DOI:
10.1039/D4TA02187H
(Paper)
J. Mater. Chem. A, 2024,
12, 14991-15005
Enhancing the healability and degradability of epoxy via synergetic steric and electron-withdrawing effects for green electrical packaging†
Received
2nd April 2024
, Accepted 15th May 2024
First published on 16th May 2024
Abstract
Pursuing healable and degradable materials without sacrificing insulation performance becomes a great challenge for developing green electrical packaging. Herein, we report the development of a new epoxy to overcome the problem via fluorine and aryl incorporation to achieve synergetic steric and electron-withdrawing effects. The epoxy possesses remarkable healing capabilities for both mechanical and electrical treeing damage, while simultaneously exhibiting a high breakdown strength (77 MV m−1), robust mechanical strength (43 MPa), and admirable glass transition temperature (113 °C, DMA). Moreover, with excellent degradability, its use is demonstrated for fabricating an insulating board matrix and high voltage resistor packaging. The epoxy can be mildly degraded to recycle intact fiber fabrics, inorganic fillers and electrical devices, making it promising for green electrical packaging applications.
1. Introduction
Epoxy resin is a commonly utilized packaging material for electrical equipment and electronic devices because of its exceptional insulation performance, thermal resistance and mechanical strength.1–3 However, epoxy typically has an intrinsically hard and brittle nature due to its crosslinked molecular structure.4 Unfortunately, this attribute triggers the formation and spread of microcracks and defects while being processed and utilized, ultimately resulting in material breakdown and drastically reducing the lifespan of electronic equipment.5 Moreover, accompanied by the miniaturization of power electronic equipment and components, insulating materials are required to withstand higher electric field intensity.6 If the applied voltage surpasses the electrical breakdown strength of the materials, various forms of electrical damage can occur to the resin. Electrical treeing is one of the most prevalent damage modes observed in polymeric insulating materials during long-time operation.7,8 It has long been considered as permanent damage, so the material, as well as the equipment, could only be abandoned until the emergence of healable polymers.9–12
In general, there are two approaches to achieving healability: extrinsic methods and intrinsic methods.13,14 Extrinsic healing involves the introduction of healing agent-encapsulating microspheres into the matrix, which gives the polymer excellent healability.15–18 However, introducing microspheres without damaging the fragile capsules is complex in real manufacturing. Moreover, microspheres provide limited healing cycles and leave voids after healing agents are used. These voids act as defects in the material and would deteriorate electric field distribution. By contrast, the intrinsic healing approach through the dynamic covalent bonds exhibits good molecular design flexibility, healing efficiency, and multiple healing capabilities. To date, numerous dynamic chemical bonds, such as hydrogen bonds, ionic bonds, Diels–Alder linkage, and ester, acetal, disulfide, imine and dynamic urea bonds, have been developed to construct healable polymers.19–24 Among them, the dynamic urea bond stands out due to its admirable healability.25 Moreover, the urea bonds usually would not influence the excellent electrical resistance and breakdown strength.26 Therefore, it is highly preferred in various types of electrical insulating and electronic packaging polymers, including but not limited to polyurethane, silicone, epoxy, etc.27–31 For example, our previous research has demonstrated that epoxy with dynamic urea bonds, formed using N,N′-di-tert-butylethylenediamine and hexamethylene diisocyanate, exhibits satisfactory healability for mechanical damage and electrical breakdown damage.32
Dynamic urea bonding proceeds via a dissociative mechanism, which involves two distinct breaking and re-forming steps.25 Therefore, manipulating the covalent bond energy of the C–N in dynamic urea bonds becomes critical to improve the reversible performance. The most common method is to control the bulk size of the substituted groups of secondary amine.28 Zhang et al. regulated the steric hindrance by varying amine substituents and investigated their influence on the healability of polyurethane.33 Similarly, Yun et al. prepared a series of healable polymers by controlling the steric hindrance of isocyanate substituents.34 Both results demonstrate the prepared materials containing dynamic urea bonds with larger steric hindrance show higher temperature sensitivity, leading to a higher rate of network rearrangement.
From the valence bond theory point of view, a covalent bond forms as the electron clouds of the adjacent atoms overlap. Rather than an exception, the dynamic covalent bond is quite sensitive to the electron density distribution.35 Therefore, the electron induction effect including electron withdrawing/donating effects would probably be another possible approach to change the reversibility of the dynamic covalent bonds, other than the steric hindrance effect, to improve the network rearrangement of the polymers. In fact, our previous study on fluorinated alcohol–carbamate bonds36,37 and phenol–carbamate bonds reported by Xu's group38 demonstrated the feasibility. Considering the structure of the urea bond, reducing the electron density of the nitrogen would probably decrease the reversible reaction energy barrier of the dynamic urea bond, therefore promoting healing, recycling and other functions of the material. Moreover, chemical groups possessing a strong electron-withdrawing effect would also benefit insulating properties.39 These groups usually contain strong electronegative atoms and would influence the local electron density distribution. In fact, this becomes more prominent when the group is adjacent to a large conjugated molecular structure, such as an aryl ring. In this way, the electron deficient structures act as electron traps to capture the charge carriers so that the breakdown strength of the material would be enhanced. For example, Yang et al. selected –CF3 to replace –CH3 in epoxy, leading to an 22.08% enhancement in breakdown strength.40 Despite these, the construction of dynamic urea bonds containing electron-withdrawing groups for developing healable polymers has rarely been reported, according to our knowledge.
In this study, healable epoxy materials containing dynamic urea bonds with electron-withdrawing groups are developed by synthesizing different secondary diamines from the reduction of Schiff bases. The influence of synergetic steric and electron-withdrawing effects on the dynamic characteristics of dynamic urea bonds was investigated by using temperature-dependent FTIR analysis and stress-relaxation analysis. The electrical properties of epoxies containing dynamic urea bonds with different electron-withdrawing groups were examined and the variation in performance was analyzed via crosslinked network analysis. Moreover, the capability of healing mechanical and electrical treeing damage was investigated while the influence of the withdrawing groups on the healability was highlighted. Additionally, the degradability of the epoxy under mild conditions was demonstrated, instead of traditional high energy-consumption methods.41 Lastly, we explored the potential applicability of the prepared material for insulating boards and encapsulation materials for power electronic devices. This study aims to present an innovative approach to developing green epoxy materials with exceptional insulation properties and healability for electrical and electronic packaging.
2. Experimental
2.1 Materials
Bisphenol-A epoxy resin (epoxy value: 0.51 eq. per 100 g) was obtained from Shandong Usolf Chemical Technology, China. Terephthalaldehyde, aniline, 4-fluoroaniline, and dibutyltin dilaurate (DBTDL) were bought from Macklin, China. 1,2-Dianilinoethane (DA), dichloromethane (CH2Cl2) and hexamethylene diisocyanate (HDI) were supplied by Meryer Chemical Technology, China. Dibutylamine (DBA) was bought from General-reagent, China. Magnesium dihydroxide (Mg(OH)2, grain diameter ≤5 μm) was supplied by Sinopharm Chemical, China. All these chemicals were directly used as received.
2.2 Synthesis of N,N′-(1,4-phenylenedimethylidyne)bis[benzenamine] (DFXDim) and N,N′-(p-phenylenedimethylidyne)bis[p-fluoroaniline] (DXDim)
DFXD and DXD were synthesized through a two-step process, of which imine intermediates (DFXDim and DXDim) were needed to be prepared first (Fig. 1). Specifically, 0.1 mol of 4-fluoroaniline was dissolved in CH2Cl2 before terephthalaldehyde (0.05 mol) was added dropwise. The reaction mixture was stirred at 50 °C for 6 h while the product precipitated. The precipitate was filtered off and rinsed with ethyl alcohol. The solid was dried in a vacuum to obtain imine intermediate DFXDim. The imine intermediate DXDim was prepared in a similar way instead of using aniline to replace 4-fluoroaniline.
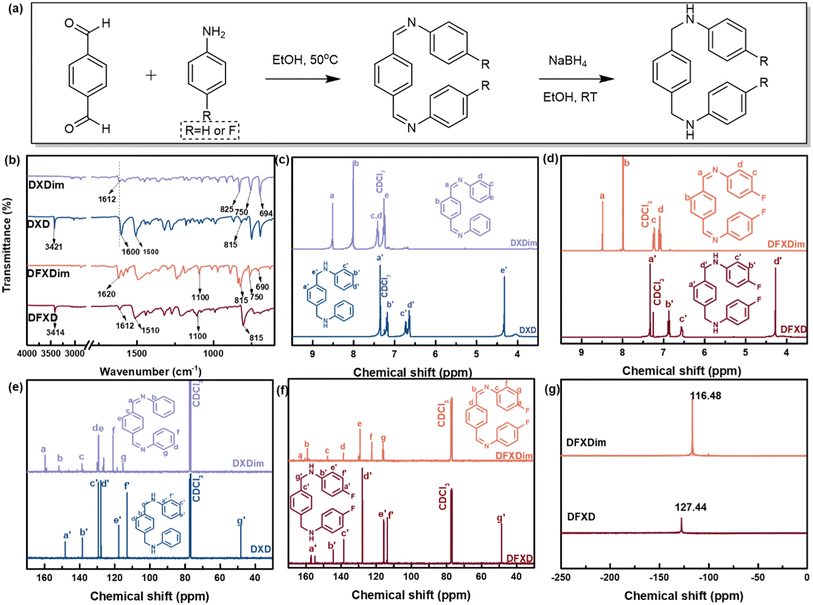 |
| Fig. 1 (a) Synthesis route of secondary diamines DFXD and DXD; (b) FTIR spectra, (c and d) 1H NMR and (e and f) 13C NMR spectra of the imine intermediates and secondary diamine products; (g) 19F NMR spectra of DFXDim and DFXD. | |
2.2.1 DFXDim.
Yield: 15.53 g, 87%. FTIR (KBr, cm−1): 1620 (–N
CH–), 1100 (Ar–F), 815 (–Ar–), 750, 690 (–Ar); 1H NMR (400 MHz, 298 K, CDCl3, TMS, ppm): 8.49 (–N
CH–, 2H), 7.99 (Ar–H, 4H), 7.23, 7.09 (Ar–H, 8H); 13C NMR (400 MHz, 298 K, CDCl3, TMS, ppm): 162.79, 147.70, 138.37, 129.20, 122.57, 115.96 (Ar), 158.96 (–N![[double bond, length as m-dash]](https://www.rsc.org/images/entities/char_e001.gif)
H–); 19F NMR (400 MHz, 298 K, CDCl3, TMS, ppm): −116.48 (Ar–F). MS (Tof-SIMS) m/z: 321.12020 [M + H]+.
2.2.2 DXDim.
Yield: 13.14 g, 82%. FTIR (KBr, cm−1): 1612 (–N
CH–), 825 (–Ar–), 750, 694 (–Ar); 1H NMR (400 MHz, 298 K, CDCl3, TMS, ppm): 8.52 (–N
C
–, 2H), 8.01 (Ar–H, 4H), 7.41, 7.26, 7.24 (–Ar–H, 10H); 13C NMR (400 MHz, 298 K, CDCl3, TMS, ppm): 151.66, 138.92, 128.95, 128.75, 126.43, 121.03 (Ar), 159.6 (–N![[double bond, length as m-dash]](https://www.rsc.org/images/entities/char_e001.gif)
H–). MS (Tof-SIMS) m/z: 285.13964 [M + H]+.
2.3 Synthesis of N,N′-di(4-fluoroarylpheny)-1,4-xylene diamine (DFXD) and N,N′-diphenyl-1,4-xylene diamine (DXD)
DFXDim (12.88 g, 0.04 mol) was suspended in ethyl alcohol (500 mL), and then NaBH4 (0.2 mol) was added in the beaker within half an hour. The mixture was stirred for 6 h at room temperature. The reaction was quenched by the addition of water and the product was extracted with CH2Cl2. The organic phase was washed with water, dried over MgSO4 and evaporated to obtain the secondary diamine product DFXD. DXD was prepared in a similar way by replacing DFXDim with DXDim.
2.3.1 DFXD.
Yield: 10.47 g, 81%. FTIR (KBr, cm−1): 3414 (–NH–), 1100 (–Ar–F), 815 (–Ar–); 1H NMR (400 MHz, 298 K, CDCl3, TMS, ppm): 7.34 (Ar–H, 4H), 6.87, 6.56 (Ar–
, 8H), 4.28 (N–C
2–Ar, 4H); 13C NMR (400 MHz, 298 K, CDCl3, TMS, ppm): 157.13, 154.79, 144.46, 138.42, 127.86, 115.75, 113.72 (Ar), 48.68 (–CH2–); 19F NMR (400 MHz, 298 K, CDCl3, TMS, ppm): −127.44 (Ar–F). MS (Tof-SIMS) m/z: 325.15195 [M + H]+.
2.3.2 DXD.
Yield: 9.83 g, 85%. FTIR (KBr, cm−1): 3421 (–NH–), 815 (–Ar–); 1H NMR (400 MHz, 298 K, CDCl3, TMS, ppm): 7.35 (Ar–H, 4H), 7.18, 6.72, 6.65 (Ar–H, 10H), 4.32 (N–C
2–Ar, 4H); 13C NMR (400 MHz, 298 K, CDCl3, TMS, ppm): 148.11, 138.50, 127.88, 129.34, 117.69, 112.94 (Ar), 48.11 (–CH2–); MS (Tof-SIMS) m/z: 289.16993 [M + H]+.
2.4 Preparation of crosslinked epoxies containing dynamic urea bonds
The preparation of crosslinked epoxies containing different dynamic urea bond structures was carried out in a one-pot analogous manner. Specifically, 0.05 mol of bisphenol-A type epoxy resin and 0.1 mol of secondary diamine (DA, DXD or DFXD) were mixed in a beaker equipped with a magnetic stirrer at room temperature for 1 h, and then heated at 100 °C for 12 h to obtain the amine-terminated linear oligomer. CH2Cl2 was introduced into the beaker to dissolve the oligomer before 0.105 mol of HDI and two drops of DBTDL were then introduced to build the dynamic urea bond-containing crosslinked epoxies. The prepared epoxy materials based on secondary diamines DA, DXD and DFXF were obtained through solution-casting and dried in an oven at 90 °C for 12 h and named EP-HUB-DA, EP-HUB-DXD and EP-HUB-DFXD, respectively.
2.5 Characterization
Fourier Transform Infrared (FTIR) spectra were recorded using a spectrometer (IN10+IZ10, America) ranging from 400 to 4000 cm−1 at room temperature with a resolution of 4 cm−1. 1H Nuclear Magnetic Resonance (NMR), 13C NMR and 19F NMR spectra were recorded using a spectrometer (JNM-ECZ400S/L1, Japan) with a frequency of 400 MHz. Temperature-dependent FTIR was performed on a spectrometer (Bruker INVENIO X) ranging from 500 to 4000 cm−1 at temperatures from 30 °C to 180 °C. The X-ray diffraction (XRD) analysis was carried out on a spectrometer (Bruker D8 ADVANCE) to study the recycling quality of composites prepared from the epoxies containing dynamic urea bonds. The mass spectrum was measured using an Ultra Performance Liquid Chromatography-Quadrupole-Time of Flight Mass Spectrometer (UPLC-Q-TOF-MS, WATERS I Class VION IMS, 1 mg mL−1 in acetonitrile). Differential scanning calorimetry (DSC) was performed on a calorimeter (DSC822e). The temperature ranged from room temperature to 200 °C with a heating rate of 10 °C min−1 under a nitrogen atmosphere. The glass transition temperature (Tg) was selected as the middle point of the step-change in thermal capacity. Dynamic mechanical analysis (DMA) was conducted on an instrument (TA Q800) in a tension film mode. Rectangular samples with a size of 15 × 4 × 0.5 mm3 were tested at a frequency of 1 Hz and a strain of 0.1%. A heating rate of 3 °C min−1 was applied from 30 °C to 200 °C. For stress relaxation analysis, experiments were performed in a strain control (2% strain) mode at a specified temperature. After equilibrating at this temperature for approximately 10 min, the stress decay was monitored. Mechanical properties were measured using a universal testing machine (CMT4503-5kN) at room temperature with a tensile speed of 2 mm min−1. Rectangular specimens with dimensions of 80 × 5 × 0.5 mm3 were prepared for the test. Details on insulating properties, reprocessing properties, healability and degradability characterization are presented in the ESI.†
3. Results and discussion
3.1 Synthesis and characterization of the epoxy network containing dynamic urea bonds
In this study, N,N′-di(4-fluoroarylpheny)-1,4-xylene diamine (DFXD) and N,N′-diphenyl-1,4-xylene diamine (DXD) were synthesized as the secondary amines to construct dynamic urea bonds. Meanwhile, a secondary amine, DA, was selected for comparison. DXD and DFXD were obtained through a two-step organic synthesis path (Fig. 1(a)), and their chemical structures were confirmed by using FTIR, 1H NMR, 13C NMR, and 19F NMR (Fig. 1(b)–(g)). Compared to the FTIR spectra of DXDim and DFXDim, those of DXD and DFXD showed characteristic absorption peaks representing –NH– at 3421 cm−1 and 3414 cm−1, respectively. Meanwhile, the absorption peaks at 1612 cm−1 (DXDim) and 1620 cm−1 (DFXDim) disappeared after reduction, respectively. This further confirmed that the imine bonds in DXDim and DFXDim were successfully reduced to obtain the desired secondary amines. The molecular structures of the amines are also confirmed by the disappearance of the resonance peaks at around 8.50 ppm as well as the appearance of a chemical shift at 4.28 ppm in the 1H NMR spectra of DXD and DFXD. The chemical shift at 127.54 ppm in the 19F NMR spectrum of DFXD verifies the presence of fluorine in the molecules while the variation in chemical shift also verifies the complete reduction of the imine to an amine.
As for the precursors with different molecular structures, the chemical structures were proved by FTIR spectra (Fig. S2†). No peak at 915 cm−1 assigned to the epoxy group is observed, which confirms the complete reaction of the amine and epoxy. This is also proved by an increased absorption peak around 1150 cm−1, which indicates the presence of hydroxyl groups formed after the epoxy ring opening. Moreover, EP-DFXD demonstrates a stronger characteristic absorption peak at 1220 cm−1, which belongs to the C–F bond. The above results verify that the precursors are synthesized as designed. HDI is further applied to react with the amine-terminated precursor to fabricate dynamic urea bond-containing materials, as shown in Fig. 2. The chemical structures of the cured epoxy were demonstrated by FTIR (Fig. 3(a)). The absence of –NCO stretching at 2260–2270 cm−1 in EP-HUB-DA, EP-HUB-DXD and EP-HUB-DFXD confirms the complete consumption of isocyanate. The consumed isocyanates were reacted with hydroxyl groups and amine groups in the precursor to form the urethane and urea bond. They are confirmed by the characteristic peaks at around 1705 cm−1 and 1640 cm−1, respectively.
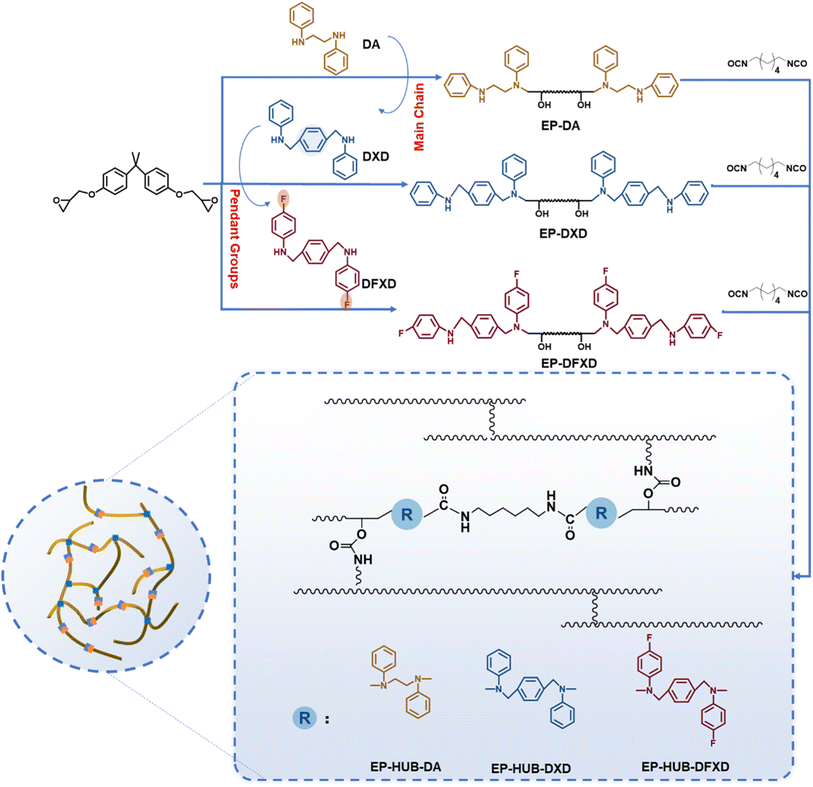 |
| Fig. 2 Schematic illustration for the fabrication of epoxy networks containing dynamic urea bonds. | |
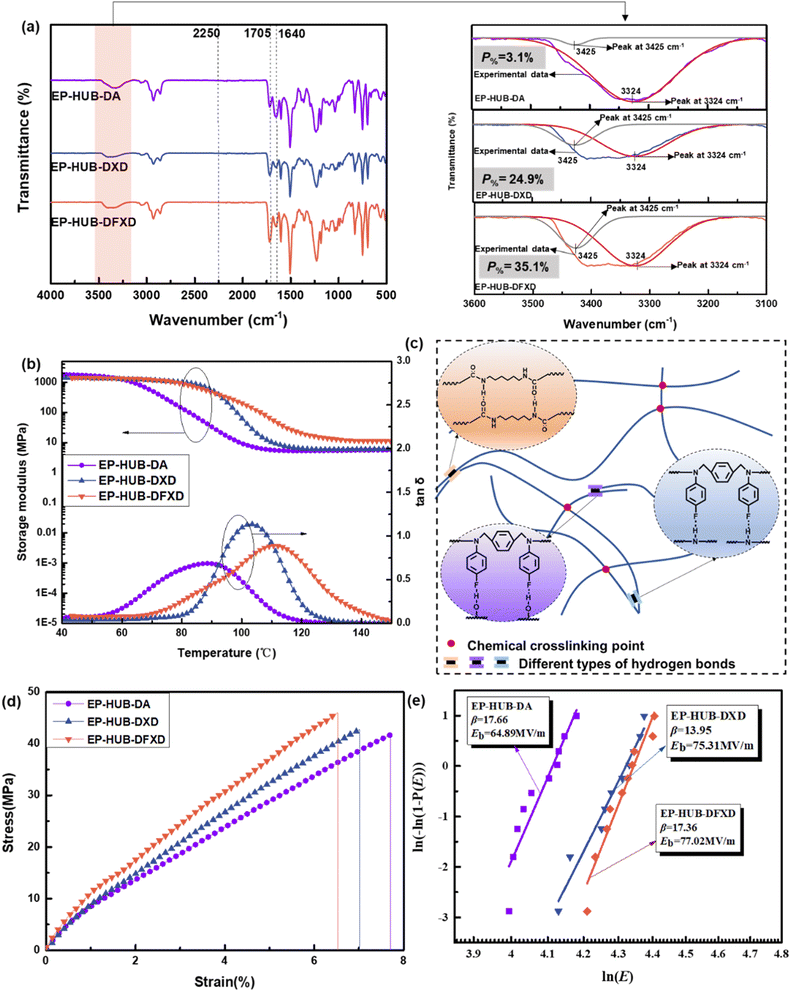 |
| Fig. 3 Epoxy containing dynamic urea bonds. (a) FTIR spectra; (b) DMA thermograms; (c) demonstration of hydrogen bonds in crosslinking networks; (d) stress–strain curves; (e) Weibull plots of the breakdown strength. | |
Complete curing is also verified by the DSC curves shown in Fig. S3,† in which there is no residual curing exothermic peak. The Tg of EP-HUB-DA is 74 °C according to the step change in thermal capacity. With the incorporation of aryl, the Tg of EP-HUB-DXD increases up to 96 °C and a further increase is observed when fluorine is introduced (EP-HUB-DFXD, 99 °C). A similar trend is found as displayed by the tan
δ curves from DMA (Fig. 3(b)). The Tgs of the samples based on mechanical stress relaxation are 89 °C (EP-HUB-DA), 103 °C (EP-HUB-DXD) and 113 °C (EP-HUB-DFXD), respectively. The results are attributed to the benzene ring (Ar-) structures in the molecular backbone, which increase the rigidity of chains. Meanwhile, fluorine substitution enhances the interaction between molecular structures so a further increase in Tg was observed. The presence of a rubbery plateau in the storage modulus thermograms of DMA confirms the presence of a crosslinked network in the materials. The crosslinking density (ve) can be calculated using eqn (1) based on the theory of rubber elasticity.
|  | (1) |
where
ve represents cross-linking density (in mol m
−3),
E is the storage modulus of the rubber platform area above
Tg,
R is the gas constant (
R = 8.314 J mol
−1K
−1), and
T is absolute temperature (
T =
Tg + 30 K).
The calculation results of the crosslinking density of various samples are shown in Fig. S4.† Theoretically, the crosslinking density of the materials would be similar due to the comparable reagent ratio and chemical structures. This inference is verified by the crosslinking density of EP-HUB-DA (513 mol m−3) and EP-HUB-DXD (554 mol m−3), the deviation of which is less than 8%. Meanwhile, the crosslinking density of EP-HUB-DFXD (1049 mol m−3) almost doubles. Considering the difference in chemical structures between EP-HUB-DFXD and EP-HUB-DXD, the additional fluorine in EP-HUB-DFXD may contribute to the increase in crosslinking density. Due to the high electronegativity of fluorine, it is easy to form hydrogen bonds with the abundant H–N structures of carbamate and urea bonds in EP-HUB-DFXD. These hydrogen bonds act as physical crosslinking points and, in this way, the crosslinking density of EP-HUB-DFXD is enhanced (Fig. 3(c)). A comprehensive analysis of FTIR spectra, especially in the wavenumber range of 3600–3100 cm−1, was further conducted to figure out the reason behind this. Peak fitting was performed at 3425 cm−1 and 3324 cm−1 using the Gaussian method, as illustrated in Fig. 3(a). Among them, the absorption peak at 3324 cm−1 corresponds to the stretching mode of N–H, whereas that at 3425 cm−1 signifies various types of hydrogen bonding.42,43 In particular, the peak intensity of the characteristic peaks of hydrogen bonds becomes stronger. Herein, variation in hydrogen bonding is described as the integrated area ratio (P%) between the peak at 3425 cm−1 and 3324 cm−1.44,45
| 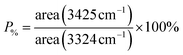 | (2) |
where area (3425 cm
−1) and area (3324 cm
−1) represent the integrated areas of the corresponding peaks.
The calculation results show that EP-HUB-DA has a P% value of 3.1%, while EP-HUB-DFXD has achieved a P% value of 35.1%. This is consistent with the aforementioned results that the incorporation of fluorine and an aryl ring could influence the formation of hydrogen bonds.
The variation in structures directly influences the mechanical properties and insulating performance of the materials. Fig. 3(d) illustrates the tensile properties of the materials containing different dynamic urea bonds. The higher elastic modulus and tensile strength of EP-HUB-DXD (σ = 41.8 MPa, E = 626 MPa) could be found as compared with EP-HUB-DA (σ = 40.6 MPa, E = 572 MPa) (Table S1†). The increase in modulus may be attributed to the replacement of the aliphatic structure with an aromatic structure. Interestingly, even though the materials contain an aliphatic chain induced by HDI, the reported strength of the materials in this study is comparable to that of conventional epoxy. This is also because the benzene ring in the side group is particularly effective in creating a stacking effect that enhances the friction between molecular chains, thus improving the mechanical strength. Furthermore, when fluorine is further incorporated into the side chain substituent groups, EP-HUB-DFXD obtains the highest elastic modulus (699 MPa) and tensile strength (43.1 MPa) compared to other samples. This is mainly due to the improved crosslinking density caused by the hydrogen bonding between fluorine and the urea bond as evidenced above. A similar trend is also evident in the insulating performance of the epoxy, as shown in Fig. 3(e). The AC breakdown strength of EP-HUB-DA is 64.89 MV m−1, which is lower than those of EP-HUB-DXD (75.31 MV m−1) and EP-HUB-DFXD (77.02 MV m−1). This is because the increase in the cross-linking density of the epoxy resin enhances its ability to inhibit leakage current, thereby improving the insulating performance. In addition, the introduction of fluorine atoms leads to the formation of more traps within the material, enhancing its capability to capture high-energy electrons. As a result, higher electrical strength can be achieved.
To compare the breakdown strength of EP-HUB-DFXD with that of other epoxy containing dynamic covalent bonds reported previously, the breakdown strength of EP-HUB-DFXD with a thickness of 1 mm was also tested, as shown in Fig. S5.† The result shows that the breakdown strength of EP-HUB-DFXD with a thickness of 1 mm is 50.02 MV m−1, which is higher than that of other reported healable epoxies (32–40 MV m−1).16–18 This further indicates that the prepared material has excellent insulating properties.
3.2 Dynamic feature of urea bond-containing epoxies with synergetic steric and electron-withdrawing effects
The dynamic feature is the foundation to achieve the network rearrangement of the materials, therefore further gaining advanced functions like healability, recyclability, and degradability, over conventional epoxies. Regarding the chemical characteristic of the dynamic urea bonds, the thermally reversible reaction was investigated by monitoring the reappearance of characteristic peaks corresponding to the dissociation and association of –NCO, while the influence of the electron-withdrawing effect on the dynamic feature was analyzed. Fig. 4(a) and S6† exhibit the FTIR curves of epoxy samples at different temperatures. It is demonstrated that an additional absorption peak assigned to –NCO groups is found between 2250 cm−1 and 2350 cm−1 for all samples when the temperature increases. Moreover, at high temperatures, the absorption intensity of this peak in EP-HUB-DFXD is stronger than in EP-HUB-DA and EP-HUB-DXD. This proves the dynamic urea bonds dissociate under thermal stimulation to generate isocyanate groups while under the influence of the aryl group and fluorine, EP-HUB-DFXD displays the largest dissociation degree.
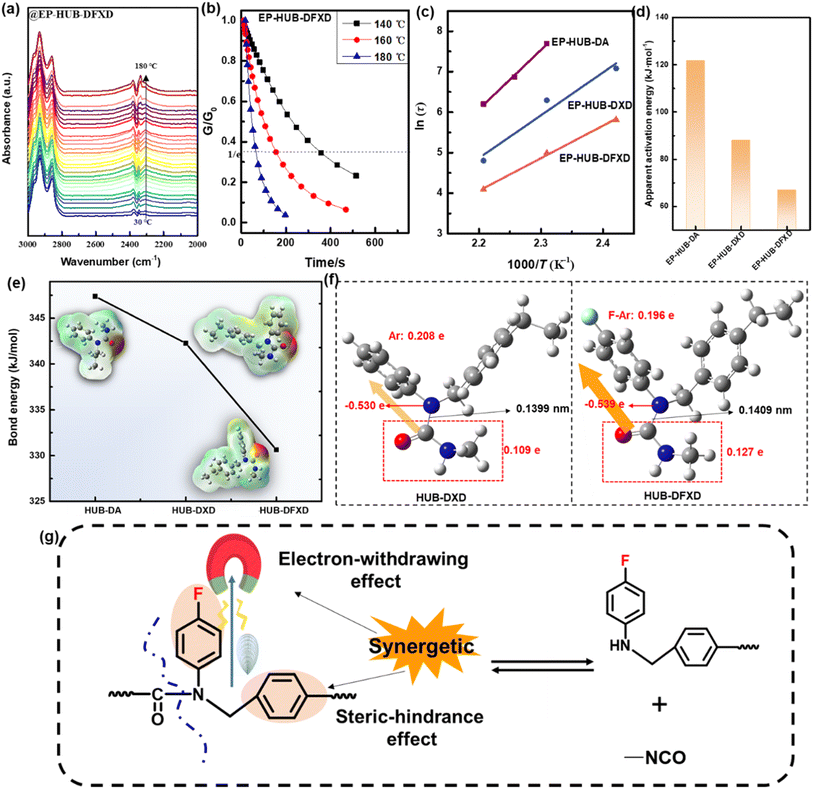 |
| Fig. 4 (a) Temperature-dependent FTIR spectra of the EP-HUB-DFXD. (b) Normalized stress relaxation curves of EP-HUB-DFXD from 140 °C to 180 °C. (c) Linear regression of the logarithm of relaxation time (ln τ) versus the reciprocal of temperature (1000·T−1). (d) Network rearrangement activation energy of epoxies with different dynamic urea bonds. (e) The calculated bond energy of hindered C–N in dynamic urea bonds with different molecular structures of electron-withdrawing groups. (f) The charge distribution of HUB-DXD and HUB-DFXD based on natural bond orbital (NBO) analysis. (g) The schematic diagram of dissociation and association of dynamic urea bonds affected by the electron-withdrawing group. | |
To further verify this observation, stress relaxation was measured via DMA and the activation energy of network rearrangement was calculated and compared. The modulus (G) of the samples was normalized by the initial value (G0), as shown in Fig. 4(b) and S7.† The characteristic relaxation time (τ) was defined as the time required for G/G0 = 1/e with an exponential decay function:
It can be found that EP-HUB-DXD and EP-HUB-DFXD fully relaxed at a temperature of about 140 °C, while a higher temperature is required for EP-HUB-DXD. The temperature dependence of the relaxation time of samples allows Arrhenius' law (Fig. 4(c)). The activation energy (Ea) of various samples can be calculated using eqn (4).46
| ln(τ) = ln(τ0) + Ea/RT | (4) |
Fig. 4(d) compares the calculated activation energy for each sample containing dynamic urea bonds with different electron withdrawing groups. EP-HUB-DFXD has the lowest network rearrangement activation energy of only 67 kJ mol−1 as compared with EP-HUB-DXD (88 kJ mol−1), and EP-HUB-DA has the highest activation energy (more than 120 kJ mol−1). To figure out the in-depth reasons, simulation of the bond energy is involved (Fig. 4(e) and Table S2†).47 Interestingly, we found that the bond energy of C–N in EP-HUB-DA is 347 kJ mol−1, while that of EP-HUB-DXD is 342 kJ mol−1. When fluorine is introduced, EP-HUB-DFXD displays the lowest bond energy of the C–N (merely 330 kJ mol−1). Considering the high electronegativity of fluorine, the electron distribution of the urea bond would be greatly influenced by the electron-withdrawing effect. This is verified by the difference in charge distribution between HUB-DXD and HUB-DFXD (Fig. 4(f)). The results demonstrate that the F–Ar side of the HUB-DFXD attracts many more electrons than the Ar side of HUB-DXD. The C–N bond length in HUB-DFXD (0.1409 nm) is longer than that in HUB-DXD (0.1399 nm), which confirms the weakening of the C–N in urea bonds via fluorine substitution. Therefore, the high dynamic reactivity of HUB-DFXD can be understood by the synergetic effect of electron withdrawing by fluorine and steric hindrance of the benzene ring, as shown in Fig. 4(g).
3.3 Reprocessing and healing based on dynamic urea bonds
Stimulation in dynamic reactivity of the urea bonds would enhance the reprocessability and healability of the epoxies. In this work, the reprocessability of epoxy-containing dynamic urea bonds was investigated through hot-pressing, as shown in Fig. 5(a). It can be found that various pulverized epoxy samples can be reprocessed into homogeneous samples under the conditions of 180 °C/20 MPa for 30 min. The mechanical properties and insulating performance of reprocessed samples were used to evaluate the processability (Fig. S8 and S9†). Fig. 5(b) further summarizes the reprocessing efficiency. For both mechanical and insulating properties, EP-HUB-DFXD exhibits the best reprocessability, while EP-HUB-DA shows the lowest recovery degree. This is consistent with the aforementioned results, indicating that a higher electron-absorbing effect of the substituent group leads to lower activation energy for network rearrangement, which benefits the properties of the reprocessed materials.
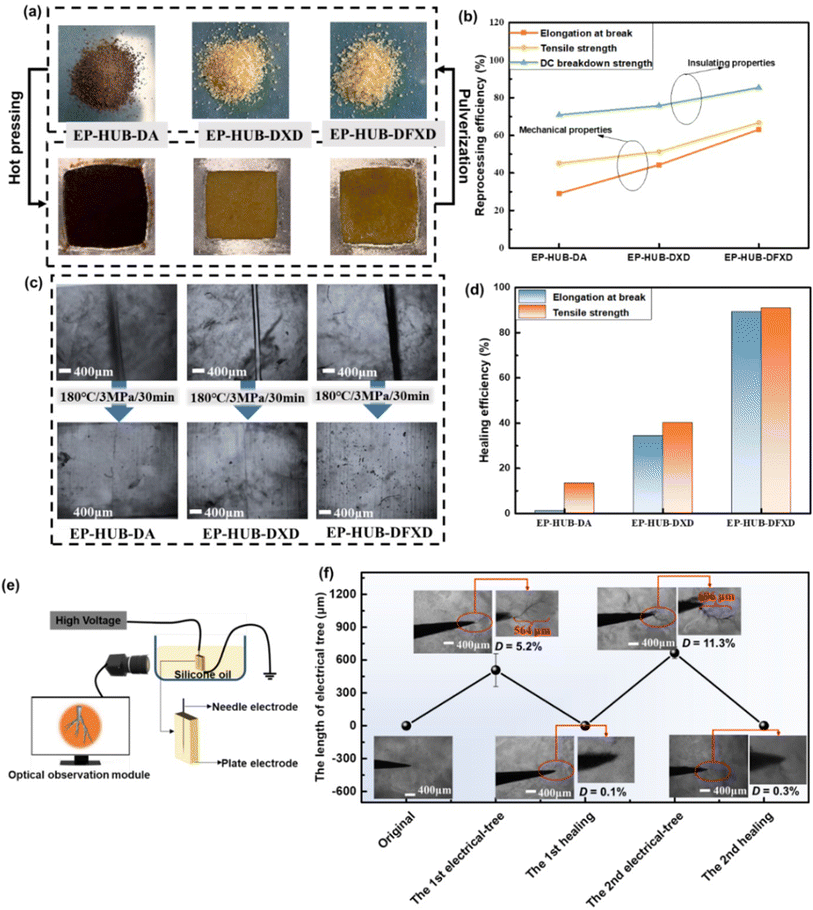 |
| Fig. 5 Reprocessing, mechanical healing and electrical treeing healing of epoxy containing dynamic urea bonds with different electron-withdrawing groups. (a) Photographs of molding epoxy powders to uniform sheets via hot pressing (180 °C, 20 MPa, 30 min); (b) reprocessing efficiencies calculated based on mechanical and insulating properties; (c) micrographs of cut samples before and after healing (180 °C, 3 MPa, 30 min); (d) healing efficiency based on tensile tests; (e) experimental system of electrical tree aging; (f) the optical images of EP-HUB-DFXD before and after healing of electrical trees. | |
Healability of mechanical damage serves as the foundation for achieving healability in electrical treeing damage. Herein, mechanical damage was evaluated via the general cut-healing performance. Fig. 5(c) and S10† show the micrographs of cut samples before and after healing at various healing times. The fractured sample was healed at 180 °C/3 MPa. When the healing time was 10 min, EP-HUB-DA and EP-HUB-DXD remained in the broken state, while the fractured EP-HUB-DFXD could be healed and the separated surface of the damaged area would be able to connect together. When further extending the healing time up to 20 min, the scratches of all samples were recovered apparently, but damage traces can still be clearly observed in EP-HUB-DA and EP-HUB-DXD. Complete recovery of these two samples requires further extension of the healing time up to 30 minutes. These phenomena are consistent with the aforementioned results. With the stimulation of the synergetic steric and electron-withdrawing effects, EP-HUB-DFXD exhibits the best healing efficiency among the samples. Furthermore, the tensile properties of the healed samples were measured to assess the impact of molecular structures on healability (Fig. S11†) and are summarized in Fig. 5(d). EP-HUB-DA exhibits the lowest healability for mechanical damage, with healing efficiencies of only 13% for tensile strength and 2% for elongation at break. When the benzene ring is introduced into the main chain, EP-HUB-DXD shows better healable performance than EP-HUB-DA because of the enhanced steric effect of the main chain. Furthermore, when electron-withdrawing groups are incorporated adjacent to the dynamic urea bond, epoxy acquires satisfactory healability. EP-HUB-DFXD containing dynamic urea bonds with fluoroaryl groups has the best healability. With the electron-withdrawing groups, high healing efficiencies based on tensile strength (91%) and elongation at break (89%) of EP-HUB-DFXD are achieved.
Electrical treeing is generally more complicated than mechanical damage, not only because of the complex damaged morphology change, but also the chemical component degradation, the latter of which is usually not observed in mechanical damage. Herein, the admirable healability in mechanical damage, as well as the enhanced breakdown resistance of EP-HUB-DFXD, convince us of its possibility to heal electrical treeing. The electrical treeing experiments were performed through a typical needle-plate electrode configuration (Fig. 5(e)). When subjected to high voltage for 15 minutes, EP-HUB-DFXD exhibited hollow damage approximately 564 μm in length within the epoxy, as shown in Fig. 5(f). The damaged samples were subsequently healed at 180 °C/15 MPa for 30 minutes. Optical images after healing revealed that the tree-like channels almost disappeared. The duty ratio (D) of electrical trees is mainly used to describe the size of the electrical tree area within a selected region of solid material. A fixed-size region (50 × 50 pixels) covering the growth range of electrical trees is selected from the electrical tree images. The duty ratio (D) of electrical trees also decreased from 5.2% to 0.1%. When subjected to a second cycle of high electric field, electrical tree damage occurred within the sample again rather than electrical breakdown. Notably, the propagation path of the second electrical treeing is different from the first, indicating the high quality of the healed area of the first electrical treeing, as it was not the weak insulation point. In addition, EP-HUB-DFXD also demonstrated multiple healing capabilities as the second electrical damage can also be completely healed under the same healing conditions.
The enhancement of healability in EP-HUB-DFXD compared to the others is reasonable. On the molecular level, the healing of the crosslinked epoxy network based on the network rearrangement capability of the dynamic exchange activity of the dynamic bonds is the dominant factor.48 As shown in Fig. 4, compared with EP-HUB-DA, the strong electronegative fluorine group greatly influences the electron distribution of the structure, thus weakening the strength of the urea bond formed by the amine and isocyanate. Since the dynamic urea bond follows the dissociation exchange mechanism, reducing the bond strength would benefit the dissociation process so as to promote network rearrangement and healability. Therefore, with a stronger electron-withdrawing group, the synergetic effect becomes more remarkable and better healing performance can be achieved. To show our advantages in healability for mechanical damage and electrical damage, recent reports on healable epoxy are summarized and compared in Table S3.† It is found that EP-HUB-DFXD possesses admirable healability for both severe fracture damage and electrical tree damage. The healing efficiency/rate of both mechanical damage and electrical damage is outstanding.
3.4 Degradation and recycling performance
The incorporation of dynamic urea bonds endows epoxy with impressive degradability. The dynamic urea bonds in the epoxy network can reversibly dissociate under the stimulation of high temperature, forming amines and isocyanate groups. Chemical solvents containing a monofunctional secondary amine can participate in the dynamic process by reacting with the generated isocyanates and produce a chain segment. With time, the crosslinked network is fragmented and the chain segments diffuse and dissolve in the solution, eventually leading to material degradation. In general, for decomposition of the dynamic covalent network based on a dynamic chemistry mechanism, the medium is required to contain specific groups which have the capability to participate in the reaction. In this study, DBA was chosen as the medium for epoxy degradation (Fig. 6(a)). DBA is a secondary amine containing butyl groups with the boiling point of 159 °C. The secondary amino structure enables the molecule to participate in the dynamic reaction with the hindered urea bond to decompose the crosslinked network. Meanwhile, the b.p. is high enough to enable the decomposition reaction to take place. EP-HUB-DFXD exhibited complete decomposition within 5 h, whereas EP-HUB-DA took more than 20 h (Fig. 6(b)). Quantitative evaluation of degradation was realized through the degradation rate, as shown in Fig. 6(c). Specifically, EP-HUB-DFXD exhibits the highest degradation rate (0.773 mg mL−1 h−1), significantly surpassing those of EP-HUB-DA (0.223 mg mL−1 h−1) and EP-HUB-DXD (0.317 mg mL−1 h−1). This disparity implies that with stronger electron-withdrawing groups, it is easier for the dynamic reaction of the urea bond to take place so the decomposition becomes faster. Meanwhile, for practical electrical/electronic applications, the materials are required to withstand acid, base or other conventional chemical solvents, such as de-flashing chemicals. This is important as numerous dynamic chemical bonds, like imine, are susceptible to acids or bases, posing challenges for dielectric employment. As depicted in Table S4,† EP-HUB-DFXD experienced a minimal mass loss of less than 3% after being immersed in various solvents at room temperature for 24 h. This observation underscores the excellent solvent resistance of the epoxy resin incorporating dynamic urea bonds. Notably, EP-HUB-DFXD did not exhibit any reactivity with DBA under ambient conditions. The selectivity in decomposition chemicals and conditions is preferred in real applications. In fact, insulating materials employed in power electronic equipment require both enhanced mechanical properties and high thermal stability, as evidenced by their tensile strength and Tg. Fig. 6(d) shows a comparison between the tensile strength and Tg of EP-HUB-DFXD and recently reported degradable epoxy incorporating various dynamic bonds. The results show that EP-HUB-DFXD exhibits both higher tensile strength (43 MPa) and Tg (113 °C). These results further highlight the superior application potential of EP-HUB-DFXD in the field of the packaging of electrical/electronic components.
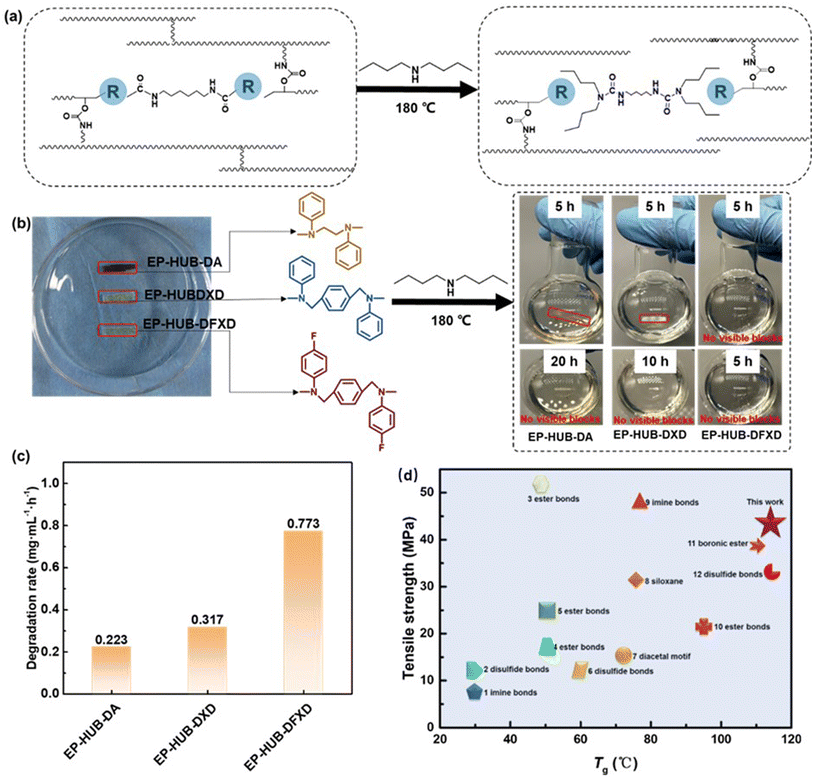 |
| Fig. 6 (a) Schematic representation of the degradation and the recycling process of the epoxy containing dynamic urea bonds; (b) degradation performance of the epoxy containing dynamic urea bonds with different electron-withdrawing groups; (c) degradation rate of the epoxy samples in DBA solution; (d) research survey on tensile strength and Tg of recently reported degradable epoxy based on dynamic chemical bonds (no. 1–12 refer to ref. 49–60). | |
3.5 Application trials in electrical insulation
The excellent insulation performance, healability and degradability of EP-HUB-DFXD imply its potential applications in the field of smart electrical insulation. Herein, the material was applied to be the polymer matrix of fiber-reinforced composite boards. EP-HUB-DFXD, glass fibers, and a 30% mass fraction of Mg(OH)2 (conventional flame retardant in insulation materials) were compounded together to prepare the insulating boards, as shown in Fig. 7(a). During the degradation process of the composite, the glass fibers and 87% of the mass of the added Mg(OH)2 particles can be recycled after 10 hours. The microscale morphology of both the fresh fibers and the reclaimed fiber fabric was examined using SEM (Fig. 7(b)). The EP-HUB-DFXD coating on the reclaimed fiber was completely eliminated, while the fabric structure remained intact. No visible damage to the fiber surface or alteration in fiber dimensions was detected. Moreover, according to the XRD patterns of the Mg(OH)2 particles shown in Fig. 7(c), the recycled particles exhibit the same crystalline structure as the original particles. Therefore, both the fibers and other inorganic fillers after recycling are retained and can be reused as their virgin counterparts.
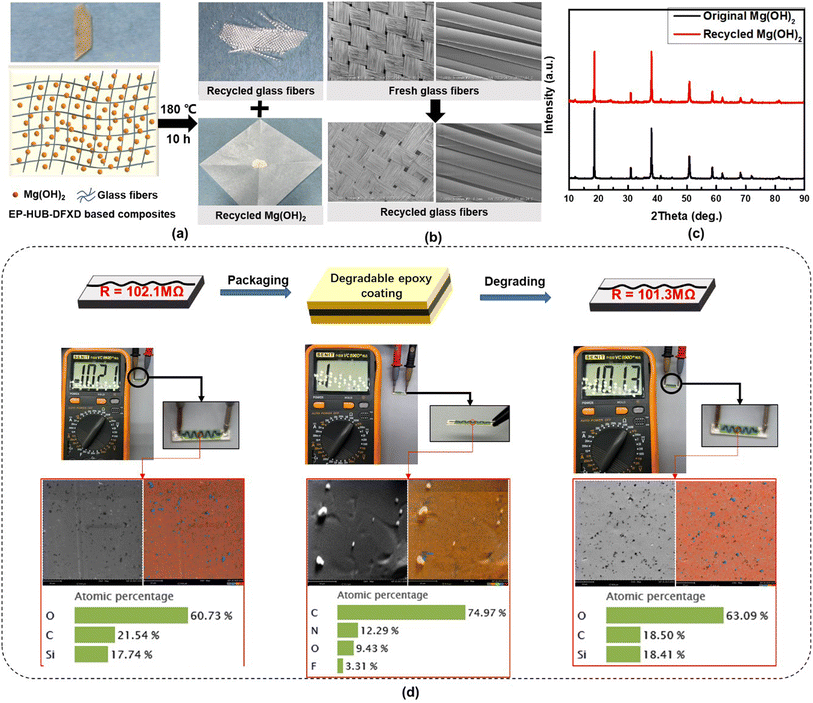 |
| Fig. 7 Applications of EP-HUB-DFXD in electrical/electronic insulation. (a) The optical microscopy images of EP-HUB-DFXD based fiber-reinforced composites containing inorganic filler Mg(OH)2. (b) The SEM images of the virgin and reused glass fibers. (c) The XRD patterns of the original and recycled Mg(OH)2 particles. (d) SEM images and EDS mapping of the high voltage resistor before packaging, after being packaged and after degradation of EP-HUB-DFXD. | |
Besides, EP-HUB-DFXD can also be used as an encapsulation material for power electronic components. Herein, high-voltage resistors were used as the devices to be encapsulated (Fig. 7(d)). The original resistance value of the resistor was 102.1 MΩ. After the surface was encapsulated with the material, the multimeter no longer detected any value, which was consistent with the attractive insulation performance of the material. Moreover, after the encapsulation was degraded in DBA, the resistance value of the component was measured to be 101.3 MΩ, which was close to the original value. SEM was first applied to observe the variation of surface morphology of the device. After packaging, the ceramic-based device was coated by an organic layer of EP-HUB-DFXD, which could be verified by the surface feature difference according to the SEM images. When the epoxy packaging was degraded, the ceramic surface appeared again, and was similar to the original one without apparent damage. To further demonstrate the packaging and degradation process, EDS mapping was used to confirm the main elements of the resistor surface. Si and O elements were detected on the original resistor surface. As for the encapsulated resistor surface, a significant increase in C percentage was observed, which confirms the successful coating of the epoxy material. Moreover, high amounts of N and F elements can be detected, which are the components of EP-HUB-DFXD. After degrading EP-HUB-DFXD, F and N were no longer detected and the element species recovered to those originally with similar element percentages. Therefore, the degradation process is verified with high efficiency. Compared with other previously reported literature (Table S5†), the epoxy containing dynamic urea bond reported in this study can not only recycle inorganic fillers such as fibers and Mg(OH)2, but also the electrical device can be recycled and used without sacrificing its properties.
4. Conclusions
In this study, we report a new epoxy with enhanced healing and degradation capabilities, together with remarkable fundamental operation performance. By incorporating fluorophenyl, not only mechanical damage but also electrical treeing damage can be healed at high efficiency via the synergetic steric and electron-withdrawing effect. Moreover, after being applied in fiber-reinforced composites and high-voltage resistor packaging, it could be conveniently degraded through the urea–amine exchange and valuable components, including fiber fabrics, inorganic fillers, and even functional electrical devices, could be readily recycled and reused. In conclusion, this research provides a convenient and scalable way to produce a new healable epoxy as a candidate with enhanced performance for applications in green electrical packaging.
Conflicts of interest
The authors declare no competing financial interest.
Acknowledgements
This work is financially supported by the Natural Science Basic Research Program of Shaanxi Province (2023-JC-QN-0401), National Natural Science Foundation of China (52130703), State Key Laboratory of Electrical Insulation and Power Equipment (EIPE22316), Key Technology Innovation Project of Xianyang (L2023-ZDKJ-JSGG-GY-022), Qinchuangyuan Innovation and Entrepreneurship Talents Project (2021QCYRC4-40) and Technology Innovation Leading Program of Shaanxi (2022KXJ-68). Prof. L. Zhang also acknowledges the support from the “High-Level Talent Introduction Plan” of Shaanxi Province. The assistance of the Instrumental Analysis Center of Xi'an Jiaotong University who provided 1H NMR data, XRD analysis, mass spectrum and temperature-dependent FTIR characterization is also acknowledged.
References
- Z. J. Sun, J. X. Li, M. C. Yu, M. Kathaperumal and C. P. Wong, A review of the thermal conductivity of silver-epoxy nanocomposites as encapsulation material for packaging applications, Chem. Eng. J., 2022, 446, 137319 CrossRef CAS
.
- Y. F. Wen, C. Chen and Y. S. Ye,
et al., Advances on thermally conductive epoxy-based composites as electronic packaging underfill materials-A review, Adv. Mater., 2022, 34(52), 2201023 CrossRef CAS PubMed
.
- C. Chen, J. X. Li and X. Wang,
et al., Transport characteristics of interfacial charge in SiC semiconductor-epoxy resin packaging materials, Front. Chem., 2022, 10, 879438 CrossRef CAS PubMed
.
- M. Dong, H. Zhang and L. Tzounis,
et al., Multifunctional epoxy nanocomposites reinforced by two-dimensional materials: A review, Carbon, 2021, 185, 57–81 CrossRef CAS
.
- G. F. Zapico, N. Ohtake, H. Akasaka and J. M. Munoz-Guijosa, Epoxy toughening through high pressure and shear rate preprocessing, Sci. Rep., 2019, 9, 17343 CrossRef PubMed
.
- X. Y. Gao, A. Kyritsakis and M. Veske,
et al., Molecular dynamics simulations of thermal evaporation and critical electric field of copper nanotips, J. Phys. D: Appl. Phys., 2021, 53(36), 365202 CrossRef
.
- J. G. Su, B. X. Du, J. Li and Z. L. Li, Electrical tree degradation in high-voltage cable insulation: progress and challenges, High Volt., 2020, 5(4), 353–364 CrossRef
.
- H. L. Zheng, S. M. Rowland, I. Iddrissu and Z. P. Lv, Electrical treeing and reverse tree growth in an epoxy resin, IEEE Trans. Dielectr. Electr. Insul., 2018, 24(6), 3966–3973 Search PubMed
.
- S. T. Li, S. H. Yu and Y. Feng, Progress in and prospects for electrical insulating materials, High Volt., 2016, 1(3), 122–129 CrossRef
.
- Y. Yang, Z. M. Dang, Q. Li and J. L. He, Self-Healing of electrical damage in polymers, Adv. Sci., 2022, 7(21), 2022131 Search PubMed
.
- Y. Zhang, H. Khanbareh, J. Roscow, M. Pan, C. Bowen and C. Y. Wan, Self-healing of materials under high electrical stress, Matter, 2020, 3(4), 989–1008 CrossRef
.
- X. Y. Huang, L. Han and X. Yang,
et al., Smart dielectric materials for next-generation electrical insulation, iEnergy, 2022, 1(1), 31 Search PubMed
.
- S. Y. Wang and M. W. Urban, Self-healing polymers, Nat. Rev. Mater., 2020, 5, 562–583 CrossRef CAS
.
- F. L. Zhang, L. Zhang and M. Yaseen, HuangK. A review on the self-healing ability of epoxy polymers, J. Appl. Polym. Sci., 2020, 138(16), e50260 CrossRef
.
- J. Y. Xie, L. Gao, J. Hu, Q. Li and J. L. He, Self-healing of electrical damage in thermoset polymers via anionic polymerization, J. Mater. Chem. C, 2020, 8(18), 6025–6033 RSC
.
- L. Gao, Y. Yang and J. Y. Xie,
et al., Autonomous self-healing of electrical degradation in dielectric polymers using in situ electroluminescence, Matter, 2020, 2(2), 451–463 CrossRef CAS
.
- W. X. Sima, C. Liang and P. T. Sun,
et al., Novel smart insulating materials achieving targeting self-Healing of electrical trees: high performance, low cost, and eco-friendliness, ACS Appl. Mater. Interfaces, 2021, 13(28), 33485–33495 CrossRef CAS PubMed
.
- P. T. Sun, M. K. Zhao and W. X. Sima,
et al., Microwave-magnetic field dual-response raspberry-like microspheres for targeted and repeated self-healing from electrical damage of insulating composites, J. Mater. Chem. C, 2022, 10(28), 10262–10270 RSC
.
- N. Zheng, Y. Xu, Q. Zhao and T. Xie, Dynamic covalent polymer networks: A molecular platform for designing functions beyond chemical recycling and self-healing, Chem. Rev., 2021, 121(3), 1716–1745 CrossRef CAS PubMed
.
- Y. Yang, Y. S. Xu, Y. Ji and Y. Wei, Functional epoxy vitrimers and composites, Prog. Mater. Sci., 2021, 120, 100710 CrossRef CAS
.
- N. Wang, X. Yang and X. X. Zhang, Ultrarobust subzero healable materials enabled by polyphenol nano-assemblies, Nat. Commun., 2023, 14, 814 CrossRef CAS PubMed
.
- Y. Y. Wang, R. Shu and X. X. Zhang, Strong, Supertough and self-healing biomimetic layered nanocomposites enabled by reversible interfacial polymer chain sliding, Angew. Chem., Int. Ed., 2023, e202303446 CAS
.
- L. Sun, L. Che, M. Li, W. G. Neal, X. Leng, Y. Long, Y. Jia, Y. Gao, M. Palma and Y. Lu, Zero-waste emission design of sustainable and programmable actuators, Susmat, 2023, 3, 207–221 CrossRef CAS
.
- S. Yu, Y. Li, S. Wu, Z. Tang, L. Zhang and B. Guo, Topological network design toward high-performance vegetable oil–based elastomers, Susmat, 2023, 3, 320–333 CrossRef CAS
.
- H. Z. Ying, Y. F. Zhang and J. J. Cheng, Dynamic urea bond for the design of reversible and self-healing polymers, Nat. Commun., 2014, 5, 3218 CrossRef PubMed
.
- S. Wu, M. R. Lin, Q. Burlingame and Q. M. Zhang, Meta-aromatic polyurea with high dipole moment and dipole density for energy storage capacitors, Appl. Phys. Lett., 2014, 104(7), 072903 CrossRef
.
- W. J. Sun, L. Zhang and S. Wang,
et al., Mechanically enhanced healable and recyclable silicone with dynamic hindered urea bond for flexible electronics, J. Mater. Chem. C, 2021, 9(27), 8579–8588 RSC
.
- Q. Zhang, S. J. Wang and B. Rao,
et al., Hindered urea bonds for dynamic polymers: An overview, React. Funct. Polym., 2021, 159, 104807 CrossRef CAS
.
- Y. F. Zhang, H. Z. Ying and K. R. Hart,
et al., Malleable and recyclable poly(urea-urethane) thermosets bearing hindered urea bonds, Adv. Mater., 2016, 28(35), 7646–7651 CrossRef CAS PubMed
.
- M. Shi, J. Liu and J. J. Qin,
et al., Reprocessed, shape-memory and self-healing robust epoxy resin by hindered urea bond, Polymer, 2024, 290, 126565 CrossRef CAS
.
- B. F. Chen, X. H. Liu and J. M. Liu,
et al., Intrinsically self-healing, reprocessable and recyclable epoxy thermosets based on dynamic reversible urea bonds, React. Funct. Polym., 2022, 172, 105184 CrossRef CAS
.
- W. J. Sun, L. Zhang and Y. J. Liang,
et al., Mechanically robust epoxy with electrical breakdown healing capability for power equipment insulation via dynamic networks, React. Funct. Polym., 2022, 176, 105307 CrossRef CAS
.
- L. H. Zhang and S. J. Rowan, Effect of sterics and degree of cross-linking on the mechanical properties of dynamic poly(alkylurea-urethane) networks, Macromolecules, 2017, 50(13), 5051–5060 CrossRef CAS
.
- S. M. Yun, H. M. Lee, S. Ahmed, G. Y. Kim, J. C. Kim and I. W. Cheong, Effect of diisocyanate structure on steric restructuring of hindered urea bonds for self-healable coating, Prog. Org. Coat., 2022, 165, 106730 CrossRef CAS
.
- L. Zhang, H. Wang, Y. Zhu, H. Xiong, Q. Wu, S. Gu, X. Liu, G. Huang and J. Wu, Electron-donating effect enabled simultaneous improvement on the mechanical and self-healing properties of bromobutyl rubber ionomers, ACS Appl. Mater. Interfaces, 2020, 12, 53239–53246 CrossRef CAS PubMed
.
- W. J. Sun, J. Z. Xu and J. H. Song,
et al., Self-healing of electrical damage in insulating robust epoxy containing dynamic fluorine-substituted carbamate bonds for green dielectrics, Mater. Horiz., 2023, 10(7), 2542–2553 RSC
.
- W. J. Sun, L. Zhang, M. K. Liu, J. Z. Xu, T. Y. Li and Y. H. Cheng, Silicone elastomer with simultaneous enhanced healing and electrical resistance via fluorine substitution for actuator dielectrics, Polymer, 2022, 255, 125125 CrossRef CAS
.
- J. X. Shi, T. Z. Zheng, Y. Zhang, B. H. Guo and J. Xu, Reprocessable cross-linked polyurethane with dynamic and tunable phenol−carbamate network, ACS Sustainable Chem. Eng., 2020, 8(50), 1207–1218 CrossRef CAS
.
- Y. W. Shi, X. R. Chen and F. B. Meng,
et al., Influence of organic additives with electron-withdrawing and electron-donating groups on insulation properties of cross-linked polyethylene at high temperatures for HVDC cable applications, J. Appl. Polym. Sci., 2022, 139(24), e52355 CrossRef
.
- K. R. Yang, W. J. Chen and Y. S. Zhao,
et al., Enhancing dielectric strength of epoxy polymers by constructing interface charge traps, ACS Appl. Mater. Interfaces, 2021, 13(22), 25850–25857 CrossRef CAS PubMed
.
- H. Y. Tsai, T. Fujita, S. Q. Wang and M. Naito, Environmentally friendly recycling system for epoxy resin with dynamic covalent bonding, Sci. Technol. Adv. Mater., 2021, 22(1), 532–543 CrossRef CAS PubMed
.
- Z. Q. Zhou, S. Y. Chen, W. C. Li, J. J. He, C. L. Yu and F. Zhang, Mechanically stable dynamic urea bond-based crosslinked polymer blend with tunable self-healable and physical properties, Macromol. Mater. Eng., 2020, 306(1), 2000527 CrossRef
.
- Y. F. Liu, R. R. Wnag and Q. An,
et al., The F center dot center dot center dot H hydrogen bonding effect on the dynamic mechanical and shape-memory properties of a fluorine-containing polybenzoxazine, Macromol. Chem. Phys., 2017, 218(15), 1700079 CrossRef
.
- J. Mattia and P. Painter, A comparison of hydrogen bonding and order in a polyurethane and poly(urethane-urea) and their blends with poly(ethylene glycol), Macromolecules, 2007, 40(5), 1546–1554 CrossRef CAS
.
- Y. M. Zhao, B. Zhang and M. Q. Liu,
et al., Effect of urethane/urea on carbonyl hydrogen bonding of polyester-polyurethane resin with mixed TDI, Polym. Bull., 2023, 36(3), 354–365 Search PubMed
.
- W. X. Liu, S. J. Yang and L. Huang,
et al., Dynamic covalent polymers enabled by reversible isocyanate chemistry, Chem. Commun., 2022, 58(89), 12399–12417 RSC
.
- Y. Li, Y. P. Wang and S. Wang,
et al., Highly tunable and robust dynamic polymer networks via conjugated-hindered urea bonds, Macromolecules, 2022, 55(20), 9091–9102 CrossRef CAS
.
- N. Zheng, Y. Xu, Q. Zhao and T. Xie, Dynamic covalent polymer networks: A Molecular platform for designing functions beyond chemical recycling and self-Healing, Chem. Rev., 2021, 121(3), 1716–1745 CrossRef CAS PubMed
.
- Y. Y. Liu, J. He, Y. D. Li, X. L. Zhao and J. B. Zhang, Biobased epoxy vitrimer from epoxidized soybean oil for reprocessable and recyclable carbon fiber reinforced composite, Compos. Commun., 2021, 22, 100445 CrossRef
.
- S. J. Shan, D. D. Mai, Y. L. Lin and A. Q. Zhang, Self-Healing, reprocessable, and degradable bio-based epoxy elastomer bearing aromatic disulfide bonds and its application in strain sensors, ACS Appl. Polym. Mater., 2021, 3(10), 5115–5124 CrossRef CAS
.
- Y. L. Liu, B. B. Wang and S. Q. Ma,
et al., Catalyst-free malleable, degradable, bio-based epoxy thermosets and its application in recyclable carbon fiber composites, Composites, Part B, 2021, 211, 108654 CrossRef CAS
.
- X. X. Yang, L. Z. Guo, X. Xu, S. B. Shang and H. Liu, A fully bio-based epoxy vitrimer: Self-healing, triple-shape memory and reprocessing triggered by dynamic covalent bond exchange, Mater. Des., 2020, 186, 108248 CrossRef CAS
.
- C. Li, Y. Z. Chen, Y. Zeng, Y. C. Wu, W. D. Liu and R. H. Qiu, Strong and recyclable soybean oil-based epoxy adhesives based on dynamic borate, Eur. Polym. J., 2022, 162, 110923 CrossRef CAS
.
- Z. Y. Ma, Y. Wang, J. Zhu, J. R. Yu and Z. M. Hu, Bio-based epoxy vitrimers: reprocessibility, controllable shape memory, and degradability, J. Polym. Sci. Polym. Chem., 2017, 55(10), 1790–1799 CrossRef CAS
.
- W. X. Zhang, F. Gao, X. J. Chen, L. Shen, Y. J. Chen and Y. J. Lin, Recyclable, degradable,
and fully bio-based covalent adaptable polymer networks enabled by a dynamic diacetal motif, ACS Sustainable Chem. Eng., 2023, 11, 3065–3073 CrossRef CAS
.
- P. B. Zhang, J. Long and K. L. Xue,
et al., Preparation of degradable bio-based silicone/epoxy hybrid resins towards low dielectric composites, Eur. Polym. J., 2023, 181, 111691 CrossRef
.
- K. Hong, Q. M. Sun and X. Y. Zhang,
et al., Fully bio-based high-performance thermosets with closed-loop recyclability, ACS Sustainable Chem. Eng., 2022, 10(2), 1036–1046 CrossRef CAS
.
- S. C. Zhou, K. F. Huang and X. W. Xu,
et al., Rigid-and-flexible, degradable, fully biobased thermosets from lignin and soybean oil: synthesis and properties, ACS Sustainable Chem. Eng., 2023, 11(8), 3466–3473 CrossRef CAS
.
- Y. N. Zeng, J. W. Li, S. X. Liu and B. Yang, Rosin-based epoxy vitrimers with dynamic boronic ester bonds, Polymers, 2021, 13(19), 3386 CrossRef CAS PubMed
.
- H. Memon and Y. Wei, Welding and reprocessing of disulfide-containing thermoset epoxy resin exhibiting behavior reminiscent of a thermoplastic, J. Appl. Polym. Sci., 2020, 137(47), e49541 CrossRef
.
|
This journal is © The Royal Society of Chemistry 2024 |