DOI:
10.1039/D3EE00841J
(Perspective)
Energy Environ. Sci., 2023,
16, 3711-3733
Circular economy for perovskite solar cells – drivers, progress and challenges
Received
15th March 2023
, Accepted 3rd July 2023
First published on 26th July 2023
Abstract
Lead halide perovskite solar cells (PSCs) are an emerging solar photovoltaic (PV) technology on the cusp of commercialisation, promising to deliver the lowest cost solar energy to date (<32 $ per MW h). Owing to the required scale of PV deployment to mitigate climate change, potential limits to deployment due to materials criticality issues, and the necessity to prevent impacts from PV waste, adoption of circular economy is essential for perovskite technologies. Here we examine 3 key themes to inform future development towards commercialisation: legislative and economic drivers for adoption of circular economy by the emerging perovskite PV industry; environmental and future materials supply issues; and current state of research which may enable remanufacturing and recycling strategies to facilitate circular utilisation of key materials in successive product generations.
Broader context
Photovoltaics (PV) are one of the fastest-growing energy technologies, with global cumulative installed capacity exceeding 1 TW by March 2022 following rapid reductions in levelised cost of energy (LCOE). To mitigate climate change, cumulative installed capacity may reach >10× this quantity by 2050. Market dominant crystalline silicon (c-Si) PV faces limits to its deployment owing to global materials security issues, and deployment to scale will generate enormous quantities of waste from which secondary materials cannot be recovered at suitable purity to feed future PV manufacturing given the state of current recycling technology. Adoption of circular economy for PV is essential to ensure these technologies are sustainable for the future. However, existing technologies suffer linear lock-in having been designed for a single lifetime with no consideration of end-of-life (EoL) outcomes. Perovskite PV is a promising emerging technology on the cusp of commercialisation, with calls for adoption of circular economy for this technology to mitigate potential impacts of Pb used in the absorber materials of these devices. To do so successfully, consideration of design with full lifecycle thinking, now, at this early pre-commercialisation stage is essential. We review economic, legislative, and environmental drivers for adoption of circular economy for perovskite technology, examining environmental and resource security issues of common materials used in device architectures, and consider strategies to enable circular retention of materials in successive product generation to facilitate circular economy.
|
Introduction
Humanity faces global environmental and energy crises.1,2 The pursuit of growth via linear economic models (i.e. the ‘take-make-waste’ economy, Fig. 1) has disrupted the Earth's natural systems to the extent we face risks from climate change, disruption of natural geochemical flows, pollution, land system change, ocean acidification and the ongoing sixth mass extinction.1,3 Despite granting prosperity and improved living standards for billions, increasing population and per-capita consumption mean we face the limits of linear economy.3–5 Finite natural resources are extracted to create products which are ultimately discarded as waste. Each stage in this process consumes fossil fuels and generates emissions and waste.6 Value is created exclusively at the point of product sale, thus economic growth is strongly coupled to primary material and energy consumption with associated emissions and waste generation. Approximately 60% of global greenhouse gas (GHG) emissions and >90% of biodiversity loss and water stress results from resource extraction.7 Achieving the Paris Agreement goal of limiting global temperature rise to 1.5 °C above pre-industrial levels will not be possible through decarbonisation of energy and transport networks alone,8 emissions from primary materials extraction, manufacturing and end-of-life (EoL) processes must also be reduced.6,7,9 There is also growing concern about access to critical raw materials (CRMs) with increasing global demand, particularly for technology metals and other essential materials needed for low carbon technologies.10,11 Many of these materials are produced only as minor by-products of other mining operations, bringing new mines on line takes decades, and CRM recycling rates from EoL products are low in general due to the dissipative nature of their applications, so no rapid solutions to demand spikes or disruption to primary supply exist.12 Due to the essential role of CRMs in green technologies for a sustainable future, global resource criticality is a major challenge to address.
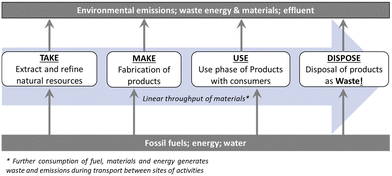 |
| Fig. 1 Material flows in the so-called ‘take-make-use-dispose’ linear economy with resource consumption, emissions and waste generation indicated. | |
Even green technologies required for net-zero cause environmental impacts during production, use, and EoL when they become waste electrical and electronic equipment (WEEE, or e-waste). WEEE is the fastest growing waste stream on the planet with 53.6 Mt per year generated globally.13 WEEE presents a major global challenge owing to its hazardous material content.14 CRM recovery rates are below 1% for many elements due to low collection rates of EoL products, the dissipative nature of their applications resulting in low recoverable value from individual products, and dissipative losses during recycling processes.12 Even recovery rates of high value materials such as Au and platinum group metals (PGMs) do not exceed ∼50%. However, despite barriers to recovery, WEEE represents a considerable opportunity as a secondary source of CRMs, many of which are present in greater concentrations than in mined ores.15
To meet the goals of the Paris Agreement, GHG emissions must be reduced across all sectors through deployment of renewable and low-carbon energy technologies.16 This will increase reliance on CRMs. Low-carbon technologies currently account for 20% of global CRMs consumption, and demand will increase with widescale deployment.17–21 To meet climate and energy targets in the EU, CRM demand is expected to increase by a factor of 20 for certain materials22 and studies projecting CRM demand in future green energy scenarios forecast multiple supply bottlenecks which may limit technology deployment and our ability to combat climate change.15,20,23–35
Cumulative global photovoltaic (PV) waste generation by 2050 has been projected as 60–78 Mt by the International Renewable Energy Agency (IRENA), with annual generation reaching 5.5–6 Mt per year.36 This projection is based on ∼4.5 TW of cumulative installed PV capacity in 2050 in line with the 2 °C scenario (2DS) for climate change mitigation proposed by the International Energy Agency (IEA).16 Strategies providing the best chance of limiting global temperature rise to 1.5 °C rely heavily on PV deployment requiring installed capacity to reach 8.5–14.0 TW by 2050.9,36,37 This suggests future PV waste generation and CRM demand for production could be considerably higher than previous estimates suggest. To address these issues, there are calls to urgently adopt circular economy in the lifecycles of PV technologies to improve their EoL outcomes and lifecycle impacts overall.
Circular economy is an industrial economy inspired by natural systems which is restorative and regenerative by design, decoupling growth from consumption to enable sustainable economic development (Fig. 2), replacing the concept of ‘waste’ with that of ‘resource’.3,38–42 Product lifetimes are extended, retaining materials at their highest possible value within the tightest possible loops of the economy for as long as possible. Thus, flow of materials through the economy is slowed and primary resource consumption is minimised by adopting waste hierarchy principles (Fig. 3). To minimise primary resource consumption and loss of materials from the economy, materials which cannot be retained within closed-product loops should be cascaded into production of other products through industrial symbiosis.12,43–51
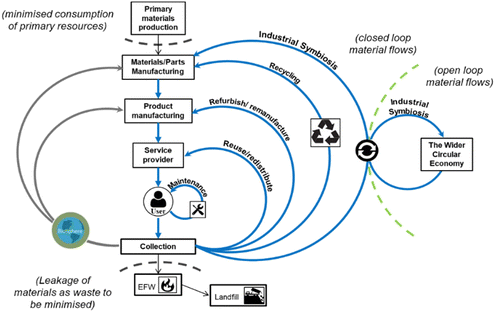 |
| Fig. 2 Material flows within a circular economy (reused with permission from Charles et al.).15 | |
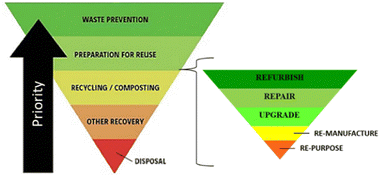 |
| Fig. 3 The waste hierarchy with refurbishment, repair, upgrade, remanufacturing, and repurposing operations incorporated with priority of actions for waste prevention indicated by the arrow. | |
Adopting circular economy successfully for established PV technology is a considerable challenge. Crystalline silicon (c-Si) technology currently accounts for ca. 95% of global PV production (2020) with cadmium telluride (CdTe) and copper indium gallium selenide (CIGS) thin-film technologies accounting for 4% and 1% respectively.52 Take-back schemes deliver EoL CdTe modules to recycling processes which recover high purity materials for new panel production preventing toxic Cd emissions while providing secondary supplies of critical Te. Promising results have also been reported for pipeline CIGS recycling processes which achieve >90% recovery rates for active materials including critical Ga and In.53,54 c-Si PV recycling generally has poor resource efficiency outcomes with significant barriers to recovery of materials at sufficient purity for use in new module production.55–57 The barriers to adoption of circular economy for c-Si PV result from the fact that these technologies suffer from ‘linear lock in’, having been designed for a linear economy with focus on product longevity over a single useful life without regard to the importance of materials retention over successive product generations. To facilitate retention of products and components requires eco-design of products and lifecycle processes in tandem. This requires, where possible, elimination of hazardous and critical materials, incorporation of low impact renewable materials, and facilitation of repair, upgrade, disassembly procedures for remanufacturing and efficient materials recovery.40,58–66 This must be guided by lifecycle assessment (LCA) to ensure environmental impacts are minimised throughout product lifecycle and not simply ‘burden shifted’, with highest impact and non-substitutable ‘critical’ components/materials retained in successive product generations.40,62,67–71 These approaches will reduce demand for primary materials, increasing secondary supply, helping to ensure green-technology deployment is not limited by supply bottlenecks.4,15,72–76 Circular design principles and holistic systems thinking must be applied from the earliest possible stage in development of emerging PV technologies to deliver truly sustainable technologies that integrate with a wider circular economy.44,76–79
Lead halide perovskite solar cells (PSCs) are an exciting emerging PV technology achieving power conversion efficiency (PCE) of 25.8% at lab scale,80 20.5% in mini-modules (63.98 cm2)81 and 17.9% at module scale (802 cm2)82 in little over a decade of development.83 The rapid rise in PSC efficiencies is unprecedented in PV technology development, competitive with PCEs of c-Si (26.7%), CIGS (23.4%) and GaAs solar cells (29.1%).84 PSCs are on the cusp of commercialisation and promise the lowest levelised cost of energy (LCOE) of any PV technology to date due to solution processability.85 Tremendous progress in scale-up has been achieved with a variety of material sets, production processes and cell architectures reported, in a race to stabilise the perovskite layer for viable commercialisation.86 Common cell architectures are presented in Fig. 4, generally comprised of a transparent conductive substrate such as transparent conductive oxide (TCO) coated glass or polyethylene terephthalate (PET) onto which an electron transport layer (ETL, usually TiO2),87,88 the perovskite, hole transport layer (HTL) and metallic contacts (typically Au via thermal evaporation) are sequentially deposited. The ETL and perovskite can be deposited as distinct layers in planar devices (Fig. 4a) or as a mesoporous ETL infiltrated by the perovskite (Fig. 4b). The most employed hole transport material (HTM) to date has been spiro-MeOTAD,89–91 although many alternatives have been reported.92–96 A variety of industrially relevant deposition techniques have been used; slot-die coating,97,98 blade coating,99–101 inkjet printing,102 spray coating103,104 and vapour deposition.105,106 Inverted P–I–N architectures (Fig. 4c), with HTL deposited directly onto the TCO, followed by the perovskite and ETL layers107–110 have been studied owing to the possibilities of easier processability and substitution of organic HTLs with low-cost, stable inorganic alternatives such as NiO.109,110 Inverted devices also benefit from less hysteresis compared with traditional planar PSCs111–113 and the possibility of replacing Au contacts with Ag or Al.109,111,112,114 Although efficiency is usually lower than traditional mesoporous PSCs, PCEs of 20.5% have been reported.108 The inverted perovskite architecture has also proven to be a better option for perovskite/tandem solar cells due to the nature of its components (better transmission of the top layer) and the compatibility of their deposition (vacuum deposition of fullerene-derived layers as ETL) with the silicon solar cell components.115 The ‘triple stack’ perovskite solar cell (Fig. 4d) has been developed as a scalable configuration in which 3 mesoporous layers consisting of an ETL (TiO2), insulating layer (ZrO2 or Al2O3) and carbon counter electrode are sequentially deposited prior to infiltration of the perovskite throughout the mesoporous framework.116 This architecture offers good scalability potential with complete screen printability of the mesoporous structure having been demonstrated, and renders metallic contacts and HTLs unnecessary.117 PCEs of 15% for lab scale devices118 and 6.6% for modules (198 cm2)119 have been reported,120 which is promising for low-cost module production.
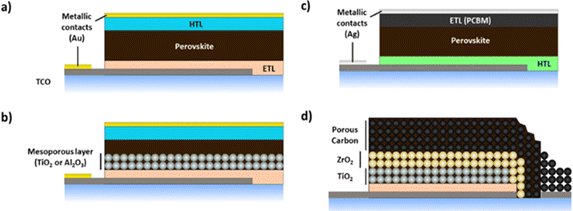 |
| Fig. 4 Perovskite solar cell configurations. Some of the most common materials employed are depicted. (a) N–I–P planar configuration; (b) N–I–P mesoporous configuration; (c) P–I–N inverted configuration; and (d) triple stack configuration. | |
Easy manipulation of the perovskite chemical composition to tune photophysical properties is possible. Gradual substitution of iodide for a smaller halide such as bromide enables band gap tuning to a value between 1.6 eV (MAPbI3) and 2.3 eV (MAPbBr3),110,121–123 a useful feature for tandem solar cell applications.124,125 Perovskite/c-Si tandem devices have been developed126–129 using wider bandgap perovskite top cells leading to PCEs of 29.8% (1cm2).80 Caesium-containing triple cation PSCs with higher thermal stability and 21.1% efficiency have also been reported, with this chemistry used as the current standard for high efficiency PSCs.90
Drivers for circular economy of perovskite solar cells
Given the significant requirement for acceleration of PV deployment, the outstanding properties of perovskite absorbers for PV, significant advancement in the scaling and stability challenges facing PSC technology and their potential use in high efficiency tandems, it is likely they can dramatically disrupt and impact the market. Couple this with the global drive for sustainability enhancement, circular economy, and better materials stewardship then the need to design perovskite devices to integrate within a circular economy is paramount. Here, we discuss in detail the drivers for establishing circular economy for perovskite PV. These include legislation, and the competitive advantage available through adoption of circular business models.
Legislative drivers
To mitigate impacts associated with WEEE, the EU introduced the WEEE directive (2012/19/EU)130 and Restriction of Hazardous Substances (RoHS) Directive (2011/65/EU)131 to enhance the industrial ecology and resource-efficiency of the EEE industry. The WEEE directive emphasises the waste hierarchy (Fig. 3) and creates a regulatory environment conducive to circular economy, banning landfilling of WEEE, establishing statutory collection, recycling and reuse targets and imposing extended producer responsibility (EPR) on electrical and electronic equipment (EEE) producers.† EPR makes producers responsible for their products’ EoL costs ensuring cost is no barrier to appropriate WEEE management. In the EU, PVCycle act as a producer responsibility organisation (PRO or compliance scheme) ensuring compliant collection and treatment of waste PV, charging members (PV producers) a fee reflecting their products’ EoL costs which is used to finance WEEE management systems and R&D to improve outcomes.132,133 China, the world's largest PV market, has equivalent legislation including PV within its scope.134,135 Japan and California (largest US PV market) have also adopted EPR for waste PV with more nations and authorities likely to follow suit in the near future. This creates an economic incentive to design for circular economy. The cost of compliance with EPR will be passed on to consumers in the price that they pay for PV, ultimately impacting LCOE. PV technologies which can undergo repair/upgrading, re-use, disassembly, remanufacturing and efficient recycling will have lower EoL costs therefore gaining a competitive LCOE advantage.
The EU RoHS directive limits permissible levels of hazardous substances in EEE to protect human health and the environment (Table 1),131 and like the WEEE directive, RoHS instruments are being globally adopted.136 RoHS limits Pb content to ≤0.1 wt% in homogeneous materials within products. The definition of ‘homogeneous material’ used in the legislation has caused debate around permissible quantities of Pb in PSCs.137 The composition of typical perovskite absorbers in lab-scale devices exceeds this limit, and if the mixture of TiO2, perovskite and spiro-MeOTAD is considered a homogeneous layer, lead content is currently 0.55 wt%, >5× the RoHS limit138 which may prevent consumer product integration. However, RoHS aims to avoid obstructing development of renewable energy technologies so PV panels to produce energy for public, commercial, industrial and residential applications are exempt. CdTe PV which contains Cd in excess of RoHS permissible limits (0.01 wt%, Table 1) holds such an exemption. This has meant that manufacturers have had to establish systems for lifecycle management of CdTe panels to prevent impacts from Cd emissions. Given that Pb-free perovskites currently offer no performance advantage over Pb perovskites,139 it is likely that Pb perovskite PV will be granted a RoHS exemption and be commercialised, accelerating the urgency to develop robust lifecycle solution to mitigate potential impacts of Pb, analogous to those adopted for CdTe PV to mitigate Cd emissions.
Table 1 Restricted substances referred to in Article 4(1) and maximum concentration values tolerated by weight in homogeneous materials as listed in ANNEX II of the RoHS directive131
Material |
Maximum concentration (wt%) |
Pb |
0.1 |
Hg |
0.1 |
Cd |
0.01 |
Hexavalent chromium (Cr VI) |
0.1 |
Polybrominated biphenyls (PBB) |
0.1 |
Polybrominated diphenyl ethers (PBDE) |
0.1 |
Competitive advantage
PV development has always focused on design for longevity over a single product lifetime as a means of improving LCOE and commercial attractiveness. This includes module lamination to prevent degradation during use. However, this feature currently prevents efficient recovery of materials from c-Si PV. Manufacturing cost analysis of perovskite solar module (PSM) production processes indicates a cost of US $107 per m2 is achievable, comparable with commercial PV technologies, and at this cost PSMs will exhibit competitive LCOE when a PCE of 18% and lifetime of 20 years is achieved.140 Current LCOE for utility scale PV is 32–44 $ per MW h,141 with techno-economic analyses of state of the art PSC manufacturing indicating a competitive LCOE of <32 $ per MW h is achievable,142 with further reductions through economies of scale once commercially established holding the potential to cement perovskite PV as a cost leader.8 Materials costs, particularly TCO coated glass substrates, significantly impact LCOE. These could potentially be reduced through recovery from EoL modules. Chen et al., successfully demonstrated the cost-effective recycling of lead, glass and TCOs from modules, calculating that materials with a value of $12 per m2 could be recovered for use in new devices consuming materials worth only $1.35 per m2 to do so.143 It is a principle of circular economy that materials cost savings result from access to recovered components and materials of sufficient purity and low toxicity to substitute purchased primary materials. Increased use of recycled content, as well as refurbishment and remanufactured devices could therefore improve perovskite PV LCOE through materials cost savings, particularly if materials are retained over successive product lifecycles, which has been demonstrated to be feasible and is discussed below.79 By capitalising on the opportunity to design PSMs with multiple lifecycles in mind at this pre-commercialisation stage of development, improved economic and environmental performance of products could be unlocked. LCOE would be further improved by valorising module components at EoL to a greater extent than is currently achievable for c-Si PV, thereby reducing EPR compliance costs which are ultimately passed on to consumers in the price they pay. Retention of embodied energy and emissions within components will also reduce module energy payback time (EPBT) and emissions associated with electricity generation (kg CO2-eq per kW h), providing a means to further decouple energy production from GHG emissions, and provide an additional marketing angle which becomes increasingly valuable as global markets become increasing environmentally conscious.137 Tian et al. have shown through lifecycle assessment that recycling strategies for perovskite PV modules could reduce energy consumption and GHG emissions associated with producing modules by >70% with the best architectures having an extremely low EPBT of 0.09 years and GHG emission factor of 13.4 gCO2-eq per kW h (compared with 1.3–2.4 years and 22.1–38.1 gCO2-eq per kW h for Si PV).144 Further advantages in this area may result from publicising circular business models, as resulted for First Solar following their adoption of recycling systems which positioned them as a leading environmentally conscious supplier in the PV industry. If perovskite technologies and lifecycle systems can be proven to be reliable, then adoption of PSS models in which producers retain ownership of PSMs, granting use of them to customers at a fee will remove capital barriers to deployment, potentially accelerating uptake. This may be particularly important for electrification in developing regions where capital outlay may be a barrier to adoption and ensuring collection at EoL to avoid impacts from informal treatment of PSMs is important.5,145
Environmental and human health risk drivers
The predominant environmental issue considered in PSC research has been potential impacts of toxic Pb. The archetypal absorber layer, MAPI, contains 1/3rd Pb by mass (∼500 nm thick layer in planar device contains <1 g per m2 Pb).137 Even if PSC modules are RoHS compliant, the solubility of the lead compounds contained results in its waste being classified as hazardous, with numerous implications for EoL treatment and export to recycling facilities. Concerns have been raised about potential impact on workers during manufacturing and recycling, and the potential for accumulation in the environment and impacts on human health if modules are damaged and exposed to rain.80,146–148 Pb is carcinogenic and causes chronic and acute damage to all organs. Children are particularly susceptible due to their vulnerable stage of ongoing development with exposure causing lifelong intellectual impairment. PbI2, a common degradation product of MAPI, has a relatively low solubility constant in water (keq = 9.8 × 10−9). In acidic media such as acid rain, solubility increases presenting a pathway for bioaccumulation.149 Pb levels in soil contaminated with rain leachate from a broken PSC module have been calculated to be 70 ppm in the first centimetre of soil,150 which is moderate compared to background levels of contamination in urban areas (400 ppm considered low-level contamination).150 Khalifa has modelled the human exposure of Pb from accidental emissions from perovskite PV modules and found the single point exposure concentrations of Pb in soil, groundwater aquifer and air even under utility scale catastrophic failure scenarios fall below EPA regulatory limits.151 However, it should be noted that there is no natural background Pb level. All detectable Pb in the environment has accumulated because of anthropogenic activities. Therefore, even undetectable emissions of Pb to the environment add to this accumulation and increasingly significant contamination. Minute traces of Pb can accumulate and concentrate in food chains, so even undetectable Pb emissions may result in acute effects in organisms at the top of food chains such as humans. It has been claimed that any detectable level in the blood is detrimental to human health.152 In the UK, the HSE set employee blood Pb action levels at which point measures to prevent further exposure must be taken and suspension levels as low as 30 μg dl−1 for women of child bearing age (Table 2).153 For these reasons, use of Pb even in such a potentially beneficial technology as PSCs is controversial, and circular economy strategies to properly manage potential impacts throughout all stages of product lifecycles will be crucial.
Table 2 Action and Suspension blood lead levels for employees set by the UK HSE153
Employee category |
Action level (μg dl−1) |
Suspension level (μg dl−1) |
General employees |
50 |
60 |
Women of child-bearing age |
25 |
30 |
Young people under 18 |
40 |
50 |
LCA studies assessing potential impacts of Pb use have concluded that impacts in production and use of PSCs do not warrant exclusion of Pb;154 with toxicity impacts from production of grid energy consumed in manufacturing far exceeding any potential impact from Pb emissions.155,156 Zhang et al. concluded that Pb in devices only accounts for ∼1% of human toxicity potential.157–159 Greatest potential impacts from Pb will occur at EoL if modules are improperly managed, and LCA has shown that with appropriate EoL infrastructure and handling to capture Pb, risk of impacts are not significant with Pb becoming a minor component of overall lifecycle impacts. Sn is one of the most promising alternatives to Pb for PSCs and under equivalent circumstances, the global warming potential (GWP) and ecotoxicity impacts of Sn production are an order of magnitude higher than for Pb and these will dominate lifecycle impacts of PSCs.160 It has also been shown that Sn(II) in perovskite materials rapidly oxidises to Sn(IV) in aqueous environments leading to HI formation; and that SnI2 exposure is more acutely toxic to zebrafish than PbI2 due to more severe acidification effects brought about by Sn2+ compared with Pb2+.161 Alternative metals investigated to replace Pb and Sn include In+, Ga+, Bi3+ and Sb3+ all of which are commonly designated as CRMs, with long-term supply concerns which may impede deployment to the scale required to achieve climate goals.161 When Pb perovskites are used, numerous strategies have been demonstrated to prevent leakage from modules including use of chelating agent additives within functional layers of cells, use of interface modifiers with hydrophilic groups and inclusion of Pb absorbing materials within encapsulation materials.162 Phosphonic and carboxylic acid compounds mixed with encapsulant materials163 and ion exchange resins incorporated in the cell structure164 have proven to be particularly effective for lead capturing, preventing lead leaking in case of cell failure.
Numerous LCA studies on production of PSCs with varying architectures and materials sets have been conducted to inform development of more environmentally friendly devices. The results of these studies however vary considerably owing to differences in methods and assumptions made. Maranghi et al. have attempted to harmonise these studies for comparison and enable ranking of architectures according to environmental impacts and identification of the materials and processes accounting for greatest impacts.165 When used in devices, Au dominates environmental impact owing to its high impacts of production, energy intensity associated with its deposition via evaporation and low deposition efficiency of this process. The same is true for Pt in cells that use this in place of Au. The lowest impact cells considered in this study use Ag or C. Both have lower embodied impacts than Au (Table 3), but Ag still contributes considerably to overall production impacts due to energy consumption in its deposition, whereas carbon may represent a lower impact deposition option with R2R solution deposition recently demonstrated.86 Final selection must be justified considering overall cell performance and net benefits afforded following consideration of avoided use of grid electricity. Should Au prove to be the most beneficial choice overall, circular economy strategies to retain Au in successive generations of PSMs will be important to mitigate ongoing impacts associated with its primary production and meet increasing demand from PSC technologies as deployment scales. Where porous carbon electrodes are used as in ‘carbon stack’ devices (Fig. 4d), the embodied energy in these layers may be retained through remanufacturing approaches which retain the carbon structure for reuse in new cells thereby retaining impacts incurred during its deposition and curing.166
Table 3 Global warming potential (GWP) resulting from mining 1 kg of metal167
Metal |
(kg CO2-eq) |
Pt |
14 704 |
Au |
12 806 |
Ag |
440 |
Cu |
3 |
Solar glass substrates represent a high proportion of embodied impacts of devices, with a net reduction in impacts afforded through substitution of indium doped tin oxide (ITO) with fluorine doped tin oxide (FTO), as is the trend in the field owing to the ‘critical’ status of In. Many LCA studies have shown relatively low impacts of substrates which is misleading as these use lifecycle impact data from the Ecoinvent database for float glass production which doesn’t account for impacts of TCO deposition which adds considerably to substrate impact.168 For these reasons, substrate retention at EoL for reuse in remanufactured devices will be important. Substitution of glass as substrate and encapsulant for lower impact or biologically derived materials may also help to address the considerable lifecycle impact associated with the use of glass. Alternative transparent plastic substrates such as PET or polyethylene naphthalate (PEN)169 which are suitable for roll-to-roll (R2R) production have been used for PSCs and polymeric encapsulants are widely used in the PV industry.57,170 However, their chemical compatibility with PSCs and behaviour in EoL processes must be considered. Delamination is a crucial step in recycling to avoid shredding and access internal components for remanufacturing/recycling. Glass substrates have the distinct advantage that they are not damaged by thermal delamination processes,56,57 whereas polymeric substrates are likely to thermally degrade preventing reuse. Where a single electrode only need be transparent, R2R production of inverted devices using flexible metal substrates has been demonstrated which could reduce consumption of glass171–174 and metal substrates will also withstand thermal delamination. Alternatively, Ke et al. successfully deposited ITO on mica to create transparent electrodes for high efficiency flexible solar cells.175 These substrates retained low electrical resistance after 1,000 bending cycles and are compatible with high temperature (450 °C) annealing, and may therefore present an interesting alternative when flexible transparent electrodes which could endure thermal delamination are required. Owing to its low-cost, biological source, recyclable and biodegradable nature, cellulose based substrates have also been used.176 Li et al. produced PSCs on cellulose paper achieving 13.2% PCE, a record for solar cells on paper substrates.177 Lei et al. produced acrylic resin coated nanocellulose paper for use in PSCs.176 Although unlikely to withstand thermal recycling processes, the renewable biological nature of cellulose and its biodegradability make it an attractive alternative to glass for flexible cells.
Although ETLs account for less of the embodied impacts in manufactured devices, these are not insignificant. SnO2 has a relatively high environmental impact due to the presence of Sn. Alternative ETLs, such as TiO2, can result in high impacts when spin-coating, heating and annealing is required resulting in relatively high energy consumption. Titania nanotubes have been used in place of mesoporous titania layers with high impacts resulting from high solvent consumption in their preparation, requiring significant efficiency and stability gains in final devices to justify their use.159,165 Strategies to retain ETLs on substrates, if viable reuse can be demonstrated, will be important for mitigating embodied impacts of Sn and high energy consumption during preparation, deposition and curing.
The impacts of HTLs in cells are dominated by energy consumption in their synthesis and materials with long/complex synthetic pathways and low final yields have higher impacts still. Where such HTMs are used, their recovery will be important, and eco-design of cells considering substitution of such HTMs with those that can be biologically sourced or have shorter/higher-yield synthetic pathways should be considered. It is clear solvent use adds considerable environmental impact to production, and that to mitigate this, solvent capture systems which prevent environmental emissions and enable solvent reuse following curing of films are necessary to mitigate these impacts. The toxicity of dimethylformamide (DMF) for perovskite deposition and chlorobenzene for HTM deposition is particularly problematic.178
Materials considerations
Resource security and materials supply constraints
Global availability of raw materials is increasingly under pressure due to growing demand and increasing likelihood of supply bottlenecks. Access to CRMs has become a priority issue for governments and industries around the world. CRMs exhibit extreme price volatility, which is problematic from the point of view of PV manufacturing as sudden increases in material costs cannot be passed on to consumers without impacting LCOE.179 Here we consider materials used in current PSC devices which have potential long-term supply risks owing to growing demand, geological abundance, geopolitical factors, and the fact that they may be produced as minor biproducts of major metals preventing scaling of primary supply with demand. Potential substitute materials which have been demonstrated in PSCs are discussed, as circular economy strategies are the most promising approach to mitigate criticality. Substitution eliminates reliance on CRMs, and where this is not possible, increasing device longevity and efficiency to reduce demand and increasing secondary supply through component reuse and recycling is essential to ensure deployment of PV is not limited by access to CRMs.
Transparent conductive oxides (TCOs)
ITO is the main TCO used in solar cells, coated onto glass to create transparent electrodes. Indium (In) has been classified as a CRM, and found to be one of the most critical elements for the PV industry using ITO in amorphous silicon and CdTe PV panels, and In in CIGS or CIS semiconductors.180,181 Other major applications of In contributing to global demand include ITO glass in flat panel displays (FPDs) and touch screens, alloys and solders, thermal interface materials, LEDs and laser diodes. In is produced as a by-product metal i.e., it is not the primary target of mining operations, rather 95% of refined primary In supply is from Zn ores processing, particularly from the mineral sphalerite. This creates problems in meeting demand spikes as primary supply depends on markets for Zn. Primary production is also concentrated in China (48%) which has high domestic In demand and a history of imposing export restrictions to conserve domestic material reserves. Although no official data is available on secondary supply, recycling from ITO production scrap is thought to be a considerable proportion of global supply, potentially exceeding primary supply.181 Recovery from EoL products however, is almost unknown. An issue with developing secondary supplies from ITO in WEEE and EoL PV is that In is present in such low quantities that economic recovery has been challenging. Processes for economic recovery did not exist until recently.182 Given the critical status of In, future lifecycle optimisation strategies should substitute ITO, and if used in commercialised devices, ensure recovery at EoL through substrate reuse or recovery from substrates making use of processes such as counter-current leaching systems proposed by Rocchetti et al. for economically viable recovery from flat-panel display glass.182 ITO is subject to registration under EU REACH and conflict minerals regulations, further reason to substitute ITO.
Although In has received much attention as a CRM, the Sn component of ITO has received far less, particularly in terms of assessing its criticality and substitution potential. The abundance of Sn in the Earth's crust is 2.1 ppm, lower than other major industrial metals such as Al, Cu and Pb; and its major applications are in Pb-free solder alloys, tinplate, tin chemicals, copper alloys and in Pb–Ca lead-acid battery grids. Global production of refined tin was approximately 361 kt per year over the period 2012–2016 with China the main producer accounting for 35% of primary production, followed by Indonesia (27%) and Myanmar (10%). Indonesia's production has plummeted since its government banned exports of unprocessed tin concentrates, and nearly all Myanmar's outputs are refined in China. Current EoL recycling input rate is approximately 31%, with recovery efficiencies depending on application. Valero et al. examined material bottlenecks in the future development of green technologies concluding that cumulative Sn demand from PV alone could exceed known reserves by 2050, highlighting the importance of circular economy practices such as substitution, dematerialization, recycling and increased resource efficiency throughout product lifecycles to ensure Sn availability does not limit PV deployment.25 This suggests substitution of SnO2 based TCOs in PSCs should be strongly considered, and where such TCOs are used, strategies to reuse coated substrates or recover the TCO must be prioritised. ITO has been successfully substituted by FTO and aluminium doped zinc oxide (AZO), both of which avoid In, but only AZO avoids use of Sn. Alternatively, flexible transparent electrodes have been produced by depositing a silver nanowire/antimony doped tin oxide (ATO) composite on PET.183 Although this avoids the use of In, it relies on replacement with Sb, itself a CRM. TCO free PSCs have been created in several ways. Sun et al., replaced the TCO with PEDOT:PSS,184 a material more commonly used as a HTM, and created flexible PSCs using graphene coated with MoO3 as the other electrode. Graphene transparent electrodes have been demonstrated by others.184,185 Numerous applications of metals to replace ITO substrates have been investigated and well-reviewed.172,186 Electrodes composed of metal nanowires, mesh, and ultrathin transparent metal films enable TCO replacement in transparent electrodes, and patterned metal electrodes in inverted devices negate the requirement for TCO substrates. Metals, can be a viable and attractive substrate candidate for preparing compact and mesoporous TiO2 layers, owing to their endurance at high temperature, a favourable characteristic for thermal delamination at EoL. However, integrating a transparent material as top electrode is necessary with metal substrates to enable light absorption. In this context, Troughton et al. produced PSCs with a nickel mesh/PET transparent electrode on commercially available titanium foil, which lends itself to R2R production of flexible PSCs.171 Impressive PCEs have been achieved by Chen et al. using Ni/Au mesh transparent electrodes,187 and Sears et al. using R2R slot-die coated silver nanowire transparent electrodes.188 However, the use of noble metals makes this a questionable strategy from a scalability point of view although a nanowire approach may reduce the quantity required for efficient cells.
Noble metals
Au, like Ag and the platinum-group metals (PGMs), is a noble and a precious metal with main applications in jewellery, bullion, coins, decoration, medicine and dentistry and as contact and conductor material in EEE. Global production in 2018 was 3502 t year−1 supplied mainly by China (14%), Australia (8%), Russia (8%) and the US (7%). Au supply is governed by conflict mineral regulations due to links between gold trade, armed conflict and civil rights abuses, introducing additional geopolitical issues to supply.24 In 2008, Morley and Eatherley found Au to be the most ‘at risk’ material for the UK of 69 assessed.167 While examining resource constraints to the renewable energy transition, Moreau et al. found known reserves could be fully depleted by 2035.24 In 2018, 26% of global supply was recycled from scrap. Mitigating depletion of primary reserves requires this rate to increase significantly but major barriers to doing so exist.189 Major applications of Au such as jewellery and bullion are viewed as precious assets handed down through generations, traded or held as reserve assets.189 Therefore much gold never becomes available for recycling. Much Au in WEEE is unrecovered due to low collection rates, dissipation in recycling, and the fact that cut-off-grades for recovery are determined by fluctuating market values.15,132 Au recovery is most usually achieved via smelting of PCBs with subsequent hydrometallurgical refinement.190,191 Au content of a PSC today is low (at ∼100 nm thickness ∼1.9 g m−2). However, cost, criticality issues and contribution to environmental impacts of PSCs form a strong case for substitution with low impact abundant materials that avoid high energy low efficiency thermal evaporation. If use of Au is shown by LCA to hold benefits despite these issues, EoL strategies for efficient recovery must be implemented, and alternative methods which enhance efficiency of deposition such as electroplating should be considered.
Global Pt demand in 2018 was 245 tonnes, with autocatalysts and jewellery the major demand sectors, followed by chemical, electronics, glass and petroleum applications.192 Its high catalytic activity is the reason for its use in many of these applications, as well as its use in counter electrode catalysts in PSCs with dye-sensitised solar cell (DSSC) like architectures.159 74% of global supply in 2018 was from mining which is highly concentrated in South Africa (67%), with additional supply from Russia (13%), Zimbabwe (9%), Canada (6%) and the US (2%). Pt is also recycled primarily from autocatalyst scrap and jewellery.193 Pt recycling is traditionally achieved through oxidative digestion in acidic chloride media, with a number of processes used to recover Pt from solution including solvent extraction, ion exchange and precipitation.194 Although little demand exists from PV, growth in demand from hydrogen fuel-cells and electrolysers,180,195–197 and the EV sector is projected.25 Pt is therefore ‘critical’ at the global level owing to high supply risk and production impacts,198 with circular mitigation strategies to decrease demand and increase secondary supply.34,198 Numerous nanostructured carbon based counter-electrodes were developed as non-precious Pt alternatives for DSSCs.199,200 Feasibly, similar innovation could avoid noble metal use in PSCs. R2R production of carbon electrodes in perovskite modules that avoid Au use has been demonstrated.86 P–I–N architectures also avoid the use of Au contacts.
Global Ag demand in 2018 was 32,145 tonnes, primarily for electronics, jewellery, coins, bullion, and c-Si PV. Only 15% of demand is met by recycling, with primary production in several countries. Only 30% of primary production is supplied from primary silver mines, >60% of reserves are polymetallic with one third of production as biproducts of Pb/Zn operations and 20% from Cu production. Ag is recovered through several processes including smelting of electronics with subsequent hydrometallurgical refinement, cupellation of jewellery, and electrolytic processes for less pure sources. Future recovery from Si-PV is a challenge due to the use of comminution to liberate materials from EVA laminate for physio-mechanical separation resulting in dissipation across material output fractions.201 Ag has viably replaced Au and Pt in PSCs, with associated cost and environmental benefits.167 GHG emissions of Ag production are ∼1/30th of GHG emissions of Au and Pt (Table 3), and market values of Ag are ∼1/40th of Pt and 1/68th of Au.‡ However, previous studies have shown Ag may be the most critical metal in future clean energy scenarios,23,27 and known reserves could be depleted by 203724 introducing very real prospects of future supply constraints.34 The use of Ag in PSCs may also be problematic due to AgI formation on contact surfaces which reduces PCE following reaction with MAI from perovskite degradation.160 Despite potential economic and environmental advantages over Au and Pt, resource criticality, price volatility and technical issues cast doubt on viability of Ag also. For these reasons, alternative abundant metals such as Al and Cu, or carbon-based materials may be the most sustainable options.117,185,202 Copper and aluminium foil are suitable substrates for R2R production of inverted PSCs.203,204 Cu in particular is known for good corrosion resistance in different environmental conditions and may be particularly promising for inverted PSC applications in which Cu has been shown to have a relatively stable interface with perovskite exhibiting little migration of Cu into the perovskite, slow chemical reaction between the two layers, and effective blocking of moisture penetration into the perovskite.202 Cr–Cu alloy electrodes have been used in high efficiency cells (23.4% PCE),205 and Cu has been used as an interelectrode in high efficiency (>26% PCE) four terminal perovskite/perovskite tandem cells.206 When inverted cell architecture is undesirable, carbon may be the front runner to replace noble metals owing to compatibility with printing for up-scaling, low-cost and environmental footprint, and abundance of carbon.86
Caesium and rubidium
New high efficiency perovskite formulations replace methylammonium with Cs and/or Rb to improve thermal stability.207–209 Cs has traditionally been an obscure metal with no formal markets and therefore difficult to price. Cs has been neglected in criticality assessments until recently. In 2018, the United States Geological Survey (USGS) added Cs to their CRM list. Concerns over Cs supply have been raised owing to limited sources and geopolitical issues associated with supply.210–212 Vidal et al. examined potential supply risks of Cs based on scarce and uncertain data concluding current rates of use could deplete known resources by 2056.213 Cs is used primarily as caesium formate in drilling fluids by the oil and gas industry. Other important applications include use as a photoelement; CsI is used in photomultiplier tubes and detectors of ionising radiation; CsI and CsBr are used to manufacture luminous tubes; Cs based catalysts are used to produce ammonium compounds, sulfuric acid, butyl alcohol, formic acid and for dehydrogenation reactions; Cs is the basis of numerous medical treatments; and Cs plasma is an important component of high-power efficiency magnetohydrodynamic generators. However, the current race to secure access to Cs has been driven by its use in atomic clocks for 5G infrastructure.214 The global Cs market was expected to grow 7%/year from 2018 to 2022,213 and production at a single mine results in considerable risk to future supply.210,211 Khalifa calculated that 1% of global Cs reserves would be sufficient to supply the entire US electricity demand from utility-scale PV to 2050 suggesting Cs demand from PV will not be a barrier to scaled deployment of PSCs.151 However, In light of growth of larger demand sectors and potential supply bottlenecks despite sufficiently large reserves to meet demand for PSCs, substitution of Cs with alternative abundant materials may be desirable. If Cs is used, CE strategies to retain Cs within PSC lifecycles may be necessary to ensure long terms supply and mitigate price volatility classically exhibited by CRMs.
Rb is a potential Cs alternative, and more abundant in the Earth's crust than common metals such as Cu, Zn and Pb, and 30 and 4 times as abundant as Cs and Li respectively, the production of which yields Rb as a by-product. Despite aforementioned risks to Cs production, normal problems associated with by-product metal supply scaling with demand may not be an issue for Rb as Li production is increasing constantly to meet demand from Li-ion batteries. Future availability of Rb may be more secure than Cs and therefore Rb may be a viable substitute for Cs in high efficiency PSCs.215
Interface engineering
Another important consideration in PSCs development has been performance and stability improvement by tuning the interface between the perovskite and active layers to improve energy level alignment between layers,106,216–220 charge separation and extraction,216,221–223 chemical interaction between selective and perovskite layers,224 to achieve surface passivation,216,220,224–227 reduce non-radiative recombination,216,220,221,228 preferential orientate perovskite crystals,216,220,229–231 increase light absorption,232 and increase of electron/hole transport capacity of materials.218,233 A range of materials and approaches have been employed for optimisation at the perovskite/ETL interface and perovskite/HTL interface (Fig. 5). Most of these improvements have been achieved through the implementation of self-assembled monolayers (SAMs),216,218,220 mainly consisting of materials such as carboxylic acids,216,234,235 phosphonic acids,216 amino acids,224,229 silanes,216,217 and fullerene derived materials,222,236 although alternative materials have also been employed.221,228 However, doping of the selective layers with materials such as Cu,237 Cs,236 In,219 Li,226,233,236 Mg,225,233 Nb233 and Sb,219 and the use of the plasmonic effect through use of noble metal nanoparticles such as Au232 to increase light absorption have also been implemented to improve the interface of perovskites with selective layers. Various quantum dot materials and composites, such as graphene, MoS2 and CsPbBr3 have also been used to improve charge transport and energy band alignment at the perovskite/HTL interface reducing charge transfer resistance while passivating defects.238–241 Issues associated with the use of Cs, In, Sb and Au have already been discussed, but Li, Mg and Nb have all be cited as critical by the EU.181 Although only required in small amounts for interface engineering, high growth in consumption from other sectors and primary supply concentration may result in future supply bottlenecks and/or price volatility. The introduction of materials in trace amounts also represent a potentially dissipative application as recovery of such small quantities will be challenging and further investigation of the fate of these materials in EoL processes is required.
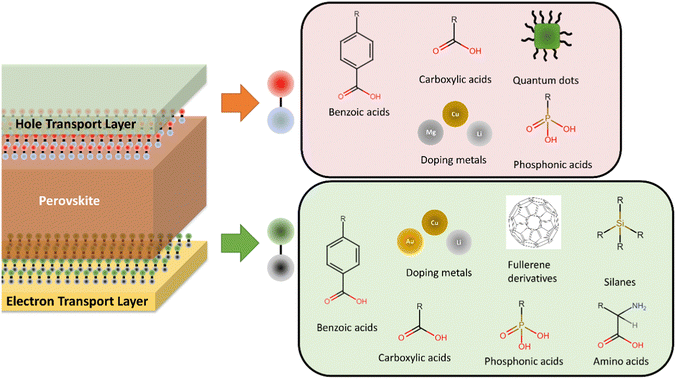 |
| Fig. 5 Summary of materials employed for interface optimisation in perovskite solar cells at the electron transport layer/perovskite interface and the hole transport layer/perovskite interface. | |
Encapsulants
The encapsulant in a PV module provides protection from the environment, structural stability, electrical insulation and resistance to UV and thermal degradation.242–246 The most successful material employed for commercial Si-PV encapsulation is ethylene vinyl acetate (EVA), representing ∼80% of the current market,245 providing high transmittance, good electrical and chemical resistance, easy processability, low cost and it has been used commercially for >20 years.242,243,245 However, degradation of EVA generates acetic acid that can induce corrosion in the PV system.243,247,248 Alternative encapsulants such as polyvinyl butyral (PVB) and silicones have also been employed less extensively than EVA.247
Selecting appropriate encapsulants for PSCs is non-trivial. In addition to aforementioned properties, challenges arise from the intrinsic nature of PSCs. Encapsulants must be chemically inert with the perovskite and selective layers of PSCs. If curing is required, the temperature must be limited to avoid perovskite degradation, which in most cases implies curing below 200 °C depending on perovskite composition.249–251 Encapsulants compatible with flexible substrates must themselves be flexible enough to protect the active layers and maintain mechanical properties of the module.252,253 Initial attempts to encapsulate PSCs with EVA,127,251,254 polyurethane (PU),255 polyolefin (POE),255 polyisobutylene (PIB),251 epoxy resins,250,251,256,257 thermoplastic polymers,127,250 Al2O3258 and other alternatives249,259,260 have resulted in varying degrees of success. However, high curing temperatures for EVA,127,242,243,251,254 delamination of thermoplastic polymers,254 chemical interaction with the perovskite layer and high costs of epoxy resins250,251,256 present significant barriers to viable PSC encapsulation.
The compatibility of encapsulants with EoL processes for PSMs must also be considered. Traditionally, two main processes for module delamination have been used: thermal degradation (mainly for Si-PV)57,261,262 and crushing for leaching of critical/valuable components (for thin film technologies).57,262 Due to their high cost, embodied impacts and CRM containing TCO coating, glass substrate should be primary targets for recovery in reusable form.137,263,264 To this end, thermal degradation is, so far, the most promising approach. However, the high temperatures required are likely to result in loss of the perovskite and any organic materials of cells. Chemical delamination of modules has been used and suggested as a promising method to selectively dissolve encapsulants, but this is yet to be proven viable for perovskite devices.57,261,265 Implementing solvent delamination must consider likely dissolution of active layers in the cells and could potentially be combined with a selective solvent dissolution approach to cell recycling. A new delamination method successfully demonstrated on CIGS modules which relies on cooling rather than heating, submerging module pieces in liquid nitrogen causing separation of EVA from glass due to their differences in thermal expansion coefficient.54 This cooling approach may be suitable for perovskite module delamination where heating is not. A potential alternative encapsulation strategy may be use of de-bondable polymers as edge sealants, which when triggered by an external stimulus (e.g. an electric/magnetic field, heating with induction or specific wavelength IR) de-bond, allowing access to cells without degradation, although this strategy has yet to be demonstrated for PV.266,267
Recent developments in the field have seen incorporation of materials into the encapsulation material to capture lead through chemisorption in the event of module failure and leakage from cells.162 Sulfonated graphene aerogel,268 sulfonic acid resins,269 phosphonic acid derivatives270,271 and ionogel272 have all been incorporated into encapsulation layers of high PCE devices demonstrating lead sequestration efficiencies of 98–99.9%. Chemisorption of Pb in this way seems to be a highly viable method of preventing Pb emissions from PSC modules while in use without compromising cell efficiency or light harvesting ability.
Solvents
Solution processability is a major advantage of PSCs presenting low-cost manufacturing options and promising prospects for cell recycling. Lifecycle impacts of hazardous solvents used in PSC manufacturing, particularly DMF (workplace exposure limit = 15 mg m−3 as a reprotoxic solvent) are a barrier to commercialisation and may hinder scalability. DMF and dimethyl acetamide (DMAc) is on the substances of very high concern (SVHC) list for consideration of restriction under Registration, Evaluation, Authorisation and Restriction of Chemicals (REACH) regulations273 and N-methyl-2-pyrrolidone (NMP) is now a restricted substance under REACH. One of the major aims of circular economy is substitution of toxic materials, and substitution of toxic solvents with less hazardous ones which don’t compromise cell performance and are suitable for scaled manufacturing techniques is a crucial challenge.274
Identifying suitable solvents requires careful consideration of solvent–solute interactions to produce high PCE devices.275 Efficient perovskite films require solvents to dissolve PbI2 to yield high concentration perovskite precursor solutions.276,277 Solvents must act as strong metal ligands,278 and MAPbI3 dissolution/deposition depends on Lewis acid–base interactions between PbI2 and dipolar aprotic solvents.279 This is also pertinent to the prospect of lead-free perovskites; SnI2 exhibits greater Lewis acidity than PbI2 requiring more highly basic chelating solvents. DMF functions well due to high dielectric constant and donicity, moderate vapour pressure and low viscosity, improving solvent removal during film curing and wettability to substrates. Desired solvent properties are highly dependent on the manufacturing method. There is a clear need for comprehensive frameworks to aid design of green low-toxicity solvent systems that attain high PCE given the number of manufacturing approaches being investigated for the various PSC architectures.280
Novel engineering solutions to design less harmful solvent systems have been demonstrated, such as dissolving methylamine gas into volatile acetonitrile to deposit perovskite at room temperature.278 The highly basic methylamine aids in solubilising the precursors, albeit at lower solution concentrations, negating the need for the solvent itself to coordinate precursors. An extension of this method bubbles methylamine through ethanol, a ‘green’ solvent which is subsequently mixed with tetrahydrofuran (THF),281 a common low-cost solvent with high vapour pressure, allowing rapid antisolvent-free crystallisation over relatively large areas. This strand of solvent system development has consequently found application in R2R manufacturing. Several issues persist with this formulation in terms of sustainability of the solvents themselves along with the added danger posed by the highly volatile chemicals THF and methylamine. It should be noted that THF is a carcinogenic chemical of concern. A recent work by Casella et al., 2023, presented a novel binary solvent system to remove methylamine from the manufacturing process.164 The novel solvent system, comprised of 2-methoxyethanol (2-ME) and THF, opens the potential for high throughput R2R manufacture via an annealing free perovskite deposition. Greater scalability and reduced embedded energy cost remains an important goal for potential commercialisation. The toxicity of 2-ME may ultimately limit the application of this system, however, this highlights the importance of ongoing research into these systems and the potential for a breakthrough on the horizon.
Recent attempts to replace the regulated solvent γ-butyrolactone (GBL) in printing carbon-based devices have been attempted. GBL is a precursor chemical which metabolises to GHB upon ingestion.282 GBL has the ability to sufficiently coordinate PbI2 in solution, leading to room temperature stable solutions. An inverse temperature-crystallisation relationship is exhibited for this solvent system wherein small MAPI crystals precipitate from solution as the temperature increases allowing infiltration of the carbon stack and pore filling at relatively low temperatures (ca. 50 °C). However, similar chemicals have been identified to perform this role, specifically the bioderived solvent γ-valerolactone (GVL), a ‘greener’ alternative unhindered by strict regulatory control.283
To aid solvent substitution, selection methodologies are needed to screen alternative solvents. Substitution must consider environmental, health and safety (EHS) factors, solvent performance in manufacturing and/or recycling, along with techno-economic performance of manufactured devices. Screening solvents based on EHS metrics provides justification for the substitution via a systematic approach. Due to the importance of solvents and quantities employed for industrial chemical processes, solvent selection guides to support improvements to process efficiency, sustainability, and safety are available. This includes those of large chemical and pharmaceutical companies including Sanofi, GSK, Astra Zeneca and Pfizer.284–294 Researchers have created unified guides consolidating this information, culminating in solvent selection frameworks such as the IMI-CHEM-21 guide.286,295–297 As a result, there is a growing body of research proposing alternative solvents, justifications for their use, and technical aspect of their impacts on the final perovskite film. Doolin et al. screened solvents based on the CHEM-21 method in conjunction with technical solvent parameters, using an approach described by the decision tree in Fig. 6 to produce cells with a mixture of DMSO:DMPU:2-MeTHF:EtOH with comparable performance to those produced with DMF.275 This framework for optimisation of greener solvent systems is a significant contribution to the field and will be an important approach to follow as new alternative solvents become available to replace traditionally hazardous ones. Doolin et al. highlighted a lack of appropriate LCA and LCIA data to inform the selection. Vidal et al. have recently published a health and environmental impact assessment of the industrial scale use of common solvents used in producing PSCs taking account of solvent production, use/removal, emissions and potential EoL treatments considering energy of evaporation for each solvent, air emission, condensation and subsequent incineration, reuse or distillation for solvent recycling.273 This is an important contribution to the knowledgebase for selection of solvents for industrial PSC production and recycling taking account of full lifecycle impacts.
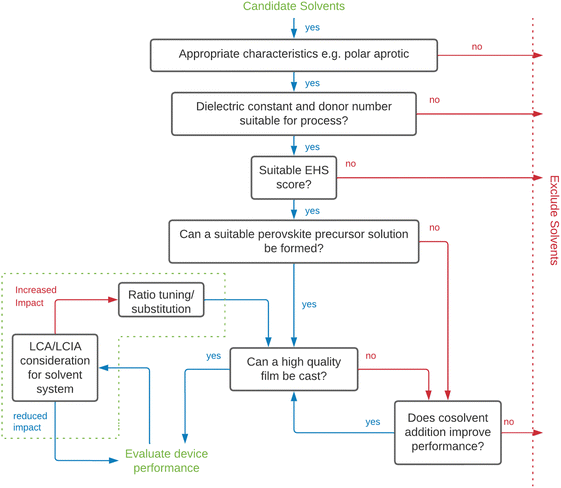 |
| Fig. 6 Solvent selection decision tree for screening and evaluation of alternative solvents for perovskite deposition (adapted from Doolin et al.).275 EHS – Environmental, health and safety, LCA – life cycle assessment, LCIA – life cycle impact assessment, MAPbI3 – methylammonium lead triiodide. | |
To date, highest efficiency devices reported have been produced using hazardous solvents, leading to conclusions that PCE and toxicity must be balanced for commercialisation.298 This implies PCE will always be compromised through use of greener solvent systems. However, Wu et al. have successfully produced high efficiency formamidinium based perovskite cells reaching PCEs of 22.4% using the green solvent triethyl phosphate.299,300 Many factors influence PCE and not all labs are able to achieve record efficiencies even with solvents such as DMF. Doolin et al. demonstrated that when a fair comparison to evaluate their green solvent systems side by side against DMF was made, comparable cell efficiencies were achieved. In an attempt to replace DMF in inks for printing perovskite, Gardner et al. evaluated cells produced with less hazardous solvent/alcohol/acid precursor systems against DMF based ones and also found efficiencies to be comparable.301 Liu et al. used a similar solvent engineering approach to Doolin et al. to develop a greener low-boiling point mixed solvent system for MAPI deposition in large area devices consisting of methylamine in ethanol and THF which when compared to DMF formed films with greater surface coverage and fewer defects yielding 0.1 cm2 and 10 cm2 cells with good PCEs of 20% and 15.6% respectively.281 This suggests fair side by side comparisons are necessary to properly evaluate performance of greener solvent systems against traditional hazardous ones and PCE needn’t be compromised for the sake of solvent toxicity.
Enabling circularity in PSCs
Take-back schemes with dedicated and efficient EoL processes will result in better outcomes for EoL PSMs than is possible through current WEEE management systems from which few materials are produced of suitable quality for closed-loop PV manufacturing. Most research toward remanufacturing and recycling of PSCs has focused on Pb recovery to prevent environmental emissions, and reutilisation of substrates. Ensuring Pb emissions are minimised throughout PSC lifecycles is essential to ensure perovskite technology does not contribute to ongoing accumulation of Pb within the environment, and EoL worker and public safety. This will be crucial to ensure favourable public perception of this important emerging technology. Establishment of appropriate business models to capture EoL modules and deal with Pb appropriately may add brand value to organisations moving early to commercialise such approaches. The take-back strategy of FirstSolar for recycling CdTe PV modules to prevent hazardous Cd emissions and secure secondary supplies of critical Te has successfully granted competitive advantage and established the company image as environmental leaders in the PV industry.302 With the trend to substitute impactful precious metals in PSCs, substrate recovery would result in retention of the most impactful and costly cell components as well as CRMs in the TCO. Tian et al. recently concluding that recovery of TCO coated glass substrates for remanufacturing could reduce EPBT and GHG emissions from new PSM production by 73 and 71% respectively.144 The study also aligns with previous LCA findings showing embedded impacts in materials far exceed impacts of manufacturing processes, and thermal processes for coating and curing account for the largest process impacts. Retention of substrates with thermally deposited functional layers for reuse in PSM remanufacturing must therefore be a priority goal of EoL strategies.
Recycling and remanufacturing approaches
If the low-cost energy promised by PSC technology are realised, successful commercialization will dramatically increase materials demand. Based on toxicity, environmental impacts, and resource efficiency consideration for materials contained in PSCs, development of circular economy strategies to capture and reuse materials from EoL PSCs are urgently required.77 Achieving this will require appropriate selection of materials sets and architectures62,65,303,304 taking account of performance during EoL treatment. The following section examines progress towards recycling and remanufacturing processing which could enable circular economy for PSCs through retention of materials/components in new devices without considerable losses in PCE. Remanufacturing represents a tighter loop of the circular economy than recycling (Fig. 2). Recycling processes recover materials at a molecular level, enabling them to be reutilised in fabrication of new cells (Fig. 7a), whereas remanufacturing seeks to create new cells from old ones utilising as much of the original cell as possible (Fig. 7b and c). Remanufacturing therefore avoids costs and environmental impacts incurred during production from raw materials (even recycled ones) by creating ‘like new’ cells using the major cost and impact components again i.e. glass substrates with mesoporous sintered layers in place.
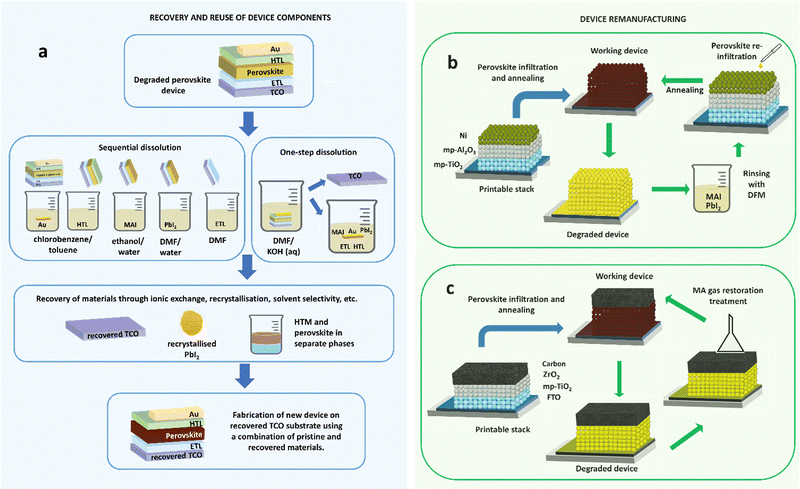 |
| Fig. 7 Methods for recovery of device components vs. remanufacturing methods: (a) multi-solvent and single-solvent approach for recycling of cells through separation, recovery and reuse of the device elements; (b) remanufacturing of a printable n-i-p stack with mesoporous nickel cathode by rinsing and re-infiltration of the perovskite material (adapted from Ku et al.);305 (c) remanufacturing of a printable carbon stack cell using a simple methylamine gas treatment to restore degraded perovskite (process described in Hong et al.).166 | |
Selective dissolution has proved an effective technique for the recovery of PSCs components for reuse in new cells without significant reduction in PCEs compared with those produced from virgin materials (Fig. 7a). Initial efforts focused on substrate retention owing to the high cost and proportion of embodied environmental impacts in these components. In an initial study by Huang et al., FTO-coated glass was recovered from ETL-free PSCs by dissolution of degraded perovskite layers and spiro-MeOTAD in DMF allowing silver counter electrodes flakes to float to the solution surface for recovery.306 Devices fabricated with the recovered substrates exhibited a PCE of 10.8%, comparable to 11.5% in devices fabricated on fresh FTO substrates. Binek et al. reported a more selective multi-solvent method where counter electrodes and spiro-MeOTAD were removed using chlorobenzene, before selective removal of methylammonium iodide from the perovskite with deionized water.263 DMF then removed remaining PbI2 and the TiO2 mesoporous film. Recovered FTO substrates were reused in new devices without loss in PCE after two cycles of recovery. Augustine et al. reported an alternative technique for recovering and reusing ITO-coated glass in inverted devices using a single inexpensive alkaline solvent while maintaining PCE in devices fabricated on recovered substrates.263 The strategy has also been successfully demonstrated for mixed cation CsPbIBr2 carbon-stack devices by Zhu et al., in which treatment with DMF enabled FTO/TiO2 recovery for use in new devices with 20% higher efficiency than virgin devices owing to the effect of residual perovskite derived species on substrates.307
Multi-solvent dissolution techniques have been successful in retaining charge-transport layers in addition to TCO-coated glass from planar308 and mesoscopic293,308–311 TiO2 devices, with promising results showing no performance loss over 10 cycles of recovery and reuse in new devices.293 Feng et al. reported the effective use of alkylamines in liquefaction of the perovskite absorber for the recovery of ITO/NiOX substrates in inverted devices without PCE loss in devices produced from recovered substrates.312 One-step dissolution with DMF has also been demonstrated to work for recovery of printable devices, as reported by Ku et al. for a full inorganic stack FTO/c-TiO2/mp-TiO2/Al2O3/NiOX where degraded perovskite was removed using DMF and reloaded into the recovered stack with a final efficiency of 12.1% versus 13.6% on a fresh stack (Fig. 7b).305 Li et al. found similar results for FTO/c-TiO2/mp-TiO2/mp-Al2O3/np-Au:NiOX stack devices, with an initial PCE of 8.6%, and PCEs of 8.2% and 7.7% for the first and second generation reused stacks.313 This approach represents a potential remanufacturing method to retain all functional layers and recondition cells through removal and reapplication of perovskites to the mesoporous structure.
To address the environmental impact of lead toxicity, works on substrate recovery have integrated strategies for effective lead capture. Kim et al. report the removal of lead from the resulting lixiviant of perovskite dissolution via solvent extraction and ion exchange, allowing 99.99% of lead removal from residual solvent.314 Binek et al. reported recovery and reuse of PbI2 by two methods: directly from the DMF lixiviant and through recrystallization of PbI2 which when used in new devices resulted in a drop in device PCE dropping only 1% compared to devices prepared with fresh PbI2.263 Zhang et al. reported lead recovery from carbon-based cells by precipitation of lead ions from DMF lixiviant as Pb(OH)2 using NH3·H2O, followed by reaction with HI to produce PbI2 with a recovery rate of 95.7%, and only 1.5% drop in PCE in devices fabricated with recovered PbI2.311 Feng et al. reported a recovery yield of 98.9% and no loss in PCE in devices fabricated from recovered NiOx/ITO substrates and precursor solutions generated from recrystallized MAPI recovered via liquefaction in alkylamines.312 Park et al. have demonstrated the use of an iron containing hydroxyapatite absorbent to recover Pb from non-aqueous solvent systems with 99.97% efficiency proposing a process for recycling modules or contaminated materials from any stage of the product lifecycle via magnetic field assisted seperation of the resulting Pb complex and recovery of PbI2 and clean solvents.315 A technique yet to be demonstrated in devices was explored by Poll et al., where lead is dissolved using a deep eutectic solvent (choline chloride and ethylene glycol) and recovered by selective electrodeposition with a yield of 99.8%.316 This all suggests that prevention of Pb emissions during EoL treatment is possible via a number of efficient recovery strategies.
An alternative approach to selective dissolution for recovery of substrate and lead is device reconditioning. Hong et al. successfully regenerated MAPI crystals within HTM free triple mesoscopic inorganic structured PSCs by post-treating devices with methylamine gas (Fig. 7c).166 After two cycles of photodegradation and regeneration of the MAPI PSCs, PCEs recovered to 91% of the initial value from 40% in the degraded state. Methylamine treatment also works well as alternative to anti-solvent to enhance performance of printed devices in manufacturing (increasing PCE from 6.67% to 15.26%).166 Another type of in-situ recovery of PbI2 has been reported for films and devices after natural or thermal-induced degradation of the perovskite film to PbI2 is reversed by spin coating of a new MAI solution onto the PbI2 film, restoring the perovskite film optical performance and resulting in an increased efficiency relative to freshly prepared devices.15,16 Such in situ strategies could potentially lead to reconditioning of cells, representing a tighter loop of the circular economy than recycling.
Although the selective dissolution of devices presents the potential for the recovery of all components, the recovery of other materials removed from the device such as spiro-MeOTAD, PCBM, and additional dopants used in the fabrication of perovskite devices have not been demonstrated for the techniques previously mentioned. Recently Wang et al. reported an innovative “one-key-reset” method for the recovery and reuse of all components in an ITO/SnO2/MAPI/spiro-MeOTAD/Au device, reaching efficiencies of 20% after the second cycle of recovery of all components, pointing at an interesting application for solvent engineering in recovery and remanufacture of high-performance devices.317 Submersion of devices in a ‘bleacher solution’ of methylamine in THF results in liberation of gold contacts, SnO2 coated substrates and a liquid fraction composed of a THF dissolved spiro phase, and liquified perovskite phase enabling all components to be reused following purification. The recovery of noble metals used as electrodes remains a challenge. Although solvent removal allows Au counter electrode recovery as HTMs are dissolved and electrodes float free, its reuse for deposition of new evaporated films is still complex. Wang et al. report recovered gold required melting at high temperatures to render it usable in deposition of new films.297 Effective ways to take advantage of noble metal properties compatible with remanufacturing have been demonstrated in reports by Li et al., where Au was applied as a dopant in the fully printable inorganic stack,313 and Yang et al., where a durable nanoporous gold film counter electrode is manufactured, recovered and reused in perovskite devices.318 Given the high cost and environmental impact of gold, substitution in commercial devices may negate the recovery challenges.
Cost-effective module recycling has been successfully demonstrated by Chen et al. who reported a method for close-loop lead recovery and remanufacture of encapsulated ITO/PTAA/Perovskite/C60/BCP/Cr/Cu modules.143 The cover glass was recovered through thermal delamination, DMF bath was used to recover ITO substrates, and a cation exchange resin bath served to recover lead iodide. The devices remanufactured with recovered substrates, lead iodide, and cover glass did not exhibit a noticeable photovoltaic performance drop. Furthermore, the cation exchange resin was regenerated with an effectiveness close to 100%. This suggests that recycling at module scale could significantly reduce lifecycle costs of PSC PV, improving competitiveness with alternative technologies. Further consideration of the sustainability and cost-effective aspects of the recovery process itself is still required for the future. Life cycle assessments of many substrate recovery techniques published up to 2021 have shown most of the impact of these techniques comes from the toxicity of solvents such as DMF.319 This suggests that further investigation of solvent based recycling strategies which rely on greener solvent systems such as that reported by Doolin et al. for device fabrication should be investigated.275
Conclusion
Adoption of circular economy throughout lifecycles of perovskite PV is necessary to minimise environmental impacts of production, ensure Pb emissions are prevented, and mitigate materials criticality issues which may limit PV deployment. There is a considerable opportunity to effectively design PSCs, PSMs and associated EoL processes in a way that will be far more difficult for established PV technology facing linear lock-in. Although legislation increasingly drives progress in this regard, the potential benefits for the technology in terms of competitiveness with established renewables are considerable.
Substitution of the most critical and costly materials of PSCs, for the most part, is technically feasible, although the impact on techno-economic performance of PSMs remains to be seen. Where this isn’t possible for techno-economic reasons, processes to retain high-value CRMs used in current architectures via cell refurbishment, remanufacture and module recycling have been demonstrated. This presents the potential to reduce production costs and environmental impacts to below levels of any other PV technology to date. The ability to valorise EoL devices to a greater extent by cycling materials back into production will result in considerably lower EoL costs compared to mechanical recycling approaches analogous to those used for Si-PV. Especially when potential decontamination strategies to mitigate lead content are also considered. The adoption of circular economy practices into lifecycles of PSMs could therefore result in the lowest LCOE from PV technologies so far.
High levels of materials retention through PSC and PSM recycling, as well as cell reconditioning has been demonstrated in the literature. Solvent dissolution of active materials for redeposition within retained mesoporous electrode structures appears a viable strategy for future commercial EoL treatment to retain most embodied costs and impacts of initial production and contained CRMs, potentially delivering second generation cells at a fraction of initial costs while mitigating the industries susceptibility to global resource security concerns. A major milestone to be demonstrated is that this can be achieved for complete carbon triple stack devices.
Barriers remain to commercial adoption for EoL treatment of PSMs. Greener solvents are required than those which have been utilised to date, although progress in this area for cell manufacturing lends itself to EoL solutions. Suitable encapsulants enabling EoL module delamination require development. Device longevity and prevention of Pb emissions is paramount for commercialisation yet leads to a dichotomy when balancing this priority with the requirement of viable delamination. Given the potential of materials retention to reduce LCOE and emissions associated with energy generation, appropriate encapsulants may sacrifice device longevity to some extent for net benefit over successive generations of PSMs afforded via retention of components/materials. Inspiration may be gained from de-bondable adhesives in development for use in alternative technologies which facilitate active disassembly.
Author contributions
RC: conceptualization, data curation, formal analysis, investigation, project administration, visualization, writing – original draft, writing – review & editing. RGR: investigation, visualization, writing original draft, writing – review & editing. AD: investigation, writing original draft, writing – review & editing. KV: investigation, visualization, writing – original draft, writing – review & editing. MD: conceptualization, funding acquisition, investigation, project administration, resources, supervision, writing original draft, writing – review & editing.
Conflicts of interest
There are no conflicts to declare.
Acknowledgements
This work was made possible by support from Engineering and Physical Science Research Council (EP/S001336/1) and through the funding of the SPECIFIC Innovation and Knowledge Centre by EPSRC (EP/N020863/1), Innovate UK [920036], and the European Regional Development Fund [c80892] through the Welsh Government. MLD and RC are also grateful for EPSRC funding for TReFCo (EP/W019167/1). RGR would like to acknowledge the IMPACT operation which has been part-funded by the European Regional Development Fund through the Welsh Government and Swansea University. MLD is also grateful for the funding from the UKRI Global Challenge Research Fund through the SUNRISE project (EP/P032591/1).
Notes and references
- W. Steffen, K. Richardson, J. Rockström, S. E. Cornell, I. Fetzer, E. M. Bennett, R. Biggs, S. R. Carpenter, W. de Vries, C. A. de Wit, C. Folke, D. Gerten, J. Heinke, G. M. Mace, L. M. Persson, V. Ramanathan, B. Reyers and S. Sörlin, Science, 2015, 347, 1259855 CrossRef PubMed.
- K. R. Shivanna, Resonance, 2020, 25, 93–109 CrossRef.
-
Ellen MacArthur Foundation, Towards a Circular Economy – Economics and business rationale for an accelerated transition, Ellen MAcArthur Foundation, http://www.ellenmacarthurfoundation.org/business/reports, 2013.
- M. P. O’Connor, J. B. Zimmerman, P. T. Anastas and D. L. Plata, ACS Sustainable Chem. Eng., 2016, 4, 5879–5888 CrossRef.
- R. G. Charles, M. L. Davies, P. Douglas, I. L. Hallin and I. Mabbett, Energy, 2019, 166, 1207–1215 CrossRef CAS.
- Circle Economy, Circularity Gap Report 2020, 2020.
- EC, Coomunication from the Commission to the European Parliament, the council, the European Economic and Social Committee of the Regions – A new Circular Economy Action Plan For a cleaner and more competitive Europe, 2020.
- Z. Song, C. L. McElvany, A. B. Phillips, I. Celik, P. W. Krantz, S. C. Watthage, G. K. Liyanage, D. Apul and M. J. Heben, Energy Environ. Sci., 2017, 10, 1297–1305 RSC.
- IRENA, World energy transitions outlook: 1.5 degrees pathway, Abu Dhabi, 2021.
- IEA, The Role of Critical Minerals in Clean Energy Transitions, OECD, Paris, 2021.
-
S. Bobba, S. Carrara, J. Huisman, F. Mathieux and C. Pavel, Critical Raw Materials for Strategic Technologies and Sectors in the EU – a Foresight Study, 2020.
- R. G. Charles, P. Douglas, J. A. Baker, M. J. Carnie, J. O. Douglas, D. J. Penney and T. M. Watson, J. Cleaner Prod., 2018, 202, 1167–1178 CrossRef CAS.
-
V. Forti, C. P. Baldé, R. Kuehr and G. Bel, The Global E-waste Monitor 2020: Quantities, flows, and the circular economy potential, Bonn/Geneva/Rotterdam, 2020.
- M. A. Charitopoulou, K. G. Kalogiannis, A. A. Lappas and D. S. Achilias, Environ. Sci. Pollut. Res., 2020, 28, 59190–59213 CrossRef PubMed.
- R. G. Charles, P. Douglas, M. Dowling, G. Liversage and M. L. Davies, Resour., Conserv. Recycl., 2020, 161, 104923 CrossRef.
- IEA, Energy Technology Perspectives 2017, OECD, 2017.
- K. T. Gradin, S. Poulikidou, A. Björklund and C. Luttropp, J. Cleaner Prod., 2018, 172, 1699–1710 CrossRef.
- E. Hache, G. S. Seck, M. Simoen, C. Bonnet and S. Carcanague, Appl. Energy, 2019, 240, 6–25 CrossRef.
- M. Hernandez, M. Messagie, M. De Gennaro and J. Van Mierlo, Resour., Conserv. Recycl., 2017, 120, 119–130 CrossRef.
- A. Månberger and B. Stenqvist, Energy Policy, 2018, 119, 226–241 CrossRef.
- W. Miyamoto, S. Kosai and S. Hashimoto, Minerals, 2019, 9, 95 CrossRef CAS.
- EC JRC, Raw Materials Scoreboard, Brussels, 2016.
- A. Elshkaki and L. Shen, Energy, 2019, 180, 903–917 CrossRef CAS.
- V. Moreau, P. Dos Reis and F. Vuille, Resources, 2019, 8, 29 CrossRef.
- A. Valero, A. Valero, G. Calvo and A. Ortego, Renewable Sustainable Energy Rev., 2018, 93, 178–200 CrossRef.
- A. Valero, A. Valero, G. Calvo, A. Ortego, S. Ascaso and J.-L. Palacios, Energy, 2018, 159, 1175–1184 CrossRef.
- L. Grandell, A. Lehtilä, M. Kivinen, T. Koljonen, S. Kihlman and L. S. Lauri, Renewable Energy, 2016, 95, 53–62 CrossRef CAS.
- A. de Koning, R. Kleijn, G. Huppes, B. Sprecher, G. van Engelen and A. Tukker, Resour., Conserv. Recycl., 2018, 129, 202–208 CrossRef.
- A. Elshkaki and T. E. Graedel, J. Cleaner Prod., 2013, 59, 260–273 CrossRef.
- Q. Wang, L. Huang, H. Yu, X. Quan, Y. Li, G. Fan and L. Li, Int. J. Hydrogen Energy, 2015, 40, 184–196 CrossRef CAS.
- R. Kleijn, E. van der Voet, G. J. Kramer, L. van Oers and C. van der Giesen, Energy, 2011, 36, 5640–5648 CrossRef CAS.
- K. Roelich, D. A. Dawson, P. Purnell, C. Knoeri, R. Revell, J. Busch and J. K. Steinberger, Appl. Energy, 2014, 123, 378–386 CrossRef.
- T. Watari, B. C. McLellan, D. Giurco, E. Dominish, E. Yamasue and K. Nansai, Resour., Conserv. Recycl., 2019, 148, 91–103 CrossRef.
- T. Watari, B. McLellan, S. Ogata and T. Tezuka, Minerals, 2018, 8, 156 CrossRef.
- N. T. Nassar, D. R. Wilburn and T. G. Goonan, Appl. Energy, 2016, 183, 1209–1226 CrossRef CAS.
-
S. Weckend, A. Wade and G. Heath, End-of-life management - Solar Photovoltaic Panels, 2016.
-
S. Teske, T. Pregger, T. Naegler, S. Simon, J. Pagenkopf, B. Van Den Adel and Ö. Deniz, in Achieving the Paris Climate Agreement Goals: Global and Regional 100% Renewable Energy Scenarios with Non-Energy GHG Pathways for +1.5C and +2C, Springer International Publishing, 2019, pp. 175–401 Search PubMed.
- Y. Kalmykova, M. Sadagopan and L. Rosado, Resour., Conserv. Recycl., 2018, 135, 190–201 CrossRef.
- D. Reike, W. J. V. Vermeulen and S. Witjes, Resour., Conserv. Recycl., 2018, 135, 246–264 CrossRef.
- N. M. P. Bocken, I. de Pauw, C. Bakker and B. van der Grinten, J. Ind. Prod. Eng., 2016, 33, 308–320 Search PubMed.
- J. Korhonen, A. Honkasalo and J. Seppälä, Ecol. Econ., 2018, 143, 37–46 CrossRef.
- F. Figge, A. S. Thorpe, P. Givry, L. Canning and E. Franklin-Johnson, Ecol. Econ., 2018, 150, 297–306 CrossRef.
- L. Dong, H. Zhang, T. Fujita, S. Ohnishi, H. Li, M. Fujii and H. Dong, J. Cleaner Prod., 2013, 59, 226–238 CrossRef.
- B. Guo, Y. Geng, T. Sterr, L. Dong and Y. Liu, J. Cleaner Prod., 2016, 135, 995–1008 CrossRef CAS.
- M. Marconi, F. Gregori, M. Germani, A. Papetti and C. Favi, Procedia Manuf., 2018, 21, 502–509 CrossRef.
- L. Sun, H. Li, L. Dong, K. Fang, J. Ren, Y. Geng, M. Fujii, W. Zhang, N. Zhang and Z. Liu, Resour., Conserv. Recycl., 2017, 119, 78–88 CrossRef.
- Z. Liu, M. Adams, R. P. Cote, Y. Geng, Q. Chen, W. Liu, L. Sun and X. Yu, Energy Policy, 2017, 102, 88–95 CrossRef CAS.
- Z. Wen and X. Meng, J. Cleaner Prod., 2015, 90, 211–219 CrossRef.
- WRAP, 2015, 2015.
-
H. Cui and C. Liu, in AIP Conference Proceedings, 2017, vol. 1864, p. 020090.
- G. C. Mantese, M. J. Bianchi and D. C. Amaral, Procedia Manuf., 2018, 21, 862–869 CrossRef.
-
I. S. E. Fraunhofer, Photovoltaics Report, Freiburg, 2021.
- D. Hu, B. Ma, X. Li, Y. Lv, Y. Chen and C. Wang, J. Cleaner Prod., 2022, 350, 131426 CrossRef CAS.
- F. W. Liu, T. M. Cheng, Y. J. Chen, K. C. Yueh, S. Y. Tang, K. Wang, C. L. Wu, H. S. Tsai, Y. J. Yu, C. H. Lai, W. S. Chen and Y. L. Chueh, Sol. Energy Mater. Sol. Cells, 2022, 241, 111691 CrossRef CAS.
- G. A. Heath, T. J. Silverman, M. Kempe, M. Deceglie, D. Ravikumar, T. Remo, H. Cui, P. Sinha, C. Libby, S. Shaw, K. Komoto, K. Wambach, E. Butler, T. Barnes and A. Wade, Nat. Energy, 2020, 5, 502–510 CrossRef CAS.
- Y. Xu, J. Li, Q. Tan, A. L. Peters and C. Yang, Waste Manage., 2018, 75, 450–458 CrossRef PubMed.
- J. Tao and S. Yu, Sol. Energy Mater. Sol. Cells, 2015, 141, 108–124 CrossRef CAS.
- A. Mestre and T. Cooper, Des. J., 2017, 20, S1620–S1635 Search PubMed.
- P. Vanegas, J. R. Peeters, D. Cattrysse, P. Tecchio, F. Ardente, F. Mathieux, W. Dewulf and J. R. Duflou, Resour., Conserv. Recycl., 2018, 135, 323–334 CrossRef PubMed.
-
N. Hunter, Designing for a circular economy, http://www.greatrecovery.org.uk/resources/designing-for-a-circular-economy/, (accessed 9 May 2022).
- J. M. F. Mendoza, M. Sharmina, A. Gallego-Schmid, G. Heyes and A. Azapagic, J. Ind. Ecol., 2017, 21, 526–544 CrossRef.
- M. D. Bovea and V. Pérez-Belis, J. Environ. Manage., 2018, 228, 483–494 CrossRef PubMed.
- M. C. den Hollander, C. A. Bakker and E. J. Hultink, J. Ind. Ecol., 2017, 21, 517–525 CrossRef.
- P. Tecchio, C. McAlister, F. Mathieux and F. Ardente, J. Cleaner Prod., 2017, 168, 1533–1546 CrossRef PubMed.
- S. Ahmad, K. Y. Wong, M. L. Tseng and W. P. Wong, Resour., Conserv. Recycl., 2018, 132, 49–61 CrossRef.
- C. Vezzoli, F. Ceschin, J. C. Diehl and C. Kohtala, J. Cleaner Prod., 2015, 97, 1–12 CrossRef.
- E. Iacovidou, C. A. Velis, P. Purnell, O. Zwirner, A. Brown, J. Hahladakis, J. Millward-Hopkins and P. T. Williams, J. Cleaner Prod., 2017, 166, 910–938 CrossRef.
- J. Mesa, I. Esparragoza and H. Maury, J. Cleaner Prod., 2018, 196, 1429–1442 CrossRef.
- M. Saidani, B. Yannou, Y. Leroy, F. Cluzel and A. Kendall, J. Cleaner Prod., 2019, 207, 542–559 CrossRef.
- M. Saidani, B. Yannou, Y. Leroy, F. Cluzel, M. Saidani, B. Yannou, Y. Leroy and F. Cluzel, Recycling, 2017, 2, 6 CrossRef.
- M. Niero and P. P. Kalbar, Resour., Conserv. Recycl., 2019, 140, 305–312 CrossRef.
- EC, Commision Staff Working document – Report on Critical Raw Materials and the circular Economy Part 2/3, Brussels, 2018.
- EC, M. Gislev and M. Grohol, Report on Critical Raw Materials and the Circular Economy, Brussels, 2016.
- D. Peck, P. Kandachar and E. Tempelman, Mater. Des., 2015, 65, 147–159 CrossRef.
-
P. Wang and S. Kara, Procedia CIRP, Elsevier B.V., 2019, vol. 80, pp. 667–672 Search PubMed.
- M. Krystofik, M. Bustamante and K. Badami, Resour., Conserv. Recycl., 2018, 135, 24–33 CrossRef.
- F.-W. Liu, G. Biesold, M. Zhang, R. Lawless, J.-P. Correa-Baena, Y.-L. Chueh and Z. Lin, Mater. Today, 2021, 43, 185–197 CrossRef CAS.
- J. Busch, D. Dawson and K. Roelich, J. Cleaner Prod., 2017, 149, 751–761 CrossRef.
-
R. G. Charles, M. L. Davies and P. Douglas, in 2016 Electronics Goes Green 2016+ (EGG), IEEE, 2016, pp. 1–8.
- H. Min, D. Y. Lee, J. Kim, G. Kim, K. S. Lee, J. Kim, M. J. Paik, Y. K. Kim, K. S. Kim, M. G. Kim, T. J. Shin and S. Il Seok, Nature, 2021, 598(7881), 444–450 CrossRef CAS PubMed.
- Wuxi Utmost Light Technology Co Ltd, China's perovskite solar module efficiency exceeds 20%, setting a new world record, https://www.prnewswire.com/news-releases/chinas-perovskite-solar-module-efficiency-exceeds-20-setting-a-new-world-record-301261431.html, (accessed 15 October 2021).
- NREL, Champion Photovoltaic Module Efficiency Chart, https://www.nrel.gov/pv/module-efficiency.html, (accessed 15 October 2021).
- A. Kojima, K. Teshima, Y. Shirai and T. Miyasaka, J. Am. Chem. Soc., 2009, 131, 6050–6051 CrossRef CAS PubMed.
- M. A. Green, E. D. Dunlop, J. Hohl-Ebinger, M. Yoshita, N. Kopidakis and A. W. Y. Ho-Baillie, Prog. Photovoltaics Res. Appl., 2020, 28, 3–15 CrossRef.
- D. Pourjafari, S. M. P. Meroni, D. P. Domínguez, R. Escalante, J. Baker, A. S. Monroy, A. Walters, T. Watson and G. Oskam, Energies, 2022, 15, 641 CrossRef CAS.
- D. Beynon, E. Parvazian, K. Hooper, J. Mcgettrick, R. Patidar, T. Dunlop, Z. Wei, P. Davies, R. Garcia Rodriguez, M. Carnie, M. Davies, T. Watson, D. Beynon, E. Parvazian, K. Hooper, J. Mcgettrick, R. Patidar, T. Dunlop, Z. Wei, M. Carnie, M. Davies, T. Watson, R. G. Rodriguez and P. Davies, Adv. Mater., 2023, 2208561 CrossRef CAS PubMed.
- E. W. Jones, P. J. Holliman, A. Connell, M. L. Davies, J. Baker, R. J. Hobbs, S. Ghosh, L. Furnell, R. Anthony and C. Pleydell-Pearce, Chem. Commun., 2016, 52, 4301–4304 RSC.
- M. M. Lee, J. Teuscher, T. Miyasaka, T. N. Murakami and H. J. Snaith, Science, 2012, 338, 643–647 CrossRef CAS PubMed.
- T. D. McFarlane, C. S. De Castro, P. J. Holliman and M. L. Davies, Chem. Commun., 2019, 55, 35–38 RSC.
- M. Saliba, T. Matsui, J.-Y. Seo, K. Domanski, J.-P. Correa-Baena, M. K. Nazeeruddin, S. M. Zakeeruddin, W. Tress, A. Abate, A. Hagfeldt and M. Grätzel, Energy Environ. Sci., 2016, 9, 1989–1997 RSC.
- M. Saliba, J.-P. Correa-Baena, C. M. Wolff, M. Stolterfoht, N. Phung, S. Albrecht, D. Neher and A. Abate, Chem. Mater., 2018, 30, 4193–4201 CrossRef CAS.
- M. L. Petrus, T. Bein, T. J. Dingemans and P. Docampo, J. Mater. Chem. A, 2015, 3, 12159–12162 RSC.
- M. L. Petrus, A. Music, A. C. Closs, J. C. Bijleveld, M. T. Sirtl, Y. Hu, T. J. Dingemans, T. Bein and P. Docampo, J. Mater. Chem. A, 2017, 5, 25200–25210 RSC.
- M. L. Petrus, K. Schutt, M. T. Sirtl, E. M. Hutter, A. C. Closs, J. M. Ball, J. C. Bijleveld, A. Petrozza, T. Bein, T. J. Dingemans, T. J. Savenije, H. Snaith and P. Docampo, Adv. Energy Mater., 2018, 8, 1801605 CrossRef.
- M. Daskeviciene, S. Paek, A. Magomedov, K. T. Cho, M. Saliba, A. Kizeleviciute, T. Malinauskas, A. Gruodis, V. Jankauskas, E. Kamarauskas, M. K. Nazeeruddin and V. Getautis, J. Mater. Chem. C, 2019, 7, 2717–2724 RSC.
- J. Liu, S. Pathak, T. Stergiopoulos, T. Leijtens, K. Wojciechowski, S. Schumann, N. Kausch-Busies and H. J. Snaith, J. Phys. Chem. Lett., 2015, 6, 1666–1673 CrossRef CAS PubMed.
- K. Hwang, Y.-S. Jung, Y.-J. Heo, F. H. Scholes, S. E. Watkins, J. Subbiah, D. J. Jones, D.-Y. Kim and D. Vak, Adv. Mater., 2015, 27, 1241–1247 CrossRef CAS PubMed.
- J. B. Whitaker, D. H. Kim, B. W. Larson, F. Zhang, J. J. Berry, M. F. A. M. van Hest and K. Zhu, Sustainable Energy Fuels, 2018, 2, 2442–2449 RSC.
- M. Yang, D. H. Kim, T. R. Klein, Z. Li, M. O. Reese, B. J. Tremolet de Villers, J. J. Berry, M. F. A. M. van Hest and K. Zhu, ACS Energy Lett., 2018, 3, 322–328 CrossRef CAS.
- S. Tang, Y. Deng, X. Zheng, Y. Bai, Y. Fang, Q. Dong, H. Wei and J. Huang, Adv. Energy Mater., 2017, 7, 1700302 CrossRef.
- Z. Yang, C.-C. Chueh, F. Zuo, J. H. Kim, P.-W. Liang and A. K.-Y. Jen, Adv. Energy Mater., 2015, 5, 1500328 CrossRef.
- X. Peng, J. Yuan, S. Shen, M. Gao, A. S. R. Chesman, H. Yin, J. Cheng, Q. Zhang and D. Angmo, Adv. Funct. Mater., 2017, 27, 1703704 CrossRef.
- A. T. Barrows, A. J. Pearson, C. K. Kwak, A. D. F. Dunbar, A. R. Buckley and D. G. Lidzey, Energy Environ. Sci., 2014, 7, 2944–2950 RSC.
- J. Griffin, A. J. Pearson, N. W. Scarratt, T. Wang, D. G. Lidzey and A. R. Buckley, Org. Electron., 2014, 15, 692–700 CrossRef CAS.
- J. Ávila, C. Momblona, P. P. Boix, M. Sessolo and H. J. Bolink, Joule, 2017, 1, 431–442 CrossRef.
- R. Swartwout, M. T. Hoerantner and V. Bulović, Energy Environ. Mater., 2019, 2, 119–145 CrossRef CAS.
- T. Liu, K. Chen, Q. Hu, R. Zhu and Q. Gong, Adv. Energy Mater., 2016, 6, 1600457 CrossRef.
- S. Yue, K. Liu, R. Xu, M. Li, M. Azam, K. Ren, J. Liu, Y. Sun, Z. Wang, D. Cao, X. Yan, S. Qu, Y. Lei and Z. Wang, Energy Environ. Sci., 2017, 10, 2570–2578 RSC.
- D. W. Ferdani, S. R. Pering, D. Ghosh, P. Kubiak, A. B. Walker, S. E. Lewis, A. L. Johnson, P. J. Baker, M. S. Islam and P. J. Cameron, Energy Environ. Sci., 2019, 12, 2264–2272 RSC.
- R. García-Rodríguez, D. Ferdani, S. Pering, P. J. Baker and P. J. Cameron, J. Mater. Chem. A, 2019, 7, 22604–22614 RSC.
- M. De Bastiani, G. Dell’Erba, M. Gandini, V. D’Innocenzo, S. Neutzner, A. R. S. Kandada, G. Grancini, M. Binda, M. Prato, J. M. Ball, M. Caironi and A. Petrozza, Adv. Energy Mater., 2016, 6, 1501453 CrossRef.
- I. Levine, P. K. Nayak, J. T.-W. Wang, N. Sakai, S. Van Reenen, T. M. Brenner, S. Mukhopadhyay, H. J. Snaith, G. Hodes and D. Cahen, J. Phys. Chem. C, 2016, 120, 16399–16411 CrossRef CAS.
- Y. Shao, Z. Xiao, C. Bi, Y. Yuan and J. Huang, Nat. Commun., 2014, 5, 5784 CrossRef CAS PubMed.
- D. Bryant, S. Wheeler, B. C. O’Regan, T. Watson, P. R. F. Barnes, D. Worsley and J. Durrant, J. Phys. Chem. Lett., 2015, 6, 3190–3194 CrossRef CAS.
- E. Aydin, J. Liu, E. Ugur, R. Azmi, G. T. Harrison, Y. Hou, B. Chen, S. Zhumagali, M. De Bastiani, M. Wang, W. Raja, T. G. Allen, A. U. Rehman, A. S. Subbiah, M. Babics, A. Babayigit, F. H. Isikgor, K. Wang, E. Van Kerschaver, L. Tsetseris, E. H. Sargent, F. Laquai and S. De Wolf, Energy Environ. Sci., 2021, 14, 4377–4390 RSC.
- Z. Ku, Y. Rong, M. Xu, T. Liu and H. Han, Sci. Rep., 2013, 3, 3132 CrossRef PubMed.
- D. Bogachuk, S. Zouhair, K. Wojciechowski, B. Yang, V. Babu, L. Wagner, B. Xu, J. Lim, S. Mastroianni, H. Pettersson, A. Hagfeldt and A. Hinsch, Energy Environ. Sci., 2020, 13, 3880–3916 RSC.
- C.-M. Tsai, G.-W. Wu, S. Narra, H.-M. Chang, N. Mohanta, H.-P. Wu, C.-L. Wang and E. W.-G. Diau, J. Mater. Chem. A, 2017, 5, 739–747 RSC.
- F. De Rossi, J. A. Baker, D. Beynon, K. E. A. Hooper, S. M. P. Meroni, D. Williams, Z. Wei, A. Yasin, C. Charbonneau, E. H. Jewell and T. M. Watson, Adv. Mater. Technol., 2018, 3, 1800156 CrossRef.
- S. M. P. Meroni, Y. Mouhamad, F. De Rossi, A. Pockett, J. Baker, R. Escalante, J. Searle, M. J. Carnie, E. Jewell, G. Oskam and T. M. Watson, Sci. Technol. Adv. Mater., 2018, 19, 1–9 CrossRef CAS.
- J. H. Noh, S. H. Im, J. H. Heo, T. N. Mandal and S. Il Seok, Nano Lett., 2013, 13, 1764–1769 CrossRef CAS PubMed.
- R. Ruess, F. Benfer, F. Böcher, M. Stumpp and D. Schlettwein, ChemPhysChem, 2016, 17, 1505–1511 CrossRef CAS PubMed.
- R. G. Niemann, A. G. Kontos, D. Palles, E. I. Kamitsos, A. Kaltzoglou, F. Brivio, P. Falaras and P. J. Cameron, J. Phys. Chem. C, 2016, 120, 2509–2519 CrossRef CAS.
- G. E. Eperon, T. Leijtens, K. A. Bush, R. Prasanna, T. Green, J. T.-W. Wang, D. P. McMeekin, G. Volonakis, R. L. Milot, R. May, A. Palmstrom, D. J. Slotcavage, R. A. Belisle, J. B. Patel, E. S. Parrott, R. J. Sutton, W. Ma, F. Moghadam, B. Conings, A. Babayigit, H.-G. Boyen, S. Bent, F. Giustino, L. M. Herz, M. B. Johnston, M. D. McGehee and H. J. Snaith, Science, 2016, 354, 861–865 CrossRef CAS PubMed.
- D. P. McMeekin, S. Mahesh, N. K. Noel, M. T. Klug, J. Lim, J. H. Warby, J. M. Ball, L. M. Herz, M. B. Johnston and H. J. Snaith, Joule, 2019, 3, 387–401 CrossRef CAS.
- J. Werner, C.-H. Weng, A. Walter, L. Fesquet, J. P. Seif, S. De Wolf, B. Niesen and C. Ballif, J. Phys. Chem. Lett., 2016, 7, 161–166 CrossRef CAS PubMed.
- K. A. Bush, A. F. Palmstrom, Z. J. Yu, M. Boccard, R. Cheacharoen, J. P. Mailoa, D. P. McMeekin, R. L. Z. Hoye, C. D. Bailie, T. Leijtens, I. M. Peters, M. C. Minichetti, N. Rolston, R. Prasanna, S. Sofia, D. Harwood, W. Ma, F. Moghadam, H. J. Snaith, T. Buonassisi, Z. C. Holman, S. F. Bent and M. D. McGehee, Nat. Energy, 2017, 2, 17009 CrossRef CAS.
- F. Sahli, J. Werner, B. A. Kamino, M. Bräuninger, R. Monnard, B. Paviet-Salomon, L. Barraud, L. Ding, J. J. Diaz Leon, D. Sacchetto, G. Cattaneo, M. Despeisse, M. Boccard, S. Nicolay, Q. Jeangros, B. Niesen and C. Ballif, Nat. Mater., 2018, 17, 820–826 CrossRef CAS PubMed.
- S. Albrecht, M. Saliba, J. P. Correa Baena, F. Lang, L. Kegelmann, M. Mews, L. Steier, A. Abate, J. Rappich, L. Korte, R. Schlatmann, M. K. Nazeeruddin, A. Hagfeldt, M. Grätzel and B. Rech, Energy Environ. Sci., 2016, 9, 81–88 RSC.
- E. C. Directive, Off. J. Eur. Communities: Legis., 2012, 55, 38–71 Search PubMed.
- E. C. Directive, Off. J. Eur. Communities: Legis., 2011, 54, 88–110 Search PubMed.
- R. G. Charles, P. Douglas, I. L. Hallin, I. Matthews and G. Liversage, Waste Manage., 2017, 60, 505–520 CrossRef CAS PubMed.
- M. R. Johnson and I. P. McCarthy, J. Eng. Technol. Manag., 2014, 34, 9–28 CrossRef.
- S. Salhofer, B. Steuer, R. Ramusch and P. Beigl, Waste Manage., 2016, 57, 27–35 CrossRef CAS PubMed.
- X. Zeng, R. Gong, W. Q. Chen and J. Li, Environ. Sci. Technol., 2016, 50, 1347–1358 CrossRef CAS PubMed.
- RoHSGuide.com, ✓ RoHS Initiatives Worldwide, https://www.rohsguide.com/rohs-future.htm, (accessed 17 November 2022).
- J. M. Kadro and A. Hagfeldt, Joule, 2017, 1, 29–46 CrossRef.
- M. A. Green, A. Ho-Baillie and H. J. Snaith, Nat. Photonics, 2014, 8, 506–514 CrossRef CAS.
- L. Serrano-Lujan, N. Espinosa, T. T. Larsen-Olsen, J. Abad, A. Urbina and F. C. Krebs, Adv. Energy Mater., 2015, 5, 1501119 CrossRef.
- N. L. Chang, A. W. Yi Ho-Baillie, P. A. Basore, T. L. Young, R. Evans and R. J. Egan, Prog. Photovoltaics Res. Appl., 2017, 25, 390–405 CrossRef.
- G. M. Wilson, M. Al-Jassim, W. K. Metzger, S. W. Glunz, P. Verlinden, G. Xiong, L. M. Mansfield, B. J. Stanbery, K. Zhu, Y. Yan, J. J. Berry, A. J. Ptak, F. Dimroth, B. M. Kayes, A. C. Tamboli, R. Peibst, K. Catchpole, M. O. Reese, C. S. Klinga, P. Denholm, M. Morjaria, M. G. Deceglie, J. M. Freeman, M. A. Mikofski, D. C. Jordan, G. Tamizhmani and D. B. Sulas-Kern, J. Phys. D: Appl. Phys., 2020, 53, 493001 CrossRef CAS.
- D. Pourjafari, S. M. P. Meroni, D. P. Domínguez, R. Escalante, J. Baker, A. S. Monroy, A. Walters, T. Watson and G. Oskam, Energies, 2022, 15, 641 CrossRef CAS.
- B. Chen, C. Fei, S. Chen, H. Gu, X. Xiao and J. Huang, Nat. Commun., 2021, 12(121), 1–10 CAS.
- X. Tian, S. D. Stranks and F. You, Nat. Sustainable, 2021, 4, 821–829 CrossRef.
-
R. G. Charles, M. L. Davies, P. Douglas and I. L. Hallin, in A Comprehensive Guide to Solar Energy Systems, ed. V. M. Fthenakis and T. Letcher, Academic Press, 2018, pp. 81–107 Search PubMed.
- Z. Jin, Z. Zhang, J. Xiu, H. Song, T. Gatti and Z. He, J. Mater. Chem. A, 2020, 8, 16166–16188 RSC.
- K. Nishimura, M. A. Kamarudin, D. Hirotani, K. Hamada, Q. Shen, S. Iikubo, T. Minemoto, K. Yoshino and S. Hayase, Nano Energy, 2020, 74, 104858 CrossRef CAS.
- S. Shao, J. Liu, G. Portale, H. H. Fang, G. R. Blake, G. H. ten Brink, L. J. A. Koster and M. A. Loi, Adv. Energy Mater., 2018, 8, 1702019 CrossRef.
- B. Hailegnaw, S. Kirmayer, E. Edri, G. Hodes and D. Cahen, J. Phys. Chem. Lett., 2015, 6, 1543–1547 CrossRef CAS PubMed.
-
R. Stehower, Lead in Residential Soils: Sources, Testing, and Reducing Exposure, https://extension.psu.edu/lead-in-residential-soils-sources-testing-and-reducing-exposure, (accessed 6 March 2023).
-
S. A. Khalifa, Drexel University, 2022.
- A. Babayigit, H.-G. Boyen and B. Conings, MRS Energy Sustainable, 2018, 5, 1–15 CrossRef.
- Health and Safety Executive, Control of Lead at Work Regulations 2002 Approved Code of Practice and guidance, HSE Books, Third edit., 2009.
- N. Espinosa, L. Serrano-Luján, A. Urbina and F. C. Krebs, Sol. Energy Mater. Sol. Cells, 2015, 137, 303–310 CrossRef CAS.
- M. Hauck, T. Ligthart, M. Schaap, E. Boukris and D. Brouwer, Renewable Energy, 2017, 111, 906–913 CrossRef CAS.
- P. Billen, E. Leccisi, S. Dastidar, S. Li, L. Lobaton, S. Spatari, A. T. Fafarman, V. M. Fthenakis and J. B. Baxter, Energy, 2019, 166, 1089–1096 CrossRef CAS.
-
J. Zhang, X. Gao, Y. Deng, Y. Zha and C. Yuan, Bio and Sustainable Manufacturing, American Society of Mechanical Engineers, 2017, vol. 4 Search PubMed.
- J. Zhang, X. Gao, Y. Deng, Y. Zha and C. Yuan, Sol. Energy Mater. Sol. Cells, 2017, 166, 9–17 CrossRef CAS.
- J. Zhang, X. Gao, Y. Deng, B. Li and C. Yuan, ChemSusChem, 2015, 8, 3882–3891 CrossRef CAS PubMed.
- L. Serrano-Lujan, N. Espinosa, T. T. Larsen-Olsen, J. Abad, A. Urbina and F. C. Krebs, Adv. Energy Mater., 2015, 5, 1501119 CrossRef.
- M. G. Ju, M. Chen, Y. Zhou, J. Dai, L. Ma, N. P. Padture and X. C. Zeng, Joule, 2018, 2, 1231–1241 CrossRef CAS.
- P. Wu and F. Zhang, Trans. Tianjin Univ., 2022, 28, 341–357 CrossRef CAS.
- X. Xiao, M. Wang, S. Chen, Y. Zhang, H. Gu, Y. Deng, G. Yang, C. Fei, B. Chen, Y. Lin, M. D. Dickey and J. Huang, Sci. Adv., 2021, 7, 8249–8278 CrossRef PubMed.
- S. Chen, Y. Deng, H. Gu, S. Xu, S. Wang, Z. Yu, V. Blum and J. Huang, Nat. Energy, 2020, 5(512), 1003–1011 CrossRef.
- S. Maranghi, M. L. Parisi, R. Basosi and A. Sinicropi, Energies, 2019, 12, 3–7 CrossRef.
- L. Hong, Y. Hu, A. Mei, Y. Sheng, P. Jiang, C. Tian, Y. Rong and H. Han, Adv. Funct. Mater., 2017, 27, 1703060 CrossRef.
-
N. Morley and D. Eatherley, Materials Security: Ensuring resource availability for the UK Economy, Resource Efficiency Knowledge Transfer Network, Chester, 2008.
- M. Monteiro Lunardi, A. Wing Yi Ho-Baillie, J. P. Alvarez-Gaitan, S. Moore and R. Corkish, Prog. Photovoltaics Res. Appl., 2017, 25, 679–695 CrossRef CAS.
- H. S. Jung, G. S. Han, N.-G. Park and M. J. Ko, Joule, 2019, 3, 1850–1880 CrossRef CAS.
- D. Sica, O. Malandrino, S. Supino, M. Testa and M. C. Lucchetti, Renewable Sustainable Energy Rev., 2018, 82, 2934–2945 CrossRef.
- J. Troughton, D. Bryant, K. Wojciechowski, M. J. Carnie, H. Snaith, D. A. Worsley and T. M. Watson, J. Mater. Chem. A, 2015, 3, 9141–9145 RSC.
- H. Lu, X. Ren, D. Ouyang and W. C. H. Choy, Small, 2018, 14, 1703140 CrossRef PubMed.
- M. Lee, Y. Ko, B. K. Min and Y. Jun, ChemSusChem, 2016, 9, 31–35 CrossRef CAS PubMed.
- Y. Xiao, G. Han, H. Zhou and J. Wu, RSC Adv., 2016, 6, 2778–2784 RSC.
- S. Ke, C. Chen, N. Fu, H. Zhou, M. Ye, P. Lin, W. Yuan, X. Zeng, L. Chen and H. Huang, ACS Appl. Mater. Interfaces, 2016, 8, 28406–28411 CrossRef CAS PubMed.
- L. Gao, L. Chao, M. Hou, J. Liang, Y. Chen, H. D. Yu and W. Huang, npj Flexible Electron., 2019, 3, 1–8 CrossRef CAS.
- H. Li, X. Li, W. Wang, J. Huang, J. Li, Y. Lu, J. Chang, J. Fang and W. Song, Sol. RRL, 2019, 3, 1800317 CrossRef.
- J.-A. Alberola-Borràs, R. Vidal and I. Mora-Seró, Sustainable Energy Fuels, 2018, 2, 1600–1609 RSC.
- A. Leader, G. Gaustad and C. Babbitt, Mater. Renew. Sustainable Energy, 2019, 8, 1–17 CrossRef.
- T. Watari, K. Nansai and K. Nakajima, Resour., Conserv. Recycl., 2020, 155, 104669 CrossRef.
- European Commission, Study on the review of the list of Critical Raw Materials (2020) – Critical Raw Materials Factsheets, Brussels, 2020.
- L. Rocchetti, A. Amato, V. Fonti, F. Vegliò and F. Beolchini, Chem. Eng. Trans., 2015, 43, 1987–1992 Search PubMed.
- S. Jon, G. Sin, G. Kim, G. Jong and J. Ri, Synth. Met., 2020, 262, 116286 CrossRef CAS.
- J. Yoon, H. Sung, G. Lee, W. Cho, N. Ahn, H. S. Jung and M. Choi, Energy Environ. Sci., 2017, 10, 337–345 RSC.
- Z. Liu, P. You, C. Xie, G. Tang and F. Yan, Nano Energy, 2016, 28, 151–157 CrossRef CAS.
- J. Ahn, H. Hwang, S. Jeong and J. Moon, Adv. Energy Mater., 2017, 7, 1602751 CrossRef.
- D. Chen, G. Fan, H. Zhang, L. Zhou, W. Zhu, H. Xi, H. Dong, S. Pang, X. He, Z. Lin, J. Zhang, C. Zhang and Y. Hao, Nanomaterials, 2019, 9, 932 CrossRef CAS PubMed.
- K. K. Sears, M. Fievez, M. Gao, H. C. Weerasinghe, C. D. Easton and D. Vak, Sol. RRL, 2017, 1, 1700059 CrossRef.
-
C. Alexander, S. Litosh, B. Alway, J. Wiebe, S. Li, D. Saha, N. Scott-Gray, F. Gay and S. Goenka, GFMS Gold Survey 2019, London, UK, 1991.
-
C. Hagelüken, in IEEE International symposium on Electronics & the Environment, San Francisco, 2006, vol. 2006, pp. 218–223.
-
R. G. Charles, P. Douglas, M. Dowling and M. L. Davies, Resour. Conserv. Recycl.
-
C. Alexander, S. Litosh, B. Alway, J. Wiebe, S. Li, N. Scott-Gray, F. Gay and D. Saha, Platinum and Palladium Survey, London, UK, 2019 Search PubMed.
-
USGS, Mineral Commodity Summaries, Washington DC, 2019 Search PubMed.
-
H. Renner, G. Schlamp, I. Kleinwächter, E. Drost, H. M. Lüschow, P. Tews, P. Panster, M. Diehl, J. Lang, T. Kreuzer, A. Knödler, K. A. Starz, K. Dermann, J. Rothaut, R. Drieselmann, C. Peter and R. Schiele, Ullmann's Encyclopedia of Industrial Chemistry, Wiley-VCH Verlag GmbH & Co. KGaA, 2001 Search PubMed.
- N. Sazali, Int. J. Hydrogen Energy, 2020, 45, 18753–18771 CrossRef CAS.
- A. Valente, D. Iribarren and J. Dufour, Int. J. Hydrogen Energy, 2019, 44, 20965–20977 CrossRef CAS.
- A. Lotrič, M. Sekavčnik, I. Kuštrin and M. Mori, Int. J. Hydrogen Energy, 2021, 46(16), 10143–10160 CrossRef.
- T. E. Graedel, E. M. Harper, N. T. Nassar, P. Nuss, B. K. Reck and B. L. Turner, Proc. Natl. Acad. Sci. U. S. A., 2015, 112, 4257–4262 CrossRef CAS PubMed.
- S. Hou, X. Cai, H. Wu, X. Yu, M. Peng, K. Yan and D. Zou, Energy Environ. Sci., 2013, 6, 3356–3362 RSC.
- X. Zheng, J. Deng, N. Wang, D. Deng, W. H. Zhang, X. Bao and C. Li, Angew. Chem., Int. Ed., 2014, 53, 7023–7027 CrossRef CAS PubMed.
- M. S. Chowdhury, K. S. Rahman, T. Chowdhury, N. Nuthammachot, K. Techato, M. Akhtaruzzaman, S. K. Tiong, K. Sopian and N. Amin, Energy Strategy Rev., 2020, 27, 100431 CrossRef.
- B. Lyu, L. Yang, Y. Luo, X. Zhang and J. Zhang, J. Mater. Chem. C, 2022, 10, 10775–10798 RSC.
- Z. Xu, Q. Zhuang, Y. Zhou, S. Lu, X. Wang, W. Cai and Z. Zang, Small Struct., 2023, 4, 2200338 CrossRef CAS.
- B. Abdollahi Nejand, P. Nazari, S. Gharibzadeh, V. Ahmadi and A. Moshaii, Chem. Commun., 2017, 53, 747–750 RSC.
- C. Li, X. Wang, E. Bi, F. Jiang, S. M. Park, Y. Li, L. Chen, Z. Wang, L. Zeng, H. Chen, Y. Liu, C. R. Grice, A. Abudulimu, J. Chung, Y. Xian, T. Zhu, H. Lai, B. Chen, R. J. Ellingson, F. Fu, D. S. Ginger, Z. Song, E. H. Sargent and Y. Yan, Science, 2023, 379, 690–694 CrossRef CAS PubMed.
- X. Hu, J. Li, C. Wang, H. Cui, Y. Liu, S. Zhou, H. Guan, W. Ke, C. Tao and G. Fang, Nano-Micro Lett., 2023, 15, 1–14 CrossRef PubMed.
- F. Bella, P. Renzi, C. Cavallo and C. Gerbaldi, Chem. – Eur. J., 2018, 24, 12183–12205 CrossRef CAS PubMed.
- M. Zhang, J. S. Yun, Q. Ma, J. Zheng, C. F. J. Lau, X. Deng, J. Kim, D. Kim, J. Seidel, M. A. Green, S. Huang and A. W. Y. Ho-Baillie, ACS Energy Lett., 2017, 2, 438–444 CrossRef CAS.
- M. Saliba, T. Matsui, K. Domanski, J. Y. Seo, A. Ummadisingu, S. M. Zakeeruddin, J. P. Correa-Baena, W. R. Tress, A. Abate, A. Hagfeldt and M. Grätzel, Science, 2016, 354, 206–209 CrossRef CAS PubMed.
- The Metal That Could Spark a New Resource War, https://www.prnewswire.co.uk/news-releases/the-metal-that-could-spark-a-new-resource-war-818713069.html, (accessed 2 February 2021).
- Cesium – The Most Important Metal Never Heard Of, https://www.prnewswire.com/news-releases/cesium---the-most-important-metal-never-heard-of-301029446.html, (accessed 2 February 2021).
- AltEnergyMag.com, 3 Rare Metals Every Investor Must Watch At This Critical Time, https://www.altenergymag.com/story/2020/02/3-rare-metals-every-investor-must-watch-at-this-critical-time-/32770/, (accessed 19 May 2022).
- R. Vidal, J.-A. Alberola-Borràs and I. Mora-Seró, Resour. Policy, 2020, 68, 101792 CrossRef.
- The Metal That Could Spark a New Resource War, https://www.prnewswire.co.uk/news-releases/the-metal-that-could-spark-a-new-resource-war-818713069.html, (accessed 16 January 2021).
- businesswire.com, Global Cesium Market 2018-2022| Growing Importance of Cesium in Cancer Treatment to Propel Demand, https://www.businesswire.com/news/home/20180814005428/en/Global-Cesium-Market-2018-2022-Growing-Importance-of-Cesium-in-Cancer-Treatment-to-Propel-Demand-Technavio, (accessed 19 May 2022).
- K. Choi, H. Choi, J. Min, T. Kim, D. Kim, S. Y. Son, G. W. Kim, J. Choi and T. Park, Sol. RRL, 2020, 4, 1900251 CrossRef.
- L. Liu, A. Mei, T. Liu, P. Jiang, Y. Sheng, L. Zhang and H. Han, J. Am. Chem. Soc., 2015, 137, 1790–1793 CrossRef CAS PubMed.
- S. Shao and M. A. Loi, Adv. Mater. Interfaces, 2020, 7, 1901469 CrossRef CAS.
- H. Wei Qiao, S. Yang, Y. Wang, X. Chen, T. Yu Wen, L. Juan Tang, Q. Cheng, Y. Hou, H. Zhao, H. Gui Yang, H. W. Qiao, X. Chen, T. Y. Wen, L. J. Tang, Q. Cheng, Y. Hou, H. G. Yang, S. Yang, Y. Wang and H. Zhao, Adv. Mater., 2019, 31, 1804217 CrossRef PubMed.
- S. Y. Kim, S. J. Cho, S. E. Byeon, X. He and H. J. Yoon, Adv. Energy Mater., 2020, 10, 2002606 CrossRef CAS.
- C. M. Wolff, L. Canil, C. Rehermann, N. Ngoc Linh, F. Zu, M. Ralaiarisoa, P. Caprioglio, L. Fiedler, M. Stolterfoht, S. Kogikoski, I. Bald, N. Koch, E. L. Unger, T. Dittrich, A. Abate and D. Neher, ACS Nano, 2020, 14, 1445–1456 CrossRef CAS PubMed.
- A. Abrusci, S. D. Stranks, P. Docampo, H. L. Yip, A. K. Y. Jen and H. J. Snaith, Nano Lett., 2013, 13, 3124–3128 CrossRef CAS PubMed.
- D. Pérez-del-Rey, D. Forgács, E. M. Hutter, T. J. Savenije, D. Nordlund, P. Schulz, J. J. Berry, M. Sessolo and H. J. Bolink, Adv. Mater., 2016, 28, 9839–9845 CrossRef PubMed.
- L. Zuo, Q. Chen, N. De Marco, Y. T. Hsieh, H. Chen, P. Sun, S. Y. Chang, H. Zhao, S. Dong and Y. Yang, Nano Lett., 2017, 17, 269–275 CrossRef CAS PubMed.
- J. Cao, B. Wu, R. Chen, Y. Wu, Y. Hui, B.-W. Mao, N. Zheng, J. Cao, R. H. Chen, Y. Y. Q. Wu, Y. Hui, B. Mao, N. F. Zheng and B. H. Wu, Adv. Mater., 2018, 30, 1705596 CrossRef PubMed.
- F. Giordano, A. Abate, J. P. Correa Baena, M. Saliba, T. Matsui, S. H. Im, S. M. Zakeeruddin, M. K. Nazeeruddin, A. Hagfeldt and M. Graetzel, Nat. Commun., 2016, 7(71), 1–6 Search PubMed.
- M. Abdi-Jalebi, Z. Andaji-Garmaroudi, S. Cacovich, C. Stavrakas, B. Philippe, J. M. Richter, M. Alsari, E. P. Booker, E. M. Hutter, A. J. Pearson, S. Lilliu, T. J. Savenije, H. Rensmo, G. Divitini, C. Ducati, R. H. Friend and S. D. Stranks, Nature, 2018, 555, 497–501 CrossRef CAS PubMed.
- I. L. Braly, D. W. Dequilettes, L. M. Pazos-Outón, S. Burke, M. E. Ziffer, D. S. Ginger and H. W. Hillhouse, Nat. Photonics, 2018, 12(126), 355–361 CrossRef CAS.
- Y.-C. Shih, Y.-B. Lan, C.-S. Li, H.-C. Hsieh, L. Wang, C.-I. Wu, K.-F. Lin, Y. Shih, H. Hsieh, K. Lin, L. Wang, Y. Lan, C. Li and C. Wu, Small, 2017, 13, 1604305 CrossRef PubMed.
- X. Wang, G. Gaustad, C. W. Babbitt, C. Bailey, M. J. Ganter and B. J. Landi, J. Environ. Manage., 2014, 135, 126–134 CrossRef PubMed.
- X. Zhang, X. Ren, B. Liu, R. Munir, X. Zhu, D. Yang, J. Li, Y. Liu, D. M. Smilgies, R. Li, Z. Yang, T. Niu, X. Wang, A. Amassian, K. Zhao and S. Liu, Energy Environ. Sci., 2017, 10, 2095–2102 RSC.
- X. Cui, Y. Chen, M. Zhang, Y. W. Harn, J. Qi, L. Gao, Z. L. Wang, J. Huang, Y. Yang and Z. Lin, Energy Environ. Sci., 2020, 13, 1743–1752 RSC.
- W. Chen, Y. Wu, Y. Yue, J. Liu, W. Zhang, X. Yang, H. Chen, E. Bi, I. Ashraful, M. Grätzel and L. Han, Science, 2015, 350, 944–948 CrossRef CAS PubMed.
- E. Yalcin, M. Can, C. Rodriguez-Seco, E. Aktas, R. Pudi, W. Cambarau, S. Demic and E. Palomares, Energy Environ. Sci., 2019, 12, 230–237 RSC.
- H. Anizelli, T. W. David, P. Tyagi, E. Laureto and J. Kettle, Sol. Energy, 2020, 203, 157–163 CrossRef CAS.
- Q. An, P. Fassl, Y. J. Hofstetter, D. Becker-Koch, A. Bausch, P. E. Hopkinson and Y. Vaynzof, Nano Energy, 2017, 39, 400–408 CrossRef CAS.
- J. Woong Jung, C.-C. Chueh, A. K.-Y. Jen, J. W. Jung, C. Chueh and A. K.-Y. Jen, Adv. Mater., 2015, 27, 7874–7880 CrossRef PubMed.
- S. Zhang, R. Guo, H. Zeng, Y. Zhao, X. Liu, S. You, M. Li, L. Luo, M. Lira-Cantu, L. Li, F. Liu, X. Zheng, G. Liao and X. Li, Energy Environ. Sci., 2022, 15, 244–253 RSC.
- X. Zheng, J. Troughton, N. Gasparini, Y. Lin, M. Wei, Y. Hou, J. Liu, K. Song, Z. Chen, C. Yang, B. Turedi, A. Y. Alsalloum, J. Pan, J. Chen, A. A. Zhumekenov, T. D. Anthopoulos, Y. Han, D. Baran, O. F. Mohammed, E. H. Sargent and O. M. Bakr, Joule, 2019, 3, 1963–1976 CrossRef CAS.
- Z. Luo, T. Guo, C. Wang, J. Zou, J. Wang, W. Dong, J. Li, W. Zhang, X. Zhang and W. Zheng, Nanomaterials, 2022, 12, 3079 CrossRef CAS PubMed.
- A. D. Al-Ghiffari, N. A. Ludin, M. L. Davies, R. M. Yunus and M. S. Suait, Mater. Today Commun., 2022, 32, 104078 CrossRef CAS.
-
E. Cuddihy, C. Coulbert, A. Gupta and R. Liang, Flat-plate solar array project. Final report. Volume VII: Module
Encapsulation, Springfield, VA, 1986.
- M. C. C. de Oliveira, A. S. A. Diniz Cardoso, M. M. Viana and V. D. F. C. Lins, Renewable Sustainable Energy Rev., 2018, 81, 2299–2317 CrossRef.
- A. Uddin, M. B. Upama, H. Yi and L. Duan, Coatings, 2019, 9, 65 CrossRef.
- S. K. Gaddam, R. Pothu and R. Boddula, undefined, 2021, 7, 920–928 Search PubMed.
- J. Ahmad, K. Bazaka, L. J. Anderson, R. D. White and M. V. Jacob, Renewable Sustainable Energy Rev., 2013, 27, 104–117 CrossRef CAS.
- C. Peike, I. Hädrich, K.-A. Weiß and I. Dürr, Photovoltaics Int., 2015, 85–92 Search PubMed.
- M. D. Kempe, G. J. Jorgensen, K. M. Terwilliger, T. J. McMahon, C. E. Kennedy and T. T. Borek, Sol. Energy Mater. Sol. Cells, 2007, 91, 315–329 CrossRef CAS.
- Y. Il Lee, N. J. Jeon, B. J. Kim, H. Shim, T. Y. Yang, S. Il Seok, J. Seo and S. G. Im, Adv. Energy Mater., 2018, 8, 1701928 CrossRef.
- F. Matteocci, L. Cinà, E. Lamanna, S. Cacovich, G. Divitini, P. A. Midgley, C. Ducati and A. Di Carlo, Nano Energy, 2016, 30, 162–172 CrossRef CAS.
- L. Shi, T. L. Young, J. Kim, Y. Sheng, L. Wang, Y. Chen, Z. Feng, M. J. Keevers, X. Hao, P. J. Verlinden, M. A. Green and A. W. Y. Ho-Baillie, ACS Appl. Mater. Interfaces, 2017, 9, 25073–25081 CrossRef CAS PubMed.
- T. S. Kim, H. J. Kim, D. M. Geum, J. H. Han, I. S. Kim, N. Hong, G. H. Ryu, J. H. Kang, W. J. Choi and K. J. Yu, ACS Appl. Mater. Interfaces, 2021, 13, 13248–13253 CrossRef CAS PubMed.
- C. Yang, J. R. Qu and Z. Y. Wu, Sol. Energy, 2021, 214, 542–550 CrossRef CAS.
- R. Cheacharoen, N. Rolston, D. Harwood, K. A. Bush, R. H. Dauskardt and M. D. McGehee, Energy Environ. Sci., 2018, 11, 144–150 RSC.
- Z. Fu, M. Xu, Y. Sheng, Z. Yan, J. Meng, C. Tong, D. Li, Z. Wan, Y. Ming, A. Mei, Y. Hu, Y. Rong, H. Han, Z. Fu, M. Xu, Y. Sheng, C. Tong, D. Li, Z. Wan, Y. Ming, A. Mei, Y. Hu, Y. Rong, H. Han, Z. Yan and J. Meng, Adv. Funct. Mater., 2019, 29, 1809129 CrossRef.
- Y. Han, S. Meyer, Y. Dkhissi, K. Weber, J. M. Pringle, U. Bach, L. Spiccia and Y. B. Cheng, J. Mater. Chem. A, 2015, 3, 8139–8147 RSC.
- S. Ma, Y. Bai, H. Wang, H. Zai, J. Wu, L. Li, S. Xiang, N. Liu, L. Liu, C. Zhu, G. Liu, X. Niu, H. Chen, H. Zhou, Y. Li and Q. Chen, Adv. Energy Mater., 2020, 10, 1902472 CrossRef CAS.
- F. J. Ramos, T. Maindron, S. Béchu, A. Rebai, M. Frégnaux, M. Bouttemy, J. Rousset, P. Schulz and N. Schneider, Sustainable Energy Fuels, 2018, 2, 2468–2479 RSC.
- J. Idígoras, F. J. Aparicio, L. Contreras-Bernal, S. Ramos-Terrón, M. Alcaire, J. R. Sánchez-Valencia, A. Borras, Á. Barranco and J. A. Anta, ACS Appl. Mater. Interfaces, 2018, 10, 11587–11594 CrossRef PubMed.
- F. Bella, G. Griffini, J. P. Correa-Baena, G. Saracco, M. Grätzel, A. Hagfeldt, S. Turri and C. Gerbaldi, Science, 2016, 354, 203–206 CrossRef CAS PubMed.
- M. F. Azeumo, G. Conte, N. M. Ippolito, F. Medici, L. Piga and S. Santilli, Sol. Energy Mater. Sol. Cells, 2019, 193, 314–319 CrossRef CAS.
- M. Marwede, W. Berger, M. Schlummer, A. Mäurer and A. Reller, Renewable Energy, 2013, 55, 220–229 CrossRef CAS.
- A. Binek, M. L. Petrus, N. Huber, H. Bristow, Y. Hu, T. Bein and P. Docampo, ACS Appl. Mater. Interfaces, 2016, 8, 12881–12886 CrossRef CAS PubMed.
- J. Gong, S. B. Darling and F. You, Energy Environ. Sci., 2015, 8, 1953–1968 RSC.
- T. Doi, I. Tsuda, H. Unagida, A. Murata, K. Sakuta and K. Kurokawa, Sol. Energy Mater. Sol. Cells, 2001, 67, 397–403 CrossRef CAS.
- M. D. Banea, Rev. Adhes. Adhes., 2019, 7, 33–50 CrossRef CAS.
- K. R. Mulcahy, A. F. R. Kilpatrick, G. D. J. Harper, A. Walton and A. P. Abbott, Green Chem., 2022, 24, 36–61 RSC.
- Z. Li, X. Wu, B. Li, S. Zhang, D. Gao, Y. Liu, X. Li, N. Zhang, X. Hu, C. Zhi, A. K.-Y. Jen, Z. Zhu, Z. Li, X. Wu, B. Li, S. Zhang, D. Gao, Y. Liu, X. Li, A. K.-Y. Jen, Z. Zhu, N. Zhang, C. Zhi and X. Hu, Adv. Energy Mater., 2022, 12, 2103236 CrossRef CAS.
- Z. Li, X. Wu, S. Wu, D. Gao, H. Dong, F. Huang, X. Hu, A. K. Y. Jen and Z. Zhu, Nano Energy, 2022, 93, 106853 CrossRef CAS.
- X. Li, F. Zhang, H. He, J. J. Berry, K. Zhu and T. Xu, Nature, 2020, 578(7796), 555–558 CrossRef CAS PubMed.
- X. Li, F. Zhang, J. Wang, J. Tong, T. Xu and K. Zhu, Nat. Sustainable, 2021, 4(412), 1038–1041 CrossRef.
- X. Xiao, M. Wang, S. Chen, Y. Zhang, H. Gu, Y. Deng, G. Yang, C. Fei, B. Chen, Y. Lin, M. D. Dickey and J. Huang, Sci. Adv., 2021, 7, 8249–8278 CrossRef PubMed.
- R. Vidal, J.-A. Alberola-Borràs, S. N. Habisreutinger, J.-L. Gimeno-Molina, D. T. Moore, T. H. Schloemer, I. Mora-Seró, J. J. Berry and J. M. Luther, Nat. Sustainable, 2020, 4, 277–285 CrossRef.
- P. J. Holliman, E. W. Jones, A. Connell, S. Ghosh, L. Furnell and R. J. Hobbs, Mater. Res. Innovations, 2015, 19, 508–511 CrossRef CAS.
- A. J. Doolin, R. G. Charles, C. S. P. De Castro, R. G. Rodriguez, E. V. Péan, R. Patidar, T. Dunlop, C. Charbonneau, T. Watson and M. L. Davies, Green Chem., 2021, 23, 2471–2486 RSC.
- J. C. Hamill, J. Schwartz and Y. L. Loo, ACS Energy Lett., 2018, 3, 92–97 CrossRef CAS.
- Z. Zhou, Z. Wang, Y. Zhou, S. Pang, D. Wang, H. Xu, Z. Liu, N. P. Padture and G. Cui, Angew. Chem., Int. Ed., 2015, 54, 9705–9709 CrossRef CAS PubMed.
- N. K. Noel, S. N. Habisreutinger, B. Wenger, M. T. Klug, M. T. Hörantner, M. B. Johnston, R. J. Nicholas, D. T. Moore and H. J. Snaith, Energy Environ. Sci., 2017, 10, 145–152 RSC.
- J. W. Lee, H. S. Kim and N. G. Park, Acc. Chem. Res., 2016, 49, 311–319 CrossRef CAS PubMed.
- S. K. Podapangi, F. Jafarzadeh, S. Mattiello, T. B. Korukonda, A. Singh, L. Beverina and T. M. Brown, RSC Adv., 2023, 13, 18165–18206 RSC.
- Q. Liu, Y. Zhao, Y. Ma, X. Sun, W. Ge, Z. Fang, H. Bai, Q. Tian, B. Fan and T. Zhang, J. Mater. Chem. A, 2019, 7, 18275–18284 RSC.
- R. B. Palmer, Toxicol. Rev., 2004, 23, 21–31 CrossRef CAS PubMed.
- C. Worsley, D. Raptis, S. Meroni, A. Doolin, R. Garcia-Rodriguez, M. Davies and T. Watson, Energy Technol., 2021, 9, 1–10 Search PubMed.
- D. Prat, O. Pardigon, H.-W. Flemming, S. Letestu, V. Ducandas, P. Isnard, E. Guntrum, T. Senac, S. Ruisseau, P. Cruciani and P. Hosek, Org. Process Res. Dev., 2013, 17, 1517–1525 CrossRef CAS.
- N. G. Anderson, Pract. Process Res. Dev., 2010, 81–111 Search PubMed.
- F. P. Byrne, S. Jin, G. Paggiola, T. H. M. Petchey, J. H. Clark, T. J. Farmer, A. J. Hunt, C. Robert McElroy and J. Sherwood, Sustainable Chem. Process., 2016, 4, 7 CrossRef.
- L. J. Diorazio, D. R. J. Hose and N. K. Adlington, Org. Process Res. Dev., 2016, 20, 760–773 CrossRef CAS.
- K. Alfonsi, J. Colberg, P. J. Dunn, T. Fevig, S. Jennings, T. A. Johnson, H. P. Kleine, C. Knight, M. A. Nagy, D. A. Perry and M. Stefaniak, Green Chem., 2008, 10, 31–36 RSC.
- C. M. Alder, J. D. Hayler, R. K. Henderson, A. M. Redman, L. Shukla, L. E. Shuster and H. F. Sneddon, Green Chem., 2016, 18, 3879–3890 RSC.
- J. Zhang, G. B. White, M. D. Ryan, A. J. Hunt and M. J. Katz, ACS Sustainable Chem. Eng., 2016, 4, 7186–7192 CrossRef CAS.
- C. Capello, U. Fischer and K. Hungerbühler, Green Chem., 2007, 9, 927–934 RSC.
- U. Tilstam, Org. Process Res. Dev., 2012, 16, 1273–1278 CrossRef CAS.
- B. J. Kim, D. H. Kim, S. L. Kwon, S. Y. Park, Z. Li, K. Zhu and H. S. Jung, Nat. Commun., 2016, 7, 11735 CrossRef CAS PubMed.
- P. G. Jessop, Green Chem., 2011, 13, 1391–1398 RSC.
- D. Prat, J. Hayler and A. Wells, Green Chem., 2014, 16, 4546–4551 RSC.
- C. J. Clarke, W. C. Tu, O. Levers, A. Bröhl and J. P. Hallett, Chem. Rev., 2018, 118, 747–800 CrossRef CAS PubMed.
-
J. L. Scott and H. F. Sneddon, Green Techniques for Organic Synthesis and Medicinal Chemistry, John Wiley & Sons, Ltd, Chichester, UK, 2018, vol. 106, pp. 21–42 Search PubMed.
- G. Ding, Y. Zheng, X. Xiao, H. Cheng, G. Zhang, Y. Shi and Y. Shao, J. Mater. Chem. A, 2022, 10, 8159–8171 RSC.
- X. Wu, Y. Zheng, J. Liang, Z. Zhang, C. Tian, Z. Zhang, Y. Hu, A. Sun, C. Wang, J. Wang, Y. Huang, Z. Zhang, K. M. Reddy and C. C. Chen, Mater. Horiz., 2023, 10, 122–135 RSC.
- X. Cao, L. Hao, Z. Liu, G. Su, X. He, Q. Zeng and J. Wei, Chem. Eng. J., 2022, 437, 135458 CrossRef CAS.
- K. L. Gardner, J. G. Tait, T. Merckx, W. Qiu, U. W. Paetzold, L. Kootstra, M. Jaysankar, R. Gehlhaar, D. Cheyns, P. Heremans and J. Poortmans, Adv. Energy Mater., 2016, 6, 1600386 CrossRef.
- First Solar, First Solar, http://www.firstsolar.com/, (accessed 4 June 2021).
- J.-P. Schöggl, R. J. Baumgartner and D. Hofer, J. Cleaner Prod., 2017, 140, 1602–1617 CrossRef.
- O. O. Akinade, L. O. Oyedele, S. O. Ajayi, M. Bilal, H. A. Alaka, H. A. Owolabi, S. A. Bello, B. E. Jaiyeoba and K. O. Kadiri, Waste Manage., 2017, 60, 3–13 CrossRef PubMed.
- Z. Ku, X. Xia, H. Shen, N. H. Tiep and H. J. Fan, Nanoscale, 2015, 7, 13363–13368 RSC.
- L. Huang, Z. Hu, J. Xu, X. Sun, Y. Du, J. Ni, H. Cai, J. Li and J. Zhang, Sol. Energy Mater. Sol. Cells, 2016, 152, 118–124 CrossRef CAS.
- W. Zhu, W. Chai, D. Chen, H. Xi, D. Chen, J. Chang, J. Zhang, C. Zhang and Y. Hao, ACS Appl. Mater. Interfaces, 2020, 12, 4549–4557 CrossRef CAS PubMed.
- L. Huang, J. Xu, X. Sun, R. Xu, Y. Du, J. Ni, H. Cai, J. Li, Z. Hu and J. Zhang, ACS Sustainable Chem. Eng., 2017, 5, 3261–3269 CrossRef CAS.
- J. M. Kadro, N. Pellet, F. Giordano, A. Ulianov, O. Müntener, J. Maier, M. Grätzel and A. Hagfeldt, Energy Environ. Sci., 2016, 9, 3172–3179 RSC.
- W. Zhu, W. Chai, D. Chen, H. Xi, D. Chen, J. Chang, J. Zhang, C. Zhang and Y. Hao, ACS Appl. Mater. Interfaces, 2020, 12, 4549–4557 CrossRef CAS PubMed.
- S. Zhang, L. Shen, M. Huang, Y. Yu, L. Lei, J. Shao, Q. Zhao, Z. Wu, J. Wang and S. Yang, ACS Sustainable Chem. Eng., 2018, 6, 7558–7564 CrossRef CAS.
- X. Feng, S. Wang, Q. Guo, Y. Zhu, J. Xiu, L. Huang, Z. Tang and Z. He, J. Phys. Chem. Lett., 2021, 12, 4735–4741 CrossRef CAS PubMed.
- M.-H. Li, Y.-S. Yang, K.-C. Wang, Y.-H. Chiang, P.-S. Shen, W.-C. Lai, T.-F. Guo and P. Chen, ACS Appl. Mater. Interfaces, 2017, 9, 41845–41854 CrossRef CAS PubMed.
- B. J. Kim, D. H. Kim, S. L. Kwon, S. Y. Park, Z. Li, K. Zhu and H. S. Jung, Nat. Commun., 2016, 7, 11735 CrossRef CAS PubMed.
- S. Y. Park, J. S. Park, B. J. Kim, H. Lee, A. Walsh, K. Zhu, D. H. Kim and H. S. Jung, Nat. Sustainable, 2020, 3, 1044–1051 CrossRef.
- C. G. Poll, G. W. Nelson, D. M. Pickup, A. V. Chadwick, D. J. Riley and D. J. Payne, Green Chem., 2016, 18, 2946–2955 RSC.
- K. Wang, T. Ye, X. Huang, Y. Hou, J. Yoon, D. Yang, X. Hu, X. Jiang, C. Wu, G. Zhou and S. Priya, Matter, 2021, 4, 2522–2541 CrossRef CAS.
- F. Yang, J. Liu, Z. Lu, P. Dai, T. Nakamura, S. Wang, L. Chen, A. Wakamiya and K. Matsuda, Adv. Sci., 2020, 7, 1902474 CrossRef CAS PubMed.
- G. Rodriguez-Garcia, E. Aydin, S. De Wolf, B. Carlson, J. Kellar and I. Celik, ACS Sustainable Chem. Eng., 2021, 9, 15239–15248 CrossRef CAS.
Footnotes |
† The producer is defined in legislation as the party responsible for placing EEE on the market which can include manufacturers or importers. |
‡ LBMA PM 29/01/21 prices. |
|
This journal is © The Royal Society of Chemistry 2023 |