DOI:
10.1039/D3MA00513E
(Paper)
Mater. Adv., 2023,
4, 4921-4928
Dicyano-functionalized indium framework as a heterogeneous catalyst for CO2 fixation in the absence of solvent and co-catalyst†
Received
8th August 2023
, Accepted 31st August 2023
First published on 4th September 2023
Abstract
Catalytic carbon dioxide (CO2) transformation into valuable products is of great interest, especially the development of innovative methods for CO2 fixation reactions. In this paper, we report the porous cyanide-functionalized MIL-68(In) metal–organic framework as a novel Lewis acid–base bifunctional catalyst. The MIL-68(In) framework was modified with different cyanide functional groups, such as 1,3-phenylene diacetonitrile and malononitrile, for the catalytic CO2 fixation reaction into cyclic carbonates. The properties of the synthesized catalysts were fully characterized using different techniques, including PXRD, FTIR, N2 adsorption, BET, SEM, XPS, TGA, NH3-TPD, and CO2-TPD. Under the optimized conditions (30 mg catalyst, 1 MPa CO2 pressure, 20 mmol epichlorohydrin, 100 °C, 10 h), MIL-68(In) functionalized with 1,3-phenylene diacetonitrile was found to afford a remarkable heterogeneous catalyst with selectivity (100%) and high conversion (99%) for the coupling reaction between CO2 and the epoxide without any co-catalyst or solvent. Moreover, the functionalized MIL-68(In) MOF also revealed applicability to other large epoxides. The enhanced activity of functionalized MIL-68(In) results from the collaboration between the unsaturated Lewis acidic indium centers and cyanide functional groups as nucleophilic sites. Furthermore, the reusability tests demonstrated that the modified MIL-68(In) was easily recycled by filtration and reusable for at least five runs with no loss in catalytic ability.
1. Introduction
Nowadays, the increasing carbon dioxide (CO2) concentration in the atmosphere resulting from fossil fuels has received much attention from the viewpoint of greenhouse gas emissions and atmospheric temperature in the 21st century.1 Therefore, it is necessary to develop effective technologies to transform CO2 from a renewable raw material (a non-toxic, and non-flammable abundant gas) into useful chemicals, aiding in greenhouse gas reduction.2–4 In particular, the coupling reaction of carbon dioxide with an epoxide is highlighted as a highly appreciated economic reaction, and the cyclic carbonate products are widely used as pharmaceutical intermediates, precursors for polycarbonates, and other polymeric materials.5–7 Because of the high thermodynamic stability of the cycloaddition reaction, the promotion of CO2–epoxide couplings requires effective catalysts and high temperature or pressure conditions.8–10 The natural solubility of homogeneous catalysts hinders the particular functions of many advanced catalysts for CO2 transformation.6 So, the utilization of heterogeneous catalysts is imperative due to their simple separation method, sample treatment, and reusability.11
Hence, catalytic systems incorporating acidic sites for epoxide electrophilic activity and basic sites as nucleophilic species are of interest for the CO2-to-epoxide coupling reaction.12
In general, metal–organic frameworks (MOFs) have attracted lots of attention in the field of catalysis due to their large specific surface areas, high CO2 adsorption capacities, tailorable porosity, diverse compositions, high catalytic performance, and controllable open channels and pores.13–16 Many MOFs have been developed for CO2-to-epoxide couplings because MOFs can provide Lewis acid–base sites, which are noted for the facilitation of CO2 cycloaddition reactions.17–21 Moreover, a co-catalyst or additives containing halide anions are frequently used in CO2 chemical conversion.22 In addition, the development of metal–organic frameworks that can be used as catalysts in CO2 cycloaddition reactions with no need for a co-catalyst or additives has gained tremendous attention.
It has been shown that indium, a metal with accessible high-level p-orbitals, is capable of receiving electrons in different Lewis acid reactions.23 Owing to this unique electronic configuration, it is reported that indium MOFs have been synthesized with a high surface area and found to possess a porous structure of high chemical and thermal stability. The use of some of them, such as CPM-23-In, CPM-200-In and In-MOF, as catalysts for selective and high CO2 uptake in the chemical fixation of CO2 with epoxides has also been demonstrated previously.23–26
The purpose of the work presented herein was to eliminate the addition of a co-catalyst, and instead incorporate nucleophilic functional groups into the structure to play the co-catalyst role for the CO2 fixation reaction. The application of different functional groups in stable MOF structures for the special properties that arise from this modification has previously been investigated.27–32
With these considerations in mind and the importance of modified MOFs, we used cyanide groups as a co-catalyst to design a novel cyanide-functionalized MIL-68(In) structure that is assembled from InO4(OH)2 octahedral units linked to each other with terephthalate ligands. Volkringer and coworkers found that MIL-68(In) displays large surface area and high thermal stability.33 MIL-68(In) showed two kinds of triangular and hexagonal channels (with pore diameters of 6.0 and 16.0 Å, respectively). In addition, the structure of MIL-68(In) leads to the arrangement of the functional groups within the pores in the modified MIL-68(In).30,34–36 Thus, the latter strategy was the synthesis of a CN-functionalized porous MIL-68(In) framework. We designed and synthesized two cyanide-functionalized MIL-68(In) MOFs with acidic and basic sites in the framework, which were then used in the catalytic CO2 transformation reaction (Scheme 1). The two new cyanide-modified MIL-68(In) MOFs were prepared by hydrothermal methods and identified by various techniques, such as PXRD, FTIR, SEM, TGA, BET, XPS, and N2 and CO2 adsorption measurements. The catalytic activity of the cyanide-modified frameworks were tested under low pressure and temperature (mild conditions) in the absence of a co-catalyst or solvent. The effects of various reaction parameters, activities over different substrates, and catalyst recyclability were investigated and are reported below. The results show that modification with cyanide groups causes a great improvement in the conversion of epoxides and CO2 to cyclic carbonates.
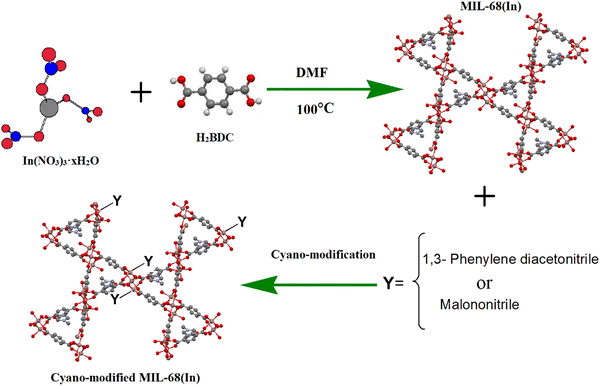 |
| Scheme 1 Schematic representation of 1,3-phenylene diacetonitrile MIL-68(In)–PhDA and MIL-68(In)–malo synthesis. | |
2. Experimental
2.1. Materials
All solvents and chemicals employed in this work are described in the ESI.†
2.2. Preparation of catalysts
2.2.1. Synthesis of MIL-68(In).
The synthesis of MIL-68(In) was done based on the previously reported method.33 In a typical process, In(NO3)3·xH2O (408.2 mg, 1.05 mmol) and 1,4-benzenedicarboxylic acid (H2BDC) (200 mg, 1.20 mmol) were added to N,N-dimethylformamide (DMF) (200 mg, 1.20 mmol). The mixture was sealed in a 15 ml Teflon-lined stainless steel autoclave and heated for 48 h at 100 °C in an oven. The obtained white precipitate consisted of needle-like crystallites that were washed with DMF and immersed in absolute ethanol for several days and the solvent was refreshed once a day to remove the guest molecules in the pores. Finally, the product was filtered and dried in a vacuum oven at 50 °C overnight.
2.2.2. Synthesis of MIL-68(In)–PhDA.
MIL-68(In)–PhDA was prepared by the post-synthetic process. Typically, 0.52 g of activated MIL-68(In) was stirred into 25 ml of toluene and suspended in 1,3-phenylene diacetonitrile (PhDA) (0.5 g, 3.20 mmol) and dichloromethane (CH2Cl2) (25 ml) and then refluxed for 20 h. Finally, the filtered precipitate was collected and dried in a vacuum oven at 90 °C for 4 h.
2.2.3. Synthesis of MIL-68(In)–malo.
This catalyst was synthesized by a similar protocol, except for the use of 0.15 g (2.27 mmol) malononitrile (malo) instead of 1,3-phenylene diacetonitrile and all other conditions were kept unaltered.
2.3. Catalytic reaction: CO2 fixation
In order to eliminate the solvent molecules, the MOF catalysts were activated at 120 °C for 12 h. In a typical run, an epoxide (20 mmol) and 30 mg of sample were put into a 25 ml autoclave. Then, the reactor was pressurized with CO2 up to 1 MPa when the system attained the point reaction temperature (100 °C for 10 h). After the end of the reaction, the reactor was slowly cooled down to room temperature and degassed. The products were extracted and analyzed by gas chromatography (GC).
3. Results and discussion
3.1. Characterization
The powder X-ray diffraction (PXRD) patterns of the synthesized MIL-68(In), MIL-68(In)–PhDA, and MIL-68(In)–malo frameworks are presented in Fig. S1 (ESI†). The diffraction peaks of the samples are similar and no differences can be observed owing to the same crystalline structures. This further verifies that modification of the framework with cyanide functional groups does not disrupt the structural integrity of MIL-68(In) and the basic diffraction peaks remain intact upon CN-functionalization.
The FTIR spectra of the synthesized MIL-68(In), MIL-68(In)–PhDA, and MIL-68(In)–malo frameworks are shown in Fig. S2 (ESI†). The typical absorption bands in the range of 1400–1700 cm−1 are related to the symmetric and asymmetric stretching vibrational modes of the carboxylate groups.37 The appearance of a cyanide (–CN) peak, related to the modified framework, becomes clear at around 2253 cm−1 and confirms the introduction of the cyanide groups into the framework.38 The observed broad band in the region of 2900–3600 cm−1 can be assigned to the stretching vibration of H2O molecules coordinated with the metal center.
To characterize the textural morphology of the as-prepared frameworks, scanning electron microscopy (SEM) analysis was performed. As shown in Fig. S3 (ESI†), all of the samples reveal needlelike structures and the morphology is preserved even after modification with cyanide groups.
The thermogravimetric analysis (TGA) was conducted under a nitrogen atmosphere and the results are shown in Fig. S4 (ESI†). The TGA curve of MIL-68(In) presents two weight losses. The first weight loss below 110 °C is due to the removal of trapped solvent molecules. The framework is stable at nearly 450 °C, then decomposes. TGA analysis was also performed on the modified frameworks. All of the modified structures are stable up to 450 °C. The first weight loss has disappeared due to the removal of trapped solvent in the modified frameworks. This obviously shows the effective elimination of the guest molecules and the successful functionalization of the frameworks.30
To verify the interaction environment of the elements and cyanide functional groups in modified Mil-68(In), X-ray photoelectron spectroscopy (XPS) analysis was performed and the results are presented in Fig. 1. As seen in Fig. 1(a), the survey spectrum of MIL-68(In)–PhDA clearly shows the main peaks of O, In, N, and C elements. In Fig. 1(b), the In 3d spectrum shows two types of peaks, In 3d5/2 (444.6 eV) and In 3d3/2 (450.4 eV).39 The two peaks for In 3d5/2 and In 3d3/2 could be resolved into satellite peaks at binding energies of 442.8 and 449.4 eV, respectively, which can be assigned to the 1,3-phenylene diacetonitrile functional groups in the modified MIL-68(In).40 As can be seen from Fig. 1(c), two types of N (denoted as N1 and N2) appeared at 399.8 (CN–C–) and 401.1 eV (C–N–In).41
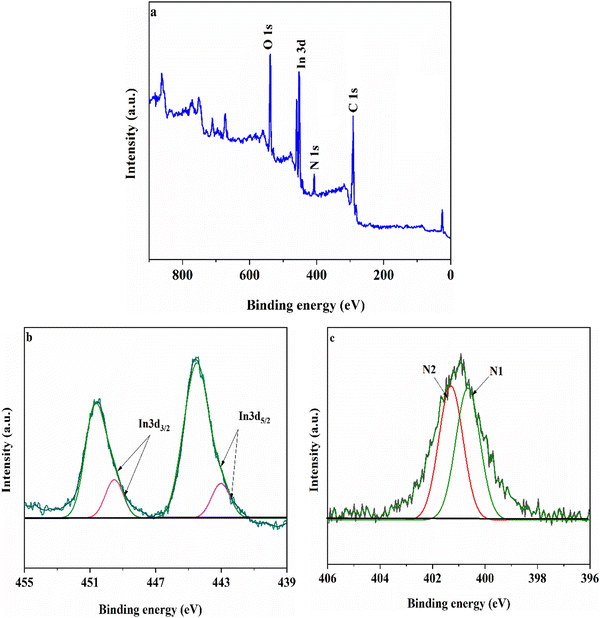 |
| Fig. 1 Typical XPS survey spectra of MIL-68(In)–PhDA (a), In 3d spectra (b) and N 1s spectra (c) of MIL-68(In)–PhDA. | |
N2 adsorption–desorption isotherms of the functionalized compounds are depicted in Fig. 2, and all of the compounds reveal a type I isotherm characteristic of the microporous nature. A Brunauer–Emmett–Teller (BET) specific surface area of 1058 m2 g−1 and pore volume of 0.59 cm3 g−1 were found for MIL-68(In), and the corresponding values for the other modified samples are shown in Table 1. The decrease in the BET surface area and pore volume supports the conclusion that the frameworks have been functionalized.
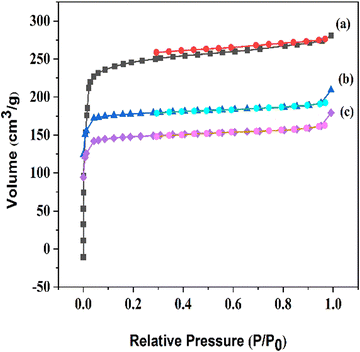 |
| Fig. 2 N2 adsorption–desorption isotherms of (a) MIL-68(In), (b) MIL-68(In)–malo, and (c) MIL-68(In)–PhDA. | |
Table 1 Textural properties of MIL-68(In), MIL-68(In)–malo, and MIL-68(In)–PhDA
Sample |
S
BET (m2 g−1) |
Pore volume (cm3 g−1) |
MIL-68(In) |
1058 |
0.59 |
MIL-68(In)–malo |
814 |
0.37 |
MIL-68(In)–PhDA |
623 |
0.29 |
To evaluate the CO2 adsorption properties of the cyanide-modified structures, CO2 measurements were performed (Fig. 3). The CO2 sorption capacity of MIL-68(In) is 35 cm3 g−1 and this increased up to 48 cm3 g−1 for MIL-68(In)–malo and 51 cm3 g−1 for MIL-68(In)–PhDA. The incorporation of the cyanide functional groups into the framework are responsible for the increase in the CO2 uptake capacity. Therefore, the high affinity of the functionalized structure for CO2 adsorption affirms the modification of the framework.
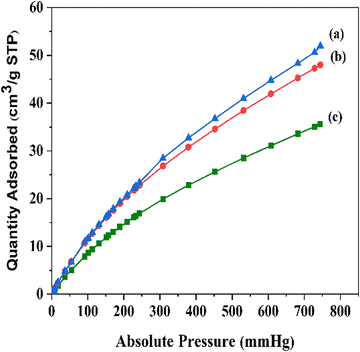 |
| Fig. 3 CO2 sorption isotherms of (a) MIL-68(In)–PhDA, (b) MIL-68(In)–malo, and (c) MIL-68(In) at 298 K. | |
To investigate the acid–base characteristics of the MOF materials, we used temperature programmed desorption (TPD) analysis. The NH3 desorption peak profile (Fig. 4a) at about 300 °C might be related to uncoordinated Lewis acid sites. Furthermore, in the case of the CO2-TPD results (Fig. 4b) for MIL-68(In)–PhDA, the peaks at about 320 °C are attributed to the strong basic sites of the cyanide functional groups in the structure.
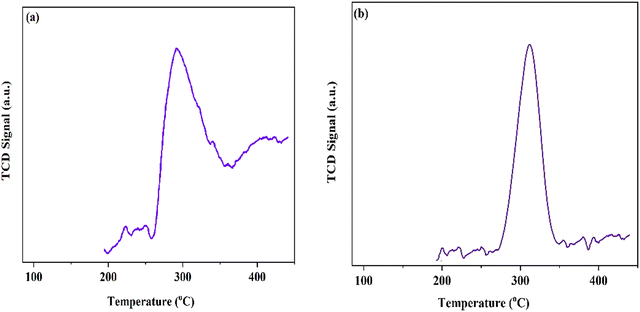 |
| Fig. 4 (a) NH3 and (b) CO2 temperature programmed desorption plots of MIL-68(In)–PhDA. | |
The C, H, and N contents of various samples were measured to determine the amount of each element and the catalyst loadings. The values of cyanide loaded in the modified samples were 22.59% (MIL-68(In)–PhDA) and 8.89% (MIL-68(In)–malo) (Table S1, ESI†), and this confirmed the modification of the structure with cyanide groups.
3.2. Catalytic activity in the CO2 fixation reaction
In order to investigate the catalytic ability of MIL-68(In), MIL-68(In)–PhDA, and MI-68(In)–malo in the CO2 fixation reaction, epichlorohydrin (ECH) epoxide was applied as the model substrate. Additionally, we clarified the role of the cyanide functional group in the modified materials as co-catalyst. The data are shown in Table 2 and evaluated against a blank experiment that was performed in the absence of a catalyst. According to the results, the reaction did not give any ECH conversion without the catalyst (Table 2, entry 1). Moreover, using the pristine MOF (MIL-68(In)) or 1,3-phenylene diacetonitrile (PhDA) alone do not lead to significant enhancement of the cycloaddition reaction (Table 2, entries 2 and 3). The conversion of catalyst was clearly enhanced by cyanide functionalization (Table 2, entry 5). Also, the physical combination of MIL-68(In) with 1,3-phenylene diacetonitrile slightly increases the conversion achieved (27%). It can be seen that modification of MIL-68(In) with cyanide functional groups improves the performance of the catalyst without adding solvent or a co-catalyst.
Table 2 The catalytic activity of different catalysts
Entry |
Catalyst |
Conv. (%) |
Reaction conditions: catalyst (30 mg), ECH (20 mmol), CO2 (1 MPa), 100 °C, 10 h. |
1 |
Blank |
— |
2 |
MIL-68(In) |
15 |
3 |
1,3-Phenylene diacetonitrile |
7 |
4 |
MIL-68(In)/PhDA |
27 |
5 |
MIL-68(In)–PhDA |
99 |
The values of CO2 pressure, reaction temperature, catalyst amount, and reaction time were optimized for the catalytic performance. The results are shown in Fig. S5–S8 (ESI†), respectively. It can be seen that the conversion of ECH to epichlorohydrin carbonate (ECHC) was 99% over MIL-68(In)–PhDA catalyst under optimal conditions.
3.3. Catalytic performance of the prepared compounds
The catalytic ability of modified catalysts (MIL-68(In)–PhDA as 1 and MIL-68(In)–malo as 2) was tested for the chemical fixation reaction. Based on the successful catalytic performance of MIL-68(In)–PhDA in the conversion of ECH, cycloaddition reactions were studied under optimized conditions using different aliphatic and aromatic epoxides, and the data are shown in Table 3. All modified catalysts (1 and 2) can efficiently convert propylene oxide (PO) to its carbonate and epoxy butane (EB) to butylene carbonate with 100% selectivity (Table 3, entries 2 and 3) due to the small size of the epoxide that can penetrate the holes and access acidic and basic sites in the functionalized catalysts. In the case of bulky epoxides, though the previously reported low conversion42 is due to the high steric hindrance of the epoxide, significant conversions with high selectivity into the related carbonates are obtained for styrene oxide (SO) and cyclohexene oxide (CHO) (Table 3, entries 5 and 7). In addition, even with an increase in the molecular size of the epoxides, such as allyl glycidyl ether (AGE) and phenyl glycidyl ether (PGE), notable conversion was afforded (Table 3, entries 4 and 6).
Table 3 Synthesis of cyclic carbonates from various epoxides
Entry |
Epoxide |
Product |
Catalyst |
Conv.a (%) |
TONb |
TOFc (h−1) |
Catalyst l: MIL-68(In)–PhDA and catalyst 2: MIL-68(In)–malo. Reaction conditions: catalyst (30 mg, 0.04 mmol cyanide groups), epoxides (20 mmol), CO2 (1 MPa), 100 °C, 10 h. TON (turnover number) is the mmol of product/mmol active cyanide site. TOF (turnover frequency) is the turnover number/reaction time. |
1 |
|
|
1
|
99 |
495 |
49.5 |
2
|
97 |
485 |
48.5 |
2 |
|
|
1
|
94 |
470 |
47 |
2
|
83 |
415 |
41.5 |
3 |
|
|
1
|
88 |
440 |
44 |
2
|
74 |
370 |
37 |
4 |
|
|
1
|
71 |
355 |
35.5 |
2
|
63 |
315 |
31.5 |
5 |
|
|
1
|
74 |
370 |
37 |
2
|
70 |
350 |
35 |
6 |
|
|
1
|
72 |
360 |
36 |
2
|
68 |
340 |
34 |
7 |
|
|
1
|
92 |
460 |
46 |
2
|
85 |
425 |
42.5 |
3.4. Possible reaction mechanism
On the basis of the experimental results and prior studies, the synergistic role of Lewis acid–base sites is necessary for the cycloaddition of CO2 and epoxides.43,44 So, a possible mechanism is suggested for the CO2 cycloaddition reaction to cyclic carbonates in Scheme 2. Accordingly, the indium atom as a Lewis acidic site initiates an electrophilic interaction with the oxygen atom of the epoxide, which is noted to activate the epoxy ring. At the same time, nucleophilic attack of the basic sites affords a sort of polar nature to the CO2 molecules (Scheme 2, route A). Now that the CO2 molecules and epoxide are activated, the ring opening of the epoxide starts with nucleophilic attack of the oxygen anion on the slightly sterically hindered epoxide side (Scheme 2, route B). Thereafter, alkyl carbonate anions are formed by the insertion of CO2 molecules (Scheme 2, route C). Finally, ring closure leads to the formation of the corresponding cyclic carbonates (Scheme 2, route D).
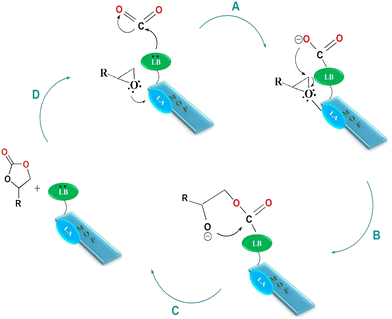 |
| Scheme 2 Proposed mechanism for cycloaddition of CO2 by modified MIL-68(In) catalyst. MOF: metal–organic framework, LA: Lewis acid, LB: Lewis base. | |
3.5. Comparison with other modified frameworks
The vital role of the cyanide functional group in the progress of the reaction has been clearly demonstrated. In comparison with catalyst 2, catalyst 1 showed the higher performance because the cyanide groups in catalyst 1 have less flexibility and are less able to rotate than in catalyst 2, so the decrease in the distance between the cyanide functional groups and the β-carbon of the epoxide facilitates the nucleophilic attack. Additionally, the high amount of CO2 gas adsorption into the cyanide groups of catalyst 1 (Fig. 3) followed by the positive effect on the nucleophilic attack leads to higher activity of the catalyst.
To specify the catalytic performance of the functionalized catalysts with other reported MOF catalysts, we compared the results of this work with other previously reported MOF heterogeneous catalysts for the CO2–epoxide coupling reaction. Details of the results are exhibited in Table 4. Some reports were carried out with higher CO2 pressure, longer reaction times, and lower TOF than our modified catalytic systems. Therefore, MIL-68(In)–PhDA can be considered as a comparable or superior catalyst to prior reported catalysts for the chemical transformation of CO2.
Table 4 The comparison of catalytic efficiency of MIL-68(In)–PhDA with previously reported MOFs
Entry |
Catalyst |
Substrate |
Co-catalyst |
Pressure (MPa) |
Temp. (°C) |
TOF (h−1) |
Ref. |
This work (TOF) (h−1) |
Reaction conditions: catalyst (30 mg, 0.04 mmol cyanide groups), epoxides (20 mmol), CO2 (1 MPa), 100 °C, 10 h. |
1 |
In-MOF |
SO |
Bu4NBr |
0.1 |
25 |
2.9 |
26
|
37 |
2 |
Mg-MOF-184 |
SO |
Bu4NBr |
0.1 |
80 |
5.5 |
49
|
37 |
3 |
MIL-68(In)-NH2 |
SO |
— |
0.8 |
150 |
1.059 |
35
|
37 |
4 |
Co-MOF-2 |
CHO |
TBAB |
0.1 |
40 |
0.33 |
47
|
46 |
5 |
(NH4)3[In3Cl2(BPDC)5] |
PO |
TBAB |
2 |
80 |
26.4 |
45
|
47 |
6 |
Zn(Bmic)(AT) |
PO |
Bu4NBr |
0.5 |
80 |
28.3 |
50
|
47 |
7 |
NH2-MIL-101(Al) |
PO |
TBAB |
1.8 |
120 |
21.7 |
51
|
47 |
8 |
CPM-200-In/Mg |
ECH |
TBAB |
1.2 |
80 |
25 |
25
|
49.5 |
9 |
CSMCRI-9 |
ECH |
Bu4NBr |
1 |
65 |
46.2 |
46
|
49.5 |
10 |
ZnMOF-1-NH2 |
ECH |
TBAB |
0.8 |
80 |
11.1 |
48
|
49.5 |
3.6. Reusability of the catalysts
The sufficiency and recyclability of the functionalized samples for the cycloaddition reaction were examined under optimal reaction conditions (Fig. S9, ESI†). MIL-68(In)–PhDA was separated from the reaction mixture by washing with dichloromethane (CH2Cl2) and vacuum drying. As shown in Fig. S9 (ESI†), based on five catalytic cycles, the catalyst is stable with no decrease in its initial activity. The XRD pattern of the recycled MOF shows the preservation of the main diffraction peaks compared to the fresh catalysts after five cycles, which indicates that the catalyst structure was not lost during the cycloaddition reaction of epoxides (Fig. S10, ESI†). The FTIR analysis results for the recovered catalysts are the same as those of the pristine catalyst, which also confirms the structural crystallinity (Fig. S11, ESI†). Furthermore, it was observed from the N2 adsorption–desorption isotherms that the structural porosity remained consistent, as indicated in Table S2 (ESI†). The results showed a slight decrease in surface area after each cycle, resulting in a minimal reduction in catalyst efficiency.
4. Conclusions
In the present study, modified MIL-68(In) with cyanide functional groups was synthesized and demonstrated appreciable catalytic results for the construction of five-membered cyclic carbonates via a cycloaddition reaction without any added solvent or co-catalyst. The modified catalysts displayed remarkable activity and high TOF with different epoxides. The high efficacy of modified MIL-68(In) is mediated by the synergetic effect of the unsaturated indium acting as Lewis acid sites and with the cyanide groups as basic sites. In addition, the catalysts were found to be recoverable during five reaction cycles without significant loss in their initial activity. This study not only develops a new modified catalyst with high conversion for the CO2 fixation reaction but also opens up new possibilities for designing efficient non-noble-metal-based cyanide-functionalized MOF catalysts.
Conflicts of interest
There are no conflicts to declare.
Acknowledgements
The authors appreciate Alzahra University Research Council for the financial support.
References
- S. Kumar, M. Y. Wani, J. Koh, J. M. Gil and A. J. F. N. Sobral, J. Environ. Sci., 2018, 69, 77–84 CrossRef CAS PubMed.
- J. R. Li, Y. Ma, M. C. McCarthy, J. Sculley, J. Yu, H. K. Jeong, P. B. Balbuena and H. C. Zhou, Coord. Chem. Rev., 2011, 255, 1791–1823 CrossRef CAS.
- M. Aresta, A. Dibenedetto and A. Angelini, Chem. Rev., 2014, 114, 1709–1742 CrossRef CAS PubMed.
- A. Rafiee, K. Rajab Khalilpour, D. Milani and M. Panahi, J. Environ. Chem. Eng., 2018, 6, 5771–5794 CrossRef CAS.
- Y. Li, X. Zhang, J. Lan, D. Li, Z. Wang, P. Xu and J. Sun, A, ACS Sustainable Chem. Eng., 2021, 9, 2795–2803 CrossRef CAS.
- A. Rehman, F. Saleem, F. Javed, A. Ikhlaq, S. W. Ahmad and A. Harvey, J. Environ. Chem. Eng., 2021, 9, 105113 CrossRef CAS.
- L. Zhang, Y. Feng, H. He, Y. Liu, J. Weng, P. Zhang and W. Huang, Catal. Today, 2021, 374, 38–43 CrossRef CAS.
- Y. Zhang, L. Liu, W. G. Xu and Z. B. Han, J. CO2 Util., 2021, 46, 101463 CrossRef CAS.
- G. Y. Hwang, R. Roshan, H. S. Ryu, H. M. Jeong, S. Ravi, M. Il Kim and D. W. Park, J. CO2 Util., 2016, 15, 123–130 CrossRef CAS.
- R. Rajjak Shaikh, S. Pornpraprom and V. D'Elia, ACS Catal., 2018, 8, 419–450 CrossRef.
- A. Helal, M. Usman, E. Arafat and M. M. Abdelnaby, J. Ind. Eng. Chem., 2020, 89, 104–110 CrossRef CAS.
- J. Li, W. J. Li, S. C. Xu, B. Li, Y. Tang and Z. F. Lin, Inorg. Chem. Commun., 2019, 106, 70–75 CrossRef CAS.
- N. Wei, Y. Zhang, L. Liu, Z. B. Han and D. Q. Yuan, Appl. Catal., B, 2017, 219, 603–610 CrossRef CAS.
- S. Zhao, Z. Liu and F. Wang, J. CO2 Util., 2020, 39, 101183 CrossRef CAS.
- X. Sun, L. Shi, H. Hu, H. Huang and T. Ma, Adv. Sustainable Syst., 2020, 4, 2000098 CrossRef CAS.
- Z. Sharifzadeh, K. Berijani and A. Morsali, Coord. Chem. Rev., 2021, 445, 214083 CrossRef CAS.
- K. Gupta, N. Guha, S. Krishnan, P. Mathur and D. K. Rai, J. CO2 Util., 2020, 39, 101173 CrossRef.
- F. N. Al-Rowaili, U. Zahid, S. Onaizi, M. Khaled, A. Jamal and E. M. AL-Mutairi, J. CO2 Util., 2021, 53, 101715 CrossRef CAS.
- Y.-H. Han, Z.-Y. Zhou, C.-B. Tian and S.-W. Du, Green Chem., 2016, 18, 4086 RSC.
- L. Zhu, X. Liu, H. Jiang and L. Sun, Chem. Rev., 2017, 117, 8129–8176 CrossRef CAS PubMed.
-
T. K. Pal, D. De and P. K. Bharadwaj, Coord. Chem. Rev., 2020, 408, 213173 Search PubMed.
- H. He, J. A. Perman, G. Zhu and S. Ma, Nano. Micro Small, 2016, 12, 6309–6324 CAS.
- Y. Yuan, J. Li, X. Sun, G. Li, Y. Liu, G. Verma and S. Ma, Chem. Mater., 2019, 31, 1084–1091 CrossRef CAS.
- S. T. Zheng, T. Wu, C. Chou, A. Fuhr, P. Feng and X. Bu, J. Am. Chem. Soc., 2012, 134, 4517–4520 CrossRef CAS PubMed.
- Y. Gu, Y. Choe and D. Park, Catalysts, 2021, 11(4), 430 CrossRef CAS.
- L. Liu, S.-M. Wang, Z.-B. Han, M. Ding, D.-Q. Yuan and H.-L. Jiang, Inorg. Chem., 2016, 55, 3558–3565 CrossRef CAS PubMed.
- J. Noh, Y. Kim, H. Park, J. Lee, M. Yoon, M. H. Park, Y. Kim and M. Kim, J. Ind. Eng. Chem., 2018, 64, 478–483 CrossRef CAS.
- M. Saghian, S. Dehghanpour and M. Sharbatdaran, J. CO2 Util., 2020, 41, 101253 CrossRef CAS.
- Q. T. Nguyen, X. H. Do, K. Y. Cho, Y. R. Lee and K. Y. Baek, J. CO2 Util., 2022, 61, 102061 CrossRef CAS.
- L. Wu, M. Xue, S. L. Qiu, G. Chaplais, A. Simon-Masseron and J. Patarin, Microporous Mesoporous Mater., 2012, 157, 75–81 CrossRef CAS.
- J. Zhang, H. Zhang, Q. Liu, D. Song, R. Li, P. Liu and J. Wang, Chem. Eng. J., 2019, 368, 951–958 CrossRef CAS.
- N. Bayati and S. Dehghanpour, J. Environ. Sci., 2023, 132, 12–21 CrossRef PubMed.
- C. Volkringer, M. Meddouri, T. Loiseau, N. Guillou, M. Haouas, F. Taulelle, N. Audebrand, M. Latroche and D. V. Saint Quentin, Inorg. Chem., 2008, 47, 11892–11901 CrossRef CAS PubMed.
- J. Zhu, H. Zhang, Q. Liu, C. Wang, Z. Sun, R. Li, P. Liu, M. Zhang and J. Wang, J. Taiwan Inst. Chem. Eng., 2019, 99, 45–52 CrossRef CAS.
- T. Lescouet and D. Farrusseng, ChemCatChem, 2012, 4(11), 1725–1728 CrossRef CAS.
- L. N. Jin, X. Y. Qian, J. G. Wang, H. Aslan and M. Dong, J. Colloid Interface Sci., 2015, 453, 270–275 CrossRef CAS PubMed.
- R. Liang, R. Huang, X. Wang, S. Ying, G. Yan and L. Wu, Appl. Surf. Sci., 2019, 464, 396–403 CrossRef CAS.
- M. Saghian, S. Dehghanpour and M. Sharbatdaran, Appl. Catal., A, 2021, 612, 117982 CrossRef CAS.
- W. Cao, Y. Yuan, C. Yang, S. Wu and J. Cheng, Chem. Eng. J., 2020, 391, 123608 CrossRef CAS.
- P. Deminskyi, P. Rouf, I. G. Ivanov, H. Pedersen, P. Deminskyi, P. Rouf, I. G. Ivanov and H. Pedersen, J. Vac. Sci. Technol., A, 2019, 37, 020926 CrossRef.
- J. Zhang, H. Zhang, Q. Liu, D. Song, R. Li, P. Liu and J. Wang, Chem. Eng. J., 2019, 368, 951–958 CrossRef CAS.
- J. F. Kurisingal, Y. Rachuri, Y. Gu, Y. Choe and D. W. Park, Chem. Eng. J., 2020, 386, 121700 CrossRef CAS.
- J. Lan, Y. Qu, X. Zhang, H. Ma, P. Xu and J. Sun, J. CO2 Util., 2020, 35, 216–224 CrossRef CAS.
- M. Liu, K. Gao, L. Liang, J. Sun, B. Li Sheng and M. Arai, Catal. Sci. Technol., 2016, 6, 6406 RSC.
- Y. H. Li, S. L. Wang, Y. C. Su, B. T. Ko, C. Y. Tsai and C. H. Lin, Dalton Trans., 2018, 47, 9474–9481 RSC.
- N. Seal, M. Singh, S. Das, R. Goswami, B. Pathak and S. Neogi, Mater. Chem. Front., 2021, 5, 979–994 RSC.
- P. Patel, B. Parmar, R. S. Pillai, A. Ansari, N. H. Khan and E. Suresh, Appl. Catal., A, 2020, 590, 117375 CrossRef CAS.
- P. Patel, B. Parmar, R. I. Kureshy, N. H. Khan and E. Suresh, Dalton Trans., 2018, 47, 8041–8051 RSC.
- Y. B. N. Tran, P. T. K. Nguyen, Q. T. Luong and K. D. Nguyen, Inorg. Chem., 2020, 59, 16747–16759 CrossRef CAS PubMed.
- Y. Li, X. Zhang, J. Lan, P. Xu and J. Sun, Inorg. Chem., 2019, 58, 13917–13926 CrossRef CAS PubMed.
- S. Senthilkumar, M. S. Maru, R. S. Somani, H. C. Bajaj and S. Neogi, Dalton Trans., 2018, 47, 418–428 RSC.
|
This journal is © The Royal Society of Chemistry 2023 |
Click here to see how this site uses Cookies. View our privacy policy here.