Building bridges between halide perovskite nanocrystals and thin-film solar cells
Received
2nd July 2018
, Accepted 14th September 2018
First published on 17th September 2018
Abstract
The development of halide perovskite (HP) based thin film solar cells has been unprecedented in the past few years, and there is significant ongoing effort aiming to make perovskite solar cells (PSCs) more efficient and stable. Parallel to the PSC research, there is growing interest in exploring the synthesis and physiochemical behaviors of HP nanocrystals (NCs). While these HP NCs inherently possess many unique properties that are suitable for the use in PSCs, the reported effort of incorporating HP NCs into PSCs is still highly limited. As a result, there is a gap between HP NC and PSC research. In this context, we provide here a brief review of the established HP NC synthesis and a discussion of the several recent studies pertaining to the use of HP NCs in PSCs. Based on these, we provide perspectives on promising directions for bridging the gap between HP NC and PSC research in the future.
1. Introduction
Halide perovskites (HPs) have been introduced recently as a new generation of semiconductor materials in the field of optoelectronics. In general, HPs exhibit a three-dimensional (3D) (pseudo-)cubic crystal structure with chemical formula ABX3, where A is methylammonium (CH3NH3+ or MA+), formamidinium (HC(NH2)2+ or FA+) or Cs+, B is Pb2+, Sn2+ or Ge2+, and X is I−, Br− or Cl− (Fig. 1).1–6 The HP family has later been extended to embrace lower-dimensional (2D, 1D and 0D) perovskites and their variants with accordingly varied chemical formulas (A2BX4, ABX4, A3B2X9, A4BX6, etc.).7–14 In the past decade of rapid development, HPs have shown great potential in a wide range of optoelectronic applications such as solar cells, light-emitting devices (LEDs), lasing, photodetectors, and X-ray imaging.15–24 Most notably, HP-based thin-film solar cells have emerged as revolutionary photovoltaic (PV) technologies that combine the merits of low materials/processing cost and high power conversion efficiency (PCE). Within a very short period of time, the PCE of perovskite solar cells (PSCs) has ramped up to 23.3% since its initial invention by Kojima et al. in 2009.25–27 The swift increase in PCE is not only attributed to the unique intrinsic properties of HP materials that include high absorption coefficients,28 suitable bandgaps,29,30 and long and balanced charge-carrier diffusion lengths,31,32 but also to the unprecedented effort in optimizing HP bulk thin film formation33–37 and device architectures.38–40 In parallel with these significant PSC developments, there is rapid growth of interest in exploring the synthesis and properties of HP nanocrystals (NCs). Compared with conventional inorganic semiconductor NCs, HP NCs exhibit many advantageous features, such as high photoluminescence quantum yields (PLQYs),41,42 narrow emission profiles, and facile bandgap tunability,43,44 as well as extreme ease in both their direct synthesis and post-synthetic treatments.45–47 While these HP NCs have been widely studied for display and light-emitting applications,48–51 there is much less effort being devoted to applying HP NCs in PSCs. In fact, merits of HP NCs including superior particle dispersity in non-polar solvents,52 ultralow defect density,53,54 and uniformity in crystal size and morphology55,56 make them inherently suitable for integration in PSCs.57,58 However, to date, these attributes have not been sufficiently explored for PV applications. In this context, the current gap between HP NC and PSC research needs to be filled.
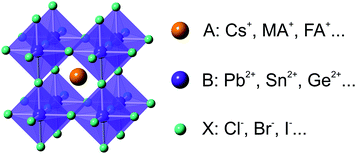 |
| Fig. 1 Schematic illustration of the crystal structure and typical compositions of halide perovskites. | |
In this article, a brief review of direct synthetic routes and post-synthetic tuning strategies for HP NCs that can enable compositional/structural control is first presented. Then, recent studies on applying HP NCs to PSC device modification and fabrication are summarized. Finally, we provide perspectives on the future research directions that may further bridge the gap between HP NC synthesis and post-treatment and their PSC applications. The objective of this perspective article is not only to highlight the many promising possibilities that HP NCs are able to offer for making efficient, stable and versatile PSCs, but also stimulate interdisciplinary researchers to further explore this young but fascinating research area.
2. Synthesis and properties of HP NCs
Synthesis of HP NCs
High-quality semiconductor NCs (also known as quantum dots, QDs) are the building blocks and vital basis in not only fundamental research, but also a spectrum of technological applications.59–64 The first demonstration of solution synthesis of HP NCs was reported in 2014 by Schmidt et al., where they synthesized methylammonium lead bromide (MAPbBr3) hybrid organic–inorganic HP NCs using a non-templating antisolvent precipitation method.65 Soon afterwards, this synthetic method was optimized by Zhang et al. who pioneered the use of a miscible solvent/antisolvent combination (e.g. dimethylformamide (DMF) and toluene) for making high-quality MA-based hybrid HP NCs with much improved optical properties.66 This so-called ligand-assisted reprecipitation (LARP) synthetic method relies on a dramatic change in solvent polarity by adding a miscible antisolvent to initiate rapid HP nucleation in solution (Fig. 2a and b). The subsequent NC growth and ripening processes can be controlled by long-chain organic ligands added to the reaction solution. Applying LARP, a wide range of high-quality HP NCs can be synthesized.67–69 Arguably, the most beneficial aspect of the LARP synthesis is the use of ambient reaction conditions (i.e. room temperature, commercially available chemicals), which enables the use of low-boiling-point solvents and chemicals, thus offering the promise of large-scale industrial-level production.70 In addition, the general ease of dissolving non-lead metal precursors (e.g. bismuth halide, silver nitrate) in coordinating solvents makes LARP attractive for synthesizing Pb-free HP NCs.71,72 Although the LARP method tends to produce relatively small NCs with an average diameter of <5 nm, larger NCs can be achieved through changing the reaction temperature and solvents.41,73 However, the low solubility of common inorganic ‘A’ cation precursors (e.g., Cs salts) in organic solvents (e.g. DMF, dimethyl sulfoxide (DMSO)) limits the generalization of LARP for fabrication of all-inorganic Cs-based HP NCs.
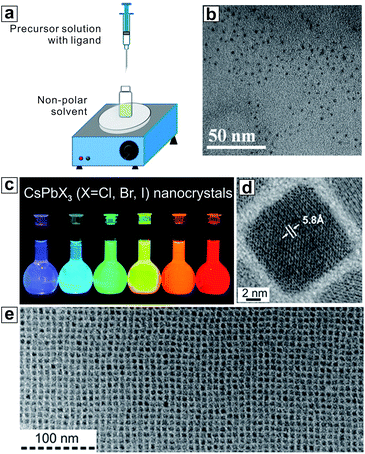 |
| Fig. 2 (a) Schematic image for the procedure of ligand-assisted reprecipitation (LARP). (b) Transmission electron microscopy (TEM) images of MAPbBr3 NCs synthesized by LARP. (c) Optical images of CsPbX3 nanocubes synthesized by the hot injection method under UV light. (d and e) TEM images of CsPbX3 nanocubes. (a) and (b) are reproduced from ref. 66 with permission from the American Chemical Society. (c–e) are reproduced from ref. 74 with permission from the American Chemical Society. | |
The hot-injection method, which is a state-of-the-art strategy for conventional NC synthesis, has been quickly adapted for the synthesis of all-inorganic HP NCs. The first example was reported by Protesescu et al. using 1-octadecene (ODE) as a solvent, PbBr2 and Cs-oleate as precursors, and oleic acid and oleylamine as capping ligands.74 Uniform CsPbX3 nanocubes with tunable edge lengths from 3.8 to 11.8 nm were synthesized using the hot-injection technique at temperatures ranging from 140 to 200 °C (Fig. 2c–e). Mixed halide NCs with precise halide ratios can be easily synthesized using a mixture of PbX2 precursors. While the general format of synthesis remains nearly unchanged, recent improvements have been made to ensure better NC monodispersity using chemically active precursors and optimized reaction conditions.55,75,76 Low-dimensional (morphologically) HP NCs are defined as HP NCs with the same crystal structure, but containing at least one dimension that is small in size. The hot-injection method is particularly suitable for synthesis of low-dimensional HP NCs, such as nanowires and nanoplatelets (Fig. 3a and b).77–81 These low-dimensional NCs are typically sensitive to polar solvents, which makes the use of the LARP synthesis very challenging. Monodisperse thickness control of nanoplatelets and nanowires is readily achieved with the control over the nucleation and growth kinetics by manipulating the ligands, temperature, and precursor ratio.82 The uniformity of as-synthesized NCs can be illustrated by their tendency to form ordered superlattices (Fig. 3c and d).83–85 Beyond inorganic HP NCs, the hot-injection technique can be adopted for synthesis of hybrid organic–inorganic HP NCs, such as FAPbX3.56,86 The low boiling point of certain organic precursors, however, limits the use of hot-injection for some hybrid HP NC syntheses (e.g., MAPbX3). Another drawback of the hot-injection technique is the use of high-boiling-point solvents with long organic hydrocarbon chains, such as ODE. These high-boiling-point solvents, together with organic ligands, may affect the uniformity and conductivity of the resultant HP NC thin film, thus limiting the final device performance. In this context, multiple rounds of purifications are required to remove these insulating components. This is challenging for HP NCs because of their instability upon interaction with polar solvents that are commonly used in purification procedures. The study on optimizing purification procedure without causing aggregation or phase transition is crucial for the incorporation of HP NCs in optoelectronic devices.
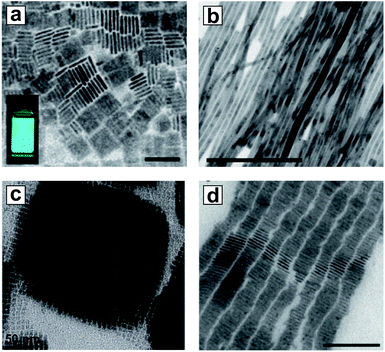 |
| Fig. 3 (a, b) TEM images of CsPbBr3 nanoplatelets and nanowires. Scale bar = 50 nm and 200 nm, respectively. (c, d) TEM images showing self-assembled superstructures for CsPbX3 nanocubes and nanoplatelets. Scale bar = 50 nm and 100 nm, respectively. (a) is reproduced from ref. 77 with permission from the American Chemical Society. (b) is reproduced from ref. 79 with permission from the American Chemical Society. (c) is reproduced from ref. 83 with permission from the Swiss Chemical Society. (d) is reproduced from ref. 80 with permission from Wiley-VCH. | |
Alternative synthetic routes offer supplementary improvements in certain aspects as compared with the two aforementioned methods. For example, a solvothermal method initiates the reaction at a mild temperature and a high pressure. The controlled nucleation and growth results in novel particle morphologies, including nanorods or nanosheets.87,88 Top-down techniques, such as mechanochemical exfoliation methods, generally reduce the use of hazardous reagents or high-boiling-point species, making them greener substitutes for large-scale production.89–92
Phase stability
HP materials are notorious for having a variety of polymorphs. The cubic or pseudocubic phases, which are only stable at elevated temperatures, have the highest absorption coefficients and optimal optical properties. Other phases with lower crystal symmetries are more stable at room temperature, at the expense of larger bandgaps and undesired optoelectronic properties.93,94 Therefore, special synthetic techniques and post-synthetic treatments are often needed to obtain and preserve the cubic phase at room temperature. As we have discussed in the previous section, HP NCs in the cubic phase can be readily synthesized due to the rapid kinetics during injection as well as the surface effects. However, being meta-stable at room temperature, cubic HPs tend to transform into the phases with lower symmetries under ambient conditions, especially for I-containing perovskites. The transformation can be accelerated by light, oxygen, moisture and polar organic solvents.95,96
While encapsulating the HP NCs with polymer, silica or glass can significantly stabilize the cubic phase, the resultant decrease in conductivity renders NCs produced in this manner unfit for PV application.97–99 Alternatively, stabilizing a desirable phase via compositional optimization has been heavily investigated. The relative abundance of halide anions is especially important for the stability of HP NCs.100,101 The stabilizing effect has been attributed to the surface abundance of a lead-halide layer, which isolates the perovskite ‘core’ from the environment. By alloying HP NCs with ions of varying sizes, it is possible to adjust the Goldschmidt tolerance factor of the perovskite102 and therefore achieve higher stability for the cubic phase. For example, in I-based HPs, Cs is too small to support cubic phases while FA is too large. Protesescu et al. synthesized Cs-FA mixed HP NCs via a hot-injection method with both high phase stability and high PL quantum yield (QY) even after 6 months of storage under ambient conditions.86 However, their mixing range was limited to the Cs-rich end, which resulted in an unfavourable bandgap. In addition to the tolerance factor adjustment, mixing ions offers a higher entropy for the cubic phase and therefore an increased phase stability.103
Bandgap tunability
The bandgap is the determining parameter for semiconductor materials. Semiconductors with different bandgaps can have different functions in PSCs (absorbers, interface modifiers, etc.). The wide bandgap tunability that HP NCs offer is of vital importance in this context.
Density of states calculations using density functional theory (DFT) have shown that the valence band (VB) of HP materials is mainly comprised of halide p orbitals, while the conduction band (CB) is dominated by ‘B’ cation frontier s and p orbitals.104 As a result, the bandgaps of HP materials are significantly influenced by B cations and halide anions. HP NCs with emission covering the full visible range of 400–730 nm can be achieved by only altering their halide composition (Cl → Br → I) (Fig. 4a).66 Specifically, as predicted by the Shockley–Queisser limit,105 the relatively lower bandgaps of I-based HPs make them more ideal absorbers for PSCs than their Cl- and Br-based analogues. The full spectrum coverage, ease of exchange, and ability of forming uniform halide alloys make halide composition control the most facile strategy to reach a certain target bandgap. Alternatively, adjusting the ‘B’ cation (e.g. replacing Pb) in HP NCs offers another effective way to alter the electronic properties, especially with the goal of further narrowing the material bandgap to achieve a better match with the solar spectrum. In this regard, Sn(II) and Ge(II) are the two potential Pb replacements that can reduce the conduction band minimum (CBM) and thus reduce band gaps.106,107 However, the synthesis of Sn- and Ge-based HP NCs is still challenging due to cation instability caused by facile oxidation of Sn(II) to Sn(IV), or Ge(II) to Ge(IV).108–110 This oxidation problem hinders the related material development. Finally, although not directly, the ‘A’ cation may also affect the bandgap tunability largely by adjusting the lattice parameter, in turn altering the orbital overlap in the VB and CB (Fig. 4d).111 When all other components are fixed, the bandgaps of bulk HPs show a decreasing trend when the ‘A’ cation radius increases from Cs (e.g. 1.73 eV for CsPbI3) to MA (e.g. 1.57 eV for MAPbI3), to FA (e.g. 1.48 eV for FAPbI3).112
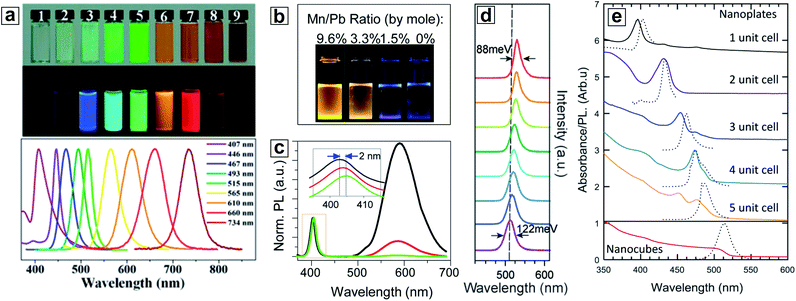 |
| Fig. 4 (a) Optical images and PL spectra of MAPbX3 nanoparticles with different halide compositions varying from MAPbCl3 (left) to MAPbBr3 (middle) to MAPbI3 (right). (b and c) Optical images and PL spectra of Mn-doped CsPbCl3 nanocubes with different doping concentrations. (d) PL spectra of MAPbBr3 (bottom) to FAPbBr3 (top) nanocubes during a cation exchange process. (e) Absorption (solid line) and PL spectra (dashed line) of CsPbBr3 nanoplatelets of atomic thickness precision and nanocubes. (a) is reproduced from ref. 66 with permission from the American Chemical Society. (b) and (c) are reproduced from ref. 113 with permission from the American Chemical Society. (d) is reproduced from ref. 111 with permission from the Royal Society of Chemistry. (e) is reproduced from ref. 77 with permission from the American Chemical Society. | |
One additional unique advantage of nanoscale HPs is the fine-tuning of bandgaps afforded by the quantum confinement effect. When the size of NCs is scaled down below the material's Bohr radius, the energy levels near the band edge become discrete, resulting in the emergence of multiple absorption features with blue-shifted profiles. Examples of this quantum confinement effect can be found for all types of HP NCs. In particular, I-containing HP NCs show the most dramatic influence due to their large Bohr radius as compared with that of their Cl and Br counterparts (e.g. 2.5 nm for CsPbCl3, 3.5 nm for CsPbBr3, and 6 nm for CsPbI3).74 As the edge length of CsPbI3 nanocubes dropped from 12.5 nm to 3.4 nm, the NC PL peak exhibited a large range blue-shift from 670 nm to 585 nm.57 The quantum confinement effect is especially more profound in low-dimensional HP NCs because they have at least one dimension significantly smaller than the Bohr radius, such as in ultra-thin nanowires and nanoplatelets. As the smallest dimension of these materials approaches a few atomic layers, adding or subtracting single monolayers results in a drastic change in their photophysical properties.68,79 For example, Bekenstein et al. found that when the thickness of CsPbBr3 nanoplatelets was changed from one to five monolayers (while maintaining the lateral size), the PL peak could be adjusted from 400 nm to 480 nm (Fig. 4e).77 This size/shape induced quantum confinement effect of HP NCs offers a composition-independent approach toward tuning the bandgap structure, providing benefits for PSC designs. This includes the possibility of their use in graded bandgap PSCs and in perovskite–perovskite tandem solar cells which cannot be easily accessed through compositional control due to possible inter-layer ion exchange processes.
Doping in HP NCs
The range of metal cations that can form HPs is limited by their valency and ionic sizes. However, it is possible to introduce small amounts of heteroatoms into the HP lattice (also known as doping). The most striking feature of doping is the introduction of extrinsic optoelectronic properties.106 For example, Mn-doped CsPbCl3 NCs exhibiting a strong emission centred at around 600 nm were successfully synthesized without significantly altering the crystal structure or the morphology of host NCs (Fig. 4b and c).113–117 In addition to Mn, rare earth ion dopants such as Yb, Eu, Dy and Ce exhibit bright emission with high QYs in CsPbCl3 HP NCs.118–120 The large Stokes shifts of dopant emission are beneficial for down-shifting high energy photons (e.g., ultraviolet light) and for reducing the photon reabsorption. Additionally, doping can alter bandgaps. For example, doping with Sn, Cd, Zn and Bi cations can cause an increased bandgap in CsPbBr3 NCs and change the PL dynamics.46,121 Mn-doped CsPbCl3 has shown enhanced PL stability compared with its undoped counterparts.122 While the detailed mechanisms are still under investigation, doping in HP NCs has shown potential in solar energy and display related applications.123,124
3. Post-synthetic treatments of HP NCs
The ‘soft’ nature (i.e. prone to change under external stimulus) of HP NCs enables a number of post-synthetic routes to modify their compositions, crystal structures, surface passivation and electronic properties much beyond what direct synthetic methods can offer. The development of such modification reactions or techniques has been an active research area fuelled by exciting discoveries. It allows for optimization of HP NC-based materials in terms of composition and structure for subsequent use in PSCs. In this section, we discuss three major post-synthetic treatments for HP NCs, which are directly related to PSC applications. Other post-synthetic treatments such as encapsulation of HP NCs in polymer or silica matrices, and ligand or ion induced crystal phase transformations will not be discussed here. We refer readers to other excellent literature studies for these related topics.47,125–131
Ion exchange reaction
The post-synthetic ion exchange method is a powerful tool commonly utilized in nanoscale research to form meta-stable phases and/or heterostructures. As discussed in the previous section, changing the halide anion can dramatically tune the bandgap of HP NCs. Unlike traditional cadmium-chalcogenide-based QDs (e.g., CdSe and CdS QDs), in which anion exchange reactions are limited by their large ionic radii and strong bonding, halide ions in HP NCs can be rapidly exchanged in either colloidal or solid phases even at room temperature.132,133 Various halide precursors have shown high reactivities during the exchange reactions, including inorganic halide salts, alkyl ammonium halides, and even HP NCs with different halide anions.43,44,134 This exchange can be achieved by simply mixing the halide precursors with NCs dispersed in their colloidal dispersion. HP NCs containing varying halide compositions (except CsPbClxI3−x, which is restricted by a large ionic radius difference43) can be achieved (Fig. 5a).43,44,135 The final particle stoichiometry is solely determined by the precursor ratio introduced into the reaction because no thermodynamic preference for halide anions has been shown.136 The high anion compatibility prevented any loss in shape or size during the process of exchange.137 Although convenient, the fast kinetics of the halide exchange reaction can also be a challenge for NC processing. For example, the uncontrollable halide exchange process hinders the formation of more complex nanostructures, or the coexistence of HP NCs of different halide compositions in colloidal solution.43 Novel methods have been developed to achieve a controllable exchange process, including photoexcited anion exchange,138 solid-state exchange,139 or surface-controlled exchange.140,141
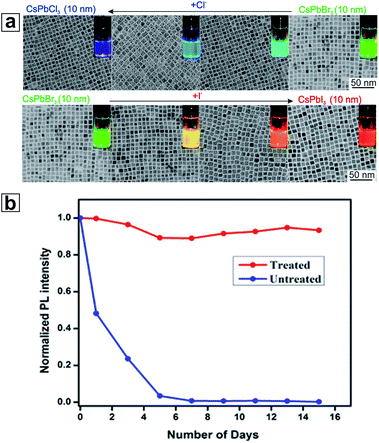 |
| Fig. 5 (a) TEM and optical images under UV light during a halide exchange reaction of CsPbX3 nanocubes. (b) Stability of CsPbI3 nanocubes with or without bidentate ligand treatment. (a) is reproduced from ref. 43 with permission from the American Chemical Society. (b) is reproduced from ref. 150 with permission from the American Chemical Society. | |
While the halide exchange is the most common and facile ion exchange reaction, cation exchange is also achievable and important in tuning the HP NC properties.46,142 Recently, Hills-Kimball et al. showed that FAPbX3 NCs, which had been difficult to obtain via direct synthesis routes, can be obtained by cation exchange from MAPbX3 HP NCs through a novel ‘solid–liquid–solid’ exchange process.111 While the reaction speed is much slower than that of the halide exchange reactions, complete transformation can still be reached. One advantage of this new ‘solid–liquid–solid’ reaction setup with slow kinetics is the possibility of intermediate reaction termination at designed mixtures of ‘A’ cation compositions for desired optical properties.111 For the ‘B’ cations, the exchange from Pb to Sn, Cd, and Zn has been demonstrated to produce CsPb1−xMxBr3.46,117,143 As is discussed above, the ‘B’ cation exchange has a profound influence on the optical properties. In the above system, a blueshift of as large as 60 nm in both absorption and PL profiles was observed. This large shift was explained by a lattice contraction effect, which is evidenced by no significant alternation in particle size or shape.
Surface ligand engineering
Organic capping ligands play a crucial role in stabilizing NCs in solution. Such ligands are highly dynamic and can be easily lost during the purification process. This loss of ligands can lead to a destabilization of the NCs, thus initiating an undesired Ostwald ripening process.144 The same ligand loss may also diminish the optical properties of the HP NCs. Therefore, optimized ligand binding and enhanced surface coverage can improve not only the colloidal stability, but also the optical properties of HP NCs. Alkyl amines and alkyl acids are the most common ligands for HP NCs. They can efficiently passivate the NCs, especially when both types of ligands are present.145,146 In addition, co-passivating the NC surface with short inorganic ligands, e.g. thiocyanate, can further promote the PL QY of HP NCs (CsPbI3 NCs) to approach unity while maintaining a high particle colloidal stability.147 It was proposed that thiocyanate can penetrate through the bulky organic ligand layer and attach to unsaturated sites on the NC surface, thus offering high surface passivation efficiency. Moreover, the use of bulky branched ligands or peptides showed a better NC compatibility with protic solvents.148,149
Another strategy to stabilize HP NCs involves adjusting the binding form between NCs and ligands. Zwitterionic ligands such as amino acids or amino-sulfonate are able to bind tightly to both cations and anions on the surface of NCs. When capped with zwitterionic ligands, superior properties of HP NCs including high colloidal solubility (50–100 mg mL−1), close-to-unity PL QY, and high colloidal stability were exhibited.52 In another example, a bidentate ligand with a short carbon chain, 2,2′-iminodibenzoic acid, was installed on the surface of CsPbI3 NCs. NCs coated with this ligand were not only stable and highly luminescent, but also showed an enhanced conductivity and electroluminescence performance when used in an LED (Fig. 5b).150 The ionic nature and rich crystal phases of the HP NCs result in the capping ligands playing additional roles as opposed to solely serving as a protective layer. For example, excess organo-amine ligands in NC solution can extract Pb cations from HP NCs, resulting in a Pb-deficient trigonal Cs4PbX6 crystal phase with a much wider bandgap and complicated photophysical properties.47,151 Further increasing the amount of amine ligands may result in the whole dissolution of HP NCs to their ionic forms.
Although HP NCs are initially part of a colloidal solution, they need to be extracted out of solution for PSC device fabrication. While long organic ligands are crucially important in the synthesis and stabilization of HP NCs in solution, these insulating organic molecules are undesirable in optoelectronic devices.152,153 Hence, these long organic ligands need to be replaced or removed for device fabrication. The replacement of long organic ligands can happen either during the formation of NCs or via a post-synthesis ligand exchange process. For example, short 1-butylamine can serve as the ligand to produce colloidal CsPbBr3 NCs used for high-voltage solar cells.70 The produced particles can be directly used to fabricate NC-based conducting films without a lengthy post-synthetic ligand treatment. In another example, a relatively short ligand of didodecyldimethylammonium bromide was used to replace oleic acid and oleylamine on CsPbBr3 NCs after synthesis. LED devices made using these treated NCs exhibited an order of magnitude higher external quantum efficiency (EQE) than that of untreated NCs (3% vs. 0.1%).154 For PSC device fabrication, a total removal of organic ligands by antisolvent washing or salt-induced coarsening is commonly applied to improve film conductivity, which will be further discussed in later sections.57,155 Studies on ligand effects in NC thin film formation and associated device performances are still limited, leaving room for future research toward the development of a wide range of ligands for HP NC-based PSC applications.
Pressure-treatment of HP NCs
Being an important thermodynamic variable, pressure casts a significant influence on the crystal structures of various materials.156–162 The dynamic structures of the HP materials promise structure–property tunability at elevated pressure. Compared with their bulk counterparts, the pressure effect on HP NCs has been much less studied. Nagaoka et al. reported the first detailed study of pressure processing on self-assembled CsPbBr3 NC superlattices.163 Through synchrotron-based in situ small/wide angle X-ray scattering (SAXS/WAXS) and optical spectroscopy measurements, the crystal phase transition, superlattice transformation and optical property evolution were simultaneously monitored. A concurrent crystal phase purification and PL enhancement were reported. Ex situ electron microscopy characterization showed an interesting 2D nanoplatelet formation through a pressure-induced oriented attachment process (Fig. 6a and b). Similar changes in both particle morphology and optical properties for MAPbBr3 NCs under pressure were also demonstrated.164 Later, a study on the same CsPbBr3 system was reported by G. Xiao et al., in which a more detailed investigation of the bandgap evolution as a function of pressure was conducted.165 This pressure processing technique has further been expanded to I-based HP NCs, such as CsPbI3 and FAPbI3, with a bandgap energy range more relevant for PSC applications (Fig. 6c).166–168 Combined with high-pressure studies on perovskite bulk materials,169–178 it can be concluded that external high-pressure-processing is capable of serving as an efficient and chemically orthogonal means to fine-tune the crystal structure, controllably engineer the bandgap and even generate new perovskite materials overcoming conventional synthetic limitations. Regardless of the promise, how to imitate the required high-pressure environment inside PSC devices remains challenging.
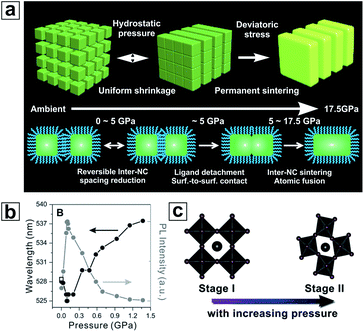 |
| Fig. 6 (a) Schematic drawing showing the pressure-sintering mechanism for CsPbBr3 nanocubes into nanoplatelets. (b) PL peak wavelength and intensity for CsPbBr3 nanocubes with increasing pressure. (c) Diagram showing the crystal structure transformation of CsPbI3 from the cubic phase to the orthorhombic phase with increasing pressure. (a) and (b) are reproduced from ref. 163 with permission from Wiley VCH. (c) is reproduced from ref. 167 with permission from the American Chemical Society. | |
4. HP NC-modified thin-film PSCs
Great progress has been made in the synthesis and post-synthetic improvement of HP NCs aimed to make them ready for further incorporation in PSC devices to either modify the HP bulk thin film or to replace it completely. In this section, we will focus our discussion on how the HP NCs improve bulk thin film-based PSC performances through one of the following two ways: (i) smoothing the PV device interfacial band alignment; and (ii) managing photon propagation using the excitonic properties of HP NCs.
Interfacial band alignment modification
The first major utilization of HP NCs for PSCs was to serve as an interface modifier for the HP bulk thin films in order to enhance band energy alignment and device integration. Compared with other modifiers such as polymers,179 and molecular species,180–183 HP NCs are unique due to their congeneric nature with the HP bulk thin film absorbers in terms of both chemical composition and crystal structure. One of the earliest studies regarding the integration of HP NCs as modifiers in PSCs was reported by Cha et al., where an interfacial layer of MAPbBr3−xIx HP NCs was introduced between the MAPbI3 HP bulk thin film and the hole-transporting material (HTM).184 Here, the MAPbBr3−xIx HP NCs were dispersed in chlorobenzene and then spin-coated on the as-crystallized MAPbI3 HP bulk thin film. It was found that by adjusting the halide ratio in MAPbBr3−xIx NCs, their VB maximum (VBM) could be tuned to be located between the VBM of the MAPbI3 bulk thin film absorber and the highest occupied molecular orbital (HOMO) of the HTM. In this context, the hole injection efficiency at the HP/HTM interface was greatly facilitated, resulting in significant improvements in all PV parameters including short-circuit photocurrent (JSC), open-circuit voltage (VOC) and fill factor (FF). The PSCs made using the HP bulk thin films modified with MAPbBr0.9I2.1 HP NCs showed 23% increase in the overall PCE compared with the HP-NC-free case. A subsequent study in a similar topic was later conducted by Zai et al., where CsPbBr3 NCs were selected as a model material to be incorporated into the FA0.85MA0.15Pb(I0.85Br0.15)3 HP bulk thin film during the antisolvent-dripping process (Fig. 7a).185 In this work, the CsPbBr3 NCs induced surface modification occurred along with the formation of the FA0.85MA0.15Pb(I0.85Br0.15)3 HP bulk thin film, which was different from the study by Cha et al. Without a significant influence on the microstructures of the final FA0.85MA0.15Pb(I0.85Br0.15)3 bulk thin film, the incorporation of NCs boosted the PSC PCE to 19.45%.185 They attributed the PCE increase to the enhanced charge collection at the NC-modified absorber/HTM interface owing to the formation of a more favourable energy alignment (Fig. 7b and c), which was in line with the conclusion drawn by Cha et al.58
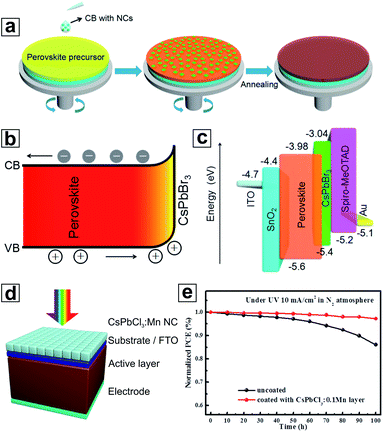 |
| Fig. 7 (a) Schematic representation of the incorporation of CsPbBr3 HP NCs into the FA0.85MA0.15Pb(I0.85Br0.15)3 HP thin film during the antisolvent-dripping step of the HP bulk thin film synthesis. (b) Energy-level diagram of the FA0.85MA0.15Pb(I0.85Br0.15)3 HP bulk thin film after CsPbBr3 NC modification. (c) Schematic diagram of energy levels in the PSCs made using FA0.85MA0.15Pb(I0.85Br0.15)3 HP bulk thin films with the CsPbBr3 NC modification, showing a graded heterojunction structure. (d) Schematic structure of solar cells coated with a thin layer of Mn-doped CsPbCl3 NCs. (e) Stability comparison of the PSCs with and without a Mn-doped CsPbCl3 NC layer under continuous UV irradiation in a N2 atmosphere. (a–c) are reproduced from ref. 185 with permission from the American Chemical Society. (d) and (e) are reproduced from ref. 187 with permission from the American Chemical Society. | |
In a recent study, Zhang et al. demonstrated a more complicated NC interfacial modification strategy through incorporation of a HP nanosheet/nanocube bilayer on top of a HP bulk thin film absorber.186 This proof-of-concept demonstration is solely based on CsPbBrI2 composition but with different morphologies (i.e., thin film, nanosheet, and nanocube). Their bandgap differences resulting from a tuned quantum confinement effect offered a preferred energy alignment in the HP bulk thin film/HTM interface. High VOC of 1.19 V was reached in the PSCs using this complex structure. Additionally, record PCE of 12.39% was reported for the CsPbBrI2 composition which has a relatively large bandgap of 1.9 eV. This study has clearly demonstrated the merits of using HP NCs as modifiers for PSCs.
Photon management
In addition to the interfacial modification using HP NCs on bulk thin films, superior optical properties, especially the PL of HP NCs can also be utilized for improving the PSCs. For example, Wang et al. introduced Mn-doped CsPbCl3 NCs, which served as a light down-conversion layer, onto the illuminated side of MAPbI3 bulk thin film PSCs (Fig. 7d).187 The Mn-doped CsPbCl3 NCs were able to enhance absorption in the UV range of sunlight while remaining transparent in the visible range. As we discussed earlier, Mn-doped CsPbCl3 NCs can efficiently convert absorbed UV light into the visible range by emitting at ∼600 nm with high EQE. This energy down-conversion process from the NC layer can significantly reduce the parasitic absorption by substrates (e.g., glass and TiO2), and thus boost the overall PCE of such devices. In addition, UV light is considered the major factor leading to destabilization of PSCs due to the photocatalytic decomposition of HP bulk thin films caused by TiO2.96 In this work, the reduction of UV light significantly enhanced the stability of PSCs as illustrated in Fig. 7e. In another approach, Chen et al. incorporated a layer of self-assembled CsPbBr3 nanowires on top of an MAPbI3 HP bulk thin film, which could recycle unabsorbed photons through a fluorescence resonance energy transfer process back to the bulk thin film absorber layer.188 They claimed that CsPbBr3 NWs here served as the localized “gratings” for the photon management, which were responsible for the enhancement of PCE by 13% compared with the NC-free case.
Luminescent solar concentrators (LSCs) are optoelectronic devices that concentrate sunlight to a small area, therefore reducing the area of solar cell devices while maintaining high power output.189–191 Mn-doped CsPbCl3 NCs have been used to fabricate large area LSCs.123 The large Stokes shift for Mn dopant PL, as discussed above, almost eliminates reabsorption in the LSCs. Together with recent advances in high-irradiance tolerant PSCs, such HP NC LSCs have great potential as a low-cost solution in practical PV applications.192
5. HP NCs-assembled thin-film PSCs
The other way of incorporating HP NCs into PSCs is to assemble them into NC thin film structures to serve as light absorber layers. Compared with their HP bulk counterparts, the HP NC-assembled thin films offer unique merits. They often exhibit high VOC compared with bulk thin-film PSCs made with the same composition.57 Other important merits include the stabilization of metastable HP phases by microstrain and the feasibility of making bilayer HP thin film structures, which will be discussed below.
The first demonstration of HP NCs-assembled thin film PSCs was reported by Swarnkar et al. in 2016, where they achieved highly stable and efficient PSCs using CsPbI3 HP NCs-assembled thin films.57 From the material aspect, there has been much interest in the CsPbI3 HP for PSC applications due to its superior thermal stability compared with its hybrid organic–inorganic counterparts and its bandgap of around 1.7 eV, which is ideal for tandem PV applications. However, the CsPbI3 HP can easily transform into a non-perovskite orthorhombic phase under ambient conditions, which has been a major hurdle that holds back the development of CsPbI3 PSCs. In this regard, significant efforts have been devoted to developing ways to stabilize CsPbI3 HPs.193–196 In the study by Swarnkar et al., a new fabrication method of CsPbI3 HP thin films was reported based on a layer-by-layer assembly of CsPbI3 HP NCs together with an effective ligand removal process using methyl acetate (Fig. 8a and b).57 The CsPbI3 HP NCs were found to remain in the NC form after the thin film fabrication. They claimed that the lattice strain of the NCs was an important factor that stabilized the cubic phase of CsPbI3 HP NCs, preventing them from transforming into the non-perovskite orthorhombic phase.57 The resultant PSC device showed high PCE of 10.77% with very impressive VOC of 1.23 V for CsPbI3 PSCs. However, this PSC showed relatively low JSC, suggesting that the electronic coupling between NCs is the PSC performance bottleneck for this structure. Potential reasons responsible for the poor electronic coupling could be attributed to the presence of capping ligands causing high electric resistance. In order to overcome this issue, in a following study reported by the same group, thin layers of halide salts (e.g., FAI, MAI, and CsI) were solution-coated on individual NCs in the CsPbI3 NCs-assembled HP NC thin films.197 This technique greatly enhanced the electronic coupling between NCs, as shown by significantly increased JSC from 9.22 to 14.37 mA cm−2 (Fig. 8c).197 In a very recent study, the ligand-removal mechanism using esters was studied by the same group.198 The in situ hydrolysis of methyl acetate was shown to be of great importance. By controlling the humidity and treatment time, oleic acid and oleylamine were effectively replaced by formamidine and acetate. The film-based ligand exchange from bulky ligands (i.e. oleic acid and oleylamine) to short ligands resulted in much higher JOC (15.4 mA cm−2). The weak NC electronic coupling in HP NCs-assembled thin films can also be mitigated by using highly conductive materials, such as carbon nanomaterials as 3D scaffolds to support the NCs-assembled HP thin films. Wang et al. employed μ-graphene to crosslink CsPbI3 NCs and formed a thin film with much improved carrier transport characteristics.199 After the μ-graphene integration, the overall PCE of the PSCs using CsPbI3 NC-assembled thin films was increased from 10.41% to 11.40%. Meanwhile, the μ-graphene integration offered additional merits by enhancing the film stability under moisture and thermal stresses, providing high device stability.
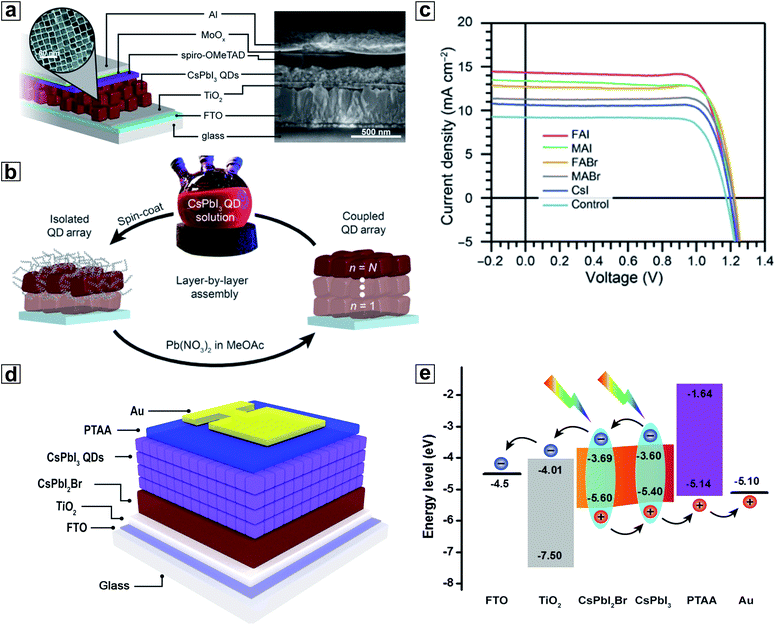 |
| Fig. 8 (a) Schematic representation of the device structure and the cross section scanning electron microscope (SEM) image of the PSC based on a CsPbI3 NC-assembled thin film. (b) Schematic of the film deposition and post-treatment procedure. (c) Current density–voltage scan of the device treated with different salt additives. (d) Schematic illustration of the graded bandgap PSC made using a bilayer of a CsPbI2Br HP bulk thin film and a CsPbI3 HP NC-assembled thin film. (e) Energy level diagram for the device in (d). (a) is reproduced from ref. 57 with permission from the American Association for the Advancement of Science. (b) and (c) are reproduced from ref. 197 with permission from the American Association for the Advancement of Science. (d) and (e) are reproduced from ref. 201 with permission from Elsevier. | |
Compared with their I-based counterparts, CsPbBr3 HPs exhibit enhanced moisture tolerance and phase stability due to the more ideal tolerance factor of the perovskite structure and stronger Pb-X bonds.200 In spite of their relatively low PCE due to the intrinsically high bandgap (2.3 eV), CsPbBr3 PSCs can potentially deliver higher VOC. Akkerman et al. reported a fast, room-temperature synthesis of high-concentration ink containing CsPbBr3 HP NCs capped by short, low-boiling-point ligands.70 This ink was used directly for making the NC-assembled HP thin films with no requirement of lengthy post-synthetic treatments. The PSCs constructed using this ink showed VOC of as high as 1.5 V and JOC of 5.7 mA cm−2. In another study by Palazon et al., CsPbBr3 HP NCs-assembled thin films were first fabricated, followed by a post treatment using thiocyanate ethyl-acetate (EA) solution. The EA solution can efficiently remove ligands, and convert the NC thin film into a compact CsPbBr3 bulk thin film.131 This method addressed challenges in preparing high-quality CsPbBr3 HP bulk thin films by using HP NCs as ‘precursors’, at moderate temperatures. It was found that by using this method, a small amount of the CsPb2Br5 phase was well-dispersed within the final CsPbBr3 HP thin film, leading to an interesting reduction in trap density. As a result, the CsPbBr3 PSC showed PCE of 6.81%, which is higher than that of CsPbBr3 PSCs made by conventional methods.
Tandem solar cell design is an important method to push device PCE beyond the Shockley–Queisser limit.105 To this end, HP NC-assembled thin films can serve as one absorbing layer combined with another layer of either HP bulk thin films or HP NCs with a complementary bandgap gradient. This is primarily attributed to the capability of depositing NC-assembled thin films using solvents which do not interact with the existing HP bulk thin films. Very recently, Bian et al. reported a proof-of-concept demonstration in this regard.201 In their study, they first fabricated a CsPbI2Br HP bulk thin film with a bandgap of 1.91 eV as the main absorber. Afterwards, a CsPbI3 NC-assembled HP thin film with a bandgap of 1.77 eV was deposited. By applying multiple strategies, including Mn cation substitution, thiocyanate capping, and FA treatment, the chemical stability and carrier mobility in the thin film could be greatly improved.201 Finally, a component-graded heterojunction was formed at the CsPbBrI2–CsPbI3 NC interface, leading to a favourable energy alignment for carrier collection as discussed earlier (Fig. 8d and e). This bilayer HP thin film with a gradient bandgap showed effective overall light harvesting and PCE of 14.45% in the final device, setting a record for purely inorganic PSCs at the time.
6. Perspectives
Development of colloidal HP NCs and their application in PSC devices have both seen rapidly growing interest. Only four years following the first synthesis of HP NCs, numerous additional discoveries have been witnessed in the community. However, these exciting discoveries have overshadowed some fundamental challenges and difficulties that need a significant amount of research effort to overcome. Therefore, in this section, we would like to provide our perspectives from both the material production and the device fabrication points of view and delineate some challenges with the potential for future directions in this fascinating research field.
Perspectives in HP NCs materials
The containing of toxic Pb is one outstanding issue for state-of-the-art HP NCs. Pb, as a poisonous heavy-metal element, has been under health and environmental regulations in many countries and regions. As a result, the development of Pb-free HP NCs is a pressing need. Although currently ongoing, the progress of development of Pb-free perovskites has still been incomparable to the development of their Pb-based counterparts. Very recently, exemplified by the Cs2AgBiX6 double perovskite, and the Cs3Sb2X9 and MA3Bi2X9 2D perovskites, Bi and Sb-based HP NCs have shown a number of promising properties including optical properties,72 high NC stability202 and controllable bandgaps.203 Success in the introduction of Bi and Sb into HP NCs presents an exciting future. However, other possible elements, such as Ge, Sn, Ti and In, that could also totally replace Pb while maintaining suitable optoelectronic properties, should not be neglected and additionally need to be paid more research attention.
While the ion exchange reactions offer facile routes toward generation of the HP NCs with mixed anion compositions, the HP NCs with mixed cations have been studied to a much lesser extent. In order to maximize the entropic stabilization effect, synthetic methods to achieve a uniform cation alloy via either direct synthesis or cation exchange need to be further developed with greater detail. Additionally, compared with their film counterparts, the physical and chemical properties of alloy HP NCs are less studied and understood. Photoinduced dealloying has been identified as a crucial source of degradation in alloy PSC films.204 Whether nano-sized confinement and surface ligands of HP NCs can provide sufficient energy barriers that are able to suppress dealloying processes is an interesting topic to explore.
Overcoating shell materials with different band energy alignments relative to the core NC is a major and fruitful research area in the conventional NC field. Inorganic shelling has been proven to be one of the most efficient ways to manipulate, modify, and improve the chemical, physical, and optical properties of NCs.60,205,206 Unfortunately, overcoating the HP NCs has proven to be a great challenge and has yet to be systematically studied and reliably developed. The material instability and ionic chemical nature of the HP NCs are responsible for the remaining hurdle that diminishes their applicability under conventional epitaxial core–shell growth conditions. Novel shell growth strategies under suitable conditions, such as room temperature solution-based atomic layer deposition, or non-epitaxial shell deposition, need to be specifically designed for this special category of NCs.
Capping ligands play a critical important role in both stabilizing the HP NCs in solution or solids, and in their performance following device fabrication. The low current density and large hysteresis in NCs solar cells are largely attributed to the presence of insulating long, organic ligands. A rationally designed ligand system could be the key to solve these problems. Current studies on fabricating NCs-based PSCs mostly rely on complete removal of the long organic ligands using an antisolvent purification procedure. Such a process, however, can cause damage to the integrity of the HP NCs. Therefore, novel methods for ligand removal during the PSC fabrication need to be developed. In another approach, before being solidified into films, HP NCs can be equipped with novel-designed ligands through solution phase ligand exchanges. The HP NCs with device-compatible ligands could then be directly applied in subsequent thin film fabrication without any additional tedious ligand removal processes. In traditional NCs-based solar cells, inorganic ligands such as thiocyanate or metal chalcogenide complexes started to be used in recent years to reduce the inter-particle distances with minimal impact on NCs-assembled film morphology.207 These inorganic molecules, with small size and ionic form, are integratable in PV devices, and should also be considered as a potential ligand set for HP NCs. In addition, the NCs printing technique requires highly concentrated NCs inks with superior particle stability and dispersity. Recent studies have demonstrated that the solubility of NCs relies on not only the chain length of ligands, but also their molecular structure.208 Therefore, modulating the interparticle interactions through ligands may be the key to achieving ideal NCs inks with high concentrations and suitable chemical and physical properties.
Thinking in advance, when aiming towards production and commercialization of HP NCs-based PSCs, HP NCs synthesis on a large scale is unavoidable. Both LARP and hot-injection procedures rely on rapid precursor injection and fast mass transport to reach an instantaneous nucleation followed by NCs growth. Although possible, neither of the two methods are ideal for scaling up to an industrial level at low cost. Therefore, more inert and low-cost precursors that can be applied to easy-to-scale-up methods, such as a non-injection heating up procedure,209,210 together with novel reactor designs could serve as a research direction that needs more development along the way.
Taking advantage of their intrinsic material nature along with more than three decades of NCs synthetic method development, HP NCs have been synthesized almost instantly with high sample uniformity. This high morphological uniformity allows for easy fabrication of HP NC superstructures from individual building blocks through self-assembly strategies. In particular, large-area HP NC superlattice thin films with a well-ordered particle close-packing possess a higher packing density and smoother film morphology than randomly packed ones. The superlattice thin film may show enhanced optoelectronic properties for PSC applications. In addition, the atomic alignments through oriented attachment,211,212 and NC substitutional doping in superlattices,213 have recently proven to be important to dramatically enhance charge transfer and thus improve the electronic properties of NC superlattice thin films. These tricks should be easily transferred to HP NC superlattice systems. Furthermore, given the flexibility in the selection of NC building blocks, HP NCs with different sizes, shapes and compositions, or even mixed with other NC types, in principle can be used for construction of HP NC superstructures with unprecedented complexity. Multi-layer tandem PSCs with highly customized and designed band energy alignments, otherwise inaccessible through HP bulk materials, become feasible. All of these studies are currently lacking in the field. Exciting discoveries should be anticipated.
Perspectives in integration of HP NCs in PSCs
Rich interactions of HP NCs with light offer great potential for their application in optoelectronic devices. Despite their superior intrinsic properties as we discussed, HP NCs need to be efficiently integrated into PSC devices with well-customized designs. As shown in Fig. 9, HP NCs can be applied in PSCs as one of the following three components: (i) the modifiers/additives for HP bulk thin films, (ii) the sole building blocks of NCs-assembled thin film light-absorbers, or (iii) the added building blocks for making graded bandgap PSCs. While some research has been done in these directions as summarized above, there is still much room to explore the potential of building PSCs with performances beyond those of the state-of-the-art devices.
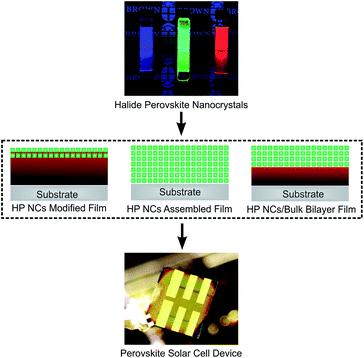 |
| Fig. 9 Schematic diagram illustrating the connection of HP NCs to solar cell devices via making three types of thin films: (i) HP NCs modified film; (ii) HP NCs assembled film; (iii) HP NCs/bulk bilayer film. | |
For the use of HP NCs as modifiers, the following research directions may emerge. First, current research has been limited to enhancing the surfaces/interfaces of the bulk HP thin films in PSCs. In fact, grain boundaries in HP bulk thin films are one of the most prominent microstructures that play a vital role in the PV performance and device stability. The congeneric nature of HP NCs allows for the modification of bulk thin film grain boundaries at minimal cost. The defects at the grain boundaries can be passivated and the band diagram may be tuned in our favour. Additionally, the HP NC-modified grain boundary could even be possibly endowed with new optical/electronic functions. Second, as discussed, the wide tunability in morphology and composition makes HP NCs ideal ‘seed’ materials for solution crystallization of HP bulk thin films. Nanocubes, nanosheets, nanowires and their ordered self-assemblies can be synthesized. They can then be introduced in the HP thin film crystallization process as heterogeneous nucleation sites. These pre-engineered NC “seeds” may help guide the HP crystallization in a controllable manner resulting in precise control over the final thin film microstructures. Nevertheless, this is still challenging considering the sensitivity of HP NCs in the perovskite precursor solutions. Such difficulty may be lifted through ligand-engineering of the HP NCs using ionic ligands or through the synthesis of polar-solvent-tolerant NCs. Third, HP NCs can also serve as dopants in the HP bulk thin films. Through innovative deposition strategies, HP NCs may be deliberately incorporated at certain locations in the bulk thin films, enabling site-specific doping. This position-controlled HP NC doping may improve the electronic properties of the HP bulk thin films, and thus the performance of the resultant PSCs.
For the use of HP NCs as the sole building blocks of the light absorber layer in PSCs, immense opportunities remain for further investigation in this direction. First, the state-of-the-art fabrication methods of HP NCs-assembled thin films are generally very tedious and are not suitable for commercial PSC production. The bottleneck for the processing of NCs-assembled thin films is the necessity of repeated deposition and ligand-washing steps, which is mainly due to the relatively low concentration of the NC inks and the unfavourably long organic ligands. By using high-concentration NC inks with short inorganic ligands as discussed earlier, the fabrication procedure can be dramatically simplified. Very recently, highly efficient LEDs were fabricated using an FAPbBr3 NC film that was synthesized by an in situ LARP process during spin-coating.214 This study may inspire new strategies for HP NC thin film fabrication in PSCs. In addition to the spin-coating method, many scalable deposition protocols, such as spray-coating, doctor-blading, and slot-die coating, may be applied for making HP NCs-assembled thin films. This represents a completely new research paradigm. Second, the as-studied HP NCs-assembled thin films and PSCs have previously only focused on using the all-inorganic HP compositions, such as CsPbI3 and CsPbBr3. These compositions exhibit bandgaps that are too large for the operation of single-junction solar cells. Therefore, lower-band-gap HP-NCs-assembled thin films need to be prepared for improving the PCE of PSCs. For example, FAPbI3 HPs show a much smaller bandgap than CsPbI3 HPs and exhibit a similar perovskite-to-non-perovskite phase transition behaviour to CsPbI3 HPs under ambient conditions. It would be interesting to see whether the NC-induced phase stabilization also applies and whether improved PCE and stability can be simultaneously achieved in the FAPbI3 NCs-assembled thin film PSCs. In addition, HP NCs may also enable the fabrication of other thin films with compositions unstable in their bulk phases (e.g. Cs2AgBiI6), which can be particularly important for developing novel Pb-free PSCs. Third, as discussed already, the electronic coupling between HP NCs is of vital importance for good charge transport dynamics in HP NCs-assembled superlattice thin films. While it has been demonstrated that overcoating NCs with suitable shell materials is a viable method for enhancing the electronic coupling of HP-NC-films,197 it may be feasible to use core–shell structured HP NCs for direct assembly of HP NC superstructured thin films with high charge mobility.
The ability to serve as the building blocks for making graded-bandgap PSCs is one of the most unique features of HP NCs. This is mainly owing to the orthogonal solvents for the deposition of HP NCs and HP bulk thin films. While a proof-of-concept study of a graded-bandgap CsPbI2+xBr1−x PSC has been reported,186 the optical bandgaps and film structures in this reported PSC device are far from being optimized. Continued research in this direction offers vast opportunities for generating PSCs with PCEs approaching the Shockley–Queisser limit.
7. Concluding remarks
The rapid development of HP materials brings exciting ideas and encouraging applications in the field of optoelectronics. The recently developed synthetic approaches for monodisperse HP NCs enabled in-depth studies of these materials for potential PSC applications. The use of HP NCs in PSC applications takes advantage of their tunable electronic properties, their well-defined crystal domains, and their crystal structural and compositional similarities to bulk HP materials. HP NCs have shown promising results both as thin film modifiers, and as light absorbers in PSC devices. We believe that this perspective article can not only provide insights into the as-made discoveries, but more importantly delineate some future directions toward connecting HP NCs to PSCs. To further advance this fascinating research direction, improvements in NC stability and surface ligand states are highly desirable. With a library of HP NC building blocks and newly developed synthetic tools, novel PSC structures and PV fabrication techniques with the integration of HP NCs are likely to emerge.
Conflicts of interest
The authors declare no conflicts of interest.
Acknowledgements
Y. Zhang, Y. Zhou and O. Chen acknowledge the support from the National Science Foundation (OIA-1538893) and Brown University's Institute for Molecular and Nanoscale Innovation Seed Program. Y. Zhou and Y. Zhang also acknowledge Prof. N. P. Padture of Brown University for the insightful discussion and the generous support. H. Yang and O. Chen acknowledge the support from the Brown University startup fund. O. Chen also acknowledges the support from the Senior Visiting Scholar Foundation of Key Laboratory at Fudan University. K. Hills-Kimball is supported by the U.S. Department of Education, GAANN Award (P200A150037).
Notes and references
- D. Weber, Z. Naturforsch. B Chem. Sci., 1978, 33, 1443–1445 Search PubMed.
- H. L. Wells, Z. Anorg. Chem., 1893, 3, 195–210 CrossRef.
- C. H. R. K. N. Møller, Nature, 1958, 182, 1436 CrossRef.
- C. C. Stoumpos, C. D. Malliakas and M. G. Kanatzidis, Inorg. Chem., 2013, 52, 9019–9038 CrossRef CAS PubMed.
- I. Chung, J. H. Song, J. Im, J. Androulakis, C. D. Malliakas, H. Li, A. J. Freeman, J. T. Kenney and M. G. Kanatzidis, J. Am. Chem. Soc., 2012, 134, 8579–8587 CrossRef CAS PubMed.
- C. C. Stoumpos, L. Frazer, D. J. Clark, Y. S. Kim, S. H. Rhim, A. J. Freeman, J. B. Ketterson, J. I. Jang and M. G. Kanatzidis, J. Am. Chem. Soc., 2015, 137, 6804–6819 CrossRef CAS PubMed.
- J. Calabrese, N. L. Jones, R. L. Harlow, N. Herron, D. L. Thorn and Y. Wang, J. Am. Chem. Soc., 1991, 113, 2328–2330 CrossRef CAS.
- T. Goto, H. Makino, T. Yao, C. H. Chia, T. Makino, Y. Segawa, G. A. Mousdis and G. C. Papavassiliou, Phys. Rev. B, 2006, 73, 115206 CrossRef.
- D. B. Mitzi, S. Wang, C. A. Feild, C. A. Chess and A. M. Guloy, Science, 1995, 267, 1473–1476 CrossRef CAS PubMed.
- R. Burnus and G. Meyer, Z. Anorg. Allg. Chem., 1991, 602, 31–37 CrossRef CAS.
- B. Saparov, F. Hong, J. P. Sun, H. S. Duan, W. Meng, S. Cameron, I. G. Hill, Y. Yan and D. B. Mitzi, Chem. Mater., 2015, 27, 5622–5632 CrossRef CAS.
- B. Lee, C. C. Stoumpos, N. Zhou, F. Hao, C. Malliakas, C. Y. Yeh, T. J. Marks, M. G. Kanatzidis and R. P. H. Chang, J. Am. Chem. Soc., 2014, 136, 15379–15385 CrossRef CAS PubMed.
- M.-G. Ju, M. Chen, Y. Zhou, J. Dai, L. Ma, N. P. Padture and X. C. Zeng, Joule, 2018, 2, 1231–1241 CrossRef CAS.
- Y. Zhou, O. S. Game, S. Pang and N. P. Padture, J. Phys. Chem. Lett., 2015, 6, 4827–4839 CrossRef CAS PubMed.
- M. Era, S. Morimoto, T. Tsutsui and S. Saito, Appl. Phys. Lett., 1994, 65, 676–678 CrossRef CAS.
- Z.-K. Tan, R. S. Moghaddam, M. L. Lai, P. Docampo, R. Higler, F. Deschler, M. Price, A. Sadhanala, L. M. Pazos, D. Credgington, F. Hanusch, T. Bein, H. J. Snaith and R. H. Friend, Nat. Nanotechnol., 2014, 9, 687–692 CrossRef CAS PubMed.
- G. Xing, N. Mathews, S. S. Lim, N. Yantara, X. Liu, D. Sabba, M. Grätzel, S. Mhaisalkar and T. C. Sum, Nat. Mater., 2014, 13, 476–480 CrossRef CAS PubMed.
- F. Deschler, M. Price, S. Pathak, L. E. Klintberg, D. D. Jarausch, R. Higler, S. Hüttner, T. Leijtens, S. D. Stranks, H. J. Snaith, M. Atatüre, R. T. Phillips and R. H. Friend, J. Phys. Chem. Lett., 2014, 5, 1421–1426 CrossRef CAS PubMed.
- L. Dou, Y. Yang, J. You, Z. Hong, W.-H. Chang, G. Li and Y. Yang, Nat. Commun., 2014, 5, 5404 CrossRef CAS PubMed.
- C. C. Stoumpos, C. D. Malliakas, J. A. Peters, Z. Liu, M. Sebastian, J. Im, T. C. Chasapis, A. C. Wibowo, D. Y. Chung, A. J. Freeman, B. W. Wessels and M. G. Kanatzidis, Cryst. Growth Des., 2013, 13, 2722–2727 CrossRef CAS.
- H. Zhu, Y. Fu, F. Meng, X. Wu, Z. Gong, Q. Ding, M. V. Gustafsson, M. T. Trinh, S. Jin and X.-Y. Zhu, Nat. Mater., 2015, 14, 636–642 CrossRef CAS PubMed.
- W. Pan, H. Wu, J. Luo, Z. Deng, C. Ge, C. Chen, X. Jiang, W.-J. Yin, G. Niu, L. Zhu, L. Yin, Y. Zhou, Q. Xie, X. Ke, M. Sui and J. Tang, Nat. Photonics, 2017, 11, 726–732 CrossRef CAS.
- S. Yakunin, M. Sytnyk, D. Kriegner, S. Shrestha, M. Richter, G. J. Matt, H. Azimi, C. J. Brabec, J. Stangl, M. V. Kovalenko and W. Heiss, Nat. Photonics, 2015, 9, 444–449 CrossRef CAS PubMed.
- H. Wei, Y. Fang, P. Mulligan, W. Chuirazzi, H.-H. Fang, C. Wang, B. R. Ecker, Y. Gao, M. A. Loi, L. Cao and J. Huang, Nat. Photonics, 2016, 10, 333–339 CrossRef CAS.
- A. Kojima, K. Teshima, Y. Shirai and T. Miyasaka, J. Am. Chem. Soc., 2009, 131, 6050–6051 CrossRef CAS PubMed.
- W. S. Yang, B.-W. Park, E. H. Jung, N. J. Jeon, Y. C. Kim, D. U. Lee, S. S. Shin, J. Seo, E. K. Kim, J. H. Noh and S. Il Seok, Science, 2017, 356, 1376–1379 CrossRef CAS PubMed.
- NREL's “Best Research-Cell Efficiencies” Chart, https://www.nrel.gov/pv/assets/pdfs/pv-efficiencies-07-17-2018.pdf, accessed on August 24, 2018.
- S. De Wolf, J. Holovsky, S. J. Moon, P. Löper, B. Niesen, M. Ledinsky, F. J. Haug, J. H. Yum and C. Ballif, J. Phys. Chem. Lett., 2014, 5, 1035–1039 CrossRef CAS PubMed.
- E. Edri, S. Kirmayer, M. Kulbak, G. Hodes and D. Cahen, J. Phys. Chem. Lett., 2014, 5, 429–433 CrossRef CAS PubMed.
- J. H. Noh, S. H. Im, J. H. Heo, T. N. Mandal and S. Il Seok, Nano Lett., 2013, 13, 1764–1769 CrossRef CAS PubMed.
- C. S. Ponseca, T. J. Savenije, M. Abdellah, K. Zheng, A. Yartsev, T. Pascher, T. Harlang, P. Chabera, T. Pullerits, A. Stepanov, J.-P. Wolf and V. Sundström, J. Am. Chem. Soc., 2014, 136, 5189–5192 CrossRef CAS PubMed.
- Q. Dong, Y. Fang, Y. Shao, P. Mulligan, J. Qiu, L. Cao and J. Huang, Science, 2015, 347, 967–970 CrossRef CAS PubMed.
- J. Burschka, N. Pellet, S. J. Moon, R. Humphry-Baker, P. Gao, M. K. Nazeeruddin and M. Grätzel, Nature, 2013, 499, 316–319 CrossRef CAS PubMed.
- D. Shi, V. Adinolfi, R. Comin, M. Yuan, E. Alarousu, A. Buin, Y. Chen, S. Hoogland, A. Rothenberger, K. Katsiev, Y. Losovyj, X. Zhang, P. A. Dowben, O. F. Mohammed, E. H. Sargent and O. M. Bakr, Science, 2015, 347, 519–522 CrossRef CAS PubMed.
- M. Liu, M. B. Johnston and H. J. Snaith, Nature, 2013, 501, 395–398 CrossRef CAS PubMed.
- W. Li, J. Fan, J. Li, Y. Mai and L. Wang, J. Am. Chem. Soc., 2015, 137, 10399–10405 CrossRef CAS PubMed.
- Y. Zhou, M. Yang, W. Wu, A. L. Vasiliev, K. Zhu and N. P. Padture, J. Mater. Chem. A, 2015, 3, 8178–8184 RSC.
- M. M. Lee, J. Teuscher, T. Miyasaka, T. N. Murakami and H. J. Snaith, Science, 2012, 338, 643–647 CrossRef CAS PubMed.
- P. Docampo, J. M. Ball, M. Darwich, G. E. Eperon and H. J. Snaith, Nat. Commun., 2013, 4, 1–6 Search PubMed.
- C. D. Bailie, M. G. Christoforo, J. P. Mailoa, A. R. Bowring, E. L. Unger, W. H. Nguyen, J. Burschka, N. Pellet, J. Z. Lee, M. Grätzel, R. Noufi, T. Buonassisi, A. Salleo and M. D. McGehee, Energy Environ. Sci., 2015, 8, 956–963 RSC.
- H. Huang, A. S. Susha, S. V. Kershaw, T. F. Hung and A. L. Rogach, Adv. Sci., 2015, 2, 1500194 CrossRef PubMed.
- F. Liu, Y. Zhang, C. Ding, S. Kobayashi, T. Izuishi, N. Nakazawa, T. Toyoda, T. Ohta, S. Hayase, T. Minemoto, K. Yoshino, S. Dai and Q. Shen, ACS Nano, 2017, 11, 10373–10383 CrossRef CAS PubMed.
- G. Nedelcu, L. Protesescu, S. Yakunin, M. I. Bodnarchuk, M. J. Grotevent and M. V. Kovalenko, Nano Lett., 2015, 15, 5635–5640 CrossRef CAS PubMed.
- Q. A. Akkerman, V. D'Innocenzo, S. Accornero, A. Scarpellini, A. Petrozza, M. Prato and L. Manna, J. Am. Chem. Soc., 2015, 137, 10276–10281 CrossRef CAS PubMed.
- F. Palazon, F. Di Stasio, S. Lauciello, R. Krahne, M. Prato and L. Manna, J. Mater. Chem. C, 2016, 4, 9179–9182 RSC.
- W. van der Stam, J. J. Geuchies, T. Altantzis, K. H. W. van den Bos, J. D. Meeldijk, S. Van Aert, S. Bals, D. Vanmaekelbergh and C. de Mello Donega, J. Am. Chem. Soc., 2017, 139, 4087–4097 CrossRef CAS PubMed.
- Z. Liu, Y. Bekenstein, X. Ye, S. C. Nguyen, J. Swabeck, D. Zhang, S.-T. Lee, P. Yang, W. Ma and A. P. Alivisatos, J. Am. Chem. Soc., 2017, 139, 5309–5312 CrossRef CAS PubMed.
- B. Wang, C. Zhang, S. Huang, Z. Li, L. Kong, L. Jin, J. Wang, K. Wu and L. Li, ACS Appl. Mater. Interfaces, 2018, 10, 23303–23310 CrossRef CAS PubMed.
- J. Song, J. Li, X. Li, L. Xu, Y. Dong and H. Zeng, Adv. Mater., 2015, 27, 7162–7167 CrossRef CAS PubMed.
- Z. Shi, Y. Li, Y. Zhang, Y. Chen, X. Li, D. Wu, T. Xu, C. Shan and G. Du, Nano Lett., 2017, 17, 313–321 CrossRef CAS PubMed.
- H. Cho, S.-H. Jeong, M.-H. Park, Y.-H. Kim, C. Wolf, C.-L. Lee, J. H. Heo, A. Sadhanala, N. Myoung, S. Yoo, S. H. Im, R. H. Friend and T.-W. Lee, Science, 2015, 350, 1222–1225 CrossRef CAS PubMed.
- F. Krieg, S. T. Ochsenbein, S. Yakunin, S. ten Brinck, P. Aellen, A. Süess, B. Clerc, D. Guggisberg, O. Nazarenko, Y. Shynkarenko, S. Kumar, C.-J. Shih, I. Infante and M. V. Kovalenko, ACS Energy Lett., 2018, 3, 641–646 CrossRef CAS PubMed.
- J. Kang and L.-W. Wang, J. Phys. Chem. Lett., 2017, 8, 489–493 CrossRef CAS PubMed.
- M. Lorenzon, L. Sortino, Q. Akkerman, S. Accornero, J. Pedrini, M. Prato, V. Pinchetti, F. Meinardi, L. Manna and S. Brovelli, Nano Lett., 2017, 17, 3844–3853 CrossRef CAS PubMed.
- Y. Dong, T. Qiao, D. Kim, D. Parobek, D. Rossi and D. H. Son, Nano Lett., 2018, 18, 3716–3722 CrossRef CAS PubMed.
- L. Protesescu, S. Yakunin, M. I. Bodnarchuk, F. Bertolotti, N. Masciocchi, A. Guagliardi and M. V. Kovalenko, J. Am. Chem. Soc., 2016, 138, 14202–14205 CrossRef CAS PubMed.
- A. Swarnkar, A. R. Marshall, E. M. Sanehira, B. D. Chernomordik, D. T. Moore, J. A. Christians, T. Chakrabarti and J. M. Luther, Science, 2016, 354, 92–95 CrossRef CAS PubMed.
- M. Cha, P. Da, J. Wang, W. Wang, Z. Chen, F. Xiu, G. Zheng and Z.-S. Wang, J. Am. Chem. Soc., 2016, 138, 8581–8587 CrossRef CAS PubMed.
- C. B. Murray, D. J. Norris and M. G. Bawendi, J. Am. Chem. Soc., 1993, 115, 8706–8715 CrossRef CAS.
- O. Chen, H. Wei, A. Maurice, M. Bawendi and P. Reiss, MRS Bull., 2013, 38, 696–702 CrossRef CAS.
- R. Plass, S. Pelet, J. Krueger, M. Grätzel and U. Bach, J. Phys. Chem. B, 2002, 106, 7578–7580 CrossRef CAS.
- K. Barnham, J. L. Marques, J. Hassard and P. O'Brien, Appl. Phys. Lett., 2000, 76, 1197–1199 CrossRef CAS.
- S. Fig, Nature, 2002, 420, 3–6 Search PubMed.
- I. L. Medintz, H. T. Uyeda, E. R. Goldman and H. Mattoussi, Nat. Mater., 2005, 4, 435–446 CrossRef CAS PubMed.
- L. C. Schmidt, A. Pertegás, S. González-Carrero, O. Malinkiewicz, S. Agouram, G. Mínguez Espallargas, H. J. Bolink, R. E. Galian and J. Pérez-Prieto, J. Am. Chem. Soc., 2014, 136, 850–853 CrossRef CAS PubMed.
- F. Zhang, H. Zhong, C. Chen, X. Wu, X. Hu, H. Huang, J. Han, B. Zou and Y. Dong, ACS Nano, 2015, 9, 4533–4542 CrossRef CAS PubMed.
- S. Sun, D. Yuan, Y. Xu, A. Wang and Z. Deng, ACS Nano, 2016, 10, 3648–3657 CrossRef CAS PubMed.
- M. C. Weidman, M. Seitz, S. D. Stranks and W. A. Tisdale, ACS Nano, 2016, 10, 7830–7839 CrossRef CAS PubMed.
- S. Bhaumik, S. A. Veldhuis, Y. F. Ng, M. Li, S. K. Muduli, T. C. Sum, B. Damodaran, S. Mhaisalkar and N. Mathews, Chem. Commun., 2016, 52, 7118–7121 RSC.
- Q. A. Akkerman, M. Gandini, F. Di Stasio, P. Rastogi, F. Palazon, G. Bertoni, J. M. Ball, M. Prato, A. Petrozza and L. Manna, Nat. Energy, 2016, 2, 16194 CrossRef.
- M. Leng, Z. Chen, Y. Yang, Z. Li, K. Zeng, K. Li, G. Niu, Y. He, Q. Zhou and J. Tang, Angew. Chem., Int. Ed., 2016, 55, 15012–15016 CrossRef CAS PubMed.
- J. Zhang, Y. Yang, H. Deng, U. Farooq, X. Yang, J. Khan, J. Tang and H. Song, ACS Nano, 2017, 11, 9294–9302 CrossRef CAS PubMed.
- F. Zhang, S. Huang, P. Wang, X. Chen, S. Zhao, Y. Dong and H. Zhong, Chem. Mater., 2017, 29, 3793–3799 CrossRef CAS.
- L. Protesescu, S. Yakunin, M. I. Bodnarchuk, F. Krieg, R. Caputo, C. H. Hendon, R. X. Yang, A. Walsh and M. V. Kovalenko, Nano Lett., 2015, 15, 3692–3696 CrossRef CAS PubMed.
- G. Almeida, L. Goldoni, Q. Akkerman, Z. Dang, A. H. Khan, S. Marras, I. Moreels and L. Manna, ACS Nano, 2018, 12, 1704–1711 CrossRef CAS PubMed.
- M. Imran, V. Caligiuri, M. Wang, L. Goldoni, M. Prato, R. Krahne, L. De Trizio and L. Manna, J. Am. Chem. Soc., 2018, 140, 2656–2664 CrossRef CAS PubMed.
- Y. Bekenstein, B. A. Koscher, S. W. Eaton, P. Yang and A. P. Alivisatos, J. Am. Chem. Soc., 2015, 137, 16008–16011 CrossRef CAS PubMed.
- Q. A. Akkerman, S. G. Motti, A. R. Srimath Kandada, E. Mosconi, V. D'Innocenzo, G. Bertoni, S. Marras, B. A. Kamino, L. Miranda, F. De Angelis, A. Petrozza, M. Prato and L. Manna, J. Am. Chem. Soc., 2016, 138, 1010–1016 CrossRef CAS PubMed.
- M. Imran, F. Di Stasio, Z. Dang, C. Canale, A. H. Khan, J. Shamsi, R. Brescia, M. Prato and L. Manna, Chem. Mater., 2016, 28, 6450–6454 CrossRef CAS PubMed.
- X. Sheng, G. Chen, C. Wang, W. Wang, J. Hui, Q. Zhang, K. Yu, W. Wei, M. Yi, M. Zhang, Y. Deng, P. Wang, X. Xu, Z. Dai, J. Bao and X. Wang, Adv. Funct. Mater., 2018, 3, 1800283 CrossRef.
- Z.-J. Li, E. Hofman, A. H. Davis, M. M. Maye and W. Zheng, Chem. Mater., 2018, 30, 3854–3860 CrossRef CAS.
- D. Zhang, S. W. Eaton, Y. Yu, L. Dou and P. Yang, J. Am. Chem. Soc., 2015, 137, 9230–9233 CrossRef CAS PubMed.
- M. V. Kovalenko and M. I. Bodnarchuk, Chim. Int. J. Chem., 2017, 71, 461–470 CrossRef CAS PubMed.
- K.-H. Wang, J.-N. Yang, Q.-K. Ni, H.-B. Yao and S.-H. Yu, Langmuir, 2018, 34, 595–602 CrossRef CAS PubMed.
- Y. Tong, E.-P. Yao, A. Manzi, E. Bladt, K. Wang, M. Döblinger, S. Bals, P. Müller-Buschbaum, A. S. Urban, L. Polavarapu and J. Feldmann, Adv. Mater., 2018, 30, 1801117 CrossRef PubMed.
- L. Protesescu, S. Yakunin, S. Kumar, J. Bär, F. Bertolotti, N. Masciocchi, A. Guagliardi, M. Grotevent, I. Shorubalko, M. I. Bodnarchuk, C.-J. Shih and M. V. Kovalenko, ACS Nano, 2017, 11, 3119–3134 CrossRef CAS PubMed.
- W. Zhai, J. Lin, Q. Li, K. Zheng, Y. Huang, Y. Yao, X. He, L. Li, C. Yu, C. Liu, Y. Fang, Z. Liu and C. Tang, Chem. Mater., 2018, 30, 3714–3721 CrossRef CAS.
- M. Chen, Y. Zou, L. Wu, Q. Pan, D. Yang, H. Hu, Y. Tan, Q. Zhong, Y. Xu, H. Liu, B. Sun and Q. Zhang, Adv. Funct. Mater., 2017, 27, 1701121 CrossRef.
- Z.-Y. Zhu, Q.-Q. Yang, L.-F. Gao, L. Zhang, A.-Y. Shi, C.-L. Sun, Q. Wang and H.-L. Zhang, J. Phys. Chem. Lett., 2017, 8, 1610–1614 CrossRef CAS PubMed.
- S. Yun, A. Kirakosyan, S.-G. Yoon and J. Choi, ACS Sustain. Chem. Eng., 2018, 6, 3733–3738 CrossRef CAS.
- L. Protesescu, S. Yakunin, O. Nazarenko, D. N. Dirin and M. V. Kovalenko, ACS Appl. Nano Mater., 2018, 1, 1300–1308 CrossRef CAS PubMed.
- D. M. Jang, D. H. Kim, K. Park, J. Park, J. W. Lee and J. K. Song, J. Mater. Chem. C, 2016, 4, 10625–10629 RSC.
- J. Almutlaq, J. Yin, O. F. Mohammed and O. M. Bakr, J. Phys. Chem. Lett., 2018, 9, 4131–4138 CrossRef CAS PubMed.
- J. S. Bechtel and A. Van der Ven, Phys. Rev. Mater., 2018, 2, 045401 CrossRef.
- S. Yang, W. Fu, Z. Zhang, H. Chen and C.-Z. Li, J. Mater. Chem. A, 2017, 5, 11462–11482 RSC.
- M. I. Asghar, J. Zhang, H. Wang and P. D. Lund, Renew. Sustain. Energy Rev., 2017, 77, 131–146 CrossRef CAS.
- K. Chen, X. Deng, G. Dodekatos and H. Tüysüz, J. Am. Chem. Soc., 2017, 139, 12267–12273 CrossRef CAS PubMed.
- S. Huang, Z. Li, L. Kong, N. Zhu, A. Shan and L. Li, J. Am. Chem. Soc., 2016, 138, 5749–5752 CrossRef CAS PubMed.
- X. Di, Z. Hu, J. Jiang, M. He, L. Zhou, W. Xiang and X. Liang, Chem. Commun., 2017, 53, 11068–11071 RSC.
- F. Di Stasio, S. Christodoulou, N. Huo and G. Konstantatos, Chem. Mater., 2017, 29, 7663–7667 CrossRef.
- J. Y. Woo, Y. Kim, J. Bae, T. G. Kim, J. W. Kim, D. C. Lee and S. Jeong, Chem. Mater., 2017, 29, 7088–7092 CrossRef CAS.
- V. M. Goldschmidt, Naturwissenschaften, 1926, 14, 477–485 CrossRef CAS.
- C. Yi, J. Luo, S. Meloni, A. Boziki, N. Ashari-Astani, C. Grätzel, S. M. Zakeeruddin, U. Röthlisberger and M. Grätzel, Energy Environ. Sci., 2016, 9, 656–662 RSC.
- J. S. Manser, J. A. Christians and P. V. Kamat, Chem. Rev., 2016, 116, 12956–13008 CrossRef CAS PubMed.
- W. Shockley and H. J. Queisser, J. Appl. Phys., 1961, 32, 510–519 CrossRef CAS.
- Y. Zhou, Z. Zhou, M. Chen, Y. Zong, J. Huang, S. Pang and N. P. Padture, J. Mater. Chem. A, 2016, 4, 17623–17635 RSC.
- Z. Xiao, Y. Zhou, H. Hosono, T. Kamiya and N. P. Padture, Chem.–Eur. J., 2018, 24, 2305–2316 CrossRef CAS PubMed.
- T. C. Jellicoe, J. M. Richter, H. F. J. Glass, M. Tabachnyk, R. Brady, S. E. Dutton, A. Rao, R. H. Friend, D. Credgington, N. C. Greenham and M. L. Böhm, J. Am. Chem. Soc., 2016, 138, 2941–2944 CrossRef CAS PubMed.
- A. B. Wong, Y. Bekenstein, J. Kang, C. S. Kley, D. Kim, N. A. Gibson, D. Zhang, Y. Yu, S. R. Leone, L. W. Wang, A. P. Alivisatos and P. Yang, Nano Lett., 2018, 18, 2060–2066 CrossRef CAS PubMed.
- X. Wu, W. Song, Q. Li, X. Zhao, D. He and Z. Quan, Chem.–Asian J., 2018, 13, 1654–1659 CrossRef CAS PubMed.
- K. Hills-Kimball, Y. Nagaoka, C. Cao, E. Chaykovsky and O. Chen, J. Mater. Chem. C, 2017, 5, 5680–5684 RSC.
- I. E. Castelli, J. M. García-Lastra, K. S. Thygesen and K. W. Jacobsen, APL Mater., 2014, 2, 081514 CrossRef.
- W. Liu, Q. Lin, H. Li, K. Wu, I. Robel, J. M. Pietryga and V. I. Klimov, J. Am. Chem. Soc., 2016, 138, 14954–14961 CrossRef CAS PubMed.
- A. De, N. Mondal and A. Samanta, Nanoscale, 2017, 9, 16722–16727 RSC.
- W. J. Mir, M. Jagadeeswararao, S. Das and A. Nag, ACS Energy Lett., 2017, 2, 537–543 CrossRef CAS.
- D. Parobek, Y. Dong, T. Qiao and D. H. Son, Chem. Mater., 2018, 30, 2939–2944 CrossRef CAS.
- G. Huang, C. Wang, S. Xu, S. Zong, J. Lu, Z. Wang, C. Lu and Y. Cui, Adv. Mater., 2017, 1700095, 10–14 Search PubMed.
- G. Pan, X. Bai, D. Yang, X. Chen, P. Jing, S. Qu, L. Zhang, D. Zhou, J. Zhu, W. Xu, B. Dong and H. Song, Nano Lett., 2017, 17, 8005–8011 CrossRef CAS PubMed.
- D. Zhou, D. Liu, G. Pan, X. Chen, D. Li, W. Xu, X. Bai and H. Song, Adv. Mater., 2017, 29, 1–6 Search PubMed.
- T. Milstein, D. Kroupa and D. R. Gamelin, Nano Lett., 2018, 18, 3792–3799 CrossRef CAS PubMed.
- R. Begum, M. R. Parida, A. L. Abdelhady, B. Murali, N. M. Alyami, G. H. Ahmed, M. N. Hedhili, O. M. Bakr and O. F. Mohammed, J. Am. Chem. Soc., 2017, 139, 731–737 CrossRef CAS PubMed.
- K. Du, Q. Tu, X. Zhang, Q. Han, J. Liu, S. Zauscher and D. B. Mitzi, Inorg. Chem., 2017, 56, 9291–9302 CrossRef CAS PubMed.
- F. Meinardi, Q. A. Akkerman, F. Bruni, S. Park, M. Mauri, Z. Dang, L. Manna and S. Brovelli, ACS Energy Lett., 2017, 2, 2368–2377 CrossRef CAS.
- S. Zou, Y. Liu, J. Li, C. Liu, R. Feng, F. Jiang, Y. Li, J. Song, H. Zeng, M. Hong and X. Chen, J. Am. Chem. Soc., 2017, 139, 11443–11450 CrossRef CAS PubMed.
- S. Yang, F. Zhang, J. Tai, Y. Li, Y. Yang, H. Wang, J. Zhang, Z. Xie, B. Xu, H. Zhong, K. Liu and B. Yang, Nanoscale, 2018, 10, 5820–5826 RSC.
- L. Gomez, C. de Weerd, J. L. Hueso and T. Gregorkiewicz, Nanoscale, 2017, 9, 631–636 RSC.
- H. C. Wang, S. Y. Lin, A. C. Tang, B. P. Singh, H. C. Tong, C. Y. Chen, Y. C. Lee, T. L. Tsai and R. S. Liu, Angew. Chem., Int. Ed., 2016, 55, 7924–7929 CrossRef CAS PubMed.
- D. N. Dirin, L. Protesescu, D. Trummer, I. V. Kochetygov, S. Yakunin, F. Krumeich, N. P. Stadie and M. V. Kovalenko, Nano Lett., 2016, 16, 5866–5874 CrossRef CAS PubMed.
- Q. A. Akkerman, S. Park, E. Radicchi, F. Nunzi, E. Mosconi, F. De Angelis, R. Brescia, P. Rastogi, M. Prato and L. Manna, Nano Lett., 2017, 17, 1924–1930 CrossRef CAS PubMed.
- S. K. Balakrishnan and P. V. Kamat, Chem. Mater., 2018, 30, 74–78 CrossRef CAS.
- F. Palazon, S. Dogan, S. Marras, F. Locardi, I. Nelli, P. Rastogi, M. Ferretti, M. Prato, R. Krahne and L. Manna, J. Phys. Chem. C, 2017, 121, 11956–11961 CrossRef CAS.
- X. Peng, Acc. Chem. Res., 2010, 43, 1387–1395 CrossRef CAS PubMed.
- J. Park, H. Zheng, Y. Jun and A. P. Alivisatos, J. Am. Chem. Soc., 2009, 131, 13943–13945 CrossRef CAS PubMed.
- S. E. Creutz, E. N. Crites, M. C. De Siena and D. R. Gamelin, Chem. Mater., 2018, 30, 4887–4891 CrossRef CAS.
- D. M. Jang, K. Park, D. H. Kim, J. Park, F. Shojaei, H. S. Kang, J. P. Ahn, J. W. Lee and J. K. Song, Nano Lett., 2015, 15, 5191–5199 CrossRef CAS PubMed.
- B. A. Koscher, N. D. Bronstein, J. H. Olshansky, Y. Bekenstein and A. P. Alivisatos, J. Am. Chem. Soc., 2016, 138, 12065–12068 CrossRef CAS PubMed.
- D. Zhang, Y. Yang, Y. Bekenstein, Y. Yu, N. A. Gibson, A. B. Wong, S. W. Eaton, N. Kornienko, Q. Kong, M. Lai, A. P. Alivisatos, S. R. Leone and P. Yang, J. Am. Chem. Soc., 2016, 138, 7236–7239 CrossRef CAS PubMed.
- D. Parobek, Y. Dong, T. Qiao, D. Rossi and D. H. Son, J. Am. Chem. Soc., 2017, 139, 4358–4361 CrossRef CAS PubMed.
- C. Guhrenz, A. Benad, C. Ziegler, D. Haubold, N. Gaponik and A. Eychmüller, Chem. Mater., 2016, 28, 9033–9040 CrossRef CAS.
- V. K. Ravi, R. A. Scheidt, A. Nag, M. Kuno and P. V. Kamat, ACS Energy Lett., 2018, 3, 1049–1055 CrossRef CAS.
- Y. Xu, S. Xu, H. Shao, H. Jiang, Y. Cui and C. Wang, Nanotechnology, 2018, 29, 235603 CrossRef PubMed.
- D. Yu, B. Cai, F. Cao, X. Li, X. Liu, Y. Zhu, J. Ji, Y. Gu and H. Zeng, Adv. Mater. Interfaces, 2017, 4, 1700441 CrossRef.
- F. Li, Z. Xia, Y. Gong, L. Gu and Q. Liu, J. Mater. Chem. C, 2017, 5, 9281–9287 RSC.
- X. Fu, C. Zhang, Z. Peng, Y. Xia, J. Zhang, W. Luo, R. Zhan, H. Li, Y. Wang and D. Zhang, J. Mater. Chem. C, 2018, 6, 1701–1708 RSC.
- V. K. Ravi, P. K. Santra, N. Joshi, J. Chugh, S. K. Singh, H. Rensmo, P. Ghosh and A. Nag, J. Phys. Chem. Lett., 2017, 8, 4988–4994 CrossRef CAS PubMed.
- J. De Roo, M. Ibáñez, P. Geiregat, G. Nedelcu, W. Walravens, J. Maes, J. C. Martins, I. Van Driessche, M. V. Kovalenko and Z. Hens, ACS Nano, 2016, 10, 2071–2081 CrossRef CAS PubMed.
- B. A. Koscher, J. K. Swabeck, N. D. Bronstein and A. P. Alivisatos, J. Am. Chem. Soc., 2017, 139, 6566–6569 CrossRef CAS PubMed.
- B. Luo, Y. C. Pu, S. A. Lindley, Y. Yang, L. Lu, Y. Li, X. Li and J. Z. Zhang, Angew. Chem., Int. Ed., 2016, 55, 8864–8868 CrossRef CAS PubMed.
- B. Luo, S. B. Naghadeh, A. Allen, X. Li and J. Z. Zhang, Adv. Funct. Mater., 2017, 27, 1604018 CrossRef.
- J. Pan, Y. Shang, J. Yin, M. De Bastiani, W. Peng, I. Dursun, L. Sinatra, A. M. El-Zohry, M. N. Hedhili, A.-H. Emwas, O. F. Mohammed, Z. Ning and O. M. Bakr, J. Am. Chem. Soc., 2018, 140, 562–565 CrossRef CAS PubMed.
- T. Udayabhaskararao, L. Houben, H. Cohen, M. Menahem, I. Pinkas, L. Avram, T. Wolf, A. Teitelboim, M. Leskes, O. Yaffe, D. Oron and M. Kazes, Chem. Mater., 2018, 30, 84–93 CrossRef CAS.
- J. B. Rivest and P. K. Jain, Chem. Soc. Rev., 2013, 42, 89–96 RSC.
- T. Chiba, K. Hoshi, Y. J. Pu, Y. Takeda, Y. Hayashi, S. Ohisa, S. Kawata and J. Kido, ACS Appl. Mater. Interfaces, 2017, 9, 18054–18060 CrossRef CAS PubMed.
- J. Pan, L. N. Quan, Y. Zhao, W. Peng, B. Murali, S. P. Sarmah, M. Yuan, L. Sinatra, N. M. Alyami, J. Liu, E. Yassitepe, Z. Yang, O. Voznyy, R. Comin, M. N. Hedhili, O. F. Mohammed, Z. H. Lu, D. H. Kim, E. H. Sargent and O. M. Bakr, Adv. Mater., 2016, 28, 8718–8725 CrossRef CAS PubMed.
- X. Zhang, Z. Jin, J. Zhang, D. Bai, H. Bian, K. Wang, J. Sun, Q. Wang and S. F. Liu, ACS Appl. Mater. Interfaces, 2018, 10, 7145–7154 CrossRef CAS PubMed.
- S. H. Tolbert and A. P. Alivisatos, J. Chem. Phys., 1995, 102, 4642–4656 CrossRef CAS.
- J. N. Wickham, A. B. Herhold and A. P. Alivisatos, Phys. Rev. Lett., 2000, 84, 923–926 CrossRef CAS PubMed.
- Z. Wang, Y. Zhao, D. Schiferl, C. S. Zha, R. T. Downs and T. Sekine, Appl. Phys. Lett., 2003, 83, 3174–3176 CrossRef CAS.
- B. Li, K. Bian, X. Zhou, P. Lu, S. Liu, I. Brener, M. Sinclair, T. Luk, H. Schunk, L. Alarid, P. G. Clem, Z. Wang and H. Fan, Sci. Adv., 2017, 3, 1–8 Search PubMed.
- B. Li, X. Wen, R. Li, Z. Wang, P. G. Clem and H. Fan, Nat. Commun., 2014, 5, 4179 CrossRef CAS PubMed.
- Z. Wang, O. Chen, C. Y. Cao, K. Finkelstein, D.-M. Smilgies, X. Lu and W. A. Bassett, Rev. Sci. Instrum., 2010, 81, 093902 CrossRef PubMed.
- H. Zhu, Y. Nagaoka, K. Hills-Kimball, R. Tan, L. Yu, Y. Fang, K. Wang, R. Li, Z. Wang and O. Chen, J. Am. Chem. Soc., 2017, 139, 8408–8411 CrossRef CAS PubMed.
- Y. Nagaoka, K. Hills-Kimball, R. Tan, R. Li, Z. Wang and O. Chen, Adv. Mater., 2017, 29, 1606666 CrossRef PubMed.
- T. Yin, Y. Fang, W. K. Chong, K. T. Ming, S. Jiang, X. Li, J. L. Kuo, J. Fang, T. C. Sum, T. J. White, J. Yan and Z. X. Shen, Adv. Mater., 2018, 30, 1–8 Search PubMed.
- G. Xiao, Y. Cao, G. Qi, L. Wang, C. Liu, Z. Ma, X. Yang, Y. Sui, W. Zheng and B. Zou, J. Am. Chem. Soc., 2017, 139, 10087–10094 CrossRef CAS PubMed.
- J. C. Beimborn, L. M. G. Hall, P. Tongying, G. Dukovic and J. M. Weber, J. Phys. Chem. C, 2018, 122, 11024–11030 CrossRef CAS.
- Y. Cao, G. Qi, C. Liu, L. Wang, Z. Ma, K. Wang, F. Du, G. Xiao and B. Zou, J. Phys. Chem. C, 2018, 122, 9332–9338 CrossRef CAS.
- H. Zhu, T. Cai, M. Que, J.-P. Song, B. M. Rubenstein, Z. Wang and O. Chen, J. Phys. Chem. Lett., 2018, 9, 4199–4205 CrossRef CAS PubMed.
- X. Lü, Y. Wang, C. C. Stoumpos, Q. Hu, X. Guo, H. Chen, L. Yang, J. S. Smith, W. Yang, Y. Zhao, H. Xu, M. G. Kanatzidis and Q. Jia, Adv. Mater., 2016, 28, 8663–8668 CrossRef PubMed.
- S. Jiang, Y. Fang, R. Li, H. Xiao, J. Crowley, C. Wang, T. J. White, W. A. Goddard, Z. Wang, T. Baikie and J. Fang, Angew. Chem., Int. Ed., 2016, 55, 6540–6544 CrossRef CAS PubMed.
- A. Jaffe, Y. Lin, C. M. Beavers, J. Voss, W. L. Mao and H. I. Karunadasa, ACS Cent. Sci., 2016, 2, 201–209 CrossRef CAS PubMed.
- L. Wang, K. Wang and B. Zou, J. Phys. Chem. Lett., 2016, 7, 2556–2562 CrossRef CAS PubMed.
- M. Szafrański and A. Katrusiak, J. Phys. Chem. Lett., 2016, 7, 3458–3466 CrossRef PubMed.
- Y. Wang, X. Lü, W. Yang, T. Wen, L. Yang, X. Ren, L. Wang, Z. Lin and Y. Zhao, J. Am. Chem. Soc., 2015, 137, 11144–11149 CrossRef CAS PubMed.
- I. Swainson, L. Chi, J.-H. Her, L. Cranswick, P. Stephens, B. Winkler, D. J. Wilson and V. Milman, Acta Crystallogr., Sect. B: Struct. Sci., 2010, 66, 422–429 CrossRef CAS PubMed.
- G. Liu, L. Kong, J. Gong, W. Yang, H. Mao, Q. Hu, Z. Liu, R. D. Schaller, D. Zhang and T. Xu, Adv. Funct. Mater., 2017, 27, 1604208 CrossRef.
- L. Zhang, Q. Zeng and K. Wang, J. Phys. Chem. Lett., 2017, 8, 3752–3758 CrossRef CAS PubMed.
- L. Zhang, L. Wang, K. Wang and B. Zou, J. Phys. Chem. C, 2018, 122, 15220–15225 CrossRef CAS.
- Y. Zong, Y. Zhou, Y. Zhang, Z. Li, L. Zhang, M.-G. Ju, M. Chen, S. Pang, X. C. Zeng and N. P. Padture, Chem, 2018, 4, 1404–1415 CAS.
- W. Q. Wu, Q. Wang, Y. Fang, Y. Shao, S. Tang, Y. Deng, H. Lu, Y. Liu, T. Li, Z. Yang, A. Gruverman and J. Huang, Nat. Commun., 2018, 9, 1–8 CrossRef PubMed.
- P. W. Liang, C. Y. Liao, C. C. Chueh, F. Zuo, S. T. Williams, X. K. Xin, J. Lin and A. K. Y. Jen, Adv. Mater., 2014, 26, 3748–3754 CrossRef CAS PubMed.
- X. Li, M. Ibrahim Dar, C. Yi, J. Luo, M. Tschumi, S. M. Zakeeruddin, M. K. Nazeeruddin, H. Han and M. Grätzel, Nat. Chem., 2015, 7, 703–711 CrossRef CAS PubMed.
- C. Zuo and L. Ding, Nanoscale, 2014, 6, 9935–9938 RSC.
- M. Cha, P. Da, J. Wang, W. Wang, Z. Chen, F. Xiu, G. Zheng and Z.-S. Wang, J. Am. Chem. Soc., 2016, 138, 8581–8587 CrossRef CAS PubMed.
- H. Zai, C. Zhu, H. Xie, Y. Zhao, C. Shi, Z. Chen, X. Ke, M. Sui, C. Chen, J. Hu, Q. Zhang, Y. Gao, H. Zhou, Y. Li and Q. Chen, ACS Energy Lett., 2017, 3, 30–38 CrossRef.
- J. Zhang, D. Bai, Z. Jin, H. Bian, K. Wang, J. Sun, Q. Wang and S. F. Liu, Adv. Energy Mater., 2018, 8, 1703246 CrossRef.
- Q. Wang, X. Zhang, Z. Jin, J. Zhang, Z. Gao, Y. Li and S. F. Liu, ACS Energy Lett., 2017, 2, 1479–1486 CrossRef CAS.
- Y. Chen, L. Li, Z. Liu, N. Zhou, Q. Chen and H. Zhou, Nano Energy, 2017, 40, 540–549 CrossRef CAS.
- W. H. Weber and J. Lambe, Appl. Opt., 1976, 15, 2299–2300 CrossRef CAS PubMed.
- F. Meinardi, A. Colombo, K. A. Velizhanin, R. Simonutti, M. Lorenzon, L. Beverina, R. Viswanatha, V. I. Klimov and S. Brovelli, Nat. Photonics, 2014, 8, 392–399 CrossRef CAS.
- F. Purcell-Milton and Y. K. Gun’ko, J. Mater. Chem., 2012, 22, 16687–16697 RSC.
-
Z. Wang, Q. Lin, B. Wenger, M. G. Christoforo, Y.-H. Lin, M. T. Klug, M. B. Johnston, L. M. Herz and H. J. Snaith, Nat. Energy, 2018, DOI:10.1038/s41560-018-0220-2.
- G. E. Eperon, G. M. Paternò, R. J. Sutton, A. Zampetti, A. A. Haghighirad, F. Cacialli and H. J. Snaith, J. Mater. Chem. A, 2015, 3, 19688–19695 RSC.
- W. Ahmad, J. Khan, G. Niu and J. Tang, Sol. RRL, 2017, 1, 1700048 CrossRef.
- Q. Wang, X. Zheng, Y. Deng, J. Zhao, Z. Chen and J. Huang, Joule, 2017, 1, 371–382 CrossRef CAS.
- P. Wang, X. Zhang, Y. Zhou, Q. Jiang, Q. Ye, Z. Chu, X. Li, X. Yang, Z. Yin and J. You, Nat. Commun., 2018, 9, 2225 CrossRef PubMed.
- E. M. Sanehira, A. R. Marshall, J. A. Christians, S. P. Harvey, P. N. Ciesielski, L. M. Wheeler, P. Schulz, L. Y. Lin, M. C. Beard and J. M. Luther, Sci. Adv., 2017, 3, eaao4204 CrossRef PubMed.
- L. M. Wheeler, E. M. Sanehira, A. R. Marshall, P. Schulz, M. Suri, N. C. Anderson, J. A. Christians, D. Nordlund, D. Sokaras, T. Kroll, S. P. Harvey, J. J. Berry, L. Y. Lin and J. M. Luther, J. Am. Chem. Soc., 2018, 140, 10504–10513 CrossRef CAS PubMed.
- Q. Wang, Z. Jin, D. Chen, D. Bai, H. Bian, J. Sun, G. Zhu, G. Wang and S. F. Liu, Adv. Energy Mater., 2018, 8, 1800007 CrossRef.
- W. Travis, E. N. K. Glover, H. Bronstein, D. O. Scanlon and R. G. Palgrave, Chem. Sci., 2016, 7, 4548–4556 RSC.
- H. Bian, D. Bai, Z. Jin, K. Wang, L. Liang, H. Wang, J. Zhang, Q. Wang and S. (Frank) Liu, Joule, 2018, 2, 1500–1510 CrossRef CAS.
- M. Leng, Y. Yang, K. Zeng, Z. Chen, Z. Tan, S. Li, J. Li, B. Xu, D. Li, M. P. Hautzinger, Y. Fu, T. Zhai, L. Xu, G. Niu, S. Jin and J. Tang, Adv. Funct. Mater., 2018, 28, 1704446 CrossRef.
- Y. Lou, M. Fang, J. Chen and Y. Zhao, Chem. Commun., 2018, 54, 3779–3782 RSC.
- J. S. Niezgoda, B. J. Foley, A. Z. Chen and J. J. Choi, ACS Energy Lett., 2017, 2, 1043–1049 CrossRef.
- P. Reiss, M. Protière and L. Li, Small, 2009, 5, 154–168 CrossRef CAS PubMed.
- O. Chen, J. Zhao, V. P. Chauhan, J. Cui, C. Wong, D. K. Harris, H. Wei, H.-S. Han, D. Fukumura, R. K. Jain and M. G. Bawendi, Nat. Mater., 2013, 12, 445–451 CrossRef CAS PubMed.
- M. V. Kovalenko, M. Scheele and D. V. Talapin, Science, 2009, 324, 1417–1420 CrossRef CAS PubMed.
- Y. Yang, H. Qin, M. Jiang, L. Lin, T. Fu, X. Dai, Z. Zhang, Y. Niu, H. Cao, Y. Jin, F. Zhao and X. Peng, Nano Lett., 2016, 16, 2133–2138 CrossRef CAS PubMed.
- X. Chen, L. Peng, K. Huang, Z. Shi, R. Xie and W. Yang, Nano Res., 2016, 9, 1994–2006 CrossRef CAS.
- O. Chen, X. Chen, Y. Yang, J. Lynch, H. Wu, J. Zhuang and Y. C. Cao, Angew. Chem., Int. Ed., 2008, 47, 8638–8641 CrossRef CAS PubMed.
- K. Whitham, J. Yang, B. H. Savitzky, L. F. Kourkoutis, F. Wise and T. Hanrath, Nat. Mater., 2016, 15, 557–563 CrossRef CAS PubMed.
- J. J. Geuchies, C. van Overbeek, W. H. Evers, B. Goris, A. de Backer, A. P. Gantapara, F. T. Rabouw, J. Hilhorst, J. L. Peters, O. Konovalov, A. V. Petukhov, M. Dijkstra, L. D. A. Siebbeles, S. van Aert, S. Bals and D. Vanmaekelbergh, Nat. Mater., 2016, 15, 1248–1254 CrossRef CAS PubMed.
- M. Cargnello, A. C. Johnston-Peck, B. T. Diroll, E. Wong, B. Datta, D. Damodhar, V. V. T. Doan-Nguyen, A. A. Herzing, C. R. Kagan and C. B. Murray, Nature, 2015, 524, 450–453 CrossRef CAS PubMed.
- D. Han, M. Imran, M. Zhang, S. Chang, X. Wu, X. Zhang, J. Tang, M. Wang, S. Ali, X. Li, G. Yu, J. Han, L. Wang, B. Zou and H.-Z. Zhong, ACS Nano, 2018, 12, 8808–8816 CrossRef CAS PubMed.
Footnote |
† These authors contributed equally to this work. |
|
This journal is © The Royal Society of Chemistry 2018 |
Click here to see how this site uses Cookies. View our privacy policy here.