DOI:
10.1039/C7RA11023E
(Review Article)
RSC Adv., 2017,
7, 54203-54212
Application of functionalized ether in lithium ion batteries
Received
7th October 2017
, Accepted 11th November 2017
First published on 27th November 2017
Abstract
Ethers can be typically categorized as chain ethers, aromatic ethers and crown ethers. Compounds with ether groups play an important role in chemistry, biology and functional materials. Ether acts as an anesthetic in medicine, and crown ethers are used to construct mechanically interlocked molecules. Lithium ion batteries are becoming more and more important in our modern life as our mobile devices such as smart phones and laptop computers need power supplies. In recent years, the ethers have been explored to improve the electrochemical properties of lithium ion batteries. Depending on the function of the ether groups, they are widely used as electrolytes, additives, binders, separators or anodes. In this paper, we review the progress that has been made in the use of functionalized ethers in lithium ion batteries and the synthesis strategies for them, and present the future research direction of functionalized ethers in lithium ion batteries.
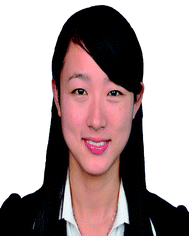 Fang Hu | Fang Hu received her Ph.D. degree from the College of Chemistry at CCNU, PR China in 2015. She joined Hanyang University as a post-doctor in 2017. She became an assistant professor at Ningbo University from 2015. Her research interests focus on lithium ion batteries, supercapacitors and electrocatalysis. |
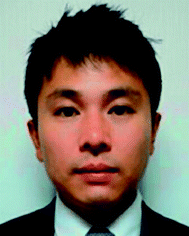 Taeseup Song | Taeseup Song received his Ph.D. degree from the Department of Materials Science and Engineering at Hanyang University, Korea in 2012. He is currently an assistant professor at Hanyang University. His research interest is mainly focused on the synthesis of nanostructured materials for energy device applications. |
Introduction
Ethers can be typically categorized as chain ethers, aromatic ethers and crown ethers. As one example of chain ether groups, alkyl ethers have been widely used as detergents, dispersants, dyeing aids and antistatic agents.1,2 Ether acts as an anesthetic in medicine. Aromatic ethers have a good solid structure, and can be used to improve a material's thermal properties and structural stability. Aromatic ether-containing epoxy resin is a type of thermosetting polymer composite with corrosion resistance and high strength.3,4 It plays an important role in industrial fields such as transistors, microchips and semiconductors. Crown ethers are used to construct mechanically interlocked molecules.5–7 Mechanically interlocked molecules are classified mainly as rotaxanes and catenanes. With the functionalization of mechanically interlocked molecules, crown ether-based molecular motor, molecular muscle and molecular shuttle have gradually been constructed. Moreover, some functionalized crown ethers, such as crown ether-based photochromic materials8 and aggregation-induced fluorescence enhancement (AIE) materials,9 have potential applications in many fields such as molecular switches and self-assembly systems.
Lithium ion batteries (LIBs) are becoming a more and more important part of our modern life. Many devices such as mobile televisions, smart phones and pocket computers need power sources, and the lithium ion battery is an excellent candidate for power and energy supply.10–14 In order to improve the performance of LIBs, some novel cathode materials, anode materials, electrolytes, additives, binders and separators have gradually been developed. Synthetic strategies are used to construct novel architecture in order to gain high energy density and good thermal stability for lithium ion batteries. For example, most inorganic compounds with high potential such as olivine-type LiNiPO4 and LiCoPO4 can be used as cathode materials.15,16 Some organic compounds such as anthraquinone can be utilized to construct novel cathode materials.17,18 Many inorganic compounds with low potential such as graphite and metal oxides are excellent candidates for anode materials.19,20 Some special organic compounds can be utilized as additives,21,22 binders23 and separators for lithium ion batteries.24,25
In recent years, ether-based lithium ion batteries have been reported widely. According to the functionalization of the ether groups, ethers are used mainly as electrolytes, additives, binders, separators or anodes in lithium ion batteries. In this paper, we review the progress of the employment of functionalized ethers in lithium ion batteries and the synthesis strategies for electrolytes, additives, binders, separators and anodes, and present the future research direction of functionalized ether in lithium ion batteries.
Electrolyte
When a lithium salt is dissolved in an organic mixed solvent, the solution can be used as an electrolyte. The normal electrolytes for lithium ion batteries (LIBs) are classified mainly as liquid electrolyte, solid electrolyte and liquid–solid electrolyte, as indicated in Scheme 1. Yang's group26 reported that ether-functionalized quaternary ammonium cation ionic liquids (1 and 2) could be used as electrolytes for lithium ion battery (Scheme 2). It was very easy to synthesize the ether-functionalized quaternary ammonium cation ionic liquids by heating the amino compounds with the corresponding halide. When these quaternary ammonium cation ionic liquids were used as electrolytes in Li/LiFePO4 batteries, these batteries showed good cycling properties. It was proved that introducing one short ether group into cation ionic liquids could reduce their melting points. The oxygen of the ether group is an electron donator, and so the electrostatic interaction of the cation would be reduced by electron donation, leading to lower melting point. More importantly, electrolytes with two ether groups had better rate properties than those with one ether group. This means that ionic liquids with low melting points were good for use in lithium ion batteries. Their electrochemical windows, viscosity and conductivity are summarized in Table 1.
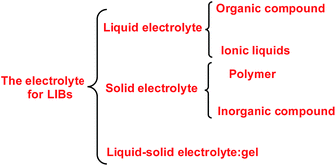 |
| Scheme 1 The electrolytes for lithium ion batteries. | |
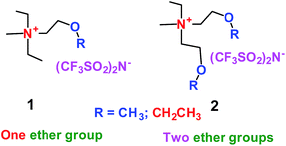 |
| Scheme 2 The structures of quaternary ammonium cation ionic liquids.26 | |
Table 1 Representative structures, electrochemical windows, viscosity (η) and conductivity (σ) of quaternary ammonium ionic liquids with two ether groups at 25 °C (ref. 26)
Structure |
Cathodic limiting potential V vs. Li/Li+ |
Anodic limiting potential V vs. Li/Li+ |
Electrochemical window V |
η (mPa s) |
σ (mS cm−1) |
 |
0.2 |
5.3 |
5.1 |
203.1 |
0.83 |
 |
0.2 |
5.2 |
5.0 |
182.3 |
0.78 |
 |
0.3 |
5.3 |
5.0 |
165.2 |
0.74 |
 |
0.2 |
5.2 |
5.0 |
230.8 |
0.70 |
 |
0.3 |
5.3 |
5.0 |
212.6 |
0.66 |
 |
0.2 |
5.3 |
5.1 |
243.1 |
0.60 |
 |
0.3 |
5.3 |
5.0 |
238.8 |
0.58 |
 |
0.3 |
5.3 |
5.0 |
231.2 |
0.54 |
 |
0.2 |
5.2 |
5.0 |
263.6 |
0.48 |
 |
0.2 |
5.3 |
5.0 |
259.3 |
0.42 |
 |
0.1 |
5.2 |
5.1 |
248.1 |
0.46 |
As well as ether-functionalized quaternary ammonium cation ionic liquids, Yang's group found that ether-functionalized trialkylimidazolium ionic liquids could also be used as electrolytes (3 and 4) (Scheme 3).27 Six ether-functionalized trialkylimidazolium ionic liquids were tested that had the same anion as in the quaternary ammonium cation ionic liquids: the bis(trifluoromethanesulfonyl)amide (TFSA) anion. These ionic liquids were used as electrolytes in Li/LiFePO4 batteries. They showed good battery performance and rate properties. Introducing the ether groups gave these ionic liquids lower viscosity, which was good for the wettability of electrodes. This means that the wettability of cation ionic liquids could be affected by the structure and viscosity, and functionalization of cation ionic liquids could improve the wettability of ionic liquid electrolytes. Interestingly, these ionic liquid electrolytes had good chemical stability with the presence of the ether group.
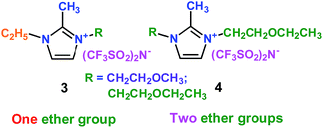 |
| Scheme 3 The structures of trialkylimidazolium ionic liquids.27 | |
Subsequently, Mandal and co-workers28 reported two imidazolium ionic liquids containing ether–siloxane (1O2O2-Im-1SiOSi) and ether–ether (1O2O2-Im-2O1) (5 and 6) (Scheme 4). When 1O2O2-Im-1SiOSi and 1O2O2-Im-2O1 were mixed with propylene carbonate (PC) as electrolytes for lithium ion batteries, they showed high electrochemical stability windows (ESWs) and good conductivity, as shown in Scheme 5. More importantly, through temperature-dependent electrochemical impedance spectroscopy (EIS), ether- and siloxane-functionalized imidazolium ionic liquids were shown to exhibit excellent thermal and electrochemical characteristics. When the imidazolium cation interacted with Li+, it would collapse the Li[TFSI]n+1n− cluster and help the Li+ ion to migrate. The functionalized imidazolium cations could also control the conductivity, viscosity and diffusion, and had the same function with the propylene carbonate.
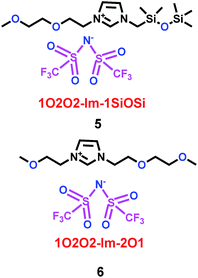 |
| Scheme 4 The structures of imidazolium ionic liquids.28 | |
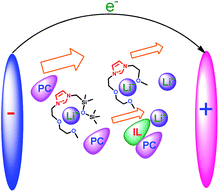 |
| Scheme 5 The electrochemical behaviors of 5 and 6 as electrolytes for LIBs.28 | |
Pyrazolium ionic liquids, which are similar to imidazolium ionic liquids, were an excellent candidate for use as electrolyte in the lithium ion battery. Yang's group have reported four novel ionic liquids (ILs) based on ether-functionalized pyrazolium cations with the counter anion bis(fluorosulfonyl) imide (FSI) (Scheme 6).29 When these four FSI-based ILs (7, 8, 9 and 10) were used as electrolytes in Li/LiFePO4 cells, they showed lower viscosity and higher conductivity, which could be due to the lower melting points and higher thermal decomposition temperatures with the presence of the ether group and FSI anion. More importantly, the PZ2o2-2-FSI with more alkyl groups possessed the lowest viscosity, while the PZ2o1-2-FSI had the highest conductivity because of the presence of the methoxy group.
 |
| Scheme 6 The structures of pyrazolium ionic liquids.29 | |
As well as some normal cation ionic liquids, guanidinium cation ionic liquids can act as electrolytes for lithium ion batteries, Yang's group found that ether-functionalized guanidinium cation ionic liquids could also be used as electrolytes (11 and 12) (Scheme 7).30 Because of the importance of viscosity for the lithium ion battery, the viscosities of 1g(2o1)(2o1)-TFSA (11) and 1g(2o1)(2o2)-TFSA (12) were checked and found to have the values of 60.2 and 58.8 mPa s respectively at 25 °C. When these ether-functionalized ionic liquids based on guanidinium cation were used as electrolytes in Li/LiFePO4 batteries, these batteries showed electrochemical stability and good cycling properties at the current rate of 0.2 C owing to the formation of a passivation layer. Moreover, without any additive, obvious lithium plating and stripping could be found on the Ni electrode when the ether-functionalized guanidinium cation ionic liquids were used as electrolytes for the lithium ion battery, which was attributed to the present of solid–electrolyte interface (SEI) film.
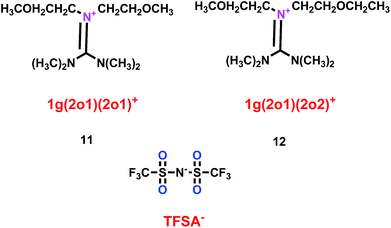 |
| Scheme 7 The structures of guanidinium cation ionic liquids.30 | |
As liquid electrolytes, ether-based cation ionic liquids with low viscosity are usually used in lithium ion batteries. Organic solvents with ether groups are also good in lithium ion batteries. Chen and co-workers found that anthraquinone (AQ) was a good candidate for the cathode material in lithium ion batteries, as shown in Scheme 8.31 For most of the inorganic compounds that are used as cathode material in lithium ion batteries, cation ionic liquids are good options. But for organic cathode compounds, some simple electrolytes such as 1,3-dioxetane (DOL) (13) and dimethyl ether (DME) (14) are useful. With LiNO3 additive and ether-based electrolyte, a lithium ion battery with anthraquinone as cathode showed good cycling and rate performance. Compared with the carbonate-based electrolyte, the discharge capacity and retention capacity of this lithium ion battery can reach 174 mA h g−1 and 84.9% after 100 cycles at 0.2 C. Furthermore, the lithium ion battery with ether-based electrolyte delivered high discharge capacities at both low and high rates. With LiNO3 additive, the ether-based electrolyte can form a protective film on the surface of the anode to prevent the SEI forming. Compared with other electrolytes, ether-based electrolytes effectively decrease the solubility of anthraquinone, which is good for lithium ion transportation. This means the introduction of an ether group can improve the high cycling and rate performance of the lithium ion battery.
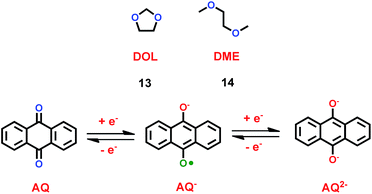 |
| Scheme 8 The structures of organic solvents with ether groups.31 | |
For cation ionic liquids, the presence of an ether group can reduce the viscosity for use in lithium ion batteries, increase the electrochemical stability and improve the cycling properties. In contrast, the organic solvents with ether groups improve the cycling and rate performance of the lithium ion battery by decreasing the solubility of the cathode.
Organic solvent alkyl ethers could be used as electrolytes. Yang and co-authors introduced the trifluoromethyl group into organic solvent alkyl ethers, and found that a mixture of diethylene glycol diethylether (15) and non-flammable methyl-nonafluorobutyl ether (16) could be employed as electrolyte for lithium ion batteries (Scheme 9).32 Compared with the conventional electrolytes, these electrolytes gave better rate, cycling and low-temperature performances for graphite/LiFePO4 cells.
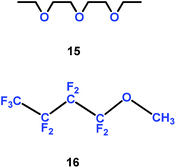 |
| Scheme 9 The structures of organic solvent alkyl ethers.32 | |
As well as cation ionic liquids and organic solvent alkyl ethers, polymers could also act as electrolytes for lithium ion batteries. Teng's group synthesized three polymers (17, 18 and 19) (Scheme 10).33 By mixing the three polymers, the P(EO-co-PO) polymeric framework of the electrolyte was gained. The P(EO-co-PO) polymeric framework exhibited high ionic conductivity. In particular, the high solvent-coordinating ability of ether groups in the P(EO-co-PO) polymeric framework created free volume for ion motion, which facilitated the transport of solvent-solvated Li+ ions through the segmental movement of polymer chains. When it was used in the graphite|GPE|LiFePO4 battery, the P(EO-co-PO) polymeric framework had high ionic conductivity and lithium transference number. Also, the P(EO-co-PO) polymeric framework exhibited smaller interfacial resistance against lithium metal. Compared with the carbonate solvent, the P(EO-co-PO) polymeric framework stabilized the solvent and suppressed the formation of thick SEI layers that hinder interfacial ion transport.
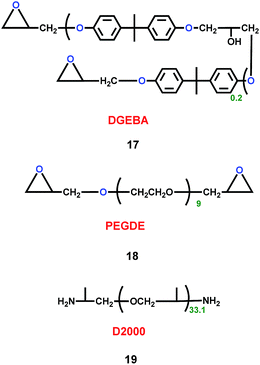 |
| Scheme 10 The structures of polymers.33 | |
Hawker's group found that the poly(allyl glycidyl ether) (PAGE) platform could be used as electrolyte (Scheme 11).34 In the structure of these electrolytes (20 and 21), the allyl ether could prevent the formation of nonconducting crystalline regions, which are bad for ion conduction. Additionally, the introduction of ethylene oxide oligomer could increase the conductivity. They found that these electrolytes have conductivities near 10−4 S cm−1 at room temperature. The properties of 21 are summarized in Tables 2 and 3.
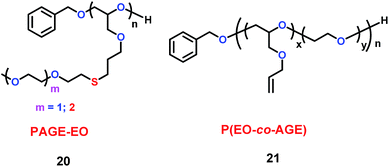 |
| Scheme 11 The structure of poly(allyl glycidyl ether).34 | |
Table 2 P(EO-co-AGE) characterization and properties34
Molar feed ratio [EO]/[AGE] |
Polymer% EO (wt) |
Mw (kg mol−1) by NMR |
Mn (kg mol−1) by GPC |
PDI |
Tg (°C) |
Xc (%) |
PEO |
100 |
n. a. |
33.7 |
1.07 |
n. a. |
86 |
7.5 |
77 |
39.4 |
29.5 |
1.12 |
−69 |
32 |
5 |
69 |
16.9 |
14.3 |
1.21 |
−70 |
23 |
4 |
61 |
14.7 |
15.8 |
1.13 |
−71 |
15 |
3 |
56 |
6.5 |
7.9 |
1.13 |
−69 |
0 |
1 |
32 |
27.5 |
17.3 |
1.11 |
−73 |
0 |
Table 3 Glass transition temperature and Vogel–Tammann–Fulcher (VTF) parameters for polymer electrolytes34
[O]/[Li] |
r = [Li]/[O] |
wLiTFSI |
Tga (°C) |
Ea (kJ mol−1) |
σ0 (S cm−1) |
Measured by differential scanning calorimetry (DSC). T0 set to Tg – 50 K in VTF fits to conductivity data. |
[Li] = 0 |
0 |
0.00 |
−78.0 |
5.96 |
6.24 × 10−7 |
90 |
0.01 |
0.05 |
−75.8 |
9.02 |
5.11 × 10−3 |
52 |
0.02 |
0.09 |
−74.0 |
9.58 |
1.97 × 10−2 |
32 |
0.03 |
0.13 |
−72.0 |
9.82 |
4.54 × 10−2 |
26 |
0.04 |
0.16 |
−67.5 |
10.4 |
1.58 × 10−1 |
16 |
0.06 |
0.24 |
−58.4 |
9.8 |
2.33 × 10−1 |
10 |
0.10 |
0.33 |
−49.3 |
9.47 |
2.79 × 10−1 |
Additive
In the lithium manganite/carbon (LMO-GR) cell, lithium manganite's activity determined the performance of the battery. Dissolved Mn ions from the positive electrode (lithium manganite) migrated to and were deposited on the negative electrode (carbon), which degraded the cell's performance for lithium ion batteries (LIBs). In order to prevent dissolved Mn ions from reaching the negative electrode, Levi's group synthesized two crown ether-based polymers, poly(undecylenyl oxymethyl-18-crown-6) (PUNOM-18C6) (22) and poly(vinylbenzo-18-crown-6) (PVB-18C6) (23) (Scheme 12).35 The PVB-18C6 polymer could trap Mn ions, which meant that the amount of manganese deposited at the negative electrode would be correspondingly reduced. Concomitantly, a 26% improvement in capacity was gained after 100 cycles of the LMO-GR. For PVB-18C6, the macrocycle and the polymer backbone were linked by the benzene ring, and the rigid link played a determining role for the Mn ion trapping ability. For PUNOM-18C6, the flexible link between the macrocycle and the polymer led to no trapping of Mn ions. Thus PVB-18C6 was better than PUNOM-18C6 as an additive for Li-ion batteries.
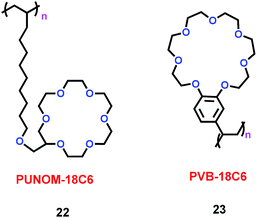 |
| Scheme 12 The structures of crown ethers-based polymers.35 | |
As well as crown ethers, alkyl ethers could also be used as additives for Li-ion batteries. By changing the ratio of ether/alkyl, Xie and co-workers synthesized three different ethers, 1,2-dimethoxyethane (DME) (24), diethylene glycol dimethyl ether (DG) (25) and triethylene glycol dimethyl ether (TEGDME) (26) (Scheme 13).36 With the presence of DME, the cell was faster to reach the stable state than with DG and TEGDME. The SEI film in DME was stable at the beginning of cycling. Moreover, the electrolytes containing DG and TEGDME had a higher resistance when the lithium ions migrated through the SEI film on the lithium electrode. The TEGDME-based electrolyte was more active for SEI film formation. This means that different ratios of the ether/alkyl moieties had a great impact on SEI formation, and determined the performance of the lithium ion battery.
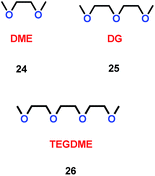 |
| Scheme 13 The structures of alkyl ethers.36 | |
As we all know, ionic liquids (ILs) could be used as electrolyte as well as additive. Yoshizawa-Fujita and co-workers synthesized one ionic liquid containing a zwitterion named 3-(1-(2-(2-methoxyethoxy)ethyl)pyrrolidin-1-ium-1-yl)propane-1-sulfonate (OE2pyps) (28) (Scheme 14).37 For the research, N-methyl-N-methoxymethylpyrrolidinium bis(fluorosulfonyl)amide ([Pyr1,1O1][FSA]) (27) and lithium bis(fluorosulfonyl)amide (LiFSA) were used as electrolytes. When the OE2pyps was used as the additive for the lithium ion battery, the electrolyte with [Pyr1,1O1][FSA]/LiFSA had a higher viscosity and lower ionic conductivity and lithium transference number. The interactions between the sulfonate groups of OE2pyps (28) and lithium ions might have a great impact on the viscosity and ionic conductivity changes. Within the cut-off voltage range of 3.0–4.3 V, the cell had better discharge capacities during the charge/discharge tests with increasing OE2pyps content. Moreover, the cycle stability became better with the addition of OE2pyps. By adding OE2pyps into the electrolytes, the interface resistance between the electrolyte and cathode was suppressed. Therefore, using this zwitterion with its long ether group as additive for Li-ion batteries could improve their charge/discharge stability. The diffusion coefficients and lithium transference numbers are summarized in Table 4.
 |
| Scheme 14 The structures of ionic liquids.37 | |
Table 4 Diffusion coefficients and lithium transference numbers for [Pyr1,1O1][FSA]/LiFSA, [Pyr1,1O1][FSA]/LiFSA/OE2pyps (5 wt%), and [Pyr1,1O1][FSA]/LiFSA/OE2pyps (10 wt%) at 40 °C (ref. 37)
Structure |
DH/m2 s−1 |
DF/m2 s−1 |
DLi/m2 s−1 |
tLi+ |
 |
5.75 × 10−11 |
5.72 × 10−11 |
4.54 × 10−11 |
0.41 |
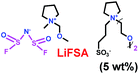 |
4.00 × 10−11 |
4.71 × 10−11 |
1.31 × 10−11 |
0.22 |
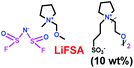 |
3.60 × 10−11 |
4.24 × 10−11 |
5.67 × 10−12 |
0.12 |
Binder
Xue and co-workers synthesized a sulfonated poly(ether-ether-ketone) with pendant lithiated fluorinated sulfonic groups (SPEEK-FSA-Li) (29) (Scheme 15), and found it was a good candidate as ionic conductivity binder.38 Compared with the binder PVDF, it had stronger adhesion and better stability. With the charge delocalization over the sulfonic chain, SPEEK-FSA-Li acted as binder with larger ionic conductivity and Li+ ion diffusion. When the SPEEK-FSA-Li binder was mixed into the electrode, the electrode exhibited smaller resistances at the solid–electrolyte interface (SEI) and lithium ion transport, which was good for lithium ion intercalation and de-intercalation. This means that the electrode had low charge plateau potential and high discharge plateau potential. The resistance values are summarized in Table 5.
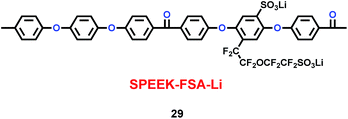 |
| Scheme 15 The structure of SPEEK-FSA-Li.38 | |
Table 5 Resistance values obtained from fitting impedance spectra38
Structure |
Rs/Ω cm−2 |
Rf/Ω cm−2 |
Rct/Ω cm−2 |
 |
2.13 |
43.76 |
147.70 |
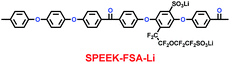 |
1.71 |
8.60 |
88.58 |
Separator
Seidel et al. found that ether-modified polysiloxanes (PSx-PEO3) (30) could act as active separators for the lithium ion battery when they were blended within a poly(vinylidene fluoride-co-hexafluoropropylene) (PVDF-HFP) matrix (Scheme 16). Moreover, when 20 wt% of PSx-PEO3 was added into the PVDF-HFP matrix, the membrane system showed better ionic conductivity and cycling results than the pure PVDF-HFP system.39
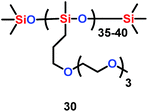 |
| Scheme 16 The structure of ether-modified polysiloxanes.39 | |
Li's group have reported a porous poly(ether-ether-ketone) (PEEK) (31) material could be used as separator in lithium ion batteries with high thermal stability and superior rate capability (Scheme 17).40 Compared with the commercial polyethylene (PE) separator, the electrolyte uptake could reach 251% when the porous PEEK membrane was used, which means that it showed excellent electrolyte wettability. More importantly, the discharge capacity could reach 124.1 mA h g−1 with the PEEK membrane acting as separator in the lithium-ion battery, which means that it showed outstanding rate performance. The physical properties of PEEK membranes and PE separators are summarized in Table 6.
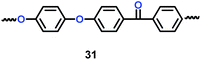 |
| Scheme 17 The structure of PEEK.40 | |
Table 6 Physical properties of PEEK membranes and PE separators40
Structure |
Thickness (μm) |
Porosity [%] |
Electrolyte contact angle [deg] |
Electrolyte uptake [%] |
Ion conductivity [S cm−1, 25 °C] |
 |
20 |
40 |
53 |
111 |
6.65 × 10−4 |
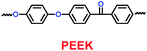 |
30 |
78 |
29 |
251 |
10.64 × 10−4 |
Kim's group have reported a kind of copolymer based on poly(arylene ether ketone) (PAEK) and poly(lactic acid) (PLA) structures (32) (Scheme 18). When various concentrations of PLA were added into the PAEK, the pore size and porosity of the copolymers were different.41 Compared with commercial poly(propylene) (PP) separator, the copolymers based on PAEK and PLA had better liquid electrolyte uptake, excellent thermal and mechanical stability, and higher lithium ion conductivity, which means the copolymers were a good candidate for separator. Based on the PAEK structure, Liu and co-workers found that phenolphthalein and allyl groups-modified PAEK (P-PAEK) (33) could also be used as an excellent composite separator for the lithium ion battery when it was mixed with PVDF (Scheme 19). It had high porosity, uniform pore distribution and low thermal shrinkage.42
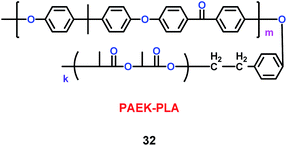 |
| Scheme 18 The structure of PAEK-PLA.41 | |
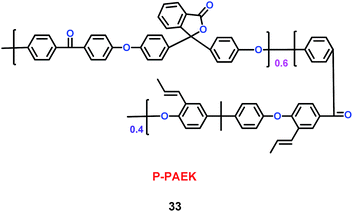 |
| Scheme 19 The structure of P-PAEK.42 | |
Anode
A microporous Zn-based metal–organic framework (MOF) containing 12-crown-4 units (Zn–MOF–Crown) (34) was constructed by Zhao's group (Scheme 20).43 This material could be used as the anode material in the lithium ion battery, with a charge capacity of 273 mA h g−1. More importantly, it retained 88% of its capacity after 500 cycles. During charge and discharge, the MOF structure integrity never was damaged because of the interaction between the Li+ ions and crown ether. Interestingly, when the Zn–MOF–Crown complexed with Li+ ions and Li+@Zn–MOF–Crown was formed, it had better electrochemical performance, with a charge capacity of 348 mA h g−1 and long-term cycling ability. This means the introduction of crown ether could improve the performance in green energy systems. The properties of different MOFs or MOF-derived materials for LIBs are summarized in Table 7. Compared with other MOF-derived materials, crown ether-based MOFs had longer-term cycling ability with high charge capacity.
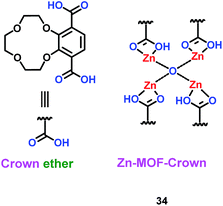 |
| Scheme 20 The structure of Zn–MOF–Crown.43 | |
Table 7 MOF or MOF-derived materials for LIBs43
Structure |
Charge capacity/discharge capacity (mA h g−1) |
Reversible capacity (mA h g−1) |
Cycle number |
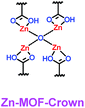 |
273/405 |
239 |
500 |
[FeIII(OH)0.8F0.2(O2CC6H4CO2)]·H2O, MIL-53 |
70/80 |
71 |
50 |
MIL-177 |
110/425 |
— |
2 |
Zn3(HCOO)6 |
693/1344 |
560 |
30 |
Co3(HCOO)6 |
870/1720 |
390 |
60 |
Zn1.5Co1.5(HCOO)6 |
930/1570 |
450 |
60 |
Mn-LCP |
610/1870 |
390 |
5 |
Co2(OH)2BDC |
1005/1385 |
650 |
50 |
Conclusions
In conclusion, ether-functionalized lithium ion batteries have been reported widely. According to the functionalization of ether groups, ethers are used mainly as electrolyte, additive, binder, separator or anode in lithium ion batteries. When functionalized cation ionic liquids were used as electrolyte, ether-based ionic liquids had better properties for LIBs, but it was very difficult to gain pure ionic liquids. Ether-based polymers could be used as electrolyte and separator. Crown ether could be utilized to construct novel additives and anodes. Compared with cation ionic liquids and polymers, crown ether was easier to synthesize, and crown ether-based metal–organic frameworks (MOFs) had better charge capacity with excellent cycling performance. Moreover, by changing the cavity size of the crown ether, it could be complexed with different metal ions such as sodium and magnesium. This means that the electrochemical performance of sodium ion batteries and magnesium ion batteries could also be improved by introducing crown ether. In the future, it will be significant to find and synthesize novel crown ether-based materials, which could be utilized to construct the anode for lithium ion batteries, sodium ion batteries and magnesium ion batteries.
Conflicts of interest
There are no conflicts to declare.
Acknowledgements
This work was supported by Basic Science Research Program through the National Research Foundation of Korea (NRF) funded by the Ministry of Science, ICT (2016R1C1B2007299) and National Natural Science Foundation of China (21602122).
Notes and references
- For selected review, see: L. He, F. Lin, X. Li, H. Sui and Z. Xu, Chem. Soc. Rev., 2015, 44, 5446–5494 RSC
. - For selected reviews, see: A. Karci, Chemosphere, 2014, 99, 1–18 CrossRef CAS PubMed
. - X. Gong, H. Kang, Y. Liu and S. Wu, RSC Adv., 2015, 5, 40269–40282 RSC
. - F. Liu, Z. Wang, D. Liu and J. Li, Polym. Int., 2009, 58, 912–918 CrossRef CAS
. - For selected reviews, see: Z. Liu, S. Nalluri and J. F. Stoddart, Chem. Soc. Rev., 2017, 46, 2459–2478 RSC
. - G. Bo, G. Dolphijn, C. McTernan and C. Leigh, J. Am. Chem. Soc., 2017, 139, 8455–8457 CrossRef PubMed
. - W. Deng, A. Flood, J. F. Stoddart and W. Goddard, J. Am. Chem. Soc., 2005, 127, 15994–15995 CrossRef CAS PubMed
. - F. Hu, J. Huang, M. Cao, Z. Chen, Y. Yang, S. H. Liu and J. Yin, Org. Biomol. Chem., 2014, 12, 7712–7720 CAS
. - X. Han, M. Cao, Z. Xu, D. Wu, Z. Chen, A. Wu, S. H. Liu and J. Yin, Org. Biomol. Chem., 2015, 13, 9767–9774 CAS
. - X. Wang, W. Han, H. Chen, J. Bai, T. Tyson, X. Yu, X. Wang and X. Yang, J. Am. Chem. Soc., 2011, 133, 20692–20695 CrossRef CAS PubMed
. - X. Wang, S. Singh, T. Ma, C. Lv, N. Chawla and H. Jiang, Chem. Mater., 2017, 29, 5831–5840 CrossRef CAS
. - A. Mascaro, Z. Wang, P. Hovington, Y. Miyahara, A. Paolella, V. Gariepy, Z. Feng, T. Enright, C. Aiken, K. Zaghib, K. Bevan and P. Grutter, Nano Lett., 2017, 17, 4489–4496 CrossRef CAS PubMed
. - For selected reviews, see: W. Li, B. Song and A. Manthiram, Chem. Soc. Rev., 2017, 46, 3006–3059 RSC
. - For selected reviews, see: Y. Tang, Y. Zhang, W. Li, B. Ma and X. Chen, Chem. Soc. Rev., 2015, 44, 5926–5940 RSC
. - Q. Truong, M. Devaraju and I. Honma, J. Mater. Chem. A, 2014, 2, 17400–17407 CAS
. - Y. Feng, H. Zhang, L. Fang, Y. Ouyang and Y. Wang, J. Mater. Chem. A, 2015, 3, 15969–15976 CAS
. - For selected reviews, see: J. Xie and Q. Zhang, J. Mater. Chem. A, 2016, 4, 7091–7106 CAS
. - L. Fédèle, F. Sauvage and M. Bécuwe, J. Mater. Chem. A, 2014, 2, 18225–18228 Search PubMed
. - H. Park, D. Shin, T. Song, W. Park and U. Paik, J. Mater. Chem. A, 2017, 5, 6958–6965 CAS
. - For selected reviews, see: T. Song and U. Paik, J. Mater. Chem. A, 2016, 4, 14–31 CAS
. - O. Wijaya, P. Hartmann, R. Younesi, I. Markovits, A. Rinaldi, J. Janek and R. Yazami, J. Mater. Chem. A, 2015, 3, 19061–19067 CAS
. - H. Fei, Y. An, J. Feng, L. Ci and S. Xiong, RSC Adv., 2016, 6, 53560–53565 RSC
. - M. Cheng, L. Li, Y. Chen, X. Guo and B. Zhong, RSC Adv., 2016, 6, 77937–77943 RSC
. - M. Xie, J. Wang, X. Wang, M. Yin, C. Wang, D. Chao and X. Liu, Macromol. Res., 2016, 24, 965–972 CrossRef CAS
. - For selected reviews, see: U. Farooqui, A. Ahmad and N. Hamid, Renewable Sustainable Energy Rev., 2017, 77, 1114–1129 CrossRef CAS
. - Y. Jin, J. Zhang, J. Song, Z. Zhang, S. Fang, L. Yang and S. Hirano, J. Power Sources, 2014, 254, 137–147 CrossRef CAS
. - Y. Jin, S. Fang, M. Chai, L. Yang, K. Tachibana and S. Hirano, J. Power Sources, 2013, 226, 210–218 CrossRef CAS
. - S. Chavan, A. Tiwari, T. Nagaiah and D. Mandal, Phys. Chem. Chem. Phys., 2016, 18, 16116–16126 RSC
. - G. Wang, S. Shen, S. Fang, D. Luo, L. Yang and S. Hirano, RSC Adv., 2016, 6, 71489–71495 RSC
. - Y. Jin, S. Fang, L. Yang, S. Hirano and K. Tachibana, J. Power Sources, 2011, 196, 10658–10666 CrossRef CAS
. - K. Zhang, C. Guo, Q. Zhao, Z. Niu and J. Chen, Adv. Sci., 2015, 2, 1500018 CrossRef PubMed
. - S. Fang, G. Wang, L. Qu, D. Luo, L. Yang and S. Hirano, J. Mater. Chem. A, 2015, 3, 21159–21166 CAS
. - L. Huang, Y. Shih, S. Wang, P. Kuo and H. Teng, J. Mater. Chem. A, 2014, 2, 10492–10501 CAS
. - K. Barteau, M. Wolffs, N. Lynd, G. Fredrickson, E. Kramer and C. Hawker, Macromolecules, 2013, 46, 8988–8994 CrossRef CAS
. - B. Ziv, N. Levy, V. Borgel, Z. Li, M. Levi, D. Aurbach, A. Pauric, G. Goward, T. Fuller, M. Balogh and I. Halalay, J. Electrochem. Soc., 2014, 161, 1213–1217 CrossRef
. - S. Xiong, Y. Diao, X. Dong, Y. Chen and K. Xie, J. Electrochem. Soc., 2014, 719, 122–126 CAS
. - S. Horiuchi, H. Zhu, M. Forsyth, Y. Takeoka, M. Rikukawa and M. Yoshizawa-Fujita, Electrochim. Acta, 2017, 241, 272–280 CrossRef CAS
. - Z. Wei, L. Xue, F. Nie, J. Sheng, Q. Shi and X. Zhao, J. Power Sources, 2014, 256, 28–31 CrossRef CAS
. - S. Seidel, S. Vettikuzha and H. Wiemhofe, Chem. Commun., 2015, 51, 12048–12051 RSC
. - D. Li, D. Shi, K. Feng, X. Li and H. Zhang, J. Membr. Sci., 2017, 530, 125–131 CrossRef CAS
. - A. Mong and D. Kim, J. Power Sources, 2016, 304, 301–310 CrossRef
. - M. Xie, M. Yin, G. Nie, J. Wang, C. Wang, D. Chao and X. Liu, Polymer Chem., 2016, 54, 2714–2721 CrossRef CAS
. - L. Bai, B. Tu, Y. Qi, Q. Gao, Z. Liu, D. Liu, L. Zhao, Q. Li and Y. Zhao, Chem. Commun., 2016, 52, 3003–3006 RSC
.
|
This journal is © The Royal Society of Chemistry 2017 |