Effective separation of metal impurities from gypsum nanosludge: synergism of mechanical force and metal species regulation†
Received
31st August 2024
, Accepted 18th October 2024
First published on 21st October 2024
Abstract
The effective separation of metal impurities from gypsum sludges is crucial for both environmental protection and resource recovery. However, it is seriously limited by their entrapment within calcium sulfate crystal lattices. This study presents a universal strategy for metal extraction through combined control of mechanical force and metal species regulation, which effectively separated P, Cr, As, Sr, Cd, and Hg from gypsum sludges with separation efficiencies all above 94.0%, especially for As (99.8%) and Hg (99.2%). Such an exciting effect was due to the precise control of a two-step dehydration–rehydration transformation of gypsum. The process initiated by the mechanical force reduced the gypsum particle size from the microscale (∼10 μm) to the nanoscale (<50 nm), which facilitated the dehydration process of gypsum–bassanite to exclude the doped metals. In the subsequent rehydration process, the nanoparticles were also beneficial for disrupting the calcium sulfate framework of bassanite, leading to the full release of entrapped metals. Additionally, the application of species-regulating agents changed the species of released metals, preventing their re-incorporation into the calcium sulfate. This approach offered a promising method for the separation and recovery of heavy metals from gypsum sludges, providing valuable insights into the treatment of heavy metal-containing solid wastes.
Environmental significance
The release of toxic metals from gypsum sludge poses a significant environmental and health risk due to their incorporation within crystal lattices, hindering efficient recovery and recycling. This study demonstrated a novel metal extraction strategy utilizing mechanical force and species regulation to achieve over 94.0% extraction efficiency for various metals, including As (99.8%) and Hg (99.2%). By enhancing the dehydration–rehydration transformation of gypsum, this approach disrupted the calcium sulfate framework and prevented metal re-incorporation, providing a sustainable solution for heavy metal separation. This work offered a valuable pathway for mitigating heavy metal pollution and advancing resource recovery from industrial waste.
|
1. Introduction
The treatment of mining wastewater, smelting wastewater,1 and coal combustion flue gas2 generates over a hundred million tons of industrial gypsum sludge annually.3 These sludges often contain fine particles (1–100 μm) that coexist with highly toxic heavy metals or impurities, including chromium (Cr),4 arsenic (As),5 mercury (Hg),6etc., thus causing severe environmental pollution and threatening human health. Therefore, the effective separation of these heavy metals is significant, not only for maintaining the environment safety, but also for the efficient recycling of gypsum sludges.
However, traditional acid or alkali leaching methods can only separate 20–65% of heavy metals from gypsum sludges,4,7 making their recycling a great challenge. Recently, advanced electrochemical methods and integrated approaches, including precipitation–electrodialysis–crystallization, have been rigorously developed for the recovery and valorization of valuable elements from gypsum and its leachates.8–11 Meanwhile, the unseparated metals, such as Cr, As, Cd, and Hg, were identified to be doped into the gypsum lattice and could not be released by simple leaching methods.4–6,12 It is known that the primary mineral phase in gypsum sludge is calcium sulfate dihydrate (DH, CaSO4·2H2O), which can be dehydrated to bassanite (calcium sulfate hemihydrate, HH, CaSO4·0.5H2O) and anhydrite (calcium sulfate anhydrite, AH, CaSO4) through dehydration at >100 °C and >200 °C, respectively.13 Recently, many methods have been studied to extract doped metals (such as Cr (ref. 4) and As (ref. 5)) from gypsum sludges through phase transformation, including decomposition by high-temperature calcination (≥800 °C)14 and hydrothermal treatment (≥120 °C, 12 hours).4 Our previous work has explored an efficient method to extract doped metals through a two-step phase transformation of dehydration–rehydration via calcination and acid leaching. Although the widespread practical application of this method is hindered by excessive energy and acid requirements, it is discovered that the metal separation efficiency of HH is much higher than that of AH, due to the re-incorporation of metals into the AH lattice.12 Therefore, the precise control of gypsum dehydrating to bassanite is the key and challenge to extract various incorporated metals from gypsum sludge.
Mechanochemistry, recognized by IUPAC as one of the ten technologies changing the world,15 includes ball-milling as its most commonly used technique. Although highly effective, ball-milling requires a substantial amount of mechanical energy, with consumption varying depending on parameters like speed and duration of operation. Ball-milling generally relies on the increase of defects, force-induced effects, and the breaking and forming of chemical bonds under mechanical energy input to facilitate reactions.16–18 It is already reported that mechanical activation methods (planetary ball mills) could transform natural gypsum into bassanite at room temperature, through grinding the particles into nano size to enhance their reactivity.19,20 Therefore, a similar process is expected to occur on gypsum sludge, which could control the dehydration of gypsum precisely to bassanite to exclude the incorporated metals. Although a few studies have noticed ball-milling as a suitable method for treating gypsum sludge,20,21 the extract efficiency could only achieve 51–70%,22 which was insufficient for the reuse of gypsum sludge. It was reported that in addition to the gypsum phase transformation, the extraction efficiency is also closely related to synergistic effects of the added agents, which could change the ionic form of metals to inhibit their re-incorporation with gypsum.4 Therefore, it is expected that ball-milling would create an initial pathway for gypsum dehydration to bassanite to exclude the doped metals, while regulating agents would facilitate the following release process in the subsequent hydration step, which synergistically offered a more complete separation of metals from gypsum sludges.
Herein, we proposed a general and effective method for extracting doped impurities from gypsum sludges, through a mechanical force-induced dehydration–rehydration process. Ball-milling was firstly employed to convert gypsum into bassanite to exclude the doped impurities, followed by the use of species-regulating agents to sequester the excluded impurities during the next rehydration step. Six typical gypsum sludges containing fine particles of P (which exhibited a binding mode in gypsum analogous to that of metals23,24), Cr, As, Sr, Cd, and Hg were chosen as probes. The mechanism of metal exclusion and separation during the two-step phase transformation was investigated by X-ray fluorescence spectrometry (XRF), X-ray diffraction (XRD), transmission electron microscopy (TEM), and density functional theory (DFT) calculations. This approach has the potential to establish a universal method for the high-efficiency separation of doped impurities from gypsum sludges, providing valuable theoretical insights into extracting metals from heavy metal-containing solid wastes.
2. Materials and methods
2.1 Materials
The pristine P(V)/Cr(VI)/As(V)/Hg(II)-containing gypsum samples were systematically procured from various locales across China (Table S1†). The Sr(II)-containing gypsum was collected from the Minqin County, Gansu Province, China. Additionally, a Cd-lattice incorporated gypsum sample was synthesized according to the methods reported in ref. 7, 25 and 26.
2.2 Preparation of metal-doped gypsum
Water-leached gypsum samples were prepared by mixing the pristine gypsum samples with distilled water at a solid-to-liquid ratio (s
:
l) of 1.5 g
:
40 mL. The mixture was stirred magnetically for 30 minutes and then allowed to settle for 2 hours before centrifugation. The supernatant was collected for inductively coupled plasma optical emission spectrometry (ICP-OES) analysis. The acid-leached gypsum samples were processed similarly, except that the distilled water was replaced with 0.2–0.5 mol L−1 dilute sulfuric acid (H2SO4) solution.
The pristine sludge samples were mixed with a sulfuric acid (H2SO4) solution (pH 3, s
:
l = 10 g
:
250 mL) and stirred. 0.1 M sodium hydroxide (NaOH) was then added to adjust the pH from 7 to 9, facilitating the removal of impurities such as NaCl, SiO2, CaCO3, and NaClO3. The samples were subsequently washed 3–5 times with distilled water to eliminate any residual alkali. Consequently, the neutralized gypsum samples containing P(V), Cr(VI), As(V), Sr(II), Cd(II), and Hg(II) were obtained. These samples were then washed with a gypsum-saturated solution (s
:
l = 10 g
:
250 mL) to remove the adsorbed metals. After washing, gypsum samples with metals incorporated into the lattice were obtained and used in the experiments. The treated metal-doped gypsum samples were designated as P-DH, Cr-DH, As-DH, Sr-DH, Cd-DH, and Hg-DH.
2.3 Mechanical force treatment for metal-doped gypsum
A specified mass of metal-doped gypsum samples was processed in a planetary ball mill (QM-3SP04, Nanjing Nanda Instruments Ltd.). The initial materials, along with 12 g of uniform agate grinding balls (colloidal aggregates of silicon dioxide, comprising approximately three 10 mm diameter balls, nineteen 6 mm diameter balls, and twenty-eight 1 mm diameter balls), were placed into the agate grinding jar. The mixture was milled under varying time intervals, with different agents and different ball-to-powder ratios. To avoid overheating, 30 minutes of grinding and a subsequent 5 minute rest mode was used. The total milling times were 10, 60, 90, 120, 180, 240, 360, 480, and 720 minutes, respectively (with no rest mode for the 10 minute milling).
2.4 Extraction of metals from milled gypsum
The milled gypsum samples were mixed with distilled water, pH 3 solutions (pH was adjusted with HCl), and certain concentration control agents (1 M HCl for As-DH and [0.01 M CuSO4
:
0.1 M Na2S2O3] solution for Hg-DH) at s
:
l = 1.5 g
:
40 mL, respectively. The mixture was stirred magnetically for a time interval (5, 10, 15, 20, 30 minutes; 1, 2, 3, 4, 6, 7 hours). The supernatant was collected for ICP-OES analysis and the solid was freeze dried for subsequent XRD characterization.
3. Results and discussion
3.1 Separation effect of various metals through the milling–leaching method
The primary phase of the six pristine gypsum samples was identified as CaSO4·2H2O, with impurities including SiO2 and CaCO3 (Fig. S1†). XRF and ICP analyses revealed a complex composition of heavy metals and impurity elements within the gypsum samples (Fig. S2†), with various contents from 548 to 16
171 mg kg−1 (Fig. S3†). To verify the elemental speciation in the gypsum samples, water washing and acid leaching were performed on all six pristine samples. After water washing, only 1–30% of the target elements (P, Cr, As, Sr, Cd, and Hg for each corresponding gypsum sample) were removed. Acid leaching extracted 30–40% of the target elements, leaving 60–70% retained in the gypsum samples, suggesting that these elements are present in a doped state (Fig. S4†). The results from the Rietveld refinement method of the treated metal-doped gypsum samples (Fig. S5 and Table S2†) revealed the doping levels of the elements of interest as follows: 0.82 wt% (P), 0.35 wt% (Cr), 1.47 wt% (As), 0.0099 wt% (Sr), 0.033 wt% (Cd), and 0.17 wt% (Hg). This suggested that most of the impurities or metals remained as lattice-incorporated states in the gypsum crystals, which were not easily removed by simple water-washing or acid-leaching. To investigate the doped speciation, XPS, FT-IR, and Raman analyses were performed (Fig. S6–S8†). The results indicated that the doped anions of P, Cr, and As were in the forms of HPO42−, CrO42−, and HAsO42−, respectively; while the doped cations were in the forms of Sr2+, Cd2+, and Hg2+, respectively. Based on the type of doped ion, the gypsum samples were categorized into anionic and cationic types. In Fig. 1a, TEM analysis of the gypsum samples showed that all the targeted elements were randomly distributed within the CaSO4·2H2O lattice. The distinct peaks observed in the metal-line profile of the EDS line scans for the gypsum samples also clearly indicated the incorporation of target elements within the gypsum crystals (Fig. 1a). Rietveld refinement of XRD showed that the corresponding incorporation ratios of P, Cr, As, Sr, Cd and Hg were 4.76 at%, 1.19 at%, 2.85 at%, 0.020 at%, 0.50 at% and 0.15 at%, respectively (Table S2†). XRF results also confirmed the presence of elements in the samples, with P, Cr, As, Sr, and Hg being 1.1%, 2.3%, 6.7%, 0.4%, and 2.9%, respectively (Fig. S2†). These results proved that the elements were not only adsorbed on the surface, but also incorporated in the gypsum samples.
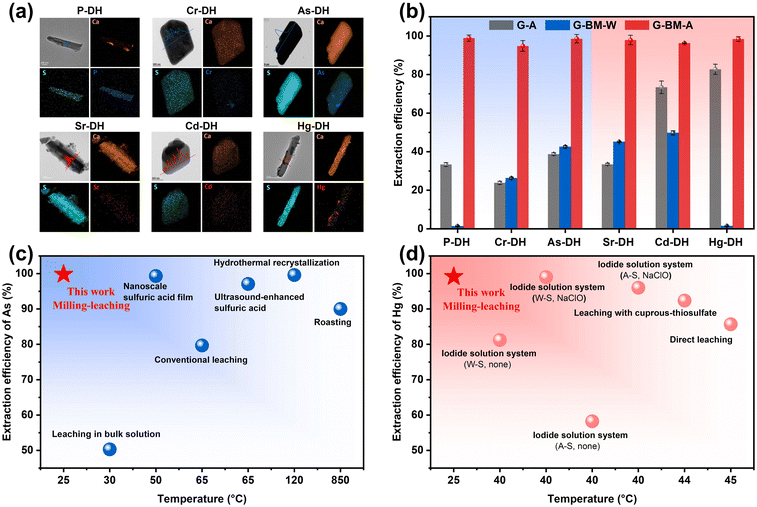 |
| Fig. 1 (a) TEM images and corresponding EDS elemental mappings of gypsum samples (curves are results of EDS line scans); (b) the corresponding extraction efficiencies of elements via different treatments; comparison of (c) As and (d) Hg extraction efficiencies between our method and other methods from the reported literature. | |
As shown in Fig. 1b, the element extraction efficiencies of treatments for gypsum ball-milled-control agent leaching (G-BM-A) was compared to: gypsum-control agent (G-A) leaching and gypsum ball-milled-water leaching (G-BM-W). The results demonstrated that the G-BM-A method achieved remarkable extraction efficiencies for various elements, with values consistently exceeding 98.9% (P), 94.8% (Cr), 99.8% (As), 97.9% (Sr), 96.3% (Cd), and 99.2% (Hg). In contrast, the extraction efficiencies of G-A were lower than 40%, while for G-BM-W, they were lower than 70%. These findings indicated that enhanced extraction could only occur through the G-BM-A method, suggesting that both milling and the control agent were necessary for higher extraction efficiency (Fig. 1b). Notably, the G-BM-A method achieved As extraction rates nearly 100%, comparable to most reported hydrothermal, ultrasonic, and nanofiltration methods (Fig. 1c and Table S3†). This performance was significantly higher than those of high-temperature methods and markedly surpassed traditional leaching techniques. For Hg extraction, the G-BM-A method also outperformed the majority of reported extraction methods (Fig. 1d and Table S4†).
3.2 Metal excluding mechanism during milling-induced dehydration
Metal excluding effect during dehydration transformation of gypsum.
The efficient extraction of the target elements from gypsum using the G-BM-A method presented a marked contrast to the G-A and G-BM-W methods. To elucidate the reasons behind these high efficiencies, the key roles of the ball-milling and agent-leaching are separately investigated. As-DH and Hg-DH were chosen as the typical anion and cation gypsum sludges to explore the contribution of the milling-induced reaction for efficient extraction. The variation of the phases for milled products at different milling times were identified by XRD analysis heat maps (Fig. 2a and b). For As-DH (Fig. 2a), the CaSO4·2H2O signals were distinctly observed during the 0–10 minutes. The diffraction peaks of CaSO4·0.5H2O began to emerge after 240 minutes, with the peaks for CaSO4·2H2O disappearing by 720 minutes. This indicated that a complete phase transformation from dihydrate to hemihydrate (designated as As-HH) occurred during the application of mechanical force. Similarly, Hg-DH also underwent a dehydration process of CaSO4·2H2O → CaSO4·2H2O and CaSO4·0.5H2O → CaSO4·0.5H2O (Fig. 2b, designated as Hg-HH). Moreover, XRD results showed that the hemihydrate phase obtained by milling was β-CaSO4·0.5H2O (Fig. S9†). This phase was consistent with that obtained when gypsum was calcined in the absence of water (Fig. S10†), suggesting that the dehydration of gypsum under mechanical force primarily followed a solid-state phase transformation mechanism, rather than a dissolution–recrystallization process.12,16,19,27
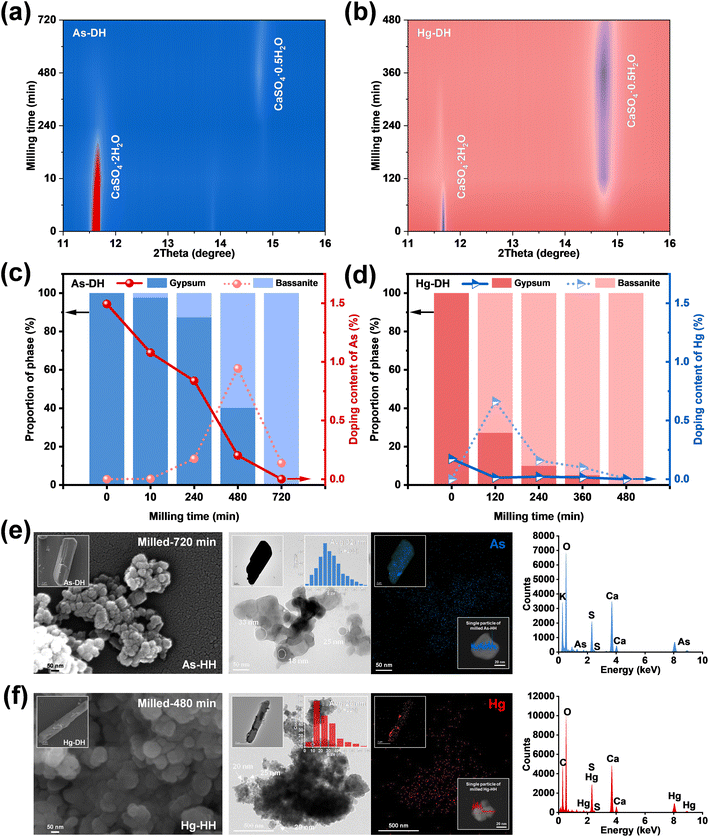 |
| Fig. 2 Heat mappings of CaSO4·2H2O and CaSO4·0.5H2O regions determined with XRD analysis for (a) As-DH and (b) Hg-DH at different times of ball-milling; the evolution of phase proportion and metal doping content for (c) As-DH and (d) Hg-DH; TEM images with elemental mapping of (e) As-HH and (f) Hg-HH obtained after 720 or 480 minutes of milling, respectively. The insets on the left depicted As-DH and Hg-DH, while the bar charts on the right presented the particle size distribution histograms for As-HH and Hg-HH obtained through ball milling. | |
Fig. 2c and d present the time-dependent metal doping content curves for As-DH and Hg-DH during milling-induced dehydration. The As-doping content in gypsum gradually decreased with the dihydrate phase converting to hemihydrate (10–720 minutes, Fig. 2c). Meanwhile, the As-doping content in bassanite increased to 0.94% at 480 minutes and then decreased to 0.14% at 720 minutes. Notably, the doped As was almost entirely excluded during the gypsum-to-bassanite transformation (90.85 ± 0.10%, Fig. S11a and S12a†), which was approximately 2.96% higher than the exclusion achieved through dehydration by calcination (88.24 ± 0.21%, Fig. S11a and S12a†). Similarly, the Hg-doping content decreased from 0.17% in gypsum to 0.0047% in bassanite after 240 minutes of milling, achieving a complete exclusion of approximately 97.30 ± 0.20% (Fig. S11b and S12b†), which was 1.70 times greater than that of calcination treatment (57.34 ± 0.25%, Fig. S11b and S12b†). Such decreased doping contents could be ascribed to the excluding effect during gypsum–bassanite transformation under mechanical force. As shown in Fig. 2e and f, the TEM images revealed that the As-HH and Hg-HH obtained via milling formed as clusters of spherical nanoparticles, with average diameters of approximately 32 nm and 26 nm, respectively. Elemental distribution analysis indicated that both arsenic (As) and mercury (Hg) were predominantly concentrated on the edges of the particles, as shown in the EDS line scans of a single particle in the insets of Fig. 2e and f. In contrast to the initial gypsum sludge, where As and Hg were homogeneously distributed (Fig. 1a), the heterogeneous distribution observed in As-HH and Hg-HH suggested that the solid-state phase transformation induced by milling converted these metals from an incorporated state within the gypsum particles to a non-incorporated state on the edges of the bassanite particles.
Structure rearrangements lead to the release of doped metals.
The above results indicated that the ball-milling induced dehydration significantly enhanced the exclusion of the doped-metal for both As-DH and Hg-DH. To gain deeper insights into the exclusion mechanism, we analyzed the micromorphology evolution and variation in structural parameters to elucidate the phase transformation and its effects on metal exclusion.
Micrometer-sized crystalline aggregates (referred to as bulks) and rods were present in the TEM and SEM results at the start of the mechanical reaction (Fig. 3a and b and S13†). XRD results showed that bassanite was formed after 10 minutes of milling (Fig. 2a and c, As-DH), while the irregular crystallites exhibited surface roughness and distorted lattice structures after 240 minutes of milling for As-DH and 120 minutes of milling for Hg-DH (Fig. 3a and b). This suggested that shear forces induced the fragmentation of calcium sulfate particles and formation of surface defects.20 Moreover, the inverse FFT of the TEM images (Fig. 3a and b, third column) showed that the lattice fringes of the original As-DH and Hg-DH samples appear to be vertically aligned. In contrast, the milled gypsum, As-DH, and Hg-DH samples after 120–720 minutes of milling consisted of irregular particles with rough surfaces and distorted crystalline lattices, highlighting the structural deformation induced by mechanical forces. The variations in lattice parameters (a, b, c) of the milled gypsum are shown in Fig. S14.† Compared to database values, the unit-cell parameters of gypsum showed anisotropic variation with milling time, which further confirms the presence of lattice distortions induced by mechanical force.28 These surface defects and lattice distortions played as the key active sites for energy transfer and accumulation, which would ignite the crystal activity to trigger the gypsum-to-bassanite transformation.29,30 Moreover, the cell volume of milled As-DH (495.47 ± 0.0037 Å3 at 480 minutes) was smaller than that of pure DH (495.60 ± 0.0039 Å3, Fig. 3c). Considering the larger ionic radius of HAsO42− (2.7 Å) compared to SO42− (2.3 Å), this decrease in cell volume could be attributed to the exclusion of HAsO42− from the gypsum lattice during the phase transformation. Initially, due to the larger size of HAsO42− incorporated into As-DH, its cell volume increased to 495.84 ± 0.0042 Å3. However, as milling progressed, the removal of HAsO42− caused the cell volume to gradually decrease, approaching that of pure DH within the first 10 minutes. Similarly, the cell volume of milled Hg-DH (495.89 ± 0.0052 Å3 at 120 minutes) was larger than that of pure DH. Despite Hg2+ having a smaller ionic radius (1.02 Å) compared to Ca2+ (1.12 Å), the increase in cell volume can be attributed to the exclusion of Hg2+ from the gypsum lattice. Over time, the cell volume of Hg-DH (initially 495.36 ± 0.0031 Å3) also converged toward the pure DH value as the Hg2+ ions were gradually removed from the crystal structure (0–120 minutes). The continuous mechanical force during milling induced lattice distortions, leading to slight fluctuations in cell volume rather than a perfect convergence to the pure DH value, as shown by the trend in Fig. 3c. Spherical clusters of nanoparticles with diameters below 40 nm were formed after 720 or 480 minutes of milling (Fig. 2e and f), while As-HH and Hg-HH obtained from the traditional calcination method (120–200 °C) maintained a micrometer scale (∼10 μm) and rod-like morphology (Fig. S15†), without any defect forming or size conversion. Moreover, the exclusion effect of calcination was lower than that of milling (Fig. S12†). Therefore, it could be concluded that milling-induced surface defects, together with the nano-size effect, could activate the lattice activity of both gypsum and bassanite, and further enhance the exclusion of doped metals.
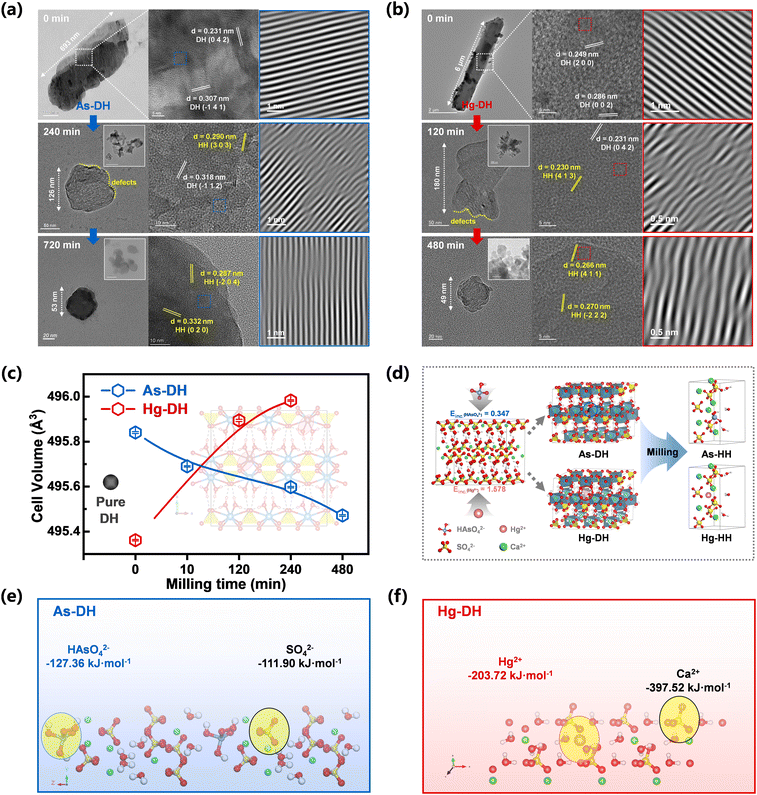 |
| Fig. 3 TEM and SEM images illustrating the micromorphology evolution of (a) As-DH and (b) Hg-DH after different milling times; the insets in the first column correspond to low-magnification TEM images of the samples at the respective time points; the second column presented the HRTEM images of the samples on the left; the third column presented inverse FFT images of TEM obtained by applying a mask. (c) Changes in the cell volume for the dihydrate phase in As-DH and Hg-DH with increasing milling time. (d) Structural diagrams of pure gypsum and metal-doped gypsum. Binding energies (Eb) of (e) SO42−/HAsO42− and (f) Ca2+/Hg2+ on the (010) crystal planes, calculated by the DFT method. | |
The exclusion mechanism was further investigated from the structural conversion of gypsum during dehydration. The crystal structure of gypsum, as shown in Fig. 3d, consists of layers of tightly bound Ca2+ and SO42− ions, which are separated by water molecules and stabilized by hydrogen bonds. The oxygen atoms in water and sulfate coordinate around the calcium ions in the CaSO4·2H2O lattice.31 Due to the similar ionic radii of metal cations (such as Cd2+,7 Hg2+ (ref. 6)) and oxyanions (like CrO42– (ref. 32) and HAsO42– (ref. 33)) to those of Ca2+ or SO42−, these ions can substitute Ca2+ or SO42− in the gypsum lattice through isomorphous substitution or interstitial doping. During dehydration, the removal of water molecules creates vacancies in the calcium or sulfate coordination sphere, causing the rearrangement of SO42−/HAsO42− oxyanions or Ca2+/Hg2+ cations, thereby compensating for calcium or sulfate coordination.34 It was reported that milling-induced shear forces could cleave gypsum crystals along the (010) plane, which facilitated structural rearrangements within the Ca2+/SO42− blocks across different CaSO4 polymorphs.20 Such rearrangement was likely to make the (010) plane pivotal for metal exclusion. The XRD diffraction patterns also showed an obvious decrease the (010) face intensity in the gypsum lattice during milling, which revealed the preferential disruption of this face in both As-DH and Hg-DH (Fig. S17a and b†). DFT calculations of binding energies (Eb) were further conducted from the (010) plane to explore the metal exclusion mechanism. As illustrated in Fig. 3e, the binding energy of SO42− with Ca2+ (−119.92 kJ mol−1) was similar to that of HAsO42− (−127.36 kJ mol−1) in As-DH. Consequently, the solid frame of the calcium sulfate lattice was destroyed under mechanical force, leading to the exclusion of As from the structure during dehydration. Fig. 3f indicates that the binding energy between Hg2+ and SO42− (−203.72 kJ mol−1) was lower than that between Ca2+ and SO42− (−397.52 kJ mol−1) in Hg-DH, suggesting that bonds with lower absolute binding energy values are more susceptible to breakage, facilitating the exclusion of Hg2+. However, due to the limitations imposed by the solid calcium sulfate framework in the solid-state phase transformation process, the atomic rearrangement during water escape was restricted.12 This constraint resulted in incomplete metal exclusion, with some metal atoms remaining confined on the edges of the CaSO4·0.5H2O lattice.
3.3 Leaching-induced rehydration enhanced metal extraction
The above results and analysis revealed that owing to the synergism of higher metal exclusion during dehydration induced by milling and the effect of control agents during the leaching process (Fig. 1b), the metal extraction efficiency for G-BM-A was considerably greater than that for G-A and G-BM-W. To ensure complete separation of metals from gypsum sludges, further release during the leaching process was also crucial. Therefore, based on the different properties of the target metals, the hemihydrate products obtained via ball-milling (marked as milled-HH) were subjected to leaching with distilled water, pH 3 solution, and specific control agents (1 M HCl for As-HH; [0.01 M Cu2+]/[0.1 M S2O32−] for Hg-HH).
Effect of milling for metal extraction.
As shown in Fig. 4a and b, XRD analysis revealed that the hemihydrate peaks of milled-HH gradually diminished, transforming completely into dihydrate in the solutions after 30 minutes. SEM images (Fig. 4c and d) further demonstrated that nanoscale particle clusters progressively transitioned into larger bulk structures, which were distinctly different from the original milled-HH. This observation suggested that a rehydration process, driven by dissolution–recrystallization, occurred. It was reported that the atom rearrangement of calcium sulfate during dissolution–recrystallization would provide a secondary pathway to release metal impurities, regardless of whether they are doped or adsorbed species.12 Therefore, the rehydration rate of bassanite to gypsum is supposed to influence the metal releasing effect significantly. In Fig. 4e, after 5 minutes of hydration in distilled water, the calcined As-HH formed only 10 ± 0.015% gypsum, whereas the milled As-HH resulted in a higher amount (13 ± 0.012%). Similarly, in Fig. 4f, the milled Hg-HH formed 90 ± 0.031% gypsum, significantly greater than the calcined Hg-HH, which formed only 72 ± 0.026% gypsum after 5 minutes. Furthermore, in solution at pH 3 or with specific control agents, hydration of the milled-HH occurred rapidly (Fig. S16†). That is to say, the rehydration rate of milled-HH was much faster than that of calcined-HH. Such accumulation could be ascribed to the smaller particle size (∼50 nm) and more surface defects of milled-HH (Fig. 4c and d) than those of calcined-HH (Fig. S15†). These findings indicated that the mechanical force applied during milling effectively reduced the particle size of As-HH/Hg-HH, which in turn accelerated the hydration rate and enhanced metal release.
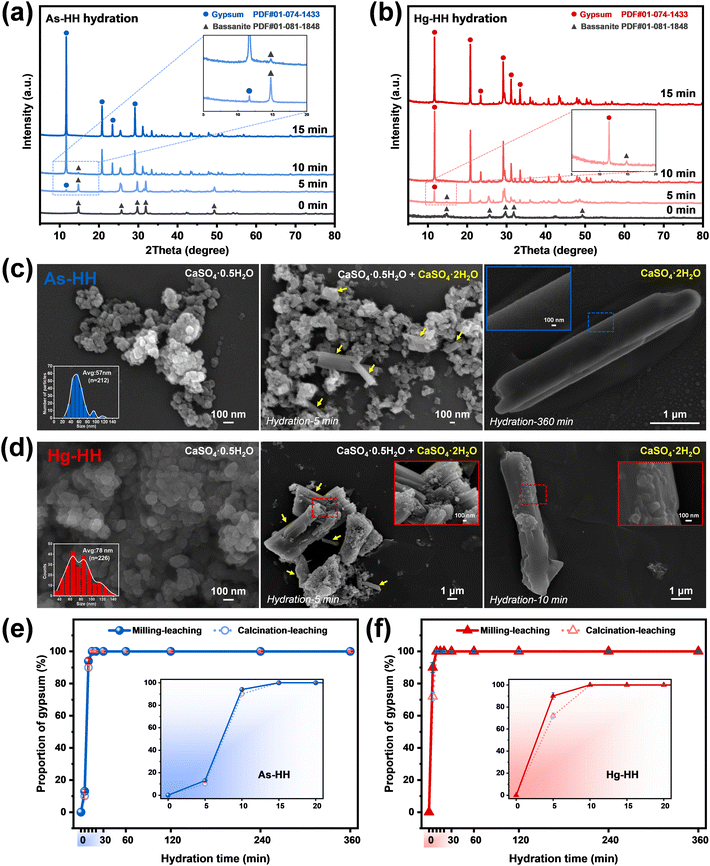 |
| Fig. 4 XRD patterns of hydration products from (a) As-HH and (b) Hg-HH obtained by milling. SEM images of hydrated CaSO4·0.5H2O for (c) As-HH and (d) Hg-HH obtained by milling; the bar charts on the left presented the particle size distribution histograms for As-HH and Hg-HH obtained through ball milling. Time-to-percentage conversion curves of hydration calcium sulfate for (e) As-HH and (f) Hg-HH, comparing milling–leaching and calcination–leaching processes; the insets magnified the results for the 0–30 minute time interval. | |
Effect of the species-regulating agent for metal extraction.
From the above discussion, it was observed that 90.85% of As was transformed into a non-incorporated state in the milled As-HH (Fig. 2c and S12†). However, only 58.58% of As was leached after As-HH rehydration back to DH in distilled water, while this value increased to 69.76% at pH 3 (Fig. 5a, 30 minutes), both of which were much lower than that of the incorporated As state in the milled As-HH. Considering that As species in both original As-DH and the milled As-HH existed in the form of HAsO42− (Fig. S6c and S18a†), it could be assumed that HAsO42− re-encapsulated back into the product of rehydration, leading to the low separation rate. Therefore, changing the species of As during rehydration was supposed to be crucial to enhance the metal extraction efficiency. Notably, when leached in an HCl solution with a concentration of 1 M H+, the As extraction efficiency significantly increased to 94.10% within 30 minutes, suggesting that re-encapsulation was inhibited in HCl solutions. It was reported that the H+ in aqueous solution could transform released HAsO42− into H3AsO4,5 as described by the following equilibrium reaction: | HAsO42− + 2H+ → H3AsO4 | (1) |
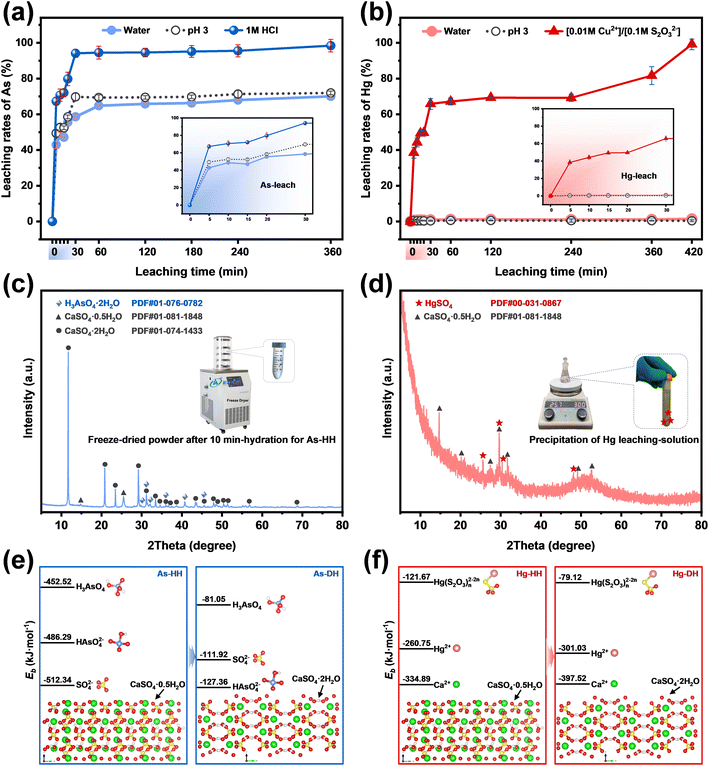 |
| Fig. 5 The metal leaching rates for (a) As-HH and (b) Hg-HH obtained via milling, subjected to leaching with distilled water, pH 3 solution, and specific control agents (1 M HCl for As-HH or [0.01 M Cu2+]/[0.1 M S2O32−] for Hg-HH), respectively; the insets magnified the results for the 0–30 minute time interval. XRD patterns for (c) freeze-dried powder after 10 minutes of hydration for As-HH (freeze-dried for 48 hours) and (d) precipitate from the leachate solution of Hg-HH (drying for 72 hours at 60 °C in a blast drying oven). (e) and (f) Binding energies (Eb) of different ion species (HAsO42−, SO42− and H3AsO4; Hg2+, Ca2+ and Hg(S2O3)n2−2n) with calcium sulfate (HH/DH) calculated by the DFT method. | |
The XRD results presented in Fig. 3c confirmed the residual H3AsO4 in the freeze-dried powder after 10 minutes of hydration of As-HH, suggesting that H3AsO4 was present in the leaching solution. This indicated that HAsO42− was successfully converted into H3AsO4 during hydration, demonstrating that the species regulation could inhibit the re-incorporation of As species into the recrystallized products via isomorphic substitution for SO42−/Ca2+, and thus improve the extraction efficiency.
As shown in Fig. 4b, similar to As extraction, the highest Hg extraction efficiency was achieved through the application of the species-regulating agent [0.01 M Cu2+]/[0.1 M S2O32−]. Leaching results for Hg-HH in pH 3 solution and distilled water were low (<2%). In contrast, in the [0.01 M Cu2+]/[0.1 M S2O32−] solution, Hg extraction gradually increased, reaching 99.15% after 720 minutes. In the sodium thiosulfate solution, Cu2+ quickly underwent redox with S2O32−, forming Cu+, which cannot remain stable as Cu2+ for long.35 The large negative Gibbs free energy for reaction S1 (ΔGS1 = −162.1 kJ mol−1, Text S6†) confirms that this process proceeds spontaneously and to completion.36
Divalent Hg2+ exhibits higher Lewis acidity than Cu+, and mercuric thiosulfate complexes, such as Hg(S2O3)46−, have larger formation constants than cuprous thiosulfate species, such as Cu(S2O3)35–.37,38 Thus, Hg2+ replaces Cu+ in the solution to form stable Hg(S2O3)n2−2n complexes. Reaction S2, with ΔGS2 = −33.35 kJ mol−1, further confirms the thermodynamic favorability of this substitution, indirectly supporting the formation of Hg(S2O3)n2−2n in solution.37
The predominant metal species in the milled Hg-HH remained Hg2+ (Fig. S18b†). XRD analysis (Fig. 5d) identified mercury sulfate (HgSO4) in the precipitated products, confirming the presence of Hg2+ in the leaching solution. The ICP results, showing a Hg2+ concentration of 957.71 mg L−1 in the leachate, further indicated that mercury exists primarily as Hg(S2O3)n2−2n, given the excess of S2O32− used in the leaching process.
Furthermore, the binding energies (Eb) of the ion species with calcium sulfate (HH/DH) were calculated using density functional theory (DFT), as detailed in the ESI† (Text S5). The binding energies were ranked as SO42− > HAsO42− ≫ H3AsO4 in As-HH, HAsO42− > SO42− ≫ H3AsO4 in As-DH (Fig. 5e), and Ca2+ > Hg2+ ≫ Hg(S2O3)n2−2n in both Hg-HH and Hg-DH (Fig. 5f). The higher Eb of HAsO42− or Hg2+ suggested that it has a stronger affinity for binding or adsorption with calcium sulfate compared to H3AsO4 or Hg(S2O3)n2−2n. The similar Eb values of HAsO42− to SO42− and Hg2+ to Ca2+, coupled with their structural and thermochemical similarities, indicated that HAsO42− or Hg2+ is prone to substituting SO42− or Ca2+ within the calcium sulfate lattice. In contrast, the lower Eb of H3AsO4 or Hg(S2O3)n2−2n implied that HAsO42− or Hg2+ was converted to H3AsO4 or Hg(S2O3)n2−2n during the leaching process (HH → DH); it became difficult for As(V) or Hg(II) to re-adsorb or re-incorporate into the calcium sulfate structure, and thus they are more readily released from calcium sulfate in the presence of SO42− or Ca2+.
3.4 Mechanism of metal release and extraction
Based on our analysis, a milling-driven mechanism for metal exclusion and release, synergized by mechanical force and control agents, has been established. As depicted in Fig. 6, during the solid-state phase transformation of gypsum dehydration, a nano-sized CaSO4·0.5H2O intermediate phase was generated due to the higher impact and friction forces involved in planetary milling, leading to the exclusion of doped metals from the gypsum structure. Subsequent rehydration in the presence of control agents was facilitated by the dissolution–recrystallization of CaSO4·0.5H2O, which broke the calcium sulfate framework and fully released the entrapped metals. Notably, this milling impact reduced the gypsum particle size from the microscale (∼10 μm) to the nanoscale (<50 nm), with gypsum crystals transforming into bassanite under shear forces. Concurrently, the metals transitioned from an incorporated state within the gypsum particles to a non-incorporated state on the bassanite particles. In As-DH and Hg-DH, doped metals were converted at 90.85% and 97.30%, respectively (Fig. 2c and d, and S12†). During the leaching process, the control agent played a crucial role by altering the form of residual impurity ions, transforming them from HAsO42−/Hg2+—which have similar binding energies and structures to SO42−/Ca2+—into species with significantly different binding energies, such as H3AsO4 and Hg(S2O3)n2−2n (Fig. 5e and f). This transformation inhibited the re-incorporation of these metals into the calcium sulfate structure, thereby achieving high metal extraction efficiencies.
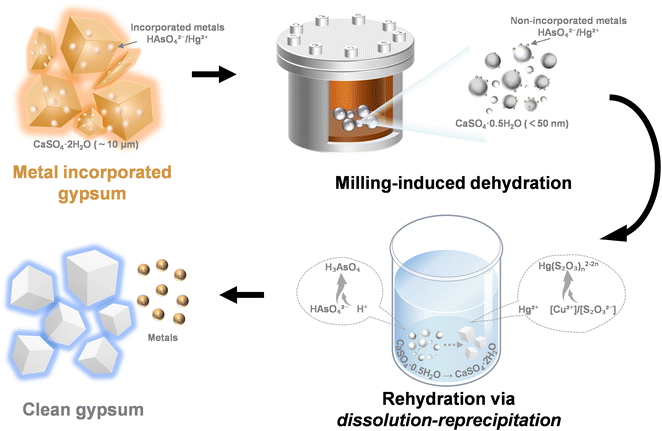 |
| Fig. 6 Mechanism of metal extraction by synergistic effects of mechanical force and metal species regulation. | |
Although the proposed method demonstrated a high efficiency in metal release and extraction from gypsum, it was important to consider the energy demanded associated with prolonged milling times. While the mechanical force facilitated metal release by inducing structural changes in the gypsum, energy consumption remained a critical factor for large-scale applications. Optimizing the milling duration based on the specific metal impurities present could mitigate some of these concerns, allowing for shorter processing times without compromising extraction efficiency. Furthermore, the use of specific leaching solutions for different elements offered a flexible approach to the selective extraction of metal impurities, although the presence of multiple impurities within the same gypsum sample may necessitate a more complex leaching strategy. In terms of the end product, the conversion of the purified gypsum into bassanite (plaster) did indeed require additional energy input. However, the value of obtaining clean gypsum suitable for industrial applications, such as construction materials, could offset these energy costs. Future work should focus on improving the energy efficiency of the process and developing integrated systems that can simultaneously address multiple contaminants while minimizing resource consumption.
4. Conclusions
In this study, we developed a general approach for metal extraction from six types of gypsum sludges, utilizing the synergistic effects of mechanical force and metal species regulation. This method effectively separated P, Cr, As, Sr, Cd, and Hg, achieving extraction efficiencies above 94.0%, with notable efficiency for As (99.8%) and Hg (99.2%), outperforming traditional methods. The mechanical force facilitated a solid-state phase transformation, reducing the gypsum particle size from the microscale (∼10 μm) to the nanoscale (<50 nm), which enhanced the gypsum-to-bassanite dehydration process and excluded doped metals. The reduced particle size further promoted the dissolution–recrystallization of CaSO4·0.5H2O during rehydration, disrupting the calcium sulfate framework and fully releasing entrapped metals. The application of species-regulating agents altered the metal species (HAsO42− → H3AsO4; Hg2+ → Hg(S2O3)n2−2n), preventing their re-incorporation into the calcium sulfate structure. This approach provided a promising method for impurity separation from gypsum sludges and might extend to other hydrous minerals, addressing the challenge of diminishing metal resources globally.
Data availability
All data supporting this study are provided in the Materials and methods section of the main manuscript and in the ESI.† This research did not involve the use of external databases or the creation of new codes.
Author contributions
Changzhou Weng: formal analysis, investigation, methodology, data curation, writing – original draft, writing – review & editing; Zhengqiang Zheng: investigation, verification, resources; Chen Tian: conceptualization, project administration, writing – review & editing; Zhang Lin: resources, supervision, writing – review & editing.
Conflicts of interest
The authors declare no competing interest.
Acknowledgements
This work was supported by the National Natural Science Foundation of China (No. 22222612, No. 22336006), the Major Program of the Natural Science Foundation of Hunan Province of China (No. 2021JC0001) and the Foundation for Innovative Research Groups of the National Natural Science Foundation of China (No. 52121004).
References
- L. Chai, Y. Ke, X. Min, B. Zhou, K. Xue and J. Chen, Separation and recovery of ZnS from sulfidized neutralization sludge via the hydration conversion of CaSO4 into bulk CaSO4·2H2O crystals, Sep. Purif. Technol., 2015, 154, 76–81 CrossRef CAS.
- S. Zhao, Y. Duan, L. Chen, Y. Li, T. Yao and S. Liu,
et al., Study on emission of hazardous trace elements in a 350 MW coal-fired power plant, Part 2. arsenic, chromium, barium, manganese, lead, Environ. Pollut., 2017, 226, 404–411 CrossRef CAS PubMed.
- C. Kang, S. Ji and H. Jo, Recycling of industrial waste gypsum using mineral carbonation, Sustainability, 2022, 14(8), 4436 CrossRef CAS.
- W. Liu, J. Zheng, X. Ou, X. Liu, Y. Song and C. Tian,
et al., Effective Extraction of Cr(VI) from Hazardous Gypsum Sludge via Controlling the Phase Transformation and Chromium Species, Environ. Sci. Technol., 2018, 52(22), 13336–13342 CrossRef CAS.
- X. Ma, S. Yao, Z. Yuan, R. Bi, X. Wu and J. Zhang,
et al., Detoxification and reclamation of hydrometallurgical arsenic- and trace metals-bearing gypsum via hydrothermal recrystallization in acid solution, Chemosphere, 2020, 250, 126290 CrossRef CAS PubMed.
- M. Sun, J. Hou, G. Cheng, S. A. Baig, L. Tan and X. Xu, The relationship between speciation and release ability of mercury in flue gas desulfurization (FGD) gypsum, Fuel, 2014, 125, 66–72 CrossRef CAS.
- X. Ma, M. A. Gomez, Z. Yuan, R. Bi, J. Zhang and S. Wang,
et al., Incorporation of trace metals Cu, Zn, and Cd into gypsum: Implication on their mobility and fate in natural and anthropogenic environments, Chem. Geol., 2020, 541, 119574 CrossRef CAS.
- X. Hu, J. Wang, F. Wu, D. Li, J. Yang and J. Chen,
et al., Phosphorus recovery and resource utilization from phosphogypsum leachate via membrane-triggered adsorption and struvite crystallization approach, Chem. Eng. J., 2023, 471, 144310 CrossRef CAS.
- X. Lou, J. Liang, S. Liu, J. Wang and H. Chen, From Grave to Cradle: Treatment, Resource Recycling, and Valorization of Phosphogypsum Wastes, Environ. Sci. Technol. Lett., 2024, 11(9), 908–919 CrossRef CAS.
- D. Li, X. Lou, J. Wang, D. Wang, P. Liao and X. Hu,
et al., An Integrated Precipitation–Electrodeposition–Electrodialysis Strategy for Efficient Close-Loop Recovery of Multiple Anions from Phosphogypsum Leachate, ACS ES&T Eng., 2024, 4(7), 1679–1689 Search PubMed.
- X. Lou, J. Wang, J. Liang, S. Liu, R. Wang and L. Deng,
et al., Sequence closed-loop recovery of fluoride, phosphate, and sulfate anions from phosphogypsum leachate via precipitation-electrodialysis-crystallization approaches, Sep. Purif. Technol., 2024, 342, 127014 CrossRef CAS.
- J. Zheng, C. Weng, C. Tian, W. Zhang, J. Qin and X. Li,
et al., Ingenious approach for retrieving valuable metals from gypsum via dehydration–rehydration two-step phase transition, Chem. Eng. J., 2024, 491, 152122 CrossRef CAS.
- S. Seufert, C. Hesse, F. Goetz-Neunhoeffer and J. Neubauer, Quantitative determination of anhydrite III from dehydrated gypsum by XRD, Cem. Concr. Res., 2009, 39(10), 936–941 CrossRef CAS.
- S. Krishnan, N. S. Zulkapli, H. Kamyab, S. M. Taib, M. F. B. M. Din and Z. A. Majid,
et al., Current technologies for recovery of metals from industrial wastes: An overview, Environ. Technol. Innovation, 2021, 22, 101525 CrossRef CAS.
- Z. Wang, X. Dong, X. Li, Y. Feng, S. Li and W. Tang,
et al., A contact-electro-catalysis process for producing reactive oxygen species by ball milling of triboelectric materials, Nat. Commun., 2024, 15(1), 757 CrossRef CAS PubMed.
- A. P. Amrute, Z. Bodziana, H. Schreyer, C. Weidenthaler and F. Schüth, High-surface-area corundum by mechanochemically induced phase transformation of boehmite, Science, 2019, 366(6464), 485–489 CrossRef CAS.
- J. Zhang, L. Xie, Q. Ma, Y. Liu, J. Li and Z. Li,
et al., Ball milling enhanced Cr(VI) removal of zero-valent iron biochar composites: Functional groups response and dominant reduction species, Chemosphere, 2023, 311, 137174 CrossRef CAS PubMed.
- P. Guo, J. Zhang, Y. Zhou, C. Tang, X. Wang and X. Gao,
et al., Remediation of Cr(VI)-contaminated soil by ball milling modified zero-valent iron biochar composites: Insights into long-term stability and microbial community, J. Environ. Chem. Eng., 2023, 11(6), 111279 CrossRef CAS.
- N. F. Kosenko, A. S. Belyakov and M. A. Smirnova, Effect of mechanical activation procedure on the phase composition of gypsum, Inorg. Mater., 2010, 46(5), 545–550 CrossRef CAS.
- M. Maslyk, Z. Dallos, M. Koziol, S. Seiffert, T. Hieke and K. Petrović,
et al., A Fast and Sustainable Route to Bassanite Nanocrystals from Gypsum, Adv. Funct. Mater., 2022, 2111852 CrossRef CAS.
- P. Baláž, M. Achimovičová, M. Baláž, K. Chen, O. Dobrozhan and E. Guilmeau,
et al., Thermoelectric Cu–S-Based Materials Synthesized via a Scalable Mechanochemical Process, ACS Sustainable Chem. Eng., 2021, 9(5), 2003–2016 CrossRef.
- D. Todorovsky, A. Terziev and M. Milanova, Influence of mechanoactivation on rare earths leaching from phosphogypsum, Hydrometallurgy, 1997, 45(1–2), 13–19 CrossRef CAS.
- F. Wu, C. Jin, R. Xie, G. Qu, B. Chen and J. Qin,
et al., Extraction and transformation of elements in phosphogypsum by electrokinetics, J. Cleaner Prod., 2023, 385, 135688 CrossRef CAS.
- Q. Guan, N. Sun, Y. Bu, R. Fan, Z. Zhang and W. Yu,
et al., Efficient extraction of impurities from phosphogypsum during crystal regulation of α-hemihydrate gypsum, J. Am. Ceram. Soc., 2023, 106(12), 7360–7374 CrossRef CAS.
- X. Sun, J. Li, X. Sun, J. Zhen, Z. Wu and W. Liu,
et al., Efficient stabilization of arsenic in the arsenic-bearing lime-ferrate sludge by zero valent iron-enhanced hydrothermal treatment, Chem. Eng. J., 2021, 129683 CrossRef CAS.
- X. Sun, M. Mao, K. Lu, Q. Hu, W. Liu and Z. Lin, One-step removal of high-concentration arsenic from wastewater to form Johnbaumite using arsenic-bearing gypsum, J. Hazard. Mater., 2022, 424, 127585 CrossRef CAS.
- J. S. Benjamin, Dispersion strengthened superalloys by mechanical alloying, Metall. Trans., 1970, 1(10), 2943–2951 CrossRef CAS.
- S. Bid and S. K. Pradhan, Preparation and microstructure characterization of ball-milled ZrO2 powder by the Rietveld method: monoclinic to cubic phase transformation without any additive, J. Appl. Crystallogr., 2002, 35(5), 517–525 CrossRef CAS.
- P. Baláž, A. Calka, A. Zorkovská and M. Baláž, Processing of Eggshell Biomaterial by Electrical Discharge Assisted Mechanical Milling (EDAMM) and High Energy Milling (HEM) Techniques, Mater. Manuf. Processes, 2013, 28(4), 343–347 CrossRef.
- O. M. Lemine, M. Sajieddine, M. Bououdina, R. Msalam, S. Mufti and A. Alyamani, Rietveld analysis and Mössbauer spectroscopy studies of nanocrystalline hematite α-Fe2O3, J. Alloys Compd., 2010, 502(2), 279–282 CrossRef CAS.
- C. Yan, J. Nishida, R. Yuan and M. D. Fayer, Water of Hydration Dynamics in Minerals Gypsum and Bassanite: Ultrafast 2D IR Spectroscopy of Rocks, J. Am. Chem. Soc., 2016, 138(30), 9694–9703 CrossRef CAS.
- J. Zheng, J. Li, L. Ling, X. Liu, S. Kong and H. Liao,
et al., Crystal regulation of gypsum via hydrothermal treatment with hydrogen ion for Cr(VI) extraction, J. Hazard. Mater., 2020, 390, 120614 CrossRef CAS.
- D. Zhang, Z. Yuan, S. Wang, Y. Jia and G. P. Demopoulos, Incorporation of arsenic into gypsum: Relevant to arsenic removal and immobilization process in hydrometallurgical industry, J. Hazard. Mater., 2015, 300, 272–280 CrossRef CAS PubMed.
- A. C. S. Jensen, S. Imberti, S. F. Parker, E. Schneck, Y. Politi and P. Fratzl,
et al., Hydrogen Bonding in Amorphous Calcium Carbonate and Molecular Reorientation Induced by Dehydration, J. Phys. Chem. C, 2018, 122(6), 3591–3598 CrossRef CAS.
-
G. S. James, Lange's handbook of chemistry, CD & W Inc, Wyoming, 2005 Search PubMed.
-
J. Carpenter, C. Bai, J. P. Escobedo-Diaz, J. Hwang, S. Ikhmayies and B. Li, et al., Characterization of Minerals, Metals, and Materials 2015, Springer, 2016 Search PubMed.
- C. Han, W. Wang, F. Xie and T. Zhang, Mechanism and kinetics of mercuric sulfide leaching with cuprous-thiosulfate solutions, Sep. Purif. Technol., 2017, 177, 223–232 CrossRef CAS.
-
T. Jiang, D. Wang, Y. B. Yang and Q. Li, Effect of Copper and Ammonia on Consumption of Thiosulfate in Gold Leaching Solutions, Characterization of Minerals, Metals, and Materials, 2013, vol. 2013, pp. 511–518 Search PubMed.
|
This journal is © The Royal Society of Chemistry 2025 |
Click here to see how this site uses Cookies. View our privacy policy here.