DOI:
10.1039/D2TA02458F
(Review Article)
J. Mater. Chem. A, 2022,
10, 19067-19089
Recent strategies for activating the basal planes of transition metal dichalcogenides towards hydrogen production
Received
27th March 2022
, Accepted 4th May 2022
First published on 20th May 2022
Abstract
The hydrogen evolution reaction (HER) presents an environmentally friendly, efficient, and cost-effective way to produce hydrogen fuel. Recently, two-dimensional (2D) transition metal dichalcogenides (TMDCs) have emerged as a fascinating class of HER materials. Their atomically thin nature acts as an interface with the possibility of maximum exposure of nearly all active sites to the reaction environment. However, for most non-metallic TMDCs, as exemplified by 2H-MoS2, 1T-PtSe2, and 1T′-ReSe2, their basal planes are usually HER-inert except for minor edges. Based on their rich chemistry, significant progress has been recently made to activate the basal planes for HER. This review provides an overview of the current activating strategies. They can be classified into internal and external regulations, depending on whether the pristine structure is altered or not. The former directly creates more active sites through doping, vacancies, phases, grain boundaries (GBs), and superlattices. On the other hand, the latter indirectly promotes the activity utilizing external methods such as the electric field, strain, substrates, and heterostructures. We discuss each strategy's principles and characteristics and highlight their enhanced catalytic activities. We finally provide personal perspectives on the challenges and opportunities in this emerging field, including a joint strategy, a phase-engineering strategy, electrical–electrocatalytic coupling, as well as the potential of “single-atom-layer” catalysis.
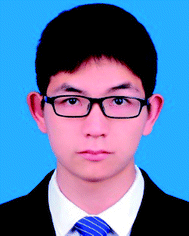 Hang Xia | Hang Xia received his B.S. degree in 2019 from Central South University. He is currently a PhD candidate in physical chemistry at Hunan University under the supervision of Professor Yongmin He. His research focuses on micro/nano electrocatalysis for water splitting. |
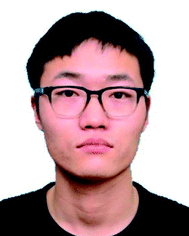 Zude Shi | Zude Shi received his M.S. degree in 2021 from Lanzhou University and his B.S. degree in 2018 from the same university. Subsequently, he joined the Yongmin He group at the College of Chemistry and Chemical Engineering, Hunan University, China. His research focuses on the surface and interface electrocatalysis of low-dimensional materials. |
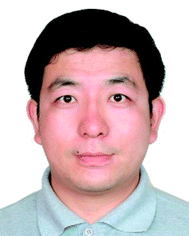 Chengshi Gong | Dr. Chengshi Gong is an associate professor at Lanzhou City University (China) andis also a visiting scholar in Prof. Yongmin He's research group at Hunan University. Dr. Gong received his PhD Degree in 2014 from Lanzhou University. His research focuses on the preparation of two-dimensional materials and their applications in water splitting. |
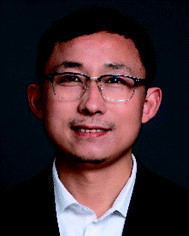 Yongmin He | Dr. Yongmin He is a professor at the College of Chemistry and Chemical Engineering at Hunan University (China). Dr. He obtained his PhD Degree at Lanzhou University in 2015 (China), and later worked in Prof. Zheng Liu and Prof. Qi Jie Wang's groups as a postdoc research fellow (2015–2021) at Nanyang Technological University (Singapore). His research interest focuses on the synthesis and structure-engineering of atom-thin materials, and their electronic or on-chip electrochemical devices, with various applications in nanoelectronics, iontronics, sensors, and electrocatalysis. |
1. Introduction
Exploring clean and renewable alternative energy technology is highly desirable to alleviate global warming and the environmental degradation caused by the excessive use of non-renewable fossil fuels.1,2 Electrochemical water splitting that converts electrical energy into hydrogen energy through the hydrogen evolution reaction (HER) is considered a promising green energy technology, exhibiting high energy density, environmental friendliness, and high product purity.3,4 Platinum (Pt) and other noble metal-based electrocatalysts give superior performance for HER;5–8 however, their scarcity and poor durability seriously hinder their large-scale application towards hydrogen production.9–11 Therefore, exploring cheap and efficient HER catalysts as an alternative to noble metals has attracted growing attention. In particular, two-dimensional (2D) transition metal dichalcogenides (TMDCs), represented by MoS2, are widely favored due to their low cost, layered structures, and fascinating electronic properties.12–14 To date, substantial research efforts have been devoted to developing highly efficient HER catalysts based on 2D TMDCs. The key advantage is that their atomically thin nature can act as an interface with the possibility of maximum exposure of nearly all active sites to the reaction environment.15–17
For a structural point of view, 2D TMDC materials are configured by X–M–X layers (M: transition metal, and X: chalcogen),18 in which M atoms are sandwiched by two X-atom planes. They have stronger ionic–covalent bonds between M and X atoms in the planes, with weaker van der Waals (vdW) interactions out of the planes. There are two primary structures in a TMDC layer: the basal plane and the edge. Both experiments and theory prove that the basal planes of most non-metallic TMDCs, for example, 2H-MoS2, 1T-PtSe2, and 1T′-ReSe2, are usually catalytically inert in HER, in sharp contrast to the HER-active edges.19–24 Considering the extremely large area in a TMDC layer (close to 100%),25,26 activating the inert basal planes presents a promising strategy to improving the overall catalytic activity of a whole layer (Fig. 1).27 The most intuitive example is that when edge-active 2H-MoS2 undergoes a phase transition into basal-plane-active 1T-MoS2, the catalytic activity is improved by orders of magnitude.28–31 Recently, significant progress has been made to activate the basal plane for HER. For example, the HER activity of the MoS2 basal plane is remarkably boosted by introducing strained vacancies, and its Tafel slope is decreased from 98 mV dec−1 to 60 mV dec−1.32 In another example, an onset potential of −25 mV and Tafel slope of 54 mV dec−1 were achieved by activating the MoS2 basal plane with ultra-high-density grain boundaries (GBs).33 Based on current achievements, it is time to offer a critical review of this topic, potentially arousing a wide range of readers for the future development of this field. Note that some excellent reviews have already been published based on 2D TMDCs for HER,31,34–39 while there is still a lack of summaries focusing only on the basal plane and its activating strategies for HER.
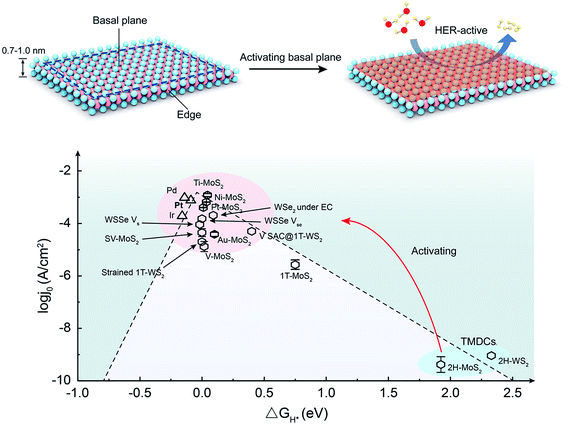 |
| Fig. 1 Activating basal planes of two-dimensional (2D) transition metal dichalcogenides (TMDCs). Top: illustration of the activating strategy of the basal planes. Bottom: volcano plot of the exchange current density as a function of the free energy of hydrogen adsorption (ΔGH*) for the original basal planes and the activated ones. Data obtained from ref. 10,19,22,32,40–46 Abbreviations: V-MoS2 for vacancy-MoS2, SV-MoS2 for strained-sulfur vacancy MoS2, WSSe Vs for the S vacancy of WSSe, WSSe Vse for the Se vacancy of WSSe, EC for the electric field, and V SAC@1T-WS2 for single-site vanadium substitution in 1T-WS2. | |
Herein, we summarize currently-developed activating strategies on TMDC basal planes toward hydrogen production (Fig. 2), discuss their principles, and highlight their advantages as well. In brief, we first introduce the HER mechanism in acidic and basic media, emphasizing the critical pH-dependent role of the free energy of hydrogen adsorption (ΔGH*) in the HER process. Then, we classify the strategies into internal or external regulations based on whether the pristine structure has been changed or not. The former is to directly create more active sites in the basal plane, including doping, vacancies, phases, GBs, and superlattices. The latter is to indirectly improve the basal–plane activity through external methods, such as the electric field, strain, substrates, and heterostructures. The underlying principles and characteristics are discussed, and each method presents several representative examples. Finally, we provided personal perspectives on the challenges and opportunities of activating TMDC basal planes to develop high-efficient HER catalysts.
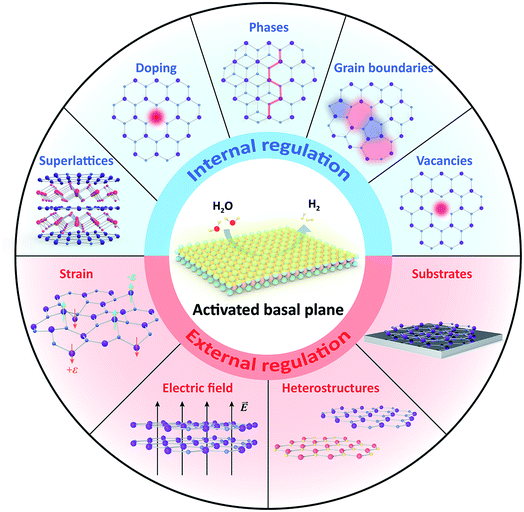 |
| Fig. 2 Overview of the currently-developed strategies for activating TMDC basal planes for the hydrogen evolution reaction (HER). The strategies are divided into internal and external regulation, depending on whether the pristine structure is altered or not. The former is inclined to directly create more active structures, including doping, vacancies, phases, GBs, and superlattices. The latter indirectly promotes the activity of the basal planes by external methods, such as the electric field, strain, substrates, and heterostructures. | |
2. HER principle and Gibbs free energy of hydrogen adsorption
There are two possible reaction pathways in the HER process: Volmer–Tafel and Volmer–Heyrovsky mechanisms.47 Taking the acidic electrolyte as a typical example (Fig. 3a), in the first Volmer step (eqn (1)), the proton obtains an electron on the electrode material (M) surface to generate an adsorbed hydrogen atom (Had) under the applied external potential. The H2 products will be generated by the following Tafel step or the Heyrovsky step. In detail, in the Tafel reaction, two neighboring Had combined on the surface of the electrode to form H2 (eqn (2)). In contrast, in the Heyrovsky reaction, another proton gets close to the Had and then receives a new electron to generate H2 (eqn (3)). | Volmer step: H3O+ + M + e− → M–Had + H2O | (1) |
| Tafel step: 2M–Had → H2 + 2M | (2) |
| Heyrovsky step: H3O+ + M–Had + e− → H2 + M + H2O | (3) |
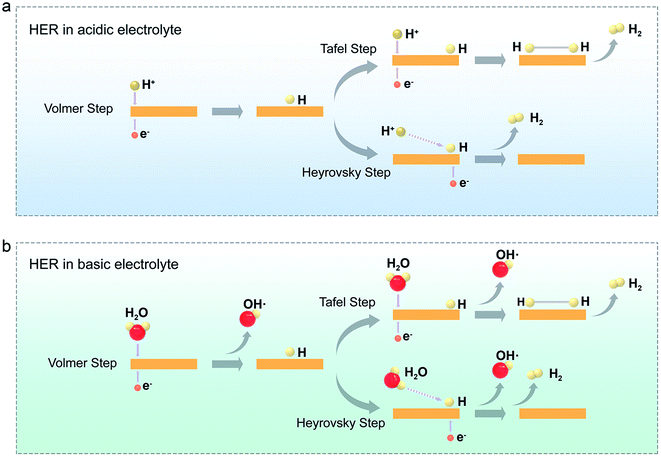 |
| Fig. 3 HER mechanism on a TMDC surface in different electrolytes: (a) acidic solution, (b) alkaline or neutral solution. Hydronium cation (H3O+) and a water molecule (H2O) serve as proton donors in the acidic and basic electrolytes, respectively. | |
No matter, which pathway HER undergoes, the adsorption of hydrogen atoms is a crucial factor. Generally, ΔGH* is recognized as an essential parameter for evaluating the HER performance, and the best HER catalysts possess ΔGH* ∼ 0.48 If ΔGH* is too negative, the conversation and desorption processes will be hindered, easily making the catalyst to be poisoned. On the other hand, a much-positive ΔGH* will weaken the adsorption, leading to inadequate H atoms in the catalytic reaction. A volcano plot is usually used to describe the relationship between ΔGH* and the exchange current density for HER catalysts (Fig. 1). It can be seen that the 2H-MoS2 basal plane, located at the right region of the volcano plots, has a poor H adsorption ability, and its rate-limiting step is the first Volmer step.22 Once the basal planes of TMDCs are activated to obtain a trade-off between adsorption and desorption, they will be consequently located in the near-central region of the volcano plots.
Notably, both, Volmer–Tafel and Volmer–Heyrovsky's steps are strongly pH-dependent. Distinct from acidic solutions with sufficient hydronium cations (H3O+) as protons, the proton source in the basic medium (alkaline or neutral) is H+, generated from the water dissociation (Fig. 3b and eqn (4)).49 As a result, the proton source in basic media is usually limited, and thus leads to a tardy HER rate compared to an acidic solution.35 Next, for the Tafel step, two Had directly combined to generate H2 (eqn (5)). For the Heyrovsky step, the Had would react with H2O and then yields H2 and OH− (eqn (6)). Note that, except for the above steps, the expense of the water molecules near the electrode surface (that is, lowering the water concentration in the electrical double layer) could push the balance of the water-involved reaction (eqn (4) and (6)) in the reverse direction.50 This phenomenon will further lower the HER rate in the basic medium, on the other hand. Therefore, the rational design of the electrocatalysts with excellent hydrogen adsorption and water dissociation is a vital direction.51
| Volmer step: H2O + M + e− → M–Had + OH− | (4) |
| Tafel step: 2M–Had → H2 + 2M | (5) |
| Heyrovsky step: H2O + M–Had + e− → H2 + OH− + M | (6) |
3. Internal regulation
This section highlights the recent advances in the internal structural regulation of TMDC's basal planes by engineering their atomic structures, such as metal/nonmetal-doping, vacancies, phases, GBs, and superlattices. These structures would act as the critical active sites in basal planes for HER.
3.1 Doping strategy
3.1.1 Metal-doping of TMDCs.
Metal-doping has been widely adopted to activate the basal plane of TMDCs in the HER. Currently, a large number of methods enable effective doping, for example, chemical vapor deposition (CVD),52–54 solvothermal method,55,56 electrochemical depositions,57,58 plasma,59,60 photoreductions,61 and self-assembly solution impregnation.62 According to the atomic structures of the doped metal atoms, this strategy presents two types: substitutional and interstitial doping, as shown in Fig. 4a. For substitutional doping, a large number of transition metals have been reported in TMDCs, such as Co, Fe, V, Cr, Pd, and Re.63,64 In theory, Tsai et al. used density functional theory (DFT) to calculate the ΔGH* on different species of transition metal-doped MoS2, providing a rational design of a new MoS2-type catalyst to strengthen or weaken the binding of key intermediates (Fig. 4b).55,65,66 However, it was found in the experiments that this doping not only affects the bond strength on doped metal atoms, but also significantly alters their coordination environment that generally introduces SV and local phase transitions of the TMDC catalysts.64 For example, Zhou et al. used the CVD approach to make two configurations of metal-doped MoS2 structures.67 As shown in Fig. 4c, Fe and Co-based configuration is usually accompanied by the generation of vacancies. Those obtained configurations can greatly improve the HER performance (3CoMo-Vs have the highest performances: a low overpotential at the current density of 10 mA cm−2 (η10 = 75 mV vs. RHE), a Tafel slope of 57 mV dec−1, and long-term durability (η10 drops by only 10 mV after 1000 cycles)), as shown in Fig. 4d. Similarly, Luo and co-workers obtained substitutional doping of Pd in the MoS2 basal plane using a solvothermal method, in which SVs were simultaneously introduced to trigger a local phase transition (Fig. 4e). It turned out to be an excellent HER performance approaching Pt/C catalysts (1% Pd–MoS2 has an exchange current density of 805 μA cm−2 and a η10 of 78 mV in Fig. 4f).62 Further, these substituted catalysts with large coordination numbers show excellent structural stability.
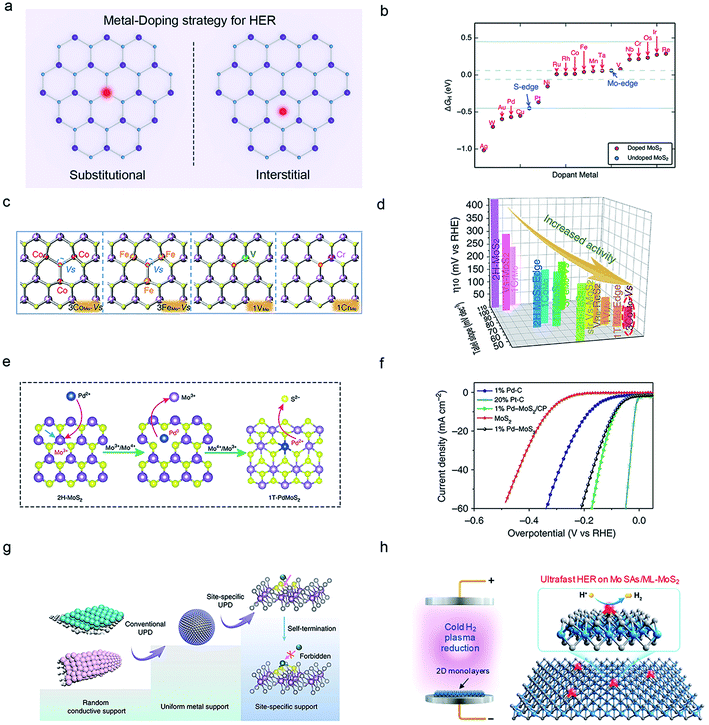 |
| Fig. 4 Metal-doping strategy of 2D-TMDCs for HER. (a) Schematic illustration of the substitutional (left) and interstitial (right) metal-doping in TMDCs. (b) Range of ΔGH* on each transition metal-doped MoS2. Reproduced with permission,65 Royal Society of Chemistry. (c) Two configurations of metal-doped MoS2 structures, in which the sulfur vacancies (SVs) are marked in blue circles and the H-bonded S atoms in red circles. (d) The corresponding η10-Tafel slope in 0.5 M H2SO4 for the HER catalysts in (c). Reproduced with permission,67 Springer Nature. Substitutional doping of Pd in the MoS2 basal plane (e) and the polarization curves of the resultant catalysts (f). Reproduced with permission,62 Springer Nature. (g) Schematic illustration of the single-atom doping on the TMDC surfaces through an electrochemical deposition method. Reproduced with permission,57 Springer Nature. (h) Schematic illustration of interstitial Mo atom doping on MoS2 using a cold hydrogen-plasma method. Reproduced with permission,59 American Chemical Society. | |
On the other hand, interstitial doping, different from the above-mentioned substitution, is located atop the basal plane instead of being confined within the crystal lattice. Currently, Pt, Rh, Pb, Bi, Pd, Sn, Nb, Mo, and Cu54,57–59 have been used as interstitial dopant atoms in TMDCs for HER. For example, Shi and co-workers obtained a variety of atomically dispersed Pt, Rh, Cu, Pb, Bi, and Sn atoms on the MoS2 surface using an electrochemical underpotential deposition (Fig. 4g).56,58 Later, Yang and co-workers reported interstitial doped 2H-Nb1.35S2 using a CVD method, which delivered an exceptionally-high current density in HER (1000 mA cm−2 at ∼370 mV and 5000 mA cm−2 at ∼420 mV).54 In addition to the above heteroatom doping, Luo et al. used a cold hydrogen plasma method to synthesize Mo-single-atom doped MoS2 (homo-atom doping), achieving an enhancement of HER activity with a Tafel slope of 36.4 mV dec−1 and a high current density of 400 mA cm−2 at ∼260 mV, as a result of the increase of hydrogen bond strength through hybridization in Fig. 4h.59
3.1.2 Nonmetal-doping of TMDCs.
It is compelling to see that many workers59,68–70 have also employed various non-metallic doping of TMDCs to activate their basal planes, such as Se,71 P,72 B,73 F,74 and N75 doping. In 2017, Zhao et al. comprehensively examined the effect and changes in the band structure of various non-metal doped TMDCs,76 theoretically providing a suitable non-metallic element for HER (Fig. 5a). Later, Pető and co-workers found that the monolayer MoS2 exposed to the ambient atmosphere at room temperature would undergo an irreversible oxygen-substitution reaction. The oxygen atoms would be dropped into the basal plane to improve the HER performance (Fig. 5b and c).77 It was also observed that oxygen doping could facilitate expanding the interlayer distance and promote the transfer of protons.78 In addition to oxygen doping, Zang and co-workers also synthesized carbon (C)-doped MoS2 (Fig. 5d), which turned out to have low overpotential in an alkaline solution, close to that of the commercial Pt/C. The reason is the C-introduced orbital modulation effect, which generates empty 2p orbitals perpendicular to the basal plane, thus facilitating the adsorption and dissociation of water in alkaline solution, as shown in Fig. 5e.79 Xiao et al. fabricated nitrogen (N)-doped MoS2 using one-step sintering method, which presents a low onset overpotential of 35 mV and Tafel slope of 41 mV dec−1. Those N dopants in MoS2 could extremely increase the number of active sites toward HER and enhance the conductivity of the catalysts as well (Fig. 5g).75 Interestingly, Janus TMDC materials (MXY, M = transition metal, X/Y = S, Se, or Te, and X ≠ Y)80 were also reported (Fig. 5f).81 They gave a better HER performance than the pristine ones, originating from the synergistic effect between the intrinsic defects and inherent structural strain in a Janus structure.82
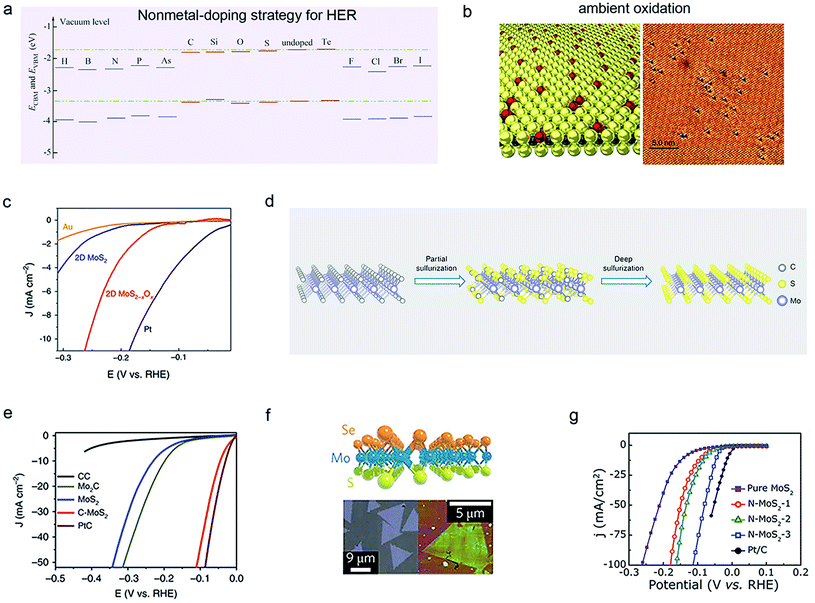 |
| Fig. 5 Nonmetal-doping strategy of 2D-TMDCs for HER. (a) The calculated ECBM and EVBM of pristine and nonmetal-doped MoSe2 monolayers. Reproduced with permission,76 Springer Nature. (b) Atomic structure (left) and scanning tunneling microscopy (STM) images (right) of the exfoliated MoS2 monolayer in the air after one month, and its corresponding HER performance (c). Reproduced with permission,77 Springer Nature. Schematic illustration of carbon (C)-doped MoS2 (d) and its corresponding HER performance in an alkaline electrolyte (e). Reproduced with permission,79 Springer Nature. (f) Janus MoS2 monolayer synthesized through a plasma-enhanced CVD method. Reproduced with permission,81 Springer Nature. (g) Polarization curves of nitrogen (N)-doped MoS2 samples. Reproduced with permission,75 Wiley-VCH. | |
Benefiting from the abundant valence states and flexible oxidation capabilities of these non-metal atoms, their doping method can finely modulate the electronic structure of TMDCs and accelerate and stabilize the HER process. Notably, the co-doping of metals and non-metals has also been tried, which improves the intrinsic performance and increases catalytic sites by alloying and synergy at different sites.67 As a whole, non-metal doping offers great potential to trigger more TMDCs-based catalyst reconstruction and optimize the reaction pathways.
3.2 Vacancy strategy
Vacancies are the commonly-found structures in TMDCs. Their distribution (isolated vacancies, di-sulfur vacancies, pair vacancies, cluster vacancies, etc.), concentration, and species83 are crucial to improving the HER-activity of the basal plane.13,70,84,85 Currently, a variety of vacancy-engineering strategies, such as Ar plasma treatment,32 electron/ion beam/laser irradiation,86 strain (physical etching),87 solvothermal growth,88 CVD annealing,83 and electrochemical desulfurization (chemical etching)89 have been developed. Those vacancies can be divided into transition metal vacancies and chalcogenide vacancies in TMDCs, as shown in Fig. 6a.
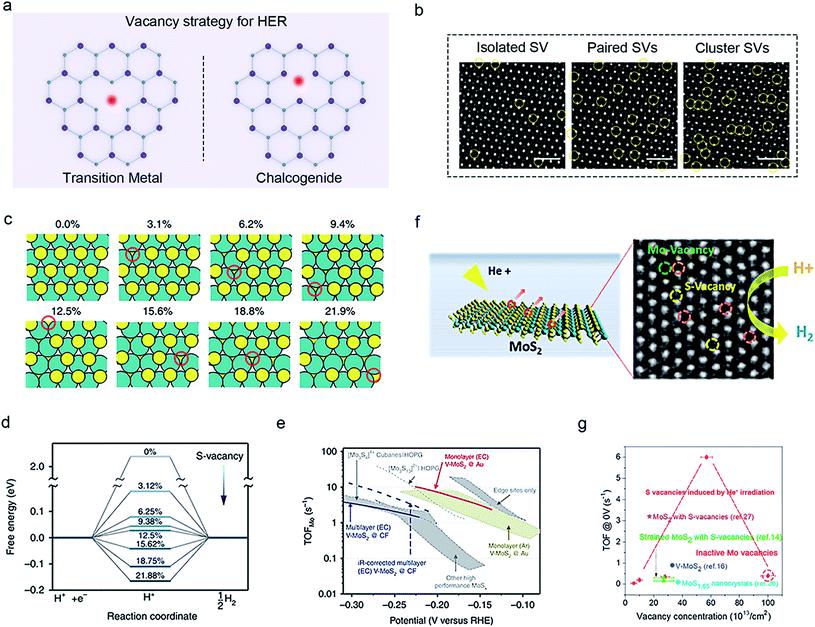 |
| Fig. 6 Vacancy strategy of 2D-TMDCs for HER. (a) Schematic illustration of two kinds of vacancies in TMDCs: transition metal vacancy (left) and chalcogenide vacancy (right). (b) Scanning transmission electron microscopy (STEM) images of the isolated S, paired S, and clustered S vacancies in a MoS2 monolayer generated by varied H2-annealing conditions. Reproduced with permission,83 Wiley-VCH. (c) Schematic illustration of the optimized structures of MoS2 with varied S-vacancy concentrations. The free energy diagram of S-vacancy sites (d) and turnover frequencies per surface Mo atom (e) for the samples in (c). Reproduced with permission,89 Springer Nature. Defective MoS2 film fabricated through a helium-ion irradiation method (f) and its corresponding turnover frequency (TOF) at varied vacancy concentrations (g). Reproduced with permission,86 American Chemical Society. | |
To investigate the influences of structures and concentrations of chalcogenide vacancies on the basal plane for HER; Zhang and co-workers employed mild H2 annealing to precisely create SVs in the monolayer MoS2 at different temperatures and achieved isolated, paired, and clustered SVs (Fig. 6b). In another example, Tsai et al. used electrochemical desulfurization to introduce SV in the basal plane of the monolayer MoS2 with a concentration of 21.9 at% (Fig. 6c). Combining the DFT calculations (Fig. 6d), the authors demonstrated that only isolated atomic vacancies can be considered localized states to maximize the charge hopping probability, and thus significantly increase the turnover frequency of Mo atoms (TOFMo = 10 s−1) of samples (Fig. 6e).83,89 Nevertheless, they also observed that a further increase in the vacancy density would form clustered SVs, which could produce deep trapping levels to lower the electronic properties, consequently degrading HER performance. To improve the vacancy density, both Lei Li and Xin Wang et al. created much higher concentrations of SVs in MoS2 compared to the above studies. They impressively found that the unsaturated Mo atoms acted as the active sites, which could introduce gap states favorable for hydrogen bonding, leading to an excellent per-site turnover frequency (1000 s−1 and 10
000 s−1 corresponding to the overpotentials of 200 mV and 300 mV in their work).88,90
On the other hand, compared with the above non-metal vacancies, Yang et al. showed that a large number of Mo vacancies were formed in CVD-grown MoS2 after Helium ion irradiation, while they found a lower HER activity (Fig. 6f and g).86 This phenomenon can be explained by the fact that the physical etching could severely damage the atomic structures of TMDC's basal planes, such as holes, cracks, and curl zones and degrade their electronic properties. Note that these non-metal vacancies would play a more positive role in improving the HER performance, as compared to the metal ones.
3.3 GB strategy
Recent studies have demonstrated that GBs possess a high catalytic activity due to the synergistic effect raised from the local strain and unsaturated sites.91 Different from the above doping and vacancies, GB is a type of 1D defect (besides edge), with dreidel-shaped dislocation cores and ringed motifs.70,85 They can be divided into homo-phase and hetero-phase structures according to their neighboring phases, as shown in Fig. 7a. The main approaches to synthesizing GBs consist of CVD,92,93 molecular beam epitaxy (MBE),94 physical vapor deposition (PVD),95,96 metal–organic chemical vapor deposition (MOCVD),97,98 hydrothermal methods,99 and plasma.93 Additionally, other factors such as the fast kinetic processes, the multiplicity of phases and ingredients, low symmetry, and crystalline substrate could also promote the formation of GBs.33,94
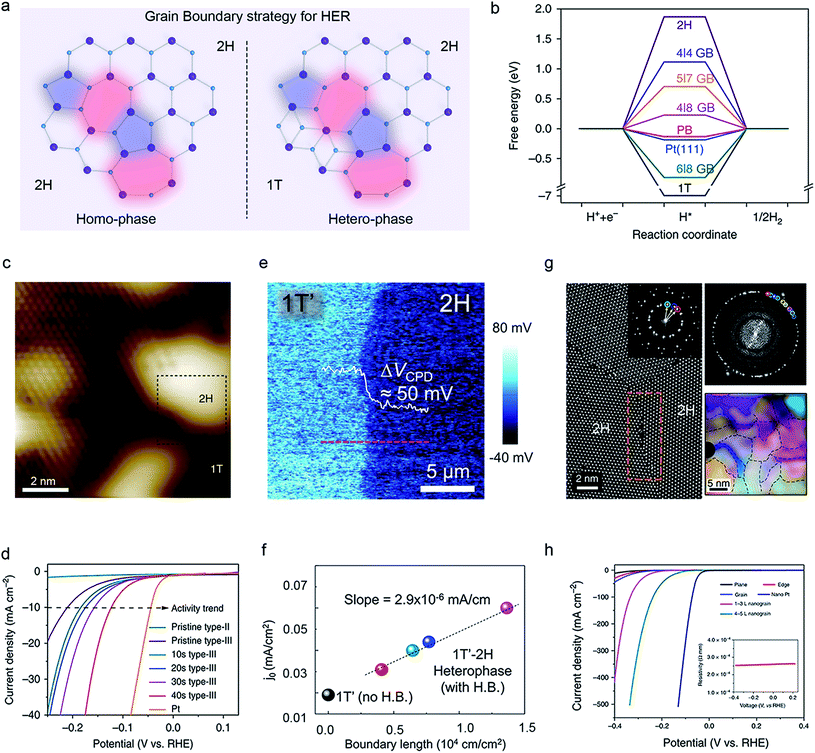 |
| Fig. 7 Grain boundary (GB) strategy of 2D-TMDCs for HER. (a) Schematic illustration of the two kinds of GBs: homo-phase and hetero-phase. (b) Comparison of the ΔGH* on 2H-MoS2, 1T-MoS2, Pt (111), and 2H–1T hetero-phase GB, and 2H–2H homo-phase GB. Reproduced with permission,93 Springer Nature. STM image of the 2H–1T hetero-phase GB of MoS2 (c) and the polarization curves with varied GB densities (d). Reproduced with permission,93 Springer Nature. Charge potential mapping across a 1T′–2H hetero-phase GB of MoTe2 (e) and its exchange-current-density as a function of the GB length (f). Reproduced with permission,92 Wiley-VCH. Atomic structures of 2H–2H homo-phase GBs in the MoS2 nanograin film (g) and their polarization curves (h) obtained from the microcells. Reproduced with permission,33 Springer Nature. | |
For example, Zhu et al. firstly calculated the Gibbs free energy of GBs in hetero/homo-phase MoS2 (Fig. 7b). 2H–1T GBs possess extremely low H adsorption energy, which improves the basal plane's activity.93 Furthermore, the authors also optimized the 2H–1T GB density of MoS2 (hundred-nanometers-size domains) by using argon plasma treatments (Fig. 7c). It turned out a very low overpotential of ∼136 mV vs. RHE, a Tafel slope of ∼73 mV dec−1, and long-term stability in acidic and alkaline conditions, as shown in Fig. 7d. Alternatively, Lee and co-workers reported the 1T′–2H hetero-phase GBs of MoTe2via CVD (Fig. 7e). They found a positive linear correlation between the exchange current density and the length of the MoTe2 2H–1T′ GBs, allowing for an excellent TOF value of 317 s−1 because of the charge accumulation and local band bending at the GBs (Fig. 7f).92 To achieve an ultra-high density of 2H–2H homo-phase GBs, in our previous work, we employed the Au-quantum-dots (QDs)-assisted vapor-phase growth in producing sub-10 nm-domain MoS2 films with a GB density up to ∼1012 cm−2 (Fig. 7g). It gave an excellent HER performance (onset potential: −25 mV vs. RHE and Tafel slope: 54 mV dec−1 in Fig. 7h).33
3.4 Phase strategy
Crystal phase-controlled synthesis of TMDCs is a promising strategy that could significantly affect catalytic activity and conductivity as well. Fig. 8a presents various polymorphs of TMDCs, including 2H, 3R, 1T, 1T′, and 1Td phases, depending on the interaction and coordination between the transition metal and chalcogen.26,100–102 Basically, the triangular prism-coordinated TMDCs are typical semiconductors (2H or 3R phase) and have a lower conductivity than metallic octahedral-coordinated ones.103,104 In the past, various strategies have been used to synthesize metal-phase group VI TMDCs, such as alkali metal intercalation,28,101,104–108 electron beam irradiation,104,109 plasma bombardment,110 pressure and strain,111 high magnetic field hydrothermal reaction,112 and electrostatic doping,.113 Using the first-principles calculations, Fan and co-workers suggested that only the basal plane of 1T′-MoS2 should be active in the HER, contrary to 2H-MoS2 (Fig. 8b).114 Unfortunately, it was found in the experiments that most 1T or 1T′-phase TMDCs are metastable and easily converted into their 2H counterparts.26,106 To abbreviate this issue, Voiry et al. adopted the Li-intercalation-based chemical-exfoliation method to produce stable 1T-MoS2 nanosheets with a negatively-charged surface. Those nanosheets exhibited an excellent catalytic activity toward HER (Fig. 8c).28 Subsequently, Liu and Yu et al. designed an alkali metal atom (K)-assisted CVD method for growing stable 1T′-TMDC monolayers (such as MoS2, WS2, WSe2, MoSe2), as shown in Fig. 8d.104,105 They claimed that the intercalation of alkali metals could significantly reduce the formation energy of the metal phase TMDCs. A better HER performance was also observed in their samples compared to that of 2H phases, as shown in Fig. 8e. To more clearly elaborate on the activity of the 1T′ phase, Yu et al. employed both thermal annealing and laser irradiation to realize a smooth phase transformation from 1T′-MoS2 to 2H-MoS2, and verify the enhanced HER activity solely based on the 1T′ basal phase using three microcells (Fig. 8f and g).104
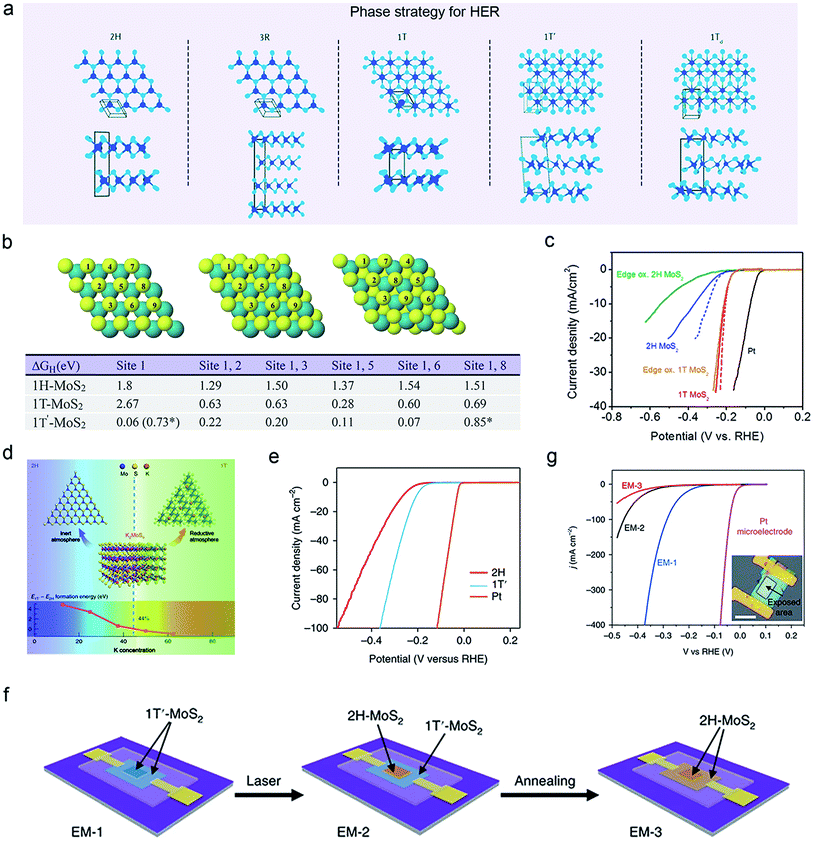 |
| Fig. 8 Phase-engineering strategy of 2D-TMDCs for HER. (a) Schematic illustration of the different phase structures of TMDCs. Reproduced with permission,26 Springer Nature. (b) The first and second H structures adsorbed on the surfaces of 1H, 1T, and 1T′ MoS2, and the correspondingly calculated Gibbs free energy, respectively. Reproduced with permission,114 Royal Society of Chemistry. (c) HER activity of solution-exfoliated 1T and 2H MoS2 nanosheets. Reproduced with permission,28 American Chemical Society. Phase-controlled CVD strategy of 1T′ MoS2 monolayer (d) and its corresponding polarization curve (e). Reproduced with permission,105 Springer Nature. The fabrication process of three types (EM-1, EM-2, and EM-3) of electrochemical microcells (f) and their corresponding HER performances. Inset: optical microscopy image of EM-1. Scale bar, 20 μm (g). Reproduced with permission,29 Springer Nature. | |
3.5 Superlattice strategy
With the help of topological physics engineering, superlattices can optimize the electronic structure and energy bands of TMDC catalysts.115–117 There are two types of superlattices: traditional (periodic stacking of different layered materials) and moiré ones (twisted structure of similar 2D bilayers), as shown in Fig. 9a. Most TMDC superlattices with different stacking orders and twists between layers have been obtained by layer-by-layer restacking,118–120 CVD,121 laser molecular beam epitaxy (LMBE),122,123 electrochemical–molecular intercalation,59,124 hydrothermal methods,125,126 capillary-force-driven rolling-up,127etc.
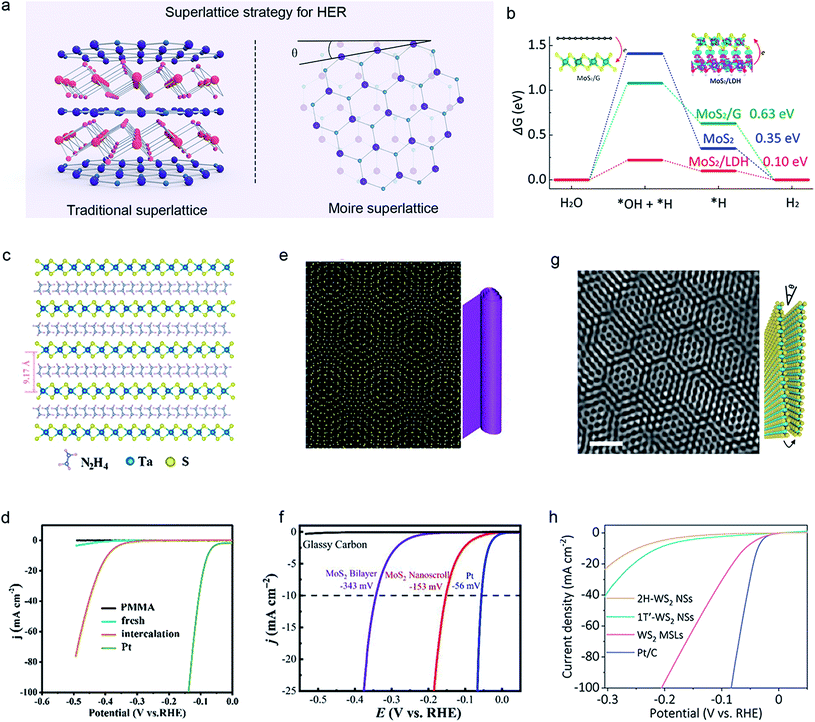 |
| Fig. 9 Superlattice strategy of 2D-TMDCs for HER. (a) Schematic illustration of two kinds of superlattices: traditional superlattice (left) and moiré superlattice (right). (b) Comparison of the Gibbs free energies of the adsorbed H on MoS2, MoS2/graphene, and MoS2/layered double hydroxide (LDH). Reproduced with permission,128 American Chemical Society. The atomic structure of the TaS2–N2H4 hybrid superlattice (c) and its corresponding HER performance (d). Reproduced with permission,59 American Chemical Society. Structures of the moiré superlattice of a MoS2 nanoscroll (e) and the corresponding polarization curves (iR-corrected) (f). Reproduced with permission,123 American Chemical Society. High-resolution transmission electron microscopy (HRTEM) image of the WS2 moiré superlattice formed by a layer-slipping method (g) and the corresponding iR-corrected polarization curves (h). Scale bar, 1 nm. Yellow and cyan balls represent S and W atoms, respectively. Reproduced with permission,126 Springer Nature. | |
In theory, Xiong et al. demonstrated the bilayer models of MoS2/graphene, layered double hydroxide (LDH)/G, and MoS2/LDH superlattices for HER. The enhanced electrocatalytic activity was observed in MoS2/LDH, attributed to significant electron accumulation at its interface that could modulate the intermediates' adsorption energies in HER pathways (Fig. 9b).128 In the experiment, Guo et al. developed an n-type TaS2–N2H4 hybrid superlattice through a spontaneous molecular-intercalation method at room temperature (Fig. 9c). It has high electrical conductivity and a low work function, confirmed by the Kelvin probe force microscope (KPFM), showing an excellent HER activity (Fig. 9d).59 On the other hand, using an LMBE technique, Jiang et al. reported a bilayer MoS2 nanoscroll (twisted angle θ ≈ 7.3°) having a moiré superlattice structure (Fig. 9e). Such a structure could extremely reduce the interlayer potential barrier to improve the hopping efficiency of electron transfer, achieving a boosted electrocatalytic performance with η10 of −153 mV vs. RHE and Tafel slope of 73 mV dec−1, as shown in Fig. 9f.123 Additionally, Xie and co-workers found a nanoconical array WS2 with moiré superlattices (Fig. 9g), showing an intriguing HER performance (the low overpotential η10 of 60 mV vs. RHE in the Fig. 9h).126 The underlying mechanism is attributed to the fact that the twisted WS2 bilayer has lower Gibbs free energy than the normal WS2. The above approaches have enriched our current toolbox for designing superlattices and provide great potential for water-splitting applications.
4. External regulation
Besides the above internal methods, external control methods, such as the electric field, strain, substrates, and heterostructures, have attracted considerable interest in activating the basal plane with a high degree of freedom.36 For example, the applied electric field and strain can realize a smooth tunning of their catalytic activities. Conductive-carbon-based or metal-based substrates provide alternatives to improving the electron-injection efficiency for HER. Constructing HER-active materials (such as hydroxides, oxides, and carbides) onto TMDC basal planes to form the heterostructures presents another promising strategy.
4.1 Electric-field strategy
Applying a vertical electric field on TMDCs could enhance the HER efficiency by increasing the electrical conductivity, reducing the ΔGH*, as well as adjusting the distribution of reactants.104,129,130 It can serve as a high-degree-of-freedom strategy for tuning the basal plane activity of TMDCs smoothly.36 In 2017, Mai et al. first explored the influence of the electric field on the MoS2 nanosheet through a back-gate microcell (Fig. 10b).131 They observed that in the absence of an electric field, a current density of 100 mA cm−2 required an overpotential of 240 mV. However, as the gate voltages increased up to 5 V, a significantly-reduced overpotential (down to 38 mV) was achieved, comparable to that of the Pt electrode, as shown in Fig. 10c. This improved HER efficiency could be attributed to lowering both MoS2 itself resistance and the Au–MoS2 contact barrier under a positive electric field. Later, a similar phenomenon was also observed in other works,132–134 further confirming that the electric field can improve the electron injection process during the HER process.
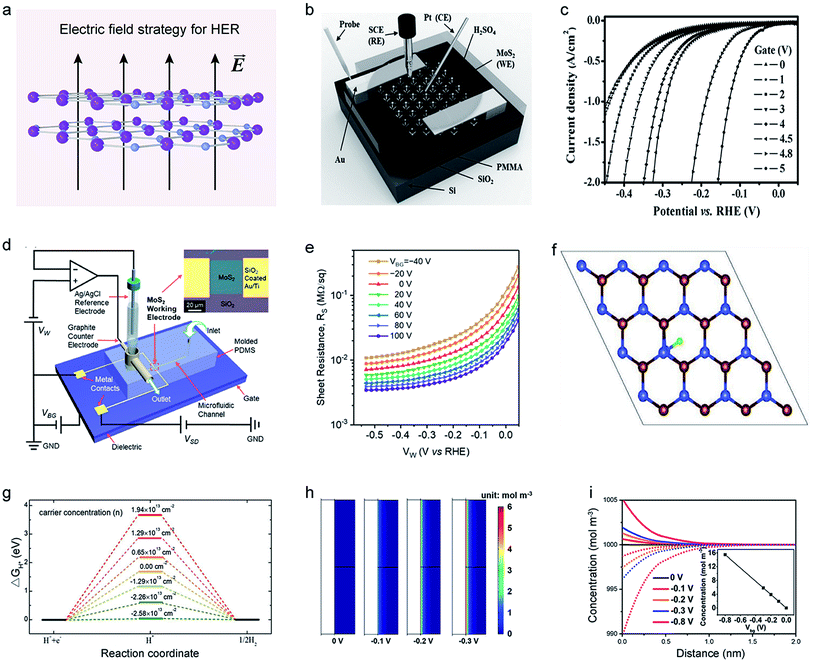 |
| Fig. 10 Electric field strategy of 2D-TMDCs for HER. (a) Schematic illustration of the electric field strategy for HER. (b) Schematic illustration of a three-electrode microcell based on a MoS2 nanosheet for HER measurement. (c) Polarization curves at varied back-gate voltages, as obtained from the micro-cell in (b). Reproduced with permission,131 Wiley-VCH. (d) The structure of a back-gated microcell. Inset: the optical images of a MoS2-monolayer electrode. (e) The normalized sheet resistance of the MoS2 electrode as a function of the electrode potential (Vw) at varied back-gate voltages (VBG). Reproduced with permission,135 American Chemical Society. (f) DFT calculation of an H-atom adsorbed on a WSe2 nanosheet charged by the back-gate voltage (blue, purple, and green balls represent Se, W, and H atoms, respectively). (g) The Gibbs free-energy diagram of WSe2 under different carrier concentrations. Reproduced with permission,45 Wiley-VCH. (h) COMSOL simulation of the net charge distribution on the surface of a VSe2 electrode at varied back-gate voltages. (i) Simulation results of charge concentrations on the surface (lines and dots represent H+ and SO42−, respectively). Inset: the net charge as a function of back-gate voltage. Reproduced with permission,110 American Chemical Society. | |
Except for the improvement of the conductivity, the electric field can also regulate the ΔGH* of the TMDCs basal planes or adjust the distribution of reactants in an electrolyte. For example, Frisbie et al. developed an electrochemical flow cell allowing the simultaneous measurements of electrical and electrochemical properties (Fig. 10d). However, they rarely observed a change in the sheet resistance of the monolayer MoS2 when increasing the back-gate voltages (Fig. 10e),135 Alternatively, a significant drop in ΔGH* was found because the Mo atoms next to the S vacancies on the basal plane accumulate excess electrons under the positive electric field, resulting in an enhanced HER performance.136 Those results suggested that the electric field dominates ΔGH* of the monolayer MoS2 rather than its conductivity in HER. A similar phenomenon was also observed in bipolar semiconductors.45Fig. 10f shows H atoms adsorbed on a WSe2 nanosheet, as obtained from the DFT calculations. The positive electric field provided more electron carriers for the bipolar WS2, reducing the free energy (Fig. 10g).
The electric field can also adjust the distribution of charged reactants at the catalyst–electrolyte interface during the HER process.137 Mai et al. used metallic VSe2 as the working electrode and found that H3O+ prefers to accumulate at the interface (Fig. 10h and i).110 Therefore, they claimed that the Volmer step in the HER process was accelerated, thus increasing the overall reaction rate. It is worth emphasizing that the electric field regulation is a complex strategy. One or more factors, such as the contact barrier of the whole system, the concentration of reactants, the conductivity of catalysts, and the transfer process of charges, would affect the reaction.
4.2 Strain strategy
Due to their atomic thickness, TMDC nanosheets are very sensitive to strain,138–140 while impressively, they can withstand up to 23 GPa (11%) mechanical strain.141 According to the d-band model,142–144 the strength of H adsorption on the catalyst is crucial to the d-band position, and a tensile strain can upshift it to reduce occupied states of antibonding orbitals, promoting the H-atom adsorption.145,146 This electronic theory could also be suitable for strained TMDCs,146 and the strain would play a vital role in the H adsorption during the HER process. Here, we discuss three strain strategies: lattice mismatch, bending substrates, and textured strain.
A lattice mismatch can induce a local strain on TMDC materials.147–149 For example, Chhowalla et al. prepared highly distorted 1T–WS2 nanosheets using an intercalation-based chemical exfoliation method.42 The STEM image shows a lattice mismatch in WS2 nanosheets (Fig. 11c), and the inset confirmed that this mismatch could cause a large area of local strain (about 3%) on the basal plane. As a result, the free energy could be tuned to be close to 0 when the strain value was 2.7%, showing an excellent performance of the highly distorted 1T–WS2 nanosheets (Fig. 11d).
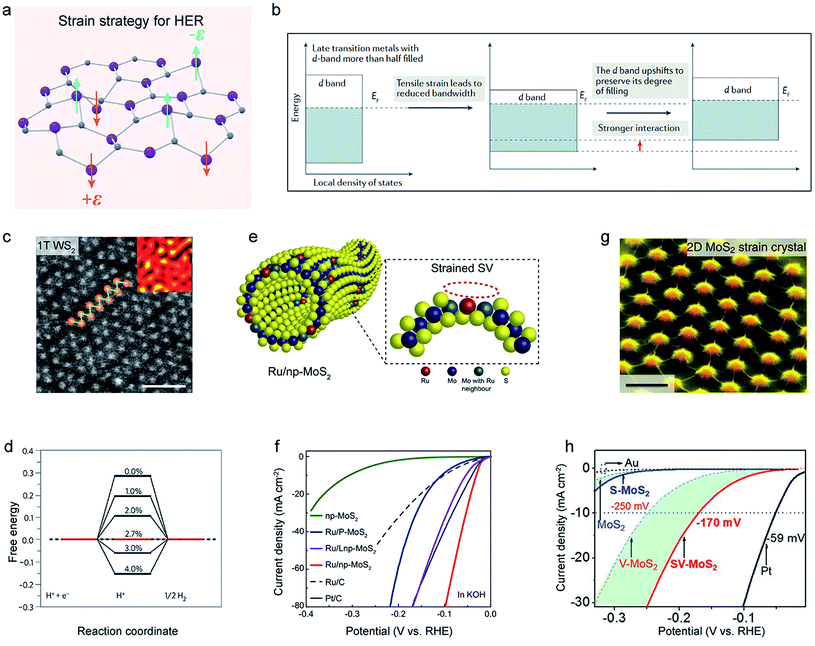 |
| Fig. 11 Strain strategy of 2D-TMDCs for HER. (a) Schematic illustration of the strain strategy for HER. (b) The energy diagrams of the influence of tensile strain on the d-band position in late transition metals. Reproduced with permission,145 Springer Nature. (c) High-resolution scanning transmission electron microscopy (STEM) images of the as-exfoliated WS2. Inset: the strain tensor mapping obtained from the STEM images (black and yellow colors correspond to compressed and tensile regions). Scale bar, 1 nm. (d) The Gibbs free energy of 1T–WS2 varied by the tensile strain. Reproduced with permission,42 Springer Nature. (e) Schematic illustration of the Ru/nanoporous MoS2 (Ru/np-MoS2). SV indicates sulfur vacancies. (f) Polarization curves of Ru/np-MoS2, in comparison to those of nanoporous MoS2 (np-MoS2), Ru/plane MoS2 (Ru/P-MoS2), and Ru/larger ligament nanoporous MoS2 (Ru/Lnp-MoS2). Reproduced with permission,151 Springer Nature. (g) False-color SEM image of a 2D strained MoS2 monolayer on a nanocone array. Scale bar, 1 μm. Reproduced with permission,154 Springer Nature. (h) Polarization curves of strained-vacancy MoS2 (SV-MoS2), in comparison to those of the Au substrate, pristine MoS2, strained MoS2 (S-MoS2), and MoS2 with vacancies (V-MoS2). Reproduced with permission,32 Springer Nature. | |
Being different from the above lattice mismatch, constructing bending strain and texture strain usually requires templates such as 3D nanoporous gold (NPG),150,151 nanofibers,152 polymer substrate,153 and nanocones.32,154 For example, Tan et al. constructed single-Ru-atom-anchored nanoporous MoS2 (denoted as Ru/np-MoS2) by NPG (Fig. 11e).151 It was found that the curved structure could introduce strain around the Ru-atom in the basal plane, the strength of which was tailored simply by the sample's ligament size. A larger strain in the Ru/np-MoS2 catalyst results in better performance, and a η10 of 30 mV, as well as a Tafel slope of 31 mV dec−1, was finally achieved, as shown in Fig. 11f. Operando X-ray absorption spectroscopy (XAS) revealed that the strain could accelerate the mass transfer from the S-vacancy sites to Ru sites, amplifying the synergetic interaction between them. In another example, Li et al. created a wide range of texture strains on the basal plane of MoS2 using a nanocone array method (Fig. 11g).32 After comparing MoS2, strain-only MoS2 (S-MoS2), and vacancy-only MoS2 (V-MoS2), strained-vacancy MoS2 (SV-MoS2) gave the best HER performance with a η10 of 170 mV, as shown in Fig. 11h (green areas referred to the contribution of strain to reactivity). They claimed that the tensile strain could narrow the MoS2 bandwidth and shift the free energy toward thermoneutrality, thus enhancing the HER activity. It is worth mentioning that the strain, in combination with other methods, e.g., vacancies,87 can provide a more flexible way to regulate the catalytic performance of the basal planes.
4.3 Substrate strategy
The underlying substrates have been confirmed to facilitate the electron injection and modify the chemical property of catalysts to improve catalytic performance, that is, the substrate effect.27,157,158 The conductive substrates can be classified into carbon materials and pure metals. The former mainly includes carbon black,159 graphenes,155,160,161 carbon nanotubes,162,163 and carbon fiber.156 The latter are Au, Ti, Ni, Pt, and so on.40 The typical substrate is graphene. Shin et al. fabricated WS2/reduced graphene oxide (WS2/rGO) hybrid nanosheets using conductive rGO as the substrate (Fig. 12b).155 Since the rGO substrate facilitates a rapid electron transfer to the WS2 catalyst, WS2/rGO nanosheets enhance HER performance compared with WS2 alone, as shown in Fig. 12c. Extending to metal substrates, Liu et al. systematically investigated the catalytic performance of TaS2 on the glass carbon plate, carbon fiber, Mo foil, and Au foil.156 Among those substrates, the authors found that Au/TaS2 has the best catalytic performance (33 mV dec−1 of Tafel plot in Fig. 12d) with the lowest ΔGH* (Fig. 12e), which results from the ideal lattice mismatch at the TaS2–Au interface (Fig. 12f).
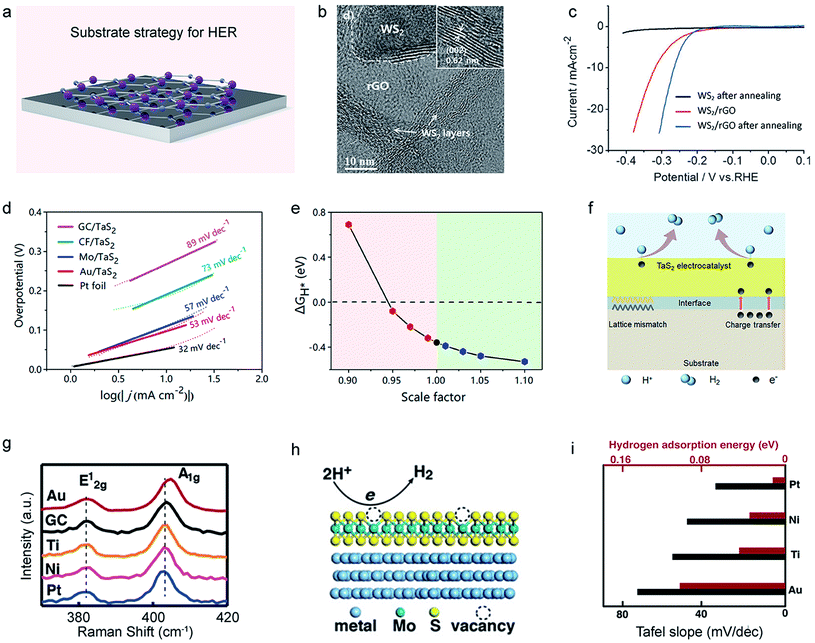 |
| Fig. 12 Substrate strategy of 2D-TMDCs for HER. (a) Schematic illustration of the substrate strategy for HER. (b) HRTEM image of the WS2/reduced graphene oxide (WS2/rGO) hybrid nanosheet. Inset: the zoom-in image of the WS2 nanosheet. (c) Polarization curves of the annealed WS2/rGO hybrid nanosheets, in comparison to those of annealed WS2 nanosheets and WS2/rGO hybrid nanosheets. Reproduced with permission,155 Wiley-VCH. (d) Tafel plots of TaS2 samples on glass carbon (GC), carbon fibers (CF), Mo, and Au substrates. (e) The ΔGH* of the TaS2 nanosheet under the lattice-mismatch condition. (f) Schematic illustration of the substrate effect on a TaS2 electrocatalyst. Reproduced with permission,156 American Chemical Society. (g) Raman spectra of monolayer MoS2 on Au, GC, Ti, Ni, and Pt substrates, showing the redshift of Pt > Ni > Ti > Au. (h) Schematic illustration of the substrate effect on a MoS2 monolayer. (i) Calculated hydrogen adsorption energies and the measured Tafel slopes of a MoS2 monolayer on Pt, Ni, Ti, and Au substrates. Reproduced with permission,40 American Chemical Society. | |
On the other hand, substrates could also induce carrier doping to modify the activity of TMDC catalysts.164,165 For instance, Cao et al. observed substrate-induced n-doping of the monolayer MoS2 through the redshift of Raman spectra (Fig. 12g).40 The DFT shows that such doping would improve the activity of the vacancies to activate the MoS2 basal plane (Fig. 12h), and a higher doping level (Pt > Ni > Ti > Au) leads to lower adsorption energy of the sample, agreeing with the experiment results (Fig. 12i).
4.4 Heterostructure strategy
Heterostructures that were rationally designed by combining the advantages of each TMDC component together would possess a higher catalytic performance than those single components.14,166,167 Here, we would discuss the synergistic effect168,169 and the interfacial charge transfer170–172 originating from heterostructures. So far, the synergistic effects have also been frequently observed in hydroxide/TMDC,173–176 TMDC/TMDC,177–180 oxide/TMDC,181–183 and others.184–187 As discussed in Section 2, the high adsorption energy of H2O hinders the generation of Had intermediates, leading to sluggish kinetics in alkaline solution. To optimize HER pathways, Jiang et al. prepared a Ni(OH)2/MoS2 heterostructure, in which Ni(OH)2 could serve as the dissociation promoter, thereafter, H2 was generated on the MoS2 basal plane.188 DFT calculations also confirmed this synergistic effect, which could lower the H2O adsorption energy from 0.75 eV to 0.05 eV, significantly accelerating the reaction kinetics. A Tafel plot of 60 mV dec−1 was finally obtained in this heterostructure, much better than that of the pristine basal plane (96 mV dec−1), as shown in Fig. 13d.
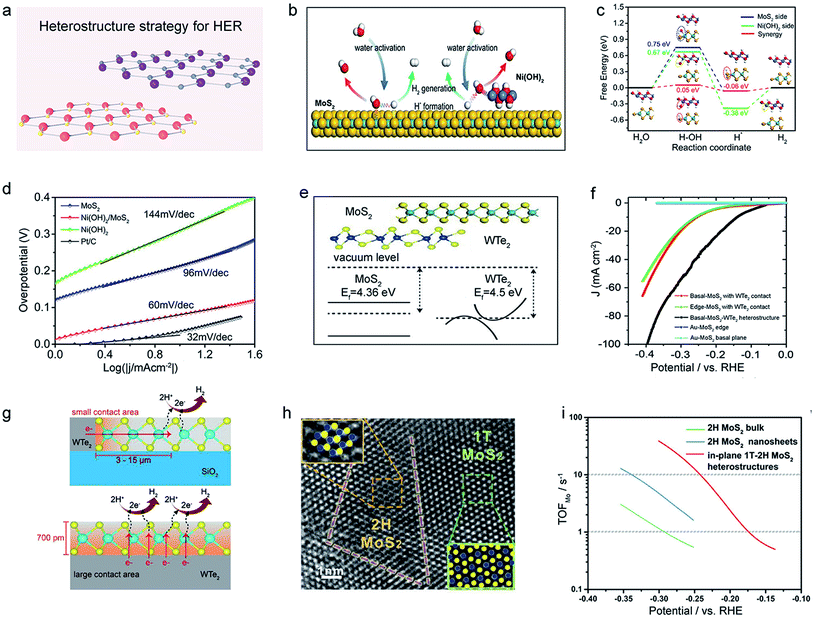 |
| Fig. 13 Heterostructure strategy of 2D-TMDCs for HER. (a) Schematic illustration of the heterostructure strategy for HER. (b) Schematic illustration of the water activation process for the Ni(OH)2/MoS2 heterostructure in an alkaline solution. H, O, Mo, S, and Ni atoms are shown in white, red, cyan, yellow, and blue, respectively. The free energy diagram (c) and the Tafel plots (d) for MoS2, Ni(OH)2, and Ni(OH)2/MoS2. Reproduced with permission,188 Elsevier. (e) The aligned band structure of the MoS2/WTe2 heterostructure. (f) The corresponding polarization curves of the MoS2/WTe2 heterostructure. (g) Comparison of the HER mechanisms of the MoS2/WTe2 heterostructure (bottom) and MoS2 with WTe2 edge-contact (top). Reproduced with permission,189 Wiley-VCH. HRTEM image (h) and the TOF(I) of the in-plane 1T-2H MoS2 heterostructure. Reproduced with permission,125 Wiley-VCH. | |
It was found that heterostructures could also optimize the electronic structure and the mass/electron transfer. For example, Cha et al. synthesized MoS2/WTe2 vertical heterostructure with semi-metallic WTe2 as the bottom layer.189 They claimed that a low Schottky barrier in the heterostructure tends to rapidly inject electrons from the bottom WTe2 to the top MoS2. Consequently, the catalytic activity of MoS2 in the heterostructure is better than that of the WTe2 edge-contacted one. That is, the former had a larger contact area than the latter (Fig. 13g), thus showing a shorter pathway of charge during the HER process. In another example, Yang et al. reported a stable in-plane 1T-2H MoS2 heterostructure using an annealing treatment method (Fig. 13h).125 They demonstrated a huge improvement in HER properties in the alkaline solution (TOF: 13.14 and 1.61 H2 s−1 at 250 mV for heterostructure and 2H-MoS2 nanosheet, respectively), as shown in Fig. 13i. This enhancement was attributed to the rapid electron transport and abundant active sites, both of which facilitate activating the inert basal plane of 2H-MoS2. It can be seen that those above heterostructures can combine the advantages of each component, significantly activating the basal plane of TMDCs. What is more, the recent emergence of machine learning could assist in screening the types and structures,190 which will be helpful in the design of high-performance heterostructure catalysts.
5. Summary and outlook
Electrocatalytic hydrogen production, basically, is an interfacial reaction, where the adsorption and desorption behavior of hydrogen atoms, that is, ΔGH* as an important parameter, dominate the reaction rate. Benefiting from their stable and atom-thin (<1 nm) nature, 2D TMDCs themselves act as an interface and possess the potential of exposing nearly all of their atoms to the electrolyte. This unique character makes 2D TMDC ideal candidates for HER catalysts and the corresponding mechanism study. Unfortunately, in respect of most non-metallic TMDCs, their basal plane is usually inert. In the past ten years, substantial studies have thus been undertaken to activate the basal plane through strategies based on internal regulation such as doping, vacancies, phases, GBs, superlattices, or external regulation, such as the electric field, strain, substrates, and heterostructures. We summarized the characteristics of all strategies mentioned above in Table 1 and enumerated their corresponding principles, active types, and representative examples. Among them, some strategies activate the basal plane by creating dispersed active sites, such as doping, vacancies, and GBs. In contrast, the others did it by modulating the whole plane's activity lane, such as phases, superlattices, the electric field, and heterostructures.
Table 1 Summary of the strategies for activating the TMDC basal planes
Strategy |
Principle |
Active types |
Examples |
Material/structure |
η
10 (mV) |
Tafel slope (mV dec−1) |
Electrolyte |
Ref. |
Doping |
Engineer locally uncoordinated active sites |
Dispersed sites |
Metal-doping |
Pd–MoS2 |
89 |
62 |
0.5 M H2SO4 |
62
|
Nonmetal-doping |
Carbon–MoS2 |
45 |
46 |
1 M KOH |
79
|
Vacancies |
Engineer locally unsaturated site |
Dispersed sites |
Isolated-S vacancies |
30 He+–MoS2 |
200 |
90 |
0.5 M H2SO4 |
86
|
Cluster-S vacancies |
Repaired 2H-MoS2 |
300 |
85 |
0.5 M H2SO4 |
88
|
Phases |
Increase the conductivity and lower the hydrogen absorption energy |
Whole plane |
1T′ phase |
1T′-MoS2 |
65 |
100 |
0.5 M H2SO4 |
29
|
1T phase |
1T-MoS2 |
230 |
45 |
0.5 M H2SO4 |
108
|
GBs |
Engineer unsaturated-site 1D channel |
Dispersed 1D sites |
2H–2H GBs |
MoS2 nanograin film |
25 |
50 |
0.5 M H2SO4 |
33
|
2H–1T GBs |
2H–1T-MoS2 GB |
260 |
85 |
0.5 M H2SO4 |
93
|
Superlattices |
Improve the activity by interfacial electronic coupling |
Whole plane |
Moiré superlattice |
WS2 moiré superlattice |
60 |
42 |
0.5 M H2SO4 |
126
|
Layer-stacked superlattice |
TaS2/N2H4 superlattice |
0.4 |
76 |
0.5 M H2SO4 |
191
|
Electric field |
Facilitate electron injection and ion-redistribution |
Whole plane |
Vertical electric field |
Monolayer MoS2 |
176 |
100 |
0.5 M H2SO4 |
135
|
Strain |
Lower the hydrogen absorption energy |
Dispersed sites |
Lattice-mismatch induced stain |
Distorted 1T WS2 |
235 |
60 |
0.5 M H2SO4 |
42
|
Bending stain |
Ru/nanoporous MoS2 |
30 |
31 |
1 M KOH |
151
|
Textured strain |
Strained-vacancy MoS2 |
131 |
48 |
0.5 M H2SO4 |
32
|
Substrates |
Enhance electron injection, and activity by doping |
Whole plane |
Metal-based substrates |
TaS2 on Au |
101 |
53 |
0.5 M H2SO4 |
156
|
Carbon-based substrates |
WS2 on rGO |
264 |
58 |
0.5 M H2SO4 |
155
|
Heterostructures |
Synergistic effect |
Whole plane |
Hydroxide/TMD heterostructure |
Ni(OH)2/MoS2 |
80 |
60 |
1 M KOH |
188
|
Accelerate interfacial charge transfer |
Whole plane |
TMD/TMD heterostructure |
MoS2/WTe2 |
135 |
40 |
0.5 M H2SO4 |
189
|
Although significant progress has been made to improve the HER activity of TMDC's basal planes, some challenges remain in the above strategies. For example, with respect to the dispersed active sites, the activating effectiveness depends largely on their intrinsic activity and density, however, a high density of the sites (for example, vacancies) will destroy the 2D layered structure. Therefore, we need to strike a balance between the activity and stability for those activating strategies since both will affect the key figure of merit of HER performances. On the other hand, adopting phase-transition, superlattices, and heterostructures enable a whole active layer of 2D TMDCs, while their structural stability and reproducibility are still challenges. For example, octahedrally-coordinated 1T-phase and intercalated hybrid superlattices have low thermodynamic stability. Alternatively, the electric field and heterostructures also lead to a whole active layer, however, their mechanisms are still challenging to clarify, such as the interlayer coupling in heterostructures, and the apparent differences among the electron injection, and electron transport, as well as ion-redistribution under the applied electric field.
Despite the above challenges, there are also many intriguing directions for efficiently activating TMDC's basal planes. Here, we provide personal perspectives on opportunities to be explored in this emerging field.
The first is a joint strategy. Such strategies have their own advantages or disadvantages, as discussed above. They would rouse a joint strategy that can combine two or three strategies to make full use of all their advantages (that is, one plus one is greater than two). A typical example is strained-S vacancies in the MoS2 basal plane.32 For only SVs, increasing their concentrations would continually lower ΔGH*, while its high level (>19%) would lead to poor stability. On the other hand, it is insufficient to activate the basal plane only by the strain strategy, even at a high strain. Interestingly, taking them together would only require ∼11% of SVs to realize an optimal condition of ΔGH* = 0 eV, which helps preserve the stability of the layered structures.
Second, phase-engineering TMDC strategy. As an important parameter of layered TMDs, the crystal phase is usually decisive to their properties. For example, most 2H TMDCs, e.g., 2H-MoS2, MoSe2, WS2, WSe2, etc., are very stable in air/water and can withstand the acidic/basic electrolyte as well as high temperatures (>400 °C in hydrogen atmosphere), while the only drawback they meet is the inertness of the basal plane for HER. On the contrary, their metallic counterparts, such as 1T-MoS2, and 1T′-MoS2, the whole basal planes are HER-active. However, their large-scale or pure-phase syntheses remain challenging to date due to their metastable nature. Therefore, under a trade-off of structural stability and HER activity, phase-engineering TMDC materials, such as 2H–1T phase transform or direct 1T phase-controlled synthesis, would present a promising strategy to activate the basal plane in a sampling manner.
The third is electrical–electrocatalytic coupling. From a charge-flowing point of view, a typical electrocatalytic process usually involves three steps, including the first charge injection step from the conductive substrate to the catalyst, the later charge transport step inner the catalyst body, and finally, the charge transfer at the sites at the solid–liquid interface. It can be seen that, besides the activity sites, both the charge injection and transport steps are the key factors affecting the reaction happens. For example, Voiry et al. improved the electron injection (the first step) from the Au electrode to the 2H-MoS2 catalyst using phase-engineered low-resistance contacts and achieved comparable performance to metallic edges and the 1T phase.30 In another example, He et al. observed a self-gating effect at the TMDC nanosheet–electrolyte interface,192 demonstrating that the electrocatalytic reaction itself can strongly modulate the conductance (the second step) of TMDC. Moreover, their semiconducting types (n, p, or bipolar) could strongly correlate with their electrocatalytic reactions (HER, OER, or both). Those typical works indicate the potential importance of electrical–electrocatalytic coupling in the HER process, which needs to be considered when exploring new activating strategies.
Last, but not least, is the potential of “single-atom-layer” catalysis. In our previous work, we reported a single-atom-layer Pt catalyst,193 fabricated by a low-temperature amorphizing strategy of 2D PtSe2 at a single-layer limit. This catalyst shows a fully-activated surface accessible to the HER, achieving high Pt-atom-utilization efficiency of up to ∼26 wt% and a nearly 100% current density relative to a pure Pt surface. As a comparison, the single-atom catalyst that has dispersed atomic sites is capable of nearly 100% of the utilization efficiency while suffering from the limitations of low mass-loadings (e.g., usually 5 wt% for Pt-based ones). Their differences can also be found in theory calculations, where the former employed H-coverage to evaluate the activity of the entire surface, while the latter only considered the H binding energy at single active sites. Based on the above discussions, it is also a desirable strategy to explore “single-atom-layer” catalysis based on 2D TMDCs because nearly all the atoms at the monolayer are accessible to catalytic reactions and are stable thermodynamically.
In summary, the activation of the TMDC basal planes can bring significant benefits to the HER. With the continuous enrichment of strategies, we anticipate that TMDCs can play a more vital role in electrochemical water splitting.
Author contributions
Y. H. conceived and initiated the project. H. X. and Z. S. carried out the literature survey, organized all the reference data, and prepared the figures. C. G. helped discuss the HER mechanism. All authors wrote the manuscript.
Conflicts of interest
There are no conflicts of interest to declare.
Acknowledgements
Y. H. acknowledges the National Key R&D Program of China (2021YFA1500900) and Fundamental Research Funds for Central Universities (531119200209).
References
- R. Dittmeyer, M. Klumpp, P. Kant and G. Ozin, Nat. Commun., 2019, 10, 1818 CrossRef PubMed
.
- F. Ueckerdt, C. Bauer, A. Dirnaichner, J. Everall, R. Sacchi and G. Luderer, Nat. Clim. Change, 2021, 11, 384–393 CrossRef CAS
.
- H. B. Wu, B. Y. Xia, L. Yu, X.-Y. Yu and X. W. Lou, Nat. Commun., 2015, 6, 6512 CrossRef CAS PubMed
.
- M. Yu, K. Wang and H. Vredenburg, Int. J. Hydrogen Energy, 2021, 46, 21261–21273 CrossRef CAS
.
- Z.-J. Chen, G.-X. Cao, L.-Y. Gan, H. Dai, N. Xu, M.-J. Zang, H.-B. Dai, H. Wu and P. Wang, ACS Catal., 2018, 8, 8866–8872 CrossRef CAS
.
- M. A. Abbas and J. H. Bang, Chem. Mater., 2015, 27, 7218–7235 CrossRef CAS
.
- D. M. F. Santos, C. A. C. Sequeira, D. Macciò, A. Saccone and J. L. Figueiredo, Int. J. Hydrogen Energy, 2013, 38, 3137–3145 CrossRef CAS
.
- P. Wang, K. Jiang, G. Wang, J. Yao and X. Huang, Angew. Chem., Int. Ed., 2016, 55, 12859–12863 CrossRef CAS PubMed
.
- A. Chalgin, C. Song, P. Tao, W. Shang, T. Deng and J. Wu, Prog. Nat. Sci.: Mater. Int., 2020, 30, 289–297 CrossRef CAS
.
- D. Liu, L. Dai, X. Lin, J.-F. Chen, J. Zhang, X. Feng, K. Müllen, X. Zhu and S. Dai, Adv. Mater., 2019, 31, 1804863 CrossRef PubMed
.
- S. Dou, X. Wang and S. Wang, Small Methods, 2019, 3, 1800211 CrossRef
.
- T. Rao, H. Wang, Y.-J. Zeng, Z. Guo, H. Zhang and W. Liao, Adv. Sci., 2021, 8, 2002284 CrossRef CAS PubMed
.
- C. Tan, X. Cao, X. J. Wu, Q. He, J. Yang, X. Zhang, J. Chen, W. Zhao, S. Han, G. H. Nam, M. Sindoro and H. Zhang, Chem. Rev., 2017, 117, 6225–6331 CrossRef CAS PubMed
.
- P. Prabhu, V. Jose and J.-M. Lee, Matter, 2020, 2, 526–553 CrossRef
.
- Q. Lu, Y. Yu, Q. Ma, B. Chen and H. Zhang, Adv. Mater., 2016, 28, 1917–1933 CrossRef CAS PubMed
.
- L. Guardia, J. I. Paredes, J. M. Munuera, S. Villar-Rodil, M. Ayán-Varela, A. Martínez-Alonso and J. M. D. Tascón, ACS Appl. Mater. Interfaces, 2014, 6, 21702–21710 CrossRef CAS PubMed
.
- M. Zhuang, L.-Y. Gan, M. Zou, Y. Dou, X. Ou, Z. Liu, Y. Ding, I. H. Abidi, A. Tyagi, M. Jalali, J. You, A. Cao and Z. Luo, J. Mater. Chem. A, 2018, 6, 2900–2907 RSC
.
- S. Manzeli, D. Ovchinnikov, D. Pasquier, O. V. Yazyev and A. Kis, Nat. Rev. Mater., 2017, 2, 17033 CrossRef CAS
.
- F. Jaramillo Thomas, P. Jørgensen Kristina, J. Bonde, H. Nielsen
Jane, S. Horch and I. Chorkendorff, Science, 2007, 317, 100–102 CrossRef CAS PubMed
.
- C. Tsai, K. Chan, J. K. Nørskov and F. Abild-Pedersen, Surf. Sci., 2015, 640, 133–140 CrossRef CAS
.
- H. Duan, C. Wang, G. Li, H. Tan, W. Hu, L. Cai, W. Liu, N. Li, Q. Ji, Y. Wang, Y. Lu, W. Yan, F. Hu, W. Zhang, Z. Sun, Z. Qi, L. Song and S. Wei, Angew. Chem., Int. Ed., 2021, 60, 7251–7258 CrossRef CAS PubMed
.
- J. Zhang, J. Wu, H. Guo, W. Chen, J. Yuan, U. Martinez, G. Gupta, A. Mohite, P. M. Ajayan and J. Lou, Adv. Mater., 2017, 29, 1701955 CrossRef PubMed
.
- L.-J. Ma and H. Shen, Appl. Surf. Sci., 2021, 545, 149013 CrossRef CAS
.
- M. Zhuang, G.-L. Xu, L.-Y. Gan, Y. Dou, C.-J. Sun, X. Ou, Y. Xie, Z. Liu, Y. Cai, Y. Ding, I. H. Abidi, A. Tyagi, K. Amine and Z. Luo, Nano Energy, 2019, 58, 660–668 CrossRef CAS
.
- C. Zhu, D. Gao, J. Ding, D. Chao and J. Wang, Chem. Soc. Rev., 2018, 47, 4332–4356 RSC
.
- Y. Chen, Z. Lai, X. Zhang, Z. Fan, Q. He, C. Tan and H. Zhang, Nat. Rev. Chem., 2020, 4, 243–256 CrossRef CAS
.
- L. Lei, D. Huang, G. Zeng, M. Cheng, D. Jiang, C. Zhou, S. Chen and W. Wang, Coord. Chem. Rev., 2019, 399, 213020 CrossRef CAS
.
- D. Voiry, M. Salehi, R. Silva, T. Fujita, M. Chen, T. Asefa, V. B. Shenoy, G. Eda and M. Chhowalla, Nano Lett., 2013, 13, 6222–6227 CrossRef CAS PubMed
.
- Y. Yu, G.-H. Nam, Q. He, X.-J. Wu, K. Zhang, Z. Yang, J. Chen, Q. Ma, M. Zhao, Z. Liu, F.-R. Ran, X. Wang, H. Li, X. Huang, B. Li, Q. Xiong, Q. Zhang, Z. Liu, L. Gu, Y. Du, W. Huang and H. Zhang, Nat. Chem., 2018, 10, 638–643 CrossRef CAS PubMed
.
- D. Voiry, R. Fullon, J. Yang, C. de Carvalho Castro e Silva, R. Kappera, I. Bozkurt, D. Kaplan, M. J. Lagos, P. E. Batson, G. Gupta, A. D. Mohite, L. Dong, D. Er, V. B. Shenoy, T. Asefa and M. Chhowalla, Nat. Mater., 2016, 15, 1003–1009 CrossRef CAS PubMed
.
- X. Wu, H. Zhang, J. Zhang and X. W. Lou, Adv. Mater., 2021, 33, 2008376 CrossRef CAS PubMed
.
- H. Li, C. Tsai, A. L. Koh, L. Cai, A. W. Contryman, A. H. Fragapane, J. Zhao, H. S. Han, H. C. Manoharan, F. Abild-Pedersen, J. K. Nørskov and X. Zheng, Nat. Mater., 2016, 15, 48–53 CrossRef CAS PubMed
.
- Y. He, P. Tang, Z. Hu, Q. He, C. Zhu, L. Wang, Q. Zeng, P. Golani, G. Gao, W. Fu, Z. Huang, C. Gao, J. Xia, X. Wang, X. Wang, C. Zhu, Q. M. Ramasse, A. Zhang, B. An, Y. Zhang, S. Martí-Sánchez, J. R. Morante, L. Wang, B. K. Tay, B. I. Yakobson, A. Trampert, H. Zhang, M. Wu, Q. J. Wang, J. Arbiol and Z. Liu, Nat. Commun., 2020, 11, 57 CrossRef CAS PubMed
.
- D. Voiry, J. Yang and M. Chhowalla, Adv. Mater., 2016, 28, 6197–6206 CrossRef CAS PubMed
.
- Q. Fu, J. Han, X. Wang, P. Xu, T. Yao, J. Zhong, W. Zhong, S. Liu, T. Gao, Z. Zhang, L. Xu and B. Song, Adv. Mater., 2021, 33, 1907818 CrossRef CAS PubMed
.
- J. Yao, W. Huang, W. Fang, M. Kuang, N. Jia, H. Ren, D. Liu, C. Lv, C. Liu, J. Xu and Q. Yan, Small Methods, 2020, 4, 2000494 CrossRef CAS
.
- L. Lin, P. Sherrell, Y. Liu, W. Lei, S. Zhang, H. Zhang, G. G. Wallace and J. Chen, Adv. Energy Mater., 2020, 10, 1903870 CrossRef CAS
.
- X. Wang, Y. Zhang, J. Wu, Z. Zhang, Q. Liao, Z. Kang and Y. Zhang, Chem. Rev., 2022, 122, 1273–1348 CrossRef CAS PubMed
.
- Y. Cao, ACS Nano, 2021, 15, 11014–11039 CrossRef CAS PubMed
.
- G. Li, Z. Chen, Y. Li, D. Zhang, W. Yang, Y. Liu and L. Cao, ACS Nano, 2020, 14, 1707–1714 CrossRef CAS PubMed
.
- L. Wu, A. J. F. van Hoof, N. Y. Dzade, L. Gao, M.-I. Richard, H. Friedrich, N. H. De Leeuw, E. J. M. Hensen and J. P. Hofmann, Phys. Chem. Chem. Phys., 2019, 21, 6071–6079 RSC
.
- D. Voiry, H. Yamaguchi, J. Li, R. Silva, D. C. B. Alves, T. Fujita, M. Chen, T. Asefa, V. B. Shenoy, G. Eda and M. Chhowalla, Nat. Mater., 2013, 12, 850–855 CrossRef CAS PubMed
.
- A. Han, X. Zhou, X. Wang, S. Liu, Q. Xiong, Q. Zhang, L. Gu, Z. Zhuang, W. Zhang, F. Li, D. Wang, L.-J. Li and Y. Li, Nat. Commun., 2021, 12, 709 CrossRef CAS PubMed
.
- D. Er, H. Ye, N. C. Frey, H. Kumar, J. Lou and V. B. Shenoy, Nano Lett., 2018, 18, 3943–3949 CrossRef CAS PubMed
.
- Z. Wang, H.-H. Wu, Q. Li, F. Besenbacher, Y. Li, X. C. Zeng and M. Dong, Adv. Sci., 2020, 7, 1901382 CrossRef CAS PubMed
.
- J. K. Noerskov, T. Bligaard, A. Logadottir, J. R. Kitchin, J. G. Chen, S. Pandelov and U. Stimming, J. Electrochem. Soc., 2005, 152, J23 CrossRef
.
- Y. Jiao, Y. Zheng, K. Davey and S.-Z. Qiao, Nat. Energy, 2016, 1, 16130 CrossRef CAS
.
- J. Greeley, T. F. Jaramillo, J. Bonde, I. Chorkendorff and J. K. Nørskov, Nat. Mater., 2006, 5, 909–913 CrossRef CAS PubMed
.
- C. G. Morales-Guio, L.-A. Stern and X. Hu, Chem. Soc. Rev., 2014, 43, 6555–6569 RSC
.
- S. Anantharaj, S. Noda, V. R. Jothi, S. Yi, M. Driess and P. W. Menezes, Angew. Chem., Int. Ed., 2021, 60, 18981–19006 CrossRef CAS PubMed
.
- C. Hu, L. Zhang and J. Gong, Energy Environ. Sci., 2019, 12, 2620–2645 RSC
.
- A. N. Enyashin, L. Yadgarov, L. Houben, I. Popov, M. Weidenbach, R. Tenne, M. Bar-Sadan and G. Seifert, J. Phys. Chem. C, 2011, 115, 24586–24591 CrossRef CAS
.
- J. Zhu, L. Hu, P. Zhao, L. Y. S. Lee and K.-Y. Wong, Chem. Rev., 2020, 120, 851–918 CrossRef CAS PubMed
.
- J. Yang, A. R. Mohmad, Y. Wang, R. Fullon, X. Song, F. Zhao, I. Bozkurt, M. Augustin, E. J. G. Santos, H. S. Shin, W. Zhang, D. Voiry, H. Y. Jeong and M. Chhowalla, Nat. Mater., 2019, 18, 1309–1314 CrossRef CAS PubMed
.
- J. Deng, H. Li, J. Xiao, Y. Tu, D. Deng, H. Yang, H. Tian, J. Li, P. Ren and X. Bao, Energy Environ. Sci., 2015, 8, 1594–1601 RSC
.
- Y. Shi, Y. Zhou, D. R. Yang, W. X. Xu, C. Wang, F. B. Wang, J. J. Xu, X. H. Xia and H. Y. Chen, J. Am. Chem. Soc., 2017, 139, 15479–15485 CrossRef CAS PubMed
.
- Y. Shi, W. M. Huang, J. Li, Y. Zhou, Z. Q. Li, Y. C. Yin and X. H. Xia, Nat. Commun., 2020, 11, 4558 CrossRef CAS PubMed
.
- Y. Shi, Z. R. Ma, Y. Y. Xiao, Y. C. Yin, W. M. Huang, Z. C. Huang, Y. Z. Zheng, F. Y. Mu, R. Huang, G. Y. Shi, Y. Y. Sun, X. H. Xia and W. Chen, Nat. Commun., 2021, 12, 3021 CrossRef PubMed
.
- Y. Luo, S. Zhang, H. Pan, S. Xiao, Z. Guo, L. Tang, U. Khan, B. F. Ding, M. Li, Z. Cai, Y. Zhao, W. Lv, Q. Feng, X. Zou, J. Lin, H. M. Cheng and B. Liu, ACS Nano, 2020, 14, 767–776 CrossRef CAS PubMed
.
- Y. R. Zheng, P. Wu, M. R. Gao, X. L. Zhang, F. Y. Gao, H. X. Ju, R. Wu, Q. Gao, R. You, W. X. Huang, S. J. Liu, S. W. Hu, J. Zhu, Z. Li and S. H. Yu, Nat. Commun., 2018, 9, 2533 CrossRef PubMed
.
- H. Li, L. Wang, Y. Dai, Z. Pu, Z. Lao, Y. Chen, M. Wang, X. Zheng, J. Zhu, W. Zhang, R. Si, C. Ma and J. Zeng, Nat. Nanotechnol., 2018, 13, 411–417 CrossRef CAS PubMed
.
- Z. Luo, Y. Ouyang, H. Zhang, M. Xiao, J. Ge, Z. Jiang, J. Wang, D. Tang, X. Cao, C. Liu and W. Xing, Nat. Commun., 2018, 9, 2120 CrossRef PubMed
.
- Y. Zhou, J. Zhang, E. Song, J. Lin, J. Zhou, K. Suenaga, W. Zhou, Z. Liu, J. Liu, J. Lou and H. J. Fan, Nat. Commun., 2020, 11, 2253 CrossRef CAS PubMed
.
- X. Tian, D. S. Kim, S. Yang, C. J. Ciccarino, Y. Gong, Y. Yang, Y. Yang, B. Duschatko, Y. Yuan, P. M. Ajayan, J. C. Idrobo, P. Narang and J. Miao, Nat. Mater., 2020, 19, 867–873 CrossRef CAS PubMed
.
- C. Tsai, K. Chan, J. K. Nørskov and F. Abild-Pedersen, Catal. Sci. Technol., 2015, 5, 246–253 RSC
.
- X. Xu, H. Xu and D. Cheng, Nanoscale, 2019, 11, 20228–20237 RSC
.
- Z. Zheng, L. Yu, M. Gao, X. Chen, W. Zhou, C. Ma, L. Wu, J. Zhu, X. Meng, J. Hu, Y. Tu, S. Wu, J. Mao, Z. Tian and D. Deng, Nat. Commun., 2020, 11, 3315 CrossRef CAS PubMed
.
- M. Rajapakse, B. Karki, U. O. Abu, S. Pishgar, M. R. K. Musa, S. M. S. Riyadh, M. Yu, G. Sumanasekera and J. B. Jasinski, npj 2D Mater. Appl., 2021, 5, 1 CrossRef
.
- D. Rhodes, S. H. Chae, R. Ribeiro-Palau and J. Hone, Nat. Mater., 2019, 18, 541–549 CrossRef CAS PubMed
.
- Z. Lin, B. R. Carvalho, E. Kahn, R. Lv, R. Rao, H. Terrones, M. A. Pimenta and M. Terrones, 2D Mater., 2016, 3, 022002 CrossRef
.
- J. Berry, S. Ristic, S. Zhou, J. Park and D. J. Srolovitz, Nat. Commun., 2019, 10, 5210 CrossRef PubMed
.
- P. Liu, J. Zhu, J. Zhang, P. Xi, K. Tao, D. Gao and D. Xue, ACS Energy Lett., 2017, 2, 745–752 CrossRef CAS
.
- D. Gao, B. Xia, C. Zhu, Y. Du, P. Xi, D. Xue, J. Ding and J. Wang, J. Mater. Chem. A, 2018, 6, 510–515 RSC
.
- S. S. Chee, H. Jang, K. Lee and M. H. Ham, ACS Appl. Mater. Interfaces, 2020, 12, 31804–31809 CrossRef CAS PubMed
.
- W. Xiao, P. Liu, J. Zhang, W. Song, Y. P. Feng, D. Gao and J. Ding, Adv. Energy Mater., 2017, 7, 1602086 CrossRef
.
- Y. Zhao, W. Wang, C. Li and L. He, Sci. Rep., 2017, 7, 17088 CrossRef PubMed
.
- J. Peto, T. Ollar, P. Vancso, Z. I. Popov, G. Z. Magda, G. Dobrik, C. Hwang, P. B. Sorokin and L. Tapaszto, Nat. Chem., 2018, 10, 1246–1251 CrossRef CAS PubMed
.
- J. Xie, J. Zhang, S. Li, F. Grote, X. Zhang, H. Zhang, R. Wang, Y. Lei, B. Pan and Y. Xie, J. Am. Chem. Soc., 2013, 135, 17881–17888 CrossRef CAS PubMed
.
- Y. Zang, S. Niu, Y. Wu, X. Zheng, J. Cai, J. Ye, Y. Xie, Y. Liu, J. Zhou, J. Zhu, X. Liu, G. Wang and Y. Qian, Nat. Commun., 2019, 10, 1217 CrossRef PubMed
.
- H. Cai, Y. Guo, H. Gao and W. Guo, Nano Energy, 2019, 56, 33–39 CrossRef CAS
.
- A. Y. Lu, H. Zhu, J. Xiao, C. P. Chuu, Y. Han, M. H. Chiu, C. C. Cheng, C. W. Yang, K. H. Wei, Y. Yang, Y. Wang, D. Sokaras, D. Nordlund, P. Yang, D. A. Muller, M. Y. Chou, X. Zhang and L. J. Li, Nat. Nanotechnol., 2017, 12, 744–749 CrossRef CAS PubMed
.
- J. Zhang, S. Jia, I. Kholmanov, L. Dong, D. Er, W. Chen, H. Guo, Z. Jin, V. B. Shenoy, L. Shi and J. Lou, ACS Nano, 2017, 11, 8192–8198 CrossRef CAS PubMed
.
- X. Zhang, Q. Liao, Z. Kang, B. Liu, X. Liu, Y. Ou, J. Xiao, J. Du, Y. Liu, L. Gao, L. Gu, M. Hong, H. Yu, Z. Zhang, X. Duan and Y. Zhang, Adv. Mater., 2021, 33, e2007051 CrossRef PubMed
.
- S. K. Kaiser, Z. Chen, D. Faust Akl, S. Mitchell and J. Perez-Ramirez, Chem. Rev., 2020, 120, 11703–11809 CrossRef CAS PubMed
.
- G. Li, D. Zhang, Q. Qiao, Y. Yu, D. Peterson, A. Zafar, R. Kumar, S. Curtarolo, F. Hunte, S. Shannon, Y. Zhu, W. Yang and L. Cao, J. Am. Chem. Soc., 2016, 138, 16632–16638 CrossRef CAS PubMed
.
- J. Yang, Y. Wang, M. J. Lagos, V. Manichev, R. Fullon, X. Song, D. Voiry, S. Chakraborty, W. Zhang, P. E. Batson, L. Feldman, T. Gustafsson and M. Chhowalla, ACS Nano, 2019, 13, 9958–9964 CrossRef CAS PubMed
.
- H. Li, M. Du, M. J. Mleczko, A. L. Koh, Y. Nishi, E. Pop, A. J. Bard and X. Zheng, J. Am. Chem. Soc., 2016, 138, 5123–5129 CrossRef CAS PubMed
.
- L. Li, Z. Qin, L. Ries, S. Hong, T. Michel, J. Yang, C. Salameh, M. Bechelany, P. Miele, D. Kaplan, M. Chhowalla and D. Voiry, ACS Nano, 2019, 13, 6824–6834 CrossRef CAS PubMed
.
- C. Tsai, H. Li, S. Park, J. Park, H. S. Han, J. K. Norskov, X. Zheng and F. Abild-Pedersen, Nat. Commun., 2017, 8, 15113 CrossRef PubMed
.
- X. Wang, Y. Zhang, H. Si, Q. Zhang, J. Wu, L. Gao, X. Wei, Y. Sun, Q. Liao, Z. Zhang, K. Ammarah, L. Gu, Z. Kang and Y. Zhang, J. Am. Chem. Soc., 2020, 142, 4298–4308 CrossRef CAS PubMed
.
- H. Zhang and Y. Han, Phys. Rev. X, 2018, 8, 041023 CAS
.
- Y. Lee, N. Ling, D. Kim, M. Zhao, Y. A. Eshete, E. Kim, S. Cho and H. Yang, Adv. Funct. Mater., 2021, 32, 2105675 CrossRef
.
- J. Zhu, Z.-C. Wang, H. Dai, Q. Wang, R. Yang, H. Yu, M. Liao, J. Zhang, W. Chen, Z. Wei, N. Li, L. Du, D. Shi, W. Wang, L. Zhang, Y. Jiang and G. Zhang, Nat. Commun., 2019, 10, 1348 CrossRef PubMed
.
- T. Kosmala, H. Coy Diaz, H.-P. Komsa, Y. Ma, A. V. Krasheninnikov, M. Batzill and S. Agnoli, Adv. Energy Mater., 2018, 8, 1800031 CrossRef
.
- Q. Feng, Y. Zhu, J. Hong, M. Zhang, W. Duan, N. Mao, J. Wu, H. Xu, F. Dong, F. Lin, C. Jin, C. Wang, J. Zhang and L. Xie, Adv. Mater., 2014, 26, 2648–2653 CrossRef CAS PubMed
.
- J. H. Huang, K. Y. Deng, P. S. Liu, C. T. Wu, C. T. Chou, W. H. Chang, Y. J. Lee and T. H. Hou, Adv. Mater. Interfaces, 2017, 4, 1700157 CrossRef
.
- K. Kang, K. H. Lee, Y. Han, H. Gao, S. Xie, D. A. Muller and J. Park, Nature, 2017, 550, 229–233 CrossRef PubMed
.
- K. Kang, S. Xie, L. Huang, Y. Han, P. Y. Huang, K. F. Mak, C. J. Kim, D. Muller and J. Park, Nature, 2015, 520, 656–660 CrossRef CAS PubMed
.
- P. D. Tran, T. V. Tran, M. Orio, S. Torelli, Q. D. Truong, K. Nayuki, Y. Sasaki, S. Y. Chiam, R. Yi, I. Honma, J. Barber and V. Artero, Nat. Mater., 2016, 15, 640–646 CrossRef CAS PubMed
.
- L. Chang, Z. Sun and Y. H. Hu, Electrochem. Energy Rev., 2021, 4, 194–218 CrossRef CAS
.
- Y. Fang, X. Hu, W. Zhao, J. Pan, D. Wang, K. Bu, Y. Mao, S. Chu, P. Liu, T. Zhai and F. Huang, J. Am. Chem. Soc., 2019, 141, 790–793 CrossRef CAS PubMed
.
- J. Zhou, J. Lin, X. Huang, Y. Zhou, Y. Chen, J. Xia, H. Wang, Y. Xie, H. Yu, J. Lei, D. Wu, F. Liu, Q. Fu, Q. Zeng, C.-H. Hsu, C. Yang, L. Lu, T. Yu, Z. Shen, H. Lin, B. I. Yakobson, Q. Liu, K. Suenaga, G. Liu and Z. Liu, Nature, 2018, 556, 355–359 CrossRef CAS PubMed
.
- X. Chia, A. Y. Eng, A. Ambrosi, S. M. Tan and M. Pumera, Chem. Rev., 2015, 115, 11941–11966 CrossRef CAS PubMed
.
- M. Yan, X. Zhou, X. Pan, J. Wang, L. Xia, K. Yu, X. Liao, X. Xu, L. He and L. Mai, Nano Res., 2018, 11, 3205–3212 CrossRef CAS
.
- L. Liu, J. Wu, L. Wu, M. Ye, X. Liu, Q. Wang, S. Hou, P. Lu, L. Sun, J. Zheng, L. Xing, L. Gu, X. Jiang, L. Xie and L. Jiao, Nat. Mater., 2018, 17, 1108–1114 CrossRef CAS PubMed
.
- K. Chang, X. Hai, H. Pang, H. Zhang, L. Shi, G. Liu, H. Liu, G. Zhao, M. Li and J. Ye, Adv. Mater., 2016, 28, 10033–10041 CrossRef CAS PubMed
.
- Z. Lai, Q. He, T. H. Tran, D. V. M. Repaka, D. D. Zhou, Y. Sun, S. Xi, Y. Li, A. Chaturvedi, C. Tan, B. Chen, G. H. Nam, B. Li, C. Ling, W. Zhai, Z. Shi, D. Hu, V. Sharma, Z. Hu, Y. Chen, Z. Zhang, Y. Yu, X. Renshaw Wang, R. V. Ramanujan, Y. Ma, K. Hippalgaonkar and H. Zhang, Nat. Mater., 2021, 20, 1113–1120 CrossRef CAS PubMed
.
- N. H. Attanayake, A. C. Thenuwara, A. Patra, Y. V. Aulin, T. M. Tran, H. Chakraborty, E. Borguet, M. L. Klein, J. P. Perdew and D. R. Strongin, ACS Energy Lett., 2018, 3, 7–13 CrossRef CAS
.
- U. J. Kim, H. Lee, W. Lee, H. Y. Jeong, H. Kim, G. H. Han, H. S. Lee, Y. Park, Y. G. Roh, Y. H. Lee, E. Lee and S. W. Hwang, Adv. Mater., 2018, 30, e1706864 CrossRef PubMed
.
- J. Zhu, Z. Wang, H. Yu, N. Li, J. Zhang, J. Meng, M. Liao, J. Zhao, X. Lu, L. Du, R. Yang, D. Shi, Y. Jiang and G. Zhang, J. Am. Chem. Soc., 2017, 139, 10216–10219 CrossRef CAS PubMed
.
- M. A. Lukowski, A. S. Daniel, F. Meng, A. Forticaux, L. Li and S. Jin, J. Am. Chem. Soc., 2013, 135, 10274–10277 CrossRef CAS PubMed
.
- W. Ding, L. Hu, J. Dai, X. Tang, R. Wei, Z. Sheng, C. Liang, D. Shao, W. Song, Q. Liu, M. Chen, X. Zhu, S. Chou, X. Zhu, Q. Chen, Y. Sun and S. X. Dou, ACS Nano, 2019, 13, 1694–1702 CAS
.
- Y. Wang, J. Xiao, H. Zhu, Y. Li, Y. Alsaid, K. Y. Fong, Y. Zhou, S. Wang, W. Shi, Y. Wang, A. Zettl, E. J. Reed and X. Zhang, Nature, 2017, 550, 487–491 CrossRef CAS PubMed
.
- X.-L. Fan, Y. Yang, P. Xiao and W.-M. Lau, J. Mater. Chem. A, 2014, 2, 20545–20551 RSC
.
- G. Abbas, Y. Li, H. Wang, W.-X. Zhang, C. Wang and H. Zhang, Adv. Funct. Mater., 2020, 30, 2000878 CrossRef CAS
.
- P. Xiong, B. Sun, N. Sakai, R. Ma, T. Sasaki, S. Wang, J. Zhang and G. Wang, Adv. Mater., 2020, 32, 1902654 CrossRef CAS PubMed
.
- L. J. McGilly, A. Kerelsky, N. R. Finney, K. Shapovalov, E.-M. Shih, A. Ghiotto, Y. Zeng, S. L. Moore, W. Wu, Y. Bai, K. Watanabe, T. Taniguchi, M. Stengel, L. Zhou, J. Hone, X. Zhu, D. N. Basov, C. Dean, C. E. Dreyer and A. N. Pasupathy, Nat. Nanotechnol., 2020, 15, 580–584 CrossRef CAS PubMed
.
- S. Masubuchi, M. Morimoto, S. Morikawa, M. Onodera, Y. Asakawa, K. Watanabe, T. Taniguchi and T. Machida, Nat. Commun., 2018, 9, 1413 CrossRef PubMed
.
- Y. Liu, Y. Huang and X. Duan, Nature, 2019, 567, 323–333 CrossRef CAS PubMed
.
- K. Kang, K.-H. Lee, Y. Han, H. Gao, S. Xie, D. A. Muller and J. Park, Nature, 2017, 550, 229–233 CrossRef PubMed
.
- R. D. Westover, J. Ditto, M. Falmbigl, Z. L. Hay and D. C. Johnson, Chem. Mater., 2015, 27, 6411–6417 CrossRef CAS
.
- X. Duan, C. Wang, J. C. Shaw, R. Cheng, Y. Chen, H. Li, X. Wu, Y. Tang, Q. Zhang, A. Pan, J. Jiang, R. Yu, Y. Huang and X. Duan, Nat. Nanotechnol., 2014, 9, 1024–1030 CrossRef CAS PubMed
.
- Z. Jiang, W. Zhou, A. Hong, M. Guo, X. Luo and C. Yuan, ACS Energy Lett., 2019, 4, 2830–2835 CrossRef CAS
.
- C. Wang, Q. He, U. Halim, Y. Liu, E. Zhu, Z. Lin, H. Xiao, X. Duan, Z. Feng, R. Cheng, N. O. Weiss, G. Ye, Y. C. Huang, H. Wu, H. C. Cheng, I. Shakir, L. Liao, X. Chen, W. A. Goddard III, Y. Huang and X. Duan, Nature, 2018, 555, 231–236 CrossRef CAS PubMed
.
- M. S. Islam, M. Kim, X. Jin, S. M. Oh, N.-S. Lee, H. Kim and S.-J. Hwang, ACS Energy Lett., 2018, 3, 952–960 CrossRef CAS
.
- L. Xie, L. Wang, W. Zhao, S. Liu, W. Huang and Q. Zhao, Nat. Commun., 2021, 12, 5070 CrossRef CAS PubMed
.
- B. Zhao, Z. Wan, Y. Liu, J. Xu, X. Yang, D. Shen, Z. Zhang, C. Guo, Q. Qian, J. Li, R. Wu, Z. Lin, X. Yan, B. Li, Z. Zhang, H. Ma, B. Li, X. Chen, Y. Qiao, I. Shakir, Z. Almutairi, F. Wei, Y. Zhang, X. Pan, Y. Huang, Y. Ping, X. Duan and X. Duan, Nature, 2021, 591, 385–390 CrossRef CAS PubMed
.
- P. Xiong, X. Zhang, H. Wan, S. Wang, Y. Zhao, J. Zhang, D. Zhou, W. Gao, R. Ma, T. Sasaki and G. Wang, Nano Lett., 2019, 19, 4518–4526 CrossRef CAS PubMed
.
- D. R. Cummins, U. Martinez, A. Sherehiy, R. Kappera, A. Martinez-Garcia, R. K. Schulze, J. Jasinski, J. Zhang, R. K. Gupta, J. Lou, M. Chhowalla, G. Sumanasekera, A. D. Mohite, M. K. Sunkara and G. Gupta, Nat. Commun., 2016, 7, 11857 CrossRef CAS PubMed
.
- W. Zhang, X. Liao, X. Pan, M. Yan, Y. Li, X. Tian, Y. Zhao, L. Xu and L. Mai, Small, 2019, 15, 1900964 CrossRef PubMed
.
- J. Wang, M. Yan, K. Zhao, X. Liao, P. Wang, X. Pan, W. Yang and L. Mai, Adv. Mater., 2017, 29, 1604464 CrossRef PubMed
.
- C. V. Nguyen, Superlattices Microstruct., 2018, 116, 79–87 CrossRef CAS
.
- T. V. Vu, N. V. Hieu, L. T. P. Thao, N. N. Hieu, H. V. Phuc, H. D. Bui, M. Idrees, B. Amin, L. M. Duc and C. V. Nguyen, Phys. Chem. Chem. Phys., 2019, 21, 22140–22148 RSC
.
- F. L. Ling, T. W. Zhou, X. Q. Liu, W. Kang, W. Zeng, Y. X. Zhang, L. Fang, Y. Lu and M. Zhou, Nanotechnology, 2017, 29, 03LT01 CrossRef PubMed
.
- Y. Wang, S. Udyavara, M. Neurock and C. D. Frisbie, Nano Lett., 2019, 19, 6118–6123 CrossRef CAS PubMed
.
- C.-H. Kim and C. D. Frisbie, J. Am. Chem. Soc., 2016, 138, 7220–7223 CrossRef CAS PubMed
.
- C. F. Gorin, E. S. Beh and M. W. Kanan, J. Am. Chem. Soc., 2012, 134, 186–189 CrossRef CAS PubMed
.
- B. You, M. T. Tang, C. Tsai, F. Abild-Pedersen, X. Zheng and H. Li, Adv. Mater., 2019, 31, 1807001 CrossRef PubMed
.
- X. Meng, T. Pandey, J. Jeong, S. Fu, J. Yang, K. Chen, A. Singh, F. He, X. Xu, J. Zhou, W.-P. Hsieh, A. K. Singh, J.-F. Lin and Y. Wang, Phys. Rev. Lett., 2019, 122, 155901 CrossRef CAS PubMed
.
- P. Johari and V. B. Shenoy, ACS Nano, 2012, 6, 5449–5456 CrossRef CAS PubMed
.
- S. Bertolazzi, J. Brivio and A. Kis, ACS Nano, 2011, 5, 9703–9709 CrossRef CAS PubMed
.
- S. Schnur and A. Groß, Phys. Rev. B, 2010, 81, 033402 CrossRef
.
- Z.-J. Zhao, S. Liu, S. Zha, D. Cheng, F. Studt, G. Henkelman and J. Gong, Nat. Rev. Mater., 2019, 4, 792–804 CrossRef
.
- J. R. Kitchin, J. K. Nørskov, M. A. Barteau and J. G. Chen, J. Chem. Phys., 2004, 120, 10240–10246 CrossRef CAS PubMed
.
- M. Luo and S. Guo, Nat. Rev. Mater., 2017, 2, 17059 CrossRef CAS
.
- C. Tsai, K. Chan, J. K. Nørskov and F. Abild-Pedersen, J. Phys. Chem. Lett., 2014, 5, 3884–3889 CrossRef CAS PubMed
.
- B. Shang, X. Cui, L. Jiao, K. Qi, Y. Wang, J. Fan, Y. Yue, H. Wang, Q. Bao, X. Fan, S. Wei, W. Song, Z. Cheng, S. Guo and W. Zheng, Nano Lett., 2019, 19, 2758–2764 CrossRef CAS PubMed
.
- K. Qi, X. Cui, L. Gu, S. Yu, X. Fan, M. Luo, S. Xu, N. Li, L. Zheng, Q. Zhang, J. Ma, Y. Gong, F. Lv, K. Wang, H. Huang, W. Zhang, S. Guo, W. Zheng and P. Liu, Nat. Commun., 2019, 10, 5231 CrossRef PubMed
.
- X. Zheng, Y. Yang, B. Sun, R. Ning, J. Sui and W. Cai, ACS Appl. Nano Mater., 2021, 4, 3493–3499 CrossRef CAS
.
- Y. Tan, P. Liu, L. Chen, W. Cong, Y. Ito, J. Han, X. Guo, Z. Tang, T. Fujita, A. Hirata and M. W. Chen, Adv. Mater., 2014, 26, 8023–8028 CrossRef CAS PubMed
.
- K. Jiang, M. Luo, Z. Liu, M. Peng, D. Chen, Y.-R. Lu, T.-S. Chan, F. M. F. de Groot and Y. Tan, Nat. Commun., 2021, 12, 1687 CrossRef CAS PubMed
.
- H. Zhu, G. Gao, M. Du, J. Zhou, K. Wang, W. Wu, X. Chen, Y. Li, P. Ma, W. Dong, F. Duan, M. Chen, G. Wu, J. Wu, H. Yang and S. Guo, Adv. Mater., 2018, 30, 1707301 CrossRef PubMed
.
- J. H. Lee, W. S. Jang, S. W. Han and H. K. Baik, Langmuir, 2014, 30, 9866–9873 CrossRef CAS PubMed
.
- H. Li, A. W. Contryman, X. Qian, S. M. Ardakani, Y. Gong, X. Wang, J. M. Weisse, C. H. Lee, J. Zhao, P. M. Ajayan, J. Li, H. C. Manoharan and X. Zheng, Nat. Commun., 2015, 6, 7381 CrossRef CAS PubMed
.
- J. Yang, D. Voiry, S. J. Ahn, D. Kang, A. Y. Kim, M. Chhowalla and H. S. Shin, Angew. Chem., Int. Ed., 2013, 52, 13751–13754 CrossRef CAS PubMed
.
- Q. Yu, Y. Luo, S. Qiu, Q. Li, Z. Cai, Z. Zhang, J. Liu, C. Sun and B. Liu, ACS Nano, 2019, 13, 11874–11881 CrossRef CAS PubMed
.
- M. Zhou, S. Bao and A. J. Bard, J. Am. Chem. Soc., 2019, 141, 7327–7332 CrossRef CAS PubMed
.
- P. Wang and B. Wang, ACS Appl. Mater. Interfaces, 2021, 13, 59593–59617 CrossRef CAS PubMed
.
- P. Cao, J. Peng, S. Liu, Y. Cui, Y. Hu, B. Chen, J. Li and M. Zhai, Sci. Rep., 2017, 7, 16048 CrossRef PubMed
.
- Y. Yan, S. Xu, H. Li, N. C. S. Selvam, J. Y. Lee, H. Lee and P. J. Yoo, Chem. Eng. J., 2021, 405, 126728 CrossRef CAS
.
- S. Mao, Z. Wen, S. Ci, X. Guo, K. Ostrikov and J. Chen, Small, 2015, 11, 414–419 CrossRef CAS PubMed
.
- L. Najafi, S. Bellani, R. Oropesa-Nuñez, A. Ansaldo, M. Prato, A. E. Del Rio Castillo and F. Bonaccorso, Adv. Energy Mater., 2018, 8, 1703212 CrossRef
.
- J. Yang, Y. Liu, C. Shi, J. Zhu, X. Yang, S. Liu, L. Li, Z. Xu, C. Zhang and T. Liu, ACS Appl. Energy Mater., 2018, 1, 7035–7045 CrossRef CAS
.
- T. G. Kelly and J. G. Chen, Chem. Soc. Rev., 2012, 41, 8021–8034 RSC
.
- G. Li, D. Zhang, Y. Yu, S. Huang, W. Yang and L. Cao, J. Am. Chem. Soc., 2017, 139, 16194–16200 CrossRef CAS PubMed
.
- C. Zhang, Y. Chen, J.-K. Huang, X. Wu, L.-J. Li, W. Yao, J. Tersoff and C.-K. Shih, Nat. Commun., 2016, 7, 10349 CrossRef PubMed
.
- J. R. Waldrop, R. W. Grant, S. P. Kowalczyk and E. A. Kraut, J. Vac. Sci. Technol., A, 1985, 3, 835–841 CrossRef CAS
.
- G. Zhao, K. Rui, S. X. Dou and W. Sun, J. Mater. Chem. A, 2020, 8, 6393–6405 RSC
.
- G. Zhao, K. Rui, S. X. Dou and W. Sun, Adv. Funct. Mater., 2018, 28, 1803291 CrossRef
.
- G. Yang, Y. Jiao, H. Yan, Y. Xie, A. Wu, X. Dong, D. Guo, C. Tian and H. Fu, Adv. Mater., 2020, 32, 2000455 CrossRef CAS PubMed
.
- L. Tao, Y. Wang, Y. Zou, N. Zhang, Y. Zhang, Y. Wu, Y. Wang, R. Chen and S. Wang, Adv. Energy Mater., 2020, 10, 1901227 CrossRef CAS
.
- H. Zhang, A. W. Maijenburg, X. Li, S. L. Schweizer and R. B. Wehrspohn, Adv. Funct. Mater., 2020, 30, 2003261 CrossRef CAS
.
- J. Hu, C. Zhang, L. Jiang, H. Lin, Y. An, D. Zhou, M. K. H. Leung and S. Yang, Joule, 2017, 1, 383–393 CrossRef CAS
.
- L. Zhang, W. Zhang, M. Wang, H. Wang, J. Zang, W. Shen, X. Huang, D. Kong, Y. Tian, T. Xu, Y. Wang and X. Li, J. Colloid Interface Sci., 2022, 614, 267–276 CrossRef CAS PubMed
.
- N. P. Dileep, P. V. Sarma, R. Prasannachandran, V. Surendran and M. M. Shaijumon, ACS Appl. Nano Mater., 2021, 4, 7206–7212 CrossRef CAS
.
- G. Zhao, Y. Lin, K. Rui, Q. Zhou, Y. Chen, S. X. Dou and W. Sun, Nanoscale, 2018, 10, 19074–19081 RSC
.
- M.-R. Gao, J.-X. Liang, Y.-R. Zheng, Y.-F. Xu, J. Jiang, Q. Gao, J. Li and S.-H. Yu, Nat. Commun., 2015, 6, 5982 CrossRef CAS PubMed
.
- X. Ma, W. Chen, Q. Li, L. Xue and C. Peng, Energy Environ. Mater., 2021, 4, 658–663 CrossRef CAS
.
- C. Yang, L. Zhou, C. Wang, W. Duan, L. Zhang, F. Zhang, J. Zhang, Y. Zhen, L. Gao, F. Fu and Y. Liang, Appl. Catal., B, 2022, 304, 120993 CrossRef CAS
.
- D. Li, J. Lao, C. Jiang, Y. Shen, C. Luo, R. Qi, H. Lin, R. Huang, G. I. N. Waterhouse and H. Peng, J. Catal., 2020, 381, 590–598 CrossRef CAS
.
- Y. Jia, Z. Wang, X.-Q. Qiao, L. Huang, S. Gan, D. Hou, J. Zhao, C. Sun and D.-S. Li, Chem. Eng. J., 2021, 424, 130368 CrossRef CAS
.
- S. Chandrasekaran, N. Li, Y. Zhuang, L. Sui, Z. Xiao, D. Fan, V. Aravindan, C. Bowen, H. Lu and Y. Liu, Chem. Eng. J., 2022, 431, 134073 CrossRef CAS
.
- Y. Yin, S. Wei, L. Zhang, Z. Guo, H. Huang, S. Sai, J. Wu, Y. Xu, Y. Liu, L. Zheng, X. Fan and X. Cui, Chem. Res. Chin. Univ., 2020, 36, 1122–1127 CrossRef CAS
.
- Z. Cheng, Y. Xiao, W. Wu, X. Zhang, Q. Fu, Y. Zhao and L. Qu, ACS Nano, 2021, 15, 11417–11427 CrossRef CAS PubMed
.
- J. Li, W. Hong, C. Jian, Q. Cai, X. He and W. Liu, J. Mater. Chem. A, 2020, 8, 6692–6698 RSC
.
- G. Li, X. Deng, P. Chen, X. Wang, J. Ma, F. Liu and S.-F. Yin, Chem. Eng. J., 2022, 433, 134505 CrossRef CAS
.
- P. Wang, X. Zhang, J. Zhang, S. Wan, S. Guo, G. Lu, J. Yao and X. Huang, Nat. Commun., 2017, 8, 14580 CrossRef CAS PubMed
.
- B. Zhang, J. Liu, J. Wang, Y. Ruan, X. Ji, K. Xu, C. Chen, H. Wan, L. Miao and J. Jiang, Nano Energy, 2017, 37, 74–80 CrossRef CAS
.
- Y. Zhou, J. V. Pondick, J. L. Silva, J. M. Woods, D. J. Hynek, G. Matthews, X. Shen, Q. Feng, W. Liu, Z. Lu, Z. Liang, B. Brena, Z. Cai, M. Wu, L. Jiao, S. Hu, H. Wang, C. M. Araujo and J. J. Cha, Small, 2019, 15, 1900078 CrossRef PubMed
.
- L. Ge, H. Yuan, Y. Min, L. Li, S. Chen, L. Xu and W. A. Goddard, J. Phys. Chem. Lett., 2020, 11, 869–876 CrossRef CAS PubMed
.
- Y. Guo, Q. Chen, A. Nie, H. Yang, W. Wang, J. Su, S. Wang, Y. Liu, S. Wang, H. Li, Z. Liu and T. Zhai, ACS Nano, 2020, 14, 1635–1644 CrossRef CAS PubMed
.
- Y. He, Q. He, L. Wang, C. Zhu, P. Golani, A. D. Handoko, X. Yu, C. Gao, M. Ding, X. Wang, F. Liu, Q. Zeng, P. Yu, S. Guo, B. I. Yakobson, L. Wang, Z. W. Seh, Z. Zhang, M. Wu, Q. J. Wang, H. Zhang and Z. Liu, Nat. Mater., 2019, 18, 1098–1104 CrossRef CAS PubMed
.
- Y. He, L. Liu, C. Zhu, S. Guo, P. Golani, B. Koo, P. Tang, Z. Zhao, M. Xu, C. Zhu, P. Yu, X. Zhou, C. Gao, X. Wang, Z. Shi, L. Zheng, J. Yang, B. Shin, J. Arbiol, H. Duan, Y. Du, M. Heggen, R. E. Dunin-Borkowski, W. Guo, Q. J. Wang, Z. Zhang and Z. Liu, Nat. Catal., 2022, 5, 212–221 CrossRef CAS
.
Footnote |
† Hang Xia and Zude Shi contributed equally to this work. |
|
This journal is © The Royal Society of Chemistry 2022 |