DOI:
10.1039/D3VA00107E
(Tutorial Review)
Environ. Sci.: Adv., 2023,
2, 1282-1301
Recent advances on value-added biocarbon preparation by the pyrolysis of renewable and waste biomass, their structure and properties: a move toward an ecofriendly alternative to carbon black
Received
29th April 2023
, Accepted 3rd July 2023
First published on 14th August 2023
Abstract
The production of renewable biocarbon from waste biomass through pyrolysis as a sustainable and ecofriendly alternative to carbon black poses major scientific challenges for value-added uses in plastic and composite industries. The need to develop new materials from sustainable resources is now globally recognized and increasingly important in view of rising greenhouse gas (GHC) emissions and climate change mitigation. Carbon black is one of the most extensively used reinforcing fillers for elastomers and colorant in the plastic industry and is produced from nonrenewable petroleum derivatives. This review reports the scope of the sustainable carbonaceous filler, biocarbon, as a reinforcing filler for polymer matrices. Herein, we focus on the physicochemical characteristics of the conventional carbon black filler and summarized the strategies to achieve these properties in sustainable biocarbon filler through the proper tuning of synthesis methodologies. Moreover, this review emphasizes on the development, challenges, and opportunities of this emerging renewable filler as a possible replacement for carbon black utilizing the immense amount of waste biomass generated in agricultural and industrial processes.
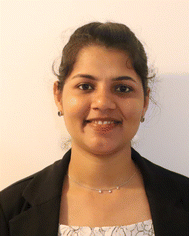 Drupitha MP | Dr Drupitha MP is currently working as a Lead Engineer-Advanced Materials, in Aliaxis Research and Technology centre Asia. Prior to her corporate entry, she gained significant experience in the field of sustainable fillers and green composites during her postdoctoral research tenure at Bioproducts Discovery and Development Centre, University of Guelph, Canada. She received her PhD from Rubber Technology Centre, Indian Institute of Technology – Kharagpur in July 2018. During her research, she worked on TPU-PDMS blend nanocomposites based on nanohydroxyapatite for tissue engineering applications. Her main research interests include synthesis of nanofillers, preparation and characterization polymer blends and nanocomposites, and developing bionanocomposites for tissue engineering applications. She has authored 9 research articles and book chapters. |
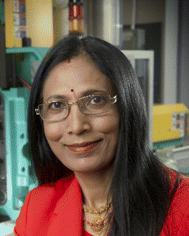 Manjusri Misra | Dr Manjusri Misra is a professor and Tier 1 Canada Research Chair (CRC) in Sustainable Biocomposites in the School of Engineering and holds a joint appointment in the Department of Plant Agriculture at the University of Guelph. She is also the Research Program Director of the Bioeconomy Panel for the Ontario Agri-Food Innovation Alliance, a program between the Ontario Ministry of Agriculture and Rural Affairs (OMAFRA) and the University of Guelph. Dr Misra completed her Bachelor's, Master's, MPhil, and PhD from Ravenshaw College at Utkal University in India focusing on Chemistry with a specialization in Polymer Chemistry and Natural Fibers during her graduate program. Dr Misra's current research focuses primarily on novel bio-based composites and nanocomposites from agricultural, forestry, and recycled resources for sustainable bioeconomy moving toward Circular Economy. She has authored more than 750 publications, including 450 peer-reviewed papers, 30 book chapters, and 55 patents. She has been the editor and co-editor of 6 books in the area of biocomposites and nanomaterials. In 2020, she was selected as one of Canada's Most Powerful Women: Top 100 Award Winner in the Manulife Science and Technology category from the Women Executive Network. She is a Fellow of the Royal Society of Chemistry (UK), the American Institute of Chemical Engineers (AIChE), and the Society of Plastic Engineers (SPE). |
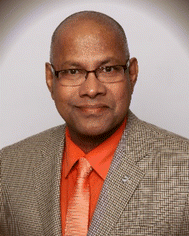 Amar Kumar Mohanty | Prof. Amar Mohanty is a Distinguished Research Chair in Sustainable Biomaterials at the Ontario Agriculture College and the Director of the Bioproducts Discovery and Development Centre. He is a professor in the Department of Plant Agriculture and School of Engineering at the University of Guelph, Ontario, Canada. Dr Mohanty is the Editor-in-Chief of Sustainable Composites @ Composites Part C – Open Access. He is one of the most cited researchers worldwide with more than 800 publications to his credit, including 463 peer-reviewed journal papers, 70 patents (awarded/applied), 6 edited books, 30 book chapters, 300+ conference papers, and over 160 plenary and keynote presentations. His Google Scholar citations count is 51959 and h-index 104 (July 24, 2023). He has received many awards, the most recent one being the prestigious Miroslaw Romanowski Medal of 2021 for his significant scientific contributions to the resolution of environmental problems from the Royal Society of Canada. He also received the Synergy Award for Innovation from Natural Sciences and Engineering Research Council of Canada (NSERC), the Andrew Chase Forest Products Division Award from the American Institute of Chemical Engineers (AIChE), and the Lifetime Achievement Award from the BioEnvironmental Polymer Society (BEPS). |
Environmental significance
Carbon black is one of the most abundantly used reinforcing filler produced from nonrenewable petroleum derivatives. With the growing concerns of global warming and dependency on nonrenewable resources, the development of alternative approaches is gaining momentum. Tuning the strategies to achieve chemical and physical characteristics of biocarbon equivalents to carbon black can lead to an economic and environment-friendly carbon filler suitable for developing sustainable composites. This review reports the scope of sustainable carbonaceous filler biocarbon as a reinforcing filler for polymer matrices. The opportunities and challenges of sustainable biocarbon over nonrenewable carbon black is summarized within the context of their preparation strategies and properties.
|
1. Introduction
Among the class of zero to three-dimensional carbon fillers, the three-dimensional carbon black is extensively used as a reinforcing filler for polymer matrices due to its cost effectiveness and morphological characteristics such as nanosize and aggregated ‘structure’.1 The extensive possibility to enhance graphitization of carbon black also places it close to the two-dimensional “wonder material” graphene.2,3 However, all these materials are based on nonrenewable petroleum-based raw materials; thus, an inevitable uncertainty looms over its availability for a long future. Taking a detour from the conventional viewpoint, sustainability can add a “fourth dimension” to the carbon family by accommodating the renewable biocarbon filler, which is the central theme of this review.4,5 As the root cause for global warming and increasing climate change issues is the excess use of nonrenewable materials, a sustainable alternative is essential to reduce the carbon footprints. Hence, the utilization of biosourced green fillers are very significant in the current scenario.6,7 The applications of biocarbon are not limited to filler and reinforcement applications; it is also advantageous for the fabrication of next-generation functional carbon materials for water treatment.8–15
Toward the replacement of petroleum-based carbon filler using sustainable biocarbon, the critical challenge lies in achieving the chemical and physical characteristics equivalent to carbon black.16,17 Even a slight change in the orbital structure or microscopic structural forms of carbon can result in an extensive range of captivating properties in terms of mechanical, electrical, and thermal characteristics. Hence, a proper understanding of the morphology and the graphitization phenomenon that causes orbital changes in biocarbon can offer a class of sustainable filler materials with a wide variety of properties, making it a sustainable alternative for carbon black.18–20 Carbon black is the most cost-effective nanocarbon with a predicted annual synthesis of 15 Mt tons by 2025. Carbon black dominates the market with all other petrobased carbonaceous fillers with an average price of $1 per kg, which is highly economic compared to carbon nanotubes ($600 per kg), graphene ($10
000 per kg), and fullerenes ($35
000 per kg).21
The term “carbon black” indicates a group of carbonaceous fillers prepared by the partial combustion or thermal decomposition of petroleum feedstock and having a spherical shape with unique aggregates forming clusters called ‘structures’.22,23 This highly structured architecture is the reason behind all the reinforcing properties of carbon black. Apart from the structure, the particle size, porosity, functionality, and graphitization properties play a significant role in the utilization of carbon black as a filler for polymer matrices.1,21,24–26 The newer sustainable version of carbon black, biocarbon or biochar, is mostly used as a microfiller for plastic matrices.27–30 The sustainability and cost-effectiveness of biocarbon over carbon black will play a vital role in its wide-scale industrial uses. Sahoo et al.31 and Bergan et al.32 have studied the cost aspects including techno-economic analysis (TEA), life-cycle assessment (LCA) of biochar, and biochar pellet production. The minimal selling price and environmental impacts of biochar were studied through TEA and cradle-to-grave LCA.32,33 The economic feasibility of biochar production was investigated using forest residues as feedstock in a small-scale portable machine. Based on their studies, the minimum selling price of biochar can be below $1000 per ton.31 An air curtain burner (ACB) portable system can manufacture biocarbon at $580 per ton from forest residues.
Biocarbon has gained a great deal of attention in recent years in energy and environment-related applications also.34–38 The nano version of this could explore the reinforcing possibility equivalent to carbon black and will be the first sustainable member in this family.
The acceptance of ecofriendly polymers is increasing due to the environmental problems associated with the disposal. Hence, sustainable plastics from renewable sources are gaining attention and these are also industrially established.30,39,40 However, carbon filler is heavily dependent on the petroleum sources.41 It was acceptable to use nonrenewable sources when we stepped into discoveries and inventions, and as we move on, it is imperative to find alternate renewable sources for a sustainable future.42 The alternatives can be any carbonaceous material, such as agricultural byproducts or industrial coproducts.43 The average global carbon emission was 33 giga tons in 2019, and the negative effect of this is doubling due to the simultaneous consumption of petroleum and emission of carbon as CO2.44 In the case of biocarbon, the positive effects are doubled due to the utilization of waste biomass for value-added applications and a reduction in petroleum dependency. Biocarbon or biochar is a terminology used for the class of carbonaceous fillers produced from renewable sources.45,46 Through this review, we explore the sustainable carbonaceous filler, biocarbon, and its challenges and opportunities as compared to the petroleum-based filler carbon black. Moreover, the scope of sustainable carbon as the next-generation energy material is also discussed based on recently reported review papers.
2. Preparation strategies of carbon black and biocarbon
Carbon black and biocarbon utilize different types of carbonization strategies and feedstock, which is responsible for the unique morphology of both. Depending on the kind of feedstock and process parameters (presence or absence of oxygen, and pressure), different types of carbonization methods are followed in the preparation of carbon black and biocarbon, which are discussed below.
2.1. Carbon black
The first version of carbon black was lamp black, introduced by Chinese for ink and lacquer formulations produced from aromatic oils and natural gas.47 Later, different types of carbon black processes were optimized to produce carbon black having different characteristics. The preparation strategies of carbon black can be mainly classified into two, namely, thermal oxidative decomposition (incomplete combustion) and thermal decomposition (pyrolysis), depending on the presence or absence of oxygen. As compared to the incomplete combustion process (98%), the pyrolysis process (2%) is less used in the preparation of carbon black. The thermal oxidative decomposition of natural gas produces channel black, and the thermal oxidative decomposition of aromatic oils of coal tar, crude oil, or natural gas at high temperature inside a furnace produces furnace black. Controlling the temperature of the feedstock (liquid feedstock) and oxygen is easier in furnace black than other blacks and hence possible to tune the morphology significantly. Thus, different types of furnace blacks are available based on the particle size, aggregate structure, porosity, etc., and widely used in elastomer-based matrices.48
2.2. Biocarbon
The primitive form of biocarbon or biochar was charcoal, which was first introduced and patented in 1897 by Ellsworth B. A. Zwoyer of Pennsylvania, and the process was further commercialized by Henry Ford, who utilized wood and sawdust byproducts from automobile manufacture as a feedstock.49 The research on biomass carbonization was started from early 1980s and were mainly focused on biooil production, and biochar and syngas obtained as byproducts were less explored.50 However, charcoal produced as a byproduct of wood fuel was used for soil amendment, water purification, and pigmentation applications from the 19th century. This was further extended globally and merged with the biomass carbonization research conducted for fuel production. The yield of biocarbon can be increased by reducing the rate of pyrolysis, and simultaneously, the biooil yield decreases. The slower heating rate promotes the uniform carbonization of biomass. However, the faster heating rate speeds up the release of condensable gases and inhibits secondary pyrolysis reactions, hence resulting in more biooil yield.50
Biocarbon/biochar is usually produced by the carbonization of wood, energy crops, agricultural and forest residues, and municipal, industrial, and food wastes, predominantly by pyrolysis and hydrothermal carbonization processes.51–53 Pyrolysis is exactly the same strategy mentioned in the case of thermal and acetylene black preparation conducted in the absence of oxygen, and the only difference is in the solid biomass used as the feedstock. Based on the heating rate of carbonization, there are two types of pyrolysis, namely, slow (10 °C min−1) and fast (100–1000 °C s−1) pyrolysis. The major products of slow pyrolysis are biocarbon along with less amounts of water and noncondensable gases, including CO, CO2, and H2. Higher heating rate promotes the biooil yield, and a lower heating rate helps in higher biochar yield.54 Hydrothermal carbonization is a heat treatment in which a wet biomass soaked in water is used as the feedstock. It mimics the coalification process and is usually conducted at a temperature less than 250 °C and high pressure so that the water remains in the liquid state.55 Zhao et al. studied biocarbon characteristics as a function of feedstock sources and pyrolysis temperatures and concluded that by the optimization of the pyrolysis condition and proper selection of feedstock, it is possible to control the biocarbon properties to different degrees. Hence, it should be possible to develop a ‘designed’ biocarbon for particular applications.56
3. Carbonization and particle formation in carbon black and biocarbon
During the conventional pyrolysis/incomplete combustion process, the formation of carbon black particles occurs through the conversion of hydrocarbon fuel molecules comprising few carbon atoms to carbonaceous agglomerates with several carbon atoms. Under high temperature, polycyclic aromatic radicals detaches the hydrogen and results in aromatic carbon rings,57 which is somewhat similar to the cyclodehydrogenation process that occurs during graphene formation through the bottom-up process.58 This can be considered as a gaseous-to-solid phase conversion. Unlike this, biocarbon formation through pyrolysis is a solid-to-solid conversion process, where the biomass is in the form of a powder or small or large pieces that are converted into the biocarbon under optimized process conditions. Also, biomass carbonization is complex in terms of its nonhomogeneity in composition. In the case of lignocellulosic biomass, it depends upon the source, cellulose, hemicellulose, and lignin ratios. The composition of a lignocellulosic biomass indicating the individual structure of biopolymers is shown in Fig. 1(a).59 The thermal degradation temperature and degradation mechanism of these three building blocks are entirely different and hence can result in different degradation products. The typical thermogravimetric analysis (TGA) curves of cellulose, hemicellulose, and lignin are depicted in Fig. 1(b).54 During the degradation of biomass, hemicellulose decomposes between 220 and 320 °C, followed by cellulose degradation. At the same time, lignin is characterized by a slow decomposition process in the range from 160 to 900 °C due to its macromolecular chain based on phenylpropanoid monomers. To have a good comparison of the biocarbon composition with respect to the carbonization temperature, the fixed carbon, volatile matter, and ash contents of oak charcoal are given in Fig. 1(c). This demonstrates the increment in fixed carbon content with carbonization temperature. A typical rotary kiln reactor used for the biochar production for soil amendment application is given in Fig. 1(d).54 These types of continuously operating pyrolyzers are easier for the preparation of larger amounts of biocarbon.60 In the case of composite applications, batch-type pyrolyzer are mostly used in the laboratory scale. Fig. 1(e) shows a type of vertical pyrolyzer used for the production of peanut hull biocarbon, and the uniformity in the biocarbon characteristics helped to improve its performance in biobased poly(trimethylene terephthalate) (PTT) matrix.4
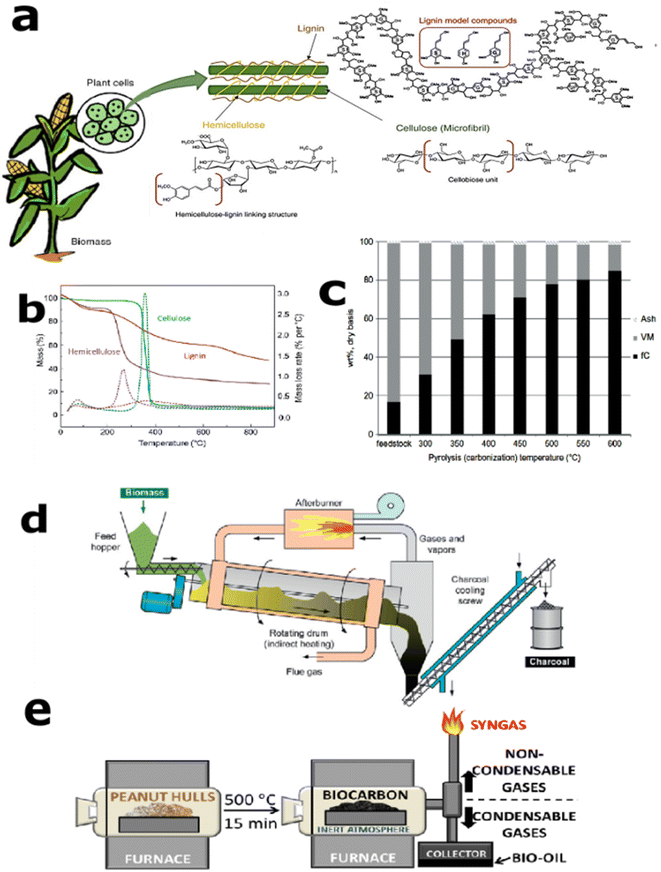 |
| Fig. 1 (a) Typical composition of lignocellulosic material demonstrating the structure of individual biopolymers, reproduced from ref. 59 (Copyright 2019, John Wiley and Sons (License number:5356640470353)), (b) the TGA and DTG (dashed lines) curves for cellulose, hemicelluloses, and lignin, reproduced from ref. 54 and 61 ((Copyright 2015, Elsevier) and (Copyright 2007, Elsevier, license number: 5356650321149)), (c) the effect of carbonization temperature on the proximate study of the resulting charcoals from oak, data adapted from ref. 54 and 62 (Copyright 2015, Elsevier, and Copyright 2001, Elsevier, license number: 5356650321149), (d) basic lay-out of a rotary retort to produce to charcoal (reproduced from ref. 54 (Copyright 2015, Elsevier, license number: 5356650321149), and (e) vertical pyrolizer used for biocarbon preparation, reproduced from ref. 4 (Copyright 2020, Springer Nature, Licensed under creative commons 4.0 International (CC BY 4.0)). | |
4. Physicochemical characteristics of carbon black and biocarbon
4.1. Particle shape and size
The morphology of carbon black and biocarbon are entirely different due to the different preparation methodologies and feedstock. Carbon black is seen as spherical nanoparticles in the form of aggregated structure, whereas biocarbon possesses random irregular shaped particles.18,63 The most significant criteria in the wide acceptance of carbon black is its variety of available grades with different particle sizes. Carbon black comprises of particles from few nanometer size to 350 nm depending on the process parameters and precursor used.64 Furnace black such as super abrasion furnace (SAF), high abrasion furnace (HAF), general purpose furnace (GPF), and semireinforcing furnace (SRF) possess lower particle size ranging from 15 to 100 nm. Thermal blacks such as fine thermal (FT) and medium thermal (MT) blacks have higher particle size in the range of 200 nm and 300 nm, respectively.65
As biocarbon follows a top-down approach of filler preparation, its particle size depends on the process of breaking the monolithic particles.63 The energy needed for breaking or milling these particles mainly depends on the characteristics of type and size of feedstock and pyrolysis conditions. Also, based on the particle size of biomass using, the rate at which heat is transferred through the particles will vary. On increasing the particle size, the distance between the surface of the input biomass and its center increases, which reduces the faster heat transmission.66 The degradation of cellulose at lower temperature (<200 °C) gives biochar, and higher temperature ends up with levoglucosan (tar).67 This temperature gradient produces different degradation products and causes secondary reactions, hence creating a gradient in the modulus properties of the particle. This gradient in modulus critically affects the post-pyrolysis steps such as ball milling; consequently, the particle size reduction process will be heterogeneous. Only a homogenous filler can compete and be reinforced such as carbon black in polymer matrices. Thus, to get a homogenous particle size in biocarbon, biomass having smaller particle size is preferred. With the reduction in particle size, the dispersibility increases. The lower particle size of the carbon black made it a reinforcing filler, and most of the mineral fillers are considered as nonreinforcing fillers due to their higher particle size.47,68
The first morphology analysis of carbon black was reported by E. F. Burton in 1940 using the first electron microscope in North America, developed by his research group. This was the classical experiment conducted for the determination of particle size and structure using thermal black.69,70 The morphology of carbon black particles (Micronex), as given in Fig. 2(a), revealed the shape of this colloidal carbon particles as spheroidal.70,71 Later, many physicists developed their own electron microscopes to explore the nanoparticle world, and carbon black was a common focus for all. In 1949, Turkevich and Hiller reported a unique image of a thin layer of carbon black prepared from graphite oxide, as shown in Fig. 2(b). The layers of carbon black resemble today's graphene. Interestingly, the birth of graphene was marked in the history by physicists almost together with electron microscopy in the name of carbon black; however, its potential was explored only after 60 years.72 The transmission electron microscopy (TEM) image of acetylene black, which is known as ecofriendly carbon black, is given in Fig. 2(c).73 Acetylene black has spherical particles with aggregated structure, which makes it conductive.47
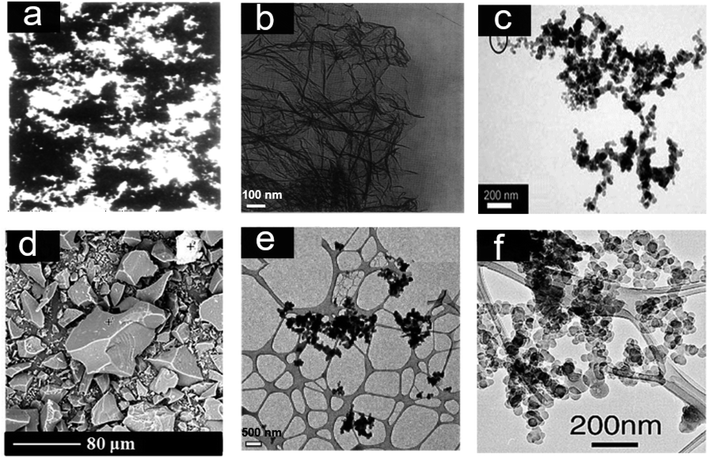 |
| Fig. 2 (a) Electron micrograph of carbon black particles (Micronex at 32400×) using first electron microscope developed in North America in 1940 (Reproduced with permission from Rubber Chemistry and Technology. Copyright © (1942)), Rubber Division, American Chemical Society, Inc, ref. 70. (b) Graphene-like carbon reported in 1949 as Carbon Black. (5000×) reproduced from ref. 72 (Copyright 1949) American Chemical Society). (c) TEM image of highly structured conducting carbon black reproduced with permission from ref. 73 (Fig. 2, chapter 19, copyright 2017, Springer Nature (License number: 5360850313496. (d) Chicken feather biocarbon 600 °C, reproduced from ref. 74 (copyright 2020, Frontiers, licensed under creative commons 4.0 International (CC BY 4.0), (e) high resolution transmission electron microscopy (HRTEM) micrographs biooil-based biocarbon prepared at 1100 °C (magnification 3000×) (Copyright 2018, reproduced from ref. 75 with permission from the Royal Society of Chemistry), (f) TEM image of soot particles collected from the biomass smoke reproduced from ref. 76 (Copyright 2004, John Wiley and license number: 5363250455534). | |
As compared to carbon black, biocarbon particles are nonhomogenous and larger in size. The higher particle size of biocarbon is due to the selection of solid feedstock and conventional pyrolysis.63,74 The scanning electron microscopy (SEM) images of biocarbon produced from the pyrolysis of chicken feather and ball milling is given in Fig. 2(d) and has a particle size that ranges from 1 μm to 80 μm. Toth et al. prepared nanosized carbon from biooil adopting the carbon black preparation method, as shown in Fig. 2(e). They utilized continuous spray pyrolysis of biooil from stem wood sawdust made from Scottish pine and Norway spruce.75 As compared to the available literature, this highlights the significance of liquid feedstock in tuning the particle size and structure. Fig. 2(f) reveals the transmission electron microscopy image of soot particles formed due to biomass and biofuel burning. The particles generated from the biomass smoke depicted carbon black-like structures and nanosized particles. Smoke is produced as a result of the carbonization of biomass in the presence of oxygen, which resulted in its structure being similar to carbon black. In addition to that, this carbon black-like morphology of soot particles opens a new scope in the utilization of smoke as a future source of carbon and hence can reduce the carbon footprint and promote circular economy.
4.2. Structure
The most unique physical characteristics of carbon black is its ‘structure’,77,78 which means the interconnected particle network formed due to the high surface energy of closely exhibited nanoparticles. The primary nanoparticles produced during the initial carbon black formation coalesce together, making the three-dimensional networks, which are known as aggregates, and these aggregates may form agglomerates linked by van der Waals forces. Based on the structure, carbon black can be classified as high structure and low structure blacks. The voids between these aggregates and agglomerates makes it porous and usually indicated as the volume of dibutylphthalate (DBP) absorbed by the carbon black. It is considered that DBP absorption mirrors the carbon black structure, which includes both aggregates and agglomerates.79 A schematic showing the surface area – structure relationship is given in the Fig. 3.73 The surface area of filler particles increases with the reduction in particle size. The lower particle size as well as higher structure promote the reinforcing ability of carbon black. Recently, Toth et al. introduced biomass-derived biooil-based sustainable carbon having nodule-like ‘structure’ similar to carbon black.75 Similarly Jiang et al. reported the synthesis of lignin based biocarbon with a ‘high structure’ similar to carbon black and hence imparted improved tensile properties to the (styrene butadiene rubber) SBR matrix.77,80
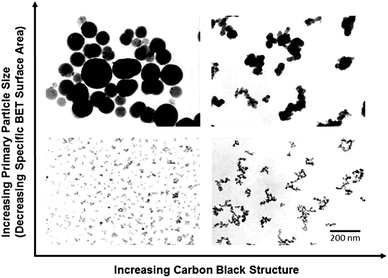 |
| Fig. 3 Morphological scheme showing the relationship between carbon black structure and primary particle size modified with permission from ref. 73 (Fig. 5, chapter 14, copyright 2017, Springer Nature, License number: 5360850466579). | |
4.3. Porosity
The porosity of carbon black and biocarbon are entirely different characteristics controlled by the process parameters and feedstock composition. The most interesting fact is that the porosity of biocarbon refers to the pores present inside the biocarbon, while carbon black porosity mainly denotes the pores present outside the individual particles or between the aggregated networks. The former is a composition dependant porosity and the latter is a structure-induced porosity. The model of biocarbon showing different types of pores such as macro, micro, and mesopores is given in Fig. 4.81 The porosity of carbon black is due to the controlled oxidation of feedstock in the reactor, whereas the biocarbon porosity is due to the compositional characteristics including the percentage of cellulose, hemicellulose, and lignin in plant-based biocarbons. Due to the selective removal of components (hemicellulose, cellulose, etc.) with increasing temperature, the plant-based biocarbon possesses higher porosity than the animal waste-based biocarbon.53 Apart from the source-related characteristics, lower heating rate, longer residence time, and moderate pyrolysis temperature also support maintaining the pore structure.53 An effective and controlled oxidation process in carbon black and a higher hemicellulose-containing biomass pyrolysis to biocarbon can result in higher porosity. Acetylene black produced in the absence of oxygen possesses adequate structure due to the characteristics of acetylene feedstock, which is exceptional and economically not feasible as compared to furnace blacks. Also, thermal black, which is produced by the pyrolysis process, depicted no structure. Cellulose dominant wood biomass showed an average porosity of 50–55% and hemicellulose dominant grass reported an 80% of porosity at the same temperature due to the lower degradation temperature of hemicellulose.82 In summary, the controlled oxidation of petroleum feedstock possess a tendency to expand its structure, which causes porosity in carbon black, and the removal of volatiles creates porosity in biocarbon. In common, a higher heat treatment temperature above ∼800 °C decreases the porosity of both carbon black and biocarbon.
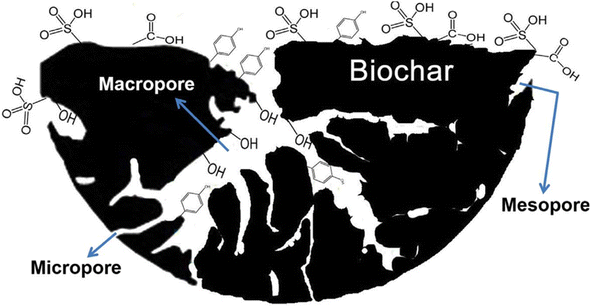 |
| Fig. 4 Model of biochar comprising various functional groups and pores (reproduced with permission from ref. 81 (Copyright 2017, Elsevier, License number: 5363231253739)). | |
The porosity of carbon material was first demonstrated by Franklin in 1949 using coal as a carbon source, where the porosity was utilized to sieve molecules and reported as ‘molecular sieve’ properties of carbon.83 Later, she conducted the carbonization of the coal at 1600 °C to analyze the change in density and found that the porosity was interestingly increased on heat treatment and that was the first carbonization study ever conducted.84 The biocarbon obtained directly after pyrolysis is reported with numerous pores on its surface and on ball milling, the breakage of particles takes place through the pores and reduces the number of pores. Prior to ball milling, the pore volume of biocarbon is found to be comparatively higher than other fillers. Even though the pore volume is sufficiently higher for individual particles, the higher particle size of these porous particles creates nonhomogeneity in the physicochemical characteristics and thereby a huge variation in mechanical properties. Also, the porosity of biocarbon was mostly studied in soil amendment applications where the particle size is not significant.85 Two types of porosity exist in carbon black, namely, open and closed porosity. Closed porosity occurs as a result of oxidative hallowing out of the centers of an individual particle within the aggregates, and the open porosity is mainly due to the pores present between the particles and aggregated structure. Total pore area for N110 (super abrasion furnace black (SAF)), N220 (intermediate SAF), and N330 (high abrasion furnace black) varies in the range of 22–25% and N330 with oxidized at 300 °C showed up to 55%.63 In the case of biocarbon, closed porosity is minimal and the open porosity contributes largely.85 The pores present in biocarbon are classified as macropores, mesopores, and micropores, where the pore diameters varies in the range of 1000–0.05 μm, 0.05–0.002 μm, and 0.002–0.0001 μm, respectively.82 Also, the pore volume of micropores showed up to a maximum value of 80% with activated biocarbons.86 These micropores present in the biocarbon acted as defects, and ball milling helped to remove these defects.87
4.3.1. Role of porosity in reinforcement.
The reinforcing mechanism in carbon black is happening due to the intake of polymer into the carbon black's structural porosity.48 The voids present in the amorphous elastomer and the carbon black porosity are mutually benefited, and thus the synergy helps in reinforcement. In the case of biocarbon composites, the porosity is not much benefited because a higher porosity was shown only with larger particles of biocarbon, while a higher particle size will affect the reinforcement negatively.88–90 Atkins91 reported that a proper selection of fillers based on porosity and according to the molecular diameter of polymers can ensure better reinforcement. High porosity in any carbonaceous filler will impart high viscosity in composite forms because the porosity allows the polymer to flow through different channels and pathways of pores, causing physically crosslinked structures. Also, with increase in the porosity, larger filler networks formation takes place in matrix and increases the percolation and hence increases the conduction properties.
4.4. Functional groups (polarity and matrix performance properties)
Even though carbon black is usually considered as inert, researchers have revealed that its surface contains many functional groups. In 1928, Johnson reported that carbon blacks contain oxygen, hydrogen, and other so-called volatile constituents. Also, the reaction with Grignard reagent showed that functional groups such as –OH, –OOH, –COOH, and >C
O are present on the carbon black surface.92 Stearns and Johnson have showed that a carbon black particle is a disordered agglomerate of polymeric benzenoid type molecules, which contain around their perimeters various functional groups, including short unsaturated hydrocarbon chains, which promote compatibility in elastomer matrices.92,93
In the case of biocarbon, the chemical characteristics of biocarbon mostly depend on the pyrolysis temperature. Biocarbon usually has abundant surface functional groups (C–O, C
O, COOH, and OH). With an increase in temperature, the functional groups start to disappear, thereby making the biocarbon more nonpolar.94 Thus, the compatibility of biocarbon and matrix can be easily controlled by the proper selection of pyrolysis temperature. Biocarbon pyrolyzed at lower temperature (300–500 °C) were revealed better interaction with polar matrices such as polyamides.95–97 Also, the high temperature treated/pyrolyzed biocarbon produced prominent improvement in a nonpolar matrix such as polypropylene (PP).97–99
Nitrogen fixation can be utilized for introducing the nitrogen complexation of biocarbon utilizing nitrogen rich biomass such as animal waste, sludge, and digestate. In addition, processing parameters such as low heating rate, lower pyrolysis temperature, and short residence time promote nitrogen fixation.53 The functionality can be measured directly from infrared spectroscopic analysis. The volatile content and pH also indicate the surface acidity coming from the oxygen functional group. X-ray photoelectron spectroscopy (XPS) analysis provides an idea about the surface composition by atomic type and some qualitative information on oxygen functionality.100
4.5. Degree of graphitization
Degree of graphitization is the most important tool in determining the properties of any carbonaceous material; more simply, it differentiates between soot and graphite. Graphite comprises of layers of hexagonally organized carbon atoms in a planar condensed ring system, which are stacked parallel to each other such that layers in which every atom has an atom directly above it are separated by one layer.22 This planar stacking sequence provides closest packing of the layer planes and is referred to as ABAB type stacking. The interlayer spacing is 0.335 nm. The c-direction is perpendicular to the hexagonal (basal) planes. Poorly graphitized carbons are described by the turbostratic model. According to this model, near-perfect segments of graphitic planes are parallel and equidistantly stacked, but there is no correlation in the position of adjacent planes. The average interlayer spacing between misoriented layers is arbitrarily considered to be 0.344 nm. Pyrolytic graphite is a monolithic graphite with a high degree of preferred crystallographic orientation obtained by the graphitization of pyrolytic carbon. Graphitic carbons are all varieties of substances in which 3D crystalline long range order can be seen by diffraction studies.48
Based on the graphitization, carbons can be classified in to graphitizing and nongraphitizing carbons. Among those, the nongraphitizable carbons that cannot be altered into graphite by high temperature are less explored and the atomic structure of those are still unclear. Most of the lignocellulosic fillers are considered as nongraphitizable carbon due to their comparatively less aromatic carbon content.101,102 Freitas et al. investigated the biomass and polyvinyl chloride (PVC) based pyrolysis process for the production of nongraphitizing and graphitizing carbons, respectively.48,101 The latter is characterized by a high degree of crosslinking and long-range isotropy. In the former case, the aromatic subunits have more tendency to orient parallel to each other and hence result in a pre-graphitic structure. The transformation of nongraphitizable carbons to isotropic and entangled carbon structures is ascribed to the comparatively large fraction of highly curved pre-graphenic layers, occurring due to the presence of nonsix carbon member rings within the carbon framework. Their development is mainly reliant on the characteristics of the carbon feedstock. The Franklin's representation of graphitizable and nongraphitizable carbon is given in Fig. 5(a) and (b).83 Also, the nongraphitizable nature of wood char was studied by Shibuya et al.103 and concluded that fullerene-like structures are present in wood charcoal and predicted that this may prevent the graphitization, as represented in Fig. 5(c).
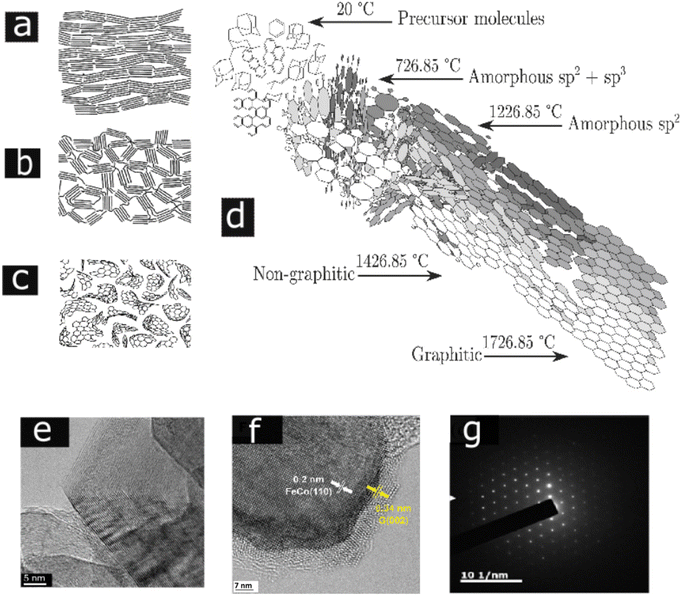 |
| Fig. 5 (a) and (b) Franklin's model for graphitizable carbon and nongraphitizable carbon, (c) model of the nongraphitizing carbons based on fullerene-like units (a), (b), and (c) are reproduced with permission from ref. 83 (Copyright 2001, Taylor & Francis, License number:4915670881135), (d) Marsh Griffith model of carbonization, reproduced with permission from ref. 112 (Copyright 2020, Elsevier, Come under creative commons (CC BY)). (e) HRTEM images of printex 25 carbon black heated at 2600 °C, reproduced with permission from ref. 3 (Copyright 2014, Elsevier, License number:5357140785094), (f) HRTEM image catalytic graphitized biomass-based graphite interface with FeCo alloy face-centered cubic structure FeCo110 and the graphene layers of graphite G(002) (licensed under Creative Commons Attribution-Noncommercial 3.0 Unported Licence, reproduced with permission from the Royal Society of Chemistry ref. 113), (g) selected area electron diffraction (SAED) patterns of graphite prepared from the rice straw reproduced with permission from ref. 114 ((Copyright 2017) American Chemical Society). | |
Similarly, the pyrolysis of silica rich biomasses such as rice husk,104,105 miscanthus and switch grasses,89 and bamboo leaves106 also result in amorphous carbons due to the presence of a higher ash content. Interestingly, these silica rich biomass-based biocarbons are well explored for supercapacitor applications and CO2 adsorption applications.105–107 Recently reported rice hull-derived silicon–carbon-based supercapacitor depicted 99% regeneration efficiency, which is very significant as a new generation sustainable energy material.108
As most of the carbon blacks were introduced for reinforcement applications in polymers specifically based on the requirements for achieving higher surface area and lower particle size, low pyrolysis temperature was chosen and hence less graphitization observed. Similar to the pyrolysis temperature, the electromechanical characteristics of the synthesis process also affect the molecular orientation in a polymer feedstock to promote its graphitization.109 The graphitization of the carbon black was well explored even from 1954 and found that the higher temperature promoted the graphitization; this was confirmed using XRD and Raman analysis.2,3,110 It was proven that the graphitization of the carbon black destroyed the compatibility with elastomer matrices.111
According to Marsh Griffith model for carbonization, aromatic carbon contents increase with temperature, as shown in Fig. 5(d). Above 700 °C temperature, carbon is present as amorphous carbon with sp1, sp2, and sp3 bonds without any stacking. When the temperature increases from 700 °C to 1200 °C, the carbon bonding changes into the sp2 hybridized state. Further increment in temperature from 1400 °C to 1700 °C causes the formation of nongraphitic carbon. Above 1700 °C, the nongraphitic carbon changes into graphene sheets, which organize in ordered stacks. Depending upon the feedstock type, this can vary due to differences in the bonding, networking abilities, and the defects present in the nongraphitic and graphitic phase. The aforementioned characteristic transformation of the various carbon phases can be scrutinized using diffraction and spectroscopic analysis.112 Raman spectroscopy is applied to study the degree of graphitization in carbonaceous materials.115 Due to the vibration of sp2 hybridized carbons, highly graphitized biocarbon materials have a sharp G peak around at about cm−1 and a symmetrical 2D peak at about 2700 cm−1 in the Raman spectra,116 whereas biocarbons dominating with ungraphitized (defect) carbons have a D peak, which appears at about 1350 cm−1.117
HRTEM images of printex 25 carbon black heated at 2500 °C is given in Fig. 5(e).3 As the biomass shows a nongraphitizable nature, an enhancement in the degree of graphitization can accompany the addition of certain inorganic and organic additives. The overall effect is to lower the temperature needed to bring about a certain degree of graphitization. Group 4 to 7 metals such as Al, Cr, Co, and Fe promote graphitization in carbonaceous materials.118Fig. 5(f) shows a graphitized biocarbon prepared from miscanthus grass by in situ generated FeCo nanoparticles.113 Xiao and Chen presented fine aromatic clusters of graphitic carbon derived from rice straw.114 The highlight of their graphitization is the removal of ash particles using suitable solvents and extracting the graphitic layers from that solution, thus converting the nongraphitizable carbon into a graphitizable one without utilizing any catalysts. To support the crystalline characteristics of a graphitic carbon prepared from rice straw, the SAED pattern is represented in Fig. 5(g).119
4.6. Ash content
The presence of ash is less than 5% in carbon black, which usually comes from the cooling water or sulfur present in the feedstock or sometimes added for controlling the structure.21 Unlike carbon black, biocarbon possesses a high amount of ash, which varies in the range of 5–30% depending upon the type of biomass.29 Biomass contains different amounts of inorganic materials, including alkali and heavy metals along with chlorine, phosphorous, and sulphur, collectively called as ash and based on biomass; the ash content follows the order sludge > animal waste > crop residues > wood.53 The ash content of biomass increases with the pyrolysis temperature and results in a lower carbon content.54 In addition to this, ash contributes in preventing the graphitization of biocarbon;83 hence, the proper washing of biomass before pyrolysis or after pyrolysis in the form of biocarbon can reduce the ash content.114
5. Applications of carbon black and biocarbon
5.1. Reinforcing filler in composites
The term ‘reinforcing filler’ denotes the action of fillers in polymer matrices, resulting in improved physicomechanical properties, especially the tensile strength and modulus properties.47 The first filler particle recognized with the reinforcing effect was carbon black in the rubber matrix. As compared to other fillers used in elastomers, carbon black is outstanding due to the excellent compatibility in hydrocarbon matrices without the use of any coupling agents.73 The factors affecting the reinforcing properties of fillers are particle size, porosity, structure, functionality, and degree of graphitization, as explained before.120 Since elastomeric matrices reveal disordered amorphous nature, the incorporation of reinforcing fillers is inevitable. The addition of biocarbon in elastomeric matrices such as natural rubber and styrene butadiene rubber were explored previously and observed a reduction in the tensile strength properties as compared to carbon black.90,121 Similarly, a recent work on the partial replacement of carbon black with biocarbon in the natural rubber matrix also revealed a reduction in tensile strength properties and lower crosslink density due to the larger particle size of biocarbon than the carbon black-filled natural rubber matrix.122 It is clear that to achieve higher tensile strength in elastomer matrices, the lower particle size is very significant and is achieved only through the utilization of pyrolysis of biooil similar to carbon black.75
As compared to the elastomer matrices, biocarbon is well explored in thermoplastic matrices.97,123 Similar to the reinforcing ability, the cost effectiveness and sustainability were the highlights of those research.124 As compared to the elastomer matrices, thermoplastic matrices showed better tensile modulus and flexural properties with the incorporation of biocarbon and which will additionally have tensile strength if both the compatibility and particle size of filler favor. However, the reinforcing ability of the biocarbon was actually observed in thermosetting plastics and comparatively crystalline matrices, where the negative effects of higher particle size was overcome by the strong intermolecular forces present between the polymer chains. Giorcelli and Bartoli reported that the coffee biochar-reinforced epoxy plastic depicted a significant increase in the tensile strength and modulus than the carbon black composites at 15 wt% of filler addition.125 Similarly, Gortari et al. studied polyphthalamide (PPA)-based thermoplastic matrix and concluded that the addition 30 phr of biocarbon revealed a slight improvement in tensile strength and excellent tensile modulus as compared to neat PPA, thus confirming the reinforcing ability of biocarbon in crystalline matrices.126
Similar to the characteristics of matrix, the matrix–filler interface is also important in determining the performance.5,127–129 Low-temperature pyrolyzed biocarbon shows good compatibility with the polar matrix and high temperature-pyrolyzed biocarbon possesses improved compatibility with nonpolar matrices.130 In addition to the functionality, physical characteristics such as size, porosity, and graphitization determine the opportunities and overall performance properties of the resulting composites. The reinforcement properties of biocarbon are not yet explored well, and the research on particle size reduction is still going on. Recently reported biooil-based biocarbon offers a huge scope in scaling up the lower-sized biocarbon particles without compromising any features of a reinforcing filler similar to carbon black.75 Even though lower-sized filler particles promote the tensile strength of polymer matrices, it is found that the impact strength properties of plastic composites based on medium-sized particles (20–75 μm) showed adequate improvement than the smaller-sized (<20 μm) biocarbon-based composites. This promotes the scope of biocarbon composites in impact strength properties even with comparatively medium-sized particles, which is also cost-effective in terms of post-processing.88
The reinforcement characteristics of carbon black is mostly explored in elastomer matrices and especially in tire applications.73,131 A plethora of literature available based on carbon black reinforcement in elastomer and plastic matrices.132,133 Carbon black is used in various range of applications and used as pigments, reinforcing filler, UV-resistant, and conductivity agent. The less amount of carbon black is found to be sufficient for coloring, conductive, and UV and thermal resistant applications, and 90% of carbon black is utilized as a reinforcing filler for elastomer matrices.1,47 The number of publications reported in the field of carbon black, biocarbon, and their composites from 1999 to 2019 are represented in Fig. 6. The research in the field of biocarbon was initiated in 1990s and slightly increased after 2009. Interestingly, based on the data available as per Web of Science, the biocarbon composites-related research articles published in the year 2019 significantly increased and reached almost half of the carbon black composites. This reveals a huge urge of the research community toward sustainable development through the utilization of green filler.
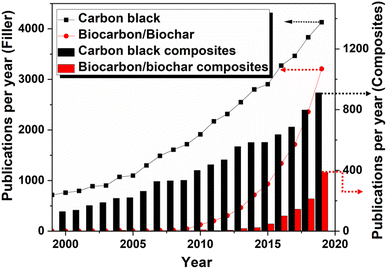 |
| Fig. 6 Number of publications per year (data acquired from Web of Science searched with keywords carbon black, biocarbon/biochar, carbon black composites, and biocarbon/biochar composites, accessed on 31st March, 2023). | |
5.2. Electrical applications of carbon black and biocarbon
Basically, the carbon black and biocarbon contains carbon present in the sp2 and sp3 hybridized state. The presence of more sp2 hybridized carbon indicates better graphitization; hence, the delocalized electron promotes electrical conductivity.134,135 Poor graphitic structure and low degree of graphitization allow less transmission of ions and electrons.136 Also, biomass has been considered as a nongraphitizing carbon precursor, Perepelkin reported an electrical conductivity increase closely by 12 orders of magnitude when increasing the heat treatment temperature of the biomass from 350 °C to 950 °C.137,138 Usually, with a decreasing amount of oxygen and sulphur-based functional groups, the conductivity rises. The conductivity was linked best with the polyaromatic nature of the carbon and aliphatic content.18 Carbon black reported an electrical conductivity from 101 to 102 S m−1, and highly-graphitized biocarbon reported a maximum of up to 102 S m−1 equivalent to biocarbon.46 The porosity of biocarbon as well as carbon black depicted a significant role in promoting the electrical resistivity due to the less packing of carbon layers, as shown in Fig. 7.138,139
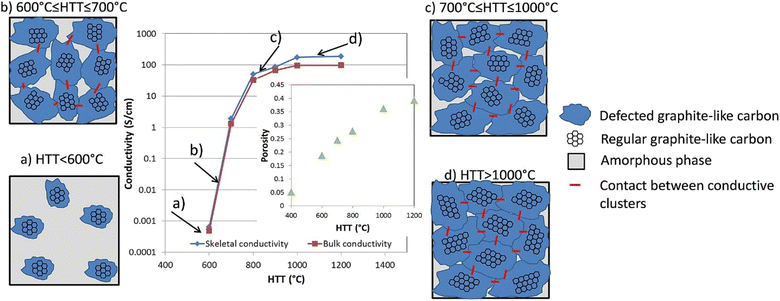 |
| Fig. 7 Scheme describing the conductivity development in biocarbons, reproduced with permission from ref. 138 (Copyright 2018, Elsevier, License number: 5357130750845). | |
In addition to the chemical characteristics of the carbon filler, its physical characteristics such as particle size and structure are also important while using it as a filler for electrical conductive applications. The lower particle size and higher structure promotes the creation of more conductive pathways in the matrix; hence, the highly structured furnace black and acetylene blacks possess very good conductivity. In both biocarbon and carbon black, the percolation threshold is an important factor, at which the conductivity of composites significantly increases due to the formation of continuous conductive networks, as shown in Fig. 8.140 Even though the pristine conductivity of biocarbon is comparable with the carbon black, the overall conductivity in polymer matrices reveals lower conductivity than carbon black due to poor dispersion.141,142
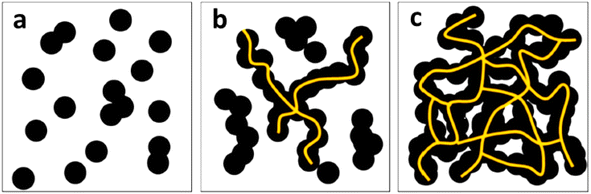 |
| Fig. 8 Schematic diagram showing the effect of filler loading and conductive network formation in carbon black composites, with (a) lower dosage, (b) medium, and (c) optimum loadings of carbon black depicting the percolation thresholds (reproduced with permission from ref. 140 (Copyright 2019, Springer Nature, licensed under a Creative Commons Attribution (CC BY) license)). | |
5.3. Thermal conductivity of carbon black and biocarbon
The thermal properties of carbon materials display a wide range of behaviors, which are related to their graphitic nature and their unique structure and size.143 The thermal conductivity of carbon materials vary from amorphous carbon to the highly crystalline carbon nanotubes (0.01 to 5000 W m−1 K−1), as shown in Fig. 9(d).144 A thermal conductivity in the range from 0.103 to 0.175 W m−1 K−1 was observed for peanut shell, miscanthus fiber, switch grass, and softwood chip-based biocarbon pyrolyzed at 500 °C.4,89 The higher thermal conductivity of 9.5 W m−1 K−1 was observed for highly graphitized wood biocarbon heat treated at high temperatures up to 2400 °C.145 The graphitization can also be achieved with catalytic way, in which metals such as Fe and Cu induce graphitization.146 In both electrical and thermal conductivities, the overall networking of filler across the matrix is the prominent factor in creating conducting channels.133,145,147 The lower particle size allows a higher dispersion of filler, and this causes enhanced conductivity with the incorporation of carbon black as compared to biochar in polymer matrices.148 When it comes to individual particles, graphitization is the major factor in allowing faster conduction.18,89
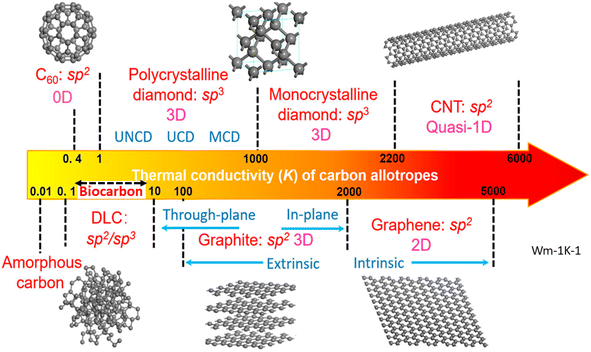 |
| Fig. 9 Thermal conductivity of carbon allotropes, modified with permission from ref. 144. (Copyright 2019, AIP Publishing, Licensed under a Creative Commons Attribution (CC BY) license). | |
5.4. Other applications
Soil amendment, energy and environmental remediation, and water purification are the widely used applications of biochar other than its composite applications.149,150 Low cost, ecofriendliness, lightness, high energy density, and long life cycle make biochar suitable for the large-scale production of lithium and sodium rechargeable batteries.151 The utilization of biochar to agriculture soil reduces the alkalinity, increases water retention capacity, and improves the soil properties, thus enhances the agriculture yields.152 The enhanced root elongation characteristics was noticed in wheat plants after the incorporation of multiwalled carbon nanotubes in growth facilities.153 Reis et al. reported the role of different biomasses in carbon electrode applications, mainly in battery and supercapacitors, and concluded that the performance of biomasses for all these applications directly depends on the characteristics of biocarbon.35 Similarly, porous carbons with controlled porosity and functionality depict a significant role as a carbon absorbent.154 As compared to modified/functionalized carbon black-based materials, biochar is advantageous in terms of the ecofriendly source and sustainable preparation strategy, and hence suitable for carbon capture and storage applications.155,156
6. Challenges and opportunities when black turns green
The main challenges associated with biomass feedstock is its nonuniformity and ash content.42 As the carbon black contains >95% carbon content, a higher carbon percentage is essential for a suitable alternative filler.21,157 Carbon black has projected an increased demand in the future as a reinforcing filler in the polymer composite application.1 While considering the nonhomogenous properties of biocarbon composites, the future of biocarbon as a reinforcing filler is challenging. To reduce the variation in the properties in terms of the mechanical characteristics, the existing solution is the proper selection of biocarbon type and dosage for specific polymer matrix. For example, the utilization of biocarbon in lower modulus amorphous matrices such as elastomers can result in a huge variation, unlike thermosetting polymers and comparatively crystalline polymers such as epoxy and polyphthalamide (PPA), respectively.87,121,126,158,159 The higher intermolecular force of attraction between the crystalline matrices cover up the nonhomogeneity in the filler shape and size; at the same time, fillers present in between the interconnected polymer crosslinks improve its load carrying capacity.
Very few literature is reported addressing the issues associated with the large scale production and technical viability of sustainable carbon filler as compared to carbon black. The macrosized biocarbon filler studied so far is scalable and very cost effective. Although biocarbon is produced in different ways to achieve carbon black equivalent properties in the past few years, there is still much to do for narrowing the gap between biocarbon and carbon black in terms of properties.86,88,160,161 The utilization of biochar in plastic matrices revealed a similar performance in terms of thermal characteristics and lower tensile strength properties. Interestingly, the modulus properties were shown significant improvement with the addition of biocarbon than the carbon black composites. Hence, biocarbon composites are utilized in automotive part fabrications and commodity plastic production. When it comes to comparable tensile strength properties similar to carbon black, especially in elastomer matrices, the compromise in technical properties (nanosize and network structure) will lead to inferior performance and hence fails as a replacement for carbon black. Recently reported nanoforms of sustainable carbons such as CNTs, graphenes, carbon black, and nanodots are appreciable in terms of their environmental friendliness, cost effectiveness, green chemistry preparation pathways, and, more importantly, the nanosize. In terms of the process, carbon black production is adaptable as it supports large scale production and hence is industrially accepted.47,162,163 The uniqueness and gravity of this issue is associated with the utilization of the liquid petro-source, which could be replaced by the waste oils or biooil produced by the pyrolysis of waste biomasses.48,164 Biooil can be prepared by the conventional pyrolysis process through fast pyrolysis. The established production strategies in the bioCNT fillers' preparation or the preparation of graphene from biographite can be used as a model for ideal nanobiocarbon synthesis.42,165,166 By replicating and modifying the existing methodologies, better sustainable strategies can be introduced. The large scale production of sustainable carbon filler is less discussed so far, which limits its acceptance and utilization in the global market. Very few research works reported the network-like morphology with a nanosize, similar to carbon black, which was also indicated as it is scalable. This is a remarkable achievement in achieving the carbon black-like technical and economic viability with less carbon footprint.
Moreover, priorities should always be given to value-added applications, especially when the hydrocarbons are utilized as a carbon source and also natural resources should not influence the food chain.167 Negotiations are also essential when the carbon architecture and its architecture-induced properties are unique and significantly depend on the source's uniformity as in hydrocarbons and the molecular freedom due to the liquid(/gas) of the feedstock. In addition to this, graphitized biocarbon can be used as a graphite source, and the exfoliation of graphite will result in graphene layers, which can be used as a better sustainable version than carbon black.168,169
Another sustainable approach to prepare carbon black-like carbon from waste is the utilization of waste tires as a feedstock for pyrolysis. Verma et al. reported the production of such ecofriendly carbon and utilized in epoxy matrix for improved mechanical properties.170
7. Conclusion
Toward the replacement of petro-based carbon filler using sustainable biocarbon, the most challenging phase is in achieving the chemical and physical characteristics equivalent to carbon black. As ‘carbon black’ includes a group of fillers having specific properties designed for particular applications, biocarbon can also be tuned based on particle size, functionality, structure, etc., through proper process optimization and selection of biomass. The biocarbon filler is beneficial than carbon black in terms of its sustainability and cost effectiveness. Moreover, biocarbon revealed better reinforcement in thermosetting plastics and crystalline matrices. However, the reinforcing ability of biocarbon in elastomer matrices are still inferior to carbon black due to larger particle size. Since the conventional biocarbon preparation utilizes a solid feedstock and follows a top-down approach of filler preparation, it is difficult to achieve smaller particles. The utilization of biomass-derived biooil as a feedstock, adopting carbon black preparation strategies, can overcome the morphological barrier of biocarbon. Similarly, lignin-derived biocarbon also revealed the network structure, which was helpful in reinforcement in the elastomeric matrix. Based on the seminal work on carbon reported in 1951 by Franklin,83,84 biomass-derived carbon was categorized as a nongraphitizable carbon. However, recent studies on pre- and post-pyrolysis treatment such as catalytic graphitization and acid washing strategies can solve the fundamental issues of nongraphitisability of biocarbon up to a certain extent. Moreover, the biooil-derived biocarbon can help in improved graphitization due to the lower percentage of minerals present as ash. In terms of functionality, biocarbon can be easily modified similar to carbon black through temperature tuning and post treatments. Tuning the strategies to achieve chemical and physical characteristics of biocarbon equivalent to carbon black can lead to an economic and environment-friendly carbon filler suitable for developing sustainable composites.
Conflicts of interest
There are no conflicts to declare.
Acknowledgements
The authors acknowledge the financial support from (i) The Natural Sciences and Engineering Research Council of Canada (NSERC), Collaborative Research and Development Grants (CRD) Program Project no. 401637 with the partner industries Prism Farms Limited and Competitive Green Technologies, Lamington, Ontario, Canada; (ii) the NSERC, Canada Research Chair (CRC) Program Project No. 460788; (iii) the NSERC, Canada Discovery Grants Project no. 401111; and (iv) the Ontario Agri-Food Innovation Alliance – Bioeconomy for Industrial Uses Research Program Project no. 100038. This study has also benefited from the facility funding to the Bioproducts Discovery and Development Centre, University of Guelph supported by FedDev Ontario, Canada; OMAFRA Canada; the Canada Foundation for Innovation (CFI); Federal Post-Secondary Institutions Strategic Investment Fund (SIF), Canada; and Bank of Montreal (BMO).
References
- N. Roy, R. Sengupta and A. K. Bhowmick, Modifications of carbon for polymer composites and nanocomposites, Prog. Polym. Sci., 2012, 37(6), 781–819, DOI:10.1016/j.progpolymsci.2012.02.002.
- C. R. Houska and B. E. Warren, X-ray study of the graphitization of carbon black, J. Appl. Phys., 1954, 25(12), 1503–1509 CrossRef CAS.
-
M. Pawlyta, J.-N. Rouzaud and S. Duber, in Raman Microspectroscopy Characterization of Carbon Blacks : Spectral Analysis and Structural Information, 2014 Search PubMed.
- M. Picard, S. Thakur, M. Misra, D. F. Mielewski and A. K. Mohanty, Biocarbon from peanut hulls and their green composites with biobased poly(trimethylene terephthalate) (PTT), Sci. Rep., 2020, 10(1), 1–14 CrossRef PubMed.
- A. K. Mohanty, S. Vivekanandhan, J. M. Pin and M. Misra, Composites from renewable and sustainable resources: Challenges and innovations, Science, 2018, 362, 536–542 CrossRef CAS PubMed.
- A. S. Barnard, Partnerships for sustainable nanotechnology, Mater. Today, 2009, 12(6), 47, DOI:10.1016/S1369-7021(09)70184-1.
- P. Tosi, G. P. M. van Klink, C. Hurel, C. Lomenech, A. Celzard and V. Fierro,
et al., Investigating the properties of humins foams, the porous carbonaceous materials derived from biorefinery by-products, Appl. Mater. Today, 2020, 20, 100622, DOI:10.1016/j.apmt.2020.100622.
- D. M. Smith, B. Hamwi and R. E. Rogers, Carbon nanomaterial-based aerogels for improved removal of copper(II), zinc(II), and lead(II) ions from water, Environ. Sci.: Adv., 2022, 1(2), 208–215 Search PubMed.
- Z. Mohammed, S. Jeelani and V. Rangari, Effective reinforcement of engineered sustainable biochar carbon for 3D printed polypropylene biocomposites, Compos., Part C: Open Access, 2022, 7, 100221, DOI:10.1016/j.jcomc.2021.100221.
- S. Babu, R. Singh, S. Kumar, S. S. R. D. Yadav, S. K. Yadav and V. Yadav,
et al., Biochar implications in cleaner agricultural production and environmental sustainability, Environ. Sci.: Adv., 2023, 115(1), 1–7 Search PubMed.
- Y. Zhang, M. He, L. Wang, J. Yan, B. Ma and X. Zhu,
et al., Biochar as construction materials for achieving carbon neutrality, Biochar, 2022, 4(1), 1–25, DOI:10.1007/s42773-022-00182-x.
- S. Ahmad, R. Singh, T. Arfin and K. Neeti, Fluoride contamination, consequences and removal techniques in water: a review, Environ. Sci.: Adv., 2022, 1(5), 620–661 Search PubMed.
- S. Cairns, A. Todd, I. Robertson, P. Byrne and T. Dunlop, Treatment of mine water for the fast removal of zinc and lead by wood ash amended biochar, Environ. Sci.: Adv., 2022, 1(4), 506–516 Search PubMed.
- T. A. Tengku Yasim-Anuar, L. N. Yee-Foong, A. A. Lawal, M. A. Ahmad Farid, M. Z. Mohd Yusuf and M. A. Hassan,
et al., Emerging application of biochar as a renewable and superior filler in polymer composites, RSC Adv., 2022, 12(22), 13938–13949 RSC.
- W. J. Liu, H. Jiang and H. Q. Yu, Development of Biochar-Based Functional Materials: Toward a Sustainable Platform Carbon Material, Chem. Rev., 2015, 115(22), 12251–12285 CrossRef CAS PubMed.
- A. Rodriguez-Uribe, M. R. Snowdon, M. A. Abdelwahab, A. Codou, M. Misra and A. K. Mohanty, Impact of renewable carbon on the properties of composites made by using three types of polymers having different polarity, J. Appl. Polym. Sci., 2020, 1–15 Search PubMed.
- E. Watt, M. A. Abdelwahab, M. R. Snowdon, A. K. Mohanty, H. Khalil and M. Misra, Hybrid biocomposites from polypropylene, sustainable biocarbon and graphene nanoplatelets, Sci. Rep., 2020, 10(1), 1–13, DOI:10.1038/s41598-020-66855-4.
- D. Pantea, H. Darmstadt, S. Kaliaguine, L. Sümmchen and C. Roy, Electrical conductivity of thermal carbon blacks: Influence of surface chemistry, Carbon, 2001, 39(8), 1147–1158 CrossRef CAS.
- D. W. Kim, H. S. Kil, J. Kim, I. Mochida, K. Nakabayashi and C. K. Rhee,
et al., Highly graphitized carbon from non-graphitizable raw material and its formation mechanism based on domain theory, Carbon, 2017, 121, 301–308, DOI:10.1016/j.carbon.2017.05.086.
- M. Demir, Z. Kahveci, B. Aksoy, N. K. R. Palapati, A. Subramanian and H. T. Cullinan,
et al., Graphitic Biocarbon from Metal-Catalyzed Hydrothermal Carbonization of Lignin, Ind. Eng. Chem. Res., 2015, 54(43), 10731–10739 CrossRef CAS.
- S. Khodabakhshi, P. F. Fulvio and E. Andreoli, Carbon black reborn: Structure and chemistry for renewable energy harnessing, Carbon, 2020, 162, 604–649, DOI:10.1016/j.carbon.2020.02.058.
- P. J. F. Harris, Structure of non-graphitising carbons, Int. Mater. Rev., 1997, 42(5), 206–218 CrossRef CAS.
- T. Koga, M. Takenaka, K. Aizawa, M. Nakamura and T. Hashimoto, Structure factors of dispersible units of carbon black filler in rubbers, Langmuir, 2005, 21(24), 11409–11413 CrossRef CAS PubMed.
- M. Wang, D. G. Roberts, M. A. Kochanek, D. J. Harris, L. Chang and C. Z. Li, Raman spectroscopic investigations into links between intrinsic reactivity and char chemical structure, Energy Fuels, 2014, 28(1), 285–290 CrossRef CAS.
- W. Xu, T. W. Zerda, H. Raab and D. Goritz, 3-D morphological characterization of carbon black aggregates using atomic force microscopy, Carbon, 1997, 35(4), 471–474 CrossRef CAS.
- Y. Sato, M. Kamo and N. Setaka, Raman spectra of carbons at 2600-3300 cm-1 region, Carbon, 1978, 16(4), 279–280 CrossRef CAS.
-
A. Mohanty, M. Manjusri, A. Rodriguez-Uribe and A. Bali, Renewable Replacement for Carbon Black in Composites and Methods of Making and Using Thereof, 2015, pp. 1–37 Search PubMed.
-
A. Mohanty, M. Manjusri, S. Vivekanandan, P. Gonugunta, T. Wang, A. Rodriguez-Uribe, et al., Methods For Creation Of Sub – Micron Biocarbon Materials From Biomass And Their Fields Of Application, 2022, pp. 1–25 Search PubMed.
- D. M. Paleri, A. Rodriguez-Uribe, M. Misra and A. K. Mohanty, Pyrolyzed biomass from corn ethanol industry coproduct and their polypropylene-based composites: Effect of heat treatment temperature on performance of the biocomposites, Composites, Part B, 2021, 215, 108714, DOI:10.1016/j.compositesb.2021.108714.
- B. P. Chang, A. K. Mohanty and M. Misra, Studies on durability of sustainable biobased composites: a review, RSC Adv., 2020, 10(31), 17955–17999 RSC.
- K. Sahoo, A. Upadhyay, T. Runge, R. Bergman, M. Puettmann and E. Bilek, Life-cycle assessment and techno-economic analysis of biochar produced from forest residues using portable system, Int. J. Life Cycle Assess., 2021, 26(1), 189–213 CrossRef.
- R. Bergman, K. Sahoo, K. Englund and S. H. Mousavi-Avval, Lifecycle Assessment and Techno-Economic Analysis of Biochar Pellet Production from Forest Residues and Field Application, Energies, 2022, 15(4), 1–18 CrossRef.
- P. Roy, A. K. Mohanty and M. Misra, Prospects of carbon capture, utilization and storage for mitigating climate change, Environ. Sci.: Adv., 2023, 2(3), 409–423 Search PubMed.
- K. Chojnacka, K. Moustakas and A. Witek-Krowiak, Bio-based fertilizers: A practical approach towards circular economy, Bioresour. Technol., 2020, 295, 122223, DOI:10.1016/j.biortech.2019.122223.
- G. S. Dos Reis, S. H. Larsson, H. P. de Oliveira, M. Thyrel and E. C. Lima, Sustainable biomass activated carbons as electrodes for battery and supercapacitors–a mini-review, Nanomaterials, 2020, 10(7), 1–22 CrossRef PubMed.
- Y. Yi, Z. Huang, B. Lu, J. Xian, E. P. Tsang and W. Cheng,
et al., Magnetic biochar for environmental remediation: A review, Bioresour. Technol., 2019, 298, 122468 CrossRef PubMed.
- R. Ahmed, G. Liu, B. Yousaf, Q. Abbas, H. Ullah and M. U. Ali, Recent advances in carbon-based renewable adsorbent for selective carbon dioxide capture and separation-A review, J. Cleaner Prod., 2020, 242, 118409, DOI:10.1016/j.jclepro.2019.118409.
- Y. Li, B. Xing, Y. Ding, X. Han and S. Wang, A critical review of the production and advanced utilization of biochar via selective pyrolysis of lignocellulosic biomass, Bioresour. Technol., 2020, 312, 123614, DOI:10.1016/j.biortech.2020.123614.
- Y. Zhu, C. Romain and C. K. Williams, Sustainable polymers from renewable resources, Nature, 2016, 540(7633), 354–362 CrossRef CAS PubMed.
- T. Narancic, F. Cerrone, N. Beagan and K. E. O’Connor, Recent advances in bioplastics: Application and biodegradation, Polymers, 2020, 12(4), 1–38 CrossRef PubMed.
- C. M. Long, M. A. Nascarella and P. A. Valberg, Carbon black vs. black carbon and other airborne materials containing elemental carbon: Physical and chemical distinctions, Environ. Pollut., 2013, 181, 271–286, DOI:10.1016/j.envpol.2013.06.009.
- Z. Wang, D. Shen, C. Wu and S. Gu, State-of-the-art on the production and application of carbon nanomaterials from biomass, Green Chem., 2018, 20(22), 5031–5057 RSC.
- K. Bazaka, M. V. Jacob and K. Ostrikov, Sustainable Life Cycles of Natural-Precursor-Derived Nanocarbons, Chem. Rev., 2016, 116(1), 163–214 CrossRef CAS PubMed.
-
IEA, Global CO2 Emissions in 2019, 2019, p. 1, Available from: https://www.iea.org/articles/global-co2-emissions-in-2019 Search PubMed.
- J. Arroyo and C. Ryan, Incorporation of Carbon Nanofillers Tunes Mechanical and Electrical Percolation in PHBV:PLA Blends, Polymers, 2018, 10(12), 1371 CrossRef PubMed.
- M. R. Snowdon, A. K. Mohanty and M. Misra, A study of carbonized lignin as an alternative to carbon black, ACS Sustainable Chem. Eng., 2014, 2(5), 1257–1263 CrossRef CAS.
- Y. Fan, G. D. Fowler and M. Zhao, The past, present and future of carbon black as a rubber reinforcing filler – A review, J. Cleaner Prod., 2020, 247, 119115, DOI:10.1016/j.jclepro.2019.119115.
-
J. B. Donnet, R. C. Bansal and M.-J. Wang. Carbon Black: Science and Technology, CRC Press, 1993, p. 461, Available from: https://books.google.com/books?id=SPpx6MkRYwMC%26pgis=1 Search PubMed.
- K.A. Aderogba and K.A. Adeniy, Charcoal Production and Energy Resources in Western Nigeria : Issues and Challenges for Sustainable Development, Savanna Journal of Basic and Applied Sciences, 2019, 1(1), 111–120 Search PubMed.
- S. Scott, On the mechanism of the rapid pyrolysis of cellulose, J. Anal. Appl. Pyrolysis, 1986, 9, 121–137 CrossRef.
- D. Matykiewicz, Biochar as an effective filler of carbon fiber reinforced bio-epoxy composites, Processes, 2020, 8(6), 1–13 CrossRef.
- M. N. F. Norrrahim, M. A. A. Farid, A. A. Lawal, T. A. Tengku Yasim-Anuar, M. H. Samsudin and A. A. Zulkifli, Emerging technologies for value-added use of oil palm biomass, Environ. Sci.: Adv., 2022, 1(3), 259–275 Search PubMed.
- L. Wang, Y. S. Ok, D. C. W. Tsang, D. S. Alessi, J. Rinklebe and H. Wang,
et al., New trends in biochar pyrolysis and modification strategies: feedstock, pyrolysis conditions, sustainability concerns and implications for soil amendment, Soil Use Manage., 2020, 36(3), 358–386 CrossRef.
-
F. Ronsse, R. W. Nachenius and W. Prins. Carbonization of
Biomass, Recent Advances in Thermochemical Conversion of Biomass, Elsevier B.V., 2015, pp. 293–324, Available from: DOI:10.1016/B978-0-444-63289-0.00011-9.
-
Biofuels and Biorefi Neries 9 Production of Materials from Sustainable Biomass Resources, ed. R. L. Smith and Z. Xiao-Feii Tian, available from: http://www.springer.com/series/11687 Search PubMed.
- L. Zhao, X. Cao, O. Mašek and A. Zimmerman, Heterogeneity of biochar properties as a function of feedstock sources and production temperatures, J. Hazard. Mater., 2013, 256–257, 1–9 CAS.
- Z. A. Mansurov, Formation of soot from polycyclic aromatic hydrocarbons as well as fullerenes and carbon nanotubes in the combustion of hydrocarbon, J. Eng. Phys. Thermophys., 2011, 84(1), 125–159 CrossRef CAS.
- C. Backes and M. Garcia-Hernandez, Production and processing of graphene and related materials, 2D Mater., 2020, 7(2), 1–282 Search PubMed.
- G. SriBala, H. H. Carstensen, K. M. Van Geem and G. B. Marin, Measuring Biomass Fast Pyrolysis Kinetics: State of the Art, Wiley Interdiscip. Rev.: Energy Environ., 2019, 8, 1–45 Search PubMed.
- W. M. Lewandowski and M. Ryms, Thermal Biomass Conversion: A Review, Processes, 2020, 8(516), 1–45 Search PubMed.
- H. Yang, R. Yan, H. Chen, D. H. Lee and C. Zheng, Characteristics of hemicellulose, cellulose and lignin pyrolysis, Fuel, 2007, 86(12–13), 1781–1788 CrossRef CAS.
- T. Cordero, F. Marquez, J. Rodriguez-Mirasol and J. Rodriguez, Predicting heating values of lignocellulosics and carbonaceous materials from proximate analysis, Fuel, 2001, 80(11), 1567–1571 CrossRef CAS.
- T. Wang, A. Rodriguez-Uribe, M. Misra and A. K. Mohanty, Sustainable Carbonaceous Biofiller from Miscanthus: Size Reduction, Characterization, and Potential Bio-composites Applications, BioResources, 2018, 13(2), 3720–3739 CAS.
- C. Jäger, T. Henning, R. Schlögl and O. Spillecke, Spectral properties of carbon black, J. Non-Cryst. Solids, 1999, 258(1), 161–179 CrossRef.
-
A. C. Sansevero and Y. Ruddy, Carbon-Containing Polymer Composites, Critical Care Nurse. Springer Singapore; 2019. vol. 16, pp. 65–98, Available from: https://link.springer.com/chapter/10.1007/978-981-13-2688-2_2%0Ahttp://link.springer.com/10.1007/978-981-13-2688-2 Search PubMed.
- M. Tripathi, J. N. Sahu and P. Ganesan, Effect of process parameters on production of biochar from biomass waste through pyrolysis: A review, Renewable Sustainable Energy Rev., 2016, 55, 467–481, DOI:10.1016/j.rser.2015.10.122.
- D. K. Shen and S. Gu, The mechanism for thermal decomposition of cellulose and its main products, Bioresour. Technol., 2009, 100(24), 6496–6504, DOI:10.1016/j.biortech.2009.06.095.
- L. Karasek and M. Sumita, Characterization of dispersion state of filler and polymer-filler interactions in rubber-carbon black composites, J. Mater. Sci., 2005, 31(2), 281–289 CrossRef.
- J. H. L. Watson, An Effect of Electron Bombardment upon Carbon Black · Contributed Original Research An Effect of Electron Bombardment upon Carbon Black, J. Appl. Phys., 2008, 153, 153–161 Search PubMed.
- W. B. Wiegand and W. A. Ladd, Colloidal Carbon as Revealed by the Electron Microscope, Rubber Chem. Technol., 1942, 15(3), 664–671 CrossRef.
- C. H. Leigh-Dugmore, Carbon black particle size, Rubber Chem. Technol., 1953, 26(4), 912–918 CrossRef CAS.
- J. Turkeyich and J. Hillier, Electron Microscopy of Colloidal Systems, Anal. Chem., 1949, 21(4), 475–485 CrossRef.
-
Fillers for Polymer Applications, ed. Rothon R., Springer, Berlin, Germany, 2017 Search PubMed.
- Z. Li, C. Reimer, M. Picard, A. K. Mohanty and M. Misra, Characterization of Chicken Feather Biocarbon for Use in Sustainable Biocomposites, Front. Mater., 2020, 7, 1–12 CrossRef.
- P. Toth, T. Vikström, R. Molinder and H. Wiinikka, Structure of carbon black continuously produced from biomass pyrolysis oil, Green Chem., 2018, 20(17), 3981–3992 RSC.
- K. Arato, J. Li, P. V. Hobbs and P. R. Buseck, Atmospheric tar balls : Particles from biomass and biofuel burning, J. Geophys. Res., 2004, 109, 1–9 Search PubMed.
- Y. Fan, G. D. Fowler and M. Zhao, The past, present and future of carbon black as a rubber reinforcing filler – A review, J. Cleaner Prod., 2020, 247, 119115 CrossRef CAS.
- W. A. Kyei-Manu, C. R. Herd, M. Chowdhury, B. JJC and L. B. Tunnicliffe, The Influence of Colloidal Properties of Carbon Black on Static and Dynamic Mechanical Properties of Natural Rubber, Polymers, 2022, 14(6), 1–19 CrossRef PubMed.
- O. A. Al-Hartomy, F. Al-Solamy, A. Al-Ghamdi, N. Dishovsky, M. Ivanov and M. Mihaylov,
et al., Influence of carbon black structure and specific surface area on the mechanical and dielectric properties of filled rubber composites, Int. J. Polym. Sci., 2011, 2011, 1–9 Search PubMed.
- C. Jiang, J. Bo, X. Xiao, S. Zhang, Z. Wang and G. Yan,
et al., Converting waste lignin into nano-biochar as a renewable substitute of carbon black for reinforcing styrene-butadiene rubber, Waste Manage., 2020, 102, 732–742, DOI:10.1016/j.wasman.2019.11.019.
- J. Lee, K. Kim and E. E. Kwon, Biochar as a Catalyst, Renewable Sustainable Energy Rev., 2017, 77, 70–79, DOI:10.1016/j.rser.2017.04.002.
- K. Weber and P. Quicker, Properties of biochar, Fuel, 2018, 217, 240–261, DOI:10.1016/j.fuel.2017.12.054.
- P. J. F. Harris, Rosalind Franklin's work on coal, carbon, and graphite, Interdiscip. Sci. Rev., 2001, 26(3), 204–209 CrossRef.
- R. E. Franklin, Study of the fine structure of carbonaceous solids by measurements of true and apparent densities: Part I. Coals, Trans. Faraday Soc., 1949, 45(668), 274–286 RSC.
-
Biochar and Soil Physical Health. Biochar - an Imperative Amendment for Soil and the Environment, ed. Abrol V. and Sharma P., Intech Open, London, UK, 2019 Search PubMed.
- W.-J. Liu, H. Jiang and H.-Q. Yu, Development of Biochar-Based Functional Materials: Toward a Sustainable Platform Carbon Material, Chem. Rev., 2015, 115(22), 12251–12285 CrossRef CAS PubMed.
- E. O. Ogunsona, M. Misra and A. K. Mohanty, Sustainable biocomposites from biobased polyamide 6,10 and biocarbon from pyrolyzed miscanthus fibers, J. Appl. Polym. Sci., 2017, 134(4), 1–11 CrossRef.
- V. Nagarajan, A. K. Mohanty and M. Misra, Biocomposites with Size-Fractionated Biocarbon: Influence of the Microstructure on Macroscopic Properties, ACS Omega, 2016, 1(4), 636–647 CrossRef CAS PubMed.
- E. Behazin, E. Ogunsona, A. Rodriguez-Uribe, A. K. Mohanty, M. Misra and A. O. Anyia, Biochars for composites, BioResources, 2016, 11(1), 1334–1348 CAS.
- L. Jong, S. C. Peterson and M. A. Jackson, Utilization of Porous Carbons Derived from Coconut Shell and Wood in Natural Rubber, J. Polym. Environ., 2014, 22(3), 289–297 CrossRef CAS.
- J. H. Atkins, Porosity and surface area of carbon black, Carbon, 1965, 3, 299–303 CrossRef CAS.
- B. C. Barton and H. M. Smallwood, Chemistry in Carbon Black Dispersion, J. Appl. Polym. Sci., 1954, XIII(134), 487–498 CrossRef.
- R. S. Stearns and B. L. Johnson, Interaction between Carbon Black and Polymer in Cured Elastomers, Ind. Eng. Chem., 1951, 43(1), 146–154 CrossRef CAS.
- S. Mandal, S. Pu, S. Adhikari, H. Ma and D. Kim, Technology Progress and future prospects in biochar composites : Application and reflection in the soil environment, Crit. Rev. Environ. Sci. Technol., 2020, 1–53, DOI:10.1080/10643389.2020.1713030.
- E. O. Ogunsona, M. Misra and A. K. Mohanty, Influence of epoxidized natural rubber on the phase structure and toughening behavior of biocarbon reinforced nylon 6 biocomposites, RSC Adv., 2017, 7(15), 8727–8739 RSC.
- E. O. Ogunsona, M. Misra and A. K. Mohanty, Accelerated hydrothermal aging of biocarbon reinforced nylon biocomposites, Polym. Degrad. Stab., 2017, 139, 76–88, DOI:10.1016/j.polymdegradstab.2017.03.013.
- A. Codou, A. Anstey, M. Misra and A. K. Mohanty, Novel compatibilized nylon-based ternary blends with polypropylene and poly(lactic acid): Morphology evolution and rheological behaviour, RSC Adv., 2018, 8(28), 15709–15724 RSC.
- M. R. Snowdon, A. K. Mohanty and M. Misra, Miscibility and Performance Evaluation of Biocomposites Made from Polypropylene/Poly(lactic acid)/Poly(hydroxybutyrate-cohydroxyvalerate) with a Sustainable Biocarbon Filler, ACS Omega, 2017, 2(10), 6446–6454 CrossRef CAS PubMed.
- E. Behazin, M. Misra and A. K. Mohanty, Compatibilization of toughened polypropylene/biocarbon biocomposites: A full factorial design optimization of mechanical properties, Polym. Test., 2017, 61, 364–372, DOI:10.1016/j.polymertesting.2017.05.031.
- G. Singh, Y. Kim, K. S. Lakhi, S. Joseph, P. Srivastava and A. Vinu, Heteroatom functionalized activated porousbiocarbons and their excellent performance for CO2 capture at high pressure, J. Mater. Chem. A, 2017, 21196–21204 RSC.
- J. C. C. Freitas, T. J. Bonagamba and F. G. Emmerich, Investigation of biomass- and polymer-based carbon materials using 13C high-resolution solid-state NMR, Carbon, 2001, 39(4), 535–545 CrossRef CAS.
- R. M. Goody, Crystallite growth in graphitizing and non-graphitizing carbons, Proc. R. Soc. London, Ser. A, 1951, 209(1097), 196–218 Search PubMed.
- M. Shibuya, M. Kato, M. Ozawa, P. H. Fang and E. Ōsawa, Detection of Buckminsterfullerene in Usual Soots and Commercial Charcoals, Fullerene Sci. Technol., 1999, 7(2), 181–193 CrossRef CAS.
- Z. Chen, X. Wang, B. Xue, W. Li, Z. Ding and X. Yang,
et al., Rice husk-based hierarchical porous carbon for high performance supercapacitors : The structure-performance relationship, Carbon, 2020, 161, 432–444, DOI:10.1016/j.carbon.2020.01.088.
- H. Xu, B. Gao, H. Cao, X. Chen, L. Yu and K. Wu,
et al., Nanoporous activated carbon derived from rice husk for high performance supercapacitor, J. Nanomater., 2014, 2014, 1–8 Search PubMed.
- Y. Zhang, C. Wang, X. Chen, X. Dong, C. Meng and C. Huang, Bamboo Leaves as Sustainable Sources for the Preparation of Amorphous Carbon/Iron Silicate Anode and Nickel–Cobalt Silicate Cathode Materials for Hybrid Supercapacitors, ACS Appl. Energy Mater., 2021, 4(9), 9328–9340 CrossRef CAS.
- F. Gana, B. Wang, J. Ziheng, L. Xie, Z. Dai and T. Zhou,
et al., From typical silicon-rich biomass to porous carbon-zeolite composite: A sustainable approach for efficient adsorption of CO2, Sci. Total Environ., 2021, 768, 144529 CrossRef PubMed.
- C. Li, H. Chen, L. Zhang, S. Jiao, H. Zhang and J. Zhang,
et al., Rice Hull-Derived Carbon for Supercapacitors: Towards Sustainable Silicon-Carbon Supercapacitors, Polymers, 2021, 13(4463), 1–16 CAS.
- M. Ghazinejad, S. Holmberg, O. Pilloni, L. Oropeza-Ramos and M. Madou, Graphitizing Non-graphitizable Carbons by Stress-induced Routes, Sci. Rep., 2017, 7(1), 1–10 CrossRef CAS PubMed.
- L. Bokobza, J.-L. Bruneel and M. Couzi, Raman Spectra of Carbon-Based Materials (from Graphite to Carbon Black) and of Some Silicone Composites, C, 2015, 1(1), 77–94 Search PubMed.
-
R. Rothon, Particulate Fillers in Elastomers, in Fillers for Polymer Applications, Springer, Berlin, Germany, 2017, pp. 125–46 Search PubMed.
- D. B. Schuepfer, F. Badaczewski, J. M. Guerra-Castro, D. M. Hofmann, C. Heiliger and B. Smarsly,
et al., Assessing the structural properties of
graphitic and non-graphitic carbons by Raman spectroscopy, Carbon, 2020, 161, 359–372, DOI:10.1016/j.carbon.2019.12.094.
- I. Major, J. M. Pin, E. Behazin, A. Rodriguez-Uribe, M. Misra and A. Mohanty, Graphitization of Miscanthus grass biocarbon enhanced by in situ generated FeCo nanoparticles, Green Chem., 2018, 20(10), 2269–2278 RSC.
- X. Xiao and B. Chen, A Direct Observation of the Fine Aromatic Clusters and Molecular Structures of Biochars, Environ. Sci. Technol., 2017, 51(10), 5473–5482 CrossRef CAS PubMed.
- X. Kong, Y. Zhu, H. Lei, C. Wang, Y. Zhao and E. Huo,
et al., Synthesis of graphene-like carbon from biomass pyrolysis and its applications, Chem. Eng. J., 2020, 399, 125808, DOI:10.1016/j.cej.2020.125808.
- S. Roscher, R. Hoffmann and O. Ambacher, Determination of the graphene-graphite ratio of graphene powder by Raman 2D band symmetry analysis, Anal. Methods, 2019, 11(9), 1180–1191 RSC.
- W. Xueshen, L. Jinjin, Z. Qing, Z. Yuan and Z. Mengke, Thermal annealing of exfoliated graphene, J. Nanomater., 2013, 2013, 1–6 CrossRef.
- H. Marsh and A. P. Warburton, Catalysis of graphitisation, J. Appl. Chem., 2007, 20(4), 133–142 CrossRef.
- C. N. S. Kumar, V. S. K. Chakravadhanula, A. Riaz, S. Dehm, D. Wang and X. Mu,
et al., Understanding the graphitization and growth of free-standing nanocrystalline graphene using: In situ transmission electron microscopy, Nanoscale, 2017, 9(35), 12835–12842 RSC.
- W. D. Schaeffer, W. R. Smith and M. H. Polley, Structure and Properties of Carbon Black - Changes Induced by Heat Treatment, Ind. Eng. Chem., 1953, 45(8), 1721–1725 CrossRef CAS.
- S. C. Peterson and S. Kim, Reducing Biochar Particle Size with Nanosilica and Its Effect on Rubber Composite Reinforcement, J. Polym. Environ., 2020, 28, 317–322, DOI:10.1007/s10924-019-01604-x.
- D. M. Paleri, A. Rodriguez-Uribe, M. Misra and A. Mohanty, Preparation and characterization of eco-friendly hybrid biocomposites from natural rubber, biocarbon, and carbon black, eXPRESS Polym. Lett., 2020, 15(3), 236–249 CrossRef.
- T. Balint, B. P. Chang, A. K. Mohanty and M. Misra, Underutilized Agricultural Co-Product as a Sustainable Biofiller for Polyamide 6,6: Effect of Carbonization Temperature, Molecules, 2020, 25(6), 1455 CrossRef CAS PubMed.
- Q. Zhang, M. U. Khan, X. Lin, H. Cai and H. Lei, Temperature varied biochar as a reinforcing filler for high-density polyethylene composites, Composites, Part B, 2019, 175, 107151, DOI:10.1016/j.compositesb.2019.107151.
- M. Giorcelli and M. Bartoli, Development of coffee biochar filler for the production of electrical conductive reinforced plastic, Polymers, 2019, 11(12), 1–17 CrossRef PubMed.
- M. Gonzalez De Gortari, A. Rodriguez-Uribe, M. Misra and A. K. Mohanty, Insights on the structure-performance relationship of polyphthalamide (PPA) composites reinforced with high-temperature produced biocarbon, RSC Adv., 2020, 10(45), 26917–26927 RSC.
- A. K. Mohanty, M. Misra and L. T. Drzal, Sustainable Bio-Composites from renewable resources: Opportunities and challenges in the green materials world, J. Polym. Environ., 2002, 10(1–2), 19–26 CrossRef CAS.
- V. Nagarajan, A. K. Mohanty and M. Misra, Perspective on Polylactic Acid (PLA) based Sustainable Materials for Durable Applications: Focus on Toughness and Heat Resistance, ACS Sustainable Chem. Eng., 2016, 4(6), 2899–2916 CrossRef CAS.
- E. O. Ogunsona, M. Misra and A. K. Mohanty, Sustainable biocomposites from biobased polyamide 6,10 and biocarbon from pyrolyzed miscanthus fibers, J. Appl. Polym. Sci., 2017, 134(4), 1–11 CrossRef.
- E. O. Ogunsona, M. Misra and A. K. Mohanty, Impact of interfacial adhesion on the microstructure and property variations of biocarbons reinforced nylon 6 biocomposites, Composites, Part A, 2017, 98, 32–44, DOI:10.1016/j.compositesa.2017.03.011.
- C. G. Robertson and N. J. Hardman, Nature of carbon black reinforcement of rubber: Perspective on the original polymer nanocomposite, Polymers, 2021, 13(4), 1–28 CrossRef PubMed.
- G. Seo, D. Kim, S. J. Kim, C. Ryu, J. Yang and Y. Kang, Reinforcement of Rubber Properties by Carbon Black and Silica Fillers, A Review, Elastomers and composites, 2017, 52(2), 1–17 Search PubMed.
- I. Balberg, A comprehensive picture of the electrical phenomena in carbon black-polymer composites, Carbon, 2002, 40(2), 139–143 CrossRef CAS.
- J. Deng, Y. You, V. Sahajwalla and R. K. Joshi, Transforming waste into carbon-based nanomaterials, Carbon, 2016, 96, 105–115, DOI:10.1016/j.carbon.2015.09.033.
- C. Das, S. Tamrakar, A. Kiziltas and X. Xie, Incorporation of biochar to improve mechanical, thermal and electrical properties of polymer composites, Polymers, 2021, 13(16), 1–32 CrossRef PubMed.
- Q. Chen, X. Tan, Y. Liu, S. Liu, M. Li and Y. Gu,
et al., Biomass-derived porous graphitic carbon materials for energy and environmental applications, J. Mater. Chem. A, 2020, 8(12), 5773–5811 RSC.
- K. E. Perepelkin, Carbon fibres with specific physical and physicochemical properties based on hydrated cellulose and polyacrylonitrile precursors. A review, Fibre Chem., 2002, 34(4), 271–280 CrossRef CAS.
- Y. Shao, C. Guizani, P. Grosseau, D. Chaussy and D. Beneventi, Biocarbons from microfibrillated cellulose/lignosulfonate precursors: A study of electrical conductivity development during slow pyrolysis, Carbon, 2018, 129, 357–366, DOI:10.1016/j.carbon.2017.12.037.
- Z. Wu, W. Li, Y. Xia, P. Webley and D. Zhao, Ordered mesoporous graphitized pyrolytic carbon materials: Synthesis, graphitization, and electrochemical properties, J. Mater. Chem., 2012, 22(18), 8835–8845 RSC.
- H. J. Choi, M. S. Kim, D. Ahn, S. Y. Yeo and S. Lee, Electrical percolation threshold of carbon black in a polymer matrix and its application to antistatic fibre, Sci. Rep., 2019, 9(1), 1–12 CrossRef PubMed.
- N. Probst and E. Grivei, Structure and electrical properties of carbon black, Carbon, 2002, 40(2), 201–205 CrossRef CAS.
- S. Gupta, O.U. Runqing and R. A. Gerhardt, Effect of the fabrication method on the electrical properties of poly(acrylonitrile-co-butadiene-co-styrene)/carbon black composites, J. Electron. Mater., 2006, 35(2), 224–229 CrossRef CAS.
- J. Hone, Phonons and Thermal Properties of Carbon Nanotubes, Carbon Nanotubes, 2007, 286, 273–286 Search PubMed.
- Q. Yuan, C. T. Lin and K. W. A. Chee, All-carbon devices based on sp 2 -on-sp 3 configuration, APL Mater., 2019, 7(3), 1–5 Search PubMed.
- M. Yu, T. Saunders, T. Su, F. Gucci and M. J. Reece, Effect of heat treatment on the properties of wood-derived biocarbon structures, Materials, 2018, 11(9), 1–9 Search PubMed.
- A. Oya and H. Marsh, Review Phenomena of catalytic graphitization, J. Mater. Sci., 1982, 17, 309–322 CrossRef CAS.
- N. Nan, D. B. DeVallance, X. Xie and J. Wang, The effect of bio-carbon addition on the electrical, mechanical, and thermal properties of polyvinyl alcohol/biochar composites, J. Compos. Mater., 2016, 50(9), 1161–1168 CrossRef CAS.
- Y. Agari and T. Uno, Thermal conductivity of polymer filled with carbon materials: Effect of conductive particle chains on thermal conductivity, J. Appl. Polym. Sci., 1985, 30(5), 2225–2235 CrossRef CAS.
- N. L. P. Ashish and P. B. L. Salvi, Comprehensive review on production and utilization of biochar, SN Appl. Sci., 2019, 1(2), 1–19, DOI:10.1007/s42452-019-0172-6.
- N. Chen and S. Pilla, A comprehensive review on transforming lignocellulosic materials into biocarbon and its utilization for composites applications, Compos., Part C: Open Access, 2022, 7, 100225, DOI:10.1016/j.jcomc.2021.100225.
- A. Pistone and C. Espro, Current trends on turning biomass wastes into carbon materials for electrochemical sensing and rechargeable battery applications, Curr. Opin. Green Sustainable Chem., 2020, 26, 100374, DOI:10.1016/j.cogsc.2020.100374.
- X. Guo, H. Liu and J. Zhang, The role of biochar in organic waste composting and soil improvement: A review, Waste Manage., 2020, 102, 884–899, DOI:10.1016/j.wasman.2019.12.003.
- X. Wang, H. Han, X. Liu, X. Gu, K. Chen and D. Lu, Multi-walled carbon nanotubes can enhance root elongation of wheat (Triticum aestivum) plants, J. Nanopart. Res., 2012, 14(6), 1–10 CrossRef.
- C. Xu and M. Strømme, Sustainable porous carbon materials derived from wood-based biopolymers for CO2 capture, Nanomaterials, 2019, 9(1), 1–13 Search PubMed.
- B. P. Chang, A. Rodriguez-Uribe, A. K. Mohanty and M. Misra, A comprehensive review of renewable and sustainable biosourced carbon through pyrolysis in biocomposites uses: current development and future opportunity, Renewable Sustainable Energy Rev., 2021, 152(111666), 111666 CrossRef CAS.
- V. Gargiulo, M. Alfè, P. Ammendola, F. Raganati and R. Chirone, CO 2 sorption on surface-modified carbonaceous support: Probing the influence of the carbon black microporosity and surface polarity, Appl. Surf. Sci., 2016, 360, 329–337, DOI:10.1016/j.apsusc.2015.11.026.
- C. M. Long, M. A. Nascarella and P. A. Valberg, Carbon black vs. black carbon and other airborne materials containing elemental carbon: Physical and chemical distinctions, Environ. Pollut., 2013, 181, 271–286, DOI:10.1016/j.envpol.2013.06.009.
- G. Chen, A. K. Mohanty and M. Misra, Progress in research and applications of Polyphenylene Sulfide blends and composites with carbons, Composites, Part B, 2020, 1–27 Search PubMed.
- S. C. Peterson, Evaluating corn starch and corn stover biochar as renewable filler in carboxylated styrene-butadiene rubber composites, J. Elastomers Plast., 2012, 44(1), 43–54 CrossRef CAS.
- M. T. Reza, J. Andert, B. Wirth, D. Busch, J. Pielert and J. G. Lynam,
et al., Hydrothermal Carbonization of Biomass for Energy and Crop Production, Appl. Bioenergy, 2014, 1(1), 11–29 Search PubMed.
- E. Behazin, M. Misra and A. K. Mohanty, Sustainable biocarbon from pyrolyzed perennial grasses and their effects on impact modified polypropylene biocomposites, Composites, Part B, 2017, 118, 116–124, DOI:10.1016/j.compositesb.2017.03.003.
- M. Javadi and M. Moghiman, Hydrogen and Carbon Black Production from Thermal Decomposition of Sub-Quality Natural Gas, Int. J. Spray Combust. Dyn., 2010, 2(1), 85–101 CrossRef CAS.
- X. Jiang, L. Zhang, F. Wang, Y. Liu, Q. Guo and C. Wang, Investigation of Carbon Black Production from Coal Tar via Chemical Looping Pyrolysis, Energy Fuels, 2016, 30(4), 3535–3540 CrossRef CAS.
- S. Arnold, A. Rodriguez-Uribe, M. Misra and A. K. Mohanty, Slow pyrolysis of bio-oil and studies on chemical and physical properties of the resulting new bio-carbon, J. Cleaner Prod., 2016, 172, 2748–2758, DOI:10.1016/j.jclepro.2017.11.137.
- S. Vivekanandhan, M. Schreiber, S. Muthuramkumar, M. Misra and A. K. Mohanty, Carbon nanotubes from renewable feedstocks: A move toward sustainable nanofabrication, J. Appl. Polym. Sci., 2017, 134(4), 1–15 CrossRef.
- A. B. Suriani, A. A. Azira, S. F. Nik, R. Md Nor and M. Rusop, Synthesis of vertically aligned carbon nanotubes using natural palm oil as carbon precursor, Mater. Lett., 2009, 63(30), 2704–2706, DOI:10.1016/j.matlet.2009.09.048.
- J. C. Colmenares, R. S. Varma and P. Lisowski, Sustainable hybrid photocatalysts: Titania immobilized on carbon materials derived from renewable and biodegradable resources, Green Chem., 2016, 18(21), 5736–5750 RSC.
- Q. Chen, X. Tan, Y. Liu, S. Liu, M. Li and Y. Gu,
et al., Biomass-derived porous graphitic carbon materials for energy and environmental applications, J. Mater. Chem. A, 2020, 8(12), 5773–5811 RSC.
- J. J. Manyà, Pyrolysis for biochar purposes: A review to establish current knowledge gaps and research needs, Environ. Sci. Technol., 2012, 46(15), 7939–7954 CrossRef PubMed.
- A. Verma, K. Baurai, M. R. Sanjay and S. Siengchin, Mechanical, microstructural, and thermal characterization insights of pyrolyzed carbon black from waste tires reinforced epoxy nanocomposites for coating application, Polym. Compos., 2020, 41(1), 338–349 CrossRef CAS.
|
This journal is © The Royal Society of Chemistry 2023 |