio, A. Perosa and M. Selva, ACS Sustainable Chem. Eng., 2018, 6, 3964–3973 CrossRef CAS.
- D. Rigo, G. Fiorani, A. Perosa and M. Selva, ACS Sustainable Chem. Eng., 2019, 7, 18810–18818 CrossRef CAS.
- R. Kakuchi, R. Ito, S. Nomura, H. Abroshan, K. Ninomiya, T. Ikai, K. Maeda, H.-J. Kim and K. Takahashi, RSC Adv., 2017, 7, 9423–9430 RSC.
- Q. Van Nguyen, S. Nomura, R. Hoshino, K. Ninomiya, K. Takada, R. Kakuchi and K. Takahashi, Polym. J., 2017, 49, 783–787 CrossRef.
- S. Suzuki, Y. Shibata, D. Hirose, T. Endo, K. Ninomiya, R. Kakuchi and K. Takahashi, RSC Adv., 2018, 8, 21768–21776 RSC.
- S. Suzuki, Y. Hamano, S. C. Hernandez, N. Wada and K. Takahashi, ACS Sustainable Chem. Eng., 2021, 9, 15249–15257 CrossRef CAS.
- S. Suzuki, S. Kurachi, N. Wada and K. Takahashi, Catalysts, 2021, 11, 120 CrossRef CAS.
- L. Szabó, R. Milotskyi, H. Ueda, T. Tsukegi, N. Wada and K. Takahashi, Chem. Eng. J., 2021, 405, 126640 CrossRef.
- S. Deb, S. R. Labafzadeh, U. Liimatainen, A. Parviainen, L. K. J. Hauru, S. Azhar, M. Lawoko, T. Kulomaa, T. Kakko, J. Fiskari, M. Borrega, H. Sixta, I. Kilpeläinen and A. W. T. King, Green Chem., 2016, 18, 3286–3294 RSC.
- S. Asaadi, T. Kakko, A. W. T. King, I. Kilpeläinen, M. Hummel and H. Sixta, ACS Sustainable Chem. Eng., 2018, 6, 9418–9426 CrossRef CAS PubMed.
- A. Sharma, S. K. Giri, K. P. Ravindranathan Kartha and R. S. Sangwan, RSC Adv., 2017, 7, 12745–12752 RSC.
- S. P. Godehard, H. Müller, C. P. S. Badenhorst, C. Stanetty, C. Suster, M. D. Mihovilovic and U. T. Bornscheuer, ACS Catal., 2021, 11, 2831–2836 CrossRef CAS.
-
https://ioncell.fi/research/
(accessed March 2022).
- K. N. Onwukamike, S. Grelier, E. Grau, H. Cramail and M. A. R. Meier, ACS Sustainable Chem. Eng., 2019, 7, 1826–1840 CrossRef CAS.
- T. Kakko, A. W. T. King and I. Kilpelainen, Cellulose, 2017, 24, 5341–5354 CrossRef CAS.
- D. Di Francesco, D. Rigo, K. R. Baddigam, A. P. Mathew, N. Hedin, M. Selva and J. S. M. Samec, ChemSusChem, 2022, 15, e202200326 CrossRef CAS PubMed.
- C. J. Chapman, C. G. Frost, J. P. Hartley and A. J. Whittle, Tetrahedron Lett., 2001, 42, 773–775 CrossRef CAS.
- D. Mukherjee, B. A. Shah, P. Gupta and S. C. Taneja, J. Org. Chem., 2007, 72, 8965–8969 CrossRef CAS PubMed.
- D. Rigo, R. Calmanti, A. Perosa and M. Selva, Green Chem., 2020, 22, 5487–5496 RSC.
- D. Rigo, N. A. Carmo Dos Santos, A. Perosa and M. Selva, Catalysts, 2021, 11, 21 CrossRef CAS.
- D. Rigo, D. Polidoro, A. Perosa and M. Selva, Mol. Catal., 2021, 514, 111838 CrossRef CAS.
|
This journal is © The Royal Society of Chemistry 2023 |