Operation of proton exchange membrane (PEM) fuel cells using natural cellulose fiber membranes†
Received
19th June 2019
, Accepted 29th July 2019
First published on 30th July 2019
Abstract
Proton exchange membranes (PEMs), such as Nafion, are still one of the reasons for the high cost of PEMFCs. Among the alternatives, cellulose, a low cost and biodegradable material, has been considered in the form of its derivatives, such as cellulose acetate, bacterial cellulose or nanocellulose, as the PEM in fuel cells. However, its use involves more chemical synthesis steps. Here, we use low-cost 1.5-micron cellulose filter paper as the scaffold and prepare membranes for PEMFCs by simply impregnating it with a 10% Nafion solution or immersing it in resorcinol bis(diphenyl phosphate) (RDP). The prepared membranes are primarily composed of cellulose, with a cellulose to Nafion or RDP ratio of 2
:
1 or 1
:
1. The membrane electrode assemblies (MEAs) incorporating the as-prepared membranes exhibit a maximum output power of 23 mW cm−2 at 80 °C for the cellulose/Nafion membrane or 10 mW cm−2 at 60 °C for the cellulose/RDP membrane with only 0.1 mg cm−2 Pt loading on the anode and cathode, when operated in air. The stability results of the membranes after 100 hours of continuous operation indicate a loss of only 10% in power for the cellulose/Nafion membrane and 20% for the cellulose/RDP membrane. It is revealed by FTIR spectroscopy that both the Nafion polymer and RDP were hydrogen bonded to the cellulose fibers, facilitating proton conduction and stabilizing them against further dissolution.
1. Introduction
PEM fuel cells are efficient and clean alternative power sources, but their high cost impedes widespread commercialization and distribution in underdeveloped areas.1–6 Two major sources which contribute to the cost are the Nafion membrane and the platinum group metal (PGM) catalyst loading. Recently a great deal of effort has been invested in trying to find alternatives.7–11 PEM fuel cells have been proposed which operate with non-PGM catalyst cathodes.12–15 The technology for producing membranes which are as durable as and with comparable conductivity to Nafion is still under development, and it is not clear whether it comes with a significant reduction in cost.16–20 Furthermore, despite the complete replacement of PGMs at the cathode, the PGM loading at the anode is still relatively high.12,13
Cellulose, a naturally occurring polymer in plants, is abundant, biodegradable and inexpensive.21–24 Because of the strong intra- and inter-molecular hydrogen bonding network, it exhibits high mechanical strength and is also potentially useful for proton conduction.25–27 Bayer et al.28 recently reported that a membrane made from crystalline nanocellulose was incorporated into an MEA to produce a maximum power of 17 mW cm−2. This represents an important breakthrough, but the process of reducing cellulose to a nanocrystalline form adds a significant expense, and the power was obtained using a relatively high total loading of 0.6 mg cm−2 of the PGM catalyst. An alternative approach was reported by Jiang et al.29 who used bacterial cellulose, without further processing, and combined it with Nafion. In this case though, a higher power, 106 mW cm−2, was obtained with a total PGM loading exceeding 2 mg cm−2, operated in pure oxygen with a Nafion/cellulose ratio of 7
:
1. To reduce the cost due to the high amount of Nafion, Jiang et al. immersed bacterial cellulose into H3PO4 or phytic acid, achieving a maximum power output of 17.9 or 23 mW cm−2, respectively.
Here we report on an alternative method, which uses standard filter paper composed of natural cellulose fibers. Two methods were attempted. First, we show that the filter paper is easily impregnated with any aqueous polyelectrolyte polymer solution simply by vacuum suction. Since both the polymer and cellulose have charged groups, when hydrated, hydrogen bonding could occur and an ion conducting membrane results which is stable without cross linking. We demonstrate the efficacy of the membrane produced by this method using a 10% Nafion solution and show that it can generate 23 mW cm−2 of power with a total combined PGM loading of only 0.2 mg cm−2, while operating in air for at least 100 hours.
To further reduce the cost of the membrane we also attempted an easy method for directly functionalizing the cellulose, and hence obviating the need for polymer impregnation. Resorcinol bis(diphenyl phosphate) (RDP), is a well-known flame retardant,30–32 and has been shown to hydrogen bond to cellulose33 enriching the fibers in PO3–H functionalities (Fig. 1). RDP is available in an inexpensive liquid form which is easily incorporated into the cellulose membrane simply by immersion. This procedure produced a stable membrane which yielded a maximum output power of 10 mW cm−2 for at least 100 hours, using only a total of 0.2 mg cm−2 PGM. Comparing our results to others reported in the literature28,29,34–37 for utilizing cellulose in PEMFC membranes, this method is very simple to implement since the membranes are easily prepared in-house using standard filter paper, without additional cross linking or further processing. This technique has the advantage that it produces MEAs at a fraction of the cost and can directly be implemented into current PEMFCs without additional modifications or re-tooling.
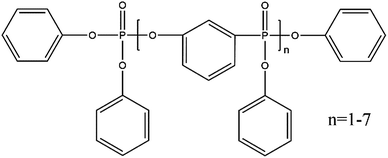 |
| Fig. 1 Chemical formula of RDP. | |
2. Experimental
2.1 Chemicals and materials
All chemicals were analytically pure and used without further purification. Cellulose filter paper, #610, with a 7.5 cm diameter and 200 μm thickness, and an average pore size of 1.5 μm, was purchased from Ahlstrom (Helsinki, Finland). Nafion 117 (183 μm), 10 wt% Nafion solution in pure distilled water and electrodes of 0.1 mg cm−2 Pt loading were purchased from FuelCellsEtc (College Station, Texas). RDP was obtained from ICL Industrial Products America (Tarrytown, NY). H2, N2 and air were purchased from Airgas (Radnor, PA).
2.2 Membrane fabrication
The cellulose/Nafion membranes were produced by placing the cellulose filters in a ceramic Büchner funnel of the same diameter, which in turn was fitted into an Erlenmeyer flask through a rubber stopper and using house (rough) vacuum. Five milliliters of Nafion were spread across the surface of the filter. The vacuum suction was maintained while the solution was spread to draw it immediately through the pores of the filter. The suction was then maintained for approximately 15 minutes or until no further solution could be observed to be drawn into the flask. The membranes were allowed to air dry overnight before assembling into the MEA. The cellulose/RDP membranes were prepared by immersing the cellulose membrane into RDP and then drying at 150 °C for 15 min.
2.3 Determination of the cellulose to Nafion or RDP ratio and membrane thickness
The cellulose filter papers were initially weighed prior to infiltration with Nafion solution or immersion in RDP, and then weighed again after drying and insertion into the MEA for testing. The thickness of different membranes was measured using a Vernier caliper (Tokyo, Japan).
2.4 Membrane characterization
The surface morphology of the membranes was imaged using scanning electron microscopy (Crossbeam340, ZEISS) for which the samples were prepared by air drying and sputter coating with a 4 nm thick layer of gold/palladium (70/30) (EM ACE600, Leica). For SEM imaging on the membrane cross sectional surface, samples were first embedded with EPO-FIX embedding resin, and then allowed to cure at room temperature overnight. The resins were trimmed using a Lecia FC-7 microtome at room temperature until the cross-sectional surface of membranes were exposed. An Energy Dispersive X-ray (EDX) detector was used to acquire the elemental distribution and content on the surface of the samples. Fourier transform infrared spectroscopy (FTIR) was performed using a PerkinElmer Frontier FT-IR spectrometer with an attenuated total reflection (ATR) accessory. Thirty-two scans were averaged to obtain each spectrum. Raman spectroscopy was performed using an InVia Renishaw system with a 514 nm laser source, 10 s collection time and 10 cycles. All spectral measurements were carried out at room temperature. The XRD results were obtained using a Rigaku Miniflex diffractometer, operating in the Bragg configuration using Cu Kα radiation (1.54 Å) with a typical scan range from 10° to 40° and using a scan rate of 1° min−1. The crystallinity of the membranes was calculated using Ic = (Itotal − Iamor)/Itotal, where Itotal is the intensity of the crystalline and amorphous parts (peak intensity of ∼22.7°) and Iamor is the intensity of the amorphous part (the minimum position between the 002 and the 101 peaks) of the sample.
2.5 Fuel cell testing
The single cell performance was evaluated on a fuel cell test station purchased from Fuel Cell Technologies, Inc. A commercial carbon cloth gas diffusion layer electrode with a Pt loading of 0.1 mg cm−2 was used as both the anode and cathode. The MEA was assembled by sandwiching the as-prepared cellulose filter membrane or Nafion 117 between the electrodes and distributing the pressure uniformly across the MEA. The testing was performed using 99.99% pure H2 with a flow rate of 50 sccm at the anode and 100 sccm of air at the cathode. The gases at both the cathode and anode were heated to five degrees above the operating temperature, to prevent condensation, and humidified with 100% relative humidity (RH). Testing was performed using an MEA having an active area of 5 cm2 at 30 °C, 60 °C, 80 °C and 90 °C.
The stability test of the cellulose/Nafion and cellulose/RDP membranes was performed by operating the test station at a constant current of 70 mA or 25 mA (corresponding to an initial voltage of 0.6 V), respectively. The voltage output was monitored for 100 hours of constant operation.
2.6 Proton conductivity measurement
The proton conductivity of the membrane was measured by using an electrochemical impedance analyzer (Bio-Logic, SP200) directly connected to the cell. H2 and N2 with 100 sccm and 100% RH were flowed through the anode and cathode side of the membrane, respectively, for 1 h at 80 °C before the measurement. The AC frequency was scanned from 5 MHz to 1 Hz at a voltage amplitude of 5 mV. The proton conductivity (S cm−1) was calculated using the following expression:
where L is the membrane thickness (cm), A is the cross-sectional area (cm2), and R is the membrane resistance derived from the high frequency intercept (Ω).
2.7 Ion exchange capacity measurement
Square pieces of each membrane were weighed before soaking for 24 h in 200 mL of 1 M H2SO4 solution, separately. Then the membrane pieces were washed thoroughly several times in order to remove excess acid. In order to replace the protons with sodium ions, the samples were placed in 50 mL of 1 M NaCl solution, heated to 40 °C, and equilibrated for at least 24 h. The remaining solution was then titrated with 0.01 N NaOH solution using pH as the indicator. The pH of 1 M NaCl solution measured using a pH meter (AB150, Accumet) was used as the standard. The IEC value (meq. g−1) was calculated using the following equation:
IEC = (VNaOH × NNaOH)/Wdry |
where VNaOH is the volume of NaOH used in the titration (mL), Wdry is the dry weight of the membrane in g, and NNaOH is the normality of NaOH solution used for titration.
3. Results and discussion
The MEA membranes prepared from the cellulose filters were first characterized with respect to their content of Nafion or RDP simply by weighing the membranes before and after suction or subsequent drying. The results are tabulated in Table 1, and represent the average of at least three membranes. From the table we can see that this method reliably produces cellulose rich membranes with a cellulose to Nafion or RDP ratio of 2.6 or 1.0, respectively, for the membranes. The thickness of the cellulose/Nafion and cellulose/RDP was measured to be 196 ± 3 um and 206 ± 2 um, respectively, while it is 198 ± 1 um for the pure cellulose filter. The crystallinity of different membranes was characterized by XRD (Fig. S1†), where the crystallinity of cellulose, cellulose/Nafion and cellulose/RDP is 90.6%, 89.5% and 77.1%, respectively.
Table 1 Weight of different types of cellulose membranes
Membranes |
Cellulose |
Cellulose/Nafion |
Cellulose/RDP |
Weight (mg) |
422 ± 6 |
583 ± 3 |
850 ± 4 |
Cellulose : Nafion (RDP) |
n/a |
2.6 : 1 |
1 : 1 |
3.1 Cellulose/nafion
The structure of the membrane surfaces was imaged using scanning electron microscopy. From Fig. 2a we can see that the bare cellulose membrane is composed of a mesh of cellulose fibers which gives the membrane its porosity. Fig. 2b shows the membrane impregnated with Nafion after vacuum suction of 10% Nafion solution and drying overnight in air. From the figure we can see that a coating appears to be covering the fibers giving them a smoother appearance and filling in the spaces between fibers. The presence of a Nafion film was confirmed using Raman spectroscopy, which was carried out for an untreated cellulose filter and a Nafion-treated cellulose filter, as shown in Fig. 2c. The Nafion-cellulose filter has many of the same peaks as the untreated cellulose, with the addition of four new prominent peaks, at 289 cm−1, 732 cm−1, 800 cm−1 and 1058 cm−1, corresponding to the CF2 twisting, CF2 symmetric stretching, CS stretching and SO3− symmetric stretching of the Nafion polymer.38 In order to determine the spatial distribution, EDX spectroscopy was carried out to examine the uniformity of the Nafion on cellulose (Fig. 3). Fluorine and sulfur are distinct elements from the sulfonic group and fluorocarbon backbone of the Nafion structure compared with cellulose. Their complete distribution throughout the image indicated that Nafion is evenly coated on the cellulose membrane.
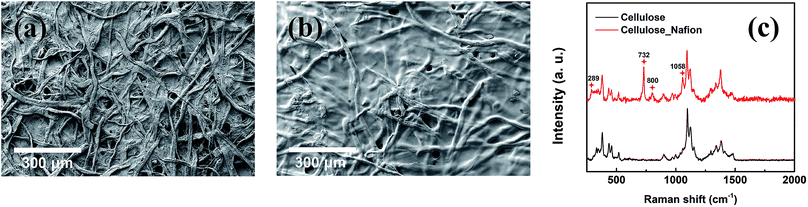 |
| Fig. 2 SEM images of (a) cellulose and (b) cellulose/Nafion membranes. (c) Raman spectra for cellulose and cellulose/Nafion membranes. | |
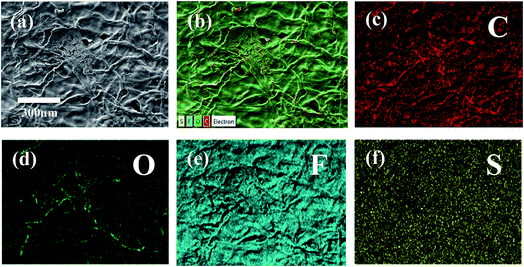 |
| Fig. 3 (a) SEM image, (b) layered elemental mapping and (c–f) corresponding carbon, oxygen, fluorine, and sulfur elemental mapping results of the cellulose/Nafion membrane. | |
The mechanical strength of the impregnated cellulose membranes was measured using DMA as a function of temperature and the data are shown in Fig. S2a.† From the figure we can see that addition of Nafion increases the storage modulus of cellulose, and the increase persists to temperatures above 100 °C. Tan delta is shown for the membranes in Fig. S2b,† where one can see a distinct peak at 105 °C in the Nafion impregnated membrane corresponding to the glass transition of Nafion. In Fig. S2d† we plot the thermal gravimetric data for the membranes, where we can see that no mass loss occurs until temperatures above 150 °C, indicating that the impregnated polymer is stable within the cellulose scaffold over the temperature range relevant for PEMFC operation.
3.2 Cellulose/RDP
To characterize and examine RDP on cellulose, FTIR spectroscopy was carried out and the results are shown in Fig. 4a. The spectrum of cellulose exhibits a peak in the 3100–3600 cm−1 region, which mainly originated from hydroxyl groups of cellulose. In the cellulose/RDP spectrum, we notice that this peak is enhanced and shifts from 3350 to 3340 cm−1, a lower wavenumber region compared to that of pure cellulose (Fig. 4b). This suggests the formation of hydrogen bonds,33,39 essential for proton conduction,40,41 between cellulose and RDP. The formation is mainly ascribed to the phosphoryl group (P
O) of RDP, as shown in Fig. 1, acting as a proton acceptor for hydrogen bonding. The same phenomenon was also observed for the cellulose/Nafion membrane (Fig. S3†). The uniformity of RDP on cellulose is confirmed from the EDX mapping results through the even distribution of the distinct phosphorous signal originating from RDP (Fig. S4†). A closer look at the mapping results (Fig. 5a–d) reveals that RDP preferentially accumulates along the cellulose fibers. This affinity of cellulose to RDP is consistent with the formation of hydrogen bonds between them. Furthermore, cross sectional SEM and EDX mapping was also carried out to gain more information on the inside of the membrane (Fig. 5e–h). The continuous and complementary distribution of RDP and the cellulose matrix further proves that RDP completely covers the abundant pores of the cellulose membrane, which is potentially beneficial for the proton conduction and the prevention of fuel crossover during the operation of PEMFCs.
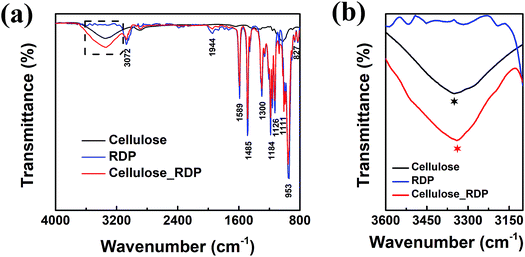 |
| Fig. 4 (a) FTIR and (b) magnified dashed square region in (a) of the cellulose membrane, RDP sample and cellulose/RDP membrane. | |
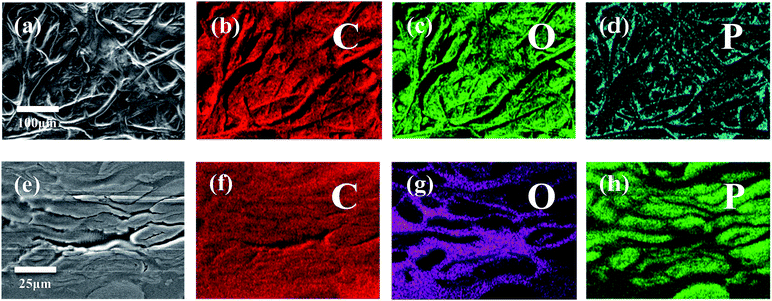 |
| Fig. 5 (a) SEM image and (b–d) corresponding carbon, oxygen, and phosphorus elemental mapping results of a typical cellulose/RDP membrane. (e) SEM image and (f–h) corresponding carbon, oxygen, and phosphorus elemental mapping results of the cross section of the cellulose/RDP membrane. | |
The mechanical strength of the cellulose/RDP membrane was also measured by DMA as a function of temperature (Fig. S2a†). From the figure we can see that addition of RDP decreases the modulus of cellulose, but it is still higher than that of the Nafion membrane (Fig. S2c†) at all temperatures and it increases with temperature. Tan delta (Fig. S2b†) shows that the peak for the RDP impregnated membrane, representing the glass transition temperature, is expected to be above 200 °C. From the thermal gravimetric analysis results for the membrane (Fig. S2d†), RDP is also stable within the cellulose scaffold over the temperature range relevant for PEMFC operation.
3.3 Fuel cell test
The assembled MEAs with the impregnated membranes were then inserted into the fuel cell test station and polarization curves were obtained as shown in Fig. 6. No power was generated with only the cellulose membrane. The addition of Nafion significantly improved the power density. Fig. 6a shows the polarization curves of the membrane impregnated with Nafion, where it can be seen that a broad plateau is reached at a maximum power density. The value at the plateau increases with temperature reaching a maximum of 23 mW cm−2 at 80 °C. When RDP was incorporated with cellulose, the maximum power output obtained was 10 mW cm−2 at 60 °C (Fig. 6b). The maximum power density is plotted as a function of temperature in Fig. 7a, where we can see that after a linear increase with temperature to 80 °C it starts to decrease at 90 °C for the cellulose/Nafion membrane while it peaked at 60 °C for the cellulose/RDP membrane. Even though the power output of the RDP impregnated membrane is lower for all temperatures compared with that of the Nafion one, the open circuit voltages of the cell at 60 and 80 °C were improved (Fig. 7b). The uniform surface may account for the prevention of hydrogen gas seeping through the membrane while permitting proton migration, hence producing a higher open circuit voltage. In Fig. S5† we plot the output voltage as a function of time, when the cell was operated in constant current mode, which achieves an initial voltage of 0.6 V. From Fig. 7c we see that the voltage decreases by only 60 mV, from 0.60 V to 0.54 V, namely 10%, over a period of 100 hours for the cellulose/Nafion membrane. This indicates that the Nafion is strongly adsorbed inside the membrane, even though it's soluble in water, and it is not eluted during operation. For the cellulose/RDP membrane, the voltage of the cell decreases to around 0.48 V, representing a decrease of 20%, after 100 hours of operation, providing a viable and cost-effective alternative in the operation of PEMFCs. The origin of the decrease is still unknown, but future measurements of the oxidative and hydrolytic stability will address this question.
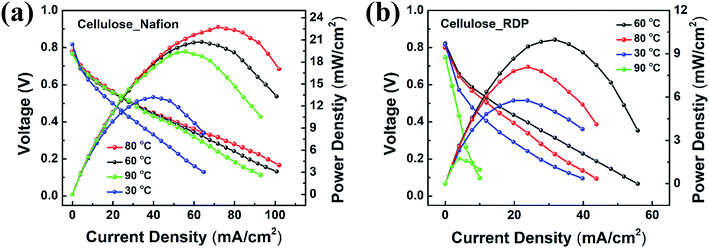 |
| Fig. 6 Polarization and power curves for (a) cellulose/Nafion and (b) cellulose/RDP membranes under various temperature conditions. | |
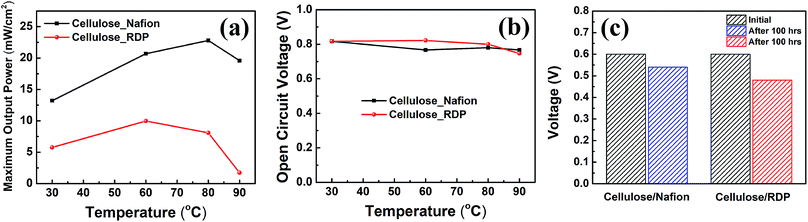 |
| Fig. 7 Comparison of (a) maximum output power and (b) open circuit voltage for cellulose/Nafion and cellulose/RDP membranes under various temperature conditions. (c) Voltage decrease of cellulose/Nafion and cellulose/RDP membranes for 100 hours of continuous operation. | |
Activation energy can be determined from the slopes of the Arrhenius plot and can provide valuable information about the possible proton conduction mechanism. Fig. 8a displays the Arrhenius plot of the conductivity of the membrane measured under variable operating temperatures. The increase of temperature from 30 °C to 90 °C increases the conductivity from 0.007 S cm−1 to 0.015 S cm−1 for the cellulose/Nafion membrane while it increases from 0.003 to 0.010 S cm−1 for the cellulose/RDP membrane. The calculated activation energy of 0.12 eV of the cellulose/Nafion membrane is similar to the value previously reported for Nafion,42,43 thus confirming that proton transport in the composite indeed occurs through Nafion where the Grotthuss mechanism is dominant at high humidity. The Grotthuss mechanism occurs via formation and cleavage of hydrogen bonds, which enable protons to hop between water molecules. The possible proton conduction pathways in the cellulose/RDP membrane are shown in Fig. 8b. Besides the Grotthuss and vehicle mechanisms, another possible proton transport mechanism is the proton-hopping along the oxygen groups of cellulose,28 promoted by the weakening of the O–H bond, as demonstrated by the red shift of the hydroxyl group peak in FTIR results. The higher activation energy of the cellulose/RDP membrane, 0.19 eV, may be due to the weaker hydrogen bonding network of cellulose/RDP compared with cellulose/Nafion considering the stronger electronegativity of the sulfonic acid group, resulting in slower Grotthuss-like proton transport.
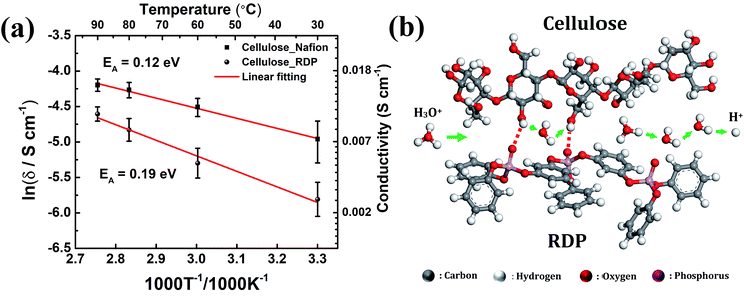 |
| Fig. 8 (a) Arrhenius plot of the conductivity of cellulose/Nafion and cellulose/RDP membranes with activation energy. The straight line is a linear fit to the Arrhenius model (error bars are for conductivity data points). (b) Schematic of the possible proton conduction mechanism in the cellulose/RDP membrane. | |
The ion exchange capacity was measured according to the protocol described in ref. 44. We found no change in pH for the remaining solution of the pure cellulose sample compared with the original NaCl solution, in agreement with the absence of power output or current in the PEMFC test. For the cellulose/Nafion membrane we obtained 0.15 meq. g−1 as compared to about 1.0 meq. g−1 for pure Nafion, which is in agreement with the approximately 8 fold increase in power observed for pure Nafion (Fig. S6†). The cellulose/RDP membrane had an ion exchange capacity of 0.04 meq. g−1 which is the amount of charge added to cellulose by RDP. Here again the power output relative to the cellulose/Nafion output approximately scales with the exchange capacity.
These results indicate that it is possible to construct an inexpensive membrane using cellulose fibers as a scaffold. Numerous polyelectrolyte polymers (oligomers) exist, including those with negative ion functionalities, which offer alternatives to Nafion, for membrane design. In addition to reducing the membrane cost, the anion polymers also permit the construction of fuel cells with non-PGM catalysts. The main drawback though is the limited amount of polymer that can be stabilized in the aqueous environment and the often-complex cross-linking chemistry that is involved. By forming strong hydrogen bonds with various charged moieties, the cellulose filters can overcome this limitation and effectively bind the polymer and stabilize it against dissolution, without interfering in the ion conduction process, hence forming a platform where a much larger set of polymers can be tested. Furthermore, in contrast to cellulose functionalized with nitric groups, such as nitrocellulose, phosphate functionalization does not appear to embrittle the fibers or make them susceptible to rapid combustion at elevated temperatures. Hence further experimentation with compounds having higher phosphorylation may be another promising approach.
4. Conclusions
In summary, we prepared membranes for PEMFCs by simply using 1.5-micron cellulose filter paper and impregnating it with a 10% Nafion solution or immersing the paper in RDP liquid. The process yielded membranes composed primarily of cellulose, with a cellulose to Nafion or RDP ratio of 2
:
1 or 1
:
1. FTIR spectroscopy indicated that both the Nafion polymer and the RDP were hydrogen bonded onto the cellulose fibers, stabilizing them against further dissolution and contributing to the charge exchange. Polarization curves obtained for the cellulose/Nafion membrane with only 0.1 mg cm−2 PGM loading at the anode and cathode, when operated in air, indicated a maximum power of 23 mW cm−2 at 80 °C. When RDP was incorporated in cellulose, a maximum power output of 10 mW cm−2 at 60 °C was achieved. The stability of the membranes was tested after 100 hours operation, and the results indicated a loss of only 10% in power for the cellulose/Nafion membrane and 20% for the cellulose/RDP membrane, demonstrating the cellulose fibers to be an effective scaffold for probing the ion conducting properties of charged polymers.
Conflicts of interest
There are no conflicts to declare.
Acknowledgements
The work at Stony Brook University was funded by the National Science Foundation, NSF-1344267 INSPIRE program. We acknowledge the access to the ThINC facility at the Advanced Energy Center, Stony Brook University. We also thank for ICL Industrial Products America (Tarrytown, NY) for providing the RDP.
References
- Y. M. Lee, Nat. Energy, 2016, 1, 16136 CrossRef.
- M. E. Scofield, Y. Zhou, S. Yue, L. Wang, D. Su, X. Tong, M. B. Vukmirovic, R. R. Adzic and S. S. Wong, ACS Catal., 2016, 6, 3895–3908 CrossRef CAS.
- M. M. Whiston, I. L. Azevedo, S. Litster, K. S. Whitefoot, C. Samaras and J. F. Whitacre, Proc. Natl. Acad. Sci. U. S. A., 2019, 116, 4899–4904 CrossRef CAS PubMed.
- W. Wang, Y. Yang, D. Huan, L. Wang, N. Shi, Y. Xie, C. Xia, R. Peng and Y. Lu, J. Mater. Chem. A, 2019, 7, 12538–12546 RSC.
- L. Wang, Y. Zhou, J. Timoshenko, S. Liu, Q. Qiao, K. Kisslinger, M. Cuiffo, Y.-C. Chuang, X. Zuo and Y. Xue, ACS Catal., 2019, 9, 1446–1456 CrossRef CAS.
- L. Wang, Y. Zhou, Y. Yang, A. Subramanian, K. Kisslinger, X. Zuo, Y.-C. Chuang, Y. Yin, C.-Y. Nam and M. H. Rafailovich, ACS Appl. Energy Mater., 2019, 2, 3479–3487 CrossRef CAS.
- M. E. Scofield, H. Liu and S. S. Wong, Chem. Soc. Rev., 2015, 44, 5836–5860 RSC.
- P. Chen, L.-K. Wang, G. Wang, M.-R. Gao, J. Ge, W.-J. Yuan, Y.-H. Shen, A.-J. Xie and S.-H. Yu, Energy Environ. Sci., 2014, 7, 4095–4103 RSC.
- G. Wang, W.-h. Wang, L.-K. Wang, W.-T. Yao, P.-F. Yao, W.-K. Zhu, P. Chen and Q.-S. Wu, J. Mater. Chem. A, 2015, 3, 17866–17873 RSC.
- M. J. Workman, A. Serov, L.-k. Tsui, P. Atanassov and K. Artyushkova, ACS Energy Lett., 2017, 2, 1489–1493 CrossRef CAS.
- W. Yuan, J. Li, L. Wang, P. Chen, A. Xie and Y. Shen, ACS Appl. Mater. Interfaces, 2014, 6, 21978–21985 CrossRef CAS PubMed.
- E. Proietti, F. Jaouen, M. Lefèvre, N. Larouche, J. Tian, J. Herranz and J.-P. Dodelet, Nat. Commun., 2011, 2, 416 CrossRef PubMed.
- A. Serov, K. Artyushkova and P. Atanassov, Adv. Energy Mater., 2014, 4, 1301735 CrossRef.
- Y. Shao, J. P. Dodelet, G. Wu and P. Zelenay, Adv. Mater., 2019, 1807615 CrossRef PubMed.
- K. Strickland, E. Miner, Q. Jia, U. Tylus, N. Ramaswamy, W. Liang, M.-T. Sougrati, F. Jaouen and S. Mukerjee, Nat. Commun., 2015, 6, 7343 CrossRef CAS PubMed.
- E. Bakangura, L. Wu, L. Ge, Z. Yang and T. Xu, Prog. Polym. Sci., 2016, 57, 103–152 CrossRef CAS.
- F. Bu, Y. Zhang, L. Hong, W. Zhao, D. Li, J. Li, H. Na and C. Zhao, J. Membr. Sci., 2018, 545, 167–175 CrossRef CAS.
- W. Gao, G. Wu, M. T. Janicke, D. A. Cullen, R. Mukundan, J. K. Baldwin, E. L. Brosha, C. Galande, P. M. Ajayan and K. L. More, Angew. Chem., Int. Ed., 2014, 53, 3588–3593 CrossRef CAS PubMed.
- K.-J. Peng, J.-Y. Lai and Y.-L. Liu, J. Membr. Sci., 2016, 514, 86–94 CrossRef CAS.
- P. Sun, Z. Li, S. Wang and X. Yin, J. Membr. Sci., 2018, 549, 660–669 CrossRef CAS.
- S. Wang, A. Lu and L. Zhang, Prog. Polym. Sci., 2016, 53, 169–206 CrossRef CAS.
- P. R. Sharma, R. Joshi, S. K. Sharma and B. S. Hsiao, Biomacromolecules, 2017, 18, 2333–2342 CrossRef CAS PubMed.
- P. R. Sharma, A. Chattopadhyay, S. K. Sharma, L. Geng, N. Amiralian, D. Martin and B. S. Hsiao, ACS Sustainable Chem. Eng., 2018, 6, 3279–3290 CrossRef CAS.
- P. R. Sharma, B. Zheng, S. K. Sharma, C. Zhan, R. Wang, S. R. Bhatia and B. S. Hsiao, ACS Appl. Nano Mater., 2018, 1, 3969–3980 CrossRef CAS.
- C. M. Lee, J. D. Kubicki, B. Fan, L. Zhong, M. C. Jarvis and S. H. Kim, J. Phys. Chem. B, 2015, 119, 15138–15149 CrossRef CAS PubMed.
- I. Smolarkiewicz, A. Rachocki, K. Pogorzelec-Glasser, R. Pankiewicz, P. Ławniczak, A. Łapiński, M. Jarek and J. Tritt-Goc, Electrochim. Acta, 2015, 155, 38–44 CrossRef CAS.
- L. Yue, Y. Xie, Y. Zheng, W. He, S. Guo, Y. Sun, T. Zhang and S. Liu, Compos. Sci. Technol., 2017, 145, 122–131 CrossRef CAS.
- T. Bayer, B. V. Cunning, R. Selyanchyn, M. Nishihara, S. Fujikawa, K. Sasaki and S. M. Lyth, Chem. Mater., 2016, 28, 4805–4814 CrossRef CAS.
- G.-p. Jiang, J. Zhang, J.-l. Qiao, Y.-m. Jiang, H. Zarrin, Z. Chen and F. Hong, J. Power Sources, 2015, 273, 697–706 CrossRef CAS.
- K. H. Pawlowski and B. Schartel, Polym. Int., 2007, 56, 1404–1414 CrossRef CAS.
- A. Toldy, P. Niedermann, Á. Pomázi, G. Marosi and B. Szolnoki, Materials, 2017, 10, 467 CrossRef PubMed.
- H. Vothi, S. Halm, C. Nguyen, I. Bae and J. Kim, Fire Mater., 2014, 38, 36–45 CrossRef CAS.
- Y. Guo, S. He, X. Zuo, Y. Xue, Z. Chen, C.-C. Chang, E. Weil and M. Rafailovich, Polym. Degrad. Stab., 2017, 144, 24–32 CrossRef CAS.
- T. D. Gadim, C. Vilela, F. J. Loureiro, A. J. Silvestre, C. S. Freire and F. M. Figueiredo, Ind. Crops Prod., 2016, 93, 212–218 CrossRef CAS.
- M. M. Hasani-Sadrabadi, E. Dashtimoghadam, R. Nasseri, A. Karkhaneh, F. S. Majedi, N. Mokarram, P. Renaud and K. I. Jacob, J. Mater. Chem. A, 2014, 2, 11334–11340 RSC.
- G. Jiang, J. Qiao and F. Hong, Int. J. Hydrogen Energy, 2012, 37, 9182–9192 CrossRef CAS.
- C. Lin, S. Liang, S. Chen and J. Lai, J. Power Sources, 2013, 232, 297–305 CrossRef CAS.
- J. L. Bribes, M. El Boukari and J. Maillols, J. Raman Spectrosc., 1991, 22, 275–279 CrossRef CAS.
- J. Joseph and E. D. Jemmis, J. Am. Chem. Soc., 2007, 129, 4620–4632 CrossRef CAS PubMed.
- J.-P. Melchior, G. Majer and K.-D. Kreuer, Phys. Chem. Chem. Phys., 2017, 19, 601–612 RSC.
- J. F. Nagle and S. Tristram-Nagle, J. Membr. Biol., 1983, 74, 1–14 CrossRef CAS PubMed.
- D. K. Paul, R. McCreery and K. Karan, J. Electrochem. Soc., 2014, 161, F1395–F1402 CrossRef CAS.
- Y. Yin, Z. Li, X. Yang, L. Cao, C. Wang, B. Zhang, H. Wu and Z. Jiang, J. Power Sources, 2016, 332, 265–273 CrossRef CAS.
- P. Kumar, K. Dutta, S. Das and P. P. Kundu, Appl. Energy, 2014, 123, 66–74 CrossRef CAS.
Footnote |
† Electronic supplementary information (ESI) available. See DOI: 10.1039/c9se00381a |
|
This journal is © The Royal Society of Chemistry 2019 |