DOI:
10.1039/D3TA06548K
(Review Article)
J. Mater. Chem. A, 2024,
12, 7351-7395
Scope, evaluation and current perspectives of MXene synthesis strategies for state of the art applications†‡
Received
26th October 2023
, Accepted 16th January 2024
First published on 20th January 2024
Abstract
MXenes have garnered considerable attention as 2D functional materials. Their application in advanced applications is linked to synthetic approaches, terminal groups (
O, –OH, and –F etc.) and multiple characteristics. Functionality and control over MXene terminations are important factors. MXenes exhibit a regular planar structure, conductivity, tuneable fabrication and structural modifications, as well as superior optical, thermal, and chemical properties. These exceptional characteristics grant MXenes and their derivatives distinction among 2D materials. MXenes have practical applications in energy conversion/storage, catalysis, sensing, water purification, drug delivery, and cancer treatments. Recent advances, with a primary focus on MXenes synthesis and terminations linked to their method of preparation, are the focus of this review. We offer potential solutions to the challenges faced by researchers during MXene synthesis. We describe the advantages, drawbacks, and mechanism associated with MXene fabrications and developments. Despite significant progress on MXene-oriented research, several challenges must be addressed before practical applications.
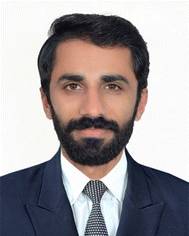 Muhammad Zeeshan Abid | Muhammad Zeeshan Abid is a doctoral student at the Institute of Chemistry, Islamia University of Bahawalpur. He is working under the supervision of Dr Ejaz Hussain. His research interests include the synthesis of MXene-derived compounds for various applications. |
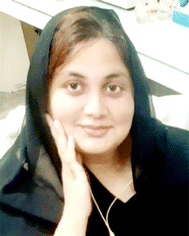 Khezina Rafiq | Dr Khezina Rafiq is Assistant Professor at the Institute of Chemistry, Islamia University of Bahawalpur. She has been awarded Global Korea Scholarship for PhD in Chemistry from Hallym University, South Korea. She has a patent invention and has published several research articles in well-known scientific journals. Her research interests include the synthesis of novel compounds for portable kidney devices, electrochemical sensing, as well as energy and environmental applications. |
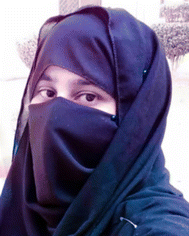 Anam Aslam | Anam Aslam is an MS student in Chemistry under the supervision of Dr Khezina Rafiq at Institute of Chemistry, Islamia University of Bahawalpur. Her research focuses on the development of advanced inorganic materials for photocatalytic applications. |
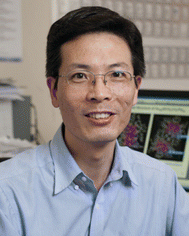 Rongchao Jin | Dr Rongchao Jin is Professor of Chemistry at Carnegie Mellon University. He received his BS in Chemical Physics from USTC in 1995, an MS in Physical Chemistry/Catalysis from the Dalian Institute of Chemical Physics in 1998, and his PhD in Chemistry from Northwestern University in 2003. After postdoctoral research at the University of Chicago, he joined the chemistry faculty of CMU in 2006. His research interests include atomically precise nanoparticles, and nanoclusters for optics and catalysis applications. |
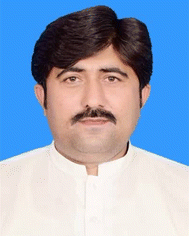 Ejaz Hussain | Dr Ejaz Hussain is an Assistant Professor in the Institute of Chemistry, Islamia University of Bahawalpur. He received his PhD from Quaid-i-Azam University. He was awarded a scholarship for advanced research at the Department of Chemistry, Carnegie Mellon University (with Professor Rongchao Jin). He was accredited with the “Best Researcher Award 2015–2016”. He is a mentor and key scientist in Inorganic Materials Laboratory 52S, and has expertise on water-splitting, renewable energy, and environmental science. |
1. Introduction
Over the past 20 years, two-dimensional (2D) materials have garnered great interest due to their extraordinary characteristics. This interest has sparked new developments in 2D materials and led to diverse applications. Materials such as MXenes, graphene, g-C3N4, metal chalcogenides and boron nitrides have attained special interest due to their appealing characteristics for practical applications.1,2 Among 2D materials, MXenes have attained special recognition not only to academic researchers but also for the industrial researchers. MXenes (pronounced “maxenes”) comprise transition-metal carbides and nitrides.3 MXenes were reported for the first time in 2011. After this discovery, synthetic protocols and applications of MXenes have been consistently improved. MXenes have been derived from etching of the MAX phase by the removal of inherited A-layers. The typical formula for the MAX phase is Mn+1AXn, where M represents early transition metals from groups III to VI (i.e., Sc, Ti, Zr, V, Nb, Ta, Cr, Mo, W). These elements can form MAX phases because they possess specific electronic configurations and a layered hexagonal close-packed (hcp) structure (in space group P63/mmc) that allows their exfoliation4. In contrast, late transition metals (i.e., Ag, Cu, Ni, Pd, Pt, Au and Zn) do not form hcp-layered structures due to their higher valence electrons (shielding). The involvement of d-electrons is important for development of the MAX phase.5 These factors significantly hinder the bonding needed to achieve the compatibility for layered structures that are essential for MAX-phase stability6. Late transition metals exhibit relatively incompatible bonding and cannot facilitate formation of stable M layers.7 Moreover, the tendency of late transition metals to form non-layered structures (strong covalent bonds) often leads to stable phases that commonly remain distinct from MAX phases.8 “A” stands for 13 or 14 element of the group. X stands for C, N and O (for oxynitrides and oxycarbides).9 In most reports, the general formula of MXenes is represented as Mn+1XnTx, where Tx stands for terminal groups (i.e.,
O, –OH, –F, –Cl, or
S). MXene terminations are the chemical functional groups over the surfaces of a MXene.10Fig. 1a represents the chemical compositions of MAX and MXenes.11
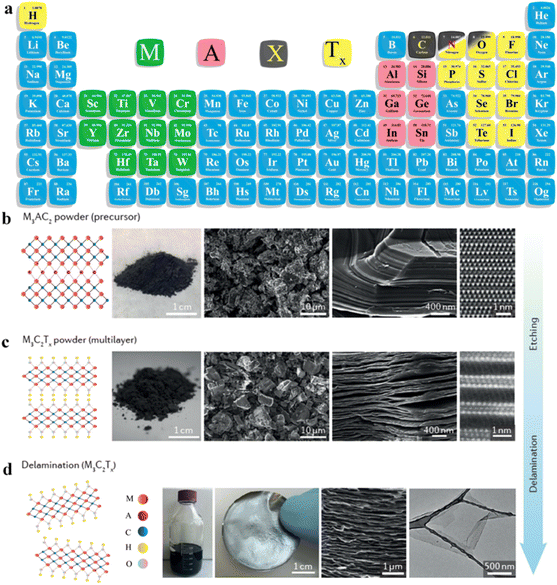 |
| Fig. 1 (a) Important elemental constituents of MAX and MXenes. The black highlight in O represents oxycarbides and oxynitrides, reproduced from ref. 11 with permission from Royal Society of Chemistry, copyright 2022. (b and c) Atomic structure, SEM and HR-STEM results of precursors of MAX (Ti3AlC2) and a multi-layered MXene (M2C2Tx). (d) SEM image of a Mo2TiC2Tx film of Ti3C2Tx in water along with a digital view and TEM image of Ti3C2Tx flakes, reproduced from ref. 60 with permission from Nature Reviews Materials, copyright 2017. | |
MXenes have been employed in various advanced applications: energy storage,12–17 electronics,18–21 environmental,22–26 sensors,27–33 catalysis34–38 and biomedicine.39,40 The advanced features and flexibility of MXene structures are the main causes of their diverse applications. The chemical and physical properties of MXenes can be modified by controlling the MXene terminations to targeted applications. MXene terminations have been altered to generate layers for “sensing” different gases or chemicals. This sensing mechanism relies upon changes in MXene electrical conductivity or capacitance due to the presence of adsorbate molecules.41 In addition, MXene terminations can affect surface properties, such as wettability, that enhance the sensing performances. MXene-based sensors have been effectively utilized for gas-, humidity-, and chemical-sensing applications. Further research is ongoing to develop more advanced MXene-based sensors with improved sensitivity and selectivity.42
The world has been facing an energy crisis but MXene-based materials have the potential to build a new hope to reduce this issue.43 There is great demand to replace conventional energy sources by developing alternative, sustainable and clean energy sources.44 The energy crisis can be overcome by solar-energy harvesting.45 For this purpose, researchers are interested in hydrogen generation via water splitting on MXenes and their substitutes.46 In this context, the characteristics of super charge-conducting materials like MXenes are crucial because these materials have potential to transfer photo-induced charges (e−/h+) to active centres. Moreover, the effectiveness of a sustainable catalytic system depends on the ability to reduce back reactions.47,48 Semiconductors exhibit low visible absorption. However, upon combination with a MXene, charge-carrier transportation is significantly enhanced.49 The efficiency of catalysts can be improved by loading MXene based co-catalysts or any noble metal. Improvement of MXene-based co-catalysts is needed to boost efficiency and scale-up photocatalytic applications.50
The functional groups (–OH,
O and –F) present on the surface of MXenes as terminations are dependent upon the type of etchant used in the synthesis.51 Direct hydrofluoric acid (HF) etching of MXenes enables changes in the proportion of –OH,
O, and –F groups on the surface of MXenes.52 In this context, titanium carbide (Ti3C2) has drawn much interest to researchers for energy conversion and energy-storage systems.53 This article provides insights on the synthetic methods for –Cl, –Br, and –I terminated MXenes by utilization of molten salts (such as ZnCl2) to erode the aluminium or “A” layer,54 which can be further modified with other terminations, like –S, –Te and –NH.55,56 A commonly utilized MXene (Ti3C2Tx) is usually terminated by
O and –OH through electrochemical corrosion.57 MXenes can be produced by the intercalation and delamination of MAX phases for algae extraction.58 Similarly, MXenes can be developed by a microenvironment method by employing organic solvents. The most effective solvents that have been identified facilitate the dispersion of substantial Ti3C2Tx nanosheets.59
This article illustrates the improvements in various syntheses and designs for MXenes and their terminations. We focus on the novel designs and approaches, structural modification, and state of the art applications of MXenes. Fig. 1b demonstrates the atomic structures along with a digital image of MAX (i.e., M3AC2), whereas Ti3AlC2 is exhibited via SEM and HR-STEM images. Consequently, HR-STEM results of Mo2TiAlC2 provide structural details. Fig. 1c presents various features of MXenes: atomic structures, digital images, and multilayer morphologies. The HR-STEM image (Fig. 1c) shows removal of the aluminium (A) layer to develop Mo2TiC2Tx. Similarly, Fig. 1d illustrates the atomic structures and TEM result of Ti3C2Tx flakes along with cross-sectional SEM results. Additionally, a digital photograph depicts 400 mL of delaminated Ti3C2Tx in water and Mo2TiC2Tx produced via vacuum-assisted filtration.60
Recent developments in MXenes have also been summarized and evaluated, focusing on their terminations and applications. These factors significantly influence the chemical properties exhibited by MXenes. Furthermore, challenges (along with their potential solutions) associated with MXene design for specific applications have been demonstrated and justified.
2. Different methods for MXene designs
The synthesis of MXenes can be achieved through various etching methods. These include in situ etching with hydrofluoric acid (i.e. HCl/LiF), direct HF etching, electrochemical etching, molten salt substitution, algae extraction, photolithography, hydrothermal methods, scalable synthesis, as well as iodine-assisted and ion-induced gelation.55,61–70 Each method has particular advantages along with disadvantages. The chemical structures and electronic properties of MXenes are dependent upon multiple aspects. These aspects may include: (i) purity of the MAX-Phase; (ii) choice of etching agent; (iii) concentration; (iv) stoichiometry of precursors; (v) method employed for preparation; (vi) reaction duration.71,72 Details of different methods used for MXene synthesis are depicted in Fig. 2.
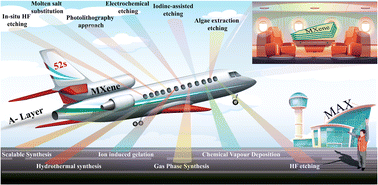 |
| Fig. 2 Synthetic methods for MXenes. | |
2.1.
In situ HF etching
This method was proposed by Ghidiu et al.56 It involves the use of different etchants (i.e., LiF/HCl, LiF/NaF, forming in situ HF)73,74 employed to eliminate the aluminium layers from a MAX-Phase. This etching process ends with the development of a layered MXene with terminations such as
O, –OH and –F (Fig. 3a).75 This method is also known as the “clay method” because the MXene obtained looks like clay paste.56 Ammonium fluoride can also be used as an etching agent to reduce the number of intercalation steps.76
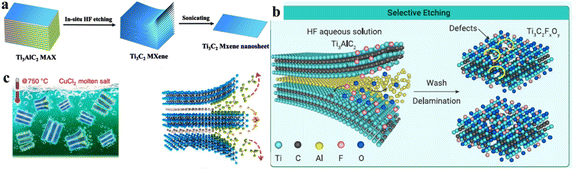 |
| Fig. 3 Synthetic schemes of MXene. (a) Ti3C2 MXene nanosheets by in situ HF etching, reproduced from ref. 75 with permission from Springer Nature, copyright, 2021. (b) Ti3C2 MXene nanosheets by HF etching, reproduced from ref. 82 with permission from ScienceDirect, copyright, 2023. (c) Development of a MXene by molten salt, reproduced from ref. 89 with permission from Nature, copyright, 2020. | |
2.1.1 Mechanism.
The in situ generation of HF from HCl and LiF facilitates etching of the A layer to form a MXene. The byproducts (i.e., LiCl, AlF3) further react with MXenes, to generate –F, –Cl, –OH and
O terminations. The etching process is depicted through eqn (1)–(5): | Ti3AlC2 + 3HCl + 3LiF = Ti3C2 + 3LiCl + AlF3 + 1.5H2 | (1) |
| Ti3C2 + 2HF = Ti3C2(F)2 + H2 | (2) |
| Ti3C2 + 2HCl = Ti3C2(Cl)2 + H2 | (3) |
| Ti3C2 + 2H2O = Ti3C2(OH)2 + H2 | (4) |
| Ti3C2 + 2H2O = Ti3C2(O)2 + 2H2 | (5) |
2.1.2 Advantages.
In situ HF etching enhances the quality of the MXene. Researchers can produce MXene films of any dimension that promise more conductive properties. Additionally, this method can be used to develop MXene ink to in situ deposits on targeted substrates. Also, there is no need for sonication for delamination.73 The yield of a MXene obtained from in situ etching method is 100%.56 Similarly, this method consumes low energy during its operation. In this method, metal cations can be embedded between MXene sheets to enhance the layered spacing to enable easier separations. The distinct advantage of this method is direct delamination of MXene sheets through intercalating fluoride ions, which provides reaction stability, higher surface area and more redox-active sites.49
2.1.3 Drawbacks.
The main drawback linked with this approach is that, due to intercalation of water molecules, the drying process can take longer time as compared with other methods.77 Furthermore, interlayer spacing can be reduced and broken during the drying process. It has been reported that, by increasing –F contents, interlayer spacing in MXene sheets can be diminished.49
2.1.4 Precautions and suggestions.
It has been suggested that in situ HF etching needs more careful handling and stoichiometry of precursors during etching and developments. Intercalation of water contents can be reduced/eradicated by using appropriate solvents.77–79
2.2. Direct HF etching
Direct HF etching is a fundamental and widely employed method for producing MXenes and derivatives. In 2011, Naguib et al. used this method to etch MAX phases.80 After HF etching, dense MAX phases were converted into loosely stacked multilayered MXenes, which contains –OH, –F and
O terminations on their surfaces (Fig. 3b).81,82 Although these terminations affected the mechanical strength and other properties, they could be controlled by the compatibility of the MXene with the polymer matrix.83 This method rendered them hydrophilic and highly dispersible in the presence of various polar solvents.60
2.2.1 Mechanism.
HF assists the etching of MAX to form MXenes. The byproduct (AlF3) and H2O react with further MXenes to generate –F, –OH and
O terminations. The etching process is depicted through eqn (6)–(9): | 2Ti3AlC2 + 6HF = 3H2 + 2Ti3C2 + 2AlF3 | (6) |
| Ti3C2 + 2HF = Ti3C2(F)2 + H2 | (7) |
| Ti3C2 + 2H2O = Ti3C2(OH)2 + 2H2 | (8) |
| Ti3C2 + 2H2O = Ti3C2(O)2 + 2H2 | (9) |
2.2.2 Advantages.
It is considered a special method if a MXene can be prepared at low or even at room temperature. This is widely recommended for its ease and simplicity of use. Using this method, the –OH group (i.e., termination) can convert Ti3C2OHxin situ to TiO2, which can extend the utility of MXenes for photocatalytic applications.49 It has been noted that fully fluorine-terminated MXenes have high resistance against oxidation, which enhances their stability. Albeit, fully iodine-terminated MXenes are considered not stable to resist oxidation.49,84 In addition, HF aqueous etching offers numerous benefits, such as complete elimination of the aluminium layer from the MAX phase, and better morphology and yield.60 Due to these advantages, researchers mostly use this approach to design MXenes and its other derivatives.85
2.2.3 Drawbacks.
HF is highly corrosive and toxic, so its direct use is restricted. MXenes produced via this method have high fluorine contents. The presence of fluorine is problematic specifically for photocatalytic reactions.49 Another major disadvantage of F-terminating groups is non-valid electrode/electrolyte interface reactions. Moreover, the interfacial resistance between electrode/electrolyte systems is enhanced, which may reduce the stability and charge-storage performance.49,86
2.2.4 Precautions and suggestions.
This method needs extra precautions due the corrosive nature of HF (etching agent)78 as well as persons familiar with safety measures. Materials must be treated appropriately after experimentation.79,87
2.3. Molten salt substitution
To avoid the etching risks in other approaches, MXenes can also be prepared using fluoride molten salts (i.e., KF, LiF, NaF, CuCl2 and bifluoride salts) (Fig. 3c). If the salt contains bromide rather than fluoride, the resulting MXene has –Br as a terminating group that can be easily substituted with other groups.88 Similarly, iodine-terminating MXenes can also be synthesized using iodine-containing molten salts. The adsorption strengths of –Br and –I are overestimated when assessed under a gas phase compared with the elemental state.84 According to Li et al., MXenes synthesized using molten salt synthesis exhibit an enhanced capacity for lithium-ion storage, which results in higher electrochemical performances.89
2.3.1 Mechanism.
The molten salt (i.e., CuCl2, ZnCl2) facilitates the etching of MAX phases by reacting with the A-layer. This reaction generates the metal as a byproduct, while the negative parts of the salt (Cl2) terminated to MXene. The etching process is depicted through eqn (10) and (11): | Ti3AlC2 + 1.5CuCl2 = Ti3CuC2 + 0.5Cu + AlCl3 | (10) |
| Ti3CuC2 + CuCl2 = Ti3C2(Cl)2 + 2Cu | (11) |
2.3.2 Advantages.
The distinct advantage is that the salt precursors of chlorine, fluorine, and iodine exhibit satisfactory binding, but the binding strength is dependent upon the surface terminations. In the case of iodine, the disparity between low and full surface terminations is comparatively large, and can reach up to 2 eV for Nb4C3.84 The other advantage of this approach is that, due to the termination of Cl, stable MXenes can be developed (which is uncommon using other methods).90 Cl-terminating groups provide excellent durability to MXenes. Additionally, molten salt etching has a broader etching range comparatively.91 Lewis-acid etching does not require the use of HF, so it is a practical and environment friendly method for generating MXenes.10
2.3.3 Drawbacks.
This approach requires a high temperature (>500 °C). The other drawback linked with this approach is the production of unwanted byproducts. In this approach, further purification may be the sole requirement. This method enhances the complexity on MXene surfaces, which may alter or affect chemical properties.49
2.3.4 Precautions and suggestions.
Appropriate heating equipment/instruments that can control and precisely measure the temperature are necessary.79,87 To obtain targeted and desired properties, extra care and expertise are mandatory for setting the required conditions (etching salt and temperature).78
2.4. Electrochemical etching
Electrochemical etching that usually performed in HCl may cause combinations of
O, –OH and –Cl terminating groups. Fig. 4a illustrates the synthesis of MXene via electrochemical etching. Yang et al.57 demonstrated that Ti3C2Tx MXenes can be synthesized through electrochemical corrosion. However, in some cases, electrochemical etching can lead to the generation of carbon-derived carbides (CDC).92 However, by altering the electrolyte composition, aluminium atoms can be substituted with OH groups. As a result, double- or single-layer Ti3C2Tx nanosheets can be generated at >90% yield.54 Three types of MXenes, namely Ti2CTx, V2CTx, and Cr2CTx, have been synthesized and reported by this method.93
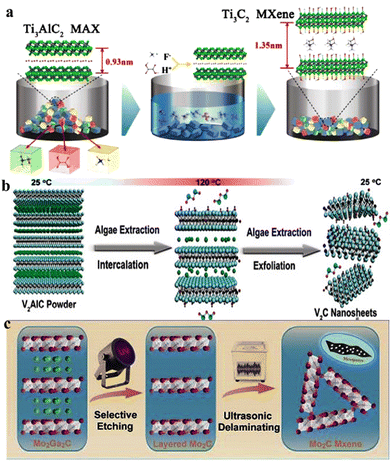 |
| Fig. 4 Synthesis of MXenes via electrochemical, algae-extraction and UV-induced selective etching methods. (a) Synthesis of MXenes via electrochemical etching, reproduced from ref. 79 with permission from Springer Nature, Elsevier, copyright 2020. (b) Production of V2C NSs via algae extraction (schematic), reproduced from ref. 58 with permission from Wiley, copyright 2020. (c) Synthesis of MXene via a UV-induced selective etching method, reproduced from ref. 96 with permission from Elsevier, copyright 2020. | |
2.4.1 Mechanism.
In the electrochemical processes, MAX reacts with chloride ions to form MXenes. Subsequently, MXenes react with water and hydroxide ions to produce –OH-terminated MXenes. The etching process is depicted through eqn (12)–(14): | Ti3AlC2 + 3Cl− − 3e− = Ti3C2 + AlCl3 | (12) |
| Ti3C2 + 2OH− − 2e− = Ti3C2(OH)2 | (13) |
| Ti3C2 + 2H2O = Ti3C2(OH)2 + H2 | (14) |
2.4.2 Advantages.
Thermal-assisted electrochemical etching provides a universal method but is also a straight forward approach to MXene synthesis that was difficult previously. The major benefit is that the proportion of active sites increases significantly by increasing the number of O-terminating groups. O-terminating groups facilitate greater adsorption of lithium ions in electrode materials.86 This approach offers a new pathway for the rapid, straightforward, and safe synthesis of MXenes.10 It is a “green” and inexpensive synthetic method. The resulting MXene can have excellent activities attributable to relatively greater lateral diameters compared with MXenes obtained in other reported methods.49
2.4.3 Drawbacks.
The significant problem associated with this method is that when Ti2AlC (MAX) is subjected to a higher cathodic potential, removal of Ti along with Al layer may occur, which can result in CDC formation. Moreover, the structures of developed MXenes can be damaged by the use of inappropriate electrolytes. A safety risk is increased due to the toxicity of the intercalation.49
2.4.4 Precautions and suggestions.
The etching setup may be altered so that wires provide electricity during experimentation.77 It has been suggested that control of key parameters (e.g., voltage, temperature, etching time, electrode preparation and handling) may significantly affect the quality of the MXene obtained.87
2.5. Algae extraction etching
Zada et al.58 introduced a new approach that emphasizes the use of vanadium carbide nanosheets (V2C NSs) to generate MXenes. This methodology involves the intercalating and delaminating of MAX with algal extraction (Fig. 4b). The V2C NSs exhibited strong structural integrity and excellent NIR absorption.94 Also, the V2C NSs exhibited effective photothermal-conversion efficiencies compared with MXenes prepared by other methods.58 However, this synthetic method has not been applied much.
2.5.1 Advantages.
The special feature of the algae extraction etching method is that it is comparatively biocompatible as compared with traditional chemical methods. Also, the raw material (algae) are relatively inexpensive and can be cultivated using sunlight.95 The quick, easy, low-cost, and high-yielding delamination process creates a novel path for breaking down MAX and creating MXenes with suitable characteristics for various applications.58 These multiple advantages make this method superior to other approaches used for MXene development.
2.5.2 Mechanism.
The MAX, when exposed to algae, transforms into a MXene. The proposed etching process is depicted in eqn (15). | V2AlC + algae = V2C + Al − algae | (15) |
2.5.3 Drawbacks.
The etching process is extremely slow and time-consuming. Moreover, control over the purity during etching and its reliability is challenging.
2.5.4 Precautions and suggestions.
The composition and properties of algae can vary and may affect the reaction for MXene synthesis. It has been suggested that the species of algae should be selected to avoid unwanted byproducts. Another suggestion is that the species of algae should be characterized before use in etching of the MAX phase.77
2.6. Photolithography
A novel and efficient UV-induced selective etching method was proposed by Mei and co-workers.96 The specialty aspect of this method is that it delivers rapid growth of MXenes in the presence of UV-light. This method propagates in 85% phosphoric acid solution (Fig. 4c). By employing this approach, an exceptional rate potential and stability can be achieved for lithium-ion batteries (LIBs) as well as sodium-ion batteries (SIBs).97 It has been reported that MXenes obtained via this approach, when used as anode material, exhibit promising results. Thus, Mo2C MXene advanced materials hold great promise for various energy-storage applications.98,99
2.6.1 Mechanism.
UV irradiation on MAX with acid leads to the formation of a MXene followed by reactions to produce –OH- and –Cl-terminated MXenes. The proposed etching process is depicted in eqn (16)–(18). | Mo2Ga2C + UV + 6HCl = Mo2C + 2GaCl3 + 3H2 | (16) |
| Mo2C + 2H2O = Mo2C(OH)2 + H2 | (17) |
| Mo2C + 2HCl = Mo2C(Cl)2 + H2 | (18) |
2.6.2 Advantages.
In this approach, use of hazardous and highly corrosive acids is avoided. MXenes obtained by this method can achieve fine structures with targeted morphologies and properties. Moreover, the product can be reproduced easily using this method. Use of MXene-based batteries can be effective, so MXenes developed by this approach can be widely utilized in energy conversion and energy-storage devices.
2.6.3 Drawbacks.
The drawbacks linked with this approach are its high cost, multiple steps and complex reaction process. The complexity of multiple processes increases the chance of errors and can lead to impurities in the final product. The chemicals used can be hazardous and more caution is needed for handling and disposal.
2.6.4 Precautions and suggestions.
The substrate must be transparent to pass the UV-light it is exposed to. Similarly, UV-protective glasses and adequate clothing should be used during experimentation. Additionally, exposure time and UV intensity must be optimized to achieve the desired results and target morphologies.87
2.7. Hydrothermal synthesis
HF is necessary in most MXene-etching processes.100 Despite being successful, some procedures are hazardous to the environment. The alkalis used for synthesis are considered to be etching agents due to the powerful affinity for amphoteric elements (i.e., Al, Ga, Pb and Sn).101 High-purity multilayer MXenes have not been prepared using traditional methods. The main challenge to obtain MXenes via alkali attack is the in situ formation of oxide or hydroxide layers.102 Li et al. reported a hydrothermal method that used NaOH for the etching of Ti3AlC2 (MAX phase) and synthesis of MXene Ti3C2Tx (where Tx is –OH,
O). The synthesis via a hydrothermal method is illustrated in Fig. 5a. Results indicated that a temperature of 270 °C led to the aluminium layer being proficiently removed with NaOH solution. Using this method, MXenes with –OH and
O terminations and 92% purity have been reported.103 Peng et al.66 synthesized Ti3C2Tx and Nb2CTx MXene using hydrothermal etching-assisted by NaBF4/HCl media.
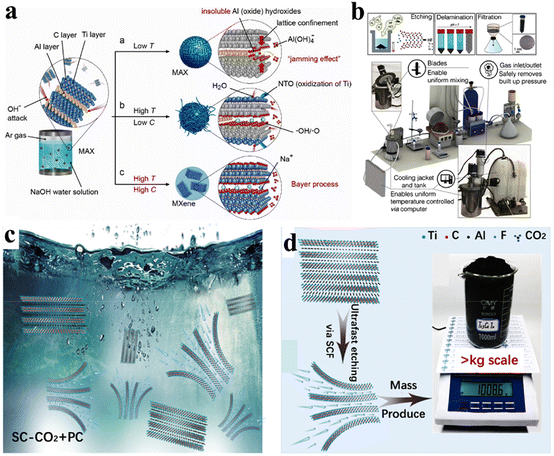 |
| Fig. 5 (a) Representation of hydrothermal synthesis, reproduced from ref. 103 with permission from Wiley, copyright 2018. (b) Synthesis of MXene via a scalable approach, reproduced from ref. 67 with permission from Wiley, copyright 2020. (c) Large-scale synthesis of MXenes via immersion of Ti3AlC2 in PC solution. (d) Etching via SCF and obtained Ti3C2Tx in kilogramme-scale, reproduced from ref. 109 with permission from Elsevier, copyright 2023. | |
2.7.1 Mechanism.
The hydrothermal reaction involves the interaction of the MAX phase with hydroxide ions and water. This results in the formation of –OH- and
O-terminated MXene, along with byproducts and H2 gas, as shown in eqn (19) and (20): | Ti3AlC2 + OH− + 5H2O = Ti3C2(OH)2 + Al(OH)−4 + 2.5H2 | (19) |
| Ti3AlC2 + OH− + 5H2O = Ti3C2O2 + Al(OH)−4 + 3.5H2 | (20) |
2.7.2 Advantages.
By employing a hydrothermal approach, MXenes can be produced quicker compared with HF-etching or other methods. The main advantage is that MXenes developed by the hydrothermal method exhibit more layers compared with that using other traditional methods. Moreover, hydrothermal is a simple and eco-friendly approach that is preferable to other approaches.104 Also, this method is based on alkali-etching precursors to produce high-purity multilayer MXenes, which is a fluorine-free approach. This method can be utilize for specific and targeted applications.103 For example, MXenes obtained via a hydrothermal method exhibit capacitance 214% greater than that of MXenes prepared by the HF-etching method.105
2.7.3 Drawbacks.
MXene synthesis via a hydrothermal approach typically requires an autoclave reactor, which requires stealth to avoid explosions. Additionally, the hydrothermal reaction requires relatively high temperatures that may oxidize the product. During the hydrothermal reaction, MXene sheets may contain multiple defects on surfaces due to the high rate of particle collision.106
2.7.4 Precautions and suggestions.
The hydrothermal approach can be dangerous due to the use of high temperatures and pressures. The morphologies of targeted MXenes may alter due to etching at high pressures and airtight environments. It has been suggested that safety measures must be engaged prior to the hydrothermal reaction. Also, a safe environment is needed to avoid explosion of the reactor due to a collapse of temperature or electricity.77
2.8. MXene synthesis via a scalable approach
Reports have suggested that the synthesis of MXenes can be scaled up to an industrial level, but experimental proof is lacking. In 2022, Shuck et al. reported a chemical reactor that was designed for scalable production of MXenes.67 Then, they compared the amounts of MXene produced using large (50 g) and small (1 g) batches. They predicted no appreciable changes between materials using large and small batches in terms of structural morphology.107 Sizes of MXene flakes (layers) between these two batches were nearly comparable. Fig. 5b demonstrates experimental setup of a 1 L MXene reactor along with a 3D model of the apparatus. This system had a cooling tank and interior jacket that ensured maintenance of temperature during the entire reaction. In this protocol, MAX powder was uniformly added using a screw feeder equipped with a gas input accessory. To prevent reactor parts from HF (which can dissolve metal or glass), the mixer and thermocouple jacket were made from a stable polymer (i.e. Teflon™).67,108 Overall, method has been advised for large-scale synthesis of MXenes.
Chen et al. developed a supercritical etching method using carbon dioxide as an etchant for the large-scale production of various MXenes (Ti3C2Tx, Nb2CTx, Ti2CTx, Mo2CTx, and Ti3CNTx) (Fig. 5c). Thermally powered supercritical carbon dioxide accelerated the etching rate and gave a yield of ∼1 kg (Fig. 5d). The prepared MXenes possessed remarkable charge-storage capacity and ∼100% coulombic efficiency.109
2.8.1 Mechanism.
The supercritical carbon dioxide-assisted reaction involves the etching of MAX with NH4HF2, which results in the formation of an –OH-terminated MXene. The proposed etching process is depicted in eqn (21). | Ti3AlC2 + CO2 + 3NH4HF2 = Ti3C2(OH)2 + (NH4)3AlF6 + 1.5H2 | (21) |
2.8.2 Advantages.
This method can be used for the large-scale synthesis of MXenes. Overall expenditures and per-unit costs can be reduced because a higher yield of product is achieved using a single-step batch reaction using this method. Also, energy consumption using this approach is less as compared with that using other methods.
2.8.3 Drawbacks.
Instrumental setup is complicated and is not commercially available. Like other methods, this approach can also be undertaken using HF and CO2, which are costly and hazardous to handle. Moreover, material disposal or residues after etching merit need extra care to ensure safety.79
2.8.4 Precautions and suggestions.
The etching process used in this method is highly exothermic, so safety measures must be adopted before starting the reaction. The flow rate of the MAX phase for HF-etching must be controlled carefully. Moreover, special safety equipment (i.e., gloves, goggles, face shield, fume hoods) is needed.
2.9. Iodine-assisted etching
Shi et al. reported this method in 2021. Fig. 6a demonstrates the preparation of MXenes using this method.110 This method involves the use of non-aqueous iodine (I2) during etching. Initially, Ti3C2Ix is formed by subjecting Ti3AlC2 to iodine etching in anhydrous acetonitrile at 100 °C. Subsequently, Ti3C2Ix is transformed to Ti3C2Tx layers, whose diameters become relatively small (∼1.8 nm). More than 71% of layers exhibit a thickness <5 nm. The resulting Ti3C2Tx flakes reveal exceptional stability even under ambient conditions.110
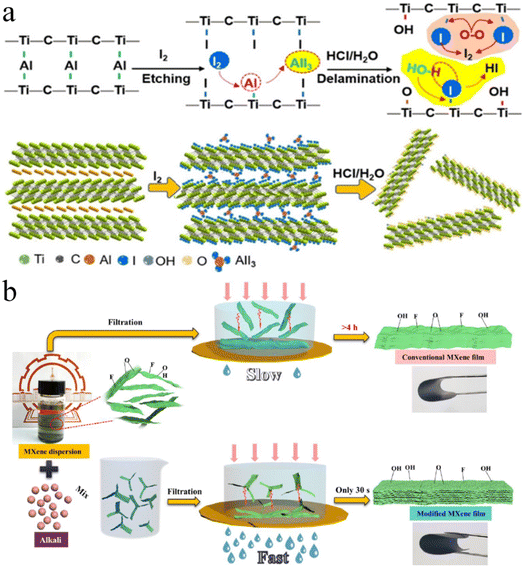 |
| Fig. 6 (a) Iodine-assisted etching and delamination of Ti3AlC2, reproduced from ref. 110 with permission from Wiley, copyright 2021. (b) Schematic illustration of synthesis, reproduced from ref. 111 with permission from Engineered Science, copyright 2021. | |
2.9.1 Mechanism.
The mechanism involves the sequential reactions of MAX with iodine, oxygen, H2O and HCl. These reactions result in the formation of an iodine-substituted MXene. Oxidation and subsequent hydrolysis gives an –OH-terminated MXene. The proposed etching process is depicted in eqn (22)–(26). | 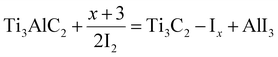 | (22) |
|  | (23) |
| Ti3C2 − Ix + xH2O = Ti3C2 − (OH)x + xHI | (24) |
| AlI3 + 3H2O = Al(OH)3 + 3HI | (25) |
| Al(OH)3 + 3HCl = AlCl3 + 3H2O | (26) |
2.9.2 Advantages.
This approach is relatively simple (in terms of handling) and cost-effective as compared with the other methods reported herein. MXenes produced by this method have high stability, purity and durability. A gelatine approach allows researchers to “fine tune” the morphology of the MXene. Moreover, this approach is protective and relatively environment friendly.
2.9.3 Drawbacks.
This approach may require more time to achieve targeted synthesis of MXene nanostructures. The precursors needed in this approach are not widely available as compared with others used in MXene syntheses. Due to its simplicity, this approach requires more attention when setting the reaction conditions.
2.9.4 Precautions and suggestions.
Handling of iodine merits attention and care because it is volatile and hazardous. Maintenance of a precise temperature during synthesis is crucial for higher output and accuracy.
2.10. Ion-induced gelation
In 2021, Wang and colleagues111 reported a quick metal ion-induced gelation approach. Using this method, Ti3C2Tx MXene could be modified with minimally intensive layer delamination (MILD). This method involves sequential steps of reactions, washing, and centrifugation to obtain a MXene with a homogeneous monolayer. Additionally, MXene micro-gels were prepared using a MXene in a KOH environment. The resulting mixture delivered a MXene membrane filter (MMF) by vacuum-assisted filtration.111Fig. 6b illustrates the scheme of this approach. The effect of MXene delamination via dimethyl sulfoxide is explained in ESI Section S1.‡
2.10.1 Mechanism.
Ion-induced gelation occurs as NaOH ions interact with Ti3C2Tx, which leads to the formation of MXene layers. This approach is depicted in eqn (27). | Ti3C2Tx + NaOH(aq) = MXene layers + byproducts | (27) |
2.10.2 Advantages.
This approach is new and easy to handle. This method is unique due to mild processing conditions (i.e., no extra-heat, no excessive solvents, or hazardous environmental toxins). Moreover, this method is tuneable so it can be handled/computed with modern accessories.
2.10.3 Drawbacks.
Scale-up of this method to an industrial setup has been done. This method has not been commercialised because it is a very recent approach (reported in 2021 by Wang and colleagues).111 MXenes prepared by this method have not been tested on modern analytical instruments.
2.10.4 Precautions and suggestions.
Selection of appropriate precursors must be compatible with an ion-induced approach.87 Laboratory-based experiments should be undertaken to optimize the synthesis parameters.77
2.11. Other synthetic methods
Various other synthetic methods, including gas-phase synthesis and chemical vapour deposition (CVD), have also been employed for the fabrication of MXenes. Each method offers distinct advantages and characteristics suitable for specific applications.
Xiang et al. utilized a fluidized bed reactor (FBR) for the synthesis of Ti2CCl2 through gas-phase synthesis (Fig. 7a). Solid TiCl3 precursors were sublimated at 770 °C and reacted with CH4 in the FBR to produce Ti2CCl2 (MXene). Approximately 100 g of MXene was generated per batch.82 The synthesis mechanism is given in eqn (28) and (29):
| 6TiCl3 + CH4 = Ti2CCl2 + 4TiCl4 + 2H2 | (28) |
| 2TiCl3 + CH4 = 2Ti2CCl2 + 4HCl | (29) |
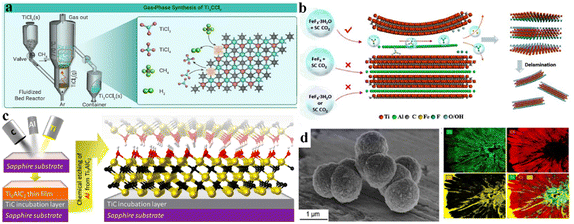 |
| Fig. 7 (a) Gas-phase synthesis of Ti2CCl2 reproduced from ref. 82 with permission from ScienceDirect, copyright 2023. (b) CO2-assisted synthesis of MXenes, reproduced from ref. 112 with permission from Royal Society of Chemistry, copyright 2023. (c) Magneto supporting for MXene synthesis, reproduced from ref. 76 with permission from American Chemical Society, copyright 2014. (d) SEM results and elemental maps of MXenes prepared via chemical vapour deposition, reproduced from ref. 113 with permission from Science, copyright 2023. | |
Feng et al. used supercritical (SC) CO2 to etch MAX in the solid phase. They observed that SC CO2 with FeF3·3H2O could synthesize and delaminate multilayer MXenes (Fig. 7b).112 The synthesis mechanism is given in eqn (30)–(33):
| Ti3AlC2 + 3FeF3·3H2O + 3xCO2 = Ti3C2 + AlF3 + 9H2O + [Fe(CO2)xF2] | (30) |
| Ti3C2 + 3FeF3·3H2O + 2xCO2 = Ti3C2(F)2 + 6H2O + 2[Fe(CO2)xF2] | (31) |
| Ti3C2 + H2O = Ti3C2(OH)2 + H2 | (32) |
| Ti3C2 + H2O = Ti3C2(O)2 + H2 | (33) |
Halim et al. reported the fabrication of Ti3C2 films via targeted removal of aluminium from sputter-deposited MAX film. Aqueous HF and NH4HF2 were used for selective etching (Fig. 7c).76 The synthesised MXene transmitted 90% of visible light and infrared light, and exhibited metallic conductivity down to 100 K. The synthesis mechanism is given in eqn (34)–(37):
| Ti3AlC2 + 3HF = Ti3C2 + AlF3 + 1.5H2 | (34) |
| Ti3C2 + 2H2O = Ti3C2(OH)2 + H2 | (35) |
| Ti3C2 + 2HF = Ti3C2F2 + H2 | (36) |
| Ti3AlC2 + 3NH4HF2 = (NH4)3AlF6 + Ti3C2 + 1.5H2 | (37) |
| Ti3C2 + aNH4HF2 + bH2O = (NH3)c(NH4)dTi3C2(OH)xFy | (38) |
MXenes are typically produced by etching MAX phases. Wang et al. introduced a novel method to synthesize MXenes by utilizing CVD, even for MXenes that have not been derived from MAX phases. They established a direct and scalable synthetic pathway for MXenes by reacting CH4 with TiCl4, ZrCl4, or ZrBr4. This approach involves the reactions of metals and metal halides with graphite, methane, or nitrogen. Direct synthesis facilitates the growth of MXenes in various diverse morphologies rather than a conventional layered structure (Fig. 7d). The synthesised MXenes from this method demonstrated impressive energy-storage capacity113
2.11.1 Advantages.
Gas-phase synthesis offers precise control for MXene synthesis without forming thermodynamically stable TiC. It allows continuous operation and scalable production to industrial levels. CVD enables the synthesis of MXenes that cannot be conventionally derived from MAX phases. CVD offers a direct route of synthesis without need for MAX phase precursors. This method leads the synthesis of MXenes with diverse morphologies beyond conventional layered structures.
2.11.2 Drawbacks.
The handling of multiple precursors can add complexity to the synthesis. Additionally, achieving uniform and controlled growth of MXenes with diverse morphologies might create challenges in maintaining consistent properties during large-scale production.
2.11.3 Precautions and suggestions.
To maintain consistent surface chemistry and excellent conductivity across batches, continuous optimization of synthesis conditions and parameters is needed. Safety protocols must be followed while operating the FBR for MXene synthesis. Reaction parameters (e.g., temperature, pressure and precursor ratios) must be standardized to maintain reproducibility and ensure consistent MXene properties. To identify ideal conditions for uniform MXene growth, systematic experimentation and testing are necessary.
Numerous methods that have been reported for the synthesis of MXene via various synthetic strategies, terminations, and characterizations for useful applications are shown in Table 1.
Table 1 Year-wise summary of different MXene materials developed via various synthetic strategies, terminations, and characterizations for useful applications
Year |
MXene |
Synthetic strategy |
MAX precursor |
Surface termination |
Film thickness (nm) |
Characterizations |
Applications |
Ref. |
2011 |
Ti3C2 |
HF treatment |
Ti3AlC2 |
–OH, –F |
1.2 |
XRD, Raman, XPS, SEM, TEM & HRTEM |
Synthesis of carbides and nitrides of Ti, V, Cr, Nb, Ta, Hf and Zr |
80
|
2012 |
Ti2C |
HF treatment |
Ti2AlC |
OH, –F |
N/A |
XRD & CV |
LIBs |
114
|
2012 |
Ti2C |
HF treatment |
Ti2AlC |
O, –F |
N/A |
SEM, BET & CV |
LIBs |
115
|
2012 |
Ti3C2 |
HF treatment |
Ti3AlC2 |
–OH, –F |
N/A |
DFT, NEB & PAW method |
LIBs |
116
|
2013 |
Nb2C |
HF treatment |
Nb2AlC |
O, –F, –OH |
N/A |
XRD, XPS, SEM |
LIBs |
117
|
2013 |
V2C |
HF treatment |
V2AlC |
O, –F, –OH |
N/A |
XRD, XPS, SEM |
LIBs |
117
|
2014 |
Ti3C2 |
HF treatment |
Ti3AlC2 |
O, –F, –OH |
<20 |
XRD, SEM, EDX, FT-IR & UV-vis-DRS |
Electrochemical biosensors |
118
|
2014 |
MXene-Cu2O |
HF treatment |
Ti3AlC2 and Cu(CH3COO)2·H2O |
O, –F, –OH |
30 ± 10 |
XRD, FESEM & TG-DSC |
Thermal decomposition of ammonium perchlorate (AP) |
119
|
2014 |
Ti3C2 |
CO2-assisted solid phase etching |
Ti3AlC2 |
–Fe, O, –F |
N/A |
SEM, TEM, AFM, XPS, & IR |
HER |
112
|
2015 |
Ti2CTx |
HF treatment |
Ti2AlC |
–OH –F O |
0.028 |
XRD, Raman, XPS, BET, SEM, TEM & HRTEM |
Super capacitors |
120
|
2015 |
(Nb0.8Ti0.2)4C3Tx |
LiF/HCl solution |
(Nb0.8Ti0.2)4AlC3 |
–OH –F O |
N/A |
XRD, SEM, TEM, & XPS |
Energy storage |
121
|
2015 |
(Nb0.8Zr0.2)4C3Tx |
HF treatment |
(Nb0.8Zr0.2)4AlC3 |
–OH –F O |
N/A |
XRD, SEM, TEM, & XPS |
Energy storage |
121
|
2015 |
Ti3C2Tx |
Dilute HF |
Ti3AlC2 |
–OH –F O |
0.9 ± 0.3 |
SEM, TEM, BET & XRD |
High performance super capacitor |
122
|
2015 |
Mo2C |
HF treatment |
Mo2Ga2C |
–OH –F O |
N/A |
SEM, TEM-EDX & XRD |
N/A |
123
|
2016 |
Mo2CTx |
HF/mixture of LiF and HCl |
Mo2Ga2C |
–OH, –F, O |
0.02 |
SEM, TEM, XRD & XPS |
LIBs and super capacitors |
124
|
2016 |
Ti3C2Tx |
Ultra-sonication |
Ti3AlC2 |
–F and O |
0.002–90 |
SEM, TEM, EDX & XRD |
Water treatment & biomedical applications |
125
|
2016 |
Zr3C2Tz |
HF treatment |
Zr3Al3C5 |
–OH, –F, O |
N/A |
XRD, SEM, TEM, TGA-DSC & XPS |
N/A |
126
|
2017 |
Ti2N |
KF + HCl |
Ti2AlN |
–OH, –F, O |
N/A |
XRD, Raman, SEM, EDX, XPS |
SERS substrate |
127
|
2017 |
Hf3C2Tz |
HF etching |
Hf3[Al(Si)]4C6 |
–OH, –F, O |
0.9 |
XRD, SEM, TEM, AFM |
Electrochemical |
128
|
2017 |
Ta4C3 |
HF etching |
Ta4AlC3 |
OH, –F, O |
1.00 |
XRD, SEM, TEM, Raman, XPS, DFT |
Anticancer |
129
|
2018 |
V2C |
NaF + HCl |
V2AlC |
–OH, –F, O |
0.854 |
XRD, SEM, EDX, Raman& TG-DTA |
Reported thermal stability of V2C |
130
|
2018 |
W1.33CTx |
LiF + HCl |
(W1.5Y0.3)2AlC |
–OH, –F, O |
— |
TEM, XRD, DFT |
HER |
131
|
2019 |
O terminated Ti3C2Tx |
HF treatment + n-butyllithium-treated method |
Ti3C2Tx |
O |
N/A |
SEM, XPS, BET & XRD |
High performance pseudo capacitors |
132
|
2020 |
Scalable synthesis of Ti3C2Tx |
HF treatment |
Ti3AlC2 |
–OH, –F, O |
0.007 |
SEM, XRD, Raman, XPS & UV-vis |
Scale-up synthesis |
67
|
2020 |
Sc2COx |
Sputtering |
— |
–OH, –F, O |
N/A |
XPS, PL, DRS |
Optical properties study |
133
|
2020 |
Cr2CTx |
FeCl3 + C6H6O6 etching |
Cr2AlC |
O, –OH |
N/A |
SEM, EDS, XRD, Raman, TEM, FTIR, XPS |
Hydrazine detection |
134
|
2020 |
Y2CF2 |
Solid-state reactions |
Y2C + YC + YF3 |
–OH, –F |
N/A |
XRD, DRS, SEM, XPS |
Photocatalytic activity |
135
|
2021 |
Ti2C, Nb2C, V2C, Mo2C, Ti3C2, and Nb4C3 |
Various chemical environments |
Ti2AlC, Nb2AlC, V2AlC, Mo2AlC, Ti3AlC2 and Nb4AlC3 |
O, OH, N, NH, NH2, S, SH, H, F, Cl, Br, and I |
N/A |
DFT, final state approximation, NEB & dimer method |
New synthesis routes |
84
|
2021 |
ZrC |
Sputtering |
— |
— |
N/A |
SEM, Raman, AFM |
Lock fiber lasers |
136
|
2021 |
Ti3C2Tx |
LiF + HCl |
Ti3AlC2 |
N/A |
N/A |
SEM, AFM, TEM, EDX & XPS |
Electrical wiring and signal transmission |
137
|
2022 |
TMSe@MXene |
HF treatment |
Ti3C2Tx & Nb2CTx |
O |
N/A |
SEM, TEM, HRTEM, STEM, XRD, XPS& BET |
ZIBs |
138
|
2022 |
MXene/CAC films |
LiF + HCl |
Ti3C2Tx |
–F, –OH |
N/A |
SEM, TEM, HRTEM, STEM, EDS, XRD, XPS, TGA, FT-IR, BET & DFT |
Super capacitors |
139
|
2023 |
PDPZ@MXene |
Vacuum-assisted filtration technology |
PDPZ and MXene |
–F, –OH |
— |
SEM, TEM, NMR, XRD, SAED, Raman & FT-IR |
Super capacitors |
140
|
2023 |
V2N |
HF treatment |
V2AlN |
–OH, –F, O |
3.7 |
SEM, TEM, XRD, XPS |
Anti-effective therapy |
141
|
2023 |
MXene@Co9S8/CoMo2S4 |
HF treatment and sulfidation |
Ti3AlC2 |
–F, –OH, S |
1.37 |
XRD, FE-SEM, EDS, TEM & XPS |
SIBs |
142
|
2023 |
GN/MXene/FeS foam |
Hydrothermal |
rGO, MXene, FeS |
–OH, –F, O |
N/A |
SEM, XRD & XPS |
Electromagnetic absorption |
143
|
2023 |
Ti2CCl2 |
CVD |
CH4 + TiCl4 |
–Cl, –Br |
N/A |
FBI-SEM, AFM, TEM, XRD, Raman, STEM, XRF, XPS |
Energy storage |
113
|
Zr2CCl2 |
CH4 + ZrCl4 |
Zr2CBr2 |
CH4 + ZrBr4 |
2024 |
Pd@Ti3C2Tx |
HF etching + wet impregnation |
Ti3AlC2 |
–OH, –F, O |
N/A |
XRD, SEM, XPS, UV-VIS/DRS |
Water splitting |
144
|
2024 |
Ti2CCl2 |
Gas phase |
TiCl3 + CH4 |
–Cl |
N/A |
XRD, SEM, AFM, STEM, HRTEM, EPR |
LSBs |
82
|
3. Insights into the doping and scope of MXene terminations
3.1. MXene terminations
Diverse compositions and a complex nature of terminations are involved in various etching methods. Despite inadequate scrutiny regarding the impact on MXene applications, researchers are striving to enhance performance by modifying the terminations linked to synthetic approaches.145 Surface variations and element doping on MXene terminations have been extensively reported, particularly for battery and supercapacitor applications. The choice of etching method is important because it can affect surface terminations.146 MXenes produced through fluorine-based etching methods typically exhibit terminations such as –OH,
O, and –F.60 Alkali and electrochemically assisted etching methods yield non-F-terminated MXenes but with lower efficiency.10 Methods involving molten salt etching generally result in the production of a single termination that can substituted via substitution reactions.55 Gas hydrolyzation has been found (Fig. 8a) to be very effective to substantially reduce F terminations.147 By employing gas hydrolyzation, oxygen (O) content remains relatively stable at ∼0.3 per unit formula of V2CTx. Some studies claim that, by doping MXenes with heteroatoms such as nitrogen (N) or sulfur (S), the electrical properties of supercapacitors are significantly enhanced.148 For example, if nitrogen is introduced into Ti3C2Tx frameworks, its thermal stability changes, thus improving its activities.149 A similar study was done for supercapacitors by annealing MXene in an ammonia environment.150Fig. 8b illustrates that simulation of nitrogen dopants in Ti3C2. LiCl, or KCl has been utilized to synthesize Cl-terminated MXenes using electrolysis. Similarly, upon addition of Li2O/Li2S to the molten state, MXenes with –O or –S have been prepared151 (see the scheme in Fig. 8c).
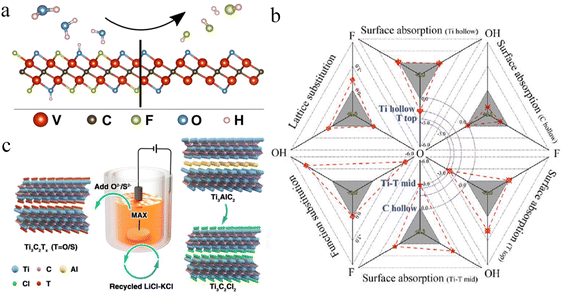 |
| Fig. 8 (a) Removal of fluoride terminations by gas hydrolyzation, reproduced from ref. 147 with permission from American Chemical Society, copyright 2022. (b) Simulation with nitrogen dopants in Ti3C2, reproduced from ref. 149 with permission from Wiley, copyright 2020. (c) MXene synthesis by molten salt etching, reproduced from ref. 151 with permission from Wiley, copyright 2021. | |
In 2019, Schultz et al. reported photoelectron spectroscopy (PES) and density functional theory (DFT) for computational studies.152 They investigated the electronic properties of Ti3C2Tx having different surface terminations. Fig. 9a demonstrates different adsorption sites on Ti3C2Tx that were computed via DFT studies.153Fig. 9b exhibits the XPS core-level spectra of Ti3C2Tx. For the three sets of spectra: one is for its loaded state (lower row); second one is for annealed MXene at 470 °C (middle row); third one is for a MXene annealed at 750 °C (upper row).152 In Fig. 9b, solid lines exhibit curve-fitting, whereas hollow circles indicate data points. The left side displays confirmation of estimated terminations at various temperatures. Fig. 9c demonstrates work functions that govern due to surface terminations with justifications about actual surface stoichiometric ratios. In Fig. 9c, the blue line represents calculated work functions, whereas red lines exhibit the experimentally determined stoichiometric values of Ti3C2O2, Ti3C2F4, Ti3C2OH2, and Ti3C2.152
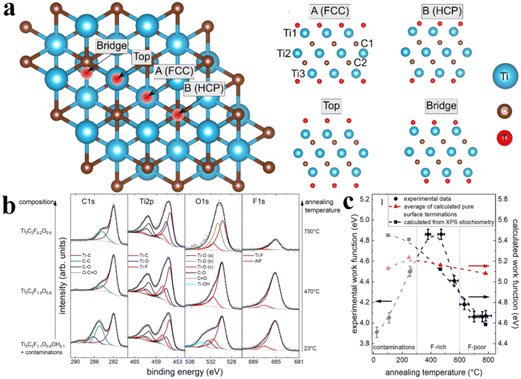 |
| Fig. 9 (a) Adsorption sites on Ti3C2Tx according to DFT calculations. The FCC adsorption site is located on top of a Ti atom in the third atomic layer. HCP was exhibited on top of a C atom in the second atomic layer. (b) XPS core-level spectra of Ti3C2Tx. (c) Work functions of different surface terminations calculated by DFT, reproduced from ref. 152 with permission from American Chemical Society, copyright 2019. | |
3.1.1 Fluorine-terminated MXenes.
The most suitable method for fabricating MXenes with F-terminations is HF etching.154 These are mostly utilized as cathodes in aqueous zinc-ion batteries. Halogenated MXenes exhibit exceptional performances as cathodes because they offer a stable platform, high energy density, and excellent rate performances.155,156 Similarly, rich F-terminated MXenes have been found to be effective electrocatalysts for the HER.51 Some studies have shown that F-terminations enhance the photocatalytic activities of Ti3C2 by increasing its hydrophilicity.157 Additionally, F-terminations aid the adsorption of various pollutants at the surface of Ti3C2.158 For example, methylene blue (MB) in wastewater can be effectively adsorbed on F-terminated Ti3C2Tx MXene (Fig. 10a). The effect of Lewis-basic halides on MXenes is explained in ESI Section S3.‡
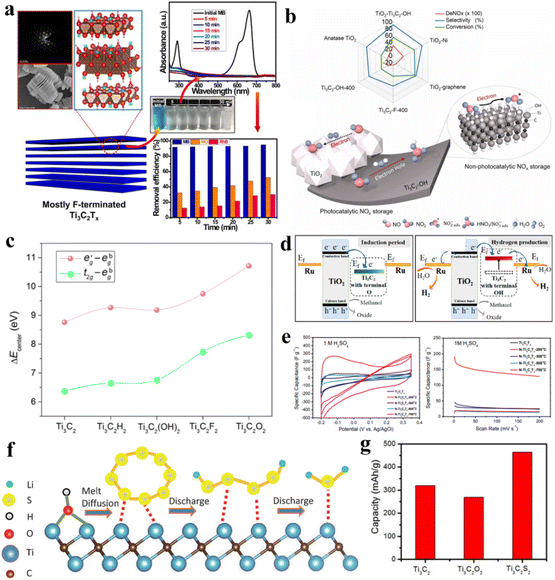 |
| Fig. 10 (a) F-terminated Ti3C2Tx MXene used for the removal of methylene blue, reproduced from ref. 358 with permission from Elsevier, copyright 2021. (b) OH-terminated MXene used for photocatalytic reactions, reproduced from ref. 160 with permission from Elsevier, copyright 2022. (c) Energy differences between Ti2 3d orbitals in unterminated and terminated MXenes along with their stability order, reproduced from ref. 162 with permission from American Chemical Society, copyright 2017. (d) Charge exchange during photoreactions, reproduced from ref. 169 with permission from American Chemical Society, copyright 2020. (e) Comparative CV results obtained at a scan rate of 1 mV s−1, reproduced from ref. 189 with permission from Elsevier copyright 2017. (f) Heat-treatment interaction with polysulfides, reproduced from ref. 188 with permission from Wiley, copyright 2015. (g) Maximum carrying capacities of Ti3C2, Ti3C2O2, and Ti3C2S2, reproduced from ref. 173 with permission from Royal Society of Chemistry, copyright 2018. | |
3.1.2 Hydroxyl-terminated MXenes.
Hydroxyl terminations can help to capture and activate CO2 molecules.159 MXenes synthesized via molten salt etching have been reported to be effective because negative electrodes are much better for applications based on electrochemical energy storage.89 In order to synthesize an –OH-terminated MXene (Ti3C2OHx), Al Mayyahi et al.160 reported a one-step hydrothermal process involving alkali-assisted aluminium etching in NaOH along with hydrazine as a delaminating agent. The special feature of Ti3C2OHx is that it exhibits strong synergism with TiO2 as a co-catalyst during the oxidation of NOx,.160 Moreover, –OH-terminations exhibit higher selectively for targets during photocatalytic reactions.161 See the –OH terminations in Fig. 10b. Quantitatively, the stability order is Ti3C2Ox > Ti3C2Fx > Ti3C2OHx > Ti3C2Hx > Ti3C2
162 (Fig. 10c).
3.1.3 Oxygen-terminated MXenes.
Oxygen termination is preferred for energy-storage applications such as supercapacitors and lithium-ion batteries.163 The surface of
O-terminated MXenes provides extra stability and electrochemical performances in energy-storage devices.164 Additionally,
O termination facilitates better interactions with electrolytes that extend charge-storage capabilities.165 Although, –OH functional groups cannot hold sufficient capacitance as compared with
O terminations. Thus, –OH functional groups can be decreased to increase capacitance by an annealing approach.166
O terminations on the surface of Ti3C2 can have a significant effect on its photocatalytic performance because
O terminations can act as electron-acceptors. Additionally,
O terminations can increase the surface area of Ti3C2, thereby providing more active sites for photocatalytic reactions to occur. H+ can be reduced with
O terminations specifically in acidic electrolytes.162,167 However, too many
O terminations can also have negative effects on photocatalytic performance.168 Excessive
O terminations can result in the formation of oxygen vacancies that can act as recombination centres. These recombination sites can affect the overall efficiencies of Ti3C2-based catalysts.169 For evaluation, see Fig. 10d. However, a moderate number of
O terminations has been suggested for optimal photocatalytic performances.170 The optimal amount of
O terminations depend on the specific application and reaction conditions.160
3.1.4 Sulfur-terminated MXenes.
Metal–sulfur batteries have high energy-storage density. Lithium–sulfur batteries have been found to be more attractive for energy-storage applications.171 Recent studies have demonstrated that S-terminated MXenes could be utilized as anode materials. Fig. 10f demonstrates heat-treatment interactions between polysulfides and Ti–OH on the surface of Ti3C2. According to Mehta et al.,172 S-terminated Mo2C (MXene) significantly boosted Li adsorption capacity that led to higher performances. Fig. 10g illustrates a comparison of the maximum charge-carrying capacities of Ti3C2, Ti3C2O2, and Ti3C2S2 (the maximum carrying capacity of a material refers to its ability to host or store a certain substance or molecule146). The presence of
S facilitates stronger adsorption/chemical reactions, enabling it to host/store a greater amount of substances, resulting in a higher maximum carrying capacity compared with Ti3C2 and Ti3C2O2.173 Extra detail of this section has been included ESI Section S4.‡
3.1.5 MXenes with mixed/other terminations.
Since the discovery of Ti3C2Tx, over 30 MXenes with diverse M and X elements have been reported. MXene properties are significantly influenced by surface terminations that offer various opportunities to optimize them for targeted applications. Natu et al. presented their perspectives on termination engineering and their impact on MXene properties.174 They stated that various terminations (e.g.,
O, –OH, –F, −Cl,
S,
NH) could be introduced to fabricate MXene surfaces (i.e., Ti3C2Clx, Ti3C2Brx, Ti3C2Sx) (Fig. 11a). Different methods have been reported to fabricate MXene surfaces, but control over MXene terminations is not possible by etching of the MAX phase through fluorine-based acids. Acid etching covers MXene surfaces with –F, –Cl, –Br, –I,
O or –OH terminations (Fig. 11b). Halogen-based surface terminations can be removed and replaced by post-etching processes. As discussed in the “Synthesis” section, molten salts such as ZnCl2 and CuCl2 can remove the A-layer by a Lewis acid–base reaction (Fig. 11c). This method facilitates obtaining homogeneous and single halogen-terminated MXenes. In 2023, Ding et al. produced MXenes with
S,
Se,
Te and Sb terminations (Fig. 11d).175
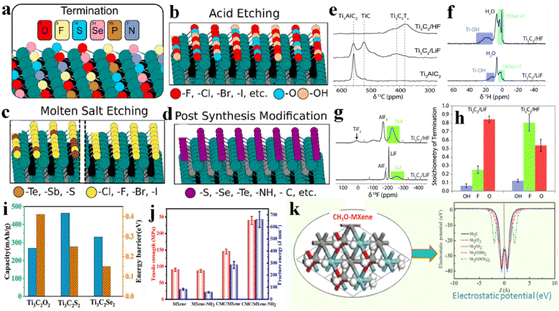 |
| Fig. 11 (a) Surface terminations of MXenes by (b) acid etching, (c) molten salt etching, and (d) post-synthesis modifications, reproduced from ref. 174 with permission from American Chemical Society, copyright 2023. (e) 13C NMR, (f) 1H NMR, and (g) 19F NMR of HF- and LiF-etched Ti3C2, and (h) comparison of surface compositions of LiF- and HF-etched Ti3C2Tx, reproduced from ref. 176 with permission from Royal Society of Chemistry, copyright 2016. (i) Comparison of storage capacity and energy barrier for O, S, and Se terminated MXenes, reproduced from ref. 177 with permission from Elsevier, copyright 2020. (j) Tensile strength and fracture energy of –NH2-terminated MXenes, reproduced from ref. 85 with permission from Elsevier, copyright 2021. (k) CH3–O-terminated Nb2C as an electrode and its potential, reproduced from ref. 178 with permission from Elsevier, copyright 2017. | |
Hope et al. quantified the surface terminations of Ti3C2Tx using 1H, 13C and 19F NMR (Fig. 11e–g). A lower concentration of –OH terminations in LiF and HF etched Ti3C2 compared with –F and
O terminations was noted. Specifically, –F terminations are more prevalent in the HF method, whereas
O terminations dominate in the LiF (in situ HF etching) method. These proportions exhibit high sensitivity to the synthetic method utilized (Fig. 11h).176
Li et al. studied the role of
O,
S,
Se and
Te terminations over Ti3C2 for Li-ion batteries. Interestingly, these terminations maintained the metallic band structure and exhibited low Li-ion diffusion barriers of 0.25 and 0.15 eV for Ti3C2S2 and Ti3C2Se2, respectively. Furthermore, these terminations improved the mechanical strength of Ti3C2 anodes, which effectively addressed the issue of electrode pulverization (Fig. 11i).177
Peng et al. compared the tensile strength and fracture energy of pristine MXenes with –NH2 terminated MXenes. –NH2 terminations increased the tensile strength (Fig. 11j). The enhanced mechanical properties were primarily attributed to the hydrogen bonding between NH2-MXene and CMC.85 The mechanism of the enhanced strength of NH2-terminated MXenes is explained in ESI Section S2.‡ Xin et al. functionalized Nb2C with –OCH3 terminations, and showed ultralow work function (1.0 eV) potential (Fig. 11k) in field emitters.178
Björk et al. theoretically explored 12 distinct terminations (
O, –OH,
N,
NH, –NH2,
S, –SH, –H, –F, –Cl, –Br, and –I) over six MXenes (Ti2C, Nb2C, V2C, Mo2C, Ti3C2, and Nb4C3). The adsorption free energies at low and full coverage (Fig. 12a and b) revealed that all species energetically favoured adsorption on MXenes, with Ti2C and Ti3C2 displaying the strongest adsorption and Mo2C the weakest. In the case of terminations, a consistent trend was observed regardless of chemical potential. Notably, –F and
O terminated MXenes exhibited the most favourable adsorption free energies.179
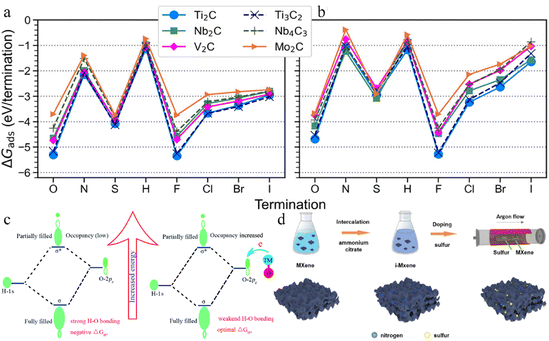 |
| Fig. 12 Adsorption free energy of various terminations over different MXenes: (a) low (x = 1/8) and (b) full coverage (x = 2), reproduced from ref. 84 with permission from American Chemical Society, copyright 2021. (c) Impact of doped metal on Cr2CO2 for the HER, reproduced from ref. 182 with permission from Royal Society of Chemistry, copyright 2018. (d) Two-step intercalation and annealing for generating N/S-doped MXenes, reproduced from ref. 184 with permission from Elsevier, copyright 2022. | |
3.2. Doped MXenes
To enhance the effectiveness of MXene for targeted applications, substituting elements (doping) at M or X sites is a promising strategy. For this purpose, various methods have been reported, such as thermal annealing, thermal sintering, solvothermal and hydrothermal approaches, coprecipitation method, and strong electrostatic adsorption.180
3.2.1 Doping in M sites.
The exceptional properties of MXenes are largely attributed to the accessible d-orbitals of metal atoms. Khazaei et al. predicted that bandgap energies decrease (e.g., Hf2CO2 > Zr2CO2 > Ti2CO2) as the size of the metal atom decreases.181 This indicates doping has the potential to alter the intrinsic properties of MXenes. The incorporation of two transition metals in MXene structures lead to exhibition of the distinct characteristics of the two transition metals. In Cr2CO2 (MXene), introduction of electron-donor transition metals can effectively reduce the ability of O* to accept extra electrons from H* (Fig. 12c), thereby weakening their interaction and eventually improving the HER activity.182
3.2.2 Doping in X sites.
Balcı et al. investigated the electronic properties of X-doped Sc2CF2 (MXene) by substituting C atoms with F, S, Si, Ge, Sn, B, N, or B + N. They demonstrated that doping caused variations in bandgap and transitions between semiconductor and metal states.183 For the co-doping of N and S, the MXene was intercalated in the presence of ammonium citrate and annealed with sulfur in an argon gas stream for 2 h (Fig. 12d)184. Despite the significant impact on MXene properties, elemental doping at X sites has garnered more attention after the discovery of oxycarbides.185
Notably, recent modifications in MXenes by partial substitution of carbon or nitrogen with oxygen from the MXene lattice are known as “oxycarbides” or “oxynitrides”. Oxycarbide MXenes reported so far exhibit <50% oxygen in their lattice. The incorporation of oxygen can control the structures and properties of MXenes. The research community has made significant progress in addressing challenges and achieving uniform surface terminations. However, further research is necessary to understand the arrangement of X-site atoms. 2D borides (MBenes or boridenes) exist as a separate group due to their distinct crystal structure.186
The development of sulfur-based electrodes in batteries addresses several challenges. Generally, sulfur is loaded onto conductive materials having a porous nature (e.g., carbon, MXene). MXenes are now regarded as the best sulfur host materials due to their success in suppressing the shuttle effect of polysulfides.187 Ti2CTx/S was initially developed as a cathode material for lithium–sulfur batteries (LSBs) by Liang et al. in 2015.188 This is the main reason why there has been increased research on utilizing MXenes in metal–sulfur batteries. A nitrogen-doped MXene, N–Ti3C2Tx, can be produced by ammonia post-etch annealing189 and with plasma treatment.190 Due to its large surface area and higher pore volume, it exhibits exceptional electrochemical capabilities for LSB applications.149 Lu et al.149 investigated the atomic positions and effects of nitrogen dopants in MXenes. DFT calculations showed that among the three sites in MXene, nitrogen (N) dopants replaced –OH terminations. It has been found that electrical double-layer and pseudo-capacitance are significantly enhanced as a result of these aforementioned replacements. Additionally, they altered the spacing and surface absorptions as an electric double-layer capacitor (EDLC). By annealing in an ammonia environment, N-doped Ti3C2Tx electrodes were reported by Wen et al.189 in 2017. N-doped Ti3C2Tx showed magnetic characteristics, and hence had a greater ability to enhance MXene properties for better performances.190 In order to enhance nitrogen dopants, a two-step pre-intercalation annealing technique has been reported along with addition of ammonium citrate (AC) as an intercalant and antioxidant addition. Subsequently, a precursor material has been subjected to annealing in an ammonia atmosphere.191 The heat treatment expands the interlayer space by incorporating nitrogen atoms into the lattice of the MXene, and additionally reduces the concentration of fluorine terminations. This treatment enhanced electrochemical capacitances with values of 192 F g−1 (1 M H2SO4 electrolyte) and 82 F g−1 (1 M MgSO4 electrolyte).146Fig. 10e demonstrates that the cyclic voltammetry (CV) profiles obtained in the presence of 1 M H2SO4 did not exhibit the perfect rectangular geometry of pure EDLC on carbon electrodes. Moreover, in the case of MXene as well as N-doped MXenes using H2SO4 electrolyte, capacitance “humps” within a potential range of −0.2 V to −0.1 V relative to an Ag/AgCl reference electrode were noted.192 Surprisingly, at high voltage, N–Ti3C2Tx exhibited robust capacitance (128 F g−1) measured at a scan rate of 200 mV s−1.189
4. Properties of MXenes and evaluation for various applications
MXenes are composed of transition-metals carbides and nitrides with variable terminations that exhibit diverse properties depending on their composition. MXene stability is associated with the number of transition-metal atoms in the unit cell. DFT calculations indicate that MXenes exhibit good stability under ambient conditions, maintaining their structure without alteration. Transition-metal carbides display superior stability as compared with their nitrides because carbon-based MXenes exhibit stronger binding energies than nitrogen-based Mxenes. The thermal stability of MXenes depends on their chemical composition and terminations. Exposed atoms on the MXene surface are often thermodynamically unstable and susceptible to oxidation in air. For example, the Ti2C (MXene) surface interacts with O2 to form TiO2, which makes it unstable in the presence of oxygen. However, their thermal stability varies based on composition, environment, and surface atoms. MXenes inherently exhibit excellent electrical conductivity due to the layered arrangement of metal atoms. Titanium-based MXenes show electrical conductivity, whereas molybdenum-based MXenes exhibit semiconducting properties. Surface terminations, defects, and lamellar scale significantly affect their conductivity. The exceptional thermal conductivity of MXenes contributes to efficient heat dissipation in electronic devices, enhancing their reliability. In terms of mechanical strength, MXenes are better than graphene in terms of elasticity and flexural strength along their plane. The nature of terminal groups and metal atoms influences their mechanical robustness. Oxygen-terminated MXenes generally exhibit higher mechanical strength than other functionalization types. MXenes, being hydrophilic, maintain a stable dispersion due to charged surfaces in water. They possess some transparency (97% at a thickness of 1 nm) and are suitable for photo-electronic applications. MXenes without surface functional groups exhibit magnetism, but the presence of functional groups diminishes it, with certain exceptions (e.g., chromium-based MXenes). These properties have led to extensive exploration of MXenes in energy storage, catalysis, electromagnetic shielding, sensing, biology, and flexible electronics. MXene properties that have led to state-of-the-art applications are illustrated in Fig. 13.
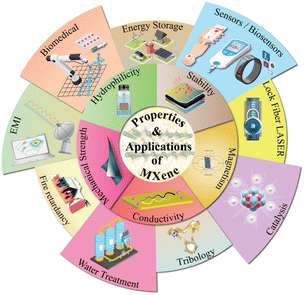 |
| Fig. 13 MXene properties that have led to state-of-the-art applications. | |
MXenes are commonly synthesized by etching the A-layer from MAX with the help of an etching agent. The choice of etching agent influences inherited terminations and subsequently impacts on the properties of MXenes for target applications. Exfoliation of MXenes is achieved by employing polar organic solvents such as dimethyl sulfoxide and isopropanol, along with multiple sonication.193–195 Ti3C2 includes terminations such as –OH,
O, and –F, and annealing of MXenes in open air can lead to their oxidation.196
Various researchers have reported advanced applications after etching of Ti3AlC2 along with functional-group linkages in the presence of HF. For example, they described the detailed mechanistic insights to functional groups mostly involved in photocatalysis. When comparing the traditional HF etching method to a hydrothermal approach using NaBF4, both methods were found to generate termination of –OH groups. However, the elemental distribution of Ti3C2 synthesized through the hydrothermal method revealed much better performances in energy-storage applications such as supercapacitors.66,197
Peng et al. explored the potential of –OH termination to enhance quick charge transfer in photocatalytic degradations of organic pollutants.198 Another investigation revealed a significant impact specifically due to –OH terminations to achieve a low work function (1.6 eV) of MXenes.199 Another study predicted that in the presence of –OH functional groups, Li-ion storage could not hold enough capacitance (which is contrary to
O terminations). It has been noted that annealing of MXenes can favour conversion of –OH functional groups which results in an increase in capacitance for various electronic applications.166 In a similar manner, annealing of MXenes in a hydrogen environment can be utilized to remove –F groups for charge-storage applications. Annealing of MXenes has proven beneficial for ion transport, so exposure of active sites is increased to involve catalytic reactions.200 Some reports have suggested that hydrophilic terminations (e.g.,
O and –OH) enable BiPiO4/Ti3C2-type semiconductors to serve as additional agents for remediation of pollutants from wastewater.201 In another study, Ti3C2 quantum dots were developed by employing TiO2/g-C3N4 for photocatalytic CO2 reduction.202 The heterojunction ability of MXenes to bond with terminations provides well-tolerated dispersion onto g-C3N4, so these quantum dots could serve as charge-transfer tracks.203
Similarly, due to inherently negative Fermi levels, Ti3C2 can deliver efficient photocatalytic H2 generation in the form of g-C3N4/Ti3C2 hybrid catalysts.204,205 Higher hydrogen activities are due to separation of charges through electron transfer from g-C3N4 to Ti3C2, which is facilitated by more conducting sites for charge transfer.206 Consequently, if this Ti3C2 material is combined with Ag3PO4, it aids photodegradation reactions.207 Zhang et al. demonstrated the significance of
O and –OH on MXenes that carry negative charges for catalytic reactions.208 Another study discovered that functional groups present in Ti3C2 may serve as “electron traps” owing to their metal-like characteristics, which serve as co-catalysts.209 Functional groups can control the morphology and surface of layers during the synthesis of composite materials.210 The incorporation of organic/MXene composites has been shown to enhance the electrochemical performance of energy-storage devices.211,212 These composites offer two key advantages. First, the high conductivity of the MXene promotes improved conductivity of organic materials, thereby enhancing material utilization.213 Second, the presence of surface multi-functional groups and large layer spacing facilitates electrolyte adsorption for ion transport.214
Ti3C2 with terminal groups is extremely effective for many applications, but few reports have focused on terminations.215,216 Study on terminations requires more attention with regard to the optimized ratio of different terminations that can enhance the characteristics and stability of Ti3C2.216Table 2 summarizes the various etching methods reported for MXene synthesis, terminations and specific applications linked to synthetic methods. Additionally, Table 2 highlights the advantages and disadvantages of reported methods for specific applications.
Table 2 Summary of etching methods, related terminations, advantages, disadvantages and applications of MXene synthetic strategies
Etching methods |
Terminations |
Advantages |
Disadvantages |
Applications |
Ref. |
HF etching |
–F, –OH |
Tunable bandgap, good conductivity and ductility |
Highly corrosive, toxic and eco-unfriendly |
Polymer composite fillers, LIBs, pseudo capacitors |
80
|
In situ HF etching |
–Cl |
Single termination |
Requires high temperature |
LIBs |
217
|
Alkali based etching |
–OH, O |
Non-toxic, corrosive resistance, excellent electrical conductivity |
Low efficiency, requires high temperature |
Catalyst support in electrochemical system |
218
|
Molten salt etching |
O, –Cl |
Exfoliated from multi- to few-layer MXene |
Aforementioned |
LIBs |
219
|
Molten salt etching followed by KOH washing |
–F, –OH |
Safe, hydrophilicity |
Aforementioned |
Energy storage |
220
|
Electrochemical assisted etching |
–OH, O |
Non-toxic, fluorine free |
Low efficiency |
Super capacitors |
57
|
Algae extraction etching |
N/A |
Cost effective, environment friendly, high yielding |
Aforementioned |
Photothermal agents |
58
|
Hydrothermal method |
–OH |
More efficient than HF etching, environmental benign |
Need expensive autoclave |
Improved adsorption properties |
221
|
In situ etching |
–OH, O |
Improved rate performance |
Aforementioned |
High performance asymmetric super capacitors |
222
|
Gas phase |
–Cl |
Aforementioned |
Aforementioned |
Energy storage |
82
|
In recent years, MXenes has been found to be suitable choices for a wide range of applications due to their distinct and desired properties: excellent electronic conductivity, chemical stability, ion intercalation, and morphology.223 MXenes have been utilized in biomedicine, energy storage, sensors, catalysis, electromagnetic-interference shielding, tribology, water treatments, fire retardancy, and lock fibre laser technologies.
4.1. Biomedical applications of MXenes
Recent research has shown that MXenes and their composites have enormous potential in the healthcare sector. MXenes are used in sensors, bone regeneration, bioimaging, antibacterial treatment, photothermal therapy, drug-delivery systems, and tissue engineering.224–228 This is due to their unique 2D structure and excellent properties, such as mechanical flexibility, hydrophilicity, light-to-heat conversion, and biocompatibility.229 Utilizing the significant surface area of SP-modified Ti3C2 nanosheets (Ti3C2-SP), the anticancer drug doxorubicin (Dox) can be effectively loaded onto the surface of MXenes230,231 (Fig. 14a). Upon endogenous or external triggering, loaded anticancer medicines can be released from MXene nanosheets for chemotherapy. The small planar nano-sizes of these Ti3C2-SP nanosheets allow them to easily circulate within the blood vessels that passively accumulate in tumour tissues,232 thereby leveraging the permeability-and-retention effect233 (Fig. 14b). A schematic of a nanoplatform, chemotherapy, photodynamic therapy, and photothermal therapy of tumours234 on Ti3C2 is illustrated in Fig. 14c. In vivo computed tomography (CT) was done by injecting 4T1 intravenously in tumour-bearing mice with TaC3-SP (20 mg kg−1).232 Surprisingly, after administering Ta4C3-SP intravenously, CT taken 24 h later showed a clear image that was only possible due to application of a MXene (Fig. 14d).129
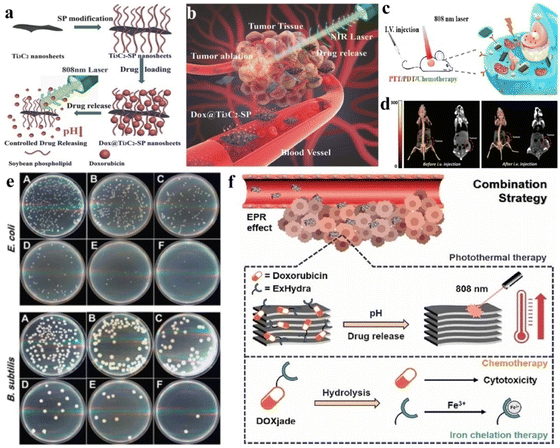 |
| Fig. 14 (a) MXene modification for drug loading and control release. (b) Use of Ti3C2 for drug delivery in vivo for photothermal and chemotherapy of cancer, reproduced from ref. 231 with permission from Wiley, copyright 2018. (c) Photothermal, photodynamic, and chemotherapy of tumours, reproduced from ref. 234 with permission from American Chemical Society, copyright 2017. (d) Evaluation of CT results for controlled tests on mice (receiving an intravenous drug at 10 mg mL−1) for 24 h, reproduced from ref. 129 with permission from Wiley, copyright 2018. (e) Images of agar plates displaying re-cultivated Escherichia coli and Bacillus subtilis after treatment with various doses of Ti3C2Tx for 4 h, reproduced from ref. 125 with permission from American Chemical Society, copyright 2016. (f) Iron chelation-based chemo-photothermal treatments, reproduced from ref. 236 with permission from Elsevier, copyright 2022. | |
Ti3C2Tx also exhibits antibacterial properties, as shown by re-cultivating Escherichia coli and Bacillus subtilis cells on agar plates after 4 h of exposure to a MXene (Fig. 14e). These images provide evidence of the antibacterial properties exhibited by Ti3C2Tx in aqueous suspensions.235Fig. 14f displays DOXjade loading onto 2D ultrathin MXene nanosheets, which enables iron chelation through chemo-photothermal treatments.236
4.1.1 Drawbacks.
From a medical viewpoint, the drawback associated with MXene-based materials is their poor dispersibility in water. This can cause obstruction of cell transit along with blood circulation.39 In addition, MXene-based materials may accumulate in the reticuloendothelial system (RES) upon intravenous injection, which can lead to toxicity.
4.1.2 Suggestions/precautions.
Defects can be resolved by altering the MXene and its surface terminations.237 It is necessary to design MXene-based compounds that are biocompatible and biologically non-toxic for medical applications.77
4.2. Energy-storage applications of MXenes
In recent decades, the world has been facing energy crises due to rising energy use and continuous decline of fossil-fuel resources.238 Hence, there is a great demand to replace these diminishing sources of energy by developing alternatives that must be clean and sustainable.239 The most common renewable energy source would be solar energy, which could be harvested by use of advances materials such as MXenes or their derivatives. Such solar-based technology would need energy conversion and appropriate storage, such as batteries and supercapacitors.240 Supercapacitors can be built to provide high power density, which is ideal for automobile and industrial applications. MXene-based batteries offer high energy density, which is advantageous for portable devices.223,241 In this context, MXene-based supercapacitors have attained significant attention as new and advanced systems. Compared with batteries, supercapacitors exhibit higher power density, charge–discharge rates, and cycle stability.223 Jiang et al.242 developed 2D MXene (titanium carbide) nanosheets for processing to develop electrochemical applications. MXene-based wafer-scale supercapacitors (MSCs) can proficiently remove a pulsed DC voltage. Besides MXenes, all-solid-state supercapacitors (SCs) utilizing polyvinyl alcohol (PVA)/KOH gel electrolyte demonstrated a density of 63 mW h cm−3 at a power density of 0.06 W cm−3, and MXene-based supercapacitors underwent 10
000 charge/discharge cycles at a current density of 5 A g−1. Their capacitance remained unchanged, indicating the sustained and stable performance of energy conversion and storage devices (ECSDs).243 Moreover, MXenes with a large surface area make good capacitors because they have double electrical layers. Fig. 15a shows a schematic representation of an in-plane ion-transport channel of MXene films. These measurements allow monitoring of the changes in the interlayer space, as illustrated in Fig. 15b for Ti3C2 electrodes as they are involved in cycling. In Fig. 15c, a comparison is presented of CV results obtained at a scan rate of 2 mV s−1 for macroporous Ti3C2 electrodes.244 These electrodes were tested in three 1 M LiTFSI organic electrolytes containing different solvents: DMSO, ACN, or PC. CV results demonstrated that the PC-based electrolyte had a higher coulombic efficiency (96%) with a wider negative voltage window of 2.4 V.245 DMSO and ACN showed a negative voltage window of 2.1 V and 2.2 V, respectively.245
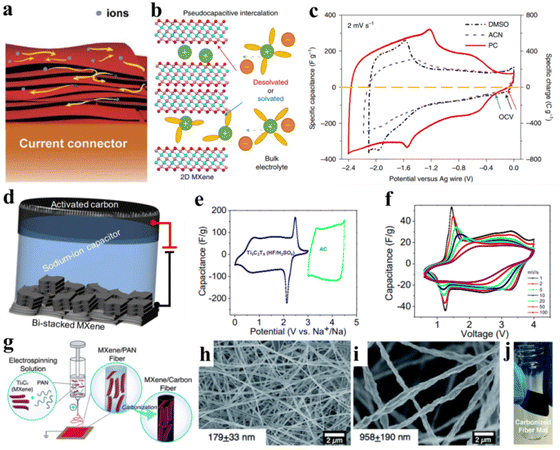 |
| Fig. 15 (a) Ion-transport channel of MXene films, reproduced from ref. 245 (b) Supercapacitor for electrolytes and MXenes (schematic). (c) CV results, reproduced from ref. 245 with permission from Nature Energy, copyright 2019. (d) High-rate energy storage using bi-stacked titanium carbide. (e) CVs of bi-stacked MXene and AC electrodes. (f) CVs of a hybrid Na-ion capacitor at various scan rates, reproduced from ref. 247 with permission from American Chemical Society, copyright 2018. (g) Scheme employed for the synthesis of MXene/carbon nanofibers. (h) SEM images of PAN fibers. (i) PAN fiber developed with a MXene (16 wt%). (j) Digital image of carbonized PAN fibers, reproduced from ref. 249 with permission from Royal Society of Chemistry, copyright 2019. | |
Fig. 15d represents a schematic diagram of Bi-stacked MXene supercapacitors and CVs of bi-stacked MXenes. AC electrodes and hybrid Na-ion capacitors in the CV curves are exhibited in Fig. 15e.246 These curves exhibit sharp redox peaks. Contrarily, CV curves for the AC electrode were rectangular. Combination of a pseudo-capacitive MXene electrode demonstrated a mixed behavior for battery and capacitor that was perhaps due to multiple layers in the MXene.247 This device could be categorized as a “hybrid” capacitor due to its unique composition.248 As shown in Fig. 15f, the lower cutoff voltage was set at 0.6 V, whereas the upper voltage limit was set at 4 V. A schematic representation of the electrospinning process for MXene/carbon nanofibers is illustrated in Fig. 15g.249 Delaminated MXene flakes were dispersed in dimethylformamide (DMF) before being combined with polyacrylonitrile (PAN) to produce MXene/PAN solutions.250 SEM results of electrospun MXene/PAN fibers are illustrated in Fig. 15h for pure PAN fibers and Fig. 15i for a MXene (10 wt%). Fig. 15j shows a fiber mat carbonized at 700 °C for 1 h using 10 wt% of Ti3C2Tx (MXene) and 8 wt% of PAN fibers.250
4.2.1 Drawbacks.
Some MXene-based electrode materials lack mechanical stability, especially if used in bendable devices. MXenes are sensitive to environmental factors such as moisture and oxygen. MXenes can undergo structural modifications that lead to reduced performance for energy-storage devices.
4.3. Use of MXene as sensors and biosensors
In the context of sensing applications, certain characteristics are required in sensing materials: sensitivity; optimized limit of detection; excellent conductivity; ability to customize required surface properties; selectivity towards specific analytes.260,261 These characteristics have been attained by MXenes and their composites for use in electrochemical biosensors. MXene-based materials possess exceptional transducing properties that make them highly suitable for a diverse range of sensors, such as bio-electrochemical, electrochemical, gas, strain, chemiluminescence, pressure, and photochemical sensors. Additionally, they exhibit stable mechanical characteristics and outstanding surface attributes.262Fig. 16a shows a chip that was specifically designed for complete blood analyses. The chip consists of four layers. The uppermost layer contains a dedicated blood-flow channel, whereas the second layer is a dialysis membrane.263 This MXene-based chip enables the passage of molecules such as urea and uric acid (UA) that are smaller than 1000 Da.250 The third layer holds a sensing chamber that controls the flow channels for isotonic solutions. The channel within this chip allows for the dialysis of blood analytes, which then accumulate within the detection chamber. In the latter, a sensing electrode (located on the bottom layer) detects analytes and generates the corresponding signals.264Fig. 16b illustrates the electrocatalytic process of UA on the MXene-modified sensor. To enhance the UA concentration at the electrode/electrolyte interface for subsequent electrocatalysis, UA molecules initially adsorb by forming hydrogen bonds with the functional groups (OH, O, and F) of MXene. Fig. 16c illustrates the concentration–time curves of UA, urea, and creatinine in blood during haemodialysis. The terms C0, t1/2, and k denote the concentration before dialysis, half-life of elimination, and the rate constant for elimination, respectively.264
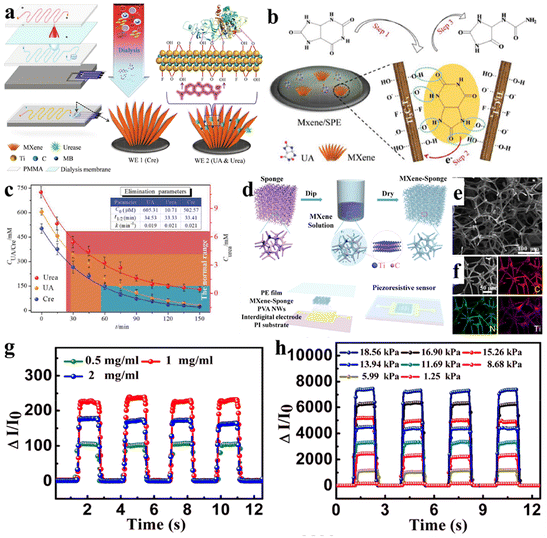 |
| Fig. 16 (a) Fabrication of a micro-fluidic chip with a MXene. (b) Scheme used for determination of uric acid on MXene/SPE. (c) Comparative curves for uric acid, urea, and creatinine in blood, reproduced from ref. 263 with permission from Wiley, copyright 2018. (d) Fabrication of a MXene-sponge. (e) SEM image of a MXene-sponge. (f) Elemental mapping of a MXene-sponge. (g) I–T curves of MXene-sponge sensors. (h) I–T curves of an MSP device. Reproduced from ref. 266 with permission from Elsevier, copyright 2018. | |
Fig. 16d represents the MXene-sponge synthetic process specifically designed for sensing applications. SEM results for the MXene-sponge and pictures of the elemental mapping for C, N, and Ti of the MXene-sponge are represented in Fig. 16e and f. Fig. 16g depicts the current–time curve of the MXene-sponge with different initial concentrations (0.5, 1, and 2 mg mL−1) under the same pressure conditions. Notably, when the initial concentration of the MXene solution is 1 mg mL−1, the MXene-based sensor exhibits the highest on/off current ratios.265,266 The current variations of the MPI-based sensor under different pressures can be seen in Fig. 16h. The current increases steadily as the pressure rises. Fig. 17a and b illustrate organ-like MXene-Ti3C2 nanomaterials encapsulating haemoglobin and cyclic voltammograms of the Nafion/Hb/Ti3C2/GC electrode, respectively.267,268
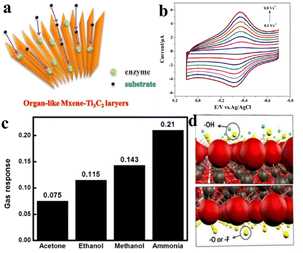 |
| Fig. 17 (a) Encapsulation of haemoglobin in an organ-like MXene. (b) CV results of a Nafion/Hb/Ti3C2/GC electrode, reproduced from ref. 267 with permission from IOP Science, copyright 2015. (c) Different terminations on MXene nanosheets. (d) Average sensing response for various gases, reproduced from ref. 269 with permission from American Chemical Society, copyright 2017. | |
Fig. 17c displays the average response of Ti3C2Tx towards the sensing of various gases, including ammonia, methanol, ethanol, and acetone. The respective response values for these gases are 0.210, 0.143, 0.115, and 0.075.269 The Ti3C2Tx sensor can be utilized for multiple sensing applications, such as sensing VOC gases, toxic organic gases, greenhouse gases (i.e. CO2, N2O), and dangerous exploratory gases (H2, CH4, C2H4, NH3) with a high response. Moreover, MXene-based sensors are widely utilized in chemical industries, food industries, electronic industries, pharmaceuticals, biomedical, and rocket or space science. In Fig. 17d, a schematic representation of a 2D Ti3C2Tx structure is presented that illustrates its surface functional groups or terminations. The structure comprises three titanium layers “sandwiched” between two carbon layers.269
4.3.1 Advantages and drawbacks.
MXene-based sensors possess high sensitivity and large surface area that allow for effective detection of biomolecules. These sensors exhibit a rapid response and can detect analytes even in trace amounts.78,270 However, drawbacks include limited stability in aqueous solutions, susceptibility to oxidation, complexity, and cost of synthesis. The limited stability in aqueous solutions (especially at extreme pH) affects the long-term performance of sensors.
4.3.2 Percussions and suggestions.
Careful surface modification is important for functionalization and surface stability.270,271 Thus, ongoing research must focus on understanding MXene–bimolecular interactions for their further sensing applications.272
Table 4 is a comparison of the solution-based electrochemical-sensing performances of MXene-derived materials, including analyte detected, sensing technique, linear range, and sensitivity. Table 5 reveals the gas-sensing performances of various recent MXene-based materials.
Table 4 Summary of solution-based electrochemical-sensing performance of MXene-derived materials, including the analyte detected, sensing technique, linear range, and sensitivity
MXene derived sensing materials |
Analyte detected |
Sensing technique |
Linear range |
LOD |
Sensitivity |
Ref. |
GOx-Au-MXene-naf/GCE |
Glucose |
Amperometry |
0.1–18 μM |
5.9 μM |
4.2 μA mM−1 cm−2 |
273
|
Tyr-MXene-chi/GCE |
Phenol |
Amperometry |
0.05–15.5 μM |
12 nM |
414.4 mA M−1 |
30
|
Hb-naf-MXene/GCE |
NO2−1 |
Amperometry |
0.5 μM–11.8 mM |
0.12 μM |
n.a. |
274
|
MXene-PtNP/GCE |
H2O2 |
Amperometry |
490 μM–53.6 mM |
448 nM |
n.a. |
275
|
MXene/GCE |
BrO3− |
Differential pulse voltammetry |
50 nM–5 μM |
41 nM |
n.a. |
276
|
MXene–FET |
DA |
Field effect transistor |
100 × 10−9–50 × 10−6 M |
100 × 10−9 M |
n.a. |
277
|
Ti3C2Tx/GCE |
H2S |
Cyclic voltammetry |
100 nM–300 μM |
16.0 nM |
0.587 μA μM−1 cm−2 |
278
|
Nafion/Hb/Ti3C2/GCE |
H2O2 |
Cyclic voltammetry |
0.1–260 μM |
20 nM |
n.a |
118
|
Ti3C2/GOD |
Glucose |
Amperometry |
39.8 μM–1.319 mM |
1.96 μM |
98.1 μA mM L−1 cm−2 |
279
|
Chit/ChOx/Ti3C2Tx/GCE |
Cholesterol |
Differential pulse voltammetry |
0.3–4.5 nM |
0.11 nM |
132.66 μA mM−1 cm−2 |
280
|
Table 5 Gas-sensing performances of various MXene-based materials
MXene derived sensing materials |
Target species |
Conc. |
Optimal temperature (°C) |
Response |
T
Res (sec) |
T
Recov (sec) |
Ref. |
W18O49 Ti3C2Tx |
Acetone |
0.17 ppm |
300 |
11.6 |
5.6 |
6 |
281
|
MoO3/WO3 |
Acetone |
0.5 ppm |
320 |
10 |
8 |
7 |
282
|
V2CTx |
Methane |
10 000 ppm |
RT |
142 |
38 |
47 |
283
|
V2CTx |
NH3 |
500 ppm |
RT |
3.41 |
41 |
109 |
284
|
Mo2CTx |
CO2 |
50 ppm |
30 |
1.14 |
30 |
45 |
285
|
4.4. Applications of MXenes in catalysis
Attention in electrochemical and photocatalytic water splitting, organic pollutants, and CO2/CO reduction has been sparked by the need to develop effective and sustainable technologies.2,286,287 High-performance catalysts play a vital part in the effective use of these technologies.45,50,288–290 Pt, Pd, Au, Ag, Cu, TiO2, CdS, RuO and IrO are the main components of conventional catalysis. However, these materials have a number of drawbacks, including high cost and limited supply.291 On the other hand, MXene-based catalysts have been employed in electrochemical and photochemical catalysis because of superior electronic conductivity and outstanding hydrophilicity.292 Moreover, MXene-derived catalysts demonstrate outstanding performances as co-catalysts that have excessive potential to replace expensive metals.223 In order to prepare MXenes having electron transport layers (ETLs) for targeted applications, a spin-coating technique has been recommended with a Ti3C2Tx colloidal dispersion (1 mg mL−1) onto ITO.293 Subsequently, such materials undergo different durations of UV-ozone treatments (0, 10, 30, or 60 min) (Fig. 18a). Devices with an architecture of ITO/ETL/CH3NH3PbI3/spiro-OMeTAD/Ag were developed to compare the performance of Ti3C2Tx as an ETL in perovskite solar cells (involved in catalysis reactions) before and after UV-ozone treatments (Fig. 18b).294
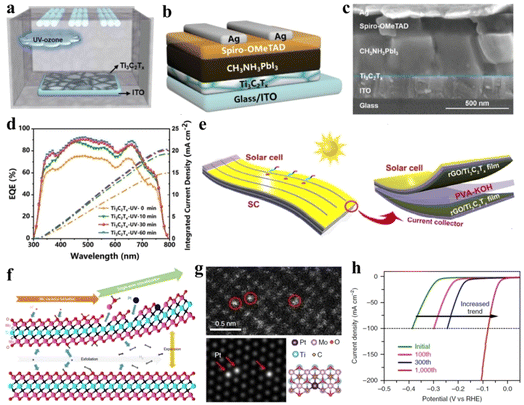 |
| Fig. 18 (a) UV-ozone treatments on a Ti3C2Tx film via spin-coating. (b) Device architecture of ITO/ETL/CH3NH3PbI3/spiro-O MeTAD/Ag on MXene. (c) SEM image of a planar perovskite solar cell (PSC). (d) Percent EQE spectra (external quantum efficiency) along with integrated current densities, reproduced from ref. 293 with permission from Wiley, copyright 2019. (e) Energy conversion and storage device (schematic), reproduced from ref. 243 with permission from Royal Society of Chemistry, copyright 2017. (f) Mechanism for the HER on Mo2TiC2O2-PtSA. (g) HAADF-STEM of Mo2TiC2Tx-PtSA. (h) HER polarization curves of Mo2TiC2Tx with a Pt foil as the counter electrode, reproduced from ref. 295 with permission from Nature, copyright 2018. | |
A typical cross-sectional SEM image of a planar PSC device fabricated using a Ti3C2Tx thin layer as ETL is shown in Fig. 18c. The SEM image demonstrates the six layers of the material (glass, ITO, ETL, CH3NH3PbI3, spiro-OMeTAD and Ag), which is extremely useful for photocatalytic reactions. Fig. 18d illustrates the computed integrated currents and external quantum efficiency (EQE) spectra for ETLs with varying UV-ozone treatment durations that correlate with performances in catalytic reactions. Finally, Fig. 18e is a schematic representation of a flexible integrated ECSD employed in catalysis. Fig. 18f illustrates the electrochemical process that facilitates hydrogen cations for reductions on the MXene surface.295 In Fig. 18g, it can be observed that Pt atoms are fixed at the Mo sites on Mo2TiC2Tx. This indicates that the Pt atoms are immobilized or anchored specifically to the Mo positions within Mo2TiC2Tx structures. The catalytic performance of the hydrogen-evolution reaction (HER) was evaluated using different cycles, with Pt serving as the counter electrode.296 The results of these evaluations are depicted in Fig. 18h, illustrating the HER catalytic performance. Other than energy-conversion applications, there are many other important applications of MXenes in catalysis, such as the HER, oxygen-evolution reaction (OER), carbon dioxide reduction reactions (CRR), nitrogen reduction reactions (NRR), organic pollutant degradation reactions (OPDR), biological catalytic reactions, Li-ion batteries, supercapacitors, and chemical/biosensing applications. Some reports have demonstrated that the microsphere structure of MQDs/ZIS/Ti(IV) resembles that of flowers, and that it can be synthesized by utilizing MXene quantum dots as co-catalysts. Fig. 19a and b demonstrate the SEM images of MQDs/ZIS/Ti(IV) microspheres. In Fig. 19c, elemental mappings reveal the uniform distribution of elements S, In, Zn, Ti, and C of MQDs/ZIS/Ti(IV) microspheres. Fig. 19d illustrates the presence of Ti(IV) nanoclusters at the edges of the MQDs/ZIS/Ti(IV). The lattice fringe interplanar spacing of 0.322 nm corresponds to the (102) plane of hexagonal ZIS, whereas 0.26 nm corresponds to the (110) plane of MQDs.297 Based on these findings, a potential mechanism is proposed in Fig. 19e that explains the high photocatalytic H2-evolution activity of the novel flower-like ZIS microsphere photocatalyst. It has been revealed that, under sunlight irradiation, electrons are photoexcited from the valence band (VB) of ZIS in MQDs/ZIS/Ti(IV) to its conduction band (CB), leaving photogenerated holes in the VB of ZIS. MQDs enhance the photocatalytic production due to the formation of a Schottky barrier at the interface of ZIS and Ti(IV) that progressively suppresses the charge recombination. Fig. 19f represents photocatalytic H2 evolution on ZIS, ZIS/Ti(IV), MQDs/ZIS, and MQDs/ZIS/Ti(IV) catalysts using sunlight irradiation.297 The H2-evolution results confirm that utilization of a MXene as a co-catalyst in the form of MQDs boosts photocatalytic activities. Abid et al. reported that Pd metal over the Ti3C2Tx surface improved the hydrogen-production activities of TiO2 by effectively quenching more electrons (Fig. 19g). The higher work function and lower Fermi levels of co-catalysts promote and facilitate higher hydrogen generation (Fig. 19h).144 These results indicate that the presence of MXene QDs and Pd@Ti3C2Tx delivers higher H2-generation efficiencies compared with other conventional catalysts in similar conditions.298
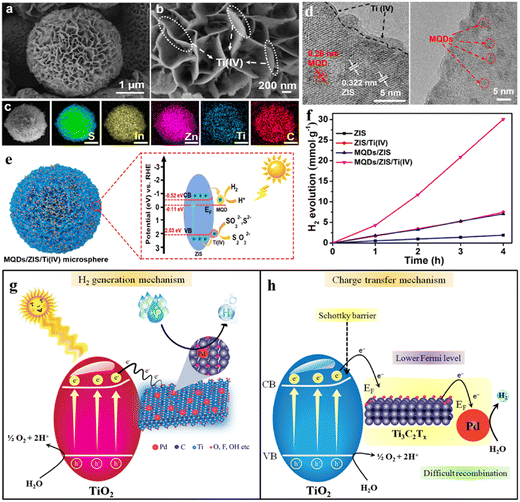 |
| Fig. 19 (a and b) SEM images of a MXene QD-supported ZIS/Ti(IV) composite. (c) Elemental mapping of S, In, Zn, Ti, and C. (d) HRTEM of MQDs/ZIS/Ti(IV). (e) Mechanism for photocatalytic H2 evolution on MQDs/ZIS/Ti(IV). (f) Comparison of photocatalytic H2 evolution on ZIS, ZIS/Ti(V), MQDs/ZIS, and MQDs/ZIS/Ti(IV), reproduced from ref. 297 with permission from MDPI, copyright 2021. (g) Hydrogen-generation mechanism and (h) charge-transfer mechanism on Pd@Ti3C2Tx-TiO2, reproduced from ref. 144 with permission from Royal Society of Chemistry, copyright 2024. | |
4.4.1 Advantages and drawbacks.
Due to their intrinsically hydrophilic nature, MXenes have distinct advantages of higher electrical conductivity and mechanical properties for catalytic reactions.299 Their conductivity is higher than that of other reported materials, such as graphene or reduced carbon nitride. MXenes have more functionalized surfaces to facilitate bonding with other species that are not available in graphene.300 Additionally, MXenes can be utilized in energy-storage devices like Li-ion batteries, pseudo-capacitors, and sensors. MXenes and their supported catalysts can be very helpful for sustainable technologies. Besides these advantages, MXenes have fundamental drawbacks: (i) agglomeration as well as poor long-term recyclability; (ii) preparation of MXenes having monolayers is complex; (iii) MXene-based catalysts can easily be oxidized in water; (iv) preparation of MXenes with few layers or targeted layers is not easy.301,302
4.4.2 Suggestions and precaution.
MXenes and MXene-supported catalysts may be ideal in many catalytic reactions.303 Ti3C2Tx has been widely utilized for the HER.304 Hydrophilic surfaces should be conducive for the charge transportation and adsorption on active sites in photocatalytic reactions. In the case of Mxenes, Gibbs free energy approaches zero infinity, which should be conducive for proton (H+) reduction reactions.301 Correct washing of MXenes is important for safe use in catalysis. Photocatalytic and pH-dependent reactions must be performed in special reactors or equipment. During washing, centrifugation, or any catalytic reaction, it is important to completely disperse the MXene or MXene-supported catalyst in the reaction mixture.79
Table 6 details evaluation of hydrogen evolution on various reported MXene-based electrocatalysts. Table 7 details various photocatalytic applications of MXene-based electrocatalysts.
Table 6 Comparative summary of H2 evolution on reported MXene-based electrocatalysts
Catalysts |
Precursors |
Over potential [η10 mV] |
Tafel slope [mV dec−1] |
Electrolyte |
Applications |
Stability |
Ref. |
MoS2/Ti3C2-MXene@C nanohybrids |
C-coated MoS2 & C-stabilized MXene |
112 |
82 |
1 M KOH |
H2 evolution and Li-storage |
>18 h |
305
|
O-terminated Ti3C2Tx |
Ti3AlC2 |
190 |
60.7 |
0.5 M H2SO4 |
H2 evolution |
24 h |
306
|
MoS2@Mo2CTx |
Mo2AlC2 |
197 |
113 |
1 M KOH |
H2 evolution |
> 8 |
307
|
Ptx Ni NWs/Ti3C2 |
PtxNi NWs and Ti3C2 |
18.55 |
13.37 |
0.5 M H2SO4 |
H2 evolution |
<2 h |
308
|
Pt/Ti3C2Tx |
TBA–Ti3C2Tx & Pt(NH3)4Cl2 |
55 |
70 |
0.5 M H2SO4 |
H2 evolution |
20 h |
309
|
Mo2CTx:Co |
β-Mo2C:Co |
180 |
59 |
1 M H2SO4 |
H2 evolution |
3 h |
310
|
NiS2/V2CTx |
V-MXene flakes |
179 |
85 |
1 M KOH |
H2 evolution |
NA |
311
|
TiOF2@Ti3C2Tx |
Ti3C2Tx & TiOF |
197 |
56.2 |
0.5 M H2SO4 |
H2 evolution and humidity sensing |
24 h |
312
|
MoS2/Ti3C2Tx |
MoS2 and Ti3C2Tx |
152 |
70 |
0.5 M H2SO4 |
H2 evolution |
12 h |
313
|
Table 7 Comparative summary of photocatalytic performances on MXene-based photocatalysts
Photocatalyst |
Synthesis method |
Photocatalytic application |
Light source |
Performance |
Ref. |
Ti3C2/g-C3N4 |
Electrostatic self-assembly approach |
H2 production |
200 W Hg lamp |
72.3 μmol g−1 h−1 |
314
|
d-Ti3C2/TiO2/g-C3N4 |
|
H2 production |
300 W Xe lamp |
1.62 mmol g−1 h−1 |
315
|
Ti3C2MXene/O-doped g-C3N4 |
Electrostatic self-assembly approach |
H2 production |
300 W Xe lamp |
25 124 μmol g−1 h−1 |
316
|
Ti3AlC2 MAX co-catalyst with proton-rich C3N4 |
Ultra-sonication method |
CO2 reduction |
35 W HID lamp |
786 μmol g−1 h−1 |
317
|
TiO2/Ti3C2 |
HF-etching |
CO2 reduction |
300 W stimulated solar Xe arc lamp |
0.22 μmol h−1 |
318
|
CdS@Ti3C2@TiO2 |
Hydrothermal method |
Dye degradation |
Visible light (λ ≥ 420 nm) |
Removal of RhB, MB, SCP and phenol at 60, 88, 88 and 150 min, respectively |
319
|
Ti3C2/CdS |
HF-etching |
H2 production |
Visible light |
825 μmol g−1 h−1 |
320
|
CHI/Ti3C2 |
HF-etching |
H2 production |
Visible to near IR |
52 ± 5 μmol g−1 h−1 |
321
|
CS@g-C3N4/MX |
Hydrothermal method |
Dye degradation |
250 W Xe lamp |
MB ∼99% and RhB∼98.5% |
322
|
Ti3C2/TiO2 nanoflowers |
HF-etching |
H2 production |
300 W Xe arc lamp |
783.11 μmol g−1 h−1 |
323
|
Pd@Ti3C2Tx-TiO2 |
HF-etching |
H2 production |
450 W Xe lamp |
35.66 mmol g−1 h−1 |
144
|
4.5. Use of MXene in electromagnetic interference (EMI) shielding
EMI is generated by various electrical devices that significantly affect the device lifespan and its environment. To reduce this problem, the common approach is employment of EMI-shielding materials. MXenes and their supported materials can act as absorbers for incoming EMI signals and protect them from the influence of the environment (e.g., moisture).223 MXenes exhibit exceptional EMI-shielding performance due to extrinsic alterations and inherent characteristics, which include dielectric inclusions, pores, or other fabrications in MXene structures.324 MXene Ti3C2Tx has been incorporated into a variety of polymeric matrices, including sodium alginate (SA), polyaniline, and ultra-high molecular weight polyethylene structures. MXene-polymeric nanocomposites display increased tensile strength but exceptional conductivity.325Fig. 20a illustrates a schematic fabrication process for robust and flexible Si-TM/BC multifunctional MXene-based films. As EMI-shielding materials, utilization of MXenes has received remarkable attention compared with other reported 2D materials. This is due to their weak mechanical properties and instability. Fig. 20b shows the surface temperature of a Si-TM/BC film over time at stable voltages of 1 to 4 V. Temperature climbed quickly before stabilization. In accordance with Joule's law, Q = I2Rt (where Q represents the generated heat, I is the applied voltage, R is the electrical resistance, and t is the working time), the temperature resulting from Joule heating is directly proportional to the applied voltage.326 The saturation temperature of the Si-TM/BC film at different driving voltages can be clearly observed in infrared thermal images (Fig. 20c). The TEM image of Ti2CTx at 500 nm is illustrated in Fig. 20d, whereas the electrical conductivity (S cm−1) of various MXene films is graphically illustrated in Fig. 20e and f. Comparison of electromagnetic interference shielding effectiveness (EMI-SE) values between transfer matrix simulation and MXene films of thickness ∼5 μm at a frequency of 10 GHz has been evaluated.327 The EMI-shielding performances of various MXene-based composites is shown in Table 8.
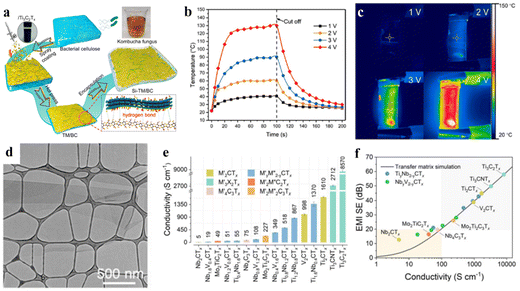 |
| Fig. 20 (a) Fabrication scheme for TM/BC and Si-TM/BC film. (b and c) Electrothermal conversion of light into heat on Si-TM50/BC, reproduced from ref. 326 with permission from American Chemical Society, copyright 2021. (d) TEM image of targeted Ti2CTx. (e) Electrical conductivity of MXene films. (f) Comparison of EMI-SE values between matrix simulation and MXene films, reproduced from ref. 327 with permission from American Chemical Society, copyright 2020. | |
Table 8 Summary of EMI-shielding performance of MXene-based composites
MXene composite |
Synthesis method |
Conductivity |
EMI shielding |
Ref. |
MXene-graphene-PVDF composite |
Spray-coating process |
13.68 S cm−1 |
53.8 dB (99.99%) |
328
|
CoPA/MXene |
Simple casting method |
1.4 × 10−2 S cm−1 |
Transparency exceeds 75% |
329
|
MXrGO@PMMA |
Electrostatic assembly |
0.98–3.96 W m−1 K−1 |
28–61 dB |
330
|
MXene/CNT |
Vacuum-assisted filtration |
1851.9 S cm−1 |
78.9 dB |
331
|
MXene/GNP |
Electro hydrodynamic atomization (EHDA) |
105 S cm−1 |
N/A |
332
|
4.5.1 Advantages and drawbacks.
MXenes and their supported materials can act as absorber for incoming EMI signals and protect the environment. Mxenes, due to their high conductivity and large surface area, can absorb electromagnetic waves effectively. This is why their demands have been increased in electronic and telecommunications. However, some drawbacks may interfere in such applications: (i) MXene compounds can be oxidized in aqueous media; (ii) hydrophilic surfaces should be conducive and non-protective for EMI shielding.
4.5.2 Suggestions and precautions.
MXene-supported IMI filters in electronic circuits can prevent the conducive interference from travelling back. MXene-polymeric nanocomposites display increased tensile strength that promotes exceptional conductivity for better performances and targeted applications.333 Nevertheless, before developing the device, testing for EMI is necessary. MXene-based electronic devices must be preserved in standard or optimized conditions of temperature, pressure, and pH.334
4.6. Role of MXene in tribology applications
Recently, MXene-derived compounds have been developed for utilization in tribology because they are excellent lubricating agents in solid and liquid forms. They have extraordinary lubricating characteristics suitable for enhancing the quality of lubricants.335 Using MXene-derived lubricants, the effectiveness of mechanical instruments is significantly improved. For an environmental viewpoint, better tribological performances are expected to minimize gas emissions for environmental hazards. Utilization of MXene-based materials in tribology is a novel and relatively unexplored area of research.223Fig. 21a is a schematic illustration of tetradecylphosphonic acid (TDPA) grafted to Ti3C2. Fig. 21b and c demonstrates that the average coefficient of friction and wear rate for three samples (castor oil, castor oil with 0.1 wt% Ti3C2, and 0.1 wt% TDPA-Ti3C2). It has been predicted that the presence of –OH groups in the MXene-EG coating causes a significant reduction in shear force.336 In turn, this reduction decreases interlayer slip during friction and facilitates the formation of a more compact friction-transfer film (Fig. 21d). The reduction in direct contact between surfaces was greater with a MXene coating, which led to a reduction in frictional characteristics.337 It has been reported that, amount of coating of The MXene also influenced friction. The coating maintained a low coefficient of friction (0.16) at 1.0 mL. This value changed to 0.6 mL during friction tests because this coating was removed quickly (Fig. 21e). The results of gradient friction tests conducted on MXene-EG coatings employing different loads on MXene-EG are shown in Fig. 21f.338 The lubrication effect of a MXene on the interlayer and substrate adhesion are illustrated in Fig. 21g. Fig. 21h illustrates the possibility for corrugation without applying an external load on homogeneous and heterogeneous MXene contacts. In this context, the weighted sum of enclosed pixels (WSEP) is a hurdle for two neighbouring layers of a MXene to slide upon each other.339Fig. 21i demonstrates how the potential corrugation changes depending on the typical stress placed on the upper slab of a MXene bilayer. This phenomenon is more commonly observed in bilayers that have –OH terminations at interfaces.340
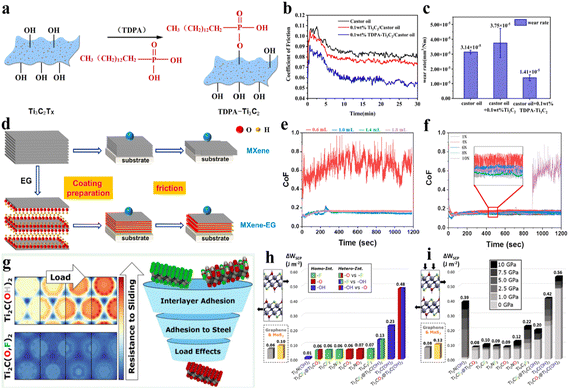 |
| Fig. 21 (a) Representation of molecules of tetradecylphosphonic acid grafted on a MXene. (b and c) Comparative coefficients of friction and wear rates of castor oil, castor oil with 0.1 wt% Ti3C2, and 0.1 wt% TDPA-Ti3C2, reproduced from ref. 336 with permission from Elsevier, copyright 2021. (d) Friction mechanism (schematic). (e) Friction tests employed for different amounts of MXene-EG coatings. (f) Friction tests performed by varying the overall load, reproduced from ref. 338 with permission from Elsevier, copyright 2021. (g) Lubrication effect of MXene-derived compounds for interlayer and substrate adhesion. (h) Potential corrugation values for homogeneous and heterogeneous MXene terminations on interfaces. (i) Potential corrugation growth as a function of applied normal load, reproduced from ref. 340 with permission from American Chemical Society, copyright 2022. | |
4.6.1 Advantages and drawbacks.
The special features of MXenes are exceptional mechanical strength and wear resistance. These characteristics make MXenes excellent candidates for applications in tribology. MXenes can enhance the durability of lubricants markedly, which leads to the long life of mechanical applications. As lubricating agents, the main features of MXenes are oxidation/destabilization in harsh tribological environments.
4.6.2 Suggestions and precautions.
MXenes require protective coatings or modifications to maintain their effectiveness under extreme conditions. Thus, conducting compatibility tests of a lubricant to other ingredients before employment in mechanical applications is a rational approach. In some cases, materials may react adversely with MXene-based lubricants. Applications of MXene reported specifically for tribological performances are shown in Table 9
Table 9 Comparative summary of tribological performances of MXene-based compounds
Types of MXene |
Friction pairs |
Testing parameters |
Lubrication mechanism |
Outcomes |
Ref. |
Ti3C2 |
Probe: MESP-HM |
30 nN–8 μN, 25–40 °C, velocity 0.2–1.0 μm, delay time 1–5 s, RH 20% |
Structure change |
The first research on micro-tribology of MXene |
341
|
Ti3C2, F-Ti3C2 & TMA-Ti3C2 |
Probe: nitride |
0–30 nN, RH 15–45%, 24 °C |
Surface properties |
Distinct tribological properties of different modified Ti3C2 dependent on hydrophilicity |
342
|
PTFE/Al3+-MXene |
Ball: GCr15, Φ 3 mm; disk: PTFE/Al3+-MXene heterogeneous coating on Si wafers |
1 N, 1 Hz, 4 mm, 27 ± 2 °C, RH 24 ± 2% |
Synergistic effect of Al3+-MXene coating and PTFE |
Preparation of friction-induced PTFE/Al3+-MXene film, and formation of secondary transfer film |
343
|
Ti3C2/graphene oxide |
Ball: AISI 52100 bearing steel; disk: copper disk (20 × 15 × 2 mm) |
1 N, 200 rpm, 2 mm |
Transferred film and evenly distributed tribolayer |
N/A |
344
|
4.7. Application of MXenes for water treatment
MXenes have been at the forefront of research on water treatments as photocatalysts or membranes to remove toxic pollutants. Wastewater containing antibiotics such as tetracycline, lincomycin, sulfonamides, and fluoroquinolones arising from animal farming, industries, and hospitals are treated with MXene-supported compounds to separate microbes.47,345–348 Water arising from mining, metal extraction and industrial processes containing hazardous metal ions (e.g., Zn2+, Cd2+, Pb2+, Cr6+ and Cu2+) can be treated to obtain natural water systems.349–354 Karthikeyan355 reported on the ability of MXenes to absorb and remove Cr(VI) and MO from water. According to Wang et al.,356 biosurfactants along with MXene nanosheets enhance the adsorption of Pb(II) from contaminated water. Similarly, removal of mercury ions (Hg2+) on nanolayered molybdenum disulfide (MoS2/MX-II)-functionalized MXene has been reported by Shahzad et al.357 Jun et al. reported successful removal of radioactive Cs+ from nuclear wastewater via a MXene.358
Furthermore, Ti2CTx has been reported to remove uranium efficiently via a sorption–reduction method. MXene nanosheets functionalized with nanolayered MoS2 have been found to be effective for the treatment of wastewater having uranium contents.359 Removal of several medicinal substances on Ti3C2Tx was reported by Yoon et al.360Fig. 22a shows the synthesis and sorption mechanisms of Ti3C2Tx. Significant adsorptive removal of radionuclides on Ti3C2Tx was achieved through a hydrated-intercalation strategy. Ti3C2Tx-DMSO-hydrated (Fig. 22b) demonstrated the highest removal (160 mg g−1) for U(VI) compared with Ti3C2Tx-dry (26 mg g−1). In particular, 1 kg of Ti3C2Tx-DMSO-hydrated could treat nearly 5000 kg of uranium-containing wastewater, reducing the residual U(VI) content to <15 μg L−1. These reports align with WHO standards for the development and delivery of safe drinking water.361 The proposed mechanism demonstrates the sorption of uranium by hydrated/dry Ti3C2Tx (Fig. 22c).361 The mechanism for the removal of toxic metals via MXenes is discussed in ESI Section S5.‡
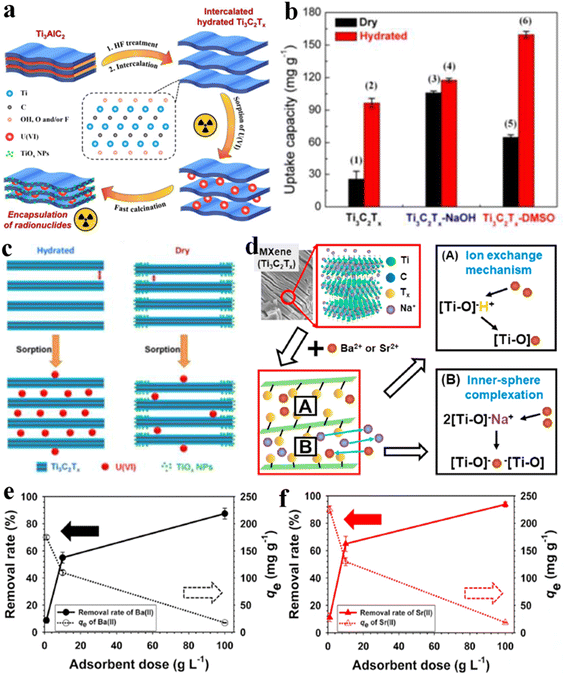 |
| Fig. 22 (a) Synthesis of Ti3C2Txvia a hydrated-intercalation approach. (b) Comparative performances obtained for Ti3C2Tx, Ti3C2Tx-NaOH, and Ti3C2Tx-DMSO. (c) Sorption of U(VI) on hydrated and dry MXenes, reproduced from ref. 361 with permission from Royal Society of Chemistry, copyright 2017. (d) Adsorption of Ba/Sr via MXene. (e) Percentage removal and qe (mg g−1) of Ba and (f) percentage removal and qe (mg g−1) of Sr by increasing the dose of MXene (g L−1), reproduced from ref. 362 with permission from Elsevier, copyright 2020. | |
MXenes have been utilized for the removal of alkaline-earth metal ions. Fig. 22d is a schematic diagram of the adsorption mechanism of Ba/Sr ions. Studies have illustrated the remarkable adsorption of Ba2+ (180 mg g−1) and Sr2+ (225 mg g−1) on MXenes, (Fig. 22e and f, respectively).362Fig. 23a and b show the relationship between the adsorption capacity of Nb2CTx and contact time for MO and MB removal.363Fig. 23c shows a dye-adsorption process that offers a promising approach for the removal of dyes from wastewater. Fig. 23d demonstrates the mechanism of degradation for RhB dye over TiO2/Ti3C2 photocatalysts.364,365 These applications demonstrate the effectiveness of MXenes for wastewater-treatment technologies.
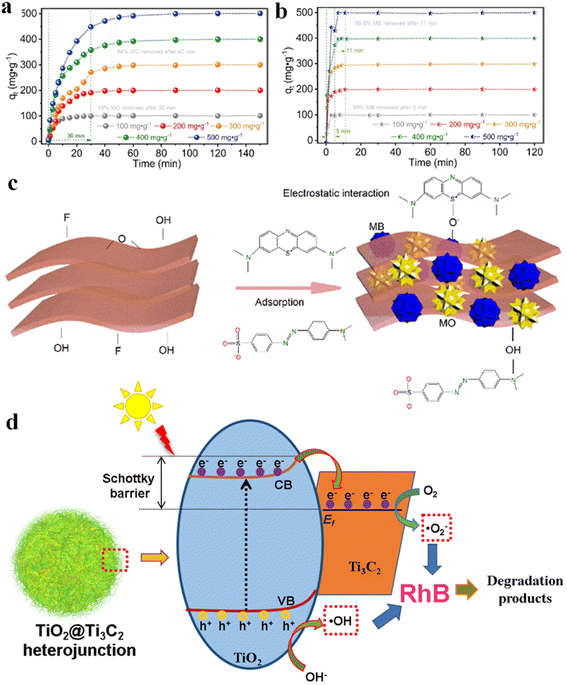 |
| Fig. 23 (a) Adsorption of methyl orange on Nb2CTx and (b) adsorption of methylene blue at various contact times. (c) Dye adsorption via electrostatic interactions, reproduced from ref. 363 with permission from American Chemical Society, copyright 2021. (d) Photocatalytic degradation of RhB via TiO2@Ti3C2, reproduced from ref. 364 with permission from Elsevier, copyright 2021. | |
4.7.1 Advantages and drawbacks.
Due to their excellent adsorption properties, MXenes can efficiently remove heavy metals, radioactive contaminants, organic pollutants, and other toxins from polluted water. Their high adsorption capacity makes them promising materials for water purification/treatment technologies. The stability and scalability of MXenes are the main limitations for large-scale applications.
4.7.2 Suggestions and precautions.
The rate of adsorption must be monitored to optimize the contact time and design for water-treatment systems. The optimized capacity is important because certain contaminants may be adsorbed more readily than others, so choosing or modifying MXenes accordingly is important.
Table 10 demonstrates the MXene-supported materials used for the removal of selected pollutants.
Table 10 MXenes employed for the removal of selected pollutants
Membrane |
Pollutant |
Conc. (mg L−1) |
Efficiency (%) |
Ref. |
Ti3C2Tx MXene nanosheets |
Cytochrome C |
20 |
97 ± 1 |
366
|
Ti3C2Tx MXene nanosheets |
Evans blue (EB) |
10 |
90 ± 1 |
366
|
Thermal cross-linked 2-D MXenes (Ti2C3Tx) |
Pb2+ |
100 |
Hydrated rejection of Pb2+: 99 |
367
|
PFDTMS-modified hydrophobic 2-D d-Ti3C2 membrane |
Cu2+ |
NA |
100 |
368
|
MXene-anchored goethite heterogeneous Fenton composite |
Hg2+ |
60 |
99.7 |
369
|
4.8. Applications of MXenes for fire retardancy/warning
MXenes exhibit great potential as flame-retardant polymers. Some reports have indicated that TiO2 formed in situ on MXene surfaces exhibits a significant fire-inhibitory effect.370 Polyethylenimine (PEI) and MXenes have been introduced to fire-retardant materials because they can efficiently slow down the speed of fires.371 Liu et al. developed a flame-resistant cotton fabric using a layer-by-layer deposition technique. These layers consisted of PEI, MXene, ammonium polyphosphate (APP) and silicone elastomer.372Fig. 24a illustrates the assembly and fireproof properties of MXene/PEI-coated fabrics. Fig. 24b and c illustrate the SEM images (at 200 and 10 μm) of pristine cotton fabric material.371 Furthermore, Fig. 24d and e demonstrate the SEM images of MXene/PEI-coated fabrics. Comparison of the fire-resistance properties of pristine cotton and MXene/PEI-coated fabric has been justified via digital photographs (Fig. 24f–h).371 Similarly, preparation of the flame-retardant materials HDBAC-Ti3C2Tx and PLA/HD-TC/SiAPP is illustrated in Fig. 25a. The flame-resistance mechanism over PLA/HD-TC/SiAPP composite has been illustrated in Fig. 25b.373 The low-temperature evaporation assembly method to synthesize MXene-polymer papers (PVP) is demonstrated in Fig. 25c.374
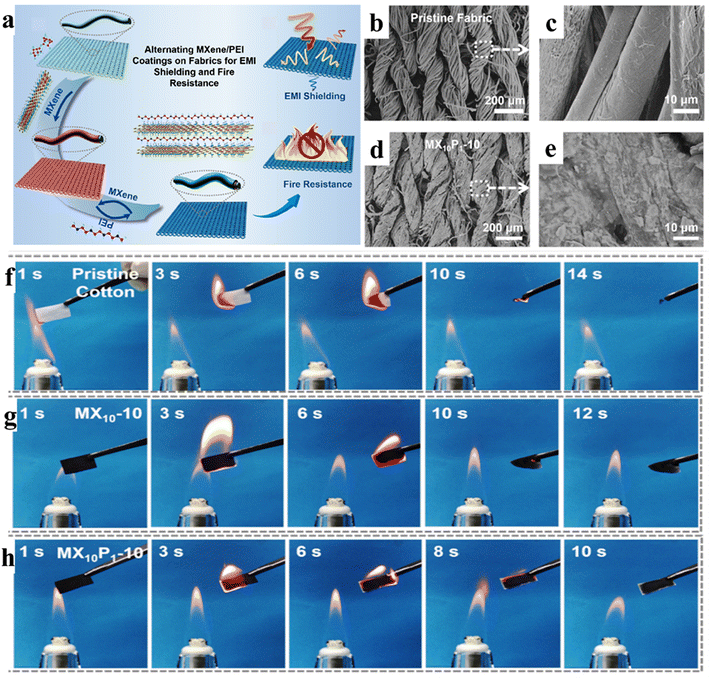 |
| Fig. 24 (a) Assembly of a MXene/PEI-coated fabric. (b and c) SEM images of pristine cotton fabric. (d and e) SEM images of MX10P1-10. (f–h) Investigation of the fireproof properties of MX10-10 and MX10P1-10 fabrics, reproduced from ref. 370 with permission from American Chemical Society, copyright 2021. | |
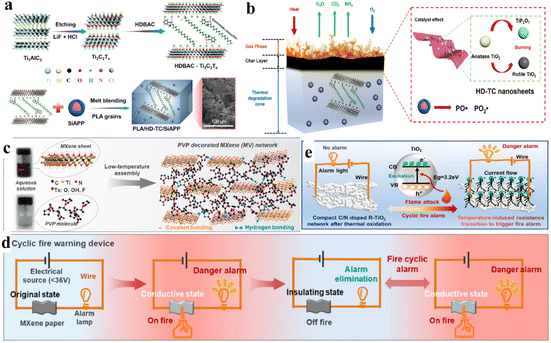 |
| Fig. 25 (a) Synthetic scheme for HDBAC-Ti3C2Tx and PLA/HD-TC/SiAPP. (b) Flame-retardant mechanism, reproduced from ref. 373 with permission from Elsevier, copyright 2022. (c) Low-temperature assembly for PVP-decorated MXene paper. (d) MXene paper-based fire-detecting sensing device (schematic). (e) Resistance transition mechanism of a C/N-doped TiO2 network, reproduced from ref. 374 with permission from Elsevier, copyright 2022. | |
Fig. 25d demonstrates a fire-warning sensor device. This device has been constructed by connecting a modified MXene paper at a low-voltage (36 V) assisted with an alarm bulb. The purpose of this setup is to detect flames. Fig. 25e is a schematic diagram illustrating the resistance mechanism of a C/N-doped TiO2 network during cyclic flame detection. When this network exposed to flames, the temperature rise leads to a change in electrical conductivity.374 This variation in conductivity results in a transition of the resistance. By monitoring resistance transition, the presence and intensity of flames can be detected.375 Various reported MXene-based flame-retardant materials with their values for thermal conductivity (W m−1 K−1), combustion performance, and PHRR reduction are represented in Table 11.
Table 11 Flame-retardant MXene-associated materials based on neat MXenes
Material |
Structure |
MXene (wt%) |
(PHRR) reduction |
Thermal conductivity (W m−1 K−1) |
Combustion performance |
Ref. |
MXene/CNF |
Film |
60 |
77.8 |
14.93 |
No ignition |
376
|
MXene/PI |
Film |
40 |
77.2 |
5.12 ± 0.37 |
Self-extinction |
377
|
MXene/GO |
Film |
40 |
97.7 |
26.49 |
No ignition |
378
|
MXene/PI |
Aerogel |
16.1 |
42.0 |
N/A |
No ignition |
379
|
Wood/MXene |
Coating |
13.1 |
58.8 |
N/A |
No ignition |
380
|
4.8.1 Advantages and drawbacks.
MXenes exhibit excellent flame-retardant properties, and can enhance the fire resistance of polymers and textiles materials. Due to their ability to form protective layers, MXenes can be preferred to other fire-retardant materials. The significant advantage is that they can provide “passive” fire protection; fewer flames spread in the case of a fire. However, the environmental impact of MXene-based fire retardant materials requires attention because these can release some harmful byproducts during combustion.
4.8.2 Suggestions and precautions.
Surface modification or blending methods are preferable for the uniform dispersion of MXenes to develop fire-retardant fabrics. Various methods can be used to integrate the MXene into polymers and textiles effectively. Advanced research on the toxicity of MXene-based fire retardants is lacking. The spread of combustion products may become more risky and challenging. Thus, no release of harmful gases or residues is mandatory during fire exposure.
4.9. Application of MXenes in mode-locked fiber lasers
MXenes have been identified as replacements of traditional saturable absorbers (SAs) such as graphene and carbon nanotubes. The major characteristics that make MXenes excellent candidates for SAs are: (i) high saturable absorption; (ii) remarkable modulation depth; (iii) flexible bandgap; (iv) electron density near to Fermi levels. According to Jhon et al.381 utilization of MXenes as SAs in mode-locked fiber lasers is a promising application. Fig. 26a illustrates the scheme of fiber laser-stacked Ti3CNTx SAs. The setup includes a polarization controller (PC), erbium-doped fiber (EDF), wavelength division multiplexer (WDM), and laser diode (LD).382 Output pulses for electrical and optical spectral results are demonstrated in Fig. 26b and c, respectively. A MXene-SA device on the stretched-pulse mode-locked fiber laser is illustrated in Fig. 26d. The radiofrequency spectrum exhibited in Fig. 26e demonstrates a signal-to-background difference of 62.4 dB.383 The typical spectrum of the mode-locked ultra-short pulse is shown in Fig. 26f. The central wavelength of the ring-cavity Tm-Ho-co-doped fiber laser system was 1550 nm along with a spectral FWHM of 42.54 nm. Fig. 26g is a schematic diagram of this fiber laser system. The Tm-Ho-codoped fiber laser system allows deep understanding of its configuration and functionality.384 Highly stacked Ti3C2Tx SAs were used to generate a relatively stable mode-locked laser system (Fig. 26h.) Analysis of the electrical spectrum revealed distinct peaks at a repetition rate of 16.77 MHz, exhibiting a signal-to-noise ratio of 66 dB. The optical spectra of pulses and fitting in the Sech2 curve for solitons is represented in Fig. 26i. The centre wavelength was determined to be 1913.7 nm, whereas the bandwidth of output pulses was 4.33 nm.385Table 12 provides a comprehensive overview of mode-locked fiber lasers derived from MXene-based SAs.
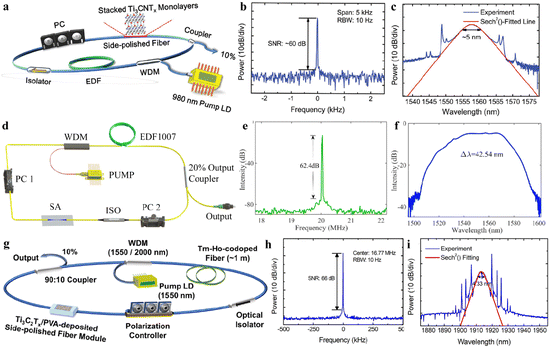 |
| Fig. 26 (a) Scheme used for a fiber laser incorporated stacked Ti3CNTx for SAs. (b) Electrical spectrum. (c) Optical spectrum of output pulses, reproduced from ref. 381 with permission from Wiley, copyright 2017. (d) Stretched-pulse mode-locked fiber laser scheme. (e) RF spectrum. (f) Optical spectra, reproduced from ref. 386 with permission from Optica, copyright 2019 (g) ring-cavity Tm-Ho-co-doped fiber laser system (schematic). (h and i) Electrical and optical spectrum of output laser pulses, reproduced from ref. 388 with permission from De Gruyter, copyright 2021. | |
Table 12 Operational parameters of a mode-locked fiber laser employing MXene-based saturable absorbers
Material |
SA structure |
Deposition technique |
λ
c (nm) |
Δλ (nm) |
SNR (db) |
Repetition rate (MHz) |
Ref. |
Ti3C2Tx |
Tapered fiber |
Optical deposition |
1564.24 |
5.21 |
55.2 |
17.9 |
386
|
Ti3C2Tx |
Tapered fiber |
Optical deposition |
1069.17 |
4.29 |
68 |
4.77 |
387
|
V2CTx |
Tapered fiber |
Optical deposition |
≈1064 |
3 |
71 |
38.5 |
383
|
Ti3C2Tx |
D-shaped fiber |
Drop casting |
1913.7 |
4.33 |
66 |
16.77 |
388
|
Ti2AlC |
Fiber ferrule |
Film attachment |
1559 |
N/A |
64.6 |
5.16 |
389
|
4.9.1 Advantages and drawbacks.
MXenes serve as SAs that enable mode-locking in fiber lasers (an advanced application). MXene-based SAs offer various advantages, such as high modulation depth, ultrafast recovery time, and stable operation. The only drawback is integration of the MXene-based components into the fiber laser system. The stability and reliability of MXene-based SAs are crucial components for practical application in fiber lasers.
4.9.2 Suggestions and precautions.
Due to unique characteristics, the use of MXene-based SAs to fiber laser systems is recommended. Necessary parameters are: (i) saturable absorption potential; (ii) modulation depth; (iii) flexible bandgap; (iv) electron density in Fermi levels should be optimized to achieve desired pulse durations for specific applications. To avoid accidental exposure to laser radiation, protective shielding and safety measures must be assured.
5. Conclusions
This review article delivers up-to-date information about the synthetic methods, mechanism, terminations, modifications, and important applications of MXenes. We highlight the advantages, drawbacks, suggestions, and precautions associated with MXene synthesis and applications. Each synthetic method has advantages and disadvantages. MXene synthesis is mostly reliant on etching of the A-layer. However, most etching methods are scientifically and economically challenging. Development of MXenes by CVD is a cost-effective and efficient “bottom-up” synthetic method. Controllable doping and surface terminations on MXenes have important roles for specific and targeted applications. The inherited properties of MXene (relatively higher thermal and electrical conductivity, mechanical strength, hydrophilicity, and structural stability) have been validated via interactions with other materials for the design of state-of-the-art applications. The composition of surface terminations is predominantly affected by the type of etching agent along with its concentration. For example, fluorine-based etching methods typically have hydrophilic terminations, such as –OH,
O, and –F, whereas electrochemical and alkali etching are less effective for some applications. MXenes with single terminations can be synthesized by molten salt etching. Sulfur terminations of MXenes exhibit remarkable performances for batteries and supercapacitors. F-terminated MXenes deliver excellent performances for electrocatalytic reactions, whereas N-doped MXenes exhibit exceptional electrochemical capabilities for LSBs and energy-storage applications.
O terminations are very effective for photocatalysis, but also for adsorption. We summarized recent developments on MXenes, terminations, and their roles in energy, catalysis, sensing, environment, medicine, water treatment, fire retardation, tribology, and EMI-shielding applications. For example, MXenes and their composites have been employed as catalysts or co-catalysts in electro/photocatalytic water-splitting reactions. Moreover, MXenes and their derived compounds exhibit strong adsorption affinities for the removal of radioisotopes, heavy-metal ions, and carcinogenic dyes from contaminated water. Additionally, MXenes and their biocompatible composites have been utilized in biosensing applications, or immobilization of enzymes to facilitate electron transfer between enzymes and electrode surfaces. MXenes and MXene-derived compounds have unique and exciting characteristics for state-of-the-art applications. Their excellent conductivity, chemical stability, and tuneable properties promise utilization in many other applications.
6. Future perspectives
• To extend the applications of MXenes, theoretical calculations and simulations need to be performed. Advanced and sophisticated experimental setups may require endorsement for new applications.
• It is essential to explore diverse terminations and their impact on properties for improving the overall performance for targeted applications.
• For precise control of the synthesis and terminations, extra attention should be given to post-etching processing.
• The interface properties of MXene nanosheets with various other materials must be investigated.
• Changes in terminations that govern applications are unclear. Hence, sophisticated technologies that can extend utilization even in humid, oxygen, or high temperatures are needed.
• Discovery of new precursors rather than the MAX phase can open new synthetic routes for MXenes.
• Alternative synthetic methods may aid the design and morphologies of MXenes for targeted applications.
• Substitutes for MXenes, such as oxycarbides and oxynitrides, may need to be discovered for state-of-the-art applications.
• The conductivity of MXenes can be controlled by employing structural changes to selective applications such as electronic, semiconductor, and sensing devices.
Abbreviations
Ti3C2 | Titanium carbide |
RhB | Rhodamine B |
EHDA | Electro hydrodynamic atomization |
MO | Methyl orange |
SE | Shielding efficiency |
DFT | Density functional theory |
NEB | Nudge elastic band |
LSBs | Lithium–sulfur batteries |
QD | Quantum dots |
MA | Microwave absorption |
MSC | Micro supercapacitor |
ECSDs | Energy conversion and storage devices |
SNR | Signal-to-noise ratio |
RBW | Resolution bandwidth |
LIBs | Lithium-ion batteries |
SIBs | Sodium-ion batteries |
CDCs | Carbon-derived carbides |
MILD | Minimally intensive layer delamination |
MMF | MXene membrane filter |
PES | Photoelectron spectroscopy |
HER | Hydrogen-evolution reaction |
EDLC | Electric double-layer capacitor |
AC | Ammonium citrate |
CV | Cyclic voltammetry |
RES | Reticuloendothelial system |
SCs | Super capacitors |
OCVs | Open-circuit voltages |
DMF | Dimethylformamide |
PAN | Polyacrylonitrile |
ACN | Acetonitrile |
PI | Polyimide |
PSC | Perovskite solar cell |
MQDs | MXene quantum dots |
EMI | Electromagnetic interference |
SA | Sodium alginate |
PANI | Polyaniline |
SAs | Saturable absorbers |
TDPA | Tetradecylphosphonic acid |
WSEP | Weighted sum of enclosed pixels |
PRBs | Permeable reactive barriers |
PVA | Polyvinyl alcohol |
ETLs | Electron transport layers |
PHRR | Peak heat release rate |
EQE | External quantum efficiency |
APP | Ammonium polyphosphate |
WDM | Wavelength division multiplexer |
PC | Polarization controller |
EDF | Erbium-doped fiber |
LD | Laser diode |
Conflicts of interest
The authors announce no conflict of financial interests.
Acknowledgements
The authors acknowledge the Higher Education Commission of Pakistan for funding support ((377/IPFP-II, Batch-I)/SRGP/NAHE/HEC/2020/27). Dr Ejaz Hussain thanks Carnegie Mellon University (USA) and Ministry of Science and Technology of Pakistan for scientific support. This scientific contribution is highly credited to the resources of the Inorganic Material Laboratory (52S), Institute of Chemistry, Islamia University of Bahawalpur, Pakistan.
References
- H. Zhang, ACS Nano, 2015, 9, 9451–9469 CrossRef CAS PubMed.
- H. D. Mai, K. Rafiq and H. Yoo, Chem.–Eur. J., 2017, 23, 5631–5651 CrossRef CAS PubMed.
- Y. Gogotsi and B. Anasori, ACS Nano, 2019, 13, 8491–8494 CrossRef CAS PubMed.
- M. Dahlqvist, M. W. Barsoum and J. Rosen, Mater. Today, 2023 DOI:10.1016/j.mattod.2023.11.010.
- M. Li, J. Lu, K. Luo, Y. Li, K. Chang, K. Chen, J. Zhou, J. Rosen, L. Hultman and P. Eklund, J. Am. Chem. Soc., 2019, 141, 4730–4737 CrossRef CAS PubMed.
- L. Fu and W. Xia, Adv. Eng. Mater., 2021, 23, 2001191 CrossRef CAS.
- R. Qin, G. Shan, M. Hu and W. Huang, Mater. Today Phys., 2021, 21, 100527 CrossRef CAS.
- K. R. G. Lim, M. Shekhirev, B. C. Wyatt, B. Anasori, Y. Gogotsi and Z. W. Seh, Nat., Synth., 2022, 1, 601–614 CrossRef.
- B. Anasori, J. Halim, J. Lu, C. A. Voigt, L. Hultman and M. W. Barsoum, Scr. Mater., 2015, 101, 5–7 CrossRef CAS.
- T. Bashir, S. A. Ismail, J. Wang, W. Zhu, J. Zhao and L. Gao, J. Energy Chem., 2023, 76, 90–104 CrossRef CAS.
- C. Lamiel, I. Hussain, O. R. Ogunsakin and K. Zhang, J. Mater. Chem. A, 2022, 10, 14247–14272 RSC.
- Y.-T. Du, X. Kan, F. Yang, L.-Y. Gan and U. Schwingenschlogl, ACS Appl. Mater. Interfaces, 2018, 10, 32867–32873 CrossRef CAS PubMed.
- J. Miao, Q. Zhu, K. Li, P. Zhang, Q. Zhao and B. Xu, J. Energy Chem., 2021, 52, 243–250 CrossRef CAS.
- J. Xu, X. Hu, X. Wang, X. Wang, Y. Ju, S. Ge, X. Lu, J. Ding, N. Yuan and Y. Gogotsi, Energy Storage Mater., 2020, 33, 382–389 CrossRef.
- L. Wang, Y. Lai, H. Tian, J. Wang, W. Zhao, Y. Wang, L. Li and L. Zhang, J. Alloys Compd., 2023, 945, 169366 CrossRef CAS.
- Y. Gao, Z. Tang, X. Chen, J. Yan, Y. Jiang, J. Xu, Z. Tao, L. Wang, Z. Liu and G. Wang, Aggregate, 2023, 4, e248 CrossRef CAS.
- Y. Wang, Z. Luo, Y. Qian, W. Zhang and L. Chen, Chem. Eng. J., 2023, 454, 140513 CrossRef CAS.
- K. Hantanasirisakul and Y. Gogotsi, Adv. Mater., 2018, 30, 1804779 CrossRef PubMed.
- M.-s. Cao, Y.-Z. Cai, P. He, J.-C. Shu, W.-Q. Cao and J. Yuan, Chem. Eng. J., 2019, 359, 1265–1302 CrossRef CAS.
- Y. Cheng, Y. Xie, Z. Liu, S. Yan, Y. Ma, Y. Yue, J. Wang, Y. Gao and L. Li, ACS Nano, 2023, 17, 1393–1402 CrossRef CAS PubMed.
- Y. Cheng, Y. Xie, Y. Ma, M. Wang, Y. Zhang, Z. Liu, S. Yan, N. Ma, M. Liu and Y. Yue, Nano Energy, 2023, 107, 108131 CrossRef CAS.
- S. Chertopalov and V. N. Mochalin, ACS Nano, 2018, 12, 6109–6116 CrossRef CAS PubMed.
- X. Zhan, C. Si, J. Zhou and Z. Sun, Nanoscale Horiz., 2020, 5, 235–258 RSC.
- X. Ma, A. Wang, J. Miao and T. Fan, Sep. Purif. Technol., 2023, 123248 CrossRef CAS.
- Y. Chen, P. Zhao, Y. Liang, Y. Ma, Y. Liu, J. Zhao, J. Hou, C. Hou and D. Huo, Talanta, 2023, 124294 CrossRef CAS PubMed.
- K. Zhao, J. W. Lee, Z. G. Yu, W. Jiang, J. W. Oh, G. Kim, H. Han, Y. Kim, K. Lee and S. Lee, ACS Nano, 2023, 17, 5472–5485 CrossRef CAS PubMed.
- A. Sinha, H. Zhao, Y. Huang, X. Lu, J. Chen and R. Jain, TrAC, Trends Anal. Chem., 2018, 105, 424–435 CrossRef CAS.
- S. Hroncekova, T. Bertok, M. Hires, E. Jane, L. Lorencova, A. Vikartovska, A. Tanvir, P. Kasak and J. Tkac, Processes, 2020, 8, 580 CrossRef CAS PubMed.
- Y. Lei, W. Zhao, Y. Zhang, Q. Jiang, J. H. He, A. J. Baeumner, O. S. Wolfbeis, Z. L. Wang, K. N. Salama and H. N. Alshareef, Small, 2019, 15, 1901190 CrossRef PubMed.
- L. Wu, X. Lu, Z.-S. Wu, Y. Dong, X. Wang, S. Zheng and J. Chen, Biosens. Bioelectron., 2018, 107, 69–75 CrossRef CAS PubMed.
- H. Gu, Y. Xing, P. Xiong, H. Tang, C. Li, S. Chen, R. Zeng, K. Han and G. Shi, ACS Appl. Nano Mater., 2019, 2, 6537–6545 CrossRef CAS.
- H. L. Chia, C. C. Mayorga-Martinez, N. Antonatos, Z. k. Sofer, J. J. Gonzalez-Julian, R. D. Webster and M. Pumera, Anal. Chem., 2020, 92, 2452–2459 CrossRef CAS PubMed.
- S. J. Kim, H.-J. Koh, C. E. Ren, O. Kwon, K. Maleski, S.-Y. Cho, B. Anasori, C.-K. Kim, Y.-K. Choi and J. Kim, ACS Nano, 2018, 12, 986–993 CrossRef CAS PubMed.
- A. Shahzad, K. Rasool, M. Nawaz, W. Miran, J. Jang, M. Moztahida, K. A. Mahmoud and D. S. Lee, Chem. Eng. J., 2018, 349, 748–755 CrossRef CAS.
- J. Peng, X. Chen, W.-J. Ong, X. Zhao and N. Li, Chem, 2019, 5, 18–50 CAS.
- Y. Wei, R. A. Soomro, X. Xie and B. Xu, J. Energy Chem., 2021, 55, 244–255 CrossRef CAS.
- Z. Li, S. Ning, F. Hu, H. Zhu, L. Zeng, L. Chen, X. Wang, T. Fujita and Y. Wei, J. Colloid Interface Sci., 2023, 629, 97–110 CrossRef CAS PubMed.
- P. D. Kolubah, H. O. Mohamed, M. Ayach, A. R. Hari, H. N. Alshareef, P. Saikaly, K.-J. Chae and P. Castaño, Chem. Eng. J., 2023, 461, 141821 CrossRef CAS.
- K. Huang, Z. Li, J. Lin, G. Han and P. Huang, Chem. Soc. Rev., 2018, 47, 5109–5124 RSC.
- J. Xu, L. Chen, S. Ding, X. Dai, Y. Dai, Y. Chen and X. Ni, Nano Today, 2023, 48, 101750 CrossRef CAS.
- Y.-U. Haq, R. Ullah, S. Mazhar, R. Khattak, A. A. Qarni, Z.-U. Haq and S. Amin, J. Sci.: Adv. Mater. Devices, 2022, 7, 100390 CAS.
- D. Chen, J. Yu, Z. Cui, Q. Zhang, X. Chen, J. Sui, H. Dong, L. Yu and L. Dong, Electrochim. Acta, 2020, 331, 135394 CrossRef CAS.
- A. Liu, X. Liang, X. Ren, W. Guan and T. Ma, Electrochem. Energy Rev., 2022, 1–33 Search PubMed.
- E. Hussain, I. Majeed, M. A. Nadeem, A. Badshah, Y. Chen, M. A. Nadeem and R. Jin, J. Phys. Chem. C, 2016, 120, 17205–17213 CrossRef CAS.
- F. Saleem, M. Z. Abid, K. Rafiq, A. Rauf, K. Ahmad, S. Iqbal, R. Jin and E. Hussain, Int. J. Hydrogen Energy, 2024, 52, 305–319 CrossRef CAS.
- Y. Liu, S. Chen, K. Li, J. Wang, P. Chen, H. Wang, J. Li and F. Dong, J. Colloid Interface Sci., 2022, 606, 1435–1444 CrossRef CAS PubMed.
- N. Wajid, K. Rafiq, M. Z. Abid, A. Ilyas, T. Najam, A. Rauf and E. Hussain, Mater. Chem. Phys., 2023, 306, 128062 CrossRef CAS.
- E. Hussain, I. Majeed, M. A. Nadeem, A. Iqbal, Y. Chen, M. Choucair, R. Jin and M. A. Nadeem, J. Environ. Chem. Eng., 2019, 7, 102729 CrossRef CAS.
- M. Tahir, A. A. Khan, S. Tasleem, R. Mansoor, A. Sherryna and B. Tahir, J. Energy Chem., 2022, 5, 18–54 CAS.
- K. U. Sahar, K. Rafiq, M. Z. Abid, A. Rauf, U. u. Rehman, M. A. Nadeem, R. Jin and E. Hussain, Colloids Surf., A, 2023, 674, 131942 CrossRef CAS.
- S. Li, P. Tuo, J. Xie, X. Zhang, J. Xu, J. Bao, B. Pan and Y. Xie, Nano Energy, 2018, 47, 512–518 CrossRef CAS.
- H. Riazi, S. K. Nemani, M. C. Grady, B. Anasori and M. Soroush, J. Mater. Chem. A, 2021, 9, 8051–8098 RSC.
- A. Ali Khan, M. Tahir and N. Khan, Energy Fuels, 2022, 36, 9821–9843 CrossRef CAS.
- S.-Y. Pang, Y.-T. Wong, S. Yuan, Y. Liu, M.-K. Tsang, Z. Yang, H. Huang, W.-T. Wong and J. Hao, J. Am. Chem. Soc., 2019, 141, 9610–9616 CrossRef CAS PubMed.
- M. Li, J. Lu, K. Luo, Y. Li, K. Chang, K. Chen, J. Zhou, J. Rosen, L. Hultman, P. Eklund, P. O. Å. Persson, S. Du, Z. Chai, Z. Huang and Q. Huang, J. Am. Chem. Soc., 2019, 141, 4730–4737 CrossRef CAS PubMed.
- M. Ghidiu, M. R. Lukatskaya, M.-Q. Zhao, Y. Gogotsi and M. W. Barsoum, Nature, 2014, 516, 78–81 CrossRef CAS PubMed.
- S. Yang, P. Zhang, F. Wang, A. G. Ricciardulli, M. R. Lohe, P. W. Blom and X. Feng, Angew. Chem., 2018, 130, 15717–15721 CrossRef.
- S. Zada, W. Dai, Z. Kai, H. Lu, X. Meng, Y. Zhang, Y. Cheng, F. Yan, P. Fu and X. Zhang, Angew. Chem., Int. Ed., 2020, 59, 6601–6606 CrossRef CAS PubMed.
- Q. Zhang, H. Lai, R. Fan, P. Ji, X. Fu and H. Li, ACS Nano, 2021, 15, 5249–5262 CrossRef CAS PubMed.
- B. Anasori, M. R. Lukatskaya and Y. Gogotsi, Nat. Rev. Mater., 2017, 2, 1–17 Search PubMed.
- X. Zhang, W. Zhang and H. Zhao, Int. J. Energy Res., 2022, 46, 15559–15570 CrossRef CAS.
- Z. Li, L. Wang, D. Sun, Y. Zhang, B. Liu, Q. Hu and A. Zhou, Mater. Sci. Eng. B, 2015, 191, 33–40 CrossRef CAS.
- W. Sun, S. A. Shah, Y. Chen, Z. Tan, H. Gao, T. Habib, M. Radovic and M. J. Green, J. Mater. Chem. A, 2017, 5, 21663–21668 RSC.
- S. Zada, W. Dai, Z. Kai, H. Lu, X. Meng, Y. Zhang, Y. Cheng, F. Yan, P. Fu, X. Zhang and H. Dong, Angew. Chem., Int. Ed., 2020, 59, 6601–6606 CrossRef CAS PubMed.
- C. Couly, M. Alhabeb, K. L. Van Aken, N. Kurra, L. Gomes, A. M. Navarro-Suárez, B. Anasori, H. N. Alshareef and Y. Gogotsi, Adv. Electron. Mater., 2018, 4, 1700339 CrossRef.
- C. Peng, P. Wei, X. Chen, Y. Zhang, F. Zhu, Y. Cao, H. Wang, H. Yu and F. Peng, Ceram. Int., 2018, 44, 18886–18893 CrossRef CAS.
- C. E. Shuck, A. Sarycheva, M. Anayee, A. Levitt, Y. Zhu, S. Uzun, V. Balitskiy, V. Zahorodna, O. Gogotsi and Y. Gogotsi, Adv. Eng. Mater., 2020, 22, 1901241 CrossRef CAS.
- S. Zhang, P. Huang, J. Wang, Z. Zhuang, Z. Zhang and W.-Q. Han, J. Phys. Chem. Lett., 2020, 11, 1247–1254 CrossRef CAS PubMed.
- H. Shi, P. Zhang, Z. Liu, S. Park, M. R. Lohe, Y. Wu, A. Shaygan Nia, S. Yang and X. Feng, Angew. Chem., Int. Ed., 2021, 60, 8689–8693 CrossRef CAS PubMed.
- G. Wang, N. Jiang, Z. Zhang, G. Wang and K. Cheng, Appl. Surf. Sci., 2022, 604, 154636 CrossRef CAS.
- M. S. Bhargava Reddy, S. Kailasa, B. C. G. Marupalli, K. K. Sadasivuni and S. Aich, ACS Sens., 2022, 7, 2132–2163 CrossRef CAS PubMed.
- V. Sharma, D. Kumar Das, R. K. Gupta, G. Yasin and A. Kumar, Inorg. Chem. Commun., 2022, 141, 109496 CrossRef CAS.
- M. Malaki, A. Maleki and R. S. Varma, J. Mater. Chem. A, 2019, 7, 10843–10857 RSC.
- V. Kotasthane, Z. Tan, J. Yun, E. B. Pentzer, J. L. Lutkenhaus, M. J. Green and M. Radovic, ACS Appl. Nano Mater., 2023, 6, 1093–1105 CrossRef CAS.
- X. Sheng, S. Li, H. Huang, Y. Zhao, Y. Chen, L. Zhang and D. Xie, J. Mater. Sci., 2021, 56, 4212–4224 CrossRef CAS.
- J. Halim, M. R. Lukatskaya, K. M. Cook, J. Lu, C. R. Smith, L.-Å. Näslund, S. J. May, L. Hultman, Y. Gogotsi and P. Eklund, Chem. Mater., 2014, 26, 2374–2381 CrossRef CAS PubMed.
- Y. Hai, S. Jiang, C. Zhou, P. Sun, Y. Huang and S. Niu, Dalton Trans., 2020, 49, 5803–5814 RSC.
- C. E. Shuck, K. Ventura-Martinez, A. Goad, S. Uzun, M. Shekhirev and Y. Gogotsi, ACS Chem. Health Saf., 2021, 28, 326–338 CrossRef CAS.
- J. Wu, Y. Wang, Y. Zhang, H. Meng, Y. Xu, Y. Han, Z. Wang, Y. Dong and X. Zhang, J. Energy Chem., 2020, 47, 203–209 CrossRef.
- M. Naguib, M. Kurtoglu, V. Presser, J. Lu, J. Niu, M. Heon, L. Hultman, Y. Gogotsi and M. W. Barsoum, Adv. Mater., 2011, 23, 4248–4253 CrossRef CAS PubMed.
- M. Tang, J. Li, Y. Wang, W. Han, S. Xu, M. Lu, W. Zhang and H. Li, Symmetry, 2022, 14, 2232 CrossRef CAS.
- M. Xiang, Z. Shen, J. Zheng, M. Song, Q. He, Y. Yang, J. Zhu, Y. Geng, F. Yue, Q. Dong, Y. Ge, R. Wang, J. Wei, W. Wang, H. Huang, H. Zhang, Q. Zhu and C. J. Zhang, Innovation, 2024, 5, 100540 CAS.
- D. Xiong, X. Li, Z. Bai and S. Lu, Small, 2018, 14, 1703419 CrossRef PubMed.
- J. Björk and J. Rosen, Chem. Mater., 2021, 33, 9108–9118 CrossRef.
- M. Peng, M. Dong, W. Wei, H. Xu, C. Liu and C. Shen, Carbon, 2021, 179, 400–407 CrossRef CAS.
- R. Jasrotia, J. Prakash, G. Kumar, R. Verma, S. Kumari, S. Kumar, V. P. Singh, A. K. Nadda and S. Kalia, Chemosphere, 2022, 294, 133706 CrossRef CAS PubMed.
- P. Lakhe, E. M. Prehn, T. Habib, J. L. Lutkenhaus, M. Radovic, M. S. Mannan and M. J. Green, Ind. Eng. Chem. Res., 2019, 58, 1570–1579 CrossRef CAS.
- T. Zhang, L. Pan, H. Tang, F. Du, Y. Guo, T. Qiu and J. Yang, J. Alloys Compd., 2017, 695, 818–826 CrossRef CAS.
- Y. Li, H. Shao, Z. Lin, J. Lu, L. Liu, B. Duployer, P. O. Persson, P. Eklund, L. Hultman and M. Li, Nat. Mater., 2020, 19, 894–899 CrossRef CAS PubMed.
- J. Lu, I. Persson, H. Lind, J. Palisaitis, M. Li, Y. Li, K. Chen, J. Zhou, S. Du and Z. Chai, Nanoscale Adv., 2019, 1, 3680–3685 RSC.
- P. Liu, P. Xiao, M. Lu, H. Wang, N. Jin and Z. Lin, Chin. Chem. Lett., 2023, 34, 107426 CrossRef CAS.
- W. Sun, S. Shah, Y. Chen, Z. Tan, H. Gao, T. Habib, M. Radovic and M. Green, J. Mater. Chem. A, 2017, 5, 21663–21668 RSC.
- D. Laishram, D. Kumar, K. P. Shejale, B. Saini, Harikrishna, R. Krishnapriya and R. K. Sharma, Heterog. Nanocatal. Energy Environ. Sustainability, 2022, 1, 165–198 Search PubMed.
- L. M. Dong, C. Ye, L. L. Zheng, Z. F. Gao and F. Xia, Nanophotonics, 2020, 9, 2125–2145 CrossRef CAS.
- F. Gao, C. Xue, T. Zhang, L. Zhang, G. Y. Zhu, C. Ou, Y. Z. Zhang and X. Dong, Adv. Mater., 2023, 2302559 CrossRef CAS PubMed.
- J. Mei, G. A. Ayoko, C. Hu, J. M. Bell and Z. Sun, Sustainable Mater. Technol., 2020, 25, e00156 CrossRef CAS.
- S. Iravani, Ceram. Int., 2022, 48, 24144–24156 CrossRef CAS.
- J. Yang, W. Bao, P. Jaumaux, S. Zhang, C. Wang and G. Wang, Adv. Mater. Interfaces, 2019, 6, 1802004 CrossRef.
- X. Xu, L. Yang, W. Zheng, H. Zhang, F. Wu, Z. Tian, P. Zhang and Z. Sun, Mater. Rep.: Energy, 2022, 100080 CAS.
- M. Alhabeb, K. Maleski, B. Anasori, P. Lelyukh, L. Clark, S. Sin and Y. Gogotsi, Chem. Mater., 2017, 29, 7633–7644 CrossRef CAS.
- H. Diebler, Inorganica Chim. Acta, 1983, 79, 93–94 CrossRef.
- G. Li, K. Jiang, S. Zaman, J. Xuan, Z. Wang and F. Geng, Inorg. Chem., 2019, 58, 9397–9403 CrossRef CAS PubMed.
- T. Li, L. Yao, Q. Liu, J. Gu, R. Luo, J. Li, X. Yan, W. Wang, P. Liu and B. Chen, Angew. Chem., Int. Ed., 2018, 57, 6115–6119 CrossRef CAS PubMed.
- N. H. Solangi, R. R. Karri, S. A. Mazari, N. M. Mubarak, A. S. Jatoi, G. Malafaia and A. K. Azad, Coord. Chem. Rev., 2023, 477, 214965 CrossRef CAS.
- Y. Dall'Agnese, M. R. Lukatskaya, K. M. Cook, P.-L. Taberna, Y. Gogotsi and P. Simon, Electrochem. Commun., 2014, 48, 118–122 CrossRef.
-
D. Sundar, L. Gurusamy, L. Karuppasamy, S. C. Barton and J. J. Wu, in Noble Metal-Free Electrocatalysts: New Trends in Electrocatalysts for Energy Applications, ACS Publications, 2022, vol. 2, pp. 151–189 Search PubMed.
- D. J. Kubicki, S. D. Stranks, C. P. Grey and L. Emsley, Nat. Rev. Chem, 2021, 5, 624–645 CrossRef CAS PubMed.
- C. E. Shuck and Y. Gogotsi, Chem. Eng. J., 2020, 401, 125786 CrossRef CAS.
- N. Chen, Z. Duan, W. Cai, Y. Wang, B. Pu, H. Huang, Y. Xie, Q. Tang, H. Zhang and W. Yang, Nano Energy, 2023, 107, 108147 CrossRef CAS.
- H. Shi, P. Zhang, Z. Liu, S. Park, M. R. Lohe, Y. Wu, A. Shaygan Nia, S. Yang and X. Feng, Angew. Chem., Int. Ed., 2021, 60, 8689–8693 CrossRef CAS PubMed.
- J. Wang, H. Kang, H. Ma, Y. Liu, Z. Xie, Y. Wang and Z. Fan, Eng. Sci., 2021, 15, 57–66 CAS.
- H. Feng, Q. Tian, J. Huang, X. Cui, J. Jiang, Y. Tian, L. Ye and Q. Xu, Green Chem., 2023, 25, 3966–3973 RSC.
- D. Wang, C. Zhou, A. S. Filatov, W. Cho, F. Lagunas, M. Wang, S. Vaikuntanathan, C. Liu, R. F. Klie and D. V. Talapin, Science, 2023, 379, 1242–1247 CrossRef CAS PubMed.
- J. Come, M. Naguib, P. Rozier, M. W. Barsoum, Y. Gogotsi, P.-L. Taberna, M. Morcrette and P. Simon, J. Electrochem. Soc., 2012, 159, A1368 CrossRef CAS.
- M. Naguib, J. Come, B. Dyatkin, V. Presser, P.-L. Taberna, P. Simon, M. W. Barsoum and Y. Gogotsi, Electrochem. Commun., 2012, 16, 61–64 CrossRef CAS.
- Q. Tang, Z. Zhou and P. Shen, J. Am. Chem. Soc., 2012, 134, 16909–16916 CrossRef CAS PubMed.
- M. Naguib, J. Halim, J. Lu, K. M. Cook, L. Hultman, Y. Gogotsi and M. W. Barsoum, J. Am. Chem. Soc., 2013, 135, 15966–15969 CrossRef CAS PubMed.
- F. Wang, C. Yang, C. Duan, D. Xiao, Y. Tang and J. Zhu, J. Electrochem. Soc., 2015, 162, B16 CrossRef CAS.
- Y. Gao, L. Wang, Z. Li, A. Zhou, Q. Hu and X. Cao, Solid State Sci., 2014, 35, 62–65 CrossRef CAS.
- R. B. Rakhi, B. Ahmed, M. N. Hedhili, D. H. Anjum and H. N. Alshareef, Chem. Mater., 2015, 27, 5314–5323 CrossRef CAS.
- J. Yang, M. Naguib, M. Ghidiu, L.-M. Pan, J. Gu, J. Nanda, J. Halim, Y. Gogotsi and M. W. Barsoum, J. Am. Ceram. Soc., 2016, 99, 660–666 CrossRef CAS.
- M. Hu, Z. Li, H. Zhang, T. Hu, C. Zhang, Z. Wu and X. Wang, Chem. Commun., 2015, 51, 13531–13533 RSC.
- R. Meshkian, L.-Å. Näslund, J. Halim, J. Lu, M. W. Barsoum and J. Rosen, Scr. Mater., 2015, 108, 147–150 CrossRef CAS.
- J. Halim, S. Kota, M. R. Lukatskaya, M. Naguib, M. Q. Zhao, E. J. Moon, J. Pitock, J. Nanda, S. J. May and Y. Gogotsi, Adv. Funct. Mater., 2016, 26, 3118–3127 CrossRef CAS.
- K. Rasool, M. Helal, A. Ali, C. E. Ren, Y. Gogotsi and K. A. Mahmoud, ACS Nano, 2016, 10, 3674–3684 CrossRef CAS PubMed.
- J. Zhou, X. Zha, F. Y. Chen, Q. Ye, P. Eklund, S. Du and Q. Huang, Angew. Chem., Int. Ed., 2016, 55, 5008–5013 CrossRef CAS PubMed.
- B. Soundiraraju and B. K. George, ACS Nano, 2017, 11, 8892–8900 CrossRef CAS PubMed.
- J. Zhou, X. Zha, X. Zhou, F. Chen, G. Gao, S. Wang, C. Shen, T. Chen, C. Zhi, P. Eklund, S. Du, J. Xue, W. Shi, Z. Chai and Q. Huang, ACS Nano, 2017, 11, 3841–3850 CrossRef CAS PubMed.
- H. Lin, Y. Wang, S. Gao, Y. Chen and J. Shi, Adv. Mater., 2018, 30, 1703284 CrossRef PubMed.
- M. Wu, B. Wang, Q. Hu, L. Wang and A. Zhou, Materials, 2018, 11, 2112 CrossRef PubMed.
- R. Meshkian, M. Dahlqvist, J. Lu, B. Wickman, J. Halim, J. Thörnberg, Q. Tao, S. Li, S. Intikhab, J. Snyder, M. W. Barsoum, M. Yildizhan, J. Palisaitis, L. Hultman, P. O. Å. Persson and J. Rosen, Adv. Mater., 2018, 30, 1706409 CrossRef PubMed.
- X. Chen, Y. Zhu, M. Zhang, J. Sui, W. Peng, Y. Li, G. Zhang, F. Zhang and X. Fan, ACS Nano, 2019, 13, 9449–9456 CrossRef CAS PubMed.
- Q. Chen, D. Zhang, J. Pan and W. Fan, Optik, 2020, 219, 165046 CrossRef CAS.
- B. Soundiraraju, R. Raghavan and B. K. George, ACS Appl. Nano Mater., 2020, 3, 11007–11016 CrossRef CAS.
- K. Maeda, H. Wakayama, Y. Washio, A. Ishikawa, M. Okazaki, H. Nakata and S. Matsuishi, J. Phys. Chem. C, 2020, 124, 14640–14645 CrossRef CAS.
- S. Liu, R. Lv, J. Wang, Y. Wang, H. Wang, H. Zhang and Y. Wang, J. Mater. Chem. C, 2021, 9, 16985–16990 RSC.
- H. Shin, W. Eom, K. H. Lee, W. Jeong, D. J. Kang and T. H. Han, ACS Nano, 2021, 15, 3320–3329 CrossRef CAS PubMed.
- M. Y. Hazman, M. E. El-Sayed, F. F. Kabil, N. A. Helmy, L. Almas, M. McFarland, A. Shams El Din and S. Burian, Agronomy, 2022, 12, 1596 CrossRef CAS.
- P. Zhang, J. Li, D. Yang, R. A. Soomro and B. Xu, Adv. Funct. Mater., 2023, 33, 2209918 CrossRef CAS.
- M. Shi, R. Wang, L. Li, N. Chen, P. Xiao, C. Yan and X. Yan, Adv. Funct. Mater., 2023, 33, 2209777 CrossRef CAS.
- X. Sun, X. He, Y. Zhu, E. Obeng, B. Zeng, H. Deng, J. Shen and R. Hu, Chem. Eng. J., 2023, 451, 138985 CrossRef CAS.
- M. Wang, X. Liu, B. Qin, Z. Li, Y. Zhang, W. Yang and H. Fan, Chem. Eng. J., 2023, 451, 138508 CrossRef CAS.
- S. Li, X. Tang, X. Zhao, S. Lu, J. Luo, Z. Chai, T. Ma, Q. Lan, P. Ma and W. Dong, J. Mater. Sci. Technol., 2023, 133, 238–248 CrossRef CAS.
- Z. Abid, K. Rafiq, A. Rauf, R. Hamed Althomali and E. Hussain, Mater. Adv., 2024 10.1039/D3MA00710C.
- H. Ahmadi, N. Shokrollah, S. Aghaei, S. Gharishvandi, M. M. Goodarzi, A. Mohebifar and N. Tightiz, J. Mater. Sci.: Mater. Electron., 2016, 27, 4689–4693 CrossRef CAS.
- Z. Bao, C. Lu, X. Cao, P. Zhang, L. Yang, H. Zhang, D. Sha, W. He, W. Zhang and L. Pan, Chin. Chem. Lett., 2021, 32, 2648–2658 CrossRef CAS.
- F. H. Fagerli, Z. Wang, T. Grande, H. Kaland, S. M. Selbach, N. P. Wagner and K. Wiik, ACS Omega, 2022, 7, 23790–23799 CrossRef CAS PubMed.
- L. Li, R. Li, S. Gai, P. Gao, F. He, M. Zhang, Y. Chen and P. Yang, J. Mater. Chem. A, 2015, 3, 15642–15649 RSC.
- C. Lu, L. Yang, B. Yan, L. Sun, P. Zhang, W. Zhang and Z. Sun, Adv. Funct. Mater., 2020, 30, 2000852 CrossRef CAS.
- H. Peçenek, S. Yetiman, F. K. Dokan, M. S. Onses, E. Yılmaz and E. Sahmetlioglu, Ceram. Int., 2022, 48, 7253–7260 CrossRef.
- M. Shen, W. Jiang, K. Liang, S. Zhao, R. Tang, L. Zhang and J.-Q. Wang, Angew. Chem., Int. Ed., 2021, 60, 27013–27018 CrossRef CAS PubMed.
- T. Schultz, N. C. Frey, K. Hantanasirisakul, S. Park, S. J. May, V. B. Shenoy, Y. Gogotsi and N. Koch, Chem. Mater., 2019, 31, 6590–6597 CrossRef CAS.
- A. Khosla, Sonu, H. T. A. Awan, K. Singh, Gaurav, R. Walvekar, Z. Zhao, A. Kaushik, M. Khalid and V. Chaudhary, Adv. Sci., 2022, 9, 2203527 CrossRef CAS PubMed.
- Z. Xie, Y. Duo, Z. Lin, T. Fan, C. Xing, L. Yu, R. Wang, M. Qiu, Y. Zhang and Y. Zhao, Adv. Sci., 2020, 7, 1902236 CrossRef CAS PubMed.
- X. Wang, Y. Wang, Y. Jiang, X. Li, Y. Liu, H. Xiao, Y. Ma, Y. y. Huang and G. Yuan, Adv. Funct. Mater., 2021, 31, 2103210 CrossRef CAS.
- M. Li, X. Li, G. Qin, K. Luo, J. Lu, Y. Li, G. Liang, Z. Huang, J. Zhou and L. Hultman, ACS Nano, 2021, 15, 1077–1085 CrossRef CAS PubMed.
- H. Zhu, B. Li, C. Y. Chan, B. L. Q. Ling, J. Tor, X. Y. Oh, W. Jiang, E. Ye, Z. Li and X. J. Loh, Adv. Drug Delivery Rev., 2022, 114644 Search PubMed.
- J. L. Hart, K. Hantanasirisakul, A. C. Lang, Y. Li, F. Mehmood, R. Pachter, A. I. Frenkel, Y. Gogotsi and M. L. Taheri, Adv. Mater. Interfaces, 2021, 8, 2001789 CrossRef CAS.
- N. Li, X. Chen, W.-J. Ong, D. R. MacFarlane, X. Zhao, A. K. Cheetham and C. Sun, ACS Nano, 2017, 11, 10825–10833 CrossRef CAS PubMed.
- A. Al Mayyahi, S. Sarker, B. M. Everhart, X. He and P. B. Amama, Mater. Today Commun., 2022, 32, 103835 CrossRef.
- X. Hu, Y. Wang, Z. Ling, H. Song, Y. Cai, Z. Li, D. Zu and C. Li, Appl. Surf. Sci., 2021, 556, 149817 CrossRef CAS.
- T. Hu, Z. Li, M. Hu, J. Wang, Q. Hu, Q. Li and X. Wang, J. Phys. Chem. C, 2017, 121, 19254–19261 CrossRef CAS.
- M. M. Baig, I. H. Gul, S. M. Baig and F. Shahzad, J. Electroanal. Chem., 2022, 904, 115920 CrossRef CAS.
- X. Xu, Y. Zhang, H. Sun, J. Zhou, F. Yang, H. Li, H. Chen, Y. Chen, Z. Liu and Z. Qiu, Adv. Electron. Mater., 2021, 7, 2000967 CrossRef CAS.
- K. Nasrin, V. Sudharshan, K. Subramani and M. Sathish, Adv. Funct. Mater., 2022, 32, 2110267 CrossRef CAS.
- Y. Xie, M. Naguib, V. N. Mochalin, M. W. Barsoum, Y. Gogotsi, X. Yu, K.-W. Nam, X.-Q. Yang, A. I. Kolesnikov and P. R. Kent, J. Am. Chem. Soc., 2014, 136, 6385–6394 CrossRef CAS PubMed.
- L. Cheng, X. Li, H. Zhang and Q. Xiang, J. Phys. Chem. Lett., 2019, 10, 3488–3494 CrossRef CAS PubMed.
- H. Wang, Y. Wu, T. Xiao, X. Yuan, G. Zeng, W. Tu, S. Wu, H. Y. Lee, Y. Z. Tan and J. W. Chew, Appl. Catal., B, 2018, 233, 213–225 CrossRef CAS.
- Y. Liu, Y.-H. Li, X. Li, Q. Zhang, H. Yu, X. Peng and F. Peng, ACS Nano, 2020, 14, 14181–14189 CrossRef CAS PubMed.
- S. Vigneshwaran, C. M. Park and S. Meenakshi, Sep. Purif. Technol., 2021, 258, 118003 CrossRef CAS.
- Y. Li and S. Guo, Matter, 2021, 4, 1142–1188 CrossRef CAS.
- V. Mehta, H. S. Saini, S. Srivastava, M. K. Kashyap and K. Tankeshwar, J. Phys. Chem. C, 2019, 123, 25052–25060 CrossRef CAS.
- Q. Meng, J. Ma, Y. Zhang, Z. Li, C. Zhi, A. Hu and J. Fan, Nanoscale, 2018, 10, 3385–3392 RSC.
- V. Natu and M. W. Barsoum, J. Phys. Chem. C, 2023, 127, 20197–20206 CrossRef CAS.
- H. Ding, Y. Li, M. Li, K. Chen, K. Liang, G. Chen, J. Lu, J. Palisaitis, P. O. Å. Persson, P. Eklund, L. Hultman, S. Du, Z. Chai, Y. Gogotsi and Q. Huang, Science, 2023, 379, 1130–1135 CrossRef CAS PubMed.
- M. A. Hope, A. C. Forse, K. J. Griffith, M. R. Lukatskaya, M. Ghidiu, Y. Gogotsi and C. P. Grey, Phys. Chem. Chem. Phys., 2016, 18, 5099–5102 RSC.
- D. Li, X. Chen, P. Xiang, H. Du and B. Xiao, Appl. Surf. Sci., 2020, 501, 144221 CrossRef CAS.
- Y. Xin and Y.-X. Yu, Mater. Des., 2017, 130, 512–520 CrossRef CAS.
- J. Björk and J. Rosen, Chem. Mater., 2021, 33, 9108–9118 CrossRef.
- R. Wang, M. Li, K. Sun, Y. Zhang, J. Li and W. Bao, Small, 2022, 18, 2201740 CrossRef CAS PubMed.
- M. Khazaei, M. Arai, T. Sasaki, C.-Y. Chung, N. S. Venkataramanan, M. Estili, Y. Sakka and Y. Kawazoe, Adv. Funct. Mater., 2013, 23, 2185–2192 CrossRef CAS.
- Y.-W. Cheng, J.-H. Dai, Y.-M. Zhang and Y. Song, J. Mater. Chem. A, 2018, 6, 20956–20965 RSC.
- E. Balcı, Ü. Ö. Akkuş and S. Berber, J. Mater. Chem. C, 2017, 5, 5956–5961 RSC.
- F. Yang, D. Hegh, D. Song, J. Zhang, K. A. S. Usman, C. Liu, Z. Wang, W. Ma, W. Yang and S. Qin, Mater. Rep.: Energy, 2022, 2, 100079 CAS.
- F. Cao, Y. Zhang, H. Wang, K. Khan, A. K. Tareen, W. Qian, H. Zhang and H. Ågren, Adv. Mater., 2022, 34, 2107554 CrossRef CAS PubMed.
- Y. Gogotsi, Chem. Mater., 2023, 35, 8767–8770 CrossRef CAS.
- Z. Xiao, Z. Li, X. Meng and R. Wang, J. Mater. Chem. A, 2019, 7, 22730–22743 RSC.
- X. Liang, A. Garsuch and L. F. Nazar, Angew. Chem., 2015, 127, 3979–3983 CrossRef.
- Y. Wen, T. E. Rufford, X. Chen, N. Li, M. Lyu, L. Dai and L. Wang, Nano Energy, 2017, 38, 368–376 CrossRef CAS.
- W. Xu, S. Li, W. Zhang, B. Ouyang, W. Yu and Y. Zhou, ACS Appl. Mater. Interfaces, 2021, 13, 49242–49253 CrossRef CAS PubMed.
- F. Yang, D. Hegh, D. Song, J. Zhang, K. A. S. Usman, Z. Wang, P. Zhang, W. Ma, W. Yang and S. Qin, J. Mater. Chem. A, 2021, 9, 6393–6401 RSC.
- B. Yang, Y. She, C. Zhang, S. Kang, J. Zhou and W. Hu, Nanomaterials, 2020, 10, 345 CrossRef CAS PubMed.
- M. Naguib, M. Kurtoglu, V. Presser, J. Lu, J. Niu, M. Heon, L. Hultman, Y. Gogotsi and M. W. Barsoum, Adv. Mater., 2011, 23, 4207 CrossRef.
- X. Zhang, Z. Zhang and Z. Zhou, J. Energy Chem., 2018, 27, 73–85 CrossRef.
- Z. Zeng, Y. Yan, J. Chen, P. Zan, Q. Tian and P. Chen, Adv. Funct. Mater., 2019, 29, 1806500 CrossRef.
- M. Han, X. Yin, H. Wu, Z. Hou, C. Song, X. Li, L. Zhang and L. Cheng, ACS Appl. Mater. Interfaces, 2016, 8, 21011–21019 CrossRef CAS PubMed.
- L. Cheng, Q. Chen, J. Li and H. Liu, Appl. Catal., B, 2020, 267, 118379 CrossRef CAS.
- C. Peng, H. Wang, H. Yu and F. Peng, Mater. Res. Bull., 2017, 89, 16–25 CrossRef CAS.
- M. Khazaei, M. Arai, T. Sasaki, A. Ranjbar, Y. Liang and S. Yunoki, Phys. Rev. B: Condens. Matter Mater. Phys., 2015, 92, 075411 CrossRef.
- M. Lu, H. Li, W. Han, J. Chen, W. Shi, J. Wang, X.-M. Meng, J. Qi, H. Li and B. Zhang, J. Energy Chem., 2019, 31, 148–153 CrossRef.
- L. Zhang, J. Yang, T. Xie, S. Feng and L. Xu, Mater. Des., 2020, 192, 108772 CrossRef CAS.
- Q. Tang, Z. Sun, S. Deng, H. Wang and Z. Wu, J. Colloid Interface Sci., 2020, 564, 406–417 CrossRef CAS PubMed.
- G. Zhao, J. Zou, X. Chen, J. Yu and F. Jiao, Chem. Eng. J., 2020, 397, 125407 CrossRef CAS.
- A. Akhoondi, M. Mirzaei, M. Y. Nassar, Z. Sabaghian, F. Hatami and M. Yusuf, Synth. Sintering, 2022, 2, 151–169 Search PubMed.
- Y. Li, L. Ding, Y. Guo, Z. Liang, H. Cui and J. Tian, ACS Appl. Mater. Interfaces, 2019, 11, 41440–41447 CrossRef CAS PubMed.
- Y. Qin, Y. Sun, Y. Li, C. Li, L. Wang and S. Guo, Chin. Chem. Lett., 2020, 31, 774–778 CrossRef CAS.
- T. Cai, L. Wang, Y. Liu, S. Zhang, W. Dong, H. Chen, X. Yi, J. Yuan, X. Xia and C. Liu, Appl. Catal., B, 2018, 239, 545–554 CrossRef CAS.
- Y. Zhang, L. Wang, N. Zhang and Z. Zhou, RSC Adv., 2018, 8, 19895–19905 RSC.
- L. Tie, S. Yang, C. Yu, H. Chen, Y. Liu, S. Dong, J. Sun and J. Sun, J. Colloid Interface Sci., 2019, 545, 63–70 CrossRef CAS PubMed.
- H. Guan, H. He, T. Zeng and C. Zhang, J. Energy Chem., 2021, 63, 633–641 CrossRef CAS.
- M. Tang, H. Sun, L. Su, Y. Gao, F. Chen, Z. Wang and C. Wang, Batteries Supercaps, 2023, 6, e202200402 CrossRef CAS.
- M. Boota, T. Hussain, L. Yang, M. Becuwe, W. Porzio, L. Barba and R. Ahuja, Adv. Electron. Mater., 2021, 7, 2001202 CrossRef CAS.
- X. Hui, P. Zhang, J. Li, D. Zhao, Z. Li, Z. Zhang, C. Wang, R. Wang and L. Yin, Adv. Energy Mater., 2022, 12, 2201393 CrossRef CAS.
- J. Li, H. Wang and X. Xiao, Energy Environ. Mater., 2020, 3, 306–322 CrossRef CAS.
- M. Tahir, A. Ali Khan, S. Tasleem, R. Mansoor and W. K. Fan, Energy Fuels, 2021, 35, 10374–10404 CrossRef CAS.
- C. Yang, Q. Tan, Q. Li, J. Zhou, J. Fan, B. Li, J. Sun and K. Lv, Appl. Catal., B, 2020, 268, 118738 CrossRef CAS.
- S. Kajiyama, L. Szabova, H. Iinuma, A. Sugahara, K. Gotoh, K. Sodeyama, Y. Tateyama, M. Okubo and A. Yamada, Adv. Energy Mater., 2017, 7, 1601873 CrossRef.
- X. Xie, Y. Xue, L. Li, S. Chen, Y. Nie, W. Ding and Z. Wei, Nanoscale, 2014, 6, 11035–11040 RSC.
- L. Liu, M. Orbay, S. Luo, S. Duluard, H. Shao, J. Harmel, P. Rozier, P.-L. Taberna and P. Simon, ACS Nano, 2021, 16, 111–118 CrossRef PubMed.
- K. Arole, J. W. Blivin, S. Saha, D. E. Holta, X. Zhao, A. Sarmah, H. Cao, M. Radovic, J. L. Lutkenhaus and M. J. Green, iScience, 2021, 24, 103403 CrossRef CAS PubMed.
- Y. Chen, T. Shi, P. Liu, X. Ma, L. Shui, C. Shang, Z. Chen, X. Wang, K. Kempa and G. Zhou, J. Mater. Chem. A, 2018, 6, 19167–19175 RSC.
- J. Xiao, J. Wen, J. Zhao, X. Ma, H. Gao and X. Zhang, Electrochim. Acta, 2020, 337, 135803 CrossRef CAS.
- N. J. Prakash and B. Kandasubramanian, J. Alloys Compd., 2021, 862, 158547 CrossRef.
- S. M. George and B. Kandasubramanian, Ceram. Int., 2020, 46, 8522–8535 CrossRef CAS.
- F. Damiri, M. H. Rahman, M. Zehravi, A. A. Awaji, M. Z. Nasrullah, H. A. Gad, M. Z. Bani-Fwaz, R. S. Varma, M. O. Germoush and H. S. Al-Malky, Materials, 2022, 15, 1666 CrossRef CAS PubMed.
- B. Lu, Z. Zhu, B. Ma, W. Wang, R. Zhu and J. Zhang, Small, 2021, 17, 2100946 CrossRef CAS PubMed.
- X. Lin, Z. Li, J. Qiu, Q. Wang, J. Wang, H. Zhang and T. Chen, Biomater. Sci., 2021, 9, 5437–5471 RSC.
- M. Soleymaniha, M. A. Shahbazi, A. R. Rafieerad, A. Maleki and A. Amiri, Adv. Healthcare Mater., 2019, 8, 1801137 CrossRef PubMed.
- C. Huang, X. Peng, D.-J. Pang, J. Li, B. S. Paulsen, F. Rise, Y.-L. Chen, Z.-L. Chen, R.-Y. Jia, L.-X. Li, X. Song, B. Feng, Z.-Q. Yin and Y.-F. Zou, Food Funct., 2021, 12, 10828–10841 RSC.
-
N. Garg and F. J. Ahmad, in MXene-Filled Polymer Nanocomposites, CRC Press, 2023, pp. 247–258 Search PubMed.
- X. Han, J. Huang, H. Lin, Z. Wang, P. Li and Y. Chen, Adv. Healthcare Mater., 2018, 7, 1701394 CrossRef PubMed.
- H. Lin, X. Wang, L. Yu, Y. Chen and J. Shi, Nano Lett., 2017, 17, 384–391 CrossRef CAS PubMed.
- Y. Zi, K. Yang, J. He, Z. Wu, J. Liu and W. Zhang, Adv. Drug Delivery Rev., 2022, 114449 CrossRef CAS PubMed.
- G. Liu, J. Zou, Q. Tang, X. Yang, Y. Zhang, Q. Zhang, W. Huang, P. Chen, J. Shao and X. Dong, ACS Appl. Mater. Interfaces, 2017, 9, 40077–40086 CrossRef CAS PubMed.
- Z. Yu, L. Jiang, R. Liu, W. Zhao, Z. Yang, J. Zhang and S. Jin, Chem. Eng. J., 2021, 426, 131914 CrossRef CAS.
- Y. Xu, Y. Wang, J. An, A. C. Sedgwick, M. Li, J. Xie, W. Hu, J. Kang, S. Sen, A. Steinbrueck, B. Zhang, L. Qiao, S. Wageh, J. F. Arambula, L. Liu, H. Zhang, J. L. Sessler and J. S. Kim, Bioact. Mater., 2022, 14, 76–85 CAS.
- L. Ou, B. Song, H. Liang, J. Liu, X. Feng, B. Deng, T. Sun and L. Shao, Part. Fibre Toxicol., 2016, 13, 1–24 CrossRef PubMed.
- Y. Guan, J. Yan, Y. Shan, Y. Zhou, Y. Hang, R. Li, Y. Liu, B. Liu, Q. Nie and B. Bruckner, Nat. Energy, 2023, 8, 304–316 CrossRef.
- M. Amin, H. H. Shah, A. G. Fareed, W. U. Khan, E. Chung, A. Zia, Z. U. R. Farooqi and C. Lee, Int. J. Hydrogen Energy, 2022, 47, 33112–33134 CrossRef CAS.
- M. Thirunavukkarasu, Y. Sawle and H. Lala, Renewable Sustainable Energy Rev., 2023, 176, 113192 CrossRef.
- T. Najam, M. K. Aslam, K. Rafiq, M. Altaf Nazir, A. u. Rehman, M. Imran, M. S. Javed, X. Cai and S. S. A. Shah, Mater. Sci. Eng. B, 2021, 273, 115417 CrossRef CAS.
- Q. Jiang, N. Kurra, K. Maleski, Y. Lei, H. Liang, Y. Zhang, Y. Gogotsi and H. N. Alshareef, Adv. Energy Mater., 2019, 9, 1901061 CrossRef.
- S. Xu, G. Wei, J. Li, W. Han and Y. Gogotsi, J. Mater. Chem. A, 2017, 5, 17442–17451 RSC.
- R. Rajeev, D. A. Thadathil and A. Varghese, Crit. Rev. Solid State Mater. Sci., 2022, 1–43 Search PubMed.
- X. Wang, T. S. Mathis, K. Li, Z. Lin, L. Vlcek, T. Torita, N. C. Osti, C. Hatter, P. Urbankowski and A. Sarycheva, Nat. Energy, 2019, 4, 241–248 CrossRef CAS.
- S. Buczek, M. L. Barsoum, S. Uzun, N. Kurra, R. Andris, E. Pomerantseva, K. A. Mahmoud and Y. Gogotsi, Energy Environ. Mater., 2020, 3, 398–404 CrossRef CAS.
- N. Kurra, M. Alhabeb, K. Maleski, C.-H. Wang, H. N. Alshareef and Y. Gogotsi, ACS Energy Lett., 2018, 3, 2094–2100 CrossRef CAS.
- C.-F. Liu, Y.-C. Liu, T.-Y. Yi and C.-C. Hu, Carbon, 2019, 145, 529–548 CrossRef CAS.
- A. S. Levitt, M. Alhabeb, C. B. Hatter, A. Sarycheva, G. Dion and Y. Gogotsi, J. Mater. Chem. A, 2019, 7, 269–277 RSC.
- R. Imsong and D. D. Purkayastha, Sep. Purif. Technol., 2023, 306, 122636 CrossRef CAS.
- L. Wang, X. Feng, L. Ren, Q. Piao, J. Zhong, Y. Wang, H. Li, Y. Chen and B. Wang, J. Am. Chem. Soc., 2015, 137, 4920–4923 CrossRef CAS PubMed.
- Q. X. Xia, N. M. Shinde, J. M. Yun, T. Zhang, R. S. Mane, S. Mathur and K. H. Kim, Electrochim. Acta, 2018, 271, 351–360 CrossRef CAS.
- M. Mahmood, A. Rasheed, I. Ayman, T. Rasheed, S. Munir, S. Ajmal, P. O. Agboola, M. F. Warsi and M. Shahid, Energy Fuels, 2021, 35, 3469–3478 CrossRef CAS.
- A. Sikdar, P. Dutta, S. K. Deb, A. Majumdar, N. Padma, S. Ghosh and U. N. Maiti, Electrochim. Acta, 2021, 391, 138959 CrossRef CAS.
- Y. Li, Z. Wang, J. Hu, S. Li, Y. Du, X. Han and P. Xu, Adv. Funct. Mater., 2020, 30, 1910498 CrossRef CAS.
- A. Sharma, P. Mane, B. Chakraborty and C. S. Rout, ACS Appl. Energy Mater., 2021, 4, 14198–14209 CrossRef CAS.
- W. Hou, Y. Sun, Y. Zhang, T. Wang, L. Wu, Y. Du and W. Zhong, J. Alloys Compd., 2021, 859, 157797 CrossRef CAS.
- A. M. Omer, G. S. Elgarhy, G. M. El-Subruiti, R. E. Khalifa and A. S. Eltaweil, Int. J. Biol. Macromol., 2020, 148, 1072–1083 CrossRef CAS PubMed.
- H. Liu, R. Hu, J. Qi, Y. Sui, Y. He, Q. Meng, F. Wei, Y. Ren, Y. Zhao and W. Wei, Adv. Mater. Interfaces, 2020, 7, 1901659 CrossRef CAS.
- A. Szuplewska, D. Kulpińska, A. Dybko, M. Chudy, A. M. Jastrzębska, A. Olszyna and Z. Brzózka, Trends Biotechnol., 2020, 38, 264–279 CrossRef CAS PubMed.
- K. Rafiq, H. D. Mai, J. K. Kim, J. M. Woo, B. M. Moon, C. H. Park and H. Yoo, Sens. Actuators, B, 2017, 251, 472–480 CrossRef CAS.
- R. A. Soomro, S. Jawaid, Q. Zhu, Z. Abbas and B. Xu, Chin. Chem. Lett., 2020, 31, 922–930 CrossRef CAS.
- J. Liu, X. Jiang, R. Zhang, Y. Zhang, L. Wu, W. Lu, J. Li, Y. Li and H. Zhang, Adv. Funct. Mater., 2019, 29, 1807326 CrossRef.
- T. Shay, M. D. Dickey and O. D. Velev, Lab Chip, 2017, 17, 710–716 RSC.
- X. Li, X. Li, T. Liu, Y. Lu, C. Shang, X. Ding, J. Zhang, Y. Feng and F.-J. Xu, ACS Appl. Mater. Interfaces, 2021, 13, 46848–46857 CrossRef CAS PubMed.
- Y. Yue, N. Liu, W. Liu, M. Li, Y. Ma, C. Luo, S. Wang, J. Rao, X. Hu, J. Su, Z. Zhang, Q. Huang and Y. Gao, Nano Energy, 2018, 50, 79–87 CrossRef CAS.
- F. Wang, C. Yang, M. Duan, Y. Tang and J. Zhu, Biosens. Bioelectron., 2015, 74, 1022–1028 CrossRef CAS PubMed.
-
P. Kalluru and R. Vankayala, 2D Functional Nanomaterials: Synthesis, Characterization and Applications, 2021, pp. 31–46 Search PubMed.
- E. Lee, A. VahidMohammadi, B. C. Prorok, Y. S. Yoon, M. Beidaghi and D.-J. Kim, ACS Appl. Mater. Interfaces, 2017, 9, 37184–37190 CrossRef CAS PubMed.
- S. Ullah, F. Shahzad, B. Qiu, X. Fang, A. Ammar, Z. Luo and S. A. Zaidi, Prog. Mater. Sci., 2022, 129, 100967 CrossRef.
- A. Rhouati, M. Berkani, Y. Vasseghian and N. Golzadeh, Chemosphere, 2022, 291, 132921 CrossRef CAS PubMed.
- B. Xu, C. Zhi and P. Shi, J. Phys.: Mater., 2020, 3, 031001 CAS.
- R. Rakhi, P. Nayak, C. Xia and H. N. Alshareef, Sci. Rep., 2016, 6, 1–10 CrossRef PubMed.
- H. Liu, C. Duan, C. Yang, W. Shen, F. Wang and Z. Zhu, Sens. Actuators, B, 2015, 218, 60–66 CrossRef CAS.
- L. Lorencova, T. Bertok, J. Filip, M. Jerigova, D. Velic, P. Kasak, K. A. Mahmoud and J. Tkac, Sens. Actuators, B, 2018, 263, 360–368 CrossRef CAS.
- P. A. Rasheed, R. P. Pandey, K. Rasool and K. A. Mahmoud, Sens. Actuators, B, 2018, 265, 652–659 CrossRef.
- B. Xu, M. Zhu, W. Zhang, X. Zhen, Z. Pei, Q. Xue, C. Zhi and P. Shi, Adv. Mater., 2016, 28, 3333–3339 CrossRef CAS PubMed.
- X. Liu, L. He, P. Li, X. Li and P. Zhang, ChemElectroChem, 2021, 8, 3658–3665 CrossRef CAS.
- R. Gao, X. Yang, Q. Yang, Y. Wu, F. Wang, Q. Xia and S.-J. Bao, Microchim. Acta, 2021, 188, 1–9 CrossRef PubMed.
- T. Xia, G. Liu, J. Wang, S. Hou and S. Hou, Biosens. Bioelectron., 2021, 183, 113243 CrossRef CAS PubMed.
- S. Sun, M. Wang, X. Chang, Y. Jiang, D. Zhang, D. Wang, Y. Zhang and Y. Lei, Sens. Actuators, B, 2020, 304, 127274 CrossRef CAS.
- Y. Sun, L. Chen, Y. Wang, Z. Zhao, P. Li, W. Zhang, Y. Leprince-Wang and J. Hu, J. Mater. Sci., 2017, 52, 1561–1572 CrossRef CAS.
- K. Matthews, T. Zhang, C. E. Shuck, A. VahidMohammadi and Y. Gogotsi, Chem. Mater., 2021, 34, 499–509 CrossRef.
- M. Wu, Y. An, R. Yang, Z. Tao, Q. Xia, Q. Hu, M. Li, K. Chen, Z. Zhang and Q. Huang, ACS Appl. Nano Mater., 2021, 4, 6257–6268 CrossRef CAS.
- T. Thomas, J. A. R. Ramon, V. Agarwal, A. Álvarez-Méndez, J. A. Martinez, Y. Kumar and K. Sanal, Microporous Mesoporous Mater., 2022, 336, 111872 CrossRef CAS.
- H. Lu, J. Tournet, K. Dastafkan, Y. Liu, Y. H. Ng, S. K. Karuturi, C. Zhao and Z. Yin, Chem. Rev., 2021, 121, 10271–10366 CrossRef CAS PubMed.
- F. Ahmad, K. Rafiq, T. Najam, E. Hussain, M. Sohail, M. Z. Abid, A. Mahmood, M. S. Javed and S. S. A. Shah, Int. J. Hydrogen Energy, 2023, 48, 35075–35111 CrossRef CAS.
- K. U. Sahar, K. Rafiq, Z. Abid, U. ur Rehman, A. Rauf and E. Hussain, React. Chem. Eng., 2023, 8, 2522–2536 RSC.
- M. Jalil, K. Rafiq, M. Z. Abid, A. Rauf, S. Wang, S. Iqbal and E. Hussain, Nanoscale Adv., 2023, 5, 3233–3246 RSC.
- M. Sabir, K. Rafiq, M. Z. Abid, U. Quyyum, S. S. A. Shah, M. Faizan, A. Rauf, S. Iqbal and E. Hussain, Fuel, 2023, 353, 129196 CrossRef CAS.
- C. V. Pham, D. Escalera-López, K. Mayrhofer, S. Cherevko and S. Thiele, Adv. Energy Mater., 2021, 11, 2101998 CrossRef CAS.
- H. Wang, Y. Wu, X. Yuan, G. Zeng, J. Zhou, X. Wang and J. W. Chew, Adv. Mater., 2018, 30, 1704561 CrossRef PubMed.
- L. Yang, C. Dall'Agnese, Y. Dall'Agnese, G. Chen, Y. Gao, Y. Sanehira, A. K. Jena, X.-F. Wang, Y. Gogotsi and T. Miyasaka, Adv. Funct. Mater., 2019, 29, 1905694 CrossRef CAS.
-
M. Bilal, Z. U. Rehman, M. Zaqa, J. Hou, F. K. Butt and A. Hussain, in Energy Applications of 2D Nanomaterials, CRC Press, 2022, pp. 185–201 Search PubMed.
- J. Zhang, Y. Zhao, X. Guo, C. Chen, C.-L. Dong, R.-S. Liu, C.-P. Han, Y. Li, Y. Gogotsi and G. Wang, Nat. Catal., 2018, 1, 985–992 CrossRef CAS.
- R. Chen, C. Yang, W. Cai, H.-Y. Wang, J. Miao, L. Zhang, S. Chen and B. Liu, ACS Energy Lett., 2017, 2, 1070–1075 CrossRef CAS.
- L. Yang, Z. Chen, X. Wang and M. Jin, Nanomaterials, 2022, 12, 542 CrossRef CAS PubMed.
- L. Ding, S. Zeng, W. Zhang, C. Guo, X. Chen, B. Peng, Z. Lv, H. Zhou and Q. Xu, ACS Appl. Energy Mater., 2022, 5, 11540–11552 CrossRef CAS.
- K. R. G. Lim, A. D. Handoko, S. K. Nemani, B. Wyatt, H.-Y. Jiang, J. Tang, B. Anasori and Z. W. Seh, ACS Nano, 2020, 14, 10834–10864 CrossRef CAS PubMed.
- X. Zhang, Z. Geng, J. Jian, Y. He, Z. Lv, X. Liu and H. Yuan, Catalysts, 2020, 10, 293 CrossRef.
- X. Li, Y. Bai, X. Shi, N. Su, G. Nie, R. Zhang, H. Nie and L. Ye, Mater. Adv., 2021, 2, 1570–1594 RSC.
- C. Xia, H. Ye, A. Kim, A. Sabahi Namini, S. Li, S. A. Delbari, J. Y. Park, D. Kim, Q. V. Le, R. S. Varma, R. Luque, A. T-Raissi, H. W. Jang and M. Shokouhimehr, Chemosphere, 2023, 325, 138323 CrossRef CAS PubMed.
- S. Chen, T. Takata and K. Domen, Nat. Rev. Mater., 2017, 2, 1–17 CrossRef PubMed.
- K. Takanabe, ACS Catal., 2017, 7, 8006–8022 CrossRef CAS.
- X. Wu, Z. Wang, M. Yu, L. Xiu and J. Qiu, Adv. Mater., 2017, 29, 1607017 CrossRef PubMed.
- Y. Jiang, T. Sun, X. Xie, W. Jiang, J. Li, B. Tian and C. Su, ChemSusChem, 2019, 12, 1368–1373 CrossRef CAS PubMed.
- J. Ren, H. Zong, Y. Sun, S. Gong, Y. Feng, Z. Wang, L. Hu, K. Yu and Z. Zhu, CrystEngComm, 2020, 22, 1395–1403 RSC.
- Y. Jiang, X. Wu, Y. Yan, S. Luo, X. Li, J. Huang, H. Zhang and D. Yang, Small, 2019, 15, 1805474 CrossRef PubMed.
- Y. Yuan, H. Li, L. Wang, L. Zhang, D. Shi, Y. Hong and J. Sun, ACS Sustain. Chem. Eng., 2019, 7, 4266–4273 CrossRef CAS.
- D. A. Kuznetsov, Z. Chen, P. V. Kumar, A. Tsoukalou, A. Kierzkowska, P. M. Abdala, O. V. Safonova, A. Fedorov and C. R. Müller, J. Am. Chem. Soc., 2019, 141, 17809–17816 CrossRef CAS PubMed.
- P. Kuang, M. He, B. Zhu, J. Yu, K. Fan and M. Jaroniec, J. Catal., 2019, 375, 8–20 CrossRef CAS.
- Y. Geng, G. Cao, L. Wang and S. Wang, PLoS One, 2019, 14, e0219512 CrossRef CAS PubMed.
- J. Liu, Y. Liu, D. Xu, Y. Zhu, W. Peng, Y. Li, F. Zhang and X. Fan, Appl. Catal., B, 2019, 241, 89–94 CrossRef CAS.
- T. Su, Z. D. Hood, M. Naguib, L. Bai, S. Luo, C. M. Rouleau, I. N. Ivanov, H. Ji, Z. Qin and Z. Wu, Nanoscale, 2019, 11, 8138–8149 RSC.
- M. Zhang, J. Qin, S. Rajendran, X. Zhang and R. Liu, ChemSusChem, 2018, 11, 4226–4236 CrossRef CAS PubMed.
- P. Lin, J. Shen, X. Yu, Q. Liu, D. Li and H. Tang, Ceram. Int., 2019, 45, 24656–24663 CrossRef CAS.
- M. Tahir and B. Tahir, Ind. Eng. Chem. Res., 2020, 59, 9841–9857 CrossRef CAS.
- J. Low, L. Zhang, T. Tong, B. Shen and J. Yu, J. Catal., 2018, 361, 255–266 CrossRef CAS.
- Q. Liu, X. Tan, S. Wang, F. Ma, H. Znad, Z. Shen, L. Liu and S. Liu, Environ. Sci.: Nano, 2019, 6, 3158–3169 RSC.
- Y. Yang, D. Zhang and Q. Xiang, Nanoscale, 2019, 11, 18797–18805 RSC.
- Y. Li, X. Chen, Y. Sun, X. Meng, Y. Dall'Agnese, G. Chen, C. Dall'Agnese, H. Ren, S. i. Sasaki and H. Tamiaki, Adv. Mater. Interfaces, 2020, 7, 1902080 CrossRef CAS.
- S. Vigneshwaran, P. Karthikeyan, C. M. Park and S. Meenakshi, J. Environ. Manage., 2020, 273, 111125 CrossRef CAS PubMed.
- Y. Li, X. Deng, J. Tian, Z. Liang and H. Cui, Appl. Mater. Today, 2018, 13, 217–227 CrossRef.
- A. Iqbal, J. Kwon, M.-K. Kim and C. Koo, Mater. Today Adv., 2021, 9, 100124 CrossRef CAS.
- Y. Zhang, L. Wang, J. Zhang, P. Song, Z. Xiao, C. Liang, H. Qiu, J. Kong and J. Gu, Compos. Sci. Technol., 2019, 183, 107833 CrossRef CAS.
- Z. Zhou, Q. Song, B. Huang, S. Feng and C. Lu, ACS Nano, 2021, 15, 12405–12417 CrossRef CAS PubMed.
- M. Han, C. E. Shuck, R. Rakhmanov, D. Parchment, B. Anasori, C. M. Koo, G. Friedman and Y. Gogotsi, ACS Nano, 2020, 14, 5008–5016 CrossRef CAS PubMed.
- K. Raagulan, R. Braveenth, H. J. Jang, Y. Seon Lee, C.-M. Yang, B. Mi Kim, J. J. Moon and K. Y. Chai, Materials, 2018, 11, 1803 CrossRef PubMed.
- A. Tanvir, P. Sobolčiak, A. Popelka, M. Mrlik, Z. Spitalsky, M. Micusik, J. Prokes and I. Krupa, Polymers, 2019, 11, 1272 CrossRef PubMed.
- M. C. Vu, D. Mani, J.-B. Kim, T.-H. Jeong, S. Park, G. Murali, I. In, J.-C. Won, D. Losic and C.-S. Lim, Composites, Part A, 2021, 149, 106574 CrossRef CAS.
- B. Zhou, Y. Li, Z. Li, J. Ma, K. Zhou, C. Liu, C. Shen and Y. Feng, J. Mater. Chem. C, 2021, 9, 10425–10434 RSC.
- B. Aïssa, A. Sinopoli, A. Ali, Y. Zakaria, A. Zekri, M. Helal, M. Nedil, F. Rosei, S. Mansour and K. Mahmoud, Carbon, 2021, 173, 528–539 CrossRef.
- K. Khan, A. K. Tareen, M. Aslam, R. Wang, Y. Zhang, A. Mahmood, Z. Ouyang, H. Zhang and Z. Guo, J. Mater. Chem. C, 2020, 8, 387–440 RSC.
- X. Hu, B. Quan, C. Zhu, H. Wen, M. Sheng, S. Liu, X. Li, H. Wu, X. Lu and J. Qu, Adv. Sci., 2023, 10, 2206835 CrossRef CAS PubMed.
- M. Liu, W. Jiang, P. Song, J. Ji and Q. Wang, Inorg. Chem. Commun., 2022, 140, 109455 CrossRef CAS.
- Q. Feng, F. Deng, K. Li, M. Dou, S. Zou and F. Huang, Colloids Surf., A, 2021, 625, 126903 CrossRef CAS.
- G. Wen, X. Wen, H. Cao, P. Bai, Y. Meng, L. Ma and Y. Tian, Appl. Nanosci., 2023, 186, 108590 CAS.
- P. Tian, G. Yu, K. Wei, Z. Zhang and N. Wang, Ceram. Int., 2021, 47, 30722–30728 CrossRef CAS.
- Z.-K. Li, Y. Wei, X. Gao, L. Ding, Z. Lu, J. Deng, X. Yang, J. Caro and H. Wang, Angew. Chem., Int. Ed., 2020, 59, 9751–9756 CrossRef CAS PubMed.
- E. Marquis, M. Cutini, B. Anasori, A. Rosenkranz and M. C. Righi, ACS Appl. Nano Mater., 2022, 5, 10516–10527 CrossRef CAS PubMed.
- Y. Guo, X. Zhou, D. Wang, X. Xu and Q. Xu, Langmuir, 2019, 35, 14481–14485 CrossRef CAS PubMed.
- Y. Guan, M. Zhang, J. Qin, X. Ma, C. Li and J. Tang, J. Phys. Chem. C, 2020, 124, 13664–13671 CrossRef CAS.
- Y. Yang, J. Zhu, K. Hou, L. Ma, Z. Li, W. Jia, H. Wang, J. Wang and S. Yang, Chem. Eng. J., 2022, 442, 136238 CrossRef CAS.
- W. Lian, X. Jie, Y. Lv and W. Yu, Appl. Nanosci., 2021, 11, 1471–1479 CrossRef CAS.
- M. E. Valdés, L. H. Santos, M. C. R. Castro, A. Giorgi, D. Barceló, S. Rodríguez-Mozaz and M. V. Amé, Environ. Pollut., 2021, 269, 116133 CrossRef PubMed.
- M. Z. Abid, K. Rafiq, A. Rauf, S. S. A. Shah, R. Jin and E. Hussain, Nanoscale Adv., 2023, 5, 3247–3259 RSC.
- A. Ilyas, K. Rafiq, M. Z. Abid, A. Rauf and E. Hussain, RSC Adv., 2023, 13, 2379–2391 RSC.
- A. Aslam, M. Z. Abid, K. Rafiq, A. Rauf and E. Hussain, Sci. Rep., 2023, 13, 6306 CrossRef CAS PubMed.
- X. Yang, Y. Liu, S. Hu, F. Yu, Z. He, G. Zeng, Z. Feng and A. Sengupta, Polym. Adv. Technol., 2021, 32, 1000–1010 CrossRef CAS.
- A. Abbas, A. M. Al-Amer, T. Laoui, M. J. Al-Marri, M. S. Nasser, M. Khraisheh and M. A. Atieh, Sep. Purif. Technol., 2016, 157, 141–161 CrossRef.
-
R. Castro-Muñoz, E. Gontarek and A. Figoli, in Current Trends and Future Developments on (Bio-) Membranes, Elsevier, 2020, pp. 125–149 Search PubMed.
- R. Castro-Muñoz, B. E. Barragán-Huerta, V. Fíla, P. C. Denis and R. Ruby-Figueroa, Waste Biomass Valorization, 2018, 9, 513–529 CrossRef.
- Z. Abid, A. Ilyas, K. Rafiq, M. A. Nadeem, A. Rauf, A. Wasim and E. Hussain, Environ. Sci.: Water Res. Technol., 2023, 9, 2238–2252 RSC.
- U. Quyyum, K. Rafiq, M. Z. Abid, F. Ahmad, A. Rauf and E. Hussain, Environ. Sci.: Water Res. Technol., 2023, 9, 1147–1160 RSC.
- P. Karthikeyan, K. Ramkumar, K. Pandi, A. Fayyaz, S. Meenakshi and C. M. Park, Ceram. Int., 2021, 47, 3692–3698 CrossRef CAS.
- S. Wang, Y. Liu, Q.-F. Lü and H. Zhuang, J. Mol. Liq., 2020, 297, 111810 CrossRef CAS.
- A. Shahzad, J. Jang, S.-R. Lim and D. S. Lee, Environ. Res., 2020, 182, 109005 CrossRef CAS PubMed.
- B.-M. Jun, M. Jang, C. M. Park, J. Han and Y. Yoon, Nucl. Eng. Technol., 2020, 52, 1201–1207 CrossRef CAS.
- L. Wang, H. Song, L. Yuan, Z. Li, Y. Zhang, J. K. Gibson, L. Zheng, Z. Chai and W. Shi, Environ. Sci. Technol., 2018, 52, 10748–10756 CrossRef CAS PubMed.
- S. Kim, F. Gholamirad, M. Yu, C. M. Park, A. Jang, M. Jang, N. Taheri-Qazvini and Y. Yoon, Chem. Eng. J., 2021, 406, 126789 CrossRef CAS.
- L. Wang, W. Tao, L. Yuan, Z. Liu, Q. Huang, Z. Chai, J. K. Gibson and W. Shi, Chem. Commun., 2017, 53, 12084–12087 RSC.
- B.-M. Jun, C. M. Park, J. Heo and Y. Yoon, J. Environ. Manage., 2020, 256, 109940 CrossRef CAS PubMed.
- Y. Yan, H. Han, Y. Dai, H. Zhu, W. Liu, X. Tang, W. Gan and H. Li, ACS Appl. Nano Mater., 2021, 4, 11763–11769 CrossRef CAS.
- V. T. Quyen, L. T. T. Ha, D. M. Thanh, Q. V. Le, N. M. Viet, N. T. Nham and P. Q. Thang, Environ. Technol. Innovation, 2021, 21, 101286 CrossRef CAS.
- N. My Tran, Q. Thanh Hoai Ta and J.-S. Noh, Appl. Surf. Sci., 2021, 538, 148023 CrossRef CAS.
- L. Ding, Y. Wei, Y. Wang, H. Chen, J. Caro and H. Wang, Angew. Chem., Int. Ed., 2017, 56, 1825–1829 CrossRef CAS PubMed.
- Y. Fan, J. Li, S. Wang, X. Meng, W. Zhang, Y. Jin, N. Yang, X. Tan, J. Li and S. Liu, Chem. Eng. J., 2020, 401, 126073 CrossRef CAS.
- J. Zhao, Y. Yang, C. Yang, Y. Tian, Y. Han, J. Liu, X. Yin and W. Que, J. Mater. Chem. A, 2018, 6, 16196–16204 RSC.
- X. Chen, X. Tong, J. Gao, L. Yang, J. Ren, W. Yang, S. Liu, M. Qi, J. Crittenden and R. Hao, Environ. Sci. Technol., 2022, 56, 4542–4552 CrossRef CAS PubMed.
- L. Zhang, Y. Huang, H. Dong, R. Xu and S. Jiang, Composites, Part B, 2021, 223, 109149 CrossRef CAS.
- C. Lan, H. Jia, M. Qiu and S. Fu, ACS Appl. Mater. Interfaces, 2021, 13, 38761–38772 CrossRef CAS PubMed.
- L. Liu, Z. Ma, M. Zhu, L. Liu, J. Dai, Y. Shi, J. Gao, T. Dinh, T. Nguyen and L.-C. Tang, J. Mater. Sci. Technol., 2023, 132, 59–68 CrossRef CAS.
- Y. Shi, Z. Wang, C. Liu, H. Wang, J. Guo, L. Fu, Y. Feng, L. Wang, F. Yang and M. Liu, Composites, Part B, 2022, 236, 109792 CrossRef CAS.
- M. Mao, K.-X. Yu, C.-F. Cao, L.-X. Gong, G.-D. Zhang, L. Zhao, P. Song, J.-F. Gao and L.-C. Tang, Chem. Eng. J., 2022, 427, 131615 CrossRef CAS.
- Z.-H. Zhang, J.-W. Zhang, C.-F. Cao, K.-Y. Guo, L. Zhao, G.-D. Zhang, J.-F. Gao and L.-C. Tang, Chem. Eng. J., 2020, 386, 123894 CrossRef CAS.
- E. Jiao, K. Wu, Y. Liu, M. Lu, Z. Hu, B. Chen, J. Shi and M. Lu, Composites, Part A, 2021, 146, 106417 CrossRef CAS.
- Y. Zhu, X. Zhao, Q. Peng, H. Zheng, F. Xue, P. Li, Z. Xu and X. He, Nanoscale Adv., 2021, 3, 5683–5693 RSC.
- Y. Liu, K. Wu, M. Lu, E. Jiao, H. Zhang, J. Shi and M. Lu, Composites, Part A, 2021, 141, 106227 CrossRef CAS.
- N.-N. Wang, H. Wang, Y.-Y. Wang, Y.-H. Wei, J.-Y. Si, A. C. Y. Yuen, J.-S. Xie, B. Yu, S.-E. Zhu and H.-D. Lu, ACS Appl. Mater. Interfaces, 2019, 11, 40512–40523 CrossRef CAS PubMed.
- Y. Jiang, X. Ru, W. Che, Z. Jiang, H. Chen, J. Hou and Y. Yu, Composites, Part B, 2022, 229, 109460 CrossRef CAS.
- Y. I. Jhon, J. Koo, B. Anasori, M. Seo, J. H. Lee, Y. Gogotsi and Y. M. Jhon, Adv. Mater., 2017, 29, 1702496 CrossRef PubMed.
-
K. Chaudhuri, Plasmonic Metasurfaces Utilizing Emerging Material Platforms, Purdue University Graduate School, 2019 Search PubMed.
- C. Ma, W. Huang, Y. Wang, J. Adams, Z. Wang, J. Liu, Y. Song, Y. Ge, Z. Guo and L. Hu, Nanophotonics, 2020, 9, 2451–2458 CrossRef CAS.
- L. Zhang, Q. Sheng, L. Chen, J. Zhang, S. Fu, Q. Fang, Y. Wang, W. Shi and J. Yao, Opt. Lett., 2022, 47, 3964–3967 CrossRef CAS PubMed.
- K. Y. Lau, X. Liu and J. Qiu, Laser Photonics Rev., 2022, 16, 2100709 CrossRef CAS.
- Q. Wu, X. Jin, S. Chen, X. Jiang, Y. Hu, Q. Jiang, L. Wu, J. Li, Z. Zheng and M. Zhang, Opt. Express, 2019, 27, 10159–10170 CrossRef CAS PubMed.
- F. Yang, Y. Ge, T. Yin, J. Guo, F. Zhang, X. Tang, M. Qiu, W. Liang, N. Xu and C. Wang, ACS Appl. Nano Mater., 2020, 3, 11850–11860 CrossRef CAS.
- Y. I. Jhon, J. Lee, Y. M. Jhon and J. H. Lee, Nanophotonics, 2021, 10, 1741–1751 CrossRef CAS.
- G. Sun, M. Feng, K. Zhang, T. Wang, Y. Li, D. Han, Y. Li and F. Song, Results Phys., 2021, 26, 104451 CrossRef.
Footnotes |
† This work has been dedicated to our son Muhammad Arhaan Ejaz on the ocassion of his 3rd birthday. |
‡ Electronic supplementary information (ESI) available. See DOI: https://doi.org/10.1039/d3ta06548k |
|
This journal is © The Royal Society of Chemistry 2024 |
Click here to see how this site uses Cookies. View our privacy policy here.