DOI:
10.1039/C3RA46351F
(Paper)
RSC Adv., 2014,
4, 13355-13360
Synthesis of a three dimensional structure of vertically aligned carbon nanotubes and graphene from a single solid carbon source
Received
2nd November 2013
, Accepted 28th January 2014
First published on 28th January 2014
Abstract
Here, we demonstrate the synthesis of a three dimensional (3D) structure of vertically aligned carbon nanotubes (VACNTs) and graphene from a single solid carbon source. Graphene growth on Cu foil is achieved using solid camphor as the carbon source, whereas the VACNTs are obtained by adding a small amount of ferrocene in the camphor feedstock with minimum contamination from the iron catalyst. Highly dense VACNTs are grown on a transferred graphene film to fabricate the hybrid structure. Raman spectroscopy, optical and scanning electron microcopy studies confirm out of plane growth of the carbon nanotubes (CNTs) from the graphene film. Current–voltage (I–V) measurements are performed to investigate the in plane and out of plane electrical characteristics of the 3D structure. Contact resistance of the VACNTs–graphene is explored taking into account the other resistive contacts in the 3D material system. Achieving a seamless contact of VACNTs–graphene film is significant for low contact resistance and thereby practical device application.
1. Introduction
Graphene, an sp2 hybridized two dimensional (2D) carbon crystal is the main building block of many other carbon allotropes, such as fullerene, CNTs and graphite.1 Graphene shows excellent electrical, mechanical, thermal and optical properties at room temperature.2–5 Similarly, the rolled graphene sheets, also known as CNTs, show extraordinary physical properties considering the unique one dimensional (1D) structure.6–9 The outstanding properties of graphene and CNTs have been exploited for the fabrication of high mobility field effect transistors, transparent conductors, field emitters, energy storage and many other device applications.10–23 Apart from the individual properties and applications of carbon materials, a hybrid structure can have significant technological advantages. Fullerene–CNTs, fullerene–graphene and graphene–CNTs hybrid systems were proposed to combine the individual properties in various applications.24–27 A hybrid structure of graphene and CNTs is significant for application in interconnects, flexible nanoelectronics and flexible field emission devices by exploiting the planar and axial directions properties.
The individual synthesis process of high quality CNTs and large-area graphene film by the chemical vapor deposition (CVD) technique has been extensively investigated.28–32 Similarly, VACNTs have been grown on various insulating substrates, such as SiO2/Si, Al2O3 and quartz by a CVD process. However, the selection of substrate significantly affects the electrical and thermal transport properties in the perpendicular direction of 1D CNTs.33 Sato et al. of Fujitsu Corp. has demonstrated the possibility of creating a 3D integrated structure of CNTs and a top few-layers graphene film.34 The catalytic growth of VACNTs with graphene-supported metal particles using graphene as a base substrate could also be significant. The transferability of CVD graphene film to an arbitrary substrate provides more flexibility for CNTs growth in a wide range of applications. Recently, Lee et al. reported an approach to grow vertically aligned multiwalled carbon nanotubes (VAMWCNTs) on reduced graphene oxide platelets and proposed its applicability as a flexible field emission device.35 Various other applications for these composite structures have been proposed, such as efficient heat radiators and wiring for very large scale integrated circuits. Again, Jeong et al. reported a flexible room temperature NO2 gas sensor consisting of a VACNTs/reduced graphene hybrid film supported by a polyimide substrate.36 Recently, Rao et al. demonstrated the synthesis of a CNTs forest on a suspended graphene monolayer and thereby extended the class of substrates for CNTs growth.37
In context with the previous reports, we demonstrate the synthesis process of a graphene–CNTs hybrid structure using a single solid carbon source in atmospheric pressure (AP) CVD. Graphene growth on Cu foil is achieved using solid camphor as the carbon source, whereas VACNTs are obtained by adding a small amount of ferrocene (1 wt%) in the feedstock. Raman spectroscopy, optical and scanning electron microcopy studies were performed to confirm the out of plane growth of CNTs from the transferred graphene film. The contact resistance of the synthesized VACNTs–graphene system was investigated by I–V measurements taking into account the other resistive contacts in the 3D structure.
2. Experimental details
2.1 Synthesis of graphene
The synthesis of the large-area graphene film was achieved using a CVD technique, as reported previously.17,38 Commercially available Cu foil with a thickness of 20 μm and purity of 99.99% (Nilaco Pvt. Ltd.) was used for the graphene synthesis in the CVD process. 1.5 mg of solid camphor powder was used as the carbon source. In the growth process, Cu foil was heated up to 1000 °C and annealed for 50 min in H2 (100 sccm) atmosphere in a high temperature furnace zone. Camphor was evaporated and introduced to the high temperature furnace by a gas mixture of Ar–H2 (98
:
2 sccm). The graphene growth was completed in 10 min and the furnace was cooled to room temperature gradually.
2.2 The transfer of graphene
The synthesized graphene film was transferred to a quartz substrate by a wet etching process to use as a base for the VACNTs growth. The as-synthesized graphene film on Cu foil was coated with the poly(methyl methacrylate) (PMMA) solution and dried at 60 °C. Fe(NO3)3 solution with a concentration of 50 mg ml−1 was used to etch the Cu foil underneath. Upon completion of the etching process, the PMMA/graphene stack was transferred onto a quartz substrate and PMMA coating was dissolved in acetone. Finally, the graphene film was treated with a diluted nitric acid solution to remove the residual Fe(NO3)3 and dried in air. Similarly, graphene layers were transferred layer by layer on the quartz substrate to obtain a low sheet resistance. VACNTs were grown on the graphene transferred quartz substrate using a Si substrate mask, such that CNTs do not grow on the entirety of the graphene film. Fig. 1 shows a schematic diagram of the VACNTs–graphene 3D structure fabrication process using solid camphor as the carbon source.
 |
| Fig. 1 Schematic diagram of the graphene and CNTs synthesis process using solid camphor and direct growth of the CNTs on the transferred graphene film for the fabrication of a 3D material system. | |
2.3 Synthesis of CNTs on graphene
A highly dense VACNTs forest was grown by the same AP-CVD process and carbon precursor. Solid camphor was mixed with ferrocene (1 wt%) and was put in the low temperature zone of the CVD furnace. The as-synthesized graphene on Cu and transferred graphene on quartz substrate were loaded into the quartz tube furnace, which was heated to a temperature of 750 °C under the flow of an Ar (80 sccm) and H2 (10 sccm) gas mixture. Heating the substrates to the growth temperature, a camphor–ferrocene mixture was introduced in the growth zone by an Ar–H2 carrier gas mixture. The growth period of the CNTs was 15 min and then the furnace was cooled to room temperature under the Ar–H2 flow. The height and density of the CNTs forest can be controlled by the quantity of the camphor–ferrocene mixture and growth duration.
2.4 Characterization of the materials
CNTs, the as-synthesized and transferred graphene films were characterized with Raman spectroscopy, optical microscopy, scanning electron microscopy (SEM) and transmission electron microscopy (TEM) studies. The morphological structures of the synthesized materials were obtained by the digital optical microscope VHX-500. SEM studies of the graphene film and CNTs were carried out with a Hitachi S-4300 at an accelerating voltage of 20 kV. Raman spectra were obtained using an NRS 3300 laser Raman spectrometer with a laser excitation energy of 532.08 nm from a green laser. The sheet resistance of the graphene film was measured by using the instrument RT-70V/RG-7C of Napson Corporation. I–V characteristics of the transferred graphene film and CNTs–graphene hybrid structure were measured at room temperature (25 °C) using a series 2400 Source Meter Keithley.
3. Results and discussion
The structural morphology of the as-synthesized and transferred graphene film was investigated by Raman and optical microscopy studies. Monolayer and few-layer graphene film can be synthesized by the developed AP-CVD process.38 In this study, few-layer graphene film was grown to be compatible with the CNTs growth on graphene film and to create a highly conducting 3D structure. Fig. 2a shows the Raman spectra of the as-synthesized graphene film on the polycrystalline Cu foil. An intense graphitic G and second order resonance double-resonance 2D peak are observed at 1584 and 2695 cm−1, respectively, whilst there is no apparent defect related D peak in the synthesized graphene film. The intensity ratios of the 2D and G peak (I2D/IG) are found to be in the range of 1.2 to 0.7, attributed to the presence of bi-layer and few-layer graphene in the deposited continuous film. Similarly, Fig. 2b shows the Raman spectra of transferred graphene on a quartz substrate. Raman peaks for the bi-layer and few-layer graphene were also detected in the transferred film. However, a low intense D peak appeared around 1330 cm−1 after chemical etching and the transferring of the graphene film on the quartz substrate. The I2D/IG ratios for the transferred graphene film are also found to be in the range of 1.02 to 0.75, the same as that of synthesized graphene on Cu foil. The wrinkle formation, as shown in Fig. 2b, as well as etchant and mechanical impact during the transfer process could contribute to the small increase in D peak. However, the overall structure and quality of the transferred graphene film did not change significantly. Fig. 2c and d show the optical microscope images of the as-synthesized and transferred graphene films. The optical image of the as-synthesized graphene film on the Cu foil shows the grain boundaries, domain structure and formation of a continuous graphene film. Similarly, the transferred graphene film remains continuous, however wrinkles formation was observed due to differences in the thermal coefficients of Cu foil and graphene film.
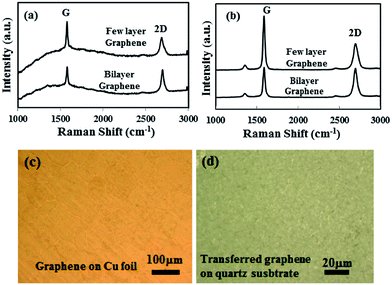 |
| Fig. 2 Raman spectra of the bi-layer and few-layer graphene for (a) as-synthesized on polycrystalline Cu foil and (b) transferred to a quartz substrate. Optical microscope images of (c) as-synthesized and (d) transferred graphene film. | |
The transferred graphene film was used as the base for the CNTs growth from the same camphor precursor with the addition of 1 wt% of ferrocene molecules. The use of the same carbon source in the AP-CVD process to grow graphene and CNTs can have symmetry in growth dynamics, thereby developing a seamless 3D structure. Fig. 3a shows an optical microscope image of the synthesized CNTs on the transferred graphene film at the edge of the masked graphene film. Some of the CNTs are scattered at the edge due to peeling off after removing the mask. As indicated in Fig. 3a, the black part shows highly dense CNTs growth, where the graphene film remains intact. Fig. 3b shows a much clearer view of the underneath graphene film at the edge of the mask. Fig. 3c shows the Raman spectra of the as-synthesized CNTs structure on the transferred graphene film. The graphitic G and second order resonance double-resonance 2D peaks are observed at 1582 and 2695 cm−1, respectively. Again, the defect related D peak is observed at 1342 cm−1, corresponding to CVD synthesized MWCNTs. At the same time, the intensity of the D peak for the underneath graphene film also increased over that of the transferred film. Increase in the D peak intensity for the graphene film can be explained with distortion of the sp2 carbon atoms with thermal stress and oxidation during the high temperature CNTs growth process. Still, the high graphitization of the graphene film with its original structure was not significantly changed. Again, it has been demonstrated that with using 13C isotope graphene Raman peaks can be visualized separately for graphene and CNTs.37 However, in our symmetric growth process with identical precursor material, shifts in the Raman peaks for graphene and CNTs are not observed.
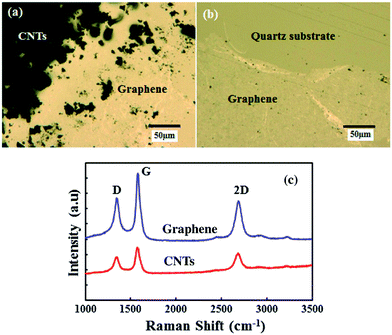 |
| Fig. 3 Optical microscope images of (a) the synthesized CNTs on the transferred graphene film and (b) the masked graphene region during the CNTs growth process, confirming that the film remains intact. (c) Raman spectra of the underneath graphene film and the as-synthesized CNTs. | |
Fig. 4a shows an SEM image of the synthesized VAMWCNTs on graphene film using a mixture of solid camphor and ferrocene molecules. In the synthesis technique, only 1 wt% of ferrocene is added with camphor, the lower catalyst concentration in the feedstock enables MWCNTs growth with low metal impurity. Whereas, in various other processes a high catalyst concentration in the feedstock leads to high metal-impurity and post-deposition purification becomes unavoidable. The growth process involves the simultaneous pyrolysis of solid camphor and ferrocene mixture in a high temperature (750 °C) furnace to obtain the VAMWCNTs. The nucleation and growth of the CNTs occurs on vapor phase catalyst sites,30 which can be significant in keeping the graphene film undamaged without the formation of metal nanoparticles. Fig. 4b shows a magnified SEM image of the VAMWCNTs synthesized on graphene film. We have scratched at one edge of the graphene–CNTs sample to observe the vertical alignment of the CNTs bundle. Some of the bundles peeled off during scratching, otherwise, the CNTs structure is robust on the basal graphene film. The highly dense structure of the VACNTs with a length of around 80 μm can be observed at the edge. The vertical column of the CNTs bundle consists of innumerous nanotubes self-organized into a dense packed structure. The observed structure of the synthesized material can be significant for high thermal and electrical conductivity.
 |
| Fig. 4 SEM images of (a) the CNTs forest grown from the solid camphor on transferred graphene film and (b) a higher magnified image confirming the vertical alignment of the CNTs bundles. | |
Fig. 5a shows a TEM image of the synthesized graphene sheet on polycrystalline Cu foil. The inset of the figure shows the SAED pattern of the graphene sheet. Multiple spots are observed in the SAED pattern. This may be due to overlapping of the two graphene sheets, or owing to a rotational stacking fault. Fig. 5b shows a high resolution TEM (HRTEM) image at the folded edge of a graphene sheet, presenting the formation of a few-layers of graphene. The synthesis of monolayer graphene and few-layer graphene can be controlled in the developed process with the camphor injection rate and growth duration. TEM results for the formation of a few-layers graphene can be correlated with Raman studies. Similarly, Fig. 5c shows a TEM of the CNTs synthesized using the camphor–ferrocene feedstock. The diameter distribution of the CNTs is observed to be in the range of 10–50 nm. Fig. 5d shows a HRTEM image of a CNT presenting more than 10 layers of graphene rolled-up to form a MWCNT structure. The rolled graphene sheets formed a tube structure with a diameter of 10 nm for the inner hole. As explained previously the ferrocene molecules act as a vapor phase catalyst for CNTs growth with decomposition, along with the solid camphor feedstock. The sp2 hybridized graphene film acts as a seeding base for the CNTs growth.
 |
| Fig. 5 (a) TEM image of the synthesized graphene on polycrystalline Cu foil. The inset figure shows the selected area electron diffraction (SAED) patterns. (b) HRTEM image at the folded edge of a graphene sheet, presenting the formation of a few-layers graphene. (c) TEM of the synthesized CNTs using the camphor–ferrocene feedstock with a diameter distribution of 10–50 nm. (d) HRTEM image of a CNT presenting more than 10 layers of graphene rolled-up to form the MWCNT structure. | |
The transferred graphene film shows a sheet resistance (Rs) of 108 Ω □−1, as measured by the four probe technique. Again, the I–V characteristic of the graphene film on an insulating substrate was investigated by a two probe setup, as shown in Fig. 6a. The device shows a linear I–V characteristic (Fig. 6b), signifying the metallic behavior of the graphene film. In previous studies, the contact resistance of VACNTs on graphene coated Cu foil has been explored.37 However, the VACNTs forest only directly on the Cu substrate can also show very low contact resistance. In this context, exploring the contact and sheet resistances of VACNTs on the graphene is quite essential for realizing a VACNTs–graphene 3D system.39 Hence, we consider a transferred graphene film on the quartz substrate integrating with VACNTs to investigate contact resistance at the VACNTs–graphene interface. Fig. 6c shows a schematic diagram of the VAMWCNTs–graphene 3D structure on quartz for electrical conductance measurements. Fig. 6d shows the I–V characteristics of the 3D structure measured by putting a probe on top of the CNTs and the other probe on the bottom graphene contact. The I–V characteristic shows linear behavior with an applied bias voltage of ±5 V, similar to an ohmic contact. A total resistance of 255 Ω was obtained in the VAMWCNTs–graphene 3D material system. The obtained resistance can be explained from the contribution of (a) probe resistance, (b) probe-CNTs contact resistance (Rprobe), (c) graphene–CNTs contact resistance (RG–CNT), (d) graphene-probe resistance (Rprobe), (e) the resistances of CNTs (RCNT) and graphene (Rs).40 The contact resistance of the highly conducting Au coated two probes is found to be 0.015 Ω, which is significantly small. Considering the low contact resistance of the two probes, we expect that the probe contact resistance on the CNTs and graphene film will be small. Previously, it has been demonstrated that the contact resistance with the Au and VACNTs film can be significantly low, although for a graphene film somewhat higher.41,42 Again, considering the effect of scattering in the CNTs forest, resistance in the CNTs bundle itself can contribute to the total resistance. Therefore, the observed contact resistance can be influenced by various other factors, rather than only the CNTs–graphene interface. This finding shows that the highly conducting 3D structure of the VAMWCNTs–graphene can be synthesized from a single solid precursor. Further studies are required in the nanoscale order to confirm the formation of a seamless junction interface with directly grown CNTs on graphene film.
 |
| Fig. 6 (a) Schematic diagram of the graphene film on an insulating substrate for I–V characteristic measurements. (b) I–V characteristics of the graphene film without any metal contact. (c) Schematic diagram of the VAMWCNTs–graphene 3D structure on quartz for I–V measurement. (d) I–V characteristic of the VAMWCNTs–graphene measured by putting a probe on the top CNTs and the other probe on the bottom graphene contact. (e) Possible contact and sheet resistances in the 3D structure. | |
4. Conclusions
In summary, we have demonstrated a symmetric synthesis process of a VAMWCNTs–graphene 3D structure using a single solid carbon source. Graphene growth on Cu foil was achieved using the solid camphor as a carbon source, whereas VAMWCNTs were obtained by adding a small amount of ferrocene (1 wt%) in the camphor feedstock with minimum contamination from the iron catalyst. CNTs growth occurs on vapor phase catalyst sites, which can be significant in keeping the graphene film undamaged without depositing metal nanoparticles. Optical microscopy and SEM studies confirmed the out of plane growth of CNTs on a transferred graphene film. TEM studies were performed to confirm the structure of CNTs and graphene in the 3D system. The carbon material structure varies significantly from the same feedstock with the addition of catalytic ferrocene molecules and control growth process. In the developed process, sp2 hybridized graphene film acted as a seeding base substrate for the VAMWCNTs growth. I–V measurements were carried out to investigate the in plane and out of plane electrical characteristics of the 3D system. The VAMWCNTs–graphene structure showed a total resistance of 255 Ω, where resistance at the probe, graphene–CNTs interface, sheet resistance and CNTs bundle resistance also contributed. Achieving a seamless contact of CNTs–graphene film may be significant for low contact resistance, and thereby practical device applications.
Acknowledgements
We would like to acknowledge the reviewers comments and suggestions to improve the paper. The first two authors contributed equally to the work. The work was supported by the funds for the development of human resources in science and technology, Japan.
References
- A. K. Geim and K. S. Novoselov, Nat. Mater., 2007, 6, 183–191 CrossRef CAS PubMed.
- A. K. Geim and P. Kim, Sci. Am., 2008, 298, 90–97 CrossRef CAS PubMed.
- R. R. Nair, P. Blake, A. N. Grigorenko, K. S. Novoselov, T. J. Booth, T. Stauber, N. M. R. Peres and A. K. Geim, Science, 2008, 320, 1308 CrossRef CAS PubMed.
- C. Lee, X. Wei, J. W. Kysar and J. Hone, Science, 2008, 321, 385–388 CrossRef CAS PubMed.
- A. A. Balandin, S. Ghosh, W. Bao, D. Teweldebrhan, F. Miao and C. N. Lau, Nano Lett., 2008, 8, 902–907 CrossRef CAS PubMed.
- S. Iijima, Nature, 1991, 354, 56–58 CrossRef CAS.
- S. J. Tans, A. R. M. Verschueren and C. Dekker, Nature, 1998, 393, 49–52 CrossRef CAS PubMed.
- P. Kim, L. Shi, A. Majumdar and P. L. McEuen, Phys. Rev. Lett., 2001, 87, 215502 CrossRef CAS.
- J. Hone, M. Whitney, C. Piskoi and A. Zettl, Phys. Rev. B: Condens. Matter Mater. Phys., 1999, 59, R2514–R2516 CrossRef CAS.
- R. H. Baughman, A. A. Zakhidov and W. A. de Heer, Science, 2002, 297, 787–792 CrossRef CAS PubMed.
- W. B. Choi, D. S. Chung, J. H. Kang, H. Y. Kim, Y. W. Jin, I. T. Han, Y. H. Lee, J. E. Jung, N. S. Lee, G. S. Park and J. M. Kim, Appl. Phys. Lett., 1999, 75, 3129–3131 CrossRef CAS PubMed.
- Y. B. Zhang, S. P. Lau, L. Huang and M. Tanemura, Appl. Phys. Lett., 2005, 86, 123115 CrossRef PubMed.
- S. V. Morozov, K. S. Novoselov, M. I. Katsnelson, F. Schedin, D. C. Elias, J. A. Jaszcak and A. K. Geim, Phys. Rev. Lett., 2008, 100, 016602 CrossRef CAS.
- K. I. Bolotin, K. J. Sikes, Z. Jiang, M. Klima, G. Fudenberg, J. Hone, P. Kim and H. L. Stormer, Solid State Commun., 2008, 146, 351–355 CrossRef CAS PubMed.
- L. Britnell, R. V. Gorbachev, R. Jalil, B. D. Belle, F. Schedin, A. Mishchenko, T. Georgiou, M. I. Katsnelson, L. Eaves, S. V. Morozov, N. M. R. Peres, J. Leist, A. K. Geim, K. S. Novoselov and L. A. Ponomarenko, Science, 2012, 335, 947–950 CrossRef CAS PubMed.
- S. Bae, H. K. Kim, Y. Lee, X. Xu, J. Park, Y. Zheng, J. Balakrishnan, D. Im, T. Lei, Y. Song, Y. Kim, K. Kim, B. Ozyimaz, J. Ahn, B. Hong and S. Iijima, Nat. Nanotechnol., 2010, 5, 574–578 CrossRef CAS PubMed.
- G. Kalita, M. Masahiro, H. Uchida, K. Wakita and M. Umeno, Mater. Lett., 2010, 64, 2180–2183 CrossRef CAS PubMed.
- A. Cao, P. L. Dickrell, W. G. Sawyer, M. N. Ghasemi-Nejhad and P. M. Ajayan, Science, 2005, 310, 1307–1310 CrossRef CAS PubMed.
- X. Yang, C. Cheng, Y. Wang, L. Qiu and D. Li, Science, 2013, 341, 534–537 CrossRef CAS PubMed.
- Z. Guo, J. Wang, F. Wang, D. Zhou, Y. Xia and Y. Wang, Adv. Funct. Mater., 2013, 23, 4840–4846 CAS.
- K. P. Loh, Q. L. Bao, G. Eda and M. Chowalla, Nat. Chem., 2010, 2, 1015–1024 CrossRef CAS PubMed.
- P. Avouris, Z. Chen and V. Perebeinos, Nat. Nanotechnol., 2007, 2, 605–615 CrossRef CAS PubMed.
- M. Zhang, S. Fang, A. A. Zakhidov, S. B. Lee, A. E. Aliev, C. D. Williams, K. R. Atkinson and R. H. Baughman, Science, 2005, 309, 1215–1219 CrossRef CAS PubMed.
- G. Kalita, S. Adhikari, H. R. Aryal, M. Umeno, R. Afre, T. Soga and M. Sharon, Appl. Phys. Lett., 2008, 92, 063508 CrossRef PubMed.
- Y. Zhang, L. Ren, S. Wang, A. Marathe, J. Chaudhuri and G. Lic, J. Mater. Chem., 2011, 21, 5386–5391 RSC.
- D. H. Lee, J. E. Kim, T. H. Han, J. W. Hwang, S. Jeon, S. Y. Choi, S. H. Hong, W. J. Lee, R. S. Ruoff and S. O. Kim, Adv. Mater., 2010, 22, 1247–1252 CrossRef CAS PubMed.
- A. Rodriguez-Manzo, F. Banhart, M. Terrones, H. Terrones, N. Grobert, P. M. Ajayan, B. G. Sumpter, V. Meunier, M. Wang, Y. Bando and D. Golberg, Proc. Natl. Acad. Sci. U. S. A., 2009, 106, 4591–4595 CrossRef PubMed.
- K. Hata, D. N. Futaba, K. Mizuno, T. Namai, M. Yumura and S. Iijima, Science, 2004, 306, 1362–1364 CrossRef CAS PubMed.
- J. Prasek, J. Drbohlavova, J. Chomoucka, J. Hubalek, O. Jasek, V. Adamc and R. Kizek, J. Mater. Chem., 2011, 21, 15872–15884 RSC.
- M. Kumar and Y. Ando, J. Nanosci. Nanotechnol., 2010, 10, 3739–3758 CrossRef CAS PubMed.
- K. S. Kim, Y. Zhao, H. Jang, S. Y. Lee, J. M. Kim, K. S. Kim, J. H. Ahn, P. Kim, J. Y. Choi and B. H. Hong, Nature, 2009, 457, 706–710 CrossRef CAS PubMed.
- X. S. Li, W. W. Cai, J. H. An, S. Kim, J. Nah, D. X. Yang, R. Piner, A. Velamakanni, I. Jung, E. Tutuc, S. K. Banerjee, L. Colombo and R. S. Ruoff, Science, 2009, 324, 1312–1314 CrossRef CAS PubMed.
- S. Talapatra, S. Kar, S. K. Pal, R. Vajtai, L. Ci, P. Victor, M. M. Shaijumon, S. Kaur, O. Nalamasu and P. M. Ajayan, Nat. Nanotechnol., 2006, 1, 112–116 CrossRef CAS PubMed.
- D. Kondo, S. Sato and Y. Awano, Appl. Phys. Express, 2008, 1, 074003 CrossRef.
- D. H. Lee, J. A. Lee, W. J. Lee and S. O. Kim, Small, 2011, 7, 95–100 CrossRef CAS PubMed.
- H. Y. Jeong, D. S. Lee, H. K. Choi, D. H. Lee, J. E. Kim, J. Y. Lee, W. J. Lee, S. O. Kim and S. Y. Choi, Appl. Phys. Lett., 2010, 96, 213105 CrossRef PubMed.
- R. Rao, G. Chen, L. M. R. Arava, K. Kalaga, M. Ishigami, T. F. Heinz, P. M. Ajayan and A. R. Harutyunyan, Sci. Rep., 2013, 3, 1891 Search PubMed.
- G. Kalita, K. Wakita and M. Umeno, Physica E, 2011, 43, 1490–1493 CrossRef CAS PubMed.
- Y. Jiang, P. Wang and L. Lin, Nanotechnology, 2011, 22, 365704 CrossRef PubMed.
- N. Chiodarelli, S. Masahito, Y. Kashiwagi, Y. Li, K. Arstila, O. Richard, D. J. Cott, M. Heyns, S. D. Gendt, G. Groeseneken and P. M. Vereecken, Nanotechnology, 2011, 22, 085302 CrossRef PubMed.
- J. W. McBride, E. M. Yunus and S. M. Spearing, Eur. Phys. J.: Appl. Phys., 2010, 50, 12904 CrossRef PubMed.
- O. Balci and C. Kocabas, Appl. Phys. Lett., 2012, 101, 243105 CrossRef PubMed.
|
This journal is © The Royal Society of Chemistry 2014 |
Click here to see how this site uses Cookies. View our privacy policy here.