DOI:
10.1039/D4QI01752H
(Research Article)
Inorg. Chem. Front., 2024,
11, 6880-6888
Cobalt and lithium recovery from spent LiCoO2 using a free-standing potassium zinc hexacyanoferrate/carbon cloth composite electrode†
Received
12th July 2024
, Accepted 21st August 2024
First published on 22nd August 2024
Abstract
Rapid rejuvenation and extensive utilization of mobile electronic devices lead to the excessive accumulation of waste lithium-ion batteries (LIBs), specifically spent LiCoO2 cathode materials. Considering the shortage of metal resources and the surging price of raw materials in the battery industry, an efficient strategy for selectively extracting valuable metals from spent LiCoO2 is urgently required. Herein, nanocube-like potassium zinc hexacyanoferrate (denoted as KZHCF) was successfully fabricated on a carbon cloth (CC) substrate for selective Co2+ adsorption from a spent LiCoO2 cathode via the combination of simple electrodeposition and hydrothermal treatment. Under optimal operational conditions, 98.6% of Co2+ was effectively extracted within 120 min at a constant potential of −0.4 V (vs. Ag/AgCl) with the CC/KZHCF composite as the working electrode, accompanied with a Co2+ electrosorption capacity of 130.9 mg g−1. Further, lithium ions in the electrolyte were separated and recovered in the form of Li2CO3via simple chemical precipitation, highlighting the feasibility of the developed electrochemical system toward cobalt and lithium recovery. Significantly, the CC/KZHCF electrode materials could be regenerated through simple potential inversion, while adsorbed Co2+ ions were facilely desorbed from the electrode surface and recovered as Co(OH)2. This work will provide a meaningful guidance for the separation and recovery of various metals from waste LIBs.
1. Introduction
LIBs have been rapidly progressing since their first commercial utilization in the 1990s and have gradually become the current mainstream energy storage batteries applied in the transport sector and portable electronic devices due to their excellent physicochemical characteristics, including light weight, long cycling lifespan and high energy density per unit weight.1–4 As a typical representative, LiCoO2 is the most commonly used cathode material in laptops, mobile phones, digital cameras and other devices.5,6 With the increasingly rapid upgradation of electronic products in the information age, numerous obsolete electronics become e-waste and are not recycled properly. It is reported that the total global e-waste is expected to reach 65.3 million tons by 2025, including 464
000 tons of waste LIBs.7,8 Considering the increasing market demand for important industrial raw materials, such as lithium, cobalt, and nickel, and the potential human health problems caused by the pollution from waste LIBs, the recovery of high value metals from spent LIBs is of great importance from both economic and environmental perspectives.9
The recycling and recovery of cobalt from waste LIBs usually begins with the pre-treatment process of physical separation for obtaining metal parts, including mechanical, mechanochemical and thermal dissolution methods.10 Subsequently, the conventional technologies for metal recovery can be divided into hydrometallurgy, pyrometallurgy and their combinations.11 Hydrometallurgical treatment comprises acid leaching and chemical precipitation processes. Inorganic and organic acids together with a reducing agent (e.g., H2O2) are usually employed to dissolve electrode material powders, followed by chemical precipitation for direct metal recovery.12 Pyrometallurgical technique involves high-temperature treatment for melting and reducing metallic components.13 Given that these techniques are characterized by massive chemical reagent use, high energy consumption associated with acid-containing wastewater discharge and toxic gas emission leading to secondary pollution, an alternative economical and environmentally friendly method is in urgent demand for cobalt recovery.14
In addition to traditional ion separation techniques including adsorption,15 chemical precipitation,16 ion exchange,17 and membrane separation,18 electrochemical sorption process19 or capacitive deionization (CDI),20 as an advanced technology was first proposed in the 1990s for removing salt ions from water. The target ions can be adsorbed when the electrode is charged and then also can be released to the bulk solution from the electrode material with short circuit or applied voltage reversal treatment.21 With the rapid development of CDI technology, the target ions have expanded from the initial alkali metal ions (K+, Ca2+, Na+, Mg2+) to some heavy metals (Cr3+, Cd2+, Pb2+, Hg2+) and rare metals (Li+, Cs+, Be2+, Ti4+).22,23 Traditional carbon-based materials, including activated carbon, graphene and carbon aerogel, have been applied as typical CDI electrodes due to their good electrical conductivity and high surface area.24 However, the mechanism of storing ions in the electrical double layer (EDL) at the interface limits the application of carbon materials in complicated systems due to their poor selectivity and low removal capacity.25 Hence, the design of novel electrode materials with high selectivity and outstanding performance during the adsorption/desorption cycles has been the focus of current CDI research.
Compared to the traditional carbon-based materials, which rely on the EDL mechanism to adsorb ions, the faradaic system with redox-active materials as the electrode with the merits of ion selectivity and high specific capacity is an alternative promising platform for environmental remediation.26 Transition metal hexacyanoferrates (TMHCFs), or Prussian blue and its derivatives (PBAs), as typical redox-active materials, usually feature a face-centred cubic lattice structure and an open framework, facilitating the rapid insertion and extraction of cations from the aqueous solution.27 Zinc hexacyanoferrate (ZnHCF), as one of the most chemically stable and low toxicity PBA analogues, has been widely applied in the field of aqueous rechargeable batteries. For instance, Niu et al. synthesized rhombohedral ZnHCF microcubes for high-voltage rechargeable sodium-ion batteries with high voltage output of 1.6 V and energy density of 59 W h kg−1.28 In another demonstration, Lu et al. modified ZnHCF nanocubes with the encapsulation of MnO2 nanosheets for an enhanced reversible capacity of 75 mA h g−1 at 1000 mA g−1.29 In addition to the applications as battery materials, ZnHCF has recently been used for the enrichment of radioactive elements from nuclear waste. Kim et al. developed a ZIF-8-derived ZnHCF composite for the enrichment of cesium ions from nuclear waste with a large Cs+ uptake capacity (204.9 mg g−1) and high selectivity towards a Na/Cs molar ratio of 1330.30 Considering the advantage of high adsorption capacity of ZnHCF materials toward cations, it is of considerable interest to utilize ZnHCF to extract Co element from waste LiCoO2 cathode materials.
In this work, the free-standing CC/KZHCF composite was synthesized through a simple electrodeposition and subsequent hydrothermal treatment for selective Co recovery from waste LiCoO2 batteries. As expected, the resulting binder-free CC/KZHCF composite can be directly employed as the working electrode, achieving excellent Co2+ adsorption/desorption capability. It is noteworthy that the sizes of KZHCF nanocubes can be modulated by varying the hydrothermal treatment time, thus giving rise to different Co2+ extraction efficiencies. The impact of several crucial factors, including applied potentials, solution pH, stability and reusability of CC/KZHCF, is evaluated during the Co2+ electrosorption process. Moreover, the plausible mechanism of Co2+ insertion/extraction behaviour in KZHCF is revealed by analyzing the variation in the valence of metal species before and after electrosorption.
2. Experimental section
2.1 Materials and characterization
The waste laptop LiCoO2 battery was purchased from the local electronic second-hand market. CC (0.34 mm in thickness) with 1.1 mΩ cm−2 through plate resistance was obtained from Shanghai Hesen Electric Co., Ltd (Shanghai, China). Hydrochloric acid (HCl, 36.0–38.0%), hydrogen peroxide (H2O2, ≥30.0%), ammonium hydroxide (NH3·H2O, 25.0–28.0%), zinc sulfate heptahydrate (ZnSO4·7H2O, ≥99.5%) and sodium sulfate (Na2SO4, ≥99.0%) were purchased from Sinopharm Chemical Reagent Co., Ltd. Boric acid (H3BO3, ≥99.5%) and potassium ferricyanide (K3[Fe(CN)6], ≥99.0%) were purchased from Aladdin Biochemical Technology Co., Ltd (Shanghai, China). The morphologies of the as-synthesized samples were characterized by scanning electron microscopy (SEM, SU-8020, Hitachi, Japan) and high-resolution transmission electron microscopy (HRTEM, JEM-2010, JEOL, Japan). X-ray diffraction patterns were recorded using an X-ray diffractometer (XRD, Panalytical Co., Netherland) with Cu Kα radiation. The chemical compositions and valence states of the surface elements of the samples were investigated by X-ray photoelectron spectroscopy (XPS, ESCALAB 250Xi, Thermo Scientific, USA) using Al-Kα radiation. The metal ions’ concentration was monitored using inductively coupled plasma optical emission (ICP-OES, Thermo Fisher Scientific ICP6300, USA) spectrometry. All electrochemical experiments were powered by a CHI 660E workstation (Chenhua, China).
2.2 Leaching experiment
The waste laptop LiCoO2 battery was first fully discharged in a 5% NaCl solution and then manually disassembled in the vacuum glove box. The cathode materials were obtained and subsequently crushed and sieved for pure LiCoO2 powder. The leaching process was performed in a 100 mL beaker with 50 mL of mixed solution containing 2.5 M HCl and 0.6% (v/v) H2O2, in which 2.5 g of LiCoO2 powder was added into the above solution and stirred for 48 h. Considering the higher reduction potential of Co3+ than that of H2O2, the presence of H2O2 here was used to reduce Co3+ to more soluble Co2+. The leaching solution was then filtered using a PTFE membrane syringe filter with 0.22 μm pore size to remove any solid impurities for subsequent ICP-OES analysis and electrochemical adsorption experiments. The leaching reaction is based on the following equation (eqn (1)).31 | 6H+ + H2O2 + 2LiCoO2 → 2Li+ + 2Co2+ + 4H2O + O2 | (1) |
2.3 Synthesis of the CC/KZHCF composite electrode
The CC/KZHCF composite electrode was fabricated through a simple electrodeposition and hydrothermal combination method according to the previous report with minor modifications.32 The commercial CC (2 × 2 cm2) was firstly treated with 3 M HNO3 for 6 h at 80 °C to obtain better hydrophilicity, followed by drying in a 60 °C oven overnight and thorough rinsing with deionized (DI) water several times. Electrodeposition was conducted with a three-electrode apparatus. Typically, 50 mL aqueous solution containing 5 g of ZnSO4·7H2O, 5 g of Na2SO4 and 1.6 g H3BO3 was used as the electrolyte. The hydrophilic CC, graphite rod and Ag/AgCl (saturated with KCl) electrodes were utilized as the working, counter and reference electrodes, respectively. The electrodeposition process was conducted under a constant current density of −50 mA cm−2 for 600 s. The obtained CC/Zn electrode was rinsed with DI water and dried in a vacuum at 60 °C overnight. Subsequently, the as-prepared CC/Zn (with Zn coating area of 1 × 2 cm2) electrode was added into a Teflon-lined stainless-steel autoclave containing 50 mL of 10 mM K3[Fe(CN)6] and heated at 60 °C for various time durations. The obtained samples under different hydrothermal treatment times were labelled as CC/KZHCF-1 (5 h), CC/KZHCF-2 (7 h), CC/KZHCF-3 (9 h) and CC/KZHCF-4 (11 h). Unless otherwise specified, CC/KZHCF signifies the product obtained at 7 h of hydrothermal treatment. Finally, the CC/KZHCF electrodes were obtained after washing with DI water several times and dried in a 60 °C oven overnight. The synthetic reaction could be described with equation (eqn (2)). |  | (2) |
2.4 Electrochemical adsorption of cobalt
Cobalt adsorption experiments were conducted in a three-electrode system in which CC/KZHCF (1 × 2 cm2), CC with the same area, and Ag/AgCl were utilized as the working electrode, counter electrode and reference electrode, respectively. The mixed solution containing Co2+ and Li+ was prepared by diluting the LiCoO2 leaching solution 1000 times with DI water. In all experiments, the electrolyte volume was 50 mL and the pH was adjusted using 0.1 M HCl and NH3·H2O. Before Co2+ adsorption experiments, the CC/KZHCF electrode was firstly pretreated in 1 mg L−1 KNO3 solution at a working potential of +1.5 V (vs. Ag/AgCl) for 30 min to discharge the K+ ions in the KZHCF and the residual K+ during the synthesis. The relevant reaction is shown as follows (eqn (3)).33 | 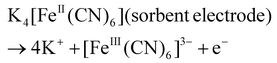 | (3) |
After the elimination of K+ ions, the CC/KZHCF electrode was transferred to the metal-containing solution for Co2+ electrosorption. The electrosorption experiments were carried out when a fixed potential was applied on the working electrode and lasted for 120 min to reach an equilibrium state. 0.5 mL of the samples were withdrawn from the reactor at predetermined time intervals and filtered for subsequent metal concentration analysis by ICP-OES. The Co recovery efficiency was calculated using the following equation (eqn (4))
|  | (4) |
and the adsorption capacity on unit mass of CC/KZHCF (
Q, mg g
−1), which was defined according to the following equation (
eqn (5))
| 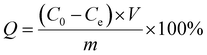 | (5) |
where
C0 (mg L
−1),
Ct (mg L
−1) and
Ce (mg L
−1) stand for the initial, time
t and final concentration of metal ions, respectively.
V and
m are the solution volume and the weight of the CC/KZHCF electrode, respectively.
2.5 Cyclic experiments
After Co2+ ions adsorption, the CC/KZHCF-Co electrode was washed with DI water and transferred to the KNO3 (1 mg L−1) electrolyte for Co2+ ions desorption and electrode regeneration. An oxidation potential of +1.5 V (vs. Ag/AgCl) was applied on the CC/KZHCF-Co electrode for 30 min. After that, the regenerated electrode was washed with DI water and dried in an oven at 60 °C overnight for the next Co recovery experiment. The cyclic experiments were repeated for 5 rounds, and the concentration of Co2+ ions was monitored by ICP-OES measurement.
3. Results and discussion
3.1 Fabrication of the CC/KZHCF composite electrode
Scheme 1 illustrates the fabrication process of the self-standing CC/KZHCF composite electrode, involving a simple electrodeposition and subsequent hydrothermal treatment. First, the commercial CC with hydrophilic surface was immersed into the electrolyte containing ZnSO4·7H2O as the precursor. In a three-electrode apparatus, Zn was in situ electrodeposited on the CC surface with a constant reduction potential at room temperature, generating a layer of Zn nanosheets. Subsequently, the as-obtained Zn nanosheets gradually grew into homogeneous KZHCF nanocubes through a redox reaction under the hydrothermal condition, in which metallic Zn can reduce Fe3+ to Fe2+ while it itself was oxidized to Zn2+, accompanied by the formation of K2Zn3[Fe(CN)6]2 (KZHCF). As a consequence, KZHCF nanocubes align densely on the CC substrate to generate the CC/KZHCF composite. It should be mentioned that the size of the composite electrode can be easily scaled up on demand.
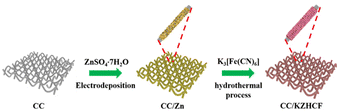 |
| Scheme 1 Schematic illustration of the preparation of the CC/KZHCF electrode. | |
As a representative, the morphology of the as-prepared CC/KZHCF-2 composite was initially characterized by SEM observation. For CC/Zn, after electrodeposition, the entire textual surface of the CC substrate was covered uniformly with a layer of densely packed nanosheets with a lateral size of 1–2 μm (Fig. 1a), indicative of the uniform coating of Zn. In the subsequent hydrothermal process, these interconnected Zn nanosheets in situ transform to homogeneous KZHCF nanocubes in the K3[Fe(CN)6] solution, which is well dispersed throughout the skeleton of the CC matrix (Fig. 1b). The microstructure of CC/KZHCF was further investigated by TEM observation. As displayed in Fig. 1c, these nanocubes possess a mean lateral dimension of 500 nm and a thickness of ca. 100 nm. Moreover, the corresponding elemental mapping images of a single KZHCF nanocube reveal that K, Zn, Fe, C and N elements are homogeneously distributed across the whole nanocube (Fig. 1d), confirming the successful fabrication of the CC/KZHCF composite. Further, the HRTEM image (Fig. 1e) demonstrates that the spacing of the interlayer lattice fringes can be identified as 5.4 Å and 4.1 Å, matching well with the (113) and (116) faces of K2Zn3[Fe(CN)6]2·9H2O (JCPDS no. 33-1061), respectively.34 Additionally, the hydrothermal treatment time plays a key role in the morphology of the fabricated CC/KZHCF composite. As demonstrated in Fig. S1,† the lateral dimension of KZHCF nanocubes gradually expands from 0.5 μm to 2 μm with increasing hydrothermal time, accompanied by a similar increase in the thickness. As a consequence, the loading masses of KZHCF nanocubes on CC substrate were calculated to be 8.5 mg, 11.3 mg, 18.8 mg and 24.2 mg for the as-fabricated CC/KZHCF-1, CC/KZHCF-2, CC/KZHCF-3, and CC/KZHCF-4 electrodes, respectively.
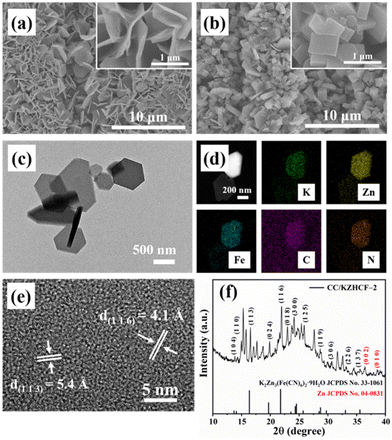 |
| Fig. 1 Morphological and structural characterization of the as-prepared samples: (a) SEM image of CC/Zn. (b) SEM image of CC/KZHCF-2. (c) TEM and (d) corresponding EDS elemental mapping of the KZHCF nanocubes. (e) HRTEM image of KZHCF; (f) XRD pattern of CC/KZHCF-2. | |
The crystalline phase of the as-prepared CC/KZHCF electrode was investigated by XRD (Fig. 1f). The diffraction peaks located at 36.3° and 39.0° are attributed to the (002) and (100) reflections from Zn nanosheets (JCPDS no. 04-0831), respectively.35 Several main characteristic diffraction peaks at 16.4°, 19.7°, 21.8°, 24.3°, 24.5° and 28.7° can be indexed to the (113), (024), (116), (214), (300) and (119) crystal facets of K2Zn3[Fe(CN)6]2·9H2O (JCPDS no. 33-1061), which is consistent with the result of HRTEM, indicating the successful synthesis of the CC/KZHCF composite electrode. In addition, the XRD patterns of CC/KZHCF-1, CC/KZHCF-3 and CC/KZHCF-4 electrodes were also examined in Fig. S2.† Compared with the other three electrodes, the characteristic peaks of the CC/KZHCF-2 electrode are sharper, indicating its better crystallinity and thus was chosen as the representative for subsequent experiments.
3.2 Electrochemical evaluation of the CC/KZHCF electrode
The electrochemically active surface area (ECSA), which was determined in the electrolyte environment rather than the atmospheric environment for BET, is utilized to characterize the ion-accessible surface in electrochemical application.36 As shown in Fig. 2a–c and Fig. S3,† the CC/KZHCF-2 electrode exhibits enhanced ECSA of 152.0 m2 g−1, superior to that of CC/KZHCF-1 (141.7 m2 g−1), CC/KZHCF-3 (144.9 m2 g−1) and CC/KZHCF-4 (144.5 m2 g−1). Evidently, the CC/KZHCF-2 electrode might provide abundant active sites that may facilitate ion storage during the electrochemical process and electrosorption of Co2+ ions on the electrode surface, thereby achieving enhanced recovery efficiency. In addition, the FeII/FeIII redox properties of the CC/KZHCF electrodes were also evaluated by the CV curves in the electrolyte containing Co2+, in which a significant pair of redox peaks appears in the CV curves for all the electrodes (Fig. 2d). A similar reduction peak at 0.55 V (vs. Ag/AgCl) was observed for Co2+ ions intercalation in the investigated four CC/KZHCF electrodes, revealing the feasibility of KZHCF electrodes toward Co2+ electrosorption. Also, the corresponding redox reaction can be described as follows (eqn (6)).37 Note that the specific capacitance of the CC/KZHCF-2 electrode toward Co2+ is higher than that of the other three electrodes. Hence, the CC/KZHCF-2 electrode is supposed to achieve the best recovery performance of Co2+. | Zn3[FeIII(CN)6]2 + 2e− + Co2+ ↔ CoZn3[FeII(CN)6]2 | (6) |
 |
| Fig. 2 (a) CV curves of the CC/KZHCF-2 electrode at different scan rates between 0.40 and 0.60 V (vs. Ag/AgCl). (b) The corresponding cathodic and anodic charging current measured at 0.50 V (vs. Ag/AgCl) plotted as a function of scan rates. (c) Calculated ECSA values of different electrodes. (d) CV curves of different electrodes in 50 mM Co2+ solution at a scan rate of 50 mV s−1. | |
3.3 Electrosorption performance of Co2+ ions on CC/KZHCF electrodes
The extraction efficiencies of Co2+ on CC/KZHCF composite electrodes were evaluated under different operational conditions. As compared to the other three composite electrodes, the CC/KZHCF-2 electrode exhibits higher extraction efficiency toward Co2+ (Fig. 3a). Approximately 98.6% of Co2+ (30 mg L−1) was electrochemically adsorbed on the CC/KZHCF-2 electrode within 120 min. From the corresponding EDS elemental mapping after Co2+ electrosorption (Fig. S4†), cobalt element was found to be uniformly distributed throughout the whole electrode surface, indicative of the successful electrosorption of Co2+ by KZHCF. By contrast, the sorption efficiencies of Co2+ on CC/KZHCF-1, CC/KZHCF-3 and CC/KZHCF-4 electrodes were about 66.0%, 86.8% and 74.0%, respectively. Further, the electrosorption capacities of Co2+ were calculated to be 116.5 mg g−1, 130.9 mg g−1, 69.3 mg g−1 and 45.9 mg g−1 for the respective CC/KZHCF-1, CC/KZHCF-2, CC/KZHCF-3 and CC/KZHCF-4. Evidently, the CC/KZHCF-2 composite electrode achieves excellent Co2+ recovery performance in terms of the recovery efficiency and uptake capacity, which might be attributed to its high ECSA accessible and active adsorption sites.
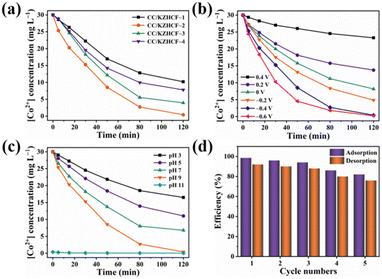 |
| Fig. 3 (a) Co2+ electrosorption by different electrodes (voltage = −0.4 V (vs. Ag/AgCl), pH = 9). (b) Effect of working voltage (pH = 9) and (c) pH value (voltage = −0.4 V (vs. Ag/AgCl)) on Co2+ electrosorption by the CC/KZHCF-2 electrode. (d) Reusability of the CC/KZHCF-2 electrode for 5 cycles. | |
The effect of the applied working potentials on the recovery efficiency of cobalt was also investigated. Considering that the side reaction of water electrolysis would occur below −0.8 V (vs. Ag/AgCl), the applied working potentials were selected from 0.4 V to −0.6 V (vs. Ag/AgCl).38 As shown in Fig. 3b, the electrosorption efficiency of Co2+ ions increased as the voltage becomes more negative, as reflected by 99.2% of the maximum value obtained at −0.6 V (vs. Ag/AgCl). Furthermore, the resulting CC/KZHCF-2 electrodes after Co2+ adsorption between −0.4 V and −0.6 V (vs. Ag/AgCl) were subjected to XRD characterization. As demonstrated in Fig. S5,† unlike that for CC/KZHCF-2 under −0.4 V (vs. Ag/AgCl), two new peaks located at 43.2° and 50.3° were detected in the CC/KZHCF-2 under −0.6 V (vs. Ag/AgCl), which can be ascribed to the representative (111) and (002) diffractions of elemental Co (JCPDS no. 01-1625).39 Thus, Co2+ ions in the solution were reduced to Co0 and deposited on the electrode surface under a potential of −0.6 V (vs. Ag/AgCl), while cobalt species were electrochemically adsorbed on the electrode surface in the form of ions under −0.4 V (vs. Ag/AgCl). Although a higher voltage might accelerate electron transfer, once Co2+ ions are reduced to elemental Co0, it is difficult for them to be oxidized into ions again and desorbed from the electrode surface into the solution. Moreover, the coating of cobalt on the KZHCF nanocubes is unfavorable for the subsequent cycling performance of the CC/KZHCF electrode. Hence, the optimal voltage toward cobalt recovery was set as −0.4 V (vs. Ag/AgCl).
Considering that Co2+ ions exist in different forms under different pH conditions, the initial solution pH value is considered as another important factor affecting the cobalt recovery efficiency. As illustrated in Fig. 3c, a remarkable improvement in the cobalt recovery efficiency is observed from 45.0% to 98.6% with increasing pH from 3 to 9. The poor recovery efficiency under acidic condition might be ascribed to the fact that the electrode surface is slightly positively charged due to the protonation, which would repel the positively charged Co2+ ions via the electrostatic repulsion effect.40 Also, the higher adsorption capacity under weak alkalinity (e.g., pH 9) can be explained by the formation of Co(NH3)63+ with 3.96 Å of hydrated radius, smaller than that of Co2+ (4.23 Å) (eqn (7) and (8)).41 As a result, Co(NH3)63+ with a smaller hydrated radius enters the KZHCF crystal lattice more easily, leading to enhanced recovery efficiency. Interestingly, it shows brown precipitation associated with Co(OH)2 colloids under strong alkaline condition (e.g., pH 11),42 causing a decrease in the Co2+ concentration in the solution, accompanied by the color variation of the electrolyte solution from light pink to colorless. These negatively charged colloids would adsorb Li+ ions in the solution, which is not conducive for the subsequent separation and recovery of Co2+.
| 6NH3·H2O + Co2+ ↔ [Co(NH3)6]2+ + 6H2O | (7) |
| 4[Co(NH3)6]2+ + O2 + 2H2O → 4[Co(NH3)6]3+ + 4OH− | (8) |
The cyclic performance and reusability of the CC/KZHCF-2 electrode were evaluated via 5 cycles of adsorption/desorption experiments, in which the spent electrode can be regenerated applying an oxidation potential of +1.5 V (vs. Ag/AgCl) in the pristine KNO3 electrolyte for next round of Co2+ electrosorption. Also, the adsorbed Co2+ ions are desorbed from the electrode surface into the above solution for subsequent recovery. As exhibited in Fig. 3d, after 5 rounds, the adsorption and desorption efficiencies of Co2+ decrease by 16.6% and 16.0%, respectively, indicating that most of the adsorbed Co2+ ions can be desorbed from the electrode and the electrosorption capability can be successfully regenerated by switching to an oxidation state. In addition, the possible release of Zn and Fe ions during multiple electrochemical cycles was detected by ICP-OES to further verify the stability of CC/KZHCF. As shown in Fig. S6,† there was almost no loss of Zn and Fe ions in the initial two absorption and desorption processes, and a trace loss appears in the third cycle. After five cycles, the concentrations of Zn and Fe ions in the solution were 0.23 ppb and 0.41 ppb, respectively, indicating that the fabricated CC/KZHCF electrode possesses excellent structural stability during the electrochemical process. Further, the stability of the CC/KZHCF-2 electrode was examined by SEM and XRD characterization. As displayed in Fig. S7,† the electrode after Co2+ desorption maintains the initial morphology with KZHCF nanocubes. In addition, the XRD pattern of the CC/KZHCF-2 electrode after Co2+ desorption is basically consistent with that of the fresh electrode material, revealing its excellent structural stability and reusability.
The selective electrosorption of Co2+ over Li+ of the CC/KZHCF electrode was further investigated. It is well acknowledged that the alkaline ions with a smaller hydrated radius would enter into the lattice channels more easily. In our case, the hydrated radii follows the order: Co2+ (4.23 Å) > Co(NH3)63+ (3.96 Å) > Li+ (3.82 Å). Considering that monovalent ions have a lower energy than divalent ions,43 a higher selectivity towards monovalent ions over divalent ions is achieved due to the dehydration energy. However, in our experiments, there is no change in the Li+ concentration before and after cobalt extraction with the initial solution containing 30 mg g−1 Co2+ and 1.5 mg g−1 Li+ (Fig. S8a†). Herein, the CV curves were introduced to evaluate the electrochemical behaviors of the CC/KZHCF electrode in different electrolyte solutions (50 mM Co2+ or Li+). As depicted in Fig. S8b,† the reduction peaks at 0.55 V and 0.78 V (vs. Ag/AgCl) were observed for Co2+ and Li+ ions insertion, respectively, illustrating a relative smaller reduction potential for Co2+ ions electrosorption in KZHCF in comparison with that of Li+ ions. In other words, it is easier for Co2+ insertion from the perspective of molecular dynamics due to its lower energy demand.44 Such a selective electrosorption of Co2+ over Li+ might be attributed to the specific pseudocapacitive characteristics of KZHCF.
3.4 The possible mechanism of Co2+ adsorption on the CC/KZHCF electrode
To gain more insight into the electrosorption mechanism of cobalt on the CC/KZHCF electrode, the chemical compositions and elemental states of CC/KZHCF before and after Co2+ adsorption were probed by XPS spectroscopy. From the survey spectrum, a new characteristic peak assigned to Co 2p appears after Co2+ adsorption as compared to the pristine CC/KZHCF electrode, indicating the successful extraction of cobalt by CC/KZHCF (Fig. S9†). The high-resolution spectrum of Fe 2p can be decomposed into two main peaks located at 721.4 and 708.6 eV, which can be assigned to the Fe 2p1/2 and Fe 2p3/2 spin-orbitals, respectively (Fig. 4a). The characteristic bands centred at 717.0 and 708.0 eV can be ascribed to the Fe2+ state, while the other two peaks located at 721.4 and 708.6 eV can be assigned to the Fe3+ state.45 After Co2+ extraction, the proportion of Fe3+ decreases from 83.1% to 62.4%, while that of Fe2+ increases from 10.6% to 27.8%. This result might be explained by the electrochemical transformation from [FeIII(CN)6]3− to [FeII(CN)6]4−. Similarly, the Co 2p spectrum after the electrosorption process is also verified in Fig. 4b, in which two main peaks at 797.1 and 781.3 eV correspond to the Co 2p1/2 and Co 2p3/2 spin-orbitals, respectively. Further, the Co 2p spectrum can be well fitted into several peaks associated with Co2+ (802.0 and 785.4 eV), Co3+ (797.1 and 781.3 eV) and satellite peaks (805.1 and 789.2 eV),46 with the respective proportions of 27.8%, 56.1% and 16.1%. Thus, it can be concluded that most Co2+ ions in the electrolyte are transformed to [Co(NH3)6]3+ under weak alkaline condition. Based on the aforementioned XPS analyses, a possible electrosorption mechanism of Co2+ on the CC/KZHCF electrode is proposed in Scheme 2. In the first step, K+ cations are extracted from the KZHCF framework upon charging in the KNO3 solution and leave large interstitial sites for the intercalation of cobalt ions. Then, Co2+ ions in the electrolyte will combine with NH3·H2O to form the [Co(NH3)6]3+ complex and further migrate into the CC/KZHCF electrode under the action of an electric field. Subsequently, [Co(NH3)6]3+ with a smaller hydrated radii than Co2+ is easy to be inserted into the KZHCF framework to maintain charge neutrality. During the desorption process, the [Co(NH3)6]3+ ions are extracted from the interstitial sites for the exchange of K+ ions in the pristine KNO3 solution under an oxidation potential.
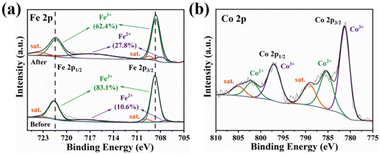 |
| Fig. 4 High-resolution spectra of CC/KZHCF-2 before and after electrosorption: (a) Fe 2p and (b) Co 2p. | |
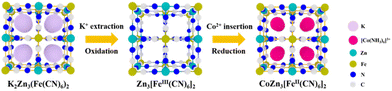 |
| Scheme 2 The electrosorption mechanism of Co2+ on the CC/KZHCF-2 electrode. | |
3.5 Simultaneous recovery of cobalt and lithium from spent LiCO2
Apart from the selective electrosorption of Co2+ from waste LiCoO2 leaching, it is necessary to convert the extracted species into important industrial raw materials. Hence, after each cycle of Co2+ electrosorption/desorption, the remaining solution containing Li+ ions are collected for evaporation and concentration treatment, followed by the addition of solid Na2CO3 under continuous stirring and heating conditions. As a consequence, Li2CO3 is generated. Upon adjusting the pH solution to 13, the filtrate containing Co2+ is collected, while Co(OH)2 precipitation is obtained in a similar way. To verify the composition of the obtained Li2CO3, the powder was subjected to XRD characterization. As illustrated in Fig. 5a, several strong peaks located at 21.3°, 30.6°, 31.8°, 34.1° and 37.0° were detected, which can be attributed to the (110), (−202), (002), (−112) and (−311) diffractions of Li2CO3 (JCPDS no. 87-0728).47 Additionally, an optical photograph intuitively reveals the white flake panorama of the obtained Li2CO3 powder (the inset in Fig. 5a). Likewise, the phase structure of the precipitated deep brown Co(OH)2 powder was also confirmed by its XRD pattern (Fig. 5b). The diffraction peaks at 19.1°, 32.6°, 38.0°, 51.5° and 58.1° can be indexed to the (001), (100), (011), (012) and (110) facets of Co(OH)2 (JCPDS no. 74-1057), respectively.48 In addition, the purity of the recovered Li2CO3 and Co(OH)2 products was detected by ICP-OES, in which Li2CO3 (1 g) and Co(OH)2 (1 g) were separately subjected to digestion treatment in aqua regia (HCl
:
HNO3 = 3
:
1) for one day, then the solution was diluted and the ion content was analyzed by ICP-OES. As displayed in Fig. S10,† the content of Li and Co was 0.186 g and 0.631 g, respectively. Accordingly, the purity of Li2CO3 and Co(OH)2 was 99% and 99.6%, respectively. All these results mentioned above indicate that the combination of selective electrosorption and chemical precipitation might be applied for the effective recovery of cobalt and lithium from waste LiCO2 cathode.
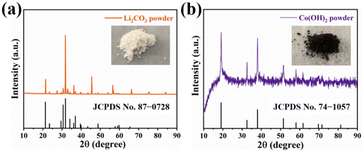 |
| Fig. 5 XRD patterns of the recovered (a) Li2CO3 and (b) Co(OH)2 powders from waste LiCoO2 cathode. | |
4. Conclusions
In summary, a free-standing CC/KZHCF composite electrode was successfully fabricated for the separation and recovery of Co2+ and Li+ from waste LiCoO2 cathode. Benefiting from the open framework structure and specific selective pseudocapacitive behavior of KZHCF, the resultant CC/KZHCF composite electrode was capable of adsorbing electrochemically active Co2+ with high efficiency and selectivity over Li+ ions. By virtue of the electrochemically-mediated adsorption and desorption properties of KZHCF, the effective separation of Co2+ and Li+ was achieved, which can be further converted into important industrial raw materials (e.g., Co(OH)2 and Li2CO3) by means of chemical precipitation. It can be predicted that this work will pave the way for the sustainable recycling of the power battery industry.
Data availability
The data supporting this article have been included as part of the ESI.†
Conflicts of interest
There are no conflicts of interest to declare.
Acknowledgements
This work was financially supported by National Natural Science Foundation of China (Grant No. 52173268 and 52371145), Anhui Provincial Natural Science Foundation (Grant No. 2308085QB73), and the HFIPS Director's Fund (Grant No. YZJJ-GGZX-2022-01).
References
- H. H. Liu, X. Zhang, H. R. Xu, W. Z. Ma, L. J. Wang, Z. H. Meng and F. Wang, Li2ZnTi3O8 anode: design from material to electrode and devices, Inorg. Chem. Front., 2023, 10, 4943–4980 RSC.
- X. B. Meng, Interface engineering of lithium metal anodes via atomic and molecular layer deposition, Inorg. Chem. Front., 2024, 11, 659–681 RSC.
- W. Lv, J. W. Meng, Y. M. Li, W. J. Yang, Y. L. Tian, X. F. Lyu, C. E. Duan, X. L. Ma and Y. Wu, Inexpensive and eco-friendly nanostructured birnessite-type δ-MnO2: A design strategy from oxygen defect engineering and K+ pre-intercalation, Nano Energy, 2022, 98, 107274 CrossRef CAS.
- W. Lv, J. W. Meng, X. D. Li, C. Xu, W. J. Yang, S. Z. Duan, Y. M. Li, X. Ju, R. S. Yuan, Y. L. Tian, M. M. Wang, X. F. Lyu, P. Y. Pan, X. L. Ma, Y. Cong and Y. Wu, Boosting zinc storage in potassium-birnessite via organic-inorganic electrolyte strategy with slight N-methyl-2-pyrrolidone additive, Energy Storage Mater., 2023, 54, 784–793 CrossRef.
- J. Chen, H. Y. Chen, S. Zhang, A. Dai, T. Y. Li, Y. Mei, L. S. Ni, X. Gao, W. T. Deng, L. Yu, G. Q. Zou, H. S. Hou, M. Dahbi, W. Q. Xu, J. G. Wen, J. Alami, T. C. Liu, K. Amine and X. B. Ji, Structure/Interface coupling effect for high-voltage LiCoO2 cathodes, Adv. Mater., 2022, 34, 2204845 CrossRef CAS PubMed.
- W. Lv, Z. L. Shen, X. D. Li, J. W. Meng, W. J. Yang, F. Ding, X. Ju, F. Ye, Y. M. Li, X. F. Lyu, M. M. Wang, Y. L. Tian and C. Xu, Discovering cathodic biocompatibility for aqueous Zn–MnO2 battery: An integrating biomass carbon strategy, Nano-Micro Lett., 2024, 16, 109 CrossRef CAS PubMed.
- S. M. Al-Salem, G. A. Leeke, M. S. El-Eskandarany and M. Van Haute, On the implementation of the circular economy route for E-waste management: A critical review and an analysis for the case of the state of Kuwait, J. Environ. Manage., 2022, 323, 116181 CrossRef CAS PubMed.
- J. J. Roy, S. Rarotra, V. Krikstolaityte, K. W. Zhuoran, Y. D. Cindy, X. Y. Tan, M. Carboni, D. Meyer, Q. Yan and M. Srinivasan, Green recycling methods to treat lithium-ion batteries E-waste: A circular approach to sustainability, Adv. Mater., 2022, 34, 2103346 CrossRef CAS PubMed.
- G. Yao, M. X. Lin, J. Yang, L. Z. Wei, H. L. Niu, Q. Q. Luo, F. C. Zheng and Q. W. Chen, Stabilizing V2O3 in carbon nanofiber flexible films for ultrastable potassium storage, Inorg. Chem. Front., 2022, 9, 1434–1445 RSC.
- J. F. Xiao, J. Li and Z. M. Xu, Challenges to future development of spent lithium ion batteries recovery from environmental and technological perspectives, Environ. Sci. Technol., 2020, 54, 9–25 CrossRef CAS PubMed.
- T. Nshizirungu, M. Rana, Y. T. Jo and J. H. Park, Rapid leaching and recovery of valuable metals from spent lithium ion batteries (LIBs) via environmentally benign subcritical nickel-containing water over chlorinated polyvinyl chloride, J. Hazard. Mater., 2020, 396, 122667 CrossRef CAS PubMed.
- Y. H. Han, X. X. Yi, R. Wang, J. F. Huang, M. J. Chen, Z. Sun, S. H. Sun and J. C. Shu, Copper extraction from waste printed circuit boards by glycine, Sep. Purif. Technol., 2020, 253, 117463 CrossRef CAS.
- J. B. Qin, Z. Qu, H. Y. Chen, Z. H. Wang, Q. Han, Y. X. Zhang, H. Zhang, Y. D. Gao, Y. Zhang, X. Z. Wang and S. Y. Zhu, Pyrometallurgy treatment of electroplating sludge, emulsion mud and coal ash: ZnAlFeO4 spinel separation and stabilization in calcium metasilicate glass, J. Environ. Manage., 2022, 329, 117101 Search PubMed.
- J. Lie and J. C. Liu, Closed-vessel microwave leaching of valuable metals from spent lithium-ion batteries (LIBs) using dual-function leaching agent: Ascorbic acid, Sep. Purif. Technol., 2021, 266, 118458 CrossRef CAS.
- H. M. Li, H. Zhang, J. F. Liu, Z. Z. Liu, H. M. Zhang, G. Z. Wang and Y. X. Zhang, Photo-enhanced precious metal recovery enabled by trithiocyanuric-linked covalent triazine frameworks, Chem. Eng. J., 2024, 495, 153494 CrossRef CAS.
- H. M. Li, M. X. Ye, Z. Fu, H. M. Zhang, G. Z. Wang and Y. X. Zhang, A freestanding, hierarchically porous poly(imine dioxime) membrane enabling selective gold recovery from e-waste with unprecedented capacity, EcoMat, 2022, e12248 CrossRef CAS.
- S. J. Li, C. W. Chen, H. J. Ge, X. Y. Guo, H. Xu, J. Zhang and Z. Y. Wu, Integration of galvanic reactions and engineered nanoconfinement in iron-copper nanocomposites for highly-efficient remediation of Cr(VI)-contaminated acidic/alkaline water, Chem. Eng. J., 2024, 484, 149533 CrossRef CAS.
- H. M. Li, M. X. Ye, Z. Z. Liu, Z. Fu, H. M. Zhang, G. Z. Wang and Y. X. Zhang, Selective Pt recovery from spent catalyst enabled by hierarchical porous poly(imine dioxime)/polyethylenimine composite membrane for recycled Pt/C catalyst, Sep. Purif. Technol., 2023, 310, 123125 CrossRef CAS.
- X. Y. Guo, Y. Zhang, H. J. Ge, J. Zhang, P. Q. Yang and Z. Y. Wu, Facile fabrication of 2D MXene loading Co-doped Prussian blue nanoparticles for ultrasensitive electrochemical assay of trace lead ions, J. Electroanal. Chem., 2023, 935, 117320 CrossRef CAS.
- Y. Yang, Q. G. Wang, S. Z. Xiong and Z. X. Song, Research progress on optimized membranes for vanadium redox flow batteries, Inorg. Chem. Front., 2024, 11, 4049–4079 RSC.
- A. Hassanvand, G. Q. Chen, P. A. Webley and S. E. Kentish, A comparison of multicomponent electrosorption in capacitive deionization and membrane capacitive deionization, Water Res., 2018, 131, 100–109 CrossRef CAS PubMed.
- W. T. Chen, X. He, Z. K. Jiang, B. Li, X. Y. Li and L. Lin, A capacitive deionization and electro-oxidation hybrid system for simultaneous removal of heavy metals and organics from wastewater, Chem. Eng. J., 2023, 451, 139071 CrossRef CAS.
- D. I. Kim, G. Gwak, P. Dorji, D. He, S. Phuntsho, S. Hong and H. Shon, Palladium recovery through membrane capacitive deionization from metal plating wastewater, ACS Sustainable Chem. Eng., 2017, 6, 1692–1701 CrossRef.
- X. Z. Zhou, A. X. Wang, X. Y. Zheng, D. F. Sun and Y. X. Yang, Uniformly anchoring Sb2O5 nanoparticles on graphene sheets via Co2+-induced deposition for enhanced lithium/sodium-ion storage, Inorg. Chem. Front., 2024, 11, 4167–4178 RSC.
- N. Kim, S. P. Hong, J. Lee, C. Kim and J. Yoon, High-desalination performance via redox couple reaction in the multichannel capacitive deionization system, ACS Sustainable Chem. Eng., 2019, 7, 16182–16189 CrossRef CAS.
- X. Su, K. J. Tan, J. Elbert, C. Rüttiger, M. Gallei, T. F. Jamison and T. A. Hatton, Asymmetric faradaic systems for selective electrochemical separations, Energy Environ. Sci., 2017, 10, 1272–1283 RSC.
- L. Q. Deng, J. L. Qu, X. G. Niu, J. Z. Liu, J. Zhang, Y. R. Hong, M. Y. Feng, J. W. Wang, M. Hu, L. Zeng, Q. F. Zhang, L. Guo and Y. J. Zhu, Defect-free potassium manganese hexacyanoferrate cathode material for high-performance potassium-ion batteries, Nat. Commun., 2021, 12, 2167 CrossRef CAS PubMed.
- L. Niu, L. Chen, J. Zhang, P. Jiang and Z. P. Liu, Revisiting the open-framework zinc hexacyanoferrate: The role of ternary electrolyte and sodium-ion intercalation mechanism, J. Power Sources, 2018, 380, 135–141 CrossRef CAS.
- K. Lu, B. Song, Y. X. Zhang, H. Y. Ma and J. T. Zhang, Encapsulation of zinc hexacyanoferrate nanocubes with manganese oxide nanosheets for high-performance rechargeable zinc ion batteries, J. Mater. Chem. A, 2017, 5, 23628–23633 RSC.
- H. Kim, H. H. Eom, Y. Kim, D. Harbottle and J. W. Lee, Reversible electro-mediated cesium ion removal using a zeolitic imidazolate framework derived zinc hexacyanoferrate composite, Chem. Eng. J., 2022, 450, 138029 CrossRef CAS.
- M. M. Cerrillo-Gonzalez, M. Villen-Guzman, C. Vereda-Alonso, J. M. Rodriguez-Maroto and J. M. Paz-Garcia, Acid leaching of LiCoO2 enhanced by reducing agent. Model formulation and validation, Chemosphere, 2022, 287, 132020 CrossRef CAS PubMed.
- B. He, P. Man, Q. C. Zhang, C. Wang, Z. Y. Zhou, C. W. Li, L. Wei and Y. G. Yao, Conversion synthesis of self-standing potassium zinc hexacyanoferrate arrays as cathodes for high-voltage flexible aqueous rechargeable sodium-ion batteries, Small, 2019, 15, 1905115 CrossRef CAS PubMed.
- R. Z. Chen, H. Tanaka, T. Kawamoto, M. Asai, C. Fukushima, H. Na, M. Kurihara, M. Watanabe, M. Arisaka and T. Nankawa, Selective removal of cesium ions from wastewater using copper hexacyanoferrate nanofilms in an electrochemical system, Electrochim. Acta, 2013, 87, 119–125 CrossRef CAS.
- Y. Y. Yuan, J. M. Xu, X. Y. Li, X. Li, X. C. Wang, X. J. Li and S. G. Dai, High-quality Prussian blue analogues K2Zn3[Fe(CN)6]2 crystals as a stable and high rate cathode material for potassium-ion batteries, J. Alloys Compd., 2022, 923, 166457 CrossRef CAS.
- Q. Q. Li, J. Wang, Y. H. Cheng and K. Chu, Zn nanosheets: An earth-abundant metallic catalyst for efficient electrochemical ammonia synthesis, J. Energy Chem., 2021, 54, 318–322 CrossRef CAS.
- M. X. Ye, C. Zhang, Z. Z. Liu, H. M. Li, Z. Fu, H. M. Zhang, G. Z. Wang and Y. X. Zhang, E-waste derived CuAu bimetallic catalysts supported on carbon cloth enabling effective degradation of bisphenol A via an electro-Fenton process, Sep. Purif. Technol., 2023, 305, 122507 CrossRef CAS.
- C. Y. Jiang, J. H. Ni and G. P. Jin, Magnetic potassium cobalt hexacyanoferrate nanocomposites for efficient adsorption of rubidium in solution, Sep. Purif. Technol., 2022, 296, 121383 CrossRef CAS.
- X. Wang, P. K. Cao, K. Zhao, S. Chen, H. T. Yu and X. Quan, Flow-through heterogeneous electro-Fenton system based on the absorbent cotton derived bulk electrode for refractory organic pollutants treatment, Sep. Purif. Technol., 2021, 276, 119266 CrossRef CAS.
- H. Feizi, R. Bagheri, Z. L. Song, J. R. Shen, S. I. Allakhverdiev and M. M. Najafpour, Cobalt/Cobalt oxide surface for water oxidation, ACS Sustainable Chem. Eng., 2019, 7, 6093–6105 CrossRef CAS.
- A. Amarray, S. El Ghachtouli, Y. Samih, M. Dahbi and M. Azzi, Enhancement of Cd(II) electrosorption using electrosorption process with manganese oxide nanomaterial electrodeposited, Desalination, 2022, 521, 115307 CrossRef CAS.
- X. X. Long, R. Z. Chen, J. H. Tan, Y. F. Lu, J. X. Wang, T. J. Huang and Q. Lei, Electrochemical recovery of cobalt using nanoparticles film of copper hexacyanoferrates from aqueous solution, J. Hazard. Mater., 2020, 384, 121252 CrossRef CAS PubMed.
- R. Solís-Rodríguez, R. Pérez-Garibay, O. Alonso-González and D. Mendieta-George, Enhancing the arsenic adsorption by controlling the zeta potential of Zn(OH)2 flocs, J. Environ. Chem. Eng., 2021, 9, 106300 CrossRef.
- Y. S. Xu, H. J. Zhou, G. Z. Wang, Y. X. Zhang, H. M. Zhang and H. J. Zhao, Selective pseudocapacitive deionization of calcium ions in copper hexacyanoferrate, ACS Appl. Mater. Interfaces, 2020, 12, 41437–41445 CrossRef CAS PubMed.
- T. H. Chen, D. V. Cuong, Y. Jang, N. Z. Khu, E. Chung and C. H. Hou, Cation selectivity of activated carbon and nickel hexacyanoferrate electrode materials in capacitive deionization: A comparison study, Chemosphere, 2022, 307, 135613 CrossRef CAS PubMed.
- Z. Z. Li, C. S. Shen, Y. B. Liu, C. Y. Ma, F. Li, B. Yang, M. H. Huang, Z. W. Wang, L. M. Dong and S. Wolfgang, Carbon nanotube filter functionalized with iron oxychloride for flow-through electro-Fenton, Appl. Catal., B, 2020, 260, 118204 CrossRef CAS.
- H. J. Zhou, H. C. Dong, J. H. Wang and Y. C. Chen, Cobalt anchored on porous N, P, S-doping core-shell with generating/activating dual reaction sites in heterogeneous electro-Fenton process, Chem. Eng. J., 2021, 406, 125990 CrossRef CAS.
- M. Shi, L. A. Diaz, J. R. Klaehn, A. D. Wilson and T. E. Lister, Li2CO3 Recovery through a carbon-negative electrodialysis of lithium-ion battery leachates, ACS Sustainable Chem. Eng., 2022, 10, 11773–11781 CrossRef CAS.
- J. J. Zhao, X. Qu, J. K. Qu, B. L. Zhang, Z. Q. Ning, H. W. Xie, X. B. Zhou, Q. S. Song, P. F. Xing and H. Y. Yin, Extraction of Co and Li2CO3 from cathode materials of spent lithium-ion batteries through a combined acid-leaching and electro-deoxidation approach, J. Hazard. Mater., 2019, 379, 120817 CrossRef CAS PubMed.
|
This journal is © the Partner Organisations 2024 |
Click here to see how this site uses Cookies. View our privacy policy here.