DOI:
10.1039/D2VA00244B
(Critical Review)
Environ. Sci.: Adv., 2023,
2, 368-396
Fabrication of biodegradable fibrous systems employing electrospinning technology for effluent treatment
Received
6th October 2022
, Accepted 23rd December 2022
First published on 28th December 2022
Abstract
The continuous industrialization with the evolution of humankind and the rapidly increasing population have led to undesirable environmental changes due to anthropogenic activities, harming the environment, especially the aquatic ecosystem. The constant discharge of different toxicogenic entities in the aquatic ecosystem globally poses one of the most significant risks to living organisms, causing virulent diseases and even death. With technological advancements, the urgent demand for pure water devoid of harmful toxins and having a sustainable ecosystem have become paramount concerns. Among the various technologies, electrospinning, which is an efficient and facile method of fabrication, has received significant attention from various research domains, especially in wastewater treatment. This is ascribed to the enhanced efficacy, structural properties, and augmented performance of the fabricated nanostructured geometry, presenting a new facet of nanotechnology. Currently, although various techniques are applied for the fabrication of materials for wastewater treatment, the electrospinning of biopolymers is emerging as a sustainable fabrication system for effluent treatment, which exhibit the advantages of biodegradability (∼ at 9–32 °C in seawater), accessibility, porosity (∼80–90%) and biocompatibility. In the present review, we comprehensively investigate different toxins and their hazardous and prevailing effects on living species, and the advantages and application of various electrospun biopolymers for effluent removal. Also, we highlight the different mechanisms, the application of biopolymers in sorption, and the kinetics and isotherms associated with fabricated nanofibers for a better understanding of electrospun biopolymers as adsorbents.
Environmental significance
The fabrication of effective systems for wastewater treatment has become a prime concern due to the presence of different pollutants globally, spreading diverse water-borne diseases. Electrospun fibers of biopolymers exhibit advantages compared to other fabricated geometries due to their porosity and accessible active sites, providing a sustainable safe operating space, truncating the environmental impact, and effectually eradicating contaminants from water. Due to the ease of access and renewable, biocompatible, biodegradable, and non-toxic nature of biopolymers compared to other material systems, they have been introduced in electrospinning, presenting a new facet of wastewater treatment. This review discusses the toxicity of various contaminants, advancements in biomaterial fabrication with electrospinning, and the recycling and regeneration of biopolymers, facilitating sustainable systems.
|
1. Introduction
Water is one of the most important and indispensable elemental constituents for the continuance of life, which plays a substantial role in diverse sectors, including agriculture, hydropower generation, industry, and mining. Nevertheless, the rapidly increasing population, urbanization, industrialization, and the higher demands for a sophisticated living standard have led to issues such as the greenhouse effect and global warming, resulting in climatic and environmental changes.1 The demand for pure water resources has amplified over the past few years, but there has been a detrimental change in the quality of water sources. The discharge of toxic contaminants directly into water bodies by humans over the last hundred years has resulted in oceans and other water bodies being severely polluted. The improper handling of waste from various industrial and agriculture sectors has led to the discharge of chemicals in the water, tremendously affecting aquatic life and unavoidably humans2 given that 60% of the human body accounts for water.3 Over a million tonnes of waste from innumerable sources, such as pharmaceutical components, dyes, oils, heavy metals, inorganic and organic pollutants, fertilizers, pesticides, phenolic compounds, and biological toxins, has been discharged in water bodies over the past few years, which is a preeminent health concern.4–6 Henceforth, obtaining pure water has become the main concern globally due to the augmented demand for freshwater and the fatal water-borne diseases accompanying water contamination, causing 48
500 diarrheal deaths annually.7
Industrial activity is one of the most significant sectors having severe negative impacts on the marine ecosystem and humans, including eutrophication, habitat destruction, augmented water flow, debris, pathogenic contamination, irritation, and metal poisoning.8 Thus, the World Health Organization (WHO) has set up protocols to regulate the concentrations of chemical pollutants in water.7 Accordingly, diverse material systems, such as biochar, zeolites, polymers and their composites, MXenes, and biodegradable polymers, including silk, starch, cellulose, and tannins, have been utilized to effectively treat discharge.9–21 However, although these materials have been extensively explored for effluent treatment, there is still a lack of combinatory approaches to enhance their properties and biodegradability. Moreover, the removal of these materials after their shelf-life is also one of the foremost challenges in the present environment-sensitive period. Specifically, the introduction of secondary pollutants after the shelf-life of materials is a concern associated with current technologies. In this framework, biopolymers play an essential role as alternatives to meet the requirements of environment-friendly wastewater treatment materials.
Biopolymers are polymeric materials manufactured from natural sources and are biocompatible and biodegradable, unlike the common polymers, which trigger numerous perceptive environmental predicaments such as pollution and global warming. Biopolymers have attracted significant attention over the last few years with a 20–30% annual growth rate and are expected to exhibit a CAGR of 13.8%, surpassing USD 33
264.7 million at the end of 2028 in terms of revenue during the forecast period (2021–2028).22 However, due to their higher price, lower performance, and limited legislative attention, their market share is less than 0.1% of the over-all plastic manufacture compared to the standard materials.22 Biopolymer-based materials, including polysaccharides,23 polypeptides, silk, alginates, polylactic acid (PLA), polyhydroxy butyrate (PHB), and poly-ε-caprolactone (PCL), have found enormous applications as advanced materials for wastewater treatment.22–26,31 Additionally, due to the advantages of biopolymers including surface modification, facile preparation and availability, biocompatibility, non-toxicity, biodegradability, and active functional groups27–30 they are gaining popularity as exceptional systems for the removal of various toxicogenic entities from effluents.
With the introduction of various material systems, researchers from various research domains are working on introducing and fabricating efficacious systems for treating effluents and removing the toxic contaminants discharged by various industries.32–34 Electrospinning is a method for the fabrication of composite fibers, which enables the fabrication of fibers as fine as 9 nm35 and is gaining significant attention in scientific research due to the prompt evolution of nanotechnology.36 This fabrication method is an efficient technique for the fabrication of various systems with exceptional properties such as high surface area and porosity, which are necessary for effluent removal.13,37,38 Furthermore, the introduction of biopolymers in electrospinning technology simplifies the fabrication process and enhances the properties of biopolymers, making them effective candidates for wastewater treatment. Electrospinning is receiving tremendous attention due to its ability to prepare complex geometries and fibrils.36,39 The fabricated electrospun nanofibers can eliminate organic and inorganic contaminants from wastewater owing to their adjustable wettability, high length-to-diameter ratio, and surface morphology.38,40 The eradication of contaminants from aqueous system utilising electrospun nanofibrous membranes involves filtration and adsorption mechanisms.
The design and fabrication of sustainable stable systems, while removing toxic entities, providing safe operating spaces, and reducing their environmental impact for the effective eradication of contaminants from water is a significant concern. The rapid increase in the population and the sophisticated living standards have caused electrospinning technology to receive significant attention from various research domains, conspicuously in wastewater treatment. Due to the ease of access and renewable, biocompatible, biodegradable, and non-toxic nature of biopolymers compared to other material systems, they have been introduced in electrospinning, presenting a new facet of wastewater treatment. Our comprehensive literature exploration on Scopus confirmed the large number of reports on effluent removal application. Fig. 1 illustrates the number of reports on electrospun biopolymers for wastewater treatment over the past ten years on Scopus. Several biopolymeric systems were reviewed for effluent treatment according to our literature review; however, very few articles provided a comprehensive investigation on the applications and progression of electrospun biopolymers and their composites for effluent treatment. The articles provided a comprehensive review on the preparation of membranes using nanotechnology and their design, functionalization, and application for the removal of various contaminants. Also, although the review article by Silva et al.41 discussed the application of electrospun chitosan for wastewater treatment, they did not explore the mechanisms involved in the removal scheme. In contrast, Xue and Wilson42 in their review article discussed the electrospinning of chitosan and modified chitosan. Nevertheless, although the existing review articles provided an in-depth analysis of various functionalized and nanoparticle-incorporated membranes for membrane filtration, none comprehensively investigated various biopolymers and their effluent removal mechanisms.
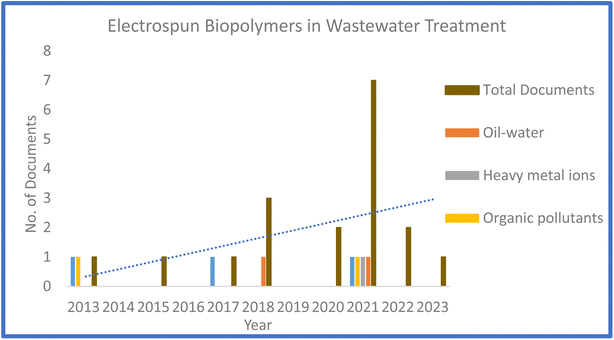 |
| Fig. 1 Available number of documents over the past ten years (number of documents per year) as of 15 November 2022 on Scopus (keywords: biopolymers, electrospinning, and wastewater treatment). | |
Moreover, the existing reviews on wastewater treatment do not provide toxicity analysis of various effluents and their hazardous effects on flora and fauna. Thus, the present work focuses on the scientific progress in the past five years in electrospun biopolymers membranes and their application in effluent removal, together with their aptitude to adsorb hazardous and toxic contaminants. Also, we present comparative ideas from the previous literature in different sections. This review article summarises the different membrane fabrication strategies and functionalization techniques and their mechanism for the adsorption of toxic contaminants. Further, we discuss the various effluent removal mechanisms by different electrospun biopolymers and composites, focusing on their adsorption mechanism, kinetics, thermodynamics, and isotherm modeling.
2. Contamination of the environment by various effluents: toxicity and hazardous effects
The existence of toxic contaminants beyond the acceptable levels due to the unimpeded release of various effluents into the marine ecosystem by oil refineries, industries, and many other sources poses a risk to all living species, which is a significant environmental and social problem, leading to an imbalance in the ecosystem.43 The toxicity of these entities, particularly from hazardous heavy metals, pharmaceutical drugs, dyes, and microplastics, is a considerable concern globally. Generally, the existing wastes can be classed as general solid waste, hazardous (generally industrial waste), and restricted solid waste by the Environmental Protection Act (EPA).44 Among them, heavy metal ions are categorized based on their toxicity as non-essential (harmful even at a low concentration) and essential (comparatively less harmful at a lower concentration) heavy metal ions.45 The USEPA (United States Environmental Protection Agency) has listed Cu, Cr, As, Cd, and Hg as primary toxic metals due to their persistency and irreversible nature, leading to their accumulation in tissues and organs of aquatic species.46 Heavy metals are highly toxic, especially to fetuses and newborn babies, damaging their brain and central nervous system (CNS), disrupting the red blood cell functionality, and even causing behavioral and psychological problems. Besides humans, severe exposure to heavy metal ions in plant species also leads to morphological and physiological changes, damage to cell function, reduced photosynthesis rate, and increased oxidation stress and mutation. Heavy metals also leads to growth obstruction in microbes.
Nickel (Ni), a heavy metal extensively employed in industrial applications for producing electrochemical nickel–cadmium batteries, is an effluent that causes major toxicity problems in the aquatic ecosystem and humans. Nickel exposure stimulates hematological effects in humans and animals. Numerous pathological effects such as lung fibrosis, skin allergies, iatrogenic nickel poisoning, and lung cancer have been reported in humans exposed to highly Ni-polluted atmospheres. Hepatic toxicity, nephrotoxicity, and dose-related changes in serum enzyme activity are also manifestations of nickel toxicity. Lead (Pb), which is one of the first metals to be discovered, is mainly discharged from industrial processes such as coal combustion, lead smelting, and battery recycling, leading to acute and chronic (>40–60 μg dL−1 in the blood) disorders in humans. Lead toxicity also causes CNS and hepatic disruption and affects the hematopoietic and renal systems. Arsenic, an abundant metal ion in underground water, is becoming prevalent in Asian countries due to arsenicosis in the Earth's crust. It combines with coenzyme complexes during respiration and causes protein coagulation after producing adenosine triphosphate and has a carcinogenic nature, which is fatal upon exposure at high levels. In contrast, mercury toxicity can cause brain disorders and complications with mobility, hearing, and speech and mercury and lead can trigger autoimmune conditions, affecting red blood cells. The maximal permissible concentrations of mercury and chromium in drinking water, as permitted by the WHO and USEPA, are 0.05 mg L−1 and 0.1 mg L−1 (chromium) and 0.001 mg L−1 and 0.002 mg L−1 (mercury), respectively.
Microplastics are fine plastic pieces with a size of less than 5 mm, which have received global attention due to their prevalent distribution in various environmental compartments, drinking water, and food.47 They are prevalent in nearly all aquatic ecosystems, occupying some planktonic organisms and size range as sediments, making them bioavailable to many aquatic organisms, including fish. Once they are ingested by fish, microplastics accumulate in the gastrointestinal tract, instigating complete digestive system obstruction and reduced feeding due to satiation. The ingestion of microplastics also prompts functional and structural deteriorations in the gastrointestinal tract, causing growth and nutritional complications in fish. Yin et al. reported that the gross energy, specific growth rate, and weight gain rate of Jacopever (Sebastes schlegelii) diminished by 9.5%, 65.9%, and 65.4%, respectively, after exposure to polystyrene microplastics (106 particles per L).48 Microplastic ingestion can induce changes in the metabolic profiles and inflammatory responses of fish and/or disrupt their innate immune system. Additionally, fine plastic particles can transmit to other organs of fish, such as their gills and liver, damaging these organs.49
With the substantial breakthroughs, the pharmaceutical industry dominates the global economy and have become the leading research sector.50 However, the direct or post-modified release of toxic contaminants by the pharmaceutical industry into the environment is a significant concern. Although various biological and physical process can lead to a reduction in pharmaceutical components in the marine ecosystem, traceable concentrations of these compounds and their metabolites have been found in several water bodies.51
The degree of toxicity in drinking water sources is low compared to industrial wastewater pollution. Nonetheless, the toxic nature of these wastes depend on their compositional concentration, which hinge on the industrial category. There are several intricate challenges associated with effluent treatment depending on its origin and type. Henceforth, based on their characteristics, numerous and precise techniques are used to handle different effluents.52Table 1 presents the various effluents, their origin, application, maximum allowable content in drinking water according to the WHO and USEPA, and their harmful effects on flora and fauna. Fig. 2 elaborates the introduction of different toxins into the water ecosystem, the consumption of these toxins by aquatic flora and fauna, the introduction of these effluents in the food chain via aquatic organisms and by water intake, and the harmful effects upon exposure to them.
Table 1 Various effluents, their origin, application, maximum allowable content in drinking water according to the WHO and USEPA, and their harmful effects on flora and fauna
Sl. No. |
Effluent |
Industry |
Applications |
Maximum allowable conc. in drinking water by WHO (mg L−1) |
Maximum allowable conc. in drinking water by USEPA (mg L−1) |
Harmful effects on exposure |
Ref. |
1 |
Nickel |
Electrochemical industries |
Electrochemical nickel–cadmium batteries |
Drinking water= < 0.1; industrial water = 2 |
0.1 |
Pathological effects, hepatic toxicity, nephrotoxicity, and fetotoxicity in animals |
53
|
2 |
Lead |
Industrial processes such as lead smelting, battery recycling |
Batteries, gasoline |
0.01 |
0.015 |
Disruption of the CNS and hepatic system and affects the hematopoietic system and renal systems, producing severe disorders |
54
|
3 |
Arsenic |
Industrial process |
Alloying agent, glass processing, metal adhesives |
Up to 0.01 |
— |
Protein coagulation and carcinogenic |
54
|
4 |
Mercury |
Natural – volcanoes & forest fire; coal-fired power plants, burning of pharmaceutical wastes |
Medicinal products, fungicides, photography |
0.001 |
0.002 |
Problems with hearing, speech, mobility, and vision. Brain disorders |
54
|
5 |
Chromium |
Tanning process |
Leather production |
0.05 |
0.1 |
Reduces seed germination, mutagenic, carcinogenic, and teratogenic |
54 and 55 |
6 |
Copper |
Smelting process |
Food storage containers |
2.0 |
1.0 |
Indian childhood cirrhosis, Wilson's disease, and idiopathic chronic toxicosis |
56 and 57 |
7 |
Cadmium |
Electrochemical industries |
Electroplating, welding. Smelting |
0.005 |
0.1 |
Kidney damage, osteoporosis, carcinogenicity, and heart diseases |
57 and 58 |
8 |
Dyes |
Textile industry |
Textiles |
— |
— |
Genotoxicity, lethal effect, carcinogenicity, mutagenicity, and tumorigenic |
59
|
9 |
Microplastics |
Plastic industries |
Packaging and textiles |
— |
— |
Blockage in the digestive and disturbs the immune system in fish |
49
|
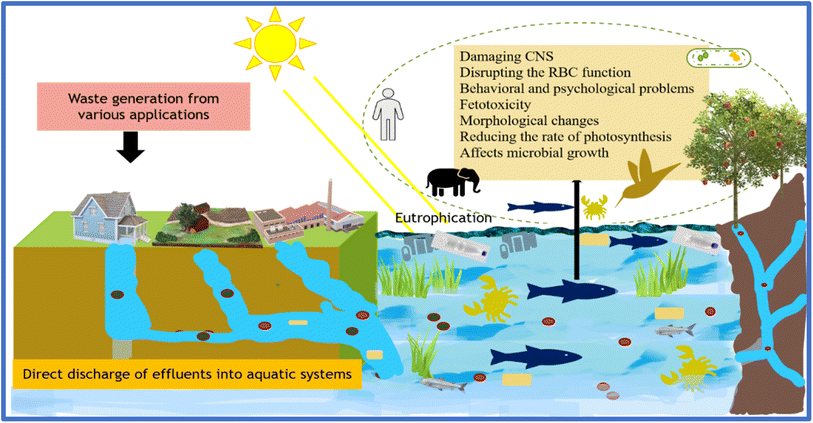 |
| Fig. 2 Introduction of different toxins in the water environment, the consumption of these toxins by aquatic flora and fauna, the introduction of these effluents in the food chain via aquatic organisms and by water intake, and the harmful effects upon exposure to them. | |
3. Effluent removal mechanism
Ion exchange, membrane technology, solvent extraction, chemical precipitation, electrochemical processes, and adsorption are the commonly employed effluent treatment methods60 (Fig. 3). Polymer-bridge formation, electrostatic patch, coagulation and direct flocculation, and adsorption are some existing and possible mechanisms employed in effluent treatment and are still applied. Coagulation/flocculation is a traditional method that generally uses long chains of non-ionic or anionic polymers as flocculants and cationic inorganic metal salts as coagulants.61 This method is extensive, effective, and facile for the treatment of various types of effluent and wastewater systems.62 In direct flocculation, a cationic polymer with medium charge density and high molecular weight is usually utilized. The two-fold function involves (1) colloidal particle charge neutralization and (2) formation of floc via the aggregated destabilized particle bridging.61 Polymer bridge formation occurs when long-chain polymers with low charge density and a high molecular weight adsorb on the surface, allowing the extension of long loops to the second surface, leading to the formation of a bridge amongst the polymers via attraction.63 The electrostatic patch mechanism includes the binding of charged polymers to an oppositely charged constituent part, initiating suspension coagulation and particle attachment via electrostatic force of attraction.63,64 Among the many removal mechanisms comprising coagulation, direct flocculation, and electronic patch, the low cost and improved efficacy of adsorption make it appealing for eradicating different toxic effluents.65 The high surface area, proficiency in processing, and porosity of biopolymers make them a feasible candidate for the biosorption of toxins via ion exchange, catalytic reduction, surface adsorption, and chelation.66
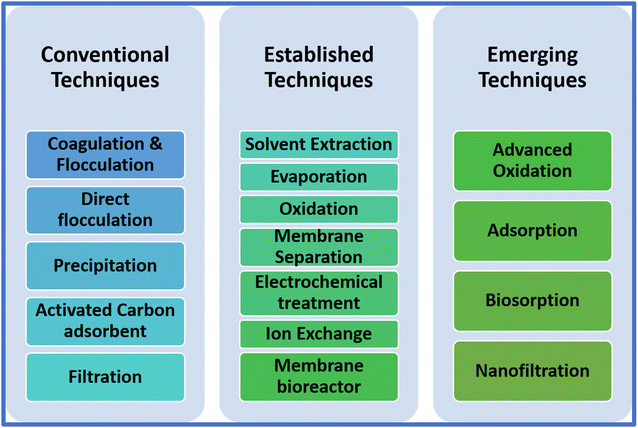 |
| Fig. 3 Classification of different technologies involved in effluent treatment. Reproduced with permission from ref. 52. Copyright 2022, Elsevier. | |
A comprehensive understanding of different thermodynamic parameters, such as changes in entropy, enthalpy, and Gibbs free energy, is mandatory to investigate the feasibility, mechanism, and biosorption performance. At equilibrium, the adsorbed adsorbate amount, qe, and the removal efficacy67 can be determined by employing the following equation:68
|  | (1) |
| 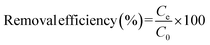 | (2) |
|  | (3) |
3.1. Adsorption isotherm
Adsorption isotherms are often adapted to demonstrate the connection between the equilibrium dosage of adsorbed adsorbate and liquid phase residual solute concentration at a constant temperature. Each isotherm model varies in the rate at which equilibrium is attained. The adsorbent in its solid stage is utilized in the adsorptive removal of solid toxicogenic entities in the liquid state. In determining and demonstrating the efficacy of a system under laboratory conditions, isotherm modeling plays a crucial role as the adsorbent–adsorbate interaction mechanism and the efficacy can be ascertained from suitable isotherm models, revealing the appropriate equation with the maximum R2 value.12,69 The various commonly employed isotherms and their equations describing adsorption mechanisms from a thermodynamic point of view are listed in Table 2.
Table 2 Commonly employed isotherms and their corresponding equations describing the adsorption mechanisms from a thermodynamic point of view
Adsorption Isotherm |
Assumptions |
Equation |
Ref. |
Freundlich |
(a) Adsorption on a heterogeneous surface |
q
c = KFC1/ne |
72
|
(b) Increase in the amount of adsorbed solute as adsorbate concentration increases |
where KF = Freundlich constant, 1/n = heterogeneity factor |
Langmuir |
(a) Monolayer adsorption, |
|
72 and 73 |
(b) no transmigration betwixt the adsorbed species |
where b = the Langmuir constant; qm = maximum adsorption capacity; Ce = equilibrium solute concentration; qe = equilibrium adsorption capacity |
(c) equivalent & identical surface sites |
(d) adsorption follows the dynamic equilibrium |
Sips |
Resulting from the limiting behavior of both Langmuir and Freundlich models |
|
74
|
where Qmax = maximum adsorption value; Ks = Sips constant; n = heterogeneity factor ranging from 0 to 1 |
BET |
Multilayer adsorption |
|
75
|
where qBET = monolayer adsorption capacity; K1 and K2 = BET constant |
Temkin |
Sorption-free energy is a function of surface coverage |
|
76
|
where θ = fractional coverage; bT = Temkin constant; AT = eqm binding constant equivalent to the maximal binding energy; T = temperature; R = universal gas constant |
Redlich–Peterson (RP) |
(a) Combines parameters of both Freundlich and Langmuir isotherms |
|
77
|
(b) Applicable for both homogeneous and heterogeneous systems |
where KR = RP constant; β = exponent ranging from 0 to 1; aPR = model constant |
Dubinin–Radushkevich |
The adsorption is associated with micropore volume filling instead of pore wall layer-by-layer adsorption |
q
e = qmax exp(−βε2) |
78
|
where qe = equilibrium adsorption capacity; β = mean adsorption-free energy; qmax = maximum adsorption capacity; ε = adsorption potential |
Harkin–Jura (HJ) |
Existence of a heterogeneous pore distribution on the adsorbent surface |
|
79
|
Halsey |
Heterogeneous active site distribution on the adsorbent surface |
|
79
|
Henry's model |
(a) Adsorption on a homogeneous surface at a lower concentration |
q
c = KHC |
75
|
(b) Linear equilibrium betwixt the concentration of the adsorbed phase and the liquid phase |
where KH = Henry's constant |
3.2. Adsorption models
The kinetic model developed by Peter Waage and Cato Guldberg in 1864 delivers details about the adsorption mechanism, transition states, and reaction rate. The adsorption kinetics gives insight into the substantial factors in the adsorption process such as the time for the removal of metal impurities, the feasible adsorption mechanism, and the reaction pathway. The residual time of the adsorbate on the adsorbent surface is also significant in estimating the maximum uptake capacity and extent of completion of the reaction.70,71
The experimental adsorption data of kinetic studies and subsequent solute removal are generally fitted with the classical pseudo-first or second-order kinetic models to determine the adsorption mechanism. The obtained experimental values precisely correspond to the equations, and the linear square regression coefficient value, R2, governs which model can be employed (higher R2 value) to clarify the adsorption kinetics. The kinetic adsorption data for modified biopolymers best suit the pseudo-second-order equation, where the values of Qt are plotted against t. Table 3 illustrates the various adsorption kinetic and kinetic equations commonly employed to estimate the reaction rate and mechanism from a thermodynamic point of view.
Table 3 Illustration of various adsorption kinetic and the kinetic equations commonly employed to estimate the reaction rate and mechanism from a thermodynamic point of view
Kinetic Model |
Description |
Kinetic equation |
Integral model |
Ref. |
Pseudo-first-order (PFO) |
Establishment of a reversible interaction equilibrium condition between two phases |
|
ln(qe − qt) = ln qe − k1t |
70 and 75 |
q
e = equilibrium adsorption capacity; k1 = rate adsorption coefficient; qt = solute adsorbed at a time, t |
Pseudo-second-order (PSO) |
Explicated as a special type of Langmuir model |
|
|
k
2 = second-order rate coefficient |
Elovich equation |
Assumptions |
|
At q = 0 |
70
|
• Energetically heterogeneous solid surface |
α and b = Elovich constants |
|
• At low surface coverage, neither desorption nor interaction can affect the adsorption kinetics |
Pseudo-nth-order |
An empirical equation without specific physical meanings |
|
(qe − qt)1−n = (n − 1)knt + qe (1 − n) |
80
|
Ritchie's equation |
First proposed for adsorption of gases on solids |
|
For n = 1, qt = qe (1 − exp−∂t) |
θ = ratio of qt & q∞, q∞ = f(Ce), obtained from the isotherm model |
If n ≠ 1, qt = qe − qe (1 + (n − 1)∂t)1/n−1 |
Boyd's diffusion model |
Adsorbate diffusion through a bounding liquid film |
|
q
t
= q∞ (1 − exp−RT) |
q
∞ = f(Ce), obtained from the isotherm model |
Frusawa and Smith model |
Assumptions |
— |
|
• Negligible intraparticle diffusion |
where kF&SS = describes the external diffusional process |
• External diffusion is the slowest step |
• Linear isotherm |
Mathews &Weber model |
Explained by the nonlinear regression method |
— |
|
S = surface coefficient |
External mass transfer model |
Assumptions |
|
— |
• film diffusion is the slowest step |
• equilibrium development on the adsorbent surface |
Weber & Morris model |
Describes the intraparticle diffusion process |
— |
q
t
= kW&Mt1/2 |
Langmuir kinetic model |
Runge–Kutta method to solve with the initial condition of q0 = 0 employing MATLAB or other programming software, making its application arduous |
|
— |
AAS model |
Based on Langmuir kinetic model |
|
— |
3.3. Thermodynamic aspect
An in-depth interpretation and illustration of different thermodynamics parameters from the isotherm models are vital to predict the mechanism and adsorption performance and the impact of changing environmental conditions on the feasibility of the process. The thermodynamic parameter ΔG° (Gibbs free energy) demonstrates the spontaneity of the chemical reaction, and the equation denoting the connection between enthalpy, free energy, and entropy is illustrated by eqn (5).75
4. Introduction to electrospinning technology
The discrepancies associated with traditional technologies and the significant evolution in the arena of nanotechnology have reinvigorated the relevance of electrospinning as an innovative approach for the fabrication of nano dimension fibrils with facile functionalization, large surface area, and superior mechanical properties. Electrospinning technology is a versatile composite fabrication approach to fabricate uniform fibers in the micro to nanometer range by employing a strong voltage supply to produce an electrically charged jet from the polymer solution.81–83 Compared to traditional spinning technologies, electrospinning emanating from integrating two words, electrostatic and spinning, uses electrostatic force to produce fibers from polymeric sources. Electrospinning is a versatile manufacturing process that can fabricate distinct structures ranging from nanofibers, hollow fibers and beads to hierarchical structures. Gooley originally patented the process of e-spin in 1902; afterward, in 1969, Taylor proposed the theoretical modeling of electrospinning.36,84 The main principle of the electrospinning technique is that the polymer droplets formed as a result of surface tension are counterattacked by the electrostatic force, forming a jet, followed by the evaporation of the solvent, forming ultrafine fibers. Numerous parameters, categorized as solution, ambient conditions, and processing parameters, govern the surface morphology of the fibers fabricated via electrospinning.
The fibers fabricated through electrospinning exhibit advantages compared to conventionally manufactured fibers, offering porosity, the ability to blend multiple polymers, enhanced mechanical properties, large specific surface area, incorporation of additives, etc. Accordingly, electrospun biopolymers have been extensively applied in effluent treatment, especially for heavy metal ion adsorption. Fig. 4 and Fig. 5 illustrate the fabrication of electrospun biopolymers via needle-based and needleless systems, respectively.
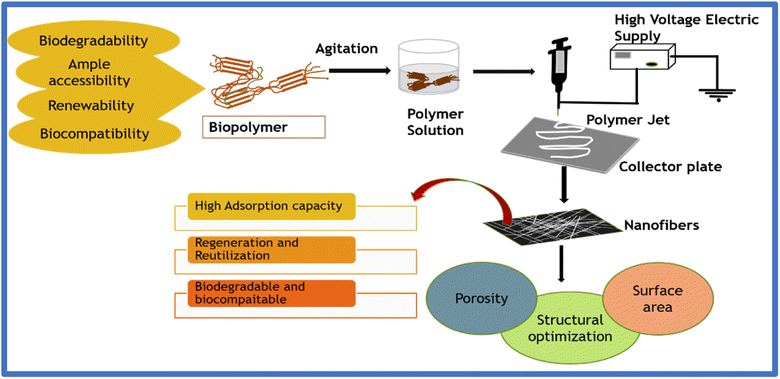 |
| Fig. 4 Electrospinning of biopolymers and the properties and utilization of nanofibers. | |
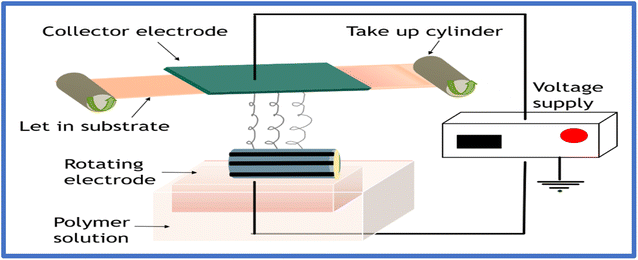 |
| Fig. 5 Needleless electrospinning of polymeric solution. | |
4.1. Effects of various parameters in the electrospinning process
The processing parameters such as feed rate, voltage, spinning distance, and capillary diameter play a significant role in determining the fiber morphology. A slight deviation in these processing parameters leads to considerable morphological changes. Among the solution parameters (polymer concentration, solvent, solution conductivity, and viscosity), solution concentration plays a significant role in fiber structure stabilization given that it influences the solution conductivity, surface tension, and viscosity. In e-spinning, the solvent used also plays a prominent role given that it affects the surface tension and the process of evaporation, where the structure and surface morphology of the nanomembrane structure depend on the solvent volatility. Environmental parameters including relative humidity and ambient temperature also play a crucial role in forming smooth and bead-free uniform fibers.85Table 4 illustrates the different parameters and their effects on fiber morphology. Taylor's mathematical expression can be used to calculate the critical voltage of a particular system at which the electrospinning process commences (eqn (5)), as follows:39 |  | (5) |
where Vc = critical voltage for electrospinning; H (cm) = spinning distance; h (cm) = liquid column length; c (Dyn cm−1) = surface tension of the spinning solution and R (cm) = spinneret inner radius. A factor of 0.09 is combined with the equation to estimate the critical voltage.
Table 4 An overview of various parameters and their effects on the electrospun fiber morphology
Parameters |
Impact on fiber morphology |
Influence |
Ref. |
Processing |
Applied voltage |
Fiber diameter |
Bead formation with an increase in the voltage beyond a critical value |
37 and 95 |
Spinning distance |
Fiber diameter |
Bead formation with short spinning distance |
37 and 87 |
Flow rate |
Fiber diameter |
With too high flow rate, beads are formed |
37 and 87 |
Environmental |
Humidity |
Fiber porosity |
Bead formation with high humidity |
87
|
Temperature |
Fiber diameter |
With an increase in temperature, there is a decrease in fiber diameter |
87
|
Solution |
Surface tension |
Fiber diameter |
Decrease in fiber pore size and diameter with low surface tension |
39 and 95 |
Solvent volatility |
Fiber porosity |
Wrapping of the capillary by fibers if very fast volatilization occurs |
Solution conductivity |
Fiber diameter |
Affects the diameter uniformity |
Concentration |
Fiber diameter |
Increase in fiber diameter as concentration increases |
4.1.1. Applied voltage.
The spinning voltage plays a vital role in forming high-performance, efficient, and moderate-diameter fibers among the other processing parameters, where a significant increase in the voltage to an optimum or critical value results in fiber uniformity, leading to ultrathin nanofibers with the formation of Tylor cones at a critical voltage. The critical voltage of a system varies from biopolymer to biopolymer. With an increase in the voltage to a critical voltage, the surface charge density of the jet increases, resulting in fiber stretching, eventually forming ultrafine fibers. However, an increase in voltage beyond the critical value leads to a phenomenon called frying, triggering a reduction in the collection efficacy of fibers37 and resulting in beads or beaded nanofiber formation. Also, there is a reduction in the Taylor cone size and increase in the jet velocity with an increase in voltage under the same flow rate, leading to an increase in the fiber diameter together with the formation of beads or beaded nanofibers. Thus, the spinning voltage is strongly correlated with bead formation in fibers, as reported by Deitzel et al.86 using a PEO/water system.
4.1.2. Flow rate.
The injection speed of the spinning solution is another imperative parameter that can be adjusted by regulating the pumping speed. A slow spinning rate indicates the extension in the time of the electrospinning process. In contrast, a high feed rate leads to the formation of fibers with large diameters or even beads.37 This is attributed to the fact that a larger solution volume is drawn out from the needle tip. Hence, there is a dire need to maintain a critical flow rate for a given voltage, which is essential to maintain the stability of the Taylor cone structure. There is a decrease in the electric charge density and an increase in electric change with a corresponding increase in flow rate. Increasing the flow rate beyond the critical value leads to the formation of beads and increase in the diameter and pore size of the fibers. Hence, it is always desirable to maintain an optimal flow rate to preserve the balance between the leaving and replaced polymer solution during jet formation.87
4.1.3. Spinning distance.
In addition to the voltage and flow rate, the distance between the collector and the capillary (spinning distance) plays a crucial role in the e-spun nanofiber morphology given that it stimulates solidification and jet extension and differs from biopolymer system to system. The morphology of nanofibers is easily influenced by the spinning distance given that it depends on the evaporation rate, deposition time, and instability interval.87 A reduction in the spinning distance is not advantageous and favorable for solvent volatilization, resulting in a decrease in the fiber performance, increase in the fiber diameter, and adhesion between fibers. Alternatively, an increment in the spinning distance leads to jet splitting and a significant reduction in the fiber diameter.88 Various studies demonstrated the effect of the spinning distance on the nanofiber morphology, which substantiated that there was a decrease in the diameter of nanofiber with an increase in spinning distance, also resulting in the formation of defective nanofibers with a larger diameter was.89 In contrast, some studies also demonstrated that no change in the nanofiber morphology occurred with an increase or decrease in the spinning distance, as illustrated by C. Zhang et al.90
4.1.4. Solution viscosity and concentration.
The solution concentration is one of the most exploited parameters in manipulating the fiber morphology in the e-spinning technique. Under the same operating or processing parameters, increasing the polymer concentration increases the fiber diameter. Due to the non-linear relationship between the solution viscosity and polymer concentration, the same non-linear relationship exists between the fiber diameter and solution viscosity. Electrospinning of the polymer/biopolymer solution with high solution viscosity produces uniform and continuous fibers given that the solution viscosity of a polymer/biopolymer is closely related to the polymer chain entanglement. The facile entanglement of polymeric chains in high molecular weight polymers leads to high solution viscosity and helps the formation of uniform fibers, whereas with low molecular weight polymers, even with the same polymer concentration, the resultant fibers formed possess a beaded morphology. With an increase in the solution concentration, there is a gradual increase in viscosity until a concentration specific or critical value, and further there is a considerable increase in viscosity.85 Alternatively, the solution concentration also affects the solution conductivity, thus influencing the charge density of the solution, and the solvent evaporation is accelerated via the stretching of a polymeric jet within tens of milliseconds (from jetting to stretching into dry fibers), overcoming the jet stretching difficulty in high molecular weight polymers.91
Also, in some cases, the improvement in fiber strength to a certain extent neutralizes the viscosity effect, resulting in a similar linear relationship between the fiber diameter and polymer concentration. However, although reducing the concentration is a straightforward method to produce nanofibers with finer dimensions, the emergence of beads and the impediment in producing ultra-fine or nanofibers with a diameter of less than 100 nm with the dilution of the solution are always a significant challenge.
4.1.5. Effect of solution conductivity and surface tension.
When exposed to an electric field, polymer solutions with lower conductivity experience low tensile forces than solutions with higher conductivity. The latter specification is advantageous for the electrospinning process given that with higher conductivity, there is a significant decrease in the diameter of fiber. Simultaneously, the application of solvents with higher viscosities and lower surface tension values leads to the formation of smooth nanofibers. Furthermore, the addition of surfactants lowers the surface tension, decreases the fiber diameter and enhances the fiber morphology.39
4.1.6. Effects of environmental parameters.
Besides the processing parameters, the ambient conditions such as relative humidity (RH) and temperature also play a significant role in controlling the fiber morphology. Changes in the nanofiber diameter are observed with a variation in humidity given that it controls the phenomena of charged jet solidification and depends on the chemical nature of the polymer or biopolymer.87 The study reported by Pelipenko et al.92 demonstrated a change in nanofiber diameter with humidity using PEO, PVA, and their blends of PEO-chitosan and PVA-hyaluronic acid. The diameter decreased from 252 nm to 75 nm and 667 nm to 161 nm for PEO and PVA, respectively, with an increase in humidity from 4% to 60%. There was a significant variation in fiber diameter with blends from 231 nm to 46 nm and 231 to 46 nm for PEO-CS and PVA-HA, respectively, when humidity was increased from 4% to 50%.
A further increase in humidity resulted in the formation of beads with individual systems and almost no e-spinning for blends. Temperature is another crucial parameter controlling the fiber properties by causing two contrasting effects in changing the fiber diameter. Temperature helps reduce the solution viscosity, and simultaneously aids an increase in the solvent evaporation rate.87 These are two opposing mechanisms; however, both lead to a decrease in the mean fiber diameter, which was substantiated by De Vrieze et al.93 using cellulose acetate and poly(vinylpyrrolidone). Low RH and increased temperature accelerate the solvent evaporation rate, forming thinner fibers. Alternatively, a decrease in temperature reduces the solution viscosity, facilitating the formation of thinner fibers. Hence, it is essential to reasonably regulate the environmental conditions to achieve the optimal fiber dimensions and uniformity in the electrospinning technique. Fig. 6 depicts the scanning electron microscopy image of electrospun nanofibers at various relative humidity.
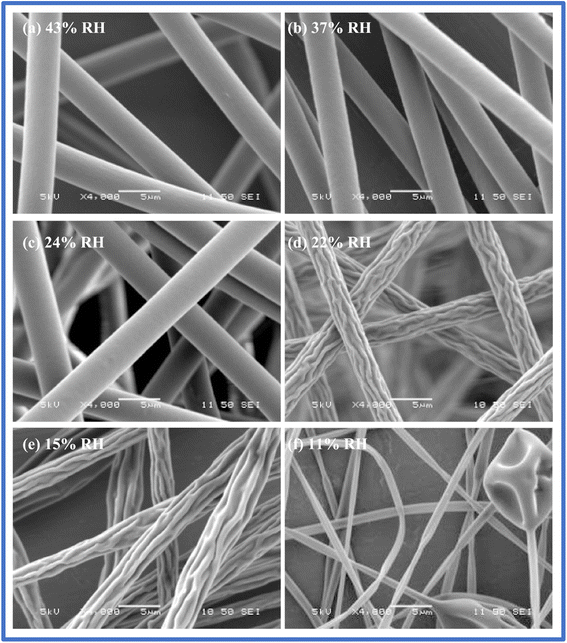 |
| Fig. 6 Scanning electron microscopy images of electrospun nanofibers at various relative humidity. Replicated with permission from ref. 94. Copyright 2009, the American Chemical Society. | |
5. Biopolymers in wastewater treatment
Over the last few decades, identifying a facile and cost-effective methodology for effluent treatment has become significant. The present technologies for wastewater treatment, which utilize carbonaceous materials, metal–organic frameworks, zeolites, nanomaterials, titanium/vanadium carbides, and polymers,10,15,96–100 induce some drawbacks despite their enhanced proficiency. This is ascribed to their non-biocompatibility, non-biodegradability, non-retrievability, and non-recyclability. These impediments in wastewater treatment concerning the existing technologies can be overcome with the introduction of biopolymers. Biopolymers have gained industrial attention as an adsorbent due to their wide availability and ability to remove contaminants from lower and higher concentrations. The presence of amine, hydroxy, and carboxyl functional groups in polysaccharides and polypeptides act as an add-on to their industrial application as adsorbent membranes, mainly for heavy metal ion adsorption.101
Natural polymers such as chitin, cellulose, starch, silk, chitosan, xanthan, collagen, gelatin, and many others have dominated in recent applications. The ample availability, biodegradability, biocompatibility, and renewability of biopolymers make them attractive in various research domains, evidently gaining prominence in effluent treatment.9,102,103 Several studies have been performed to investigate the adsorptive capture of heavy metals, dyes, pharmaceutical wastes, and other toxins using biopolymeric systems and successfully employed them in wastewater treatment.104 Their high surface area and porosities are advantages for their enhanced application and are either directly combined or reinforced using an additive to increase their bioactivity.105Fig. 7 illustrates the commonly employed biopolymers in wastewater treatment and their source of origin.
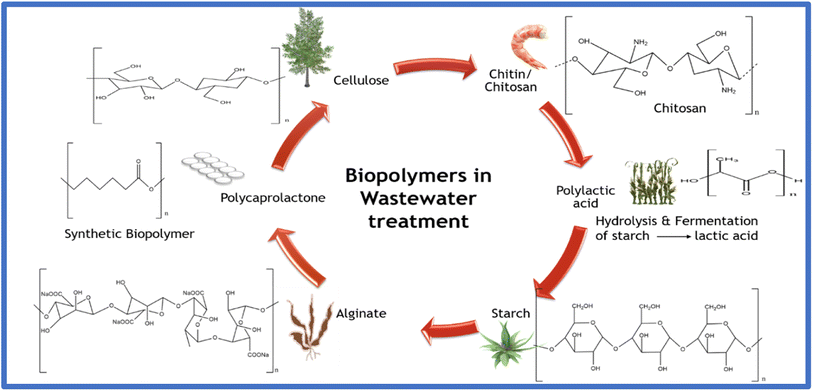 |
| Fig. 7 Commonly employed biopolymers in wastewater treatment. | |
5.1. Functionalization of electrospun biopolymers
Functionalization is the most suitable strategy to alter the selectivity, extraction efficacy, and physicochemical properties of nanofibers. The encapsulation of nanoparticles in electrospun fibers to produce functional materials is a method that has been investigated and effectively utilized in many arenas. The most commonly used nanofiber modification technologies include co-axial electrospinning, polymer mixing and doping of nanoparticles. Chemical modification, which includes incorporating different functional groups such as amino, acetyl, benzoyl, thiol, and carboxyl and antimicrobial or antibacterial agents, and or the addition of nano-additives has found extensive application, especially in wastewater treatment to achieve selectivity. Several antibiotics or antimicrobial agents are incorporated in the electrospun fibrous mats to introduce antimicrobial properties, thus preventing microbial infections and contaminations by inhibiting microbial growth. Hence, introducing nanomaterials such as silver nanoparticles, zinc oxide, titanium dioxide, and carbon nanotubes has found extensive application as antimicrobial agents for microbial inhibition.106,107Table 5 illustrates the various functionalization strategies used in effluent treatment.
Table 5 The various functionalization strategies used in various effluent treatmentsa
Material |
Surface Modification |
Functional Group |
Effluent |
Q
m
|
Mechanism |
Isotherm |
Reference |
CA: cellulose acetate; CS: chitosan; PEI: polyethylenimine; and PGMA: poly(glycidyl methacrylate).
|
Cellulose |
Carboxylation |
Carboxyl |
Pb2+ |
81.3 |
Adsorption & filtration |
Langmuir |
110
|
MB |
76.92 |
CA |
PMMA |
Carboxyl |
Cd2+ |
2.2 |
Adsorption-chelation |
— |
111
|
Hg2+ |
5.2 |
Cu2+ |
2.7 |
Cellulose |
Citric acid |
Carboxyl |
Cu2+ |
399.14 |
Adsorption–ion exchange |
Langmuir & Freundlich |
112
|
CA/polyvinylpyrrolidone |
Thioglycolic acid |
Sulfhydryl |
Cd2+ |
34.70 |
Adsorption |
Langmuir |
113
|
Pb2+ |
30.96 |
Cu2+ |
19.63 |
CS |
PGMA & PEI |
|
Cr2+ |
138.96 |
Adsorption |
Langmuir |
114
|
Cu2+ |
69.27 |
Co2+ |
68.31 |
CS/poly(ethylene oxide) |
Phosphorylated nanocellulose |
Phosphate |
Cd2+ |
232.55 |
Adsorption |
Langmuir |
115
|
Cellulose |
Cysteine |
Thiol |
Cr2+ |
87.5 |
Adsorption |
Langmuir |
116
|
Pb2+ |
137.7 |
Besides antibiotics, adding immobilized bacteria to the electrospun nanofibrous web is another modification strategy to prepare bio-composite membranes for wastewater treatment. Sarioglu et al.108 introduced a bacteria-immobilized electrospun nanofibrous web of PCL, and PLA was directly added to Clavibacter michiganensis cells for the removal of Setazol Blue BRF-X textile dye. Their study also demonstrated the improvement in removal rate with an increase in viable bacteria, and the strong attachment of the bacteria cells made the biocomposites reusable. Surface modification using plasma treatment is another excellent technique widely employed to treat electrospun membranes before their application in water remediation. The activation of surface groups without affecting the bulk property of the electrospun membranes and the fact that the chemical and physical properties of the adsorbent can be modified considerably by varying the system variables make it applicable in water treatment. Carbon dioxide plasma treatment is one example, where upon the exposure of electrospun membranes to plasma, the surface characteristics of the membrane, such as hydrophilicity, increase, introducing a smooth surface. Upon CO2 plasma treatment, highly negative carboxylate (COO–) groups are formed on the membrane surface.109 The grafting and electro-spraying techniques are other modification techniques that introduce specific properties in a membrane system. Fig. 8 presents a schematic illustration of the different methods for the modification of electrospun nanofibers including modification technology of nanofibers, surface modification of nanofibers and thin film composite nanofiber membranes.
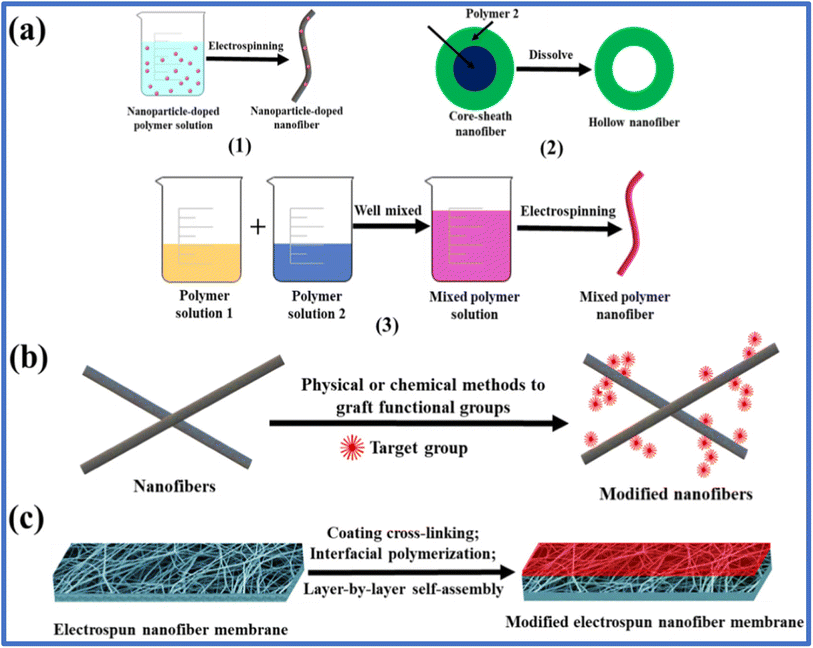 |
| Fig. 8 Schematic illustration of the different methods for the modification of electrospun nanofibers. (a) Modification technology of nanofibers. (b) Surface modification of nanofibers. (c) Thin film composite nanofiber membranes. Replicated with permission from ref. 107. Copyright 2020, Elsevier. | |
6. Electrospun biopolymer membranes in wastewater treatment
The primary removal mechanism of electrospun biopolymers is adsorptive removal, which involves either physisorption or chemisorption based on the type of adsorbent and adsorbate employed. The adsorptive removal efficiency of electrospun biopolymers is due to their interconnected pore structures, high aspect ratio, specific surface area, and tailorable properties such as surface roughness. The removal mechanism of various effluents and their applicability are discussed in the following sections.
6.1. Oil-filtration and adsorption mechanism
The nanofibers fabricated using electrospinning technology possess hierarchical tailorable structures, interconnected pore structures, and high surface area, and wetting properties (superhydrophobic/superoleophilic and superhydrophilic/superoleophobic) by tailoring their surface roughness, making them a suitable candidate for oil–water separation. The filtration and absorption of water or oil from an oil–water emulsion with different densities is possible using different wettability electrospun selective nanofibers. The Laplace equation is employed to estimate the intrusion pressure (Δp) according to the wetting model, as follows: | 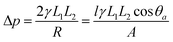 | (6) |
where θa = advanced membrane contact angle; a = membrane pore circumference; R = radius of meniscus; A = membrane pore area; and γL1L2 = surface tension.
When the prepared membrane shows superoleophilic nature in the air, i.e., θa ≈ 0, the Δp of the electrospun membrane will be less than zero, indicating that the fabricated membrane cannot support the oil pressure, thereby spontaneously permeating the oil under gravity and forming a stable solid/oil interface before water contact. Thereafter, enriching the repellency between the membrane and water given that oil occupies the hierarchical structure and water resides in an opposing state, enables the separation of heavy oil–water emulsions. In contrast, lipophobic and superhydrophilic nanofibers can separate heavy water-oil mixtures. In this process, the polarity of the membrane enhances the water permeability, thereby leading to oil repulsion.117
The lipophilic and hydrophobic nature of membranes make them excellent materials, with excellent capacity, stability, and reusability for treating oil spillages and oil–water emulsions. The low energy barrier is due to the compatibility of the oil (decrease in oil contact angle and surface tension), and the fibrous membrane facilitates oil penetration into the fibers. Moreover, the high specific area and porosity of e-spun fibers further improve the removal efficiency, acting as an excellent adsorbent material for oil recovery from water. Fig. 9 illustrates the oil–water emulsion mixture removal mechanism.
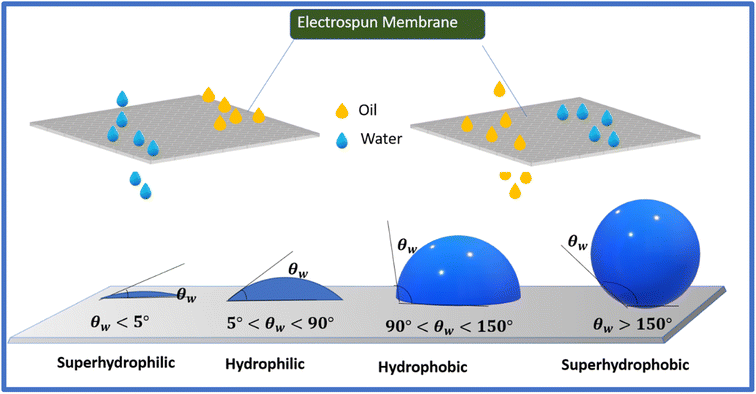 |
| Fig. 9 Oil–water emulsion separation mechanism. | |
Oil spills are one of the most significant contaminations arising from anthropogenic and natural disasters, leading to the liberation of petrochemical oil and massive accumulative hazardous impacts on the coastal marine and coastline ecosystems and soil. The results of oil spillages are disastrous in that they can directly eliminate wildlife and microbial ecosystems such as plankton due to the high oil concentration.118 Low separation efficiency, generation of secondary pollutants, process complication, and high energy consumption are some drawbacks of the existing oil–water emulsion separation technology, including condensation, biological treatment, and air flotation. Hence, the adsorption and filtration mechanisms have been applied in recent years owing to their facile nature and high removal efficiency. The existence of uniform and interconnected nanopores in electrospun membranes overcomes the limitation of the low flux of conventional membranes, making them an excellent choice for a pressure-driven removal mechanism.
A nanofibrous cellulose (NFC) membrane with a uniform and interconnected porous structure was fabricated using the wet electrospinning technique, demonstrating a high oil intrusion pressure and separation flux. The membrane system was proficient for oil–water separation application due to its superoleophilic nature (WCA = 0°), outstanding chemical stability, and separation efficacy exceeding 99% by both pressure and gravity-driven oil/water separation.119 Motivated by powder metallurgy, Jing et al.120 sintered the annealed electrospun membrane of poly-L-lactic acid/poly-D-lactic acid (1/1) for 30 min at 200 °C and 1 MPa. The sintering significantly enhanced the Young's modulus and tensile strength of the nanofiber membranes from 23.7 and 0.9 MPa to 546.2 and 11.1 MPa, respectively. Another crucial factor involved in the preparation of oil–water separation membranes is the surface wettability, such as hydrophilic/oleophobic or hydrophobic/lipophilic according to the Cassie–Baxter and Wenzel models. The introduction of a rough surface with a hierarchical structure is critical for fabricating a superoleophilic surface. A hierarchical surface-modified electrospun PLA nanofiber coated with silver nanoparticles and polydopamine (PDA) demonstrated superhydrophobicity with a water contact angle of 158.6° ± 1.2° and was efficiently utilized for the separation of an oil and water emulsion. The membrane illustrated a separation efficiency of 98%, permeation flux of 2664.3 L/m2h and antibacterial activity of 99% during gravity-driven separation.121 In all these cases, the nanofibrous membranes fabricated using electrospinning demonstrated excellent potential as oil–water separation membranes. Nevertheless, they are presently limited to the laboratory scale owing to the difficulty in industrial fabrication, which hinders their large-scale applications, opening up a new aspect for further exploration.
6.2. Microbial removal
Microorganisms such as bacteria, fungi, protozoa, worms, and viruses, which are commonly found in wastewater, are introduced in the aquatic environment, changing the color, turbidity, and odor of the water, requiring constant vigilance, even in well-developed countries. These pathogenic organisms include viruses, which are more deadly than bacteria and fungi. Accordingly, several technologies, such as nanomaterials, are introduced in bioremediation.122 Microbes that are useful in biotechnology and bioengineering can diminish the performance ability of filtration membranes, spreading fatal and infectious diseases, which have received global attention. Bacterial pathogens such as Vibrio cholerae Escherichia coli O157:H7, Shigella dysenteriae, Campylobacter jejuni, and bacterium belonging to the Legionella genus are the most prevalent bacteria involved in the outbreak of cholera, cryptosporidiosis, giardiasis and gastroenteritis, respectively.123
In most cases, the average diameter of water-borne bacteria is from 0.2 μm (E. coli size = 0.5–2.0 μm)124 to the largest cell of the colorless sulfur bacteria Thiomargarita namibiensis, which is ∼750 μm in diameter.125,126 Chlorination, one of the most common techniques used for inhibiting microbial growth and nullifying contamination, introduces chlorine in large amounts in water systems, and thus the WHO has introduced controlled and permitable chlorine in the water. To introduce a chlorine-free system, research has been focused on the application of antimicrobial agents, which lead to new diseases due to pathogenic actions. The advantages of electrospun nanofibers with large porosity, surface roughness, zeta potential, pore diameter, and surface area make them a prominent candidate as pre-filters in pressure-driven membrane filtration technology.127 Besides, the advantage of the facile incorporation of antiviral, antibacterial, and bioactive agents in nanofibers through the e-spinning technique is an addition advantage.128 The two procedures employed in removing different pathogens and bacteria from water are adsorption and size exclusion,129 which can be categorized as initial, principal, and supplemental.130 The initial step involves the removal of microbial pathogens before or as they enter the treatment plant, reducing the microbial loading in the subsequent treatment. This includes bank filtration, micro strainers, pre-sedimentation with coagulation, off-stream storage, and rough filtration. In the second stage, which is the principal process, the microbes present in the water are treated, removing a significant percentage of microbes via high-rate granular media filtration, flotation, and sedimentation. A supplemental removal stage using membrane filtration, cartridge filtration, slow sand filtration, bag filtration, or precoat filtration is either used as a supplemental process to enhance the drinking water quality or as alternative to the principal removal process.130
Marova et al.131 used electrospun nanofibers of polyhydroxyalkanoates (PHA) and demonstrated the efficiency of the biopolymeric system for microbial removal using Micrococcus luteus, Saccharomyces cerevisiae, Escherichia coli and Bacillus subtilis. The electrospun membrane exhibited a greater removal efficiency towards B. subtilis with approximately 90% removal efficiency. The study demonstrated that e-spun biopolymer membranes can be efficiently utilized for the adsorptive removal of microbes without harming the environment.
6.3. Metal ion adsorption
Biopolymers are rich in different functional groups, exhibiting high adsorption affinity towards heavy metals and dyes, and are directly electrospun into nanofibers for the adsorptive removal of these contaminants from wastewater.24 The mechanism by which electrospun biopolymers remove heavy metal ions and dyes from wastewater involves physisorption and chemisorption or their combination. Physisorption involves trapping toxic pollutants on the surface or within the pores by intermolecular (van der Waals) or electrostatic force between the adsorbent matrix and adsorbate. Physisorption can also occur as a multilayer, where the adsorbate molecules adsorb on the adsorbent system as a multilayer at a suitable temperature and pressure. The specific surface area of the adsorbent is a crucial parameter in determining the its physisorption ability; hence, many studies illustrate the incorporation of functional materials in e-spun fibrous membranes to increase the adsorbent surface area.
In contrast, chemisorption or chemical adsorption involves either the formation of stable chemical bonds between the adsorbate and adsorbent or a redox reaction to remove effluents from water. Hence, the surface chemical properties of adsorbents are one of the critical parameters to describe effective adsorption. Functionalization or surface modification, including incorporating functional groups or adding reducing agents to the membrane surface via grafting, is an efficient method to incorporate specific surface properties together with high performance and stability in the fabricated membrane.37Fig. 10 illustrates the adsorption and heavy metal removal mechanism by employing an electrospun biopolymer.
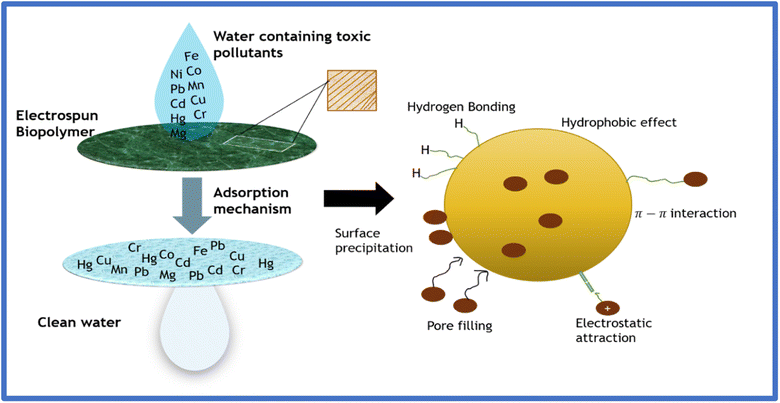 |
| Fig. 10 Adsorptive removal mechanism involving heavy metal ions by employing an electrospun biopolymer. | |
Among the various removal strategies, including reverse osmosis, chemical precipitation, ion exchange, and adsorption, the adsorption mechanism has received considerable attention due to its high efficiency, low cost, and facile operation. The enhancement in the number of adsorption sites and adsorption efficiency coupled with regeneration and recycling provides a new opportunity to utilize electrospun biopolymer membranes as efficient filtration membranes. Electrospun round-shaped nanofibers from a graphene oxide-reinforced alginate biopolymer were employed to proficiently remove Pb2+ and Cu2+ ions from wastewater. The nanofibers exhibited an adsorption efficiency of 102.4 mg g−1 for Cu2+ and 386.2 mg g−1 for Pb2+, at an optimal pH of 4–7. The adsorption followed the pseudo-second-order model, and the adsorption removal mechanism was found to be the chemical coordination of O2 and ion exchange.132 It was reported that PVA/protein nanofibers employed to eradicate NSAIDs and carbamazepine exhibited adsorption efficiency of 84.5–97.4% for a standard mixture and 77.8–96.1% for actual wastewater under optimum parameters of 60 min contact time, 27 °C temperature, 0.25 mg L−1 initial adsorbate concentration, pH of 5.5, and 35 mg adsorbent dosage. The adsorption interaction predominately occurred via chemisorption and followed the Freundlich adsorption isotherm, and the maximal adsorption capability was 31.25 to 333.33 mg
g−1.133
Diethylenetriaminepentaacetic acid-modified chitosan/polyethylene oxide nanofibers fabricated by electrospinning were employed for the adsorption of Ni2+, Pb2+, and Cu2+. The fabricated nanofibers retained their adsorption capability even after five consecutive desorption–adsorption cycles and exhibited the maximum adsorption efficacy of 177, 142, and 56 mg g−1 for Cu2+, Pb2+, and Ni2+, respectively. The measured thermodynamic parameters, i.e., ΔS° ΔH°, and ΔG°, demonstrated that the adsorption of this system was feasible, spontaneous, and endothermic, respectively, and the adsorption studies illustrated that the adsorption follows monolayer adsorption, best fitting the Langmuir adsorption isotherm. The indication of the physical nature of ion adsorption by free energy and heat of adsorption values based on the DR and Temkin models adds to the compatibility of an adsorbent for widespread application in the continuous adsorption process.134 An NH2-functionalized cellulose acetate/silica composite nanofibrous membrane, efficaciously fabricated using a combined methodology by employing electrospinning and sol–gel process, was analyzed for its ability to remediate a Cr6+ ion aqueous solution. The fabricated porous and rough membranes demonstrated a maximum adsorption efficacy of 19.46 mg g−1 and illustrated a BET surface area of 126.49 m2 g−1, which was much higher than the maximum surface area of electrospun fibers of 80 m2 g−1. The removal efficacy of the nanofiber membrane was higher than that of hematite hollow microspheres (6.8 mg g−1), porous polyacrylonitrile/ferrous chloride composite nanofibers (4.4 mg g−1), and α-Fe2O3 nanofibers (16.17 mg g−1), which is ascribed to its high specific surface area and surface active sites.135
6.4. Dye and pigment adsorption
Dyes can be classified as ionic or non-ionic based on their existence in the ionic or non-ionic form in solution. The adsorption of nonionic dyes involves chemisorption, where a potent surface complex/ligand or chemical bond is formed between the adsorbent surface functional groups and dye molecules. In addition to chemisorption, the removal of ionic dyes involves physisorption and ion exchange methods, where an intermolecular or electrostatic bond is formed between the cationic or anionic dye and the adsorbent via physisorption. Ion exchange depends on the adsorbent efficacy in adsorbing the same amount of ionic dye, while releasing ions, thus removing dyes in water. Materials such as graphene oxide, β-cyclodextrin (β-CD), magnetic nanoparticles, and polydopamine (PDA) have been widely used for dye removal from water. However, the agglomeration of these adsorbents results in less adsorption than expected. Electrospun nanofibers, as the support of these adsorbent materials, not only decrease the agglomeration probability, but further increase the adsorbent-specific surface area, thereby effectually increasing the efficacy and rate of adsorption.37
The nonwoven mesh of cellulose acetate with a fiber diameter ranging from 200 nm to 1 μm fabricated by electrospinning demonstrated enhanced structure integrity coupled with mechanical behavior on thermal treatment for 1 h at 208 °C. The nanofibrous mesh was chemically modified using alkali to obtain a RC nanofibrous mesh, which was then surface functionalized with Cibacron Blue F3GA, a common affinity dye ligand, for biomolecular separation without any considerable reduction in mechanical properties. The resultant nanofibers with a CB content of 130 μmol g−1 demonstrated a capture capacity of 13 and 4 mg g−1 for both bovine serum albumin and bilirubin, respectively, illustrating regeneration and re-utilization ability for three consecutive cycles and reported a lower permeation flux compared to other commercially available microfilters.136
6.5. Other organic pollutants
Organic pollutants such as pharmaceutical drugs, including antibiotics, antidepressants, antiallergens, adversely affect living organisms. The primary removal mechanism associated with these pollutants involves adsorptive removal, which involves physisorption and chemisorption. In physisorption, the adsorbate forms a physical bond with the surface groups of the adsorbent via electrostatic interaction or intermolecular van der Waals forces. In chemisorption, the effluents are removed from the wastewater via a chelating ligand or by redox reaction between the adsorbate and adsorbent surface groups.
Electrospinning technology and thermal curing were employed to fabricate a polybenzoxazine-based cross-linked CA nanofibrous membrane with a maximum adsorption efficacy of 552 μg g−1 and removal efficacy of 92%, which are much higher than that of the pristine cellulose acetate nanofibrous membrane towards aromatic hydrocarbon. The membrane also demonstrated a superior Young's modulus of 213.87 ± 30.79 MPa and tensile strength of 8.64 ± 0.63 MPa.137 The electrospun chitosan/polyethylene oxide (PEO) nanofiber was applied for the removal of the anti-inflammatory drug ibuprofen under the optimized processing parameters of voltage (12–17 kV) and flow rate (0.6 mL h−1), where 70% of the initial drug concentration was removed with 25 g of nanofibers after 20 min. The adsorption obeyed the Freundlich and pseudo-second-order models and illustrated an equilibrium adsorption capacity of 141.21 under the optimum pH of 4–5.138 The electrospun nanofibers fabricated using PEO/carboxymethyl chitosan was used to eliminate fluoxetine,139 which revealed the probable chemisorption mechanism with electrostatic bonding for the nanofiber. The fabricated protein/PVA nanofibers via electrospinning from a blend of PVA and protein extracted from Moringa stenopetala seeds with a diameter of 232.87 ± 59.35 nm under optimum parameters including voltage of 5 kV, flow rate of 5 μL min−1 and spinning distance of 12.5 cm exhibited thermal stability up to 170 °C, making them a favorable candidate for effluent removal.140
Table 6 presents a summary of different electrospun nanofibers for the treatment of various effluents, their removal mechanism, maximum adsorption efficacy, modeling, removal efficacy, equilibrium adsorption capability, and properties.
Table 6 Different electrospun nanofibers for the treatment of various effluents, their removal mechanism, maximum adsorption efficacy, modeling, removal efficacy, equilibrium adsorption capability, and propertiesa
Sr. No |
Material |
Processing parameters |
Effluent |
Removal mechanism |
Adsorption capacity (mg g−1) |
Isotherm model |
Kinetic model |
Optimum removal parameters |
Removal efficiency |
Eqm adsorption capacity (mg g−1) |
Properties |
Ref. |
PSO – pseudo-second order and PFO – pseudo-first order.
|
1 |
Alginate/GO |
Flow rate = 1.5 mL h−1; spinning distance = 20 cm; V = 16 kV |
Pb2+ & Cu2+ |
Adsorption–ion exchange & chemical coordination of O2 |
Cu2+ = 102.4; Pb2+ = 386.2 |
— |
PSO |
pH = 4 to 7 |
— |
Pb2+ = 286.89; Cu2+ = 68.19 |
Simple regeneration process, low-cost, and low-temperature sensitivity |
132
|
2 |
PVA/protein |
Flow rate = 5 μL min−1; spinning distance = 12 cm |
NSAIDs & carbamazepine |
Chemisorption |
31.2 ± 0.21–333.33 ± 0.93 |
Freundlich |
PSO |
Initial adsorbate conc. = 0.25 mg L−1; t = 60 min; T = 27 °C; pH = 5.5; adsorbent dosage = 35 mg |
Standard mixture = 84.5–97.4% |
0.0353–0.0406 |
Relative standard deviation = 6.2–12.6% |
133
|
V = 25 kV |
Real water = 77.8–96.1% |
3 |
Acid-modified chitosan/polyethylene oxide |
Flow rate = 0.01 mL min−1; V = 40 kV; spinning distance = 15 cm |
Ni2+, Pb2+, & Cu2+ |
Physisorption (illustrated by DR and Temkin models) |
Ni2+ = 56; Pb2+ = 142; Cu2+ = 177 |
Langmuir |
PSO |
t = 90 min |
— |
Ni2+ = 55; Pb2+ = 136; Cu2+ = 168 |
Excellent regeneration and reusability even after 5 cycles |
134
|
4 |
Lignin/PVA nanofibers |
Flow rate = 0.5–0.6 mL h−1; V = 10–20 kV; spinning distance = 10–20 cm |
Fluoxetine |
Adsorption |
29 |
— |
PFO |
t = 0–150 min; adsorbate concentration = 25 mg |
Unmodified fiber = 30%; thermally modified fiber = 70% |
110–125 |
Fiber dia = 156 nm |
141
|
5 |
Nanofibrous cellulose |
Spinning distance = 10 cm; V = 19 kV |
Oil–water separation |
Gravity & pressure-driven separation |
— |
— |
— |
— |
99% |
— |
Permeation flux = 120 000 L m−2 h−1; durable; withstand harsh environment |
119
|
6 |
Cellulose acetate |
Flow rate = 4 mL h−1; V = 25 kV |
Bovine serum albumin & bilirubin |
Adsorption |
Bovine serum albumin = 13; bilirubin = 4 |
— |
— |
— |
— |
— |
No. Of cycles = 3; fiber dia = 200 nm to 1 μm |
136
|
7 |
Bacterial web/PLA |
Flow rate = 0.5 mL h−1; V = 10–15 kV; spinning = 10–12 cm |
Setazol Blue BRF-X |
Biological removal |
1.77 × 103 |
Toth model |
Zero-order |
t = 48 h; initial dye concentration = 50 mg L−1 |
89.57% |
112.15 |
Reusable for continuous remediation |
108
|
Bacterial web/PCL |
3.24 × 103 |
87.88% |
109.75 |
8 |
NH2-functionalized cellulose acetate/silica |
— |
Cr6+ |
Adsorption |
19.46 |
— |
— |
— |
— |
— |
BET surface area = 126.49 m2 g−1; nanorod length = 200–400 nm |
135
|
9 |
Fe2O3 NP coated CA/Chitosan |
Spinning distance = 15 cm; flow rate = 0.3 mL h−1; V = 12.5–20 kV |
Phenol, Cr(IV) and Ni(II) |
Adsorption – chelation & electrostatic attraction |
Phenol = 163.5; Cr(IV) = 193.2; & Ni(II) = 143.3 |
RP |
PSO |
T = 25 °C; contact time of 0.5–6 h; adsorbent dosage of 0.2–1 g L−1; pH = 3–8 |
|
Cr(IV) = 155.3; phenol = 136.8; & Ni(II) = 103.4 |
Physical stability even after 5 cycles |
142
|
10 |
CA/Chitosan |
Cr(IV), phenol, and Ni(II) |
Adsorption – chelation & electrostatic attraction |
Cr(IV) = 181.6; phenol = 157.7; & Ni(II) = 135.7 |
RP |
PSO |
— |
Cr(IV) = 150.6; phenol = 135.5; & Ni(II) = 102.2 |
Good physical stability for 5 consecutive cycles |
11 |
Chitosan/PEO |
Flow rate = 0.6 mL h−1; V = 12–17 kV; spinning distance = 10 cm |
Ibuprofen |
Adsorption |
70 ± 2 |
Freundlich |
PSO |
pH = 4–5 |
70% |
141.21 |
Increased potential with chemical modifications |
138
|
7. Engineered electrospun membranes for effluent removal
Various fascinating topologies can be fabricated by either tuning the electrospinning parameters, tuning the polymer composition, and conducting post-treatment or designing numerous collectors and spinnerets. According to the logical relationship, the topologies are categorized into (1) individual electrospun nanomaterials with various surface or inner morphologies, (2) hybrid electrospun nanomaterials by integrating functional components or nanomaterials into individual topologies, and (3) assemblies, which are electrospun hierarchical structures congregated from individuals and/or hybrids, and further each category is divided into several clusters.84
7.1. Core-shell and hollow nanofibers
Compared with conventional e-spun nanofibers, the synergistic advantage of the shell and core material geometry of core–shell nanofibers, exhibiting enhanced properties, makes them more efficient. Inspired by the production of microcapsules from a coaxial jet proposed by Loscertales et al.143 in 2002, two coaxially arranged spinnerets were used to fabricate continuous core–shell nanofibers. This introduced the fabrication of complex internal structured multi-channel nanofibers. Core-shell nanofibers can also be produced directly from a homogeneous polymer solution with a single needle according to the phase separation principle, as illustrated by Zhang et al.144 However, handling more groups of solution and the difficulties in solving the interaction between fluids hinder the application of these spinning methods, which can be overcome by introducing practical design for spinnerets. The three-spinneret e-spun device designed by Jiang et al.145 solved the fluid interactions by introducing an inert fluid in the intermediate spinneret, producing distinct core–shell nanofibers. Due to the improvement in mechanical properties with a core–shell nanofiber geometry, they have been introduced in industrial wastewater treatment applications. Ma et al.146 fabricated core–shell-structured cellulose acetate–polycaprolactone/chitosan (CA–PCL/CS) nanofibers via the coaxial electrospinning technique with a core-to-shell ratio of 0.442 to eliminate Cr(VI) with a maximum removal efficiency of 126
mg g−1 at room temperature. The adsorption kinetics illustrated the mechanism of chemisorption with possible transferring, sharing, or exchange of electrons with the adsorbate and adsorbent.
The fabrication of hollow nanofibers involves the application of two concentrically aligned spinnerets to introduce a hollow geometry. Hollow nanofiber membranes have the advantages of a high aspect ratio, capability of self-support, and higher packing density compared to other flat sheet membranes and are cost-effective for industrial applications.147
7.2. Porous membranes
By controlling the environmental parameters such as temperature and relative humidity (controlling the solvent evaporation rate helps in regulating the pore size), the fabrication of porous fibers is possible to induce phase separation via the electrospinning process. When the relative humidity exceeds 30%, the generation of pores on the fiber surfaces with a non-uniform pore size distribution was illustrated by Casper et al.148 Post-processing treatments such as surface modification or functionalization can also introduce pores in a mixed polymer system, making them an excellent candidate for the selective and adsorptive removal of effluents with an increase in the number of active sites and surface area. The selective evaporation of the solvent phase via supercritical drying is another method to form a mesoporous membrane structure. A cryogenic liquid bath followed by subsequent vacuum drying induces the formation of a porous structure given that immersing the fibers in a cryogenic liquid freezes the solvent islands formed in the fibers due to phase separation.84 The fabrication of a macro-level 3-D polymer network was possible using the electrospinning process, where the micro-cage, a particular type of porous structure, was connected by fibers, unlike the micro-cage solid cores prepared via polymer emulsion. The micro-cage was formed due to the difference in the evaporation rate of the solvents via the e-spinning of a polymer blend emulsion with phase separation.149
7.3. Aligned nanofibers
Aligned or uniform and highly oriented nanofibers fabricated using the electrospinning process have attracted significant attention for wastewater treatment. Uniaxially aligned nanofibers can be collected either by introducing a gap in the conventional collectors to introduce parallelly arranged fibers or by specifically designed collectors such as drum collectors. To annihilate the impediments in the large-scale fabrication of aligned fibers, Yang et al.150 introduced two magnets in the plate collector and used the magnetic field to drive the preparation of large-area polymer nanofibers. In contrast, Liu et al.151 prepared ordered, aligned straight and wavy nanofibers with unique wetting properties, enhanced separation flux and antifouling properties by introducing two magnets in the collector region of the traditional collector plate, enabling their application in wastewater treatment.
7.4. Hybrid nanofibers
Hybrid nanofibers or nanofibrous membranes prepared via electrospinning have received great attention over the past decades owing to their properties and facile fabrication techniques. Co-polymerization and blending are two methods involved in forming hybrid nanofibers, incorporating synergistic properties in the fibrous system. Besides the co-polymerization and blending techniques, composite fabrication via electrospinning have also gotten attention in wastewater treatment. Gopi et al.152 successfully demonstrated the application of electrospun hybrid nanofibers by incorporating chitosan nano-whiskers in a polymer matrix. The incorporation of chitosan nano-whiskers introduced thermal stability, permeation flux, and enhanced oil–water removal efficiency. Moreover, Gopi et al.,153 in another study, demonstrated the application and efficiency of the same hybrid system for the removal of indigo carmine. Their study also disclosed that this system can be applied for the adsorption of various viruses, hormones, and proteins.
8. Regeneration and reutilization of electrospun fibers
The regeneration process encompasses the recovery and recycling of used nanofibrous bio-adsorbents to ascertain the reutilizing efficiency of the adsorbent over a sequence of adsorption cycles. Various biological, chemical and physical methodologies are used to regenerate the utilized biosorbents. The type, nature, processing feasibility, and efficiency of the adsorbent–adsorbate system determine the appropriate strategy for regeneration. Generally, chemical processes mainly involving alkali and acid reagents are the most efficient and commonly employed techniques due to their simplicity and cost-effectiveness.154 Various chemicals such as sodium hydroxide, hydrochloric acid, and nitric acid are used to understand the regenerating and recycling ability of the adsorbent via desorption studies. Biological treatment was found to demonstrate an improvised recycling ability than the chemical process.
Fabricated electrospun cellulose acetate mesh nanofibers, after the adsorption of bilirubin and bovine serum albumin, were regenerated with 0.1 M sodium hydroxide in a 1
:
4 ethanol–water mixture for 24 h and were reutilized for adsorption in three consecutive cycles.136 Acid-modified chitosan/polyethylene oxide was treated with 0.01 M HCl, leading to the repulsion between metal ions and –COO and –NH2 groups due to the protonation of the COO and –NH2 groups. The treatment of the nanofibers with NaOH solution neutralized the excess acid, activating the surface groups and leading to effective adsorption and successful re-utilization for five consecutive adsorption–desorption cycles. However, the reduction in the number of active sites with adsorption caused a decrease in the adsorption efficacy by 12%, 20%, and 17% for Ni2+, Pb2+, and Cu2+ ions after five cycles, respectively.134 The carboxyl-functionalized cellulose acetate, after utilization for adsorptive removal, could be quickly recovered by metal ion desorption using a saturated ethylenedinitrilotetraacetic acid solution and could be reutilized for metal ion adsorption, providing economic sustainability and enabling the recyclability of the adsorbent system.111
Regeneration and recycling ability are important parameters, which ensure the application of electrospun biopolymers, enabling a circular economy. The applicability and ability of the system can also be determined by analyzing the regeneration and reutilization via adsorption–desorption cycles. Improvisation in electrospun biopolymer properties via surface modification and functionalization leads to more active sites by opening the closed pores, leading to an increase in removal capacity and mechanical properties.
9. Biodegradation kinetics
Biodegradation plays a crucial role in comprehending the long-term performance of biosorbents given that the information of the adsorbent after its application in effluent removal acts as a driving element in their treatment, where the characteristics of the system and the kinetics of cell growth/hydrolysis play a crucial role. Biopolymers are commonly disposed of in the natural environment without any secondary treatment. This is followed by their degradation by the direct action of microbes, which includes biodeterioration, depolymerization, assimilation, and mineralization, as shown in Fig. 11.
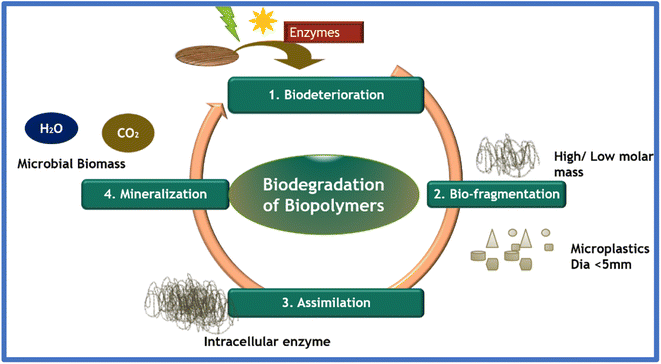 |
| Fig. 11 Illustration of the biodegradation mechanism by the direct action of microbes. | |
Michaelis–Menten proposed zero-order, first-order, half-order and mixed-order models to describe the biodegradation kinetics in soil by fitting the theoretical data. Eqn (7) shows the theoretical approach in the power rate model with time t, rate constant k and concentration of substrate C.
|  | (7) |
where
n = fitting parameter.
This model can accept substrate–disappearance curves by changing n and k until a good fit is achieved. According to eqn (7), it is noticeable that k is proportional to the power of C. The model obeys first-order kinetics when n = 1 and is generally used in the same form.
The kinetics of cell growth by Monod can be used to understand the microbial degradation kinetics of organic matters and is written as follows:
|  | (8) |
where
μmax = maximum specific growth rate;
Ks = constant, which signifies the concentration of the substrate when the growth rate is half-reaction;
S = substrate concentration; and
μ = specific growth rate of bacteria.
10. Industrial-scale application and challenges
The application of electrospun membranes has changed the realm of nanotechnology with their applicability in wastewater treatment, and the advanced properties and ease of the fabrication of membranes with desired characteristics are added advantages. The flexibility in the fabrication of nanofibers by blending, electro-spraying, or other post-treatments such as grafting, plasma treatment, and chemical and physical vapor deposition techniques enhances their application in effluent treatment due to their tunable properties. The introduction of biopolymers in electrospinning is beneficial for the fabrication of more biocompatible, biodegradable, and non-toxic nanofibrous membranes with efficient tunable properties and functionalities. However, although many techniques are used to improve the properties of electrospun biopolymer membranes, there is still room for improvement in their large-scale applicability and production. Although large-scale manufacturing techniques involving needless and multi-nozzle electrospinning techniques are available, by increasing the rapidity, the fibers formed are not always homogeneous. Hence, more studies are required to improve the large-scale production of electrospun biopolymer membranes with homogenous properties and uniformity. Self-cleaning membranes with anti-wetting and anti-fouling properties are another area that needs direct attention, together with membranes with enhanced mechanical properties with long-term stability and recyclability, which can sustain the force induced by laminar flow.155
Alternatively, the material specificity is a factor that needs attention in wastewater treatment, which hinders the large-scale applicability of biopolymers on an industrial scale. The non-enzymatic hydrolysis of bio-polyesters such as PCL releases microplastic into the marine ecosystem much faster than conventional polymers, causing secondary pollution and impeding the application of biopolymers.24 Hence, more research is required in the case of electrospun biopolymers for their vast and efficient applicability on an industrial scale.
11. Conclusion and future outlook
The upsurge in population growth and the sophisticated living standards together with the augmentation in industrial production have resulted in the discharge of various toxic entities directly into the ecosystem without proper treatment channels. In this context, efficient systems that are facile and simple to fabricate, and simultaneously cause no secondary harmful effects are necessary, and substantially eliminating toxins is a great concern. Although various efficacious methodologies and material systems have been introduced for competent toxin removal, the biodegradation of the system coupled with biocompatible properties is a prime concern. Among the diverse materials, biopolymers have received global consideration in wastewater treatment due to their biodegradability, renewability, ample availability, and facile accessibility.
Electrospinning is a facile and straightforward fabrication technology that endows the fabricated nanostructured geometry with enhanced structural properties, performance, and efficacy, emerging as a new attribute of nanotechnology. The introduction of biopolymers, which are biodegradable and biocompatible, in electrospinning technology, has presented a new strategy to effectually fabricate nanofibers with enhanced surface area, porosity, and functionalization. The current challenges of introducing the property of specificity in an adsorbent for a particular toxin can be overcome by employing the electrospinning technique because it facilitates the fabrication of composites. Moreover, fibers made from biopolymers tend to have biodegradation capability and can be easily retrieved, regenerated, and reutilized more successfully than conventional polymers.
The present review highlighted the application of electrospun biopolymeric systems to eliminate perilous and fatal toxicogenic matter from water. The toxic adverse effects of various pollutants on terrestrial and aquatic flora and fauna and the application of biopolymers electrospun biopolymers in effluent treatment were discussed. Biopolymers have attracted tremendous attention over the past decades from diverse research domains due to their biocompatibility and biodegradability. The deductions from numerous studies substantiated that biopolymers are promising adsorbents and flocculants with high efficiency for the removal of harmful waste materials from water. However, the large-scale industrial application of electrospun biopolymers requires more research to understand the capability of electrospun biopolymer membranes in water treatment. Furthermore, although biopolymers have been effectively employed as filtration membranes or adsorbent materials in multifarious effluent systems, few articles investigated the fabrication of biopolymer nanofibers via electrospinning for the removal of various toxins.
Moreover, no article explored the applicability of these materials after their usage and their biodegradation analysis under a natural atmosphere. The discussion on the degradation kinetics of electrospun biopolymeric materials opens up a new path to their comprehensive understanding. However, a thorough and comprehensive analysis is still necessary to determine the complete potential of electrospun biopolymeric systems for wastewater treatment beyond the present-day perception.
Ethical statement
The submitted article complies with the journal's ethical guidelines and does not contain the results of studies involving humans and/or animals.
Data availability
All data generated or analyzed during this study are included in the submitted manuscript.
Author contributions
Alsha Subash contributed to Material preparation, data collection analysis, and article writing. Minoo Naebe and Xungai Wang contributed to the writing – review, and editing of the article before submission. Balasubramanian Kandasubramanian contributed substantially to conceptualization and discussion and reviewed the manuscript before submission.
Conflicts of interest
The authors declare no conflict of interest.
Acknowledgements
The authors acknowledge research support from DIAT (DU) and Deakin University under the Deakin India Research Initiative (DIRI). The first author acknowledges Dr Amrita Nighojkar, Miss. Niranjana J. P, Mr Jigar Patadiya, Miss. Neelaambhigai Mayilswamy, Mr Alok Kumar, and Miss. Shruti Gupta for their unwavering technical support throughout the review writing. The authors are thankful to the editor and anonymous reviewers who have helped to improve the quality of the manuscript.
References
- Z. Huang, S. Zheng, Y. Liu, X. Zhao, X. Qiao, C. Liu, B. Zheng and D. Yin, Distribution, toxicity load, and risk assessment of dissolved metal in surface and overlying water at the Xiangjiang River in southern China, Sci. Rep., 2021, 11, 109 CrossRef CAS PubMed.
-
I. Bashir, F. A. Lone, R. A. Bhat, S. A. Mir, Z. A. Dar and S. A. Dar, in Bioremediation and Biotechnology, Springer International Publishing, Cham, 2020, pp. 1–26 Search PubMed.
- W. C. Chumlea, S. S. Guo, C. M. Zeller, N. V. Reo and R. M. Siervogel, Total body water data for white adults 18 to 64 years of age: The Fels Longitudinal Study, Kidney Int., 1999, 56, 244–252 CrossRef CAS PubMed.
- S. P. Goutam, G. Saxena, V. Singh, A. K. Yadav, R. N. Bharagava and K. B. Thapa, Green synthesis of TiO2 nanoparticles using leaf extract of Jatropha curcas L. for photocatalytic degradation of tannery wastewater, Chem. Eng. J., 2018, 336, 386–396 CrossRef CAS.
- P. Chowdhary, A. Raj and R. N. Bharagava, Environmental pollution and health hazards from distillery wastewater and treatment approaches to combat the environmental threats: A review, Chemosphere, 2018, 194, 229–246 CrossRef CAS PubMed.
- M. Patel, R. Kumar, K. Kishor, T. Mlsna, C. U. Pittman and D. Mohan, Pharmaceuticals of Emerging Concern in Aquatic Systems: Chemistry, Occurrence, Effects, and Removal Methods, Chem. Rev., 2019, 119, 3510–3673 CrossRef CAS.
- J. A. Cotruvo, 2017 WHO Guidelines for Drinking Water Quality: First Addendum to the Fourth Edition, J. Am. Water Works Assoc., 2017, 109, 44–51 CrossRef.
-
O. B. Akpor, Wastewater Effluent Discharge: Effects and Treatment Processes, 3rd Int. Conf. Chem. Biol. Environ. Eng., 2011, vol. 20, pp. 85–91 Search PubMed.
-
J. Pandey, Biopolymers and Their Application in Wastewater Treatment, Emerging Eco-friendly Green Technologies for Wastewater Treatment, 2020, pp. 245–266 Search PubMed.
- S. M. Fakhrhoseini, B. Czech, K. Shirvanimoghaddam and M. Naebe, Ultrafast microwave assisted development of magnetic carbon microtube from cotton waste for wastewater treatment, Colloids Surf., A, 2020, 606, 125449 CrossRef CAS.
- A. Rajhans, P. M. Gore, S. K. Siddique and B. Kandasubramanian, Ion-imprinted nanofibers of PVDF/1-butyl-3-methylimidazolium tetrafluoroborate for dynamic recovery of europium (III) ions from mimicked effluent, J. Environ. Chem. Eng., 2019, 7, 103068 CrossRef CAS.
-
R. B. Amal Raj, R. R. Gonte and K. Balasubramanian, in Enhancing Cleanup of Environmental Pollutants, Springer International Publishing, Cham, 2017, pp. 255–295 Search PubMed.
- P. Gore, M. Khraisheh and B. Kandasubramanian, Nanofibers of resorcinol–formaldehyde for effective adsorption of As (III) ions from mimicked effluents, Environ. Sci. Pollut. Res., 2018, 25, 11729–11745 CrossRef CAS PubMed.
- K. Shirvanimoghaddam, B. Czech, G. Wójcik and M. Naebe, The light enhanced removal of Bisphenol A from wastewater using cotton waste derived carbon microtubes, J. Colloid Interface Sci., 2019, 539, 425–432 CrossRef CAS.
- S. Wang and Y. Peng, Natural zeolites as effective adsorbents in water and wastewater treatment, Chem. Eng. J., 2010, 156, 11–24 CrossRef CAS.
- F. Dixit, K. Zimmermann, R. Dutta, N. J. Prakash, B. Barbeau, M. Mohseni and B. Kandasubramanian, Application of MXenes for water treatment and energy-efficient desalination: A review, J. Hazard. Mater., 2022, 423, 127050 CrossRef CAS PubMed.
- F. Dixit, G. Munoz, M. Mirzaei, B. Barbeau, J. Liu, S. V. Duy, S. Sauvé, B. Kandasubramanian and M. Mohseni, Removal of Zwitterionic PFAS by MXenes: Comparisons with Anionic, Nonionic, and PFAS-Specific Resins, Environ. Sci. Technol., 2022, 56, 6212–6222 CrossRef CAS PubMed.
- P. M. Gore, M. Naebe, X. Wang and B. Kandasubramanian, Progress in silk materials for integrated water treatments: Fabrication, modification and applications, Chem. Eng. J., 2019, 374, 437–470 CrossRef CAS.
- P. M. Gore, M. Naebe, X. Wang and B. Kandasubramanian, Silk fibres exhibiting biodegradability & superhydrophobicity for recovery of petroleum oils from oily wastewater, J. Hazard. Mater., 2020, 389, 121823 CrossRef CAS.
- K. V. Udayakumar, P. M. Gore and B. Kandasubramanian, Foamed materials for oil–water separation, Chem. Eng. J. Adv., 2021, 5, 100076 CrossRef CAS.
- A. Purabgola, N. Mayilswamy and B. Kandasubramanian, Graphene-based TiO2 composites for photocatalysis & environmental remediation: synthesis and progress, Environ. Sci. Pollut. Res., 2022, 29, 32305–32325 CrossRef CAS PubMed.
-
Coherent Market Insights Pvt Ltd, Biopolymers Market Analysis, http://www.coherentmarketinsights.com/.
- P. Rule, B. Kandasubramanian and R. R. Gonte, Uranium(VI) remediation from aqueous environment using impregnated cellulose beads, J. Environ. Radioact., 2014, 136, 22–29 CrossRef CAS PubMed.
- A. Subash, M. Naebe, X. Wang and B. Kandasubramanian, Biopolymer – A sustainable and efficacious material system for effluent removal, J. Hazard. Mater., 2023, 443, 130168 CrossRef CAS PubMed.
-
P. M. Gore, M. Naebe, X. Wang and B. Kandasubramanian, in ACS Symposium Series, 2022, vol. 1408, pp. 107–123 Search PubMed.
- P. M. Gore, M. Naebe, X. Wang and B. Kandasubramanian, Nano-fluoro dispersion functionalized superhydrophobic degummed & waste silk fabric for sustained recovery of petroleum oils & organic solvents from wastewater, J. Hazard. Mater., 2022, 426, 127822 CrossRef CAS PubMed.
- V. U. Kavitha and B. Kandasubramanian, Tannins for wastewater treatment, SN Appl. Sci., 2020, 2, 1081 CrossRef CAS.
- G. P. Udayakumar, S. Muthusamy, B. Selvaganesh, N. Sivarajasekar, K. Rambabu, S. Sivamani, N. Sivakumar, J. P. Maran and A. Hosseini-Bandegharaei, Ecofriendly biopolymers and composites: Preparation and their applications in water-treatment, Biotechnol. Adv., 2021, 52, 107815 CrossRef CAS PubMed.
- M. Hassan, J. Bai and D.-Q. Dou, Biopolymers; Definition, Classification and Applications, Egypt. J. Chem., 2019 Search PubMed.
- S. Rastogi and B. Kandasubramanian, Progressive trends in heavy metal ions and dyes adsorption using silk fibroin composites, Environ. Sci. Pollut. Res., 2020, 27, 210–237 CrossRef CAS PubMed.
- P. M. Gore, L. Khurana, R. Dixit and B. Kandasubramanian, Keratin-Nylon 6 engineered microbeads for adsorption of Th (IV) ions from liquid effluents, J. Environ. Chem. Eng., 2017, 5, 5655–5667 CrossRef CAS.
- M. N. Issac and B. Kandasubramanian, Review of manufacturing three-dimensional-printed membranes for water treatment, Environ. Sci. Pollut. Res., 2020, 27, 36091–36108 CrossRef CAS PubMed.
- A. Nighojkar, V. K. Sangal, F. Dixit and B. Kandasubramanian, Sustainable conversion of saturated adsorbents (SAs) from wastewater into value-added products: future prospects and challenges with toxic per- and poly-fluoroalkyl substances (PFAS), Environ. Sci. Pollut. Res., 2022, 29, 78207–78227 CrossRef CAS PubMed.
- A. Nighojkar, K. Zimmermann, M. Ateia, B. Barbeau, M. Mohseni, S. Krishnamurthy, F. Dixit and B. Kandasubramanian, Application of neural network in metal adsorption using biomaterials (BMs): a review, Environ. Sci. Adv., 2023, 2(1), 11–38 Search PubMed.
- S.-H. Tan, R. Inai, M. Kotaki and S. Ramakrishna, Systematic parameter study for ultra-fine fiber fabrication via electrospinning process, Polymer, 2005, 46, 6128–6134 CrossRef CAS.
- N. A. Patil, P. M. Gore, N. Jaya Prakash, P. Govindaraj, R. Yadav, V. Verma, D. Shanmugarajan, S. Patil, A. Kore and B. Kandasubramanian, Needleless electrospun phytochemicals encapsulated nanofibre based 3-ply biodegradable mask for combating COVID-19 pandemic, Chem. Eng. J., 2021, 416, 129152 CrossRef CAS PubMed.
- J. Cui, F. Li, Y. Wang, Q. Zhang, W. Ma and C. Huang, Electrospun nanofiber membranes for wastewater treatment applications, Sep. Purif. Technol., 2020, 250, 117116 CrossRef CAS.
- S. Simon and K. Balasubramanian, Facile Immobilization of Camphor Soot on Electrospun Hydrophobic Membrane for Oil-Water Separation, Mater. Focus, 2018, 7, 295–303 CrossRef CAS.
- N. Mayilswamy, N. Jaya Prakash and B. Kandasubramanian, Design and fabrication of biodegradable electrospun nanofibers loaded with biocidal agents, Int. J. Polym. Mater. Polym. Biomater., 2022, 1–27 Search PubMed.
- P. M. Gore, L. Khurana, S. Siddique, A. Panicker and B. Kandasubramanian, Ion-imprinted electrospun nanofibers of chitosan/1-butyl-3-methylimidazolium tetrafluoroborate for the dynamic expulsion of thorium (IV) ions from mimicked effluents, Environ. Sci. Pollut. Res., 2018, 25, 3320–3334 CrossRef CAS PubMed.
- A. O. Silva, R. S. Cunha, D. Hotza and R. A. F. Machado, Chitosan as a matrix of nanocomposites: A review on nanostructures, processes, properties, and applications, Carbohydr. Polym., 2021, 272, 118472 CrossRef CAS PubMed.
- C. Xue and L. D. Wilson, An Overview of the Design of Chitosan-Based Fiber Composite Materials, J. Compos. Sci., 2021, 5, 160 CrossRef CAS.
-
C. M. Hussain and R. Keçili, in Modern Environmental Analysis Techniques for Pollutants, Elsevier, 2020, pp. 1–36 Search PubMed.
-
A. Gürses, K. Güneş and E. Şahin, in Green Chemistry and Water Remediation: Research and Applications, Elsevier, 2021, pp. 135–187 Search PubMed.
- M. Jaishankar, T. Tseten, N. Anbalagan, B. B. Mathew and K. N. Beeregowda, Toxicity, mechanism and health effects of some heavy metals, Interdiscip. Toxicol., 2014, 7, 60–72 CrossRef PubMed.
- J.-J. Kim, Y.-S. Kim and V. Kumar, Heavy metal toxicity: An update of chelating therapeutic strategies, J. Trace Elem. Med. Biol., 2019, 54, 226–231 CrossRef CAS PubMed.
- M. N. Issac and B. Kandasubramanian, Effect of microplastics in water and aquatic systems, Environ. Sci. Pollut. Res., 2021, 28, 19544–19562 CrossRef CAS PubMed.
- L. Yin, B. Chen, B. Xia, X. Shi and K. Qu, Polystyrene microplastics alter the behavior, energy reserve and nutritional composition of marine jacopever (Sebastes schlegelii), J. Hazard. Mater., 2018, 360, 97–105 CrossRef CAS.
- W. Wang, J. Ge and X. Yu, Bioavailability and toxicity of microplastics to fish species: A review, Ecotoxicol. Environ. Saf., 2020, 189, 109913 CrossRef CAS PubMed.
- D. N. Lakdawalla, Economics of the Pharmaceutical Industry, J. Econ. Lit., 2018, 56, 397–449 CrossRef.
- C. B. Patneedi and K. Durga Prasadu, Impact of pharmaceutical wastes on human life and environment, Rasayan J. Chem., 2015, 8, 67–70 CAS.
- G. Crini and E. Lichtfouse, Advantages and disadvantages of techniques used for wastewater treatment, Environ. Chem. Lett., 2019, 17, 145–155 CrossRef CAS.
- H. N. Muhammad Ekramul Mahmud, A. K. O. Huq and R. binti Yahya, The removal of heavy metal ions from wastewater/aqueous solution using polypyrrole-based adsorbents: a review, RSC Adv., 2016, 6, 14778–14791 RSC.
- S. J. Aldin Ebrahimi, A. Eslami and L. Ebrahimzadeh, Evaluation of heavy metals concentration in the drinking water distribution network in Kurdistan villages in the year 2012, Res. J. Pharm., Biol. Chem. Sci., 2015, 6, 55–61 Search PubMed.
- A. A. Belay, Impacts of Chromium from Tannery Effluent and Evaluation of Alternative Treatment Options, J. Environ. Prot., 2010, 01, 53–58 CrossRef CAS.
- D. L. de Romaña, M. Olivares, R. Uauy and M. Araya, Risks and benefits of copper in light of new insights of copper homeostasis, J. Trace Elem. Med. Biol., 2011, 25, 3–13 CrossRef PubMed.
-
R. K. Gautam, S. K. Sharma, S. Mahiya and M. C. Chattopadhyaya, in Heavy Metals in Water, Royal Society of Chemistry, Cambridge, 2014, pp. 1–24 Search PubMed.
- Z. Shamsollahi and A. Partovinia, Recent advances on pollutants removal by rice husk as a bio-based adsorbent: A critical review, J. Environ. Manage., 2019, 246, 314–323 CrossRef CAS PubMed.
- G. J. Nohynek, R. Fautz, F. Benech-Kieffer and H. Toutain, Toxicity and human health risk of hair dyes, Food Chem. Toxicol., 2004, 42, 517–543 CrossRef CAS PubMed.
- M. Sarkar, A. K. M. L. Rahman and N. C. Bhoumik, Remediation of chromium and copper on water hyacinth (E. crassipes) shoot powder, Water Resour. Ind., 2017, 17, 1–6 CrossRef.
-
M. F. Chong, in Advances in Water Treatment and Pollution Prevention, Springer Netherlands, Dordrecht, 2012, pp. 201–230 Search PubMed.
- O. AMUDA and I. AMOO, Coagulation/flocculation process and sludge conditioning in beverage industrial wastewater treatment, J. Hazard. Mater., 2007, 141, 778–783 CrossRef CAS PubMed.
- M. Agunbiade, C. Pohl and A. Ashafa, A Review of the Application of Biofloccualnts in Wastewater Treatment, Pol. J. Environ. Stud., 2016, 25, 1381–1389 CrossRef CAS.
- B. Bolto and J. Gregory, Organic polyelectrolytes in water treatment, Water Res., 2007, 41, 2301–2324 CrossRef CAS.
- S. H. Mousavi, F. Shokoofehpoor and A. Mohammadi, Synthesis and Characterization of γ-CD-Modified TiO2 Nanoparticles and Its Adsorption Performance for Different Types of Organic Dyes, J. Chem. Eng. Data, 2019, 64, 135–149 CrossRef CAS.
- R. Zhang and Y. Tian, Characteristics of natural biopolymers and their derivative as sorbents for chromium adsorption: a review, J. Leather Sci. Eng., 2020, 2, 24 CrossRef.
- A. L. Taka, E. Fosso-Kankeu, K. Pillay and X. Y. Mbianda, Removal of cobalt and lead ions from wastewater samples using an insoluble nanosponge biopolymer composite: adsorption isotherm, kinetic, thermodynamic, and regeneration studies, Environ. Sci. Pollut. Res., 2018, 25, 21752–21767 CrossRef CAS PubMed.
- H. Shahbeig, N. Bagheri, S. A. Ghorbanian, A. Hallajisani and S. Poorkarimi, A new adsorption isotherm model of aqueous solutions on granular activated carbon, World J. Model. Simul., 2013, 9, 243–254 Search PubMed.
-
Adsorption Processes for Water Treatment and Purification, ed. A. Bonilla-Petriciolet, D. I. Mendoza-Castillo and H. E. Reynel-Ávila, Springer International Publishing, Cham, 2017 Search PubMed.
- S. Sen Gupta and K. G. Bhattacharyya, Kinetics of adsorption of metal ions on inorganic materials: A review, Adv. Colloid Interface Sci., 2011, 162, 39–58 CrossRef CAS PubMed.
- R. Gonte and K. Balasubramanian, Heavy and toxic metal uptake by mesoporous hypercrosslinked SMA beads: Isotherms and kinetics, J. Saudi Chem. Soc., 2016, 20, S579–S590 CrossRef CAS.
- K. Y. Foo and B. H. Hameed, Insights into the modeling of adsorption isotherm systems, Chem. Eng. J., 2010, 156, 2–10 CrossRef CAS.
- P. S. Ghosal and A. K. Gupta, Determination of thermodynamic parameters from Langmuir isotherm constant-revisited, J. Mol. Liq., 2017, 225, 137–146 CrossRef CAS.
- N. T. R. N. Kumara, N. Hamdan, M. I. Petra, K. U. Tennakoon and P. Ekanayake, Equilibrium Isotherm Studies of Adsorption of Pigments Extracted from Kuduk–kuduk (malabathricum L.) Pulp onto TiO2 Nanoparticles, J. Chem., 2014, 2014, 1–6 CrossRef.
- A. Pillai and B. Kandasubramanian, Carbon Xerogels for Effluent Treatment, J. Chem. Eng. Data, 2020, 65, 2255–2270 CrossRef CAS.
- Z. Chen, W. Ma and M. Han, Biosorption of nickel and copper onto treated alga (Undaria pinnatifida): Application of isotherm and kinetic models, J. Hazard. Mater., 2008, 155, 327–333 CrossRef CAS PubMed.
- C. R. Girish, Int. J. Civ. Eng. Technol., 2017, 8, 80–86 Search PubMed.
- Q. Hu and Z. Zhang, Application of Dubinin–Radushkevich isotherm model at the solid/solution interface: A theoretical analysis, J. Mol. Liq., 2019, 277, 646–648 CrossRef CAS.
- O. Chijioke Elijah, O. Nonso Collins, O. Callistus Obumneme and N.-B. Jessica, Application of Modified Agricultural Waste in the Adsorption of Bromocresol Green Dye, Asian J. Chem. Sci., 2020, 15–24 CrossRef.
- J. Wang and X. Guo, Adsorption kinetic models: Physical meanings, applications, and solving methods, J. Hazard. Mater., 2020, 390, 122156 CrossRef CAS PubMed.
- Y. Badhe and K. Balasubramanian, Nanoencapsulated Core and Shell Electrospun Fibers of Resorcinol Formaldehyde, Ind. Eng. Chem. Res., 2015, 54, 7614–7622 CrossRef CAS.
- R. Yadav and K. Balasubramanian, Metallization of Electrospun PAN Nanofibers via Electroless Gold plating, RSC Adv., 2015, 5, 24990–24996 RSC.
- J. Tahalyani, K. K. Rahangdale, R. Aepuru, B. Kandasubramanian and S. Datar, Dielectric investigation of a conducting fibrous nonwoven porous mat fabricated by a one-step facile electrospinning process, RSC Adv., 2016, 6, 36588–36598 RSC.
- J. Han, L. Xiong, X. Jiang, X. Yuan, Y. Zhao and D. Yang, Bio-functional electrospun nanomaterials: From topology design to biological applications, Prog. Polym. Sci., 2019, 91, 1–28 CrossRef CAS.
- B. Bera, Literature Review on Electrospinning Process, Imp. J. Interdiscip. Res., 2016, 2, 972–984 Search PubMed.
- J. Deitzel, J. Kleinmeyer, D. Harris and N. Beck Tan, The effect of processing variables on the morphology of electrospun nanofibers and textiles, Polymer, 2001, 42, 261–272 CrossRef CAS.
- A. Haider, S. Haider and I.-K. Kang, A comprehensive review summarizing the effect of electrospinning parameters and potential applications of nanofibers in biomedical and biotechnology, Arabian J. Chem., 2018, 11, 1165–1188 CrossRef CAS.
- L. Hou, N. Wang, J. Wu, Z. Cui, L. Jiang and Y. Zhao, Bioinspired Superwettability Electrospun Micro/Nanofibers and Their Applications, Adv. Funct. Mater., 2018, 28, 1801114 CrossRef.
- T. Wang and S. Kumar, Electrospinning of polyacrylonitrile nanofibers, J. Appl. Polym. Sci., 2006, 102, 1023–1029 CrossRef CAS.
- C. Zhang, X. Yuan, L. Wu, Y. Han and J. Sheng, Study on morphology of electrospun poly(vinyl alcohol) mats, Eur. Polym. J., 2005, 41, 423–432 CrossRef CAS.
- T. Lin, H. Wang, H. Wang and X. Wang, The charge effect of cationic surfactants on the elimination of fibre beads in the electrospinning of polystyrene, Nanotechnology, 2004, 15, 1375–1381 CrossRef CAS.
- J. Pelipenko, J. Kristl, B. Janković, S. Baumgartner and P. Kocbek, The impact of relative humidity during electrospinning on the morphology and mechanical properties of nanofibers, Int. J. Pharm., 2013, 456, 125–134 CrossRef CAS PubMed.
- S. De Vrieze, T. Van Camp, A. Nelvig, B. Hagström, P. Westbroek and K. De Clerck, The effect of temperature and humidity on electrospinning, J. Mater. Sci., 2009, 44, 1357–1362 CrossRef CAS.
- C.-L. Pai, M. C. Boyce and G. C. Rutledge, Morphology of Porous and Wrinkled Fibers of Polystyrene Electrospun from Dimethylformamide, Macromolecules, 2009, 42, 2102–2114 CrossRef CAS.
- T. J. Sill and H. A. von Recum, Electrospinning: Applications in drug delivery and tissue engineering, Biomaterials, 2008, 29, 1989–2006 CrossRef CAS PubMed.
- H. Saini, E. Otyepková, A. Schneemann, R. Zbořil, M. Otyepka, R. A. Fischer and K. Jayaramulu, Hierarchical porous metal–organic framework materials for efficient oil–water separation, J. Mater. Chem. A, 2022, 10, 2751–2785 RSC.
- K. Thakur and B. Kandasubramanian, Graphene and Graphene Oxide-Based Composites for Removal of Organic Pollutants: A Review, J. Chem. Eng. Data, 2019, 64, 833–867 CrossRef CAS.
- H. E. Karahan, K. Goh, C. John, E. Y. Zhang, C. Yıldırım, C. Y. Chuah, M. G. Ahunbay, J. Lee, Ş. B. Tantekin-Ersolmaz, Y. Chen and T. Bae, MXene Materials for Designing Advanced Separation Membranes, Adv. Mater., 2020, 32, 1906697 CrossRef CAS PubMed.
- W. Xiang, X. Zhang, J. Chen, W. Zou, F. He, X. Hu, D. C. W. Tsang, Y. S. Ok and B. Gao, Biochar technology in wastewater treatment: A critical review, Chemosphere, 2020, 252, 126539 CrossRef CAS PubMed.
- K. Shirvanimoghaddam, B. Czech, M. M. Abolhasani and M. Naebe, Sustainable periodically patterned carbon nanotube for environmental application: Introducing the cheetah skin structure, J. Cleaner Prod., 2018, 179, 429–440 CrossRef CAS.
- L. de Souza Neves Ellendersen, M. C. Milinsk, M. Feroldi, I. Volkweis Zadinelo, L. Dena dos Santos, G. I. Bolzón de Muniz, L. J. Gasparrini and H. J. Alves, Biopolymer foam for remediation of aquatic environments contaminated with particulates and heavy metals, J. Environ. Chem. Eng., 2018, 6, 6131–6138 CrossRef CAS.
- A. Hojjati-Najafabadi, M. Mansoorianfar, T. Liang, K. Shahin, Y. Wen, A. Bahrami, C. Karaman, N. Zare, H. Karimi-Maleh and Y. Vasseghian, Magnetic-MXene-based nanocomposites for water and wastewater treatment: A review, J. Water Process Eng., 2022, 47, 102696 CrossRef.
- R. Das, T. Lindström, P. R. Sharma, K. Chi and B. S. Hsiao, Nanocellulose for Sustainable Water Purification, Chem. Rev., 2022, 122, 8936–9031 CrossRef CAS PubMed.
- B. Liu, D. Wang, G. Yu and X. Meng, Adsorption of heavy metal ions, dyes and proteins by chitosan composites and derivatives — A review, J. Ocean Univ. China, 2013, 12, 500–508 CrossRef CAS.
-
A. Aravamudhan, D. M. Ramos, A. A. Nada and S. G. Kumbar, in Natural and Synthetic Biomedical Polymers, Elsevier, 2014, pp. 67–89 Search PubMed.
- A. F. de Faria, F. Perreault, E. Shaulsky, L. H. Arias Chavez and M. Elimelech, Antimicrobial Electrospun Biopolymer Nanofiber Mats Functionalized with Graphene Oxide–Silver Nanocomposites, ACS Appl. Mater. Interfaces, 2015, 7, 12751–12759 CrossRef CAS PubMed.
- H. Chen, M. Huang, Y. Liu, L. Meng and M. Ma, Functionalized electrospun nanofiber membranes for water treatment: A review, Sci. Total Environ., 2020, 739, 139944 CrossRef CAS PubMed.
- O. F. Sarioglu, N. O. San Keskin, A. Celebioglu, T. Tekinay and T. Uyar, Bacteria immobilized electrospun polycaprolactone and polylactic acid fibrous webs for remediation of textile dyes in water, Chemosphere, 2017, 184, 393–399 CrossRef CAS PubMed.
- D. A. Gopakumar, V. Arumukhan, R. V. Gelamo, D. Pasquini, L. C. de Morais, S. Rizal, D. Hermawan, A. Nzihou and H. P. A. Khalil, Carbon dioxide plasma treated PVDF electrospun membrane for the removal of crystal violet dyes and iron oxide nanoparticles from water, Nano-Struct. Nano-Objects, 2019, 18, 100268 CrossRef.
- C. Li, H. Ma, S. Venkateswaran and B. S. Hsiao, Highly efficient and sustainable carboxylated cellulose filters for removal of cationic dyes/heavy metals ions, Chem. Eng. J., 2020, 389, 123458 CrossRef CAS.
- Y. Tian, M. Wu, R. Liu, Y. Li, D. Wang, J. Tan, R. Wu and Y. Huang, Electrospun membrane of cellulose acetate for heavy metal ion adsorption in water treatment, Carbohydr. Polym., 2011, 83, 743–748 CrossRef CAS.
- K. Zhang, Z. Li, N. Deng, J. Ju, Y. Li, B. Cheng, W. Kang and J. Yan, Tree-like cellulose nanofiber membranes modified by citric acid for heavy metal ion (Cu2+) removal, Cellulose, 2019, 26, 945–958 CrossRef CAS.
- T. Xiang, Z. Zhang, H. Liu, Z. Yin, L. Li and X. Liu, Characterization of cellulose-based electrospun nanofiber membrane and its adsorptive behaviours using Cu(II), Cd(II), Pb(II) as models, Sci. China Chem., 2013, 56, 567–575 CrossRef CAS.
- D. Yang, L. Li, B. Chen, S. Shi, J. Nie and G. Ma, Functionalized chitosan electrospun nanofiber membranes for heavy-metal removal, Polymer, 2019, 163, 74–85 CrossRef CAS.
- R. Brandes, D. Belosinschi, F. Brouillette and B. Chabot, A new electrospun chitosan/phosphorylated nanocellulose biosorbent for the removal of cadmium ions from aqueous solutions, J. Environ. Chem. Eng., 2019, 7, 103477 CrossRef CAS.
- R. Yang, K. B. Aubrecht, H. Ma, R. Wang, R. B. Grubbs, B. S. Hsiao and B. Chu, Thiol-modified cellulose nanofibrous composite membranes for chromium (VI) and lead (II) adsorption, Polymer, 2014, 55, 1167–1176 CrossRef CAS.
- W. Ma, Y. Ding, M. Zhang, S. Gao, Y. Li, C. Huang and G. Fu, Nature-inspired chemistry toward hierarchical superhydrophobic, antibacterial and biocompatible nanofibrous membranes for effective UV-shielding, self-cleaning and oil-water separation, J. Hazard. Mater., 2020, 384, 121476 CrossRef CAS PubMed.
- A. M. P. Madhubashani, D. A. Giannakoudakis, B. M. W. P. K. Amarasinghe, A. U. Rajapaksha, P. B. T. Pradeep Kumara, K. S. Triantafyllidis and M. Vithanage, Propensity and appraisal of biochar performance in removal of oil spills: A comprehensive review, Environ. Pollut., 2021, 288, 117676 CrossRef CAS PubMed.
- S. K. Hong, S. Bae, H. Jeon, M. Kim, S. J. Cho and G. Lim, An underwater superoleophobic nanofibrous cellulosic membrane for oil/water separation with high separation flux and high chemical stability, Nanoscale, 2018, 10, 3037–3045 RSC.
- Y. Jing, L. Zhang, R. Huang, D. Bai, H. Bai, Q. Zhang and Q. Fu, Ultrahigh-performance electrospun polylactide membranes with excellent oil/water separation ability via interfacial stereocomplex crystallization, J. Mater. Chem. A, 2017, 5, 19729–19737 RSC.
- L. Liu and W. Yuan, A hierarchical functionalized biodegradable PLA electrospun nanofibrous membrane with superhydrophobicity and antibacterial properties for oil/water separation, New J. Chem., 2018, 42, 17615–17624 RSC.
- A. Chithra, R. Sekar, P. Senthil Kumar and G. Padmalaya, A review on removal strategies of microorganisms from water environment using nanomaterials and their behavioural characteristics, Chemosphere, 2022, 295, 133915 CrossRef CAS PubMed.
- S. Fahimirad, Z. Fahimirad and M. Sillanpää, Efficient removal of water bacteria and viruses using electrospun nanofibers, Sci. Total Environ., 2021, 751, 141673 CrossRef CAS PubMed.
-
National Research Council (US), Steering Group for the Workshop on Size Limits of Very Small Microorganisms, in Size Limits of Very Small Microorganisms, National Academies Press (US), Washington (DC), 1999 Search PubMed.
- H. N. Schulz and B. B. Jørgensen, Big Bacteria, Annu. Rev. Microbiol., 2001, 55, 105–137 CrossRef CAS PubMed.
- P. A. Levin and E. R. Angert, Small but Mighty: Cell Size and Bacteria, Cold Spring Harbor Perspect. Biol., 2015, 7, a019216 CrossRef PubMed.
- R. Wang, Y. Liu, B. Li, B. S. Hsiao and B. Chu, Electrospun nanofibrous membranes for high flux microfiltration, J. Membr. Sci., 2012, 392–393, 167–174 CrossRef CAS.
- M. Mukherjee and S. De, Antibacterial polymeric membranes: a short review, Environ. Sci.: Water Res. Technol., 2018, 4, 1078–1104 RSC.
- A. Lee, J. W. Elam and S. B. Darling, Membrane materials for water purification: design, development, and application, Environ. Sci.: Water Res. Technol., 2016, 2, 17–42 RSC.
-
K.-K. Au, in Water Encyclopedia, John Wiley & Sons, Inc., Hoboken, NJ, USA, 2005 Search PubMed.
-
I. Marova, V. Kundrat, P. Benesova, P. Matouskova and S. Obruca, in 2015 IEEE 15th International Conference on Nanotechnology IEEE-NANO, IEEE, 2015, pp. 204–206 Search PubMed.
- L. Pan, Z. Wang, X. Zhao and H. He, Efficient removal of lead and copper ions from water by enhanced strength-toughness alginate composite fibers, Int. J. Biol. Macromol., 2019, 134, 223–229 CrossRef CAS PubMed.
- T. G. Kebede, S. Dube and M. M. Nindi, Biopolymer electrospun nanofibres for the adsorption of pharmaceuticals from water systems, J. Environ. Chem. Eng., 2019, 7, 103330 CrossRef CAS.
- N. S. Surgutskaia, A. Di Martino, J. Zednik, K. Ozaltin, L. Lovecká, E. D. Bergerová, D. Kimmer, J. Svoboda and V. Sedlarik, Efficient Cu2+, Pb2+ and Ni2+ ion removal from wastewater using electrospun DTPA-modified chitosan/polyethylene oxide nanofibers, Sep. Purif. Technol., 2020, 247, 116914 CrossRef CAS.
- J. Li, X. Lai, C. Xing and D. Wang, One-Pot Synthesis of Porous Hematite Hollow Microspheres and Their Application in Water Treatment, J. Nanosci. Nanotechnol., 2010, 10, 7707–7710 CrossRef CAS PubMed.
- Z. Ma, M. Kotaki and S. Ramakrishna, Electrospun cellulose nanofiber as affinity membrane, J. Membr. Sci., 2005, 265, 115–123 CrossRef CAS.
- Y. Ertas and T. Uyar, Fabrication of cellulose acetate/polybenzoxazine cross-linked electrospun nanofibrous membrane for water treatment, Carbohydr. Polym., 2017, 177, 378–387 CrossRef CAS PubMed.
- L. Paradis-Tanguay, A. Camiré, M. Renaud, B. Chabot and A. Lajeunesse, Sorption capacities of chitosan/polyethylene oxide (PEO) electrospun nanofibers used to remove ibuprofen in water, J. Polym. Eng., 2019, 39, 207–215 CrossRef CAS.
- A. H. I. Khierallah, I. I. C. Bates, B. Chabot and A. Lajeunesse, Adsorption of Pharmaceutical Contaminants from Aqueous Solutions Using N,O-Carboxymethyl Chitosan/Polyethylene Oxide (PEO) Electrospun Nanofibers, J. Mater. Sci. Chem. Eng., 2021, 09, 15–38 CAS.
- T. M. Stanne, L. L. E. Sjögren, S. Koussevitzky and A. K. Clarke, Identification of new protein substrates for the chloroplast ATP-dependent Clp protease supports its constitutive role in Arabidopsis, Biochem. J., 2009, 417, 257–269 CrossRef CAS PubMed.
- A. Camiré, J. Espinasse, B. Chabot and A. Lajeunesse, Development of electrospun lignin nanofibers for the adsorption of pharmaceutical contaminants in wastewater, Environ. Sci. Pollut. Res., 2020, 27, 3560–3573 CrossRef PubMed.
- A. Karamipour, P. Khadiv Parsi, P. Zahedi and S. M. A. Moosavian, Using Fe3O4-coated nanofibers based on cellulose acetate/chitosan for adsorption of Cr(VI), Ni(II) and phenol from aqueous solutions, Int. J. Biol. Macromol., 2020, 154, 1132–1139 CrossRef CAS PubMed.
- I. G. Loscertales, A. Barrero, I. Guerrero, R. Cortijo, M. Marquez and A. M. Gañán-Calvo, Micro/Nano Encapsulation via Electrified Coaxial Liquid Jets, Science, 2002, 295, 1695–1698 CrossRef CAS PubMed.
- J.-F. Zhang, D.-Z. Yang, F. Xu, Z.-P. Zhang, R.-X. Yin and J. Nie, Electrospun Core–Shell Structure Nanofibers from Homogeneous Solution of Poly(ethylene oxide)/Chitosan, Macromolecules, 2009, 42, 5278–5284 CrossRef CAS.
- H. Chen, N. Wang, J. Di, Y. Zhao, Y. Song and L. Jiang, Nanowire-in-Microtube Structured Core/Shell Fibers via Multifluidic Coaxial Electrospinning, Langmuir, 2010, 26, 11291–11296 CrossRef CAS PubMed.
- L. Ma, X. Shi, X. Zhang, S. Dong and L. Li, Electrospun Cellulose Acetate–Polycaprolactone/Chitosan Core–Shell Nanofibers for the Removal of Cr(VI), Phys. Status Solidi, 2019, 216, 1900379 CrossRef CAS.
- S. Bandehali, F. Parvizian, H. Ruan, A. Moghadassi, J. Shen, A. Figoli, A. S. Adeleye, N. Hilal, T. Matsuura, E. Drioli and S. M. Hosseini, A planned review on designing of high-performance nanocomposite nanofiltration membranes for pollutants removal from water, J. Ind. Eng. Chem., 2021, 101, 78–125 CrossRef CAS.
- C. L. Casper, J. S. Stephens, N. G. Tassi, D. B. Chase and J. F. Rabolt, Controlling Surface Morphology of Electrospun Polystyrene Fibers: Effect of Humidity and Molecular Weight in the Electrospinning Process, Macromolecules, 2004, 37, 573–578 CrossRef CAS.
- Y. Zhu, D. Yang and H. Ma, One-step fabrication of porous polymeric microcage via electrified jetting, Nanoscale, 2010, 2, 910 RSC.
- D. Yang, B. Lu, Y. Zhao and X. Jiang, Fabrication of Aligned Fibrous Arrays by Magnetic Electrospinning, Adv. Mater., 2007, 19, 3702–3706 CrossRef CAS.
- Y. Liu, X. Zhang, Y. Xia and H. Yang, Magnetic-Field-Assisted Electrospinning of Aligned Straight and Wavy Polymeric Nanofibers, Adv. Mater., 2010, 22, 2454–2457 CrossRef CAS PubMed.
- S. Gopi, R. Kargl, K. S. Kleinschek, A. Pius and S. Thomas, Chitin nanowhisker – Inspired electrospun PVDF membrane for enhanced oil-water separation, J. Environ. Manage., 2018, 228, 249–259 CrossRef CAS PubMed.
- S. Gopi, P. Balakrishnan, A. Pius and S. Thomas, Chitin nanowhisker (ChNW)-functionalized electrospun PVDF membrane for enhanced removal of Indigo carmine, Carbohydr. Polym., 2017, 165, 115–122 CrossRef CAS PubMed.
- P. R. Yaashikaa, P. Senthil Kumar and S. Karishma, Review on biopolymers and composites – Evolving material as adsorbents in removal of environmental pollutants, Environ. Res., 2022, 212, 113114 CrossRef CAS PubMed.
- L. Francis, F. E. Ahmed and N. Hilal, Electrospun membranes for membrane distillation: The state of play and recent advances, Desalination, 2022, 526, 115511 CrossRef CAS.
|
This journal is © The Royal Society of Chemistry 2023 |
Click here to see how this site uses Cookies. View our privacy policy here.