DOI:
10.1039/D1NH00594D
(Review Article)
Nanoscale Horiz., 2022,
7, 141-167
Applications of liquid metals in nanotechnology
Received
12th November 2021
, Accepted 23rd December 2021
First published on 23rd December 2021
Abstract
Post-transition liquid metals (LMs) offer new opportunities for accessing exciting dynamics for nanomaterials. As entities with free electrons and ions as well as fluidity, LM-based nanomaterials are fundamentally different from their solid counterparts. The low melting points of most post-transition metals (less than 330 °C) allow for the formation of nanodroplets from bulk metal melts under mild mechanical and chemical conditions. At the nanoscale, these liquid state nanodroplets simultaneously offer high electrical and thermal conductivities, tunable reactivities and useful physicochemical properties. They also offer specific alloying and dealloying conditions for the formation of multi-elemental liquid based nanoalloys or the synthesis of engineered solid nanomaterials. To date, while only a few nanosized LM materials have been investigated, extraordinary properties have been observed for such systems. Multi-elemental nanoalloys have shown controllable homogeneous or heterogeneous core and surface compositions with interfacial ordering at the nanoscale. The interactions and synergies of nanosized LMs with polymeric, inorganic and bio-materials have also resulted in new compounds. This review highlights recent progress and future directions for the synthesis and applications of post-transition LMs and their alloys. The review presents the unique properties of these LM nanodroplets for developing functional materials for electronics, sensors, catalysts, energy systems, and nanomedicine and biomedical applications, as well as other functional systems engineered at the nanoscale.
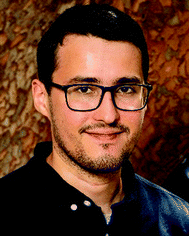
Francois-Marie Allioux
| Francois-Marie Allioux is a postdoctoral fellow at the School of Chemical Engineering, University of New South Wales (UNSW), Sydney, Australia. He completed his PhD in Material Science in 2017 at Deakin University, Geelong, Australia. Prior to that, Dr Allioux received his Master of Chemical Engineering from the Paul Sabatier University in Toulouse, France. Dr Allioux's research interests include the fundamental and applications of low-melting point and liquid metals for environmental processes and technologies. His current research focuses on the formation of liquid metal nanostructures. |
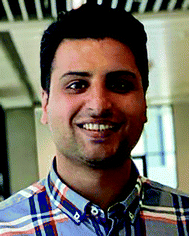
Mohammad B. Ghasemian
| Mohammad Bagher Ghasemian is a postdoctoral fellow in the Center for Advanced Solid and Liquid based Electronics and Optics (CASLEO) in the School of Chemical Engineering, University of New South Wales (UNSW), Australia. He received his PhD degree in Materials Science & Engineering from UNSW in 2018. Dr Ghasemian's research interests include the fundamentals and applications of liquid metals in 2D materials, piezoelectric materials, sensors, and additive manufacturing. |
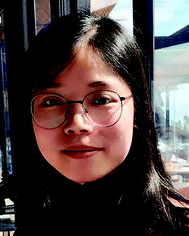
Wanjie Xie
| Wanjie Xie completed her PhD in 2020 at Deakin University, Australia. She then became a postdoctoral researcher at the School of Chemical Engineering, University of New South Wales (UNSW), Australia, where she focused on investigating the synthesis of functional nanocomposites based on gallium-based liquid metals. |
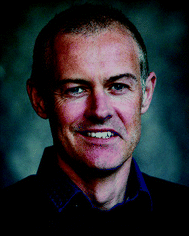
Anthony P. O'Mullane
| Anthony O’Mullane received his BSc Chemistry degree (1997) and PhD degree (2001) from University College Cork (Ireland). He is a Fellow of the Royal Society of Chemistry, the Royal Australian Chemical Institute and Queensland Academy of Arts and Sciences. He is the immediate past-Chair of the Electrochemistry Division of the RACI and served as vice chair of the Physical Electrochemistry Division of the International Society of Electrochemistry. He is an Editorial Board Member of ChemElectroChem. His work focuses on the electrochemical fabrication, characterisation and application of a wide range of materials including liquid metals with energy and environmental remediation applications. |
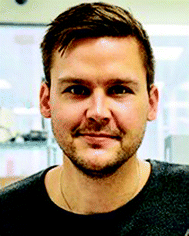
Torben Daeneke
| Torben Daeneke received his PhD in Chemistry from Monash University, Australia in 2012. After graduating he held postdoctoral appointments at the CSIRO and at RMIT University (Australia). In 2018 he joined RMIT's School of Engineering as a faculty member where he is now an Associate Professor. Dr Daeneke has authored over 100 peer-reviewed journal articles and has been awarded several fellowships and grants, including an ARC Discovery Early Career Researcher Award (DECRA) and a RMIT VC postdoctoral fellowship. His research focuses on studying the chemistry of liquid metals, the synthesis of 2D materials and the development of novel catalysts. |
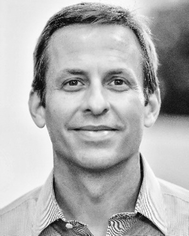
Michael D. Dickey
| Michael Dickey received a BS in Chemical Engineering from Georgia Institute of Technology (1999) and a PhD from the University of Texas (2006) under the guidance of Professor Grant Willson. From 2006–2008 he was a post-doctoral fellow in the lab of Professor George Whitesides at Harvard University. He is currently the Camille and Henry Dreyfus Professor in the Department of Chemical & Biomolecular Engineering at NC State University. He completed a sabbatical at Microsoft in 2016. Michael's research interests include soft matter (liquid metals, gels, polymers) for soft and stretchable devices (electronics, energy harvesters, textiles, and soft robotics). |
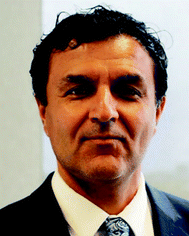
Kourosh Kalantar-Zadeh
| Kourosh Kalantar-Zadeh is a professor of Chemical Engineering at the University of New South Wales (UNSW), Sydney, Australia. He is involved in research in the fields of materials sciences, electronics, and transducers. He is best known for his works on two-dimensional semiconductors, ingestible sensors and liquid metals. He led his group to the invention of an ingestible chemical sensor: human gas sensing capsule. |
1. Introduction
Mercury (Hg) is traditionally the most recognized liquid metal (LM) that remains a liquid well below room temperature (melting point: −38.8 °C). However, due to its high toxicity, high vapor pressure, and low boiling point (356.7 °C), Hg is being increasingly phased out for most industrial, consumer or research applications. Other near room temperature melting point LMs include the highly pyrophoric rubidium (Rb, melting point: 39.3 °C) and caesium (Cs, melting point: 28.4 °C). Therefore, research on LMs is now more than ever centered around the low melting point post-transition metal gallium (Ga), which has a melting point of 29.8 °C. Unlike liquid Hg, liquid Ga presents unusual properties due to the high degree of covalent bonding within the bulk of its LM matrix, which results in it staying in the liquid state over a range of 2000 °C. It also has a low vapor pressure below 1500 °C.10–12 At near room temperature, the effectively zero vapor pressure allows for safe and routine operation in common research environments and also applications in high vacuum environments.21 To expand the family of LMs, research is now expanding from that of Ga and Ga alloys to other post-transition metals including indium (In, melting point: 156.6 °C), tin (Sn, melting point: 231.9 °C) and bismuth (Bi, melting point: 271.4 °C) that all melt below 330 °C.21 Cadmium (Cd, melting point: 321.1 °C), thallium (Tl, melting point: 304.0 °C) and lead (Pb, melting point: 327.5 °C) are also considered in this family of low melting point post-transition metals but, due to their high toxicity, are often not incorporated in general research areas and applications.
The bulk structure of low melting point post-transition LMs and their alloys is particularly hard to characterize as they are dense and impermeable to many characterization techniques. Bulk LMs present a matrix lacking any crystalline features formed of free ions and electrons, which provide metallic behavior including high thermal and electrical conductivity and also a water-like viscosity.32
Surface layering phenomena, which correspond to an atomic-scale ordering in the interfacial top layers, can occur in post-transition LMs and alloys. The study of the surface structure and composition of Ga and Ga-based LMs have been the subject of numerous investigations using advanced reflectivity, scattering techniques and nanotopography assessments.10,11,34 The surface of Ga and Ga-based LMs have been demonstrated to be composed of an atomically smooth surface comprised of a sea of quasi-free electrons and positive ions.11,35,36 Despite having an atomically smooth surface free of any crystalline structure, liquid Ga has been shown to possess a lamellar ordered surface, which is a few atomic diameters thick.10,11,35 However, differences between LMs also exist, for instance, liquid Ga presents localized electrons in the bulk matrix as opposed to liquid In, which shows more uniformly distributed free electrons.37 Liquid Sn was also reported to exhibit such atomic surface layering.38 In addition, liquid Ga, and many of its most common liquid alloys, in air at ambient conditions, establishes an atomically thin self-limiting oxide layer following a Mott–Cabrera model that is often reported to be between 0.5 and 3 nm thick.39,40 In contrast, the oxide layers of liquid In, Sn and Bi grow into thicker coatings when exposed to oxygen.41–44
LMs and their alloys can be synthesized at the nanoscales using various agitation methods. Nanoparticles composed of at least two different metallic elements are typically referred to as nanoalloys.45 Liquid nanoalloys can be used for the synthesis of different solid, liquid and liquid/solid nanostructures such as core/shell, stratified, high and low entropy and fully phase separated nanoparticles.14,23,28 LM-based nanoalloys have been integrated into nanocomposites of organic and inorganic materials, which properties have been explored in polymeric matrices and also their interactions with biomaterials have been investigated.3,17,20,46,47 Altogether multi-elemental nanocompounds and nanocomposites, made of LMs, have been shown to offer interesting physical and chemical properties that originated from the liquid state of these entities.
Finally, the incorporation of nano-sized liquid particles is rapidly emerging in exciting applications. Their utilization has been shown to enhance catalytic activity, provide the possibility of self-healing in electronics, improve sensing (mechanical, gas, and biological), and harvest energy. They have also been used in nanomedicine and biotechnology, e.g. for drug delivery and targeting applications with responses that are not seen in solid nanoparticles.
This review aims at providing insights into how low melting point post-transition LMs and alloys influence nanotechnology. The methods utilized for the formation of LM-based nanostructures and nanoparticles are presented. The review discusses multi-elemental LM nanodroplets and their solidification, which relates to their entropy and environmental stimuli. The reactivity, surface composition, interfacial layering and nanodomains at the dynamic surface of LM alloys are also reported. The very recent and emerging applications of LMs for the synthesis of nanomaterials, energy production and storage, electronics, sensing, catalysis and in nanomedicine are then presented. Finally, some future prospects for the application of LMs in nanotechnology are discussed.
2. Characteristics of post-transition metals and alloys at the nanoscale
2.1 Post-transition metals and alloys
Post-transition metals share common properties such as low melting point, electrical conductivity, mixed metallic and covalent bonds, and are softer compared to transition metals. However, a universal definition for post-transition metals remains only partially accepted. Fig. 1a shows the group of elements defined as post-transition metals considered in this review with the addition of the elements in the zinc group due to their importance in this review. In a similar way to transition metals, post-transition metals also form a multitude of alloys. Alloying of post-transition metals forms low melting point alloys with tunable properties and phase compositions. In addition, post-transition metals also form eutectic alloys in the liquid state, which have melting points lower than their respective single elements. For instance, a eutectic binary alloy formed of 75.0 wt% Ga and 25.0 wt% In (EGaIn) has a melting point of 15.6 °C, which is lower than the respective melting points of each element. Another example of a post-transition eutectic alloy is Galinstan, which has a reported melting point of around ∼10 °C, and is a ternary alloy of 68.5 wt% Ga, 21.5 wt% In, and 10.0 wt% Sn.48 A plethora of other eutectic binary alloys of relatively low temperature melting points can be formed from post-transition metals such as EBiSn (57 wt% Bi and 43 wt% Sn, melting point 139.8 °C), and ternary alloys, including Field's metal (51 wt% In, 32.5 wt% Bi, 16.5 wt% Sn, melting point 62 °C), and even quinary alloys that include Pb and/or Cd elements.23,28,32 The representative eutectic post-transition metal alloys are presented in Table 1.
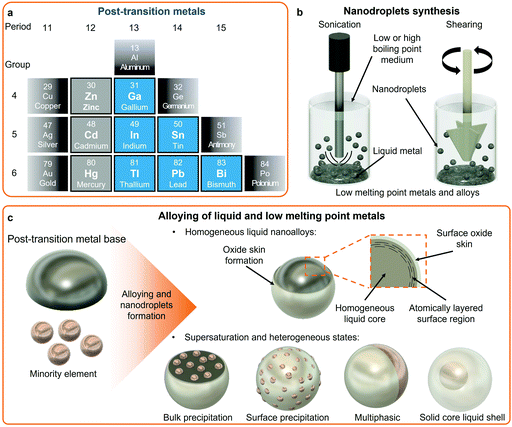 |
| Fig. 1 (a) Portion of the periodic table showing the elements defined as post-transition metals (in blue) and zinc group (in gray) due to the importance to this paper. (b) Representation of the sonication and shearing methods used for the synthesis of LM nanodroplets from low melting point metals and alloys. (c) Illustration of the surface oxide and atomic layering phenomena in LMs and the reported nanostructure variations in LM nanodroplets. | |
Table 1 Composition of some important low melting point post-transition eutectic alloys
Alloy name |
Eutectic composition (wt%) |
Eutectic melting point (°C) |
Density (g cm−3) |
Eutectic alloy containing toxic metals (Pb, Cd and Tl), In is considered less toxic in comparison.
|
EGaIn |
Ga78In22 |
15.5 |
6.28 |
EGaSn |
Ga86.5Sn13.5 |
20.5 |
— |
EBiCda |
Bi60Cd40 |
146.0 |
10.49 |
EBiSn |
Bi57Sn43 |
139.0 |
8.12 |
EBiIn |
Bi49In51 |
68.1 |
6.34 |
EBiPba |
Bi55.5Pb44.5 |
125.5 |
10.52 |
ECdIna |
Cd25.6In74.4 |
126.0 |
— |
ECdPba |
Cd17.5Pb82.5 |
246.0 |
10.40 |
ECdSna |
Cd32.3Sn67.7 |
176.0 |
7.68 |
ECdTla |
Cd17Tl83 |
203.5 |
11.35 |
EPbSna |
Pb37Sn63 |
183.0 |
8.40 |
ESnTla |
Sn57Tl43 |
166.0 |
8.59 |
EGaSnZn53 |
Ga86Sn11Zn3 |
14.9 |
6.14 |
EBiPbSna |
Bi52.5Pb32Sn15.5 |
95.0 |
9.69 |
Galinstan |
Ga68.5In21.5Sn10 |
∼10.0 |
6.44 |
Field's metal |
Bi32.5In51Sn16.5 |
62.0 |
7.88 |
Wood's metala |
Bi50Pb26.7Sn13.3 |
70.0 |
9.67 |
GaSnZn + In54 |
EGaSnZn + In21.4 |
15.9 |
6.20 |
EBiPbInSna |
Bi49Pb18In21Sn12 |
58.0 |
8.58 |
Cerrolow 117a |
Bi44.7Pb22.6Sn8.3Cd5.3In19.1 |
47.2 |
8.86 |
Post-transition metals are now increasingly considered as universal platforms for alloying with other metallic elements including other post-transition, transition, and alkali metals, and also rare earth elements.21,32,49 Considering the concept of high entropy alloys, elemental combinations of post-transition metals and their resulting structures are nearly limitless. LM alloys can form liquid monophasic and multiphasic liquid–solid alloys. Elements in liquid monophasic alloys are homogenously distributed within the LM matrix as opposed to multiphasic alloys, where segregated solid domains exist in various forms. The low melting points of the post-transition metals provide facile paths for the synthesis of nanoalloys and multi-elemental nanoparticles using a variety of processes applied to the alloy melts. Despite all these possibilities, systematic alloying of post-transition metals based on well-designed elemental libraries and the study of their nanostructures remain largely unexplored.
2.2 Surface chemistry of post-transition LMs and alloys and surface layering
Single and multi-elemental LM phases exhibit extraordinary surface enrichment phenomena which are increasingly becoming recognized for the synthesis of nanostructured materials.50 In LM matrices, it is understood that elements naturally compete to appear at the surface of LMs. Therefore, the surface composition might vary dramatically in comparison to the bulk. As an example, Ga-based LMs form a self-limiting passivating oxide skin layer, the composition of which is determined by the makeup of the Ga-based alloy and conditions of the environment at the interface with the LM.50 Typically in the air, the oxide skin layer of LMs such as Ga, EGaIn or Galinstan is composed of amorphous gallium oxide (Ga2O3).51 However, alloying with other elements in the bulk LM can drastically change the elemental composition of the oxide layer. For example, when very small amounts (∼1 wt%) of aluminum (Al), gadolinium (Gd) or hafnium (Hf) are mixed with Ga, the surface of the liquid Ga is occupied with their oxides, namely aluminum oxide (Al2O3), gadolinium oxide (Gd2O3) and hafnium oxide (HfO2), respectively, rather than Ga2O3, indicating the higher tendency of Al, Gd and Hf for enriching the surface of the alloy as compared to Ga.50 The surface composition follows the preferential oxide formation of the alloyed materials that offer the lowest Gibbs free energy for oxide formation.50,52
Indium tin oxide (ITO) sheets were also synthesized and collected through a squeeze-print process from the surface of InSn liquid alloys confirming the contribution of both In and Sn in the surface layer. However, the ratios of In/Sn in the collected sheets differed significantly from their initial ratios in the bulk. Sn showed a higher tendency than In to migrate to the surface and contribute to the oxide layer.55 This competitive elemental migration from the core to the surface of liquid alloys can selectively dope such 2D metal oxides. By using liquid alloys with various ratios of Bi and Sn, it is possible to obtain Bi2O3 doped 2D SnO. Sn showed much stronger preference than Bi for migration to the interface of liquid alloys, even at very low Sn concentrations. In this case, Bi2O3-doped SnO nanosheets with the highest atomic percentage of 0.7% for Bi were collected from the surface of liquid alloys while the atomic percentage of Bi in the bulk alloy was around 90%.56 Melts of Bi alloys can also show preferential oxidation phenomenon. As an example, the formation and collection of antimony oxide (Sb2O3) nanosheets were reported on BiSb alloy melt that presented a α-Sb2O3 dominated surface oxide layer.57
In addition, oxide layers can be collected via gas injection into LM melts in aqueous, organic or inorganic electrolyte solutions.50,58,59 As examples, SnO nanosheets and SnOx nanoflakes were collected from Sn melt (>260 °C) and EBiSn melt (>139 °C), respectively.58,59 The use of electrolyte solutions with various degree of acidity and alkalinity allow to gain access to the subsurface of the LM alloys and therefore collecting non-favorably formed 2D transition metal oxide nanosheets that would otherwise be covered by Ga2O3. Titanium dioxide (TiO2) and cobalt oxides (CoOx) nanosheets were formed from GaTi alloys and Ga-based alloys containing Co particles, respectively, using such method.60,61 Other stamping, brushing, squeegeeing and high shear methods were devised for oxide skin collection from LM melts.62–68
The ultra-smooth and reactive surface of LMs can also be used for templating 2D materials. In contrast to solid metals, LMs possess a dynamic electrical double layer (EDL).26,69 The physicochemical properties of the EDL of LMs can be manipulated with surface modifications, particle coatings and changes in the electrolyte interface.26 Manganese dioxide (MnO2) and molybdenum sulfide (MoS2) monolayers were formed on the surface of EGaIn using galvanic replacement reactions between the surface of the LM and a permanganate (potassium permanganate) or molybdenum (ammonium tetrathiomolybdate) ionic source, respectively, in aqueous media.70,71 Similarly, highly crystalline bismuth telluride (Bi2Te3) nanostructured platelets were synthesized at the surface of EGaIn drops.72 As another example, the formation of layered double oxides was also achieved using a room temperature liquid alloy of Ga, In and Al.73 In this study, the Al-containing LM alloy was placed in an aqueous solution containing divalent cationic species including Ni2+ or Co2+ ions. Low-dimensional aluminum hydroxides formed spontaneously on the surface of the LM drop when immersed, and subsequently reacted with the cations present in solution. Following a hydrothermal process, the layered double oxides were formed.73
2.3 Nanopatterns from the solidification of LM surfaces
Solidification of post-transition LM systems can result in the formation of nanosized surface patterns and also phase separation during bulk solidification. Bulk phase separation during liquid to solid transition in molten metals is a well-known phenomenon of classical metallurgy.
The solidification and nanophase separation phenomena were investigated for the Bi–Ga system, including the dilute eutectic BiGa (Bi0.0022Ga0.9978) that resulted in Turing-like patterns when the surface was agitated and a solidification front was produced that propagated from the point of agitation.7 During the solidification process, a Bi surface enrichment (up to 25 times) was reported to occur, which was associated with the formation of highly ordered Bi nanoscale patterns on the surface as presented in scanning electron microscopy (SEM) images and energy-dispersive X-ray spectroscopy (EDS) elemental mappings (Fig. 2a). The nanopatterns of Bi were reported at the subsurface of the solid alloy confined under the natural Ga oxide layer that protected them from oxidation. Similarly, nanopatterning was also found for other dilute binary and ternary Ga, Sn and Bi-based alloys.7 In addition, post-transition/transition metal systems, such as Bi0.01Cu0.99, were also shown to present surface phase ordering at the sub-micron scale emerging during solidification.7 The formation of surface nanopatterns was found to be dependent on multiple factors specific to each alloy including crystalline structures, solidification and oxidation thermodynamics. In another set of investigations, nanoscale patterns were observed on a Bi monolayer grown on niobium diselenide (NbSe2) that also resulted in Turing-like patterns (presented in Fig. 2b).15,74
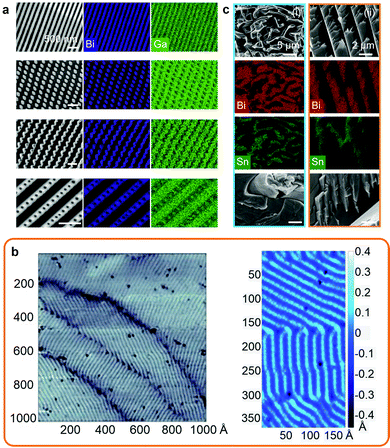 |
| Fig. 2 (a) SEM images and EDS mapping showing the surface nanoscale BiGa patterns including lamellae, rods, transitional and lamella-rod. Scale bars: 500 nm. Adapted with permission.7 Copyright 2021, Springer Nature. (b) Surface topography of a single Bi monolayer grown on NbSe2. Adapted with permission.15 Copyright 2018, AAAS. (c) SEM images and EDS mapping of the solidification patterns in the bulk of Bi0.4Sn0.6 (i) and EBiSn (ii) alloys. Adapted with permission.23 Copyright 2019, Springer Nature. | |
In comparison, bulk solidification of post-transition metal alloys generally results in standard micron to sub-micron patterns of separated phases of fibrous, lamellar or rod shape structures. An example is presented for the solidification of BiSn alloys at the eutectic composition and also below and above the eutectic composition as presented in Fig. 2c. At the eutectic BiSn composition (57 wt% Bi), mostly fibrous structures were observed, which was attributed to solidification from the higher entropy system as opposed to non-eutectic ratios that solidified over a range of temperatures into more ordered lamellar and rod shape structures.23
2.4 Synthesis of nanoalloys and multi-elemental nanoparticles of post-transition LMs
By using LMs, nanoalloys and multi-elemental metallic nanoparticles can be synthesized based on a variety of metallurgical processes. In this regard, for synthesizing and designing nanoalloys and multi-elemental nanoparticles, synergetic physical and chemical properties between the added elements should be carefully considered.75 In addition, strategies that have been used for the creation of ‘transition metal-based nanoalloys and nanoparticles’ can be adopted for post-transition metals.76 During synthesis, considerations such as phase separation, formation of multiphasic structures and multiple interfaces were reported to be thermodynamically driven, leading to the lowest energy of the system that determine the morphologies and crystal phases after solidification and phase separation.77
To date, multiple nanoalloy synthesis methods for creating ‘transition metal-based systems’ have been investigated including chemical reactions in aqueous or organic solutions combined with thermal reduction, microwave or laser irradiation, and sonochemistry.78 Many of these methods rely on processes that incorporate precursors that are decomposed to establish nanoalloys. These growth processes generally require a combination of redox pathways, ligand assisted reactions and de-solvation steps. These steps can have a profound impact on crystal growth, directing the growth along certain crystal facets and impeding natural crystal expansion along others. In contrast, the synthesis of nanoalloys and nanostructured interfaces using ‘post-transition LM focused pathways’ have received less attention.7,23,28
LM nanodroplets synthesis.
Room temperature liquid and low melting point post-transition metals and alloys can be dispersed and shaped into nanodroplets using a variety of techniques. Top-down approaches have so far been the most popular techniques for the formation of such nanodroplets. They include mechanical agitation and sonication as illustrated in Fig. 1b.79 Other mechanical synthesis and dispersion methods have also been reported including microfluidic, shearing, nebulization, extrusion and patterning of LMs.80–83 Microfluidic approaches can produce more monodispersed yet relatively large micron-sized droplets (50 to 200 μm), while nebulization results in droplet dimensions below 200 nm with a narrow size distribution.80,81,84 Shearing methods are particularly promising for the synthesis of micro to nano size droplet of LMs from low melting point alloys.82,85 However to date, sonication methods based on probe sonicators and ultrasonic baths have remained the main techniques for synthesizing dispersions of LM micro and nanodroplets. Patterning and extrusion techniques have also been used for the formation of LM drops, some of which offer narrow size distributions; however, the obtainable LM droplet dimensions generally remain in the microscale ranges.83,86,87
Post-transition LMs such as EGaIn and Galinstan have been routinely processed into nanoscale entities using sonication techniques. The sonication temperature, choice of the solvent, pH conditions and addition of stabilizer molecules were reported to drastically influence the resulting dimensions of the nanodroplets and of materials which are co-produced in the process.79 Without the usage of surfactants, sonication of liquid Ga and its alloys generally result in the formation of droplets that are covered with Ga2O3 or monohydroxide (GaOOH) coatings, depending on the surrounding solvent. However, with excess sonication time (usually more than 20 minutes), these liquid Ga and its alloys may totally transform into Ga2O3 and GaOOH nanoflakes, nanoplate or nanorod crystals.88–90 The transformation is due to the heat generated by the sonicator rather than sonochemistry.89 On another note, Ga itself has appeared to be a catalytic material that can break strong covalent bonds during sonication even those of stable molecules such as N2.91 In this regard, nitridation of Ga-based alloys has been reported via sonication in the presence of nitrogen-rich precursors such as N2 gas or polyvinylpyrrolidone (PVP) surfactant resulting in the formation of mixed gallium nitride (GaN) and GaOOH nanocrystallites.91
Besides the sonication duration and power intensity, other factors such as temperature and the presence of charged molecules or surfactants were reported to induce shape transformation of LM nanodroplets. For example, dealloying phenomena were shown to occur in Ga-based nanodroplets via moderate heating either during or after sonication or via sonication in alkaline solution.89,97 EGaIn nanospheres were observed to transform into individual GaOOH nanorods together with solid In nanoparticles by heating the solution to 70 °C. In this case, the heating could drive the transformation of EGaIn nanodroplets from liquid to solid via selective dealloying of Ga through its oxidation into GaOOH nanorods. Interestingly, the use of surfactants was shown to prevent dealloying during heat treatment.89
A drawback of sonication is the broad particle size distribution of the produced nanodroplets. To minimize the size distribution of the nanodroplets, different strategies, such as combined on-chip sonication, dynamic temperature control and centrifugation were proposed.92,93 Other techniques, such as coupling laser irradiation and sonication approaches, were also reported that resulted in remarkable size reduction of droplets to below 10 nm.94,95 A brief description of the different nanodroplet preparation techniques is presented in Table 2.
Table 2 Post-transition LM nanodroplets synthesis techniques
Synthesis technique |
Ga-based LM droplets size range |
In situ functionalization |
Applicability to other low-melting point metals and alloys |
Sonication coupled with laser irradiation.
Microfluidic coupled with sonication.
|
Sonication81,92–96 |
<10 nm,a 50 to 1000 nm |
Yes |
Yes |
Shearing82,85 |
∼10 nm and below 10 μm |
Yes |
Yes |
Microfluidic80,84,93 |
50 to 1000 nm,b 50 to 200 μm |
Yes |
Not reported |
Patterning83 |
50 to 500 μm and more |
Not reported |
Not reported |
Extrusion40,87 |
10 to 500 μm and more |
Not reported |
Not reported |
LM nanodroplets functionalization.
LM nanodroplets can be functionalized in situ during sonication using a variety of molecules to prevent their nucleation, control their particle size distribution or promote their colloidal stability.96,98 LM nanodroplets can be functionalized during their synthesis via direct grafting of organic materials on their bare reactive surface or via anchoring of molecules on the hydroxyl groups present on the oxide layer.79 Functionalization of LM nanodroplets was reported through a range of molecules bearing functional anchoring groups such as silane, amine, thiol, catechol, phosphate, trithiocarbonate, and other acidic groups.46,81,93,96,99–105 As an example, diblock copolymers with short poly(acrylic acid) anchoring segments were attached to the Ga oxide skin of EGaIn nanodroplets to form polymer brushes.106 These polymer brushes/EGaIn nanodroplets exhibited good re-dispersibility with narrow size distribution in a variety of solvents. The surfactants and organic materials that are incorporated on the surface of LM droplets can have significant effect on the properties of the nanodroplets, granting them specific bio-functionalities, especially in biotechnology and nanomedicine applications.3,107 Such coatings can also improve the stability of suspensions of these nanodroplets. It has been reported that grafting of a hydrophobic polymer layer comprising of poly(1-octadecene-alt-maleic anhydride) on the surface of LM nanodroplets enabled them to remain stable for more than 60 days in a buffer solution without oxidation-induced aggregation.105 Altogether, functionalization of LM nanodroplets present great opportunities for tuning their properties for various applications.
Heterogenous nanostructures formation.
Post-transition LM alloys provide the possibility of creating a range of interfacial heterostructures via controlling the alloy composition and alteration of the ambient conditions.8,90 Heterogeneous multiphasic LMs were reported in supersaturated states, when a solute element, above its maximum solubility, is added into a LM as the solvent.8,108 The concentration limit at which the LM alloy remains liquid is specified by the relevant phase diagrams.109 Although, it should be considered that observations might significantly diverge from classical phase diagrams when the dimensions of droplets becomes smaller. Additionally, LM nanodroplets can exhibit homogeneous or heterogenous cores and surfaces of various compounds, depending on how they were designed and synthesized. Supersaturation and then cooling can produce secondary solid phases in the LM pool. As an example, cerium (Ce) crystals were synthesized inside liquid Ga or Galinstan droplets using this method.8 Below the Ce solubility limit, the LM alloy presented a homogenous core matrix and atomically smooth surface, while above the Ce solubility limit, self-forming solid Ce nanoparticles emerged encapsulated within the liquid Ga-based core matrix.8
Information from phase diagrams can be used for the creation of interesting solid–liquid nanoparticles. For instance, intermetallic compounds can be formed, based on phase diagrams, by bringing a secondary metal into intimate contact with LMs. This method can be used with metals that are not soluble in the LM of interest, such as nickel (Ni), molybdenum (Mo) and copper (Cu) in LM Ga. As an example, it was demonstrated that by dispersing solid Cu particles in Ga-based LMs, intermetallic Cu2Ga crystals were produced.110,111 Interestingly, the Cu2Ga crystals were seen to diffuse into the LM matrix in time.110 The formation of Cu2Ga intermetallic was also reported in Galinstan sandwiched between two Cu current collectors and upon applying a high DC current.112
Solidification of LM nanodroplets.
Sonication of LM melts to form particles combined with subsequent solidification offers unique opportunities for synthesizing solid nanoparticles of post-transition metals and the observation of phenomenon such as supercooling (i.e. materials that remain liquid below their melting point). These processes allow to study surface physicochemistry, oxide formation mechanisms and catalytic micro-kinetics occurring at the dynamic surface of LM nanodroplets. Significantly, the formation of LM nanodroplets and their subsequent solidification, can also lead to altered thermodynamics with perturbed core and interfacial chemistries at the nanoscale, as compared to bulk LM melts.
An interesting co-existence of liquid and solid phases has been reported below the melting point of post-transition metals. Such examples were demonstrated with the simultaneous existence of solid Ga crystals within liquid Ga encapsulations at the nanoscale.1 It has been suggested that the reactivity of the support utilized during the deposition of the Ga nanodroplets played a crucial role in the nucleation of the solid Ga phase within the Ga liquid. In this case, Ga nanodroplets deposited on sapphire (c-Al2O3) produced solid Ga nanoparticles within the liquid encapsulation.1 However, on amorphous glass substrates, only a Ga liquid phase was observed, which was ascribed to the weaker wetting of liquid Ga on glass in comparison to sapphire and also to the high activation energy of Ga diffusion into the glass. On more reactive substrates, such as silicon (Si), Ga dissolves into the Si matrix forming an interfacial layer of gallium silicide.1 The solid Ga particles and encapsulating liquid Ga nanodroplets formed on the different substrates are shown in Fig. 3a as characterized using high angle annular dark field scanning transmission electron microscopy (HAADF-STEM) and EDS mapping.1
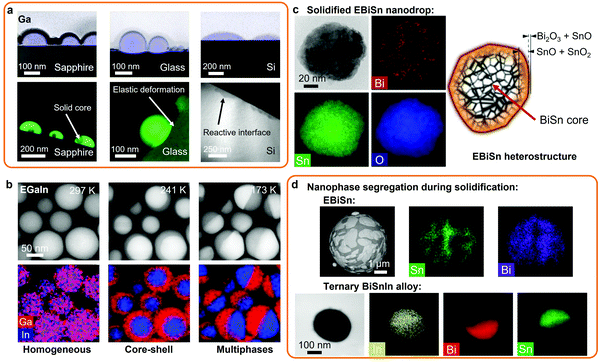 |
| Fig. 3 (a) Solid core liquid shell Ga nanodroplets formed on crystalline, amorphous or reactive substrates (HAADF-STEM images and Ga EDS mapping). Adapted with permission.1 Copyright 2016, Springer Nature. (b) Homogeneous and heterogeneous EGaIn nanodroplets formed via thermal cycling (HAADF-STEM images and EDS mapping). Adapted with permission.14 Copyright 2019, Elsevier. (c) Solidified EBiSn nanodrop presenting a metal core and a complex oxide shell structure (TEM image and EDS mapping). Adapted with permission.23 Copyright 2019, Springer Nature. (d) Nanophase distribution across EBiSn (SEM image and EDS mapping) and ternary BiSnIn alloys (TEM image and EDS mapping). Adapted with permission.28 Copyright 2020, ACS Publications. | |
In another interesting observation, controlled phase transitions in homogeneous binary EGaIn nanodroplets were demonstrated via thermal cycling.14 Multiple phase transitions were observed, from an In solid core in a Ga liquid shell to a Janus type material with both solid In and Ga phase separated as presented in Fig. 3b. This phenomenon was also shown in ternary Ga–In–Sn alloys with the formation of a solid bi-crystal cores of In and Sn in solid Ga shells, which indicated the importance of the concentration of the minority element in the Ga liquid base for the formation of specific liquid/solid nanostructures.14 In addition, supercooling was reported to be exacerbated by the size reduction of bulk LM to micro and nanodroplets.113,114
Taking advantage of the solidification of LM nanodroplets of post-transition metals also provide great opportunities for creating solid metal and metal oxide nanoparticles. For synthesizing nanodroplets of post-transition metals and alloys of higher melting point than Ga, sonication or shearing processes can be conducted in appropriate high boiling point solutions. The sonication of molten Sn, Bi and their alloys (eutectic and non-eutectic) was reported in silicone oil, which has a boiling point above the respective melting points of each of the metals.23 In this case, Bi and Sn nanoparticles were formed with sizes below 200 nm. When the eutectic BiSn alloy was used, the synthetized nanoparticles showed intricate structures of BiSn metallic core, multiple shells of Sn oxides (SnO and SnO2) and a surface oxide shell of mixed SnO and bismuth oxide (Bi2O3), as represented in Fig. 3c.23 In this example, the eutectic BiSn nanoalloys showed more lines and surface defects, edge dislocations and increased boundaries in comparison to other BiSn nanoalloys.23 Additionally, this study revealed that agitation resulted in the formation of more diverse surface oxides on nanodroplets rather than simply SnO present on the surface of bulk of BiSn alloys due to the change of the thermodynamic conditions.
The formation of eutectic BiSn microparticles with nanosized separated domains of Bi and Sn is presented in Fig. 3d.23,28 Furthermore, the addition of 2 wt% In into the eutectic BiSn alloy (Bi56Sn42In2 alloy) was reported to dramatically decrease the particles size distribution during sonication, which presented perfect separation of the Sn and Bi domains and In coating (Fig. 3d).28
In another example, low-melting point ternary nanoalloys were formed via sonication in glycerol or DI water.19,115 Here, Field's metal melt was processed into nanoparticles with an average size of 250 nm. The synthesized nanoparticles presented spherical core/shell metal/metal oxide heterostructures including In(OH)3 oxide phase, binary BiIn2 and Sn0.8In0.2 metallic phases after solidification, which indicated phase separation during the solidification of the liquid alloy.115
The principles of nanometallurgy applied to post-transition-based liquid and alloys is only beginning to be realized for the formation of nanoalloys. Sonication and solidification of low melting point alloys provide new routes for the creation of functional micro and nano features and chemistries that are otherwise not accessible in bulk LM melts. While some valuable effects of nano-ordering phenomena in the core and at the interfacial oxide layer have been observed in single and multi-elemental LMs, the realization of many more possibilities remains to be achieved.
3. Nanocomposites based on LMs
In this section, the possibility of creating composites, with nanostructured fillers, using LMs are presented. The LM nanocomposites that are discussed here can be made of nanosized LMs dispersed into polymeric materials, grafted with polymeric networks, or made of nanodimensional inorganic solid particles dispersed into a LM phase. The composites can be made in liquid, solid, or heterogeneous states and formed into matrices such as elastomers, hydrogels, foams and semisolids.
3.1 LM polymer and organic material nanocomposites
In the previous sections, we described how LM nanodroplets can be synthesized. These nanodroplets can then be encased into polymers to form LM polymer nanocomposites with several useful properties. Their formation is often reported to follow a one-pot mixing method with direct synthesis of the LM nanodroplets into a pre-polymeric liquid before casting and curing.
LM polymer nanocomposites based on non-conductive matrices present high initial electrical resistivity (>kΩ m), even with a high-volume fraction of LM nanodroplets (Φ ≥ 50%) due to the presence of a naturally insulating surface oxide layer on the LMs and a thin layer of polymer that separates the LM nanodroplets.20,116–121 The composite can be rendered conductive by a mechanical compression step that ruptures the oxide layer and/or polymer coating, and merges the LM nanodroplets.20,119,120 Laser irradiation, or any other heat sources, can also achieve electrical percolation by merging the LM droplets via thermal expansion.122,123 To partially prevent the oxidation of the LM nanodroplets, they can be synthesized ex situ in a solvent containing a trace amount of an acidic or basic mediator.119,122 Co-fillers can also be mixed together with the LM nanodroplets to simultaneously provide enhanced conductivity as well as new properties to the nanocomposites.16,119,124 In one example, the addition of graphene flakes was shown to augment both the electrical conductivity and increase the mechanical integrity of the matrix.119 In another example, the formation of anisotropic LM-based nanocomposite with enhanced conductivity was reported via the magnetic alignment of solid magnetic co-fillers before curing of the elastomer matrix.124
Polymers with specific functional groups can be used for dispersing and stabilizing the nanodroplets resulting in electrically conductive LM composites without the need for mechanical activation. Such examples are seen for LM hydrogel composites which provide ionic conductive coatings.47,125–129 In addition when hydrated, the hydrogel matrix and LM phase demonstrate flexibility, stretchability and self-healing properties. As an example, EGaIn nanodroplets with an average size of 220 nm, were synthesized in situ in an aqueous poly(vinyl alcohol) (PVA) solution prior to cross-linking.47 Other hydrogels with distinct responsive properties remain to be investigated as functional matrices for the synthesis of LM nanocomposites.130
The co-addition of functional molecules, such as thermochromic pigments, in the elastomer matrix was also reported. In such case, Joule heating of the LM phase induced a color change across the LM composite.131 A wide range of functional molecules as co-additives in LM composites and nanocomposites systems remain to be studied.132
Organic materials can be reacted on the surface of LM nanodroplets, during or after their synthesis, to form LM organic networks. During their synthesis, the reactive surfaces of the nanodroplets can be manipulated resulting in the grafting and polymerization of organic compounds. The in situ formation of LM nanodroplets was reported to directly initiate the polymerization of various monomers.5,133–135 As an example, the synthesis of EGaIn nanodroplets via sonication was shown to initiate free radical polymerization reaction of vinyl monomers in an aqueous solution (Fig. 4a).5 Alternatively, LM nanodroplets can be dispersed into a monomeric solution before the polymerization reaction and utilized as nucleation sites. For example, polyaniline (PANI) nanofibers were synthesized at the surface of EGaIn nanodrops leading to EGaIn/PANI nanocomposites as characterized with SEM and transmission electron microscopy (TEM) (Fig. 4b).18 In another example, the oxide layer on the surface of EGaIn nanodroplets was covalently functionalized with poly(methyl methacrylate) (PMMA).24 The TEM images of the PMMA-grafted EGaIn nanodroplets are presented in Fig. 4c along with the resulting EGaIn/PMMA composite, which was compared to a EGaIn/PDMS composite prepared by mechanical dispersion. Similarly, in situ polymerization of EGaIn/lactones nanocomposites were reported.134 Such approaches may lead to more homogeneity across the composite as compared to mechanical mixing.24 In a different approach, EGaIn droplets functionalized with acrylate ligands were cross-linked into a LM organic network with a high weight fraction of LM (>99.9 wt%), which presented stretchability and electrical conductivity under strain as shown in Fig. 4d.27
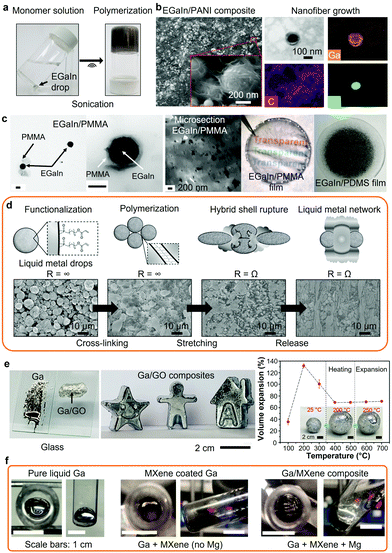 |
| Fig. 4 (a) EGaIn-initiated free radical polymerization reaction of a vinyl-based monomer. Adapted with permission.5 Copyright 2019, ACS Publications. (b) EGaIn/PANI nanocomposite with EGaIn nanodroplets integrated into the PANI nanofiber network (SEM images and TEM/EDS mapping). Adapted with permission.18 Copyright 2020, ACS Publications. (c) TEM images of the PMMA-grafted EGaIn nanodroplets and photographs of the resulting EGaIn/PMMA nanocomposite and compared to a EGaIn/PDMS nanocomposite prepared by mechanical dispersion. Adapted with permission.24 Copyright 2019, Springer Nature. (d) Polymerization of functionalized EGaIn nanodroplets forming a LM network and subsequent mechanical activation with associated SEM images. Adapted with permission.27 Copyright 2019, Wiley-VCH. (e) Photographs of liquid Ga and Ga/GO putty on glass, examples of shaped Ga/GO putties and volume expansion of the Ga/GO putty as a function of temperature with optical photos showing the expanded putties. Adapted with permission.29 Copyright 2021, AAAS. (f) Photographs of the top and side of Ga/MXene composite after ultrasonic agitation with or without addition of Mg. Adapted with permission.31 Copyright 2019, ACS Publications. | |
3.2 LM inorganic nanocomposites
Inorganic materials can also be mixed with nanosized or bulk LMs to form LM inorganic nanocomposites. The LM phase can offer distinct advantages in comparison to conventional media including an oxygen free environment, high thermal and electrical conductivities, and high catalytic activity. These characteristics provide both opportunities and challenges for establishing inorganic nanocomposites with LMs.
LM nanodroplets can be modified during its synthesis for the formation of inorganic nanocomposites. As an example, Galinstan micro and nano droplets with solid silver (Ag) and gold (Au) inclusions were synthesized during sonication of Galinstan in AgNO3 and KAuBr4 solutions, respectively.136 In another example, micro and nanodroplets of Galinstan were utilized as surface templates for the formation of copper species including CuO, Cu2O and Cu via galvanic replacement using CuSO4 as the precursor.137 The crystals stoichiometry and growth could be controlled by adjusting the pH and reaction time. In a similar approach, EGaIn and manganese dioxide core/shell nanostructures were synthesized via sonication using KMnO4 as the Mn source.70 Co-sonication of EGaIn and 2D tungsten oxide (WO3) flakes was also performed for synthesizing EGaIn/WO3 nanocomposites.138 The presence of WO3 flakes during sonication also increased the shearing forces resulting in EGaIn droplets with reduced sizes. Furthermore, EGaIn micro and nanodroplets were encapsulated by 2D graphene materials including GO, reduced GO (rGO) and functionalized GO post-synthesis or during synthesis.139,140 In such cases, sonication of EGaIn in a GO solution resulted in EGaIn nanodroplets encapsulated with rGO and the reduction of the GO flakes were taking place at the same time.139 Encapsulation of EGaIn nanodroplets with metal–organic frameworks (MOFs), such as ZIF-8, was also reported.141
The surface of LM droplets can be functionalized with micro and nanoparticles of metals, metal oxides, carbon-based and also with some organic materials, resulting in the formation of the so called ‘LM marbles’.26,69,142,143 LM marbles are typically synthesized by rolling a LM droplet on a bed of particles or by immersion in a colloidal suspension.26 The particles then adhere to the LM surface. LM marbles were coated with semiconductor particles, such as ZnO and WO3, insulators, such as Teflon and SiO2, and also with carbon nanotubes.26,69,142,143
Bulk LMs can be utilized for the dispersion of inorganic particles forming LM inorganic nanocomposites with enhanced mechanical strength and/or thermal properties, and also with other functionalities such as the modulation of supercooling.29,144–146 In such cases, strong shear forces should be applied to assist in wrapping the incorporated particles into the LM bulk. To date, Ga and Ga-based inorganic nanocomposites have been synthesized with 2D transition-metal carbides and nitrides (MXenes), functionalized carbon nanotubes, graphene, graphene oxide, graphite, diamond, tungsten and silicon carbide for a variety of applications.29,31,144,147,148 Similar to any other liquid media, mixing of particles in LMs requires interfacial and dimensional compatibility.29 As an example, large GO flakes (>10 μm) were dispersed in Ga-based LMs forming stable inorganic nanocomposites that could be shaped into various forms as shown in Fig. 4e.29 Furthermore, thermal post-treatment of Ga/GO LM nanocomposites allowed for the formation of Ga-based foams. Elemental addition, such as Mg in Ga-based LMs, was also reported to facilitate the binding and wetting of MXenes at the LM interface (Fig. 4f).31
4. Emerging applications of nanostructured LMs
In this section, the use of nanostructured LMs in different emerging applications are presented. The main subsections are dedicated to the most researched applications including soft electronics, sensors, catalysis, energy, nanomedicine and biomedical applications, while a final subsection is presented for other applications.
4.1 LM soft electronics
Soft electronics is an emerging class of electronics able to operate under mechanical deformation, which are critical for the formation of soft junctions, artificial skins, soft robotics and wearable electronics. Unlike rigid electronic materials, such as Au and Cu, LMs are intrinsically stretchable with mechanical properties close to other liquids. LMs and LM nanodroplets present fluidity and deformability; bulk LMs flow readily like water, although the presence of solid surface species (e.g. oxides) complicates the rheological behavior, but also offers opportunities for shaping the metal. All those properties are particularly valuable characteristics for the formation of soft electronics.2,20,118,119,149–151 During stretching and deformation, LM and LM nanodroplets can deform in the direction of the applied strain, in contrast to solids, as illustrated in Fig. 5a.2,9
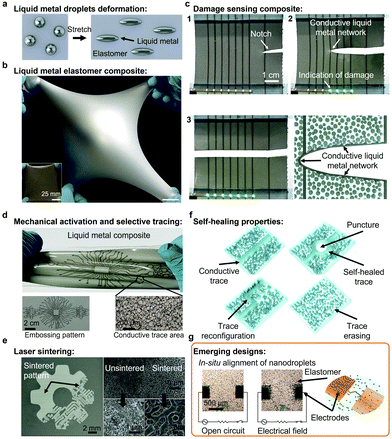 |
| Fig. 5 (a) Schematic illustration of the deformation of LM droplets in the direction of the stretching. (b) Stretchable LM elastomer composite. Adapted with permission.2 Copyright 2017, National Academy of Sciences. (c) Propagation of a cut in a LM composite and formation of conductive LM network indicating of the damage. Adapted with permission.9 Copyright 2019, Wiley-VCH. (d) Intricate embossing pattern of electrically conductive LM traces in an elastomer-based composite. Adapted with permission.20 Copyright 2018, Springer Nature. (e) Electrically conductive LM trace formed via laser sintering on an elastomer matrix (SEM images). Adapted with permission.25 Copyright 2018, ACS Publications. (f) Illustration of the self-healing properties of a LM elastomer nanocomposite. Adapted with permission.30 Copyright 2021, Springer Nature. (g) Dielectrophoretic process for in situ alignment of LM nanodroplets in an elastomer matrix. Adapted with permission.33 Copyright 2020, Wiley-VCH. | |
The very high surface tensions of LMs (∼724 nM m−1 for bare Ga and ∼624 nM m−1 for bare EGaIn152,153) represent an important challenge for the formation of stable non-spherical shapes, such as wires and sharp features, at the nanoscale. LM wires formed by 3D printing remain in the micro range (∼2 μm in width), while the direct patterning of LMs can, in theory, achieve sub-micron resolution.154,155 To date, sub-micron scale EGaIn patterns were achieved with features as small as ∼180 nm using a hybrid electron-beam and soft lithography method.156 In comparison, sub 10 nm LM nanodroplets have been reported using mechanical agitation methods.82,94
LM probes can be employed as soft junctions and for surface electrical characterization.26,157,158 As examples, LM marbles coated with semiconducting particles were utilized for the formation of soft contacts with LM–semiconductor junctions.26 LM nanotips, with sharp apexes between 10 and 100 nm, shaped by pulling (tensile forces) a drop of LM, can be used as soft electronic contacts to surfaces.157
Biphasic liquid/solid LM nanocomposites can be synthesized with the addition of secondary materials, such as Cu, Ag, Ni particles or CNTs, as previously mentioned, and can present enhanced electrical and thermal conductivities, and also altered rheological characteristics as compared to the plain LM phase. Biphasic LM nanocomposites were extruded, printed or painted on substrates forming electronic components and soft contacts.110,144,147,159–162 As an example, LM/CNTs nanocomposite was 3D printed into soft electrically conductive wires (5 μm in diameter) with 3D interconnections that were made possible by the enhanced stability of the printed patterns with the LM/CNTs nanocomposite as compared to plain LM.144
LM nanodroplet inks and slurries can be directly utilized for the writing or printing of soft electronic patterns on flexible substrates.163–166 A mechanical activation step is required as the polymer coating or oxide layer on the LM nanodroplets is electrically insulating and makes the printed pattern non-conductive. Alternatively, spraying process of LM can generate sufficient kinetic energy to merge the LM droplets on impact producing conductive paths.167
The insulating nature of the LM nanodroplets can constitute an advantage for soft electronic device fabrication. As an example, the selective mechanical merging of LM nanodroplets allows for the formation of tunable antennas for wireless communication.150 In this work, the operating frequency of the antenna was tuned by controlling the merging length across of EGaIn slurry injected into microchannels. Biphasic liquid/solid conductive traces can also be formed from the thermal treatment of a sprayed EGaIn nanodroplets slurry.168 The resulting traces presented a LM phase contained by a crystalline solid top layer, which provided an enhanced interface with the formed solid particles as compared to biphasic LM inorganic nanocomposites.
EGaIn and Galinstan nanodroplets were also proposed as electron transport materials and self-healing metal contacts in perovskite, flexible perovskite and organic solar cells.94,95,169,170 As an example, LM nanodroplets were shown to facilitate the electron-transfer process and also provide temporary electron storage at the grain boundaries of perovskite materials.94
LM inks are typically based on LM nanodroplets functionalized with a range of polymeric compounds, such as polysaccharides or tannic acid, that provide adhesion properties to the LM inks.46,171 In one example, coils and electrode arrays were fabricated by inkjet printing of a Galinstan nanodroplets dispersion on flexible PDMS substrates.166 Additionally, complex conductive patterns could be drawn using ballpoint systems. LM patterns were also formed via maskless UV photolithography process using a EGaIn/photoresist nanodispersion.172 The EGaIn/photoresist patterns were then mechanically activated to produce conductive traces with a resolution of 10 μm, which included sharp features.
Highly stretchable LM polymer nanocomposites that maintain conductivity up to 1200% strain were reported.2,6,30,121 An example of a LM polymer soft composite system is presented in Fig. 5b.9 As previously mentioned, mechanical activation of LM polymer nanocomposites is required to form electrically conductive materials. Mechanical activation can be non-selective across the whole material or selective for the formation of functional conductive LM traces. As an example, an array of conductive traces on a soft elastomer was demonstrated as sensors of mechanical damage (Fig. 5c).9 An innovative strategy to form complex soft electronic circuits is based on embossing techniques, where a specific pattern is pressed on the material. Elaborate embossed LM patterns were formed with metallic conductivity (Fig. 5d).20,30 Complexes patterns can also be formed using direct laser writing (Fig. 5e).122,123 In specific cases, the mechanical patterning and activation process can be reversed while the traces can be reconfigured using chemical treatments.30 In addition, LM traces formed on hydrogel-based soft electronics can be formed in the dry state and then erased with hydration of the hydrogel.127
LM traces formed from merging LM nanodroplets exhibit self-healing properties. In an early study, encapsulated EGaIn microdroplets (∼3 μm) into a urea-formaldehyde resin acted as a healing agent restoring the conductivity of the gold circuitry upon mechanical fracture.173 Similarly, the self-healing properties of LM traces were shown within elastomers with reconfiguration of the LM conductive pathways across cutting, tearing and puncture damage as illustrated in Fig. 5f.20,30 Functionalized LM nanodroplets can also provide self-healing properties to the base polymer material.174 Additionally, LM soft electronics present exceptional resistance to crack and tear propagation due to the deformable nature of the LM additives, which can redirect stress away from the crack.175
LM soft electronics with reversible insulating and conductor behavior were also synthesized.121,176 As an example, a LM soft electronic circuit containing EGaIn droplets showed insulating behavior above the melting point of the alloy and conducting behavior during the freezing cycle due to the expansion of the Ga droplets creating a conductive percolation path across the insulating polymeric matrix.121 The recyclability of LM-based soft electronics is also emerging via the dissolution of the polymer matrix and separation of the LM phase under mechanical agitation.30,176 However, the formation of conductors from LM nanodroplets usually requires a high loading of nanodroplets to achieve percolation. To reduce the loading of LMs, the alignment and sintering of EGaIn LM nanodroplets into liquid microwires was demonstrated by dielectrophoresis in a stretchable silicone matrix before curing (Fig. 5g).33 These particle-based inks can also be used as self-healing inks that can be assembled in situ to repair broken electrical pathways.
4.2 Sensors
Nanosized LMs present great opportunities as sensing materials due to their variable electrical resistance under mechanical deformation, tunable semiconducting oxide layer, ease of synthesis and unique interaction phenomena with heavy metal ions. Nanostructured LMs and nanocomposites were utilized as pressure and motion sensors, for the sensing of electromagnetic fields, gases and vapors, heavy metal ions, and also utilized as plasmonic-based sensors (Table 3). In addition, nanostructured LMs present great opportunities for biomedical imaging and biosensing.
Table 3 Sensing applications of LMs and LM composites
Sensor type |
LM |
Media |
Ref. |
Pressure and motion |
EGaIn |
Elastomer, hydrogel, polymeric foam |
6, 20, 46, 119, 128, 165, 178 and 182
|
EGaIn/graphene |
|
Galinstan |
|
EGaIn/Ni |
|
Ga/rGO |
|
Electromagnetic |
EGaIn and Fe |
Elastomer |
16
|
Gases and vapors |
Oxidized Galinstan |
Selected gases (H2, NO2, H2S, NH3, CH4, acidic vapors) |
18, 22, 100, 138 and 192
|
Oxidized GaIn, GaSn and GaZn |
EGaIn/WO3 |
EGaIn/PANI |
EGaIn-Based/polydopamine |
Heavy metal ions |
Galinstan(bulk)/WO3(nano) |
Electrolyte (Pb2+, Cd2+) |
26, 46, 139 and 197
|
Galinstan(nano)/WO3(nano) |
EGaIn/tannic acid |
EGaIn/rGO |
Plasmonic-based |
Ga |
Substrate supported, suspension |
7, 91, 198 and 201–203
|
EGaIn |
GaN/GaOOH |
BiGa and AgGa nanopatterns |
Pressure and motion sensors.
Soft and deformable LM micro and nanocomposites present variable electrical conductivities under various mechanical deformation processes, such as stretching, pressing and twisting. In contrast to most composites integrating solid conductive fillers, LM-based composites exhibit positive piezoconductivity, which corresponds to an increase of conductivity upon strain.16,124,177 These changes in electrical properties under mechanical loads are particularly useful for the formation of pressure and motion sensing LM/polymer composites.20,119,149 Porous foam-like LM nanocomposites can also be prepared, which showed increased electrical conductivity when pressed.178 Additionally, a LM-based elastomer foam integrating micron-sized LM droplets and presenting positive piezopermittivity was utilized as pressure and touch sensor based on the change of capacitance across the material under various deformations.179 In addition, glues incorporating Galinstan nanodroplets were reported for pressure sensitive connections.180 Other LM-based materials, such as LM hydrogel nanocomposites and microscale LM printing on stretchable substrates, were incorporated in strain sensors.128,165 Furthermore, LM-based nanocomposites with advanced designs can be employed as strain sensors with the ability to record motions when integrated with different objects and wearables such as gloves (Fig. 6a).6,179
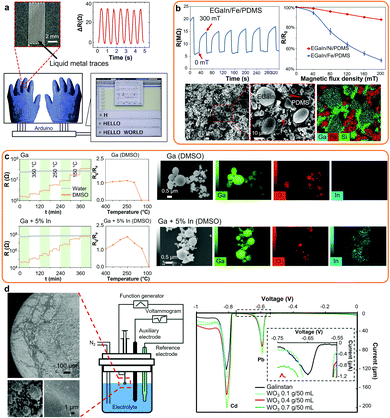 |
| Fig. 6 (a) Photo of a LM-based strain sensor with corresponding electrical signals from finger bending and straightening, and LM integrated sensors in wearable gloves functioning as keyboard. Adapted with permission.6 Copyright 2018, Elsevier. (b) Response of magnetic LM composites to magnetic field with cyclic resistance changes of the LM/Fe composite, resistance changes of the Fe and Ni LM composites and corresponding SEM and SEM/EDS images of LM/Fe magnetic composites. Adapted with permission.16 Copyright 2019, Springer Nature. (c) Response and response factors of the Ga and GaIn-based sensors made in DMSO or Milli-Q water post-annealing towards NO2, and SEM/EDS elemental mapping of the nanodroplets. Adapted with permission.22 Copyright 2020, ACS Publications. (d) SEM images of the Galinstan-based heavy metal ion sensor showing the WO3 surface nanocoatings, experimental setup and differential pulse voltammograms of Pb2+ and Cd2+ (10 mmol L−1 each) obtained on the Galinstan(bulk)/WO3(nano) electrode as a function of initial WO3 concentration during LM marble synthesis. Adapted with permission.26 Copyright 2012, Wiley-VCH. | |
Electromagnetic sensing.
LMs were shown to react to magnetic field stimulation and also present magnetocaloric properties.181 The magnetic properties of LMs can be significantly altered with the dispersion of magnetic micro and nanoparticles into or with LMs forming composite materials with high electrical conductivity and, at the same time, magnetic sensitivity.108,124,142,182–185 Magnetic LM-based elastomer micro and nanocomposites were also synthesized.16,47,186 As an example, EGaIn was dispersed along with micro Fe or Ni particles in a PDMS matrix forming magnetic stretchable conductors, which were demonstrated as magnetic field sensors.16 Responses of the magnetic LM-based material to a magnetic field and its structure are shown in Fig. 6b. In this example, changes in electrical resistance were attributed to the alignment of the magnetic particles in the direction of the magnetic field and to the mechanical deformation of the micro/nanocomposite reducing the spacing between the conductive particles.
LM-based antennas present reversible deformability upon mechanical deformations, self-healing capabilities, frequency tuneability via stretching and can also act as remote strain sensors.187,188 LM-based antennas are typically formed by injecting LMs into elastomers, but can also be synthesized from the mechanical merging of LM nanodroplets encased into elastomeric microchannels.150
Gases and vapors sensing.
Semiconducting metal oxides can be used to sense oxidizing and reducing gases via chemisorption mechanisms at elevated temperatures.189 However, at low temperatures these interactions can be associated to physisorption. For example, in presence of oxygen (O2) and above 800 °C, the resistivity of Ga2O3 thin films changes as the O2 concentration increases in the material.190,191 Galinstan micro and nanodroplets, presenting a native skin of semiconducting amorphous Ga2O3, allowed for the low temperature sensing of nitrogen dioxide (NO2), ammonia (NH3) and methane (CH4) gases below 150 °C via a proposed physisorption mechanism.192 Doping and mixtures of Ga2O3-based materials were also shown to enhance and tune the gas sensing properties via the formation of specific heterostructures at the contact between the Ga2O3 phase and the dopant materials.189,191,193,194 LM-based processes, such as low temperature alloying and transformation at the nanoscale, can also be used for controlling the doping into metal oxides of post-transition metals that can be used for sensing applications. In one example, the formation of binary GaIn, GaSn and GaZn micro and nanodroplets, and secondary annealing step, was investigated for sensing NO2 and hydrogen (H2).22 Metal oxides obtained from binary Ga-based nanodroplets were seen to greatly influence the gas sensing properties due to the formation of specific morphologies, particle size, grain and crystal structures. The response and response factors of post-annealed Ga and GaIn-based sensors towards NO2 and their SEM images and EDS elemental mappings are presented in Fig. 6c. In another example, EGaIn/WO3 nanocomposites were assembled into gas sensing devices which presented selective chemisorption sensing for H2 as compared to NO2 and hydrogen sulfide (H2S).138 In addition, physisorptive sensors can also be established from composites with post-transition metals. For examples, EGaIn/PANI and EGaIn-based/polydopamine nanocomposites were reported for the sensing of acid vapors and NO2via changes in the material conductivities, respectively, at room temperature.18,100 Gas sensing materials can also be synthesized at the surface of LMs.56,72 For example, Bi2O3-doped SnO nanosheets with controlled Bi2O3 doping showed selective conductivity responses to NO2 and H2.56
Heavy metal ions sensing.
LMs have historically played important roles in the sensing of ions, especially heavy metal ions, in solution, likely due to similarities in the atomic orbitals of post-transition metals and heavy metal ions.195,196 Such sensors are generally based on stripping voltammetry in which the target ions are preconcentrated into LMs, by applying a negative voltage, and then oxidized when the voltage is reversed and the current is measured. The most common LM used as the electrode for stripping voltammetry is Hg. However due to Hg toxicity, other solid and liquid post-transition metal electrodes are being investigated including Ga, EGaIn and Galinstan.26,195 Increasing the surface to volume ratio of the electrode can increase the sensitivity for such sensors and various methods have been used for implementing nanostructures within the context of LMs for such applications. As an example, Galinstan(bulk)/WO3(nano) LM marbles were utilized for sensing Pb2+ and Cd2+.26 The LM marbles presented enhanced sensitivity to Pb2+ and Cd2+ as compared to plain unmodified Galinstan due to increased surface area and interfacial amplification of the electrical field that were gained through incorporating WO3 nanoparticles onto the surface of the LM. The structure of the LM marble, the experimental setup and differential pulse voltammograms of Pb2+ and Cd2+ are shown in Fig. 6d. In another example, WO3 nanoparticles were coated on Galinstan nanodroplets for the sensing of Pb2+.197 Here, they both increased the surface to volume ratio and also stabilized the micro and nanodroplets of LMs. Tannic acid-functionalized EGaIn nanodroplets were also demonstrated for the electrochemical sensing of heavy metal ions.46
Plasmonic-based sensing materials.
LMs and LM nanodroplets show promise as plasmonic structures with tunable optical absorption in the UV, visible and near-IR (NIR) ranges.198–200 Liquid Ga nanodroplets were previously demonstrated as plasmonic materials which exhibit size-dependent resonances spanning from the UV to the NIR.201,202 In addition, EGaIn nanodroplet suspensions have been shown to demonstrate both strong UV and visible range plasmonic resonance.200,203 Plasmonic properties of LMs can also be used together with metal oxides. Galinstan/Ga2O3 LM/metal oxide (LM/MO) micro to nanostructures were also demonstrated to have plasmonic responses that can be tuned depending on the size of the LM droplets.197 In addition, solidification nanopatterns observed on the surface of dilute BiGa and AgGa LM alloys were demonstrated as plasmonic structures for surface-enhanced Raman spectroscopy.7
Biosensing.
LM nanodroplets present many opportunities for biosensing due to their surface chemistry, plasmonic and electrochemical properties.203–205 As discussed previously nanostructured Ga-based materials exhibit tunable resonance energy from the UV to the IR range, as a function of their shapes and sizes.200,204,205 As biosensing examples, Ga nanodroplets were reported for the sensing of DNA sequences and other molecules.204,206 In addition, LM nanodroplets can be tracked in vivo.101,107,207–211 Biosensing using fluorescent Ga-based crystallite nanostructures, such as GaN, has also been reported.91,212,213
4.3 Catalysis
LMs for catalysis present many advantages due to their liquid and dynamic interfaces which are resistant to deactivation (coking) and morphological changes as compared to solid catalysts.8,49,214 In addition, liquid Ga is an important soft substrate for catalytic transition and other rare and/or expensive elements. The application of bulk post-transition LMs for thermal catalysis and electrocatalysis, such as for gas conversion, will not be reported in this review as they were recently reviewed elsewhere.49 LMs, either in bulk or nano morphologies, have been used with nano oxide particles as co-contributors for photocatalysis.197,215 LM micro and nanodroplets were also in situ synthesized and demonstrated as sonochemical catalysts for the degradation of organic dyes.216 LMs can also be used with other metals to enhance catalysis. Liquid Ga and Galinstan with Ce nanoparticles were demonstrated as catalysts resistant to coking for carbon dioxide (CO2) electro-reduction due to the low van der Waals force at the liquid interface between the LM and the solid carbon products (Fig. 7a).8 In another example, a mechanically-induced catalytic process using a suspension of Ga nanodroplets and Ag/Ga intermetallic nanorods were utilized for the reduction of CO2 into solid carbonaceous products and O2 at room temperature.217 GaPt nanoparticles created by galvanic replacement have also been used for the oxidation of methanol and ethanol.218 In another report, a GaPt catalytic system was prepared by galvanic replacement of Pt salts on Ga on an alumina matrix for propane dehydrogenation at 350 to 450 °C.219 Pd has also been used with a Ga support for dehydrogenation of organic compounds at elevated temperatures.214
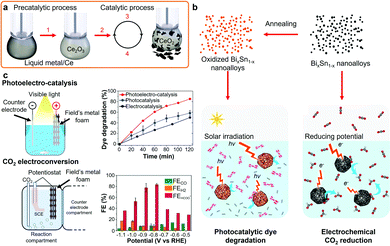 |
| Fig. 7 (a) Room temperature catalytic process of CO2 reduction to solid carbon on LM/Ce electrodes. Adapted with permission.8 Copyright 2019, Springer Nature. (b) Schematics representing the solidified BiSn nanoalloys utilized for photocatalytic dye degradation or CO2 electrochemical reduction. Adapted with permission.19 Copyright 2019, Springer Nature. (c) Photoelectrocatalysis and CO2 electrochemical conversion using a metallic foam formed from the assembly of Field's metal nanodroplets and corresponding dye degradation and CO2 conversion rates, respectively. Adapted with permission.23 Copyright 2019, Wiley-VCH. | |
Nanoparticles obtained using various LM solidification processes also present attractive catalytic properties due to the controllable polycrystallinity, grain sizes, nanodomains and surface oxide decoration.19,23,28,115 For example, eutectic BiSn nanoalloys showed higher photocatalytic and electrocatalytic performance as compared to non-eutectic BiSn nanoalloys, for the degradation of organic dyes and CO2 reduction reaction, respectively.23 The schematic representation of the solidified BiSn nanoalloys and their catalytic applications are presented Fig. 7b. The specific formation of catalytic surface oxides, such as mixed In2O3, SnO and SnO2 nanocrystals, was also demonstrated during the foaming and solidification of Field's metal nanodroplets for the photoelectrocatalysis of organic dyes and CO2 electrochemical reduction as presented in Fig. 7c.19
Oxidation of LM micro and nanodroplets can also lead to the formation of catalytically active nanomaterials.90,197 As an example, hexagonal α-Ga2O3 nanoflakes with photocatalytic activity have been prepared by the sonication of liquid Ga for up to 60 minutes in DI water followed by annealing.90 In addition, LM nanocomposites were shown to present high photocatalytic activity.70,136,137,215 For example, EGaIn/MnO2 nanocomposites presented high photocatalytic activity for the degradation of organic dyes.70
4.4 Energy applications
Energy storage devices.
Post-transition metals and alloys are increasingly considered as electrode materials in LM batteries, electrode nanocomposites in lithium-ion and sodium-ion batteries and as conductive media. Sn and Ga present high theoretical specific capacity of 990 mA h g−1 and 769 mA h g−1, for the discharge products of Li2Ga and LixSn (0 ≤ x ≤ 4.4), respectively.220,221 In particular, Ga shows exceptional lithiation properties as one Ga atom can host two lithium atoms, and potentially presents self-healing properties during lithiation/delithiation cycles.4,220,222 During lithiation, liquid to solid phase transition occurs with the formation of LiGa alloys and particularly of Li2Ga, which is a solid product with a melting point of ∼288 °C. The lithiation process of a Ga nanodroplet (∼300 nm) is shown in Fig. 8a.4 Similarly, Ga can form NaGa alloys during sodiation cycles. Ga shows a theoretical capacity of 217 mA h g−1 with the formation of Na22Ga39, while it should be considered that GaNa phases require very high temperature for melting.223 Altogether, lithiation and sodiation are associated with the loss of the liquid/liquid interface and important volume expansion, of up to ∼160% and ∼260% respectively, which remains problematic for the mechanical stability of the electrode material.4,224
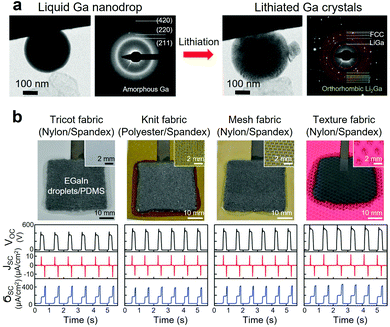 |
| Fig. 8 (a) Phase transformation of an amorphous liquid Ga nanodrop before and after lithiation (TEM images). Adapted with permission.4 Copyright 2013, ACS Publications. (b) Wearable triboelectric nanogenerator based on EGaIn/PDMS elastomer composite integrated with stretchable fabrics and corresponding electrical outputs. Adapted with permission.13 Copyright 2020, Wiley-VCH. | |
LM batteries typically refer to batteries operating at high (above 400 °C) or intermediate (240 °C) temperatures which consist of two high melting point LM electrodes separated by a molten salt electrolyte.223,225 LM batteries show superior electrode charge-transfer kinetics due to their liquid/liquid interfaces, are immune to dendrite formation due to the solubility of the deposited species, possess long lifetimes and low cost depending on the metals and alloys chosen, but require high temperature operation and can only be used for static storage in large scale applications.225–227 The advances and current understanding of LM batteries were recently reviewed elsewhere.223 Ga-Based room temperature LM batteries were also reported, which present many advantages in terms of thermal management and reduction of parasitic reactions that occur at high temperatures.223 Room temperature LM batteries can also be applied to portable and soft electronics due to the stretchability of the LMs. Nanostructures in the LM type electrolytes can potentially play an important role for enhancing their properties, a topic that can be widely explored in the future.
Ga-Based liquid alloys have also been used as electrode materials for the development of soft batteries which allowed for some degree of flexibility and stretchability.228–230 Soft and deformable LM-based supercapacitors were synthetized based on EGaIn or Galinstan films.231,232 In one example, CNTs were coated on the surface of microtextured EGaIn films on a PDMS substrate to achieve a soft and stretchable supercapacitor which was able to retain its capacitance under 30% strain.232
Nanosized Ga-based LM fillers were also investigated for lithium-ion and sodium-ion batteries.220,233–238 As an example, GaSn nanodroplets stabilized with rGO and CNTs were synthesized as a nanocomposite slurry and coated on Cu foils to form anode materials, which demonstrated self-healing capability and retained capacity after 4000 cycles with a capacity of ∼400 mA h g−1 at 4000 mA g−1.220 In another example, core/shell nanocomposite of LM nanodroplets contained in hollow carbon fibers was investigated to alleviate the volume expansion during lithiation and delithiation cycles.239
Energy harvesting.
Soft LM polymer micro and nanocomposites were investigated as stretchable thermoelectric generators and triboelectric nanogenerators energy harvesting devices.13,154,240–242 EGaIn-Based elastomers with integrated thermoelectric elements were demonstrated as a stretchable and flexible thermoelectric devices.240,242 LM/PDMS triboelectric nanogenerator composites (Fig. 8b) were also proposed for harvesting energy from body motions presenting high stretchability (strain limit above 500%).13 In addition, the ability to mechanically change the surface area of LMs in electrolytes (e.g. hydrogels) was demonstrated and which resulted in variable area capacitors for mechanical-to-electrical energy harvesting.243 This concept could be further extended to nanoscale LM components.
Thermal management.
Bulk LMs are excellent thermal management materials due to their high thermal conductivity and liquid interface providing an intimate contact between substrates.244 LM nanocomposites and nanodroplets were also investigated as thermal pathways for heat dissipation.2,29,108,110,245,246 For example, a EGaIn LM soft micro/nanocomposite with high maximum strain (∼600%) exhibited exceptional thermal conductivity.2 The thermal conductivity was shown to increase to a metal-like conductivity under strain due to the deformation of the LM droplets forming thermally conductive pathways in the stretching direction.
4.5 Nanomedicine and biomedical applications
Selected post-transition metals and alloys, all based on Ga-based alloys, are liquid within the range of human body temperature, which present an unprecedented opportunity of using metallic fluids for biomedical applications and nanomedicine. Unlike Hg, Ga-based alloys are considered to have a low level of toxicity. As an example of biocompatibility, both Ga and EGaIn were investigated as microelectrodes for neural tissue stimulation.247 Subsequently, the biocompatibility of the LM microelectrodes was demonstrated on long-term hippocampal neurons cultures.
Ga-Based nanodroplets are increasingly considered as functional biomaterials. The interest in developing functionalized Ga-based nanodroplets lies in the synergies between their LM cores, fluidity and ease of functionalization and synthesis at the nanoscale.3,208,209,211 Functionalized EGaIn nanodroplets also presented good biodegradability and low toxicity in mice.3 Functionalized LM nanodroplets can respond to a wide range of physical stimuli including acoustic and electromagnetic waves, light and thermal stimulations and also chemical stimuli for drug delivery, tumor cell treatment, biosensing and bioimaging as summarized in Fig. 9a.3,101,181,203,204,207–211,248–250
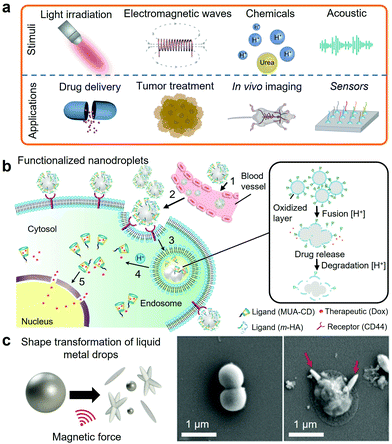 |
| Fig. 9 (a) Illustration of the reported stimuli and applications of LM nanodroplets in nanomedicine. (b) Illustration of the acid-triggered drug delivery mechanism using functionalized EGaIn nanodroplets. Adapted with permission.3 Copyright 2015, Springer Nature. (c) Representation of the magnetically induced shape transformation of magnetic LM nanoparticles and SEM images of the bacteria before and after magnetic activation. Adapted with permission.17 Copyright 2020, ACS Publications. | |
It should be considered that during the synthesis of Ga-based nanodroplets via mechanical agitation, such as EGaIn, the release of Ga and In ions was reported, which presented significant toxicity to a series of human cell cultures.251 Washing or functionalization steps post synthesis can alleviate this effect. Compared to Hg or Cd ions, Ga and In ions show much lower toxicity.251,252 In addition, some Ga salts, such as gallium nitrate (Ga(NO3)3), are authorized drugs and used as an iron(III) analogue in cancer therapy and also proposed as therapeutics for the treatment of antibiotic-resistant bacteria, as Ga(III) ions were shown to disrupt the iron-dependent metabolic pathways of bacteria.253–257 Ga compounds are also routinely used as contrast agents in nuclear medicine and oncology.248,258 However, we note reports of toxic exposure to Ga complexes, such as halide complexes, and airborne In compounds, related to electronic component manufacturing, that can induce significant toxicity concerns and threat to human health.259,260
Drug delivery and tumor therapy.
The therapeutics application of Ga-based nanodroplets were recently reviewed.248 The more recent developments of functional nanodroplets for biomedical applications are focused on multi-synergic processes, that take advantage of multifunctional coatings and the metallic properties of the nanodroplets.107,211 LM nanodroplets have been demonstrated as drug carriers that allow the release of therapeutic agents via chemical stimuli, such as in intracellular acidic environments, or via physical stimuli, including thermal deformation under NIR irradiation, acoustic or electromagnetic stimulation, or using a combination of chemical and physical stimuli.3,107,261 As one of the pioneering examples, functionalized EGaIn nanodroplets, with thiolated polymeric shells, were utilized as drug delivery systems, which released the therapeutic molecules after cellular internalization and fusion in the mild acidic conditions (Fig. 9b).3 Advantageously, the EGaIn materials also presented enhanced contrast capability for X-ray imaging at the same time. There are many examples of LM nanodroplets functionalized with enzyme, proteins, nanoparticles and polymer coatings that were investigated for tumor therapy.107,207–209,211,262–265 In many of these examples, the local temperature in the vicinity of the functionalized EGaIn nanodroplets could be remotely increased via NIR irradiation providing photothermal therapy both in laboratory and animal models.
Antimicrobial agent.
Ga-Based nanodroplets were shown to release Ga3+ ions upon oxidation in acidic and basic environments, which can provide antibacterial properties in biological systems.251,256 The use of micro and nanodroplets can enhance the diffusion mixing rate of Ga3+ released from Ga-based materials. To date, LM nanoalloys and stimuli-responsive nanocomposites have been investigated as antimicrobial and biofilms remediation materials.17,266 Ga nanodroplets (∼300 nm) were utilized as adhesive nucleation sites on fabric materials for the formation of GaCu nanoalloys via galvanic replacement which presented antibacterial, antifungal and antiviral properties.266 In another example, the shape transformation of magnetic Galinstan micro and nanodroplets were induced via magnetic activation and presented nanosharp edges that physically ruptured bacteria cells and the biofilm matrix (Fig. 9c).17
4.6 Other applications
The other applications that utilize the surface tension, solvation, electrical and thermal conductivities, surface functionalization, reflectivity, fluidity, or reactivity of LMs are presented in this section and summarized in Table 4.
Table 4 Other applications of nanostructured LMs
Application |
LM |
Media |
Ref. |
LM-based actuators |
EGaIn and Galinstan droplet |
Electrolyte, H2O2 solution, polymer matrix |
2, 69, 143, 268, 270, 271 and 274
|
LM marbles |
LM composites |
Magnetic fluids and LM-based actuators |
EGaIn/Ni |
Air, polymer matrix |
47, 108, 182–186 and 283
|
EGaIn/NdFeB Ga/Ni |
Galinstan/Fe |
Galinstan/Gd |
LM marble |
EMI shielding |
EGaIn |
Polymer matrix |
29 and 284–287
|
EGaIn/Ni |
LM composite |
Ga/rGO |
Micromirrors |
Galinstan |
Electrolyte |
288 and 289
|
EGaIn |
Separation |
Field's metal |
Electrolyte, polymer matrix |
18, 19 and 290
|
In and Ga oxides |
EGaIn/PANI |
Thermal management |
Functionalized Ga |
Silicone oil, air, polymer matrix |
2, 29, 108, 110 and 244–246
|
EGaIn |
Ga/Cu composite |
Ga/diamond composite |
Galinstan/Gd |
Nanothermometers |
Ga/CNTs |
Vacuum |
291 and 292
|
Nanomaterial synthesis using LMs |
Ga alloys |
Electrolytes |
22 and 293–296
|
LM-based actuators.
The interfacial tension of LMs can be chemically and electrochemically manipulated for actuation in electrolyte solutions at low voltages, as shown in examples with mm- and sub-mm sized LM drops.267–273 At the nanoscale, nanocoating of mm-sized LM drops was shown to drastically affect the surface tension induced forces. As examples, actuation of nanocoated LM marbles was reported via electro- and photochemical methods, where the nanocoating altered the surface tension and capacitance of the LM marbles or acted as a photocatalyst triggering a chemical reaction, respectively.69,143 Soft actuators based on thermally and electrically conductive LM nanocomposites were also developed for soft robotics taking advantage of the deformable and soft nature of the LM nanodroplets, or extrusion ability, incorporated into responsive elastomers.2,274–277 Particularly, a nanocomposite based on EGaIn nanodroplets and a liquid crystal polymer was demonstrated to provide shape-morphing capabilities via electro- or photo-thermal actuation.278 Adaptative materials, such as liquid crystalline systems, present great opportunities for the development of soft actuators and other functional LM-based nanocomposites.279–281
Magnetic LM fluids.
Magnetic micro and nanoparticles, such as gadolinium (Gd), Ni, Fe, Fe2O3 and neodymium–iron–boron (NdFeB), were incorporated into LMs which provided magnetic properties to the LM phase.108,124,183,184 In one example, a Gd supersaturated Ga-based LM presented nanoprecipitates of Gd, which enabled the magnetic properties for the base LM alloy and also presented high magnetocaloric effect at room temperature.
Magnetic LM-based actuators.
Magnetic LM fluids, polymeric, micro and nanocomposites can be magnetically actuated.142,182–185,282,283 Magnetization and demagnetization cycles were shown to align the dispersed magnetic particles and enable actuation of the nanocomposites with potential applications as magnetic switches and for soft robotic actuation.47,185 For example, LM soft nanocomposites based on mixed nanosized EGaIn/Fe3O4 nanoparticles showed combined remote magnetic actuation capabilities and high electrical conductivity.47
EMI shielding.
LM composites and nanocomposites were investigated as stretchable electromagnetic interference (EMI) shielding materials which could provide both high electrical and thermal conductivities.284–287 The LM phase can act as a continuous conductive phase absorbing and efficiently dissipating the incoming electromagnetic waves, as the mixed matrix surface enhanced the electromagnetic waves reflection. As an example, a LM-based EGaIn/Ni micro/nanocomposite was coated on various stretchable substrates for added EMI shielding properties.287 In another example, a EGaIn elastomer composite was synthesized by mechanically mixing bulk EGaIn into a PDMS base to provide EMI shielding at low temperatures.284
Micromirrors.
Reflective LM surfaces present useful properties for optical applications, particularly with the dynamic control of their surfaces that allow switching between concave and convex shapes at the milli- and micrometer scales.289 Micromirrors and micromirrors array with tunable reflectivity were demonstrated with a dimension of 100 μm.288 The formation of nanomirrors from LM traces and nanodroplets remains to be demonstrated.
Separation.
LMs and post-transition metals can be used for the synthesis of size exclusion or ionic separation materials thanks to their ease of synthesis into porous and mixed polymeric structures, and to their interactions with alkali and heavy metal ions. As an example of a size separation material, solidified Field's metal nanodroplets were sintered by a mild exothermic chemical reaction into microporous foam structures.19 In another example, lithium ion selective nanocomposites were also formed via the in situ dealloying of EGaIn nanodroplets in a polymeric matrix.290 The dealloying products, Ga oxides and In metal nanoparticles, provided selective binding sites for Li+ and mechanical cohesion to the polymer nanocomposites, respectively.
Nanothermometers.
Ga can be confined at the nanoscale within carbon nanotubes (diameter between 40 to 200 nm), which were utilized as nanothermometers operating between −80 °C and 500 °C.291,292 Such concepts can be extended for the formation of many other thermally sensitive functional nanodevices.
Nanomaterials synthesis using LMs.
Collection of the oxide layer of LMs was shown to yield a range of functional low-dimensional materials as previously presented in Section 2.2. LM-based synthesis of inorganic nanomaterials can also be achieved via the controlled thermal, electrochemical or acoustic expulsion of alloyed and dissolved elements in LMs.22,293,294,296,297 For example, fast electrochemical perturbations in the surface tension of Ga-based LM alloys can trigger the expulsion of alloyed elements, such as Sn, In, Bi and Zn from the LM base into nanostructured metallic or metal oxide materials.293,295 A few major examples regarding different methods for preparing nanomaterials from LM alloys are presented in Table 5.
Table 5 Nanomaterials synthesis using LMs
Method |
LM |
Advantages and disadvantages |
Collected materials and references |
Touch-print |
Ga-Based and molten post-transition metals and alloys |
Limited to favorably formed oxides, heterostructure formation, thermal post-treatment transformation, substrate-dependent, possible LM residues |
Ga2O350,68 |
HfO2, Al2O3, Gd2O350 |
SnO43 |
Bi2O344 |
SnO/In2O3 heterostructures298 |
Bi2O3 doped SnO56 |
Sb2O357 |
ZnO299,300 |
Stamping, squeezing, patterning and spreading |
Ga-Based and molten post-transition metals and alloys |
|
Ga2O362,63,65–67,301,302 |
|
In2O365 |
|
PbO303 |
|
ITO55 |
|
SnO65 |
Agitation |
Ga-Based alloys |
High yield |
Ga2O364 |
Gas injection |
Ga-Based and molten post-transition metals and alloys |
Access to favorably and non-favorably formed oxides |
HfO2, Ga2O350 |
TiO261 |
CoOx60 |
SnO and SnOx58,59 |
Surface templating and reactive methods |
Ga-Based alloys |
Near room temperature reactive process, formation of monolayers and crystals, limited to specific ionic precursors and solvent environments, thermal post-treatment transformation |
MnO270 |
Mn3O4297 |
MoS271,297 |
Bi2Te372 |
CuO, Cu2O and Cu137 |
Carbon materials296,297 |
Layered double oxides73 |
Sn, ZnO, In/In2O3, Bi/Bi2O3 nanostructures293,295 |
5. Conclusion and future perspectives
In this review, we reported the advances of room temperature and low melting point LMs and alloys in nanotechnology. We showed that the core and surface of LMs can be engineered at the nanoscale to offer fascinating solid/liquid core/shell structures, nanoparticle inclusions, surface decorations and nanopatterns, and deviate from the formation of thermodynamically favored metal oxides during mechanical agitation.
The synthesis of LM nanodroplets is of particular interest due to the low melting points of the post-transition metals and alloys that allow processing under mild mechanical conditions. However, the realization of nanodroplets with a narrow size distribution and which are liquid at the sub-10 nm scales still represents a significant challenge. To date still relatively few binary and ternary LM systems have been investigated at the nanoscale. Many possibilities of multi-elemental LM nanoalloys and high entropy liquid alloys are yet to be investigated with the potential for machine learning approaches leading to materials with exciting new properties.
LM based nanocomposites can be designed to present enhanced mechanical properties, electrical and thermal conductivities, as well as hybrid capabilities. The LMs can act as reactive phases to solvate nanoadditives and participate in their chemical reactions. Such capabilities also highlight the widely expanded usages of LMs as liquid media for physicochemical transformations of solutes at the nanoscale.
LMs are used in soft electronic components due to their intrinsic stretchability characteristics. Nanoscale patterning of LM traces and wires are currently limited to advanced lithography techniques with the best reported resolution of ∼180 nm. However, LM nanodroplets in composites can potentially offer better resolution traces. Advantageously, LM nanodroplets can be particularly well integrated with elastomers for soft electronic applications. Nevertheless, for the development of such advanced soft electronics, the controlled dispersion and specific interfacial compatibility of LM nanodroplets within polymers remain to be fully investigated.
LMs and solidified LMs present many opportunities for catalytic applications at the nanoscale. Nano-dimensional LMs have been shown to exhibit a good degree of catalytic activity and can be used as soft supports to other catalytic and reactive elements, while presenting nonpolar liquid interfaces resistant to deactivation and coking. However, understanding the surface elemental distribution still needs to be addressed for the synthesis of catalytic LM alloys. Solidified nano-dimensional LMs, made from LM synthesis processes, also present many advantages for creating highly catalytically active nanostructures with engineered oxide representation. However, solidification mechanisms leading to catalytically favorable morphologies and crystal phases remain to be uncovered.
Nanostructured LMs also show potential for the development of the next generation of flexible energy storage devices both as components of electrodes and electrolytes. Some challenges remain, such as control of the volume expansion during charge/discharge cycles, increasing the charge capacity of the systems and understanding the interfacial electrochemical reactions. LM nanodroplets also enable wearable energy harvesting devices, such as using triboelectric nanogenerators, that are based on the fluidity and softness of the LMs. The next generation of LM nanocomposites will witness their integration into more multifunctional devices integrating energy generation, electronic, sensing and actuation capabilities.
Finally, selected Ga-based LM nanodroplets present great opportunities in biotechnology and nanomedicine due to their low toxicity and liquid states below or at the temperature of the human body. Such Ga based LM nano entities offer the opportunities of becoming platforms for the design of multifunctional nanodevices with synergetic functionalities for drug delivery, cancer therapy and imaging. To date, the inclusion of many other inorganic and metallic elements in the Ga-based LM based bio-systems has not been investigated, which would offer new synergetic effects for enhanced imaging, sensing and therapeutic capabilities.
Author contributions
Francois-Marie Allioux: writing – original draft, and review and editing. Mohammad B. Ghasemian: writing – original draft. Wanjie Xie: writing – original draft. Anthony P. O'Mullane: review and editing. Torben Daeneke: review and editing. Michael D. Dickey: review and editing. Kourosh Kalantar-Zadeh: supervision, writing – original draft, and review & editing.
Conflicts of interest
There are no conflicts to declare.
Acknowledgements
The authors would like to acknowledge the Australian Research Council (ARC) Laureate Fellowship grant (FL180100053) for financial support for this work.
References
- M. Losurdo, A. Suvorova, S. Rubanov, K. Hingerl and A. S. Brown, Nat. Mater., 2016, 15, 995–1002 CrossRef CAS PubMed
.
- M. D. Bartlett, N. Kazem, M. J. Powell-Palm, X. Huang, W. Sun, J. A. Malen and C. Majidi, Proc. Natl. Acad. Sci. U. S. A., 2017, 114, 2143–2148 CrossRef CAS PubMed
.
- Y. Lu, Q. Hu, Y. Lin, D. B. Pacardo, C. Wang, W. Sun, F. S. Ligler, M. D. Dickey and Z. Gu, Nat. Commun., 2015, 6, 10066 CrossRef CAS PubMed
.
- W. Liang, L. Hong, H. Yang, F. Fan, Y. Liu, H. Li, J. Li, J. Y. Huang, L.-Q. Chen, T. Zhu and S. Zhang, Nano Lett., 2013, 13, 5212–5217 CrossRef CAS PubMed
.
- J. Ma, Y. Lin, Y.-W. Kim, Y. Ko, J. Kim, K. H. Oh, J.-Y. Sun, C. B. Gorman, M. A. Voinov, A. I. Smirnov, J. Genzer and M. D. Dickey, ACS Macro Lett., 2019, 8, 1522–1527 CrossRef CAS
.
- L. Tang, S. Cheng, L. Zhang, H. Mi, L. Mou, S. Yang, Z. Huang, X. Shi and X. Jiang, iScience, 2018, 4, 302–311 CrossRef CAS PubMed
.
- J. Tang, S. Lambie, N. Meftahi, A. J. Christofferson, J. Yang, M. B. Ghasemian, J. Han, F.-M. Allioux, M. A. Rahim, M. Mayyas, T. Daeneke, C. F. McConville, K. G. Steenbergen, R. B. Kaner, S. P. Russo, N. Gaston and K. Kalantar-Zadeh, Nat. Nanotechnol., 2021, 16, 431–439 CrossRef CAS PubMed
.
- D. Esrafilzadeh, A. Zavabeti, R. Jalili, P. Atkin, J. Choi, B. J. Carey, R. Brkljača, A. P. O’Mullane, M. D. Dickey, D. L. Officer, D. R. MacFarlane, T. Daeneke and K. Kalantar-Zadeh, Nat. Commun., 2019, 10, 865 CrossRef PubMed
.
- E. J. Markvicka, R. Tutika, M. D. Bartlett and C. Majidi, Adv. Funct. Mater., 2019, 29, 1900160 CrossRef
.
- M. J. Regan, E. H. Kawamoto, S. Lee, P. S. Pershan, N. Maskil, M. Deutsch, O. M. Magnussen, B. M. Ocko and L. E. Berman, Phys. Rev. Lett., 1995, 75, 2498–2501 CrossRef CAS PubMed
.
- P. S. Pershan, J. Appl. Phys., 2014, 116, 222201 CrossRef
.
- S.-F. Tsay and S. Wang, Phys. Rev. B: Condens. Matter Mater. Phys., 1994, 50, 108–112 CrossRef CAS PubMed
.
- C. Pan, D. Liu, M. J. Ford and C. Majidi, Adv. Mater. Technol., 2020, 5, 2000754 CrossRef CAS
.
- S.-Y. Tang, D. R. G. Mitchell, Q. Zhao, D. Yuan, G. Yun, Y. Zhang, R. Qiao, Y. Lin, M. D. Dickey and W. Li, Matter, 2019, 1, 192–204 CrossRef
.
- A. Fang, C. Adamo, S. Jia, R. J. Cava, S.-C. Wu, C. Felser and A. Kapitulnik, Sci. Adv., 2018, 4, eaaq0330 CrossRef PubMed
.
- G. Yun, S.-Y. Tang, S. Sun, D. Yuan, Q. Zhao, L. Deng, S. Yan, H. Du, M. D. Dickey and W. Li, Nat. Commun., 2019, 10, 1300 CrossRef PubMed
.
- A. Elbourne, S. Cheeseman, P. Atkin, N. P. Truong, N. Syed, A. Zavabeti, M. Mohiuddin, D. Esrafilzadeh, D. Cozzolino, C. F. McConville, M. D. Dickey, R. J. Crawford, K. Kalantar-Zadeh, J. Chapman, T. Daeneke and V. K. Truong, ACS Nano, 2020, 14, 802–817 CrossRef CAS PubMed
.
- C. Zhang, F.-M. Allioux, M. A. Rahim, J. Han, J. Tang, M. B. Ghasemian, S.-Y. Tang, M. Mayyas, T. Daeneke, P. Le-Clech, R. B. Kaner, D. Esrafilzadeh and K. Kalantar-Zadeh, Chem. Mater., 2020, 32, 4808–4819 CrossRef CAS
.
- F.-M. Allioux, S. Merhebi, J. Tang, S. A. Idrus-Saidi, R. Abbasi, M. G. Saborio, M. B. Ghasemian, J. Han, R. Namivandi-Zangeneh, A. P. O'Mullane, P. Koshy, R. Daiyan, R. Amal, C. Boyer and K. Kalantar-Zadeh, Adv. Funct. Mater., 2020, 30, 1907879 CrossRef CAS
.
- E. J. Markvicka, M. D. Bartlett, X. Huang and C. Majidi, Nat. Mater., 2018, 17, 618–624 CrossRef CAS PubMed
.
- K. Kalantar-Zadeh, J. Tang, T. Daeneke, A. P. O’Mullane, L. A. Stewart, J. Liu, C. Majidi, R. S. Ruoff, P. S. Weiss and M. D. Dickey, ACS Nano, 2019, 13, 7388–7395 CrossRef CAS PubMed
.
- S. A. Idrus-Saidi, J. Tang, J. Yang, J. Han, T. Daeneke, A. P. O’Mullane and K. Kalantar-Zadeh, ACS Sens., 2020, 5, 1177–1189 CrossRef CAS PubMed
.
- J. Tang, R. Daiyan, M. B. Ghasemian, S. A. Idrus-Saidi, A. Zavabeti, T. Daeneke, J. Yang, P. Koshy, S. Cheong, R. D. Tilley, R. B. Kaner, R. Amal and K. Kalantar-Zadeh, Nat. Commun., 2019, 10, 4645 CrossRef PubMed
.
- J. Yan, M. H. Malakooti, Z. Lu, Z. Wang, N. Kazem, C. Pan, M. R. Bockstaller, C. Majidi and K. Matyjaszewski, Nat. Nanotechnol., 2019, 14, 684–690 CrossRef CAS PubMed
.
- S. Liu, M. C. Yuen, E. L. White, J. W. Boley, B. Deng, G. J. Cheng and R. Kramer-Bottiglio, ACS Appl. Mater. Interfaces, 2018, 10, 28232–28241 CrossRef CAS PubMed
.
- V. Sivan, S.-Y. Tang, A. P. O'Mullane, P. Petersen, N. Eshtiaghi, K. Kalantar-zadeh and A. Mitchell, Adv. Funct. Mater., 2013, 23, 144–152 CrossRef CAS
.
- C. J. Thrasher, Z. J. Farrell, N. J. Morris, C. L. Willey and C. E. Tabor, Adv. Mater., 2019, 31, 1903864 CrossRef CAS PubMed
.
- F.-M. Allioux, S. Merhebi, M. B. Ghasemian, J. Tang, A. Merenda, R. Abbasi, M. Mayyas, T. Daeneke, A. P. O’Mullane, R. Daiyan, R. Amal and K. Kalantar-Zadeh, Nano Lett., 2020, 20, 4403–4409 CrossRef CAS PubMed
.
- C. Wang, Y. Gong, B. V. Cunning, S. Lee, Q. Le, S. R. Joshi, O. Buyukcakir, H. Zhang, W. K. Seong, M. Huang, M. Wang, J. Lee, G.-H. Kim and R. S. Ruoff, Sci. Adv., 2021, 7, eabe3767 CrossRef CAS PubMed
.
- R. Tutika, A. B. M. T. Haque and M. D. Bartlett, Commun. Mater., 2021, 2, 64 CrossRef
.
- V. Kamysbayev, N. M. James, A. S. Filatov, V. Srivastava, B. Anasori, H. M. Jaeger, Y. Gogotsi and D. V. Talapin, ACS Nano, 2019, 13, 12415–12424 CrossRef CAS PubMed
.
- T. Daeneke, K. Khoshmanesh, N. Mahmood, I. A. de Castro, D. Esrafilzadeh, S. J. Barrow, M. D. Dickey and K. Kalantar-Zadeh, Chem. Soc. Rev., 2018, 47, 4073–4111 RSC
.
- F. Krisnadi, L. L. Nguyen, Ankit, J. Ma, M. R. Kulkarni, N. Mathews and M. D. Dickey, Adv. Mater., 2020, 32, 2001642 CrossRef CAS PubMed
.
- T. R. Lear, S.-H. Hyun, J. W. Boley, E. L. White, D. H. Thompson and R. K. Kramer, Extreme Mech. Lett., 2017, 13, 126–134 CrossRef
.
- M. J. Regan, P. S. Pershan, O. M. Magnussen, B. M. Ocko, M. Deutsch and L. E. Berman, Phys. Rev. B: Condens. Matter Mater. Phys., 1996, 54, 9730–9733 CrossRef CAS PubMed
.
- K. S. Vahvaselkä, Phys. Scr., 1980, 22, 647–652 CrossRef
.
- C. J. Powell, Adv. Phys., 1967, 16, 203–213 CrossRef CAS
.
- O. G. Shpyrko, A. Y. Grigoriev, C. Steimer, P. S. Pershan, B. Lin, M. Meron, T. Graber, J. Gerbhardt, B. Ocko and M. Deutsch, Phys. Rev. B: Condens. Matter Mater. Phys., 2004, 70, 224206 CrossRef
.
- M. J. Regan, H. Tostmann, P. S. Pershan, O. M. Magnussen, E. DiMasi, B. M. Ocko and M. Deutsch, Phys. Rev. B: Condens. Matter Mater. Phys., 1997, 55, 10786–10790 CrossRef CAS
.
- M. D. Dickey, ACS Appl. Mater. Interfaces, 2014, 6, 18369–18379 CrossRef CAS PubMed
.
- J. F. García Martín, S. Sánchez and R. Metz, Oxid. Met., 2012, 77, 1–7 CrossRef
.
- E. Ricci, T. Lanata, D. Giuranno and E. Arato, J. Mater. Sci., 2008, 43, 2971–2977 CrossRef CAS
.
- T. Daeneke, P. Atkin, R. Orrell-Trigg, A. Zavabeti, T. Ahmed, S. Walia, M. Liu, Y. Tachibana, M. Javaid, A. D. Greentree, S. P. Russo, R. B. Kaner and K. Kalantar-Zadeh, ACS Nano, 2017, 11, 10974–10983 CrossRef CAS PubMed
.
- K. A. Messalea, B. J. Carey, A. Jannat, N. Syed, M. Mohiuddin, B. Y. Zhang, A. Zavabeti, T. Ahmed, N. Mahmood, E. Della Gaspera, K. Khoshmanesh, K. Kalantar-Zadeh and T. Daeneke, Nanoscale, 2018, 10, 15615–15623 RSC
.
- K. Tiwari, M. Manolata Devi, K. Biswas and K. Chattopadhyay, Prog. Mater. Sci., 2021, 121, 100794 CrossRef CAS
.
- M. A. Rahim, F. Centurion, J. Han, R. Abbasi, M. Mayyas, J. Sun, M. J. Christoe, D. Esrafilzadeh, F.-M. Allioux, M. B. Ghasemian, J. Yang, J. Tang, T. Daeneke, S. Mettu, J. Zhang, M. H. Uddin, R. Jalili and K. Kalantar-Zadeh, Adv. Funct. Mater., 2021, 31, 2007336 CrossRef CAS
.
- S. Merhebi, M. Mayyas, R. Abbasi, M. J. Christoe, J. Han, J. Tang, M. A. Rahim, J. Yang, T. T. Tan, D. Chu, J. Zhang, S. Li, C. H. Wang, K. Kalantar-Zadeh and F.-M. Allioux, ACS Appl. Mater. Interfaces, 2020, 12, 20119–20128 CrossRef CAS PubMed
.
- S.-Y. Tang, C. Tabor, K. Kalantar-Zadeh and M. D. Dickey, Annu. Rev. Mater. Res., 2021, 51, 381–408 CrossRef CAS
.
- K. Zuraiqi, A. Zavabeti, F.-M. Allioux, J. Tang, C. K. Nguyen, P. Tafazolymotie, M. Mayyas, A. V. Ramarao, M. Spencer, K. Shah, C. F. McConville, K. Kalantar-Zadeh, K. Chiang and T. Daeneke, Joule, 2020, 4, 2290–2321 CrossRef CAS
.
- A. Zavabeti, J. Z. Ou, B. J. Carey, N. Syed, R. Orrell-Trigg, E. L. H. Mayes, C. Xu, O. Kavehei, A. P. O’Mullane, R. B. Kaner, K. Kalantar-zadeh and T. Daeneke, Science, 2017, 358, 332–335 CrossRef CAS PubMed
.
- M. Wurdack, T. Yun, E. Estrecho, N. Syed, S. Bhattacharyya, M. Pieczarka, A. Zavabeti, S.-Y. Chen, B. Haas, J. Müller, M. N. Lockrey, Q. Bao, C. Schneider, Y. Lu, M. S. Fuhrer, A. G. Truscott, T. Daeneke and E. A. Ostrovskaya, Adv. Mater., 2021, 33, 2005732 CrossRef CAS PubMed
.
- A. Goff, P. Aukarasereenont, C. K. Nguyen, R. Grant, N. Syed, A. Zavabeti, A. Elbourne and T. Daeneke, Dalton Trans., 2021, 50, 7513–7526 RSC
.
- A. Dobosz, Y. Plevachuk, V. Sklyarchuk, B. Sokoliuk and T. Gancarz, Fluid Phase Equilib., 2018, 465, 1–9 CrossRef CAS
.
- A. Dobosz, Y. Plevachuk, V. Sklyarchuk, B. Sokoliuk, O. Tkach and T. Gancarz, J. Mol. Liq., 2018, 271, 942–948 CrossRef CAS
.
- R. S. Datta, N. Syed, A. Zavabeti, A. Jannat, M. Mohiuddin, M. Rokunuzzaman, B. Yue Zhang, M. A. Rahman, P. Atkin, K. A. Messalea, M. B. Ghasemian, E. D. Gaspera, S. Bhattacharyya, M. S. Fuhrer, S. P. Russo, C. F. McConville, D. Esrafilzadeh, K. Kalantar-Zadeh and T. Daeneke, Nat. Electron., 2020, 3, 51–58 CrossRef CAS
.
- M. B. Ghasemian, A. Zavabeti, M. Mousavi, B. J. Murdoch, A. J. Christofferson, N. Meftahi, J. Tang, J. Han, R. Jalili, F.-M. Allioux, M. Mayyas, Z. Chen, A. Elbourne, C. F. McConville, S. P. Russo, S. Ringer and K. Kalantar-Zadeh, Adv. Mater., 2021, 33, 2104793 CrossRef CAS PubMed
.
- K. A. Messalea, N. Syed, A. Zavabeti, M. Mohiuddin, A. Jannat, P. Aukarasereenont, C. K. Nguyen, M. X. Low, S. Walia, B. Haas, C. T. Koch, N. Mahmood, K. Khoshmanesh, K. Kalantar-Zadeh and T. Daeneke, ACS Nano, 2021, 15, 16067–16075 CrossRef CAS PubMed
.
- Z. Hu, T. Yuan, H. Li, Y. Qiu, W. Zhou, J. Zhang, Y. Zhao and S. Hu, Nano Res., 2021, 14, 4795–4801 CrossRef CAS
.
- T. Yuan, Z. Hu, Y. Zhao, J. Fang, J. Lv, Q. Zhang, Z. Zhuang, L. Gu and S. Hu, Nano Lett., 2020, 20, 2916–2922 CrossRef CAS PubMed
.
- J. Crawford, A. Cowman and A. P. O'Mullane, RSC Adv., 2020, 10, 29181–29186 RSC
.
- T. Alkathiri, N. Dhar, A. Jannat, N. Syed, M. Mohiuddin, M. M. Y. A. Alsaif, R. S. Datta, K. A. Messalea, B. Y. Zhang, M. W. Khan, A. Elbourne, N. Pillai, J. Z. Ou, A. Zavabeti and T. Daeneke, Chem. Commun., 2020, 56, 4914–4917 RSC
.
- V. Kochat, A. Samanta, Y. Zhang, S. Bhowmick, P. Manimunda, S. A. S. Asif, A. S. Stender, R. Vajtai, A. K. Singh, C. S. Tiwary and P. M. Ajayan, Sci. Adv., 2018, 4, e1701373 CrossRef PubMed
.
- J. Li, X. Zhang, B. Yang, C. Zhang, T. Xu, L. Chen, L. Yang, X. Jin and B. Liu, Chem. Mater., 2021, 33, 4568–4577 CrossRef CAS
.
- K. Vimalanathan, T. Palmer, Z. Gardner, I. Ling, S. Rahpeima, S. Elmas, J. R. Gascooke, C. T. Gibson, Q. Sun, J. Zou, M. R. Andersson, N. Darwish and C. L. Raston, Nanoscale Adv., 2021, 3, 5785–5792 RSC
.
- Q. Li, J. Lin, T.-Y. Liu, X.-Y. Zhu, W.-H. Yao and J. Liu, npj 2D Mater. Appl., 2021, 5, 36 CrossRef CAS
.
- J. Cooke, L. Ghadbeigi, R. Sun, A. Bhattacharyya, Y. Wang, M. A. Scarpulla, S. Krishnamoorthy and B. Sensale-Rodriguez, Phys. Status Solidi A, 2020, 217, 1901007 CrossRef CAS
.
- R. Lin, W. Zheng, D. Zhang, Y. Li and F. Huang, ACS Appl. Electron. Mater., 2019, 1, 2166–2173 CrossRef CAS
.
- J. Lin, Q. Li, T.-Y. Liu, Y. Cui, H. Zheng and J. Liu, Phys. Status Solidi RRL, 2019, 13, 1900271 CrossRef
.
- S.-Y. Tang, V. Sivan, K. Khoshmanesh, A. P. O'Mullane, X. Tang, B. Gol, N. Eshtiaghi, F. Lieder, P. Petersen, A. Mitchell and K. Kalantar-zadeh, Nanoscale, 2013, 5, 5949–5957 RSC
.
- M. B. Ghasemian, M. Mayyas, S. A. Idrus-Saidi, M. A. Jamal, J. Yang, S. S. Mofarah, E. Adabifiroozjaei, J. Tang, N. Syed, A. P. O'Mullane, T. Daeneke and K. Kalantar-Zadeh, Adv. Funct. Mater., 2019, 29, 1901649 CrossRef
.
- Y. Wang, M. Mayyas, J. Yang, J. Tang, M. B. Ghasemian, J. Han, A. Elbourne, T. Daeneke, R. B. Kaner and K. Kalantar-Zadeh, Adv. Funct. Mater., 2021, 31, 2005866 CrossRef CAS
.
- M. Mousavi, M. B. Ghasemian, J. Han, Y. Wang, R. Abbasi, J. Yang, J. Tang, S. A. Idrus-Saidi, X. Guan, M. J. Christoe, S. Merhebi, C. Zhang, J. Tang, R. Jalili, T. Daeneke, T. Wu, K. Kalantar-Zadeh and M. Mayyas, Appl. Mater. Today, 2021, 22, 100954 CrossRef
.
- X. Zhang, L. Xu, J. Zhou, W. Zheng, H. Jiang, K. Zuraiqi, G. K. Li, J. Liu and A. Zavabeti, ACS Appl. Nano Mater., 2021, 4, 9200–9212 CrossRef CAS
.
- Y. Fuseya, H. Katsuno, K. Behnia and A. Kapitulnik, Nat. Phys., 2021, 17, 1031–1036 Search PubMed
.
- W.-T. Koo, J. E. Millstone, P. S. Weiss and I.-D. Kim, ACS Nano, 2020, 14, 6407–6413 CrossRef CAS PubMed
.
- P.-C. Chen, X. Liu, J. L. Hedrick, Z. Xie, S. Wang, Q.-Y. Lin, M. C. Hersam, V. P. Dravid and C. A. Mirkin, Science, 2016, 352, 1565–1569 CrossRef CAS PubMed
.
- P.-C. Chen, M. Liu, J. S. Du, B. Meckes, S. Wang, H. Lin, V. P. Dravid, C. Wolverton and C. A. Mirkin, Science, 2019, 363, 959–964 CrossRef CAS PubMed
.
-
P. Ferrari, G. Sanzone, J. Yin and E. Janssens, Chapter 1 – Physical Synthesis of Nanoalloys, Elsevier, Oxford, 2020 Search PubMed
.
- Y. Lin, J. Genzer and M. D. Dickey, Adv. Sci., 2020, 7, 2000192 CrossRef CAS PubMed
.
- J. Thelen, M. D. Dickey and T. Ward, Lab Chip, 2012, 12, 3961–3967 RSC
.
- S.-Y. Tang, R. Qiao, Y. Lin, Y. Li, Q. Zhao, D. Yuan, G. Yun, J. Guo, M. D. Dickey, T. J. Huang, T. P. Davis, K. Kalantar-Zadeh and W. Li, Adv. Mater. Technol., 2019, 4, 1800420 CrossRef
.
- I. D. Tevis, L. B. Newcomb and M. Thuo, Langmuir, 2014, 30, 14308–14313 CrossRef CAS PubMed
.
- M. G. Mohammed, A. Xenakis and M. D. Dickey, Metals, 2014, 4, 465–476 CrossRef
.
- S.-Y. Tang, I. D. Joshipura, Y. Lin, K. Kalantar-Zadeh, A. Mitchell, K. Khoshmanesh and M. D. Dickey, Adv. Mater., 2016, 28, 604–609 CrossRef CAS PubMed
.
- S. Çınar, I. D. Tevis, J. Chen and M. Thuo, Sci. Rep., 2016, 6, 21864 CrossRef PubMed
.
- T. V. Neumann and M. D. Dickey, Adv. Mater. Technol., 2020, 5, 2000070 CrossRef CAS
.
- C. Ladd, J.-H. So, J. Muth and M. D. Dickey, Adv. Mater., 2013, 25, 5081–5085 CrossRef CAS PubMed
.
- M. A. Creighton, M. C. Yuen, M. A. Susner, Z. Farrell, B. Maruyama and C. E. Tabor, Langmuir, 2020, 36, 12933–12941 CrossRef CAS PubMed
.
- Y. Lin, Y. Liu, J. Genzer and M. D. Dickey, Chem. Sci., 2017, 8, 3832–3837 RSC
.
- N. Syed, A. Zavabeti, M. Mohiuddin, B. Zhang, Y. Wang, R. S. Datta, P. Atkin, B. J. Carey, C. Tan, J. van Embden, A. S. R. Chesman, J. Z. Ou, T. Daeneke and K. Kalantar-zadeh, Adv. Funct. Mater., 2017, 27, 1702295 CrossRef
.
- S. Cai, M. Mayyas, M. G. Saborio, M. B. Ghasemian, J. Tang, T. Daeneke, J. Han, A. A. Esmailpour, F.-M. Allioux and K. Kalantar-Zadeh, J. Mater. Chem. C, 2020, 8, 16593–16602 RSC
.
- H. Lu, S.-Y. Tang, Z. Dong, D. Liu, Y. Zhang, C. Zhang, G. Yun, Q. Zhao, K. Kalantar-Zadeh, R. Qiao and W. Li, ACS Appl. Nano Mater., 2020, 3, 6905–6914 CrossRef CAS
.
- S.-Y. Tang, R. Qiao, S. Yan, D. Yuan, Q. Zhao, G. Yun, T. P. Davis and W. Li, Small, 2018, 14, 1800118 CrossRef PubMed
.
- H. Yu, W. Zhao, L. Ren, H. Wang, P. Guo, X. Yang, Q. Ye, D. Shchukin, Y. Du, S. Dou and H. Wang, Adv. Mater., 2020, 32, 2001571 CrossRef CAS PubMed
.
- S. Li, Y. Li, K. Liu, M. Chen, W. Peng, Y. Yang and X. Li, Appl. Surf. Sci., 2021, 565, 150470 CrossRef CAS
.
- J. N. Hohman, M. Kim, G. A. Wadsworth, H. R. Bednar, J. Jiang, M. A. LeThai and P. S. Weiss, Nano Lett., 2011, 11, 5104–5110 CrossRef CAS PubMed
.
- F. Hoshyargar, H. Khan, K. Kalantar-zadeh and A. P. O'Mullane, Chem. Commun., 2015, 51, 14026–14029 RSC
.
- S. Handschuh-Wang, M. Rauf, T. Gan, W. Shang and X. Zhou, ChemistrySelect, 2021, 6, 10625–10636 CrossRef CAS
.
- Z. J. Farrell, C. J. Thrasher, A. E. Flynn and C. E. Tabor, ACS Appl. Nano Mater., 2020, 3, 6297–6303 CrossRef CAS
.
- W. Xie, F.-M. Allioux, R. Namivandi-Zangeneh, M. B. Ghasemian, J. Han, M. A. Rahim, J. Tang, J. Yang, M. Mousavi, M. Mayyas, Z. Cao, F. Centurion, M. J. Christoe, C. Zhang, Y. Wang, S. Merhebi, M. Baharfar, G. Ng, D. Esrafilzadeh, C. Boyer and K. Kalantar-Zadeh, ACS Nano, 2021, 15, 16839–16850 CrossRef CAS PubMed
.
- S. A. Chechetka, Y. Yu, X. Zhen, M. Pramanik, K. Pu and E. Miyako, Nat. Commun., 2017, 8, 15432 CrossRef CAS PubMed
.
- Z. J. Farrell and C. Tabor, Langmuir, 2018, 34, 234–240 CrossRef CAS PubMed
.
- F. Centurion, M. G. Saborío, F.-M. Allioux, S. Cai, M. B. Ghasemian, K. Kalantar-Zadeh and M. A. Rahim, Chem. Commun., 2019, 55, 11291–11294 RSC
.
- Z. J. Farrell, N. Reger, I. Anderson, E. Gawalt and C. Tabor, J. Phys. Chem. C, 2018, 122, 26393–26400 CrossRef CAS
.
- Y. Lin, J. Genzer, W. Li, R. Qiao, M. D. Dickey and S.-Y. Tang, Nanoscale, 2018, 10, 19871–19878 RSC
.
- Q. Wei, M. Sun, Z. Wang, J. Yan, R. Yuan, T. Liu, C. Majidi and K. Matyjaszewski, ACS Nano, 2020, 14, 9884–9893 CrossRef CAS PubMed
.
- D. Xu, J. Hu, X. Pan, S. Sánchez, X. Yan and X. Ma, ACS Nano, 2021, 15, 11543–11554 CrossRef CAS PubMed
.
- I. A. de Castro, A. F. Chrimes, A. Zavabeti, K. J. Berean, B. J. Carey, J. Zhuang, Y. Du, S. X. Dou, K. Suzuki, R. A. Shanks, R. Nixon-Luke, G. Bryant, K. Khoshmanesh, K. Kalantar-zadeh and T. Daeneke, Nano Lett., 2017, 17, 7831–7838 CrossRef PubMed
.
-
H. Okamoto and H. Okamoto, Phase diagrams for binary alloys, ASM International, Materials Park, OH, 2000 Search PubMed
.
- J. Tang, X. Zhao, J. Li, R. Guo, Y. Zhou and J. Liu, ACS Appl. Mater. Interfaces, 2017, 9, 35977–35987 CrossRef CAS PubMed
.
- D. P. Parekh, C. M. Fancher, M. G. Mohammed, T. V. Neumann, D. Saini, J. Guerrier, C. Ladd, E. Hubbard, J. L. Jones and M. D. Dickey, ACS Appl. Nano Mater., 2020, 3, 12064–12070 CrossRef CAS
.
- D. K. Sarfo, R. R. Taylor and A. P. O’Mullane, ACS Appl. Electron. Mater., 2020, 2, 2921–2928 CrossRef CAS
.
- A. Yamaguchi, Y. Mashima and T. Iyoda, Angew. Chem., Int. Ed., 2015, 54, 12809–12813 CrossRef CAS PubMed
.
- V. B. Kumar, Z. e. Porat and A. Gedanken, J. Therm. Anal. Calorim., 2015, 119, 1587–1592 CrossRef CAS
.
- S. A. Idrus-Saidi, J. Tang, M. B. Ghasemian, J. Yang, J. Han, N. Syed, T. Daeneke, R. Abbasi, P. Koshy, A. P. O'Mullane and K. Kalantar-Zadeh, J. Mater. Chem. A, 2019, 7, 17876–17887 RSC
.
- M. D. Dickey, Adv. Mater., 2017, 29, 1606425 CrossRef PubMed
.
- N. Kazem, T. Hellebrekers and C. Majidi, Adv. Mater., 2017, 29, 1605985 CrossRef PubMed
.
- A. Fassler and C. Majidi, Adv. Mater., 2015, 27, 1928–1932 CrossRef CAS PubMed
.
- M. G. Saborio, S. Cai, J. Tang, M. B. Ghasemian, M. Mayyas, J. Han, M. J. Christoe, S. Peng, P. Koshy, D. Esrafilzadeh, R. Jalili, C. H. Wang and K. Kalantar-Zadeh, Small, 2020, 16, 1903753 CrossRef CAS PubMed
.
- J. W. Boley, E. L. White and R. K. Kramer, Adv. Mater., 2015, 27, 2355–2360 CrossRef CAS PubMed
.
- H. Wang, Y. Yao, Z. He, W. Rao, L. Hu, S. Chen, J. Lin, J. Gao, P. Zhang, X. Sun, X. Wang, Y. Cui, Q. Wang, S. Dong, G. Chen and J. Liu, Adv. Mater., 2019, 31, 1901337 CrossRef PubMed
.
- S. Liu, S. Y. Kim, K. E. Henry, D. S. Shah and R. Kramer-Bottiglio, ACS Appl. Mater. Interfaces, 2021, 13, 28729–28736 CrossRef CAS PubMed
.
- S. Liu, S. N. Reed, M. J. Higgins, M. S. Titus and R. Kramer-Bottiglio, Nanoscale, 2019, 11, 17615–17629 RSC
.
- G. Yun, S.-Y. Tang, Q. Zhao, Y. Zhang, H. Lu, D. Yuan, S. Sun, L. Deng, M. D. Dickey and W. Li, Matter, 2020, 3, 824–841 CrossRef
.
- M. Liao, H. Liao, J. Ye, P. Wan and L. Zhang, ACS Appl. Mater. Interfaces, 2019, 11, 47358–47364 CrossRef CAS PubMed
.
- J. Xu, Z. Wang, J. You, X. Li, M. Li, X. Wu and C. Li, Chem. Eng. J., 2020, 392, 123788 CrossRef CAS
.
- J.-E. Park, H. S. Kang, J. Baek, T. H. Park, S. Oh, H. Lee, M. Koo and C. Park, ACS Nano, 2019, 13, 9122–9130 CrossRef CAS PubMed
.
- Z. Zhang, L. Tang, C. Chen, H. Yu, H. Bai, L. Wang, M. Qin, Y. Feng and W. Feng, J. Mater. Chem. A, 2021, 9, 875–883 RSC
.
- P. Zhang, Q. Wang, R. Guo, M. Zhang, S. Wang, C. Lu, M. Xue, J. Fan, Z. He and W. Rao, Mater. Horiz., 2019, 6, 1643–1653 RSC
.
- L. Tang, L. Wang, X. Yang, Y. Feng, Y. Li and W. Feng, Prog. Mater. Sci., 2021, 115, 100702 CrossRef CAS
.
- Y. Jin, Y. Lin, A. Kiani, I. D. Joshipura, M. Ge and M. D. Dickey, Nat. Commun., 2019, 10, 4187 CrossRef PubMed
.
- L. Wang and Q. Li, Chem. Soc. Rev., 2018, 47, 1044–1097 RSC
.
- T. Gan, S. Handschuh-Wang, W. Shang, J. Shen, L. Zhu, Q. Xiao, S. Hu and X. Zhou, Macromol. Rapid Commun., 2019, 40, 1900537 CrossRef CAS PubMed
.
- X. Li, M. Li, Q. Shou, L. Zhou, A. Ge, D. Pei and C. Li, Adv. Mater., 2020, 32, 2003553 CrossRef CAS PubMed
.
- F. Centurion, R. Namivandi-Zangeneh, N. Flores, M. Tajik, S. Merhebi, R. Abbasi, M. Mayyas, F.-M. Allioux, J. Tang, W.
A. Donald, C. Boyer, M. D. Dickey, K. Kalantar-Zadeh and M. A. Rahim, ACS Appl. Nano Mater., 2021, 4, 2987–2998 CrossRef CAS
.
- F. Hoshyargar, J. Crawford and A. P. O’Mullane, J. Am. Chem. Soc., 2017, 139, 1464–1471 CrossRef CAS PubMed
.
- H. Li, R. Abbasi, Y. Wang, F. M. Allioux, P. Koshy, S. A. Idrus-Saidi, M. A. Rahim, J. Yang, M. Mousavi, J. Tang, M. B. Ghasemian, R. Jalili, K. Kalantar-Zadeh and M. Mayyas, J. Mater. Chem. C, 2020, 8, 1656–1665 RSC
.
- J. Han, J. Yang, J. Tang, M. B. Ghasemian, L. J. Hubble, N. Syed, T. Daeneke and K. Kalantar-Zadeh, J. Mater. Chem. C, 2019, 7, 6375–6382 RSC
.
- Y. Wang, S. Wang, H. Chang and W. Rao, Adv. Mater. Interfaces, 2020, 7, 2000626 CrossRef CAS
.
- M. A. Creighton, M. C. Yuen, N. J. Morris and C. E. Tabor, Nanoscale, 2020, 12, 23995–24005 RSC
.
- Y. Liu, Q. Wang, J. Deng and W. Zhang, Chem. Commun., 2020, 56, 1851–1854 RSC
.
- R. Chen, Q. Xiong, R.-Z. Song, K.-L. Li, Y.-X. Zhang, C. Fang and J.-L. Guo, Adv. Mater. Interfaces, 2019, 6, 1901057 CrossRef CAS
.
- X. Tang, S.-Y. Tang, V. Sivan, W. Zhang, A. Mitchell, K. Kalantar-zadeh and K. Khoshmanesh, Appl. Phys. Lett., 2013, 103, 174104 CrossRef
.
- Y.-G. Park, H. Min, H. Kim, A. Zhexembekova, C. Y. Lee and J.-U. Park, Nano Lett., 2019, 19, 4866–4872 CrossRef CAS PubMed
.
- C. Zhang, L. Li, X. Yang, J. Shi, L. Gui and J. Liu, Int. J. Heat Mass Transfer, 2020, 148, 119055 CrossRef CAS
.
- L. Cao, H. Park, G. Dodbiba, K. Ono, C. Tokoro and T. Fujita, Appl. Phys. Lett., 2011, 99, 143120 CrossRef
.
- W. Kong, Z. Wang, M. Wang, K. C. Manning, A. Uppal, M. D. Green, R. Y. Wang and K. Rykaczewski, Adv. Mater., 2019, 31, 1904309 CrossRef CAS PubMed
.
- C. Wei, H. Fei, Y. Tian, Y. An, G. Zeng, J. Feng and Y. Qian, Small, 2019, 15, 1903214 CrossRef CAS PubMed
.
- P. Won, S. Jeong, C. Majidi and S. H. Ko, iScience, 2021, 24, 102698 CrossRef CAS PubMed
.
- Y. Lin, C. Cooper, M. Wang, J. J. Adams, J. Genzer and M. D. Dickey, Small, 2015, 11, 6397–6403 CrossRef CAS PubMed
.
- M. J. Ford, C. P. Ambulo, T. A. Kent, E. J. Markvicka, C. Pan, J. Malen, T. H. Ware and C. Majidi, Proc. Natl. Acad. Sci. U. S. A., 2019, 116, 21438–21444 CrossRef CAS PubMed
.
- M. D. Dickey, R. C. Chiechi, R. J. Larsen, E. A. Weiss, D. A. Weitz and G. M. Whitesides, Adv. Funct. Mater., 2008, 18, 1097–1104 CrossRef CAS
.
- G. J. Abbaschian, J. Less-Common Met., 1975, 40, 329–333 CrossRef CAS
.
- T. H. Park, J.-H. Kim and S. Seo, Adv. Funct. Mater., 2020, 30, 2003694 CrossRef CAS
.
- Y.-G. Park, H. S. An, J.-Y. Kim and J.-U. Park, Sci. Adv., 2019, 5, eaaw2844 CrossRef CAS PubMed
.
- M.-g. Kim, D. K. Brown and O. Brand, Nat. Commun., 2020, 11, 1002 CrossRef CAS PubMed
.
- F.-M. Allioux, J. Han, J. Tang, S. Merhebi, S. Cai, J. Tang, R. Abbasi, F. Centurion, M. Mousavi, C. Zhang, W. Xie, M. Mayyas, M. A. Rahim, M. B. Ghasemian and K. Kalantar-Zadeh, ACS Appl. Mater. Interfaces, 2021, 13, 43247–43257 CrossRef CAS PubMed
.
- R. C. Chiechi, E. A. Weiss, M. D. Dickey and G. M. Whitesides, Angew. Chem., Int. Ed., 2008, 47, 142–144 CrossRef CAS PubMed
.
- R. Tutika, S. H. Zhou, R. E. Napolitano and M. D. Bartlett, Adv. Funct. Mater., 2018, 28, 1804336 CrossRef
.
- R. Guo, X. Wang, H. Chang, W. Yu, S. Liang, W. Rao and J. Liu, Adv. Eng. Mater., 2018, 20, 1800054 CrossRef
.
- M. Tavakoli, M. H. Malakooti, H. Paisana, Y. Ohm, D. Green Marques, P. Alhais Lopes, A. P. Piedade, A. T. de Almeida and C. Majidi, Adv. Mater., 2018, 30, 1801852 CrossRef PubMed
.
- U. Daalkhaijav, O. D. Yirmibesoglu, S. Walker and Y. Mengüç, Adv. Mater. Technol., 2018, 3, 1700351 CrossRef
.
- Q. Zhang, Y. Gao and J. Liu, Appl. Phys. A: Mater. Sci. Process., 2014, 116, 1091–1097 CrossRef CAS
.
- J. L. Melcher, K. S. Elassy, R. C. Ordonez, C. Hayashi, A. T. Ohta and D. Garmire, Micromachines, 2019, 10, 54 CrossRef PubMed
.
- A. Sahlberg, F. Nilsson, A. Berglund, H. Nguyen, K. Hjort and S. H. Jeong, Adv. Mater. Technol., 2018, 3, 1700330 CrossRef
.
- L. Ren, J. Zhuang, G. Casillas, H. Feng, Y. Liu, X. Xu, Y. Liu, J. Chen, Y. Du, L. Jiang and S. X. Dou, Adv. Funct. Mater., 2016, 26, 8111–8118 CrossRef CAS
.
- T. V. Neumann, B. Kara, Y. Sargolzaeiaval, S. Im, J. Ma, J. Yang, M. C. Ozturk and M. D. Dickey, Micromachines, 2021, 12, 146 CrossRef PubMed
.
- S. Liu, D. S. Shah and R. Kramer-Bottiglio, Nat. Mater., 2021, 20, 851–858 CrossRef CAS PubMed
.
- F. Ongul, S. A. Yuksel, S. Bozar, G. Cakmak, H. Y. Guney, D. A. M. Egbe and S. Gunes, J. Phys. D: Appl. Phys., 2015, 48, 175102 CrossRef
.
- K. Chu, B. G. Song, H.-I. Yang, D.-M. Kim, C. S. Lee, M. Park and C.-M. Chung, Adv. Funct. Mater., 2018, 28, 1800110 CrossRef
.
- X. Li, M. Li, L. Zong, X. Wu, J. You, P. Du and C. Li, Adv. Funct. Mater., 2018, 28, 1804197 CrossRef
.
- R. Abbasi, M. Mayyas, M. B. Ghasemian, F. Centurion, J. Yang, M. Saborio, F.-M. Allioux, J. Han, J. Tang, M. J. Christoe, K. M. Mohibul Kabir, K. Kalantar-Zadeh and M. A. Rahim, J. Mater. Chem. C, 2020, 8, 7805–7811 RSC
.
- B. J. Blaiszik, S. L. B. Kramer, M. E. Grady, D. A. McIlroy, J. S. Moore, N. R. Sottos and S. R. White, Adv. Mater., 2012, 24, 398–401 CrossRef CAS PubMed
.
- B. He, Y. Du, B. Wang, X. Zhao, S. Liu, Q. Ye and F. Zhou, Chem. Eng. J., 2022, 427, 131019 CrossRef CAS
.
- N. Kazem, M. D. Bartlett and C. Majidi, Adv. Mater., 2018, 30, 1706594 CrossRef PubMed
.
- Y. Xin, J. Lan, J. Xu, D. Wu and J. Zhang, ACS Appl. Mater. Interfaces, 2021, 13, 19351–19359 CrossRef CAS PubMed
.
- G. Yun, S.-Y. Tang, H. Lu, S. Zhang, M. D. Dickey and W. Li, Small Sci., 2021, 1, 2000080 CrossRef
.
- Y. Peng, H. Liu, T. Li and J. Zhang, ACS Appl. Mater. Interfaces, 2020, 12, 6489–6495 CrossRef CAS PubMed
.
- J. Yang, D. Tang, J. Ao, T. Ghosh, T. V. Neumann, D. Zhang, Y. Piskarev, T. Yu, V. K. Truong, K. Xie, Y.-C. Lai, Y. Li and M. D. Dickey, Adv. Funct. Mater., 2020, 30, 2002611 CrossRef CAS
.
- G. Bo, H. Yu, L. Ren, N. Cheng, H. Feng, X. Xu, S. X. Dou, H. Wang and Y. Du, ACS Appl. Nano Mater., 2021, 4, 550–557 CrossRef CAS
.
- Y. Yu and E. Miyako, iScience, 2018, 3, 134–148 CrossRef CAS PubMed
.
- B. Ma, C. Xu, J. Chi, J. Chen, C. Zhao and H. Liu, Adv. Funct. Mater., 2019, 29, 1901370 CrossRef
.
- L. Ren, S. Sun, G. Casillas-Garcia, M. Nancarrow, G. Peleckis, M. Turdy, K. Du, X. Xu, W. Li, L. Jiang, S. X. Dou and Y. Du, Adv. Mater., 2018, 30, 1802595 CrossRef PubMed
.
- M. Xiong, Y. Gao and J. Liu, J. Magn. Magn. Mater., 2014, 354, 279–283 CrossRef CAS
.
- L. Cao, D. Yu, Z. Xia, H. Wan, C. Liu, T. Yin and Z. He, Adv. Mater., 2020, 32, 2000827 CrossRef CAS PubMed
.
- R. Guo, X. Sun, B. Yuan, H. Wang and J. Liu, Adv. Sci., 2019, 6, 1901478 CrossRef CAS PubMed
.
- J.-H. So, J. Thelen, A. Qusba, G. J. Hayes, G. Lazzi and M. D. Dickey, Adv. Funct. Mater., 2009, 19, 3632–3637 CrossRef CAS
.
- K. N. Paracha, A. D. Butt, A. S. Alghamdi, S. A. Babale and P. J. Soh, Sensors, 2020, 20, 177 CrossRef PubMed
.
- Y. Li, A. Trinchi, W. Wlodarski, K. Galatsis and K. Kalantar-zadeh, Sens. Actuators, B, 2003, 93, 431–434 CrossRef CAS
.
- M. Ogita, K. Higo, Y. Nakanishi and Y. Hatanaka, Appl. Surf. Sci., 2001, 175–176, 721–725 CrossRef CAS
.
- J. Frank, M. Fleischer and H. Meixner, Sens. Actuators, B, 1996, 34, 373–377 CrossRef CAS
.
- M. Shafiei, F. Hoshyargar, N. Motta and A. P. O'Mullane, Mater. Des., 2017, 122, 288–295 CrossRef CAS
.
- Z. Wei, M. K. Akbari, Z. Hai, R. K. Ramachandran, C. Detavernier, F. Verpoort, E. Kats, H. Xu, J. Hu and S. Zhuiykov, Sens. Actuators, B, 2019, 287, 147–156 CrossRef CAS
.
- J. Frank, M. Fleischer and H. Meixner, Sens. Actuators, B, 1998, 48, 318–321 CrossRef CAS
.
- P. Surmann and H. Zeyat, Anal. Bioanal. Chem., 2005, 383, 1009–1013 CrossRef CAS PubMed
.
- J. Zheng, M. A. Rahim, J. Tang, F.-M. Allioux and K. Kalantar-Zadeh, Adv. Mater. Technol., 2021, 2100760 CrossRef
.
- W. Zhang, J. Z. Ou, S.-Y. Tang, V. Sivan, D. D. Yao, K. Latham, K. Khoshmanesh, A. Mitchell, A. P. O'Mullane and K. Kalantar-Zadeh, Adv. Funct. Mater., 2014, 24, 3799–3807 CrossRef CAS
.
- Y. Yang, N. Akozbek, T.-H. Kim, J. M. Sanz, F. Moreno, M. Losurdo, A. S. Brown and H. O. Everitt, ACS Photonics, 2014, 1, 582–589 CrossRef CAS
.
- J. M. Sanz, D. Ortiz, R. Alcaraz de la Osa, J. M. Saiz, F. González, A. S. Brown, M. Losurdo, H. O. Everitt and F. Moreno, J. Phys. Chem. C, 2013, 117, 19606–19615 CrossRef CAS
.
- P. C. Wu, T.-H. Kim, A. S. Brown, M. Losurdo, G. Bruno and H. O. Everitt, Appl. Phys. Lett., 2007, 90, 103119 CrossRef
.
- M. W. Knight, T. Coenen, Y. Yang, B. J. M. Brenny, M. Losurdo, A. S. Brown, H. O. Everitt and A. Polman, ACS Nano, 2015, 9, 2049–2060 CrossRef CAS PubMed
.
- P. C. Wu, C. G. Khoury, T.-H. Kim, Y. Yang, M. Losurdo, G. V. Bianco, T. Vo-Dinh, A. S. Brown and H. O. Everitt, J. Am. Chem. Soc., 2009, 131, 12032–12033 CrossRef CAS PubMed
.
- P. Reineck, Y. Lin, B. C. Gibson, M. D. Dickey, A. D. Greentree and I. S. Maksymov, Sci. Rep., 2019, 9, 5345 CrossRef PubMed
.
- A. G. Marín, T. García-Mendiola, C. N. Bernabeu, M. J. Hernández, J. Piqueras, J. L. Pau, F. Pariente and E. Lorenzo, Nanoscale, 2016, 8, 9842–9851 RSC
.
- P. Albella, B. Garcia-Cueto, F. González, F. Moreno, P. C. Wu, T.-H. Kim, A. Brown, Y. Yang, H. O. Everitt and G. Videen, Nano Lett., 2011, 11, 3531–3537 CrossRef CAS PubMed
.
- A. García Marín, M. J. Hernández, E. Ruiz, J. M. Abad, E. Lorenzo, J. Piqueras and J. L. Pau, Biosens. Bioelectron., 2015, 74, 1069–1075 CrossRef PubMed
.
- X. Sun, B. Cui, B. Yuan, X. Wang, L. Fan, D. Yu, Z. He, L. Sheng, J. Liu and J. Lu, Adv. Funct. Mater., 2020, 30, 2003359 CrossRef CAS
.
- J. Yan, X. Zhang, Y. Liu, Y. Ye, J. Yu, Q. Chen, J. Wang, Y. Zhang, Q. Hu, Y. Kang, M. Yang and Z. Gu, Nano Res., 2019, 12, 1313–1320 CrossRef CAS
.
- X. Sun, M. Sun, M. Liu, B. Yuan, W. Gao, W. Rao and J. Liu, Nanoscale, 2019, 11, 2655–2667 RSC
.
- D. Wang, W. Xie, Q. Gao, H. Yan, J. Zhang, J. Lu, B. Liaw, Z. Guo, F. Gao, L. Yin, G. Zhang and L. Zhao, Small, 2019, 15, 1900511 CrossRef PubMed
.
- J.-J. Hu, M.-D. Liu, F. Gao, Y. Chen, S.-Y. Peng, Z.-H. Li, H. Cheng and X.-Z. Zhang, Biomaterials, 2019, 217, 119303 CrossRef CAS PubMed
.
- K. Adolfsson, H. Persson, J. Wallentin, S. Oredsson, L. Samuelson, J. O. Tegenfeldt, M. T. Borgström and C. N. Prinz, Nano Lett., 2013, 13, 4728–4732 CrossRef CAS PubMed
.
- Q. Liu, T. Yang, Y. Ye, P. Chen, X. Ren, A. Rao, Y. Wan, B. Wang and Z. Luo, J. Mater. Chem. B, 2019, 7, 1442–1449 RSC
.
- N. Taccardi, M. Grabau, J. Debuschewitz, M. Distaso, M. Brandl, R. Hock, F. Maier, C. Papp, J. Erhard, C. Neiss, W. Peukert, A. Görling, H. P. Steinrück and P. Wasserscheid, Nat. Chem., 2017, 9, 862–867 CrossRef CAS PubMed
.
- W. Zhang, B. S. Naidu, J. Z. Ou, A. P. O’Mullane, A. F. Chrimes, B. J. Carey, Y. Wang, S.-Y. Tang, V. Sivan, A. Mitchell, S. K. Bhargava and K. Kalantar-zadeh, ACS Appl. Mater. Interfaces, 2015, 7, 1943–1948 CrossRef CAS PubMed
.
- O. Oloye, J. D. Riches and A. P. O’Mullane, Chem. Commun., 2021, 57, 9296–9299 RSC
.
- J. Tang, J. Tang, M. Mayyas, M. B. Ghasemian, J. Sun, M. A. Rahim, J. Yang, J. Han, D. J. Lawes, R. Jalili, T. Daeneke, Z. Cao, C. A. Echeverria, F.-M. Allioux, A. Zavabeti, J. Hamilton, V. Mitchell, A. P. O’Mullane, R. B. Kaner, D. Esrafilzadeh, M. D. Dickey and K. Kalantar-Zadeh, Adv. Mater., 2021, 2105789 CrossRef PubMed
.
- O. Oloye, C. Tang, A. Du, G. Will and A. P. O'Mullane, Nanoscale, 2019, 11, 9705–9715 RSC
.
- T. Bauer, S. Maisel, D. Blaumeiser, J. Vecchietti, N. Taccardi, P. Wasserscheid, A. Bonivardi, A. Görling and J. Libuda, ACS Catal., 2019, 9, 2842–2853 CrossRef CAS PubMed
.
- Y. Wu, L. Huang, X. Huang, X. Guo, D. Liu, D. Zheng, X. Zhang, R. Ren, D. Qu and J. Chen, Energy Environ. Sci., 2017, 10, 1854–1861 RSC
.
- K. T. Lee, Y. S. Jung and S. M. Oh, J. Am. Chem. Soc., 2003, 125, 5652–5653 CrossRef CAS PubMed
.
- C. J. Wen and R. A. Huggins, J. Electrochem. Soc., 1981, 128, 1636–1641 CrossRef CAS
.
- S. Zhang, Y. Liu, Q. Fan, C. Zhang, T. Zhou, K. Kalantar-Zadeh and Z. Guo, Energy Environ. Sci., 2021, 14, 4177–4202 RSC
.
- R. D. Deshpande, J. Li, Y.-T. Cheng and M. W. Verbrugge, J. Electrochem. Soc., 2011, 158, A845 CrossRef CAS
.
- Y. Jin, K. Liu, J. Lang, D. Zhuo, Z. Huang, C.-A. Wang, H. Wu and Y. Cui, Nat. Energy, 2018, 3, 732–738 CrossRef CAS
.
- H. Kim, D. A. Boysen, J. M. Newhouse, B. L. Spatocco, B. Chung, P. J. Burke, D. J. Bradwell, K. Jiang, A. A. Tomaszowska, K. Wang, W. Wei, L. A. Ortiz, S. A. Barriga, S. M. Poizeau and D. R. Sadoway, Chem. Rev., 2013, 113, 2075–2099 CrossRef CAS PubMed
.
- Y. Ding, X. Guo, Y. Qian, L. Xue, A. Dolocan and G. Yu, Adv. Mater., 2020, 32, 2002577 CrossRef CAS PubMed
.
- G. Liu, J. Y. Kim, M. Wang, J.-Y. Woo, L. Wang, D. Zou and J. K. Lee, Adv. Energy Mater., 2018, 8, 1703652 CrossRef
.
- Y. Wang, X. Wang, M. Xue, Q. Li, Y. Zhang, D. Liu, J. Liu and W. Rao, Chem. Eng. J., 2021, 409, 128160 CrossRef CAS
.
- D. Liu, L. Su, J. Liao, B. Reeja-Jayan and C. Majidi, Adv. Energy Mater., 2019, 9, 1902798 CrossRef CAS
.
- J. Yun, Y. Lim, H. Lee, G. Lee, H. Park, S. Y. Hong, S. W. Jin, Y. H. Lee, S.-S. Lee and J. S. Ha, Adv. Funct. Mater., 2017, 27, 1700135 CrossRef
.
- M.-g. Kim, B. Lee, M. Li, S. Noda, C. Kim, J. Kim, W.-J. Song, S. W. Lee and O. Brand, ACS Nano, 2020, 14, 5659–5667 CrossRef CAS PubMed
.
- X. Guo, Y. Ding, L. Xue, L. Zhang, C. Zhang, J. B. Goodenough and G. Yu, Adv. Funct. Mater., 2018, 28, 1804649 CrossRef
.
- B. Han, Y. Yang, X. Shi, G. Zhang, L. Gong, D. Xu, H. Zeng, C. Wang, M. Gu and Y. Deng, Nano Energy, 2018, 50, 359–366 CrossRef CAS
.
- M. Zhu, S. Li, B. Li and S. Yang, Nanoscale, 2019, 11, 412–417 RSC
.
- Y. Liu, L.-P. Yue, P. Lou, G.-H. Xu, J. Liang, P. Guo, J. Wang, R. Tao, Y.-C. Cao and L. Shi, Mater. Lett., 2020, 258, 126803 CrossRef CAS
.
- G. Zhang, H. Deng, R. Tao, B. Xiao, T. Hou, S. Yue, N. Shida, Q. Cheng, W. Zhang and J. Liang, Mater. Lett., 2020, 262, 127194 CrossRef CAS
.
- C. Huang, X. Wang, Q. Cao, D. Zhang and J.-Z. Jiang, ACS Appl. Energy Mater., 2021, 4, 12224–12231 CrossRef CAS
.
- J. Zhu, Y. Wu, X. Huang, L. Huang, M. Cao, G. Song, X. Guo, X. Sui, R. Ren and J. Chen, Nano Energy, 2019, 62, 883–889 CrossRef CAS
.
- M. Zadan, M. H. Malakooti and C. Majidi, ACS Appl. Mater. Interfaces, 2020, 12, 17921–17928 CrossRef CAS PubMed
.
- V. Vallem, Y. Sargolzaeiaval, M. Ozturk, Y.-C. Lai and M. D. Dickey, Adv. Mater., 2021, 33, 2004832 CrossRef CAS PubMed
.
- F. Suarez, D. P. Parekh, C. Ladd, D. Vashaee, M. D. Dickey and M. C. Öztürk, Appl. Energy, 2017, 202, 736–745 CrossRef
.
- V. Vallem, E. Roosa, T. Ledinh, W. Jung, T.-I. Kim, S. Rashid-Nadimi, A. Kiani and M. D. Dickey, Adv. Mater., 2021, 33, 2103142 CrossRef CAS PubMed
.
- Y. Gao and J. Liu, Appl. Phys. A: Mater. Sci. Process., 2012, 107, 701–708 CrossRef CAS
.
- P. Fan, Z. Sun, Y. Wang, H. Chang, P. Zhang, S. Yao, C. Lu, W. Rao and J. Liu, RSC Adv., 2018, 8, 16232–16242 RSC
.
- J. Mingear, Z. Farrell, D. Hartl and C. Tabor, Nanoscale, 2021, 13, 730–738 RSC
.
- N. Hallfors, A. Khan, M. D. Dickey and A. M. Taylor, Lab Chip, 2013, 13, 522–526 RSC
.
- W. Xie, F.-M. Allioux, J. Z. Ou, E. Miyako, S.-Y. Tang and K. Kalantar-Zadeh, Trends Biotechnol., 2021, 39, 624–640 CrossRef CAS PubMed
.
- P. Zhu, S. Gao, H. Lin, X. Lu, B. Yang, L. Zhang, Y. Chen and J. Shi, Nano Lett., 2019, 19, 2128–2137 CrossRef CAS PubMed
.
- Q. Wu, N. Xia, D. Long, L. Tan, W. Rao, J. Yu, C. Fu, X. Ren, H. Li, L. Gou, P. Liang, J. Ren, L. Li and X. Meng, Nano Lett., 2019, 19, 5277–5286 CrossRef CAS PubMed
.
- J.-H. Kim, S. Kim, J.-H. So, K. Kim and H.-J. Koo, ACS Appl. Mater. Interfaces, 2018, 10, 17448–17454 CrossRef CAS PubMed
.
- J. E. Chandler, H. H. Messer and G. Ellender, J. Dent. Res., 1994, 73, 1554–1559 CrossRef CAS PubMed
.
- H. Quezada, M. Martínez-Vázquez, E. López-Jácome, B. González-Pedrajo, Á. Andrade, A. M. Fernández-Presas, A. Tovar-García and R. García-Contreras, Expert Rev. Anti-Infect. Ther., 2020, 18, 609–612 CrossRef CAS PubMed
.
- L. C. S. Antunes, F. Imperi, F. Minandri and P. Visca, Antimicrob. Agents Chemother., 2012, 56, 5961–5970 CrossRef CAS PubMed
.
- S. Hijazi, D. Visaggio, M. Pirolo, E. Frangipani, L. Bernstein and P. Visca, Front. Cell. Infect. Microbiol., 2018, 8, 316 CrossRef PubMed
.
- C. H. Goss, Y. Kaneko, L. Khuu, G. D. Anderson, S. Ravishankar, M. L. Aitken, N. Lechtzin, G. Zhou, D. M. Czyz, K. McLean, O. Olakanmi, H. A. Shuman, M. Teresi, E. Wilhelm, E. Caldwell, S. J. Salipante, D. B. Hornick, R. J. Siehnel, L. Becker, B. E. Britigan and P. K. Singh, Sci. Transl. Med., 2018, 10, eaat7520 CrossRef PubMed
.
- Z. Xu, X. Zhao, X. Chen, Z. Chen and Z. Xia, RSC Adv., 2017, 7, 52266–52273 RSC
.
- L. Kostakoglu, J. P. Leonard, I. Kuji, M. Coleman, S. Vallabhajosula and S. J. Goldsmith, Cancer, 2002, 94, 879–888 CrossRef PubMed
.
- C. S. Ivanoff, A. E. Ivanoff and T. L. Hottel, Food Chem. Toxicol., 2012, 50, 212–215 CrossRef CAS PubMed
.
- K. J. Cummings, M. Nakano, K. Omae, K. Takeuchi, T. Chonan, Y.-L. Xiao, R. A. Harley, V. L. Roggli, A. Hebisawa, R. J. Tallaksen, B. C. Trapnell, G. A. Day, R. Saito, M. L. Stanton, E. Suarthana and K. Kreiss, Chest, 2012, 141, 1512–1521 CrossRef PubMed
.
- Y. Lu, Y. Lin, Z. Chen, Q. Hu, Y. Liu, S. Yu, W. Gao, M. D. Dickey and Z. Gu, Nano Lett., 2017, 17, 2138–2145 CrossRef CAS PubMed
.
- Z. Guo, J. Lu, D. Wang, W. Xie, Y. Chi, J. Xu, N. Takuya, J. Zhang, W. Xu, F. Gao, H. Wu and L. Zhao, Bioact. Mater., 2021, 6, 602–612 CrossRef CAS PubMed
.
- N. Yang, F. Gong, Y. Zhou, Y. Hao, Z. Dong, H. Lei, L. Zhong, X. Yang, X. Wang, Y. Zhao, Z. Liu and L. Cheng, Biomaterials, 2021, 277, 121125 CrossRef CAS PubMed
.
- T. Liu, Y. Song, Z. Huang, X. Pu, Y. Wang, G. Yin, L. Gou, J. Weng and X. Meng, Colloids Surf., B, 2021, 207, 112023 CrossRef CAS PubMed
.
- D. Wang, Q. Wu, R. Guo, C. Lu, M. Niu and W. Rao, Nanoscale, 2021, 13, 8817–8836 RSC
.
- K. Y. Kwon, S. Cheeseman, A. Frias-De-Diego, H. Hong, J. Yang, W. Jung, H. Yin, B. J. Murdoch, F. Scholle, N. Crook, E. Crisci, M. D. Dickey, V. K. Truong and T.-I. Kim, Adv. Mater., 2021, 33, 2104298 CrossRef CAS PubMed
.
- C. B. Eaker and M. D. Dickey, Appl. Phys. Rev., 2016, 3, 031103 Search PubMed
.
- J. Liao and C. Majidi, Soft Matter, 2021, 17, 1921–1928 RSC
.
- G. Li, J. Du, A. Zhang and D.-W. Lee, J. Appl. Phys., 2019, 126, 084505 CrossRef
.
- L. Hu, L. Wang, Y. Ding, S. Zhan and J. Liu, Adv. Mater., 2016, 28, 9210–9217 CrossRef CAS PubMed
.
- J. Wissman, M. D. Dickey and C. Majidi, Adv. Sci., 2017, 4, 1700169 CrossRef PubMed
.
- S.-Y. Tang, V. Sivan, P. Petersen, W. Zhang, P. D. Morrison, K. Kalantar-zadeh, A. Mitchell and K. Khoshmanesh, Adv. Funct. Mater., 2014, 24, 5851–5858 CrossRef CAS
.
- J. Shu, D.-A. Ge, E. Wang, H. Ren, T. Cole, S.-Y. Tang, X. Li, X. Zhou, R. Li, H. Jin, W. Li, M. D. Dickey and S. Zhang, Adv. Mater., 2021, 33, 2103062 CrossRef CAS PubMed
.
- C. Pan, E. J. Markvicka, M. H. Malakooti, J. Yan, L. Hu, K. Matyjaszewski and C. Majidi, Adv. Mater., 2019, 31, 1900663 CrossRef PubMed
.
- A. Kotikian, J. M. Morales, A. Lu, J. Mueller, Z. S. Davidson, J. W. Boley and J. A. Lewis, Adv. Mater., 2021, 33, 2101814 CrossRef CAS PubMed
.
- Y. Chen, J. Yang, X. Zhang, Y. Feng, H. Zeng, L. Wang and W. Feng, Mater. Horiz., 2021, 8, 728–757 RSC
.
- C. P. Ambulo, M. J. Ford, K. Searles, C. Majidi and T. H. Ware, ACS Appl. Mater. Interfaces, 2021, 13, 12805–12813 CrossRef CAS PubMed
.
- P. Lv, X. Yang, H. K. Bisoyi, H. Zeng, X. Zhang, Y. Chen, P. Xue, S. Shi, A. Priimagi, L. Wang, W. Feng and Q. Li, Mater. Horiz., 2021, 8, 2475–2484 RSC
.
- J. Yang, X. Zhang, X. Zhang, L. Wang, W. Feng and Q. Li, Adv. Mater., 2021, 33, 2004754 CrossRef CAS PubMed
.
- P. Lv, X. Lu, L. Wang and W. Feng, Adv. Funct. Mater., 2021, 31, 2104991 CrossRef CAS
.
- L. Wang, A. M. Urbas and Q. Li, Adv. Mater., 2020, 32, 1801335 CrossRef CAS PubMed
.
- J. Jeon, J. Lee, S. K. Chung and D. Kim, J. Microelectromech. Syst., 2016, 25, 1050–1057 CAS
.
- R. Guo, H. Wang, M. Duan, W. Yu, X. Wang and J. Liu, Smart Mater. Struct., 2018, 27, 085022 CrossRef
.
- M. Zhang, P. Zhang, C. Zhang, Y. Wang, H. Chang and W. Rao, Appl. Mater. Today, 2020, 19, 100612 CrossRef
.
- D. Yu, Y. Liao, Y. Song, S. Wang, H. Wan, Y. Zeng, T. Yin, W. Yang and Z. He, Adv. Sci., 2020, 7, 2000177 CrossRef CAS PubMed
.
- B. Yao, W. Hong, T. Chen, Z. Han, X. Xu, R. Hu, J. Hao, C. Li, H. Li, S. E. Perini, M. T. Lanagan, S. Zhang, Q. Wang and H. Wang, Adv. Mater., 2020, 32, 1907499 CrossRef CAS PubMed
.
- M. Zhang, P. Zhang, Q. Wang, L. Li, S. Dong, J. Liu and W. Rao, J. Mater. Chem. C, 2019, 7, 10331–10337 RSC
.
- Z. Wan, H. Zeng and A. Feinerman, Appl. Phys. Lett., 2006, 89, 201107 CrossRef
.
- K. Nakakubo, H. Yoshioka, K. Morita, R. Ishimatsu, A. Kiani, H. Hallen, M. D. Dickey and Y. Oki, Opt. Mater. Express, 2021, 11, 2099–2108 CrossRef CAS
.
- S. Merhebi, M. Mohammad, M. Mayyas, R. Abbasi, C. Zhang, S. Cai, F. Centurion, W. Xie, Z. Cao, J. Tang, M. A. Rahim, J. Zhang, A. Razmjou, G. Leslie, K. Kalantar-Zadeh, J. Tang and F.-M. Allioux, J. Mater. Chem. A, 2021, 9, 19854–19864 RSC
.
- Y. Gao and Y. Bando, Nature, 2002, 415, 599 CrossRef CAS PubMed
.
- Z. Liu, Y. Bando, M. Mitome and J. Zhan, Phys. Rev. Lett., 2004, 93, 095504 CrossRef PubMed
.
- M. Mayyas, M. Mousavi, M. B. Ghasemian, R. Abbasi, H. Li, M. J. Christoe, J. Han, Y. Wang, C. Zhang, M. A. Rahim, J. Tang, J. Yang, D. Esrafilzadeh, R. Jalili, F.-M. Allioux, A. P. O’Mullane and K. Kalantar-Zadeh, ACS Nano, 2020, 14, 14070–14079 CrossRef CAS PubMed
.
- B. Lertanantawong, P. Lertsathitphong and A. P. O'Mullane, Electrochem. Commun., 2018, 93, 15–19 CrossRef CAS
.
- M. Mayyas, K. Khoshmanesh, P. Kumar, M. Mousavi, J. Tang, M. B. Ghasemian, J. Yang, Y. Wang, M. Baharfar, M. A. Rahim, W. Xie, F.-M. Allioux, R. Daiyan, R. Jalili, D. Esrafilzadeh and K. Kalantar-Zadeh, Adv. Funct. Mater., 2021, 2108673 CrossRef
.
- M. Mayyas, H. Li, P. Kumar, M. B. Ghasemian, J. Yang, Y. Wang, D. J. Lawes, J. Han, M. G. Saborio, J. Tang, R. Jalili, S. H. Lee, W. K. Seong, S. P. Russo, D. Esrafilzadeh, T. Daeneke, R. B. Kaner, R. S. Ruoff and K. Kalantar-Zadeh, Adv. Mater., 2020, 32, 2001997 CrossRef CAS PubMed
.
- J. Han, M. Mayyas, J. Tang, M. Mousavi, S. A. Idrus-Saidi, S. Cai, Z. Cao, Y. Wang, J. Tang, R. Jalili, A. P. O'Mullane, R. B. Kaner, K. Khoshmanesh and K. Kalantar-Zadeh, Matter, 2021, 4, 4022–4041 CrossRef
.
- M. M. Y. A. Alsaif, S. Kuriakose, S. Walia, N. Syed, A. Jannat, B. Y. Zhang, F. Haque, M. Mohiuddin, T. Alkathiri, N. Pillai, T. Daeneke, J. Z. Ou and A. Zavabeti, Adv. Mater. Interfaces, 2019, 6, 1900007 CrossRef CAS
.
- V. Krishnamurthi, T. Ahmed, M. Mohiuddin, A. Zavabeti, N. Pillai, C. F. McConville, N. Mahmood and S. Walia, Adv. Opt. Mater., 2021, 2100449 CrossRef CAS
.
- N. Mahmood, H. Khan, K. Tran, P. Kuppe, A. Zavabeti, P. Atkin, M. B. Ghasemian, J. Yang, C. Xu, S. A. Tawfik, M. J. S. Spencer, J. Z. Ou, K. Khoshmanesh, C. F. McConville, Y. Li and K. Kalantar-Zadeh, Mater. Today, 2021, 44, 69–77 CrossRef CAS
.
- N. Syed, A. Zavabeti, K. A. Messalea, E. Della Gaspera, A. Elbourne, A. Jannat, M. Mohiuddin, B. Y. Zhang, G. Zheng, L. Wang, S. P. Russo, E. Dorna, C. F. McConville, K. Kalantar-Zadeh and T. Daeneke, J. Am. Chem. Soc., 2019, 141, 104–108 CrossRef CAS PubMed
.
- B. J. Carey, J. Z. Ou, R. M. Clark, K. J. Berean, A. Zavabeti, A. S. R. Chesman, S. P. Russo, D. W. M. Lau, Z.-Q. Xu, Q. Bao, O. Kavehei, B. C. Gibson, M. D. Dickey, R. B. Kaner, T. Daeneke and K. Kalantar-Zadeh, Nat. Commun., 2017, 8, 14482 CrossRef CAS PubMed
.
- M. B. Ghasemian, A. Zavabeti, R. Abbasi, P. V. Kumar, N. Syed, Y. Yao, J. Tang, Y. Wang, A. Elbourne, J. Han, M. Mousavi, T. Daeneke and K. Kalantar-Zadeh, J. Mater. Chem. A, 2020, 8, 19434–19443 RSC
.
|
This journal is © The Royal Society of Chemistry 2022 |