Surface-modified ultrafiltration and nanofiltration membranes for the selective removal of heavy metals and inorganic groundwater contaminants: a review
Received
17th April 2023
, Accepted 22nd August 2023
First published on 31st August 2023
Abstract
Groundwater contamination due to heavy metals and inorganic contaminants is a growing concern worldwide. Exposure to toxic elements, such as arsenic, chromium, copper, cadmium, fluoride, and nitrate, can pose significant health risks to humans and wildlife. Owing to its low footprint, cost-effectiveness, and automation, membrane technology has emerged as an effective technique for removing these contaminants. However, membrane fouling and the trade-off between membrane selectivity and permeability for charge-specific contaminants remain key challenges. To address these issues, this study comprehensively reviews various membrane surface modification techniques for the selective removal of heavy metals and inorganic contaminants. This review starts with the surface modification methods for ultrafiltration and nanofiltration membranes, including strategies, such as pore tuning, nanocomposites-based surface modifications, and membrane surface charge modifications by blending, coating, and chemical grafting. Furthermore, different metal/metal-oxide nanoparticles, hybrid nanomaterials, carbon nanotubes, graphene oxide, and metal–organic framework-based nanofillers in membrane blends and coats are also explored. Thereafter, it highlights the mechanisms behind removing different contaminants. The last section discusses the challenges and future prospects of such surface-modified membranes, which highlighted the area requiring extensive research, including the cost-economics, scale-up, and application of membranes in a real-time groundwater matrix, and how new-generation surface modification methods of membranes have shown promising results. This review provides valuable insights into the current state of knowledge in the membrane technology field, and its findings can guide future research and development efforts to address the challenges in heavy metals and inorganic contaminants from groundwater.
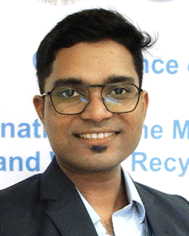 Mitil Meghanath Koli | Mitil Meghanath Koli holds a B.E. in Civil Engineering from University of Mumbai, India and M.Tech. in Civil-Environmental Engineering from Walchand College of Engineering, Sangli, India. Currently, he is a Ph.D. student at the Environmental Science and Engineering Department, Indian Institute of Technology, Bombay, India. His research focuses on the development of new generation ultrafiltration and nanofiltration membranes for groundwater treatment and advanced oxidation processes for emerging contaminant removal. He is the recipient of the prestigious Prime Ministers Research Fellowship (PMRF) for his doctoral research by the Ministry of Education, Govt. of India and the Sir Ratan Tata Trust Scholarship. |
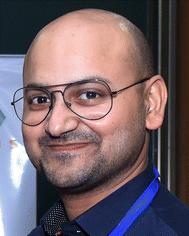 Swatantra Pratap Singh | Dr. Swatantra Pratap Singh is Associate Professor at the Indian Institute of Technology Bombay in the Environmental Science and Engineering Department and leads the interdisciplinary Environmental Nanotechnology Lab (ENano). He is also Professor-in-Charge for the Centre of Excellence on Membrane Technologies for Desalination, Brine Management, and Water Recycling (DeSaltM) at IIT Bombay, supported by the DST, India. He received his Ph.D. and M.Tech from the Indian Institute of Technology Kanpur, India, in Environmental Engineering and was a post-doctoral scholar at Zuckerberg Institute of Water Research, Ben-Gurion University of the Negev, Israel. He won the INAE Young Engineer Award (2020) and ISEES Young Scientists Award (2020). His current research interests are desalination and wastewater treatment by membrane technology and nanomaterials for environmental remediation. |
Water impact
Groundwater contamination due to heavy metals and inorganic pollutants is a pressing challenge around the globe, and their mitigation by new-generation surface-modified polymeric membranes is an emerging research field. This review focuses on novel fabrication techniques and action mechanisms for the removal of contaminants by ultrafiltration and nanofiltration membranes, further highlighting their associated challenges and future prospects for scaling up these membranes.
|
1. Introduction
Groundwater has often been considered a stable and reliable resource because it is buffered from short-term variability in weather patterns.1 Groundwater quality generally ranges from good potable fresh water to medium for domestic and industrial usage or inappropriate quality for any purpose.1–3 It depends on various anthropogenic and natural factors that are responsible for further pollution and contamination.2–4 Groundwater contaminants can be broadly classified into three major types: chemical, biological, and radioactive.3,5 Chemical contaminants of inorganic nature include nitrogen compounds, anions and oxyanions of F−, SO42−, and Cl−, and major cations, such as Ca2+ and Mg2+, typically found in groundwater.6–9 Zinc, lead, mercury, chromium, cadmium, and copper, and metalloids, such as selenium and arsenic, are some other chemical elements contaminating groundwater.5–12 Organic contaminants, such as hydrocarbons, halogenated compounds, plasticizers, pesticides, pharmaceuticals, personal care products, and natural estrogens, are also emerging from groundwater. Since these contaminants, especially heavy metals, are toxic over a specific exposure limit, the United States Environmental Protection Agency (USEPA) and the Bureau of Indian Standards (BIS) have suggested specific limits for their presence in drinking water.13
Heavy-scale industrialization has caused frequent environmental hazards due to heavy metals in many developing countries. Hexavalent chromium [Cr(VI)] is the most frequent type of heavy metal found in water streams and is extremely poisonous.14,15 Hazardous combustion emissions, sewage sludge, landfills, the metal industry, and mining are all sources of anthropogenic cadmium in groundwater.10,16 Similarly, arsenic (As) and fluoride (F) pollution of groundwaters caused by various factors, including water–rock interactions, anthropogenic activities, and groundwater recharge, has harmed millions of people around the world.6,17–23 Agricultural and urban runoff, excessive pesticide use, inappropriate treatment, and leaching of industrial waste and sewage effluents into groundwater all contribute to nitrogen in the form of inorganic nitrates (NO3−) entering aquatic systems.24–26 Acidic liquid discharge and effluent from industries using copper as a base metal for manufacturing can leach toxic compounds into the ecosystem and adversely affect human health.9,27,28 An excess of these inorganic pollutants and heavy metals in groundwater for any living species could be deadly and sometimes cancerous.29 Conventional remediation techniques for potentially removing these contaminants are chemical precipitation, oxidation using chemicals/photocatalysts, coagulation–flocculation, biosorption, adsorption and ion-exchange electrocoagulation, electrodialysis, phytoremediation, phytovolatilization, electrical remediation and thermal desorption methods, membrane technology, etc.15,17,22,24,26,30–34 Most of these technologies have a high carbon footprint and demand increased energy and cost, especially for the construction of civil units. The total cost of chemicals for processes such as coagulation and flocculation is also very high, and these chemicals require precision in handling their dosage.35 Hence, a need arises for a low-footprint, user-friendly, and less energy-intensive technology for the global community.
Membrane technology is a state-of-the-art process with a low footprint, excellent effluent quality, automated operating system,36–38 and therefore an appealing approach for overcoming the potential shortcomings of conventional water treatment systems. However, there is a need to tailor the membrane surface due to limits such as selectivity and permeability trade-offs and high-pressure requirements.39–42 A literature survey revealed no focused review based on surface modifications for UF and NF membranes for the selective removal of groundwater-contaminating heavy metals and inorganic contaminants. However, few reviews focus on improving the permeability and fouling resistance of membranes and improving the salt rejection capabilities of NF and RO membranes.43–48 Therefore, a focused review highlighting UF and NF membrane modifications for the selective removal of groundwater-contaminating heavy metals and inorganic ions such as arsenic, copper, cadmium, chromium, fluoride, and nitrate is still lacking. Accordingly, this review focuses on conventional and smart fabrication methods for developing surface-modified membranes (SMMs) to remove these contaminants from water. Furthermore, the paper also describes the unique properties of diverse nanomaterials and nanocomposites based on metal and carbon elements. The performance of SMMs of UF and NF are focused separately for the rejection of each contaminant. The challenges and future scope of such SMMs are described at last and shall benefit the membrane-research community by targeting the selectivity enhancement of the membranes.
2. UF and NF membrane process and limitations
Pressure-driven polymeric membranes are classified as microfiltration (MF), ultrafiltration (UF), nanofiltration (NF), and reverse osmosis (RO) membranes depending upon their pore size, as shown in Fig. 1(a).37 UF membranes are typically asymmetrically porous in cross-section with pore-size in the range of 0.02–0.1 μm (ref. 49 and 50) and reject solute molecules by adsorption, size exclusion or screening, and pollutant deposition, leading to fouling on the membrane surface.51,52 NF membranes are porous, asymmetric membranes often called ‘loose’ RO membranes because they provide higher water flux and lower trans-membrane pressure. NF membranes are able to achieve the removal of multivalent ions and, to an extent, monovalent ions.53 The membrane surface charge can be tuned as positive or negative, which can influence the selective penetration of ionic-charged components of various salts.58 Hence, these membranes can be efficiently employed for different charged ion removal applications. Despite their ease of production and high quality of permeate water, UF and NF membranes have constraints, such as hydrophobicity,54–56 and membrane fouling of organic, inorganic, and biological form,27,28,57,58 which would eventually cause a reduction in permeability.59 Additionally, membrane fouling deteriorates the membrane integrity, decreases the lifespan, and increases the maintenance cost.60 Selectivity and permeability trade-off is a major hindrance that dominates the performance of both UF and NF membrane.40,61,62 The balance between selectivity and permeance poses a significant challenge to the widespread implementation of NF membranes on a large scale since improving the membrane selectivity often results in a reduction in permeance, making it difficult to achieve both simultaneously.41
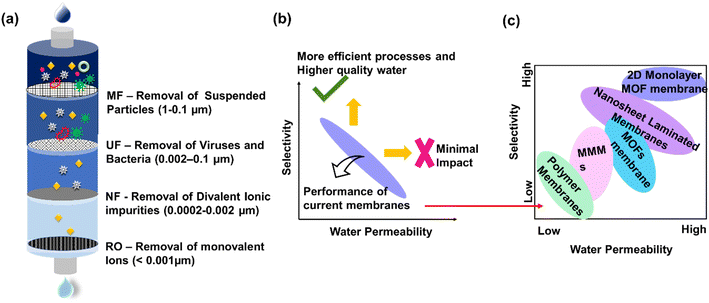 |
| Fig. 1 (a) Membrane process spectrum with pore size distribution. (b) Selectivity-permeability trade-off for conventional membranes [reproduced and modified from ref. 86 with permission from American Chemical Society, copyright 2023]. (c) The possible modifications to improvise the membrane performance [reproduced and modified from ref. 87 with permission from Elsevier, copyright 2023]. | |
Hydration radii and ion-diffusivity are two important parameters that affect the rejection performance of the membrane.52,63,64 The typical hydration radii of heavy metal ions and elements lie below the UF range. For instance, the hydration radii of different contaminants, as shown in Table 1, are all smaller in size compared to the pore size of UF and thereby are difficult to be rejected by mere screening mechanism.65–69 The size of these contaminants also is pH-dependent, and comprehensive information on the speciation of different ions with pH is given in Table 1.
Table 1 pH vs. speciation for different contaminants found in groundwater
Element |
pH range |
Speciation |
Hydration radii (nm) |
Ref. |
As(III) (in reducing environment) |
<9.2 |
H3AsO3 |
— |
70
|
9.2–12.1 |
HAsO32− |
— |
12.1–13.4 |
AsO33− |
— |
As(V) (in oxidizing environment) |
<2.24 |
H3AsO4 |
— |
71–74
|
2.24–6.9 |
H2AsO4− |
0.352 |
6.9–11.5 |
HAsO42− |
0.27 |
>11.5 |
AsO43− |
— |
Cd |
<9 |
Cd2+ |
0.426 |
8, 9 |
|
9–10 |
Otavite |
— |
|
|
>10 |
Cd(OH)3− |
— |
|
Cr(VI) |
<6.5 |
HCrO4− |
0.242 |
75, 76 |
6.5–10 |
CrO42− |
0.375 |
Cu |
<7.5 |
Cu2+ |
0.410-0.419 |
77, 78 |
9–12 |
Cu(OH)2 |
— |
|
|
>12 |
Cu(OH)42− |
— |
|
F |
<3.2 |
HF |
— |
79
|
>3.2 |
F− |
0.352 |
NO3− |
Entire pH range |
NO3− |
0.316-340 |
25, 80, 81 |
The hydration radii and the associated charge of divalent ions are greater than monovalent ions and hence are rejected significantly better by an NF membrane. For example, Gonzalez et al. examined the removal of inorganic contaminants from groundwater using an NF membrane.82 The order of rejection for anions (SO42− > HAsO42− > HCO3− > Cl−) and cations was (Mg2+ > Ca2+ > K+ > Na+). However, the rejection of anions does not always follow a similar pattern as per the hydration radii.63,82 A more complex phenomenon, such as the diffusivity coefficient, also plays an important role in deciding the rejection pattern.83,84 The higher the diffusivity, the greater the solute permeability and, subsequently, the lower rejection of ions.85 Hence, specific modifications for UF and NF membranes are necessary to overcome these limitations and serve the excellent perm-selectivity purpose.
3. SMMs synthesis and fabrication
The characteristic surface property and the membrane surface structure govern the selective nature of UF and NF membranes. Surface modification of polymeric membranes aims to control membrane fouling, improving the membrane's selectivity for desired applications and simultaneously improving the flux. Popular methods for surface modification include tuning pore size and manipulating surface charge by techniques, viz., coating, blending, radical grafting, composite, chemical, and combined methods.44,88,89 A general scheme of the surface modification methods and their removal mechanisms for UF and NF membranes are illustrated in Fig. 2 and 3, respectively. Further, a list of highly efficient SMMs, along with their fabrication techniques and action mechanisms, are summarized in Table 2.
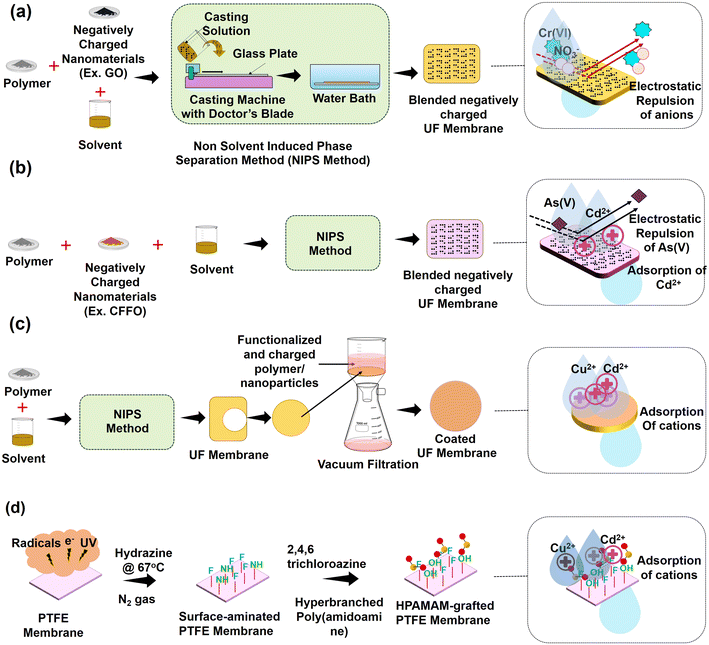 |
| Fig. 2 (a) Typical scheme of the selective fabrication of UF membrane and removal mechanism of Cr(VI) and NO3− removal by blending approach. (b) Typical scheme of selective fabrication of UF membrane and removal mechanism of Cu2+ and Cd2+ removal by coating approach via vacuum filtration. (c) Typical scheme of selective fabrication of UF membrane and removal mechanism of positively charged Cd2+ or negatively charged As(V) by the blending approach. (d) Grafting approach scheme of UF membrane surface modification for cations removal [reproduced and modified using ref. 163 with permission from Elsevier, copyright 2023]. | |
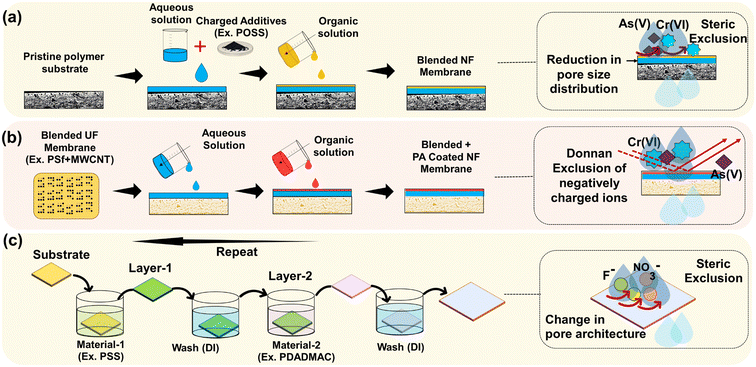 |
| Fig. 3 NF membranes surface modification methods and action mechanism by (a) blending, (b) coating, (c) layer-by-layer dipping method for the rejection of different contaminants. | |
Table 2 Summary of nanomaterials used for membrane surface modifications for high removal of contaminants and corresponding removal mechanisms
Contaminant (WHO guideline) |
Membrane fabrication method |
Nanomaterials used |
Contaminant removal (%) |
Removal mechanism |
Ref. |
Arsenic (0.01 mg L−1) |
UF membranes |
Mixed matrix NIPS |
Organoclay, arginine modified montmorillonite, Cu2Fe2O4, Cu2Fe2O4/CNT, UiO-66, GO |
>98% |
Adsorption |
90–94
|
NF membranes |
Blending and interfacial polymerization |
Na-CQD, POSS, P[MPC-co-AEMA], GO, UiO-66 in PA layer |
>98.5% |
Donnan exclusion and pore size reduction |
95–99
|
Coating |
SPEEK on PA |
Donnan exclusion |
38
|
Cadmium (0.003 mg L−1) |
UF membranes |
Mixed matrix NIPS |
Polycarbonate + hydrous MgO + alumina, CFFO, CND, MWCNT |
>98% |
Adsorption |
33, 100–103 |
NF membranes |
Blending and interfacial polymerization |
Hyperbranched PEI-cystamine |
>98% |
Donnan exclusion and steric hindrance |
104
|
Chromium (0.05 mg L−1) |
UF membranes |
Mixed matrix NIPS |
CS + PVA + MMT, epoxy functionalized PES, UiO66-NH2, GO |
>95% |
Adsorption |
54, 105–109 |
NF membranes |
Blending and interfacial polymerization |
2,5-Diaminobenzenesulfonic acid, poly(m-phenylene isophthalamide) |
>96% |
Donnan exclusion and steric hindrance |
110, 111 |
Mixed matrix NIPS |
Carboxylated GO (98), PEG + GO |
>96% |
112–114
|
LBL assembly |
nZVI@TiO2, nZVI@TiO2 on CS/alginate |
115, 116 |
Chemical grafting |
2-Acrylamido-2-methylpropanesulfonic acid on PSf |
117
|
Dip coating |
CS + PEI + GO |
118
|
Copper (2 mg L−1) |
UF membranes |
Mixed matrix NIPS |
α-ZrP, biochar, ZIF67/carboxylated GO |
>98% |
Adsorption |
119–123
|
NF membranes |
Vacuum filtration followed by interfacial polymerization |
PEI + cellulose |
>96% |
Adsorption and Donnan exclusion |
124
|
Mixed matrix NIPS and interfacial polymerization |
Modified Fe2O3 in PES NF |
125
|
Fluoride (1.5 mg L−1) |
UF membranes |
Mixed matrix NIPS |
PVDF + maifanite and activate alumina |
>88% |
Adsorption |
126
|
Coating |
Activated alumina fillers coated on CA phthalate |
>90% |
127
|
NF membranes |
Blending and interfacial polymerization |
GO layer on PES TFC |
>80% |
Donnan exclusion |
99
|
Nitrate (50 mg L−1) |
UF membranes |
Mixed matrix NIPS |
CS biopolymers |
100% |
Adsorption |
128
|
NF membranes |
Coating |
PSS coated on commercial NF |
88.8% |
Donnan exclusion |
129
|
3.1 Arsenic
UF membranes are tailored using different methods to sequester arsenic ions from the water matrix. The removal of arsenic can be obtained by blending different metal and carbon-based nanomaterials with polymers. Zhang et al. followed a mixed matrix approach wherein the phase inversion induced by immersion precipitation was applied to prepare Fe3O4-blended polyethersulfone (PES) membrane.130 The PES flakes with Fe3O4 microspheres and PVP was added to the DMF solution and stirred until complete dissolution. The casting solution was uniformly covered on a glass plate with a glass rod and immersed at room temperature in a deionized water coagulation bath. The As(V) ions from the water could easily bind to the Fe3O4 microspheres in the blended membrane, resulting in purified water. A similar approach of introducing clay nanoparticles such as organoclay,90 montmorillonite,91 kaolinite,131 and metal oxide nanoparticles such as Fe–Mn binary oxide,132 Zr,133 TNT,134 Y2O3,135 Al–TiO2,136 ZnO,137 APTES-Al2O3,138 and HINM139 in different polymers have been explored to remove arsenic by adsorptive technique. Organometallic nanoparticles such as MOFs are hybrid organic–inorganic solid materials composed of metal ions or metal ion clusters and organic ligands.140,141 MOFs such as UiO-66 have been used as potential sorbents for arsenate by introducing them in the PVDF membrane matrix by the phase inversion method.93
The presence of surface charge on the membrane or membrane pores plays a crucial role in the rejection of anions such as arsenic. This charge is derived from the ionizable functional groups present on the membrane surface and within its pore structure.142 The nature of the polymer as well as the additive materials used in the fabrication of UF or NF membranes, determines whether the surface groups are positive, negative, or zwitterionic. The dissociation of these surface groups is highly influenced by the pH of the solution that comes into contact with the membrane surface.72 Graphene oxide (GO), a chemical derivative of graphene with a reactive oxygen functional group,143 has attracted interest due to its superior water permeation, molecular sieving properties, and realistic prospects for industrial-scale production and presence of different functional groups with tunable charges.144 A significant benefit of GO over conventional graphene materials is that it can be bulk produced via well-established oxidation routes and graphitic flakes.143 Ions or molecules can be selectively transported through the interlayer spacing of multi-layered 2D GO.145 A study on GO-based UF membranes was carried out by Namdar et al., wherein pristine GO nanosheets were functionalized by aspartic acid and then dispersed in NMP.146 PVC polymer and a pore-inducing agent, PEG were further added to the solution in specific proportions. The doping solution was then used to cast the membrane using the NIPS method, as shown in Fig. 2(a). Other carbon-based nanomaterials like CNTs are synthetic carbon-based nanotubes composed of cylindrical graphite sheets rolled up in a tube-like structure with the appearance of a latticework fence. It provides frictionless transport of water molecules, making them suitable for developing high fluxing removal techniques.147 CNTs have been used to remove various heavy metals and dyes from wastewater and desalination.147–149 Functionalizing the hydrophobic tips of pristine CNTs can enhance the hydrophilicity as well as enhance their ion selectivity.150 Hence, CNTs are also used as additives in polymer solutions, and the developed mixed matrix membranes were used for selective arsenic removal.151 Further, a blended membrane with ferrous sulfide (FeS) and carboxyl-functionalized ferro-ferric oxide (CFFO) nanoparticles was fabricated via NIPS and was efficient for negatively charged HAsO4− as well as positively charged Cd2+ removal by electrostatic repulsion and adsorption, respectively, as illustrated in Fig. 2(b).101
The membrane's pore size was tuned by fabricating a thin film composite (TFC) selective membrane for arsenate removal by incorporating different co-polymers and nanoparticles in the active or substrate layer.62 Yingran et al. demonstrated using a water-soluble co-polymer P[MPC-co-AEMA] by introducing it in the PA layer by the interfacial polymerization method.96 The substrate layer was fabricated using the NIPS method. For preparing the selective layer, the PES substrate was first immersed in a solution containing known proportions of P[MPC-co-AEMA] and PIP solution for 2 min. The membrane was then thoroughly dried with filter paper. A 0.15 wt% TMC/hexane solution was poured on top of the former support for 1 min. The as-prepared TFC membrane was dried in air for 5 min. The synthesized membrane was both hydrophilic and had a small pore size, leading to excellent arsenic removal by steric exclusion without compromising the pure water permeance. About 99.8% arsenic was rejected by a TFC membrane modified with sodium carbon quantum dots.95 Functionalized polymers like sulfonated polyether ketone (SPEEK) and polyhedral oligomeric silsesquioxane (POSS) are also demonstrated for arsenic removal.38,152 Briefly, SPEEK coating in methanol was filtered and dip-coated onto the inner surface of the hollow fiber PES UF membrane. The initial composite membrane was dried and cured for an hour at 65 °C and stored in deionized water for further use. The membrane enhanced the negative charge density, leading to a higher arsenate rejection.
An NF membrane with GO nanosheets was fabricated by the cross-linking method on a PA support using a PES-5 UF membrane as a substrate layer. The GO nanosheets were incorporated in a cross-linking reagent, namely, TMC (1,3,5-benzenetricarbonyl trichloride), and m-phenylenediamine (MPD) was used as an amine monomer.99 The as-prepared membrane had a high negative charge due to the presence of oxygenated functional groups of epoxide, hydroxyl, carbonyl, and carboxylic acids on the basal planes, leading to arsenic rejection. Rezaee et al., however, used a mixed matrix approach to fabricate a GO-blended polysulfone (PSf) membrane, which could attain an As(V) rejection up to 85% at 8.5 pH.153 The rejection of membranes could also be enhanced by incorporating negatively charged moieties like ZnO and ZnO–MgO in the membrane either in blended form or active layer coating.154,155 Another emerging class of carbonaceous nanomaterials is carbon quantum dots (CQDs), which have excellent water dispensability and low toxicity. Moreover, these CQDs can be tuned to have various hydrophilic and charged functional groups such as amino, hydroxyl, carboxyl, carbonyl, and other oxygenous groups, which can enhance the permeance and membrane surface charge properties.156,157 For example, a sodium ion-modified CQD was incorporated as a filler in the organic phase while fabricating a TFC membrane, and the as-prepared membrane showed a high negative zeta potential and narrow pore-size distribution, resulting in the excellent removal of arsenic ions.158
3.2 Copper
Copper is a cationic pollutant that can be easily removed by fabricating an adsorptive membrane. For example, Abdulkarem et al. developed a highly negatively charged MMM by blending PVDF and α-ZrP nanoparticles using a simple phase inversion method.119 The negatively charged –H2PO3− moieties effectively adsorbed the Cu2+ ions. A typical procedure of the fabrication for such membranes is shown in Fig. 2(c). Other nanoparticles such as alumina, TiO2, and Fe3O4 nanoparticles were modified by immobilizing silica, metformin, and amine, as well as biochar and activated carbon have successfully demonstrated their usage as nanofillers in polymer matrix for the fabrication of MMM via the phase inversion process.120–122,125,159 The selective fabrication could also be achieved by exposing the bare membrane to a solution of nanoparticles through a vacuum filtration apparatus, as implemented by Zeng et al. The layered double hydroxide-LDH/GO composite solution was diluted in 50 mL DI water and was sonicated to achieve homogenous dispersion. The uniform solution was then vacuum filtered through a bare PVDF membrane and used for experimental purposes. More than 80% removal was achieved.160 Further, UF membranes fabricated using the phase inversion method with GO nanoplates functionalized with POSS and ZIF-67/carboxylated-GO have shown promising results for Cu2+ removal from the water matrix.123,152
UF surface modification for removing Cu2+ is also possible by UV irritation grafting, as demonstrated by Yoo et al. Typically, the membranes were fabricated by the surface amination of PTFE membranes with hydrazine, followed by chemical coupling with the hydrophilic chelating agent hyperbranched poly(amidoamine) (HPAMAM), as illustrated in Fig. 2(d). High rejection of Cu2+ can be facilitated by modifying the surface of the TFC membrane into a positively charged NF membrane. Hoang et al. fabricated such a membrane by modifying the PES substrate using a cellulose nanocrystals (CNCs) coating by vacuum filtration.124 Further, the IP method was used to prepare the TFC membrane using PEI and TMC n-hexane as the aqueous and organic mediums, respectively. More than 98% rejection of copper was obtained with this membrane. An enhanced Cu2+ rejection is also possible by tailoring the active layer of the TFC membrane. IRMOF-3/GO, mesoporous synthetic hectorite (MSH), and a composite of MSH and MOF (UiO-66-NH2) were first dispersed into the aqueous monomer solution and then doped on the substrate layer.161,162 Such deposition enhanced the rejection of copper cations by the synergistic effect of Donnan exclusion and dielectric repulsion.
3.3 Cadmium
Selective cadmium removal is possible via UF membranes using a solvent-casting method. The poly(ε-caprolactone)/Ag-MMT solution was cast on a glass plate and kept for 24 h for drying. The dried film was subjected to chloroform evaporation, dried in a vacuum oven for 3 days at 40 °C, and then used for experiments.164 The mixed matrix approach was also applied by adding activated carbon to the polymer matrix via NIPS.165 These membranes could target more than 88% pollutant removal. Sam et al. demonstrated the green synthesis of CQDs from oats. The CQDs were incorporated in the PES polymer, and the mixed matrix membrane was fabricated using the NIPS method. The addition of CQDs enhanced the hydrophilicity of the membrane due to the introduction of new functional groups of –OH and –COO–. GO and MWCNTs are also a few carbon-based nanoparticles that can fabricate adsorptive membranes to remove such positively charged cadmium ions.33,103,166 A TFC membrane was fabricated by considering PES as a support layer and solution of hyperbranched polyethyleneimine (HPEI) in DI water (aqueous phase) and TMC-hexane (organic phase). The as-prepared membranes were soaked immediately into the cysteamine mixture to functionalize the selective layer further. The attachment of –SH on the membrane enhances the selectivity and subsequently increases the Cd2+ removal efficacy.104 The pore size of a TFC membrane can also be tuned by incorporating PEI in the membrane substrate and/or by water-soluble glutaraldehyde and epichlorohydrin, which yielded high CdCl2 rejections.167
3.4 Chromium
Inorganic fillers such as MMT have been successfully incorporated in a MMM for the selective adsorption of hexavalent chromium.105,106 A study demonstrated where the polymer PSf itself was functionalized using chlorosulfonic acid. The sulfonation reformed the hydrophobic PSf into a hydrophilic one, increasing the water flux. Further, the sPSf was incorporated with nano-TiO2. At lower pH values, the surface charge of TiO2 induces a fixed charge on the membrane; since Cr exists in its anionic form, there is a strong electrostatic interaction between TiO2 and Cr ions, resulting in maximum rejection. At higher pH values, both TiO2 and Cr exist in anionic forms, leading to a possible repulsion.54 Similar studies on functionalizing polymers were carried out by Jayalakshmi et al.107 Nanoparticles such as SiO2, UiO-66-NH2, and ZIF-8 have been used in different polymer matrices for fabricating MMMs by the phase inversion method for enhanced Cr(VI) rejection.108,168
Negatively charged GO nanosheets as well as functionalized GO have also been investigated with promising results for Cr(VI) rejection through a MMM.109,146 Certain functionalized nanoparticle polymer coatings such as L-cysteine POSS applied on TFC membranes are also effective in Cr(VI) rejection due to the negatively charged functionalities of –COO– and –O–, which repel the anionic Cr(VI) metal ions.169 Nanoparticles of TiO2, nZVI@TiO2, and carboxylated GO have demonstrated significant effectiveness in Cr(VI) removal.54,112,115 These nanoparticles are added to the active layer solution of the TFC membrane and fabricated using the interfacial-polymerization technique, as shown in Fig. 3(a). Another approach to NF modification is by tailoring the substrate layer using different polymer concentrations or adding hydrophilic and charged nanoparticles and then coating with the PA layer via interfacial polymerization. For example, Wang et al. demonstrated the efficient removal of Cr(VI) by developing a TFC membrane over the MWCNT-blended PES membrane, as illustrated in Fig. 3(b).
3.5 Fluoride
Monovalent F− is challenging to reject by membranes due to its small hydration size. Hence, adsorptive UF membranes have been fabricated for their efficient removal. Studies on PVDF membrane blended with maifanite (MFS) and activated alumina (AA), Fe–Al–Mn@chitosan (CS) in CA, exfoliated Mg–Al–Fe layered double hydroxides (LDHs) incorporated in PES have indicated high adsorption affinity toward fluoride ions due to their inherent positive charge.126,170,171 A porous alumina-supported NF membrane was fabricated by depositing 4.5-bilayer poly(styrene sulfonate) (PSS)/poly(diallyldimethylammonium chloride) (PDADMAC) films by a layer-by-layer technique, as shown in Fig. 3(c).172 The fabricated NF membrane resulted in F− rejection extending up to 73%. Interestingly, size exclusion played an essential role in increasing the rejection rate of F− ions. The selectivity of PSS/PDADMAC membranes is a strong function of the number of deposited layers, indicating that NF properties are susceptible to film structure. A graphene-based nanocomposite membrane was synthesized by interfacial polymerization through the chemical bonding of the GO layer to the PES surface.99
3.6 Nitrate
UF membranes for effective nitrate removal can be fabricated using the non-solvent induced phase inversion method by incorporating charged and hydrophilic nanoparticles such as α-Fe2O3,173,174 CS nano-biopolymers in the polymer matrix of polyacrylonitrile (PAN), and PES polymers.128 A study on NO3− removal was carried out using carbon-based nanoparticles such as GO.175 However, the MMM developed was not much effective due to low rejection. A commercial NF membrane was modified using poly(sodium 4-styrenesulfonate) (PSS) to improve the nitrate rejection from groundwater.129 The coating of PSS onto the virgin membrane enhanced the surface negative charge density. The modified membrane achieved a nitrate rejection rate of up to 88.8% and a permeate flux of 27 LMH.
4. Action mechanism of surface-modified UF and NF membranes for contaminant removal
The modifications made on the UF and NF membrane surface reject different contaminants by adsorption, size exclusion or sieving, Donnan exclusion, or dielectric repulsion.176 Size exclusion is one of the main rejection mechanisms commonly described in the rejection of solutes using porous UF membranes. The molecular weight cut-off (MWCO) often quantifies the rejection of a solute and is defined as the molecular weight of a solute that can be rejected at 90%. This concept is based on the observation that the size of molecules is typically larger as their MW increases.177 However, in the case of UF membranes, the applicability of this concept is only limited to the rejection of colloids and organics such as protein molecules, bacteria, and viruses. Researchers have addressed the limitations of ultrafiltration (UF) membranes in retaining nano-sized cations and anions by developing UF adsorptive membranes, blended/mixed matrix membranes, or through polymer-enhanced coagulation and separation.178–180 The contaminated water, when pre-treated with surfactants, ligand complexes, or coagulating agents and passed through UF membranes, has shown high rejection efficiency and flux in removing heavy metals like chromium.180 However, the proper disposal of heavy metals and complex molecules has led to secondary pollution through sludge formation, which limits their usage.181
Adsorptive UF membranes utilize functional groups on the membrane or incorporate sorbents to adsorb contaminants while allowing wastewater to permeate through. The adsorption mechanism involves electrostatic interaction, hydrogen bonding, and complexation.182 Modifying the surface charge of UF membranes via a mixed matrix membrane approach is another approach to ion removal, with the fixed charge model used to describe the rejection of charged membranes.183 When wastewater containing heavy metal ions and organic molecules comes into contact with the diffuse layer of an adsorptive UF membrane, certain molecules larger than the membrane's pore size are rejected through a process called molecular sieving. Furthermore, within the diffuse layer, a portion of the small molecules and ions are also rejected due to repulsive forces between them and the charged membrane surface. The charged membrane creates an electrostatic barrier that repels these particles, preventing them from passing through the membrane. However, some small molecules and ions overcome the repulsive forces and pass through the diffuse layer, reaching the stern layer of the membrane. In the stern layer, these molecules and ions undergo adsorption, a process where they bind to the adsorbent material present in the membrane.178,184,185 The adsorbent material, which may contain functional groups like carboxylate (–COO–) or hydroxyl (–OH), interacts with the ions through various mechanisms such as electrostatic interactions, hydrogen bonding, or complexation.185 Heavy metals form ionic bonds with the adsorbents anchored on the membrane, while water molecules pass through the porous structure with low transport resistance, resulting in high-quality treated water suitable for consumption.37
The removal properties and fouling tendency of UF membranes are greatly influenced by the charges on the membrane, which interact with ionic solutes. The fixed charge model, proposed by Teorell, Meyer, and Sievers (TMS model), has been used to describe the rejection of charged UF membrane, which assumes a fixed wall charge density and a uniform radius.186 However, the actual pore radius is often smaller than the pore radius calculated by MWCO experiments, indicating the partial blocking of the pores by solutes. The blocking of pores and modification of the wall charge affect the flow pattern, which has been described in the literature and used to explain the removal of chromic acid by membranes with larger pore radius.187 The membrane charge can be positive or negative, depending on the specific surface modification process. The surface modification of the PAN UF membrane reduces the pore size through the formation of COO– on the membrane surface and pore wall. The modified PAN membrane exhibits stronger repulsion toward divalent anionic solutes compared to monovalent anionic solutes due to higher volumetric charge densities, which is also dependent on solute concentration. However, the effective volumetric charge density decreases with decreasing pH as the isoelectric point of these membranes is located at a lower pH region, resulting in repulsion between ions and the membrane surface.188,189
NF membranes generally have a thin film composite structure consisting of porous asymmetric membranes as a support layer and an ultrathin PA selective layer formed on the support having pores in the sub-nanometer range, i.e., 0.2–2 nm.37,190,191 When the membrane separates neutral or uncharged solutes, the removal is primarily governed by steric hindrance, more commonly referred to as size exclusion.186 Hence, the sieving mechanism dominates the rejection of neutrally charged ions of As(III). Studies have shown a positive correlation between the rejection rate and the molecular size of the solute.192 However, a hindrance can occur in the rejection based primarily on size exclusion if an ion is present with the same hydrated radii193 because the hydrated radius of the contaminant is smaller than the pore radius. Organic micropollutants do not dissociate at near neutral pH and thus do not have any ionic charge interaction with the membrane surface; therefore, their rejection is majorly governed by steric exclusion.37,194 The surface charge on the membrane surface and pore wall is another crucial factor in the transport of ions through the UF and NF membrane. NF membranes typically have charged capillary-like pores.186 By Donnan exclusion, a membrane with a strong negative charge can readily bind cationic impurities while rejecting anions. The opposite is valid for a membrane with a strong positive charge. Emamjomeh et al. determined that the removal mechanism in the NF membrane especially involved the size of the molecules and the electrical response between the surface of the membrane and the ions in the feed solution.195 Furthermore, Donnan exclusion occurs due to electrostatic interactions between ionic solutes and the membrane matrix's fixed electric charges.196 The rejection trends shown in their study demonstrate that the ion removal is governed by size exclusion and Donnan exclusion as the observed trends do not correspond to the size of the hydrated ions.
Yaroshchuk et al. introduced dielectric exclusion during the removal process by providing an in-depth analysis of this mechanism.197 The investigators claimed that when an ion interacts with the bound electrical charges generated by an ion at the interface of the membrane and solvent, dielectric exclusion takes place due to the difference in their dielectric constants. Technically, the contaminant ion in the solvent creates polarization charge distribution at the discontinuity surface between the solvent and membrane surface, depending on their individual dielectric constants. The interaction between the ion and membrane across the planar interface is termed as the ‘image’ force. Therefore, if the solvent has a higher dielectric constant than the membrane, the image force will be repulsive for both anions and cations.198 Another theory considers the dielectric constant within the membrane pores. It suggests that if the pore dielectric constant pores decrease, it eventually approaches the dielectric exclusion of bulk solution, and the pore reduces in size.199 This creates an extra energy barrier for the ions to penetrate the pores, thereby excluding them. The hydrated radii of ions are of great importance as it is one of the governing parameters for ion rejection. Generally, divalent ions have two layers, the dense inner layer and the outer elastic layer, that weakly connect with nuclear ions. The water molecules modify their outer hydration shell so that the inner hydration shell can pass through the pore, allowing ions with a radius greater than the pore size to still flow through. The initial hydration shell can readily pass through the pore because the outer hydration shell has replenished several water molecules. The second hydration shell collects more water molecules in the permeated area after exiting the pore to create a new hydration shell.200 Such membranes have a dense layer that only allows water to diffuse to the permeate, rejecting the ions on the feed side via the solution–diffusion mechanism and concentration gradient.196 The diffusion process and ion selectivity depend on the solubility and diffusivity of the specific ions in the membrane material.
5. Performance of surface-modified UF and NF membranes for contaminant removal
5.1 UF membranes for arsenic removal
Existing pristine UF membranes face limitations in effectively removing arsenic from water, primarily due to their larger pore-size, typically ranging between 0.02 and 0.1 μm. However, innovative membrane surface modification techniques offer promising solutions to eliminate arsenic from polluted water. As mentioned earlier, one such effective approach involves creating adsorptive membranes by incorporating various organic or inorganic adsorbents into the membrane matrix through blending or coating. The tailored adsorptive properties of the modified membranes enable them to selectively capture arsenic ions while maintaining their high water permeability. For example, Shokri et al. studied the performance of organoclay as an inorganic adsorbent in a PSf composite UF membrane for As(V) removal from surface water.90 The enhanced miscibility of organoclay with the non-solvent water due to the hydrophilic chain of organoclay molecules led to macrovoid extension across the entire membrane, which increased the overall membrane porosity and, subsequently, the permeability. A dynamic adsorption assessment of the membrane with 1.5 wt% organoclay content resulted in more than 90% removal of 100 ppb As(V) contaminated water. The completely separated layers of fully exfoliated organoclays, as well as the intercalated structures in the membrane matrix, provided accessibility for As(V) adsorption. The zwitterionic charged properties of montmorillonite (MMT) modified with arginine amino acid (Mt-arginine) were investigated by incorporating in PSf.91 Due to dominating dual charges, i.e., positive by amino acids and negative by carboxylic species, the PSf/MMT-Arg membrane showed more than 98% As(V) removal efficiency over pH 3-7. The electrostatic interaction between MMt-Arg and As(V) anions significantly adsorbed the arsenate species. Another adsorptive UF membrane using PES blended with iron oxide (Fe3O4) microspheres was synthesized to remove arsenic.201 When passed through the membrane, the arsenic-contaminated water developed a complex with Fe3O4, producing a low arsenic permeate. As(III) removal was explored using Fe–Mn binary oxide (FMBO), nanoparticle doped on polyether sulfone (PES) hollow fiber membrane.132 About 90% of As(III) could be removed up to a pH 9 of the water sample with an adsorption capacity of 73.5 mg g−1, as illustrated in Fig. 4(a). The incorporation of FMBO nanoparticles enhanced the mean surface roughness of the membrane along with the number of pores and simultaneously reduced the pore size, enabling an increased arsenite removal efficiency. The desorption of the adsorbed As(III) on the saturated membranes can be successfully done by increasing the pH above 11 so that the membrane adsorption capability can be recovered.
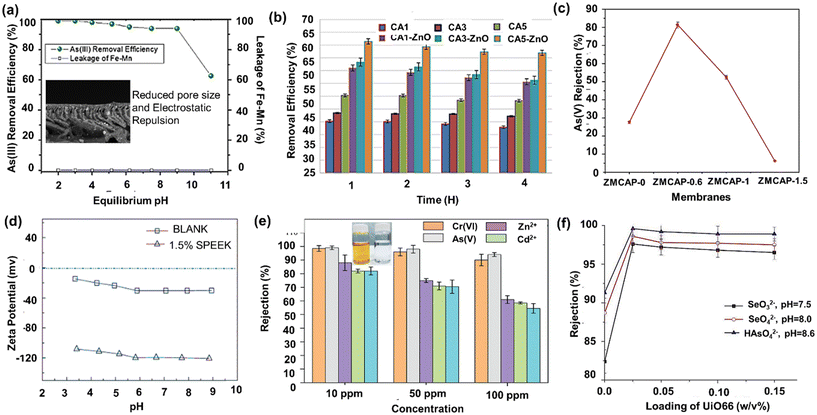 |
| Fig. 4 (a) As(III) removal performance by PES/Fe–Mn binary oxide UF mixed matrix membrane [reproduced from ref. 132 with permission from Elsevier, copyright 2023]. (b) As(V) removal performance by cellulose acetate–zinc oxide nanoparticle mixed matrix membrane [reproduced from ref. 154 with permission from Elsevier, copyright 2023]. (c) As(V) removal performance by binary zinc–magnesium oxides on polyphenylsulfone/cellulose acetate derivatives [reproduced and modified from ref. 204 with permission from Elsevier, copyright 2023]. (d) Increment in negative zeta potential by SPEEK addition [reproduced from ref. 38 with permission from Meri, copyright 2023]. (e) Carboxylated-PPSU mixed matrix membrane [reproduced and modified from ref. 112 with permission from Royal Society of Chemistry, copyright 2023]. (f) UiO66-incorporated TFC Membrane [reproduced from ref. 98 with permission from Elsevier, copyright 2023]. | |
Luan et al. developed multi-walled CNT (MWCNT) deposited on a conventional polymeric PVDF membrane.92 CuFe2O4 nanoparticles were intercalated into the carboxylated and hydroxylated CNT, and a sonicated dispersion was filtered into a PVDF membrane surface. The CuFe2O4/CNT composite removed As(III) by initial adsorption, followed by the oxidation of As(III) to As(V) by the CuFe2O4 particles and subsequently adsorbed onto the CuFe2O4/CNT membrane. Overall, a high adsorptive effect (>90%) at less than 0.01 bar pressure over a pH range 5–9 was achieved with effective regeneration using 0.001 M NaOH. A mixed matrix PVDF hollow fiber membrane was fabricated by embedding UiO-66 particles to remove arsenate from aqueous solutions, which showed 267 mg g−1 over a pH of 4.7.93 The sorption could occur on different sites on UiO-66 particles, with oxygen in Zr–O–C being the most favorable site for sorption. At higher pH, the surface of UiO-66 becomes negatively charged, and the removal mechanism is dominated by electrostatic repulsion than adsorption. Kumar et al. explored CS-modified GO achieving 71.9 mg g−1 arsenic adsorption over three regeneration cycles.94 The possible removal mechanisms were attributed to interactions such as cation–π interaction, RNH3+-aromatic π system, electrostatic interaction (H2AsO4−, HAsO42−–+NH3R), inter and intermolecular hydrogen bonding, as well as anion–π interaction (R–COO−-aromatic π system and R–O−-aromatic π system).
It is also possible to tune membranes by inducing charged nanoparticles onto the membrane surface/into the membrane so that negatively charged anions of arsenic get repelled due to electrostatic repulsion. MMM with ZnO nanoparticles was explored in a varied composition of cellulose acetate (CA), acetone, and formamide to synthesize UF and NF membranes for arsenic removal.154Fig. 4(b) illustrates the membrane performance for 4 h duration, indicating more than 58.77% removal efficiency after embedding ZnO nanoparticles in the membrane due to the steric exclusion phenomenon at near neutral pH. Embedding ZnO nanoparticles in the CA membranes decreased the pore size pertaining to a greater straining effect on the arsenic ions and enhancing their removal compared to the lone CA membranes.202,203 A polyphenyl sulfone (PPSU) UF hollow fiber membrane was fabricated using CA and CA phthalate (CAP) by varying additive concentrations.204 The PPSU/CAP 5 wt% membrane gave optimum performance, permeability of 40.11 LMH bar−1, and 41% arsenic rejection over a wide pH range. The removal was enhanced two-fold after introducing binary zinc–magnesium oxide (ZnO–MgO) nanoparticles into the PPSU/CA and PPSU/CAP hollow fiber membrane [Fig. 4(c)]. Enhancement occurred due to arsenite oxidation to arsenate oxide and steric repulsion by the ZnO–MgO nanoparticles embedded in the negatively charged membrane surface.
5.2 NF membranes for arsenic removal
Conventional thin film composite (TFC) membranes are tailored by introducing certain co-polymers for increasing both flux and rejection of arsenic ions due to simultaneous improvement in the hydrophilic nature of the membrane and reduction in the pore size. A water-soluble co-polymer, P[MPC-co-AEMA], which is zwitterionic in nature, was synthesized via a free-radical polymerization between 2-methacryloyloxyethyl phosphorylcholine (MPC) and 2-aminoethyl methacrylate hydrochloride (AEMA). The P[MPC-co-AEMA] co-polymer was introduced in the PA selective layer of TFC membranes exhibiting permeability of 8.5 LMH bar−1 and 99.8% arsenic (HAsO42−) rejection due to an increment in hydrophilicity and reduced pore size of the membrane.205 The P[MPC-co-AEMA] forms a hydration layer containing both positive and negative charge over the membrane surface, which aids the electrostatic repulsion effect for both charged ions. Additionally, the co-polymer fills the free volume of the membrane, thereby reducing the pore-size of the selective layer and restricting the passage of arsenic ions. A further enhancement was achieved by functionalizing the CQD with sodium ions, revealing a permeability of 10.4 LMH bar−1 and 99.5% arsenic rejection.95 An enhanced degree of rejection was attributed to the molecular sieving and electrostatic repulsive theory due to small pore size and narrow pore-size distribution. Functionalized polymers are an attractive solution for enhancing the rejection capability of the membranes. Song et al. explored the modification of the NF membrane using thin sulfonated polyether ether ketone (SPEEK).206 The novel composite hollow fiber membrane could achieve As(V) rejection over 95% and superior permeability of 11 LMH bar−1. The incorporation of SPEEK increased the negative zeta potential of the membrane, as shown in Fig. 4(d). This helped to reject arsenate ions by more than 90% via the Donnan exclusion mechanism. The performance of a TFN membrane containing polyhedral oligomeric silsesquioxane (POSS) was investigated for the removal of arsenic.207 The presence of POSS in the PA membrane tightened the pores, thereby narrowing the pore size distribution. High rejections of arsenic (97.4%) over a wide pH range were achieved mainly due to size exclusion and steric repulsion with a permeability of 5.4 LMH bar−1. Similarly, a poly(m-phenylene isophthalamide)-based NF membrane reached up to 99% rejection due to the Donnan charge exclusion behavior of the membrane.208 Interestingly, it was found that the addition of NaCl enhanced the As(V) rejection while adding Na2SO4 reduced the rejection by 8%. This could be explained by the phenomenon of preferential passage of more mobile co-ions and the predominantly strong steric-effect of SO42− ions over the arsenate ions.
A novel GO nanocomposite was investigated in a flat membrane module with a cross-flow pattern by Pal et al.99 The membrane exhibited excellent selectivity for the removal of arsenic (98.5%) along with other contaminants such as fluoride, iron, and suspended solids from groundwater at an optimum pH of 8.0, an operating pressure of 14 bar, and an hourly cross-flow of 800 L. Similarly, a nanocomposite membrane using GO thin layer coated on a microporous flat-sheet PES support resulted in a flux of 398.5 LMH and 86.7% As(V) removal.209 The negative hydrophilic functional groups, such as hydroxyl and carboxylic in GO, reportedly induced a negative charge. They created a high negative zeta potential on the surface of the membrane, which increased the Donnan exclusion effect between the negatively charged membrane surface and the negative charge of arsenate. Furthermore, the membranes modified by GO provided active sites and functional groups such as –OH and –COOH to form metal ion complexes, thereby enhancing the rejection of arsenate ions. A PPSU/carboxylated GO-incorporated PPSU membrane showed more than 98% As(V) removal at initial concentrations of 10, 50, and 100 ppm due to the enhanced charge properties of GO210 [Fig. 4(e)].
MOFs such as UiO-66, a type of Zr-MOF, have recently gained much attention, especially in water application.211 UiO-66 nanoparticles with 30 nm UiO-66 and 0.15 wt% incorporated in the PA layer exhibited the highest flux of 11.5 LMH bar−1 and rejection of 98.6% toward HAsO42−, as shown in Fig. 4(f). The composite TFN membrane exhibits negative charges in the pH range of 2–12 due to the deprotonation of carboxyl groups on the surfaces of the PA layer and UiO-66 particles. Further, Tajuddin et al. demonstrated the fabrication of a MMM using 0.5 wt% UiO-66 integrated into PSf membrane as a nanofiller with a TFC, dense PA layer formed on top of the substrate layer.212 An As(V) removal of 87.5% was exhibited by the 0.5 wt% UiO-66 fabricated membrane. These TFN membranes may efficiently reject the negative ions due to the Donnan effect as well as size exclusion. The enhanced permeability is attributed to the aperture of UiO-66 particles, allowing water to permeate smoothly while repelling the solutes selectively.
5.3 UF membranes for copper removal
Adsorptive UF membranes for Cu2+ removal were explored by Abdulkarem and team by fabricating a blend of PVDF and α-ZrP.119 The negative charge on the membrane surface was enhanced after implanting a large number of α-ZrP nanoparticles due to the introduction of negatively charged (–H2PO3−) moieties, which could easily adsorb Cu2+ ions along with other positively charged cations, as shown in Fig. 5(a). Furthermore, their incorporation increased the ion exchange capacity between the membranes and the metal ions of different hydrolysis constants. Likewise, biochar composed of carboxyl, hydroxyl, and phosphorus groups, along with some light metals, was incorporated in PSf MMM hollow fiber membrane for Cu2+ adsorption and exhibited excellent results.120 Their corresponding contributions to the adsorption process follow the order: complexation accompanied with H+ ion exchange > cation exchange > precipitation with phosphorus. Ghaemi et al. investigated Cu2+ removal by introducing Al2O3 nanoparticles in the PES matrix, which revealed high water permeance and Cu2+ ions adsorption.159 The negatively charged alumina nanoparticles were dispersed on the surface and in the backbone of the nanocomposite membrane, increasing the available active sites to adsorb Cu2+ ions on the membrane surface. A TiO2 and polyaniline (PANi)-containing PES composite membrane could reject 94% Cu2+ from the aqueous solution.121 Since TiO2 is pH sensitive, the results indicated that Cu2+ removal at low pH was dominated by cationic repulsion, whereas at higher pH (>6), the negatively charged particles are removed via ion exchange. PANi coating also further improved the adsorption capacity via its chelating property.
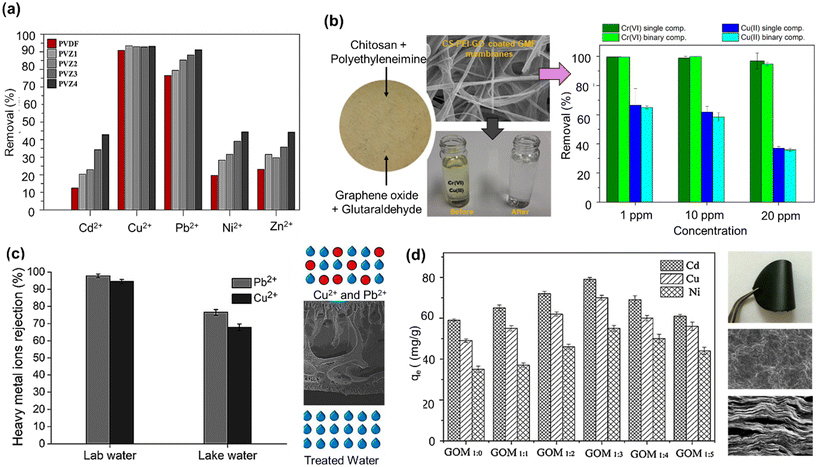 |
| Fig. 5 (a) Copper and cadmium removal performance by PVDF-a-ZrP mixed matrix membrane [reproduced from ref. 119 with permission from Elsevier, copyright 2023]. (b) Copper removal by CS, polyethyleneimine, GO, and glutaraldehyde to produce a multifunctional nano-composite membrane coating [reproduced and modified from ref. 118 with permission from American Chemical Society, copyright 2023]. (c) Copper removal performance and mechanism by ZIF-67/cGO incorporated in polyethersulfone hollow fiber membrane [reproduced from ref. 123 with permission from Elsevier, copyright 2023]. (d) GO membranes (GOM) for cadmium removal (inset: digital images of GOM membrane and SEM micrographs of surface and cross-section) [reproduced from ref. 166 with permission from Elsevier, copyright 2023]. | |
A layered double hydroxide-LDH/GO/PVDF composite membrane was prepared via a self-assembly technique to investigate their potential for removing Cu2+.160 Since the membrane contains a hydroxyl group on the surface, it gets chelated with Cu2+ and increases the removal efficiency (>80%) based on the GO membrane by surface complexation. GO nanoplate surface was functionalized by glycidyl polyhedral oligosilsesquioxane (POSS), a 3D nanoparticle with a rigid cage structure, and was used to fabricate polyetherimide (PEI) membrane.213 An excellent flux of 32 LMH for the blended membrane with 0.01 wt% glycidyl-POSS (PG) could be achieved with 51–55% Cu(NO3)2 rejection. The formation of more active site due to the cage structure of POSS, tuning the size of membrane pores, good dispersion of PG into the membrane structure, and the presence of negative charges on the membrane surface are the critical reasons for Cu(NO3)2 rejection. CS + PEI coated with GO dispersion showed excellent rejection of Cu2+, more than 95% in a single ion solution, and satisfactory removal in a binary mixture with Cr(VI) at different concentrations [Fig. 5(b)]. Here, the Cu2+ ions formed a surface complex with the amine groups by sharing a vacant electron pair from the nitrogen atoms, subsequently leading to the enhanced removal of copper. A novel approach of using Jatropha oil-based polyol (JOL) blended with hexamethylene diisocyanate (HDI) was studied by Harun et al.214 The fabricated JPU membrane was further blended with GO to form Jatropha/GO composite membrane (JPU/GO), which could reject Cu2+ up to 71.60% by complex formation. A zeolitic imidazolate framework-67-carboxylated GO (ZIF-67/cGO) was synthesized and incorporated in PSf, resulting in a high flux and 66.4 ± 3.2 mg g−1 for Cu2+ adsorption, which is illustrated in Fig. 5(c).123 The electrostatic interaction between the positively charged heavy metal ions and the negatively charged hollow fiber membrane surface enabled adsorption due to the incorporation of ZIF-67/cGO in the membrane matrix.
5.4 NF membranes for copper removal
Cu2+ rejection can be facilitated through a TFC membrane prepared by PEI and cellulose nanoparticles.124 The flux of fabricated TFN was 23.92 LMH, and the rejection was 98.0% and 96.5% of CuSO4 and CuCl2, respectively. Since the hydration radii of Cu2+ was 0.419 nm, the rejection of ions could be attributed to the size exclusion phenomenon. Fe3O4 nanoparticles were modified by immobilizing silica, metformine, and amine and then embedded in the PES NF membrane to give 92% removal.125 Considering the chemical structure of these nanoparticles, many N atoms are around each particle, offering active adsorption sites through their lone electron pairs. A composite of MOF and GO is also explored for Cu2+ sequestration. IRMOF-3/GO was doped on polydopamine-coated PSf substrate and was demonstrated for Cu2+ removal.161 More than 90% Cu2+ rejection was achieved while maintaining a relatively high flux of 31 LMH. The improvements in heavy metal ions rejections could be attributed to the enhancement of positive membrane surface zeta potential (Donnan exclusion) and the high adsorption capacity of IRMOF-3/GO. Mesoporous synthetic hectorite (MSH) and a composite of MSH and UiO-66-NH2 nanoparticles incorporation in piperazine aqueous monomer solution were studied.162 The membrane exhibited 60.86 LMH flux and 84.62% CuSO4 rejection due to the synergistic effect of the strong Donnan exclusion and dielectric repulsion of the ions. Another PEI hybrid TFC membrane was fabricated using L-cysteine-functionalized POSS nanoparticles and methyl-methacrylate as monomers. The membrane could adsorb more than 79% Cu2+ due to ions collisions with the surface of membranes, leading to more adsorption ions on the membrane by active sites. Additionally, the diagonal distance between the Si-atoms of the POSS nanoparticles is about 0.53 nm, and the adjacent distance of Si atoms is about 0.32 nm. Thus, the adsorption capacity of the metal ions based on ion radius due to trapping and adsorbing into the POSS structure is enhanced.213,215
5.5 UF membranes for cadmium removal
Cadmium can be sequestered via UF membranes using nanomaterials such as poly(ε-caprolactone), i.e., PCL and silver exchanged MMT for adsorption.164 The membranes exhibited homogeneous sponge microstructures, increased surface hydrophilicity, and adsorbed 61.11% Cd2+ ions. The composite membrane has an initial positive charge and thus promotes the fixation of anions, and then different cations like Cd2+ are transferred from the bulk solution to the membrane surface. A similar structure was observed in an MMM developed by mixing activated carbon (AC), polyethyleneimine, and silver nitrate, which resulted in 35% Cd2+ adsorption.165 Further, enhanced elimination of both Cd2+ and Cu2+ up to 97% was obtained using polycarbonate (PC) with hydrous manganese oxide (HMO) and alumina nanoparticles in an MMM. The nanoparticles provided higher active adsorption sites and removal for cadmium ions at elevated pH values, whereas they tend to form a positively charged layer at acidic pH, reducing the adsorption efficiency. A ferrous sulfide and carboxyl-functionalized ferro-ferric oxide nanoparticles-blended PVDF membrane resulted in 99% Cd2+ removal.101 The composite membrane developed ionized FeO− and –COO forms, which were deemed responsible for enhanced negative charge throughout the membrane by adsorption and charge repulsion. Carbon nanodots (CNDs) synthesized from oats and embedded on the PES membrane demonstrated excellent Cd2+ removal due to the presence of –OH, –C–O–, and –COO–, which improved membrane hydrophilicity along with increasing negative zeta potential.33 A 0.5% CNDs/PES rejected 99.78% of Cd2+ at pH 5 with at least four cycles and >95% efficiency due to the electrostatic interaction between the positively charged cadmium and negatively charged membrane. Eco-friendly photoluminescent carbon dots (CDs) produced from carboxymethylcellulose-CMC and poly(ethyleneimine) (PEI) contain abundant oxygen and nitrogen species and a high graphitization index.102 The resulting membrane showed a Cd2+ removal percentage of 91.1%, attributed to the PVA-CDs film that favored the rapid adsorption of Cd2+ by providing more –OH sites for the target metal ions. Also, hydrogen bonds were formed, facilitating increased electrostatic exchange with Cd2+ and thus improved adsorption.
Carbon-based nanoparticles such as GO membranes for Cd2 and Cu2+ have demonstrated a highly ordered layered GO membrane with a larger interlayer spacing, which can be observed in the scanning electron microscope image in Fig. 5(d).166 The maximum adsorption capacities of the fabricated GO–PVA membranes for Cu2+, Cd2+, and Ni2+ were approximately 72.6, 83.8, and 62.3 mg g−1, respectively. The excellent adsorption ability of the GO membranes can be attributed to the presence of abundant oxygen-containing functional groups on the surface and interlayer of the GO membranes that can easily bind heavy metal ions through a Lewis base–acid type phenomenon. A functionalized MWCNT/PSf composite membrane was fabricated using DMF and water with isopropanol as a coagulant.103 Functional groups such as –COOH, –OH due to membranes' surface oxidation, –CONH and –CH2NH2 due to amide functionalization, and –CON3 due to azide functionalization are generated on the membrane surface, which shows complex formation with Cd2+ ions. The amide-functionalized MWCNT/PSf composite membranes gave 94.2% removal for Cr(VI) and 78.2% for Cd2+. At acidic pH, protons compete with the heavy metal ions, thus providing maximum rejection. An increase in the rejection of both metal ions was noted, possibly due to a decreased pore size as well as an increase in the number of active adsorption sites on the functionalized CNTs. Interestingly, a pronounced metal rejection was noted for amide and azide groups since they have a better binding capacity compared to the carboxylic groups.
A hyperbranched polyethyleneimine (HPEI) integrated with PES, TMC, and cystamine was investigated for Cd2+ removal.104 Because of the presence of peripheral tertiary amine groups from the HPEI polymer, the membrane had a ridge-valley and noodle morphology with improved surface roughness. The presence of thiol groups played a vital role in complexing the metal ion on the modified membrane surface, allowing the PES/HPEI-SH membrane to attenuate Cd2+ to a degree of 99%. Peydayesh and the team demonstrated Cd2+ and Cu2+ removal from a mix of heavy metal ions. They fabricated an NF membrane with self-assembled ethylenediamine (ED)-grafted multi-walled carbon nanotube (ED-g-MWCNT) on the top layer of asymmetric PES.216 The fabricated membrane was positively charged, and the rejection rate of Cd and Cu was 92.4% and 91.9%, respectively. The rejection mechanism was dominated by the collaborative effect of Donnan exclusion and steric hindrance of the ions with larger hydrated radii. The membrane showed excellent removal of other metal ions as well [Zn (96.7%), Mg (95.01%), Ca (91.3%), Ni (90.7%), and Pb (90.5%)]. Also, specific localized interactions may occur between heavy metals and amine residues on the surface of ED-g-MWCNT, leading to their adsorption. A high flux of 80.5 LMH was achieved due to the incorporation of nanotubes with a loading ratio of 0.6 wt%.
5.6 UF membranes for chromium removal
Toxic Cr(VI) removal was demonstrated by fabricating an adsorptive PSf/MMT mixed matrix UF membranes and MMT modified with methyl dihydroxy ethyl hydrogenated tallow ammonium (mMMT).105 The composite membrane enhanced Cr(VI) removal by 89% and 95% due to the presence of quaternary ammonium, which contains cations-adsorbed Cr(VI). The development of an eco-friendly organic–inorganic hybrid membrane using CS, polyvinyl alcohol (PVA), and MMT clay to remediate Cr(VI) was reported by Sangeetha et al.106 The CS/PVA/MMT membrane showed higher rejection of Cr(VI), i.e., 84–88%, at a pH of 7 and Cr(VI) concentration of 50 ppm. At acidic pH, the membrane surface becomes positively charged due to the protonation of the amine group, which rejected the Cr6+ ions dominant in that pH. In contrast, at alkaline pH, the membrane surface is negatively charged due to excess hydroxyl groups and zero protonation, resulting in a lower rejection rate of Cr(VI), as illustrated in Fig. 6(a). A hydrophobic PSf was reformed into a hydrophilic polymer by sulphonation and made into a composite by incorporating nano titania.54 The hydrophilicity of the composite membrane was significantly increased by sulphonation, whereas titania formed a fixed negative charge on the membrane surface, which supported ionic interactions and facilitated the rejection of Cr(VI) ions. The rejection of Cr(VI) extended up to 98% due to both steric repulsion and photocatalytic reduction processes.
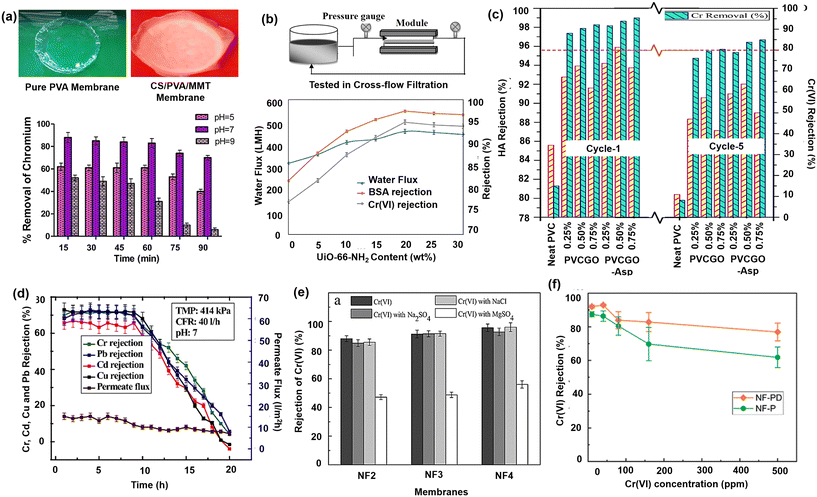 |
| Fig. 6 Chromium removal performance by (a) CS/PVA/MMT membrane (inset: digital images of pure PVA and CS/PVA/MMT membrane) [reproduced and modified from ref. 106 with permission from Elsevier, copyright 2023]. (b) PVDF/CS/UiO-66-NH2 membrane via cross flow filtration [reproduced and modified from ref. 108 with permission from Elsevier, copyright 2023]. (c) Aspartic acid-functionalized GO present in polyvinylchloride MMMs [reproduced and modified from ref. 146 with permission from Elsevier, copyright 2023]. (d) GO + PSf impregnated membrane [reproduced from ref. 109 with permission from Elsevier, copyright 2023]. (e) 2-Acrylamido-2-methylpropanesulfonic acid (AMPS) grafted onto a PSf UF hollow fiber membrane [reproduced from ref. 117 with permission from Elsevier, copyright 2023]. (f) 2,5-Diaminobenzenesulfonic acid (DABSA)-incorporated polyamide layer TFC membrane [reproduced from ref. 110 with permission from Elsevier, copyright 2023]. | |
Habibi et al. investigated the performance of SiO2 nano-particles and/or polydopamine layer-modified PSF membrane for Cr(VI) removal.168 A lower rejection of the order of 40% was achieved for the membranes at higher pH, presumably due to the rejection being more charge repulsion-dominated between the negatively charged hydroxyl groups of the silica nanoparticles. At lower pH, the protonation of amide groups leads to an enhanced adsorptive capacity on the polydopamine selective layer, which is now positively charged. Additionally, the macro-voids of the hybrid membranes were suppressed by the addition of polydopamine, thereby aiding in the retention of chromium ions by steric hindrance. Improved connectivity of pores between the sub-layer and bottom layer with increased hydrophilicity was obtained by CA-MMM with epoxy-functionalized PES.107 The percentage rejection of Cr(VI) at CA/EPS 80/20 wt% blend composition was 98.3%, attributed to the formation of sponge-like pore morphology as well as complexation between chromium ions and PEI. The MOFs such as UiO-66 NH2 and ZIF-8 were introduced in the PVDF membrane and coated with CS nanofibers.108 The PVDF/CS nanofibrous membrane containing 20 wt% UiO-66-NH2 exhibited a maximum water flux of 470 LMH and 95.6% Cr(VI) rejection [Fig. 6(b)]. Further, grafting the nano-crystallites of UiO-66-NH2 MOF on cellulose fibers immobilized on filter paper demonstrated more than 84% Cr(VI) removal.211 The grafting process was facilitated by surface functionalization of the cellulose fibers to express terminal carboxylate groups that act as anchoring sites to coordinate Zr(IV) ions. An approach to tune the pore size and membrane surface charge of the PAN membrane by hydrolysis using NaOH was developed by Muthumareeswaran et al. The hydrolyzed PAN membranes showed >90% rejection of Cr(VI) mainly due to the Donnan repulsion by the COO− functional groups present in the pore wall as well as the membrane surface.189
Aspartic acid-functionalized GO nanolayers were synthesized to fabricate polyvinylchloride (PVC) composite membranes to remove chromium from a humic acid (HA) mixed feed water.146 It showed the bridging effect of Cr cation between HA molecules as an electrostatic interaction, leading to the formation of large-size HA–Cr complexes, resulting in an increment in Cr removal using membrane filtration, as shown in Fig. 6(c). Also, the ligand and metal ions undergo associative substitution, forming stable chelate rings during the filtration process and increasing the lone Cr removal. Further, Mukherjee et al. demonstrated the use of pure GO-based MMM wherein 0.2 wt% GO-impregnated PSF membrane resulted in the removal of Cr6+ ions to the extent of 154 mg g−1 at pH 3.9.109 The electrostatic interaction between the negatively charged membrane surface and positively charged metal ions facilitated the adsorption, leading to high rejection. The membrane also effectively removed other ions, such as Cd, Cu, and Pb, as indicated in Fig. 6(d). Zhang et al. developed GO framework-based (GOF) membrane using isophorone diisocyanate (IPDI) as a cross-linker.217 The results of filtration experiments and microstructure characterization confirmed that IPDI cross-linking GO enhanced the structural stability and enlarged the nano-channels among GO sheets for higher water permeability of 100 LMH. It was also noticed that an increase in pH increased the carboxyl and hydroxyl group dissociation within the GO sheets, thereby leading to a higher density of negative charges. Thus, the membrane showed excellent rejection for Cr3+ ions (89.6%) at pH > 9.6 due to the electrostatic interaction of GO via adsorption.
5.7 NF membranes for chromium removal
An MMM was prepared using L-cysteine functionalized POSS and methyl-methacrylate (MMA) applied on a polyether-imide-TFN membrane.213 The presence of POSS strongly enhanced the adsorption of prepared membranes due to increased adsorption sites and affinity of POSS nanoparticles for metal ions. The functional groups with negative charges, such as –COO– and –O–, repel divalent anions. The flux could reach up to 70.63 LMH, and the rejection of chromium was 81%. Porous amine-functionalized MCM-41 nanoparticles (NH2-MCM-41) were grafted on a PVDF-TFC UF membrane as it formed a hydrophilic and adsorptive layer on the membrane surface.218 The electrostatic interaction between Cr(VI) anions and protonated amino groups in an acidic solution was the driving force that led to a maximum adsorption capacity of 2.8 mg g−1. Due to its small pore size and enhanced surface hydrophilicity, the modified UF membrane acted as a barrier to effectively restrict the large NOM molecules and reduced their direct adsorption on the membrane surface.218,219 A novel NF hollow fiber membrane with a high negative charge and permeate flux prepared by the grafting of 2-acrylamido-2-methylpropanesulfonic acid (AMPS) onto a PSf UF hollow fiber membrane also showed excellent high Cr(VI) rejection even in the presence of salts of Na2SO4 and NaCl, as indicated in Fig. 6(e).220 The presence of sulfonic groups on the membrane surface showed a stronger electrostatic repulsion effect on chromium's divalent and monovalent ions. The negative charge of the membrane could also be increased by introducing 2,5-diaminobenzenesulfonic acid (DABSA)110 or poly(m-phenylene isophthalamide) (PMIA)111 over the NF membrane substrate layer. The membrane was negatively charged over a wide pH range and showed rejection >80%, as indicated in Fig. 6(f), due to the charge repulsion phenomenon in both synthetic and industrial wastewater. PMIA is an aromatic polyamide possessing self-charged characteristics that increase the NF membrane's negative surface charge and thus result in increased ion removal by Donnan exclusion.
TiO2 nanoparticles have also shown applicability in NF membranes due to their hydrophilic, photocatalytic, and charged properties. Accordingly, CS thin films were developed on plain PSf and PSf/TiO2 membrane substrates using PVA as a binder. The composite membrane achieved about 100% reduction of Cr(VI) to Cr(III) through electrons and protons donated from the OH and NH2 groups of the CS layer and further got adsorbed to give chromium-free water.54 A photocatalytic TFC membrane was modified by a layer of CS as an adsorbent and then coated with a layer of zerovalent iron@titanium dioxide (nZVI@TiO2) nanoparticles via layer-by-layer technology.116 The presence of the nanofillers improved the hydrophilicity of the membrane and consequently, flux up to 39.7 LMH was achieved. The presence of an additional layer of CS and nZVI@TiO2 nanoparticles on the TFC membrane caused more resistance to Cr(VI) ions' penetration into the membrane, causing a significantly higher rejection (97.63%). Similarly, the PAN membrane with TiO2 fillers could also reject chromium up to 83.27% with 71.801 LMH permeability. A polyphenylsulfone (PPSU) NF membrane with carboxylated-GO has demonstrated more than 98% removal of both As(V) and Cr(VI) with a flux of 27 LMH due to the enhanced negative charge of the membrane surface.221 Bagheripour et al. investigated the performance of an NF membrane by incorporating composite GO/CS (GOC) nanoplates.114 The GOC-modified membranes showed higher hydrophilicity, flux and rejection, and a smoother surface. Increased membrane hydrophilicity also improves the wettability of the membrane surface, which enhances the ion's collisions with the membrane surface, thereby improving the possibility of solute adsorption on active sites of composite nanoplates. Additionally, the high affinity of chitosan for metal ions adsorption enhances the rejection and overall produces a high-quality permeate. GO was further used along with PEI as a cationic polymer and glutaraldehyde as a cross-linking agent, and more than 90% Cr(VI) removal efficiency was achieved.118
5.8 UF membranes for fluoride removal
An adsorptive UF composite PVDF membrane blended with maifanite (MFS) and activated alumina (AA) named MFS-AAPVDF was investigated for fluoride removal from water.170 The composite membrane reported 84.04% removal of fluoride at an initial concentration of 12.37 mg L−1 due to the development of protonated membrane surface, stimulating the adsorption of fluoride ions at lower pH. CA-based MMM was prepared using mixed Fe–Al–Mn@CS as a nanofiller with increased fluoride ion adsorption capacity, as shown in Fig. 7(a).171 Interestingly, after the subsequent adsorption of fluoride ions, the membrane surface developed a negative charge, and further enhancement in rejection occurred due to the electrostatic repulsion phenomenon. Similarly, an iron oxide-modified PES/CA membrane for fluoride adsorption was developed with 18 wt% PES, 2 wt% CA, and 0.5 wt% Fe2O3 nanoparticles, exhibiting a maximum pure water flux of 156 LMH and fluoride removal efficiency of 70.3%.222 The membrane also demonstrated reusability for 8 cycles with a constant rejection rate, indicating durability, and showed promising results in fluoride-contaminated real water samples. Based on the fluoride removal studies, it was determined that adsorption is the primary mechanism for removing fluoride ions, and the quantity and dispersion of Fe2O3 nanoparticles are crucial for membrane performance. The presence of a higher amount of iron oxide nanoparticles led to increased defects and heterogeneity in the membranes, and the subsequent agglomeration of nanoparticles reduced the available surface area for fluoride adsorption, resulting in lower fluoride removal efficiency.
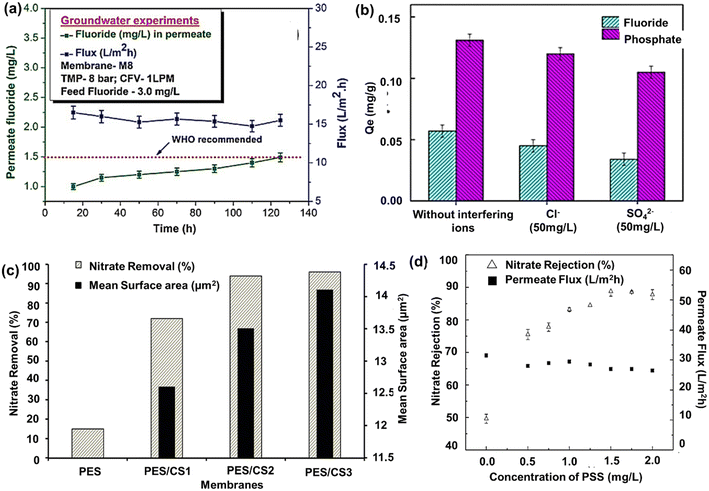 |
| Fig. 7 Fluoride removal performance by (a) Fe–Al–Mn@CS-based metal oxides blended cellulose acetate MMM [reproduced from ref. 171 with permission from Elsevier, copyright 2023]. (b) Exfoliated Mg–Al–Fe layered double hydroxides/PES membranes [reproduced from ref. 126 with permission from Elsevier, copyright 2023]. Nitrate removal performance by (c) commercial NF membrane modified using PSS [reproduced from ref. 129 with permission from Springer Nature, copyright 2023]. (d) PES NF membrane-embedded by CS nanoparticles [reproduced from ref. 128 with permission from Elsevier, copyright 2023]. | |
An MMM of exfoliated Mg–Al–Fe layered double hydroxides (LDHs) incorporated in PES displayed a much higher adsorption capacity for fluoride (1.61 mg g−1).126 Fluoride ion is a hard base due to its high electronegativity and small ionic size and therefore displays a strong affinity for electropositive multivalent metal ions (Al3+, Fe3+) on LDHs. It was also observed that removal was slightly affected due to the presence of chloride and sulfate ions due to the ion-interference phenomenon [Fig. 7(b)]. Karmakar et al. developed an aluminium fumarate (AlFu) metal–organic framework-polyacrylonitrile hollow fiber MMM for selective fluoride removal from real-time groundwater. The MMM with 10 wt% AlFu could withstand for more than 20 h and achieved about 205 mg g−1 adsorption capacity and 20 LMH of permeate flux. The MOF's positive charge at lower pH promotes fluoride adsorption by replacing OH− ions, and the smaller hydrated fluoride atoms readily bond with polar Al atoms through electrostatic interaction, leading to greater adsorption.223 Chatterjee and De demonstrated an efficient removal of fluoride using activated alumina fillers doped on CAP membrane.127 The CAP membrane could reject fluoride in the range of 88–92% at a feed concentration of 12 mg L−1. It was observed that at pH < pHZPC, the MMM surface became positively charged, favoring the attraction of negatively charged fluoride ions. Thus, the adsorption phenomenon seemed dominant concerning the fluoride removal mechanism, but it was significantly influenced by electrostatic interaction and the pH of the solution. It was also noted that low trans-membrane pressure and higher cross-flow rate favored the adsorption-dominated filtration.
Another novel synthesis of crystalline TiO2 nanoparticles using Bacillus licheniformis bacteria was done by their modification with an alumina precursor to form an Al2O3/TiO2 nanocomposite. This hybrid nanocomposite was impregnated onto thermoplastic polyurethane nanofibers. Fluoride adsorption onto the nanocomposite is attributed to the formation of surface complexes, and the extent of adsorption depends on the number of exchangeable surface hydroxyl groups.224 Carbonized bone meal CBM-impregnated UF grade hollow fiber MMM for fluoride removal from groundwater was checked by Chatterjee et al. Incorporating calcium and phosphate groups into the membrane significantly increases the fluoride uptake capacity compared to a pure polymeric membrane.225 Fluoride ions are sorbed on the surface of the MMM and interact with the calcium and phosphate groups in CBM, facilitating their removal and extending up to 5 mg g−1. The limited removal by the pure polymeric membrane is attributed to electrostatic repulsion between fluoride ions and the sulfone group in the membrane.
5.9 NF membranes for fluoride removal
Monovalent F− are difficult to reject by NF membranes due to their small hydration size. A porous alumina-supported NF membrane was fabricated by depositing 4.5-bilayer poly(styrene sulfonate) (PSS)/poly(diallyldimethylammonium chloride) (PDADMAC) films by a layer-by-layer technique.172 The fabricated NF membrane resulted in F− rejection extending up to 73%. Interestingly, size exclusion played an important role in increasing the rejection rate of F− ions. The selectivity of PSS/PDADMAC membranes is a strong function of the number of deposited layers, indicating that the NF properties are very sensitive to the film structure. A graphene-based nanocomposite membrane was synthesized by interfacial polymerization through the chemical bonding of the GO layer to the PES surface.99 The membrane was operated in a cross-flow mode, revealing more than 98% arsenic and 80% fluoride removal. A significant finding was that the removal occurred while selectively retaining the useful calcium and magnesium minerals in drinking water. The membrane module had a flux of about 150 LMH during operation over long hours (>150 h) with a pressure of about 15 bar. The membrane module had only a 3–5% drop in flux, indicating antifouling characteristics.
5.10 UF membranes for nitrate removal
Bahmani et al. studied an adsorptive UF-MMM, consisting of PAN and α-Fe2O3 nanoparticles, developed for removing nitrate (NO3−) from aqueous solutions.173 α-Fe2O3 nanoparticles are hydrophilic, and the accumulation of such functional groups attracts water molecules to the membrane surface, allowing easy diffusion of water into the membrane matrix. At lower pH, the H+ ion concentration increased, which made the membrane surface positively charged. Thus, negative charged NO3− was removed to the extent of 85% in the pH range of 3–4. Breida et al. investigated the use of γ-Al2O3 ultrafiltration (UF) membrane for the removal of NO3− from aqueous solutions containing 50 mg L−1 NO3− in tangential filtration mode.226 The γ-Al2O3 membrane displayed amphoteric properties, with its surface charge varying with pH. When the pH of the solution was lower than the pHpzc (8.5) of the membrane, the membrane surface became positively charged, leading to the rejection of cations. As a result of electroneutrality, NO3− ions were also rejected. The charge of the cations played a significant role, with the rejection rate surpassing 80% for the divalent cation Mg(NO3)2 and reaching 50% for the monovalent cation NaNO3. CS nano-biopolymers (CS-NPs) were synthesized using tripolyphosphate and transferred into the organic solvent via the solvent exchange method and integrated into the PES membrane.128 Almost complete removal of nitrate ions was achieved using the MMM having CS-NPs for 20 mg L−1 nitrate-contaminated water at 0.45 MPa pressure, as seen in Fig. 7(c). It was reported that the removal of nitrate by the composite membranes embedded by CS nanoparticles is dominantly governed by the adsorption process. Hollow fiber MMM of PAN and 5 wt% Al2O3 was investigated by Mukherjee and De, leading to enhanced hydrophilicity and nitrate adsorption capacity (15 mg g−1).174 The dominant mechanism was suggested to be adsorption on increased active sites in MMM due to the strong presence of alumina particles. MMMs fabricated using PSf and GO nanosheets created a porous structure, increasing the flux to 49.92 LMH with 39% nitrate removal efficiency.175 The dominant mechanism of nitrate removal is rejecting the ions from the membrane surface by electrostatic repulsion or the Donnan effect.
5.11 NF membranes for nitrate removal
A commercial NF membrane was modified using poly(sodium 4-styrenesulfonate) (PSS) to improve the nitrate rejection from groundwater.129 Coating of PSS onto the virgin membrane enhanced the surface negative charge density. The rejection increased with an increase in PSS concentration, with 1.5 mg L−1 giving optimum results, as observed in Fig. 7(d). The as-modified membrane achieved a nitrate rejection rate of up to 88.8% and a permeate flux of 27 LMH. Notably, the membrane showed little deviation in the rejection rate over a wide pH range. In the process of surface modification of the virgin NF membrane, PA was hydrolyzed by sodium hydroxide, which generated carboxyl and amino groups. The amino group might be protonated at low pH, causing an electrostatic repulsion between the charged groups. This repulsion may reduce the pore size and thus maintain high nitrate rejection at lower pH.
6. Effect and mechanism of mixed ions on membrane performance
The presence of co- and counter ions in real-time groundwater can affect the filtration performance of any membrane due to their interference with the charges of the targeted contaminant ion and the membrane's charge. The presence of cations such as Ca2+ can enhance the removal of the anionic contaminants because it can interact with the membrane, reducing its negative charge and causing lesser electrostatic repulsion between the negatively charged sites within the membrane structure. Additionally, the membrane pores are compressed to a narrower size that restricts the passage of the anions, leading to a higher removal efficiency.227 In contrast, the presence of monovalent sodium ions (Na+) as sodium chloride (NaCl) salt could decrease the rejection as they tend to weaken the charge exclusion process, which is a dominant rejection mechanism for anions such as arsenate and chromate.72 For example, the impact on the presence of coexisting ions alongside Cr(VI) was investigated by H. Xu et al. using a solution containing 1 mM Cr(VI) along with Na2SO4, NaCl, or MgSO4 salts at concentrations of 1.5 mM, 3 mM, and 1.5 mM, respectively. The presence of NaCl and MgSO4 inhibited the retention by the NF membranes, respectively, since the divalent cation Mg2+ enhanced the shielding effect on membrane charges, facilitating the transfer of anionic Cr(VI) ions by reducing the electrostatic interaction between the negative charges on the membrane and anions in the solution.220
The adsorption of metal ions on the membrane surface is influenced by their electronegativity and positive charge density.216,228 Metal ions with higher electronegativity and positive charge density tend to exhibit higher adsorption. For example, Pb2+ with an electronegativity value = 2.3 showed higher adsorption compared to Cu2+ with an electronegativity value = 1.9 due to the higher electronegativity of Pb. Additionally, Pb has lower hydration energy and a lower first hydrolysis constant (pK1) compared to Cu, which favors the formation of MOH+ and enhances adsorption on the membrane surface. These variations in the rejection of toxic heavy metal ions in different feed solutions can be attributed to the presence of various organic and inorganic components, particularly cations, in the water composition. These components act as shields, affecting the interaction between the heavy metal ions and the membrane surface.123 A study was conducted to investigate the impact of chloride, sulfate, pH, and temperature on groundwater defluoridation using a nanofiltration (NF) membrane, as well as the occurrence of membrane fouling. Among the various ions present in the groundwater, sulfate exhibited the highest rejection rate. This can be attributed to the electronegative nanomembrane having a Donnan repulsion effect, where ions with higher charge values experience stronger repulsion from the membrane. Additionally, the rejection rate of ions with the same charge value varied depending on their radius, with smaller ions being more effectively rejected. For instance, the rejection ratio of NO3− was higher than that of NO2−. Fluoride and chloride, belonging to the halogen family, displayed an increase in the atomic radius with nuclear charge and electronic shell, similar to their corresponding ions. However, as the ion radius increased, the negative charge value decreased, and consequently, the rejection ratio of fluoride decreased steadily. In addition to the Donnan repulsion effect, other transport mechanisms contributing to ion rejection were convection and diffusion, which depended on the thickness of the membrane's active layer. While convection mechanisms were more prominent at low transmembrane pressure, diffusion mechanisms became predominant, especially when using the PPSU/carboxylated-GO membrane.112
The rejection and selectivity of different ions in a mixed solution depend on several ionic characteristics such as hydrated radius, hydration-free energy, fluidity of near membrane boundary layer, and flexibility of the hydration shell.80,82 The apparent size of ions in water is determined by their hydrated radius rather than their ionic radius. During membrane transport, ions with weak hydration potential can temporarily rearrange the water molecules in their hydration shells due to shear stress from transmembrane pressure.80 The arrangement of water molecules around charged ions is highly structured and dependent on the ionic charge. Anions, having more electrons in their outermost shells, are generally larger than cations with similar atomic numbers. However, the hydrated radii of anions are typically smaller because they can hold fewer water molecules in their hydration shells due to the closer positioning of hydrogen atoms.229 For cations such as Ca2+ and Mg2+, hydrated radii decrease with increasing ionic radii, but there is no clear correlation between the hydrated radii and ionic radii for anions.230 Hydration free energy measures the stability of hydrated ions compared to their unhydrated forms. During membrane filtration, higher transmembrane pressures can lead to a loss or rearrangement of water molecules in the hydration shells.231 Ions with lower hydration energies (cations) have soft hydration shells, can more easily lose the water molecules in their hydration shells, and permeate through the membrane compared to some anions. In the case of negatively charged NF membranes, cations are less retained than anions due to the attractive interactions between the solute and membrane that facilitate their passage. Thus, useful cations like Ca2+ and Mg2+ were found to be retained by highly negatively charged GO-coated PES NF membrane for decontaminating fluoride and arsenic-polluted groundwater.232,233
7. Challenges and future direction
Although having remarkable properties, membrane technology still faces multiple challenges in terms of simultaneous enhancement of selective ions removal and flux at a lower pressure. A few of the challenges and future prospects are highlighted in Fig. 8. Mixed matrix or blended membranes incorporated with nanofillers have evidenced better rejection of heavy metal ions and improved flux. However, a key bottleneck to nanotechnology applications for water purification is the availability of suppliers to provide large quantities of nanomaterials at economically viable prices.234 The bulk synthesis of such nanofillers/nanoparticles on a laboratory scale is a strenuous task; thereby, there is a need to explore facile methods of synthesizing nanoparticles at a greater scale. Other typical challenges faced while fabricating blended membranes are the possibility of agglomeration of nanofillers in the membrane matrix due to improper adhesion and homogeneous particle distribution,235 leakage in the permeate,236 toxic nature of filler materials,237 and development of interfacial and surface pattern defect on the membranes.238
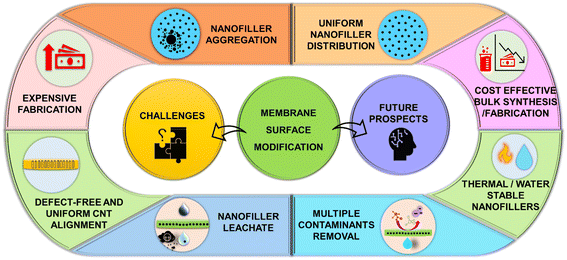 |
| Fig. 8 Typical challenges and future scope for the surface-modified membranes. | |
Carbon-based nanomaterials, such as CNTs and GO, have been extensively investigated for use in polymer composite membranes for water purification applications. Despite their abundant charged functional groups, fabricating and synthesizing these membranes at a commercial scale can be challenging as pristine CNT and GO membranes often exhibit poor mechanical and aqueous stability, aggregation, and reduced flexibility.150 Furthermore, CNT synthesis is complex and expensive, and the alignment of CNTs within composite membranes can significantly impact the membrane selectivity and flux. Increasing CNT concentration and alignment within polymer matrices is crucial for successfully commercializing CNT composite membranes.150,239 In graphene-based membranes, the design of channel pores is critical to prevent the passage of ions. However, achieving a precise control of the pore size remains challenging in membrane design.
Additionally, there is a significant knowledge gap in the ecotoxicological effects of graphene-based materials. Poor adhesion between GO layers and the underlying polymeric membrane is another obstacle in the development of GO membranes. Surface functionalization and activation techniques require further studies to develop unique protocols for GO membrane fabrication on a larger scale. Furthermore, although GO exhibits excellent chemical resistance, solvent-based applications require both the support and selective layer to resist the medium of operation, limiting the choice of porous substrates available for membrane fabrication.240–242
MOFs present a bright future as selective materials due to their tunable nature of the pore, selectivity, appended functionality, fast capture kinetics, and regeneration capacity.243 However, the performance of MOF-functionalized membranes should be evaluated in real-world conditions to validate their effectiveness and feasibility for large-scale water and wastewater treatment applications. This includes studying the membrane's performance under variable operating conditions, such as changes in pH, temperature, and ionic strength.244,245 Furthermore, the selectivity and permeability of the membrane should be optimized for specific applications, such as removing specific contaminants or recovering specific nutrients. Another important consideration is the environmental impact of MOF-functionalized membranes, particularly in terms of their disposal at the end of their useful life. Studies should be conducted to evaluate the potential risks associated with releasing MOF fillers into the environment as well as the feasibility of recycling or repurposing the membranes. Finally, it is important to consider the economic feasibility of MOF-functionalized membranes. While they offer promising advantages in terms of selectivity and permeability, the cost of MOF fillers and their incorporation into membranes must be carefully considered. Studies should be conducted to evaluate the cost-effectiveness of MOF-functionalized membranes compared to conventional TFC membranes and other advanced membrane technologies. In summary, while MOF-functionalized membranes offer promising potential for water and wastewater treatment applications, there are still several challenges that need to be addressed, including optimizing the synthesis and incorporation of MOFs into membranes, ensuring long-term stability and water resistance, understanding the transport properties of the membrane, and evaluating the environmental and economic impacts of the technology.140,246–248
The economic aspect is essential in the futuristic development of surface-modified UF and NF membranes. The cost economics of ultrafiltration (UF) and nanofiltration (NF) membrane modification can vary depending on several factors, including the type of modification, nanomaterial used, scale of the project, and specific application. UF membranes are low-pressure driven membrane processes due to their cost-effectiveness in terms of CAPEX and OPEX. Strategies such as adsorptive UF membranes can significantly enhance the structural porosity and require much lower working pressure to achieve high water flux and, thus, the operating cost of the membrane system.249 While composite materials have the superior advantage of combining the properties and functionalities of both organic and inorganic materials, their preparation procedures are often complex and costly. Materials such as TiO2 and ZnO nanoparticles have been extensively used in membrane modifications wherein ZnO nanoparticles are estimated to have one-fourth cost compared to TiO2.250 Additionally, they possess strong hydrophilicity as well as charged functional groups like –OH, –SO3H, and –COOH,202 which make them suitable for large-scale applications. Clayey materials have emerged as promising nano-engineered materials due to their cost-effective and environment-friendly nature, making them excellent candidates for blended polymeric membranes. A comprehensive study on four different types of nanomaterials was conducted by Shoshaa et al. by gauging them on their separation performance, antifouling properties, leaching toxicity, preparation simplicity, and cost-effectiveness. The inorganic fillers were deemed more cost-friendly, followed by carbon-based nanomaterials and composite-based nanomaterials.251
One of the most prominent disadvantages of commercially available membrane systems is the fouling issue, which contributes to a higher OPEX. As per a study by Jafari et al., the cost of fouling as a fraction of OPEX is about 11% for anoxic groundwater treatment by NF membranes.252 Hence, developing membranes with high antifouling ability and separation performance by different surface modification methods has become imperative. Recently, Song et al., performed a cost-evaluation of a novel NF membrane prepared by coating sulfonated poly(ether ether ketone) over UF membrane for arsenic removal from groundwater.38 A preliminary cost estimation for arsenic rejection from the water source was set, assuming a working time of 300 days per year and a treatment capacity of 1000 m3 h−1. The total cost of producing drinking water was 0.15 $ per m3, considering factors such as membrane permeability, module geometry, recovery rate, lifetime of the membrane system, labor cost, and cost of electricity. Generally, the market price of NF membranes is higher than that of UF membranes. However, in this case, the cost of the modified NF membrane module was marginally higher than the market price of UF membrane module (35–50 $ per m2)253,254 with excellent quality water. However, this study was limited to pentavalent arsenic removal without considering the antiscalant cost, and further extensive study is needed with trivalent arsenic removal. Since pilot-scale studies on real-time applications for SMMs are very limited, it is very difficult to conduct the techno-economic analysis of these membranes, and more future pilot-scale studies are required for a better estimate.
Understanding the structure–property–performance relationship is essential for developing membranes with improved selectivity and performance. There is a growing demand for efficient and cost-effective membranes for water treatment, especially for the simultaneous removal of mixed heavy metal ions from aqueous solutions. Therefore, research efforts must be directed toward developing membranes that can selectively remove heavy metal ions, even in the presence of other ions. In addition, developing membranes for real-time groundwater treatment is another area that needs attention. These membranes must have high selectivity, high permeability, and good stability under varying conditions. Moreover, long-term stability and durability are critical for membranes in water treatment applications. Therefore, research efforts must also focus on developing membranes that can withstand harsh environments and maintain their performance over extended periods. Scaling up membrane manufacturing is another challenge that needs to be addressed. To make these membranes commercially viable, developing cost-effective and scalable manufacturing processes is essential. Additionally, efforts must be directed toward developing membranes that can be easily integrated into existing water treatment processes. Overall, there is a need for interdisciplinary collaborations to develop membranes with improved selectivity, performance, and scalability for water treatment applications.
8. Conclusion
Membrane filtration is a promising technology for the removal of toxic groundwater contaminants such as arsenic, cadmium, chromium, copper, fluoride, and nitrate. Cost and space constraints often challenge traditional technologies, making membrane technology an attractive alternative. However, there is a trade-off between selectivity and permeability for membranes. One emerging field in membrane science and technology is tuning the membrane surface for the selective removal of metal ions, improving flux, and enhancing fouling mitigation capacity. Surface modifications of membranes can be achieved through blending, coating, grafting, and tuning pore size. The blending of polymers with nanofillers and/or other supporting polymers in a mixed matrix/composite membrane approach is a facile method for improving the selective nature of membranes without compromising flux. Nanoparticles such as SiO2, MgO, ZnO, and FeS have been widely explored with promising results for the surface modification of membranes. These nanoparticles possess high hydrophilicity, charged functional groups, and pore-tightening ability, which can be incorporated into polymers for tuning their surfaces and enhancing the rejection of ionic heavy metals and contaminants. Carbon-based nanomaterial membranes, such as CNT and GO-based membranes, have the potential to sequester major heavy metal ions. The functionalization of CNTs and GO and their integration into a polymer matrix add hydroxylic, carboxylic, and amidic groups, which are predominantly responsible for the rejection of metal ions.
Different surface modification methods can be used for anionic and cationic metal ions. Ions of arsenic, chromium, fluoride, and nitrate are anionic; hence, Donnan exclusion and steric repulsion govern their rejection, followed by adsorption on active sites. In contrast, it is anticipated that cations of cadmium and copper are dominated by the adsorption phenomenon on negatively charged porous membranes. MOFs are novel nanocrystalline cage-like structured nanoparticles that exhibit superior water permeability and high selectivity toward different metal ions. Coating MOFs on membrane surfaces can improve pure-water flux due to the presence of a highly hydrophilic aperture of the MOFs. Due to charged nodes and concise apertures, the targeted metal ions are rejected through the Donnan exclusion phenomenon, making MOF-based membranes extensively studied and showing better opportunities for their development in water purification technologies. Overall, investigating different surface modifications for UF and NF membranes is desirable to lower the excess demand of energy and cost required by high pressure-driven membrane systems such as reverse osmosis systems. Knowledge of the properties of different nanomaterials, nanocomposites, and cost-effective fabrication methods of such selective membranes can contribute to developing new-generation membranes with tunable surfaces.
Conflicts of interest
There are no conflicts to declare.
Acknowledgements
We gratefully acknowledge the Department of Science and Technology (DST; Grant No. DST/TMD-EWO/WTI/2K19/EWFH/2019/395(C1); SP/YO/2019/1579(G)) and the Indian Institute of Technology Bombay (IITB) for their financial support. Mitil. M. Koli acknowledges the Ministry of Education, India, for the Prime Minister Research Fellowship (PMRF) support, and Swatantra P. Singh acknowledges the DST-Inspire Faculty Award for the support.
References
-
A. J. Jakeman, O. Barreteau, R. J. Hunt, J. D. Rinaudo and A. Ross, Integrated Groundwater Management: Concepts, Approaches and Challenges, 2016, pp. 1–762 Search PubMed
.
- A. I. Stefanakis, D. Zouzias and A. Marsellos, Environ. Eng. Sci., 2015, 4, 82–102 Search PubMed
.
- M. S. Díaz-Cruz and D. Barceló, Chemosphere, 2008, 72, 333–342 CrossRef PubMed
.
- A. O. Talabi and T. J. Kayode, J. Water Resour. Prot., 2019, 11, 1–19 CrossRef CAS
.
- R. M. Coyte, K. L. McKinley, S. Jiang, J. Karr, G. S. Dwyer, A. J. Keyworth, C. C. Davis, A. J. Kondash and A. Vengosh, Sci. Total Environ., 2020, 711, 135135 CrossRef CAS PubMed
.
- E. Shaji, M. Santosh, K. V. Sarath, P. Prakash, V. Deepchand and B. V. Divya, Geosci. Front., 2021, 12, 101079 CrossRef CAS
.
- M. Sen, A. Manna and P. Pal, J. Membr. Sci., 2010, 354, 108–113 CrossRef CAS
.
-
A. Kubier, Ph.D. Dissertation, Universität Bremen, 2019 Search PubMed
.
- A. Kubier, R. T. Wilkin and T. Pichler, Appl. Geochem., 2019, 108, 104388 CrossRef CAS PubMed
.
- N. Idrees, B. Tabassum, E. F. Abd Allah, A. Hashem, R. Sarah and M. Hashim, Saudi J. Biol. Sci., 2018, 25, 1365–1368 CrossRef CAS PubMed
.
- S. Mani Tripathi and S. R. Chaurasia, Eng. Sci. Technol. Int. J., 2020, 23, 1153–1161 Search PubMed
.
- P. Li, D. Karunanidhi, T. Subramani and K. Srinivasamoorthy, Arch. Environ. Contam. Toxicol., 2021, 80, 1–10 CrossRef CAS PubMed
.
-
C. D. Palmer and R. W. Puls, EPA Groundwater Issue: Natural Attenuation of Hexavalent Chromium in Groundwater and SoilsUnited States Environmental Protection Agency, 1994 Search PubMed.
-
In situ treatment of soil and groundwater contamination with chromium, National Risk Management Research Laboratory, United States Environmental Protection Agency, Cincinnati, Ohio, 2000 Search PubMed.
- S. K. Sharma, B. Petrusevski and G. Amy, J. Water Supply: Res. Technol.--AQUA, 2008, 57, 541–553 CrossRef CAS
.
- F. Burke, S. Hamza, S. Naseem, S. Nawaz-ul-Huda, M. Azam and I. Khan, SAGE Open, 2016, 6, 215824401663440 CrossRef
.
- S. Alka, S. Shahir, N. Ibrahim, M. J. Ndejiko, D. V. N. Vo and F. A. Manan, J. Cleaner Prod., 2021, 278, 123805 CrossRef CAS
.
-
K. Brindha and L. Elango, Fluoride: Properties, Applications and Environmental Management, 2011, pp. 113–136 Search PubMed
.
- M. M. Damtie, Y. C. Woo, B. Kim, R. H. Hailemariam, K. D. Park, H. K. Shon, C. Park and J. S. Choi, J. Environ. Manage., 2019, 251, 109524 CrossRef CAS PubMed
.
- J. Hao, M. J. Han, S. Han, X. Meng, T. L. Su and Q. K. Wang, J. Environ. Sci., 2015, 36, 152–162 CrossRef CAS PubMed
.
- Y. He, J. Liu, Y. Duan, X. Yuan, L. Ma, R. Dhar and Y. Zheng, J. Environ. Sci., 2023, 125, 453–469 CrossRef PubMed
.
- S. V. Jadhav, E. Bringas, G. D. Yadav, V. K. Rathod, I. Ortiz and K. V. Marathe, J. Environ. Manage., 2015, 162, 306–325 CrossRef CAS PubMed
.
- P. L. Smedley and D. G. Kinniburgh, Appl. Geochem., 2002, 17, 517–568 CrossRef CAS
.
- S. K. M. Huno, E. R. Rene, E. D. Van Hullebusch and A. P. Annachhatre, J. Water Supply: Res. Technol.--AQUA, 2018, 67, 885–902 CrossRef
.
- E. Sacchi, M. Acutis, M. Bartoli, S. Brenna, C. A. Delconte, A. Laini and M. Pennisi, Appl. Geochem., 2013, 34, 164–180 CrossRef CAS
.
- S. Tyagi, D. Rawtani, N. Khatri and M. Tharmavaram, J. Water Process. Eng., 2018, 21, 84–95 CrossRef
.
- H. Xu, K. Xiao, X. Wang, S. Liang, C. Wei, X. Wen and X. Huang, Front. Chem., 2020, 8, 1–14 CrossRef PubMed
.
- T. Nguyen, F. A. Roddick and L. Fan, Membranes, 2012, 2, 804–840 CrossRef CAS PubMed
.
-
A. L. Srivastav and M. Ranjan, Inorganic Pollutants in Water, 2020, pp. 1–15 Search PubMed
.
- A. Hafiane, D. Lemordant and M. Dhahbi, Desalination, 2000, 130, 305–312 CrossRef CAS
.
- M. Tahaikt, R. el Habbani, A. Ait Haddou, I. Achary, Z. Amor, M. Taky, A. Alami, A. Boughriba, M. Hafsi and A. Elmidaoui, Desalination, 2007, 212, 46–53 CrossRef CAS
.
- I. Ali, T. A. Khan and M. Asim, Sep. Purif. Rev., 2011, 40, 25–42 CrossRef CAS
.
- S. Sam, S. P. Malinga and N. Mabuba, Membranes, 2021, 11, 1–21 Search PubMed
.
- B. Yu, Y. Zhang, A. Shukla, S. S. Shukla and K. L. Dorris, J. Hazard. Mater., 2000, 80, 33–42 CrossRef CAS PubMed
.
- X. Yeoh, S. N. A. M. Jamil, F. Syukri, M. Koyama and M. Nourouzi Mobarekeh, Water, 2022, 14, 3778 CrossRef
.
- X. Liu, Z. Ren, H. H. Ngo, X. He, P. Desmond and A. Ding, Water Cycle, 2021, 2, 51–63 CrossRef
.
- N. S. Suhalim, N. Kasim, E. Mahmoudi, I. J. Shamsudin, A. W. Mohammad, F. M. Zuki and N. L. A. Jamari, Nanomaterials, 2022, 12, 3 CrossRef PubMed
.
- J. Song, M. Zhang, A. Figoli, Y. Yin, B. Zhao, X. M. Li and T. He, Environ. Sci.: Water Res. Technol., 2015, 1, 839–845 RSC
.
- Z. Liang, J. Wang, Q. Zhang, T. Zhuang, C. Zhao, Y. Fu, Y. Zhang and F. Yang, Sep. Purif. Technol., 2021, 276, 119308 CrossRef CAS
.
- H. B. Park, J. Kamcev, L. M. Robeson, M. Elimelech and B. D. Freeman, Science, 2017, 356, 1138–1148 CrossRef PubMed
.
- H. Zhang, Q. He, J. Luo, Y. Wan and S. B. Darling, ACS Appl. Mater. Interfaces, 2020, 12, 39948–39966 CrossRef CAS PubMed
.
- B. Corry, J. Phys. Chem. B, 2008, 112, 1427–1434 CrossRef CAS PubMed
.
- G. R. Xu, J. N. Wang and C. J. Li, Desalination, 2013, 328, 83–100 CrossRef CAS
.
- N. Nady, M. C. R. Franssen, H. Zuilhof, M. S. M. Eldin, R. Boom and K. Schroën, Desalination, 2011, 275, 1–9 CrossRef CAS
.
- A. Elrasheedy, N. Nady and M. Bassyouni, Membranes, 2019, 9, 1–31 CrossRef PubMed
.
- M. R. Esfahani, S. A. Aktij, Z. Dabaghian, M. D. Firouzjaei, A. Rahimpour, J. Eke, I. C. Escobar, M. Abolhassani, L. F. Greenlee, A. R. Esfahani, A. Sadmani and N. Koutahzadeh, Sep. Purif. Technol., 2019, 213, 465–499 CrossRef CAS
.
-
S. M. J. Zaidi, K. A. Mauritz and M. K. Hassan, Functional Biopolymers, Springer Cham, Switzerland, 2019, pp. 391–416 Search PubMed
.
- D. J. Miller, D. R. Dreyer, C. W. Bielawski, D. R. Paul and B. D. Freeman, Angew. Chem., Int. Ed., 2017, 56, 4662–4711 CrossRef CAS PubMed
.
-
B. Spivakov and V. Shkinev, Encyclopedia of Analytical Science, 2nd edn, 2004, pp. 524–530 Search PubMed
.
-
R. Singh and N. P. Hankins, Introduction to Membrane Processes for Water Treatment, Elsevier B.V., 2016 Search PubMed
.
- S. H. Mohamad, M. I. Idris, H. Z. Abdullah and A. F. Ismail, Adv. Mater. Res., 2013, 795, 318–323 Search PubMed
.
-
E. Nagy, Basic Equations of Mass Transport Through a Membrane Layer, 2019, pp. 1–10 Search PubMed
.
- C. N. Worou, Z. L. Chen and T. Bacharou, Water Pract. Technol., 2021, 16, 291–319 CrossRef
.
- M. S. Jyothi, M. Padaki, R. Geetha Balakrishna and R. Krishna Pai, J. Mater. Res., 2014, 29, 1537–1545 CrossRef CAS
.
- A. Marjani, A. T. Nakhjiri, M. Adimi, H. F. Jirandehi and S. Shirazian, Sci. Rep., 2020, 10, 1–11 CrossRef PubMed
.
- N. Nady, M. C. R. Franssen, H. Zuilhof, M. S. M. Eldin, R. Boom and K. Schroën, Desalination, 2011, 275, 1–9 CrossRef CAS
.
- D. Pichardo-Romero, Z. P. Garcia-Arce, A. Zavala-Ramírez and R. Castro-Muñoz, Processes, 2020, 8, 1–22 CrossRef
.
- L. I. Moran Ayala, M. Paquet, K. Janowska, P. Jamard, C. A. Quist-Jensen, G. N. Bosio, D. O. Mártire, D. Fabbri and V. Boffa, Ind. Eng. Chem. Res., 2018, 57, 14740–14748 CrossRef CAS
.
- C. Y. Tang, Q. S. Fu, C. S. Criddle and J. O. Leckie, Environ. Sci. Technol., 2007, 41, 2008–2014 CrossRef CAS PubMed
.
- Z. Yang, P. F. Sun, X. Li, B. Gan, L. Wang, X. Song, H. D. Park and C. Y. Tang, Environ. Sci. Technol., 2020, 54, 15563–15583 CrossRef CAS PubMed
.
- R. M. DuChanois, C. J. Porter, C. Violet, R. Verduzco and M. Elimelech, Adv. Mater., 2021, 33, 210131262 CrossRef CAS PubMed
; Z. Yang, P. F. Sun, X. Li, B. Gan, L. Wang, X. Song, H. D. Park and C. Y. Tang, Environ. Sci. Technol., 2020, 54, 15563–15583 CrossRef PubMed
.
- Z. Yang, P. F. Sun, X. Li, B. Gan, L. Wang, X. Song, H. D. Park and C. Y. Tang, Environ. Sci. Technol., 2020, 54, 15563–15583 CrossRef CAS PubMed
.
- B. Tansel, J. Sager, T. Rector, J. Garland, R. F. Strayer, L. Levine, M. Roberts, M. Hummerick and J. Bauer, Sep. Purif. Technol., 2006, 51, 40–47 CrossRef CAS
.
- A. G. Volkov, S. Paula and D. W. Deamer, Bioelectrochem. Bioenerg., 1997, 42, 153–160 CrossRef CAS
.
- J. Yoon, G. Amy, J. Chung, J. Sohn and Y. Yoon, Chemosphere, 2009, 77, 228–235 CrossRef CAS PubMed
.
- E. R. Nightingale, J. Phys. Chem., 1959, 63, 1381–1387 CrossRef CAS
.
- J. de Carvalho Izidoro, D. A. Fungaro and S. B. Wang, Adv. Mater. Res., 2011, 356–360, 1900–1908 Search PubMed
.
- D. Fanou, B. Yao, S. Siaka and G. Ado, J. Appl. Sci., 2007, 7(2), 310–313 CrossRef CAS
.
- F. Guesmi, C. Hannachi and B. Hamrouni, Desalin. Water Treat., 2010, 23, 32–38 CrossRef CAS
.
- V. K. Sharma and M. Sohn, Environ. Int., 2009, 35, 743–759 CrossRef CAS PubMed
.
- T. Mokhena, M. Mochane, M. Tshwafo, L. Linganiso, O. Thekisoe and S. Songca, Intech, 2016, 225–240 Search PubMed
.
- T. A. Siddique, N. K. Dutta and N. R. Choudhury, Nanomaterials, 2020, 10, 1–37 Search PubMed
.
- Y. Yoon, G. Amy and J. Yoon, Desalination, 2005, 177, 217–227 CrossRef CAS
.
- J. Mähler, I. Persson and R. B. Herbert, Dalton Trans., 2013, 42, 1364–1377 RSC
.
- L. S. McNeill, J. E. McLean, J. L. Parks and M. A. Edwards, J. – Am. Water Works Assoc., 2012, 104, 7 CrossRef
.
- D. C. Sharma and C. F. Forster, Bioresour. Technol., 1994, 49, 31–40 CrossRef CAS
.
- W. P. Zhu, J. Gao, S. P. Sun, S. Zhang and T. S. Chung, J. Membr. Sci., 2015, 487, 117–126 CrossRef CAS
.
- J. Pei, L. Huang, H. Jiang, H. Liu, X. Liu and X. Hu, Sep. Purif. Technol., 2019, 210, 651–658 CrossRef CAS
.
- Y. Deng, D. K. Nordstrom and R. Blaine McCleskey, Geochim. Cosmochim. Acta, 2011, 75, 4476–4489 CrossRef CAS
.
- B. Tansel, Sep. Purif. Technol., 2012, 86, 119–126 CrossRef CAS
.
- B. Yang, X. Tong, Z. Deng and X. Lv, J. Chem., 2016, 2016, 2–8 Search PubMed
.
- B. Gonzalez, S. G. J. Heijman, L. C. Rietveld and D. van Halem, Sci. Total Environ., 2019, 667, 297–305 CrossRef CAS PubMed
.
- A. Seidel, J. J. Waypa and M. Elimelech, Environ. Eng. Sci., 2001, 18, 105–113 CrossRef CAS
.
- J. J. Waypa, M. Elimelech and J. G. Hering, J. – Am. Water Works Assoc., 1997, 89, 102–114 CrossRef CAS
.
- L. B. Chaudhari and Z. V. P. Murthy, J. Hazard. Mater., 2010, 180, 309–315 CrossRef CAS PubMed
.
- J. R. Werber, A. Deshmukh and M. Elimelech, Environ. Sci. Technol. Lett., 2016, 3, 112–120 CrossRef CAS
.
-
B. Achiou, M. Karunakaran, M. R. Tchalala and Y. Belmabkhout, in Advances in Carbon Capture, Elsevier, 2020, pp. 331–355 Search PubMed
.
- M. Bigalke, A. Ulrich, A. Rehmus and A. Keller, Environ. Pollut., 2017, 221, 85–93 CrossRef CAS PubMed
.
- U. W. R. Siagian, K. Khoiruddin, A. K. Wardani, P. T. P. Aryanti, I. N. Widiasa, G. Qiu, Y. P. Ting and I. G. Wenten, Curr. Pollut. Rep., 2021, 7, 448–462 CrossRef CAS
.
- E. Shokri, R. Yegani, B. Pourabbas and N. Kazemian, Appl. Clay Sci., 2016, 132–133, 611–620 CrossRef CAS
.
- E. Shokri, R. Yegani and A. Akbarzadeh, Appl. Clay Sci., 2017, 144, 141–149 CrossRef CAS
.
- H. Luan, B. Teychene and H. Huang, Chem. Eng. J., 2019, 355, 341–350 CrossRef CAS
.
- P. Wan, M. Yuan, X. Yu, Z. Zhang and B. Deng, Chem. Eng. J., 2020, 382, 122921 CrossRef CAS
.
- A. S. K. Kumar and S. J. Jiang, J. Environ. Chem. Eng., 2016, 4, 1698–1713 CrossRef CAS
.
- Y. He, D. L. Zhao and T. S. Chung, J. Membr. Sci., 2018, 564, 483–491 CrossRef CAS
.
- Y. He, Y. Pan Tang and T. S. Chung, Ind. Eng. Chem. Res., 2016, 55, 12929–12938 CrossRef CAS
.
- Y. He, J. Liu, G. Han and T. S. Chung, J. Membr. Sci., 2018, 555, 299–306 CrossRef CAS
.
- Y. He, Y. P. Tang, D. Ma and T. S. Chung, J. Membr. Sci., 2017, 541, 262–270 CrossRef CAS
.
- M. Pal, M. K. Mondal, T. K. Paine and P. Pal, Environ. Sci. Pollut. Res., 2018, 25, 16579–16589 CrossRef CAS PubMed
.
- M. Delavar, G. Bakeri and M. Hosseini, Chem. Eng. Res. Des., 2017, 120, 240–253 CrossRef CAS
.
- S. Mishra, A. K. Singh and J. K. Singh, J. Membr. Sci., 2020, 593, 117422 CrossRef
.
- M. Abdullah Issa and Z. Z. Abidin, Molecules, 2020, 25, 3541 CrossRef PubMed
.
- P. Shah and C. N. Murthy, J. Membr. Sci., 2013, 437, 90–98 CrossRef CAS
.
- B. E. Mosikatsi, N. Mabuba and S. P. Malinga, J. Water Process. Eng., 2019, 30, 100686 CrossRef
.
- L. Jacob, S. Joseph and L. A. Varghese, Arabian J. Sci. Eng., 2020, 45, 7611–7620 CrossRef CAS
.
- K. Sangeetha, P. Angelin Vinodhini, P. N. Sudha, A. Faleh and A. Sukumaran, Int. J. Biol. Macromol., 2019, 132, 939–953 CrossRef PubMed
.
- A. Jayalakshmi, S. Rajesh, S. Senthilkumar and D. Mohan, Sep. Purif. Technol., 2012, 90, 120–132 CrossRef CAS
.
- M. Pishnamazi, S. Koushkbaghi, S. S. Hosseini, M. Darabi, A. Yousefi and M. Irani, J. Mol. Liq., 2020, 317(3), 437 Search PubMed
.
- R. Mukherjee, P. Bhunia and S. De, Chem. Eng. J., 2016, 292, 284–297 CrossRef CAS
.
- X. Z. Wei, Z. Q. Gan, Y. J. Shen, Z. L. Qiu, L. F. Fang and B. K. Zhu, J. Colloid Interface Sci., 2019, 553, 475–483 CrossRef CAS PubMed
.
- X. Ren, C. Zhao, S. Du, T. Wang, Z. Luan, J. Wang and D. Hou, J. Environ. Sci., 2010, 22, 1335–1341 CrossRef CAS PubMed
.
- A. K. Shukla, J. Alam, M. Alhoshan, L. A. Dass and M. R. Muthumareeswaran, Sci. Rep., 2017, 7, 1–12 CrossRef PubMed
.
- A. Saeedi-Jurkuyeh, A. J. Jafari, R. R. Kalantary and A. Esrafili, React. Funct. Polym., 2020, 146, 104397 CrossRef CAS
.
- E. Bagheripour, A. R. Moghadassi, S. M. Hosseini, B. Van der Bruggen and F. Parvizian, J. Ind. Eng. Chem., 2018, 62, 311–320 CrossRef CAS
.
- M. Kazemi, M. Jahanshahi and M. Peyravi, J. Hazard. Mater., 2018, 344, 12–22 CrossRef CAS PubMed
.
- M. Kazemi, M. Peyravi and M. Jahanshahi, J. Water Process. Eng., 2020, 37, 101183 CrossRef
.
- H. M. Xu, J. F. Wei and X. L. Wang, Desalination, 2014, 346, 122–130 CrossRef CAS
.
- P. C. Bandara, E. T. Nadres and D. F. Rodrigues, ACS Appl. Mater. Interfaces, 2019, 11, 17784–17795 CrossRef CAS PubMed
.
- E. Abdulkarem, Y. Ibrahim, M. Kumar, H. A. Arafat, V. Naddeo, F. Banat and S. W. Hasan, Chemosphere, 2021, 267, 128896 CrossRef CAS PubMed
.
- J. He, Y. Song and J. P. Chen, Chemosphere, 2017, 186, 1033–1045 CrossRef CAS PubMed
.
- A. Pakdel Mojdehi, M. Pourafshari Chenar, M. Namvar-Mahboub and M. Eftekhari, Colloids Surf., A, 2019, 583, 123931 CrossRef CAS
.
- S. M. Hosseini, S. H. Amini, A. R. Khodabakhshi, E. Bagheripour and B. Van der Bruggen, J. Taiwan Inst. Chem. Eng., 2018, 82, 169–178 CrossRef CAS
.
- A. Modi and J. Bellare, Sep. Purif. Technol., 2020, 249, 117160 CrossRef CAS
.
- M. T. Hoang, T. D. Pham, D. Verheyen, M. K. Nguyen, T. T. Pham, J. Zhu and B. Van der Bruggen, Chem. Eng. Sci., 2020, 228, 115998 CrossRef CAS
.
- N. Ghaemi, S. S. Madaeni, P. Daraei, H. Rajabi, S. Zinadini, A. Alizadeh, R. Heydari, M. Beygzadeh and S. Ghouzivand, Chem. Eng. J., 2015, 263, 101–112 CrossRef CAS
.
- Z. Jia, S. Hao and X. Lu, J. Environ. Sci., 2018, 70, 63–73 CrossRef CAS PubMed
.
- S. Chatterjee and S. De, Sep. Purif. Technol., 2014, 125, 223–238 CrossRef CAS
.
- N. Ghaemi, P. Daraei and F. S. Akhlaghi, Carbohydr. Polym., 2018, 191, 142–151 CrossRef CAS PubMed
.
- L. Zou, S. Zhang, J. Liu, Y. Cao, G. Qian, Y. Y. Li and Z. P. Xu, Environ. Sci. Pollut. Res., 2019, 26, 34197–34204 CrossRef CAS PubMed
.
- X. Zhang, X. Fang, J. Li, S. Pan, X. Sun, J. Shen, W. Han, L. Wang and S. Zhao, J. Colloid Interface Sci., 2018, 514, 760–768 CrossRef CAS PubMed
.
- T. Marino, F. Russo, L. Rezzouk, A. Bouzid and A. Figoli, Membranes, 2017, 7, 1–15 CrossRef PubMed
.
- R. Jamshidi Gohari, W. J. Lau, T. Matsuura and A. F. Ismail, Sep. Purif. Technol., 2013, 118, 64–72 CrossRef CAS
.
- J. He, T. Matsuura and J. P. Chen, J. Membr. Sci., 2014, 452, 433–445 CrossRef CAS
.
- R. J. Gohari, W. J. Lau, E. Halakoo, A. F. Ismail, F. Korminouri, T. Matsuura, M. S. Jamshidi Gohari and M. N. K. Chowdhury, New J. Chem., 2015, 39, 8263–8272 RSC
.
- Y. Yu, L. Yu, C. Wang and J. P. Chen, J. Colloid Interface Sci., 2018, 530, 658–666 CrossRef CAS PubMed
.
- K. Sunil, G. Karunakaran, S. Yadav, M. Padaki, V. Zadorozhnyy and R. K. Pai, Chem. Eng. J., 2018, 348, 678–684 CrossRef CAS
.
- C. Potla Durthi, S. B. Rajulapati, A. A. Palliparambi, A. K. Kola and S. H. Sonawane, Int. Nano Lett., 2018, 8, 201–211 CrossRef CAS
.
- J. Rowley and N. H. Abu-Zahra, J. Environ. Chem. Eng., 2019, 7, 102875 CrossRef
.
- M. S. Sri Abirami Saraswathi, D. Rana, N. J. Kaleekkal, K. Divya and A. Nagendran, J. Environ. Chem. Eng., 2020, 8, 104426 CrossRef CAS
.
- M. Gao, G. Liu, Y. Gao, G. Chen, X. Huang, X. Xu, J. Wang, X. Yang and D. Xu, TrAC, Trends Anal. Chem., 2021, 137, 116226 CrossRef CAS
.
- B. Yin, L. Sun, S. Tang and H. Zhou, Ind. Eng. Chem. Res., 2020, 59, 19689–19697 CrossRef CAS
.
- S. I. Siddiqui and S. A. Chaudhry, Process Saf. Environ. Prot., 2018, 119, 138–163 CrossRef CAS
.
- D. R. Dreyer, S. Park, C. W. Bielawski and R. S. Ruoff, Chem. Soc. Rev., 2019, 31, 228–240 Search PubMed
.
- Y. Wei, Y. Zhang, X. Gao, Z. Ma, X. Wang and C. Gao, Carbon, 2018, 139, 964–981 CrossRef CAS
.
- S. Dervin, D. D. Dionysiou and S. C. Pillai, Nanoscale, 2016, 8, 15115 RSC
.
- H. Namdar, A. Akbari, R. Yegani and H. Roghani-Mamaqani, J. Environ. Chem. Eng., 2021, 9, 104685 CrossRef CAS
.
- R. Das, M. E. Ali, S. B. A. Hamid, S. Ramakrishna and Z. Z. Chowdhury, Desalination, 2014, 336, 97–109 CrossRef CAS
.
- Y. H. Li, X. Zhang, J. Wei, C. Xu, D. Wu, S. Wang, Z. Luan and B. Wei, Environ. Technol., 2003, 24, 391–398 CrossRef CAS PubMed
.
- T. Madrakian, A. Afkhami, M. Ahmadi and H. Bagheri, J. Hazard. Mater., 2011, 196, 109–114 CrossRef CAS PubMed
.
- C. H. Ahn, Y. Baek, C. Lee, S. O. Kim, S. Kim, S. Lee, S. H. Kim, S. S. Bae, J. Park and J. Yoon, J. Ind. Eng. Chem., 2012, 18, 1551–1559 CrossRef CAS
.
- S. Addo Ntim and S. Mitra, J. Colloid Interface Sci., 2012, 375, 154–159 CrossRef CAS PubMed
.
- S. Leaper, E. Oscar Avendan, J. Miguel Luque-Alled, S. H. Cartmell and P. Gorgojo, ACS Appl. Polym. Mater., 2021, 3, 1854–1865 CrossRef CAS PubMed
.
- R. Rezaee, S. Nasseri, A. Hossein Mahvi, R. Nabizadeh, S. Abbas Mousavi, A. Rashidi, A. Jafari and S. Nazmara, J. Environ. Health Sci. Eng., 2015, 13(1), 61 CrossRef PubMed
.
- C. Potla Durthi, S. B. Rajulapati, A. A. Palliparambi, A. K. Kola and S. H. Sonawane, Int. Nano Lett., 2018, 8, 201–211 CrossRef CAS
.
- M. Kumar, A. M. Isloor, S. R. Todeti, H. S. Nagaraja, A. F. Ismail and R. Susanti, Chem. Eng. J., 2021, 405, 126809 CrossRef CAS
.
- D. L. Zhao and T. S. Chung, Water Res., 2018, 147, 43–49 CrossRef CAS PubMed
.
- H. Feng, J. Liu, Y. Mu, N. Lu, S. Zhang, M. Zhang, J. Luan and G. Wang, Sep. Purif. Technol., 2021, 266, 118586 CrossRef CAS
.
- Y. He, D. L. Zhao and T. S. Chung, J. Membr. Sci., 2018, 564, 483–491 CrossRef CAS
.
- N. Ghaemi, Appl. Surf. Sci., 2016, 364, 221–228 CrossRef CAS
.
- H. Zeng, Z. Yu, Y. Peng and L. Zhu, Appl. Clay Sci., 2019, 183, 105322 CrossRef CAS
.
- Z. Rao, K. Feng, B. Tang and P. Wu, ACS Appl. Mater. Interfaces, 2017, 9(3), 2594–2605 CrossRef CAS PubMed
.
- M. B. Gohain, R. R. Pawar, S. Karki, A. Hazarika, S. Hazarika and P. G. Ingole, J. Membr. Sci., 2020, 609, 118212 CrossRef CAS
.
- H. Yoo and S. Y. Kwak, J. Membr. Sci., 2013, 448, 125–134 CrossRef CAS
.
- F. Benhacine, N. Abdellaoui, O. Arous and A. S. Hadj-Hamou, Environ. Technol., 2020, 41, 2049–2060 CrossRef CAS PubMed
.
-
K. A. M. Said, G. G. George, N. A. M. Alipah, N. Z. Ismail and R. L. Jama, in MATEC Web of Conferences, 2016, p. 87 Search PubMed.
- P. Tan, J. Sun, Y. Hu, Z. Fang, Q. Bi, Y. Chen and J. Cheng, J. Hazard. Mater., 2015, 297, 251–260 CrossRef CAS PubMed
.
- J. Gao, S. P. Sun, W. P. Zhu and T. S. Chung, J. Membr. Sci., 2016, 499, 361–369 CrossRef CAS
.
- S. Habibi, A. Nematollahzadeh and S. A. Mousavi, Chem. Eng. J., 2015, 267, 306–316 CrossRef CAS
.
- S. Bandehali, F. Parvizian, A. R. Moghadassi, S. M. Hosseini and J. N. Shen, J. Polym. Res., 2020, 27, 94 CrossRef CAS
.
- C. Meng, X. Zheng, J. Hou and C. Wang, Water, Air, Soil Pollut., 2020, 231, 46 CrossRef CAS
.
- M. Chaudhary and A. Maiti, J. Membr. Sci., 2020, 611, 118372 CrossRef CAS
.
- S. Uk Hong, R. Malaisamy and M. L. Bruening, Langmuir, 2007, 23(4), 1716–1722 CrossRef PubMed
.
- P. Bahmani, A. Maleki, H. Daraei, M. Khamforoush, S. Dehestani Athar and F. Gharibi, J. Mol. Liq., 2018, 271, 557–570 CrossRef CAS
.
- R. Mukherjee and S. De, J. Membr. Sci., 2014, 466, 281–292 CrossRef CAS
.
- R. Rezaee, S. Nasseri, A. H. Mahvi, R. Nabizadeh, S. A. Mousavi, A. Maleki, M. Alimohammadi, A. Jafari and S. Hemmati Borji, Chem. Eng. Commun., 2019, 206, 495–508 CrossRef CAS
.
- H. K. Shon, S. Phuntsho, D. S. Chaudhary, S. Vigneswaran and J. Cho, Drinking Water Eng. Sci., 2013, 6, 47–53 CrossRef CAS
.
-
E. Alonso, Master of Science Thesis, King Abdullah University of Science and Technology, 2020 Search PubMed
.
- T. Yu, J. Zhou, F. Liu, B. M. Xu and Y. Pan, Membranes, 2022, 12, 1–10 Search PubMed
.
- I. Kammakakam and Z. Lai, Chemosphere, 2023, 316, 137669 CrossRef CAS PubMed
.
- M. F. Hamid, N. Yusof, N. M. Ismail and M. A. Azali, J. Appl. Membr. Sci. Technol., 2020, 24, 39–49 Search PubMed
.
- J. Zhou, Z. Fan, Q. Tian, S. Zhao and Y. Jiang, Micro Nano Lett., 2020, 15, 903–906 CrossRef CAS
.
- K. C. Khulbe and T. Matsuura, Appl. Water Sci., 2018, 8, 1–30 CrossRef CAS
.
- Y. Liang, Y. Zhu, C. Liu, K. R. Lee, W. S. Hung, Z. Wang, Y. Li, M. Elimelech, J. Jin and S. Lin, Nat. Commun., 2020, 11, 1–10 CrossRef PubMed
.
- S. Hao, Z. Jia, J. Wen, S. Li, W. Peng, R. Huang and X. Xu, Sep. Purif. Technol., 2021, 255, 117772 CrossRef CAS
.
- Z. Q. Huang and Z. F. Cheng, J. Appl. Polym. Sci., 2020, 137(13) DOI:10.1002/app.48579
.
- X. L. Wang, T. Tsuru, S. I. Nakao and S. Kimura, J. Membr. Sci., 1997, 135, 19–32 CrossRef CAS
.
- G. Pugazhenthi, S. Sachan, N. Kishore and A. Kumar, J. Membr. Sci., 2005, 254, 229–239 CrossRef CAS
.
-
M. R. Muthumareeswaran, PhD Thesis, Indian Institute of Technology Delhi, 2014 Search PubMed
.
- M. R. Muthumareeswaran, M. Alhoshan and G. P. Agarwal, Sci. Rep., 2017, 7, 1–12 CrossRef PubMed
.
-
P. Chuntanalerg, S. Bureekaew, C. Klaysom, W. J. Lau and K. Faungnawakij, Nanomaterial-incorporated nanofiltration membranes for organic solvent recovery, Elsevier Inc., 2018 Search PubMed
.
-
M. A. Alaei Shahmirzadi and A. Kargari, Nanocomposite membranes, Elsevier Inc., 2018 Search PubMed
.
- S. Wang, L. Li, S. Yu, B. Dong, N. Gao and X. Wang, Chem. Eng. J., 2021, 406, 126722 CrossRef CAS
.
- R. Epsztein, E. Shaulsky, N. Dizge, D. M. Warsinger and M. Elimelech, Environ. Sci. Technol., 2018, 52, 4108–4116 CrossRef CAS PubMed
.
- L. Zhu, J. Chem., 2015, 2015, 1–9 Search PubMed
.
- M. M. Emamjomeh, H. Torabi, M. Mousazadeh, M. H. Alijani and F. Gohari, Appl. Water Sci., 2019, 9(4), 71 CrossRef
.
- L. Y. Ng, A. W. Mohammad and C. Y. Ng, Adv. Colloid Interface Sci., 2013, 197–198, 85–107 CrossRef CAS PubMed
.
- A. E. Yaroshchuk, Adv. Colloid Interface Sci., 2000, 85, 193–230 CrossRef CAS PubMed
.
-
J. N. Israelachvili, Intermolecular and surface forces, Elsevier, 3rd edn, 2011 Search PubMed
.
- D. L. Oatley, L. Llenas, R. Pérez, P. M. Williams, X. Martínez-Lladó and M. Rovira, Adv. Colloid Interface Sci., 2012, 173, 1–11 CrossRef CAS PubMed
.
- S. S. Dukhin, N. v. Churaev, V. N. Shilov and V. M. Starov, Russ. Chem. Rev., 1988, 57(6), 1010–1030 CAS
.
- X. Zhang, X. Fang, J. Li, S. Pan, X. Sun, J. Shen, W. Han, L. Wang and S. Zhao, J. Colloid Interface Sci., 2018, 514, 760–768 CrossRef CAS PubMed
.
- L. Shen, Z. Huang, Y. Liu, R. Li, Y. Xu, G. Jakaj and H. Lin, Front. Chem., 2020, 8, 224 CrossRef CAS PubMed
.
- T. D. Dipheko, K. P. Matabola, K. Kotlhao, R. M. Moutloali and M. Klink, Int. J. Polym. Sci., 2017, 2017, 1–8 CrossRef
.
- M. Kumar, S. RaoT, A. M. Isloor, G. P. S. Ibrahim, Inamuddin, N. Ismail, A. F. Ismail and A. M. Asiri, Int. J. Biol. Macromol., 2019, 129, 715–727 CrossRef CAS PubMed
.
- Y. He, J. Liu, G. Han and T. S. Chung, J. Membr. Sci., 2018, 555, 299–306 CrossRef CAS
.
- J. Song, M. Zhang, A. Figoli, Y. Yin, B. Zhao, X.-M. Li and T. He, Environ. Sci.: Water Res. Technol., 2014, 1, 839 RSC
.
- Y. He, Y. Pan Tang and T. S. Chung, Ind. Eng. Chem. Res., 2016, 55(50), 12929–12938 CrossRef CAS
.
- C. Zhao, S. Du, T. Wang, J. Zhang and Z. Luan, Adv. Chem. Eng. Sci., 2012, 02, 366–371 CrossRef CAS
.
- R. Rezaee, S. Nasseri, A. H. Mahvi, A. Jafari, M. Safari and B. Shahmoradi, J. Adv. Environ. Health Res., 2016, 4, 169–175 CAS
.
- A. K. Shukla, J. Alam, M. Alhoshan, L. Arockiasamy Dass, F. A. A. Ali, M. R. Muthumareeswaran, U. Mishra and M. A. Ansari, Environ. Sci.: Water Res. Technol., 2018, 4, 438–448 RSC
.
- T. Hashem, A. H. Ibrahim, C. Wöll and M. H. Alkordi, ACS Appl. Nano Mater., 2019, 2, 5804–5808 CrossRef CAS
.
- M. H. A. Tajuddin, J. Jaafar, N. A. H. Md Nordin, A. F. Ismail, M. H. D. Othman and M. A. Rahman, Malays. J. Fundam. Appl. Sci., 2020, 16, 359–362 CrossRef
.
- S. Bandehali, F. Parvizian, A. R. Moghadassi and S. M. Hosseini, J. Polym. Res., 2019, 26 Search PubMed
.
- N. Haninah Harun, Z. Zainal Abidin, A. Halim Abdullah and R. Othaman, Processes, 2020, 8(2), 230 CrossRef
.
- S. Bandehali, A. Moghadassi, F. Parvizian, Y. Zhang, S. M. Hosseini and J. Shen, Sep. Purif. Technol., 2020, 242, 116745 CrossRef CAS
.
- M. Peydayesh, T. Mohammadi and S. K. Nikouzad, J. Membr. Sci., 2020, 611, 118205 CrossRef CAS
.
- P. Zhang, J. L. Gong, G. M. Zeng, C. H. Deng, H. C. Yang, H. Y. Liu and S. Y. Huan, Chem. Eng. J., 2017, 322, 657–666 CrossRef CAS
.
- Y. Bao, X. Yan, W. Du, X. Xie, Z. Pan, J. Zhou and L. Li, Chem. Eng. J., 2015, 281, 460–467 CrossRef CAS
.
- M. Kumar, H. M. Baniowda, N. Sreedhar, E. Curcio and H. A. Arafat, Chem. Eng. J., 2021, 408, 127300 CrossRef CAS
.
- H. M. Xu, J. F. Wei and X. L. Wang, Desalination, 2014, 346, 122–130 CrossRef CAS
.
- A. K. Shukla, J. Alam, M. Alhoshan, L. Arockiasamy Dass, F. A. A. Ali, M. R. Muthumareeswaran, U. Mishra and M. A. Ansari, Environ. Sci.: Water Res. Technol., 2018, 4, 438–448 RSC
.
- C. Evangeline, V. Pragasam, K. Rambabu, S. Velu, P. Monash, G. Arthanareeswaran and F. Banat, Desalin. Water Treat., 2019, 156, 177–188 CrossRef CAS
.
- S. Karmakar, S. Bhattacharjee and S. De, Chem. Eng. J., 2018, 334, 41–53 CrossRef CAS
.
- S. P. Suriyaraj and R. Selvakumar, RSC Adv., 2016, 6, 10565–10583 RSC
.
- S. Chatterjee, M. Mukherjee and S. De, J. Water Process Eng., 2020, 33, 101002 CrossRef
.
- M. Breida, S. Alami Younssi, A. Bouazizi, B. Achiou, M. Ouammou and M. El Rhazi, Heliyon, 2018, 4, e00498 CrossRef CAS PubMed
.
- J. J. Waypa, M. Elimelech and J. G. Hering, J. – Am. Water Works Assoc., 1997, 89, 102–114 CrossRef CAS
.
- Y. Ibrahim, V. S. Wadi, M. Ouda, V. Naddeo, F. Banat and S. W. Hasan, Chem. Eng. J., 2022, 428, 131267 CrossRef CAS
.
- B. Hribar, N. T. Southall, V. Vlachy and K. A. Dill, J. Am. Chem. Soc., 2002, 124, 12302–12311 CrossRef CAS PubMed
.
- B. Tansel, J. Sager, T. Rector, J. Garland, R. F. Strayer, L. Levine, M. Roberts, M. Hummerick and J. Bauer, Sep. Purif. Technol., 2006, 51, 40–47 CrossRef CAS
.
- M. Mota, J. A. Teixeira and A. Yelshin, Sep. Purif. Technol., 2002, 27, 137–144 CrossRef CAS
.
- M. Pal, S. Chakrabortty, J. Nayak and P. Pal, Int. J. Environ. Sci. Technol., 2019, 16, 4583–4594 CrossRef CAS
.
- A. Ramdani, A. Deratani, S. Taleb, N. Drouiche and H. Lounici, Desalin. Water Treat., 2021, 212, 286–296 CrossRef CAS
.
- N. Savage and M. S. Diallo, J. Nanopart. Res., 2005, 7, 331–342 CrossRef CAS
.
- Y. Li, W. B. Krantz and T.-S. Chung, AIChE J., 2007, 53(9), 2470–2475 CrossRef CAS
.
- A. Wang, P. Lu, X. Wen Cheng, L. Shen, Z. Huang, Y. Liu, R. Li, Y. Xu, G. Jakaj and H. Lin, Front. Chem., 2020, 8, 224 CrossRef PubMed
.
- D. Qadir, H. Mukhtar and L. K. Keong, Sep. Purif. Rev., 2017, 46, 62–80 CrossRef
.
- R. Nasir, H. Mukhtar, Z. Man and D. F. Mohshim, Chem. Eng. Technol., 2013, 36, 717–727 CrossRef CAS
.
-
J. Lee, Carbon Nanotube-Based Membranes for Water Purification, Elsevier Inc., 2018 Search PubMed
.
- O. Abdalla, M. A. Wahab and A. Abdala, Curr. Pharm. Biotechnol., 2020, 22, 1686–1704 Search PubMed
.
- Y. Jiang, P. Biswas and J. D. Fortner, Environ. Sci.: Water Res. Technol., 2016, 2, 915–922 RSC
.
- G. Liu and W. Jin, Sci. China Mater., 2018, 61, 1021–1026 CrossRef CAS
.
-
A. V. Desai, S. Sharma and S. K. Ghosh, 4-Metal-organic frameworks for recognition and sequestration of toxic anionic pollutants, Elsevier Inc., 2019 Search PubMed
.
- R. Li, J. P. Chen and V. Freger, J. Membr. Sci., 2023, 121357 CrossRef CAS
.
- W. A. El-Mehalmey, Y. Safwat, M. Bassyouni and M. H. Alkordi, ACS Appl. Mater. Interfaces, 2020, 12, 27625–27631 CrossRef CAS PubMed
.
- T. Le, X. Chen, H. Dong, W. Tarpeh, A. Perea-Cachero, J. Coronas, S. M. Martin, M. Mohammad, A. Razmjou, A. R. Esfahani, N. Koutahzadeh, P. Cheng, P. R. Kidambi and M. R. Esfahani, Ind. Eng. Chem. Res., 2021, 60, 6869–6907 CrossRef CAS
.
- J. Li, H. Wang, X. Yuan, J. Zhang and J. W. Chew, Coord. Chem. Rev., 2020, 404, 213116 CrossRef CAS
.
- R. Lin, B. Villacorta Hernandez, L. Ge and Z. Zhu, J. Mater. Chem. A, 2018, 6(2), 293–312 RSC
.
- S. Shahrin, W. J. Lau, P. S. Goh, A. F. Ismail and J. Jaafar, Composites, Part B, 2019, 175, 107150 CrossRef CAS
.
- J. Hong and Y. He, Desalination, 2014, 332, 67–75 CrossRef CAS
.
- R. Shoshaa, M. Y. Ashfaq and M. A. Al-Ghouti, Environ. Technol. Innovation, 2023, 31, 103162 CrossRef CAS
.
- M. Jafari, M. Vanoppen, J. M. C. van Agtmaal, E. R. Cornelissen, J. S. Vrouwenvelder, A. Verliefde, M. C. M. van Loosdrecht and C. Picioreanu, Desalination, 2021, 500, 114865 CrossRef CAS
.
- S. Judd, Membr. Technol., 2003, 13–74 Search PubMed
.
- C. M. Nguyen, S. Bang, J. Cho and K. W. Kim, Desalination, 2009, 245, 82–94 CrossRef CAS
.
|
This journal is © The Royal Society of Chemistry 2023 |