Non-aqueous direct leaching using a reusable nickel-selective amic-acid extractant for efficient lithium-ion battery recycling†
Received
24th July 2024
, Accepted 6th October 2024
First published on 7th October 2024
Abstract
The demand for lithium-ion secondary batteries (LiBs) is rapidly increasing in pursuit of the Sustainable Development Goals. In particular, the recycling of nickel-based cathodes is attracting attention owing to the growth of the electric vehicle market. There are concerns surrounding conventional LiB recycling processes regarding environmental pollution because of their complexity and the discharge of large amounts of acidic wastewater. In this study, we used an alternative recycling process that directly leaches the cathode materials using a non-aqueous hydrophobic solvent instead of inorganic acids. This method enables simultaneous leaching and extraction, which are typically performed in two stages in conventional recycling, to be performed in a single step. To enhance the leaching of nickel-based cathodes, N-[N,N-di(2-ethylhexyl) aminocarbonyl methyl] glycine (D2EHAG), which has high affinity for nickel and cobalt, was used to prepare the leaching solvent. More than 96% of the nickel and cobalt in a nickel-based cathode was successfully leached into the D2EHAG solvent system, while typical industrial metal extractants showed very poor leaching performance. The addition of ascorbic acid and water into the leaching solvent synergistically enhanced the leaching efficiency, demonstrating a crucial role in the leaching process. After leaching, the leached metals could be selectively separated and recovered by stripping. Furthermore, the reusability of the leaching solvent was demonstrated for at least three leaching–stripping cycles. These findings will contribute to the development of a more simple recycling process for nickel-based automotive LiBs with a reduced amount of acidic wastewater.
Sustainability spotlight
The transition from gasoline-powered vehicles, major contributors to global warming, to electric vehicles is being encouraged. With the increasing demand for electric vehicles, the recycling of lithium-ion batteries (LiBs) becomes crucial. However, there are concerns surrounding traditional recycling methods for LiBs regarding their high environmental impact. This study aims to develop an environmentally friendly LiB recycling process surpassing conventional methods. Using N-[N,N-di(2-ethylhexyl) aminocarbonyl methyl] glycine as a leaching agent, the metals were efficiently leached from LiB cathode materials. Furthermore, the proposed approach eliminates the need for inorganic acids, simplifying the process. Upon realization, this process will contribute to society in various aspects, including environmental, economic, and social aspects. This process aligns with SDGs 7, 11, and 13.
|
1 Introduction
In recent years, lithium-ion batteries (LiBs) have attracted significant attention in the pursuit of achieving the Sustainable Development Goals, which are recognized as universal challenges worldwide.1–3 LiBs, as secondary batteries, use a metal oxide such as lithium cobalt oxide (LCO) or lithium nickel cobalt manganese oxide (NMC) as the cathode, graphite as the anode, and a metal such as copper (Cu) or aluminum (Al) as the current collector. Through the movement of lithium ions, these batteries undergo charging and discharging processes.4,5 The cathode material of LiBs is expected to transition from LCO to NMC because NMC is more cost-effective than LCO and offers equivalent or superior structural stability, specific capacity, and discharge voltage.6,7 The LiB market is estimated to expand from $41.1 billion in 2021 to $116.6 billion by 2030.8 The lifespan of lithium-ion batteries (LiBs) is 8–10 years, leading to a large number of spent LiBs in the future. It is estimated that more than 11 million tons of spent LiBs will be generated by 2030.9
The positive electrode materials of LiBs contain several important metals, such as lithium (Li), cobalt (Co), nickel (Ni), and manganese (Mn).10 The resources of these metals are constantly being challenged by issues such as geographical concentration in producing countries and resource depletion.11,12 The current growth rate of LiBs places significant pressure on the supply of the rare metals for battery materials, leading to potential severe scarcity of these rare metals in the future.13 In addition to resource issues, there are environmental problems and potential safety concerns stemming from spent LiBs.14,15 Therefore, it is essential to recycle the important metals from spent LiBs.
Conventional LiB recycling methods include direct recycling, pyrometallurgy, and hydrometallurgy.16 Direct recycling is considered to be economically and environmentally advantageous over other methods. However, if the electrode materials contain structural defects, their repair is generally challenging, leading to slight degradation of the battery performance.17,18 Pyrometallurgy involves treating the cathode material at high temperatures (1400–1700 °C) to recover the desired metals (Co, Ni, and Cu). However, Li, Mn, and Al form slag, resulting in production loss of the target metals. Moreover, these processes require significant energy and emit toxic pollutants, posing environmental challenges.19,20 Hydrometallurgy involves leaching the cathode material in an inorganic acid followed by solvent extraction to recover the desired metals. Compared with pyrometallurgy, hydrometallurgy has lower energy consumption for recycling, resulting in reduced environmental impact.21 Therefore, research on hydrometallurgy is being actively performed,22–24 and many companies have incorporated hydrometallurgical processes into their operations.25–27 However, concerns have been raised regarding the environmental impact stemming from the generation of large amounts of acidic wastewater and toxic gases during leaching, as well as the complex and lengthy process. As a result, there is a pressing demand for the development of environmentally friendly recycling processes for LiBs.
In recent years, researchers have proposed new recycling processes using hydrophobic solvents, such as organic solvents and hydrophobic deep eutectic solvents, as alternatives to inorganic acid solutions to address the above issues.28–35 Processes using non-aqueous solvents for refinement have been historically described as lyometallurgy, but in recent years they have been referred to as solvometallurgy or ionometallurgy depending on the solvent used.36,37 The use of hydrophobic solvents enables combination of the leaching and extraction operations, which are typically performed in two different stages, facilitating direct stripping. Thus, simplifying the process not only reduces the running costs, but it also improves the process safety and reduces the energy consumption. Additionally, by not using inorganic acids during leaching, the generation of harmful gases and corrosion of the equipment can be avoided.37 Therefore, these methods offer potential advantages in terms of economics, environmental impact, and safety. Peeters et al.32 reported LiB cathode material recycling via hydrophobic solvent leaching using the industrial extractant di-(2-ethylhexyl) phosphoric acid (D2EHPA) for the direct leaching and stripping of LCO for metal separation. Carreira et al.31 reported that a hydrophobic deep eutectic solvent composed of decanoic acid and trioctylphosphine oxide can selectively recover rare metals from NMC by concentrating HCl. However, challenges remain, such as the incomplete elimination of the inorganic acids during leaching and the low recycling efficiency of NMC, and there is the potential for future development.31,32
In this study, to achieve a more environmentally friendly recycling process applicable to all types of LiB cathode materials, we propose a recycling process using an organic extractant and an organic solvent for the direct leaching of the metals from LiB cathode materials. This process uses N-[N,N-di(2-ethylhexyl) amino carbonyl methyl] glycine (D2EHAG), which was developed in our laboratory, as the organic extractant.38–40 This extractant, a proton-dissociating tridentate ligand, exhibits specific metal selectivity for Co, Ni, and Mn in LiBs owing to the hard and soft acids and bases principle and chelation effect.41,42 Quantum chemical calculations using density functional theory have demonstrated its high affinity for Ni(II) and Co(II), showing its excellent separation performance for Ni, Co, and Mn.43n-Dodecane, which possesses similar chemical properties to commercially used kerosene, was used as the organic solvent, along with the natural additive ascorbic acid and water as an additive agent. These additives were used to enhance the leaching efficiency and achieve high-efficiency leaching of the target metals. Following leaching, selective separation and recovery of the rare metals were accomplished through stripping by contact with acidic aqueous solutions with different pH values. Finally, to investigate the sustainability of this process, the reuse of the organic phase was demonstrated for a maximum of three leaching cycles. A new flow sheet for sustainable LiB recycling based on organic extractants and organic solvents was established. Furthermore, this process was applied to actual spent LiBs, demonstrating the potential impact of this recycling process on the future LiB industry (Fig. 1).
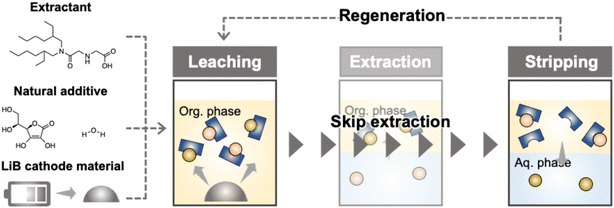 |
| Fig. 1 Schematic illustration of the LiB cathode material recycling process proposed in this study. | |
2 Materials and methods
2.1. Reagents and chemicals
D2EHAG was designed in our laboratory, and its large-scale synthesis was commissioned to Koei Chemical Co., Ltd (Osaka, Japan). D2EHPA was purchased from Tokyo Chemical Industry Co., Ltd (Tokyo, Japan). N-decanoic acid was obtained from Japan Epoxy Resin Co., Ltd (Tokyo, Japan). A standard solution of Li, Co, Ni, Mn, and Y, lithium nickel manganese cobalt oxide (NMC111), and ascorbic acid were purchased from FUJIFILM Wako Pure Chemical Co. (Osaka. Japan). Hydrochloric acid (HCl, 10 mol dm−3), sulfuric acid (H2SO4, 5 mol dm−3), and 1-propanol were obtained from Kishida Chemical Co., Ltd (Osaka, Japan). Sodium hydroxide solution (NaOH, 1 mol dm−3) was purchased from Nacalai Tesque, Inc. (Osaka, Japan). Milli-Q water was used to prepare the aqueous solutions for all of the experiments.
2.2. Leaching experiments
The experiments were performed in triplicate unless otherwise stated. A mixture of n-dodecane and water with a volume ratio of 1
:
1 containing an adjusted concentration of the extractant (D2EHAG, D2EHPA, or Versatic10) was subjected to vortexing for 1 min followed by vigorous shaking at room temperature and 1500 rpm for 1 h. The aqueous phase was saturated with water in the organic phase. Subsequently, centrifugation was performed at 293 K and 5500 rpm for 1 min to separate the organic and aqueous phases. The upper phase, containing the water-saturated organic solvent, was collected and used as the leaching solution. The organic solvent and NMC were placed in a vial to achieve a solid-to-liquid (S/L) ratio of 10 g L−1. A known concentration of ascorbic acid was then added. The leaching tests were performed at 333 K for 24 h with stirring at 400 rpm, unless otherwise stated. After leaching, centrifugation was performed at 293 K for 10 min at 20
000g to precipitate the solids, and the supernatant was collected. The metal concentration in the organic phase after leaching was measured by inductively coupled plasma optical emission spectroscopy (ICP-OES: Optima 8300, PerkinElmer). The ICP samples were prepared by diluting with 1-propanol containing yttrium as an internal standard at a ratio of 50
:
1. The ICP-OES apparatus was equipped with a Peltier-cooled organic sample introduction kit and an injector with a reduced inner diameter of 1 mm for direct measurement of organic samples. To generate a stable plasma during the measurements, the flow rates of the plasma and nebulizer gas were adjusted to 10 and 0.5 L min−1, respectively. Under these conditions, the correlation coefficient of the calibration curve for each analyzed element was above 0.999. To evaluate the leaching performance, the leaching efficiency (% L) was defined as follows:
where CL,M,Org, WM,NMC, and V are the concentration of any metal M in the organic phase after leaching, the initial weight of NMC, and the volume of the organic phase, respectively. Additionally, to investigate the formation of reverse-micellar droplets in the organic phase, dynamic light scattering was performed with a Zetasizer Nano analyzer. A Karl-Fischer CA-200/VA-0200 moisture meter was used to determine the amount of water in the organic phase. This experiment was performed in quintuplicate (n = 5).
2.3. Stripping experiments
To recover the metals, the organic phase after leaching was brought into contact with dilute aqueous sulfuric acid solution of known concentration at an aqueous/organic phase ratio (A/O) of 1
:
1 for 1 h at 1500 rpm. Subsequently, centrifugation was performed at 298 K for 1 min at 5500 rpm to separate the organic and aqueous phases. The metal concentration in the organic solvent after stripping was measured by ICP-OES, following the same procedure as in the leaching experiment. To evaluate the stripping extraction performance, the stripping extraction efficiency (% S) was defined as follows:
where CS,M,Org is the concentration of any metal M remaining in the organic phase after stripping.
2.4. Reusability test of the extractant and organic phase
To establish a sustainable recycling process, the reusability of the organic phase was investigated. After stripping, a regeneration step was introduced to restore the leaching performance of the organic phase. In the regeneration step, the organic phase was brought into contact with aqueous ammonia solution of known concentration at a volume ratio of 1
:
1 for 1 h at 1500 rpm. Subsequently, centrifugation was performed at 298 K for 1 min at 5500 rpm to remove the aqueous phase. Subsequently, using the recovered regenerated organic solvent, leaching and stripping were repeated using the same conditions and methods, as described in Sections 2.2 (leaching experiments) and 2.3 (stripping experiments). The leaching performance of each cycle was evaluated based on the leaching efficiency.
3 Results and discussion
3.1. Leaching
The target model LiB cathode material was LiNi1/3Mn1/3Co1/3O2 (NMC), and direct leaching using different extractants was investigated. The chemical structures of the acidic extractants used in this study are shown in Fig. 2. These extractants were dissolved in n-dodecane and used as leaching solvents, with ascorbic acid and water added as environmentally friendly additives. The effect of the extractant concentration on the leaching efficiency of NMC into the organic solvent is shown in Fig. 3. Regardless of the extractant concentration, D2EHAG showed significantly better leaching performance than the other extractants. A previous study found that the chelating ability of the leaching solvent affects the leaching of metal oxides.44 Versatic10 exhibited low liquid–liquid extraction efficiencies for the four LiB-containing metals, as shown in Fig. S1.† Consequently, most of the metals were not leached from the LiB cathode material. D2EHAG, which was designed to have high affinity for Ni and Co, showed good liquid–liquid extraction behavior. The affinity for the metals was in the order Ni, Co, Mn, and Li, as shown in Fig. S2.†41 In this study, the metals were leached in the order Ni
Co ≫ Mn
Li, suggesting that the high coordination ability of D2EHAG promoted metal leaching. In contrast, the liquid–liquid extraction behavior of D2EHPA showed an extraction order of Mn, Co, and Ni when excluding Li, with Ni showing the lowest affinity for D2EHPA (Fig. S3†). This is attributed to the complete absence of Ni leaching in the leaching tests using D2EHPA. Furthermore, there was not much correlation between the concentration of the extractant and the Li leaching efficiency. Considering the layered structure of NMC, interlayer Li ions and protons in the system leach through a substitution reaction.45
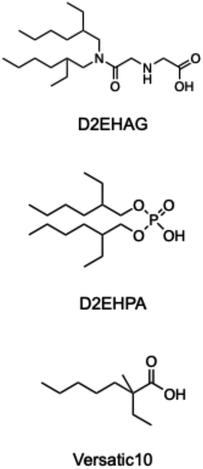 |
| Fig. 2 Chemical structures of the evaluated extractants. | |
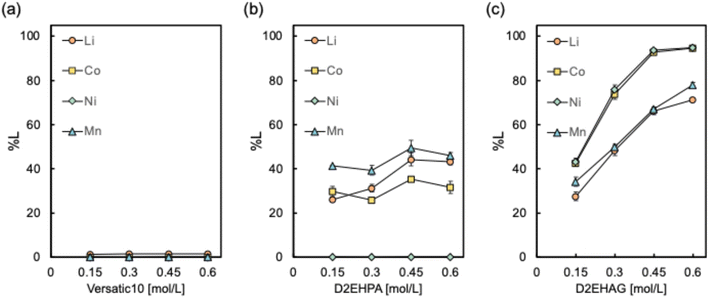 |
| Fig. 3 Leaching efficiencies of the metals from NMC by different concentrations of (a) Versatic10, (b) D2EHPA, and (c) D2EHAG diluted in n-dodecane with 0.1 mol per L ascorbic acid and a saturated amount of water. Experimental conditions: S/L = 10 g L−1, heating at 333 K at 400 rpm for 24 h. | |
Subsequently, the saturated water content in the organic solvent at various extractant concentrations was measured (Fig. 4(a) and (b)). The water content increased in a concentration-dependent manner for all of the extractants. At 0.6 mol per L D2EHPA, D2EHPA contained 0.16 vol% water. In contrast, 0.6 mol per L D2EHAG contained 3.3 vol% water. This indicates that D2EHAG can retain approximately 13 times more water than D2EHPA.
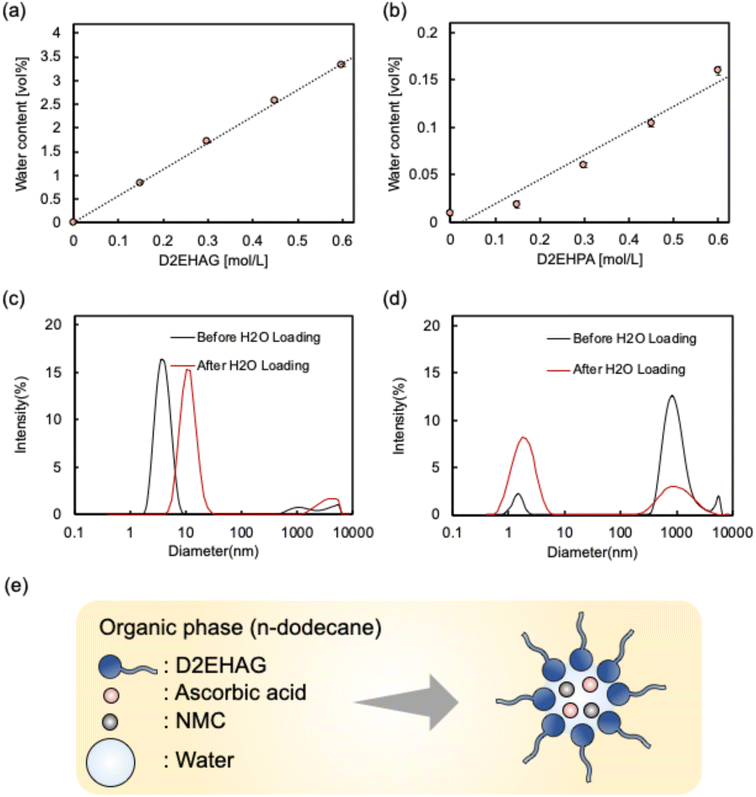 |
| Fig. 4 Saturated water contents in n-dodecane containing the extractants (a) D2EHAG and (b) D2EHPA. Particle diameters in n-dodecane containing the extractants (c) D2EHAG and (d) D2EHPA. (e) Schematic representation of the expected extractant and water state in the organic solvent. | |
The particle sizes in the organic solvent before and after the addition of the saturation amount of water were measured, and the results are shown in Fig. 4(c) and (d). It has been reported that D2EHPA, which is already used as an industrial extractant, forms reverse micelle structures in organic solvents.46 Similarly, D2EHAG showed peaks in the range of several nanometers to several tens of nanometers, indicating the formation of reverse micelle structures. The peaks for D2EHAG were of higher intensity and larger particle size than those of D2EHPA, allowing it to retain more water. The differences in the water contents and particle sizes are due to the structures of D2EHAG and D2EHPA. The hydrophilic part of D2EHAG has alternating charges, resulting in attractive forces between D2EHAG molecules. Conversely, D2EHPA has a positive central element surrounded by negative charges, causing repulsive forces between D2EHPA molecules. Therefore, D2EHAG forms reverse micelles more readily than D2EHPA, enabling it to encapsulate more water than D2EHPA.
We also investigated the effects of the additives on NMC leaching. Considering the environmental impact, naturally derived ascorbic acid and water were used as the additives in this study. First, the effect of the amount of water was investigated (Fig. 5(a)). As the amount of water in the organic solvent increased, the leaching efficiencies of the metals improved, with the maximum leaching efficiencies were achieved when water was added at the saturation level. The effect of the water present in the organic solvent on metal leaching has not been previously elucidated owing to limited previous studies. It is known that lithium ions strongly associate with water and are one of the most easily hydrated metal ion species.47 Therefore, considering that D2EHAG does not exhibit affinity for lithium, water may be involved in stabilizing lithium ions in the organic solvent. Additionally, reverse micelles have been reported to be crucial reaction sites in various fields.48,49 Water-soluble reactants dissolve in the water phase of reverse micelles. Consequently, given the proximity of the reaction sites owing to the aggregation of the reaction sites of D2EHAG, ascorbic acid, and NMC within the reverse micelles, processes such as ligand exchange reactions and redox reactions could potentially be used.
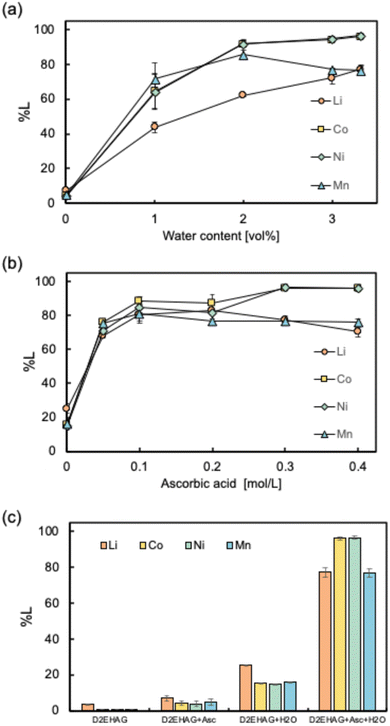 |
| Fig. 5 Effects of the (a) amount of water with 0.1 mol per L ascorbic acid and (b) ascorbic acid concentration with the saturated amount of water on the leaching of the metals from NMC by 0.6 mol per L D2EHAG diluted in n-dodecane. (c) Summary of the effects of D2EHAG and the additives on the leaching efficiency. Experimental conditions: S/L = 10 g L−1, heating at 333 K at 400 rpm for 24 h. | |
The effect of the amount of ascorbic acid on the leaching efficiencies of the metals was investigated. In this study, ascorbic acid was used as a reducing agent. Generally, additional reducing agents are required for the leaching of LiB cathode materials, such as NaHSO3, Cu, H2O2, and ascorbic acid.50–53 However, reducing agents containing metals, such as NaHSO3 and Cu, result in contamination of impurity metal ions during the process. Additionally, H2O2 is highly unstable and explosive, posing a safety hazard.54 Owing to these factors, ascorbic acid, a naturally derived organic compound, was selected. The results of experiments with different amounts of ascorbic acid are shown in Fig. 5(b). The leaching efficiencies of the metals were the highest for 0.3 mol per L ascorbic acid. The increases in the metal recovery efficiencies of Co and Mn are attributed to the reduction of Co(III) to Co(II) and Mn(IV) to Mn(II), which is consistent with a previous study.55 In other words, the addition of ascorbic acid promotes the leaching of the metals by reducing the insoluble metal species to soluble metal ions.
Finally, the effects of D2EHAG, ascorbic acid, and water are shown in Fig. 5(c). When only D2EHAG or D2EHAG and one of the additives was added, the leaching of the target metals was minimal. However, high leaching performance was achieved by adding both ascorbic acid and water to D2EHAG. The maximum leaching efficiencies of Li, Co, Ni, and Mn were 77.2%, 95.6%, 96.0%, and 75.8%, respectively. These results demonstrate the synergistic effect of D2EHAG, ascorbic acid, and water.
So far, we have investigated the leaching behavior of NMC as a model LiB cathode material. However, actual LiBs are composed of various components, including not only the cathode material, but also the anode material, current collector, and other materials.10 Additionally, the separation process for each component is problematic because of the differences in the product specifications and cost considerations.56 Therefore, this recycling process was applied to the LiB black mass obtained by crushing actual spent LiBs. We characterized the black mass in a previous study, and its composition is given in Table S1.†29 The results of leaching the black mass under the optimized conditions are shown in Fig. 6. Similar to the results obtained for NMC, the metals Co, Ni, and Mn were efficiently leached. However, the leaching efficiency of Li was lower than that for NMC. Interestingly, impurity metals such as Cu and Al were not efficiently dissolved and remained in the residue. These findings suggest the possibility of selectively leaching the important metals from LiB black mass using the proposed recycling system.
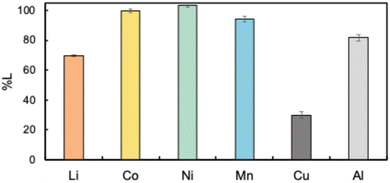 |
| Fig. 6 Leaching efficiencies of the metals from the LiB black mass by 0.6 mol per L D2EHAG in n-dodecane with 0.3 mol per L ascorbic acid and a saturated amount of water. Experimental conditions: S/L = 10 g L−1, heating at 333 K at 400 rpm for 24 h. | |
3.2. Stripping
To recover and separate each metal, a stripping process was performed by contacting the metal-loaded organic phase with dilute aqueous sulfuric acid solution. The stripping of Li, Co, Ni and Mn was performed by controlling the sulfuric acid concentration, and the results are shown in Fig. 7. Through stripping, each metal was selectively separated and recovered depending on the sulfuric acid concentration. Li almost quantitatively migrated to the aqueous phase at low sulfuric acid concentration, followed by the recovery of Mn, Co, and Ni as the sulfuric acid concentration increased, in that order. This is consistent with the order of the affinities of the metals with D2EHAG. Generally, when stripping with acidic extractants, proton exchange occurs between the organic and aqueous phases upon contact with acidic aqueous solution.57 As a result, the coordination structure between the acidic extractant and the metal is disrupted, releasing the metals with low affinity. Similarly, in the case of D2EHAG, the protons of the carboxylic acid at the metal binding sites are regenerated, preventing the coordination of metals and causing their release.41 Therefore, it is suggested that the metals with low affinity for D2EHAG migrated to the aqueous phase. Furthermore, for stripping with 1 mol per L sulfuric acid, almost all of the metals were removed from the organic phase, and the percentages of the metals remaining in the organic phase were all below approximately 3%. However, it is not possible to completely separate individual metals in a single stripping process. This could be resolved by repeating liquid–liquid extraction, which is expected to purify the metals.
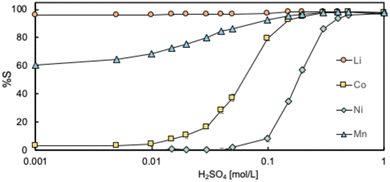 |
| Fig. 7 Stripping efficiencies of the metals from loaded D2EHAG in n-dodecane at different concentrations of sulfuric acid. Experimental conditions: A/O = 1/1, shaking at room temperature at 1500 rpm for 1 h. | |
3.3. Reusability
The reusability of the organic phase is one of the most important aspects of sustainable recycling processes. Therefore, the reusability of D2EHAG as a leaching solvent was investigated. The organic phase, from which all of the metals were removed after stripping, underwent a regeneration process by contact with aqueous ammonia solution and was reused as the leaching solvent. The aqueous ammonia solution was used to neutralize the abundant protons in the organic solvent and to maintain an environment in which metals can coordinate with D2EHAG. The results of the leaching tests up to the third cycle under the same conditions of leaching and stripping are shown in Fig. 8. The leaching efficiencies of Li, Co, Ni, and Mn in the third cycle were 81.7%, 97.8%, 99.4%, and 72.2%, respectively. That is, D2EHAG continued to efficiently leach Li, Ni, and Mn even after three cycles. Regarding Mn, there was a slight decrease in the leaching performance with cycle repetition. However, compared with the other metals, Mn production is stable, and its recycling priority is lower than those of the other metals. Therefore, D2EHAG demonstrated high reusability, indicating the sustainability of this recycling process.
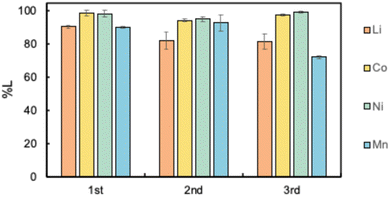 |
| Fig. 8 Reusability of the organic solvent using 0.6 mol per L D2EHAG as the leaching agent. Before each leaching, 0.3 mol per L ascorbic acid was added to the organic solvent. Leaching experiment conditions: S/L = 10 g L−1, heating at 333 K at 400 rpm for 24 h. After leaching, the organic phase was stripped by 1.00 mol per L H2SO4. Stripping experiment conditions: A/O = 1 : 1, shaking at room temperature at 1500 rpm for 1 h. | |
4 Conclusion
In this study, the acidic extractant D2EHAG was used to separate and recover the important metals from LiB cathode materials. This newly proposed recycling process reduces the use of inorganic acids in conventional processes and allows for the omission of extraction steps. Under the optimized mild leaching conditions (60 °C, 400 rpm, 24 h), using 0.6 mol per L D2EHAG with 0.3 mol per L ascorbic acid and the saturated amount of water (∼3.3 vol%) as the leaching solvent, the leaching efficiencies of Li, Co, Ni, and Mn from NMC reached 77.2%, 96.1%, 96.5%, and 76.6%, respectively. In contrast, conventional industrial extractants, such as Versatic 10 and D2EHPA, showed negligible leaching. This exceptional leaching performance is attributed to the excellent affinity of D2EHAG for metals. Following leaching, selective separation and recovery of the metals can be achieved by contacting the metal-containing organic phase with aqueous sulfuric acid solution of various concentrations. Furthermore, the organic phase for leaching can be regenerated by neutralizing it with aqueous ammonia solution after stripping. D2EHAG demonstrated excellent leaching performance for three cycles. These results demonstrate an environmentally friendly and sustainable recycling process for LiB cathode materials through direct leaching using D2EHAG.
Data availability
The data supporting this article have been included as part of the manuscript and ESI.†
Author contributions
Takejirou Matsui: conceptualization, data curation, writing – original draft preparation, reviewing, and editing. Takafumi Hanada: conceptualization, reviewing, and editing. Masahiro Goto: conceptualization, supervision, and editing. All authors have read and agreed to the final version of the manuscript.
Conflicts of interest
There are no conflicts of interest to declare.
Acknowledgements
This study was supported by JST, CREST Grant Number JPMJCR24S2, Japan and the Environment Research and Technology Development Fund (Grant No. JPMEERF2023002) from the Ministry of the Environment of Japan. We thank Edanz (https://jp.edanz.com/ac) for editing a draft of this manuscript.
References
- M. S. H. Lipu, A. Al Mamun, S. Ansari, M. S. Miah, K. Hasan, S. T. Meraj, M. G. M. Abdolrasol, T. Rahman, M. H. Maruf, M. R. Sarker, A. Aljanad and N. M. L. Tan, Batteries, 2022, 8, 199 CrossRef.
- M. A. Cusenza, F. Guarino, S. Longo, M. Ferraro and M. Cellura, J. Energy Storage, 2019, 25, 100845 CrossRef.
- E. Fan, L. Li, Z. Wang, J. Lin, Y. Huang, Y. Yao, R. Chen and F. Wu, Chem. Rev., 2020, 120, 7020–7063 CrossRef CAS PubMed.
- G. E. Blomgren, J. Electrochem. Soc., 2017, 164, A5019–A5025 CrossRef CAS.
- D. L. Thompson, J. M. Hartley, S. M. Lambert, M. Shiref, G. D. J. Harper, E. Kendrick, P. Anderson, K. S. Ryder, L. Gaines and A. P. Abbott, Green Chem., 2020, 22, 7585–7603 RSC.
- N. Nitta, F. Wu, J. T. Lee and G. Yushin, Mater. Today, 2015, 18, 252–264 CrossRef CAS.
- U. Saleem, B. Joshi and S. Bandyopadhyay, J. Sustainable Metall., 2023, 9, 950–971 CrossRef.
- T. Raj, K. Chandrasekhar, A. N. Kumar, P. Sharma, A. Pandey, M. Jang, B. H. Jeon, S. Varjani and S. H. Kim, J. Hazard. Mater., 2022, 429, 128312 CrossRef CAS PubMed.
- M. He, X. Jin, X. Zhang, X. Duan, P. Zhang, L. Teng, Q. Liu and W. Liu, Green Chem., 2023, 25, 6561–6580 RSC.
- M. Li, J. Lu, Z. Chen and K. Amine, Adv. Mater., 2018, 30, 1800561 CrossRef PubMed.
- E. A. Olivetti, G. Ceder, G. G. Gaustad and X. Fu, Joule, 2017, 1, 229–243 CrossRef.
- J. F. Peters and M. Weil, Resources, 2016, 5, 46 CrossRef.
- H. U. Sverdrup, Resour., Conserv. Recycl., 2016, 114, 112–129 CrossRef.
- W. Mrozik, M. A. Rajaeifar, O. Heidrich and P. Christensen, Energy Environ. Sci., 2021, 14, 6099–6121 RSC.
- N. Bolan, S. A. Hoang, M. Tanveer, L. Wang, S. Bolan, P. Sooriyakumar, B. Robinson, H. Wijesekara, M. Wijesooriya, S. Keerthanan, M. Vithanage, B. Markert, S. Fränzle, S. Wünschmann, B. Sarkar, A. Vinu, M. B. Kirkham, K. H. M. Siddique and J. Rinklebe, Environ. Pollut., 2021, 290, 118067 CrossRef CAS PubMed.
- F. Larouche, F. Tedjar, K. Amouzegar, G. Houlachi, P. Bouchard, G. P. Demopoulos and K. Zaghib, Materials, 2020, 13, 801 CrossRef CAS PubMed.
- Y. Lu, K. Peng and L. Zhang, ACS ES&T Eng., 2022, 2, 586–605 Search PubMed.
- J. Wu, M. Zheng, T. Liu, Y. Wang, Y. Liu, J. Nai, L. Zhang, S. Zhang and X. Tao, Energy Storage Mater., 2023, 54, 120–134 CrossRef CAS.
- A. Cornelio, A. Zanoletti and E. Bontempi, Curr. Opin. Green Sustainable Chem., 2024, 46, 100881 CrossRef CAS.
- B. Makuza, Q. Tian, X. Guo, K. Chattopadhyay and D. Yu, J. Power Sources, 2021, 491, 229622 CrossRef CAS.
- K. Davis and G. P. Demopoulos, RSC Sustainability, 2023, 1, 1932–1951 RSC.
- P. Meshram, A. Mishra, Abhilash and R. Sahu, Chemosphere, 2020, 242, 125291 CrossRef CAS PubMed.
- J. Wang, Y. Lyu, R. Zeng, S. Zhang, K. Davey, J. Mao and Z. Guo, Energy Environ. Sci., 2023, 17, 867–884 RSC.
- C. Cai, A. T. N. Fajar, T. Hanada, R. Wakabayashi and M. Goto, ACS Omega, 2023, 8, 3198–3206 CrossRef CAS PubMed.
- W. Lv, Z. Wang, H. Cao, Y. Sun, Y. Zhang and Z. Sun, ACS Sustain. Chem. Eng., 2018, 6, 1504–1521 CrossRef CAS.
- B. He, H. Zheng, K. Tang, P. Xi, M. Li, L. Wei and Q. Guan, Recycling, 2024, 9, 9 CrossRef.
- L. Li, X. Zhang, M. Li, R. Chen, F. Wu, K. Amine and J. Lu, Electrochem. Energy Rev., 2018, 1, 461–482 CrossRef CAS.
- S. Wellens, T. Vander Hoogerstraete, C. Möller, B. Thijs, J. Luyten and K. Binnemans, Hydrometallurgy, 2014, 144–145, 27–33 CrossRef CAS.
- T. Hanada and M. Goto, Green Chem., 2022, 24, 5107–5115 RSC.
- T. Sakamoto, T. Hanada, H. Sato, M. Kamisono and M. Goto, Sep. Purif. Technol., 2024, 331, 125619 CrossRef CAS.
- A. R. F. Carreira, A. Nogueira, A. P. S. Crema, H. Passos, N. Schaeffer and J. A. P. Coutinho, Chem. Eng. J., 2023, 475, 146374 CrossRef CAS.
- N. Peeters, K. Binnemans and S. Riaño, Green Chem., 2022, 24, 2839–2852 RSC.
- E. K. Kopkova, E. A. Shchelokova and P. B. Gromov, Hydrometallurgy, 2015, 156, 21–27 CrossRef CAS.
- M. Kamisono, T. Hanada and M. Goto, ACS Sustainable Resour. Manage., 2024, 1, 1021–1028 CrossRef CAS.
- L. Gijsemans, J. Roosen, S. Riaño, P. T. Jones and K. Binnemans, J. Sustainable Metall., 2020, 6, 589–598 CrossRef.
- A. P. Abbott, G. Frisch, S. J. Gurman, A. R. Hillman, J. Hartley, F. Holyoak and K. S. Ryder, Chem. Commun., 2011, 47, 10031–10033 RSC.
- K. Binnemans and P. T. Jones, J. Sustainable Metall., 2017, 3, 570–600 CrossRef.
- W. Yoshida, Y. Baba, F. Kubota, N. Kamiya and M. Goto, J. Chem. Eng. Jpn., 2017, 50, 521–526 CrossRef CAS.
- F. Kubota, R. Kono, W. Yoshida, M. Sharaf, S. D. Kolev and M. Goto, Sep. Purif. Technol., 2019, 214, 156–161 CrossRef CAS.
- W. Yoshida, Y. Baba, F. Kubota, S. D. Kolev and M. Goto, J. Membr. Sci., 2019, 572, 291–299 CrossRef CAS.
- Y. Baba, F. Kubota, N. Kamiya and M. Goto, Ind. Eng. Chem. Res., 2014, 53, 812–818 CrossRef CAS.
- Y. Baba, F. Kubota, M. Goto, R. W. Cattrall and S. D. Kolev, J. Chem. Technol. Biotechnol., 2016, 91, 1320–1326 CrossRef CAS.
- T. Hanada, K. Seo, W. Yoshida, A. T. N. Fajar and M. Goto, Sep. Purif. Technol., 2022, 281, 119898 CrossRef CAS.
- R. Golmohammadzadeh, F. Faraji and F. Rashchi, Resour., Conserv. Recycl., 2018, 136, 418–435 CrossRef CAS.
- S. Tang, M. Zhang and M. Guo, ACS Sustain. Chem. Eng., 2022, 10, 975–985 CrossRef CAS.
- D. Wang, Y. Li, J. Wu and G. Xu, Solvent Extr. Ion Exch., 1996, 14, 585–601 CrossRef CAS.
- D. M. Wilkins, D. E. Manolopoulos and L. X. Dang, J. Chem. Phys., 2015, 142, 064509 CrossRef PubMed.
- J. Eastoe, M. J. Hollamby and L. Hudson, Adv. Colloid Interface Sci., 2006, 128–130, 5–15 CrossRef CAS PubMed.
- K. Holmberg, Adv. Colloid Interface Sci., 1994, 51, 137–174 CrossRef CAS.
- P. Meshram, B. D. Pandey and T. R. Mankhand, Chem. Eng. J., 2015, 281, 418–427 CrossRef CAS.
- M. Joulié, E. Billy, R. Laucournet and D. Meyer, Hydrometallurgy, 2017, 169, 426–432 CrossRef.
- S. M. Shin, N. H. Kim, J. S. Sohn, D. H. Yang and Y. H. Kim, Hydrometallurgy, 2005, 79, 172–181 CrossRef CAS.
- L. Li, J. Lu, Y. Ren, X. X. Zhang, R. J. Chen, F. Wu and K. Amine, J. Power Sources, 2012, 218, 21–27 CrossRef CAS.
- G. Zeng, J. Yao, C. Liu, X. Luo, H. Ji, X. Mi and C. Deng, ACS Sustain. Chem. Eng., 2021, 9, 16133–16142 CrossRef CAS.
- J. Lie, S. Tanda and J. C. Liu, Molecules, 2020, 25, 2166 CrossRef CAS PubMed.
- S. Wu, N. Kaden and K. Dröder, Batteries, 2023, 9, 297 CrossRef CAS.
- A. M. Wilson, P. J. Bailey, P. A. Tasker, J. R. Turkington, R. A. Grant and J. B. Love, Chem. Soc. Rev., 2014, 43, 123–134 RSC.
|
This journal is © The Royal Society of Chemistry 2025 |
Click here to see how this site uses Cookies. View our privacy policy here.